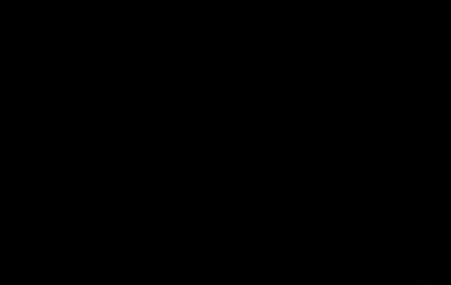




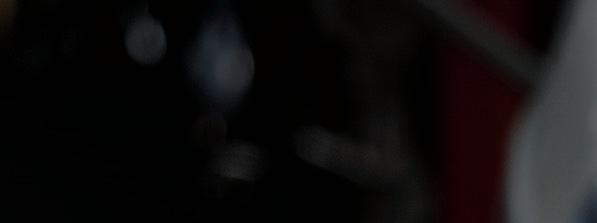
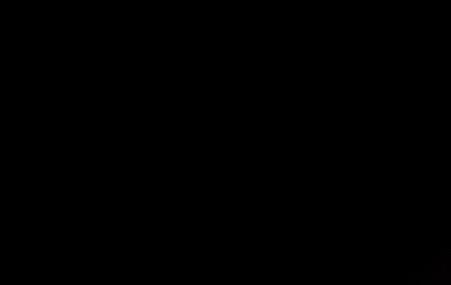
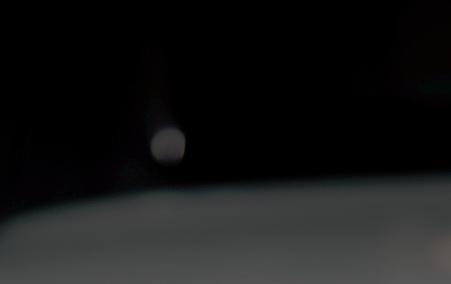



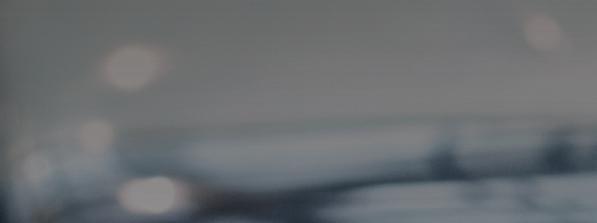
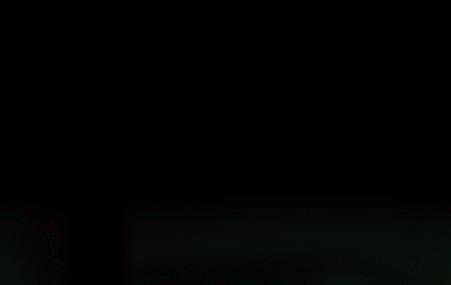
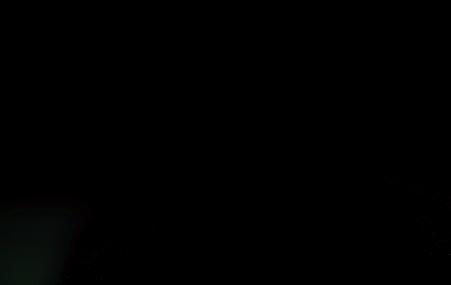


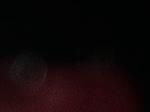


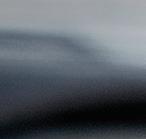
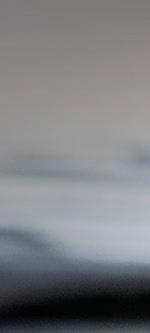
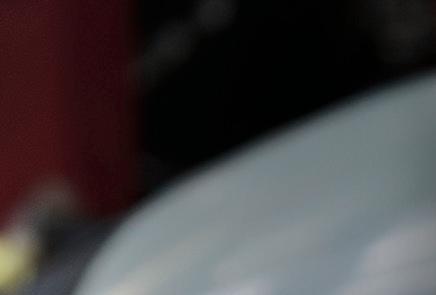



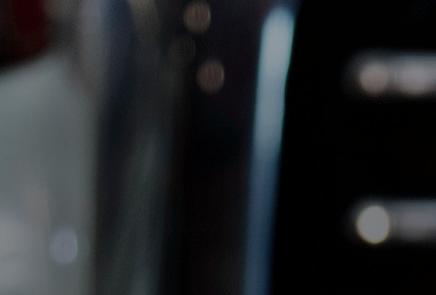
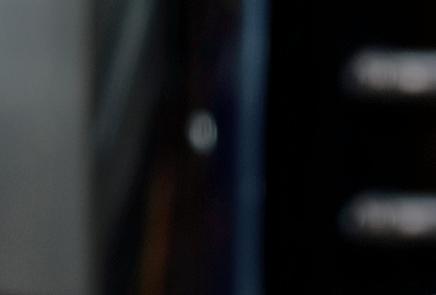
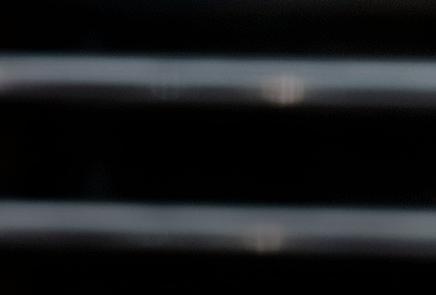

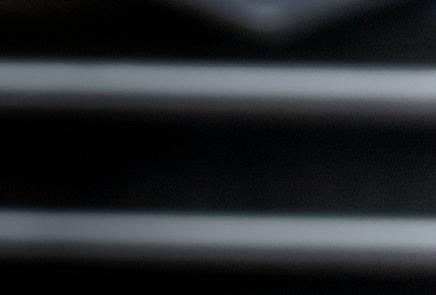
It’s go time!
Now with built-in CAN FD and DoIP protocols.
Featuring built-in CAN FD and DoIP protocols and easy connectivity to Bluetooth, Wi-Fi and USB, the latest USB-Link™ 3 is our most advanced VCI adapter to date—with compatibility for a wide range of OEM diagnostics software. Visit nexiq.com to learn more.
Equipment
Prebuy 2027:
The procurement predicament
With a major round of emissions regulations coming to heavy-duty trucking in 2027, and MY2026 booked up, fleets aren’t left with many procurement options.
An engine overhaul could be a fleet’s best bet when looking to squeeze a few more years of life out of a truck. And going all in can help ensure the quality and reliability they’re hoping for.
Failure to communicate
If information isn’t passed down the right way from leadership to coworkers to customers, that’s a problem you need to fix right away—and you can’t do it with a wrench.
Certain
management industry.
no more; OEM rebrands to International Motors To simplify its identity in the industry for the future, as well as go back to its roots, Traton is sunsetting Navistar, giving rise to International Motors. FleetMaintenance. com/55142617
Pullapalooza: Revved up at the National Tractor Pulling Championships In all of motorsports, tractor pulling is regarded as the most powerful, and Fleet Maintenance went to this year’s 57th National Tractor Pulling Championships to find out what kind of maintenance is needed to obtain that power. FleetMaintenance.com/55139738
Vol. 28, No. 8
FLEET MAINTENANCE
Market Leader - Commercial Vehicle Group Dyanna Hurley 248-705-3505 | dhurley@fleetmaintenance.com
Editorial Director Kevin Jones kevin@fleetmaintenance.com
Editor-in-Chief John Hitch john@fleetmaintenance.com
Associate Editor Alex Keenan alex@fleetmaintenance.com
Associate Editor Lucas Roberto lucas@fleetmaintenance.com
Contributors Seth Skydel, Gregg Wartgow, Mindy Long, Missy Albin, Jeremy Wolfe
Fleet Maintenance Multimedia Account Executives
Multimedia Account Executive - West Michael Simone 973-713-0094 | michael-s@fleetmaintenance.com
Multimedia Account Executive - Southeast Peter Lovato 231-233-2660 | peter@fleetmaintenance.com
Multimedia Account Executive - Northeast Larry Schlagheck 248-444-1320 | larry@fleetmaintenance.com
Tool & Equipment Multimedia Account Executives
Multimedia Account Executive - Midwest Diane Braden 920-568-8364 | diane@fleetmaintenance.com
Multimedia Account Executive - West Mattie Gorman-Greuel 920-563-1636 | mattie@fleetmaintenance.com
Multimedia Account Executive - East Cortni Jones 920-568-8391 | cortni@fleetmaintenance.com
Production Manager Patricia Brown Ad Services Manager Karen Runion
Art Director Erin Brown List Rental
CUSTOMER
847-559-7598 Circ.fleetmag@omeda.com PO Box 3257 • Northbrook IL 60065-3257
ARTICLE REPRINTS reprints@endeavorb2b.com
Fleet Maintenance (USPS 020-239; ISSN 2150-4911print; ISSN 2150-492Xonline) is published nine times a year in January/February, March, April, May, June, July, September, October, and November/December by Endeavor Business Media, LLC. 201 N Main St 5th Floor, Fort Atkinson, WI 53538. Periodicals postage paid at Fort Atkinson, WI 53538 and additional mailing offices. Postmaster: Send address changes to Fleet Maintenance PO Box 3257, Northbrook, IL 60065-3257.
Subscriptions: Publisher reserves the right to reject non-qualified subscriptions. Subscription prices: U.S. $75 per year; Canada/Mexico $110 per year; All other countries $162 per year. All subscriptions are payable in U.S. funds. Send subscription inquiries to Fleet Maintenance, PO Box 3257, Northbrook, IL 60065-3257. Customer service can
Older trucks cost more because of maintenance. New trucks will cost more because of regulations. The age-old question is what to do about it?
By John Hitch Editor-in-chief
A truck hitting 500,000 miles is like a person turning 40. I’m not sure about you, but that’s when I noticed I lost a step, and the ones I took always hurt because my knee cartilage was all worn down from waiting tables and running from my past. My neck and ankles started to crack at the slightest rotation. And my metabolism slowed, too.
What happens to heavy-duty trucks at the half-million-mark ain’t all that di erent. As Brian Antonellis, current SVP of fleet operations at Fleet Advantage, describes in our story on prebuy pandemonium and procurement planning (Pg. 10), “you start to see mpg drop o and the [repair and maintenance] cost curve increases around 450,000 miles.”
When you start to trot that truck out past then, you’ll notice the a ertreatment system needs more attention, the suspension might need work, and electrical wires could be a bit askew from absorbing all those road vibrations. As a truck ascends toward being over the hill, each mile gets a little more expensive. Your drivers fuel up a little more o en, and the trucks are in the shop more. ese almost-middle-aged trucks add as much as 15 cents/mile for maintenance alone, Antonellis said, based o a large pool of Fleet Advantage customers’ maintenance data.
It’s a good thing trucks aren’t really like people, because at this point Antonellis recommends you just get rid of the thing when it gets too old, which he defi nes as 450,000-500,000 miles, and trade it in for a hot new number— probably something with great big ol’ luminous LED headlights, a sleek aerodynamic body, and an integrated powertrain to boot. Oh, and it probably weighs less, too. at would totally devastate the current truck’s self-esteem.
But trucks don’t have feelings, so you don’t have to feel bad dumping them when they start to age. It’s a typical big-fleet mentality to sell o older trucks, but not everyone has the luxury of trading in models when they start to get a few wrinkles, like they’re Leo DiCaprio or something. e little guys and gals don’t have as many options, especially with the diminishing returns on trade-ins and high interest rates. O en they are stuck with the truck they’ve got and hope to stay ahead of the maintenance items and pray it generates more revenue than it costs to run and repair.
ose costs rise every year over 500,000 miles, so the law of diminishing returns kicks in. And it’s probably kicking in for a lot of fleets right now, as 2019 was the modern highpoint for Class 8 sales with 276,000, while semis averaged 100,000 miles a year.
Such is life for a company that derives profits from commercial vehicles, and they know about the cyclical nature of trucking, cutthroat rates, and omnipresent threat of downtime. I doubt they’re looking for pity. I’d wager most just want to get by doing what they do until they sell—either due to success or age, going bankrupt, or dying.
Or until new laws kick in when the government decides to change things up and demand better results on the emissions front. e next big one is the Environmental Protection Agency’s 2027 NOx fi nal rule to nearly eliminate the harmful fumes. e agency throws out big numbers on how much money will be saved by how much child asthma will allegedly be eliminated by 2045. Who knows how much of that is true, as cockroaches are also linked to child asthma. Why not attack them and leave trucking alone for awhile?
at aside, whoever makes those EPA projections will never be held accountable if found untrue. But fleets do have to account for how to a ord all the new emissions systems coming in MY2027 and beyond, which could increase the price of a truck by $20,000-30,000, Antonellis said. And they have months to figure out how to refresh their fleets before the regulation takes e ect, even as they try to maintain their current aging a ertreatment systems.
“Without a doubt, the most di cult part of the industry is either going to be the repairs and maintenance or the rules and regulations,” asserted Christopher DeFeo, president of a small stone wholesaler called DeFeo Materials. His 2019 trucks are also starting to show their age, but he only has one maintenance person,
and in this economy he’s not sure what to do. Some in his position may opt to prebuy if they can, or turn to leasing. Or maybe keep running those trucks into their golden years and overhaul the engines. It’s becoming less common, but we show you how on Pg. 16. And according to Jim Madich, engine service supervisor at Blaine Brothers, engine rebuilds could be needed anytime a er 500,000. “Lately we’ve seen that a lot of trucks with a ertreatment systems are not lasting that long,” he said.
What is becoming more common is getting someone else to handle all the hassles.
As Jim Lager, EVP of sales and rental at Penske Truck Leasing pointed out, “ e more complex and expensive equipment gets, the more fleet operators need a partner,” which is true and a good plug for leasing, or at least, contract maintenance.
“Diagnosing on today’s equipment is impossible to do if you don’t have the right equipment,” he added. And for all-makes fleets like DeFeo’s it’s even harder. (And that’s a good plug for why you should check out our special section on diagnostics, starting on Pg. 31.)
ere are no defi nitive answers, but it’s never been more important to focus on maintenance, whether that’s in-house or outsourced.
“Uptime is paramount,” Lager asserted, though added, “A lot of fleets don’t even know how to calculate that. ey don’t even really know what that is.”
With your current trucks not getting any younger, and new ones coming out not getting any cheaper, that should be a top priority in the next year so your business doesn’t also lose a step going forward.
Launch Tech USA, a leader in the automotive diagnostic tool industry, is proud to announce a strategic partnership with the National Automotive Service Task Force (NASTF). This collaboration is set to revolutionize the automotive industry by addressing critical issues surrounding vehicle security and the integrity of automotive repair services.
Launch Tech USA and NASTF will work together to implement advanced technologies and protocols that aid in reducing car theft and keeping vehicles where they belong; with their owners.
PREVENTING TOOL AND PROPERTY LOSSES
Through this partnership, Launch Tech USA and NASTF will work to reduce these risks by ensuring that locksmiths have access to secure and reliable tools, minimizing their exposure to potential threats.
Through this partnership, Launch Tech USA and NASTF will work to reduce these risks by ensuring that locksmiths have access to secure and reliable tools, minimizing their exposure to potential threats.
In today’s fast-paced world, where almost everything is available at the click of a button, success for companies is no longer just about what they sell—it’s about what they deliver. This shift is particularly evident in the fl eet maintenance industry, where challenges like workforce retention, inadequate training, and subpar working conditions don’t make it easy.
In this demanding environment, it’s not just the products that set a company apart but the value-added services that truly make a diff erence. In this context, the tools used in fl eet maintenance can either add to these burdens or help alleviate them. Take all-makes diagnostics, for example. In today’s fl eet industry, where a single truck often integrates systems from various manufacturers, having an all-makes diagnostic tool is essential—it’s a given. Every fl eet depends on these tools for comprehensive coverage, regardless of the OEM software they might also use. In this crowded market, where many diagnostic tools seem interchangeable
at fi rst glance, the real diff erence lies in the support and services that accompany them—services that turn a good product into a great solution.
Let’s break out the pillars that elevate a standard diagnostic tool into an essential asset for fl eet maintenance.
Implementation is often the fi rst major hurdle when integrating new software. Fleet managers and technicians often wrestle with IT issues, adding stress to an already challenging job. Recognizing these diffi culties, Cojali has designed the implementation of Jaltest Diagnostics to be as smooth as possible. The process is supported by the Cojali team and its distributors, who provide extensive assistance during setup, including on-site support to ensure a seamless and effi cient transition.
However, implementation is only the beginning. Proper training is crucial; without it, even the most advanced tools can remain underutilized. Jaltest Diagnostics stands out not only for its intuitive interface and embedded diagnostic features but also for the exten-
sive training support that is provided. From onboarding new users or off ering ongoing education, Cojali ensures every user is prepared to make the most of Jaltest’s capabilities.
And what happens when a technician hits a roadblock? Advanced technical support becomes crucial. Picture this: It’s 4 PM, and a truck rolls into the shop with a laundry list of symptoms. The technician plugs in the diagnostic tool, gets a fault code report but gets stuck trying to run a cylinder cut-out test. This is where Jaltest Advanced Technical Support becomes invaluable. With a team of ASE-certifi ed technicians just a phone call away, ready to remote in and assist, the technician can quickly get back on track, solving the issue efficiently and confi dently.
Traditionally, tasks like ECU revision updates could only be handled by dealers, resulting in delays, higher costs, and a loss of control over the repair process. Cojali changes that narrative with Jaltest Central Services, off ering streamlined solutions for actions like Cummins revision updates, Detroit Diesel recalibrations, Paccar parameter changes, and International body controller updates. These services are available through the same diagnostic tool that technicians use daily, eliminating the need to rely on dealers and restoring control back into the hands of the fl eet manager.
