
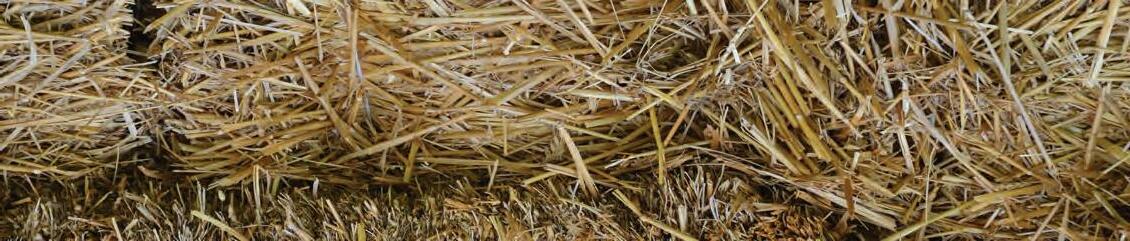
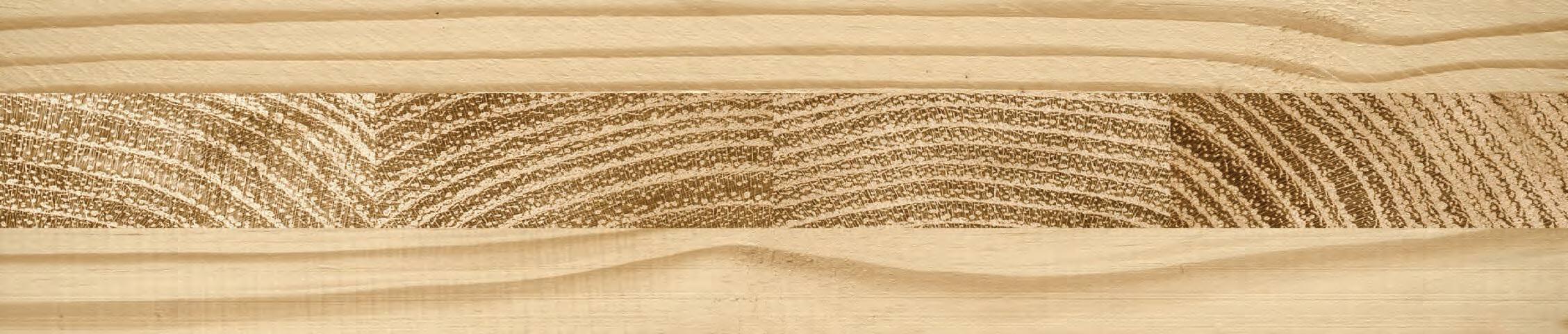
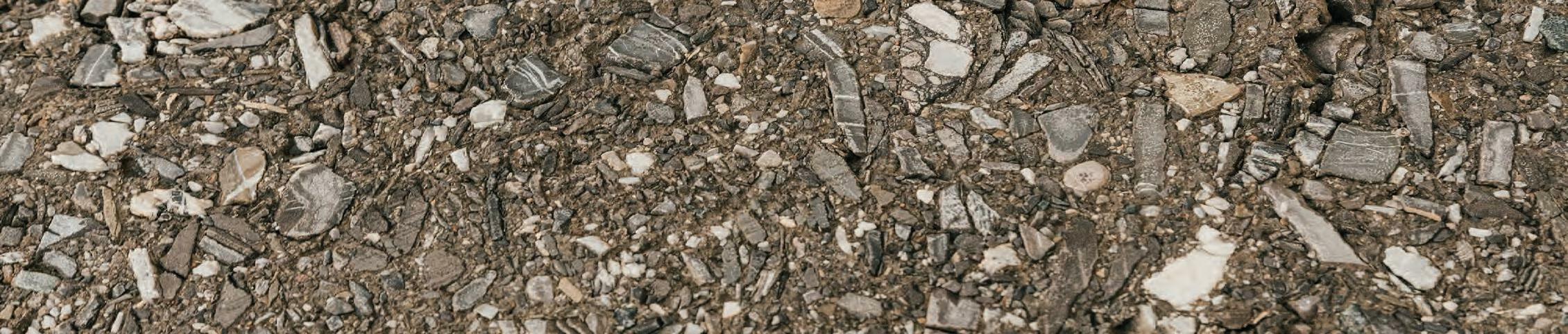
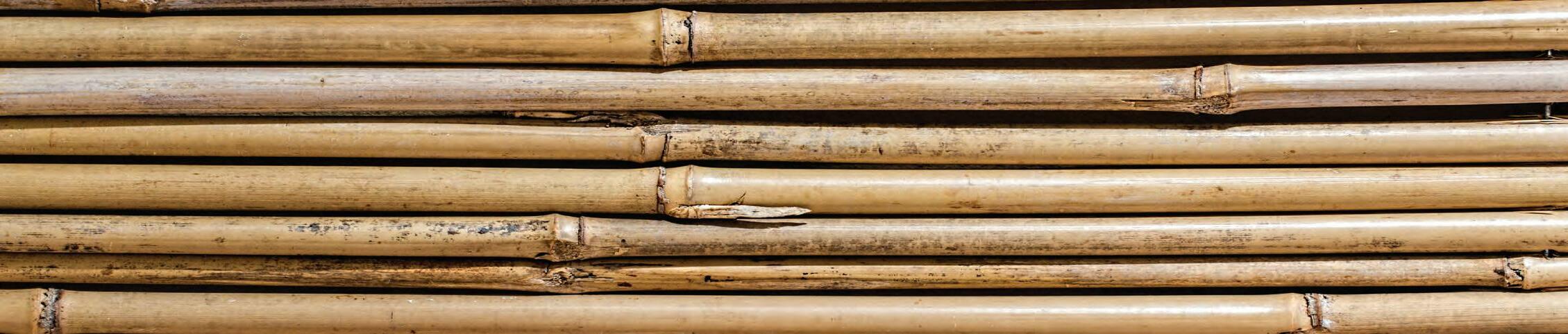


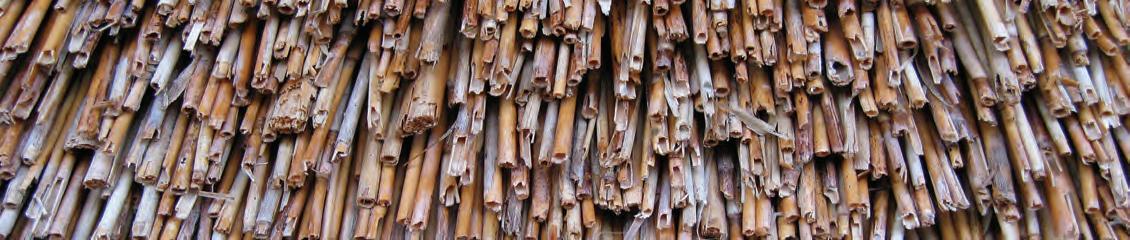
The five small houses documented in this publication are designs by LTL Architects (Lewis.Tsurumaki.Lewis) that use biogenic material assemblies as the catalyst for building form, domestic organization, and spatial seduction. Our goal with these concept houses is to demonstrate the creative opportunities for rethinking domestic dwelling by embracing biogenic materials and their full life cycle as integral to the design process. By doing so, we seek to amplify the call for architects, developers, and builders to integrate carbon sequestering materials in constructing the approximately one million homes built every year in North America1 and to address the challenge of housing the growing population globally.
This design work serves as a coda to our recent book, Manual of Biogenic House Sections, which asserts that the most viable means to radically reduce embodied carbon in buildings is to use plant and earth-based materials.2 In that book we illustrated 55 built houses from around the world to demonstrate that this work is not only possible, but has a global presence and impact. We made cross-sectional perspectives for each of the 55 houses to show the intersection of spatial invention with material assemblages broken into chapters on wood frame, mass timber, bamboo, straw, hemp, cork, earth, brick, stone, and reuse.
