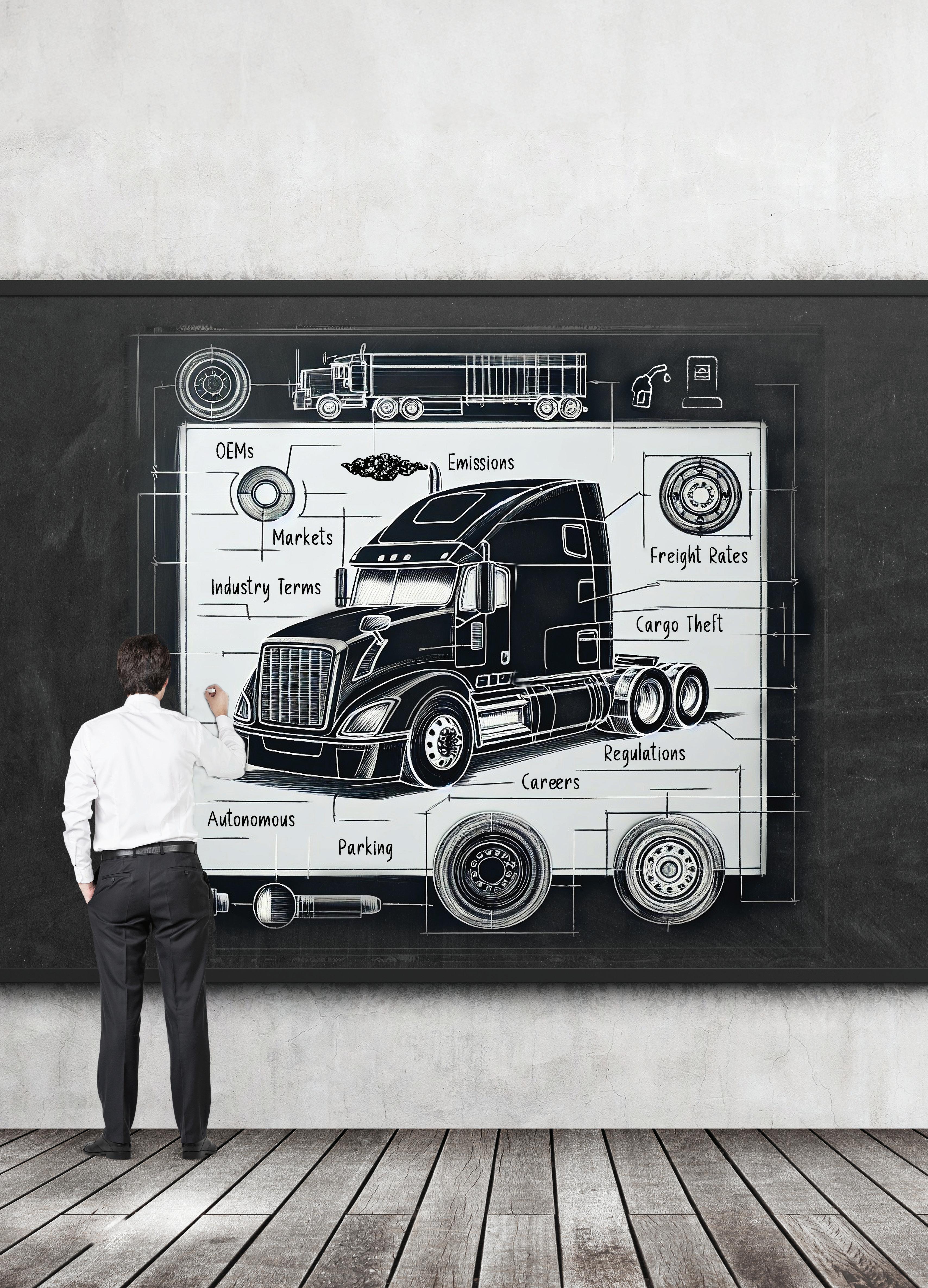

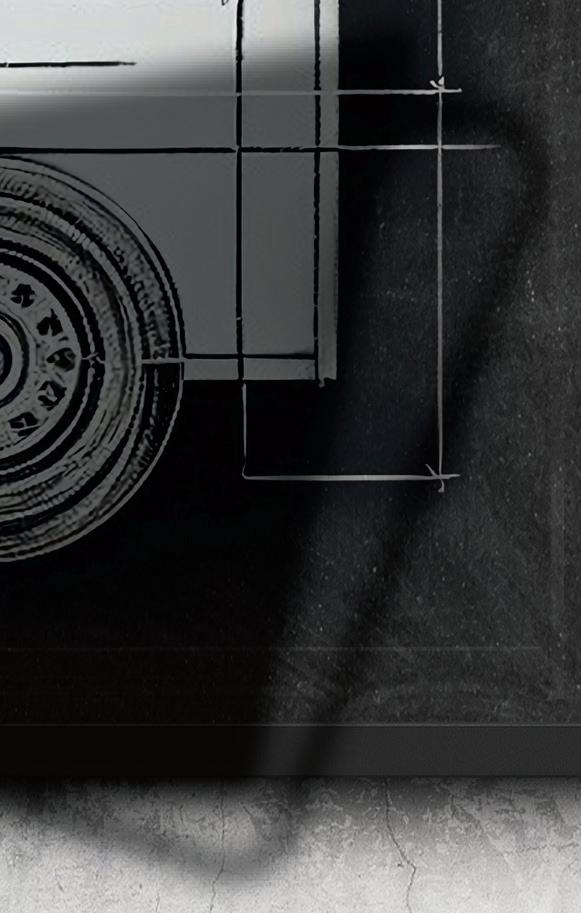
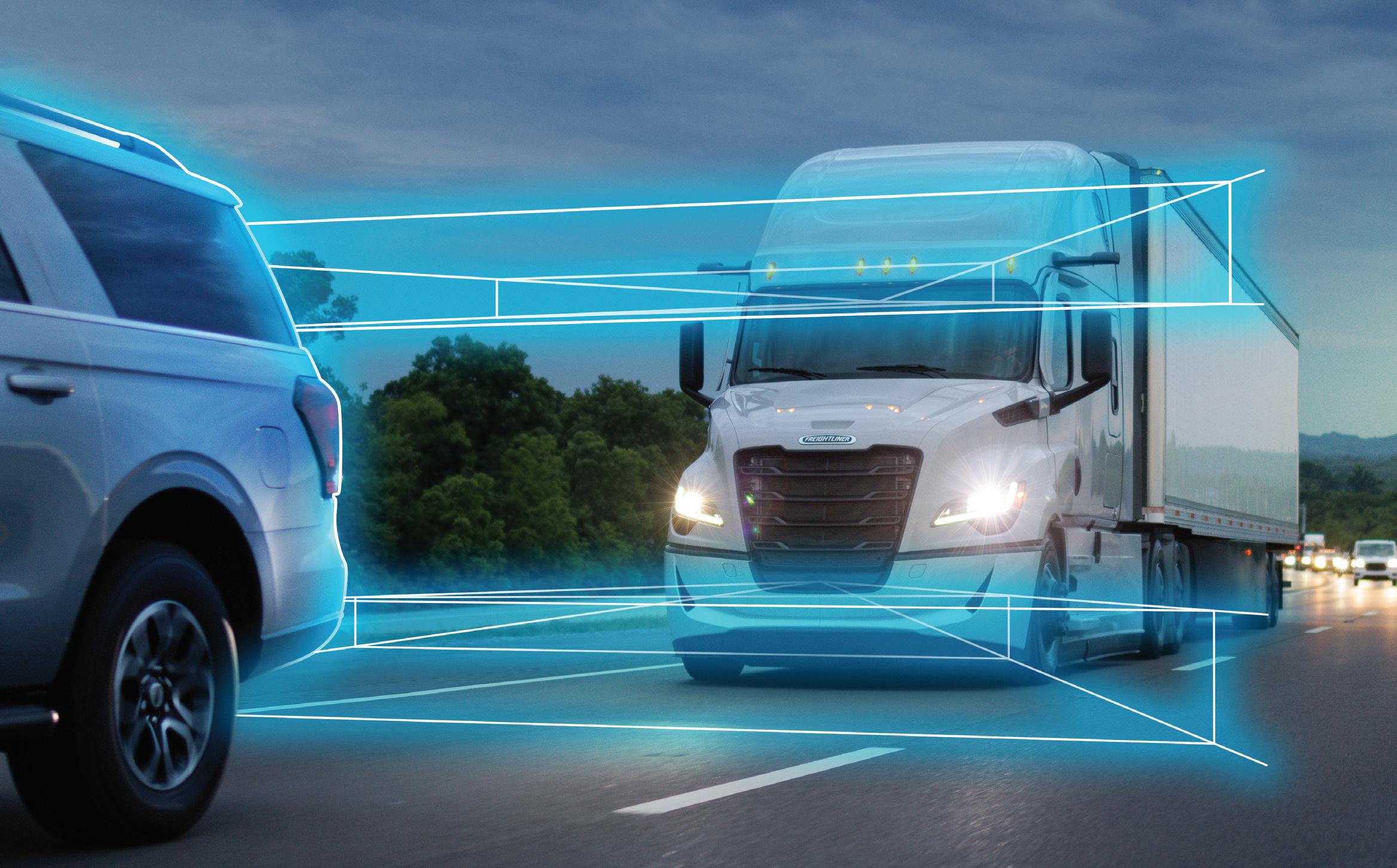
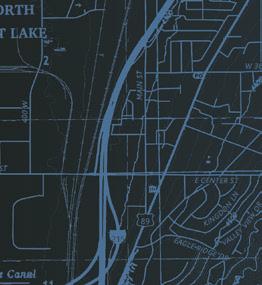
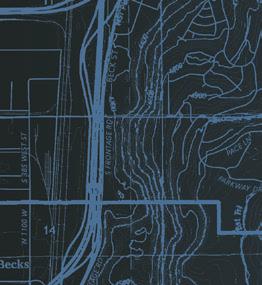
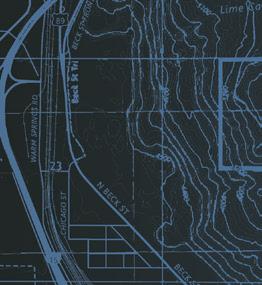
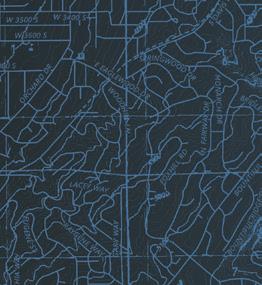
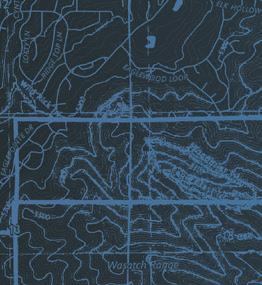

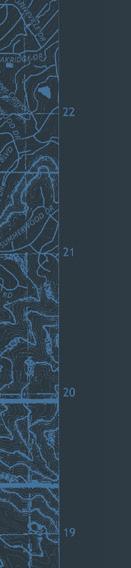
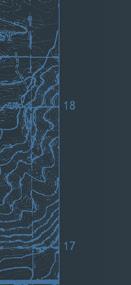

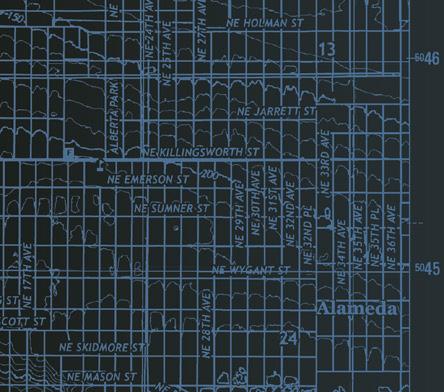
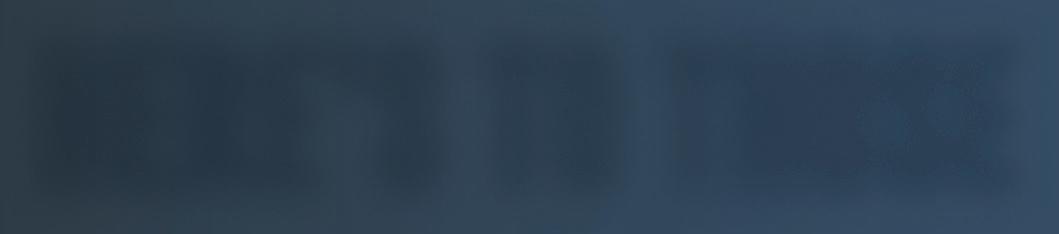

The Fifth Generation Cascadia from Freightliner unlocks a new level of safety and confidence in your drive. Minimize close calls utilizing Detroit Assurance® with Active Brake Assist 6 (ABA6), reduce blind spots with the factory-installed MirrorCam System, and experience smoother stops with the advanced Intelligent Braking Control System. From early mornings to late nights, the Fifth Generation Cascadia is always ready for what’s next.
THE FIFTH GENERATION
Border operations can require di erent types of trucks, certifications, documentations, drivers, and planning to move freight into and out of the U.S.
New Models
8 Meet Mack’s ‘badass’ highway truck Safety 411 16 Let’s weigh out the ramifications
Class 8 trucks are complicated. Here’s a basic guide to what to consider for your fleet when equipment shopping.