In an overcrowded market of allmakes diagnostic tools, it’s not just about covering the makes and models or having an extensive library of technical information. Jaltest Diagnostics excels in those areas, but what truly sets it apart is the comprehensive support package that backs the fl eet. From smooth implementation and thorough training to on-demand technical support and dealer-exclusive actions, Jaltest provides the tools, resources, and expertise that fl eet managers and technicians need to thrive. It’s not just about what we sell— it’s about what we off er: everything needed to keep fl eets running smoothly, effi ciently, and independently.
Technical Information
agra tion
All technical information including wiring diagrams, troubleshooting, component locations and pictures...
All-Systems Scan Engine, Aftertreatment, Transmission, Brakes, Cab Controllers, and Hydraulics
Dealer Level Capabilities
DPF Filter Regen and Resets, Injector Coding, Transmissions calibrations...
Afte sion rs, an ler abil ilter esets g, Tra tions
Wide Coverage
All makes diagnostic coverage on all systems, on any kind of vehicles (Including Off road Equipment)
Advanced Technical
US-based certified diesel technicians, assisting in executing actions and interpreting technical information for users
Central Services
Perform Cummins Revisions Updates, International Body Controller Updates, Paccar Parameter Change MX PCI EPA 13-17, and Detroit Diesel ACM / CPC / MCM / TCM Recalibration
With a major round of emissions regulations coming to heavy-duty trucking in 2027, and MY2026 booked up, fleets aren’t left with many procurement options.
By John Hitch
n heavy-duty trucking, the profit margins are slim and the margin for error is even slimmer. And even the mightiest fleets with the best drivers can be brought down by weak accounting and a poor procurement strategy.
But what do you do when the pockmarked roads, intense weather, and time itself take their toll, and fleets need to refresh their ranks? ere are several options, from buying new or used to leasing or renting. en you must decide how long you’ll keep the asset, or as the odometer creeps up over half a million miles, perhaps overhaul and try to hit a million or more miles.
at’s the question many are asking right now as their regular trade-out cycle approaches. But they also must prepare for the Environmental Protection Agency’s ultra-low NOx fi nal rule that takes e ect for model year 2027 heavy-duty trucks. Called “Control of Air Pollution from New Motor Vehicles: Heavy-Duty Engine and Vehicle Standards,” the regulation reduces NOx down to near zero. And the cost and uncertainty over the new emissions-compliant technology will have fleets changing things up in the next few years.
For starters, the new technology has made MY2025 and MY2026 trucks, which won’t cost as much as MY2027 and later vehicles and use familiar technology, an attractive (and frankly downright gorgeous) potential alternative. Known as a pre-buy, the strategy is a way for fleets to hit the snooze button on unproven new emissions systems that otherwise might keep them up at night.
And the last time regulations forced OEMs to install new emissions systems, “it didn’t go well; those trucks really weren’t reliable,” noted Jim Lager, EVP of sales and rental at Penske Truck Leasing.
Many of Lager’s contemporaries can still vividly recall scores of their diesel trucks being down at any given time because of faulty selective catalyst reduction and engine gas recirculation systems.
“ ere are scars in the industry from that,” o ered Brian Antonellis, current SVP of fleet operations at Fleet Advantage, who was a director of PepsiCo’s fleet in the early 2010s when downtime due to a ertreatment issues was an epidemic. “It was very challenging … people just assumed the technology was going to work.”
Skepticism is far more rampant now. As one of the largest logistics and leasing companies out there, Penske works closely with the OEMs, and Lager feels confident the industry has learned from that initial emissions system rollout.
“I don’t think reliability is going to be that big a problem,” Lager assured, though he has been around long enough, starting as a trailer mechanic, to expect the unexpected. “But it could be. en you’ve got uptime problems and costs and a lot of other things that go along with that unknown commodity.”
If you’ve been napping through all the latest developments, we’ll catch you up so you can get closer to knowing how to proceed with your procurement strategy.
As you may recall, 2019 was an idyllic time, almost like a Renaissance painting came to life, where everything seemed to make sense, people got along and even talked to each other in person. It was also a
banner year for Class 8 truck makers, who notched 276,000 sales. That was five years ago, and so all those trucks—figuring they average 100,000 miles a year—are reaching a depressing milestone.
“When you’re managing the life cycle, you start to see mpg drop off and the [repair and maintenance] cost curve increases around 450,000 miles,” Antonellis explained, “So we target that 450,000 to 500,000 miles as a time to replace.”
Antonellis emphasized that fleets should consider the total cost of ownership more than acquisition costs, especially as fuel degradation kicks in and components need to be replaced.
“Think about it,” he offered. “About 75% of the total cost of operating a truck is in fuel and maintenance, and 61% of it is in fuel … Being able to target that replacement cycle and get it pretty close so you don’t run an extra year with an R&M cost that increases up to 13, 14, 15 cents a mile is crucial.”
That target isn’t as easy to hit for most fleets right now. Back in 2019, the economy was great, and the interest rate set by the Federal Reserve was under 2%. Even with the first rate decrease since March 2020, it’s still around 5%.
The EPA regulations looming just a few years away are calling for OEMs to produce more efficient, longer-lasting engines, driving down current NOx standards by 80%. An earlier 2007 rule limited NOx to 1.2-1.5 grams per horsepower-hour during normal operation. The new requirement during operation is 0.035 g/bhp-hr, or 98% less. The emission system useful life has increased to 650,000 miles from the current 435,000 miles.
To meet stricter EPA and CARB standards, OEMs have already started to make changes. Paccar’s MX-13 engine, for example, will include a compact twin assembly featuring an electric heater powered by a 48-volt generator in the flywheel of the MX-13 to provide lower NOx output, as well as lengthen the SCR, according to Joe Vatalaro, director of maintenance at PacLease.
To avoid having to deal with the more expensive and complex engines and new emissions systems that meet those requirements, the heavy-duty sector saw a huge prebuy in 2006: 284,000 units. In 2026, the industry is bracing for the same.
Hadley Benton, VP of business development for Fleet Advantage, suggests prebuying mitigates two risks. “There’s the risk of the new technology: ‘If it breaks down, what do I do?” he said. “The other risk is the increased cost. We’re talking about a $30,000 premium, and we just learned [in August] that the majority of that increase is related to warranty.”
According to Penske’s Lager, MY2027 Class 8 trucks will cost 3-4% more.
On the positive side for MY2027, Benton noted, “The newer equipment is going to be more efficient, so you should get better mpg, and obviously, you’ll have lower maintenance and repair costs because it’s new.”
In this economy, that extra money per truck, combined with the interest on that truck, might not be offset by slightly better fuel economy, and the maintenance savings could be canceled out if a problem with the new system causes downtime.
So what should be done? Prebuy in 2026 and everything will work out, right? But time is running out for that choice.
Lager said at Penske, account representatives who once helped fleet customers look six months out now need to start planning 18 months ahead at minimum, but three years would be better.
“The general guideline in the past has been that you need to plan ahead six to 12 months, but I think that is changing when you’re looking at prebuys for the emission standards,” said Vatalaro, citing potential production delays and extended lead times.
And many took that advice based on the MY2026 order books, another reason to act fast.
“Everybody believes this is going to be the largest prebuy,” Antonellis told Fleet Maintenance back in March. “Talking to a lot of the OEMs, they’re already saying they’re pretty much sold out in 2026.”
Magnus Koeck, VP of strategy, marketing and brand management at Volvo Trucks, also predicted that “In 2026 the total market could be the highest we have ever seen.”
Also, last March, retiring Daimler Truck CEO Martin Daum said the market leader will increase its capacity to meet demand: “If we see in 2025 and 2026 a pull-forward effect, we’ll go from there.”
There is still a little time left.
“I think we’re going to see availability in the first half, and we’re going to see demand tightening and going back to allocation in the second half of calendar year 2025,” Antonellis stated.
As you make your plans, these experts advise that you educate yourself not only on EPA rules but also on the separate rules set by the California Air Resources Board. And don’t let the snooze button deter you from taking action.
“This prebuy is really setting up as another event like COVID, only we know it’s coming, so everybody can be prepared,” Fleet Advantage’s Benton noted. “You don’t want to wait till the last minute. You really have to start now. If companies haven’t been thinking about this already and started planning their procurement strategy, they’re almost behind the eight ball.”
Every solution right now in trucking is like a monkey’s paw, none problem-free. But if you’re careful with what you wish for and make a very calculated wish, you should still be in business in 2028. (No one ever said trucking was for the faint of heart.)
“It’s a scary decision to make,” explained Christopher DeFeo, owner and president of DeFeo
» This Peterbilt 389 is one of DeFeo Materials’ five vocational trucks. They are all coming up on 500,000 miles, so owner Christopher DeFeo has to decide what his next move will be. DeFeo Materials
Materials, a river stone wholesaler in Connecticut. “The new truck market is very high—and not going to come down—matched with very high interest rates. That right there is keeping me from ordering trucks.”
The Federal Reserve eased the interest rate by 0.5 percentage points in September, though DeFeo believes he has about four to six months to make a decision. Perhaps after the election, the rate will drop another 1.5%, he opined; however, buying a new truck is about more than just interest rates.
“You have to look at your debt-to-income ratio … and is the cash flow going to be there to continue to support making these massive payments?” the 29-year-old business owner asked. “Not to mention, are we going to sell a truck that has a 60- or 72-month loan after three or four years— when we already paid mostly interest and now we’re on the equity portion?”
He said when deciding to purchase or lease, review the amortization schedule to calculate the remaining loan balance at estimated time of replacement or sale.
DeFeo, whose trucking career started at age 15 driving on a wheat farm, has been around long enough to not act impulsively and stretch beyond his means. He believes dealers’ push to prebuy are hiding a more clear-and-present danger.
“They’re trying to scare [fleet customers] more about what could happen with 2027 emissions instead of the actual reality. Is there even going to be enough profit or business to justify buying a new truck at the current prices?” DeFeo questioned. “Forget about the next 30 grand.”
What makes this more difficult is that for fleets with under 10 trucks, which is about 95% of them, the owner has to fill several roles.
“You have to be everything: a debt manager, a mechanic, a driver, employee manager,” DeFeo said, adding people in his position must also monitor records and keep up on rules and regulations. For now, DeFeo has enough to get by with a quarry lease, five vocational trucks—a 2004 Kenworth W900, three 2019 Peterbilt 389s with tri-axle dump beds, and a Western Star 49X, plus more than 15 pieces of heavy equipment
With Continental’s newest metro urban tire – Conti HAU 5 – urban buses can be sure they provide their passengers with the smoothest and safest ride. As an EV-compatible tire, the Conti HAU 5 meets the special requirements of EV/Hybrid and those of combustion engine buses. With 3 Peak Mountain Snowflake and Mud & Snow designations, the Conti HAU 5 delivers superior performance in all weather conditions, giving you confidence at every turn. Visit us at www.continental-truck.com for more information.
and 80-plus rail cars. He also has his sights on expanding the stone business to other regions and trying to rely less on the trucks to bring revenue.
But he can’t ignore the trucks or their TCO.
These trucks are all around the 500,000-mile mark, and operating in a quarry hauling rocks is the vehicle equivalent to working on a chain gang. It wears you down.
DeFeo is already seeing the early signs. Emissions issues on a few of his trucks gave the company fits in spring, which had the foreman handle what diagnostics and preventive maintenance he could; the rest was outsourced. That gives him pause in considering the used market.
“You’re either paying the bank or you’re paying the mechanic and the bank because you still have a payment on a used truck,” DeFeo said. “This is why we went to newer trucks because the downtime was eating us alive.”
Newer trucks are also less likely to be put out of service by inspectors. Those violations cost money to pay for repairs, fines, and insurance increases, he said.
So, should DeFeo sell the used trucks he has and go new?
“Right now is not the time to sell because of how bad the used-truck market is,” he said.
According to Benton, he’s right. “Used-truck prices are at an all-time low,” he explained. “We’re kind of coming out of the bottom of that cycle right now.”
The top of the cycle was during the middle of the pandemic, when OEMs were playing catch-up after shutting down, and the lack of key parts such as semiconductors kept orders from being fulfilled, raising the demand for existing vehicles. And the prebuy may create a similar situation.
“We anticipate that there will be a surge in the used market,” Benton said. “If you’ve got used equipment that is in good working condition, and we’re sold out in ’26 as everybody expects us to be, then we should end up back in a situation like where we were with COVID.”
New and used trucks both have their pros and cons. But at least for the next few years, leasing might end up being the most attractive because this procurement strategy answers the most important question for overburdened fleet managers: “Can’t somebody else do it?”
In short, leasing takes the hassle out of running a fleet, especially if you do full service, which includes maintenance. Instead of paying off a loan, you pay a fixed amount to a bank or leasing company’s financial arm for an agreed-upon number of months. At the end of the term, you hand the keys back and can upgrade to the new model year, which will have the latest safety, efficiency, and driver comfort features. They also can handle the minutia of truck ownership, such as licensing, fuel tax, and permits.
“Does your logistics department want to manage all of the truck maintenance, technician training, and capital expense of these ever-changing vehicles, or do you want more of a full-service lease with PacLease, with manufacture-trained technicians, where we can take care of everything?” asked Vatalaro, adding account reps will also help with debt, capitalization, and overall finances.
» Joe Vatalaro, director of maintenance for PacLease, said the lessor offers companies flexible leasing options and customized spec’d Peterbilt and Kenworth equipment, which will provide flexibility for fleets to become comfortable with 2027 engine technology. PacLease
This lets executives and owners of any fleet focus on their actual raison d’être, whether that’s hauling pebbles or delivering pharmaceuticals.
“What they really care about is what is the most cost-effective way that allows them to deliver their product from point A to point B that also provides the highest level of service to their customer base and gives them a competitive advantage in their market,” NationaLease President Dean Vicha said.
Lessors provide the scale and adaptability small fleets need to compete with larger competitors and have partnerships with maintenance providers who can service all makes and models.
For owners like DeFeo, this is helpful. “Without a doubt, the most difficult part of the industry is either going to be the repairs and maintenance or the rules and regulations,” he noted.
This will become even more important as the planning phase for the next wave of GHG Phase 3 regulations that emphasize zero-emission powertrains ramp up at the end of the decade.
“We’ve got people dedicated to this,” Lager said of handling regulations. “This is their job. They do nothing but meet with regulators or meet with manufacturers to dive into the maintenance aspect.”
Another difference is with leasing, you just re-up a new lease or walk away. Ownership, though, allows fleets to build equity and depreciate an asset’s value at tax time, which DeFeo noted would be more savings if profits were high. But that doesn’t always work out in a bad economy.
“Companies that have been selling equipment over the last few years have been getting kicked in the gut a lot because they’re upside down depending on how quickly they depreciated the asset,” Benton said. “The faster you depreciated them the lower your loss, but still a loss.”
There’s also residual value to take into account, which is the value of a truck that has been completely depreciated. In leasing, fleets don’t have to worry about depreciation or residual value. The lessor assumes all that.
Benton advises spending on items that are “accretive to your bottom line.” DeFeo Materials, for example, is investing in a maintenance facility at the quarry so equipment can be worked on indoors.
In cases like that, where capex is spoken for, leasing avoids dealing with complicated accounting. “I’m probably not going to put [capex] into a depreciating asset like a truck, so that has a big impact on whether I purchase it or whether I lease it,” he said.
Fleet Advantage offers an early exchange program without penalty and uses data analytics to predict when the best time to exchange is, factoring in things like fuel efficiency and maintenance costs.
That is helping fleets plan their prebuy strategy.
“Probably 50% of our asset base is already committed to early exchanges,” Benton said. “So what that means is for those terminations [set to expire] in ’27 and ’28, we’ve already started coaching those customers through replacements in ’25 and ’26.”
Lager said that based on mileage and utilization of the asset, customers can help extend past 2028 to “ride through the introduction of the new equipment.”
According to the latest benchmarking survey from the National Private Truck Council, 28% of private fleets in the Class 8 sector lease the majority of their fleet, while 38% own more than 90% of their fleet. About one in three does a combination of owning and leasing.
“We are seeing more market share moving to full-service leasing in the private fleet arena,” NationaLease’s Vicha noted. “As vehicles continue to become more complex and capital intensive, I expect this to continue.”
And in planning for the future, Fleet Advantage also just announced a new program that provides battery-electric trucks and yard tractors at essentially the same cost as diesel trucks, which could result in a $3,000 saving per month. The lessor absorbs those costs.
“By taking some financial risk, we think we can convince the early adopters to take on some operational risk and help move the needle on the transition to alternative fuels,” Benton said.
Questioning whether a fleet should lease or buy “is an exercise that all companies should be going through on a regular basis because there are lots of factors that go into that cost of funds,” Benton explained. He added it’s not uncommon for fleets to switch back and forth depending on the economy and fleet financial situation.
For DeFeo, a lease would protect against major repair costs, because the lessor handles maintenance, and the fleet would always have the latest, most efficient technology. Leasing also offers shorter terms than loans and accounting overall is simplified.
But on the con side, along with not building equity, fleets that require specialty equipment to do their jobs might have limited options and modifications might be prohibited. DeFeo’s trucks needs wetline PTOs, for example. Vatalaro said PacLease does work with fleets to customize Peterbilt and Kenworth trucks.
In the end, availability is what matters most. And according to a recent discussion with one OEM, Benton believes customers should make a decision by Q2 2025 “to ensure you have allocation for 2026 and 2027.”
For related content go to FleetMaintenance.com/equipment
PC-based software provides comprehensive support for commercial vehicles
The most successful commercial vehicle repair operations typically possess one common trait—the ability to complete repairs quickly. They understand that a truck sidelined for any length of time can directly impact the profitability of a trucking operation.
