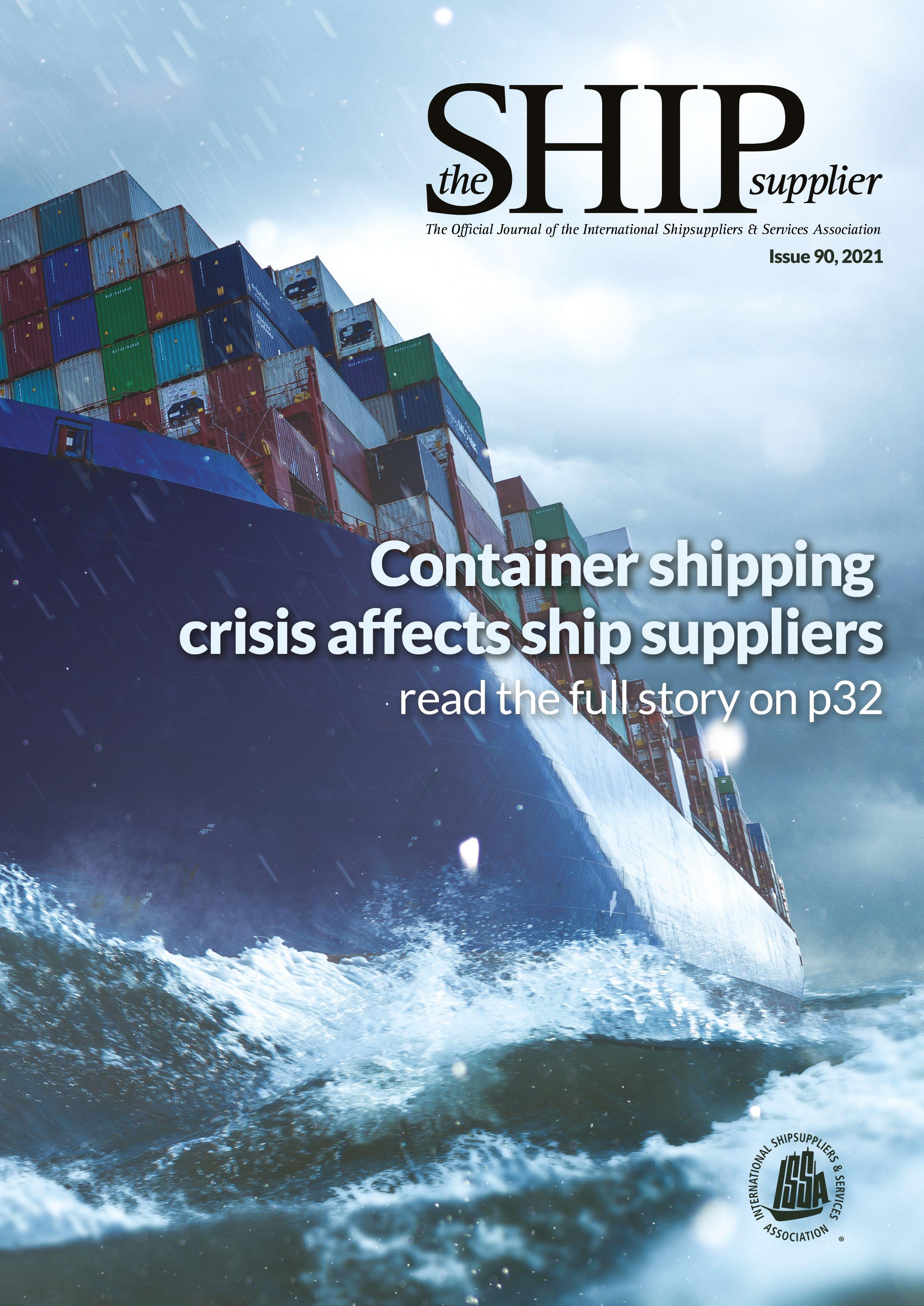
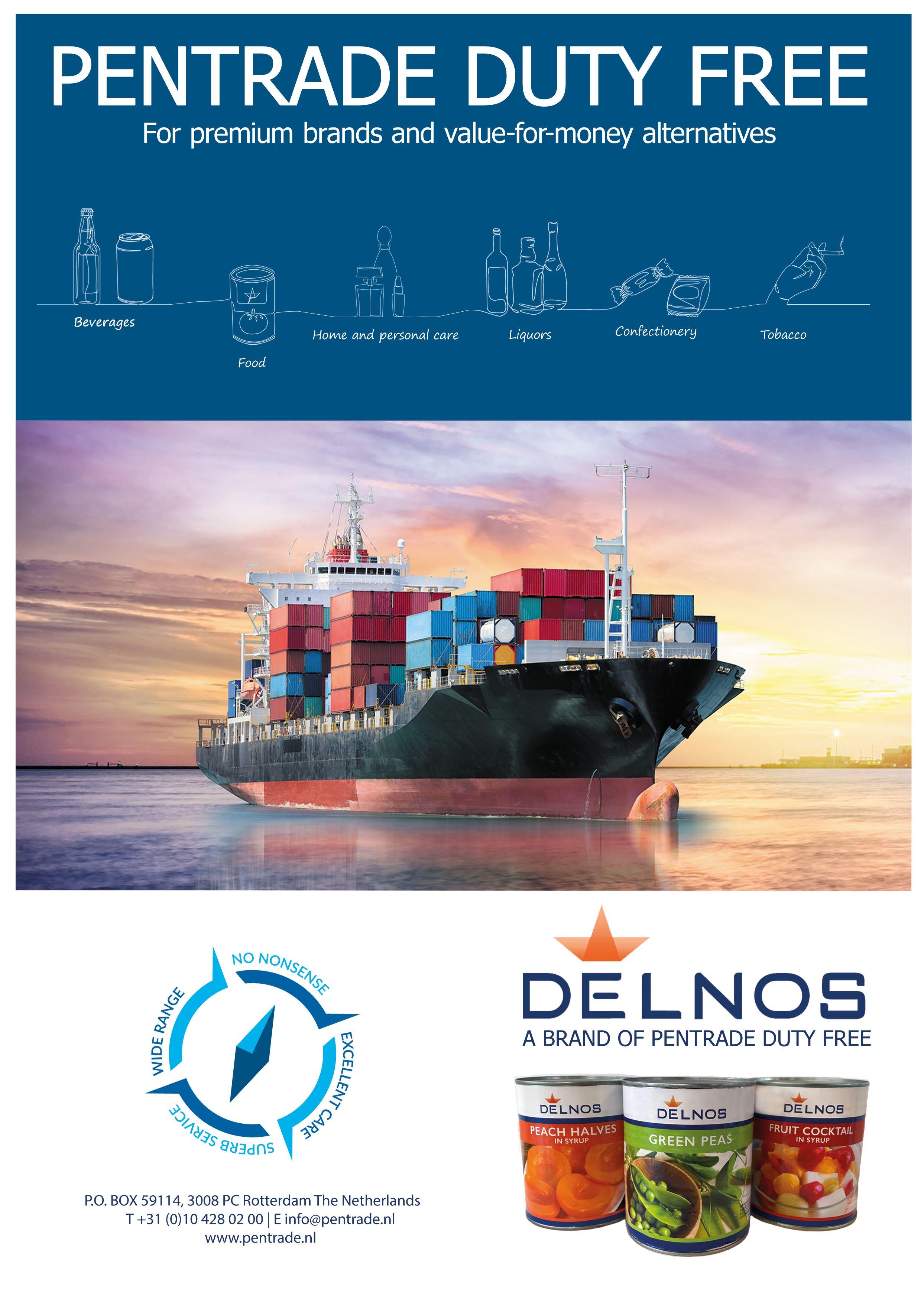
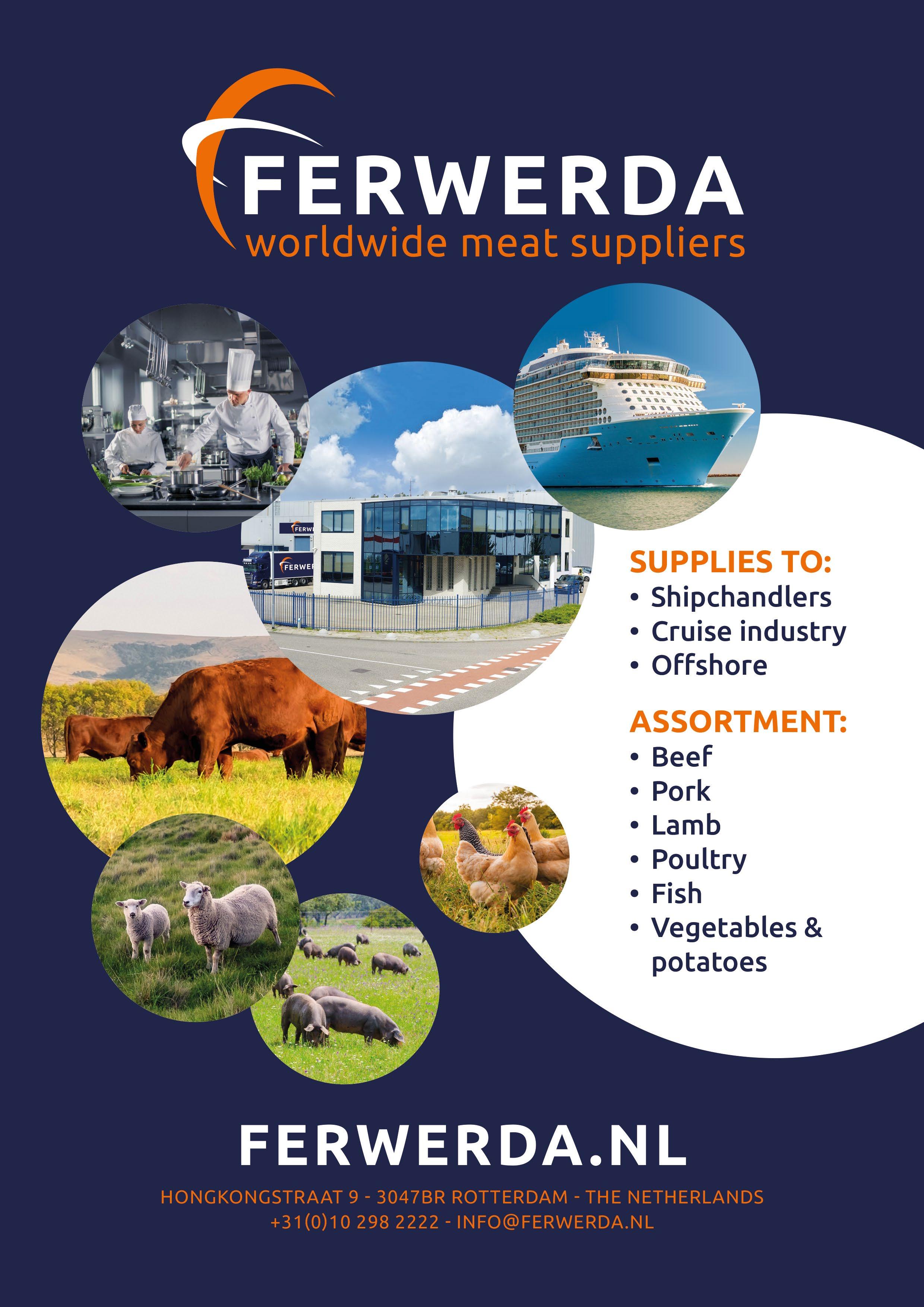




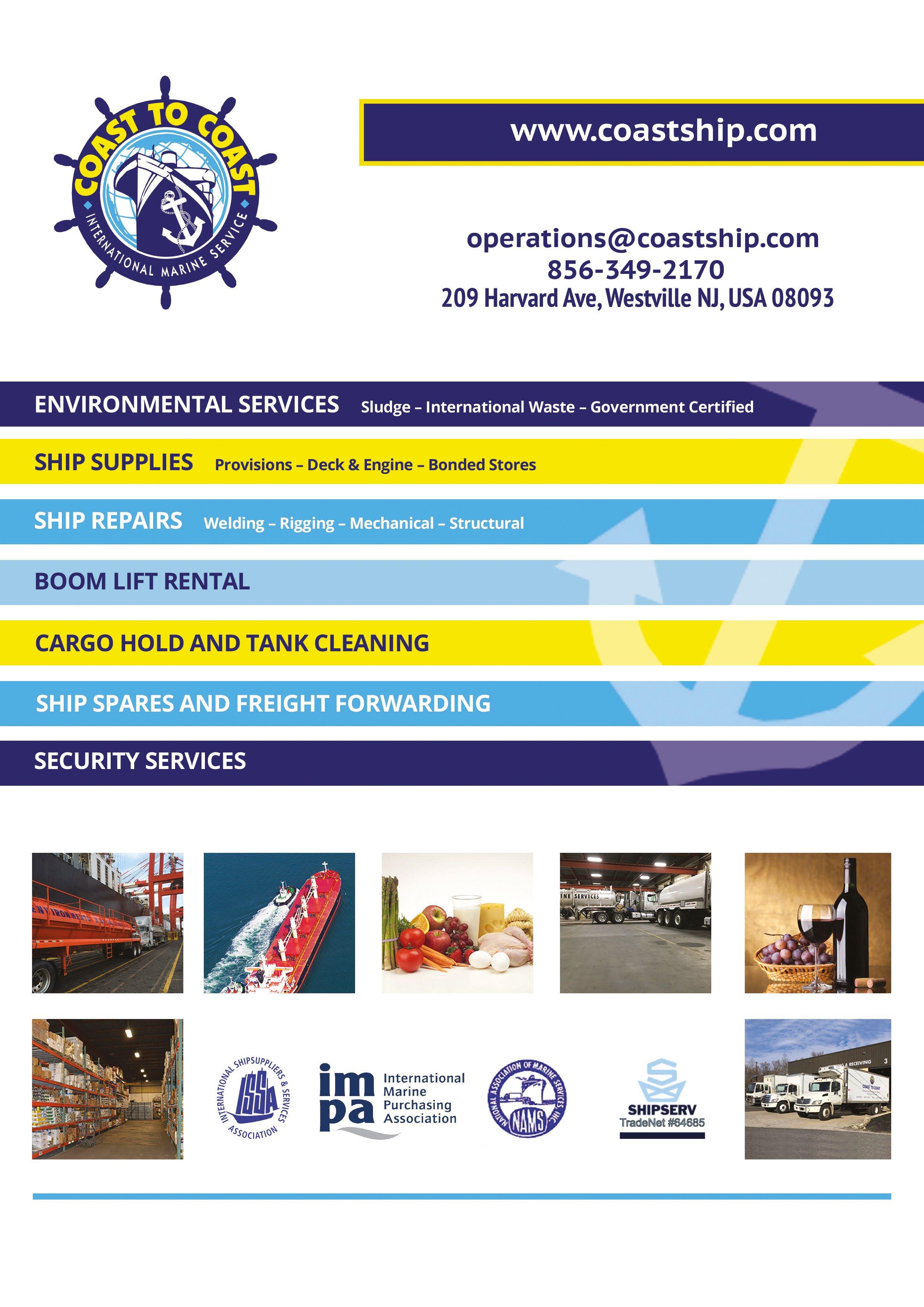
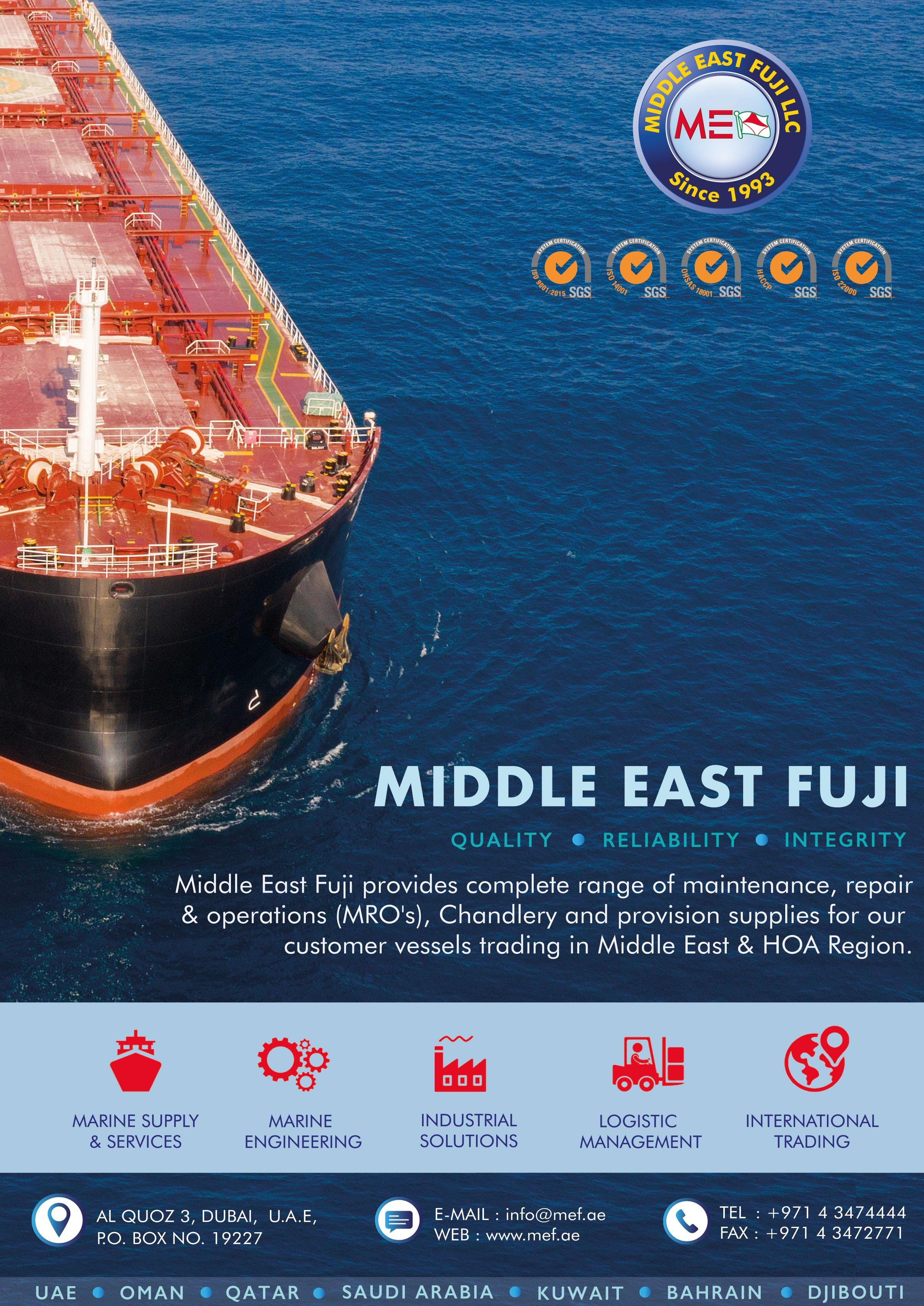
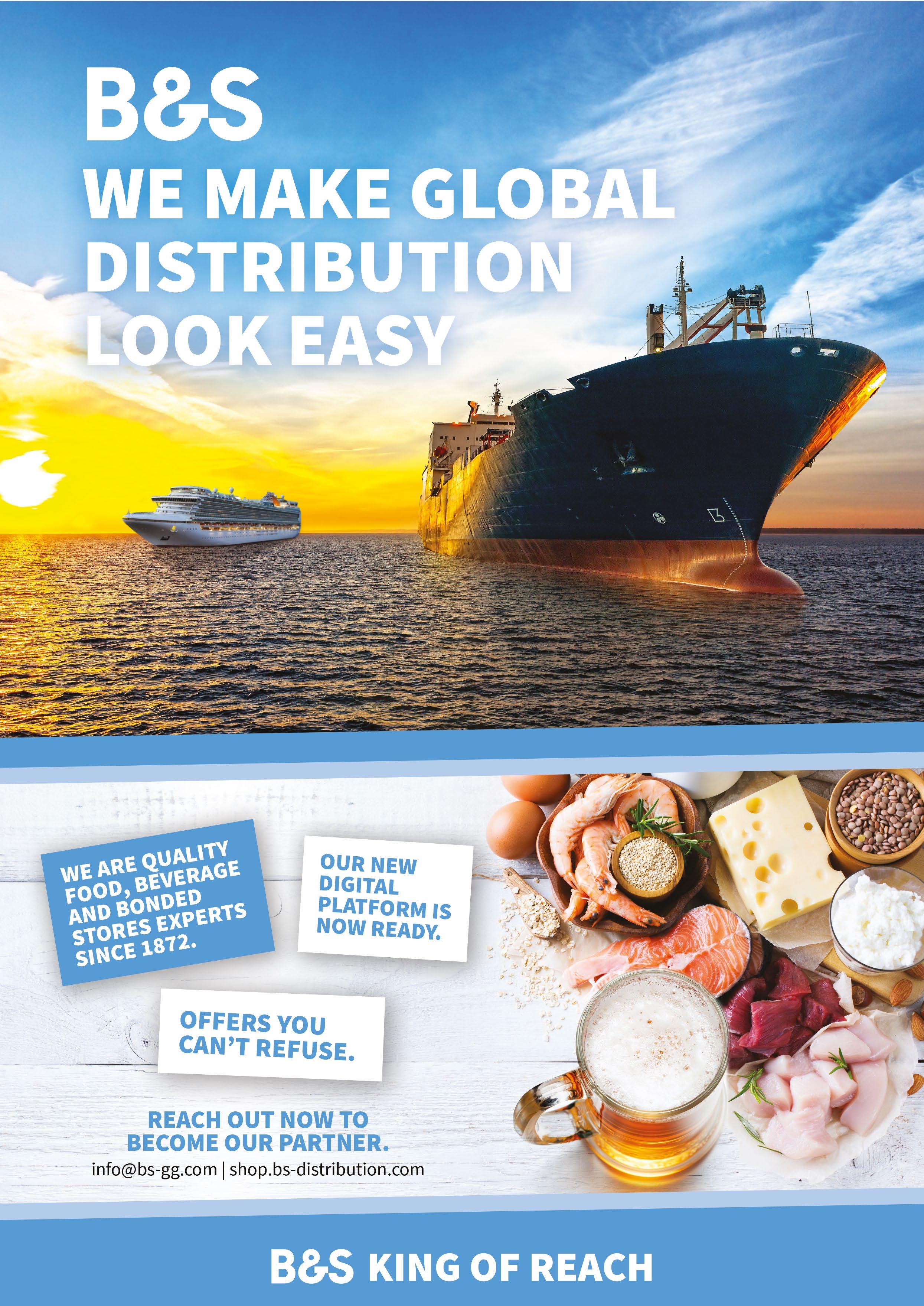
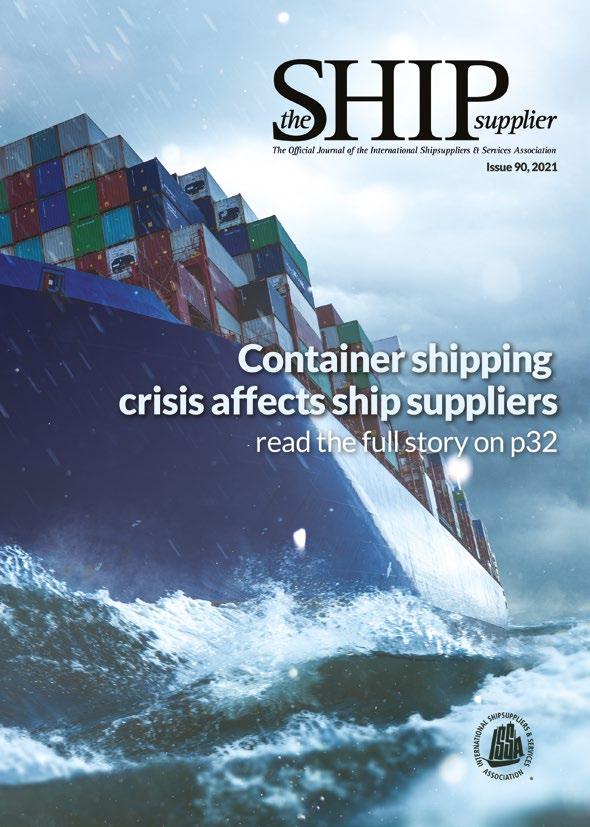

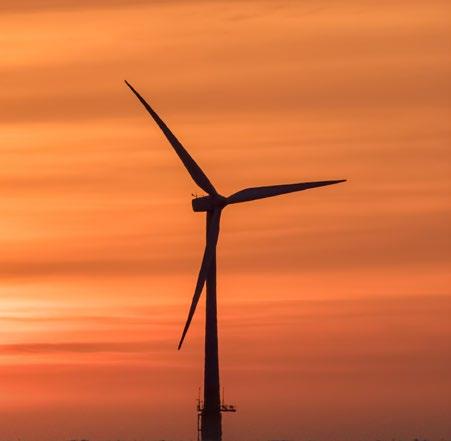

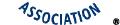
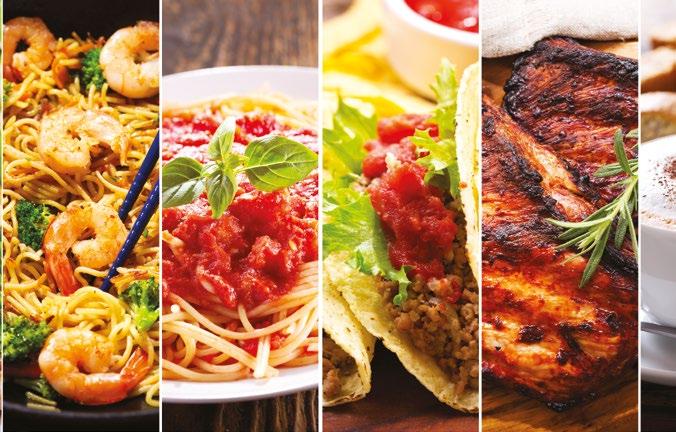
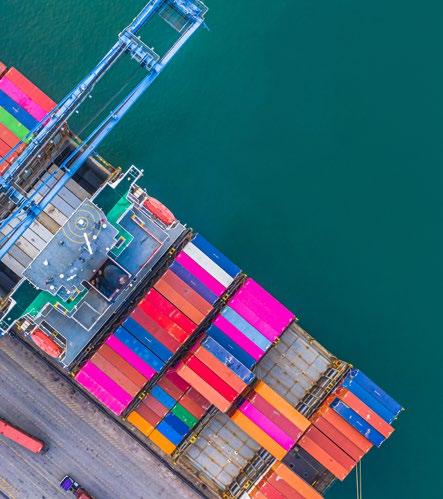
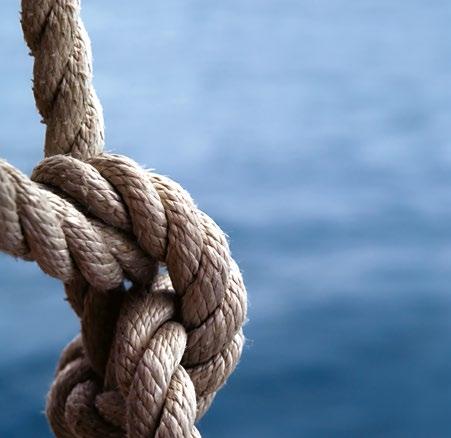
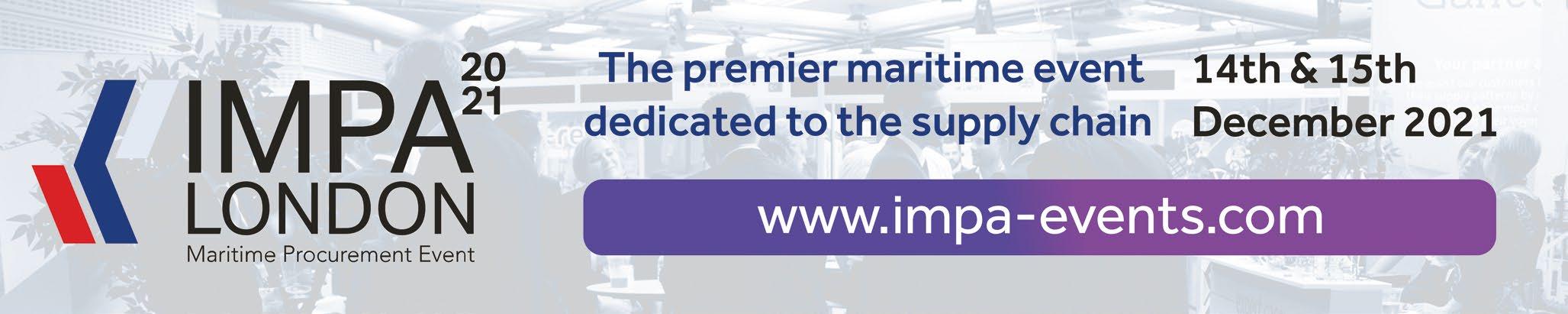
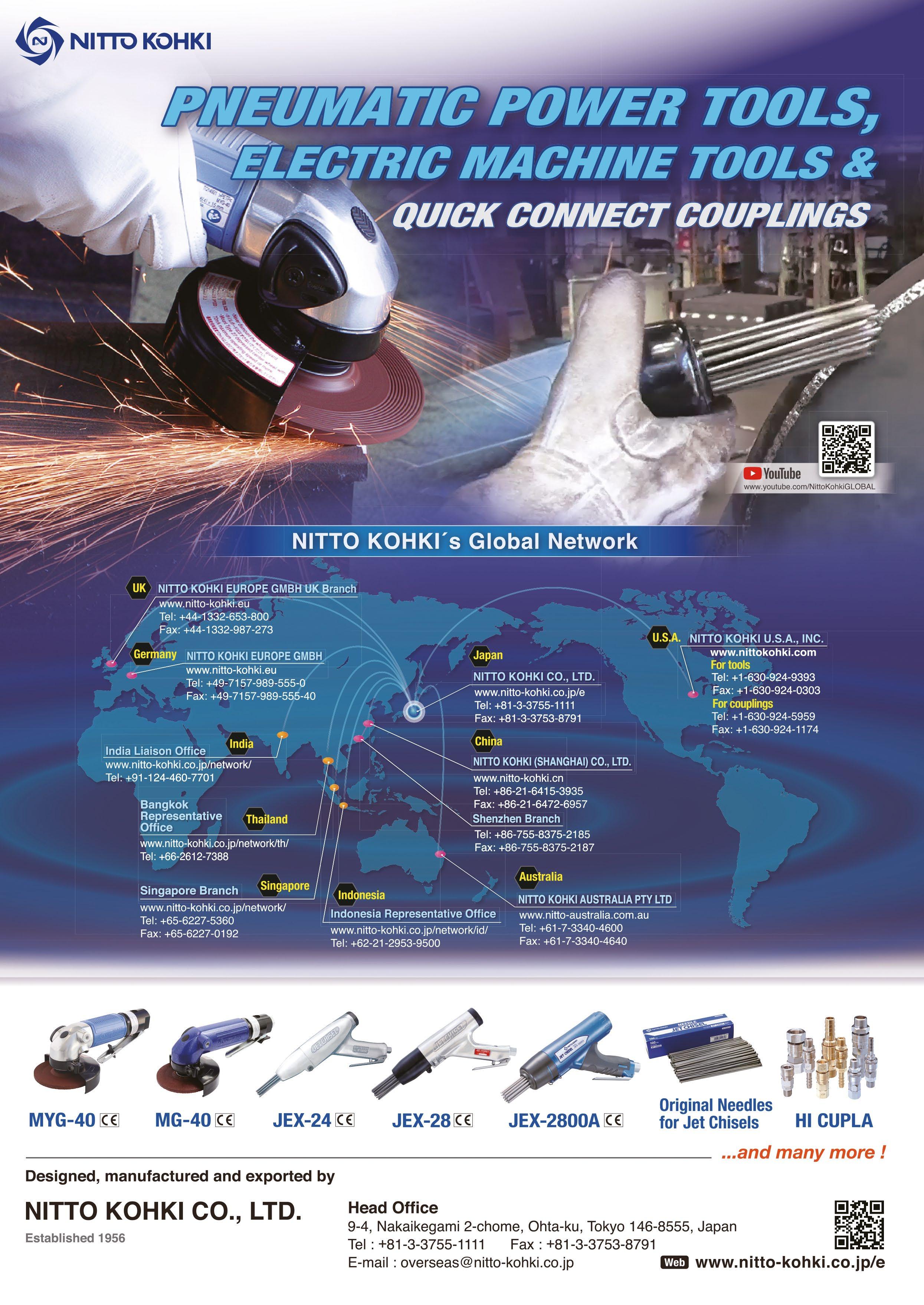

elcome to the latest issue of The Ship Supplier. I can’t believe we are already entering the last quarter of the year, and what a year it has been.
The world is slowly emerging from the ravages of the Covid pandemic, with many economies gradually opening-up. It won’t be too long before we all start to leave our Zoom screens and meet once again in person. Something I am certainly looking forward to.
But as we come to the end of a second year of Covid, shipping continues to prove its resilience. Trade is continuing at a pace, more so in some sectors such as containers, and the embattled cruise sector which so severely bore the brunt of the impact of the national lockdowns, has thankfully started to open-up. A welcome move for our ISSA members in that sector.
And ISSA is strongly in position to take advantage of the return to normality. When you consider all the hard work that we have done here at ISSA during the past 18 months, it is going to be an exciting 2022.
One immediate initiative we will be launching is the ISSA Education Programme, and we have enlisted the help of a major player in the field who will work with us to deliver cutting edge training courses for suppliers and buyers. These courses will be embracing the smart technology and will be virtual but will be designed to help you, as ISSA members, develop and train your staff to the high standards you meet. We are at the early stages of launching this initiative, but we will keep you all informed of progress.
