A Proud History Mike Schoonover has carried on his family’s legacy through personal and standardschallengesprofessionalwhilemaintaininghighandbeingavisiblememberofhisMinnesotacommunity.
WINNERAWARDFENDERBENDERTHECELEBRATING2022 PAGE 32 LEADINGTHEWAY FENDERBENDER.COM / SEPTEMBER 2022 EXPANSIONEXAMINING PAGE 62 WITHCOMMUNICATINGCUSTOMERS PAGE 60 SPREADINGYOURMESSAGE PAGE 70

VEHICLEEMISSIONCONTROLINFORMATIONConformstoregulations:2016 MY California: Not for sale in states with California emissions standards. TWC/HO2S/WR-HO2S/CAC/TC/DFIU.S.EPA:T2B4 FED2.3L-Group:LDVGFMXV02.3VJWEvap:GFMXR0125NBVNoadjustmentsOBDII Fuel: Gasoline ABZ VEHICLEMFD.BYFORDMOTORCO.INU.S.A. DATE: EXTPNT: RC: DS0: WB BRK INTTR TP/PS R AXLE TR SPR 114 4 GP K 45 V DB F05 UTC THISVEHICLECONFORMSTOALLAPPLICABLEFEDERALMOTORVEHICLESAFETYSTANDARDSINEFFECTONTHEDATEOFMANUFACTURESHOWNABOVE.01/03 VIN:TYPE:00000000000000000 MPV FRONTGAWR: 2735LB AT AT 205 kPa/30 240 kPa/35 1240KGP235/70R16SL16X7.0J REARGAWR: 3325LB 1508KGP235/70R16SL16X7.0JGVWR: 5880LB/2667KG WITHTIRESRIMSPSICOLD WITHTIRESRIMSPSICOLD F0085T0183 UA 13 3U51B P265/70R17REARSPARE CONTROLVEHICLEEMISSIONINFORMATION Conformstoregulations: 2015 Fuel: Gasoline U.S.EPAclass/stds: LDV/TIER2 Californiaclass/stds: PC/ULEVqualified Group: FGMXV01.80111.2L Evap:SFI/HO2S/TWC,FGMXR0095805OBD:II 00000000 FRONTREARSPARE 215/55R1697H215/55R1697HT125/85R1699 SEATINGCAPACITY TOTAL 4 FRONT 2 REAR 2 Thecombinedweightofoccupantsandcargoshouldneverexceed352kgor776lbs.240kPa,35PSI240kPa,35PSI420kPa,60PSISEEOWNER’SMANUALFORADDITIONALINFORMATIONTIREANDLOADINGINFORMATION TIRE SIZE COLDTIREPRESSURE COUSSINSRSSIDEAIRBAGGONFLABLELATÉRAL(SRS) TOAVOIDSERIOUSINJURYORDEATH:•Donotleanagainstthedoor.•Donotuseseatcoversthatblocksideairbagdeployment.Seeowner’smanualformoreinformation.POURÉVITERDESBLESSURESGRAVESOUMORTELLES:•Nevousappuyezpascontrelaporte.•N’utilizezpasuncouvre-siègequipeutbloquerledéploiementducoussingonflablelatéral.Voirlemanuelduconducteurpourdeplusamplesrenseignements. WARNINGAVERTISSEMENT VEHICLE MFD.BY: TOYOTA MOTOR MANUFACTURING, GVWR 4233LB GAWR FR 2668LB RR 2668LB THIS VEHICLE CONFORMS TO ALL APPLICABLE FEDERAL MOTOR VEHICLE SAFETY , BUMPER , AND THEFT PREVENTION STANDARDS IN EFFECT ON THE DATE OF MANUFACTURE SHOWN ABOVE . PASS. CAR C⁄ TR : 4Q2 ⁄ LA43 ACV30L --CEPGKA A ⁄TM: --01A ⁄ U241E MADE IN U.S.A. 08270KENTUCKY,00000000000000000INC.02 ⁄ 04 STK A Contact Us : Contact your LKQ/Keystone Local Sales Rep Upload your photos to the Website: www.AutoDataLabels.com Email your photos: Labels@AutoDataLabels.com DELIVERY IN 1-3 DAYS! SUPPLY CHAIN ISSUES COSTING YOU TIME & MONEY? AUTO DATA LABELS ARE CUSTOM DESIGNED AND MADE IN AMERICA Place Your Label Order Via One of These 3 Easy Ordering Options: To Visit Our Website SCAN HERE FOR ADDITIONAL INFORMATION ABOUT AUTO DATA LABELS: Visit Our Website At www.AutoDataLabels.com Email Us At labels@AutoDataLabels.com Or Call Us At (631) 667-2382 ©2022 Auto Data Labels an LKQ Company. Visit us at Shop.LKQcorp.com and LKQcorp.com Vin Labels AC Labels Caution LabelsEmission Labels Tire Pressure Labels Paint Code Labels SRS SIDE AIRBAG COUSSIN GONFLABLE LATÉRAL (SRS) TO AVOID SERIOUS INJURY OR DEATH: Do not lean against the door.•Do not use seat covers that block side air bag deployment.See owner’s manual for more information. POUR ÉVITER DES BLESSURES GRAVES OU MORTELLES: Ne vous appuyez pas contre la porte. N’utilizez pas un couvre-siège qui peut bloquer le déploiement du coussin gonflable latéral. Voir le manuel du conducteur pour de plus amples renseignements. AVERTISSEMENTWARNING TIRE AND LOADING INFORMATION TIRE SIZE COLD TIRE PRESSURE 303kpa 44psi 303kpa 44psi 303kpa 44psi The combined weight of occupants and cargo should never exceed 505 Kg or 1114 Lbs. P265/70R17P265/70R17P265/70R17FRONTREARSPARE SEE INFORMATIONMANUALOWNERSFORADDITIONAL SEATING CAPACITY TOTAL 3 FRONT 3REAR 0 VEHICLE EMISSION CONTROL INFORMATION Conforms to regulations: 2016 MY California: Not for sale in states with California emissions standards. TWC/HO2S/WR-HO2S/CAC/TC/DFI U.S. EPA: T2B4 LDV 2.3L-Group: GFMXV02.3VJW Evap: GFMXR0125NBV No adjustments needed. FED OBD II Fuel: Gasoline ABZ VEHICLE MFD. BY FORD MOTOR CO. IN U.S.A. DATE:EXTPNT: RC: DS0: WB BRK INT TR TP PS AXLE TR SPR 114 4 GP K 45 V DB F05 UTC THIS VEHICLE CONFORMS TO ALL APPLICABLE FEDERAL MOTOR VEHICLE SAFETY STANDARDS IN EFFECT ON THE DATE OF MANUFACTURE SHOWN ABOVE. 01/ 03 TYPE:VIN: 00000000000000000FRONTMPVGAWR: 2735LB AT AT205 kP 30 240 kP 35 16X7.0JP231240KG570R16SL REAR GAWR: 3325LB 16X7.0JP231508KG70R16SL GVWR: 5880LB 2667KG PSIRIMSWITHIRESCOLD PSIRIMSWITHIRESCOLD T0183F0085 UA 13 3U51B
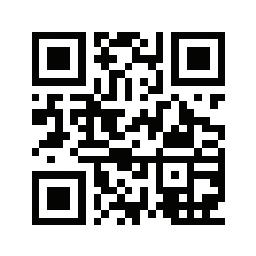
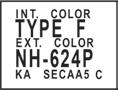
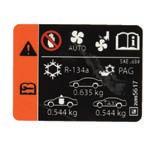
Go for performance. Leave the dust behind. 3M™ Cubitron™ II Net AbrasivesForIntroducingAutomotive Repair Get the job done sooner with 3M™ Cubitron™ II Net Abrasives, the fastest-cutting and longestlasting net abrasive discs and sheets in the world. This family of net abrasives delivers 2X the cut rate and 2X the life of other leading net abrasive families. All the while, letting dust extractors perform their best by leaving virtually no dust on the work surface and in the environment. 3MCollision.com/Net For additional information, including important safety and warranty information regarding 3M Automotive Aftermarket products, visit www.3Mcollision.com/info. Copyright 2022 by 3M. All rights reserved. 3M and Cubitron are trademarks of 3M Company.
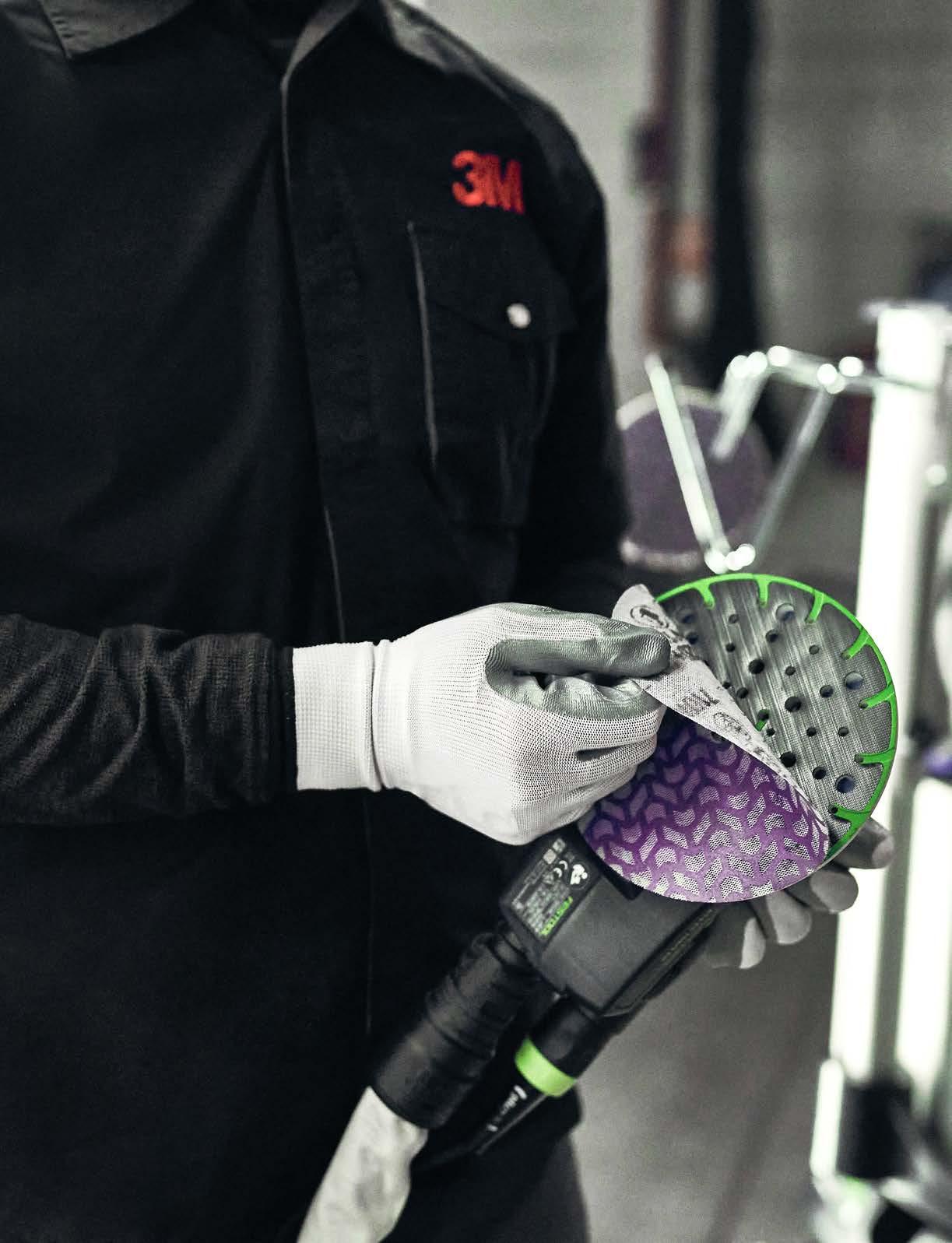

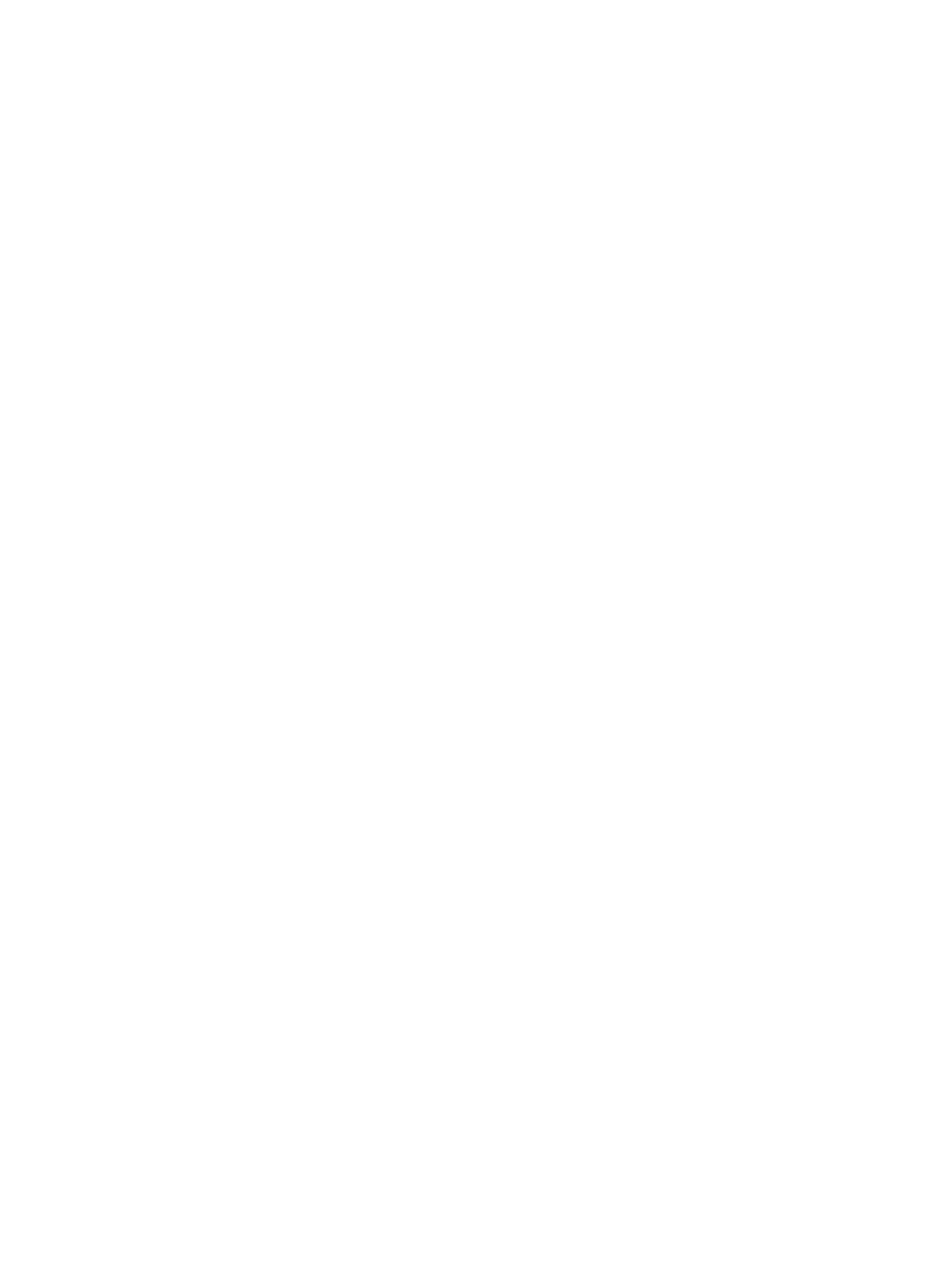
5September 2022 fenderbender.com Printed in the U.S.A. COPYRIGHT ©2022 BY 10 Missions Media LLC. All rights reserved. FenderBender (ISSN 1937-7150) is published monthly by 10 Missions Media, LLC, 571 Snelling Avenue North, St. Paul, MN 55104. FenderBender content may not be photocopied, reproduced or redistributed without the consent of the publisher. Periodicals postage paid at St. Paul, MN, and additional mailing offices. POSTMASTERS Send address changes to: FenderBender, 571 Snelling Avenue North, St. Paul, MN 55104. 32 2022MIKEAWARDFENDERBENDERWINNERSCHOONOVER Community and family legacy are priorities for this Minnesota operator BY MATT HUDSON 09.22 | VOLUME 24 | NUMBER 09 CONTENTS SEPTEMBER

QUICK FIX DRIVERS10 SEAT Celebratingnominees 11 PAST THE PAGE Two MSOs make big news BREAKDOWN13 Power teamworkof NUMBERS18 The state of certs 21 13 CONTENTS SEPTEMBER
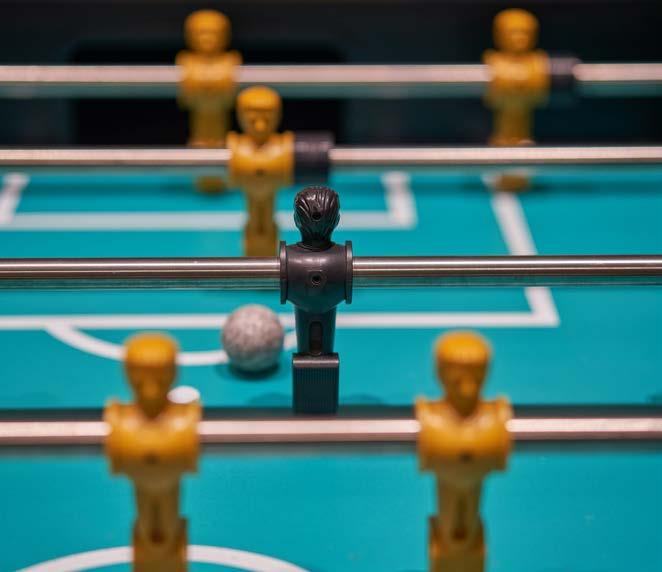
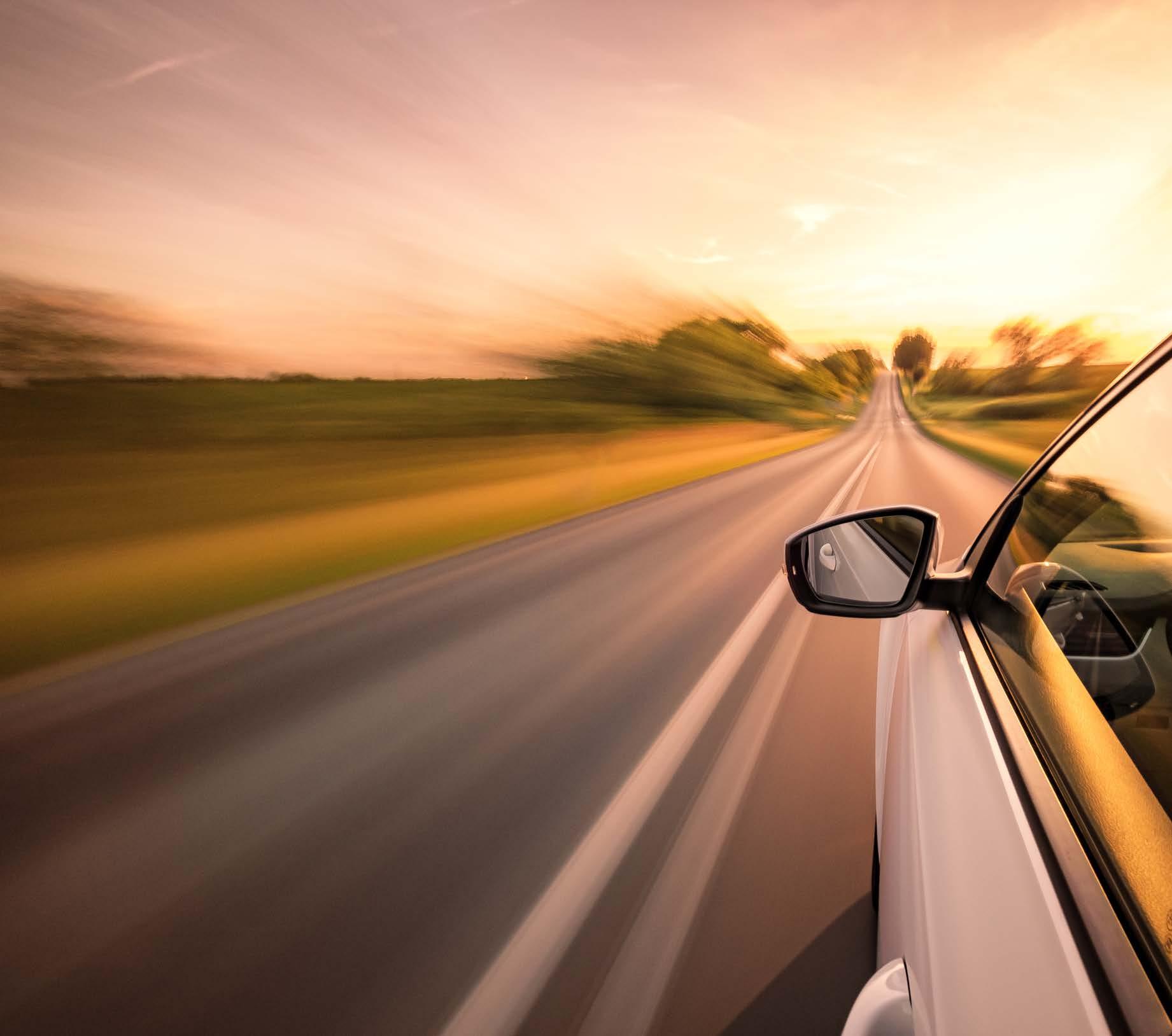
7September 2022 fenderbender.com STRATEGY COLUMNS 29 THE BIG IDEA Examining your shop’s culture BY KEVIN RAINS COLLISION72COURSE Making the difficult decisions BY TIFFANY MENEFEE THE58SOP Thinking about certs LEADERSHIP60 Wide communicationopen CASE62STUDY Looking at expansion ADAPT65 Tech and the aftermarket SALES+MARKETING70 Gaining media coverage THEOUTSIDE74LINES Following the rules BY JASON BOGGS 62 MAKE EVERY JOB A JOB WELL DONE. Copyright © 2022 Axalta Coating Systems, LLC and all affiliates. All rights reserved. metalux.us Metalux LV is a new Low VOC paint that delivers collision-quality color at an affordable price. Backed by Axalta, it’s easy to use and provides the high-quality results you’ve come to expect from Metalux. VALUE YOU CAN COUNT ON.
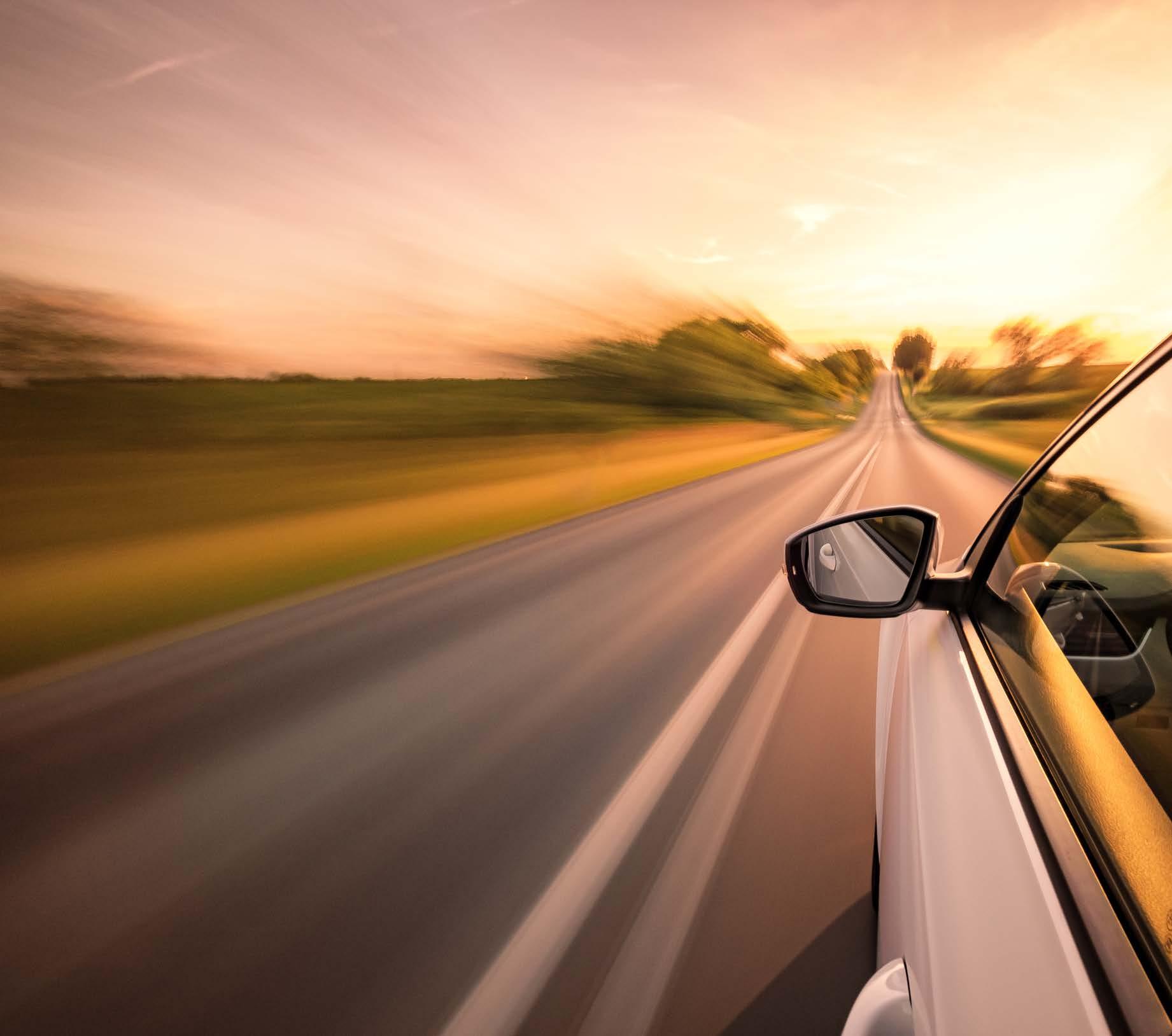
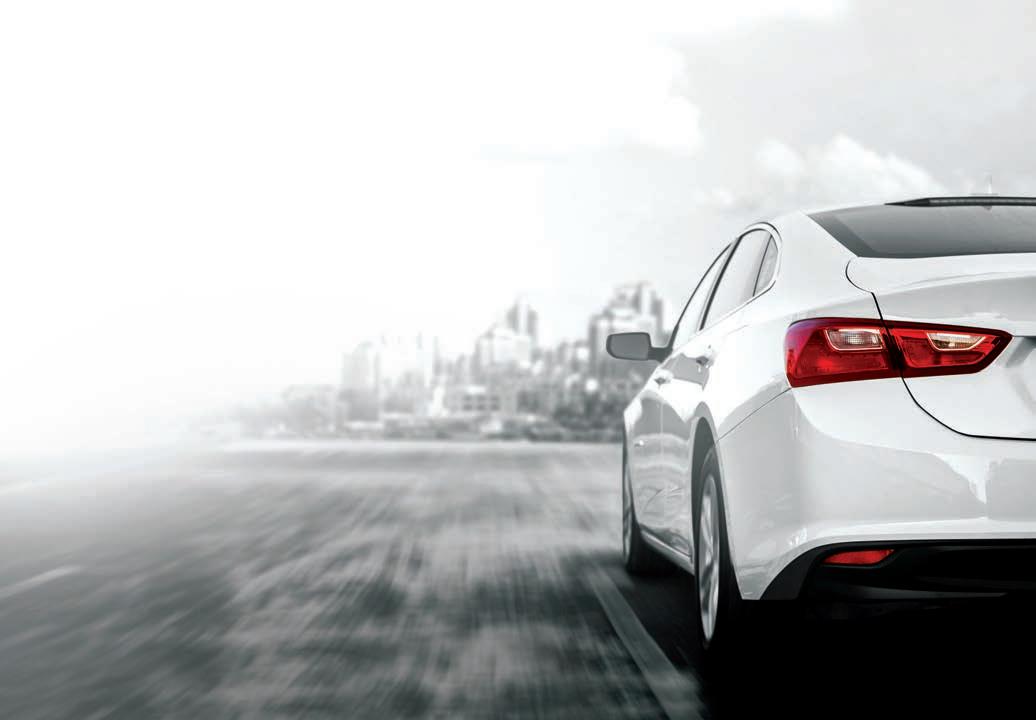
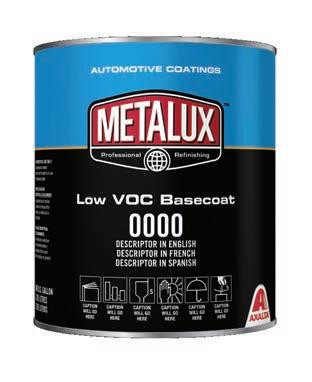
AssociatedALLDATA3MBank Kent Automotive ATA/Dan-Am Company CLICK ON THE LOGO BELOW FOR PRODUCT INFORMATION CONTENTS ONLINE EXTRAS AUTEL Axalta Coating Systems Auto Data Labels TechForce Foundation LKQFinishMasterCorporation SpanesiPPGAmericas Mitsubishi ProColor Collision Equalizer SUN CollisionMaaco Bosch Launch Tech USA AAAAkzoNobelAutoParts Pro SpotPodiumInternationalKeco Body Repair ProductsADAPT
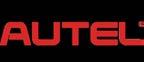



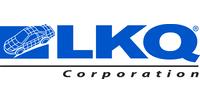

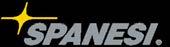

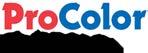


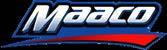
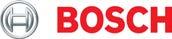
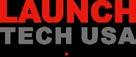


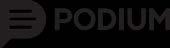






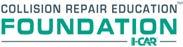
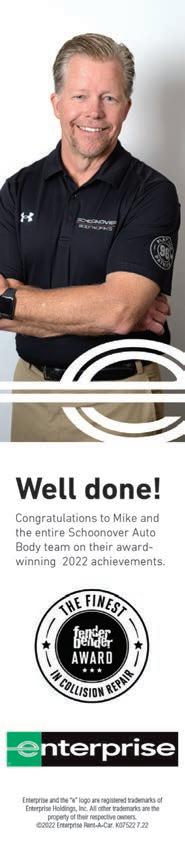
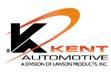
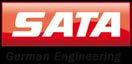

READ WHAT THE PROS READ
FENDERBENDER.COM/SUBSCRIBE to
9September 2022 fenderbender.com EDITORIAL Matt Hudson Content Director Todd Kortemeier Editor Hanna Bubser Digital Reporter Leah Marxhausen Special Projects Editor Jason Boggs Contributing Writer Noah Brown Contributing Writer Lindsey Gainer Contributing Writer Tiffany Menefee Contributing Writer Mike Munzenrider Contributing Writer Kevin Rains Contributing Writer Peter Suciu Contributing Writer EDITORIAL ADVISORY BOARD Jordan Beshears Steve’s Auto Body Sheryl Driggers Universal Collision Greg Lobsiger Loren’s Body Shop John Magowan Ernie’s Auto Body Stan Medina Certified Collision Works ART AND PRODUCTION
Mariah Straub General Manager and Production Manager Meghann Moore Bookkeeper and Client Service Specialist Meghan Horan Community Development Associate Tiffany Fowler Senior Digital Media Strategist Karley Betzler Administrative Assistant HOW TO REACH US 571
TO SUBSCRIBE OR RENEW AT
“The opportunity
Zach Pate Jonathan Ricketts SALES
read about ways to improve your business from credible owners and manufacturers is priceless.” —Stan Medina, Owner, Certified Collision Works, Corpus Christi, Texas
Snelling Avenue North, St. Paul, MN 55104 tel 651.224.6207 fax 651.224.6212 web 10missions.com The annual subscription rate is $72 (U.S.A. only) for companies not qualified to receive complimentary copies of FenderBender BACK ISSUES Past issue single copies are $8. Go to fenderbender.com/backissues LETTERS TO THE EDITOR editor@fenderbender.com ARTICLE REPRINTS For high-quality reprints or e-prints of articles in this issue call 651.846.9488 or email reprints@fenderbender.com. Opinions expressed in FenderBender are not necessarily those of Endeavor Business Media, and Endeavor Business Media does not accept responsibility for advertising content.
Chris Messer Vice President and Publisher 651.846.9462 / cmesser@10missions.com Andrew Johnson Associate Publisher 651.846.9459 / ajohnson@10missions.com Marianne Dyal Marketing Strategist (National Accounts) 706.344.1388 / mdyal@10missions.com Chad Hjellming Marketing Strategist (National Accounts) 651.846.9463 / chjellming@10missions.com Bob Marinez Marketing Strategist (National Accounts) 216.533.8747 / bmarinez@10missions.com
FENDERBENDER
Martha Severson Marketing Strategist (National Accounts) 651.846.9452 / mseverson@10missions.com Kyle Shaw Marketing Strategist (National Accounts) 651.846.8480 / kshaw@10missions.com Dan Thornton Marketing Strategist (National Accounts) 734.676.9135 / dthornton@10missions.com Sean Thornton Marketing Strategist (National Accounts) 269.449.0257 / sthornton@10missions.com Kenzie Verschoor Associate Marketing Strategist (National Accounts) 651.846.9472 / kverschoor@10missions.com Matt Harper Regional Sales Manager 651.846.9551 / mharper@10missions.com Melody Todd Senior Marketing Strategist (Regional Accounts) 651.846.9468 / mtodd@10missions.com Autumn Morey Customer Success Representative 651.846.9460 / amorey@10missions.com Jen George Client Service Specialist 651.846.9465 / jgeorge@10missions.com
Art Director Olivia Curti Graphic Designer Morgan Glisczinski Graphic Designer Emme Osmonson Graphic Designer
Creative Services Director


