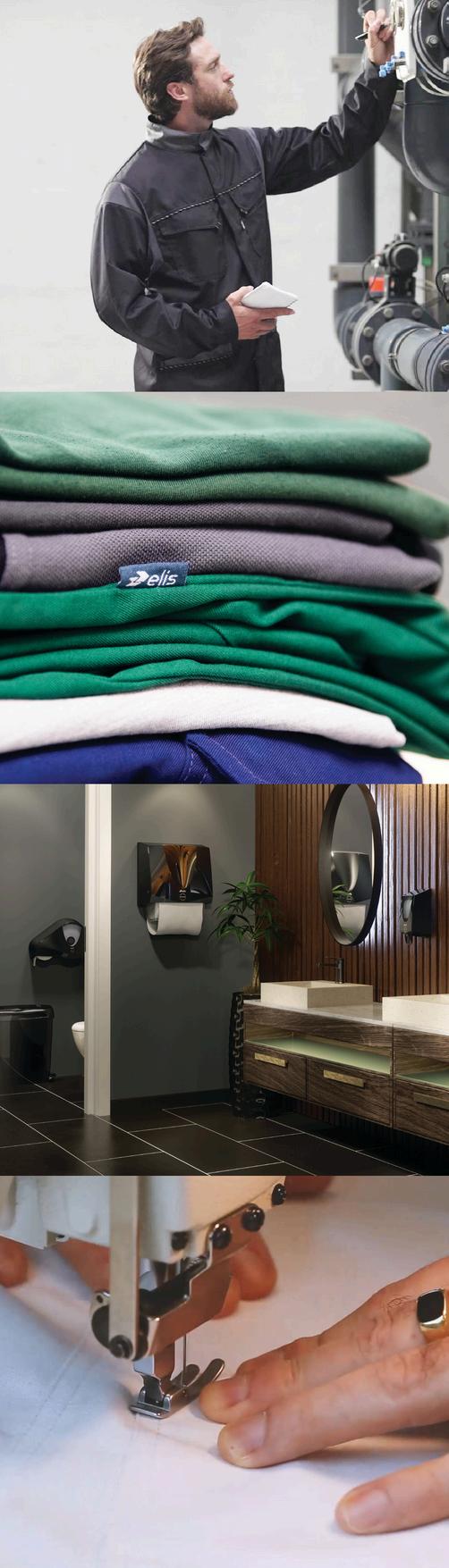
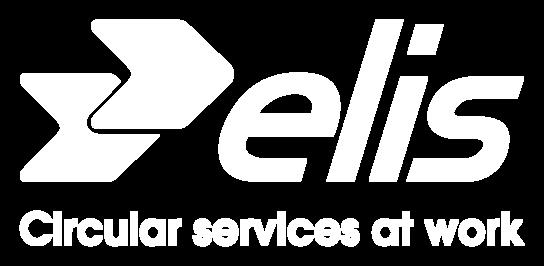
protection and development of our employees We are committed to supporting our direct suppliers and their communities, as well as contributing to local causes and initiatives.
At Elis our is Group CSR in integrated with both governance and management, the governance structure is overseen by the Chairman of the Management Board and led by the CSR Director, who reports directly to the Chairman.
The Elis Group CSR Committee monitors and anticipates CSR issues as they relate to both setting and implementing our Group strategy. Meeting bi-annually they deliver an annual report on the sustainable development program within Universal Registration Document, URD.
The CSR Committee is made up of four members and each member of the CSR committee has responsibility for specific objectives. Locally our Environmental Management System is maintained by our WECO team and each General Managers. The WECO (Water, Electricity, Chemical Optimisation) team hold weekly meetings to monitor the ongoing key efficiencies for water, gas, electricity and chemical usage.
All WECO results are reviewed by the General Managers across the country on a weekly basis and then consolidated to be presented to the BoM monthly, and shared with HQ based in France Our CSR Ambassador also reports on results in a quarterly report sent to the CSR Director at Elis HQ.
