
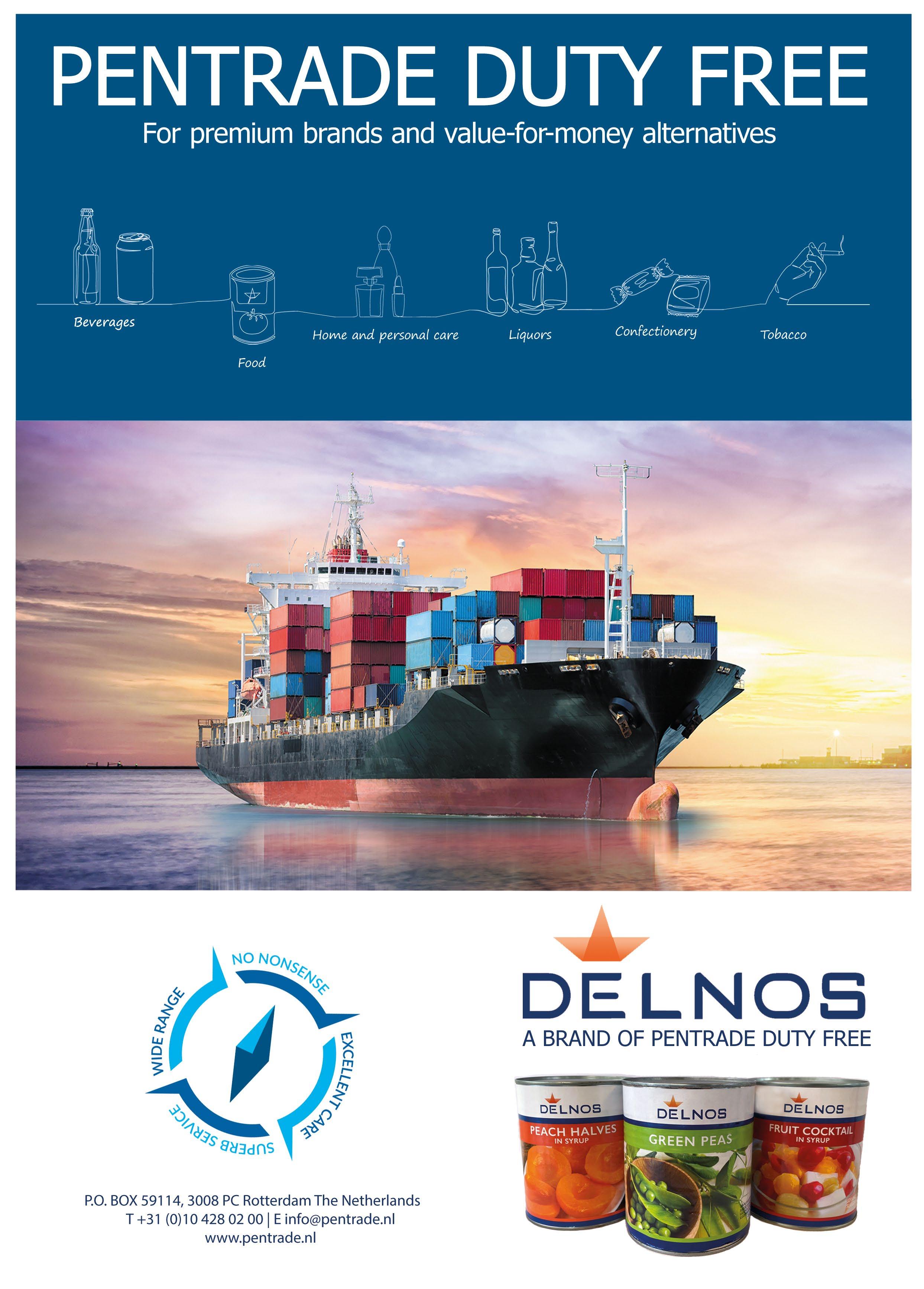
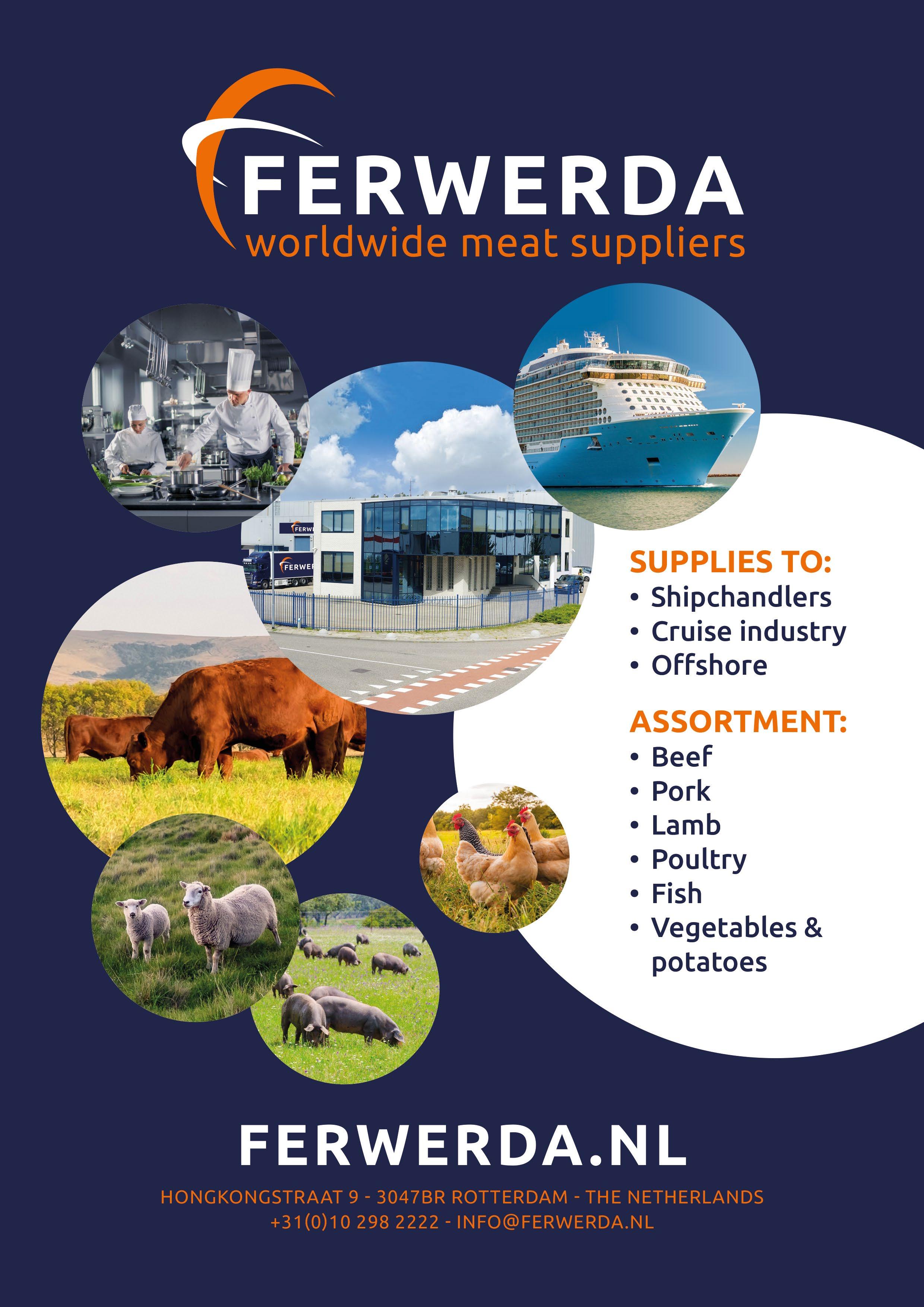



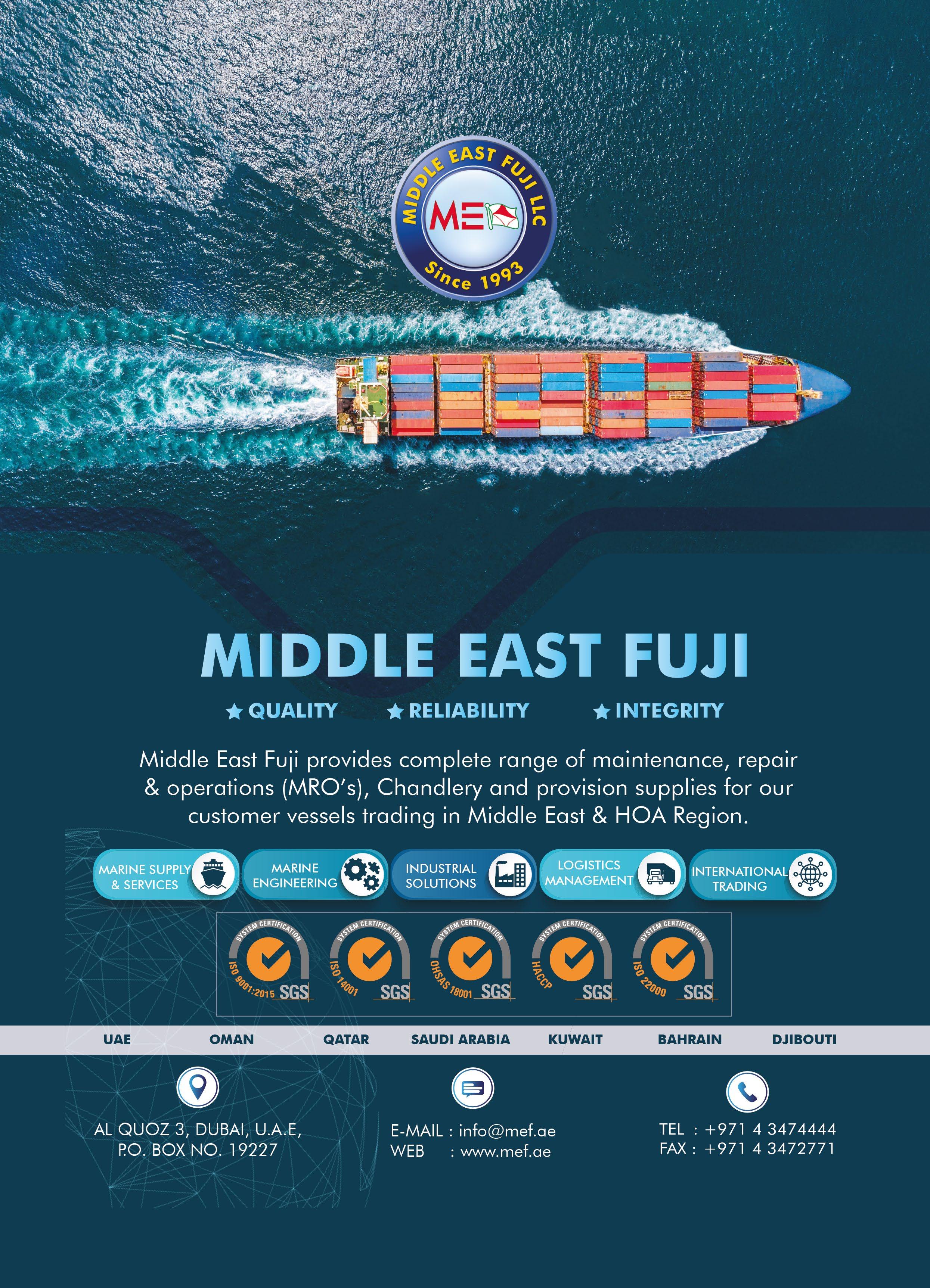
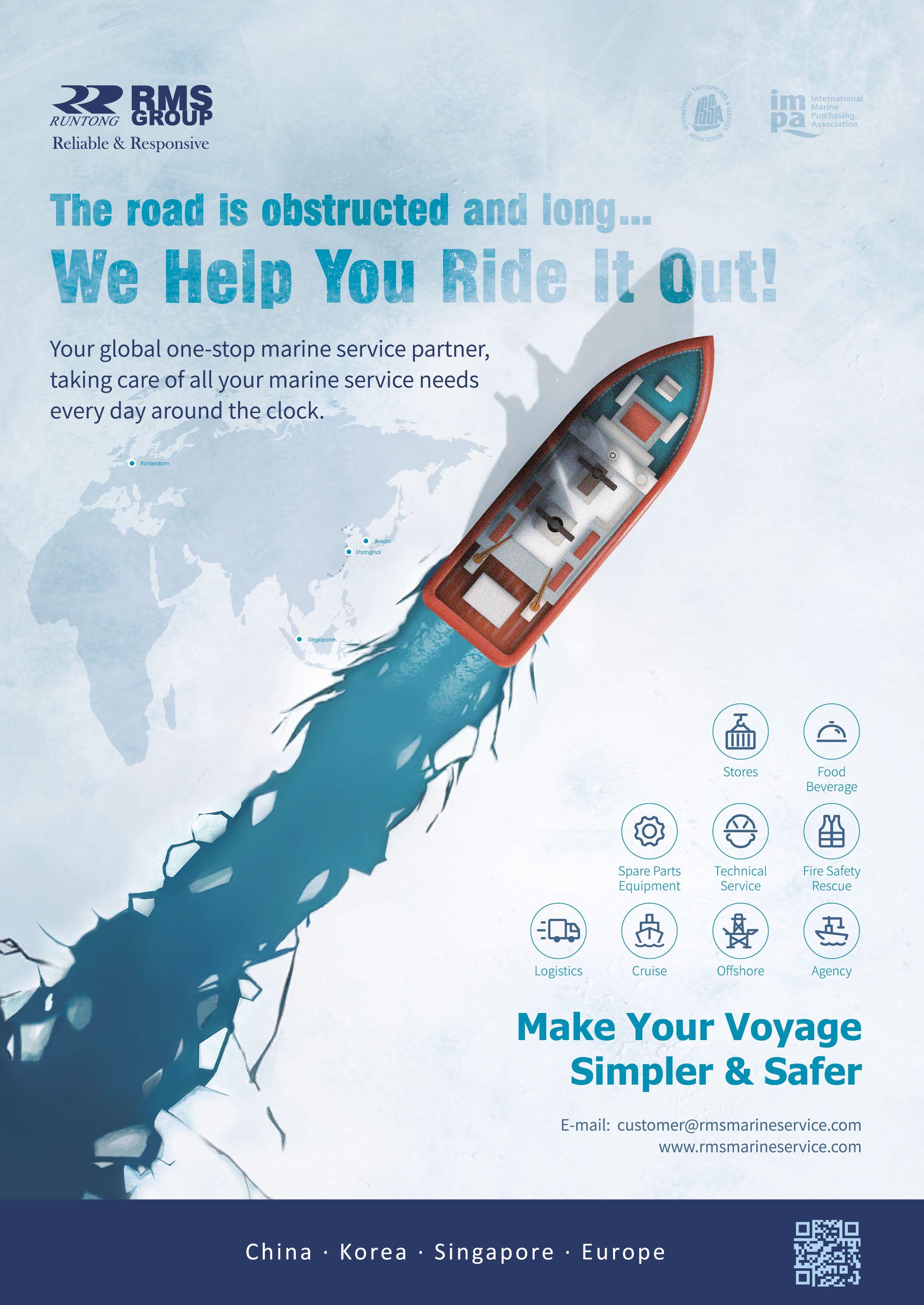
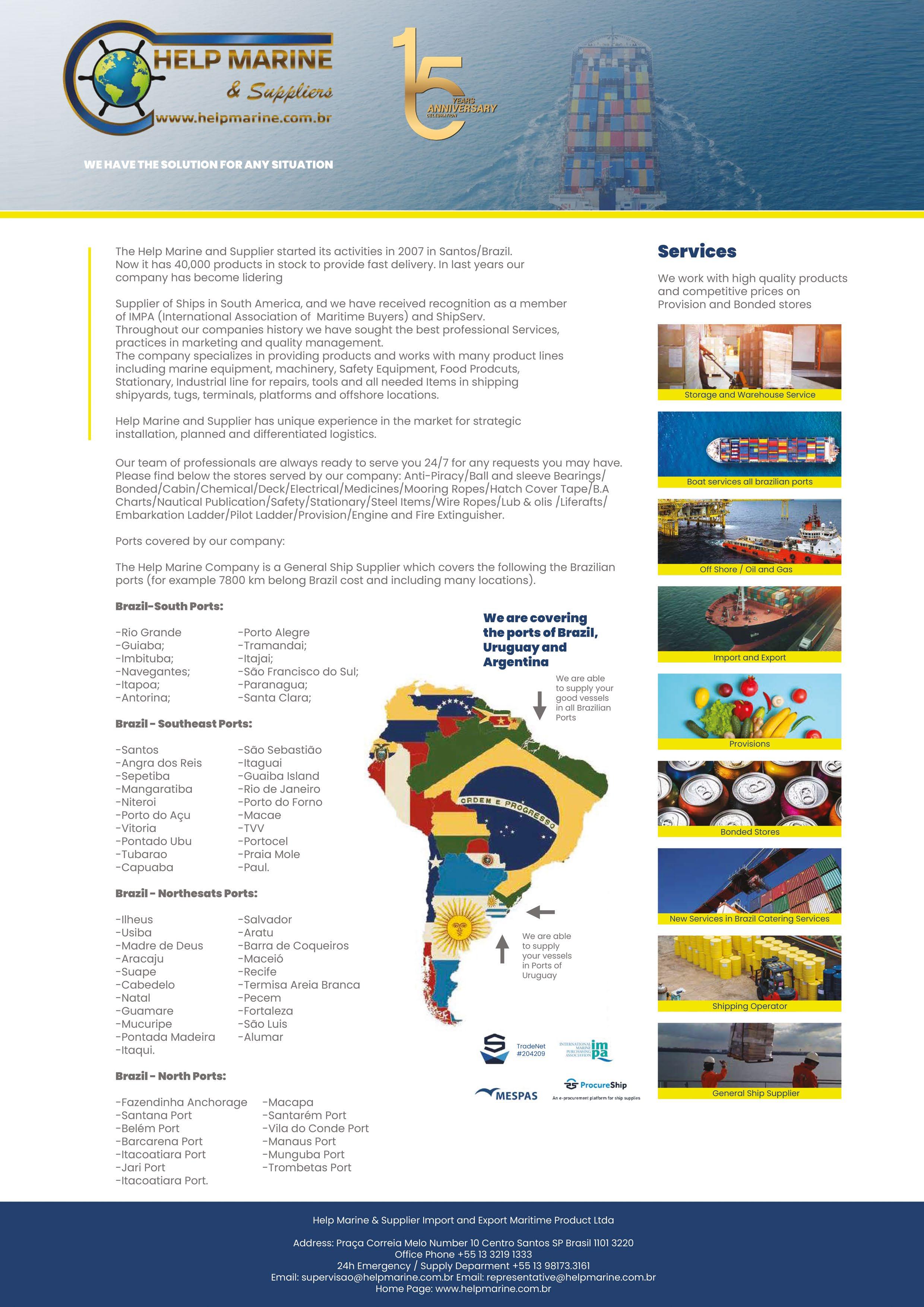