To help fleets and independent truck owners minimize the downtime of vehicles in need of repair, more and more repair operations are utilizing eTechnician diagnostic software from NEXIQ Technologies. Designed to improve the speed, efficiency and accuracy of the vehicle diagnostic phase, eTechnician has become an essential tool for shops committed to delivering fast, high quality repair work. In a business where time truly is money, this can go a long way in building a base of loyal customers.
Technicians of all skill levels appreciate eTechnician for its ability to deliver comprehensive coverage across a wide range of commercial vehicles. This includes critical diagnostic capability for engines, transmissions, brakes, body, chassis and more. To provide fleet managers and repair facilities with valuable insight on the many benefits of eTechnician, Dave Shock, product manager, Snap-on Business Solutions/ NEXIQ Technologies, has provided answers to a number of important questions regarding commercial vehicle diagnostics and NEXIQ’s advanced PC-based software application, which he helped develop.
What are today’s technicians looking for when it comes to vehicle diagnostics?
Simplicity. Rather than searching multiple applications for the information they need, technicians want to have everything right at their fingertips. This includes the collection of service information, which can be a challenge.
What source does eTechnician use to obtain its service and repair information?
eTechnician uses web services from Mitchell1 to acquire fault code troubleshooting information. By partnering with this highly reputable source, eTechnician provides techs with the support they need to diagnose a vehicle quickly and accurately.
What type of vehicles does eTechnician support?
I think it’s safe to say that if a truck rolls into a commercial vehicle repair facility, there’s a very good chance that eTechnician has it covered. This includes consumer pickup trucks and vans, all the way up to commercial service vans, transit buses, work trucks and Class 8 semis. And I’m not just referring to a wide range of vehicles from a single manufacture, but rather the ability to provide diagnostics across all major brands. When it comes to engine support specifically, eTechnician covers all commercial
on-highway diesel and gasoline engine equipped vehicles.
Which bi-directional tests does eTechnician support?
eTechnician provides unprecedented bi-directional support, including changeable parameters and thousands of special tests such as DPF Regen, Injector Cutout and SCR performance/ system testing, to name a few. It’s also important to note that eTechnician provides testing designed to help the technician get vehicles out of derate.
Does eTechnician include a vehicle history component?
Yes. eTechnician provides the ability to generate cloud-based, fleet-wide vehicle history reports that provide shops with access to data for every diagnostic session for every vehicle serviced using our tool, regardless of location. Reports include special test results, component details, technician notes, recordings and life/trip data.
Do you have to be an experienced tech to use eTechnician?
Not at all. We designed eTechnician around the people who use it—technicians. By consulting with techs from day one of the software’s development, we created an intuitive, technician-focused diagnostic tool that’s simple to learn and easy to use.
Does NEXIQ offer a free trial for repair operations interested in taking eTechnician for a test drive?
Absolutely. Repair operations can start a 14-day free trial by visiting nexiq.com/ freetrial.
How can readers learn more about eTechnician?
It’s easy. Simply visit the eTechnician product page at nexiq.com.
An engine overhaul could be a fleet’s best bet when looking to squeeze a few more years of life out of a truck. And going all in can help ensure the quality and reliability they’re hoping for.
EBy Gregg Wartgow [ IN
VEHICLE ]
mission regulations will become more stringent in 2027, and the cost of new trucks will rise even higher. Interest rates are already high. And remember when you sell your current trucks that used prices have tumbled from their eye-popping highs from a couple of years ago. In other words, there are several reasons to encourage fleets to hang on to their trucks a bit longer than in the past.
Data suggests some already are. e average life cycle of a truck-tractor has crept up into a prime overhaul window. According to a June 2024 report published by the American Transportation Research Institute (ATRI), the average trade cycle on a truck/tractor is 7.5 years (673,995 miles).
If this trend continues, could that lead to an increased demand for engine overhauls over the next several years? at’s tough to say at the end of 2024.
» As an alternative to an in-frame overhaul, swinging a reman engine is another option for fleets looking to extend the life of a vehicle. Remanufactured engines are factory-assembled and tested by the OE. Pictured is a technician in a Detroit reman center.
Still, it’s likely to be a viable option for fleets to evaluate and one of the many variables that collectively play into the overall ROI equation for a fleet asset, including ownership costs, maintenance and repair costs, uptime and reliability, fuel e ciency, safety, etc. In some instances, the best ROI could point to an overhaul.
“If you can maintain a fleet really well so trucks are able to operate long past the initial expenditure, it can be a huge boon to cash flow,” said Alejandro Paret, owner of Diesel Rebuild Kits, a distributor of top a ermarket parts brands.
For fleets that run the numbers and make an educated decision to keep a truck in operation longer, it’s important to know what their options are. If an engine hasn’t su ered major damage and is only showing signs of normal wear and tear, an overhaul is one of those options.
Mileage is the fi rst indicator.
“It always used to be that million-mile mark,” said Jim Madich, engine service supervisor at Blaine Brothers, based in Blaine, Minnesota, which provides parts, repair, maintenance, and towing services in the region. “Lately, we’ve seen that a lot of trucks with a ertreatment systems are not lasting that long. We advise our customers to start watching for signs that an overhaul could be needed any time a er 500,000 miles.”
What are some of those signs?
Michael Young, powertrain product marketing manager at Daimler Truck North America (DTNA), said drivers will o en complain about power loss and reduced fuel mileage. Increased oil consumption and coolant usage are also at the top of the list. Madich added that fleets that do oil sampling may learn there is a lot of iron, copper, or metals in the oil.
Other signs that an overhaul is needed include blue, black, or white exhaust; engine knocking; poor engine braking; and low oil pressure.
In addition, it’s important to understand the condition of the rest of the vehicle before making an overhaul investment. Overhauling an engine might not make sense if the transmission is also on the verge of failure, the chassis is in rough shape, or other costly repairs will be needed in the coming months. If one or more of these is the case, it might make more sense to invest in a new truck. But if all of those other items check out okay, and the fleet is looking to get at least a few more years of service out of the truck, an engine overhaul could provide a solid ROI.
When performing an overhaul, a technician must disassemble the engine and inspect vital components to determine what needs replacing. en they’ll put it all back together again. A successful overhaul hinges on a technician having the right skills and training along with the right tools and parts.
With respect to the parts, both OEs and a ermarket companies o er overhaul kits to make it
easy for the technician to get their hands on the key items that need to be replaced. For example, on the OE side, the Mack Trucks Re-Power program o ers several options for fleets looking to “refresh” an engine, including an engine overhaul. Mack o ers an in-frame overhaul kit using genuine new parts as well as a remanufactured overhaul kit.
“We load our REMACK (remanufactured) overhaul kit with a remanufactured connecting rod, and we’ll preload a cylinder kit so it’s easier to install,” said Sherman Williams, director of remanufacturing and parts product development at Mack Trucks. “ e customer has the choice of having a Mack dealer handle the installation or buying the kit over the counter and doing it themselves. It’s not an easy task, though, which is why we tend to lean customers toward our dealers to make sure the installation is done correctly.”
In the case of Detroit, its StepUp Overhaul program has four progressive levels. Using the DD15 engine as an example, Step 1 is a basic overhaul kit that includes the following:
Ü Six cylinder kits, which include pistons, rings, pins and bushings, cylinder liners, and seals
Ü Connecting rods
Ü EGR actuator linkage nut
Ü Oil pump, oil fi lter, oil pan gasket
Ü Coolant fi lter
Ü Fuel line kit, fuel fi lter kit
Ü Lower-end bearing kit
Ü Cylinder head bolt set
Ü Cylinder head gasket kit
Ü Block gasket kit
Step 2, the Super Overhaul, adds a high-pressure fuel pump, cylinder head assembly, and coolant thermostat. Step 3, the Complete Overhaul, adds a turbocharger, axial power turbine and turbine gearbox, water pump, and set of six fuel injectors.
“Choosing the right package comes down to the type of wear the technician is seeing in the engine,” Young said. “It also comes down to how much of the engine a fleet wants to overhaul based
Are your trucks getting up there in years, but you still want to hold onto them? Here are a few things to know:
• Engines ranging from 500,000 to 1 million miles, or comparable work hours, could be considered.
• Make sure the transmission is in good condition.
• Make sure you have capable technicians or a trusted rebuilder to perform the overhaul.
• Internal warning signs include:
» Power loss
» Reduced mpg
» More oil consumption
» More coolant usage
» Low oil pressure
Signs the driver would notice:
• Seeing blue, black, or white exhaust
• Hearing engine knocking
• Feeling poor engine braking
on the expectations they have for how long they expect to continue running the engine.”
Madich said Blaine Brothers typically encourages its fleet customers to opt for the highest level of overhaul kit, regardless of make or model. “If one of the components fails that you didn’t replace, it would be a real shame to wipe out an overhauled engine just for trying to save a few bucks,” Madich said, adding that it’s also important to know how the warranty might be a ected by not replacing certain components.
A ermarket overhaul kits are another option for fleets. In the case of Diesel Rebuild Kits, Paret said they ask for an engine serial number. “ is allows us to determine which specific components are needed for the overhaul, which allows us to provide the fleet with a 100% match for what it needs,” he explained.
STANDARD ADAS CALIBRATION SYSTEMS
MA600 ADAS CALIBRATION SYSTEMS
In the case of a routine in-frame overhaul— where the technician pops the head off and installs new pistons, liners, bearings, and rings— Paret said it’s a relatively quick procedure for a good technician. “More importantly, it helps bring you back to zero-hour operation of the engine,” he added. “The technician also wants to address the cylinder head to make sure it still has a flat surface. They could take it to a machine shop to make sure it’s still in spec.”
As a distributor for major U.S. aftermarket manufacturers like Interstate-McBee, IPD, PAI, FP Diesel, and AFA, Paret said Diesel Rebuild Kits incorporate components that are more affordable than genuine OE but not of lesser quality.
“The parts we use are designed to meet or exceed the OE part,” Paret said. “And in some cases, we actually offer a better warranty.”
The Diesel Rebuild Kits’ website says most of their brands come with a two-year warranty, though some components that feature a high-performance coating are warrantied for three years. That is generally in line with what many OEs offer.
An in-frame overhaul is not a fleet’s only cost-effective option for “refreshing” an engine, however. In fact, Mack’s Williams has witnessed a trend away from in-frames. Part of that is technician-driven, meaning that many of today’s technicians don’t have the time, skills, or desire to perform a complete in-frame rebuild. The bigger factor, however, relates to reliability.
“When you move up the tiers of repower overhauls, from a basic in-frame overhaul to either a remanufactured 3/4 or 7/8 swing engine, you’re getting a much higher-quality product,” Williams said. Thus, along with its overhaul kit, Mack Trucks also offers two reman engine packages. One is a 7/8 engine, complete transmission, and carrier. The other is a basic 3/4 engine and short transmission if the fleet wants to refresh the entire powertrain.
Step 4 of Detroit’s StepUp program also happens to be a reman engine replacement.
“ If one of the components fails that you didn’t replace, it would be a real shame to wipe out an overhauled engine just for trying to save a few bucks. ”
Jim
“A remanufactured engine is factory-assembled and tested,” Williams explained. “And because it is all done at our factory, we have all the applicable updates to implement all engineering changes that have come about since the engine was first produced.”
Compared to an in-frame rebuild, reman engines typically have faster installation turnarounds.
“Our customers want to increase their vehicle’s utilization,” Williams said. “When you’re going from an in-frame overhaul to swinging an engine, you’re decreasing downtime. You’re also increasing the quality of what you’re getting. When you have a factory-remanufactured 7/8 engine that’s dyno-tested, along with up to three years of warranty coverage, there’s a lot of value there.”
If a fleet still determines that an in-frame overhaul is the most desirable option, it can minimize downtime by making sure a reputable service provider handles the procedure.
DTNA’s Young said it’s important to work with a rebuild provider that is within the service network for that particular brand of engine. “These rebuilds are complex and require special tools,” he said. “Also, working with a certified in-network service provider will usually help a fleet maximize the warranties.”
In the case of Detroit, a basic overhaul has a one-year warranty, a super overhaul has a
one-year/100,000-mile with an option for a two-year/200,000-mile warranty, and a complete overhaul has a two-year/200,000-mile with an option for a three-year/300,000-mile warranty. The caveat is that all overhauls must be performed by an authorized Detroit service outlet.
In the case of Mack Trucks’ Re-Power program, a two-year parts warranty is included, although a three-year/350,000-mile warranty is offered when the overhaul kit is installed by a Mack dealer.
Up in Minnesota and Wisconsin, Blaine Brothers is an authorized dealer for CAT and Cummins engines. But they’ll work on just about anything that comes their way. That requires a serious commitment to tooling and training. When considering an independent shop to perform an overhaul, fleets should look for these types of credentials and capabilities.
Madich said Blaine Brothers always takes advantage of training opportunities offered by Cummins. To help fill in the blanks with the other makes and models their technicians touch, Blaine Brothers seeks out reputable third-party training providers. They’ve found a good one in Texas that they regularly send technicians to.
“The classes cover brands like Detroit and Paccar, and they usually last around four days,” Madich said. “They’re really popular and usually book full. So anytime there is an opening, we’ll send guys down there, depending on what the class is and what our training needs are in terms of make, model, and EPA year.”
Blaine Brothers identifies a few technicians at each of its four truck repair locations to become rebuild specialists. “It’s a very skilled job that you can’t just give to anybody,” said Jason Kendrick, director of service operations. “Those specialists are the techs who are sent to training classes.”
Additionally, when Blaine Brothers hires a new technician who may have just finished up their schooling, they identify those who have an interest in becoming a rebuild specialist. “After a few months on the job, we can usually tell if someone has the potential to advance into more advanced work like an overhaul,” Madich added.
Those with potential are groomed on the job by current rebuild specialists. “They’re essentially training their replacements,” Kendrick said. When the time comes for those new technicians to step in to the role of specialist, they’ll start partaking in those external training sessions to stay at the forefront of knowledge.
Engine rebuild specialists also require some specialized tools that a typical “maintenance shop” likely won’t have.
“Some of these tools get pretty expensive, so it’s typically the shop that will buy them,” said Howard Durfee, assistant coordinator for the diesel technology and advanced diesel programs at WyoTech, a trade school in Laramie, Wyoming. Examples include cylinder liner pullers and tools to reinstall liners correctly; tools for liner holdouts to make sure they aren’t sitting too far in or out; and brand-specific tools for cam bearings, taking blocks out of frames, lifting cylinder heads off, and more.
As one of the premier diesel training centers in the country, WyoTech has invested in these types of specialty tools to help train the future generation of diesel technicians. Even though they’re located in a small, remote city, the reputation of their program helps draw students from all over the country. Durfee said class size ranges from 40-100 students. For select students, a portion of the 12-week advanced diesel curriculum includes rebuilding an engine for a local fleet.
With so much attention on new technology and diagnostics in recent years, Durfee said it’s encouraging to see that young, up-and-coming technicians are also eager to roll up their sleeves on the mechanical side of things. When an engine rebuild comes into the class, quite a few hands go up to participate.
“We generally like to have three students working on a rebuild,” Durfee explained. “We like to pick the more gung-ho students.
“They also have to meet certain requirements, like having at least near-perfect attendance, and need to be very detail-oriented,” he continued.
“You cannot rush with a rebuild.”
Fleets shouldn’t rush with their decision to invest in a rebuild, either. Sometimes a remanned
replacement engine is the best option, and sometimes investing in a brand-new truck will make the most sense. But if a fleet has a truck in the 500,000- to 700,000-mile range and is looking to squeeze a few more years of reliable service out of it, an overhaul can prove to be a good bet.
For related content go to FleetMaintenance.com/in-the-bay
One benefi t of electric vehicles for fl eets is the promise of reduced maintenance. But “less maintenance” doesn’t mean “no maintenance,” and fl eets still need to perform routine tasks like tire rotations, brake service, and fi lter changes on their EVs. In fact, due to the near-instant torque EVs off er, they may need new tires more often than their gas-powered counterparts. Whether you’re doing a battery swap or just swapping tires, here are 5 tips for safely lifting an EV for service.
1. Use a lift with suffi cient rated capacity. Thanks to their high-voltage battery packs, most EVs are heavier than their internal combustion engine (ICE) counterparts. Check the vehicle weight and make sure the lift you’re
planning to use has suffi cient rated capacity to raise it for service.
2. Don’t guess at the lifting points. It’s critical that your frame-engaging lift contacts an EV only at the vehicle manufacturer’s recommended lifting points. Most EVs are designed with their battery packs under the vehicle. The battery packs are large – taking up most of the undercarriage – and heavy. As a result, the OEM-recommended lifting points are often on the far edges of the vehicle frame. Some two-post lift arms will not extend or retract far enough or have a low enough profi le to reach these points. If your lift can’t reach the manufacturer-recommended lifting points, don’t put your safety at risk. Use a diff erent lift.
3. Choose the right adapters. Flip-up adapters are convenient, but not precise. Stackable screw pad adapters can be adjusted up or down to ensure level lifting and more precise and secure frame engagement. Gouge- and tear-resistant polyurethane pads reduce risk of vehicle damage. Never use wood blocks or homemade adapters.
4. Rock before you roll (or lift). If using a two-post lift, after the lift arms are positioned, raise the lift until just before the adapters contact the lifting points. Make sure the arm restraint gears on all four arms are engaged, and then raise the lift until the vehicle tires are a few inches off the ground. Stop and verify that all four adapters are making solid contact with the recommended lifting points. If they are not, lower the vehicle and start over. If the adapters appear to be making secure contact, gently rock the vehicle to make sure it is stable and balanced before proceeding.