Tire Tracks
Mount a better TPMS solution
There’s more than one way to power a fleet. Here’s how various traditional and alternative internal combustion engine fuels work.
36
Ashley Kordish leads Ralph Moyle into a
Combining best practices with hard data can help all stakeholders enhance food quality and safety.
Energy E cient Technologies targets TRU ine ciency with patented liquid nanotechnology.
John Poindexter addresses the JBPCO team and other business units at NTEA’s Work Truck Week.
How JB Poindexter built a $2.5B truck body empire JB Poindexter and Co., a manufacturing conglomerate of work truck and van products, has grown into one of the industry’s most vital suppliers, according to founder John Poindexter, who is celebrating 40 years in business. He told FleetOwner that if JBPCO and its nine business units were “vaporized today,” the industry would be in a state of “severe distress.”
Read more at FleetOwner.com/JBPCO40.
Webinars
Benchmark to win: Join us this month to discuss creating data-driven, realistic KPIs that align with industry benchmarks and lead to measurable results. Learn how to leverage benchmarking data to contextualize your fleet’s performance and apply optimization strategies that drive continuous improvement. FleetOwner.com/BenchmarkWebinar
Tariffs
While tariff uncertainty and impacts loom, we have regular updates on how decisions in D.C. and abroad are impacting freight, trucking, and your business.
FleetOwner.com/tariffs
Delivered to your inbox, FleetOwner newsletters provide regular industry news and event updates, and breaking news alerts. Manage your email subscriptions at FleetOwner.com/subscribe.
Market Leader
Commercial Vehicle Group
Dyanna Hurley
dhurley@endeavorb2b.com
Editorial Director
Kevin Jones kevin@fleetowner.com @KevinJonesTBB
Editor in Chief
Josh Fisher josh@fleetowner.com @TrucksAtWork
Senior Editor
Jade Brasher jade@fleetowner.com
Editor Jeremy Wolfe jeremy@fleetowner.com
Digital Editor Jenna Hume jenna@fleetowner.com
Art Director Eric Van Egeren
Audience Development Manager Laura Moulton
Production Manager
Patricia Brown patti@fleetowner.com
Ad Services Manager
Karen Runion
Contributors
David Heller
Dan Knauer
Jason McDaniel
Gary Petty, Private Fleets
Editor Kevin Rohlwing
Seth Skydel
Endeavor Business Media, LLC
CEO Chris Ferrell
COO Patrick Rains
CRO Paul Andrews
CDO Jacquie Niemiec
CALO Tracy Kane
CMO Amanda Landsaw
EVP/Transportation
Kylie Hirko
linkedin.com/fleetowner facebook.com/fleetowner x.com/fleetowner
Access comprehensive reports, engaging industry topics, and exclusive multimedia content...and best of all...it’s FREE. Register at FleetOwner.com/members.
May 2025
Published by
LLC
30 Burton Hills Blvd., Suite 185 Nashville, TN 37215
800-547-7377
When it comes to transporting perishable goods, timing is everything. Continental truck tires and our Digital Tire Monitoring Solutions ensure your refrigeration fleet reaches its destination on schedule, maintaining the integrity of your cargo.
One year later, the Fleets Explained series is just getting going [ Lane Shift Ahead ]
By Josh Fisher Editor in Chief
@TrucksAtWork
We’ve
heard from many of you that you’re using these articles to help new hires get up to speed. With intern season getting underway, we wanted to highlight this online library.
WHETHER YOU’RE JUST getting started in the industry or have been around for decades, trucking and fleet management can be complicated.
A year ago, we launched Fleets Explained to give a general overview of how these vital industries function.Our growing library has 20 entries so far, each designed to help demystify everything from how freight rates work and fuel prices are determined to defining common industry abbreviations and explaining the rich American history of trucking. And we have a dozen more in the works.
On the following pages, you’ll find three of those Fleets Explained articles (focusing on fuel types, cross-border operations, and spec’ing trucks; and we have a quiz for Last Word). We’ve heard from many of you that you’re using these articles to help new hires get up to speed. With intern season getting underway, we wanted to highlight this online library at FleetOwner.com/fleets-explained We’re also looking for feedback and ideas for future Fleets Explained articles. Feel free to pass that on via explained@fleetowner.com. Below are what we’ve focused on and direct links to those entries.
Trucking segments: Freight can be categorized by carrier types, cargo types, and various commodities, reflecting this complex industry. FleetOwner.com/SegmentsExplained
How EVs differ: The more than 3 million EVs in operation make up just 1% of vehicles on the road. FleetOwner.com/EVsExplained How does TMS work? For fleets, a transportation management system acts as a centralized program that coordinates data collection and automates tasks. FleetOwner.com/TMSExplained
How freight rates work: Trucking segments have slightly different rates, particularly between spot and contract freight. All rates experience cyclical boom and bust phases. FleetOwner.com/RatesExplained Industry careers: There’s more to trucking
than driving. Industry careers showcase opportunities for various skills and experiences. FleetOwner.com/CareersExplained
How emissions are regulated: Heavy-duty vehicle emission regulations fall under two major authorities. FleetOwner.com/EmissionsExplained
History of truck OEMs: Seven brands from four global companies account for 99.9% of Class 8 truck sales. Here’s how they got there. FleetOwner.com/OEMhistory
Industry organizations: Trucking organizations advocate for the industry or specific segments and workers. FleetOwner.com/TradeOrgs
Industry abbreviations: Here’s a guide to common trucking abbreviations. FleetOwner.com/TruckingTerms
How NOx and DEF work: NOx is a significant air pollutant, and diesel exhaust fluid is a critical treatment method. FleetOwner.com/NOxExplained
How to prevent cargo theft: There are different kinds of cargo theft in the trucking industry, distinguishing between straight and strategic theft. FleetOwner.com/CargoTheft
How AVs work: Autonomous vehicles have the potential to revolutionize truck operations. FleetOwner.com/AVsExplained
Truck parking explained: There are 11 truck drivers for every truck parking space in the U.S. FleetOwner.com/ParkingExplained
Distracted driving impacts: Truck drivers must remain vigilant against their distractions and those of other drivers. FleetOwner.com/DistractedDriving
How fuel prices work: Fuel prices make up a quarter of carriers operating costs. FleetOwner.com/FuelPrices
U.S. Interstate System history: Before the First World War, rail was the quickest way to move freight—or anything else. Today, freight relies on trucks and the divided highways crisscrossing the vast nation. FleetOwner.com/HighwaysExplained FO
High-tech Pioneer launches in city where company began 125 years ago by
Josh Fisher
BROOKLYN, New York—For 125 years, Mack Trucks has been synonymous with American power and toughness. But the trucking pioneer wanted its next truck to meet its own B.A. test.
“What is the ‘B.A. test’?” Fernando Couceiro, Mack Trucks’ highway and product VP, asked industry media before the new Mack Pioneer truck was unveiled to the public here. “It has to look badass … We don’t like pretty or cute. We like badass.”
Mack used its New York City roots as the backdrop to debut the most aerodynamic highway truck in its history, creating 11% better fuel efficiency than the Mack Anthem. The Pioneer is designed for efficiency that makes hardworking drivers’ jobs easier, Couceiro said hours before the truck was unveiled.
The Pioneer, which will be produced as the Bulldog’s premier long-haul highway truck, will be available in various sleeper and day cab configurations in the U.S. and Canada. The OEM, which was founded by two brothers here in Brooklyn in 1900, began developing the Pioneer in 2017, the same year the Anthem highway model debuted.
Mack leaders said the Anthem, which has found more success as a day cab, will continue in production as they look to grow long-haul market share among North American fleets. Full production begins this summer.
Couceiro’s pitch to fleets that might have overlooked Mack for long haul in the past is that the OEM has always been about uptime. “That’s never been a problem for us,” he said. “I think we’ve always been known for reliability, durability, and things like that—so much that people almost take it for granted.”
And while the Anthem highway truck was “a competitive product on safety, fuel efficiency, and comfort, we have high ambitions to grow the on-highway
market. Just being competitive wasn’t enough. We need to be leaders, take share from our competitors. We have to be better than that. This is really what we are doing with the Pioneer—we’re really taking it into a leading position in these three elements: safety, fuel efficiency, and driver comfort.”
Before the Pioneer’s debut drew hundreds to the Brooklyn Navy Yard (and thousands more for the live virtual unveiling), Mack engineers detailed what went into the new Class 8 truck’s design that they said includes several
industry-first and cutting-edge features.
The Pioneer’s brand bridge in the grille creates a new signature Mack look for the tractor that integrates headlamps with the grille trim. The OEM also repositioned its bulldog hood ornament, removing it from its pedestal to incorporate it into the body to help manage airflow under the hood, according to Lukas Yates, Mack’s expert chief designer.
The grille is made of fiberglass-reinforced plastic with metal-formed mesh that makes it strong and lightweight. The headlamps include a standard defrost function that pushes hot air into the lens to prevent ice buildup, a first for Mack vehicles.
The cabin features metal handles and extrusions at all touch points that make
it durable and improve drivers’ tactile experience, giving it that tough work truck feel, OEM engineers said.
“The Mack Pioneer represents our commitment to innovation and excellence in the highway segment,” Jonathan Randall, president of Mack Trucks North America, said before the unveiling. “This truck tells the Mack story—it’s bold, iconic, strong, and timeless, embodying our DNA and character while taking our customers into the future with advanced design that prioritizes both driver experience and operational efficiency.” FO
CUT COSTS AND DOWNTIME WITHOUT SACRIFICING
Propane autogas is a proven solution for fleet owners and managers focused on efficiency and performance. It delivers the lowest total cost of ownership of any fuel, cutting fuel expenses, reducing maintenance, limiting downtime, and offering affordable refueling infrastructure that scales with your needs. Compared to diesel, it’s a cleaner, more costeffective way to power your fleet without compromising power or reliability. From medium-duty trucks to delivery vans, propane autogas is the smarter way to keep your fleet moving and your business operating at its best.
Discover how propane autogas can drive efficiencies for your fleet at propane.com/fleets.
Auto transport shakeup continues
Proficient Auto Logistics continues to increase its capacity through acquisitions as the vehicle-hauling market remains in flux since Jack Cooper Transport’s demise earlier this year.
Proficient leaders said its Brothers Auto Transport purchase adds 13% more capacity to the fleet, which
debuted at No. 136 on the 2025 FleetOwner 500: For Hire list less than a year after its initial public offering. Based in Pennsylvania, Brothers has 110 transporters and terminals in Pennsylvania, New York, Maryland, Ohio, and Virginia.
“This acquisition is an important milestone in our growth strategy,” Proficient CEO Richard O’Dell said in a statement.
¶ Visual inspection relating to damage
¶ Cracked welds
¶ Retention pin holes oblong-shaped
¶ Correct retention pins
¶ Readable decals and placards
¶ Compromised
“The operational and geographic synergies between our companies will allow us to provide a higher level of service to our customers while elevating our presence in the Northeast.”
Jack Cooper, whose abrupt closure in February came after it lost Ford and General Motors contracts, opened up auto-hauling market potential.
¶ Visual inspection relating to damage
¶ Excessive wear
¶ Missing components
¶ Leaks
¶ Complete functional test
¶ Readable decals and placards
¶ Visual inspection relating to damage
¶ Leaking fluids
¶ Non-OEM conforming, tampered with or missing components
¶ Readable decals and placards
Visual inspection relating to damage
Cracked welds
Excessive wear
Missing components
Complete functional test
Readable decals and placards
Compromised
“The immediate result of [Jack Cooper going out of business] has been a redistribution among market participants of a significant amount of OEM contract business,” PAL executives said in a Q2 earning statement. “New contract business in place at Proficient is representative of the company’s overall market share and is expected to ramp up over the remainder of 2025.”
Insufficient nationwide truck parking is receiving more attention at the state and federal levels. However, there is just one truck parking space for every 11 truck drivers, according to the American Transportation Research Institute’s recently released research highlighting insights and strategies for expanding truck parking at public rest areas. The average U.S. rest area has 19 truck parking spaces. Southern states average 25 per rest area, while the Northeast averages just 15.
Conducted with the American Association of State Highway and Transportation Officials, researchers surveyed all state DOTs about public truck parking costs and components, took parking space inventory, and other data. The study also included input from more than 500 drivers.
Case study topics include truck parking information systems, repurposing state-owned facilities for truck parking, and truck parking provision in the event of severe weather conditions.
ATRI used the state DOT survey to create a public truck parking dashboard available on ATRI’s website.
Carriers across the industry join NACFE’s ‘Messy Middle’ Run
Alternative powertrain pioneers are preparing for this year’s major freight efficiency showcase. The North American Council for Freight Efficiency announced 13 carriers will take part in its latest freight efficiency demonstration: Run on Less – Messy Middle.
“I’m thrilled with the participation,” Mike Roeth, NACFE’s executive director, told FleetOwner. “I’m excited to help these pioneering fleets tell their stories—that’s what the Run is all about.”
Run on Less – Messy Middle will begin September 8 and last three weeks. The Run will explore realworld, long-haul runs of four different power types: diesel, natural gas, battery electric, and hydrogen.
