MANUFACTURING SOLUTIONS FOR MACHINING DIFFERENTIAL HOUSINGS

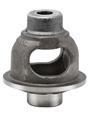
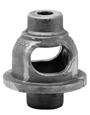
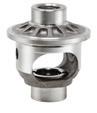



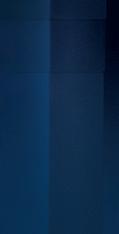

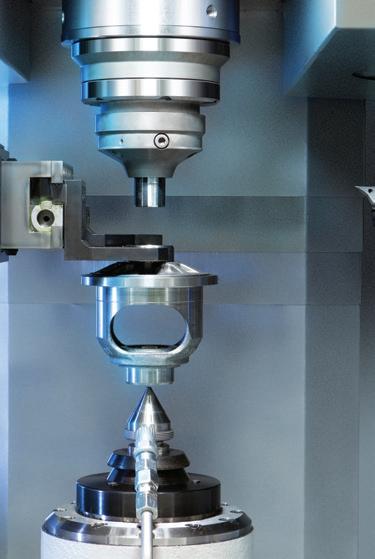
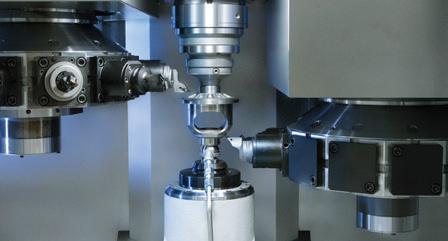

HIGH POTENTIAL FOR ALL DRIVE CONCEPTS! HIGH-PERFORMANCE
HIGH POTENTIAL FOR ALL DRIVE CONCEPTS! HIGH-PERFORMANCE
for internal combustion engines, electric motors or hybrid engines.
According to a recent study, McKinsey has estimated that global automobile production will grow by approximately two percent annually until 2030. The differential is a perfect example of how these increasing quantities can be tackled effectively despite the high quality requirements. This central component is crucial for all types of drive concept – whether internal combustion engine, electric motor or hybrid engine. Therefore, its production requirements continue to steadily rise. The machining of the differential housing, however, is extremely challenging. For years, the EMAG Group has been working to create the perfect solution.
The EMAG Group has developed a manufacturing solution for the production of differential housings that focuses on maximum productivity and process reliability.
This solution uses machines from EMAG’s modular product range which provide maximum efficiency with a comparatively low investment cost.
The flange side of the housing is machined in OP 10. This is known as the flange side because later the ring gear will be welded to it. The complete internal and external machining of the axle mount takes place in this operation using a bell tool to ensure high-speed machining processes.
Turning the cage side (OP 20) Turning the flange side (OP 10)CLAMPING DEVICE: 2 x 2-JAW CLAMPING CHUCK
The internal machining of the cage side of the differential housing and the external machining of the axle mount is performed in OP 20 using a bell tool - the borehole is also drilled. To ensure excellent machining quality, customized EMAG chucks are used in both processes and guarantee a secure hold.
OP 30 includes the complete external machining of the differential housing. By using a VT 4 for the four-axis machining of the housing, high-quality is guaranteed and machining times are dramatically reduced. Machining in a single clamping operation rules out the possibility of re-clamping errors, and the high rigidity of the two tool turrets and the clamping fixture ensures high tolerances.
In OP 40, the first thing you see is the impressive clamping device, which was developed by EMAG specifically for the production of differential housings. In this operation, the boreholes are cleaned and the spherical cap is initially scrubbed internally using a banana tool and then dressed.
The vertical pick-up turning machines of the VL-Series are part of the EMAG Group’s Modular Machine line.
The vertical pick-up turning machines in the VL-series were developed specifically for the precision manufacturing of chucked parts. To cover the widest possible range of parts, the VL-series is available in four versions and can machine workpieces ranging from 10 – 400 mm (0.4 – 16 in) in diameter.
