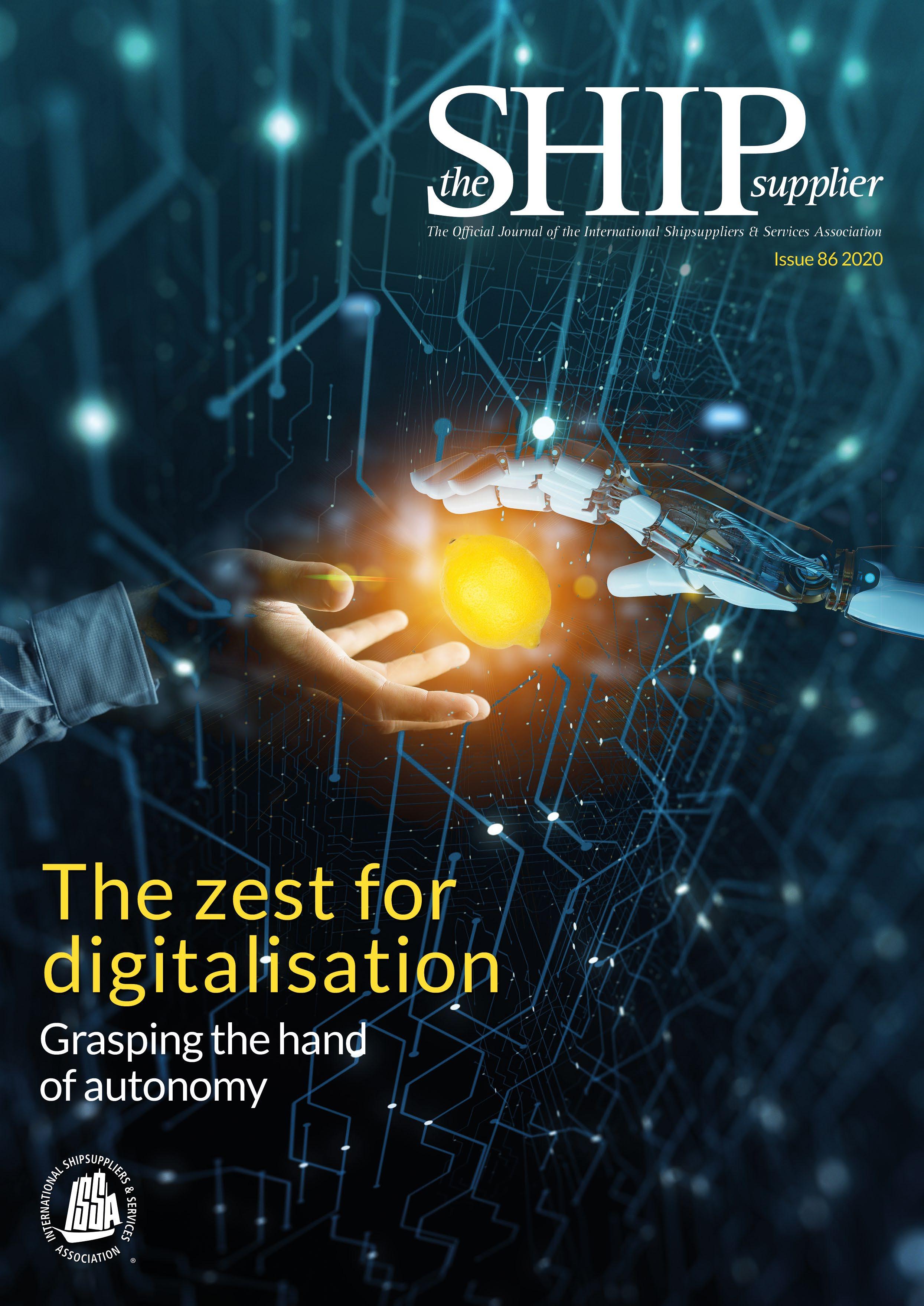
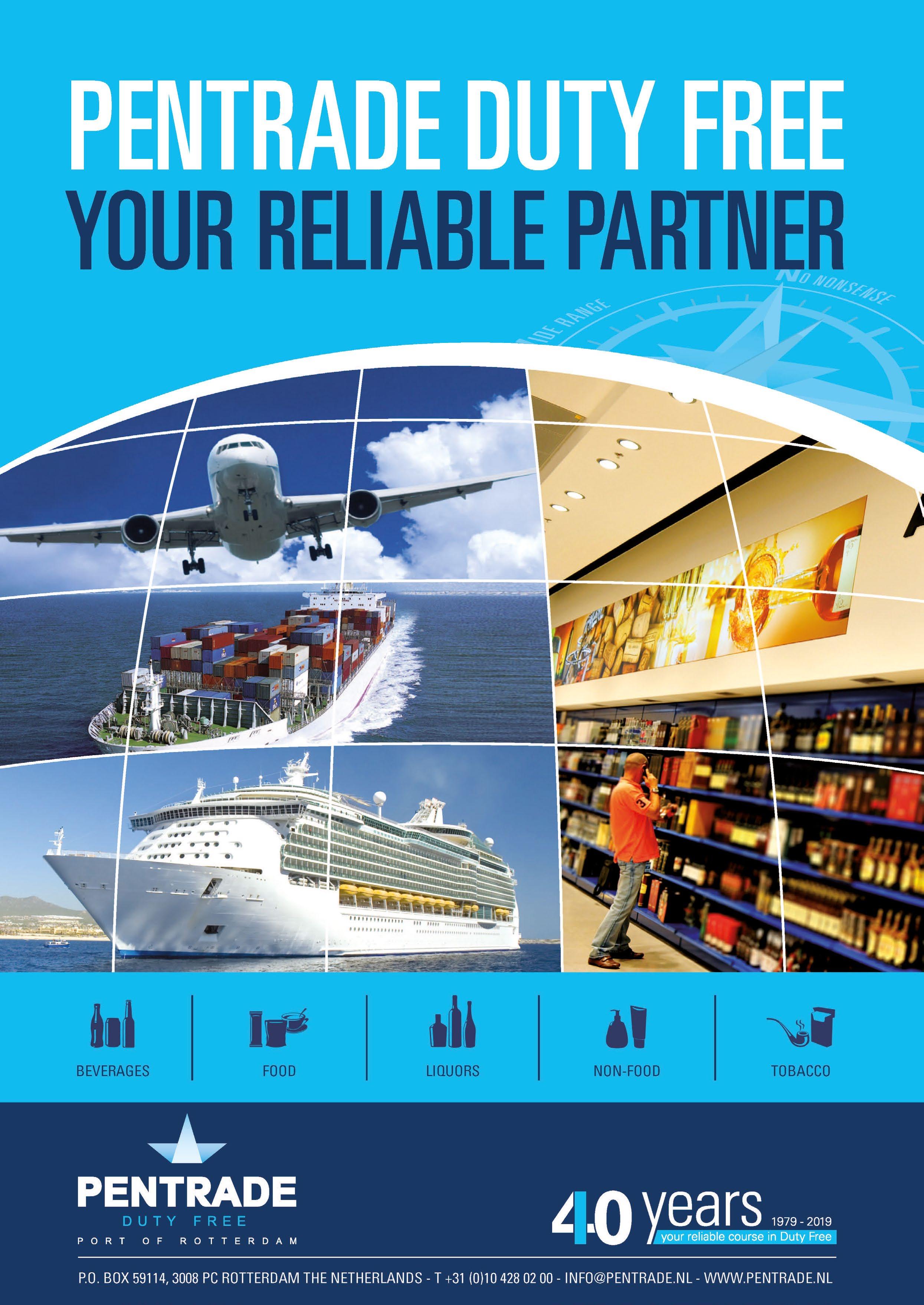
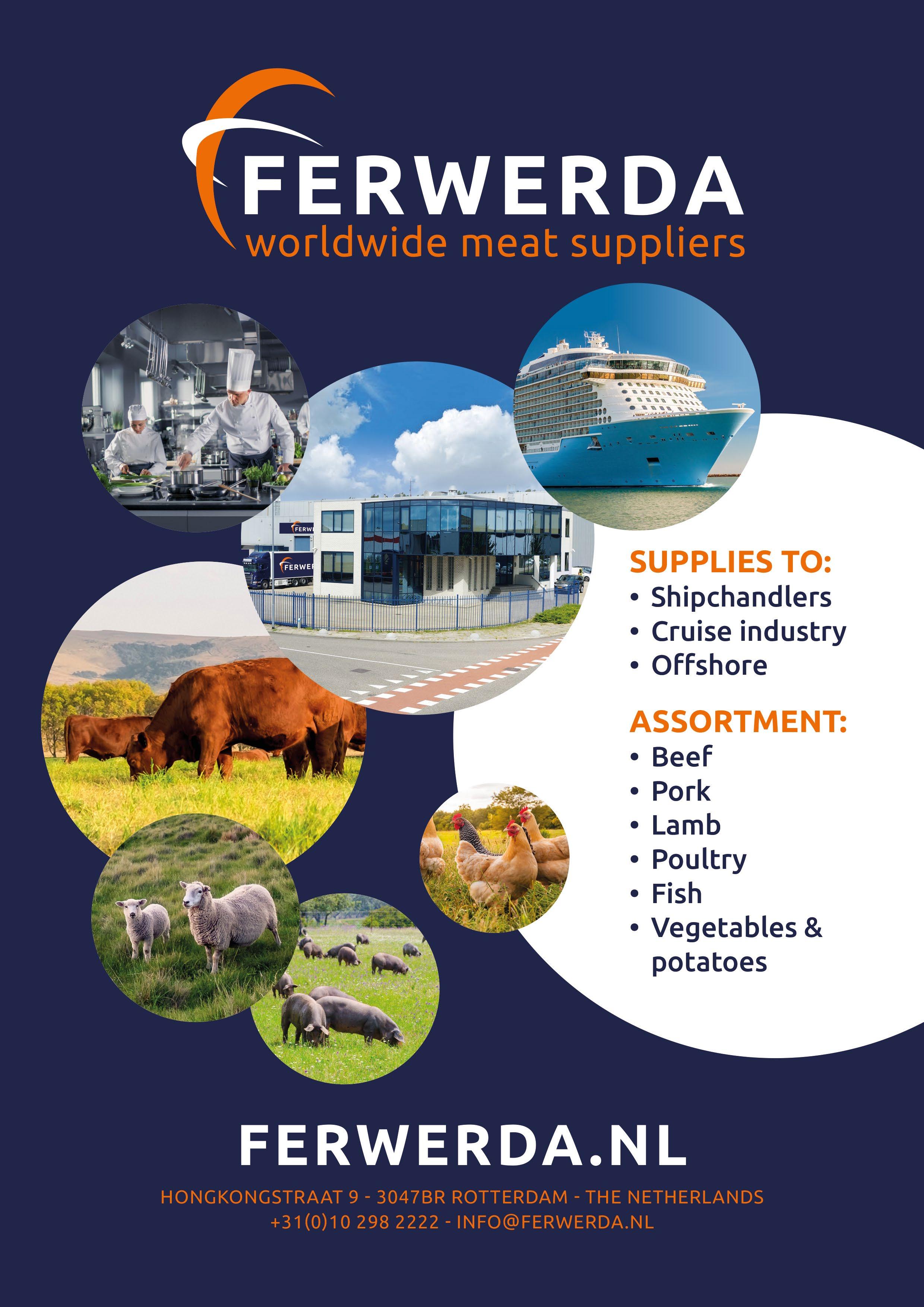
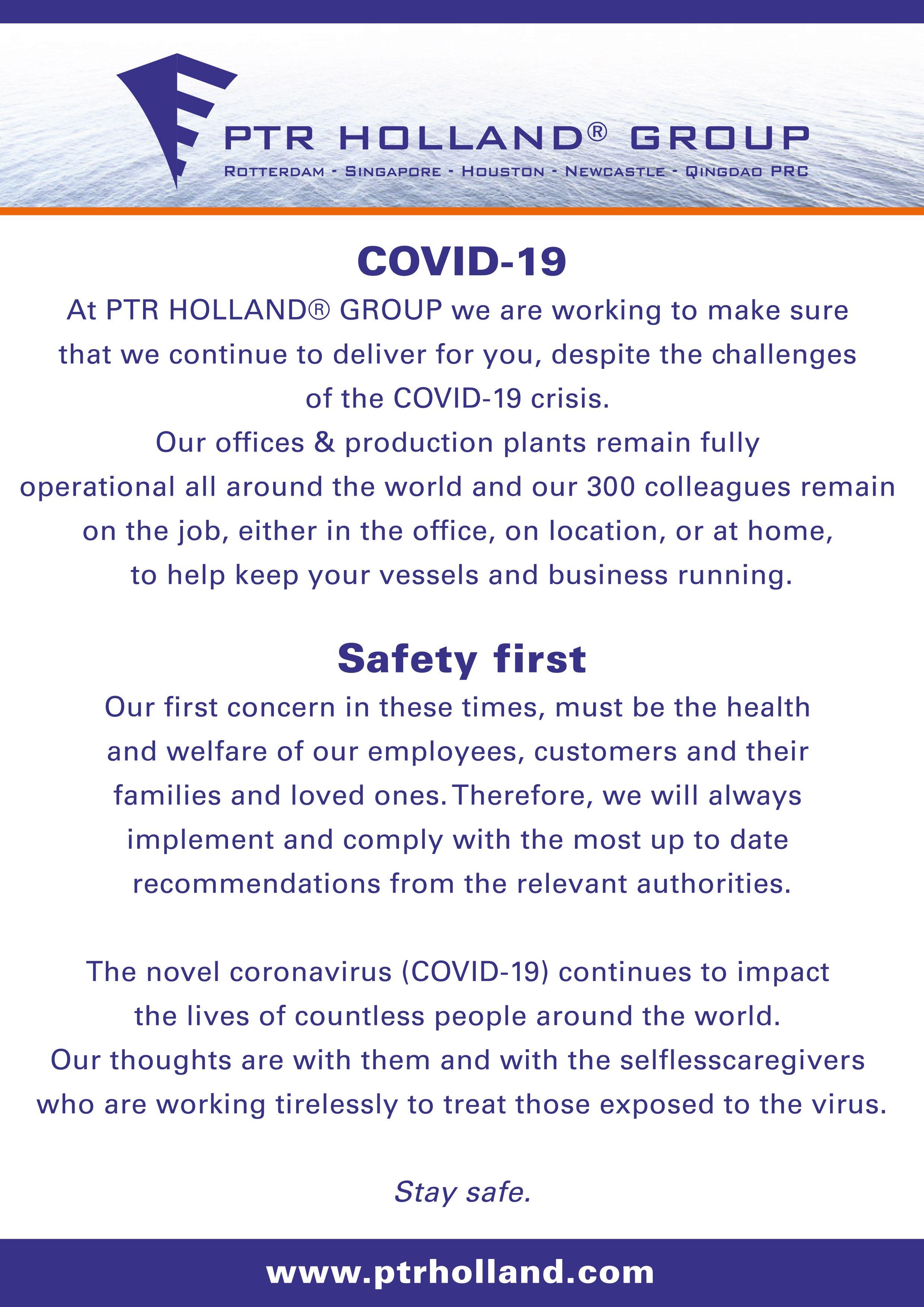
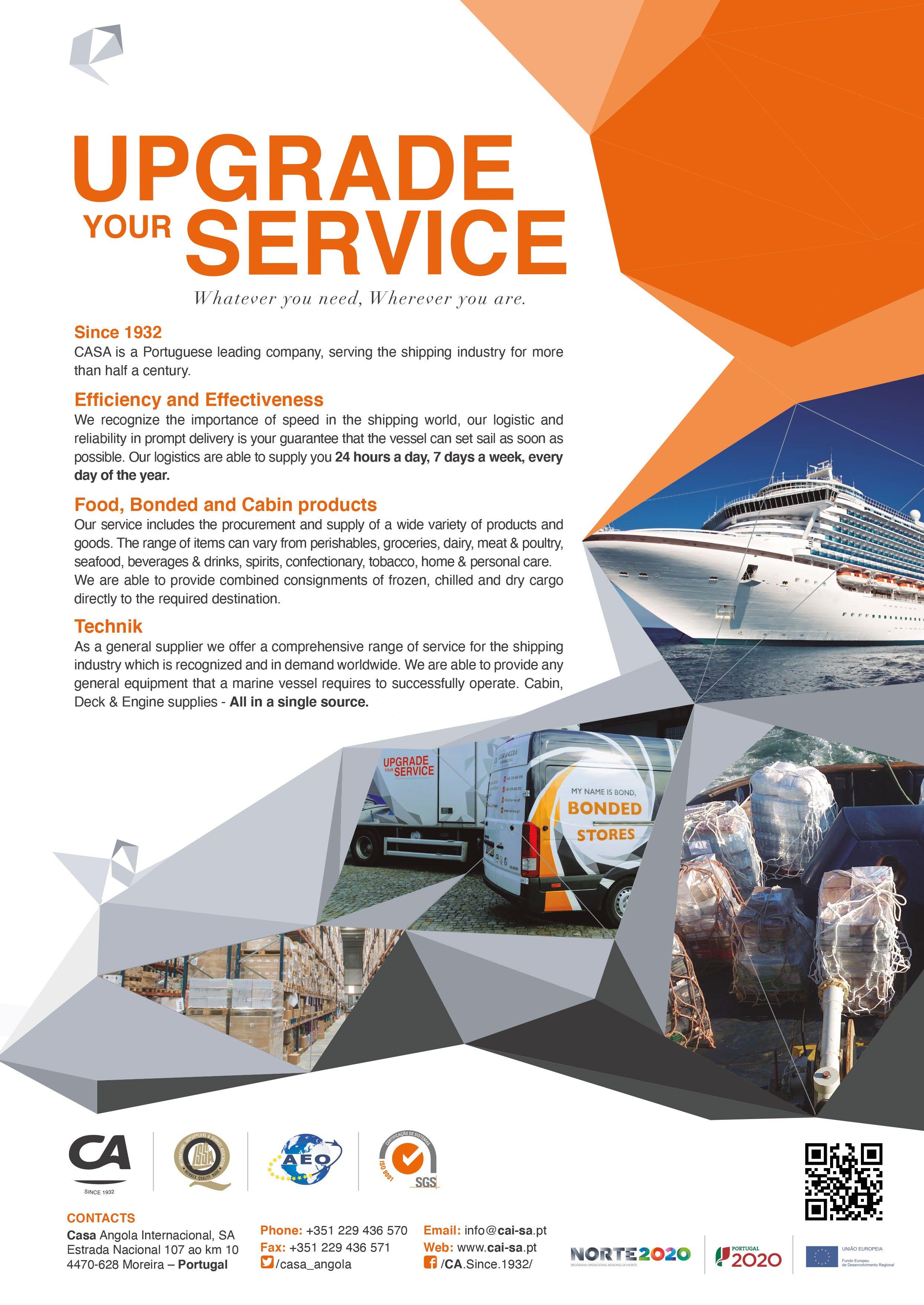

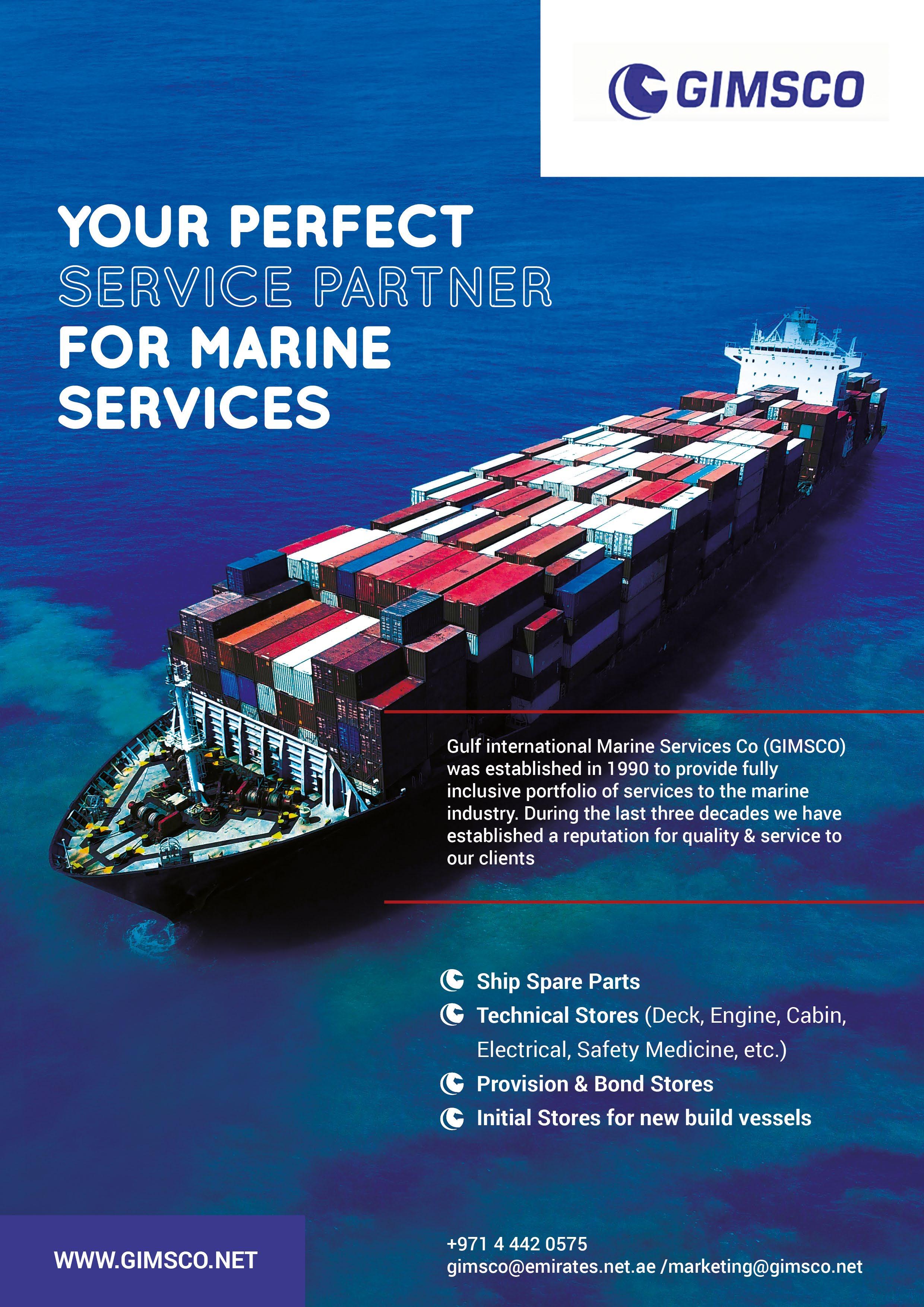
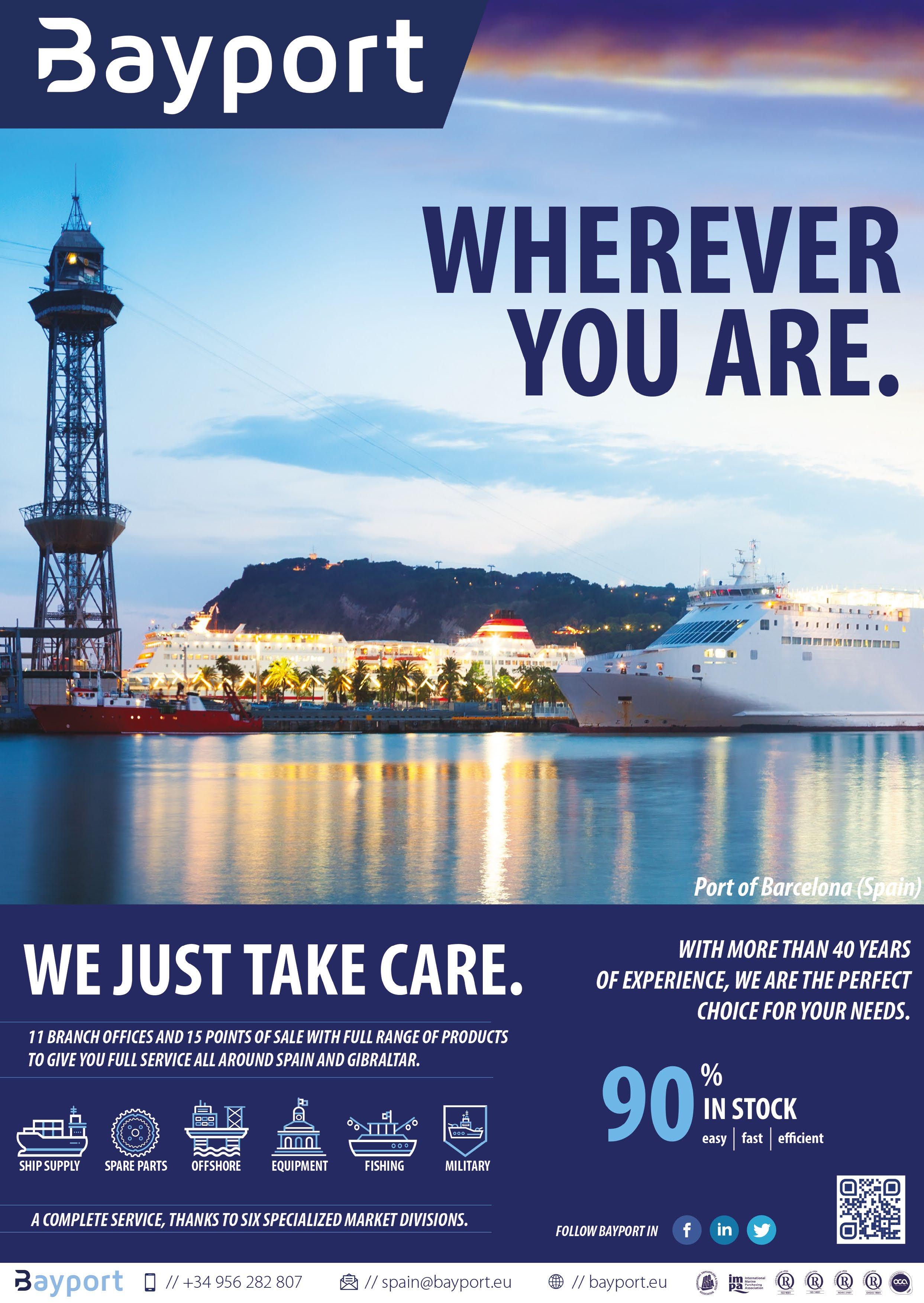
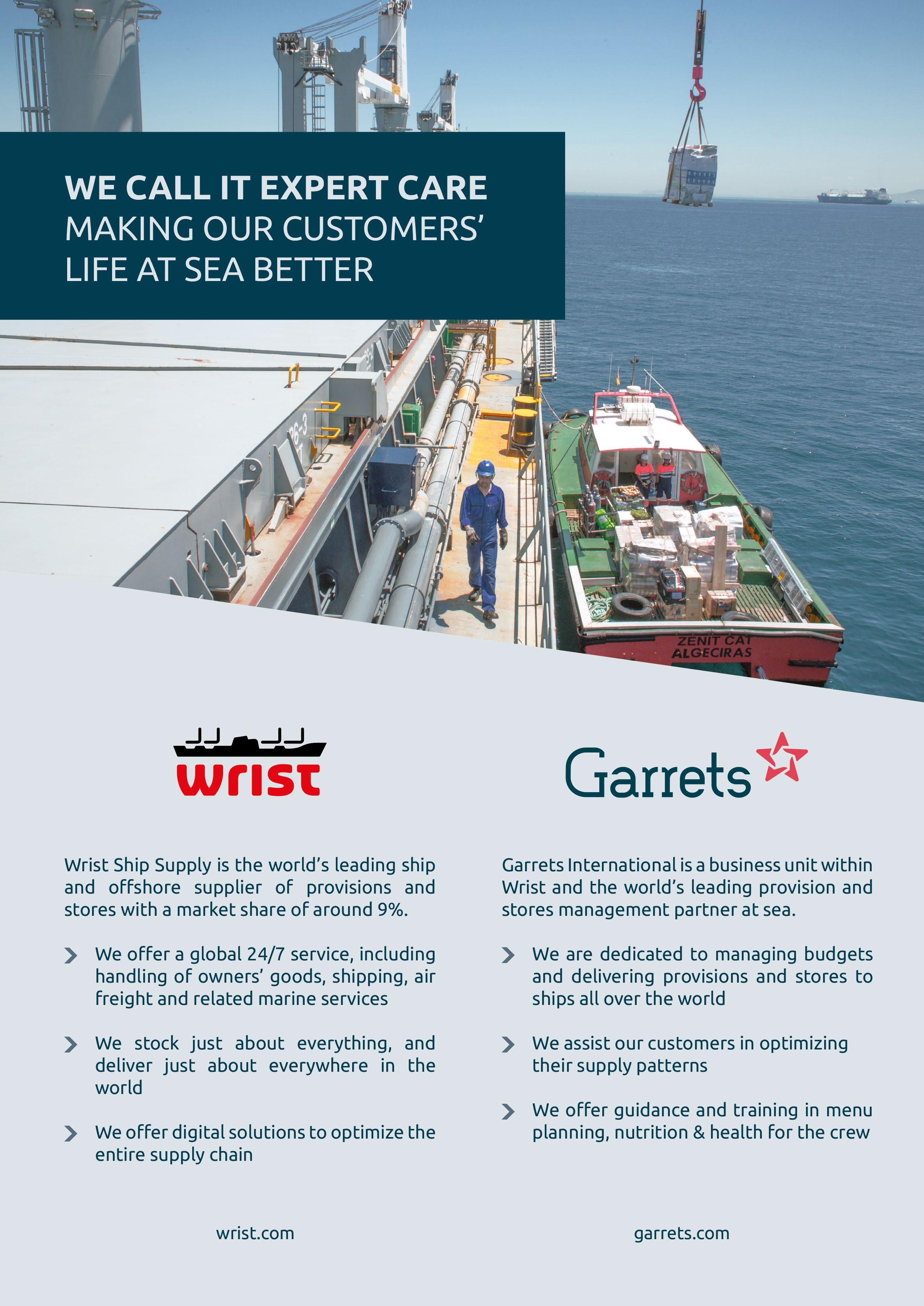
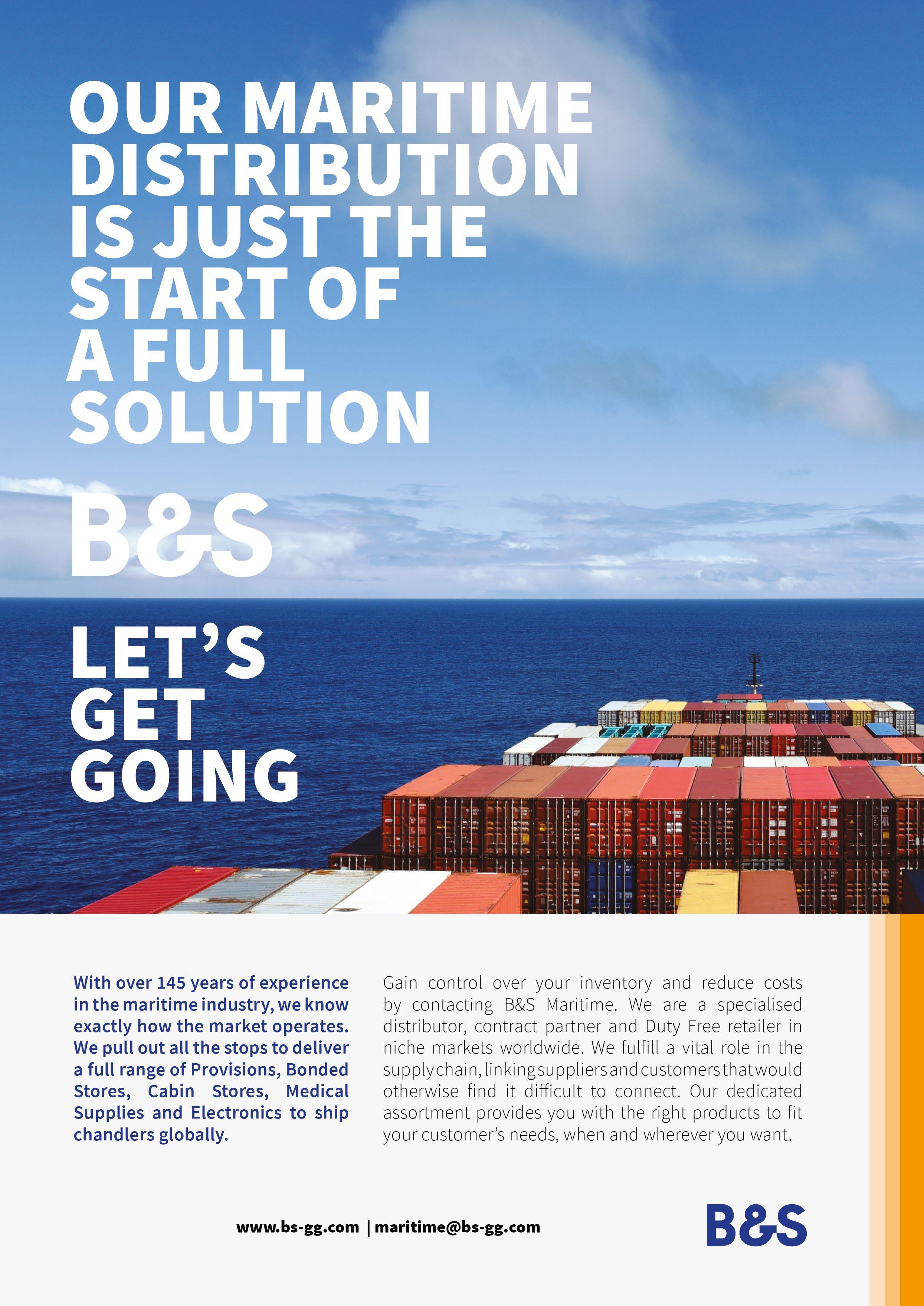

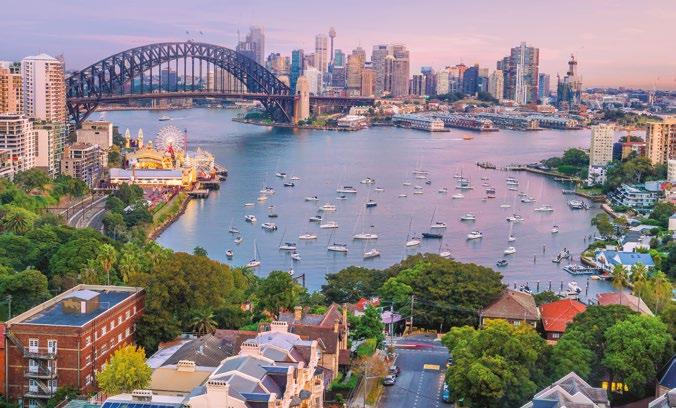
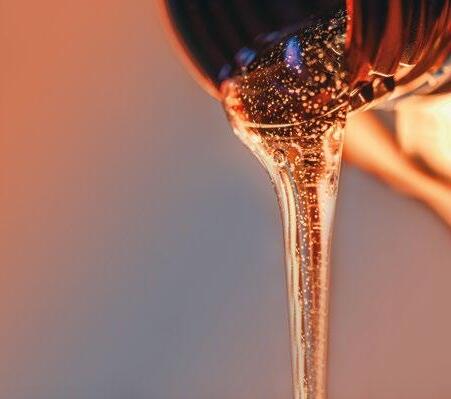
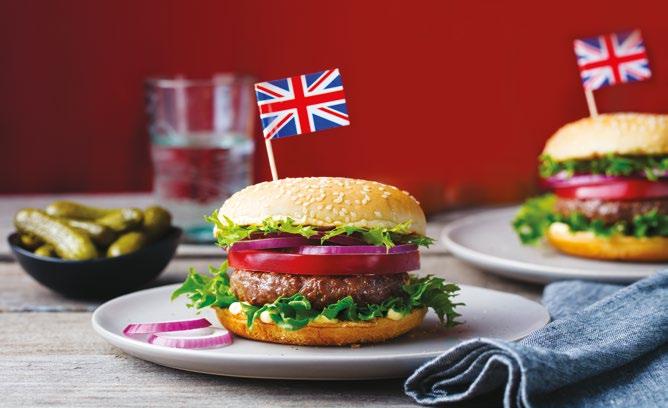
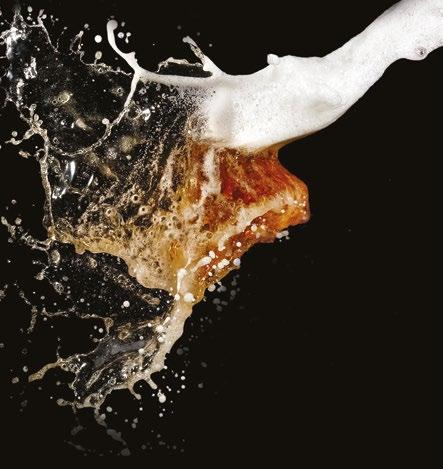
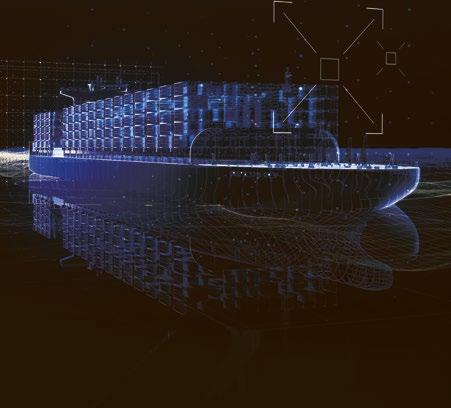
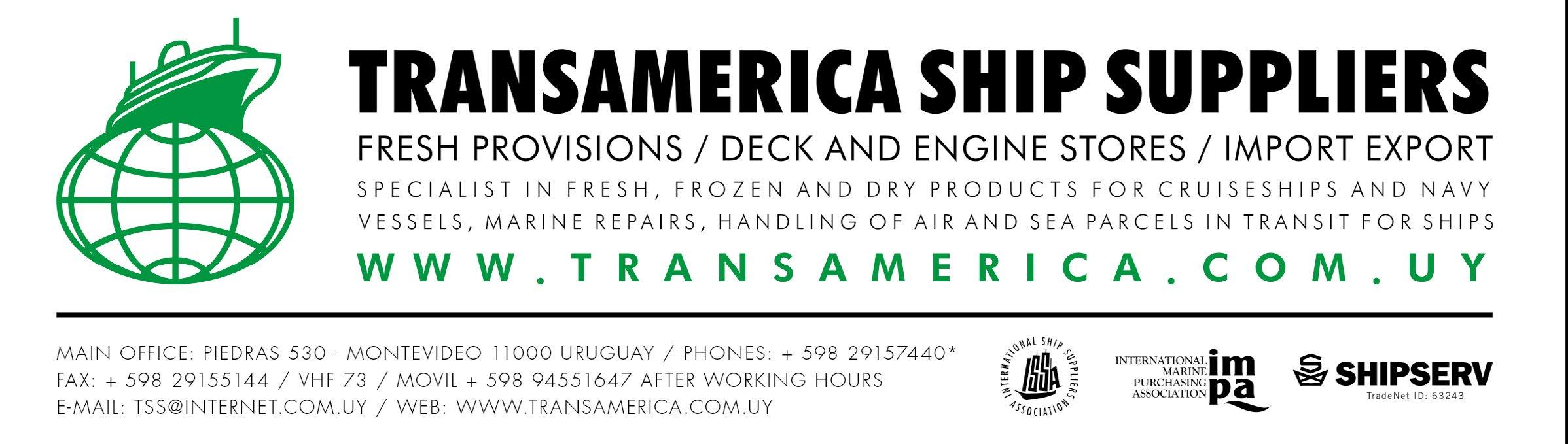
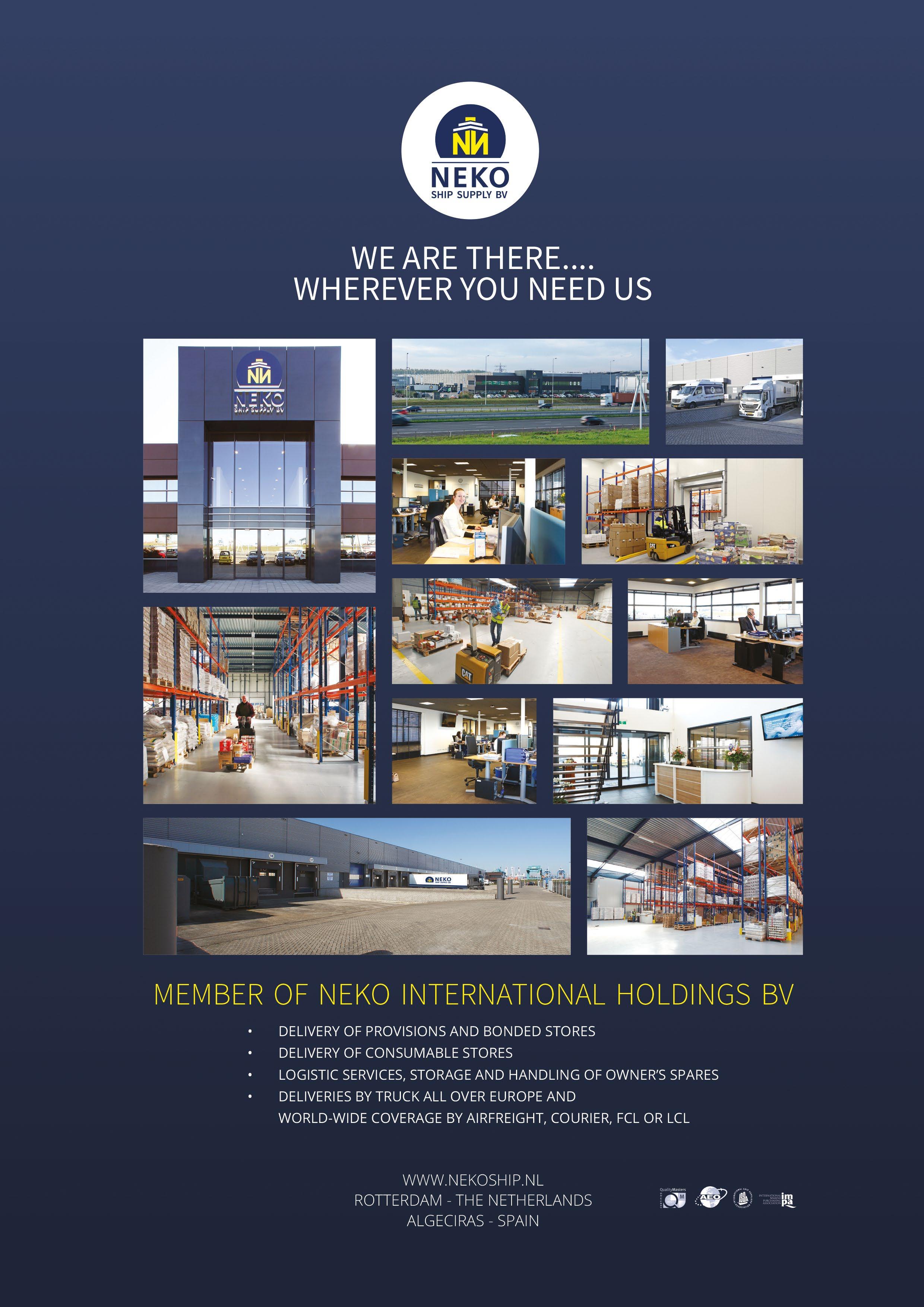
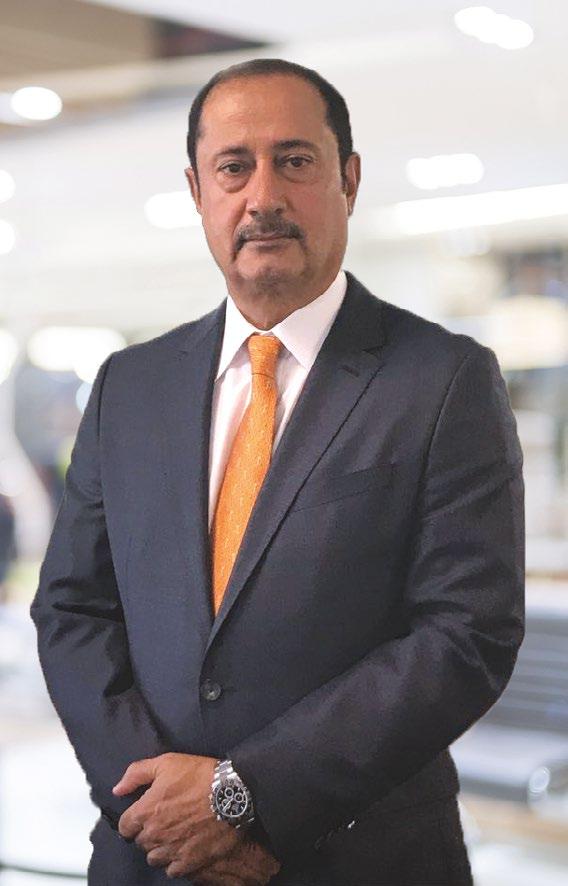
ear ISSA Members and Maritime Colleagues,
This very strange year has been racing by and while many of us find ourselves in and out of COVID-19 lockdown, industry and trade is continuing regardless.
Ships are still plying their trades and they still need supplying which underlines our view here at ISSA, that ship suppliers and seafarers should be regarded as key workers because of the hard and essential work they do. By being awarded this status, suppliers would find their movement from warehouse to ship and back unimpeded. They would also be free to move unhindered from country to country in pursuit of their profession.
We will continue to press home these demands and work with our owning and management colleagues in the industry to place the right amount of pressure on the regulators to highlight the important role our members play.
It has been a very busy three months especially in our work to update the ISSA Articles of Association. This is an important task because it ensures that ISSA is bang up-to-date when it comes to the rules surrounding its governance. We are also looking forward to developing our own ISSA App and work is progressing at a fast rate to have that ready by the end of the year. The ISSA App is an important tool as it will mean all our ISSA members can access everything they need from the ISSA portal at the click of a button on their mobile device. Exciting stuff.
I can’t write this Foreword without important reference to the two ISSA Catalogues which have now been printed and are ready for dispatch to ISSA Associate and National Association Members. And great thanks to my Executive Board colleague, Alfredo Tosato, and his team for their hard work here.
You can keep up to date with the latest news on the ISSA website at www.shipsupply.org and send in your comments and views to the ISSA Secretariat either by phone on +44 (0)20 7626 6236; Fax +44 (0)20 7626 6234 or alternatively email secretariat@shipsupply.org
The ISSA Ship Stores Catalogue is crammed with up to 60,000 items including new sections for The Polar Code and Superyachts. Priced at only €180 with discounts for multiple purchases, it represents great value for money. While the Provisions & Bonded Stores Catalogue, priced at only €150, again with multiple buy discounts, is the first of its kind in the industry and is full with up to 4,000 items and accompanying photographs. Anyone wishing to place an order please email the secretariat@shipsupply.org
Saeed al Malik ISSA PresidentThe President of the Australian Ship Suppliers Association says the ship supply market in Australia is “getting back to normal” from the COVID-19 pandemic which saw the cancellation of ISSA’s annual Convention, which was this year due to take place in Sydney.