5. Always consider center of gravity. It’s crucial to your safety that any vehicle you raise on a lift remains stable and balanced. On a two-post lift, vehicle weight should be evenly distributed across all four lift arms. If work requires removing or installing heavy vehicle components that may aff ect the vehicle’s center of gravity, use high-reach support stands.
BendPak
30440 Agoura Road Agoura Hills, CA 91301 (800) 253-2363
www.bendpak.com
Ifinformationisn’tpasseddown
the right
wayfromleadershiptocoworkerstocustomers, that’s a
There’s nothing quite like the stomach-dropping feeling of realizing that you’ve forgotten something important, especially when that something is a Peterbilt 378. But that’s what happened to Jamie Wendt, CEO of HM Repairs and Services, and also alignment shop Madison Spring, both based in Wisconsin.
It was a busy Monday morning, and Wendt was expecting a customer’s truck to roll in that day. In preparation, he told the shop manager to get the vehicle on the schedule before it arrived.
“Well, he probably got busy, so it didn’t get put on the schedule, and the driver didn’t talk to [the employee], so the truck got forgotten,” Wendt recalled.
Two and a half hours passed before the customer called the shop to check on their vehicle. Realizing what had happened, Wendt pushed back another project and assigned two technicians to the truck to make up for lost time. ey worked late to get the vehicle fi xed that very evening, and the truck was picked up fi rst thing on Tuesday morning.
While Wendt was able to save the situation with the Peterbilt, looking back, the CEO noted that he could have chosen another method of notifying his scheduler of the incoming vehicle, such as an instant message, so the shop manager would have been reminded of the task that needed to be done.
Such reminders are important when shops and fleets have to keep track of innu-
merable critical details on several vehicles at once. is can be especially di cult for shops like HM Repairs that have grown from a small operation to a busier one.
For example, while Wendt used to be the one fielding customer calls, they must now be directed to the service writer. But even so, longtime customers still may reach out to him about their vehicles, providing all the information that needs to be ferried to the service writer anyway, said the shop owner’s wife Jessica Wendt, who is CFO of both shops.
“ e more people who you have on your team, the more important communication is to be able to make sure that everybody knows [critical information],” Jessica explained. “And I think that was a struggle for us initially—and still is a struggle here, too.”
But HM Repairs is not alone in experiencing miscommunication problems that a ect the business. According to Forbes Advisor’s 2024 report on workplace communication, nearly half of workers surveyed said ine ective communication hampers their productivity.
And it’s even more important for leadership to cultivate their communication skills. at Forbes report noted 43% of on-site workers lost trust in leaders who could not e ectively connect with them.
Having strong communication is not only critical for those in operations but also between those in the back o ce and on the shop floor. Without it, busy technicians may rush to fi x a truck without getting enough information from the driver.
664692950|KariHoglund,851416354|phattaraphumGettyImages
“Balancing communication and technical skills has a huge impact on both company success and each individual employee’s success,” said Ryon Packer, chief product o cer at Motus, a vehicle management and reimbursement so ware provider. “But I think every manager has at least one story about the great technician who upset customers, was challenging for peers to work with, and ultimately wasn’t technically good enough to overcome the negative issues.”
How can a fleet juggle all of these moving pieces when it comes to communication? While ‘improving their communication’ might seem redundant, it is true, as long as we are aware of the various areas communication can be improved, from day-to-day notes to big-picture plans.
Matthew Copot, VP of fleet management for Saia, a less-than-truckload fleet out of Georgia, believes the basics of good communication start with clarity.
“You’ve got to be clear when you’re communicating, and do it o en,” he advised.
According to Copot, this clarity and repetition helps employees understand their jobs and responsibilities, which increases their overall engagement with the company.
Motus’ Packer leans on three basic tenets to communicate clearly:
Ü Answers fi rst—Make sure the main point is the fi rst thing communicated.
Ü Just say it—Use simple language and focus on being understood.
Ü Make it clear when you’re changing things.
“A lot of communication is the admission that we’ve decided we’re doing something wrong and now want to do it di erently. Own it!” Packer asserted.
Make sure that you follow through on what you have promised, said Amanda Schuier, strategic maintenance director at Jetco Delivery and the 2024-2025 general chairman and treasurer for American Trucking Associations’ Technology and Maintenance Council. She also emphasized the importance of using simple, easy-to-understand language, particularly in instances when a
technician may have far more information about a truck than the customer or senior leader they’re speaking with.
“From a technical standpoint, you can’t always assume that people know what you’re talking about,” Jetco’s Schuier noted. “So, if you’re typing up a super technical email, always say, ‘Let me know what needs clarifying.’”
As for what not to do when communicating, Packer again emphasized the need for simplicity and a direct approach:
Ü Don’t justify—Stick to the ask or directive, not the story behind it.
Ü Don’t use your own language—Deliver the message the way your audience is going to hear it.
Ü Don’t assume that because it matters to you, it matters to everyone.
e next step beyond the right words to say is knowing the right medium through which to say them. e Forbes Advisor report noted that for on-site workers, 38% found mobile phones to be the most e ective way to communicate, with landline phones and Zoom following up at 22% and 21%. But that doesn’t necessarily mean any of these methods will be the best way to communicate in every situation your fleet encounters or for every person in your fleet.
“I think you have to have a good blend,” Saia’s Copot explained. “You have to read the room well and understand which piece of communication is best.”
As an example, for informal messages that only need a quick response, perhaps a text message is best. But if you have a longer message or need a more in-depth plan, a phone call may be better. If you want to retain your message and the response for later reference, then an email could be the way to go.
Fleets should also take into account their recipient’s preferred form of communication and the content of the message they need to deliver.
“I do not like text or email for any kind of communication where you’re trying to address an issue that could be sensitive,” Wendt explained,
While having a ‘strong culture’ can feel like meaningless buzzwords in today’s commercial repair shops, their true meaning is much simpler and more impactful, according to Beverly Beuermann-King, workplace culture and resiliency speaker and expert at Work Smart Live Smart.
“When we talk about the culture that we’re trying to create, generally, whether we use the words or not, it’s about respect,” Beuermann-King explained. “It’s about productivity. It’s about allowing people to bring the best of themselves to the workplace.”
Regardless of what you call a positive workplace, this culture and respect can quickly degrade due to the poor behavior of one person, making it harder for your other employees to stay healthy, engaged, and productive in the shop or fleet. Whether this behavior presents in passive-aggressive comments or withholding needed information, even by accident, the best way to deal with it is with direct communication, Beuermann-King said. But how do you prepare for such a loaded conversation?
First, it helps to understand the motivation behind the toxic behavior or at least have an idea of where it might be coming from.
“What do people get from being negative, difficult, gossiping, or toxic?” BeuermannKing asked.
While a shop manager might not be able to help with external factors causing this behavior, such as difficulties at home or a stressful move, they can help meet these needs in a more appropriate way in the shop.
all levels can be heard.
“because it can sound so nice and so compassionate in your head, but when they read it, there’s one word in there that triggers something.”
At HM Repairs, they use a mix of texting, phone calls, Microso Teams, and walkie-talkie radios for delivery drivers. Additionally, for some training matters and company-wide communications, they also use their payroll platform, Paylocity.
But to reach that point, managers need to successfully navigate an open discussion with the employee in question. To start, be prepared to address the employee’s positive behaviors as well as their negative ones so that you’re offering balanced feedback, Beuermann-King said. Managers also need to anticipate how the person they’re speaking with may respond to being called out. Planning ahead for bluster, blaming, or even an attempt to leave the discussion allows the manager to be able to redirect this response back to the conversation at hand, and focus on solutions instead of deflection.
“ When you look at emergencies, we have what we call ‘critical situations’ that require immediate notification.”
Matthew Copot, VP of fleet management, Saia
“Not everybody in a truck repair shop is going to have a company email,” Jessica Wendt stated. “And our technicians aren’t going to have a company-wide email that they’re going to be checking during the day. But everybody gets paid, right?” is makes Paylocity ideal for polling employees on their meeting availability and rolling out safety training because the platform allows managers to see when employees complete the training.
or even an attempt to leave the discussion
Then, if the employee seems willing to work with leadership, be ready to outline future expectations for the employee and what you can do to support them. Don’t forget to establish follow-ups with this person, too, to make sure the behavioral change is holding, and there are no additional issues.
On a more personal level, it’s just as important to understand what your listener needs to hear, Jetco’s Schuier added.
“My boss, for example, is very numbers-driven,” she explained. “So when I talk to him, I know that I need to approach him with facts and fi gures, whereas for me, I’m more of a big-picture, emotive thinker.”
“The problem is we know that sustaining performance is about checking in,” Beuermann-King emphasized.
“It’s about holding people accountable.” —AK
e amount of ways to communicate within a fleet is a long list by itself, let alone when considering the sheer amount of messages and data that a shop or fleet might exchange every day. While AI technology can help fleet and maintenance managers fi lter vehicle data, shi ing through data from people, in all its forms, is a bit trickier.
“The most common issue I hear is that between email, text, word of mouth, Slack, ticket systems, etc., issues just get lost in the noise,” Packer added. Instead, as businesses grow, leadership may only be able to stay on top of day-to-day issues by creating a single, easy-to-use tracking system, and then reminding people to use it consistently, he continued.
Additionally, managers may need to reassess their communication strategies if they’re feeling overwhelmed. After all, getting too much information from your peers may be due to a lack of clarity in what you need, resulting in an overabundance of data instead.
“Try to be specific in what you’re asking,” Saia’s Copot advised. Then, if you’re getting too much data, provide feedback on what you do and don’t need.
Specificity is especially important when it comes to fleet emergencies. Preferably, a shop should know what it needs and which people need to know what information before a problem occurs.
“When you look at emergencies, we have what we call ‘critical situations’ that require immediate notification,” Copot commented. “As cliche as it may seem, we lay out scenarios so you know the ‘who’ and the ‘how’ of the communication is based upon different types of situations that might exist.”
For example, if a technician is injured in the shop, Saia outlines the priorities of the situation, starting with caring for the injured person, followed by what level of communication needs to be upheld and who will monitor that communication.
However, fleet communication has to include more than a single shop’s disaster plans or the distribution of safety training to the company. It also must encompass communication between the technicians on the ground and the decision-makers at the top. And this can be tricky, especially when maintenance is both costly and critical.
Jetco’s Schuier is often in the position of needing to be the link between shop management and company executives, a job which may include explaining why a truck’s maintenance costs are rising. Communication between these two spheres is especially important in these situations, when a solution on paper may not translate to the shop floor or vice versa.
“Sometimes in the office, we see a solution, but then in the shop, we’re able to say, ‘Okay, this will or won’t work’ because we’re able to back it up with technical information,” Schuier noted.
As an example, Jetco wanted to save money on tire costs. Schuier investigated using super single tires on a vehicle but found that because of the permitted load of the truck, the tires weren’t going to achieve the company’s goal.
This kind of communication requires that leadership and shop technicians are not siloed with executives up in a glass-paned tower while techs remain down in the trenches.
It is for this reason that Copot keeps an open line of communication.
“A technician is free to make a phone call to me or directors or regional managers,” he stated. “And regional managers, directors, and I are
¶ Visual inspection relating to damage
¶ Cracked welds
¶ Retention pin holes oblong-shaped
¶ Correct retention pins
¶ Readable decals and placards
¶ Compromised
¶ Visual inspection relating to damage
¶ Leaking fluids
¶ Non-OEM conforming, tampered with or missing components
¶ Readable decals and placards
¶ Visual inspection relating to damage
¶ Excessive wear
¶ Missing components
¶ Leaks
¶ Complete functional test
¶ Readable decals and placards
¶ Cracked welds
¶ Visual inspection relating to damage
¶ Excessive wear
¶ Missing components
¶ Complete functional test
¶ Readable decals and placards
¶ Compromised
always walking shop floors to talk to people and find out what’s happening.”
As an example, Copot once struck up a conversation with a driver while leaving Saia’s corporate office and heard about his needs regarding the pallet jack he was using. Unbeknownst to the driver, Copot was working on sourcing more of what he needed, which allowed the driver to have the clarity he required right away.
Both Jetco and HM Repairs facilitate this kind of interdepartment communication with regular meetings. HM Repairs holds shared Microsoft Teams meetings between its two locations each month, allowing everyone to share the room at the same time.
Jetco has consistent shop and operations meetings with attendees from shops, operations, and senior leadership, with Schuier further spreading the information from each meeting by sending out agendas and summaries before and after each event. “Even if you didn’t attend the meeting, you still know what happened,” she explained.
If a shop or fleet can’t coordinate direct meetings between technicians and executives, that’s where middle management’s communication skills become critical in making sure that technicians feel heard.
“What your team needs to know is that you’re at the table vying for them and that you’re stepping up with your bosses and your leaders and saying, ‘We need these types of resources for our
teams to do the job that they need to do,’” said Beverly Beuermann-King, workplace culture and resiliency speaker and expert at Work Smart Live Smart. The consulting company works with organizations to improve personnel management and satisfaction.
Finally, there’s no situation in which communication is more important than conflict. And in a chicken-and-egg way, conflict also tends to grow from poor communication.
“Toxicity grows; it becomes more pervasive the longer we allow it,” Beuermann-King warned. Toxic behaviors can include passive-aggressiveness, backstabbing, withholding information, blaming, and the silent treatment—all of which can cause havoc to a fleet’s communication streams and the business at large.
But although more difficult than a standard notification or conversation, communication can help defuse these situations as long as the participants figure out how to communicate more effectively and how to address the underlying issues, Beuermann-King said.
This requires understanding the ‘payoff’ of negative behavior, be it contrariness or gossiping.
“Because there’s always a payoff, whether it’s
for
and that you’re stepping up with your bosses and your leaders.”
Beverly Beuermann-King, Work Smart Live Smart
recognition or control or attention, and when we understand that, then we can meet those needs in a much more appropriate way,” BeuermannKing explained.
Addressing this requires a personalized conversation with the employee in question as well as a system for feedback and accountability.
“It’s important to take that person aside and say, ‘This is what we want the mission and values of the company to be, and we need you to stop doing X and become more part of this,’” HM Repairs’ Jessica Wendt concluded.
For related content go to FleetMaintenance. com/shop-operations
by John Hitch
Welcome to the 2024 Fleet Diagnostics special section. This hasn’t been a ground-breaking year for new tools or ways of doing things, but it has been a huge one in terms of how the industry has coalesced time-proven strategies with new technologies.
We’ve been writing for awhile about how more and more technicians will be relying on diagnostic tools, tablets, and laptops to get the job done. Over the last few years, the ratio of tools to techs has narrowed from 1:6 in 2016 to about 1:3 now, according to Noregon. And as Mindy Long reports in our cover story on page 34, there will be one diagnostic tool per tech in the next five years.
For some shops, it could be even sooner. Over in Portsmouth, Virginia, at American Fleet Service, there’s a diagnostic tool for every 1.5 techs, company president Butch Cassel said.
Does this mean your lube techs will need a new ruggedized tablet to change an oil filter? We’re not there yet, but it does mean fleets need a wider array of tools for their more experienced techs and, of course, diagnostic specialists. This could range from your typical scan tools and electric testing units to more niche ones like borescopes and thermal images.
And for some gear, like computers, you’ll want extras in case one breaks down. The last thing you want is two techs bare-knuckle boxing over the last laptop. (This is something
we’ve heard happened before most fleet managers realized investing in diagnostics was necessary.) So take a look at the piece and see if you are adequately prepared.
We also asked our resident diagnostic bestie, senior master tech Missy Albin, to see if TMC’s incoming RP on root cause analysis meets the expectations the group’s leadership have hyped it up to be. Albin bravely accepted the challenge and used the key elements of the RP, the fishbone diagram and 5 Whys, to troubleshoot a truck that wouldn’t shut off. The results will not only change how Albin does her job going forward but likely will for many others as well. (My wife even tried to use it to get me to shut up, but so far that’s been ineffective.)
Finally, Jeremy Wolfe dives into the world of remote diagnostics, which continues to grow more accurate and informational. Now a staple feature for heavy-duty trucks, remote diagnostics are helping fleet employees understand the nature and severity of fault codes—including which problems can wait and which ones need urgent attention.
We’re positive you’ll find some value in each of these stories, which should set you up to meet your own expectations for uptime in the coming years. And to help even more, check out the many new diagnostic tools included at the end.
Thanks for reading and happy troubleshooting!
Diagnostic tool demand is hitting a critical mass, with experts predicting a 1:1 tech-to-tool ratio by decade’s end.
by Mindy Long
Eight years ago, a commercial vehicle shop, on average, had one diagnostic tool per six technicians, according to Noregon Systems. By the end of this year, the diagnostic solution provider estimates the ratio will be 1:3.
Bruno Gattamorta, chief commercial officer for Cojali, which makes Jaltest diagnostic tools, thinks the ratio will be 1:1 by 2030. “You’re not going to be able to do anything without these tools in the future. As time goes on, there are more sensors and more ECMs,” he said.
With increased demand for maintaining and repairing more sophisticated commercial vehicle systems and components, in some places, a 1:1 ratio is just around the corner.
Butch Cassel, president of American Fleet Service, based in Portsmouth, Virginia, said the shop has one tool per every 1.5 techs. He’ll invest in additional tools if it takes too long for techs to get results—or if the shop picks up a new fleet customer with specific
engines that need to be diagnosed. “Especially in a small, independent heavy-duty shop, there is a fine line to balance tool expense versus return,” he explained.
As fleets and maintenance managers plan their budgets for 2025 and beyond, it is a fine line they will walk all the same. The technicians will need to learn the basics of modern troubleshooting and have the tools necessary to do so unless they want to market themselves as a boutique antique truck repair facility.
A tech likely needs one of these tools for most jobs, from replacing a radio to an oil change (because they need to reset sensors). And because most systems communicate, the added wires, sensors, and processors may require some level of diagnostics.
