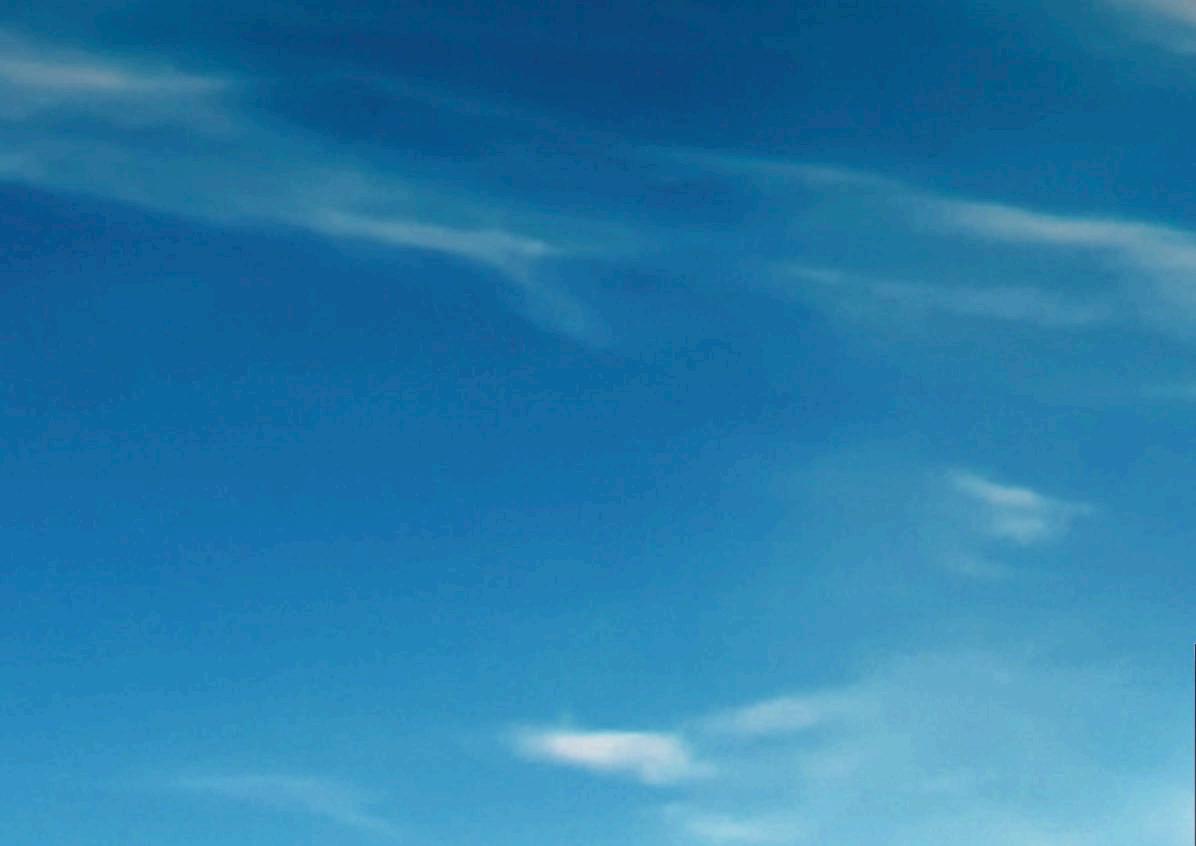
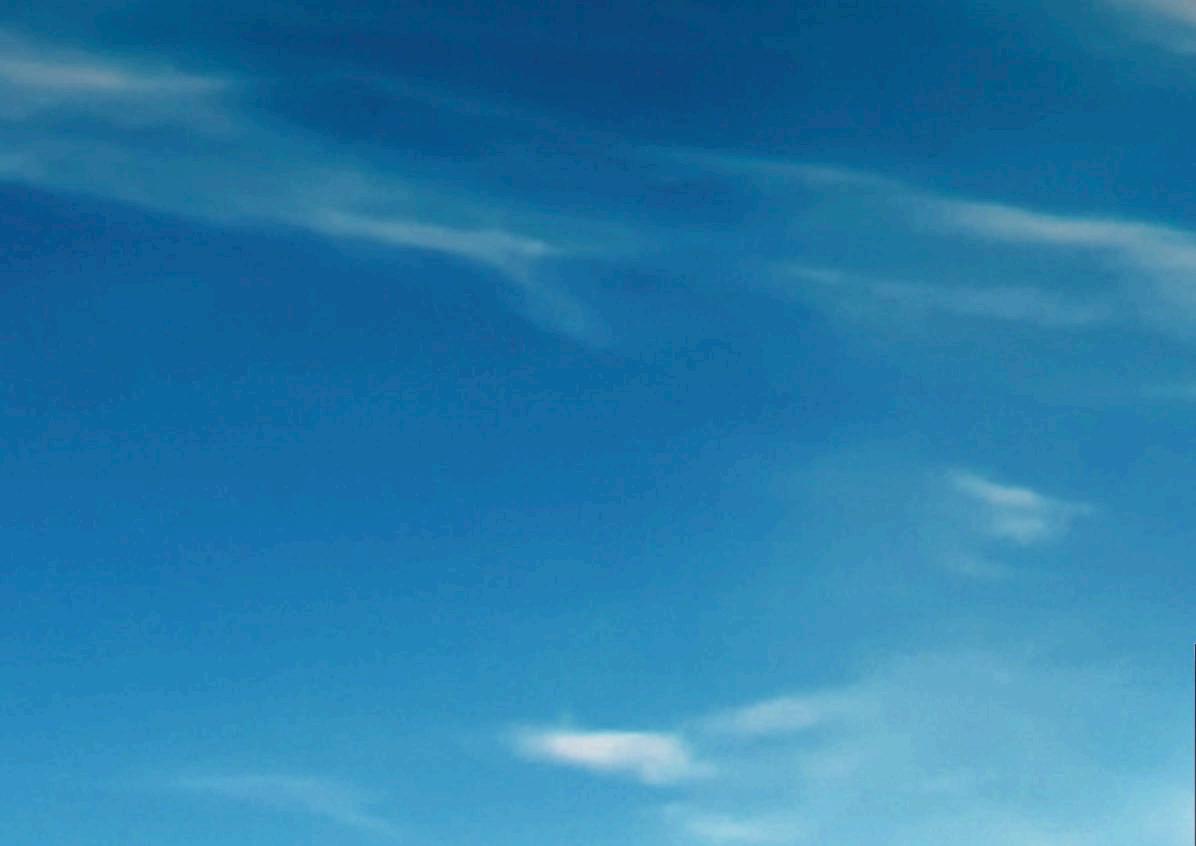
AI AGE OF
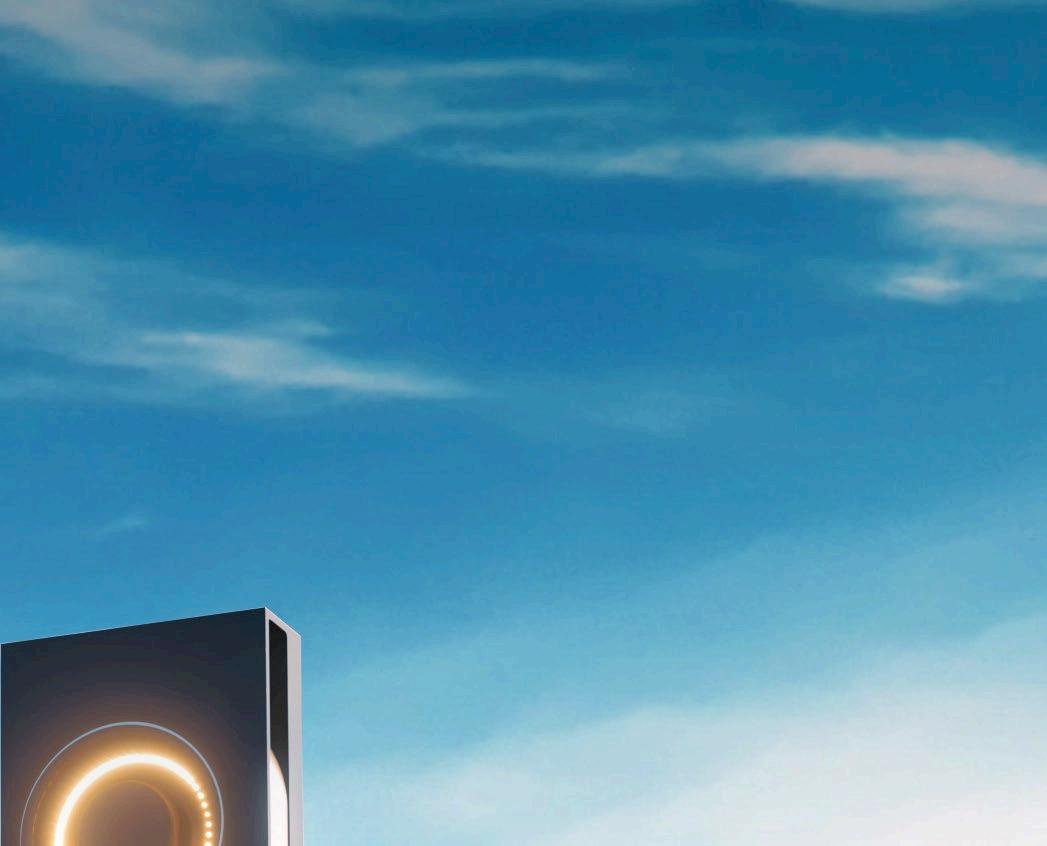

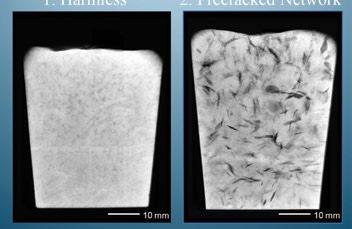
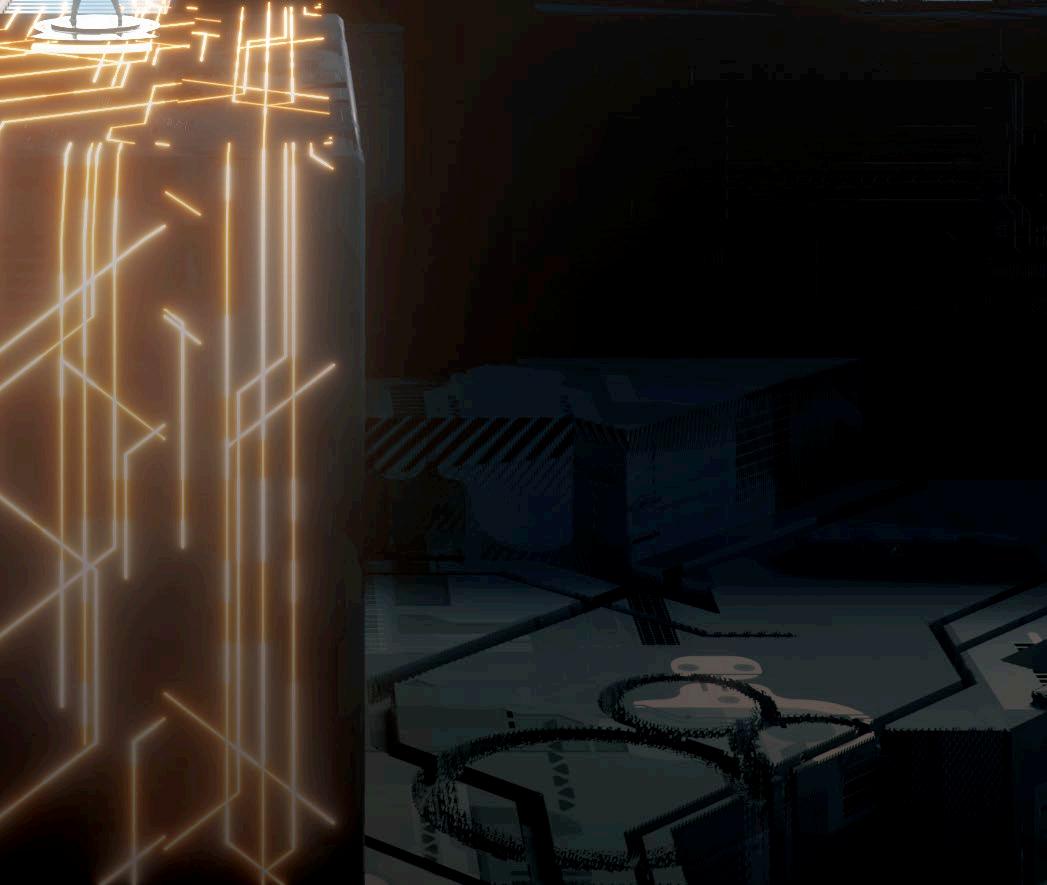

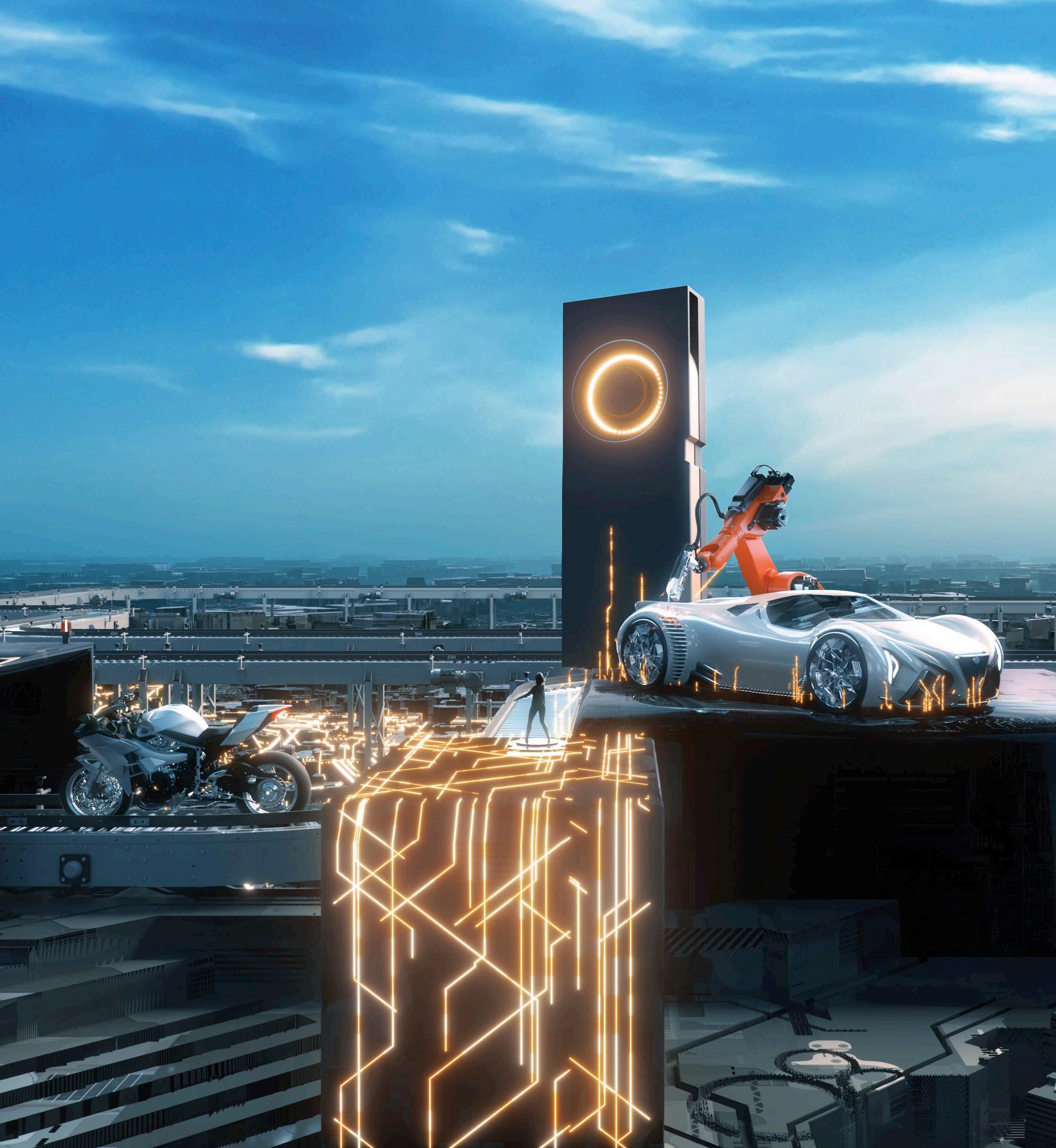
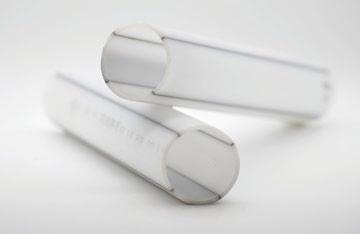
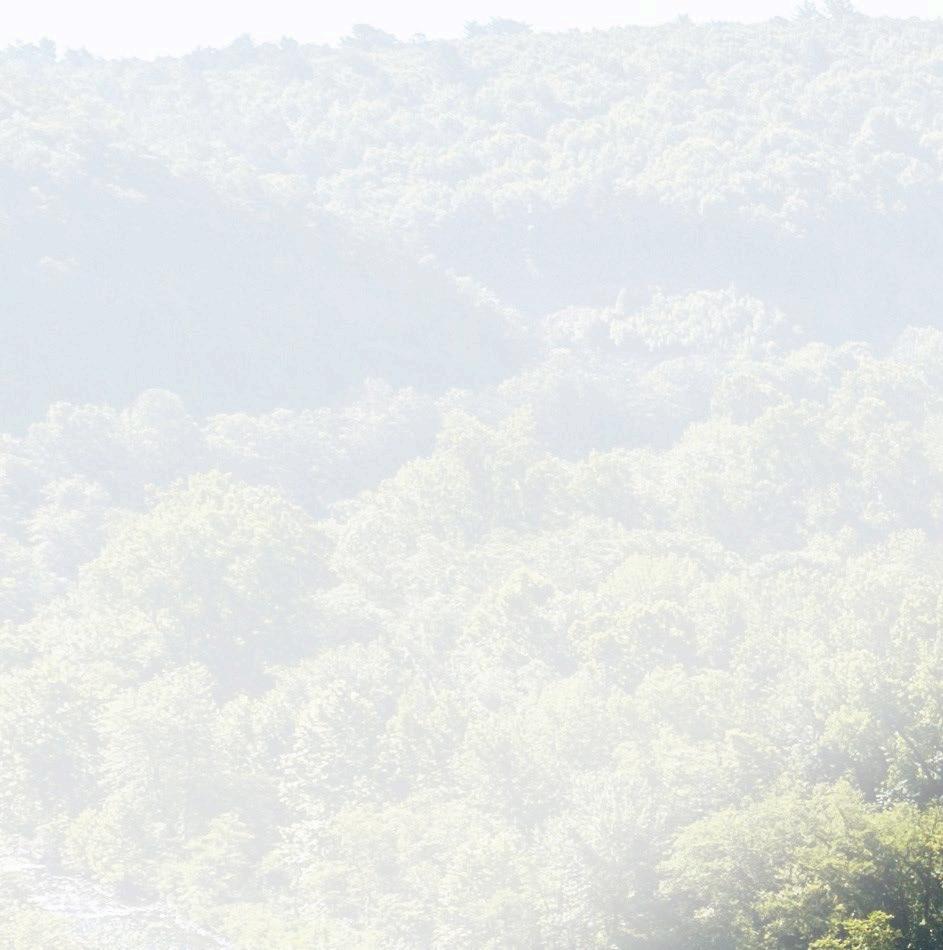
Fluoroelastomers
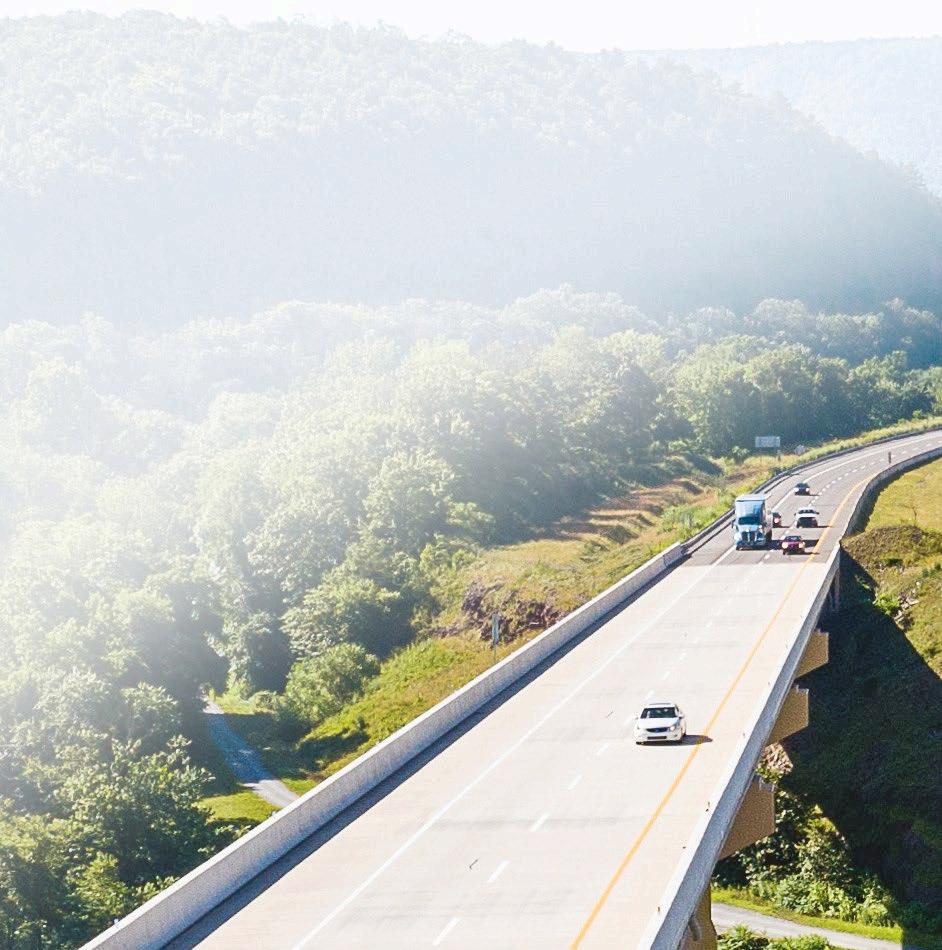


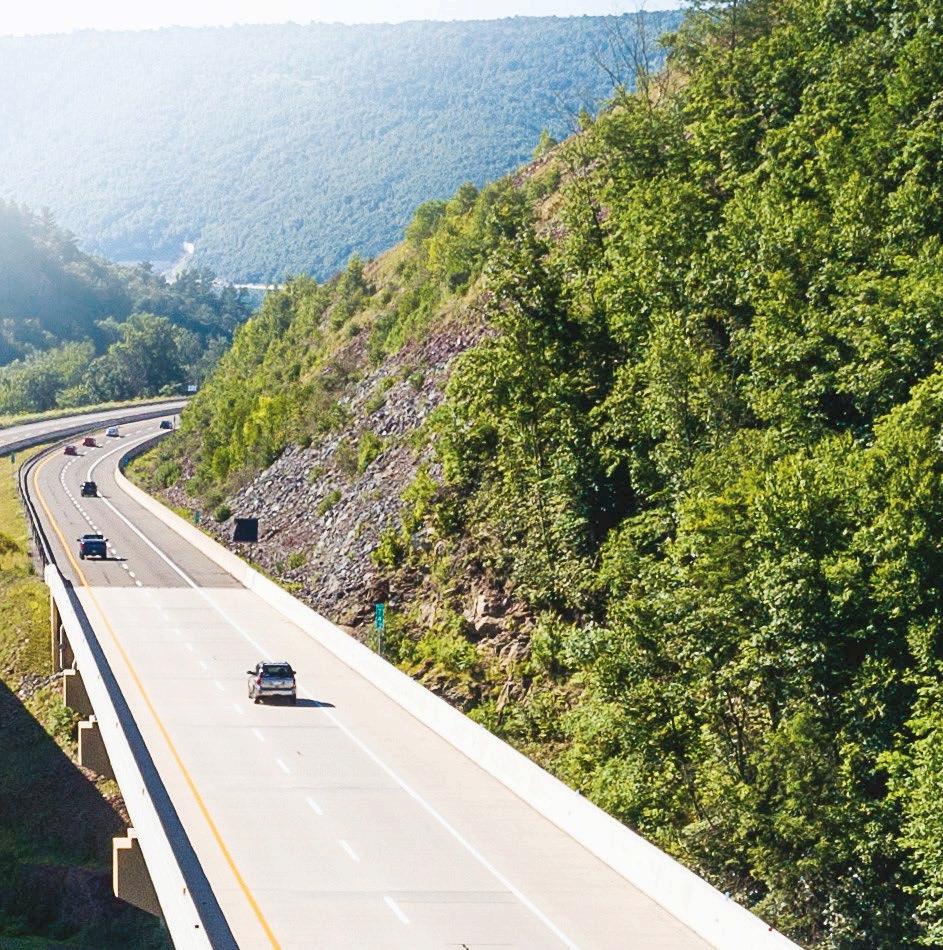
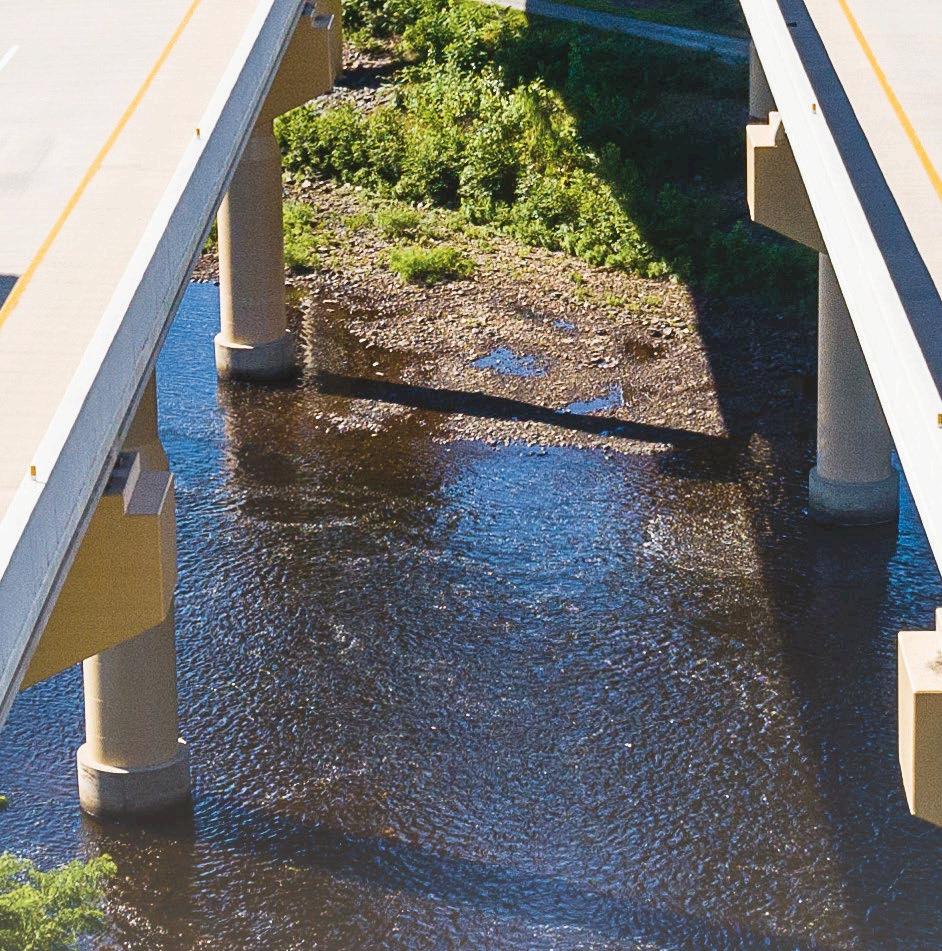
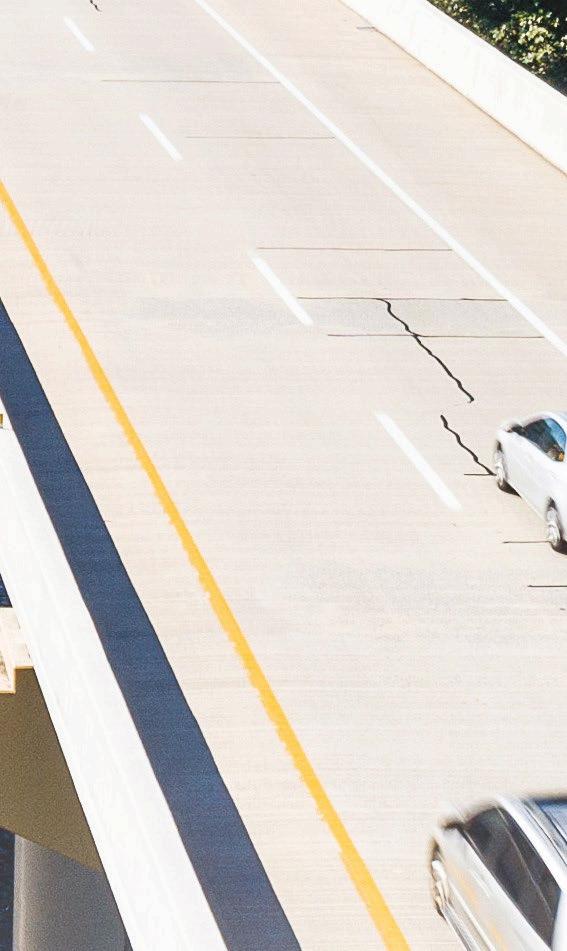

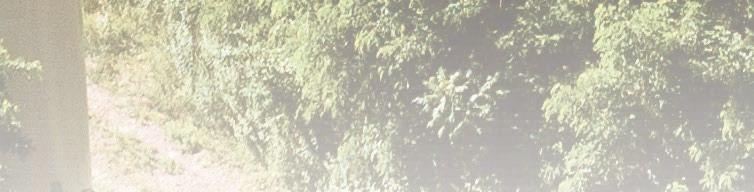
Viton™ FWRD APA Fluoroelastomers
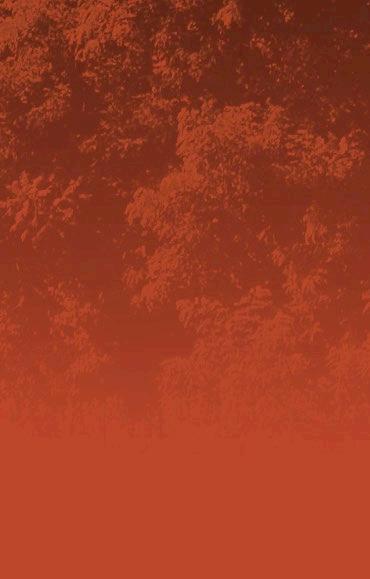
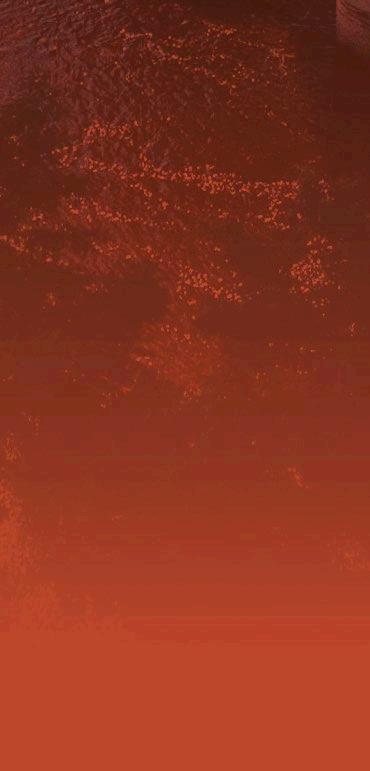
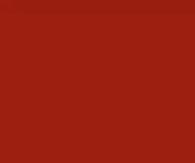
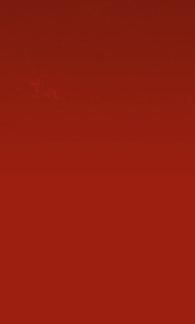
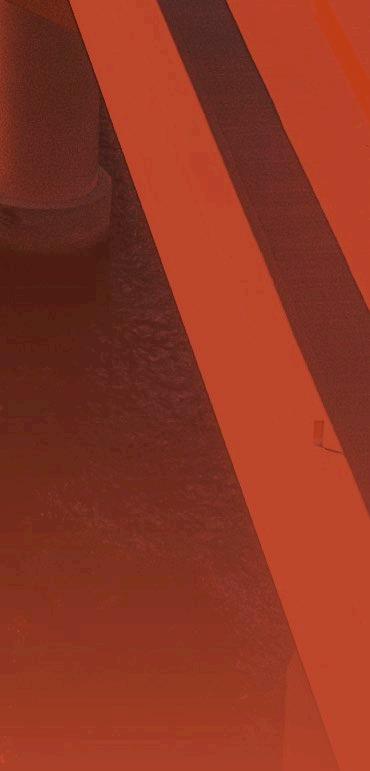
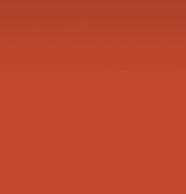
Our process for manufacturing Viton™ FWRD APA fluoroelastomers has been upgraded, by formulating without the use of a fluorinated surfactant. We innovate to meet your performance needs and ensure continued supply, in the face of a rapidly evolving regulatory landscape.
Internal testing, as well as customer testing, have confirmed Viton™ FWRD APA fluoroelastomers made using our new process at a commercial scale production plant, have comparable performance to the current grades.
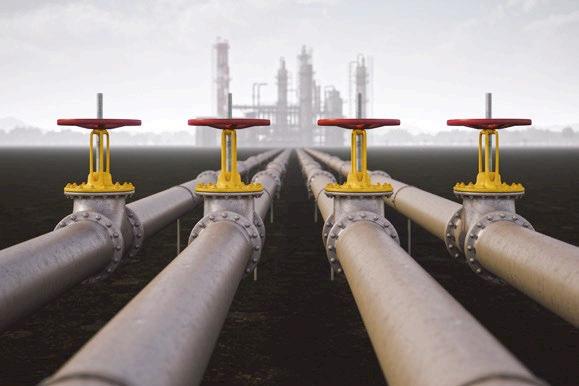
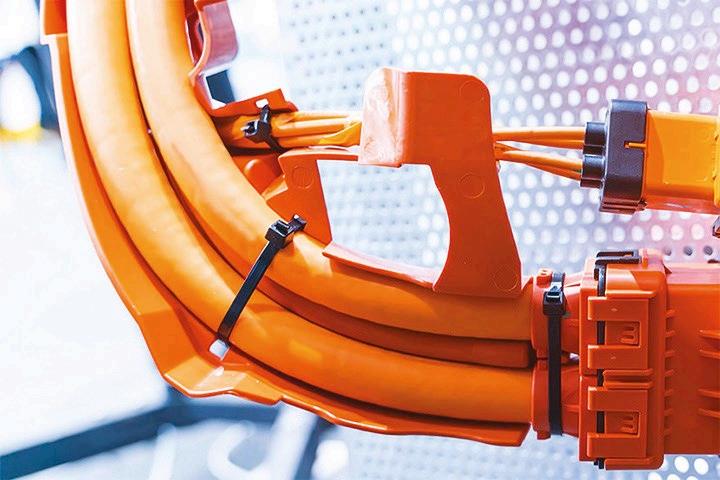
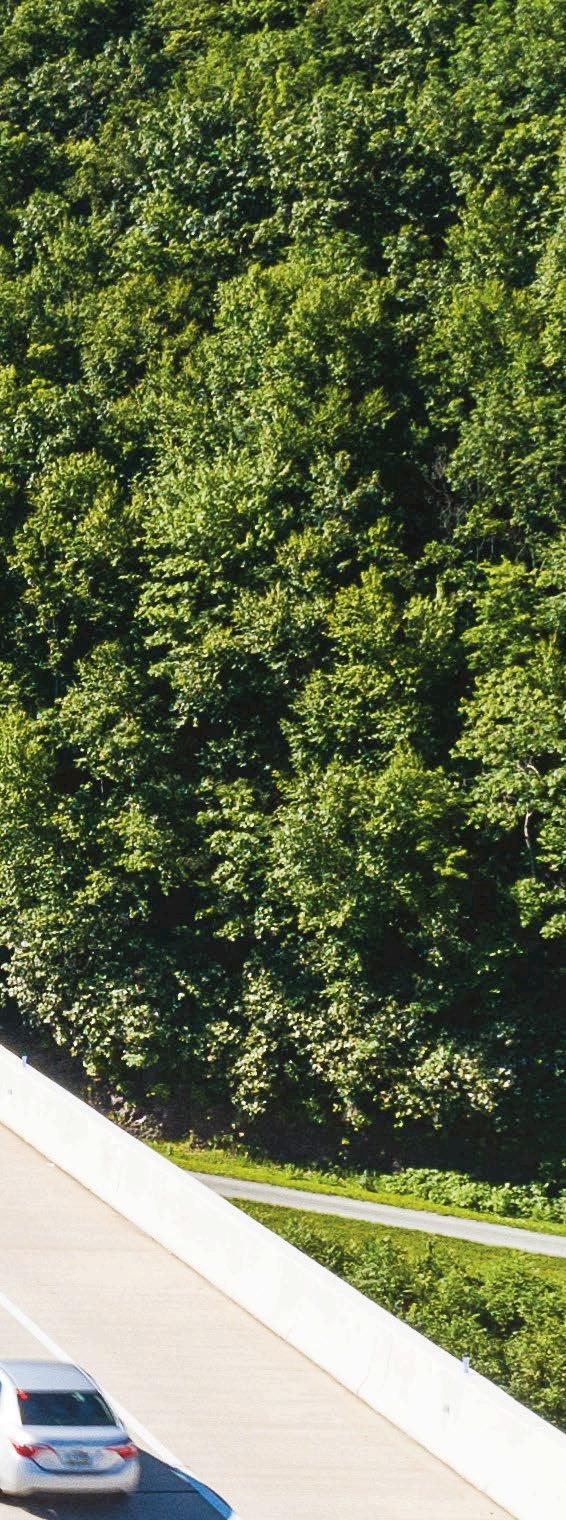
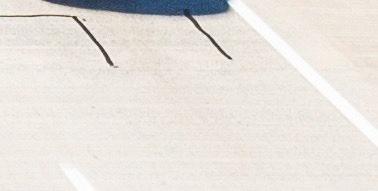

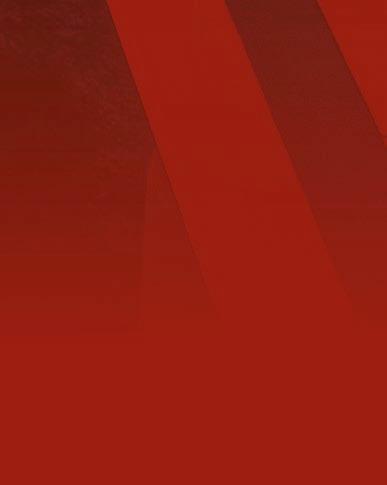
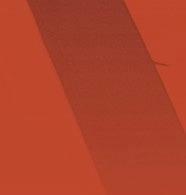

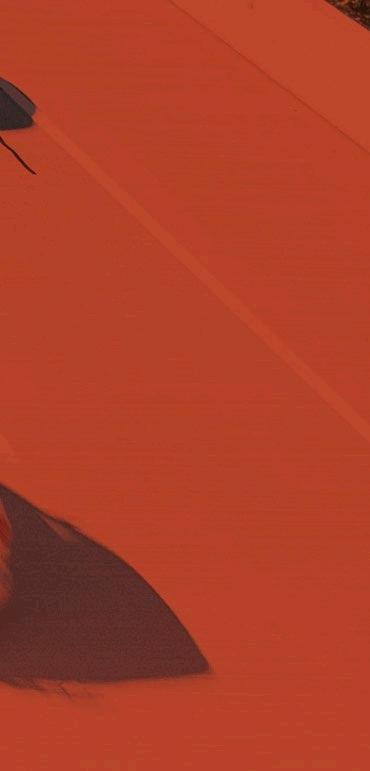

viton.com
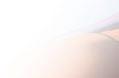





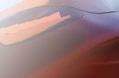

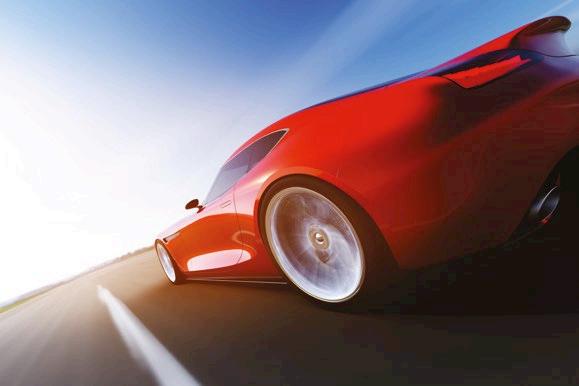





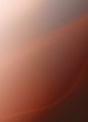
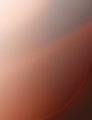
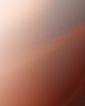
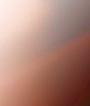






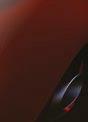
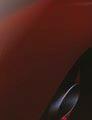
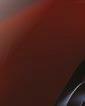

The increasing complexities of modern manufacturing are placing growing demands on design engineers across the globe. Hailed by some as the next industrial revolution, artificial intelligence (AI) is already having a significant influence on how products and systems are designed and delivered. While the potential value of the technology is clear to many, the pace and success of adoption across industrial sectors depends on a multitude of factors.
Our cover story Age of AI (pages 6-13) takes a deep dive into the trends, challenges, barriers and future outlook for AI in design and manufacturing, featuring insights from those spearheading the technology forward. We’ve picked the brains of experts from the likes of Schneider Electric, Autodesk, NVIDIA and others to see whether the rapid adoption of AI could really prove to be a paradigm shift for the design engineering field.
From software to materials, this issue also delves into the fascinating world of composites (pages 33-38). We bring you the latest advancements in composite products, technologies and materials straight from the show floor of JEC World 2025. As we inch towards a more sustainable world, circular composite innovations will become increasingly vital for designers as they seek to balance performance, efficiency, cost and environmental considerations within their products.
Lastly, our new regular Skills zone section rounds up the latest training and education opportunities for design engineers. If you’re looking to upskill, flip to page 48.
Hayley Everett Editor
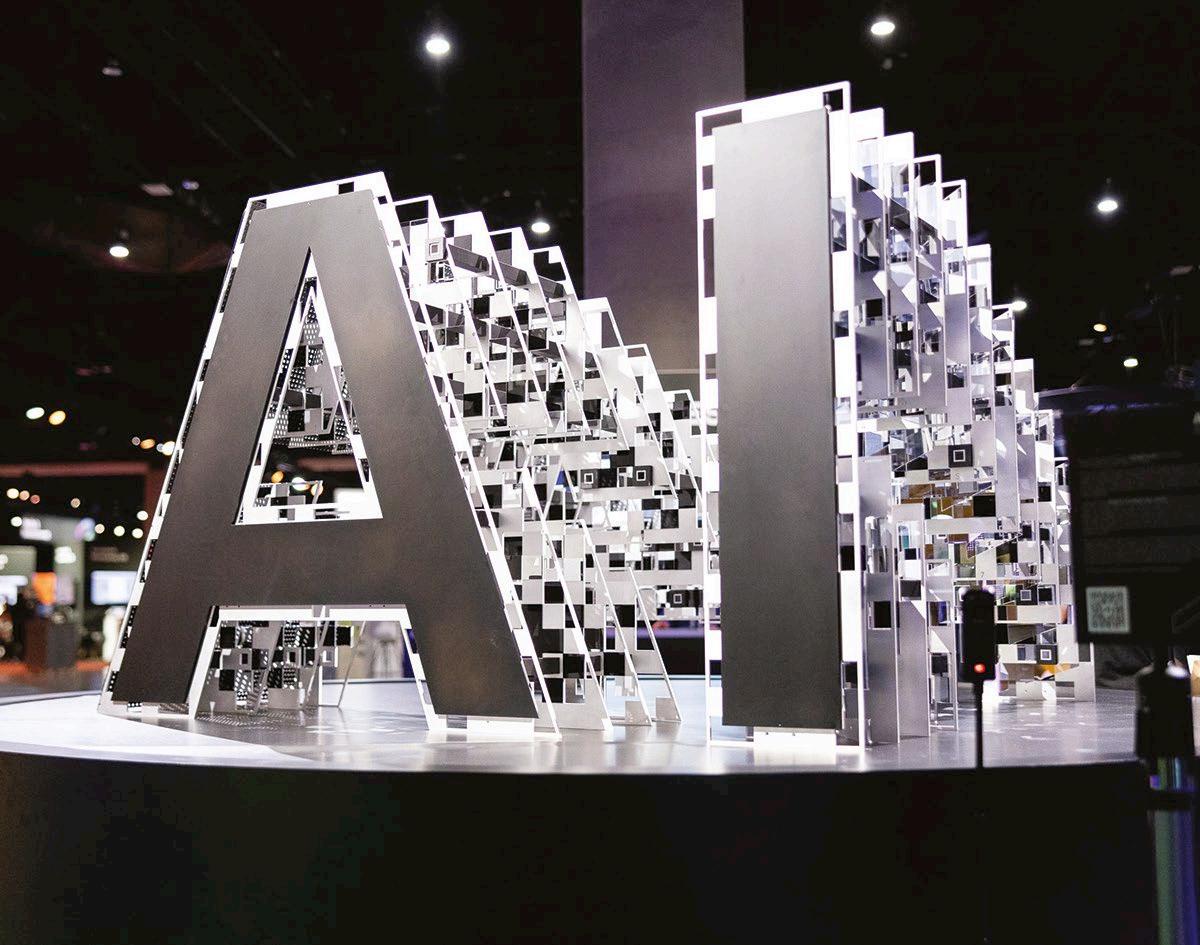
AI is changing the engineering landscape as we know it. In this special feature, leading companies reveal how they are integrating the technology as a more sustainable world beckons
DESIGN
Taking the heat out
Overcoming the challenges of EV wallbox design
How
Redefining
& ELECTRONICS
20 Sensing the future
Exploring the latest developments in sensor technology
22 Reliable connections
The importance of delivering connector reliability in harsh environments
25 Quality control
Safeguarding the quality of precision products
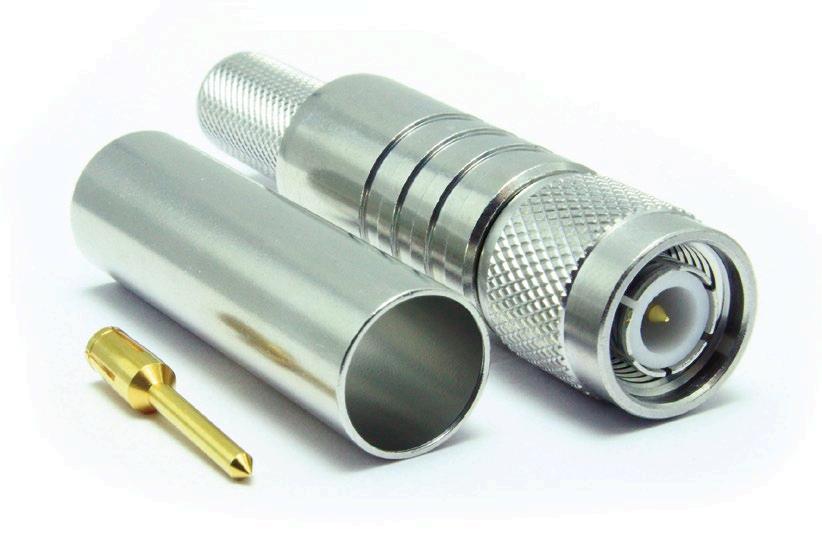
28 The fundamental flaw
Is anti-gravity casting the silver bullet for crack-free metal structures?
30 On guard
The crucial role of corrosion protection products in steel production
COMPOSITES
33
Circular innovation
The latest advances in composites as seen at JEC World 2025
FASTENERS & SEALING
39 The evolution of the trapezoidal thread
Innovative thread technology has delivered a new lease of life to traditional trapezoidal threads
MOTORS, DRIVES & CONTROLS
42
Attractive proposition
Recycling and reusing the magnets used in motors
46
Discussing Donuts
How a new generation electric motor family is offering unprecedented performance
PUBLISHER
Jerry Ramsdale
EDITOR
Hayley Everett heverett@setform.com
STAFF WRITER
Jake Holmes jholmes@setform.com
DESIGN – Dan Bennett, Jill Harris
HEAD OF MARKETING
Shona Hayes shayes@setform.com
HEAD OF PRODUCTION
Luke Wikner production@setform.com
BUSINESS MANAGERS
John Abey | Darren Ringer
ADVERTISEMENT EXECUTIVES
Paul Maher, Iain Fletcher, Peter King, Adam Croft, Marina Grant, David Pattison
e advertising@setform.com
CONTACT US...
t +44 (0) 207 253 2545
e mail@setform.com
SKILLS ZONE
48
Investing in tomorrow
Rounding up the latest training and education opportunities in design engineering
SHOW PREVIEW
49 CWIEME returns to Berlin
The event for coil winding, insulation and electrical manufacturing takes place 3-5 June
Smart Manufacturing in Birmingham
The ‘largest festival of advanced manufacturing’ kicks off 4-5 June

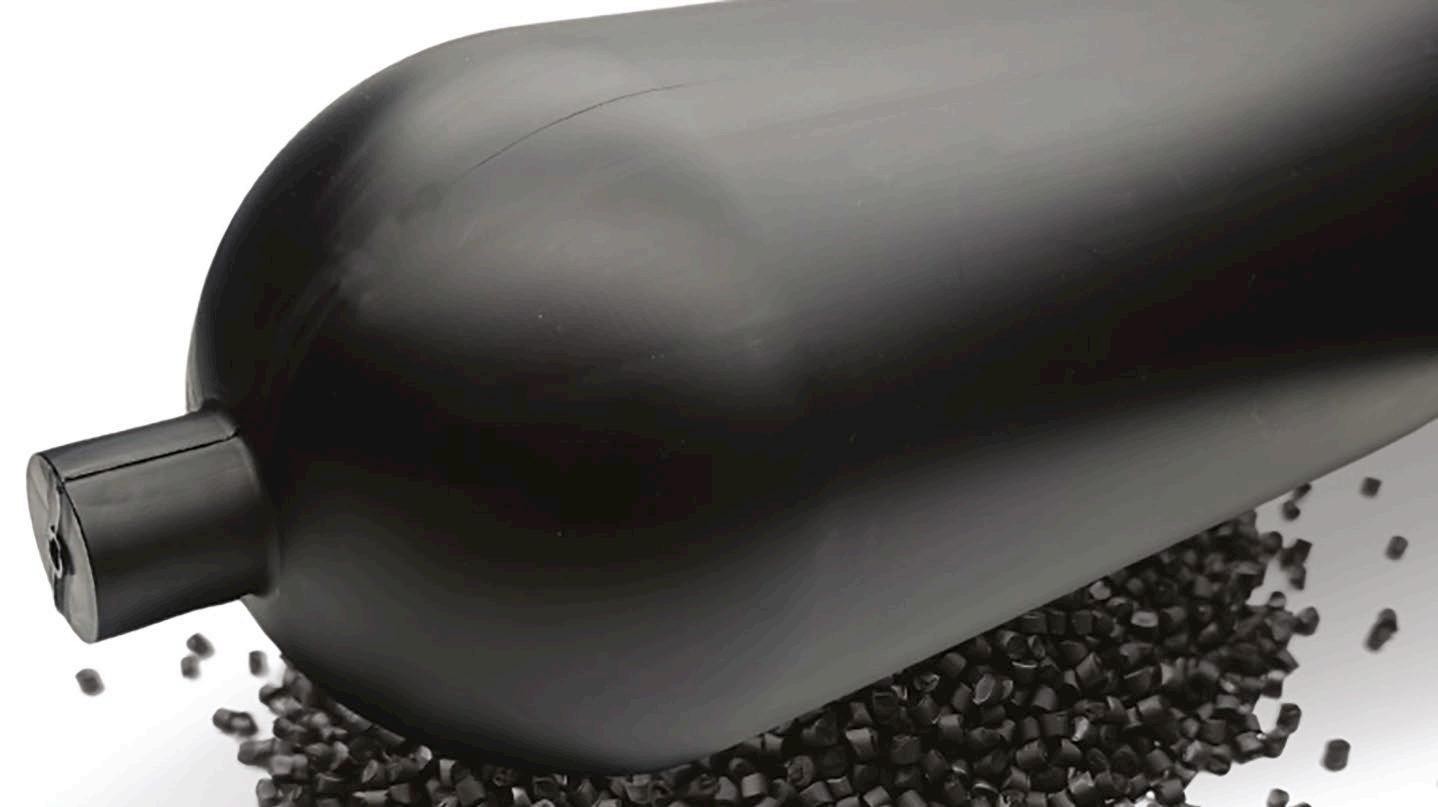
Setform’s international magazines for engineers are published quarterly and distributed to senior engineers throughout the world. Other titles in the company portfolio focus on Oil & Gas, Design, Transport, Mining, Energy and Power.
The publishers do not sponsor or otherwise support any substance or service advertised or mentioned in this book; nor is the publisher responsible for the accuracy of any statement in this publication. ©2025. The entire content of this publication is protected by copyright, full details of which are available from the publishers. All rights reserved. No part of this publication may be reproduced, stored in a retrieval system, or transmitted in any form or by any means, electronic, mechanical, photocopying, recording or otherwise, without the prior permission of the copyright owner.
Setform Limited | 6 Brownlow Mews, London, WC1N 2LD, United Kingdom
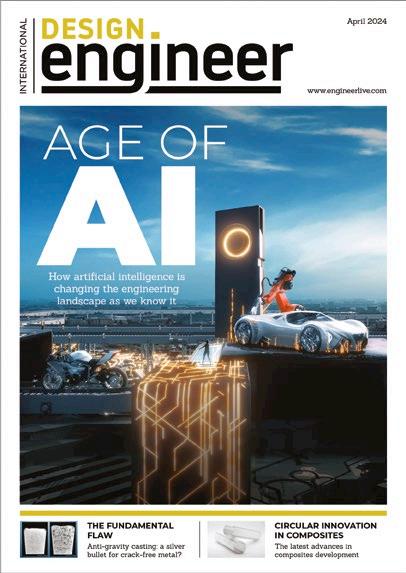
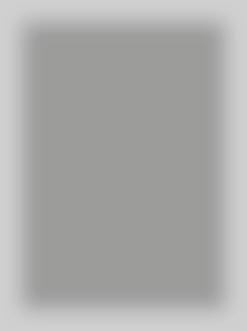
artificial intelligence is changing the engineering landscape as we know it
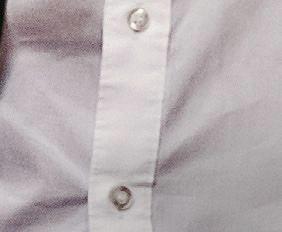
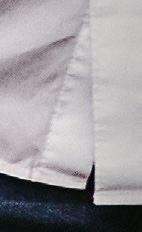