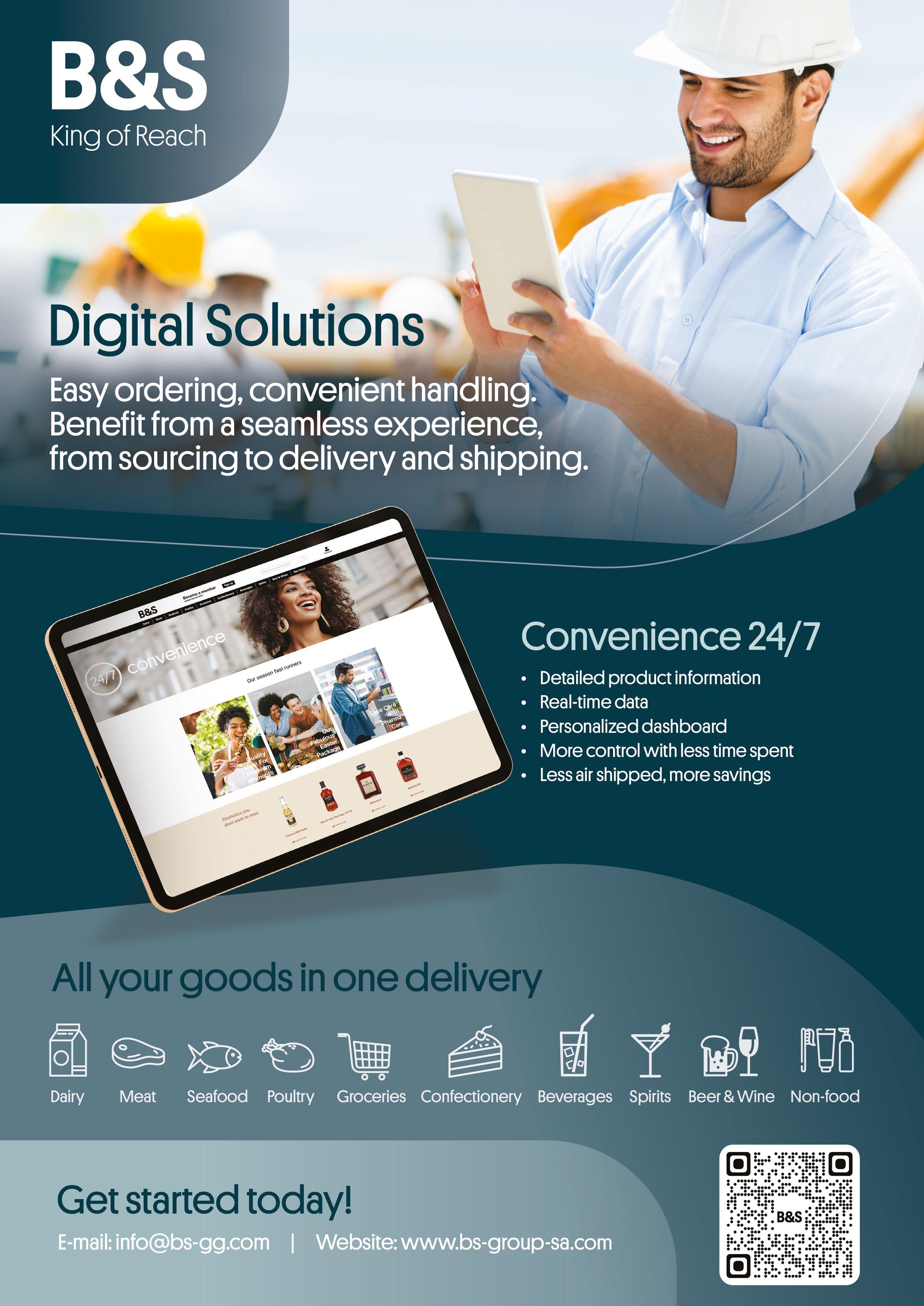
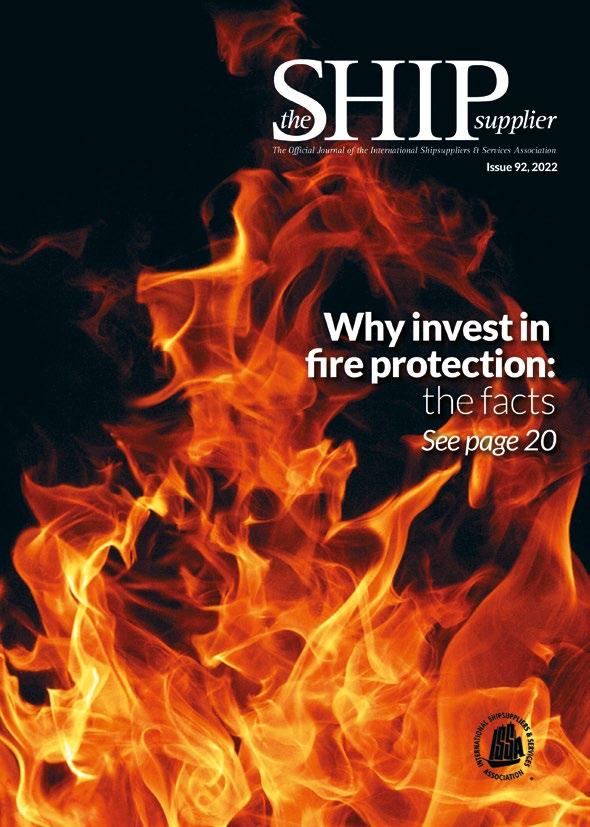
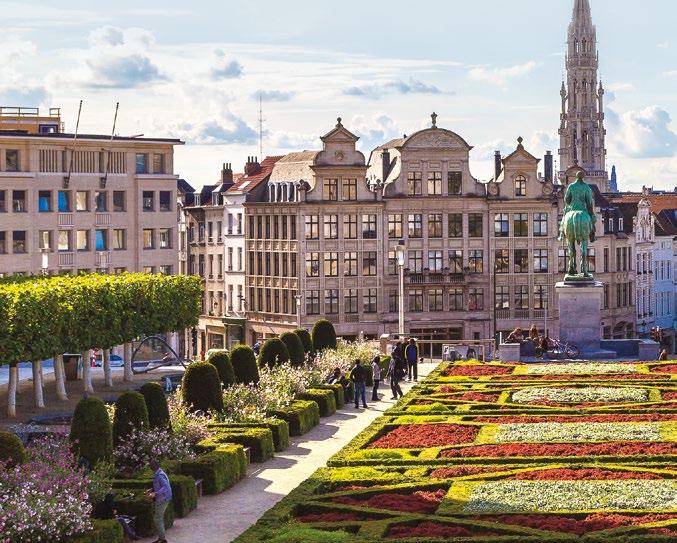
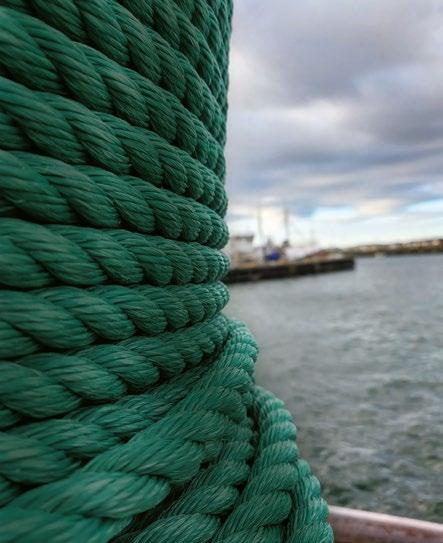
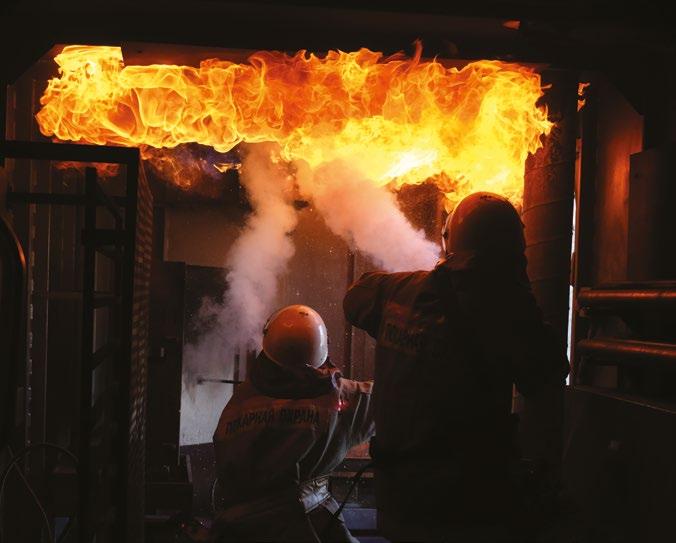
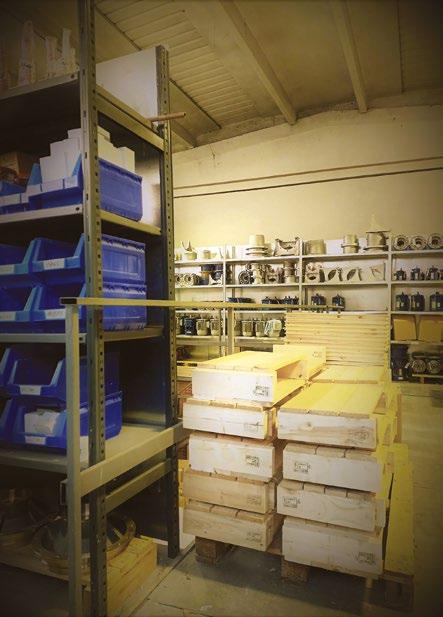