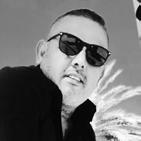
fenderbender.com
Going forward, Crash Champions will oversee and manage the acquired network of shops. In the press release, José E. Feliciano, co-founder and managing partner, and Colin Leonard, partner of Clearlake, offered the following statement:
“Today is an exciting day for Crash Champions and another major milestone in our growth story,” said Matt Ebert, founder and CEO of Crash Champions, in the release. “This strategic combination further enhances our ability to serve our customers and insurance partners while creating advancement opportunities for our team members across bothTheorganizations.”investmentfrom Clearlake is described as growth capital and marks the investment firm’s second transaction in the collision repair industry, the release says. Clearlake was a main partner in Service King’s prior debt recapitalization.
10September 2022 fenderbender.com
@fenderbendermag @fenderbendermag @fenderbendermag fenderbender.com/linkedin
CRASH CHAMPIONS ANNOUNCED that it will acquire Service King Collision with the help of a strategic investment from Clearlake Capital Group.
PAST THE PAGE VIDEOS | PODCASTS | WEBINARS | NEWS
The deal gives Crash Champions a total network of 550 locations across 35 states and the District of Columbia, according to a press release. The total company workforce will be more than 9,200. All locations will operate under the Crash Champions name.
“This investment was driven by our thematic-based approach to investing in the automotive aftermarket and our specific identification of the collision repair sector as an ecosystem at a historical inflection point. The proliferation of vehicle technology has put unique demands on the shop operators to invest in OEM certifications, equipment, and most importantly their personnel to deliver safe and efficient service. We are impressed by Matt and the Crash Champions leadership team and admire their commitment to customer service and re-investment in both their operations and talent. It is exciting to partner with them to create this differentiated national platform, and we look forward to utilizing our O.P.S. framework to unlock the inherent value of this combination and position the platform for continued strong growth.” Prior to the deal, the Crash Champions network extended to 20 states with more than 200 locations. The press release noted that no operational disruptions are expected. More details of the transaction were not disclosed. CRASH CHAMPIONS ABSORBS SERVICE KING WITH NEW INVESTMENT
UNSPLASH
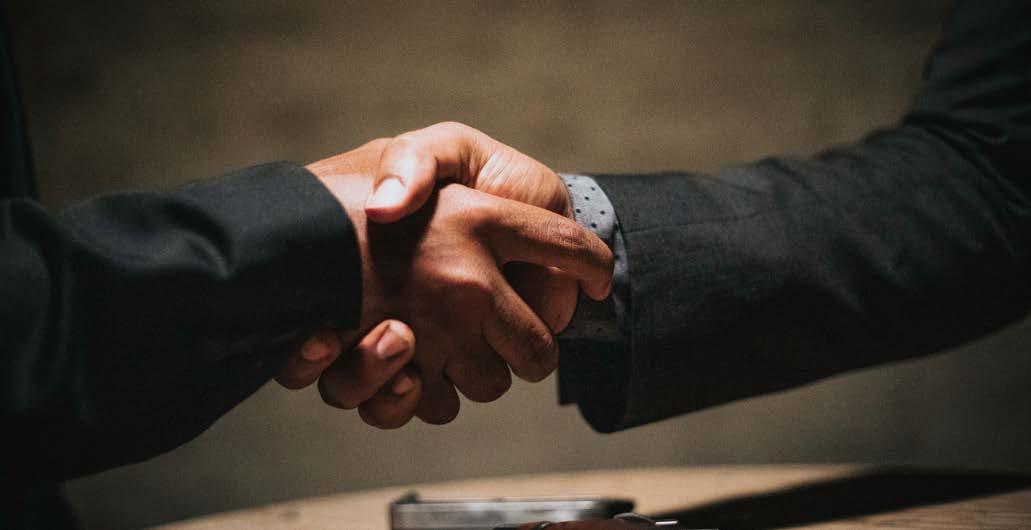
TODD KORTEMEIER EDITOR tkortemeier@endeavorb2b.com
A COMMUNITY OF WINNERS
THERE’S AN IMPLICIT understanding that comes with handing out awards. The per son who wins is of course deserving, but so are their fellow nominees. “It’s an honor just to be nominated,” goes the gracious response, and depending on your level of cynicism you may take that at face value or dismiss it as cliche, but it’s true. Anyone in the conversation for an award should feel honored, not just 2022 FenderBender Award winner Mike Schoonover (p. 52) but also runners-up Ryan DeMarco (p. 74) and Cliff Sullivan (p. 76), as well as all the other distin guished owners and operators nominated by their colleagues. There are cases to be made for so many people, cases that were made passionately in nominations. In these challenging times there are a myr iad of owners who have overcome profes sional and personal setbacks to succeed. But there can only be one winner, of course, and Mike Schoonover exemplifies that resiliency owners have had to have over the past few years. Carrying on the family business, growing it through tough times, is a story I think you’ll enjoy reading.
11September 2022 fenderbender.com DRIVER’S SEAT
The same goes for Cliff Sullivan, who may have been nominated specifically for how he successfully navigated the COVID-19 pandemic, but who was able to do so be cause of the culture he’d established across decades. And then there’s Ryan DeMarco, an owner still in his late 20s who has al ready made a name for himself with early success. I hope you’ll join me in celebrating their achievements. In addition to taking some time to honor our award winner, you’ll find more of our resources for the day-to-day operations of your shop in the rest of this month’s pag es. They don’t hand out awards simply for showing up to work each day, but maybe they should. Thanks for showing up for your employees and your customers each and every day.
This month we celebrate a few owners by name and many more helping to raise up the collision repair industry

THE COUNTDOWN TO THE 2023 TECHNOLOGYAUTOMOTIVEADAPTSUMMITSTARTSNOW DATES AND LOCATION FOR 2023 ADAPT SUMMIT WILL BE ANNOUNCED SOON! JOIN THE UPDATES LIST TO GET FIRST ACCESS TO NEWS. LEARN MORE AT ADAPTSUMMIT.COM Au t omotive Te chnology Summit
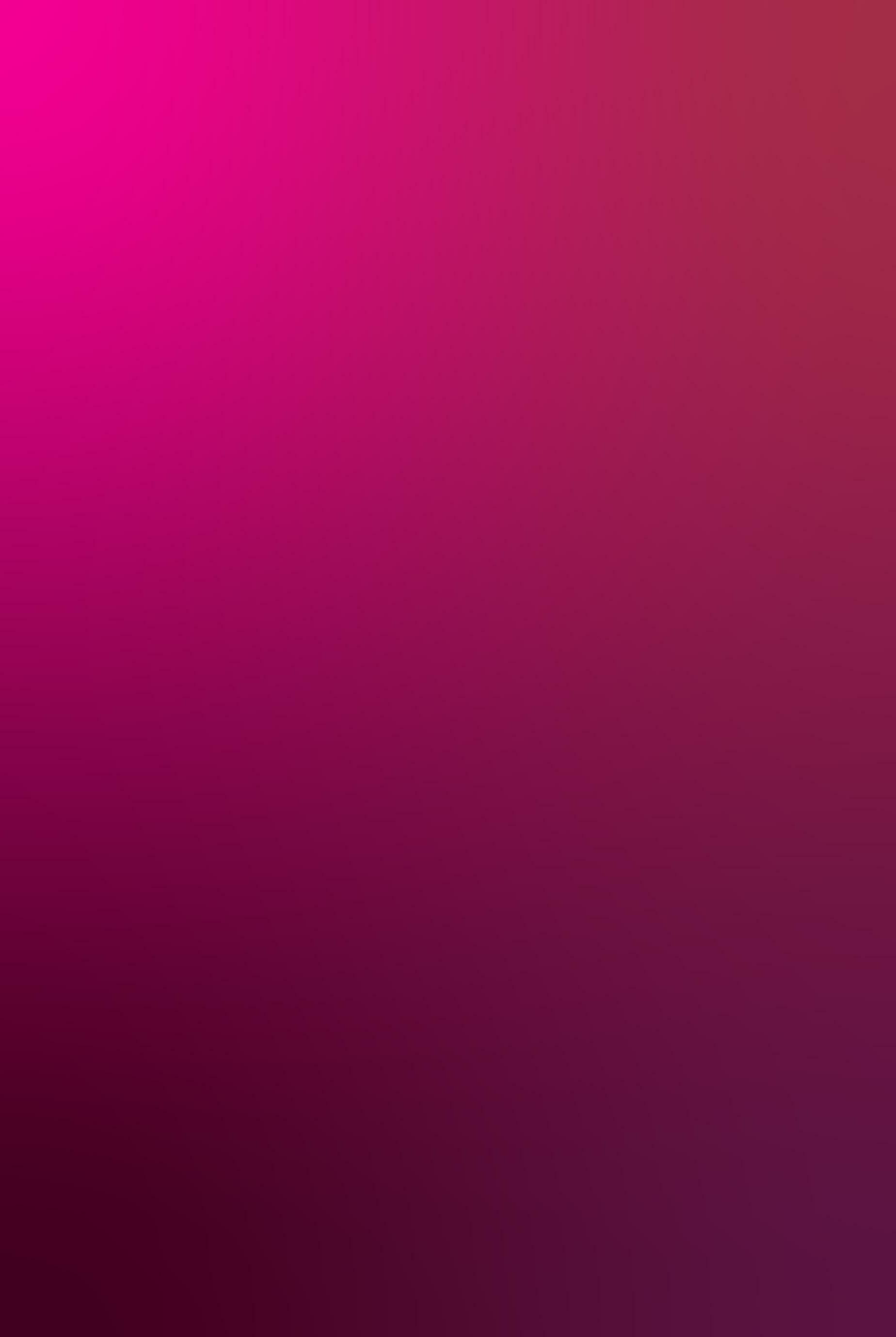
13September 2022 fenderbender.com QUICK FIX UNSPLASH NEWS | IDEAS | PEOPLE | TRENDS
TEAMWORK MAKES DREAM WORK
THE
IT’S THE BEGINNING of a new school year, and that means that class is in session. For technical schools like Lincoln Tech, this goes beyond getting students back into a classroom.It’sabout setting students up to succeed in a career, which the school approaches in a multitude of ways.
Lincoln Tech establishes partnerships with brands to expand upon the hands-on training offered to its students
By HANNA BUBSER ANALYSIS
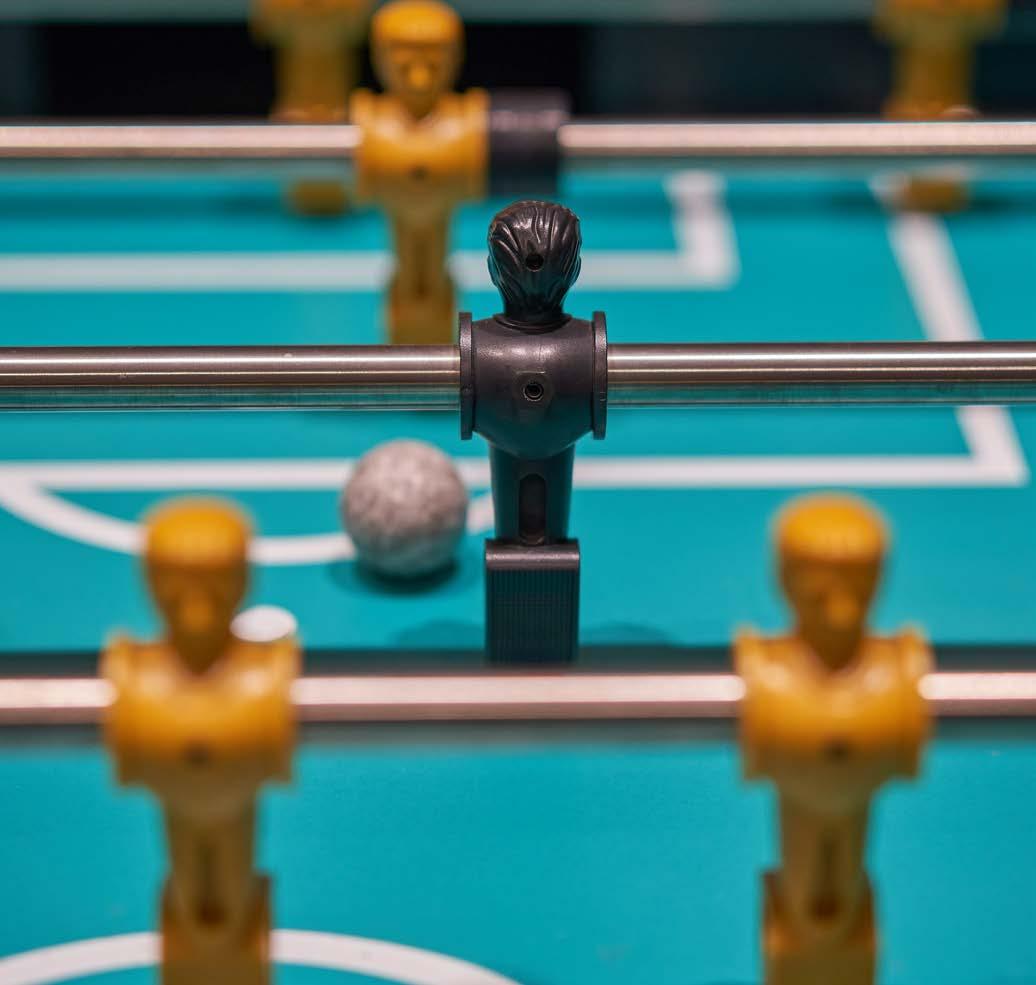
NEXT YEAR’S DATES AND LOCATION WILL BE ANNOUNCED SHORTLY! JOIN THE UPDATE LIST FOR NEWS ON THE TOP BUSINESS BUILDING EVENT FOR THE COLLISION REPAIR INDUSTRY. FENDERBENDERCONFERENCE.COM ARE YOU READY FOR THE FENDERBENDER2023MANAGEMENTCONFERENCE?
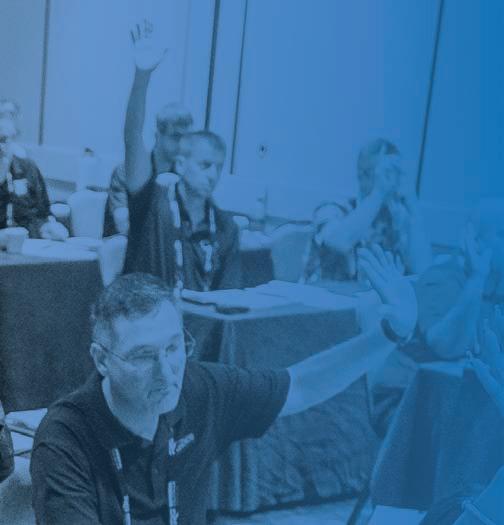
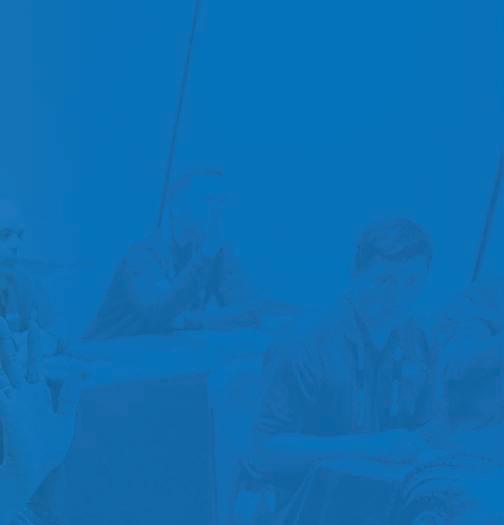
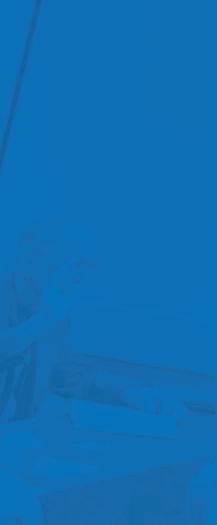


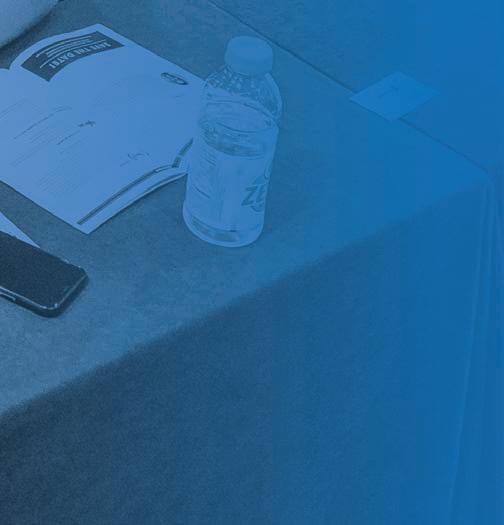
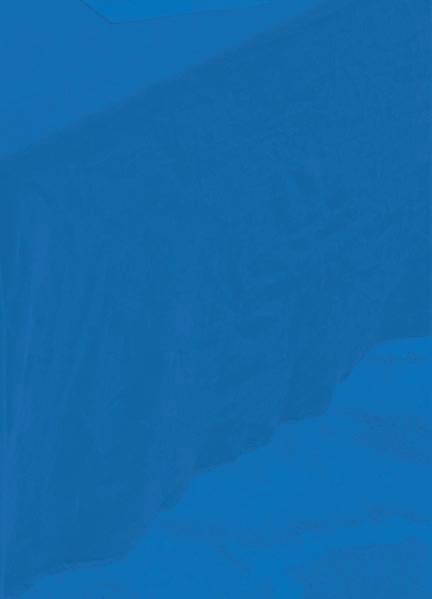

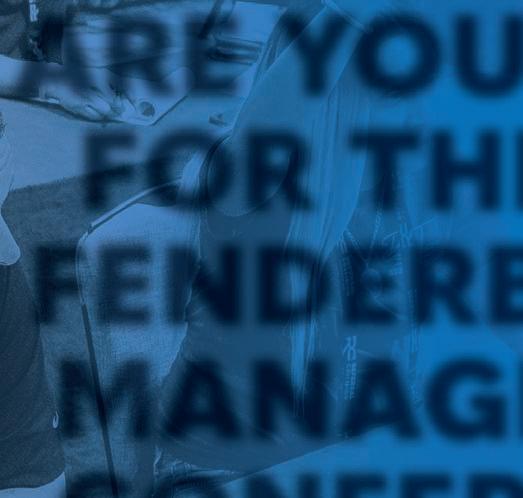
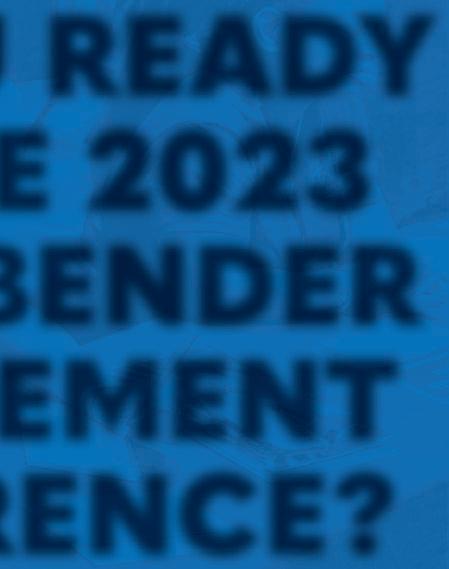

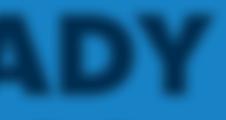

“The ultimate goal is that we want to gather feedback from the Lincoln Tech students about the performance and the usability of our equipment,” Watkins says. “Having never before used automotive painting equipment or anything like that, students will bring a fresh perspective and give us some ideas.” GFS will also train Lincoln Tech in structors on its REVO Accelerated Curing Systems at all six of the campuses that offer collision repair programs.
15September 2022 fenderbender.com
QUICK FIX Lincoln Tech’s campuses. This includes two side downdraft paint booths and a paint mix room that were re cently installed at Lincoln Tech’s Denver loca tion, and GFS products that will soon be in stalled at the Lincoln Tech Nashville campus.
“By them teaching these kids already how to use accelerated curing, and what the benefit of that is, I think that’s a huge ku dos to Lincoln Tech for making that invest ment,” Watkins says. Overall, Watkins is confident that work ing with Lincoln Tech to bring GFS prod ucts to students will have a positive impact.
In addition to products, AkzoNobel will also provide Lincoln Tech with technical training that complements the collision program and the AkzoNobel Acoat Selected e-learning training academy, which is a suite of online learning classes. these relationships and being associated with these premium brands is helpful.”
UNSPLASH
Fill a Critical Need AkzoNobel is another example of a Lin coln Tech partner as the school’s exclusive source for paints and refinish coatings. This partnership will apply to all six of the Lincoln Tech locations that of fer collision repair programming. It’s a partnership that came naturally as Rich DeCamp, district sales manager at Ak zoNobel, explains. “We were already servicing two lo cations for a number of years and had a strong relationship with them, as well as a track record of support,” DeCamp says.
“Whether you’re a student who attends our East Windsor campus in collision, or whether you’re a student who attends our Grand Prairie campus, what you experience over the program and the products you use … are virtually identical,” Nyce explains.
“It’s important to us because all of these students that will be going through the Lincoln Tech program are not only getting trained properly, which is the most impor tant thing,” Watkins says. “But they are also getting to use GFS equipment, [which] is also very important.”
Discover New Perspectives Global Finishing Solutions, a manufac turer that provides paint booths and finishing environments for multiple in dustries, is in one such partnership that brings the brand’s products to some of Founded in 1946 in Newark, New Jersey, the school came into existence through the motivation of helping World War II vet erans find jobs. Initially, this focused on the automotive and diesel industries. Today, Lincoln Tech offers areas of study that include transportation, auto motive, collision, heavy equipment repair, skilled trades such as welding and electri cal and even cosmetology and medicaloriented fields of study.
“It’s very similar to how a franchise model would work.”
The partnerships help Lincoln Tech to keep things consistent across all of the campuses that have collision repair pro grams, which includes six of its 22 campus es across the country. These locations include: East Windsor, Connecticut; Grand Prairie, Texas; India napolis; Melrose Park, Illinois; Nashville, Tennessee; and Denver.
Lincoln Tech has a network that al lows them to support their students. This includes establishing partnerships with trusted industry brands. Chad Nyce, Lincoln Tech’s chief innovation of ficer, explains how this is applicable to the school’s collision repair and refin ishing“Studentsprogramming.wantto know that, when they’re coming to Lincoln Tech, they’re go ing to be using some of the best tools and equipment and products that are on the market,” Nyce says. “That really does make a difference. We believe that they’re liter ally the best in their industry, so, having
Lance Watkins, senior territory man ager at Global Finishing Solutions, sees this collaboration as mutually beneficial.
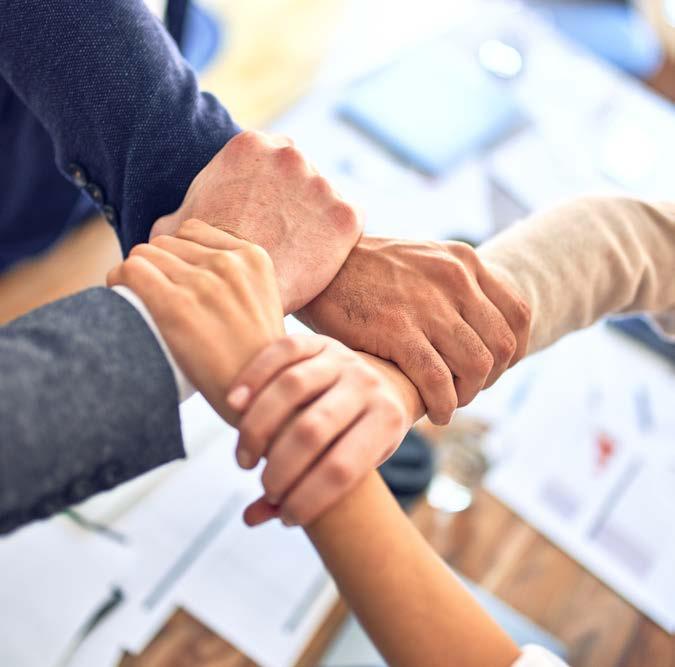
“We have a history of providing more than just a can of paint,” DeCamp says. “Providing hands-on training as well as ed ucational services is what we specialize in, and that’s a good fit for what Lincoln Tech is trying to do.” The reach that Lincoln Tech has in re gards to training future technicians is a motivating factor for AkzoNobel, as it not only utilizes the brand but also supports the industry overall. “We’re looking to support the industry as much as we can, especially at a critical time with the technician shortage, and ulti mately create more interest in the industry and the critical roles the trades play in our workforce,” DeCamp says. Global Finishing Solutions and Ak zoNobel will also provide product support to Lincoln Tech’s Kindig Academy, which is a six-week fabrication and finishing course held at Lincoln Tech’s Denver cam pus. Both brands have a partnership his tory with Dave Kindig of Kindig It Design.
16September 2022 fenderbender.com whatever it might be, we’re always trying to create that environment that mimics the real world that they’re going to face once they get out of school.”
Another hope for promoting these hands-on product and project experiences for students is that Lincoln Tech can effec tively set up its student body for a lasting career. This is especially crucial these days, considering the on-going labor shortage in the “Whenindustry.students come to us and are in terested in any of our programs, we really take a lot of time to help them understand what the jobs in these different industries look like. The last thing we want to do is have a student come, and we train them for a year, and then they get out into the job and they’re like, ‘Oh my gosh, this is not anything like I thought it was going to be,’” Nyce says. “We really do spend a lot of time making sure that our students understand the job prospects that are out there for them and the different types of places they could work.”
tion at Kindig Academy that acts as a safe and controlled environment for sanding, priming and some painting. AkzoNobel has worked with Kindig on the Modern Classikk paint line. This line is derived from the Sikkens refinish brand from AkzoNobel, which will be used at Kindig Academy.
Understand the Impact Global Finishing Solutions and Ak zoNobel are not the only partnership pursuits of Lincoln Tech, but they are two examples that show the impact of teaming up. Peter Tahinos, senior vice president of marketing at Lincoln Tech, points out that bringing successful brands into the educational sphere allows for realistic ex periences to occur. “We try to create a real world environ ment in our schools so that students are using the same equipment that they’ll use in the field once they graduate,” Ta hinos says. “Whether it’s paint or tools or
GFS is providing an Excel Worksta
QUICK FIX CONNECT WITH FENDERBENDER FOR THE LATEST COLLISION REPAIR CONTENT FOLLOW WHAT THE LEADERS FOLLOW
17September 2022 fenderbender.com FOLLOW.LEADERSTHEWHATFOLLOW CONNECT WITH FENDERBENDER FOR THE LATEST COLLISION REPAIR CONTENT
18September 2022 fenderbender.com QUICK FIX (Percent of overall survey respondents) No certifications 47% 14% 1 certification 8% 16% Nobutcertifications,planningtogetsome 9% 5% THE 2022 FENDERBENDER INDUSTRY SURVEY revealed much about the state of the industry and where things are trending. And while the largest segment of responders—34 percent—reported no revenue from DRPs, more than half also reported having no OEM certifications. Here’s a breakdown of where shops stand on certs in 2022. NUMBERS STATE OF THE CERTS Become Today!GlassCertifiedAAutoTechnician AUTOGLASSACADEMY.COM512-807-3526




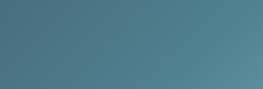


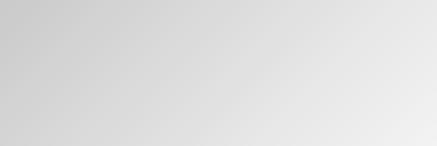



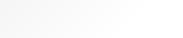


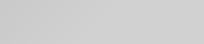
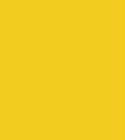