Each participating carrier selects one vehicle to participate in the event, sharing operational information and its telematics data along the Run.
This Run will feature four diesel, three natural gas, four battery electric, and two hydrogen vehicles. The vehicles and their engines cover both major and minor OEMs. Among the named carriers are major fleets dominating the latest FleetOwner 500 lists. The demonstration goes beyond covering different powertrains: The event will capture a wide range of companies, manufacturers, routes, loads, and geographies.
Throughout 2025 and 2026, RunOnLess.com will feature a growing collection of stories and data points.
In August, the Run on Less website will feature profiles for each participant leading up to Stories from the Run and data streaming from each truck in September. NACFE will visit each of the participants’ sites with video crews to record the carriers’ stories. As the Run gets underway, the group will publish the carriers’
operational data on different dashboards for each of the four powertrain options, sharing key statistics such as miles per kilogram of fuel.
Once the Run concludes, NACFE will share its immediate findings in early October. Throughout the rest of 2025 and into 2026, the group will share deeper analysis and produce reports on its learnings. FO
Moving freight across U.S. borders by truck can be complicated and require various equipment, certifications, and documentation. by Jade
Total imports to the U.S. from Mexico grew by 4.9% in 2024, and in January 2025, total crossings from the southern and northern borders of the U.S. rose 8.2% year over year, according to C.H. Robinson. While on-again, off-again tariffs impact imports (and exports) in North America, eets still have plenty of opportunities to get in on the action.
Trucks can move freight across the border in three ways, said Mark Vickers, Reliance Partners’ EVP and head of international logistics. The most
straightforward way is a through shipment. Freight can also move across the border with a transloaded shipment.
With a through shipment, “cargo is loaded, say in Chicago, and it’s kept in that same box and moved in that same truck from Chicago all the way to Monterrey,” Vickers said as an example. “There is no movement of that cargo outside of the box.”
While straightforward, Vickers said a through shipment is the most expensive way to move freight across the border. Therefore, he and his team advise their customers to learn the transloading process.
Brasher
Shipments can be moved via transload in two ways, Vickers said, using the same Chicago-to-Monterrey, Mexico, example. The rst way involves a U.S. carrier using a U.S. truck and trailer to carry a load from Chicago to the border. Once at the border, the trailer will be moved to a U.S.-based border warehouse for inspection. After inspection, it’s moved across the border to a warehouse based in Mexico via a drayage partner. Finally, a Mexican carrier using a Mexican truck will pull the U.S. carrier’s trailer to its nal destination.
“At least ve parties are going to touch that [load], so a lot can happen
there,” Vickers said. He explained that the other transloading process is a “true transloading” process. This is when the cargo is unloaded from the U.S. trailer at the border, placed in a warehouse, put onto a new trailer, and moved across the border to a warehouse in Mexico via drayage. Once there, it’s inspected again before being placed onto a Mexican trailer for a Mexican truck to take the load to its final destination, Vickers said.
Cross-border documentation and certification
Carriers must have a carte porte— essentially a bill of lading—to move freight across the border via shipment or transloading.
A carte porte, required for customs clearance, includes “detailed information about that shipment—what type of product it is, what route it might take, the vehicle that’s used—and serves as an invoice for transportation,” Jason Merck, a TMS manager for Syfan Logistics, said. A carte porte also provides information for Mexican tax collection and fraud mitigation.
Then there’s certification with the Customs-Trade Partnership Against Terrorism, which Matt Silver, founder and CEO of cross-border load board Cargado, said is the “main security protocol” that most trucking companies and shippers use to move freight from Mexico to the United States.
Companies that are CTPAT certified will have enhanced facility security. Silver explained that individuals who wish to gain access to those facilities will have their identification checked and their fingerprints scanned.
“Most cross-border trucking companies are either CTPAT certified, or their partner carriers in Mexico are CTPAT certified,” Silver said. “Most shippers moving freight out of Mexico expect CTPAT-certified carriers, and so traditionally, [CTPAT certification] has become the norm.”
Freight moved by a company that isn’t
Trend in U.S. - North American Freight Since January 2006 to February 2025 - Value (in millions)
Total U.S. - North American Freight Flows
U.S. Freight Flows with Canada and Mexico
These graphs represent the increase in transborder trucking freight between the United States and Mexico and Canada since 2006. Source: U.S. Department of Transportation
CTPAT certified will be more difficult to insure, Silver said, as lax security measures could pose risks to U.S. national security.
Warren Transport, a CTPAT-certified carrier, regularly ships freight across the border. Its business model involves an asset-based contract with CTPAT-certified Mexican carriers, also known as an interchange agreement.
“An interchange agreement is basically that you allow your U.S. equipment to go in and out of Mexico with a partnership with a Mexican carrier,” Jerry Maldonado, Warren Transport’s director of Laredo and Mexico operations, said.
Through an interchange agreement, Warren Transport carries a trailer to the border where a Mexican carrier will take that exact trailer and all its contents to its final destination in Mexico. That carrier will then bring the trailer back.
The agreement Warren Transport has with CTPAT-certified Mexican carriers
places sole responsibility for the trailer on the Mexican carrier that signs the agreement. The contract provides trailer details to ensure it returns in the same condition as it left.
If the Mexican carrier returns the trailer damaged, Warren Transport bills the Mexican carrier for the damage. In some instances, this has encouraged the carrier partner to train their drivers to ensure they take care of the equipment, Maldonado said.
U.S. carriers can also insure the trailers sent across the border, Vickers explained, which is popular among Reliance Partners’ large, asset-based carrier customers that send trailers into Mexico.
Motor carriers with these certifications, partnership agreements, and insurance should feel confident operating across the border. FO
Read more about this at
East Refuse Trailers are built to stay on the job longer, providing you the strength to handle the stresses of hauling refuse all day every day. By incorporating lightweight and longer-lasting components into each and every trailer, East has earned the reputation of time-tested performance and higher resale value. The East Genesis® design uses highquality aluminum with 33% more yield strength than the industry standard. The unique 2-inch thick, double-wall extruded aluminum panels are tongue-and-groove and robotically welded together, vertically inside and out, for superior strength, easier repair and resistance to twisting.
by David Heller
I COULD BARELY BELIEVE it when I realized I’ve been writing this column for 15 years. I was recently looking through my files and reflecting, when I also realized that while time has marched on, many of our industry’s issues remain. You could pick up a 2010 trade publication and find articles relevant to 2025.
Heavier trucks wouldn’t just travel on interstates. About one in five U.S. bridges would need to be replaced or strengthened to handle six-axle trucks. Can our infrastructure afford that?
Congress needs to hear from us when these issues are considered. At a recent U.S. House Highways and Transit subcommittee hearing about how trucking boosts American communities, increasing truck weight was discussed. It seems, once again, that the message of raising the weight limits from 80,000 lb. on five axles to 91,000 lb. on six axles is about improving productivity.
Regardless of the divisiveness of the trucking industry on this issue (the Truckload Carriers Association remains opposed to any increase), increasing truck weight by 11,000 lb. is not that simple. A 53-ft. trailer is not built with Legos. Adding a sixth axle is not as simple as just snapping it on. The trucking industry would bear the cost of adding a sixth axle. And don’t forget about the impact on our roads and bridges.
The discussions about adding weight to trucks are happening simultaneously as complaints continue about our infrastructure’s disrepair and lack of funding. The U.S. Department of Transportation studied the impact of various longer and heavier truck configurations on interstates and U.S. highways and found that the additional cost of damage to roads and bridges would require billions of dollars in new federal spending, adding even more to our budget deficit. The Highway Trust Fund remains underfunded simply because the fuel tax has never been adjusted to reflect inflation, the changing world of miles per gallon, and the growth of electric vehicles.
Heavier trucks wouldn’t just travel on interstates either. Increases in truck weight would have especially severe consequences for local roads and bridges. These heavier trucks need to run on state and local roads to pick up and drop off freight and for “reasonable access” for fuel, food, and other necessities.
Local roads and bridges face significantly more damage than interstates because they might be older, not built to the same standards, or already in poor condition—issues rarely acknowledged by heavier-weight advocates. One recent study identified 474,266 local bridges in the U.S. The research found that 87,455 of those structures would be “at risk” of needing to be replaced or strengthened
to accommodate heavier configurations, nearly one in five.
The interesting thing about discussions surrounding increasing weight is that nobody acknowledges that we already have carriers in this country that specialize in hauling heavier weights. They use specialized trailers and obtain state permits to transport heavier loads.
My point is that there are professional trucking companies that specialize in hauling heavier weights safely. If increasing weight was as paramount to productivity increases as many claim, why wouldn’t they already haul it?
This brings me to the issue of safety. The USDOT study mentioned earlier found that heavier trucks with six axles had higher crash rates in the three states with sufficient data. As an industry dedicated to reducing accidents and improving a carrier’s safety performance, hauling heavier weights should be left to those who specialize. In the event that overall weight limits are increased, it may create an environment in which care and caution may not be taken when hauling.
In reality, any increase to the overall 80,000-lb. limit would be fraught with problems. As an industry that thrives on its operation flexibility, there are other ways in which productivity can be increased. Reduced detention time or increased split sleeper breaks could bring about just that. Averaging a mere 6.5 -7 hours of drive time out of the federally regulated 11 hours shows that changes can be made in an effort to keep our driving population driving. Increasing weight should not be among those options. FO
David Heller | Dheller@truckload.org
David Heller, CDS, is senior VP of safety and governmental affairs for the Truckload Carriers Association. He is responsible for interpreting and communicating industry-related legislation to TCA members.
THE NEXT GENERATION
With up to 200 miles of range, better configurability, faster charging, and more power—the next generation T680E isn’t your typical battery-electric truck. It’s The Worlds Best.™
Spec’ing a truck should include thoughtful communication with key stakeholders, such as technicians and drivers.
There are as many different truck speci cations as there are commercial vehicle eets in operation today.
Each business has its own speci c needs, options, budget, and driver preferences—and each truck has hundreds of components that can be ne-tuned for that business.
Spec’ing a Class 8 truck means diving into all the gritty details of both eet needs and truck components.
Identify business needs:
Three ‘C’s
Choosing the right truck means rst de ning what “right” means. Each eet
Class 8 trucks are complicated. Here’s a basic guide to what to consider for your fleet when equipment shopping. by Jeremy Wolfe
has its own de nition of “right,” and shaping that de nition is the rst step in spec’ing trucks.
Three factors can help de ne “right” for your operation: duty cycle, compliance, and communication.
If a eet manager goes to a dealer looking for new equipment, the rst question they will hear is “what is your duty cycle?”
Truck speci cations depend entirely on the application. When it comes to duty cycle, the most important factors to consider are weight, location, speed, and annual mileage.
Fleet vehicles must comply with state and federal laws. This includes reporting and licensing across several agencies. If a carrier plans to haul hazardous materials, for example, its equipment must comply with unique laws that are speci c to that application.
Most stock tractor-trailers from dealerships comply with existing laws, but highly customized equipment can easily run afoul of the law. Falling out of compliance has disastrous consequences, so spec’ing should always ensure compliance with the federal Department of Transportation’s agencies, state DOTs, and any other relevant groups.
Spec’ing is not just about components but also business relationships. Communication is one of the most critical steps in specifying the ideal truck. Choosing a truck’s con guration should involve dialogue with every party, from dealers to drivers.
Fleet managers should prepare wellthought-out questions about any relevant aspect of their operation before engaging stakeholders.
It is crucial to listen to the feedback from drivers and technicians, as they are the professionals who use this equipment the most. Did drivers experience problems with current or past vehicles, or have they reported dissatisfaction with in-cab amenities? Do technicians report speci c components failing more often than expected, or do they nd that a certain manufacturer makes repairs unnecessarily dif cult?
Dealerships often have highly technical information about speci c truck components, which can help decide whether a particular component ts a particular duty cycle.
Top considerations for finding the right truck
Trucks are complicated. Each component choice has implications for several essential aspects of its operation. Choosing a truck or component is more likely to be correct when it satis es the factors below.
Fuel is the biggest per-mile cost for commercial carriers besides driver pay. The right truck spec should be as fuel ef cient as possible for its duty cycle. The truck’s powertrain, tires, and aerodynamics can maximize fuel ef ciency.
If a truck is in the shop, it is not making money. Fleets should aim to spec a truck for the greatest reliability and life cycle that falls within their equipment replacement schedule.
When spec’ing a new truck, the eet’s previous vehicle maintenance records can identify areas of improvement. Repeat failures can mean that a component is under-spec’d.
Some OEMs, like Volvo, might also include upkeep packages or warranties to help maximize uptime and ensure their customers are satis ed.
The payload is one of the most essential parts of a duty cycle. It is important that the truck is equipped with a chassis and powertrain designed speci cally for the type of freight it is hauling. A truck’s GVWR, payload capacity, and towing capacity are some of the variables that can determine whether it matches the duty cycle of a eet.
Terrain has major implications for truck operations. Highways and unpaved roads can require very different tires. Steep inclines might need greater torque to haul goods. The truck might need particularly high ground clearance for uneven terrain, or low clearance for special loading. The vehicle’s wheelbase or track might need to be more compact for urban maneuverability.
Cost is one of the most important factors in choosing a truck.
