Building Iconic Spaces:
Top Considerations for Public Assembly Facilities
General
1. FACILITY INSURANCE REVIEW
• Verify the facility insurance carriers have reviewed and approved the materials and specifications of work to be completed on renovations and expansions of existing properties.
2. FIELD CONDITION SURVEYS
• Conduct comprehensive surveys for trades working against existing structures, ensuring any impacts are coordinated with ongoing occupied activities.
• Noise pollution violations are on the rise. Consider placing Sound Decibel Meters at areas adjacent to residential neighborhoods.
3. WARRANTY PROVISIONS
• Review and coordinate Warranty Provisions of materials and scope where dissimilar materials meet and create an exterior watertight seal.
4. GEOTECHNICAL REPORT INCLUSION
• Include geotechnical findings to preempt foundation-related challenges.
5. CRITICAL LOGIC TIES
• Plan for scope completion dependencies such as completing exterior roofing before installing interior spray-on fireproofing on the underside of a roof’s metal decking.
6. OWNER AND DEVELOPER RESPONSIBILITIES
• Clarify utility responsibilities, financial aspects (insurance, contingencies, design fees, financing, legal matters), and plan checks. Address geotechnical reports, land acquisition, permits, infrastructure, and specialty consultants. Integrate program management, PR, marketing, and utility costs for a holistic approach.
Vegas Convention Center, (LVCC) Phase 2 Expansion, Las Vegas, NV
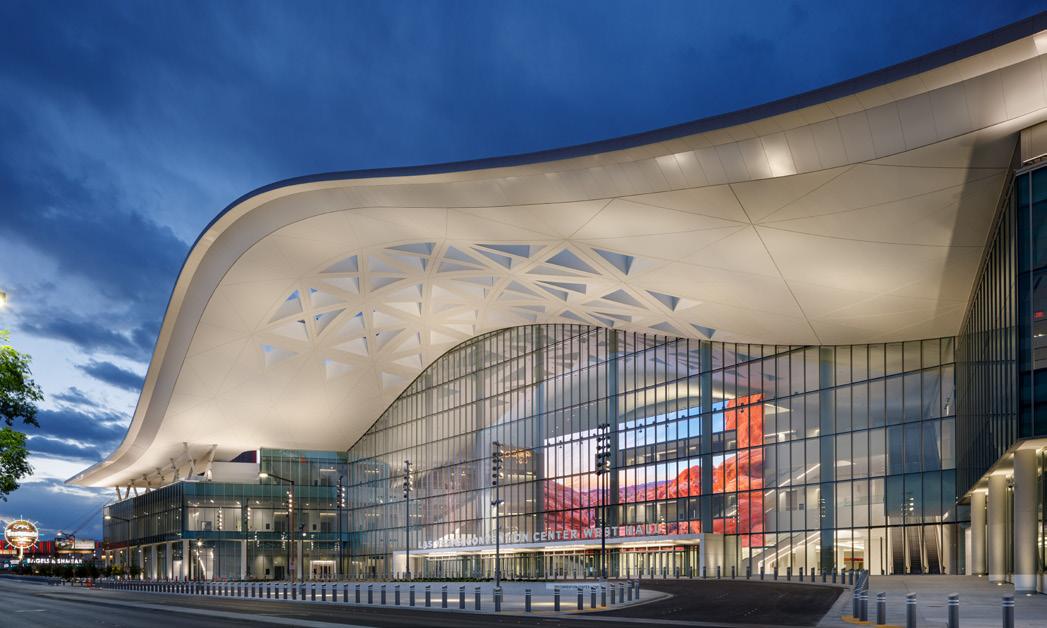
Schedule
1. PHASED PROJECTS
• Identify dependencies and impacts for phased projects.
Example: The LVCC West Hall Expansion followed a phased construction strategy that accelerated critical paths for early trade mobilization.
2. DESIGN ASSIST
• A design-assist approach enables CMAR to bid early, collaborate with trades, and control costs. Early trade selection ensures timely material procurement, crucial for convention centers where mezzanine-housed mechanical equipment must be hoisted during structural erection.
3. LOGISTICAL CONSTRAINTS
• Address constraints driven by show scheduling and exhibitor load-in and load-out activities. Construction swing shifts, off-hours loading and unloading, truck-to-hook strategies, and offcampus storage are just a few approaches to improving efficiency.
Example: The JJCC marshaling facility addressed urban congestion by relocating truck staging operations to an onsite facility, freeing surrounding streets.
4. DESIGN INFORMATION ROAD MAP
• Determine the design phase schedule, establish the submittal process timeline, and define RFI response parameters to ensure a structured and efficient workflow.