For now, as is the ISSA tradition, I would like to wish you all continued success in the always exciting world of ship supply.
You can keep up to date with the latest news on the ISSA website at www.shipsupply.org and send in your comments and views to the ISSA Secretariat either by phone on +44 (0)20 7626 6236; Fax +44 (0)20 7626 6234 or alternatively email secretariat@shipsupply.org
Saeed Al Malik ISSA PresidentACOVID-19 outbreak for the ship supply industry is undoubtedly a test.
Global trade, which has been shaken by the “black swan” of the pandemic, has plunged into a great recession and negative growth.
Everyone is looking forward to an early recovery.
China’s ship supply industry faces a great test from the pandemic due to the high level of prevention and control requirements, the business for transmission and a longer logistic time.
These increase costs. However, it is worth it to control the outbreak and ensure the flow of supplies and shipping.
Covid has taken its toll causing some shipping enterprises that were hit hard to withdraw from the market.
In the first half of 2021, China’s transportation economy was accelerating to return to the pre-pandemic position. The main indicators are stabilization/, strengthening and improving.
Cargo volume and port cargo throughput has maintained rapid growth. In the first half of this year, the port cargo
throughput was 7.64 billion tons, up 13.2% from the same period in 2020 and 13.9% from the same period in 2019.
The container throughput was 140 million TEUS, an increase of 15.0% over the same period in 2020 and 8.8% over the same period in 2019.
During this period, the ship supply industry, while overcoming various difficulties to ensure the supply of ships, has made great efforts to strengthen pandemic prevention and control.
Closed management was strictly implemented within the ship supply service process.
In addition operational procedures were strengthened for the management of vehicles and personnel, to ensure that the identification, temperature, health status, health code (to show if the person has been to COVID-19 affected area), travel code and other information was checked and found to be satisfactory.
Steps were taken to strengthen the control of the shipshore interface, strictly delimit the “three zones” (polluted area, semi-polluted area and clean area) at the operation site, and make the three zones the closed loop.
It was agreed ship suppliers would adhere to the principle of “no boarding unless necessary”, strictly control the personnel boarding and disembarking, and carefully register relevant information of those who must board and disembark, so that they can be known, controlled and traceable.
All personnel were properly provided with personal protective equipment to achieve delivery as far as practicable.
If it is necessary to board the ship, the person on board shall standardise the operational process of disinfection first and then apply further disinfection measures before boarding and after disembarcation.
All foreign-related front-line workers entering the dock must complete 100% vaccination and nucleic acid test every three days, and strictly implement the requirements of secondary protection during their work. Relevant protective substances are included in infectious medical waste management after use, and transferred and disposed of according to regulations.
