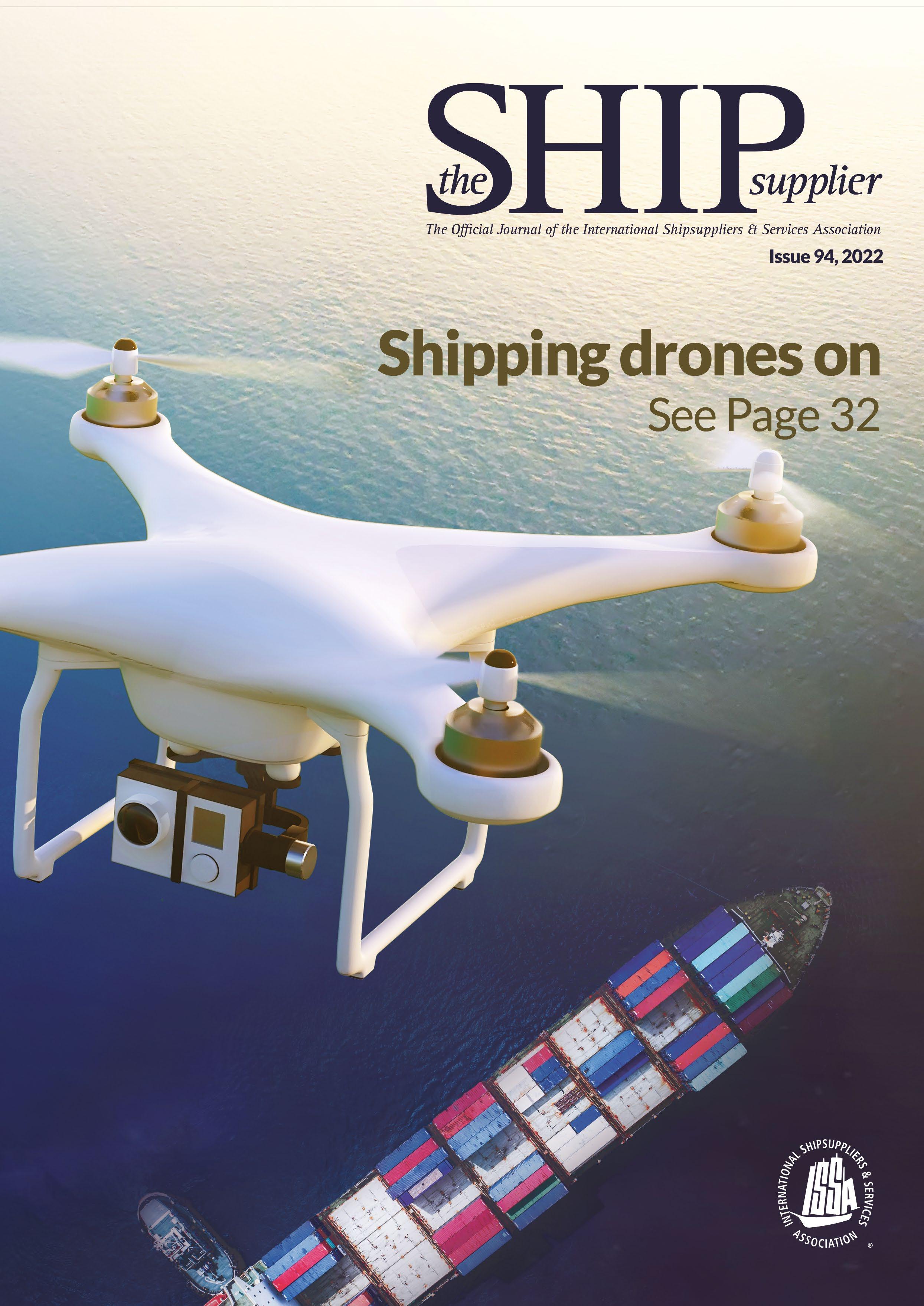
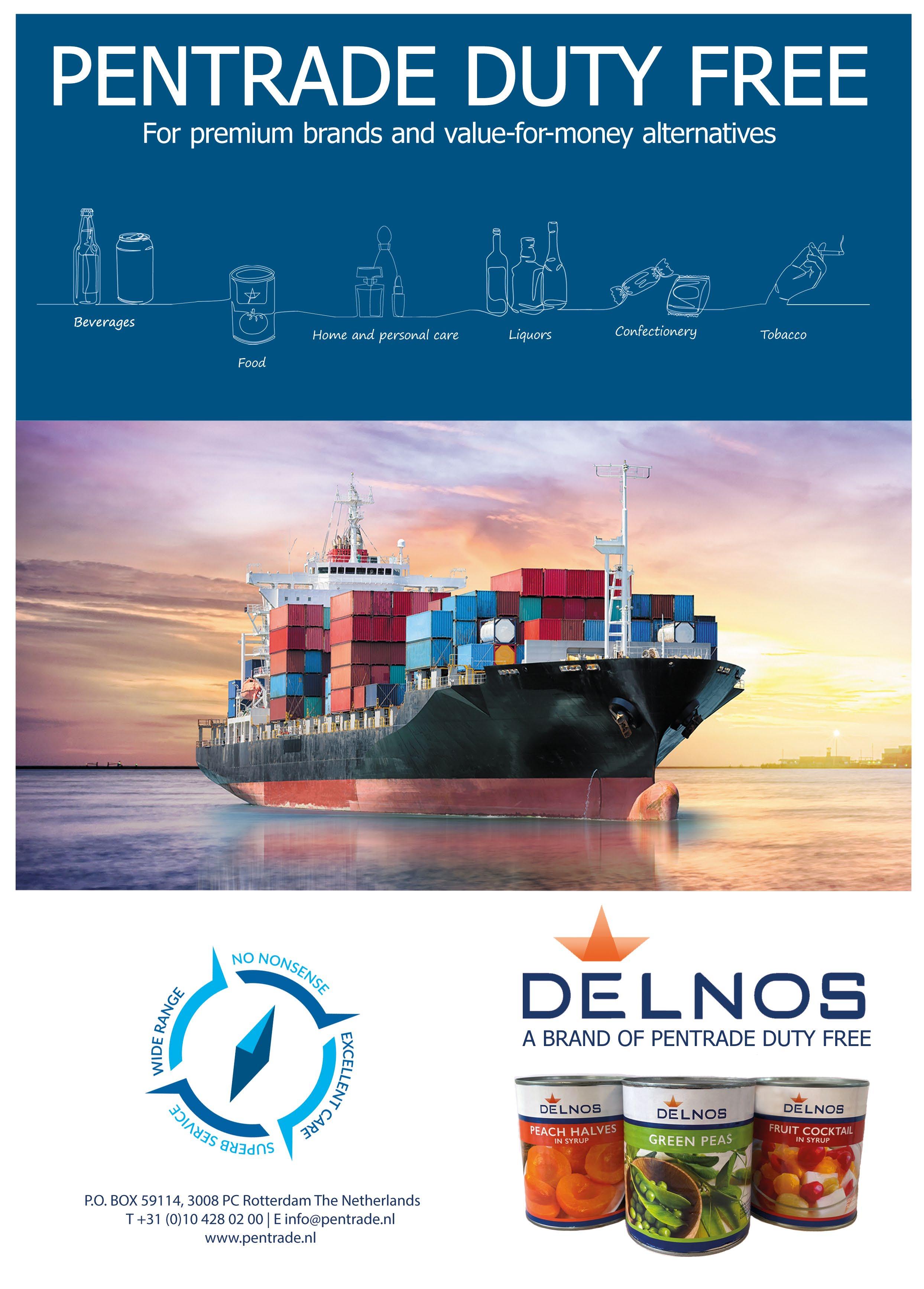

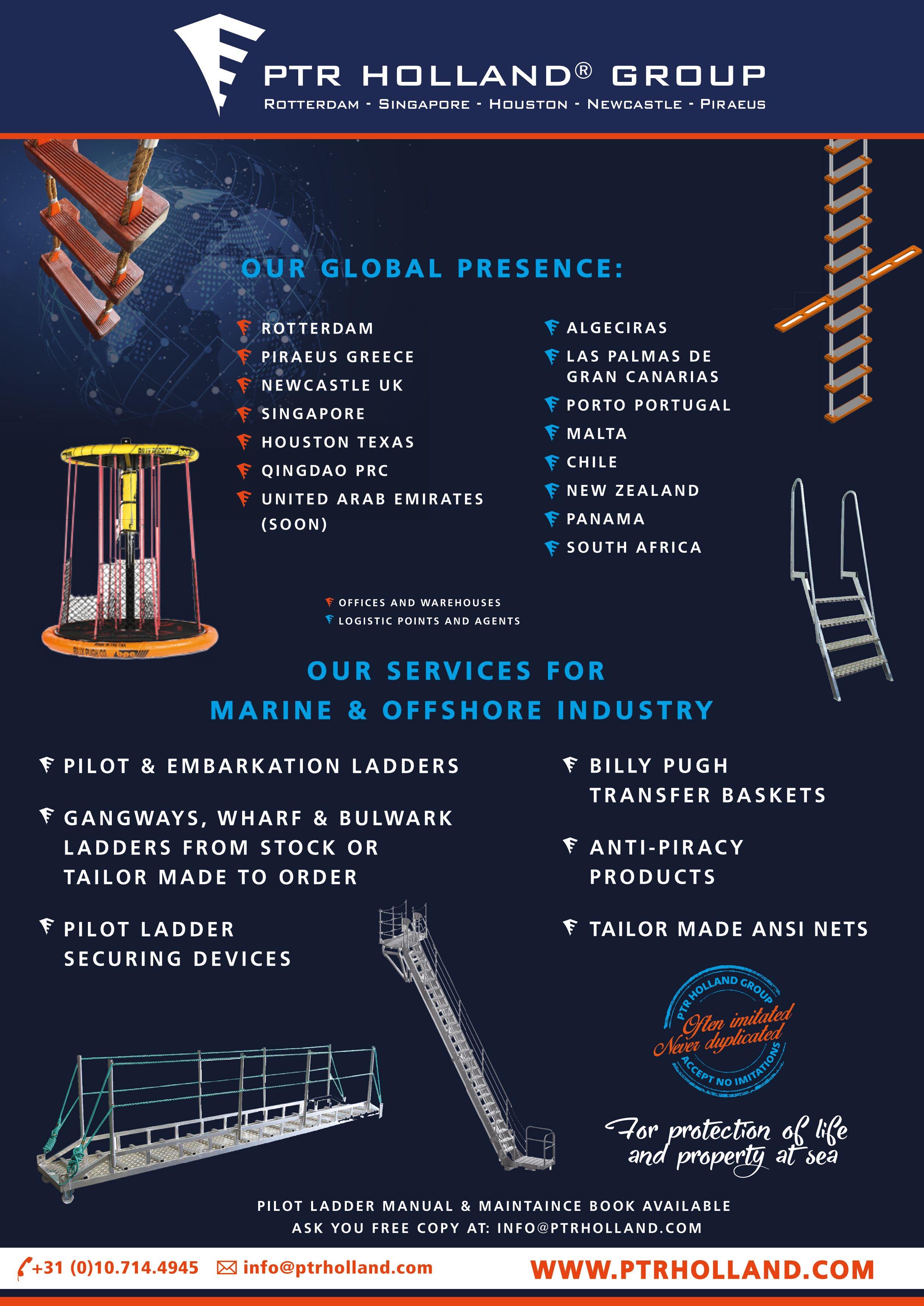

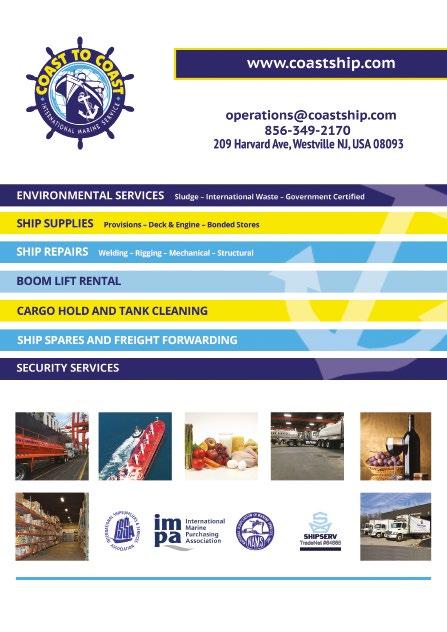


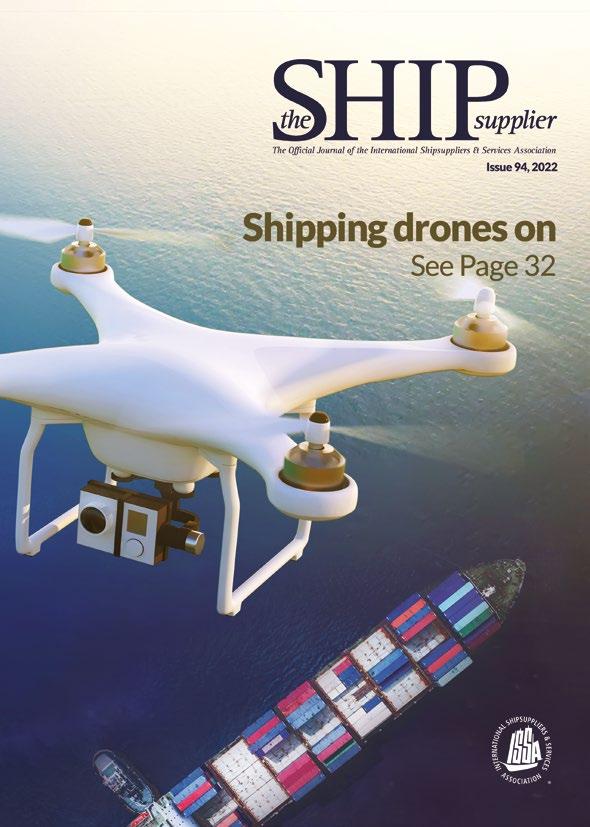
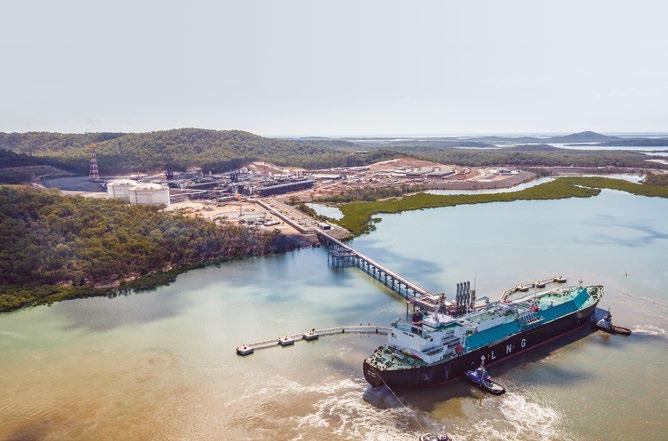
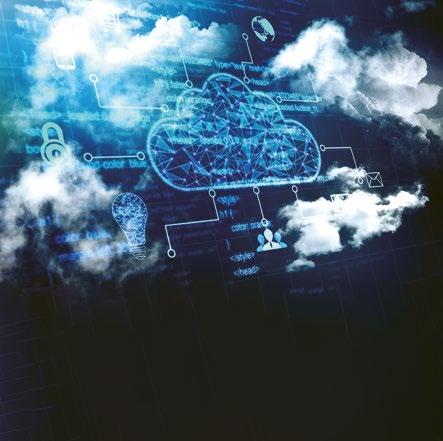

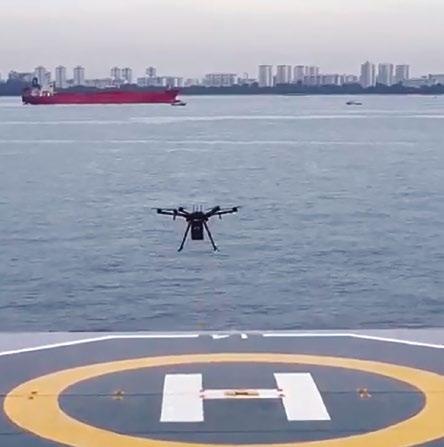
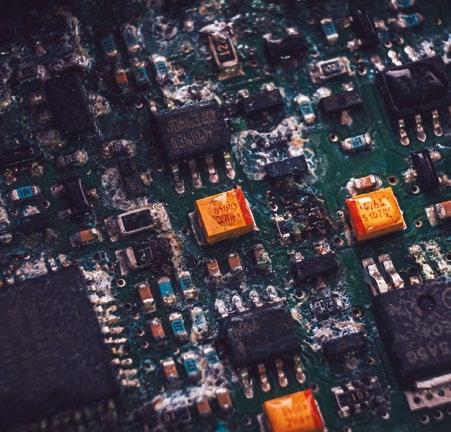

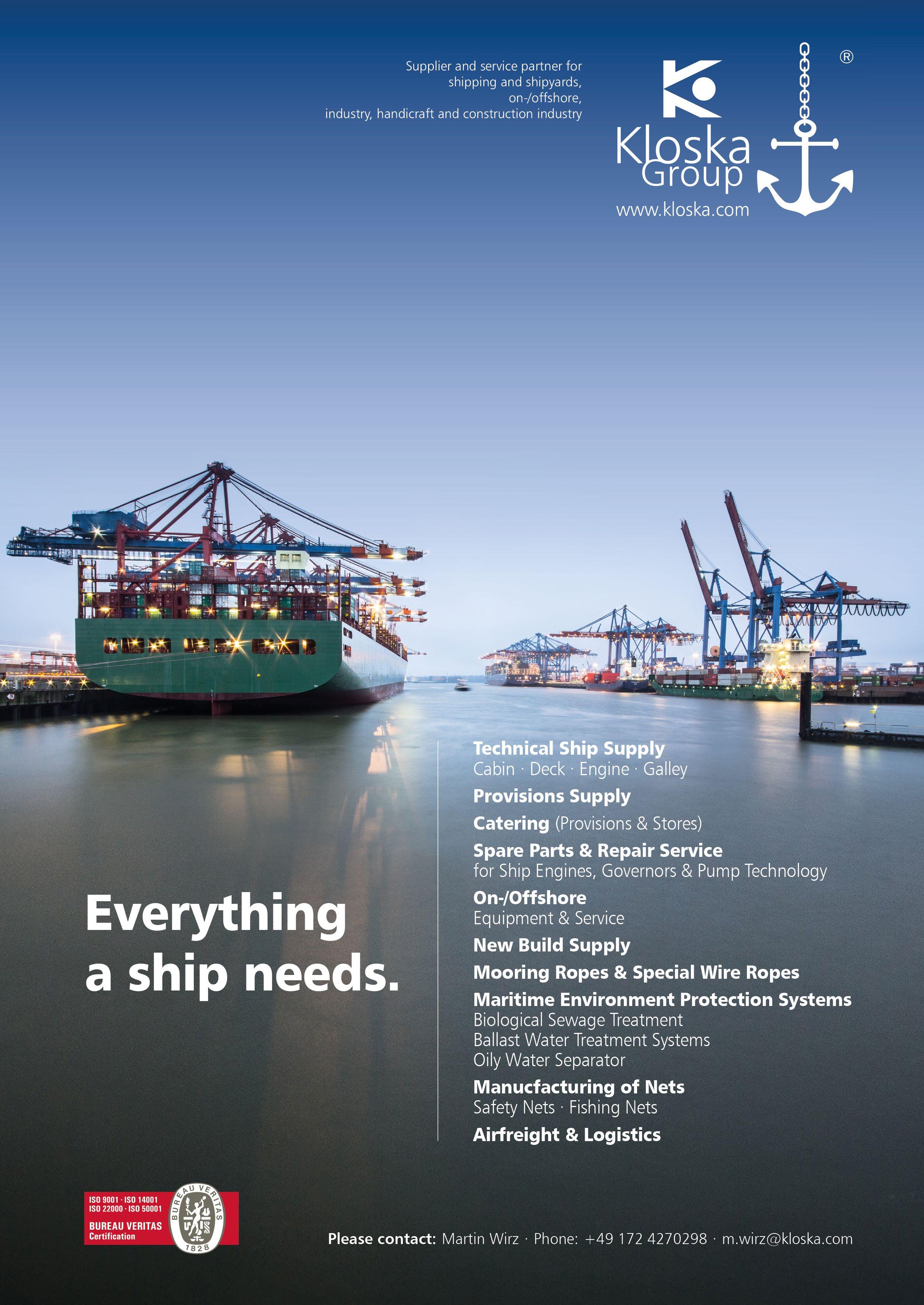
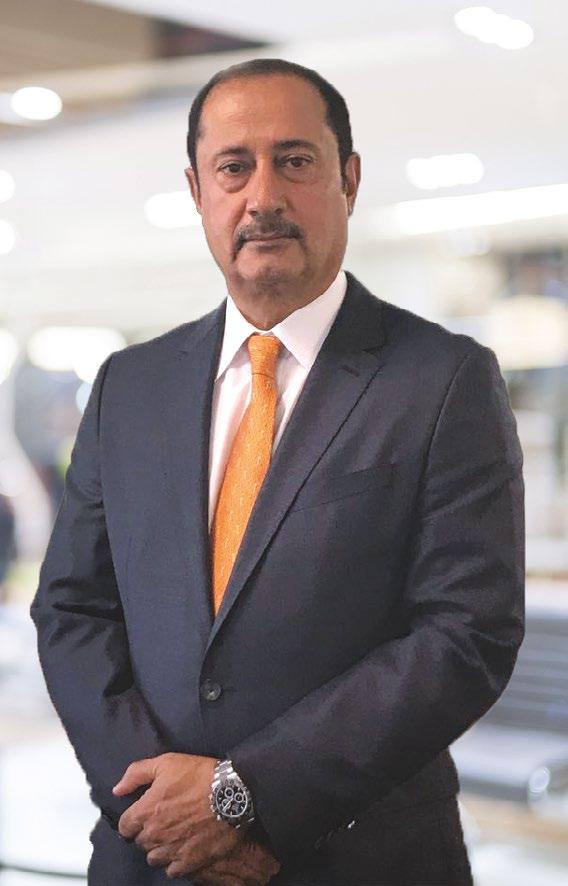
Welcome to the latest edition of The Ship Suppler, once again crammed full of news, views and comments about global ship supply.
As you start to flick through the pages, myself, my fellow Executive Vice Presidents as well as representatives from ISSA National Associations, will have completed our first ISSA Assembly meeting since the 2019 ISSA Convention in Busan. It was truly a delight to see many of my ISSA friends and colleagues in London in the flesh, so to speak, during mid-September and it proved to be the ideal opportunity to debate a myriad of issues and initiatives that are underway at ISSA.