“Most repairs use some type of diagnostic tool to verify the complaint, confirm the cause, or make the correction,” noted Dan Carrano, VP of fleet maintenance for A. Duie Pyle, a less-than-truckload carrier based in West Chester, Pennsylvania.
Daniel Mustafa, director of technical service for TravelCenters of America, said that over the past 20 years, electronics have been incorporated into virtually every vehicle system. “While this gives excellent visibility to vehicle issues, it makes electronic diagnostic tools a requirement for most vehicle systems,” he said.
This is true even in the body repair sector. According to Tom McGuire, CEO of Precision Diagnostics, a maker of tools for the collision sector, technicians can no longer “bare-knuckle” their way through repairs anymore.
Because advanced driver assistance systems (ADAS) are now integrated into many vehicles, diagnostic tools are now essential, even for simple tasks like replacing a windshield or bumper.
“Technicians today are working on computers, processors, and communication networks that are integrated into the vehicle architecture,” he explained.
OK, so we know they’re needed. But what are these tools really providing, and why can’t we go back to those simpler, more analog times from two decades ago? For starters, all those additional sensors and ECUs paired with telematics lead to commercial vehicles producing and sharing more data than ever before.
So much, in fact, that “the vehicle itself is becoming a diagnostic tool,” said Robert Braswell, executive director of the American Trucking Associations Technology & Maintenance Council. “With telematics, you’re anticipating faults before they happen,” he said. With the next stage in diagnostic evolution, predictive maintenance, AI programs can cross-reference a truck’s symptoms (or fault codes) against similar cases, alerting management when a truck might have to “call off” for health reasons. That gives you enough lead time to make changes and not disrupt operations.
But as you may have guessed when that truck rolls into the bay, “you need some sort of tool in the shop bay to figure out what is wrong,” Braswell said.
The best anyone could do without tools is guess at the root cause, Aaron McCoy, fleet performance manager for FleetNet America, said. “Not every failure or its cause can be directly seen or heard,” he said.
Diving in without a tool increases the odds that a customer will get their vehicle back with the same problem or even in worse condition. “That causes reputational damage not only to the technician but also the shop as a whole, and in some shops, [this] can even result in the technician being forced to work without compensation if they have to do rework or if they go over the quoted labor time,” McCoy said.
Danny Colon, co-owner of Dedicated Diagnostics, said the tools also save time, particularly when diagnosing complex, multi-system issues. He explained that JPRO’s enhanced fault guidance provides detailed, step-by-step instructions for diagnosing and repairing faults based on specific diagnostic trouble codes.
“This feature streamlines the diagnostic process, allowing our technicians to quickly identify and resolve issues without needing to consult multiple sources,” Colon explained.
In a modern truck, a cranking/starting system has a minimum of three computers and their associated switches and sensors. “You can very quickly
determine if a starter is receiving voltage or not, but if not, why? To answer that question without diagnostic software is likely impossible,” Mustafa, TravelCenters of America, said.
Another example is lighting. “In [older] vehicles, the only way to know if the exterior lights were working was to get out and look. On the modern truck, it sets a fault code and communicates that to the driver through the instrument cluster info screen,” Mustafa explained, adding that lighting faults have made TA’s top 10 fault code list.
Even the radio communicates with the collision mitigation and lane departure warning systems to give drivers audible alerts. “Years ago, if the radio went bad, you’d pull it out and put a new one in there. If you do that now, you have to program the modules in the truck to say there is a new radio and provide the code. Otherwise, it will get a check engine light,” Carrano, A. Duie Pyle, said, adding that any electrical fault or issue that causes a check engine light requires diagnostic software.
Aven Blozan, a technician for Iron Buffalo, which operates shops in Colorado and Montana, said 100,000 things can go wrong on a truck. “If you had to guess which one of those things was causing the check engine light, you would just be replacing the truck,” he said.
More and more tools are providing a one-stopshop experience for technicians. “There was once a time that you retrieved the fault code from the tool, but if you needed service information, you had to go to another source. After you identified the needed
parts, you had to go to another source to look up the parts,” Mustafa said. “In the leading software manufacturers, all these functions have been built in.”
ATA’s Braswell said shop managers need to know which handheld tool, tablet, or laptop is needed for a repair. “They need to be aware to schedule the repairs so techs can complete the repairs and verify that the repair was completed properly,” he said.
As tool functionality increases, shops may be able to streamline the overall number of tools needed. “The proprietary nature of tooling is starting to melt away, so you can have one brand that can cover multiple models,” Braswell said.
A versatile, comprehensive tool means technicians can address various problems across multiple vehicle systems without switching between different tools, enabling faster diagnostics and repairs, reducing downtime, and improving overall service efficiency.
“As a newer company, this strategy helps us maximize our operational efficiency and deliver superior service to our clients,” Colon, Dedicated Diagnostics, said. It is also necessary for each shop to have a tablet or laptop to connect to as well as sufficient scan tools.
Jason Hedman, Noregon, is seeing increased functionality influence purchases. “You don’t have to have as many individual tools because our tool services multi-brands, but you do have more laptops per service center,” he said. “If you’ve only got one machine in the shop with 12 technicians, somebody’s always waiting on a machine.”
Carrano has experienced the increased need for laptops firsthand. “Where we needed one laptop, now we have two. Where we had three, now we have five. It is hard to do anything without a laptop,” he said.
Additionally, some services can tie up a laptop for extended periods. At A. Duie Pyle, technicians always check soot levels in exhaust aftertreatment systems and may conduct a forced regen, which can take a half hour or more, to prevent drivers from having to do it while on the road.
“You need a laptop the entire time to do a forced regen. When you think about how many PMs we do a week, the forced regens can tie up the tool,” Carrano said.
Iron Buffalo’s Blozan added that nearly any repair on an aftertreatment system requires a diagnostic tool. “Since it is a federally regulated part of the vehicle, you have to go through certain procedures to clear the derate and the check engine light,” he explained.
To aid technicians, tool providers are adding more features. TEXA has added a guided diagnosis feature to increase technician efficiency. “This new IDC5 functionality directs the technician through the vehicle problem, with step-by-step interactive instructions that begin at the diagnostic code and complete with recommended repair solutions,” Fabio Mazzon, technical manager for TEXA USA, said.
Cojali has added more dealer-level features, which can save time and drive ROI on the tool. “We can do remote calibrations of ECMs or ECUs. Before, you’d have to go to the dealer, wait for them to do the install, and update your software,” Cojali’s Gattamorta explained.
Noregon has added coverage on Cummins-powered equipment, CAT-powered equipment, Paccar, and
International. “It isn’t shiny or sexy, but our customers want new features, and they really want to fix their trucks,” he said.
Noregon has rolled out Truck Check Up software to perform and submit heavy-duty vehicle inspections required by the California Air Resources Board’s clean fleet regulations, which apply to any vehicle traveling in California. TA plans to support the CARB program and will likely begin offering the service at California locations and possibly other surrounding states next year.
When Mustafa researched CARB-certified inspection tools, he was excited to see that TA’s primary tool supplier, Noregon, had a solution. “The advantage of their tool is that not only can it be used for the CARB inspections but also for diagnostics. This alleviates the burdens of purchasing a new tool and having to manage two different tools.”
“ As a technician, I frequently considered a shop’s tooling and equipment as a factor in whether I would accept an offer to work for that shop in the first place. ”
Aaron McCoy, fleet performance manager, FleetNet America
While the tools are becoming essential, they don’t replace the skills technicians need. “One of the big misnomers is you have this fancy robust scan tool that solves all the issues. It doesn’t, but it is a great data resource,” Precision Diagnostics’ McGuire explained. “The worst thing you can do is have really good tooling and underdeveloped technicians. We learned a long time ago that you have to marry the two.”
One of the challenges is that today’s trucks are getting more complex quicker than the fleet technicians can scale. “The issue is not just having the software and the laptop. It’s having techs who know how to use it,” Blozan said, adding that techs also need to know when to question the data. “You can get led down the wrong path if you’re blindly trusting the information a tool is giving.”
As a result, training on tools and overall maintenance is essential. “The tool will lead you, but the fleet tech still has to make that final decision,” Carrano said. A. Duie Pyle taps into OEM training, creates handouts and training videos, and has trainers in the field.
With the ongoing technician shortage in the industry, shops must focus both on retention and recruitment.
“Having proper equipment and diagnostic tools available is a big factor in retaining experienced technicians and attracting new ones,” FleetNet America’s McCoy said. “As a technician, I frequently considered a shop’s tooling and equipment as a factor in whether I would accept an offer to work for that shop in the first place.”
Tools can also boost a technician’s confidence. “They might see 25 different brands of vehicles. They’re not going to know how to fix them all. We give them the step-by-step instructions on what they have to do to fix it, and then that, combined with their knowledge and experience, gives them the solution,” Gattamorta explained.
versatile,
tools, reducing
Mustafa added that some of the most sophisticated systems even offer just-in-time training specifically suited to the troubleshooting steps needed.
Cojali offers its customers access to advanced diesel technicians who can help other technicians over the phone. “When the user becomes the hero of the story and solves the problem, they become engaged,” Gattamorta said.
Because diagnostic equipment and tooling improves the ability of technicians to diagnose and repair customer vehicles, techs can make more money and experience fewer on-the-job frustrations. “There is an added advantage of the technician being able to
educate themselves and improve their workmanship quality as they gain experience,” McCoy said.
Shops unable to invest in new scan tools or update existing software coverage often find their master technicians leaving in search of better work. “It’s unfortunate, but it is a story we hear more often,” Mazzon said.
Gattamorta pointed out that most technicians only use a fraction of what the tools are capable of, and it can be difficult for them to recognize they are not using the tools to their full potential. Technicians are offered weekly training sessions by Cojali, and customized training is available based on the requirements of individual shops. ●
by Missy Albin
Recommended Practice 551: Root Cause Analysis (RCA) was introduced at the American Trucking Associations’ 2023 Technology & Maintenance Council Annual Meeting, and after much study and debate, it is tentatively slated for publication in the 2025 manual. It was championed as a formal way to troubleshoot using the scientific method and logic. After using it on a real job, I found it may be one of my most essential tools as a diagnostic technician.
Essentially, the RP provides guidance on two root cause methodologies: the fishbone diagram and 5 Whys. Though I’ve worked on trucks since 2004 and have been diagnosing them for about a decade, I had never heard of these tools before. Curious about how these could help me at the International dealership where I work, I set out to learn more.
My first step was getting a primer from Mike Parnitzke, owner/principal of Parnitzke Consulting Group. The former rocket scientist for Pratt Whitney is spearheading efforts to evolve the RP guidance from
TMC’s pending RP 551 on root cause analysis will change the game for troubleshooting problems in the bay and office, and we had one technician take it for a test drive.
paper (or web viewer) into functional digital tools that could be used “in the garage and back office.” This will likely involve augmented reality and artificial intelligence and is a ways off. For now, I just wanted to use the basics to help me find the root cause of equipment failures and to make quality repairs to create lasting solutions.
So let’s start with the basics of RCA, which Parnitzke stressed “is not rocket science.” (And he would know.) It’s just the scientific method and asks the tech to define the problem, collect data to confirm root causes, and finally establish ways to eliminate them for good.
He explained it’s going from “Houston, we have a problem …” to “Houston, we have an understanding of the problem.”
This begins with the fishbone diagram, created by Dr. Kaoru Ishikawa, a Japanese quality control expert, in the 1960s. It maps the real possibility of failure for various categories that branch off from the spine. When you are all done, it looks like a fish skeleton.
“The fishbone diagram is a brainstorming-centric tool and has several steps in it to help you focus and also organize your thoughts,” Parnitzke explained.
You start by creating the problem statement and quantify what is happening, not why. The RP uses the example of high maintenance expenses with wheel bolt hole cracking as a leading expenditure. If you don’t put enough information and thought into the head of your diagram, you’ll find yourself floundering later, so don’t rush.
Using technical manuals and other resources based on the categories, you then create general cause categories, such as processes, policies, people, equipment, and so on. Brainstorm the subcategories, such as “irregular tire wear” and “lack of proper lube” under equipment, and ask why each is happening. Then cull the root causes from these by determining if the “cause” is removed or corrected, then the issue stops. Validate with other subject-matter experts as a “sanity check.”
The next step is to look at the 5 Whys, a simple and direct line of successive questions that a team
Aftermarket install ECM
» Someone tied into the ignition circuit
› Could be shorting to power
› Backfeed to ignition from device
» Communication codes would be present
» Loss of power 1117, power supply loss with ignition on codes may be present
» Popping fuse
» Internal short
» Weak/bad ground
» The new switch is bad
» Ignition relays
» Ignition wire from switch to fuse panel shorting to battery power
Ignition circuit short to battery
» Accessory circuit
» Aftertreatment circuits
» A ftertreatment PDM :
› I gnition relays and aftertreatmen t
f use and relays shorte d
› Water caused shor t
› P DM wire and plug side exposed to element s
° P DM plugs and seals poor integrit y
Problem/Effect:
Will not shut down with ignition key
» Component shorting internally
» Loss of communication
» Bad ground
» Likely root cause(s) Ignition switch Module controller or component
of SMEs can use to identify a root cause. It’s best used when there is before and after data/evidence for a problem. Once everyone is gathered, they must define the problem effect, and put it at the top of a flipchart or whiteboard. Keep asking why that happened and then what made that happen until your fifth “why” in the chain and the root cause is revealed. At each step, you likely have to discuss multiple possible pathways.
After discussing this with Parnitzke, I realized I do all of this informally in my head. I question the driver, review repair and warranty histories, read fault codes (and everything written about them), and use fault code trees when available. By using a process of elimination—my favorite is the FMI hierarchy—I narrow it down and finally identify the root cause.
The problem is that when I convert my diagnostic process from my head to paper, it becomes what I call “technician hieroglyphics.” I understand it, but others do not. At times, this causes friction when my service writer needs an answer key to decipher my personal language.
Although validating to know I’ve been intuitively using similar strategies to what TMC advises, I figured adding some tips from the RP to my diagnostic tool bag would help me find the root cause in a more focused way on paper.
Fortunately, I got my chance when a 2016 International ProStar with a problem rolled into the shop. The driver reported this truck just didn’t know when to quit; the engine and everything stayed on even when the key was turned off.
First, I verified the entire truck would stay live with the key in the “off” position and out of the ignition. The engine stayed running, the radio played, and the dash lit up with ABS traction control, trailer, and “electrical fault.”
It was time to utilize a fishbone diagram, I thought. This job did not have a diagnostic path written and no active codes to chase. All I had was a major symptom, which became my “effect.” Now, I needed to find the “root cause.”
As I was writing out the path, another diagnostic tech, Dave Caponigro, asked what I was doing.
My brief explanation had piqued his interest. (Lured him right in.) He even prompted his ChatGPT to make a fishbone diagram for my exact effect, but the AI bot could not do it. It was up to me, and it turned out to be exactly the type of job that reminds me why I am so passionate about what I do. Charting each major category branch, or bone, I was able to visualize what my next steps were going to be in testing and eliminating theories.
After thinking about it, I decided the problem effect was: “Will not shut down with ignition key.” The major categories were: “aftermarket install,” “ignition switch,” “ECM,” “module component,” and “battery short to ignition.” After reviewing it with my service manager, Joe Dougherty, he added a few more subcategories, which were tested strategically as I moved down to the spine.
I verified the replaced key switch was not the cause of the problem and that the installed aftermarket devices did not come with any “creatively added” circuits. Those theories were eliminated.
Next, I pulled the ECM fuse from the panel. The engine shut down, but the electrical stayed on. I repeated the same procedure for the body and Bendix controllers, and after that pulled ignition fuses one at
a time. Finally, when the F5-F aftertreatment fuse was pulled, everything shut off. This was my first theory but last branch in my fishbone, as the box is difficult to get to on this chassis at ground level.
I lifted the truck to access the several panels to reach the PDM. I peeled open the box, and there it was—filled with water and cyan-colored from the corrosion—exactly what I expected to find and the true root cause. I rebuilt the entire PDM with a new updated, sealed PDM and mounted it by reversing the clips and bolt heads on the top rather than bottom.
To ensure I could permanently fix the issue, I did a 5 Whys analysis asking how the PDM went bad. In the end, I determined that the box design led to the failure and that if I simply replaced it with a similar version, the problem would reoccur. So I used a better designed box that completely sealed except for 26 empty terminal slots.
The fishbone diagram was so helpful that I have used it on multiple jobs since then. I am certain I will use these tools in every complex diagnostic I get going forward. It kept me focused and organized while I was able to change my technician hieroglyphics into a legible story.
Now I just sit here with one more why. Why has this not been a part of my diagnosis all along? ●
Remote diagnostics have boosted shop efficiency and reduced fleet downtime by adding actionable insights to fault code data.
by Jeremy Wolfe
Telematics provide fleets and shops with a wealth of information, from engine health to efficiency and performance metrics, though not every employee knows how to cash in on the information age’s oft-misunderstood digital currency.
They likely understand that fault codes, for example, indicate a problem on a truck. But is it minor or major, and will it impact the business—or is it merely technological white noise?
To help alleviate this, modern remote diagnostics go a step further than sharing technical error codes. Remote diagnostics use a vehicle’s telematics gateway to communicate fault codes and vehicle data, such as location or mileage, to a remote database.
The database shares this information with the customer through SMS alerts, emails, or on a proprietary platform. However, remote diagnostics go beyond simple error codes, as Paul Smith, VP of business development for custom solutions at Noregon, explained.