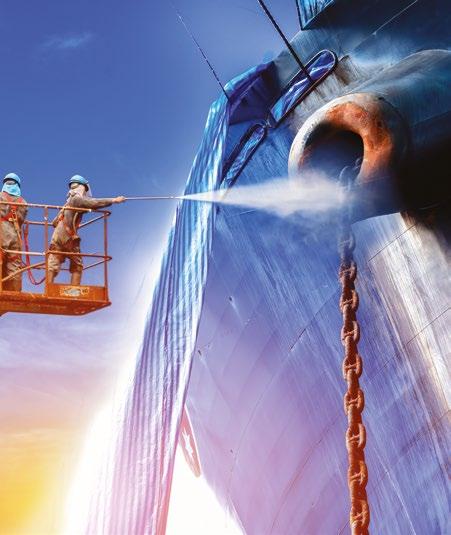
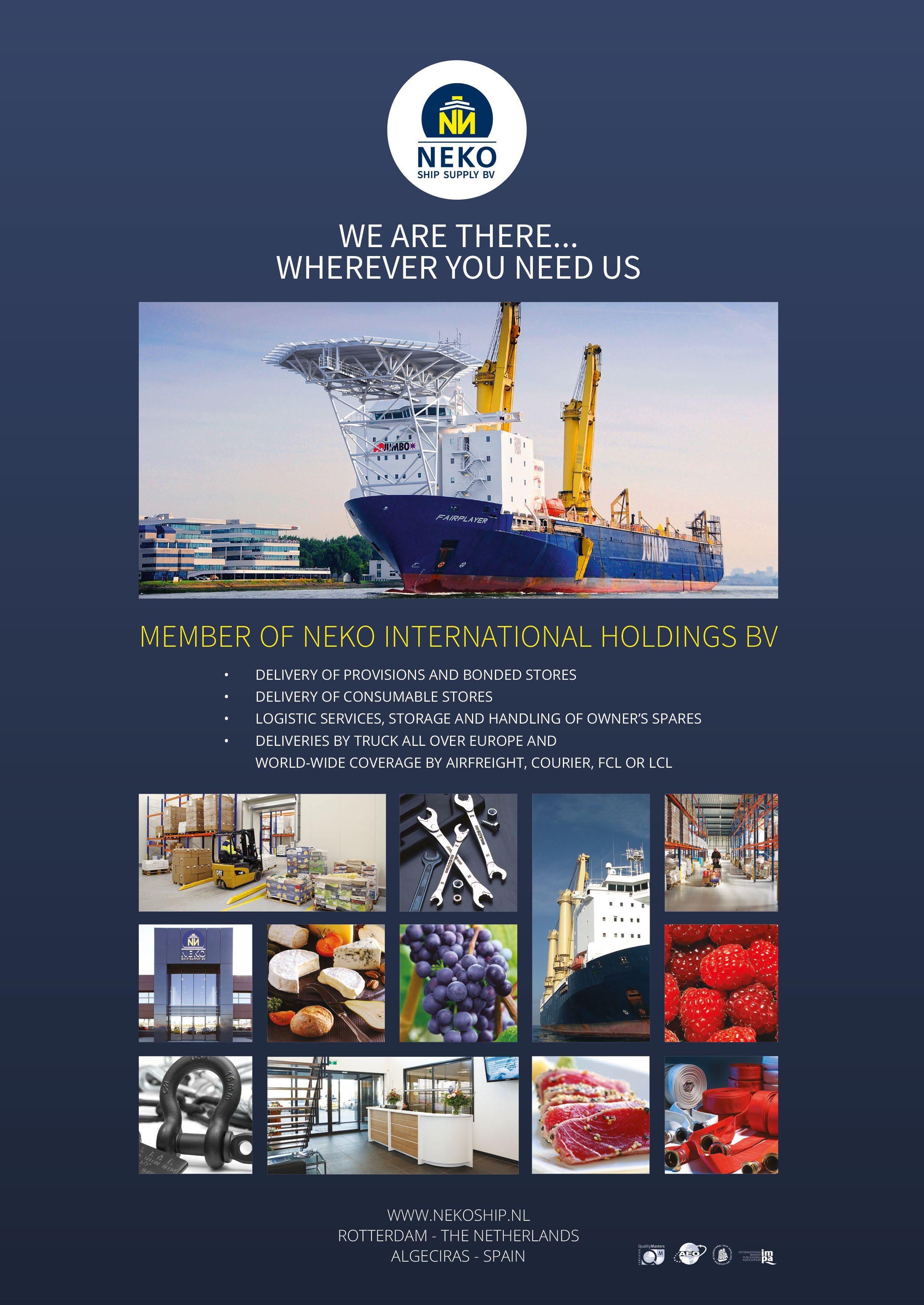
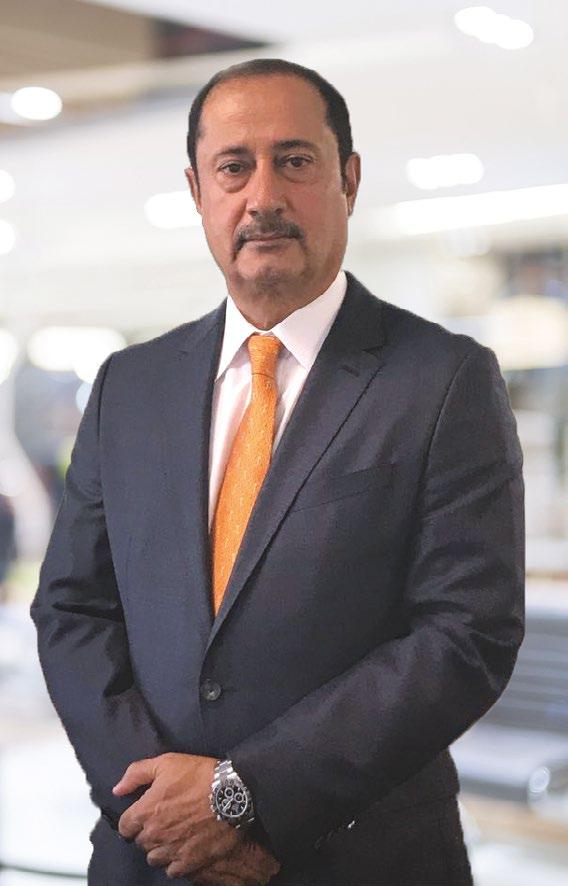
hope this message finds you well despite the difficult times the shipping industry is facing.