And what a time and place to hold the meeting, so soon after the sad passing of Her Majesty Queen Elizabeth II. We were a little concerned about whether our Assembly meeting would go ahead following her passing, because news had started to come through that the IMPA show had been cancelled because of the impending funeral arrangements. We were lucky however, in that our meeting rooms were some distance away from Westminster and so were largely unaffected by what was going on.
You can keep up to date with the latest news on the ISSA website at www.shipsupply.org and send in your comments and views to the ISSA Secretariat either by phone on +44 (0)20 7626 6236; Fax +44 (0)20 7626 6234 or alternatively email secretariat@shipsupply.org
The meeting did give us the opportunity we needed to discuss the state of the ship supply sector and the effective role that ISSA can play in protecting the interests of the ship suppliers. There is a lot happening in global shipping at the moment and I know that many of our members were represented at the SMM Exhibition in Hamburg in early September. The halls and stands were full and with shipping markets standing at their strongest level for many years, the future looks good. But we all need to remain competitive, relevant and compelling to our clients and the industry at large.
Plans are already afoot to stage next year’s ISSA Convention in person and we will keep ISSA members abreast of developments as they happen. u
Happy reading.
Saeed Al Malik ISSA PresidentAustralian Ship Suppliers & Services Association Chairman and ISSA Executive Vice- President Jim Costalos reflects on a challenging period “down under” and reports on those illusive green shoots of recovery
2021 proved to be more difficult that 2020 for the Australian Ship Supply industry. Covid continued and so did restrictions. The Borders remained closed until 2022.
Business again continued at a lower stage through 2021 but improved drastically in 2022, with the ongoing problems in China, assisting the Australian suppliers.
ASSA lost two members and gained one new member.
Interport, sadly went out of business, whilst Kollaras’ business went into another direction. The new member was technical supplier Mazu Marine in Melbourne.
Australia now stands at 14 full members, one associate member and two life-time members.
ASSA started in 1980 with 8 members, of which two continue to be members today: Australian Providoring & Sealanes – both were awarded Longevity Acknowledgement during the ISSA convention of 2015 in Singapore.
With the unrest and war in Europe, we have seen the cost of goods increase dramatically. Keeping a fixed term pricelist is now a very difficult proposition.
With travel now permitted ASSA will be holding its AGM in Singapore later in 2022. The first time since 2019, the Australians have been able to meet “face to face”.
ASSA is pleased to announce that long time ASSA Secretary, Paul Begg, was inducted in the Baseball South Australia, Hall of Fame. Paul was instrumental in the ISSA convention of 2000 in Sydney.
Australian members continue to struggle with IHM MD/ SDoC. Hopefully the good work ISSA are undertaking will assist in this area.
As always our members continue to be cautious with credit terms, especially when new customers approach for the first time. Members are enforcing continued strict credit control. u
Secretary-General of CFESA – Ms. Li Li – reports on ship supply in China and the on-going Pandemic challenges for members
In 2022, the new Covid-19 has still not left us.
Faced with a complex and severe Covid-19 prevention and control situation, Chinese ship suppliers are all in the same boat: fighting Covid-19 together.
The industry is a chess game, up and down, as it jointly builds a solid Covid-19 prevention and control network.
Since March this year, the outbreak of Covid-19 in Shenzhen, Shanghai and other Chinese Ports, has led to strict containment measures being adopted. This has had a certain impact on the ship supply business.
Doing a good job in Covid-19 prevention and control is the basic premise for ensuring smooth operations.
Faced with Covid-19, the industry has always adhered to the general strategies of ‘external prevention of imports, internal prevention of rebound’ and ‘prevention of people, materials and the environment’, and insisted on relying on the system to manage people and minimise the impact of Covid-19 on the ship supply business.
Over the past few months, in the face of the impact of Covid-19, Chinese ship suppliers have always responded to
changes, brokered through adversity, and established a “one ship, one gear” control mechanism.
At the same time, there has been a strengthening of the centralised management of personnel and implementation of control measures such as personnel management, special vehicle transfer, environmental sanitising, and nucleic acid testing.
During the implementation of the ship supply business service, all the “three-piece set” protection was introduced effectively to build a solid line of defence against Covid-19.
Accurately controlling changes in everything was essential, viz. vehicles, materials, and the environment. This has truly achieved “one net” for Covid-19 prevention and control, and “one chain” for the implementation of responsibility.
On the one hand, CFESA’s members have paid close attention to the Covid-19 situation and prevention and control requirements, urging employees to co-operate with the requirements of local communities and prevention and control departments, and strictly implement Covid-19 preventative measures.
This has ensured the health and safety of employees.
On the other hand, ship suppliers in China have fully considered the impact that the development of Covid-19 may have on specific business operations.
This has meant the need to make preparations in advance, assemble field personnel, and strengthen communication with cargo owners, shipowners and terminals, analyse the arrival of ships, properly layout, and pre-station field personnel and business vehicles to business points, create conditions for business operations, and fully ensure the smooth development of key businesses.
Once a ship says it needs temporary off-site supply, operators have been urged to contact CFESA as soon as possible to complete the supply through mutual help among the members of the association.
The new round of Covid-19 has had a significant impact on the shipping industry, and most of our member companies are small and medium-sized enterprises. These are the main force of national economic and social development, playing an important role in promoting growth, ensuring employment, activating the market, and improving people’s livelihood.
Only when the enterprises are good will the Chinese economy be good. Only when the enterprise is strong will the regional economy be strong. In this regard, the relevant departments of the state and local governments have successively introduced a series of policies. CFESA
summarises these policies and sends them to their members, hoping that everyone can make full use of their own specific conditions and local policies to provide some help to all.
The efforts and persistence of the industry make us dare to face more severe challenges. Everyone is working and innovating, so that we can find the dawn of hope and continue to move forward.
Covid-19 will eventually pass, and the light is just around the corner. u
storing underway in China under controlled conditions.
says Abdul Hameed Hajah long-time resident and ship supplier in the island state and ISSA’s Senior Executive Vice-President
The maritime sector in Singapore is one that is constantly evolving to ensure the city-state remains one of the most efficient ports in the world from which to procure services and goods.
Amidst the global manpower crunch, The Maritime and Port Authority of Singapore (MPA), together with local port operators Jurong Port
(JP) and Port of Singapore Authority (PSA) have invested significant resources in ensuring digitalisation and automation are at the forefront of their future developments. These efforts are also aided by Enterprise Singapore, the government agency that champions enterprise development and provides various grants and other forms of advisory support to local firms.
The Tuas Mega port, which will become the world’s largest fully automated container port once operational, was planned with the pragmatism that has defined Singapore’s growth over the years.
Container handling demand continues to soar across the globe and given Singapore’s position as an important maritime and trading hub, the continues
development of this new port is a clear signal to the world that Singapore is ready to welcome additional container traffic by ramping up its handling capacity.
Some of the highlights at this port include unmanned vehicles, data analytics, driverless trucks for port transport, combined with a digital ecosystem designed to reduce significantly paperwork and overcrowding at the ports. The first phase of the port was recently opened and as it continues to expand operations, is expected to be a key engine of growth for Singapore in the future.
Another ambitious project, the largest collaboration across different sectors within the shipping industry in Singapore, is the Singapore Trade Data Exchange (SGTradex).
SGTradex hopes to be the digital highway that connects stakeholders with each other, with information being exchanged between willing parties seamlessly.
This is done in a secure and confidential manner between consenting parties and allows for the different digital
platforms used by individual companies to be connected to a single system where data can be shared.
The data highway will also be connected to LTConnect, which is Jurong Port’s digital platform for port-related services. SGTradex has since its inception engaged many different stakeholders who can contribute to the building of such an all-encompassing digital infrastructure.
In this way it is hoped that it would one day be possible to conduct the entire flow of operation from order placement till delivery of goods through a single platform, making it easier for various stakeholders including agents, barge operators, ship chandlers and shipowners to interact and exchange information.
Since 2018, an annual event called the Smart Port Challenge has been held, helmed by the Pier71 Port Innovation Ecosystem Reimagined @ Block 71 team, a joint collaboration amongst MPA, PSA and NUS (National University of Singapore) Enterprise.
Various problem statements are sought from industry players and these are then shared with interested companies who then produce solutions to tackle these issues. These are then debated by a panel and the best solutions are then eventually funded by the government agencies to produce prototypes in close consultation with the relevant parties.
Through this programme, innovative solutions like drone deliveries to vessels, Electronic Delivery Order systems and optimisation of barges are currently being explored and expected to be available for use in the near future.
It is in this dynamic environment that focuses on innovation that drives the maritime industry in Singapore and helps to ensure its reputation as a one stop centre for all things shipping. u
Here is food for thought: what happens to waste generated by cleaning hulls?
Marine coatings experts AkzoNobel believes such waste needs to be reclaimed and disposed of responsibly if the maritime industry is to enjoy a clean and sustainable future.
The firm absolutely subscribes to the notion that those whose business takes them to our seas and oceans must embrace the modern buzz words, viz. social responsibility, social governance and sustainability – to name but three.
Regulators recognise the delicate state of the planet’s ecosystem and need them to introduce meaningful regulations to ensure best practice that protects the sea and the marine life that dwells therein.
Underwater ship hull cleaning is sometimes a necessary activity for many vessel owners but is one that can result in substantial amounts of waste being produced.
This is why recovering waste material or reclamation is vital for the sustainable future of the industry.
Reclaiming the waste generated from hull cleaning operations provides assurance to vessel operators that materials resulting from their operations are handled in a sustainable, environmentally and socially responsible manner.
Without reclamation, it’s fair to say that no-one can be truly serious about their sustainability credentials.
By doing this, any paint debris and biofouling arising from the cleaning operation is gathered and can be safely disposed of, rather than accumulating in the area where the hull cleaning has been undertaken. This minimises the potential for any invasive biofouling species moving to a new place where it does not belong.
This is a crucial aspect and one that is firmly in the spotlight of the International Maritime Organisation (IMO) guidance, as well as other initiatives such as the recently launched Clean Hull initiative (CHI).
CHI is being led by the Bellona Foundation to create a new standard, focusing on ‘proactive hull cleaning’,
which by definition is a standard which vessel owners can choose to adopt or not, it is not a regulation.
AkzoNobel confirm that, as a marine coatings manufacturer, it intends to take part in this initiative, but will always insist that reclamation is part of the process.
In 2020, the Baltic and International Maritime Council (BIMCO) developed the first global standard for ship hull cleaning, that focused on the need for reclamation, diver safety and maintaining the performance of the fouling control coating applied onto a ship’s hull.
The IMO has also embarked on the Glofouling initiative to review both the commercial impact of biofouling accumulation on hulls and the potential for shipping to act as a vector for the translocation of invasive species.
This may result in the introduction of new regulatory rules to maintain clean hulls, depending on the outcome of the study.
With all this industry activity, the importance of reclamation in the hull
cleaning process is clear both now and for the future. Indeed, some ports including Southampton and Rotterdam do not allow cleaning without reclamation which means that any non-compliant systems (either shorebased or deployed onboard vessels) are effectively banned from use.
Chris Birkert, Marine Segment Manager at AkzoNobel, says: “The proactive and optimised cleaning regime is designed to maintain performance over the operational cycle of deep-sea trading vessels, while they are conducting their normal operations.
“Unlike diver operated brush cleaning methods which can increase the risk of damage and potentially reduce the effective scheme life of a fouling control system, our Intertrac HullCare system uses technology which
cleans the surface with water jets and reclamation with sustainable waste disposal routes.
