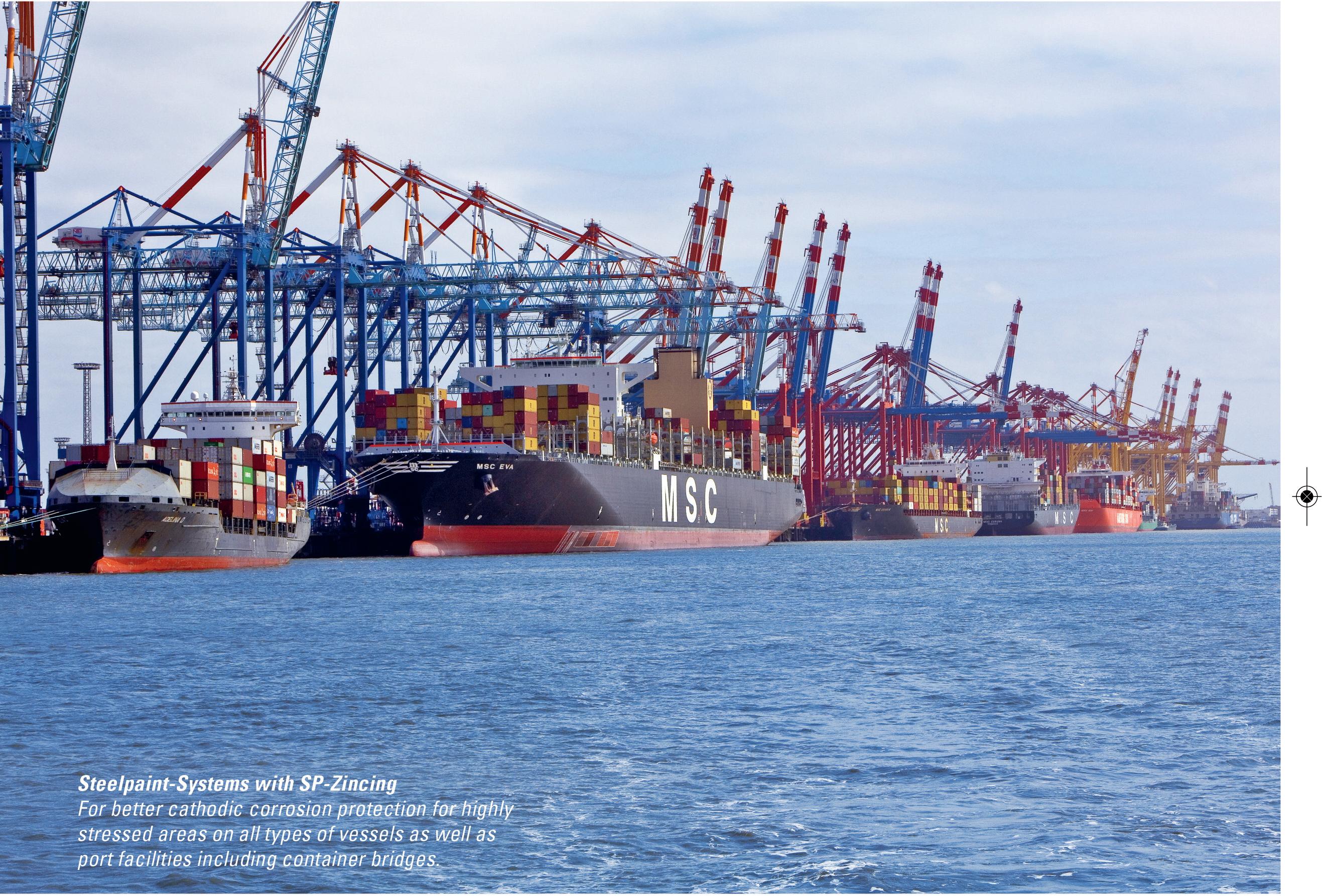

Andrew Hucker-Brown andrew@dc-int.com
EDITORIAL
Louise Dodds-Ely Editor
Jay Venter Deputy Editor
Samantha Smith
SALES
Matthew Currin Senior Sales sales2@dc-int.com Executive
Zack Venter Advertisement Sales sales@dc-int.com Executive
CORRESPONDENTS
Brazil Patrick Knight
India Kunal Bose
Europe Barry Cross
UK Maria Cappuccio
UK Michael King
UK
Richard Scott
ADMINISTRATIVE OFFICE
Business Publishing International
Corporate Park, 11 Sinembe Crescent
La Lucia Ridge, South Africa, 4051
Tel: +27 31 583 4360
Fax: +27 31 566 4502
Email: info@dc-int.com
Twitter: twitter.com/drycargomag
HEAD OFFICE
Trade Publishing International Limited
Clover House, 24 Drury Road, Colchester, Essex CO2 7UX, UK
Tel: +44 (0)1206 562552
Email: info@dc-int.com
Website: www.drycargomag.com
Twitter: twitter.com/drycargomag
ISSN 1466-3643
Insta: www.instagram.com/drycargointernational
Trade Publishing International Ltd does not guarantee the information contained in Dry Cargo International, nor does it accept responsibility for errors or omissions or their consequences. Opinions expressed herein are not necessarily those of Trade Publishing International Ltd
© Trade Publishing Int’l Ltd 2024
Following last year’s resumed growth, commodity import demand may lose some momentum over the next twelve months, based on recent signs. As a result a slowing tendency in world seaborne dry bulk trade seems likely.
Currently a pickup in global economic activity’s growth rate that could boost dry bulk trade volume substantially in 2024 is not expected, but some positive influences are visible. In particular interest rates in many countries appear set to begin a downwards trend in the fairly near future, amid retreating inflation, with benefits for spending patterns. But there is great uncertainty about China’s progress, and how much this will contribute to the wider import demand trend.
The outlook for steel industry raw materials trade — iron ore and coking coal — in the next twelve months suggests further growth may prove elusive. After last year’s increase, iron ore movements in particular probably will experience restraints. Lower imports into China, seen as quite likely could offset or more than offset any increases among other countries.
Annual 2023 steel production figures published by the World Steel Association emphasize contrasting changes among the main raw materials importers. Compared with the previous year South Korea’s crude steel output was 1% higher at 66.7mt (million tonnes), while
China’s total was unchanged at 1,019.1mt. In Japan a 3% reduction to 87.0mt was recorded, and the European Union experienced a much larger 7% decline to 126.3mt.
Calculations for world seaborne coal trade in 2023 as a whole point to an increase of 5–6%, a remarkably robust performance after almost no growth in the previous twelve months. The huge expansion of imports into China more than offset weakness among other prominent importing countries.
A continuation of this trend during 2024 looks unlikely based on recent indications. Prospects for importers are mixed. Some, including India and several smaller Asian buyers such as Vietnam are expected to raise their volumes.
Others, including China, Japan and the EU may see flat or lower volumes purchased. In China an especially large reduction is seen as a possibility because the combination of influences resulting in last year’s upsurge may be absent.
Among grain and soya importing countries positive changes are evident. Higher volumes are emerging in a number of areas. These could contribute to an overall 22mt or 3% increase in world grain and soya trade in the current 2023/24 year based on US Department of Agriculture estimates
published in mid-January, raising the total to 687mt, compared with 665mt in the preceding 2022/23 period.
Expected additional wheat and coarse grains volumes in most importing areas are a feature of the outlook for the 2023/24 year ending third quarter 2024. An increase in Asia’s regional total is predicted by USDA, with the East Asia sub-region seeing a 7.7mt (9%) rise to 97mt, while Southeast Asia sees a 2.6mt (6%) rise to 45.8mt. In other areas including the Middle East, North Africa and sub-Saharan Africa growth is also predicted, although by contrast European Union imports may be lower.
Steel products (coil, plate, sheet and other items) form one of the biggest minor bulk trade elements. In 2023 these movements apparently increased modestly by about 2% after falling steeply to around 360mt in the previous twelve months. Another rise may be achieved in 2024 according to some forecasts.
New carrying capacity added to the world fleet of bulk carriers is detailed in table 2. Calculations based on Clarksons Research data suggest that bulk carrier newbuilding deliveries of all sizes increased by over a tenth in 2023 to 35 million deadweight tonnes after falling in the previous twelve months. This year’s newbuilding total added may be flat.
A strong global coal trade performance unfolded during the past twelve months, contrasting with a flat outcome in the previous year. But signs suggest that a continuation of the resumed growth may not be seen in 2024 and a downturn seems more likely to occur. An especially significant reason is that the huge boost from additional imports into China last year could be partly reversed in the period ahead.
Provisional estimates based on incomplete information suggest that the world total for seaborne steam and coking coal trade was about 80mt (million tonnes) higher in 2023, reaching well over 300mt. Imports into China, one of the largest buyers on the world market, apparently increased by more than half. This additional volume was partly offset by lower imports into the European Union and a weakening pattern among other buyers. Among
export suppliers many benefited from growth but Russia’s exports evidently decreased.
Import demand around the world last year derived continued support from emphasis on coal as a valuable contributor to energy security, enhanced by great upheaval in the previous year when Russian pipeline natural gas supplies into European countries were curtailed. Nevertheless numerous buyers reduced purchases. This trend was influenced by the priority of cutting carbon emissions and shifting energy supplies towards cleaner energy sources, as part of a longer term process likely to diminish coal consumption and trade.
During the past twelve months the progress of economic activity affecting energy use varied among coal consuming
and importing countries. In China and Japan economic growth accelerated, while in India and Europe slowdowns were recorded. The broad indicator of gross domestic product (GDP) for the world economy as a whole grew by 3.1% in 2023 from the previous year, based on International Monetary Fund calculations, below the 3.5% seen in 2022. Estimates suggest a similar 3.1% growth rate could be seen this year.
Widely varying performances were a feature of the past year. After the ending of strict pandemic controls, China’s economy rebounded in 2023 from a low 3.0% GDP increase in the preceding twelve months, to a 5.2% growth rate. Japan also achieved a marked acceleration from 1.0% to 1.9%. By contrast, the European Union’s growth in 2023 plummeted from 3.6% to a minimal 0.6% and India’s progress slackened by half a percentage point to 6.7%. In the year
* Bulk Shipping Analysis 2023 estimate ** 2023 estimate compared with previous year source: Clarksons Research and Bulk Shipping Analysis, January 2024
ahead a recent IMF forecast indicates a modest pickup in Europe accompanied by slowing tendencies in China, India and Japan.
Influences that could prove supportive are indicated by the IMF’s update report published last month, entitled ‘Moderating inflation and steady growth open path to soft landing’. After some difficulties encountered in the past twelve months IMF analysts suggest that “the clouds are beginning to part”. World GDP this year could maintain the 3.1% growth seen last year. While the global performance deteriorated in 2023, recovery from events including the pandemic, Russia’s invasion of Ukraine, and the cost-of-living crisis is proving “surprisingly resilient”.
Broad economic activity patterns are likely to be reflected in energy demand. Assuming that energy costs remain well below those seen previously (especially in
2022 and into last year, when gas prices rose to exceptionally high levels), energy consumption trends may be firmly supported. Nevertheless an ongoing emphasis on renewable energy supplies — particularly wind and solar, but also nuclear and hydro-power — implies that any benefits for coal consumption and import demand will be limited.
Energy usage with implications for coal is likely to be affected in the year ahead and longer term by national and regional policy implementation resulting from political decisions in numerous countries. The move towards an increasing embrace for zerocarbon fuels and power sources, amid the decarbonization imperative to counteract global warming, is having a very prominent impact. Government measures, especially among the largest coal importing countries, to limit and eventually eliminate carbon emissions while also cutting air pollution in
urban areas is having increasingly large repercussions.
Provisional calculations show world seaborne coal trade growing robustly last year, compared with the preceding twelve months, following the previous year’s almost unchanged volume. In 2023 resumed expansion was facilitated by rapid growth in China’s imports, contrasting with weakness elsewhere among importers. Volumes of trade in both steam and coking coal segments increased, although extra steam coal quantities comprised most of the advance.
Trends in the largest importers and for world trade as a whole are shown in the table above, based on historical data compiled by Clarksons Research and calculations by Bulk Shipping Analysis. During 2022 world seaborne coal trade
• Monospiral and Level-Wind configurations
• Rugged and dependable magnetic coupler for dusty environments
• Corrosion-resistant, long-life rollers; precision sealed bearings
• Systems customized for the application
• Preassembled option, for easy installation
Slip Rings
• Allow infinite rotation
• Combined power, control and media (water, air, oil, vacuum, other)
• Available with ATEX and SIL 3 certification
Conductix-Wampfler has one critical mission: To keep your bulk material handling operations running 24 / 7 / 365. You need proven, worryfree energy solutions - and Conductix-Wampfler has them. Our systems provide reliable electric power and water to stacker/reclaimers, barge and ship loaders/unloaders, bulk conveyors, tripper systems, and gantry cranes. Conductix-Wampfler systems are rugged, low maintenance, and timetested in tough, dusty environments. All products are backed by the largest sales and service network worldwide!
www.conductix.com
Motor Driven Reels Cable Festoongrew by 3mt to 1,229mt, followed by a large 79mt or 6% increase in 2023. Tentative expectations for 2024 suggest that a small decline is likely.
A pessimistic estimate was published in late December by the Australian Government’s Department of Industry, Science and Resources, suggesting a lower outcome for the current year. This calculation, showing a 1,337mt total for 2024, after an estimated 1,360mt last year, is based on all international coal trade including movements on overland routes (although the majority is seaborne), and so is not directly comparable.
The smaller category, coking coal, comprising around one-fifth of all seaborne coal movements, was restrained by lower or no increase in steel production in a number of countries last year, while a larger proportion of China’s imports were overland shipments. Within the dominant steam coal category, comprising the remaining four-fifths of trade, import volumes were mainly supported by China’s upsurge, partly offset by lower volumes imported for power generation by other buyers.
Percentage changes last year in the two biggest importing countries, shown in the table underline contrasting outcomes. India’s imports were quite stable at 239mt amid an improved contribution from domestic coal mines. In China, the effects of reviving economic activity and energy demand coupled with a lagging upwards trend in domestic coal production, lower hydro-power generation and energy security priorities was instrumental in boosting the seaborne imports 2023 total by about 130mt or 55%, to reach over 360mt.
In the past twelve months steam coal purchases by a group of five smaller Asian importers — Malaysia, Pakistan, Philippines, Thailand and Vietnam — evidently increased by around 3mt, to 128mt, after a decline in the preceding year. This group has become a prominent trade segment amid rising power station capacity and continued electricity demand growth.
Sharply reduced seaborne imports into Europe were a feature of last year’s coal trade patterns. The European Union and United Kingdom together are estimated to have seen a decline of about 25mt or 20%, to below 100mt, reversing much of the previous year’s growth. Amid an easing of natural gas supplies after the disruption occurring after pipeline supplies from Russia were mostly ended, earlier downwards pressures on coal consumption and imports resumed.
Among coal suppliers to the world market, numerous changes have been occurring, affecting the geographical pattern of global coal trade. Final 2023 figures are awaited but some annual variations are already visible. In the coking coal segment, Australia’s dominant exports decreased. Changes among steam coal exporters saw a strong increase in Indonesia’s volume, accompanied by growth in Australia and USA, contrasting with lower exports from Russia.
Compared with many expectations at the beginning of the period, last year’s growth in global coal trade was surprisingly strong. Is the upwards trend sustainable through 2024, or are some influences likely to become negative and result in a downturn? Signs suggest further growth will be difficult
to achieve.
A common feature applicable to several major and some smaller coal importing countries is that future changes in several influences determining the outcome — whether imports are up or down, and by how much, or unchanged — are surrounded by great uncertainties. Annual forecasts are often informed guesses of what result may arise, and consequently are subject to continuous modification as the year progresses. The outlook for some countries’ coal markets and domestic production (where relevant) is unclear, sometimes because political influences are unpredictable, emphasizing the nature of the puzzle.
One complicating influence impinging on the current outlook during 2024 and beyond is the significance of China’s coal imports surge in the past twelve months. Part of this 2023 expansion represented a recovery from an unusually low volume in the preceding year when, among other influences, imports from Indonesia were curtailed at the beginning of 2022. However, there is justification for doubts about potential for further growth or even a maintained level, and a reduction this year seems a more plausible expectation.
Import demand in China is one of the most prominent uncertainties affecting international coal trade in future years. Estimates of annual volumes are largely conjectural. While buying on international markets reflects commercial factors, shortterm government policy decisions and controls often intervene, complicating analysis and intensifying doubts. General indications about these policies are known, or may be envisaged, but the timing and magnitude of effects on coal imports are much less obvious. Short-term trade flows may change rapidly.
Looking at factors affecting the longerterm trend of world coal trade, negative impulses pervade the international coal market and maintain ongoing downwards pressure. These influences severely constrain potential for coal trade to strengthen in 2024 or subsequent years. National and regional policies on energy supplies, within which the broad strategy is visible but the timing and extent of specific measures is often less clear, are likely to adversely affect coal use and movements. The global impact of policy trends is set to drive a decline in coal trade over the decade ahead.
More specifically, measures introduced with the intention of benefiting the environment have prioritized switching away from coal-fired power generation,
Our bespoke solutions are designed to meet each customer’s specific requirements from a tool kit of proven components, utilising the expertise of a team of specialist in house design engineers.
We lead the loading chute industry & set the standard for dust emissions and environmental pollution control in dry bulk handling.
Our worldwide reputation is built on high quality, well-engineered, robust, high performance chutes, backed up by excellent customer service and global lifetime product support.
towards cleaner natural gas or the often preferred choice of renewable energy supplies. In European countries in particular the emphasis has greatly reduced coal-fired power plant capacity and electricity generation and decimated the coal market.
Amid these imponderables forecasts of world seaborne coal trade in 2024 incorporate speculation and guesses, albeit informed by perceptions about underlying trends. Current signs point towards weaker import demand in some countries during the next twelve months, which may be only partly offset by rises elsewhere.
An analysis already referred to, published recently by the Australian Government’s Industry Department, adds to a range of negative views of the outlook for coal trade this year. The calculations show world trade in steam and coking coal totalling 1337mt in 2024, a 23mt or 2% decrease from last year’s estimated 1,360mt volume. These figures include some land movements but are mostly seaborne. Steam coal trade this year is expected to decline by about 2%, while coking coal trade marginally decreases by under 1%.
Changes among the main buyers are expected to vary. Contrasting with negative predictions elsewhere for 2024, India’s imports are expected to see a 39mt or 18% increase to 259mt, including a rise of almost a quarter in steam coal imports and a smaller increase in coking coal volume. Conversely China’s imports are expected to fall by 105mt (28%) this year to 275mt, caused by lower steam and coking coal requirements. These two countries together comprise over two
fifths of the world total.
Further growth in India’s import demand is envisaged, partly compensating for weakening trends in many other importing countries and acting as a vital support for global trade. The positive view of India’s purchases in the twelve months ahead is based on rising coal use, exceeding growth in domestic coal production and available supplies. But a national policy of reducing dependence on foreign supplies, by boosting output from domestic mines and improving availability, results in uncertainty about the direction of the trend.
A specific estimate for Europe’s entire coal imports is not included in this forecast. Alternative calculations from other analysts suggest that the short term boost seen over the past two years, and already weakening in 2023, has disappeared and a downwards trend has resumed.
Coal trade’s progress in 2024 and beyond will reflect several influences. The pace and composition of global economic activity and its consequences for energy demand will be significant. Also, coal’s competitiveness with alternative energy supplies, and the extent of pressure from decarbonization policies are likely to be instrumental.
When these factors are evaluated the conclusion is that the recent robust trend in world seaborne coal trade will not prove sustainable. There seems to be limited potential for positive changes in influences to have an impact during 2024. Much greater scope for negative changes could be enough to reduce world seaborne coal trade substantially. What appears to have
been a peak volume resulting from last year’s upturn probably will be followed by a downwards trend.
Accordingly, an analysis published at the end of last year by the International Energy Agency concluded that “global coal trade is expected to contract as demand declines in the years ahead”. Two especially influential aspects likely to be seen in the next few years were highlighted as drivers. These were summarized as first, growing domestic production in coal-intensive economies such as China and India and second, coal phase-out plans elsewhere, such as in Europe. IEA analysts suggest that the result could be a 12% decline in world coal trade through to 2026, including a 16% fall in the steam coal trade component and a 2% decrease in coking coal movements.
Yet, while the direction of the trend seems clear, and the approximate magnitude of changes may appear quantifiable, there is still uncertainty about the pace. The IEA acknowledges that coal “has a central role in the world economy”, remaining the largest energy source for power generation, steelmaking and cement production. Questions raised are ”when the peak in (coal) demand will occur, at what level, and how fast consumption will decline after that point”.
What seems clear is that the impact of the ‘normal’ economic and commercial drivers of coal use and imports will be modified by the effects of environmental policies adopted by governments, and of the attitudes and actions of businesses and consumers. The outcome of these additional drivers is likely to be visible as an influence constraining and probably ultimately reducing global coal trade.
Swiss marine power company WinGD and Japanese shipbuilder and technology developer Mitsubishi Shipbuilding Co., Ltd. have completed the initial design of an ammonia fuel supply system (AFSS) for vessels powered by WinGD’s X DF A ammonia-fuelled engines.
The AFSS design is the first result of a wide-ranging partnership announced last year that will develop solutions for ammonia engines and fuel systems that can be applied across a range of vessel designs. The project will now proceed to the detailed design phase, ensuring that ammonia capability is available to ocean going vessel operators ahead of regulatory requirements to reduce greenhouse gas emissions.
As well as the fuel supply system — including a fuel valve unit, fuel conditioning and all related piping — the concept includes several features to enable the safe use of ammonia as a marine fuel. These include an ammonia catching system as well as purging and venting arrangements.
Manabu Kawakado, Head of Marine
Engineering Centre, Mitsubishi Shipbuilding Co., Ltd. said: “Our partnership with WinGD has made rapid progress in less than a year since we launched the cooperation. Concluding the initial AFSS design at this stage puts us in a strong position to offer a complete fuel system to ship operators as demand for carbon-free ammonia fuel grows over the coming years.”
Sebastian Hensel, Director R&D, WinGD said: “At present, our primary focus is on advancing the technology of our clean-fuel solutions including our ammoniapowered X-DF-A engines, with the first delivery expected in Q2 2025. This collaboration will make sure that the auxiliary systems and integration capability are in place to apply our engine designs, and developing the fuel supply system concept is a crucial step in bringing ammonia fuel capability to the marine market.”
Under the partnership, WinGD will develop X-DF-A engines at appropriate sizes for a range of vessel designs, providing
the shipbuilder with the specifications for installing the engines and the requirements for all auxiliary fuel systems. Mitsubishi will design the vessels, set performance parameters for the engines and further develop its existing AFSS for use with WinGD’s ammonia engines.
WinGD advances the decarbonization of marine transportation through sustainable energy systems using the most advanced technologies in emissions reduction, fuel efficiency, hybridization and digital optimization. With their two-stroke lowspeed engines at the heart of the power equation, WinGD sets the industry standard for reliability, safety, efficiency and environmental design, backed by a global network of service and support. Headquartered in Winterthur, Switzerland since its origin as the Sulzer Diesel Engine business in 1893, today it is powering the transformation to a sustainable future.
WinGD is a CSSC Group company.
NORDEN is acquiring four Capesize newbuildings to meet strong demands from customers looking to unlock economies of scale by sizing up to improve efficiencies while lowering emissions.
With the latest investments, adding to the five owned and seven chartered Capesize vessels, NORDEN gradually moves closer to its ambition to operate between 20–25 Capesizes, supporting its full-service approach by creating a truly unique customer offering across all dry cargo sizes. The investments are furthermore a testament to the long-term opportunities that NORDEN is seeing in the dry cargo markets.
Besides giving customers the opportunity to upsize to improve supply-chain efficiencies, Capesizes also enables NORDEN to enhance the scope of current and future logistics projects, all while strengthening the ambitions to decarbonize its customers’ supply chains.
“With our latest investments in not only Capesizes but also in Projects & Parcelling and logistics, we are now able to provide our customers with a truly unique full-service approach across all dry cargo segments, with a strong focus on decarbonization,” says Jan Rindbo, CEO of NORDEN.
The four state-of-the-art vessels are expected to be delivered between 2025–2027.
Capesize bulk carriers are usually between 150,000–210,000 tonnes in deadweight with a length of 289 metres. The vessels are 45 metres wide with a draught of about 18 metres when fully loaded. The name Capesize originates from a time when the vessels were too large to transit the Suez Canal and Panama Canal and instead had to traverse between oceans via either Cape of Good Hope or Cape Horn.
Working in potentially explosive atmospheres has a lot of strict and complex rules, regulations and procedures – especially when it comes to inspections using ‘Hot Tools’ that can cause ignition.
The Cygnus 1 Ex is different to any ultrasonic testing (UT) equipment on the market. Here’s why…
Carrying out inspections with testing equipment certified to a suitable protection level is vital to ensuring the testing operation does not jeopardize the safety of hazardous environments. It is important to understand which is the correct equipment, and where to use it.
The Cygnus 1 Ex uses the Intrinsically Safe protection to ensure that under both normal uses and with applied fault conditions, no arc or spark can be generated, and no component can heat up enough to cause an explosion. Therefore, the 1 Ex can be safely used in ‘Zone 0’ hazardous areas such as oil and gas refineries, mines and fuel depots.
Another plus to the Intrinsic Safety (IS) design of the 1 Ex is that it is able to perform live testing safely within hazardous areas without the need for a Hot Work Permit or plant shutdown, making it ideal for anyone working around open flames and heat application. The Cygnus 1 Ex is in a league of its own. This unique advantage saves time and money which can be spent elsewhere whilst allowing users to take wall thickness surveys anytime.
The entire gauge, from how it sits in the hand to taking and storing measurements, is geared towards the best user experience, making inspection quick and simple despite challenging environments, such as mines.