Accurate records are vital.. Everyone on board ships navigating internationally and the receiving units of the ship’s pollutants such as garbage and domestic sewage have set up special working classes to operate the closed loop management of the whole process of operation, traffic and life.
We are working together with the rest of the world to overcome the pandemic. However, the market changes and impacts brought by the epidemic are real.
To cope with such changes and their impact there needs to be a deep understanding of these variables. Positive responses and proactive actions can help ship suppliers maintain the safe operation of the ship supply chain.
The ship supply industry’s hard time will pass finally. We are all looking forward to that day! u
ISSA Executive Vice-President and ASSA Chairman Jim Costalos casts his critical eye over Australia’s struggle with Covid-19 but with an optimistic future view
The Australian ship suppliers have not escaped the effects of the COVID-19 Pandemic.
After a difficult 2020, everyone was hopeful for a better 2021. Alas, 2021 has proven to be even more difficult than the previous year.
Australia, as a whole, has handled the Pandemic rather well compared to many parts of the world. However, the
constant state of border closures given at limited notice, continues to cause havoc in everyday life. The Australian Government continue to keep our International Border closed without any ray of sunshine as to when it will re-open.
Current vaccinations in Australia are very low compared to most Western nations. However our Prime Minister believes the majority of Australians will be vaccinated by the end of the year.
The Australian ITF has been arranging care packages for ships’ crews at various ports. This is in an effort to assist the crew members that are not allowed ashore in this country and have been stuck on vessels for many months without an opportunity for repatriation.
Australia was awarded the 2020 ISSA convention to be held in November 2020 in Sydney only to be forced to cancel. The Australian Ship Suppliers Association also cancelled their 2020 AGM and with continuing uncertainty were forced to postpone the 2021 AGM.
There certainly has been a downturn in business during 2021.
Ship Owners have been reducing the volume of their purchasing down under. Whilst the Government has not deemed our industry as essential, our members have managed to continue to operate and offer our invaluable services to the international vessels calling at Australia’s 40 ports.
The role of the ship supplier, especially in Australia, is generally un-noticed & un-appreciated, until the emergency hits and we are the first people contacted. It was pleasing to see that the ASSA members have managed to adapt and survive in these difficult times.
A difficult situation facing our members is the new regulations IHM MD/SDoC that require the supplier to certify / declare dangerous goods. As Australia is not a major supplier nor manufacturer of ships’ technical goods, this area is causing stress amongst our members and their ability to comply. As an Association with the assistance of the International body (ISSA) we are looking for ways to overcome the problem
The Australian Association was formed in 1980 in Adelaide with 8 original members. Today all major suppliers are members with the number now at 15 full members, 2 Associate members and 2 Lifetime individual members (for long & invaluable service).
The membership has been keen to assist with Environmental Aspects and are seeking cleaner forms of delivery & packaging: basically in line with ISO. The Association has commenced working closely with MIAL (Maritime Industry Australia), in an bid to gain a louder voice in Canberra.
We trust & look forward to relative normality returning in 2022. u
Despite the challenges and risks posed by Covid-19, Singapore has remained open for business, underlining her status as a premier port trusted by ship owners all over the world.
So says the island state’s Black Sea Marine & Trading Pte Ltd principal Abdul Hameed Hajah.
While the recovery of other ports in the region has increased competition, Singapore remains well positioned (quite literally!) as a global shipping hub that has taken a meticulous, multi-pronged approach in ensuring the safety of all across the entire supply chain.
In addition to requiring all port users to be tested regularly and tracked upon entry into the ports, Enhanced Port Measures have been implemented at container terminals, requiring deliveries to vessels to be completed with minimal contact with crew.
Boarding officers are presently also not allowed to board vessels at both the terminals as well as at anchorage. Failure to adhere to these regulations comes with heavy penalties.
The pandemic has impacted many companies in terms of manpower shortages due to enforced Work-From-
Home (WFH) arrangements, increased costs of freight when importing goods and shipment delays, as well as various restrictions on port entry and delivery of supplies.
However, the stringent policies implemented by local authorities have been detrimental in Singapore’s general success in controlling the spread of the virus within its shores and ensuring that ship suppliers are able to operate safely.
Even as restrictions are slowly eased, masks and social distancing remain a mandatory requirement in all public places. The country has also ramped up testing and contact tracing capabilities and boats the highest proportion of vaccinated population in the world.
The covid-19 situation has highlighted the need for the industry to tap into technology to digitalise the port experience and shift away from an over-reliance on physical documents.
The Maritime Port Authority of Singapore, assisted by SASS, is currently exploring innovative opportunities in transforming the role of boarding officers with the hope to digitalise the port experience. u
Safety is unquestionably a critical consideration in most modern ports and terminals.
However, there are still grey areas where a lack of unified regulation or guidance leaves certain operations vulnerable to incidents.
Take lighting for example. There are currently no global standards for lighting levels despite lighting being fundamental to the safety of workers, the efficiency of operations and port security.
In fact, the International Maritime Organization (IMO) has never regulated or published recommended guidelines.
While we cannot disregard the value of existing port lighting standards in the UK, set by the Health and Safety Executive (HSE) and by those in the European Union, alongside ISO requirements, the lack of regulation from a global body has impacted the overall quality of lighting in ports.
As a result, there are legacy lighting systems present in many terminals around the world falling short of the standards that should be acceptable today. This in turn poses a serious and avoidable threat to those working within ports as well as to the reputations and profitability of operators.
This lack of clarity around lighting best practice is becoming increasingly important as more operations are exposed to volatile weather conditions, such as high heat and high winds, meaning inadequate lighting is more likely to fail and lead to a dangerous working environment.
With major insurance provider, TT Club, defining lighting as a significant factor in the top 10 risks posed in container ports to workers, it is up to owners and operators to act now.
The solutions to improve lighting in ports are accessible for owners, no matter what size or location. Such investments are also guaranteed to offer economic payback, increased security and the sustainability of operations.
Currently, many ports and terminals still use underperforming lighting solutions, such as high-pressure sodium, metal halide, or other similarly dated technologies. Due to their design, these solutions can lead to diminished visibility and are prone to breaking.
There are however alternative solutions on the market.
Unlike metal halide lamps, that degrade quickly and require replacing every 1-2 years, LED bulbs last for a minimum of 10.
The durability of LED lighting also means less workers are required to ascend masts and poles; significantly reducing risk. Similarly, the greater visibility of up to and above 50%, helps prevent the occurrence of avoidable accidents.
A reputable manufacturer should also offer a service to tailor lighting solutions to an environment. For instance, accurately positioning lighting can ensure it can withstand extreme weather conditions.
It is critical to remember that an accident could not only be harmful to workers but catastrophic for a port’s reputation. Were a broken lightbulb, or insufficient lighting, found at the scene of an accident, the port or terminal operator would be liable. As a minimum, this type of insurance claim would result in the issuing of a very large pay-out and, in some countries, like Russia, the port operator could be criminally prosecuted.
A lack of guidance around lighting standards and a subsequent awareness of the significant and accessible efficiency gains that upgrading lighting solutions can achieve has been overlooked for too long.
In addition an accident should never be the catalyst for much needed infrastructural upgrades. Upgrades, especially the use of LED lighting solutions are simple, effective and, most importantly, a vital asset to protect both owners and employees. u
IMajor UK Meats & Food Supplier Cavendish Ships Stores Ltd are experiencing pinch points in the supply chain. Managing Director JOHN DAVEY details the problems
SSA Executive Vice-President and major UK ship supplier MD, John Davey, is well used to the ups and downs of the ship supply industry.
With the Pandemic raging for the past 18 months and the bottom falling out of the cruise industry (one of his major business segments) life has been very challenging.
From his Headquarters in Fareham, Hampshire – close to the major port of Southampton (a busy cruise ship port) he has a ringside seat on the current difficulties.
“UK supply chains are currently fragmented for a number of reasons. Demand has increased with the relaxation of Covid restrictions but this in turn has placed pressure on a weak infrastructure.
“The longer supply routes in themselves are impacted by the significant freight increases coupled with longer lead times particularly from the Far and Middle East.
“In addition there is the added problem of a lack of containers in the key hubs.
“Protein from Australia and New Zealand is particularly tight and some lines are now exposed to import tariffs.
“Closer to home, Brexit has in turn had an impact with movements to and from the European Union now being classed as exports and imports with the relative associated paperwork.
“Once again border Vet checks and Customs
formalities are slowing down the process and in some instances non unified controls are creating a misunderstanding which results in loads getting rejected.
“Within the UK there is an acute shortage of qualified Heavy Goods Vehicle (HGV) drivers with many returning to their native countries at the start of the Pandemic.
“Many cannot, or are reluctant, to return.
“This has resulted in a backlog of deliveries within the UK and the UK Government relaxing some driver regulations in an attempt to ease the problem, but it is too little too late.
“Supermarket shelves are uncommonly bare in certain areas as a result of this “perfect storm”.
All in all this has created numerous problems for Ship Suppliers who on one hand are elated with the increase in business after such a torrid 18 months, whilst on the other hand are frustrated with the fragmented supply chains which do not help a “just in time” business model. u
Tony Broadhead from Turner-Price Shipping & Offshore pays tribute to the firm’s loyal staff
Turner-Price, like all companies, has gone through a very challenging 18 months.
We have had to adapt quickly to a very different world.
I feel we have been very fortunate that we have achieved this by having a very dedicated and passionate team who have gone that extra mile to maintain our success.
During the past 18 months we have had to re-group and re-think our strategy while still being able to keep our focus on what has been fundamental to our success through very trying times: QUALITY, SERVICE and PRICING.
I believe QUALITY & SERVICE in the current situation has surpassed PRICING although this is still very important to our customers who are paying the bill and something we are constantly monitoring.
Over the past few years there has been a big change to focus on Crew wellbeing and healthy eating.
This is becoming more important than ever to our customers and something we have been pushing for some time. Vessels and vessel owners/managers are also noticing that by having better Quality and Service levels they are reducing the amount of food wastage by around 10% - 15%a significant saving.
As it stands, we have a good solid supply chain on all meats and ambient goods which are mainly sourced from within the UK supply chain.
One thing we have noticed is that fresh produce is much more expensive now compared to previously. When speaking to other suppliers within the industry they all have the same issue.
We are also finding ourselves having to reject more delicate produce like salad items as the quality has not been to the standard we expect. We have been given many different reasons for this situation from Brexit, Covid and the lack of people to pick the produce or the fact the products just aren’t available at the moment.
I would like to think this is only a short-term issue and as things are slowly getting back to normal we are hoping this issue will also go back to how it was prior to the pandemic.
We now also transport our fresh produce secured on pallets using net wrapping to enable produce to breathe during transportation. If required, our drivers will carry regular pallet wrap and toppers should the customer require fully wrapped pallets to lift the product onboard.
We are trying our best to help in this area. We offer a large selection of paper, cardboard and wooden alternatives in packing and usage of single use plastics.
I know many companies are struggling with staffing and driver shortage and we have not gone untouched by this situation but as I stated earlier, we are very fortunate to have dedicated and loyal staff who have given us the ability to succeed and provide the quality service we give to our customers. u
Rotor Sails were first fitted to a vessel over a century ago.
However, with sustainability now at the forefront of all shipowners’ minds, Anemoi - a global provider of proven wind technology - has successfully reimagined the concept as a modern-day solution that can help aid decarbonisation.
Anemoi believes Rotor Sails, which were originally known as Flettner Rotors, offer an immediate and compelling solution for the maritime community. These unique, tall cylindrical sails can be installed on the main ship deck, bow or elsewhere with sufficient space. An electric motor is used to rotate the sails to harness the renewable power of the wind and propel the ship.
It has been estimated that if Anemoi Rotor Sails were installed on every suitable vessel in the world fleet, the average savings per year would be 17m tonnes of fuel and 56m tonnes of carbon – this is no mean feat.
Rotor Sails make use of the aerodynamic phenomenon known as the ‘Magnus Effect’. As the cylinder rotates within an airflow, a forward thrust force perpendicular to the apparent wind direction is created, which delivers additional thrust to the vessel. The thrust generated can either provide additional vessel speed or maintain vessel speed by reducing power from the main engine. The obvious benefit from this is less fuel burned and reduced emissions.