The right truck choice matches the eet’s needs for the lowest reasonable price. Under-spec’ing a truck can lead
to increased downtime and maintenance costs, but over-spec’ing a truck is often an immediate waste of money.
Fleets should consider the following:
• What are the upfront vehicle costs?
• Will cheaper speci cations still satisfy the eet’s standards?
• Will a cheaper option compromise safety?
• Can the company receive nancing from lenders?
• How much will the asset’s value deteriorate over time?
• Will the truck order’s lead time work for the eet’s needs?
As super cial as it may be, a truck’s look can be as important as ef ciency when it comes to winning over clients.
Many trucks on the road today look worn, dirty, and are decorated with pictures of inappropriately dressed women. Many more trucks look sleek, clean, and are coordinated to match the carrier’s brand colors. Which eet vehicle would a customer prefer to have in their yard, facing the public, potentially for several hours?
A commercial vehicle’s primary function is its ability to move goods from one place to another. Engines, gear trains, axles, brakes, and tires are the foundations of every eet’s business.
Here are a few of the most important powertrain components when spec’ing a truck.
With fewer moving parts, they’re easier to
BendPak’s new 16AP and 20AP Series super-duty two-post lifts are the ultimate solution for mixed fleets, handling Class 1 through 5 vehicles with ease—from passenger vehicles to school
and more
to run. Maximize your shop’s uptime with BendPak’s superior performance and unbeatable value. To learn more, visit bendpak.com or call us at 1-800-253-2363.
A typical internal combustion engine burns fuel to produce the energy that moves loads. The most important outputs of the engine are its torque (the rotational energy applied) and its horsepower (energy and distance over time).
The engine can vary its output by burning fuel more quickly, measured as rotations per minute. A higher rpm tends to produce more horsepower and torque, but each engine has its sweet spot for the most ef cient rpm.
Some of the most critical factors in spec’ing an engine are its power output, fuel ef ciency, size, and reliability. Inef cient engine spec’ing can increase operating costs through unnecessary fuel consumption or engine wear.
Alternative powertrains introduce many more questions. Battery electric and hydrogen fuel cell vehicles use electric motors instead of combustion
engines, and natural gas combustion differs from diesel combustion.
These differences have impacts on the vehicle’s suitable duty cycles.
The transmission uses a set of gears to better adjust the engine’s produced speed and torque. By adjusting a truck’s gearing in real time, the transmission can raise either the torque or horsepower. The transmission choice has implications for payload capacity, fuel ef ciency, and ease of maintenance.
Automated gearboxes tend to be standard for today’s transmissions, but manuals can still be practical in very heavy applications. For most duty cycles, automated transmissions are the optimal choice to lengthen clutch life, improve fuel economy, and reduce driver strain.
Some key factors in choosing a transmission are torque, slow-speed maneuverability, forward speed, reverse speed, maximum grades, power takeoff compatibility, and maintenance needs.
Today’s transmissions work very closely with their engines. Manufacturers tend to sell these components together. When in doubt, eets should choose engines and transmissions that were speci cally designed to work together by an OEM’s engineers.
Many OEMs develop integrated powertrains. The Cummins X15 Integrated Powertrain includes the engine, transmission, driveshaft, di erentials, axles, and brakes—all designed to work smoothly together.
Photo: Cummins
Another important factor is a vehicle’s axle makeup. This decides how the tractor supports a load’s weight and how the powertrain sends power to the wheels.
A vehicle’s gross axle weight rating has important regulatory implications. The right axle spec requires that the truck’s hauls never exceed its GAWR.
There are many options in choosing how many axles the chassis has, how they receive power (powered axles), and which ones are used to steer (steering axles). These options comprise the axle con guration, also known as the chassis con guration.
The most common axle con guration terms used in over-the-road trucking are 6x4 and 6x2. These names describe the composition of powered axles and steering axles. A 6x4 con guration is the most traditional for trucks: A 6x4 chassis has six total wheels and four drive wheels (three total axles, with two drive axles). A 6x2 has six total wheels but only two drive wheels.
With more drive wheels, the 6x4 produces greater torque for hauling heavy loads or negotiating rough terrain. Compared against the 6x2, however, more drive axles mean greater rolling resistance, leading to worse fuel economy—about 2.5% less ef cient than that of a 6x2.
The chassis axles not only determine performance but also have signi cant regulatory implications for weight compliance and registration. Other important factors include axle
spacing/grouping, suspension articulation points, and lift axles: A carrier’s specific operations and jurisdiction will shape these choices.
The axle ratio is an important factor in torque and fuel efficiency. The axle ratio refers to the gearing in a truck’s differential, which dictates how many driveshaft revolutions translate to wheel revolutions. Similar to transmission gearing, the differential’s gearing multiplies the torque applied to the wheels—but unlike the transmission, this gear ratio does not change.
An axle ratio of 2.79:1 provides less torque and greater fuel efficiency, while a ratio of 3.73:1 provides greater torque at the cost of speed and fuel efficiency. Lower ratios can be suitable for most on-highway loads below 80,000 lb. Steep terrain and heavy hauls may require higher axle ratios.
The truck’s tire choice has significant impact on its longevity, grip, fuel efficiency, speed, and maximum weight. These factors are determined by the tire’s material makeup, tread design, rolling resistance, dimensions, and more.
Different tire compositions suit specific seasons, geographies, road environments, costs, and repair frequencies.
Tires are also one of the more safety-critical components of a truck. Tire failures can cause disastrous accidents, so their reliability should be much more important than affordability.
The most safety-critical parts of the truck are the brakes.
Trucks use either air brakes or hydraulic brakes. Most long-haul trucks use air brake systems—either disc brakes or drum brakes—which use compressed air to apply pressure to the brakes.
Hydraulic brakes use hydraulic fluid to apply pressure. Air brakes are more popular and are easier to maintain, but they apply less power than hydraulic brakes. Federal standards require brake systems to fully stop tractor-trailers in no more than 250 ft. when loaded to their GVWR at 60 mph.
These components are far from an exhaustive list. Even the components listed have many slight variations not mentioned here.
Other important parts of a truck can include its cabin interior, driver amenities, trailer, air system, fuel tanks, idle limiting, electrical systems, driver assistance tech, frame rating, telematics systems, and more.
As long as the fleet has a clear definition of what the “right” equipment entails, it will be able to navigate spec’ing across any other components. FO
by Kevin Rohlwing
I’VE STRONGLY SUPPORTED truck and trailer TPMS (tire pressure monitoring systems) for as long as I can remember. When the first ATIS (automatic tire inflation system) was introduced, there was no doubt in my mind that it would be successful. Trailer tires are by far the most neglected in any fleet, so providing a constant source of regulated air to each wheel position seemed like a no-brainer at the time. It still does.
To say TPMS is a curveball to mounted tire programs is a disservice to curveballs. If a good baseball player knows the curveball is coming, it’s easier to hit it.
The interchangeability of tire and wheel assemblies makes ATIS on trailers popular. The components and mechanics of connecting the air supply to the tires may differ, but a 295/75R22.5 on a 10-hole hub-pilot wheel with a standard valve stem can be used with any ATIS currently on the market. Nothing “extra” or “special” is required.
But TPMS is a completely different story. With multiple systems from various manufacturers, the truck tire
industry is where passenger and light trucks were two decades ago.
When the federally mandated TPMS phase-in started in 2006 vehicles, questions outnumbered answers by 10 to 1 as the industry struggled with damaged sensors and systems that wouldn’t reset after service. Truck tire industry challenges could be more daunting.
Mounted tire programs have become incredibly popular because carriers can maintain a bank of steer, drive, and trailer tires that are inflated and ready to be installed by maintenance personnel. The only difference is the tread and the wheel (steel or aluminum). Worn or damaged tires are returned to the vendor for replacement and returned to the bank. It’s a great system for both parties.
To say TPMS is a curveball to mounted tire programs is a disservice to curveballs. If a good baseball player knows the curveball is coming, it’s easier to hit it. If the curveball is one of three or four pitches on the way, it can be tougher to hit. For mounted tire programs, TPMS can potentially be a radio-controlled anti-gravity pitch that defies the laws of physics. Sometimes, it may be unhittable.
Fleet technicians do not care where the tires come from when they replace them on a tractor in a mounted tire program. Sprinkle in some TPMS, and now the fleet has to identify the year, make, and model on every tire that comes off a truck. As if that’s not enough, the bank of tires will need assemblies with TPMS sensors that match the tractor’s year, make, and model. Therefore, the fleet will need to purchase additional TPMS sensors. How many depends on a number of known and unknown factors.
Truck tire vendors and retreaders also face known and unknown challenges of picking up assemblies with sensors, removing them, storing them, and then
reinstalling them in rims before they are mounted, inflated, and delivered. The vendor must somehow communicate the year, make, and model to the fleet so the customer knows where to install the sensors. Fleets operating different makes and models may need more tires in the bank to keep the TPMS operational under the present mounted tire model.
One solution is to abandon mounted tires for tractors with TPMS. Based on experience, if the sensors stay with the truck in the same wheel positions after a tire change, the TPMS will resume normal functioning. The truck will be shut down for longer with extra expense, but the TPMS will continue to operate as designed and warn the driver when a tire is underinflated. It’s the best way to guarantee that everything works after changing the tires.
Fleets should also expect higher costs to manage TPMS in a mounted tire program. Currently, the demounting, mounting, and inflation process is quick, simple, and efficient. Add TPMS sensors, and it takes more time to demount the tire without damaging the sensor or the beads. Removing and reinstalling the sensor is another time drain in the mounted tire department, while the process of inventory management for customer sensors hasn’t even been considered.
The American Trucking Associations’ Technology & Maintenance Council has formed a new task force to develop recommended practices for managing TPMS in a mounted tire program. Fleets, tire manufacturers, and commercial tire dealers should work together to create solutions that work for each other. FO
Kevin Rohlwing | krohlwing@tireindustry.org
Kevin Rohlwing is the chief technical officer for the Tire Industry Association. He has more than 40 years of experience in the tire industry and has created programs to help train more than 220,000 technicians.
Cenex diesel fuels are formulated to deliver optimal power, performance, and protection. The enhanced additive package includes an aggressive detergency package that Cenex says effectively removes engine deposits and keeps injectors clean. In addition, Cenex Roadmaster XL protects equipment from contaminants, improves engine performance with a total water management system, and increases power and fuel ef ciency with a more complete fuel burn. Cenex says its on-road diesel fuel can improve engine performance and fuel economy while reducing downtime and maintenance costs.
Hot Shot’s Secret says its Everyday Diesel Treatment (EDT) can maximize fuel
ef ciency and diesel engine longevity. According to the manufacturer, the treatment can improve fuel economy up to 7.3%, increase cetane levels by 7 points, and enhance overall combustion ef ciency. EDT can also prevent injector deposits, reduce DPF regens, and maximize lubricity to protect fuel system components from wear.
Lucas Oil says its CK-4 diesel oil blend is built to protect today’s modern diesel engines. Formulated with API Group II and Group III base oils and a cutting-edge additive package, the manufacturer says CK-4 delivers
performance, durability, and ef ciency. It meets Cummins CES20086 standards, so it is capable of delivering protection under severe operating conditions. Available in synthetic blend and petroleum options, CK-4 ghts soot, resists oxidation, extends oil life, and helps reduce lter maintenance.
Rislone’s Diesel DEF Treatment Super Concentrate is a formula designed to improve selective catalytic reduction system ef ciency, stabilize diesel exhaust uid, and prevent AdBlue/DEF crystallization. As crystals build up, they can clog the SCR system and cause performance problems. Rislone says regular use of its DEF Treatment protects the tank, pump, heater, sender, lines, injector, and mixer against harmful crystal deposits. FO
GM Jacob Montero takes over the Paccar OEM amid uncertain times
by Josh Fisher
DENTON, Texas—The trucking industry’s newest chief executive is taking over an iconic truck maker during uncertain economic and regulatory times. New Peterbilt GM Jacob Montero said his brand and its Paccar parent company have been through it before, and he and his leadership team are ready for the moment.
“We’ve been in business going back to 1905,” he said of Paccar. “That spans 21 presidents, 29 election cycles, multiple technology transitions, and since the ’70s 33 different federal emissions and fuel standards. Regulatory change is part of what we do.”
Montero was promoted in January as the U.S. freight market still waits for its
post-pandemic rebalance as fleets and truck buyers seek clarity on emissions regulations that the Trump administration wants to revise or repeal. This and unstable tariff policies have made long-term business planning difficult.
Montero said Peterbilt has used this time to stay close to customers and educate them. With a manufacturing presence here in Texas and elsewhere in the U.S., Canada, and Mexico, Montero said that Paccar is ready to adjust to whatever the supply chain throws at the company.
“It’s a partnership, right?” Montero told industry journalists during a roundtable Q&A with Peterbilt’s new executive leadership team on April 13. “You can’t predict the future, but we can stay very close with them and advise them and try to assist them as they look and set their purchase plans over the next few years.”
Peterbilt officials noted the OEM led with 21.2% market share in the vocational and refuse markets. Its overall Class 8 sales rose to No. 2 in the U.S.
