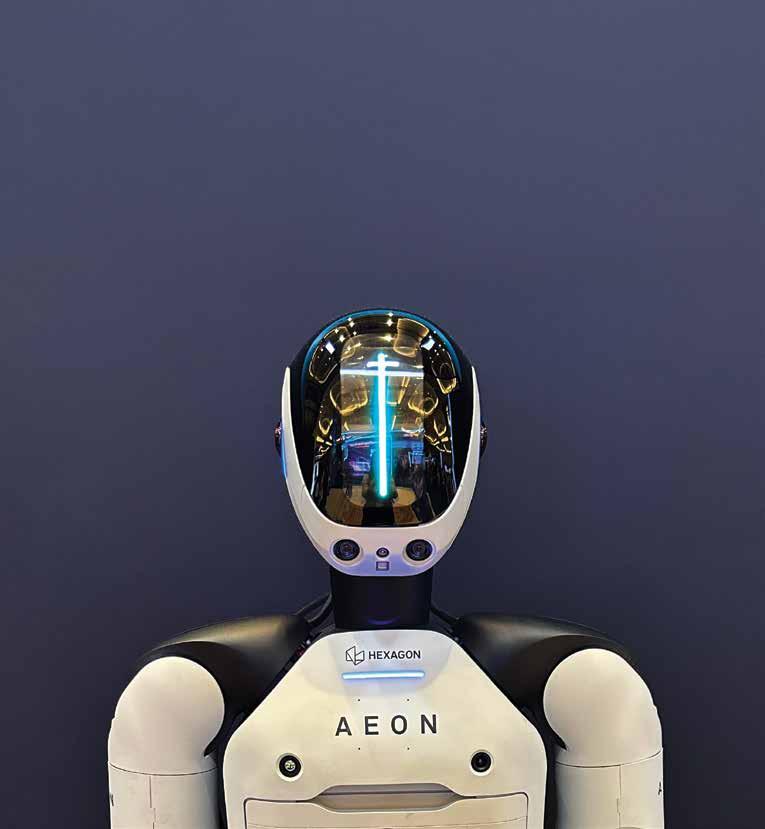
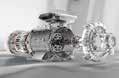
Autonomy is rapidly advancing, driven by innovations in AI, robotics and sensor technologies. As design engineers embrace this technological shift, autonomous systems are becoming integral within sectors such as aerospace, automotive and manufacturing. This issue’s cover story (from page 6) embodies this trend as we bring you the latest from Hexagon Live 2025, the headline of which was the unveiling of an autonomous humanoid robot, Aeon, prompting the question: Could we soon be on the brink of a fullyintegrated human-robot workforce?
Autonomy remains a key theme throughout this issue, from smarter sensors in additive manufacturing operations (page 16), and shifting simulation left (page 38), to the ways AI is enabling improved ease-ofuse in electronics design (page 20). Elsewhere, we cover the evolution of prototyping in product design (page 14), new material opportunities for space flight (page 24) and how one company is playing its part in shaping the future of composite manufacturing (page 30).
Our regular Skills Zone feature (from page 44) is jampacked for this issue, featuring fresh investments in upskilling, upcoming training opportunities and recent events that highlight the critical role of education in manufacturing. The show preview section, meanwhile, previews three important trade shows in the electronic industry’s calendar, flip to page 48 to find out more.
Hayley Everett Head of Editorial
18
How advances in measurement and automation are helping businesses unlock new levels of insight, performance, and possibility
Shaping the future of highperformance engineering
Discussing
How
Medtech training
How Stratasys 3D printing technology is enhancing medical training
INSTRUMENTATION & ELECTRONICS
20
AI is here to help AI is revolutionising ease of use within electronics design
22
The art of soldering
Recognising the source of defects in soldering within electronics production
24 To infinity
How inflatable aerodynamic decelerators could offer radically new material opportunities for space flight
28 Circular challenges
Overcoming obstacles to integrating circular economy practices
COMPOSITES
30 Closing the loop
Shaping the future of composites manufacturing FASTENERS & SEALING
34 Plastic performance
Discussing the performance expectations for threaded inserts
35 Good grades
The different grades and types of stainless steel used in fasteners
MOTORS, DRIVES & CONTROLS
38 Simulation shift
How simulation technology is powering a human-centred approached to manufacturing
PUBLISHER
Jerry Ramsdale
EDITOR
Hayley Everett heverett@setform.com
STAFF WRITER
Jake Holmes jholmes@setform.com
DESIGN – Dan Bennett, Jill Harris
HEAD OF PRODUCTION
Luke Wikner production@setform.com
BUSINESS MANAGERS
John Abey | Darren Ringer
ADVERTISEMENT EXECUTIVES
Paul Maher, Iain Fletcher, Peter King, Marina Grant
e advertising@setform.com
CONTACT US...
t +44 (0) 207 253 2545
e mail@setform.com
41 Energy efficient
Tackling global energy challenges with highefficiency motors
SKILLS ZONE
44 Engineering the future
Two recent events highlight the critical role of education and training
46 Composites in focus
Fresh investment and training opportunities are taking the UK composites sector from strength to strength
SHOW PREVIEW
48
Electronics in focus
ECS welcomes design engineers to Oxford in September
On the microscale Microelectonics UK brings together the microelectronics, semiconductor and photonics industries
Electronic & embedded design
EDS returns to Coventry in October
41
Setform’s international magazines for engineers are published quarterly and distributed to senior engineers throughout the world. Other titles in the company portfolio focus on Oil & Gas, Process, Transport, Mining, Energy and Power.
The publishers do not sponsor or otherwise support any substance or service advertised or mentioned in this book; nor is the publisher responsible for the accuracy of any statement in this publication. ©2025. The entire content of this publication is protected by copyright, full details of which are available from the publishers. All rights reserved. No part of this publication may be reproduced, stored in a retrieval system, or transmitted in any form or by any means, electronic, mechanical, photocopying, recording or otherwise, without the prior permission of the copyright owner.
ROAD TO AUTONOMY
Unlocking new levels of insight, performance and possibility Setform Limited | 6 Brownlow Mews, London, WC1N 2LD, United Kingdom
International Design Engineer was on the ground at Hexagon Live 2025 to discover how advances in measurement and autonomy are helping businesses unlock new levels of insight, performance, and possibility
Stepping out of the 44°C Las Vegas heat and into the (thankfully) air-conditioned lobby of the strip’s newest swanky hotel, the Fountainebleau, it seemed like a fitting setting for this year’s Hexagon Live conference. Indeed, the following few days promised a wealth of new innovations and cutting-edge technology announcements, as the company celebrated its 25th anniversary.
Automation was the key theme of the conference, from the unveiling of Hexagon’s sci-fi-esque humanoid robot to the launch of a fully autonomous metrology suite. Attendees also got an early preview of the findings from the company’s global manufacturing survey, which offered a detailed look at the state of the industry, and its mounting challenges.
In the opening keynote, Chairman of the Board Ola Rollén reflected on how far Hexagon has come in the last 25 years, since the pivotal moment in June 2000 when the company acquired Brown & Sharpe Manufacturing Company in Rhode Island - a deal that marked the company’s entry into precision measurement.
“What I’ve learned, and what I’ve always believed in, is that the only constant in life is change,” he said. “We’ve lived through financial crisis, we’ve lived through COVID and all sorts of things, and companies, organisations and individuals must always learn and change. This is why late last year, the Board of Directors decided to spin off our Asset Lifecycle Intelligence and Safety, Infrastructure and Geospatial divisions, as well as ETQ and Bricsys, into a separate company independent to Hexagon, called Octave.”
He handed over to the CEO of the new company, Mattias Stenberg, who added, “We are introducing Octave to unleash intelligence at scale, to sharpen our strategic focus, accelerate growth and ultimately unlock greater value for both companies. We are combining four leading software divisions: ALI with its portfolio of design, construction operations and asset management software; SIG, the clear leader in public safety, physical security and geospatial solutions; ETQ
which analysts rank as the world leader in the quality space; and finally our rebel disruptor in the CAD space with Bricsys.
“By combining these capabilities, we’re raising the bar,” he continued. “Octave will have the flexibility to focus on our own operating strategies, accelerate innovation and continue developing a powerful platform for the future.”
According to Stenberg, Octave will be a ‘unicorn company’ from day one, making it different from most other startups. Defining Octave’s scope, he said, “we’re in the business of designing, building, operating and protecting the world’s most missioncritical assets, including energy and processing complexes, electric generation and grid infrastructure, advanced production facilities, critical transport hubs and missioncritical data and control centres. The advantage we have is that the company will be born truly digital, and will be a software-first company.”
The headline announcement of the conference was undoubtedly the unveiling of Hexagon’s autonomous humanoid robot, Aeon. Introduced by Arnaud Robert, president of Hexagon’s robotics division, Aeon is a versatile, agile and intelligent humanoid robot that the company believes will signal a new era in industrial automation. Designed for dynamic environments such as factories and warehouses, Aeon represents what Robert described as a “massive transition from automation to autonomy.”
In his keynote address, Robert traced the evolution of industrial robotics: from stationary, single-task robots to autonomous mobile robots (AMRs), and now to multipurpose humanoids like Aeon.
“We are entering the age of humanoids,” Robert told the audience. “Versatile, multi-purpose robots that bring real autonomy into industrial settings.”
Two key technological
breakthroughs, both achieved within the last 18 to 24 months, have made humanoids like Aeon viable. “First, we’ve seen extremely high-performing actuators come to market,” said Robert. “They allow robots to move smoothly and quickly. And second, bionic hands have become significantly more dexterous. Two years ago, a robot would struggle to pick up a bolt – now, it can do so with ease.”
Another major enabler of humanoid capability is physical AI, a field that combines sensor technology, machine learning, and real-world interaction. “We’re now seeing foundational models for robots, similar to large language models like ChatGPT,” Robert explained. “These models teach a robot how to reason. If the task is to ‘scan the door,’ the model breaks it down: find the door, approach it, scan it, return.”
He also highlighted Visual Language Action Models (VLAMs), which further deconstruct tasks into motion
commands: “Move the arm forward, up, down… every detail, handled by the model, not hard-coded.”
Adding to the autonomy leap is edge AI computing. “Two years ago, everything had to be done in the cloud,” Robert said. “Now, Aeon contains two full AI computers onboard, making decisions in near real-time. This changes the autonomy game completely.”
Robert described Aeon’s design around three core pillars: agility, awareness, and versatility.
Agility, he said, is a combination of dexterity and locomotion. “Aeon has 34 degrees of freedom,” he noted. “Think of an elbow with one, a wrist with two – Aeon can move with human-like fluidity.” For motion, the team opted for wheels over legs or belts, given their efficiency in industrial layouts.
Awareness, or more specifically spatial intelligence, is powered by Aeon’s 22 sensors, including 12 cameras, microphones, and infrared
sensors. “Most humanoids can’t match our sensor suite,” Robert said. “But the challenge is not just gathering data. It’s knowing which sensors to prioritise in real time. We solve that through multi-modal sensor fusion.”
Versatility is achieved through innovative training methods. “We use simulation, reinforcement learning, and imitation learning,” Robert explained. “With imitation learning, the robot watches a human and copies their actions. No code needed. What used to take weeks of programming, we now achieve in hours.”
