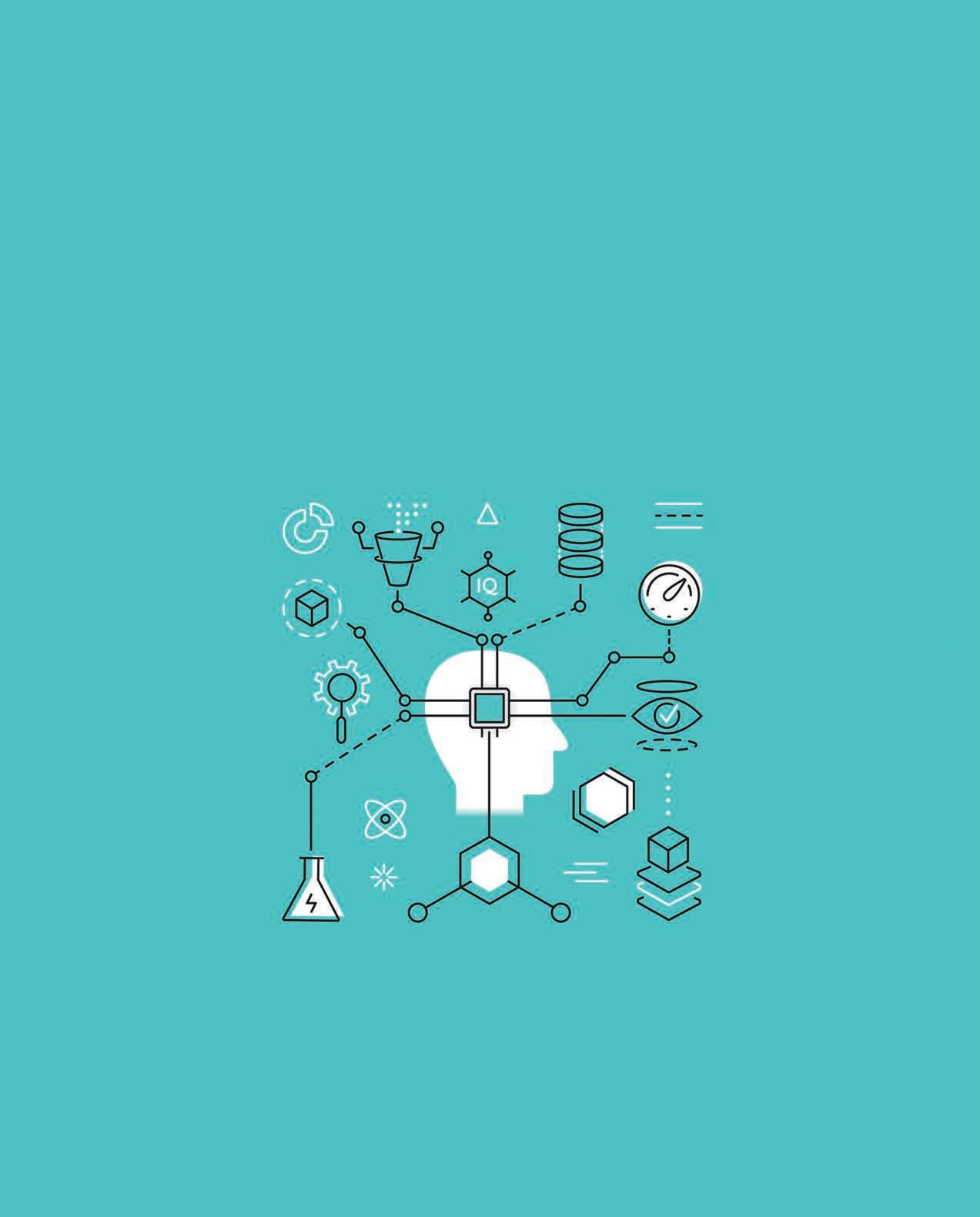
16 minute read
IL MODELLO DATA-DRIVEN APPLICATO ALLA MANUTENZIONE
a cura di Michela Del Pizzo
LA CRESCENTE DIFFUSIONE DEI SENSORI SUI SINGOLI MACCHINARI E SULLE LINEE DI PRODUZIONE, LA POSSIBILITÀ DI SFRUTTARE “ON DEMAND” RISORSE REMOTE PER L’ARCHIVIAZIONE, L’ELABORAZIONE E L’ACCESSO AI DATI, ECC., SONO TUTTE INNOVAZIONI CHE PERMETTONO OGGI DI DIGITALIZZARE QUANTO PIÙ POSSIBILE LE ATTIVITÀ DI MANUTENZIONE DEGLI IMPIANTI CHIMICI, PETROLCHIMICI E FARMACEUTICI
Advertisement
SPECIALE
MANUTENZIONE 4.0
Il tema della manutenzione diventa fondamentale per garantire non solo il corretto funzionamento delle architetture di automazione industriale, ma anche la necessità imperativa di mantenimento nel tempo attuale e futuro (predittività) dell’operatività dei sistemi, per le eventuali riconfigurazioni e cambi di produzione generati dagli output degli algoritmi evoluti di analisi dei dati fabbrica con le variabili provenienti dal web e sul filo conduttore delle necessità di smart manufacturing.