“We are disappointed we needed to cancel the ISSA 2020 Convention in Sydney to mark the 65th year of ISSA and the 40th of ASSA,” said Mr Costalos. “I believe we were one of the first to cancel an event during the year, but it has proved that our decision was correct. Australia missed the
opportunity to showcase our beautiful country to the world. However, I am sure we will try again sometime in the future.”
Mr Costalos said that during the height of the pandemic between March and June, all Australian suppliers were inundated with orders. The numbers of ships calling had not altered, however the orders had increased threefold.
“Due to the uncertainty of quality available around the world, ship owners took the initiative to store in Australia,” Mr Costalos told The Ship Supplier. “Australia is well known as one of, if not the best for quality, safety and true to label goods
in the world. Of course, Australia is considered a little more expensive than some major storing ports around the world, however many owners understand this but realise in Australia there is value for money. With Australian goods, they have longer lasting quality products thus reducing the amount of wastage, which at times purchasers do not take into account.”
He said the weaker Australian dollar had also helped further reduce any difference.
COVID-19 has affected the Australian market both positively and negatively. From a provision supply perspective, although business increased there were
minor concerns with the availability of technical goods. With border closures and cancellation of flights, the availabllity and easy access to specialised technical items became difficult. Nevertheless, the “never say die” attitude of Australian suppliers prevailed to complete supplies to the upmost satisfaction of the ship owners and managers. Owners’ ships’ spares from overseas also became an issue due to limited flights, however members assisted as much as possible.
The cruise market was also an area that hurt many Australian suppliers. In some instances, cruise operators entering liquidation caused losses for members, whilst many surviving cruise operators caused serious delays in their payment for goods taken in Australia, causing cash flow situations.
“I am sure this is the same around the world and not unique to Australia,” Mr Costalos said. “General shipping also faced difficulties and, as we all know, if the ship owners suffer, so do the ship suppliers. Australian suppliers are now monitoring credit terms and conditions closer and
ISSA is also taking a positive step on this to assist its members worldwide.”
There have also been difficulties with crew changes due to restrictions on entering the country.
“Unfortunately, the seafarers have endured a difficult time. Further, our boarding officers are not permitted to board any vessels, thus causing slight difficulties in the industry,” explained Mr Costalos.
Australians are currently not allowed to travel overseas without approval from Canberra whilst persons entering Australia are prohibited unless they are Australians or have special reasons. The borders between states are also closed. Especially to Victoria, New South Wales, Tasmania & the Australian Capital Territory where COVID-19 continues to be active. Queensland, Western Australia, South Australia and the Northern Territory are relatively safer places.