As the world starts to open following the passing through of the global pandemic, we find ourselves starting to look to new opportunities that may lie ahead. Borders are opening-up and business meetings are starting to be held faceto-face, as opposed to via video conference, so we could be looking at a definite return to normality.
However, putting geopolitics aside, shipping and its respective industry sectors will have to continue to keep its nose to the grindstone and press firmly aheadsomething that ISSA is doing with conviction.
We are starting to work on a lot of important projects, not least of all the efforts to secure agreement with the industry over IHM Material Declarations. This is an important issue as it affects all of us as ship suppliers and the Secretariat is working hard on this with the ISSA lawyer to secure a pathway ahead.
I have touched on the issue of ISSA Education before, and I am delighted to announce that progress is continuing at pace. We are working very closely with our partners in the programme, the World Maritime Academy, to start putting the programme together and all ISSA members will soon receive a survey from the WMA asking such important questions such as: what is your topic preferences for digital courses?
You can keep up to date with the latest news on the ISSA website at www.shipsupply.org and send in your comments and views to the ISSA Secretariat either by phone on +44 (0)20 7626 6236; Fax +44 (0)20 7626 6234 or alternatively email secretariat@shipsupply.org
This is a very exciting initiative for ISSA as it means we can help our members ensure new employees entering the industry are trained to the necessary standards. As mentioned before, these courses will be digital so accessible by students when the time is right for them. u
Happy Reading!
Saeed Al Malik ISSA PresidentWhat is OCEAN doing for shipsuppliers in the European Union? Chairman Wolfgang Sump explains.
OCEAN was founded in 1976 and has been taking care of the interests of European ever since.
The key reason for the formation of OCEAN was to monitor the new European Common Market and its institution’s effect on our industry.
On 17th July 1975, the European Economic Community (EEC) published the first draft “Regulation on the customs procedure for the supply of ships, aeroplanes and trains in the international traffic”, which aimed at setting harmonised rules for ship supply in the Common Market of the EEC.
At the same time, the European Commission had made it clear that official contacts would only be made with associations from European Community (EC) countries. This point alone made it justifiable to form an organisation inside the International Ship Suppliers Association (ISSA) and it was decided to name the organization O.C.E.A.N., from the French “Organisation de la Communite Europeenne des Avitailleurs des Navires”.
Over the years the EC – today the European Uniongrew with new members and so did OCEAN. Today OCEAN consists of 16 EU-shipsuppliers associations plus Turkey as an associate member. Unfortunately the United Kingdom left OCEAN as a result of BREXIT.
One of OCEAN’s main concerns has always been and still is the fact that the Shipsupply business is unique and needs a lot of explanation.
When new legislation is written by EU officials, there is always the need for close communication between OCEAN and the EU Commission.
Therefore OCEAN working groups and the Secretariat in Brussels have established a close relationship with many Directorates General, e.g. DG Sante for health legislation or DG Taxud for customs and taxes.
To name one of the big success stories: OCEAN was able to give the ship supply industry a place in the Union Custom Code through the EU ship supply guidance.
For 2022 and the coming years OCEAN has a wide range of subjects on the agenda.
The main idea is to build a road map, which clearly shows OCEAN’s targets for the next 4 years. In 2026 OCEAN will celebrate its 50th anniversary and this is a very good milestone to prepare for the medium and long-term future of our proud organisation.
In our last Board meeting in November 2021 the Board installed a sub-group consisting of OCEAN Chairman Wolfgang Sump, Vice Chairman Costantino Zavoianni and the Swedish delegate Carl Forsman.
The Board asked the group to present a first draft of this challenging task (the Road Map) by the end of February 2022. This draft will be discussed in the next Board Meeting in May.
Without revealing too many secrets at this stage, let me mention a few keywords from the document, which currently is named “Agenda.50” as a working title:
• OCEAN will of course continue to work on making a shipsupplier’s life as easy as possible by supporting the industry regarding customs, VAT, excise duties, health regulation and so on.
• A strong presence and visibility to the European decision makers will remain of utmost importance.
• At the same time OCEAN will closely monitor new future subjects such as digitalisation, diversification and the environment.
Furthermore OCEAN will take a special look at a modern internal structure, networking activities and financial stability with clearly defined timeframes and responsibilities.
All this will help to guarantee that OCEAN is well prepared for the next 50 years! u
Gives a comprehensive review of ship supply operations in Southern Europe
As with all other businesses even the Southern European ship supply industry is living through a turbulent historical period experiencing an interesting mix of threats and opportunities.
Generally, the traditional habits of our industry - flexibility and resilience - are helping our companies to recover from the
pandemic’s tough time and facing the current war scenario.
It may well be that the average small size of Southern European suppliers risks having a critical impact in the medium term.
High rise of inflation on food products will surely create budget “headaches” to catering companies and to their
suppliers such as to fixed prices contracts which will now need to be all renegotiated.
The Cruise segment is expected to restart in 2022 summer season while ferry boats and merchant vessels, especially with Container and Tanker vessels, are consolidating their trading already relaunched starting from mid 2021.
In Italy a new national VAT exemption rule, enacted in August 2021, is affecting the daily operation with additional bureaucratic burdens which involve customers and suppliers.
The supply chain is always a key factor in the success of the operational process with new additional challenges coming from stricter port safety rules.
We see more and more deliveries are needed by barge with consequent increase in costs and extra time needed due to organisational procedures.
Finally we feel that the digitalisation pushed by owners and managers is a real opportunity but suppliers are still struggling to adapt - especially small companies which have more difficulties to instal new IT and to launch relevant investments.
In Greece we see as national problem the non-exemption from duties and taxes for certain categories of ships, such as foreign warships and commercial cruise ships which, in order to procure supplies without duties and taxes, bypass Greek logistics companies and order supplies from companies in other countries.
Also restriction of the exemption in certain cases, such as the sale to ship-based operators other than the shipowner, due to the interpretation of the provisions by the competent customs authorities.
In Spain a cost increase in the energy resources is affecting our industry very hard. This makes the difficult situation in the logistic sector even worse, with very serious problems in the logistic supply chain with lack of stock of many articles and the high cost of shipping freight that we all are suffering from for months now.
Speaking about customs matters: the interest among our members in the certification as AEO is increasing.
In Bulgaria main difficulties that arise are both the increase in shipping cost, which of course makes our products more expensive for our clients, and the lengthy delays can cause the missing of important deadlines for arrival at the final destination.
Any amendments that have been made and adopted locally in Bulgaria are ensuring faster clearance procedures with less
paper trail and a more Electronic environment, which enables both Customs Authorities and Customs agents/brokers to handle faster Import and Export procedures.
Finally we would say that enthusiasm and the magic of our job is still well kept despite the hard challenges our members daily face but with recognized benefits coming from our membership of the EU. u
“Do the maths”!
“Make fire protection an investment not a cost” – so says Dr Carl Stephen Patrick Hunter OBE, Chairman, Coltraco Ultrasonics
The fire industry uses scientific principles to enable its very existence.
However, fire engineering designs are often based on formulae that technicians have no way of verifying as accurate.
Fire engineers do not always understand the physical properties of the clean agents or fire suppression agent that they use. For example, Novec™ 1230 Fire Protection Fluid, a clean agent fire extinguishant, is an organic compound which deteriorates quickly to a point of non-effectiveness if poorly handled and stored.
The value of the assets that fire extinguishing systems protect is increasing rapidly, whilst market pressures lead to the delivery of ever-cheaper systems. Too often fire protection is seen as a cost rather than an investment.
These problems, and many more, may be solved in the fire industry by the application of fundamental scientific principles.
Headquartered in London, Coltraco Ultrasonics is a global company and is principally engaged in the research, design, development, manufacture, integration and sustainment of highexporting advanced technology systems, products and services.
Coltraco Ultrasonics is the global leader in the fields of contents monitoring of gaseous extinguishing systems and watertight/airtight integrity monitoring, all of which are integral to the success of any fire suppression system.
The firm designs ultrasonic technologies to “see the sounds that others cannot hear” and, in their acoustic and mechanical systems, to “measure the hitherto unmeasurable”.
An emphasis on fundamental science in “practical scholarship” and sustained, innovation, invention, and discovery continues to underpin Coltraco’s research, development, design, and ergonomics program.
Our technologies take advantage of the fundamental characteristics and properties of sound waves to monitor and measure an array of specialised environments across 25 diverse market sectors, including the fire industry, delivering the Safesite™ on land and the Safeship™ at sea.
For instance, where it would previously have taken a 2-man team 15 minutes to dismantle, weigh, and reinstall one 45kg CO2 fire extinguishing gas cylinder on a large ship, that may have up to 600, Coltraco Ultrasonics’ science-led technologies allow one person to monitor the contents of that fire suppression gas cylinder in the gas suppression system in 15 seconds.
Within this vision of the Safesite™ on land and the Safeship™ at sea, the firm’s technologies allow customers to justify actively engaging in going above and beyond existing regulations as an integrated and essential element to their business activity. Customers, personnel, and assets alike will be better for it.
Clean agents are pressurised liquified or non-liquified fire suppression gas, that is pressurised on actuation, and commonly used in the fire industry.
CO2, frequently used in a gas fire suppression system, is permanently under 720 psi or 49 bar of pressure, nearly 50 times atmospheric pressure.
Pressurised fire extinguishing gas cylinders are often considered by the fire industry as single and passive columns of solid material, from the perspective of their monitoring following installation.
However, as these cylinders are constantly under pressure, with this pressure changing due to variations in temperature, they should be considered active, dynamic systems, that require constant monitoring. Indeed, all good engineering demands the monitoring of dynamic structures, such as highly pressurised cylinders, that are designed to protect critical infrastructure and assets.