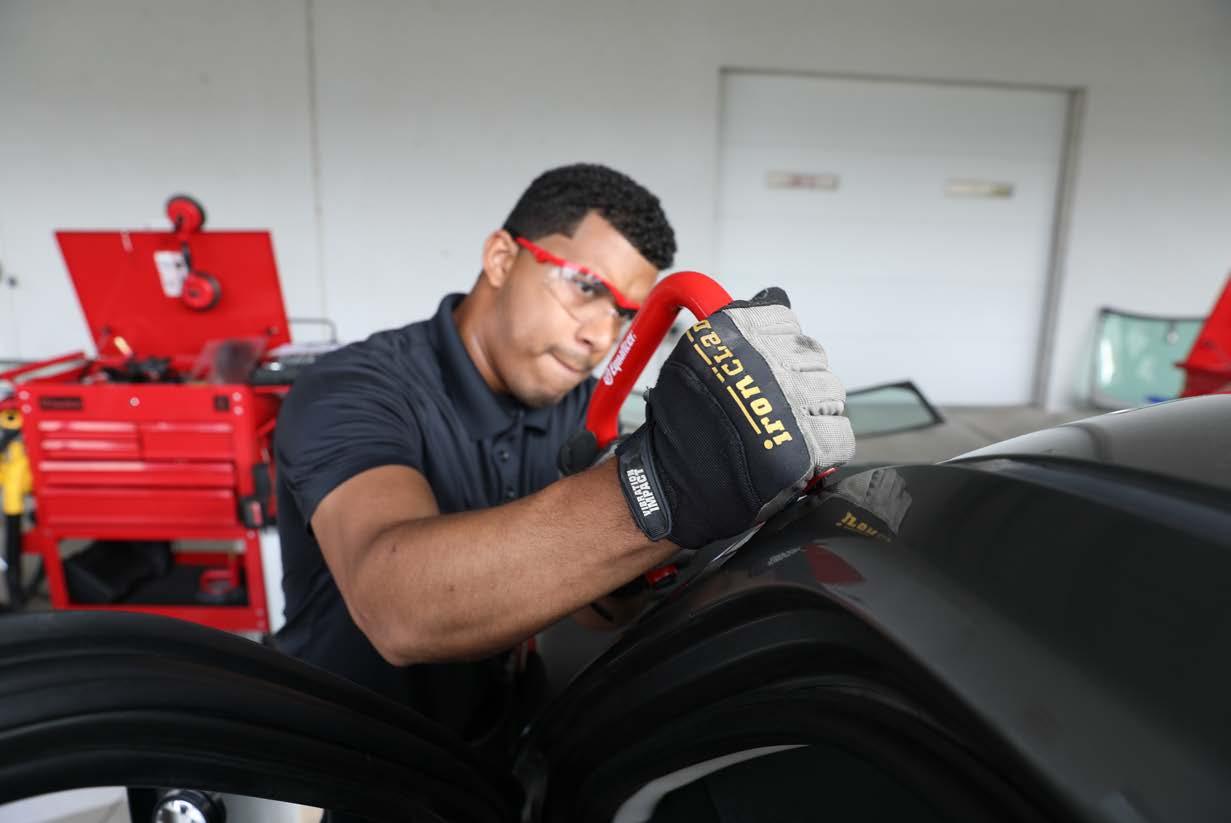
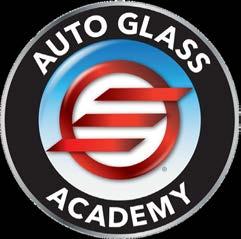
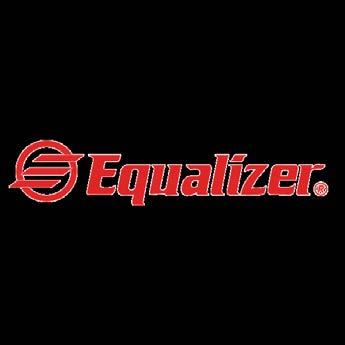
“With the help of PPG’s Trend Tracker, we went from losing money on paint and materials to making a profit and keeping our P&M down to around 5.5%.” “ We system.”Envirobaseusingreducedgreatlyredosthe “PPG is more like a family relationship— they’re always on your side and will go out of their way to help.” PERFORMANCE YOU CAN COUNT ON BUSINESS PROFILE WHY FRANK’S COLLISION MADE THE SWITCH FRANK’SCOLLISIONColumbus,GeorgiaFrankWilcox~Owner The PPG Logo, Envirobase and the Multiple Cubes Geometric Design are registered trademarks of PPG Industries Ohio, Inc. ©2022 PPG Industries, Inc. All rights reserved. www.envirobase.com 4 LOCATIONS 40 EMPLOYEES 5 PAINTERS 5 PAINT BOOTHS 69 VEHICLES PER WEEK Frank Wilcox
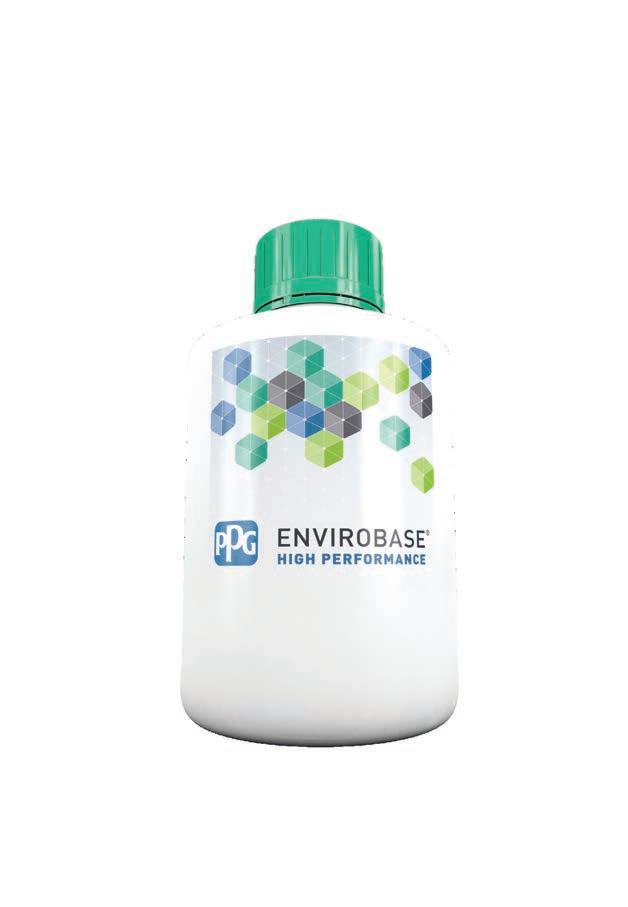


PERFECT FINISH. PERFECT FIT. Mitsubishi not only offers quality vehicles but quality crash parts too! Choose Genuine Mitsubishi Parts for quick, efficient delivery to help keep you and your customers happy. For inventory information and to find out about price reductions on all models, contact your local dealer today. GENUINE MITSUBISHI PARTS.
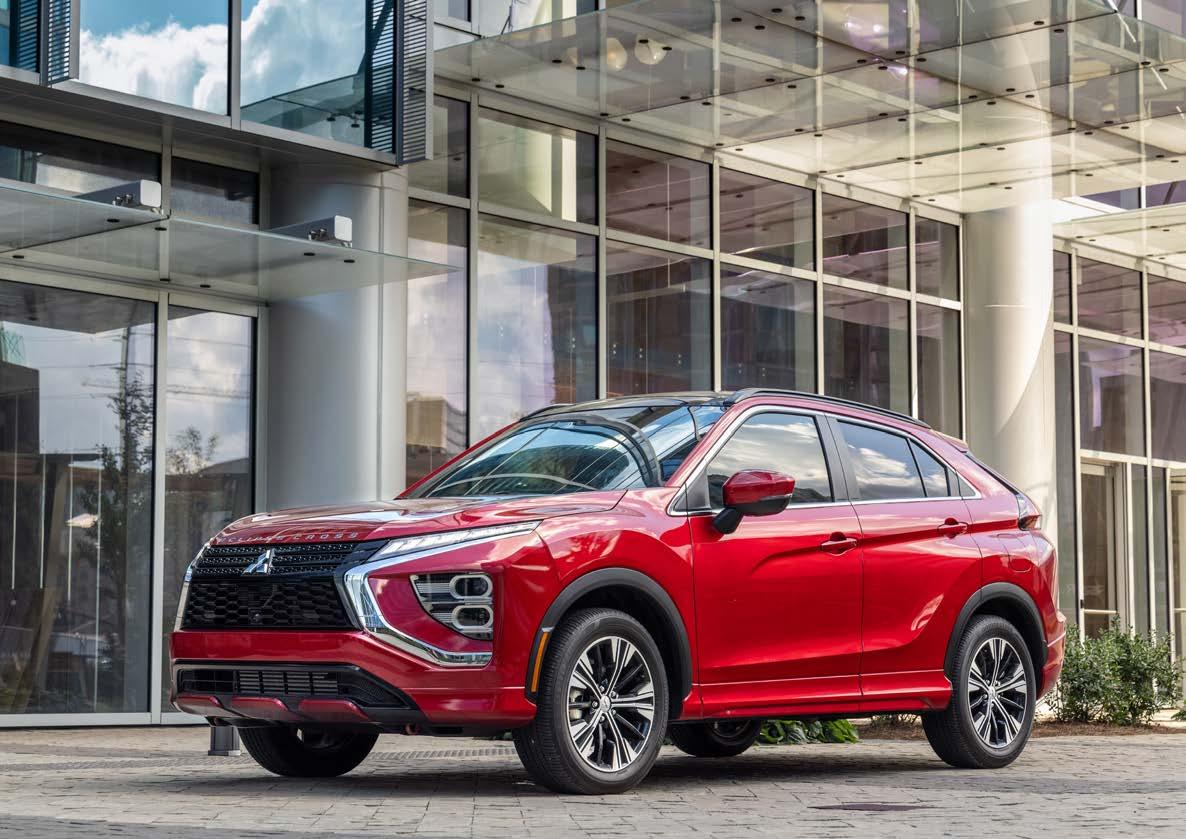
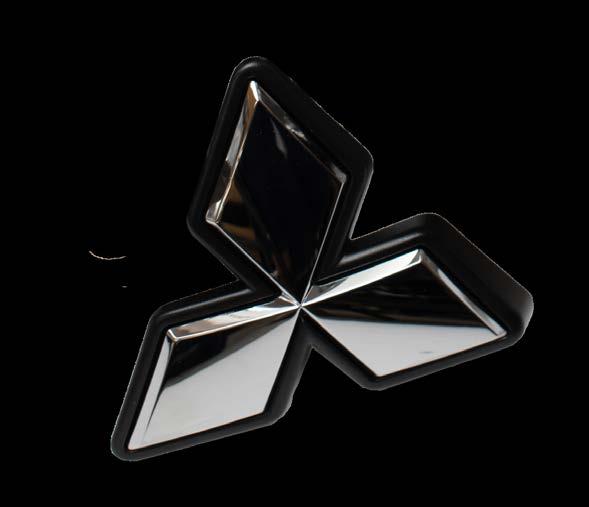

The Canadian 2022 Franchisee of the Year was announced to be the CARSTAR Centennial Auto Group, which is led by Ezra, David and Robert Kember.
Power of Education
Wong joined CARSTAR in 2018 and has locations in San Jose and San Francisco, California.
The Hudson Valley Community College collision repair program offers an education in a wide spectrum of specialties in the industry.
“I spent a lot of time with my grandfather growing up,” Julius said to WNYT. “He had a lot of older cars and tractors and he’d always talk about fixing them up and all of the cars that he had when he was growing up. I loved it. I loved the idea of that.”
QUICK FIX 19-YEAR-OLD FINDS CAREER OPPORTUNITY THROUGH HUDSON VALLEY COMMUNITY COLLEGE
JASON WONG AWARDED US CARSTAR FRANCHISEE OF THE YEAR CARSTAR has announced Jason Wong as the United States 2022 Franchisee of theAccordingYear. to a press release, the honor was bestowed upon Wong at the opening ceremonies of the CARSTAR Conference 2022 at the Gaylord Opryland Resort and Convention Center in Nashville on July 13, 2022. “This is incredible, what an honor to LIGHT HITS be named as the CARSTAR Franchisee of the Year,” said Wong in the press release. “Thank you to the team at CARSTAR—the leadership from Michael Macaluso and Dean Fisher, the operations team and our team at CARSTAR Auto World Collision. I texted them first thing to say it was a team award, not the franchisee of the year award but the FRANCHISE of the year. This shows that the CARSTAR way works and all the CSI and KPI measurements prove the performance.”
The Hudson Valley Community College program covers many different components of collision repair, from detailing to structural to non-structural repair and Althoughmore.the automotive aftermarket is mostly male-dominated, Julius doesn’t necessarily give much thought to gender in the field.
GIORDANO/HVCCVINCENT
“I never really had a problem with it. I never really looked at it as an obstacle.” JuliusJuliussaid.is still a student, but she is already working in the industry. Hudson Valley Community College is hopeful that more young people like Julius will follow suit and explore repair-oriented opportunities.
21September 2022 fenderbender.com
Despite the industry-wide labor shortage, young people like Mya Julius are still motivated to carve out their careers in collision repair. According to WNYT News 13, the 19-year-old Julius is enrolled in the Hudson Valley Community College Automotive Technical ServicesAutobody Repair associate degree program. The school is in Troy, New York. Julius, who grew up in Cambridge, has loved working on cars since she was young thanks to the influence of her grandfather.

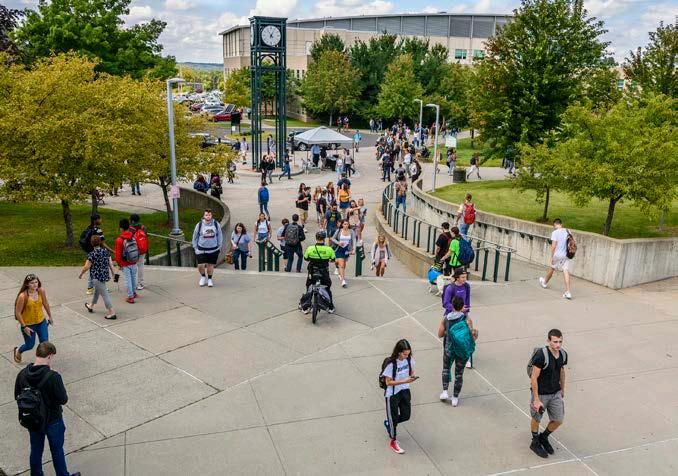
• CCA 2021 Painter of the Year – Kirt Martin of Palmetto Paint and Body Works in Camden, South Carolina
Your
QUICK FIX SOUTHEAST COLLISION CONFERENCE HONORS INDUSTRY PROFESSIONALS
The Southeast Collision Conference honored 10 industry professionals at an awardsAccordingceremony.toa press release, the recently held conference was hosted by the Carolinas Collision Association, Gulf States Collision Association, and Tennessee Collision Repairers Association in late June 2022 in Richburg, South Carolina.
• GSCA 2021 Most Improved Shop of the Year, Mississippi – Richie’s Collision Center of Hattiesburg, Mississippi • TCRA 2021 Most Improved Shop of the Year, Tennessee – Wallace Collision Center of Bristol, Tennessee
ADAS Information
• CCA 2021 Tech of the Year – Marc John of Statesville Collision Center in Statesville, North Carolina
The three associations chose a collective of 10 collision repair professionals to honor at the conference’s opening awards ceremony. Those individuals included:
Wiring Diagrams h Real-World
SUN is a trademark, registered in the United States and other countries of Snap-on Incorporated.
22September 2022 fenderbender.com
• CCA 2021 Detailer of the Year – Zack McClure of Starnes Collision Center in Charlotte, North Carolina • CCA 2021 CSR of the Year – Ashley Stukes of Big Chris Collision in Aiken, South Carolina
• CCA 2021 Estimator of the Year –Michaela Hood of Galeana’s Collision Center in Columbia, South Carolina
• CCA 2021 Most Improved Shop of the Year, North Carolina – Statesville Collision Center of Statesville, North Carolina
• CCA 2021 Most Improved Shop of the Year, South Carolina – Prestige Collision Services of Pendleton, South Carolina • CCA 2021 Board Member of the Year – Ted Martin of Bill Black Chevrolet in Greensboro, North Carolina
Materials SUN Collision Repair Information COMPLETE COLLISION & MECHANICAL DATA YOU CAN TRUST LEARN MORE AND GET A FREE DEMO Call 877-840-1973 or visit SUNcollision.com
“The greatest act of love and community that you can show is selflessness, and I think everybody here understands the importance of that,” CCA President Kyle Bradshaw said at the ceremony, according to the press release. “Seven years ago, there was nowhere we could go to network and bounce ideas off each other. But a couple people employed selflessness to get this association started, and others gave selflessly—our members and sponsors have given their time and financial resources. We want to reward those who are selfless in their organizations.” Those chosen to be recognized were selected based upon their motivation and efforts to “do the right thing,” according to the press release. This year was the inaugural year of the Southeast Collision Conference and plans are underway for another event in 2023. trusted source for comprehensive, accurate OEM data to diagnose the issue and complete the repair with maximum efficiency h Body and Frame h Paint and Finish h h h Insights


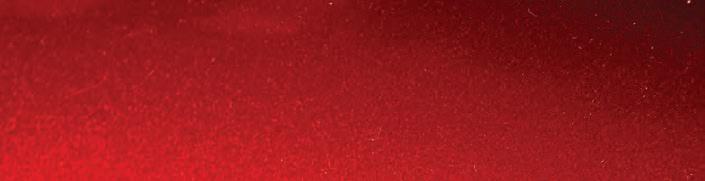
JOIN NETWORKTHE A proven business model for 20 years, ProColor Collision is growing! Independent body shop owners driving their business forward are choosing ProColor. Standardized operations, management tools and consolidated technology solutions improve performance. The ProColor team of industry professionals are dedicated to performance excellence offering the sales, operational and marketing support needed to take business to the next level. ProColor Collision is committed to helping shop owners grow their business locally while leveraging established relationships with global insurers, suppliers, and fleet companies. The ProColor PROcess is a winning formula. Find out more at procolor.com ProColor Collision franchises are not currently being offered for locations in Hawaii, Indiana, Kentucky, Maryland, Minnesota, Nebraska, New York, North Dakota, Rhode Island, South Dakota, Texas, Utah, Washington or Wisconsin, or to residents of these states. ProColor Collision USA LLC, 650 Pelham Blvd, Suite 100, St. Paul, MN 55114 ® Registered Trademark of MONDOFIX INC.
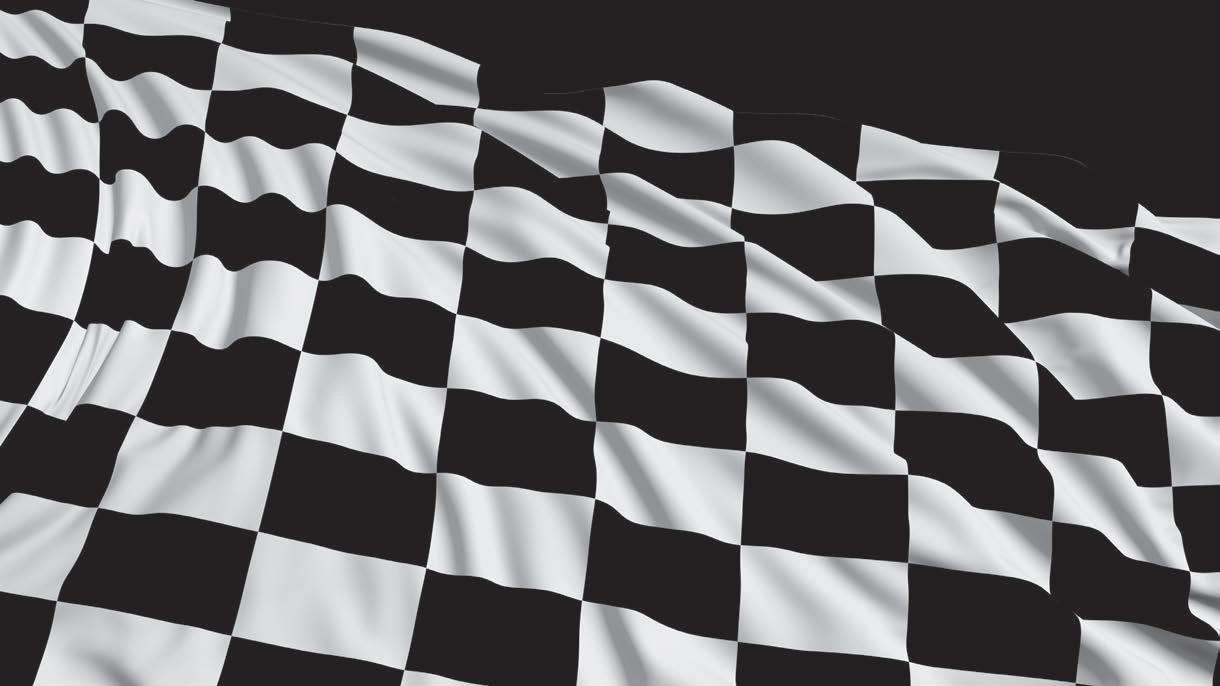
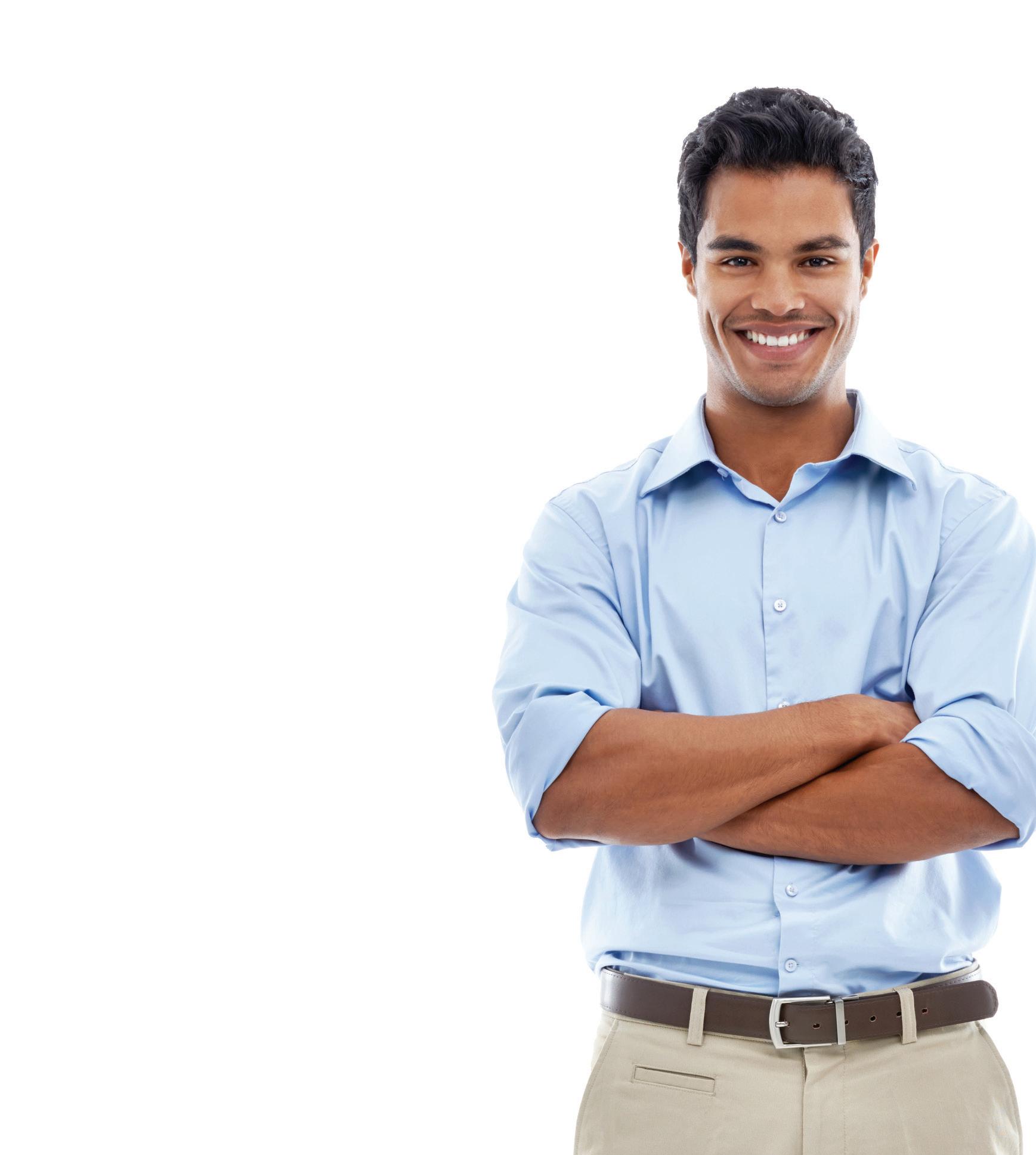
The goal of events such as these is to help first responders have a full understanding of everything from advanced vehicle technologies to latemodel vehicles in order to help them with rescue and emergency situations.
UNSPLASH
A survey from AAA has revealed that onequarter of Americans are likely to buy an electric vehicle for their next car purchase. According to the Lane Report, the greatest percentage of the individuals who responded to the AAA survey are millennials, making up 30 percent of those who would buy an EV. The AAA survey showed that 77 percent of people desiring the EV route want to do so because of high gas prices. Overall, the survey found that one in four Americans want their next car to be fully electric. “The increase in gas prices over the last six months has pushed consumers to consider going electric, especially vehicle owners within that 26- to 41-year-old age group,” said Lori Weaver Hawkins, public affairs manager, AAA Blue Grass, according to the Lane Report. “They are looking for ways to save and automakers continue to incorporate sought-after styling and the latest cutting-edge technology into electric vehicles, which appeals to this group of drivers in Regardlessparticular.”ofthe intention to go electric, the survey showcased certain hesitancies as well. Range anxiety is still prevalent, with 58 percent of respondents concerned about running out of a charge whileAdditionally,driving. 60 percent cited high purchase prices as a concern, 55 percent said the cost of battery replacement, and 31 percent said the inability to install a charging station where they live. Fifty-five percent of respondents fear that EVs are not suitable for long-distance traveling, and 60 percent worry that there are not enough places to charge the vehicle.
First responders are the first people on the scene of an accident, so understanding how a vehicle works can be crucial in helping them achieve their mission. The NABC F.R.E.E program aims to help them navigate these challenges. This event took place on June 25. Gerber Collision & Glass in Nashville hosted the event at its location. Nissan North America provided the vehicles that were used, and Genesis Rescue System provided the classroom education as well as the extrication demonstration.
In June, the National Auto Body Council through its F.R.E.E. program hosted a hands-on extrication demonstration for Nashville first responders. According to a press release, the event was put on by the NABC First Responder Emergency Extrication program as well as Gerber Collision & Glass, Nissan North America, and Genesis Rescue Programs. Over 30 first responders were in attendance from the Nashville Fire Department and other nearby areas. “As a Nashville resident, this NABC F.R.E.E. event was extra special,” said Kyle Mederios, chair of the NABC F.R.E.E. committee. “Being able to witness firsthand the scenarios first responders are presented with and the quick, precise thinking they must perform gave me an even greater respect for them. As a result of this event and our great partnerships with Gerber Collision & Glass, Nissan North America, and Genesis Rescue Systems, we’re already working to host another event soon.”
QUICK FIX DRIVEN BRANDS ELECTS JOSE TOMÁS TO BOARD OF DIRECTORS
24September 2022 fenderbender.com
QUARTER OF AMERICANS WANT AN EV, SURVEY SAYS
Driven Brands has announced that Jose Tomás has been elected to its board of directors.According to a press release, Tomás is the chief administrative officer for TelevisaUnivision, which is the leading Spanish language content and media company in the world. He also has a bachelor’s degree in business administration and a master’s degree in management from Florida International University.Theelection of Tomás, which went into effect on July 11, 2022, brings the board’s total to nine members. “We’re thrilled to have Jose join our board of directors,” said Jonathan Fitzpatrick, CEO and president of Driven Brands, in the press release. “He brings a wide breadth of experience, diverse perspective and keen focus on operations, people and culture that will be invaluable as we continue to grow Driven. His election also marks an important milestone in Driven’s journey as a public company as the majority of our directors are now independent.”Additionally, the board has changed the Compensation Committee and Nominating and Corporate Governance Committee to have only independent directors. Tomás will serve on both committees.
NABC HOSTS EMERGENCY EXTRICATION DEMONSTRATION IN NASHVILLE
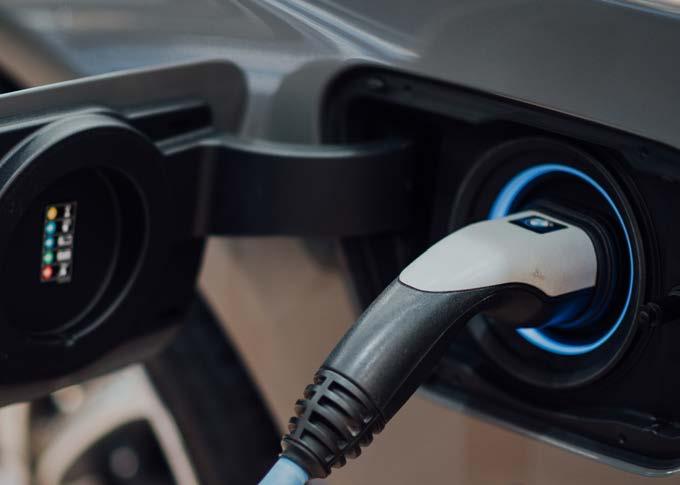
Solutions for every job.
The complete solution that enables shops to recalibrate vehicle camera and radar systems with confidence, speed, efficiency, precision and a vision for the future. the next generation of vehicle sensors with major OEMs means your ADAS equipment is ready for the vehicles of today and of the future. You can count on Bosch, the global leader in diagnostics, to deliver a full range of solutions that work together to make your service process precise and simple.
Bosch SystemCalibrationADAS
boschdiagnostics.com
Co-developing
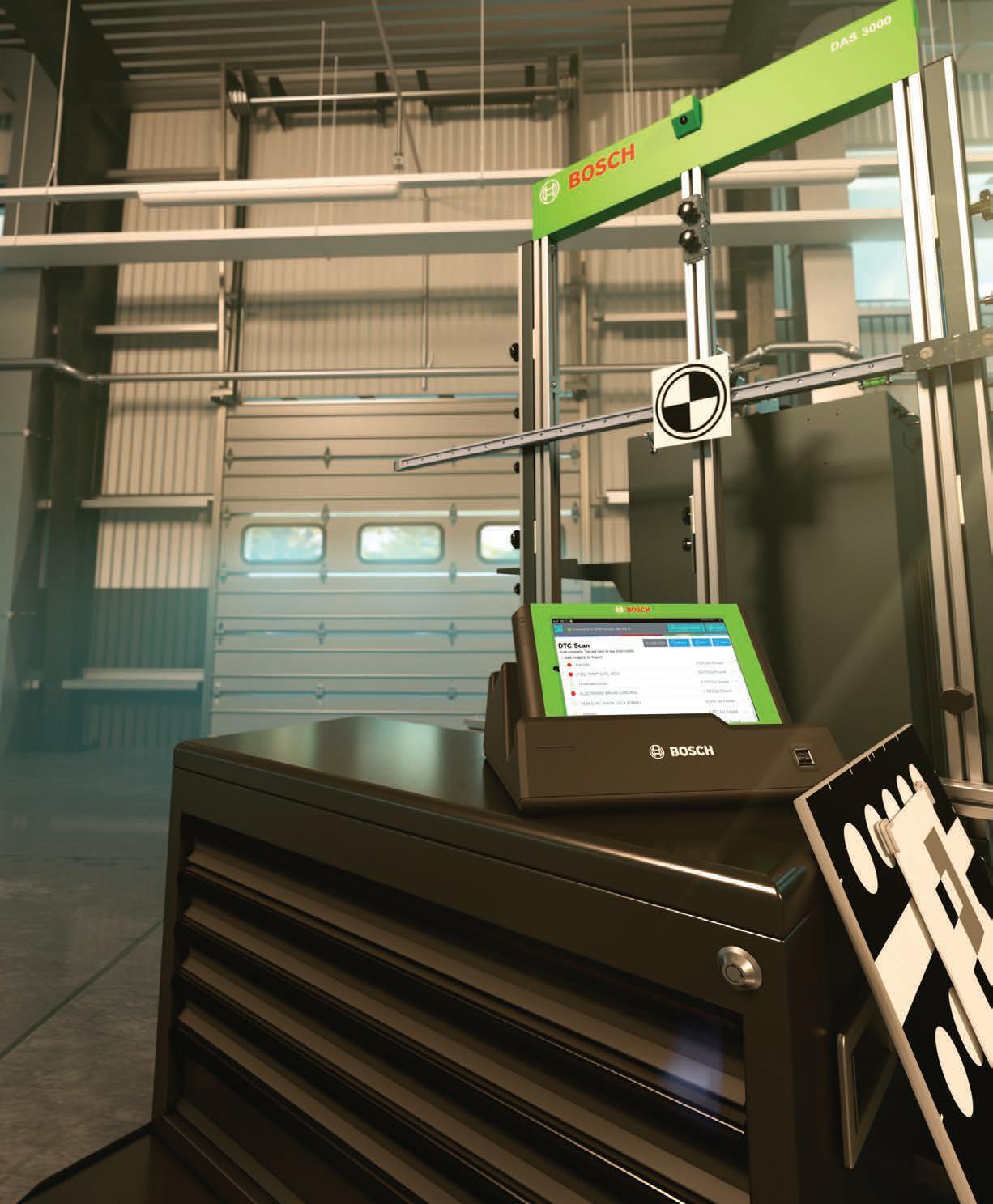
26September 2022 fenderbender.com QUICK FIX
NO MATTER HOW refined the approach a tech takes to research, information gaps in the automotive aftermarket are inevi table. Seeking out up-to-date and relevant information is a huge part of conducting a successful repair on every vehicle these days, but the research process can be a daunting task to complete on top of all the other daily demands.
SPARE PARTS UNSPLASH
REPAIRSTREAMLININGRESEARCH
By NOAH BROWN AND HANNA BUBSER