Despite uncertainty, Montero is optimistic: “There is no great time, no worse time. It’s just what it is. I’m super excited about the future of Peterbilt, the products we have, and the customers that we’ve been able to partner with.” FO
There’s more than one way to power a fleet. Here’s how various traditional and alternative internal combustion engine fuels work.
by Jade Brasher
There are multiple fuel types available for vehicles. Some alternatives can immediately be direct replacements for your eet’s current fuel. That is, if you can nd them.
This FleetOwner Fleets Explained article details the different types of fuels powering trucking and commercial eets. Some have been around for more than a century, and others are emerging as transportation considers
alternatives to traditional power. You can nd even more detail at FleetOwner. com/FuelExplained.
What is diesel?
Diesel is trucking’s favorite fuel. It powers 97% of Class 8 trucks and 75% of smaller medium-duty trucks. It’s a popular fuel for heavier applications because of its performance and ef ciency, offering a “greater energy density than other liquid fuels,” providing more “useful energy
per unit of volume,” the U.S. Energy Information Administration states.
But diesel produces harmful tailpipe emissions. Diesel particulate matter, tiny particles containing chemicals, can lead to health problems, according to the California Air Resources Board. Diesel also emits oxides of nitrogen, which can harm the environment.
Diesel-powered vehicles are getting cleaner, however. The American Trucking Associations stated: “Over the last three decades, emissions from new trucks have been reduced by more than 98%.”
With the Environmental Protection Agency’s Clean Trucks Plan, those diesel emissions will be decreased even further for truck models beginning in 2027. The Clean Trucks Plan is a string of regulations seeking to decrease overall emissions from trucks. For example, EPA’s latest NOx regulation under the plan seeks to decrease NOx emissions, which are already near-zero at 0.20
grams per brake horsepower-hour, by 82% to 0.035 g/bhp-hr, Allen Schaeffer, Engine Technology Forum executive director, told FleetOwner-affiliate Fleet Maintenance in 2023.
Diesel also suffers significant price volatility. It’s one of a fleet’s highest expenses and one of the most unpredictable.
Gasoline powers 22% of all commercial vehicles in the U.S., according to the Engine Technology Forum. Gasoline engines don’t produce as much torque as diesel engines because of lower compression ratios, combustion speed, diesel fuel’s energy density, and more; therefore, gasoline-powered vehicles shine in applications where a diesel engine’s higher efficiency is not necessary or where maintenance is more challenging, such as urban driving.
Gas-powered vehicles also have the upper hand with maintenance.
Diesel-powered vehicles have a diesel particulate filter, which requires regular maintenance. This can add up over time and negate any efficiency advantages of a diesel engine.
Gasoline, like diesel, is refined from fossil fuels and has environmental drawbacks. Gasoline could be even more harmful than diesel because of its inefficiency. However, gasoline engines emit less nitrous oxide than diesel engines.
As with diesel, gasoline is a commodity with unpredictable pricing.
Ethanol is made from starch- or sugar-based materials known as feedstocks. This feedstock is converted into fuel through fermentation at an ethanol production facility, then used with a gasoline blend. The most common ethanol blend is E10, made up of 90% gasoline and 10% ethanol. However, ethanol blends can reach as high as 83%
ethanol, known as E85, according to the U.S. Department of Energy.
The EPA approved the use of E10 in all internal combustion gasoline engines and the use of E15 fuel (a blend of 10.5% to 15% ethanol) in gasoline vehicles MY2001 and newer. The use of E85 requires a exible-fuel vehicle.
According to EIA, ethanol was the most produced and consumed biofuel in the U.S. in 2022. This is likely because of its widespread availability—the fuel is available at more than 4,200 public fueling stations across 44 states, according to DOE—and because it’s compatible with many light-duty vehicle engines straight from the factory. While the most produced and consumed alternative fuel, ethanol is also used in nearly all gasoline sold in the U.S., according to EIA, which contributes to its consumption beyond the strict use of E10, E15, and E85.
Ethanol fuel is generally less expensive than 100% gasoline fuel; however, lower cost doesn’t necessarily make it a more cost-effective option. Ethanol consumers typically experience fewer miles per gallon of ethanol-blend fuel than pure gasoline.
While also considered a fossil fuel, natural gas, both compressed natural gas and lique ed natural gas, burns cleaner than traditional fuels while offering a similar performance.
While compressed natural gas offers performance similar to traditional fuels with acceleration, cruise speed, and horsepower, it’s a bit less ef cient than conventional gasoline and diesel fuel because of its decreased density.
LNG is nearly as ef cient as gasoline or diesel in terms of performance and range, and according to Cummins, one tank of LNG allows a vehicle to travel more distance than one tank of CNG. But while it’s more ef cient, it’s more complex. LNG “is created by purifying natural gas and cooling it to negative-260 degrees Fahrenheit,” according to Shipley Energy. Keeping it cooled to
This graph illustrates the volatility of various fuel types over the course of 24 years.
Source: U.S. Department of Energy | Alternative Fuels
EV charging stations aside, biodiesel has shown the largest alternate fuel station growth over the past several years. Ethanol fueling station growth has remained steady, while propane has experienced a slight decline, according to the U.S. Department of Energy. Source: U.S. Department of Energy
this temperature is imperative for its transport and use. As of 2023, the U.S. has roughly 50 LNG fueling stations compared to CNG’s 700-plus, according to DOE.
Fueling with either CNG or LNG requires a speci c powertrain, which can be purchased directly from the factory or which eet owners can convert from existing gasoline- and diesel-powered light- and medium-duty vehicles.
What is propane?
Lique ed petroleum gas, also known as LPG or propane autogas, is a byproduct
of natural gas and crude oil processing and re ning. It is an odorless, colorless liquid stored in tanks under pressure. Once that pressure is released, “the liquid propane vaporizes and turns into gas that is used in combustion” engines, according to DOE.
Fueling with propane requires a speci c engine. While no OEMs build propane-powered vehicles, both Ford and General Motors offer prep packages for an aftermarket propane conversion.
Propane autogas is less ef cient than gasoline and diesel, with DOE stating that one gallon of the fuel provides 27%
less energy than one gallon of gas. Yet propane-powered vehicles are easier to maintain because of their clean burn, and “low carbon and low contamination characteristics may result in longer engine life,” DOE states.
Fleets operating propane-powered vehicles might find it easier to fuel on-site, and propane infrastructure is easier to develop than other alternative fuels. Propane fuel suppliers will often lease the tank, pump, and dispensing equipment necessary for eets to fuel on-site, DOE states. This leaves the eet responsible for additional costs, such as the concrete pad for the equipment and an electrical line to supply any electrical needs to the equipment.
What is hydrogen fuel?
While hydrogen is the most abundant element in the universe, found in water, ammonia, and sugar, it must be isolated from element compounds and converted to useful energy. It takes more energy to isolate hydrogen than hydrogen produces, EIA states, but because hydrogen is more ef cient than gasoline and diesel and also presents a clean burn, there is a push to see it become a widely used fuel.
Hydrogen fuel is compressed into a gas and stored in tanks onboard a
vehicle. Tanks are re lled in private and public fueling stations, of which there are few, with most concentrated in California.
Hydrogen has failed to gain widespread adoption, primarily because of cost. Hydrogen has high production and
Biodiesel Production, Exports, and Consupmtion
This graph showcases the production and consumption of biodiesel. Aside from a few outliers, the U.S. has consistently produced biodiesel relative to its demand.
Source: U.S. Department of Energy
transport costs, which trickle down to the consumer. Sold in kilograms, S&P reported hydrogen prices for light-duty vehicles rose up to $36 per kilogram in 2024. Although 1 kg of hydrogen produces the ef ciency of 2.8 kg of gasoline, this price difference is enough to scare most consumers and eets from hydrogen-powered vehicles.
Also contributing to hydrogen’s hefty price tag could be that the industry has failed to decide which form of hydrogen to produce and transport more broadly. Hydrogen is transported and stored in two ways: liquid or gas. And each method has different requirements.
Made from used vegetable oils, animal fats, and recycled restaurant grease, biodiesel is a more sustainable alternative to diesel fuel. It is often mixed with petroleum diesel, according to DOE, and B5 biodiesel refers to blends with up to 5% biodiesel and 95% petroleum diesel. B20 refers to blends with 6% to 20% biodiesel.
“The e four driver – the 2025 NPTC Driver Hall of Fame inductee – embody all the characteri tic , kill and attitude that are the heart of what enable the private fleet to continue to deliver exceptional level of cu tomer ervice. They are amba ador , not only for their company, but for the entire private fleet community.” NPTC President and CEO Gary Petty
JD began his driving career in 1969 and in those 55 years he has racked up 5.8 million miles without an accident or a moving violation. He began his career driving for Constellation Finishing, where he worked for five years before joining Rogers Finishing as a Shipping Supervisor. He joined Shaw Industries Group, Inc. 29 years ago where he has recorded three million of those safe driving miles hauling flooring. Currently, he works 12 hours a day shuttling trailers around Dalton, GA.
“As a dedicated truck driver, I’ve strived to exceed expectations in all aspects of my job over the years,” he says. “I understand the importance of maintaining my own personal wellness, practicing safe driving habits, and upholding the highest standards of professionalism and courtesy.These are essential not only for my own well-being but also for the safety of everyone I encounter on the road daily. Regular exercise, eating well, and getting plenty of sleep are key parts of my daily routine and help me stay alert and fit.”
Scottie began driving for Poland Springs (now Primo Brands) in 1991 and in those 32 years he has achieved 3.2 million miles hauling bulk spring water in a six-axle tractor-trailer combination (unbaffled food product tanker) with a gross combined vehicle weight of 99,000 pounds. He has only one non-preventable accident on his record and no moving violations.
He began working with heavyduty trucks and equipment in the logging industry, where his father ran a family business. Once he was of legal driving age, he moved into driving the family pulp truck, hauling logs and firewood. At 21, he joined Poland Spring, starting as a yard truck driver. There, he gained valuable experience in maneuvering tractor-trailers and shifted over to the transport division, where he remains to this day working 10-12 hours per day, 5-6 days a week, covering 390-460 miles daily.
A volunteer with the Harrison, Maine Fire Department, Scottie says, “I strive to maintain a positive attitude and always offer help to others. “
Zanesville, OH
Kenny began his career behind the wheel 61 years ago and has driven for 3.5 million miles without an accident, injury or moving violation. He joined AutoZone 27 years ago, where he has accumulated more than two million of those safe driving miles.Typically he delivers to AutoZone stores often with challenging parking lot conditions including parked cars, landscaping items, and other fixed hazards.
Kenny is a past Trustee and current member of The Christian Missionary Alliance Church of Zanesville, Ohio where he had maintained their landscaping for 25 years. He is also the president of the local Donut Shop retirees daily gathering.
“I am very big on having a plan and working it.When possible, I do a complete inspection the night before and another inspection in the morning. I plan my routes and directions the day before and do my best to get a good night's sleep. I strive to be safe every day because I want to come home to my family and not ever hurt anyone. I thank God for watching over me every day and keeping me safe.”
Marathon Petroleum Co. LP Columbus, OH
In 44 years of driving, Todd has driven 3,050,000 miles without an accident, injury or moving violation. He started his driving career in the United States Marine Corps (USMC) in 1981 driving straight trucks and tractor trailer combination units.Todd was also employed as a school bus driver for the city of Hilliard and Dublin Ohio for a year before joining Marathon Petroleum in 1986 as a Transport Driver.
Todd is a certified Smith Driving System trainer. He volunteers for the American Red Cross delivering blood and products through out the state of Ohio. Todd often volunteers his time during natural disasters. For example, after 2024 Hurricane Helen,Todd and his wife loaded up their personal pickup truck with more than $1,000 worth of propane heaters and headed south and donated supplies and helped with relief efforts.
“As a professional driver, it is essential to arrive to work each shift well rested and prepared mentally and physically for the task at hand,” Todd says.
Fleet owners and drivers might already be using B5 in their vehicles without being aware of it, since it is not mandatory to label B5 fuels at the pump explicitly, DOE states. On the other hand, B20 must be labeled and is compatible with most light- and medium-duty engines and performs similarly to 100% or B5 diesel.
Blends of 20% biodiesel and 80% petroleum diesel will offer 1% to 2% less efficiency than pure diesel, and blends with a higher percentage of biodiesel will have even less ef ciency.
While biodiesel blends are a more sustainable fuel, DOE states they produce a similar amount of air-quality emissions as petroleum diesel. However, a higher blend of biodiesel produces fewer greenhouse emissions.
What is renewable diesel?
Like biodiesel, renewable diesel comes from animal fats and vegetable oils. But unlike biodiesel, renewable diesel is processed to be chemically identical to petroleum diesel, DOE states. Renewable diesel is a drop-in fuel that can power any diesel vehicles immediately— no modi cations are necessary.
“
Because of its equivalent chemical makeup, renewable diesel can be blended, transported, and coprocessed with petroleum diesel as well as transported in existing petroleum diesel pipelines. Existing diesel refineries can also be converted into renewable diesel production facilities with little associated cost.”
There are multiple ways to produce renewable diesel, and production plants are growing. While most facilities are in West Coast states, there are renewable diesel production plants in Kansas, North Dakota, and Oklahoma.
EIA states that renewable diesel can be blended, transported, and co-processed with petroleum diesel because of its equivalent chemical makeup. Renewable diesel can also be transported in existing petroleum diesel pipelines, and existing diesel re neries can be converted into renewable diesel production facilities with little associated cost, EIA states.