Coltraco Ultrasonics’ Portalevel® ultrasonic liquid level indicators are capable of measuring the level of liquified and non-liquified fire suppression gas in a gaseous fire extinguisher to +/-1.5mm accuracy. This level of accuracy has never been achieved before.
These technologies are complemented by the Permalevel® Featherweight, which allows for the constant monitoring of a gas suppression system from these fixed monitoring sites and can be tracked centrally at the customer location and remotely globally, and our Portascanner® AIRTIGHT 520. Without constant monitoring, a risk is generated in the very environment for which it is designed to reduce risk.
Coltraco Ultrasonics’ retrofittable devices allow users to go above and beyond existing safety regulations, combining the ease of retrofitting with the highest accuracy of constant monitoring, capable of monitoring both liquified and nonliquified gas fire suppression systems.
Coltraco Ultrasonics at the Forefront of Room Integrity Monitoring with the Portascanner® AIRTIGHT 520.
Our Portascanner® AIRTIGHT 520 ultrasonic airtightness and leak detection instrument is able to detect leak sites as small as 0.06mm, with a tolerance of 0.02mm. This is an unparalleled level of accuracy, and Coltraco Ultrasonics is the only company world-wide able whose instruments are able to monitor level and precisely identify, measure, and quantify the size, extent, and severity of leaks.
Coltraco has been a part of the Working Group on British and International Standards Organisation (ISO) Standards Safety Engineering since 2016.
Room integrity monitoring is essential under ISO 14520 where gaseous extinguishing systems have to be designed in relation to the discharging agent hold-time and discharging
agent peak pressure, to ensure that fire extinguishing gases do not leak, and that fires are not replenished with fresh oxygen.
Whilst room integrity is frequently monitored at the design stage of a fire suppression system through positive pressurisation, such as with a Door Fan Test or Pulse Test, it is common for further tests to be completed infrequently once this initial inspection has been passed. A building is like a ship at sea. It turns and bends as any structure does, and during this aging, leak sites develop.
A new British invention, following the colocation of the company’s Physicists and Scientists at Durham University, a globally outstanding centre of teaching and research excellence, the Portascanner® AIRTIGHT 520 builds on Coltraco Ultrasonics’ long history in watertight integrity monitoring for the Royal Navy.
The Portascanner® AIRTIGHT 520 allows for the ultrasonic quantification of leak sites in a depressurised environment, which is a unique capability globally.
Regular, simple, and accurate room integrity testing with the Portascanner® AIRTIGHT 520 will allow the fire industry to make sharper decisions, verify technical specifications, and reveal possible defects in
a complementary manner to periodic Door Fan or Pulse room integrity testing.
Ultrasonic measuring solutions are a better-fastercheaper method of ensuring safe fire engineering practices are adhered to.
• Better: Ultrasonic technology is non-invasive, nondestructive, and non-disruptive, meaning it is safer for personnel and does not require the user to shut down the fire suppression system during inspection.
• Faster: The non-disruptive, non-invasive nature of ultrasonic contents monitoring allows testing to take place when the fire suppression system is in-situ and operational. Likewise, the absence of any need for pressurisation, and simple-to-use instruments, allow for rapid, regular room integrity inspections, with little previous training required.
• Cheaper: Enabling inspection to take place without disruption to the fire suppression system means no shut-down, saving time, and no requirement for multiple operators, saving labour costs.
This facilitates the implementation of a comprehensive maintenance program as part of a strategic approach to business continuity, reducing the risk of accidental or ineffective discharges and leaks not being picked up, creating additional value, leading to revenue reward.
It is the firm’s vision that this industrial integration of technological solutions to provide a bulwark against wider industry misrepresentation and minimal, even occasional and flagrant disregard in the application of standards and good global engineering will create standards which all can understand and apply.
The mathematics of its failure are high, whether in the application and understanding of the formulae used to calculate design concentrations of gases or flow rates, or in the deployment of fundamental engineering principles to protect dynamic pressurised systems and the structures they are working so hard to protect against fire. u
The fire risks associated with alternative marine fuels and the carriage of electric cars and lithium-ion batteries will need to be addressed if the next generation of sustainable, autonomous ships are to be safe, according to global Survival Technology specialist Survitec.
Speaking to The Ship Supplier, Finn Lende-Harung, Commercial Director, Fire Solutions at Survitec explained that while existing fire extinguishing technologies and mediums are highly effective in dealing with gas and methanol-fuelled fires, batteries, ammonia and hydrogen throw up their own challenges.
“The consequence of a fire from these alternative fuels can be substantial as seen in recent accidents both on land and at sea. This requires higher focus on fire prevention through the use of inert gas systems and very early detection of monitoring gas pressures and temperatures,” he said.
Rafal Kolodziejski, Head of Product Support and Development – Fire Systems at Survitec, agreed that if there is a fire in a ship’s battery room, boundary cooling could even be an issue given the potentially high temperatures involved.
“At the same time, toxic gases being produced out of battery modules exposed to high temperature and fire is another critical aspect. It creates new barriers for implementing currently available mediums like Novec or other clean agents being used onboard a ship.”
Referring to a fire aboard a car carrier, which sank in March, Mr Kolodziejski said it took more than eight days for fire-fighting systems (and fire tugs) to contain and extinguish a fire fuelled by the lithium-ion batteries in the electric cars carried onboard.
“Electric car cargoes or containers carrying lithium-ion batteries are a real concern and we are seeing more fires with these types of cargoes, which are very difficult to extinguish,” Mr Kolodziejski said.
Another emergent risk is the influx of substandard spare parts and services.
“The separation of the technical from the procurement department is resulting in a greater need for quality assurance and greater controls to ensure components and consumables are from trusted suppliers. This is crucial.”
Mr Kolodziejski referred to several incidents where CO2 hoses, for example, have not been fit for purpose or properly tested, despite certificates and stickers suggesting otherwise.
“This is placing people and assets at risk,” he said.
Mr Lende-Harung also revealed that the maritime industry’s response to COVID-19 has seen a “massive surge in demand” for remote system diagnostics and condition monitoring, resulting in Survitec’s Maritime Protection brand developing and recently introducing a remote support service for its inert gas systems.
The equipment consists of a remote VPN gateway that connects to the inert gas system operator panel via an ethernet cable or Wi-Fi. Through the secure gateway, Survitec fire safety experts can then monitor, operate, adjust, and troubleshoot the system shoreside without having to physically attend the ship.
“We can connect at short notice in case of issues threatening normal operation or to provide training to ship crews.
“We can help a system operator tune-up the IG system to reduce fuel consumption and increase system stability.
“For ship managers it reduces the maintenance spend and reduces lead times substantially when support and assistance is required,” said Mr Lende-Harung.
Indeed, following the success of Survitec designed fire system for Yara Birkeland, the world’s first fully autonomous containership, Mr Lende-Harung believes that remote diagnostics and the monitoring of fire safety equipment will become a major factor in the swing towards autonomous shipping.
“Even though a fire onboard an autonomous ship may not directly harm the shoreside crew it still presents a catastrophic risk to the ship, the cargo, the environment,” concluded Mr Lende-Harung. u
www.survitecgroup.com
Swedish ship supplier creates the first circular economy for plastic ropes. The ship supplier, and ISSA-member, DFS has created the world’s first plastic rope that is part of a circular economy. Does this new rope, ReLine™, have the potential to change the market for plastic ropes as a whole? We’ve asked Carl Forsman, Project Manager at DFS, to give his thoughts on this groundbreaking innovation.
According to the IUCN, about 14 million metric tons of plastic ends up in the ocean each year.
That makes up roughly 80% of all marine debris found from surface waters to deep-sea sediments. This problem has even created large “garbage patches” in the middle of our oceans.
Recent studies suggest that a very large part of these patches are made up from discarded fishing gear. Furthermore, the WWF warns that the scale of “ocean plastic pollution” might quadruple by the year 2050.
I believe we all agree that this is a major issue, and that everyone must help mitigate this problem.
For us, a ship supplier with our headquarters located in northern Europe, we saw an opportunity to make a difference within both our industry and immediate geographical area.
You see, today DFS is Sweden’s largest ship supplier and we deliver all types of goods to all types of vessels but if you go back to when we were founded (1950) our core business concerned fishing gear.
“
to reduce CO2-emissions and plastic pollution within ship supply through innovation, collaboration and concrete action
Naturally, even if a lot has changed since then, we have always had a close relationship with the local fishing industry and we still have a passion for ropes, trawls, nets and all other types of fishing gear.
As we realised that this part of our customer base was facing the overwhelming challenge of plastic pollution, we also realized that we had a responsibility to help them out as much as possible.
A couple of years ago we started our environmental initiative, called “Green Link”. Our goal with the initiative states “to reduce CO2-emissions and plastic pollution within ship supply through innovation, collaboration and concrete action”.
Our work with “Green Link”, combined with our realisation that there was a gap to fill within the fishing industry, led us to the idea of creating a circular economy for the most used plastic products within our market – rope.
At this point we had already established a good relationship with a Danish company called Plastix AS. They are world leading when it comes to gathering, processing and recycling discarded plastic ropes and nets. Their final product is called OceanIX rPPC, plastic pellets that are completely made from discarded plastic waste from the maritime industry.
Our idea was quite simple: what if we used OceanIX rPPC to create new ropes?
It had not been done before, mainly because the recycled plastic pellets have some different characteristics than virgin plastic but also because the general interest of the manufacturers still remained low.
The path from idea to reality was not without its problems. It took us about 18 months before we finally managed to create our first version of (what is now known as) ReLine™.
Since then we have refined our process and created two more versions of the rope, the “final” one was delivered in November of 2021 and we already have orders from a lot of different customers within the Scandinavian fishing industry.
It’s not enough just to sell ropes that are made from old ropes however. Sure the product itself is “circular” (since it’s made from an older version of itself) but really to “close the loop” you also have to make sure that ropes make it back to Plastix.
This is why we have launched co-operation with several different parties to make sure that discarded fishing gear from our customers is also handled appropriately.
This is only the beginning of our journey with ReLine™ but we are very happy with the fact that the groundwork is done. If all parties included stay focused we might actually have a chance of impacting the market of plastic ropes in a really significant way.
Looking forward we are also planning on creating another version of ReLine™: a mix of OceanIX rPPC and virgin plastics.
It might seem strange to introduce non-recycled material to a product that is already 100% recycled but it is necessary to meet certain requirements within different markets.
Because ReLine™ is made from 100% recycled ropes and nets its MBL (minimum breaking load) is about 20% lower than equivalent ropes made from virgin plastics.
In most industries this is not an issue since the MBL is higher than it needs to be anyway. However, for certain markets the rope is required to meet certain standards (mainly ISO-standards) and then the current MBL of ReLine™ is too low.
That is why we are currently developing the ReLine™ Mix, a rope made from 70% OceanIX rPPC and 30% virgin plastic. This version will meet the requirements of various ISO-standards and can then be used on a much broader scale within all industries.
Our journey with ReLine™ has only begun but it has already been inspiring, educating and fun.