Each site has specific targets based on the industry norms in addition to sitespecific expectations. The WECO team also conducts in depth energy audit annually.
Our sustainability policy is reviewed on an annual basis to ensure sustainable procedures are implemented on a day-to-day/operational level. We monitor all aspects of service delivery to ensure we can assess clear, detailed data regarding our performance to illustrate where improvements can be made within our organisation to improve our sustainability and environmental impacts.
We continually seek to improve our energy efficiency and reduce our environmental impact throughout our plants and our equipment, regularly evaluating our stance on delivering a sustainable and environmentally sound service. Our rental maintenance business model inherently reduces resource consumption and extends product life
In September 2023, the Elis CO2 emission reduction targets were approved by the Science Based Targets initiative (SBTi) These objectives are fully in line with the objectives of the 2015 Paris Climate Agreements to contribute to restrict global warming to less than 1.5°C compared to pre-industrial levels on Scope 1 and 2, and below 2°C on Scope 3.
The Science Based Targets initiative (SBTi) is an international recognised framework to support companies in setting their CO2 emission reduction targets consistent with scientific knowledge to maintain temperature rise below 1.5°C. Taking 2019 as our base year, we are committing to a reduction in SCOPE 1&2 CO2 emissions of 47.5%, by 2030. This aims to reduce to absolute GHG emissions from direct emissions and indirect emissions - e g : electricity, gas, and diesel Our SCOPE 3 CO2 emissions target is a reduction of 28% by 2030. A reduction in absolute GHG emissions from purchased goods and services, fuel and energy related activities, upstream transportation and distribution, employee commuting, and end-of-life treatment of sold products.
Our CSR targets are outlined in our roadmap, to deliver on our ambition of becoming carbon net zero.
We recognise our corporate and social responsibilities and confirm our commitment to achieving this target As a company, we are conscious of our carbon emissions and have a variety of procedures in place to ensure our carbon output is minimised, ensuring our service delivery on our contracts will not adversely affect our client’s aim of becoming carbon net zero.
Our climate change agreement requires us to reduce our energy use and carbon dioxide (CO2) emissions in line with government targets; our internal goal is to achieve or exceed these, with the following targets:
Reducing (CO2) emissions by 20% by 2025
Reduce water consumption per kg of linen delivered between 2010 and 2025 by 50%
Reducing water use by 2.5% year-on-year.
Offering at least one collection composed of sustainable materials for each product family, an example: the Phoenix washroom collection composed of 78-95% recycled materials.
Increase the number of eco-friendly vehicles and EVs.
As part of this commitment, we drive continuous improvement for all our sites with comprehensive data collated and monitored for all our processing sites. All our management procedures, data recording and emissions reductions are integrated within our day-to-day/operational processes.
Annual Environmental Reporting to Elis Group includes data on usage of gas, electricity, and water, in addition to waste and recycling data, breaches of operating license and environmental events including water and effluent spillages.
An important feature of the submission is site initiatives which afford the opportunity to flag new processes, projects and advances in CSR and Environmental goals These are then shared across the Elis Group for wider implementation.
All Elis facilities have annual targets focusing on sustainability of operations, supporting greater energy efficiencies through investments that include heat reclaiming equipment, latest-generation machinery that requires fewer natural resources (gas, electric, water, and detergents) for the production and hygienic laundering of textiles, and eco-conscious warehouse and office lighting In addition, all cleaning formulas and detergents are 100% environmentally friendly.
Water Electricity, Chemical Optimisation is an industrial division developed by Elis for all 440+ plants across the world The WECO team in Ireland, led by Sean Porter ensure that all plants are clear on the process principles as set out by Group, providing information on washing technologies, water & energy treatment and how to optimise equipment. They conduct weekly review meetings (via TEAMS) with all sites to ensure that they are running within range and conduct physical internal audits reporting on efficiency across all key areas
Each General Manager is required to input the water, power ( electricity and gas) and chemical usage within their plant, the following KPIs are tracked:
Litres of water used per kg of linen/workwear processed.