That’s why I-CAR has the Repairability Technical Support system. It is an online database that takes the guesswork out of repair research by providing access to vast amounts of information to help guide even the toughest repair questions.
VanHulle explains that finding a re pair procedure with the RTS system could take five minutes compared to blindly re searching for three hours or more.
That is why the RTS system goes straight to the source and refers heavily to OEM“Ourprocedure.mainfocus is always ‘what does the OEM say? What does the OEM pro vide?’ So [that’s what] we are always go ing for … directing people how to get to that information and how to interpret that information,” VanHulle says.
The rise in ADAS prevalence and new vehicle technology often not only re quires an individual to absorb new infor mation, but also could require adapting some of the repair procedures that are already familiar.
27September 2022 fenderbender.com
“We gathered together this informa tion after thousands and thousands of hours of research from all these different areas that might trigger some of these dif ferent calibration events,” VanHulle ex plains. “And [we] put it into one location so that when you’re writing that repair order … you can find that information upfront and you’re not trying to scramble on a Friday afternoon.” A massive pull for utilizing the RTS system is that it offers a more stream lined approach to research, which in turn saves time.
In fact, you rarely have time for that. But at the end of the day, you still deserve access to the information that can help you towards a job done.
“Every one of these vehicles is differ ent. Each model year is different … we pride ourselves on only having up-to-date information.” He says.
Time is not always on your side. As a working professional in this industry, you don’t always have hours to dedicate to getting an answer on a complex repair or guidance on difficult detail.
The Inter-Industry Conference on Auto Collision Repair understands not only the existence of knowledge gaps, but also takes into account something else: how precious time is when it comes to conducting a repair.
Hopping on a computer and clicking onto the first online search engine that pops up can seem like the easiest route, but on a platform as vast as the world wide web the options are endless—and in this case, that isn’t always a good thing.
“A simple job is no longer simple with all the calibrations that need to be done,” VanHulle says.
VanHulle notes that the system has updated information that gets refined through the input of its users. This sys tem is open to anyone for use and does not currently require a login.
VanHulle sees the value in resources such as these and believes that the RTS system can be one such tool.
“It’s really there to help people find the information that’s out there and iden tify any of those gaps and help get those closed,” he says.
Scott VanHulle, manager of RTS and OEM relations for I-CAR, says that having this kind of vetted information is incred ibly helpful in the long run. “There are a lot of things that if you’re not doing it and you’re missing it, you may not have a problem for a while,” Van Hulle says. “But one day it will happen, and that’s going to be a problem that you don’t want to have.”
Ultimately, the best strategy for stay ing informed starts with knowing where to do your research and using those tools to your advantage. You never know what changes could happen next in the after market.“Ifyou’re not using the RTS website, you’re going to be missing some of those important steps because the amount of in formation out there is a little overwhelm ing at times,” VanHulle says. “So you re ally need to dive down to make sure that you’re not missing a vital step when all of the sudden systems aren’t available or something’s not working properly.”
Basically, it can do some of the initial grunt work for the user. Across an in dustry where information is constantly changing, it is important to have re sources in your back pocket that provide guidance and solutions to more than one problem at a time.
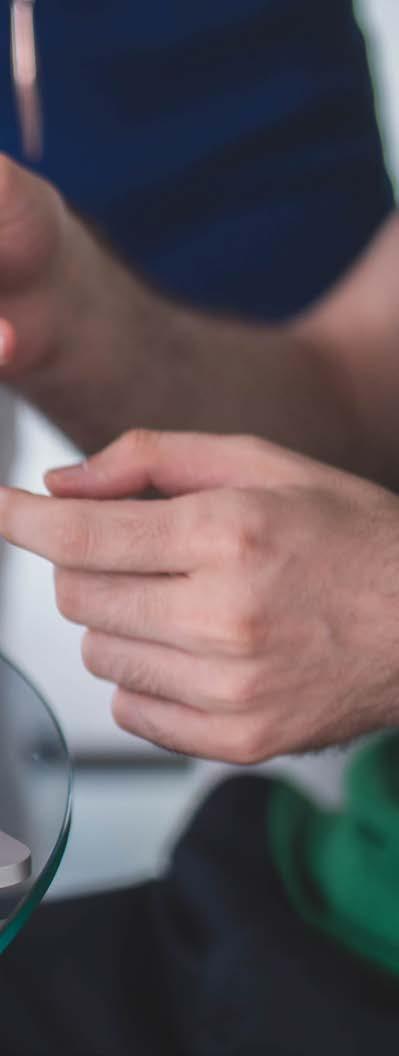
CELEBRATING 50 YEARS AS AMERICA’S BODY SHOP! CELEBRATING 50 YEARS AS AMERICA’S BODY SHOP! Maaco is 50 and better than ever thanks to our thriving franchise family! See why everyone is talking about joining Maaco now at MaacoFranchise.com

Attracting and retaining talent through intentional culture building
COLUMNS THE BIG IDEA
I want to return in this month’s column to a topic I used to talk about a lot but haven’t in a long time: culture. Culture is a word that is getting thrown around a lot these days—and for good rea son! I think we are discovering the truth of what Peter Drucker said long ago, “Culture eats strategy for breakfast.” If you have the secret sauce of a great culture, the strategy will take care of itself. Another reason culture is so important is the talent pool of workers seems to be shrinking. Per haps that’s a generational thing. Or maybe it’s be cause so many people got a life reset when COVID hit. I’m sure there are many reasons. I’m also sure this situation is way more complex than any one thing or some simple explanation. But the reality remains: the talent pool is shrinking. And this is hitting our industry especially hard. Many of us have been fighting for years to find and keep enough workers to do the work that was coming at us. But what is it that draws and then keeps people engaged with a shop? In a word, culture. Fewer people are willing to just work a job for a paycheck. They want the environment they work in to be fulfilling, fun even. They want their job to have meaning and be tied to a higher purpose than simply making the owners more money! And they want to be productive. They really do! People aren’t wired for meaningless work where they sit around and just do the minimum to col lect a check. If that’s your view of people then you are the problem. Deep down people want to be productive but they need the tools, the oppor tunity, the affirmation, and the environment to support that. So, if our plan is simply to just “pay more and expect more,” we are going to lose in the end. No matter how much marketing and sales we do, if we don’t have talent to get the work out it won’t matter. We’ll just have the same issue: more opportunity than capacity. We have to get culture right. Our shop’s longterm survival depends on it. But how? How do we get culture right? Only two things are needed: 1. Understand what culture is 2. Understand how to influence it First, what is culture? Every shop has values. Sometimes these values are not stated. Other times they are declared but not adhered to. But in the best shops, they are both clear and reinforced regularly throughout the organization. That is culture—living out the values and scaling them throughout the whole shop. Things like quality craftsmanship, caring for customers with empa thy, being generous to the communities we work in, and offering opportunities for our team to get training and advance in their careers. These are all examples of values. And these values get com municated in the way we hire, fire, review and retain talent. They get expressed by good bound aries—like what we will or will not tolerate. And keep in mind, values are not aspirational (that’s vision) Values are more discovered than made. You already have them. Now it’s time to see if they really represent who you are and will help you build the kind of team and business the world needs more of. And one that will attract and re tainSo,talent.how do we influence it? Here’s my very simple perspective on influenc ing Allculture.businesses have leaders. Call them found ers, owners, managers—it doesn’t matter. There is someone influencing others in the organization at scale. Let’s say a shop has 12 people working in it from front to back. Someone’s job touches all 12 of those people and that person is calling the shots. On any team there are players and there are coach es. The coaches define the culture. Culture starts with a leader. And for the record, if you’re reading this, that’s likely you. In some capacity, you are leading others. And people are watching you and listening to you for cues on how to work—what to do next, how things get done, what you will tolerate and what you won’t. And leaders have both character and tasks. It’s the com bo of who they are and what they do. Both of these influence the culture. Are you casting a vision more significant than “let’s just make it to Friday so we can play on the weekends!” Are you cutting corners on repairs to get it out the door or are you reinforcing high quality through rigorous quality control checks all along the way as vehicles move from one department to the next? Your shop has a culture and it’s made up of your values. Your values determine what you will and will not tolerate, what you expect, how the work gets done, and why it gets done in the way it does. These are all things under your direct con trol. And these are the very things that make up your culture.
KEVIN RAINS After 18 years in the industry, Kevin Rains sold his network of shops. He now coaches body shop owners and leaders and is the author of the upcoming book Launch to Legacy: The Small Business Roadmap to Success and Significance. You can reach Kevin kevinrains@gmail.comat EMAIL: kevinrains@gmail.com ARCHIVE: fenderbender.com/rains
29September 2022 fenderbender.com MATTHEWSJILL The Secret Sauce of Culture


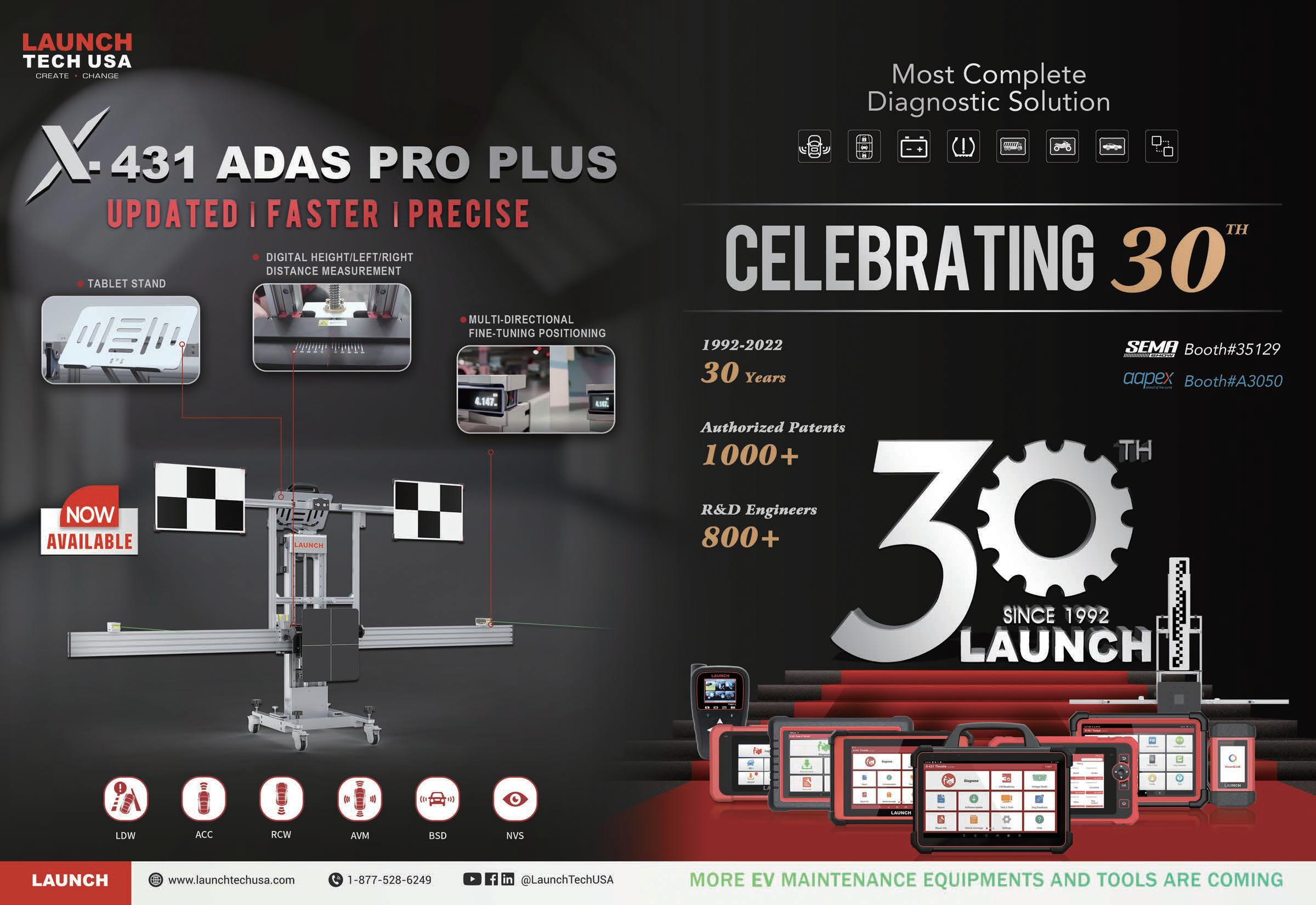
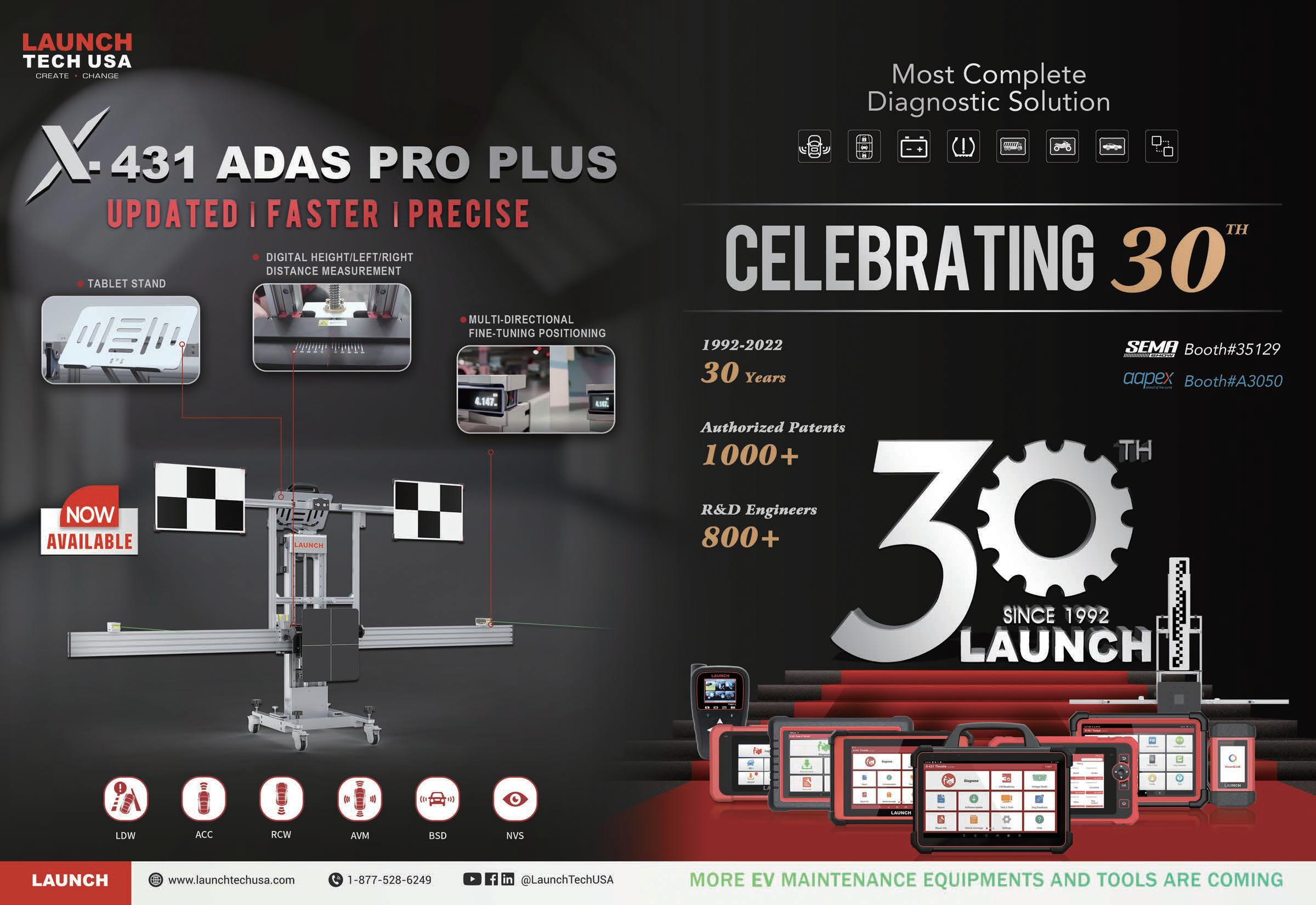
MCGEEBREE FENDERBENDER AWARD Mike Schoonover FENDERBENDERAWARDWINNER:2022
32September 2022 fenderbender.com This operator focuses on family ties, quality work, and community service
By MATT HUDSON
September 2022 fenderbender.com

FENDERBENDER AWARD
“I grew up in the business,” he says. “As a kid, I would ride with dad whenever he would go into the office on the weekends and just kind of hang out.”
34September 2022 fenderbender.com
After college, Schoonover went to work at the shop. At various times, he was a shop runner, cleaner, parts manager, production manager, sales and front office, and executive at the company. He and Gayle officially took over as owners in 2000. Thus began an impressive ownership history for Schoonover. Not only has The Family Business Mike Schoonover and his wife Gayle are stewards of the shop started by Mike’s grandfather in the 1930s.
WHICH HISTORY to start with? Schoonover Bodyworks has an impressive one, starting in 1938 when Chuck Schoonover borrowed $50 from a Saint Paul, Minnesota, business owner to help launch the Schoonover AutoTheRebuild.collision repair shop has been in family hands ever since. Mike Schoonover is the third-generation owner alongside his wife, Gayle. Schoonover’s own history is intertwined with the shop.

MikeCongratulationsSchoonover and the Schoonover Bodyworks and Glass team
Mike Schoonover with Maria Taylor (CCC)
To learn more about the Patrick Schoonover Heart Foundation, visit playforpatrick.org. CCC is proud to work with Schoonover Bodyworks and Glass. Mike Schoonover embodies the best of our industry with his outstanding service to his customers, and his commitment to making heart scans more accessible and affordable through the Patrick Schoonover Heart Foundation.
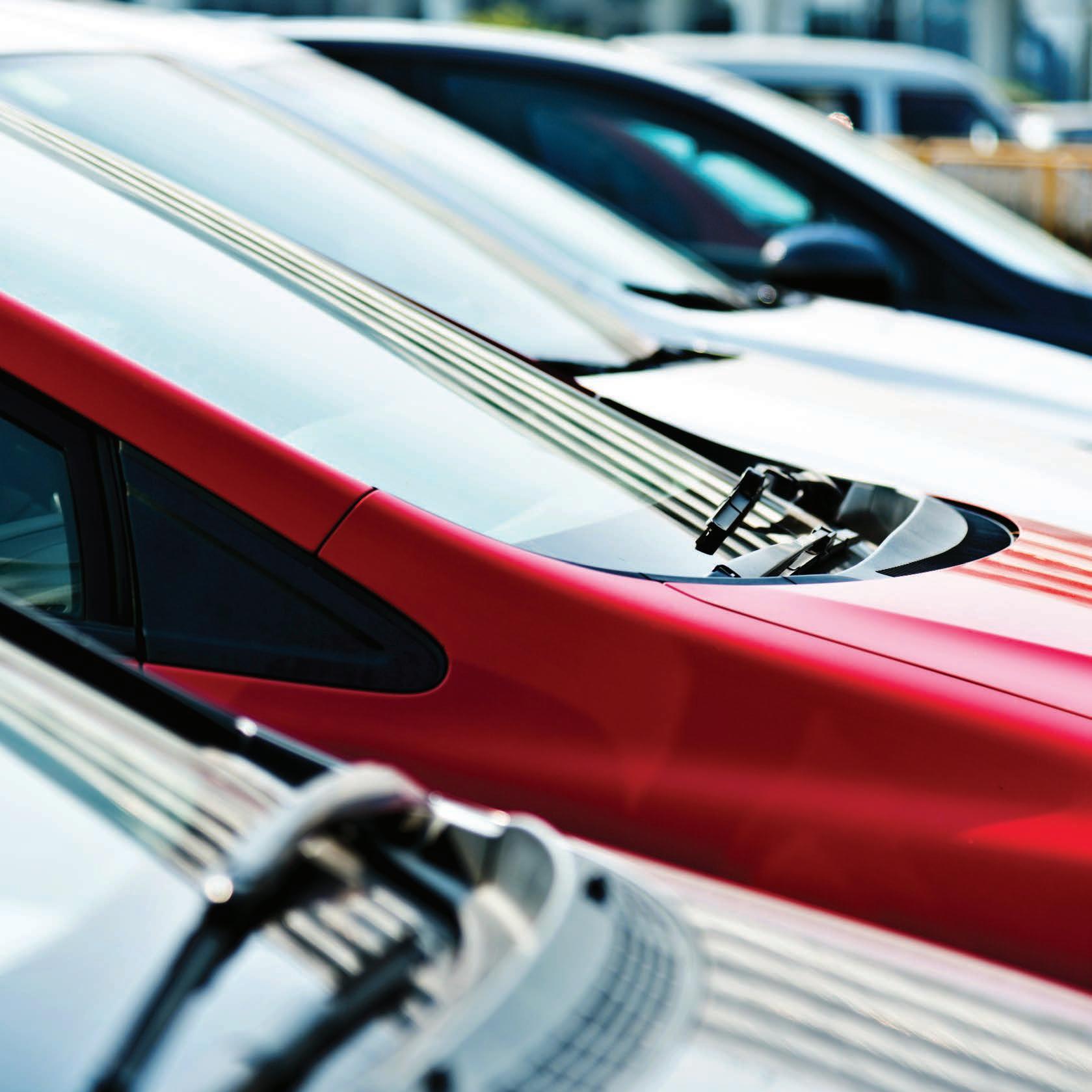


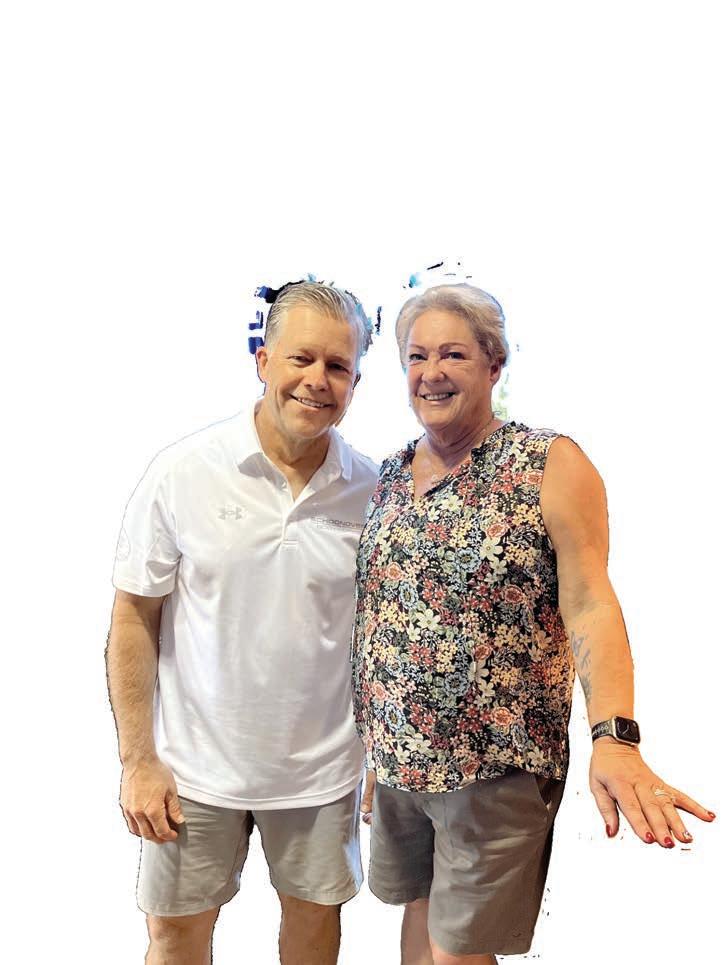
Today, Schoonover Bodyworks remains a successful, local, single-shop operation that’s going through a bit of a growth spurt. Schoonover is actively testing his expertise and leadership along the “Growingway.this business is challenging,” he says. “We’re having to add more people. Gayle does the books, pays the bills, and she’s also the partner in this business and trying to make your life away from work easy—and still you know you’ve got the challenges ahead of adding more people and stress and workload.”
What shows through all those histories is a dedication to customer service and quality repair. And in the case of Schoonover Bodyworks, that dedication has stood the test of time. That’s the mark of a solid collision repair business, and this year, it’s the setting for the 2022 FenderBender Award winner, Mike Schoonover. A Community Landmark Schoonover’s shop is known not only for quality repairs but its community involvement.
36September 2022 fenderbender.com
he built the operation into a modern powerhouse, he sought to help guide the future of collision repair at large. His industry ties include serving on the I-CAR Board of Directors, CAPA Technical Committee and Board of Directors, ASA Collision Division, AASPMN Collision Committee and that Board of Directors.Themost impactful part of the Schoonovers’ history was the 2014 death of their son, Patrick, from a heart condition. In the wake of that deeply painful event, the Schoonover family has helped to raise awareness of heart health and screened thousands of kids through a foundation.
FENDERBENDER AWARD
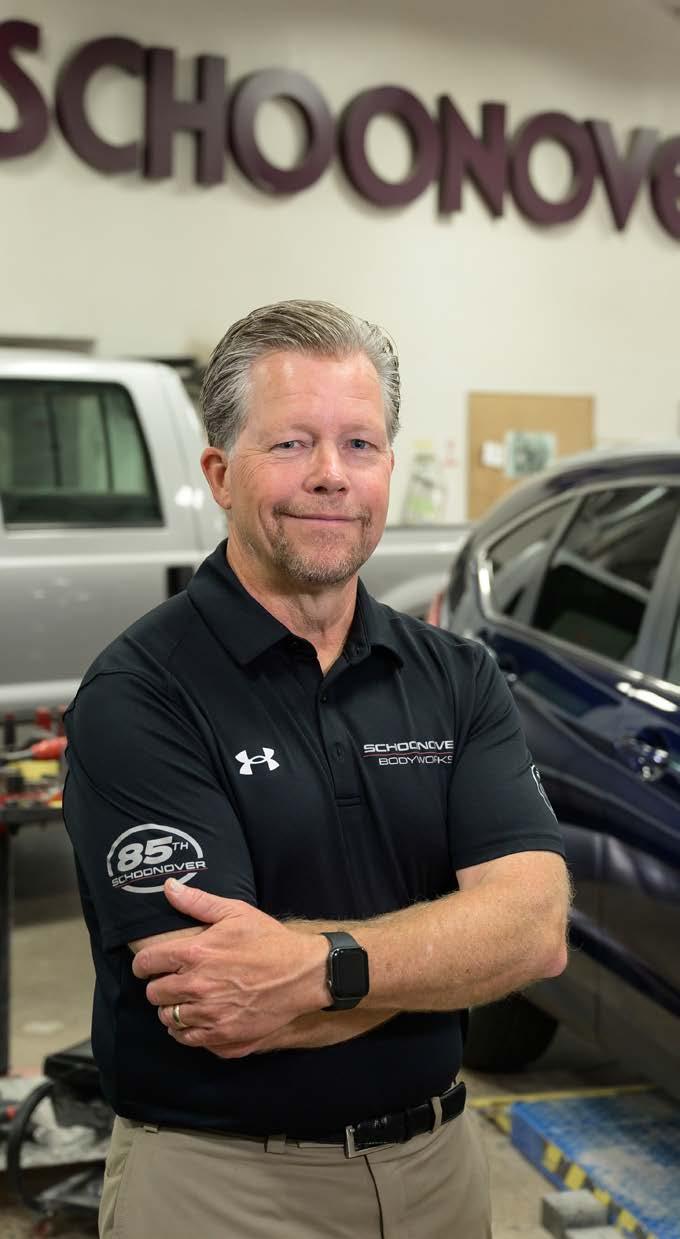
Congratulations Schoonover Bodyworks and Glass! We are proud to be your partner in paint.
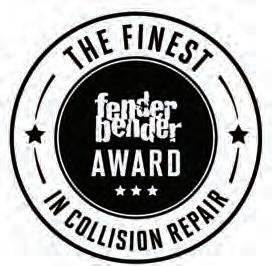
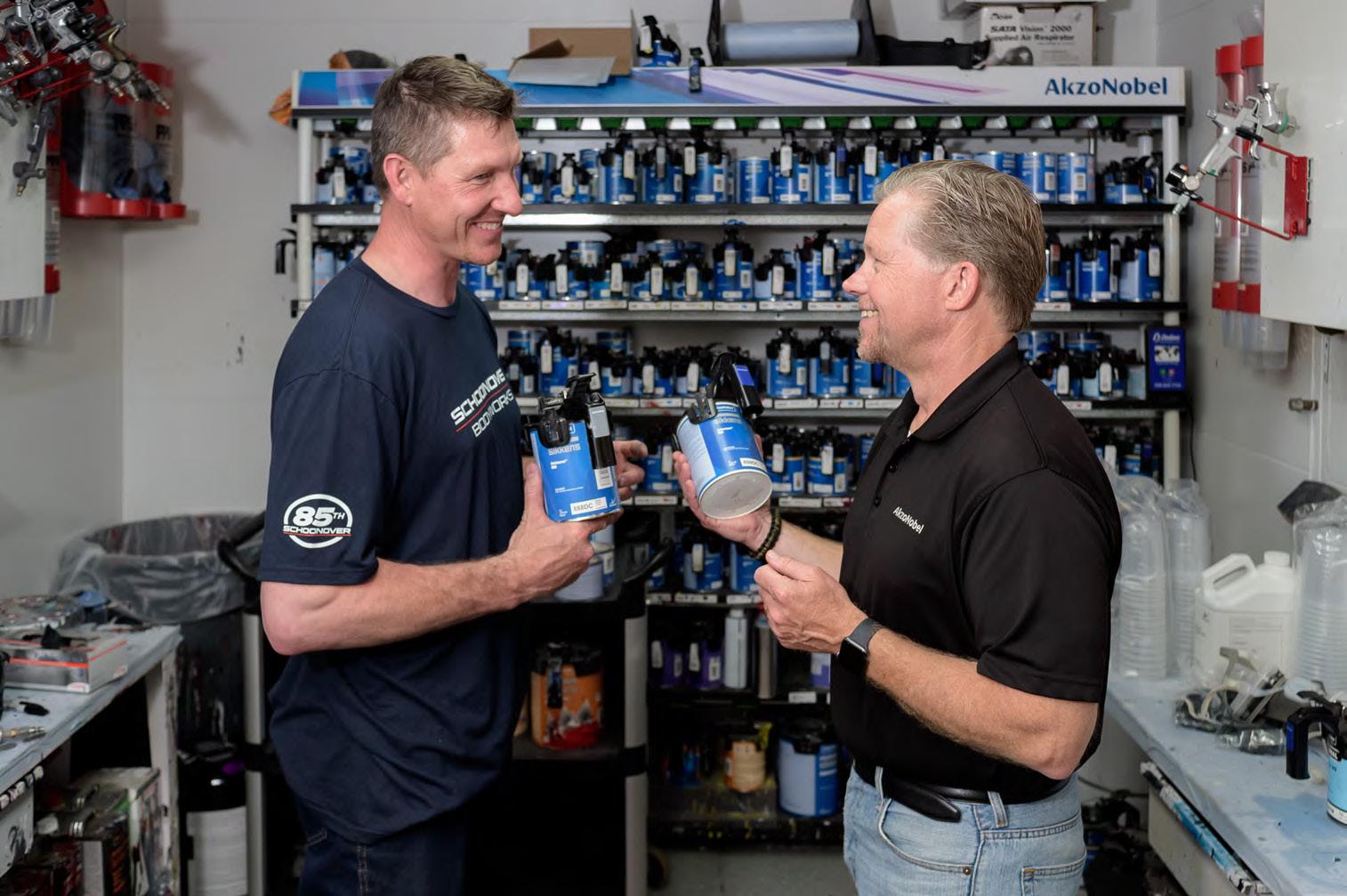
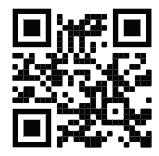
FENDERBENDER AWARD 38September 2022 fenderbender.com
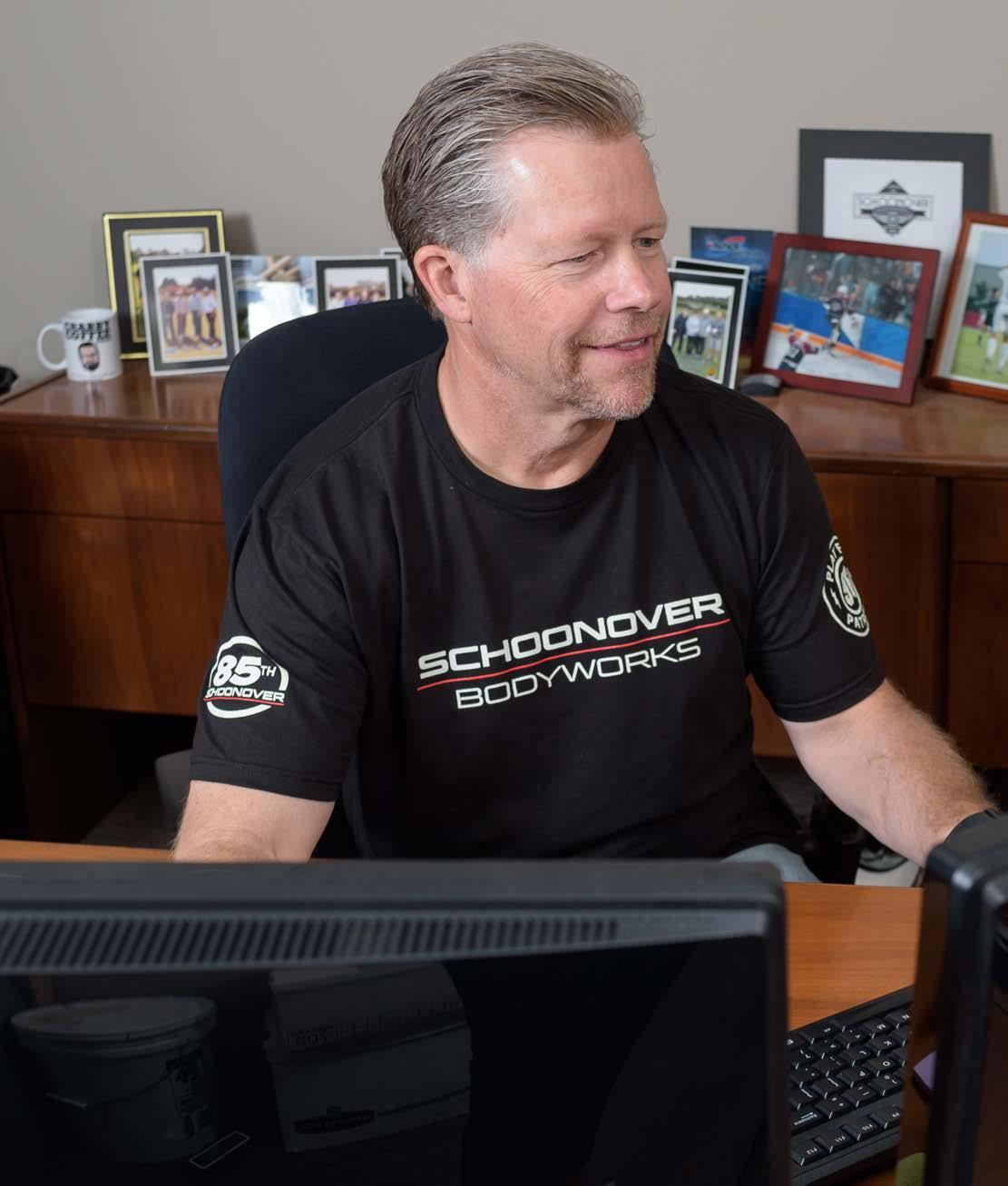
Schoonover’s team became really thrifty with space when they started work ing on ADAS components about five years ago. The shop became an early adopter of in-house ADAS work. “We started doing that stuff in-house maybe four or five years ago,” Schoonover says. “We do the pre-and post-scans and are able to do most calibrations in-house.”
STAFF SIZE: 18 AVERAGE SHOP SIZE: 14,000 SQUARE FEET AVERAGE MONTHLY CAR COUNT: 132 ARO: $2,250 TOTAL ANNUAL REVENUE: $3.5 MILLION
“That kind of turned into, ‘As long as your car is here, we can change your oil or rotate your tires,’” he says.
39September 2022 fenderbender.com
Schoonover started offering some maintenance services, creating a true onestop shop that’s not as common for collision repairers. The shop offers air conditioning service, alignments, brake work, oil chang es, shock and strut replacement, steering and suspension work, and more. It was a lot to take on for the 14,000-square-foot busi ness in Shoreview, Minnesota.
SCHOONOVER BODYWORKS AND GLASS LOCATION: SHOREVIEW,
Space concerns become acute when working with ADAS. Schoonover says that they often plan a shop day around calibra tion work in order to clear the space re quired to perform them.
The Name on the Building A Schoonover has presided over the ever-growing business since Chuck Schoonover founded the company in 1938.
The motivation to bring all these processes into the shop stems from the idea that true quality control is to have MN
An Evolving Brand Schoonover Bodyworks maintained its high level of quality after Mike Schoonover took over as owner. But he wasn’t afraid to make some changes. After experimenting with a mobile glass repair and installation setup, Schoonover brought glass in-house. That coincided with another change.