The display offers four screen views: Measurement, AScan, Data-logging, and B-Scan, which can be easily rotated using the left and right navigation keys. Four dynamic function keys are purposely integrated to match screens, maximizing ease and speed of control. And users can quickly switch the screen between a light or dark background to adapt to indoor and outdoor lighting. What’s more, the gauge’s Manual Measurement Mode allows gates and gain to be configured to suit the application. For post-inspection analysis, users can transfer data and generate reports seamlessly using CygLink, easily connected via Bluetooth™ or a data port.
This heavy-duty device also uses the Cygnus-pioneered Multiple-Echo technique which ignores protective coatings — negating the need and time for removing important, expensive coatings or epoxy that safeguard against external or internal corrosion.
Furthermore, Cygnus’ Deep-Coat feature allows the gauge to make the leap from measuring substrates through the standard 3mm (0.12”) coatings, up to 20mm (0.8”) thick coatings.
The Cygnus 1 Ex, like all Cygnus products, is manufactured in the UK and has a 3-year warranty.
Bedeschi S.p.a. has announced the finalization of a new contract for a coal transshipment system (a similar system can be seen, right), and is delighted to have gained the trust of a new esteemed customer in Indonesia.
A large shipyard will build this tailormade solution in the Guangdong district with Indonesia as the final destination.
The scope of supply includes two receiving hoppers with associated belt feeder extractors, one coal blending mixer, belt conveyors and one slewing luffing telescopic shiploader.
The system is controlled by multiple levelling sensors to monitor the quantity of coal in the hoppers and optimize blending
performance.
Transshipments are an essential part of materials handling on the open sea to avoid bottlenecks inside ports, and are a big part of the offshore solutions offered by Bedeschi.
This is another important step in Bedeschi’s globalization strategy with Bedeschi Far East, its widespread network in the Far East and its team based in Hong Kong with Indonesia and China Mainland offices.
Bedeschi offers more than a century of expertise. Bedeschi SpA was established in 1908 and is today one of the oldest
European companies specialized in the creation of turn-key solutions for bulk handling material, container logistics and bricks.
Bedeschi was founded by Guglielmo Bedeschi, and today the fourth generation is running the company — which has expanded to such an extent that it is now comparable to the biggest players in the industries.
The current know-how in design, engineering and manufacturing are the result of more than 100 years of experience. Bedeschi nowadays can provide its customers with complete turnkey solutions for different product industries.
Renowned conveyor roller and accessory manufacturer Rulmeca is heavily involved in the transshipment market through its participation in the Nord Gabon floating transfer station project.
This project, headed by Sammi, facilitates the handling of bulk cargo at sea, without the need to berth at a port. This makes operations simpler, as it obviates the need for a receiving port and/or specialized equipment.
Sammi specializes in the design and manufacture of solutions and systems for bulk material handling in Italy and abroad.
Design and construction of a turn-key system installed on an FTS (Floating Transfer Station) to handle dry bulk materials. The handling solution consists of two receiving hoppers (fed by two grab cranes), respectively, placed on the port side of the FTS. From each of the two hoppers, the product is extracted by means of two belt feeders (1,500tph [tonnes per hour] capacity each) and conveyed into a collecting belt conveyor (2,500tph capacity) placed longitudinally on the port side of the and, from here, onto across belt conveyor (2,500tph capacity) installed at the stern of the FTS. Then, the material is conveyed to a longitudinal conveyor (2,500tph capacity) installed on the starboard side of the FTS, which transfers the material to a shiploader boom conveyor (2,500tph capacity) fitted on the starboard side of the FTS. All shiploader functions include, but are not limited to: boom luffing, boom slewing,
shuttle extraction, discharge chute rotation and trim, dozer winch. Belt feeders have provision (i.e. support beams bolted type) for the future installation of load cells in order to monitor the product flow extracted from each hopper. On the first belt conveyor, a belt scale is installed for the purpose of monitoring of material flow. The operation of the conveyor system is carried out from a cargo control room
located in the wheelhouse on the bridge deck. All equipment (constituting the conveyor system) has the possibility to be operated from a main pulpit included in cargo control room or from a local control station close to the drive unit for maintenance purpose.
Possibility of installing high-performance
essionProf b b b ompanies in more than nal c
V
hhhihli ff
orldwide w ountries w 110 c d bili ork with becauseourgrabso erstegengrabs e Ve gen grabs, cause our grabs o best productivity. Combining our ext the feedback from our loyal custome materials and unloading situations. W
ooking f L foorincreasedreliability and an extended lifespan? Let us know, b
offerthemthehighestrelia er them the highest relia tensive knowledge and exp ers results in optimized gra We call this ‘Grab Intelligen productivity, lower mainte because together we can m
bilityand y and perience with bs f foorallbulk nce’.
enance costs and ove mountains.
solutions for heavy duty application in extremely aggressive environmental conditions.
The collaboration with Rulmeca gave to the customer the possibility to choose among a wide range of products to find the best that suits its needs. Rulmeca products used in the project include:
Guide rollers for conveyor: these v units offer very solid high wall thickness, and are resistant to belt edge wear. They have a top closed tight shell and smooth rotation due to contactless seals.
For various reasons, the conveyor belt may tend to drift laterally at times. In these cases, to limit the problem, it’s possible to use vertical rollers with cantilevered spindles, generally known as belt guide rollers. These special rollers for conveyors allow a continuous and immediate alignment of the belt, despite the stress to be beard due to the transportation of heavy loads.
There are multiple advantages associated with the installation of guide rollers for conveyors and the provided alignment of the belt. Their use allows a more efficient, long-lasting and safer functioning of the conveyor system. To keep the belt in the right running helps to avoid slips and fall risks of the conveyed materials for operators during functioning and reduce the waste of resources. Of course, this also cut downtimes and unplanned maintenance interventions of the belt. Another advantage is that the use of guide rollers for conveyor can noticeably increase production — and therefore the profits — of the industry in question.
However, it’s necessary to pay particular attention to the use of such rollers for conveyors, so that the forces on the guide roller by the belt do not damage the belt edge. In other words, guide rollers do not eliminate
the true reason for the belt tracking off; therefore, the belt may consequently ride over the guide roller or become distorted against it. For these reasons, it’s advisable to always use guide rollers on the so called self-centralizing transoms which rotate automatically whenever the belt tracks off conveyor centre and selfcorrects.
temperature variation. For instance, the working temperature of PSV rollers is defined as between –20°C and +100°C with standard greased components, but it’s possible to reach also temperatures outside of this range using special grease, bearings and seals.
v these top quality heavy duty conveyor rollers with hermetic sealing system are robust, precise, and have welded construction, shafts of 20mm, 25mm, 30mm and 40mm. They offer a very long life, even in heavy and dirty working conditions.
Due to an accurate design and manufacturing, series PSV meets the utmost standards of quality and performance of heavy-duty conveyor rollers expected by many equipment manufacturers or end-users dealing with automated systems for bulk material handling.
PSV rollers are specifically designed as heavy-duty conveyor rollers intended to operate in very difficult conditions of the most varied bulk handling applications: mines, caves, cement works, coal-fired electric utilities and dock installations. Different configurations are available with shaft diameter from 20 to 40mm and tube diameter from 63 to 194 sharing a robust steel construction and an hermetic sealing system with multiple labyrinth seals. These provide extremely high load capacity and resistance to impact, corrosion and abrasion of bulk materials, pollutants and other aggressive elements during conveyance.
Therefore, this unique design perfectly fits for the double challenge that heavy-duty conveyor rollers are usually called to. First, it allows for the transportation of heavy and large lump size bulk materials. Moreover, it’s the solution to the environmental challenges of dust, dirt, water, low and high temperatures or strong day/night
While they are heavy-duty conveyor rollers meant to work in such harmful and challenging conditions, PSV rollers are also able to offer maximum effectiveness and productivity, furthermore combined with commonly desired energy savings, long working life and minimal maintenance over time.
Impact rollers with rubber rings: v these higher quality rubber rings stand out from their competitors. They use solid rubber rings fixed by high steel stop ring, welded to the shell. They are a highly efficient and hermetically sealed system, which results in a roller with a long life.
The shock absorbing rollers, more often known as ‘impact rollers’ consist of a base steel roller design, on which are fitted rings, designed to resist and absorb the pressures given by the impact of materials onto the belt.
These rollers are positioned in the carrying section of the belt, corresponding to the point of loading where the material falls onto it.
Italian equipment manufacturer SAMMI offers a wide range of products and services, including: Mechanical conveyors: belt v conveyors; pipe conveyors; tripper car; spillage chains; and bucket elevators. Mobile bulk handling equipment: v radial stackers; reclaimers; shiploaders; and barge loaders/unloaders. Other equipment/ services: hoppers; v crushing & screening; dust control/suppression; drives & controls; weighing; sampling & inspection; storage systems; and engineering consultancy.
Of particular note is SAMMI’s experience in designing complete cargo handling solutions for floating transfer stations (FTS), for a range of cargoes: coal, iron ore sulphur, clinker, limestone, etc. These technologies include: turnkey solutions for hoppers; belt feeders and conveyors; shiploaders (with conveyor capacities of up to 2,500tph [tonnes per hour]; and electrical & automation control systems.
Below are just a few examples of SAMMI transshipment projects:
In 2005, SAMMI supplied fixed belts v for transshipper Bulk Pioneer The work, was for customer Shipping Services S.r.l., for end-user Berau Mining Coal, and took place in Indonesia. It comprised: a solution for bulk material, extractors, hoppers, shiploaders, and belt conveyors. A system of conveyor belts for coal transport was supplied, with a capacity of 1,000tph, capable of loading Capesize vessels from 180,000dwt to nine holds and Panamax vessels from 80,000dwt to seven holds, through the two loading hoppers, extractors, fixed belts conveyor up to the two
mobile shiploaders.
In 2010/11, SAMMI worked for Capo v Noli Transportes Maritimos Lda, with end-user Berau Mining Coal. It supplied a raw material transfer conveyor system for transshipper Bulk Java, in Indonesia. This solution was for bulk material, extractors, hoppers, shiploaders, and belt conveyors. The project encompassed a new transfer conveyor system of raw material installed on new geared pontoon Bulk Java (the transshipper) for coal transport. The capacity is 2,000tph, capable of loading Capesize vessels from 180,000dwt to nine holds and Panamax vessels from 80,000dwt to seven holds.
DETAILS
The conveyor system is equipped with two shiploaders, one installed at fore and one at aft. When loading oceangoing vessels (OGVs), the shiploaders have the chute
axis distant 30m from the centre of the foundation column and a jib inclination ranging from +12° to –10° (that can be controlled by means of hydraulic cylinders). The rotation speed at the top of the shiploader is approximately 10m/min and the acceleration/ deceleration time is five seconds.
The rotation is controlled by three hydraulic gearboxes fed by a hydraulic power pack. The equipment is provided with a hydraulic brake system, used while in operating conditions, and with a mechanical brake while in rest conditions (‘service brake’). In operating conditions the rotation range of the shiploader is about –43° from the transversal position. The rotation of the shiploaders is limited by two magnetic limit switches (for each unit): the first generates an acoustic signal and a deceleration of the shiploader, the second stops the shiploader within the above mentioned braking time. The shiploader is installed on a high thickness steel column; the seat of the slewing bearing is placed on
the top of this column.
The slewing bearing is provided with an internal teeth-range. The rotating part consists of a platform placed on top of the slewing bearing on which the support structure of the shiploader is installed. A hydraulic cylinder, manually calibrated, is provided for belt tensioning. While in rest position the shiploader is supported by two rest saddles.
In 2011/12, SAMMI worked v for Sinoway International Company Limited, with enduser Berau Mining Coal. The project, in Indonesia, was a self-unloading system for transshipper Bulk Borneo, and comprised a solution for bulk material, extractors, hoppers, shiploaders, and belt conveyors. The plant concerned a transshipment system to be installed on new geared pontoon Bulk Borneo (the transshipper) for coal transport, with a capacity of 2,000tph, capable of loading Capesize vessels from 180,000dwt to nine holds and Panamax vessels from 80,000dwt to seven holds. Operations take place through the two grab cranes which feed the receiving hoppers TR1/TR2 and from each hopper the handled material is extracted by means of two belt conveyors BC1/BC2 and conveyed into a single belt conveyor BC3 transversely placed extractors.
DETAILS
modes: manual mode, for plant maintenance and start-up tuning. In this case the plant is fully under control of the operator, whom have the responsibility and can operate the plant both from control cabin and locally by means of a remote control. Semi-automatic mode. The single machines run in automatic mode under PLC supervision, start and stop are manually commanded from main operator panel, boom luffing and rotation of shiploaders by means of a remote control (under PLC supervision). Selection of operating modes no.1 and no.2 is made by manual selector installed on the main operator panel.
to discharge the material on two belt conveyors BC4/BC5, each of which feeds a shiploader (SHP1 e SHP2). The air draught of the shiploaders from sea level is approximately 18.5m. When operating to load Panamax and Capesize vessels, the plant operates with two shiploaders having a span between supporting column and chute axis of approximately 30m. The material flow can be divided on both shiploaders SHP1 and SHP2.
On the discharging section of conveyor BC3 a flow-regulating by-pass is provided to discharge the material on two belt conveyors BC4/BC5, each of which feeds a shiploader (SHP1 e SHP2). The air draught of the shiploaders from sea level is approximately 18.5m. When operating to load Panamax and Capesize vessels, the plant operates with two shiploader having span between supporting column and chute axis of approximately 30m, and the material flow can be divided on both shiploaders SHP1 and SHP2.
On belt conveyor BC3 a belt scale is provided for the monitoring of material flow. On both conveyors BC1 and BC2 a metal detector is provided to detect unexpected metal parts. When detecting a ferrous part or component, metal detectors control unit generate a signal which will stop the line. A sampling system is provided on belt conveyor BC3.
The plant can operate in the following
In 2011/12, SAMMI worked for v Sinoway International Company Limited, with end-user Berau Mining Coal. The solution was for a selfunloading system for transshipper Bulk Sumatra, and comprised a solution for bulk material, extractors, hoppers, shiploaders, belt conveyors. The project comprised design, full supply (MEC-ELE-AUT-OLE) and commissioning of belt conveyor system Bulk Sumatra for coal transport. The capacity was 2,400tph, capable of loading Capesize vessels from 180,000dwt to nine holds and Panamax vessels from 80,000dwt to seven holds, through the two grab cranes which feed the receiving hoppers TR1/TR2 and from each hopper the handled material is extracted by means of two belt conveyors BC1/BC2 and conveyed into a single belt conveyor BC3 placed transversely extractors.
On the discharging section of conveyor BC3 a flow-regulating by-pass is provided
On belt conveyor BC3 a belt scale is provided for the monitoring of material flow. On both conveyors BC1 and BC2 a metal detector is provided to detect unexpected metal parts. When detecting a ferrous part or component, metal detectors control unit generate a signal which will stop the line. A sampling system is provided on belt conveyor BC3.
On plant start-up, the operator can select three different operating cycles, as described below:
o discharge on vessel’s bulk with shiploader SHP1 and conveyors BC1/BC2 working at 600tph each (total 1,200tph);
o discharge on vessel’s bulk with shiploader SHP2 and conveyors BC1/BC2 working at 600tph each (total 1,200tph);
o discharge on vessel’s bulk with shiploader SHP1 and SHP2, conveyors BC1/BC2 working at 1,200tph each (total 2,400tph).
o Otherwise the operator can select a ‘special cycle’ and, depending on the line selected (i.e. working with a single or both shiploaders), manually input the corresponding speed of conveyors BC1–BC2 by means of inverters. Selection of the four operating cycles above mentioned can be made by push button placed on the main operator panel.
In 2011/12, SAMMI worked for v Coeclerici Logistics S.p.a, with endusers Limited Liability Company and Coeclerici Logistics Russia. The solution was a 750tph offshore conveyor belt system for transshipper Bulk Kremi, with continuous shiploader (crusher & prilled sulphur handling). This was for bulk materials, shiploaders, hoppers, belt conveyors, and extractors. The project in Ukraine comprised a complete material handling system for FTS Bulk Kremi 1. The work included design, full supply (MEC-ELE-AUT), commissioning and service. The equipment was installed on a 14,000dwt flat top pontoon crane. The transshipper is equipped with two cranes, two hoppers, two extractors, one longitudinal belt, one transversal belt, one longitudinal belt and a loader. It is designed for a capacity of 750tph of sulphur, but also able to transport coal and iron ore in different specific weights, using the inverters in the extractors, treating mainly 90% sulphur, 5% carbon and 5% iron ore. The system allows the loading of OGV up to Panamax, so an 18m air draught with a draught at full load of 6.5m. The shiploader can be traversed up to 50° to step over cranes between holds of ships with cranes and allows the loading using a retractable chute.
SAMMI in 2010 applied in design and supply of an offshore vessel loading system. The scope of work included a complete handling and shiploading system which is suitable to transport and load sulphur on vessels from Handy up to Panamax size. The plant will be installed on the Bulk Kremi transshipper and includes hoppers, belt conveyors and a shiploader, with a total span of 30 metres when fully extended. System specifications:
o boom with slewing, shuttling and luffing functions;
o material transfer from the feed chute at the pivot structure to the boom tip;
o retractable loading chute, for efficient material distribution and to reduce dust emissions;
o luffing angle up to 50°
to pass over vessel’s mast or cranes to enable quick hold changes during loading; and
o design fully in accordance with directive Atex 94/9/EC regulations.
In 2011, the company was awarded a contract for the design and supply of a turnkey coal handling for a rated capacity of 2,000tph of coal, to be installed in a new transshipper presently under construction. As for the project Bulk Java, the system will include double charging hoppers, belt conveyors and two continuous shiploaders both slewing and luffing-type. Operational tests were carried out in which the shiploader was completely assembled in the workshop together with its electrical and hydraulic power elements, to test that all slewing, luffing and shuttle functions operate as they should.
The main advantage of carrying out these types of workshop tests is that they significantly reduce the time required in the shipyard for the assembly, commissioning and fine-tuning of the system. This further underscores SAMMI’s commitment to meeting all the expectations of its customers. SAMMI’s technical solutions are all engineered to offer reliable, efficient and cost-effective operations.
In 2010/11, SAMMI worked for Capo v Noli Transportes Maritimos Lda, with end-user Berau Mining Coal. The project was a transfer conveyor system of raw material for transshipper Bulk Java. The solution was for bulk material, extractors, hoppers, shiploaders, and belt conveyors. The project included a new transfer conveyor system of raw material installed on new geared pontoon Bulk Java (the transshipper) for coal transport, capacity 2,000tph,
capable of loading Cape Size from 180,000dwt to nine holds and Panamax from 80,000dwt to seven holds. It took place in Indonesia.
The conveyor system is equipped with two shiploaders, one installed at fore and one at aft. When loading OGVs, the shiploaders have the chute axis distant 30m from the centre of the foundation column and a jib inclination ranging from +12° to –10° (that can be controlled by means of hydraulic cylinders). The rotation speed at the top of the shiploader is approximately 10m/min and the acceleration/deceleration time is five seconds.
The rotation is controlled by three hydraulic gearboxes fed by a hydraulic power pack. The equipment is provided with a hydraulic brake system, used while in operating conditions, and with a mechanical brake while in rest conditions (‘service brake’).
In operating conditions the rotation range of the shiploader is about –43° from the transversal position. The rotation of the shiploaders is limited by two magnetic limit switches (for each unit): the first generates an acoustic signal and a deceleration of the shiploader, the second stops the shiploader within the above mentioned braking time. The shiploader is installed on a high thickness steel column; the seat of the slewing bearing is placed on the top of this column.
The slewing bearing is provided with an internal teeth-range. The rotating part consists of a platform placed on top of the slewing bearing on which the support structure of the shiploader is installed. A hydraulic cylinder, manually calibrated, is provided for belt tensioning. While in rest position the shiploader is supported by two rest saddles.
CSL has announced a 20-year strategic partnership with Adelaide Brighton Cement Ltd. (Adbri) to build and operate the world’s first fully electric battery capable self-unloading vessel.
The custom-designed ship will replace Adbri’s Accolade II and will support the company’s limestone operations in South Australia with a focus on enhanced efficiency and environmental responsibility. The ship will carry up to 2.7 million tonnes of limestone per year, which represents a 35% increase over the existing vessel’s carrying capacity.
“Developed in line with CSL and Adbri’s shared decarbonization vision, this groundbreaking vessel will initially run on a hybrid diesel and battery system, replacing 25% of diesel with electric power and lowering Scope 1 emissions by 40% compared to Accolade II,” explains Louis Martel, CSL President and CEO. “By 2031, we aim to run the ship entirely on electric power, further reducing Scope 1 emissions to less than 10%.”
The design of the 11,000dwt self-loading and self-discharging bulk carrier has been optimized to provide a fully integrated
limestone supply chain for Adbri. The hybrid diesel-electric propulsion system combined with one of the most advanced battery installations on a bulk carrier globally provides a pathway to decarbonize shipping operations. Approximately 50% of the vessel’s energy requirements will be provided by a combination of shore power and battery energy storage, with plans to install sufficient batteries in the future to allow 100% electric operations.
“Adbri is excited to have one of the
world’s first 100% battery electric capable cargo vessels as our limestone carrier,” said Mark Irwin, Adbri Chief Executive Officer.
“The new vessel, owned and operated by CSL, will support Adbri to increase cement volumes at Birkenhead, while also supporting the production of lower carbon products such as EvoCem™ that uses limestone as a clinker substitute.”
Construction of the new vessel will begin in 2024 and delivery is expected in early 2026.
Emissions into the environment are nowadays the focal point for almost all industries across the world, including maritime logistics which contributes to about 80% of world trade and with dry bulk commodities accounting for more than 50% of the seaborne trade.
Transshippers, which are a vital part of the offshore logistics of dry bulk commodities, must fulfill its part in the ongoing pursuit of sustainability and efficiency.
Shi.E.L.D. Services, thanks to its extensive experience in the field, is
committed to guaranteeing optimal efficiency of the transshippers providing the ship owners with actionable insights into lower carbon emissions without affecting the overall performance.
Lower emissions can be achieved in the first place by replacing fossil fuels with carbon-neutral fuels. However, as much as these alternative fuels are emerging and becoming more available, their implementation and distribution networks are not
growing fast enough to meet the equivalent economies of fossil fuels. It may take an ample amount of time before these alternative sources become an effective solution.
Another factor to be considered is that offshore logistics projects usually take place in remote locations where the availability of traditional fuel is often critical, and the procurement of alternative fuels would be even more challenging.
Among all dry bulk cargoes being transported, coal makes up a major percentage as a primary source of raw
Transshipment operation in West Africa.
materials. As of today’s outlook of the market, it is impossible to overlook its industrial significance despite the contrasting demands of decarbonization. However, industries and owners can still find an efficient way to reduce emissions into the environment due to its uses.
While still working towards the implementation of alternative energy sources on board transshippers, Shi.E.L.D. Services, as designer and technical manager of transshippers that handles coal besides other commodities, is pursuing other ways to reduce emissions while maintaining and even improving the efficiency of its managed assets. Of the many, three main attributes of this plan are discussed below.
Offshore logistics is composed of different phases. In case of export of cargo, the most important activities are:
loading shuttle vessels at the jetty; v transporting cargo from the jetty to v the offshore location; transferring the cargo from the shuttle v vessels into the bulk carriers; the back-and-forth voyages of the v shuttle vessels between the port and the OGV.
Monitoring this entire supply chain helps identify bottlenecks or activities that slow down the process and are not directly connected to the operational activities.
“A smooth operational flow is the deciding factor for good performance; hence each phase needs to be performed at its maximum efficiency. To ensure this, we adopt a variety of strategies and tools, one of these tools being Spinergie .This helps us monitor in real time the status of each asset of the fleet and allows us to promptly identify those activities which are delaying the operations. The possibility to intervene in a short time to assess the root causes of delays makes it possible to rectify and reduce the downtime,” explains Guglielmo Tersalvi, Director of Operations at Shi.E.L.D. Services.
“Additionally, fuel expenses make up a significant portion of operational costs. This may as well leave the owners with a higher probability of investing in fuel-saving equipment on a vessel. Thinking forward, we appraise our client’s budget to allow them to meet the sustainable needs onboard with optimized investments aimed at reducing fuel consumption and the relevant operational costs.
“In short, even transshippers operating in remote areas can target lower emissions by achieving a smooth operational flow with no delays and reducing the specific fuel
consumption, which is the quantity of fuel used for each tonne of cargo handled. In the same industry, we are also recording demands for investing in fuel-saving equipment which we support.’, concludes Tersalvi.
Transshippers require extensive maintenance, and the costs may go up very quickly if equipment breaks down at sea and in remote locations, calling for emergency repairs. This leads to interruptions in the transshipment operations accompanied by additional costs due to fuel consumed in the meantime. In a wider lens, the operational progress of the entire fleet of vessels depends on efficient repair.
A maintenance plan, which is custom developed by Shi.E.L.D. Services engineers for each vessel system, includes simple dayto-day activities and more complex maintenance jobs or replacement of critical components to be carried out at longer intervals.
The maintenance strategy adopted by Shi.E.L.D. Services proactively relies on a combination of the following recognized industry standards:
Preventive (or planned) mainten- v ance , which is carried out at predetermined intervals, usually according to the instructions of the manufacturer.
Risk-based maintenance, where the v equipment is considered in a wider context of operation, environmental, and process conditions, based on which the maintenance programme is defined.
Predictive (or condition-based) v maintenance, where the performance of the equipment is monitored, and maintenance is carried out when the observed parameters deviate from the set baseline.
In addition to the above-discussed parameters which are widely used in the industry, laytime and shipments are also important but less discussed topics today. Efficient and cumulative shipments assure both timely availability of the components onboard and reduction of emissions throughout the supplying process.
Over time, the efficiency of systems degrades. This can be seen not only in terms of lower performance but also in higher specific fuel consumption. Therefore, every component of the vessel system is monitored and maintained according to the tailored maintenance plan developed for it.