Initially, the primary use cases for Aeon will be within manipulation, inspection, reality capture and operating tasks. In a live demo, Aeon sorted objects using both hands independently, traditionally a complex challenge in robotics. “Sorting isn’t new,” said Robert, “but doing it with two hands, independently, with awareness of task continuation –that’s a feat.”
For inspection, Aeon scanned a
car door using a high-resolution 3D scanner. “We trained Aeon to do this using imitation learning,” said Robert. “During the demonstration, it not only scanned the door but detected a missed section and returned to rescan it autonomously.”
Aeon also excels at reality capture, using its sensor array to build a medium-fidelity digital twin of its environment. “It’s perfect for inventory management,” Robert added.
To bring Eon to life, Hexagon Robotics formed strategic partnerships with Microsoft, Maxon, and NVIDIA.
“With Microsoft, we leverage Azure for cloud training and edge deployment,” said Robert. “With Maxon, we’re developing the next generation of actuators, which are essential to Aeon’s agility. And with NVIDIA, we use their AI supercomputers for training, Omniverse for simulation, and edge GPUs for onboard autonomy.”
During the conference session, Hexagon announced two pilot
With labour shortages and an aging population, humanoids will allow industry to prosper by taking on repetitive tasks
deployments of Aeon: one with Pilatus Aircraft, and another with Schaeffler Group. All being well, the robot will complement human workers, but isn’t designed to replace them. “With labour shortages and an aging population, humanoids will allow industry to prosper by taking on repetitive and physically demanding tasks,” Robert added.
“This is just the beginning. You’ve seen the agility, versatility and awareness of Aeon today, but imagine what is possible in the next 12 months.”
Another key unveiling during Hexagon Live 2025 was the company’s new autonomous metrology suite, capable of cutting coordinate measuring machine (CMM) programming time from days to hours. Based on Hexagon’s cloud-based Nexus platform, the software removes all
coding from CMM workflows to help manufacturers speed up critical R&D and manufacturing processes.
Across automotive, aerospace and general engineering sectors, shorter product lifecycles and frequent design revisions have increased the need for high-accuracy measurement. However, there are now fewer skilled CMM programmers and quality data is scattered and underutilised. The Autonomous Metrology Suite is designed to tackle this problem through the integration of digital twins. In practice, a digital twin of every connected CMM synchronises seamlessly with its physical counterpart, so the correct inspection programme always reaches the right machine, helping to eliminate possible human error. All quality, utilisation and environmental information flows straight to a cloud dashboard, creating a continuous digital thread that supports datadriven decisions on the shop floor.
Hexagon first introduced Nexus as a platform to encourage collaboration between individuals and departments in order to improve agility within organisations. The platform is built to connect various technologies and people working across different disciplines, featuring an extensive range of digital technologies. International Design Engineer sat down with Stephen Graham, executive vice president and general manager at Hexagon Manufacturing Intelligence, to discuss how Nexus’ latest developments are helping to connect the dots in manufacturing processes worldwide.
Q: WHAT KIND OF TRACTION HAS NEXUS SEEN SO FAR IN THE MARKET?
SG: To be honest, Nexus has seen more traction in the engineering space than in manufacturing so far. That’s why we’re focusing more heavily on production and metrology here at Hexagon Live - to push adoption further into the manufacturing side. There’s something about the discipline of design engineering where people tend to “get it” more easily, so we’ve been developing workflows to connect engineers and streamline simulation at scale.
Q: HOW ARE CUSTOMERS USING NEXUS IN THEIR MANUFACTURING OPERATIONS?
SG: One example is a large automotive customer of ours that currently has around 100 engineers using a simulator and wants to scale that up to 200. That presents two challenges: needing more compute infrastructure and managing twice as much data. So, we’re building workflows that run simulations in the cloud via Nexus, capture the data, and enable easier analysis. Another common use case - especially in aerospace - involves getting engineers from different disciplines to collaborate, like fluid dynamics and structural engineers, who need to exchange data quickly and efficiently. Nexus helps bridge those workflows.
Q: HOW DOES THE 3D WHITEBOARD FIT INTO NEXUS?
SG: The 3D whiteboard is a great visual representation of Nexus’s collaborative capabilities, but at its core, Nexus is about connectivity. It connects different engineering tools and even links design to the shop floor. Engineers don’t need to abandon the tools they’re familiar with; they can keep using them while sharing
data seamlessly between departments. The 3D Whiteboard then makes this visible and tangible.
Q: AND SO THIS IMPROVES EFFICIENCY ACROSS THE VARIOUS DEVELOPMENT STAGES?
SG: Exactly. Take the example of an aerodynamics engineer and a structural engineer. Traditionally, their work is iterative - back and forth. But if they can collaborate in real time through Nexus, that loop becomes much faster. So yes, collaboration directly drives agility and helps design teams move faster.
Q: WHAT UNDERPINS THE NEXUS CLOUD PLATFORM IN TERMS OF SECURITY?
SG: Security isn’t traditionally our expertise, so we’ve partnered closely with Microsoft on this. Nexus runs on Azure as a multi-tenant public cloud solution, and we’re confident in its security for all applications. Some customers, especially in aerospace, want private cloud implementations, and again, we work with Microsoft to support that.
Q: HOW DOES VTDX BENEFIT FROM NEXUS?
SG: VTdX is a complete rewrite of our Virtual Test Drive tool, designed specifically to run natively in the cloud. For autonomous vehicle systems, you need to simulate thousands of driving years to ensure safety. VTdX uses Nexus Compute to run tens of thousands of simulations in parallel, something that simply wouldn’t be feasible otherwise.
Q: WHAT’S THE ROLE OF MATERIALS ENRICH IN THE DESIGN PROCESS?
SG: Materials Enrich helps design engineers by providing richer material datasets. It combines simulation and AI to interpolate or extrapolate material behaviour beyond what’s been physically measured, saving time and cost while improving simulation accuracy.
Q: FINALLY, WHAT’S NEXT FOR NEXUS?
SG: We have a long roadmap of capabilities in the works, but the bigger vision is end-to-end collaboration from design through to production and quality inspection. We want to see workflows grow organically within customers. Start small, prove value, and then expand.
During Hexagon Live 2025, Paul Miller, vice president and principal analyst of Forrester Research, presented the key findings from a global manufacturing survey commissioned by Hexagon and conducted by Forrester Consulting. The study captured insights from over 1,000 manufacturing decision-makers across APAC, EMEA, North America, and Latin America, offering a detailed look at the state of the industry, and its mounting challenges.
“Lack of agility was a top-five challenge across every role and every region – and for the C-suite, it was number one,” Miller said. “Manufacturing infrastructure takes time to build. You can’t just read about a new tariff and respond by building a new factory tomorrow.” The cost and complexity of bringing new products to market was another critical concern, he noted, “In Latin America and North America, the high cost of new product introduction wasn’t just the top issue, it was ten points clear of anything else.”
However, digital transformation continues to evolve, with 71% of respondents citing digital twins as delivering large or transformational benefits, although widespread adoption remains elusive. “91% reported problems with digital transformation and 90% encountered barriers to digital twin implementation,” said Miller. The biggest challenges? A lack of real-world measurement data, too many analogue processes, and insufficient in-house skills.
Sustainability remains central, albeit framed more economically than idealistically. “Reducing waste, scrap, and rework provides a direct bottom-line benefit,” said Miller. Digital simulations are also proving critical, with 42% of respondents selecting early simulation as the most effective way to improve environmental sustainability.
Miller highlighted the need to balance hardware, software, and human roles in what Forrester calls the ‘automation triangle’. “For years to come, almost every task will be a combination of robots, software, and people,” he said. “The key is understanding how to deploy each together, not in isolation.”
In the fast-paced world of Formula One, where every millisecond counts and the margin for error is razor-thin, innovation is crucial. Red Bull Racing’s long-standing partnership with Hexagon has become an influential alliance in the world of motorsport, one which is are now being applied to design, engineering, simulation and production capabilities beyond the racetrack by the former’s sister company, Red Bull Advanced Technologies.
Since 2006, Hexagon’s advanced metrology and manufacturing equipment has played an integral part of Red Bull Racing’s pursuit of performance. From the pit lane to the factory floor, Hexagon’s equipment has powered the kind of
high-precision measurement and inspection capabilities that modern Formula One demands. As Rob Gray, technical director of Red Bull Advanced Technologies, explains, this partnership extends deep into the workflow of both car development and race-day operations.
“We use Hexagon products across five or six core areas, like inspection and build, but also trackside,” Gray says. “We don’t have an exact count, but it’s probably dozens of systems in constant use globally.”
One example of the impact of Hexagon’s technology was the introduction of its laser tracking system, which drastically altered how Red Bull sets up and maintains its cars.
“Before, set up was done manually –strings, rulers, the old-fashioned way,” Gray explains. “Switching to the tracker saved time and increased accuracy. On
a Friday evening, the car gets pulled apart, checked and rebuilt. Saving even a few minutes during that turnaround means our people get more sleep, and our cars get better performance.”
Other key tools include portable CMMs and 3D scanners, which help Red Bull’s engineers ensure dimensional accuracy at every stage. These systems are used both for validating parts against CAD models and for monitoring fit and alignment during assembly. When damage or misalignment is suspected, technicians can scan the car and compare it to factory CAD data in real-time.
Red Bull Advanced Technologies is taking these learnings from Formula One and applying them to a wide range of challenges in broader engineering and manufacturing
sectors. Simulation is a key tool used by the company’s engineering teams to understand the balance of tradeoffs between competing requirements and ensuring the optimum product is delivered for a specific application. In particular, the company focuses on improving vehicle aerodynamics, mechanical, composite and electrical design, structural analysis, simulation and modelling, control systems and software development, and manufacturing.
Red Bull Advanced Technologies’ latest venture is the RB17 hypercar, which has been designed to blur the lines between an F1 racing vehicle and a high-performance road vehicle. First unveiled at the Goodwood Festival of Speed in 2024, the vehicle incorporates Formula One thinking at every level, and it too draws on Hexagon’s suite of solutions.
“The RB17 shares a lot of DNA with our F1 cars, and we plan to use Hexagon tools in the same way,” Gray expands. “From component measurement to bodywork scanning – and now even robotic inspection –we’re pushing what’s possible.”
In particular, robotic quality assurance holds promise for automating the inspection of panel gaps and finish tolerances, offering a leap forward in efficiency for high-end production.
Despite its racing pedigree, the RB17 is designed to be accessible to more than just professional drivers. With 1,200 horsepower and active suspension, the car can be tailored to suit the skills of its driver, even novices.
“We can tone it down,” Gray says. “Set it for understeer, make it safe
and predictable. Then as drivers gain experience - whether in the simulator or on the track - they can turn it up. It becomes a tool for driver development as much as a performance machine.”
From developing the initial concept through to the delivery of the finished RB17 to customers, Red Bull Advanced Technologies is responsible for the entire process of designing and building the hypercar, of which there are only 50 that will be sold.
The vehicle’s electric motor enables weight-saving design decisions, like removing the starter motor, alternator, and reverse gear, while still giving drivers performance and convenience.
“We’ve taken on some ridiculous challenges,” Gray says. “But we tend to deliver. Whether it’s building our own F1 engine or designing the RB17, it’s that mindset—if we commit to something, we can make it happen.”