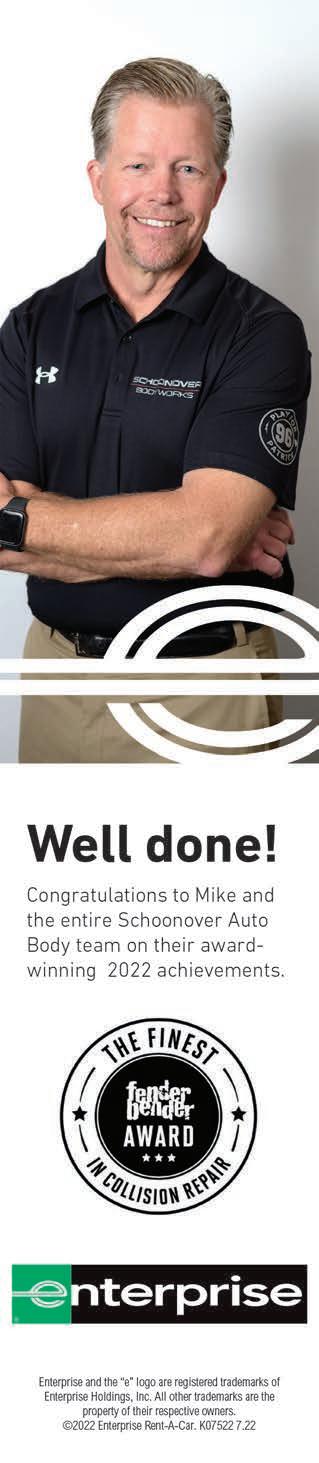
“Years ago, we had a need to grow, be cause our business was flourishing,” he says. “We wanted to add more people, we were running into backlogs.”
In 2020, the Schoonovers finally pur chased the building. But then came another decision. They received multiple buyout of fers for the longtime family business. The incentives to take the cash and exit can be tempting. But with all the foundation the A One-Stop Shop Schoonover has worked to add a wide range of services to his shop’s offerings.
40September 2022 fenderbender.com FENDERBENDER AWARD
those processes happen at your business. Schoonover doesn’t want to stake his business’ reputation on outsourced work or processes.“Dadtaught me this at a young age: The more you can do under one roof, the better you can be,” he says. Given the ambitious service menu at Schoonover Bodyworks, it’s no wonder that the shop is due for an expansion. It wasn’t a straightforward process. For years, Schoonover’s father still owned the building. He says that it wasn’t right to push for an expansion without ownership of the real estate. They ended up turning down business when the backlog grew too large.
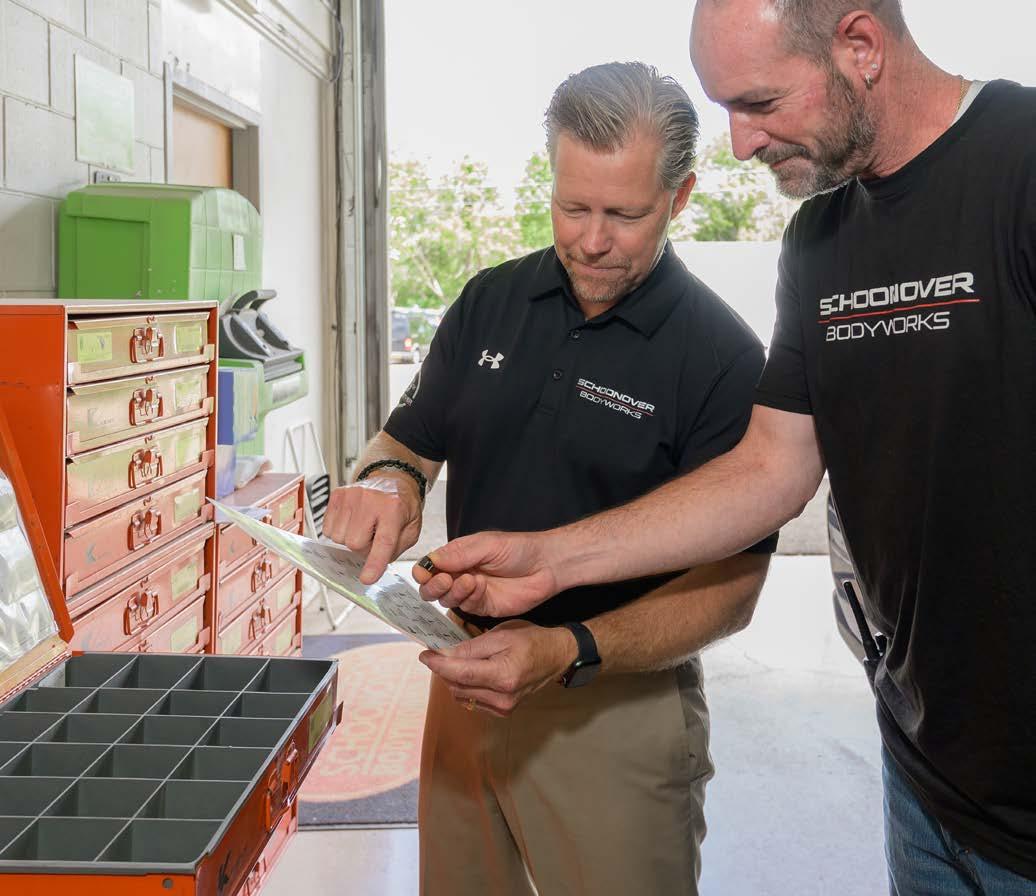
Green is more than just a color to us.
Beginning mid-September, while supplies last. Watch for more info.
Phone: www.satausa.com800-533-8016 E-mail: satajet@satausa.com www.sata.com/x5500futureINFO
The exclusive independent distributor of SATA products in the US and Puerto Rico
The green SATAjet X 5500 FUTURE is not only a reference to nature, it is also a symbol for harmony and hope and especially for the future! We are striving for a sustainable and connected future that makes the most out of the potentials of the digital transformation. The globe-shaped circuits on the spray gun represent the technology which is connecting people and thus enables the globalized world of the future. The radiant green color with the black components not only looks harmonious, it stands for aligning our actions with sustainability and the preservation of nature.
Congratulations Mike ~ Schoonover Bodyworks & Glass on being chosen 2022 collision repair shop
Phone: www.satausa.com800-533-8016 E-mail: satajet@satausa.com
Thank you for using SATA equipment in your shop! We value your commitment and dedication to using quality SATA products.
SATA, SATAjet and/or other SATA products referenced herein are either registered trademarks or trade marks of SATA GmbH & Co. KG in the U.S. and/or other countries.
As a manufacturing company, sustainable growth is of great importance to us and an integral part of our daily activities. This includes the consistent conservation of resources and avoidance of waste. As an example, we produce part of our electricity with our own solar power and have reduced our waste volume by around 20% in the last five years.
The exclusive independent distributor of SATA products in the US and Puerto Rico

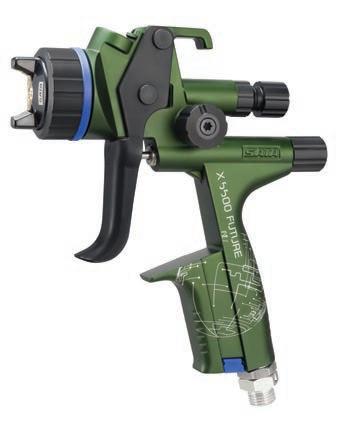
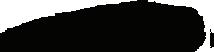

42September 2022 fenderbender.com FENDERBENDER AWARD

Industry Growth Schoonover has a long list of industry af filiations, both locally and nationally. Around 2007, he got an opportunity to join the prestigious I-CAR Board of Directors as On the Rise Schoonover Bodyworks and its team of 18 employees is in the midst of an expansion.
“I THINK IT WOULD BE COOL TO SEE WHAT THE BUSINESS CAN DO WITH THE DREAM THAT WE HAD OF MAKING IT BIGGER AND BETTER.”
MIKE SCHOONOVER owner, Schoonover Bodyworks
“I think it would be cool to see what this business can do with the dream that we had of making it bigger and better,” Schoonover says. He and Gayle remained in place and made plans to create the space for their am bitious one-stop shop outlook. This sum mer, those plans turned into action, and crews broke ground to add an additional 7,000 square feet or so to the space. The shop continues to evolve in a competitive marketplace.“Ithink our customers have ap preciated it. We welcome competition,” Schoonover says. “A lot of folks said back in the day that big consolidators are going to drive us out of business, and I don’t think that’s the case at all. Consolidators have pushed us to be better.”
43September 2022 fenderbender.com
Schoonovers had made in the business, it wasn’t realistic to walk away.

FENDERBENDER AWARD a representative from the Automotive Ser viceAAssociation.TwinCities colleague asked Schoonover to take on that role. It was Darrell Amberson, president of operations for LaMettry’s Collision. Around 2007, Amberson had established his tenure at ASA leadership, and a board position opened up at I-CAR to represent ASA. Schoonover says he was honored to be asked to join, and he took the op portunity. The experience turned out to be worthwhile.“Beingapart of the I-CAR board of di
Doing More Schoonover has taken on leadership roles in industry associations such as I-CAR.
44September 2022 fenderbender.com
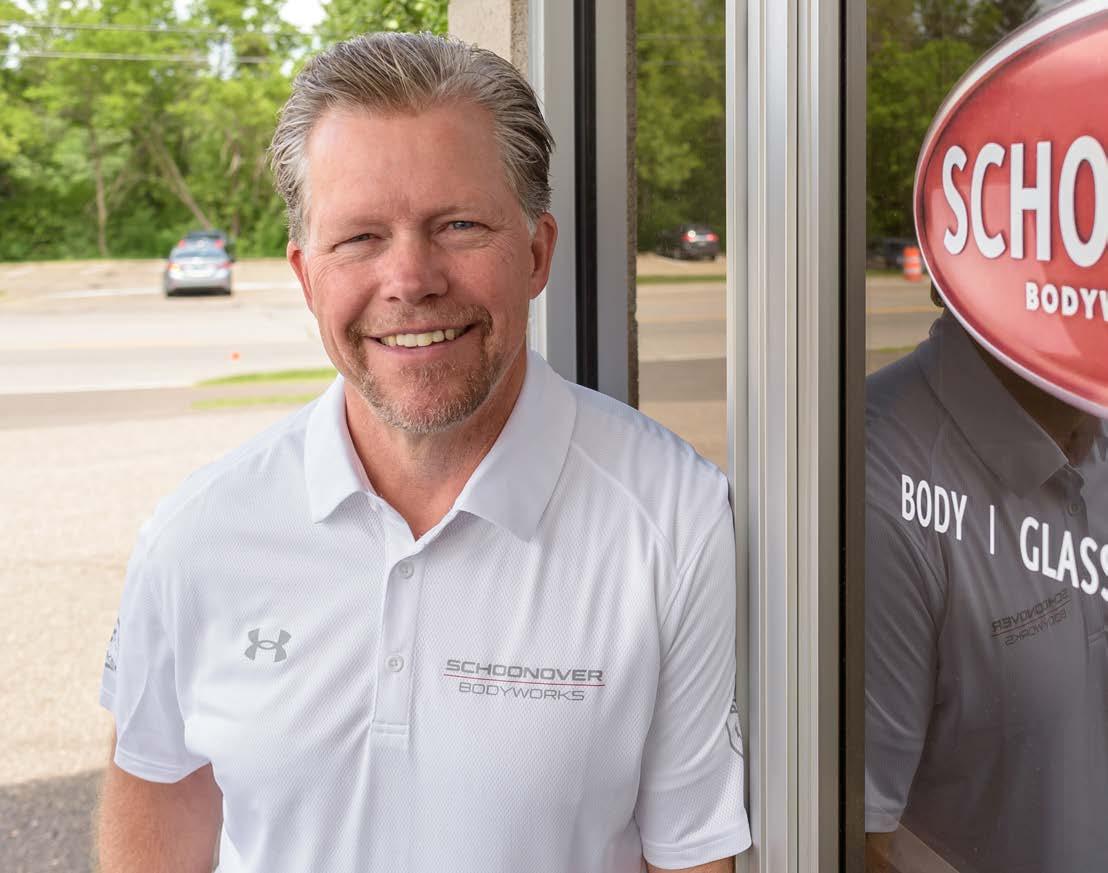
45September 2022 fenderbender.com
5pm 20418 HWY 65 NE • East Bethel, MN 55011aaaparts.comStandard6-MonthNoHasslePartReplacementWarrantyExtendedLaborWarrantiesAvailableUponRequestInventoryavailableonline(Car-Part,CCC,PartsTrader,APU)Remanufactured&AftermarketoptionsavailableBuyingused&unwantedvehiclesataaaautoparts&U-PullR-PartsDropofforpick-upoptionsavailableuponrequest 2 LOCATIONS FOR ALL YOUR RECYCLED AUTO PART NEEDS PROUDLY SERVING NORTH METRO & SOUTH METRO AREAS! CongratulationsSchoonoverBodyworks! FROM AAA AUTO PARTS AND THE TEAM PRP AUTOMOTIVE RECYCLERS
rectors on behalf of ASA was probably my most favorite, just because there were a lot of people on the board who were way smarter than me,” Schoonover says. “Exec utives from different companies that serve the collision repair industry. Those people wereAmbersonbrilliant.” says that Schoonover was perfect for the position. “Very good operator, very conscien tious,” Amberson says of Schoonover. “Very high standards of integrity and intelli gence. He loves the business.” Amberson says that the high standard of professionalism runs in the Schoonover family. Schoonover’s father, Dick, was among a group of Twin Cities collision re pair operators who sought to elevate the profile of the industry, battling the percep tion of the “grease monkey” and promoting one of intelligent business leaders. Dick Schoonover passed away in 2020. Amberson says that Mike Schoonover carries that torch, acting with profession alism and pride in the work. Part of that characteristic is the inability to let mistakes pass. Amberson tells one story about a shop visit years ago in Michigan. The visit was Call your sales rep for details! -
(800) 238-6664 2871 160th St.W • Rosemount, MN 55068 Mon-Fri 8am
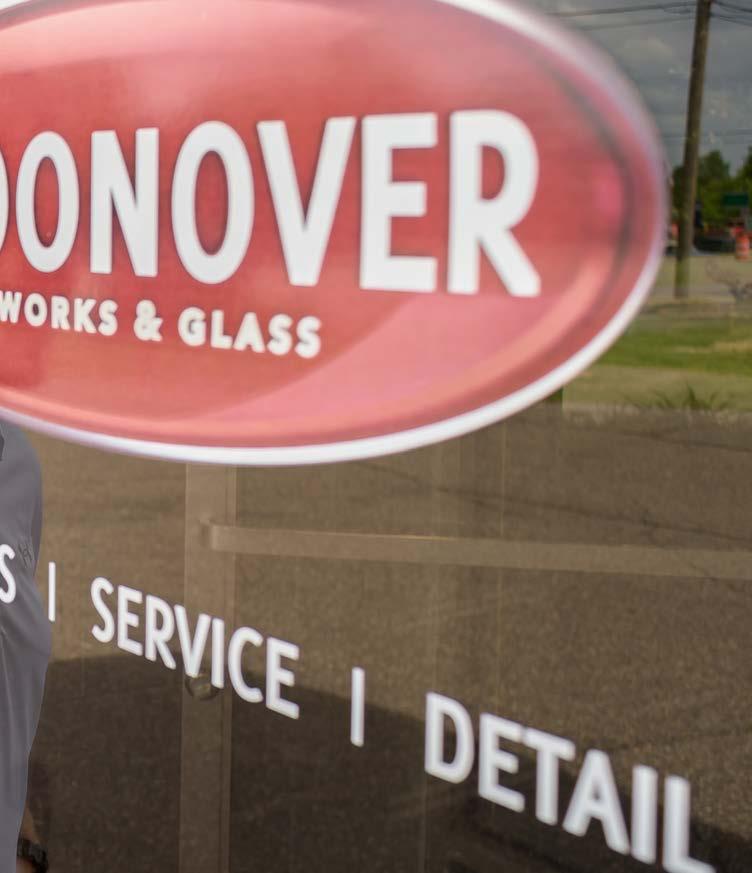

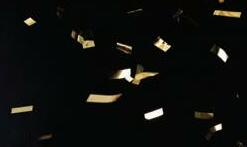
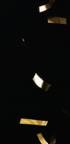
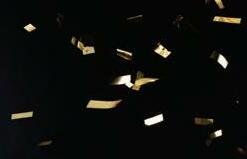
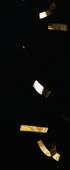

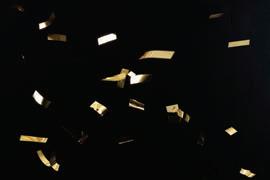
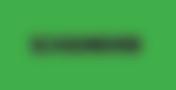
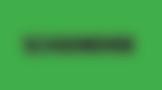






















46September 2022 fenderbender.com FENDERBENDER AWARD

Collision CONGRATS, SCHOONOVER BODYWORKS! All of us Associatedat Bank would like CollisonBender2022receivingBodyworksofMikecongratulatetoSchoonoverSchoonoverontheFenderFinestinRepair. Member FDIC. (8/22) PO6984
for
ALL BE WORKING ON MAKING THE INDUSTRY BETTER, MAKING
47September 2022 fenderbender.com part of a CAPA committee, and the hosting shop belonged to the CEO at the time. Part of the visit included a look at test fitting for parts to ensure that they meet strict OEM specifications for thickness, cor rosion resistance, and other factors. “We’re in this room, and pretty soon Mike speaks up and says, ‘Look at this hood over here,’” Amberson says. The hood wasn’t fitting as it should dur ing this parts fitting presentation. It was a bit of an embarrassment for the host, but it showed Shoonover’s dedication to quality. Though Amberson and Schoonover oper ate in the same metro area, it’s the larger goal of elevating an industry that binds them. “It’s what we should be doing. When it comes to competing with the customer, we’re each going to try and make the sale,” Amberson says. “But at the same time, we should all be working on making the indus try better, making it safer, and doing right by the consumer.”
SAFER, AND DOING RIGHT BY
AMBERSON
DARRELL president of operations LaMettry’s
Play For Patrick Patrick Schoonover scored the first goal in a youth hockey game on Nov. 14, 2014. Schoonover and Gayle were at the game. Moments after the goal, Patrick died on the ice. He had complications related to an un detected heart defect. “When they brought him to the hos The Quality’s the Thing Schoonover has established a reputation for quality and accuracy in completing repairs. SHOULD IT THE CUSTOMER.”
“WE
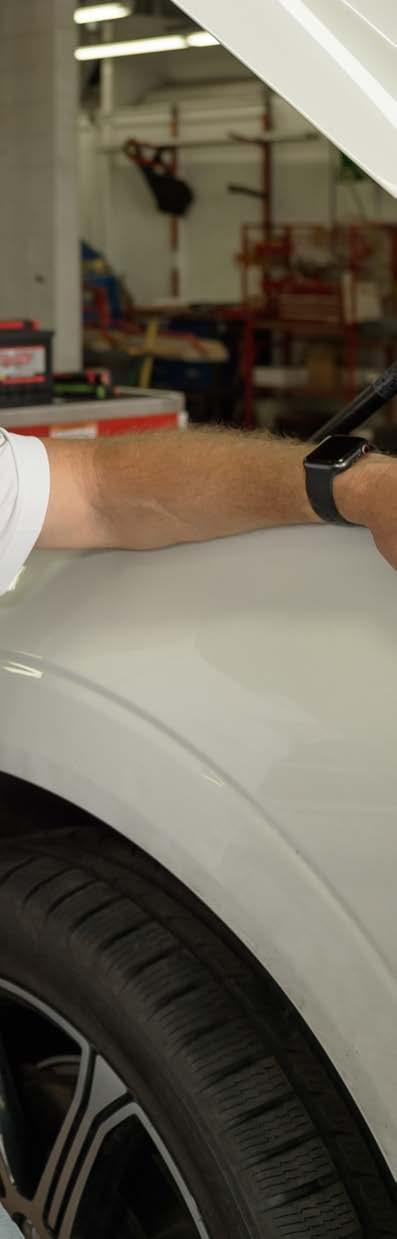
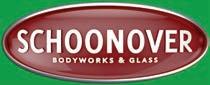
48September 2022 fenderbender.com FENDERBENDER AWARD pital, they weren’t able to revive him,” Schoonover says. “He had two issues with his heart, and even if it happened when he was in an emergency room and that hap pened with his heart, they wouldn’t have been able to bring him back.” It was a devastating blow to the fam ily, their friends, and the Minnesota youth hockey community. Through the pain and healing processes, a community of profes sionals started rallying around the case. A family member was seeing a cardiologist, who offered to help educate others on heart
Play for Patrick Out of the tragic death of the Schoonovers’ son Patrick came a foundation to help identify similar life-threatening heart conditions in children.
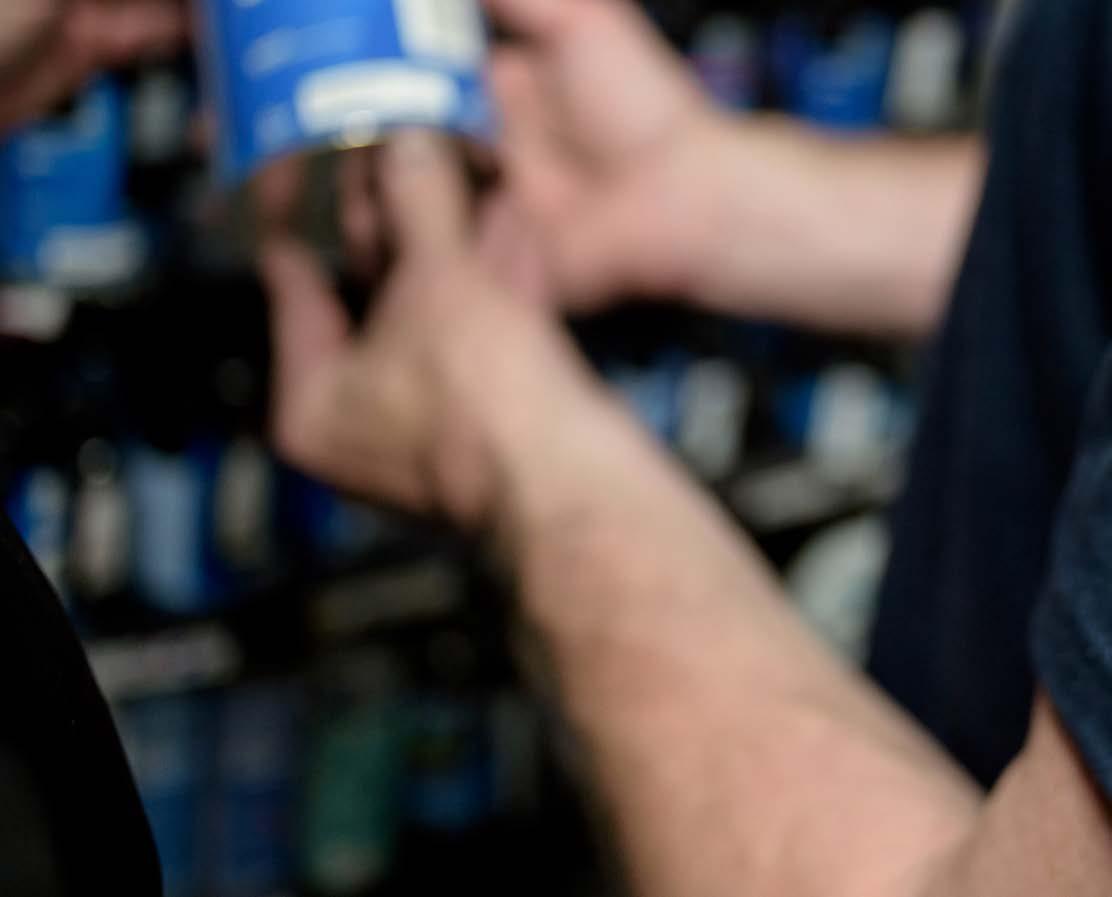
49September 2022 fenderbender.com health and regular checks. That’s how the Foundation started. “That was when we met with that cardi ologist, and we decided that we didn’t want another family to feel what we were going through,” Schoonover says. “We started a foundation in Patrick's name and started doing heart screenings.” The Patrick Schoonover Heart Foun dation is the result of the work by the Schoonovers, volunteer cardiologists, and a network of supporters. The Foundation sets up heart screening events for kids to iden tify potential issues—like the one that went undetected in Patrick. Through spring 2022, the Foundation has held 25 screens for 4,178 kids. More than 500 of those kids were found to have elevated blood pressure or some signs of an abnormality, leading them to pursue other health checks that are potentially life-saving.“Those4,100 kids have been screened. A lot of them have been screened and they know that they’re OK,” Schoonover says. “And there are more kids who now know
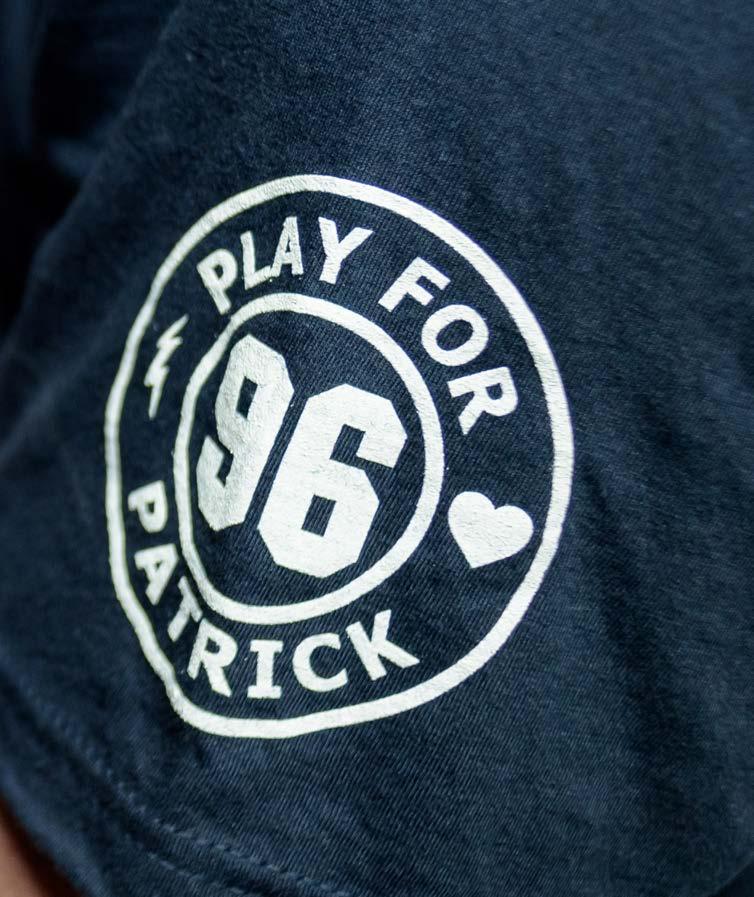

