
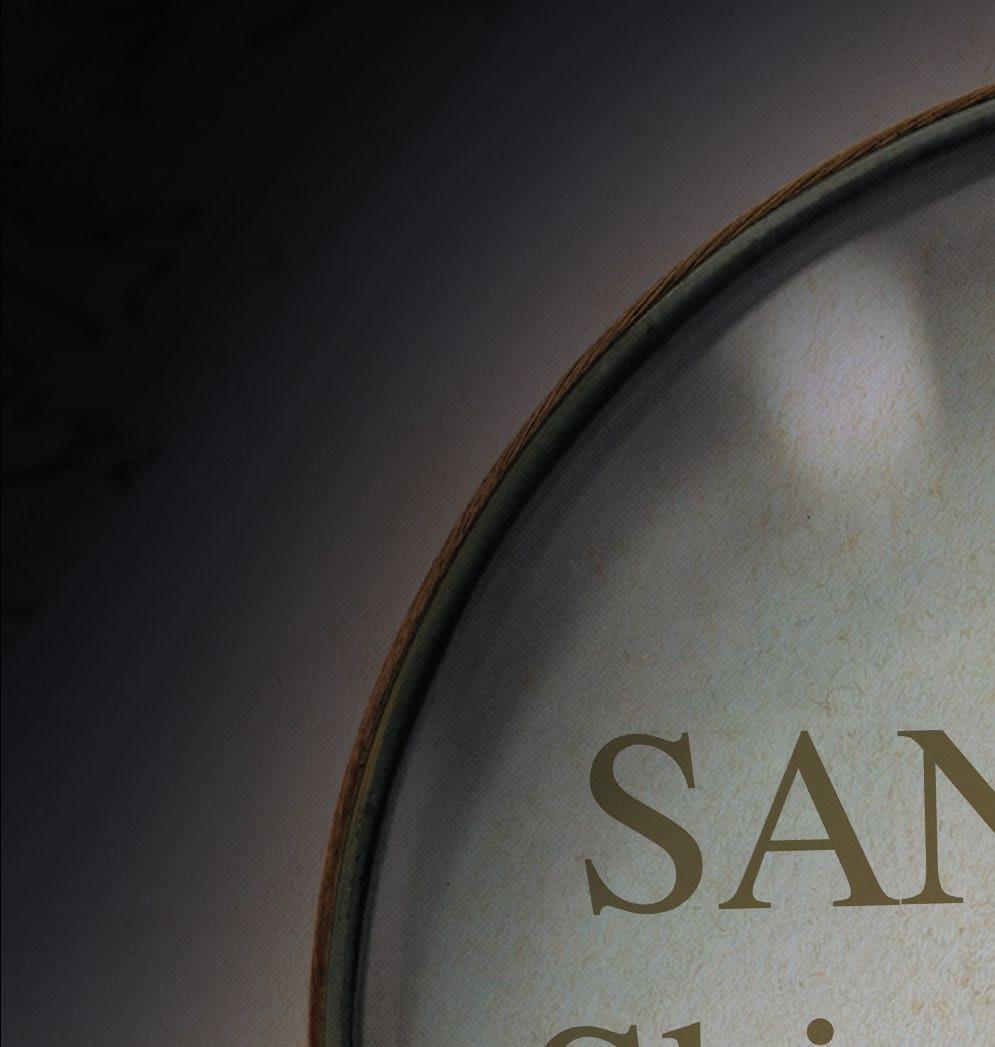
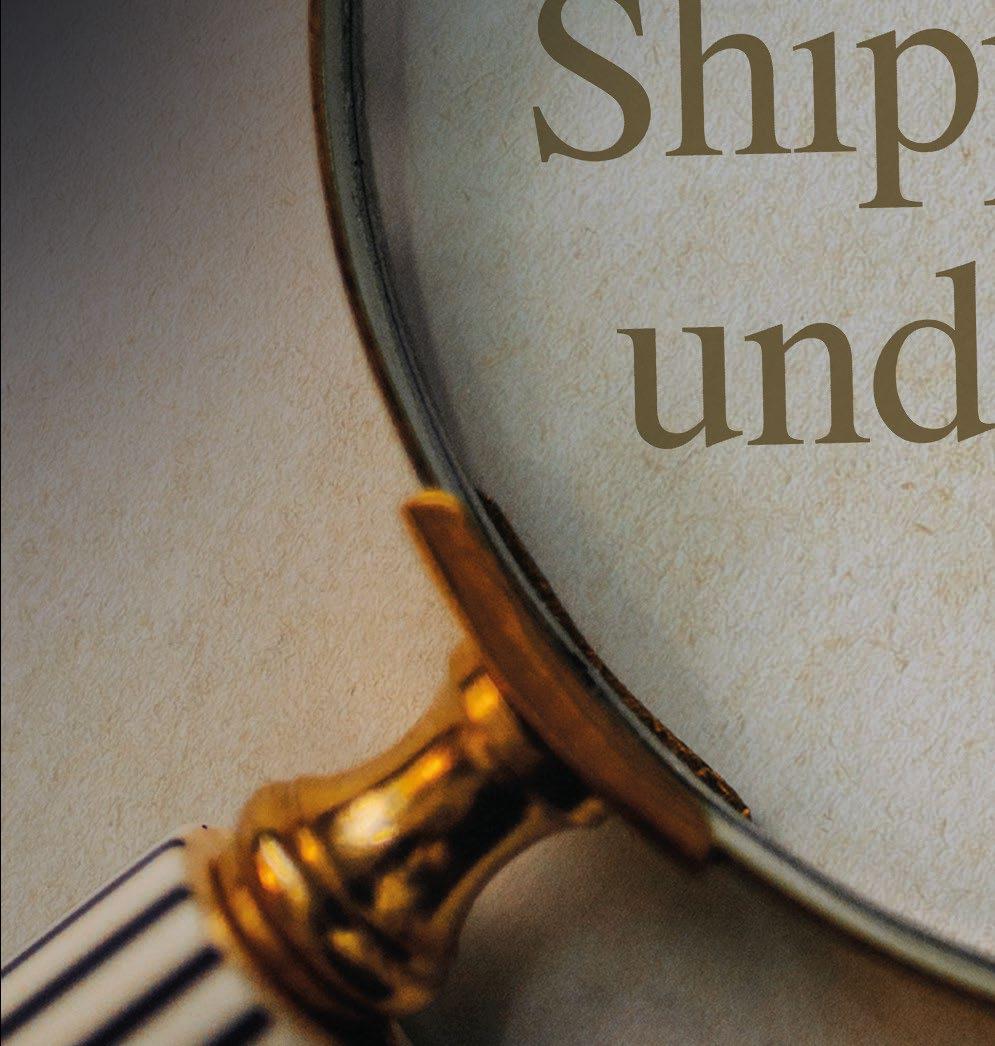
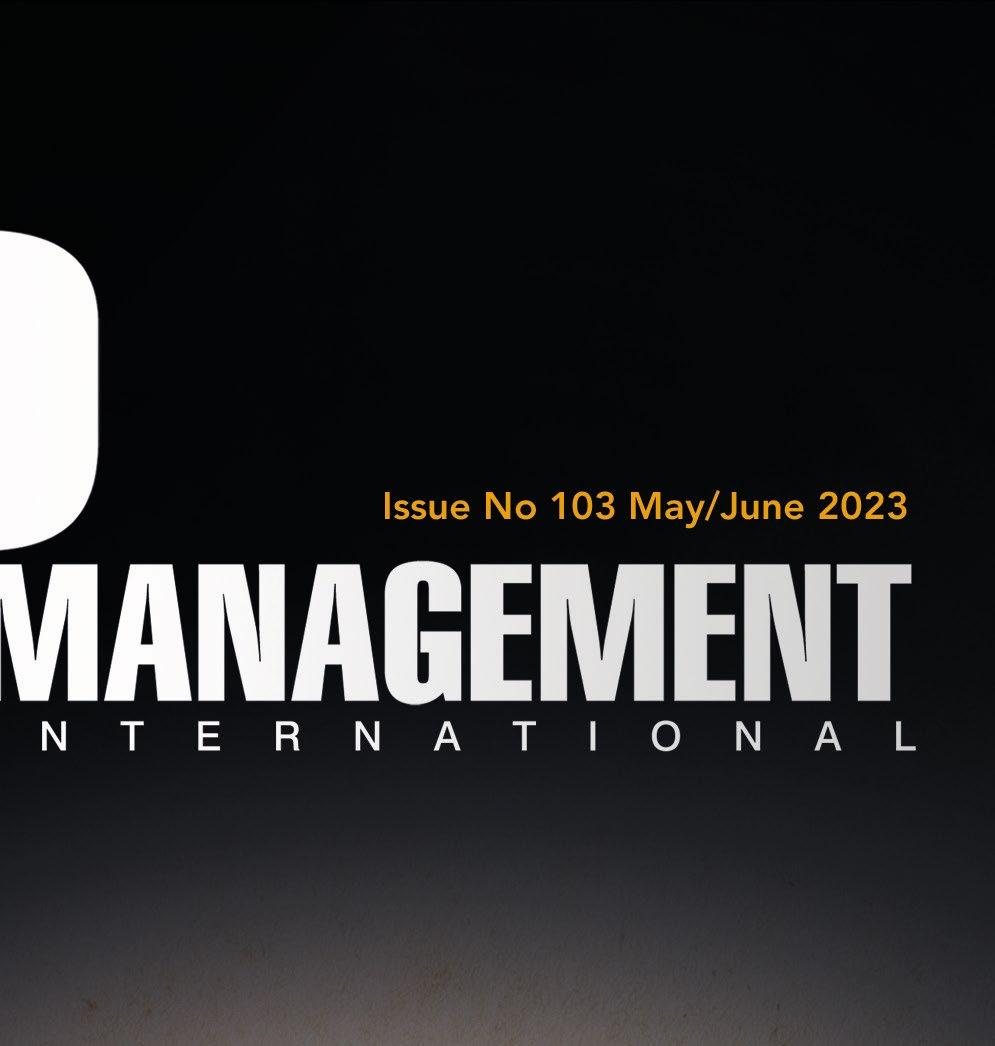
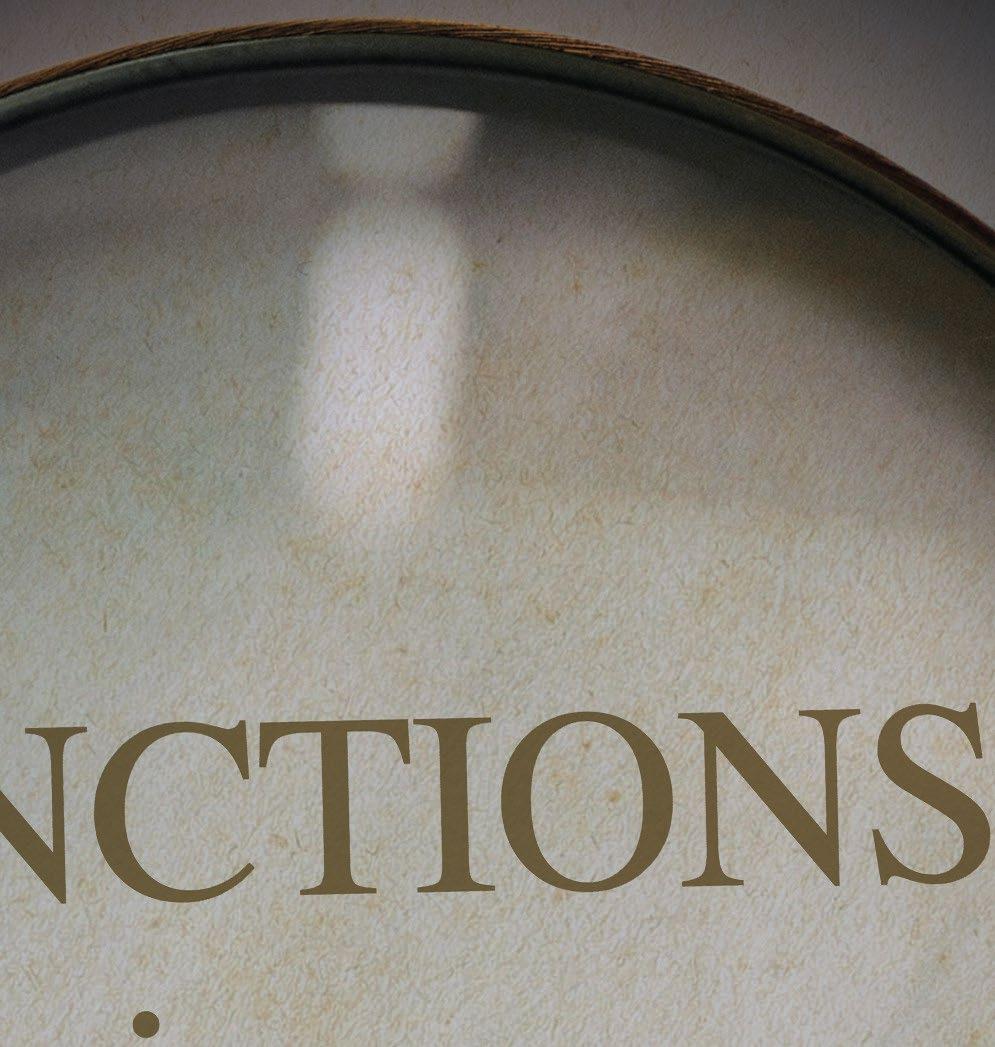
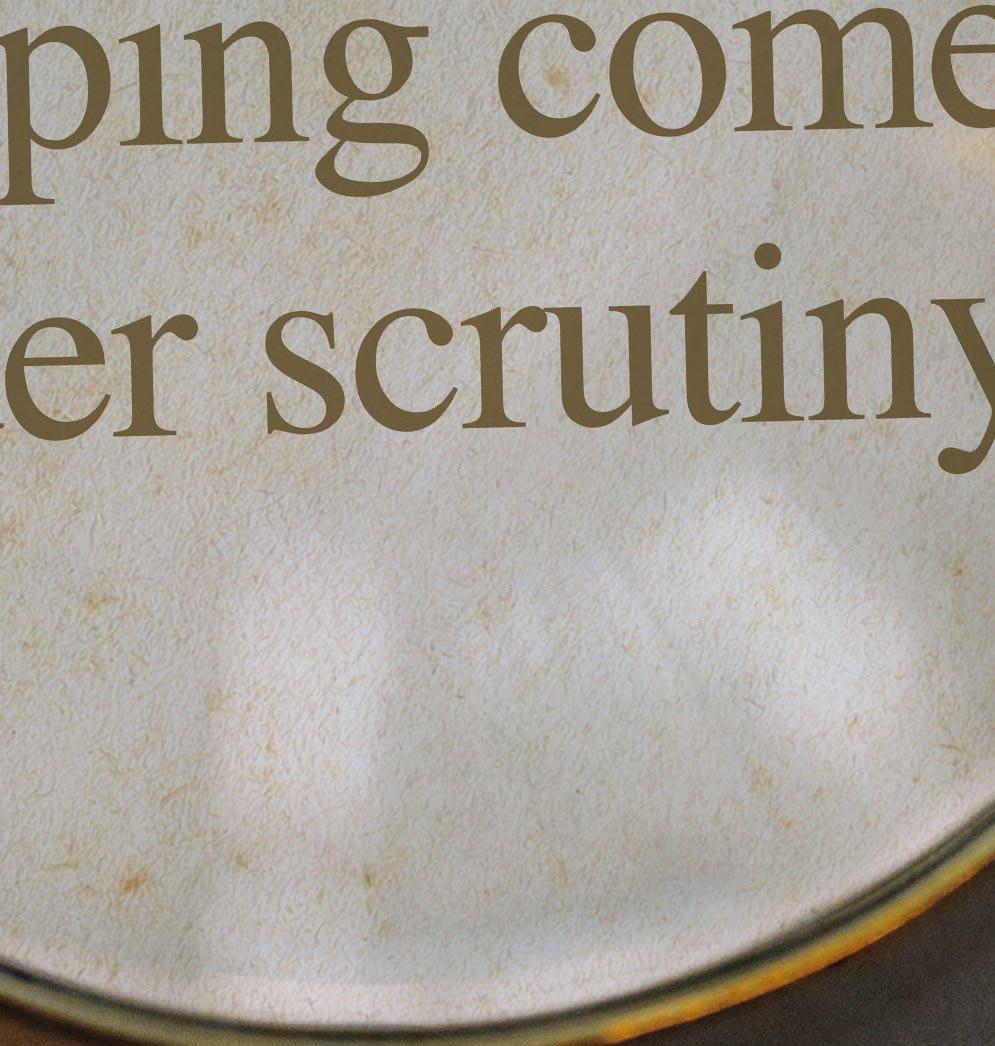
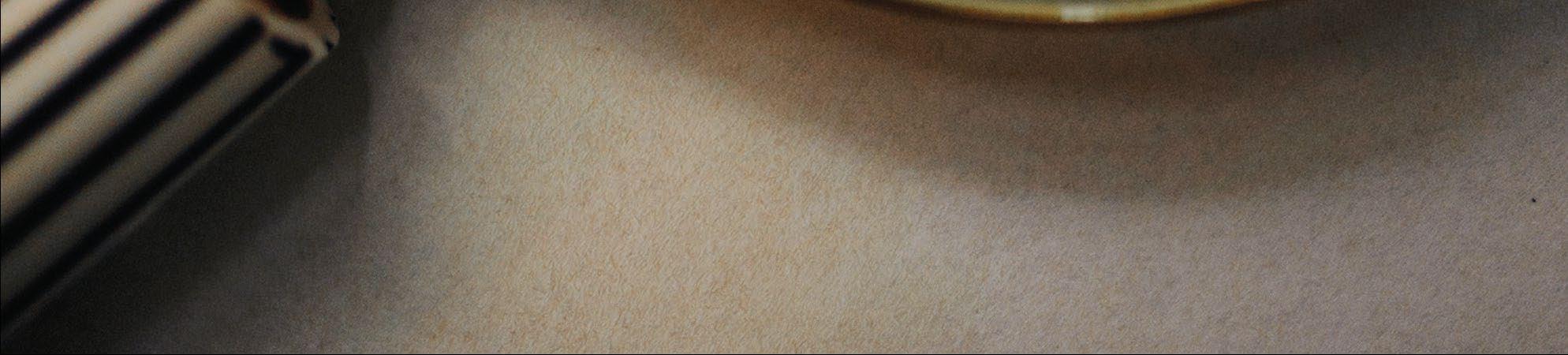
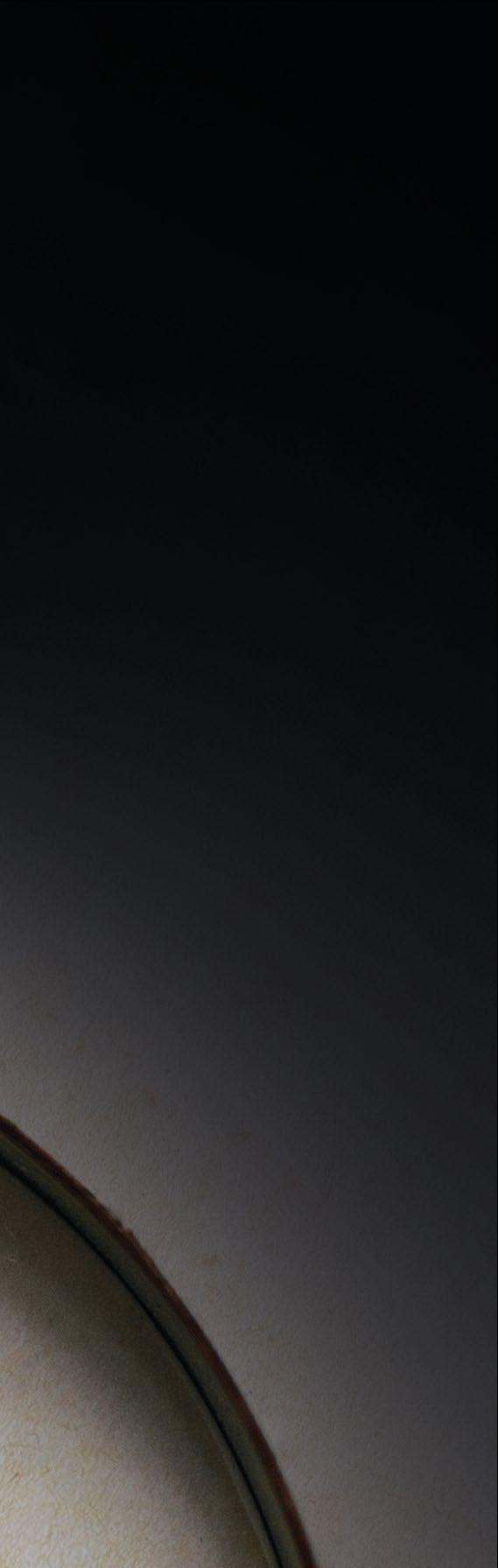
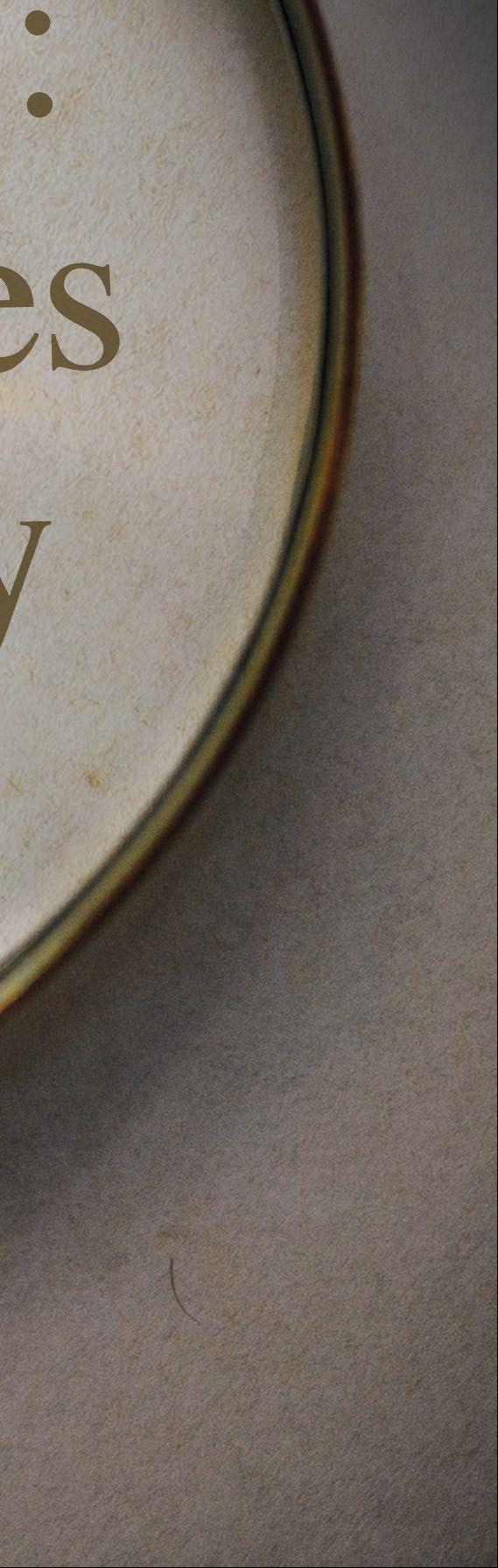
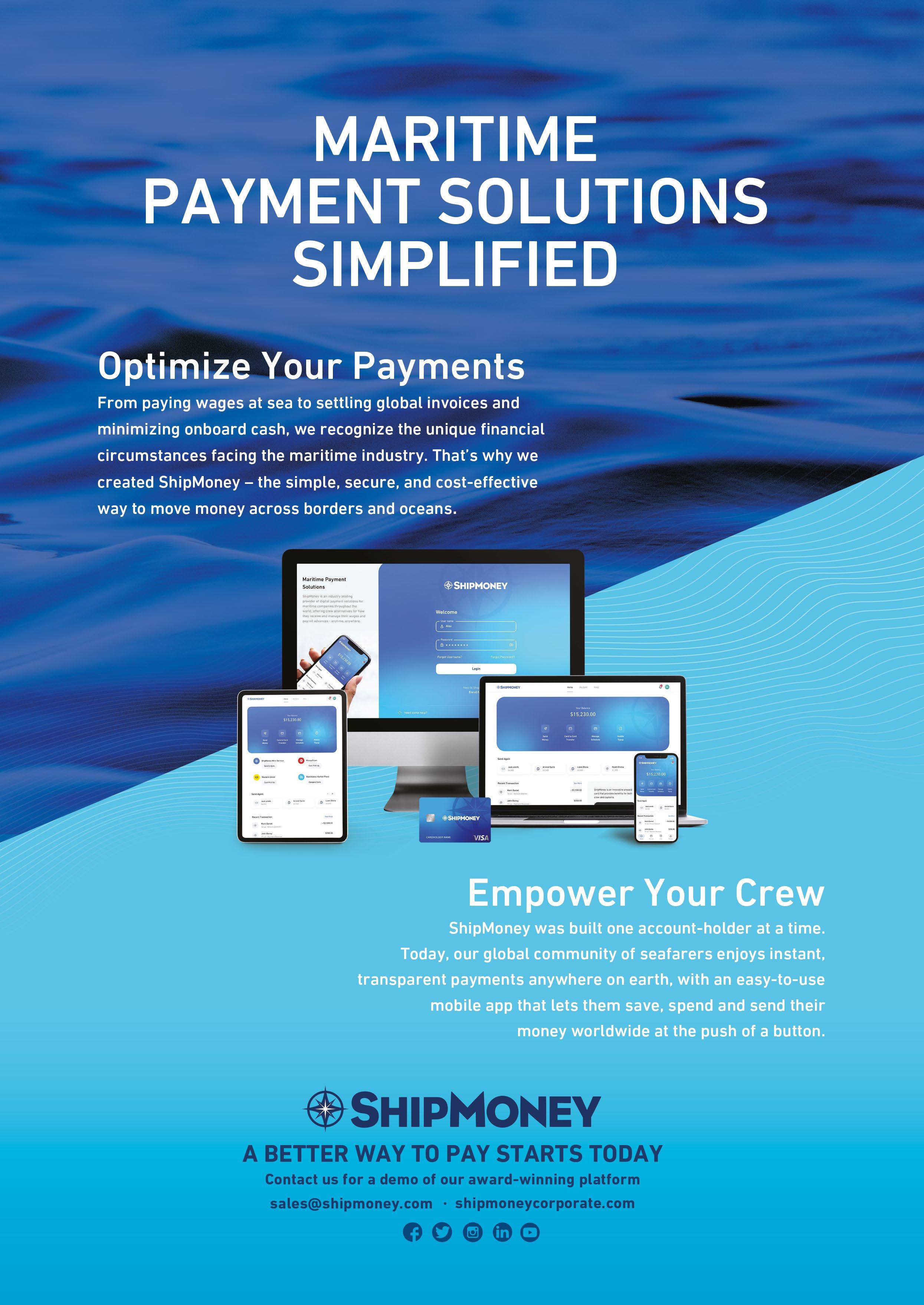
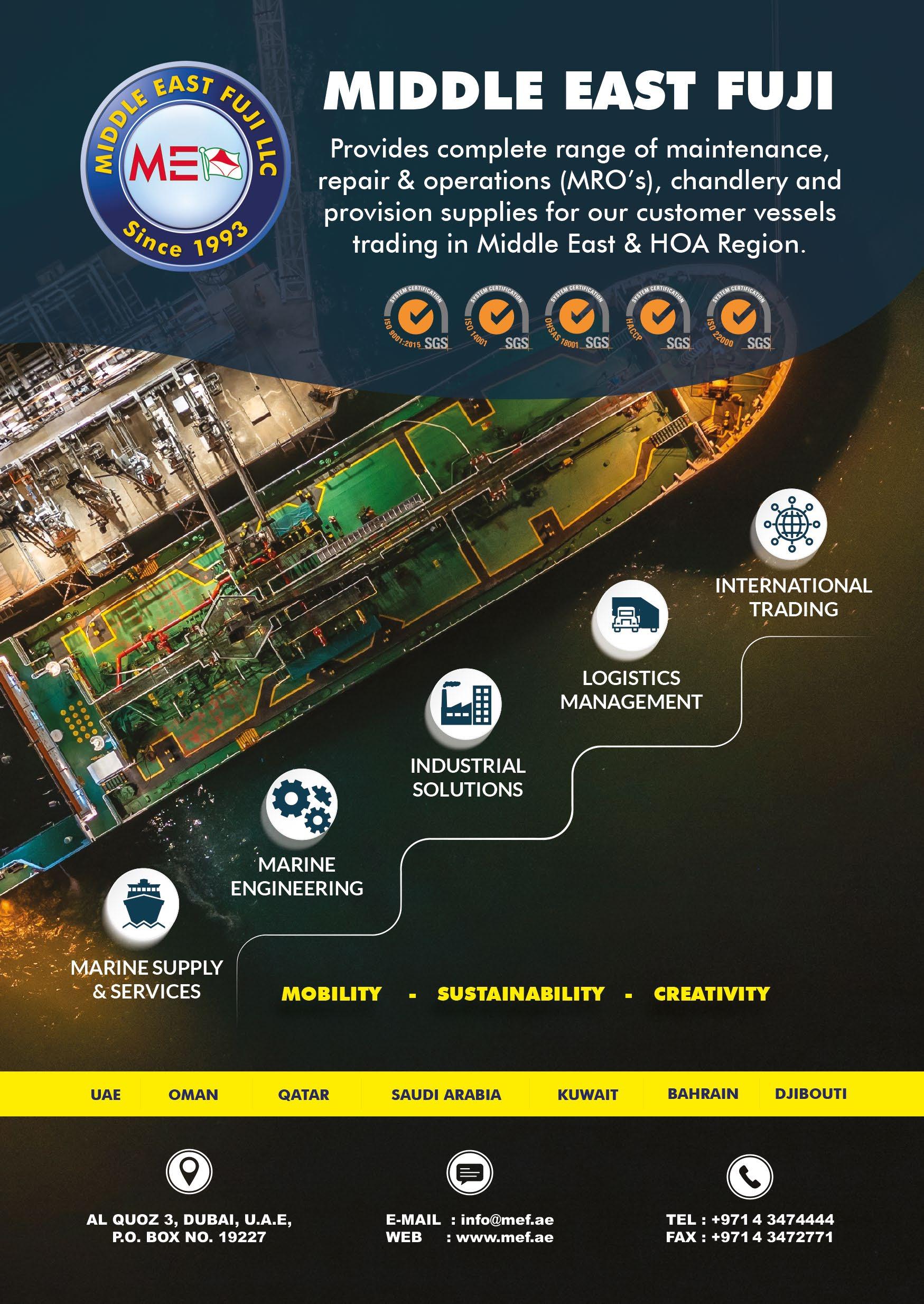
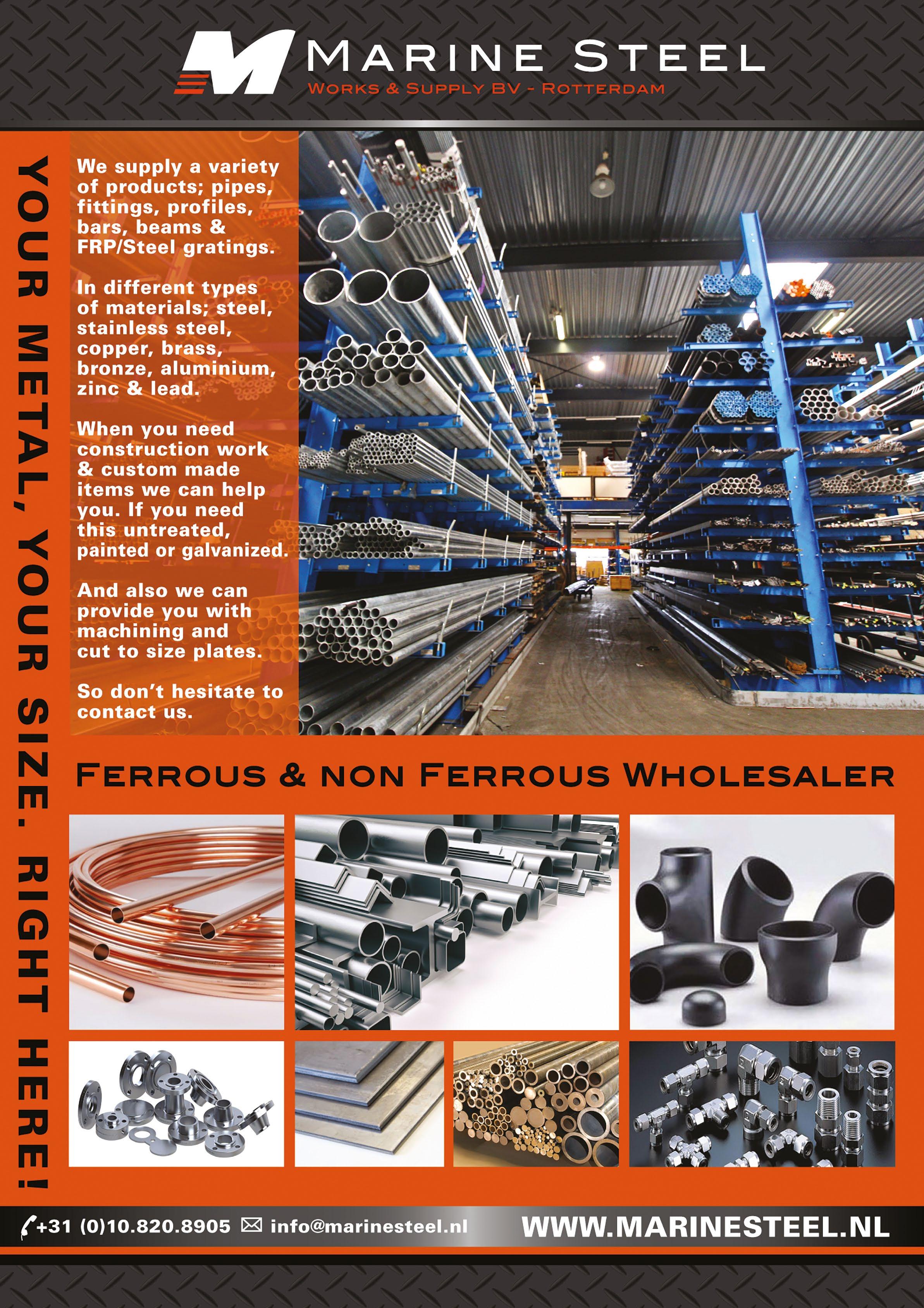
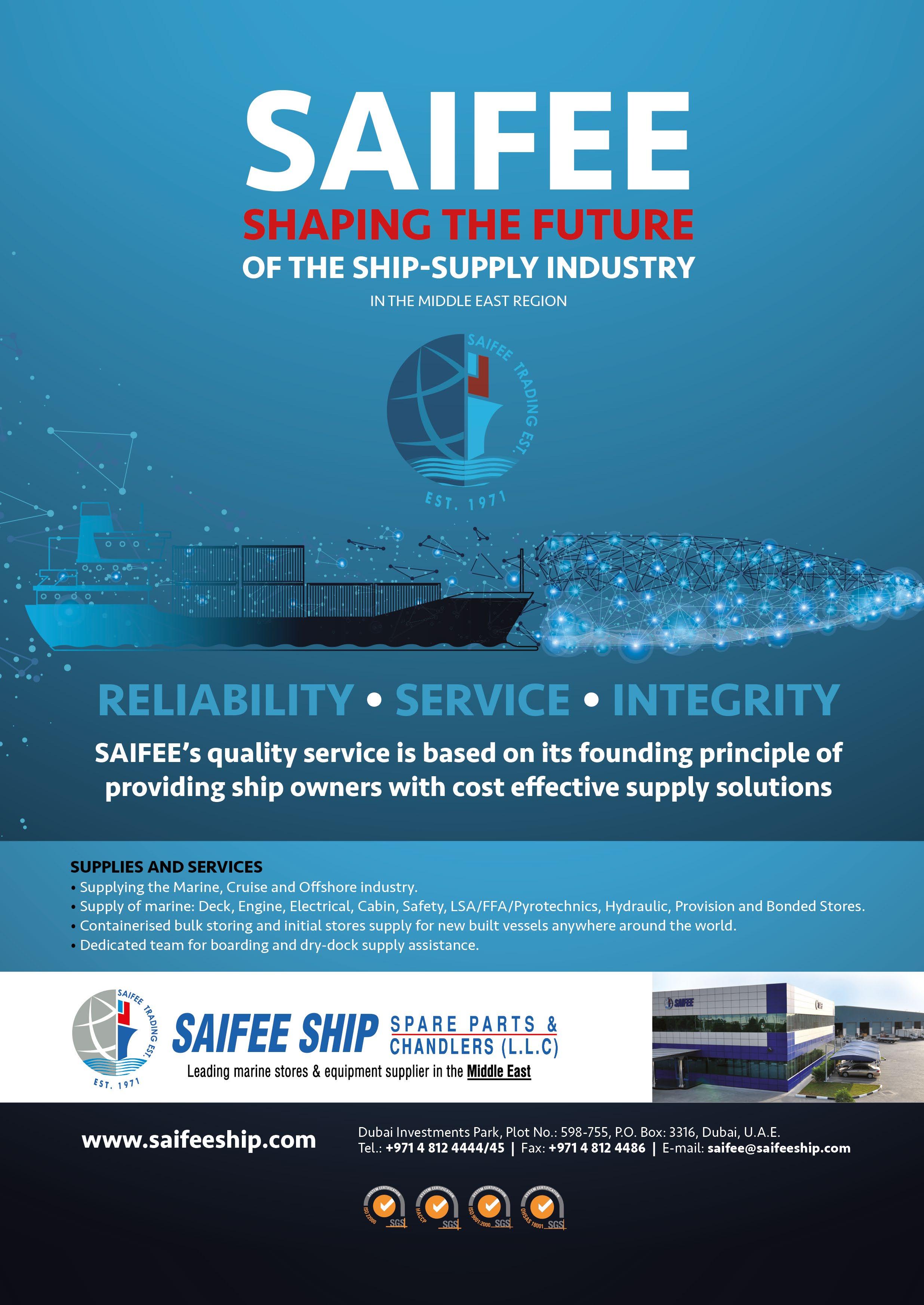
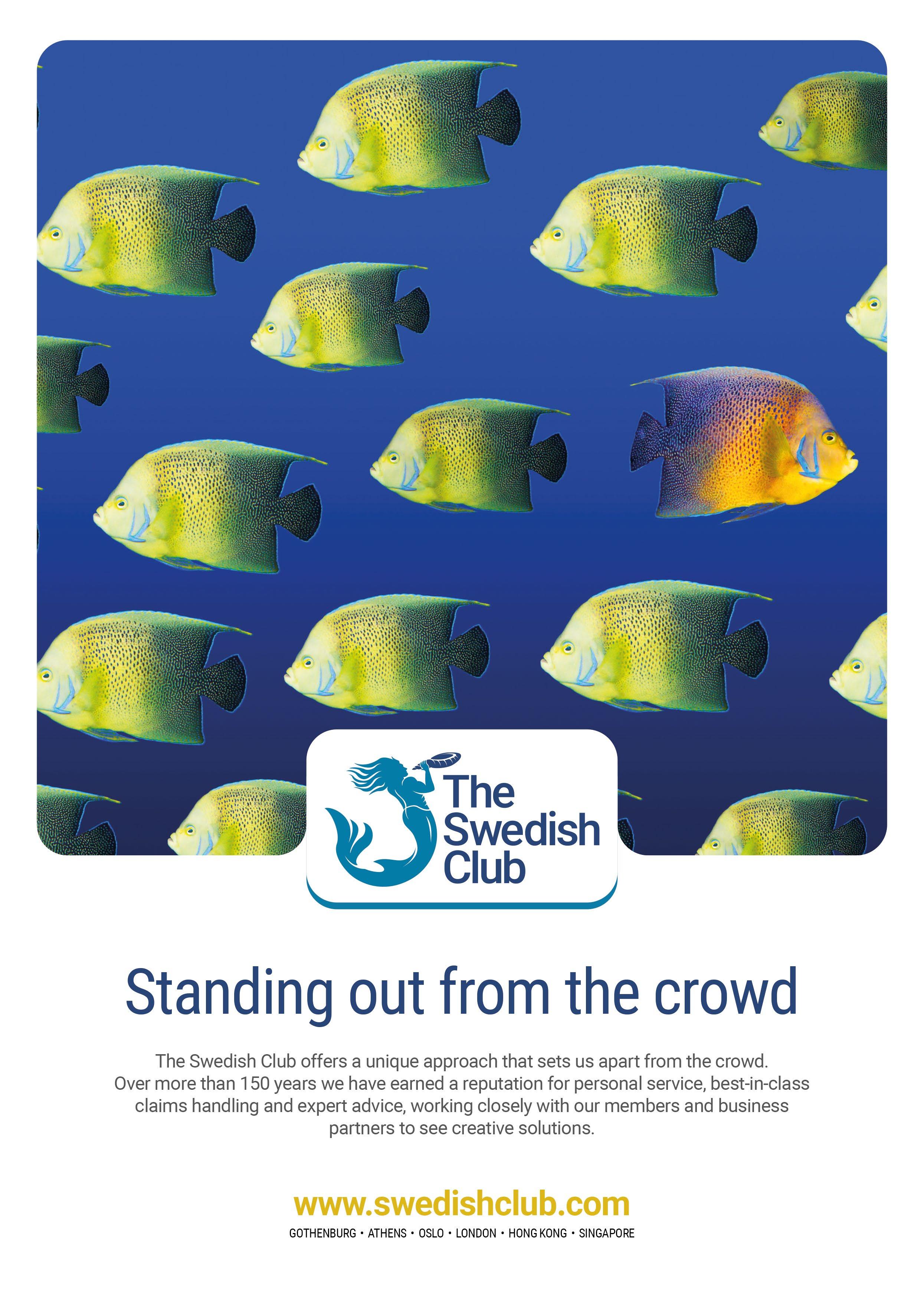

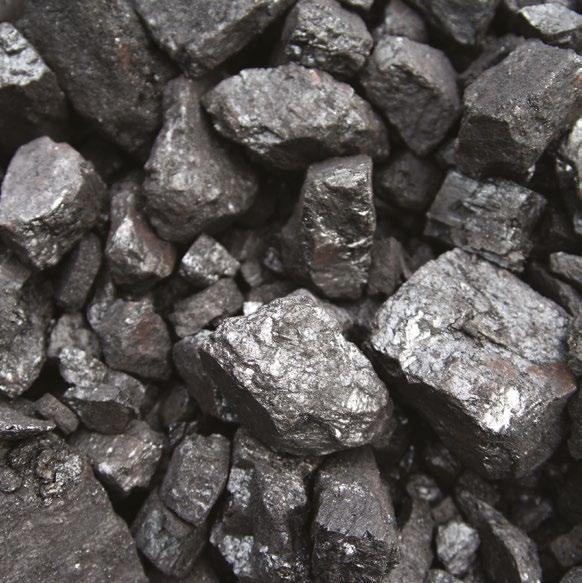
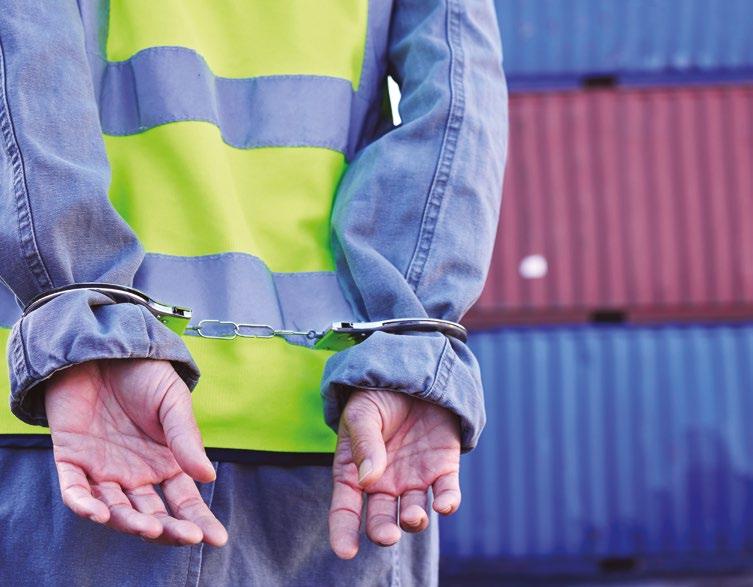
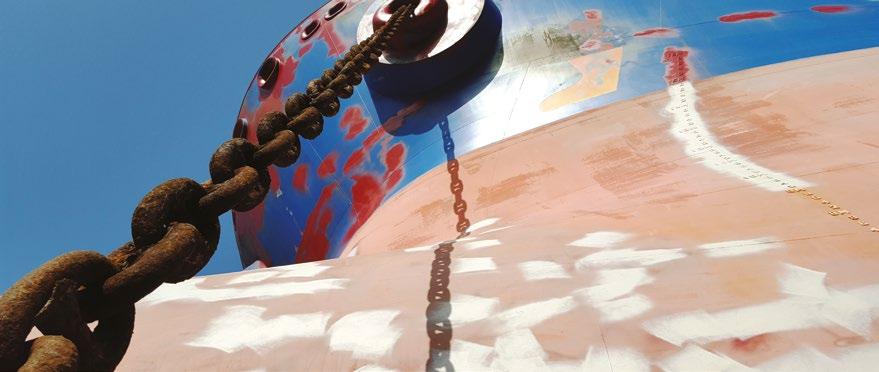
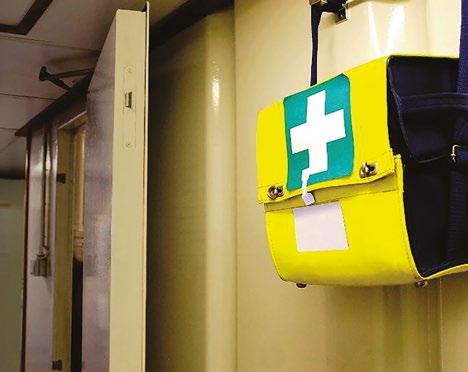
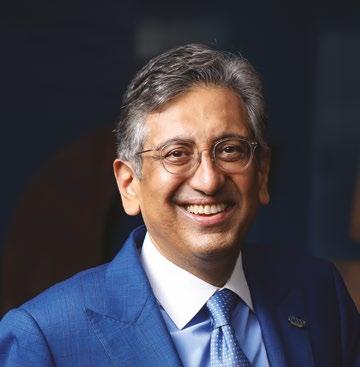

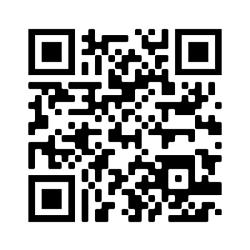
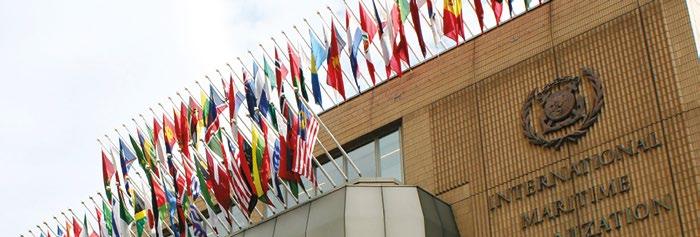
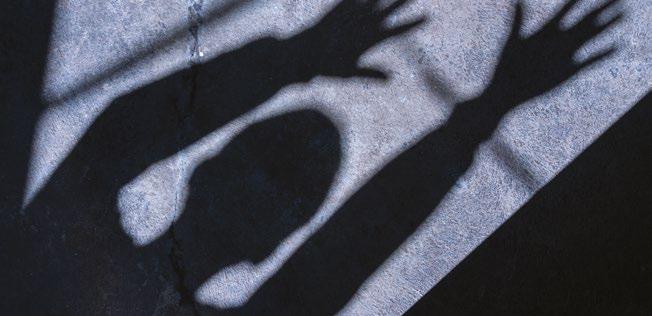
‘Meeting management’
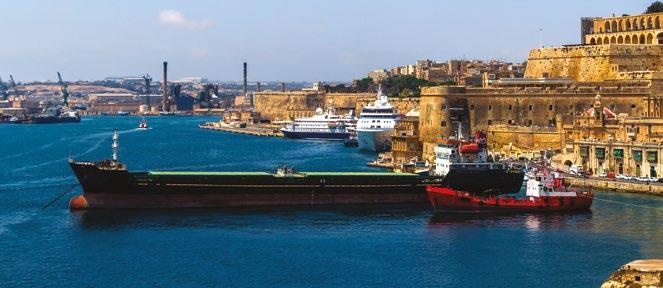
Sanctions and their impact on

FUTURE
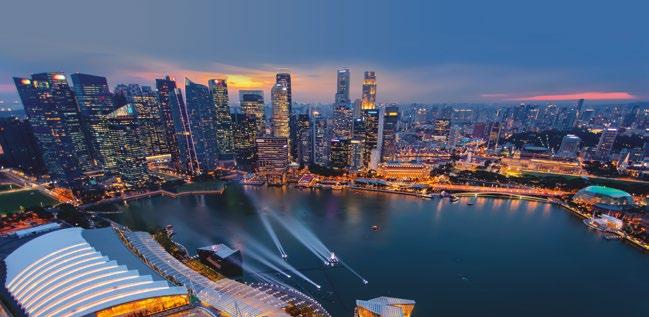
Predicting the future:
nothing short of a guessing game
Growth is on the cards for M.T.M. but at the right
Property inflation puts spotlight on Singapore cluster dominance

‘Meeting management’
Sanctions and their impact on
Predicting the future:
nothing short of a guessing game
Growth is on the cards for M.T.M. but at the right
Property inflation puts spotlight on Singapore cluster dominance
Sanctions compliance in the maritime industry has become far more onerous and complex than ever before since Russia’s invasion of Ukraine over a year ago, as panellists highlighted in the recent SMI round table on the subject, edited excerpts of which are included in these pages. Previous restrictions already applied to a host of other regimes in different jurisdictions.
Latest sanctions apply not only to companies and individuals operating ships and transporting cargoes to and from Russia but to all those providing the above with ancillary services – such as ports, flags, class societies, bunker suppliers, ship agents, brokers & financiers, insurers, lawyers … and so forth.