For the five house designs shown within this document, we deliberately foregrounded section as the privileged representational means of design, exploring the relationship between site and material, and rendering visible the issues of gravity, climate, and the human occupation of space. In addition, we have woven the process of assembly and disassembly into the design of these houses, embracing the full life-cycles of the building materials as integral to the form and composition of the house. This is a direct challenge to the legacy of modernity that sought to focus architectural practice on the objecthood of architecture, privileging the industrial fabrication of building products and resulting in the dissociation of buildings from site and material processes. Our current climate crisis is a consequence of this framing–a conceptualization of design practices as concurrent with linear systems of extraction, building, and then demolition. The dependence on fossil fuels underwrites this dissociation of architecture from the creative possibilities of regenerative and dynamic life cycles. In these five projects we are arguing for a new direction for discourse, one in which architectural practice embraces and is in turn informed by dynamic and regenerative cycles of material use.
Yet, when plant- or earth-based building materials are discussed in architectural discourse, there is often an inherent nostalgia for the traditional forms of building historically associated with a given material. For instance, earth-based buildings are associated with traditional adobe houses and straw constructions conjure images of utilitarian agrarian sheds. These couplings, while a resultant of past practices that are valuable for study, unfortunately function as a deterrent toward innovation and the creation of new and seductive projects that can galvanize broader public adoption of biogenic materials. Moreover, it is not our intent to simply replace low performing standards with more environmentally friendly materials as such substitutions have limited capacity to make fundamental change over time without a transformation in the size, form, and performance of the house.
Rather, these projects demonstrate our optimism about architecture’s agency when engaging biogenic materials in the move towards a regenerative future. The houses all use low-processed materials that sequester significant amounts of carbon and can be locally sourced from the selected sites. The positive impact to human health, by removing highly-processed building materials derived through the petrochemical industry from homes, is significant.3 These houses challenge the binary between the house as object and its site, and embrace the consequences of time, in terms of biogenic growth and decay, as integral to their conception. The interior of these houses are compact and small, with the spatial organization of domestic life rethought from the standpoint of the biogenic material assemblies. As such, these five houses exemplify the use of limited available resources for maximum performative and spatial potential, and summarized by a simple phrase echoing the words of Michael Pollan: Live in physical spaces. Not too big. Made from plants.
1 “Housing Starts End 2020 Strong: Risks Ahead,” Press Release, National Association of Home Builders (January 21, 2021). https://nahb.org/news-and-economics/industry-news/ press-releases/2021/01/Housing-Starts-End-2020-Strong-Risks-Ahead
2 Paul Lewis, Marc Tsurumaki, and David J. Lewis, Manual of Biogenic House Sections (ORO Editions, 2022).
3 See the work of the Healthy Materials Lab at Parsons School of Design, https://healthymaterialslab.org/
Clay Plaster
Clay Plaster Wood
Wood Horizontal Batten Natural Stained
Plywood Subfloor
Thickness is often conceived in negative terms in contemporary architecture, indicative of a lack of material optimization and therefore inefficient. However, biogenic materials, particularly those derived from agricultural waste products, like straw, invert those logics, reasserting the performative and spatial benefits of plant-based mass that is plentiful, cheap, relatively lightweight, and carbon-sequestering. This project capitalizes on the potentials of this biogenic thickness and illustrates a dialogue between two methods of stacking jumbo straw-bales.