La nuova frontiera della manutenzione preventiva e predittiva è legata al modello data-driven in anello chiuso-closed loop analytics. Milioni di dati di processo vengono generati durante i cicli di produzione a livello OT (Operation Technology) da sensori, controllori, telecamere, contattori, ecc.
La maggior parte di essi viene utilizzata nel programma di sequenza del PLC (controllore logico programmabile), ma questi dati hanno molto più potenziale come semplice input di una funzione if/ else. Questa mole di informazioni può quindi essere sfruttata in automazione per la manutenzione predittiva: ma come?
Nelle prossime pagine, vedremo diversi progetti di manutenzione ad alta innovazione, questo perché le tecnologie che fino a qualche anno fa sembravano avveneristiche sono in realtà ampiamente utilizzate dall’industria per cercare di guadagnare sempre maggiore efficienza dai processi produttivi.
MANUTENZIONE PREDITTIVA NEL CLOUD
La digitalizzazione e i suoi benefici nell’ambito della manutenzione degli impianti aziendali riguardano innanzitutto la connettività e l’accesso rapido alle informazioni relative alle manutenzioni, e anche il monitoraggio diretto delle macchine, che può avvenire anche da remoto, con la possibilità di predirne il comportamento. Sono le soluzioni e i vantaggi della manutenzione predittiva: disponibilità più facile e immediata delle informazioni necessarie per la manutenzione, che si traduce in maggiore velocità nella soluzione dei problemi e dei fermi macchina; possibilità di monitoraggio diretto, anche da remoto; e, infine, predizione sul comportamento di macchine e impianti, grazie alla disponibilità di Data base relativi allo storico o a funzionalità disponibili di auto-apprendimento (Machine learning). Queste ultime si integrano al supporto tecnico del fornitore e includono soluzioni rapide per identificare e reperire le parti di ricambio. Tutto ciò permette alle aziende una riduzione dei rischi di fermi macchina non previsti, la pianificazione della manutenzione basata su dati oggettivi, e l’ottimizzazione dei magazzini ricambi strategici e dei costi di manutenzione.

ODiN (Online Diagnostic Network) è la piattaforma cloud-based di Bosch Rexroth di analisi predittiva su sistemi oleodinamici. Il suo funzionamento consiste nella raccolta dei dati delle macchine dai sensori installati (fase di data collection), nel trasferimento con modalità sicura (fase di data transfer), attraverso uno IoT gateway e un router pre-configurato con una SIM card, al cloud disponibile nel data center Bosch. Qui gli algoritmi di machine learning scansionano i dati (fase di data processing) per individuare eventuali anomalie, che vengono sottoposte al vaglio di un esperto in grado di decidere le azioni preventive più opportune da eseguire e concordare con il cliente. ODiN è attualmente impiegato in decine di stabilimenti in almeno 11 Paesi nel mondo, con un rilevamento medio di 11 milioni di misure al giorno per ogni stabilimento. La piattaforma consente di aumentare la tempestività dell’intervento manutentivo di circa il 50%.
