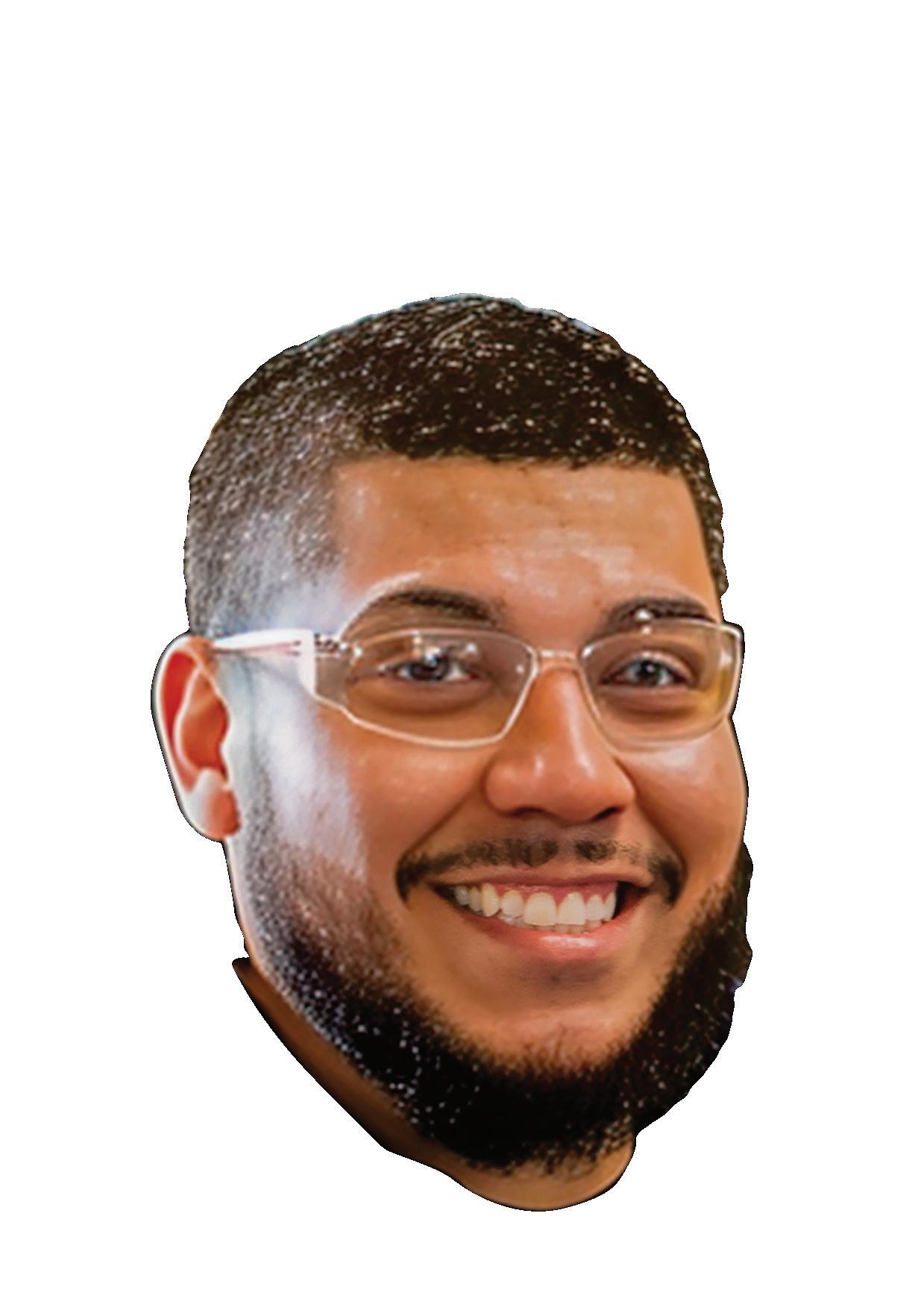
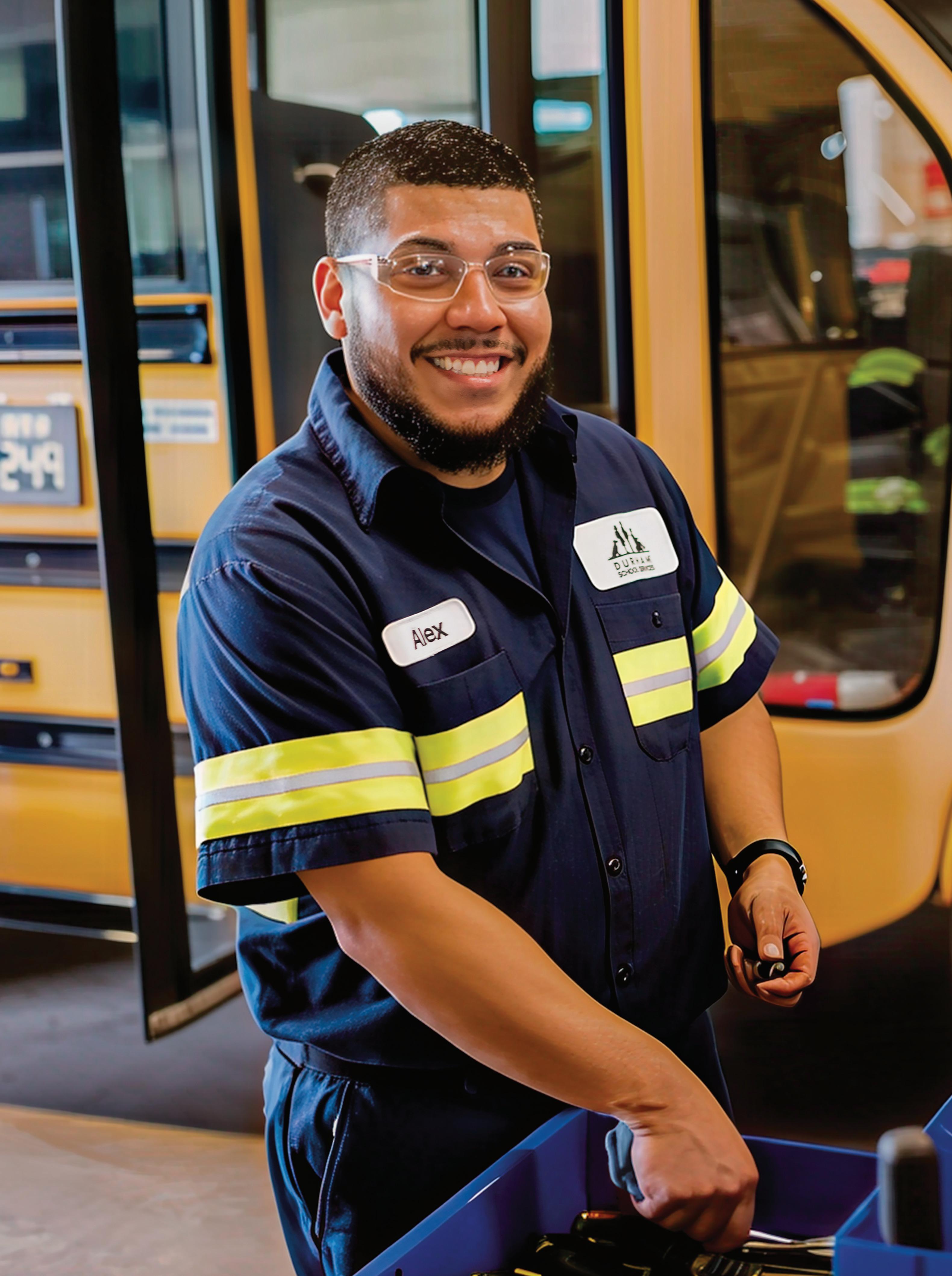
PRO-LINK+, built for servicing a complete range of commercial vehicles, makes Benny more than just a pitstop technician - it makes him an efficiency expert.
Under the hood, PRO-LINK+ delivers:
• OEM-specific coverage for engines, transmissions, chassis, and brakes
• Code-specific information with detailed testing procedures, component photos and wiring diagrams
Take control with over 200 special tests and 600 user-configurable parameters. Built tough for medium and heavy-duty trucks, PRO-LINK+ is your essential diagnostic companion.
Emissions critical
Uptime takes a big hit when technicians struggle to diagnose problems in the aftertreatment system. This is a top maintenance challenge for many fleets, requiring a concerted focus on tools, training, and analytical skills.
In The Bay Is your shop ready for its close-up?
More shops are turning to video to improve their training and outreach. Here’s how to start your own program.
Shop Operations
The great compensation compromise
Most technicians want a predictable paycheck. Shops want efficiency and accountability. There are ways to deliver both without fully committing to flat rate or hourly.
Putting a stop to your shop’s revolving door
Perfecting your hiring practices doesn’t mean much if you can’t retain your techs. Here are five tactics to help mitigate turnover.
Truly protecting technicians’ hands and eyes in the shop takes more than making sure they have safety glasses and rubber gloves.
Shop Technology
Tired of tire service? Robot wheel changer is on the way What happens when engineers
for
Vol. 28, No. 5
FLEET MAINTENANCE
Market Leader - Commercial Vehicle Group Dyanna Hurley 248-705-3505 | dhurley@fleetmaintenance.com
Editorial Director Kevin Jones kevin@fleetmaintenance.com
Editor-in-Chief John Hitch john@fleetmaintenance.com
Stay up-to-date on industry news and events, new product launches, and more. FleetMaintenance.com/subscribe
SuperRigs Results: ‘Scrapin By’ edges out competition
Shell Rotella’s 43rd annual SuperRigs truck beauty contest may have started with rain, but the trucks still brought the shine. FleetMaintenance.com/55294052
ARTICLE
Allison acquires Dana’s off-highway unit for $2.7B
The move will strengthen Allison’s position with customers in construction, mining, and ag, while allowing Dana to streamline its commercial vehicle product lines. FleetMaintenance.com/55297321
READ ANYTIME, ANYWHERE
Read the digital edition online at FleetMaintenance.com/ magazine/78606
Want your own issue?
There are two simple steps to get a free subscription:
1. Go online to: FleetMaintenance.com/ subscribe
2. Complete the online subscription form. That’s all there is to it.
5 steps to find root causes and increase uptime
Visit the official website of Fleet Maintenance for more information from stories in this issue, plus online exclusives on pertinent topics in the fleet maintenance management industry. ARTICLE
While every maintenance department is working to get trucks back on the road as quickly as possible, taking a bit more time to solve an issue, and not patch it, will do more for overall fleet uptime. FleetMaintenance. com/55295132
Associate Editor Alex Keenan alex@fleetmaintenance.com
Associate Editor Lucas Roberto lucas@fleetmaintenance.com
Contributors Seth Skydel, Gregg Wartgow, John Baxter Sales Development Representative Sachin Sinha sachin@fleetmaintenance.com
Fleet Maintenance Multimedia Account Executives
Multimedia Account Executive - West Michael Simone 973-713-0094 | michael-s@fleetmaintenance.com
Multimedia Account Executive - Southeast Peter Lovato 231-233-2660 | peter@fleetmaintenance.com
Multimedia Account Executive - Northeast Larry Schlagheck 248-444-1320 | larry@fleetmaintenance.com
Tool & Equipment Multimedia Account Executives
Multimedia Account Executive - Midwest Diane Braden 920-568-8364 | diane@fleetmaintenance.com
Multimedia Account Executive - West Mattie Gorman-Greuel 920-563-1636 | mattie@fleetmaintenance.com
Multimedia Account Executive - East Cortni Jones 920-568-8391 | cortni@fleetmaintenance.com
Production Manager Patricia Brown
Ad Services Manager Karen Runion
Art Director Erin Brown
Ryder to scale Tow4Tech platform
The platform “brings speed, transparency, and automation to a process that has ... lacked all three,” Ryder VP Jenn Dixon said. FleetMaintenance. com/55294670
PO Box 3257 • Northbrook IL 60065-3257
REPRINTS
Happiness is the most important shop KPI you don’t measure—but should.
By John Hitch Editor-in-chief
Last year’s Technician Issue featured a rather sullen cover model wearing a hoodie and burying his face in his hands. It seemed to best represent one of the biggest threats to uptime— unaddressed physical and mental health problems. And like with any issue in the shop, we did our best to troubleshoot why this malaise continues to fester.
Joshua Taylor, a Canadian shop manager-turned-podcaster, surmised the root cause was poor leadership. More specifically, the “Wrench Turners” host, who o en talks about techs’ mental health, blames managers and supervisors who don’t listen, and those lacking the power to instill positive changes when techs do open up.
According to Training Industry, bad bosses in general cost companies $500,000 annually due to lost onboarding and training costs when employees can’t take it anymore. is also factors in additional health costs from stress-related maladies and lost productivity when workers waste time agonizing about their o ce oppressor or hiding from them.
But this year I thought we should focus more on the positive aspects of being a tech, hence the smiling tech on this issue’s cover. I want readers to feel happy, not hopeless.
In a conversation I had with my oldest friend and most trusted master tech, John O’Brien, on happiness and how bosses a ect that, he noted in the past, managers have asked him to accommodate the dealership’s customers who just bought a new vehicle. He recalled a recent one where he had to address an issue with the Bluetooth speaker.
“You have to give yourself a crash course and become an expert in this one thing that nobody’s ever seen, nobody’s ever heard about,” the fl at-rater said of this warranty work, which pulls him from far more profitable jobs.
e overall dealership wins by earning a customer’s loyalty, but depending on the manager, it could cost O’Brien’s wages.
“You’ll have some managers that are cool and flag some internal time for that, and you’ll have some managers that are [ducking chicks] about it,” he explained. He believes the motive for the latter type of manager not giving him a fairer rate is “that it will raise their unapplied labor rate and a ect their bonus because it digs into profits.”
is isn’t the case with his new manager, who is great about quickly approving things
like li repairs and costly scan tool updates, but it has happened in the past. As his friend for decades, I’ve known exactly when he has a good or bad boss by his mood o the clock.
at’s a powerful ability leaders wield, and weak leaders who refuse to provide the tools techs need, or care more about their bonus than what they are paid to do—support their techs—should absolutely be accountable. As the saying goes, “Sunlight is the best disinfectant.”
ere can be many ways to reinterpret this maxim, fi rst attributed to U.S. Supreme Court Justice Louis Brandeis and made about corporate and government corruption and transparency. What if as a fleet maintenance leader, you prioritize beaming sunshine—in the form of proactive decisions—on employees not to disinfect the bad, but to promote the growth of what’s good in the shop? In short, focus more of your energy on the positive than the negative.
A er all, do you want to be the boss who goes around pointing out every ticky-tacky way a tech is being inecient by having a messy toolbox, or the one who rewards a tech who cleverly confi gured their rolling diagnostic cart to improve troubleshooting and repair time?
In the former scenario, you are shining a light on something technically ine cient, but likely infecting that worker with resentment towards you and leadership in general, with them wasting even more time ranting to coworkers about what a jerk you are. In the positive situation, the rewarded tech gets their e cient and creative behavior reinforced—something that messy tech might want to mimic (Grease monkey see; grease monkey do). And the cost is a minute of your time and that $25 gi card to Chili’s your boss gave you.
I have no way to quantify the happiness you’d bring into the shop with such a little-rayof-sunshine-type gesture, but there are ways to track this unconventional KPI by looking at how certain decisions impact measurable KPIs. e obvious one is productivity. We address that on Pg. 18, where we tackle the flat rate vs. hourly debate. One shop bases individual pay structure on skill level, while another submits to the techs’ preference. In both cases, the techs are happy with the arrangement. You can survey your techs and see how they want to be
paid. If productivity and profits go up a er, you can assume the techs are happier. Or instead of assuming, just ask them.
Another is safety. In our PPE story on Pg. 26, we talk about how compliance starts with focusing on what best protects the tech, while also being comfortable enough to wear all the time. e converse is techs don’t wear gloves or safety glasses, and could get hurt and miss time. Here, you can talk to your distributor and test out a few brands and styles to fi nd what works best. Such an emphasis on safety culture tends to trickle down into better throughput, fewer comebacks, and higher morale. Plus, we cover several ways you can improve retention (Pg. 24), the top metric for technician happiness. If you follow our experts’ advice and mostly try not to be a [ducking chick], I’m confident it will lead to brighter days for your shop (and career), too.