When it comes to installing Anemoi technology, wholesale changes to the vessel structure - or dry docking - are not necessary. Rotor Sails and all associated equipment are delivered to the dockside, ready for installation. The Anemoi’s highly trained team then supervise the full process.
Once the integration work is complete to make the vessel ‘wind-ready’, each Rotor is installed in a single crane lift and connected to the foundation on the ship’s deck.
Before this takes place, a feasibility study will have been conducted to determine the optimal positioning of the Rotor Sails. This is to maximise performance within the vessel constraints and the required Deployment System for the ship.
Key considerations will include: cargo operations, available deck space, proximity to existing structures that may affect aerodynamic performance and the structural
arrangement of a vessel’s deck for the development of the foundation structure.
Safety and regulatory considerations that must also be addressed include compliance checks related to stability, navigation (visibility, navigation lights and radar), helicopter operations and safe access on deck.
The vessel integration stage is crucial to the process and clients are supported at every stage, including the design and installation of the structural foundations and the electrical cabling from the vessel main switchboard to each Rotor Sail.
The vessel integration can be completed during the construction phase of a newbuild vessel, or during a survey at a shipyard for a retrofit vessel.
Once the Rotor Sails are installed and all cables are connected, final commissioning of the system is completed prior to handover.
This fundamental stage ensures safe operation and compliance with Class requirements through stringent testing. u
Many ship suppliers are closely involved in sending and receiving shipping containers world-wide.
The contents ranges from technical stores, provisions and bonded stores to inventory destined for new builds.
Until relatively recently this was a cheap and efficient method of transporting goods across thousands of miles of ocean.
Not at the moment though. The cost of shipping a 40’ container from the Far East to Germany has shot up some 800% in the last 12 months – and there is no sign of the $20,000+ rate slowing or reversing.
To understand why this latest problem has arisen The Ship Supplier approached industry expert Alexandros Karydis.
Alex is Director of Chartering and S & P at Hanse Bereederung GmbH, the in-house chartering and S&P broker outfit of Columbia Shipmanagement.
We began by asking what the root cause is of the eye-watering hike in container shipping rates.
Alex confirmed that the initial cause was the Covid-19 Pandemic. However by the Spring of 2020 scepticism had taken over and it was no longer thought this was the case.
“Then came the “miracle” of demand surge when lock-down caused a significant increase in consumer spending. Multiply this by the billions of items exported from China and this translated into a big demand for boxes,” he said.
Alex continued: “There was an economy of scale before the Pandemic that showed as an over supply of tonnage combined with low freight rates. Ship owners were operating on an un-sustainable breakeven basis.
“Shipping companies needed to charter in from a smaller pool of tonnage. Suddenly suitable vessels were fixing from three to five years when previously they had been fixed for six months. Scrapping slowed down and the view was taken that older ships could be retained and chartered at a significantly increased daily rate.”
It was well known that this translated into very high profits.
The second factor affecting rates was a “perfect storm” of the container behemoth Ever Given being stranded in the Suez Canal and before that problems in the supply chain. In addition there were port-side delays combined with Covid induced delays that resulted in closed ports and ships moving to try and berth at nearby alternatives.
Both Shenzhen and Ningbo Ports clusters were closed for extensive periods adding to the insipient chaos.
Time ticks by and now traders are worrying about Black Friday, Thanksgiving and Christmas stock and whether it will all arrive on time.
“This problem is wider than just shipping,” said Alex. “The whole supply chain globally (with or without pandemic) is affected with enormous paperwork: Customs formalities, bureacracy and delays adding to the crisis.”
When asked about a box cost reducing, Alex snorted that a reduction
would come in time and would stabilise but at nowhere near the previous $2,000 level.
He also offered little comfort to ship suppliers anxious to get their boxes to and from the Far East. Air freight was mentioned but only for light weight and high value consignments.
The container train from Shanghai to Hamburg was fast but very expensive –as we mentioned: a perfect storm.
Alex was firm in his view that there is no evidence shipping companies are profiteering from these unique conditions. “Everyone is used to cheap freight so all this has come as a huge shock to merchants,” he said.
“Another major contributory factor adding fuel to the fire is the lack of boxes available for stuffing. Shippers have been complaining loudly to the European Union about the situation. Contributory causes are recognised but definitely do not include any sort of cartel.”
To try and circumvent the problems some shippers are chartering in their own dedicated vessels but there is talk that a 1700 TEU ship can secure time charters at $150,000 a day! (albeit for short term periods) That, says Alex, makes no economic sense.
“This has turned from a headache to a migraine,” was how Alex succinctly summed up the situation.
He went on: “Take heart – container shipping is of the utmost importance for the industry for the next many years.”
Offering comfort to ship suppliers in particular Alex went on: “This situation is temporary. Many players are presently facing situations they can’t control but I believe market forces will correct the imbalance.
“Ship suppliers are not the only sector facing such difficulties but I can tell you that charterers are trying very hard to correct the imbalance for the benefit of all.” A glimmer of hope then. u
In just one year LALIZAS Safety and Inspection experts have built a highly successful presence in the Middle East.
Their state-of-the-art facility at Fujairah, UAE has established an enviable reputation with a solid customer base.
Despite operating in challenging conditions, LALIZAS’ highly skilled team of experts provides any vessel or oil rig/ platform with LSA/FFE inspections & services that meet the highest standards.
Their “one stop” Service Station provides marine safety services and supply requirements, approved by International Association of Classification Societies, ABS, RINA, LR, NKK, DNV-GL, IRS and Local Authority of United Arab Emirates.
The Service Station covers a wide range of inspections in all Gulf Cooperation Council (GCC) ports and anchorages, namely, Saudi Arabia, Kuwait, the United Arab Emirates, Qatar, Bahrain, and Oman.
The scale and breadth of their Service is very impressive. It includes servicing and supply for life rafts, life jackets,
immersion suits, chemical suits, breathing devices and fire extinguishers.
In addition all types of firefighting systems on board vessels fall under their servicing and supply scope.
An experienced team also provides inspection of lifeboats, rescue boats and their launching appliances.
Load testing of cranes and gangways, annual inspection and testing of elevators and automation services are also provided.
Their first anniversary is just the beginning of this firm’s breath-taking venture into the rigorous operational climate of the Middle East.
Giving truth to their corporate motto - “Safety is not just a product, it’s an ongoing process.” – it seems a racing certainty demand for their expertise will just keep growing.
https://www.lalizas.com/
Two important sectors of the shipping industry have experienced a remarkable turn-around in recent months. Demand and freight rates have soared due to a surge in consumer demand. This has come from the success of vaccines in curtailing the COVID-19 pandemic in many developed countries. Demand suppressed over the past 18 months has been released and there is increasing confidence that the worst effects of the disease are now behind us.
The jump in freight rates for container ships and bulk carriers follows years when ship owners had scaled back orders for newbuildings. Additionally, in the doldrums of the last year, record numbers of ships have been sold for scrap. Consequently, as shippers have sought to respond to the recent surge in demand, they have found fewer vessels available and freight rates have soared.
The biggest jump has been in the container ship sector, where the shortage of vessels has been severely compounded by congestion in major ports, particularly in China and the United States. This has resulted in numerous ships lying idle at anchorages, unable to load or discharge, due to the ports’ inability to process containers. Freight rates are now so high, that bulk carriers are being hired to carry containers. Shortages of vessels and port capacity are not problems that cannot be quickly fixed. Consequently, most commentators believe what is now being described as a “boom” will last, at least until the end of 2022.
Naturally, the spike in freight rates has triggered multiple vessel sales as ship owners, both old and new, have sought to get in on the action. Dramatic rises in the value of assets have not deterred buyers. No doubt some have diverted too much money to acquisitions, leaving them short of sufficient working capital to pay operating costs in a timely manner. They will expect ship suppliers and other creditors to grant extended credit to cover the shortfall.
Although buyers anticipate benefiting from the current good freight rates, they will need to service leases and mortgages with high interest rates attached. There is a danger that, when freight rates stabilise, owners will find themselves struggling to keep up payments. High freight rates tend to cause owners to postpone dry-docking for as long as possible. If funds have not been set aside to cover such expenditure, this can result in the perfect storm of high costs needing to be met at a time when the vessels are off-hire and due to re-enter a now weakening market.
Crew shortages and the extra complexities of crewing a larger fleet, exacerbated by ongoing crew change difficulties in many parts of the world, will see more owners turn to third-party ship managers. Such managers are keen to take on extra clients, especially as there is very little risk from their point of view.
Since they act “as agents only” or “as managers only”, they have minimal exposure should an owner get into financial difficulties. An owner in that situation can rely upon the managers’ discretion and, most likely, forbearance in the knowledge that ship suppliers and other creditors are carrying the risk.
The natural inclination is to celebrate when customers take on additional vessels but ship suppliers must continue to exercise caution. Larger fleets may mean more frequent orders but they may also conceal increased risks and new hazards. u
The Covid pandemic has been particularly damaging to the cruise industry.
Whilst the largest operators have, so far, been able to keep themselves afloat a number of smaller operators have collapsed. One such operator was Cruise & Maritime Voyages, whose vessels were managed by Global Cruise Line Inc in Greece (“Global”). Three were owned by CMV, two were on bare-boat charter (with option to buy) from Carnival and one was time-chartered in.
Many ship suppliers around the world had been happy to supply their vessels for many years. When Covid hit, the vessels were brought to England to be laid-up, while CMV sought to raise the finance that would be necessary to see them through the pandemic. When they failed to do so, they entered into insolvency.
The three owned vessels were mortgaged to Macquarie Bank and were arrested by the Bank and sold by the English Court. The Bank was entitled to all the proceeds of sale, and trade creditors of those vessels were left empty handed.
The two bare-boat chartered vessels (“Vasco da Gama” and “Columbus”) were arrested by their owner and were also sold by the Court. These vessels were not mortgaged, so the proceeds of sale were available to those who made claims without risk of a mortgagee claiming the proceeds in priority.
Many creditors issued claims at Court. Disputes broke out between those creditors and the Port of Tilbury, concerning the extent of the Port’s charges (which had a priority over trade creditors). This dispute was resolved by the Court, and the Port’s claim reduced significantly.
Vasco da Gama sold for US$10.4 million and Columbus for US$5.5 million. Whilst the proceeds of sale would not be sufficient to satisfy all the claims, after significant work to reduce the claims of the Port and Carnival, trade creditors of Vasco da Gama were paid 95% of their claim value, and 50% on the Columbus.
However, there were several creditors who chose to play the waiting game, apparently preferring to see whether the vessels would sell for sufficient to offer them a worthwhile recovery before commencing proceedings.
Upon the realisation that worthwhile recoveries may in fact be possible, proceedings were commenced. However, they failed to commence proceedings before Carnival terminated the bare-boat charters, and after a contested hearing in the English Admiralty Court it was held that this delay was fatal to their claims.
This was certainly an unusual case, where trade creditors recovered significant sums following the judicial sales. Typically, when vessels are sold in such manner the proceeds are wholly consumed by banks/lenders and other priority claimants (the port and crew). In this case, a more positive outcome was possible, owing to the absence of mortgages and the values of the vessels.
Those creditors who took advice from the right lawyers and made good choices were able to make good recoveries. Others acted too late, or not at all, perhaps put off by the wrong advice or a lack of faith in the advice they received.
The lesson to learn is that it is always worth taking early advice from the right people, and to trust that advice. Salvus Law acted for 15 creditors who recovered more than $6.5 million dollars. u
Engine lubricants must handle the potential issues related to each fuel mix available to any operator today. They must also provide a level of qualification in the reliability of the emission treatment systems that are coupled to the engine, and the new fuels of tomorrow. Nikolaos Kotakis, Technical Manager from Lubmarine at TotalEnergies brings simplicity to the complex world of sustainable shipping and clean engine technology.
‘E
missions’ is the buzz word across the shipping industry this decade and is likely to be well into the next.
When we look at emissions, the IMO 2020 sulphur cap, which limited the sulphur in fuel oil used on board ships operating outside designated Emission Control Areas to 0.50% m/m (mass by mass), was a significant regulation and global movement to reduce air emissions from shipping.
Since its implementation on 1 January 2020, one of the biggest takeaways we have experienced from the last 18 months is the importance of engine cleanliness, which has been confirmed by a number of sea trials.