Over the past two decades, prototyping has gradually shifted away from labourintensive processes thanks to the emergence of new technologies, which have helped to compress timescales and reduce costs. Today, the prototyping process is often a hybrid one, combining multiple methods and technologies in order to better meet specific product requirements and industry needs.
Matt White, business development and sales manager at Ogle Models & Prototypes, shared his insights into this trend during TCT3Sixty, particularly in regards to how CAD, CNC machining and 3D printing technologies have impacted the process.
“The major shift we saw was with the invention and adoption of CAD in particular, which led to CNC machining and later, 3D printing technologies,” he confirmed. “Ultimately, these technologies have allowed us to compress timescales considerably. You can test more, you learn, you can make quicker and better decisions to move forward with your product development, ultimately de-risking and avoiding costly mistakes.”
As a result, higher quality products can make it to market much quicker. However, choosing the right process for individual projects is essential, White adds: “Choosing the right process, material and finish at each stage can significantly reduce the risk of project failure. Often, you might need to utilise multiple processes to fully test your product and utilise multiple prototypes together to get to your conclusion.”
So, how does 3D printing fit into the prototyping process? “There’s sometimes a misconception of the prototyping process being just 3D printing and that you will get the part in your hands within hours. But this is rarely the case,” White explained. “The real value lies in what happened before and after the print, so embracing all these technologies and, of course, a human touch as well.”
When prototyping, White believes design engineers should always think about how to add value. “Speaking to experienced teams around a machine to get design advice and feasibility insight can limit early mistakes and identify any manufacturing issues,” he advised. “This will save costly delays down the line and then it’s time to consider material and process selection. Is the process or the material chosen going to give you the results you require? This can unlock further insights and prompt interventions, even at this very early stage of development.”
As such, leveraging a few different processes during the prototyping phase is vital. “Utilising processes such as CNC machining has the benefit of lowering costs for large models, however it may not be applicable
if there are lots of fine details and complex geometry,” he added. “So that’s where advances on multiple processes are combined to save cost and lead times, allowing more tests to be done without sacrificing on cost or quality.
3D printing can be used to incorporate finer detailed sections while CNC machining could be used for the more simple and larger sections where tighter tolerances are required. Then postprocessing is a great way to add value and bring models to life, and at speed.
“Prototyping is about more than just 3D printing,” White concluded. “It’s about transforming ideas into the physical reality that persuade, perform and validate as well. Think carefully about what you want to achieve from each stage and where you can add value to consider all processes to save time, money and mitigate risks.”
During AM processes, quick and precise adjustments are crucial during production
Ross Turnbull, director of product engineering and business development at Swindon Silicon Systems, shares how smarter sensors can overcome barriers to additive manufacturing adoption
Analysis by additive manufacturing (AM) consultancy group, Wohlers, shows that in 2024 the global AM industry grew to $21.8 billion. Despite this growth, the report indicates that 2024 was a year of mixed performance, suggesting barriers still prevent mass uptake. Mixed-signal ASIC design company Swindon Silicon Systems is addressing these hurdles through the development of smarter sensors.
As industrial demands evolve, customers are increasingly seeking solutions tailored to specific performance and functional requirements. AM technologies help meet these needs.
Thanks to its layer-by-layer assembly process, AM can create
highly complex shapes and geometries in a single step. This capability accelerates the journey from digital concept to physical prototype and eliminates the need for specialised moulds or tooling. Furthermore, when parts must fit precisely within tight spaces or alongside other components, AM enables early verification of fit and function without the expense of fullscale manufacturing.
AM technologies also enable manufacturers to be more flexible and tailor products to specific needs, supporting differentiation and stronger customer-manufacturer relationships. However, challenges still remain in successfully implementing and using this technology.
Research conducted by the World Economic Forum highlights that 53% of companies surveyed saw quality assurance and qualification as the primary barrier to adopting AM. Poor layer adhesion, cracks and warping are common problems. In large-scale production, especially in aerospace and automotive sectors, even minor discrepancies in product quality can have serious consequences. Such defects often lead to elevated costs, production delays and costly recalls that could damage a manufacturer’s reputation. Due to this risk, manufacturers need better visibility over their processes. Tracking process parameters allows defects to be detected and corrected
An Application Specific IC (ASIC) is a bespoke chip that can be designed to meet precise performance and environmental requirements
before compromising a component’s structural integrity or performance. Optical sensors are well-suited to AM, providing detailed insight into surface characteristics and internal features. Technologies like monochrome or colour CCD and CMOS sensors can detect surface flaws and irregularities during production. While this technology has come a long way, it still faces limitations in AM processes. In these environments, sensors must produce clear, low-noise data for accurate signal interpretation and informed decision-making. So, how can we ensure this?
To answer that, we need to examine the sensors’ components more closely. In most sensors, the sensing element is typically combined with one or more integrated circuits (ICs) that serve as the interface. These ICs handle signal conversion, processing tasks and translate light intensities into electronic signals that can then be interpreted and acted on by other devices.
However, standard ICs can struggle with precise signal processing, resulting in unreliable data. This is
a serious drawback in advanced AM processes when accurate feedback is critical for closed-loop control and automation. In addition, inconsistent performance and limited reliability make it difficult to meet the rigorous quality assurance and qualification standards expected in industrial environments.
A more effective approach is to use a custom-built solution tailored to the application. An Application Specific IC (ASIC) is a bespoke chip that can be designed to meet precise performance and environmental requirements, including overcoming the aforementioned challenges.
In AM, quick, precise adjustments are essential during production to ensure layer consistency, maintain dimensional accuracy and prevent defects that compromise part quality.
An ASICs design allows for optimised on-chip processing, supporting these adjustments without relying on external systems. This makes them especially valuable in closed-loop control systems, where real-time feedback is critical for maintaining quality and process stability.
ASICs can also be fine-tuned with sensor-specific protocols to deliver
superior image clarity and resolution. This level of customisation enables the sensor to identify even the smallest inconsistencies in a build layer, such as porosity, warping or minor structural anomalies that can compromise the integrity of a component. By providing this targeted performance, ASICs ensure more reliable data acquisition and significantly reduce the risk of quality issues in AM production.
Full control over the ASIC’s design also means the component has a smaller footprint than other solutions, making the sensor easier to integrate into existing machinery. With a customisable choice of wired and wireless communication protocols available, ASICs can support both new and legacy equipment.
Additive manufacturing has the potential to transform large-scale production by enabling complex components to be machined from a wide range of materials in a single step. However, sensing systems must be enhanced for this technology to be widely adopted. Here, ASICs offer a key advantage, providing tailored solutions to address specific AM process sensor needs.
3D printing can provide surgeons – and their patients – with confidence when carrying out new procedures
TissueMatrix claims to be the softest commercially available 3D printing material
Jake Holmes learns how Stratasys 3D printing technology is helping to enhance medical training
For some time now, 3D printing has been transforming the nature of medical training by providing affordable, customisable and ultra-realistic anatomical models for education and surgical practice. Created from patient-specific data, these models allow medical professionals to plan and practice surgical procedures and techniques with increased accuracy and confidence.
At TCT3Sixty, Arnaud Toutain, business manager of medical EMEA at Stratasys, outlined the different ways additive manufacturing can be useful within medical training settings.
The phrase, ‘this is my first time doing this,’ is not what most people want to hear from their surgeon just before going under the knife. Thankfully, 3D printing can provide surgeons – and their patients - with confidence when carrying out new procedures.
Current mainstream medical training diverges down one of three routes: plastic mannequins, deceased humans or cadavers, and animals. All three of these have their own unique problems, but the overarching one is they all lack the exact realism akin to what medical professionals face in a real-world setting.
However, students can be supplied with more lifelike practice resources through 3D printing, which allows for real feel and feedback of the materials and simulates almost exactly how live human bodies react and respond. Practice is vital in medical training, and being able to readily print these resources allows far more opportunities for students to learn, so when they are eventually confronted with conducting the procedure for the first time, they will already be experienced and confident.
“Now we’re getting to a level of expertise where we can bring the colour, texture and haptic feedback,
adding to the realism… if it is in the body, we can probably mimic it,” Toutain said. “The good thing is we have a great technology called PolyJet, it fits pretty much perfectly with what we are trying to achieve here. It is a multicoloured, multi-material high-resolution printer that can print everything in one go. This is our go-to solution for this type of training.”
Stratasys’ J850 Digital Anatomy is the company’s most advanced medical modelling printer, giving users the ability to create biomechanically accurate anatomical models, as well as radio-realistic phantoms and models.
No assembly or painting is required after printing, as the PolyJet technology is capable of printing the complete model in one go. Super soft materials developed by Stratasys are being used for cardiovascular printing in particular, but can be used throughout the body.
Stratasys’ BoneMatrix was developed to simulate bone, and GelMatrix is used to print the soft abdominal organs, such as kidneys and livers. The company’s TissueMatrix claims to be the softest commercially available 3D printing material, creating models that respond like native organ tissue when force is applied. These materials are what gives the 3D printed models their human-like feel and haptic feedback, enabling it to be used for medical training purposes.
Traditional training methods, such as operating on cadavers, has its limitations. There is little haptic feedback, and there is little room for customisation or specific issue training.
Toutain explained: “A dead human might be close to what people would experience in real life, but in the meantime it’s dead tissue, so it’s dry. It does not feel like a human, and most likely won’t have the pathology we are looking for. If you want to train someone on a very specific fracture, for example to install a plate, you will have to recreate the fracture, which is not easy to recreate the exact way you want it.”
3D printing alleviates these issues as trainees can be given 3D printed models dealing with the exact scenarios they will face to practise on, with haptic feedback.
“There is freedom if you need to
BoneMatrix simulates human bone in anatomical models
GelMatrix is used to produce soft abdominal organ models
create a specific fracture, or if you need a specific tumour in the brain, you just need to design it,” Toutain added. “Then you can have it in your digital inventory and you can print it.”
Using 3D printing also allows for consistent training. Human bodies have variations per person, meaning 10 different surgeons will have 10 different training experiences if using cadavers. By implementing 3D printed models instead, consistent training can be implemented across the board, making it easier for training managers to help students.
Human bodies are expensive, not necessarily the cost of the body
itself, but due to the transportation and storage of them. They need to be kept frozen, and due to a lack of availability, sometimes have to be shipped from other countries. The scarcity of bodies can be an issue for training purposes.
At a time of budget squeezes for hospitals, and in countries such as the UK where there is growing healthcare demand, reducing costs is critical. 3D printing can help hospitals that need to reduce their overhead costs or are looking to make their budget stretch further. The improved benefits of 3D printed models, such as haptic feedback and specific injuries, can also allow for better educated professionals, raising the standards of medical care.
Holmes discovers how AI is revolutionising ease of use within electronics
Artificial intelligence (AI) has monopolised headlines in recent years with its promise of revolutionising design, engineering and manufacturing practices. While some find the prospect of AI in the workplace daunting, others have already cottoned on to the technology’s potential benefits and have started integrating it into their operations. In electronics engineering in particular, AI offers many opportunities for streamlining and improving operations.
Alin Dragan, team lead for product
management at WSCAD, presented at Smart Manufacturing Week to educate attendees on how AI can - and istransforming electrical design.