The benefits are evident. Effective maintenance ensures that the equipment lasts longer, the inventory is optimized, and reduces unplanned maintenance in favour of scheduled maintenance, which is easier to manage and more effective to control. But it also gives a few advantages in terms of fuel savings as well:
Fewer breakdowns result in less v specific fuel consumption for the period when the transshipper and the other vessels are in operation. Higher efficiency of the equipment v means that less power, and therefore less fuel, is required for the equipment to produce the same amount of work.
Material handling on a transshipper requires various pieces of equipment like cranes, grabs, hoppers, conveyors, generators etc. to transfer cargo from one vessel to another. The selection of the equipment therefore plays a role in the transshipment performance which causes fuel consumption reduction.
For example, a grab of new design which provides a higher payload and lower opening/closing times, guarantees a higher quantity of cargo handled for each crane cycle. This results in less specific fuel consumption and overall lower emissions.
‘The same principle applies to all other main equipment being it a crane with higher hoisting and lowering speeds or a properly designed conveyor system. Selecting efficient equipment gives an indubitable return on the investment.’, says Tersalvi.
Shi.E.L.D. Services’ approach to achieving higher efficiency through optimization of the operations, proper maintenance plans, and selection of effective equipment gives the company’s clients the advantage in the current transitional and competitive
market. Despite the increasing restrictions imposed by the international regulations, it is still possible to achieve the desired high performance ensuring lower operational costs and carbon emissions, thanks to accurate management and use of the proper tools.
Shi.E.L.D. Services is a logistics management consulting services company that helps commodity traders, bulk shipping companies, port owners/operators, and other stakeholders in the dry bulk logistics sector.
supply chain workflows, reduce operating costs, and maximize profitability. The company specializes in designing innovative and bespoke dry bulk logistics solutions and comprehensive technical consultancy that help unlock new opportunities.
Shi.E.L.D. Services’ expertise in logistics consulting services is deeply rooted in the dry bulk shipping sector. Its team of dry bulk shipping leaders and professionals has served in the core leadership at Coeclerici, one of the world’s leading industry players. It has, since then, built a reputation for excellence, reliability, and efficiency in the
As trusted partners in the operation of bulk carriers and transshippers, Shi.E.L.D. Services ensures the continuity of the logistics chain in challenging environments, providing critical first and last-mile connectivity with its fleet of custom-built transshipment vessels and feeder barges. It has worked on several groundbreaking projects in Asia, Africa, and the Middle East, including the world’s first transshipment of granulated sulphur in the Black Sea.
Shi.E.L.D. Services is the consecutive winner in the ‘Bulk Logistics Excellence’ category at the IBJ awards 2019 and 2022, followed by the ‘Lifetime Achievement
Loading of the oceangoing vessel.
MacGregor’s new gravity self-unloading system eases the discharge of coarse materials from cargo holds, allowing bulk carriers to transport a wider variety of materials in greater volume.
The gravity self-unloading system is a time-tested means of discharging cargo from bulk carriers, with sloping cargo-hold walls designed to facilitate material flow. While a low slope angle is sufficient for unloading free-flowing material such as dry sand, a higher angle is required to effectively discharge coarser material like wood chips — at the expense of reduced storage space. Since the slope angle is decided at the vessel design phase, bulk carriers are typically limited to transporting
one type of cargo.
Drawing on decades of experience in self-unloader design and materials research, MacGregor, part of Cargotec, has pioneered a new system that will allow bulk-carrier operators to overcome this limitation and unlock new opportunities.
The augmented system ‘MacGregor GravityVibeTM’, features a patent-pending vibrating unloader that reduces internal friction to ease the discharge of coarse material. While the automated unloading sequence remains a gravity-based operation, GravityVibeTM deploys the vibrating panels as needed to shift any remnants or break the ‘bridges’ that form when cohesive cargo binds together to
block the outlet. As a result, the system effectively discharges cargo using a slope angle of just 15–20° — far lower than the 35–60° angle required in a conventional gravity self-unloading configuration.
Bulk carriers equipped with GravityVibeTM will therefore be able to handle not only a wider variety of materials but also a greater overall volume of cargo. This will consequently increase earning potential for the operator while reducing carbon dioxide emissions per carried cargo tonne to support compliance with environmental regulations.
“Bulk carrier cargo holds are typically designed to handle a specific kind of material, meaning the ship owner is
somewhat limited in the type of assignments they can take on,” commented Mikael Hägglund, Sales Manager, General Cargo Cranes, Transloading and Self unloaders, MacGregor. “MacGregor
GravityVibeTM overcomes these limitations to afford owners greater flexibility when taking on new contracts, but it also boosts earning potential and environmental performance by optimizing cargo capacity.”
Whereas conventional self-unloaders feature two longitudinal and two transfer conveyors, GravityVibeTM’s low slope angles mean that it functions with just one longitudinal conveyor. With fewer components, the system is less complex, which means its maintenance and spare-
parts requirements are reduced, in combination with the increased flexibility, resulting in improved cost efficiency. The streamlined set-up also minimizes spillage and the need for cleaning, with crew benefiting from a lighter workload and improved safety.
Crucially, with another patent-pending component from MacGregor isolating the vibrating panels from the hull structure, GravityVibeTM minimizes the transfer of vibrations and noise to other parts of the ship. This helps to protect the vessel and its critical machinery from stress-related damage while ensuring comfortable working conditions for personnel.
“As the culmination of decades of
experience in self-unloading systems and years of targeted research, MacGregor GravityVibeTM is our most advanced selfunloader yet,” said Tomas Wallin, Senior Product Owner, Self-Unloaders, MacGregor. “We developed the system according to established best practice, using textbook understanding of material behaviour in combination with a decisive innovation on how to handle cargo types with different properties. We have also tested it in collaboration with leading universities.”
While GravityVibeTM is primarily envisaged as an onboard installation, MacGregor’s studies have shown the technology to be equally applicable to
hoppers, where the action of the vibrating panels would minimize the reliance on gravity alone, allowing a lower height and wider inlet. This would in turn make it easier for crane operators to transfer
cargo into the hopper for more accurate and efficient operations, while the smaller dimensions would also mean a lower overall investment.
MacGregor is offering customers the
opportunity to validate GravityVibeTM’s handling of their chosen materials in fullscale mock-up demonstrations at the company’s test facilities.
Louis Dreyfus Ports and Logistics (LDPL) is a specialist subsidiary of Louis Dreyfus Armateurs’ (LDA), a French family-owned company founded in 1851. LDPL’s focus is logistics, maritime and port operations, in particular for the dry bulk cargo industry.
Over the past 30 years, LDPL has run several different projects in different continents and offered to its clients tailor-
made industrial maritime solutions, from the mining site to the end-users. This has given the company great expertise that covers the entire value chain — from port operations to barging, transshipment and shipping — and it can therefore provide technical advice and marine solutions for the most complex logistical challenges, thus making a real difference.
LDA and LDPL, being conscious of their
responsibility in reducing carbon emissions in shipping, are actively working on alternative fuels as well on wind-assisted propulsion vessels which will reduce industry greenhouse gas emissions. LDPL, among others, has been granted an Approval In Principle from an IACS class society and is currently developing a maritime logistics solution dedicated to green ammonia and hydrogen, called FRESH (Fresh Renewable Energy Solution for Hydrogen).
Not everybody is with what dry bulk transshipment is exactly, and why it is necessary in many cases for the export and/or import of dry bulk cargoes. We explain briefly below the nature of transshipment, and how it has significantly developed during the last decades.
There is no doubt that the nature of trades in dry bulk commodities has evolved, generating challenges and so creating opportunities throughout the global supply chain; this is especially true when it comes to scale of shipping commodities to the end-users.
Dry bulk cargo trades have changed, in terms of market requirements for different commodity types. Seaborne transportation has more than doubled during the last 25 years and become bigger and bigger in terms of shipments sizes. This has required exporters and importers to adapt their operations and develop solutions that can make the supply of raw resources viable from an economical perspective. The main dry bulk cargoes — like grain, coal, iron ore, bauxite and manganese — are today mostly transported in large-sized bulk carriers, like Capesizes and Newcastlemaxes. The sizes and draughts of these vessels do not, in many cases, fit with the conditions at the ports where exporters and importers operate. These are typical scenarios where dry bulk transshipment is needed. Transshipment makes it possible to eliminate constraints relating to vessel sizes in areas where port draughts and infrastructures are limited.
In these cases, solutions including floating cranes, transshippers, tugs & barges and self-propelled barges are required to facilitate the large-scale export and/or
import of dry bulk cargoes. Tugs & barges and self-propelled barges make it possible to load and/or unload cargoes at ports with restrictions and limitations, while floating cranes and transshippers make it possible to load and/or unload them offshore to/from the oceangoing vessels. These type of operations normally require customized solutions which, while each is different from the other, make it possible to overcome infrastructure challenges in a tailored, practical and reliable logistics way.
Dry bulk transshipment is one of the native activities of Louis Dreyfus Ports and Logistics commencing in the early 1990s with deployment of floating cranes in Indonesia for the transhipment of coal.
LDPL rapidly expanded its dry bulk transshipment business comprising of floating cranes, transshippers, tugs & barges and self-propelled barges worldwide from
Asia to South America working in Indonesia, India, United Arab Emirates, Sierra Leone, Guinea, Colombia and Dominican Republic among others. Notable customers include NOMAC, Adaro, Kideco, Sinarmas, Fomento, Emirates Global Aluminum, Harbin Electric International, Glencore, Vale and Banpu to name a few.
The biggest strength of LDPL is its ability to study, develop and provide solutions in short periods of time and in a
contractual format acceptable to its clients. It has provided customized shipping solutions to large reputed industrial customers in contractual formats such as EPC, O&M, take or pay, joint ventures, time charters and is always open to evaluate newer and different viable options.
While the choice for the type of transshipment system to be employed is critically determined by cargo volumes, weather working days, infrastructural restrictions, cargo characteristics, operational needs and targeted handling rates, LDPL has developed an in-house software, specific for dry bulk transshipment operations modelling. This software uses simulation optimization to provide a comprehensive range of solutions for study, design and optimization of any dry bulk transshipment project. This software is able to determine the best modelling complying with an extensive list of operational constraints within a few seconds. It calculates and suggests the best way to manage all deployed assets and provides accurate results and outcomes of the operations, using Monte-Carlo method algorithms.
Simulations include an extensive list of parameters which model every single manoeuvre and marine operation.
LDPL is also involved in shore handling projects where it acts as port operator for operation and maintenance of harbour cranes employed for loading/unloading dry bulk cargo for example in Dubai and Indonesia. It also offers consulting
and ship management services to third party ship owners. This makes LDPL a niche full marine logistics service provider capable of offering a one-stop-shop to meet all the transportation and transshipment needs of its clients.
Mineral Resources (MinRes) has commissioned its first transshipper — MinRes Airlie — after successfully completing sea trials.
The innovative transshippers are an integral part of the transport solution for MinRes’ Onslow Iron project, which will unlock billions of tonnes of stranded iron ore in the west Pilbara region.
Sea trials included testing the Articulated Tug and Barge (ATB) system, with the tug successfully interlocking to the barge to power the transshipper.
Other manoeuvres tested included speed, turning angles, time to stop and checks of the navigation and mechanical systems, with trials held off the coast of Ningbo Zhoushan port in China.
MinRes Executive General Manager Marine Jeff Weber said it was fantastic to commission the first bespoke transshipper.
“This is an important milestone for the Onslow Iron project, with the delivery of our first transshipper on time and on budget, with the ATB system proven technology,” Weber said.
“The sea trials are an opportunity for us to ensure all systems are working as they are intended to, with safe operations our utmost priority.
“The shallow-draught transshippers are pivotal to making the Onslow Iron viable, with transshippers significantly reducing the project’s environmental footprint and capital investment, compared to dredging a deep-water port.”
Sea trials for the remaining transshippers will occur in a staged approach, with the first two vessels due to arrive at the Port of Ashburton in the coming months to commence operations mid-year.
The transshippers, named after islands off the Pilbara coast, were designed by MinRes with the support of naval architects and engineering firms based in Australia and Canada. Once fully operational, the fleet of seven transshippers will be one of the largest and most sophisticated transshipping operations in Australia.
Onslow Iron is projected to ship around 35 million tonnes of iron ore per year, with an expected mine life of more than 30 years.
MinRes’ Onslow Iron project is set to redefine mining in Western Australia through world-first autonomous road trains, industry leading dust free transport and resort-style workforce accommodation. The transformational Onslow Iron project is one of the largest iron ore projects currently under development in Australia.
Onslow Iron is being developed by MinRes, in a joint venture partnership with Red Hill Iron Joint Venture (RHIJV) partners Baowu, AMCI and POSCO.
MinRes will deliver all mining services and infrastructure for the project, including a crushing plant and haulage, port and
transshipping services to facilitate the export of the product.
The project will have the shortest pitto-port distance in the industry, with iron ore transported 150km from the mine site to the port. In a world first, the product will be transported by jumbo autonomous road trains via a dedicated fenced and sealed haulage road. Once the product reaches the Port of Ashburton, it will be shipped via fully enclosed transshippers to Capesize vessels anchored 40km off the coast.
The Onslow Iron project’s game-changing innovations — designed and developed by MinRes — will minimize the project’s environmental footprint and increase efficiencies. This includes:
NextGen modular crushing plants that v produce significantly lower dust and noise emissions than traditional crushers;
world’s largest autonomous road v trains that will enhance road safety and increase operational efficiencies; transition of autonomous road trains v from diesel to electric, reducing carbon emissions; and transshippers that enable MinRes to v export iron ore from the Port of Ashburton without needing a deepwater port, significantly reducing the environmental impact and capital cost.
DCi
Despite an upbeat end to 2023, the start of the year has been rocky for the dry bulk sector in many countries, and ship agents are being called on to provide stability in increasingly turbulent times.
Dry bulk players are looking at a turbulent start to 2024. They are facing a ‘perfect storm’ of geopolitical events creating waves that impact major trade routes, a slowdown in the Chinese economy leading to fewer bulk cargo imports to the world’s second-biggest market, and concerns involving the Suez and Panama Canals causing bulk carriers to reevaluate their journeys. Adding to these global headwinds, individual countries grapple with their domestic challenges that further complicate the dry bulk landscape.
It was not long ago that the sentiment was much more optimistic. The Baltic Dry Index saw a peak in freight rates in December 2023, while Panamax, Supramax and Handysize vessels indices reached recent highs. But the growing number of ships tied up at ports or rerouting due to issues in Panama and the Red Sea has tempered that optimism early this year.
While global instability is affecting almost all players across the supply chain, issues for the dry bulk sector are compounded by local and regional hurdles and supply-demand trends.
Geopolitics present a constant challenge to shipping. For example. in July 2022, a grain corridor was opened for a year in the Black Sea. It allowed ships calling at the Ukrainian ports of Chornomorsk, Odessa and Pivdennyi to navigate to the Istanbul anchorage area, after inspections. GAC Turkey provided
daily updates and agency support and helped guide vessels chartered by the United Nations’ World Food Programme through the inspection process.
The industry has to draw on its resilience to weather the storm. Ship agents play an important role in helping the dry bulk sector overcome the challenges, particularly when wildly fluctuating market trends make effective long-term planning incredibly difficult.
“Major dry bulk players face multiple challenges to ensure their vessels and cargo make their destination on time and on budget. That’s why it is vital for agents to have presence at both load and discharge ports,” says Lars Hardeland, Operations Director – Shipping at GAC Group, the global ship agent.
“Shipping agencies must exercise flexibility to adapt to supply chain disruption, either local, regional or global. To do so, they need robust contingency plans supported by a global Business Continuity Plan for port call management and financial controls, to give ship owners and managers the reassurance they need in uncertain times.”
GAC has more than 60 years of experience handling dry bulk commodities and vessels. With its global reach of more than 300 offices in over 50 countries, it is ideally placed to support global dry bulk players to ensure vessel turnaround times are kept to a minimum.
GAC works with dry bulk shippers around the world, including: steel, iron ore and coal at major China v
ports;
South Africa for coal at Richards Bay v and iron ore at Saldanha Bay: coal and iron ore at Australian key v ports, particularly in Queensland; a range of commodities throughout v the Middle East; iron ore, petcoke, coal and bauxite at v Trinidad’s deep draught Chaguaramas hub.
The group continues to expand its global footprint, with new offices opening in Germany, Greece, the United States, Malaysia and Vietnam in 2023 in response to growing demand for its services.
“From monitoring port conditions to loading and unloading vessels to keeping updated on port authority requirements, GAC remains committed to supporting our customers and driving their success regardless of the challenge,” adds Hardeland. Its free daily Hot Port News e-bulletin is a trusted source of global port intelligence from GAC’s network of offices and agents since 1998.
GAC adapts and innovates to keep pace with emerging challenges, including the adoption of digital platforms to boost operational efficiencies and help its dry bulk customers overcome some of the hurdles they face.
It developed its Pegasus portal to provide real-time information about port infrastructure, services, mishaps, accidents, delays and turnaround times. With access to data on 220,000 vessels and ports globally, customers can predict port congestion, pick the best routes and make
informed voyage decisions based on efficiency, time and financial considerations even before booking shipping services. Technology is also embraced by GAC’s local operations.
“Increasingly, we are using data analytic tools to gain insights related to shipping routes, weather conditions, market trends and operational performance,” said Selcuk Ozer, Head of Shipping at GAC Turkey.
“That helps us to make more informed decisions and improve our overall efficiencies, while also improving our ability to communicate with everyone involved in the supply chain, including shippers, carriers and port authorities.
“That data, and the operational transparency it brings, correlates directly with customer confidence. We see that particularly in the dry cargo sector where operators are using digital platforms and software for real-time tracking of their cargo. To complete the picture, we need to
support that with our own data.”
At the same time ship owners are confronted with the implications of geopolitics on their business and a growing stack of regulations that must be adhered to, locally and internationally. Ship agents make significant difference by applying their understanding of the rules governing dry bulk to guide their customers to ensure compliance.
“Ship owners face increasing pressure to comply with international standards related to emissions, ballast water treatment, and other environmental concerns, and it is vital we support them to ensure they remain compliant no matter where they are in the world,” adds Ozer.
“Our dry bulk experts are continuously updated on international regulations that affect all our customers. And it’s yet another reason why the role of a shipping
Twelve years ago, Navonus Group started as a port agency and cargo survey company all rolled into one.
“When Navonus steps on board a ship, one of our agents visits the captain, while our surveyor goes to the chief officer for inspection of the cargo.” says Josie Peiffer, Manager Supervision, Navonus NV.
“We are certainly service-oriented,” he adds, “our triumphs are embodied by a hard-working crew of professionals, and we stand for a local, honest, first-class service.”
The Head-office of Navonus is in Ghent with branch offices in Antwerp, Zeebrugge, Rotterdam, Hamburg and Aarhus/ Denmark.
The actual head count for the group is 30 employees, for Netherlands, Denmark, Germany, and Belgium.
The Navonus Agency department, using all modern technology of port-call software, offers a 24/7 service with one goal in mind, to give the captain and his crew a good local service.
A young team of boarding agents and operators giving old-fashioned agency service to all their ships, clients, shipowners, and service providers.
The Navonus Cargo Survey department, being “your eyes, ears and nose”, can guarantee the quality of clients’ product, whether they are buying, selling, or merely transporting.
The company’s tightly knit team of surveyors has more than a century of experience and its competence is deeply
agent is so important — with the right agent, you know they have your back.”
That close relationship between a dry bulk operator and their agent is even more critical in uncertain times with constantly changing market conditions. The volatile nature of the industry makes the ability to adapt rapidly to change essential to survival. Also, supportive and effective partners can help.
rooted in the GAFTA, FOSFA and ISO 17020 accreditations and recommendations.
The service include supervision during loading and unloading of dry agri bulk and liquid products, draught survey, hold condition survey, pre-shipment survey, and weight control.
Navonus experienced a steady growth and the company does not in intend to give up its level of personal service. “While expanding our company we carefully analyse customers’ needs and how we can best facilitate them.” explains Peiffer, “So, we can service our clients precisely as they expect.”
Working with this perspective gives it the advantage to act locally and think globally.
The Navonus Group is proud to proclaim itself a reliable, independent ships agent and dedicated co-maker in quality,
superintendence, and logistics.
If something unexpectedly goes wrong because of the hazards of the sea, Navonus’ team of experts knows how to safeguard its clients’ interest against ocean carriers, cargo underwriters, etc.
The agenda of the Navonus Group in
AND PROFESSIONALISM
SUPPORTED BY YEARS OF EXPERIENCE . With unique experience stretching back over 70 years, MORSKA AGENCJA GDYNIA (MAG) remains a major player in the Polish maritime sector, with a wide scope of services and expertise.
MAG was founded in 1951 and is one of the oldest enterprises from the sectors of transport and logistics operating in the Polish market. In Polish ports and shipyards, the company is providing agency services for Polish vessels and foreign flags. Over time, the company extended its range of activity to include chartering ships, port operations and container shipments as well as an employment agency for Polish mariners on ships under foreign flags.
MAG represents foreign shipping lines, shipowners and insurance clubs (P&I) in Poland and is a member of The Baltic International Maritime Council (BIMCO) and The Ship Agent and Brokers Association at Gdynia.
MAG offers complete package of logistic services like freight forwarding as well as transport solutions. No matter where customers need to transport (deliver cargo) with their experience, they can be assured about the safety of the cargo and order fulfilment. The dynamic growth of logistics works mentioned above resulted in the employment of additional staff in dedicated department to handle these issues.
MAG is present in Gdansk, Szczecin, Swinoujscie, Darlowo and all other Polish see ports and is an important player in the market. MAG ship agency’s experienced team is at the disposal of shipowners and ship crews calling at all Polish ports 24 hours a day, all year round.
MAG scope of activities includes, among others include: assistance when vessels v enter the port and when putting the sea; supervision over port v operations; organization of all v repairs;
inspections and controls; v keeping of ship documentation; v providing emergency agency services v for international insurance companies, supporting them in the process of damage adjustments in road, railway, and sea transport; change of crew; v assistance in emergencies which v require for example medical care; and assistance in all forwarding and v customs procedures.
MAG acts for both ships’ agent and freight forwarders for principals operating in the ports/port terminals in the field of a wide range of bulk goods, both dry and liquid/ calling at Polish ports and port terminals such as: agri products, coal, coke, limestone, biomass, aggregates, cement, fertilizers, wheat pellets, chemical products, wood logs, wood chips and others.
MAG serves over 1,250 vessels from coasters to Panamax and Capesize vessels. Dry bulk constitutes approximately 32% of the agency’s ships volume. Total volume of bulk cargoes amounts approximately two million tonnes.
Beyond traditional ship agency services MAG offers different logistics services: freight forwarding; v forwarding services documentation; v warehousing; v transshipment and storage; v tracking; v reporting regarding cargo handled at v the port; supervising port operations loading v and reporting regarding cargo being handled at the port rail and road transport; custom clearance, customs v documentation; and consultancy and representation of v other companies in cargo transshipment and forwarding.
MAG’s comprehensive services in the field of organization sea, road, rail, rivers transport and management of transport and logistics chain of project cargo type goods in export, import and transit are provided to Polish and foreign customers.
MAG co-operates with shipowners who have extensive experience in carrying such objects and operate specialist Heavy Lift type vessels.
MAG manages its own universal terminal, in the middle of the Polish coastline in Dar ł owo, with its own transshipment quays and offers storehouses and hard-surface storage yards. In the port, MAG organizes the
handling and storage of cereal grains, fertilizers, wood, aggregates, coal, steel as well as palletized and bagged goods. Due to its location the terminal is also dedicated as hub and service port for offshore wind farms in Polish waters.
Morska Agencja Gdynia has its own warehouses in a strategic location in Poland. Storage space can function like bonded warehouse, temporary storage warehouse or reloading place under customs supervision which also meet all safety standards.
The range of services offered in the field of warehousing include: storage; v handling bulk goods, general cargoes, v project cargoes/heavy goods; collection; v co-packing; and v domestic and foreign distribution. v
MAG provides agency services and a wide range of complimentary services and is always ready to find solutions in a challenging market. On a day-to-day basis, the team co-ordinates dozens of logistics and transport operations and guarantees professional service in all aspects of bulk goods transshipped in all Polish ports and always strives to meet the highest standards.
To strengthen the company’s position in the competitive market, MAG focuses on complex cargo services in international and domestic transport. MAG is very versatile company, operating in many different areas and always open to new projects.
To sum up, Morska Agencja Gdynia is characterized by flexibility and diversification as well as a guarantee of meeting clients’ expectations in order to achieve their business goals.
World Marine, headquartered in Glyfada, Athens, Greece, headed by Alexios Arnokouros, has been servicing the shipping industry consistently since 1985, with its Ship Agency and Representation services in Egyptian Ports-Suez Canal, P.R. China and S.A.R Hong Kong.
WORLD MARINE EGYPT
Maintains own offices in Port Said, v Suez, Alexandria and in Cairo. Awarded with ISO 9001 offering v better services at lower cost. Specialized on Suez Canal Tolls v Reduction Scheme, in case of Alternative Route.
Is licensed to handle owners matters v including crew change, superintendent and technician attendance, medical assistance, cash to master, spare parts, supplies and provisions, fresh water supply, waste disposal, sludge and bilge waters, repairs, class and P&I attendance and sscec renewal to all Egyptian ports/terminals. Offers round the clock Ship Agency v solutions for vessels calling Egypt, transiting Suez Canal, loading or discharging, attending husbandry matters in the Egyptian territory.
WORLD MARINE CHINA
With a sustained presence in v servicing all Chinese ports and shipyards for more than 33 years, World Marine is ready to offer its services to vessels and owners on a 24/7 basis through its expanded network of associates.