According to the U.S. Department of Energy, the U.S. transportation industry consumes more biodiesel than it produces.
Source: U.S. Department of Energy | Alternative Fuels Data Center
Renewable diesel is made from sustainable sources and offers environmental bene ts over petroleum diesel. DOE mentions one study that indicated renewable diesel produces less carbon dioxide and nitrogen oxide than petroleum diesel, which “reduces carbon intensity on average by 65% when compared with petroleum diesel.”
What is renewable natural gas?
Another drop-in fuel, renewable natural gas can power conventional natural gas engines, both CNG and LNG. Biogas produced from the decomposition of organic matter and renewable natural gas can come from land lls, livestock operations, and wastewater treatment facilities. According to DOE, biogas produced from land lls is often used to produce electricity, whereas biogas from livestock operations and wastewater treatment facilities can power vehicles.
The National Association of Clean Water Agencies released a study estimating that renewable natural gas derived from wastewater treatment plants could produce enough energy to cover 12% of the nation’s electricity needs, but of the more than 16,000 wastewater treatment plants in the U.S., only about 1,200 of them are producing renewable natural gas.
While these numbers appear low, Coherent Market Insights predicts that the market for biogas will grow by more than $10 billion by 2032. FO
FleetOwner zeroes in on refrigerated fleets and technologies in this special section from Refrigerated Transporter —the trusted resource for temperature-controlled transportation and logistics professionals.
Kordish leads Ralph Moyle into a new trucking era by
Jason McDaniel
Ralph Moyle Inc. (RMI) CEO
Ashley Kordish grew up on a small farm in Mattawan, Michigan, where her grandfather, RMI’s namesake founder, started their refrigerated trucking business. Her earliest, and most fond, memories involve playing in the backyard of the family farmhouse and watching heavyduty trucks pull into and out of the fuel island behind the fence.
So, diesel is in her blood. However, she was not always sure if trucking was in her heart.
The Moyles also are a family of teachers, so she was considering pursuing a career in teaching in high school. Then she served as a volunteer re ghter and EMT at the Mattawan Fire Department while also working part-time at RMI and attending college. And after securing a bachelor’s degree in integrated supply management at Western Michigan University, she spent nearly three years at American Axle and Manufacturing in quality control and material planning.
That’s when a passion for transportation seized her soul.
“That was a pivotal time for me,” she recalled. “I was trying to gure out if the family business was truly where I wanted to be. And I can de nitively say my time away solidi ed that I belong here.”
Kordish returned in 2015 as an operations manager, where she honed her trucking expertise, then worked her way up to VP of operations in 2018 and CEO in 2022. Now, 10 years into her tenure, she’s fully committed to overhauling operations and eet management, navigating a challenging environment, and preserving the company’s culture.
“Seeing her grow, and really jump into that leadership role full-time, has been fantastic,” Clarice Talaga, associate director of operations, said. “She’s definitely risen to the occasion.”
A woman in transportation Kordish’s RMI sabbatical did more than provide career clarity. It also shaped her management perspective, made her tougher, and set a precedent for family members coming up behind her. Younger sister Olivia Moyle worked at J.B. Hunt before joining RMI as a transportation account manager. “I had to become more assertive while working at American Axle, and that was a good thing for me because I was a little shy when I started,” Kordish said.
Her father, CSO Michael Moyle, and uncle, CFO Jonathon Moyle—Ralph’s sons who still share ownership of the company—didn’t hand her anything either. She swept out trailers as a teenager, drove a forklift in RMI’s warehouse when she was older, and spent time in dispatching, billing, and the shop. “That was critical,” Kordish said. “It helped me gain credibility and respect, especially as a female in this industry—and the first female leader in our organization.”
Steve Bolf, fleet and facilities manager—and a 22-year RMI veteran— agrees. “I’ve always thought taking the time to work in every part of the company, and learn what they do, was
a very noble thing,” he said.
Kordish always felt like she had to work harder to prove herself in a traditionally male-dominated industry. Now one of the Women in Trucking Association’s Top Women to Watch in Transportation for 2023, she’s working hard to further their feminine cause and help other women realize their trucking dreams.
“I’m extremely proud to be a woman in trucking,” Kordish said. “We’re active members in the Women in Trucking Association, and I go to all the conferences. Representing women in this industry is something I think about a lot.”
Maintaining RMI’s small-town values, and keeping the business in the family, are equally important to Kordish. Bolf said she’s excelling there, too. The job has changed significantly since Ralph and his sons ran the show, but the company’s emphasis on personalized customer service and open-door employee communication remains RMI’s greatest differentiator.
“She’s really helped promote a culture and space where everyone has an opportunity,” Talaga agreed. “Can you do the work? At the end of the day, nothing else matters.”
RMI’s roots date to 1945, when then 13-year-old Ralph began hauling grapes from local farms for Welch’s.
He purchased his first tractor in 1952 and incorporated Ralph Moyle Inc. in 1966. Michael, who took the lead growing RMI’s warehousing operation, and Jonathon joined their father in the early 1990s, and Ralph started stepping back from the business in the early 2000s, although he continued to visit their Mattawan terminal long after he retired.
The founder of RMI died Jan. 11, 2022—but not before learning of Kordish’s intention to join, and one day lead, his company.
“I’m grateful he knew that before he passed away,” Kordish said.
Today, RMI hauls juice, beer, and tea with 60 trucks, 90 reefer trailers, and 186 dry van trailers, and corn syrup in six tank trailers. It also maintains a 400,000-sq.-ft. ambient-temperature warehouse in nearby Paw Paw. The company delivered almost 17,000 loads to customers across 38 states in 2024, despite dealing with a rate-suppressing freight recession.
“Last year was the roughest year I’ve seen in my career, and even my uncle said it was one of the worst years in his career,” Kordish said. “So we just buckled down and worked toward surviving.
“Our warehouse operation really is what kept us moving.”
Diversification is the key to managing trucking’s ups and downs, Talaga added. So are consistent, close-knit relationships, and nearly 90% of RMI’s transport business involves contracted hauls and dedicated services. Those partnerships also help RMI avoid heading home empty, with only a 14% weekly deadhead rate, Kordish shared. Still, leaders are doing their best to adjust to the evolving landscape, this year cutting 10 trucks and tightening RMI’s Midwest footprint.
“We’re trying to keep those drivers who increasingly want more home time,” Kordish said. “But the Midwest region also seems to be our sweet spot as a company. That’s where we’re landing nice lanes.”
RMI also leans on associations like WIT and the Truckload Carriers Association to stay informed on industry issues and learn new ways to operate more efficiently. The company participates in the TCA Profitability Program (TPP), and Kordish is in line to chair TCA’s Refrigerated Division. “TCA has been incredible,” Kordish said. “I love that organization. It’s great for small family-owned carriers like us who want to connect with like-minded companies.”
The most important individuals in any trucking enterprise are the drivers. That’s why Kordish also obtained her commercial driver’s license. “I really want to understand our drivers, and what they’re going through so I can help make conditions better for them,” she explained.
RMI employs 40 regional and shorthaul drivers, nine local drivers, and nine drivers dedicated to shuttling and spotting equipment for key customers like Coca-Cola—one of Ralph’s original accounts—Knouse Foods, and Gordon Food Service. And RMI drivers tend to stick around. The company boasts a 12.5% year-to-date turnover rate thanks to its approach to caring for drivers. “They appreciate the culture here more than anything else,” Talaga said.
In addition to constant communication, first-name relationships, and responsive maintenance services, RMI pays its company drivers by percentage of load to incentivize selection of longer, higher-paying runs. “It creates more autonomy for our drivers in terms of load selection,” Talaga said. “Also, when we’re negotiating contracts with customers, and rates go up, they get a raise, too, because their percentage increases.”
Word of mouth still is the best recruiting tool. But RMI also is connected to The Michigan Works! Association and administers its own apprenticeship program to help young drivers obtain their CDL. RMI prefers candidates over the age of 21 but will take on prospects as young as 18. The two-phase training
includes CDL prep and 4-6 weeks of on-road instruction. Two drivers who recently completed the program jumped right into critical roles.
“All the things I’m typically worried about with new hires, they have under control,” Talaga said. “It’s nice having a reliable driver pipeline.”
RMI utilizes Smith System training and recently implemented Trakstar’s learning management system to make ongoing education easier for drivers on the go. And to promote continuous improvement, the carrier leans on Netradyne’s forward-, inward-, and side-facing cameras and GreenZone scoring system, which generates excitement for performance improvement. “Our drivers’ abilities, and their safe-driving skills, have really increased since we started using it,” Talaga said. “And we catch crazy things on these cameras.
“I’ll have a driver I know and trust call with an outlandish story, and I’m thinking, surely they’re pulling my leg. And they’re like, ‘No, check the camera. That’s what happened.’ And sure enough, it is.”
Updated equipment strategy
Today’s drivers also gravitate toward newer, well-maintained equipment, so RMI is adjusting its equipment strategy, too. “Ralph used to buy anything
that ran in an auction,” Kordish said. “People used to call us the rainbow fleet because we ran trucks of all different types and colors.
“About 10 years ago, we started buying new trucks and trailers.”
RMI’s fleet now primarily consists of Volvo trucks sourced from M&K Truck Centers in Kalamazoo, Michigan, and Freightliners from Freightliner of Kalamazoo, which is across the street from its Mattawan terminal. Most trucks are sleepers, but RMI also runs a mix of leased and purchased tractors to protect them from any recall issues and provide more fleet flexibility.
The carrier rotated in 15 newly leased Freightliner Cascadias last year.
“Freightliner offers the ParkSmart bunk system, which acts as a factory-installed APU (auxiliary power unit),” Bolf said. “Not having to idle trucks to keep drivers cool on breaks is a huge plus.”
New dry van and reefer trailers are Hyundai Transleads from Trailer Equipment in Grand Rapids. For the first time in RMI history, the company last year added nine brand-new Hyundai refrigerated trailers with new Carrier Transicold X4 7500 transport refrigeration units (TRUs).
“We’ve stuck with Carrier because when the emissions regulations started to hit, they did the smart thing and
detuned their horsepower below 25 so they didn’t need a diesel oxidation catalyst, EGR (exhaust gas recirculation), and all the engine electronics,” Bolf said.
RMI’s terminal includes a 20,000sq.-ft., eight-bay shop for truck and TRU maintenance, and a 6,400-sq.-ft. shop with three drive-through bays for heavy-duty trailer work, like frame and ducted floor repairs. RMI is certified to perform in-house warranty service on its Freightliner and Volvo tractors, and it employs a full-time reefer technician to boost TRU uptime.
New Freightliners feature full Detroit powertrains and Assurance safety systems as well as Samsara electronic logging devices. New trailers feature Hendrickson suspensions and TireMaax tire pressure control systems, Orbcomm GPS tracking and load sensors, and Carrier Lynx Fleet telematics.
“We run equipment from the vendors who treat us best,” Bolf summarized.
RMI is not planning to buy any new trucks and trailers this year because of the uncertainty surrounding tariffs and the Trump administration’s plans to roll back engine emissions regulations. Instead, it’s focusing on extending trade cycles while refining processes and procedures, expanding warehouse services, and gearing up for what they hope is an improving market.
“We’re seeing signs of hope,” Kordish said. “Brokers are reaching out to us, calling and emailing about available loads, which tells me capacity is opening up.”
In another positive signal, more experienced drivers are approaching RMI about work, Talaga said, and their Midwest lanes are rebounding faster than other lanes, so the carrier is well-positioned to take advantage of an uptick in business. But Kordish said they’ll continue to proceed cautiously.
“Oftentimes, trucking companies will buckle down in a freight recession and then, when things are good,
they forget to keep monitoring their expenses,” she said. “We’ve decided we’re not doing that. We’re going to stay buckled down.”
RMI also is committed to furthering its family feel while Kordish prepares the next generation of leadership in trucking—her two children, 7-year-old Valeria and 5-year-old Xander.
“One day, I would love for them to enter the family business,” she said. “They already know the difference between a dry van and reefer, and they love hanging around trucks and coming to the office. But I’m going to take the same approach my family took with me.
“I want them to decide where they belong.”
markets a full-line of hydraulic liftgates for light, medium, and heavy-duty trucks and trailers. Toplifters, Stowaways, Railgates, Sideloaders, and Conventional models are all part of the THIEMAN line-up. For many years, THIEMAN has been customizing liftgates to meet specific needs. If a special need arises, give us a call. From 1000 lb. to 6600 lb. lifting capacities, THIEMAN can provide a liftgate for almost every application.
SCombining best practices with hard data can help all stakeholders enhance food quality and safety. by Dan Knauer
hipping meat and seafood within the perishable cold chain is a high-stakes proposition for grocers, restaurants, and their supplier networks. Temperature abuse can lead to the formation of bacteria and the potential for foodborne illness. Protecting consumers from this possibility is the top priority. In addition, stakeholders must guard against nancial losses from rejected loads, legal entanglements, and reputational damage.
Proper refrigeration and robust temperature management programs are the foundation of quality assurance (QA) initiatives. In particular, temperature consistency is critical to help prevent spoilage and the growth of microorganisms.