FENDERBENDER AWARD 50September 2022 fenderbender.com

“With everything that’s gone on in the past couple years in the world, the appre ciation for family-owned businesses has gone up dramatically,” Schoonover says. While it can be a selling point to have ownership under the same shop roof as the customer, it also means that the engine for The Family Legacy Schoonover values his shop’s history as a family-owned business and what that means to his customers.
The foundation encourages those ath letic kids to Play for Patrick. That extension of help to others is right in line with Pat rick’s character, Schoonver says. “We like to think that he’s helping and looking out for other kids,” he says. “In real life, he was one that would look out for other kids or other teammates. Just a competitor and great all-around kid. We feel as though he would be happy.”
51September 2022 fenderbender.com that they have an issue that needs to be dealt with, either severe or minor. And they’re going to pay attention.”
“WE GOINGWHATFAMILYWANTTHATDECIDEDWEDIDN’TANOTHERTOFEELWEWERETHROUGH.”
The Family Business Schoonover is extremely proud of the fam ily business. He says that their focus is to sharpen their single-shop operation to be the best and most comprehensive offering for the local clientele, who view local own ership as a strong incentive.
MIKE SCHOONOVER owner, Schoonover Bodyworks
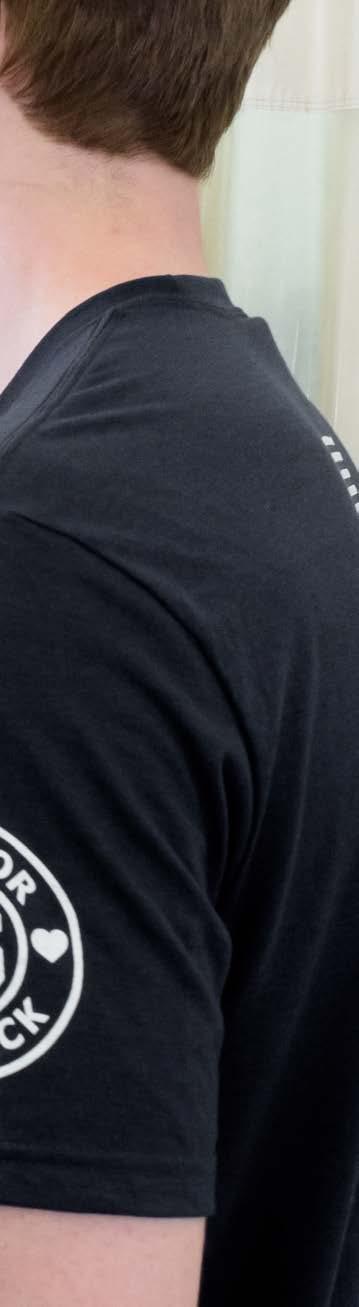
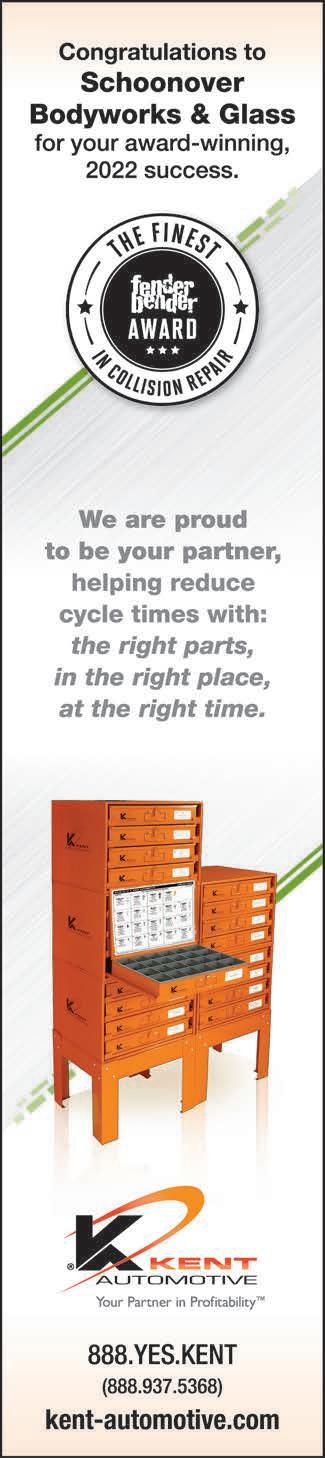
52September 2022 fenderbender.com
A Hands-On Approach Schoonover takes pride in keeping a close eye on the details of operations in his shop.
growth must come from within. That’s the challenge for detail-oriented, driven opera tors like the Schoonovers. The family business is flourishing, and it’s also extending into other industries. It’s funny how life events ripple over time. Back in 2014, the Schoonovers’ daughter, Anna, played in a high school lacrosse tournament days after Patrick’s death. It was an emotion al time, but that tournament helped her to land a spot on a Division I college team. That college education helped Anna to develop and pursue a passion for car diac care. Now a working professional, she works for Medtronic, a large medical device company, helping to improve the cardiac products there. “Her whole purpose was her brother,” Schoonover says. “And now she’s in car diac care, and now Medtronic is aware of what we’re doing through Play for Patrick andSoAnna.”what is the family business for the Schoonovers? It might not be limited to one line of work, but when a Schoonover sets their mind on a task, the track record shows that they will do it right.
FENDERBENDER AWARD

CONGRATULATIONS!
premium
Thank You for your ongoing partnership with the FinishMaster
WE ARE HERE TO HELP, FROM START TO FINISH! follow us @finishmasterinc AWARD THE F I NEST INCOLLISI ON REPAIR 866-711-5235 • FINISHMASTER.COM/WECANHELP
for the 2022 FenderBender Finest in Collision Repair Award!
and Glass
Mike Schoonover and Bodyworks Team selected
for being
FinishMaster has been serving Schoonover Bodyworks and Glass since 2015 as their trusted distribution partner. It is an honor to support this well-respected, family-owned collision repair shop, and to see the positive impact they continue to make on other families’ lives through the Patrick Schoonover Heart Foundation. are committed to continue being the key factor in their success through our team’s support, services, and product offerings. Team!
We
the Schoonover
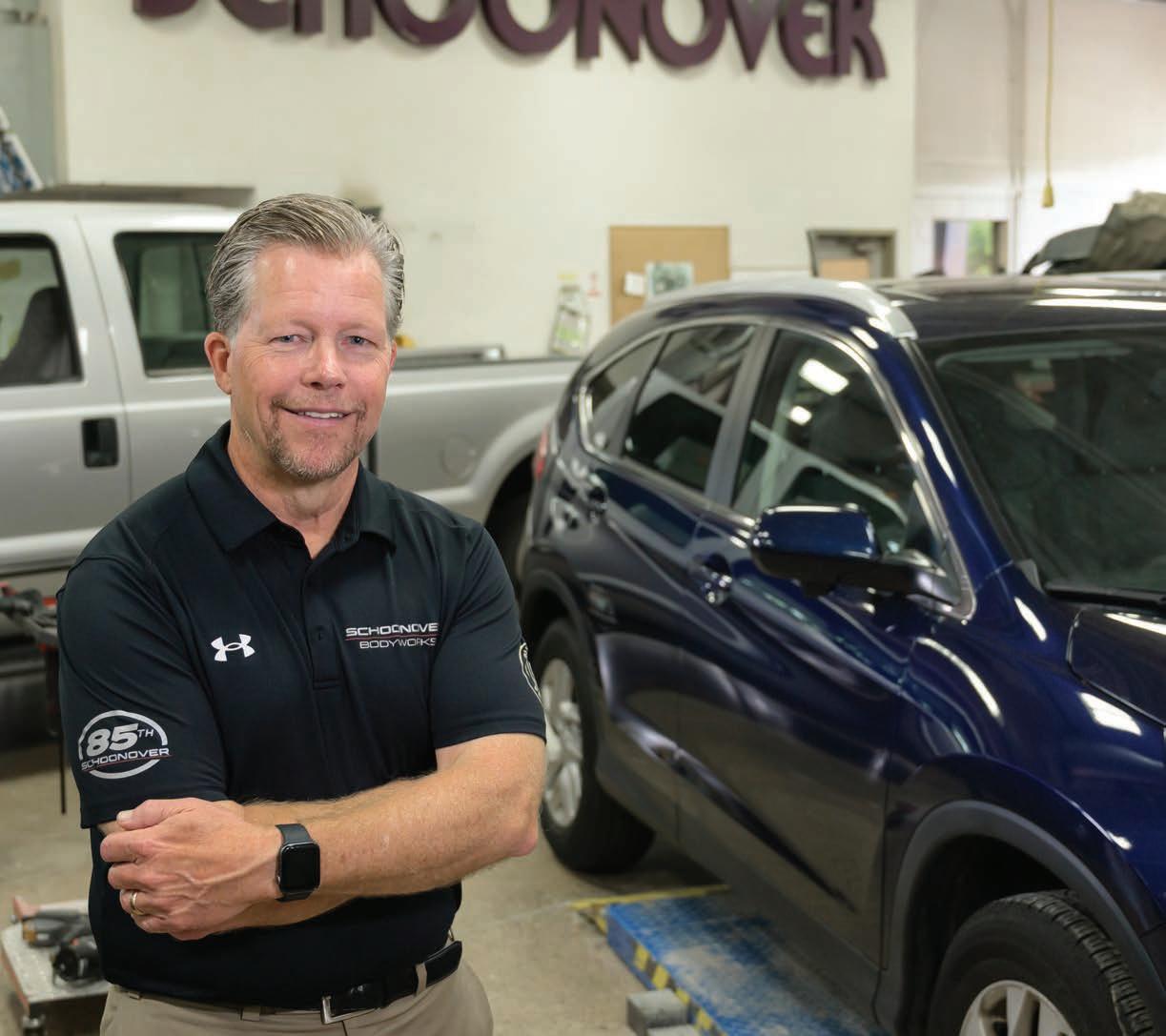
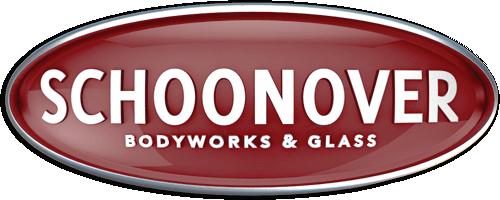
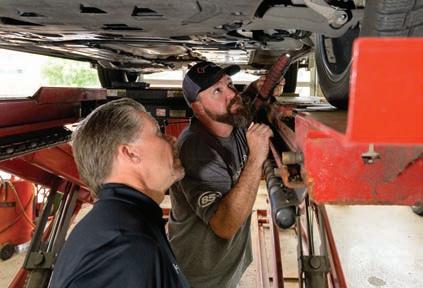

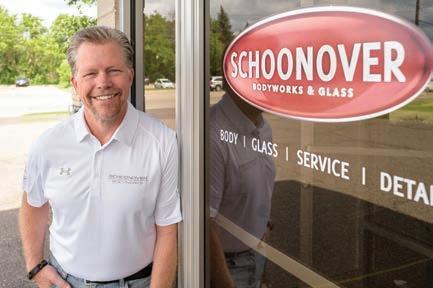
father, Richard, opened the Eustis, Florida, shop two years before De Marco was born. He grew up in and around the business. So it was no wonder that by age 18, DeMarco went to work there. “I was working as an apprentice under one of the body men,” DeMarco says. He had plans to train up for a techni cian role, but Richard had other plans, urging DeMarco to go off to college. He did that and earned his degree before return ing to All County. Upon his return, DeMarco was officially the shop’s estimator. But he was handling all aspects of the operation. “I like to call it baptism by fire, but by six months he kind of tossed everything at me and stepped back,” DeMarco says about taking the reins from his father. “And it’s been a learning process from there.”
By MATT HUDSON
FENDERBENDER AWARD RUNNER UP: Ryan DeMarco
RYAN DEMARCO started at All County Col lision when he was 18 years old. But his re lationship in the family business went back muchDeMarco’sfurther.
ship role at 27 years old. And through his hard work, close studying, and leadership skills, the shop has seen impressive revenue growth and sets a standard as an I-CAR Gold Class shop. Big Ambitions DeMarco is a young shop owner, but he credits the experience within his shop that’s helped them succeed.
“When I was estimating, I was lucky to have a 20-year tech in the shop,” he says.
“So that if I had a heavy hit I could take the time and go over it with him.” That kind of attitude helped him win the respect of his colleagues. DeMarco has found that leadership respect doesn’t adhere to age, but he needs to be on his Agame to succeed in a competitive industry. DeMarco represents the next generation who will take the industry forward. “It is a cool feeling,” he says. “I think I'm at a bit of an advantage in my age. A lot of competitors are thinking of retirement.”
54September 2022 fenderbender.com FENDERBENDER AWARD RUNNER UP
“I hired a parts manager to take the time to search instead of just calling and ordering parts, we have a flowchart to check the OEM,” he says.
“Recognizing and setting SOPs to in crease cycle time. Maintaining the high est level of customer satisfaction,” Richard DeMarco wrote. “Works 7 a.m. to 6 p.m. then works on any unfinished estimates or supplements at home until late.”
In late 2021, he took over the owner This impressive young operator gets results
The shop is seeing results from DeMar co’s leadership. Operating in a growing area just outside of Orlando, the shop has expanded its customer base and maxi mized process efficiencies.
“We’ve improved the process to handle higher capacity,” DeMarco says. “There were times at $1 million in rev enue when it seemed that it was all we couldDeMarcodo.” brought excellent techs to the team and trained them to write their own supplements, he says. The company im proved its DRP scores to get work that way. He also spearheaded an effort to increase marketing, in particular on the review and referral fronts. When competitors have 20 or so reviews, All County Collision has 200 mostly positive reviews online. Finally, DeMarco got serious about sourcing parts.
Under DeMarco’s leadership, All County Collision went from being a mil lion-dollar shop to a $1.6 million shop. Now it's on track to surpass $2.5 million in revenue.Innominating DeMarco for an award, Richard DeMarco chalked the success up to a dedication to process.

Congratulations to Mike and the entire team over at Schoonover Bodyworks for winning the 2022 FenderBender Award. This only confirms what we at Podium and the Shoreview, MN community already knew: Schoonover just does it better. They’ve combined the personal touch of a family-owned business with tools like Podium to create an unmatched experience. We can’t wait to watch as Schoonover Bodyworks continues to raise the bar for body shops everywhere.
- Mike Schoonover, Owner podium.com/schoonover
Congrats, Schoonover Bodyworks!
“Podium makes things more efficient for us. We’re more productive. A five minute phone call is now just a quick text.
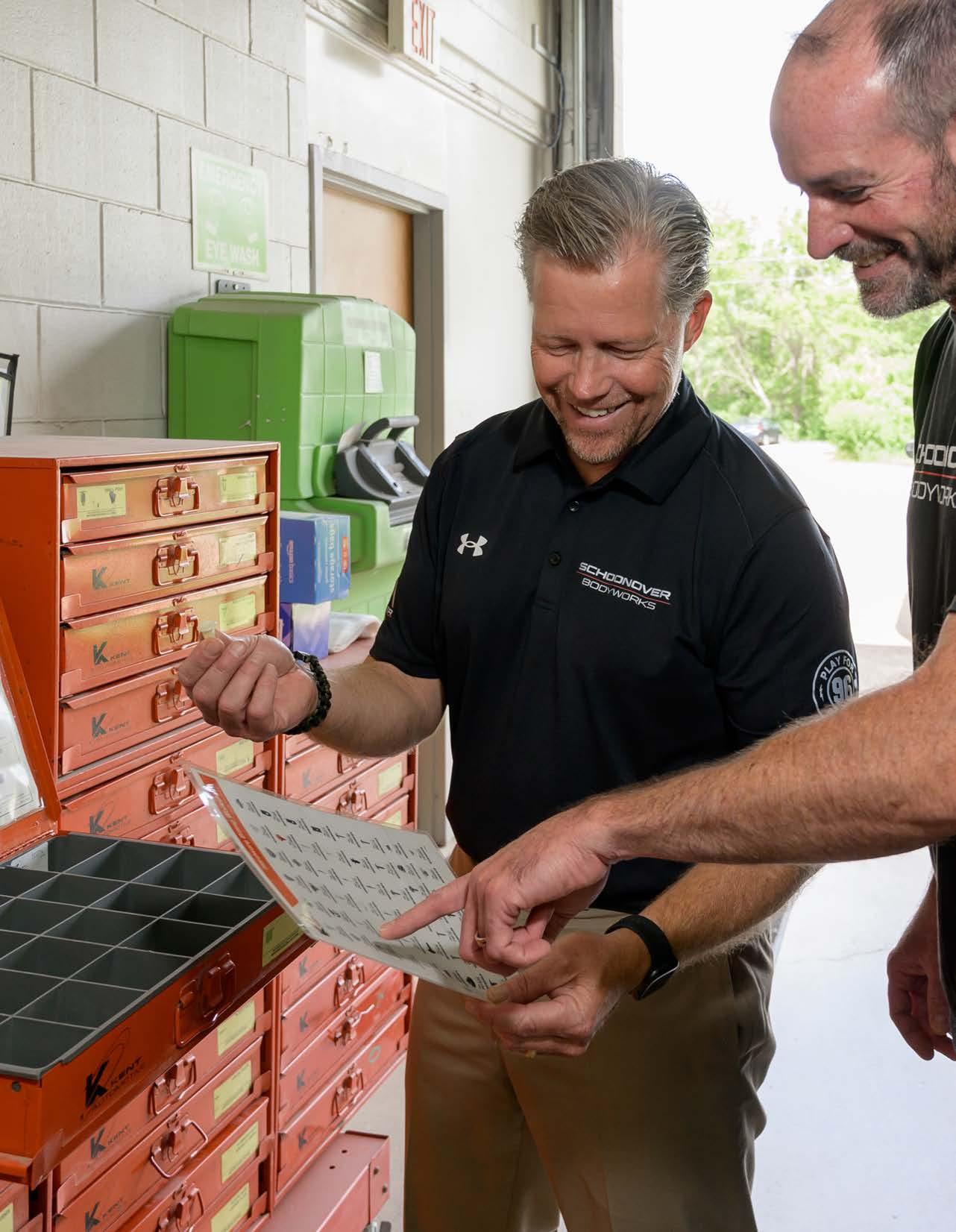
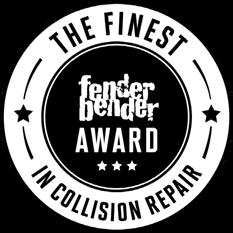
Sullivan says he was set to retire three years ago but his kids asked him to stick around. Whenever that day of retirement comes, Sullivan knows he’ll be leaving Pre mier safe and in good hands. “I’m not bragging, I’m just being honest,” he says. “I’ll put this shop up against any shop in the nation on quality, speed, cus tomer service, you name it. We’ll beat ‘em.”
By TODD KORTEMEIER
Unprecedented Times Sullivan says that without getting his em ployees to buy in, nothing that he came up with in his office on March 15, 2020, to handle the emerging pandemic would have mattered. But Sullivan did have a plan and it centered around one word: touchless. Staying apart was the only way to keep em ployees and guests safe. For employees, Sullivan broke co-work ers into teams to limit the possibility of spread. For customers, Sullivan had to find a way for guests to bring their cars in with out any face-to-face contact. Through presterilized rental cars, bagged and sanitized keys, electronically signed documents and so much more, the shop pulled it off and never had to shut down.
With two locations in Ventura County, and possibly a third on the horizon, Pre mier is a fixture within the community.
“The only person that didn’t collect a check for about 13 months is me,” Sullivan says. “We gained people through that.”
Cliff Sullivan
Part of the Community To Sullivan, serving the community is a responsibility. And that’s not only through providing repair services. It means donat ing pallets of water to local high schools for football games. It’s sponsoring the GIVE –MENTOR – LOVE Foundation benefitting victims of human trafficking.
ing to run this business, and keep not only the staffing and our facility safe but equally if not more important, the guests safe.”
56September 2022 fenderbender.com FENDERBENDER AWARD RUNNER UP
TOUCH TIME IS one KPI that any shop owner is familiar with. But the concept of touch took on new meaning to operators and to the world at large upon the onset of the COVID-19 pandemic. When it came to touch time in the sense of interaction between employees, between customers, that metric by necessity had to go to zero in MarchCliff2020.Sullivan remembers it well. The owner of Premier Coach Automotive in Thousand Oaks and Camarillo, California, even remembers the day. It was March 15, a Sunday. It was the day before Ventura County—sandwiched between Santa Bar bara and Los Angeles—was to implement its form of lockdown restrictions. It also happened to be the day Sullivan’s grandson was“Sundayborn. at about noon, I went upstairs in my office, closed the door, and I spent about four hours,” Sullivan recalls now. “My goal, the end goal, was to figure out how am I going to run our business, how are we go A leader in good times and bad
FENDERBENDER AWARD RUNNER UP:
The story of how Sullivan was able to do that is part of the reason why he’s a 2022 FenderBender Award runner-up. But it’s be cause of all the decisions, all the processes, all the team-building that came before in his nearly three decades running Premier that allowed the shop to not just survive but thrive through COVID. That broader story is why Sullivan is so-honored this year.
A People Business Sullivan’s orientation to collision repair came early on when he entered the indus try at the age of 24. Now 53, Sullivan admits he could barely change a tire or perform an oil change then, but he realized something early on that allowed him to be successful very“Whenquickly.Igot into this business I realized very, very early on that it’s not a car busi ness,” Sullivan says. “It never has been a car business. It’s a people business … And once I recognized that, the rest of the business be cameThateasier.”focus on people continues to guide Premier, which Sullivan bought by the time he was 26. That goes for guests—never “cli ents” or “customers”—as well as employees. Sullivan reports that 80 percent of his crew have worked there 10 or more years, and 20 percent have been there at least 20 years.
“Over the years we’ve done a good enough job, and a good enough job, and a good enough job, and an outstanding job, and an outstanding job and now it’s just not a question. They come see us,” Sullivan says.