Uptime takes a big hit when technicians struggle to diagnose problems in the aftertreatment system. This is a top maintenance challenge for many fleets, requiring a concerted focus on tools, training, and analytical skills.
By John Baxter [ DIAGNOSTICS ]
Aertreatment systems have improved by leaps and bounds since 2010 when diesel particulate fi lters and selective catalytic reduction became standard on heavy-duty diesel trucks. ese systems capture more harmful emissions and are more reliable, while fleets better understand what it takes to keep them performing properly.
“We have learned a lot about monitoring a ertreatment systems and optimizing preventive maintenance practices, and understand that using quality replacement parts, scheduling, and managing idle hours are critical,” explained Joe Pu , VP of truck technology and maintenance at NationaLease.
Still, Pu explained that training techs and drivers remains “the biggest a ertreatment challenge today.”
at’s because as these systems evolve, technicians need to stay up-to-date on all their service and component changes, as well as new issues that can spring up while staying proficient on previous versions. Even experienced troubleshooters can’t hit all of these moving targets.
It’s a reason why on diagnostic solutions provider Noregon’s 2025 “Unpacking the Commercial Vehicle Diagnostics Industry” report, 38% of the vetted respondents pointed to the a ertreatment system as the most challenging component to work on, just 2% behind the top answer, vehicle electronics, which stretch across the entire truck.
But for uptime to stay consistent, fleets must rise to meet the emissions challenges.
“Knowing how to properly diagnose and repair these systems is critical given how easily they can reduce an engine’s power output or shut it down entirely,” explained Jason Hedman, product manager at Noregon.
For example, at any time, a deterioration in the emission system’s performance may cause a truck to go into derate. is forces the driver to stop and manually force the emissions system to complete a regeneration cycle to burn o soot collected in the diesel particulate filter. Unless the derate was due to the engine not getting up to the correct temperature due to an on-road factor, such as excessive idling or an ill-timed tra c jam, there’s a problem only a proper diagnosis can sus out.
» Engines and aftertreatment maintenance is a dirty and challenging job, but somebody’s gotta do it. Shops can help them out by providing the latest diagnostic tools.
Finding out what the root cause is requires both properly trained techs and the right tools that can detect and repair issues on modern emissions systems. And even more changes are on the way to meet 2027 NOx standards. ey also have to keep up with older trucks too, as Noregon’s report noted that 75% of heavy-duty trucks are already eight years old or more. Without the training, critical thinking skills, and tools, no fleet running diesel trucks will get very far. at’s why we caught up with several diagnostic experts to explain why all three are vital.
e most glaring issue is keeping shop techs up to speed on the evolving systems. Longer diagnostic time leads to a backlog of work in the shop.
Sandeep Kar, chief strategy officer at Noregon, attributes high shop dwell times for trucks to a generational skills gap and lack of proper troubleshooting devices. “Older technicians are having a hard time fi guring out what these electronics are really spitting out in terms of information and insights, and younger technicians don’t have the right tools,” he told Fleet Maintenance
But where should shops start? Diagnostic eciency is likely a good place. Hedman explained that techs sometimes have a wasteful approach to troubleshooting and repair.
“A common mistake we see with a ertreatment system maintenance is technicians rushing to force a regen when they see an a ertreatment fault, rather than performing a proper diagnosis,” he said. “Unfortunately, an unnecessary regen can take a bit of time, burn fuel, and render the system too hot to work on for a while, so it leads to ine ciencies and lost profits in the shop.”
Not having enough training resources available seems to be another source of ine cient troubleshooting.
“One of the main challenges is the di culty in accessing resources that make it easier to understand and resolve both mechanical and electronic issues, which are o en very complex,” noted Jorge Verdejo, sales director at Cojali USA. “ ese resources go beyond tools—they include training or even online expert services that technicians can consult when needed.”
Cojali o ers various in-person and online training through Jaltest University. Courses range from the scan tool basics to more direct training on DEF systems and NOx sensors.
More online and in-person training with vendors is the long-term solution, but that takes time. For immediate training triage, the OEMs o er expert help through uptime call centers. On the vendor side, Noregon o ers Technicians as a Service. is connects technicians stuck on a di cult job with remote experts who can walk them through that specific task while providing some teaching tips so they are more prepared for the next one.
» Software such as Snap-On’s SureTrack provide parts information and expert guidance from other technicians to help troubleshooters target the root cause faster and get trucks back on the road. Snap-On
Source: Noregon Research
Below is a diagram of most current aftertreatment systems, including the DPF, SCR, and more.
“ Diagnosis is more about understanding the system; it’s not just one box or component, it’s multiple components from the turbo and EGR valve to the seventh injector and the DEF doser for the SCR system. ”
Michael DeMarinis, training and development manager at Boss Truck Shops
Most diagnsotics can be performed by scan tools that connect to the vehicle, but don’t forget about the other helpful devices a tech can use to troubleshoot issues.
Sam Lord, director of maintenance and telematics at Kirk NationaLease, said laser thermometers and thermal imagers “not only provide quicker identification and
verification of issues, but also provide the technician with a better understanding of the operation of these modern systems.”
And Luke Powell explained borescopes can also be useful, especially when locating DEF doser problems. When the doser is stuck open, excess DEF won’t react with the NOx generated by
the engine, but instead will crystallize. Powell said he will unfasten the three bolts to remove the doser and slide the borescope’s camera end into the system to confirm if crystallization occured. Crystals may also appear if the urea is of poor quality, so fleets should also test the DEF when crystals are present to improve the system’s NOx reduction.
“ is reduces the need for less experienced mechanics to pull away a coworker from another job while ensuring the vehicle doesn’t face additional unplanned downtime,” Hedman said.
But phoning a friend can’t be the default solution. For techs to advance as diagnosticians, they need to figure things out for themselves. To do that, they need to know how pumps, wires, and valves all interact with one another. But that doesn’t come easy.
“ e biggest challenge is understanding how it all works,” o ered Luke Powell, a technician at Fleet Pride in Lancaster, Pennsylvania.
Without figuring this aspect out, a technician will never see the full picture, and thus never achieve their full troubleshooting potential.
“Diagnosis is more about understanding the system; it’s not just one box or component, it’s multiple components from the turbo and EGR valve to the seventh injector and the DEF doser for the SCR system,” explained Michael DeMarinis, training and development manager at Boss Truck Shops.
DeMarinis noted all these systems are interconnected, requiring a tech to identify all the issues so they can properly perform a root-cause analysis.
“If you get a NOx sensor code, you can’t just replace that sensor,” he said. “You must fi rst diagnose the problem that caused the high NOx. Just replacing a sensor when it’s only providing an indication of trouble ends up being frustrating for both the technician and customer.”
A fleet that does this not only spends hundreds on the sensor but must also factor in the downtime and labor costs. And the worst part is that the problem, hiding somewhere upstream undiagnosed, has not been resolved, either.
Powell noted such problems can range all the way from an exhaust system leak that deprives the DOC and DPF of necessary exhaust heat to a failed air dryer desiccant filter. Debris from that filter can clog the air supply, which enables the fuel doser (or seventh injector) to work, thus interfering with the doser’s job of keeping the DOC and DPF hot. ese two interlinked components must remain hot enough to burn o hydrocarbons, and especially particulate that’s trapped by the DPF until it combusts. Powell said another root cause may be an EGR valve not closing properly, which can result in excessive soot clogging the DPF.
Intimately knowing the system, combined with experience, helps techs like Powell dig down to the root cause more quickly.
It also involves upgrading the most valuable diagnostic tool at your disposal: your tech’s brain. e ability to logically trace the symptoms to the root cause takes a specific mindset. Two methodologies, the fi shbone diagram and the 5 whys, can help a tech organize their thoughts—and possible causes and e ects—more clearly to systematically discern the root cause. To best apply these strategies for a ertreatment or any kind of troubleshooting, take a look at Technology & Maintenance Council Recommended Practice 551: Root Cause Analysis, which was approved this year.
Even when a tech is highly trained and knows how to get to the root cause, they still need accurate data coming from the vehicle via vehicle health data and diagnostic trouble codes. And to interface with all that data, the shops need the right tools to take their diagnosticians to the next level.
On the vehicle, this starts with remote diagnostics, which OEMs made a standard feature in 2011, shortly after the modern emissions system mandates. For example, Daimler Truck North America (DTNA) has Virtual Technician, Mack has Guard Dog Connect, and Kenworth and Peterbilt use Paccar’s SmartLINQ. International’s was OnCommand Connection, but with the rebrand it’s My International now. Volvo just calls it Remote Diagnostic (those Swedes are a direct bunch). These all provide realtime health, fault codes, and historical sensor data from the engine and aftertreatment systems. They also give techs a headstart.
“Alongside fault data, remote diagnostics solutions also share convenient, accessible information about the code: what it means, how urgent it might be, and the likely parts and services necessary for repairs,” related Magnus Gustafson, VP of connected service at Volvo Trucks North America.
The DTCs—one code or a specific combination—could also trigger an alert in a fleet maintenance platform integrated with predictive maintenance. Based on the severity, the driver might be directed to pull over or venture to the nearest repair facility to avoid catastrophic engine failure.
In less severe cases, this information still helps fleet managers and technicians speed up intake and increase uptime, noted Patrick Wallace, Peterbilt marketing manager for zero-emission and connected trucks.
Dealers, large fleets, and leading third-party repair vendors may also have access to certain OEM-specific scan tools and software to speed up troubleshooting.
For example, DTNA has developed an AI-powered tool for its Uptime Management Suite called Techlane. According to the company, this tool helps techs speed up troubleshooting and root cause analysis, repair, and warranty processes. The generative AI also helps techs complete repair orders and invoices.
“Techlane maximizes uptime for customers by consolidating AI-based diagnostics, technical information, and repair processes specific to the vehicle being repaired,” offered Paul Romanaggi, GM of CX and Service at DTNA. “With this new technology, we
Though not an immediate priority, shops should think about how and when they will train techs for the MY2027 engines and aftertreatment systems.
Cummins, for example, is adding a Twin Module Aftertreatment System (two SCRs), which comes with a separate belt-driven 48V alternator to heat the aftertreatment components. Among new variations, in-cylinder (late injection) will also be used at times to raise exhaust temps.
Daniel Meadows, Cummins HD VPI Customer Care, said the new electric heating system won’t require scheduled maintenance.
“Troubleshooting will be handled with a combination of Control Systems Diagnostics, similar to current product support today through measurements taken by the ECM, MGU, & HCU sensors,” Meadows said. “Through the outof-mission service bay diagnostic tests, the performance of the heaters and 48V systems will be run through a standard cycle, then measured against how they perform against the respective heating cycles. Standard wire harness troubleshooting will be used in the instances of shorted wiring.”
Learning all this sounds complicated, but techs already certified on the X15 engine only need to complete Cummins’ Virtual College and Virtual Short course trainings to become certified on the new engine, Meadows added. Hands-on training will also be available.
The other OEMs will reveal more details on their compliant engines closer to launch, but Nick Smith, International’s media relations manager, did say the S13 “will retain approximately 90% of its current componentry, so changes to tools and training are expected to be minimal.”
are not only driving increased efficiency for existing technicians but also attracting a new generation of technicians who thrive on this technology.”
The solution is already deployed at more than 500 dealers and used by several thousand techs.
“For our new or less experienced technicians, the true benefit in Techlane is bringing resources to a
◾ OE-level heavy-duty coverage without expensive individual OEM subscriptions
◾ All-in-one subscription unlocks access to repair information for all makes and models
◾ Manufacturer coverage: Freightliner, International, Kenworth, Mack, Volvo, Peterbilt, Sterling, Western Star, and more
◾ Engine coverage: PACCAR, Cummins, Perkins, Detroit DieselMBE, Mack, Navistar, Caterpillar, Deutz, MTU, and more
◾ System coverage: transmissions, brake systems, exhaust treatment, audio systems, and more
◾ Diagnostic capabilities: Enhanced bidirectional controls including Injector coding, forced DPF regen, VGT relearning, special tests, component actuations & more. Also includes live datastream and full color-wiring diagrams
◾ OHW upgrade kit available for agricultural, construction, stationary vehicles and more
◾ One year warranty
Rapid DTC scan powers all-system DTC scans
◾ Complete pre- and post-reporting with wireless printing
◾ Topology view OE-level network information
◾ Seamless Solutions for Secure Gateway Access: Unlock access to OEM Secure Gateway Modules (SGW) for Ford/Lincoln, FCA/ Stellantis, Honda/Acura, Hyundai, Kia, Genesis, Nissan, Subaru, Mercedes, Porsche, Volkswagen, and Volvo vehicles; Access solution varies by OEM (directly on-tool software, via AutoAuth, and more)
◾ OEM full-color wiring diagrams & enhanced bi-directional testing with Enhanced subscription
Access to Repair Source – 100% OEM-licensed repair information library with the most expansive, reliable, and up-to-date vehicle coverage and information, right from the source with Enhanced subscription
◾ Access to Code-Assist™ top reported fixes by Identifix
◾Quick links to Identifix, Mitchell, AllData and more
◾ On-tool and online training videos
◾ All new Android 11 OS+ software with access to Google Play Store
◾ First year software subscription free plus 30-day trial of Enhanced subscription
central location so they don’t have to constantly hunt for answers,” said Jerry Kocan, president and GM of Four Star Freightliner in Alabama. “They can reduce time spent out of the bay and be more productive. For our highly experienced technicians, we are seeing an average of 10% efficiency increase, with some achieving an even greater increase of 25% or more.”
While this advanced solution is just getting started with the Class 8 market leader’s dealer techs, it won’t be long until the AI-enabled diagnostic technology trickles down to smaller fleets and independent repair shops. The aftermarket already provides tools such as all-make remote diagnostics to get ahead of issues like an unexpected derate, such as Jaltest Telematics or Noregon TripVision.
And because of the prevalence of mixed fleets, shops are trending toward adopting all-makes scan tools. OEMs had 100% market share in 1990, but according to Noregon estimates, the aftermarket will be even by 2028.
“All-make multi-protocol scan tools are very intuitive in today’s market; the techs get the advantage of one software interface to learn instead of multiple different operations and layouts of OEM software per brand,” NationaLease’s Sam Lord, director of maintenance and telematics at Kirk NationaLease, noted.
He explained that OEMs use multiple branded components between the ABS, transmission, and powertrain systems, and each has its own interface. Aftermarket tools, meanwhile, offer a comprehensive and efficient alternative.
“With all-make software such as Jaltest, there is no reconnecting different software for each component and the functions, layout, and operations remain the same through a single connected interface session,” Lord said.
He added the all-makes scan tools help the NationaLease shop “troubleshoot issues and complaints faster and more accurately with features like guided diagnostics,” as well as perform vehicle VIN decoding, bidirectional commands for resets, and forced regens.
It should be mentioned that the number of diagnostic tools is rising. As of last year, Noregon estimated the diag tool-to-tech ratio was 1:3, with an even distribution coming by the end of the decade.
Bruno Gattamorta, chief commercial officer for Cojali, agreed the ratio will be 1:1 by 2030. “You’re not going to be able to do anything without these tools in the future. As time goes on, there are more sensors and more ECMs,” he told Fleet Maintenance last year.
Lord thinks this is a “fair estimation.” He added, “From our team’s standpoint, the diagnostic tool is a required shop tool no different from a jack or tire tool, and we will continue to provide our team with the best and most complete software tooling available today as a shared resource.”
And the aftermarket is starting to consolidate all that all-makes data. For instance, Noregon made a big move last year by releasing its shop management platform, ShopPulse, to bring vehicle and repair data into one platform, helping
Aftermarket tools
OE tools
“ From our team’s standpoint, the diagnostic tool is a required shop tool no different from a jack or tire tool, and we will continue to provide our team with the best and most complete software tooling available today as a shared resource.”
Sam Lord, NationaLease
managers get a better overall view of vehicle and technician efficiency.
Noregon believes this is the future for aftermarket repair, one where “shops complete diagnostics and service automation in a single pane of glass.”