MINERALIT® polymer concrete machine base
Z-axis
X-axis
Main spindle
Measuring system (optional)
NOW AVAILABLE:
SIEMENS 840D SOLUTION LINE
Turret with 12 tool positions (optional Y-axis)
Automation
HIGHLIGHTS:
MAXIMUM PRECISION –DIRECT POSITION MEASURING SYSTEMS
THE PATENTED EMAG TURRET
Max. workpiece diameter: 100 mm | 4 in
Max. workpiece length: 150 mm | 6 in
+ HIGH STRENGTH
Large working spindle bearing diameter + machine body made of MINERALIT®
+ COMPLETE AUTOMATION
Including raw and finished parts storage areas
+ SIMPLE HANDLING
All the service units are easy to reach
+ MINIMUM FOOTPRINT
Compact machine design
+ MAXIMUM PERFORMANCE
Short travel times between the machining area and pickup automation system Machines shown with optional decorative sheet kit
When it comes to producing a high quantity of differential housings, fast manufacturing processes are crucial. In order to achieve this, the loading and unloading of the machines must be done very quickly. The VT 2 and VT 4 machines guarantee maximum performance with their four axes, short travel distances and powerful main spindle.
The benefits of this machine platform are obvious when the machine is required to produce high part volumes. Since this platform can machine the workpiece from two sides, the production time is dramatically reduced allowing for more parts to be machined, quicker. The machines flexibility is also guaranteed by the two tool turrets, each with eleven tool stations, that can be equipped with turning or driven tools.
Example of typical workpieces machined on VT systems.
MINERALIT® polymer concrete machine base
Main spindle
Tool turret 1
Tool turret 2
Control system (Fanuc)
Automation
NOW AVAILABLE:
840D
» Six second workpiece changeover time.
» Comes ready for integration with EMAG TrackMotion automation system.
+ REDUCED MACHINING TIMES
thanks to four-axis machining
+ SHORTER IDLE TIMES
thanks to simultaneous loading and unloading of components
+ DECREASED INVESTMENT COSTS
thanks to integrated automation
On VL machines, the working spindle is used to both machine workpieces and load/unload them. With the customizable carrier prisms, the costs to change parts for different components are extremely low. The carrier prisms are simply inserted in the conveyor belt and the necessary transport-related data is updated on the control unit.
The VT 2 is loaded and unloaded by the turrets. While one workpiece gripper moves a new component into the turning machine, the other removes the finished workpiece. This entire process takes only six seconds.
TrackMotion combines the concept of conveyor belts integrated with gantries into one single automation solution.
The TrackMotion is a track that runs through multiple machines with a TransLift unit attached. The TransLift will grip parts, even parts with different heights, correctly position them and if necessary turn the part over. The way the TrackMotion is set up allows it to link a variety of machines very easily. To decrease cycle times even further, multiple TransLift units can be added.
Laser welding is now an established technology for the production of automotive powertrain components. With its technological expertise, EMAG was able to gain an early reputation in this sector as a major systems supplier for customized manufacturing lines for the welding of differentials, differential housing and ring gears.
Currently, the industry is experiencing a technological shift. Vehicles with hybrid drive systems are on the rise, all-wheel-drive vehicles are continuing to improve and the pressure to reduce overall vehicle weight is increasing. These demands all rely on the manufacturer’s ability to produce weight-optimized differential gears that are smaller than those in rear axle differentials on luxury vehicles.
To meet these demands, the ELC 160 from EMAG with an enhanced automation cell is offering an optimized solution for these applications with small differentials. This manufacturing system is setting new industry standards in terms of productivity and economic efficiency.
Precise
Workpieces are checked ultrasonically after each operation to ensure complete process control.
EMAG Salach GmbH
Salach
Austrasse 24
73084 Salach
Germany
Phone: +49 7162 17-0
Fax: +49 7162 17-4027
E-mail: info@salach.emag.com
Frankfurt
Martin-Behaim-Strasse 12
63263 Neu-Isenburg
Germany
Phone: +49 6102 88245-0
Fax: +49 6102 88245-412
E-mail: info@frankfurt.emag.com
Leipzig
Pittlerstrasse 26
04159 Leipzig
Germany
Phone: +49 341 4666-0
Fax: +49 341 4666-2114
E-mail: info@leipzig.emag.com
Munich
Zamdorferstrasse 100
81677 München
Germany
Phone: +49 89 99886-250
Fax: +49 89 99886-160
E-mail: info@muenchen.emag.com
Austria
Glaneckerweg 1
5400 Hallein
Austria
Phone: +43 6245 76023-0
Fax: +43 6245 76023-20
E-mail: info@austria.emag.com
Denmark
Horsvangen 31
7120 Vejle Ø
Denmark
Phone: +45 75 854854
Fax: +45 75 816276
E-mail: info@daenemark.emag.com
Market Companies
EUROPE
EMAG MILANO S.r.l.