Engine cleanliness is of course essential in this new operating regime. It requires a high level of in-depth technical awareness, support and solutions for all ship operators and OEM’s to ensure they implement the right lubricants and fuels strategy – and are using the right combination of solutions to operate successfully.
It is one of the reasons why our technical experts are focused on ensuring all our customers use lubricants and monitoring tools that deliver optimal engine performance and engine cleanliness.
What is clear, however, is that the shipping industry will continue to face changes with initiatives that deep dive further into energy efficiency, emissions and greenhouse gas targets, as industry’s knowledge and experience of new fuels evolve.
In line with TotalEnergies’ net-zero climate ambition, our team from Lubmarine at TotalEnergies and our colleagues at TotalEnergies Marine Fuels are developing multiple low- and zero-carbon marine fuel and lubricant solutions to help advance decarbonisation across the industry.
Yet, we strongly believe that the sector should act now and not wait for these technologies to be commercially ready.
In terms of fuel options to reduce the environmental footprint of maritime transport, compared to conventional fuel, LNG is presently the cleanest available marine fuel at scale and paves the way towards carbon-neutral bioLNG.
As one of the first movers in the supply of marine LNG, TotalEnergies Marine Fuels has actively invested infrastructure in Rotterdam, Marseille and Singapore to serve shipping customers that have chosen LNG as the cleaner fuel choice.
Their goal is to extend the company’s LNG supply chain across strategic bunkering hubs.
With increasing demand for LNG bunkering that is now seen in the number of new LNG-powered vessels on the order books, clearly the shipping market has confidence in LNG – in its infrastructure, practicality, availability and flexibility.
TotalEnergies anticipates that global LNG bunkering demand may rise to 10Mt per annum by 2025, and represent more than 10% of the bunkering market in 2030.
Likewise in the area of engine lubrication, we all must anticipate the demand and be ready to propose sustainable solutions in engine lubrication that will most likely be flexible enough to run on several types of fuels.
At Lubmarine we continue to strengthen our work with OEMs and the marine lubricants supply chain partners on how best to develop new formulations of cylinder lubricants and Trunk Piston Engine Oils appropriate to the new fuels of the future, and their application for both 2 stroke and 4 stroke engines.
Success has been achieved in qualifying products such as Talusia Universal, which is developed using a unique chemistry that helps the neutralization process and the control of engine deposit growth in the pistons, rings, and liners.
We received a No Objection Letter (NOL) for Talusia Universal (BN57) by WinGD for use with all fuels with a sulphur content 0.00%S to 1.50%S (including LNG and Dual Fuels), and late last year by MAN Energy Solutions for the same product following rigorous tests carried out on two different vessels fitted with W6X72 engines.
In this new, low-sulphur era, the traditional lubricant indicator of base number (BN)—used to quantify acid neutralization capability—will be only part of the equation. New refinery processes and fuel blend stocks used to produce VLSFOs, that could have led to engine condition challenges, can only be tackled effectively with innovative chemistries.
While existing lubricant oils are designed to achieve the reliability of engines running on today’s conventional low sulphur fuel oils, it is reasonable to expect increased research and development into lubricants that will handle alternative fuels of the future.
As knowledge and experience of new fuels evolves, we will continue to develop new formulations of engine lubricants appropriate to the fuel and its application. We will not consider just the sulphur content of the fuel used but also the engine characteristics, emission control and energy saving systems, and the operating conditions so we can
create solutions designed to help further reduce CO2 emissions.
Low and zero sulphur fuels bring with them their own lubrication challenges, however we understand fully that new fuel and new engine technologies need new types of lubricants.
It is one of the reasons why we believe that low ash chemistry can be the
basis for the next generation of engine oils, particularly for dual-fuel engines or those diesel engines fitted with selective catalytic reduction systems.
We have pioneered this strategy with Talusia Optima – a product that uses Ash Free Neutralizing Molecules. This is a unique and patented technology that provides fast and effective acid neutralization without mineral deposit build-up from the most demanding two-stroke engines. This revolutionary lubricant was developed through intensive R&D at our renowned Solaize Research Center.
Looking to the future, with engine technology continually evolving, we need to remain agile. We work to find efficient and cost-effective solutions to the challenges ship owners face in the lead up to 2030 and 2050.
Everyone has a part to play in the transition to a cleaner, better performing industry. It is a period in our time which represents incredible evolution through fuel innovation and engine oil advancement, and it’s exciting. u
Rope Manufacturing is one of the oldest professions in the world.
The Pyramids were built using them, and in many ways not that much has changed. However, one of the biggest changes over the last 100 years has been the move to man-made fibres (Polyester, Nylon and Polypropylene), and away from natural fibres such as hemp and cotton.
The benefits in performance have been significant; however, they have come at a cost. Modern fibres’ reliance on oil-based raw materials has posed many questions for rope manufacturers looking to reduce their carbon footprint.
As a UK manufacturer of synthetic ropes, this is an issue that English Braids is looking to tackle head on. The company has adopted a sustainability program (R5 Philosophy details found at https://www.englishbraids.com/ r5sustainableropes ) which, in part, has included a review of possible raw material alternatives. Recycled fibres are starting to become a real option. However there are still limitations in performance, supply, and price point.
One of the most significant advancements in manmade fibres has been around the replacement of steel wire with high-tech HMPE fibres. The fibre is the same strength as steel but 1/7th of the weight.
The reduction in weight and subsequent
increase in safety (due to lack of stretch and therefore reduced kinetic energy), has driven the adoption of this product in many markets.
It was therefore significant when DSM Dyneema® introduced the first green alternative to the HMPE market.
The company has changed the fibre feedstock from fossil fuels to that of plant origin. The oil used, crude tall oil (CTO), is a by-product of the paper industry, yet offers no reduction in performance when used in ropes.
Thus, coupled with tight environmental policies, the company has been able to demonstrate huge carbon reductions when compared both to steel wire and alternative HMPE’s.
However, the fibre is only part of the story. For the market to realise these savings it relies on the adoption of the rope manufacturer and the subsequent education of the end users.
To this end, English Braids have looked to promote the fibre as part of their “Steelsafe” range. This range of HMPE based 12-strand lines are specifically targeted at high performance applications, where steel wire would have originally been the preferred option. Due to the increased performance demands the adoption is now eroding the traditional polyester markets as limitations are reached in diameter and weight.
“It is essential that the end users understand more about the product that they are purchasing, starting with,
who manufacturers the rope” says Henry Earp, Sales Director of English Braids.
“This is the only way in which buyers will be able to make informed decisions, allowing them to meet or influence their carbon targets.
“All too often we see specifications that are no more than a breaking load with the manufacturer and fibre being unknown.
“Not only does this make sustainable decisions very difficult, but it also exposes the end user in the event of issues with the product in application. A piece of paper, in the form of a C of C will not resolve a critical failure”.
English Braids believes that working closely with the manufacturer will bring the best possible benefits to the overall supply chain. The environmental benefit is furthered when the manufacturer is local to the supply chain, thus decreasing carbon involved in distribution.
English Braids manufactures HMPE (Dyneema®) ropes up to 120mm in diameter in lengths ranging from less than 1m up to many thousands of meters in continuous lengths. Hence our statement, “Going to any lengths for our customers”.
The focus markets include renewables, lifting, offshore and civil engineering with an emphasis around the North Sea and North Atlantic waters and northern European operators. u
www.englishbraids.com
Vessels are increasingly using electrical systems to power across oceans, but a component’s design must account for these extreme conditions. Here, David Atkins , project director at marine resistor manufacturer Cressall, investigates offshore resistor design.
Whether for main propulsion propellors, crane or lifting systems, or cable laying, electrical drives can be found at the heart of many marine operations, offering increased control, reliability and mechanical simplicity.
Dynamic braking resistors (DBRs) are an essential part of an electric drive system that remove excess energy from the system when braking.
When designing electrical components for offshore applications, material selection is key from the start of the process to guarantee that equipment will perform under harsh conditions.
Engineers tasked with designing resistors for marine applications must consider material choice, structural stability and cooling method.
Corrosion-resistant materials
Sea water and the saline atmosphere are corrosive.
Due to this, stainless steel, combined with special paint systems, is typically used for the enclosure metalwork for resistor elements.
With materials containing at least 10.5 per cent chromium, stainless steel reacts with oxygen in the air to produce a protective layer on its surface to prevent corrosion if not painted.
There are many grades of stainless steel that can offer high corrosion resistance, which can be further enhanced by the addition of extra elements.
For below-deck applications, 316 and 304 stainless steel contain nickel to broaden the protective layer created by the chromium, and can be used in unpainted condition.
“Design
engineers need to ensure that there is enough mechanical support in the structure to stabilise the resistors for safe operation when it is subjected to these forces.
Cressall can conduct finite element analysis (FEA) to help ensure structural stability”
However, for above-deck components, 316 stainless steel has a higher nickel quantity and added molybdenum, so the resistor unit’s metalwork receives optimum protection against the marine atmosphere.
However in some conditions, painting will also be required.
Cressall’s resistor enclosures for the EV2 resistor terminal cover boast at least an IP56 ingress protection rating, certifying that sea water cannot enter the unit to cause harm.
In addition to the exterior, it is important that the resistor’s element can withstand the harsh conditions.
For these applications, Alloy 825 sheathed mineral-insulated elements are less vulnerable to atmospheric corrosion.
As the element is encased within the mineral insulated sheathing, the sheath is at earth potential, so if water or high humidity is present this will prevent accidental contact with
the live element, making them a much safer choice for marine applications.
Considering the impact of a vessel’s rotational motions — its sideto-side motion, or pitch, and its frontto-back motion, or roll, is crucial.
Design engineers need to ensure that there is enough mechanical support in the structure to stabilise the resistors for safe operation when it is subjected to these forces.
Cressall can conduct finite element analysis (FEA) to help ensure structural stability.
FEA allows design engineers to predict a product’s performance in the real world, then see the impact of forces and make changes accordingly. This ensures the resistor performs well in the potentially extreme weather conditions.
It’s also important to consider the size constraints of marine
applications. In contrast to onshore units, offshore electrical components must fit into a compact area, so the size of the unit’s support structures must be minimised without compromising durability.
An essential part of a resistor is its cooling system. Since the resistor dissipates excess energy as heat, the cooling system is responsible for cooling the resistor element to ensure continued operation. Depending on the layout and resources of the system, resistors can be naturally or forced air or water-cooled.
Air-cooled resistors come in two types — forced and naturally cooled systems.
Forced cooling systems use a fan to dissipate heat in a compact space. These units are suitable for deck mounting and can be secured using anti-vibration mounts.
Natural cooling is the most common in marine applications, offering a higher power rating and can be mounted in machinery spaces, protected environments or on deck. For machinery spaces or protected areas, consideration should be given to how the hot air released from the resistors should be evacuated to ensure other equipment mounted locally does not overheat.
Alternatively, the cooling system can use the vessel’s chilled water system, which circulates cool water for air conditioning and equipment cooling. If the chilled system uses sea water, titanium-sheathed elements with super duplex steel metalwork can be incorporated, for continuous use in acidic, tropical sea water and downgraded to 316 stainless steel for freshwater systems.
The ocean is a valuable asset for energy, transport and trade. Ongoing development of electric drives for marine applications can be challenging, but taking these conditions and energy savings into account makes them a viable and advantageous option for powering vessel and for use in offshore structures.
Cressall offers a bespoke resistor design service to help with individual applications. u www.cressall.com
Over 90 percent of world trade is carried across the world’s oceans by some 90,000 marine vessels. According to the International Maritime Organization, maritime transport worldwide is responsible for almost 2.5 % of total greenhouse gas (GHG) emissions, it produces one billion tons of CO2 each year — and the industry continues to grow rapidly.
In the past decade, faced with the requirement to reduce NOx and SOx pollution in emission control areas (ECA) along coastlines, vessel operators have primarily turned to low-sulphur fuels such as LNG to fulfil the requirement, as well as invest in installing scrubbers to clean tail-pipe gases. The demand for pure electric and hybrid vessels globally have also grown steadily and is expected to accelerate after 2020, mainly driven by the now-confirmed global sulphur regulations- enforced by the International Maritime Organisation (IMO).