We urge all our friends within this industry to launch their own initiatives and projects concerning sustainability. We have to if we are to overcome the enormous challenges of climate change and pollution. u
With more emphasis placed on Maritime Decarbonization and Sustainable Shipping, the trend of vessel owners worldwide designating more expenditure into delivering energy savings is growing rapidly- with many owners looking to retrofit conventional lighting on their vessels with LED Lighting.
SOPEX Innovations, a Singapore based company and GL Lighting Holding are in a strategic partnership of which the latter- has more than 20 years of experience in the Research and Development, Design and Manufacture of technological advanced and innovative Green LED Lighting solutions and has more than 500 ODM and OEM projects for renowned international lighting companies.
SOPEX Innovations places emphasis on the design and development of ideal LED solutions- providing green and innovative energy-efficient technologies and meeting the demands of the harsh Marine environment at the same time.
LED optimises energy consumption as compared to conventional lighting, reduces maintenance through improved durability, and allows great savings to one’s electricity consumption. SOPEX pledges to deliver the highest-quality range of reliable LED lighting, allowing you to maximise your investment in operations and reduce your maintenance needed. Their Green Initiatives plan involves working with vessel owners to retrofit conventional lighting to LED lights with maximum luminosity and the shortest Return-on-Investment.
Be it a new vessel or a retrofit, “Going Green” is one of the ways you can amortise your investment within 1-2 years.
This approach is proven, cost-effective, and can be achieved within 12 to 24 months. Let us work collaboratively to do something real, measurable, and impactful. Write to us at info@sop-led.com and we will be glad to provide you with a workable solution.
GL Lighting Holding has one of the best and most up-to-date luminaire factories in Asia. The manufacturing facilities consist of an 11,000M2 mechanical plant and an 11,500M2 electronic plant, which come with cutting-edge production facilities of fully automated SMT line, clouds enabled electronics manufacturing setup, advanced powder coating line, and CNC/laser/plastic injection/cold-forged/aerospace welding.
SOPEX Innovations had the opportunity to work with BW Hafnia on the conversion of conventional lightings to LED for one of their vessels BW Orinoco, a crude oil tanker sailing under the Singapore flag. The team had successfully retrofitted 28 pieces of IEC 60533 certified Marine floodlights- providing the shipowner with up to 90% energy savings and 55% CO2 emission reduction with less than 2 years of ROI. Crew were delighted with the brightness and coverage of the outdoor LED Floodlights and being able to do without monthly consumables replacement.
Most of the Floating Dock’s outdoor lights were fitted with SOP 6 Module LED Floodlights, ensuring that the entire deck of the floating dock is provided with adequate illumination to enable work seamlessly, regardless of whether it is the day, night, or bad weather. SOP 6 Module LED Floodlights are equivalent to 2x400W MH/ 2x250W HPS / 1000W Mercury.
Asia World Port Terminal
Asia World Port Terminal located along Yangon city river in Myanmar upgraded their high mast conventional lighting to a brighter, more reliable, and energyefficient SOP LED lighting system to reduce their maintenance and electric utility cost. They enjoyed energy savings of up to 76% per year while attaining the return on LED Investment in just 1.8 years
Giorgia Viaggi - from Italian supplier REXNAVI – gives some helpful advice on managing your inventory
In the last two years the world has changed.
We have new needs as individuals and professionals. We always hear ‘heavy words’ like pandemics, sustainability, and smart-working. We are going through changes and facing new regulations - and the shipping sector is not untouched.
Coping with this ‘new normal’ we may lose track of the basics. And what is one of these basics to keep your vessels running? Spare parts!
Spare parts are, of course, constituents of bigger machinery and are designed to be easily removed and fitted. They are often overlooked but they are vital for vessel operations as they play a major role in the functioning of equipment.
Managing spares from the purchasing and technical department side is hard work. Think of demand forecasting: the part manager must take into consideration not only “how many pieces” but also “when” and “where”, acting either on a predictive or on a reactive position.
Sometimes you can plan your purchases. Equally sometimes parts get broken or worn out and the vessel crew were unable to predict it.
Reaction is key during a crisis – not only the crew and the part manager must react, but also the spare part supplier.
As a pertinent example
Just think of pump spare parts. Pumps are included in the auxiliary machinery group and yet they are very important as they assist in the propulsion system – so they play a key role as a back-up of bigger or higher ranking systems.
Where can you source your pump spare parts? There is a wide choice of companies that can support you in this. Besides
the original pump brand (known as the maker or in some countries as OEM), you can contact companies dealing with compatible spare parts (also known as OEM in some countries – yes, OEM is a tricky name but this is another story!).
The end users have many options and various sources of supply depending on their budget, policy, delivery time and location.
What does a good spare parts manufacturer/supplier do?
• Market analysis;
• Manages offers, orders and claims;
• Inventory and warehouse management;
• Sources raw materials;
• Follows in-house and out-sourced production;
• Research and development;
• Logistics;
• Invoicing;
• Handles requested documents (MDs, SDocs, Certificates…).
Yes, spare parts are vital but it is clearly not all about the product. As John Ruskin once said, “Quality is never an accident. It is always the result of intelligent effort”.
When you look for a spare parts supplier check on their product quality, check on their price, but do not forget to check on their service.
Look for suppliers who care for your spare parts and your vessel; who put themselves in your shoes and where customer service permeates the entire company. u
https://www.rexnavi.it/en/
At AkzoNobel, we supply the sustainable and innovative paints and coatings that our customers, communities – and the environment – are increasingly reliant on. That’s why everything we do starts with People. Planet. Paint.
It has seen us commit to using reduced, re-used and recycled material where possible, while still offering long-lasting, excellent performance that customers have come to expect from our Marine Coatings division throughout its 140-year history.
Our sustainability efforts have seen us ranked at the top of several major indices. For example, AkzoNobel has received the highest possible MSCI rating (AAA) for six consecutive years and is part of the Clean 2000 – a ranking of the companies with the highest revenue from sustainable solutions.
As testament to our continuous investment and commitment - we have been consistently ranked at the top of many different external indices which rank corporate sustainability performance.
In 2021, we also proudly announced as the first paints and coatings company to have received approval by the Science-Based Targets initiative (SBTi) for our carbon reduction targets.
As you would expect, as a business we take an active role in supporting initiatives in our surrounding areas, outside of our business. We are actively providing support and resources to a number of great initiatives including The Ocean CleanUp, Polar Pod and the Water Revolution Foundation – each different, but each taking steps to help protect and better understand biodiversity and our ecosystem.
And our internal experts are working alongside industry leaders on a number of strategies, including the IMO’s GloFouling initiative to minimise translocation of invasive species from ships’ hulls and to create the industry’s first cleaning standard with a focus on performance and sustainability - BIMCO.
We are also delivering new ways to help our customers with their vessel efficiency and environmental performance while supporting the industry’s carbonneutral journey as a whole.
One key way we have achieved this is through the launch of Intertrac® HullCare - the industry’s most environmentally sustainable hull management package to date.
As fleet operators today face an increasingly complex set of operational and legislative challenges, the solution offers an opportunity to reduce operational uncertainty, boost operational performance metrics and extend service lifetimes beyond solutions currently available in the market.
Available as a 5 or 10-year scheme, it combines high-performance hull coating technology from our International®
We are mainly a service-based company specializing in different types of services like catering services (Offshore/Onshore), Ship Chandelling services, Industrial Support Services and we are also engaged in management of restaurants which operates inside the Ras Laffan industrial city
range, cutting-edge ROV (remote operating vehicle) inspection, and big data performance monitoring, with proven hull cleaning techniques aligned with the BIMCO industry standard.
By ensuring that smooth, clean hulls are maintained, Intertrac® HullCare can help operators achieve step-change reductions in CO2 emissions of up to 34,000 tonnes and fuel savings of €4.6m over a 10-year period, in comparison to a typical five-year fouling control system.
The scheme optimises paint consumption and maintenance while having the lowest environmental footprint of any similar scheme, as well as future-proofing against environmental legislation.
To further drive sustainability in the industry, our ambition is to provide coverage in the most frequently used ports and anchorage locations, with ROVs deployed in 2021 and further locations planned, including provisions via third parties, throughout 2022.
The inclusion of proactive hull cleaning as part of Intertrac® HullCare also helps to increase savings during the dry-docking cycle. And in a further boost to sustainability, all cleaning is aligned to the BIMCO industry standard, so it is conducted using cleaning technology with reclamation as standard.
Not only are we committed to investing in sustainability in our company, but we are also helping our industry partners, as tackling the ecological impact of the shipping industry is a priority we share with operators worldwide.
As well as setting new standards for operational efficiencies, Intertrac® HullCare exemplifies how we are actively collaborating with customers to provide solutions that further their financial and sustainability performance as well as that of the marine industry as a whole. The advanced remote inspection and cleaning technologies used have been developed and tested in close collaboration with leading global equipment suppliers over the last five years.
And to reinforce our commitment to supporting the marine industry on its carbon-neutral journey, we have recently appointed our first-ever Global HullCare Manager. Colin Mercer takes on the role after 23 years of experience delivering sustainability goals across multiple AkzoNobel business units.
In his role, Colin is tasked with building a seamless management program for owner partners, allowing them to effortlessly manage the performance of their vessels, while helping them to remain compliant with any impending legislation around EEDI, EEXI and CII.
As the industry faces an ever more stringent regulatory environment, our focus and ambition going forward is to provide our owner partners with stand-out, end-to-end support as well as develop the most innovative sustainable marine industry services in the marketplace.
Through Intertrac® HullCare we offer the experience, technology and data to maximise a fleet’s operational efficiency, driving forward our customers’ carbon-neutral journey with uncompromising performance. u
Possible major antifouling scientific break-through announced
The Danish biotech company Cysbio may have broken the code on how to eliminate copper in ship’s paint. The copper is replaced with sustainable and biodegradable eelgrass acid.
Virtually all vessels plying the world’s oceans daily are coated with antifouling paint, which prevents invasive species from attacking the ships’ hull, thereby increasing the ships’ water resistance.
Unfortunately, there are many harmful chemicals in the paints available today, one of which is copper.
The Danish company Cysbio has found the solution. They have developed and patented a fermentation technology to produce chemicals that are difficult to manufacture such as eelgrass acid.
It’s a quantum leap in research, as eelgrass acid can be used to prevent all kinds of microbes and even larger organisms from attaching to surfaces. It can therefore be used in antifouling paint for ships, thereby avoiding the use of environmentally harmful materials.
Current antifouling paint is primarily based on older technology in the form of traditional heavy metal containing biocides, primarily copper, and it’s proved difficult to produce a more sustainable substitute.
However in nature, there’s a plant that holds the solution to the problem: namely eelgrass, which has its own antifouling mechanism to eliminate unwanted micro-organisms by producing eelgrass acid, says Henrik Meyer, CEO of Cysbio. He adds:
“Eelgrass only produces a tiny amount of eelgrass acid, so extraction directly from the eelgrass plant material is not affordable and production by chemical synthesis is also too expensive to allow commercial use.
“However, by brewing the acid, much like brewing beer, using our genetically engineered microorganisms to make eelgrass acid, we can make production much cheaper and based on renewable carbon sources, thereby making the whole process and the antifouling products fully sustainable.”