Charging forward to the next generation of e cient transportation
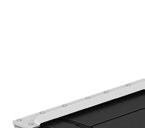
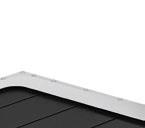
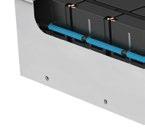

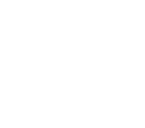
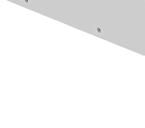

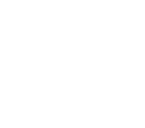
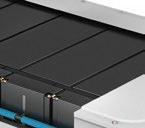

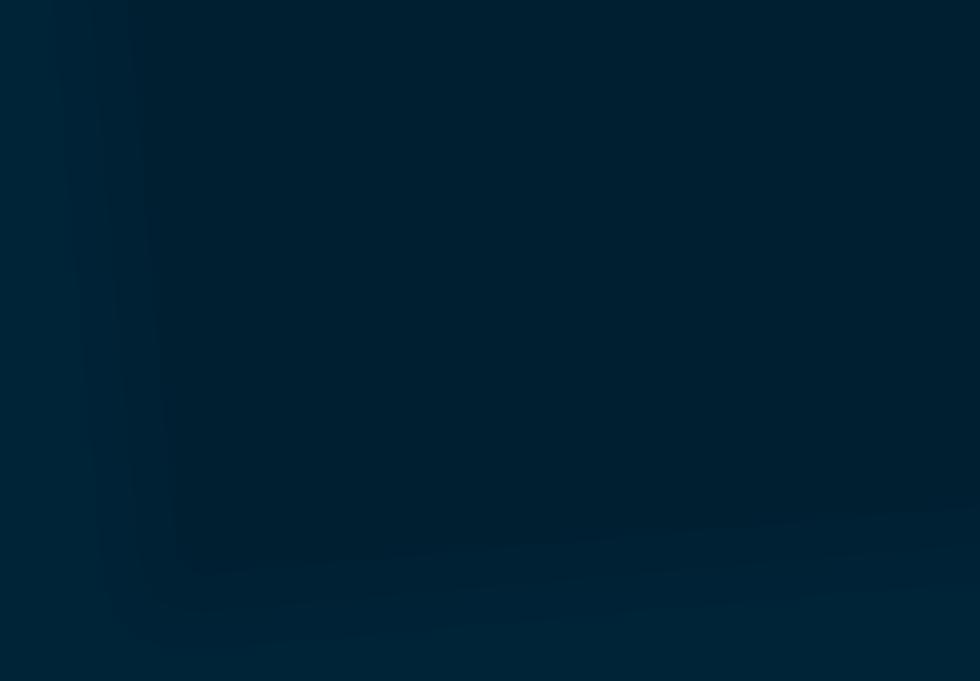
and
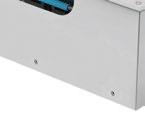
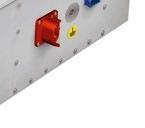
AGE OF AI
How the rapid adoption of artificial intelligence is proving to be a paradigm shift for design engineering

Framework for a target AI portfolio
Modern manufacturing is becoming ever more complex in the pursuit of innovation. Design engineers are, as a result, facing continual challenges in order to walk the tightrope between efficiency, function, form and sustainability within their products. The rapid adoption of artificial intelligence (AI) is already vastly altering how ideas are conceived, systems are designed and solutions are delivered. The potential value of the technology is clear to many, but the path to truly harnessing its benefits and embedding it within our workflows remains unclear.
This special Age of AI feature (pages 6-13) takes a deep dive into the challenges, trends, use cases and insights into how AI can influence the design engineering landscape, both
now and in the future. Across the following pages, we hear from some of the leading companies in this area who are proactively adopting AI into their processes and transforming the way they design and make products as we transition to a more sustainable world.
HARNESSING AI
According to a recent study by international management consulting firm Arthur D. Little (ADL), the challenge of AI adoption is not just about adding new tools, but about “systematically reshaping the very foundations of how organisations create value from innovation.”
Titled “Moving innovation forward: How to harness AI to transform development & engineering,” the report is the result of a collaboration between ADL, the Netherlands Academy of
Engineering (NAE), the Royal Swedish Academy of Engineering Sciences (IVA) and the Koninklijk Instituut van Ingenieurs (KIVI). The report draws insights from over 900 AI and technology use cases, as well as input from leading companies across six industries, in a bid to summarise the practical steps necessary to move beyond experimentation to scalable and meaningful AI integration.
NAVIGATING AI’S IMPACT ON ENGINEERING
In the study, development and engineering comprises activities along the entire innovation cycle, including intelligence gathering, idea generation, R&D, design, prototyping, scale-up and launch. “Deploying AI can seem like drinking water from a fire hose,” the
Source: Arthur D. Little
report states. “AI applications already exist that are applicable for every step of the development and engineering cycle from intelligence through to commercialisation. Prioritisation involves making difficult trade-offs between what’s important versus urgent, what’s easy/low impact versus difficult/high impact, and what’s noregret versus speculative.”
TRENDS AND CHALLENGES
According to the report, there are several key trends and challenges that are radically changing the nature of development and engineering.
The first challenge is what ADL refers to as demand-side challenges – increasing complexity, stricter compliance requirements, and a shift toward integrated, technologyrich solutions as consumers demand smarter, more personalised products. On the supply side, the report identifies skill shortages in AI and software engineering, poor data quality and persistent supply chain disruptions as hindrances to companies’ abilities to innovate.
From a trends perspective, ADL predicts new capabilities in knowledge integration, data management and collaborative innovations will be essential to meet rising technological and regulatory demands. As a “transformative enabler”, AI can augment engineering capabilities, streamline workflows and drive innovation in order to address the growing demands of modern engineering.
The report states: “Traditional approaches are inadequate, adopting AI and other advanced methods is critical to overcoming challenges and maintaining competitiveness.”
PEOPLE BEFORE TECHNOLOGY
Next, the report looked at the potential of current AI tools and the existing barriers to faster adoption, stating: “AI clearly emerges as the technology with the highest potential to transform engineering. Recent developments in AI give it the potential to enhance capabilities across tasks such as design, planning, and problem solving.”
A lack of skills and data, lack of trust and impact of regulations are some of the perceived risks
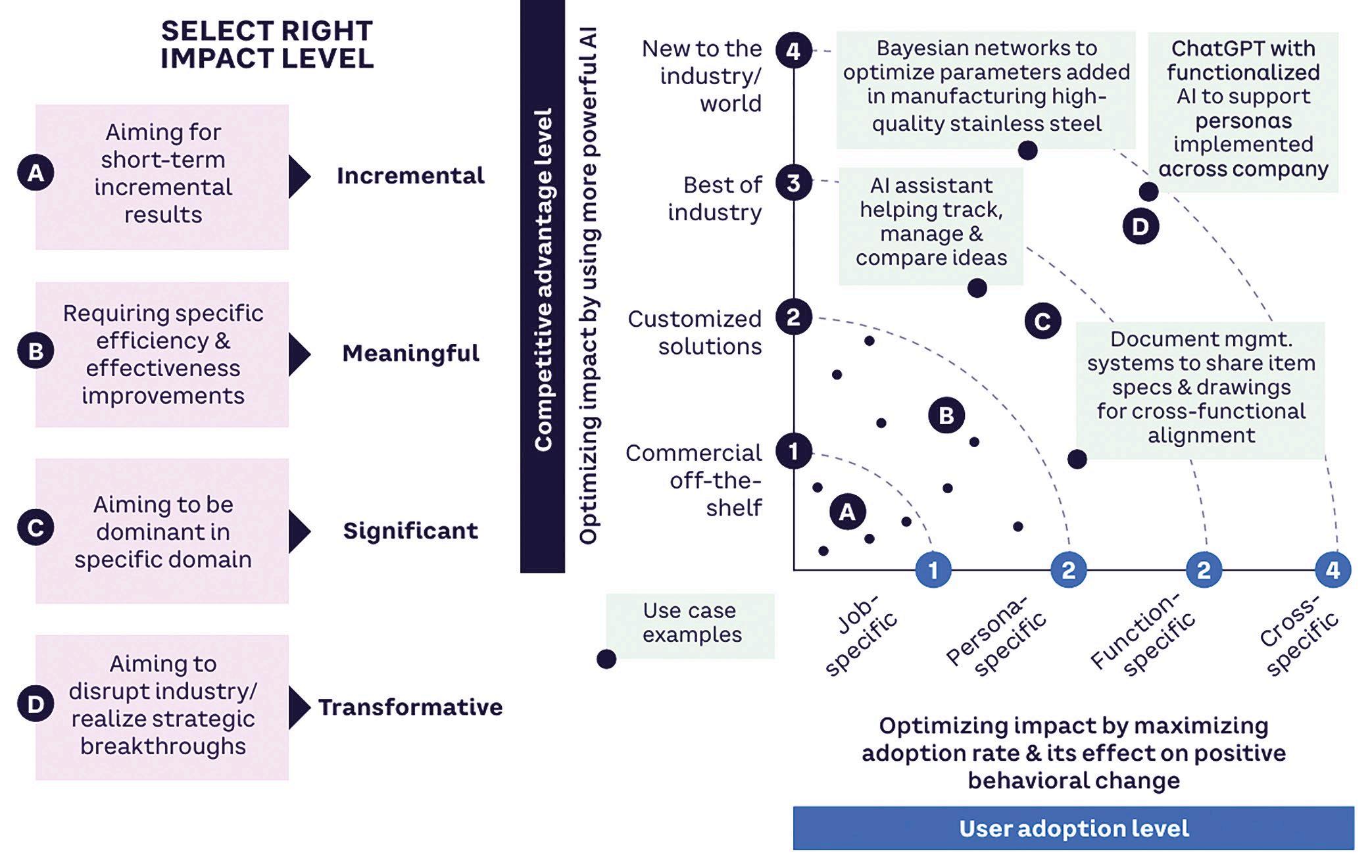
Source: Arthur D. Little
Prioritisation by considering impact and adoption
of deploying AI in engineering and development according to the companies surveyed for the report. ADL also cites user attitudes and behaviours as potential barriers to the technology’s adoption, meaning a people-centric approach is crucial.
“If we look at the future challenges of development and engineering, the potential of AI to help address these challenges, and the risks and barriers around effective integration, we see that, more often than not, the issues are about people – engineers and innovators – rather than systems or technologies,” the report states. “If people are so essential to making progress in AI-enhanced engineering and innovation, it follows that the approach for integrating AI should be similarly people-focused.”
CAPTURING THE FULL VALUE
The report concludes by outlining a practical approach to ensure the alignment of AI integration with the broader development and engineering technology portfolio, which ADL says is vital to ensuring that AI is being deployed to its full value. The report
states that a strategic approach is key: “It is important to prioritise potential AI investments, aiming for competitive advantage to key user personas and their specific needs.” However, this is a balancing act: “Properly integrating various priorities requires a careful collaboration of the desired target situation – where should we aim high and where are incremental improvements good enough?”
Therefore, an integrated roadmap is needed: “A successful way forward aligns with the broader technology strategy, considers leading-edge AI developments and those that are more mature, and allocates implementation priorities based on impact, adoption, and return on investment (ROI).

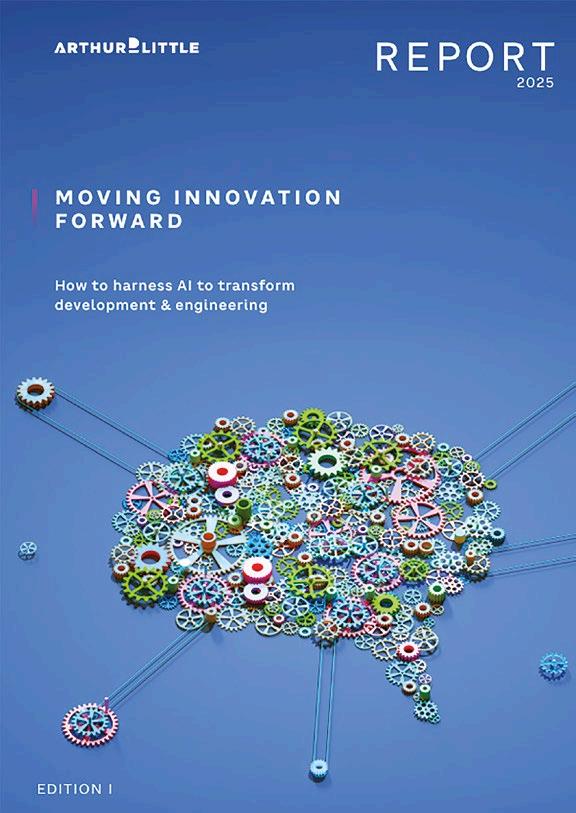

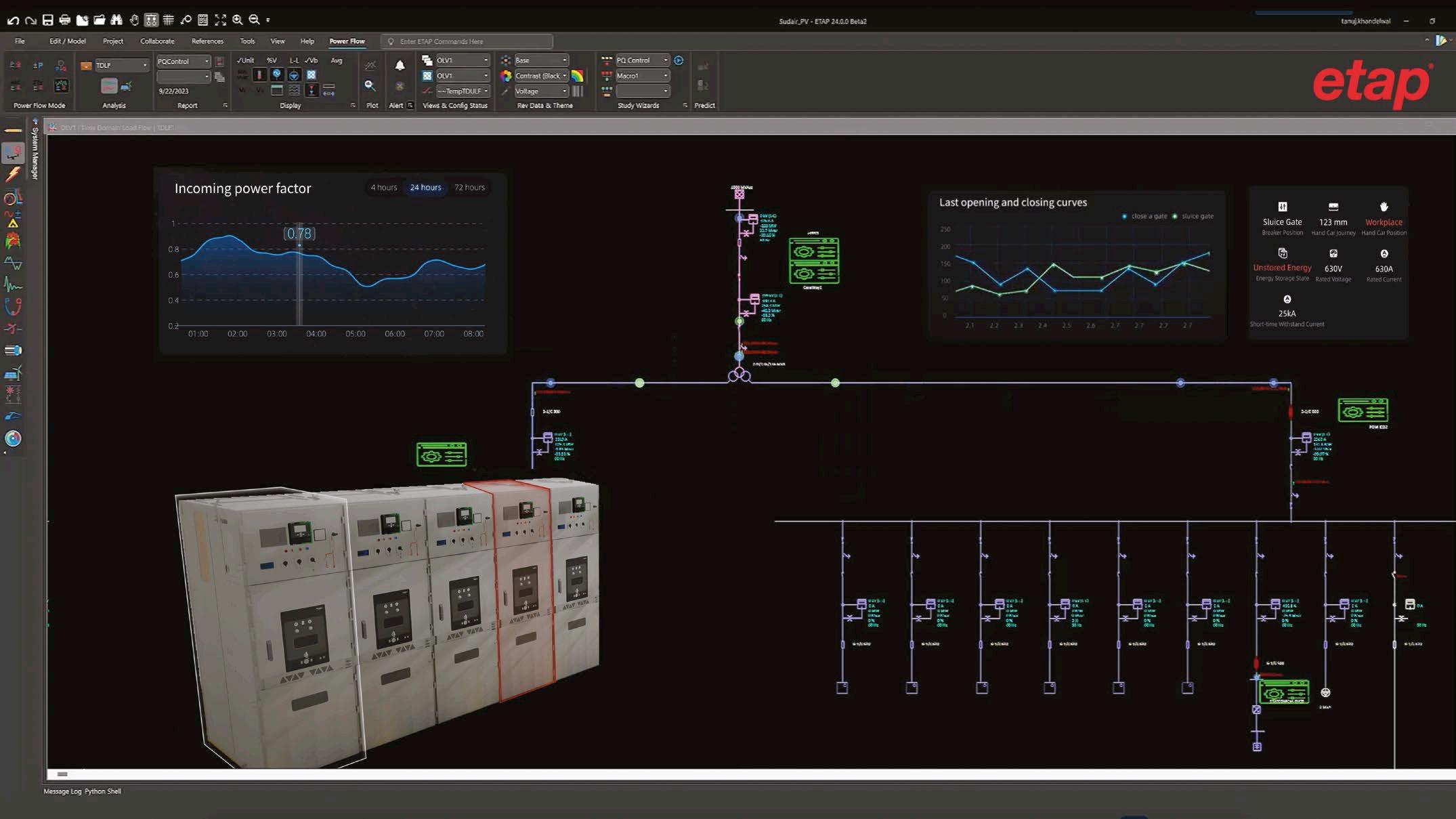
ETAP and Schneider Electric recently unveiled the world’s first digital twin to simulate AI factory power requirements from grid to chip level using NVIDIA Omniverse
A TECHNOLOGY ENABLER
Using AI as a tool to cut through the complexity of current industrial practices and drive automation in energy management
AI is not just a technological advancement; it is a strategic enabler that can help businesses enhance efficiency, reduce emissions, and drive economic growth. Those are the words of Maria Tjader, head of government affairs UK and Ireland at Schneider Electric. The company’s own AIbased solutions have been engineered with the aim of transforming energy management and automation as it pursues its ambitious sustainability and industrial efficiency goals.
“AI really is going to be, and currently already is, the next industrial revolution,” Tjader continues. “By integrating AI into industrial operations, companies can futureproof their business and contribute to the UK’s sustainability and innovation goals.”
With four international ‘AI Hubs’ in India, France, the US and China, Schneider has fully embraced its own
digitalisation journey, within which AI is playing an increasingly important role. In light of recent advances in Industry 4.0, the company is now calling for the potential of AI to be fully harnessed in the industrial space to correctly utilise data, streamline production lines and contribute to predictive maintenance strategies.
“The Labour government came
into power last year with notable policy priorities,” Tjader says. “One is Clean Power 2030 to decarbonise the power system, and the other big flagship policy is an industrial policy with the aim to reboot UK industry and make it more competitive. In January, the government published an AI opportunities action plan, which sets out its belief that AI is going to
AI really is going to be, and currently already is, the next industrial revolution
be a huge component in delivering its policy priorities.”
The opportunity to optimise with AI across vital sectors such as healthcare, education and manufacturing is huge, Tjader says. According to the International Monetary fund (IMF), fully adopting AI could increase productivity by up to 1.5 percentage points annually, potentially contributing an average of £47 billion per year to the UK economy over the next decade.
“If you deploy AI in the energy grid, you’re going to be able to monitor and optimise energy consumption and energy use, ultimately leading to being able to reduce energy and optimise and improve energy efficiency,” Says Tjader. “It’s also going to help to integrate renewable sources better. On the industrial strategy side, industries can use AI to optimise, plan and predict demand and output. It can also be used to manage the supply chain both for industry and in the energy system and to forecast energy demand and production.”
AI FOR INDUSTRY
Schneider Electric recognised the need to become an AI-driven company early on, establishing its Global AI Hub shortly after 2016. Today, the hub is filled with over 350 AI specialists.
“This strategic investment enabled us to develop and deploy AI capabilities internally across our own production lines, distribution centres and facilities,” says Francois Disch, digital transformation delivery lead

at Schneider Electric. “Now, we are extending this expertise to assist other businesses to harness AI for industrial automation, energy management and sustainability in the most responsible way possible. Government strategies provide a strong direction for industry and support solution providers and end users in committing to innovation to reach a more sustainable, profitable future.”
As Disch explains, AI can impact industrial automation in numerous ways. Within asset management, AI enables remaining part lifetime estimation, economic strategy optimisation and maintenance planning, while also identifying opportunities for waste reduction. Meanwhile, AI can improve process yield optimisation via throughput maximisation, while the technology’s automation capabilities can aid in anomaly detection, risk estimation,

risk source identification, patter recognition, and preventative action recommendation.
Elsewhere, AI can enhance data analysis and data value identification, in addition to optimising production plans and forecasting production consumption to adapt optimal power supply planning. In short, there are countless opportunities for AI to make a sizeable impact within industrial production sites and supply chains across the globe.
SUSTAINABLE AI
Crucial to the continued acceleration of AI is managing the technology’s energy consumption, however, and sustainable AI is an area Schneider Electric is fully focused on. To ensure sustainable growth of AI, the company believes technological advancement must be balanced with environmental stewardship. Achieving this will not only require efficient and resilient digital infrastructure, but also incentives for AI adoption, quantifying, assessing and prioritising AI’s impact on sustainability, and establishing and maintaining robust AI governance frameworks.
“It’s really important that businesses, governments and academia continue to assess and quantify what the impact is of AI on sustainability, the environment and the planet,” says Tjader. “At the moment, this feels like the biggest challenge, considering the volatility of geopolitics at the moment, but it is something that is going to be critical if we’re going to be able to use AI for sustainability, energy and industry without negative effects.”
How AI can impact industrial automation KPIs
How AI can impact energy management KPIs
Autodesk is employing a comprehensive crossindustry AI strategy for its product portfolio
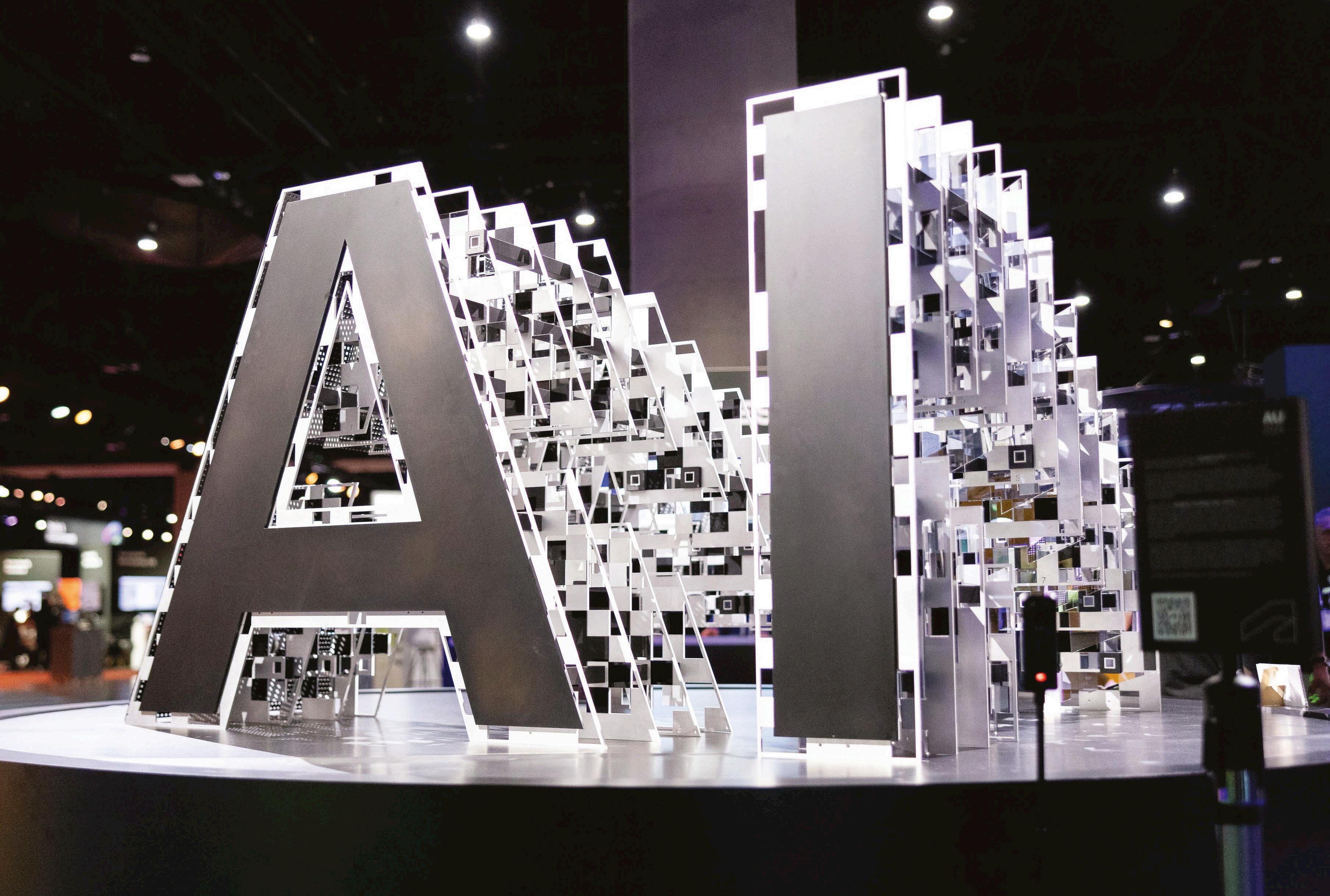
GENERATIVE GEOMETRY
Autodesk’s Daron Green provides an update on the company’s experimental Project Bernini for generative AI 3D shape generation
For design engineers, accuracy and productivity in 3D modelling is vital for the success of digital designs. Generative artificial intelligence (AI) has captured the attention of businesses across a wide range of industries, and while the use of generative AI tools is becoming more common the technology is still in its early stages.
Despite its infancy the potential of generative AI is huge, garnering
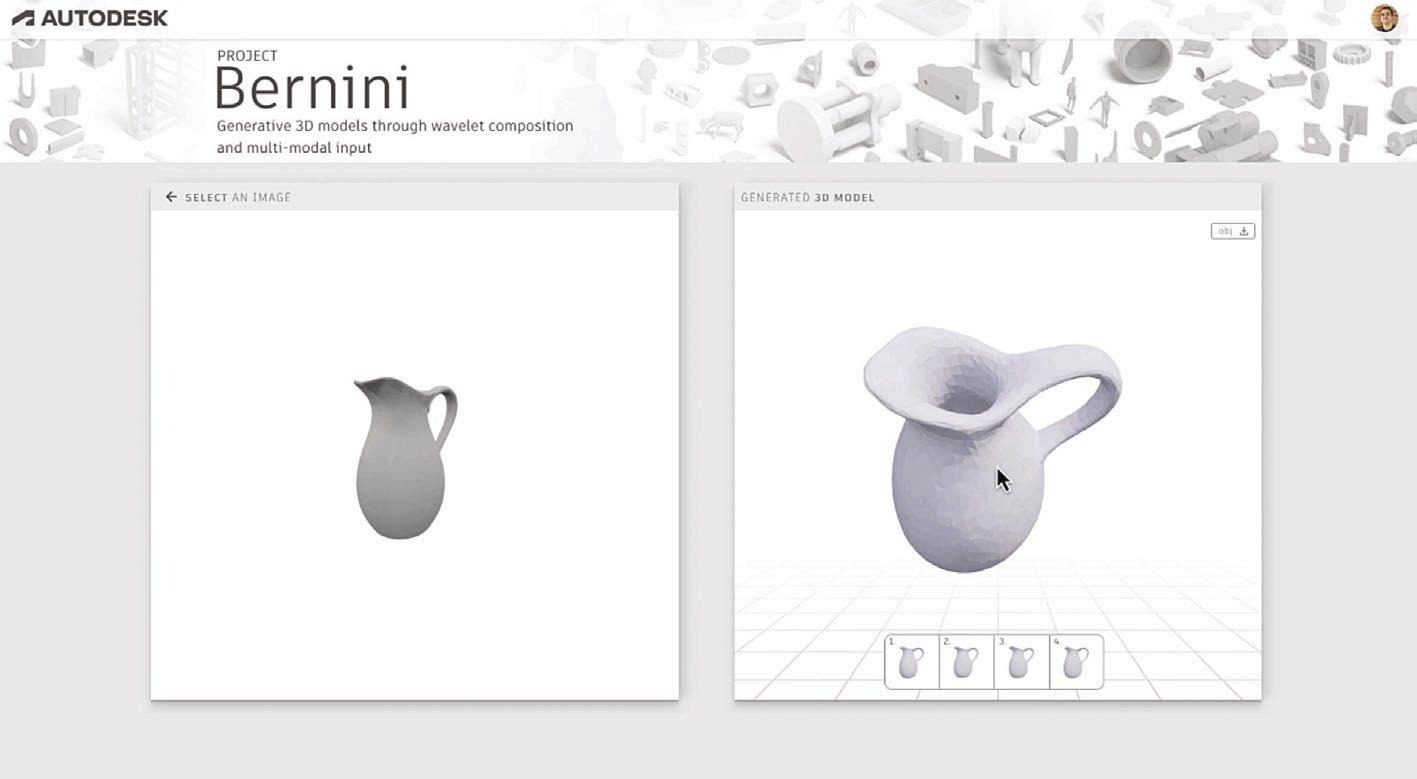
A water pitcher generated on the Bernini AI model
the interest of large global players in the software sector. Autodesk is one of those names, having launched its experimental generative AI proof-ofconcept project, Bernini, last year. The model operates by rapidly generating superior 3D shapes from a variety of inputs including a single 2D image, multiple images showing different views of an object, point clouds, voxels and text.
The aim? To form the basis of generative models that can be
applied for different use cases across architecture, product design, entertainment, and much more.
“Autodesk launched a new Fusion feature in January that employs generative AI to create sketch constraints,” explains Daron Green, chief scientist at Autodesk. “This is a notoriously time-consuming, non-creative and error-prone task. We expect to see more productivity enhancements powered by generative AI like this in the future. Project
Bernini is an experimental generative AI proof-of-concept trained of the world’s largest training dataset of 3D shapes. The lessons Autodesk’s AI researchers learned when developing Bernini have helped the team immensely as they pursue additional generative models.”
FUTURE-PROOFING DESIGN AND MAKE
While Bernini was developed purely as proof-of-concept with no plan for commercialisation, the model offers a promising outlook for generative AI within the future of product design.
According to Autodesk’s 2024 State of Design & Make report, 78% of business leaders believe AI will enhance their industry and 79% agree that AI will make their industry more creative.
“Project Bernini points to a future when professionals will sketch or describe an object using natural language and the technology quickly generates geometry that a designer could import and begin to edit and adapt for their needs,” Green says.
Through Bernini, Autodesk’s engineers focused on generating functional 3D structures that could work in the real world and serve the purpose that the designer has in mind.
GENERATIVE CAPABILITIES
So how does the model work? “Project Bernini accepts a variety of unput modes including natural language text prompts, 2D sketches, point clouds, voxels and more to generate 3D shapes,” Green explains. “We continue to research new input modes and ways to enhance precision and more.”
To best illustrate the model’s capabilities, the example of a water pitcher is given. While other 3D generative models might produce shapes that look like the pitcher with textures that improve their superficial appearance in a specific lighting environment, the Bernini model generates shape and texture separately and does not confuse or meld those variables. Therefore, water pitchers generated by Bernini would be hollow in the middle and could actually hold water, as any real-world pitcher would need to do.
Autodesk’s AI Lab and Research teams trained the Bernini model on
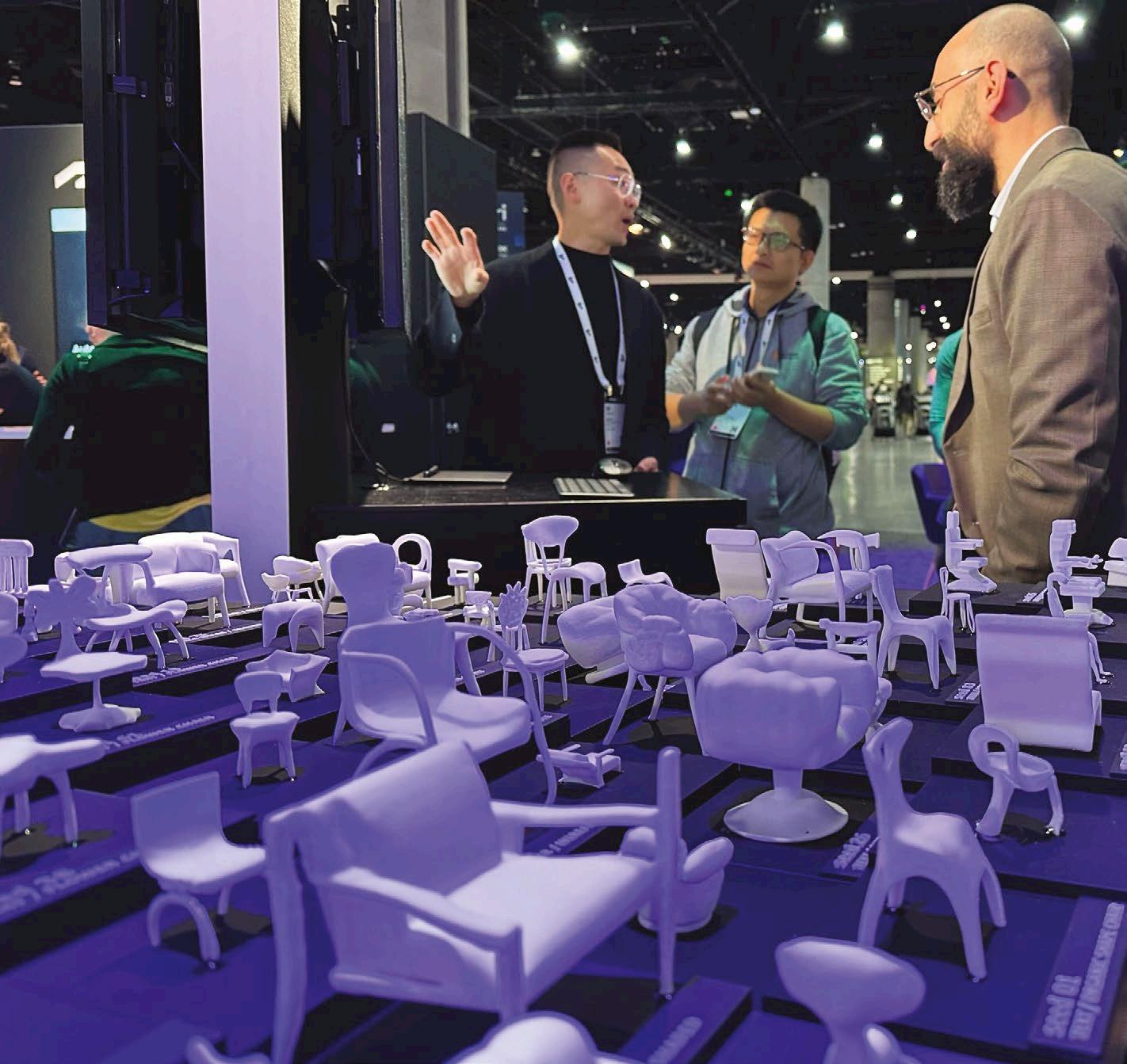
a dataset of 10 million diverse 3D shapes, made up of publicly available data, a mixture of CAD objets and organic shapes.
“The research team learned how to collect and curate the world’s largest training dataset of 3D shapes, train the model, balance compute resources, and evolve the inference results,” Green continues. “These are all valuable lessons as they continue to focus on topical research efforts in generative AI.”
LOOKING AHEAD
While Project Bernini is exciting and at the leading edge of generative AI, Autodesk states its models will become increasingly useful when trained on larger, higher-quality professional datasets. But how disruptive could generative AI be to the product design and engineering process as a whole?
“Initially, we expect to see many time-consuming, tedious tasks automated to such a degree that much of the non-creative and less valuable tedium designers face today with these tools is streamlined or eliminated altogether,” Green predicts. “The
efficiency gains will represent a type of disruption. However, the greater disruptions will come when designers and engineers are able to partner more fully with the software to generate unique designs and systems not only faster but in unique ways.”
In fact, Project Bernini is just one aspect of a much larger AI strategy that Autodesk is deploying, focused on delivering intelligent assistance and generative capabilities across its entire cross-industry product portfolio.
“Today, the design of a physical product is the result of often many thousands of small steps within existing design software,” Green adds. “For example, a cylinder might be extruded and then narrowed. Each step represents a software command. Imagine a future that allows a product to be created from an AIgenerated series of commands where these commands are automatically inferred purely from the designer’s description. There will be disruptions, but the optimistic view is that pairing human ingenuity with generative AIenabled systems will create capacity for this partnership to achieve more.”
Demonstrating Project Bernini
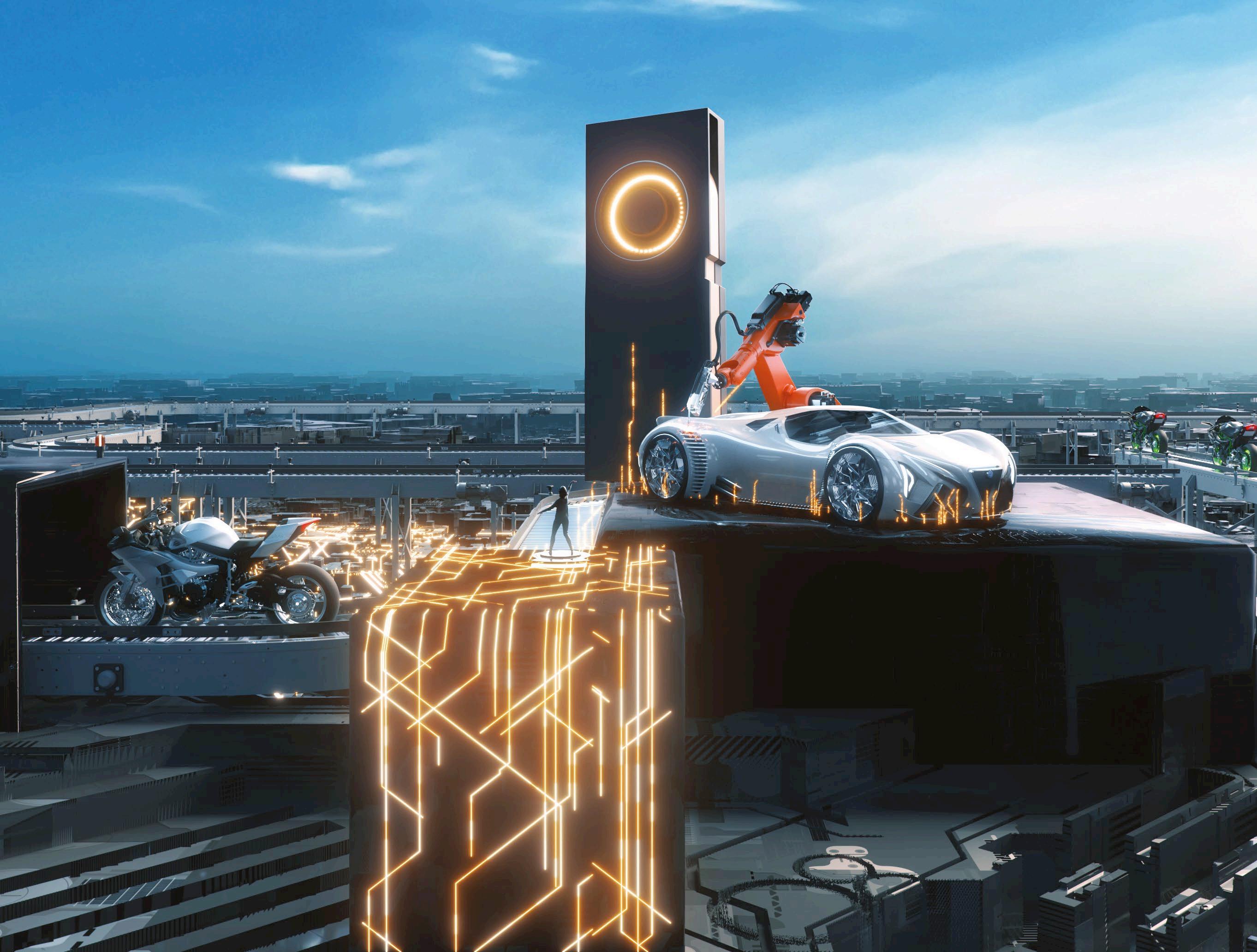
CHANGING THE GAME
NVIDIA’s John Linford gives his take on how generative AI is influencing product design and engineering
Having pioneered accelerated computing since the early 1990s, NVIDIA has become one of the largest and most influential companies in the artificial intelligence (AI) space. With arguably the world’s most advanced platform for generative AI, the firm is enabling industries across the globe to deploy generative AI applications into production at scale.
As such, there are few better placed to provide insight on AI’s current and future impact on product design than NVIDIA’s principal technical product manager, John Linford. International Design Engineer picked his brains on the progress made so far in AI design tools and their application.
“Designers are now using AI-
enhanced tools to create products for industries like automotive, manufacturing, aerospace and energy,” he says. “AI is helping optimise material layouts for maximum strength and minimal weight while taking into account physical constraints like stress, strain, fatigue and thermal limits. AI surrogate models for thermal diffusion, fluid flow and linear deformation provide real-time product performance feedback as the design evolves and enable designers to anticipate physical figures-of-merit like drag or surface pressure before high fidelity simulations are performed.”
Simulation-based design processes are also undergoing transformation, with AI reducing computation
time and improving accuracy in simulations of complex physical systems, he adds: “Everything manufactured is first simulated, and physics-informed neural networks (PINNs) enable simulations that are orders-of-magnitude faster than traditional approaches. PINNs enhance AI models by incorporating the governing equations of physics directly into the machine learning framework. This produces surrogate models that combine physics-based causality with simulation and observed data, enabling real-time prediction. NVIDIA PhysicsNeMo includes PINN architectures appropriate for external aerodynamics, fluid flow and other applications.”
Physics-inspired AI is transforming automotive, manufacturing, aerospace and energy

AI DESIGN TOOL ADVANCEMENTS
The capabilities of generative AI – the ability of algorithms to create new text, images, sounds, animations, 3D models and computer code – are moving at incredible speed. By employing large language models (LLMs), the technology can substantially reduce the time people devote to manual tasks like searching for and compiling information, for instance.
Within more industry-focused scenarios, “Generative AI is changing the game in semiconductor manufacturing, for instance LLMs enhancing code generation in the design space,” Linford offers. “For example, NVIDIA uses ChipNeMo, a domain specific foundation model trained on NVIDIA data, to help our internal design work. Engineering assistant copilots are helping design chips, design systems and optimise fab operations. Agentic workflows combine multiple AI agents to execute complex tasks, like bug summarisation and analysis on multi-modal data such as text, images and video.”
He continues, “At NVIDIA, we build AI to build chips for AI! Over the last
6 years, we have done many AI for chip design research projects and several of these are in production use today. Our projects cover a wide spectrum of design areas, such as architecture design, RTL, verification, synthesis, cell design, physical design – including placement, route and optimisation – as well as analogue design and lithography.”
INDUSTRY OUTLOOK
Generative AI is rapidly finding its feet in a wide range of industrial sectors, Linford says. For instance, streamlining vehicle design and manufacturing in the automotive industry, powering a new wave of healthcare innovation through drug discovery and enhancing the operational efficiency of telecommunications.
“Physics-inspired AI is transforming the automotive, manufacturing, aerospace and energy industries,” he continues. “For example, Siemens Gamesa used the NVIDIA PhysicsNeMo framework to train a PINN that led to 4,000 times faster wind turbine wake optimisation compared with traditional approaches. This speed increase enables large-scale, detailed wind farm layouts that optimise turbine placement and maximise energy output.”
Real-time digital twins (RTDTs) are the cutting edge of computeraided engineering (CAE) simulation, because they enable immediate feedback in the engineering design loop. RTDTs have soared in demand within the aerospace, automotive and electronic design industries in particular.
“Siemens Energy uses digital twins to maximise uptime for heat recovery steam generators,” Linford says. “These massive machines use hot exhaust gases to boil water. The exhaust gases can cause corrosion, leading to downtime for system maintenance. High-fidelity simulations of multiphase turbulent flow help predict where and when corrosion occurs. Physics-informed AI can infer this flow in seconds, making these simulations feasible. With simulation, unplanned downtime is reduced by up to 70%, saving the industry $1.7 billion per year.
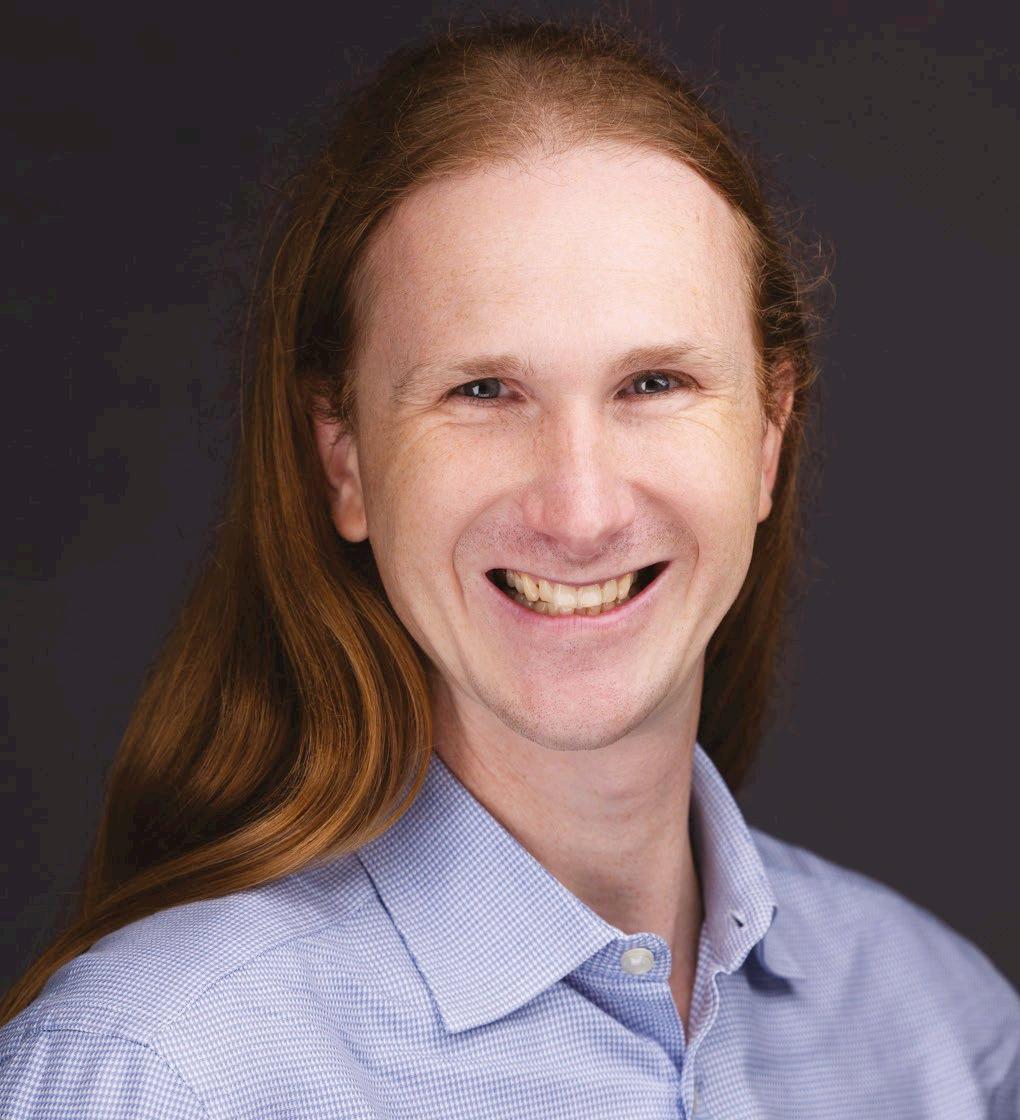
Linford, principal technical product manager at NVIDIA
A LOOK INTO THE FUTURE
According to Linford, generative AI will have a pivotal role to play in how design engineering processes of the future will operate.
“Advanced warehouses and factories use fleets of hundreds of autonomous mobile robots, robotic arm manipulators and humanoid robots working alongside people,” he says. “Implementations of increasingly complex systems of sensor and robot autonomy require coordinated AI training in simulation to optimise operations, help ensure safety and avoid disruptions.”
And what about from NVIDIA’s perspective? “NVIDIA offers enterprises a reference architecture of NVIDIA accelerated computing, AI NVIDIA Isaac and NVIDIA Omniverse technologies to develop and test digital twins for A-powered robot ‘brains’ that drive robots, video analytics AI agents, equipment and more for handling enormous complexity and scale,” he offers. “This framework brings software-defined capabilities to physical facilities, enabling continuous development, testing, optimisation and deployment.”
“Accelerated computing enables AI, and AI enables quantum computing. AI models trained on quantum data generated from simulators and physical hardware are expected to unlock useful quantum computing. Broad adoption of AI ultimately leads to data generation and model training at scales that were previously impossible, transforming industries and enabling new opportunities.”
John
TAKING THE HEAT OUT
In recent years the design of electric vehicle charging wallboxes has been transformed, with devices packing more power and faster charging speeds than ever into increasingly compact housing. This makes managing and mitigating temperatures inside the wallbox a major challenge for design engineers, as Steve Drumm explains
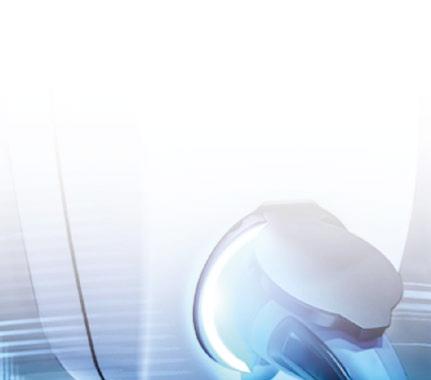
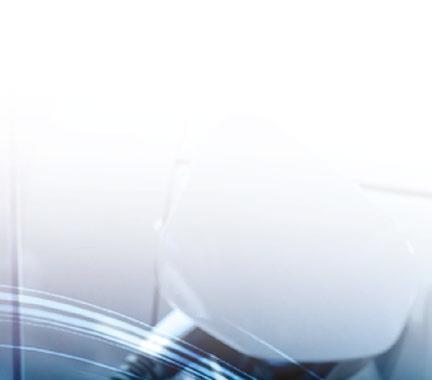
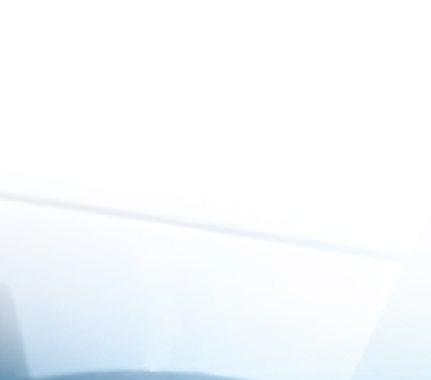
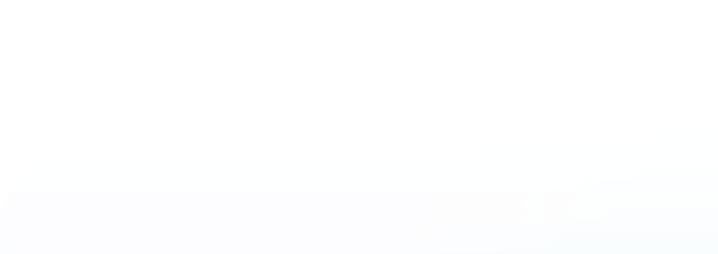
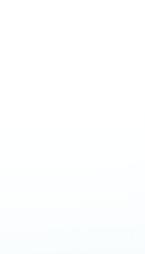