The aftermarket continues to integrate shop management platforms with repair guidance. Most recently, Fullbay, a platform used by many heavy-duty independent shops, integrated with Mitchell 1. This allows users to standardize labor estimates, diagnostics data, and interactive wiring diagrams to further cut time-consuming actions in the shop, which will help managers track key performance metrics better and take a bite out of dwell time.
Looking ahead, the next best diag tools could be worn by the technician. This year Cojali unveiled Jaltest Diagnostics AR, an augmented reality platform running off the Magic Leap 2 smart goggles. This allows techs to work on the vehicle without losing sight of the computer screen, which appears on the wearable device’s lenses. The tech can interface with that screen with hand gestures, and at some point, via voice commands.
“Imagine a repair on a Cummins engine related to the SCR system, such as a fault code 3232, which refers to NOx sensors,” Cojali’s Verdejo said. “Thanks to Jaltest AR, the technician can clearly identify the sensor and verify whether it’s connected correctly. They can view its exact location, what it looks like, and where it should be connected, including wires, pins, and connections.”
Expected in shops in 2026 or ‘27, the AR tool also could help with uptime and recruiting.
“When we look at the new generations, we need to speak to them in their own language...digital, fast, and hands-on—making it easier to diagnose and fix emissions problems from day one,” Verdejo said. “There’s no way they will read a PDF to learn, but they love videogames. The augmented reality experience, interactive steps, and visual guides create a gamified, intuitive workflow that speeds up learning and improves accuracy.”
Equalization System
Failsafe mechanical system delivers equal lifting and a stable, level vehicle for operators.
Extended Height
The extended-height top beam on 192 models provides greater clearance.
Hydraulic Cylinders
Dual-drive hydraulic cylinders deliver smooth operation and rise higher than those in comparable lifts.
UHMW Polyethylene Load Bearings Evenly distribute radial and axial forces during operation.
Column Safety Locks Placed every four inches in the columns and engage automatically when lifting.
A versatile choice for mixed fleets, BendPak’s
and 20AP
super-duty two-post lifts easily take on Class 1 through 5 vehicles, from passenger cars to commercial trucks and vans. They reach further, lift higher and deliver greater stability than other lifts, all while protecting technicians with unmatched safety systems and ergonomics. With fewer moving parts, they’re easier to maintain, less prone to wear, and more cost-effective to operate. Maximize your uptime and efficiency with BendPak’s super-duty lifts — delivering superior performance and unmatched value. To learn more or to shop now, visit bendpak.com or call us at 1-800-253-2363
Safety Lock Failsafe mechanisms secure the lifting carriages and arm assemblies during operation.
Multi-face Metal Columns Innovative design better withstands twisting and biaxial loading forces to minimize movement for greater stability.
Lift Dampener Precision controls allow operators to manage descent speed.
But if natural light isn’t an option, Heath recommends an Amaran and Aputure lantern or LED lighting setups. Even lights that might already be lying around the shop can work, like the Milwaukee Tool M18 Magnetic Extendable Boom Light.
Albin has a more readily available solution in her guerrilla-style production process.
“I use flashlights for light, and will point them around my work to record while using the flash on the phone,” she illustrated. “That will help remove shadows in dark areas.”
Now that you’ve acquired your gear setup, even if it’s made up of equipment you already have, it’s time to come up with a strategy. Going in blind can result in frustration and wasted time.
“Number one, have a plan,” said Howat. “So much of it is prep work. The filming shouldn’t be the challenge; the filming is the easy part.”
The first step is identifying a topic or specific repair to focus on, which Heath said becomes no problem once you have an eye for what would make a good video.
“The advantage of being in a shop environment is that you have new stuff coming in all the time, new things happening all the time, new problems,” he explained, “so you have to train yourself to be aware of things that are happening that would help other people, solutions that other people might not know, tips that people might find valuable. Once you start to see those, you just never run out of ideas.”
Howat emphasized the importance of having someone knowledgeable assist in writing the video script, if it has one.
“You have to work closely with your subject matter experts as you prepare the project,” he said. “We do what’s called a mock-through early in production, where our writers and our SMEs are at the unit. They walk through the procedure, and everyone understands what it’s going to be.”
Another factor to consider is safety. When documenting an entire repair process, it’s essential to adhere to best safety practices not only to keep yourself safe but to avoid liability.
“You need to understand your company’s safety policies and the OSHA requirements around what you do, because that little video has big ripples. You’re sending a message to your associates about
how important you think safety is, and your goal is to create a culture of safety,” Howat continued.
Forgetting to put safety glasses back on between takes or leaving sweat on your brow will all be noticeable to the viewer, he explained.
Albin concurred, offering that careful thought about the process you want recorded before you even pick up the wrench can streamline filming.
“Definitely go in with a plan,” she said. “If you have a certain job and you know you’re going to be rebuilding something, think about having your camera overhead while you’re rebuilding it. Think about camera placements prior to whatever you’re going into.”
The plan is in place—Now it’s time to get behind the lens. With the right foresight, shooting should be a breeze, but there are some general guidelines, tips, and tricks that can make the process a bit easier and make your final product easier on the eyes. Shot variety is a key part of this.
“We do multiple takes, because we’ll shoot from different angles,” Penske’s Howat detailed. “So we’ll start with a wide shot, and then we’ll come in tight. It’s the same process, it’s just now you see where the wrench is going exactly.”
And taking into consideration the unpredictability of a shop environment, where anything can roll through the bay doors, it’s easy to see how ad-libbing here and there might be necessary.
» When it comes to filming in the shop, preparation is half the battle. Make sure that you and your team know the process you want to film, any related safety concerns, and where you want the camera.
“We are always improvising because everything changes with each shoot,” Rock said. “The topic, person being filmed, location, environment, equipment, etc.”
Day discussed some strategies, offering that sometimes you have to work with what you’ve got.
“Many videos involve being inside or under a truck with small, cramped spaces and little natural light,” he explained. “Sometimes we take the camera off the tripod and maneuver it up and through the truck axle. At times, we make do with our phone’s flashlight to accommodate the tight quarters.”
Albin said it’s best “to never let the camera and your recording interfere with your work.”
Another overlooked factor is that someone has to be on camera, and vo-techs aren’t known for their drama clubs.
“These people aren’t actors,” Howat said. “They’re technicians, they’re subject matter experts.”
He offered some strategies for warming up, like tossing a Nerf ball back and forth before filming to get some of those pre-show jitters out, or planning out the first shot with some stage direction.
“We start with movement,” he explained. “Usually, the first shot, they’re walking into frame. It just gives the nervous system a chance to burn off some of that extra energy at the start.”
Not to fear, though, as he emphasized that initial stage fright usually wears off quickly.
“Everyone gets better during the shoot. So if they start off nervous, they will get their feet under them in about five minutes, and then from there, they’re fine,” he continued.
Gaffin had similar thoughts on getting more comfortable in front of the camera, sharing that despite his shyness in public speaking, he can overcome these hesitations when filming himself.
“It’s definitely mental,” he said. “I get in my own head every time. I don’t like the sound of my own voice, I don’t like watching myself back.”
The key is to relax and the audience will follow.
“You’ve got to pretend you’re just having a regular conversation. You’ve got to get out of your own head and not worry about sounding stupid,” he suggested.
Your video is shot, but what now? Depending on the goal of your video, you can have from a few minutes to a few hours (for more complex repairs) of raw footage to trim down to a watchable piece of content, and there are a few ways to do this.
Many companies, like Bendix and Diesel Laptops, use paid subscription-based editing software like the applications offered through the Adobe Creative Cloud suite, while other creators use the free software built into platforms like TikTok.
“I would say 99% of [our editing] is done in [Adobe] Premiere Pro or After Effects, or a
combination of both of those,” Diesel Laptops’ Heath said, adding that they use a website called Kapwing.com to auto-generate captions.
Free options include iMovie and CapCut, which are user friendly and can be picked up in minutes.
DaVinci Resolve, also free, is more intermediate with a bit of a learning curve, but offers more features and control. All can be solid options, with some requiring more of an initial time investment.
Penske captions their videos for convenience.
“All of our videos are closed captioned because the work environment can be loud,” Howat explained. “We also include the transcripts of some of our videos so they can print them out and keep them for taking notes or their own reference.”
Another thing to consider is that different editing styles are better for certain jobs. For longer repairs, Albin suggested something like a timelapse video to speed things up for the viewer.
“You can always go in and dub that over with music, or you can talk and explain what you’re doing in those moments,” she offered. “Then that doesn’t interrupt your workflow.”
While editing can entail more detail-oriented processes like color grading, multi-cam sync, and refining audio and lighting, it can also mean simply cutting out dead space in an iPhone clip. The goal is to create a more polished end product.
“I try not to have any boring time in my video,” Gaffin said. “I’ll edit stuff right up to the second, so there’s no lag time where you’re just waiting for something to happen.”
When the final .MP4 file sits in the export folder, the final step is determining where to distribute it. Is the video for onboarding and training purposes? Then maybe it’d be most effective shared internally. But if the objective of the project is to reach a new audience or attract customers, then it needs to go somewhere publicly accessible.
Gaffin’s main focus is YouTube, where his videos average anywhere from 15 minutes to over an hour, but he utilizes Instagram and TikTok to boost and promote his longer work.
Albin said YouTube’s “rules are more difficult to adhere to if you’re making videos on another platform, especially with music,” mentioning potential copyright issues when transferring videos from platform to platform.
Bendix’s approach involves their own site rather than a public outlet.
“Bendix has a successful and popular—over 200,000 users—online education portal, brake-school.com. Most of the videos we create in-house go there and are used by technicians,” Day outlined. “These videos have helped bolster our reputation and establish Bendix as an industry leader when it comes to online training.”
This keeps Bendix’s content consolidated and available to customers while making it easy to get feedback.
“We often hear from techs and mechanics who say how much they like
the videos,” Day continued. “When a truck is down, every minute is critical to getting it back on the road, so technicians appreciate that most of our videos are only five to seven minutes and often point them to the supporting technical documents, as applicable.”
National Express’ Rock emphasized the importance of viewer feedback.
“Start small, keep it simple for both the creators and the audience, gain feedback on what worked and didn’t work, and constantly adapt to make the process easier and the end product more beneficial for your audience,” he concluded.
And as Penske’s Gerke pointed out, the only way to get input on video content is if people see it.
“We can create content, and we will only get feedback if we put that video somewhere where it’s accessible,” she said, “in a place where it’s useful for whoever it is you’re shooting it for.”
Creating video in-house can bring many benefits to shops and techs, but it’s undeniably difficult to start. However, the best video is the one you make.
“When you go in to edit and to upload it, it comes along with a little bit of humiliation at first, because you’re uncertain,” Albin related.
The process itself is daunting, let alone having to put yourself out there on camera.
“All of that is intimidating, but I think once you break the ice, you get genuine feedback,” she continued. “Sometimes you have to sift through the comments, but there are wonderful people out there who enjoy this type of content.”
Sometimes the best way in is to “just throw it out there,” Diesel Laptops’ Heath recommended.
“At the beginning, you’re going to suck, and only over time can you improve,” he said. “My two tips would be: one, start recording, get out there, and two, be consistent with it.”
Raw
Fast, authentic, and real
• No barrier to entry
• Might come off rough around the edges
Polished
• More professional
Better for brand strength
Requires time, learning, and budget
If your content journey involves a larger-scale plan to build an audience and foster brand growth, establishing a cohesive and recognizable style for your videos can help viewers quickly identify your work in the infinite sea of online content.
“The first thing we did was develop our look or our brand to our videos, and this means we use Penske units and we use the approved Penske colors,” explained Andy Howat, manager of maintenance training solutions at Penske Truck Leasing. “We often turn the contrast levels up just a little bit on the camera to get extra clarity in our base when we’re filming. We use a lot of pan-style shots and extreme close-ups in our videos. So that’s kind of our style, that’s our brand, and my team knows to do that.”
For related content go to FleetMaintenance.com/in-the-bay
Professional Power in Your Hands
“Access to live data, tests and calibrations for all makes of engines, transmissions, brakes and body control systems is critical today with everything being electronic. The comprehensive coverage and ability to go from code to diagnostic procedure, component location and wiring diagram make PRO-LINK+ the best diagnostic system I’ve ever used.”
Frankie Mendoza
Owner Frankie’s Truck Repair Nogales, AZ
Most technicians want a predictable paycheck. Shops want e ciency and accountability. There are ways to deliver both without fully committing to flat rate or hourly.
By Gregg Wartgow
]
If it always worked out perfectly, shops would just pay technicians a flat rate, where pay is dependent on billable hours. is scenario incentivizes technicians to be more productive; they only earn when the shop is getting paid. Furthermore, it promotes technician e ciency. If a tech can get a four-hour job done in three hours, they still get paid for all four. Super e cient and proficient technicians can make a lot of money. at’s great for the top techs in the shop, but less appealing for everyone else. at’s a reason flat rate seems to be falling out of favor versus set
“Very few shops are doing flat rate anymore, and it’s almost nonexistent in heavy duty,” said Peter Cooper, CEO of Ascend Consulting and a brand ambassador for Fullbay shop management soware. “ e main reason why is that most shops won’t be able to get buy-in from the employees.”
Industry veteran Ken Eggen believes flat rate can still work under the right circumstances. It just takes the right technicians with the right experience and mindset. It’s also helpful when the SRTs (standard repair times) are embraced with open arms.
“Years ago when I was helping manage a 1,000-vehicle fleet, we looked at average repair times across our three shops to develop our own internal repair times,” said Eggen, who today is COO at Wolf River Express, a transportation company with o ces in Tennessee, Ohio, and Illinois. Eggen also has a maintenance consulting business, K.M.E. Services. “We got really good buy-in because the technicians felt like they participated in the creation of those standard job times. e high achievement-minded technicians get what flat rate can do.”
In Taylor, Texas, Guzman Automotive, which services consumer and Classes 1-6 commercial vehicles, has been able to make fl at rate work.
e two-year-old shop is co-owned by longtime auto shop manager James Guzman, company CEO, and his son, Joe Gonzales, company president, who treat their techs like family. In this structure, the older, more experienced A and B techs are flat rate, while the C techs make an hourly wage.
“Every 90 days, we are looking at what our C-level apprentice technicians have been producing, what they’ve learned, and which certifications
they’re pursuing,” Gonzales said. “We want everybody striving for that next tier. at’s why we also encourage our C-level apprentices to help out the A-level master technicians.”
Not every technician is built the same way, though, which is why many shops have found hybrid pay structures to be very e ective. By combining an hourly wage with some form of incentivized compensation, shops can provide predictability while also o ering opportunity, which is an e ective way to drive productivity and profitability.
One of the downsides of flat rate is that a technician doesn’t get paid unless there’s work to be had. at can lead to income volatility, especially during slow periods or when engaged in highly complex jobs. Not every technician will be accepting of this. In fact, Cooper said most won’t—particularly when working for the typical independent repair shop.
“If I were a technician looking for a job, I just don’t know that I would trust a small, independent shop to keep me busy,” Cooper related. “Flat rate is just too risky for most technicians.”
Flat rate also presents some potential downsides from the shop’s perspective. Since emphasis is on speed, shops could see an uptick in misdiagnosis and comebacks. At a dealership or independent repair shop, a technician has to eat that comeback time, so it sort of polices itself. But for a fleet’s internal maintenance department, the manager o en needs to do quite a bit of policing.
“In a fleet shop, there needs to be consistent measuring, monitoring, and coaching of the technicians to remind them that they need to do the jobs the right way and not get in too much of a hurry,” Eggen said.
Another potential downside of paying flat rate is that morale could su er if some technicians feel like others are getting all the good jobs. Morale could also take a hit if technicians feel like the SRTs are unrealistic. at’s why Eggen said developing your own times is not a bad idea. If that isn’t practical, rely on SRTs from a reputable, independent source such as the Technology & Maintenance Council (TMC), MOTOR, ALLDATA, Mitchell 1, Diesel Laptops, and/or others.