For these parties, ‘due diligence’ and investigation of matters such as a ship’s Ultimate Beneficial Ownership and voyage plan have become order of the day, for fear of imparting services to any of so-called ‘dark fleet’ of tankers and other vessels illicitly serving Russian interests. Ignorance of such matters will not be an excuse unless active attempts at discovery can be shown to have taken place.
But all this transparency goes against the grain for much of a shipping industry long imbued with a degree of obfuscation, either for reasons of competitive secrecy or the fiscal discretion of a uniquely ‘offshore’ business.
And as panellists at the round table pointed out, it’s not just a matter of
wilful deception. The very nature of tramp shipping means many masters arriving in port or at anchorage are simply unaware of their ship’s next port of call and therefore unable to provide that information to the authorities requesting it.
All of which smacks of the old conundrum: What happens when an irresistible force meets an immovable object?
One thing seems clear, however, as everyone at the round table agreed. Today’s enhanced and rapidly evolving sanctions landscape is not going to go way anytime soon, and the shipping industry just has to find a modus operandi in this ‘new reality’. l May/June 2023
Ship managers are urging the European Commission to follow the ‘polluter pays’ approach when finalising legislation intended to reduce greenhouse gas emissions from shipping in European waters.
They have highlighted concerns that proposed legislation could miss its mark if it holds ship management firms accountable for emissions reductions rather than target the parties who control key pollutionrelated aspects of ship operation such as fuel, machinery and vessel speed.
The Commission is set to finalise legislation which will include GHG emissions from maritime transport within the EU Emissions Trading Scheme (EU-ETS) and ship management association InterManager, which represents 80% of the world’s largest ship management companies, has submitted a position paper to inform this discussion. Its concerns centre on the definition of the entity responsible for ETS compliance.
In its submission InterManager stated: “The huge financial risk imposed on ship managers by the revised ETS Directive is disproportionate to the negligible influence managers have in respect of the emissions generation by maritime transport. By directing compliance and enforcement measures at a party which is neither the polluter nor able to exert significant influence on the polluter, the current form of the revised ETS Directive significantly dilutes the incentives for polluters to reduce emissions. This is in direct conflict with the ‘polluter pays’ principle, which is a key tenet of EU environmental policy.”
InterManager stressed that it recognises the importance of reducing greenhouse gas emissions from maritime transport and welcomes regulations designed to enable the shipping industry to decarbonise, including revisions to the EU-ETS to include maritime transport emissions within its scope.
However, it urged the Commission to word the regulation carefully to ensure the correct parties are in focus: “Under a Polluter Pays Scheme such as EUETS, the default responsible party should be the one controlling the highest number of emissions relevant aspects, not the one with the lowest.”
“As technical ship managers we take care of repairs, maintenance and crewing for, and on behalf, as agents of our customers the shipowners. Most of a vessel’s emission relevant key aspects are outside our remit – the speed, predominantly determining the consumption, as well as the trading area of the vessels are contractually agreed between shipowner and charterer in the Charter Party Contract, without involvement of the technical ship manager. The type of fuel used, the engines and other machinery installed on the vessels are decided by the shipowner when ordering or buying the vessel, also outside our remit,” it wrote.
InterManager Secretary General, Capt. Kuba Szymanski commented: “It would be patently unjust if the EU legislation forcibly imposed that the ship manager shall be the regulated entity, this would be similar to holding the facility manager responsible, not the factory owner.”
Noting the EU’s efforts to align the EU-ETS legislation with the shipping industry’s ISM Code, InterManager’s submission points out: “ISM is concerned with the safety of vessel operations in which we, as technical managers, do have a say as we provide the crew that operates the vessel in a safe manner as well as the procedural framework that allows them to do so. EU ETS is not geared towards safety but aims at reducing the environmental impact of shipping, which will require different fuels, different machinery and/or lower speeds - all decisions outside the remit of the technical ship manager.” l
Anglo Dutch logistics and shipping agency group
VertomCory Group announced the acquisition of Monson Agencies from Five V Capital, creating a market leading shipping agency group and accelerating VertomCory’s strategy of international expansion.
Established in 1981, Monson Agencies is Australia’s leading technology-enabled shipping agency. The company specialises in dry and wet-bulk commodities, servicing some of the world’s largest industrial producers and traders and covering some of the fastest growing bulk export and import markets in the Asia Pacific region. Five V Capital had invested alongside founder Dale Monson to strengthen and expand Monson Agencies’ core offering into new regions and invest in its proprietary agency ERP technology.
The executive team of VertomCory said the deal established VertomCory as a market leader in shipping agency. “We will now be able to compete on size-for-size basis with the world’s largest shipping agencies given our greater global presence and expansion into the Asia Pacific. We will offer our customers expanded global shipping services, superior technology and decades of experience. The alignment of values and reputation between our organisations makes Monson an excellent fit and will establish VertomCory as number one in the eyes of clients.
“Monson was the final piece of the puzzle to enable VertomCory become a global player in port agency, and we are grateful for Monson’s and Five V ‘s decision to sell the business back to the shipping industry.”
Justin England, Five V Capital, said the transaction made “clear commercial sense given VertomCory’s strong shipping history, alignment of culture, capabilities and dedication to customer experience. The acquisition by VertomCory will establish a key link between the
Northern and Southern Hemispheres, enhancing client service and providing incredible opportunities for the staff and clients of Monson Agencies.”
Rob Davis, Chief Executive Officer of Monson, also welcomed the transaction, saying: “We are excited to join VertomCory. This is a great step forward for Monson Agencies to be joining a shipping company with such strong standing in Europe. I look forward to working with the new owners and expanding our capacity across global shipping ports, with the investment, scale and experience that VertomCory brings.
“Our clients will be delighted too, and they will continue to enjoy high-quality service and also gain access to a wider set of expertise, capabilities and geographic coverage,” he added.
Dale Monson, who retained a minority interest after Five V invested in the business, said he was delighted with the transaction. “As the industry consolidates, I welcome VertomCory as a tremendous custodian of the business given it is an established leading operator which will continue to drive Monson Agencies’ growth.”
VertomCory Group is made up several of Europe’s strongest logistics and shipping agency companies, including Rotterdam-based Vertom Agencies and UKbased Cory Brothers, established as long ago as 1842. l
After 14 years since its adoption, the Hong Kong International Convention for the Safe and Environmentally Sound Recycling of Ships (the Hong Kong Convention) is set to finally enter into force on June 26, 2025, following ratification by major recycling country Bangladesh and flag state Liberia.
The HKC was due to enter into force 24 months after three criteria were met - namely ratification by not less than 15 States, not less than 40% of the world’s merchant shipping by gross tonnage, and ship recycling capacity of not less than 3% of the gross tonnage of the combined merchant shipping of those States mentioned above – all of which have now been achieved.
Her Excellency Ms. Saida Muna Tasneem, High Commissioner, Permanent Representative of Bangladesh to the IMO, deposited the instrument of accession at IMO Headquarters in London on June 26, while the same day The Honourable Lenn Eugene Nagbe, Commissioner and CEO of the Liberia Maritime Authority, did the same.
Secretary-General Kitack Lim commended Bangladesh and Liberia for their accessions to the Hong Kong Convention, calling it “a momentous day for IMO, and it is indeed a historical development for the international shipping industry, for the marine environment, and especially for workers and local communities in ship recycling countries globally.”
Mr. Lim also thanked the Government of Norway for its continued support to the IMO-implemented project on Safe and Environmentally Sound Ship Recycling in Bangladesh (SENSREC), which had helped to make this accession possible, he added, inviting other Member States who have not yet become a party to the HKC to do so as soon as possible.
H.E. Ms. Tasneem said: “The Government of Prime Minister Sheikh Hasina has once again demonstrated
Bangladesh’s global leadership and commitment as a major ship recycling country to environmentally safe and sustainable ship recycling by acceding to the Hong Kong Convention.”
As a pre-eminent maritime player, Liberia is proud to have ratified the HKC “thus attaining the required threshold for this critically important international convention to finally come into force,” said The Hon. Lenn Eugene Nagbe, adding: “Today is indeed a great and historic day for world shipping.”
The HKC was adopted at a diplomatic conference held in Hong Kong, China, in 2009. It embraces the “cradle to grave” concept, addressing all environmental and safety aspects relating to ship recycling, from the ship design stage through to the end of the ship’s life, including also the responsible management and disposal of associated waste streams in a safe and environmentally sound manner. It places responsibilities and obligations on all parties concerned – including shipowners, ship building yards, ship recycling facilities, flag States, port States, recycling States.
Upon entry into force of the HKC, ships to be sent for recycling will be required to carry onboard an Inventory of Hazardous Materials. Ship recycling facilities authorized by Competent Authorities will be required to provide a Ship Recycling Plan, specific to each individual vessel to be recycled. Additionally, Governments will be required to ensure that recycling facilities under their jurisdiction comply with the Convention.
Entry into force of the Convention was welcomed enthusiastically by international shipping bodies including the International Chamber of Shipping, Asian Shipowners’ Association and BIMCO, the latter calling on ship owners not only to observe the HKC when it takes effect but also to recycle ships responsibly in the meantime. l
Ahead of the closing of the European Commission’s public consultation on evaluation of the EU Ship Recycling Regulation (SRR) in early June, the Cyprus Shipping Deputy Ministry welcomed the review as a welcome opportunity to address what it calls “a significant loophole” in the SRR.
In addition to the circumvention from obligations of SRR, the fundamental problem is that while on paper the total is enough, in reality there is insufficient approved and costeffective recycling capacity to meet the requirements of the regulation, it believes.
Ioannis Estratiou, Director of Safety & Environmental Protection at the Shipping Deputy Ministry (SDM), told SMI: “There is an urgent need to revise that regulation since, in my considered view, it fails to fulfil its purpose, namely ensuring the safe and environmentally sound recycling of ships.”
He explained that there are currently only 44 approved facilities under the SRR, “the majority in Europe, one in the USA, three in the UK and six in Turkey”, whereas the vast majority of recycling takes place in Asia, in countries like India, Pakistan, Bangladesh and China. Many EU flag ships therefore reflag to a non-EU register for their final voyage to avoid the EU regulations, thereby confounding the SRR’s objective.
Many Indian yards have applied for EU SRR approval, he adds, but are prevented from obtaining it by EU waste shipment regulations that include the Basel Convention banning export of hazardous waste from OECD countries to non-OCED countries (like India), a technicality that the Legal Services of the European Commission has been trying to find ways to work round but so far without success.
The SDM believes that this latest review of the SRR should include a constructive dialogue
among EU partners in order to make the regulation “robust, effective and sustainable”. Use of financial mechanisms might be considered to incentivise owners of EU-flagged ships to use approved yards, says Estratiou, rather than compelling them to do so. With the Hong Kong Convention now due to enter into force in June 2025 (see separate story), the continued need for the EU SRR might be reviewed after that date, he suggests. l
ITIC has a long association with Cyprus, from providing cover to the first ship managers nearly 40 years ago to opening our European office there this year. Over the years, ITIC’s cover has been shaped, as the industry has developed – to include cover for crew management, commercial and pool management.
One of the specialities of Cyprus is crew management, and ITIC has seen a steady increase in the number of claims made against ship and crew managers that have arisen purely from crew negligence. P&I or hull insurers should cover claims arising from crew negligence. They are not the responsibility of the supplier of the crew, namely the crew manager. For example, in the event that a fully certificated and qualified chief engineer cause damage to a main engine due to an error, the claim should fall against the hull and machinery underwriters. The fact that the chief engineer made a mistake does not mean the manager was negligent.
It is a condition of ITIC’s insurance that BIMCO CREWMAN or SHIPMAN is used. These documents state: “…managers shall not be liable for any acts or omissions of the Crew, even if such acts or omissions are negligent, grossly negligent or wilful…”
This was very important in the following claim where the manager took on a ship, including the provision of the crew.
The ship was heading towards Shanghai, and the master reported that she had experienced excessive vibration after passing close to a buoy marking a wreck. The manager subsequently received an anonymous message from the vessel advising that she had hit a wreck. When the ship reached its final destination, it was dry-docked and damage was noticed.
The manager was co-assured on the hull policy, but the owner commenced arbitration proceedings claiming that substantial additional costs had been incurred.
The claim was based on an allegation that the manager was vicariously liable for the actions of the master. The manager’s defence was simply that, under the terms of the agreement, they had no liability for the crew’s negligence. The manager’s sole obligation was to provide an appropriately qualified crew.
Negotiations and investigations by experts and lawyers continued for the next five years, and substantial costs were incurred. The arbitration hearing was scheduled to take place; however, the owner (probably realising that his claim for crew negligence was unlikely to succeed) served an entirely revised claim backed by a lengthy report from an expert. The claim was fundamentally altered and was now focused on the manager’s application of the ISM code and the role of the DPA. A further allegation was made that the bridge team suffered from fatigue at the time of the incident and that the manager should have been aware of this.
By this time, the costs of investigation and preparing the defence had reached US$ 1,000,000. A defence was submitted, and the manager’s lawyers were confident that the claim could be successfully defended. Still, it was recognised that the hearing could last up to seven days, resulting in legal costs in the region of US$ 750,000, in addition to the US$ 1,000,000 already spent in preparing the defence.
The owner offered to settle the claim on a “drop hands” basis, with both sides bearing their costs.
Although the manager felt they had been presented with an extremely weak case, they could not rule out the possibility of adverse findings. Accordingly, the offer was accepted.
This case shows how important it is to use the correct contract and to have insurance to cover the legal costs of defending even weak claims. The defence of a manager is always expensive. l
Representing the global shipmanagement sector at international level is a crucial role of InterManager, explains its Secretary General Capt. Kuba Szymanski.
Shipping is a worldwide industry and as the representative for the global shipmanagement sector, InterManager speaks to international regulators and over-arching bodies on behalf of ship managers to ensure the voice of ship managers is heard and taken into account.
Speaking with ‘One Voice’ in this way is crucial to secure a level playing field and to make sure that global regulators understand the role of ship managers in the international supply chain.
InterManager regularly attends and contributes to the work of the International Maritime Organization (IMO). In fact, for the past 13 years InterManager has been one the most active Non-Governmental Organisations (NGOs), greatly helped by the fact we have our own Accredited Representative in Capt. Paddy McKnight, who not only represents us but also facilitates all our work.
Paddy has now been joined by Capt. Gary Hallet working on a projectby-project basis for InterManager to further strengthen our IMO team. In addition, some of our members also take a proactive approach and send their representatives to participate in IMO committee work which is very beneficial.
Informed discussions require accurate information on which to base decisions.
To facilitate this in areas which impact our work, over the past four years InterManager has taken on the role of statistician in order to enhance the information recorded by the IMO’s Global Integrated Shipping Information System (GISIS) which we
believe is statistically somewhat deficient due to the underreporting of accidents by some Flag States.
On behalf of the entire shipping industry InterManager collects data on lifeboat accidents in order to feed into debates on safety matters, particularly through the Human Element Industry Group (HEIG). We are fortunate that our member Capt. Ajay Tripathi from MMS Singapore is championing this project and spends an enormous amount of time searching through many sources to identify as many accidents as possible.
As a result, our comprehensive database now stretches back to the 1980s. Sadly it shows 508 fatalities, 391 serious injuries, and 142 minor injuries have been sustained in 503 accidents involving lifeboats and rescue boats. Obviously this is absolutely appalling for an industry which prides itself on safety and InterManager is working with partner organisations and the IMO to do all we can to improve this.
Another area of special interest is enclosed spaces onboard ships. InterManager’s statistics here run from 1996 and show that 356 people lost their lives in enclosed spaces – 259
seafarers and 97 shore personnel in 183 accidents.
In addition, InterManager has scrutinised the statistics for falls on ships. These figures stretch back to 2015 and show that 56% of all accidental falls on ships resulted in a person falling from height, while 44% of accidental falls on ships resulted in a person falling from the ship into the sea. Pilots account for 5% of the total who have lost their lives due to falls during the period studied.
InterManager has submitted these fall statistics in three separate documents using a new instrument created recently by the IMO called ‘Lessons Learned and Safety Issues Identified from the Analysis of Marine Safety Investigation Reports’. These documents have been submitted for consideration by the Sub-Committee on Implementation of IMO Instruments (III) at its 9th session.
This makes it possible for the shipping industry to access these documents and make use of our findings. InterManager strongly believes that it is only possible to manage something which is measurable. By having up-to-date statistics we are able to monitor the impact of IMO rules and regulations. l
The Panama Ship Registry, administered by the Panama Maritime Authority (AMP), for the first time has become eligible for the US Coast Guard’s Qualship 21 Program, which has been in existence for more than 20 years. This represents a milestone for the Panama Ship Registry and demonstrates the institution´s effort and its human resources in changing working methods and fleet monitoring.
The Qualship 21 program was established by the USCG on January 1 2002, designed to ensure safe and environmentally friendly maritime commerce. To qualify for this program, vessels must comply with the established requirements, demonstrating compliance and good environmental management.
For Panama to gain Qualship 21 acceptance a series of measures was implemented to guarantee the reduction of possible detentions upon arrival of its flagged vessels in ports of the US. This included it being made mandatory for all Panamanian flag vessels transiting or visiting ports in
Panama prior to their arrival in the United States to undergo a Flag State Inspection as soon as they arrive at any port terminal or anchorage area in Panama.
Effective August 1, 2022, the AMP also initiated a special flag inspection program for vessels arriving at US ports whose PSC history made them liable for a Port State Control Inspection by the US Coast Guard.
The General Directorate of Merchant Marine of the AMP, via the Department of Navigation and Maritime Safety, in conjunction with Flag Inspectors, Recognized Organizations, and the Segumar Technical Offices located in the US and Panama among other regions, all worked together to achieve this great objective.
The national government of the Republic of Panama and this Maritime Administration, encourage ship owners, operators, and ship captains to maintain the highest standards to ensure a safe as possible, innovative and sustainable industry, always having as principle the protection of the human life at sea and the environment. l
SMI talks to industry leaders and asks the question How do you keep up with the rigours of the shipping industry?
Ahead of the expected entry into force, of the Hong Kong Convention for Ship Recycling (HKC), with India having already ratified the IMO regulation and Bangladesh pledged to do so, GMS chief executive Anil Sharma can reflect with quiet satisfaction on the role he and his company have played in advancing responsible ship recycling on the Indian Subcontinent.
There’s been no looking back for Sharma since he abandoned a comfortable life in American academia in the early 1990s to seize an early opportunity in India’s ship recycling market. Following his company’s foundation in 1992, it has introduced innovations that have become recycling best practices, and then industry standards, as well as diversifying into shipowning based on the sustainability principles that guide GMS business.
Today, Sharma believes that those same combination of qualities – an eye for a deal, fearless innovation and social responsibility – position the company well to navigate the complexities of the future ship recycling and ship-owning markets.
GMS (originally Global Marketing Systems) has come a long way since the early entrepreneurial days when Sharma was convinced by friends in Bhavnagar to buy mothballed US naval vessels for scrapping in the fledgling recycling hub of nearby Alang.
In fact, the company didn’t even exist until years after he signed his first vessel purchase in 1992.
“These were high-value vessels due to their high non-ferrous content,” he recalls. “Since GMS was not born yet, I bid under my name, despite the seemingly daunting size, scope and liabilities.”
Sharma successfully delivered the vessel to Alang for recycling, following that success by buying six of the eight retired vessels being offloaded by MARAD that year. In a bizarre, post-Cold War twist, MARAD recommended Sharma to the Russian consulate in Washington, and in 1993 he found himself contributing to the dismantling of naval vessels for the rival superpowers, already towing vessels across both the Atlantic and Pacific oceans.
Some 30 years later, GMS is a ship recycling powerhouse, headquartered in Dubai rather than Washington or Alang, and with a formidable record of more than 4,000 successful transactions.
Over the past seven years the company has accounted for 30% of vessel scrapping in the Indian subcontinent, by weight. Of those transactions, more than 1,100 vessels were bought on an ‘as is where is’ basis with the buyer responsible for getting them to recycling facilities wherever in the world.
Having the Hong Kong Convention ratified in Bangladesh will raise the profile of the Indian subcontinent for responsible ship recycling
Anil SharmaOne contributing factor to GMS’ growth story has been Sharma’s willingness to take a fresh perspective on the business of ship recycling. For example, in March 2017 the company closed its first digital deal made through an app, which it had developed in-house in an attempt to connect the many siloed systems involved in the recycling process.
“We are aiming to digitalize the entire ship recycling process,” says Sharma. “It’s time for the industry to incorporate artificial intelligence, machine learning and all the other digital advances that can bring this vital industry to a place where we are ready for tomorrow.”
The GMS app epitomises the company’s approach to transparency and its long quest to add value for ship owners while simplifying the process of recycling.
In the coming years, Sharma also has big plans to increase GMS’ activities in India, “I call it the land of opportunities,” he says.
Looking forward to the next 20 years, Sharma is optimistic about the chance to bring about positive change in the recycling industry, not only in sustainability but in safer and more responsible work practices. “I sincerely hope that one of the big changes will be the ratification of the Hong Kong Convention, which will demonstrate that yards in the Indian subcontinent are leading the way on green ship recycling,” he explains.
A big proponent of the HKC, Sharma has been campaigning for years to have it ratified in Bangladesh, a long-held hope that he feels is likely to be realised mid-2023. When other states, as expected, follow Bangladesh’s example, the mandatory regulation will come into force two years later.
Sharma’s support for the HKC has been invaluable to driving adoption of standards. Virtually all the yards in India are already HKC compliant, and an increasing number of Bangladeshi yards are working towards compliance. “This is an issue close to my heart and one we have been campaigning for a long time at GMS and in the work being carried out via our Sustainable Ship Recycling Programme (SSORP).
As part of SSORP, GMS offers training to workers free of cost for the yards to raise work practice standards. Meanwhile, for shipowners that choose to use the programme, GMS documents that the work in the yard is up to HKC compliance levels.
“Having the HKC ratified in Bangladesh will raise the profile of the Indian subcontinent for responsible ship recycling. We have long been anticipating this day and have worked hard to make sure workers are prepared and that it is as easy as possible for shipowners using these yards to ensure that vessels are being recycled in compliance with HKC ,’’ adds Sharma.
Both Sharma’s values in pushing forward industry best practice, and in particular the belief in sustainable recycling practices, has led GMS to some interesting business opportunities. One consequence is its shipowning arm, Lila Global, which was formed in 2006 and specialises in extending the life of older vessels which may not appeal to some vessel operators focused on modernising their fleets (see later article in Middle East report).
Sharma explains that the company has conducted conclusive research into the impact of extending the life of vessels compared to scrapping and building new tonnage to meet capacity. “As long as vessels continue to burn fossil fuels, extending the life of a perfectly good vessel creates lower carbon emissions than building new ships,” he says. “In some cases, the sellers wish to monetise their investments in vessels, in which case we are happy to extend the vessel’s life by undertaking mid-life upgrades and continuing to trade the unit under our fleet.”
Sharma is not afraid of diversification beyond shipping if it feeds his passions. A prime example of this is his love of team sports, specifically football. Since 2016, GMS has been the majority owner of the Odisha Football Club (formerly called the Delhi Dynamos FC), which competes in the Indian Super League, the top flight of soccer in that country.
While his maritime and football interests may seem disparate, a common thread that Sharma feels connects the two is the need to take calculated risks and the need to work as a team in order to deliver the best results. He recognises that institutions are only as strong as their weakest links - a reason why GMS places so much emphasis on training and good communication.
Just as his team were crowned Super Cup champions in April 2023, Sharma believes that once the HKC is ratified, the ship recycling yards on the Indian subcontinent will also be capable of mixing it with, and prevailing against, the very best. l
023 is an important milestone for the Wallem Group as it will be the Hong Kong-based manager’s 120th Anniversary. A milestone indeed. But as John-Kaare Aune, CEO, told SMI, growing its managed fleet from its current level of 180 ships to somewhere nearer 250-300, is at the heart of its strategy.
“We’re very proud of our history, and we have a very strong name in the market. have just returned from China where Wallem is synonymous with ship management I would say. So, we’re trying to come out more in the market again and be much more visible as well,” he said.
“We’re looking at a 50% growth level in the years to come on it, but we want a sustainable type of growth. We’re positioning ourselves as a kind of medium-sized ship management company, able to provide tailormade solutions that we don’t think that the biggest ship management companies are able to provide. They say that they can, but I don’t really believe they’re able to give that attention to the owners that we can give as a medium-sized player. Our key focus is understanding our ship owners’ strategy and growth plans, and seeing how best we can partner with them to support them and help them achieve
their targets and goals. And, of course, support them to make money and to meet their financial targets,” he said.
And as he contends, it is all about being transparent.
It’s about playing with open cards with the ship owners and working as their asset partner. “It’s not about us coming and telling them that this is the Wallem way. It’s more about seeing how we understand how they do business and how we can then add value and help support them to do it in a more efficient and better way,” he said.
The market is also changing, with digitalisation at the forefront of the industry’s mind and the fuel of the future dominating discussion. But as Mr Aune stresses, Wallem has been a central part of shipping’s development over the years, moving from sail to steam, into conventional engines and onto electronic engines. “Now, we’re taking on our first dual-fuel LNG tankers coming out next month.
So, I think it’s all been part of our history and been part of ship management. You get new technologies, you have the people to actually look at how we can best use the tools and it’s very much about being able to use them as tools.
I don’t think that digitalisation is going to take over the human interaction.”