Kilowatts per hour used per kg of linen/workwear processed Mili-litres of chemicals used per kg of linen/workwear processed.
This information is fed into a report presented to the Elis Ireland ELT and ultimately to the Operations team at Elis HQ in France.
The WECO team are also tasked with exploring, developing and testing technologies that can positively impact operational efficiencies. Bi-annual training is conducted by the WECO team for all Managers, Engineers, Maintenance teams and Production Managers and any staff members nominated by these managers.
The Elis WECO team work with our partners to ensure that detergents used in the wash process are free from harmful chemicals such as phosphorus, and materials such as VOCs and microplastics. No products manufactured or supplied by our partners contain Microplastics or PFAS.
Practical awareness training is provided to all staff to enable them to contribute to our goal of maximising process energy efficiency. The training covers areas such as correct loading and operating speeds of machines, choosing the appropriate programs to process items, the importance of cleaning and hygiene, reporting equipment faults and the importance of teamwork.
The Elis Pest Control Academy ensures that each technician is always aware of the latest innovations within the industry, updates and new legislation in addition to new operating methods. There is always a focus on sustainability and the responsible use of rodenticide as we actively work on solutions that reduce usage and protect wildlife and the environment.
Through the Elis Academy and our dedicated Methods team (operations and engineering specialists) staff are informed how to optimise use and consumption of resources, maximise efficiency and deliver on our commitment to our customers of fulfilling orders on time. We equip the engineering team with the support, knowledge, tools, and resources to safely maintain and operate the facility and to exceed our energy efficiency targets. Irish operations are benchmarked against our European partners and are recognised as consistently ranking highly in all categories.
Each plant has a Sustainability Champions to promote sustainability across all aspects of employee’s lives at both work and home. Within KLAXOON (a web platform that allows our teams to access training modules developed in the Elis Group and customised by each country – see sample below) there are CSR training modules which outline our CSR objectives, and workshops to better understand the issues of sustainability, these are promoted by our Sustainablity Champion
Our Sustainability Champion for Elis Pest Control is Mae Ortiz. We are currently rolling out Climate FRESK workshops – these aim to raise awareness and understanding about climate change and encourage impactful positive actions at the personal and business level The workshops are based on IPCC (Intergovernmental Panel on Climate Change) reports and the aim of these workshops is to provide or teams with a better understanding of the causes and consequences of climate change.
We track energy usage as one of our KPIs, ensuring we can use this data to make improvements accordingly.
Energy usage is collated as follows:
Site energy use data, to review and identify patterns or trends
Monthly performance data, giving site performance against target, divisional position, and historical performance. Divisional summaries, showing sites ranked on a year-to-date basis and against the preceding three years The figures are compared against targets that reflect our Climate Change Agreement reduction requirements.
Pottery Rd and all Irish plants are benchmarked against our European partners and ‘best in class’ figures identified and aspired to.
Initiatives we have introduced include:
On-site infrastructural improvements totaling over €1.3m in value began in January 2024 and include the installation of a new ironer feeder/ folder, increasing throughput of sheets by approximately 350 per hour, the increase in efficiencies delivers and reduced associated gas and electricity costs.
Q3 will see a full upgrade of the dryers on-site, increasing capacity with less machines which will provide energy savings of 8 7%
Change-over to LED within the Pottery Rd has a projected annual CO2 savings of almost 30 tonnes.
Pottery Rd’s plant and offices are powered by 100% renewable energy. Continuous heat recovery from both effluent and heat generated by other equipment which is fed back into fresh water supplies
Improving efficiency of steam-raising boilers by installing flue gas economisers and more controllable burners.
Installing high-efficiency burners to steam-raising boilers, which reduces gas consumption and nitrous oxide emissions.
We track all water consumption across all Elis sites according to individual site targets. We monitor consumption, to identify methods of reducing consumption where possible, in the following ways:
Weekly water meter readings taken by each site and expressed against volume of items processed
Invoice values which are reconciled with usage from meter readings
Monthly water use, which provides us with individual site performance against target, relative position within division and historical performance
External chemical supply companies validate the wash process monthly against expected water efficiency
Irish operations are benchmarked against our European partners for water use. European ‘best-in-class’ figures are identified and aspired to.