“Technicians also have to be given the right tools in the right place so they can do their jobs the right way,” Eggen added. “ e parts room is a huge factor. If the right parts aren’t in inventory, how do you expect the technician to keep moving and get paid?”
e role of the service writer is also important. e service writer, Eggen pointed out, is typically the fi rst person to have a conversation with the driver. “ e writer must do a good initial diagnosis to get that express assessment done correctly and written up clearly,” Eggen said. “ en the technician can get a good jump on what they need to do.”
Could all of this lead to a shop culture where support sta develop animosity for the technicians? It certainly could if things were le to fester.
Guzman Auto’s Gonzales noted a time when a service advisor mistyped labor times and then had an hourly C-level tech perform the work to
The parts room is a huge factor. If the right parts aren’t in inventory, how do you expect the technician to keep moving and get paid? ”
Ken Eggen, COO, Wolf River Express
decrease the labor cost, instead of communicating
“ is frustrated the A technician who completed the diagnosis because it would short his labor time,” Gonzales said. Of course, the shop owner quickly addressed this, telling the advisor he would have to pay for mistakes like that out of his own pocket in the future, and not take money from the tech.
“ at’s not a fun conversation to have, but you’re taking food o a hardworking man’s table when you do that,” Gonzales asserted.
Another thing to watch is having fl at-rate techs perform jobs outside of their primary role of producing revenue, such as trying to fi nd an elusive repair part.
“Why on earth would a shop have its technicians running around chasing parts?” Cooper
asked. “Techs shouldn’t be doing anything that takes a wrench out of their hand, and everyone needs to understand that.”
That’s not to suggest that a flat-rate pay structure is the only way to achieve maximum productivity. When you think about the main objectives of paying techs flat rate in the first place, hybrid compensation structures also make a lot of sense.
“With a hybrid pay plan, you pay an hourly wage along with a production bonus,” Cooper explained. “That’s the best of both worlds because you’re incentivizing technicians to perform, but their base paycheck is also predictable.”
According to Zane Clark, director of technician relations at TechForce Foundation, hybrid pay plans can only be effective when roles and pay expectations are clearly defined. Additionally, there must be open communication regarding how work is assigned, performance must be consistently tracked, and technician feedback must be solicited so any necessary adjustments can be implemented.
“Ultimately, success hinges on mutual trust and aligning the pay structure with each technician’s strengths and motivations,” Clark said.
Success also hinges on how the shop as a whole will benefit. According to Cooper, it starts with determining what the shop can afford to pay its technicians. As a general rule, technician wages should be around 17-20% of a shop’s gross income.
Fullbay’s “State of Heavy-Duty Repair” report suggests that the median shop labor rate is $134. So as an example, a shop charging $134 should be able to pay technicians anywhere from $22.78 to $26.80 per hour.
Cooper said a good threshold for kicking in premium pay is 70-75% efficiency. “If a technician is billing 30 hours a week, the shop is likely making money off of that technician,” Cooper said. “Once a technician hits 32 hours (80% efficiency), everything beyond that is typically profit.”
Vincent Myles, owner of Myles Truck Repair, worked with Cooper to develop a hybrid pay structure across his three diesel repair shops in Georgia. Technicians work a maximum of 40 hours a week. If they can bill 35 of those hours (87.5% efficiency), they get an extra $2 per hour for that week. The higher the efficiency rating, the higher the pay premium for the week. “Our tier system actually goes as high as making an extra $24 per hour on top of their hourly wage,” Myles pointed out.
It should be noted that Myles Truck Repair does have one technician who’s still on flat rate, and that’s because the technician has requested it. “He’s a very driven person who understands that flat rate can mean feast or famine,” Myles pointed out. That technician is a rarity though. Myles said 90% of techs have no interest in flat rate pay. He doesn’t think flat rate is in the best interest of the typical shop, either.
“We tried flat rate in the past and it really hurt us,” Myles related. “The techs had no feeling of stability from one week to the next. That led to more errors because they felt like they had to hurry to make a decent paycheck. With this hybrid system,
New technicians won’t be tearing down diesel engines, but they can assist senior techs on less complex but important jobs such as making sure jack stands are placed correctly.
1. Inconsistent amount of work leads to inconsistent and unpredictable paychecks
2. Morale goes down when some techs feel like others are getting all the good jobs
our techs don’t feel like they have to work a ton of hours to make decent money. They make money and the shop makes money by being more efficient.”
The tiered system at Guzman Auto seems to alleviate some of this. Gonzales said the A-level techs get around $55 per flat hour, B-level techs get around $35 per flat hour, and C-level techs earn an hourly wage of $20 to $25 per hour. Leadership explains upon hiring why and how this system works to discourage animosity among the C-level techs who will routinely assist the A-level guys making more than double their pay.
Part of these junior techs’ compensation is that invaluable mentorship that will someday help them improve their SRTs and bill more hours in the day.
“The role of a C-level apprentice technician is clearly defined, and part of that role is gaining
3. There’s a feeling that SRTs are unrealistic and unfair
4. Techs feel like they aren’t being set up for success with the right tools and overall work environment
5. Poor parts inventory management can slow techs down and impact their paychecks
6. Service writers don’t do a good job with their initial assessments, which causes techs to get off to a slow start
valuable on-the-job experience by helping our A-level master technicians,” Gonzales explained.
“Our C-level techs realize how this will make them more valuable 12 months down the road. They also get a taste of what working on these bigger jobs is like, and how much money they could end up making if they got bumped up to flat rate. Now they want to learn and grow as quickly as humanly possible.”
This structure has also helped Guzman Automotive keep their A-level technicians in the game. As Gonzales explained, a lot of these experienced technicians are really sharp, but their bodies are wearing down faster than their minds. With assistance from the C-level apprentices, the older master technicians don’t have to worry about lifting heavy things and potentially getting injured.
C-level apprentices are incentivized in their own right. They often get an hourly premium for every hour beyond the 20 they bill. As for the B-level technicians, they are able to earn a solid flat rate while continuing to hone their skills and learn to become more efficient. They also see the opportunity to evolve to the A level, where they’ll be granted a “helper” so they can bill even more hours and make even more money. That provides a lot of motivation.
“This program has had a huge impact on productivity, profitability, and morale,” Gonzales said. “It eliminates the thinking that one tech is taking work away from another. Everyone is gaining from helping each other.”
Offering premium pay or bonuses based on efficiency and throughput is typically the most common way of incentivizing technicians. But it’s not the only way.
“In a fleet shop, it’s all about uptime,” Eggen said. “So standards and incentives around how long vehicles are in the shop, no comebacks, no worker comp injuries, attendance, etc. can feed into some really good incentive plans that could be paid on a quarterly basis. The fleet should identify upfront how much money is available and what needs to happen to earn the incentive. Then everybody in the shop can share equally. When it works correctly, the technicians all pull their weight and start to manage each other.”
A healthy, predictable paycheck is certainly essential to recruiting and retaining technicians today. But it’s only one piece of the puzzle.
Think about a young person just starting their career. In fact, take another step back and think about why they even enrolled in a diesel program at a technical college in the first place. According to Tyler Rhodes, education manager at the Universal Technical Institute campus in Avondale, Arizona, many students were told they could make a good living as a diesel technician and would have an easy time landing a job.
“Beyond that, there isn’t a whole lot of thought that goes into how they are going to earn this great living,” Rhodes said.
To that point, most emerging technicians don’t really understand what flat rate is, according to Rhodes. But they do understand what being valued feels like.
“When I first got into the auto repair industry many years ago, there were no tool allowances or tuition reimburse
$30 PER HOUR
The median technician pay in Q4 of 2024
3.4% YOY
How much technician pay grew throughout 2024
$32 PER HOUR
The hourly technician rate grew from $31 to $32 from 2023-2024
Source: Fullbay’s 2024-2025 State of Heavy Duty Repair Report
64% of diesel technicians prefer hourly or salaried pay
5% of diesel technicians prefer traditional flat-rate pay
Source: WrenchWay’s Voice of Technician Report
ments,” Rhodes said. “In today’s world, many employers are offering these types of things in some form, along with things like relocation allowances. Everyone is competing for the same technicians. In most cases, everybody knows what they need to be paying as a starting wage. So those other types of benefits can help.”
According to data presented in Fullbay’s report, two-thirds of shops offer health insurance and provide bonus opportunities for technicians, 59% provide some level of assistance for purchasing tools, 44% offer flexible scheduling, and 36% provide a matching 401k program.
Ready for one more statistic? The Fullbay report suggests that roughly two-thirds of technicians would prefer to stay right where they are. Given that, it’s really up to a shop to give technicians a reason to stay.
“We have to think past the binary idea that compensation is either hourly or flat rate,” TechForce Foundation’s Clark said. “The more systemic issue is how we elevate the technician profession by improving workplace culture, conditions, and total compensation. That means aligning the need for skilled labor with the needs of skilled labor—ensuring that techs are respected, supported, and inspired to stay and grow in the industry.”
For related content go to FleetMaintenance.com/ shop-operations
Perfecting your hiring practices doesn’t mean much if you can’t retain your technicians. Here are five tactics to help mitigate turnover.
By Alex Keenan
For all the time and money you spend bringing new technicians into the shop and getting them up to speed, it’s all for naught if they can’t be retained within your walls. Turnover is a problem across the industry, notably with drivers, but having a revolving door where techs are out as fast as they come in may have the biggest impact on uptime.
“When a good technician leaves, they do not just walk out with their tools,” said Jim Eisenberger, a former technician and founder and CEO of Pinpoint, a platform to assist techs with diagnostics and repairs. “ ey take years of experience and real-world problem-solving knowledge with them.” at kind of loss creates a “ripple e ect” that can take three to five years to recover from, Eisenberger said. at’s how much time it can take to train new techs to build the diagnostic intuition and skills they need.
“Most do not make it that far,” he said.
Around 14% of technicians le their jobs in the fi rst two years, according to Fleet Maintenance a liate Ratchet+Wrench’s 2023 Industry Survey Report. A 2021 ASE Education Foundation study put that at 41%.
Techs have dozens of reasons to leave (life
happens), but there’s one big mistake shops make, according to Bill Black, CEO and president of National Fleet Management Inc.
“ e problem with turnover is typically during the selection process, not the actual employment process,” Black said. Simply put, shops don’t properly screen candidates.
He said techs might also exaggerate their skill level or become disenchanted with the pay structure. Or maybe both parties fi nd out the relationship is a bad fit and need to break up.
But that can’t be the reason why turnover is as bad as it is. Leadership must have some control and accountability over the situation. e fact is turning wrenches is a hard job, one made harder with poor management and stagnant pay. Add to that increasing complexity and competition in the shop, it’s not di cult to understand why that revolving door exists.
“ at is what the job has become,” Eisenberger asserted. “And for many, it is just not worth it anymore.”
So, the question now is how can management make the job worth it? Here are five areas to address in your shop.
Competitive hourly pay, or steady hours for fl at-raters, is step one to keeping techs in your shop, according to Matt Trapp, VP of operations at Fleet Services by Cox Automotive.
“ e technicians want to be busy,” Trapp noted. “And when they start to see a slowdown, or they see an area where it dries up, then they start getting nervous and look for other opportunities.”
And while it is on a technician to make sure they’re working e ciently and getting jobs done on time, it’s not their job to hunt for work.
“Keeping them full, having them attain their hours and earn overtime—those are meaningful to the technicians,” Trapp emphasized.
On a related note, stagnant wages are a quick way to drive technicians out your door, added Arthur Lon, sr. director of talent management at Fleet Services. It’s basic advice, but sometimes the easiest solutions are also the most accurate.
“It is, unfortunately, a lot easier to get a higher pay bump by switching companies, as opposed to sticking around and waiting for that annual increase, if that’s even a thing,” Lon said. So one way to keep technicians in your shop is to make sure this isn’t true. O er your techs pay transparency, so they know what metrics impact their pay, understand what they need to do to get a raise, and know how much they’ll get.
And, in some cases, this provides just cause to reexamine how you compensate employees, too.
“ at means designing a pay structure that actually works for the people fi xing the cars,” Eisenberger said. “It means treating techs like humans, not machines with a socket in their hand.”
Of course, along with pay, a competitive benefits package is critical. Some of the most basic options to o er include healthcare and dental insurance, as well as a 401K match. But a bad plan that requires high premiums might not make up for a slightly higher wage, forcing a tech to fi nd higher take-home pay elsewhere. In Wrench Way’s most recent Voice of Technician survey, 47% of respondents said their shop did not provide good benefits. So make sure your benefits are in line with or better than other shops in the region.
You can also set yourself apart with tool insurance, which Transervice Logistics o ers, according to Kari Beeson, VP of recruitment and risk management.
“Because it’s so minimal, it’s part of our overall insurance program that we have to have in order to operate,” Beeson explained. “It never hurts to have, and it’s great to know that you have additional coverage.”
You could even o er pet insurance.
“[Pet insurance is] something that stands out to people,” said Jacob Leach, sr. mobile diesel technician at Cox Automotive. “I won’t say that that’s one of the most important benefits, but I’ll say that defi nitely helps them stand out as a company.”
ese benefits sweeten the pot for techs and show that you care about their overall well-being.
For Voice of Technician respondents, having adequate tools and equipment in the shop was the top thing students and techs looked for in a potential shop. At Cox Automotive, that extends into making sure that their mobile technicians have what they need and that they’ll be comfortable in their service trucks.
“It ties together to ensure that the employee feels that they are valued and they want to stick around,” Lon explained.
This means getting their technicians’ input on making sure their vehicles’ doors open well, that the drawers allow them to easily store their tools, and that the trucks are secure places to keep parts and components.
Additionally, keeping your technicians onboard may mean updating your systems, too. Leach recalled how one of the reasons he returned to work for Fleet Services after trying another company was that the service trucks weren’t properly set up as a virtual office.
“We were using our personal telephones for work,” he said. “And then on top of that, we were using paper. They weren’t really set up for the tools and resources as much as we are here.”
Beyond functional equipment, some more cosmetic additions never hurt, too, in terms of keeping technicians happy. For instance, Lon said Cox’s technicians have enjoyed using Apple’s CarPlay to listen to their music in their trucks, and that Remote Start is great to cope with the weather.
For other gift ideas, National Fleet Management’s Black said that his employees really appreciate the annual Christmas party and summer event the company puts on for them and their families. Not only are the “epic” parties a blast for the kids, with the Christmas festivities including gifts, a magic show, face paint, and a visit from Santa Claus, but the adults can win prizes, too. Black noted that they’ve raffled off a week-long resort trip to Disney World (plus spending money), four-day weekends at resorts with $400-$500 of spending money, and the ever-popular big-screen TV.
“It’s funny, because the prize everybody wants to win is the big-screen TV, and it’s usually the least-expensive gift,” Black laughed.
But if those exceed your budget, easier gifts can include tool allowances and outerwear for your techs. Beeson noted that their tool allowance ranges from $500-$1,000, and that they offer boot allowances and provide (and wash) their techs’ uniforms, too. And when winter rolls around, Transervice offers new outerwear as well.
Beeson noted that, especially for the next generation of technicians, career advancement is a necessity.
“They’re really looking for that career path to grow,” she explained. “And if they can’t find it, they will jump ship very fast… if you can’t compensate and keep up with their growing, then they’ll go somewhere else.”
Luckily, there are plenty of options to show techs a path to their future. Lon explained that Cox allows technicians to try assignments on
» Keeping techs happy in the shop doesn’t just mean posting shout-outs online when a tech does well. You should make sure they feel heard and that management supports them.
National Express
Turnover and worker loss in the trades: TechForce Foundation found that replacing positions due to turnover and retirement outpaced those due to growth at a rate of 4:1 in 2024.
The cost of hiring: Boulo, a recruiting service, found it costs an average of $5,000 to hire a new person.
Productivity loss due to hiring: Growthforce reported that it takes up to five months for new hires to reach full productivity.
No path to success: In WrenchWay’s 2025 Voice of Technician survey, only 35% of diesel techs said their shop offered a well-laid-out career path, 21% fewer than in 2024.
Work week: According to WrenchWay, 93% of technicians don’t like working on the weekends.
various other teams, such as in billing or estimating, so that as wrenching wears on their bodies, techs know that they still have other options at the company.
Meanwhile at Transervice, Beeson said that they not only help their techs get their ASE certifications and help pay for tests, but also will actively
guide techs toward management roles through higher education.