“I believe the main lesson from the COVID situation is the importance of local manufacture. I can see the Australian government looking at re-establishing
manufacturing in Australia, something that unfortunately has been declining for many years,” said Mr Costalos. “Obviously hygiene needs to be maintained at a high level at all times. A positive from COVID was the reduction of the Flu and other contagious diseases.”
Discussing the immediate future, Mr Costalos said he believed there would be a general improvement in business during the next year and it would hopefully be back to normal sometime in 2021. “It will continue to be difficult and the ship supplier will need to be active in many areas, better purchasing, better cost control, higher vetting of customers credit terms, higher and more services offered as value for money to our customers, and general improvement in operational control,” he said.
Unfortunately, the Australian Ship Suppliers & Services Association, which has been in a healthy and steady condition for a number of years , lost a ‘services’ member due to COVID-19 bringing the total number to 17 members ( 15 full & two Associate) . u
While the COVID-19 pandemic has hit many suppliers hard, the ship supply sector in Singapore has remained relatively stable during the last few months with a spike in volumes during the first half of 2020.
“This is likely because many of the major ports were closed during the height of the pandemic and Singapore was a good choice to take supplies given its control over the situation,” said Danny Lien, President of Singapore Association of Shipsuppliers & Services (SASS).
However, he said that suppliers were facing an uncertain global economic outlook that will hurt consumption, which in turn will hurt international trade. Another external challenge is the tensions of trade wars among countries such as America, China, Australia, Korea and Japan. “This will further depress international trade which will have a major impact on cargo shipments,” he said.
Mr Lien said the fear of shipping companies defaulting on payments and late payments from customers because of various reasons all add to the cash flow challenges ship suppliers are facing.
“Many SASS members are already experiencing longer than usual payment from their customers while the
suppliers to ship suppliers are pressing for prompt payment which can potentially create cash flow gaps,” said Mr Lien.
As well as external challenges he said members were experiencing some more specific to Singapore including the perennial shortage of labour. As Singapore ship suppliers are very dependent on foreign workers, the travel restrictions have created a shortfall of staff and the poaching of competitors’ employees has inadvertently driven up staff costs which has added to the already high operating costs in Singapore.
Mr Lien said the outlook for the next 12 to 18 months remained challenging with many countries experiencing a second or third wave of infections.
“Ship suppliers need to transform their businesses to remain agile and less labour intensive while at the same time being able to operate in the new normal of working from home as well as practising social distancing,” he said.
“The new normal will require businesses to be digitally connected to their customers and their suppliers to leverage on technology as their cutting edge.”