And where will this growth come from geographically and what will be the driver for generating more business? According to Mr Aune, concentrating on historical areas like Asia and Europe makes sense “because we are located there” but Wallem also has a small representation in the US servicing clients there. “But it’s definitely the European and Asian markets where we will see growth coming from.”
The plethora of new regulations, especially when it comes to emissions and decarbonisation, is seen as an area where Mr Aune believes Wallem can add value to shipowner clients. “It’s much more difficult for a ship owner with 10 or 20 ships in its fleet to be able to stay on top of the regulation and manage the law makers’ requirements. We also want to be there as their technical partner when they are looking for new solutions to energy saving devices.”
What are the owners and principals saying to you when you ask them what they want from a third-party manager? “It’s different, from owner to owner. Especially like if you look at the Chinese market, it’s quite different than the European markets I would say. Many of the Chinese clients are looking at de-risking a bit, just making sure that they actually have a manager that’s taking the kind of full control over the vessel management side of things. While I would say that many of the European
owners are looking at us as an extension of their technical teams and working much more closely on a day-to-day basis as well,” he said.
And what about the challenges moving forward? “I think it depends a little bit on the markets as well, which areas you look at. But of course, there are certain parts of the market that are very cost-sensitive. I wouldn’t call it a challenge, it’s an opportunity. The traditional relationship between the owner and the manager has changed. Many owners now, don’t want the traditional relationship that we had. It’s more of a hybrid approach, it’s more of a ‘we are here to help you’. There are certain things they want to keep control of and there are certain things that they can leverage. We see this more and more, it’s more of a partnership than we are handing over our ships for management. And it changes the whole dynamic actually.
“I think one thing that’s changed a bit as well in the last four to five years is that we do see some owners that have a preference on making sure that their team is sitting fairly close to where they are. There’s synergies of course between having the technical and operational teams in the same time zone, being fairly close to the chartering teams and have that kind of level of communication to ensure the business operates efficiently,” he said. l
While kidnap will always be traumatic, action can be taken to mitigate the impacts on crews according to Mental Health Support Solutions
Although ship managers and owners are taking ever greater steps to protect their crews, the fact is that piracy is rife throughout parts of Asia, Africa and the Americas and it is likely that on any day of the year, a vessel will have been boarded by pirates and the crew subjected to a nightmare experience.
Any crew suffering this chilling event will be impacted for an extended period of time, as will their families. But there are steps that can be taken by both hostages and their employers that will help to minimise the negative impact, according to Charles Watkins, Founder of Mental Health Support Solutions (MHSS).
“Sadly, this is not an uncommon occurrence. Recently we have seen an incident on the Monjasa Reformer, a Danish oil tanker which was boarded in March, forcing the crew of 16 to lock themselves away in the ship’s safe room. They have just been rescued after more than five weeks under exceptionally challenging circumstances and my thoughts are with them and their loved ones. I hope that their employers and families understand that every individual will have a different response to the events and recovery will take place at a different pace for each of them,” he said.
MHSS has worked with many seafarers following traumatic situations and has seen that the consequences may take as long as six months after the event to appear. The emotions felt during the ordeal, fear of death, extreme anxiety, helplessness, sadness, anger, a strong longing to escape the situation, and a sense of being out of control, can all lead to short- and long-term effects. Short term some may suffer nightmares, compulsions, or an array of emotions like fear, horror, anger, guilt, or shame. Others may experience feelings of detachment, dissociative reactions (e.g. flashbacks), depersonalisation (feelings of being removed from themselves), and being overly aware of potential threats.
Long-term effects may be even more debilitating in that they can persist over a much longer period, these can include an inability to experience positive emotions, avoiding going back to sea all together, or being treated differently by colleagues onboard after returning to work.
He added: “It is really important for hostages to seek support from clinical psychologists and therapists once their ordeal is over. Doing this at an early stage can stabilise and start to decrease the symptoms of post-traumatic stress and help with understanding the connection between body and mind which, in itself, will help to alleviate feelings of anxiety and helplessness. What is more, talking to a professional can help them to understand that their responses are normal and that others go through similar periods of adjustment with similar symptoms. Equally important is learning how to focus on breathing when experiencing fear - fear changes the normal breathing patterns, which in turn can exacerbate feelings of anxiety.
“In addition to talking with a clinician, they should accept any help and support offered by friends and family. They may be inclined to protect their friends and families from hearing about their experiences but it is actually beneficial for everyone if they can talk with their loved ones,” he stressed.
It is not only the hostages themselves who are affected by the ordeal, but also their loved ones waiting at home for news. Ship managers and owners should ensure that they keep very close contact with the families throughout the course of the kidnap situation. Even if there is no new information, they should respond to families swiftly and regularly. Companies should be equally aware of the impact on crew working on their other vessels who may be friends of the hostages or have sailed with them in the past. It is a difficult circumstance for everyone involved so communication is key as is demonstrating that preventative strategies have been put in place to ensure crew security in the future. l
Voyage decision-making solution provider OneOcean has provided the following commentary on the recent United Nations High Seas Treaty on ocean conservation.
On 4 March, UN negotiators agreed the first ever treaty to protect the world’s oceans that lie outside national boundaries. The Biodiversity Beyond National Jurisdiction (BBNJ) agreement, known as the High Seas Treaty, will inevitably have implications for international shipping, but exactly what those implications will be is unclear.
There are some 219 million square kilometres of ocean, known as the ‘high seas’, that lie outside the exclusive economic zones of national jurisdiction. That’s almost two-thirds of the world’s oceans currently without protected status. The new UN treaty is aimed at establishing a legal framework to change this. Before this enters into force 60 countries will need to ratify the treaty, so the impacts are not imminent. The shipping industry has been alerted to the fact that changes to its ways of operating may be coming. What those changes are is still unclear.
What we know about the High Seas Treaty
The IMO points out that “ships plying their trade across the world’s oceans are subject to stringent environmental, safety and security rules, which apply throughout their voyage.”
While the Flag State has jurisdiction on ships sailing the high seas, enforcement of many maritime rules tends to be weak or uncoordinated. Ships operating on the high seas can also carry
out activities that may not be subject to any regulations and, if they are, monitoring is not always enough. This inevitably opens the door to infractions.
The BBNJ treaty is most certainly well intentioned. It provides a framework for managing ocean resources. It will also promote realisation of the target to establish 30 percent of the world’s oceans as marine protected areas (MPAs) by 2030. The aim is to change the current situation where states are limited to declaring MPAs solely within their own national jurisdiction.
The treaty requires oversight on high seas activities. Environmental risk assessments will be needed, with input coming from all relevant stakeholders. All in all, the treaty is designed to support the United Nations Convention on the Law of the Sea (UNCLOS) by establishing a holistic approach to protect the marine environment.
The agreement does not apply to warships or naval auxiliary vessels. They are, however, expected to operate in a manner consistent with the agreement.
There are many aspects of the treaty’s effects on shipping that we don’t know yet. For example, while oversight on high seas activities is the plan, how exactly this will be imposed is unclear. We don’t know what, if any, new regulations on shipping will be legalised.
The most likely marine sectors to be affected appear to be commercial fishing, deep sea mining and operations that create ocean noise pollution. The same is true for shipping lanes, which may also be affected.
But perhaps the biggest question mark is the one relating to open loop scrubber systems. Will the new treaty have an impact on their use? There is already debate within the industry on the effectiveness of these systems in reducing overall environmental harm, and it is possible that the UN Ocean Treaty will revive this.
Under the IMO’s existing regulations on scrubber systems, Flag States are responsible for monitoring their use. One important requirement is that they “shall endeavour not to impair or damage its environment, human health, property, or resources, or those of other states”. There are no guidelines issued for their use beyond national jurisdiction. Nor does the BBNJ treaty include any specific regulations having a direct effect on shipping operations or equipment installed onboard vessels.
There is speculation that the IMO’s Marine Environment Protection Committee will approve a new plan for harmonizing the rules for scrubber washwater discharging. This might be an opportunity for aligning new rules to the ambitions of the treaty.
There appears to be general enthusiasm for the aims of the new High Seas Treaty, but the devil might lie in the details. The current environmental legislation is centred on coastal and specific emission control areas. How this legislation will be extended to include ocean areas beyond national jurisdiction has not been explained.
If new regulations are introduced, questions will arise regarding their implementation and enforcement. Will shipping companies be responsible for self-reporting? If so, what onboard mechanisms will be needed, and what new considerations need to be addressed?
However, it seems clear that the importance of operators being able to plan and monitor complete voyages in full compliance across the high seas will increase. OneOcean
is here to help you prepare for this eventuality using our EnviroManager and Regs4ships solutions.
EnviroManager and EnviroManager+ provide end-to-end clarity on environmental regulations in force around the world and along voyage routes, accurately calculated from the correct baseline. If new environmental regulations do come into effect and new MPAs are designated, they will be incorporated into the solution. This tool will provide clarity on the regulations in effect on the high seas and which operational actions are allowed, restricted or prohibited.
Our Regs4ships solution contains an intelligent database of regulatory documents from the IMO, ILO, Flag States and other official regulatory bodies. Any new regulations that come from the UN Ocean Treaty will be incorporated into the solution as soon as they are published. This will give companies the maximum time to read through and prepare for compliance, adjust operations and procedures as needed.
Although the new treaty poses more questions than answers, the industry nevertheless needs to be prepared. OneOcean’s advanced digital solutions are a good place to start. l
The following is an edited version of an article by psychologists Ivan Doulgerof (pictured bottom) and Frank Lamberg Nielsen (pictured top)
The ability to manage or lead meetings is a vastly underestimated part of the leadership repertoire, on board ship as much as in land-based office environments, and regardless of whether the meeting is taking place virtually or in person.
Meetings on board vessels are not just time-limited social forums through which maritime leaders are weighed and measured by their crew. Through meetings, maritime leaders can also gain important insight into crew members, as well as influencing their perceptions and attitudes.
We would argue that the quality of meeting management on board vessels is reflected directly on the financial bottom line – including the social part of the bottom line. The crew members’ perception of meeting efficiency on board has a direct impact on their moods and emotions, on their general motivation and work ethics, on their attitudes towards their jobs, as well as on degree of job satisfaction.
Poor quality of meeting management can have major consequences for crew members’ relationships with their leaders and land organisations. It leads to decline in productivity, increased dissatisfaction, negative attitudes, low levels of creativity, as well as less qualified decisions – which, in turn, affects all crew members and their land organisations negatively. Plus, of course, there are safety considerations that come with poor performance.
Conversely, well-structured meetings and qualified meeting management strengthens the trust between maritime leaders and their crew members. It is precisely through well-orchestrated meeting management that leaders can have a positive impact on their crew members and can handle group dynamics in such a manner that the internal cohesion of vessel departments are strengthened.
As we highlight in our upcoming book, ‘The Emergency Preparedness Manual – An Operational Maritime Leadership Perspective’, maritime leaders should reflect on how they can make good use of meetings as unique opportunities to interact both appropriately and efficiently with meeting participants. Before any meeting, maritime leaders should be clear as to what it is they wish to achieve. Other points to consider include:
• Convening meetings well in advance – so that participants can plan their other tasks without perceiving the meeting as a disruptive factor;
• Starting them on time – to avoid negative social reactions;
• Setting clear frameworks, formulating purposes and clear goals for meetings – including revisiting ‘rules of engagement’ during meetings when necessary;
• Being clear about the extent to which participants are part of the decision-making process, to avoid any false expectations;
• Involving all participants as much as possible and facilitating dialogue so that meeting participants have an opportunity to contribute and learn from each other;
• Dealing with any friction during meetings – or managing surfacing conflicts in an adequate manner;
• Evaluating the meeting process together with the participants –both for learning purposes, and to identify need for changes regarding future meetings.
Managed correctly, meeting management in maritime environments can be exercised as an integration of what we call ‘Leadership Type 1’ and ‘Leadership Type 2’: the former is oriented towards results, entails coordination of a common effort towards a common goal, and is, as such, operational in its character; while the latter is oriented towards relations, and among other things entails influencing perceptions and attitudes of others, care-taking behaviour, as well as development of others.
If maritime leaders exercise both results- and relationshiporiented types of leadership during meetings, they will experience completely different kinds of group dynamics and of commitment from participants. Well managed meetings lead to effective decisions characterized by both their quality and degree of acceptance. l
SMI’s latest round table debate focused on the important issue of international sanctions and their implications, from the perspective of the Malta maritime cluster, strategically located in the central Mediterranean and home to the largest Ship Registry in the European Union. Below are edited excerpts from the discussion, a full recorded version of which can be viewed on the SMI website.
Panellists included:
Dr. Jan Rossi, Senior Associate - Ganado Advocates Malta; Capt. David Bugeja, Chief Officer and Harbour Master - Ports & Yachting Directorate (Transport Malta); Ms. Genevra Forwood, Partner - White & Case (Brussels); and Riccardo Landini, CEO NAI International (Navigazione Montanari SpA). Moderated by Sean Moloney, CEO of Elaborate Communications.
Sean Moloney
Welcome everybody to the latest in our series of SMI, Ship Management International round tables, this one run in association with Ganado Advocates of Malta, so I shall ask Ganado’s Dr Jan Rossi to kindly introduce the debate.
Jan Rossi
Good day and thank you, Sean. I’m a shipping lawyer with Ganado Advocates’ shipping practice here in Malta and over the past year, like many other people, we’ve had to face a lot of queries from our clients, essentially shipowners and yacht owners as well as brokers and operators on how the day to day activities are impacted, or shall be impacted, by the current sanctions regime which is constantly evolving and changing. Primarily, the reason why Malta is so affected by this is twofold. Firstly, from a geographical point of view, the sanctions do affect certain operations such as bunkering, ship to ship transfers and the like that are carried out here in Malta by the local marine services industry for reasons of our strategic location, and secondly due to the large amount of shipping organisations and vessels that are registered under Malta as a leading flag.
Sean Moloney
Thank you very much, Jan. Can I ask the other panellists to please introduce themselves and give an opening perspective?
David Bugeja
Hello everyone and thank you for inviting me to participate in this interesting debate. I am a master mariner by profession and have been doing the job of harbour master for the last 25 years. As people may appreciate, in Malta that not only covers
one port but all the ports and also, as rightly mentioned by Jan, all the activities and commercial operations taking place in our local and territorial waters and therefore we are the interface through the local ship agents in respect of clearing ships to carry out services and operations in Maltese ports. Normally we are dealing with safety of navigation issues and coordinating ship movements without having to deal with this new tier of diligence and verifications prior to us clearing the numerous vessels and the enquiries we receive.
Genevra Forwood
My name’s Genevra Forwood and I’m a partner at White & Case, which is an international law firm and I lead the EU and the UK sanctions teams within our firm. We work very closely with colleagues in Washington DC and various other jurisdictions as well to provide joined-up advice on sanctions and so my perspective is as a sanctions lawyer emerging from the avalanche of sanctions that we’ve just been coping with in this last year following the Ukraine invasion. From our perspective, it’s unbelievable the number of ways in which various companies have been impacted by these sanctions. What’s clear is that sanctions have moved into the mainstream of compliance and risk management of any company, whatever the sector. It’s no longer a niche area that you only need to be concerned with if you are dealing in specific sensitive activities or jurisdictions.
Riccardo Landini
My name is Riccardo Landini, I’m the CEO of NAI International in Malta, which is a company part of the Malta NAI Group and Italian Shipowners. We own 20 tankers so we are very, very impacted by the sanctions in the transporting of oil and its
products. We have a daily work to be done to make sure that our voyages, our transportation are not under sanctions so the due diligence that we are forced to do adheres to everything.
Sean Moloney
Thank you, everyone. So before we come onto our first question can I ask you please Genevra to provide an overview of where we are in the sanctions space?
Genevra Forwood
Ok, this is not going to be exhaustive because of time constraints but I’d like to set the scene by saying what’s changed: why everyone is talking about sanctions now, what’s different from a couple of years ago and what’s changed in terms of how sanctions are adopted and enforced.
When we’re talking about EU sanctions, as a foreign policy instrument they’re very specific and a matter of EU law because it’s a combined exercise by the EU on the one hand and the 27 Member States on the other. So, in terms of adopting sanctions, they have to be adopted by unanimity by the 27 Member States and they’re enforced at the national level by the different competent authorities, so it’s not as easy as just one country like the UK or the US taking a view and adopting the sanctions that they see necessary. One thing that we’ve really seen in the last year is the alignment between the EU and its G7 partners and other aligned jurisdictions and this is where it gets tricky - you can’t assume that just because you’re okay under one set of sanctions, you’re okay under the other because while there’s a lot of devil in the detail, there’s also a lot of broad alignment.
Then on the sanctions themselves, there’s the sheer number and intensity of the sanctions packages that we’ve seen. We’re now awaiting the 11th EU sanctions package against Russia and just to put that into perspective, in 2014 after the Crimean invasion, there was just two packages and very quickly people were able to figure out what those meant and move on. Now what we’re having is the landscape changing every two or three months and just when you think you’ve figured out what you can and you can’t do, then it all changes again. So it’s just this constant, constant effort to keep up and the burden on internal compliance teams has just been massive.
Also I think what’s worth flagging is that we’ve not just got these kind of classic sanctions with blacklisted parties subject to an asset freeze in the EU or a SDN (Specially Designated National) in the US where you’re checking off a list and then you think okay, there’s no sanction person involved, I’m fine. That’s absolutely not the case. First of all, you need to look back at your ownerships to make sure that there’s no one in the background who owns or controls the person you’re dealing
with, which throws up a number of challenges but also there are many, many other sanctions that have been developed, which are specially designed now to target the Russian economy in various ways.
So again, just gliding over them all, we’ve got export bans on massive numbers of goods and technologies to Russia and then you’ve got import bans so goods coming out the other way and what’s important to flag here in the maritime sector, it’s not just the actual export in itself, it’s all the associated services that you might find, such as providing insurance or financing or brokering and technical assistance and other what we might call peripheral activities that are targeted as well.
Sean Moloney
Okay, thank you very much Genevra. Now I’m going to bring in Riccardo on this. You’re a shipowner, you’re involved in the tanker sector… what are your thoughts on the extent to which the industry is aware of what it’s facing?
Riccardo Landini
Well, I have to say that independently on our personal take on the war, we must be aware of the sanctions and on the implication in not following the rules. The transport of goods, as Genevra was saying, is clearly affected by the sanctions and we have to see many aspects and many sides of the business, going deeply into the diligence we are forced to do to perform on any kind of voyage because at the end, any genuine mistake can have disastrous consequences for any company involved in transporting goods by sea.
Sean Moloney
David, with your background and current responsibilities, how concerned are you about the level to which the industry is aware of all of this?
David Bugeja
Well, I think the shipping industry is aware, but I don’t think it is aware of the severity of the situation in some areas. What we experience is that shipowners and ship managers like Riccardo and similar operations, they are taking this quite seriously and doing all the due diligence because as was rightly mentioned, the repercussions can be very, very serious. But the problem we face, I think, is with the intermediaries, the service providers, the ship agents, the ship chandlers, the bunker operators in respect of support services. I think in those areas, these service providers may sometimes be assuming that they do not have to do anything because someone else has done it for them and if I’m getting a request and the authority is clearing it or the shipowner is asking for it, then it means that everything is alright and we should go ahead and if we are stopped, why are
we stopped? So I firmly believe that there are the, let’s say, real shipowners, the managers and maybe the legal firms that take this seriously and check the authorisation but there is a range of other players within the sector that maybe are not dedicating enough effort to be part of the due diligence process.
Sean Moloney
Thank you, David. Jan, as part of Malta’s legal profession how are you dealing with this and what are you saying to clients in transactions like transfer of ownership of vessels or the registration of vessels under the Maltese flag?
Jan Rossi
Well, initially what I have observed is a total shift in approach towards the sanctions. So whereas in the initial months, many shipowners and operators in the industry attempted to work within the remit of those sanctions and keep that function to Russia and Russian interests, few were the ones that would actually keep up. Instead, many players decided to shift their business elsewhere, even if that resulted in a loss of income, purely because they were wary of the consequences of breaching sanctions and also because they did not have the resources available to ensure that their operations are in line with the sanctions, especially the smaller individuals which David refers to, such as ship agents. For a lot of businesses that work in and around the port, it is very difficult for them to keep up with the barrage of sanctions that are constantly published.
Insofar as transaction work in concerned, yes, it did definitely affect how this is done. Firstly, sellers in any S&P (Sale & Purchase) transaction are requesting additional documents on their buyers and who owns their buyers in order to ensure that any of those buyers are not sanctioned or not connected to the sanctions. Additionally, questions are also asked where the vessels will be used because certain sanctions also extend to the geographical use of those assets so that is one perspective. When it comes to yachts, these are specifically targeted because yachts are considered to be luxury goods so the specific prohibition are the same of yachts to Russian interests or for use here around Russia. So yes, I mean, I believe that whereas the early days perhaps not everybody was abreast of the sanctions, I would say that for the large part it is very difficult not to be aware of them 14, 15 months down the line.
Sean MoloneyThanks, Jan. Looking at how sanctions have shaped the way the ship registries operate and with the Russian ‘dark fleet’ hitting the headline on an almost daily basis, what steps should a jurisdiction like Malta be taking to ensure that it is not flagging vessels involved?
Jan Rossi
Well firstly - and this was a novelty - the Registry now seems to be screening parties to S&P transactions whereas in the past, this was not being done. You now approach the Registry with a bill of sale or other details of both the seller and particularly the buyer, which will be a new client of the Registry and is being screened versus sanctions. So that is something which is rather novel.
Secondly, many Russian shipowners used to use the Malta flag because it was very popular with Russian interests as an underlying registry with subsequent registration in Russia as the overlying registry particularly in navigation of routes which are within Russia’s internal waters. Many of those clients, to describe them that way, have voluntarily left the Registry or have been asked to leave the Registry and find an alternative flag or have been advised by people such as myself that look, unfortunately your time working with EU jurisdiction is up, you need to start thinking of alternative options before the loop gets tighter and tighter and then there’s no way out.
Genevra Forwood
On the point of screening and ownership checks, we all know in theory what needs to be done but actually doing that in practice can really be extremely difficult actually to find out who’s behind it when you have complex structures, many layers, trusts etc. So you have these situations when you can only get to a place where you’re comfortable saying ‘well, I don’t have reason to suspect that this person owns or controls this entity despite their involvement’ and so you do get very difficult judgment calls to make there.
Unfortunately, the approach that we would all like in theory is to be able to go to an authority and get a clear view - are we or are we not able, is this person covered or not covered? - and that’s not really a fruitful avenue just because the authorities are not necessarily providing that sort of guidance. So it does leave companies themselves having to take a view there and having to document having reached a particular conclusion.
Sean Moloney
Just moving on from what Genevra said there, Riccardo, you’re a shipowner involved with the carriage of crude oil, how have sanctions impacted your interaction with other actors in the industry such as charterers and insurers?
Riccardo Landini
Well, our Maltese flag fleet is carrying both crude and refined products and this sanction that heavily impacted the day-today operation and activity in our companies. We have been forced to increase procedures in prefixing voyages like accurate due diligences, use of a specialised structure of intelligence, producing new sanction clause also to be inserted in the charter
party and collecting a declaration from our clients. That seems a lot of paper to be asked for and obtained and it is indeed.
Also, because shipping has always been a sector where privacy has been used makes this a bigger point to be overcome when you perform due diligences because not all our clients are ready to disclose the information we are requesting. So every day it’s difficult to decide and to choose what our ships have to carry and which clients are to be followed in their activities.
Sean Moloney
David, let me bring you in on this because you talked earlier about the interaction with agents and also with ship chandlers. How has this changed and what sort of questions are you now asking, what sorts of checks and balances and inspection are you doing to ensure that everything is as it should be?
David Bugeja
Well, actually the first challenge was internal and by internal, I mean when we’re talking with our own personnel mainly in functions like port operations and vessel traffic services, which start questioning even from an employment point of view whether this is our job. You know, we’re here to do a safety of navigation task to manage shipping movement and now you’re asking us to be detectives or to do all this and so that’s the first challenge that you’re changing the functions of your personnel but one way or another, that can be dealt with.
In respect of the other one, it can be quite difficult or you see, you know, why are you doing this because prior to such detailed, complex functions, for example, for a loaded tanker to be provided bunkers was a very straightforward situation. You notify that you are a loaded tanker with a product X loaded in a particular port, you’re coming here to anchor for 12 hours to receive bunkers, the bunker barge goes provides you and within 12 hours the job is done and you depart to your next port. Now, the moment that we say ‘but we want more details of your cargo and the origin and the owners and the beneficiaries and the next port’, where sometimes the reality of the business is they do not have an export, and they are still waiting for instructions whether to discharge this in A or B port or whether they are going to proceed,’ it all becomes very complex and very sensitive.
Importantly, for a country like Malta, we all need to appreciate that in respect of the local harbour and port-related and anchorage operations, these value-added services that we provide, these services of bunkering, of changing crews out at sea, of facilitating the provisions of stores, of doing transhipment operations, they are a core part of our economy because our domestic market is very, very small. So if, for example, you have a bunker operator who’s employing 40 people ashore and have
three bunker barges with crew and everything, the moment you start disrupting their service, the client can say ‘oh, it was too complex there, I will go to the next place, I’ll just navigate a couple of hundred miles to the east or to the south or whatever and I’ll get the job done’ so that’s what this means for us.