“The combination of ultra performance fouling control coatings and pro-active hull cleaning with fouling reclamation as standard, boosts fuel and emissions savings and makes Intertrac HullCare, we believe, one of the most sustainable hull performance packages in the marine industry.
“All of this is achieved with minimal impact to vessel operations and without upfront capital investment or vessel modification.”
Not all organisations in the marine industry see the importance of reclamation as part of the hull cleaning process. Many speak earnestly about sustainability and protecting the environment, while failing to mention
the importance of reclamation.
However, as the industry becomes ever more focused on providing a sustainable future, this lack of a focus on reclamation is short-sighted according to Birkert.
He says: “If waste debris is not handled properly and disposed of in a responsible manner, it has the potential to accumulate steadily in ports and harbours and may cause unintended harm.
As the ship supply industry is heavily involved in facilitating hull cleaning and anti-fouling delivery – and as part of ISSA’s on-going Green ISSA policy – this focus on reclamation of waste generated by hull cleaning activity ought to pique the interest of the supply side. u
www.international-marine.com/ in-focus/intertrac-hullcare
Van Ameyde Marine, the global marine consultancy and surveying firm, is advising ship managers to remain Covid aware and ensure that crews are fully vaccinated amid the prospect of a further wave of infections from a new strain of the virus.
Michael Robertson, a senior marine consultant with the company’s McAuslands division, said: “With reports in Europe and Asia pointing to an increase in the number of Covid cases, ship managers and crews should not let their guard down.
“If there is another wave this winter, we could see ships and crews quarantined again and trade disrupted. There are reports of a new strain of the virus emerging in China, so I don’t think Covid is going away any time soon.”
While a Covid infection may be less severe for a fully vaccinated individual, Van Ameyde McAuslands’ crew care team is concerned that some seafarers have yet to receive their booster jabs.
Charlotte Malkin, Crew Care Coordinator, Van Ameyde McAuslands, said: “While Neptune Declaration statistics point to a seafarer vaccination rate of 89.3%, which is probably an over estimation, we are finding that some crew members have only had one or two of the doses and missed boosters when they were at sea. We’re arranging a lot of vaccinations and tests at the moment.”
While travel entry requirements for many countries have eased, the crew welfare team is arranging more and more in
Antigen tests arranged for crews at airports, with results sent directly to the ship manger and individual within 30 minutes.
“When travelling to Asia, a PCR test is still a travel entry requirement. We continue to carry out PCRs for crews travelling back home to the Philippines, for example. Chinese Embassy approved PCRs are also required if vessels are scheduled to visit Chinese ports or if crews are flying back home from China,” said Malkin.
The marine consultancy is also advising ship operators to keep managers and crews abreast of the rapidly developing monkeypox situation and how to mitigate against the risk of infection.
Katy Peters, Founder and CEO of 360 Health, said: “Similar to Covid-19, monkeypox infection is likely to bring on flu-like symptoms – fever, headaches etc. but the incubation period could be up to 21 days.
“A rash usually appears within one to five days after the onset of symptoms and this could be on the face, inside the mouth, and on other parts of the body, like hands, feet, chest, genitals or anus. The illness will typically last between 2-4 weeks.”
“Ship operators should advise their P&I Clubs immediately if they suspect they have a case on monkeypox on board one of their vessels,” said Robertson.
The World Health Organization (WHO) has determined that the multi-country outbreak of monkeypox constitutes a Public Health Emergency of International Concern. u
Danish-based marine electronics company, Daniamant, announces the latest development of its lifesaving product: lifejacket lights.
Daniamant offers lifejacket lights with lithium or alkaline batteries, designed to be compatible with all variations of life jackets in any size, thanks to its fit-forpurpose light clip design.
The lithium-based technology has an extremely long lifetime and is able to work at extreme temperatures, whilst having a longer lifespan when activated.
Once operated, Daniamant’s lithium lights will last for almost 90 hours and well above the required 0.75cd light output.
The firm has also been busy showcasing its alkaline technology, which meets regulatory standards of SOLAS and the Marine Equipment Directive.
This gives customers the option to choose an alkaline light instead of a Lithium-based light.
Recognising the issue of disposal of Lithium, as well as increasing transportation costs, Daniamant’s innovative product design allows seagoers to choose a lifejacket light
depending on individual priorities of transport, disposal and performance.
The alkaline technology has an impressive lifetime of 60 hours once activated and above the required 0.75cd.
Daniamant offers a broad range of electronic marine safety equipment, from its breadth of alarm systems, such as nautical alarms, oil level alarms, salinometers, and bridge watch alarms, to navigational safety systems including its Forward-Looking Sonar and Inclinometers.
Kevin Rough, CEO at Daniamant, sais: “Keeping people safe at sea is what drives us at Daniamant, and we continuously strive to create products that not only meet standards but exceed them.
“Our vast product range of safety equipment is part of our mission to ensure the safety of everyone at sea, whilst maximising our contribution to the safety of the marine industry.” u
www.daniamant.com
Embracing digitalisation key to maximising shipping’s potential, says
Shipping is an industry in the midst of an unprecedent shift towards adopting new technologies and methods of working to meet ambitious decarbonisation goals and net-zero targets.
However, a barrier remains for the adoption and shift to digital technologies and platforms, which can seem daunting, but are designed to maximise efficiency, reduce workloads, ease supply chain congestion, lower emissions and provide greater scale, depth and insights into how your business is operating.
For people without a digital background, the transfer to the digital age can appear overwhelming. Following the initial impacts of COVID-19, businesses quickly realised they lacked the capabilities and digital infrastructure to work efficiently, when office life was put on hold due to lockdowns and safety concerns.
In turn, this spurred the realisation of the importance of embracing digitalisation to meet these new challenges and drive greater efficiency across their businesses.
Traditionally, the approach of ship suppliers and port agencies involves multiple contacts, pricing structures and complex communication processes, which can involve a plethora of messaging platforms, making it easier for key information to be missed.
This is where digitalisation shines, with the ability for all communications and critical information to be safely stored in one place, with a simple to use single systems interface.
Managing these long and often difficult supply chains using traditional methods negatively impacts the productivity of those working both onboard and onshore.
For businesses to maximise the efficiency of workloads, digitalisation is critical to reduce the amount of tedious
manual tasks, leading to more fulfilling and efficient work for those involved and provide more time utilising their specialist skills.
For many operating on a vessel, they have years of experience and areas of vital expertise. Digitalising rudimentary administrative tasks allows them to provide maximum value to owners and operators.
Over the past few years, the shipping industry faced a perfect storm of more vessels, yet with less cargo and increased delays.
For ship suppliers this meant rapidly changing agendas and requirements from clients.
Digitalisation will bring a wide range of benefits to combat these challenges, particularly addressing business efficiency through increased agility and visibility to all team members.
Optimising key processes allows for real-time decision making, countering some of the complexities that arise, minimising delays and more effectively servicing clients.
By adopting digital platforms and integrating them across the company, businesses can harness the power of data. By using sophisticated data analytics tool platforms, such as S5 Agency World, businesses can identify the highest quality suppliers and find the most competitive prices across the international supply chain.
These services are continually updated to monitor performance and ensure optimum efficiency, thus providing the edge needed to outperform the competition.
Recently, S5 Agency World held a summit in Hamburg, which brought together influential leaders from across the maritime supply chain to help demystify the digital transformation and discuss how we can promote the advantages and increased usage of optimised services.
When embracing digitalisation, one of the most important issues raised by the panel was the importance of using digital platforms that are fully integrated.
For example, one panellist explained how they chose to take the leap to digitise their business, but ended up choosing multiple software packages, which although vertically optimised, were not fully integrated leading to information silos losing important data insights.
This highlights the importance of partnering with industry experts when making the transition to ensure standardisation and transparency between platforms.
As the global supply chain becomes more complicated, with ever-increasing logistical, legislative and regulatory demands, adopting digital solutions can ensure accountability and compliance, and help teams to continue to manage complex supply chains smoothly.
Environmental legislation and the shipping industry’s broader decarbonisation goals create additional considerations for owners, operators and crew alike.
A greater uptake in digitalised and optimised services can help alleviate some of these new challenges while also helping the industry move closer to a greener, cleaner future.
Now is the time for the shipping industry to embrace fully greater standardisation and transparency to meet the needs of the industry today and in the future.
By facilitating a successful digital transformation, the industry will be prepared to meet the coming challenges of the next decade and beyond. The changing landscape coupled with environmental targets means that changes need to be made, but with the correct approach.
Digitalisation, collaboration and maximizing the skillset of all those who work within the industry gives shipping an opportunity to play a major role in helping to decarbonise the global supply chain. u
www.s5agencyworld.com
During the Covid-19 pandemic, some ship suppliers and ship agents turned to drones to boost the efficiency of ship supply deliveries whilst safeguarding the well-being of crew
However, such technology could have a much wider impact for the future of ship supply services. Daniel Nordberg, GAC Group Vice-President Asia Pacific and Indian Sub-Continent describes the benefits.
major energy customers recently approved the use of F-Drones for deliveries.
We hope to scale up deliveries of courier parcels and spare parts of up to 10 kg for them when the opportunity arises.
Maritime crews around the world had to adapt to a myriad of unprecedented challenges presented to them by the Covid-19 pandemic.
One of the greatest challenges was crew change. At the height of the pandemic, constantly changing health directives kept shipowners and managers on their toes – and in some cases trapped crew members onboard, unable to leave after they completed their tour of duty.
Sanitation requirements and social distancing measures also delayed or impeded husbandry services, adding another obstacle to the task of keeping a vessel stocked with supplies.
To overcome such disruption, some ship agents and ship suppliers turned to developing technologies. Among them was our global shipping and logistics service provider GAC, which in 2020 joined forces with Singapore-based start-up F-Drones to develop large-scale drones capable of carrying 100 kg of cargo more than 100 km out to sea to ships and offshore platforms.
Drones offer a contactless and flexible alternative to traditional transportation methods, eliminating the need for social distancing during delivery. They are also fully electric, making them environmentally
friendly with a lower carbon emission footprint for ship supply operations.
Though many countries have now gradually lifted most Covid-19-related restrictions, and shipping protocols and operations are returning to prepandemic levels, the legacy of lessons learned during the pandemic remains. At GAC we have seen the long-term benefits of drone technology for our shipping and logistics services and we are set to deepen our investment.
“GAC is always looking for new and unique technological developments that can benefit our customers and the wider shipping and logistics industries,” says my colleague Sofie Bager, Managing Director of GAC Singapore.
“Our partnership with F-Drones is a perfect example of our desire to help create state-of-the-art technology that will improve the welfare of crews, make shipping more sustainable and ultimately keep vessels moving.”
GAC has also used drones to collect bunker fuel samples from vessels – an operation that typically takes two hours or longer with a launch boat, but only 15 minutes with drones – while one of our
For ship suppliers, drones could be a gamechanger. They offer an attractive, cheaper alternative to launch vessels and helicopters that traditionally supply vessels, particularly when it comes to ondemand or time critical deliveries.
By eliminating the need to send an entire vessel and crew out to deliver supplies, risks of accidents to personnel boarding vessels are mitigated. The comparatively small size of drones also allows them to land precisely on a vessel that may have limited deck space.
The technology has been proven to work at night, enabling ship suppliers to offer 24/7 access to ship supplies without having to dock.
For operators and managers, drones can improve the bottom line at a time when supply chains are increasingly under tremendous strain.
Improving the turnaround time of a vessel, even only by an hour, can have a positive knock-on effect on the wider industry and GAC is keen to ensure our services are as efficient as possible to keep ships on track.