“We offer classes for them to take, especially for [Microsoft] Excel, because when you start getting to the management level, you’re talking P&Ls, and you’re talking a financial acumen that you should have,” Beeson explained. “So if they want to take courses, even if they don’t want to get a degree, to better understand business, then we’ll reimburse them for that.”
While having a strong shop culture sounds like a vague retention tactic at the best of times, it’s still one that works.
“We’ve had people where they left because of money, but then they came back because the culture wasn’t there,” Beeson asserted.
That means making sure that managers know how to coach their techs, and that your techs can easily communicate with their managers about their concerns.
“The best shops invite technicians into process decisions,” Eisenberger added. “That kind of respect goes further than any bonus ever could.”
And while having a strong culture does mean making sure leadership and management are qualified and communicative with their technicians, shops can also be creative in making sure their techs feel taken care of in other ways. For Black, that means having a chaplain come by once a week to offer their technicians support.
“It’s kind of like a mental-health type thing, it’s not just about God or church,” Black said. “It’s more about counseling.”
All of this can help increase a technician’s stability and decrease their stress, showing them that their shop is one that wants them there for the long haul.
“The number-one reason that I came back is there’s a lot more stability here,” Leach concluded on why he returned to Cox Automotive. “I can be happier and be way more efficient as a technician, and if you’re not being efficient, then you can’t be happy, in my personal opinion.”
Truly protecting technicians’ hands and eyes in the shop takes more than making sure they have safety glasses and rubber gloves.
By
Seth Skydel
Gerry Mead, VP of truck service at TravelCenters of America, has worked in the commercial vehicle maintenance industry since the mid-’90s, leading maintenance e orts for some of the largest fleets in the country. At this point, he’s regarded as a top fleet maintenance expert who can spot problems in the shop from a mile away. It wasn’t always this way. Early in his career, one oversight nearly cost him an eye.
“While replacing the decking on a gooseneck trailer, I was drilling out fasteners from underneath when a metal shaving ended up lodging in my eye,” Mead recalled. “I initially didn’t realize it, but it led to an emergency eye irrigation, followed by surgical removal of the shaving and a bu ng procedure.”
Mead said he was wearing safety glasses at the time, though he admits sealed safety goggles would have prevented the injury. Looking back, he said this incident was a “tough but important reminder that working safely means you should “match the right PPE to the specific hazard, not just check the box.”
Mead’s pain penance was relatively light, considering he kept his vision. But accidents like this are far too common in the shop, despite OSHA mandates regarding the use of proper personal protective equipment, such as face shields for welding and gloves for handling lubricants. And it’s the duty of shop leadership to ensure that the right type of PPE is always used for specific work.
“Technicians work in high-risk environments every day,” Mead o ered. “Hands and eyes are
“For example, for hand protection, it’s important to remember that meeting dexterity needs is as critical as cut protection,” Kelly continued. “A glove that has a high level of cut protection could reduce dexterity. If technicians use rotational tools like impact hammers and screw guns, polyurethane will be a better choice because it has good grip but isn’t as sticky as foam nitrile, so it reduces the risk of a glove becoming wrapped around the rotating tool.” e important thing to remember is that the PPE should shield your workers from the worstcase scenario.
“Sometimes glasses aren’t enough,” Kelly stated. “ ere’s potential for stored energy in many vehicle maintenance applications. ere are belts that have a tensioner, which can suddenly break free. Antifreeze is under pressure at high temperatures, so you may need full-face protection to reduce the risk of catastrophic injury, whether from an extreme burn or object impact.”
at may seem like an overabundance of caution, as your techs likely perform the same type of jobs hundreds of times without incident, but the managers’ job is to mitigate risk. As the saying goes, “Accidents happen.”
at’s why at Fleet Fast, an Akron, Ohio-based commercial vehicle body shop, using the proper hand and eye protection is non-negotiable, noted Brian Joseph, the company’s operations manager. ere’s rarely a moment when someone isn’t using power tools to grind, cut, weld, or paint.
“It’s not just about compliance; it’s about making sure our team gets home safely every day,” Joseph said. “We’ve seen fi rsthand how a small mistake can turn into a serious injury if the right PPE isn’t being used.”
two of the most vulnerable parts of the body in a shop—and injuries aren’t just painful; they can be permanently disabling. Protecting these areas is critical not just for safety but also for the long-term sustainability of operations, because safe technicians are also productive technicians.”
“ Beyond dollars and cents, non-compliance erodes safety culture.”
Gerry Mead, VP, TravelCenters of America
Kyle Anderson, group manager of product marketing at Milwaukee Tool, agreed, noting, “Statistics show that hand injuries account for a significant portion of nonfatal workplace incidents, leading to lost workdays, while eye injuries remain a daily concern.
“Where there are hazards such as flying debris, chemical splashes, and sharp objects, without proper protective gear, technicians face serious injuries that can impact both their safety and productivity,” he continued.
John Kelly, safety sales specialist at Brass Knuckle Protection, noted there is not a one-sizefits-all approach to PPE. Each task should be evaluated individually based on adequate protection and performance.
e cost of not having hand and eye protection programs or non-compliance by technicians is staggering on multiple levels, Mead noted. “From a human standpoint, one serious eye injury or hand laceration can change someone’s life,” he said, “and from a business perspective, OSHA fi nes, workers’ compensation claims, and lost productivity due to injuries add up quickly.
“But beyond dollars and cents, non-compliance erodes the safety culture,” Mead added. “When one technician cuts corners, it can set a precedent, and soon others follow. at’s why we don’t treat PPE as optional.”
Kevin Botosan, Fleet Fast’s production coordinator, added injuries lead to lost time and unnecessary liability. “One eye injury or deep hand laceration can put a technician out for weeks,” he said. “ at a ects not just the employee, but the entire flow of the shop. We run on quick turnarounds and tight deadlines, so keeping our people protected keeps the business running smoothly, too.”
Failing to implement proper hand and eye protection programs can result in costly consequences for both workers and businesses, including medical expenses, lost productivity, and potential legal liabilities, Anderson pointed out. “Safety investments are a necessary precaution that not only comply with regulations but also foster a culture of protection, ensuring technicians can work confidently without the fear of injury,” he said.
“There are a number of ways to consider costs,” said Kelly. “You need to factor in medical care, lost time and productivity, and workers’ comp claims. There’s also the possibility of increases in insurance costs and the loss of reputation, or even loss of business due to negative publicity.
“According to an OSHA calculator, the average cost of a laceration injury is $46,000 and for vision loss, the cost exceeds $200,000,” Kelly continued. “It seems clear that a little prevention goes a long way.”
Advancements in hand and eye PPE continue to enhance worker safety. At the same time guidelines and certification standards can help make effective choices.
Guidelines for protective gloves and eyewear help shop management choose the right equipment to prevent injuries, noted Austin Dorman, group manager of product marketing at Milwaukee Tool. For instance, OSHA highlights the importance of coated fabric gloves that improve grip and resistance to abrasions, while ANSI Cut Level and EN388 certifications are important benchmarks for selecting gloves that balance durability and performance.
“For hand protection, new glove technologies focus on providing both safety and performance,” Dorman related. “They balance dexterity and durability for maintaining precision handling while ensuring sufficient protection.”
Made with an 18-gauge knit construction, Milwaukee Tool’s High-Dexterity ANSI/ISEA 105-2016 Cut Level 2 Nitrile Dipped Gloves have been tested using the EN388 puncture standard. The gloves feature a reinforced nitrile coating between the thumb and index finger to strengthen durability in high-wear areas.
Regardless of a glove’s protective abilities, it still has to be functional enough to achieve compliance. If the tech has to keep taking the gloves off to access a tablet to find a work order or instructions, they may just leave them off.
A “game-changer” at TA’s shops has been the implementation of “tech nology-friendly gloves” that employ conductive threads in the fingertips that allow for full touchscreen use “without sacrificing protection or dexterity,” Mead said.
The gloves still need to stand up to the rigors of the job. Mead highlighted the introduction of HPPE (high perfor mance polyethylene) and enhanced grip coatings like sandy nitrile or foam latex. These promote protection and flexibility, allowing for a secure hold on oily or wet components, reducing both injury risk and dropped parts. Compliance is equally important at eye level. If eye protection obscures vision or is uncomfortable, that too will not be utilized enough. Advancements have been made in that area as well. For example, some designs feature adjustable nose bridges, lightweight frames, and anti-fog coatings, Mead explained. Some even come with blue
light filtering, which helps reduce eye fatigue when using diagnostic tablets or digital service tools.
“Technology has significantly improved eye protection with innovations such as advanced lens coatings that resist scratches and fogging, increasing durability and user satisfaction,” Dorman said. “Gasketed safety glasses are becoming more popular due to their superior debris protection, while stylish, lifestyle-oriented designs ensure consistent usage.”
Mead could have used those as an up-and-coming shop supervisor.
Comfort and fit are also factors to weigh when selecting protective eye gear, Dorman added, also citing adjustable nose bridges and temples that conform to various face shapes. There are full coverage designs to help prevent foreign objects from entering and gasketed eyewear when exposure to dust or chemicals is considered.
For eye protection, Brass Knuckle offers Midnight safety glasses featuring a removable gasket. “It’s a dust goggle with a foam filter that fills the gap
between the glasses and the face that can be quickly converted to traditional impact protection safety eyewear,” Kelly said. It can also be fitted with SideShield earpieces for wraparound protection.
“Midnight safety glasses also have our BK-AntiFOG+ protection that is impregnated into the lens so it won’t wash or wipe off,” Kelly added. “It lasts long enough for any fluctuation in heat and humidity to regulate, which means lenses stay clear.”
With a face shield attached to the goggles instead of a hard hat so the mask moves with the wearer, Brass Knuckle offers the Vader Combo for full-face protection. The product also fits over most prescription eyeglasses and provides 99.9% UV protection.
At Fleet Fast, PPE choices include 3M Virtua Safety Glasses with antifogging features. “These are affordable everyday safety glasses that are perfect for purchasing in bulk to keep around the shop for technicians if they need a pair, and for visitors,” Joseph said.
“We also use the Dewalt DPG82 Concealer AntiFog Dual Mold Safety Goggle to provide eye protection from all angles and to allow technicians to wear prescription glasses,” Joseph added. “These goggles are perfect when technicians need to drill out rivets from a box truck or trailer side panel as they block metal shavings from getting behind their glasses.”
For work gloves, Joseph also noted that Fleet Fast has found that polyurethane-coated designs offer excellent dexterity and grip, especially when handling small parts or performing tasks that require precision.
The big thing is to always stay up-to-date on new PPE innovations.
“PPE is evolving fast, and we’re always evaluating new options that enhance performance while keeping our teams protected,” Mead concluded. “If it helps keep hands and eyes safe, and keeps technicians comfortable and compliant, we’re paying attention.”
TMC OFFICERS
General Chairman / Treasurer
RADU MIHAI
BURNCO Rock Products
Vice Chairman / Meetings Chairman
MARK KENNEDY
Knight Swift Transportation, Inc.
Chairman, Study Groups
JOEY YOUNG Publix Supermarkets, Inc.
Chairman, Associates Advisory Group
ROGER MAYE ConMet
Chairman, Membership & Publicity
LARRY RAMBEAUX Purkeys
Immediate Past Chairman
AMANDA SCHUIER Jetco Delivery
Executive Director
ROBERT BRASWELL
TMC DIRECTORS
JUSTIN ANDERSON ZF
SCOTT BARTLEIN Truck Fleet Management
CHRIS DISANTIS Aim Transportation Solutions
BRENT HILTON
Maverick Transportation, LLC
KEN MARKO US Foods
ANTHONY MARSHALL United Parcel Service, Inc.
KEVIN TOMLINSON Shrader Tire & Oil Co.
Dear Trucking Industry Professional:
TMC MEETINGS
RALEIGH, N.C.
September 14-18, 2025
2025 Fall Meeting & National Technician Skills Competitions Raleigh Convention Center
NASHVILLE, TENN.
March 16-19, 2026
2026 Annual Meeting & Transportation Technology Exhibition Music City Center
June 1, 2025
ATA’s Technology & Maintenance Council (TMC) invites you to join us for our 2025 Fall Meeting, Sept. 14-18, at the Raleigh Convention Center in Raleigh, N.C. Once again, TMC’s Fall Meeting features a strong slate of educational sessions for equipment professionals, as well as a host of activity geared for truck technicians.
The theme of TMC’s 2025 Fall Meeting — Ensuring Trucking’s Future Success — centers around finding solutions to the technical, economic, personnel and regulatory challenges that face our industry. Many of our educational sessions will address these topics, as explained in our fall meeting promotion.
In addition, TMC is holding North America’s 20th annual National Technician Skills Competitions September 14-16. The event — TMCSuperTech 2025 — will feature a single professional track for all types of technicians. The event showcases our industry’s commercial vehicle technicians, who will compete across two-days for top honors and valuable prizes as they demonstrate their diagnostic abilities through a series of skills stations. Organized by TMC’s Technician & Educator Committee (TEC), TMCSuperTech 2025 will this year start Sunday morning and conclude Monday evening. Awards will be given to the top technicians and skills station winners during Tuesday evening’s Awards Banquet. This year also features our 10th Student Technician Skills Competition, TMCFutureTech 2025. All meeting attendees are welcome to observe the competitions.
The Council is also offering the TEC Technician Training Fair. The fair will take place on Tuesday, Sept. 16. For details, please review the material provided in our meeting brochure, found on TMC’s event website: https://tmcfall.trucking.org. For information, call (703) 838-1763 or email tmc@trucking.org.
On behalf of TMC’s Board of Directors, I encourage you to take advantage of this opportunity and join us at TMC’s 2025 Fall Meeting. We look forward to seeing you in Raleigh!
Sincerely,
Robert Braswell TMC Executive Director
80 M Street, Se, Suite 800 • WaShington, DC 20003 (703) 838-1763 • e-Mail: tMC@truCking org http://tMC truCking org
By Jack Poster
The trucking industry is currently going through an exciting period of technological change; new systems are being put into place to improve eciency and power better decision making. At times like this, it’s good to review the many aspects and e ciencies associated with the industry’s foundational system that make all types of comparisons and maintenance tracking possible—Vehicle Maintenance Reporting Standards (VMRS). Managed by the American Trucking Associations’ Technology & Maintenance Council (TMC), VMRS has been the ultimate building block for maintenance and equipment reporting for more than 50 years.
VMRS provides a methodology for tracking parts, equipment, labor costs, and vehicle maintenance issues across the entire transportation industry. It provides an important data layer that enables manufacturers and fleets to compare maintenance information to make intelligent business decisions.
It’s o en said that the best technology is the kind you never see working. at’s the case with VMRS. It’s been thoroughly integrated into various equipment maintenance so ware packages used by many fleets, no matter their size or vocation, and VMRS continues to expand and add new codes on an ongoing basis, adapting to the many changes in the industry.
e flow of maintenance information starts with technicians; they are the fi rst step in collecting the correct data. For a fleet to operate smoothly, the data must be precise and the repair order complete. If the incorrect information is collected on the repair order, eventually the wrong information will be portrayed as factual.
Fleets using VMRS have a standard by which they can analyze their entire portfolio of maintenance and operational costs, including historical data. VMRS can help pinpoint areas of excess expense and premature failure, increasing eciency and equipment utilization. VMRS is also a valuable tool for benchmarking equipment expenses and the overall performance of the maintenance department.
VMRS provides a sound basis for budget preparation and forecasting based on fleet mix, projected utilization, and historic performance. VMRS helps control costs by providing detailed records of where monies were spent and at what point a piece of equipment might be ready to be decommissioned.
Any size of fleet can benefit by implementing VMRS into its daily maintenance routine. VMRS codes help track labor distribution, covering both direct and indirect labor. VMRS provides complete details as to parts usage, identifying which part should be inventoried and which should be procured on an “as needed” basis. VMRS creates a single process to document when, why, and how maintenance is performed on equipment.
VMRS gives the user the ability to track repair data for use in forecasting, setting a realistic budget, and to proactively schedule maintenance procedures. e collection of substantial amounts of information can become confusing and chaotic if you do not have structure, but VMRS brings clarity to the process.