Having entered a very demanding and v competitive era where the need for qualitative but also low cost services is highly sought by all parties involved in shipping, the company is continuously upgrading its network so as to keep the standards of its company high towards its clientèle. Services vessels calling China or Hong v Kong, that are in need of Ship Agency solutions for cargo operations, dry dock, repairs, delivery (S&P),
husbandry matters, new building supervision and scrubbers fitting follow-up.
A ship agent, like World Marine Corp., represents a vital part in shipping operations, usually servicing charterers, ship owners, and operators when the ship is at port. The main duty and role of a ship agent is to be principal’s office extension, where the ship calls and a reliable party in front of local authorities.
As it is not feasible for any party to be represented globally, with its own office in every port, a ship owner/charterer (or other party interested on a ship’s prospective port call) is choosing during a port call, a local ship agent, the most suitable to physical attend his vessel, ensuring its smooth operation at port.
This role includes the accomplishment of all ship formalities and settlements with local authorities before-during-after the ship’s part call.
The agent must provide up-to date detailed information on port restrictions, conditions and tariffs, taxation, environmental (ballast policy, law sulphur), as well cargo- specific information, export documents, receipts, OBL — issuance for loading operation-availability-copies, receivers arrangements for to receive cargo-discharging operations.
Additional duties include dealing with crew changes, cash to master — CTM, spares clearance/collection/delivery, repairs, provisions, water, bunkers, medical, underwater inspection, and ship’s delivery.
All activities require an experienced agent’s coordination for a professional and timely attendance, as every process involves several parties interaction with local and international interests.
In Egypt: all ports of Egypt and with v own offices in Port Said, Suez, Alexandria and Cairo.
In PR China: all ports over China and v with own basis in Shanghai.
World Marine’s main competitors in Egypt and China are all major public and private owned shipping agency companies.
According to World Marine Department Heads of Egypt and China operations desk, where the company offers agency services, its businesses relates:
Egypt 60% in total and China 40% in v total operations.
In Egyptian ports 40% to dry bulk and v 60% to tankers (transits).
In Chinese ports 20% dry dock v services and 80% owner’s matters handling.
MAIN CHALLENGES OF WORLD MARINE ARE
Compliance with the increasing digital v progress of the maritime sector. To differentiate itself in competitive v environments, promoting the environmentally friendly practices, such as adopting electric vehicles or modern/green launches.
Adaptation to steadily changing v security, legal and operational requirements of global shipping (IMO, ILO and the latest conventions etc) along with the observation of the worldwide political/economical conditions.
Open to possible joint ventures, v synergies and strategic alliances with local and global shipping services providers.
The Suez Canal Authority (SCA) offers Rebate on tolls whenever there is an alternative route (via Cape of Good Hope or Panama or Northern Sea Route) in order to attract ships to pass via Suez Canal. SCA policy is not fixed, as they study each case individually; taking into consideration various factors, i.e. present freight market, bunkers cost, vessels consumption and speed, duration of voyage, etc.
World Marine is experienced with the Suez Canal Authority (SCA) rebates policy, with $9,000,000 in returns to its clients for 2023, with over 700 applications and 300 successful rebates.
As the year 2024 started, it is now time to look at the year 2023 and what happened during that year, writes Jonas Funck, Ship Agency Manager, Inkoo Shipping Oy Ab.
The world situation has changed; we managed Covid-19 and after that, other crises appeared. This meant that we had to think once again about solutions to problems independent of us.
What we did was to reorganize the way we agents worked separately, to a team that handles everything, regardless of where you are located. From being three in Inkoo who handled the traffic in Inkoo and two in Parainen who handled the traffic in Parainen, there are now five of us who handle all the traffic. In this way, we can keep our expertise at a high level and the work is distributed more evenly between all of us. We handle clearances along the entire coast, not just in Parainen, Inkoo and Kantvik. With the customer in focus, we build a concept that makes visiting a Finnish port smooth.
The world situation has also made companies to think greener and be more independent from countries, that are on the blacklist regarding trade. This has meant for Inkoo harbour, that instead of fossil fuels, such as hard coal, petcoke etc., it has received more biofuels for power plants such as wood chips, energy wood and wood pellets. On average, six ships a month arrive with biofuel at Inkoo and Kantvik harbor. Also, the floating LNG terminal Exemplar, which arrived in Inkoo at the end of December 2022, provides us with various tasks.
Inchcape Shipping Services (ISS) has been traditionally very strong in the liquids and gas markets in China but is expanding fast in dry bulk, which has become a massive industry over recent decades thanks to China's economic boom. Here, ISS China's David Young, Area General Manager, Northeast Asia, and Joseph Shi, Operations Manager Dry Bulk, shed light on the agent's role in managing port calls and some common challenges they face.
In a nutshell, Inchcape's chief task as a shipping agent working for dry bulk customers is supervising cargo operations and ensuring an efficient port call. “As the agent we handle all in-water formalities to ensure the smooth berthing of bulk carriers in port and the safe and efficient discharge of their cargo. This includes managing all related documentation, such as bills of lading (BLs), and ensuring compliance with regulations. We then take care of cargo loading and all the outward formalities related to a vessel's departure,” David Young explains.
Inchcape also offers extended services such as supporting vessel masters with port captain functions including cargo stowage, draft issues and discharge planning. “The port captain is especially relevant when handling valuable cargoes and for planning the discharge of multipart parcel cargoes in different locations. We also arrange ship surveys and inspections including off-hire surveys when a vessel is redelivered from charter, as well as follow up supply chain issues thanks to our local presence in ports both in importing and exporting countries,” Young adds.
Husbandry issues are also in Inchcape's remit if requested by the vessel owner or operator. These range from simple provisioning or organising a crew change to delivering spare parts, arranging for onboard repairs and organising bunkering.
In China, Inchcape employs 64 people and is responsible for managing approximately 5,950 port calls annually on behalf of major global charterers. The chief dry bulk import commodities are iron ore, coal and grain. “We have our own offices in Dalian, Tianjin, Shanghai, Guangzhou and Qingdao, but supervise local agents handling cargo operations in other locations. A particular advantage of working with Inchcape is that we can act as a single contact point for
client vessels calling anywhere in the country. There are over 70 ports in China and we cover all of them,” Young says.
“Procedurally, customers typically approach us when they have, or are about to, fix a vessel to ascertain the estimated costs for a particular port call. Based on our comprehensive local knowledge, we will provide them with a pro forma DA (disbursement account) detailing those costs. They then appoint us as the protective or sole/general agent for the port call.”
Cargo receivers generally nominate their own preferred agents in local ports, whom Inchcape then appoints as subagents subject to its supervision. “The local agent's focus is protecting the interests of the receiver or shipper but we need to look after our own client's interests. If cargo ops are suspended for some reason, for example a stowage issue or problem with the ship's gear, we need to keep close tabs on the sub-agent in order to safeguard our own customers,” Young says.
Shi stresses that working with a global agency provides foreign principals with peace of mind, thanks Inchcape's robust governance and compliance procedures, local insight and fast response time. “In each region we have a Regional Operations Centre where customers can send inquiries and get feedback usually within the same working day. It's also far easier for customers to use one provider, with a single statement of account, than having to deal with multiple different agents in different ports.”
This approach also mitigates risk. It is not uncommon for critical errors to occur with the local receivers appointed agents –for example releasing a cargo without the original BLs. “Such cases can end up in smaller shops declaring bankruptcy. Unfortunately, they often continue to trade but under a different name, making it very tricky for foreign litigants to recoup their losses,” says Shi.
One key operational challenge in dry bulk shipping is that there can be a lot of schedule changes while vessels are at sea that will impact cargo operations. “This might lead to congestion at ports and competition for berths, while issues such as labour disputes and equipment problems can further complicate matters,” Young says. “In these kinds of scenarios, it
is crucial to constantly monitor schedules and communicate with both port administrations and receivers to seize opportunities for berth availability. This demands strong mathematical skills and a sharp mind.”
Other potential glitches include damage to a vessel during cargo operations, which is a particular risk in shuttle operations using grabs. “In the event of an incident, we have to coordinate with the ship owner, charterer and whatever party has been responsible for the damage. And vice versa, sometimes there can be impurities in a cargo that might cause damage to a conveyor belt. All these kinds of small things we are trained to look out for and handle,” says Shi.
“Working as an agent on the ground can be stressful but it's fun as well.You have to juggle a lot of balls while interacting with all sorts of different people. My motivation is providing the best possible service to our clients,” he adds.
To give a sense of the quantities Inchcape is responsible for, in 2023 it handled a total of 46 port calls for coal with a total volume of 3mt (million metric tonnes). In grain, it handled 25 shipments during the year with a total volume of 1.5mt. On the iron ore front it manages around 50 port calls per month for a major iron ore producer in Brazil, with a total volume of around 7mt, and 60 monthly shipments for a major iron ore producer in Australia with a total volume of around 10mt.
“These volumes are substantial but capacity-wise we are eager to do more, backed by our solid reputation in the market as a trustworthy, long-term partner,” Young concludes.
Joseph Shi, Operations Manager Dry Bulk, at Inchcape Shipping Services.For the past 16 years, Safina Shipping Agency has been at the forefront of maritime expertise, evolving into one of the top 20 shipping agencies in Egypt. As a pivotal member of the ICAA group, Safina was established to manage the group’s vessels and containers. However, the company’s strategic shift in 2009 has not only broadened its scope but also elevated its status within the shipping industry. Born in a ship owning group of companies, Safina prides itself on being an agent that truly understands the wants and needs of the principle.
Safina’s success story is marked by its ability to attract top bulk producers in Egypt, leading to the addition of various verticals, including metals, cement, fertilizers, copper, coal, mill scale and pellet fines.
Over the last decade, Safina has seamlessly operated across diverse industries, collaborating with leaders in each sector and establishing an impressive track record.
With over 50 satisfied customers in the last five years and engagement with toptier clients in different bulk industries for a decade, Safina has become a trusted partner in Egypt’s shipping industry. Handling around 5.5mt (million tonnes) in 2023 across different commodities, Safina has solidified its position as a key player, commanding 30% of the iron ore market, 27% of the clinker market, and 23% of the steel scrap market.
Safina’s influence extends beyond Egypt as it covers all ports within the country, with plans to expand its footprint in Jordan, KSA, and Sudan.
This strategic expansion aims to further strengthen Safina’s position as a leading shipping agency in the region.
Safina offers a comprehensive range of services, including vessel supply, protective agency, bunker call agency, port agency, dry docking, maintenance and repair, canal transit services, and maritime logistics such as liner husbandry service, chartering service, break bulk and project logistics, and liner and NVOCC (Non-Vessel Operating Common Carrier) agency.
The diversity of Safina’s operations is mirrored in the types of vessels it operates, ranging from container ships, bulk vessels, and multi-purpose vessels to liquid and gas carriers, as well as luxury super yachts.
Safina’s commitment to excellence is evident in its numerous certifications, including ISO 9001/2000 for quality management, OHSAS 18001 for occupational health and safety, ISO 14001 for environmental management, and an Anti-bribery Compliance certification from TRACE. These distinctions underscore Safina’s dedication to maintaining the highest standards in its operations.
Safina actively participates in industry forums and organizations, holding distinguished memberships in institutions such as The Baltic and International Maritime Council (BIMCO), and the main shipping chambers in Egypt.
As Safina Shipping Agency continues to navigate the seas of excellence, its unwavering commitment to quality, safety, and client satisfaction sets it apart in the competitive maritime landscape. With a rich history, a diverse portfolio of services, a global presence, and a focus on industry best practices, Safina is well-poised to remain a key player and a trusted partner in the ever-evolving world of shipping.
Crossing international waters can be complex, demanding local knowledge and seamless coordination. At WaterFront Maritime Services, the company bridges the gap between global reach and local expertise, ensuring maritime operations navigate smoothly and efficiently.
WaterFront Maritime Services’ expansive network stretches across 490+ offices in over 90 countries, giving clients access to deep, in-depth local knowledge wherever their journey takes them. The company’s team members cultivate strong relationships with local authorities and port officials, ensuring efficient handling and reducing potential delays.
As a local representative, WaterFront Maritime Services acts as a trusted advisor and advocate, navigating the intricacies of each port call. It leverages its local expertise to handle all aspects of port and agency requirements, saving the client valuable time and resources and giving them peace of mind, knowing they have a dedicated team on the ground, anticipating their needs and ensuring a seamless experience.
Owned by two industry leaders, Sharaf Shipping and Ben Line Agencies, WaterFront boasts a proven track record of success. The company operates as ship agents in over 490 offices worldwide, serving some of the largest mining and oil companies, trading houses, ship owners, and ship managers globally. Its key numbers speak for themselves, reflecting its commitment to excellence and efficiency.
Whether a client is chartering a vessel, managing a fleet, or transporting essential commodities, WaterFront Maritime Services customizes its solutions to their specific needs. The company’s global reach ensures consistent quality and service, while its local expertise guarantees the client navigates each port with confidence. This translates to tangible results: saved time, reduced costs, and mitigated risks.
WaterFront Maritime Services’ strategically located office in Panama City provides immediate access to both canal entrances and exits, minimizing transit times and ensuring efficient cargo movement.
Its dedicated Panama team has over 30 years of experience, specializing in navigating the intricacies of Panama Canal operations. The company secures optimal
transit slots at competitive rates, ensuring seamless compliance with all canal authority requirements, and delivering reliable transit guarantees for peace of mind.
Benefits of WaterFront Maritime Services’ Panama expertise:
Transit slot auctions: WaterFront v Maritime Services’ team leverages indepth knowledge of canal traffic patterns and auction strategies to secure its clients’ vessels’ most efficient and cost-effective slots.
Vessel compliance: The company v meticulously handles all documentation and procedures, ensuring vessels meet the strictest canal authority regulations and avoid delays and potential fines.
Transit Guarantees: With v WaterFront Maritime Services’ extensive network and established relationships, it offers reliable transit guarantees, minimizing uncertainties and maximizing schedule predictability.
WaterFront Maritime Services offers comprehensive value-added services that empower charterers, ship owners, and ship managers to navigate the maritime industry confidently, efficiently, and sustainably. Tailored Solutions for Every Voyage:
Health, Safety & Environment v (HSE): Ensure crew wellbeing, vessel readiness, and environmental compliance with expert guidance and training.
Compliance: simplify regulatory v complexities through its global network, expertise, and digital tools, mitigating risks and avoiding costly delays.
Payment solutions: streamline v
financial transactions with secure, transparent, timely payments across borders.
Cargo security: protect valuable v cargo with robust security protocols, real-time tracking, and risk mitigation strategies.
ESG reporting: meet evolving v environmental and social governance requirements with accurate, comprehensive reporting solutions. Operational optimization: v maximize profitability and minimize downtime with efficient route planning, fuel management, and datadriven insights.
Market intelligence: stay ahead of v the curve with timely market updates, trend analyses, and competitor insights, making informed decisions for your vessels.
Cargo document management: v ensure seamless cargo movement with accurate and timely documentation handling, minimizing errors and streamlining processes.
With a presence in over 90 countries, WaterFront Maritime Services seamlessly connect clients across load and discharge ports, ensuring the most efficient execution of cargo, vessel, or crew operations.
Dedicated experts: WaterFront Maritime Services has a team of maritime professionals with in-depth industry knowledge and understanding of its clients’ specific needs.
Technology-driven solutions: v cutting-edge technology platforms that streamline operations, optimize efficiency, and enhance visibility.
Global network: seamless v connectivity across continents, ensuring smooth navigation and efficient resource allocation.
Unwavering commitment: a v dedication to your success, safety, and the environment every step of the way.
v
WaterFront is 100% committed to the highest level of Corporate Compliance, covering Anti-Bribery & Corruption,
Health and Safety & Environmental Management, and adherence to International Sanctions. Benchmarked against the UK Bribery Act of 2010 and the US FCPA, we are active Maritime AntiCorruption Network (MACN) and TRACE Certified members. Holding ISO Certifications:
SO 9001: 2015 (Quality Management v
System);
ISO 14001: 2015 (Environmental v Management System); and
ISO 45001: 2018 (Occupational v Health & Safety System).
WaterFront Maritime Services manages all aspects of cargo and vessel operations, finance, documentation, compliance, and vendor management. From co-ordinating terminal activities to handling bunkering, repairs, and crew changes, the company’s services encompass the entire port agency spectrum, offering efficiency and reliability to clients worldwide.
Founded in 1945, the Tampa-based maritime services firm A.R. Savage Company LLC is pleased to announce that it has accepted a substantial investment into three of its operating companies from the international shipping services company Agunsa USA, AGS.
This includes investments in the A.R. Savage & Son organization that operates a premiere ship agency, as well as Tampa Bay Ship Services that provides line handling services, waste removal, hold cleaning and other port services, and A.R. Savage & Son Advisory Services that provides seasoned counsel to logistics and transportation firms across the nation.
In recent years, the company’s leadership team has helped fuel an expansion of these services from Tampa Bay to a dozen U.S. ports.
“Our customers have come to know they can rely on our companies for exceptional service, tremendous value and objective advice,” said A.R. Savage Company President & CEO Arthur Savage. “Now the same high-quality ship agency services will be available to them throughout the nation, as we remain focused on superior port call management that brings them the best results.”
AGS, based in Florida, operates as the subsidiary of AGUNSA for North America and is an integral part of GEN Companies, a publicly traded corporation with more than 90 years of experience in the logistics,
Specializing in cargo operations, bunkering, and husbandry, IMGS Group ensures the seamless management of vessels, crews, cargo, and more.
With a full spectrum of services, including port agency, protective agency, husbandry agency, cargo agency, and crew support, IMGS Group stands as a beacon of reliability. Their real-time local knowledge and operational expertise guarantee efficient port calls, making them a dependable choice for maritime needs.
Beyond the basics, IMGS Group offers an array of other related services, including port handling, transportation, and vessel chartering. From the discharge and loading of various cargo types to safe and timely
movements worldwide, IMGS Group ensures a seamless experience.
Operating throughout Africa and South Asia, IMGS Ship Agency provides comprehensive coverage and support on local, regional, and global scales. Noteworthy among their achievements are the impactful projects of last year. Imagine 19,000 (metric) tonnes. of lentils and 21,000 tonnes of chickpeas distributed across Pakistan, courtesy of IMGS Group. This not only facilitated essential food supply but also marked a significant contribution to the Middle East, discharging and distributing fertilizer across the region.
Additionally, IMGS Group played a
maritime, and port sectors. AGS and AGUNSA provide specialized maritime agency services in more than 20 countries, covering the Americas, Asia, and Europe. In addition, they expand their offerings with infrastructure concession services, logistics operations, and air solutions, among others.
Both companies, A.R. Savage Company and AGS AGUNSA, stand out for sharing a strong foundation of ethical values and commitment, focusing on integration and service excellence to clients, with the goal of exceeding their expectations.
“We are excited to help Agunsa expand into United States markets,” Savage said, “especially as this growth will originate from our headquarters right here in Tampa.”
pivotal role in Djibouti by welcoming its first-ever cruise liners —Cloud and Diana — setting the stage and bolstering the country’s tourism sector.
Highlighting last year’s triumphs and this year’s endeavours, IMGS Group continues to excel. The Liberty Glory recently discharged over 30,000 tonnes of sorghum for USAID & WFP, addressing the needs of drought-affected populations in the Horn of Africa — a humanitarian initiative to feed approximately two million people for a month. Similarly, with PAGODA at the helm, IMGS Group executed a seamless operation — unloading 9,000 tonnes of wheat for Falconbridge Resources in Djibouti.
DCi
More than two million tonnes of trade have passed through the Port of Mackay in Queensland, Australia, in just seven months, underlying the publicly owned port’s versatility and importance to the region. The port has already clocked up 2.218 million tonnes of cargo, surpassing throughput in the same period of the previous financial year (2,070,495).
North Queensland Bulk Ports Corporation (NQBP) CEO Brendan Webb said the top three traded commodities were petroleum (1,115,656 tonnes) sugar (636,196 tonnes) and grain (223,221 tonnes).
“The strong trade performance at the Port of Mackay reflects its pivotal role as a leading service centre for agricultural and mining industries,” Webb said.
The port provides an essential connection between regional Queensland and the world boasting trading links to neighbouring countries in Asia as well as New Zealand and North America.”
As well as supporting the trades of today, the Port of Mackay is ready to play its part in supporting the Queensland Government’s Jobs and Energy Plan.
“As a publicly owned multi-commodity port, Mackay can play a role supporting the energy transformation underway through the importation of renewable energy infrastructure,” Webb said.
“We’re continuing to invest in Port of Mackay infrastructure to boost our capabilities. The Port of Mackay can also help with the decarbonization of the industrial supply chain, by moving break bulk and containerized cargo away from long-distance road travel.”
The Port of Mackay is one of four ports NQBP is responsible for, collectively facilitating around half of Queensland’s trade by tonnage.
“NQBP is one of Australia’s key gateways to trade, providing security, growth, and prosperity for our local North Queensland communities,” Webb said.
“Our ports are flexible and capable of sustainably addressing the trade requirements of Queensland and the communities and stakeholders we serve.”
Regional, national and international logisticians count on Port Milwaukee for a turnkey approach to solve their transportation and supply chain needs. Strategically located in the industrial center of the U.S., Port Milwaukee provides premier access to domestic and world markets.
Geopolitical and economic challenges weighed on throughput in all North Range ports in 2023. The declining development of the German economy and the subdued consumer sentiment also affected the business of Germany’s largest all-purpose port. In 2023, container throughput declined in comparison to the previous year, although a slight recovery occurred in the second half of the year. Bulk cargo throughput, however, remained largely stable, ensuring a consistent supply for Germany’s economy. There was a positive development in trade with several American and Southeast Asian countries. Compared to its Northern European competitors, the decline in containerized cargo in Hamburg was less pronounced, allowing the Port of Hamburg to maintain its market share.
In 2023, the terminals in the Port of Hamburg handled a total of 114.3mt (million tonnes) of goods. Seaborne cargo throughput is thus 4.7% below the level of the previous year. Container throughput amounted to 7.7 million TEU, decreasing by 6.9%. In the first half of 2023, the decline in container throughput amounted to as much as 11.7% compared to the same period in the previous year. “When we look at the development of our throughput figures, we are on the same level as our
Northern European competitors and are holding our own well compared to other ports. The decline is primarily due to the difficult geopolitical and economic situation that we all are facing,” explains Axel Mattern, CEO of Port of Hamburg Marketing.
Bulk cargo throughput, which is important for the supply of the German economy and industry, remained stable in 2023 at 36.2mt (–0.2% compared to the previous year). With an increase of 8.4% to 6.6mt, the agribulk business in particular recorded strong growth. In the area of liquid cargo, companies increased throughput to 10.6mt. This equates to a gain of 6.6% compared to the previous year. Conversely, the throughput of grabbable cargo fell by 6.2% to 19mt. This was due to reduced power generation from coal as well as an inspection at a steelworks connected to the Port of Hamburg.
USA traffic continued its positive development of the previous years. In total, 653,000 TEU were handled in 2023 with what has become the Port of Hamburg’s second strongest trading partner. This corresponds to a gain of 8% compared to 2022. Throughput with India also developed positively. In direct traffic alone,
191,000 TEU — 5.6% more containers — were handled with the world’s most populous country in the past year. India thus became the Port of Hamburg’s eighth most important trading partner. China continues to lead the list with 2.2 million TEUs handled in 2023.
Hinterland traffic to and from the Port of Hamburg turned out relatively robust in 2023, despite the decline in total cargo throughput. With a volume of 5.1 million TEU, a decrease of only 4.7% was recorded. Transshipment traffic declined more significantly (2.6 million TEU, –10.9% compared to the previous year), after already exhibiting volatility in the past.
Despite operational challenges, such as strikes and poor weather conditions, rail transported a total of 45.6mt (–3.6%) of goods and products via Europe’s largest rail port. In terms of modal split, with a share of 53.5%, rail transport is clearly ahead of truck (38.1%) and barge transport (8.4%).
Container cargo mirrors this trend. In the previous year, 2.5 million TEU were transported to or from the hinterland of the Port of Hamburg by rail, marking a 6.4% decline. Rail transport constituted nearly half (49.7%) of all containers in hinterland traffic, with road transport representing 47.9% and inland waterways making up 2.4%.
Ports of Indiana shipped 12.6mt (million tonnes) of cargo in 2023, the secondhighest tonnage in its 63-year history. This is a 6% increase over 2022 and second only to 2018, when Indiana’s three ports handled 14.8mt of cargo. The largest single cargo increase in 2023 was coal exports from Mount Vernon, which jumped 78%. Fertilizer increased more than 11% overall, with double-digit gains at Mount Vernon and Jeffersonville, while soy products, minerals, ethanol, DDGs and cement also increased.
“At Ports of Indiana, we are privileged to partner with a group of world-class companies that ship critical cargoes to and from our regional economies,” said Ports of Indiana CEO Jody Peacock. “The dedication and hard work of these businesses is why Indiana ranks 12th in the nation for maritime shipping and why our maritime economy is booming. The 2023 cargo volumes were even more impressive considering some of the major challenges facing our industry this past year with low water levels and lock closures.”
Indiana’s three-port system maintained substantial tonnages despite several factors that stymied the US inland maritime industry as a whole: an extended lock closure on the Illinois River, nearrecord low water levels on the Mississippi River, and a weeklong work stoppage by Canadian St. Lawrence Seaway employees.
Ports of Indiana also experienced significant growth in rail shipments during
2023, with rail carloads increasing 28% year over year. All three ports increased rail shipments as Mount Vernon led the way with 39,909 rail cars, a 42% increase from 2022. Overall, Ports of Indiana handled 65,141 railcars in 2023.
The 2023 business results also indicate that Ports of Indiana’s economic impact increased year over year. A 2023 study found that Indiana’s three ports supported more than 49,000 jobs and generated $8.7 billion annually for the state’s economy, $3.5 billion in annual wages, and $536 million in state and local taxes.