Via dei Mille 31
20098 San Giuliano Milanese (Mi)
Italy
Phone: +39 02 905942-1
Fax: +39 02 905942-24
E-mail: info.milano@emag.com
EMAG MILANO S.r.l.
Succursale en France
5 Avenue de L'Europe – BP 22
18150 La Guerche sur L'Aubois
France
Phone: +33 248 7711-00
Fax: +33 248 7111-29
E-Mail: info.france@emag.com
EMAG MILANO S.r.l.
Sucursal en España
Pasaje Arrahona, n° 18
Polígono Industrial Santiga
08210 Barberà del Vallès (Barcelona)
Spain
Phone: +34 93 7195080
Fax: +34 93 7297107
E-mail: info.spain@emag.com
EMAG UK Ltd.
Chestnut House
Kingswood Business Park
Holyhead Road
Albrighton
Wolverhampton WV7 3AU
Great Britain
Phone: +44 1902 37609-0
Fax: +44 1902 37609-1
E-mail: info@uk.emag.com
EMAG OOO
ul. Akademika Chelomeya 3/2
117630 Moscow
Russia
Phone: +7 495 287 0960
Fax: +7 495 287 0962
E-mail: info@russia.emag.com
AMERICA
EMAG L.L.C. USA
38800 Grand River Avenue
Farmington Hills, MI 48335
USA
Phone: +1 248 477-7440
Fax: +1 248 477-7784
E-mail: info@usa.emag.com
EMAG MEXICO
Maquinaria EMAG Mexico S de RL de CV
Av. Hercules 301 Nave 1
Poligono Empresarial Santa Rosa
76220 Santa Rosa Jauregui, Querétaro
Mexico
Phone: +52 442 291 1552
E-mail: info@mexico.emag.com
EMAG DO BRASIL
Edifício Neo Corporate Offices, CJ 1503
Rua Enxovia, 472
04711-030 São Paulo SP
Brazil
Phone: +55 11 38370145
Fax: +55 11 38370145
E-mail: info@brasil.emag.com
Turning Milling Grinding Gear Hobbing Power SkivingSweden
Glasgatan 19B
73130 Köping
Sweden
Phone: +46 221 40305
E-mail: info@sweden.emag.com
Hungary
Gerenda 10
1163 Budapest
Hungary
Phone: +36 30 9362-416
E-mail: lbujaki@emag.com
Czech Republic
Lolkova 766
103 00 Praha 10 – Kolovraty
Czech Republic
Phone: +420 731 476070
E-mail: mdelis@emag.com
Poland
ul. Krzycka 71A / 6
53-020 Wrocław
Poland
Phone: +48 728 389 989
E-mail: info@poland.emag.com
Turkey
Sanayi Cad. No.: 44
Nish İstanbul Sitesi D Blok
D: 155 Yenibosna – Istanbul
Turkey
Phone: +90 532 694 54 44
E-mail: ckoc@emag.com
EMAG (China) Machinery Co., Ltd.
Building A3 & B7 Cangneng
Europe & America Technology Park
No. 8 Loujiang Rd. (N.)
215400 Taicang
Jiangsu, China
Phone: +86 512 5357-4098
Fax: +86 512 5357-5399
E-mail: info@emag-china.com
EMAG (Chongqing) Machinery Co., Ltd.
No. 10th Lailong Road
Yongchuan District
402160 Chongqing
China
Phone: +86 23 49783399
Fax: +86 23 49783388
E-mail: info@emag-china.com
TAKAMAZ EMAG Ltd.
1-8 Asahigaoka Hakusan-City
Ishikawa Japan, 924-0004 Japan
Phone: +81 76 274-1409
Fax: +81 76 274-8530
E-mail: info@takamaz.emag.com
EMAG INDIA Pvt. Ltd.
Technology Centre
No. 17/G/46-3, Industrial Suburb, 2nd Stage, Yeshwantpur, Bengaluru – 560 022
India
Phone: +91 80 50050163
E-mail: info@india.emag.com
EMAG KOREA Ltd.
Rm204, Biz center, SKn Technopark, 124 Sagimakgol-ro, Sangdaewon-dong, Jungwon-gu, Seongnam City, Gyeonggi-do, 462-721
South Korea
Phone: +82 31 776-4415
Fax: +82 31 776-4419
E-mail: info@korea.emag.com