In response to VMRS user requests and changes in technologies, TMC has made several upgrades to the VMRS database and added and expanded the Code Keys that comprise VMRS. In 2023, TMC announced the addition of the VMRS Services Portal, an online tool where the complete VMRS
database is housed, giving VMRS licensees realtime access to the codes.
e VMRS Services Portal is a unique one-stop location for everything VMRS. It o ers access to the codes, an online copy of TMC’s VMRS Implementation Handbook, a way to request new codes, a way to communicate directly with TMC concerning any questions, and much more about VMRS. It is a long-awaited upgrade for the many VMRS licensees.
New codes are added to VMRS on a continual basis; the latest examples are for Electric Vehicle components. TMC has been working with major truck manufacturers and other original equipment parts manufacturers to ensure the new codes are valid and ready for the VMRS community to use. ere are currently more than five hundred electric vehicle (EV) codes in Code Key 33. Each such code has “electric vehicle” at the end of the component’s description. In addition to the EV components, codes for an EV charging station have been added, making VMRS ready for use by any company currently using EVs as part of their fleet. ere are times when new VMRS codes are needed that o er greater flexibility when describing maintenance events. e VMRS Codes Task Force determined such new codes were needed to describe maintenance alerts and repair priorities. A er much deliberation, TMC successfully approved a new separate Code Key, entitled Code Key 25: Maintenance Labor Alerts.
Historically, VMRS has been used during or a er a service event, usually when completing a repair order or warranty claim. Code Key 25 is a departure from the normal method of using VMRS, as the new Code Key reflects work that needs to be performed in advance of a scheduled activity. Code Key 25 serves as a notice that the labor in question is due to be performed at specified intervals determined by the fleet, service provider, vehicle and/or component manufacturer. e maintenance alert codes in Code Key 25 defi ne a single description and code to represent a bundle of activities that are associated with a given maintenance task. Code Key 25 gives the capability of providing standardized alerts prior to the actual maintenance task being performed, adding a new aspect to VMRS.
In 2025, TMC’s S.5 Fleet Maintenance Management Study Group, working through its Health Ready Component Status Task Force, proposed the development of a new Instruction Set for the purpose of establishing linkage between key VMRS component codes and SAE fault codes.
Proposed Instruction Set 17 allows each SAE Fault Code (also known as Diagnostic Trouble Codes) to be directly mapped to a specific VMRS Component Code (Code Key 33), giving additional meaning and consistency to each individual fault code and reducing the need for subject matter experts to make the connection between faults and their respective components from the original equipment manufacturer (OEM) fault descriptions. Data following the schema in VMRS Instruction Set 17 can enable fleet managers to conduct analytics based on mission-specific experiential data. e mapping fi le based on Instruction Set 17 can provide a starting point for fleets, third-party maintenance providers, and OEMs to expand
their data science and analytics capabilities for maintenance and operations.
VMRS Instruction Sets are composite codes, derived from combinations of various Code Keys and/or other data elements. These Instruction Sets are numerical sentences, using individual Code Keys as building blocks or “words” to describe various aspects of equipment specification or labor activity.
In the balloting process in the summer of 2025, Instruction Set 17 is featured in the latest update of TMC RP 802G. Instruction Set 17 is composed of the following data elements:
1. SAE Fault Code Type — The type can be one of the following:
• Suspect Parameter Number (SPN) which identifies a specific component or system
• Subsystem Identifier (SID) which identifies a subsystem
• Parameter Identifier (PID) which identifies a specific parameter
• On-Board Diagnostics (OBD), which refers to the system that monitors and reports vehicle faults
2. SAE Fault Code — This is a numeric data element.
3. SAE Fault Code Description — This is an alpha data element.
4. SAE Protocol — This can be J1939, J1587, OBDII, and others.
5. VMRS Component Code — This is a nine-digit numeric code from Code Key 33 which identifies a component at the system, assembly, and component level (Code and Description).
6. VMRS Technician Failure Code (optional) — This identifies the apparent failure of a suspect component, as determined by the technician/ supervisor (Code and Description).
Proposed Instruction Set 17 has several potential uses. For example, Instruction Set 17 can:
• Help fleet managers realize a significant increase in warranty claim approvals
• Help submit relevant fault codes with each repair claim
• Enable enhanced predictive analytics opportunities
• Identify system repair trends
• Help fleet managers better understand financial trends within each system, assembly, and component
• Enable further downstream tool capabilities
• Unlock greater potential for data science teams
• Identify technician training opportunities
• Shed light on where technicians
are not correctly diagnosing certain systems
• Identify repeat repairs/failures
If the new changes are adopted by Council membership, TMC will create and maintain a populated list of codes following the Instruction Set 17 schema which will be entitled “Instruction Set 17 SAE/TMC Fault-to-Component-Code Mapping Digital Annex.”
As mapping develops, the digital annex will be
As new technologies are developed and equipment requires new methods of maintenance, VMRS will continue to reflect those changes. VMRS had been an integral part of equipment maintenance for many years and will continue to be an important aspect of maintenance for many more years.
Technical Session #1
Next Generation TractorTrailer Connector: What Fleets Want
Wednesday, September 17 8-9:30 a.m.
For the past several meetings, Technology & Maintenance Council (TMC) Task Forces have been evaluating various proposals for the next generation tractor-trailer electrical connector, which will be critical for the development of future combination vehicle designs. Now the time has come for decisions to be made by the industry and there remains a lack of consensus for a future single standard going forward. Fleets must make their preferences known; otherwise, an undesirable solution will be thrust upon them. Is connector chaos unavoidable? This session, organized by TMC’s S.1 Electrical Study Group, will pick up where the Council’s last Shop Talk session on this important subject left off. During this session, our fleet-only panel will present survey feedback on connector design preferences as well as review available test data from fleets who have tried some of the various proposed solutions under consideration. Panelists will help attendees understand how this substantial change in asset interconnectivity will affect their acquisition and maintenance costs by model year 2030 and beyond, which is when whatever solution is adopted—perhaps even a “no standard” solution—is anticipated to emerge. If your fleet relies on combination vehicles in its operation, this is a must-attend session. Your input is critical to shaping what the future will hold for tomorrow’s articulated vehicles. Help shape our operation’s future before it’s too late. As the old saying goes, “if you’re not at the table, you’re on the menu.”
Technical Session #2 CAN Do! Simplifying Network Communications
Troubleshooting
Thursday, September 18 9:30-11 a.m.
Today’s complex commercial vehi-
cles rely on a sophisticated network of on-board communications collectively called the Controlled Area Network, or CAN Bus. It is the nerve center of the entire combination vehicle, playing a direct role in nearly every on-board system. Correctly diagnosing CAN bus-related fault codes, errors, and maintenance alerts is essential for properly managing vehicle safety, performance, and asset availability. Not following proper troubleshooting guidelines will invariably cost fleets time, money, and downtime because of an inability to pinpoint the root cause of databus-related maintenance and repair issues. During this session, our expert panel will provide attendees with critical information and practical skills necessary to effectively diagnose common and uncommon issues in the CAN bus system. Attendees will gain an in-depth understanding of CAN bus communication protocols, common failure modes, and modern diagnostic tools needed to troubleshoot these complex circuits. This will feature a dynamic discussion on how the CAN bus operates, followed by an interactive demonstration with pre-recorded videos to highlight the most effective testing methods used to locate and solve CAN bus issues. Armed with the right information, your technicians “CAN do” when it comes to CAN bus troubleshooting.
technician must face. Equipment users/fleets expect to be able to return a downed unit to service in a timely manner without purchasing unneeded components, paying for wasted labor, or risking another related equipment failure due to inaccurate/incomplete troubleshooting. What’s more, technicians working on the roadside performing emergency breakdown service or in a parking lot performing scheduled mobile maintenance are often working alone and must take extra precautions to work safely. Tire service at roadside presents its own set of unique challenges. The tire road service vehicle, for example, must be adequately equipped to handle whatever repairs are needed to get the vehicle operational. Cutting corners in equipment and supplies at best will be inefficient, and at worst, can be deadly. Proper procedures must also be known and followed to ensure timely and safe repairs.
ATA’s Technology & Maintenance Council has developed the industry’s best collection of recommended practices covering the service, repair, and maintenance of tires and wheels. During this session, panelists will review what fleets should know when it comes to roadside servicing of tire and wheel systems. We’ll review repair procedures, tooling, lifting and jacking, and other safety-related practices every technician should know when performing a road service call on tires and wheels for commercial vehicles. We’ll also cover proper tire specification and maintenance to minimize roadside breakdowns, as well as what information should be gathered when roadside calls come in so as to ensure an efficient, effective repair.
Engine & Motor Study Group
S.2 Recommended Practices for Tire Road Service Tire & Wheel Study Group
Wednesday, September 17
9:45-11:15 a.m.
Performing maintenance service at roadside presents significant challenges. Working outside along the roadways or in parking lots presents dangers that are unique to those situations, which are not always addressed when training for working in the shop. Uneven terrain, inclement weather, different types of surfaces, traffic patterns, and animal interaction are just some challenges the road service
Wednesday, September 17 1:15-2:45 p.m.
Today’s heavy-duty trucks run hotter than their predecessors, and that’s why it’s important to stay on top of your cooling system maintenance. Failure to do so can lead to major repairs caused by exhaust gas recirculation (EGR) cooler issues, heat exchanger inefficiency, and other coolant-related breakdowns. Proper cooling system performance starts with proper coolant selection and maintenance. Is your operation making the most out of today’s high-performance organic acid technology (OAT) formulations? During this session, panelists will cover identification
and tracking of common repairs and coolant pump replacements to help determine the root cause of engine-related failures among the various manufacturers. We also will provide training take-aways for technicians to prevent commonly encountered issues from escalating into serious maintenance concerns. Presenters will review the various types of coolants used in today’s heavy-duty power units, the consequences of improper coolant service, and the impact of electrolysis and drive system issues on cooling system performance. We’ll also cover recommended practices for preventing water pump failures and replacements, which can be a significant yet preventable expense for fleet operations. If cooling system issues are heating up your maintenance operation, this session is for you.
Regulatory
for Fleets: Emissions, OSHA, FMCSA, & Other Alphabet Soup Fleet Maintenance Management Study Group Wednesday, September 17 3-4:30 p.m.
If you think you know what’s going on in the world of federal and state regulation—think again. Changes in presidential administrations always bring some measure of shift in policy and regulation, but the changes presented by the second Trump administration have been unprecedented. That has left manufacturers, suppliers, and equipment users reeling from the sudden uncertainty that’s following a fouryear period of increasingly stringent emissions, manufacturing, safety, and labor regulation. The California Air Resources Board’s (CARB) Advanced Clean Truck (ACT) Regulation was designed to transition medium- and heavy-duty vehicles from diesel-based to zero-emission powertrains and the process had already begun in 2024, with the percentage of Class 7 & 8 truck-tractors required to be zero-emission-based rising to 40% by 2032. However, with the U.S. Environmental Protection Agency (EPA) announcing it is “reconsidering” heavy-duty truck emissions standards—as well as EPA’s authority to regulate greenhouse gases altogether—CARB has announced it has withdrawn its request from EPA for a waiver to implement its proposed Advanced Clean Fleet initiative (ACF) that would drive fleet demand for zero-emission vehicles. Similar uncertainty exists in other federal agencies such as the Federal
Motor Safety Administration (FMCSA), National Highway Traffic Safety Administration (NHTSA), Occupational Health and Safety Administration (OSHA), etc. What once was a certain pathway to increasingly stringent emissions, equipment, and labor regulation has been turned on its head, but for how long? Attend this session as we map out the volatile state of regulatory implementation and the effects it will have on your operation. Actionable information will be shared so fleets can plan and execute effective plans with your organization’s C-level leaders, administrative team, maintenance management, and technicians.
Chassis & Brake Systems Study Group
Thursday, September 18
7:45-9:15 a.m.
Air disc brakes have the potential to provide Classes 7-8 vehicles greater braking power, shorter stopping distances, and improved safety. They are becoming increasingly common on new tractors and trailers, but just as is the case with traditional Air Chamber S-cam brakes, proper specification and maintenance is a must for optimal performance, service life, and return on investment. Manufacturers promote the fact that today’s air disc brakes have longer service intervals and reduced maintenance costs than their earlier generation predecessors that help lower cost and downtime. Some fleets say otherwise because of reports of shorter service life intervals and increased maintenance costs as compared to the latest generation S-cam drum brakes. In some cases, such shortcomings are attributable to improper maintenance and repair, and if a fleet struggled to maintain S-cams, they likely will struggle to maintain air disc brakes also. ATA’s Technology & Maintenance Council (TMC) has developed a number of recommended practices designed to help fleet managers spec and maintain air disc brake systems. During this session, panelists from our S.6 Chassis & Brake Systems Study Group will review these practices in depth and provide their expert guidance on how to get the most out of disc brake technology.
S.7 Liftgate Preventive Maintenance: Raising the Bar Trailers, Bodies & Material Handling Study Group
Thursday, September 18 7:45-9:15 a.m.
Power liftgates provide trucking operations great benefit and value for the work they can perform and simplify. A variety of configurations and designs ensure liftgates can be successfully applied to a variety of industry vocations, including coldchain logistics, pickup and delivery operations, and urban city delivery, just to name a few. Yet as with any technology, attaining the maximum benefit and service life from liftgates relies on proper preventive maintenance. If your operation relies on liftgates to get the job done, are you maintaining these systems properly? ATA’s Technology & Maintenance Council has developed a series of recommended practices on liftgate specification, charging, and maintenance. Of these, TMC RP 733, Liftgate Preventive Maintenance Inspection, offers guidelines for liftgate preventive maintenance inspection (PMI) procedures, based on fleet usage and time schedules. The document covers liftgate identification, structural inspection and lubrication, hydraulic inspection, and electrical inspection. Attend this session as our expert panel provides an in-depth look at this recommended practice and offers guidelines for raising the bar on your operations liftgate PMI program.
Sustainability & Environmental Technologies Study Group Wednesday, September 17 1:15-2:45 p.m.
The U.S. economy will face monumental challenges as the nation transitions to a less carbon-intensive economy. Although the recent change in presidential administration has slowed interest in electric vehicle (EV) adoption to decarbonize the economy, fleet electrification will continue to progress, but only if the required infrastructure is available. Experts agree the U.S. electrical grid will take a beating as adoption of EVs expand, with a huge uptick in power required to power cars, homes, and the rest of the country. The process is not quick, either. Most fleets report lead times of two to four years to bring EV charging infrastructure online in their depots. Fleets need to use a careful step-by-step process when engaging utilities and the governing jurisdiction, as the energy needs for heavy-duty EVs are far larger and more complex than in a “normal” commercial facility. Fleet managers should expect to develop and work from a
checklist of all the energy needs of a fleet when working with utilities and the governing jurisdictions. Three factors collectively determine how much it will cost a fleet to operate its EVs—kilowatts, kilowatt hours, and time. ATA’s Technology & Maintenance Council (TMC), in cooperation with other industry groups and stakeholders, has developed guidelines to help fleet managers interested in adopting EVs execute the necessary charging infrastructure planning and optimization required for successful implementation. Attend this session as our panel of experts will offer proven guidance on how to bring EV charging infrastructure online in fleet operations.
Collision & Corrosion Control Study Group
Wednesday, September 17 9:45-11:15 a.m.
Aggressive corrosion caused by formulations of road-ice clearing chemicals is a serious maintenance problem for many equipment users. Use of magnesium chloride and calcium chloride-based products by certain states is especially associated with increased incidence of corrosion on vehicles, causing damage in as little as a single winter season. The scope of the problem is far-reaching, representing a multibillion-dollar toll on the entire trucking industry. This does not include the damage caused to highways, local roads, and other public utility infrastructures in North America. To reduce this problem, the Technology & Maintenance Council (TMC) of American Trucking Associations (ATA) has developed recommended practices to help equipment managers and users combat this serious problem. During this session, our expert panel will present proactive corrosion protection strategies that equipment users can employ in their operations so they can minimize the amount of corrosion-related damage sustained before it gets a chance to emerge and spread. We’ll offer guidelines on effective specifications, maintenance practices, and washing techniques to help your fleet get ahead of corrosion before it destroys your equipment.