Un caso applicativo è, ad esempio, quello della tedesca Lollar Guss GmbH, azienda specializzata in prodotti in fusione per un’ampia gamma di settori. In passato, Lollar Guss ha subito alcuni tempi di fermo imprevisti nell’impianto di stampaggio causati da malfunzionamenti a carico del sistema idraulico centrale. La macchina per stampaggio è un elemento fondamentale
del processo di fusione. Le sue notevoli dimensioni rendono difficile effettuare la manutenzione nonché individuare eventuali malfunzionamenti. Inoltre, le tempistiche consentite per la ricerca e la soluzione di eventuali problematiche sono estremamente limitate, considerato che la produzione avviene su tre turni. Lollar Guss ha quindi deciso di monitorare le pompe del sistema idraulico della macchina per stampaggio utilizzando la soluzione Online Diagnostic Network. Sono stati installati 48 sensori in totale per raccogliere dati su pressione, temperatura, portata, temperatura ambiente, correnti del motore e purezza dell’olio. Il DAQ Box invia ogni settimana a ODiN diversi gigabyte di dati per essere analizzati. Nel caso in cui ODiN rilevi delle anomalie, gli esperti in manutenzione di Bosch Rexroth informano Lollar Guss suggerendo i provvedimenti da adottare.
Che si tratti dunque di impianti produttivi, industriali o di impianti di gestione dell’energia, l’obiettivo comune di chi ne ha la gestione è sempre cercare di fare efficienza, a partire dalla valorizzazione dell’esistente e possibilmente in un’ottica sostenibile di interconnessione: concepire il lavoro come una serie di passi interconnessi, come fossero maglie di una catena, presuppone che il miglioramento di una qualunque maglia valorizzi l’ottimizzazione di ognuna delle altre. Tre sono quindi i concetti alla base della cosiddetta “fabbrica predittiva”: efficienza, perché è possibile ottimizzare la gestione di persone, materiali e risorse finanziarie; sostenibilità, perché si sfruttano dati già esistenti per progettare nuovi modi di lavorare (l’intelligenza artificiale si automigliora); inclusività, in quanto la diversità (età, visione, genere, etnia) e l’accoglienza di nuovi contributi di fatto accrescono il valore di un processo esistente.
Cefla, con MIPU, ha recentemente sviluppato due nuove piattaforme di manutenzione predittiva, C-cogenS e C-Platform, dedicate rispettivamente agli impianti di produzione di energia e agli impianti tecnologici in plant industriali. Tramite l’IoT (Internet of Things), attraverso la rete internet (e non tramite lan del cliente), potenzialmente ogni oggetto del plant industriale ha una sua identità nel mondo digitale e può dare informazione di funzionamento al servizio di manutenzione. Tutta la progettazione e l’ingegnerizzazione dei processi passa così attraverso sensori digitali, intelligenti e interconnessi, che con protocolli lan free trasmettono dati ad una piattaforma cloud che dialoga con i sistemi Cefla e del cliente (nel caso venga richiesta l’interfaccia).
EFFICIENZA GESTIONALE E DIGITAL TWIN