Nested in a cleft along a rocky coastline in a northerly climate, the house is insulated from the ground by a terraced mound of straw that echoes the slope of the hill. A corbelled wall of vertically stacked strawbales defines the other side of the house. The primary collective space of the house is captured between these two elements and capped by a roof of wooden beams that tie the two forms of straw-bales into a stable assembly. The hillside mass serves as a counterweight for the stacked wall. A continuous linear skylight separates the two systems while providing illumination for the primary collective spaces of the house below. The terraced bales are surfaced internally by a cork lining, rendering the interior as an inhabitable topography for domestic life. More private spaces, bedrooms, and a bathroom are burrowed into the thickness of the straw mound while carved voids connect the interior to apertures in the roof above. The wall of straw-bale begins outside the enclosure of the house in the rugged site, extending to link the entry path, front door, main living area, and view into a linear sequence. Taking advantage of the modular form of the straw-bales, the wall rises from two bales to eighteen bales high while it tilts incrementally outward at the base, corbelling like masonry to accommodate a wider living space toward the sea. While the wall is surfaced in clay-based plaster and shingled with hemp fiber corrugated sheets, the roof is covered by an unprotected exterior layer of straw, allowed to decompose over time and slowly merging building and site.
200k
180k
140k
120k 100k 80k
-20k
-40k
-60k
-80k
-100k
-120k
-140k
40k 20k -160k
-180k
160k 60k -220k
220k -240k
The growth cycle of straw is less than a year, and straw is a waste product of the food grains they produce.
Stone, steel, cork and hemp can be disassembled and reused in other projects. Reused biogenic materials continue to sequester carbon.
Bundled straw and jumbo sized bundles serve as the preset modular unit of the house and inform its design.
Reusable helical piles, adjusted to the topography of the site, provide a level datum for the installation a stone floor that is lifted off the ground.
Cork Stake Straw-bale
Plywood
plaster
Clay plaster and a layer of cork protect the straw, creating the interior surface of the house.
Jumbo bales of straw, staggered into a terraced step or corbeled as a retaining wall form the shapes of the house.
PREFABRICATED CEILING
Timber boxes, filled with straw-bales are assembled off-site and provide structural span integrated with insulation.
The structural timber box beams span between the wall and the terraced mass to enclose the interior space.
Corrugated hemp panels
Battens
Clay plaster
Straw-bale
HEMP CLAD STRAW-BALES
Corrugated hemp fiber panels provide an additional weather protection on top of clay plaster adhered to straw-bales.
In addition to the corrugated hemp cladding, wood siding is used to protect the clay and straw exterior. On the roof, the straw is left to decompose, forming the growing medium for the green roof.
Bedroom 1 Bedroom 2
Open Living Space
Bathroom
Kitchen
Rammed Earth Wall Bamboo Lamella Wood Framing Plywood Sheathing Weather Resistant Barrier
Thatch Roof Wood Sill
Glulam Sill Rammed Earth Wall Mud Tile Stone Footing Foam Glass Insulation
Rammed Earth Floor Trass Lime Floor Slab
Two distinct structures and materials are brought together in this project to create a multi-layered, reciprocal house that embraces and retains the agricultural origins of housing sites. A barn-like shed at 292-feet long and 32-feet high made from bamboo provides the primary exterior enclosure. This exterior shell mitigates the impact from rain and moisture on the rammed earth house below while also providing insulation and solar warmth. The consistent temperature of the thick earthwork spaces offsets diurnal changes of the shell, and integrates the living quarters of the house into the material of the agrarian site.
The structure for the shell is based on a lamella system, where the use of standard 8-foot lengths of bamboo are arranged into a diagrid pattern based on the repetition of a single joint. This system maximizes the structural capacity of smaller pieces, thus efficiently using materials to create large vault-like enclosures. The south side of the lamella structure is clad in bio-based polycarbonate to create a large greenhouse for the residential garden below that can be planted year-round. The north side is wrapped in thatch, derived from layers of stacked and woven grasses, providing insulation and weather protection against the prevailing north winds. Cables from the ridge beam support vines and vertical growth that help distinguish the garden from the living area and provide an internal shade layer. The ends of the shed follow the diagonal pattern of the lamella system and provide entrance and adjustable apertures to modulate cross ventilation along the length of the shell.
Set into the ground below the topsoil are the rammed earth living quarters that stretch linearly along a single sloped corridor paralleling the shape of the shell above. These spaces are made by the same earth excavated in the process of carving the house into the site. At the east end is the semi-conditioned outdoor gathering area framed by amphitheater seats that are built up over the living areas behind. Taking advantage of the thermally modifying capacity of earth, the kitchen, dining and bedroom zones are recessed into the ground. The earthen roof doubles as a work and gathering area, with elevated views over the garden and out to the landscape beyond.