“This is an exciting time at Ports of Indiana,” said Peacock. “We’re going through a transformational period as we build up our internal resources to spur
port growth and work through transitions of key terminal operators at all three ports. We’re cautiously optimistic about the 2024 cargo outlook, but we’re more excited about how our team is positioning Indiana’s port system for long-term future growth.”
Ports of Indiana is a statewide port authority operating three ports on the Ohio River and Lake Michigan. Established in 1961, Ports of Indiana is a self-funded enterprise dedicated to growing Indiana’s economy by developing and maintaining a world-class port system, and by serving as a statewide resource for maritime issues, international trade, and multimodal logistics.
TAssociated British Ports (ABP) has given a lease to Enicor who have a multi-millionpound deal with British Steel to take 400,000 tonnes of skim iron, sometimes known as pig iron skulls, and export it overseas.
Two deep sea vessels have been organized for a total of 47,000 metric tonnes to ship the by-product to international markets. This is the largest scrap export shipment within the last few years. The first vessel arrived in port midJanuary to collect the first shipment.
Simon Bird, Regional Director for the Humber ports said: “We’re delighted that Enicor recognize the importance of Immingham as a gateway to the rest of the world. The Port of Immingham is ideally located with excellent links to global markets and will be vital in helping them fulfil their plans as a business.”
James Bowers, CEO of Enicor said: “Enicor has gone from strength to strength in recent years seeing turnover exceed £100m and tonnages exported reaching new levels.
“The opening of our Immingham dock operations is a milestone moment for the company allowing us to sell deep sea cargos worldwide. We understand that our first vessel of scrap exported will be the largest in recent years. We hope to maintain a
close relationship with ABP over the coming years and push to execute vessels of similar size every four to six weeks. We would like to thank ABP for their support thus far.”
Enicor was founded in 2023 after KJB Consulting acquired BW Riddle, a metal recycling business and is based in Lincolnshire.
ABP Humber Ports complex form the UK’s busiest trading gateway. The four ports of Immingham, Grimsby, Goole, and Hull handle more than 58mt (million tonnes) of cargo between them each year worth approximately £75 billion. Across the Humber, the ports support 34,900 jobs and contribute £2.5 billion to the UK economy.
ABP Humber’s major investment programme ensures the ports offer state-of the-art cargo handling infrastructure and equipment, alongside a highly skilled team who can handle a vast array of cargo safely, efficiently, and sustainably.
ABP Humber works collaboratively to build long-term partnerships and deliver the right supply chain solutions for customers, including value-added services and new facilities tailored to suit their business needs.
Its Port Operations are complemented by its Pilotage Service and Vessel Traffic Service which ensure vessels are safely navigated through the Humber Estuary.
ABP Humber offers 364 hectares of development land across its port locations
capable of attracting investment and delivering transformational benefits for the economy both locally and nationally.
The ports are all part of the new Humber Freeport, which offers three tax sites with an exceptionally business-friendly tax and regulatory environment for potential manufacturing investors.
ABP Humber supports its local communities. The ABP Humber Coastal Half Marathon and 10k is now in its 7th year and complements ABP’s race sponsorship across the country.
Associated British Ports (ABP) is the UK’s leading ports group, with 21 ports and other transport-related businesses, creating a unique national network capable of handling a vast array of cargo. It is driving growth, contributing £15 billion to the UK economy every year and supporting over 200,000 jobs.
ABP is redefining what Keeping Britain Trading means in the greener, cleaner economy.
ABP IN NUMBERS
~90mt of cargo handled each year; v 4,000 hectares of port estate owned; v 38% reduction in GHG emissions v from 2014–2021; 18 out of 21 ports have renewable v energy generation projects; and >£55 million investment made in low v emission and renewable energy generation technologies.
For testing purposes before handoff to a client, LBS cranes are still mounted on the more common LHM undercarriage so they can be moved more easily.
The contract for the purchase of four cranes was signed during the Intermodal event in São Paulo in 2022. The cranes were delivered in September and are now part of a fleet of 16 barge-slewing cranes in operation at the port. Founded in 1987, Porto Chibatão in Brazil plays a crucial role in the logistical operations and economic impact on the regional economy. It serves the Manaus industrial park, also known as the Manaus free trade zone, and is essential for processing increasing cargo volumes in the region.
Since 2007, Liebherr and Porto Chibatão have been building upon a successful and growing business partnership. It has been characterized by a growth strategy that included an early adoption of Liebherr FCC and LBS type cranes at the port, trendsetting in the world. Porto Chibatão today is the biggest private port and Liebherr port equipment customer in Latin America, featuring 42 different cranes, including gantry cranes, fixed cargo cranes, and barge-slewing cranes.
The port spans an impressive one million square metres. Its static load capacity stands at a staggering 40,000 TEUs, demonstrating its ability to handle substantial cargo volumes with ease. The
four LBS 800 are equipped for container handling and have a turnover of up to 35 containers per hour and can lift up to 104 tonnes. To accommodate improved visibility during operations, the cranes were also built with a tower extension. Based on the latest Liebherr mobile harbour crane design, the cranes also feature an updated interior cabin and a more digital architecture overall that paves the way for partial automation and future assistance systems.
Shipping and port logistics continue to play a key role in the global supply chain. Porto Chibatão’s berthing facility consists of 1,026-metres-long floating pier or quay for embarking and disembarking ships coming from long-haul navigation and cabotage. It has the capacity to simultaneously operate eight vessels with draughts of up to 20 metres. Among the important shipping companies that use the harbour are Hamburg Süd, Maersk Mercosul Line, LogIn, CMA-CGM, MSC, and general cargo ships and steel products destined for the Manaus Industrial Pole. Products include materials from the textile industry, electronics, and two-wheelers, among many other goods.
“As a leading port operator in Brazil, we are always looking for innovative solutions to improve our performance and sustainability,” notes Jhony Fidelis, General Executive Director of Grupo Chibatão. “These particular LBS 800 cranes from Liebherr are a perfect fit for our vision, as they offer high productivity and low emissions. We are proud to work with Liebherr, a company that shares our commitment to excellence and fostering environmental responsibility.”
In recent years, Porto Chibatão received the go-ahead from Antaq, Brazil’s ports and waterways regulatory agency, to move forward with its 98 million reals — about €18.3 million — expansion plan to lengthen the floating pier from 710 metres to 1,026 metres. The expansion is needed to process increasing cargo volumes in the Manaus industrial park.
The trend for transporting commodities is ultimately towards larger and more goods, overall. Successful ports orient themselves around an effective growth strategy. It’s been almost ten years since the first LBS 600 was delivered to Porto Chibatão. With the LBS 800, a new marker has been set. And the needs of the future can be effectively met, today.
Maputo Port Development Company (MPDC) has announced its annual results, highlighting significant growth in various metrics, consolidating its position as one of the region’s main economic drivers.
Of the 31.2mt (million tonnes) handled, approximately 25mt were made up of various ores, including chromium, ferrochrome, magnetite, coal, phosphate ore, vanadium, titanium, copper, vermiculite, among others. “The handling of these cargoes reflects the diversification strategy on which the Port of Maputo has focused in recent years,” says Osório Lucas, MPDC’s Chief Executive Officer.
One point to highlight is the more balanced distribution of the volumes transported. While 61% was handled by road, 39% was transported by rail, indicating a significant increase of 8.4% in rail use compared to the previous year, thus also
setting a new record for the Port of Maputo.
“The sustainable growth of the transportation corridor continues to be a concern for MPDC. Although there is growth in rail handling, demand for the port has grown exponentially and so we will continue to work with CFM to seek a better balance between rail and road cargo,” explains the Executive Director. Another of the measures adopted by MPDC during 2023 to mitigate road congestion was the opening of the Truck Traffic Management Park in Pessene, which opened in November.
The substantial increase in the volume of cargo has had a direct impact on the value of the fixed and variable fees paid to the Government of Mozambique. In this context, the Port of Maputo contributed more than $41 million dollars (excluding taxes and dividends to shareholders),
marking a growth of 29% on last year. This financial increase consolidates the Port’s economic contribution to the country’s development.
The year 2023 was also marked by a strong investment in Mozambican culture. The various celebrations associated with the Port of Maputo (20th anniversary of the concession to MPDC, 120 years of the Port of Maputo in partnership with CFM and the end of the year in partnership with Rádio Moçambique) were marked with unique musical shows, accessible to the general public, with a strong focus on national musicians and artists. The social investment component included support for Kanyaka, with participation in the rehabilitation of the passenger transport vessel and investment in the executive project that will allow work to begin on the rehabilitation of the Kanyaka jetty in 2024.
HOPA Ports has released results for the 2023 navigation season, reporting a combined total cargo of 11,293,179 metric tonnes through the ports of Hamilton and Oshawa. The 2023 total was a 9% increase from 2022, marking the second-highest volume in the past decade. The season saw a total of 665 vessels, with 603 in Hamilton and 62 in Oshawa, taking advantage of the longest ever Seaway shipping season.
Commodities transiting the Ports of Hamilton and Oshawa represent approximately 30% of total cargoes transiting the Canada–US Great-Lakes Seaway system. HOPA’s cargo totals rose by 9% in 2023 versus a 3.38% increase in system cargo as a whole.
“Commodities fluctuate year-to-year driven by market and other external forces that are often beyond our control; that’s why we are focused on future trends. Our investments in trade-enabling infrastructure, and those of our tenants and partners are the engines of longer-term performance,” said Ian Hamilton, President & CEO of HOPA Ports.
Over the past 15 years, HOPA and partners have invested close to $1 billion in transportation infrastructure and terminals that have enabled the steady growth of key commodities. This trend continues with the recent announcements of a $135 million sugar refinery, a new rail container facility, a new flour mill, and HOPA capital works for 2024 exceeding $40 million.
In 2023, agri-food commodities through the Ports of Hamilton and Oshawa reached a combined total of 3.5mt (million metric tonnes), an increase of 5% over 2023. Agrifood represented 31% of total HOPA cargo in 2023, compared to an agri-food total of 18% in 2013, and just 10% in 2009. This growth has been driven by major investments in agricultural-related terminal infrastructure. Over the past 15 years, the port has attracted $500 million in new investments by agri-food companies, including grain handling terminals, fertilizer terminals, and Ontario’s leading mid-size brewery. HOPA kicked off 2024 by announcing even more agri-food investment, in the form of a new flour mill, to be constructed by Parrish & Heimbecker, and a new sugar refinery, to be constructed by SucroCan.
“Food processing is a $4.8 billion sector in Ontario, and we’re delighted to be providing the key ingredients to grow this sector further, in the form of the location
and logistics solutions that food manufacturers need,” said Hamilton.
At the Port of Oshawa, plans for a new grain export terminal are now under way. “We hope to have shovels in the ground in the coming months to enhance export capacity for grain grown in Durham, Kawartha and other GTA-east grain producing regions. The new export terminal is expected to be ready for the fall 2024 harvest,” said Hamilton.
Steel and steel-making commodities had a stellar year in 2023, exceeding 6.2mt, a 13% increase compared to the previous year.
HOPA continues to invest in capacity for the value-added steel-related manufacturing supply chain. In 2023, construction of a $10 million, 60,000ft2 rail transload facility for steel products proceeded on-track. This facility, to be operated by NSD Warehouse & Distribution and supported in part by the National Trade Corridors Fund, will make new connections between transportation modes and add more than 100,000 metric tonnes of new steel handling capacity at the Port of Hamilton.
Cement, asphalt and aggregates led the cargo mix at the Port of Oshawa in 2023. “These commodities are critical to infrastructure, housing and manufacturing –everything we need to keep our regional economy humming,” said Hamilton. “It is our job to make sure we have the supply chains in place to move these essential goods reliably and efficiently.”
HOPA continued to advance its Niagara Ports strategy, which now encompasses more than 600 acres of industrial space in Niagara. In 2023, three new parcels of land were transferred by Transport Canada to HOPA management: two at the Thorold Multimodal Hub and one in Port Colborne, creating more opportunities for businesses to locate and grow as part of HOPA’s Great Lakes port network. The Thorold
2023 Tonnage – Hamilton & Oshawa
Multimodal Hub welcomed its 20th tenant in 2023, and the Hub was awarded a Canadian Urban Institute ‘Brownie’ Brownfield Redevelopment Award for its innovative approach to repurposing a legacy industrial site for modern uses.
HOPA was also thrilled to be recognized in 2023 as Bulk Port of the Year by International Bulk Journal. “Our ports are essential trade gateways to Canada’s largest and most dynamic economic region,” said Hamilton. “Through expanded industrial lands and a comprehensive range of multimodal services, we contribute to economic prosperity and a resilient, futureready supply chain.”
As an integrated port network, the Hamilton Oshawa Port Authority (HOPA) offers port and marine assets in Hamilton, Oshawa and Niagara, to support Ontario industries and facilitate trade. By investing in high-quality infrastructure and prioritizing sustainability, HOPA helps build prosperous working waterfronts in Ontario communities. Overseeing more than 1,400 acres and more than 180 tenant companies, 40,000 Ontario jobs are connected to the cargo that passes through HOPA’s integrated ports.
At its New Year cocktail party, the Port of Sept-Îles revealed that it had reached an alltime high with 36.6mt (million metric tonnes) of cargo handled at its facilities in 2023. The previous record was set in 1979 with 34.9mt.
“This new milestone is of national significance and makes the Port of Sept-Îles one of the leading ports in the country,”
said Pierre D. Gagnon, President and CEO of the Port of Sept-Îles. “Thanks to this new record, we have proudly reclaimed second place among Canadian ports in terms of annual volume of operations, ahead of the Port of Montréal and behind Vancouver. We have also reaffirmed our status as the largest mineral port in North America.”
The Port of Sept-Îles experienced new momentum in 2023, including an overhaul of its mission statements, vision, values, and strategic priorities. Numerous community stakeholders were involved in the process that led to these changes.
To guide future development and with the intention of opening a dialogue with the
community, in October 2023 the Port of Sept-Îles also launched an online public consultation entitled “Ré-imaginez le coeur de Sept-Îles” (Re-imagine the Heart of Sept-Îles). This innovative approach to collecting development ideas for the harmonization of riverfront spaces in the lower town was a great success: 6,819 participants, 55 projects submitted, and 748 votes on the specially designed platform.
“We would like to thank all the stakeholders and citizens who participated in our two consultation processes. Your contribution is essential to guide the future development of your Port. With 2024 marking the 25th anniversary of the port authority’s autonomy, we can get the next quarter century off to a strong start thanks to a transparent and sustainable connection with our communities,” said Pierre D. Gagnon and Bernard Lynch, Chairman of the Board of Directors.
In 2023 and with the support of the Government of Québec, economic players in the region, namely the Port of Sept-Îles and the economic development corporations of Sept-Îles and Port-Cartier,
were able to proceed with the consolidation of Port-Cartier-Sept-Îles industrial port zones. The creation of this large new area will help make certain sectors with strong industrial potential more attractive to developers worldwide, especially in the global context of energy transition and opportunities related to decarbonization.
“Considering that the maritime activity of the industrial port zone of Port-CartierSept-Îles represents 50% of the total operations on the St. Lawrence River as well as 15% of the commercial value of Québec’s annual exports, it goes without saying that we have a world-class industrial ecosystem that we must promote on a large scale,” said Pierre Gagnon.
The current interest of major steel companies in high-purity iron from the Labrador Trough to accelerate the iron industry’s decarbonization efforts is also a unique opportunity.
International developers are already targeting the region as a base for their green projects.
“We have all the right assets to allow
our iron products to be processed locally and to shift towards the production of green steel here in the region. Now more than ever is the perfect time for all socioeconomic players in the region to support everything that needs to be done to make the most of these unmissable opportunities!” said Pierre Gagnon and Bernard Lynch.
Boasting diverse, state-of-the-art facilities, the Port of Sept-Îles is North America’s largest ore-handling port, with a projected volume for 2024 of more than 40mt. It is also recognized as the largest primary aluminum port terminal in the Americas in terms of operational volume. The facilities at the Port of Sept-Îles play a vital and strategic role in the economy of Eastern Canada.
The port is also deeply committed to sustainable development and has pioneered the first environmental observatory on the St. Lawrence Seaway System to monitor the marine ecosystem as well as a research chair with Université Laval to study coastal ecosystems and port operations.
Marcor Stevedoring’s eagerly awaited new mobile harbour crane was delivered onto shore at the Hartel Terminal mid-February 2024.
Marcor expressed its gratitude to UWL and the crew of Bravewind for her safe voyage and good cooperation during the discharge.
The stevedoring company’s first Liebherr LHM 800e, with its 64m reach and peak capacity exceeding 2,000tph (tonnes per hour), perfectly aligns with its bulk, bagged and containerized operations.
The crane is not only unique in its performance and capabilities. It is also the first of its kind to operate fully electrified.
The new LHM 800e purchased by Marcor Stevedoring will play a key role in contributing to more economical and environmentally friendly operations at its forthcoming dry bulk terminal. The bulk cargo capacity of this giant is also unique at up to 2,300tph. Technical innovations in Liebherr’s latest-generation mobile harbour crane — including its electric drive unit, updated cabin, and more digital infrastructure — help ensure that current and future demands by the terminal can be effectively met. For example, it’s equipped for digitalized operating management and the integration of future assistance and partial automation systems. These benefits contribute to a more streamlined operation of the crane, saving time and costs for the operator.
At the signing ceremony, held in Rotterdam on 21 February 2023, Ulf Boll, CEO at C. Steinweg Group, said “Our acquisition of a Liebherr LHM 800 for the Steinweg Hartel Terminal is an important step for us in ensuring that our bulk operations and services maintain strong growth. We commenced the development of a new 160,000 cubic metre quay-bound bulk warehouse, and these are directly reachable through a single manipulation crane grab. Size, performance, and mobility were therefore important factors in our investment decision. The crane’s electric motor and Liebherr’s service offering rounded off this package. The fact that it’s fully electric is also aligned with our ESG strategy and our path to a carbon neutral operation. We’re excited to see the LHM 800 in action at our terminal and look forward to a productive future with Liebherr as a partner.”
In this third and final blog of the series, conveyor belt specialist Bob Nelson explains how some conveyor belt manufacturers are cutting costs by supplying belts that do not meet the promised specification.
As any conveyor operator will know, industrial conveyor belts consist of two parts — an inner carcass protected by an outer layer of rubber commonly known as ‘covers’. The most popular type of construction uses a carcass consisting of layers of synthetic fabric.
These can range from single and dualply constructions right through to multiply belts that contain five or more layers of fabric, each with thin layer (skim) of rubber in between that bonds the layers together and helps to absorb impact energy. The second but much less
commonplace type of construction is mostly reserved for long distance conveying and uses strong steel cords that are completely encompassed by rubber.
The most commonly used construction are multi-ply belts that, as the name implies, use multiple (three or more) layers of synthetic fabric. Within that, the most popular synthetic fabric consists of a mixture of nylon and polyester (EP). This is because, for multiply belts at least, polyester and nylon fabric have the best balance of mechanical properties including allowing the belt to run straight and true, to trough, to flex round pulleys and drums and stretch while at the same time
Running straight and true — for multi-ply belts, polyester and nylon fabric have the best balance of mechanical properties.
Fraudulent practice — the use of totally polyester (EE) fabric instead of the specified polyester/nylon mix (EP) in multi-ply belts can cause multiple problems.
A multi-ply construction belt.
providing sufficient transversal rigidity and longitudinal strength.
However, although they may be the same basic specification, there are often huge differences in the quality of the fabric plies between one belt and another. This is because, in an effort to offer the lowest possible price, manufacturers use cheaper, lower quality fabrics where the more costly nylon transversal weft material is kept to a minimum. Although the required tensile strength may be achieved, rip and tear resistance is noticeably reduced and the elongation (elasticity) is insufficient. Splice joint unreliability and steering and handling problems are all symptomatic of cheap, low-grade fabric.
An increasingly common and even more blatant deception involves the use of totally polyester (EE) fabric plies in a carcass that is claimed to be an EP carcass construction. This is a particularly important point because the manufacturer is deliberately not supplying the specification of belt that the customer asked and paid for. The reason for the deception is that polyester (EE) fabrics cost around 30% less than EP so it is a big help in creating the perception of a lower ‘like for like’ price. Although the use of totally polyester (EE) fabric in multiple ply belts compromises a whole range of essential mechanical properties, the manufacturer knows that it is highly unlikely that the unsuspecting end-user will have laboratory tests carried out that would reveal their fraudulent behaviour. The same principle, of course, also applies to the quality of the rubber covers.
It is important to bear in mind that polyester (EE) fabric plies very much have their place in certain belt types and constructions. Traditionally, their use was mostly limited to industry-specific belts such as sawmills for example. Ironically, however, huge advances in single and dual-ply belt technology where uniquely designed full-polyester
Superior Industries, Inc., a US-based manufacturer and global supplier of bulk material processing and handling systems, has unveiled the most significant redesign to conveyor idlers in decades. This update is backed by a substantial $4.5 million investment in cutting-edge idler manufacturing equipment at its American production locations.
According to Superior Industries, a uniquely vertically integrated manufacturer of conveying equipment and components, these are the key innovations of the new idler design:
Ironclad weld joint at tube to end v disc: flush end disc prevents material entrapment between roll and frame. Weld bead is securely housed within the roll’s structure, ensuring added durability. Modern, robotic welding for greater weld penetration and extreme consistency.
Revamped designs of idler bearing v seals: a decade of rigorous testing results in an unmatched bearing protection system. Lifespan of standard bearing seals surpasses all other models tested. Premium Titanium® Seal provides extended longevity for demanding applications. Major upgrade to idler v manufacturing: improving industryleading pace, Superior achieves new heights in manufacturing speed. Manufacturing production rate of standard and custom idlers sees 35% increase. Integration of robotic manufacturing ensures a level of consistency previously unseen.
fabrics have been developed are proving to be a game changer. When weaved in a specific design, polyester provides a single-ply belt with greater support and rigidity.
Fenner Dunlop in Europe and North America with Ultra X and Nova X are the leading exponents in this field. What they do not do, of course, is claim that a belt is EP when in reality it is EE.
They say that cheats never prosper but, as I have hopefully explained over this ‘mini-series’ of blogs, there are many manufacturers out there who are cheating and who are profiting at the expense of their customers who think they are getting a bargain. As the old but still very true saying goes, you only get what you pay for.
Bob Nelson“Tens of thousands of Superior idlers are installed on our own conveyors every year, so roll performance really, really matters,” emphasizes Jason Adams, president of Superior. “The new idler exceeds our own high performance standards and we’re excited for other conveyor owners and operators to benefit from this upgrade.”
From Rock Face to Load Out®, Superior Industries engineers and manufactures
Lemniscate
groundbreaking bulk material processing and handling equipment plus cutting-edge components.
The 52-year-old manufacturer supplies bulk crushing, screening, washing and conveying systems plus all related parts and services for industries like aggregates and mining. In addition to manufacturing from its hometown in Morris, Minnesota, USA, Superior operates four additional US facilities, plus operations in South America and Asia.
©2023 Martin Engineering).
Are you just checking the boxes by doing required training hours, or is your goal to get a return on your investment? There can be huge improvements in production, maintenance labour, risk avoidance and cashflow by training employees on how to safely control fugitive materials in bulk material handling and then implementing changes, writes R. Todd Swinderman, President Emeritus/Martin Engineering. Unfortunately, half measures don’t get half results, so training alone won’t be sufficient. Following through on what has been learned is the key.
Training should be robust enough to
break the “We’ve always done it that way” mentality and encourage creativity in problem solving with safety at the forefront of the design. Companies that place a priority on safety — and address fugitive material problems seriously — benefit from fewer safety incidents, less regulatory oversight and higher productivity and profits.
Everyone operating, cleaning or maintaining conveyors should be trained in the hazards of belt conveyors and bulk material handling. Operators and cleaning crews
should have a basic understanding of what is normal conveyor operation and what the common problems are, so they can be aware that there are ways to reduce dayto-day problems such as spillage and belt wander.
Basic training includes topics such as guarding, identifying problems and safe work practices. Appropriate safety training emphasizes how the belt can store elastic energy even when Lock-Out Tag-Out procedures are followed and why additional securing of the belt is required. Further, with the retirement of many experienced operators and mechanics —
and the difficulty in finding new workers — it becomes critical that new employees understand the basics of conveyor design and operation.
The engineering and maintenance staff should be additionally trained in fundamental conveyor design concepts, so they can analyse cause-and-effect relationships. Quite often the visible signs of poor conveyor operation are not the root cause of the problem. For example, using guide rollers to force the belt to track does not address the fundamental reason for the belt mistracking and usually results in belt edge damage.
Sometimes training is on a specific piece of equipment with the goal of creating trainers who can educate the rest of the maintenance department. This approach works well with certain types of equipment but ends up with one or two motivated and well-versed technicians who can troubleshoot.
A mechanic trained in installing problem solving components will run into a myriad of physical constraints. First, the original conveyor design and subsequent modifications can make it impossible to install equipment according to the manufacturer’s instructions without a complete redesign. Second, often
structural obstructions or conveyor arrangements don’t allow enough room for installation, clear views for inspection or access for safe and easy maintenance access according to industry standards.
Conveyor design training for engineers and mechanics is critical so they can diagnose problems with an understanding of fundamental design methods. Systems are incrementally modified over time to minimize problems when belt speed and capacity exceed the original design specifications. No two conveyors are identical and even twin conveyors side by side can act differently. So, adhering to standard design methods allows one technician to make these slight adjustments and another technician to recognize the intentions even without the prior technician present.
Training alone rarely results in meaningful actions to improve conveyor performance. When management understands the clear links between safety, cleanliness and productivity, it is much easier to turn training into results. There are many variations of how this can work, but most success stories have common threads:
basic training in conveyor hazards and v the methods for controlling fugitive
materials; training in conveyor design v fundamentals and the root causes of common problems; management participation in the v training to show support; a pilot programme and measured v results; and a long-term plan implemented from a v successful pilot programme.