Consider the following scenario for a typical grocery or restaurant QA team.
A load of beef arrives at the local distribution hub a few days before the Fourth of July holiday weekend. Although the refrigerated trailer temperature is still within the high end of the acceptable temperature range, the QA staff notices several red ags of temperature abuse:
• Pulp temperature readings are slightly above the safe maximum temperature for beef.
• The product packaging contains an excessive purge of blood and moisture, suggesting that some thawing and/or warming occurred.
To con rm their suspicions, the QA staff checks the trip data from the onboard data logger. They discover that the trailer holding temperature rose to 47 degrees Fahrenheit for more than four hours earlier that day—well above the safe range for beef. This could indicate several possibilities:
• The driver turned off the refrigeration unit, likely to save on fuel consumption and expenses.
• In a multi-drop load scenario, the driver may have left the doors open too long while dropping off other products before this delivery.
• A malfunctioning reefer unit
• Insuf cient trailer insulation
• Air chute issues
Whatever the cause, the QA staff is left with no other choice than to reject the load, which may be valued at more than $100,000.
Even though the customer doesn’t end up paying for a bad load, the product loss results in opportunity costs. A grocer may suffer lost revenue and empty shelves until the next load of beef arrives—which could be up to a week. If
the client is a restaurant, it could potentially take one of the most pro table items off their menu during a holiday weekend, disappointing customers and indirectly encouraging them to dine elsewhere. The incident will also weaken the food supplier’s relationship with its customer. The supplier must scramble to replace the lost product in time or risk losing business to a competitor.
Of course, the next step in this unfortunate scenario is to determine the parties responsible for the product loss.
Cold chain safety is a shared responsibility
Producers (shippers), carriers (truck drivers), logistics companies, distribution centers, and retailers all share responsibilities when it comes to ensuring cold chain safety. The potential for temperature abuse of meat and seafood can occur at any phase of the shipping process, especially whenever product changes hands.
It’s critical for stakeholders to understand the regulations governing the meat and seafood industry cold chain, follow shipping best practices, and take preventive measures to promote food safety.
Federal guidelines and regulations
Depending on the product, the distance from its origin to destination, and its intended use, various commodities are shipped fresh, frozen, or somewhere in between.
Per recommended guidelines from the U.S. Department of Agriculture (USDA), proper refrigeration during transit is necessary to address food safety concerns and preserve the freshness of highly perishable meat and seafood. These standards are intended to help minimize the potential growth of harmful bacteria and microorganisms, preserve the fresh physical appearance and necessary hydration levels for quality, and maximize the useful shelf life.
USDA guidelines recommend speci c temperature ranges for various types of products, with optimum ranges allowing little room for deviations. In addition, the Food Safety Modernization Act (FSMA) authorizes the FDA’s requirement for producers to specify the required temperature range for each perishable shipment.
If a carrier is suspected of temperature abuse or deviating from the standard, they are responsible for verifying proper holding temperatures were maintained during transit while the product was under their purview.
Use of third-party temperature-monitoring devices—such as real-time trackers and loggers—is the most effective way to automatically and effectively capture this data. Without this information, carriers can be at risk if a temperature abuse dispute occurs. Discharge and return-air temperatures from the trailer’s refrigeration unit may not be admissible by courts in every state. By contrast, third-party monitors provide an objective record of shipping conditions.
For meat and seafood stakeholders, effective temperature management requires careful attention to a full spectrum of perishable shipping processes and best practices.
• Preparation establishes a temperature baseline. Before shipping, product is packaged fresh or frozen and loaded into a refrigerated trailer that is pre-cooled to a speci ed temperature range. The insulating effect of boxes and packaging makes it imperative that both the product and the trailer are at the desired temperature when packed, stacked, and loaded.
Once product is loaded, it’s too late to try and cool it further. The trailer and its refrigeration unit aren’t designed to remove unwanted heat or pull temperatures down to desired ranges. Make sure the refrigeration unit is set for continuous run mode for the duration of the cold chain journey.
• Maintain proper holding temperature ranges in transit. Refrigerated trailers are designed only to maintain proper holding temperatures, so they should be thoroughly inspected before each shipment. Check the walls and insulation for tears, especially since there are many older trailers on the road today that can have degraded R-values. Ensure that there is suf cient air ow and proper operation of the trailer’s air chute, if one is present, and verify proper door sealing to create a refrigerated compartment.
Meats are porous and can absorb odors, which could result in spoilage or poor product taste. To help prevent this, clean, sanitize, and deodorize the trailer to help protect against potential cross-contamination with previous loads. Don’t mix loads with other odor-emitting products.
Load, arrange, and stack product and pallets to help reduce heat transfer from the exterior walls of the trailer to the payload. Follow a centerline pattern to support proper air ow and avoid over-stacking meats, which can cause unwanted purges. Ensure temperatures are consistent from the front to the back of the trailer.
• Understand the shipping method. Freight on board (FOB) shipments fall into two categories, and it’s important to be aware of the differences between them.
• FOB origin: The buyer assumes ownership of the goods when they leave the seller’s facility. The seller still has a stake in the quality, however, as this impacts their brand’s reputation. The purchaser also cares in this scenario because they have nancial ownership of the product. In the event of loss, they would have to work with the carrier and insurance provider to determine who is at fault.
• FOB destination: The shipper retains ownership of the goods until they’re delivered. The seller’s stake in the cold chain is higher in this scenario because ensuring the quality of the product upon delivery is their responsibility. The purchaser bene ts from detailed temperature data; they wouldn’t want to accept product that’s suffered temperature abuse and would therefore have a shorter shelf life.
Consumers don’t know or care who owns the shipment at any given point. But the quality of the food they eat matters a great deal, and they’ll ultimately blame the brand if the product doesn’t meet expectations.
• Shipment size considerations. Full truckload shipments with only one pickup and drop destination are less susceptible to temperature deviations caused by doors opening and closing. Regardless of what shipping method is chosen, this option provides the most predictability and relatively fewer risks.
Partial truckload shipments typically ll more than half of the trailer but leave room for another company’s product as long as it’s being delivered to the same destination. Although this can save shipping costs, it comes with some risks. Product from the other company may be loaded at a different temperature range. In addition, cold air can escape during loading or unloading, potentially leaving product susceptible to heat for an extended period.
Less-than-truckload (LTL) is a designation for smaller shipments, typically handled with a “hub-and-spoke” model. One truck picks up the shipment, which is consolidated at a third-party facility and loaded onto a different truck for delivery. This multi-leg supply chain adds more risks because multiple refrigeration units need to be operating correctly.
LTL loads can take longer to build. This can extend the time required to maintain proper shipping temperatures. It can also result in poorly arranged loads that negatively impact air ow, stacking, temperatures, and food quality.
No matter the size of the shipment, multiple stops for pickups and deliveries introduce more opportunities for opening doors during loading and unloading, and ultimately, more risk of temperature abuse.
In the meat and seafood cold chain, proper measurement can only be accomplished with robust third-party monitoring capabilities, which provide the means for validating temperature data with objectivity and urgency.
An ideal solution is comprised of integrated hardware and software, including:
• Real-time tracking devices that leverage cellular networks to provide live location and temperature information
• Data loggers that provide a history of in-transit temperatures after a shipment arrives
• Cloud-based software that can aggregate shipping data into a centralized platform and transform it into deep cold chain insights and intuitive dashboards
Real-time trackers are ideal for those seeking a proactive approach to temperature management or who need to track delivery arrival times. Stakeholders are alerted precisely when and where temperature abuse is occurring, enabling them to take immediate action to prevent loss, rather than waiting for a shipment to arrive. Location data can help users anticipate delayed shipments, making it possible to reroute trucks or take other precautions to help prevent supply disruptions.
Historic data loggers provide an objective record of in-transit temperatures, which can be downloaded upon receipt of the shipment at a facility. This objective record provides evidence of any temperature abuse, which can be used to make more informed decisions about whether to accept or reject loads. They’re also valuable resources when resolving claims disputes. Since data logs can’t be tampered with, they’re admissible as evidence in a dispute.
Cloud-based software combines all data streams into one location. This helps provide complete visibility into current cold chain activities while uncovering historic performance trends. Consolidated data enables more informed decision-making while assisting users to create preferred carrier lists and improve perishable temperature management.
cient
by Jason McDaniel
Oil fouling is a well-known issue in all refrigeration equipment, including transport refrigeration units (TRUs). This gradual buildup of compressor lubricating oil inside the walls of refrigerant tubing forces pumps to work harder and hinders heat transfer, reducing cooling equipment ef ciency and lifespan.
Energy Ef cient Technologies (EET) offers a compelling solution—but reefer carriers have been cautiously pessimistic.
“The biggest problem we face every time is people saying, ‘This sounds too good to be true,’” lamented Joe Mearman, EET president and CEO. “But it is realistic, and once people nally install this product in a few of their refrigeration systems, they tend to incorporate it throughout their portfolios.”
The product in question is CryoGenX4, a patented liquid nanotechnology that is designed to eliminate and prevent this pervasive problem the American Society of Heating, Refrigerating and Air-Conditioning Engineers rst documented in 2005. And thousands of hours of validation across diverse industries, including restaurants, hotels, data centers, cold chain distribution, and temperature-controlled transportation,
indicate it delivers considerable savings in fuel, maintenance, and equipment-replacement expenses while also helping carriers meet shippers’ goals to curtail Scope 3 GHG emissions.
“The savings are more than just ‘signi cant,’” maintained Chris Bramble, EET national sales director. “It’s almost like, ‘How do you not do this?’”
‘Like
Mearman spent 20 years with the Navy identifying more ef cient equipment technologies in submarines, warships, and facilities as a civilian research and development engineer. He and a partner founded EET in 2007 to pursue that passion on a grand scale.
“Our goal was to nd known and repeatable technology we could put into larger footprints to make a global difference in climate change,” Mearman said. “We rmly believe CryoGenX4 is the answer. So we’ve been moving up the chain, deploying it in larger and larger installations.”
Mearman met the inventor of CryoGenX4, Tri-S Technologies CEO Tony Sgarbi, in 2008 at a conference in Baltimore,
where EET is based. Sgarbi worked with Mobil 1 and Dura Lube early in his career. He perfected polarized refrigerant oil additive (PROA) technology with PolarShield before patenting his unique solution in the early 2000s. CryoGenX4, the product’s fourth evolution, utilizes electromagnetically charged particles to penetrate the invasive oil and embed itself on the interior surfaces of refrigeration systems, removing and preventing oil buildup.
“It has a stronger attraction and smaller particles than the oil that sticks to the walls inside the machine, so it pushes past the oil and adheres to the metal’s lattice structure,” Sgarbi explained. “It acts like Te on in a frying pan—and attaches like a magnet.”
EET, which boasts 11,000 installers under contract, now is the largest global distributor of CryoGenX4, which is inside 158,000 machines in 100 countries across six continents, Mearman said. The company also offers 200 other technologies and processes for improving energy ef ciency.
‘Transformative’ potential Mearman’s team started with HVACR systems in restaurants, grocery stores, and data centers. Those efforts led to hotels, assisted living centers, convenience stores, beer distribution facilities, and more. EET now features 70 case studies across 18 industries on its website, esquaredt.com. Marriott International is one of its largest customers, along with Omega Healthcare, Cogent Communications, a McDonald’s food distributor, Anheuser-Busch Companies, and Molson Coors Beverage Company.
Reefer transport is a newer target—and CryoGenX4 boasts “transformative” potential.
EET estimates cold chain transporters use 4 million refrigerated trucks and trailers, 500,000 refrigerated railcars, and 1.5 million reefer containers globally. By adopting CryoGenX4, they could realize “billions” of dollars in fuel savings and eliminate “millions” of metric tons of carbon dioxide emissions each year.
Starbucks distributor DPI tested CryoGenX4 in a 4-yearold Carrier Transicold Vector 8600MT TRU on a 53-ft. reefer trailer at its Mid-Atlantic distribution center in Capitol Heights, Maryland. The study showed a 20% increase in fuel ef ciency—compared to the same delivery route over a two-month period without CryoGenX4—and corresponding 20% average fuel savings. DPI also realized a 24% increase in freezer ef ciency and 42% boost in cooler ef ciency, helping it reduce food spoilage by better maintaining setpoints during transport and decreasing “pull-down” times after reefer doors open.
“Twenty-percent average fuel savings in refrigerated trucking is very signi cant,” Mearman said. “Fuel costs more than electricity, so it’s a faster payback. It’s more challenging to deploy, because if you have 1,000 trucks, we need to track
them all down. But it’s an incredibly powerful opportunity for cold chain transportation.”
The return on a eet’s investment in CryoGenX4 will depend on the age of the equipment—performance improves more dramatically in older units, but with less run time remaining—how often it operates, and the price of fuel. “A one- to two-year payback across the board is easy,” Mearman said. “Some will be faster. If TRUs are running 20 hours a day in areas with high fuel rates, it’s probably less than a year.”
The DPI evaluation suggested the company could save $343,000 every year for the next seven years—or $2.1 million total—by deploying CryoGenX4 in all of its 256 reefer trailers, assuming $3 a gallon for diesel.
“We’re going to get savings every time that reefer runs,” Mearman said.