During the pandemic we had the extra challenge of ensuring all crews were tested, vaccinated and quarantined in line with government rules, which added to turnaround time. In response, we looked to technology – including drones – to boost efficiency elsewhere. u
Chevron Marine Lubricants has announced the launch of its Clarity Synthetic EA Grease 0, an anhydrous calcium thickened lubricating grease based on biodegradable synthetic esters that meet the parameters specified in the 2013 Vessel General Permit (VGP) rules for environmentally acceptable lubricants issued by the U.S. Environmental Protection agency (EPA).
The high-performance grease is suitable for a variety of marine applications where an NLGI 0 EA grease is required, including rudder carrier pumps, slides, hinges, and propeller caps.
The grease contains antioxidants, corrosion inhibitors, and Extreme Pressure and Anti Wear (EP/AW) additives.
The calcium thickener, together with the biodegradable esters, makes
the product particularly suitable for lubricating heavily loaded bearings.
It features excellent adhesion and water resistance and is designed for extreme applications in wet and corrosive environments, even at low temperatures.
“This is an important addition to our product portfolio as it expands our range of EAL solutions to meet customers’ requirements,” commented Martin Roessner, technical field specialist, Chevron.
“Wherever the application involves a risk of contamination to the water, soil or channels, this new Clarity Synthetic EA Grease 0 is recommended.”
It is readily biodegradable and is easily pumpable in most modern centralized lubrication systems. u
www.chevronmarineproducts.com
important part of future
The maritime industry has been working on developing strategies to address climate change.
The majority of these strategies are being shaped by the decarbonisation regulatory frameworks introduced by the International Maritime Organisation (IMO).
As a result, shipping companies consider new fuels to meet IMO decarbonisation requirements.
While doing so, one risk they may face is the engine damage if they do not also consider their choice of cylinder lubricant.
The performance of new fuels is yet to be extensively tested on marine engines at sea, and this can create uncertainty about lubricant choice and operational changes that could place an extra burden on seafarers.
Castrol is a trusted partner that can help companies navigate these uncertainties. The company’s global network of experts supports shipping companies with the optimum lubricant choices, with its services centred around scheduling, monitoring and consultancy.
The scheduling service works to discover the right solutions for key players in the maritime industry based on the equipment and model of their vessel. Castrol’s scheduling services ensure every moving part on a vessel is optimised for performance and reliability.
Cassandra Higham, Marketing Director, Global Marine and Energy, at Castrol said: “Castrol’s experts are leaders in their fields, and use their decades of industry experience, eye for detail and technical expertise to identify potential barriers to asset optimisation, improve efficiencies, and create competitive advantage for the customers they work alongside.
“They focus on the areas where they can create proven value for their customers.”
The monitoring service ensures that lubricants are performing to the highest standards, thus supporting a vessel’s everyday operations.
Castrol offers useful insight into the ship’s performance thanks to its online Used Oil Analysis data (UOA), on-board solutions, test kits and expert condition monitoring advice.
A useful tool is Castrol’s LabCheck Digital Portal which enables staff to access the latest ship’s data and provides maintenance suggestions.
As crews differ from one vessel to another, experts are always reevaluating analytical data to provide the best tailored solutions.
The consultancy service enables shipping companies to access high-end personalised advice and maximise the efficient cooperation between lubricants and the ship’s assets.
Castrol’s global network of Technical Services Engineers (TSEs) are always available to solve issues anywhere in the world at any time of the day and improve the efficiency of operations.
The TSEs are also fluent in multiple languages to ensure they can communicate effectively and cater to the many different requirements of customers around the world.
Ms. Higham said: “Castrol is constantly accessible to support its customers, not only with a fit for purpose high-performing lubricant, but also to interpret used oil analysis and OEM trends and advise how best to deal with associated engine wear issues.”
The company is constantly referencing the latest regulatory trends and developments in the maritime industry to ensure its products are innovative and effective.
For example, Castrol’s Cyltech 40 XDC cylinder oil recently obtained a Category II No Objection Letter from MAN Energy Solutions following thorough field testing.
The Cyltech range has been developed to reduce wear within different components of the engine. The Category II requires cylinder oils to have excellent performance and cleaning ability, suitable for use under different fuel sulphur levels.
The maritime industry is still trialling products to accelerate the transition towards carbon-neutral shipping and Castrol seeks to provide the best support to facilitate this.
There is potential for shipping companies to be more sustainable with low sulphur fossil fuels along with new prospects unlocked by alternative fuels (eg. LNG, methanol, hydrogen, ammonia).
As high-end technologies allow experts to develop more fuel options with different properties, ensuring the engine is protected is essential.
This means that lubricants will become increasingly important for the maritime industry as the pressure to meet the IMO’s environmental targets grows.
Being one of the leading manufacturers and providers of lubricants in the industry, and with its technical experts always available, Castrol can support ships and their teams to make the best choices to increase engine efficiency and optimise performance.
Focusing on sustainability will help companies with the delivery of operations and benefit the companies‘ competitiveness in terms of reputation, efficiency and innovations.
The sooner companies acknowledge this is the way forward, the better prospects they will have to compete in a future environmentally responsible market. u
www.castrol.com
The maritime industry is embarking on a journey towards carbon reduction. The urgency of situation is heightened through measures set by the International Maritime Organization, to reduce carbon intensity of all ships by 40% by 2030.
Following market trends, the maritime industry is expecting an increase in demand for greener ships. Many ship owners attend to the demand by retrofitting their vessels with green LED lights. These LED Lights help vessels to optimise their energy consumption leading to an overall reduction carbon emission from energy use. Comparatively longer service life couple with the reduced need for maintenance results in lesser material wastage and increased savings in the long run.
Singapore based companies, SOPEX Innovations Ltd (“SOPEX”), are in a strategic partnership with GL Lighting Holdings, to “Save Our Planet” through reliable and innovative energy-efficient technologies for normal and hazardous areas. SOPEX work hand in hand with shop owners and ship chandlers worldwide to contribute to maritime sustainable development in energy efficiency and decarbonisation. The group’s vision of supplying lighting that can withstand harsh environments and achieving sustainable development through energy optimization and waste minimization, brings them hope for a reduction of 65% in carbon footprint through the process.
GL Lighting Holdings is a specialist in R&D, Design and manufacturing of Green LED solutions and have been in the business for more than 20 years. Having completed over 500 ODM and OEM projects for renowned international lighting companies including Philips and OSRAM. They own one of the best most up-to-date luminaire factories in Asia which consist of an 8,500m2 mechanical plant and a 11,000m2 electronic plant that are equipped with cutting-edge production facilities of fully automated SMT line, clouds enable electronic manufacturing setup, advanced powder coating line, and CNC/laser/plastic injection/cold-forged/aerospace welding.
Together, SOPEX encourages customers’ adoption by performing onboard assessments of lighting requirements, generating inspection reports on Return on Investments and Total Cost of Ownership, and providing recommendations on LED lightings with the right technical specifications appropriate for each vessel.
SOP has recently developed their new line of Modular Floodlights, the SQ6 Series, consisting of 1, 2 and 4 Modules. Designed to be an improved version of their popular SQ5 Series, the development team has placed emphasis on improving the performance based on the minimum Lux requirements at Deck Areas onboard vessel without compromising on energy savings.
A good example would be a 1 Module unit (Medium Beam Angle) from SQ6 can easily replace a 3 or 4 Modules unit
(Narrow Beam Angle) from SQ5 based on projection distance and illumination area. The sturdy design of the SQ6 Series has qualified it to be EMC and IEC Compliant. Not only that, but it is also IP67 rated.
SOPEX places emphasis on the continual research, design, and development of ideal LED solutions to provide green, innovative, and sustainable technologies that can meet the unique demands of Marine environments.
IKAN LANDUK – IKAN LANDUK is a Bulk Carrier, built in 2013 (9 years old), sailing under the flag of Singapore. The performance of the pre-existing traditional lighting system was failing, and the captain decided to change out the traditional lights for SOP brand Heavy Duty LED Floodlights and Modular LED Floodlights to help save energy whilst improving overall brightness and visibility when at sea. Captain remarks that the performance of the SOP lights is very good. The intensity and the brightness of the LED (flood) light are much better than previous reflector light, and that SOP LED lights do not produce too much heat even during long periods of use.
DENKO BRIGHT – DENKO BRIGHT is a Liquid Bulk Carrier, built in 2015 (7 years old), sailing under the flag of Singapore. During Denko Bright’s port call in Singapore, she was required to replace 2 units of Ex-proof Modular Floodlight and SOPEX Innovations had the opportunity to supply to the vessel for immediate replacement to avoid any discrepancies during her Class Survey. Norstar Ship management and the Vessel is very satisfied with the performance of the lights, the design, brightness and area the Floodlight is able to illuminate.
MSC POLARIS - MSC POLARIS is a Container Ship built in 1995 (27 years old) and currently sailing under the flag of Liberia. She was in Sembawang Shipyard, Singapore for repair job from year 2021 to 2022. Despite her age, Owners MSC went ahead to change out pre-existing 2 Feet Fluorescent Lights and Pendant Lights with 155 units of SOP SUS316
LSW Series 2 Feet LED Lights and 27 Units of SOP Wall / Ceiling Mounted Pendant Light for the outdoor area and 32 units of Recessed and Surface Linear Module Lights for indoor locations within the superstructure, for more savings in energy and consumables, taking a huge step forward in reducing the carbon footprint. u
Write to us at info@sop-led.com or call us at +65 6210 2371 and we will be glad to provide you with a workable solution specially catered to your needs.
In the last edition of The Ship Supplier we discussed the significance of ensuring that you understand you customer – who they are and what is their relationship to the vessel.
An interesting case from the US 4th Circuit of Appeals (SING FUELS PTE LTD v M/V LILA SHANGHAI) serves to illustrate this point very well indeed.
But why is a US Court of Appeal decision interesting to ISSA members, who may be sitting on the other side of the world?
The answer to that question lies in the ISSA Conditions of Sale, which apply US law to all contracts formed pursuant to them. The reason for this is that US law is very favourable to ship suppliers, because of the maritime lien that arises under US law in favour of the supplier of “necessaries”.
If problems arise in collecting payment, the US law maritime lien can sometimes be the difference between collecting or not collecting what is owed (though many other factors will also be relevant in determining outcomes).
In the recent case, a bunker supplier failed in its efforts to assert a US law maritime lien over the vessel to whom it supplied bunkers (to a value of US$530,000).
The bunker supplier asserted that it had supplied the bunkers at the request of a charterer of the vessel, through the agency of the charterer’s agent (a bunker broker). Had it been able to establish that the broker through whom the trade was conducted was indeed the agent of a charterer then a maritime lien would have arisen and the vessel and its owner would have been liable to pay (subject to a secondary argument around whether the bunker supplier had delayed too long in bringing its claim).
The Court held that the bunker supplier had not established that the broker was the agent of the charterer.
The bunker supplier had not obtained any direct confirmation from the charterer that the broker was acting as their agent. It appeared that there was in fact another entity in the sales chain, sitting between the bunker supplier and the charterer. The bunker supplier had never sought to identify that party, or their relationship with the vessel.
The Court noted that it is not enough that the alleged agent describes itself as such. The principal (in this case the charterer) must itself have held out to the bunker supplier (or the world at large) that it had authorised the broker to act on its behalf.
The case is an important reminder of how vital it is to be very clear about who you are transacting with, and what is their role in the transaction.