We have implemented the following measures in response to data collected, to reduce water consumption:
Installation of Blue Ocean™ Laundry Water Filtration System in a number of our sites has enabled operations to reduce water consumed per kg of linen delivered from 10 litres to 4.5 litres.
Up to 75% of water is now reclaimed and reused through water recovery systems allows the processing of any linen type in any continuous batch washer compartment without affecting background colour
Widespread use of heavy-duty tunnel washers: equipped with separate compartments, they allow laundry to progress through different processing stages by moving from one compartment to another Regular monitoring of water meters to prevent any losses
Conducting water- and energy-related audits
Optimisation of washing equipment (fine-tuning of water flow monitoring) and related washing programs
Water use is monitored centrally by our GM and WECO teams and used to identify discrepancies and build the business case for improvements. These measures have resulted in the following reduced levels of water consumption:
A 50% reduction in water usage since 2005 whilst ensuring finished quality is not unfavourably affected.
Secondary water recovery and filtration allowing us to operate our foul and infected disinfection process at zero litres/kg.
We recognise the distance travelled between our sites and our client’s is a key Environmental factor which is why in all thirty countries that we operate proximity to our clients is of prime importance.
Elis operations at Pottery Rd are continuously reviewed - routes for deliveries and collections are optimised to improve the quality of service to all clients. Our fleet is HVO (Hydrotreated Vegetable Oil) powered reducing carbon emissions by up to 92%, up to 30% in NOx emissions, up to 85% in particle matter and up to 90% on Greenhouse gases. Since the introduction of HVO to the fleet in August 2023, the site has saved 160 tonnes of CO2 against the company’s reduction targets.
Distribution Manager Ken Keating manages a team of 18 in-house drivers, with no 3rd party drivers. All drivers have been eco-driving trained. The “Eco-HDV” research project initiated by the Environmental Protection Agency evaluated the impacts of the adaptation of eco-driving in the Irish heavy-duty fleet, as per the vehicles currently used by Elis and found that eco-driving and related practices improve fuel efficiency and reduce vehicle emissions and the overall impact on air quality. Fuel use is monitored in the form of Kg of linen delivered per litre of fuel and Kg of CO2 per Kg of linen delivered.
Our recently installed GLAD system - Global Logistics Assistance for Deliveries enables our Distribution Manager, Ken Keating in Pottery Rd to optimise and track routes and customers in real time enabling customer service to predict actual delivery time based on previous deliveries. This enhances our service to our customers and provides confidence to our drivers that routes are always optimised This optimisation ensures routes are at their most efficient, decreases km per route and reduces Co2 emissions.
Distribution is further supported by CameraMatics, a driver-centric cloud platform that continuously improves performance and safety with enhanced visibility and digitised smart processes The platform translates data from onboard sensors, smart cameras, and driver apps to support driver safety, load security and continuous learning and improvement. Enhancing training regarding collections to site, vehicle security, driver training, accident prevention and analysis of driver’s behaviour. The platform has been deployed to the entire Pottery Rd fleet and translates data from onboard sensors, smart cameras, and driver apps to support driver safety, load security and continuous learning and improvement. Allowing Ken Keating to access recorded playback for the previous month in addition to LIVE coverage and is spot checked daily. The system has enhanced training regarding collections to site, vehicle security, driver training, accident prevention and analysis of driver’s behaviour and has been positively received by our insurance company.
Pottery Road is the first Elis in laundry in Ireland to implement laundry cage tracking Each trolley is individually tagged with an RFID tag and barcode and assigned to a specific customer at the time of dispatch and then scanned back into the laundry automatically upon return from the customer. The aim of the project is improved linen management, identifying customers with large linen inventories to support with order management, more accurately identify when linen is returned from customers to give improved traceability and assist with safe loading of vehicles based on routing demands.
specify the products sourced to ensure our textiles match our CSR objectives: minimising their environmental impact and increasing sustainability.