Singapore has set a goal of reducing its greenhouse gas emissions intensity by 36% compared to 2005 levels by 2030. Singapore is also working towards stabilising its emissions with the aim of peaking around 2030. These are ambitious targets and as per Chairman of the InterMinisterial Committee on Climate Change, Minister Teo Chee Hean “Our goal of building a more carbonefficient and climate-resilient Singapore can
only be achieved when the community and businesses work together with the government in making climate-friendly habits and practices a way of life.”
There is approximately 2000 harbour craft operating in Singapore waters, emitting poisonous Greenhouse gases (GHG). The Engineering arm of BH Global Group, Sea Forrest Power Solutions (SFP) has successfully delivered Singapore’s First Hybrid-Powered Ship - The “Penguin Tenaga” with project partners and is
currently engaging in further R&D activities towards the design of the Green Infrastructure and construction of hybrid electric propulsion vessels.
The ships of the future will run on electricity and SFP aims to provide innovation green solutions to address emissions globally and around Singapore waters- contributing to Singapore’s 2030 decarbonization target. “Electrifying harbour craft vessels operating in and around Singapore waters will significantly help to reduce Singapore’s emissions footprint. Equipped with the technical know-how and relevant experience, BH Global, together with our subsidiary Sea Forrest, will endeavour to participate in and contribute towards realising this national vision.” Mr Vincent Lim, Chairman of BH Global Group stated.
Electrification and Hybridization can be done for both new-builds and retrofits. Sea Forrest is currently working on the development of Full Electric Ready (FER) Systems for the Harbour and inland watercrafts and will expand to Offshore support vessels in the near future. The FER System ease the transformation of a hybrid vessel to full electric vessel by offering step-changes to key contributors- Lowered battery prices, comprehensive Charging Infrastructure, Improved Battery density.
SFP aims to improve the efficiency of existing energy assets and to upgrade and modernize wherever possible with
its green technology and solutions. As an alternative to conventional oil products, Sea Forrest’s Parallel Hybrid Design and a flagship Full Electric Ready (FER) propulsion solution contribute to a reduction in carbon emissions of potentially up to 20% as compared to current solutions in the market. Other notable products Sea Forrest has developed include the Energy Cube (Energy Storage System) incorporated into a vessel’s power system, allowing it to store energy for later use; unique charging solutions that allows marine vessels to easily transfer power from shore to ship; and remote AI pilotageuse of Machine Learning and Artificial Intelligence to boost the incorporation of propulsion systems.
“We aim to achieve a complete ecosystem for Singapore’s electric-hybrid and pure electric propulsion systems, ranging from shore chargers to on-board systems.” said Mr George Lee, CEO of Sea Forrest. Sea Forrest will continue to spearhead further collaboration with owners, operators, suppliers and the authorities and drive initiatives towards the electrification and digitalisation of vessel operations.
Encompassing future technologies and the ecosystem approach, Sea Forrest endeavours to offer a clear route to Decarbonisation and also the potential for zero emission vessels. u
Middle East Fuji has commissioned its solar power plant, with all necessary approvals from the authorities and connected to the Dubai power grid.
The plant has been placed on the rooftop of the new logistics hub of MEF.
Speaking at the commissioning event, Mr. Saeed Al Malik, President & CEO of Middle East Fuji said: “MEF remains committed to environmental causes and this is one of our major steps in our journey towards carbon neutral operations.”
He said that the 178 KW plant will reduce its carbon footprint by many tons of carbon during the estimated useful life of the plant. The company has also invested in hybrid vehicles, VRF systems for air-conditioning and many other initiatives to reduce its carbon footprint.
Middle East Fuji also inaugurated its new logistics hub in April 2021.
Mr. Ryusaku Hayashi, Managing Director of MEF, said that the new logistics hub helps MEF to improve its operational efficiency and increase its logistics capacity significantly.
It is a fully airconditioned facility with advanced technologies such as VNA trucks connected with WMS systems to automate storing and picking operations.
Mr Hayashi continued: “Considering the effect of hot temperatures in UAE and its impact on the products and our staff, we decided to go for a fully airconditioned facility for the consumable storage, although it adds to our operational cost.
“This, however, improves our staff productivity and boosted their morale.”
MEF continued to grow even during the difficult time of 2020-2021 and the construction of the logistics hub was fully undertaken during the height of the pandemic.
Mr Hayashi concluded: “We are committed to providing
the right products and best solutions to our customers and this very commitment helped us to continue operating and grow even during this period.
“We are blessed with the confidence of our customers, which makes us more responsible and committed towards their needs each and every time. u
Gibbons International , a thirdgeneration ship supplier based in Seaham, County Durham, UK, is celebrating 100 years of trading.
Ian Gibbons, Director and grandson of the man who established Gibbons International, says: “Over the last 100 years we have enjoyed fantastic success for a small, familyrun business and have built up a loyal clientele including major offshore, renewable, oil and gas, bulk, container passenger ferry and cruise line operators. We also send goods to the Falkland Islands.”
The story of how Gibbons International was formed and grew to become one of the country’s leading ship suppliers is an interesting one. Once a corner shop business in Sunderland, it’s now an International Company supplying vessels throughout the UK, Europe and beyond.
The business was set up by Ian’s grandfather, Albert George Gibbons, after he returned to Sunderland
from World War 1in 1921. Born in Sunderland in 1895, Albert enlisted as a soldier in the first world war where he was lucky to survive after being shot at Aveluy Wood, during the battle of the Somme.
Ian picks up the story: “Grandad served in the East Yorkshire regiment and as well as being shot, through the stomach into his back, he was also gassed. It’s a small miracle he made it home.”
But when he did, Albert spent several years working at Glebe pit before deciding to set up a business on his own, which is when he opened his first butcher’s shop in Coronation Street later moving to 70 High Street East, both in Sunderland’s East End.
Ian continues: “Due to the busy nature of the port, butchers would also supply meat for the ships’ crew, and many became known as ‘shipping butchers’. This is where the marine connection began for Gibbons International. My father was born in 1922. He went to sea as a galley boy
at the age of 15, first joining the vessel “Reynolds” in Sunderland bound for Australia in the late 1930s.”
“As World War 2 began, my father, also named Albert George, but betterknown to his customers as Albie, was planning to join the RAF as a rear gunner on a Lancaster bomber and was about to travel to Scotland for training. He sought the advice of my grandfather who told him that with his experience he’d be better joining the merchant navy, so he took that advice and became a cook serving on various vessels, including those supplying the war effort on the Atlantic convoys.”
Albert’s involvement in the business picked up again at the end of the war, by which time the new shop at 138 High Street West, had opened. By 1945 he was more interested in expanding the marine element of the business to cover all aspects of ship supply food, cabin stores, engine stores and duty-free goods.
Over the next 35 years, he concentrated on building a great reputation for service as in the 1940s and 50s, there were a couple of dozen ‘shipping butchers’ and ‘ship chandlers’
plying their trade in Sunderland, so competition was fierce.
“My father recounted some nights he would wait all night long at the docks, with other competitors, to be the first to meet the captain of the vessel early in the morning when he awoke,” says Ian. “This determination would pay off as by the end of the 1970s the competition on a local level, at least, had all but gone.”
Meanwhile, Ian’s grandfather had become a prominent councillor in Sunderland and was Deputy Mayor for a time in the 1960s. When he closed the 70 High Street East shop to concentrate on 138 High Street West, he arranged a treat for his loyal customers and their families by chartering several coaches for a day trip to Redcar, reported to acclaim in the local press.
Fast-track to 1984 and Ian had left school and joined the business, working there whilst still studying part-time for a degree in business management.
“In 1992 we moved the marine supply and catering butcher side of the operation from the central city location to a brownfield site in Southwick,” continues Ian. “In 2000, Lisa, my wife, joined the
business and is now director, running the marine supply business. I assist and run the financial side while Ian Trotter, our sales manager who has spent all his working life in ship supply, joined us in 2000.”
In 2017, the business moved to a modern unit at Spectrum Business Park, Seaham overlooking the sea from which they still operate today.
As members of the International Shipsuppliers & Services Association (ISSA), International Marine Purchasing Association (IMPA) and British Association of Ship Suppliers (BASS), Gibbons International is well respected in the industry, not least because of the personal touch customers receive, which Ian says is mainly down to the business staying in the same family for three generations.
Ian concludes: “Over the past 100 years our values have remained the same – offering a high level of customer service and building relationships to provide a reliable and cost-effective solution in the marine supply chain. This ethos has been at the heart of our success over the years, and we look forward to many more successful decades of operation.” u
ISSA is sad to announce that former Singapore Association of Shipsuppliers & Services President and well-known Singapore ship chandler Col How Seen Shing has died.
He was SASS President from 1988 to 1991 during which time the annual ISSA Convention was staged in Singapore in October 1990 under his Chairmanship. He urged delegates to take time out from the busy Conference and Trade Exhibition to explore the delights of his country.
Col How Seen Shing was the former representative of the ship chandler Kenwell.
He enjoyed attending ISSA Conventions and was accompanied to Athens in 1987 by colleagues Abdul Hameed Hajah and Tay Teng Hong.
SASS President Danny Lien and the Board expressed their sincere condolences to his family.
Among many other colleagues and friends expressing their condolences and deep sympathy to the family were: Tissa Fernando, Jonny Lok, Choy Cheok Wing, Francois Le Blanc, Tay Teng Hong and Abdul Hameed Hajah. u
ISSA Member China Friendship External Supplier Association of Commerce (CFESA) has elected long-standing Association Secretary-General Ms. Li Li to be their new President.
Taking over the Presidency from her distinguished predecessor Mr Liu Shengju, Li Li is well known to the ISSA Family from her regular attendance over many years at Convention and representing China on the ISSA Assembly.
Members will be pleased to hear that Mr Liu was voted by CFESA to take up the post of Secretary-General.
In another development CFESA has moved its Office from its longtime home in China Commerce Tower to new premises at: Room 720-2 Guangyao Oriental Plaza, No.18 Yangfangdian Road, Haidian District, Beijing, China 100038. u
The Association’s e-mail address remains the same: cfesa@cei.cn
This year’s general meeting of the Association of German Ship Suppliers (VDS) was held in Hamburg on September 17, 2021. 28 people from 30 member companies took part.
The previous board was unanimously re-elected: Jens Pfeiffer, Hamburg –Chairman, Wolfgang Sump, Hamburg - Deputy Chairman, Mathias Overhaus, Emden - Treasurer and five other members from Bremen, Hamburg, Kiel and Rostock.
The previous auditors were unanimously re-elected.
Due to the challenging situation of the association as a result of various unfavourable developments in recent years, examples being a consolidation on both the customer and member side, the corona pandemic and steadily increasing demands on ship suppliers from the authorities, the board and secretary decided unanimously on a package of measures to improve the association’s situation, which was proposed for voting.
This includes the membership of the Association as a member of the WGA Wholesale and Foreign Trade Association Hamburg e.V, which has now been decided by the members. This new co-operation should lead to a “win-win situation” for both associations, from which both can benefit extensively.
The association’s chairman, Mr Jens Pfeiffer, reported on the results of the annual internal survey on the market situation in the ship supply industry in 2020 and on current challenges and opportunities.
Despite the corona pandemic, there have been good company developments. In 2020, however, the “ship supply sector” in particular has declined sharply.
Unfortunately, cruise lines and other shipping companies have ordered very cautiously and some of the businesses have shifted abroad.
Short-time working was widely used by companies. A sharp decline in new orders and sales losses of up to 70% were recorded, especially in the cruise segment,
and unfortunately staff had to be cut in some areas.
Compared to the previous year, the price pressure remained generally unchanged and the relationship with suppliers had become more difficult in some cases because obligations no longer have to be met due to the loss of sales.
Brexit had little or no negative impact in general, as ship chandlers always had to carry out export procedures for their ship deliveries anyway. Only a few procedures have become more complex with Brexit. The current situation again gives cause for hope.
The shipping markets have recovered in many segments. Further adjustments in the business processes and markets of the members as well as a currently reasonably well-controlled corona situation have currently led to profitable business again, in some cases at pre-crisis level.
Nevertheless, further consolidation of the market participants is possible.
Significantly negative business developments compared to the previous year had been reported for “tax-free trade” due to the travel restrictions caused by the corona pandemic.