©2022 ALLDATA LLC. ALLDATA, ALLDATA Repair, ALLDATA Collision, ALLDATA Diagnostics, ALLDATA Shop Manager, ALLDATA Tech-Assist and ALLDATA Mobile are registered trademarks and Automotive Intelligence, ALLDATA Manage and ALLDATA Community are marks of ALLDATA LLC. AutoZone is a registered trademark of AutoZone Parts, Inc. All other marks are property of their respective owners. Visit ALLDATA.com or call (888) 531-4092 ALLDATA applauds you and your team for this well-deserved win! We’re so proud to have served for more than 15 years as your collision repair information provider and are truly honored to be recognized as your “Preferred Partner.” Please accept ALLDATA’s enthusiastic congratulations. We wish you every success as you continue to inspire the entire industry with your innovation and commitment. Mike Schoonover Schoonover Bodyworks & Glass ALLDATA Collision® The #1 choice for collision repair information. Everything you need for safe and accurate repairs, direct from the OEMs. CONGRATULATIONS
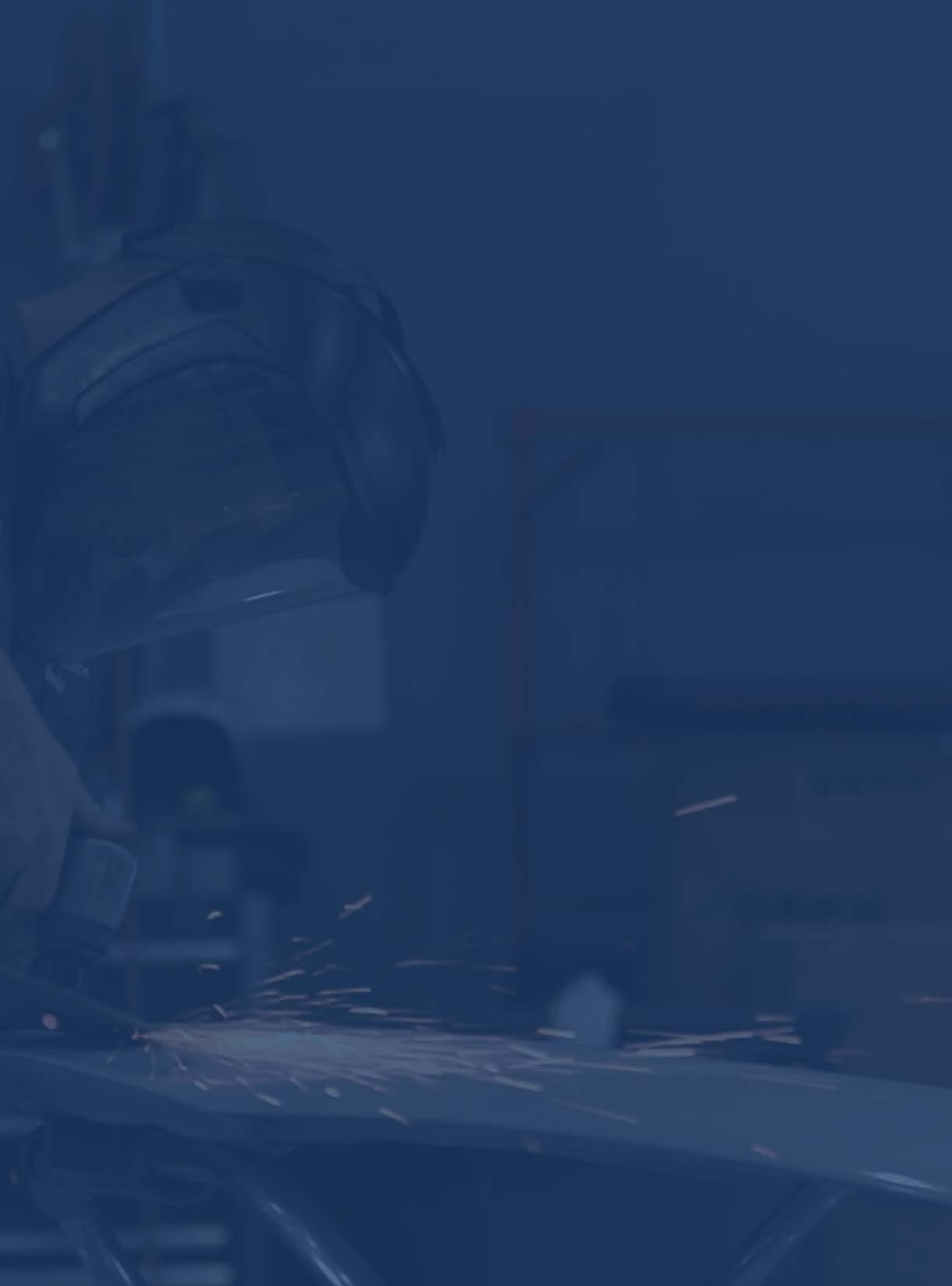
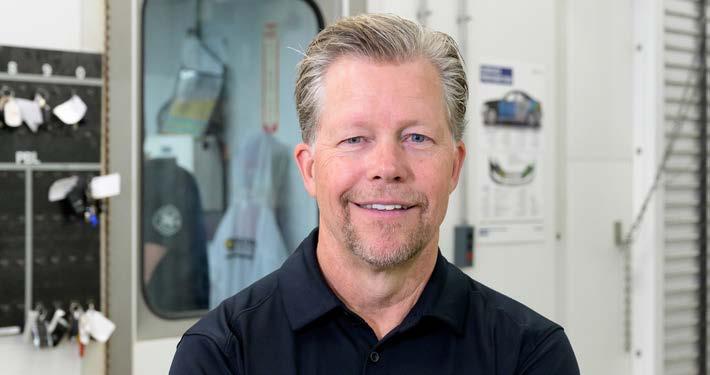
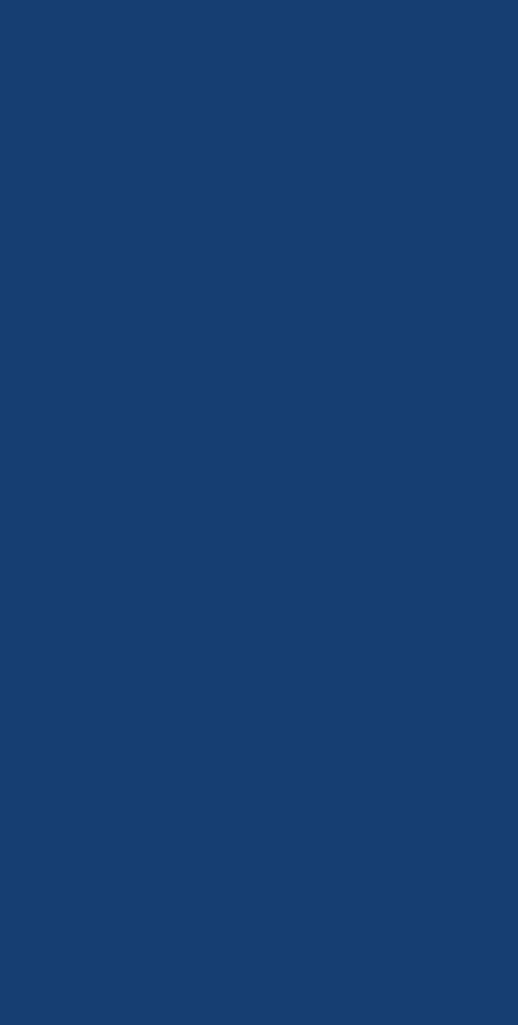
58September 2022 fenderbender.com
Make sure getting certified makes sense for your shop
Becoming OEM-certified is one way of doing that, but there’s much to think about before you put in the time and money pursuing certification from the
STRATEGY LEARN | GROW | WORK SMARTER THE SOP
WHAT TO CONSIDER WHEN CONSIDERING OEM CERTIFICATION
IN A QUICKLY EVOLVING collision repair industry, one of the best things you can do for your body shop is to make it stand out.
59September 2022 fenderbender.com
Human Factor Training is another cost to consider. You need to determine who you’d want to train, their time away for that training, the ongoing costs for future training, and again, how you can recoup that cost.
hottest new EV line, or your favorite luxury vehicle maker.
“There’s nothing guaranteed, like referrals, from being on a certification program, but it is something that can help separate your business as a repair professional from the body shop down the street,” says Tony Adams, who, prior to becoming a business services consultant for AkzoNobel Coatings, spent more than 30 years at Weaver’s Auto Center in Shawnee, Kansas, in a variety of administrative roles. Before beginning a path toward certification, Adams says, shops need to consider the fleet of vehicles in their area, what capital investments they’d need to make, how to recoup their investment, and more. Here’s what to consider when you’re considering certification.
UNSPLASH
As told to MIKE MUNZENRIDER Brand Choice
The first thing I would look at is the current fleet of vehicles that I’m working on–what brands come through my shop most often. If my No. 1 brand is Ford, then I’m looking into becoming part of the Ford Certified Collision Network. If my No. 2 brand is Nis san, I’m looking into Nissan certification, and so Anotheron. angle is to see what opportuni ties are out there. Let’s say I have a strong relationship with the Volkswagen dealer ship down the road. Could I leverage that connection to get more business by becom ing VW-certified?
Equipment Costs
Remember, it’s not just an equipment in vestment, there’s also an important hu man factor.
Self Promotion Here’s a big piece that shops often forget about: They put a lot of work into OEM cer tifications and they think the work is just going to come in the door, but you have to work and let consumers know that you have that specialized training and tooling for that specific automaker. Mike Anderson at his events will often call a certified shop, tell them he needs work done for one of their OEs, and the per son on the other end of the line never says the shop is certified! Shops really need to promote their certifications and their ad vanced training and everything else that comes with it. Again, leverage dealer relationships too, communicate with those service de partments, those service advisors, let them know you’re their certified shop.
Market Thoughts If pursuing certification makes sense in terms of the cars on which you work, or there’s a clear opportunity, the next thing to consider is if there’s enough demand in the market for you to recoup your invest ment. If you’re in a market with lots of higher-end vehicles, maybe it can sustain another Jaguar-certified shop alongside a competitor who is already certified. If you’re in a different market, perhaps a rural area, probably not. Also, certified work may not be the same as your retail rate, you may need a specialty rate to make up the costs.
What costs need to be considered? There’s the investment in equipment and tooling, and there are strategic ways to approach it. Does your existing equipment align with the required equipment for a given certi fication? If I’m going to look into multiple certifications, I want to know if a particular squeeze-type resistance spot welder is go ing to work for all three in order to avoid buying multiple welders.
Bottom Line There’s no rule of thumb or a formula to make sure certification makes sense for your shop, but if you consider your market, your investment and how to recoup it, and then promote the certification once you have it, your shop should benefit.
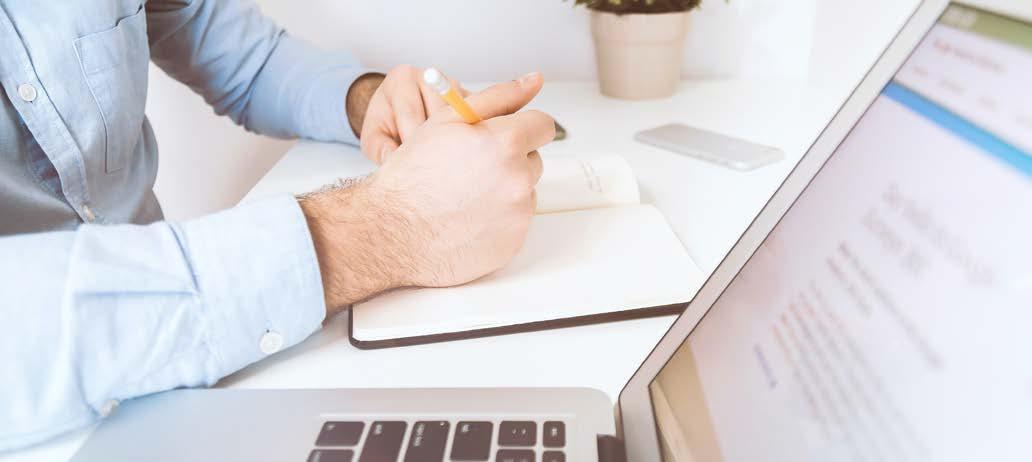
While accidents and restoration proj ects may bring people into the shop, it’s the experience they have once they’re there that will determine whether they return. “It can make or break your business,” says Bob Sloan, owner of Sloan Product, a custom body shop in North Canton, Ohio. “Communicating with your customers creates a relationship and brings loyalty. Once you’ve earned their trust and re spect, you have a life-long client for what ever they need.”
“Customers have accidents one out of ev ery seven years, and most are not familiar with the vehicle repair process,” reminds Mark Probst, owner of Probst Auto Body in Dieterich, Illinois. “As a collision shop, we need to take time with our customers and explain the process.”
In the auto body repair industry, open, honest communication is of the utmost importance. When someone has been in an accident, emotions and stress are at an all-time high. They need to know they can trust you and your shop to help them through the entire vehicle repair process from start to finish, and keep them in formed at regular intervals along the way.
KEEPING THE LINES OF COMMUNICATION OPEN to effectively communicate with customers to build trust and profitability
By LINDSEY GAINER
STRATEGY UNSPLASH LEADERSHIP
Honesty is the best policy. Both Probst and Sloan agree that being up front and honest in every customer inter
60September 2022 fenderbender.com
How
AS WITH ANY RELATIONSHIP in life, the success of a relationship between a busi ness owner and their customers is largely dependent on effective communication. Communication opens doors—it’s what lands you the job, builds customer rela tionships and makes a business thrive.
“The first phone call or visit should focus on showing empathy, assuring the customer you’ll take care of everything,” he says. “Part of the process may be explained, along with getting them in another form of transportation and getting them sched uled. A second conversation should happen once insurance information is verified, and to remind them of their appointment. Fi nally, on the day of drop-off, any concerns they have should be addressed. This would also be a great time to address how the re pair process is handled. The more commu nication and preparation you have up-front the better you can ‘set the stage’ for what all should happen and address potential prob lems you could run into.”
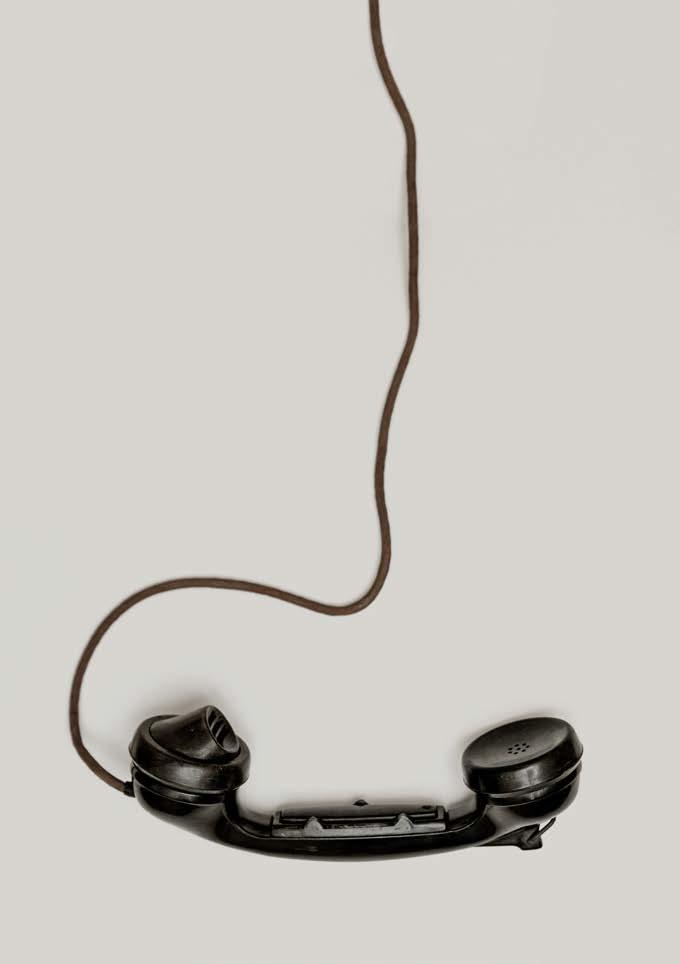
“Our first, main contact point with ev ery customer happens after we do a com plete teardown and blueprint of what is needed to repair the car,” he says. “This helps us set the stage for the rest of the re pair. During the next few days we are wait ing on confirmation of insurance approval and parts delivery times. Once these items are confirmed, we update the customer with a better idea of repair times. When re pairs are started and everything has been approved and verified, we update the cus tomer on a case-by-case basis. This could be once a week, twice a week, etc.” Probst’s team holds daily release meetings to review every vehicle in pro cess, to give the customer service repre sentative the information she needs to decide who to update. Then, when they’re close to finishing the repair, they let the customer know the vehicle should be ready to pick up within a couple days so they can plan accordingly.
Once a customer has dropped off their car, they’re fully relying on you to keep them updated, something Probst and Sloan both make a “Notpriority.onlydoes communication build trust, it also helps the customer understand the repair process … it’s all part of exceed ing expectations,” says Sloan. “I provide an overview of how the pro cess will go for their particular job from the start,” he adds. “Once the vehicle gets through the first step of the repair—typi cally when body work is complete and it’s ready to be scheduled for the paint booth—I let the customer know. At that point, I give them an ETA for completion day. Then, a day or two prior to completion, I provide another update via phone, email, or text—whatever they prefer. Most of our customers these days prefer to be con tacted via email or text. We determine that from the very first communication when they request a repair estimate.” Emails and texts allow Sloan to send progress photos to customers throughout the repair process, providing a more per sonalized approach. “It gives them a behind-the-scenes look at their repair, which people really appreci ate,” he says. “The amount of information I share really just depends on the client and what the repair or project is and how exten sive it is, but being able to text or email pho to updates helps me keep a good balance of communicating and being able to answer questions and educate the customer about the Forprocess.”larger projects or repairs, Sloan also invites his customers to stop by the shop and check on the progress in person. Probst also maintains certain “touch points” dur ing the repair, but leaves room for flexibil ity depending on the circumstance.
61September 2022 fenderbender.com action is imperative—especially if some thing has changed or not gone according to plan.“Honest communication is always best,” says Probst. “No question, always reach out to the customers as soon as something changes or goes wrong during the process that may contradict something you origi nally told them. Most people understand that stuff goes wrong and you may be de livering them bad news, but what people aren’t OK with is when something goes wrong and no one has communicated to them what happened.” Probst recalled a time when one of his staff members accidentally scratched a panel on a truck that was in the shop for re pair, in an area that was nowhere near the original damage. They began repairs on the scratch without notifying the customer, but the customer happened to stop in to check on progress and saw what had happened. He later told Probst that he wasn’t upset the truck was scratched, but was upset no one had notified him. “This is a perfect example of why it’s always best to communicate with the cus tomer and be honest,” says Probst. “Typi cally if you’re honest and don’t make ex cuses, customers will understand. They may not always be happy about what hap pened, but the fact you were honest lets them know you have integrity and no mat ter what you’re doing the right thing.” Sloan agrees, adding that you should never over-promise and under-deliver. “Always be upfront and honest from the very beginning of a repair or project.”
“I was very hesitant at first to make the transition,” he admits. “I wasn’t sure how I would pay another person and I wasn’t sure what my ‘new role’ would be if I wasn’t involved with the customer. Once I did re move myself, though, I found I had more time to spend on marketing, community relations, finance, production issues, etc.
Who should handle customer communication?
Probst and Sloan take two different ap proaches, both equally effective for the na ture and scale of their operations.
Communicate during the repair.
As a shop owner, the choice to handle custom er communication yourself or delegate the role to another person on your team certainly isn’t an easy one, and each option has pros and cons. One way isn’t better or worse than the other—the key is finding what works best for you personally, based on your preferences and goals for your business.
There are great coaches out there to sharp en your skills, which will make you a bet ter person/owner.”
Looking back, it was one of the best deci sions I ever made to hire people to handle the front Howeveroffice.”you decide to do it, Probst recommends all owners develop their communication skills through education, training, and mentorship/consulting.
As for what details Probst shares? “We go over repair concerns first and any information related to the length of repair time,” he says. “This may include quality of parts, any necessary OEM re quired procedures, sublet repairs that are needed, anything denied by insurance, any possible delays we could encounter, etc. We try to make sure there are no sur prises for the customer. I don’t believe there is a need to get ‘too technical’ unless the customer asks for more information.”
Sloan runs what he describes as a “small-ish family shop,” and handles the majority of contact with custom ers himself. He likes that it keeps him closely connected to his clientele and his community, but everyone on his team is cross-trained to communicate with cus tomers when Probst—whoneeded.runs a larger shop with multiple locations—handled customer communication directly for a long time, but decided to step away from it at the rec ommendation of a consultant to focus on other areas of the business.
“Read books and learn about people and personalities,” he says. “I highly rec ommend enlisting the help of consultants and mentors, and attending trainings.
“We see many aftermarket tools that claim to be factory approved, but frankly we see some issue with it,” says Amber son. “Some equipment was off by any where from 1 mm to 10 mm and required correction. This is why you also need thatTrainingtraining.”certainly needs to be a con siderable part of that plan—otherwise, shops can be left with equipment that can’t be properly employed. Moreover, it is also impossible, say the experts, to invest in everything at once. Even if the budget would allow for it, such an expan sion may not be advisable.
“A lot of what you are investing in will also be outdated in a couple of years,” says Amberson.Thefinal consideration in any expan
While there are certainly no crystal balls, and honestly who could have foreseen a global pandemic, followed by massive inflation and record-high gasoline prices, shop owners still need to consider how to address an expansion with what they already know.
By PETER SUCIU ANYONE LOOKING TO TAKE ON an expansion is reminded that Rome wasn’t built in a day. However, what is often forgotten is that the Eternal City grew haphazardly with no clear-cut plan. That resulted in a terrible fire that destroyed much of the city, while floods were a constantThoughfear.we can hope that a shop owner won’t face actual fires or floods (or attacks by barbarians), a lack of a plan when considering an expansion could still lead to untold stress and headaches.
Considering where you want to be in that world is the question. That can even in clude what cars you may want to see roll into your shop, and which ones you’ll have to turn away.
The Challenge We can’t predict if there’ll be another pandemic, and we don’t know if the pain at the pump will result in drivers ditch ing their big trucks, but we do know that the automotive world is always evolving.
“Is there a particular brand or brands you want to work with, and you can go from there,” Amberson tells FenderBend er. “But, do you also hope to rely on the dealer to perform some of the work, such as calibration?”Thatisavery big part of the conversa tion, adds Bud Center, I-CAR director for technical products and curriculum.
The failure to address the future can also spell doom for a shop. “In a nutshell, you have to consider what you hope to accomplish,” explains Darrell Amberson, president of operations, LaMettry’s Collision. “There are a lot of ways to tackle this.”
62September 2022 fenderbender.com CASE STRATEGYSTUDY GETTY
“Shop owners need to have a plan,” says Center. “And they need to consider what mix of cars is coming in the door today. We often hear of shop owners investing in equipment without properly analyzing their current business and the market place and then not seeing those vehicles come in to allow them to utilize the equip ment. You have to have a plan, and you have to know your market.” In addition to the market conditions, you need to make sure the equipment you actually choose can handle the job.
Simply put, where do you see the business in five or 10 years, and how do you plan to get there?
It’s time to start thinking about investments—but don’t get overwhelmed
APPROACHING ADVANCED VEHICLE REPAIR
“About one in five calibrations fail,” Cen ter also warns.
“This could include working with rent al car companies, or glass companies that do replacements and then you can provide the calibration,” says Anderson.
“You have to think about your facility,” says Center. “Not every location is going to have the space required to perform ADAS calibrations.” The Solution With the plan in place, shop owners can determine what equipment they’ll use, and what training they’ll need to provide to ac tually use it. This can begin with knowing the market, and the demographics.
PEXELS
“EV stalls will need to be larger,” says Center. “It is safe to say you’ll need, at min imum, one and half the amount of space for an EV stall.”
“I don’t think there is really ever a case where training is wasted,” says Amberson. “And when it comes to equipment, if you approach this conservatively, at best you purchase something you don’t use as much as you may have thought you would. It is still necessary to take these risks, but also understand that expansion is something that is going to be ongoing and that in time things will need to be replaced.” Such upgrades and expansion should be seen for the opportunities that they can provide.
63September 2022 fenderbender.com sion is making sure you even have the room to handle any new equipment you might be considering.
“You need to consider what are the most common vehicles in the area, as well as what you’re already commonly working on, and then you can start your growth from there,” says Mike Anderson, owner/ president of CollisionAdvice Consulting Services. “It is also important to note that not investing isn’t an option. This is espe cially true of the calibration tools. If you are doing $150,000 or more in monthly business, there should be no reason not to invest in the tools and technology.” There also needs to be that consid eration of aftermarket vs. factory scan tools, and today there are a number of manufacturers that will sell the tools to do the calibrations. Choosing a quality scan tool is critical, otherwise, the mon ey could be wasted.
The Takeaway A well-planned and well-executed expansion can allow a shop to grow, and provide quality service to the customer for years to come.
“You have to understand where you want your business to go,” concludes Center. “You could dive in and you can tackle multiple vehicle lines, and even EVs, but you have to remember that every vehicle you choose to service may require an investment in spe cialized equipment and training.”
“You can start with the aftermarket calibration tools, and based on your needs and finances and willingness to grow you can determine what brand to focus on,” suggests“ManyAmberson.shopswill find that they’re go ing to invest in the equipment for the cars they’re most commonly fixing,” adds An derson. “This will have other advantages. Repetition is key, and the more you do, the better you’ll get at it.”
Shops should also take advantage of whatever opportunities that the OEMs are currently“Thereproviding.isalot of training available from the OEMs for both certified and non-certified shops,” Anderson contin ues. “Training is absolutely necessary, and you may have to do some research because there are so many myths around calibration.”“I-CAR’s educational programming includes an optional ADAS role which in cludes 14 online courses and two handson courses where students receive expert instruction in ideal learning conditions including all of the necessary tools, equip ment, and facilities,” says Center. Once those facets are understood, the next step is focusing on how any equipment can be incorporated into the shop.
The Aftermath Following any upgrade or expansion, there will likely be some second-guessing on whether the right decisions were made. Yet, this is where proper planning also helps— so that you don’t feel like equipment ac quisitions and the requisite training that comes with it were wasted effort.
With these investments in the shop, the business can also expand its services.
“This is where we recommend ‘bland’ walls, dimmable lights, and of course plen ty of space,” adds Amberson. And if you’re even thinking about tak ing on electric vehicles (EVs) in the shop, there are other considerations that will need to be addressed.
“It should be the best replacement when possible,” says Amberson. “It may not matter whose tools that you use, but you need to get the target in the exact spot the manufacturer specifies. Most OEM scan tools would be able to do that, but some aftermarket products won’t have the ability to get into all the modules on a ve hicle. It may not even be clear which mod ules you’re not getting into.”

IMPROVE SHOP EFFICIENCY & PROFITABILITY • PRECISE OPTICAL MEASUREMENT WITH 6 HIGH RESOLUTION CAMERAS • SELF CALIBRATING CAMERAS, ALWAYS ACCURATE, EVERY TIME • CAMERAS AUTOMATICALLY TRACK VEHICLE HEIGHT ON LIFT • MAXISYS INTERFACE FOR WHEEL ALIGNMENT INTELLIGENT ADAS IA900WA FRAME The Next Step In ADAS Calibration Now Includes Wheel Alignment Technology. One Frame To Perform 4-Wheel Alignment & ADAS Calibration. ADAS CALIBRATION SELF-CALIBRATING AUTO HEIGHT TRACKING6 HI-RES CAMERASWHEEL ALIGNMENT TWICE AS NICE THE ONLY FRAME TO PERFORM ADAS CALIBRATIONS & WHEEL ALIGNMENTS SUPPORT: 1.855.288.3587 FOLLOW US @AUTELTOOLS VIEW MARKETING MATERIAL: ISSUU.COM/AUTEL2 EMAIL: USSUPPORT@AUTEL.COM | WEB: AUTEL.COM
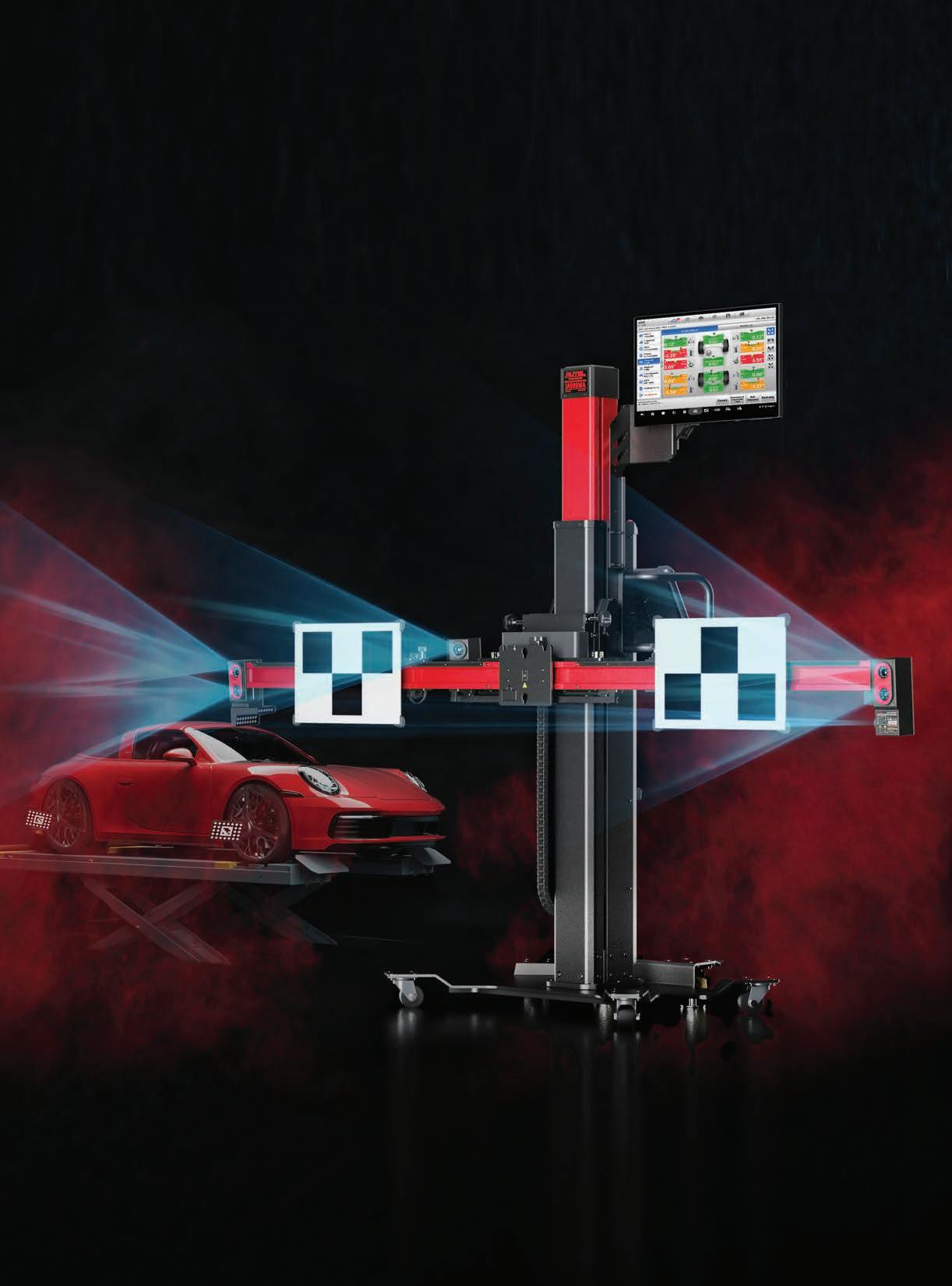
65September 2022 fenderbender.com
STRATEGYADAPT UNSPLASH
INDUSTRY-WIDE CHANGE is not some thing that can be taken in all at once. Rap idly shifting technologies and the pro cesses that bind those shifts are vast and feel more and more frequent these days. When looking at this phenomenon in the context of a repair shop environment,
THE
AFTERMARKET EFFECT
Mike Tanner of the Auto Care Association explains how emerging technology could be an aftermarket advantage
By HANNA BUBSER AND NOAH BROWN
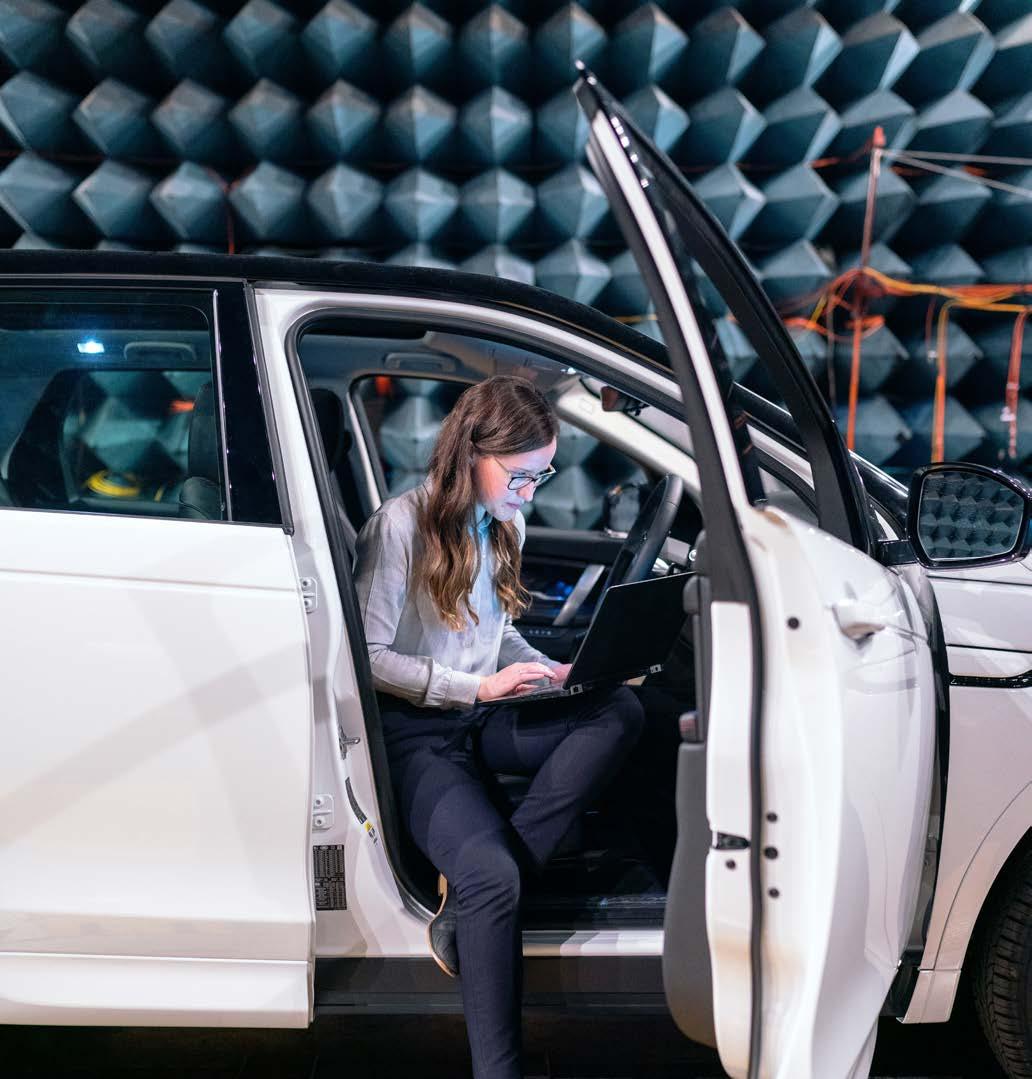
Stop by our booth to meet the CARSTAR family or let us know if you’re coming by emailing Aaron at arodrigue@carstar.com CAN’T WAIT TO SEE YOU AT THE FENDER BENDER CONFERENCE!MANAGEMENT

JOIN NOW! Unlock your full potential with the only social network 100% dedicated to working and future technicians. Use TechForce to connect with other techs, host events, access resources for your future, and more. JOINTECHFORCE.ORG Education&TrainingCompetitions&GamesCareers Scholarships&
STRATEGY PIXABAY
Hearing from the aftermarket in terms of new vehicle design is especially impor tant, Tanner says, because repair is an in evitable and overlooked part of the process.
“[The manufacturers] don’t always look at how this vehicle is going to be repaired or … how it’s going to be maintained after it’s out of warranty.” Tanner says.
67September 2022 fenderbender.com it can be difficult to determine the best place to start. Preparing for the future can be a daunting task, especially when some of the most impactful changes, such as ICE vehicles becoming more obsolete, won’t be seen for several decades.
Mike Tanner, director of vehicle com munications with the Auto Care Associa
Working alongside the emerging tech nology committee, which is made up of ACA members, the group determines what technologies are high and low risk and then performs research to establish an approach.Twoareas that the group has deter mined to be priorities include access to

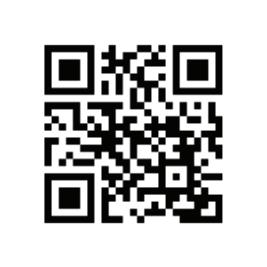

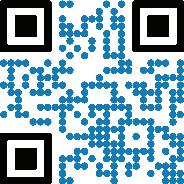

68September 2022 fenderbender.com into play, which is an element that Tanner says is important to both the repair shops and the customers alike.
“It’s important to remember that there are a lot of challenges out there, and the aftermarket will evolve,” Tanner says.
“Our proposal is to implement standardization for secure data architec ture,” Tanner says. Tanner explains that this standard ization is far-reaching as well, because as we look to the future there are still many services that the aftermarket can STRATEGY provide to electric vehicles and softwaredefined vehicles alike, such as tires, ADAS calibration, brake services, battery servic es, battery coolant, steering, suspension and“Allmore.of those areas will still be there, and then there’s other things that we’re not even aware of yet,” Tanner says. But at the end of the day, it all comes back to data. “If we don’t have access to that data, there’s nothing that we’ll be able to do.” TannerTheresays.is reason to be hopeful, Tan ner explains. The technology to connect vehicle data to those who are repairing it is already at play in the industry. Tanner says that, at this point, it’s about getting sectors to come together in a more collab orative way. “All of the technology exists in the vehicle today to do that. They have hard ware security modules in the vehicle that would support this,” Tanner says. “We feel like it’s just a matter of everyone getting together and agreeing on the policies and governance. But the technology is no lon ger an excuse for not allowing access to the aftermarket to maintenance repair data.” When looking into the future, Tan ner believes that this kind of openness to communication is vital. Discussions among industry members can be a great jumping-off point, and Tanner will have the opportunity to help conduct such a conversation at the ADAPT: Automotive Technology Summit this fall in DallasFort Worth, Texas. He will have a spot on the “Securing High-Tech Repairs” panel, during which panelists will discuss how to maintain cybersecurity for all repairers, and how to keep customer data safe. As overwhelming as that topic may sound, Tanner wants all of the Summit at tendees to know that the aftermarket is re silient, and there is plenty to look forward to.
Built ByJoin the Movement! To create awareness of talent opportunities within the collision industry by educating the population as a whole on the ample opportunities, success stories and segments within the industry. Donate to the Movement! GRAND PRIZE RAFFLE Driving Talent Forward FINGERTIPSCOLLISIONREPAIRNEWSATYOUR FENDERBENDER.COM
“The vehicle manufacturers have been saying for years that the vehicle is basically a computer on wheels … if that’s the case, then vehicle owners are used to having control over who has access to their data that’s created by their phone or their computer. It shouldn’t change just because it’s a vehicle,” Tanner says. Ensuring that this data can be accessed fairly is a big component of the Right to Repair movement, which continues to be a hot topic across the industry. Tanner wants to see all sectors of the automotive industry come together over these stan dards to make the largest impact possible.









































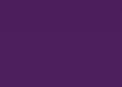
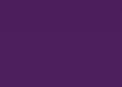










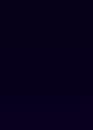
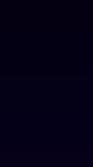







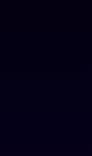
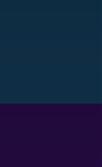














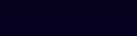











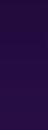
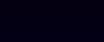
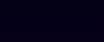



































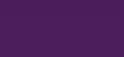
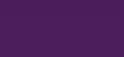


















