He added that Singapore ship suppliers were now being encouraged by Government agencies to digitalise their business to remain competitive
and efficient. SASS remains a strong proponent of digitalising the ship supply industry in Singapore, he said, and now works very closely with all the Government agencies and ports to help the industry adopt digitalisation.
Mr Lien said one positive during the pandemic was that SASS’s membership had grown when many businesses were required to shut down to prevent the spread of the virus.
“Many suppliers to the ship suppliers who were not SASS members turned to SASS for assistance and support to obtain the permit to continue operating,” he said. “SASS was able to lobby the Government agencies and the suppliers were allowed permits to operate within the guidelines stipulated by the authorities.” u
Abdul Hameed Hajah, Senior Executive Vice-President of ISSA and an advisor to SASS, highlighted how substantial Government assistance and good cooperation between industry partners greatly helped companies in Singapore to get through the challenges presented by COVID-19.
SASS had worked closely with the Maritime Port Authority of Singapore and many of its members were given permission to continue operating during the partial lockdown as they were classified as essential services. Other members were in direct contact with the relevant ministries, thereby speeding up the process for approval. The pandemic highlighted the importance of industry cooperation within the shipping fraternity and the interdependence between ship suppliers and related service providers.
Likewise, at the international level, the IMO had accepted ISSA’s request to include ship supplies as essential services in their letter to member countries. This made it easier for members around the world to continue with their operations despite the worsening Coronavirus situation.
Once it became clear that the Coronavirus situation in Singapore had to be contained with more drastic measures, the Government doubled up efforts to ensure there was additional assistance to facilitate working from home and accommodating Malaysian workers who were unable to return home due to border closures. Companies also received wage support and a period of rental relief in order to help them get through the crisis.
Agreeing with Mr Lien, he believes that one consequence of this pandemic is a realisation that telecommuting and working remotely are not impossible to implement and may in fact result in greater cost savings for the company. If companies can harness the technology available today to improve their work processes in the future, it may forever change the way we do business. u
On no account “make it snappy”
Snap Back. No, not a feisty conversational response but a highly dangerous phenomenon. When a ship’s mooring rope “snaps” it flies “back” at speeds up to 500mph with often lethal consequences to anyone standing in the wrong spot – hence Snap Back.
The statistics highlighting mooring ropes activities have been brought into stark relief by P&I Club, the respected UK marine insurer.
The Club’s released data shows over half of all reported injuries over the past 20 years occurred during mooring.
Some 40% of serious accidents were due to lines breaking or tightening unexpectedly with an estimate that seafarers had a one in four chance of losing a limb and one in seven chance of death from a rope accident.