Sales are falling sharply and profits have developed negatively in line with sales. Due to the corona pandemic, hardly any travellers had travelled to third countries from April 2020.
Partially closed borders, restrictions and related travel warnings have contributed to this. Brexit also caused problems in this area when importing and exporting to Great Britain (GB).
For 2021, further losses in sales are expected as a result of the corona pandemic and further consolidations at airlines and travel agents.
In his final speech, Mr. Pfeiffer emphasized the importance of ship suppliers in the supply chain for the safe and efficient operation of a commercial ship.
Despite advancing digitization and consolidation, reliable suppliers who offer that certain extra service are an important success factor in a business such as shipping that is characterised by time and price pressure and flexibility.
At the end of 2020, the association had 114 members. These were general ship suppliers, technical ship suppliers (office supplies, deck equipment, wire ropes, IT, electronics, paints, fishing equipment, IT companies, paints, lamps, machine repairs, ship and object fittings, nautical charts, distress equipment, sail making, ropes), food suppliers , Manufacturers and suppliers of luxury foods, manufacturers and suppliers of wellness, cosmetic and hygiene products, cleaning agents, manufacturers and suppliers of technical devices, duty-free shops, shops on cruise ships. u
One of the tenets of ISSA is the declared ambition to foster ever closer relationships with key international players in the maritime industry. Articles 4.1.(c) and 4.2.(a) oblige the Association to take active steps to promote itself and its members to a wide range of maritime industry and government organisations. One method now employed by ISSA to achieve this is to invite key organisations, ship owners, ship managers and commercial firms of note to join the Association as Honorary Members.
The following are now elected as Honorary Members and ISSA extends the warmest of welcomes to them and looks forward to working closely together going forward.
Castor Marine, a growing global coastal and offshore connectivity provider has signed a reseller agreement with Tampnet, the largest offshore 4G LTE network operator in the North Sea.
After signing, Castor Marine immediately went to work for its first 4G Tampnet client: The Walk-to-Work vessel Keizersborg went live and now has seamless 4G LTE offshore connectivity.
With this deal, Castor Marine is now an official Tampnet Activation Point, adding value to its customers’ operations.
In the past, vessels supported by Castor Marine automatically switched to the VSAT connection of the company’s own network when moving outside of 4G coverage and vice versa. Now, full 4G coverage for ship and crew is guaranteed.
Other benefits are that customers who want Tampnet access can simply add them to their connectivity package with one telephone call; customers have less administration in relation to managing connectivity for their fleet; they benefit from higher bandwidth enabling dedicated 4G connections in the North-Sea or a high level of North Sea redundancy, ensuring more uptime.
Castor Marine already delivers fleetwide connectivity services for the fleet of Wagenborg, where it also remotely monitors and manages all onboard equipment 24/7, ensuring the continuous operation of all the vessels.
As Wagenborg’s North Sea offshore wind operations depend on a continuous and correct flow of information – both between people and machines – the company decided to go live with the new low-latency connection for its Walk-to-Work vessel Keizersborg as soon as possible.
Ivo Veldkamp, CEO of Castor Marine, said: “The expansion of our services with Tampnet 4G is part of our growth strategy and our mission to ensure the best vessel connectivity anywhere in the world.
“The seamless integration of Voyager VSAT with 4G LTE services from Tampnet ensures high availability for businesscritical operations, reducing downtime and associated costs for all our clients.” u
www.castormarine.com
SHIPMOOR, a new ship mooring tool that performs static and dynamic ship mooring analyses in a rapid, user friendly and intuitive manner, has been launched by HR Wallingford and Witherbys.
Created to make the assessment of mooring an LNG carrier a straightforward and user driven process, SHIPMOOR uses the power of cloud-based servers to undertake live mooring analysis for each ship.
The internet based tool offers an efficient solution for the significant amount of calculation and processing required in this sort of analysis.
With mooring errors and disconnections often causing lengthy delays, SHIPMOOR mitigates the input of incorrect data by hosting an up to date, standardised database of LNG port information, enabling live sharing of information between all parties involved in the mooring of a ship, from the operator through to the assessments office and the team at the berthing location.
In providing transparency and accurate data alongside a 3D
visualisation of any arrangement, the program provides safer and more efficient berthing.
Dr Mark McBride, Ships and Dredging Group Manager at HR Wallingford, said: “SHIPMOOR can be used for all types of ships to validate their mooring arrangements against the conditions they will encounter. In the case of LNG carriers, the results can be validated against industry specific environmental criteria.
“SHIPMOOR improves safety by mitigating the risk of mooring line failure, excessive ship movement and emergency disconnection of the loading arms.”
Developed with security at its heart, SHIPMOOR runs within an internet browser and meets the IMO’s newly introduced cybersecurity requirements.
Technical Director at Witherbys, Johan Machtelinckx, added: “With traditional methods for preparing the mooring of LNG carriers often causing errors and delays, SHIPMOOR is truly a 21st century solution for mooring analysis.
“By optimising a process that usually requires a lengthy and data intensive setup, SHIPMOOR saves vast amounts of time for each mooring operation.”
HR Wallingford is an independent organisation, established for more than 70 years, offering specialist consultancy and applied research services in civil engineering and environmental hydraulics to clients worldwide.
The company has an international reputation for scientific and engineering excellence, and delivers practical solutions to complex water related challenges faced by its international clients and partners. A dynamic research programme underpins its work, ensuring it is at the leading edge of the industry.
Based in Edinburgh, Scotland, Witherbys is one of Scotland’s largest and most successful publishing companies, exporting a portfolio of more 400 specialist titles in the shipping sector to more than 110 countries. u https://www.shipmoor.com.
Elcome International, one of the world’s largest distributors of nautical charts and publications, has created a new secure tool to prevent viruses, malware or corrupted files from being introduced into ships’ navigational computers.
Dubbed Elcome Bridge Protect, it provides a simple and cost-efficient method of ensuring safe transfer of files without the need for passwords or fingerprint checks.
The package includes a special protected USB 3.0 flash drive and custom client software that makes it impossible for infected files to be introduced into the ECDIS and other networked ship systems when uploading electronic charts and updates.
The shipping industry’s growing reliance on automation electronics and digitization increases the danger of cyber “bugs” being introduced into ships and shoreside infrastructure.
Cyber attacks in the maritime industry have risen by over 900% in the last three years, ranging from malware introductions causing navigational errors to full-blown accessdenial ransomware.
“A primary potential point of entry for shipboard cyber infections is downloads from shoreside networks,” explained Kostiantyn Matvieiev, Elcome’s senior manager, charts and publications.
“Electronic Nautical Charts (ENC), Notices to Mariners (NtM) and software updates are delivered to the ship by satellite links when underway or on a DVD when in port.
A USB flash drive is generally used to load these files into the ECDIS computer. If an off-the-shelf unprotected USB is used, it can potentially introduce corrupted files, which can spread throughout the ship’s interconnected network with devastating results.”
The innovative design of the Bridge Protect client software automatically locks the flash drive with a low-level file system that leaves no empty memory space in the USB storage medium, thereby preventing transfer of harmful files inadvertently into the ship’s computer.
An added bonus is that Bridge Protect can be incorporated as part of the Safety Management System stipulated by the International Maritime Organization (IMO) Resolution MSC 428 (98) and becomes a mandatory part of the annual verification of the company’s Document of Compliance, which came into effect 1 January 2021.
“As the shipping industry transitions from paper charts and publications to electronic media, there is increasing danger of disabling cyber attacks that can threaten the ship’s safety at sea.
“Elcome is committed to harnessing cutting-edge technologies to protect ships’ systems and ease the workload for crews without compromising safety of navigation,” said Jimmy Grewal, executive director of Elcome. u
When you need a morning boost or a flavanol-rich post-gym pick me up, you’re just 2.5 minutes away from barista-grade hot chocolate. The Velvetiser delivers the hot chocolate you crave for – and it’s totally portable! Just choose your flavour, add flakes of real chocolate to your choice of dairy, plant milk or water. Then press the button and let the patented “velvetising” process deliver luxurious cloud-like chocolate velvet. The Velvetiser takes up the same space as a kettle and adjusts easily for a left or right hand pour. The classic copper clad Velvetiser is chic, stylish and on-trend, with looks good enough to grace any kitchen countertop – or hotel room kitchenette (if travel is ever allowed again of course!). £99.95 from www.hotelchocolat.com
Today’s tech — from smartphones and tablets to streaming devices and smartwatches — all require a Wi-Fi connection. That makes the wireless router one of the most important home appliances that no one ever seems to talk about. Routers are pretty much your key to accessing the internet, and if yours frequently requires resetting, it might be time for you to make an upgrade.No 1 recommended WiFi Router to upgrade to is the TP-Link Archer AX50 Wi-Fi 6 Router. The Archer AX50 is among the best Wi-Fi 6 routers available on the market today. Its dual bands deliver 2,402 and 574 Mbps speeds, so it’s an excellent option for users who stream lots of videos or play video games online. Available from amazon.com at $127.13
HMV – His Master’s Voice. Was ever there a more iconic music label than that? A Master Class in identifying, signing and managing musicians, HMV with its iconic London West End store was for years the leader of the pack. Now to celebrate this famous legacy comes a box set of 5 CDs plainly titled: “Now That’s What I Call HMV”. One hundred celebrities celebrate the Company’s Centenary. They’re all there: Queen, Elvis Presley, John Lennon, Paul McCartney – the list goes on and on. When you read this, the Box Set will just have launched. If the children go hungry and you need to pawn the dog order this literally once in a lifetime Set and prepare to laugh, cry and be dazzled. www.hmv.com
The two deepest, most soul-searching of Rachmaninov’s purely orchestral works, and an orchestra nurtured in the ‘Rachmaninov sound’ by Stokowski and Ormandy during the composer’s lifetime: what a gift for a great interpreter of our times. You need not only a sensitivity to the special string warmth but also an ideal flexibility for the tempo rubato implied when not explicitly requested in so much of Rachmaninov’s music.
Rachmaninov
Symphony No. 1; Symphonic Dances Philadelphia Orchestra/Yannick Nézet-Séguin
With thanks and acknowledgement to www.classical-music.com
At a time when travel was difficult, dangerous and expensive, Albrecht Dürer was rarely still, criss-crossing Europe in the late 15th and early 16th centuries gathering ideas and techniques, making contacts among artists and clients, and steadily spreading his own fame. An exhibition at London’s National Gallery will be the first to track the importance of Dürer’s excursions, to places like Italy and the Low Countries, for the development of his work and their wider influence. The show will include small sketches that Dürer made in silverpoint of landscapes, plants, animals and people during his travels. Many of the works will be on display in the UK for the first time. One highlight will be Christ Among the Doctors (1506) from the Thyssen-Bornemisza Museum. With thanks and acknowledgement to The Art Newspaper Suermondt-Ludwig-Museum, Aachen, 18 July-24 October; National Gallery, London, 20 November-27 February 2022
SIn the ninth and latest addition to the New York Times bestselling Spy School series, Ben Ripley faces his nemesis, Murray Hill, on the high seas. Thanks to the evidence Ben uncovered in his investigation of the Croatian, the CIA has tracked his nemesis, Murray Hill, to Central America, where they believe he is boarding the world’s biggest cruise ship, The Emperor of the Seas, on its maiden voyage around the world. His mission: Pose as part of a family, with Alexander and Catherine Hale as his parents, Erica as his sister, and his best friend Mike as his brother, to find out what Murray is plotting. At first, it sounds exciting to have a mission on the most glamorous ocean liner on earth, but as usual, nothing goes according to plan. There is action, danger, and plenty of surprises as Ben and his team quickly find themselves in hot water.
Spy School At Sea
By Stuart Gibbswww.SimonandSchuster.com
With thanks to Book Club Chat
Noma, the pioneering Copenhagen restaurant, which shuttered its doors in early 2017 and has since relocated to a new location in the city, continues to dazzle and remains a chart topper. The menu is heavily seasonal, focusing on seafood during the winter, vegetables during the spring/summer and game come autumn. Heading, as we are, into Autumn, Noma confirms the pattern continues. “This menu will be a celebration of fall abundance and the period of the year when meat will play a starring role at Noma. “Expect lots of preserved greens and flowers that we have foraged over the summer, together with mushrooms, berries and everything the forest has to offer.”