“It’s not just a matter of knowing if a vehicle needs repairs; you have to know where you can send it for repair,” Smith told Fleet Maintenance. “With TripVision, you can accurately diagnose issues, identify the needed repairs, and use that information to schedule an appointment, reserve a bay, and have the part ordered before the vehicle even arrives at the shop.”
The investment can reduce downtime and maintenance expenses, according to Nick DiPietro, director of
asset optimization and procurement at Lazer Logistics, a yard management services provider.
“Remote diagnostics undoubtedly represent a worthwhile investment for Lazer Logistics,” DiPietro said. “The ability to monitor vehicle health remotely helps prevent costly breakdowns and reduces maintenance expenses.”
A decade ago, fleets received access to an overwhelming amount of technical data for each vehicle. An important characteristic of modern remote diagnostics is making this data usable and accessible.
Remote diagnostics have a shared role across providers: sharing vehicle error codes, identifying potential problems, and facilitating their repairs.
From Kenworth to Western Star, every major heavyduty truck brand offers its own remote diagnostics solution. Other providers, like Jaltest Telematics, offer brand-agnostic diagnostics for fleets using a mix of trucks or platforms.
User-friendly diagnostics solutions help to elevate less technically skilled staff understand fault code relationships, follow complex operations, and recognize the urgency of certain repairs.
“It was a task to understand the data and what insights could be derived,” Noregon’s Smith explained. “But now remote diagnostics is at the forefront of dealer
and fleet maintenance strategies—and they’re being used in ways that they’ve never been used before.”
According to DiPietro, Lazer Logistics has seen significant value in using Noregon’s remote diagnostics solution over the last decade.
“We began utilizing telematics and remote diagnostics in 2015, integrating TripVision across our entire fleet,” DiPietro said. “One of the most important initiatives to come out of this new technology was the ability for real-time monitoring and diagnostics of vehicles and equipment.”
A major function of today’s telematics solutions is remote diagnostics. Based on a survey of fleets conducted by Noregon in 2023, remote diagnostics was identified as the most crucial telematicsenabled feature.
Since mid-2012, Volvo Trucks North America has made remote diagnostics standard on every one of its vehicles. According to Magnus Gustafson, VTNA VP of connected services, the main benefit is concisely “to add context.”
“Alongside fault data, remote diagnostics solutions also share convenient, accessible information about the code: what it means, how urgent it might be, and the likely parts and services necessary for repairs,” Gustafson explained.
Remote diagnostics also help users understand their vehicles’ problems without thorough expertise.
“It’s difficult to diagnose issues by just looking at fault codes, so you have to look at patterns. You have to look at operational values,” Gustafson said.
“You take a third-party solution, and you say, ‘I have this fault code’—that may mean something. But if it’s this code with that code with something else, that may mean something different.”
Volvo has an analytics engine that monitors truck data and follows logic rules dictating remote diagnostics behavior. This rule engine allows the OEM to be highly accurate in its diagnoses, according to Gustafson.
“We take those complicated SAE industry explanations for fault codes and we actually tell you how it’s affecting your vehicle,” Noregon’s Smith said. “We make some recommendations and then we spell out an action plan.”
Fault urgency guidance is a staple feature of remote diagnostics solutions. A solution’s urgency rating helps users understand the impact an error will have on the vehicle.
“If you’re using it the way it’s designed, it’s an early warning system,” Smith said.
VTNA’s urgency classification, for example, has two color-coded categories: yellow and red.
“We do yellow cases, which means you need to attend to this issue, but the truck can finish its mission, versus a red case, or alert, which is something that requires immediate attention and probably will end up diverting that truck,” Gustafson explained.
Other providers, like Kenworth and Noregon, use a four-color classification system: green, yellow, orange, and red.
When a vehicle stops running, it costs a fleet money. Broad, color-coded urgency categories help users understand quickly whether they can keep operating the vehicle. Many non-urgent repairs can be added to existing planned services, easily reducing downtime.
Many remote diagnostics platforms can connect fleets to support staff or nearby shops to facilitate repairs. This can reduce a fleet’s downtime and enhance a shop’s efficiency.
“You don’t have to take the truck out of service if you don’t have to; that’s the ultimate benefit,” Gustafson said. “The second is if the truck gets diverted to a dealership for a repair. What we see is, because it’s prediagnosed, it’s about 20 to 22% faster turnaround time.”
The result for maintenance staff is saved time, swift repairs, and well-planned operations.
Lazer Logistics’ DiPietro finds that remote diagnostics boost the company’s efficiency by enabling proactive maintenance. Basing maintenance intervals on the vehicle’s actual condition rather than on fixed intervals can lead to savings in both time and money.
“Moreover, remote diagnostics contribute to overall fleet safety by identifying potential issues before they escalate, thereby enhancing driver and public safety on the roads,” DiPietro said. “This early notification allows us to dispatch maintenance crews equipped with the necessary tools and parts to the
exact location of the breakdown swiftly. By diagnosing issues remotely, we minimize downtime significantly, ensuring that operations remain efficient and disruptions are kept to a minimum.”
Over time, remote diagnostics solutions have incrementally become more accurate, informational, and valuable for fleets and shops.
Remote diagnostic logic is continuously improving, resulting in a reduction in false alerts. And vehicles are still becoming smarter each year, adding significant new data streams on critical assets outside the powertrain.
“Every time I turn around, there’s a new sensor on a vehicle that’s delivering data to someone’s cloud or someone’s user interface,” Smith said. “There’s lots of room to grow in the future with remote diagnostics
as we start to incorporate things like intelligent trailer data, tracker data, and advanced driver assistance systems data.”
VTNA’s new VNL tractor, for example, introduces a 24-volt electrical architecture that Gustafson said will enable faster and more accurate diagnostics operations.
Looking further ahead, Noregon’s Smith thinks that artificial intelligence could find even more accurate diagnostics from the growing wealth of asset data available. Perhaps even vehicles that make their own appointments.
“And then we start talking way into the future with autonomy. Imagine a vehicle that can self-diagnose and self-schedule its own maintenance appointment,” Smith said. ”A technician in a shop walks into the bay, and his schedule is already planned out because vehicles are automatically scheduling their maintenance. Isn’t that something?” ●
Calibrate ADAS on light-, medium-, and heavy-duty vehicles
Perform static front camera calibrations, including Lane Departure Warning system calibrations, on applicable light-, medium-, and heavy-duty vehicles with the just-released MA600 CV ADAS Packages and the Standard CV ADAS Packages from Autel . Each frame system solution includes patterns and targets for performing static calibrations on Mercedes-Benz Sprinter and Ram ProMaster vans and heavy-duty vehicles equipped with the Bendix Wingman system. Packages are available with or without the required MaxiSYS MS909CV tablet, which supports dynamic calibration on Class 3-5 vehicles and Class 6-8 vehicles, as well as static calibration setup and software.
For more information visit FleetMaintenance.com/55129618
Turnkey diagnostic solution includes rugged tablet
The TEXA Axone Nemo Plus Truck Diagnostic Kit with Multihub from TEXA USA is a comprehensive, turnkey troubleshooting solution that includes the tablet, TEXA IDC5 software, and Multihub interface. The rugged 11.6” Axone tablet features an Intel N100 processor, 16 GB RAM, and 250 GB SSD storage. It can connect to Wi-Fi and Bluetooth 5.3 modules for connection to the TEXA vehicle interfaces. A built-in camera allows the user to capture details during maintenance operations and create reports that can be given to customers or sent to technical assistance. Also includes a secure case, OBD 9-pin adapter Type II, and a oneyear TEXPACK subscription.
For more information visit FleetMaintenance.com/55136502
Compatible with all major OE diagnostic applications
The DLA+ 3.0 Vehicle Interface Adapter from Noregon supports on-highway vehicles and off-highway equipment. The adapter offers an improved microprocessor to increase speed and programming capabilities and includes Smart Cable technology to auto-detect what cable is plugged into the device. The tool also incorporates upcoming CAN FD and DoIP integrations for better reliability. The DLA+ 3.0 is available for purchase as a standalone option or in kits paired with a Panasonic Toughbook and JPRO, NextStep Repair, and more. For more information visit FleetMaintenance.com/55001081
One platform does it all
Whether you’re a master technician or working to become one, every tech needs accurate information and the latest technology to get the job done right—and quickly. Say hello to eTechnician , a software tool developed by NEXIQ and designed to diagnose any truck that comes into your shop, from light- to heavy-duty, with special features including animated DPF regen, full system scans, a cloud-based vehicle history, and bidirectional support. Request a 14-day free trial available at nexiq.com/freetrial.
For more information visit FleetMaintenance.com/21277606
11’ long tube
The Vividia BD-5030i Borescope from Oasis Scientific is a semi-rigid USB borescope with a 0.19” diameter probe head and an 11’ long tube. It is equipped with both a front and side camera on the head and is designed to integrate seamlessly with the “USEE Camera” app (available on iPhone, iPad, and Android). Users can switch between both cameras and adjust their LED brightnesses within the app. Pictures and videos can be saved to connected devices.
For more information visit FleetMaintenance.com/55089262
All-makes, all-systems diagnostic solution used by 25,000+ shops
The Jaltest Commercial Vehicles diagnostic tool by Cojali is an all-makes, all-systems solution for light-, medium-, and heavy-duty vehicles, including trucks, vans, buses, trailers, as well as agricultural, off-highway, and material handling equipment. It provides advanced electromechanics coverage for all ECMs, including aftertreatment systems, and supports actions such as regenerations, resets, and injector calibrations. This tool features an extensive diesel technical encyclopedia embedded into the software. Users benefit from expert support by certified diesel technicians for remote assistance during repairs. It also enables OEM-exclusive functions like Cummins Revision Updates and Paccar Parameter Changes, among others, through the Jaltest link.
For more information visit FleetMaintenance.com/21277492
10x faster vehicle scans
The X-431 Throttle V from Launch Tech USA is designed to deliver a combination of automotive intelligence, quick navigation, and ergonomic handling for optimal efficiency. According to Launch Tech, the Throttle V is the most powerful scan tool in the X-431 family, providing fast performance during diagnostics and vehicle repair. With access to X-431 FIX and CODE ASSIST carline repair information, the Throttle V aims to accelerate the diagnostic repair process.
For more information visit FleetMaintenance.com/55136499
The Zenith Z7 from EZDS is a diagnostic scanner that features OE-level functionality as well as ADAS functionality and access to security gateways for FCA, Nissan, Ford, and Hyundai vehicles. With built-in J2534 pass-thru capability, along with support for DoIP, CAN FD, and Topology scans, it is designed to be an all-in-one solution for diagnostics. Additionally, the scanner has bidirectional communication with 24V commercial trucks and inclusive remote diagnostic support.
For more information visit FleetMaintenance.com/55089255
The Diesel Tablet 2 from Diesel Laptops is suited for work on commercial trucks, RVs, yard trucks, and more with over 5,000 dealer commands. It includes graphical system views for real-time sensor, actuator, and component data, as well as a smart VCI for self-diagnosis with diagnostic port voltage and databus traffic information. The Tablet 2 is also IP65-rated, dustproof, and water-resistant, and it includes Tech2Tech for remote diagnostic sessions. The tablet includes a year of Diesel Repair Standard and a perpetual license software with automatic updates. For more information visit FleetMaintenance.com/55125994
The latest ADS and ADS X Software Update from Bosch includes MY 2024 coverage and ADAS calibrations with over 2,000 new special tests and system applications. This includes a new Topology View and battery voltage indicator for ADS X series scan tools, plus improved scan tool speed, the company stated. The Topology View offers a visual representation of vehicle controllers organized along the vehicle’s bus lines, including the bus name and pin, while the increased 2018-2024 vehicle coverage supports DTC, data, and bidirectional functions. Bosch ADS X users with an active subscription can install the update after automatically receiving the download.
For more information visit FleetMaintenance.com/55133823
The HD Pro Tab II from CanDo is a sleek, fast IP65-rated tablet with a large memory that allows technicians to perform DPF regeneration, SCR/NOx resets, injector programming, change and set parameters, and offer full bidirectional controls. The HD Pro Tab II covers more than 60 manufacturers, including Detroit, Cummins, Paccar, John Deere, Caterpillar, and Volvo. A full suite of connectors comes with the kit, along with a docking station and two years of updates.
For more information visit FleetMaintenance.com/55056564
The i50HD Heavy Duty Diagnostic and Diesel Engine Scanner from Foxwell is compatible with Android 9.0 operating systems for global markets and features wireless connection and one-touch update. It offers a comprehensive and affordable diagnostic solution for pickups, trucks, and buses from manufacturers such as Caterpillar, Paccar, International, Detroit, Hino, and Ford, Chrysler. The i50HD performs general diagnostics like reading code/erasing code, live data, active test, and ECU information as well as DP regeneration, injector cutoff, and speed limit settings. It can also run bidirectional tests and automatically read VINs.
For more information visit FleetMaintenance.com/55041141
Supported by Cojali and modeled on Jaltest software
ACom AE from Bendix Commercial Vehicle Systems is the newest generation of the company’s diagnostic software is the newest generation of the company’s diagnostic software for its electronics systems, past and present, and includes its Global Scalable Brake Control and Global Scalable Air Treatment technology. Supported by Cojali and modeled on Jaltest software, ACom AE detects and gathers active and inactive diagnostic troubleshooting codes from various vehicle ECUs. It can also assist techs with diagnosing and troubleshooting tractor and trailer electronic products, and features DTC reporting and bidirectional communication.
For more information visit FleetMaintenance.com/55141852
Perfect for heavy-, medium-, and some light-duty vehicles
DG Technologies said its flagship DPA XL scanner diagnoses and reprograms heavy-duty vehicles with the most manufacturer software compatibility on the market today. It’s a TMC RP1210compliant Dearborn Protocol Adapter (DPA) with current and future technologies built in for years of shop service, and used for diagnostics and reprogramming of heavy-duty, medium-duty, and some light-duty vehicles. It also covers over-the-road, bus, construction, agricultural, military, industrial stationary equipment, and fleet vehicle segments. CyberGuard is included, and it’s built in the U.S.
For more information visit FleetMaintenance.com/53069141
All-in-one, mobile, advanced diagnostic trailer tester and inspection system
Innovative Products of America ’s Alpha MUTT (2nd Gen) with ABS and Tablet #5710A-T10, is an all-in-one, mobile, advanced diagnostic trailer tester and inspection system for both vehicles and trailers. IPA said its proprietary technology provides unparalleled results, drastically improving inspection accuracy, shop performance, and safety, as well as all aspects of lighting, air brake, ABS inspections, and repair. Made in the U.S., this easy-to-use trailer tester with advanced ABS, lights, and digital air brake diagnostics requires no setup or monthly fees.
For more information visit FleetMaintenance.com/55129624 , No.
The BCT-468 from Auto Meter is a handheld electrical system tester specifically designed for heavy-duty trucks. The tester uses a separable tablet and control module along with Auto Meter’s optional AMPNET cloud data management services to deliver accurate and fast testing results. Features include automatic voltage drop testing on starter, alternator, and liftgate cables and connectors; step-by-step graphical troubleshooting instructions; and a ruggedized control module with an 8” viewing angle touchscreen user interface. Wi-Fi enabled for automatic real-time data collection and customer communications.
For more information visit FleetMaintenance.com/55139326
Certain tools require regular calibration to ensure that repairs and replacements remain accurate in measurement, performance, and reliability.
By Lucas Roberto
Even a skilled and careful technician can be undone if their tools, such as torque wrenches, aren’t properly calibrated, which is why shop managers need to have a plan in place to verify that each piece of equipment is receiving regular checkups.
Not all tools in the shop require calibration, but technicians and supervisors need to know which ones require regular calibration to ensure repairs and replacements remain accurate in
measurement, performance, and reliability. This includes everything from torque wrenches and pressure gauges to diagnostic equipment like multimeters and oscilloscopes.
“Calibration is important for any precision instrument,” explained Kevin Rohlwing, chief technical officer for the Tire Industry Association. “If measurements are incorrect, then the perceived solution may not solve the problem.”
It’s important to remember some tools, like torque wrenches, can become out of calibration through daily wear or from being dropped.
“When tools lose accuracy due to wear, mishandling, or environmental factors, the results can be catastrophic— and costly,” warned Justin Franchuk, office and HR manager at Team Torque, which tests, repairs, and calibrates various torque tools. “When your tools fail to deliver the correct torque, you’re playing a dangerous game with both product integrity and human safety.”
For example, over- or under-tightened wheel-end lug nuts can and have caused entire wheels to slip off many a truck and trailer on the road, leading to serious injury and death.
Wheel-off events happen “on average about three times a day somewhere here in North America,” said Rod Imhoff, key account manager at Chicago Pneumatic. “Now, granted, it normally goes off into a cornfield or the woods and we don’t need to hear about
“ When torque control devices go out of calibration, it usually means the actualtorque is less than whatever the tool is set for. ”
Kevin Rohlwing, chief technical officer, Tire Industry Association
» Some specialized smart tools can use an algorithm to track their own calibration dates.
it, but it’s those times when it does hit some private property, a car, a building, or God forbid, a person, and you actually have a fatality.”
He added that “a fatality can be complete bankruptcy to a company that owned that vehicle when [the wheel] came off.”
But being mindful of torque wrench accuracy can ensure that these events are mitigated.
Torquing to a specific calibration level means stretching a stud just enough to where it wants to return to its original yield point, Imhoff explained.
“When you exceed that and you go too high, you can stretch that stud beyond a yield point; visibly, you may not even notice it, but you would certainly notice it over time,” he said.
He likened the situation to wearing a tube sock. “You might get up and put your tube sock on, and it goes up to about mid-calf, and it’s fine. But by
lunchtime, it’s falling down around your ankle,” he illustrated. “Now, why is that? Because it was stretched beyond its yield point at some point.”