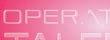

















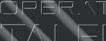


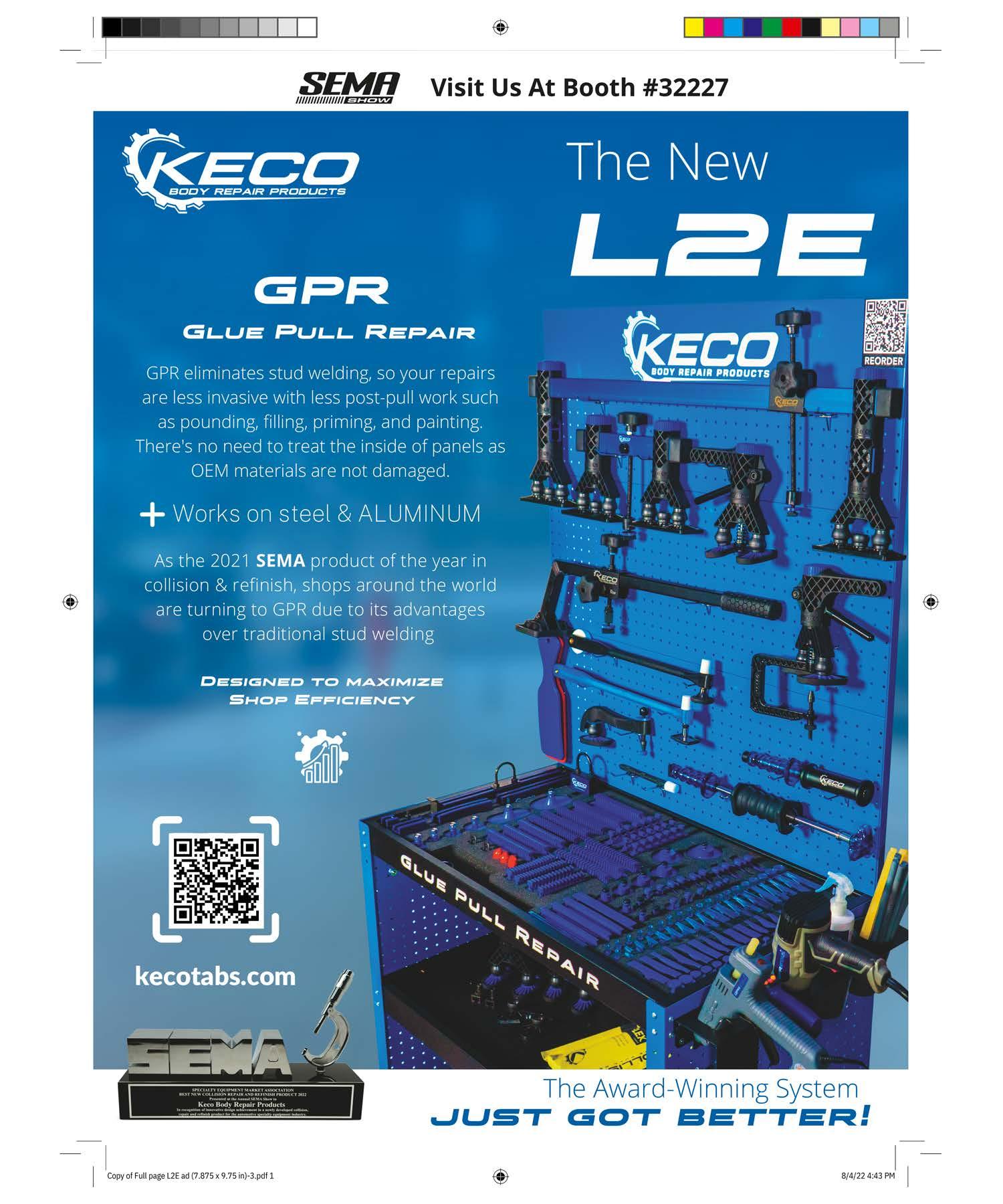
PEXELS
A
THE MORE PEOPLE WHO ARE familiar with your business and the services you offer, the more potential customers you can attract. It’s simple math! And these days, the way most people get to know a brand or service is through media out lets—places like social media channels (e.g. Facebook, Instagram, YouTube, and Twitter), local news stations, print publi
STRATEGYSALES+MARKETING
SECURING MEDIA COVERAGE FOR YOUR SHOP step-by-step guide
70September 2022 fenderbender.com
By LINDSEY GAINER
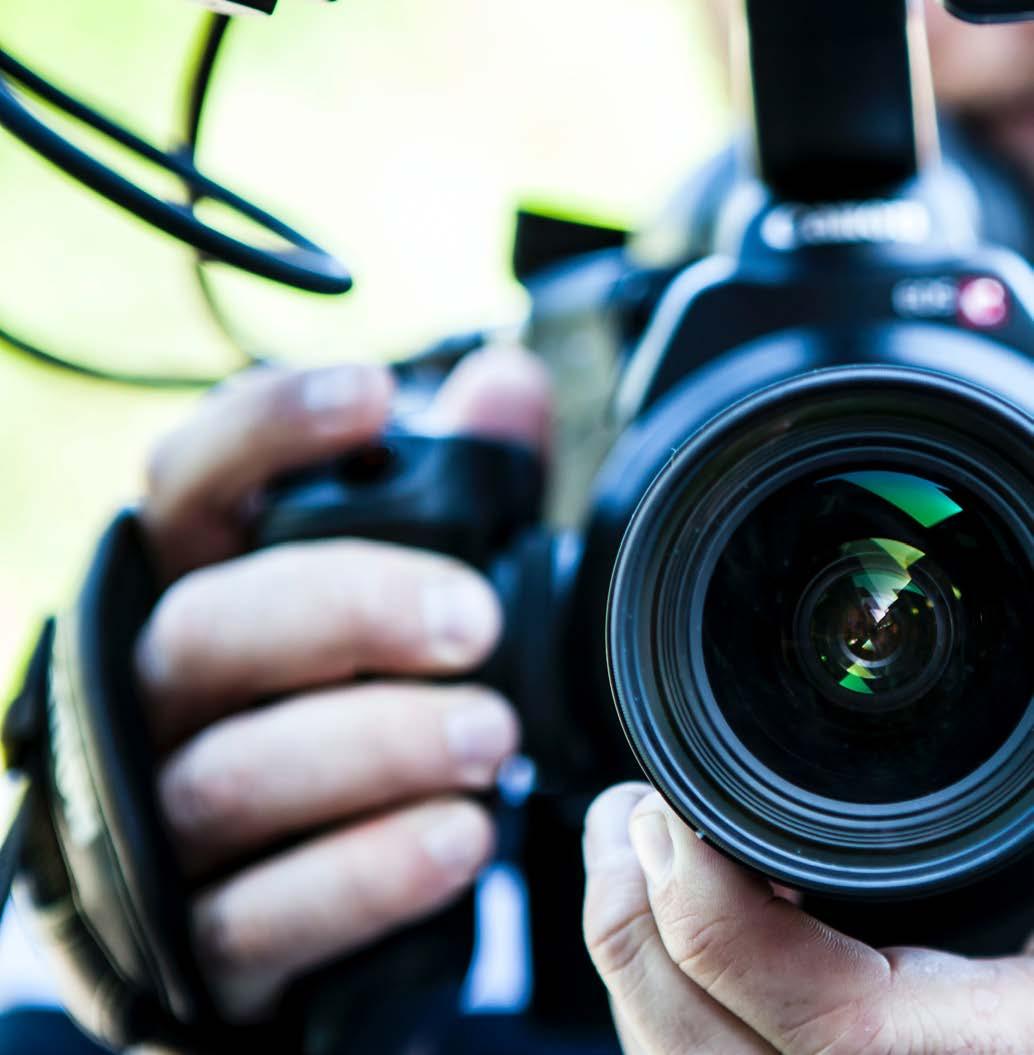
“Small shops tend to lack time to fo cus on media, so they can definitely use help from experts. Therefore, shop owners should consider hiring a marketing agency or contractor whose sole focus is to promote their business. Outsourcing is not only like ly to produce better results, but a firm or contractor will also come with fewer strings attached than a full-time employee.” cations and their corresponding websites, radio and podcasts. Forging a connection with potential customers through these channels is essential for success, and it’s not as hard as you may think to put your shop on the media map. Don’t be shy.
Traditional media coverage by a TV sta tion or print publication happens in one of two ways—you either seek it out your self by initiating contact and “pitching” yourself to a media outlet, or the outlet it self takes an interest in something you’re doing and contacts you directly to feature your shop in a segment or article they’re creating. While the second option is cer tainly enticing, it’s not how you should expect to gain most of your traction. In order to get your shop on people’s radar, you need to actively pursue opportunities for media coverage.
Additionally, consider signing up as a source on a website like Help A Reporter, which matches reporters with sources who possess expertise in the subject matter they’re working on. If your skillset and ex pertise match a journalist’s need, they may contact you to contribute to their story.
Regardless of what kind of coverage you secure, though, be sure to get the most “bang for your buck” by sharing it on your website and social media channels once it airs or is published.
You may also want to consider putting together a short press release that shares all the details with the reporter up front, as Sapp did. He recommends doing a quick Google search to find a template online, or finding someone willing to write it for you if you choose to go that route.
If these suggestions sound great but you just don’t know how you’ll find the time to implement them, consider hiring someone to focus on your media coverage and mar keting initiatives. “If you are a shop with multiple loca tions or have big revenue goals, you might have an in-house person who can handle everything for you,” says Filzen. “However, if that in-house person is doing other things for your business, they will lack the time and attention necessary to do a terrific job promoting your media.
“Securing this kind of press coverage is a great way to stay involved in the commu nity,” adds Sapp. “When you get press it puts your shop at the front of people’s minds, and they’ll be more likely to remember you when they need the services of a body shop. It also adds legitimacy to your business in the eyes of potential customers.” How to reach out and secure coverage. Once you’ve identified one or two ideas you’d like to pitch, start by considering whether you know anyone directly or through an ac quaintance who works for a media outlet in your area, like Sapp did. If you do, use that connection as a starting point and work from there. If you don’t, that’s OK. Think of local TV and radio stations, newspapers, magazines, or websites that might be interested in what you have to share, and visit their websites to find their contact information (often found at the
Following up is important too, some thing Sapp did several times to ensure he was on the media outlet’s radar. Media coverage can also be purchased when you invest in advertising. If you find you’re unable to gain traction through “free” coverage, it’s worth exploring paid avenues.
If you’ve never pitched yourself or your shop in this way before it can be intimidating at first. Keep in mind, how ever, that you’re doing the media outlet a service by informing them of something that might be of interest to their audience … so they’ll be happy to hear from you. Pitching a media outlet directly saves them the work of having to discover the idea themselves—it’s a win-win situa tion for you both! They have a great story for their audience, and you’re increasing your shop’s visibility and brand aware ness at the same time. What should you pitch? When it comes to deciding what types of things to pitch, marketing expert Jennifer Filzen—owner of Rock Star Marketing in Monterey, California—suggests looking for opportunities that will present value to an outlet’s audience.
Consider hiring help.
71September 2022 fenderbender.com very bottom of the site, in the small print).
Some will have general email addresses or numbers you can call, and many will list directories of their reporters, writers, hosts, etc. along with their contact infor mation—go ahead and send an email or give them a call directly.
“The best thing you can do is lead with value,” she says. “If your story offers val ue to the community—like a celebration where everyone’s invited, or the attendees get to learn something new, or if the story helps people feel safer—chances are better that you’ll pique the outlet’s interest for a time slot or article.” Is your shop celebrating a milestone anniversary? Just opening and having an open house for the community? Hosting a customer appreciation day or holiday cel ebration? Offering a new service or spe cial that people can’t find anywhere else? Or perhaps you’re growing your business or expanding to additional locations, or you’ve recently won an award or partici pated in community service … these are all great (and valuable) opportunities for mediaWhencoverage.Modern Body Shop in Athens, Georgia, recently celebrated its 50th an niversary, it secured both digital and print coverage on the cover of the local Sunday newspaper simply by sending out a press release. Jake Sapp, assistant manager and grandson of the shop’s founder, Gene Sapp, says it was important to the family that they set aside a day to invite the community to come together and celebrate the milestone. And, having worked in the nonprofit world before joining the team at the shop, he knew how important it was to gain public ity around the event. Sapp already had contacts at a couple of the local papers, so he emailed them a press release directly and his efforts paid off in a big “Theway. Athens Banner-Herald decided to run a nice profile on the shop and event,” Sapp says. “It was featured on their website and the front page of the Sunday paper. We shared the link to the online feature on our social media channels and I sent it to some contacts directly as well. It definitely helped bring awareness to the event.”
ARCHIVE: fenderbender.com/menefee TIFFANY MENEFEE has more than 20 years experience in the insurance business and now runs a collision repair shop in El Paso, Texas.
I cannot state enough the importance of hav ing good skilled collision repair technicians, but along the same lines we know how critical it is to have a good shop culture. Shop culture affects our entire shop and in my personal opinion it can criti cally affect shop flow and employee retention. So what happens when one of your best technicians is wreaking havoc on your shop culture? Well let me tell you that’s what I had to deal with at my shop. My best technician had been with me for al most five years and I depended on him heavily. If I needed something done on a car right then he would do it. If I needed him to come early or stay late or come in on a weekend he would do it. He was fast. He was skilled. He was committed to the shop. All the other technicians and staff seemed to like him. Overall he was an excellent repair technician. So why did I fire him? Dynamic is the word that comes to mind. His dynamic within the shop was throwing everything elseItoff.started off very small where I didn’t see what was happening, but he started to believe that the shop and myself needed him more than he needed the shop and the job. If you’ve been in the industry long you all can think of one technician that comes to mind when I say this. He started to become a playboy, strutting around the shop like a rooster preening his feathers. It began with taking small liberties of the freedom I allotted him because he was such a good technician and someone I relied on. Those small liberties began to grow. When I saw what was happening I put a stop to it. I spoke to him. I addressed the issues and was hoping that would resolve things but his energy had changed. Everything seemed to be running smoothly and the same as before but it wasn’t. He wasn’t happy. He felt like I was now taking advan tage of him because I put a stop to those liberties he was taking. His energy and how he felt about the shop changed, which changed the whole dynamic in my shop. But it was so hard to pinpoint because everything seemed normal. I was terrified to fire him. What if I was wrong and he wasn’t the issue with the shop? I didn’t know when and where I would find another skilled technician. I didn’t know how the other employees would react. I was afraid that it would make them feel insecure in their positions at the shop if I was firing my best technician. I was con cerned about shop flow and if we would be able to get the same amount of vehicles out that we were used to. I was worried about the shop culture. I was just worried that I hadn’t tried all I could do to save this valuable employee and that I was go ing to make a wrong decision.
The collision repair industry is hurting for skilled technicians and firing a skilled tech is pretty unfathomable for most shops. I am always reading articles and blogs about how to attract skilled technicians, how to cross train, apprentenc ing technicians and how there is just a general lack of collision repair schools. We can all agree good technicians are just hard to come by.
Moral of the story is don’t let one employee, even if it is your best technician, hold your shop back. Yes, it is scary to let someone you really de pend on go, but you and your shop will rebound. Letting my best technician go was one of the best decisions I have made because my shop and my team are stronger now than we ever were.
COLUMNS COLLISION COURSE
Finally though, I did fire him. He started taking liberties again and I couldn’t justify keeping him. It was affecting morale, affecting shop flow and caus ing me a huge amount of stress. And it was one of the best decisions I have made in the shop to date. I had no idea how one person and their per sonality and energy could so negatively affect a shop. I was worried about the shop’s productivity but everyone, without me having to ask, pulled together and we kept our shop flow the same. Yes we had to work some extra hours until we found a replacement technician, but everyone stepped up and did that willingly. The shop morale and shop culture changed for the better within one week of my letting my best technician go. The employees are closer knit now and morale and culture is bet ter than it ever has been. It still leaves me dumb founded how I can let my best technician go and the effect it had on the shop was an instant ben efit, not a drawback.
EMAIL: tiffanykaymenefee@gmail.com
Sometimes the most unimaginable move is the right one
72September 2022 fenderbender.com
How Firing My Best Technician Liberated My Shop
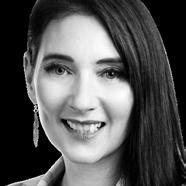

THE 2022 FENDERBENDER INDUSTRY SURVEY IS HERE KPI TECH+TOOLS LEADERSHIP Learn more and get the report today! SPONSORED BY Get key insights into the collision industry, including shop owner demographics, shop revenue, what technology shops are investing in, and how they're marketing their businesses.

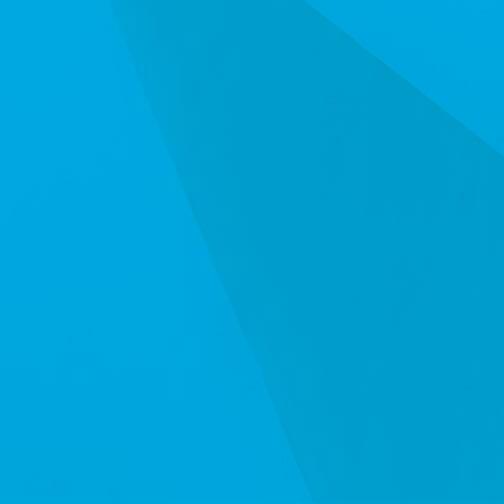
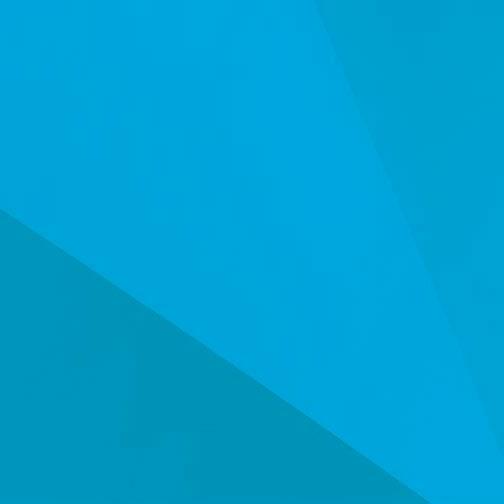
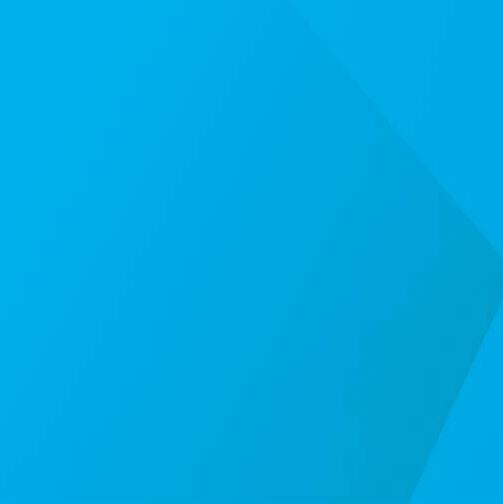

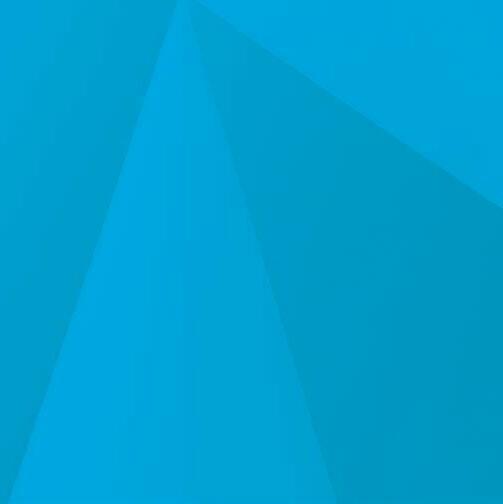

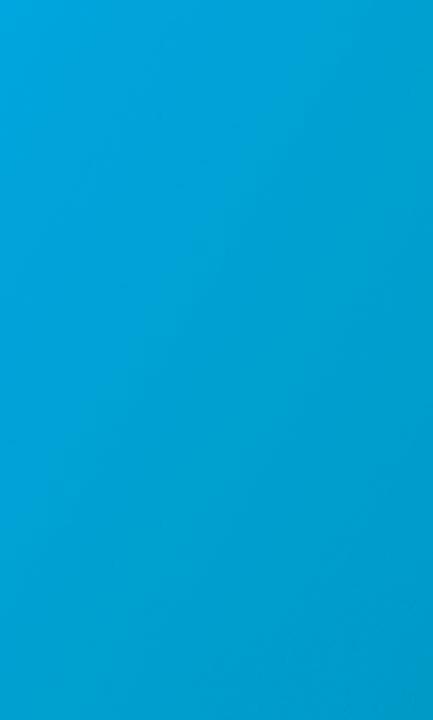
74September 2022 fenderbender.com PARKSSTEVEN COLUMNS OUTSIDE THE LINES
In July of this year I spent two weeks in Poland and the Czech Republic working with Ukrainian refugees. It was an amazing trip and hopefully someday I’ll discuss the trip in this column. How ever this month I want to talk about my travel ex perience as I flew in and out of Berlin, Germany. There was a church in Berlin which offered us the use of their van during the trip. We gave away 50,000 free books to children and the van was perfect for our mission. Driving in Germany is a pure joy. My wife has relatives in Germany so I’ve visited and driven there before. Everyone, and I mean everyone, follows the rules there. German efficiency is not just a saying, it’s poetry in motion. The left lane in Germany is purely for passing drivers. They move over immediately after passing a vehicle. I live in New Jersey, and every lane is considered a pass ing lane here. And we also get those drivers who do the speed limit while cruising in the left lane. Even bicycle riders in Germany use hand signals to let people know when they are turning. And the best part about it is everything works smoothly. I’ve never experienced a traffic jam in Germany. With everyone obeying traffic laws, people just move along without getting in anyone else’s way. When I was walking with a German friend on the sidewalk I accidently stepped into the bike path. He let me know, immediately, that if I didn’t get off the bike path that I would be hearing the bikers ring their bells letting me know I was in their way. I would not mind driving for a profession in Germany. To put that into perspective, I lived a quarter mile from our collision center, and if I could afford it I’d fly there every day instead of driving. Driving is not an activity I enjoy. Yet with everyone following the rules in Germany it be comes a very enjoyable endeavor. So, it got me thinking about how well we fol low rules in the shop, from a rule as simple as where, or where not, to park a vehicle to some thing like mixing the paint for the repair in the beginning of the repair process versus making the paint while the vehicle is sitting masked up in the booth. Every time we would break rules in the shop it would hurt our efficiency. I can’t tell you how many times I wanted to blow a gasket because a vehicle would be sitting in the paint booth masked up while the paint team was struggling to get the color matched. We made the decision in 2008 to verify the color and mix the paint for each repair during the blueprint stage. Yet in 2022, with mostly the same team, we would find ourselves breaking the rules and pay ing the Anotherprice.example of me breaking the rules came in our hiring processes. I learned to in terview people at least five times before hiring them. It worked out so well that I hired a bunch of people, following our hiring rules, between 20042006 and then we didn’t need to hire anyone for over a decade after that. We would hire someone if the right person came along, but that was just adding to the team, not filing a void. In 2020 a body tech moved into our area from out of state. I went through our normal interviewing process and eventually hired him. He turned out to be one of the best hires I ever made. Just after deciding to hire him a painter moved into our area from out of state as well and asked to interview with us. Feeling like things were going so good for us, I broke the rules and hired him during the second interview. That hire did not turn out well. I had to fire him after a frustrating year. So why do we break the rules? I think our cul ture accepts rule breaking. In fact sometimes it’s even rewarded. I think we don’t realize the conse quences of breaking rules until it’s quite painful. The Germans figured out a long time ago that fol lowing the rules, even the tiny ones, was benefi cial for all. I think we are such an individualistic society that we do what’s best for us, not the good of theWhenwhole.Ilook back over the best periods of our company, it’s when we are following our own rules that we wrote together as a team. We would often stop the system, sit together and talk when the pain of not following the rules had become unbearable. We’d all agree that we weren’t go ing to let it happen again. Somehow we’d find ourselves having the same conversation again a yearIt’slater.likely that there are rules, or processes, your team has devised together that aren’t get ting followed on a regular basis at your shop. If you are wishing your team efficiency was better, take a look at what rules are not being taken se riously. Have a review with the team about why those rules are in place and commit to sticking to them before the pain gets too difficult to bear. It will pay huge dividends in the long run.
EMAIL: jason@boggsauto.com ARCHIVE: fenderbender.com/boggs
JASON BOGGS ran Boggs Auto Collision Rebuilders in Woodbury, N.J., for nearly 25 years. He has attended the Disney Institute and Discover Leadership, and has studied lean manufacturing processes.
The Importance of Rule Following Remember why your shop has rules in the first place
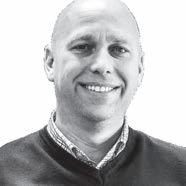
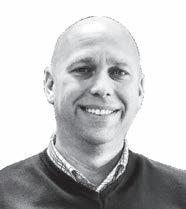
The men and women of LKQ are passionate about parts and providing the best possible service to our customers. Our world-class product sourcing, recycling, and remanufacturing operations and our more than 20,000 North American employees are the difference between delivering a part that’s just OK and one that’s just right for the job. Feel the passion and find your next replacement part at www.LKQcorp.com Call Us : 866-LKQ-CORP Visit Us Online : www.LKQCorp.com The PartsPassionatePeople New Aftermarket | Recycled OE | Remanufactured Engines & Transmissions | Paint Products
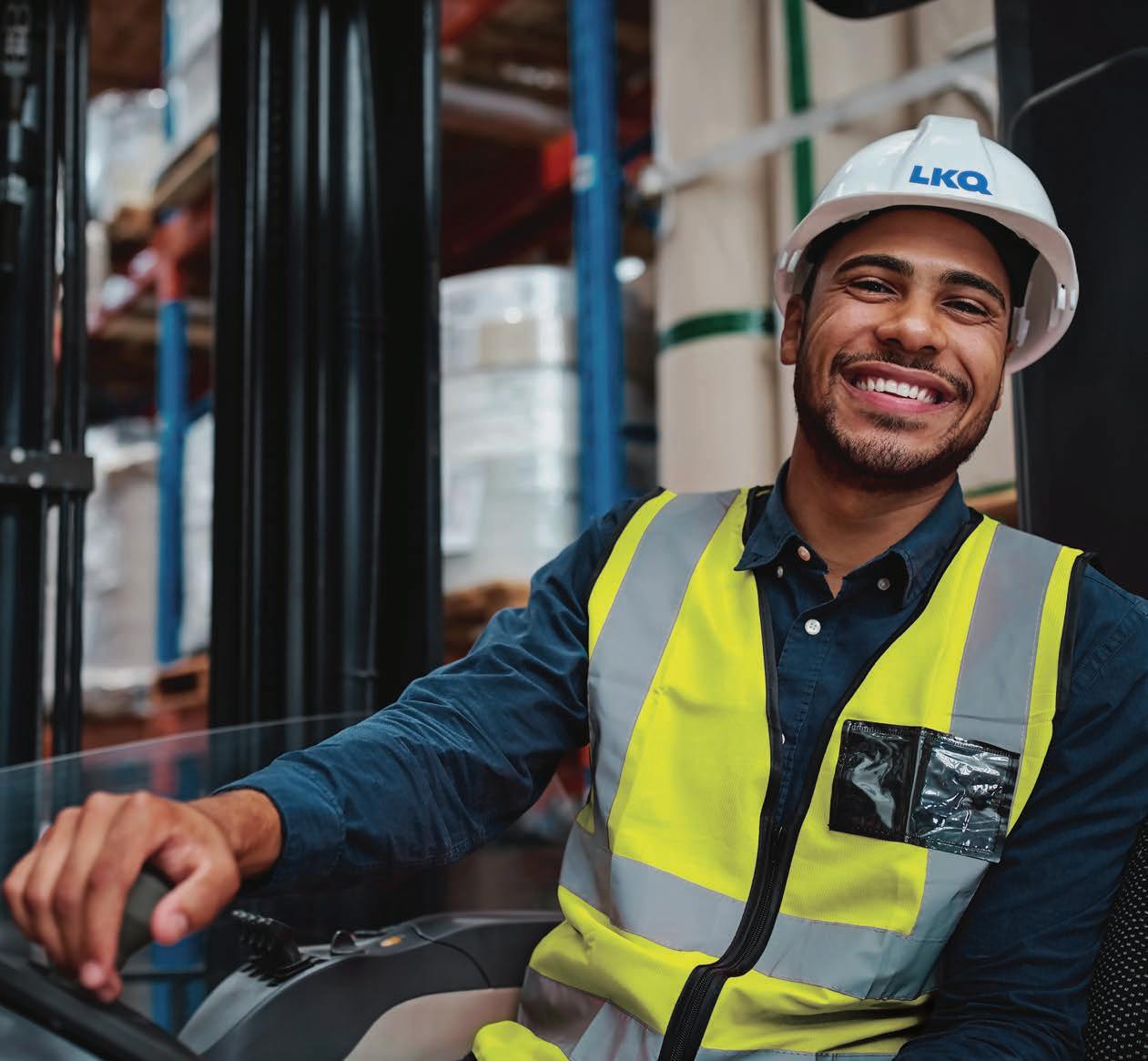
224-SPANESI (224-772-6374) www.spanesi-americas.com facebook.com/spanesiamericas Spanesi Americas, Inc. 123 Ambassador Dr. STE 107 Naperville, IL 60540 The Blueprint is Right in Front of You. The Spanesi® Touch Electronic Measuring System and Multibench Structural Repair Workstation are designed to work together seamlessly. The Multibench allows technicians to drive most vehicles directly onto its low-profile ramps. After the vehicle is disassembled to evaluate the damage, the Touch rolls right up, letting the technicians gather measurement data in no time. With its 10-ton pulling column, the Multibench also serves as a single-bay repair solution. Finally, technicians use Touch to check structural repairs and ensure proper OEM specifications are achieved. Touch Electronic Measuring System: Comparative Measurements Complete SuspensionMechanicalDocumentationPartsMeasurementsPartsMeasurements User Added Points with Photos Vehicle Frame and Structural Items Wheel and Tire Alignment Checks Multibench Structural Repair Workstation: Loading Capacity 3,175kg (7,000lbs) Lifting Height 1.45m (4’ 9”) Lift Time (Ascension) 45 seconds Pulling Force 10 Tons MULTIBENCH Structural Repair Workstation TOUCH Electronic Measuring System Learn More Now
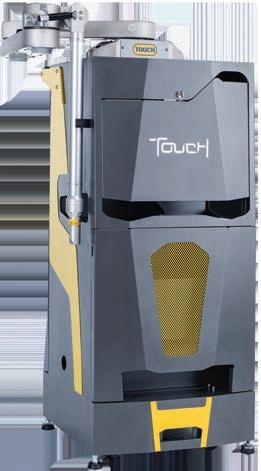
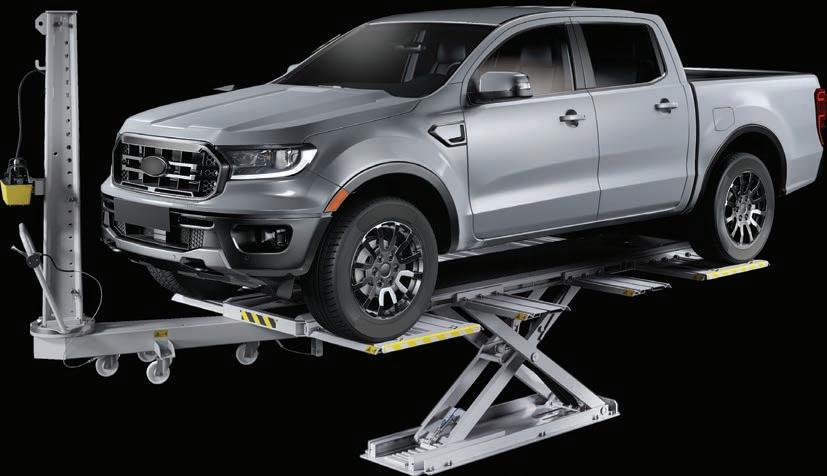
OUTSIDE BACK COVER 4.625” FOLD Ready. Set. GetI-CAR.com/GTGCtoTheFastestandMostAffordableWayforaShoptoGetStartedonitsTrainingJourney!This Customized Package Gives Shops: • A Discount on Gold Class Required Training • Limited Turnover Protection • An In-Shop Knowledge Assessment™ • A Dedicated Customer Care Representative • Flexible Monthly or Pay-in-Full Payment Options

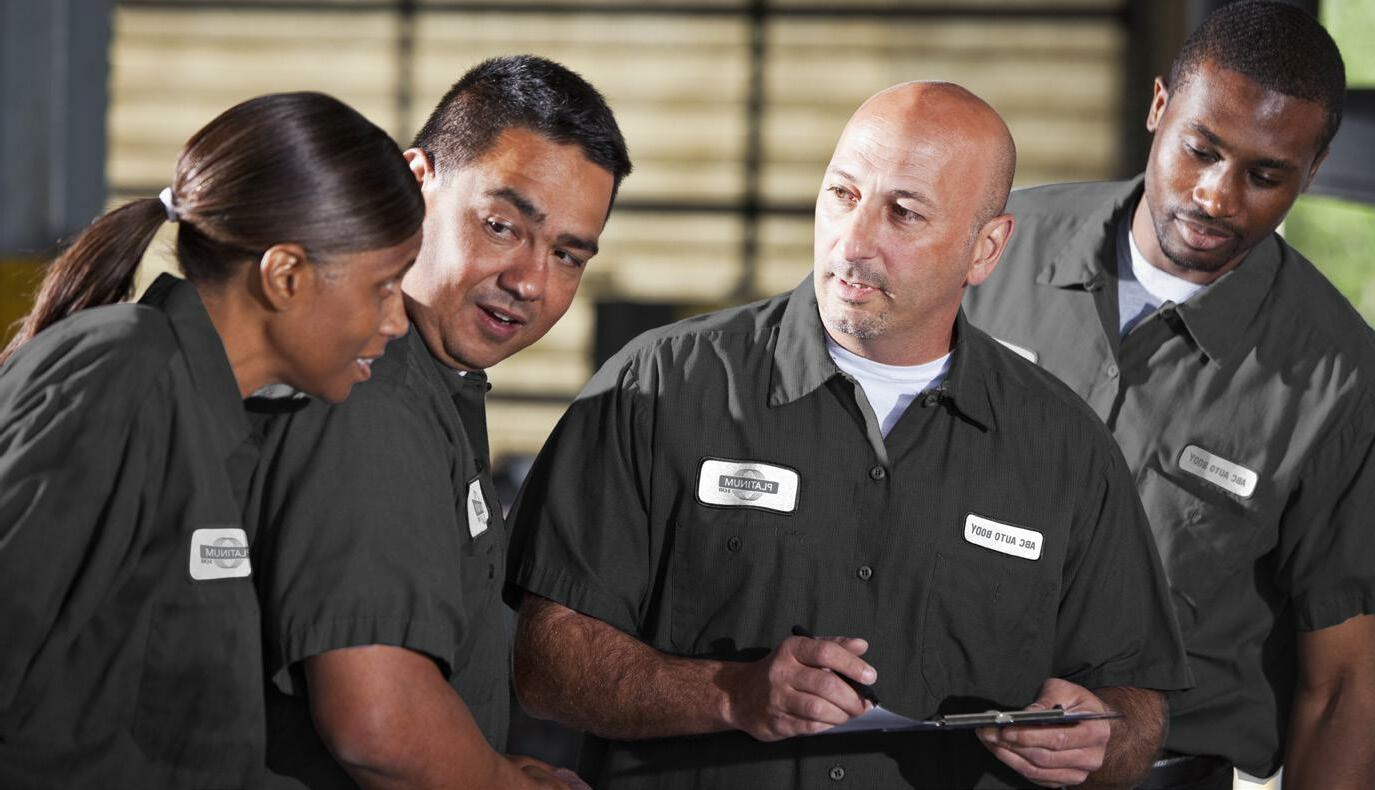