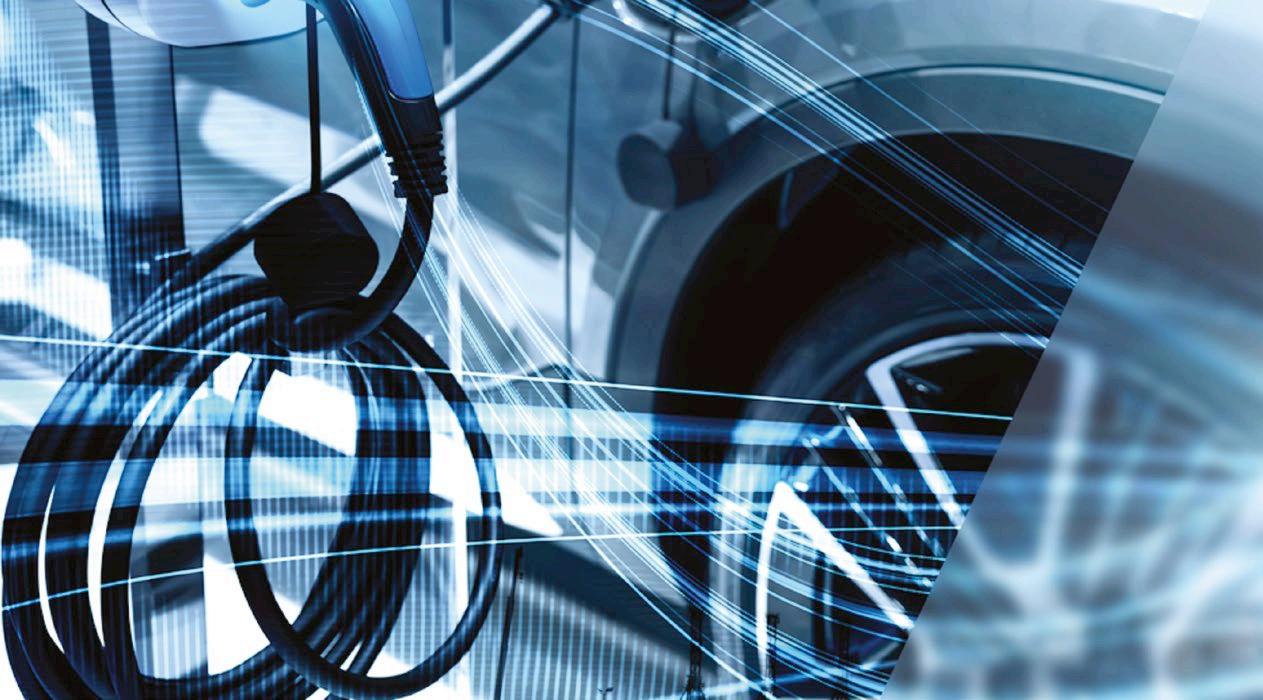
operating temperature
Electric vehicle (EV) charging wallboxes are an increasingly common sight at homes, businesses, public parking areas and petrol stations. With the EV market set to continue its rapid growth in the coming years, wallbox manufacturers are eager to make their devices the most appealing, namely by making them as compact as possible, while providing safety, efficiency, and the fastest possible charging speeds.
The problem here is that packing high power electronics into increasingly small spaces creates more heat. Heat is one of the top enemies of wallbox design. If temperatures are too high then this will have an effect on charging speed and efficiency, and will cause components to wear prematurely. On a particularly hot day, or if a fault is causing the wallbox to overheat, then it may not be able to function at all. Chargers are often in continuous use, or may be used by a series of vehicles in rapid succession, giving the wallbox no opportunity
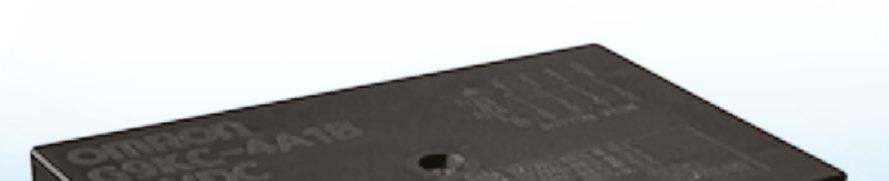
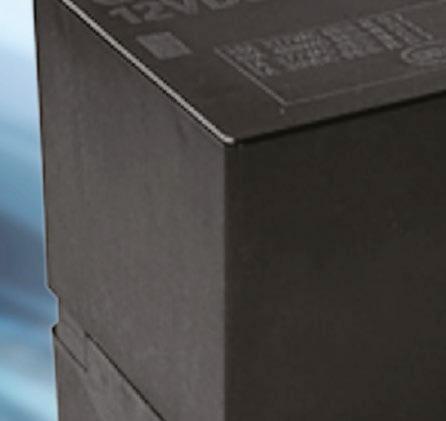
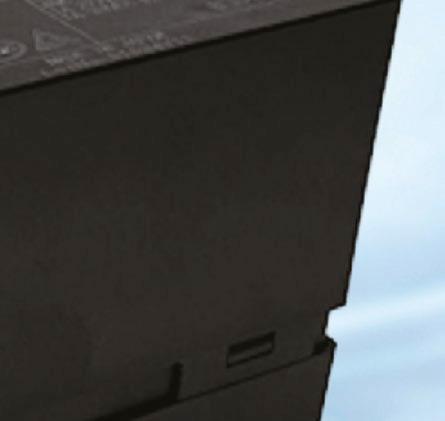
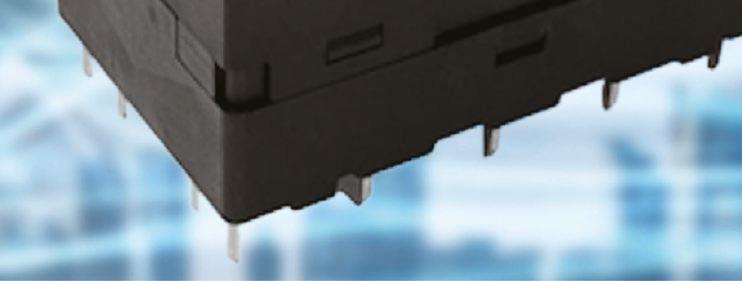
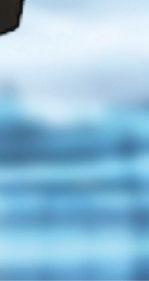
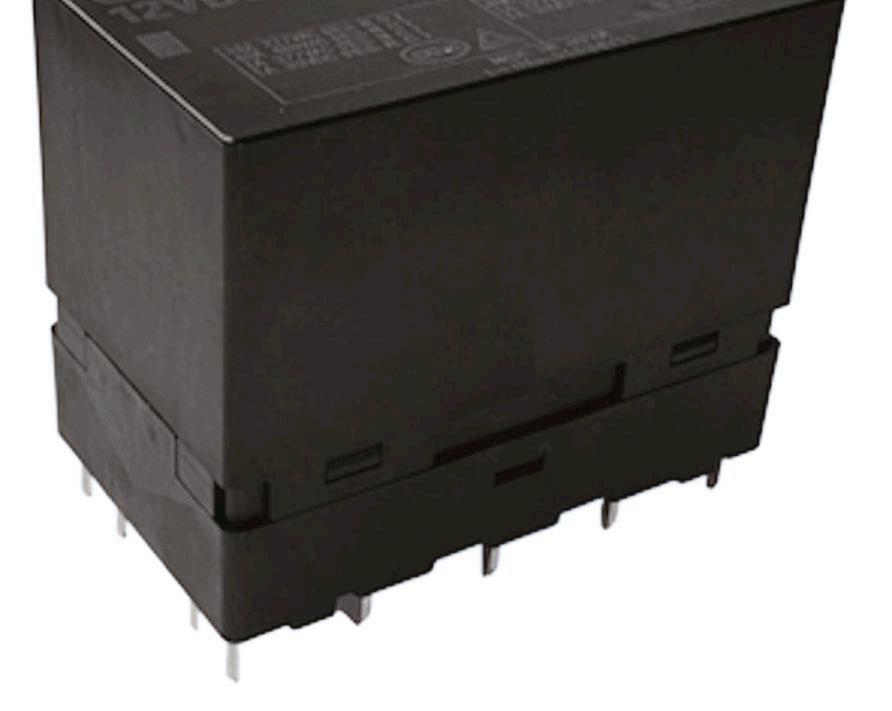
to cool down between charges. In direct sunlight, a wallbox’s internal temperature can easily reach 70-80˚C, and cycle through 50-60˚C variances within the space of a couple of hours. Many chargers will have temperature sensors which will activate a reduction in charging current in overtemperature conditions. While this is good for safety, it means slower charging rates and more inconvenience for the end user.
CHARGER TYPES EXPLAINED
Wallboxes are Mode 3 type chargers. Electric vehicle supply equipment (EVSE) is classified into four different modes: Mode 1, Mode 2, Mode 3 and Mode 4. Mode 1 is the least widely adopted because it does not have safety communication with the EV, and as such is not permitted in some countries, nor is it supported by the majority of EV manufacturers. Mode 2 involves using a charging cable equipped with an in-cable control and protection device, connected
to a household socket. While this is considered safer than Mode 1, charging speeds are still poor compared to Modes 3 and 4.
Mode 3 AC chargers are by far the most common in homes and businesses. While these do not achieve the same charging speeds as the Mode 4 DC fast chargers found at public charging points, they provide safe and secure slow charging – ideal for charging overnight or during the working day. However, since these devices are installed in homes and businesses, space and aesthetics are highly important, and become a key differentiator between manufacturers.
BALANCING PERFORMANCE AGAINST HEAT DISSIPATION
With manufacturers therefore eager to make their devices as compact as possible, while also delivering as much power as possible, this creates a fundamental conflict. The electronics
The G9KC’s lower
reduces the likelihood of reaching current throttling thresholds
within a wallbox will generate heat simply through normal operation, and the higher their power, the more heat is generated. Improved charging speeds can be achieved by using higher charging currents, however this requires the use of higher rated electronic components, resulting in more heat generated inside the wallbox enclosure. It therefore requires careful design to manage and mitigate temperatures to ensure optimum performance and longevity, without compromising on the amount of space required to deliver it.
Power relays are one of the prime culprits for heat inside wallboxes. As such, any reduction in their operating temperature can make a significant difference to the efficiency and longevity of the wider system. Specifically, the contact resistance of the relay is often crucial to the amount of heat it generates. Even a one milliohm increase in contact resistance can equate to up to 18˚C or more in increased load terminal temperature rise.
Omron’s G9KC PCB relay approaches this problem by using a mechanically coupled double-break contact ensuring full compliance to the coming revision IEC 61851 Ed.4. The structure is the result of meticulous development optimised specifically for AC wallbox charging. An optimal copper content with a performance enhanced contact card (cradle) design significantly improves energy efficiency while reducing heat dissipation. As a result, with good overall charger design, operating temperatures in a typical 22kW 32A wallbox can be reduced by as much as 10˚C. This not only facilitates faster, more efficient charging, but also unlocks new possibilities for wallbox designers to develop more compact and robust designs.
The relay’s 4-pole structure means that a single device can replace larger multi-pole contactors and three or four single-pole relays with a single G9KC, reducing the footprint required. It has an extremely low contact resistance, with a guaranteed initial contact resistance of less than 6 milliohms – roughly half that of any equivalent solution on the market. This significantly reduces hotspots caused by flowing current. As well
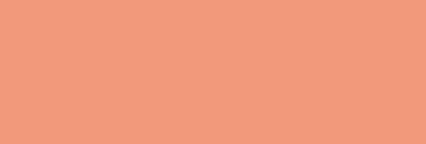

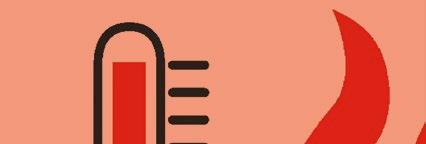
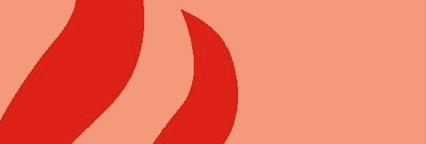
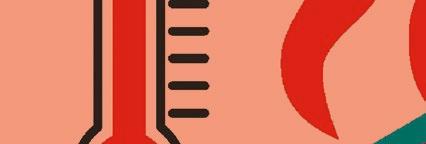
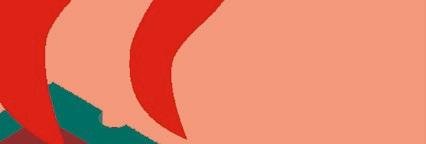

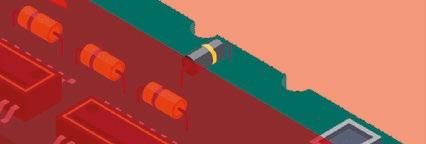
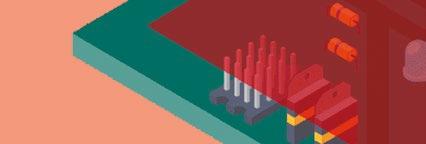

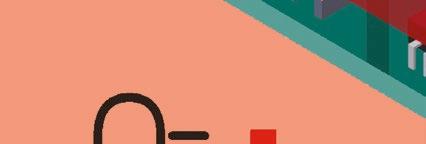
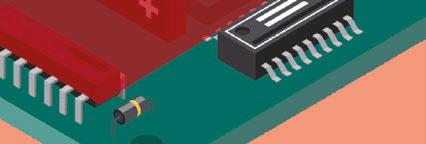
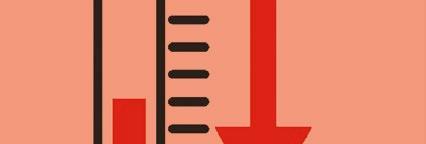
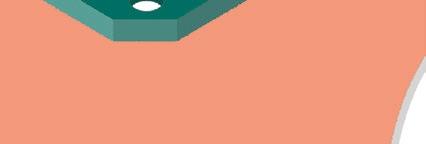
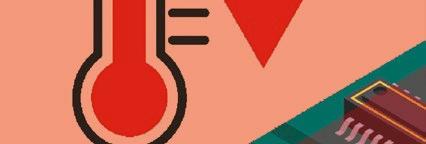
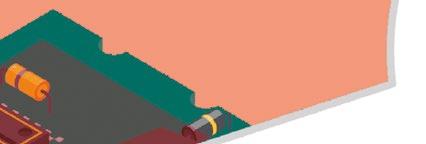
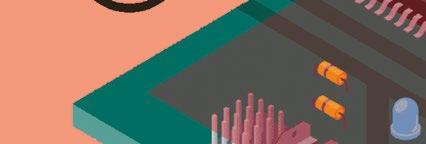
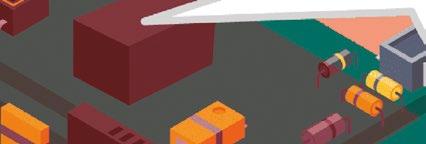
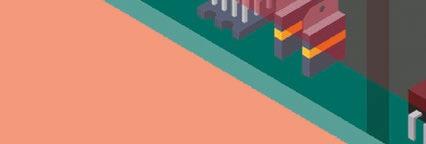
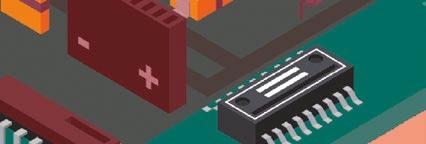
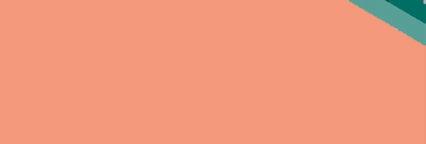
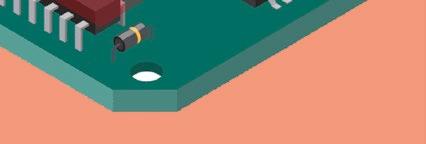
as improving charging efficiency and performance, the G9KC’s lower operating temperature reduces the likelihood of reaching current throttling thresholds, while also contributing to improved reliability and longevity of the relays themselves, as well as surrounding components. Crucially, as well as a low initial contact resistance, the relay retains a low contact resistance throughout its lifetime. This is particularly important given that wallboxes will typically have an operational lifetime of several years or more.
THE FUTURE OF WALLBOX DESIGN
It is widely acknowledged that charging infrastructure must improve quickly to accommodate the rapidly
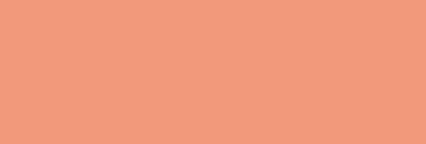
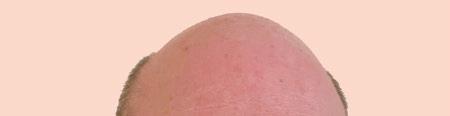
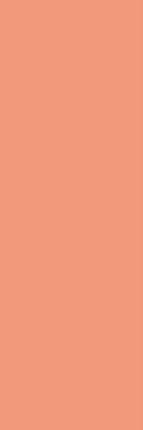
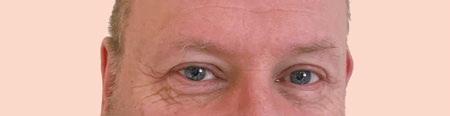
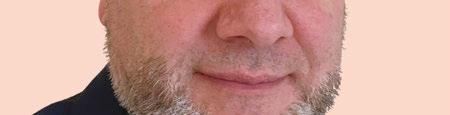
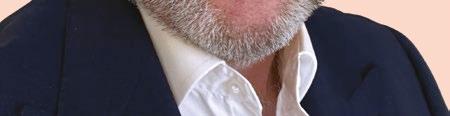
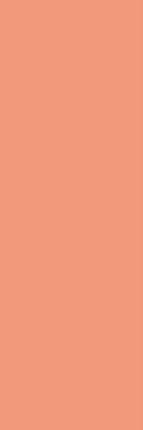
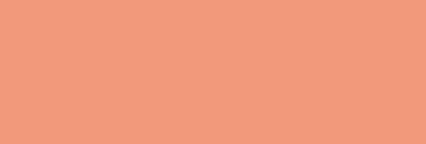

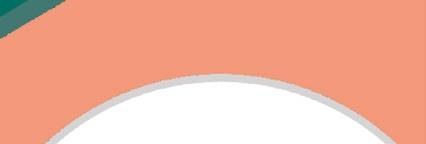
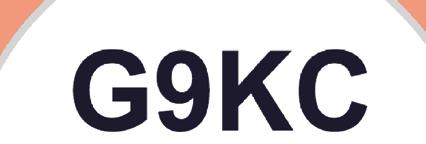
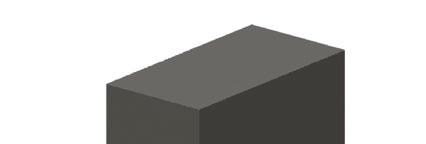
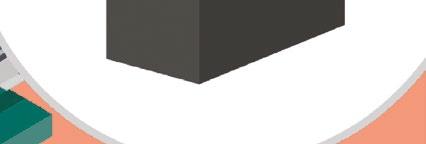
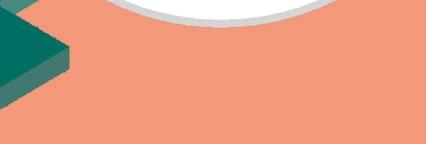
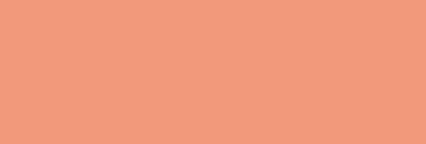
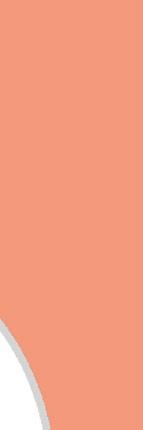
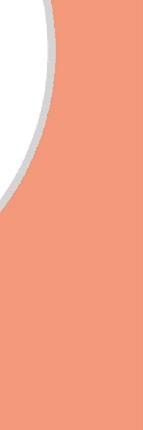
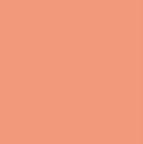
growing EV market. Wallboxes in general offer a low-cost and safe solution for EV range anxiety, which continues to be cited by motorists as a reason not to switch to electric. With new developments in relay technology, they can also be designed to be unobtrusive and fit in with the aesthetics of where it is installed. As well as permitting faster charging, the use of lower heat generating components can facilitate the inclusion of more functionality into wallbox designs, incorporating sensors to monitor charging speeds, and potentially even new developments in wireless charging. Even so, passively managing heat will continue to be an energy efficient and competitive approach to one of the most critical design challenges.
The G9KC PCB Relay
Steve Drumm is at Omron Electronic Components Europe BV
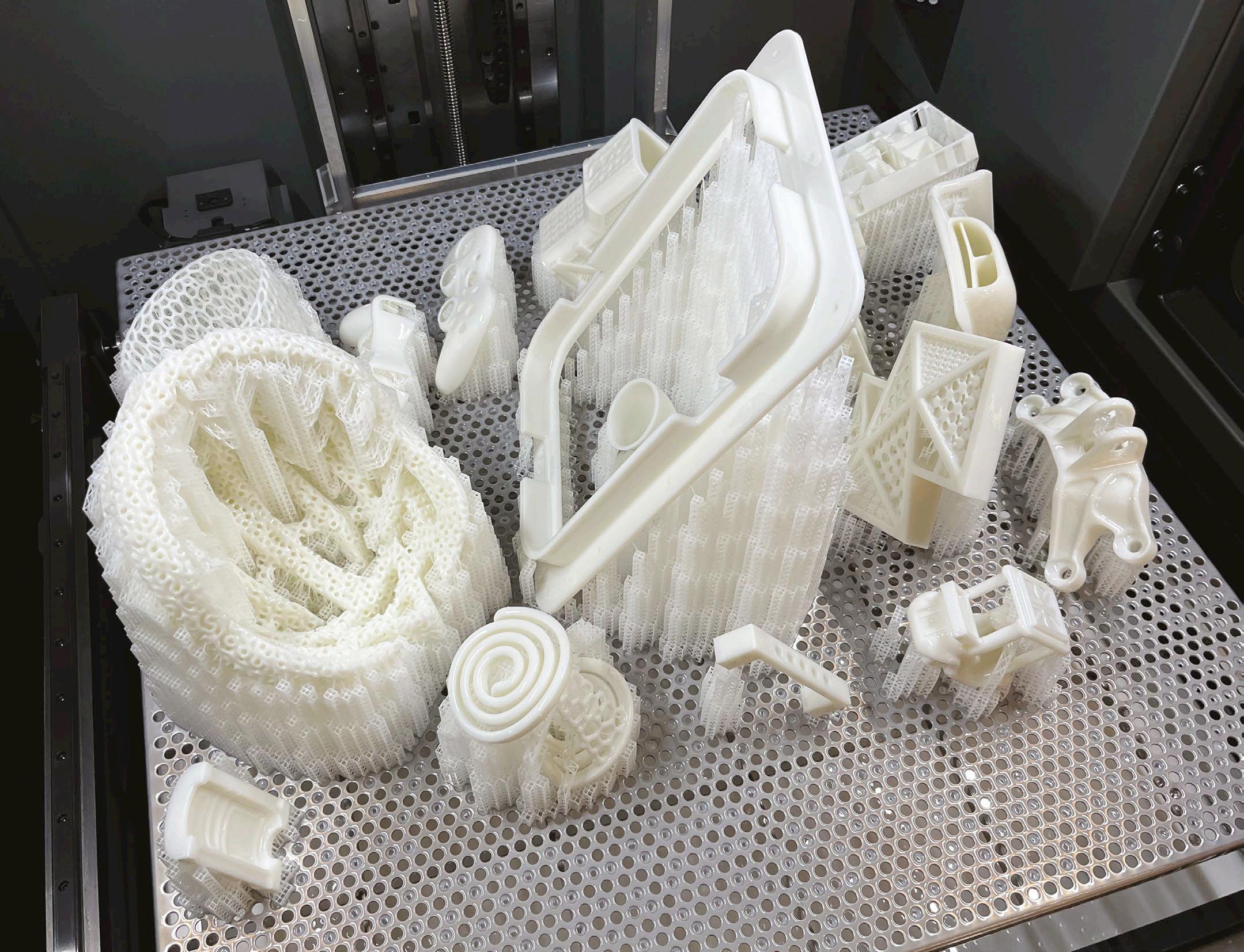
FROM PRINT TO ROAD
Jake Holmes speaks with Andrea Langford and Fadi Abro to discover how additive manufacturing can benefit OEMs
Change will always inspire one of the following two: fear or opportunity. When working with modern technology, change is inevitable. The automotive industry is at the forefront of change, partly through legislation and partly through the advancement of technology and the ever-growing expectations of customers.
Additive manufacturing is currently being used in the automotive industry in three broad cases; prototyping and product development, manufacturing support, and finally production parts such as spare parts or after-market parts.
Fadi Abro, global director of transportation at Stratasys, says:
“I think everyone inherently knows the benefits of 3D printing for product development. You can make parts really quickly and you can do design verification, and the benefits of that are still immense because you’re going to stop problems from happening downstream. The product development is still incredibly important for automotive.”
Abro adds: “Manufacturing support is where you are helping manufacture the product, not necessarily taking a part, manufacturing it and putting it in the car, but using a tool or a fixture of
some kind to help make the assembly process in the manufacturing process more effective and efficient and save some money along the way.”
AFTER-MARKET MODIFYING
After-market manufacturing can have large benefits to all parties involved. Roush Performance is an after-market car modifier, with one of its more famous ranges being adaptations to a Ford F-150. The company was able to achieve cost savings through using additive manufacturing, as it only required 2,000 units of its mounting brackets.
GrabCAD Print is now available for use on the Neo SLA platform
The company’s SAF ReLife solution can efficiently repurpose waste PA12 powder from powder bed fusion printers
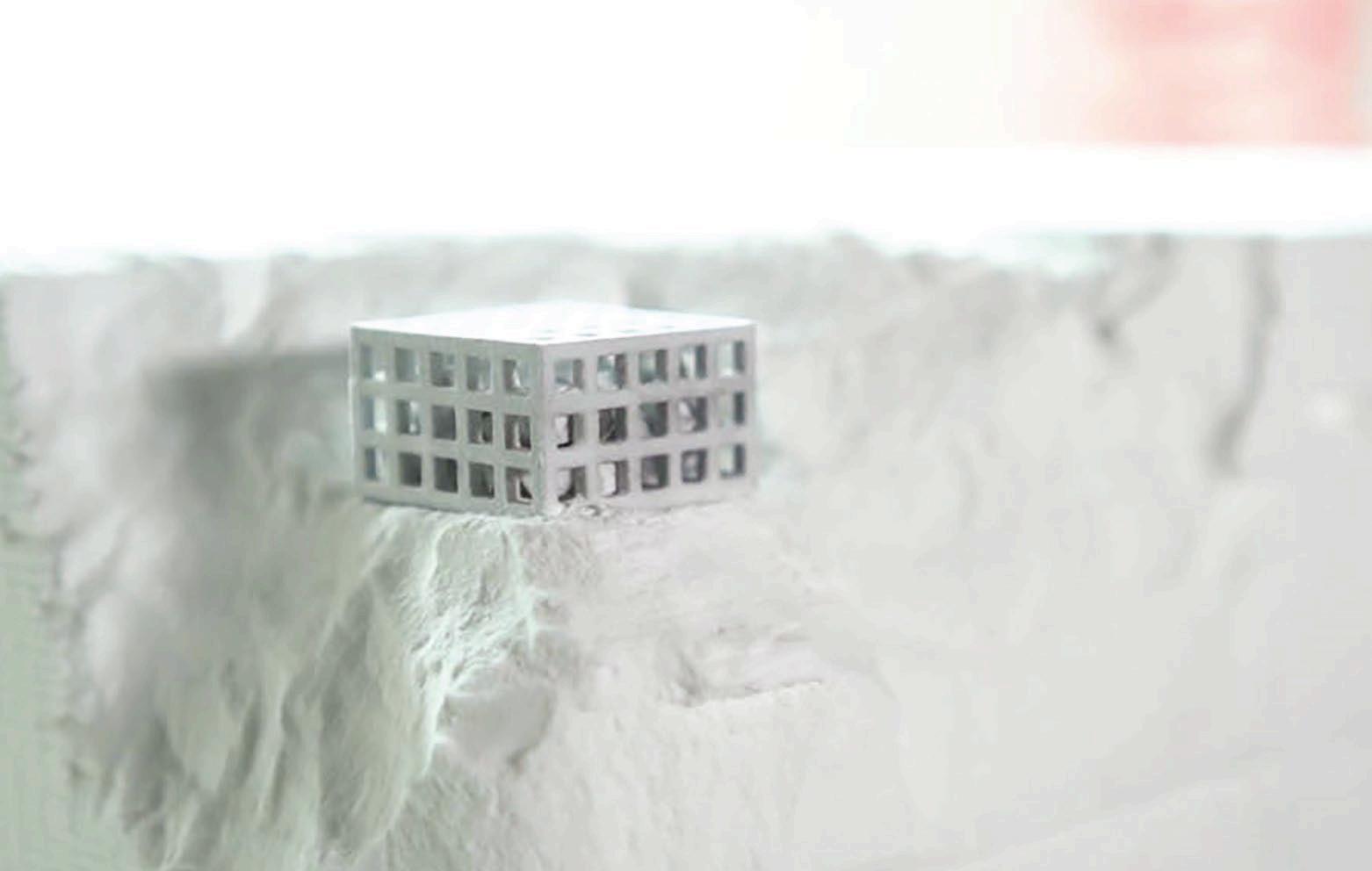
However, the big benefit for Roush Performance came in lead times. The company fits 50 car kits per week. All 50 kits can be made in 10 hours using additive manufacturing techniques, whereas traditional manufacturing could take months for the products to arrive on site.
After-market parts are not just limited to modifications but also repairs and replacements.
Abro explains: “Today OEMs have warehouses filled with parts for every single product line they represent in service, in all of the years. If you need a new grill, they have to go into the inventory and get it.” If the spare part isn’t available, OEMs will have to order a batch of injection moulded replacement parts, rather than being able to just make what is required.
Using Stratasys’ printers and design for additive manufacturing (DFAM) capabilities, OEMs can print on demand the exact parts which are required, leading to no waste and much faster lead times. Currently, the biggest limiting factor in the widespread use of this process is the paperwork involved in replacing parts with materials different to the original materials used.
A NEW WAY TO MANUFACTURE
Andreas Langfeld, EMEA President
at Stratasys, outlines how additive manufacturing can take its next steps forward. Langfeld says: “The next step of the evolution, that is also happening today, is you are not just using additive manufacturing for tooling, jigs, and fixtures but as an alternative to traditional manufacturing methods or end-use components.”
Langfeld cites how spare parts of trains, both for exterior and interior use, are being made using additive manufacturing – made possible by the availability of materials which meet the EN 455/2 standard required. McLaren’s race teams are also taking advantage of this technology, with Langfeld saying wind-tunnel tests are being conducted using products manufactured via 3D printing.
Abro adds: “The ability to iterate and change designs quickly gets you to market first.”
The use of additive manufacturing, even if it is not directly used in the finished product, can have large benefits for an OEM, and hence is a massive incentive for manufacturers to incorporate into their processes.
LICENSE TO PRINT
Langfeld says: “The training of the operators is not a problem, it’s a machine and they [engineers] are used to working with machines. It’s less complex than other heavy machinery
The ability to iterate and change designs quickly gets you to market first
that you will find on the shop floor.”
The challenge is design, before additive practices make it to the shop floor. Company’s mindsets will need to move towards additive manufacturing to deliver lightweight structures and complex geometries that cannot be achieved through other manufacturing methods.
Langfeld expands: “Increasing that mindset, that’s the real challenge in terms of education, and that’s where the market still has a gap. There is not a huge range of design services for specific industries.”
Stratasys has partnered with aerospace company AMcraft to provide certified designs in aerospace. The combination of certified aerospace designs from AMcraft and certified 3D prints from Stratasys creates a full package for clients.
MANUFACTURING TOMORROW
Although it is unlikely complete vehicles will ever be 3D printed, the influence of the process is going to grow, especially as automotive companies look to cut costs and lead times whilst offering more personalisation.
As waiting times start becoming more harmful to businesses’ sales and customer satisfaction, the appeal of additive manufacturing will grow.

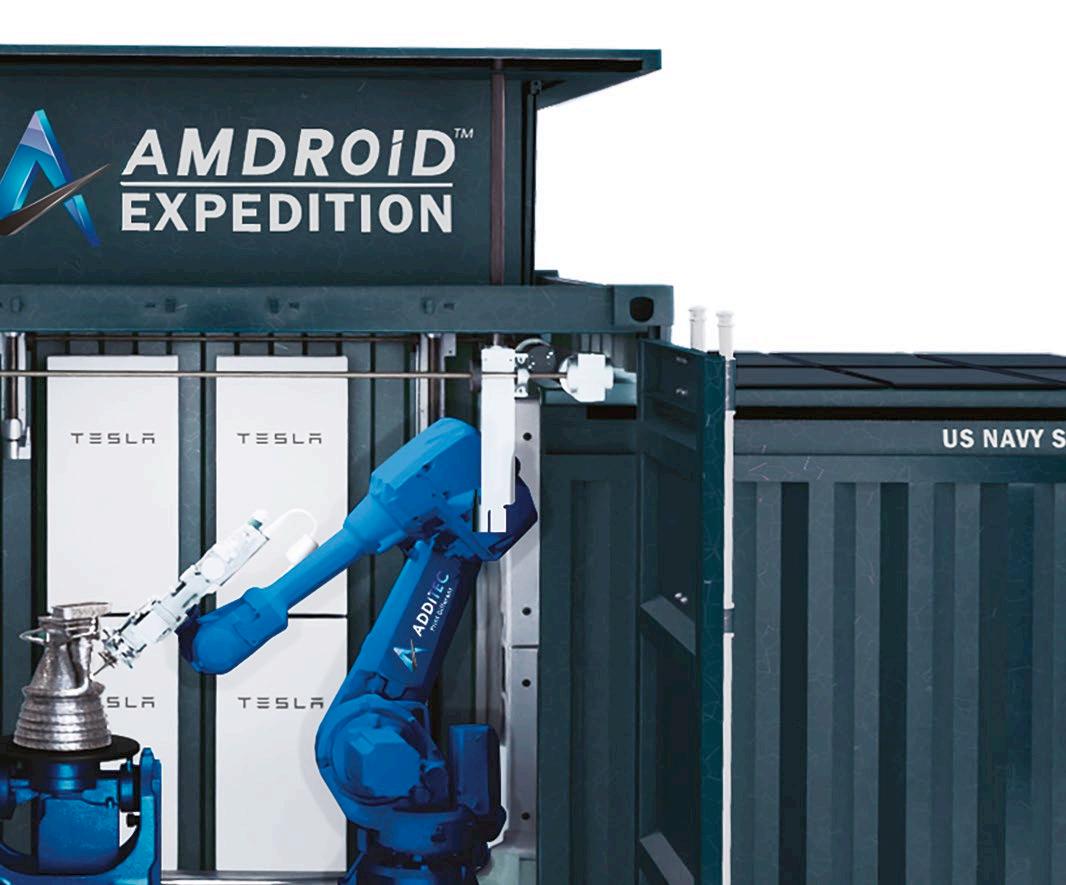
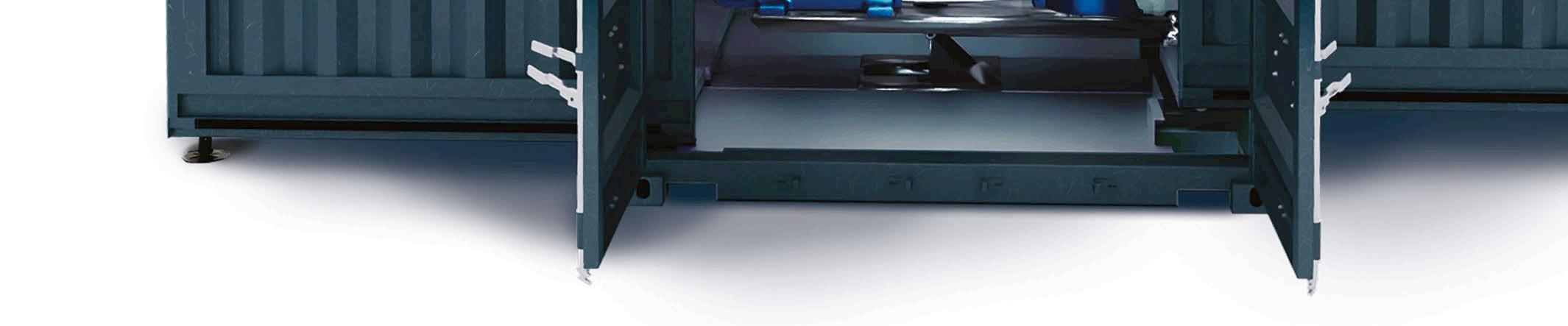
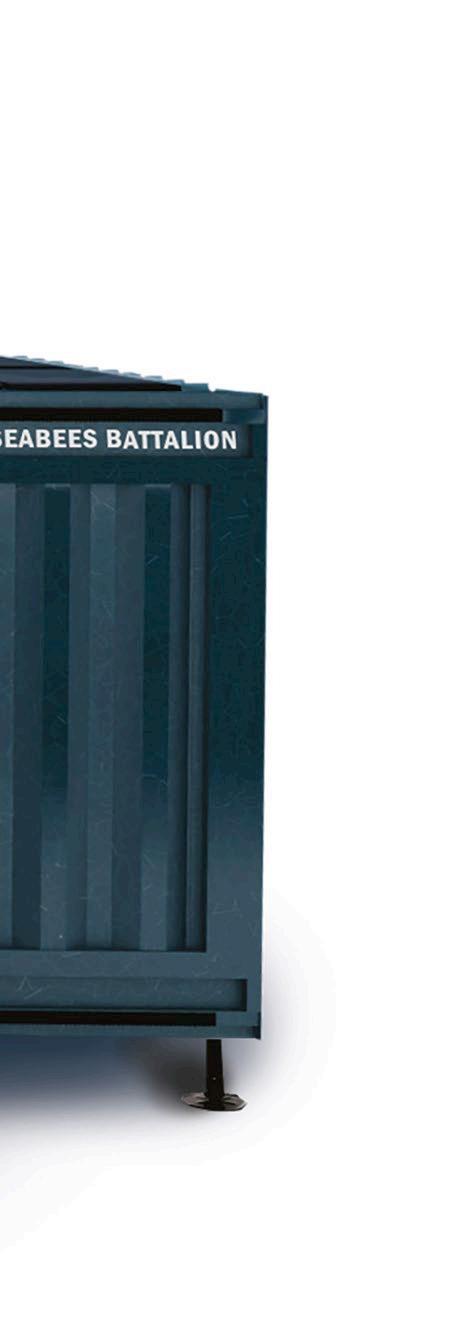
REMOTE REPAIRS
Introducing a new LDED solution poised to redefine point-of-demand manufacturing and metal repair
Remote manufacturing is becoming increasingly important for efficiency, flexibility and cost savings in the modern manufacturing landscape. Improved resource utilisation goes hand in hand with this, as does lessening the carbon footprint of manufacturing operations as global industries work towards their net zero goals.
Additive manufacturing is one technology that is changing the game here, particularly through enabling on-demand production in remote or challenging environments. A recent string in the technology’s bow is Additec’s new Amdroid X laser directed energy deposition (LDED) turnkey solution, designed for the defence, construction, energy and emergency response industries.
MISSION-CRITICAL MANUFACTURING
Built for rapid deployment, the Amdroid X enables manufacturing and repairs to metal parts in remote and off-grid locations. The machine’s portability, efficiency and autonomy is poised to transform manufacturing in areas such as offshore oil platforms, temporary construction sites, and disaster recovery zones where traditional manufacturing
methods fall short.
“The Amdroid X is a true pointof-demand manufacturing solution, tailored for the defence sector and unmatched in the market,” says Brian Matthews, Additec’s CEO. “Its advanced features, adaptability and rapid deployment capabilities address critical needs across multiple industries. This self-sufficient system operates with minimal external resources, making it invaluable in remote and off-grid environments.”
DELVING INTO THE TECH
The Amdroid X’s portable modular design is certainly eye-catching –the technology is housed in a 10foot container expandable to 169 square feet. Included in the footprint is an integrated command centre for seamless operation in harsh conditions, an advanced energy system, self-sustaining gas supply and user-friendly software tools.
Featuring an optional ultra high power 12kW fibre laser, the system is capable of producing large-scale metal components from stainless steel, aluminium, copper and other materials.
“The Amdroid X streamlines the prototyping process by enabling fast,
on-site production of metal parts,” an Additec engineer explains. “With its powerful 6kW fibre laser – upgradeable to 12kW – it achieves deposition rates of up to 4kg/h, allowing engineers to iterate designs quickly and cut development time. Its multi-axis robotic system handles complex geometries with precision, reducing the need for post-processing and enabling faster evaluation on prototypes.”
Meanwhile, 54kWh of storage across four ‘power walls’ make up the container’s advanced energy system, which is fully rechargeable via solar technology to ensure reliable off-grid performance. The container also has a self-sustaining gas supply by means of a built-in nitrogen generator that extracts nitrogen from ambient air, eliminating the need for external shielding gas in most applications.
“The Amdroid X can manufacture a wide range of high-performance metal components, including engine components such as turbine blades, housings, and other critical aerospace and energy parts,” continues Additec’s engineer. “The system can also manufacture structural parts such as support brackets, frames and loadbearing components for industrial applications, and maritime hardware
The Amdroid X LDED solution for remote manufacturing
like propeller blades and hull reinforcements. The machine can also produce specialised tools and moulds tailored for specific manufacturing needs.”
WIDE APPEAL
“The Amdroid X’s versatility makes it a game-changer across multiple industries,” says the Additec engineer. “In defence, it enables on-site production and repair of missioncritical parts in remote locations, keeping operations running smoothly. In aerospace, it supports the production of lightweight, complex parts and enables field repairs, reducing downtime and supply chain dependency. The Amdroid X is also designed for use on ships and offshore platforms, making maintenance and repairs more efficient. Finally, in the energy and mining sector, it can assist in fabricating and repairing large metal components for oil rigs and infrastructure, ensuring minimal downtime.”
By enabling on-site production, the Amdroid X could help to eliminate supply chain delays and accelerate repair times. This capability is crucial in situations where fast turnaround is essential, such as military operations to ensure mission readiness, remote energy installations for reduced downtime, or disaster response for the rapid fabrication of essential components to restore damaged infrastructure quickly.
VERSATILE MANUFACTURING
Alongside its remote manufacturing capabilities, the Amdroid X can also provide benefits for in-house production sites, says Additec’s engineer.
“While it excels in field deployment, the Amdroid X is also a valuable addition to factory floors,” they confirm. “Its compact footprint and fast setup make it perfect for producing small batches, custom components or on-demand replacements without disrupting existing production lines. We also have the Amdroid 3D printer which is specifically designed for that environment.”
So, how will portable technologies like the Amdroid X influence how we manufacture parts in the future?
“Portable, self-contained
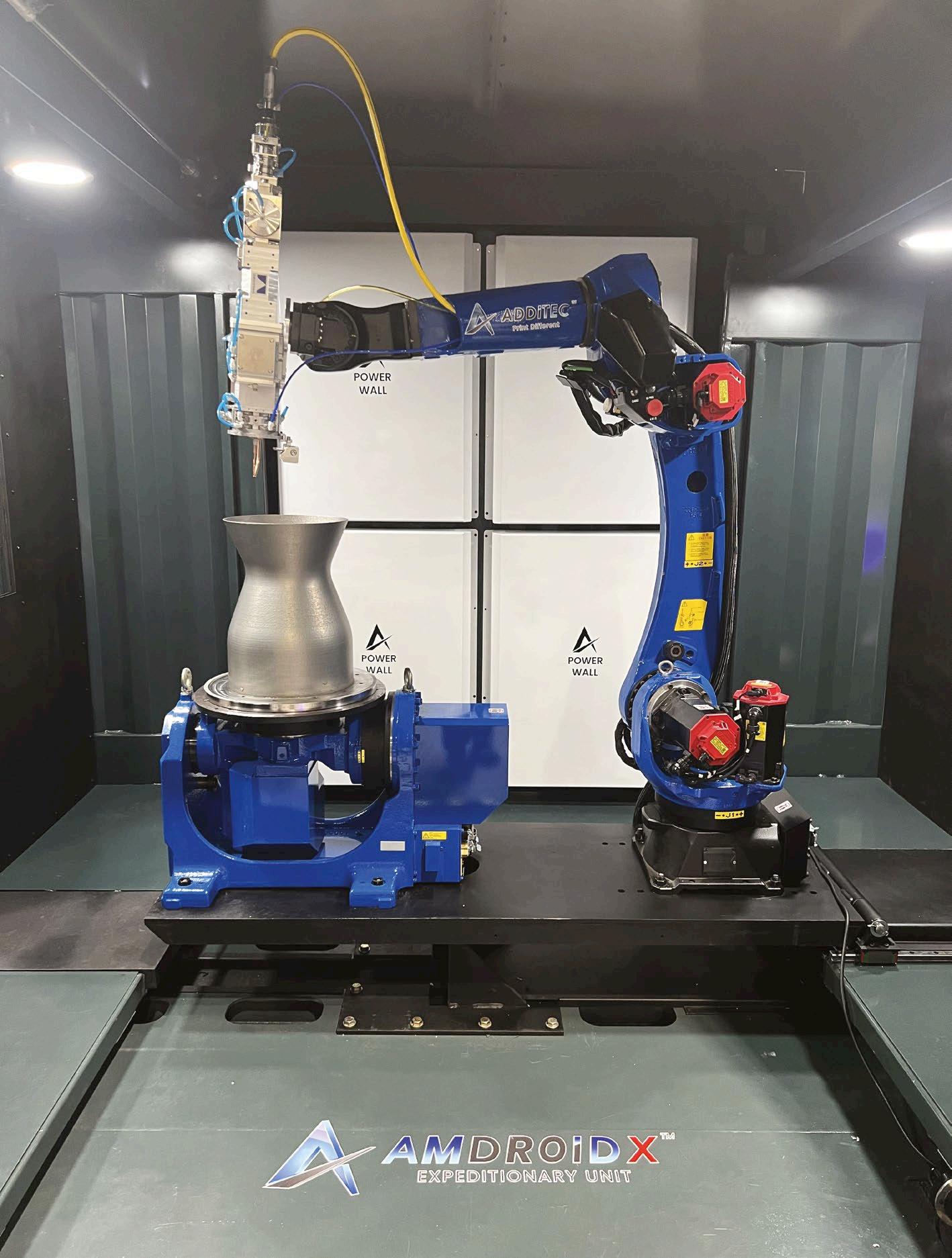

manufacturing solutions are changing the game by decentralising production and bringing manufacturing closer to the point of need,” Additec’s engineer says. “They are also enhancing agility and enabling quick adaptation to new challenges and reducing downtime. Lowering costs is another factor, through cutting transportation expenses, lead times and material cost and waste. The Amdroid X uses wire feedstock and doesn’t need argon or nitrogen for specific applications, as it uses the nitrogen generator.
“In short, the Amdroid X is redefining how industries approach manufacturing, making on-site production more efficient, costeffective and adaptable – especially in challenging environments.”
The system can produce a wide range of high-performance metal components
The system is equipped with user-friendly software tools
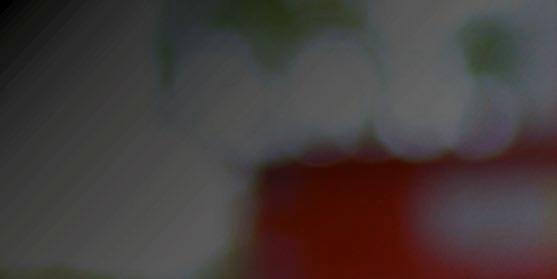
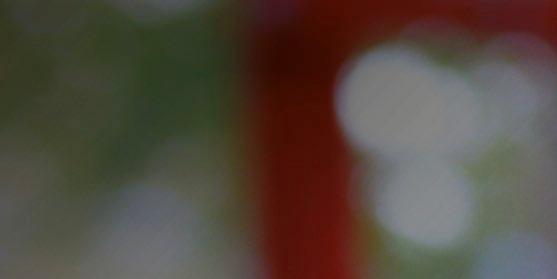
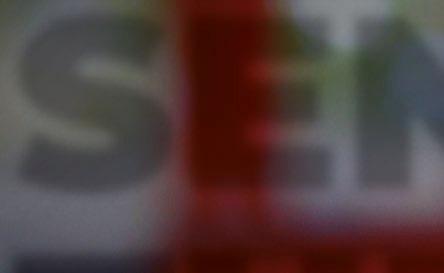
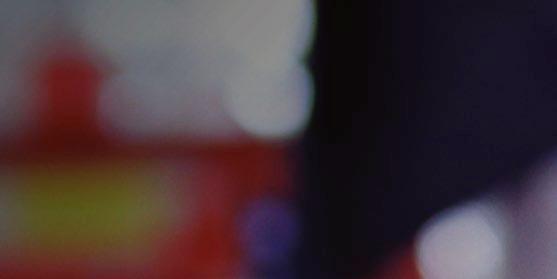
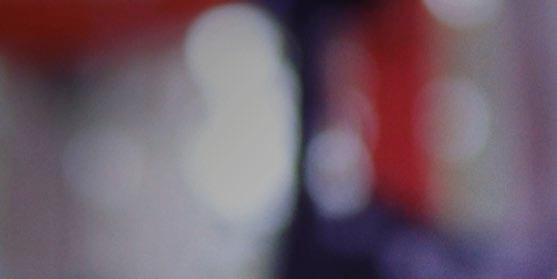
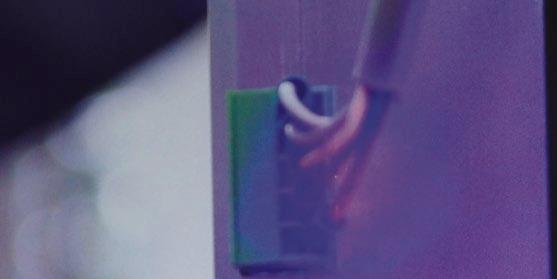
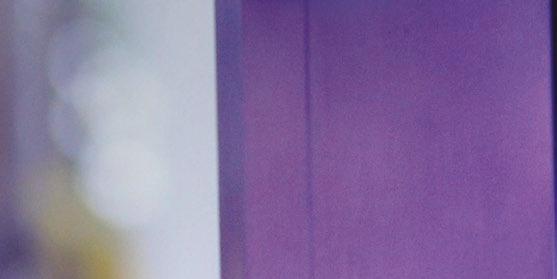

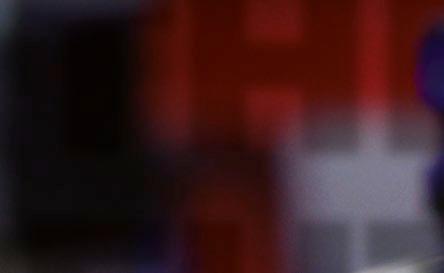
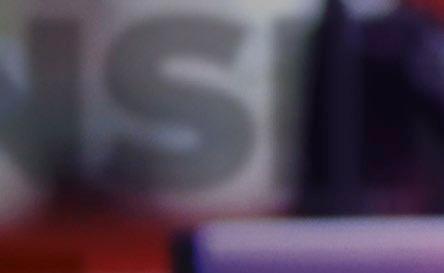
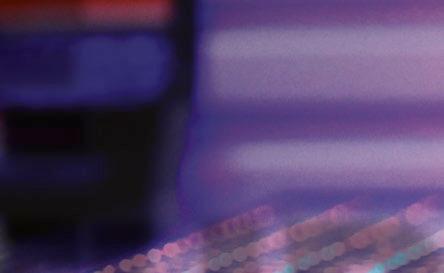
SENSING THE FUTURE

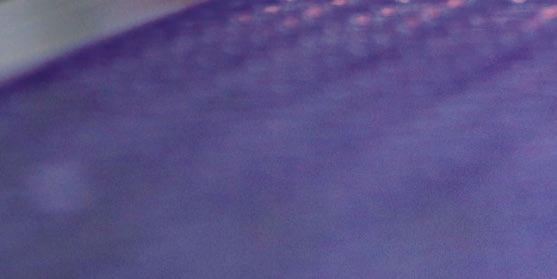
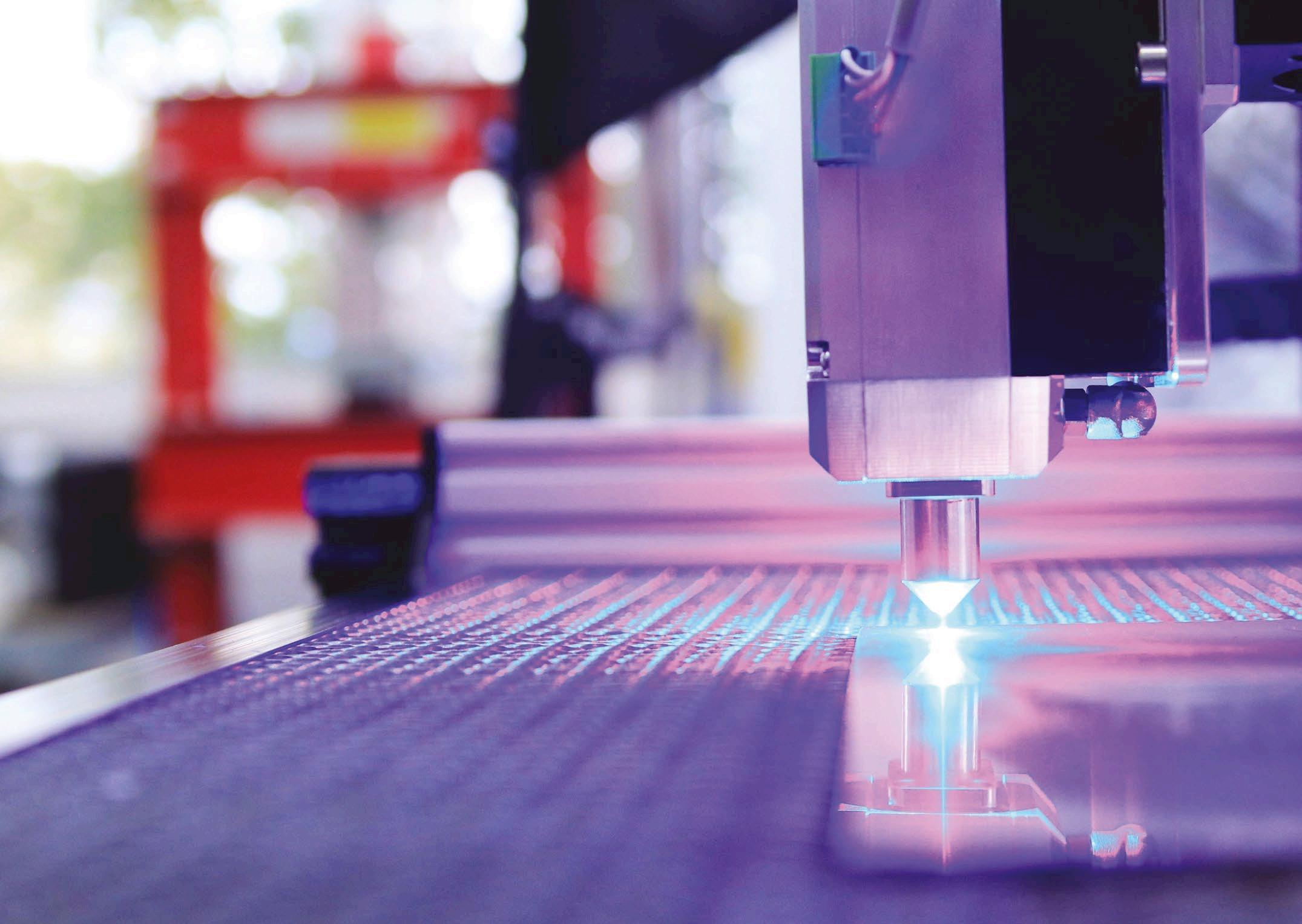
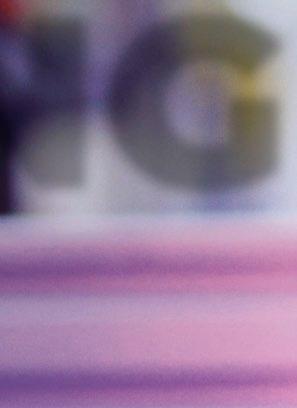
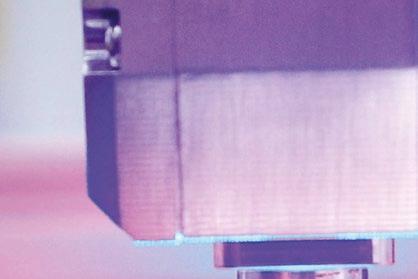
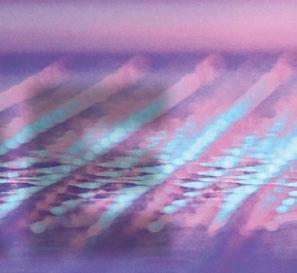
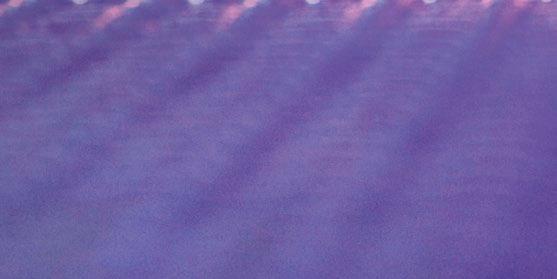
Exploring the latest developments in sensor technology within design engineering

Miniaturisation, integration, and biocompatibility are just some of the recent trends in sensor technology that have got people talking. Additionally, the rise of smart vision sensors and the increased use of 5G for data transmission have been key topics of discussion at various global industry events in recent months, alongside the fascinating fi eld of ‘sensor fusion’.
This article looks in greater detail at some of the latest product and technology developments within the sector.