Sean Moloney
That brings it onto the important point of the effectiveness of sanctions. Are they doing more damage to European interests than the effect they’re having on the intended targets such as Russia? Jan, let me bring you in on this. It seems that there’s an awful lot of work for lawyers dealing with all of this. What are your thoughts on that point about the effectiveness of sanctions and who’s winning and who’s losing?
Jan Rossi
Well, that’s a very tricky question and I’ll reply based on what I’ve seen so far as our legal practice is concerned. Yes, as you correctly point out, initially the sanctions brought in a lot of work insofar as legal advice and services. I myself, unlike Genevra, am not specialised in sanctions so I had to learn as I went along in advising my clients because essentially I’m a shipping lawyer. However, that type of work is starting to fizzle out. Why? Because as David correctly pointed out, many operators are choosing alternative places to do business, alternative jurisdictions, which are less complex. Complexity increases costs, it increases stress levels and businesses will always go for the easier option. So, whilst initially yes, it did create a flurry of legal activity and legal work, what I am now starting to see is that potential clients are moving elsewhere, including outside the European Union, which automatically means that certain business has decreased.
Sean Moloney
So, are we going to be seeing then a shift in this type of flagging activity to Open Registries away from the European flags, because of what Genevra said earlier about once the EU or the Commission decides on something, it is binding across all EU Member States?
Jan Rossi
believe so, yes. It’s already happening and I believe it will continue to happen.
Riccardo Landini
One thing that Jan said really rings true. That is the high cost that every company is facing now to comply with sanction. We are being forced to hire new resources to set up a sanction compliance programme and legal costs are usually increased by the sanction.
Genevra Forwood
Yes, there is a tendency to say ‘well it’s going to cost us too much
to figure out these rules, let’s just de-risk completely, let’s just stop all business with Russia or Belarus or whatever’. But there may be things that you can do legitimately and then having the absolutely right advice to be able to take that position can become a competitive advantage.
Riccardo Landini
Correct but to say ‘we are not heading to Russia or from Russia’ is not the solution because wherever you go, you have to still comply with the sanctions.
Sean Moloney
So what are the challenges and problems for jurisdictions like Malta surrounding these geopolitical issues?
David Bugeja
I think the first thing we need to realise that the world is a very big place and if the European markets and in particular our Mediterranean region becomes too visible and too complex, as we have already mentioned business will move elsewhere. For the European shipowners, ship operators and shipping ports, there’s going to be some of us who will lose dearly or are already doing so - and once you lose certain business, it’s very difficult to bring it back – while there are other places where circumventing is the order of the day.
Genevra Forwood
Yes, it’s a very real challenge having a common understanding of these sanctions and I have to say that another thing you see with sanctions is that it’s never a black line. There’s always an area of grey and where it’s grey because of the risks inherent in sanctions it’s sort of de facto that people don’t go there anyway. So, actually the effect of sanctions is even broader than what’s written in the regulations in practice.
Sean Moloney
And what if a stakeholder within the shipping industry, a chandler or bunker supplier, has fallen foul of sanctions unwittingly?
Genevra Forwood
There is a provision in the EU Sanctions Regulations which says that you will not be liable if you did not know and had no reason to suspect that what you were doing on contravenes sanctions. So it’s called the due diligence defence, which is good, and so it’s not strict liability, which is already something but in order to invoke that, you have to show that you took reasonable steps, right? So, when we’re talking about the screening of counterparties, it’s not enough just to say well, oh you didn’t pop up on a list, a reasonable diligence would be to ask ‘who’s your UBO (ultimate beneficial owner)’ and do what you can to find out who’s behind the operation and then screen those persons as well. So a sort of wilful blindness is not going to get you out, you really have to make efforts to be able to invoke that defence.
Sean Moloney
Jan, can I bring you in on this? What is the process here in Malta on that?
Jan Rossi
Yes, so the competent authority here in Malta is the Sanctions Monitoring Board and that is the competent authority that is referred to in the EU Regulation. The Sanctions Board is set up in virtue of law in terms of the National Interest (Enabling Powers) Act and amongst many functions, one of its key functions is awarding rulings on whether certain proposed transactions fall within the remit of the sanctions or not. So definitely over the past 12 to 15 months, the amount of requests for guidance as well as formal resubmitted applications has increased significantly. In addition to ad hoc rulings, the Board periodically publishes guidance notes and FAQ’s which assist players within the local industry. And to also latch onto what Genevra mentioned, the other side of the coin is that if you are willing to understand what’s going on, there’s definitely a competitive advantage both as a player in the industry in the shipping world and also as a legal services provider.
Sean Moloney
Okay, thank you all very much indeed for what has been a really good debate. l
it’s nothing short of a guessing game
The impact of geopolitics on global trade, digitalisation and future fuels came under the spotlight during April’s Singapore Maritime Week with industry leaders all jostling for position to be the first to stick their fingers in the air and try to second guess the future.
Addressing the 5th Annual Capital Link Forum, Jeremy Nixon, Global CEO of Ocean Network Express, said that in addition to the UK and Russia conflict, the situation between the US and China continues to ratchet up economically. But the shipping industry will continue to keep moving and products will continue to find their way like water running down a hill to the bottom of the valley, he told delegates; they will just move through different gateways or different operations or different hubs and that will continue.
“But, I think what we can say from the contentious side at least, is that we are seeing a de-leveraging in trade between the US and China. Just 12 months ago, the US was importing about 45% of its imports in containers from China, that’s down to about 35% today. Many companies in the US are looking to reduce the amount of imports they’ve got coming from China; of course the beneficiaries from South East Asia, typically Vietnam, Indonesia, Malaysia, India are already coming on very, very strongly as well, and of course Japan and Korea have done well as well,” he said.
“My own feeling on this is that it will start to bottom-out in due course, simply because as we all know there’s a certain amount of production in the world and we can’t just turn it off and move it so easily, and all the ships and all the ports won’t be able to cope. But the nearshoring is going on as we see in the areas of sustainability and alternative energy; an area we are going to see huge change in the next 5-10 years.”
Mark O’Neil, President and CEO of the Columbia Group, and President of InterManager, said the industry needed to “be relevant and compelling and look ahead and be client-facing. We need to see ourselves more as an activity servicing our respective clients rather than as a sector-specific. The sector is so fragmented and so specialised now, is it actually a sector at all, or is it an activity serving its client sectors, be they in commodities, be they in leisure, be they in energy. And I really do think that we are at that Nokia moment as a centre – there is no way that one regulation is going to apply to each and every jurisdiction involved in shipping, or each and every different specialised sector in shipping.
“And I think in all of our various client sectors we have to optimise, we have to optimise everything, we have to optimise the maintenance of our vessels and adopt preventative maintenance techniques, we have to optimise the bunker supplies to those vessels, optimise supplies to those vessels and we have to optimise the training of our crews, the specialised training of our crews on individual different vessel types and individual different specialised vessel sectors, harnessing the technologies that we have available to us now, the e-learning systems, the virtual reality training systems that we have and can utilise.
“We have to optimise the recruitment process and perhaps over different models, recruiting our seafarers. Our seafarers are all on social media, they’re all very well able and taught how to use social media and look to social media for movement within the industry and we have to optimise obviously the operation of our vessels. But of course people are what is really important and I think we all need to put people at the front, the middle and at the end of whatever we do,” he said.
Picking up the baton, Nick Brown, CEO of Lloyd’s Register, turned his attention to the environment and
the forthcoming MEPC 80 meeting at the IMO. “While everyone has high expectations for MEPC 80, what we’ve seen in recent days is the EU not slowing down; it is moving ahead with emission trading schemes and looking to increase the scope of the MRV regulations to not only look at CO2 but cover methane and Nox. It is looking to try and close the gap between the commercial affordability of tomorrow’s fuels to the commercial affordability of today’s fuels and trying to stimulate investment in green fuels or renewables such as the requirements going forward for vessels going into Europe around renewable fuels and the non-biological origin.
“Unfortunately, while I am certain that every single person in this room would prefer to see one set of regulations, it should be global and the IMO should be a big advantage for our industry in any form of transition, I think we’re heading headlong towards regional regulations in the short-term. That said, we only have to look back three years, it doesn’t seem that long ago since IMO 2020 and the move to those sorts of fuels, where we were given enough warning and if we have all of the stakeholders involved, fuel producers, ports, bunkering, suppliers, ship management
companies, shipping companies, crewing, training centres etc. we’ve proven that we can move the entire industry from one fuel to another fuel overnight. So, things are not impossible. do hope that the European regulations will assist us in getting greener ships, new engines, new fuels tested, piloting or green corridors or clean energy hubs, but I don’t believe that we can expect a global regulation for all of this to follow in the short-term,” he said.
Singapore is the world’s largest bunkering centre and so the fuel debate is of massive importance, and according to Rahul Choudhuri, Regional Director AMEA for VPS, Singapore is taking a very strong position with biofuels. Indeed, they supplied 140,000 tonnes last year and are looking at exceeding, going beyond that number this year.
“The Singapore Shipping Association (SSA) in the middle of last year developed a document for biofuels, to give a start point for those who will come in bunker in Singapore, what you need to know. Some very general stuff about biofuels. Then the Singapore Standards Development organisation took this role to develop a biofuel standard, to sort of align with where Singapore is going. So this is a really hot topic. And internally this is something we are spending pretty much this whole year looking at. Because we’ve tested in excess of 1,000 biofuel samples throughout the last year and a half. And this work, I was trying to see, I think approximately we have increased our work over the last two years something like 14, 15 times.”
According to Mr Choudhuri, the industry has a good feel of what these biofuels look like. And we’re going out to the industry saying that this is what we see, this is what you need to do, how do you need to prepare. They are very good fuels but they are not your normal fuels, they need to be handled in a different way.
“Now the other angle to this, is that we have been on a one-year project with the Global Centre for Maritime Decarbonisation. And we have been dealing with them on the biofuel project. So, everything they’ve done on biofuel project, we’ve been testing it, from source to supply. For example, the two projects we’ve completed, basically they are trying to build a framework for a green channel. So, a lot of these biofuels are coming from China now, how do you move them securely to Singapore and then you blend them here and supply it. And is this chain secure? Is the product secure? Does the product last this travel and blending or not?
And the final piece of the puzzle is that we are involved in an ongoing project with GCMD right now, working extremely closely with them, to look at fingerprinting of biofuels. Because in the industry, if you ask anybody, so how do I know that this is made of soy or palm? There is no way, there’s nothing in the industry that can give you, once it’s in the supply chain, to know what is the origin. So we’re trying to do some very ground-breaking work on, can we actually find a methodology which is something like again forensic science, to give some fingerprinting.” l
NorthStandard has opened the doors of the Singapore office that establishes its new headquarters in Asia.
Located in expanded and fully refurbished premises at the former North address of Springleaf Tower, Anson Road, the establishment of a single office was marked out as a priority during the merger between North P&I and The Standard Club, given the significance of regional members and the pivotal role of Singapore based service delivery.
Establishing a combined P&I business that is considered to be more extensive than any other within the Lion City, NorthStandard has identified continuity of customer relationships as its first priority across the region. The consolidated office is led by David Roberts, former Standard Asia Managing Director and James Moran, former North Director (Singapore).
Roberts, who has been appointed Head of Asia-Pacific, said: “Singapore’s maritime industries are accustomed to hearing about the benefits of scale, but we are also fully aware that members and brokers put the highest value on the
relationships we have with them. We have acted at pace to launch NorthStandard in Singapore to confirm our commitment to continuity of service in Asia delivered by our combined team.
“The personal contacts and relationships that members value, remain firmly in position within the new organisation.
Members will also welcome the fact that a far broader service portfolio is available to them within the region than was previously the case through either North or Standard,” added James Moran, who was recently confirmed as NorthStandard’s Chief Operating Officer, Asia Pacific/Head of P&I Claims – Asia Pacific. “Service levels will benefit from the combination of resources and inhouse capabilities: arguably, we offer the widest service provision in P&I based in this time zone,” he said.
Consolidation in Singapore provides a basis for a regionally led response from NorthStandard to the challenges of decarbonisation, digitalisation, regulation, and recruitment, said Roberts. The Club’s regional specialities include management of the Singapore War Risks Mutual (SWRM) (Singapore’s national war pool), Strike & Delay Class cover, a particularly strong position in FD&D, fast-growing owners’ fixed premium lines of business and a dedicated Coastal & Inland Class.
According to David Roberts (pictured left), pre-merger they had 20-23 people on the north side and 35 people on the southern side, so bringing the two together under one roof creates the largest P&I Club in Asia and certainly Singapore. And what are the opportunities? “It is a size thing, but to us it’s much more about servicing our members and in the scale to do that effectively… and using that to improve our competitive market position.
“You asked the question about what are we looking to achieve here in Asia? I think the answer to that is, you know, really closely interlinked with the growth of Asia Pacific generally. Asia Pacific is currently about 50% of global shipping, but it’s actually growing at a faster rate than the rest of the world. So, from a NorthStandard Group’s point of view, it’s logical to have a strong focus in this region. Both clubs have historic strong positions in Asia Pacific, and if we put that together and we’re certainly one of the premier clubs in Asia Pacific.
“We’re talking about, not only conventional P&I, you know, cover, you know, related to Charterers Clubs, but we’re also talking about a squeeze of additional speciality clubs that the group offers, and if you put all that together, we believe that it’s a non-rivalled package of covers that we can offer the market,” he said. l
Competition authorities have approved the merger of OSM Maritime Group and the Singapore-based Thome Group. The merged company, OSM Thome, will be a power house in the international ship management market, represented in 22 countries and headquartered in Arendal, Norway.
“This is a big day for OSM Thome,” said Finn Amund Nordbye, CEO of OSM Thome.
“Our merger is now formally and finally approved. The merged company combines proud traditions with high ambitions. Our business is based on Norwegian maritime skills and with skilful employees in leading shipping locations across the world, we will strengthen our position as an innovative and worldleading supplier of ship management services. We have built a company for the future, with safe, efficient and sustainable management of ships as our DNA. That will give added value for our customers and for our colleagues,” he said.
Several of the world’s leading shipping companies are customers of OSM Thome, and the fleet includes various segments such as tank, bulk, container, car ships and offshore vessels. The company handles ship management for nearly 450 ships and is responsible for crewing on about 550 additional ships.
“We are respectful about, and appreciate, the trust shown to us by our customers, which we will do our utmost to maintain through our around the clock operations on the seven seas.
We know our customers’ needs and our skilled and dedicated colleagues, both on land and on sea, are crucial for us to be able to provide the best solutions. We have the skills and the ability to continue growing. We will do so by offering competitive solutions and taking good care of our existing as well as new customers. We will remain leading within safe and efficient management as well as within important areas such as digitalisation, cyber security and green shipping,” Mr Norbye added.
The integration process has been thoroughly planned and now, as the merger finally is approved, the work of joining the two organisations can begin. Through this process, the daily run of the ships and attention to our customers remain the top priority. The integration process will be done in a fast and proper manner and in good dialogue with employees at the various offices. “It’s all about people” has been OSM’s mark for many years, and remains a core credo for the merged company. l
Singapore will weather the post effects of the Covid pandemic and the current cost inflation issue and will continue to grow, purely because of the kind of maritime footprint that it has, according to Manish Jain, COO of Womar Tanker Pools.
And while the Covid pandemic had an impact on Singapore and other maritime clusters with people working from home and even relocating away from the City State, Mr Jain is convinced that Singapore will continue its role as the world’s number one international maritime centre.
“When you look back at the COVID situation and the way that Singapore reacted to it, it is not easy to compare Singapore to the bigger countries because Singapore can implement rules here, that other bigger countries would struggle to implement. And people here in Singapore were very much in line with what the government was doing and compliant with that. When you look at other countries like the
UK and you ask somebody to quarantine how can you be sure they’re doing it because the country is so big, but it’s different here in Singapore,” he said.
Did Singapore see lots of people move because of the COVID pandemic? Manish Jain again: “No because shipping is very resilient and worked through the COVID situation. There is no doubt about it that shipping was not affected..
“When you look at the cost levels in all the maritime centres around the world, like Copenhagen, London, New York, Dubai, none of them are cheap,” he told SMI. Singapore will continue to grow because of the sheer number and diversity of maritime businesses that are here - shipowners shipmanagers charterers bunker suppliers, brokers technology and software providers, ship repair etc. They are all are here. You can dismantle the infrastructure. The government had to take decisions during Covid and it impacted some people, but Singapore is a country very quick to change course,” he said. l
MTM Shipmanagement has set itself a very realistic growth target of 100 plus managed vessels, an increase from its current managed fleet of 70, and operating a fully-fledged shipmanagement service from its Greece office in addition to (Singapore and Mumbai ) this year is at the heart of its growth strategy.
But according to Capt Rajiv Singhal, Managing Director of M.T.M. Ship Management, any growth must be slow and gradual and focused on quality rather than just quantity, with a strong emphasis on clients with a global rather than a regional presence.
M.T.M. is one of those unique breed of ship managers who despite having a pedigree owning ships, also offer third party shipmanagement services. “We are managing about 70 plus ships now and our ship management business is growing in the Far East, South East Asia and the Middle East. So, the focus has to be on a client who is global and not concentrated in just one region,” he told SMI during a recent visit to Singapore.
M.T.M.’s presnce in the Far East, US, Europe and Japan will add the necessary resource that a larger internationallyoperating principal will be looking for, he believes.
The company’s managed fleet is quite specialised, comprising of oil product tankers, chemical tankers & MR
tankers. The company has also experience in managing Aframax tanker and LPG tankers. On the dry side it is managing bulk carriers from handy size to Kamsarmax, and Capes. According to Capt Singhal, M.T.M. has past experience in managing container ships as well.
“We undertake ship management services from our offices in Singapore and Mumbai. Ship management from Greece is expected to start this year. 99 % of our manning and Training needs are met by in house offices worldwide” he said.
“I want the company to concentrate on operating at a global level. This includes Japan, which is a large shipowning country, as well as Scandinavia and Greece,” he said.
The fragmented nature of the shipping industry, with only a small percentage, thought to be 20%, of owned vessels managed by third party managers, must be seen as positives by companies like M.T.M. Indeed, managers who are well resourced, with a strong global presence, can offer the service demanded by owners facing even more regulation coming through.
“We have that capability,” he stressed. “So, the owner doesn’t have to worry about compliance with new or existing environmental regulations. They don’t have to
worry about crewing or technical management because we can provide the necessary service. Gone are the days of conventional ship management, now the industry expects ship managers to provide to provide a range of services that can help the owners. It is about giving them the confidence that they can give their asset to us and we can not only serve them but also serve their customers, the charterers.”
Conservative in its approach to the market is at the heart of M.T.M.’s growth strategy, and its management reach is focused on product and chemical tankers and bulk carriers, but it believes it has to be dynamic, continuously evolving the services it offers. According to Capt Singhal, it is not about becoming big for the sake of it, “but if we have an owner who is like-minded, like MTM, and who believes that asset management and agrees in maintaining a fleet under rules required by maritime regulations then we will look to take on the management of ships from other sectors such as containerships and gas carriers.
“Of course, we are owners and we run the managed vessels as if we owned them ourselves. We go out into the market, run them like an owned vessel, with the aim of helping the owner to propel their business and to meet the needs of their charterers. We don’t consider ourselves as third-party managers, but as owner’s managers. We want to
run the ships as owners and maintain their asset value and commercial viability to the highest quartile,” he said.
M.T.M. has a total crew pool of approximately 4,000 seafarers. Of this amount, Burmese are about 30%; Filipinos about 26%; a high level being Indian; with the remainder European - Georgians and Ukrainians.
And what about Singapore as a base to operate from? How has it been affected by the past three years of Covid pandemic?
Capt Singhal again: “I think Singapore is a very shipping friendly nation. And the government and the government bodies here are supporting the shipping industry very well through their vision programme, through their bunkering programme, through the environment programme. It’s a very, very friendly country to do ship management and you receive good support from the government and the regulatory bodies.”
Costs are going up, he conceded, and that is becoming a challenge. “Because the cost of living is increasing, this is having an impact on the cost of property and renting. But Singapore will continue to grow as a maritime cluster because of the support it gets from the government and the regulatory bodies here. And historically it has been placed in a strategic location but some correction will be required in the property prices and inflation here.” l
Singapore is acknowledged as the number one international maritime centre but the after-effects of the Covid pandemic have resulted in a significant rise in costs, more notably house rental costs. And there are fears that unless something is done to curb the property cost inflation, it could impact on Singapore’s attraction as a place to do business from.
But according to one Singapore source, the important role that maritime plays in the Singapore economy remains high, driven by a thriving international maritime cluster inn the City state.
“The maritime sector is undoubtedly a key economic pillar of Singapore contributing significantly to Gross Domestic Product and job creation,” said Murali Pany, Managing Partner at Joseph Tan Jude Benny, Advocates and Solicitors in Singapore.
“As a global hub port and international maritime centre, there is a deep and thriving maritime ecosystem here with a large concentration of international shipping groups,
offshore and marine engineering companies and maritime service providers.
“As a law firm with a specialisation in maritime and international trade law for over 35 years, we are part of this ecosystem and a considerable portion of our work comes from this sector,” he stressed.
According to Mr Pany, the industry is changing and some traditional streams of legal work have reduced as companies handle more legal issues in-house. “But other streams remain and there are always new areas and opportunities, especially with tightening environmental, fiscal, and financial regulations. We see growth in strategic advisory and restructuring work. Law firms will need to recalibrate their offering and find their value add for clients.
“The key lessons learnt from the pandemic are importance of innovation and adopting technology. This will improve efficiency, provide flexibility to respond to changes and ultimately maintain Singapore’s competitiveness as an IMC,” he added. l
Saudi Arabia has set itself the ambitious target of attaining national port throughput of 40m teu by 2030, a quadrupling of the current figure. While fears of a global economic slowdown and growing inflation have stymied recent progress, the Kingdom saw a boost in container throughput in the first quarter, up 17.6%, after a modest performance in fullyear 2022, when total throughput rose only 3%.
At the same time, Saudi Arabia has jumped 17 places in the World Bank’s Logistics Performance Index (LPI), rising from a position of 55 in 2018 to 38 this year, underlining the progress made in building out the Kingdom’s logistics infrastructure. Saudi Arabia’s ranking was matched by those of India, Lithuania, Portugal and Turkey, also all ranked 38.
Saudi Arabia also ranked 21st in the United Nations Conference on Trade and Development’s (UNCTAD) Liner Shipping Connectivity Index in the fourth quarter of 2022. Saudi ports’ container throughput totalled 2.01m TEU in the first quarter of the year, compared to 1.71m TEU in Q1 2022, the Saudi Ports Authority (Mawani) reported.
Quarterly container statistics further showed a 16.1% spike in exported TEU attaining a total of 0.56m TEU against the backdrop of last year’s first quarter volume of 0.51m TEU. Imported containers performed better, with a year-on-year rise of 22.4% from 0.52m TEU to 0.64m TEU. Meanwhile, transhipment received a 15.0% boost to volumes last quarter, growing from 0.68m TEU to 0.78m TEU.
For full year 2022, Saudi ports handled 10.36m TEU, a 3.2% rise compared to 10.04m TEU in 2021. Outbound and inbound
containers amounted to 4.84m TEU, a 5% increase on the 4.63m TEU of 2021, while transhipment volumes rose 2% y-o-y to 5.52m TEU.
However, Saudi Global Ports (SGP), which is the sole operator at Dammam, claimed to have handled 2m TEU at the port in 2022, a 13.0% rise on the previous year. “This is a milestone for King Abdulaziz Port and a first amongst ports in the Eastern Province,” a company statement on social media said. “This is also a testament to our continued commitment to invest in newer technologies, developing facilities and upskilling our workforce to enable SGP to better serve customers with increased operational efficiency and future-ready capabilities to facilitate larger vessels.”
Last September saw inauguration of the Port of Jazan City for Primary and Downstream Industries (JCPDI Port) , operated and managed by Hutchison Ports. An alumina refinery alongside
run by Chinese concern Hangzhou Jinjiang will have an investment capital estimated at $1.07 billion.
President of the Royal Commission for Jubail and Yanbu, Eng. Khalid Al-Salem, said the port, in its first phase, would consist of three industrial berths, and single point mooring providing services to Saudi Aramco Refinery, three commercial berths for handling containers including general cargo and bulk goods, in addition to storage yards with special areas for storing and monitoring refrigerated containers.
The port’s berth has a depth of 16.5 metres, with a capacity of 21,000 containers, and can also handle general cargo and bulk cargo ships with a capacity of more than 100,000 tons per ship.
“We have been in Saudi Arabia for 22 years, and it is a very important market for Hutchison Ports. This marks a new chapter for us in the Kingdom and we look forward to working closely with the Royal Commission to make Hutchison Ports Jazan a success and help JCPDI reach its full potential and contribute to the Saudi Vision 2030,” said Eric Ip, Group Managing Director, Hutchison Ports.
Greenfield ports are also planned in the second half of the decade at Oxagon, to serve the new Neom giga-project, with a final capacity of 9m TEU, and Dhiba, further up the northwest coast, with a planned capacity of 3.5m TEU.
With additional plans to create up to 60 logistics hubs, the Kingdom is intent on becoming a global centre for trade. Given their strategic location, GCC countriesespecially Saudi Arabia - are positioned to serve as logistics hubs with some already established centres like Dubai leading the way. However, logistics service providers need to improve their operational efficiency when it comes to last-mile deliveries and optimising asset performance and digitalisation, local observers have noted.