Riuscire a organizzare e digitalizzare le informazioni relative a tutti i processi interni - dalla produzione stessa fino alla pianificazione e gestione dei turni di lavoro - e rendere tutti questi dati condivisibili e disponibili sul cloud è un tema chiave per molte aziende. Con questo obiettivo Vertiv ha accelerato il processo di trasformazione digitale dei propri stabilimenti più strategici in
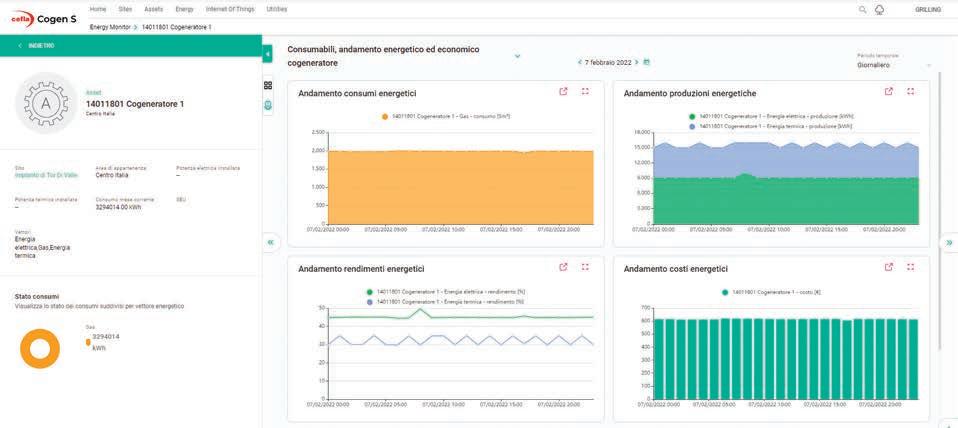
SPECIALE
MANUTENZIONE 4.0
A cura di Antonio Curri consulente di ally Consulting
MANUTENZIONE DA REMOTO DEGLI IMPIANTI INDUSTRIALI
OGGI POTREBBE NON ESSERE PIÙ NECESSARIO AVERE DEI TECNICI MANUTENTORI ESPERTI DA MANDARE IN SITO, POICHÉ CON I SISTEMI ATTUALI DI MICRO-VISUALIZZAZIONE UN QUALSIASI TECNICO COLLEGATO DA REMOTO PUÒ “DIRIGERE” L’INTERVENTO DI MANUTENZIONE E/O DI RIPARAZIONE, LASCIANDO LO SPOSTAMENTO FISICO SOLO NEL CASO DI SOSTITUZIONI DI ATTIVITÀ E/O RICAMBI CRITICI
Nella corsa alla digitalizzazione e all’Internet delle cose (IoT), anche le attività che coinvolgono la manutenzione degli impianti sta subendo una trasformazione epocale. Infatti, se la disponibilità di connessioni ed integrazioni sempre più massicce e a larga banda da un lato, e dall’altro di applicazioni software sempre più in grado di controllare ogni singolo elemento costitutivo di un impianto, la manutenzione oggi è sempre più semplice da effettuarsi. La semplicità è dovuta alla possibilità di analizzare ogni singolo dato sia di ciascun componente dell’impianto, sia delle condizioni di esercizio dello stesso. Infatti, la profusione di elettronica cablata a tutti i livelli e l’informatizzazione di tutti gli elementi permettono di conservare la storia del funzionamento dell’impianto stesso, arricchito anche da dati e variabili “ambientali”, ovvero esterne all’impianto ma che ne raccontano la storia dell’esercizio (esempi sono la temperatura ambiente, il grado di umidità, …). In questo modo le attività di manutenzione si trasformano da una modalità quasi artigianale fino alla sua evoluzione ingegneristica, cui compete la ricerca migliorativa, controllando ed assicurando la buona efficienza degli impianti e dei suoi componenti, con attività coordinate di ispezioni, di raccolta di dati storici, di analisi dei guasti.
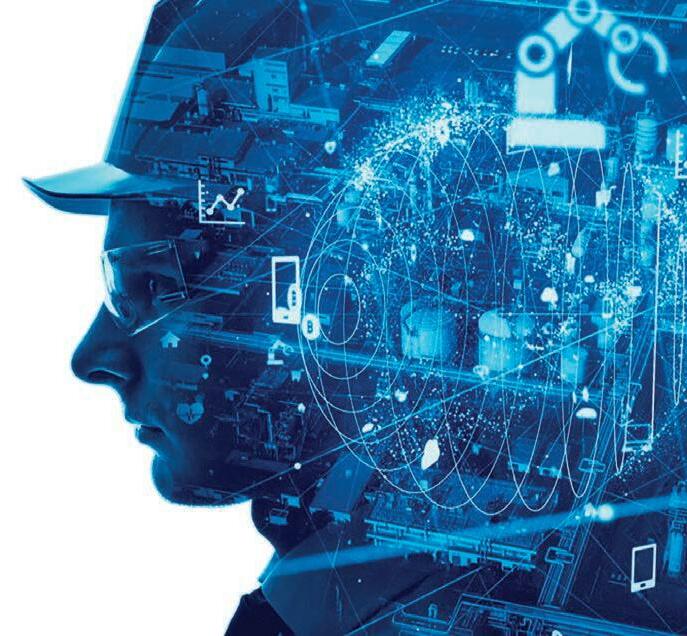
Ormai vi sono applicazioni che sono in grado di archiviare i dati e metterli a disposizione di applicazioni per creare relazioni tra questi dati ed eventi caratteristici del funzionamento dell’impianto stesso. Tali relazioni descrivono lo “stato” di ogni singolo pezzo dell’impianto (valvole, reostati, attuatori, trasduttori, ecc.) fornendo informazioni analitiche e relazioni tra eventi (sia di funzionamento, sia di anomalie e/o guasti). Tali informazioni sono preziose per coloro che si occupano sia della progettazione dell’impianto, sia per coloro che si occupano della manutenzione preventiva. Infatti, le correlazioni esistenti tra gli stati degli elementi dell’impianto e la sua efficienza e i suoi “guasti” permettono di comprendere meglio i comportamenti che precedono un guasto o che hanno una certa rilevanza statistica tale da far presumere la possibilità di tale evento.