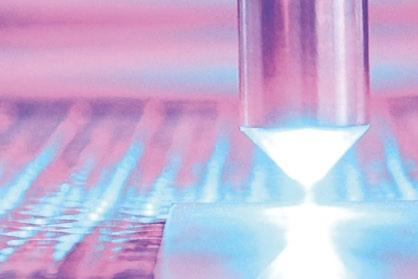
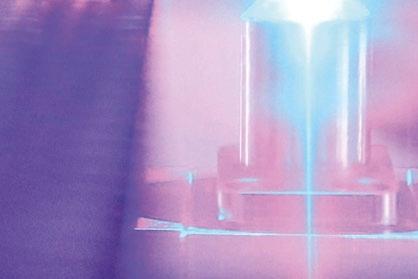
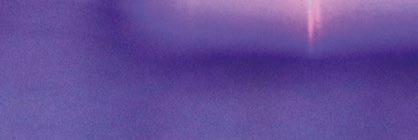
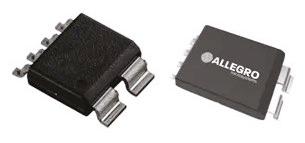
MASS-MARKET MEMS
Omnitron Sensors has secured $13 million in funding to accelerate the mass production of its microelectromechanical systems (MEMS) scanning mirror.
The production of MEMS sensors has long been limited by expensive, labour-intensive manufacturing
Innovative piezoelectric and triboelectric manufacturing enhances tactile sensors, enabling sensitivity, flexibility, and efficiency for robotics, wearables, and interactive systems
Allegra MicroSystems’ new ACS37030MY current sensor IC
methods, however the company’s fabrication IP could be poised to change this. The IP acts as a critical enabler for optical cross-connects (OXCs) in artificial intelligence (AI) data centres, optical subsystems in long-range LiDAR for autonomous navigation, see-through displays in extended reality (XR) headsets, and precision laser spectrometry for methane gas detection.
“Omnitron Sensors has achieved the quantum leap in MEMS fabrication technology for which the industry has been waiting,” says Mark Hart III, CEO of Corriente Advisors – one of the investors in firm’s Series A funding round. “By inventing a process of fabricating mass-market MEMS sensors that are higher-performance,
more affordable and more durable than existing sensors, Omnitron is uniquely able to satisfy unmet needs in long-stifled markets with enormous potential which have hit a will due to the longstanding limitations in sensor technology and the inability of legacy MEMS manufacturing techniques to address those constraints.”
PUSHING THE BOUNDARIES
Meanwhile, Allegro MicroSystems has boldly claimed to “redefine sensing” with the launch of two new current sensor ICs. The ACS37030MY and the ACS37220MZ leverage the company’s cutting-edge sensing technology to provide low internal conductor resistance, high operating bandwidth and reliable performance across a wide range of automotive, industrial and consumer applications.
“We’re excited to introduce our latest current sensor ICs, as Allegro continues to push the boundaries of sensor IC technology,” says Ram Sathappan, vice president of global marketing and applications at Allegro MicroSystems. “Our newest sensors establish new standards for precision and reliability, empowering customers to overcome design and efficiency standards, while also demonstrating how our technology is driving a smarter, more efficient future.”
Designed for precise current sensing in a compact and durable package, the new current sensor ICs deliver higher isolation in a 40% smaller footprint compared to the existing 16pin packages on the market. The new innovative designs also incorporate lower resistance, which helps to reduce power dissipation.
SPREAD YOUR WINGS
From the world of research, scientists at the Institute of Science Tokyo
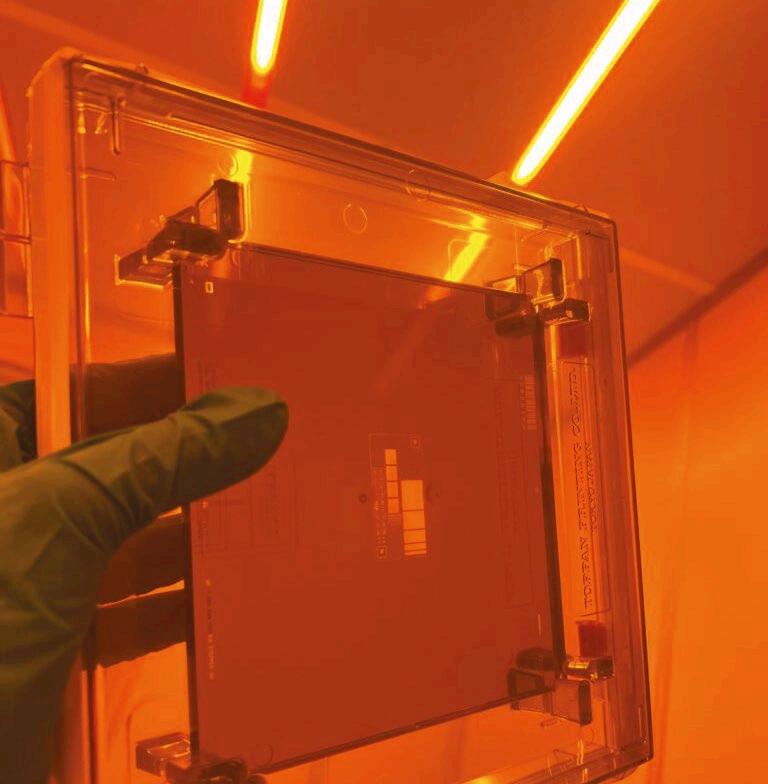
have designed a hummingbirdinspired flapping-wing robot capable of detecting the direction of weak airflow through machine learning of wing strain data. The researchers were able to detect wind direction with 99% accuracy using seven strain gauges on the flapping wing and convolutional neural network model.
The breakthrough was inspired by natural strain receptors within the wings of flying insects and birds that collect strain sensory data to aid their flight control. The researchers applied this idea to their study (published in Advanced Intelligent Systems) to investigate the use of strain sensors on hummingbird-mimetic flexible wings to accurately detect flow directions during tethered flapping in a wind tunnel simulating hovering flight under gentle wind conditions.
“Small aerial robots cannot afford conventional flow-sensing apparatus due to severe limitations in weight and size,” explains associate professor Hiroto Tanaka. “Hence, it would be beneficial is simple wing strain sensing could be utilised to directly recognise flow conditions without additional dedicated devices. This study contributes to the growing understanding that hovering birds and insects may sensitively perceive wind through strain sensing of their flapping wings, which would be
We’re excited to introduce our latest current sensor ICs, as Allegro continues to push the boundaries of sensor IC technology
Omnitron Sensors’ fabrication IP enables OXCs in long-range LiDAR for autonomous navigation systems
beneficial for responsive flight control. A similar system can be realised in biomimetic flapping-wing aerial robots using simple strain gauges.”
SELF-POWERED SENSORS
In South Korea, researchers have been researching ways to improve the manufacturing and performance of self-powered tactile sensors for robotics. The team at Chung-Ang University have been focusing on both piezoelectric and triboelectric tactile sensors which generate their own power. Although both sensor types offer self-powered functionality, piezoelectric sensors leverage voltage generation through mechanical stress in non-centrosymmetric materials, such as quartz and polyvinylidene fluoride (PVDF), while triboelectric sensors operate on contact-induced charge transfer.
Previously, the manufacturing of these types of sensors was limited by material brittleness and environmental limitations. However, the researchers’ new novel manufacturing process has overcome these challenges, combining innovative material engineering and advanced fabrication techniques to deliver multi-modal sensing and realtime interaction capabilities to sensors.
“Our study explains the materials and device fabrication strategies for tactile sensors using piezoelectric and triboelectric effects, as well as the types of sensory recognition,” says professor Hanjun Ryu. “These strategies aimed to enable the development of high-performance sensors for applications in robotics, wearable devices and healthcare systems. It is anticipated that AIbased multi-sensory sensors will make innovative contributions to such advancements in various fields.”
RELIABLE CONNECTIONS
The importance of delivering connector reliability in harsh environments
In the world of engineering, connectors are the unsung heroes that ensure the seamless operation of complex systems. For harsh environments, connector design and selection are critical. Delivering long-term reliable connector performance will involve mitigating one or multiple risks posed by the operational environment, such as environmental temperature, vibration and shock, exposure to water and dirt, access restrictions, and hazardous or corrosive substances connectors might be exposed to.
TOLERATING TEMPERATURE CHANGES
Connectors for outdoor telecom equipment need to withstand exposure to the elements while maintaining high data transmission rates. Components must be manufactured from suitable materials to tolerate temperature extremes yet not suffer cracking or damage. Changes in temperature can cause connector and cable materials to expand and contract, affecting connector performance through loss or degradation of signal. However, clever connector design can overcome some of these challenges.
Anti-piston or anti-rifling connectors with a 2-part contact design (such as the one in figure A) allow the centre conductor to slide within the connector, where expansion and contraction of the cable centre conductor due to temperature changes is found. In this example, a white bronze connector body in place of the normal nickel body plating of a TNC offers enhanced corrosion resistance.
AVOIDING DAMAGE FROM DIRT
Connectors for use on agricultural equipment will be regularly subjected to liquid and/or dust which could damage equipment and negatively impact the RF signal. Selecting
a connector or adaptor with an appropriate Ingress Protection (IP) rating is critical. An IP67 rating provides dust-tight protection against the ingress of solid contaminants for two to eight hours of continual exposure and protection against water ingress when immersed in depths of 15cm to 1m for up to 30 minutes, whereas IP68 provides the same protection from solids, but protects against long-term immersion up to specified depths and water pressures.
VIBRATION PROTECTION
Environmental shock and vibration can negatively affect signal transmission quality by causing connectors to come loose, or even disconnect, resulting in partial to total signal loss. Secure locking mechanisms, like threaded and bayonet options, provide positive mating and a constant signal path. BNC, TNC, SMA, and N-Type RF connector variants feature a silicone gasket that helps protect the locking mechanism against vibration, making them more suitable for industrial applications than push-fit designs which are more likely to spin during vibration, resulting in reduced performance.
RF connectors made with stronger base materials, such as stainless steel, generally permit rougher handling without the risk of reduced performance. Pictured above (top right) is an SMA adaptor made from stainless steel permitting a tighter torque and featuring a silicone gasket to protect the locking mechanism against vibration.
CONNECTOR DESIGN
Reputable connector manufacturers will be able to provide in depth technical information and specifications for each of their products and will be knowledgeable about how to overcome the design
SMA IP68 stainless steel right angle plug to jack adaptor
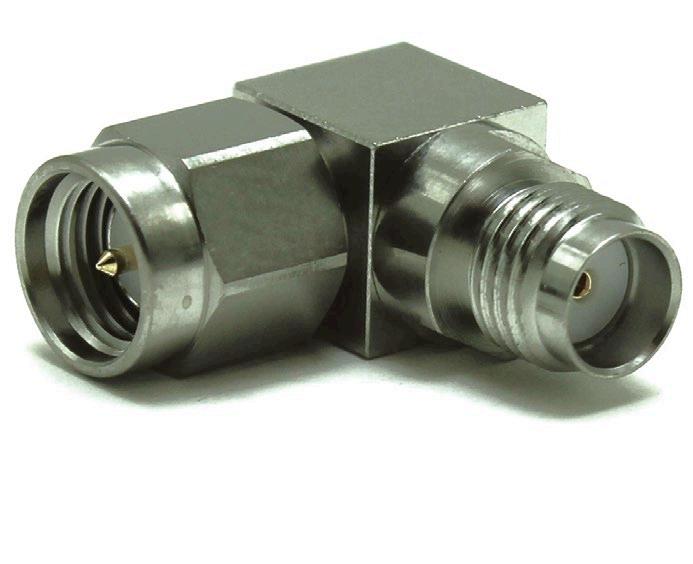
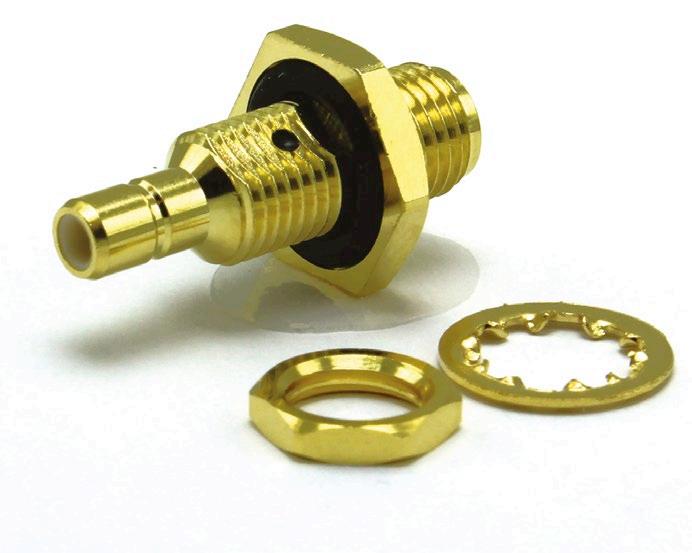
IP68 hermetically sealed RP SMA to SMB adaptor tested to 50 metres
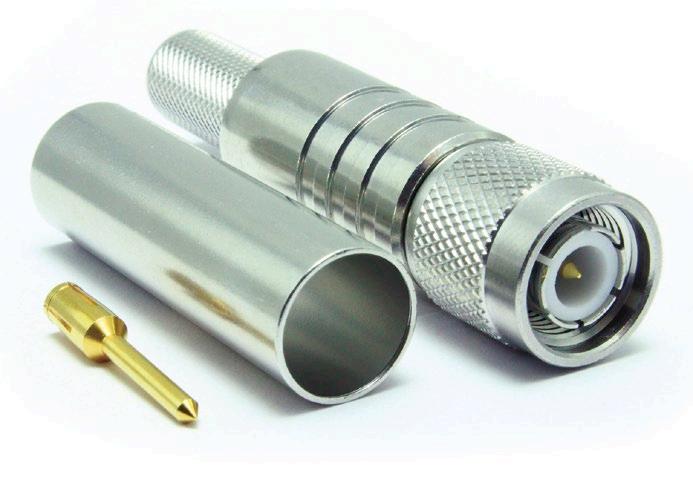
(Figure A) The COAX Pro 50 TNC straight plug with easy fit antipiston contact
challenges that harsh environments may present. Armed with the information customers provide, they will be able suggest off-theshelf connector or cable assembly suitability. Where a bespoke solution is required, they will be able to work with customers from initial design concepts to the supply of a fully qualified production part.
Emma Ashton is with COAX Connectors. www.coax-connectors.com

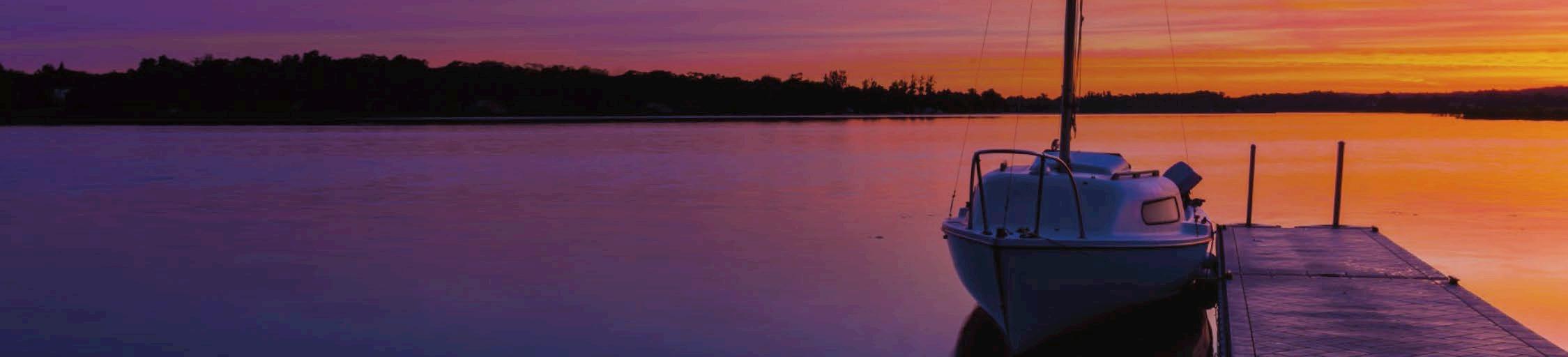


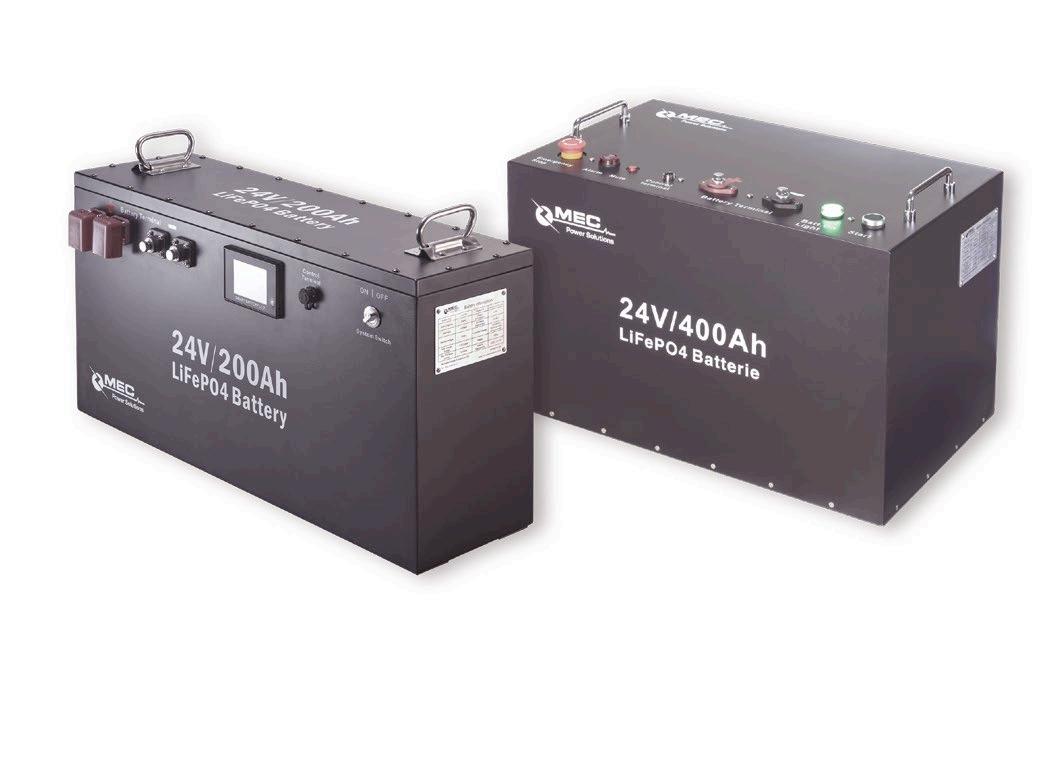

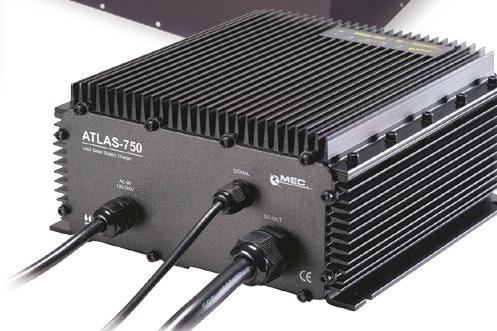
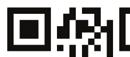

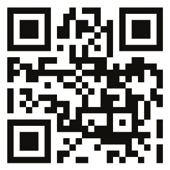
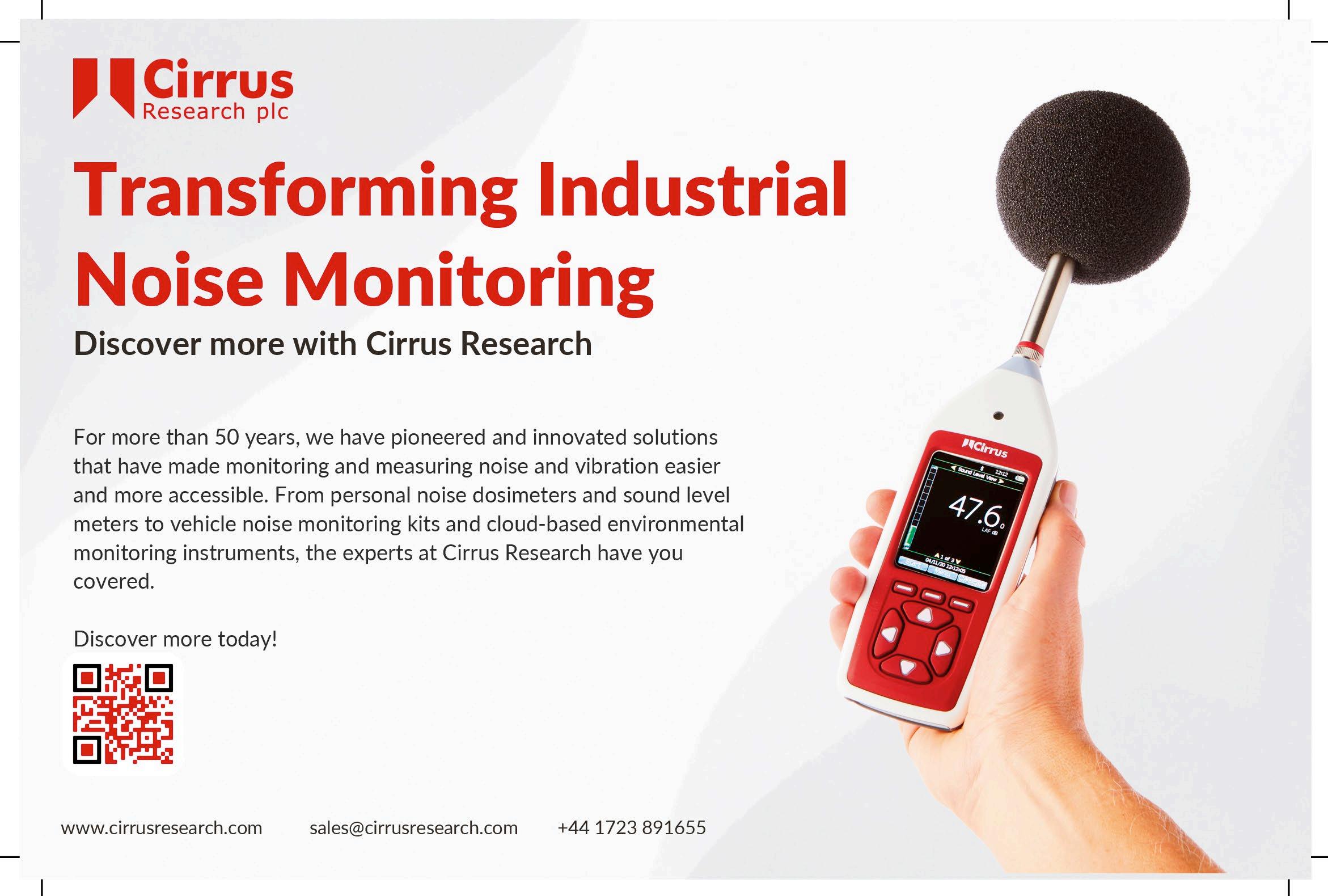
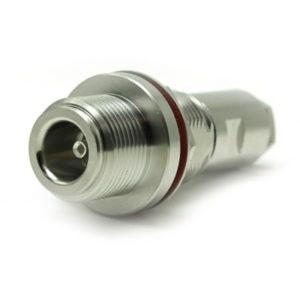
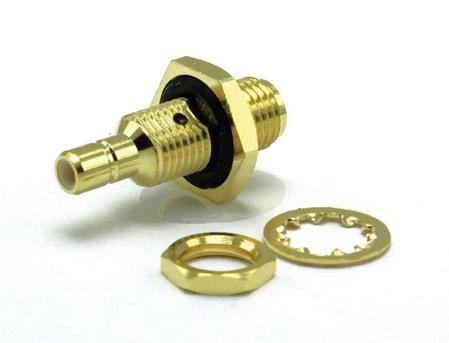
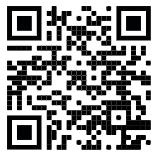
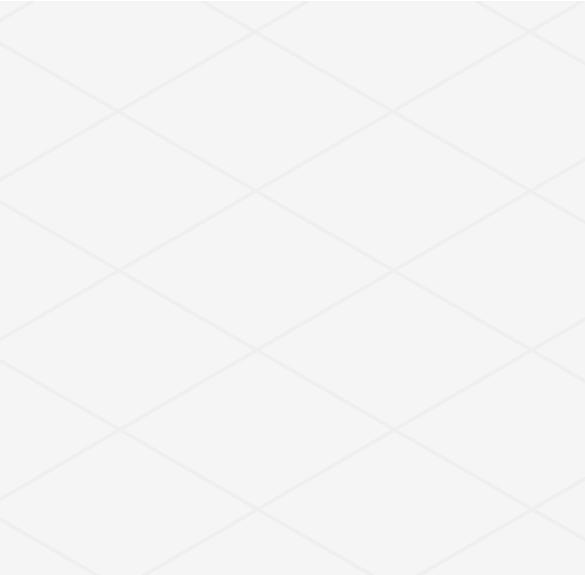

•
•
•
•

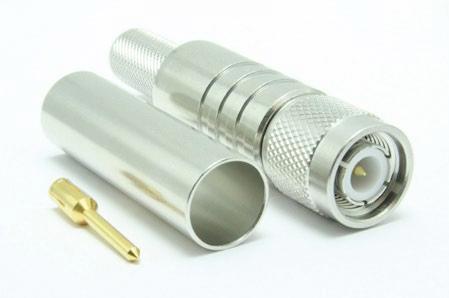





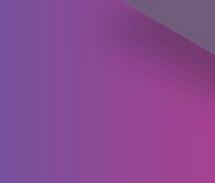


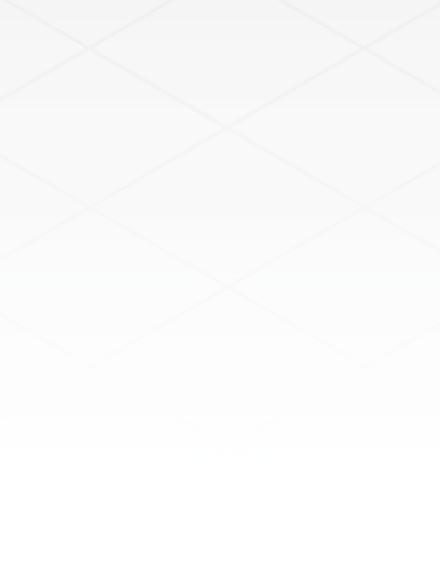
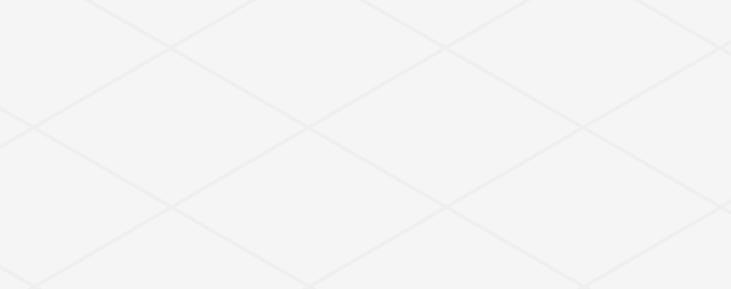
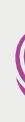
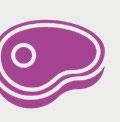
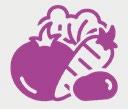
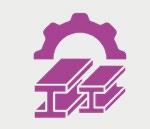
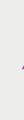
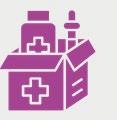
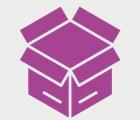

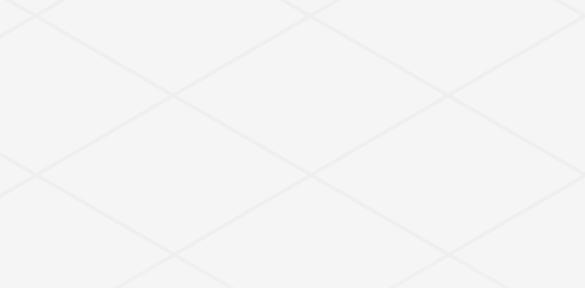
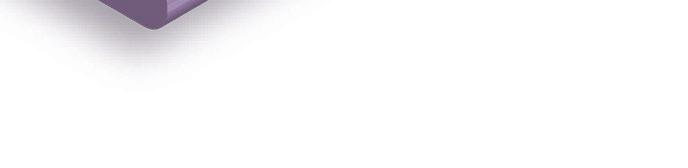
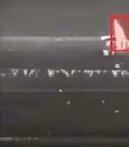
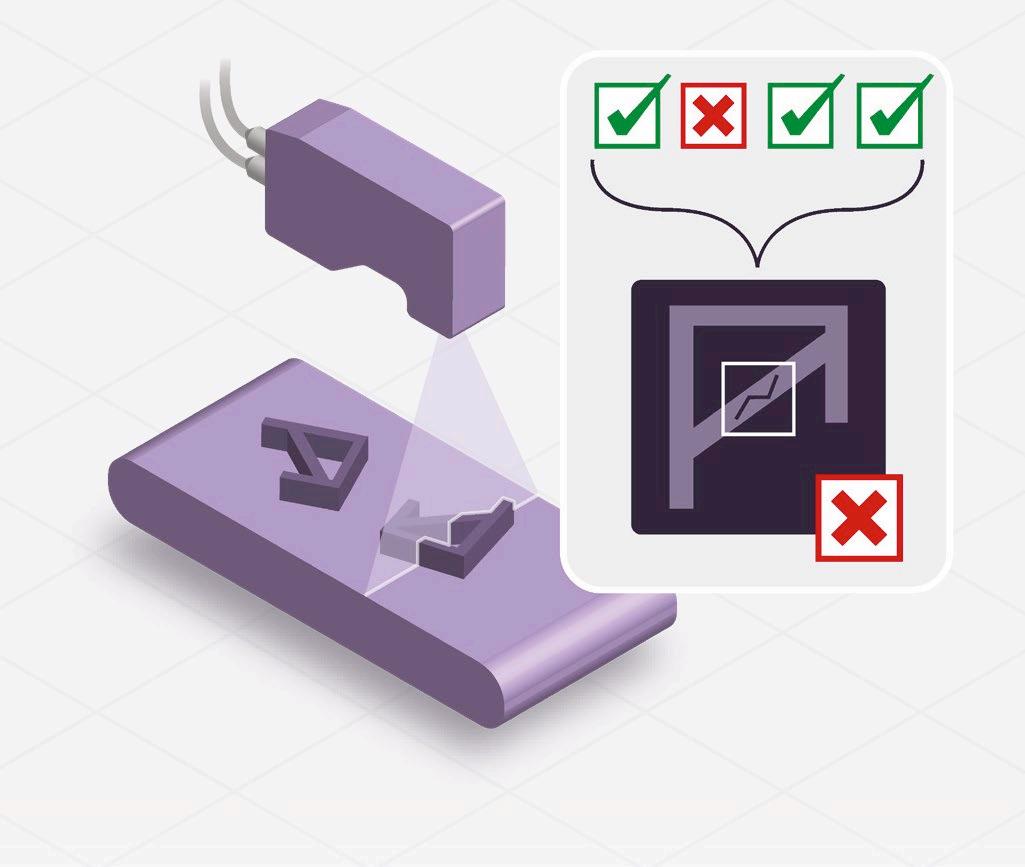




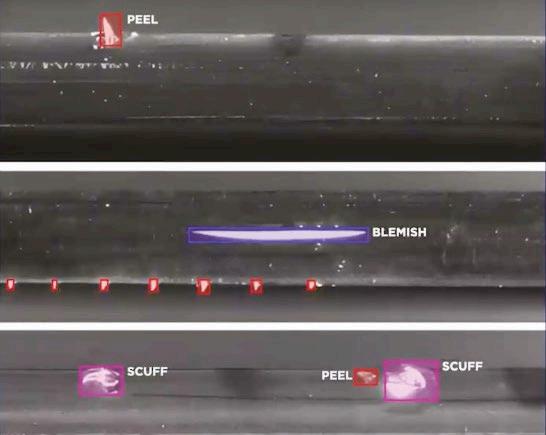
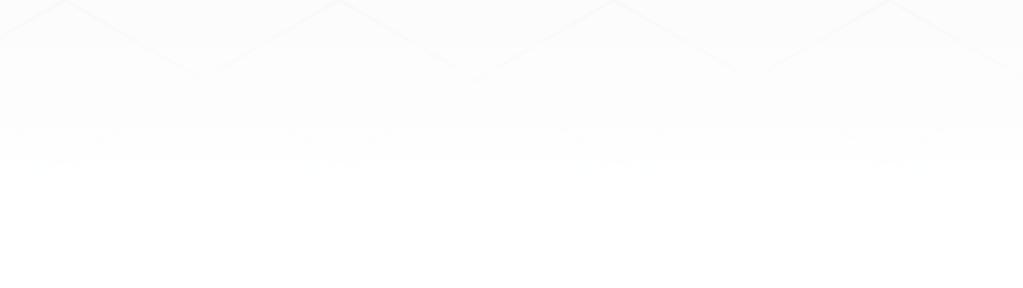

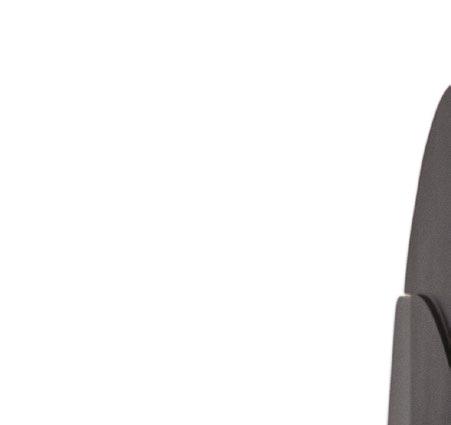
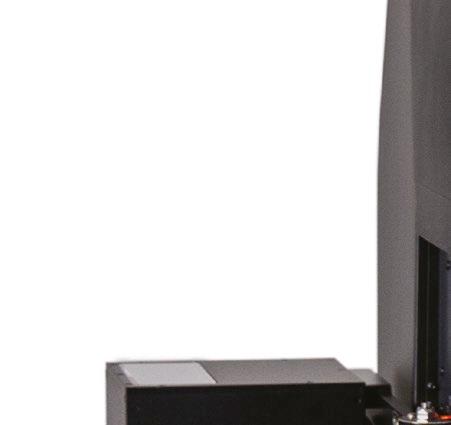
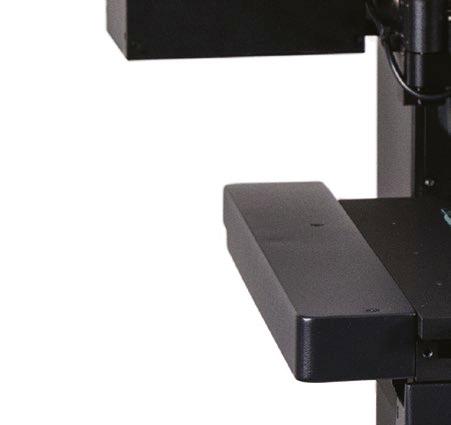
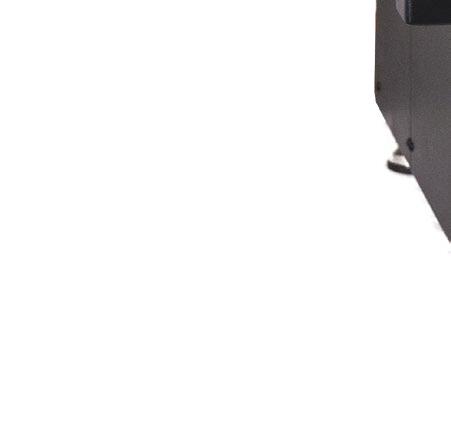
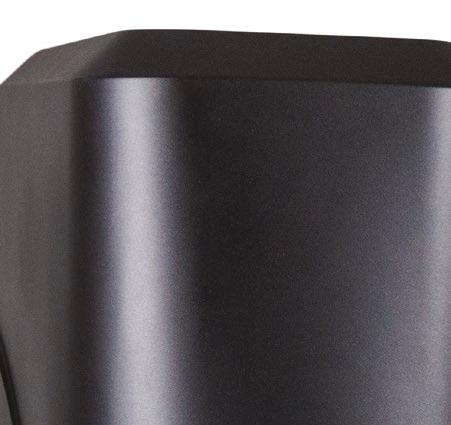
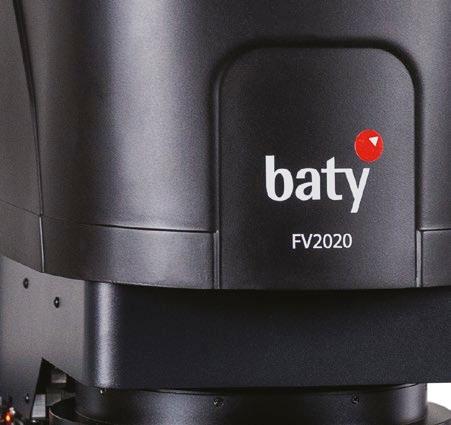
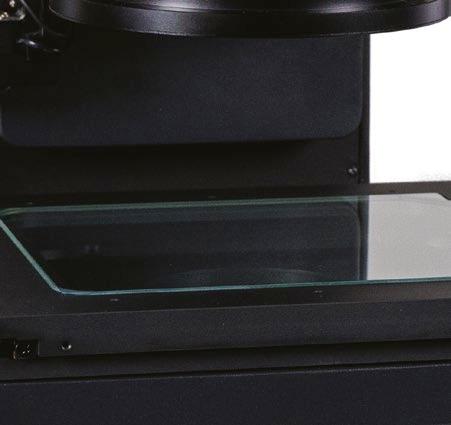
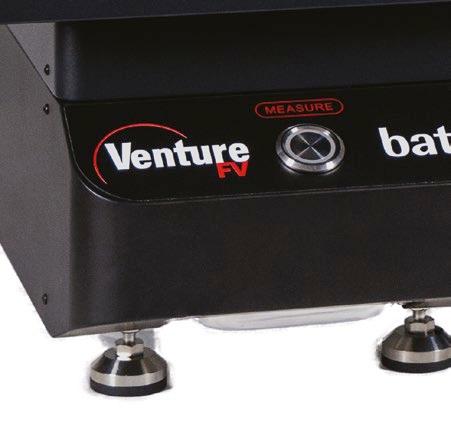
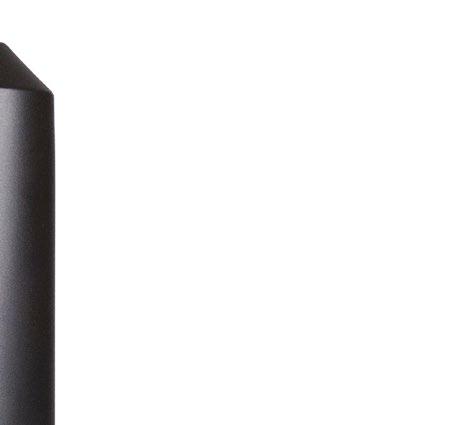



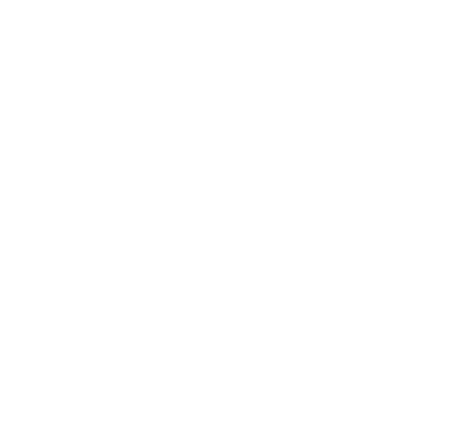

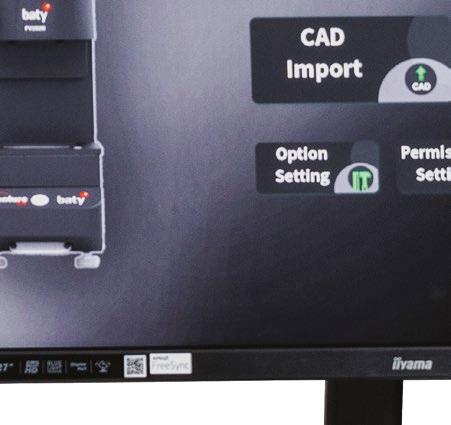

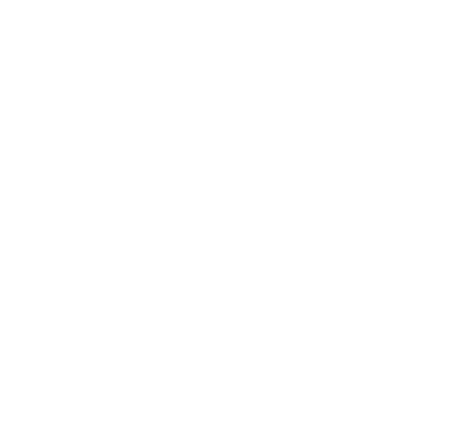
The machine is mainly designed for control and quality checks, ensuring all product dimensions are accurate
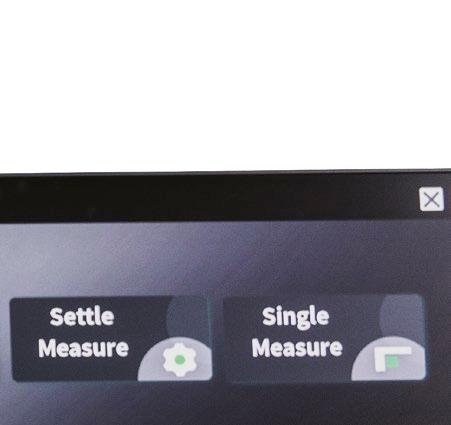