Without antifoulants in the paint, invasive organisms attack the ship’s hull, which increases the ship’s frictional resistance, decreases speed, while fuel usage and shipping costs skyrocket.
The ship also emits more CO2 and risks spreading invasive micro-organisms from one ecosystem to another. For these reasons, there haven’t been any financial or environmental advantages in eliminating biocides in antifouling paints.
Henrik Meyer continued: “The problem is that the harmful effects of not using antifouling agents have been so great that we have chosen to live with copper accumulation.
“But now, as we can produce eelgrass acid, we can use more environmentally friendly chemistry and thereby avoid copper and other harmful components in our seawater.”
Jens Tørslev from the independent research organization, DHI Water Environment Health, which specializes in aquaculture, agrees that the pros and cons of antifouling ship’s paint make for a hard balance. He notes that developments in antifouling will help the shipping industry and, in the long run, the environment.
“The industry is aware of the paint’s unwanted effects, and earlier, there have been attempts to tighten the regulation for the use of chemical substances in ship’s paint.
“However the paint still contains some copper, and too much copper in the water can show their effects on the ecosystem. Now, there are alternatives for the industry, and that’s positive,” Jens Tørsløv explains.
Prohibition is gaining ground
Due to the lack of alternatives, antifouling paints containing copper are still permitted, but environmental authorities the world over have started to counteract.
Sweden has fully banned ships with copper paint in the Bay of Bothnia and freshwater lakes, while the Netherlands and California have introduced restrictions that prohibit the sale of ship paint with high concentrations of copper for yachts and recreational vessels.
Henrik Meyer again: “It’s crucial that corporations and politicians drive this development. Companies that produce ship’s paint must take part in product development, as they will actively be using these new chemicals in the future.
“It will take some development work, but it will create great market value for the first companies who enter the market with these new products, and we are prepared to help and co-operate with them.”
He adds: “The current method with chemical and copper-containing paint is expensive and unsustainable, so it makes both economic and environmental sense to replace these less wanted components with more environmentally friendly solutions.”
Cysbio uses advanced technology to produce cheap and sustainable biochemicals by modifying micro-organisms with the ability to convert simple sugars to biochemical products. Cysbio is a spin-out of Novo Nordisk Foundation Center for Biosustainability at DTU (Technological University of Denmark). u Read
Posidonia 2022 will be held this summer from June 6-10, with the 27th staging of the world’s most prestigious shipping event gearing up to welcome the international maritime community back to its Athens Metropolitan Expo venue, following the pandemicinduced disruption of the 2020 event.
Already, nearly 90% of the exhibition floor is committed, and as new bookings continue, Posidonia 2022 is on course to match, if not overcome, its exhibitor record set in the pre-pandemic staging of 2018, which had registered 2,009 exhibitors and 22,000 visitors from 92 countries.
The majority of this year’s confirmed Posidonia exhibition space has again been reserved by international companies, and at least 85 of the total number of exhibitors will be making their Posidonia debuts.
Theodore Vokos, Managing Director, Posidonia Exhibitions, the event’s organiser, said: “We are ready for the great reset of the shipping industry.
“We are delighted to witness such strong demand and feel the desire of the international maritime community for Posidonia’s physical resumption.
“As the home of the Greek shipping community, Posidonia has always been a popular destination to network with leaders of industry, showcase the latest in maritime engineering and
technologies, and engage in discussions that shape the international discourse on the sector’s most important issues,” said Mr Vokos.
The booming dry bulk and container markets, the decarbonisation debate, new technological challenges and how they reshape the industry, the initial impact of Covid-19 and the subsequent rebound from it, as well as the uncertainty of what the future holds in a post-pandemic world, will be some of the topics to be addressed during the conference programme of Posidonia 2022.
With Posidonia 2022 fast approaching, the recently elected President of the Union of Greek Shipowners (UGS) Mrs. Melina Travlos lends her support to the organization of the event: “The long-standing and globally well-established shipping exhibition, Posidonia, comes back this year after 4 years of absence due to the pandemic, with solid foundations not only to live up to the raised expectations of the international maritime community, but to also exceed them.
“Having been honoured to be at the helm of our historic Association, the institutional representative of Greek shipping
which owns 20% of global tonnage and 59% of the EUcontrolled fleet and on behalf of the Board of Directors too, we are certain of the successful conduct of this important for the international shipping industry event, the lynchpin of global trade and economic growth”, Mrs. Travlos stated.
“Posidonia 2022 offers the opportunity to unite the international maritime community and rally it behind commonly accepted principles and mutually beneficial strategies for an environmentally friendly and sustainable shipping sector, both in the short and long term”, Mrs. Travlos concluded.
The conference agenda is still being shaped, but already the flagship Tradewinds Shipowners Forum is confirmed, along with the Global Maritime Summit, organised by Seatrade in conjunction with the Global Maritime Club, and the Capital Link Investor Forum.
Other confirmed events, highlighting the international participation at Posidonia, include the Japan Ship Exporters Association seminar, the 3rd Korea-Greece Hellenic Maritime Cooperation Forum and a conference by the Polish Embassy in Greece.
Posidonia is also proud to support HELMEPA, WISTA Hellas, the Yes Forum youth project, the Hellenic Institute of Maritime Technology, Isalos.net and the Institute of Chartered Shipbrokers, who will also be organising conferences and seminars at Posidonia 2022.
The signature Posidonia Games will again be an essential part of the Posidonia experience, with hundreds of exhibitors expected to participate in the multidisciplinary sporting calendar which include the sailing Regatta Posidonia Cup, the Posidonia Running Event, the Posidonia Shipsoccer Tournament, the Posidonia Golf Tournament and the all new Posidonia 3on3 Basketball.
Posidonia is organised under the auspices of the Ministry of Maritime Affairs & Insular Policy, the Union of Greek Shipowners and the Hellenic Chamber of Shipping and with the support of the Municipality of Piraeus and the Greek Shipping Co-operation Committee. u
https://posidonia-events.com/
Global ship supplier and longterm ISSA Member Wrist has announced its acquisition of Panama-based ISSA Member Centralam Panama further extending their global network.
Jens Holger Nielsen, Group CEO of the Wrist Group, says “We’re looking forward to initiating our co-operation with Centralam Panama at one of the world’s most important maritime hubs.
“Centralam Panama’s management team is experienced and competent, and our companies share the same core values and business principles.
“Our customers, and thereby ourselves, will benefit from the combined
experience and capability in the ship supply market”.
“In becoming part of the Wrist Group, Centralam Panama will benefit from Wrist’s global reach, scale, and digital platforms, providing vastly expanded opportunities for our customers and business partners.
“Panama has historically been an area that vessel operators try to avoid with regard to services and supplies. With the presence of Wrist, this will no longer be the case,” says Thomas Rold, owner and CEO of Centralam Panama.
Mr Rold will continue to manage the business as part of Wrist.
Presently Centralam Panama
annually serves more than 2,500 vessels passing through the Atlantic and Pacific ports of Panama, providing customers with provisions, technical goods and stores, owners’ goods and spare parts handling as well as storage, distribution and other services.
The company’s operations are based around large and modern warehouses located centrally in the main port areas at the Pacific entrance to the Panama Canal and only a 70 km drive from the main ports on the Atlantic coast.
It is part of Wrist’s strategy to take a leading role in the global consolidation and development of the ship supply industry. Consequently, Wrist is continuously exploring new opportunities for serving customers through innovation and technology, thereby fuelling both organic growth and acquisitions. In December 2021, Wrist founded and financed Source2Sea, an independent digital sourcing marketplace facilitating online marine procurement and supply between maritime buyers and suppliers. More recent expansions of the Wrist Group include the acquisition of Wrist Valencia in 2020, Van Hulle in Antwerp in 2019, and Klevenberg in Rotterdam in 2018. Further acquisitions are expected in 2022. u
CMA D. ARGOUDELIS & CO S.A. is pleased to announce the establishment of a new subsidiary outside of Greece, D. ARGOUDELIS & CO LTD.
CMA Group is one of the largest Automation groups in Greece and Cyprus. The group consists of CMA D. ARGOUDELIS & CO S.A. in Greece and the new sister company D. ARGOUDELIS & CO LTD, based in Nicosia, Cyprus. The parent company was established in 1987.
The new company has its headquarters in Nicosia (Themistokli Dervi 41, HAWAII NICOSIA TOWER) and the main
goal of the company is to provide for the Cypriot market all the solutions, products, and services that the company has in Greece, tailored for local needs. At the same time, it offers the ability to cover the needs of companies and organizations operating in both countries, with a unified way of sales & technical support.
D. ARGOUDELIS & CO LTD has partnerships with the world largest manufacturers such as: Bosch Rexroth, Emerson Aventics, Danfoss, DEIF, FESTO, PR Electronics, Siemens, Klay Instruments, Brannstrom, Lumel, etc., thus offering a wide range of solutions for the majority of companies in the Cypriot market. u
We were very sad to learn of the sudden and unexpected death of Sharon Sennett in February 2022. Sharon was known to many ship suppliers, owners, managers and Masters as an excellent marine catering professional and as a loyal friend.
After time served as a Purser on passenger vessels, Sharon joined Garrets International in 1996. Sharon’s father, Paul Mullett, was Garrets’ Operations Director. Sharon quickly learned to take responsibility as Paul was often away visiting contracted ships. She was relentlessly hard-working but always cheerful and happy to talk. As the company grew, she remained committed to supporting the ships assigned to her, ensuring their crews were well fed and within budget.
Following a change in Garrets’ ownership, Sharon left in 2015 to join SeaStar, the catering arm of Wrist Ship Supply. The next year Wrist acquired Garrets, so Sharon soon found herself back at Garrets. As cost-cutting followed, Sharon’s post was made redundant. However, she was then snapped up by Oceanic, the catering arm of V.Ships, were she worked studiously for the last four years.
Suppliers knew Sharon understood the practicalities of delivering to ships. Always friendly, she was astute, practical and always focused on meeting the needs of the vessel. Her skills and abilities earned her respect both ashore and at sea.
Sharon had a great love of friends and family, and she was immensely proud of her three daughters, Georgia, Emily and Erin. We extend our sincere condolences to them. u
ISSA extends a warm welcome to its two newest members: Recollect Soluciones Offshore and Al Samad Enterprises.
Based in Cartagena, Colombia, Recollect Soluciones Offshore is a well established general ship supplier providing the full range of services. In addition they are also suppliers of navigational charts and publications.
A further offering is environmental services to the highest IMO MARPOL standards.
In addition to serving Cartagena, Recollect Soluciones Offshore’s services are available in Barranquilla, Buenaventura, Covenas, Tolu and Santa Marta.
www.recollect.com.co
With its Head Office in Karachi, Pakistan, Al Samad Enterprises is very well positioned to supply maritime chemicals and oils, the firm’s speciality.
Port Qasim and Gawadar (Outer Anchorage) are also served by the company.
However as well as its speciality supply business, the company also supplies the full range of goods and services to be expected of the general ship supplier.
They are also able to carry out annual inspections.
https://alsamadent.com
Both members sport the ISSA Quality Certificate as well as a range of ISO Certifications. u
The International Maritime Organisation (IMO) has announced this year’s celebratory days. World Maritime Day will be celebrated at IMO HQ on the 29th September 2022.