Installation is fast and simple. CryoGenX4 is injected into the system through the refrigerant port at a rate of 1 oz. per ton of refrigeration in a process that takes only a few minutes, Mearman said. “And the beauty of this is that it’s a one-time application for the life of the equipment,” Bramble added.
Every deployment is insured for $1 million, though no one has ever used the policy, and using CryoGenX4 will not void the manufacturer’s warranty, Mearman said. “It is illegal for a company to void a warranty for using a technology they haven’t tested,” he explained. “That’s the Magnuson-Moss Warranty Act—and we have seen zero voided warranties in over 158,000 global installations to date.”
EET also makes adoption affordable with low-interest nancing options.
“We’re a national contractor with the National Energy Improvement Fund,” Mearman said. “They’re the largest nancier of projects across the country. So there’s no money out of pocket, and the nancing costs are 1.5-2% of the lifetime savings you can extract out of these projects. It’s nothing. You get to keep the other 98% of the savings—and you get to start saving money and increasing pro t right away.
“It’s cash-positive immediately.”
by Gary Petty
Private fleet drivers inducted into the NPTC/International
THE NATIONAL PRIVATE Truck Council has inducted four top private fleet truck drivers into its Driver Hall of Fame each year since 1987. At May’s NPTC annual conference, James “JD” Chasteen, Shaw Industries Group, Dalton, Georgia; Scott “Scottie” Edwards, Primo Brands Corp., Portland, Maine; Kenny White, AutoZone, Zanesville, Ohio; and Donald “Todd” Young, Marathon Petroleum Co., Columbus, Ohio, were honored as the “best of the best” truck drivers in the industry.
Each driver possesses an elite record of millions of miles of safe driving practices; a reputation of earned respect and admiration among fellow drivers, supervisors, and customers for exemplary professional standards; and personal qualities of honor, integrity, willingness to help others and kindness. Here are snapshots of each driver.
James “JD” Chasteen began his truck driver career in 1969 and has driven 5.8 million miles in 54 years, three million of those miles with Shaw Industries Group over 29 years. He puts in eightto 12-hour days, 40-50 hours per week, and drives locally around Dalton, Georgia, northern Georgia, and Tennessee. He has zero accidents over more than five decades, a three-year record of no-moving violations, and has a career-long practice of using the Smith System of defensive driving system daily.
Chasteen was awarded the National Safety Council’s Best Safe Driver of the Year in 2022 for the Atlantic Region and has been recognized by Shaw each year for his safe driving experience. He loves metal-detecting for Civil War items, loves attending his church, and cherishes time spent with grandkids when they were younger.
Scott “Scottie” Edwards has been driving nearly his entire trucking industry
career with his current company—31.5 years and 3.1 million miles. He began working with heavy-duty trucks and equipment in the logging industry with a family business run by his father before starting out as a yard truck driver with his current employer at age 21.
Edwards operates a six-axle tractor-trailer with a GCVW of 93,000 lb. and typically works 10-12 hours per day, five to six days a week covering 390 to 460 miles at various cities in Maine and Massachusetts. He has had no-moving violations in his 32-year career and has been honored several times as driver of the month.
Edwards has delivered more than 3,600 wreaths to Arlington Cemetery as part of the Wreaths Across America organization and was awarded a President’s Award from his company.
Kenny White has been a driver for 61 years (27 years with his current company) and driven 3.5 million total miles for his entire career, which involved no injuries or collisions. He has a three-year no-moving violations history and has earned multiple safe driving awards for millions of miles of safe driving.
White is married to wife Susan and has two children, seven grandchildren, and 13 great-grandchildren. He is an enthusiast of vintage and muscle cars. White is a former trustee and a current member of his church where he has taken care of the landscaping for 25 years. He is a current member of the Zanesville Eagles F.O.E. 302.
Donald “Todd” Young has 44 total years as a driver (38 years with his current company) and over 3 million miles with Marathon. He began his career in the U.S. Marine Corps driving straight trucks and tractor-trailers, then later worked as a school bus driver before joining Marathon.
Young’s typical workweek is four shifts per week, 12 hours per shift. In addition to Young’s three years of no-moving violations, he also has a career-long record of no preventable accidents, and he has previously been named a National Driver All-Star by NPTC. He has extensive
Each driver possesses an elite record of millions of miles of safe driving practices and a reputation of earned respect.
training in defensive driving, first aid, CPR/AED, fire extinguisher training, industrial workplace ergonomics, hazard communication, and DOT hazmat security awareness. Young is also a certified Smith Driving System trainer. He volunteers for the American Red Cross to deliver blood and products throughout Ohio and often volunteers for relief efforts during natural disasters.
Congratulations to JD, Scottie, Kenny, and Todd as 2025 NPTC Driver Hall of Fame winners! FO
How Ryder helps Southern Glazer’s optimize alcohol distribution nationwide
by Seth Skydel
The delivery operation at Southern Glazer’s Wine & Spirits has taken various approaches over the years. “It’s been a journey working with different fleet and maintenance partners and learning what’s best for our business,”
Mike Bratcher, VP of operational transformation at the Miami-based alcohol distributor, said. “With equipment coast to coast making direct store deliveries, we landed on a model in which Ryder procures vehicles to our specs and provides and maintains them under a full-service lease.”
About 3,500 trucks, tractors, and trailers with the Southern Glazer’s logo operate across the country. Most of the fleet, about 2,200 units, consists of Class 7 International straight trucks with 18-ft. Wabash bodies. The fleet includes Class 6 trucks and tractors, Ford Transit Connect vans, and Great Dane trailers. Because its cargo weighs about 30 lb. per case, trucks are spec’d with ramps instead of liftgates to reduce weight.
For Southern Glazer’s, keeping deliveries flowing is essential to maintaining a competitive edge. While timely and efficient product distribution is integral to remaining competitive, visibility into inbound transportation of more than 11,000 brands from 1,600 wine and spirits suppliers is also essential.
Southern Glazer’s had some inbound supply chain challenges over tracking and monitoring goods from suppliers to distribution centers. The far-reaching consequences included less visibility, making it challenging to address disruptions promptly and satisfy customers.
“Because of our relationship with Ryder on the vehicle lease and maintenance side, it was a natural next step to take advantage of their supply chain solutions and technology as well as their expertise in managing carriers,” Bratcher
Southern Glazer’s logo appears on more than 3,500 trucks, tractors, and trailers that operate across the country.
said. “Through the RyderShare transportation management solution, we were able to restructure inbound transportation and make our supply chain more efficient and resilient.”
With RyderShare, Southern Glazer’s has data to plan and optimize loads through predictive analytics. With clearer visibility, on-time deliveries improved to over 98%, and on-time pickups have jumped to 80%. In addition, labor efficiency savings doubled.
“Historically, we could see when freight wasn’t moving, but we didn’t know why or how to fix it,” Drew Vermilion, SVP of supply chain and chief of staff, related. “With RyderShare, we know the source and severity of delays and can hold partners and internal business teams accountable to prevent them. In addition, there is added granularity. Under our previous systems and processes, multi-leg moves were only shown as one haul. Now, we can track loads from the first leg through final delivery.”
RyderShare allows Southern Glazer’s to optimize its network, Vermilion noted. “We used to have seven people chasing POs,” he said. “Now, we have execution-focused calls with Ryder to ensure the freight is moving and address any exceptions. We’re managing the freight; the freight isn’t managing us.”
Even the best distribution approach doesn’t work without good drivers, Mike Bratcher pointed out. “We hire our own drivers in each market, as regulations surrounding alcohol distribution don’t allow us to deliver across state lines,” he said. “The vast majority of our drivers return home each evening, and that gives us a retention advantage.”
“We are looking ahead, however, because a portion of our driver workforce is retiring in the next five years,” Bratcher added. “We’ve initiated pilot programs aimed at training warehouse associates who want to drive as a career.”
Southern Glazer’s, a multi-generational, family-owned company, offers a healthy work-life balance with four-day workweeks as well as “fun and friendly competition” among drivers. With Ryder’s support, for example, annual truck driving rodeos are held at all of the company’s distribution centers
“These are family events where everyone can show off their skills, and we can show our appreciation for their dedication and hard work,” Bratcher said.
“Across the board, it’s about relationship and solutions,” he emphasized. “At Southern Glazer’s Wine & Spirits, we are benefiting from our partners’ expertise and everyone’s unwavering commitment to continuous improvement.” FO
30 Burton Hills Blvd., Suite 185 Nashville, TN 37215 800-547-7377 fleetowner.com
Kylie Hirko EVP/Transportation kylie@fleetowner.com
Dyanna Hurley
Market Leader/Commercial Vehicle Group 248-705-3505
dhurley@endeavorb2b.com
Peter Lovato Associate Publisher 231-233-2660 peter@fleetowner.com AL, GA, FL, LA, MS, NC, OK, SC, TX
Michael Simone Western Territory 973-713-0094
michael-s@fleetowner.com
AR, AZ, CA, CO, IA, ID, IL, KS MN, MO, ND, NE, NM, NV, OR, SD, UT, WA, WI, WY
Larry Schlagheck Northeastern Territory 248-444-1320 larry@fleetowner.com
CT, DE, IN, KY, MA, MD, ME, MI, NH, NJ, NY, OH, PA, RI, TN, VA, VT, WV
Richard A. White Business Operations Manager richard@fleetowner.com
Laura Moulton Audience Development Manager lmoulton@endeavorb2b.com
FleetOwner, (USPS Permit 200040, ISSN 1070-194X print, ISSN 2771-5205 online) is published nine times a year in January/February, March, April, May, June, July/ August, September, October, and November/December by Endeavor Business Media, LLC. 201 N Main St 5th Floor, Fort Atkinson, WI 53538. Periodicals postage paid at Fort Atkinson, WI, and additional mailing o ces. POSTMASTER: Send address changes to FleetOwner, P.O. Box 3257, Northbrook, IL 60065-3257.
SUBSCRIPTIONS: Publisher reserves the right to reject non-qualified subscriptions. Subscription prices: U.S. $118 per year; Canada $138 per year; All other countries $175 per year. All subscriptions are payable in U.S. funds. Send subscription inquiries to FleetOwner, PO Box 3257, Northbrook, IL 60065-3257. Customer service can be reached toll-free at 877-382-9187 or at fleetowner@omeda.com for magazine subscription assistance or questions.
Printed in the USA. Copyright 2025 Endeavor Business Media, LLC. All rights reserved. No part of this publication may be reproduced or transmitted in any form or by any means, electronic or mechanical, including photocopies, recordings, or any information storage or retrieval system without permission from the publisher. Endeavor Business Media, LLC does not assume and hereby disclaims any liability to any person or company for any loss or damage caused by errors or omissions in the material herein, regardless of whether such errors result from negligence, accident, or any other cause whatsoever. The views and opinions in the articles herein are not to be taken as o cial expressions of the publishers, unless so stated. The publishers do not warrant either expressly or by implication, the factual accuracy of the articles herein, nor do they so warrant any views or opinions by the authors of said articles. Volume 122, Issue 4
Article Reprints — For reprints and licensing, please contact reprints@endeavorb2b.com.
Photocopies: Authorization to photocopy articles for internal corporate, personal or instructional use may be obtained from the Copyright Clearance Center (CCC) at 978-750-8400. Obtain further information at copyright.com.
Archives and Microform: This magazine is available for research and retrieval of selected archived articles from leading electronic databases and online search services, including Factiva, LexisNexis and Proquest.
Mailing Lists: Endeavor makes portions of our magazine subscriber lists available to carefully selected companies
that o er products and services directly related to the industries we cover. Subscribers who do not wish to receive such mailings should contact the Endeavor Business Media subscriber services at 800-547-7377, ext. 1500.
Privacy Policy: Your privacy is a priority to us. For a detailed policy statement about privacy and information dissemination practices related to Endeavor Business Media products, please visit our website at www.endeavorbusinessmedia.com.
This index is a service to readers. Every e ort is made to maintain accuracy, but FleetOwner cannot assume responsibility for errors or omissions.
A. Ford Motor
B. Volvo Group
C. Kenworth
A. White
B. Peterbilt
C. Kenworth
D. Brockway
C. Western Star
A. Kenworth
B. Tesla
C. Nikola
D. Mack Trucks
D. International Motors
B. Consolidated Freightways
D. International Harvester
A. Navistar International Corporation
1. Which company sold its heavy-duty truck line to Freightliner in the late 1990s?
2. Which company introduced the first truck sleeper cab?
3. What is the original name of the company that rebranded itself as International Motors in 2024?
5. Which company is famous for inventing the three-point seat belt?
A. Chrysler
B. Ford
C. Volvo
D. General Motors
4. Which company was the first to o er a Class 8 hydrogen fuel cell tractor in the U.S.?
6. Who gave Mack Trucks its Bulldog nickname?
A. An unknown truck driver who drove long haul with his bulldog Walter in the cab
B. British soldiers who used Mack Trucks during World War I
C. President Eisenhower when Mack trucks were used to help build the early highways
D. The Mack Brothers, who raised English bulldogs as a hobby
7. Who built the first Peterbilt trucks?
A. T.A. Peterman
B. Roger P. Sterling
C. Norm Peterson
D. Peter Fageol
As the clouds of uncertainty gather on the horizon, rise above them with the power, efficiency and unflinching reliability of the most trusted engine in the industry.