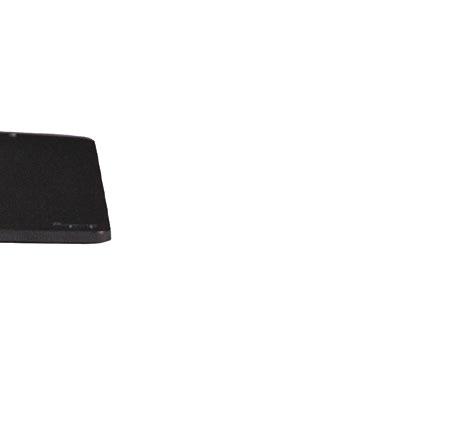

QUALITY CONTROL
Jake Holmes looks at some of the machinery safeguarding the quality of precision products
As product designs grow increasingly complex, the need to check and validate these designs continues to grow. Precision parts manufacturers can design parts that are measured in nanometres, a scale too small to be assessed with the human eye.
The desire for efficiency has led designers to maximise all space available to them, meaning a single nanometre can be the difference between a part working and failing. Having a high level of quality assurance on parts is also becoming
increasingly vital to companies.
Bowers Group has developed its new Baty Venture FV series, a range of inspection machines. The field-of-view machine standout is the FV3020, named as such for its measuring range of 300 by 200 along the XY axis.
FV3020 features a dual field of view which has a three-micron accuracy on its large field of view, or a one-micron accuracy on its small field of view. The machine is mainly designed for control and quality checks, ensuring all product dimensions are accurate.
SPEED IS KEY
The FV3020 stands out due to the speed with which it can capture information and assess parts. In high-volume production environments, quality assurance mechanisms need to match the speed of production to avoid creating a bottleneck effect. With the machine, it only takes a single second to capture a thousand dimensions of a product or part, speeding up the quality control process significantly. Meanwhile, batch inspections can be completed in seconds.
The Baty Venture FV series field of view inspection machine
INSTRUMENTATION ELECTRONICS
The de-skilled nature of the process also helps reduce costs. Not needing to have an employee standby and assess each product nor operate the machine reduces costs and increases efficiency. The only labour required is moving parts on and off the field of view platform.
In-built to the machine is the software that allows the deskilled operation. It can detect parts that have been placed onto the stage, going through its library to identify parts and then assess them. A scan of parts needs to be uploaded to the machines library to do this, but once uploaded the machine can accurately detect parts and complete quality assurance checks.
If multiple fields of view are required for a reading, the stage is required to stitch together the data, however, if only one field of view is required for inspection then it is possible to attach a conveyor belt to the operation.
ROTARY VIEW
Full scans are possible using the FV3020, and this is what the optional additional rotary is for. Multifaceted
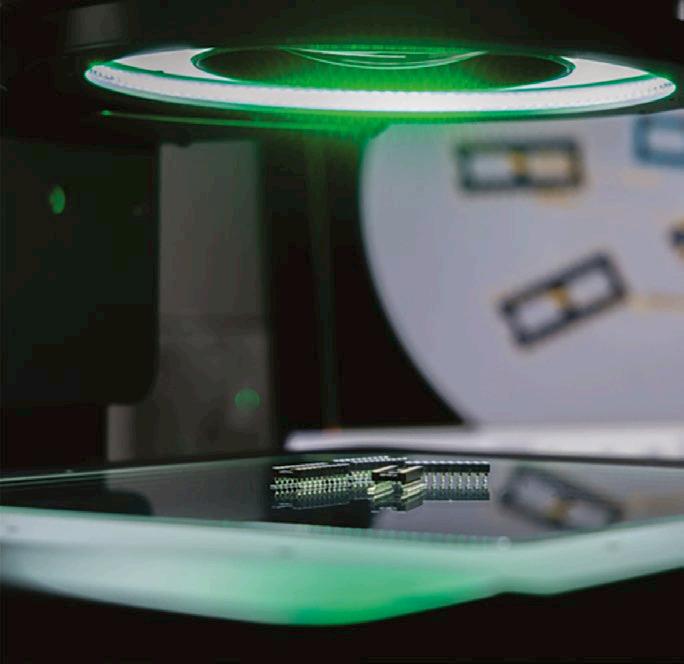
parts can be scanned using the rotary attachment, allowing multiple sides of a part to be shown to the optic for inspection. This allows the process to be automated rather than an employee changing the rotation of the part after every scan.
3D parts can be scanned in using the rotary option, allowing one inspection shot to collect all the necessary data without constant repositioning from a user. This remains a deskilled process. Multiple
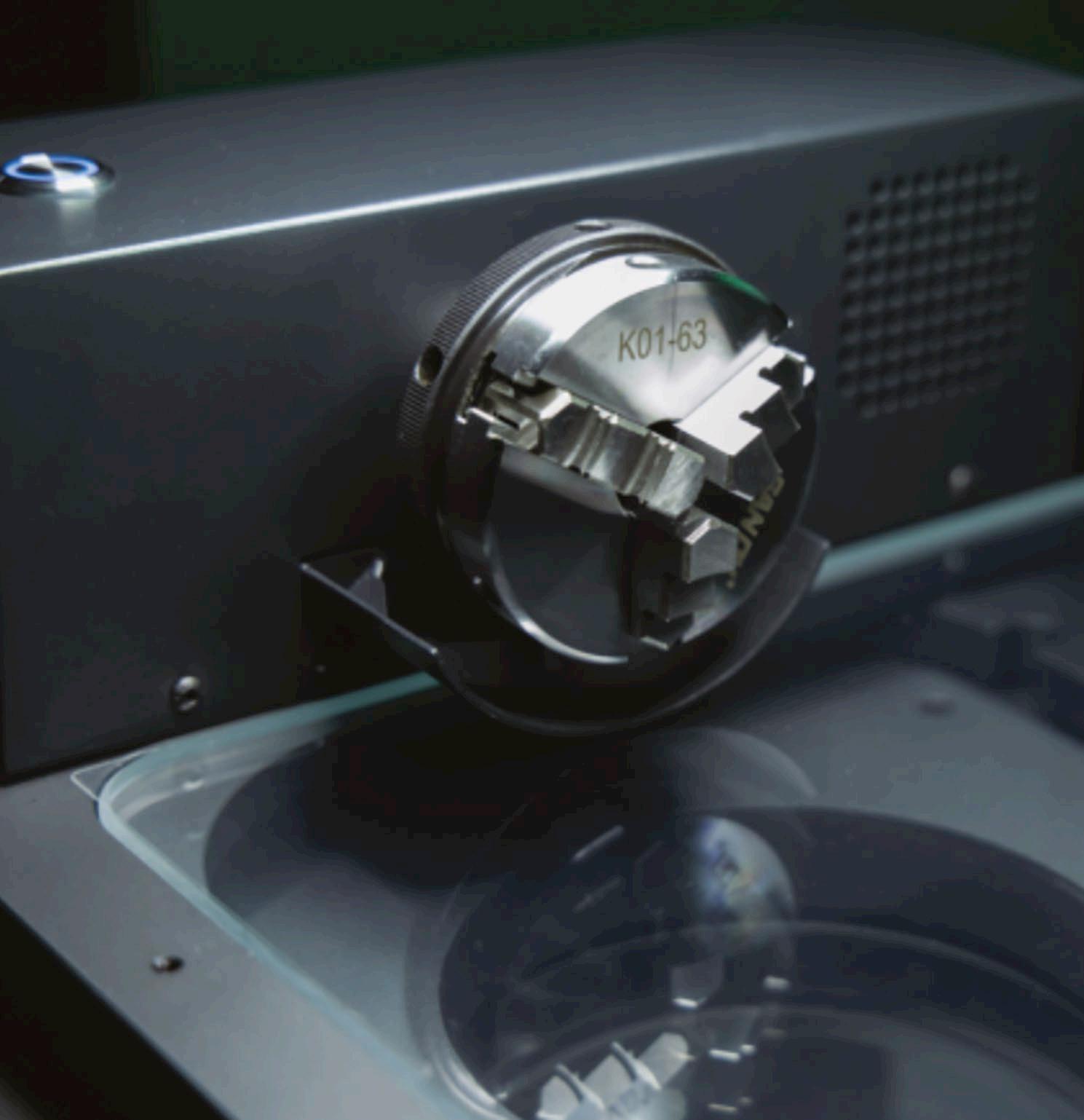
scans can be taken per rotation to build an accurate image of the piece.
The stage can use different lighting to highlight different features of the part, allowing more accurate measurements to be taken. This can be done whilst the rotary part is in action, allowing silhouette to help create measurements. CNC rotary indexing is enabled via the rotary axis, allowing automated inspection programs to operate on cylindrical parts.
CONFOCAL PRO
An additional optional confocal pro laser probe, the SB-FVHPS-1, can be added to the FV3020 granting the machine Z-axis measurement capabilities. This can be used to assess pocket heights.
The laser is focused at a certain working height, shooting out a 65-micron diameter micron spot. A range of surfaces work with the laser, including transparent materials, giving it an advantage over traditional touch probes. It boasts an accuracy of 2.5 microns.
In addition to the stage lighting, the confocal laser is working underneath the rotary to measure points to assess flatness of the part. It is well suited to assessing surface height, flatness, and thickness. The confocal laser enables 3D functionality on an otherwise 2D scanner, providing additional Z-axis measurements in detail to go along with the XY measurements taken from the camera lens. Data is captured from both the top and bottom surfaces by the probe, allowing it to assess thickness in a single measurement. This makes it a versatile solution for a range of measurements.
ASSESSING PROGRESS
As technology becomes more advanced and machinery becomes more intricate, the need to correctly assess parts is becoming ever more important. Progress cannot be made unless what we are producing is functional.
Investing in quality assurance can help prevent future errors, breakdowns, bottlenecks, and lead to more reliable machinery. Reduction in human involvement will not only reduce costs but can also take human error out of the equation.
The Baty Venture FV series is designed for control and quality checks
The FV3020 can be fitted with a rotary axis for increased automation
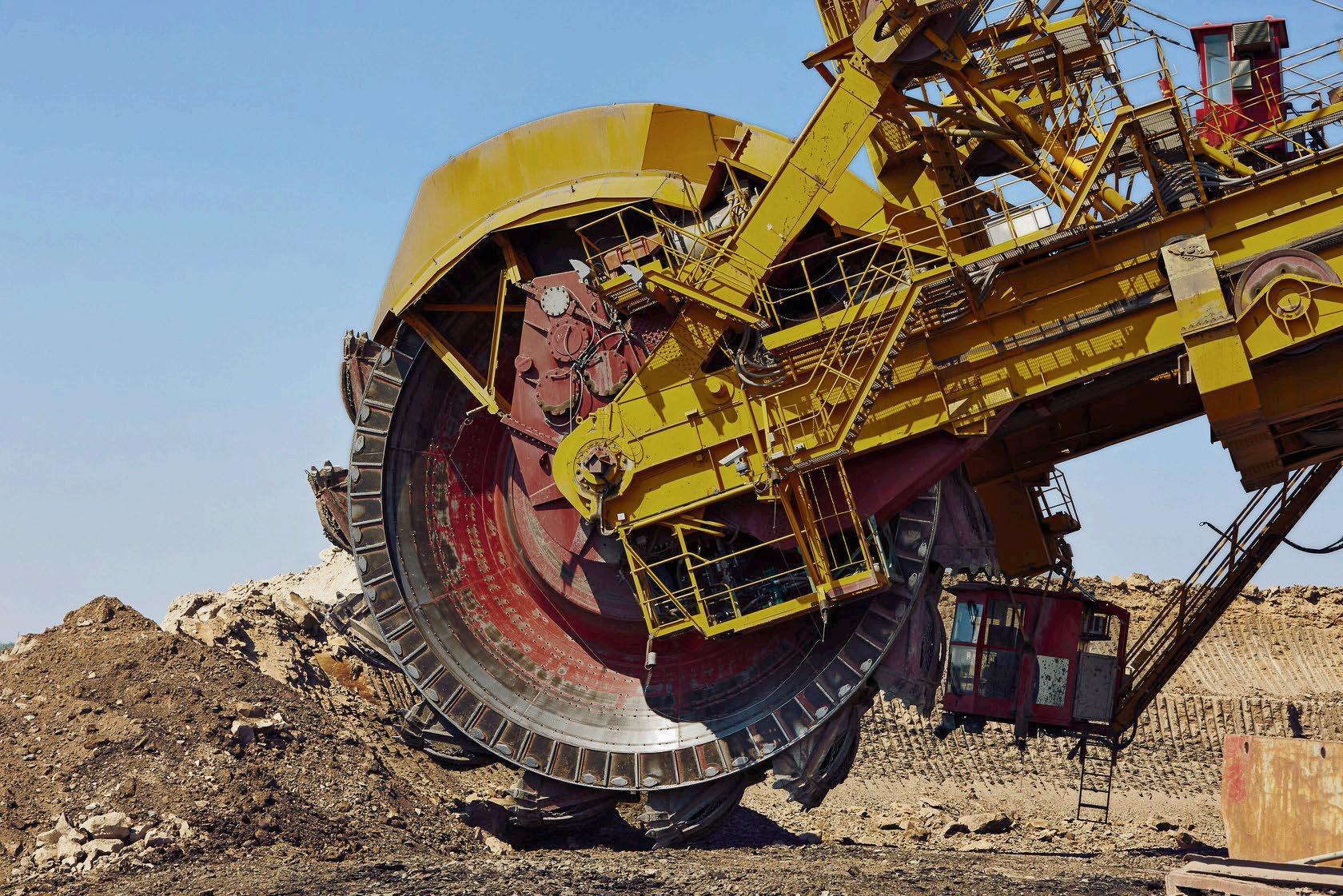

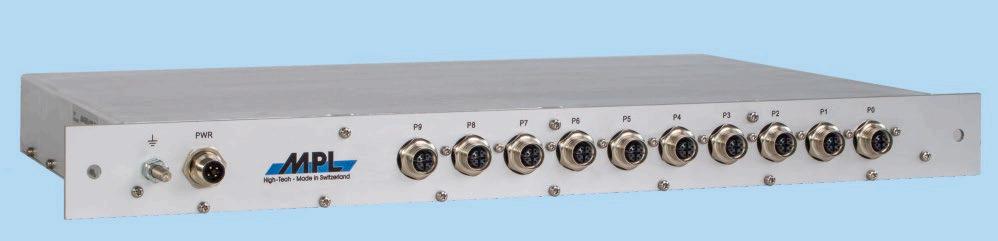






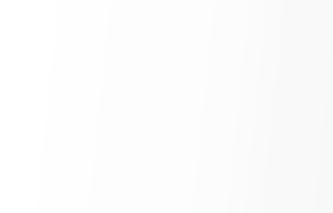

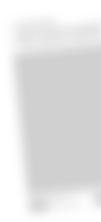
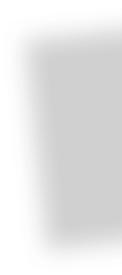
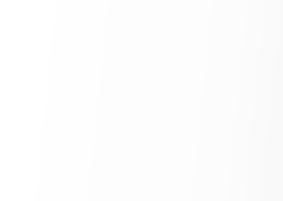








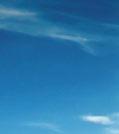
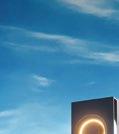
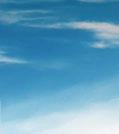
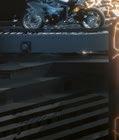
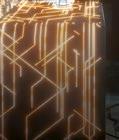
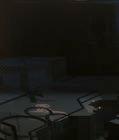
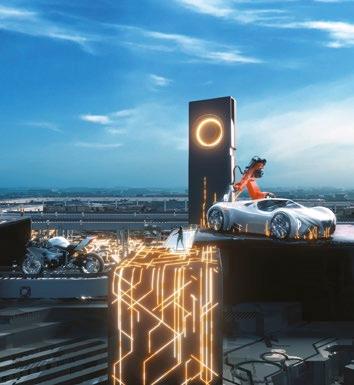


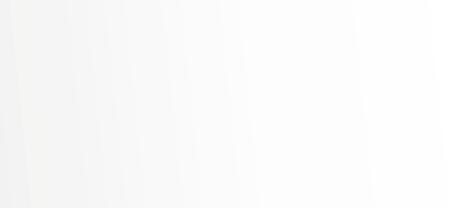
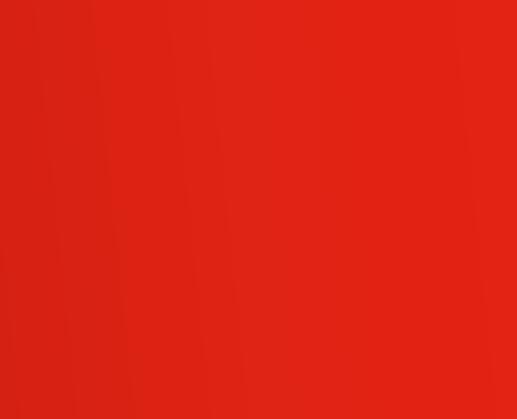



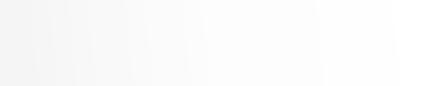





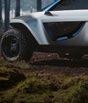
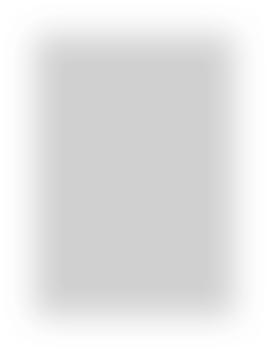
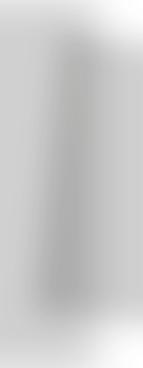

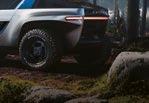

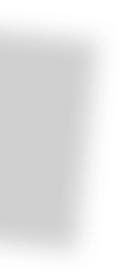
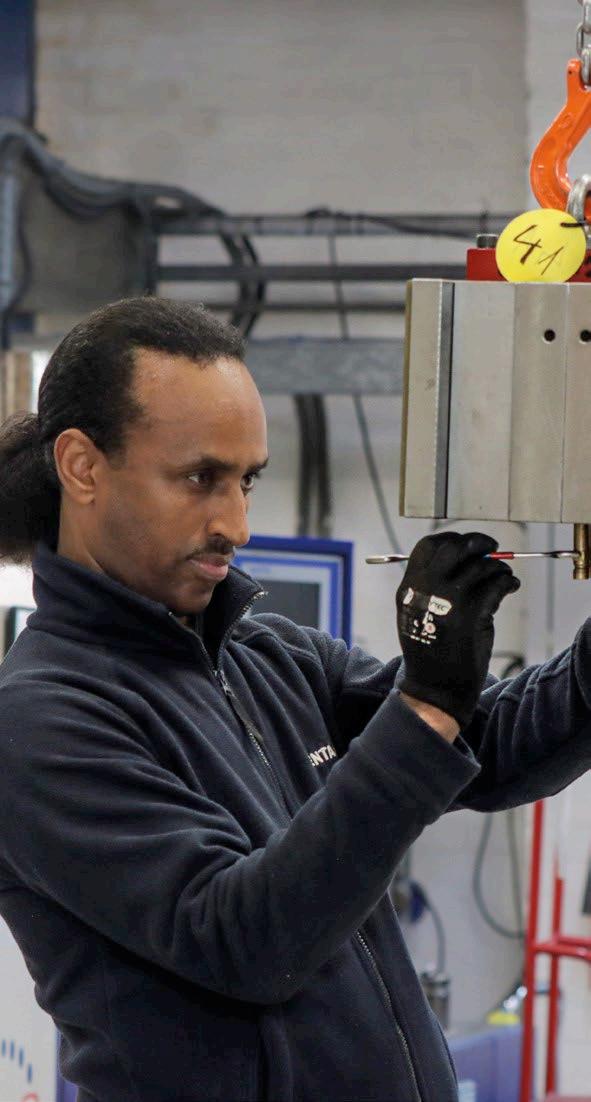

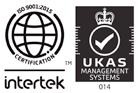
THE FUNDAMENTAL FLAW
Could anti-gravity casting prove to be the silver bullet for crack-free metal casting? Despite industry-wide scepticism, this professor believes so...
“No one has really understood why metal castings are unreliable when compared to forging, until recently. What I’m about to reveal today is being denied by millions,”
Professor John Campbell, professor emeritus of casting technology at the University of Birmingham, states to a room full of journalists. We’re at a First Friday Club media briefing hosted by Cadence, and Campbell has been invited to share his decades of work on anti-gravity metal casting.
“The fundamental issue of making good metal is simply this: the surface of the liquid metal itself,” Campbell continues. “On the surface of liquid metal is a very thin film created by contact with the air around it. When the metal is poured turbulently during casting, the slightly drier surface is folded over itself and you have two oxide surfaces which will never bond. So, what you now have going off into the liquid metal is a crack, as these two surfaces comes apart extremely easily.”
This crack in the liquid state is what Campbell calls a ‘bifilm’ and, while they require the right technology and equipment to identify, they are apparently prevalent in many traditionally cast metal structures. Bifilms can be fairly harmless if they result in a convoluted crack, Campbell says, but in the cases where
Top-poured turbulent casting process
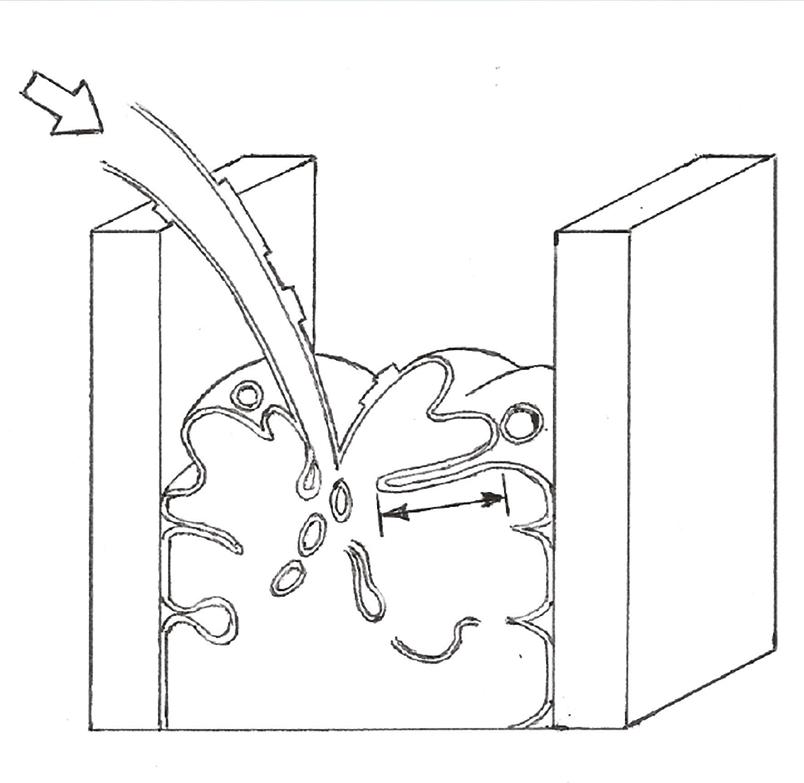
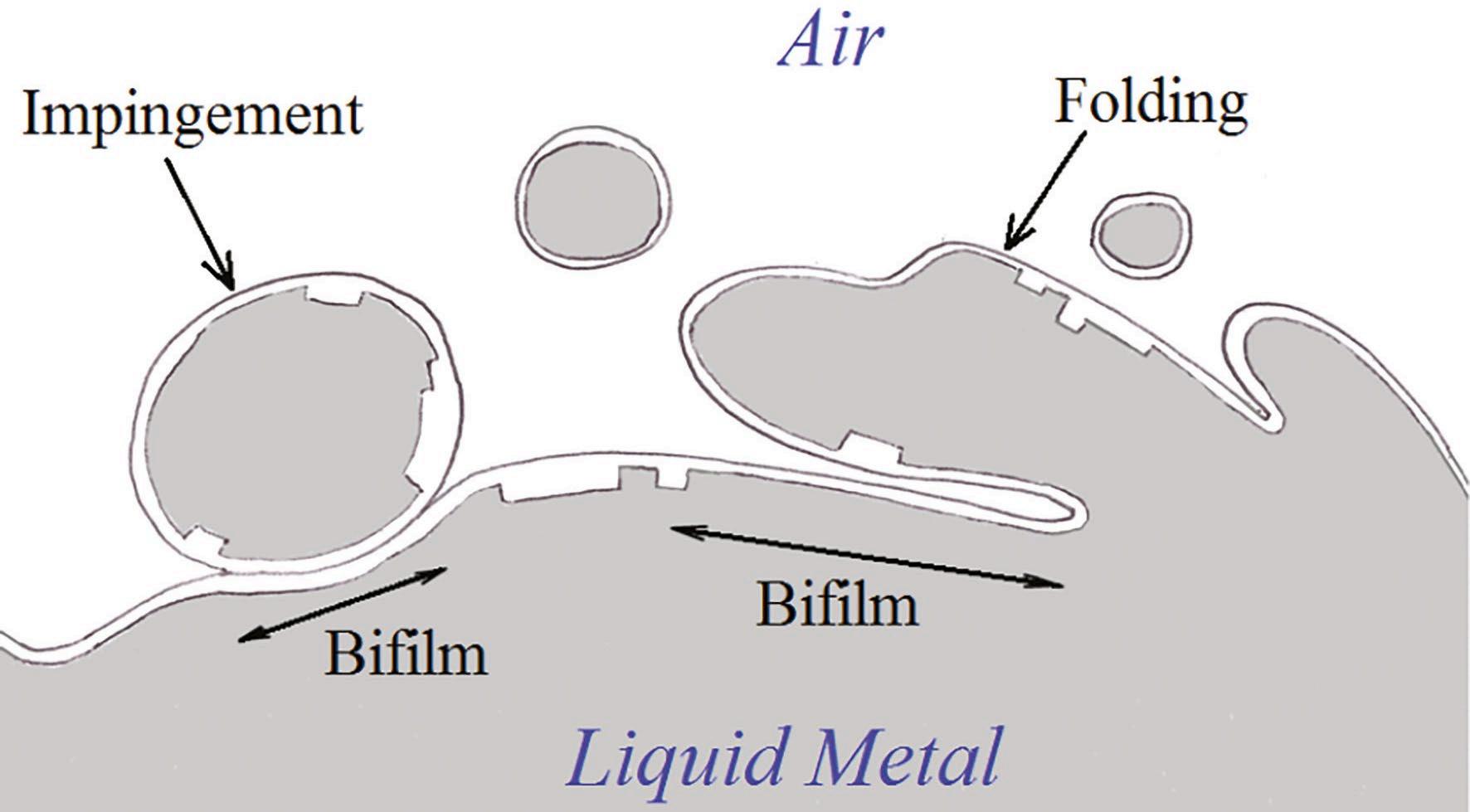
Surface turbulence generating bifilm cracks in the liquid metal
gas diffuses into the solid metal they can become expanded cracks up to 10 times the size of what they were originally, which can lead to significant consequences.
“With this knowledge, we can go on to understand for the first time many things which have bugged metallurgists, such as hydrogen embrittlement,” Campbell continues. “Because hydrogen
can diffuse into the interior of a metal – against all the rules – through these bifilms which act as open pathways for the hydrogen to move throughout the structure. So, when you have a situation where a structure has lots of bifilms and therefore lots of diffusion paths for the hydrogen, the tensile strength can open up these cracks further until the metal fatigues.”
The contact pour casting method explained


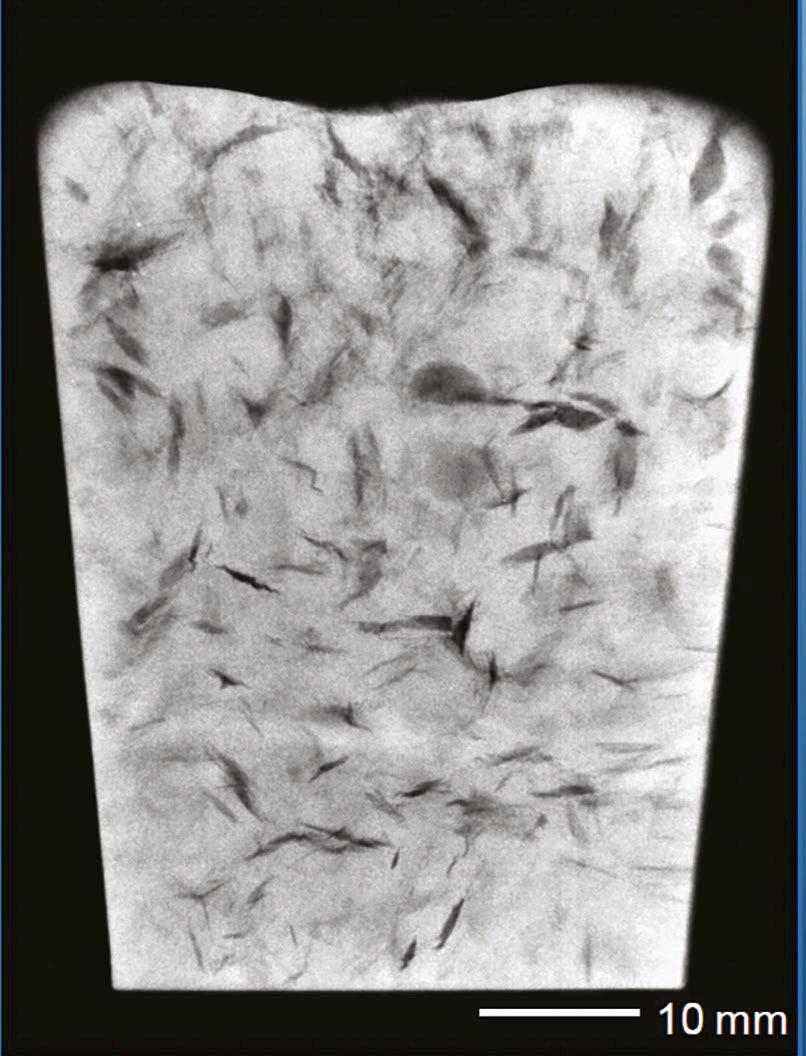
The two formats for bifilms (left) harmless (right) pre-cracked network
OUT WITH THE OLD
“The main problems with metals are the entrainment defects of the liquid state: bifilms and bubbles,” Campbell says. “They’re both rather similar, but there’s more air in the bubble. Now, there’s a lot of continuous casting, which is better than how steel was made before, but it’s still not perfect. Special steels are generally cast as an ingot which is top-poured because that is the cheapest way to fill an ingot mould. More expensive ingots, which are said to be better, are poured through a conical pouring basin and filled from the bottom.”
These are currently the two principal ways of casting steel,
but according to Campbell these techniques are “fundamentally bad.”
“With the conical pouring basin, the basin takes in air and concentrates it, putting in about 50% air into the metal which maximises the population of bifilms,” he explains.
So, what is the alternative?
“The real way to cast steels is what I call the contact pour situation, where the gap between the basin and the running system is eliminated,” Campbell says. “This is a system of melting and casting in which the liquid metal is never poured. It either moves horizontally or uphill and then fills the ingot, rather than being poured in. With this, you suddenly get a
(Left) top-pour casting (middle) bottom gating casting (right) contact pour casting methods
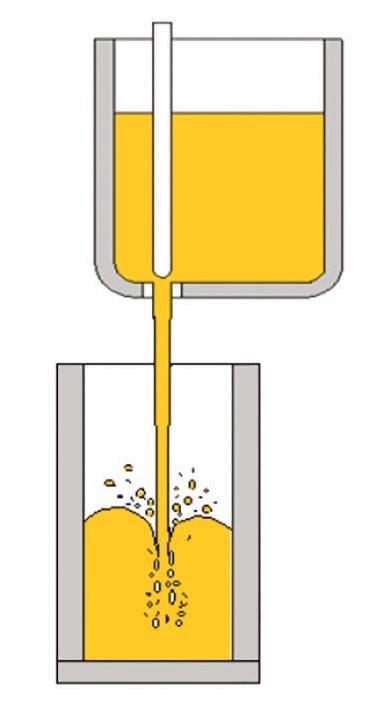
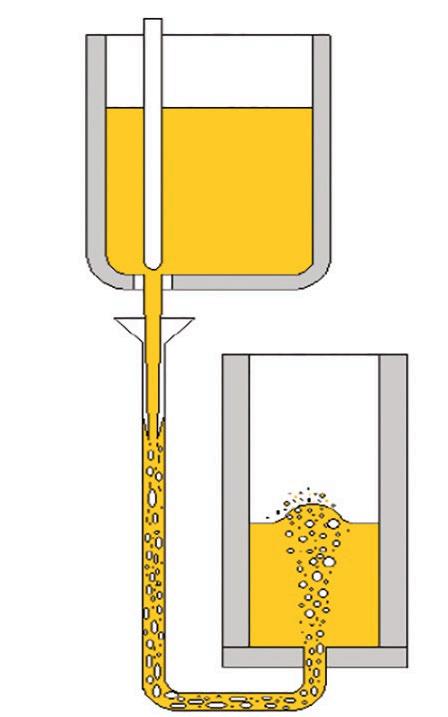
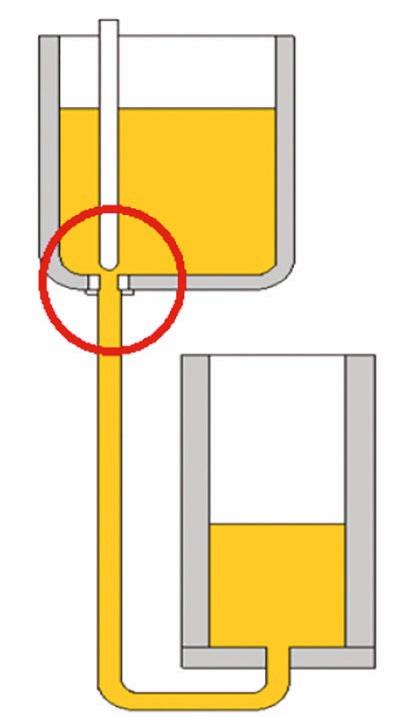
fantastic jump in the steel’s properties: it’s no longer full of bifilms and the steel now achieves its full strength. Plus, it wouldn’t suffer hydrogen embrittlement, as it wouldn’t suffer the corrosion we currently see because there are no bifilms to transport it.”
This begs the question, why isn’t this method widespread throughout metal production? Campbell says he has worked with several reputable companies to install his system, namely Rolls Royce and Cosworth, but there is industry scepticism around the existence of bifilms altogether.
“People look at cracks which have caused failures and they just say, oh yes, it’s a fatigue crack,” he shrugs. “We just give something a name and think that we’ve explained it. The trouble with bifilms is that they’re very, very thin oxide films that come together as closed cracks – they don’t show up on radiology. It’s hard work to reverse decades of thinking.”
And how is it that Campbell is able to identify the existence of bifilms, when others can’t? “It’s easier for me because I’ve realised they’re there,” he answers. “You can design inspection techniques to find them, and then you see them immediately. We have to slim down the metal to make it ultrasensitive to x-rays, then they start to show up clearly. But most people wouldn’t have bothered to slim down the metal that much.”
Now that Campbell has retired from the University of Birmingham, he has made it his mission to try to change the narrative on bilfims within the metal production space.
“The future is interesting, because we could solve problems with our metals that we’ve lived with for years, like hydrogen embrittlement, in which hydrogen pressure vessels explode unexpectedly, or pipelines which explode due to stress, corrosion and cracking,” he concludes. “These things need not happen, with simple changes to eliminate bifilms we would live in a happier, more efficient world. The whole business of bifilms in metals is affecting our lives all the time, not only because of the huge inefficiencies of working with metals, which are less good than they could be, but some of them are so bad as to be dangerous, and none of them need be. All of them could be better.”
By extending the lifespan of steel structures, Avantguard coatings reduce the frequency of replacements and repairs and enable cost savings
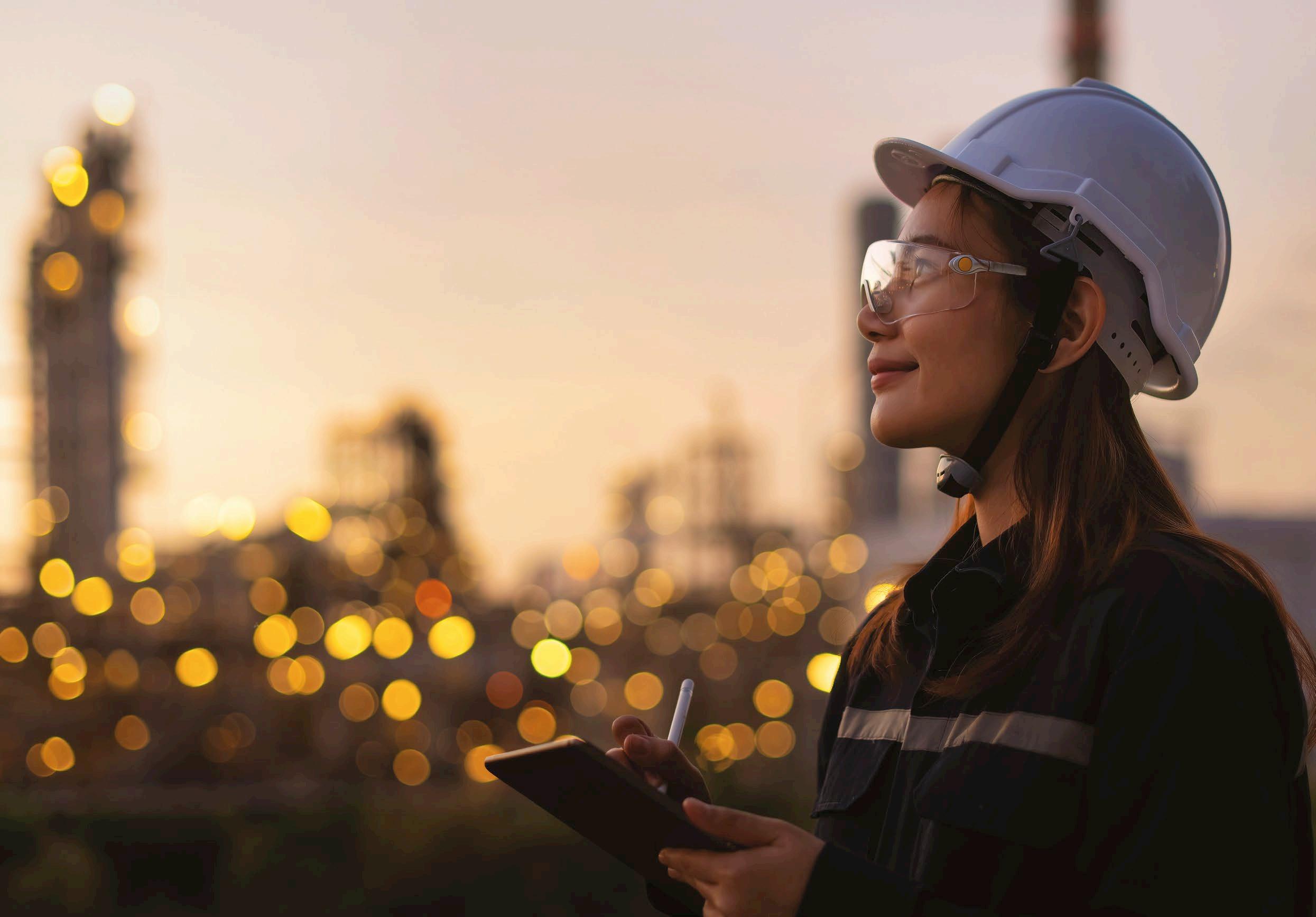
SON GUARD
Jose Fernandes discusses the crucial role of corrosion protection products in steel production and maintenance
teel, while known for its strength, is susceptible to corrosion, especially when exposed to moisture, chemicals, and other environmental factors. Therefore, ensuring suitable corrosion protection for steel during production, and later throughout maintenance, is crucial in prolonging the material’s lifespan, reducing cost and ensuring the reliability of steel structures and equipment.
Coatings specialist Hempel A/S has introduced its latest innovation in steel protection, Avantguard 750 Pro, with the aim of addressing critical environmental and economic challenges through improving steel durability.
“Corrosion protection products such as Avantguard 750 Pro play a crucial role in enhancing both environmental and economic outcomes in steel production and maintenance,” says Jose Fernandes, product manager corrosion protection at Hempel. “By extending the lifespan of steel structures – recommended for protection beyond 35 years – these coatings reduce the frequency of replacements and repairs, leading to significant cost savings.”
Aside from the business benefits, corrosion protection can also mean big green wins, too. “Environmentally, improved durability translates to a decrease in steel
production demand, thereby lowering CO2 emissions associated with manufacturing,” Fernandes adds.
“Moreover, Avantguard 750 Pro’s high solids content and low volatile organic compound (VOC) emissions contribute to a reduced environmental footprint during application.”
Corrosion protection products such as Avantguard 750 Pro play a crucial role in enhancing both environmental and economic outcomes in steel production and maintenance.
TRIPLE THREAT
Avantguard 750 Pro is built upon more than a decade of Hempel’s patented Avantguard technology.
“Hempel’s Avantguard technology stands out due to its patented Triple Activation process, which enhances corrosion protection by activating all three methods: barrier effect, inhibitor effect, and galvanic effect,” Fernandes explains. “It combines zinc, hollow glass spheres and a proprietary activator in our unique patented technology. The result is superior corrosion protection with higher durability compared to standard zinc-rich primers.”
This approach ensures improved durability and helps to extend the lifespan of steel structures. “Additionally, Avantguard 750 Pro has been formulated with high solids content, resulting in lower VOC emissions, contributing to more sustainable solutions,” Fernandes adds.
EXTREME ENVIRONMENTS
In particular, Avantguard 750 Pro is designed for the longterm protection of steel structures and equipment that operate in severely corrosive environments. The solution is therefore suited to a range of harsh environments, from protecting upstream and downstream infrastructure from critical conditions in the oil and gas industry to safeguarding onshore and offshore wind turbine towers against corrosion.
The coating can also be applied within infrastructure to ensure the longevity of bridges, civil structures and port equipment that may be exposed to aggressive elements, and within thermal power plants to maintain the integrity of steel structures subjected to high temperatures and corrosive agents. Meanwhile, the solution can offer enhanced protection to ship topsides in aggressive marine environments.
“Avantguard’s versatility also makes it suitable for both new constructions and maintenance projects, offering excellent crack resistance even in complex geometries,” Fernandes adds.
WEIGHING THE BENEFITS
As Fernandes explains, Avantguard 750 Pro offers several long-term benefits across a wide range of industries. One such advantage is extending asset lifespan: “Prolonged protection reduces the need for frequent maintenance and replacements, ensuring continuous operation and flexibility,” he says.
Improved cost efficiency is another beneficial factor, he continues: “Lower maintenance requirements and extended intervals between repairs result in reduced operational costs over time.”
Environmental sustainability is also an advantage, as the decreased need for steel production and maintenance activities could lead to a reduction in CO2 emissions and resource consumption. Additionally, the coating’s ability to cure at temperatures as low as -10°C and its tolerance to high humidity during application allow for year-round application in diverse environmental conditions.
Fernandes adds: “These advantages collectively enhance the performance, sustainability and profitability of operations across sectors such as oil and gas, renewable energy and infrastructure.”

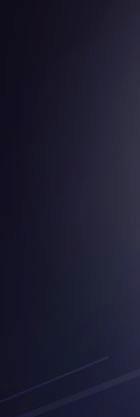

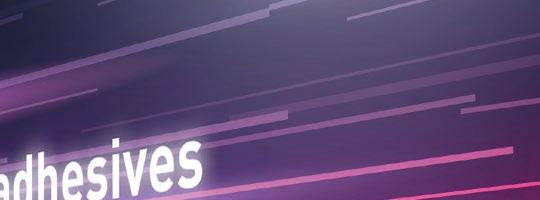
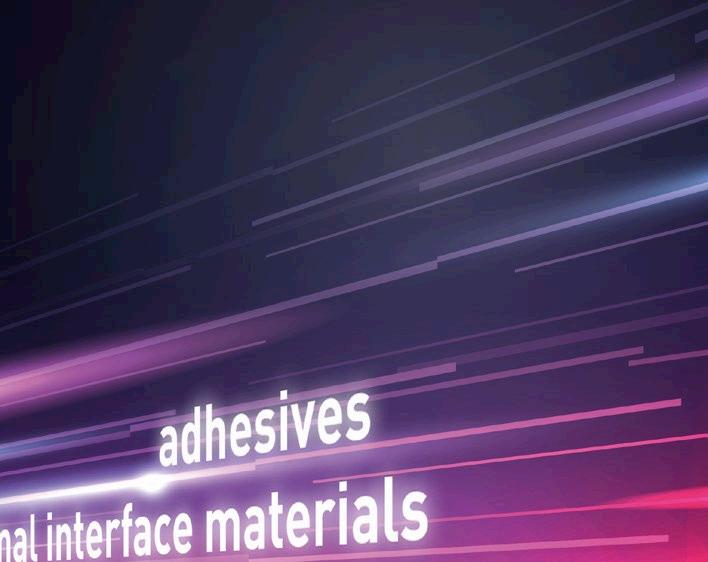

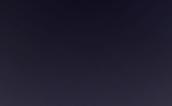


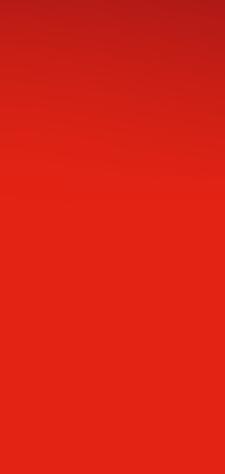
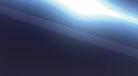
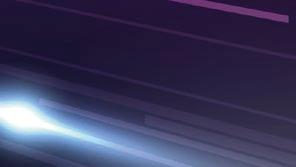
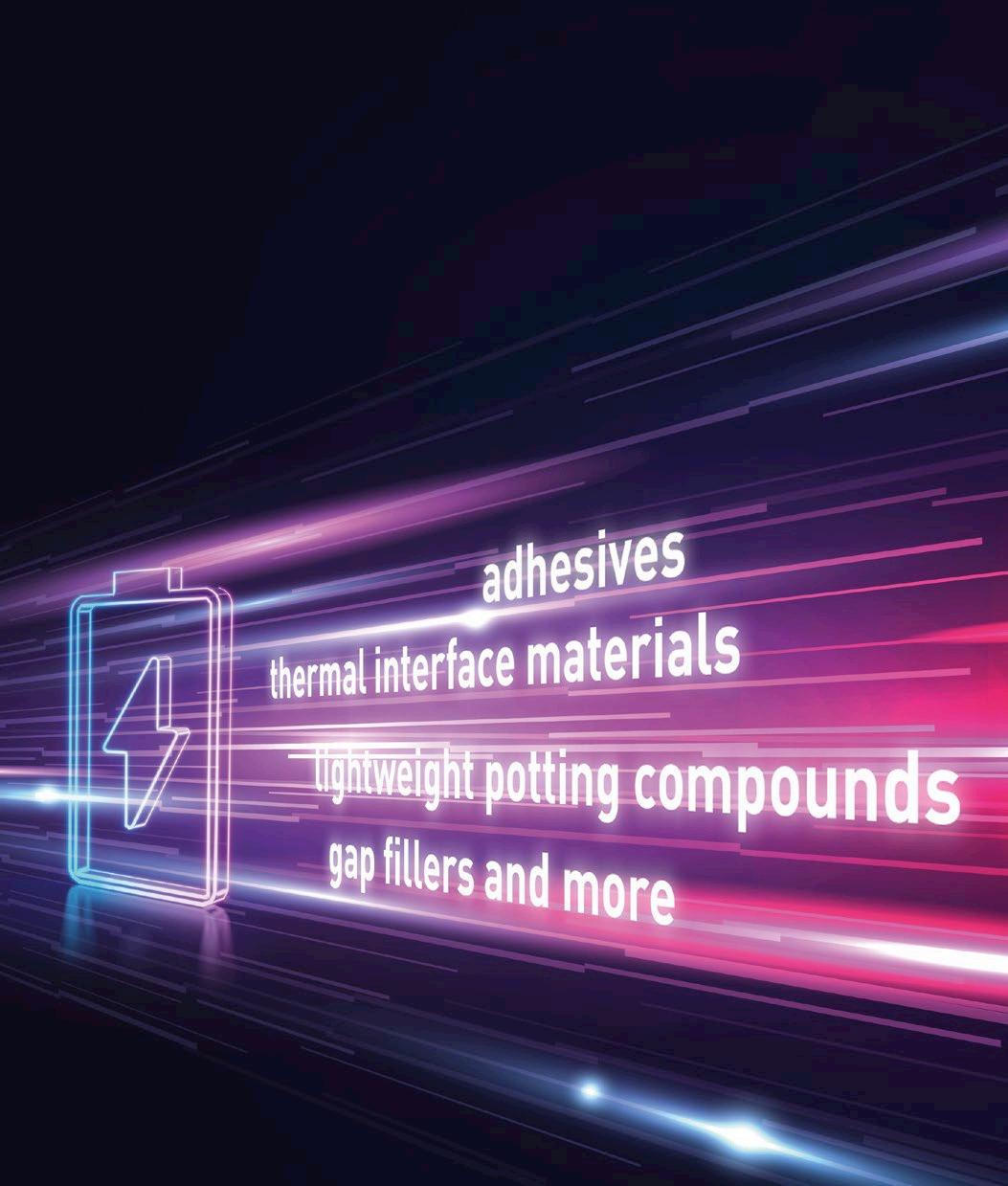
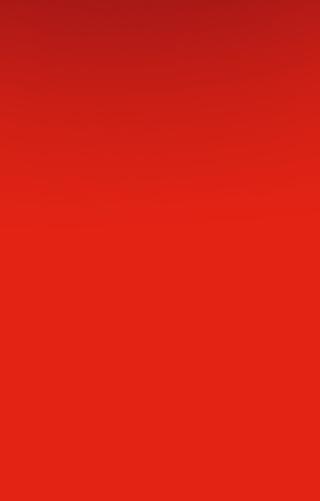
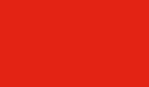
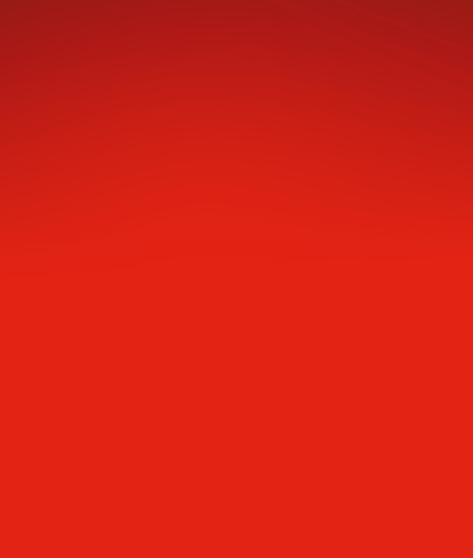


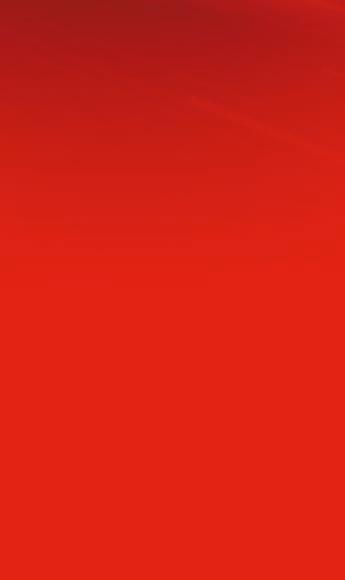
SOLUTIONS FOR EV BATTERIES
SPECIAL SILICONES FOR SAFE AND SUSTAINABLE BATTERY ASSEMBLIES
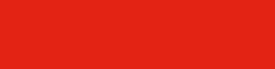
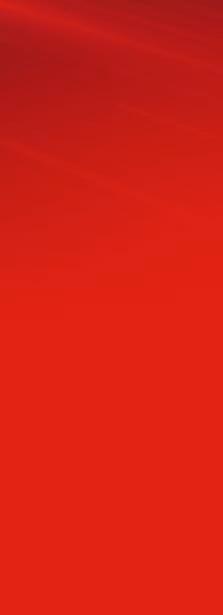
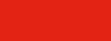
Without adequate battery protection, EV batteries may experience reduced performance, malfunction or in the worst case thermal runaway events. We provide performance materials for reliable function, safety and best power of battery modules and packs. CHT offers a comprehensive package of solutions for thermal management, lightweight potting compounds, gap fillers and high performance adhesives for assembly and gasketing of battery packs. In addition, we offer customized products to meet your individual design and functional requirements. Benefit from our expertise and experience in silicones.
More: cht-silicones.com


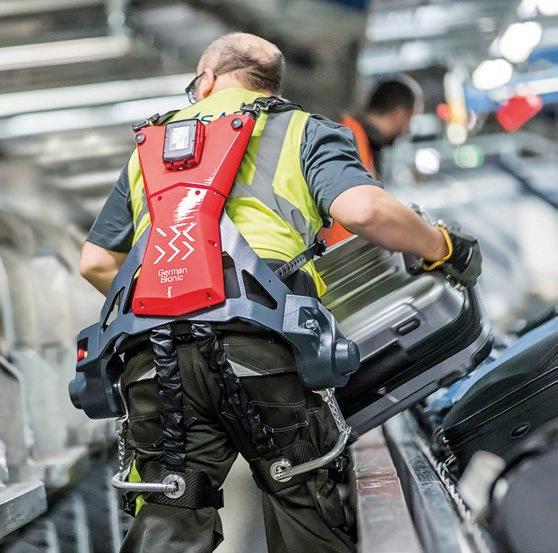
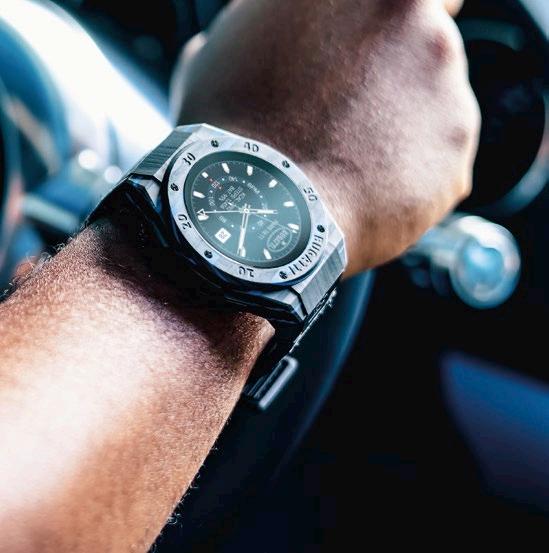
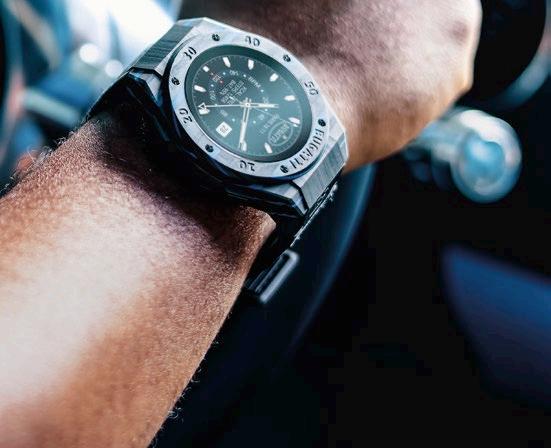
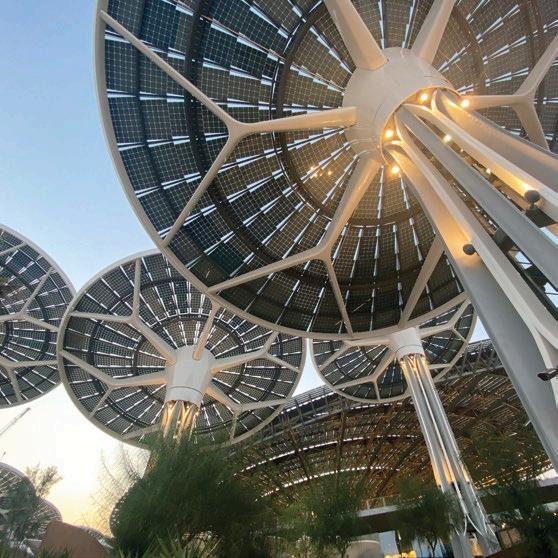
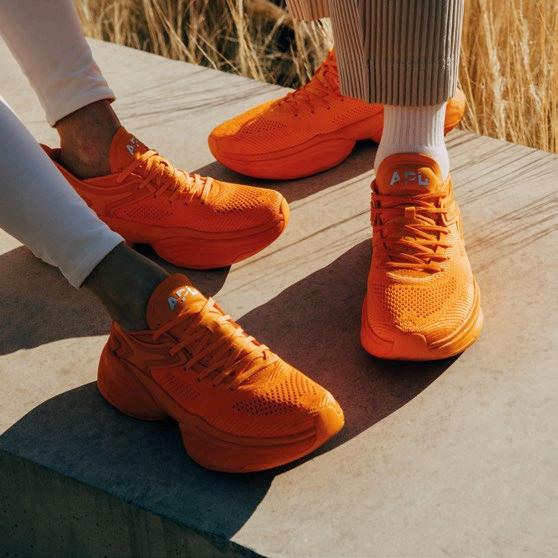
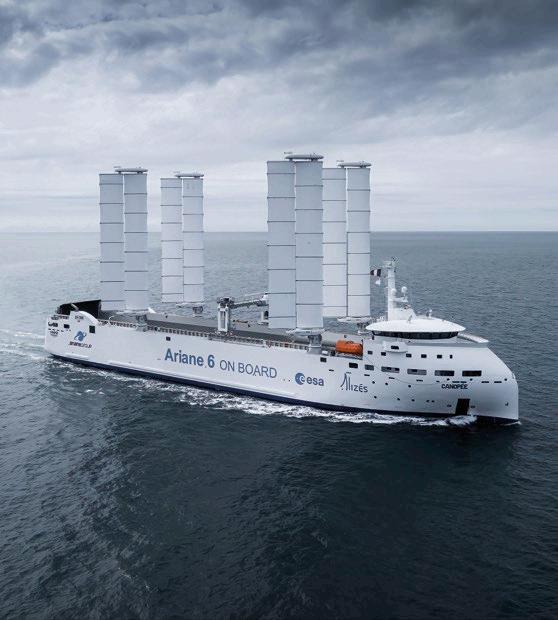
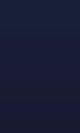
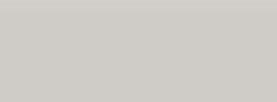