ISSA members will generally not be concerned with charterers in the way that bunker suppliers often are.
Whilst charterers frequently purchase bunkers, it is much more unusual that they would be purchasing the items typically provided by ISSA members (which generally fall to the owner’s responsibility).
It is nevertheless important that when transacting with anyone that is not the legal owner of the ship that you understand who they are, and what relationship they have with the vessel. If there is not a clear and obvious agency between the owner and the party with whom you are dealing, you should consider seeking confirmation from the owner that they authorise the agent to act on their behalf.
It may often be the case that you are dealing with someone who is not authorised by the owner to act on their behalf (for example, a caterer or another ISSA member).
In such cases, it is important to understand who is responsible for payment and rate your risk accordingly.
This recent case does not change the law, but it reminds us all that the maritime lien (and right to arrest a vessel) can easily be lost if care is not taken. u
Bruce Hailey is a Solicitor specialising in maritime law and based in Manchester, UK www.salvuslaw.com
Bromley Abbott unpicks the knots to reveal the diversity of rope and its importance to the maritime industry
When it comes to ropes it is clear there is a plethora of applications to consider.
A significant employer of rope technology is the maritime industry and a leading player that covers the spectrum of such technology is Dynamica Ropes.
This Danish manufacturer of high-performance synthetic fibre solutions replace steel wire and chains with lighter, safer and stronger alternatives.
The firm’s flagship products are HMPE/ Dyneema and Dyneema – both registered trademarks – the World’s strongest man-made fibre.
Dyneema® is also called ultra-high molecular weight polyethylene (UHMWPE) and is used for manufacturing several types of ropes, slings and tethers.
The Company commented: “At Dynamica Ropes, we manufacture our rope solutions with HMPE/Dyneema® to offer our customers the lightest, strongest and most reliable solution possible.
“In fact, our rope solutions have such high strength performance, that they are replacing steel wire and chains for heavy lifting operations both on- and offshore.”
Spanning 10 declared industrial sectors it may come as a surprise at just how diverse the subject of rope has become.
Of course, we all know it was the ancient Egyptians who developed rope-making techniques way back in 2,500 BC.
Unbelievably a lot of their techniques are still employed today.
Interestingly a real no-no when it comes to ropes is tying knots. Consider the heading of this article merely illustrative as no knots should be present to unpick!
Instead, advises the company, opt for splices. A properly spliced rope by an expert fitter will result in a 10% maximum loss in strength whereas a knot results in a 60% loss in strength. Who knew?
To illustrate the points made in more depth we have chosen two case studies to focus upon from the many applications offered by the company:
• Mooring
• Towing
Floating production storage and offloading (FPSO) solution
When it came to the specifications for an FPSO solution there were five key factors to consider:
• Strength
• Reduced size
• Low weight
• Easy handling
• Low backlash energy
The solution also needed to ensure it would not be affected by sea-water conditions and the stress related to permanent mooring.
Dynamica SK78 mooring ropes were the perfect match as all the boxes of characteristics required for permanent mooring were ticked.
To reinforce the efficacy of the solution the FPSO Master concerned said: “We have been using Dynamica SK78 mooring ropes as our permanent mooring ropes for our FSU.
“We have been using it for over 5 years now and are very happy to share that these ropes have performed beyond our expectations.
“Worth mentioning qualities are the easy handling and the maintenance free ropes plus the fact the deck is always clean.
The Master particularly praised the ease of handling – loved by the crew – and the major advantage of the rope being free from whiplash so very safe to use.
Towing – retired after 3,997 jobs!
Another major use of rope in the maritime industry is, of course, towing.
And if it is longevity you worry about then the case of the Svitzer Tug that has recently retired its main towing rope after 3,997 jobs should fill you with confidence in this remarkable product.
What came as something of a surprise was the proud statement that after 2,000 successful towage jobs the rope was “turned” end to end and went on to be used in the remaining 1,997 trouble-free towing jobs before retirement.
With a full history of the line’s service, number of towage jobs and active escorts etc. the rope was retired after 3997 jobs and the tug operator ordered its replacement.
In fact, our rope solutions have such high strength performance, that they are replacing steel wire and chains for heavy lifting operations both on- and offshore
Dynamica explained: “According to our mutual agreement the rope was returned to us for product testing and evaluation since it is of interest for the tug operators to find out the residual strength and condition of the line.
“The visual inspection showed that the rope and cover was in very good shape, much better than could be expected - it was clear that it had been taken good care of.
“The cover on the eye was found to be in a good state. The eye ‘neck’ and cover was compressed due to the cowhitch.
The compression forced the cover to open up down the eye.
“In some places, the tow rope was twisted around its axis meaning the rope was deformed and had a ‘square’ shape.
“This most likely happened as a result of burring on the winch. The compression of rope, can influence the breaking strength of the rope.”
Different break tests were performed:
• Outer eye (cow hitch eye) + new eye
• Inner eye
• Tests approx. 60 m down the rope from each eye end (2 new splices)
This hard-working rope passed these tests with flying colours and no loss of integrity was discovered. In the test results below “X” marks where the rope parted:
Dynamica explained how this remarkable result was achieved: “The extra 1997 jobs with no issues were possible due to our manufacturing process.
“The tow lines are manufactured with genuine HMPE/Dyneema® and pre-stretched in the heat stretching unit, thereby gaining strength when under
repeated tension as the fibres are organised due to the heat and tension applied.”
The Master of the Svitzer Tug added: “We are very pleased with the performance of our Dynamica Tow lines.
“They have been in service since installation and have completed 3997 jobs.
“The bespoke main line is additionally connected to a working pennant (20 m x 56 mm Dynamica jacketed line).
“These pennants are replaced every 2000 jobs (end for ended after 1000 jobs).”
Having had the good fortune to examine Dynamica’s product offerings in depth it seems sensible to suggest owners, operators and ship suppliers should take a look at the diversity on offer and the advantages to be had using the company’s innovative approach. u
https://dynamica-ropes.com
If we talk about supplying ships in Spain, we have to talk about Bayport. With 9 delegations spread along the coast and a large percentage of products in stock available, it is the partner in which more and more customers entrust their supply needs.
In the last few years, they have shown an enormous exponential growth that is evident in the milestones they have reached as a company: new branches, new business segments and new ways of optimizing their daily operations to offer their customers an increasingly excellent service.
This year, Bayport inaugurates a new headquarters with more than 29,000m2 in Cadiz (Spain). A new logistics platform that boosts not only its ship supply division, but also its thirdparty logistics division. The increase in available space, storage and distribution capacity with new and efficient vehicles, make it possible for the company to offer its services in an increasingly optimal way.
In addition, in line with this process optimization, there is a continuous search for sustainability. In recent years, more and more companies are thinking green in order to grow their business in a green and environmentally responsible way. For this reason, Bayport has launched a campaign to reduce CO2 emissions and its carbon footprint through different tools.
One of them, the most important, is the self-supply of energy for its new Logistics Centre. Thanks to an impressive installation of photovoltaic panels on the roof of the industrial building, energy consumption will be reduced by the equivalent of more than 240 tons of CO2, the equivalent of planting 13,500 trees.
However, they also focus their efforts on issues related to Corporate Social Responsibility. During this year, they have obtained the NT 165001 certification accredited by IVAC, which certifies the good practices and the correct performance of the companies in the field of CSR - CSR. Bayport currently has agreements with UNICEF through
the Business Alliances programme, and with the Spanish Red Cross, as well as specific aid agreements such as in the recent Ukraine-Russia conflict, where they supported a solidarity shipment of basic necessities.
Thanks to an efficient solar panel installation, Bayport will reduce more than 240 tons of CO2 emisions to the atmosphere.
In short, Bayport continues to advance as it has been doing for more than 43 years, when it began as “Puerto Y Bahía” as a small ship supply company. Today, it is an indispensable component in the logistics chain for its clients, thanks to the fact that it offers solutions adapted to each client, and proof of this is its increasingly wide range of services, without losing quality and efficiency in any of them. “We know that our customers need their needs to be met as quickly as possible, as well as possible and at the best possible price”. u
Humidity, salt spray, moisture, and extreme temperatures combine to create a perfect recipe for corrosion on electricals and electronics in marine environments.
Two of the most serious consequences are equipment failure and costly replacement.
Global corrosion protection experts Cortec Corporation have an innovative solution to the problems associated with delicate electronics and a salty environment: their VPCI Emitters.
While marine environments create a perfect recipe for corrosion, Cortec VpCI Emitters are an easy recipe for successful corrosion prevention inside electronic and electrical cabinets aboard ships or offshore platforms.
VpCI Emitters release Vapour phase Corrosion Inhibitors that fill the electrical or electronic enclosure and form a molecular protective film on the metal surfaces within.
This molecular layer does not interfere with equipment operation, but it does interfere with the normal corrosion reaction that takes place in the presence of metal, oxygen, and an electrolyte.
VpCI Emitters come in three basic sizes. The last number of each name signifies the volume of space protected:
• VpCI -101 Device (self-adhesive foam piece that protects 1 cubic feet [28 L] of enclosed space)
• VpCI -105 Emitter (self-adhesive cup that protects 5 cubic feet [0.14 m³] of enclosed space)
• VpCI -111 Emitter (self-adhesive cup that protects 11 cubic feet [0.31 m³] of enclosed space)
Cortec also offers a variety of VpCI -130 Series Foam Emitters available in sizes that protect up to 10 cubic feet (0.3 m³/m²) of space per unit (VpCI-137), perfect for preserving large rooms of electrical equipment during shutdown.
VpCI Emitters are often used during layup or mothballing of offshore rigs or oceangoing vessels. They are an important part of a good strategy to ensure equipment is ready to use at start-up.
The fact that VpCI Emitters are easy to remove or do not need to be removed at all before bringing equipment back online gives users maximum convenience and minimum downtime.
This also means VpCI Emitters can often be used during active operation to minimize corrosion related electrical/ electronic repairs and service interruptions.
Preventative maintenance is key to avoiding expensive down-time for sensitive electronics.
Whatever situation you find yourself in, remember the advantages of preventative maintenance. u
an innovative technologybased solution for controlling biofouling on ships’ hulls.
From the minute a vessel is launched, biofouling is a problem. It impacts fuel efficiency, vessel speed and performance, and contributes adversely to the impact on the environment. For this reason, the management and control of microfouling before it progresses to more serious levels of biofouling is key, but represents a major challenge for vessel owners and operators.
Fortunately, technology-based solutions for controlling biofouling are increasingly entering the market, offering owners and operators options to tackle the problem of biofouling early on.
Adopting a proactive in-water cleaning plan is the biggest step that a vessel owner or operator can take to improve vessel performance and overall fleet readiness.
Armach’s proactive in-water cleaning approach can be taken for all vessels, whether those already operational or new.
Once built and painted, the hull needs to be kept as clean as possible, as any growth on the hull will have a negative impact on performance, including increasing fuel consumption and emissions.
A recent report published by the IMO’s GloFouling Partnership has indicated that a very thin layer of slime (approx 0.5mm thick) covering 50% of the hull can increase emissions as much as 20-25%. Such a level of growth can occur rapidly in warm waters and is not easily detected.
A common approach to trying to prevent, or reduce the speed of biofouling, is through the use of advanced hull antifouling coating.
These coatings work one of two ways, either through the biocidal removal of growth, or by limiting the adhesion of growth to the hull and using the vessel’s own movement through the water to remove the only loosely attached growth.