Dragan explained how implementing AI into electrical schematics can create ease of use for operators, reducing downtime required for training and potentially preventing costly mistakes from occurring on a user-input level.
By creating software that is easily user-friendly, sales opportunities grow
vastly as more customers are satisfied with the product. Dragan says: “Our mission is to build, to develop software, to develop tools. That helps our users win back time.”
Dragan lays out the benefits to engineers: “They don’t spend too much time on their electrical design, reduce stress, which is also a very important topic, and obviously also work smarter.”
When developing electrical Computer-Assisted Translation (CAT) software, most clients selected ‘ease of use’ as a driving factor, reflecting the market demand. A limiting factor to
Very simply, the more that is being produced, the more there is to sell, which translates directly into increased profits
technology and its adoption can often be human limitation or human error. Simply, to err is human. Despite the power of technology, if a person does not know how to use it, or instead forgets about inbuilt features, it will not be as efficient or functional.
“It does not matter how powerful a CAT software is, if it’s not easy to use the feature you need to solve your issue or to save money, or the feature is not discoverable, it might as well not exist,” Dragan stated.
WSCAD has been able to implement AI into its operations due to its policy of reinvesting revenue into the company’s infrastructure. Dragan reports 24% of company revenue is reinvested into research and development efforts, allowing for WSCAD to become an expert in its field and build on 35 years of experience.
Introducing AI into CAT systems will
not simply make all issues disappear, however, as Dragan explained: “Engineering CAT is a complex thing, and complex problems often require complex solutions.”
One of the limitations WSCAD faces when creating its systems is the broad range of applications its clients require the systems for, from doughnut machines to rocket ships. By making a system with a variety of functions to cover all bases, the system becomes less user-friendly due to the sheer volume of functions.
“The more features you add, the more you tend to lose usability,” Dragan added. According to him, being immediately discoverable and understandable are the two key pillars of usability. AI will, by its very nature, know its system better than a human can, and can operate it quicker as well. Implementing AI can allow complex systems to appear easy to use due to the interface.
Last year, WSCAD introduced
Electrix AI, what the company claims is the world’s first AI-powered electrical CAD solution, eliminating tedious manual steps and completing tasks in seconds to slash design time by up to 99%.
By making task completion quicker, it allows employees to crack on with other projects they have, speeding up operations across the board. Very simply, the more that is being produced, the more there is to sell, which translates directly into increased profits. Rather than having staff contacting support, or researching how to use software, those hours of unproductivity can be minimised by an AI-powered system which knows the solutions when posed with a problem by the operator.
WASCD has introduced an AIpowered co-pilot into its Electrix AI software, a new chatbot feature that allows users to type what they want into the system, and it will make the changes itself. This saves time and effort in learning the intricacies of the software and achieves the same outcome, allowing employees to conduct more tasks in the same amount of time.
Error checking is also a useful feature, with employees able to check their work using AI. The system can point out any gaps in information and alert users to any data points that need to be filled. This saves hours of scrolling through documents and manually checking for errors.
Engineering, research and development can be very expensive. But gaining a competitive edge on the market can be achieved by costsaving practices, such as integrating AI at the start of the design and manufacturing stage. Bringing costs down can either reduce product or service price for clients, or the spare revenue can be reinvested to make further improvements to a particular product or service. Both outcomes can result in far greater client satisfaction and therefore higher customer retention and sales
While soldering is an indispensable technique in current electronics production processes, defects can still occur. These defects can lead to unreliable solder connections and potentially the malfunction or failure of the end product. Specialising in thermal system solutions, Rehm Thermal systems develops reflow soldering systems for convection, condensation and contact soldering, coating and drying systems. With 30 years’ experience behind it, the company has shared its latest guidance on reflow soldering, and how companies can recognise and avoid the sources of defects during the soldering process. With a long history dating back to ancient Egypt, soldering plays a crucial role in the manufacture of electronics today. Despite considerable developments in soldering technology, however, defects can still result in electronic components not being reliably connected. In addition to causing malfunctions and failures, faulty solder connections can also result in high electrical resistance and increased heat generation, which can damage components or even cause fires.
Unreliable end products can damage a company’s reputation and customer confidence in the brand, therefore it is essential for manufacturers to identify soldering defects during the production process and repair any faulty PCBs. Rehm also advises that the probability of soldering defects can be reduced before and during the soldering process.
Tombstones occur as soon as one solder joint of two-pole components (such as capacitors or resistors) melts before the other. The resulting wetting forces and surface tension cause the element to lift on one side. Therefore, with a solder paste with a lower surface tension, the weight force
of the component is sufficient to hold it in position and the occurrence of tombstones can be reduced.
In contrast, lead-free solders have a higher surface tension and lower tombstone rates, and several studies speak in favour of a correlation between increasing wetting time and decreasing tombstone rates, Rehm Thermal Systems summarises.
To counteract the asynchronous melting of solder joints and the formation of tombstones, larger quantity differences between the pastes of both connection pads can be prevented, as the smaller one always melts before the larger solder deposit. Conveyor speed can also counteract the tombstone effect; the higher the speed, the greater the risk that the soldering material is not
heated through evenly and that one solder joint melts earlier than the other. In addition, the soldering profile can influence tombstone formation as depending on the solder paste formulation, the PCB design and placement tolerances, tombstones can occur in both linear and saddleshaped profiles. To counteract this effect, Rehm Thermal Systems says, the saddle profile can be advantageous because it homogenises the temperature distribution in the assembly through the holding phase.
The company produces multiple technology manuals that deal with many topics related to reflow soldering, from the reliability of soft solder joints and other soldering defects to the technology and engineering of soft soldering processes.
Off the back of the Pheonix 1 launch, IDTechEx’s Mika Takahashi sits down with Jake Holmes to discuss how inflatable aerodynamic decelerators could offer radically new material opportunities for space flight
Space travel has remained a fascination to humankind, with Neil Armstrong’s infamous ‘one small step for a man, one giant leap for mankind’ etched into the minds of an entire species. Previously, economic restrictions limited space travel to just a select few, but with the latest technological developments, prices may allow more of us to embark on the final frontier.
The successful inaugural flight of Atmos Space Cargo’s Pheonix 1 re-entry capsule has much wider implications for space travel, thanks to its novel inflatable heat shield that allows it to re-enter the Earth’s atmosphere for recovery. Mika Takahashi from IDTechEx was able to explain the technologies involved and what this means for the sector.
The reason you need a heat shield is because spacecraft travel very fast, and the heat shield is the way they slow themselves down
“The reason you need a heat shield is because spacecraft travel very fast, and the heat shield is the way they slow themselves down,” Takahashi says. “Spacecraft travel quickly, either orbiting Earth or travelling from another planet. As they return to Earth, instead of aerodynamically entering the atmosphere, the goal is to slow down.”
“Spacecraft enter with a blunt body and use the drag of the atmosphere to slow themselves down, and in a sense that’s an energy conversion from energy as velocity to energy as heat” he adds. “This generates significant amounts of heat, we call this aerothermic heating.”
Historically, two varying methods have been used to deal with this
More advanced thermal protection systems will require growth in material demand
intense heat: ablative heat shields and tile-based systems.
Ablative heat shields are designed to wick away heat as they evaporate. The material burns itself up in the process of re-entering the atmosphere and its descent to Earth, protecting the spacecraft behind the shields from the intense temperatures. These are single-use and were most famously used on the Apollo space missions.
Tile-based systems are low-density silicon installation tiles that absorb heat but are not conductive through their surface and reject the heat out. This means the material is not consumed in the process of slowing down the spacecraft.
This is where the heat shield design of the Phoenix 1 is unique and changes established practices in the industry.
Takahashi says: “Pheonix 1 takes a different approach. The way thermodynamics works, if you have a larger surface area of your heat shield, you’re going to have less intense heating. Typically, the surface area of your heat shield is limited by the rocket payload cone.
“What Phoenix has done is have a small, stowed heat shield but upon re-entry, the heat shield is inflated, giving a much larger surface area and then the heating will be less intense, therefore there’s less restrictions about
What Phoenix has reportedly done, and there’s not a huge amount of technical data they’ve released about this, but it’s using the hot gas in the upper atmosphere to inflate the heat shield
what sort of materials we can use.”
This is a fairly new technology; NASA previously tested a similar project named Lofted in a low-orbit flight test demonstrator in 2022. For this project, NASA took a large nitrogen gas tank up to inflate the shield in space. However, this takes up both weight and space on the spacecraft, and also requires extra tubing and decompression valves.
“What Phoenix has reportedly done, and there’s not a huge amount of technical data they’ve released about this, but it’s using the hot gas in the upper atmosphere to inflate the heat shield,” Takahashi explains. “So rather than taking compressed gas with them and then reregulating that and inflating the heat shield, instead they have some sort of inlet valve which they open upon re-entry and hot gases from the upper atmosphere inflate that heat shield. Again, there is very little technical and concrete data about that, but if they were able to achieve that, it’s quite a unique development.”
Atmos Space Cargo has yet to unveil what specific materials it is using in their initial Pheonix 1 capsule, but
NASA has been transparent about its use of materials, and it’s likely to be similar to what the former is using, according to Takahashi.
The Thermal Protective System (TPS) is twofold. It needs to be able to be compacted and stowed away, but also needs to protect against temperatures of 1400°C, and not conduct that heat through to the spacecraft.
Takahashi says: “Typically, you’d see an outer layer of ceramic fibre, the purpose being to structurally and mechanically withstand the high temperatures. That’s going to be the outermost layer. Beneath that, you have an insulator, with one of the upcoming materials in this field being an aerogel. An aerogel is a very lowdensity and low-conductivity material. The role of the aerogel insulator is to protect the delicate parts underneath from the hot ceramic fibre.”
For the inflatable structure, a braided fabric yarn is used, as it has very strong fibres and features a gasproof laminate, allowing the structure to inflate and preventing hot gases from the atmospheric heating from getting inside. NASA filled this section with nitrogen, whilst Atmos Space Cargo claims to have filled it with hot gases from the upper atmosphere.
Another layer of braided fabric is underneath this, creating a concentric ring design for NASA’s deployment of the technology.
The materials need to fill three functions to be suitable for use in TPS applications: high temperature resistance, low thermal conductivity and being flexible and stable under inflation.
Atmos Space Cargo has announced that for its second rendition of the Pheonix project it will be adding re-entry direction control, meaning operators can control where the capsule lands. This allows for landing near to the launch site, speeding up recovery of the capsule and the time taken to prepare for a new launch. SpaceX has found this niche with landing components of its spacecraft for later reuse, allowing its Falcon Nine system to launch at a far higher regularity.
This elevates the current issue of landing in the ocean. Salt water is corrosive to heat shields and capsules and can cause them considerable damage, leading to costly and timeconsuming repairs. Further to this, there are the associated costs with moving capsules from where they
happen to land, such as the Indian ocean, to the launch site.
By not having to rebuild capsules and instead being able to reuse previously used models, launches could be increased from one to two a year up to five or six times this number of launches. This is a dramatic increase in operations, as capsules can take between six to eight months to produce, whereas reusing capsules allows them to be used on a four-week cycle.
Industry can also take advantage of the cheapening of space travel.
Manufacturers of high-value goods are looking at micro-gravity manufacturing at these altitudes. We do not have the capacity for high volumes yet, therefore production is limited to very high-value products. Companies such as American enterprise VADA are currently developing products in the field.