This includes assessing products to ensure they meet key criteria, such as:
Specifying durable products which are suitable for reuse.
Reducing in-use impacts
Specifying lower impact fibres and those with recycled content
Minimising hazardous chemicals.
To support ethical trading, we are signatories to the UNITED NATIONS GLOBAL COMPACT (members since 2006) and we are also a member of the global collaboration platform SEDEX, which works to improve working conditions in global supply chains, further supporting our approach to ethical trading. Our Supplier code for Elis Ireland is ZC1082780
Our design team has introduced several innovations to extend the durability and reduce the impact of our products over the lifetime of the items including creating new textile blends which are more durable and less prone to holes and shrinking than 100% cotton items. This means replacement of items and rejection of items are lower, reducing environmental impact with longer life cycles.
As of 2023, 94.8% of our procurement spend is with direct suppliers that have undergone a CSR assessment in last 3 years this will be 95% by 2025, with 100% monitored via a CSR strategy.
All suppliers that are assessed through a CSR audit are monitored to ensure that the action plans that were created are implemented. As of 2023 almost 30% of direct workwear suppliers are based in Europe and more than 90% of direct hygiene and well-being suppliers are based in Europe and 58% of all product collections have at least one collection composed of sustainable materials, and we aim to have at least one sustainable collection in all categories by 2025
Key values for Elis are: respect for others, exemplary behaviour, integrity, and responsibility. These key values are the foundation for all our actions and choices These key values are part of a larger framework which includes the United Nations (UN) Universal Declaration on Human Rights, the United Nations Convention on the Rights of the Child, the European Convention on Human Rights, the United Nation Global Compact, and the International Labour Organization (ILO) fundamental conventions.
Respecting, promoting, and preventing human rights violations are at the heart of corporate social responsibility. Elis has formalised its commitment to Human Rights under the Code of Ethics based on the Group’s values of integrity, responsibility, exemplarity in its commercial environment, and respect for all its employees, suppliers, customers and stakeholders or any 3rd party. Elis define fairness in our practices, our purchasing policy and respect for free competition. Within each section there are questions posed and answered to ensure that all employees have relevant examples of unacceptable practices and what to do when they experience this or witness an action contra to our code of ethics.
Elis is fully committed to the fight against corruption and influence peddling in addition to prevention of conflicts of interest and lobbying, guidelines are provided within our code along with an acknowledgment of our responsibilities surrounding producing accurate and sincere documentation, the protection of personal data, protection of capital and assets and a respect for confidentiality. The Sustainable and Ethical Purchasing Charter, also sets out the following: Commitments to Human Rights and fair Labour practices
Commitments against corruption, anti-competitive practices, and influence peddling
Whistle-blower procedure
The Whistle-blower procedure is also included within our code of conduct. Should an employee confronted with a situation likely to breach a law, a regulation or the principles laid down within our Code of Ethics. An alert system, enabling anyone confidentially report any situation is available via https://report.whistleb.com/elis. Elis guarantees the confidentiality of the identity of the person raising the alert and the disclosure of facts may be reported only through strict compliance with applicable regulations, This and all HR policies are shared as refresher campaigns throughout the business monthly. The whistle blowing procedure was most recently shared in May 2024
Our business model is based on the concept of offering product (workwear, mats, washroom facilities) as a service and offering a range of high-quality, sustainable products and services rather than disposable products or products with planned obsolescence.
We encourage business partners to comply with international standards or norms related to environmental assessment and certification for the products they process or produce. Elis Business Partners of textile products must obtain OekoTex® standard-100 certification for all textile products delivered and we encourage our partners to use following labels or standards whenever possible in their own operations.
EU Ecolabel (http://ec.europa.eu/environment/ecolabel/)
Nordic Swan (https://www.nordicecolabel.org/) for environmentally friendly design and/or use of products;
Fairtrade (https://www.fairtrade.net/) certification through Flo-CERT (https://www flocert net/);
BCI (Better Cotton Initiative) (https://bettercotton.org/) label for products containing cotton/ suppliers involved in cotton processing
GOTS (https://www.global-standard.org/) certification for products containing organic fibres.