In questo caso si può parlare addirittura di manutenzione predittiva, nel senso che si è in grado di costruire un modello analitico di comportamento del componente in osservazione che sfrutta alcuni modelli probabilistici come: • Modello di Weibull, distribuzione che si può applicare a tutte le fasi del ciclo di vita utile dell’impianto; • Modello di Gauss, che può tener conto dei fenomeni di usura; • Modello di Poisson, che può aiutare nell’analisi dei guasti accidentali.
Ciò permette di attivare tutte quelle azioni che, se effettuate prima del verificarsi del guasto, ne attenuano la portata o addirittura lo evitano. Queste informazioni possono essere analizzate anche a livello di progettazione dell’impianto in modo da poter considerare al meglio gli eventi che limitano il funzionamento di quel componente, in termini di efficienza e dell’impatto che funzionamenti fuori dalla norma possono indurre sull’efficienza totale dell’impianto.
Un altro capitolo importante, sempre legato alla manutenzione, è quello che riguarda l’effettuazione del suo intervento.
Oggi potrebbe non essere più necessario avere dei tecnici manutentori esperti di quell’impianto da mandare in sito, poiché con i sistemi attuali di microvisualizzazione (occhiali 3D, occhiali con fotocamera e display incorporati) un qualsiasi tecnico collegato da remoto a questi strumenti, magari in possesso al gestore dell’impianto, può “dirigere” l’intervento di manutenzione e/o di riparazione usando anche delle apposite check list dettagliate, fino a dei veri e propri piani manutentivi, lasciando lo spostamento fisico solo nel caso di sostituzioni di attività e/o ricambi critici. In alcune circostanze si può addirittura creare dei sistemi di allerta che al verificarsi di determinate condizioni o al superamento di certe soglie di valori, avvertono l’addetto a quella parte dell’impianto di effettuare specifiche attività di manutenzione per evitare guasti e/o imprevisti.
La disponibilità di questi “nuovi strumenti digitali” sta spostando il focus da interventi a posteriori a interventi a priori, minimizzando sia le probabilità di fermo impianti, sia l’impatto di questi. In questo caso, è evidente l’aumento di efficienza che tale tipo di manutenzione è in grado di dare, sia al produttore del componente/impianto, sia al gestore dell’impianto stesso. Infatti, i tempi di risposta decrescono in maniera esponenziale, soprattutto quelli per il fermo impianto e i costi delle attività si riducono, eliminando almeno quelli relativi alle trasferte dei tecnici. Ma soprattutto “liberano tempo” alle attività preventive di manutenzione: potendo fare manutenzione predittiva e preventiva (ispezioni, lubrificazione, riparazioni, aggiornamenti software, ...) nei tempi corretti, anche gli interventi straordinari si riducono, con benefici economici per tutti.
Quindi tali strumenti permettono oggi di differenziare quelle aziende che usano componenti ed impianti connessi perché in grado di avere performance ed efficienze migliori e quindi costi più bassi e produttività più alte, ma anche i produttori di componenti e impianti che fornendo prodotti già in grado di essere “internetizzati”, possono offrire un servizio di assistenza best of breed.
EMEA. Il progetto porterà nei prossimi anni a una totale integrazione e sinergia tra gli stabilimenti chiave dell’azienda all’interno della Regione EMEA. Vertiv ha adottato la piattaforma di Brick Reply per gestire tutti i processi produttivi e comunicare con i sistemi gestionali già in uso oltre che con le linee di produzione. Brick Reply offre differenti soluzioni per il miglioramento dei processi produttivi, compreso quello che ha rappresentato uno degli aspetti più innovativi del processo di digitalizzazione promosso da Vertiv: la creazione di un digital twin. Il digital twin consiste nella realizzazione di un modello digitale in grado di studiare e simulare il comportamento reale dell’impianto produttivo, abilitando analisi strutturate che permettono di simulare diversi scenari che potrebbero condurre a una diversa organizzazione dell’impianto stesso.
Con il supporto di Concept Reply - il centro di ricerca e sviluppo di Reply sull’Internet of Things – è stato possibile integrare processi e macchine grazie a un’azione di “retrofitting”. Questo ha consentito a Vertiv di ottenere informazioni strategiche dai macchinari, come l’utilizzo della potenza elettrica, la temperatura e lo stato di attività, e utilizzare queste informazioni per gestire la produzione e impostare azioni di manutenzione predittiva.