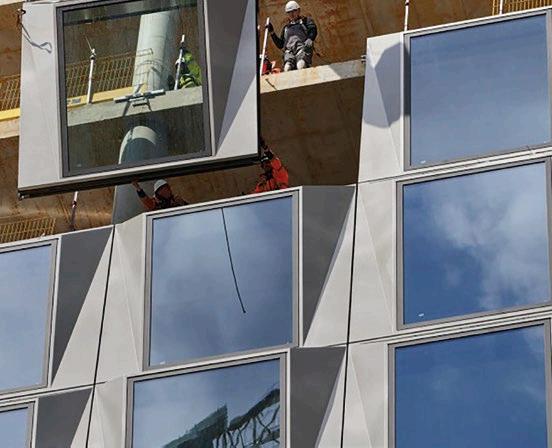
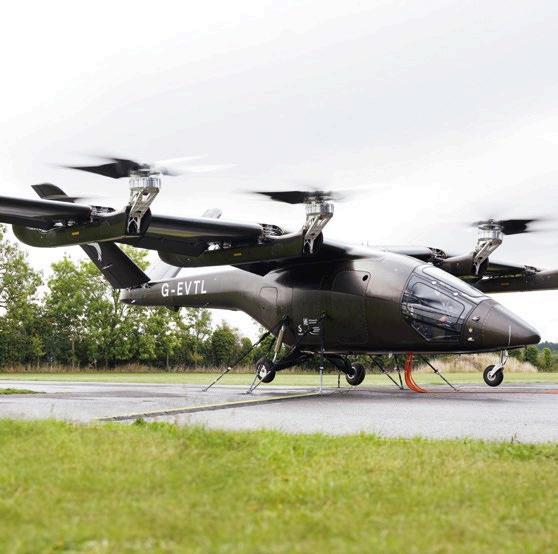
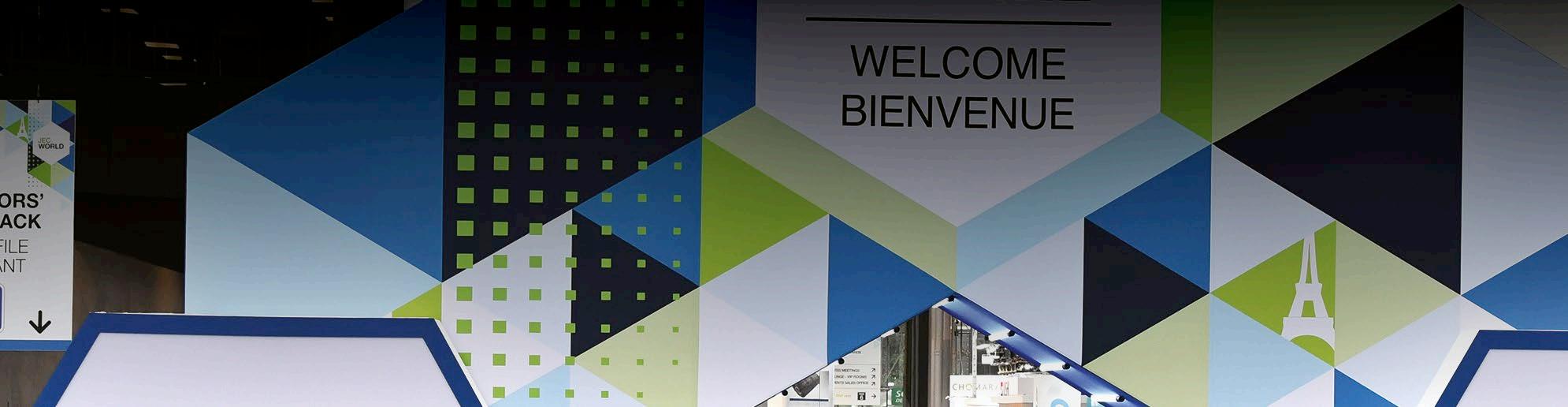
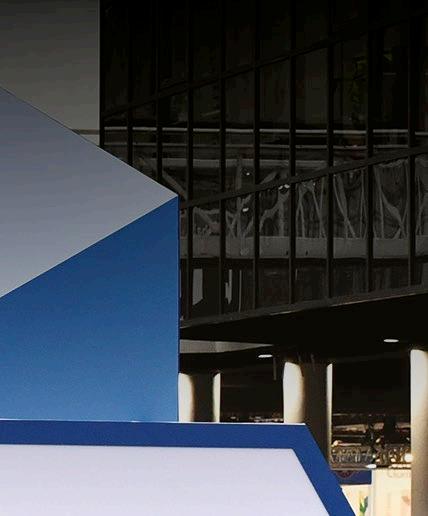
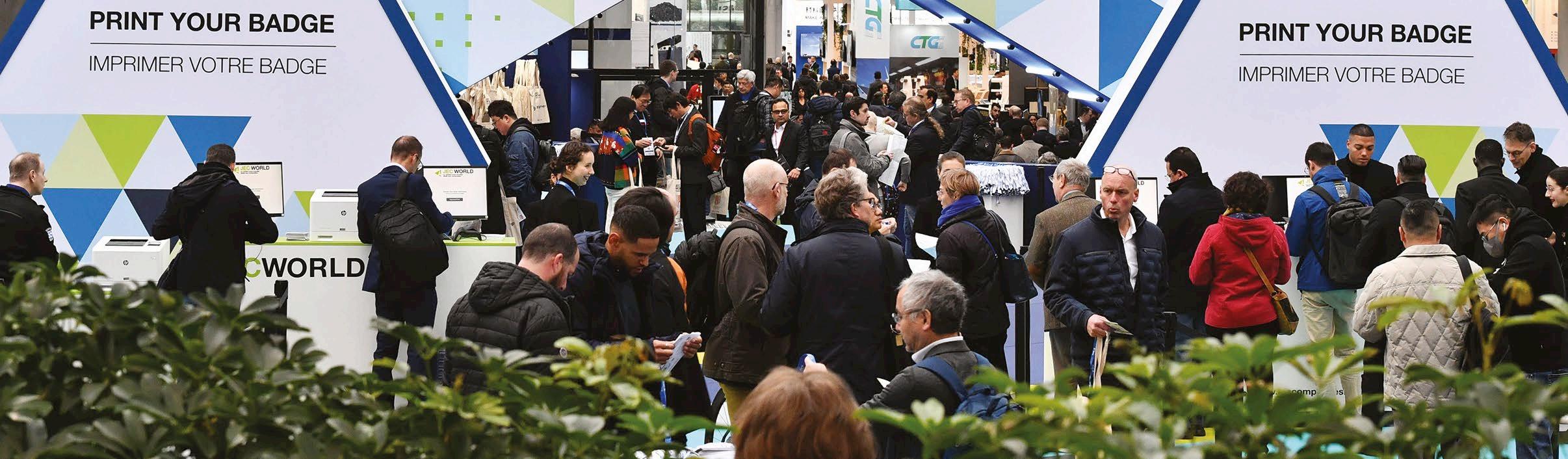
CIRCULAR INNOVATION
Bringing you the latest advances from across the composites sector, straight from the show floor of JEC World 2025
Pushing the limits was the overarching theme of JEC World 2025, which brought together the global composites sector to showcase the latest innovations that are redefining lightweighting, performance and design possibilities in industrial applications.
The 60th edition of the show was the largest to date, attracting over 45,000 professionals from 94 countries. More than 1,350 exhibitors displayed their cutting-edge products and technology advances, while thought leaders discussed a range of topics key to composite innovation, such as circular economy principles.
In total, more than 600 new products were launched during JEC World 2025, giving a positive indication to the pace of development within the composites industry. The Live Demo zone, meanwhile, highlighted automated and robotised processes, including large-scale manufacturing technologies.
CELEBRATING INNOVATION
This year’s JEC Composites Innovation Awards recognised 11 collaborative achievements across the composites spectrum, which the organiser says reflects the industry’s dedication to providing new solutions for all application sectors. The competition is open to any company, university or R&D centre with a compelling collaborative innovation or
concept to showcase.
Running through the winners, Airbus took first place in the Aerospace –Parts category for its Multifunctional Fuselage Demonstrator (MFFD), made out of thermoplastic composite materials covering novel design and build concepts and delivering lower CO2 emissions, dustless joining and material and process time reduction. Also in the aerospace category, Loop Technology’s FibreLINE technology was awarded in the Process category for its high-rate manufacturing of composite structures. Jaguar Land Rover took the Automotive and Road Transportation category for its Sustainably Optimised Composite Automotive (SOCA) project for decarbonising the manufacturing of composite automotive parts, while Fraunhofer IMWS’ thermoplastic sandwich moulding technology won the Process category for enabling the fully automated production of 3D moulded components in a material-efficient lightweight sandwich construction.
Other award winners included: Building and Civil Engineering – TechnoCarbon technologies; Circularity and Recycling – ILSUNG Composites Corporation; Design, Furniture and Home – Cobra International; Digital, AI and Data –New Frontier Technologies; Maritime Transportation and Shipbuilding –International Centre for Numerical Methods in engineering (CIMNE); Renewable Energies – IRT Jules Verne; Sport, Leisure and Recreation – The Gun Sails von Osterhausen
ALLIANCES MADE
JEC World also saw the launch of the European Circular Composites Alliance (ECCA), an initiative dedicated to establishing a circular economy for composites in Europe. The alliance is the result of a partnership between JEC and the European Composites Industry Association (EuCIA), and will set targets on the use of recovered and recycled composites, develop standards for circular product design, and provide a forum for industry voices.
“ECCA is an essential step towards a wider circular economy for the whole of Europe,” said Professor Roberto Frassine, EuCIA’s President, “Combining the collective will and ambition of our composites manufacturers, associations and end-users into one voice will accelerate our journey to net-zero.”

JEC World 2025 brought together the entire composites supply chain
The launch of ECCA at JEC World
SUSTAINABILITY IN FOCUS
In line with the theme of circular sustainability, Syensqo introduced its ReGen portfolio of sustainable composite materials at this year’s show. Containing a controlled blend and/or mass-balanced renewable feedstocks, the materials offer the same performance as their parent equivalents but with added sustainability credentials.
During the event, Syensqo’s new SolvaLite 714 ReGen, MTM 57 ReGen and MTM 58B ReGen materials were launched for the automotive market. The company says its ReGen portfolio is a response to market desire for circular composites, without the need to make modifications to existing manufacturing processes.
The Synesqo booth also highlighted several innovative components and flagship products within the composites space, such as the first fully composite electric car battery box enclosure to meet all major automotive mechanical and fire safety hazards, which the company designed in partnership with Ricardo and Airborne. The firm also showcased a wing spar from Ascendance’s ATEA VTOL prototype created from Syensqo’s MTM 45-1 epoxy resin system for its high-performance and flexible curing properties, and micro launcher components manufactured by Orbex using the Syensqo’s CYCOM 5320-1 thermoset resin system coupled with THORNEL T650 fabric. These parts play a key role in Orbex’s novel carbon fibre coaxial tank, specifically designed for its BioLPG
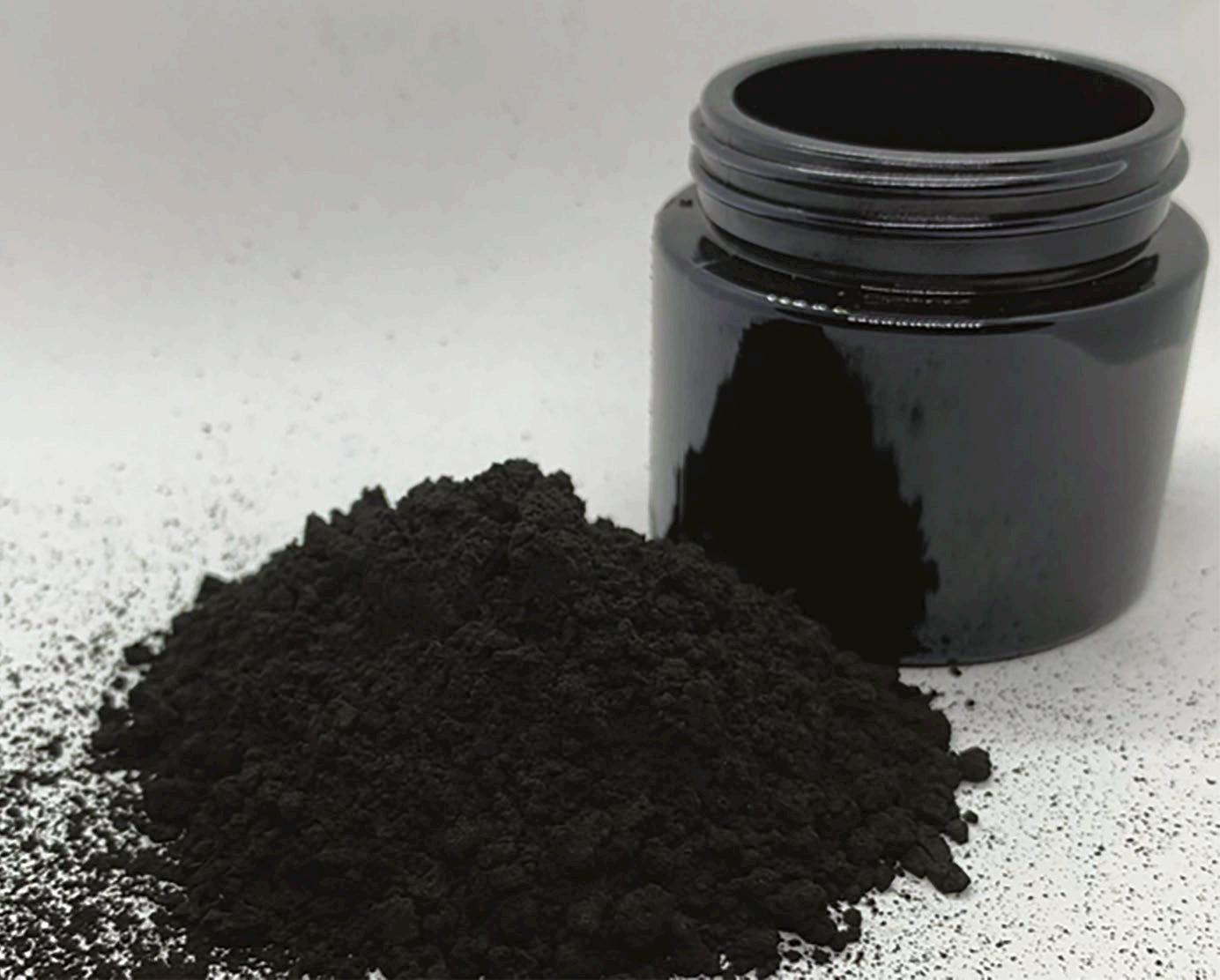
fuel system for sustainable space exploration.
CARBON-NEGATIVE COMPOSITES
Elsewhere, Dama Bioplastics unveiled its innovative carbon-negative material, Dama Black, designed specifically for the plastics, rubbers and composite sectors. Derived from waste biomass, the biomaterial locks away three tonnes of CO2 per ton produced, delivering a carbonnegative impact while enhancing product performance.
Dama Black can be seamlessly integrated into existing manufacturing processes across high-performance automotive components to consumer goods
Providing increased lightweight, thermal stability, UV stabilisation and mechanical strength, Dama Black can be seamlessly integrated into existing manufacturing processes across highperformance automotive components to consumer goods. According to the firm, Dama Black is capable of doubling the strength of plastic composites and increasing the strength of concrete by 20%. The material is made entirely from plant waste and could therefore act as a sustainable drop-in replacement for petroleumbased Carbon Black. Dama Black has both automotive and construction grades, but is suited to applications across a wide range of sectors ranging from bioplastics, paint, food and beverage, oil and gas, and medical.
“2025 marks a pivotal year for Dama and the industries we serve,” says Cole Gibbs, founder and CEO of Dama Bioplastics. “Dama Black represents the future of sustainable materials, combining environmental responsibility with innovative performance.”
Dama Black is carbon-negative
Graphene-infused polymer pellets and hydrogen liner
THE GOLDEN AGE OF GRAPHENE?
Initially dubbed the revolutionary ‘wonder material’ of the past decade, graphene is well-known in the engineering community for its superior strength, electrical conductivity and transparency. So far, though, the material has struggled to live up to the initial hype surrounding it due to challenges in production and scaling up. As seen at JEC World, one company is working hard to change that, however, with very promising success.
Founded in 2017 by Dr Mamoun Taher, Graphmatech is an innovative Sweden-based materials company that infuses graphene into polymers and metals to create composite materials with remarkable properties. The key to success for the company’s multifunctional hybrid materials is its novel infusion process, says Cecilia Arhammar, head of research and development at Graphmatech.
“We have developed a blending process via extrusion where we heat up the plastic polymer and blend in the graphene in a way that is key to maintaining the material’s properties,” she explains. “To do this on a large scale is very complex. We have therefore designed a machine that enables a very good blend between the polymer thermoplastic material and the graphene, achieving good separation of the graphene plates.”
The process for infusing metals with graphene is slightly different, she continues, “We cover metal particles
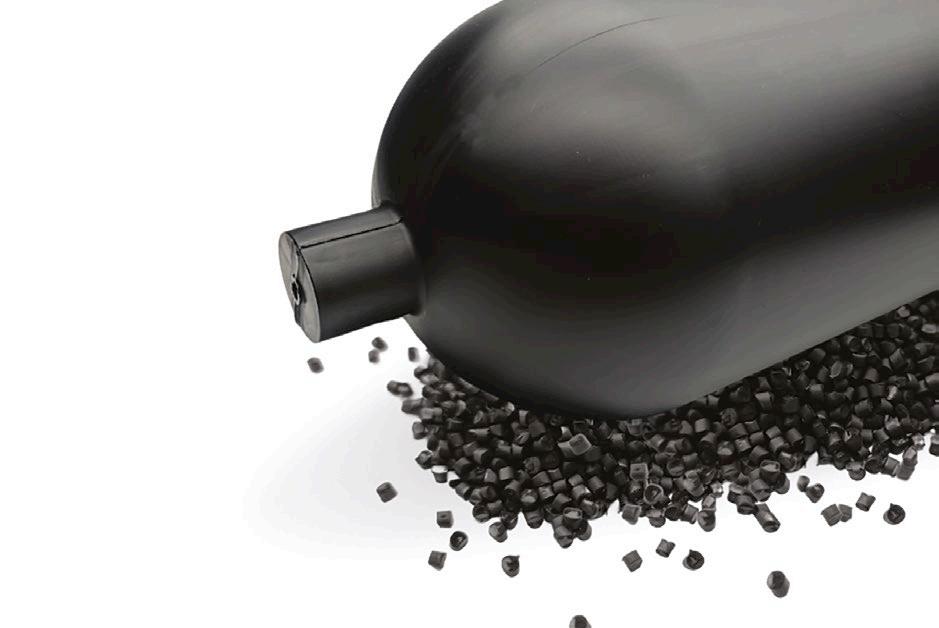
with very thin sheets of graphene which enables us to fine-tune the properties of the metal powder. We have refined the process so that we can apply this to any process where powder is used.”
WIDESPREAD APPLICATIONS
Graphmatech’s resulting polymergraphene composites have the potential to reshape a wide range of applications, from conductive pipes and hydrogen infrastructure to industrial packaging.
“Within aerospace, for example, graphene can enhance the polymer vessels used for hydrogen storage,” Arhammar says. “This results in minimal leakage. As well as hydrogen storage tanks, graphene-infused thermoplastics could be widely used in applications like regular gasoline tanks and pressure vessels – any component that requires higher thermal and mechanical load would benefit from graphene-infused polymers. Protecting electronics is also a key area that we’re looking at. Additionally, there are currently a lot of limiting factors with packaging protection, such as oxygen, where graphene-infused composites could really make a difference.”
LESS HYPE, MORE REALITY
The driving force for Graphmatech
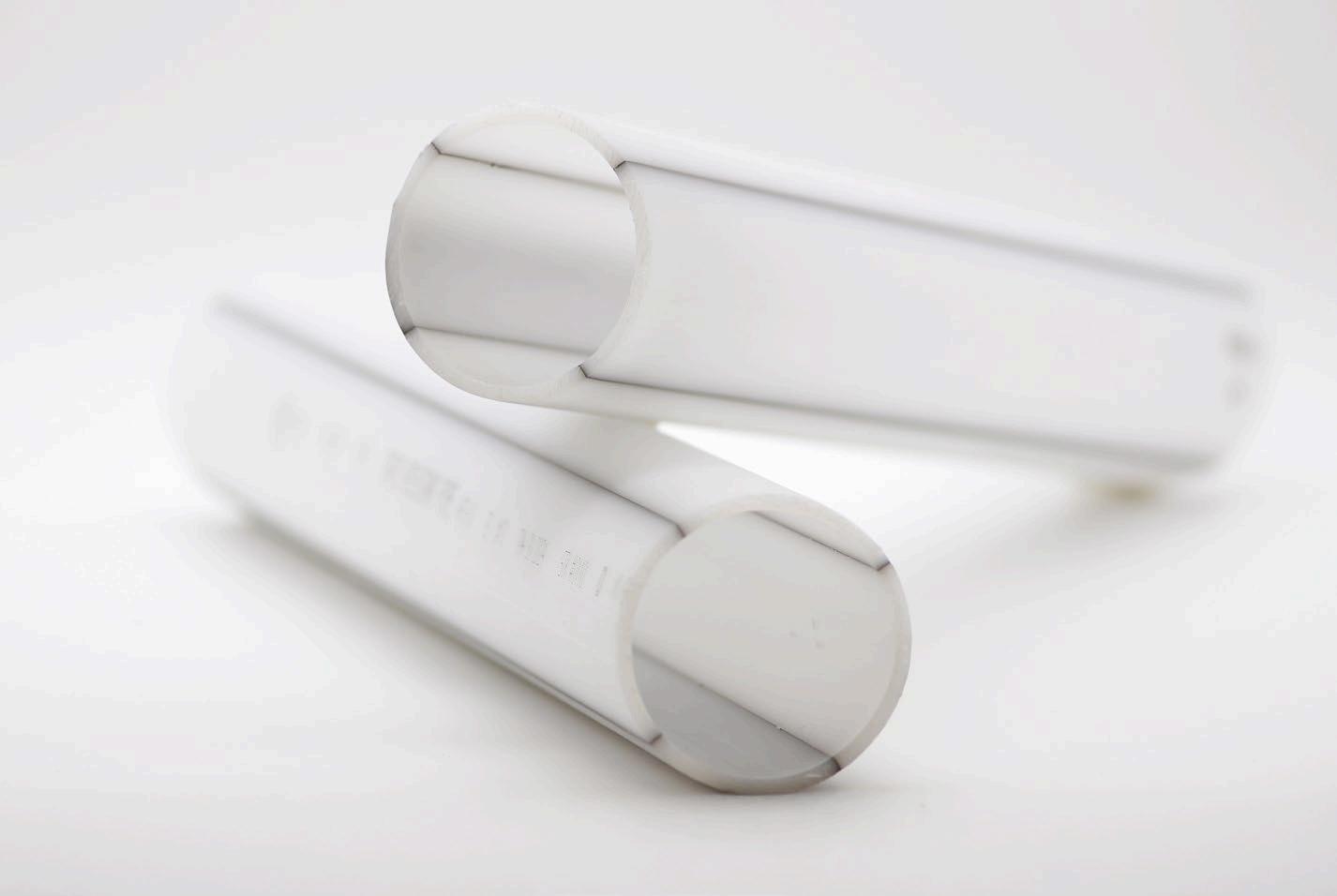
is not just to push the boundaries of existing materials’ capabilities, but to also unlock new markets in pursuit of a greener industrial future.
“We are positioned well in the value chain as we focus solely on the application of graphene in polymers and metals in line with our customers’ needs,” Arhammar says. “The key is in managing our polymer extrusion process, which is very scalable with the right investment.”
So, what’s next for Graphmatech as the company looks to ramp up its capabilities? “Scaling up is key for us in order to provide the market with the materials that are needed,” she continues. “Beyond that, being able to improve, test and demonstrate new polymer parts in collaboration with our partners will be important. Certification is also key in this area. Looking at hydrogen specifically, there are a number of regulations that must be followed, and proof-of-concept for products will be vital here.”
The company recently received a Swedish grant for its hydrogenfocused solutions, prompting the company to set the goal of implementing its graphene-infused composites within 1,000 light commercial vehicles and 500 heavy commercial vehicles by 2027. Through this, the company hopes to reduce carbon dioxide emissions by over 50,000lbs per year.
“Many people do not know that hydrogen is actually an indirect greenhouse gas,” Arhammar adds. “It has a potential impact on the environment that is 11 times higher than that of CO2 over a 100-year period. This has to do with how methane is being contained within the atmosphere due to hydrogen preventing it from breaking down over time.”
Therefore, the hydrogen sector will form a key part of the company’s research and development efforts going forwards, as it seeks to play a pivotal role in the green transition towards smarter materials.
Graphene-infused conductive pipes
BIOBASED SOLUTIONS
JEC World also saw Wessex Resins and Adhesives launch its new BIOinfusion epoxy resin system specifically engineered for composite manufacturing. The firm hails the launch as a significant advancement in sustainable materials that offers manufacturers a “compelling” alternative to traditional petroleum-based resins.
BIOinfusion resin is 32% biobased and formulated with renewable resources, lowering the material’s environmental impact while maintaining the strength and durability the company’s Entropy Resin products are known for. The resin is suitable for use within a wide range of industries, from lightweight components in automotive vehicles to wind energy turbine blades and marine applications.
“We are very pleased to introduce BIOinfusion to the market,” says Sam Oliver, operations director at Wessex Resins and Adhesives. “This biobased epoxy resin system represents a significant milestone for the composite manufacturing industry. By providing a high-performance,
sustainable solution, BIOinfusion enables manufacturers to reduce their environmental impact while maintaining the exceptional quality they require.”
FORTIFIED FOAM
The use of foam cores within composite material applications has been increasing recently as a means to reduce weight and increase the stiffness of parts in a range of industries.
Autoclave methods for manufacturing composites such as prepeg compression moulding (PCM) and resin transfer moulding (RTM), however, generally require high heat resistance of over 100°C during the process. This has traditionally meant that the number of applicable foams is limited, with most of the high heat-resistant foams in sheet form. This requires pre-cutting, which leads to high processing costs and can impact productivity.
At JEC World, Asahi Kasei showcased its new SunForce particle beads foam based on the engineering plastic modified polyphenylene ether (m-PPE). The foam combines the desirable aspects of m-PPE such as
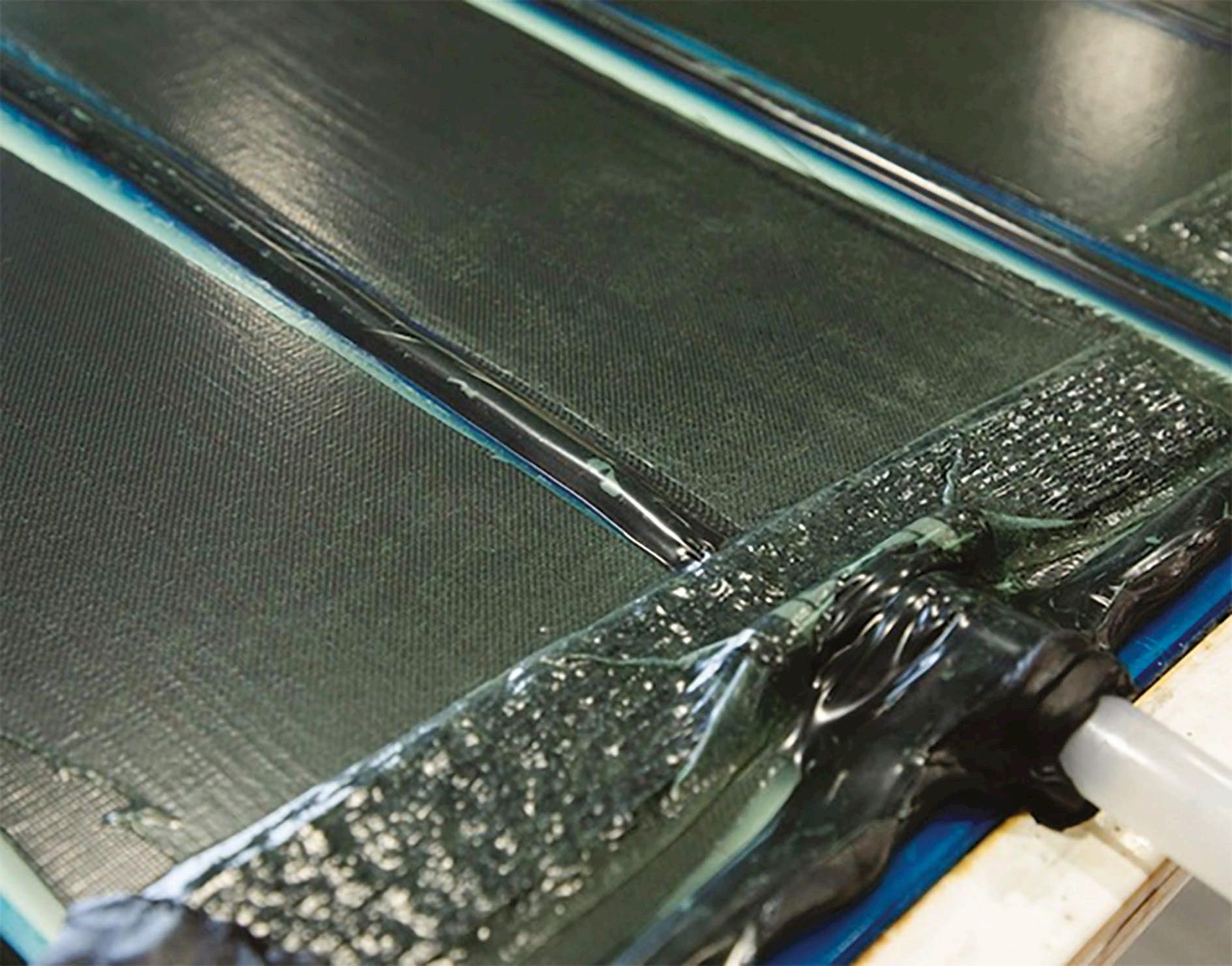
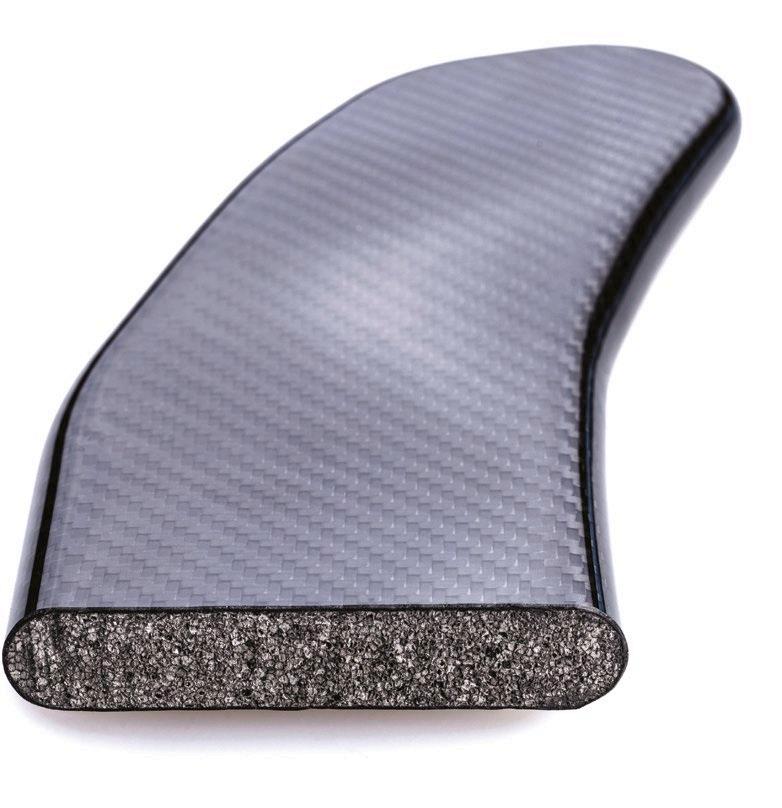
The cross section of a demonstrator spoiler made of CFRP and SunForce
heat resistance, dimensional stability and low water absorption, with the lightweight, thermal insulation and formability benefits of bead foam. SunForce beads can be moulded by in-mould forming leveraging the steam chest moulding process. In combination with the smallsized beads, the process allows for medium to high-volume production of composite core parts with accurate, complex and curved shapes, without the need for additional milling. Thanks to these properties, SunForce can be used as a foam core or sandwich material for a variety of applications in the medical, industrial, aeronautical and sports industries.
This biobased epoxy resin system represents a significant milestone for the composite manufacturing industry
The BIOinfusion epoxy resin system
A NEW DIMENSION
As industries increasingly prioritise sustainability, an environmentally responsible material that also offers high durability, good lifespan and energy-efficient production is crucial. Industrial Summit Technology (IST) Corporation believes its newly launched advanced polyimide fibre Imiditex fulfils this brief.
The material is designed to work in synergy with traditional glass and carbon fibres to enhance their performance and unlock “unprecedented” applications, all while offering a high 3.0GPa tensile strength, a continuous use temperature exceeding 250°C, and an ultra-low water absorption rate of less than 0.9%.
“One of the most unique characteristics of Imiditex is its vibration damping and shock absorption,” says Toshiko Sakane, CEO and president of IST Corporation. “As well as its high temperature and UV resistance, it is lighter than both glass fibre and carbon fibre so when combined with these materials it can form much lighter composite parts.”
When using conventional materials, design engineers are often faced with trade-offs between strength, weight and flexibility. Imiditex, however, can be integrated seamlessly into composite structures to complement and expand the functional capabilities of existing parts. When combined with carbon or glass fibres, the material provides superior vibration damping, improved impact resistance and significant weight reduction without compromising the structural integrity of the part, and without replacing conventional composite fibres.
“We have had lots of enquiries from the automotive and aerospace sectors for reducing vibration issues, such as engine wing vibration or spoiler wing vibration,” Sakane says. “Also, far less energy is needed to produce Imiditex when compared to carbon fibre, for instance.”
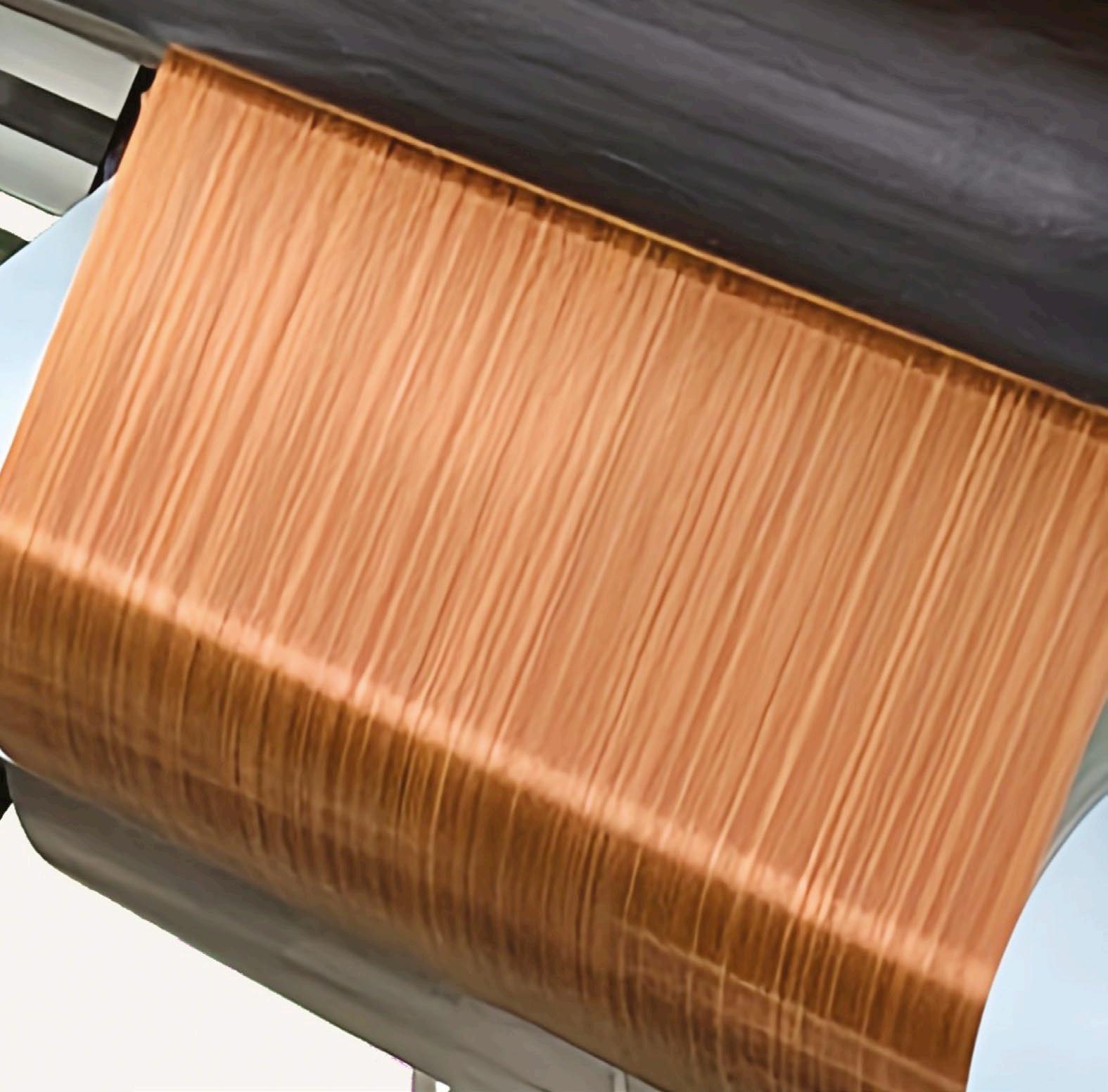
Imiditex
provides numerous performance enhancements to existing composite materials
ENHANCE OVER REPLACE
When incorporated into composite structures, Imiditex can provide numerous performance enhancements through its excellent electromagnetic transparency, low transmission loss, and high impact resistance and durability.
“Essentially, Imiditex retains the existing properties of polyimide such as heat resistance, low water absorption and high strength which makes it ideal for high-performance composite applications,” Sakane continues.
By enhancing rather than replacing existing composites, Imiditex is poised to unlock new possibilities across a wide range of applications, such as telecommunication devices, sports equipment, automotive and mobility components, infrastructure, medical devices, and aerospace and satellite technologies.
VERSATILE APPLICATIONS
Within the field of aerospace, saving weight while ensuring structural integrity is a crucial requirement for composite components. Imiditex
fulfils both of these demands, leading to improved fuel efficiency and ensuring durability in extreme environments. The fibre’s vibration damping properties improve part stability, while its electromagnetic transparency make it well suited to applications in which radio wave transmission is essential, such as aircraft communication systems and satellite components.
Lightweight and durable materials are also highly sort after within the automotive sector as the industry looks to improve its sustainability credentials. Imiditex enhances vehicle components by reducing weight and improving impact resilience, leading to better fuel efficiency and lower emissions. According to Sakane, integrating the fibre into automotive composite parts will support the next generation of transportation innovations.
Contributing to longer-lasting composite structures, Imiditex reduces material waste and minimises the need for replacement parts. Production of the fibre is also considerably more energyefficient than other composite fibres, generating approximately one fifth of the CO2 emissions associated with carbon fibre manufacturing.
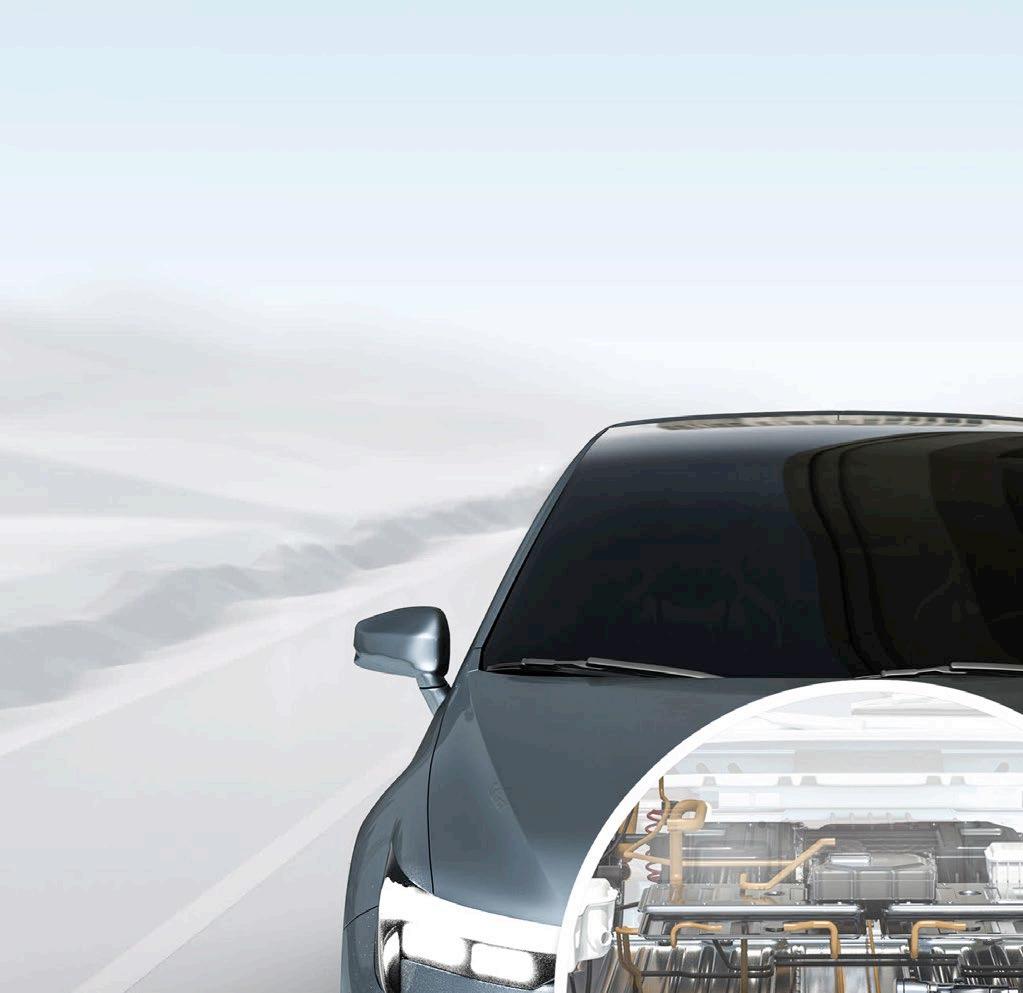

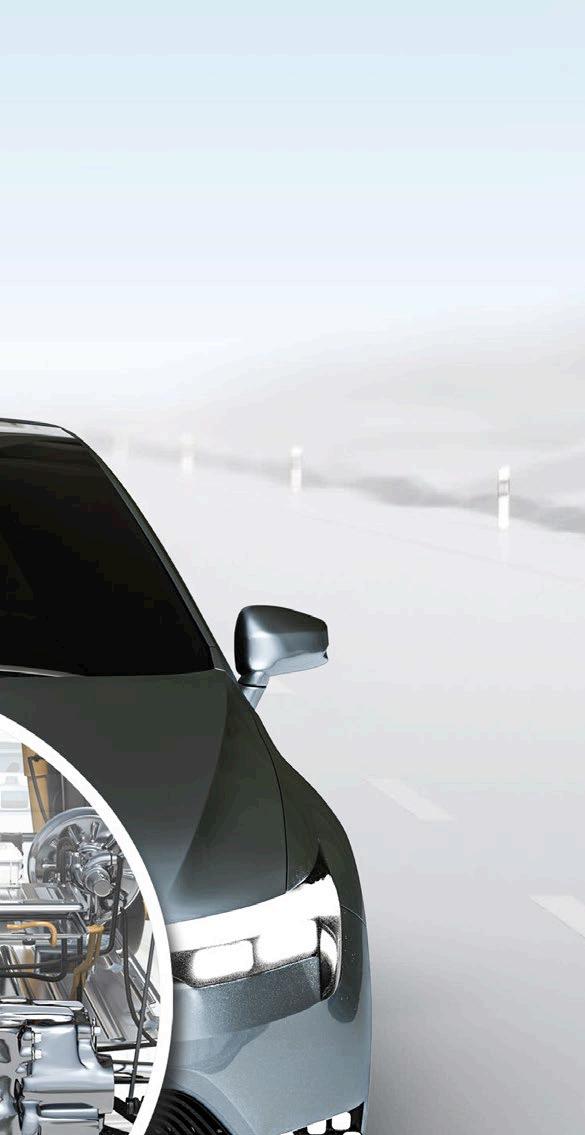
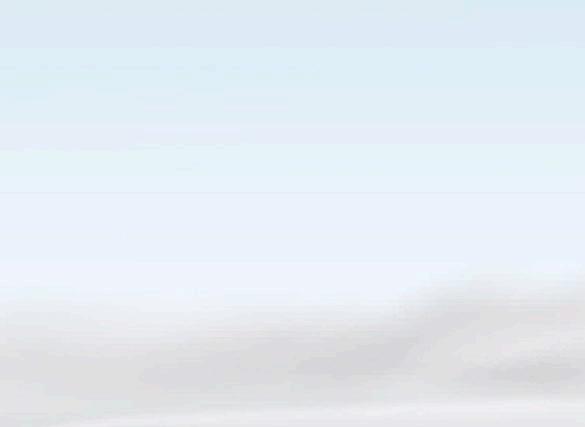
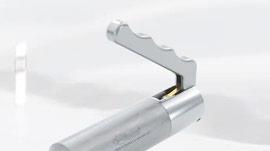
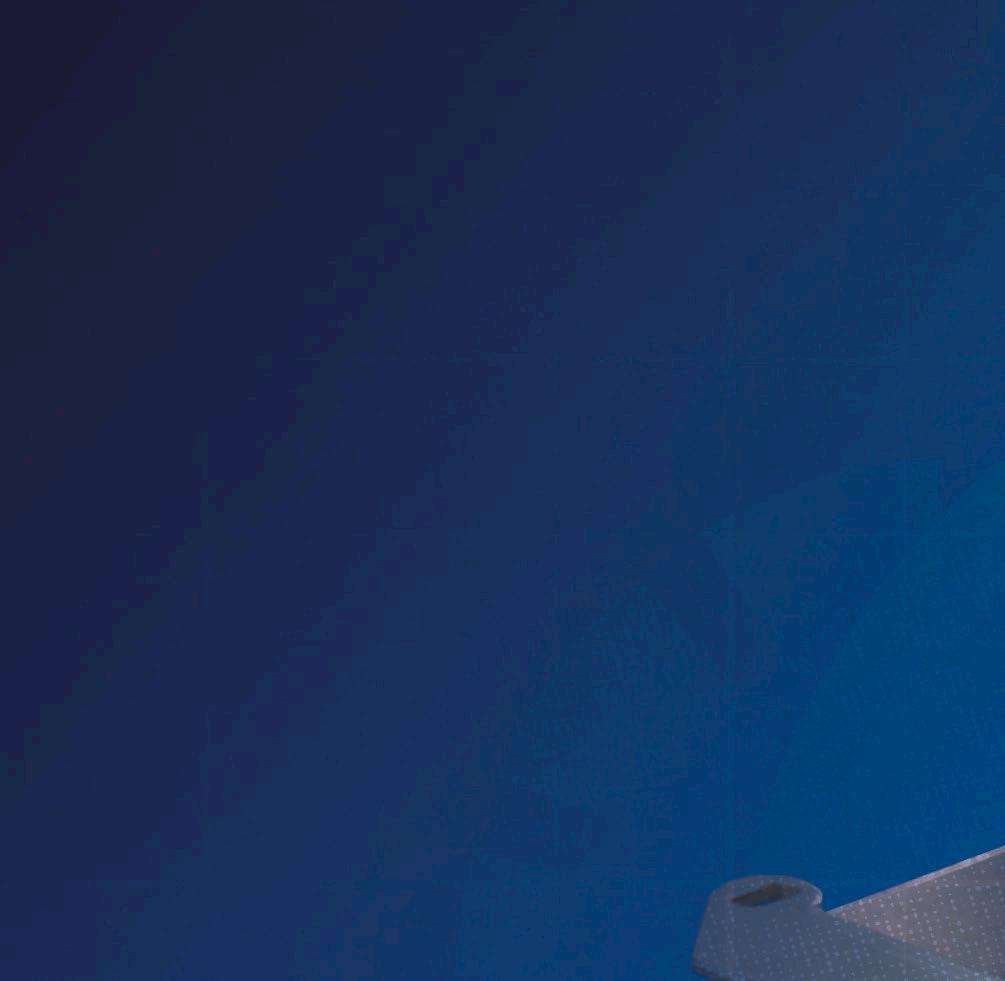
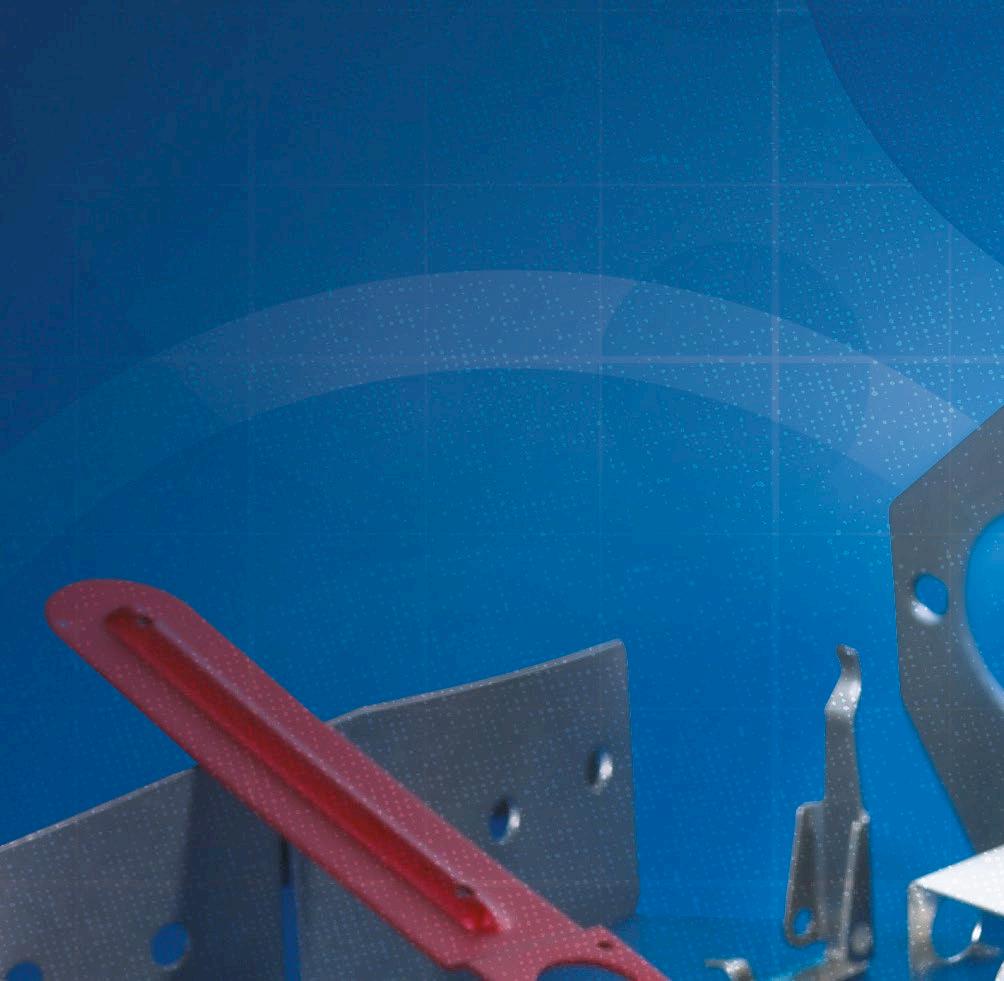
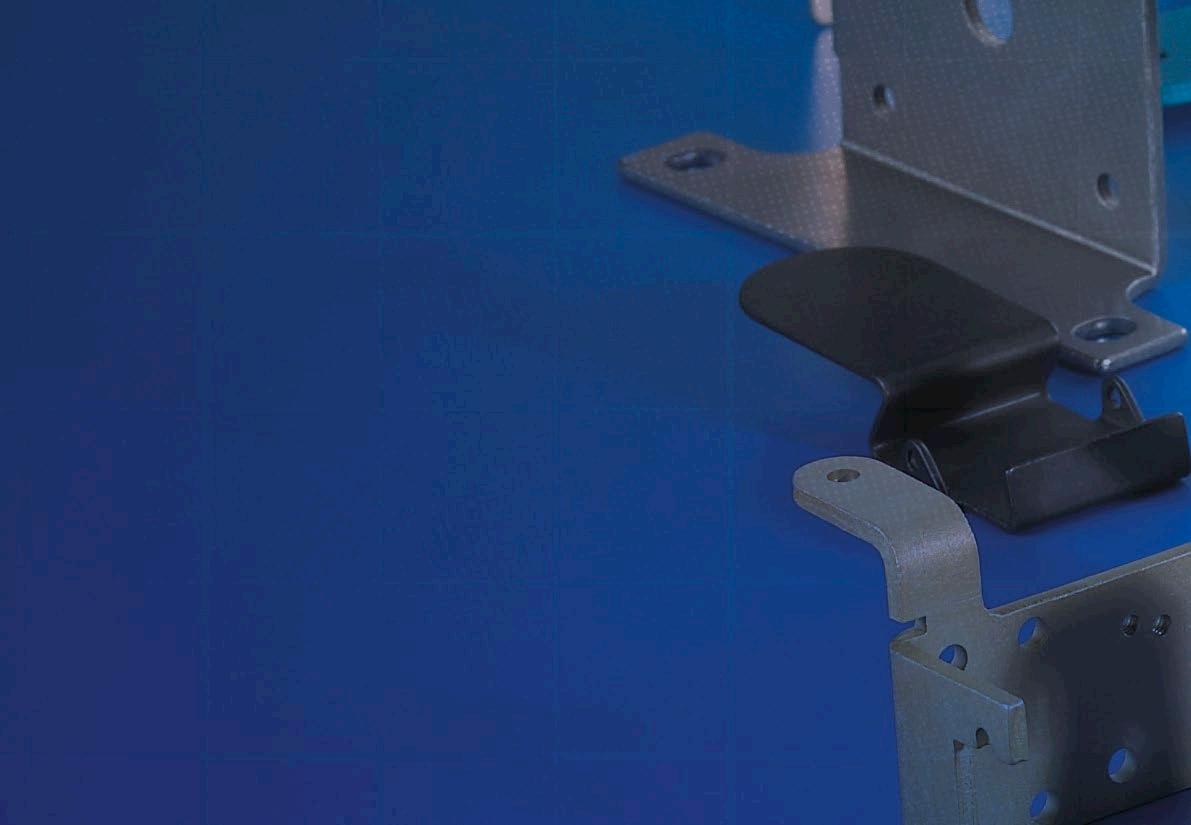
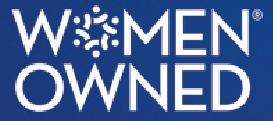
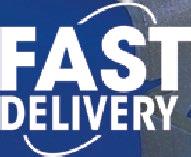
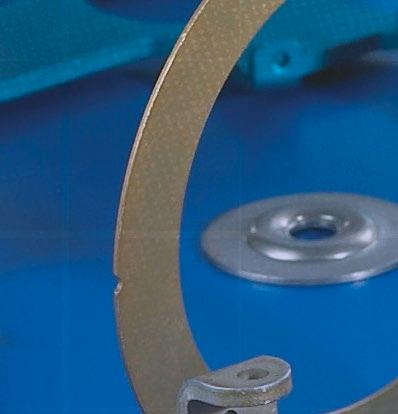
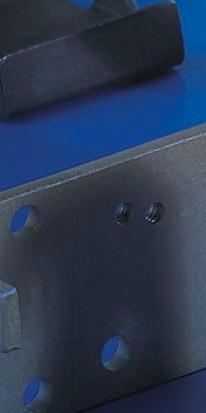
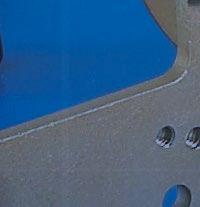
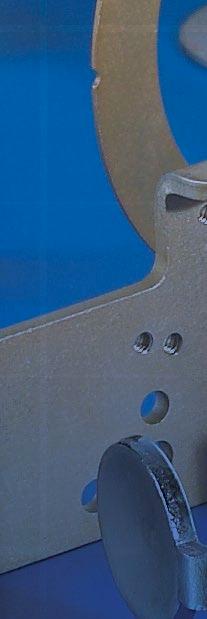
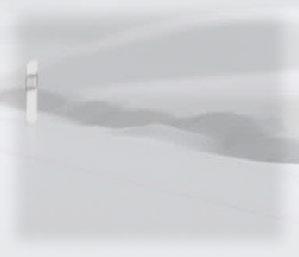
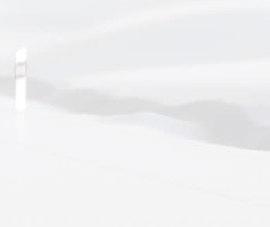
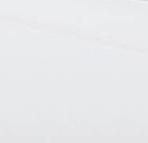
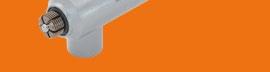
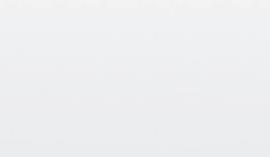