We are committed to increasing the volume of certified materials and items to our ranges teaming up with suppliers to identify the best certifications for each product type. E.g., OEKO-TEX certification for the textiles, FSC-labelled paper products, Lyocell fibre: the TENCEL™ brand Lyocell fibre made from wood grown in sustainably managed and FSC-certified forests.
Within our facility service, we are continually reworking designs to ensure that they work more effectively and have less chance of breakage increasing their lifespan within the washroom environment.
In Ireland, within our Washroom Collec manufactured using 78% - 95% recycle plastics and produced using 4# times l studies) and FUSION which is Cradle to
Recycling and reusing end-of-life products is a priority for Elis, and we have set a target to recycle or reuse 80% of our end-of-life textiles by 2025. We are striving to identify the best recycling or recovery routes and the technologies available, preferring textile-to-textile recycling and reuse.
End of life linens are re-purposed at a recycling centre based in Dublin, used as cleaning materials for garages etc. Currently end of life workwear is used for energy recovery in the form of SRF. We are currently in negotiations with a company to ensure that our workwear can also be repurposed or recycled as insulation in 2025.
Ireland along with the other 193 UN countries has signed up to a resolution to help eliminate marine litter and micro-plastics in the sea. We are continually looking into ways to change our processes so that our products are better protected during transport, storage/handling without the use of plastics. Since March 2023 Pottery Rd have saved the equivalent of 50,000 500ml bottles through the introduction of reusable water bottles for all staff and water cooler throughout the plant
Microplastics are typically considered plastic particles smaller than 5mm. Primary sources of microplastics include microbeads, microfiber and plastic pellets, secondary sources are from the decomposition of larger plastics. Elis are working with our textile manufacturing partners to better understand impact of different fabrics and innovations. We are conducting tests to improve our understanding of micro- plastics and are contributing to progress draft European regulations on this issue. Detergents used in the wash process within Eis plants are free from microplastics. No products manufactured or supplied by our chemical suppliers contain microplastics or PFAS.
We provide both logo mats and standard mats to customers using recycled plastics, In 2023 over 109,000 500ml plastic beverage bottles from the environment were used to create new logo mats ensuring they did not arrive at landfill or pollute our oceans.
We are currently working with our suppliers on removing zinc and phthalates from the rubber backing of our mats and launched a mat manufactured using 100% recycled fibres in 2023. Elis Ireland utilise a mat repair service offered by Elis Latvia that prolongs the lifespan of the mats by up to 2 years and reduces waste. 98% of the mat processed are repaired or resized. We are currently in negotiation with a plant in Rotterdam to take out end of life mats to produce playground and gym flooring.
Elis have partnered with Shabra Plastics & Recycling, taking Elis used (clean) plastic bags returned by our customers and general packaging and recycling it into new bags for our customers – these are branded Elis and state that they are produced with 100% recycled plastic
Elis are actively exploring the development of a trolley system that utilises reusable cage liners within the delivery trolley, this initiative aims to reduce the environmental impact of single-use plastics within our service delivery model which are currently used in sites to wrap both workwear and linen.
Cage liners, made from recycled polyester and can be laundered can now be used to protect linen as it is being delivered. We appreciate that this may not be suitable for all customers and in instances where cage liners are deemed unsuitable, the soiled linen return bags used are 100% recycled plastic. Additionally, we have begun recycling plastic cages that are beyond repair These are melted down, and repurposed, supporting a circular economy
PICTOGRAM OF PROCESS
Elis Pest Control offers our customers an integrated approach that involves a comprehensive audit of customer’s sites to identify current or potential pest infestations/ threats, enabling us to create a strategic pest management program.
Pest management is an essential service provided to organisations and industry to ensure they offer quality goods and services to their customers while providing and safe and healthy environment for their employees. In recent years Ireland has seen a dramatic increase in pest activity including a 94% increase in rodent callouts and a 42% increase in cockroach activity.