In un’ottica di Industria 4.0, in cui tutti gli elementi all’interno del sito produttivo devono avere un approccio digitale, è stato essenziale implementare una soluzione che alla fine permettesse ai macchinari di essere dotati di “intelligenza”. Con l’azione di retrofitting sviluppata da Concept
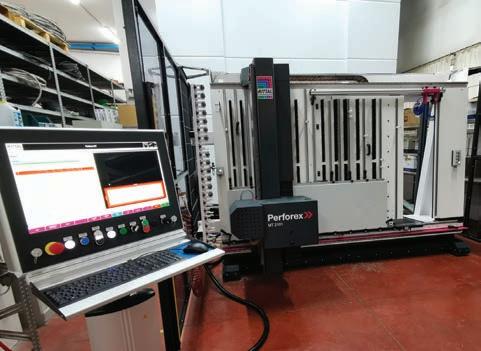
SPECIALE
MANUTENZIONE 4.0
Reply, le macchine critiche sono state quindi dotate di una “sensibilità” IoT attraverso l’utilizzo di sensori ad hoc. Inoltre, grazie a un approccio di edge computing, è stato possibile lavorare sulla conversione dei protocolli. La soluzione Concept Edge Industrial IoT è infatti in grado di “dialogare” con la piattaforma Brick Reply, permettendo il controllo e il monitoraggio delle singole macchine, selezionando i dati localmente e inviando al cloud solo le informazioni strategiche, fondamentali per favorire un migliore sinergia tra tutti gli impianti.
ELEVARE GLI STANDARD QUALITATIVI
La ricerca continua di nuovi prodotti da proporre al mercato, il dinamismo e una particolare attenzione agli aspetti organizzativi fanno di Logel un’azienda competitiva nel settore delle automazioni elettriche ed elettroniche che offre un servizio a 360 gradi. Con l’utilizzo di Eplan Pro Panel è possibile creare una visualizzazione digitale completa degli schemi e un gemello digitale per la progettazione del quadro elettrico. Grazie al “gemello digitale” l’operatore sa quale percorso far seguire al singolo filo, a quale morsetto collegarlo e in quale canalina deve passare. Questo processo assicura la realizzazione di uno o più quadri elettrici conformi al progetto originale, privi di errori e completamente rispondenti alle richieste del cliente. Successivamente è possibile “collegare” il progetto con i centri di lavoro, ad esempio Rittal Perforex MT, per realizzare un ambiente “Cad-CAM” dedicato. Il software che genera il progetto 3D, invia un input al centro di lavoro che fora le piastre e prepara le feritoie degli armadi e delle cassette.
Il centro di lavoro Perforex MT, Milling Terminal, diminuisce drasticamente i tempi di lavorazione meccanica (circa 80%): dagli armadi compatti a quelli di grandi dimensioni. Effettua forature, filettature e fresature di tutti i materiali comunemente utilizzati, come lamiera di acciaio verniciata o zincata, acciaio inox, alluminio, rame e plastica.
REALTÀ AUMENTATA PER L’ASSISTENZA DA REMOTO
Le applicazioni che utilizzano l’AR consentono di agevolare la collaborazione a distanza, fornendo enormi potenzialità soprattutto per quanto riguarda le attività di service. AB si è avvalsa recentemente della collaborazione di Vuforia Chalk, la soluzione di PTC basata sulla tecnologia AR (Augmented Reality), per gestire gli interventi di assistenza in remoto in modo rapido ed efficace. Nel 2016 AB avvia un importante processo di riorganizzazione in ottica internazionale, che le impone di rispondere in modo adeguato alle nuove necessità che nascevano dall’ampliamento dei mercati, dalla richiesta di soluzioni ad elevata customizzazione e da time-to-market sempre più pressanti. Viene così dato il via a un progetto interno di ampio respiro, che coinvolge anche le risorse umane per affrontare le mutate esigenze di formazione del personale. Prende corpo lo sviluppo di una nuova piattaforma (Product Configurator), che via via si amplierà includendo altri pilastri – tra cui il PLM – ed evolvendo in una vera roadmap di trasformazione digitale.