Step forward mighty Maersk who have risen to the challenge to reduce or even eliminate these alarming statistics so far as their own mooring operations are concerned.
How? By implementing an innovation called Snap Back Arrestor (SBA) ropes on the mooring lines used to hold vessels in place while docked in port for loading and unloading.
Maersk has chosen Norwegian-based manufacturer TIMM ROPES (part of industry giant Wilhelmsen) that offers new mooring rope technology featuring a special core that elongates more than the surrounding rope, acting to absorb and dampen the tremendous energy released when mooring ropes break while under strain.
As a result, instead of snapping back in unpredictable ways at great speed, a broken SBA rope will simply drop to the ground.
The new ropes are also coloured with a Maersk blue colour stripe, making it easier for operators to spot any damage or twists in the rope that could affect breakage.
Maersk confirms this is another important visual feature developed to enhance the safety of those involved in ship mooring operations.
“This SBA rope technology embraces one of the fundamental elements of our “Safety Differently approach,
This new technology and innovative approach enables us to safely transform the mooring rope approach in our industry and help lead by example to protect our seafarer community and our dockworkers ashore
by building in capacity to safeguard people,” said Aslak Ross, Maersk’s Head of Marine Standards.
Each year Maersk buys and replaces some 1,000 mooring ropes – an annual expense of nearly $2 million.
Maersk will be implementing an exchange program in which their current mooring ropes will be replaced at the end of their five-year lifecycle with SBA enhanced ropes and Maersk anticipates that full fleet implementation of the new SBA ropes will be completed within five years.
“This new technology and innovative approach enables us to safely transform the mooring rope approach in our industry and help lead by example to protect our seafarer community and our dockworkers ashore,” added Ross.
The Timm SBA has been in development for seven years.
It now has DNV GL verification and Timm say it is the first rope on the market with human-centred design at its core.
It is this unique design feature that looks set to eliminate over time the injuries and fatalities presently to be seen in the mooring operations of ships worldwide.
(With acknowledgement to Maritime Executive and Timm Ropes/Wilhelmsen Norway). u
Ballast Water Management System (BWMS) provider Ecochlor has set up its first location for spare parts outside of the US, in Singapore.
Michael Madely, VP of Global Service at Ecochlor, says it will be the first of many planned locations for Ecochlor’s spare parts support network.
“Having an inventory of spare parts located in Singapore will provide a faster response time to all vessels in Asia with our system onboard. Our goal is to have parts located in the three main time zones – Asia, Europe and the US – in an effort to provide real-time response to our customers’ requirements for maximum system operation with minimum downtime.”
Ecochlor has just completed the shipment of more than USD 117,000 in spare parts to Singapore to better support clients in Asia during installations and service calls for their vessel’s ballast water management system (BWMS).
Ecochlor’s global growth and strong after-sale service support programs are a big factor in the company’s continued success in the BWMS industry.
The company recently received Type Approval from the Norwegian Maritime Authority (NMA) for the IMO BWMS Code (MEPC.300(72) / revised 2016 G8)
standards. The new certification applies to the entire range of Ecochlor BWMS, with flow rates of between 500 m3/hr. and 16,200 m3/hr., meaning that vessel owners may continue to install Ecochlor’s BWMS after the IMO BWMS Code October 28, 2020 deadline. The company completed the additional testing required for active substance technologies for full approval in marine, brackish and fresh waters earlier in the year. The tests confirmed that no changes in equipment or in the operation of the Ecochlor BWMS were required.
Ecochlor’s BWMS uses a two-step treatment process to treat ballast water; filtration and chlorine dioxide. Treatment is during uptake only, with no discharge neutralisation step required. The company has the capability to supply, service and support its
systems worldwide and has a reputation for delivering an easy-to-use system for ship crews. The system requires minimal crew involvement during operation and does not have any TRO components, which can cause interruption to both ballasting and de-ballasting operations. Treatment dosage and efficacy are not affected by salinity, temperature or “dirty” water - all factors that result in uncertainty as to the efficacy of other technologies. The system energy requirement is very low, possibly the lowest of any BWMS on the market.
After 28th October 2020, all vessels installing a BWMS must comply with the international BWMS Code. Approval pursuant to the previous G8 guidelines (MEPC.174(58)) will no longer be acceptable.
“This latest regulatory approval is another example of Ecochlor’s unwavering commitment to obtain and maintain regulatory approvals from Class Societies and Flag Administrations across the globe, even as the requirements continue to evolve,” said Steve Candito, Ecochlor’s CEO. u
The Asia region continues to be a key destination for UK exports of meat and dairy, with the UK and Japan recently agreeing an historic free-trade agreement which will help growth opportunities in this high-value market.
That’s according to Dr Phil Hadley (pictured right), International Market Development Director for the Agriculture and Horticulture Development Board (AHDB), the levy board which represents farmers, growers and others in the supply chain.
“While Japan is a relatively new market for our beef and lamb, having only secured market access last year, our beef exports for the first six months of 2020 were worth £4.7 million,” he told The Ship Supplier
He said that throughout 2020, and despite the COVID-19 pandemic, there had been strong demand for UK products as well as stable trade to the EU and the main reason for this is the quality and provenance involved.
“UK products are considered by many as being high quality, natural and produced with integrity. They are not sold as ‘cheap’ products, but as high end, desirable and premium products, commanding a price accordingly. With our livestock being grass fed and the UK operating to some of the highest welfare and food safety standards in the world, we are able to compete with countries around the world.”
However, the pandemic has caused some short-term disruptions and price rises for
containers due to delay in unloading and returns, which has hampered trade, and exports destined for the food service sector, although recovering slowly, have not yet achieved preCOVID levels and may not for some time, warned Dr Hadley.
Despite these challenges, AHDB has still been able to ship its products around the world and the issues being faced are now largely resolved. In fact, red meat exports were worth £733 million in the first six months of the year – up nearly 3% on the same period last year.
Dr Hadley said in certain markets there is still a strong desire from specific consumer segments for particular products which tend to be products that are clearly labelled and sold at a very high premium such as antiobiotic free, grass fed and high welfare.
There is a strong trade for dairy and meat to the EU and Asia, as well as growing opportunities to North American markets.
With Brexit just around the corner, he said that there were obviously ongoing Government negotiations but from an export perspective, the EU is a long-established and valuable market. “Therefore, it is vitally important that we have favourable terms of trade to mitigate the disruption to the EU,” he said.
The AHDB currently holds over 80 export health certificates in the livestock sector.
In terms of future growth and expansion, Dr Hadley said the US and Canada offer real potential for growth, with exports of pork, lamb and beef to the North American market enjoying a strong start to the year.
In the first six months of the year, its beef shipments to Canada had grown to 968 tonnes from a modest 26 tonnes during the same period last year, and exports of total pig meat, including offal, increased by more than 400% to just over 500 tonnes, with lamb export volumes up by a staggering 1,800%.
“Despite the volumes being lower than other markets, the figures show the potential to grow our red meat exports in this all-important region,” said Dr Hadley.
He explained that the US market had been more of a challenge for exporters since the 25% tariff on pork was introduced in October last year. However, shipments had been steadily increasing since February from a low 137 tonnes to 724 tonnes in June – just 28 tonnes below the same period last year. The UK is also on the cusp of seeing its beef shipped to the US for the first time in over 20 years, with the market estimated to be worth £66 million in the first five years alone.
“We are also expecting to see growth opportunities in the Middle East and, in the medium-longer term, emerging markets such as India hold real potential for our red meat exports,” said Dr Hadley.
Overall, he added, UK meat products remained in strong demand with wholesalers and ship chandlers due to the recognised quality. u
The recognised quality of our products mean they remain in strong demand
Shipping companies can apply their own environmental procedures in an instant with the launch of OneOcean’s new add-on to EnviroManager.
EnviroManager+ allows users to deliver timely, positionbased information and clarity across the fleet with location specific policies.
Available to commercial maritime companies as well as cruise and superyacht operators, EnviroManager+ allows company-specific regulations to be applied across a full fleet, a select group, vessel type or location. Updates can be added and deployed within minutes to reflect company policies and ensure position-based data is delivered quickly. This ensures crews have the right information at the right time to make the best decisions.
Today’s ever-changing environmental regulations mean companies must ensure vessels are operating efficiently to avoid penalties incurred for non-compliance. EnviroManager+ has been developed to help mitigate the risk of making costly errors such as straying into territorial waters, for example, extra buffers and instructions can be added to indicate when and where it is best to drop anchor. By incorporating bespoke procedures and regulations,
EnviroManager+ enables ship operators and management companies to go above and beyond minimum regulation requirements whilst demonstrating that they are doing their bit to promote environmental awareness.
“We are delighted to announce the roll out of EnviroManager+ to the maritime industry,” said OneOcean’s CEO, Martin Taylor. “Through insights gathered from customer input, we identified a need for shoreside teams to provide onboard crew with clear guidance around company policies quickly and timely. Understanding what actions can be undertaken based on company policies, in relation to maritime legislation and the location of a vessel, is a big task for onboard crew. Our aim is to help the shipping industry go above and beyond minimum regulatory requirements, providing customers with a practical way to enforce company policies and reduce risk.”
EnviroManager+ can instruct vessels to carry out a number of checks and procedures before entering local or environmentally controlled zones such as US Waters. Customised messages can be created and displayed alongside the regulations within EnviroManager for the company’s crew to see. u
More oxygen is needed onboard ships.
So says Survitec, a global leader in safety and survival solutions to the maritime industry and others.
Focus has switched to re-assessing the quantity of oxygen needed onboard different vessels in case of a COVID-19 outbreak or other respiratory infection.
Presently the IMDG Code and MFAG guidelines specify as a minimum 44 litres of medical grade oxygen at 200 bar to be carried.
“The current minimum may not be enough in the event of a new outbreak,” said Jan-Oskar Lid, Survitec’s Global Technical Sales Manager – Fire, Rescue & Safety.
The present minimum oxygen quantity carried will be enough for one COVID-19 patient to be treated for just over five hours.
“Obviously the present levels of oxygen carried on board will not be nearly enough to treat a number of virus-infected persons,” said Mr Lid.
He urges all operators and owners to increase the number of oxygen cylinders currently carried onboard.
Seafarers, while working on board, have the right under the Maritime Labour Convention to the same level of medical care as comparable as possible to that available to workers ashore.
Mr Lid reminds the industry that medical oxygen is a prescription drug and an integral part of outfitting of any vessel.
In a bid to support its customers, Survitec has partnered with Netherlands-based Lagaay International offering its ISO 9809-1:2019 compliant MedOx medical oxygen cylinders.
Anticipating a significant increase in demand
Joris Alberda, Lagaay’s Managing Director said: “We will now work with Survitec to ensure maritime industry demand for medical oxygen can be met.”
Mr Lid added an important point: “Lagaay’s MedOx cylinders are filled to 200 bar as recommended by IMO. Other regions globally have different maximum filling pressures. In the USA it is 150 bar and in some Asian countries it is 128 bar.”
Details of installation standards and variations between Flag States may be obtained direct from Survitec.
Lagaay’s is the closest to a globally acceptable valve standard, specifically for medical oxygen delivery. u
LNG is presently the best fuel available to ship owners because it has been technologically proven to significantly reduce the environmental footprint of maritime transport. However, refined low-sulphur products and blended very-low sulphur fuel oils are becoming increasingly important.
Total began developing 0.5% sulphur fuels a few years ago in collaboration with partners across our industrial set-up, including research centres and our customers. The biggest takeaway is that engine cleanliness is essential, which has been confirmed by several sea trials. This requires our technical experts to provide a high level of in-depth technical awareness, support and solutions to ship operators to ensure they implement the right lubricants, monitoring tools and fuels strategy to achieve optimal engine performance and cleanliness.
Modern ships must have reliable engines that run quietly and meet strict environmental emission limits. Operators also seek to minimise operating costs, and this is why we have developed a comprehensive range of solutions.
Working with OEMs we have qualified products such as Talusia Universal that are developed using a unique chemistry that helps the neutralisation process and the control of engine deposit growth in the pistons, rings, and liners. In March we received a No Objection Letter (NOL) for Talusia Universal (BN57)
by WinGD for use with all fuels with a sulphur content 0.00%S to 1.50%S, and by MAN Energy Solutions for the same product following rigorous tests carried out on two different vessels fitted with W6X72 engines. For certain sectors of the industry we also provide a range trunk piston oils suitable for high to medium-speed four-stroke diesel engines. For example, our Aurelia and Disola products guarantee high safety margins, high levels of engine cleanliness and compatibility with all main fuel types, including low sulphur fuel oil, LNG, distillates, marine diesel oil and gas oil.
Total Lubmarine provides a comprehensive range of synthetic ester environmentally acceptable lubricants to comply with regional environmental regulations for sectors including cruise and ferry passenger ships, as well as bio lubricants and greases that fulfil Vessel General Permit requirements for oil-to-sea interfaces. We also provide technical support services and bespoke training for operators on topics such as better lubrication management.
What is clear, however, is that the shipping industry will continue to face changes with initiatives that deep dive further in to energy efficiency, emissions and greenhouse gas targets as industry’s knowledge and experience of new fuels evolve. We continue to strengthen our work with OEMs and the supply chain on how best to develop new formulations of cylinder lubricants and oils appropriate to the new fuels
of the future, and their application for both 2 stroke and 4 stroke engines. We are also looking at engine characteristics, energy saving systems, and operating conditions that can be enhanced to further reduce carbon dioxide emissions. u
Modern ships must have reliable engines that run quietly and meet strict environmental emission limits. Operators also seek to minimise operating costs, and this is why we have developed a comprehensive range of solutions
Global lubricants supplier Castrol says the role of marine lubricants has become increasingly important with the evolution of new fuels and engine technology.
More efficient engines, new and varied fuels, and recent changes to leading OEM cylinder oil strategies are making lubricant choice a more important and complex decision.