The Day of the Seafarer has been fixed for 22nd June 2022.
This year’s World Maritime theme is “New technologies for greener shipping”. Members are encouraged to organise or join in any local celebrations of either or both dedicated days and further information on the parameters of celebrations is available from the ISSA Secretariat.
A spokesman for the IMO has drawn attention to plans for the Day of the Seafarer.
“For 2022, the focus of the Day of the Seafarer campaign, as usual, will highlight the key role of seafarers, while thanking them for their invaluable contribution.
“It will also link to the World Maritime theme and a social media campaign will be organised to mark the Day.
“Details of the campaign and how to participate, together with a variety of materials and “content opportunities” to assist participation, will be posted on the IMO website (www.imo.org) in due course.” u
PSW Power & Automation has ordered three compact Zinus cable handling systems that will supply shore power at the Port of Helgeland’s facilities in Sandnessjøen, Norway.
Zinus’ delivery consists of three Shore Power Compact cable handling units, which can deliver a total power of 2.5 megawatts.
The equipment will be delivered in Q3 2022. PSW is total supplier of the entire shore power plant and has the turnkey contract for electrification of the port.
“The cable handling units will primarily supply lowvoltage shore power to platform supply vessels servicing
offshore installations in the Norwegian Sea but can also serve other types of vessels visiting Sandnessjøen,” Norwegian Zinus said.
‘This delivery is yet another confirmation of the qualities offered by our technology, and we are pleased once again to be shown confidence in a market with ever stronger competition,” said Ronny Olson, Sales Director at Zinus.
“The fact that the contract is with PSW Power & Automation is particularly gratifying. PSW was one of our very first customers back in 2018 and continues to be a faithful and important partner.” u
Like everyone else, the shipping industry is doing its best to combat climate change and address the thorny subject of reducing plastic waste at sea.
Now along comes long established and well known Dutch water company Hatenboer-Water translating words into action.
They have developed their Plastic Free @Sea concept –and this simple idea has attracted wide-spread praise from ship owners, operators and crew on board.
Embracing this innovative idea, and the technology behind it, shipowners can reduce the tens of thousands of plastic water bottles on board to virtually zero, saving cost and handling time as a bonus.
The system consists of a contact free water bottle filling station, a filtration unit to guarantee quality drinking water and reusable bottles.
Each water fountain features easy hands-free sensor activation, providing users with a sanitary, touchless bottle filling experience.
The key components have an antimicrobial protection
that inhibits the growth of mould and mildew. In addition, as crew members are often reluctant to drink tap water from the water tanks due to their past experience, HatenboerWater provides on- and off-line training and information to get all crew acquainted with the ins and outs of the system.
Several regulatory bodies have laid down ambitious sustainability programmes. To take this forward fleet owners have to overcome crew concerns about the quality of new drinking water systems.
Hatenboer-Water acknowledges this and addresses it by providing each crew with visual information (posters, infographics), a digital magazine explaining the Plastic Free @Sea concept in (technical) detail, a practical manual and dedicated training if so desired.
By design, the units are easy to maintain and the dispenser clearly indicates when filters need to be changed. Tests with first clients have shown that crew members quickly grow confident and even fond of drinking water from the tap. u
Opsealog (the French performance management company) and Identec Solutions (the Austrian wireless solutions provider) have joined forces to provide accurate and reliable tracking of support vessels.
During a pilot project with Shell’s fleet in Nigeria the new team achieved unprecedented precision.
The new partnership aims to enhance their services to the offshore oil and gas sector. This will help companies further optimise the operations of their support fleets, reducing their emissions and maximising safety and security in harsh environments.
The partnership combines Identec Solutions’ GPS trackers with Opsealog’s data integration and analysis service, Marinsights.
The GPS trackers collect precise and real-time data on the positioning of each vessel, which is processed and analysed by the Marinsights platform to provide meaningful insights that can improve safety, optimise operations, and reduce fuel consumption.
The combined solution was successfully tested during a pilot project which was completed in collaboration with Shell companies in Nigeria.
Nine vessels were equipped with an i-Q350LX GPS-SAT removable transponder of Identec Solutions. These were configured to send the vessel position automatically every 30 minutes through the Globalstar network. This helped Shell overcome the challenges related to the tracking of its support vessel fleet in the winding rivers of the Niger delta, where in addition to the unavailability of the Automatic Identification System (AIS), bad weather conditions can pose a challenge for satellite reception.
The data was then analysed by Opsealog’s marine consultants and presented on the Marinsights platform, which enabled the company to visualise its fleet on a map in real time, with specific information for each vessel. The software also generated reports on routes and position quality, as well as alerts when a vessel was immobilised for a certain duration or when it crossed a geofenced area.
Opsealog’s founder and managing director Arnaud Dianoux said: “The remarkable results of this pilot project with Identec Solutions for Shell Nigeria demonstrate the power of digital solutions and illustrate what can be achieved when a wealth of high-quality data combines with state-of-the-art performance management service.
“Having a comprehensive portrait of support vessels operations is an essential component of a strong security strategy, and can also unlock efficiencies that support companies’ decarbonisation efforts.”
Dr. Urban Siller, CEO at Identec Solutions added: “We strongly believe that good visibility of onshore and offshore operations delivers safety and productivity.
“As the industry seeks to become safer, greener and more efficient, having a precise understanding of the activities of each vessel is vital. This is where our cutting-edge technology comes into play, and we are proud to partner with Opsealog on this journey that will support the offshore oil and gas sector as it moves towards sustainability.” u
With thanks to Esquire Magazine ©
Finding it hard to sleep? It might be that you’re struggling to turn your brain off. There are plenty of mindfulness methods you can apply to fix that, but Dodow is perhaps the simplest tech-based approach. It’s a simple device that projects a blue light onto your ceiling at a metronomic pace (for 8 to 20 minutes), which you match to your breath. Take a breath in when it expands, and breath out when it retracts. You should find that focussing your attention on the exercise calms your mind, and you’ll be off to sleep in no time.
Dodow sleep device
https://www.mydodow.com
Few devices are as original as the Samsung Freestyle, introduced during CES 2022. That’s because it’s more than just another projector. For starters, it’s one of the most versatile projectors around with its no-fuss operation — featuring auto image adjustment and colour correction. Point and project, it doesn’t get easier than that. Furthermore, it doubles as a powerful smart speaker powered by Samsung’s Bixby and Amazon Alexa. Throw in some fancy smart lighting modes into the fold, and the Samsung Freestyle is a projector like no other before it.
Samsung Freestyle
With thanks to https:spy.com
https://www.samsung.com/uk/projectors/the-freestyle/the-freestyle-sp-lsp3blaxxu/
© Samsung (with thanks)
‘Dubbed by NME “a soundtrack to life after lockdown”, Bastille’s fourth album builds on their reputation for boundless optimism. Or as the band puts it: as the band put it: “Who knows what the future holds? Doesn’t matter if I got you”
In these difficult times never has such optimism been needed more. By design Bastille have always found optimism in end times. 2016’s ‘Wild World’ was a barbed attack on political corruption and fake news while a string of mixtapes, collaborative singles and their stringled ReOrchestrated live shows saw the four-piece champion community.
All those hopeful threads come together on ‘Give Me The Future’, a sleek pop record that explores millennial anxiety in a world of rapidly evolving tech.
Released on 4th January 2022 by Virgin Records
With thanks to Ali Shutler and https://www.nme.com ©
Certain performers seem to find a Being John Malkovich-like secret portal to the brain of every composer they play. Marc-André Hamelin is certainly among them. And when the brain is that of the maverick of the Bach dynasty, Carl Philipp Emanuel, we can expect extraordinary things. With music that is rooted in his father’s legacy yet looks as far ahead as Brahms and Schumann, CPE is one of those figures who challenges the linear view of music history. Hamelin’s two generously filled discs make a strong case not only for the composer’s historic significance but also for the modern piano’s suitability to his limitless flights of imagination and unsettling juxtapositions. In this Hamelin joins Danny Driver (Hyperion) and Mikhail Pletnev (DG) among the most distinguished of modern exponents.
CPE BACH Sonatas & Rondos (Marc-André Hamelin)
Hyperion CDA68381-2
With thanks to Gramophone Magazine
https://www.gramophone.co.uk/review/cpe-bach-sonatas-and-rondos-marc-andr-hamelin ©
Donatello’s marble bas relief
“Madonna and Child (1420-25).”
Credit: © Antje Voigt/ SMB Skulpturensammlung
In his own time, the 15th-century Florentine sculptor Donatello was regarded as “the master of masters.” Despite this, there has been no major exhibition devoted to the sculptor’s work for nearly 40 years. That is set to change in March when a sweeping survey of Donatello’s work opens in Florence at Palazzo Strozzi and at the nearby Museo Nazionale del Bargello, which houses the most important collection of works by the sculptor, including “David” (circa 1440). Smaller incarnations of the show will be seen at the Gemäldegalerie in Berlin in September and the Victoria and Albert Museum in London next year. - Cristina Ruiz. After such a lengthy absence from public viewing and enjoyment if you can get to Italy we urge you to do so – in case there is another 40 year gap!
“Donatello: the Renaissance”
Palazzo Strozzi and Museo del Bargello, Florence; Gemäldegalerie, Berlin
March 19-July 31 (Florence); September 2-January 8, 2023 (Berlin)
With thanks to CNN ©
Richard M. Nixon: arguably the most divisive President the USA has ever elected. Watergate – his nemesis – has intrigued people ever since Nixon departed Washington DC in disgrace aboard the Presidential helicopter. Now comes a startling book with access to so-far unpublished documents and transcripts. This is the gift that keeps on giving.Garrett Graff, the New York Times bestselling author of The Only Plane in the Sky, provides the first definitive narrative history of Watergate—“the best and fullest account of the crisis, one unlikely to be surpassed anytime soon” (Kirkus Reviews, starred review)—exploring the full scope of the scandal through the politicians, investigators, journalists, and informants who made it the most influential political event of the modern era. For sure this will not be the last word on the subject but after 50 years a scholarly and historical view is to be welcomed. “Watergate – a new history” by Garrett M. Graff
Published by Avid Reader Press
An imprint of Simon & Schuster Inc.
Released 22nd March 2022
With thanks to The New York Times ©
With thanks to Tripadvisor ©
What better recommendation for this much-loved Japanese restaurant than the comment of one diner on Tripadvisor: “What better way to experience the heart of a community and culture than to survey various flavour profiles and preparations… all paired with the local libations?” No wonder Ise Sueyoshi is 3 in Tripadvisor’s 2021 List of Best Restaurants world-wide. The Tokyo restaurant is located between Roppongi and Hiroo and serves traditional “Kaiseki” style Japanese cuisine.
Yuuki Tanaka, the owner chef, was born in Mie prefecture and trained in “Kikunoi”restaurant in Tokyo. After training, he spent a year in Toronto, Canada and undertook further training around the world. A key feature of the restaurant is that all the fresh luxury ingredients are transported directly from Ise, Mie prefecture.
Ise Sueyoshi
4-2-15 Mizuno Bldg., 3F Nishiazabu, Minato 106-0031 Tokyo Prefecture
Web site: http://isesueyoshi.blog.fc2.com/ .