A walkdown of one or two ‘problem belts’ and a review of goals the day before the training help the instructor focus on sitespecific problems and management’s expectations. The survey and interview usually take a few hours to half a day. The goal is for the instructor to have actual examples to show the class their problems are not necessarily unique. An experienced teacher will most likely have examples showing similar problems and their solutions.
The first day typically starts with reviewing the typical problems and getting the class to talk about their specific challenges. The class identifies a couple of problem conveyors and the class splits into small teams. Each team can look at the same problem or select different ones. Photos and videos of the issues are taken to be used in the problem-solving
discussions.
The rest of day one and the start of day two review basic design principles that relate to the problem conveyors. The discussion centres on possible root causes and solutions. Once the teams reach an agreement on a way forward, they prepare a short presentation with the help of the instructor, using their actual conveyor problems and the knowledge they gained. The presentations may also include an estimate of the cost of the proposed solutions.
At the end of day two, management is invited to listen to the team presentations and solutions. By participating in the class presentations, management shows a commitment to making improvements and has an opportunity to ask questions. The trainees, by making the presentations, show the knowledge they gained and support for the proposed solutions. The photos, videos and inspection sheets help shed light on issues and solutions crews experience every day.
It is critical at this step that the manager(s) who attend the presentations have the authority to act on the proposals and are willing to commit to a pilot program to prove the theoretical results can be turned into reality.
One or more conveyors are selected for a
trial program. While it is normal to select the “worst” conveyor, keep in mind that half measures do not get half results, so consider the project’s scope. Once a conveyor(s) has been selected, detailed proposals for retrofit can be obtained. An experienced person from the selected equipment supplier should overview the designs, offer feedback, and supervise the installation. Either outside contractors or in-house personnel can be used. Sufficient
downtime must be allocated to properly modify the conveyor.
Measuring results from improvements is important but relatively easy to do. Photos and videos of before and after must be taken. Dust levels are measured using common instrumentation, spillage can be measured by placing buckets or trays in appropriate locations and carryback is measured by placing a tarp under several return idlers close to the discharge pulley.
A
The collected fugitive materials are weighed for comparison after the conveyor has been modified. Dust and spillage sampling locations should be marked so the tests can be accurately repeated after retrofitting and an improvement percentage can be calculated.
The length of time for collecting samples can vary from a day to a week and should give a good representation of the average or typical operating environment and weather conditions. It is important to keep the dust monitor running even if the conveyor is running empty, as maximum fugitive dust levels are often detected when running conveyors empty long enough that the carryback dries out and becomes airborne.
Usually, the results of the pilot program are immediately noticeable, but there is a temptation to assume the problem has been fixed and to revert back to delaying maintenance without follow-up maintenance, causing the results to deteriorate. Therefore, the test period should extend to the next scheduled maintenance shutdown with periodic inspections and adjustments made by the equipment supplier in the interim to ensure optimum efficiency.
To demonstrate the benefit of safety to a company’s bottom line, the U.S. Occupational Safety and Health Administration (OSHA) created the online tool, ‘$afety Pays,’ which uses companyspecific economic information to assess the potential economic impact of occupational injuries on that firm’s profitability. The program estimates direct costs (claim cost estimates provided by the National Council
on Compensation Insurance) and indirect costs (provided by the Stanford University Department of Civil Engineering) and weighs them against financial details supplied by the company.
Experience has shown that the motivation to take action developed in the classroom often defaults back to prior habits. Sometimes it is a lack of funding, an understaffed maintenance department or a ‘run-till-broke’ mentality. The pressure to get back into production overwhelms the training that emphasizes the understanding of the root causes of inefficiency and injuries such as fugitive materials. A production-at-all-costs approach means the problems and safety concerns never go away, and employees just have to accept the poor performance and added risks, which demoralizes them.
It is incumbent upon management to take the safety and maintenance training as seriously as the staff, listen to the concerns of employees and fix the problem correctly the first time. As research has shown, companies that prioritize safety, training, and updating equipment enjoy fewer safety incidents, less regulatory oversight, higher productivity and greater long-term profits.
R. Todd Swinderman earned his B.S. from the University of Illinois, joining Martin Engineering’s Conveyor Products division in 1979 and subsequently serving as V.P. and General Manager, President, CEO and Chief Technology Officer. Swinderman has authored dozens of articles and papers, presenting at conferences and customer facilities around the world and holding
more than 140 active patents. He served as President of the Conveyor Equipment Manufacturers’ Association (CEMA) was the editor of CEMA’s 6th and 7th editions of Belt Conveyors for Bulk Materials, The Design Guide for Belt Conveyors. Swinderman is active on several CEMA committees including Chair of the Bulk Safety Committee and is a member of the ASME B20 committee on conveyor safety which set US conveyor safety standards. Swinderman retired from Martin Engineering to establish his own engineering firm, currently serving the company as an independent consultant.
Martin Engineering has been a global innovator in the bulk material handling industry for more than 80 years, developing new solutions to common problems and participating in industry organizations to improve safety and productivity. The company’s series of Foundations books is an internationally recognized resource for safety, maintenance and operations training — with more than 22,000 print copies in circulation around the world. The 500+ page reference books are available in several languages and have been downloaded thousands of times as free PDFs from the Martin website. Martin Engineering products, sales, service and training are available from 17 factoryowned facilities worldwide, with whollyowned business units in Australia, Brazil, China, Colombia, France, Germany, India, Indonesia, Italy, Malaysia, Mexico, Peru, Spain, South Africa, Turkey, the USA and UK. The firm employs more than 1,000 people, approximately 400 of whom hold advanced degrees. DCi
A paradigm shift can be defined as a fundamental change in basic concepts and experimental practices, and it happens when usually it is replaced by a new and different concept.
Some of the solutions currently in place for reclaiming bulk material from storage piles were developed over a hundred years ago, with the first bucket-wheel excavators used in lignite mining being manufactured in the 1920s. The main function of these machines was continuous digging in largescale open-pit mining operations, removing thousands of tonnes of overburden a day.
The bucketwheel design on boom excavators has been extended to the reclaiming process, and today these machines are used to pick up bulk materials which have been stockpiled by a stacker, for onward transport of the materials to a processing plant. These processes can have low, medium and high material flow rates.
The main issue with bucketwheel technology on boom reclaimers is low efficiency, because there are large variations
in the tonnes per hour reclaiming rate due to the need to reclaim material from different benches of the stockpile.
Reclaiming the top benches of the stockpile is a challenge, and this has a detrimental influence on the average capacity in tons per hour to reclaim an entire pile. Also, reclaiming of the two halfcones at each end of the stockpile is inefficient and produces a low reclaiming capacity. Another problem is that bucketwheel reclaimers leave a trail of material which is not reclaimed and remains on the storage yard floor. For these reasons SCHADE presents a far more efficient concept for reclaiming stockpiles.
The BWR reclaims the material from the pile by benches, which depending on the height of the pile, will regularly be 4 up to 5
benches, as shown in figure 1.
The BWR boom performs a slewing action to reclaim the benches, with predefined angles and rotation for each bench. The boom slew determines the material cutting contour of the bucketwheel as www.drycargomag.com
Slew
Bench start angle end angle
1 12.5° 77.5°
2 22.5° 65.0°
3 30.0° 52.5°
4 47.5° 37.5°
shown in figure 2.
The reclaim angles of the stacked material per bench are defined in figure 3.
Reclaiming the pile by slewing the boom in each bench and pushing back the BWR creates the configuration shown in figure 4.
Reclaiming the benches in the sequence
1, 2, 3 and 4, is carried out with synchronized movements of the bucketwheel moving forwards (1–2), backwards (2–3), lowering the boom (3–4) and repeating the movements in the lower benches, as shown in figure 5.
The PSR reclaims material from one side of the pile using two parallel booms with scraper conveyors equipped with shovels and chains. The material is reclaimed in layers by scraping the side of the pile with progressive filling of the shovels, and by moving the portal forward against the stockpile at a constant speed, see figure 6.
The shovels and scraper chains are the most important mechanical components of the PSR, and their configuration determines the PSR reclaiming efficiency, see figures 7 and 8.
To reach reclaiming capacities above 3,000tph (tonnes per hour), two booms equipped with scraper conveyors are required, see figure 9.
The machine is a portal reclaimer. It is used for removing stockpiles of bulk material. The machine scrapes the bulk material from the pile and transports it through transfer chutes onto the discharge conveyor belt. It can be used to remove the entire stockpile or individual sections of the stockpile. The travel path inside the area of operation is limited by switches in the software, and can be readjusted to new stockpile boundaries when areas of the stockyard have been completely emptied.
The pile is reclaimed by the scraper boom. The scraper boom is fastened to the travel drive side with bearings and suspended on the cantilever beam by means of a hoist. The scraper boom is raised and lowered with the hoist. To reclaim the bulk material the boom is equipped with continuous chains to which the scraper blades are attached. The machine moves on rails installed along the length of the stockyard.
During the reclaiming process the chain is driven by the chain drive, and travels around the scraper boom within the chain guides. At the same time the complete machine moves at working speed along the pile. The bulk material is reclaimed by the scraper blades and transported into the feeding chute at the end of the scraper
boom through the drag trough. The bulk material then drops onto the feeding roller table and is fed to the discharge belt. The discharge belt transports the bulk material to the following process, see figure 10.
When the machine has reached the end of a pile it stops for a short time. The scraper boom is lowered by the hoist. The machine subsequently continues operating in the opposite direction. This process is repeated until the pile has been fully reclaimed. Whether in manual or automatic mode the scraper boom is always lowered in stages according to preset values. These values are part of the machine control system. The machine’s performance depends principally on three factors; the immersion depth of the scraper blades into the bulk material, the chain speed, and the travel speed. These parameters are defined during commissioning.
The portal reclaimer’s range of movement is monitored electronically and is limited at the ends by mechanical limit switches. Monitoring prevents the range of movement of the stacker from intersecting that of the portal reclaimer. This ensures that the stacker does not convey material onto the portal reclaimer. To avoid
collisions between a portal reclaimer and a stacker operating in the same storage area the distance between these machines is continuously measured.
If a risk of collision arises the control software initiates the appropriate actions, see figure 11.
For increased clarity we have prepared a technical study to compare the application of a bucketwheel on boom reclaimer against a portal scraper reclaimer with double boom, under the same operating conditions, the results and conclusions of which will be shown below. The characteristics of the bulk material to be handled are described in figure 12.
The chosen stockyard machine is a bucketwheel reclaimer on boom, the operating conditions of which are shown in figure 13.
The BWR construction project firstly involves the definition of the peak reclaiming capacity, which depends on the optimization of the nominal capacities reclaimed for each bench. There is specific software for the application which defines all the design characteristics of the BWR as shown in figure 14.
The most significant variable in this input is the factor K, which defines the force to cut the pile, and is determined by the material characteristics and the lump size, see figure 15.
The output of the software calculates the nominal capacities obtained in each
contour depending on the slewing boom angle for each bench, see figure 16.
With this effective reclaiming capacity data an evaluation of the total reclaiming time of the complete stockpile, measuring 243m long x 40m wide x 17m high, is carried out, see output figure 17.
The resulting time to reclaim a complete stockpile is shown in figure 18.
The main data of the PSR is shown in figure 19.
With this effective reclaiming capacity data an evaluation of the total reclaiming time of the complete stockpile can be carried out, as shown in figure 20.
The above calculation is carried out until the stockpile has been completely reclaimed. The result is shown in figure 21.
Figure 22 shows the main details of the comparison between BWR and PSR.
After reclaiming with a BWR the stockpile is very disorganized, see figure 23.
After reclaiming with a PSR the stockpile is flat and clean, see figure 24.
The chart in figure 25 shows the variability of the reclaiming capacity when performed by a BWR, and the following conditions:
uneven material flow v optimized design of the yard belt v conveyor not possible
average rate of reclaim approx. 70% v of nominal capacity
The chart in the Figure 26 shows the reclaiming capacity when performed by a PSR, and the following conditions:
constant material flow v optimized design of the yard belt v conveyor
average rate of reclaim >90% of v nominal capacity
SCHADE can demonstrate the following conclusions:
The BWR 12,000tph peak capacity is v much higher than the PSR 6,050tph peak capacity.
Average reclaiming capacities are v virtually the same for both reclaimers, which means that the PSR is much more efficient.
The material to be reclaimed, sinter v
Our serv did i tk ry and commissioning – from consulti support ry specific solutions ange of bulk handling r
• e and spare parts hotlin l After Sales Support dwide service network
ices include e
equipment Servic • Globa • us on LinkedIn and join our community! Visit
ng through to
feed and pellet feed, has a low grain size range, 6–18mm, which is not challenging to reclaim and allows the application of a lighter reclaimer machine.
Large grain sizes up to 32mm, such v as lump ore, can also be reclaimed by a PSR.
The reclaiming time for the entire v stockpile is practically the same for both machines, once again showing the relative efficiency of the PSR for the same type of work.
The BWR leaves unrecovered v residual material of at least 2% after finishing storage pile reclaiming. This volume of residual material could be even larger if an efficient method is not applied for reclaiming the two half-cones at each end of
Martin manufactures railcar connectors, industrial vibrators and railcar openers that help evacuate bulk materials like coal, aggregate or grain more efficiently. From the railcar through the unloading gate and onto an under-track conveyor system — these tough, long-lasting products allow you to transfer more cargo with shorter discharging times, deliver better material containment to prevent spillage and eliminate the risk of sending a worker under the gate.
the pile. The measure to combat this is to use a shorter reclaiming step advance.
The BWR is at least 37% heavier than v the PSR, not including the counterweight.
The BWR needs a counterweight (120 v tonnes) to balance the machine, while the PSR is already a balanced machine and does not need any counterweight.
A PSR has a more compact design, less v civil work is required.
The power consumption of the BWR v is at least 28% higher than the PSR, resulting in higher operating costs.
The BWR manoeuvring area is around v 43% larger than the PSR, as it needs to have a greater push back area when operating with the boom at an angle of 12° to reclaim the lower benches.
The duty cycle of the BWR v bucketwheel is twice that of the PSR scraper. The result is much greater wear on the wheel parts (lips and teeth of the buckets) in contact with the reclaimed material versus the scraper parts (lateral plates and teeth of the blades).
The peripheral speed of the BWR v bucketwheel is 5 times the speed of the PSR scraper shovels.
A BWR has high dynamic loads on the v steel structure caused by periodic digging action, which may result in structural failures and cracks later on.
Established in 1976 with an original capacity of 12mt (million tonnes) per year, South Africa’s Richards Bay Coal Terminal (RBCT) has grown into one of the world’s leading handlers of bulk materials. The terminal, which serves a long list of shareholders, is a vital export link in the South African economy. Today it has a nameplate capacity of 91mt per year, and Hägglunds hydraulic direct drive systems are integral to the material flow.
Among terminals for bulk materials handling, few compare with RBCT in either size or pace. The terminal owns 70km of rail network, and its tipplers offload incoming trains at a rate of 5,500tph (tonnes per hour). At the port end, there are four shiploaders with capacities of 10,000–12,000tph serving berths that can hold five Capesize vessels at any given time. At the centre of it all are 75km of conveyors and ten stockyard machines — one reclaimer, two stackers and seven stacker reclaimers — in a stockyard whose capacity is 8.2mt.
Kubendren Naidoo, General Manager, Asset Management, who has been with RBCT for 20 years, takes pride in the terminal’s control over these assets. All equipment is managed and maintained by RBCT staff, who have accumulated vast technical and procedural knowledge. Naidoo and his team are frequently consulted by visitors, who are particularly
curious about the Hägglunds hydraulic direct drive systems from Bosch Rexroth.
“RBCT is seen as the flagship of Hägglunds technology within the country,” Naidoo says. “We get visits from stateowned entities and other terminals around the world, who want to understand the technology we use. And many of them are amazed. Subsequent to seeing the Hägglunds hydraulic technology on our machines, many have retrofitted it on theirs.”
Back in 2005, Naidoo led RBCT’s own investigation into Hägglunds technology. As head of a development programme focused on stacker reclaimers, he explored the feasibility of moving away from traditional electromechanical bucketwheel drive systems. The business case for a Hägglunds solution was strong, indicating both higher uptime and payback within four to five years. Thus, it was implemented some years later when procuring a new stacker reclaimer.
In 2010, SR6 went into operation with a Hägglunds MB motor on the bucketwheel. “That was our first stacker reclaimer to have a Hägglunds drive system, and it was the first in Africa as well,” Naidoo says. “We ran that motor for ten years with no challenges and no downtime.”
In 2020, the motor was proactively
upgraded to a Hägglunds CBm. This motor type had been installed on SR1 and SR2, two new stacker reclaimers procured in 2019. “Our only reason for changing it out was that a new model was available, and to standardize with our other machines,” says Naidoo of the decision.
“We’d seen great reliability with that motor.”
Over the years, RBCT has not only installed Hägglunds drive systems on new machines. Since 2015, the terminal has retrofitted several older stacker reclaimers, replacing their electromechanical bucketwheel drives with Hägglunds solutions. The first of them, which was 37 years old at the time, was the first Hägglunds retrofit performed in Africa. The others have ranged from 32 to 41 years old when retrofitted.
“Since we were retrofitting on machines in excess of 35 years old, structural integrity and fatigue played a critical role in our decision-making,” says Naidoo. He notes the power density of the Hägglunds motors, which provide exceptional output with little size or weight. Continuing, he explains, “Our stacker reclaimers have a boom length of 60 metres. The lighter, more compact bucketwheel drive system removed up to ten tonnes off the boom tip, which had a significant impact on the stress patterns. It was a key factor in ensuring
materials you move. With our compact Hägglunds direct drive systems, you can adapt easily to the job at hand, taking advantage of full torque at an infinite range of speeds. And should an overload try to stop you, the drives’ low moment of inertia and quick response will keep your machines protected. We’ll support you too, with an agile global network and smart connectivity to bring you peace of mind. Driven to the core.
Hägglunds is a brand of Rexroth. www.hagglunds.com
that we get extended life from our stacker reclaimers.”
In effect, Naidoo points out, the advantages of power density are doubled on this type of machine. “There’s counterweight mass on a stacker reclaimer, so the reduction in weight on the boom is balanced by a reduction in counterweight mass,” he says. “Overall, the reduction in weight on our stacker reclaimers is significant.
That’s less weight to be carried around, so there’s also an element of energy efficiency.”
Today, RBCT has Hägglunds hydraulic direct drive systems on the bucketwheels of all but one stacker reclaimer. A major reason for this is the desire to protect uptime. Minimizing the time spent on bucketwheel service has been a top priority.
“When the gearboxes on our stacker reclaimers failed, it would take us up to seven days to replace them,” says Naidoo. “Now, with the Hägglunds systems, we can replace a motor in one shift, which is eight hours at most. Working with the Hägglunds team, we’re looking at opportunities to reduce it further — possibly to four hours.”
In addition, RBCT is experiencing more uptime during regular operation in the stockyard. This is due to the built-in overload protection, which allows the
Hägglunds drives to recover immediately after a stall.
“If a machine stalls, the operator can luff the machine out of the stockpile face and the system will start up again,” Naidoo says. “It detects that there’s less load and restarts automatically. With previous systems, we would need to get a technician to the machine to inspect and reset it. Once again, an improvement in turnaround time.”
Having seen success on the bucketwheels, RBCT is looking into the feasibility of Hägglunds systems in other stacker reclaimer positions, such as slewing drives. In addition, the terminal is using them elsewhere on site: on the rail tippler indexers. Here, Hägglunds systems replaced 24 outdated hydraulic motors that had long been prone to failure.
“Between 2010 and 2014, we implemented a process of improving the hydraulic filtration systems and introducing Hägglunds CA motors,” Naidoo relates. “We see greater equipment uptime and improved life expectancy from the Hägglunds motors. Given the cost we were incurring due to the high failure rate in those applications, there’s been financial payback.”
Just as on stacker reclaimers, uptime is crucial on the tippler indexers — especially
in light of the limited national rail capacity. “We face a constrained environment in terms of export volumes due to rail challenges,” says Naidoo. “Higher uptime is extremely beneficial to the value chain within South Africa, and to our shareholders.”
Overall, the impact of uptime in RBCT operations cannot be underestimated. “In our business, where time is critical, we want to eliminate any sort of delay,” Naidoo says. “Keeping a vessel waiting outside because of an unplanned failure results in significant demurrage charges that our shareholders pay. And that’s only the cost of the vessel itself. There are other indirect costs, so the numbers can add up quickly.”
Just as every minute of downtime costs, every minute of uptime means potential. The terminal’s nameplate capacity is 250,000 tonnes per day, but RBCT can far exceed this during shorter periods. To date, the record is 415,000 tonnes in 24 hours.
“When the vessels, trains and stock on the ground all align, we’re able to hit huge capacities in a short space of time,” Naidoo says. “The Hägglunds drive systems provide high availability, and that reliability is very cost effective. They probably represent five percent of the business of our machines. But while they’re a small component of our
With over 35 global installations, the CommTrac bulk terminal operating system (TOS) is TBA Group’s integrated software solution for bulk and breakbulk cargo. CommTrac is the award-winning way to plan, track and manage all types of noncontainerized bulk and breakbulk cargo. Highly scalable, it manages manual machinery and people while controlling the automated assets across a terminal, or terminal network, in real-time. It provides the tools, precision and management information required to simplify cargo operations. CommTrac maximizes revenue, profitability, compliance and growth potential while reducing risk.
CommTrac is used by large coal terminals around the world to drive operational performance and provide a robust inventory. In fact, one of CommTrac’s earliest installations, and longest standing customers, is Associated British Ports (ABP) which, in 2005, commissioned CommTrac for use at its Humber International Terminal.
Constructed in 2000, the Humber International Terminal (HIT) was a $45 million investment and facilitated the seamless transfer of imported coal from ships to the stockyard and further to the newly constructed rail load-out facilities. The terminal utilized a traditional crane/grab system, channelling products
As the system had previously been used primarily for grain cargoes, CommTrac worked closely with Associated British Ports to develop the additional functionality needed to handle coal at the Humber International Terminal.
onto the open conveyor system via hoppers. Semi-automatic stacker reclaimers were employed to deposit the products into the terminal’s dedicated stockyard. With a capacity to hold up to one million tonnes of coal, the stockyard utilized GPS mapping to ensure the segregation of each customer’s product.
Up until this point, CommTrac had been used primarily to manage grain and feed operations, and so the development team worked closely with ABP to develop the additional functionality necessitated by coal. The terminal environment included ship-to-shore cranes, stacker reclaimers, rail loading and truck operations, all of which were managed by CommTrac. The system was also responsible for inventory management, automation and integration with the site’s weighbridge.
While the focus at HIT has since shifted to wood pellets, CommTrac’s flexibility means that the site’s operators are still able to utilize its functionality, and this experience with coal handling allowed TBA to assist other coal terminals around the world, including Nectar Group’s Beira Terminal.
CommTrac’s most recent experience in the coal handling sector is Trigon Terminals in Canada. Established in 1978, Trigon Pacific Terminals serves as a crucial export hub for the abundant reserves of
metallurgical and thermal coal located in northern British Columbia and Alberta.
Privately owned by AMCI Group, Riverside Holdings, and the Lax Kw’alaams Band and Metlakatla First Nation, Trigon Pacific Terminals has earned recognition for its cost-effective operations. With the help of CommTrac, the facility operates around the clock, providing high-quality and efficient services. It can unload trains at a rate of 6,000tph (tonnes per hour) and load vessels at an impressive 9,000tph. In addition to handling petroleum coke, the terminal has the capacity to accommodate additional bulk volumes, with an annual shipping capacity of 18mt (million tonnes).
In 2023, Trigon handled 10.6mt (metric) of dry and liquid bulk products, accounting for just under half of the Prince Rupert Port Authority export volumes, an increase of 36% on 2022.
One of the key areas where CommTrac has made a real difference to all these terminals is stockpile management. Optimizing the available space and managing the routing of conveyors are crucial to the success of any coal terminal.
Efficient stockpile management helps coal terminals maintain optimal inventory levels. This involves balancing the supply and demand for coal, preventing overstocking or understocking situations. Maintaining appropriate inventory levels
ensures that the terminal can meet customer demands without excessive storage costs or supply shortages.
Coal quality can vary, and different customers may have specific requirements. Proper stockpile management allows terminals to segregate coal based on quality characteristics, such as calorific value or sulphur content. This ensures that customers receive the specific grade of coal they need, improving customer satisfaction and maintaining the terminal’s reputation.
Clearly, one of the unique characteristics of coal is that it is prone to combustion and the creation of dust. Properly managed stockpiles reduce these risks by controlling factors such as coal particle size, moisture content, and proper ventilation. Minimizing dust emissions not only contributes to environmental compliance but also enhances workplace safety.
And ultimately, properly managed stockpiles contribute to a safer working environment. A well-organized stockyard minimizes the risk of accidents, such as coal avalanches or collapse of stockpiles. This is crucial for protecting the safety of terminal personnel and preventing damage to equipment.
Key to CommTrac’s success has been its adaptability to a wide range of bulk and general cargo settings. As well as ensuring that the software can be adapted for use in a wide range of scenarios, its development team also have deep understanding and experience of all of the different environments and understand the unique challenges presented by each one, and this is especially true of coal handling.
Many coal terminals around the world are still dependant on several separate systems to manage operations. While every terminal will use IT to some extent, what’s often missing is a central hub. Instead, they are overly reliant on spreadsheets and manual processes — such as phone calls and emails. The problem with this approach is that there is no ‘single source of truth’, no one place that everyone in the organization can refer to for accurate and real-time data. This can make it difficult to analyse performance and plan for the future and can lead to major inefficiencies.