Castrol’s survey of marine owners, operators and managers, earlier this year, revealed that 30% of those surveyed had undertaken no or limited planning to prepare for these new fuels.
When the dynamic between engine, fuel and lubricant isn’t right it could result in reduced efficiency, dirtier engines, and damage to cylinders, while increasing costs.
The changes mean owners and operators should consult closely with lubricant providers to find solutions for engines that have a good balance of both cleaning and neutralising power.
Cassandra Higham (pictured), Marketing Director, Global Marine & Energy, Castrol, commented: “The sulphur cap means we have entered a new era of complexity in the engine room. In addition, the journey to decarbonisation will mean an increasingly diverse fuel mix, where lubricant choice becomes more critical.
“Increasing stress on engines, a focus on cost, and more blended fuels mean that previous assumptions in the choice of lubricants no longer apply. Castrol supports a new, collaborative approach, with an emphasis on engine cleanliness, in this more challenging operating environment.”
For years, the measure of performance of a cylinder oil has been largely based on its alkalinity, or base number (BN). However, with lower sulphur levels in fuels, cylinder oils need to have both cleaning and neutralising power to protect engine hardware. Castrol Cyltech 40SX was formulated with a bespoke detergency system specifically for use with low sulphur fuels.
Ms Higham added: “It is vital that lubricant providers, engine manufacturers, ship owners, fuel suppliers and technical staff come together to smooth the road for shipping. The current challenges are only the tip of the iceberg, as the shipping industry aims to transition to new lower carbon fuels and energy.”
Castrol is working with the whole sector to help change the way the market views marine lubricants. Part of this includes a programme of consultative operational and technical improvements that can ultimately drive efficiencies across the engine room – an initiative called ‘SmartGains’.
“As the industry works to stabilise, we’re encouraging the conversations,” concluded Ms Higham. u
The popularity of craft beers has been rising in recent years, and this trend has been lapped up by cruise ship passengers.
One such company which has seen sales rise in such products is international brewing giants Molson Coors Beverage Company, which operates through Molson Coors North America and Molson Coors Europe.
Jiri Rais, of the company’s Americas Travel Retail team, told The Ship Supplier : “The study of local markets and cruise passengers has allowed us to strategically target new up and coming trends. Over the past few years, we have seen the rise of craft beer onboard cruise lines. Molson Coors was able to take advantage of this movement and
bring great brands such as Blue Moon and Leinenkugels into the hands of passengers. It has become very apparent over the years that innovation will be key for cruise lines and their customers, hence why Molson Coors is exploring new beer segments such as seltzers and craft mixed drinks.”
Molson Coors has been brewing for more than two centuries. From Coors Light, Miller Lite, Molson Canadian, Carling and Staropramen to Coors Banquet, Blue Moon Belgian White, Leinenkugels’ Summer Shandy, Creemore Springs and more, the brewing company produces some of the most loved and iconic beer brands. But while the company’s history is rooted in beer, it also offers a modern portfolio that expands beyond beers with sparkling cocktails, canned wine, kombucha, cider and more.
Prior to the COVID-19 pandemic, Molson Coors saw a robust expansion of its flagship brands such as Coors Light, Blue Moon and Miller Lite in the cruise lines industry. Regional brands also played an important role for the company with the growth of brands such as Aspall Cyder around the UK and St Archer’s Gold for sailings from California. With regards to commercial vessels, Molson Coors has also been able to provide a balanced portfolio of beers to match the needs of crew and guests onboard.
However, the pandemic has undoubtedly affected the company’s different business units around the world, with the cruise industry impacted by a global shutdown which has put vessels out of action for many months.
“With the onset of COVID-19, we are in the same boat as all beverage suppliers; waiting for business to return to normal,” said Mr Rais. “We have been able to weather the storm with our partners and prepare game plans for growth once business resumes.”
One prominent trend the company has seen since the pandemic began is the rise in people drinking more at home, which has meant a significant increase in demand for packaging more typical in the off-premise market, typically cans, while there has been a corresponding decline in demand for onpremise packaging, such as kegs.
“Overall, this has created a bottle neck in the supply chain, that we’ve worked hard to adapt to, so that we can maintain consistent supply,” said Mr Rais.
“As countries have started to come out of lockdown, the on-premise business has started to gain some traction again, though it is very different to how it was before.”
When the cruise business opens up again it is expected that Miller Lite, Coors Light and Blue Moon will continue to be some of the most popular products among passengers. “They are core brands that every consumer enjoys and loves to drink while onboard,” said Mr Rais.
Recently, Molson Coors expanded its craft programme and started to include more regional and craft breweries from specific cruise itineraries. For example, it offered its Terrapin brand from Athens, Georgia to ships in the Caribbean, Saint Archers Brewing to ships sailing Mexican Riviera itinerates, and beers and cyders from Sharp’s and Aspall’s to ships sailing from the UK.
“Other than in craft, the rise of seltzers in the US and parts of Europe has become an important part of our strategy in the business,” said Mr Rais. “One trend we have seen develop over the past few years is the ‘better for you category’. The brands appeal to a growing consumer base that want simple, pure and organic ingredients in their beverages.”
Along with a change in tastes, environmental sustainability has been a key pillar that Molson Coors has been tackling for many years now and it was something consumers were valuing more and more each day.
“Protecting the environment and lowering our carbon footprint has been an important pillar in our company. We have significantly invested in decreasing our carbon footprint and lowering the amount of water we use to brew our beers. We have set up numerous initiatives across our company to save the environment and do our part in protecting our earth from harm,” said James Thacker, Travel Retail Senior Manager, Molson Coors.
Despite the pandemic currently affecting the cruise business, Molson Coors is confident that sales will bounce back.
“We believe the cruise business will come back even stronger than before,” said Mr Thacker.
“It might take time as we adjust to the post-COVID environment, however, we believe we have the right brands to succeed in the market. Molson Coors are expanding into new markets around the world, and we are doing the same in shipping and cruise – improving distribution to our brands, to deliver consistent availability around the globe. As we do this, we will continue to work with our customers to meet their needs across all channels.” u
One of the major post-COVID consumer expectations will be health and hygiene and brewer Anadolu EFES has taken this onboard by addressing concerns through its protective foil innovation on EFES cans.
The fifth largest brewer in Europe and 10th largest in the world says it has rolled out the innovation to every can in the EFES portfolio as part of its corporate responsibility to customers and consumers.
“Our 100% recyclable and easy-to-remove protective foils ensure the top of the can is untouched against dirt, dust and microbes,” explained Sertaç Karşı - Overseas Market Development Manager.
It is just one of the challenges the industry is having to adapt to since the start of the pandemic which has seen visible effects on ship supply.
“The cruise channel is significantly affected due to health concerns, yet the case is a bit different for commercial vessels,” said Mr Karşı. He said the initial reaction for commercial vessel ship supply was led by concerns regarding the continuation of access to supplies.
“We have seen vessel management teams stocking up for potential discontinuation of supply. However, this fluctuation is neutralised and the overall commercial vessel supply has seen less damaging effects compared to the cruise channel, which has ground to a halt since the early months of the year.”
He said despite the market challenges posed by COVD-19, the company remained optimistic for the future of ship supply.
Anadolu EFES boasts a portfolio consisting of highquality alcoholic and non-alcoholic beer brands in more than 70 countries worldwide. EFES Pilsener is the flagship brand for the ship supply channel and is a smooth and easy drinking lager brewed with premium quality and natural ingredients.
Mr Karşı said maritime was a multi-cultural industry where many consumers, staff and suppliers from different countries and backgrounds meet and the international nature of the industry makes it suitable for brands with international footprint and brand awareness.
“More specifically for beer, international lager brands are the most popular offerings in this channel,” said Mr Karşı. “EFES Portfolio is very suited to accommodate the large spectrum of demand with a wide range of international brand offerings and pack formats.”
He said health and wellness has been a defining trend for consumer categories for over a decade, and driven by this EFES is expecting increased availability of nonalcohol offerings within the channel. u
The EU Ship Recycling Regulations (SRR) come into force at the start of 2021, based broadly on the IMO’s MEPC 269. The SRR place certain obligations on ship owners with regard to the records they must keep in relation to prescribed hazardous materials present on their vessel.
Ship owners/managers are placing requirements upon their own suppliers to supply information in relation to hazardous materials in a belief (often mistaken) that it is necessary in order to comply with their obligations. Increasingly it is being seen that owners are requiring suppliers to provide a “declaration” that items supplied contain no hazardous materials (or where they do, to declare them).
In fact, owners are not obliged by the SRR to obtain such declarations for almost all of the items that are supplied by the vast majority of their suppliers. This would be necessary only for items that are incorporated into the structure or equipment of the vessel, usually at the build stage or during a significant modification.
The requirement to maintain any kind of register for hazardous materials beyond those incorporated into the vessels structure or equipment only arises upon a decision being made to re-cycle (scrap) a vessel and even then, the level of detail required of such a register is quite limited.
Nevertheless, owners are being encouraged to seek declarations of content of hazardous materials for every single item supplied to a vessel during its operation. The usefulness of such information is highly doubtful, since without a highly sophisticated stock control system and very careful processing of all declarations
it will be impossible to identify the item supplied to the declaration, throughout its life-cycle on the vessel.
The difficulty for ship chandlers is that a typical supply to a vessel will include hundreds of line items, many of which are not manufactured specifically for use at sea. The manufacturer will not produce a hazardous materials specification aligned with the SRR and therefore the supplier cannot know whether there is hazardous material content.
The concern for suppliers is they will be under pressure to provide declarations that there are no hazardous materials (or declare those items where there are) without certain knowledge of whether this is the case. Theoretically, claims could lie against a supplier who fails to correctly declare hazardous materials, if an owner relies on that declaration and the owner (or a third party) suffers injury or loss as a consequence.
It is understood suppliers will find it difficult/impossible in some cases and onerous in all cases to provide a line-by-line declaration of the hazardous content of every item supplied. Nevertheless, such declarations should not be provided lightly, without a clear understanding of the risks and with proper systems in place to ensure their accuracy.
ISSA is seeking to take this issue up with the IMO, in the hope they may at least clarify the requirements that arise upon a decision to scrap a vessel, and make clear this does not entail a item-by-item declaration of all hazardous materials.
In the meantime, careful consideration needs to be given to whether such a declaration can be properly given. u
Getting closer to your partners in order to understand their needs and be able to serve them in the best possible way is everyone’s goal. For the safety industry, it is absolutely necessary to agree that the main focus must be given on the human life, so as to ensure its safety at sea; extensive knowledge is the key. Building expertise is a long journey that needs effort, constant training and focus on market needs and feedback.
Honest synergies with appreciated partners have been a great asset during our pathway. In an effort to stay close with them by sharing our expertise, LALIZAS decided to organize several trainings on the Inspection of Immersion Suit ‘Neptune’ to Technical Departments of Maritime Companies we are closely cooperating with. LALIZAS highly skilled technicians explained step by step how to inspect
the Immersion Suit ‘Neptune’ and why this procedure is of major importance.
In this way, our partners get the practical knowledge they might need, being able to maintain, service and extend the lifetime of their lifesaving equipment on board. Additionally, they are able to understand whether the work in the service stations has been done properly, ensuring that their equipment will be totally operational when duty calls. Details about the proper maintenance, thus operation, of lifesaving equipment are not well-known, although it is of extreme importance.
“Our aim is to provide a 360° support to all people who put their trust in us. We try to maintain a continued relationship with all our partners by offering extensive aftersales support and training on the proper use of our lifesaving equipment”, commented by Mr. Iasonas
Lalizas, Marketing & Communication Manager of the LALIZAS Group.
Since 1982, LALIZAS has focused on optimizing its operations in order to provide maritime industries, inshore as well as offshore, with the most up to date safety solutions, keeping maritime professionals safe. u
Safety is not just a product; it is an ongoing process.
Trainings took place in LALIZAS manufacturing premises in Greece with all necessary precautions.
“The fourth industrial revolution is upon us now and we ignore it at our peril!”
These stark words from John Beck, Vice President, Procurement – Wilhelmsen Ship Management Singapore and President eGenie Forum, was just one of the calls to action in a digital debate discussing the digitalisation of the ship supply sector.
The webinar – Journey to eGenie 4.0 – posed the question ‘Do we really need big data and robotics to buy lemons?’ and was hosted by the Singapore-based eGenie Forum, whose core purpose is to be the ‘voice of the industry’ shaping the future through creative innovation and focusing on the digitalisation of the procurement and supply chain function. The Forum, which has received support from Singapore’s Agency for Science, Technology and Research (A*STAR) was initiated in May 2018 by Captain Peter Machado and BK Lim and currently has 35 members.
“New tools are now available to allow buyers and suppliers to analyse and manipulate data in greater detail than ever
before but my feeling is that the marine supply chain is lagging a bit behind,” said Mr Beck.
“There are many reasons for that but what is very clear is that the quality of the data available in the industry is generally quite poor. The industry is highly transactional in nature and poor data means that the order process is inefficient, not just for buyers, but also for suppliers.”
Mr Beck spoke about the need for standardisation of the data to allow both suppliers and buyers to automate transactions, saving costs and time and cited how the likes of Amazon and Alibaba had changed the nature of buying goods.
The webinar, which attracted 200 delegates from across the world, was moderated by Danny Lien, Managing Director, Amos International and President of Singapore Association of Shipsuppliers and Services, who spoke of the need to transform the industry.
Panellist Kenneth Lim, Chief Technical Officer, Maritime Port Authority Singapore, also spoke about the need for
standardisation, and the MPA’s recent launch of the Digital OCEANS initiative with like-minded partners with the aim of standardising the way vessels do port clearance in every port.
“It is very much like the challenge you have between the buyer and the supplier,” he told the webinar. “What is exciting is the way business transactions will be transformed.”