By developing more costeffective methods of re-entering the atmosphere, through re-usability, the space sector can open the door for more regular trips to the stars. This can be utilised by explorers, researchers, and industry, all having their own unique reasons for why they want to explore space’s untapped potential.
engineeringtectosisarecognizedpartnerandhas automotivebeenakeyplayerinthetestingworldfor20years: •Founded2004inGraz,Austria •50engineers/technicians/mechanics •In-houseprecisionmachiningandmanufacturing •4dedicatedengineandbalancingtestbenches •StrongNVHandacousticsexpertisefrom componentleveltovehiclemeasurement
Contactustodayandlettectos “Therefuelyoursuccess! is either a solution or we create one.”
Jake Holmes reports from Smart Manufacturing Week on the obstacles facing manufacturers working to integrate circular economy practices within their operations
In a nutshell, the circular economy refers to an economic system based on the reuse and regeneration of materials or products, as a means of continuing production in a sustainable way. Understanding the role circular economy practices can play within engineering can protect supply chains and help manufacturers plan for the future.
At Smart Manufacturing Week, Alister Morris – managing director of Accu – moderated a panel on the topic, particularly the challenges facing manufacturers as they seek to integrate circular economy principles into their businesses. He was on hand to interview Sandra Gaspar, head of recycling at Eurocell, and Nick Kemp, head of design X50 at Brompton Bicycles.
Kemp cited how in the bike industry, there is plentiful choice of aluminium to choose from at the design stage, however mixing and matching these different grades can cause recycling difficulties at the end of a product’s life. “If you start going for the weird, rare and exotic trying to save that extra 0.2% of weight, you are limiting the potential of recycling downstream,” he said.
Speaking from Eurocell’s perspective, Gaspar added, “our products are fully recyclable and are designed to be disassembled easily.” Eurocell’s products, such as windows, doors and cladding, are constructed of 32% recycled content, which can be recycled up to 10 times. For a product with a 20 to 30-year lifecycle, this gives the material a very long life.
A lingering preconception around sustainable materials it that they add large costs to the manufacturing process. Morris asked the panel how their businesses remain profitable despite this.
Despite the initial large investment Eurocell required to upgrade from 19%
recycled materials to now 32%, Gasper reported the companies KPI’s are all still profitable.
Although, not passing on the costs of investing in new processes was a challenge for Brompton Bicycles. The brand’s reputation means customers expect it to use sustainable practices, so in order to maintain sales the company must move in this direction, Kemp said, “leadership is absolute, if you don’t have someone at the top saying ‘Yes, I believe it resonates with our company’s values’ then its dead in the water.”
According to Kemp, Brompton Bicycles’ biggest limitation when implementing circular economy practices is the transition phase. Having recently introduced 100% post-consumer recycled wheel rims, the company had to learn far more about the value chain of the product compared to previous processes.
“Ordinarily, we would order this particular shape, send it off to a rim manufacturer, and it would turn up,” Kemp explained. “Instead, we got involved right down to the scrapyard, where the material came from.”
Gasper has built a network across the UK, including a service where Eurocell will collect windows from customers’ homes for recycling, and recycle centres where the company can buy 300 tonnes of material, allowing it to operate across the UK. “One of our biggest challenges is to collect the performance-fit stock material,” she said. “Performance-fit stock is a challenge because there’s lots of variations, such as construction, waste management and scrap metal dealers.” Education remains an issue not just for consumers, but for supply chains, as Brompton Bicycles discovered. Having strong supply chain relationships can help alleviate some of the issues, allowing for processes to be established. “We found the problems came from not where we were expecting,” Kemp added. “The postconsumer recycled metal we expected to cause all the problems, it didn’t. It was the little add-on processes.” As such, Brompton Bicycles has changed some of its add-on processes to align with its new materials. According to the panel, efforts to become carbon neutral and use responsible, reusable materials comes with its challenges. Changing production methods and material sources has its associated costs, along with the disruption of supply chains having to adapt to new demands. However, the payoff can be worth it. Having established sustainable practices allows companies to operate knowing material shortages and new legislation should not affect them, keeping operations flowing and establishing strong supply chains to protect against an uncertain future.
“Composites UK has been really important to us as a company over the last few years. It provides access to industry specific advice that an SME like us would struggle to source otherwise. Additionally, the networking opportunities give us a place to keep upto-date with industry developments.”
Lyndon Sanders, Director, Far-UK
Composites UK is the Trade Association for the UK composites industry.
Across the UK each member of Composites UK receives the opportunity to:
• Save money
• Save time
• Boost their impact
• Expand their network
• Secure their future
Capitalise on the growth of the Global composites market and join the expanding list of Composites UK member companies today.
“Our visibility across the composites community has not only increased since becoming members but also continues to allow us to deepen our knowledge about this innovative sector by working with our industry peers and specialists. Everyone at Composites UK is a pleasure to work with and we are looking forward to what is next in store.”
Julia Loeser, Sales and Marketing, DK Holdings
Hot on the heels of an award win, Alun Reece, CEO of Loop Technology, tells Louise Davis how his company’s joined-up approach is shaping the future of composites manufacturing
Like many engineering sectors, the composites industry is gradually embracing the benefits delivered by greater automation. And UK company
Loop Technology is one of the pioneers here: its expertise lies in bringing automation to composite manufacturing – with a special focus on the highly demanding aerospace sector. “Aircraft manufacturers are aiming to build lighter, more aerodynamic, fuel-efficient aircraft using composite materials to address the unmet demand and record backlog,” explains Alun Reece, CEO of Loop Technology.
So, how does automation come into play? “In aerospace manufacturing, automation systems have to be able to perform myriad complex tasks, often
on very large-scale structures to a tight tolerance,” answers Reece. “The innovation in robotics around scale, precision and collaborative working is continually opening up opportunities in aerospace and the momentum within the industry is gathering pace. The versatility offered by modern robotics is redefining the way manufacturing tasks are done, driving down costs while driving quality up,” he observes. This versatility is perfectly illustrated by Loop Technology’s flagship FibreLine system. In January 2025, it was recognised in the Aerospace Process category of the JEC Composites Innovation Awards. Reece describes the award-winning solution as an end-to-end automated composite preforming system that, “delivers a step change in production
rates for composite parts and components such as aircraft wings and wind turbine blades.” Additionally, FibreLine 2x1 is a different configuration that builds smaller composites parts – such as fairings, wing tips and automotive panels.
The FibreLine system cuts, sorts and sequences large plies of carbon fibre and other composite material. It then picks, forms and places this material into the designated mould with extremely high accuracy, without damage. The material is inspected to verify ply position and integrity, before tacking, consolidation and then moving to the next stage of the process. Reece points out that FibreLine “drastically” reduces the number of pieces that need to be brought together to make a part. “The
Alun Reece, CEO, Loop Technology
system lays up much larger, multilayer plies than other methods and material is placed into the mould at a record speed. This is an enabling solution for the composites industry that offers a way to meet the growing demand for parts and components in several different sectors,” he states.
Although Loop Technology works with a variety of global manufacturers and Tier 1 OEMs across industries such as automotive, renewables and defence, the aerospace sector is becoming a particularly enthusiastic customer of its solutions. “FibreLine is being used to automate dry fibre layup and inspection in projects that aim to facilitate the manufacture of lighter, more fuel-efficient aircraft and meet the growing demand within aerospace,” explains Reece. “One system is currently installed at the National Composites Centre as part of the Airbus ‘Wing of Tomorrow’ programme. Another system will
shortly be installed at the Innovation facility at the University of Sheffield’s Advanced Manufacturing Research Centre (AMRC), which is part of the Composites at Speed and Scale (COMPASS) programme. The inaugural project at this Innovation facility is the Isothermic High-Rate Sustainable Structures (IHSS) project, led by Boeing, alongside Sprit AeroSystems, AMRC and Loop Technology.”
Because automation for fibrereinforced composites is a burgeoning area, R&D projects such as the above form a critical part of Loop Technology’s everyday work.
Commenting on this aspect, Reece notes: “FibreLine is being used in several high-profile R&D projects that have the ultimate goal of using automation to increase the production rate of composite aerostructures. Additionally, at our HQ we have our own R&D facility, which is being used to continually evolve the FibreLine system as well as to test customers’ components and parts.”
One example of Loop Technology’s future-focused, integrated approach is the use of its FibreLine system as part of the Ultra HighRate Deposition System at the National Composites Centre (NCC), which is used on the Airbus ‘Wing of Tomorrow’ programme. On this, Reece comments: “The initiative is designed to increase the performance and production rate for the next generation of fuel-efficient, low-emission aircraft.” Indeed, the programme is designed to explore radical new approaches to the design and manufacture of aircraft wings, with composites being a key focus area.
On this programme, a complete ply stack of dry fibre piece parts (approximately 170 individual dry fibre pieces) were deposited and some of the full 17m length plies were deposited at close to maximum rate, equating to approximately 30 seconds for an individual 17m ply. Reece notes: “Since its installation in 2020, the NCC has used the Ultra High-Rate Composite Deposition System to make huge leaps forward in composite manufacturing. They are on track to deliver a dryfibre deposition rate in excess of 350kg per hour – 75% more than the initial targets.”
Reece is also focused on R&D on the AI front – and Loop Technology already uses AI within its product offerings. “Our composite inspection system, FibreEye, leverages advanced imaging techniques with AI to create a comprehensive inspection ecosystem and document defect characteristics and locations,” Reece explains.
Another popular area of Loop’s expertise lies in composite grippers; a solution that quickly became a
necessity in composite manufacturing due to the risks involved in composite handling. For safety-critical aerospace engineering applications, damage or deformation of composite plies caused by handling simply cannot be tolerated. The FiberLine system includes FibreForm, an advanced composite gripper system that manipulates much larger plies than many other methods.
“Our FibreForm system uses high flow vacuum generator grippers to create lift on the composite fabric whilst managing shear forces to ensure no damage is done to the material,” details Reece. “It then forms the composite plies into a wide range of shapes including concave, convex, omega and double curvature profiles. It does this, where necessary, to match the highly complex geometric surfaces of the mould, placing the ply precisely on the surface. This sophisticated layup system has developed and evolved over a number of years, through the dedication and hard work of our engineers.”
As well as selling products, Reece has adopted a service-driven business model from the off, reflecting his belief that a properly integrated approach will ultimately benefit all players in the broader composites industry. Highlighting Loop’s offerings here, he says: “Our service and support team provide targeted training, expert servicing through maintenance visits and callouts, extended warranties, advice on future upgrades and more, on a range of our products and systems.”
As well as FibreLine for high-rate composite preforming, the company also delivers systems and software across the advanced manufacturing industry. “We specialise in industrial robotics, motion control and machine vision and have expertise in fields such as assembly, metrology, labelling and machining,” explains Reece.
Automation is at the heart of all of the company’s efforts; and a further example is that Loop Technology
The National Composites Centre in Bristol has a FibreLine system as part of the Ultra High-Rate Deposition System
provides automated laser cleaning systems and distribution of CleanLaser models, providing full training and an optional laser safety training course for its customers. “Additionally, we are the UK reseller for Robotmaster offline programming, providing training and support in that regard as well,” Reece notes. “This software provides manufacturers with the ability to quickly and easily program robots to perform manufacturing tasks, making robotic automation accessible to a much wider audience.”