In recent years our awareness of the need for better stewardship of rodenticides to prevent risks to wildlife species has meant that we have now entered a new era in Pest Control – where the service provider and client are working together to protect not only the business but also the environment only using toxic bait as a last resort and minimising its exposure to wildlife.
At Elis Pest Control we recognised that we needed work ‘smarter,’ using technology to do the monitoring and the skill and knowledge of our technicians to resolve the issues. Identifying issues sooner, before an infestation takes hold provides the client with the best outcome; resolutions are achieved faster with less disruption to the site and the business.
Elis CONNECT provides a SMART approach – our sensors track movement, our algorithm identifying the species. What differentiates Elis CONNECT from other systems is that it can identify a rodent from a spider ensuing that there are no ‘false positives or unwarranted trips to site. Using our sensor technology LIVE alerts are possible with no reliance on traps or bait being activated to provide evidence of activity and crucially provides an overview of trends on a site seasonally, by location and by the hour.
This award-winning system provides the technician with an insight into what is happening on site and issues that may be leading to infestations. As we gain an insight into the activity of our clients’ sites using Elis CONNECT, we can quantify how this SMART system better serves our customers and protect the environment:
By identifying that a pest issue has arisen on a site earlier and understanding the causes we can resolve problems more effectively – reducing the number of call outs it takes to resolve an issue, on average, from 7 to 4 follow up visits.
This not only reduces the risk to staff and stock on site but also reduces carbon emissions by up to 42%
By pinpointing where activity is taking place, there is no requirement to place toxic bait throughout a site and we have been able to reduce our rodenticide by 46% on Elis CONNECT sites.
False alerts have been irradicated and this has reduced the number of visits required to site. Where appropriate the number of physical visits to sites has also been reduced by 75% - contributing to reducing Scope 3 emissions for our clients
Our portal allows our clients to keep all reports, certifications, and records together in one location without the need for everything to be held on paper – a greener solution.
Employee welfare is a pillar of our CSR strategy, recognising that the well-being and development of our workforce are essential to our success. Our commitment to employee welfare includes comprehensive health and safety programs, continuous professional development opportunities, competitive compensation, and a supportive work environment that fosters diversity and inclusion. We believe that investing in our employees not only enhances their quality of life but also drives innovation and productivity within our organisation.
The importance of supporting the wellbeing of employees and the access to nutritious food, which can improve our teams’ overall health and energy levels is recognised at Elis and we have a number of initiatives in operations: fruit boxes which are made available twice weekly; cereals and a hot lunch (homemade soups, pasta dishes with brown bread) available each day (free of charge) and ‘Pizza Friday’ on the last Friday of each month as a monthly treat!
Our Code of Ethics, outlines the ethical principles shared at Elis, setting out the application of this code and the role all employees take within it. It details our rules of conduct and the importance of the protection of employees, suppliers, and stakeholders. Respect for all persons, regard for health and safety policies and the need to act with integrity, responsibility, endeavouring to always set an example for all stakeholders is at the heart of the code.
HR conduct refreshers of key HR policies each month including Diversity, Inclusion, Equity and Personal Data Protection. These refreshers are conducted to ensure compliance and reinforcement of key policies and highlight any updates/changes, providing consistency across the organisation and preventing complacency.
At Elis we believe that respect for individuals and equal opportunities are fundamental values, and we endeavour to foster harmonious and high-quality personal and professional relationships, regardless of seniority and function, with fairness and respect for all. In tandem with this we have a Disability Charter, which sets out our commitment to diversity and inclusion. This charter is in line with the non-discrimination, diversity and equal opportunities policy implemented by Elis, via our Code of Ethics
Educational campaigns are held each November during Disability Awareness month, and International Disability Day December 3rd. HR and Marketing have completed inclusive recruitment practices training, including information regarding interviewing, job specs and all managers across all functions have completed Disability Awareness Training including Reasonable Accommodation Training which was initiated was April 2024 and will be supported with on-going refresher training.