He added that an ecosystem approach was hugely important and the ship supply sector in Singapore had made the cluster what it is – a transhipment hub and a bunkering hub –and was worth around S$2 billion.
The webinar very much explored the issue that those who embrace digitalisation will do better, and those who ignore it will get left behind.
Law Chung Ming, Director, Transport and Logistics, Enterprise Singapore said the current COVID-19 pandemic had affected the global economy tremendously and disrupted the supply chain but evidence showed that those who had responded quickly had fared much better.
“COVID-19 has presented an opportunity for us to rethink our business model,” he said. “We must be prepared for even more demanding changes and expectations from our customers as the whole business community transits into a post-COVID world. We must gear up for the new normal.”
He said people needed to realise the benefits of digital platforms.
“I am very much aware that Singapore Association of Shipsuppliers and Services has been working very hard with the respective Government agencies on various initiatives to help get digitalisation and innovation in the ship supply sector and introduce new ways of doing business more efficiently, more effectively, and more productively,” he said.
Mr Beck said with so much data out there, some companies had felt overwhelmed and the industry needed to get it into some form of order to use it. He cited Wilhelmsen’s sustainability drive, as an example, where data had allowed the company – as part of its plastics initiative – to analyse bottled
water consumption by vessel and to take steps to change behaviour and perceptions onboard.
eGenie is aiming to help ship suppliers, and buyers, with two products it is currently working on as part of its Work Process (WP2) Group, headed up by Peter Schellenberger, Vice President, Product Development and Innovation, eGenie Forum and Vice President, Supply Chain, Thome Ship Management.
The objective of WP2 is to enable the standardisation of data specification and format in the maritime product catalogue for better alignment between buyers and suppliers. The first product is a tender list that clearly describes items so they can be clearly identified by buyer and supplier for a tender quotation, while the second is a simple catalogue, aimed at providing the missing link between what is chosen by the company and what is actually delivered to make sure the specifications are the same.
“We have been trying to get the industry movement going by getting a lot of the industry players onboard,” explained Mr Schellenberger.
Many ship managers, owners and suppliers, are involved in the eGenie and A*STAR data collection initiative, and he said it was very important to share information and data. Contributors include Columbia Shipmanagement, Thome Group, Wilhelmsen Ship Management, OSM/ OSERV and suppliers such as Seven Seas, Con-Lash, Amos International, BH Global and Saifee. The WP2 plans to roll out its results soon.
A panel discussion followed on ‘Strive, Thrive and Drive New Business Model in Challenging Times’, again moderated by Mr Lien and with five further panellists.
Saw Kok Wei, President, Business Units at Jorong Port (JP) said 65% of vessels that come to Singapore do so for bunkering, to take on supplies and for crew changes and the only way to grow the market was to become more efficient
We have been trying to get the industry movement going by getting a lot of the industry players onboard “
Peter Schellenberger
and turn the vessels round quicker. He added that JP were happy to work on eGenie Maritime 4.0 because they believe it will provide even greater efficiency.
Mr Lien posed the question ‘ is digitalisation the silver bullet for companies during these challenging times?’
Law Chung Ming said digitalisation was an important bullet but it was not the only bullet and one important one was manpower and talent.
“As we embark on digitalisation, let’s not forget the impact on manpower and if we do the digitalisation well, the impact on manpower and talent will be very positive,” he said. “But, if we don’t do it well it could be negative.”
Dr Puay Siew Tan, Director Manufacturing Systems Division, Model Factory@SIMTech (Singapore Institute of Manufacturing Technology), A*STAR SIMTech said technologies were now available and COVID-19 had provided the opportunity for companies to realise the importance of digitalisation and how they can change the business model.
Ole Anton Gulsvik, CEO of ship supplier Seven Seas, spoke about how ready his company was when the pandemic hit, in terms of digitalisation.
“Obviously, being a global business, digitalisation is a very, very important part for us. From a communication point of view, we had a benefit in the beginning because we were used to communicating over digital platforms. Looking back, I would not say we were super prepared but by default, because of our set-up, we handled the situation very well.
Jamie Ng, Director Digital Transformation, at another ship supplier, Con-Lash, said as a company they were in the midst of a digital transformation, however some of the challenges they have faced is lack of knowledge or talent with digital skills.
“Even though we knew the problems we wanted to solve we didn’t know which solutions were the right fit for us,” she said.
Ms Ng added that off-the-shelf solutions tended to work in silos, and also digitalisation involved a lot of capital, along with a change in mindset “as the people needed to be onboard”.
“In a traditional business like ship supply, there is bound to be some level of resistance,” she said. “It’s very important to reassure that technology isn’t here to replace anyone. It empowers workers to work more productively.” u
Fire safety has become a major concern in the container shipping industry, in particular, with vessels of 20,000-TEU and more entering the market. A fire in just one container can have catastrophic implications for the whole of the cargo. The very nature of container shipping means that the cargoes are in general finished goods of high value.
Insurer Allianz gives the example of a March 2018 fire onboard the Maersk Honam southeast of Oman. At the time the ship was carrying 7,860 containers, corresponding to 12,416 TEU. Although the ship was less than a year old at the time of the incident, and consequently was fitted with the latest fire-fighting equipment, the damage to ship and cargo was severe, with five fatalities among the crew members.
The incident was one of the largest general claims on record, thought to be in the hundreds of millions of US dollars - Allianz said a total loss would have seen damages of over $1 billion. The fire was not totally extinguished for weeks, and the salvage operation involved a further seven weeks before the ship could be towed to a port of refuge.
This is just one example from a growing list of large container ship fires in the last decade.
One of the major difficulties is that, despite IMO regulations, cargo is not being properly declared, so firefighters can never be certain just what they are dealing with. Insurers, including Allianz and the International Union of Marine Insurance (IUMI) say both ship design and regulations governing fire-fighting equipment need updating to take into account the growing capacity of ultra-large containerships, minimising fire risk and making it easier to extinguish and contain fires.
The rule-makers at IMO are aware of this - the Guidelines for Formal Safety Assessment for use in the International Maritime Organisation’s rule-making process say that fire protection of new cargo ships with containerised cargo on deck should be improved. But implementation of such rules, and their subsequent entry into force, can stretch to many years.
Marine safety and lifesaving equipment specialist Survitec believes such improved safety measures should be considered from the outset and should form the basis of the design process of any new
container vessel. But it is not just ship design and equipment standards – the potential dangers of fire, and successful crisis management in the event of an explosion or conflagration must be embedded into the mindset of the crew.
Although SOLAS regulations specify what type of firefighting system should be onboard a specific ship type, UIMI points out the rules were formulated with older, smaller general cargo vessels in mind, and haven’t kept pace with the size of many current ships.
Many containerships still carry CO2 deployment systems installed onboard, which many now deem to be ineffective where container fires are concerned. Below deck, CO2 systems are often effective and in common use. However, the gas cannot penetrate container walls and oxygen sealed inside containers will encourage fires to burn resulting in an re-ignition.
A lack of fire detection on deck is another potential problem. Reduced manning levels mean crew members are not able to keep a regular check on container temperatures.
Following the Maersk Honam fire, Maersk and ABS carried out their own evaluation on hazards which are not addressed in the IMDG code. As a result, Maersk’s own procedures have been modified – for example any container identified as carrying dangerous goods is not stowed near crew accommodation or the engine
room, and fire-resistant cargo is stowed above deck. But these depend on cargoes being correctly declared.
Although some authorities check random containers and impose penalties for misdeclaration – a common practice to avoid higher cargo rates - in many cases such dangers are overlooked, with potentially serious consequences. As the number of containers on board increases, then inspection gets harder, and the chances of inadvertently stowing dangerous goods in an inappropriate location increase.
SOLAS says that containerships built after 1st January 2016 must have at least one water mist lance capable of penetrating a container wall, while if five or more tiers of containers are carried on deck, ships up to 30m wide need at least two mobile water monitors, and over 30m they need four.
There are SOLAS-compliant water mist lances that rely on a pointed hammer to penetrate the container door – not only unbalanced and ineffective, but it has been found that the resulting hole is not large enough for the lance to penetrate fully. In some cases, it has needed a second crew member with a sledgehammer – exposing two personnel to a hazardous situation. Some use battery powered drills or saws, fine if well maintained and fully charged. The portable monitors need to be carried, up tall ladders, by a crew member wearing full protective equipment and breathing apparatus.
Insurance companies are highlighting this issue with the latest reference being a presentation at IMO sub-committee SSE7. We believe additional measures will be required in a foreseeable future. What these will be is unclear at this stage, but Survitec is following this closely to be able to develop new safe fire products to serve our customers, says Erik Christensen, Technical Director Water and Inergen, Novenco Fire Fighting, a Survitec Group Company.
Survitec’s Novenco Fire Fighting (NFF) XFlow Mobile Water Monitor is used to protect the container deck area and the associated Water Mist Lance is used to protect container bays. In the event of a fire in a container, the water mist lance and the water monitor can be used together or independently.
The water mist lance tool case contains a battery-operated drill, a fire hose and the lance itself. The equipment can easily be carried, mounted and operated by one person. The lance is connected to the fire main using the hose in the tool case. The drill is fast and safe to operate, contrary to a spike and hammer, and
easy-to-use, but for maximum effect the hole needs to be drilled at a significant height. The lance is then inserted in the hole and can then operate unattended for as long as needed.
The water monitor is easy to carry and assemble by an individual and can be placed on deck or any other horizontal surface without any straps or fastening devices. The monitor is connected to the fire mains with a standard fire hose which starts operating as soon as the hydrant valve is opened.
In terms of mobility, the lightweight Water Mist Lance comes in a practical tool case for easy storage and use, which is easily carried to significant heights of the top containers. Survitec’s water spray is discharged both vertically to protect crew from the heat, and horizontally to suppress the fire. Similarly, the Mobile Water Monitor boasts a nozzle pressure of 4.0 bar, the throwing distance is 40m and the monitor can protect up to 10 tiers of containers, and even more at high pressure.
The flexibility of Survitec’s Water Mist Lance means the system can reach cabins, waste bin etc. and cars onboard the container ship and is equipped with a drill to penetrate the container wall quickly and safely. Requiring only one crew member to operate reduces the risk of danger to fellow crew members.
With only one waterway connection for fast response time from alarm to operation, the Mobile Water Monitor saves crew members time unlike alternative systems which require the crew having to hoist the device up using a telescopic lift to hit accurately the doors of the burning container. With hydrant adaptors available, the dual-purpose nozzle is available for spray and jet functionality. The easy elevation features of both the Water Mist and Mist Lance mean that Survitec’s systems ensure precise and efficient firefighting u
ISSA has been saddened to learn of the death of Rubens de Souza, General Supply Manager at G.Pierotti Ship Supplier in Brazil.
Mr de Souza dedicated his whole life to the ship supply business and built a remarkable reputation in the industry.
Gustavo Pierotti, Commercial Director, G.Pierotti Ship Supplier, Brazil told The Ship Supplier, on behalf of the G.Pierotti team: “It is with the most profound regret that we inform you that José Rubens de Souza, our Rubens (or Rubinho), passed away on Saturday, August15th 2020.
“Rubens was with us for more than 40 years, being our General Supply Manager for most of its period. Honest, hard-working and polite, he inspired many and was a true icon in the ship supply industry. May our Lord receive his soul and comfort his loved ones.” u
Redmar (Redsea Mediterranean Marine Services Co)
8 Palestine Str., Massagrie Bld.
P.O Box 1171 Port Said
Egypt
Tel: 20 66 326 1112 / 3 / 4
Fax: 20 66 326 1115
e-mail: operation@redmar.com.eg/ purchasing@ redmar.com.eg
Port Coverage:
Ain Sokhna, Alexandria, Damietta, Port Said, Port Suez, Red Sea Remote Ports, Safaga, Sidi Kerir, Suez Canal
Gulf Agency Company (Egypt) Limited
Villa No.1
El Mosheir
Ahmed Ismail Street
Sheraton Helipolos District Cairo Egypt 11799
Phone: +203 484 0256/+203 483 2510
Fax: +203 484 8480
A-SPE Europe is your global supply partner with years of experience in providing safety marking products to marine, offshore and oil & gas industries.
This year we are celebrating our 15th anniversary. Our company is another year older and another year wiser. Throughout these years we have acquired knowledge and experience to deliver the highest standards, making strong and professional relationships along the way. We also learned that we are not afraid to innovate and our team, going together and working side by side, can make it happen.
Our field of expertise is production of photoluminescent IMO Safety Signs, Low Location Lighting Systems, Pipe Marking Tapes and other specialized technical tapes to equip vessels in compliance with all relevant marine standards and regulations.
Today, in addition to our regular choice of marine safety signage, we have adapted our production facility and launched the new range of #stopCOVID-19 products to fill the gap of social distancing Floor Marking and self-disinfecting solutions, like AS-100 Anti Microb Tape.
Over the 15 years, we have been honoured to be trusted by shipyards, ship chandlers and industrial customers from more than 70 countries worldwide, and their satisfaction is the best recommendation of our company. u
I wanted to personally thank all our customers, partners and employees for supporting A-SPE, for your incredible loyalty and for making us part of your journey all these years. We greatly value your trust and confidence and we look forward to an exciting future.
Irek Mianowski General ManagerAn ambitious and comprehensive MOU has been signed by Wilhelmsen and Hyundai Glovis allowing the two companies to exchange expertise and competency to improve existing technology and service areas, along with looking for new opportunities to shape the future of the maritime industry.
This new phase of a business relationship, which has been in place since 2004, will see the companies work together practically to explore both short, and longer-term opportunities such as those within the global gas shipping market, along with conducting research into alternative vessel fuels, such as liquefied hydrogen.
Commenting on the announcement Thomas Wilhelmsen, CEO of the Wilhelmsen group said: “We have always been interested in leveraging potential synergies between the two companies, but it’s our shared focus on developing hydrogen as a fuel for the future that has acted as the real catalyst. Starting an in-depth discussion, which has unlocked a number of areas where we can share competence, expertise and ambition, this framework agreement is just the beginning.”