Meanwhile, International Maritime Industries’ (IMI) new mega-yard at Ras Al Khair yard for newbuildings is planned
to go fully live before the end of 2023. The focus is now on training a workforce which is expected to number around 80,000 when fully rostered. In February, IMI signed agreements worth almost $350m as part of the In-Kingdom Total Value Add 2023 (IKTVA) Programme.
“Six of the agreements, signed with industry-leading companies ESAB, Gulf Cryo, Euroblast, Acceleron, and ElectroMech, are focused on enhancing IMI’s business operations across a range of areas including shipbuilding, ship repair, and marine engineering,” IMI said.
Other agreements were signed with leading Saudi training institutions including the National Industrial Training Institute (NITI), Saudi Petroleum Services Polytechnic (SPSP), National Maritime Academy (NMA), and National Power Academy (NPA), to enhance IMI’s apprenticeship programme.
The Kingdom also plans to increase oil production capacity from 12-13m barrels per day (bpd) by 2027 and expand its offshore support vessel (OSV) fleet by 50% over the next four years. State-owned oil giant Aramco already posted a record net income of $161.1 billion (+ 46% y-o-y) in 2022 - making it ‘the world’s richest company’ by some accounts - followed by another $31.9 billion (-19%) in Q1.
All this augurs well for continued fleet renewal and expansion at Aramco’s shipping arm Bahri (National Shipping Company of Saudi Arabia) - as do current inflated energy prices for all shipping companies linked to oil and gas majors in the Middle East. Indeed, Bahri in March reported that it had signed a non-binding MoU with the Suez Canal Authority to look into setting up a joint maritime transport company in Egypt, interpreted as a desire by Saudi Arabia to increase its strategic shipping presence in the Middle East region.
Bahri currently operates a fleet of 96 vessels totalling over 13.5m dwt, including 40 VLCCs. Future tanker newbuilding and repair work is set to take place at IMI, in which it holds an important ownership stake. l
In a move designed to put the contribution of the United Arab Emirates capital on a par with other major shipping hubs around the world, the initial public offering of Abu Dhabi Ports (ADP) Group launched on the Abu Dhabi Securities Exchange in early 2022 has had a salutary effect on the group’s fortunes. Ever since, it has made a regular stream of announcements, including international port development projects, a move into tankers and the expansion of its dry bulk fleet.
The group’s 2022 annual report said that total container capacity at ADP’s Khalifa Port is 8.5m TEU. With the land available for industrial zone development around it being seven times larger than that adjoining nearby Jebel Ali Port in Dubai, the region’s largest shipping hub potentially has a real future competitor on its doorstep.
Indeed, the world’s biggest shipping line, MSC, became a joint venture partner with a local entity for the creation of expanded terminal operator, Abu Dhabi Terminals, in 2018. Agreements with Cosco and CMA CGM now mean that incremental capacity will be bolted on in rapid fashion, in contrast to the organic development that Jebel Ali has seen over the years.
Throughput at Khalifa Port Container Terminal is already rising rapidly with 2022 volumes up 28% from 3.39m TEU in 2021 to 4.33m TEU last year. Further growth is forecast for next year when CMA CGM is expected to bring its new facility at the port on-line.
Progress at Jebel Ali Port was less striking, with full-year throughput up 1.7%, from 13.74m teu in 2021 to 13.97m last year. Analysts say that the lack of growth in recent years—volumes were 15.40m teu in 2017 and 15.59m teu in 2015—is attributable to the departure of MSC and Cosco services to Abu Dhabi.
However, it would be a mistake to write off DP World, which has become a colossus, ranked among the world’s top-five port operators. Today, DP World operates 350 business units in 75 countries. Revenues have more than quadrupled since 2015, when they were $4bn, to $17.1bn in 2022. In contrast, AD Ports Group’s reported revenues for full-year 2022 were $1.5bn.
Gross throughput in the DP World global terminal portfolio was 79m TEU last year. After languishing below 80% since 2012, it saw gross capacity utilisation jump to 84.9% in 2021, before rising to 85.5% last year. In the first quarter, DP World reported gross volume growth of 3.7%
on a like-for-like basis, when it handled 19.5m TEU across its global portfolio of container terminals.
In March, DP World said it had invested more than $10 billion in the global logistics sector since 2012, making it one of the top five overseas investors in this period, according to the latest foreign direct investment (FDI) data released by industry consultants.
Also, in January this year DP World announced that Jebel Ali Port has entered a long-term partnership with Maersk through which both parties will collaborate on various aspects of service delivery and work towards a common goal of decarbonising logistics and serving their customers better.
At the opening of the Seatrade Maritime Logistics Middle East event held as part of UAE Maritime Week in May this year, H.E. Eng. Hassan Mohammed Juma Al Mansouri, Undersecretary for Infrastructure and Transport Affairs at the MOEI, spoke of the UAE’s vision and strategic plan to advance its maritime and logistics sectors’ growth and development. During his speech, he highlighted the UAE’s significant progress in expanding and modernising its ports, increasing cargo volumes, and strengthening its position as a global trade hub.
“Capitalising on the capabilities of our state-of-
the-art ports, several of which rank amongst the top 10 globally, we have been able to handle over 25,000 port calls, and more than 19 million TEUs annually, cementing our position as a preferred destination for international trade,” he said, also contributing AED 90 billion ($24.5 billion) to the national economy.
Meanwhile, last December the UAE government announced the formation of the Emirates Shipping Association (ESA), to replace the long-moribund UAE Shipping Association. An official statement said the ESA had become a full member of the International Chamber of Shipping.
“The UAE is among the most influential countries in developing the maritime industry and has established its pioneering status among the leading maritime hubs globally,” said Hessa Al Malek, Advisor to the Minister for Maritime Transport Affairs, a unit of the UAE Ministry of Energy and Infrastructure (MOEI).
“With a mission to bring together ship owners, industry suppliers and key decision-makers in the sector through strategic networking opportunities and closed-door leadership roundtables, Emirates Shipping Association aims to help its members promote, secure and expand the global maritime industry.” l
APM Terminals Bahrain, the operator of Khalifa Bin Salman Port, has announced the launch of a ground-breaking solar power project worth approximately $10m to make the port energy self-sufficient by the end of 2023.
By implementing this project, the terminal will reduce its carbon emissions by 65% while also securing a reliable and sustainable source of energy, effectively making Khalifa Bin Salman Port energy-sufficient.
“We are very excited to take the first major step in our decarbonisation plans, which will make Khalifa Bin Salman Port the region’s first seaport to be fully powered by renewable energy,”
shared Farooq Zuberi, CFO and interim MD, APM Terminals Bahrain. “Our decarbonisation strategy for the port is in line with the vision of HM The King and the commitment of HRH the Crown Prince and Prime Minister for Bahrain.”
By the end of the solar implementation project, APM Terminals Bahrain will have installed 20,000
solar photovoltaic panels capable of generating 18.5 Gigawatts of electricity per year. This renewable energy source will produce clean and sustainable energy for powering various port operations, including container handling, crane operations, and lighting, setting an example for the entire maritime industry. l
Lila
Vessels reaching the end of their design life are ordinarily phased out, as part of a responsible fleet management strategy. However, Dubai-based Lila Global, an integrated vessel owner and operator, linked to the GMS group (see earlier article) and led since January 2023 by seasoned CEO Steve Kunzer, has dared to do differently.
Determined to ‘do more with less’, rather than prematurely recycle vessels and create additional GHG emissions during the shipbuilding process for newbuild replacements, Lila Global believes in the possibility of extending the lives of high-quality mid-age (> 15 years) vessels and operating them as safely and efficiently as newbuilds.
Currently Lila operates 39 vessels including bulk carriers, VLCCs and containerships, transporting over 30 million tonnes of cargo annually.
The company’s mantra is that older vessels are not automatically more accident prone or polluting and that operational and environmental risk can be managed, in part, by adhering to strict maintenance schedules and operating procedures, and carrying out mid-life upgrades to ships’
equipment. Lila Global also continues to invest heavily in crew training and welfare, which, as a corollary, is helping to mitigate the recruitment and retention problems the wider industry is facing.
“It’s an exciting time to be at the helm of Lila Global as we look to solidify our position as the premier owner and operator of mid-age vessels”, says Kunzer. “I am especially proud to lead a team that is committed to demonstrating, on a daily basis, that it is possible to run a safe and profitable fleet while adhering to environmental sustainability principles.”
Bringing a wealth of C-suite experience of managing quality fleets and developing and implementing business strategy, Steve Kunzer will provide a guiding hand as the company continues to diversify its fleet and portfolio of services in lockstep with a rapidly decarbonising and digitising industry. l
The Middle East is increasingly being seen as an important transportation hub linking Asia and Europe. Digitalisation is driving the efforts to boost efficiency across the entire supply chain, with smart ports popping up across the region.
Sensors, cameras and communications systems fully integrated with port infrastructure put remote control and automated use of cranes and vehicles, as well as real-time tracking of shipments and goods, at their fingertips.
Such data-driven operations offer ship managers and operators a greater understanding of their vessels and cargo, whilst enabling ship agents to up their game and improve the traditional on-the-ground services they provide.
“An important part of a ship agent’s role is to offer their local knowledge and experience to aid owners and operators that can’t be at every vessel call,” says Fredrik Nystrom, Group Vice President for Middle East, GAC Group. “Technological advances, such as automation and artificial intelligence, will enable them to collect and analyse more data than ever before, improving their position as the main information hub for local regulations and requirements, such as crew requirements, customs checks and documentation.”
GAC is one of the region’s longest-serving ship agencies. It started in 1956 when Swedish entrepreneur Bengt Lindwall signed an agreement with two Kuwaiti businessmen to provide professional ship agency services in the country. Today, Kuwait’s Shipping License ‘No.1’ is proudly displayed at GAC Kuwait’s office in Farwaniya.
Since then, the shipping, logistics and marine services provider has expanded its coverage across ports in the Middle East, weathering many storms to keep global trade moving.
It is now embracing the benefits of disruption in the form of technological advances that are shaking some of the traditional tasks of ship agencies. Nystrom says the long-term advantages will pass on operational benefits to their customers.
“Change is inevitable. What is crucial is that we, as ship agents, adapt with technology and utilise it to improve our services and offer better value for our clients,” he adds.
“This means embracing innovations that can improve vessel turnaround times or using automation to offer better communication on port regulations or weather conditions to help customers save time and money and plan better.”
Ports in the region are now primed to lead these technological advances. According to the 2022 Global Container Port Performance Index, the ports of Salalah in Oman and Khalifa in the UAE were in the top five most efficient ports in the world due, in part, to their increased use of technology.
“Ship agents have the chance to become the primary information hub for smart ports by becoming digitally connected and having a greater understanding of all the elements of a successful port call. And while technology can improve operational efficiencies, the local presence of ship agents on the ground will still be vital even in a digital world,” says Nystrom. l
The Middle East forms a key market for salvage experts
Marine Masters, who have been active in the region since the company was set up in the Netherlands in 2016. Foregoing the traditional ownership of expensive equipment that then needs to be deployed globally, impacting cost and project time, Marine Masters delivers complex operations using locally available resources.
Its most recent success involved deploying to the Persian Gulf and utilising a local heavy-lift vessel to refloat a CALM buoy. The buoy was inoperable, posed a hazard to safe navigation and the hoses connected to it were full of hydrocarbons that could have negatively impacted the environment if released into the water. Marine Masters’ ability to respond faster than other marine salvors, in addition to its reputation for practical solutions and affordability, was a key consideration for the end client.
Henk Smith, co-owner and cofounder of Marine Masters said: “We are known for our quick, safe and innovative solutions. These qualities enable us to mobilise quickly, in response to an incident, and to work effectively in challenging operational environments, for example busy shipping lanes and sensitive marine areas. Our skills and experience came to the fore during our recent deployment, and I’m glad to say our plan to refloat the buoy was executed perfectly.”
Rapid response, a key ingredient of effective incident management, is facilitated by sourcing equipment from regional entities and by working closely with local partners
and contractors. The commercial advantages of this approach, and Marine Masters’ ability to deliver pragmatic salvage plans, is evident in the company’s record of managing more than 60 successful emergency responses, with zero incidents and no pollution, since it was established.
The advantages of its business model go beyond commercial and safety considerations. The model also operationalises the company’s commitment to ESG principles: sourcing equipment locally reduces emissions related to salvage operations thereby contributing to the maritime sector’s decarbonisation goal; and paying fair wages and offering internationally recognised training continues to benefit workers after the salvage contract.
Agility and pragmatism are highly prized by customers and the ability to assess incidents on their merits and develop specific plans of action will become ever more important as vessels become larger and more complex and HFO is gradually phased out in favour of alternative fuels. Adapting tried and tested salvage techniques and developing, testing and implementing new ones is key to the future of the salvage industry, and Marine Masters has stolen a march on others.
After its successful deployment to the Persian Gulf, the company continues to engage in new markets and is actively looking to apply its expertise to new service areas, including the development of offshore wind farm decommissioning techniques. l
Dubai-based Drydocks World, part of DP World, recently celebrated its 40th anniversary, which coincided with successful completion of its 20,000th project for marine and energy clients.
At a gala dinner to mark the anniversary, DP World
Chairman and Group CEO Sultan Ahmed Bin Sulayem described Drydocks World’s evolution over the past four decades as “a testament to the strength of the brand, its people and the commitment so many have shown over the past four decades.”
Spearheading that commitment is current Drydocks World CEO, Capt. Rado Antolovic, PhD. He says the company is “steadfast in its commitment to being at the forefront of the maritime industry.
After 40 years of leveraging our unparalleled resources, access, location, and skillsets, we have made the UAE a focal point for the global maritime industry attracting customers from all four corners of the world. Drydocks World, with the support of DP World, has helped to put Dubai at the centre of the maritime services world.”
Notable milestones during Drydocks World’s first 40 years have included the expansion from its initial focus on ship repair and maintenance to include new building and fabrication of marine vessels on 1994. Subsequently, conversion capabilities for the energy industry were introduced in 1996, which were further expanded in 2004 to cater to offshore energy customers. The company is now continuing to evolve its business offering, with the addition of comprehensive engineering, procurement, and construction (EPC) services. It is also expanding its facilities in Dubai with the new South Yard development providing dedicated fabrication facilities, and has a newly established presence in Mumbai, India, as well as a yard for superyacht work in the Mediterranean, in Montenegro.
Capt. Antolovic explains to SMI that South Yard expansion in Dubai is aimed at increasing the company’s fabrication capacity
by equipping the Yard with new technology that will offer improved services to its clients and customers. The 70,000sqm South Yard is a dedicated facility for new building projects that will feature “cutting-edge equipment, a much leaner execution process and a completely new load-out facility, which includes a new rig jetty to cater to the increasing demand from the rig, oil, and gas market for heavy structures to fit renewable energy clients’ needs,” he says.
“In a vital evolution of the Drydocks World’s business, just last year the company signed a service level agreement with the DP World Subcontinent Region office in Mumbai,” he continues.
“We selected Mumbai because the skills and manpower in India is world-leading and allows us to tap into the right engineering workforce to take our offering to the next level. The Engineering Centre in Mumbai supports our own Engineering office in Dubai, advancing day-to-day operations with digitally native capabilities, while seamlessly enhancing our footprint in India to cater to specialised services in the Indian subcontinent.
“The agreement now provides Drydocks World with a ‘Centre of Excellence for Engineering’ within our group that allows us to advance our brand, our strengths and our offering to customers from around the world who are relying on us to evolve their own assets and capabilities.”
Yards at Drydocks World have are now able to work on 42 projects simultaneously, informs Capt, Antolovic, “which means that we’re capable of handling any project – from commercial merchant ship repairs and conversions to FPSO repairs for our valued customers.
“We are excited to deliver on a few projects, including upgrade projects that will be retrofitted with various sustainable technologies. Just earlier this year, the FPSO Firenze sailed
South Yard to have cutting-edge equipment, a much leaner execution process and new load-out facility
Capt. Rado Antolovic PhD, CEO, Drydocks Worldaway from our yard to operate in the Baleine Field, off the Ivory Coast. This major renovation project was a huge undertaking by the Drydocks team and had crossed four million LTI (lost time incident)-free manhours by January 2023. This is just one of the many merchant ship repairs and conversions that we are able to work on at the same time.
“We are also set to begin work on upgrading the FPSO Petrojarl Knarr floating production storage and offloading (FPSO) vessel for deployment at the Rosebank field offshore the UK. The contract is a joint venture with Aker Solutions, and under the agreement, we’ll be responsible for the construction and life extension of the FPSO vessel, which will operate for 25 years at the Rosebank field without drydocking.”
While once it was feared that yard overcapacity was looming in the ship repair sector, now the problem is rather the reverse, says Capt. Antolovic, with “a huge amount of backlog in refurbishment and maintenance in the maritime industry’ including “plenty of demand for upgrading existing fleets to extend the lifespan.” With so much new tonnage also coming online, especially from China, “the market is very healthy”, he says.
Another factor has been pent-up demand for ship repair work that built up during Covid but Capt. Antolovic points out that Drydocks World remained open throughout the pandemic, unlike yards in China that form the Dubai-based company’s main rivals.
Since the start of 2023, Drydocks World has been operating “at full capacity thanks to a steady flow of orders and consistent bookings,” he continues. “So far, we have received more than 60 confirmed repair orders in Q1 of 2023, sold out yard occupancy until the end of August 2023, and received an increased number of inquiries stretching out later into the year.”
The Drydocks World CEO concludes by underscoring the importance of sustainability and the need for shipping industry players to step up to the challenge. “Providers like us are also playing this field,” he emphasises, “not just because it’s good for business – as we are always striving to support our customers’ needs, whatever they may be – but because it’s the right thing to do.” l
To try and gain a global view of the current state of the ship repair industry, SMI put the same set of questions to two different yards groups whose activities span some of the world’s major ship repair locations: International Ship Repair FZE of Fujairah, UAE and the Newport Shipping Group, which comprises a network of 15 different yards located mainly in Turkey and China. Questions covered the state of the ship repair market, main types of work being undertaken, and the demand for environmental retrofits. For the companies’ very illuminating answers please read on…
Q) How would you describe the shiprepair market in general at the moment and how is your recent, current and forward workload looking? How has the re-entry of Chinese yards into the international market following the lifting of the Covid pandemic affected the overall supply/demand situation?
International Ship Repair FZE
The Ship repair market is currently on the upscale. With many of the vessels earlier running under long extensions are now falling due for docking, resulting in overload of vessels in the shipyards. We are also getting quite a significant share of the Afloat repairs before docking in UAE. With over 1200 skilled technicians at our stake we take up major afloat jobs. Going forward the future looks only positive and buoyant for ship repair in UAE.
Newport Shipping
We do see Chinese yards receiving more inquires after Covid restrictions being lifted. Some owners may still be hesitant to go back to China for docking but I believe eventually Chinese yards will see interest back to normal. One thing that is noticeable is the overall cost inflation in Chinese yards which can have some impact on competitiveness of Chinese yards.
Q) What types of vessel and repair & retrofit/conversion works are you carrying out at present? Are there any recent reference projects that you would like to detail?
International Ship Repair FZE
Well, we repair all sorts of vessels from AHTs to ocean going VLCCs. Our specialization is Pre-Docking & Post Docking afloat repair work. Since we have huge skilled workforce of 1200 technicians in UAE, we are the one stop solution for all the major afloat repair needs. Owner/Managers are finding it economical to get the afloat jobs done prior docking. We have carried out major afloat jobs on 10 of the container vessels including Steel, Piping, Mechanical works, Crane Repair including the Jib, Cabin, Boom & BWTS Retrofit work.
We are also currently engaged with one of the Chinese Scrubber Manufacturer on the Scrubber retrofitting. We have recently installed the Open Loop Scrubber (Deck house) on one of the Cyprus based Container vessel at Khorfakkan Port. We have the resources & infrastructure to undertake Scrubber Retrofit work in UAE.
Newport Shipping
We are currently very busy with normal dockings as usual with both our Cicek and partner yards. (Lianghui Xia, Managing Director).
In 2023, there is a trend of chemical tankers undergoing Newport Shipping drydocks. We do not think there is a particular
reason for this but those projects are more complicated than other type of vessels’ docking processes so this might show that our ability to carry out drydocking and ship repair services at its 15 shipyards with 38 dry-docks globally, together with the offer of attractive prices with long term payment options, leads decision makers to choose Newport Shipping. Also, there is another trend we get projects from the same owner again and again and this shows us customer satisfaction. (Erdal Turk, Sales Manager)
Q) Are you seeing an uptick of demand for ‘green’ modification and retrofit work to comply with EEXI and CII, and if so of what type? Likewise are you carrying out Ballast Water Treatment System installations and is demand for these rising?
International Ship Repair FZE
Yes, we find that the demand for green modification will rise in the near future. As regards Ballast Water Treatment System, we have so far installed more than 100 systems on container + bulk carriers. We continue to support the owner/managers on the retrofit side.
Newport Shipping
There are couple of projects we have done in our Istanbul yard for Bulbous Bow modification and Mewis duct upgrades. (Turgay Colak, Head of R&D)
We still did not have a retrofit project yet related to fuel consumption or EEXI and CII. However, the number BWTS installation projects so far in 2023 has increased by approximately 15% -compared to the 12 months of 2022 - in just the first five months of the year. (Erdal Turk, Sales Manager)
As regards Newport’s provision of financing for major environmental retrofits/conversions, we are in frequent dialogues with financial institutions who showed strong interest to support our projects for environmental retrofits and conversions. The support from the financial market is unbroken. But we also notice a kind of ‘wait and see’ approach from the shipowner’s side. The reasons for this are manyfold. However, applying such a mentality to your journey to be in line with regulatory requirements can lead to longer lead times with delays in project timelines and missed opportunities to reap the financial rewards. (Ingmar Loges, Managing Director)
Also worth noting is that Newport Shipping recently agreed a cooperation agreement with NSB Group to install the latter’s WIDENING concept for containerships, which not only increases vessels’ load carrying capacity but also reduces their EEXI and CII in the process.
Newport Shipping says it is working on new developments for the shipping industry that will enable existing vessels to be more sustainable in the future and meet more stringent green regulations. l
Gemak Group of Companies is one of the pioneer companies in Turkey’s ship repair, ship conversion, and newbuilding field with its technology-based services, operational efficiency, and the importance it has assigned to innovation over the past 50 years.
As one of the biggest shipyard groups in Turkey, Gemak has completed more than 3,000 projects to date from various shipowners for different vessel types and sizes.
Since 2022, Gemak Group has provided services to a wide range of vessels from bulk carriers to container vessels, Ro-Ro/passenger vessels, pure car carriers, and dredger vessels. A broad scope of the works includes docking & general services, cleaning & painting works, steel works, pipe renewals; steel & mechanical outfitting repairs, electrical repairs, refurbishment works, ballast water system installation, and scrubber system retrofit projects.
Apart from the normal dry-docking and repairs, Gemak Group has carried out different new building and conversion projects including:
• Conversion project of a PSV to live fish carrier besides increasing the length of the vessel by 7.6 metres;
• Upgrading of a vessel by increasing the jacking height by about 10 metres and performance of structural modifications for new crane installation;
• New building of an offshore wind energy platform;
• New building of an offshore wind turbine; and
• New building of the world’s biggest live fish farm.
With extensive technical infrastructure, engineering quality, and relevant work experience, Gemak strives its best to keep its position as a preferred yard in the Mediterranean area for unique projects and vessels.
Strategically located at the heart of the Mediterranean, the group matches Turkey’s rising position with its evolving development and increasing investment in its facilities to provide the best to its clients.
It maintains a permanent team of in-house designers and engineers who represent the backbone of its design philosophy and culture. These emerging stars are supported by multidisciplinary teams at the TGE Research and Development Center, Turkey’s first R&D centre for the maritime industry.
In addition to all its industrial activities, Gemak Group is proud to be the first shipyard in Turkey to start a sustainability programme and plans.
For its future development Gemak Group has competitive strategies and activities that will strengthen its market focus, enhance its service quality, and improve its management efficiency as it continues to expand its scope of business as it has successfully done ever since its establishment in 1969. l
MarineShaft makes great use of the welding technique of Laser Cladding in repairing rudder and propeller equipment. During the past six years, a robot has carried out repairs that were previously impossible, as well as general welding tasks, which has resulted in a shorter delivery time when using the technology, as the company explains.
Danish-based MarineShaft A/S specializes in classapproved repairs of rudder arrangements and propeller equipment. Since the purchase of the robot, the company has worked purposefully on getting the classification societies’ approval of the welding technique.
“From Day One, our goal has been to achieve full class approval to use laser cladding on various materials, and we have achieved our goal,” says Peter Pallesen, Senior Project Manager.
MarineShaft has class approvals to apply laser cladding to:
In terms of advantages, the lower heat input of the laser cladding method brings two important benefits:
Firstly, the classification societies will approve laser cladding of items where they normally do not permit welding, e.g. welding of couplings, bearings, bearing journals on propeller shafts, and other rotating parts.
Secondly, post-weld heat treatment can be omitted after laser cladding, which reduces the delivery time with several days.
Technique & scope
Laser cladding technique consists of use of a numerically controlled robot arm, which provides several geometric possibilities for the application of the material, where mechanical advancement as in a lathe only makes it possible to apply the material in a continuous string. The technique ensures very precise and accurate welding, where the surrounding areas remain unaffected by the minimal heat input.