Elis provides the EAP, a confidential service designed to assist staff should they be dealing with personal and professional problems that could be affecting their home life or work life, health, and general wellbeing. This service is available free of charge to every member of staff who have been with Elis for over one year.
To understand the issues that are facing our staff a company survey, is conducted on a bi-annual basis provides everyone with the opportunity to share their thoughts and opinions about the practices within Elis and evaluate our performance. In our most recent survey in May 2023, Pottery Rd had a 95% participation rate and while we scored highest in the category relating to teams’ commitment to our customers, it was noted that engagement required improvement, to address this ‘Employee Voice’ meeting were initiated.
Employee Voice meetings comprise of a committee of elected members from each department relevant to the plant, for Pottery Rd this is: Production, Operations, Distribution, Customer Service and Office. Each member is asked to be the ears and voice of their fellow employees creating a two-way communication between management and all staff. Information regarding the Group and Elis Ireland is shared, issues concerning the site, employee of the month, social activities, suggested charity initiatives and community involvement are discussed along with suggestions from departments on how we can improve things. This has led to the introduction of a Prayer Room at Pottery Rd, more vegetarian options for the lunch offering and additional fans on the floor during periods of warmer weather.
At Elis we have created a Group program: CHEVRONS recognising exemplary employees. CHEVRONS are nominated from our production and maintenance teams and are invited to an all-expenses paid trip to a European destination (previous destinations: Paris, Barcelona and Lisbon) with their partner. The itinerary includes receptions, cultural trips, entertainment and banquets, celebrating their contribution to Elis.
Employees of the Month are nominated by the General Manager on each site; chosen for embodying our core values, this person can be from any part of the business and is rewarded with a hamper and their photo added to each
During Wellness Week and Sustainablity Week events such as yoga, self-defence, stretching and mediation session are hosted. To accommodate drivers, MLS staff and technicians who are unable to partake in these activities as they take place on-site and their work has them on the road/off-site, a series of 15-minute meditation and breathwork videos designed to impart practical mindfulness skills to destress and relax our teams which can be used in daily life have been created They also feature self-reflection journaling prompts; these are accessible all year round.
Wellbeing events: yoga, on-line meditation, talks and self-defence classes
Contributing to local communities and supporting causes is a vital aspect of our corporate social responsibility (CSR) policy. We believe that by actively engaging in and supporting the communities where we operate, we create a positive impact that extends beyond our business. This commitment not only helps to address local needs and challenges but also strengthens our relationships with stakeholders, fostering a sense of shared purpose and responsibility
We are delighted to be supporting St. Angela’s College of ATU with ’reject linen’ from our linen plants. These linens, with flaws such as discoloration, tears etc. are used by students in their fashion designs to stunning effect. This has saved the college purchasing new linens and freed up budget for additional resources
We have been proudly supporting MOVE (Medical Overseas Voluntary Elective) a charity run by third-year medical students in Trinity College Dublin for several years. M.O.V.E's aim is to raise money for underfunded, understaffed and underprivileged hospitals in developing countries. Elis support this charity by supply scrubs, some new and some almost new
Reject linens, including blankets are made available to local charities including homeless shelters and animal rescue centres in both Dublin and Cork We also make end of life mats available to animal rescue centres.
Blankets and mats for shelters
Noise surveys are carried out annually at each site, they are also carried out when any site makes a significant change to its operating model, either in terms of hours worked or equipment. Any breaches or increase in noise levels are reported to our QSE team and actioned promptly.
Our rental maintenance Services include
Elis is an international textile, hygiene & facilities services business, operating in 29 countries across the globe, delivering a complete textile rental and laundry service We offer everything from workwear to mats, mops, bed and bath linen, hygiene supplies and pest control services
With plants and distribution hubs across Ireland, Elis offers an unrivalled level of nationwide service with accredited systems and a commitment to the highest infection control standards Our 1,400+ workforce, proudly support over 10,000 Irish businesses, delivering quality products and services Our circular services help clients stay focused on their core business while allowing them to reduce their environmental footprint