TMC New Technology Presentations New Technology Presentations Wednesday, September 17 3-4:30 p.m.
TMC’s New Technology Presentations inform Council members of innovative features or applications of new technologies without engaging in blatant merchandising, advertising, or harmful competitive references. This session, exclusive to TMC’s Fall Meeting, provides manufacturers of innovative products and services the opportunity to give a 10-minute presentation on the virtues and benefits of their most cutting-edge offerings. As many as eight presentations will be offered during this popular educational session. Products presented should be in production and available to the industry at the time the request is made. Products on the market for more than two years will not normally be considered. Products shown must be a component, tool, or service used in the commercial transportation industry that is conceptually unique in its design from a manufacturer or service supplier company that has an active TMC member in good standing. Marginal improvements or upgrades of existing products will not be considered for presentation.
Tuesday, September 16 4-4:30 p.m.
Several TMC Study Groups will not hold separate educational sessions at TMC’s 2025 Fall Meeting, but they still need your input. The following Study Groups will hold business sessions in Raleigh at which they will update attendees on their task force activity, as well as solicit input and approval for new task forces to study pressing issues facing today’s fleets:
• S.1 Electrical
• S.4 Cab & Controls
• S.12 On-board Vehicle Electronics
• S.14 Last-mile & Vocational Vehicles
• S.16 Service Provider
• S.18 Automated & Electric Vehicles Your attendance and participation is important in identifying what projects and topics are to be pursued in TMC’s various sessions.
LIST OF SKILLS STATIONS (subject to change)
SUNDAY
Day 1 Rounds
There will be a total of 15 skill stations in Sunday’s Day 1 Rounds. Each station, featuring hands-on and/or tabletop equipment mock-ups, will be divided into 7 substations (subject to change). Each station rotation will last 22 minutes followed by an eight-minute reset/rotation/instruction period. At the end of 22 minutes, with the appropriate signal, competitors will be escorted to next contest within rotation.
The 15 stations are:
PT1: RP Manual
PT2: Lubricants & Fuels
PT3: Coolants & DEF
PT4. Electronic Engine Diagnostics
PT5: Electrical Circuits
PT6: Fasteners
PT7: Service Information
PT8: Cybersecurity
PT9: Trailer Lighting
PT10: Tire & Wheel
PT11: Advanced Driver Assistance Systems (ADAS)
PT12: Central Tire Inflation
PT13: Wheel End
PT14: Trailer Alignment
PT0: ASE Written Test (separate from the skills station rotations, takes place from 3-4 p.m.
Day 1 will also feature one holding pen, two breaks, and a lunch period.
LIST OF SKILLS STATIONS (subject to change)
SUNDAY
FT0: ASE Written Test
MONDAY
The Student Competition Skill Stations will consist of a total of 15 skill stations plus an opening ASE Written Test. The stations will be:
FT1: RP Manual
FT2: Lubricants & Fuels
FT3: Coolants & DEF
FT4. Electronic Engine Diagnostics
FT5: Electrical Circuits
FT6: Fasteners
FT7: Service Information
FT8: Cybersecurity
MONDAY
Day 2 Rounds
There will be a total of 13 skill stations in Monday’s Day 2 Rounds. Each station will be divided into 6 substations (subject to change). Each station will last 22 minutes including an opening two-minute instruction period. The 13 stations will be:
PT15: Brakes
PT16: Trailer Electrical Corrosion
PT17: Liftgates
PT18: Automated Manual Transmissions
PT19: HVAC
PT20: Remote Diagnostics
PT21: Starting & Charging
PT22: Steering & Suspension
PT23: Emissions & Aftertreatment
PT24: Rollup Doors
PT25: Wiring Diagrams
PT26: Electric Vehicle Safety
PT27: Fifth Wheel
Twenty-two minutes will be allotted to each cycle. Each station rotation will last 22 minutes followed by an eight-minute reset/rotation/instruction period. At the end of 22 minutes, with the appropriate signal, competitors will be escorted to next contest within rotation.
Day 2 will also feature one holding pen, two breaks, and a lunch period.
The Technology & Maintenance Council (TMC) of American Trucking Associations is proposing adoption of the following Recommended Practices:
• RP 139D(T), Battery Selection Criteria — This Recommended Practice (RP) offers guidelines for selecting batteries to be used in Class 7-8 commercial vehicles.
• RP 169A(T), Road Service Diagnostic Evaluation Process — This RP offers guidelines for troubleshooting electrical, starting, and charging issues at roadside.
• RP 201F(T), Tire Flap and Rim Dimensions — This RP offers guidelines on tire flap and rim dimensions for tires used on Class 7-8 commercial vehicles.
• RP 205E(T), Use of Tire Bead Lubricants — This RP offers guidelines on tire bead lubricants for tires used on Class 7-8 commercial vehicles.
• RP 214F(T)v2, Tire/Wheel End Balance and Runout — This RP offers guidelines on tire and wheel end balance and runout for tires/wheels used on Class 7-8 commercial vehicles.
• RP 220F(T), Tire Tread Design Selection — This RP offers guidelines on tire tread design and selection for tires used on Class 7-8 commercial vehicles.
• RP 253B(T), Usage Guidelines for Retreaded Steer Axle Tires — This RPoffers guidelines for retreaded steer axle tires used on Class 7-8 commercial vehicles.
• RP 254B(T), Usage Guidelines for Repaired Steer Axle Tires — This RP offers guidelines for repaired steer axle tires used on Class 7-8 commercial vehicles.
• RP 404C(T)v2, Truck and Truck Tractor Access Systems — This RP offers guidelines for entry and egress of Class 7-8 commercial trucks and truck-tractors.
• RP 363B(T), Underhood Thermal Event Prevention — This RP offers guidelines on underhood thermal event prevention on Class 7-8 commercial vehicles.
• RP 379(T), Battery Electric Vehicle (BEV) Coolant Selection — This RP offers guidelines for selecting coolants for battery electric vehicles used in commercial service.
• RP 446(T), In-Cab Gas Detector Specifications — This RP offers guidelines for spec’ing in-cab gas detectors for commercial vehicles.
• RP 554(T), Pre-Trip Inspection for Battery Electric Vehicles (BEVs) — This RP offers guidelines for conducting pre-trip inspections for battery electric vehicles used in commercial service.
• RP 622C(T), Wheel Seal and Bearing Removal, Installation and Maintenance — This RP offers guidelines for conducting wheel seal and bearing removal, installation and maintenance.
• RP 650A(T), Guidelines for Fifth Wheel Pre-Delivery Inspection, Preventive Maintenance and Troubleshooting — This RP offers guidelines for conducting fi fth wheel pre-delivery inspection, preventive maintenance and troubleshooting.
• RP 659A(T), Air Release Fifth Wheel Function Guidelines — This RP offers guidelines for air release systems used on fi fth wheels for Class 7-8 commercial vehicles.
FT9: Trailer Lighting
FT10: Tire & Wheel
FT11: ADAS
FT12: Central Tire Inflation
FT13: Wheel End
FT14: Fifth Wheel
HP1: Holding Pen
Twenty-two minutes will be allotted to each cycle. Task completion will occur within this time allotment. At the end of 22 minutes, with the appropriate signal, competitors will be escorted to the next contest within rotation and will receive instructions. The day will also feature one holding pen, two breaks, and a lunch period.
• RP 710B(T), Overhead Door Selection and Installation for a Dry Van or Body — This RP offers guidelines for overhead door selection and installation for a dry van or body used in commercial service.
• RP 761A(T), Overhead Door Maintenance Guidelines for a Dry Van or Body — This RP offers guidelines for overhead door maintenance for a dry van or body used in commercial service.
• RP 1113A(T), Guidelines for Driver Incentive Programs — This RP offers guidelines for driver incentive programs for commercial vehicle fleets.
• RP 1120(T), Guidelines for Charge Cycle Optimization and Energy Management in Battery Electric Commercial Vehicles (BEV) — This RP offers guidelines for charge cycle optimization and energy management in battery electric commercial vehicles.
• RP 1121(T), Guidelines for Electric Vehicle Charging Infrastructure Planning, Installation and Operation — This RP offers guidelines for charge cycle optimization and energy management in battery electric commercial vehicles.
Any party may submit a written request of appeal of a proposed Recommended Practice (RP). However, the request must be received by the Technology & Maintenance Council within 90 days of publication of this notice. If no appeals are made at the end of the 90 days, the RP will be formally adopted by TMC. (The suffi x “T” indicates an RP is proposed.) With the printing of this issue, the following RPs are now open to the 90-day appeal process. Written appeals can be sent to TMC Technical Director Jack Legler, 80 M Street, SE, Suite 800, Washington, DC 20003. Phone: (703) 838-7956; jlegler@trucking.org.
The following Task Forces of the Technology & Maintenance Council (TMC) will meet in open session on Tuesday, September 16, 2025 at the Raleigh Convention Center in Raleigh, N.C. Task Force meetings are scheduled for approximately one hour and will take place between 8 am and 4 pm eastern. Parties wishing information on how to attend specific Task Forces should contact TMC headquarters at (703) 838-1763 or visit https://tmcfall.trucking.org.
S.1 Electrical
• Future Electrical/Electronic Systems (Joint FT/S.1)
• Microgrids and Battery Storage (Joint S.1/S.11)
• Next Generation Tractor-Trailer Electrical Interface
Rear-facing LED Out-of-Service Criteria Wireless EV Charging Standards and Recommendations
• RP 137D Update (Antilock Electrical Supply)
• RP 141A Update (Trailer ABS Supply)
• Exploring Trailer Voltage Drop for Current & Future Demands (Joint
S.1/S.7)
• Post-Pilot Review Specification Inspection Guidelines
RP Updates (S.1)
RP 107C/RP 159 Update (Tractor-Trailer Connector Maintenance/Spec’ing)
• RP 185 Update (Reefer Shorepower Guidelines)
S.2 Tire & Wheel
• RP Updates (S.2)
• Proper Tire Mounting With Tire Pressure Monitoring Systems (TPMS)
• Tire Maintenance Management Systems Tire Conditions Analysis Guide for Light Commercial Vehicles (Joint S.2/S.14)
• Tire Information & Lifecycle Data Service Requirements
• Managing TPMS Sensors in Mounted Tire Programs
S.3 Engine & Motor
• RP 322B Update (Coolant Pump Failure Modes)
• Guidelines for Testing and Leak Detection for Electric Vehicle Powertrain Systems
• RP 301D Update (Air Intake System Maintenance)
• RP Updates (S.3)
• Engine Diagnostics & Emissions Using SNAPAcceleration Smoke Testing Procedures
• Lubrication for Electric Vehicles
S.4 Cab & Controls
RP Updates (S.4)
• RP 430 Update (Guidelines for Collision Warning)
• Conversion of Rearview Mirrors to Cameras
• RP 429 (Windshield Replacement & Repair)
• Battery/Hybrid Truck Cab A/C Specifications Truck Cab Occupant Protection Specifications
• Rearview Camera Monitoring Systems
S.5 Fleet Maintenance Management
• RP Updates (S.5)
• VMRS Codes
• Health Ready Components Standards
• Cybersecurity Issues (Joint S.5/S.12)
• RP 531A Update (Parts Inventory Mgmt Guidelines)
Personal Protection Equipment & Technician Wellness
Root Cause Analysis
• Decommissioning Equipment
• Inspection Document Quality Control
S.6 Chassis & Brake Systems
• RP Updates (Brake-Related RPs)
• RP 628D Update (Aftermarket Brake
Lining Classification)
• RP 629A Update (Brake Lining Contamination)
RP Updates (Chassis -Related RPs)
RP 619B Update (Air System Inspection Procedure)
• Spindle Condition Analysis
• RP 656B Update (Hub and Spoke Fastener Maintenance)
S.7 Trailers, Bodies & Material Handling
• RP Updates (S.7)
• Brake-Activated Pulsating Lamps
RP 730 Update (Air Line Antifreeze Recommendations)
• RP 731A Update (Lube Free Coupling Guidelines)
• RP 707A Update (Rear Bumper Dimensions)
• Exploring Trailer Voltage Drop for Current & Future Demands (Joint S.1/S.7)
• Trailer Refrigeration Unit Charging Onboard Specifications
S.11 Sustainability & Environmental Technology
• RP Updates (S.11)
• Energy Efficiency Test Procedures for Electric Vehicles
• Fleet Expectations and Guidelines for Spec’ing Electric Vehicles
• Understanding Electric Vehicle Efficiency Performance
• TCO Calculator for Electric Vehicles SmartWay Activities
Energy Conservation/Industry
Sustainability Update
• Trailer Refrigeration Unit Charging Infrastructure
• Trucking Duty Cycles (Defining
Operation Segmentation)
S.12 On-Board Vehicle Electronics
RP Updates (S.12)
• RP 1230 Messaging Standardization Revisions
• RP 1210D Update (Windows API)
• Communication Network Troubleshooting
• ADAS Data Messaging
• Regulatory Reporting Standards
• Device Security
• Guidance to RP 1226 Connection Transfer of Asset Ownership Predictive Maintenance
S.14 Last Mile & Vocational Vehicles
• RP Updates (S.14)
• Class 2-6 Electric Vehicle Inspection Standards
• Commercial Electric Vehicle Body Inspection and Upfitting
• Guidelines for Quality Control of Body/ Equipment Upfitters
Maintenance Considerations for High Consumption Vocational Air Systems
S.16 Service Provider
• Guidelines for Effective Repair Order Documentation
• Repairing Customer Relationships Following Repair Disagreements
• Spec’ing Service Vehicles to Match Scope of Service
• Electric Vehicle Battery End of Life Handling, Retention & Disposal Implementing TMC RPs in Fleet & Service Provider Operations
• Service Provider Standards of Excellence
• RP 1612 Update (Service Event Data Transparency)
• RP Updates (S.16)
S.17 Collision & Corrosion Control
• Corrosion Manual Update
• Heavy-Duty Collision Repair Roadmap
• Frame Correction
• RP Updates (S.17)
S.18 Automated Vehicles Automated Driving System Selection
• Process Technician & Maintenance Shop Requirements for Automated Vehicles
• Trailer Specification for Automated Power Units
• Optimization of Driver Training for ADAS/ADS
• Automated Vehicle Industry Updates
• Cybersecurity for Automated Driving Systems
Technician & Educator Committee
• Future Technician Scholarships
• Educator Involvement/Progression From Tech to Educator
Future Truck Committee
• Future Electrical/Electronic Systems (Joint FT/S.1)
• Augmented and Virtual Training
• Future Cab and Driver Interface
• Future Trailer Productivity Future Tire Reliability/Durability
• Energy Conservation/Industry Sustainability Update
• Future Data Science in Trucking
• Future Chassis and Brake Systems
What happens when engineers known for missile defense systems and giant robot battle suits take on a time-consuming, repetitive shop job? An automated lift that swaps four wheels in 15 minutes, of course.
By John Hitch
When you get too much wear and tear on your tires or brakes, you simply swap them out. And that requires a technician to physically remove up to four heavy wheel assemblies, and then replace them when they’re done. It’s one of the most common—and physically demanding—jobs in the shop, leading to plenty of wear and tear on your tech’s upper body. And those are not so easy to swap out. Even in the best-case scenario, low-value jobs like rotating all four tires take up precious shop space and your tech’s valuable time, while the repetitive, high-strain work slowly rips and pulls at their muscles and ligaments.
According to a startup called PitPro Automation, this is the perfect job for robots. Not the humanoid Optimus developed by Tesla, mind you, but an automated wheel changer that’s equal parts NASA and NASCAR, comprising a traditional off-theshelf alignment lift with two gantry robots that can torque and untorque lug nuts with steely precision, and remove and replace the wheels without breaking a sweat. Pre-loaded new wheel assemblies are stocked on an attached carousel. A tech still manually controls the lift and positioning of jacks, but the robot drastically slashes repair time.
“We can access all four wheels, take them off, [and] put them back on in 15 minutes,” CEO and founder Jeremy Conrad told Fleet Maintenance
The MIT graduate tested weapons-grade lasers for missile defense systems as an Air Force officer before starting a robotics venture capital fund.