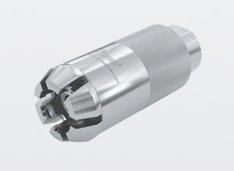
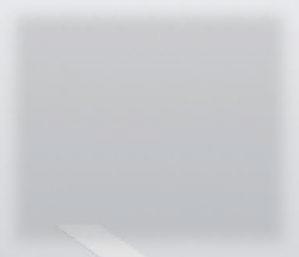


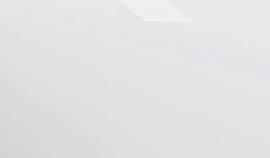
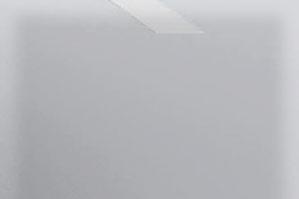
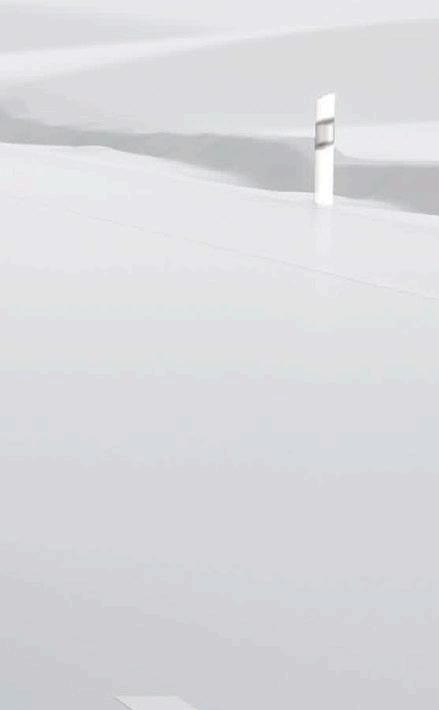
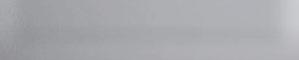
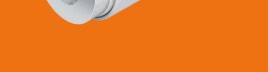


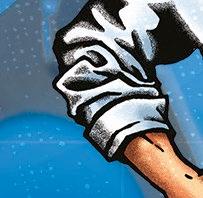
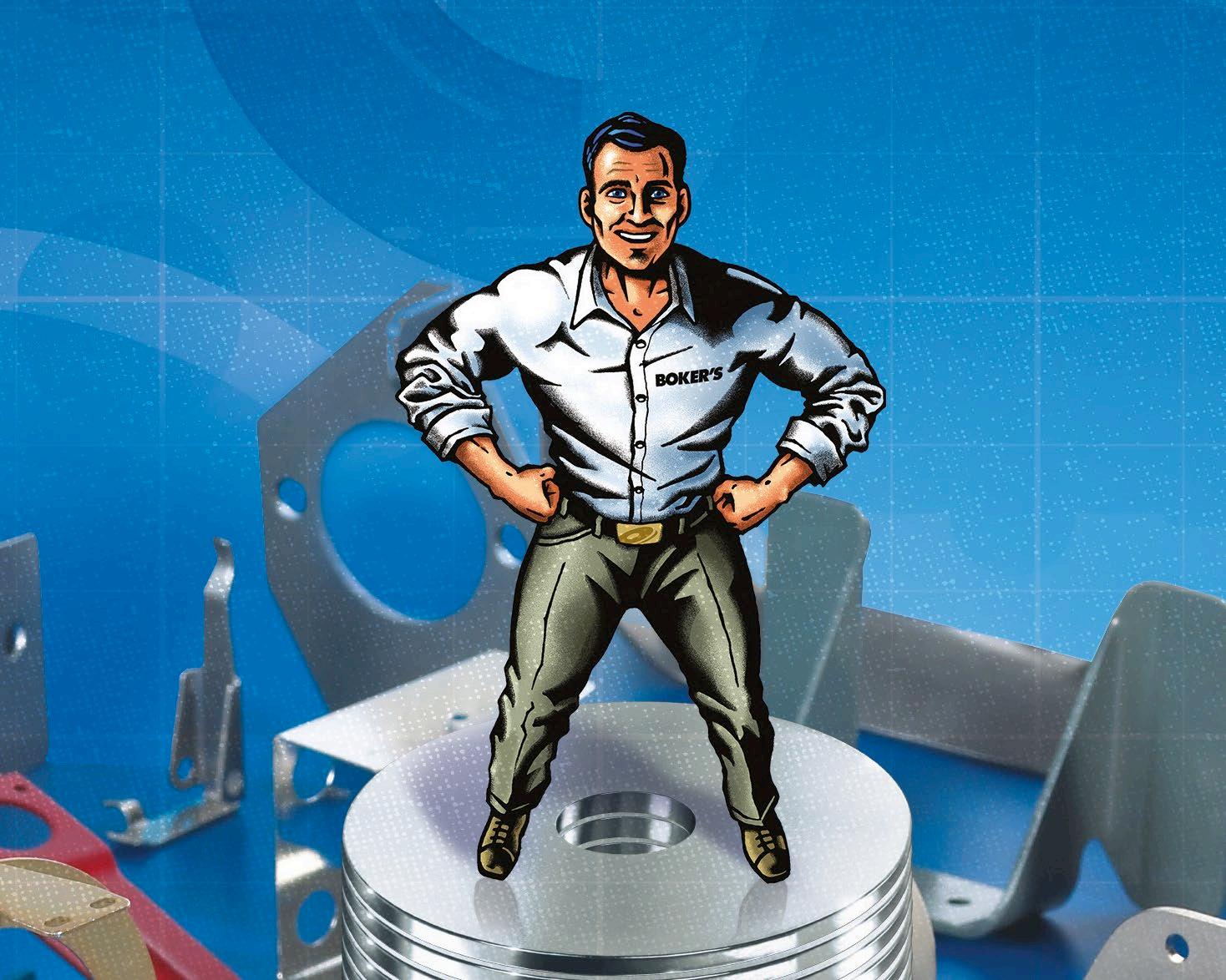
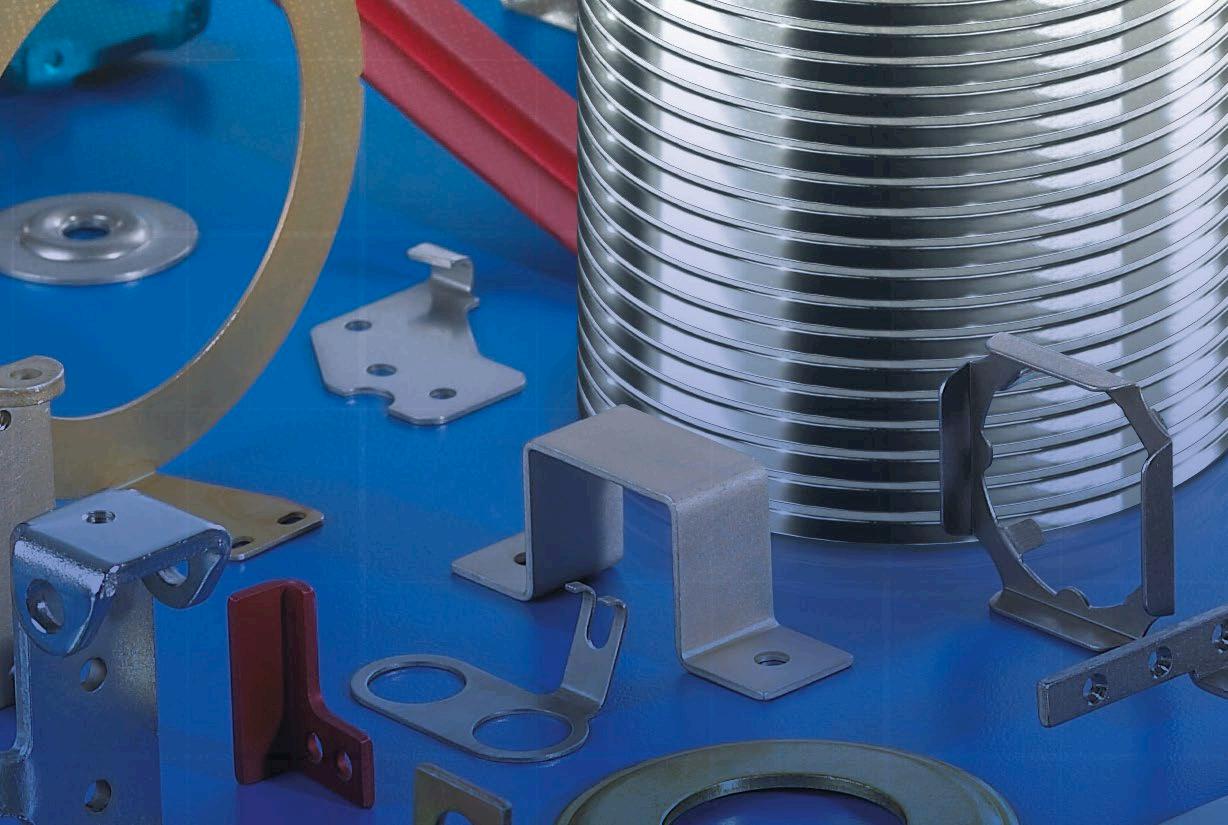

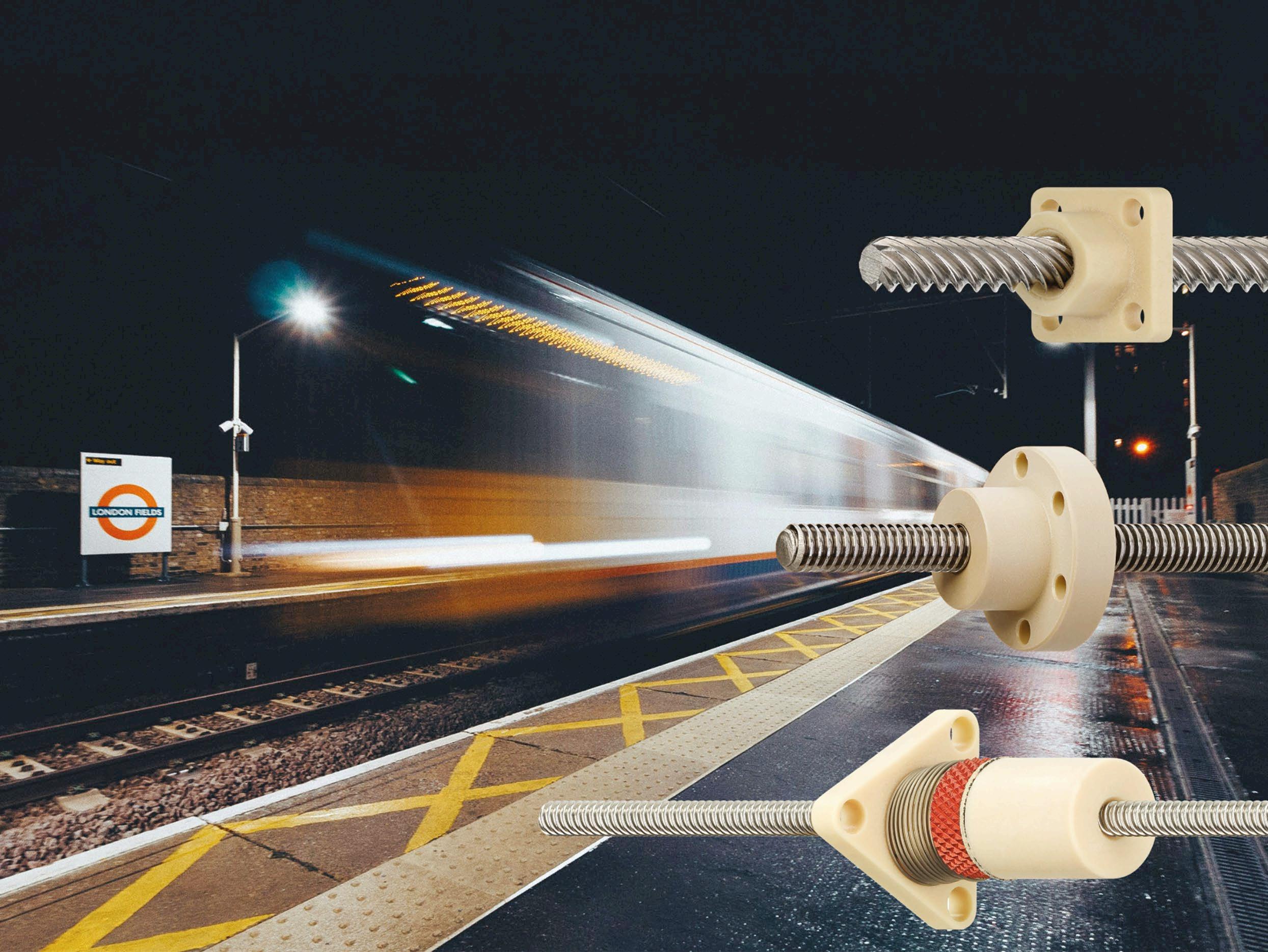
THE EVOLUTION OF THE TRAPEZOIDAL THREAD
How one company has given a new lease of life to traditional trapezoidal threads with its innovative thread technology
Akey component of mechanical engineering applications for decades, trapezoidal threads convert rotational movement into linear motion. However, even the most reliable technologies have room for improvement, says Robert Day, dryspin product manager at Igus.
“Working at Igus means daring to take an industry standard component and say: It can be even better,” he says. Specialising in motion plastics, Igus initially developed and patented its dryspin thread technology in 1996 as an alternative to high helix pitch threads. Over 50 variations
are now available, ranging from matched screws and threaded nuts to dimensions with low pitches for quick one-to-one replacement of old trapezoidal threads.
The company has applied its dryspin technology to trapezoidal threads in order to provide longer service life, improved efficiency, reduced wear and quieter operation to applications. Day and his team have achieved this by optimising the interaction between the leadscrew and polymer threaded nut, resulting in a 30% longer service life and 82% improvement in efficiency.
“You might ask yourself, what
difference does the geometry make to a leadscrew, and the answer is quite a lot,” he explains. “The dryspin geometry has flatter thread angles, rounded teeth, and is asymmetrical. The contact surface between the lead screw and the lead screw nut is reduced, which decreases noise and vibration. And, being asymmetrical rather than symmetrical means that we can increase the distance between the thread pitches of the screw, meaning more high-performance plastic and tribologically optimised material can be used in the second part of the lead screw for power optimisation, which reduces friction and wear.”
Dryspin leadscrew technology has found success in the rail sector
FASTENERS & SEALINGS

Dryspin technology optimises the interaction between the leadscrew and polymer threaded nut
NEAR SILENT OPERATION
Alongside its durability and efficiency credentials, dryspin leadscrew technology is also quieter than most conventional trapezoidal threads. This is due to the teeth being rounded rather than square, so the contact surface between the threaded nut and the screw is reduced. This leads to fewer vibrations and therefore minuses rattling or squeaking.
“The tighter manufacturing tolerance of the lead screws compared to DIN 103 7e also ensures more precise running behaviour and significantly higher speeds in the application,” Day adds.
SUSTAINABILITY ADVANTAGES
“The seven standard materials we use as lead screw nuts have been optimised to gve us the lowest coefficient of wear and friction possible,” Day continues. “And much like our bearing technology, it depends on the application as to which material and lead screw option is best suited to our customers.”
Not only does dryspin offer mechanical advantages over traditional lead screws, but it also delivers sustainability wins too, he says.
“Both parts of the lead screw are fully recyclable,” he explains. “The screws are also lubricationfree which means they require no maintenance and have a much longer life than traditional options.
This means that we’re minimising waste, producing less parts, and reducing our carbon footprint.”
The dryspin screw technology also enables sustainability benefits within the lifecycle of products, too. “The leadscrews are also lightweight, so in a car for instance we are lowering the weight of parts that go in it and therefore helping to reduce the carbon footprint of those applications.”
MANUFACTURING CAPABILITIES
Igus manufactures its lead screws using three methods. For standard products, the firm opts for injection moulding. For special parts or to customise a part to a customer’s design, CNC machining is another port of call. Thirdly, for rapid prototyping or proof-of-concept applications, the company can 3D print parts to aid in the design and specification of the lead screw system.
“Customers can input their application details, such as loads, speeds and so on, and our system will tell them the best material and pitch size for the application, as well as the predicted lifetime of the part and the drive requirements,” Day adds. “Once the customer has specified and designed the part, the details can be uploaded to our online shops where they will be provided with instant pricing and fast checkout. With our online tools, our sustainability and mechanical advantages, dryspin has been successful in many industries.”
ON THE RAILS
“One industry we have had a lot of success with our dryspin technology is the railway industry,” Day says. “Rail manufacturers need a reliable, robust solution that requires minimum maintenance, so with the help of our online design tools and our expert system, we are able to specify to correct parts to ensure they have a robust product that is reliable and has a predictable lifetime.”
In particular, dryspin technology has been successfully applied to improve a leading rail operator’s sliding step mechanism. Traditional sliding step mechanisms – which bridge the gap between the train and the platform to ensure safe boarding and alighting for passengers – often face problems such as sticking, misalignment and high maintenance costs. The use of Igus’ dryspin lead screw drives paired with its iglidur J nuts enabled the system to function without fault despite high temperature fluctuations and exposure to dirt and moisture. The simplified guidance system eliminated sticking while the maintenance-free design reduced life cycle costs.
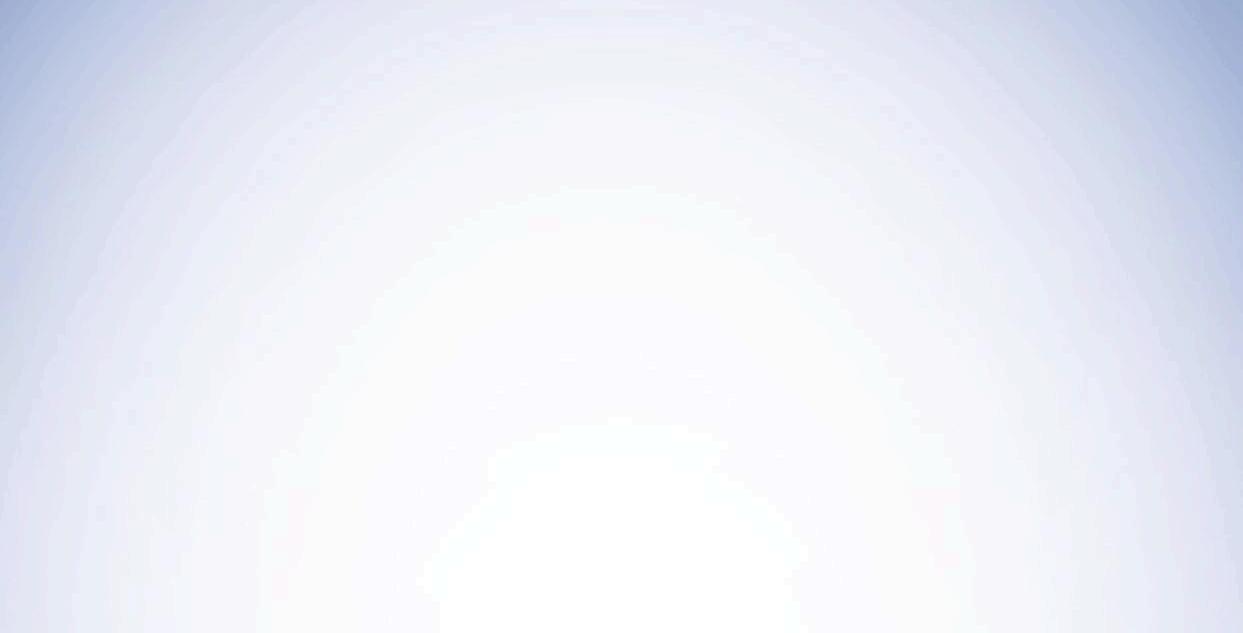
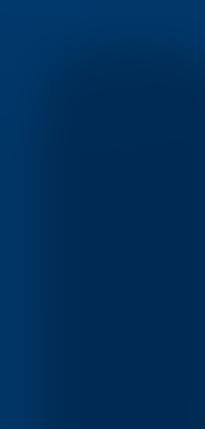

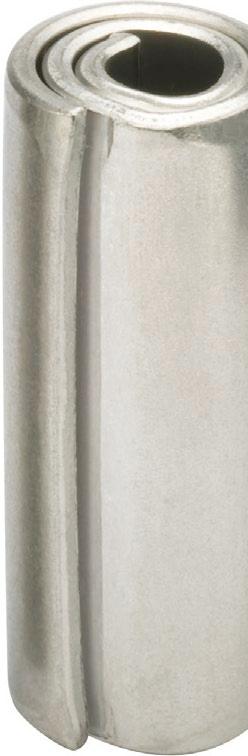
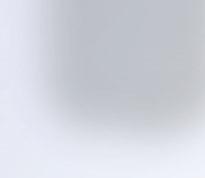
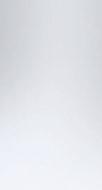

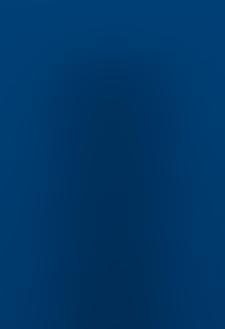

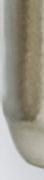
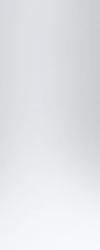

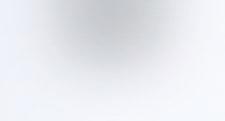


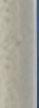
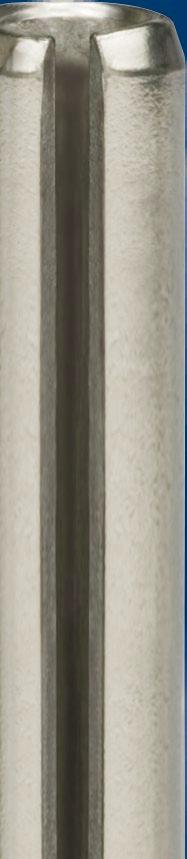

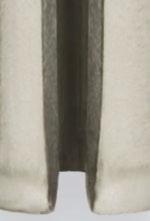
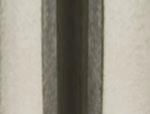


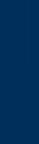

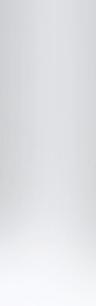


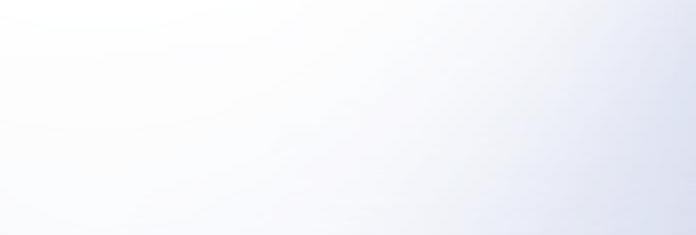
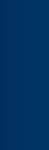
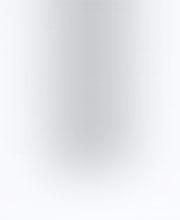

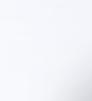

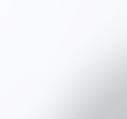

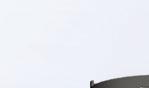

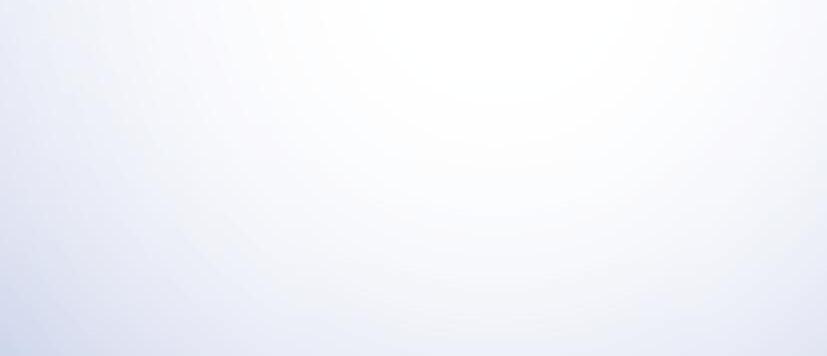


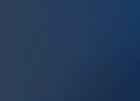

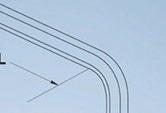
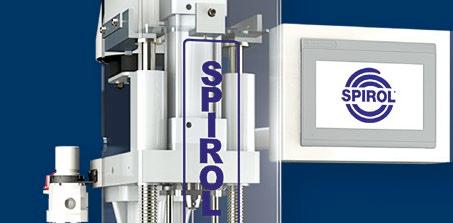
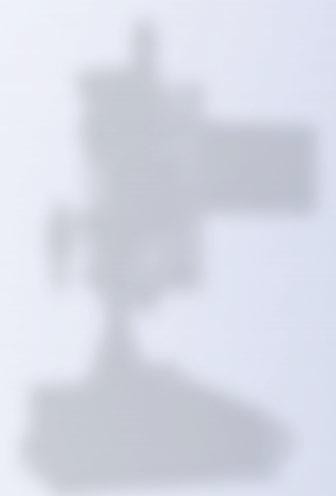
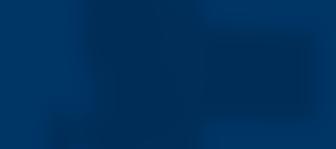
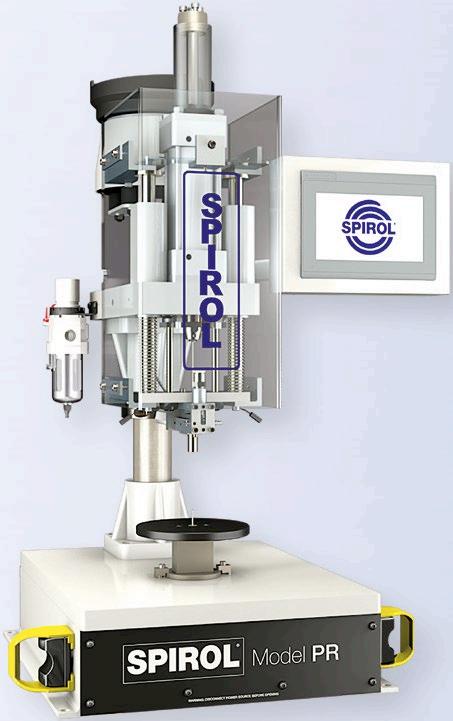
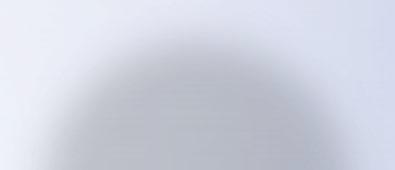

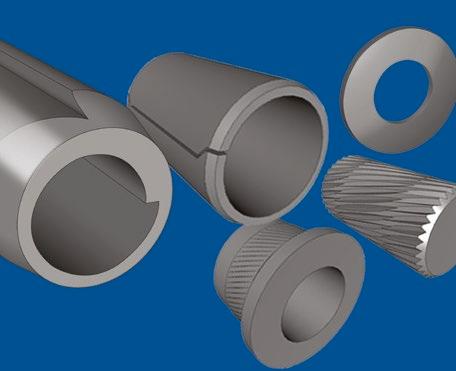
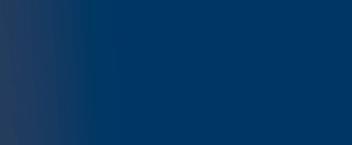
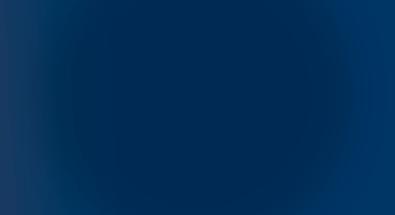


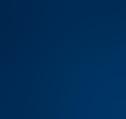
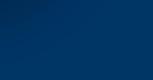
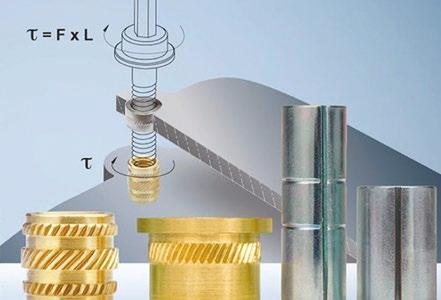
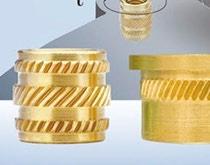
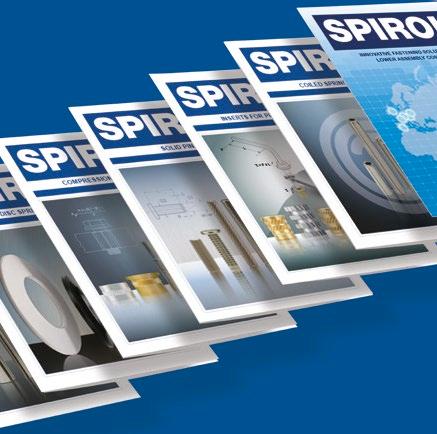
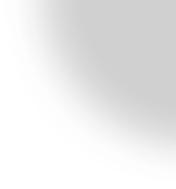
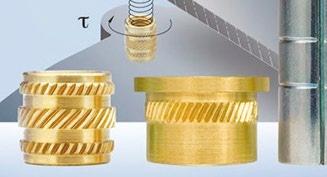
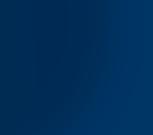

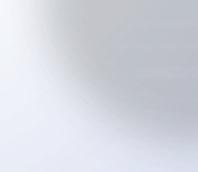
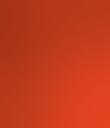
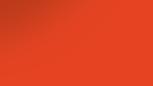

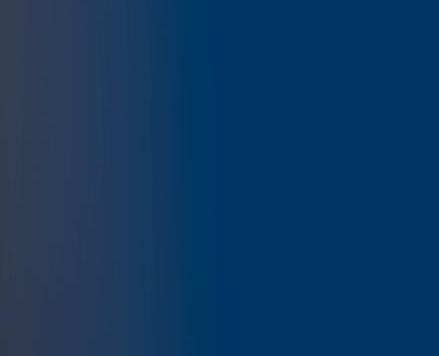
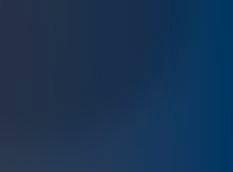


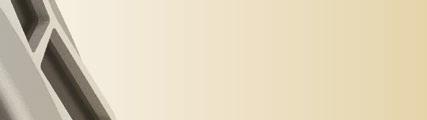
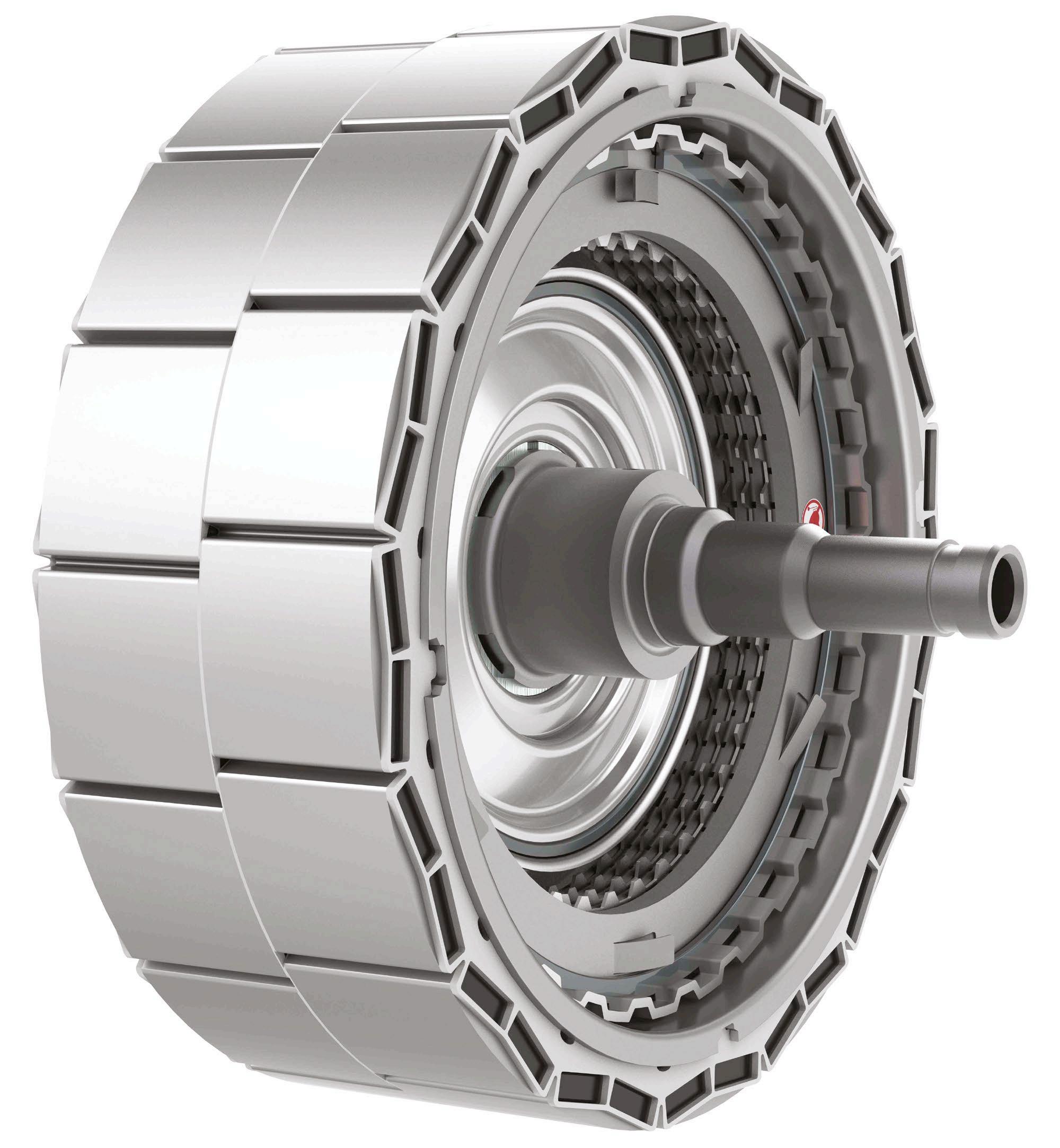
ATTRACTIVE PROPOSITION
Dr David Moule, an expert in electric drives with a passion for sustainability, tells Louise Davis about some valuable work focused on recycling and reusing the magnets used in motors

EDr David Moule, electric drives technical specialist, ZF
lectric drives technical specialist at ZF’s Servo Drives Centre of Competence, Dr David Moule, recalls how a shared interest in best practices concerning magnet recycling led to a major European project on the recycling and reuse of rare earth materials. “ZF has worked with the University of Birmingham around magnets and related technologies for some time. Around 10 years ago Professor Allan Walton and I started discussing the technologies the university had developed for the recycling of magnets using hydrogen,” begins Moule.
Discussing his own inspiration, Moule notes: “I understood that in future, the ability to recycle magnets efficiently would be very useful. I remembered when insufficient facilities were available to deal with the environmentally damaging gases present in end-of-life fridges and freezers in the early 2000s – resulting in ‘fridge mountains’ awaiting safe processing. Technologies would be needed to ensure that the same mistakes weren’t made as we aimed to electrify transport.”
Moule explains that, following the university pioneering the use of hydrogen in the manufacture of magnets, “ZF subsequently joined a consortium that Professor Walton was assembling to bid for a European project. That became SUSMAGPRO, which stands for Sustainable Recovery, Reprocessing and Reuse of Rare Earth Magnets in a European Circular Economy.”
The work of the four-year project – and that Moule and his team at ZF continue to focus on – centred on the recycling of systems such as motors containing neodymium (known as NdFeB) magnets. Metallic elements such as neodymium and other rare earth metals are classed
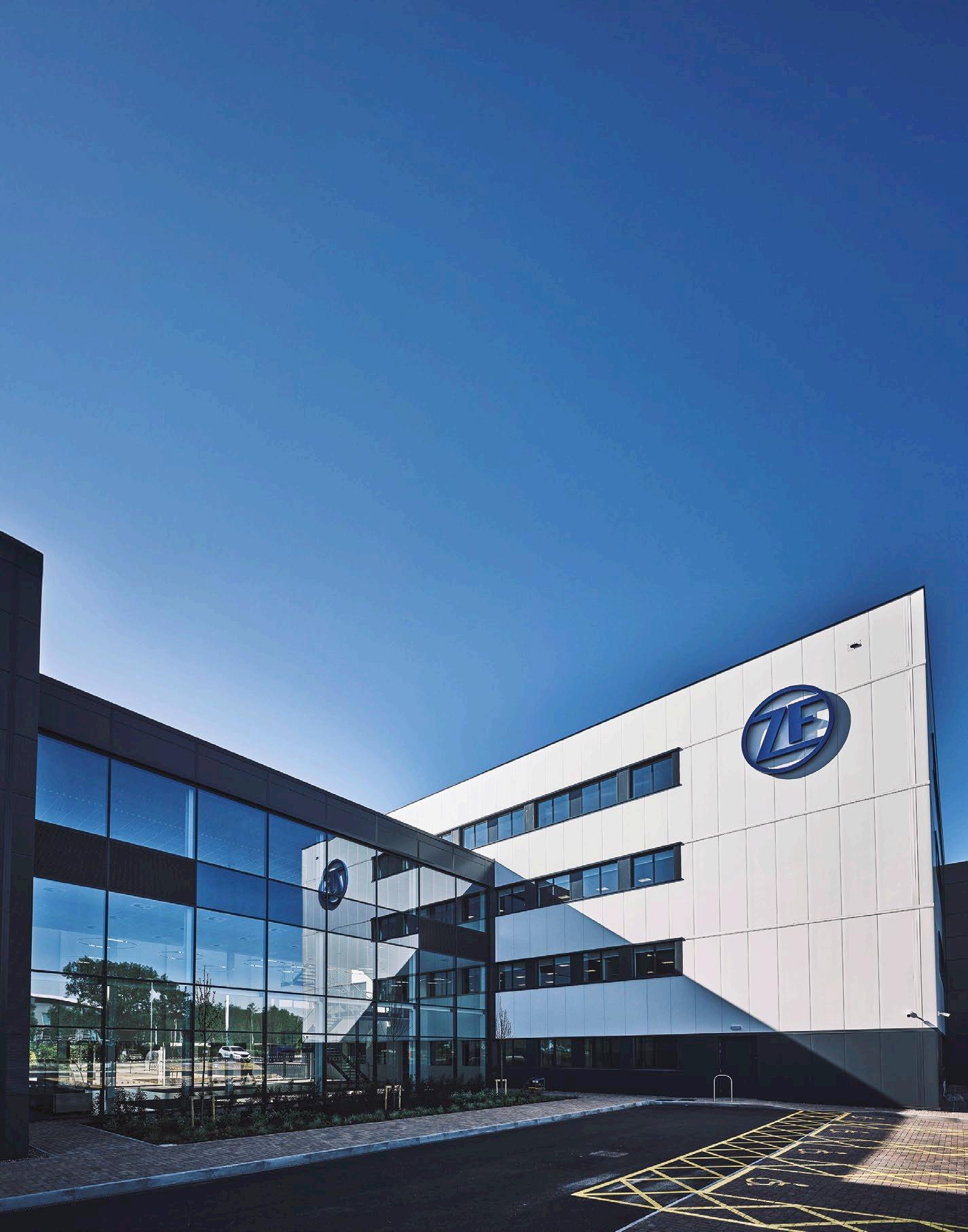
Metallic elements such as neodymium and other rare earth metals are classed as critical raw materials by the EU
as critical raw materials by the EU. “These magnets find considerable use in automotive applications such as traction motors, and auxiliaries such as high-performance steering and braking systems. The same materials are also used in wind power generators, hard disk drives, loudspeakers, and many other motor applications,” details Moule. “Through the work with Professor Walton and his team we wished to understand how rare earth metals used in magnets could be efficiently recycled. To do this we needed to understand the process – and the things that will contaminate the process. This understanding would enable us to make design changes to our products, allowing them to be more easily recycled at scale many years in the
future once they reach the end of their useful lives in vehicles.”
The SUSMAGPRO project ended in 2023 and Moule reveals that, towards the end, its partners had achieved a major milestone: “Recycled magnets produced from secondary material via the patented hydrogen-processing of magnet scrap (HPMS) approach, developed by the University of Birmingham, were tested in rotors produced by ZF. The performance of these recycled magnets was nearly identical to that of virgin materials, demonstrating the feasibility of largescale rare earth element recycling.”
And Moule reports that the insights gained by ZF designers from the project, primarily around the magnets’ improved recyclability, “are being incorporated into the designs of new
ZF’s facility near Solihull supported its activities within the SUSMAGPRO project
MOTORS, DRIVES, CONTROLS
ZF motors – which in turn supports our sustainability strategy.”
POLES APART
Although well known for its automotive products, ZF manufactures motors for a large, diverse range of industries, all of which rely on rare earth metals. And the company has a dual focus in this sustainability work: both in the technology involved in putting recycled materials to work and in how to design its own motors so they can be more easily recycled. Which of those two areas is the most important to Moule? “Well, it’s really a single focus,” he asserts. “It’s not possible to separate the two goals of using recycled materials and having motors that are more easily recyclable; they support each other. As more products are recycled, there will be a greater amount of recycled material available for use in motors.”
Moule explains that if the properties of recycled magnets differ from those
obtained from virgin material, then design changes may be necessary to enable the use of that increasing supply of recycled material. “Conversely, if motors are more easily recyclable to allow magnets to be more easily recycled – either through mechanical changes allowing easier access to the magnets, or elimination of sources of contamination that may cause degradation in the magnet properties – then there will be more recycled magnets available,” he points out.
Ultimately, Moule says, “By understanding the recycling process, we can make changes to the designs that will improve the efficiency and yield of the recycling process.”
DESIGN FOR LIFE
Successfully juggling various requirements is key to progress here. “Design engineers and recycling engineers frequently have different perspectives on a solution,” Moule observes. “A design engineer will often
think in terms of having the smallest, lightest, most appropriate materials to fulfil a function. A recycling engineer is looking to have only materials compatible with a recycling process, not wanting anything present that will contaminate a process. A design engineer focuses on one unit and has lots of detailed data in regard to its make-up. A recycling engineer, presented with that same part in years to come will likely have it included in a mix of parts to process – and have much less detailed information to hand. A design engineer is often thinking about how to make millions of parts in the same place, whereas the recycling engineer is looking to process tonnes of material that has come from many different places.”
Rather than regarding these differing aims as a source of conflict, Moule reports that, “By understanding the various perspectives and considering a whole life cycle rather than just one aspect, our

engineers are now able to design and manufacture products that are far more sustainable.”
This collaborative approach is reflected in the engineering expertise that ZF is relying on for this crossdisciplinary R&D work. “We have a range of people involved – from those holding a PhD with years of experience, through to those who have left school much more recently and are currently studying,” details Moule. “The principal skills are those of magnet and motor experts combined. However, the additional skills of the prototype engineers bring added value.”
Expanding on the firm’s in-house expertise, Moule describes how ZF in the UK has a long-established magnetic materials laboratory capable of characterising permanent magnets and soft magnetic materials such as electrical steels. “This unique facility is used not only for understanding the behaviour of magnetic components in our own products but is also offered
as a service to external customers.
“During permanent magnet tests we can investigate their behaviour when they are subjected to magnetic fields and temperatures that may demagnetise them, such as those within an electric motor operating at high torque.”
Moule mentions that permanent magnets, such as NdFeB or ferrites, are also used in linear actuators, sensors and electronic components: “ZF engineers are particularly active in assessing options for the use of recycled magnets in motors and sensors,” he says. “Our motor designers are interested in the properties that are achieved by recycled magnets and are well able to determine the impact of these properties on the performance of a motor. They can take the magnet characterisation data obtained from our magnetic materials laboratory and use it in finite element electromagnetic simulations to predict motor performance.”
Following the simulation work, Moule explains that, “Our prototype laboratories assemble motors and sensors for testing using recycled magnets. This allows us to gain not only theoretical but practical confidence in the resulting tests.”
Moving from testing to realworld applications, Moule confirms that insights gained from both the SUSMAGPRO project and ZF’s own development work are being comprehensively applied. “One of the less tangible and harder to measure impacts has been the greater awareness of sustainability amongst the design engineers,” he comments. “It’s been quite subtle: design engineers have started work on a project then stopped and said to a colleague, ‘is this going to be a good idea for the future – it’s OK for now but how is it for sustainability?’ And this wouldn’t have happened before we adopted the more holistic approach to design.”
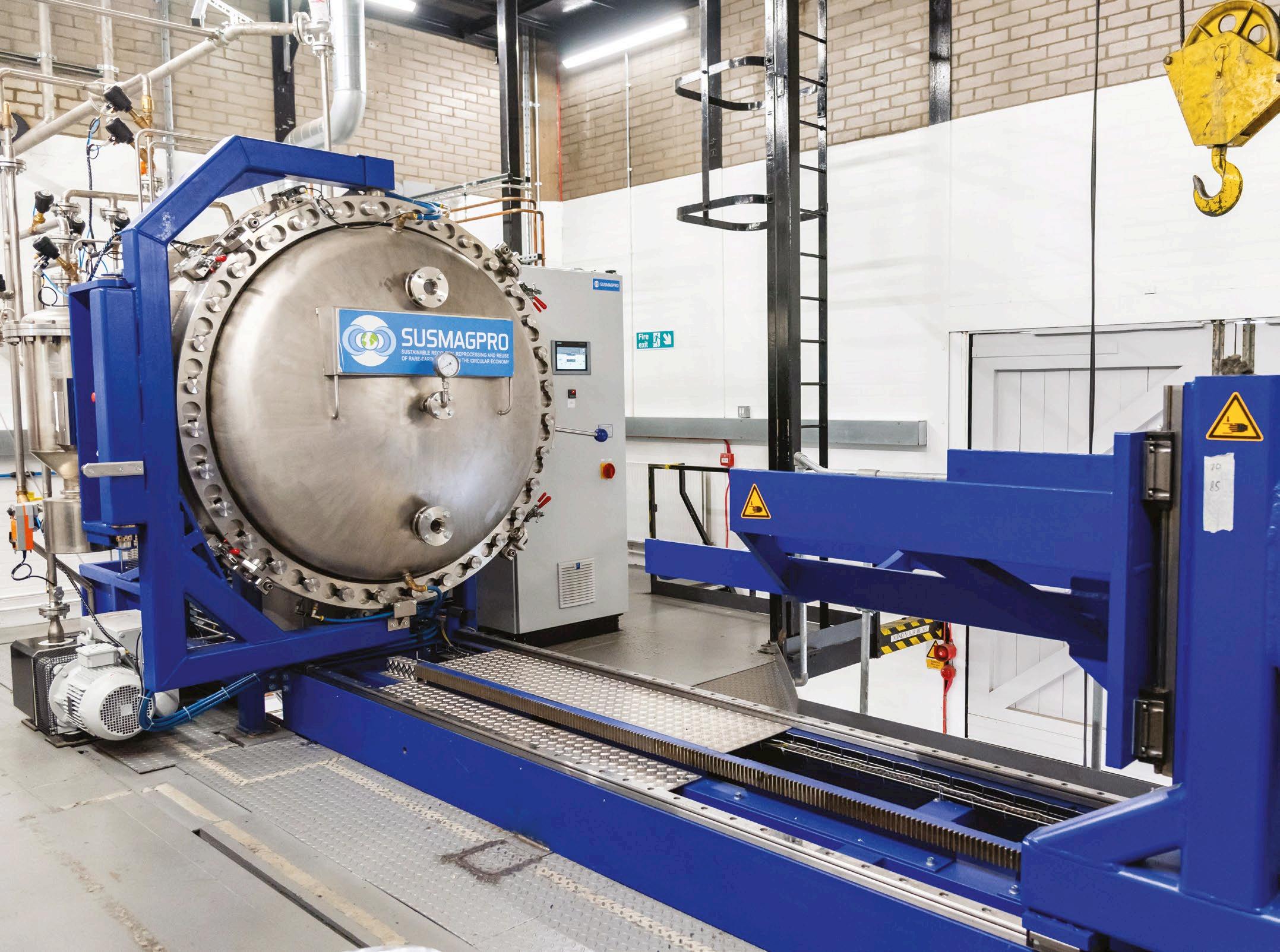
The University of Birmingham’s hydrogen reaction vessel for the processing of magnetic scrap. Image courtesy of the University of Birmingham
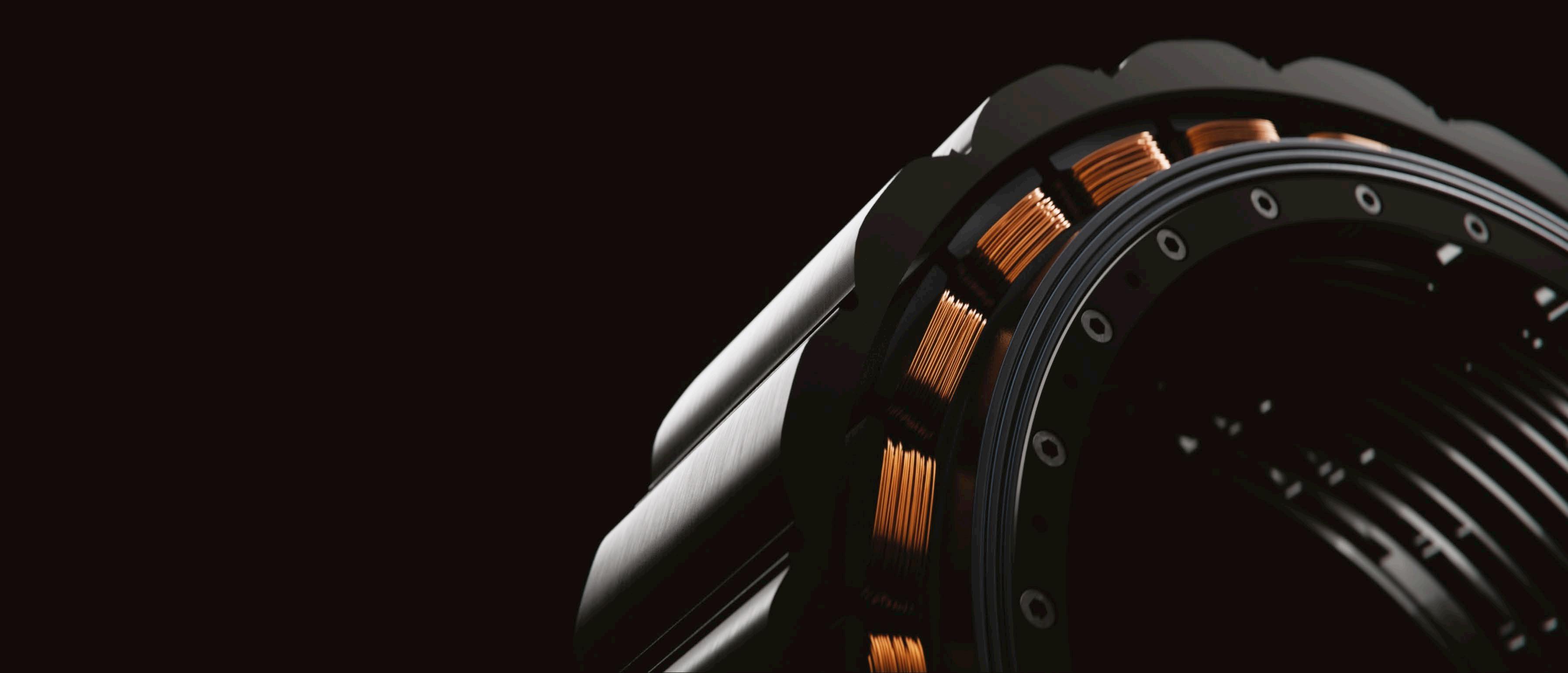
DISCUSSING DONUTS
Jake Holmes delves into how this new generation electric motor family is offering unprecedented performance and cost efficiency
The starting gun has gone on the race to create a more compatible world. Ease of use has become a big factor for companies when deciding what products to incorporate into their designs. By creating and using technologies with improved compatibility it allows for faster production and reduced costs, as less skilled labour is required to build the finished product.
Donut Lab is one company at the forefront of this effort, having recently introduced its modular technology platform which includes an electric motor family that “completely eliminates the need for power transmission.”
In addition to the motor, the important components of the modular Donut platform are battery modules, computer units and software that controls the vehicle. Zero manual integration work is required to combine these components, reducing development time in electric vehicles (EVs). The Donut platform is just the start, with the company announcing at CES trade show it plans to speed up vehicle software development by 10fold with its latest software update.
MOTOR INNOVATION
One of the main components of the Donut platform is a donut motor that can be placed directly into the tyre
and which has now been expanded into a motor family. Traditional powertrain systems have made EVs expensive to manufacture and maintain, while reducing vehicle performance and increasing weight and complexity.
The firm’s donut motor integrated directly with the tyre eliminates the need for power transmission entirely, making vehicles considerably lighter, more economical, and easier to manufacture. In addition, the second significant advantage of a donut motor is that it makes unsprung mass completely irrelevant.
“Great unsprung mass has been the most important reason why everyone hasn’t used motors integrated with the tyre in their vehicles,” says Marko Lehtimäki, Donut Lab’s CEO. “Through the torque and power density we’ve now achieved, the relative weight of the motor is so small that for the first time the unsprung mass is insignificant. For these reasons, we’ve also invested a lot of time into patenting our inventions, because we believe that these motors will change the whole industry.”
STREAMLINING HMIS
CES also saw Donut Lab and international software company Qt introduce the latter’s new Qt Accelerate solution as part of a strategic partnership between the two companies.
“With the help of Qt Accelerate, the development of HMIs (humanmachine interfaces) will become automated and significantly more efficient. The technology to be integrated into the Donut platform will recognise the vehicle configuration and will be able to create an HMI that matches the vehicle’s actual features,” says Petteri Holländer, senior vice president of Ventures at Qt Group. “This takes place completely automatically and therefore requires no manual work.”
“With the help of an intelligent software layer, we can automatically integrate physical components, but in addition to this, we are now developing future software development solutions that will make vehicle development significantly more efficient and agile,” adds Lehtimäki. “At the core of all of this is advanced artificial intelligence, and in the future, the artificial intelligence features of the Donut platform will improve vehicle design, development, testing and validation in unimaginable ways.”
Qt Accelerate aims to streamline HMI for users in EVs. This simplifies the user experience and makes EVs easier to use, increasing the accessibility of the technology. This reduces the level of technical training someone needs to operate these machines.
The Donut Motor eliminates the need for power transmission