Beyond the obvious reduction in administrative burdens and enhancements in customer communications, the true return on investing in a TOS within a coal terminal lies in leveraging data to diminish demurrage costs and bolster operational efficiency. By monitoring the loading and unloading
of vessels, trains and trucks, as well as analysing stoppage events, the terminal gains a transparent perspective of their commercial situation. This data-driven approach enables informed decisionmaking, such as process modifications, additional shifts, or resource allocations, all grounded in facts rather than speculative guesswork.
Analysing this data retrospectively allows the coal terminal to identify the root causes of performance setbacks, fostering a culture of continuous improvement. Meanwhile, streamlining vessel turnarounds and optimizing storage utilization allows for increased capacity.
Based in Oro-Medonte, Ontario, Canada, BATEMAN is an industry leader in the creation and fabrication of material handling products designed to support the recycling, demolition, waste, industrial, port, railway, and forestry industries.
Founded in 1989, BATEMAN has over 30 years of experience in attachment manufacturing and continues to rapidly expand. In 2019, BATEMAN was acquired by GRYB International, a material handling attachments manufacturer, based in Victoriaville, Quebec.
GRYB International derives from GRYB Attachments, which was founded in 2007 and continues to expand with the additional acquisitions of Winkle Industries, Shearex, Serco Loaders, e-Trak, RadTech, and DalkoTech. GRYB International is a group of manufacturing companies that develop, design, and manufacture products
for a wide range of industries. Today, GRYB International employs over 400 individuals.
BATEMAN is proud to manufacture both hydraulic and self-contained diesel clamshell buckets for coal handling. The best solution for re-handling and digging, BATEMAN clamshell buckets help streamline processes. Its hydraulic clamshell buckets are available in light, medium, and heavy-duty configurations with either open or closed back designs. All clamshell buckets come equipped with BATEMAN’s severe-duty rotator with continuous 360° rotation and internal hydraulic relief.
BATEMAN rotators also feature fully sealed moving parts for submersion in water. Customers that are looking for something specific are welcomed, and invited to work with BATEMAN’s team to
design a custom bucket that is just right for their specific needs.
BATEMAN’s major clients include those in the waterway dredging, road salt, wood chip, and coal handling industries, as well as many more. In order to better serve its customers, BATEMAN also offers installation and support services, when needed, for all attachment purchases. The BATEMAN team additionally offers personalized and customized on-site installation services and training so that users and their teams can safely and properly operate their new handling equipment.
BATEMAN’s team also provides repair and refurbishment services for existing handling equipment — whether the original is BATEMAN brand or not — with remarkable efficiency. BATEMAN has an on-the-road service team that can repair
customers’ handling equipment, magnets, or generators. Its service team specializes in solving complex problems for any type of installation.
For customers that have just ordered a new BATEMAN attachment, BATEMAN can handle every aspect of the delivery, including customs clearance anywhere in the world. Its high volume of deliveries allows it to offer competitive rates to its customers. The delivery is flexible, provided the destination has capabilities to
receive and offload heavy equipment.
In order to stay competitive in the market, BATEMAN is continually investing in research and development to improve its products and actively innovate new, highquality material handling attachments. After years in the grapple business, BATEMAN decided to bring over some of its grabs’ strongest features to its clamshell buckets’ design such as rotations, pin design and retention, cylinder design, and frame design to provide customers with the dexterity of
an orange peel grapple.
In the past year BATEMAN is proud to have created, designed, and fabricated an all-new addition to its line up — the levelcut clamshell bucket. The level-cut clamshell bucket allows operators to dredge the bottom of waterways. What makes this clam so special? The bowls are designed to extract a specific amount of sediment from the bottom of bodies of water, all while leaving a flush surface to save operators time and money.
Coal mines and thermal power plants have used Rulmeca motorized pulley conveyor belt drives for more than 60 years. The Westmoreland coal mine is one of the many projects that relies on Rulmeca’s technologies.
Coal mines and thermal power plants have used Rulmeca Motorized Pulley conveyor belt drives for more than 60 years. From Kazakhstan to the US to Thailand, on every continent, mine and plant operators have learned that Motorized Pulley technology is reliable, safe, and easy to install. The Westmoreland Kemmerer, Inc. coal and lignite mine in Kemmerer, Wyoming is a 13,400 acre opencast mine complex which currently produces coal in three active areas from 12 primary seams and splits. It opened in 1881 as the Twin Creek underground mine to work the Adaville Formation and opened the Elkol Underground Mine in 1950. The mine supplies approximately 2.8mt (million tonnes) per year to a 700 megawatt thermal power plant, adjacent to the mine, via a 4,200 ft long overland conveyor.
Faced with an ageing silo reclaim conveyor and 20 years of coal in reserve, the mine decided to improve plant efficiency and plan for the future, by upgrading a problematic drive system on the 450ft-long 54in-wide inclined #130 conveyor in 2015. Fed by three weigh belt feeders beneath three silos at a rate of 1,600tph (tonnes per hour), this convex conveyor feeds the overland conveyor as well as a truck loader.
Eventually, the exposed drive system became unreliable due to chronic coupling failures (requiring weekly re-welding) and occasional pulley slippage. Slippage was most prevalent during winter weather temperature, which can approach –30°F.
In addition to improving conveyor reliability and performance, mine management has a strong desire to improve working conditions for plant personnel while reducing the cost of maintenance as much as possible.
Conveyors & Equipment of Salt Lake City, UT suggested that Kemmerer Mine consider a Rulmeca Motorized Pulley to replace the ageing #130 conveyor drive in 2015. By December of that year, one 180 HP model 800HD Rulmeca Motorized Pulley was installed in the conveyor head position. The installation
crew only required one shift to install the 5,700 lb Motorized Pulley thanks to the pulleys’ compact size, light weight, and ease of alignment. Time-consuming drive component alignment was unnecessary because all drive components are internal and pre-aligned.
Kemmerer Mine Maintenance Superintendent, Jerry Schinke, said, “The actual install of the Rulmeca Motorized Pulley was quick and painless. There was a noticeable drop in the noise level and I am looking forward to the heat from the pulley keeping the belt ice free.”
Motorized Pulleys, in general, increase system reliability, lower maintenance expense, improve personnel safety, save space, and reduce power consumption because they enclose all drive components within an oil-filled and hermetically sealed pulley shell.
The Kemmerer Mine’s adoption of Motorized Pulley technology is part of a local trend, which began in the trona mines in southwestern Wyoming several years ago in both surface and underground conveyors. The acceptance of Motorized Pulley technology throughout the US, across Europe, and in Asia began slowly in the 1980s but has accelerated in this century.
Rulmeca units used in this project include:
Motorized Pulley 1000H & 1000HD: v this is compact, offers equal weight distribution; and resistance against external influences. This RULMECA
motorized pulley type 1000HD is a highly developed reliable and strong drive with an outstanding power range of 160–250kW. It is able to take a high radial load and is robust in design. Therefore it is especially developed for use in: mining conveyors, excavators, stackers, reclaimers, and heavy loaded conveyors in gravel and sand.
The motorized pulley 1000HD is designed for tough, irregular, extreme and brutal working conditions. The compact design allows the design engineers to save material and cost when developing the conveyor. A high protection rate connected with the standard labyrinth sealing system it can be used in all ambient conditions.
Motorized Pulley 138LS, Ø 138mm: v this unit, with machined helical gear box, performs an efficiency, in a compact diameter of 138mm only. With a min RL of 300mm and powers ranging from 0.10 to 0.75kW this size of motorized pulley is suitable for most duties requiring such a small diameter — e.g.: light agriculture and bulk solids handling conveyors, mobile or portable conveyors; and as a drive unit for brush cleaners etc. The Motorized Pulley 138E has standard IP66/67 enclosure and is available in complete stainless steel execution for wash down applications.
Motorized Pulley 165LS, Ø 165mm: v with machined helical gear box, performs an efficiency, in a compact diameter of 165mm only. With a min RL of 400mm and powers ranging from 0.11kW to 1.5kW this size of motorized pulley is suitable for most duties requiring such a small diameter – e.g.: light agriculture and bulk solids handling conveyors; mobile or portable conveyors; as a drive unit for brush cleaners etc.. It has a standard IP66/67 enclosure and is available in complete stainless steel execution for wash down application.
Since 1971, Kinshofer GmbH has been a major manufacturer of high-quality attachments for truck-mounted cranes and it is now also becoming one of the preeminent producers of attachments.
In the last two decades, KINSHOFER has become more and more involved in the re-handling business, producing large orange peel grabs (P-Series) for excavators with an operating weight of up to 120 tonnes and re-handling clamshell buckets (C-Series) for excavators and carriers with an operating weight from 18 tonnes of up to 100 tonnes.
The durable KINSHOFER re-handling clamshell buckets of the C-Series have been developed especially for the loading and unloading of bulk materials in large amounts — including coal and coke. The widely spaced pivots and the flat closing curve provide maximum volume and the ground surface is protected when discharging from e. g. boat or train carriages. The two shells are driven by sturdy hydraulic cylinders.
The cylinder-version of the C-series is
available for excavators with 18t up to 100t operating weight. The smaller versions up to 65t are equipped with two vertical
The P-series of orange peel grabs with fullly closing tines is ideal for coal.
cylinders, the C100VHD up to 100t with four cylinders. The shells are very robust to withstand highly abrasive materials and the integrated endless rotation guarantees the precise positioning of the grab.
An alternative to the clamshell buckets is the KINSHOFER orange peel grab
P-series. Sizes range from the smallest P22V for excavators from 16 tonnes operating weight up to the huge P120VHD with a staggering volume of 3,500 litres in the largest variant. Different shell designs — narrow or wide, half or fully closing tines — make it possible to match the grab to the task. These heavy duty, sturdy grabs are often used to handle scrap, waste or rocks. As the C-series, the orange peel grabs are equipped with a robust 360° rotation. Accurate fittings eliminate tine distortion, the end stops for closing and opening are especially solid. Bolts are reinforced and have a large bearing surface. The hydraulic cylinders that operate the arms are protected by replaceable piston rod protections.
KINSHOFER sticks strictly to innovation and quality. Thomas Friedrich, President & CEO of the Kinshofer Group, says: “Kinshofer continues its strategy to provide the industry with a ‘one-stop-shop’ solution of outstandingly engineered products to increase efficiency and, more importantly, profitability of our customers.”
Now that we are well into the first quarter of the 21st century, we no longer expect to find material handling systems — especially coal handling systems — without adequate and efficient dust control systems. Raring Corp is celebrating 40 years in the dust control market this year with its ADSTM Dry Fog suppression technologies and Conditioning systems technologies.
The Raring Corp’s (TRC’s) participation
in the coal industry material handling market has always been significant. Since the beginning of its history, it has been involved in thermoelectric projects and coal mines that continue to supply electric power to the USA. This is mainly explained due to the fact that TRC is an American company located in the state of Washington, which allows it to be close to the industry and end-users within its
country. TRC’s presence in India, through its long and close relationship with F. Harley, in the coal handling industry, is also important. TRC’s projects there have not only been focused on the mining stage, but also on transporting and unloading the material to and from India’s thermoelectric power plants, a source of generation that represents more than 50% of its energy matrix today.
The coal industry can be dangerous. The fact remains that coal is a fuel, and is by nature an explosive material. It can generate sparks during transportation. It is
therefore vital to use the best dust control technologies, supplied by companies like TRC, that offer the most appropriate solutions for tackling the dust issues under
these extreme conditions.
During the handling and transportation process, coal is classified as explosive in some areas of extractive and power
generation plants. When suctioning and transporting coal dust particles at high velocities inside suction ducts, the particles tend to collide, spark and ignite and can burn the bags or plates inside bag houses or electrostatic precipitators respectively. This can be highly dangerous and costly to repair. However, this is not the case when using ADSTM Dry Fog or TRC’s wetting systems for the following reasons: dust is not being sucked; v dust is not being transported; v dust generation is suppressed in-situ; v no by-product is generated; and v the dust generated is settled down into the v material handling equipment.
Additionally, and as was previously mentioned, there are classified areas in the plants where coal material handling takes place, which translates into highly explosive areas where precautions must be taken to prevent explosions from occurring. TRC’s suppression systems can be completely pneumatic, thus avoiding the possibility of sparks and meeting stringent requirements in these areas. Both the company’s Conditioning and ADSTM Dry Fog suppression technologies can efficiently operate under these conditions, while still meeting the environmental demands required for each site, providing a highly competitive solution that is easy to install, operate, maintain and very efficient in controlling coal handling dust.
Davide Gambarotta, CEO of GAMBAROTTA GSCHWENDT, explains, “Our mission is to offer customers our experience, knowledge and innovation to render the exceptional products that we design and produce available all over the world, thus creating value for all those who participate in the company and share its objectives.”
GAMBAROTTA GSCHWENDT SRL is a family-owned company which was founded in 1919 by Umberto Gambarotta Senior in Trento after World War I. At that time, its main business was general mechanical work such as truck fixing, modifications transforming trucks from fixed to tipping, repairs to mining equipment, forge jobs, etc. Steel parts were recovered from World War I remnants, since the region had been deeply affected by the conflict.
In 1958 Umberto Gambarotta Jr. (father of the current CEO, Davide Gambarotta) joined the family business and actively contributed to the real first corporate turning point: the truck repair business was replaced by the industrial activity of designing and supplying systems for cement plants, mines and magnesium.
GAMBAROTTA GSCHWENDT transformed itself from a mechanical repair shop, with exclusively local clientèle, to an entity dedicated to the design and supply of conveyor systems for process plants.
From the 80s to the 90s there was great international expansion of the company: from a European industrial reality (especially in Germany, ever since 1958),
GAMBAROTTA GSCHWENDT acquired a wide-ranging presence, by getting important foreign orders that led to the opening of commercial offices, first in the Americas, in Asia and then in Africa and Australia.
The new establishment of the Gambarotta Group, led by the current CEO, Davide Gambarotta, took place between 2019 and 2020 and is made up of five leading companies in the sector and about 130 people specialized in 44 different fields.
The companies involved are:
GAMBAROTTA GSCHWENDT SRL; GAMBAROTTA AUSTRALIA; v MDG HANDLING SOLUTIONS SRL; v MDG AMERICA INC.; and v OSSITAGLIO SRL. v
Today, GAMBAROTTA GSCHWENDT’s main products include bucket elevators,
Lateral view of the special drag chain conveyor and its hopper.
screw conveyors, drag chain conveyors, pan conveyors, apron feeders, loading bellows, rotary valves, slide gates and top-quality spare parts for above mentioned equipment.
Many industrial sectors need to convey bulk materials, and GAMBAROTTA GSCHWENDT’s drag chain conveyors are an ideal solution.
Among the materials being handled are coal, coal dust and petcoke. For these applications GAMBAROTTA GSCHWENDT designs its equipment according to ATEX regulations.
But how does a drag chain conveyor work? Drag chains carry bulk material along the machine’s casing, which is composed of a steel box with rectangular cross-section and hermetically sealed cover.
The toothed wheels at the drive station drive the chains fitted with appropriate scrapers.
At the same time, the chains convey a material layer, which can sometimes be higher than the scrapers themselves. This happens when the lower layer of the material, which is transported directly by the scrapers, supports and carries the upper, thus creating a continuous material flow moving as fast as the chain.
This type of conveyor is appreciated for its ecological impacts, it being completely closed and hence avoiding dust pollution.
GAMBAROTTA GSCHWENDT’s product range includes several types of drag chain conveyors, such as:
TRS — drag chain conveyor with single v drop forged chain: suitable for hauling fine-grained or small-sized material
and relatively small capacities at any inclination (even up to 90°).
TRD — drag chain conveyor with v double drop forged chain: suitable for hauling lumps and medium to large capacities, generally with inclination <20°.
TRA — drag chain conveyor with v double round steel chain: perfect for the same uses as the TRD, with the added advantage of having a lower vertical extension.
TRP — scraper-paddle conveyor with v double chain with rollers: for the same uses as the TRD, but can be operated at high speeds (0.7m/sec) thanks to the mobile parts supported by the chain rollers that roll on guides.
TRC — submerged drag chain v conveyor: to recover slag and ash immersed in water as a result of various industrial processes (e.g. extinguishing of boiler ash).
TRL — cleaning drag chain conveyor v with linear axis: suitable for recovering
dust beneath main conveyors such as pan or belt conveyors.
TRLC — cleaning drag chain conveyor v with curved axis: suitable for recovering dust beneath main conveyors and recycling them on the latter.
GAMBAROTTA GSCHWENDT designs and produces brand-new equipment as well as upgrading solutions and modifications of any existing machine. Moreover, the
company provides its customers with any kind of original high-quality spare part.
GAMBAROTTA GSCHWENDT has recently developed a drag chain conveyor for raw coal. In this case the material bulk density was 1t/m3 and its grain size 0–200mm.
This machine has a centre-to-centre distance of 15 metres and the layout is horizontal. Its capacity is 700m3/h and the
The drag chain conveyor includes 160 scrapers plus 12 cleaning scrapers and their distance is 720mm.
The final destination of this conveyor is subject to cold temperatures, which lead coal to solidification into big material pieces. Because of the need to transport very large coal pieces this drag chain conveyor has been equipped with a wide hopper and bottom sheet, hosting five drag chains and two drive stations.
from
thyssenkrupp Polysius has decades of experience in the field of storages for various materials for the cement, fertilizer and woodchips industry. While the stockyard machines required a high degree of manual operation in the past, thyssenkrupp Polysius introduced the first fully automated stockyard in 2017. High process and operating reliability, reduced OPEX costs and increased safety for personnel are the reasons why many customers have opted for the fully automated storage since its market launch. This technology is not only advantageous in the cement sector, but also for many other storage applications.
Calling on its extensive know-how in the automation of machines and systems, thyssenkrupp Polysius tackled the challenge of finding the best possible automated storage solution — with particular consideration given to occupational health and safety requirements. As a company certified to ISO 45001, the international standard for assessing occupational health and safety
management systems, thyssenkrupp Polysius was determined that the same high standards it applies internally should be reflected in this bulk storage system as well.
The outcome of thyssenkrupp Polysius research and development efforts can be seen at a cement plant in Turkey. Here, the first bulk storage system started operation in mid-2017. As the first-ever fully automated solution in the cement industry, it was a technical breakthrough.
Correctives for raw meal grinding are stored on one side of the facility and additives for cement grinding on the other. A 180° slewing belt stacker installed in the middle runs up and down on rails to stack the additives and correctives into piles. Two portal scrapers, one on each outer side, reclaim the materials as required. For operators the fully automated, longitudinal storage system offers a number of operational benefits: more precise, efficient and above all health-friendly stockyard management in production plants.
Operator health is a key issue with conventional storage solutions for the bulk
handling. Every time the equipment that stacks the raw materials into piles has to be moved to a different pile, somebody has to enter the dust-filled storage facility to operate the machine. The same is true for the reclaimer, the machine used to remove the required quantity of the bulk material. The dust levels in a conventional facility can be a health risk, and in many countries the relevant occupational health and safety regulations have become much stricter in recent years. The fully automated storage system developed by thyssenkrupp Polysius ensures operators no longer need to be in the dusty air inside the storage facility.
The new bulk storage system from thyssenkrupp Polysius enables four key tasks to be carried out automatically: moving the stacker from pile to pile; moving the reclaimer from pile to pile and precisely undertaking the first cut; avoiding any collisions between the stacker and reclaimer; and determining the respective pile volume.
A key aspect of this state-of-the-art
storage solution is the intelligent radar sensor technology, which collects reliable data on the pile shape and positioning of the equipment.
As an example, with conventional systems the first cut is always tricky to perform because after stacking, the pile surfaces are not even. But as the system software precisely knows the height and shape of each pile, it automatically directs the reclaimer to exactly the right position to start operation.
Designing an automated solution for bulk storage was only possible by means of a smart software solution. Intelligent software tools ensure safe operation of the equipment. Operation, handling and
interaction between the machines are fully automated. One key factor for the success of this fully automatic operation was the development of an ACM (anti-collision module).
By collecting and evaluating all necessary information on the position of the stacker and reclaimer, the ACM monitors internal and external collision safety independent of the technological processes and thus protects the machines in any operating mode. Communication between the stacker and the reclaimer takes place via a fixed ACM interface, which was specially developed to ensure safe and collision-free passing of the machines.
To this end, different situations have to be taken into account by the ACM. The task in developing the software was to
ensure no collisions occur between the stacker and the reclaimer while including a solution and preference for crossing and passing. One particular challenge resulting from the parallel storage design was to protect the belt stacker on both sides during rotation and also to take the intermediate walls between the bulk storage into account.
The manpower savings achieved by using this fully automated system are a key factor in high-wage economies, for example. Another advantage is that the software also allows the volume of the piles to be determined. This makes stockyard management more efficient. Being able to determine the volume of each pile is particularly useful because it provides an overview of the used and remaining quantities of additives and correctives, thus facilitating the forecasting of future demand. Last but not least, the compact design of this automated storage system saves space, which also helps to reduce bulk storage costs.
The thyssenkrupp Polysius fully automated solution is designed for storing the bulk materials required in production lines in a healthy, safe and more efficient manner. Its successful operation demonstrates how industry-leading know-how can be deployed to deliver operational efficiency benefits while at the same time reducing the occupational health and safety risks to operating personnel.
Since wheat, corn, canola, soybeans, and the like are sensitive to moisture and temperature changes, an airtight structure that wards off water and controls the interior environment is the best way to ensure quality control. Here, Dome Technology explains a few considerations when planning a grain-storage facility:
Oftentimes those who buy land on a port get less property for their money, requiring decisions on how to get the necessary storage on a smaller parcel of land.
“If a port does not have height restrictions, which some do, the most efficient thing is to go vertical instead of horizontal,” Dome Technology sales manager Lane Roberts said.
Because of its height, a dome allows companies to stack product deeper, taking up less property at the site. The double curvature of a dome lends itself to the ability to build up, rather than out, and that curve provides strength at all points of the structure, even near the apex. The entire interior of a dome, then, can be used to contain product.
Facilities storing grain should be robust enough to tolerate frequent loading and unloading. “The storage facility needs to be able to hold a high volume and be able to handle its throughput. A dome can handle
that because of its structural integrity, (but) steel bins after a certain amount of time wear out. Steel bins are not built for high throughput,” Dome Technology sales manager James Stoker said.
That’s because steel bins are built with fasteners or welded seams to secure metal sections together. Frequent loading and unloading cycles fatigue the bin at bolt holes or weld imperfections until a crack develops at these locations and causes structural failure. Filling and emptying will stress a dome too, but a dome’s rebar can accept the force without the same fatigue problems; the stress is not channeled to weak spots like bolts or seams because there aren’t any.
Insulation doesn’t come standard with traditional storage facilities like bins and silos, and fluctuations in external and internal temperature, plus the possibility of moisture or condensation inside the structure, can compromise product integrity and pose a danger for volatile materials.
In contrast, a dome staves off some boundary issues other structures face. First, the airform covering the entire dome prevents water and moisture from seeping in. Important for moisture-affected products, this feature eliminates introduction of outside water into the pile.
Secondly, the combination of waterproof membrane, reinforced concrete shell, and continuous layer of polyurethane foam prevents extreme interior temperature fluctuation; these features reduce heating and cooling of the walls and air inside, preventing condensation.
Aeration systems, and a cable array of moisture meters and temperature cables ensure internal conditions are ideal.
Heat spoils grain, which spoils a company’s bottom line. But grain can also be combustible — the dust especially — and explosion happens when an ignition source lights a dust cloud generated by moving product. “The dust is very explosive, so you’re trying to control ignition sources through correct wiring methods, making sure it’s rated for the area or minimizing the amount of electrical equipment in the area,” Aagard said. Dome Technology’s team of experts will help customers identify the right equipment for a dome and the ideal places to put it.
Food-safe paint is necessary when storing products intended for human consumption. It’s an expensive but necessary finish for food products headed directly to customers. The paint creates a barrier between product and concrete.
As the global energy landscape undergoes a massive shift towards sustainability, one renewable resource in particular has attracted considerable attention - wood pellets. Low in carbon footprint and efficient in combustion, wood pellets have rapidly gained prominence as a cleaner alternative to traditional fossil fuels like coal. The demand for these ‘green’ energy sources is surging, sparking a corresponding need for efficient and safe storage solutions. Enter Eurosilo, a system designed to tackle common challenges of wood pellet storage while adhering to global standards.
The world is witnessing a green energy revolution and wood pellets are at the heart of this change. Their popularity has led to a
dramatic increase in production and storage needs across the globe. To ensure the quality of wood pellets and safety during handling, efficient storage techniques are of utmost importance. Furthermore, sustainable storage methods can prevent potential environmental hazards.
The traditional methods of wood pellet storage often present challenges that compromise both safety and operational efficiency. Combustible dust formation during loading, self-heating risks, pellet segregation and issues related to worker exposure are significant areas of concern. In addition, effective temperature monitoring is needed to prevent fire hazards.
This is where the Eurosilo system comes into play. By meeting NEN-ENISO 20024 standards, it provides a comprehensive approach to enhance safety, efficiency, and sustainability in the storage of wood pellets.
The Eurosilo system exhibits a robust approach to managing combustible dust. It replaces traditional free-drop methods, which contribute to high dust formation, with a telescopic chute that significantly curbs this problem. This crucial feature aligns the system with stringent safety standards, such as ATEX/NFPA.
In the realm of safety, the Eurosilo system stands tall with its cuttingedge temperature monitoring and CO detection capabilities. Employing infrared cameras, multiple sensors, and a rotation mechanism, it facilitates comprehensive temperature and CO monitoring.
This advanced system outperforms traditional methods that offer limited coverage.
Operational efficiency is a key focus in the global development of pellet storage. To this end, the Eurosilo system’s screw conveyor ensures controlled discharge, thereby preventing avalanches during normal operations. This contrasts starkly with gravity flow systems that are prone to avalanches, leading to potential safety risks and operational challenges.