Jung-Hoon Kim, CEO from Hyundai Glovis said: “We are pleased to strengthen our partnership with Wilhelmsen Group. This MOU that we are signing today will leverage on each company’s strengths to maximize synergies
Espen Gjerde, Director Strategy and M&A, Wilh. Wilhelmsen
Holding ASA, Thomas Wilhelmsen, CEO of the Wilhelmsen group and Jan Eyvin Wang, Senior Vice President Industrial Investments, Wilh. Wilhelmsen Holding ASA
and provide competitive options for both companies to respond rapidly growing global gas demands and tightened environmental regulations.”
With over 25 years’ experience in the gas shipping market, Wilhelmsen Ship Management’s expertise, managing both LNG and LPG vessels will prove invaluable to Hyundai’s growth ambitions in this segment. Helping to strengthen ship safety management, while streamlining operational costs through strategic cooperation and innovation.
Providing specialised management expertise and insights on targeted technical areas, such as ballast water and scrubbers, in addition Wilhelmsen will share several their digital initiatives for potential trial on Hyundai Glovis vessels. Beneficial for both companies, whether it is their vessel performance monitoring system, digital mooring application, or onboard IT infrastructure, Wilhelmsen will be able to benchmark and refine their innovations alongside a willing partner.
In addition to shipmanagement services and digital initiatives, Hyundai Glovis will also look for opportunities to cooperate with Wilhelmsen’s agency division to achieve operational efficiencies across their global port operations. u
Fire is any seafarer’s worst nightmare – indeed everyone’s worse nightmare.
But, when you own the world’s biggest superyacht, provision of state-of-the art fire protection equipment is absolutely vital.
Step forward British-based Bull Products which has won a contract to protect m/v REV Ocean from any chance of fire onboard during its current fitting-out programme.
Working with Vestcom, a major wireless communication supplier in Norway, Bull Products will supply more than 25 of its Cygnus Wireless Alarms to protect the ship until completion in 2021.
The units installed on the ship include 25 Cygnus Fire Call Point Alarms and a range of first aid, heat, smoke and water detectors.
The alarm system also connects to Bull’s 3G Auto Dialler that allows site managers to programme up to 50 phone numbers of responsible persons in an emergency who are then notified by SMS if an activation or intrusion has occurred.
Matt Trigwell, Sales Director at Bull Products, said: “Shipyards provide unique challenges to fire safety and have a number of high risks including hazardous materials, welding operations and electrical dangers.
“Our wireless fire alarms are key to protecting workers and the ship around the clock. We are delighted to support such a prestigious project.”
REV Ocean is the world’s largest superyacht build by the Norwegian yard, Vard Brattvaag. u
Anew sustainable clothing brand – All At Sea –has launched.
Nothing unique about that – except the brand is seeking to raise awareness of the challenges and opportunities that the seafaring life can offer.
The founders have experienced life at sea in both the Royal Navy and the Merchant Navy and are well qualified to turn that experience into a unique twist using the clothing brand as the peg.
All At Sea Director of Sales and former Royal Navy veteran Alastair Taylor said: “For most people life at sea is invisible.
“Through our brand we hope to create a community both on and off line that breaks down the barriers to seeing, experiencing and understanding such a lifestyle.”
The firm has pledged that a percentage of profits will go to Human Rights At Sea (HRAS), a charity committed to ending human rights abuses globally.
Sustainability is the brand’s watch-word. They have teamed up with sustainable clothing supplier Tee Mill to ensure sustainability at every point of the retail process.
Co-founder Joe Marsh, a former professional mariner added: “Having lived and worked on or by the sea our whole lives we
are passionate about protecting it and know that tackling plastic pollution and the fast fashion industry is paramount to this.”
The clothes are designed to be practical and fashionable for life on and off a ship. The added bonus is educating the wider world to shipping and seafarers’ lives and the vital global service they provide.
The current clothing line will include unisex and women’s t-shirts, jumpers, hoodies and bags. More garments and new ranges will be available in due course. u
Let’s face it no-one likes a wrinkly and ill-fitting floor – least of all on a luxury cruise ship.
Enter F. Ball and Co, at the up-coming Cruise Ship Interiors Expo Europe with their range of market-leading flooring adhesives and floor levelling compounds.
Use Ball’s products, they claim, and optimise the aesthetic appearance of installed floor coverings on your cruise ship.
An added bonus: the integrity of your installation is maintained throughout its working life.
Installations using Ball’s products range from some of the world’s most prestigious cruise ships and Mediterranean-based superyachts to polar exploration vessels, iconic New Orleans paddle steamer show boats as well as offshore oil rigs.
Amongst the key products for marine applications are Stopgap 700 Superflex and Stopgap 1200 Pro levelling compounds.These are recommended for substrates subject to flexing or movement with temperature changes, including steel decking.
When it comes to the need to maintain the look in an area subject to a wide temperature range, the company recommends Styccobond F49 Hybrid PS temperature tolerant vinyl adhesive.
Impressively this product is able to withstand extreme changes in temperature, from -20°C to +60°C, and is resistant to water.
Cruise Ship Interiors Expo Europe runs from 2nd to 3rd December 2020 at Excel, London and is co-located with Cruise Ship Hospitality Expo Europe. u
Global ship supplier Wrist is expanding its already significant Spanish presence.
New facilities are opening in Valencia on 1st September to support customer needs along the entire Spanish east coast.
Linked to Wrist’s Europe-wide Shuttle truck network, customers of this major supplier in Spain can look forward to a slicker response to their needs and demands in the region.
The Valencia facility will extend and support existing operations in Algeciras and Las Palmas.
In turn this increased operational efficiency will lead to more competitive prices and better service, says the firm.
Although Wrist has a local partnership presence already in Valencia, the opening of its new facility will mean their customers benefit from the firm’s global logistics network. This extends
beyond the Spanish east coast ports to key European ports.
The Port of Valencia is a key player not only in Europe but globally and has increased its connectivity during this year. It was a natural choice for Wrist to locate its new facility there.
Heading the operation will be Jens Lundin, Wrist’s General Manager (Spain).
He said: “We are proud to expand our customer reach in Spain with new facilities in Valencia.
“We are ready to live by our mission of making life at sea better for our seafarers and we are looking forward to welcoming our customers with our services in Valencia and the entire Spanish east coast.”
Further afield Wrist has facilities in the three other largest and most important European Ports, viz. Rotterdam, Antwerp and Hamburg, cementing its position as one of the world’s leading ship suppliers. u
No other sector of the shipping industry has been as badly affected by the COVID-19 pandemic as cruise. After decades of continuous growth, cruising was brought to an abrupt end in March this year. It has now experienced six months of enforced idleness, during which time many crew members and suppliers have remained unpaid.
At the time of writing, four international cruise companies have gone out of business. Almost all others have been obliged to take drastic steps to stay in business. The biggest failure to date has been Cruise and Maritime Voyages (CMV), a line with six vessels managed out of Greece by Global Cruise Lines Ltd. (GCL). The ships are all under arrest in the U.K., with five scheduled to be auctioned by the Court in October. Looking at the large number of claims
filed against the vessels, it is clear the business was reliant upon extended credit from suppliers for much of its cash flow.
Christian Verhounig, who was jointly CMV’s CEO and GCL’s COO, has recently established a new company, CVI Group Limited, to acquire CMV’s mailing list and other office assets from the Administrators appointed by the Court. Should he be able to get back in business, he may find suppliers reluctant to grant credit terms.
Elsewhere, the major cruise lines are hoping they are viewed as “too big to fail” by lenders and investors. However, they are all bleeding cash as governments around the world still advise against any form of cruise travel. Uniquely in the shipping industry, cruise companies are fully paid before the start of every voyage. They are now enduring the pain of being forced to return much of that cash. All claim many disappointed passengers accept credit notes instead of cash, but it still hurts.
Carnival, the biggest cruise company, with more than 100 vessels, is fast disposing of ships, with many going straight to the breaker’s yard. Ships formerly thought of as merely “middle-aged”, have been sold, with the sale proceeds deemed less important than halting the monthly outgoings on the vessels. The company will ditch at least 20 ships in a 12-month period.
The second biggest company, Royal Caribbean, has dropped the word, ‘Cruise’ from its name. It was the first to pull the plug, foreclosing on Pullmantur, Spain and sending three of that brand’s four ships to scrap. The company is now pinning high hopes on its private island resort in the Caribbean, with cruise as just the way of ferrying holidaymakers to it.
Genting, owner of the brands, Crystal Cruises, Dream Cruises and Star Cruises, was already struggling before the outbreak of COVID-19. It is now in discussions with creditors as it attempts to restructure.
In Europe, various lines have attempted to resume cruising but with only limited success to date. Circular, so called “blue water” cruises, (without any port calls between joining and leaving the ship), have limited appeal. Short cruises with few passengers on board may have been uneventful but deepen losses and do not fit with the, “We always sail full” mantra of the cruise bosses.
Naturally, when cruise lines sneeze, their suppliers catch a cold. Ship managers and catering contractors focused on the cruise industry share their clients’ pain. Most have low overheads, so will stay in business. Just don’t rely on their judgement when assessing risk. Otherwise, you may get more than a bruising! u
Trust those canny folk at Bose to come up with another “must have” from the world of sound: cool and fashionable sunglasses with built in sound!
Well used now to noise-cancelling headphones that allow you to fly in silence, the sunglasses give you connectivity to your play list without anyone knowing.
Operated through the Bose Connect App you can set up the sunglasses to your own personal preferences.
There are a variety of styles to suit everyone and once you have set them up it should be a case of “wear and enjoy”.
Bose Sunglasses
£199
www.bose.co.uk
Experts believe water is what we will be fighting over – and sooner than you think. It makes sense, therefore, to look at ways of conserving and re-cycling this most vital of resources and The Hydraloop might well be a gadget to consider. This device—it’s big, like a refrigerator—recycles and cleans about 85% of the water you use in your home, while its app keeps you updated on the recycling process and your total water usage. The device covers all water usage areas including, showers, washing-up, laundry, your swimming pool or whatever.
It’s not cheap – new technology seldom is - and the upfront cost at $4,000 is significant. The claim is that your water bill will probably reduce and you will have the satisfaction of making a contribution to the greener and environmentally-friendly planet we all aspire to. www.hydraloop.com
Inclusivity, choice, and togetherness are just some words that chime loudly with Pillow Queens. Their new single “Handsome Wife” arrives at a time when those words have rarely had more impact. The track is on their new album “In Waiting”. In what everyone is calling unprecedented times, “Handsome Wife” looks at the importance of life’s often under-appreciated moments, as the band explains: “Handsome Wife begins with a glimpse into an emotional homecoming, one that intensifies and romanticises the seemingly insignificant. The album releases on 25th September.
For Beethoven fans 2020 is his year – the 250th anniversary of his birth. It seems only right, therefore, to draw attention to the sometimes over-looked corner of this mighty composer’s output – the short-form Bagatelles. And who better to introduce us to them than virtuoso pianist Paul Lewis who is the type of musician that can take the most mundane musical phrase and bring it to life - and all without exaggeration or sounding affected. Once again he displays his high degree of musicianship in his rendition of these shortform Bagatelles by Ludwig van Beethoven.
Beethoven: ‘für Elise’, Bagatelles, Opp. 33, 119 & 126 Harmonia Mundi
Her Majesty Queen Elizabeth II’s feisty younger sister – HRH Princess Margaret – always divided opinion.
Now her equally feisty Lady in Waiting Anne Glenconner pulls aside the curtain to give a glimpse of this lesser-known member of the British Royal Family.
However Lady in Waiting: My extraordinary life in the shadow of The Crown tells us much more than spending 25 years dancing attendance on The Queen’s sister.
It reveals the life of a wonderfully diverse member of the British aristocracy with enough tales of her own to fill several more volumes.
With a close-up view of Princess Margaret’s life for decades these two childhood friends supported each other throughout their long lives.
A degree of sadness and some wistfulness mingles with moments of great joy and stunning history, It is a book that will leave you begging for more.
Lady in Waiting: My Extraordinary Life in the Shadow of the Crown
By Anne Glenconner Hodder & StoughtonAcclaimed Turkish chef Fatih Tutak, who has worked everywhere from Copenhagen to Hong Kong, is returning to his roots by opening his first restaurant in Istanbul.
By working closely with Turkish fishermen, farmers and artisanal producers, Tutak promises to celebrate his country’s diversity of produce.
Served in a modern, light-filled setting, the food here merges the chef’s extensive travels and overseas experience with historic Turkish techniques to re-interpret traditional flavours. This means multi-layered dishes that include bulgur wheat with miso, veal and radish, or a main of duck with sour cherries and chestnuts. Desserts on offer include a “snow’” of lemon verbena and persimmon, while all the wines served are Turkish. www.turkft.com
Postponed due to COVID-19, the stunning “Masterpieces from The National Gallery, London” Exhibition is now under way in Osaka, Japan.
The National Museum of Western Art has advance time slot admissions available online for this rare glimpse of some of the British National Gallery’s treasures.
This exhibition introduces 61 masterpieces from the Gallery’s collection ranging in date from the Renaissance to the Post-Impressionists.
It is the first large-scale presentation of works from the National Gallery outside Great Britain, and features the first Japanese display of all of the works, including Carlo Crivelli’s The Annunciation, with Saint Emidius and Van Gogh’s Sunflowers.
The collection of the National Gallery, unlike other major European museums based on their country’s royal collections, was assembled by the people for the people.
The broad ranging and inclusive collection, which contains works that date from the latter half of the 13th century through the beginning of the 20th century, can be considered a “textbook of the history of European painting.”
Ulysses deriding Polyphemus - Homer’s Odyssey
Joseph Mallord William Turner 1829
www.nmwa.go.jp