While over-torquing can stress a lugnut, leading to it cracking and not doing its job to keep the wheel attached to the spindle, Rohlwing said it’s more common for an imprecise wrench to not provide enough torque.
“When torque control devices go out of calibration, it usually means the actual torque is less than whatever the tool is set for,” he said. “If they are dropped, improperly stored, or damaged, the end result may not be accurate.”
Whatever the case, when a wheel off causes injury or death, the last shop recorded to have touched that wheel will face severe scrutiny in court.
“In the event of a wheel-off accident, the plaintiff’s lawyer will consider everything that may have contributed to the accident,” Rohlwing explained. “Was the technician properly trained to install the wheel with the correct torque and clamping force? Did they follow industry-recommended practices? Was the torque control device calibrated? Is there a certificate of calibration to verify the accuracy?”
Although calibration will always be an essential aspect of repair work, taking good care of tools can minimize inaccurate performance mid-repair and the need for unscheduled calibrations. Things like rough handling and overuse can impact the ability of a tool to do its job properly.
“Especially with the torque wrench—If you drop it, set it down too hard, if it falls off the truck,” said Dillon Grimes, a mobile diesel mechanic with Cox Automotive. “I’d say that nine times out of 10 if something loses calibration, it’s probably mishandling.”
Rod Imhoff, key account manager for Chicago Pneumatic, noted that for certain tools, everything down to the specifics of storage can have an impact on the tool’s calibration, explaining that a standard click wrench, for example, shouldn’t be left “loaded.”
“You don’t want to leave it set, because the spring that’s controlling the setting of the torque when left in that position weakens over time or loses its retention,” he cautioned, “so you need to leave it unset.”
This is because if a technician were to find a tool already set in the shop, there are a number of unknowns that can influence its accuracy.
“You don’t know how long it’s been in that position; you don’t know if the tool’s been dropped or if it was laid down,” he continued.
“There’s really no way of ever knowing from looking at the tool or just generally using the
APPLICATIONS:
> Auto Glass Removal
> Spray-In Bedliners
> Bonded SMC Panels
> Metal Bond Adhesives
> SMC Panels
> Undercoating
Remove auto glass in minutes with the Inductor® Series: Glass Blaster. Release urethane in hard-toreach areas where other glass tools can’t go, with no damage to the encapsulate or frit.
tool if it’s at 10%, 5%, 50% of the torque that it’s specifically set at.”
The environment within the shop is another element to consider.
“It isn’t easy to keep wheel torque tools clean and dry, but it plays a big role,” Kevin Rohlwing, chief technical officer for the Tire Industry Association, stated.
Regarding humidity, for example, Imhoff explained that as with any metal item, “whether it be aluminum or steel, you’re going to get some expansion and shrinkage and temperature change in [a humid environment], not to mention what the moisture can do to the inside of a tool as well.”
He offered a few solutions, such as investing in high-quality, industrial-strength tools that are water-resistant and sealed as well as controlling the shop environment as best as possible for tool longevity.
» To stay on top of tool calibration, there should be a designated person to keep shop tools in spec, and technicians should be sure to check their personal tools against another from time to time to make sure both are functioning properly.
Rohlwing has seen this kind of interrogation firsthand as an expert witness.
“I’ve been in civil cases where these types of questions are always asked,” he recalled. “An untrained technician who doesn’t follow industry guidelines and uses a torque control method that has never been calibrated is difficult to defend,” he cautioned. “The reverse is also true in that a well-trained tech that follows the guidelines and uses a calibrated torque control device is easier to defend.”
Regular tool calibration is the remedy, but an effective calibration program requires an understanding of which tools require calibration and how often. This information almost always comes directly from the manufacturer.
To keep track, shops should assign a designated person or team responsible for keeping these tools in spec.
A complete six piece kit to crimp and release the Deutsch terminals found throughout the industry on trucks, construction equipment, motorcycles, race cars, agricultural and marine equipment, heavy duty vehicles and other vehicles and equipment subject to excessive vibration and wherever an environmentally sealed connection is used.
Extra long reach 14” dual head chuck with internal lock on threads inflates in both straight and offset positions. Easy to read, dual calibrated scales (0-160 PSI and 0-1100 kPa). Protective rubber boot surrounds dial gage. Ideal for use with heavy duty trucks, buses, RV’s and motor homes. 13” long hose with 360 degree swivel.
Dillon Grimes, a mobile diesel mechanic for Cox Automotive, explained that it’s a bit of a joint effort where he works. Whereas the company itself is responsible for keeping torque wrenches and other similar tools calibrated, the responsibility for air and tire pressure gauges falls to the technicians themselves.
“Whenever [a gauge] shows sign of wear, you test it against two or three different devices,” he said, “and if it registers differently, then we either recalibrate or replace those.”
DJ Painter, a former technician and now Noregon technician as a service lead, advised management to ensure all relevant shared shop tools are calibrated annually and to red tag those that aren’t. To motivate techs to also keep their personal tools calibrated according to schedule, he suggested using an incentive program.
Grimes explained that ensuring some devices are calibrated can be easily incorporated into typical repair processes without expending too much extra time.
“Every so often, I’ll go out of my way and instead of just the normal air pressure gauge I use, I’ll grab two just to verify that they’re both reading correctly.”
Many newer tools let you know when they require calibration, like the CP86 series from Chicago Pneumatic. While users should still get the tool calibrated on an annual basis or per manufacturer guidelines, these smart tools will alert you if something changes via an app on a cell phone or tablet that allows monitoring.
“If you use the tool on really high-level torques, or maybe you use the tool frequently enough, or you drop the tool, it records all of that kind of information and does its own algorithm to figure out when calibration is due,” Imhoff outlined.
For other tools, this isn’t always possible or practical, especially if the intricacies of the tool demand a higher attention to detail.
“When you think about pneumatic tools, calibration is more than just making sure it’s torquing properly,” Imhoff explained. “It’s ensuring that the rings, springs, and valves are working appropriately too. So there are some parts that can have some wear and tear and need to be replaced regularly as well.”
There are other factors that make taking care of regular calibration in house a less-than-ideal solution.
“A lot of companies will put stickers on their tools when cali-
bration is due, but let’s call it what it is,” Imhoff remarked. “[A shop] environment is not the best for stickers to stay on things the way they should. It’s a greasy, oily environment with a lot of different cleaning chemicals and things, so it doesn’t really work so well.”
All that said, the safest way to stay on top of your calibration and ensure that your tools are holding up their end of the bargain is to regularly
schedule them as per OEM guidelines.
Imhoff recommends outsourcing to a reputable third-party company instead of investing in calibration equipment and training in-house.
“If you can get a company that’s going to do an annual calibration—I call it a birthday card— they’ll send you a reminder that it’s coming up on your annual time to get calibrated,” he concluded.
“That’s the best way to do it.”
By Seth Skydel
Fuel and fi lter quality, as well as following OEM guidelines for fuel system maintenance, play a key role in keeping engines running e ciently and reliably. In addition, vehicle maintenance teams must not overlook the importance of fuel injectors, designed to keep the fuel supply running smoothly. When an injector experiences a problem, the whole engine su ers the consequences.
“Injector operation is required for not only eciency but also emissions standards as well,” said Chad Six, Ohio Valley regional supervisor, maintenance operations, transport & rail, at Marathon Petroleum.
It helps that the system itself typically handles injector upkeep.
“Fuel injectors are lubed and cleaned by diesel fuel during normal operation,” Six said. “As this is done under normal operation, they don’t become dirty or need to be removed and cleaned.”
But injectors are not only utilized for engine
operation, Six stated. “Emissions system components rely on fuel to catalyze and clean the diesel particulate fi lter,” he said. “If fuel injector operation is compromised, so is the e ciency of the emissions system.”
Six added that general engine maintenance goes a long way to ensure this happens consistently, saying “fuel injector fi ltration and fuel quality are important for [an injector’s] life cycle.”
Brad Queen, content group manager and vehicle electronics specialist at Noregon, agreed.
“Fuel quality plays an important role in the operation and longevity of fuel injectors,” Queen, an ASE-Certified Master Technician, said. “Higherquality fuel improves injector reliability and causes less wear on components, limits corrosion from water intrusion, and provides better performance and fuel mileage across the entire fuel system due to better combustion than poorer quality fuel.”
Mark Ulrich, Cummins director of customer
»
support, noted the leading diesel engine manufacturer does not have specific diesel injector maintenance requirements aside from ensuring the fuel and fi lters are up to snu .
“For best fuel system performance and health, we recommend customers follow prescribed fuel fi lter maintenance intervals with the correct micron fi lter ratings as outlined in the Cummins operation and maintenance manual for a given engine product,” he stated. “We have not been made aware of any issues with our fuel system components when fleets use commercially available sources of fuel. Following these guidelines ensures that engines meet needs and expectations on performance, e ciency, and reliability”.
But what happens when diesel injectors start to underperform?
“Diesel injectors are crucial for engine e ciency, and dirty injectors can cause poor combustion, reducing performance and increasing fuel consumption,” Scott Meek, diesel training director at Diesel Laptops, said. “Low-quality fuel can clog injectors, speeding up wear and lowering reliability, so clean, high-quality fuel is essential for maintaining injector e ciency.”
Noregon’s Queen pointed out that the buildup of internal and external deposits in diesel injectors can lead to a variety of problems. ose include weakened or total loss of engine power, decreased fuel economy, and an increased need for regens due to high soot levels.
Dirty or malfunctioning fuel injectors can also a ect engine longevity, noted Clay Parks, VP of
development at Rislone. “If injectors are not spraying fuel as a fi ne atomization—like fuel droplets—the fuel will not completely burn, and it will either be pushed out the exhaust or some of it will end up in the oil,” he explained. “ at also reduces the life of the engine and emissions components. A dirty or defective fuel injector should give fleet managers many concerns.”
Just as injectors have many benefits, they can also fail in several ways, Marathon’s Six said.
“ ey can fail internally in the seat of the injector and not atomize fuel correctly, leak by returning too much fuel, and ‘dribble’ or have compression pass through,” the maintenance manager explained. “ is will allow compression from the piston to introduce air into the fuel system return.”
e injector O-rings at the cylinder head can also fail and lead to internal fuel leaks, Six continued.
An electronic failure could also occur where the injector meters how much fuel feeds the cylinder. ese can be di cult to predict, and according to Six, “electronics can fail at any time for any reason.”
But how can you tell what’s wrong and why?
“Injector problems require visual checks, performance tests, and electronic diagnostics,” Dan Nynas, chief operating o cer at Diesel Laptops, explained. “Using advanced tools can pinpoint issues early, preventing bigger engine problems.”
With a combination of OEM or a ermarket so ware, injector flow and spray pattern testing, as well as sending out injectors to be tested, fleets can diagnose injector problems, noted Rislone’s Parks.
Not all shops stock these tools, though, Six noted.
“That being said, diagnostic software is required to set trim codes when or if a fuel injector is replaced,” Six added. “ e trim code tells the engine control module where that injector metered so if just one is replaced, it knows how to meter and balance that injector to the rest.”
e diagnosis will also depend on the failure point, Six said. “If the injector fails, the standard cylinder cut-out test would be the fi rst diagnostic procedure,” he stated. “If the problem is a low eciency, drivability, or fuel usage issue, a cylinder balance test would be the procedure to utilize to see if the injectors are atomizing fuel correctly.
“A cylinder contribution test can also be run to identify the same issue as well as a leaking O-ring seal,” he continued. “A er these tests are done and proper diagnosis is established, the failed injector should be inspected to see if the electrical connections are intact, and nothing abnormal is seen on the surface.”
Noregon’s Queen recommended using an advanced diagnostic tool, such as a troubleshoot-
ing module, that guides the users down a series of procedures until the root cause of the issue is discovered.
By keeping up on preventive maintenance, fleets can stay ahead of injector issues.
ere are a number of factors that come into play when determining how o en fuel injectors should be cleaned and/or replaced, and it will vary by fleet.
“Cleaning and replacement intervals depend on engine type, conditions, and fuel quality,” Meek said. “Typically, injectors should be serviced every 20,000 to 30,000 miles.”
Chris Johnson, business development manager at Diesel Laptops, recommended using ultrasonic cleaners and flow testers “to ensure thorough cleaning” as well as high-quality cleaning solutions.
Employing premium cleaners at regular intervals will help injectors stay clean and improve their lifespan, Rislone’s Park noted.
“We recommend an injector cleaner that includes a top lube to prevent sticking and allow greater power and performance,” he added. Fortunately, avoiding O-ring issues requires far less frequent attention.
“Removing and re-sealing the injector O-rings should be completed around the 500,000-mile mark, but most fleets do not perform this task if there is no issue,” Six noted. “ e standard practice is to replace the failed injector, and on high-mileage vehicles, it makes sense to replace all injectors. If one is worn out, the rest are more than likely to fail as well.”
When replacing a fuel injector, Noregon’s Queen said it is important to ensure that you program the new one correctly.
“ is is o en overlooked because not all OEs require programming codes, but even in instances where the engine seems to run fi ne, there could be a decrease in fuel economy due to not being properly programmed,” he explained further. “Shops should give technicians step-by-step instructions for removing the old injector and installing the new one.”
While exact numbers could vary depending on how a fleet uses its diesel equipment or trucks, keeping injectors clean could provide a 2-5% fuel economy improvement, Clay Parks noted.
“Fleets can quantify the benefits of keeping injectors clean by considering the consequences,” Noregon’s Queen said. “When an injector can’t function properly, the risks include roadside breakdowns, unsafe driving conditions, and increased fuel consumption.”
“Clean injectors can boost fuel economy by as much as 5% to 10%, depending on conditions,” Mark Lipinski, diesel tech trainer at Diesel Laptops, stated. “ ey also reduce engine wear, lowering maintenance costs and extending component life. Over time, this translates to significant savings for fleets.”
Modern-day propane fuel systems inject propane as a liquid through fuel injectors like modern-day gasoline fuel injection systems, related Mario Genovese, director of customer success for ROUSH CleanTech, the clean technology division of Roush Enterprises.
“Liquid propane is held in on-board tanks and then pressurized to the fuel injection system via a fuel pump assembly mounted inside the fuel tank,” Genovese explained.
“The liquid propane is injected into the engine’s intake manifold to be atomized with oxygen and burned through the engine’s combustion chamber, exactly how gasoline fuel injection systems work.
“With this fuel injection system, powertrain maintenance intervals and specifications are unchanged from the OEM manufacturers’ recommendations,” Genovese continued. “All engine oil, filter, spark plug, coolant, and transmission fluid maintenance intervals remain the same, and fleets are instructed to follow the vehicle operator’s guidelines for these types of routine maintenance procedures.”
The propane fuel system does contain two fuel filters that are both rated to be changed at 50,000 miles, Genovese pointed out. The first filter is in line between the vehicle’s fuel door/ fill valve and the propane tank; the second filter is in line between the vehicle’s fuel tank and the engine’s fuel injection system.
“All ROUSH CleanTech propane autogas fuel systems are OBD-II compliant, which means that any automotive diagnostic tool can connect to the vehicle’s port and perform basic diagnostic functions just like a gasoline vehicle,” Genovese said. “This includes reading and clearing diagnostic trouble codes, viewing and recording various engine and fuel system parameters, and performing certain functional diagnostic tests.
“Liquid injection propane autogas fuel systems can provide the same reliability to start and perform in all climates and temperatures,” he continued. “They are also maintained, diagnosed, and repaired in the same fashion as a gasoline fuel system. All of this leads to faster turnaround time for repairs, keeping vehicles on the road and improving uptime for fleets.”
Kitsap Transit, a public transport fleet in Washington, is a longtime ROUSH CleanTech customer and noted the specific benefits of propane versus diesel fuel injectors, as they experienced with their Ford E-450s with a Roush propane conversion.
After more than seven years and 150,000+ miles, they had just begun to swap the propane injectors, Dennis Griffey, Kitsap director of maintenance, told Fleet Maintenance in 2023. This is far less frequent than the buses with Duramax engines.
“They fight over working on the Fords [with propane systems], and people push off working on the GM chassis [with Duramax] as much as they can,” Griffey said.
When it comes to running a successful fleet in the mobile maintenance and service industry, making sure your vehicles are up to the task means equipping them with the right assortment of tools and ensuring that the trucks themselves are upfitted to your needs. By taking the time to upfit your vehicles properly, you’re setting your fleet up to operate smoothly and achieve better performance, safety, and efficiency, which can provide you with a competitive edge.
To start, customizing your vehicles to accommodate the right tools and storage solutions boosts efficiency, minimizes downtime, and extends vehicle lifespan. By reducing wear and tear and potentially lowering fuel costs, upfitting can directly benefit your bottom line. Additionally, upfitting lets you standardize vehicles across the fleet, equipping them with uniform features and equipment. This uniformity simplifies operations, facilitates training, and makes maintenance more manageable, leading to cost reductions and enhancing the overall management of the fleet.
But if an upfit is designed incorrectly, it can result in significant issues, such as mismatched
By Chris Johnston FLEET OPERATIONS MANAGER, SHORT TERM
VEHICLE ORDERING, MERCHANTS FLEET
Johnston has over 15 years of experience in the fleet industry with a focus on upfitting. Prior to joining Merchants Fleet, Johnston created chassis and upfit specifications for light-duty vehicles as truck & upfit consultant at Element Fleet Management. He also spent more than a decade at GE Capital managing truck purchases and customer bailment pools, recommended upfit packages, and provided coaching, team building, and assistance to team members.
components that degrade vehicle performance and safety, a lack of standardization that complicates maintenance and increases costs, and inadequate planning that leads to costly future modifications. Plus, poor integration with vehicle systems can cause operational disruptions and frequent maintenance needs, further driving up costs. Proper planning and execution are essential to avoid this. Some key considerations are important when upfitting a mobile service vehicle specifically, including safety and specificity for your fleet’s operations.