Laser cladding is performed with several types of powder, depending on the base material and function needed. MarineShaft uses the powder types bronze, stellite 21 and Inconel 625. All powder types fuse 100% to the base material and has been thoroughly tested by Force Technology.
With laser cladding, applying a material that gives a harder surface and thus extends the item’s strength and lifespan is possible. Laser cladding is thus a price-reducing and environmentally friendly repair.
Malfunctions and causalities often cause damage to vital ship parts. At MarineShaft, several couplings, chrome liners, blade carriers, propeller shafts etc. have been repaired using laser cladding.
Laser cladding can easily restore parts with wear and other damages, such as cylinder head for valve seats, bearing journals on the propeller shaft, propeller shaft seal liners, blade carriers, propeller hub, etc.
MarineShaft offers laser cladding of:
• Propeller shafts
• Propeller equipment/components
• Stabilizer fins
• Gear component
• Thruster components
• Engine parts
• Components for the wind turbine industry
• Industrial components
MarineShaft has recently ordered a new compact mini laser cladding equipment, adding to its existing resources and it is anticipated for delivery in autumn 2023.
Also, the company mainly operates laser cladding in its workshops located in Hirtshals, but this is about to change.
Distinguished by its crawler chassis, the newly purchased mini equipment offers enhanced mobility and flexibility. This innovative feature enables MarineShaft to extend its laser cladding services more easily to on-site and mobile applications, catering to the specific needs and requirements of its valued clients.
“Our equipment is in daily use in the workshops in Hirtshals”, says Pallesen, adding: “With yet another piece of equipment, we free up capacity, which is essential for a company like ours, where we have a continuous flow of damaged parts, and where the repair should preferably be completed yesterday.
At the same time, the new extra equipment enables us to offer our customers on-site laser cladding.”
Staying at the forefront of technological advancements entails more than just embracing lasercladding technology. MarineShaft has also recently made a strategic investment in state-of-the-art 3D scanning equipment.
Right now, MarineShaft is fully engaged in training and practicing the use of this 3D scanning equipment. “We are excited to expand our portfolio of service competences and offer our customers 3D scanning solutions both in-house and on-site”, says Pallesen.
This cutting-edge, portable, and handheld device will enable the company to offer a wide range of new on-site services, further expanding MarineShaft’s extensive portfolio of on-site repair solutions and for the benefit of its valued customers.
The equipment can be used for various purposes, including measurement of propeller blades, fixed propellers, propeller shaft cones, rudder blade cones, crane foundations, and much, much more. l
Shipowners and operators that overlook Artificial Intelligence (AI) technology when it comes to managing their operational expenditure may pay a heavy price, writes Osher Perry, CEO and Co-Founder of ShipIn Systems
Running a ship is expensive enough for owners and operators in calm economic waters – but even more so when buffeted by the headwinds of inflationary pressures.
The latest report from maritime research consultancy Drewry shows that daily operating costs (Opex) increased for the fifth consecutive year in 2022, climbing by 2.2% to US$7,474. Drewry attributed the rise to price inflation in goods and services across the shipping sector, and to supply chain disruption caused by the Covid-19 pandemic.
Shipping companies hit with increased costs face a major challenge: how to manage Opex as inflation drives up the price of crewing and crew-related fees, lubes, repair and maintenance, management and administration, and insurance. For an industry now operating in a digital era, the answer is artificial intelligence (AI).
An AI-powered platform or system that monitors and shares insights into multiple Opex categories can optimise a ship’s operations while enhancing efficiencies and reducing expenditure. This technology gives owners and operators the means to constantly track operational costs such as repairs and maintenance, or stores, spares and lubes across their entire fleet on a daily, monthly or yearly basis. Additionally, the data can be gathered concurrently rather than through siloed departments or teams that use different mechanisms and tools.
Maritime technology such as the current generation of AI platforms also provides enhanced communication and collaboration possibilities between ship crew and shore, increased knowledge sharing, and the ability to drive continuous improvements across the entire fleet.
Taking a holistic view makes economic sense, while a fragmented approach where various systems work independently to monitor different operational costs is counterintuitive. Rather than reducing their outgoings, a shipping company will spend more on greater headcount and various tracking tools to gather and assess data that could be retrieved through a single, integrated system.
Shipping is inundated with a wealth of digital solutions to manage various aspects of operational expenditure, encouraging siloed teams to become even more disconnected from other business units. This, in turn, creates unmanageable volumes of data, meaning owners and operators fall short of their operational goals. Having teams operating independently can also lead to missed opportunities to reduce costs due to ineffective or sometimes almost non-existent communication between departments.
As KPMG’s ‘Digital Transformation in the Shipping Industry is here’ report reveals, investing in technology can reduce a shipping company’s Opex by up to 15%.
Michael Papageorgiou, Senior Manager, Advisory Department, KPMG, believes tech has reinvigorated the maritime sector, with new applications helping to streamline operations, improve the customer experience and enhance efficiency. Tools enabling ship owners and operators to monitor data in real-time such as digital platforms, blockchain and the Internet of Things are disrupting and reshaping maritime, he adds.
McKinsey, the management consulting firm, also advocates shipowners and operators investing in technology to optimise costs and reduce Opex. In a 2022 article on how to transform a shipping company, the firm makes several recommendations such as collecting and analysing data and building digital applications to inform decision-making. The firm also makes the case that digital tools can support cost efficiencies by helping to identify Opex trends; this, in turn, enables shipping companies to optimise crewing spend and overall procurement processes (spares, stores and provisions), and streamline repair, maintenance, port, drydocking and bunkering costs.
With the right analytical tools, shipowners can gain greater visibility of onboard operations to make crewing and crew-related costs more efficient. The technology enables them to assess behavioural competencies and identify improvement areas and training needs. They can also monitor the effects of training on the company’s safety culture, and drive retention by providing crew with AI-powered tools to do their jobs more safely and efficiently.
The Opex-related benefits of investing in technology from a repair and maintenance standpoint include the easy monitoring of routine onboard activities such as engine or steer gear inspections, or tracking planned versus actual activities. An AI-powered system will establish whether a job has been fully completed and if, for example, personal protective equipment was used.
For stores, spares and lubes, companies can use one or a few digital tools to ensure all equipment onboard a vessel is properly maintained, and to track the use of spares and lube oils to avoid over-consumption. Automatically detecting, digitally logging and auditing stock is another benefit.
Elsewhere, digital tools can improve management and administration by simplifying onboard or shoreside processes, monitoring internal regulations and procedures for easier compliance, and making incident and claims management far more straightforward. An AI-powered CCTV system like ShipIn’s FleetVision platform can automatically log and categorise events after detecting them, providing evidence in near real-time and eliminating the need for someone to trawl many hours of footage following an incident.
From a loss prevention perspective, reducing insurance claims is another Opex-related issue that can be improved using technology. A digital platform will highlight areas of investment for improving fleet safety and security while mitigating risks, provide early hazard detection through visual analytics, and offer increased insights and analytics, helping companies to drive improvement and enhance their safety culture.
The savings and cost efficiencies available to shipping companies that adopt AI are clear, as a recent ShipIn case study proves. ShipIn worked with a dry bulk operator that was spending around US$2.7 million yearly on operating a post-panamax vessel, with crew and crew-related costs accounting for their biggest outlay (37%). The rest was going towards stores, spares and lubes (17.8%), management and administration (16%), repair and maintenance (14%), and insurance (7%).
After installing FleetVision™, an AI-powered platform that plugs into a ship’s CCTV, the shipping company reduced Opex on that vessel by almost $400,000 a year. The system continuously monitors, detects, and logs any onboard events, alerting seafarers and shoreside colleagues to anomalies, hazards and inefficiencies related to security, safety, maintenance, navigation, cargo, and other operations.
In a digital age where technology can provide a holistic view of a shipping company’s operational expenditure, embracing AI should be a priority. Owners and operators that do so will have access to data highlighting Opex-related inefficiencies, which they can address – creating a more streamlined, productive and cost-effective operation at sea and onshore. l
Singapore-based liner grouping Ocean Network Express (ONE) is proud to be sponsoring Penguin Cove in Bird Paradise, Singapore’s new bird park by the Mandai Wildlife Group. In January this year, Jurong Bird Park closed after 52 years of operations and a new chapter began in May with opening of the brand-new Bird Paradise, located in the Mandai Wildlife Reserve, an integrated nature and wildlife destination in Singapore. Home to 3,500 birds from 400 species, the 17-hectare park features highlights like the eight large walk-through aviaries that reflect different habitats around the world, a 2,000-seat Sky Amphitheatre, and a state-ofthe-art Ocean Network Express Penguin Cove. The 3,000m2 facility also has two salt-water acrylic tanks, amongst the largest in the world, and features a lighting setup that mimics the day and night cycles of the Sub-Antarctic Falkland Islands, a key welfare enhancement for the birds and facilitates their breeding cycles. l
At end-April around 300 guests from the maritime industry attended a cocktail reception to celebrate 25 years of Bernhard Schulte Shipmanagement (BSM) in Singapore. Speakers emphasised the pioneering role of BSM, which was one of the first third-party ship managers in Singapore. Eurasia, member of the Schulte Group and one of the predecessors of today’s BSM, started its ship management activities in Singapore 25 years ago. With this foundation, the Schulte Group established a second foothold in East Asia besides Hong Kong. In 2008, the four Schulte Group ship management companies – Eurasia Group, Hanseatic Shipping, Dorchester Atlantic Marine, Vorsetzen Bereederungs- und Schiffahrtskontor – merged under the single brand BSM. Pictured is Johann Schulte, majority shareholder of the Schulte Group, receiving a commemorative plaque from Ms Tan Beng Tee, Executive Director of the Singapore Maritime Foundation. l
Woell Marine GmbH, a German family company only founded in 2015, is already sponsoring WS Racing and its ‘GIRLS ONLY’ team, which competed at this year’s 24-hour race at the Nürburgring. The family business started out supplying life-saving equipment and now carries out underwater ROV inspections as well. “We are very excited and are keeping our fingers crossed for the WS Racing Team,” says company boss Sascha Woell. “In our daily work we know only too well the importance of efficiency and teamwork.” l
Nor-Shipping 2023 clocked up a record turnout at the exhibition, big names at the conferences and a social scene that basked in unbroken sunshine all week long.
The organisers reported a total of around 30,000 entries into the exhibition halls, where visitors experienced around 892 exhibiting companies, and total participant numbers of over 50,000, including those at conferences, networking events and official social gatherings.
In terms of knowledge sharing activity, the level of speakers, including US diplomat John F. Kerry (pictured), Dr Andrew Forrest of Fortescue Metals Group, Nobel laureate Joseph E. Stiglitz, and IMO Secretary-General Kitack Lim, all of whom appeared at the Ocean Leadership conference. Danish tanker operator Tärntank won the 2023 Nor-Shipping Next Generation Ship Award for its hybrid tankers under construction, with technology and engineering provided by Kongsberg Maritime, while wind power pioneer AlfaWall Oceanbird and Bound4Blue Co-founder and COO Cristina Aleixendri Munoz also scooped awards. The next Nor-Shipping, the 30th edition, will take place in Lillestrøm and Oslo, Norway on 2-6 June 2025. l
Adventure Race Japan raises $1.3m for seafarer welfare
The Mission to Seafarers (MtS) has successfully completed its Adventure Race Japan (ARJ) fundraising challenge, raising a total of US$1.3m through team registrations, corporate sponsorships, and other fundraising efforts. The highly anticipated Adventure Race Japan (ARJ) challenge took place from 18-21 May 2023 on the Izu Peninsula, Japan, and witnessed an exhilarating display of determination and camaraderie as 64 teams from 19 countries fearlessly tackled the ‘Green Dragon’ and ‘Black Dragon’ races in support of MtS. Green Dragon Race overall winner - with the highest fundraising amount and fastest completion time - was BW Hikers, while the Black Dragon Race overall winner was BSM Global. A closing Awards Ceremony and Gala Dinner welcomed distinguished guests, including MOL President & CEO Takeshi Hashimoto and Yukito Higaki, President of Shoei Kisen Kaisha, both Japanese companies being among Gold Sponsors of the event. l
Within the Gibraltar report in last issue (SMI 102, p.70), the captions to the photos of Tyrone Payas and Ernest Morillo were inadvertently transposed, and are reprinted correctly here.
Tyrone Payas is Managing Director of Global Agency Company or Global Group of Companies, a wellestablished ship agent, providing specialist shipping and associated services to international clients from its base in Gibraltar, not to be confused with Gulf Agency Company (GAC) based in Dubai. Mr Payas informs that his company recently completed a successful LNG Ship to Ship (STS) transfer in Gibraltar’s Western Anchorage that finished on 11 June.
Ernest Morillo is Branch Manager of Alfaship, a company with more than 30 years of experience delivering efficient bunker agency services in the Canary Islands and Gibraltar Strait. Alfaship was one of the sponsors of Maritime Week Gibraltar and says its agents from the Gibraltar branch are highly experienced in the maritime sector and are able to assist the needs of calling vessels under any possible setback.
SMI apologies for any inconvenience caused by the misidentifications. l
In the film ‘Rain Man’, Dustin Hoffman plays a charming but autistic individual who constantly tells his brother Charlie Babbage, played by Tom Cruise, that “I’m an excellent driver”. But all he really does is steer the family car round the drive. Then Charlie discovers that Rain Man has another excellent attribute, which he puts to work winning money in Las Vegas!
In last issue’s Alternative Viewpoint article Michael Grey argued that the overworked officers on the bridge are increasingly distracted from their potentially dangerous job, by streams of demanding messages. Mostly this is a stressful irritation, but occasionally it’s the last straw. Too few people, trying to do too much, in too little time, lose control and disaster strikes. This sort of thing has been going on for decades. Almost 50 years ago THE Torrey Canyon oil spill was caused by a tired master, on a difficult passage, with a badly designed autopilot lever.
Michael’s conclusion, that the communications jungle will make it even worse, has merit. You can buy a ‘pay as you go’ Inmarsat SIM card on Amazon, so texts can now be scanned almost anywhere. But as we head into an era of innovation, instead of looking at this as an irritation, we could see it as an opportunity to resolve these ancient watchkeeping problems, by using digital technology and communications to make the whole process safer and more efficient.
The digital revolution has been building critical mass since the cable revolution in the 1860’s. The explosive growth of cable traffic peaked in the early 1900s and finally petered out in 1980 when telephones and fax took its place. Today we are on the cusp of an even more dramatic change that will, with a bit of luck, solve the problems Michael is rightly concerned with. In February, Inmarsat launched its latest I6-F2 satellite, another massive step forward. The
ability to link information systems in real time and process key operational information with well-placed automation, can make many more operations automatic (just as it did in the engine room 30 years ago).
This is not really a novel suggestion. A couple of years ago I attended a lecture by one of the programmers working on the Google car. Her job was to program “changing lanes” and her message was the importance of endlessly checking code. This sort of fastidious system development ensure that systems are safe and effective. Most cars nowadays have a very high degree of automation, and a growing number can drive themselves quite competently. On 28 May, Edinburgh UK started an autonomous bus service, and it still seems to be running okay. Early reports say it seems very safe, but a bit jerky!
The aim is not to remove the crew, it is simply to make sure that the watch keeper can do exactly that - focus on the safety and efficiency of the ship, whilst enjoying a cup of coffee.
The reality is that you can’t resist this wave of change. Why? Because the ‘driven to distraction’ problems that Michael identified are all real and they must be solved. This great wave of information management is already here, and the industry is busy putting it to work. But it is not easy. The challenge for shipping companies and ship managers is to accept that in some ways people are not such ‘excellent drivers’ and well-designed automated systems will be better. So there is an opportunity to emulate Charlie Babbage, by diverting the superior human skills to things they excel at and use automated systems where they excel.
Like Rain Man we need to play off our strengths and, as Michael argues so eloquently, driving ships when you are tired and deluged with messages, is not one of them. But digital systems love it, especially the messages! l
In this Market Report, SMI takes a look at the state of play in the large LNG carrier (LNGC) sector. By Ian Cochran
Large Liquefied Natural Gas Carriers (LNGCs) range from a capacity of 120,000 cubic metres (cbm) to the so-called Q-Max size of around 260,000 cbm.
They are usually split into three categories, depending on their propulsion units - steam turbine, tri-fuel dieselelectric (TFDE) and the latest 2-stroke duel-fuel engine types, in which MAN and WinGD dominate the market.
As for tank containment systems, there are two main types - the MOSS and the membrane system. The number of membrane containment systems far outweigh the MOSS types, which found favour with Japanese shipowners in the early days.
Today, most if not all of the LNGC newbuildings will be fitted with a membrane system or a derivative, many of which are designed by French engineering company, GTT, under various licensing agreements with shipbuilding yards, mainly in South Korea and China – the two countries now pre-eminent in LNGC newbuilding.
Partly due to the opening of the new Panama Canal lock system, the favoured size of vessel among operators and owners is around 174,000-175,000 cbm capacity. This size range currently dominates the orderbook and is the benchmark for commercial decisions.
Turning to spot charter rates for an average size LNGC, they have proved very volatile in recent years. For example, the Baltic Exchange’s BLNG1 index (AustraliaJapan round voyage) moved from a peak of $430,000 per day in November 2021, down to $31,000 per day in February 2022, and again rising to over $500,000 per day in November 2022 before falling to $70,000 per day in March of this year, according to a report from Banchero Costa, which covered the first three months of this year.
Primarily due to the seasonal nature of LNG trades, rates had retreated still further to around $40,000 per day by the end of May, according to the latest figures from Fearnleys. Poten & Partners said recently in a webinar that the severe peaks and troughs seen in the past couple of years were unlikely to be repeated this year or next.
Banchero Costa also said that at the end of March, indicative 15-year plus timecharter rates for a standard LNGC were in the region of $110,000 per day, where they have roughly remained since. However, shorter term charters of around 12 months garnered about $70,000 per day.
At the end of May, VesselsValue reported that there were 317 large LNGCs on the orderbook, a number that has been steadily rising over the past few years on the back of forecasts of increasing supply and demand. At the same time, 566 large LNGCs were on the water.
At the end of the first quarter of this year, a newbuilding would set you back around $271 mill. However, since then the cost has come down slightly to around $260 mill today. The high prices compared to just a couple of years ago are down to several factors, including a lack of newbuilding slots at shipyards for up to 2027 deliveries, plus rising material costs and equipment supply chain issues.
Banchero Costa estimated that around 35 new LNGCs would enter the market this year in all size ranges. Between January and March 2023, there were at least nine units delivered, up 67% on the same period in 2022. This included eight standard-sized units and just one LNGC of below 120,000 cbm capacity.
Despite new IMO regulations creating a drive for greater vessel operating efficiency, recycling of elderly LNGCs remains subdued. There have only been a couple vessels reported sold for demolition, thus far and the Italian broking house thought there would only be three in total this year.
Due to the number of deliveries estimated for this year, Banchero Costa forecast that net fleet growth in the standard size sector will be around 6% year-on-year, accelerating to around 12% in 2024. This compares with a fleet growth of 5% y-o-y in 2022.
Partly due to the knock-on effect of Russia’s invasion of Ukraine, LNG trade volumes remain very positive, with a 5.9% growth in ship loadings seen in the first three months of 2023, to 106.5m tonnes, the report said.
While Australia and Qatar showed a percentage rise in export shipments during the quarter, Russia dropped by 7.8% y-o-y to 8.2m tonnes.
Mainly due to the switch away from Russian gas, European Union (27) LNG imports surged by 13.6% to 25.2m tonnes, while the UK imported some 6.4% more LNG during the period.
However, due to an economic slowdown, China imported 2.2% y-o-y less totalling 16.4m tonnes.
Due to their high technical specifications, the ownership profile tends to be with a few highly specialist companies, including some of the world’s energy majors. For example, at the end of March, about 21% of the trading LNGC fleet was owned by Japanese concerns, around 16% by Greek-based companies, 11% by Mainland Chinese interests, the Gulf Co-operation Council states accounted for another 9%, while South Korea interests were responsible for about 7% of the fleet, according to Banchero Costa’s report. l
By April this year, more than 100 vessels under construction or on order had been specified with propulsion machinery designed to allow operation on methanol fuel, and interest is continuing to grow. Methanol is seen as a viable, immediate way of cutting emissions that also offers a pathway to more ambitious environmental goals.
However, the manner of the accelerated recourse to the alternative fuel testifies to the blend of business verve and pragmatism that characterises the shipping industry and its technologically bolder members, since all existing applications and new commitments to methanol so far have been within the realm of dual-fuel engine technology. The option that such machinery offers of using and effecting immediate switchover to marine diesel oil (MDO), marine gas oil (MGO), or heavy fuel oil (HFO) constitutes a vital and effective risk mitigation factor for shipowners seeking a viable energy transition route.
Classification society DNV has pointed out that methanol dual-fuel vessel designs tend to be less complex than comparable ships engineered for LNG fuel, inferring lower build prices. Nonetheless, the premium involved with a methanol-capable prime mover is still significant. Moreover, in the light of incoming and evolving greenhouse gas (GHG) regulations, a switch from standard( ‘grey’) to ‘green’ methanol will be required much sooner than for a vessel powered by LNG. Salient in this context, the fuel can be produced in the so-called power-to-X process, in which CO2 is captured from the air.
While its calorific value is about half that of marine distillates, the energy density of methanol is comparable to other alternative fuels, and its liquid state facilitates storage and bunkering at ambient temperatures. Moreover, and most importantly from a shipping industry perspective, methanol is cost-competitive and can be supplied to a great extent using existing infrastructure.
Methanol has corrosive properties and very low viscosity but is sulphurfree and commands a much lower price than distillate. As well as virtually eliminating SOx and particulate matter (PM) emissions, the combustion of methanol yields significantly reduced nitrogen oxides (NOx), thereby eliminating the need for complex SCR exhaust gas aftertreatment. Unlike ammonia, methanol presents fewer safety considerations as it is not highly toxi, and allows flexibility in the positioning of fuel tanks in the ship, affording design and cost benefits.
A pioneer in the uptake of methanol in ocean-going vessels, the Canadian company Waterfront Shipping has been operating product tankers of the 50,000dwt category powered by methanol dual-fuel main engines since 2016. Seven such vessels entered service that year, powered by 500mm-bore ME-LGI, two-stroke dual-fuel engines developed by MAN to run on methanol, heavy fuel oil (HFO), marine diesel oil (MDO) or marine gas oil (MGO), and allowing seamless switching between fuels.
In methanol mode, the engine uses HFO, MDO or MGO as a pilot fuel for initial ignition. A subsidiary of world-
leading methanol producer Methanex Corporation, the Vancouver-based operator ensures cargo flows from the parent’s plants in Canada, Chile, Egypt, New Zealand, Trinidad & Tobago, and the USA.
During 2020, with 11 methanolfuelled tankers already under its wing, Waterfront entered into agreements covering orders placed by various shipowners with Hyundai Mipo Dockyard for eight further, methanolpowered vessels of 49,999dwt. Duly delivered through 2021 and 2022, the newbuilds incorporate secondgeneration ME-LGIM two-stroke MAN propulsion engines.
Stena has forged a relationship with Switzerland-headquartered Proman, the second largest producer of methanol, by way of a joint venture shipping enterprise, Proman Stena Bulk. The partners have invested in a newbuild series of six methanolfuelled, 49,900dwt chemical/product carriers, four of which have been commissioned to date.
The versatile, IMO Type 2 vessels ordered from Guangzhou Shipyard International encapsulate the IMOIIMeMAX design, an enhanced, dual-fuel version of the innovative
IMOIIMAX class delivered to Stena between 2015 and 2018. Each of the original type is fitted with an MAN 6S50ME-B9.3 two-stroke diesel engine, featuring low-load optimisation and exhaust gas bypass. Using a similar engine structure and footprint, the new Proman Stena Bulk tankers are powered by the latest iteration of MAN’s ME-LGIM dual-fuel machinery, the LGIM-W variant, which uses a methanol/water emulsion.
The IMOIIMeMAX flotilla can transport methanol and other cargoes from Proman’s production hubs in Trinidad & Tobago, Texas and Oman to markets around the world, and is able to maximise the scope to handle a broad variety of products for backhauling or repositioning. The design is attributed with an EEDI 11% below the 2025 Phase 3 requirements. Proman also currently has a biomethanol plant under construction in Canada, scheduled to commence operations in 2025.
Long in the vanguard of developments in the ferry sector, the Stena organisation owns and operates a ro-pax vessel, Stena Germanica, that has used methanol as main engine fuel since conversion and return to service in March 2015. Under a project effected at the Remontowa yard in Poland, one of the ship’s four Wartsila(originally Sulzer design) medium-speed main engines was adapted to burn methanol. Fuel piping and ancillary equipment was installed to allow subsequent, consecutive conversions of the other three engines in the course of the vessel’s regular service between Gothenburg and Kiel.
Experience gained with the Stena Germanica has fed into a new investment for the group’s short-sea network, whereby two ro-ros ordered in China will feature hybrid propulsion systems using machinery that can be run on methanol. The bespoke
vessel design, dubbed the NewMax type, offers a 2,800 linear-metre freight payload that will boost capacity on the Heysham/Belfast run by 80% in 2025. Stena plans to secure future volumes of e-methanol to meet a corporate goal of a 30% reduction in CO2 emissions by 2030.