In a further nod to his focus on automation, Reece also reveals that Loop Technology has recently announced a partnership with Kobots, a firm that provides smart automation solutions to the construction industry. Loop will be selling Kobots’ automation systems in the UK. “We will also provide training, service and support for these automation systems that deliver increased efficiency as well as a reduction in health and safety hazards for the dry lining sector,” he confirms.
Unique ‘know how’ based composite training solutions
Courses in Composite Design, Analysis and Manufacture
Specialist in Aerospace, Marine, Rail and Automotive sectors
Cleanroom Solutions and Equipment Supply
Design, specification and supply of cleanroom equipment
OEM for composite curing and repair equipment
Specialised equipment supply for composite manufacturing
Ready to expand your horizons Visit our website
www.northcompositesengineering.co.uk
PU/PE
Precision
Slide
Precision
Insert performance is a common concern in the design engineering process
The use of threaded inserts in plastic assemblies allows designers to replace machined and cast metal components with plastic to achieve significant cost and weight savings without any loss of joint strength. Insert performance — resistance to rotational torque and tensile loading (also known as pull-out) — is a common concern in design, but answering how an insert will perform is rarely a simple ‘yes or no.’ Insert performance is only partially influenced by the insert itself. Other factors include:
• Plastic material and filler composition
• Design and quality of the plastic components including hole consistency
• Installation process and resultant quality
• Alignment of the mating component and how it supports the installed insert With so many different combinations of insert materials, plastic types, and assembly configurations it’s impossible to determine what performance could be achieved in a specific application without understanding these factors. In fact, up to 75% of the insert’s performance is a direct result of how
well it was installed.
To establish a benchmark for an application, it’s critical to assemble and test the joint under the application’s production environment. Since questions surrounding performance often arise earlier in the design process, it is important to consider which of the previously listed factors may be easily adjusted compared to those with a more significant impact if modified. An insert can be recommended to meet a specific application’s requirements in the design stage, and/or modifications can be proposed to an existing assembly to optimise performance based on prior experience and extensive performance data. In some cases, it is preferred to test the insert in the application to determine the installation criteria that will yield the best performance. Ultimately, acceptance of any threaded insert is subject to testing and evaluation to confirm performance in the actual application.
Once a benchmark has been established and the application moves into production, it is imperative to remember that variation to any of the aforementioned factors may affect the insert’s ability to resist rotational
torque and pull-out. Limiting the number of suppliers involved with an assembly can also minimise variables that affect performance. Therefore, if possible, purchase both the threaded inserts and installation equipment from the same supplier.
Many insert manufacturers provide performance data in their product catalogue. This data should be used solely as a comparative guide for insert types and sizes. It should not be used to compare across manufacturers since testing methods and materials are not consistent, nor should it be used to estimate a performance benchmark.
Given the variety of plastic materials, fillers, and the complexity of component design, it is impossible to provide insert performance data which can be applied to specific applications. It is recommended that designers partner with application engineering experts who specialise in threaded inserts for plastics as early as possible in the design stage to determine the most appropriate insert for their assembly. Final approval of the threaded insert should always be based on testing and approval in the actual application.
Stainless steel fasteners are typically made from austenitic, ferritic or martensitic grades
Patrick Faulkner, lead engineer at precision engineering component distributor Accu, looks at the different grades and types of stainless steel used in fasteners
tainless steel fasteners are widely used across many industries due to their excellent corrosion resistance, strength, durability and performance.
All these factors combine to make stainless steel fasteners suitable for applications including marine, automotive and chemical processing, which can involve exposure to moisture, chemicals or weathering. Their high strength and durability mean they can withstand heavy loads and extreme temperatures
without weakening or corroding. They also require minimal maintenance and retain their clean and polished appearance over time.
However, the specific strength, corrosion resistance and overall performance of a stainless steel fastener can vary depending on its internal crystal structure and grade.
Stainless steel fasteners are
typically made from austenitic, ferritic or martensitic grades, each with a distinct crystal structure. By understanding these structures, engineers can select fasteners with the right properties to ensure longterm performance.
Austenitic steel forms when ferrite is heated to 912oC, causing a transformation in its crystal structure, from body-centred cubic crystal to
face-centred cubic. A face-centred cubic structure can absorb up to 2% carbon. When cooled, austenite reverts to its original ferrite form. However, by adding chemical additives like nickel and manganese found in many austenitic stainless steels, the structure can be retained at lower temperatures. While austenitic stainless steels cannot be significantly hardened through heat treatment, they can be strengthened through cold working. Their exceptional corrosion resistance and durability in aggressive environments makes them a popular choice in many applications, especially in stainless steel screws. At Accu, this grade is used for the majority of stainless steel fasteners, due to its reliable performance and versatility.
Martensitic steel features a bodycentred cubic crystal structure formed when heated austenite is rapidly cooled by quenching. This fast-cooling process prevents the formation of cementite and traps carbon atoms within the crystal layers, forming a very hard material.
Unlike austenitic grades, martensitic stainless steels can be hardened through heat treatment, although austenitic grades do offer better corrosion resistance. The high hardness and durability of martensitic steel make it ideal for applications where cutting performance and wear resistance are essential, such as surgical instruments and specific industrial tools.
A1 stainless steel
A1 stainless steel is a free machining grade designed for improved machinability and ease of fabrication. While it does not offer the same level of corrosion resistance as highergrade stainless steels used in marine or harsh environments, it excels in applications where machinability and adaptability are key.
A2 stainless steel
One of the most common stainless steel grades used for fasteners is A2 Stainless steel. This grade offers a well-balanced mix of resistance
Stainless steel fasteners are widely used across many industries
to corrosion and oxidation and mechanical performance. A2 graded stainless steel fasteners are resistant to liquids and foodstuffs as well as inorganic chemicals. Although this grade is resistant to corrosion in water, it can tarnish over time in humid environments.
A4 stainless steel
For environments that are more corrosive and with high chloride content, A4 stainless steel is the preferred option. This grade includes levels of nickel and molybdenum, which significantly enhance resistance against aggressive environments containing chlorides and sulphur dioxide. As a result, A4 stainless steels are commonly used in marine environments. The increased amount of chromium in these components also gives them a slightly brighter appearance.
The most common types of stainless steel fasteners include bolts, screws, nuts, washers and rivets, which can be manufactured from different stainless steel grades that influence their properties and performance.
Stainless steel screws come in various types, from machine screws designed for metal-to-metal fastening to self-tapping screws used in wood or plastic. Most screws are made from austenitic grades, which provide excellent corrosion resistance, strength and durability. Similarly, bolts made from austenitic stainless steel are ideal for outdoor or marine environments due to their excellent resistance to rust.
Stainless steel nuts manufactured from ferritic or martensitic grades provide magnetic properties and higher hardness, while those made from austenitic grades excel in corrosion resistance. Washers and rivets, often made from austenitic stainless steel A2 grades, are common due to their superior corrosion resistance and durability, performing well in chemically aggressive environments.
Choosing the right material and grade of stainless steel is vitally important. Understanding the properties of each type results in a better-performing fastener.
Understanding the crystal structure of stainless steel grades allows engineers to select fasteners with the correct properties
Shifting simulation left enables product design teams to gain critical insights
Scott Parent, VP and field CTO, and Peter Slattman, senior enterprise account executive, at simulation specialist Ansys give their take on how simulation technology is powering innovation from the beginning of the design phase right through to the end of the manufacturing process.
The transition from Industry 4.0 to 5.0 represents a significant shift in manufacturing’s approach to technology. Whilst automation continues to generate anxiety amongst those who fear that technologies like artificial intelligence (AI) or robotics will replace humans in the workforce, the fifth industrial revolution emphasises human interaction and collaboration with technology. The European Commission describes it as more comprehensive than 4.0, with pillars for sustainability, human centricity, and resilience.
Smart manufacturing encompasses the efficient orchestration of factories and the physical and digital processes within plants. These systems are collaborative, information driven, and event driven, creating integrated processes that are monitored and continuously evaluated with the sensing, information, analytical models, and workflows needed to automate routine actions and prescribe action
for non-routine situations.
The manufacturing landscape increasingly demands systems that can respond dynamically to changing conditions whilst maintaining optimal performance. Traditional manufacturing approaches struggle to adapt to the variability and complexity that characterises modern production requirements. Smart factories address these challenges by implementing interconnected systems that continuously gather data, analyse performance patterns, and adjust operations accordingly.
Multiphysics simulation provides critical insight and predictive accuracy to support the sensing data and analytical models that define smart manufacturing. This technology addresses multiple physics phenomena simultaneously, enabling comprehensive understanding of complex manufacturing processes. It integrates with AI and machine learning algorithms to support advanced technologies like digital twins, additive manufacturing, and automation. This integration enables manufacturing systems to operate with greater effectiveness and efficiency across diverse operating conditions.
Solutions that link simulation, data, and resources across organisations create the digital thread that extends throughout product lifecycles. This enables real-time decision making based on current operational data and predictive insights derived from simulation models. The digital thread connects design intent with manufacturing reality, ensuring that theoretical models align with practical implementation requirements.
Product development teams increasingly support data fusion by shifting simulation left, integrating simulation earlier in design and development. This strategic approach fundamentally changes how manufacturing systems are conceived and developed. By introducing simulation earlier, development teams gain critical insights to inform design, prevent product failure, decrease spending, and reduce time to market. This early integration allows engineers to explore design alternatives and optimise performance before committing to physical prototypes. The shift towards earlier simulation implementation represents a fundamental change in manufacturing methodology. Traditional approaches
Simulation-powered digital engineering is driving smart factory development worldwide often relegated simulation to validation roles late in development cycles, but modern smart manufacturing demands predictive insights from the earliest design stages. This transformation enables development teams to identify potential issues and optimisation opportunities when changes remain cost-effective and implementable.
Through digital twins, smart factories maximise simulation during operations and maintenance. This delivers benefits like real-time systems analysis and predictive maintenance, enabling machine operators to detect issues sooner. Advanced monitoring systems continuously assess equipment performance, identifying patterns that indicate potential failures before they occur.
This supports asset health performance and lifecycle optimisation whilst reducing equipment downtime and related repair costs, increasing sustainability with insights encouraging fuel efficiency and carbon reduction. Manufacturers implementing predictive maintenance strategies report significant improvements in equipment reliability and operational continuity. The ability to schedule maintenance
activities during planned downtime, rather than responding to unexpected failures, transforms operational efficiency and cost management.
Simulation empowers advanced technologies like additive manufacturing, which plays an increasingly important role in modern smart factories. This technology supports sustainability by increasing the success rate of first-attempt printing results, which reduces the time, energy consumption, material waste, and costs of trial-and-error printing. The precision enabled by simulation-guided additive manufacturing processes significantly improves resource utilisation and environmental impact.
Additive manufacturing also helps secure supply chains with its ability to produce parts locally, at scale, and on demand. This localised production capability reduces transportation requirements and enables more responsive manufacturing systems. The combination of simulation-guided design and additive manufacturing creates opportunities for optimised, sustainable production that would be impossible through traditional manufacturing approaches.