Modern coating systems work extremely well in reducing the speed in which biofouling occurs, but this assumes the vessel operates within the specifications of the coating. However, extended idling or pier side time will challenge the capabilities of even the best coatings. In either case, they are more effective at dealing with macro-fouling.
Micro-fouling can be considered the bigger issue. It is either too new to the hull to have absorbed the biocide or is light enough to remain attached to the fouling release coating, and micro-fouling can start impacting performance in days. Currently, practices for inwater cleaning are either reactive, whereby the hull is cleaned once the situation is deemed ‘bad enough’ to warrant it, or scheduled at extended periods.
These cleaning cycles tend to be fairly intensive events, requiring an investment of at least one day along with the use of large equipment. Further, if removing macrofouling, the current reactive cleaning techniques can be aggressive and may cause damage to the coating system. In addition, it is not economically
attractive, as the cost for the reactive solution will be the same, whether it’s removing slime or barnacles.
Armach Robotics (Armach), however, is offering a dedicated proactive cleaning solution that overcomes the shortfalls of current methods. The Armach Robotics cleaning methodology is optimised for removal of early stage microfouling. A vessel can be completely cleaned in a single day, and through the use of autonomy and reduced onsite infrastructure and manpower, the annual cost is significantly lower than a reactive solution.
Armach achieves all this through the use of their new Hull Service Robot (HSR).
The HSR is a single man deployed hybrid flying and hull crawling robot, approximately 1 meter long and weighs less than 35kgs that can clean approx 650 sq meters (7,000 sq feet) per hour.
The brushes used on the cleaning head have been extensively tested to ensure they work optimally with the coating system being cleaned, effectively removing the microfouling while not damaging or accelerating the wear rate of the coating. The HSR is equipped with a forward-looking sonar, and forward and rear looking cameras to document the condition of the hull, pre and post cleaning.
Armach’s ultimate differentiator is the use of autonomy and precision on-hull navigation to overcome all barriers presented by current methods.
If the HSR knows its exact location on the hull at all times, it can be programmed to cover the hull efficiently and prove that it provided complete coverage of the hull.
Providing efficient hull coverage is critical to a successful proactive cleaning approach. If areas are missed, the microfouling can quickly develop into macrofouling, defeating the purpose of proactive cleaning.
Due to the true autonomy of the HSR, there is no need for it to be actively piloted. Whereas a reactive system may require multiple people to oversee the operation of a single system, multiple Armach HSRs can be monitored by a single person, and due to the small size of the HSR, no significant infrastructure is required for its launch, operation and recovery.
The value of Armach’s pre and post cleaning report data cannot be overstated. It provides proof to the owner and operator that the complete hull was addressed, and that the service paid for was the service received.
These factors all combine to create a more economical solution compared to the proactive use of a traditional cleaning system. Proactive in water cleaning is the future of hull maintenance. u
www.armachrobotics.com
Whilst all sectors of the shipping industry have been impacted by COVID-19 pandemic, the worst affected has been the cruise sector.
Despite much optimism, events this year have shown that suppliers need to remain vigilant when granting credit. Regardless of size, most companies in the sector have not yet returned to profitable trading.
The start of this year saw the bankruptcy of the three cruise lines owned by Genting Hong Kong Limited: Star Cruises, Crystal Cruises and Dream Cruises.
When the three fleets where combined, they represented the world’s 4th largest cruise business, after Carnival, Royal Caribbean and Norwegian Cruise Line. These three behemoths incurred massive losses during the pandemic and have been obliged to borrow money at increasingly high rates of interest.
All the companies are reporting increased bookings, but their figures conceal a dark secret. Many cruisers booking now are
paying with credits received after cruises booked in 2020 and 2021 were cancelled.
During the height of the pandemic, all cruise companies resisted requests for refunds on cancelled cruises. Instead, most holiday makers were persuaded to accept credits, often representing 125% or higher of the amount paid. The cash was used to keep the cruise companies afloat during the pandemic. Now the companies must provide “free-of charge”, the cruises paid for two or three years ago. At the same time, fuel, a major cost, is much more expensive than it was before and during the pandemic.
What do investors think? Here is how the share prices of the big three have changed over the past three years,
As the above figures show, all the companies’ shares rebounded in 2021 from the hammering they endured in 2020. However, in the past year, confidence has drained away again, with all the shares now trading at prices 50% or more lower than they were a year ago.
The figures are important, not because of what they reveal about individual companies but what they say about confidence in the cruise industry in general.
The numerous smaller cruise companies will be experiencing most of the problems grappled with by the big three: providing cruises paid for with credit notes, rising fuel prices, increasing costs of borrowing, declining investor confidence.
Within the last month, two single-ship companies have suspended operations: Tradewind Voyages and Island Escape Cruises. For the former, this is linked to financial problems with its parent. The latter is in Receivership and its vessel arrested.
The largest early casualty of the pandemic was Cruise & Maritime Voyages and its six-ship fleet managed by Global Cruise Lines.
Subsequently, several people involved in that business established Ambassador Cruise Line (ACL), which now has two ships, contracted out to third party management by Bernhard Schulte Cruise Services. ACL has just announced that one of its vessels will take up a charter with the Scottish government for the housing of refugees. Dependable income for at least six-months is preferable to uncertain passenger bookings.
The cruise sector can provide ship suppliers with largeorders, but they can come with big headaches for the unwary. u
Many readers will know of Paul Begg, the longest serving Secretary of the Australian Ship Suppliers & Services Association.
Now to add lustre to his already burnished reputation we are delighted to report that Paul has been inducted into the Baseball SA Hall of Fame after 60 years involvement with the game.
The Induction Ceremony Citation reads: “For continuous and passionate impact on South Australian Baseball through excellence in Umpiring and Baseball Administration”.
Paul started his illustrious career in the 1960s playing for Enfield and after a short spell in Northern Territory returned to South Australia to become the SABL Auditor in 1973/74.
For 20 years Paul umpired over 3,500 local, State, ABL and
International games with 16 of those years umpiring Claxton Shield and ABL games. He retired from umpiring in 2000.
He then became CEO of the South Australia Baseball League (2000 to 2002) and for many years in his early career he was involved with the Baseball Umpire Association of SA.
In addition he was a leading light in the Australian Baseball Federation as well as spanning the entire spectrum of umpiring duties throughout the game in South Australia and beyond.
Notable amongst his umpiring duties was his selection as Australian Umpire for the 2000 Olympic Games in Sydney, where he was elected Olympic Umpire of the Year.
In 2002 he was elected a Life Member of the SA Baseball League. u
Nordic is pleased to announce a strategic partnership with the AVS Group.
The AVS group has a history of 37 years in shipping and is active in ship supplies, ship catering, seafarer training, and ship management.
The company headquarters is based in Istanbul with branch offices and activities in Greece, Holland, Singapore and Liberia.
AVS currently employs 180 including staff located ashore/offshore and on local catering projects.
Nordic’s investment in the AVS Group is consistent with its strategy to diversify, expand and develop further in the business, focusing on optimizing procurement competitiveness.
In addition, Nordic will benefit from AVS’s strong local network, while both companies will do their best to explore existing and upcoming business opportunities.
Nordic intends strategically to develop crewing activities in Turkey to diversify its still growing crew pool and actively co-operate with universities and training facilities such as EKOL Shipping (maritime education and training centre owned by AVS Group) that provides training and career opportunities to Turkish seafarers but also to other nationalities.
The new strategic co-operation provides Nordic with a strong partner in Istanbul and marks another step in the group’s resolve to increase its international expansion and presence in the industry. u
Amaritime industry safety milestone has been reached: 40 years of LALIZAS building a safety culture and adding value to the maritime community.
Returning to Posidonia, the company’s team took the opportunity afforded by this famous Exhibition to introduce the latest lifesaving solutions to keep everyone safe on board.
In recent years the firm’s focus has turned to providing safety orientated services as well as its renowned suite of products.
These include the Fire Safety Rescue (FSR) Service & the Fast & Independent Liferaft Exchange (F&I).
Through FSR they can support a vessel’s needs at almost any port, offering service and replacement on all LSA and FFE at any place and any time with minimum port stay.
F&I is a radical game-changer in the life-raft market, a unique proposal to Ship Owners/ Managers for a simple & fast life-raft exchange to keep the vessels compliant and in service.
F&I is managing life-raft compliance, through exchange, in the world’s key ports as a managed service - for a single fixed fee - without need of a contract and with no single OEM brand restriction.
The company’s oft-quoted boast is that “safety is not just a product it is an on-going process”.
Well known in the shipping and yachting sectors, a flick through the company’s extensive Catalogue reveals a wide and comprehensive range of safety-related products and services.
The Ship Supplier salutes this bastion of arguably the most important area of maritime supply. u
www.lalizas.com
Finnish maritime behemoth Wärtsilä has installed its SPECS camera system on board Brittany Ferries’ “Salamanca” passenger vessel for more efficient and safer operations.
This innovative system – full title Smart Panoramic Edge Camera System (SPECS) – provides the latest situational awareness solution in support of crew in difficult weather conditions and manoeuvring in tight berths.
Navigating busy ports and berthing are two of the most challenging aspects of ferry operations. Increased vessel size, introduced in line with ‘safe return to port’ regulations, and challenging weather conditions mean the margin for error during these manoeuvres is tiny.
The SPECS super-wide cameras will give the crew a 360° view, from the edge of the hull to the horizon, streamed directly to the bridge in real-time. Live distance indications to objects around the vessel reduce risks of a collision, protecting passengers, crew and the ferry, while improved visibility helps Masters navigate rough seas.
With busy schedules to keep, minutes used manoeuvring on each side of a voyage can also quickly increase costs. The efficiencies achieved thanks to the assistance of the SPECS system can maximise trading time and minimise fuel consumption. By saving fuel, Brittany Ferries is also reducing its greenhouse gas emissions, advancing the company’s sustainability strategy.
Arnaud Le Poulichet, Director of Engineering and Maintenance, Brittany Ferries said: “When the captain is confident in manoeuvring it improves safety, saves time and fuel.
“This clear and strong return on investment makes adopting SPECS an obvious decision. But there is more to embracing digitalisation. Using the latest technology also plays an important role in attracting high-quality crew. By having innovative technology onboard, we make seafaring attractive to a new generation of seafarers – who we must engage in the industry.”
Sasha Heriot, Head of Product, Assistance Systems, Wärtsilä Voyage commented: “The company’s proactivity in adopting cutting-edge technology is impressive and will ensure it remains one of the leading cross-channel ferry operators.
“It is also encouraging that Brittany Ferries shares our vision of a high-tech future for bridge systems and is excited about not only the benefits SPECS can bring today, but also how technology will advance and develop into the future.
“SPECS provides the core situational data that will make this vision a reality and we are delighted to be partners with Brittany Ferries on this digital journey.”
SPECS also enables a host of other functions. Processed data can be exported for use in simulation and training.
Brittany Ferries plans to use the data to show other crew how manoeuvring can be performed in specific conditions and ports. Export to simulation facilities can also allow for close investigation into any vessel incidents and thus reduce the risk of similar occurrences. u
www.wartsila.com
Mark W. Barker, the first new U.S flagged Great Lakes bulker in almost 40 years, has successfully completed sea trials and will now begin trading throughout the freshwater lakes and river networks with oil-free propeller shaft bearings from Thordon Bearings.
Built in Sturgeon Bay, Wisconsin, by Fincantieri Bay Shipbuilding for The Interlake Steamship Company, Thordon’s scope of supply includes a water lubricated RiverTough bearing, Nickel-Chromium-Boron (NCB) alloy liner for a propeller shaft diameter of 445mm (17.5in), and two Thordon Water Quality Packages.