The Eurosilo system offers an automated operating mode that parallels the principle of first in first out (FIFO) gravity flow systems, but without the associated limitations. With its integrated automatic control system, complete silo emptying is achieved, eliminating the need for manual cleanup that is often required after traditional gravity flow operations. This automation not only enhances efficiency and reduces reliance on manual labour, but also streamlines the workflow and mitigates safety risks associated with manual intervention.
As safety regulations evolve worldwide, the Eurosilo system stays ahead of the curve with its innovative inertization technique. The system continuously inertizes with nitrogen gas at the bottom of the silo, aligning with the highest safety standards and contributing to the global
effort to ensure safe storage and handling of wood pellets.
When selecting an appropriate storage facility for wood pellets, it is paramount to consider various parameters that ensure the safety and efficiency of the operations. Criteria such as the availability of space, stringent fire safety measures, and operation flexibility are the cornerstone of a wellfunctioning storage system. The recently drafted DIN 20024 serves as a valuable aid in this evaluative process, offering a clear framework that aligns with industry-wide expectations. The Eurosilo system stands at the forefront of these considerations, bringing forward numerous advantages in the realm of space optimization, operational dexterity, and fire safety. Integrating state-of-the-art technology and complying with global safety directives, the Eurosilo system emerges as the optimal choice for those who seek a dependable and forward-thinking solution in wood pellet storage.
In an industry dictated by time, climate, and quality control, covered storage facilities serve as guardians, ensuring the integrity of dry bulk commodities from origin to destination.
The paramount protection provided by enclosed storage becomes crucial, safeguarding goods against adverse weather conditions, temperature fluctuations, and potential contaminants to maintain optimal conditions.
Moreover, covered storage mitigates risks associated with open-air storage, addressing spoilage, degradation, and pilferage. This is particularly critical for commodities like grains, where quality preservation is not only economically significant but also pivotal for global food security.
IMGS’s unwavering commitment to advancing covered storage technologies aligns seamlessly with the industry’s pursuit of efficiency, safety, and sustainability. As we delve into the subsequent sections, we explore the features of IMGS’s Multipurpose Cargo Terminals and the innovative Grain Bunker System, highlighting their transformative impact on covered storage for dry bulk commodities.
IMGS MULTIPURPOSE CARGO TERMINALS: STREAMLINED ALL-IN- ONE FACILITY
IMGS Group’s Terminal and Silo Management provides a holistic solution, streamlining cargo handling, storage,
processing, and transportation. Key features include:
Storage: utilizing high-grade stainless v steel silos with automated monitoring for optimal preservation.
Processing/blending: high-speed v facilities cater to various commodities, ensuring efficient operations. Handling: efficient management of v cereals, pulses, animal feeds, fertilizers, and more.
Bagging/packaging: remarkable v capacity for swift bagging and packaging processes.
Warehousing: strategically located v facilities catering to bulk and breakbulk cargo needs.
Transportation and delivery: v seamless end-to-end deliveries facilitated through a global network. Collateral/stock management: v flexible solutions to minimize operating risks.
Strategically situated in Pakistan, UAE, Saudi Arabia, and various parts of Africa, IMGS Group’s Multipurpose Cargo Terminals provide efficient and convenient cargo movement solutions on a global scale.
In response to challenges posed by traditional grain storage, IMGS Group introduces the Grain Bunker Storage System — an economical solution for short
to medium-term storage. Key features include:
Modular flexibility: storage capacity v ranging from 500 tonnes to 30,000 tonnes, providing adaptability.
Portability: transportable in kit form, v offering flexibility in relocation.
Rapid assembly: quick setup, with a v 10,000 tonnes bunker installable within four to five days. Preservation features: equipped with aeration, fumigation, and temperature monitoring systems for optimal grain preservation.
IMGS Group offers comprehensive
services, covering construction oversight, cargo stacking, bunker coverage, management, survey, testing, and discharging/disassembly. The system has seen successful global implementation in locations like Perth, Saskatoon, Birmingham Country, Natal Province, and the UAE.
IMGS Group’s Covered Storage Systems stand as a revolutionary solution, offering efficiency, cost-effectiveness, and adaptability for short to long-term grain storage. With a global presence and unwavering commitment to innovation, IMGS Group redefines grain storage, providing sustainable solutions to meet the evolving needs of the industry.
As Hudig & Veder Group, we are keen on creating an ultimate logistical plan for our customers by combining different departments and disciplines within our ABC-concept.
Our ABC-concept can therefore be best described as an existing supply chain under control of Hudig & Veder.
Agencies, Chartering, Forwarding, Bulk & Projects, we offer the optimal collaboration between our business departments.
SAMMI s.r.l. specializes in the design and manufacturing of solutions for bulk materials handling, providing complete support, from engineering to implementation, through to commissioning, of tailor-made installations (both for the development of new plants or revamping existing ones). SAMMI’s goal is for its customers to achieve maximum return on investment in the shortest possible time, minimizing plant downtime and impacts on maintenance and spare parts activities. Below are details of two projects undertaken by SAMMI involving the covered storage of dry bulk material.
2848 – HANDLING AND STOCKYARD SYSTEM 600TPH FOR GRAIN TERMINAL SOLUTION FOR BULK MATERIALS, BELT CONVEYORS, BUCKET ELEVATORS, TRIPPER CARS, HOPPERS Design, supply, transport, assembly and commissioning of mechanical works for the extension of the lifting and transport system of bulk grains from dock by belt or trucks to be stored inside the existing warehouses. Implementation according to Atex standards. Line capacity of 600tph (tonnes per hour) of cereals.
Job number: 2848
Sector: Food industry / port terminals
End user: Eurodocks
Customer: Gruppo Setramar
Location: Italy
Year: 2011–2012
DETAILS
Belt conveyor capacity 600tph; v Belt bucket elevator height 36.5m. v The project consisted of a complete handling and storage system to be installed
in the existing warehouses of grain terminal in Ravenna, Italy. The system includes a truck unloading station, receiving hopper, bag type dust-suppression filters, belt feeder for material recover from hopper and to feed one 600tph bucket elevator which transports the material to a set of belt conveyors to feed either the existing conveyor lines or to transfer the material onto the new tripper conveyor, which will be installed in height inside an existing building to stock grain, cereals and flours.
This plant has been designed to fully comply with directive ATEX 94/9/EC regulations for equipment installed in potentially explosive atmospheres.
To reduce potentially dangerous dust spillage, each conveyor is provided with cover hoods for the whole length and pocket filters on both loading and discharge sections.
The rated capacity of the conveyor system is 1,200tph for a total storage capacity of about 15,000 tonnes inside the building (covered area). The peculiarity is that the system is almost entirely installed underground, in view of a quarry expansion project: a new vertical tunnel of height 150m and diameter 4m, chamber and horizontal tunnel have been excavated. Inside the underground chamber one hopper for limestone vertical receiving, feeder and crushing mill will be installed.
After being reduced in size, material will be transported via belt conveyor system to the outside.
In addition to that, the belt conveyor which transports limestone to the outside is plaincurved with a radius of 600m, to fit
the geometry of the excavation.
3101 – BPLK214 LOTOS COKING UNIT, HANDLING SYSTEM AND SCRAPER
RECLAIMER
SOLUTION FOR BULK MATERIALS, STOCKYARD, STACKER , BELT CONVEYORS
Design, full supply (MEC-ELE-AUT) and commissioning of petcoke handling storage, reclaiming and truck loading system.
Job number: 3101
Sector: Oil & gas
End user: Lotos Asfalt Sp. z o.o.
Customer: KT KINETICS
TECHNOLOGY S.p.a. (part of Maire Tecnimont Group)
Location: Poland
Year: 2016–2017
DETAILS
v
Conveyor capacity up to 200tph.
The project concerns the manufacturing of the coke storage and loading facilities system, which’s function is to handle the coke product from the closed coke slurry system to the storage stockpile and then from this one to the truck loading station. The coke from the CCSS Unit is delivered to the storage bulk hall, where a shuttle conveyor allows for the distribution of material through building length. To prevent against dispersions of explosive coke dusts, a loading bellows is provided under the shuttle.
From the stockpile, the coke is delivered to the truck loading system by means of a semi portal scraper that keep materials, sending it to a conveyor chain up to truck loading station. In case of
to the
Moreover, it is important to underline that all the systems are ATEX certified for
guarantee of security and suitable to working temperatures from –25°C. The first level control system is performed by a fully redundant PLC.
All the steps of the project have been
followed by SAMMI from the beginning, with the initial design to the following main phases, such as production, monitoring, final assembly.
THE NEW HES GDYNIA FLAT WAREHOUSE FOR THE ADDITIONAL 64,000 TONNES OF GRAINS IS SHAPING UP
Construction works for the grain storage facility extension at Slaskie Quay started on 18 of May 2023.
Most of the underground work and infrastructure for bottom discharge
operations will soon be fully completed, getting the walls up is still in progress and the roof and other conveyor system is to follow. The facility will be up and running at the end of the year.
With the extra capacity HES Gdynia will be able to offer higher level of efficiency, quality and capabilities to play an essential role in logistical supply chains,
underpinning the terminal as the reliable logistic grain partner, strategically positioned for domestic and non-domestic supplies.
The terminal in Gdynia is well located to support grain and animal feed trade, along with a diverse range of bulk commodities being exported and imported to worldwide destinations.
Laidig Systems, Inc., a bulk material reclaim equipment designer and manufacturer based in the United States, proudly announces its recent ATEX and CE certifications for its line of Cone-Bottom reclaimers. These designations allow Laidig to broaden its global presence by providing material handling solutions for partners across Europe.
The ATEX certification ensures that Laidig’s Cone-Bottom reclaimer line is able to be installed in potentially explosive dust atmospheres in accordance with a strict set of health and safety standards. The CE certification indicates Laidig’s machines have been deemed to meet the European Union’s safety, health, and environmental protection requirements. Both certifications were awarded to Laidig following stringent testing and independent verification purposes.
“Having ATEX/CE certifications on Laidig Cone-Bottom reclaimers allows these very versatile machines to be used in more locations around the world,” said Daniel Laidig, owner and CEO of Laidig Systems, Inc.
“Additionally, it provides every operating partner peace of mind that Laidig equipment has undergone detailed engineering and rigorous testing to comply with EU directives.”
Laidig’s entire line of Cone-Bottom reclaimers, including its 4300 Series, 5300 Series, 8300 Series, 9300 Series, and 9600 Series is now ATEX-certified as Category 1/2 equipment. The equipment, including its design and construction, has been found to comply with the Essential Health and Safety Requirements set forth by the European Parliament.
Laidig’s line of Cone-Bottom reclaimers is now CE-certified. In a review, the machinery was found to comply with the listed standards within the EU Machinery and Great Britain Supply of Machinery regulations. All Laidig Cone-Bottom reclaimers, where applicable, will be marked with the ‘CE’ logo.
“We are excited to be able to utilize the CE and ATEX marks on Laidig Cone-
Bottom reclaimers. The marks underline the approach we take in providing worldclass solutions for our customers,” said Vice President of Engineering Tom Lindenman.
Before these designations, Laidig’s Cone-Bottom reclaimers were already known worldwide for their versatility and dependability across dozens of industries. Laidig has worked diligently to acquire these certifications for an EU marketplace that demands them; now a much larger group of industries can utilize them.
“Coupling these certifications with the already-proven Cone-Bottom designs will allow Laidig to be able to provide these solutions to a much broader base of business partners within the EU,” said International Sales Manager John Koorn. “It truly is a very exciting moment for us here at Laidig.”
The reclaimer series was also designed with serviceability in mind, with all motors, drive components, and maintenance points situated outside of the material hopper. The Cone- Bottom’s heavy-duty auger and reclaim drive ensure that the equipment can operate and unload a silo even in the harshest conditions. It is ideal for the reclamation of countless materials, including dry bulk meals, flours, brans, powders, and recyclables or wastes.
A pioneer in belt conveyor accessories has launched the next generation of tracking technology for a global marketplace. Martin Engineering designed the highly responsive Martin® Tracker™ HD (heavyduty) belt conveyor alignment system with widely available plate steel to increase availability and affordability across all six continents it serves. A mistracking belt produces excessive spillage which increases labor costs for clean-up and may cause contact with the mainframe. This seriously damages both the belt and the structure and increases the potential for a friction fire. The Martin Tracker HD upper and lower units provide immediate, continuous, and precise adjustment of the mistracking belt. The result is greater productivity with less unscheduled downtime from both equipment replacement and spillage cleanup for a lower cost of operation.
“Since most OEM mistracking devices are only designed to prevent contact with the stringer and don’t actually realign the belt, operators can spend a lot of time monitoring the system and adjusting idlers to achieve consistent alignment,” explained Dave Mueller, Product Manager for Martin Engineering. “With enough manual adjusting, operators find that idlers must be
re-centred if there’s a change in cargo characteristics or to install a new belt. The Tracker HD automates the alignment process, eliminating the need for constant monitoring and manual adjustments, reducing the labour and downtime for maintenance.”
The Martin Tracker HD’s unrivalled precision comes from sensing rollers that ride either side of the belt edge and are
attached to the end of an arm assembly. As the rollers detect slight variations in the belt path, the force of the wandering belt causes the arms to automatically position a pivoting idler in the opposite direction of the misalignment. The lever action requires less force to initiate the correction and only slight adjustments mean the consistent contact between the belt and idlers reduces the energy needed to bring the belt back into alignment.
“Certain countries can’t buy the square
www.drycargomag.com
tubing, so we’re now manufacturing the equipment from readily available plate steel without any changes to the performance or life of the unit,” Mueller pointed out. “This allows the Tracker HD to be produced and supplied across all global business units.”
Easy to install and designed to withstand the stress associated with wider, thicker belts moving at higher speeds and carrying heavier loads, the Martin Tracker HD is suitable for a belt thickness up to 1.125in (28.5mm) and speeds up to 800fpm (4m/s). Both the upper and lower units accommodate belt widths of 36–72in (915–1,828 mm) with an effective tracking distance of 150ft (45.72m).
upper unit before the discharge, operators ensure the belt is centred on the head pulley allowing for optimal belt cleaning with maximum cargo discharge.
Available in 20°, 35°, and 45° trough angles, there are options for the addition of a Martin® Trac-Mount™ Idler, which allows the entire troughed idler unit to be slid away from the mainframe and safely serviced from outside of the system by a single worker. This important safety element can considerably reduce the amount of labor and maintenance time for the replacement of broken or frozen idlers. Also available are rubber-lagged rollers on the lower tracker and a grease kit for both the upper and lower assemblies. The unit is not suitable for reversing conveyors, belts with substantial rollback, or paddle or chevron belts.
PROPER PLACEMENT IS THE KEY
It is recommended operators install Martin Tracker HDs after the load zone on belts wider than 24in (610mm) with additional units placed down the system to keep the belt centred and tracking. By placing an
The lower tracker has been redesigned to include an extra safety feature not found in competitor units. Regardless of the conveyor, return rollers have been known to detach and drop, creating a serious safety issue, so the Martin Tracker HD has been equipped with safety guarding on the steering roll to prevent the roller from coming off or putting workers in harm’s way. On the return, it is recommended to place a tracker after the discharge zone or take-up pulley, as well as periodically down the system depending on length. To ensure centred loading, the belt must enter the loading zone aligned, so installing a lower unit approximately five times the belt’s width in distance from the tail pulley will support an efficient loading process.
FIELD TESTED AND APPROVED
Since the basic design of the Martin Tracker HD is similar to that of its predecessors with square tube construction, the testing
focused on performance, durability and installation time. Tested in bulk handling operations including mining and cement where mistracking leading to spillage had historically been a concern, the unit performed up to Martin Engineering’s high standards.
“Martin Engineering believes safety should be a core function in any conveyor accessory we design, and the Tracker HD is no different,” Mueller said. “By automating consistent belt tracking, this solution reduces equipment wear, maintenance time, and downtime. These factors lower the cost of operation offering the best return on investment of any tracker on the market.”
Martin Engineering has been a global innovator in the bulk material handling industry for more than 80 years, developing new solutions to common problems and participating in industry organizations to improve safety and productivity. The company’s series of Foundations books is an internationally recognized resource for safety, maintenance and operations training — with more than 22,000 print copies in circulation around the world. The 500+ page reference books are available in several languages and have been downloaded thousands of times as free PDFs from the Martin website. Martin Engineering products, sales, service and training are available from 17 factory-owned facilities worldwide, with wholly-owned business units in Australia, Brazil, China, Colombia, France, Germany, India, Indonesia, Italy, Malaysia, Mexico, Peru, Spain, South Africa, Turkey, the USA and UK. The firm employs more than 1,000 people, approximately 400 of whom hold advanced degrees.
Cooper Marine is a part of behemoth bulk handling specialist The Cooper Group. It serves the US inland waterway system, and has a significant presence in the US Gulf.
Cooper Marine consists of a fleet of 41 towing vessels (up to 4,600HP) and 450 barges. The company’s barge affreightment and towing footprint includes the Tennessee–Tombigbee waterway, Mississippi River, Gulf Intracoastal Waterway, Black Warrior River, Tennessee River, Tombigbee River, Mobile River, Ohio
River, Illinois River, Arkansas River, and Cumberland River.
Cooper Marine operates the largest barge fleeting footprint in the United States, including barge fleets on the Lower Mississippi River, Port of Mobile, Yellow Creek State Inland Port, and numerous private terminal barge fleets along the US inland waterway system.
Cooper Marine operates one of the country's largest fleet of dry bulk gantry and floating derrick cranes. The company’s world-class stevedoring operations consist
of two deep-draught private cargo terminals in the Port of Mobile, operations at public cargo terminals in the Port of Corpus Christi and Port of Mobile, and numerous private inland marine terminals throughout the states of Alabama and Mississippi.
Cooper Marine’s private terminals in the Port of Mobile include 35 acres of storage area to support cargo transloading operations to and from ship, barge, and truck, and a reclaim and conveyor system for transloading wood pellets from bottom-dump trucks into covered barges.
www.drycargomag.com
Established in 1905, The Cooper Group has operations on all three US coasts and international operations in Mexico. The company maintains ownership in numerous satellite companies, forming The Cooper Group, including warehousing, terminal operations, tugboats, push boats, barging, barge fleeting, floating terminals, logistics, forestry operations, vessel repair and restaurants.
The Cooper Group’s experienced, action-oriented people, state of the art
equipment and automated facilities provide customers with fast, efficient and cost effective movement of cargo anywhere.
The Cooper Group is anchored by one of America’s oldest and largest stevedoring and maritime firms, with operations on all three US coasts and internationally.
Port of Corpus Christi customers moved record tonnage through waterway in 2023, surpassing 200m tonnes for first time
Port of Corpus Christi customers set a new high mark in annual tonnage during 2023, moving more than 200mt (million tonnes) of goods through the Corpus Christi Ship Channel for the first time in its history.
The 203mt moved in 2023 was an 8.1% increase from the prior year. The new high mark primarily can be attributed to a jump in crude oil exports to 126.1mt in 2023, a 12.5% increase compared to 2022. The Port of Corpus Christi also saw a nearly 13.5% increase in agricultural commodities to a little over 2.2mt, as well as a slight increase in refined products to 42.5mt. A record volume of liquefied natural gas (LNG) — 16.3mt — moved through the Corpus Christi Ship Channel in 2023, as well.
Port of Corpus Christi customers
moved 51.8mt through the gateway during the fourth quarter of 2023, a 4.4% increase from the same period in 2022. The leading commodities during this period were crude oil, refined products and LNG. A record volume of crude oil — 12.2mt — moved through the waterway in December 2023, 10.1% higher than the prior record set in September 2023.
“The reaching of this newest milestone in the Port of Corpus Christi’s lengthy history is a testament to the strength and commitment of our customers, who supply much-needed goods to our trading partners around the world,” said Kent Britton, Chief Executive Officer for the Port of Corpus Christi. “Closing out 2023 on such a strong note sets the right tone as we go into 2024, which we expect to be another solid year for our customers.”
In September, the U.S. Army Corps of Engineers awarded the final contract for the Corpus Christi Ship Channel Improvement Project to Callan Marine, Ltd. Phases one and two have concluded, with the third estimated for completion later this year. The fourth and final phase of the CIP is projected to be complete in early 2025.
The Port of Corpus Christi also has several other infrastructure projects in development or under construction, including improvements to its Bulk Terminal docks, upgrades to Cargo Dock 9 — which handles breakbulk cargo, like wind farm components — and expansion of Oil Dock 1. The latter project will make Oil Dock 1 the first of the Port’s Inner Harbor docks to accommodate the new 54-foot depth.
“On behalf of my fellow Port of Corpus Christi commissioners, I congratulate our customers and staff for achieving this incredible milestone in 2023,” said David Engel, Chairman of the Port of Corpus Christi Commission. “We remain committed to investing in our infrastructure to ensure our customers are able to continue and expand their success, which will allow for further economic development in South Texas.
As a leader in US energy export ports and a major economic engine of Texas and the nation, the Port of Corpus Christi is the largest port in the United States in total revenue tonnage. Strategically located on the western Gulf of Mexico with a 36-mile, soon to be 54-foot (MLLW) deep channel, the Port of Corpus Christi is a major gateway to international and domestic maritime commerce.
The Port of Corpus Christi has excellent railroad and highway network connectivity via three North American Class-1 railroads and two major interstate highways. With an outstanding staff overseen by its seven-member commission, the Port of Corpus Christi is ‘Moving America’s Energy’.
t r o p p e o h e t t a i c e r p p e a We W
. u o h y t i k w r o o w y t t i n u
g n i ow ll , a s e i g o l o n h c e e t tiv ova n n r i u d o n e a l p o e r p u e o r hs a t g n e tr r s u O
m a e r t u . O e r fo e r b ve n e a h ly t t n e ci i f f e e r o d m n r a fe a s s o g r e ca ov o m s t u
n o ti a t r o nsp ra e t n r o b r te a ’ w s r e m to s u r c u t o e e o m y t a y d r ve s e ive tr s
. p i sh d r tewa l s a t n e m n ro i nv d e n y a t fe a n s s i r e d a e g l n i e o b s l e a l i h s w d e e n
. e o w r d e ith e d n n , a s p to r s eve e n rc e m m o e c n r o b r te Wa
m o c . s l a n i m r e dt e t ia c o s as . w. w w w
is 19 miles from the Gulf of Mexico with 24-hour channel and dock accessibility.
Less than two hours from sea to transit, the Port of Port Arthur is North America’s ultimate direct transfer facility positioned on the Gulf of Mexico to competitively handle any type of commodity.
Port of Port Arthur is strategically located midway on the barge shipping routes of the intercoastal waterway that extends from St. Marks, Florida to Brownsville, Texas. The Sabine-Neches Ship Channel is part of that system with channel depths to safely accommodate large petrochemical tankers and cargo ships. The Port
The Port of Port Arthur (POPA) is highly experienced in handling all types of cargo, specifically:
Breakbulk: POPA specializes in v handling breakbulk cargo for various customers, such as forest products, aluminium, steel, and military cargo. With its ongoing improvements to infrastructure there is a logistic advantage in coming to Port Arthur.
Project cargo & heavy lift: POPA is v an experienced port capable of handling heavy, and oversize cargo.
Centrally located on the Sabine Neches Waterway, the port is well
equipped to handle the project cargo needs of its customers.
Energy: the port is located on the v Sabine Neches Waterway that is home to the nation’s third-largest waterway, and the #1 bulk liquid cargo waterway. With its local tenant, Low Sulphur Diesel is exported around the world from the docks in Port Arthur.
Roll-on/roll-off (Ro-Ro): when it v comes to Ro-Ro cargo, the port is equipped with an 80ft Ro-Ro dock and 100ft apron — with POPA’s direct on dock rail access, it creates a win-win situation for customers.
Containers. v
Intermodal: the Port of Port Arthur’s v transportation support system is impressive. Upon arrival at the port,
customers’ cargo can utilize an extensive array of barge waterways, railroad, roadways, and ocean carriers. Barge shipping routes include the Sabine-Neches Ship Channel, Gulf of Mexico Intracoastal Waterway, and numerous in-land rivers and canals. Railroad support includes: KCS Railroad, CN Railroad, UP Railroad, BNSF Railroad, Tex Mex, and TFM.
Direct Transfer Facility: the ultimate direct transfer facility for international shipping. The Port of Port Arthur completed in the year 2000 an expansion that included all the operating features demanded by the maritime industry. The total dock length at the terminal is 3,000 linear feet; Berth 5 (completed early 2021)
offers 600 linear feet, and Berth 6, which was due to complete last year (2023) offers 1,000 linear feet. There is total shed storage of 550,000ft2, and open storage of 25 acres asphalt surface.
Transit shed: the forest products industry wanted — and got — the finest transit shed to protect newsprint, linerboard, woodpulp, paperboard, plywood and lumber. To give them what they wanted, the Port of Port Arthur not only duplicated the superior quality of its existing shed, it also added extra large hanger type doors (36ft wide x 24ft high); state-of-the-art lighting for ’round-theclock safe traffic; an enclosed rail and truck apron for all-weather operations; and a storm water drain system throughout the apron dock that includes 36x12ft door gratings.
Open storage: the metals industry wanted more open storage and rail accommodations. What they got was an extension of the existing 50-car dockside capacity to 150 railcars for direct transfer; and an asphalt surfaced open storage up to 18 acres.
Rail transportation: the port is connected to the KCS Railroad providing direct intermodal service to and from major markets of the United States and Canada.
Truck transportation: convenient access to interstate highways.
Port equipment: the port is equipped to handle any type breakbulk general cargo, including, but not limited to: forest products; iron and steel products; dry bulk cargoes; project and military cargo; and bagged and bailed goods. DCi
Our bespoke solutions are designed to meet each customer’s specific requirements from a tool kit of proven components, utilising the expertise of a team of specialist in house design engineers.
We lead the loading chute industry & set the standard for dust emissions and environmental pollution control in dry bulk handling.
Our worldwide reputation is built on high quality, well-engineered, robust, high performance chutes, backed up by excellent customer service and global lifetime product support.