Nearly 200 manufacturers have demonstrated their dedication to efficiency and cutting-edge technology by joining the World Economic Forum’s Global Lighthouse Network. To earn Lighthouse designation, manufacturers must apply Industry 4.0 technologies at scale to drive step-change financial, operational, and sustainability improvements.
Powered by simulation, digital engineering is driving smart factory development worldwide, impacting manufacturing in nearly every industry from construction and transportation to automotive and aerospace. The smart factory market is estimated at £389.14 billion in 2025 and is forecasted to reach £619.34 billion by 2030, reflecting widespread recognition of these technologies’ transformative potential.
This expansion demonstrates manufacturing’s recognition that simulation-powered digital engineering provides the foundation for navigating complex product requirements whilst meeting sustainability goals. Smart manufacturing success will depend on how it can leverage multiphysics simulation to enhance human problemsolving capabilities, enabling faster innovation and more sustainable production processes.
The
In recent years, industrial decarbonisation has become both a necessity and a competitive advantage for businesses. With electric motors consuming nearly half of the world’s electricity and expected to double in number by 2040, ABB is taking a missiondriven approach to lead the energy transition. The company’s innovations in motor technology, combined with the learnings from its recent industry survey on decarbonisation through energy efficiency, are positioning the company as a key enabler of sustainable industrial transformation.
“We’re entering a new era of efficiency,” says Stefan Floeck, division president of IEC LV Motors at ABB Motion. “Everything that moves or flows in industrial processes is powered by electric motors. While often hidden, they consume around 45% of the world’s electricity. This is why increasing their efficiency has such massive potential.”
ABB’s innovative motor technologies, such as its ultra-efficient SynRM
Everything that moves or flows in industrial processes is powered by electric motors.
While often hidden, they consume around 45% of the world’s electricity
(Synchronous Reluctance Motor), address the most demanding applications - from water treatment to food production and hazardous chemical environments. “Our motors have the power to cut global electricity consumption by up to 10%,” Floeck notes. “That’s a serious impact.”
Despite the progress made in optimising the energy efficiency of electric motors so far, the global energy intensity metric – the energy required to produce one US dollar of GDP – has plateaued at around 2% improvement per year.
“That’s not good enough,” says Ivor Vidjen, global head of strategy and business development for IEC LV Motors. “The IEA recently called on all of us to double down and increase efficiency gains to 4% annually. Time might be on our side in terms of our business case becoming stronger, but this is not a luxury we can afford to waste.”
To ensure ABB’s strategic vision aligns with market realities, the company conducted a wide-reaching survey of 3,000 industry stakeholders in late 2024, including 2,400 technical experts across various industrial sectors.
“We wanted to stress-test our assumptions,” Vidjen explains. “What we found was incredibly encouraging. About 94% of respondents said they are either actively investing or planning to invest in energy efficiency. When you include the undecideds, our strategy is applicable to about 99% of the market.”
Importantly, the motivations behind those investments are changing. A decade ago, energy efficiency was largely driven by regulation. Today, the momentum is internal. “We’re seeing a real shift,” says Vidjen. “Businesses are now motivated by sustainability goals, brand value, and operational resilience. The pressure is no longer just from regulators - it’s coming from within.”
One of ABB’s consistent messages has been the strategic importance of electric motors in industrial
decarbonisation. That message, it seems, is gaining traction.
“It’s gratifying to see what we’ve been saying for years is now widely understood,” Vidjen shares. “Optimising your motors is not just a sustainability win, it’s the best return on investment many plant managers can make.”
However, despite the clear long-term benefits, a common hurdle remains: upfront cost. High-efficiency motors often carry a premium, which can be a sticking point for procurement teams. ABB is tackling this by reframing the conversation around Total Cost of Ownership (TCO).
“When you look at a motor’s entire lifecycle, the energy cost far outweighs the initial purchase price,” says Vidjen. “Educating our customers about that – changing the mindset –that’s our daily challenge and also our greatest opportunity.”
ABB prides itself on offering the broadest motor portfolio in the industry, spanning every major application and
ABB’s facility in Vaasa, Finland
segment. But it’s not just about having the widest selection – it’s about building trust through reliability.
“Our motors are chosen for the most critical applications under the harshest conditions,” adds Daniel Eberli, head of product management for IEC LV Motors.
“That’s no coincidence – it’s our design philosophy. Reliability isn’t just a buzzword for us; it’s embedded in every motor we produce.”
Ease of use is another hallmark of ABB’s engineering approach.
“We’ve engineered hundreds of preconfigured options, and when that’s not enough, we step in with tailored solutions,” Eberli says. “It’s how we build expertise and deepen our customer relationships.”
Among ABB’s most advanced innovations is its synchronous reluctance (SynRM) motor technology, launched in 2011 and now entering its next generation.
“We were the first to introduce this
Captions to go here
Not using rare earths makes these motors easier to recycle, easier to service, and more sustainable overall
technology commercially, and we’ve continued to lead,” Eberli says. “It took time, but the market has come to understand and trust SynRM as a safe, efficient, and highly reliable choice.”
Thanks to surging energy prices, interest in ultra-efficient motors like SynRM has soared. “Efficiency matters more than ever,” he notes. “That’s why we’ve expanded the SynRM portfolio to include water-cooled versions for higher power density, and even variants for explosive environments.”
This year, ABB became the first to launch a magnet-free IE6 efficiencyclass SynRM motor. While IE6 is not yet officially defined, ABB applies the consistent logic of 20% loss reduction per class.
“When we say IE6, we mean 20% fewer losses than IE5 – just as IE5 is 20% more efficient than IE4,” explains Eberli. “Compared to IE3 motors, we’re talking about 50% less energy loss. That’s huge.”
Lower losses also mean cooler motors, with bearing temperatures up to 15% lower than standard designs. This directly improves the longevity and reliability of the motor. “The two most common failure points in motors are bearings and insulation,” Eberli adds. “Lower temperature means longer life.”
ABB’s SynRM motors also avoid the use of rare earth metals, and have a magnet-free rotor, which brings both sustainability and supply chain advantages.
“Not using rare earths makes these motors easier to recycle, easier to service, and more sustainable overall,” says Eberli. “We even use low-carbon copper for our SynRM models, thanks to partnerships with specialised suppliers.”
And because they match traditional IEC frame sizes, SynRM motors are drop-in replacements for existing induction motors, offering significant benefits for companies looking to retrofit and upgrade their existing
operations. Still, ABB recognises that SynRM isn’t always the only answer. “We’re technology agnostic,” Eberli adds. “Whether it’s magnet-assisted designs or permanent magnet solutions, we pick the best technology for each customer’s specific need.”
ABB is also serious about walking the talk on sustainability. “98% of a motor’s materials are recyclable,” Eberli notes. “We’re already running take-back schemes in many countries. And our Environmental Product Declarations (EPDs) give customers full transparency on embedded carbon and resource use.”
ABB was the first in its category to publish EPDs for electric motorsdefining the product category rules and setting benchmarks. As such, a key part of ABB’s strategy is being proactive rather than reactive.
“When someone asks for an IE3 motor, we say, ‘You could have this IE4 or even IE5 alternative.’ Yes, it may cost 10% more upfront, but the payback time is six months to two years,” Floeck says. “That’s how we build trust and shift mindsets.”
Applications involving pumps, fans, and extruders – where motors rarely run at full load – represent major opportunities for efficiency gains. Floeck says that using frequency converters with ABB’s motors can significantly reduce both mechanical complexity and energy consumption. “You reduce the motor consumption, and with an IE5 motor, the efficiency under partial load is far superior. That’s where the real energy savings are.”
ABB’s ability to offer both motors and drives as part of a complete package also gives the company an edge. “Many competitors offer either motors or drives. We have both –with the same tools, same pricing
Ivor Vidjen, global head of strategy and business development for IEC LV Motors
structures, and integrated support,” Floeck adds.
Looking ahead, ABB is aligning itself with the EU’s climate-neutral targets through Scope 1, 2, and 3 emissions strategies. “We’re doing well on Scope 2,” Floeck says. “Scope 3 is more complex, because it involves the energy our products consume during use. But even there, we believe we’re part of the solution – not the problem. We’re helping the world save energy, and that’s core to ABB’s mission.”
As Europe looks to secure its technological future and inspire the next generation of engineers, two recent events highlight the critical role of education and training
From rockets and Mars rovers to advanced chip design, recent innovations in design engineering have showcased the impact new and emerging talent in the sector can have on the way we approach design challenges. This article rounds up some of the latest advances and opportunities across the engineering landscape.
In May, the University of Bath, UK, hosted its 60th Engineering Design and Project Exhibition, a vibrant showcase of student creativity and technical skill.
Feauturing final-year individual and group projects from the Departments of Mechanical Engineering and Electronic & Electrical Engineering, the event offered a glimpse into how Bath students are tackling real-world problems through design and ingenuity.
The exhibition featured an impressive range of student-built prototypes and concepts, from rockets and jet-powered aircraft to sustainable mobility solutions, drug delivery systems, and even an artificial heart. Projects reflected some of today’s most pressing global challenges, such as environmental sustainability, public health and
space exploration. Among the notable student teams were:
• Team Bath Heart, creators of a total artificial heart and two-time world champions at the Heart Hackathon
• Team Bath Racing Electric, who design and race battery-powered race cars in Europe’s Formula Student competitions
• Team Bath Roving, builders of Mars and Lunar rovers
• Team Bath Drones, ranked Europe’s top drone team in 2024
• Bath Hydrogen, working to adapt internal combustion engines for hydrogen fuel
The exhibition also spotlighted
University of Bath graduates Navjot Sawhney and Hélène Verhaeghe, who delivered the Joseph Black keynote lecture sharing the journey of The Washing Machine Project. Launched in 2019, the project has brought handpowered, water-efficient washing machines to over 15 countries, improving the lives of more than 46,000 people.
“Bath was crucial in helping me develop The Washing Machine Project,” said Sawhney. “It’s emotional to return to where this journey began. I hope our story inspires students to use their skills to solve real-world problems.”
UK Member of Parliament Wera Hobhouse also attended the event, presenting an award to Team Bath Heart for its contributions to equality, diversity, and inclusion. “In a world facing immense challenges, it’s fantastic to see our own engineers from Bath leading the way,” she said.
While the UK celebrates grassroots engineering talent, Europe’s semiconductor sector is taking a bold step forward with the launch of the FAMES Academy - an educational and training initiative designed to equip engineers with the skills needed to harness FD-SOI and other cuttingedge chip technologies.
Launched during the CEA-Leti Innovation Days – LID World Summit in Grenoble, France, in June, the FAMES Academy is a flagship training program of the FAMES Pilot Line, which supports the EU’s commitment to semiconductor self-sufficiency under the European Chips Act.
“The FAMES Academy is a cornerstone of our mission to equip Europe’s microelectronics community with the skills needed to leverage FDSOI technology,” said Laurent Fesquet, project manager and deputy director of the TIMA Laboratory.
The academy is built around three core objectives:
• Supporting skill transfer to European industry for next-generation chip development
• Attracting new talent into Europe’s microelectronics sector
• Training professionals to design
and characterise advanced semiconductor nodes
Over the next four years, the FAMES Academy will offer training sessions, workshops, and theoretical courses, including hands-on access to FDSOI, eNVM, RF, 3D integration, and PMIC technologies. The academy complements the FAMES OpenAccess platform, giving professionals access not just to equipment and labs, but also to the knowledge required to use them effectively.