The San Francisco-based company, which revealed the automated wheel changer in late
June, estimates this is 80 to 90% faster than a human, ultimately savings fleets up to $300 in downtime costs per tire service.
“Managing service operations across 10,000+ Ford dealers, I saw how downtime and technician shortages cripple fleet profitability daily,” stated former Ford Pro CEO Ted Cannis, who previously worked with Conrad. “PitPro’s fleet-focused automation directly solves these operational challenges that impact customer deliveries while improving efficiency.”
The robotic technology can also sense tire tread depth and psi, as well as detect broken or stripped nuts. The shop also shouldn’t worry about wheeloffs, as the system torques within 1% of OEM specification and records the data.
The company is targeting fleet customers with Class 3 or lower pickups and vans, so under 14,000 lbs. GVWR. They can modify the design based on a customer’s needs, with the largest version for Sprinter vans (170-in. wheelbase) spanning about 15 ft. across and 35 ft. long, explained Gui Cavalcanti, PitPro’s head of engineering. It was designed to fit into your typical commercial vehicle bay, “hugging the sides of the vehicle with only a couple inches gap,” Cavalcanti explained, adding a laser curtain can be added as a safety measure to shut the machine off if a worker or foreign object breaks the plane. The lifts anchor into the ground with no infrastructure changes required.
Cavalcanti, who spent his formative years at Boston Dynamics developing what would become Atlas, then co-founded a short-lived-but-fascinat-
ing giant robot fight club called MegaBots, said the company’s future ambitions include bulking up to handle Classes 5-8 tires, and even balance tires and change brakes. (Coincidentally, NASA and NASCAR were actually involved in the development of MegaBot’s Eagle Prime, which Cavalcanti co-piloted in a battle of honor against a Gundamstyle Japanese robot.)
But for now the company is looking for service centers with 10-20 bays or fleet depots with 200+ light-duty assets to pilot the technology early next year. These scaled-down pilot versions “are basically a hydraulic robot that looks like a very fancy moving version of any other lift to their shop,” he said, noting the machine will use “the same basic tech shops are used to seeing, like cylinders, cables, and chains.” The system can run off 208V three-phase or 240V single-phase power.
And don’t let the high-tech gadgetry fool you; the automated platform exists to make technicians’ and shop managers’ lives much easier.
“If you have a de-scoped, constrained problem set, like for fleets working with lots of the same vehicles, you can actually make the robot really, really good at that thing,” Cavalcanti assured.
In preparation for inventing the wheel changer, both Conrad and Cavalcanti earned “higher level certification” from the Tire Industry Association and talked to several tire shops. The biggest advantage Conrad believes this machine offers them is “taking some of that heavy lifting away from the technicians, so they can focus on higher value work like working on an engine.”
Removing this burden also mitigates the risk for shop injuries related to mishandling commercial tires, such as a fractured foot or sprained wrist, as well as ones caused by repetitive lifting, such as a slipped disc or torn labrum.
“People just can’t stay in it very long without literally breaking their backs,” Cavalcanti added, noting wheel assemblies “are getting heavier and heavier,” with a Ford Transit’s assemblies each weighing nearly 80 lbs. “If you’re doing two cars an hour for a full workday, you’re done after two or three years.”
Conrad said one national chain considering becoming an early adopter admitted their turnover was around 120%.
“Even beyond the musculoskeletal stuff, it’s just a brutal profession,” Conrad asserted, citing anecdotes from shop managers like trying to handle frozen lug nuts in the winter or working in a sweltering Florida shop without climate control.
Finally, automation like this opens up roles for techs willing to join the trade but not built for the physical demands.
“If you can’t lift those big tires, male or female, whatever, it just means you can’t get to that next level—and so I certainly think that this is the technology that really can open it up,” Conrad said. “There are lots of different ways to adjust for the tech shortage, and I really think we’re going to have to try all of them, or this is a field that’s going to continue to struggle.”
Can mount on the truck or trailer side or nose
Phillips Industries ’ REAR-VU installation kits are designed to help fleets easily install the REAR-VU camera system. The latest kits come in three models: the Trailer Side Mount Antenna Kit (No. 78-1200), the Trailer Nose Mount Antenna Kit (No. 78-1201), and the Truck Mount Kit (No. 78-1202). The Side Mount Antenna Kit includes REAR-VU with a mounting bracket, directional antenna, and a side-mount installation hardware kit, and installs in 15-20 minutes. The Trailer Nose kit can install in the trailer roof seam with the included retaining clips and includes REAR-VU, a mounting bracket, nose antenna, extended cable, and an install kit. It can be installed in 30-50 minutes, depending on available shop equipment. The Truck Mount Kit includes REAR-VU with a back-of-cab moutning bracket, omni-direcitonal antenna, and an installation hardware kit, and can install in 15-20 minutes. For more information visit FleetMaintenance.com/55294913
Hellwig Products ’ Helper Springs for 2024-25 Ford Super Duty F-250 and F-350 pickups provide better support and higher-level load capacities than factory contact leaf springs alone. With two springs designed to work with the rear OEM contact leaf springs, they offer more support under heavy loads to ensure a level truck and a more comfortable ride. The contact helpers mount atop the factory leaf springs to offer an additional 2,000 lbs. of load support. Manufactured and designed to offer an OEM-style fitment and made in the U.S. with heat-treated 4140 chromoly steel, each kit includes all the necessary hardware for installation and can be installed in a few hours with simple hand tools and jacks.
For more information visit FleetMaintenance.com/55297355
The MyMack Driver App from Mack Trucks is a driver application for the Mack Pioneer highway model. The app is available to download from the Apple Store and Google Play, and allows drivers to remotely monitor their truck’s fuel level, Diesel Exhaust Fluid (DEF) level, oil level, and check the status of their vehicle’s lights. Additionally, the app lets drivers remotely activate their climate control system when equipped with Mack’s Integrated Parking Cooler.
For more information visit FleetMaintenance.com/55293094
Dorman ’s Headlight Bulb Retainer provides a longer-lasting and more affordable repair solution for Ram ProMaster vans. The socket features a patent-pending reinforced locking tab that solidly secures the bulb, simplifies future replacements, reduces maintenance costs, and helps ensure safer driving conditions. The retainer is designed to replace the OE headlight bulb pigtail locking tab, which the company says has insufficient holding power and causes the headlight bulb to loosen and disconnect. When the locking tab breaks, the hot halogen bulb can fall out of the socket entirely, landing inside and melting the plastic headlight housing.
For more information visit FleetMaintenance.com/55298068
The CT5 TIME TO GO from CTEK features a series of LED lights that indicate different charging stages, and how long (in hours) the battery needs before it’s charged. The CT5 uses advanced technology, giving the user three charging and maintenance programs—normal, AGM charging, and record. The charger is fully automatic; it can be connected directly to the battery indefinitely, if required; and it won’t over or undercharge.
For more information visit FleetMaintenance.com/55293103
Kinedyne ’s Transport Grade 70 Chain is a strong, secure, efficient, and reliable cargo securement method built to deal with rougher cargo. Manufactured from heat-treated carbon steel for industrial strength, this chain has the durability to handle the rough tie-down jobs that would damage web tie-down assemblies. The Transport Grade 70 Chain is available in the following sizes: 1/4”, 5/16”, 3/8”, and 1/2”. Each size comes in bulk in a barrel or pre-cut in a barrel or box. All Kinedyne Chains are manufactured in compliance with the recommendations set forth by the National Association of Chain Manufacturers (NACM).
For more information visit FleetMaintenance.com/55298073
Offers extended recommended service intervals
Hendrickson ’s advancements to their STEERTEK NXT steer axles on Blue Bird school buses bring further weight reduction to the student transportation sector. The company has reduced the weight compared to the previous generation’s steer axles, improving weight savings by an additional 25 lbs. to increase payload capacity and improve fuel efficiency. Additional benefits of the STEERTEK NXT axles include a two-piece knuckle designed for easier, cost-effective service, and extended recommended service intervals, helping to reduce downtime and maintenance frequency. Axles are assembled and fabricated in the U.S.
For more information visit FleetMaintenance.com/55297358
The Surfsight AI-14 dash cam from Lytx provides both audio and visual realtime alerts to help keep drivers focused. The dash cam includes an integrated LCD touchscreen for efficient installation, and it features flexible audio recording for both inside and outside the vehicle. The AI-14 provides road-facing ADAS features such as following distance, critical distance, and rolling stop, with pedestrian detection and red-light detection on the way soon. The camera itself is tamper-resistant, and features convenient record buttons for drivers to mark key events and includes over-the-air firmware updates.
For more information visit FleetMaintenance.com/55296848
Provides multi-surface traction
OTR ’s LIFTBOSS A/T nondirectional tire is designed for telehandlers operating in construction and material handling environments, providing multi-surface traction across asphalt, concrete, and gravel. Featuring a step-down tread and mud breakers for self-cleaning, as well as integrated sipes for enhanced traction, this tire ensures safety and durability. Other advantages include low rolling resistance for reduced fuel consumption, a self-cleaning design for shedding mud, and a low profile for enhanced stability and sidewall protection. The LIFTBOSS A/T also has a non-directional tread pattern for greater versatility and easy ordering.
For more information visit FleetMaintenance.com/55298056
The 1,000V CAT III Hybrid Multimeter with Insulation Resistance Test from OTC allows technicians to perform insulation and high-voltage electrical tests on modern vehicles with ease. This full-function multimeter incorporates an insulation test feature to test for voltage leaks through insulation found on hybrid and electric vehicles. The tool includes heavy-duty class III test leads with alligator clips, short lead, K-Type temperature adapter, and a soft-sided carry case.
For more information visit FleetMaintenance.com/55293857
The Grip-on 10-pc Essential Locking Pliers Set , No. EK-SET10, from Dynamic Tools includes 10 essential designs and sizes to be employed where strong, temporary grip is needed. The epoxy resin coating is 10 times more corrosion resistant than nickel and provides superior resistance to welding spatter. No-pinch easy release lever eliminates painful accidental pinching of hands and fingers. Drop-forged jaws ensure long-term durability. A piano wire spring ensures superior tool life and reliable opening and closing of the tool. Improved design reduces the gap between the lever and handle, protecting the spring from damage. Includes a metal storage rack. For more information visit FleetMaintenance.com/55296262
The Cal-Van Tools 5-pc Lug & Lock Flip Socket Set , No. 96100, features sockets designed with six fluted twists for gripping damaged lug nuts. The flip socket on the opposite end has 12 fluted twists for wheel locks, and all of the set’s flip sockets have a 1/2” drive design. The set includes a 7/8” Lug & Lock Flip Socket, a 21mm Lug & Lock Flip Socket, a 19mm-3/4” Lug & Lock Flip Socket, a 17mm Lug & Lock Flip Socket, and a 1/2” drive 3” extension bar.
For more information visit FleetMaintenance.com/55297368
Services various Cummins engines from 1989 to current
The CTA Tools Cummins Front & Rear Crankshaft Seal Remover & Installer Master Kit , No. 5085, is a comprehensive kit for installing and removing the front and rear crankshaft seals on Cummins engines, including ISB, ISC, ISL, QSB, and B and C Series models from 1989 to the current day. It’s compatible with factory OE seals and wear sleeves. The kit includes a Cummins USB front crank seal removal and installation tool, a Cummins crankshaft seal installer, a Cummins wear sleeve install tool, a rear crankshaft seal removal and installation tool, and a Cummins B and C Series rear crank seal/wear sleeve installer.
For more information visit FleetMaintenance.com/55297726
ProMAXX Tool ’s PMXPWP915 Series line of air hammer–powered fuel injector removal kits is designed to eliminate engine teardown during Ford EcoBoost injector replacements. Saving up to 15 labor hours, the line offers a faster, safer method to remove seized injectors without removing the engine or cylinder head. These professional-grade kits are compatible with Ford 1.0L, 1.5L, 3.5L, and 3.7L EcoBoost engines, including applications in the Transit and F-150. Each kit includes ProMAXX Tool’s exclusive precision-engineered jig with machine shop grade tooling that eliminates the hassle and lost productivity in pulling a head. For more information visit FleetMaintenance.com/55297737
Makes oscilloscope diagnostics faster and easier
Pico Technology ’s latest update to PicoScope 7 Automotive simplifies setup with the all-new Setup Wizard, expands Guided Tests to cover more vehicle systems, enhances Demo Mode for hands-on learning, and introduces new tracking rulers for real-time waveform analysis. Improvements to the math channels, serial decoding, and extended timebases provide deeper insights into signal behavior, helping workshops quickly diagnose issues.
For more information visit FleetMaintenance.com/55297363
The Gray Manufacturing WPLS50 Light Duty Mobile Column Lift offers a 5,000-lb. lifting capacity per lift. It features a T-handle designed for easy maneuverability, even in tight workspaces, and a self-contained modular design. The WPLS-50 also includes lockable swivel casters, adjustable lift forks, a blinking light system for self-directing operational setup, and a color-coded display background to indicate lift status. The WPLS-50 is an ALI-certified lift.
For more information visit FleetMaintenance.com/55296254
Allows users to attach cup holders, phone holders, and more
Matco Tools ’s 38” x 24” MSCX SIDEKICK Ready Tool Cart equipped with rails ready for the SIDEKICK modular organization al system, sold separately, that allows users to attach cup holders, phone holders, power tool holders, and more to their cart. It features expanded side storage and a top till cutout that provides a clear view into the top till area and eliminates the need to reach over the cart’s lip. The cart is available in blue, green, black, or gray.
For more information visit FleetMaintenance.com/55297373
Reads, checks, and programs TPMS sensors
Cojali ’s Jaltest TPMS is a device to help technicians maintain and manage their tire pressure monitoring systems (TPMS) in commercial vehicles. The tool is compact and easy to use, and is compatible with OE and alternative and universal sensors. Offering coverage for trucks, buses, trailers, and light commercial vehicles, Jaltest TPMS can read sensor data such as pressure, temperature, battery level, and sensor ID number. It can also program and clone universal sensors, provide detailed information on compatible references, relearn processes in TPMS control units, and consult work reports and scan by code. Provided with an active software license for the first year.
For more information visit FleetMaintenance.com/55293855
Mobile design allows for quick relocation
The ARI-Hetra WS-MobileAlign is a cutting-edge mobile alignment machine designed to simplify alignment for vehicles of all sizes, from heavy-duty trucks and buses to motorcoaches and cars. Designed and engineered for flexibility and mobility, the WS-MobileAlign features advanced 3D imaging and HD cameras. Wheelmounted targets help to ensure precise calculations and alignment results. Works on the ground or on various lift types, including four-post, scissor, and platform lifts while retaining calibration during elevation. Users can operate the system remotely from any tablet for added convenience. A secondary monitor enhances visibility when working at ground level.
For more information visit FleetMaintenance.com/55296855
Includes adjustable hooks for hands-free placement
Coxreels ’s line of three industrial duty LED lights is now available on PC10 reels. Features include a variety of industrial-grade features and options, including a 50,000-hour rating, internal light diffusers, shatter-resistant polycarbonate lenses, and adjustable steel hooks for hands-free placement. The line is made up of a compact LED light feature (-M), an LED light with the additional power source (-K), and an industrial-duty, UL Listed LED light (-H).
For more information visit FleetMaintenance.com/55297367
Seamlessly mounts to hats, safety helmets, and more Streamlight ’s SL-SideSaddle series of lighting systems is designed to seamlessly mount to a wide range of hats, hard hats, and safety helmets. Available in both USB rechargeable and alkaline battery-powered models, the SL-SideSaddle is built for use in demanding environments, providing reliable, hands-free lighting. Offers selectable spot, flood, or spot/ flood combination modes and a rear-facing blue LED taillight. The lightweight, impact-resistant lights integrate without interfering with other headgear accessories, such as visors or hearing protection, and are easily detachable for handheld use. The lights feature a tough polycarbonate thermoplastic construction and an unbreakable polycarbonate lens that is impervious to shock and drop tested to withstand 2-meter impact. Available in high-visibility yellow or black.
For more information visit FleetMaintenance.com/55297742