Designed to transport salt, iron ore, stone, and other bulk cargoes throughout some of the narrowest rivers in North America’s Great Lakes region, including the tight bends of the Cuyahoga River, the single screw Mark W. Barker is the 6th Interlake Steamship vessel that Thordon’s proprietary polymer bearings have been installed.
“Interlake has had a lot of success with our propeller shaft bearings,” said Jason Perry, Thordon’s Regional Manager, North America. “Their vessels operate in some of the region’s narrowest, shallowest waterways which means vessels are unable to turn and instead must reverse using bow and tunnel thrusters.
When operating at lower shaft speeds, the RiverTough polymer formulation reduces friction and bearing wear. The material can also withstand operations in highly abrasive, very sandy environments.”
Wear rates for RiverTough are typically less than half that of rubber bearings based on ship owner feedback. Offering increased resilience, easier shaft alignment and less edge loading, lubricants in the polymer material reduce friction levels during nearly-dry starts, significantly eliminating stick-slip and vibration at low shaft speeds. Results from shipowners have shown wear rates of 0.075mm to 0.100mm (0.003in to 0.004in) in 6000 to 7000 hours of annual use.
With a hull optimized for energy efficiency the 28,000dwt River-class bulker is powered by a pair of 400HP main engines driving a single controllable pitch propeller through twin-input, single out-put reduction gearbox. It is the first ship to operate on the Great Lakes with engines that meet EPA Tier 4 emissions standards.
EPA Tier 4 standards entered into force in January 2017, requiring marine engines rated at 600kW and above to be fitted with technologies capable of significantly reducing nitrogen oxide (NOx), sulphur dioxide (SOx) and particulate matter (PM).
Craig Carter, Vice President Business Development added: “Mark W. Barker is truly a milestone ship for Interlake and we are proud to be associated with what is arguably one of the most advanced, energy efficient selfunloading bulkers to operate on the Great Lakes.
“Our relationship with Interlake Steamship and Bay Shipbuilding dates back to 1998 when we installed propeller shaft bearings to the 25,000dwt Kaye E. Barker. Since then, we have enjoyed a very productive, collaborative relationship with both owner and yard and look forward to working together on future projects.” u
https://thordonbearings.com
Demand in the Deepwell cargo pump market is still being driven by cost and service support but owners and managers are reluctant to compromise on product quality or put up with poor after sales service, which is why companies like Cargo Care Solutions have seen a near tripling in business levels during the past three years.
According to Peter Peltenburg, CEO of the Dutch-based company, strong growth in the shipping markets has been behind the surge in orders. However, products need to be priced at the correct level and the right dialogue needs to be entered into with the market to ensure the right products are delivered, at the right quality and at the right price.
“We see our role as being a crucial element in the partnership that exists with the ship owner and the manager.
“We offer a complete alternative solution when it comes to the maintenance and support of a number of marketsupplied Deepwell cargo pumping systems, and our value proposition covers spares, service and support.
“Our vision is to allow our customers to operate their equipment in a safe, reliable and cost-efficient way.
“Yes, it is combination of price and service support but what we are starting to see is a need for an alternative in the market,” he said.
“Over the last years, we have significantly scaled our scope of supply, service activities and service locations, so we can keep accommodating the growing global demands of our customers.
“As a result, we can offer our clients global support from Rotterdam, Houston and Singapore with high quality spare
parts and local service from engineers with a long history at the original maker or extensive in-house training,” he added.
Cargo Care Solutions operates service stations in Rotterdam, Houston and Singapore where it offers parts and servicing for Deepwell cargo pumps.
“For vessels preparing for survey we can make a big difference when we are able to handle the complete project: pre-dock inspection, spare parts and service. In general, we offer all types of inspections - annual or pre-dock, we offer dry dock assistance for overhaul and maintenance of the cargo systems, on board troubleshooting and remote support on the complete cargo pumps system.”
But according to Mr Peltenburg, many of his competitors took their eye off the ball when it came to delivering the service levels demanded by the market and this paved the way for his firm to fill the gap.
“The volumes we buy in are sometimes smaller than our competitors, but we are still able to reduce our costs and make the money we need to make. Before, the market operated with an ethic of really expensive and very good service. Now with some companies it is still an ethic of expensive but with a poor service, and that isn’t good enough,” he said.
Cargo Care Solutions has offices in The Netherlands, Germany, Singapore, Denmark, China and the US and has its own Research & Development and test facility at its Rotterdam headquarters. u
www.cargocaresolutions.com
Anew life jacket that will increase survival time in cold water has been developed jointly by one of the UK’s largest port operators and a specialist safety supplier.
The personal floatation device has been two years in the making, filling a gap in the market for marine pilots and could be rolled out to other workers in water-based roles.
Peel Ports Group – working in partnership with Mullion Survival Technology, a producer of marine safety equipment – developed the jacket after undertaking an audit of similar products available on the market and concluded that existing jackets would not protect against the threat of cold-water shock.
Following two years of research, prototype testing and end-user consultations, the pilot jacket is now rolling off the production line, with Liverpool Pilotage Services Limited (LPSL) receiving the first order and Marine teams across Peel Ports Group expecting their jackets in the coming weeks.
A selection of other major ports and offshore companies have also tagged onto Peel Ports’ initial order to test the jacket.
The launch of the new pilot jacket forms part of a wider project led by Peel Ports Group’s Marine team to review the end-to-end process of boarding and landing of personnel to and from ships.
As well as the design and production of a new pilot jacket, the project has led to the development of a brand-new pilot ladder safety training course that is now being recognised by other major ports, and the introduction of regular ‘wet’ safety drills.
Nicole Read, Group Marine Projects Manager at Peel Ports Group said: “It has been fantastic to lead this innovative project, which represents an important step in further improving safety standards for marine pilots.
“The project involved listening to the needs of marine pilots and providing them with solutions and technologies that mean that if they are faced with an incident, they know they are safe.
“We’re very pleased to have developed a next-generation marine safety jacket, with three prototypes created over the course of two years in order to perfect the final product.”
The jacket boasts many innovative features, including some inspired by protective clothing encountered by Nicole Read when climbing and mountain biking, such as a helmetcompatible hood and back protector.
The device features a 150N integrated automatic life jacket, an AIS personal locator beacon and neoprene seals at the neck, waist and wrists to reduce the threat of cold-water shock.
Gary Doyle, Group Harbour Master at Peel Ports Group said: “I am delighted with the way this project has developed as a collaborative venture with Mullion. The intent was to improve safety and manage the impact of cold-water shock as much as possible. After extensive trials, it is pleasing to see that we have achieved this.”
Tim Meakin, Northern Regional Sales Manager for Mullion said: “It has been a pleasure to work with Nicole Read on this exciting project. She has devoted many hours, along with her partners in the industry, to help develop a product which we feel sure will set new standards in marine safety. Her input is hugely valued”. u
www.peelports.com
© Wikipedia https://en.wikipedia.org/ wiki/The_Blonde_%26_Pink_Albums
The Blonde & Pink Albums are a double album and collectively the fourth studio album by American drag queen and singer-songwriter Trixie Mattel. Released on June 24, 2022, the album was promoted by the singles “Hello Hello”, “This Town”, and “C’mon Loretta” prior to release and includes collaborations with Shakey Graves and Michelle Branch. The Blonde & Pink Albums primarily consist of power pop, pop rock and alternative rock songs, a departure from her earlier country and folk style. AllMusic contributor Matt Collar commented: “Part of Mattel’s appeal is that while her drag style is often over-the-top high-concept glam, her music is charmingly straightforward and The Blonde & Pink Albums are hooky, sugar-coated pop fun”. Surely there is nothing comparable to the mighty Cathedral Organ. From haunting penny whistle to mighty roof-raising bass there is no louder - or finer - sound in the musical realm than a pipe organ at full throttle. The purpose of this recording is to celebrate the 50th anniversary of the organ in Blackburn Cathedral, UK, with works that chronologically coincide with the instrument’s history. John Robinson is the Organist and Director of Music at Blackburn Cathedral, as well as the Director of the Blackburn Music Society and the Blackburn Chamber Choir. All the pieces on this recording are played with assured musicianship.
© Esquire - www.esquire.com
LAUS DEO - Various Composers - Blackburn Cathedral Organ - John Robinson (Organ) - 802561056126 - Released: August 2022 - Regent REGCD561
If you can’t bring yourself to buy an influencer-style ring light for your daily Zoom calls, then this is the perfect alternative. Logitech’s Litra Glow clips to the top of your laptop, emitting a wide and soft glow, and while it’s technically designed for streamers – i.e. Twitch gamers who haven’t slept in two days and would benefit from some flattering lighting – it’ll more than do the job for everyday work meetings. You can adjust the brightness and colour temperatures to find the best light for your skin tone, too.
Logitech Litra Glow, £59
The brand Nothing (best known for headphones so far) has had the world of tech enthusiasts patiently waiting for the reveal of their new smartphone. They promised something a little bit different, and they delivered on that. The back of the device is transparent, allowing you to see the inner workings of the device. In addition it features a number of LED lights that the company has called ‘Glyphs’. These lights flash in different ways to inform you of incoming calls, texts, social media notifications and plenty of other alerts on your device. Elsewhere, the team at Nothing have fitted in a solid battery, strong camera performance and a good display.
© Science Focus - www.sciencefocus.com
Considered one of the greatest contemporary Australian artists of the past two decades, Sally Gabori began painting in 2005, around the age of eighty, and rapidly achieved national and international renown as an artist. In just a few short years of a rare creative intensity, and prior to her death in 2015, she developed a unique, vibrantly colourful body of work with no apparent ties to other aesthetic currents, particularly within contemporary Aboriginal painting. Bringing together some thirty monumental paintings, this exhibition is organised in close collaboration with the artist’s family and the Kaiadilt community, alongside the foremost specialists in Kaiadilt art and culture. They were present in Paris for its opening to pay tribute to this artist.
Tue-Sun 10am-8pm until Sunday 6th November 2022
With thanks to www.galleriesnow.net
Every day, Travis Devine puts on a cheap suit, grabs his faux-leather briefcase, and boards the 6:20 commuter train to Manhattan, where he works as an entry-level analyst at the city’s most prestigious investment firm. Then one morning Devine’s tedious routine is shattered by an anonymous email: She is dead. Sara Ewes, Devine’s co-worker and former girlfriend, has been found hanging in a storage room of his office building—presumably a suicide, prompting the NYPD to come calling on him. If that wasn’t enough, Devine receives another ominous visit, a confrontation that threatens to dredge up grim secrets from his past. This treacherous role will take Travis from the impossibly glittering lives he once saw only through a train window, to the darkest corners of the country’s economic halls of power.
“The 6:20 Man” by David Baldacci © Grand Central Publishing
With thanks to www.cntraveller.com
Thanks to www.goodreads.com
The bar at the newly transformed Maybourne Hotel is the old world glam we all need after years of sweatpants and cocktails at home, a real destination in the heart of Beverly Hills. Designed by architect and interior designer André Fu, known for his work at the ultra-sleek Upper House in Hong Kong, neither the interiors nor the cocktails, which nod to British classics with a SoCal twist, disappoint. No expense was spared when it came to building out the space which gives off old world European money meets Beverly Hills energy. The highlight of the room is the bar carved out of solid Turkish silver onyx paneled with ivory and walnut. Soft golden lighting hits the nickel backbar, giving everyone a sexy glow in this jewel box of a watering hole.