The process starts with selecting the appropriate vehicles based on their size, payload capacity, fuel efficiency, and maneuverability. Each vehicle should be viewed as a tool designed for specific tasks, ensuring drivers have the right equipment to execute their jobs effectively.
Safety enhancements are among the most significant benefits of upfitting. Advanced safety features such as backup cameras, improved lighting, and collision avoidance systems can protect drivers and reduce accident rates, especially on a busy job site. These upgrades are crucial for safety and help minimize the company’s liability risks.
But the upfitted truck must also comply with current safety regulations and industry standards. Make sure that any upfitter you work with is up to date on these standards and can integrate essential safety features into vehicles that are upfitted for your company. This commitment to safety helps minimize the
risk of accidents and enhances the welfare of the workforce.
Additionally, the overall design of the vehicle should be considered when upfitting. The design of fleet vehicles, including considerations like vehicle weight, significantly impacts their operational efficiency. Lightweight materials like aluminum or composites and modular components that serve multiple functions can reduce the weight of an upfitted vehicle. Eliminating redundant equipment and optimizing storage solutions can also reduce weight and increase the available space in a vehicle. Advanced design practices can further reduce weight by minimizing excess material while maintaining structural integrity.
Managing vehicle weight optimizes fuel efficiency, maximizes payload capacity, and improves handling and performance. It also ensures compliance with regulations and reduces maintenance costs by minimizing wear and tear.
There are many things to consider when upfitting a vehicle for use in mobile maintenance. This includes modifications designed to enhance functionality, safety, and efficiency. Here is a list of items that may be included when upfitting:
Storage solutions:
Ü Toolboxes: Secure and weather-resistant units for storing hand and power tools.
Ü Shelving Units: Custom configurations to efficiently organize materials and tools.
Ü Rack Systems: Used for transporting larger equipment.
Safety features:
Ü Beacon Lights: Enhances visibility on the road or at a job site, especially in poor lighting conditions.
Ü Backup Alarms: Alerts others when the vehicle reverses, which is crucial for preventing accidents.
Ü Safety Partitions: Installs between the cab and cargo area to protect occupants from shifting loads during transport.
Heavy-duty upgrades:
Ü Heavy-Duty Suspension: Reinforced to support additional weight from equipment and supplies.
Ü Reinforced Tires: Designed for rough terrains and are puncture-resistant with the proper load rating.
Ü Engine Upgrades: Enhanced cooling systems and larger engine sizes can be considered for vehicles used for heavy loads or those needing added towing capacity.
Power and electrical modifications:
Ü External Power Outlets: Facilitate using electrical tools without additional power sources.
Ü Upgraded Electrical Systems: Support additional lighting and electronic equipment.
Exterior and interior modifications:
Ü Towing Packages: Include hitch receivers and trailer wiring for towing.
Ü Utility Racks: For transporting bulky or oversized items.
Ü Durable Floor Linings: Protect the interior from damage and make cleaning easier.
Ü Ergonomic Seating: Supports long hours of driving or operation with enhanced comfort.
Ü Custom Paint or Graphics: To include company branding and enhance visibility.
Communication and navigation systems:
Ü GPS Tracking: For efficient fleet management and navigation to job sites.
Ü Mobile Communication Systems: Include twoway radios or cellular boosters for improved communication in varied environments.
Custom tailoring for specific needs:
Ü Crane and Winch Systems: For lifting and moving heavy materials.
Ü Compressed Air Systems: Integrated compressors for powering pneumatic tools. Choosing durable materials for these items and vehicle components ensures that they can endure daily operations and adverse conditions, extending the vehicle’s lifespan and reducing the frequency and costs of maintenance.
Fleets may also want to consider integrating telematics with upfitting solutions. This includes real-time data from GPS tracking, sensors, and onboard diagnostics that provide insights to enable route optimization, predictive maintenance, and enhanced driver performance monitoring.
Data and analytics also play a crucial role in optimizing the overall upfitting process. By analyzing vehicle performance data and market trends, fleet managers can make informed decisions that improve efficiency and productivity. This data-driven approach allows for continual adjustments and enhancements to fleet strategies.
Effective cost management is crucial when upfitting vehicles used for mobile maintenance. Despite the initial investment required, doing research to identify cost-effective upfitting solutions can help manage expenses without compromising safety or quality. Reducing downtime is another critical consideration while upfitting vehicles. Planning to do upfitting work during off-peak hours or aligning it
Full-Color Wiring Diagrams (without the monthly fees):
f View 3D models to see a full picture of the exact vehicle, its system components — including critical sensors, actuators and more
f Embedded repair information & quick one touch links to guided diagnostics
Live Data Stream:
f System display breaks down complicated systems into smaller subsystems for an easily digestible view of the vehicle, so techs know exactly what’s in the vehicle and what to expect during repair
Extended License Subscription:
f Diagnostic functions continue after subscription expiration
f Optional Off-Highway software and cable kit for working on stationary generators, forklifts, combines, cranes and everything in between
with scheduled maintenance can significantly reduce operational disruptions.
Integrating advanced technologies like AI and automation may further revolutionize vehicle upfitting. Innovations in smart sensors and autonomous capabilities could enhance monitoring, maintenance, and efficiency, paving the way for more innovative, safer, and cost-effective fleet operations.
Fleet managers can analyze vehicle performance data and market trends in real time by evaluating which of these technologies is right for their upfits. Using this information, they can make informed decisions that can continually improve their fleets, ensuring they remain adaptable and efficient.
Vehicle upfitting is essential to helping mobile maintenance companies maximize their performance and reliability. By embracing new technologies, prioritizing safety, and utilizing data analytics, fleet managers can ensure their fleets are equipped to meet today’s challenges and are prepared for the future. Through a well-designed upfitting process using an experienced partner, higher efficiency, enhanced safety, and greater business success can be achieved.
f HDS 1000 touchscreen Windows® 10 tablet
f Ruggedized drop-tested tablet designed for the garage environment
f Enhanced bidirectional controls
Injector coding, forced DPF regen, VGT relearning, special tests, component actuations & more
f Standardized software user interface
f Scan procedures the same for a Sprinter van to a Terex Titan dump truck
f All-in-one subscription unlocks access to repair information for all makes and models
f Handy soft-sided carrying bag for easy transport between vehicles and sites
f Live tech support
f Industry leading nationwide field support
The Haldex DBT22LD Air
Disc Brake from SAF-Holland features a large-diameter single piston with an integrated thrust plate as well as lube-free, stainless-steel pins and PTFE-coated steel bushings to reduce seizing risks and increase service life. The brake can fit common integrated steer axle torque plates and provides the brake force to support up to a 23,000-lb. gross axle weight rating. Its boltless pad simplifies maintenance and requires no extra tools for service.
For more information visit FleetMaintenance.com/55134865
The AeroFender from FlowBelow offers a streamlined design for the quarter fender to improve fuel efficiency and reduce drag. Applicable for both single- and dual-axle power units, the AeroFender reduces turbulence around tractor and trailer wheels to increase fuel economy. The device works on any truck and can be installed aftermarket, and complements other aerodynamic devices for added savings.
For more information visit FleetMaintenance.com/55135829
For more information visit FleetMaintenance.com/55142340
The Fleetguard Air Breather is a desiccant filter for use on bulk fluid storage tanks. Desiccant breathers are designed to replace standard tank-installed vents and filters during system operation and shutdown, according to the company. Composed of silica gel beads, polyurethane foam, and high-efficiency media, desiccant air breathers work to capture moisture and other harmful contaminants in fluid tanks from particle intrusion.
For more information visit FleetMaintenance.com/55142380
extending alternator life. Whether charging liftgate or pallet
Eliminate idling and enhance the performance and lifespan of your battery banks with the Phantom-30 Charging System from Power! Ideal for managing two battery banks (12V and 24V), it ensures efficient charging from up to two power sources, such as solar and a vehicle’s alternator. The system prioritizes solar power, reducing fuel consumption and extending alternator life. Whether charging liftgate or pallet jack batteries, the Phantom-30 keeps equipment ready and reliable, eliminating idling and drastically reducing fuel costs.
Velociti Inc. partnered with RAM Mounts to provide In-Cab Mounting for the company’s service solutions. Velociti offers its VeloCare health monitoring and support program, which proactively identifies vehicle issues and offers health reporting and automatic service tickets. RAM Mounts offers mounting solutions for phones, tablets, cameras, GPS systems, laptops, scanners and printers, radios, and other electronic components. Designed to protect against shock, vibration, dirt and debris, the modular, configurable components help keep VeloCare’s insights at a driver’s fingertips in the cab. Included are IntelliSkin sleeves for phones and tablets that allow users to securely charge and sync devices using the RAM Mounts’ GDS vehicle docks.
For more information visit FleetMaintenance.com/53071998
I-Series Gen 2 line of upgraded truck tires includes the I-31M, I-42W, I-28D, and the I-52A. The I-31M versatile, all-position tire for rugged on- and off-highway use features stone ejectors and a curb wall to protect against penetration and impacts. The I-42W wide-based option enhances traction with better cut-and-chip resistance. The I-28D regional and long-haul drive tire with zig-zag sipes and grooves offers superior traction in adverse weather conditions. The I-52A tire is engineered to endure the demands of stop-and-start regional routes with increased fuel economy. A Peace of Mind Warranty covers defects in workmanship and materials for all of the tires and includes a casing allowance for two retreads for six years.
For more information visit FleetMaintenance.com/55137710
monitors fueling devices from any location
Dover Fueling Solutions ’ PetroVend Synergy Fuel
Site Controller is a singular platform that allows fleets to remotely monitor and manage their fueling devices via a PC, tablet, or mobile device. Using a required DX Fleet subscription, the device offers visibility into site operations, transactions, and alerts. It also offers PCF capabilities that allow managers to set specific fueling rules based on vehicle type, time of day, and fuel type for fuel distribution. The PetroVend integrates dispenser communications into the controller, including IP gateway functions and DFS EDGE IoT functions, and offers card management features such as multi-product quantity restrictions and expanded prompt capabilities.
For more information visit FleetMaintenance.com/55128425
Goliath Carts ’ Weld Stand allows technicians to set up weld test coupons at any position or angle for safe and effective use. Each stand includes a shelf, weld gun holder, welding plier holder, wet and dry bucket, white board, and metal thickness gauge, with the stand coming in two different models. The GWS-MOB1 is mobilized and includes a Goliath-branded base with two polyurethane wheels for accessibility and mobility; the GWS-FL1 is floor-bolted and requires three bolts for fastening. Additionally, a mobile base accessory (GWS-B1) can turn the floor-bolted stand into a mobilized unit.
For more information visit FleetMaintenance.com/53077221
Eaton ’s Advantage series automated diaphragm spring clutches are for all makes and models of automated manual transmissions in the EMEA market. The clutches are built to strict OEM quality standards and minimize idling noise while reducing severe vibrations and delivering extended clutch life.
For more information visit FleetMaintenance.com/55142368
The BendPak Octa-Flex Series offers the functionality of a traditional twopost lift with the added versatility of a second set of powered assist arms for lifting and maneuvering large or heavy vehicle components such as EV battery packs. The overall size of the lift has been reduced without affecting drivethrough clearance and lifting height, and the series now uses direct drive for faster and smoother assist arm use. The Octa-Flex series also has a single power unit and controller for better efficiency and maintenance.
For more information visit FleetMaintenance.com/55142374
Eberspächer offers a diverse selection of fueloperated heaters, including the high-performance Airtronic S3 Commercial/M air heater and the innovative Hydronic S3 Commercial water heater, ensuring driver comfort in any environment.
The 13,000W Tri-Fuel Portable Generator from Harbor Freight has a 458cc engine designed to provide backup power for the jobsite. For increased mobility over tough terrain, the generator includes 10” flat-free wheels and a foldable handle. The push-button electric start allows the user to turn the unit on or off with no manual choke required, and a key fob is included so that the generator can be remotely started and switched off from up to 100’ away. A single fuel-selector switch allows the user to choose between gasoline, propane, or natural gas. The generator is backup ready with 240V/120V, 50A, and 30A outlets.
For more information visit FleetMaintenance.com/53099131
The 3/16” Orbital Palm Sander, No. SXSN6P01, from SUNEX Tools features Kevlar-impregnated rotor blades that the company says increase the tool’s lifespan by 50%. It operates at 11,000 rpm and uses a comfortable rubber over-mold and precision-balanced pad to increase grip and reduce vibrations. It also has a lightweight design, weighing only 2.78 lbs., and has integrated wrist support that both reduces user fatigue and directs exhaust air away from the sander. The sander also uses a low-noise muffler design for quiet operation at 81.2 dB.
For more information visit FleetMaintenance.com/55142355
The Wheeler Digital F.A.T. Wrench is designed to offer precise torque settings, allowing the user to apply repeatable, accurate torque settings to scope bases and rings, action screws, and more. Additionally, audible and visual indicators let the user know when the desired torque setting has been achieved. The wrench has a range of 5-100 lbs.-in. to aid in accurately torquing screws to recommended specifications, and it includes 10 bits made from phosphate-coated S2 tool steel hardened to 56-58 Rockwell C. The included custom-molded case safely stores both the wrench and bits when they are not in use.
For more information visit FleetMaintenance.com/55088484
The Snap-on Speed Demon EPIQ 68” Roll Cab, No. KETP682A3WHZ, is a limited-edition roll cab featuring a Speed Demon emblem and skull outfitted with a piston mohawk, turbocharged horns, and teeth made of Snap-on bits and sockets. The Speed Demon includes a SpeeDrawer for access to small parts, a PowerDrawer for secure charging, and a PowerTop with an LED light spanning the entire length of the drawers. To expand storage capacity, users can create a complete Speed Demon system by adding a matching work center and side lockers.
For more information visit FleetMaintenance.com/53098908
The MAXXAIR MSX3030 refrigerant recovery machine was engineered to handle both R134a and 1234yf effortlessly, servicing units ranging from light-duty vehicles to high-capacity HD systems. The MSX3030 also provides the flexibility to upgrade to larger tanks for expanded capabilities. It boasts a robust tubular steel chassis designed for durability and long-lasting performance in demanding environments and features a High-Capacity Oilless Compressor. The 7” color touch screen simplifies every procedure with intuitive navigation, ensuring precision and ease for every technician. Built in the U.S.
For more information visit FleetMaintenance.com/55133010
The Flexzilla X3 11-pc Blow Gun Kit , No. AG1211FZ, from Legacy Manufacturing features an ergonomic gun body for maximum comfort and control, reducing operator fatigue. A variable flow trigger regulates air volume precisely with maximum flow. The modular accessories system allows the Flexilla blow guns to be customized for extension length and tips needed for various jobs. Flexzilla blow gun safety nozzles are labeled to meet or exceed OSHA standards.
For more information visit FleetMaintenance.com/55141863
The Electrical Connector Pliers , No. 37990, from Lisle Corporation feature narrow knurled tips that provide extra grip when removing connectors in tight spaces. The tool is designed to remove many of the single and double connectors found in commercial vehicles. The pliers are 8” long and made from forged carbon steel for extra strength and durability. A spring in the handle allows the user to work one-handed, and dual materials grips provide additional comfort.
For more information visit FleetMaintenance.com/55141858
DXS Impact Sockets from Ingersoll Rand replace the traditional square drive of other sockets with a spline-type interface for a tighter fit, more load-bearing surface, and easier access to tight spaces. The sockets are made from chrome molybdenum alloy steel, feature a ball nose retention pin for quick, tool-free installation and removal, and come with a lifetime limited warranty. The sockets are available both individually and in four sets: SAE, metric, standard, and deep.
For more information visit FleetMaintenance.com/55142372
The Coast RL35R Voice Activated Headlamp features voice-recognition technology that allows full hands-free use of the light with spoken commands for power on/off, lighting output, beam shape, beam color, and other functions. It also has manual controls and the Coast Variable Light Control dial for even more precise adjustments. It provides up to 1,100 lm with a 613’ beam at maximum power with a 2.5-hour runtime. The RL35R includes a silicone-lined strap made of non-slip mesh and a detachable, rechargeable battery pack that can be used as a power bank. It’s IP54 water- and dust-resistant and comes with a lifetime warranty.
For more information visit FleetMaintenance.com/55141866
FleetCross by MOTOR is a comprehensive single source for mediumand heavy-duty part numbers and truck part cross-references, labor times, and repair information in the U.S. and Canada, including diagnostic trouble codes, wiring diagrams, maintenance schedules, and more. Features include web training, fast and accurate search results with flexible search options, and access to all makes plus additional aftermarket part numbers and illustrations.
For more information visit FleetMaintenance.com/55142333
The Brass Knuckle SmartFlex 400 Series gloves are comfortable, general-purpose work gloves that provide abrasion resistance and maximum dexterity. There are three gloves in the 400 Series, each suited for a different style of work. The BK401 is black nylon with a gray coating to conceal dirt and grime; the BK402 is white-on-white, making it easy to identify foreign particles on the glove for inspectors and quality control; and the BK403 is black nylon with a black coating, a tough-looking concealer for grimy projects. The lightweight, 13-gauge nylon shell facilitates dexterity and grip, and the grip is further enhanced by a polyurethane coating on the palm and fingers that provides maximum grip strength without being sticky.
For more information visit FleetMaintenance.com/55089563
The Universal Suspension Arm Lever from Pichler Tools is designed to push down the wishbone when removing the drive shaft, changing the axle boots, or before replacing the wheel bearings. The lever is made for one-person operation, allowing the suspension arm to carry out the required work. The tool locks the lower arm down and allows for controlled alignment for reassembly.
For more information visit FleetMaintenance.com/53096675
•