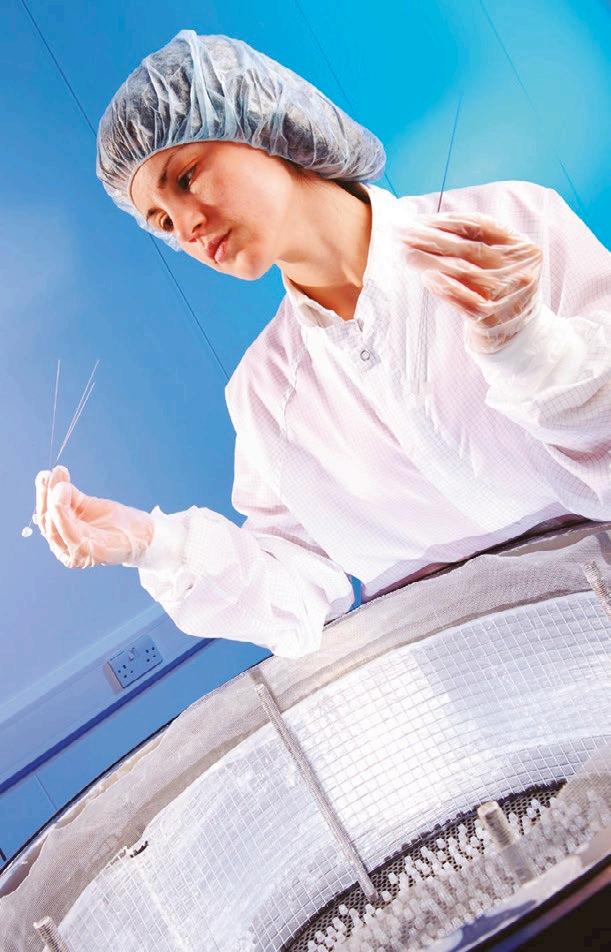

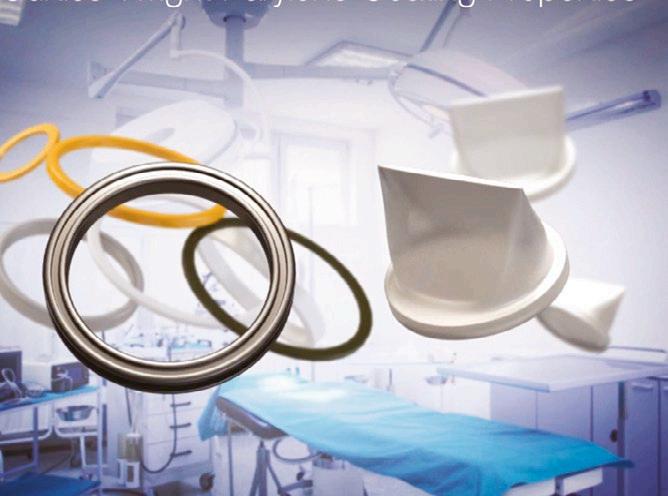
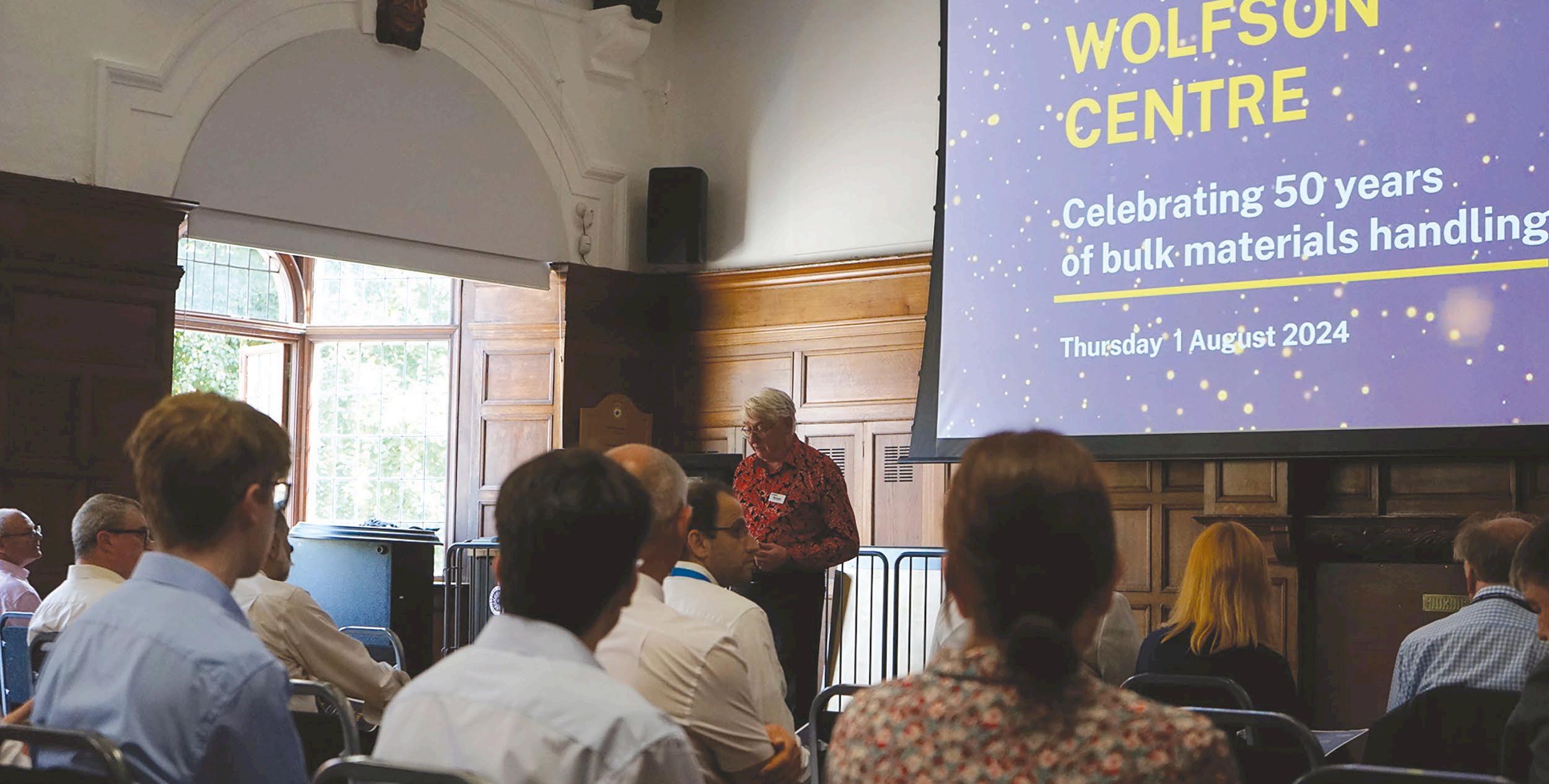
The Wolfson Centre currently has a range of training courses available
INVESTING IN TOMORROW
Jake Holmes rounds up the latest training and education opportunities in the design engineering space
Kaizen - the Japanese philosophy of continuous improvement - is not just for machines and processes but for people also. Without proper training and job growth, employees can become unproductive and disenfranchised.
Keeping a workforce motivated and educated is the key to maintaining high productivity and reducing labour turnover. Investing in training can help reduce future costs from high staff turnover or mistakes leading to downtime.
DATES FOR YOUR DIARY
As ever, the Wolfson Centre has a range of courses available. Starting on 10th June 2025 is the ‘Fire Prevention and Management in Biomass and Bulk Materials Storage’ course hosted at the University of Greenwich Medway campus. In September, the Wolfson Centre is supporting the FEFIA Conference, taking place 10-12 September at the University of Leeds. The FERIA Conference will bring together interested parties in fuel and energy research, with a focus on biomass, waste, and fossil fuels. The
focus of the conference will be to align domestic and international objectives. Meanwhile, between 14-17 September Glasgow will play host to the Euro PM2025 Congress and Exhibition. This year’s edition will feature special interest seminars with a focus on innovation, trends, and markets. Adding to this, the latest developments from the global PM supply chain will be on display.
CAD COVERED
The Institution of Engineering Designers (IED) approves and accredits courses to give peace of mind to attendees that what they are learning is correct and useful in the working world. One of their approved providers is Pentagon Solutions.
Software is growing increasingly important, and Pentagon’s course for a Plant 3D Project educates attendees on how to use AutoCAD, AutoCAD Plant 3D, and Autodesk Navisworks software packages. The five-day course covers basics and modelling, allowing users to get an understanding of the software.
Man and Machine is another IEDaccredited course provider, offering
a course in Inventor Introduction to Solid Modelling. The four-day course runs on the 3rd, 10th, 17th, and 24th of June and is held remotely. Attendees will benefit from a hands-on learning experience on how to design models from conceptual sketching, up to solid modelling and assembly design.
GET EDUCATED ON ELECTRIFICATION
In the electrification sector, the Electrification Revolution Skills (ERS) Hub launched 20 months ago and offers an interactive platform for both careers and up-skilling opportunities in the UK electrification space. Professionals can benchmark their capabilities using the website’s Electrification Self-Assessment Tool, useful for professionals who want to highlight their shortcomings for improvement.
According to leading recruitment experts, 2025 is a pivotal year for attracting new talent into the electrification sector. Matt Devine of Michael Page notes his companies Talent Trends indicates an opportunity for companies looking to plug the skills gap within the sector.
CWIEME RETURNS TO BERLIN
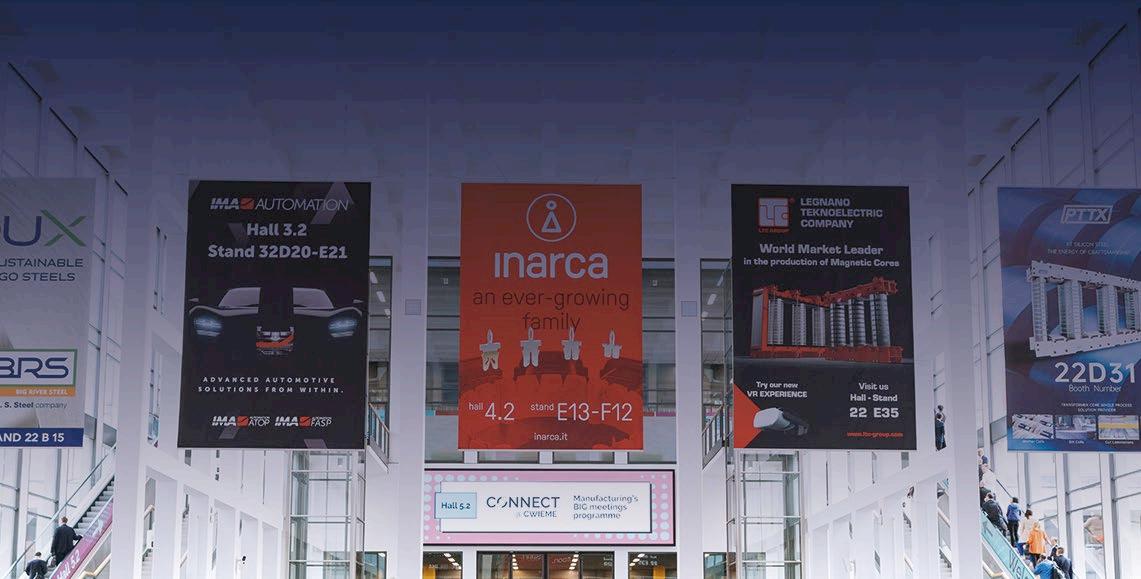
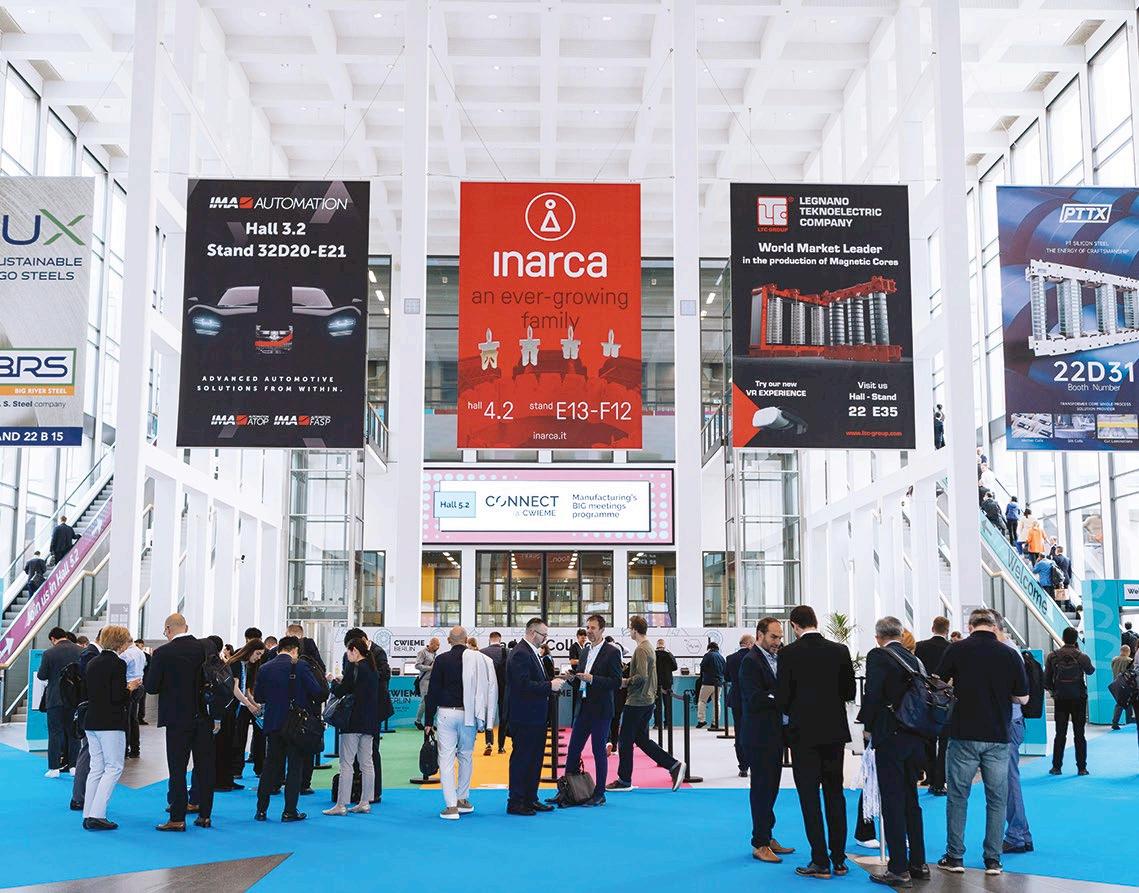
The world’s longest running event for coil winding, insulation and electrical manufacturing –CWIEME – will take place in Berlin, Germany, from 3-5 June 2025.
Over 6,000 engineers and professionals are expected to descend on the three-day event, where they will discover cutting-edge products and services from more than 600 suppliers across components, raw materials, and process machinery. The exhibition covers a wide range of sectors, including coil winding, transformers, generators, electric motors, materials and e-mobility.
The show’s Innovation Zone will showcase the latest product developments in these fields, while attendees will have the opportunity to gain insights from industry experts across over 70 sessions. 16% of this year’s agenda will be focused on eco-friendly innovations in line with manufacturing’s transition to a more sustainable future. In 2025, the show will introduce its inaugural Start-Up Zone, providing a first-hand look at groundbreaking ideas. Meanwhile, the show’s Future Engineers Programme will run parallel to the main event with the objective of building a programme that addresses the talent gap, draws in young talent to the industry, and provides them with a plethora of career opportunities.
SMART MANUFACTURING IN BIRMINGHAM
Smart Manufacturing Week will kick off in Birmingham once again this year, taking place 4-5 June 2025 at the NEC. Self-billed as the “largest festival of advanced manufacturing” that 2025 has to offer, Smart Manufacturing Week will bring together some 13,500 expert speakers, industry-shaping influencers and visitors from around the world to observe and discuss the latest solution across the design, engineering, manufacturing and maintenance fields.
Across the Drives & Controls, Design + Engineering Expo, Maintec and Smart Factory Expo sections, the event will see more than 450 suppliers showcase their latest products and technologies across the two days. The show’s Practical Solution Theatres will feature a wide range of supplier-led presentations to deliver practical solutions to design, engineering, manufacturing and maintenance challenges. Alongside this the event will once again feature a conference and summit programme offering technical presentations, panel discussions and debates delivered by experts from the world of smart factory manufacturing, design engineering and maintenance engineering. The 2025 event will be carbon neutral, with one tree planted for every attendee.
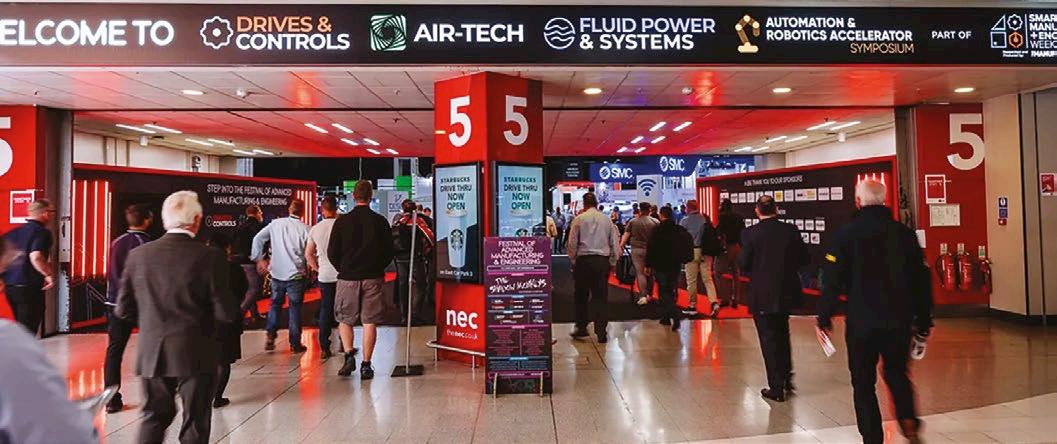
Boker’s Inc.
Boker’s, Inc., is a full-service manufacturer of precision metal stampings, washers, spacers and shims. Since 1919, nearly every industry around the world has trusted Boker’s to provide quality made-to-order components, world-class service and fast delivery.
T +1 612 729 9365
E sales@bokers.com
W bokers.com
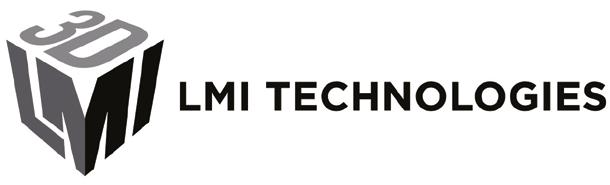
LMI Technologies
As the global leader in 3D scanning and inspection, LMI Technologies works to advance quality and productivity with 3D sensor technology.
E contact@lmi3d.com
W lmi3d.com
GET
t +44 (0)207 253 2545
RECOM Power
RECOM produces standard and custom DC/ DC, AC/DC converters, switching regulators, and LED drivers from sub-1W to tens of kW. Headquartered in Gmunden, Austria, RECOM is known for quality, innovation, wand excellent customer service.
T +43 7612 883 25 700
E info@recom-power.com
W recom-power.com

Gold & Wassall Hinges
With over two centuries of experience in the hinges industry, Gold and Wassall provides a fully comprehensive design and manufacturing service for any kind of hinge for practically any application.
T +44 (0)1827 63391
E enquiries@goldwassallhinges.co.uk
W goldwassallhinges.co.uk
Nano Dimension
Nano Dimension (Nasdaq: NNDM) aims to revolutionise electronics and mechanical manufacturing through precision additive manufacturing and AI-driven solutions, enabling on-demand production and managing a distributed manufacturing network.
T +1 857-557-8022
E sales@nano-di.com
W nano-di.com
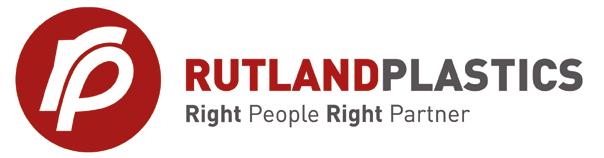
Rutland Plastics
With over 65 years of experience, we offer a full range of plastic injection moulding services across all sectors with the ability to make plastic parts from 1g to 45kg and up to 1.5m in size.
T 01572 723476
E enquiries@rutlandplastics.co.uk
W www.rutlandplastics.co.uk

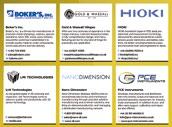
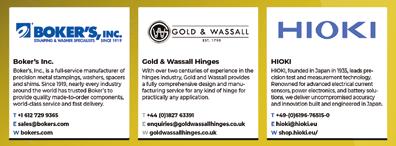
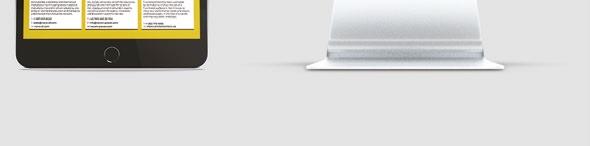
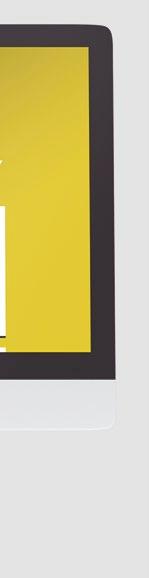

HIOKI
HIOKI, founded in Japan in 1935, leads precision test and measurement technology. Renowned for advanced electrical current sensors, power electronics, and battery solutions, we deliver uncompromised accuracy and innovation built and engineered in Japan.
T +49-(0)6196-76515-0
E hioki@hioki.eu
W shop.hioki.eu/
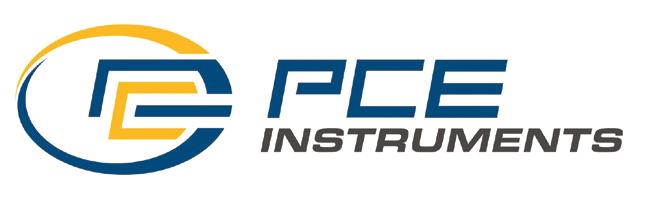
PCE Instruments
Develops, manufactures and distributes test instruments, scales and balances and selected laboratory equipment for industry, trade and research. In addition to pre- and after-sales support, calibration and repair are also offered.
T +44 (0) 161 464902 0
E info@pce-instruments.co.uk
W www.pce-instruments.com
Viton™
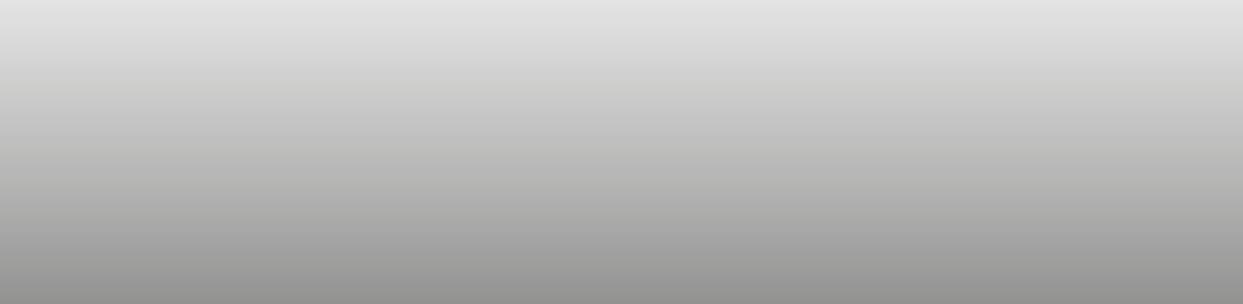
Our process for manufacturing Viton™ fluoroelastomers has been upgraded, by formulating without the use of a fluorinated surfactant. We innovate to meet your performance needs and ensure continued supply, in the face of a rapidly evolving regulatory landscape.
T +1 302 773 1000
W viton.com/en/contact-us

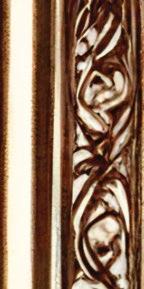
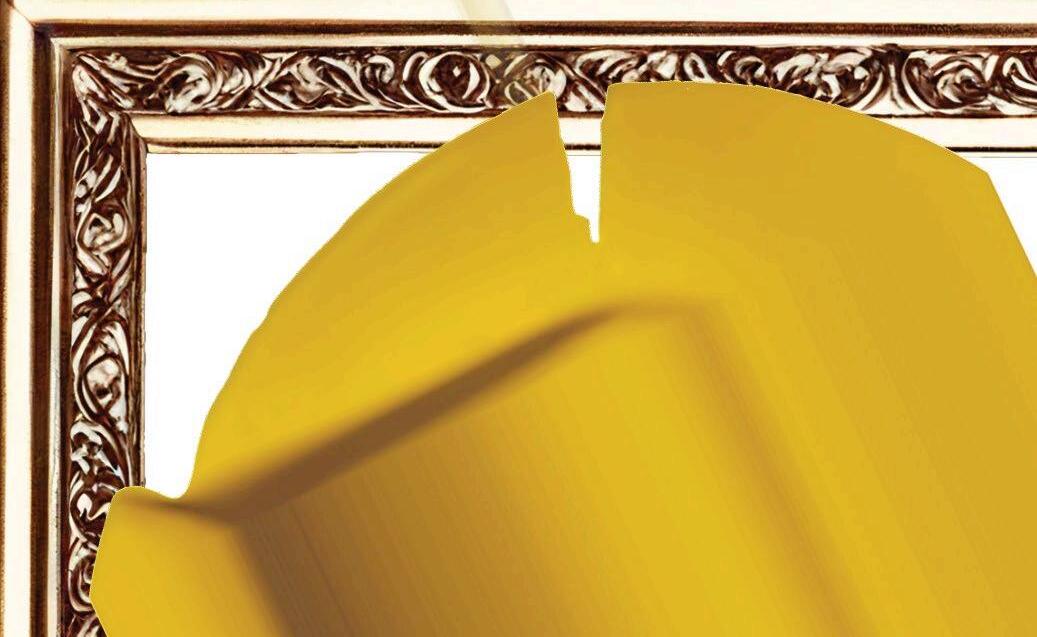


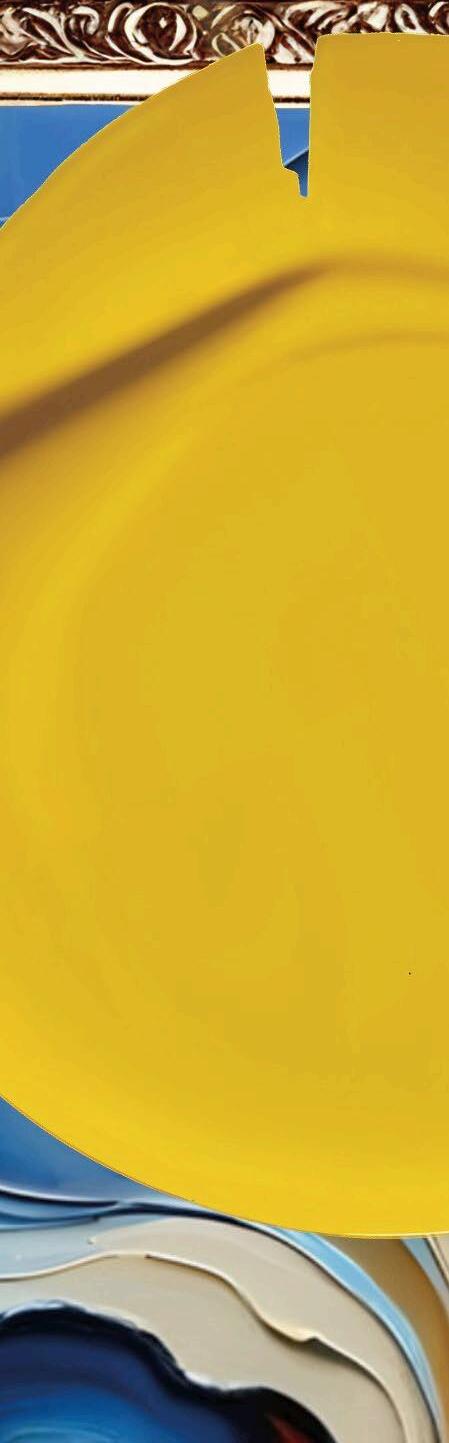
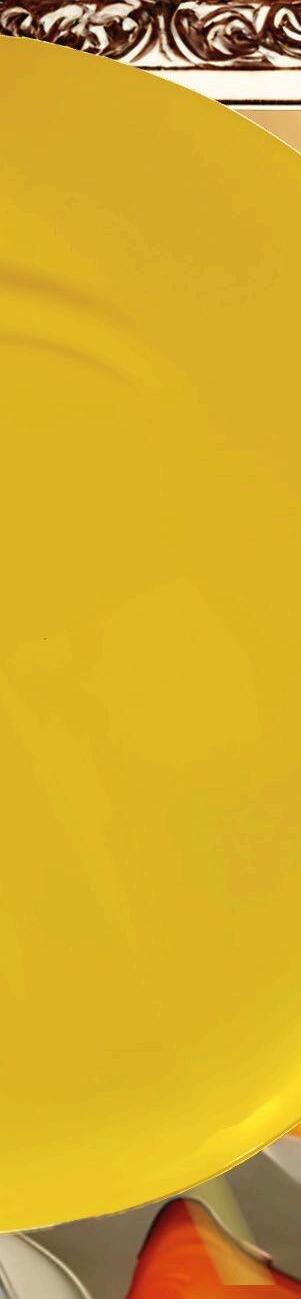

engineeringtectosisarecognizedpartnerandhas automotivebeenakeyplayerinthetestingworldfor20years: •Founded2004inGraz,Austria •50engineers/technicians/mechanics •In-houseprecisionmachiningandmanufacturing •4dedicatedengineandbalancingtestbenches •StrongNVHandacousticsexpertisefrom componentleveltovehiclemeasurement
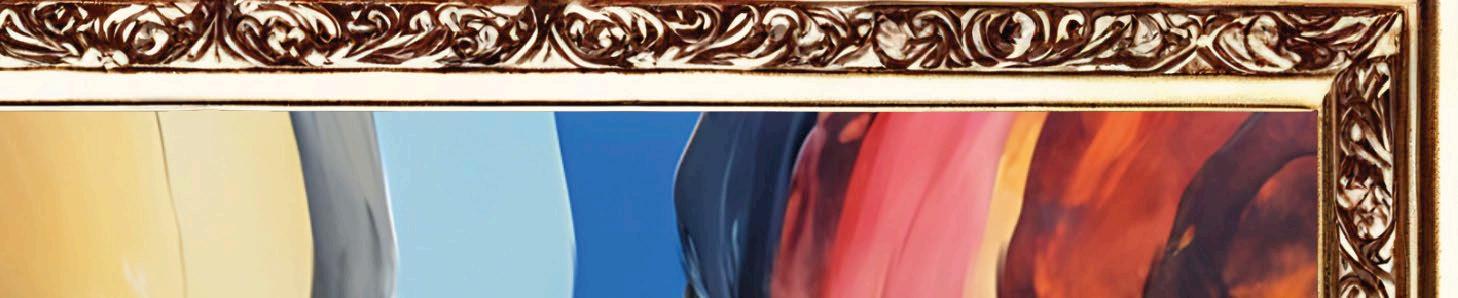
Contactustodayandlettectos “Therefuelyoursuccess! is either a solution or we create one.”

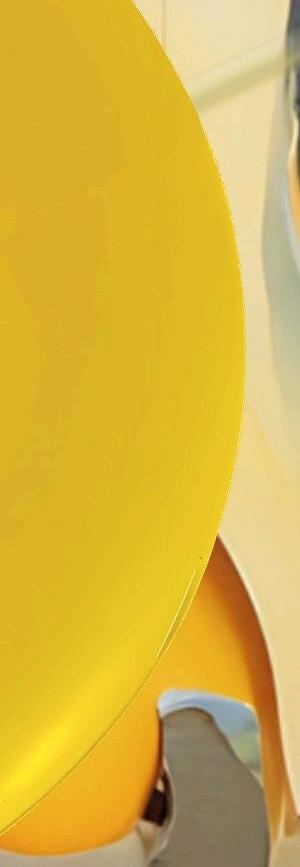
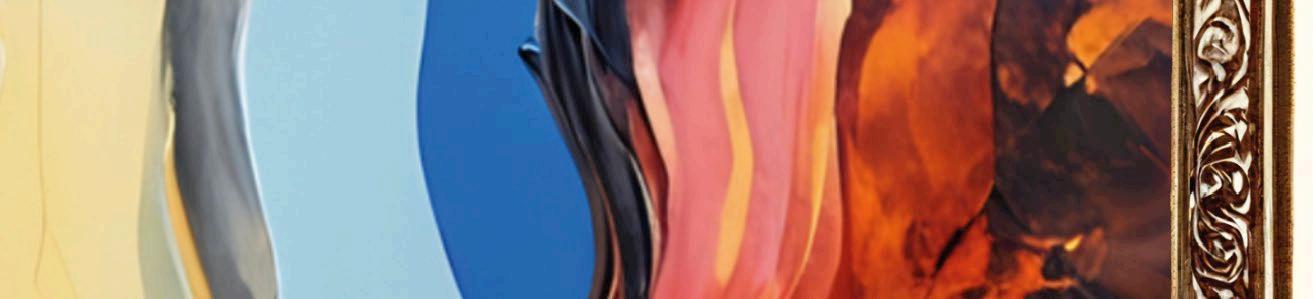

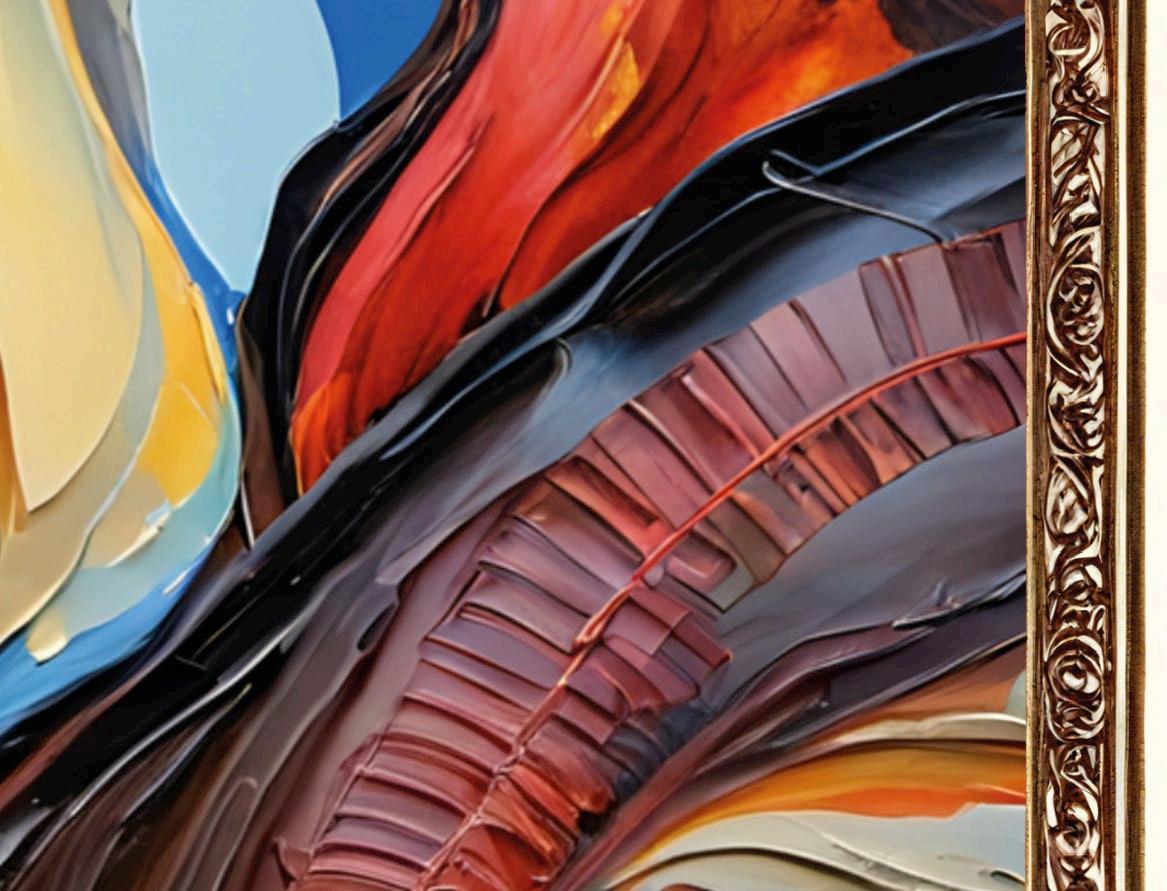
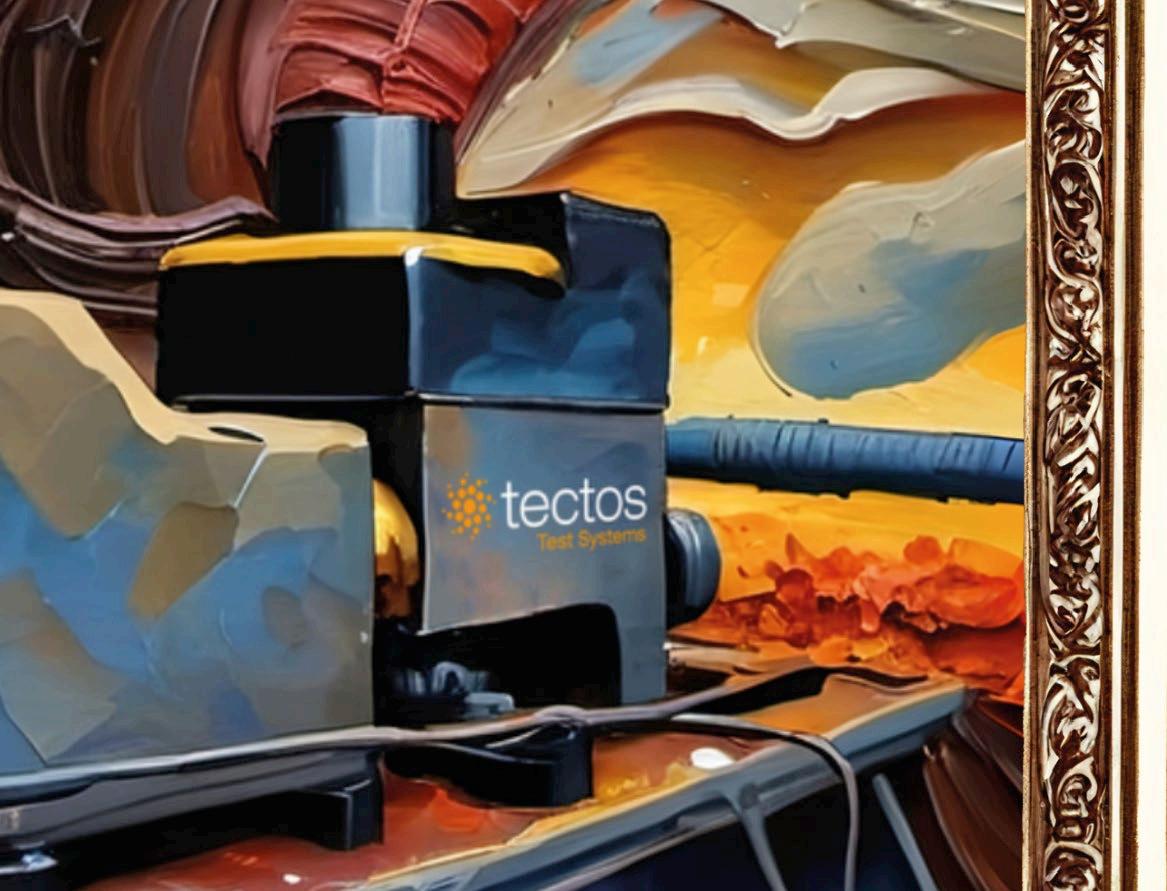
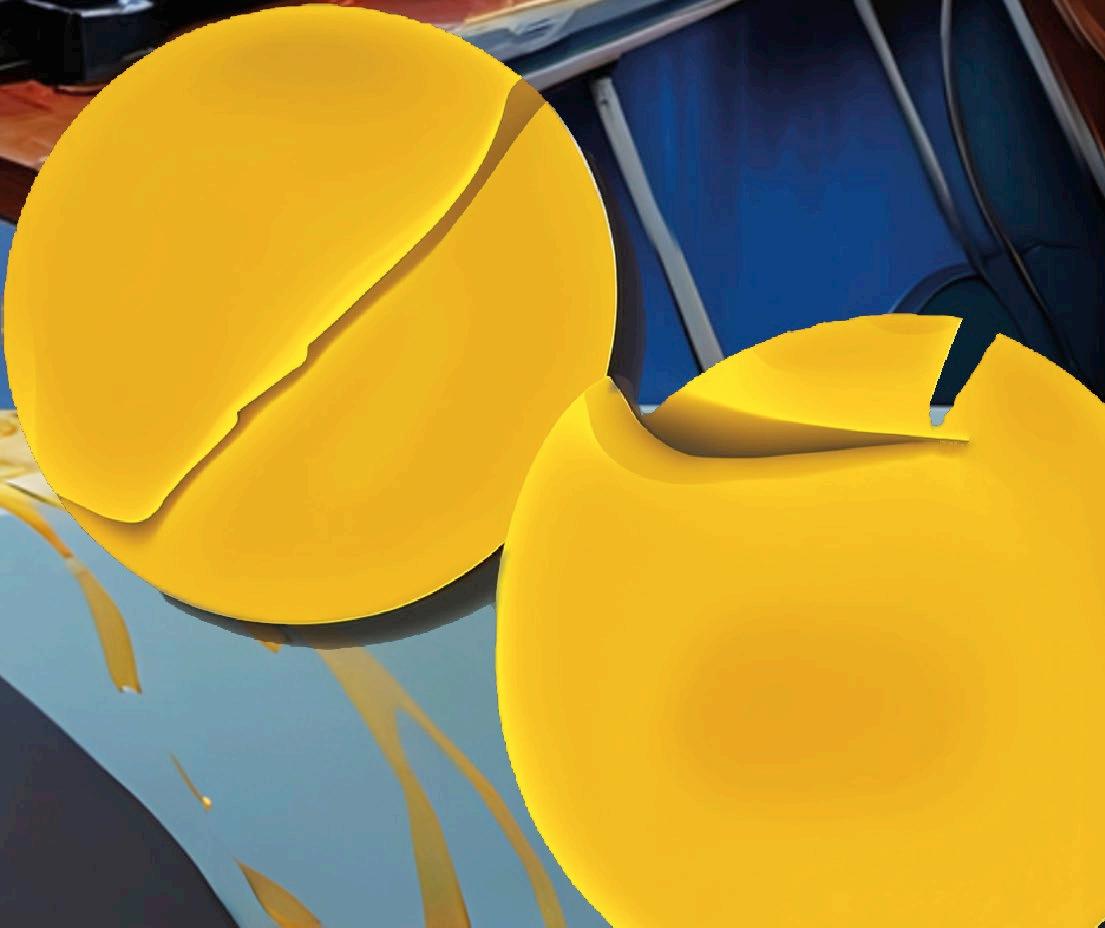



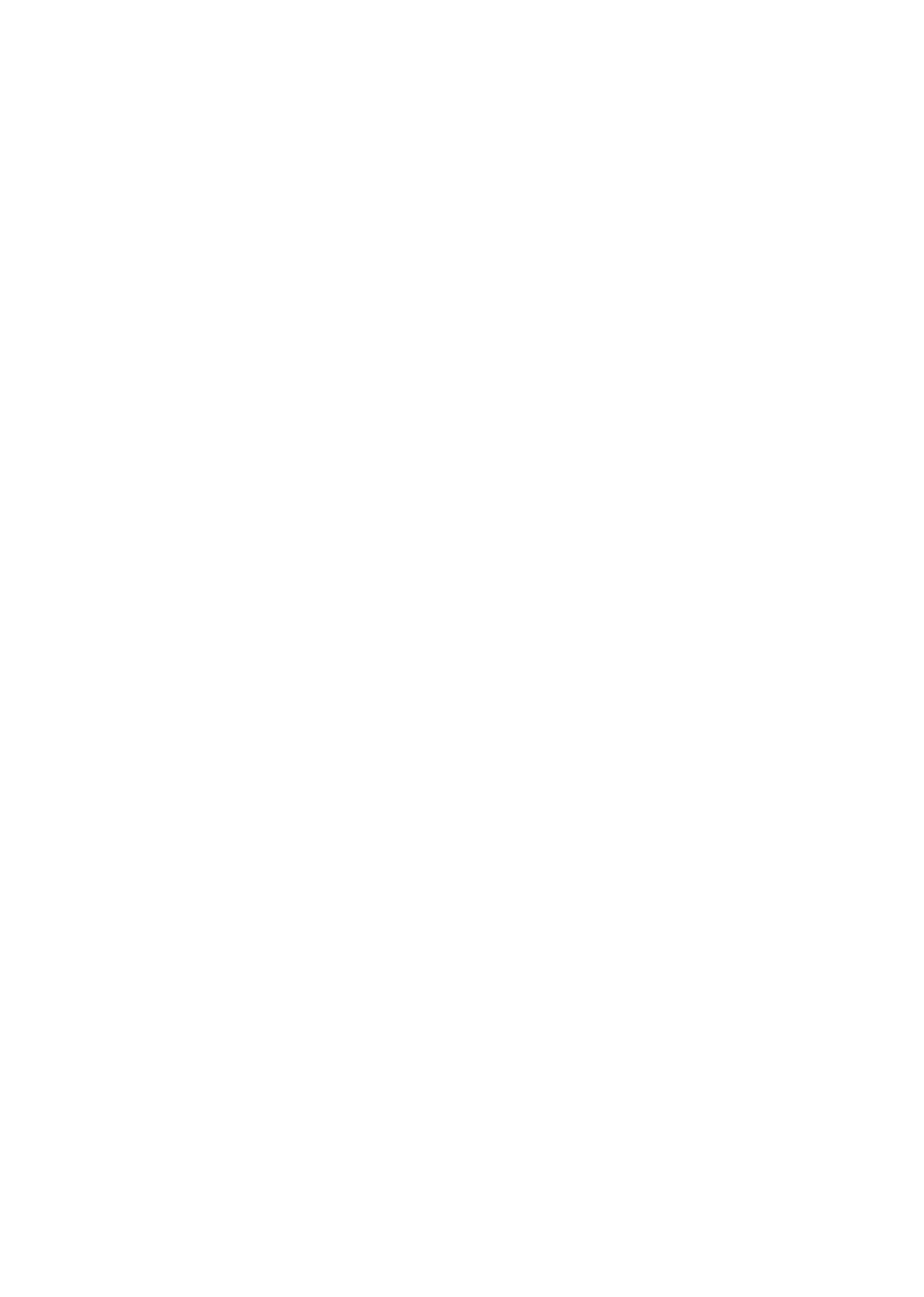