STRUMENTI DIGITALI PER MIGLIORARE L’OPERATIVITÀ DEGLI IMPIANTI
Siemens Italia e il Gruppo Maire Tecnimont attraverso Tecnimont SpA il suo principale EPC contractor, hanno firmato un accordo per offrire servizi digitali all’avanguar-

dia per la manutenzione predittiva e aiutare così i clienti ad aumentare l’operatività degli impianti e ridurre i costi di manutenzione.
L’accordo prevede che le due aziende lavorino insieme su un determinato numero di studi di fattibilità e identifichino una lista di clienti a cui indirizzare una proposta commerciale congiunta, in modo da promuovere l’applicazione della tecnologia di manutenzione predittiva per monitorare gli asset critici degli impianti. Siemens Predictive Analytics si basa su algoritmi di apprendimento automatico che identificano le normali condizioni operative e di guasto, sulla base dei dati storici raccolti dall’asset, e forniscono un alert per identificare potenziali guasti alle apparecchiature prima che diventino un problema e causino la perdita dell’asset e, nel peggiore dei casi, la perdita di produzione dell’impianto.

DATI IN TEMPO REALE PER GARANTIRE LA CONTINUITÀ OPERATIVA
Schneider Electric ha fornito a BASF le sue soluzioni software EcoStruxure Asset Advisor per monitorare e gestiMaire Tecnimont sfrutterà la sua esperienza come contrac- re in tempo reale i suoi asset, così da garantire la massima tor di ingegneria, procurement e costruzione (EPC) nel funzionalità, continuità operativa lungo tutto il ciclo di vita. settore della trasformazione delle risorse naturali, per for- BASF ha rinnovato la sottostazione elettrica del suo impiannire ai proprietari di impianti applicazioni di intelligen- to di Beaumont, in Texas, scegliendo tecnologie con cui za artificiale, basate su tecnologie di Predictive ottenere una maggiore visibilità sulle operations. Analytics di Siemens, per il monitoraggio Questo impianto, che fa parte della divisione degli asset, la valutazione delle prestazio- dell’azienda rivolta all’agricoltura, ora ha ni e la manutenzione delle attrezzature. a disposizione un “cruscotto digitale” e Questo approccio di innovazione aper- un supporto esperto per monitorare lo ta fa leva su tecnologie chiave per tro- status dei suoi asset critici 24 ore su 24, vare le migliori soluzioni per le esigenze sette giorni su sette. La nuova sottostaspecifiche dei proprietari degli impian- zione fornisce elettricità a tutto l’impianti. I risultati sono benefici tangibili come to e grazie alle soluzioni e ai servizi Schuna migliore efficienza produttiva, una neider BASF riesce a monitorare lo stato manutenzione più efficace, un ambiente di degli asset misurando oltre 100 variabili su 63 lavoro più sicuro, un controllo più agevole delle asset connessi. Il software EcoStruxure Asset Ademissioni e migliora il livello di training per gli operatori visor, che offre monitoraggio condition based e analytics dell’impianto. predittive è lo strumento chiave che consente di ottenere Con questo accordo, il Gruppo Maire Tecnimont conti- questi vantaggi, migliorando anche la sicurezza nell’impiannua a migliorare il portafoglio di servizi digitali, al fine di to e l’efficienza operativa. Inoltre, grazie ai servizi profesoffrire ai clienti una nuova value proposition per aiutarli a sionali di Schneider Electric Services Bureau, BASF ottiene supportate la transizione energetica aumentando l’efficien- indicazioni personalizzate e raccomandazioni proattive che za degli impianti, nonché assicurando processi e prodotti prevengono i guasti e ottimizzano le strategie di manutencon la massima performance dal punto di vista ambientale. zione. Il servizio basato su cloud combina una piattaforma Siemens conferma, a sua volta, il posizionamento unico data driven con l’esperienza di Schneider Electric in tutte le a supporto delle aziende e, grazie a innovative soluzioni aree dei servizi sul campo. Sfrutta l’emergere dell’IoT, insiesoftware e di automazione, permette alle aziende di trar- me alle innovazioni nella connettività, nella tecnologia dei re il massimo dalla digitalizzazione, in particolar modo in sensori e nell’analisi predittiva. EcoStruxure Asset Advisor termini di riduzione del time-to-market, aumento della valuta i dati reali degli asset critici connessi e applica l’analisi flessibilità e dell’efficienza. avanzata per identificare le potenziali minacce.
Questo impianto ora ha a disposizione un “cruscotto digitale” e un supporto esperto per monitorare lo status dei suoi asset critici 24 ore su 24