A milestone was recently reached in the roll-out of powerful methanol propulsion technology through the factory acceptance test (FAT) of the world’s largest methanol two-stroke engine. The 950mm-bore G95ME-C10.5-LGIM ‘cathedral’ engine, design rated for a nominal maximum continuous output of 6,870kW per cylinder that equates to 82,440kW in the 12-cylinder model, was put through its paces during April at the Ulsan works of Hyundai Heavy Industries, a prolific licensee of MAN Energy Solutions.
At the 500mm-bore size, the ME-LGIM engine series cut its teeth at sea in 2016. At the time of the G95 version’s FAT, the sales tally for the type as a whole exceeded 100 units, over 50 of which involve newbuilds specified with the potent G95ME-C10.5-LGIM. A.P. Moller-Maersk has nominated the latter for its 16,000 TEU generation ordered from HHI’s shipbuilding division. Booked by the Danish carrier in three tranches, the newbuild series currently extends to 18 vessels of the design, covering delivery slots through 2024 and 2025.
South Korean integrated logistics group Hyundai Merchant Marine (HMM) confirmed earlier this year that nine 9,000 TEU boxships booked at domestic yards would be powered by 800mm-bore models of the methanol dual-fuel ME-LGIM engine.
Also in the top echelon of the marine power range, the Chinese-owned Swiss two-stroke specialist Winterthur Gas & Diesel (WinGD) launched a project with Korean licensee HSD Engine last year to develop methanol-capable variants of the largest engine sizes(920mm- and 820mm-bore) in its two-stroke portfolio. A subsequent collaboration entered into with Chinese licensee CSSC CMD was followed by an opening contract for the first X92DF-M methanol dual-fuel engines in China, to power four 16,000 TEU boxships to be built at Yangzhou for COSCO Shipping Lines. The lead vessel is due in 2025.
Meanwhile, Maersk has stolen a march on its competitors with the impending introduction this summer of a 2,100 TEU intra-regional boxship powered by an MAN G50ME-LGIM engine designed to run on methanol or very low sulphur fuel oil. The 17-knot feeder, ordered from Hyundai Mipo Dockyard, will provide valuable operating experience with methanol in advance of the commissioning of the first of the group’s 16,000 TEU newbuild vessels. Take-up in the liner sector gained new dimension with the inclusion of 12 methanol dual-fuel boxships of 15,000 TEU in CMA CGM’s recently formalised deal with China State Shipbuilding Corporation (CSSC). The French
carrier had previously embraced LNG as transition fuel on a large scale, and the latest programme includes further investment in LNG dual-fuel tonnage at the 23,000TEU ‘ultra’ capacity rating.
Further endorsement by the bulk shipping sector of methanol-based propulsion has been expressed this year through a raft of contracts awarded to Tsuneishi Shipbuilding of Japan, one of the world’s most prolific constructors of bulker tonnage. Two Kamsarmax-class newbuilds ordered by trading house Mitsui & Co and a pair booked by Copenhagen-headquartered J.Lauritzen have all been specified with methanol-capable, dual-fuel two-stroke installations. Common to both projects, entailing deliveries beginning during the second half of 2025, are long-term charter arrangements with Cargill Ocean Transportation.
The gearless 81,200dwt vessels under the Danish contract, which will be assigned to Cargill’s trade for seven years, will be owned by newly-established Lauritzen NextGen Shipping, set up as a platform for future investments by J.Lauritzen and Lauritzen Bulkers in zero carbon emission and otherwise future-proof assets. The dual-fuel machinery to be adopted will enable the bulkers to operate without producing carbon emissions when running on ‘green’ methanol, or potentially on bio-diesel.
Tsuneishi has also landed an order from undisclosed interests for an Ultramax bulker fitted with an MAN methanol dual-fuel main engine.
While what may be termed conventional methanol is already widely available, investment in sustainable methanol production is growing year-on-year, meaning that shipowners adopting methanol fuel now will benefit from a clear decarbonisation pathway as increasing quantities of low-carbon ‘blue’ and carbon-neutral ‘green’ methanol become accessible. l
MAN licensee HHI has rolled-out the world’s largest methanol-burning engine, the G95ME-C10.5-LGIM (credit: MAN ES).
Steve Esau, Chief Operating Officer at SEA-LNG, provides a status update on bio-LNG and explains why the LNG pathway can deliver, and is delivering, decarbonisation today.
Maritime decarbonisation is likely to be an incremental process as recognised in the recent agreement in Brussels on FuelEU Maritime, the European legislation which sets out probably the world’s most ambitious path to maritime decarbonisation.
FuelEU Maritime defines greenhouse gas (GHG) intensity targets for the energy used on board ships (of greater than 5,000 gross tonnes) for all energy used on intra-EU voyages and 50% of the energy used on ships sailing to or from ports outside the EU.
The trajectory specified starts with a 2% reduction by 2025, 6% by 2030, 14.5% by 2035, 31% by 2040, 62% by 2045 and 80% by 2050. The deal also includes a provisional 2% renewable fuels usage target by 2034.
The use of LNG as a marine fuel enables vessels to be compliant with the well-to-wake GHG intensity targets proposed under the legislation until 2035. The use of a 20% drop-in blend of bio-LNG can extend compliance until beyond 2040. Thereafter, compliance can be achieved through increasing use of bio-LNG and its electro-fuel cousin, renewable synthetic (e-) LNG as and when it becomes available.
Bio-LNG is biomethane that has been liquefied. Currently the main way to produce biomethane is through anaerobic
digestion of waste biomass such as manure. The waste biomass is put into a digester where it produces biogas. Impurities are then removed from this biogas, resulting in streams of pure biomethane and biogenic CO2. Biomethane is then used directly as a fuel or liquefied into bio-LNG. The CO2 can be used, for example, in greenhouses to promote crop growth or as a feedstock for synthetic fuels, such as e-LNG.
Methane is naturally produced alongside CO2 when agricultural waste is spread in its unprocessed form as fertiliser on the land – organic matter breaks down and methane is emitted into the atmosphere. When this agricultural waste is used to produce biomethane, the anaerobic digestion process effectively captures the methane that would otherwise be released into the atmosphere, resulting in a fuel that is net-zero and can even have negative-emissions on a full life-cycle basis. Additionally, an output of the anaerobic digestion process is fertiliser, which means that bio-LNG production can more broadly support the circular economy.
Bio-LNG is already commercially available to the shipping industry in both Europe and North America. There are also significant and growing numbers of bio-LNG production (or biomethane liquefaction) plants coming online worldwide.
The shipping industry is making newbuild investment decisions right now that will impact emissions today and for the next 25-30 years, the typical lifetime of a deep-sea vessel. Shipowners and operators need factual analysis that compares alternative fuel pathways on a like-for-like and full lifecycle, wellto-wake basis. They also need research that evaluates the costs and practical implications of the entire pathway, not simply a fuel in isolation.
Bearing all the above in mind, many regulators, suppliers, shipowners and ship operators recognise that LNG offers a lowcost, low-risk incremental pathway to decarbonisation, and that bio-LNG is a key steppingstone on that pathway. l
Slips and trips are the most common cause of injury at work and can lead to other types of serious accident such as falls from height and falls into machinery. One new type of durable non-skid safety coating designed to prevent slips and trips is Form-A-Tread, offered by RGF Materials of the US.
Described as a durable, high-tech, full epoxy coating that dramatically increases traction, Form-A-Tread is suitable for a wide range of slip and fall prone areas such as decks, docks, and gangways.
A traditional technique for preventing slip and fall accidents in maritime applications is through the application of non-skid adhesive tape or reduced epoxy coatings embedded with aggregate, explains the company. However, with continual exposure to the sea and sun, tapes can peel off. Coatings and aggregate can also abrade away quickly, leading to frequent reapplication to maintain safety standards.
Form-A-Tread is designed to last for years even in harsh marine environments, which reduces the need for maintenance and replacement. The coating type can be quickly and easily applied without a primer, even over welds or other non-flat irregularities, and is typically reader for use in under 4 hours, thereby minimising cost and disruption, according to RGF Materials.
The coating provides a very durable, slip-resistant surface on maritime walking surfaces like vessel decks and gangways as well as other large areas. It can be applied to aluminium, steel, wood, and other porous and non-porous substrates. The formulation, along with topically applied aggregate, lasts for years even when exposed to extreme
weather, temperature, sea spray, sunlight, and chemicals.
Recently IRI (International Registries, Inc.), administrator of the Republic of the Marshall Islands (RMI) flag, had to replace a worn conventional non-skid application on an old aluminium Coast Guard Defender-class boat because the non-skid adhesive tape previously applied to the decks and gunwales of the all-aluminium boat had degraded to the point where it no longer provided the traction necessary to safely take the inspectors out to the larger vessels they were evaluating.
Christian Worch, IRI’s Ship Desk Coordinator, operates the Defender-class boat at the Annapolis Anchorage in the Chesapeake Bay to transport inspectors to and from RMI-flagged vessels. He relates how as a solution, IRI had a non-skid coating Form-A-Tread SL (Self Levelling) applied to the workboat in the same areas and patterns as the previous non-skid material. The all-epoxy safety product is a combination of a low-to-medium viscosity, 100% solids epoxy binder and a specialised aggregate. After minimal surface preparation, the application of the epoxy only took one day.
In addition, another epoxy formulation designed to increase traction on stairs and ladders, called Form-A-Tread Original, was applied in specific areas such as the vessel operator’s footrest.
“I have seen many different variations of non-skid applications and I really like the non-skid, all epoxy product applied to our workboat,” comments Worch. “The application was very neat, clean, and even across the boat. It looks very professional. After about six months, it looks like it was just applied yesterday.” l
» Discovered treasures
Finding beauty in the lost and found, bespoke jewellery maker Serra Malta has always been intrigued by an object’s history and the mark the user leaves behind. Inspired by anything natural or manmade, Serra’s creations begin by being washed up on a beach or found on a woodland walk. She is particularly fascinated by attitudes to consumables in our throwaway world and challenges the meaning of usefulness. Using lost wax casting, the objects are carved, filed and shaped before taking the form of metal. The jewellery, that was once a discarded object, becomes something to treasure. Bottle- tops or fragments of a shell form some of her exquisite work.
On application Malta99.wixsite.com
» Cinema on-the-go
This 2-in-1 portable full HD projector with speaker will amaze and entertain always. It is ‘the’ new way to listen to and watch entertainment without restrictions. It’s smart, sleek, and adventuresavvy and it’s designed for entertainment anywhere. A unique fusion of technology and aesthetics, this authentic audio pleasure, custombuilt by Harman Kardon, provides 100” immersive visual feast from the comfort wherever you are. With built-in battery and cable-free with Wi-Fi & Bluetooth.
For an almost luxurious way to play this Olympic sport in the comfort of your own home, this fabulous football table, from Impatia’s Derby collection, is a visionary football table with glass top, which dedicates itself to Italy; in-particular, to the city of Milano, where the game of football holds great prominence. This design masterpiece is representing a modern reinterpretation of a popular game, made with meticulous care through the highest exponents of Italian craftsmanship.
The Derby
£14,058.00 impatia.com
VIVE reality
There is no place in the world quite like India and nowhere better to unlock its treasures and unravel its mysteries than at The Leela. Whether you’re drawn to the serene lake views of Udaipur, the still Kerala outback or the bustling lanes of Delhi, just as every city and region of this beautifully diverse country is unique, so is every Leela hotel. The Leela Palace Trail offers multi-day itineraries to six exquisite awardwinning palaces in New Delhi, Jaipur, Udaipur, Bengaluru, Chennai and Kovalam. Each astonishing you with its unique architecture and exquisite environs. Explore lively bazaars with The Leela Palace New Delhi or restore inner balance with the ancient science of Ayurveda at The Leela Kovalam, a Raviz Hotel.
HTC Vive takes business to the next level with the new all-in-one VIVE Focus 3 for business VR. Combining outstanding visuals with superior audio and next level inside-out tracking and controllers, this headset delivers superior comfort, with a new strap design a curved swapable battery pack allowing you to keep going all day and a quick charge function. An L.E.D indicator lets you know how much power you have left, a wide range and fine-adjustable Inter Pupillary Distance range, a quick-release button and easily removable magnetic front and rear face gaskets and comes with two-year VIVE Business Warranty and Services.
VIVE Focus 3
€1099.00 nomvdic.io
£1,350.00 vive.com/vive-focus3
» 100% luxury
BRABUS Marine is devoted to luxury day through building and developing an ultra-exclusive, exciting range of luxury tenders and day boats. Outstanding performance, power and superior acceleration, top class drivability, in its recognizable design forms the DNA of a BRABUS Shadow boat. Uncompromising marine highperformance, the BRABUS Shadow 900 range is perfect for anyone willing to push the boundaries. Models include the Shadow 900 Spyder, the fully open BRABUS Shadow 900 Sun-Top (pictured) and an ultra-luxurious SUV of the Sea and fully enclosed Cabin cruiser.
Shadow 900 Sun-Top
£447,500.00 brabus.com
Black Rock City, USA
August 24 - 7 September 2023
It doesn’t get any more hair-curling, baton-twirling, mind-swirlingly spectacular than Burning Man, which has been described as a ‘City of Art’. For one week this experimental community in Nevada‘s Black Rock Desert challenges its 60,000 ‘participants’ to express themselves and rely on one another while incorporating the annual theme in some way – think performances and art installations to otherworldly costumes and handmade gifts from strangers. Held from August 24 until 7 September 2023.
The antidote to be pharma and fast foods, this revised edition of Dr Sarah Myhill’s comprehensive guide to health care for health practitioners and motivated patients alike – armed with this knowledge, wellness and an optimal health-span should be within our grasp and the grasp of all those we care for. Easy to follow, logical and evidence based, Dr Myhill shows how, if we can get the basics right, disease specific benefits will follow. She doesn’t pretend it’s easy but the incentives are undeniable. A range of case histories show how to apply the theory in this book to us and to those we care for.
Jon Cleave www.newyonder.earth/ page/corporatepackages
9 Rue Francois Rocca, 13008, Marseille alexandre-mazzia.com
Introducing you to a new global streaming service, multi award-winning film studios (Albert certified carbon-neutral sustainable productions) and Certified B Corp®, that inspires, informs and helps restore our planet. Newyonder was established in October 2020 by Founder and CEO Jon Cleave, who has worked on documentaries which have aired on the BBC, Netflix and Amazon Prime, as well as directing award-winning Three Moons of Biyangdo. Newyonder’s content and impact are interlinked, from oceans to woodlands, they categorise the stories they tell with impact projects using nature-based themes and beyond. The collective journey to a wilder planet has already begun – in our oceans. Alongside the B2C Streaming Service, Jon is expanding into B2B partnerships through Corporate Benefits Packages. As businesses and corporations are looking towards a more sustainable future, company employees can also be inspired, educated and informed through the power of story. With its ever-growing catalogue of films, this can form a truly inspiring part of an employees’ benefits packages. For more information on this for your employees visit www.newyonder.earth/ page/corporatepackages . Call 07917 616 513.
Until 5 November
If you happen to find yourself in Copenhagen this year, pay a visit to the National Gallery of Denmark where you will see 60 paintings, 20 paperworks and two sculptures in a display entitled ‘Baroque’, conveying the story of the Baroque period in Europe as it unfolded.
Visitors can expect to see values of the time reflected in the pieces, such as religious ideology being challenged in favour of philosophy and science.
The treatise ‘On the Soul’, by Aristotle in antiquity, reveals that man becomes alive by discovering the five senses, knowledge and passion. Alexandre Mazzia welcomes all to share his soul, through his exquisite restaurant boasting three Michelin stars. It offers an exclusive signature menu delivering the chef’s finest creations, where guests can dine in the form of a ‘carte blanche’ giving free rein to the creation and imagination of the chef, and offering sea and plants that dominate this sensory stroll. The menu provides one immersive pairing (wine, champagne and sake tasting) per person from our sommelier’s selection, water and hot drinks and will cost around €1,280 for two people. Call +33 (0) 491 248 363 for reservations and go online for a more in-depth understanding of this unique dining experience.
“Do you remember when you used to check the coronavirus charts in the newspaper every day and wonder whether the world would ever get back to normal? Gosh, those were good times,” opined
Andrew Tuck, editor of Monocle.
It’s no longer a pandemic, said the World Health Organization, but we cannot (yet; if ever?) return to the status quo ante-covid because a host of morbid symptoms has since sprung up and our fight-flight response to them has made us wappered, bumfuzzled and unmoored. The world has opened up again and we crave, silently, to move on to sunnier uplands, but we are scarcely the same people.
If it is not yet an epidemic of unhappiness and deterioration of wellbeing bordering on depression – which Winston Churchill famously referred to as his ‘black dog’ - the daily bulletin-bombardment of angst, hard yards and fury will soon make it so. The cost-of-living crisis and rocketing inflation have made us poorer. Huw Pill, chief economist of the Bank of England, in a bracing moment of candour during a podcast, told us to suck it up. “Somehow in the UK,
someone needs to accept that they’re worse off and stop trying to maintain their real spending power by bidding up prices,” he said. He was roundly pilloried, compelled to apologise.
In mid-May the Office of National Statistics reported a record number of 2.6m Britons are out of work due to long-term sickness, while 7.3m are waiting to be seen and treated. There are currently 8.7m economically inactive people, aged 16 to 64, in the UK. NHS data revealed that in 2021 alone, 8.3m patients were prescribed antidepressants in England – 22% more than in 2015-16. OECD’s 2022 figures show that Greece, France, Italy and Spain recorded significantly higher than average numbers of 18-24 year olds who were neither studying nor working. They are called ninis in Spain (ni estudia, ni trabaja); neets in the UK –neither in employment, education nor training; ninjas in the US – no income, no job, no assets.
Diagnosing symptoms and taking the temperature of the nation – let alone the world – can tie you up in a hot knot of anguish. Psychologists call this all-around feeling of blah and bleurgh, stuck in a rut and impotence ‘lifestyle fatigue’ or ‘languishing’ – the opposite of flourishing and thriving.
“Languishing,” wrote Wharton School professor of psychology Adam Grant in The New York Times “is a sense of stagnation and emptiness. As if you’re muddling through your days, looking at your life through a foggy windshield. You might not notice the dulling of delight or the dwindling of drive; you don’t catch yourself slipping slowly into solitude, you’re indifferent to your indifference.”
Grant adds: “In psychology we think about mental health on a spectrum from depression to flourishing, the peak of wellbeing. Depression is the valley of illbeing...and languishing is the neglected middle child of mental health, the void between depression and flourishing. You’re not functioning at full capacity; it’s disrupting your ability and focus, and triples the odds that you’ll cut back on work.”
It resembles anhedonia – a feeling of malaise, the inability to feel pleasure and a loss of interest in activities and relationships that one used to enjoy. It is exacerbated by feeling burnt-out, the subject of a study by the think tank Onward, which probed the causes of rising numbers of people feeling overwhelmed and exhausted. “The blurring of the work-personal life distinction is the leading cause of burnout. Workers who bring work into their personal life are less likely to do activities that help them relax, contributing to higher levels of exhaustion.
Many of us feel too burnt-out and under pressure to participate in civic life,” Jenevieve Treadwell, the report’s author, said. We feel less motivated, with languishing turning into anguish. “When you’re lacking the energy to do things, finding there are things that you feel you should do but don’t have the desire to anymore. The enjoyment isn’t there in the same way it used to be,” said Dr Elaina DellaCava, psychiatrist at Weill Cornell Medicine in New York.
“Quiet quitting” became a big buzzword in 2022/23: workers making a conscious decision to reduce the importance of their jobs and careers to their lives; prioritising their out-of-work life. The long lockdowns and working from home gave people the time and space to contemplate the empty husks of their ambitions and to evaluate their work lives, workplaces and job satisfaction. And for many, the result was disenchantment and disconnect.
“They’re fed up – with crap work, crap pay and high bills. Many jobs don’t provide a reliable, stable or liveable income. If working harder doesn’t bring promised rewards because of the way the economy is structured, with power and wealth flowing upwards rather than being shared, why work furiously hard?”
wrote Amelia Horgan in “Lost in Work: Escaping Capitalism”.
A recent poll conducted by the coaching platform BetterUp showed that one in three UK workers identify as quiet quitters who have made a trade-off between work engagement and their wellbeing. Quiet quitters showed that what
they make up for in wellbeing, they lack in a sense of belonging and a commitment to the organisation, and thus have less of a sense of purpose and motivation to continue to learn and grow. Not expecting too much, attempting too little; just doing the bare minimum so as not to get fired.
Dan Pontefract, leadership strategist, wrote in Forbes: “The long-term aspirations of people were misaligned. Many believed that climbing the ladder and adding more assignments was core to life. All of it, for some, has now become an unsuitable endgame. Unfortunately, it may be the only good thing to come out of the pandemic. That is not to say work isn’t central to our being; we all must pay the rent or mortgage. But our core is changing; work is not core; the core is now you.”
At the prospect of a teachers’ strike, Homer Simpson pontificated: “If you don’t like your job, you don’t strike; you just go in every day and do it really half-assed.” A new trend going viral on TikTok is “bare-minimum Mondays, a way of practising self-care at the start of the week and a cure for the Sunday scaries,” says news website Axios. Ivan Misner, ceo of businessnetworking BNI, countered: “Bare-minimum Monday is a great way to get fired.” Employers have begun to use surveillance tech and tactics to track their employees’ productivity which will, inevitably for some, lead to “quiet firing.”
Elon Musk, who fired 6,000 Twitter employees (down from 8,000) following his acquisition of the company, famously said: “As soon as it is obvious you aren’t adding value, it’s not rude to leave. It is rude to make someone stay and waste their time.”
The Chinese equivalent of quiet quitting is bai-lan – literally, “to let it rot”, to embrace a hopeless situation rather than make efforts to turn it around. Xi Jinping once said: “China’s hope lies in its youth.” But faced with an economic slowdown, a lack of social and career mobility in a very competitive and materialistic society, the youth are turning their backs on high societal expectations and the grind of the ‘996 regimen’ (i.e., work from 9am to 9pm, 6 days a week). They are turning their backs on cheng jia li ye – the Chinese ideal of having a family and a decent career, owning an apartment. The prevalence of tang ping (lying flat) – an adjunct of bai-lan – is marked by a loss of hope which is prompting many young Chinese to give up highly paid, stressful white-collar jobs for manual labour, choosing to live in a state of precarity.
In Japan, some 1.5m people, between the ages of 15 and 64, are living in a more or less permanent state of self-imposed lockdown or hikikomori, brought on by the pandemic and the loss of jobs during lockdowns. They have become recluses, unable and unwilling to leave their homes and to engage with the world. Japanese also call it the ‘80:50 problem’ – with parents in their ‘80s looking after children in their ‘50s. We are emerging into sunlight, but many of us appear not to bounce back. “Studies show that one thing human beings hate more than almost anything is uncertainty, the sense that
our lives are subject to forces we do not control,” wrote Mathew Syed in The Sunday Times. The interminable lockdowns and self-isolating have made people feel anxious, overwhelmed and wary of having to – once again – present the best versions of their well-dressed, fragrant selves at all times.
In December last year, some 400,000 English speakers around the world cast their vote in a poll conducted by Oxford Languages, which publishes the Oxford English Dictionary, to crown the word of 2022. ‘Goblin mode’ encapsulates the zeitgeist and is a “type of behaviour which is unapologetically self-indulgent, lazy, slovenly and greedy, typically in a way that rejects social norms and expectations.” It is the unashamed shedding of all kinds of masks.
Caspar Grathwohl, president of Oxford Languages, explains: “Given the year we’ve just experienced, ‘goblin mode’ resonated with all of us who are feeling a little overwhelmed. It’s a relief to acknowledge that we’re not always the idealised, curated selves that we’re encouraged to present.” Goblin mode disregards societal norms and rejects the prospect of returning to what we once knew as “normal life”, to embrace what The Guardian’s Kari Paul wrote as “the comforts of depravity.”
Slobbing out in pyjamas on the sofa where very little happens but repeatedly. Not showering. Pizza and bento boxes strewn all over the kitchen floor. Doomscrolling and lapping up to maximum-eyeball overload a mind-numbing online diet of trivia, influencer culture, gore, micro-aggressions and inanities.
A sack of woe staying indoors day after blursday, getting weird and anti-social. “It’s a state you enter after watching an entire season of a show in one sitting. Wearing the same shirt you slept in the night before and then fall asleep in it again. Eating handfuls of shredded cheese over the sink,” wrote Mia Mercado in The Cut. “In goblin mode, your posture must be so bad you are essentially lying down...leaving the house wearing sweats, wearing them to work, to school.” Sweatpants - the bane of Karl Lagerfeld - who described them as a “sign of defeat. You lost control of your life so you bought sweatpants.”
Tom Whipple, The Times’ health editor, wrote: “We are experiencing an unexpected kind of globalisation: the globalisation of emotion. From Albania to Zambia, New Zealand to New Guinea. The world is more united than ever before in feeling sad, worried and angry.”
Shouldn’t there be more to life than this? Everyone now seems to be in therapy or into self-care. Or jacking it all in to move to Puerto Rico or Portugal, to surf, scubadive, escape. But to render the world explicable, we have to keep moving, for who knows what the morrow brings? These too will pass, so have something to look forward to and build resilience around it. Take a leaf out of Dolly Parton’s book. “Never get so busy making a living,” said the philosopher manquée of Tennessee, “that you forget to make a life.” l