Upcoming training events include:
• FAMES FD-SOI Design School (EFDS) in Grenoble, 25–30 January, 2026
• A two-day chip design course at Ireland’s Tyndall Institute, 24–25 November, 2025
• Ongoing e-learning modules and tutorials accessible online
Courses will focus on real-world design trade-offs in areas such as automotive, artificial intelligence (AI), and high-performance computing (HPC), including topics like energy efficiency, system performance, and integration complexity.
“We want to give European engineers and researchers the tools to succeed in a rapidly evolving field,” said Dominique Noguet, FAMES Pilot Line coordinator. “That means more than access
to hardware—it means access to hands-on learning, mentorship, and practical experience.”
The FAMES Academy and Pilot Line are supported by a broad European consortium, including CEA-Leti (France), imec (Belgium), Fraunhofer (Germany), Tyndall (Ireland), VTT (Finland), CEZAMAT WUT (Poland), UCLouvain (Belgium), Silicon Austria Labs, the SiNANO Institute, Grenoble INP, and the University of Granada (Spain).
By aligning academic training with industry needs, the FAMES initiative aims to bolster Europe’s chip design ecosystem and safeguard its position in global technology supply chains.
Whether through student-built drones and Mars rovers or Europe’s strategic training programs in advanced chip design, one thing is clear: engineering is at the forefront of tackling today’s most complex challenges.
While Bath’s exhibition captured the power of early-stage innovation and student passion, the FAMES Academy represents the next step - ensuring that those students, and the wider European workforce, are equipped to design and build the technologies of tomorrow.
Fresh investment and training opportunities are taking the UK composites sector from strength to strength
In June, the UK Government announced its Modern Industrial Strategy, promising a “new approach for a new era” of manufacturing. Recognised by the Government as being the ‘highest growth opportunity areas for the economy and business’ the Industrial Strategy focuses on key sectors, namely: advanced manufacturing, aerospace, clean energy, defence and digital technologies.
Notably for the UK composites sector, the strategy goes as far as to commit to “scaling up R&D in composites, including through support for government-backed centres such as the National Composite Centre (NCC) in Bristol.”
Richard Oldfield, CEO of NCC, welcomes the announcement. “Already an innovation partner to industry, we are expanding our capabilities to deliver more impact for the nation,” he says. “This includes collaborating to develop the future materials, products and processes that will secure UK technology leadership for next-generation aircraft platforms and anchor future industries in support of the UK’s energy transition. The alliance between the High Value Manufacturing Catapult and MOD [recently] announced is also testament to NCC’s status as a centre of excellence for defence innovation.”
Katherine Bennett CBE, CEO of the High Value Manufacturing Catapult, echoes Oldfield’s support for the strategy, adding: “The publication of the modern industrial strategy is a pivotal step towards transforming the UK into an industrial powerhouse. The High Value Manufacturing Catapult has a proven track record of turning policy into progress, investing more than £1 billion in a nationwide network of research and development facilities.”
On a mission to help the UK composites sector embrace digital technologies and boost its productivity, NCC has launched its Made Smarter Great South West programme across Cornwall, Devon, Somerset and Dorset. Funded by the Department for Business and Trade, the programme will run until the end of March, 2026.
SMEs in the region will benefit from up to 50% match funding for digital tech adoption, fully funded digital leadership and champion training, paid digital internships and personalised one-to-one digital roadmaps.
“We’re delighted that SMEs across the Great South West region can now take advantage of the Made Smarter programme to accelerate their digital transformation journeys,” says Katy Riddington, chief portfolio officer at NCC. “NCC has helped hundreds of SMEs de-risk and scale new technologies for faster market adoption, greater efficiency and competitive advantage. As a lead delivery partner for Made Smarter, we look forward to working with our partners SWMAS and UWE to demonstrate how digital technologies can help businesses stay competitive, sustainable and future-ready.”
June also saw NCC announce the initial location of its open-access carbon fibre development facility at Cygnet Texkimp’s site in Northwich, Cheshire. Recognised in the UK Government’s Industrial Strategy and Advanced Manufacturing Sector Plan, the initiative will support the UK’s strategic growth sectors.
The facility will house two digitallyenabled development lines for manufacturing carbon fibre and act as a critical stepping stone to further develop and industrialise advanced material manufacturing capability in the UK. Businesses accessing the facility will be able to leverage worldclass on-site materials expertise and collaborate closely with the North West’s leading chemical and materials cluster and the West of England’s leadership in advanced engineering. In addition to enabling carbon fibre innovation, the facility will train future generations of chemists and engineers. Initial testing at the facility is scheduled to start in Autumn 2025 before it becomes fully operational in Spring 2026.
Elsewhere, Composites UK – the trade association for companies working in the UK’s fibre-reinforced polymer composite supply chain –has announced a series of webinars to provide vital education and training for engineers working with composite materials.
The first, titled ‘Introduction to life cycle analysis (LCA) for composites’, will take place on 15th June, at 11am BST. The webinar, presented by Composite UK’s sustainability manager Malcolm Forsyth, will offer a foundational overview of LCA with a particular focus on composite materials. Participants will gain insight into why and how LCA is used to assess the impacts of composites across their full lifecycle – from raw material sourcing and manufacturing through to usephase and end-of-life scenarios. The webinar will cover key considerations such as data quality, system boundaries and functional units, along with specific challenges when considering composite materials. According to Composites UK, the webinar will benefit engineers, material scientists and
sustainability professionals looking to gain a good understanding of how to start integrating LCA into their product development and business decisionmaking processes.
The second, titled ‘Get ahead with environmental product declarations’, will take place on 30th July at 9:30am BST. Environmental product declarations (EPDs) are fast becoming essential for selling composite parts in today’s environmentally conscious markets. But for many companies, the process of understanding and preparing EPDs is still unclear. To help SMEs stay competitive and meet growing customer demands, Composites UK is partnering with business service network partner Decerna to host a three-hour live webinar to demystify EPDs and give attendees the knowledge and confidence to engage with providers and navigate the EPD process effectively.
With the UK composites sector valued at £13.36 billion as of the latest available data from Composites UK, nearly 50,000 people are now employed across the industry. This reflects the high-value, skilled roles that composites support across the country, the association says. As such, the need to reduce market barriers for the composites sector, such as addressing the skills gap and investing in sustainability and recycling, has never been as important as it is today.
Recognised by the Government as being the ‘highest growth opportunity areas for the economy and business’ the Industrial Strategy focuses on key sectors, namely: advanced manufacturing, aerospace, clean energy, defence and digital technologies
The Electronic Component Show (ECS) will welcome design engineers and purchasing professionals to the Kassam Stadium in Oxford in September. Taking place on the 18th September, the one-day exhibition
Sand conference will give attendees the opportunity to meet to discuss the latest components, services and projects that engineers and purchasers are working on.
The conference programme will feature the latest trends in electronics,
how they can be implemented into product design, and provide a platform for engineers to engage with fellow industry experts. With the event running just 10am-3pm, it bills itself as the ‘perfect solution’ for those with busy schedules.
Register to attend at: www.electronic-component-show.co.uk
ticking within the realms of electronics, Microelectronics UK will bring together entire value chains from across the microelectronics, semiconductor and photonics industries to showcase the UK’s world-class expertise in R&D, design innovation and advanced manufacturing. Taking place 24-25th September at the London’s Excel Arena, the event is expecting over 4,000 visitors across the two days, while over a hundred speakers will discuss the latest industry trends
Microelectronics UK is expecting over 4,000 visitors in 2025
and technology advances across four separate content tracks.
The UK’s microelectronics and semiconductor industry is poised for significant growth, driven by strategic government initiatives and increasing demand across key sectors such as automotive, telecommunications, and healthcare. Given this robust outlook, Microelectronics UK believes it has a pivotal role to play in showcasing cutting-edge innovations, fostering collaboration, expediting domestic and international trade, while highlighting
the UK’s leadership in niche areas such as compound semiconductors and semiconductor design. Attendees will gain insights into market trends, establish and explore strategic and commercial partnerships, and leverage emerging opportunities in a rapidly evolving global landscape.
Book your place at: www.microelectronicsuk.com
The Engineering Design Show (EDS) will return to Coventry Building Society Arena across 8-9th October, offering a platform for design engineers looking for direct access to the electronic and embedded design sector’s latest products, services and
innovations. Visitors to the event will be able to explore hundreds of UK and international suppliers, including those for CAD software, product design, mechanical design and more.
Alongside the exhibition, more than 50 conference sessions and technical workshops are poised
to provide topical content on the challenges and opportunities for the engineering sector.
Visitors will also benefit from keynote speeches from industry leaders and live demonstrations, in addition to numerous networking opportunities.
Boker’s, Inc., is a full-service manufacturer of precision metal stampings, washers, spacers and shims. Since 1919, nearly every industry around the world has trusted Boker’s to provide quality made-to-order components, world-class service and fast delivery.
T +1 612 729 9365
E sales@bokers.com
W bokers.com
As the global leader in 3D scanning and inspection, LMI Technologies works to advance quality and productivity with 3D sensor technology.
E contact@lmi3d.com
W lmi3d.com
e advertising@setform.com
t +44 (0)207 253 2545
With over two centuries of experience in the hinges industry, Gold and Wassall provides a fully comprehensive design and manufacturing service for any kind of hinge for practically any application.
T +44 (0)1827 63391
E enquiries@goldwassallhinges.co.uk
W goldwassallhinges.co.uk
HIOKI, founded in Japan in 1935, leads precision test and measurement technology. Renowned for advanced electrical current sensors, power electronics, and battery solutions, we deliver uncompromised accuracy and innovation built and engineered in Japan.
T +49-(0)6196-76515-0
E hioki@hioki.eu
W shop.hioki.eu/
Nano Dimension (Nasdaq: NNDM) aims to revolutionise electronics and mechanical manufacturing through precision additive manufacturing and AI-driven solutions, enabling on-demand production and managing a distributed manufacturing network.
T +1 857-557-8022
E sales@nano-di.com
W nano-di.com
RECOM produces standard and custom DC/ DC, AC/DC converters, switching regulators, and LED drivers from sub-1W to tens of kW. Headquartered in Gmunden, Austria, RECOM is known for quality, innovation, wand excellent customer service.
T +43 7612 883 25 700
E info@recom-power.com
W recom-power.com
With over 65 years of experience, we offer a full range of plastic injection moulding services across all sectors with the ability to make plastic parts from 1g to 45kg and up to 1.5m in size.
T 01572 723476
E enquiries@rutlandplastics.co.uk
W www.rutlandplastics.co.uk
Develops, manufactures and distributes test instruments, scales and balances and selected laboratory equipment for industry, trade and research. In addition to pre- and after-sales support, calibration and repair are also offered.
T +44 (0) 161 464902 0
E info@pce-instruments.co.uk
W www.pce-instruments.com
Viton™
Our process for manufacturing Viton™ fluoroelastomers has been upgraded, by formulating without the use of a fluorinated surfactant. We innovate to meet your performance needs and ensure continued supply, in the face of a rapidly evolving regulatory landscape.
T +1 302 773 1000
W viton.com/en/contact-us