200k
180k
47.8k emitted
140k
120k 100k 80k
polycarbonate glass trass lime mortar
cement foam glass
rammed earth
steel clay plaster stone
straw/reed plywood dimensional lumber glulam
bamboo
0 -34.1k net -81.9k stored
-20k
-40k
-60k
-80k
-100k
-120k
-140k
40k 20k -160k
-180k
-200k
160k 60k -220k
220k -240k
Earth material used for construction is found at or close to the bulding site to minimize transportation costs. Topsoil should not be used as it holds organic material. Earth can be reused from previous constructions.
Bamboo and polycarbonate can be disassembled and reused in other projects. Reused biogenic materials continue to sequester carbon.
The growth cycle of reeds is rapid and sequesters carbon. The availability of reeds for use in roofing has declined as focus of agriculture is on seed production with shorter and less viable stalks.
Bamboo growth is prolific, achieving a usable size in years. Bamboo grows in a diversity of climates and can flourish in degraded land.
The genius of the system is the use of the repetitive joint that turns identical, short, 8' lengths of bamboo into a large-spanning, economical structure.
BAMBOOBundles of thatch are secured to secondary wood members and furring strips in layers and tied to the lamella structure.
Temporary formwork is used to compact the earthen mixture into its final shape.
Repetitive short bamboo culms form the outer structure. The two halves meet at a ridge beam thus forming a pointed arch in section.
The north side is covered in a thick reed thatch providing insulation and protection against prevailing winds. The south side remains open and clad with a bio-based polycarbonate, creating a greenhouse.
Tucked under the warm thatch layer, and heated by the sun, an interior core of rammed earth contains the primary programmatic elements of the house. The soil used comes from the excavation of the immediate site.
Semi-conditioned Patio Kitchen/Dining Bedroom Garden
This project uses the unusual size of the standard cross laminated timber (CLT) panel to rethink the A-frame cabin. Rather than cutting CLT to replicate the box shape of a typical rectangular house, this project exploits the elongated dimensions of a typical CLT panel to form a tall structure. The manufacturing dimensions of CLT are set by the size of the glue and press bed which are designed to create very long mass timber panels at a given width. For this house, standard panels are used with minimal tooling and the assembly process is based on the efficiency of minimal parts to maximum effect. Here, 10 pieces of 5-ply CLT panels, each 10’ x 50’ long, oriented vertically, are used to build and shape the house. The resulting tall space is used to reorganize domestic life and engage the conditions of a wooded site.
A single panel forms the plan of the house with five pairs of panels tipped into place on the east and west sides. The northernmost set of panels anchor into a prefabricated staircase made from CLT and serves as the structural core of the project, providing necessary shear resistance. The front pair of panels form an isosceles triangle, and define an A-frame facade. Three pairs of panels fill in the middle and are staggered equally in their angle of orientation from the triangle in the front to the rectangle in the back. Horizontal planks of CLT extend from the staircase to create spaces for sleeping, working and gathering, organized to work within the tall spaces formed by the pairs of tall timber planks. A serrated and stepped CLT panel forms the roof enclosure and provides an occupiable roof deck with integrated seating located high among the treetops.
Wood-based building materials are used throughout to complement the CLT structure, creating a single material wall, and maximizing the sequestered carbon of the house. Wood fiber insulation mixed with paraffin provides the thermal and vapor barrier on the outside of the CLT. Wood planks set on timber purlins comprise the exterior rainscreen. At the front, a louvered glass facade can be adjusted to control ventilation, using the interior height to maximize cooling from stack effect while ensuring solar gain during winter months. On the inside, the CLT forms the interior surface, and is treated with natural oils for protection and durability. Use of slender pier foundations create a minimal foundation, lifting the CLT away from the ground, and limiting disturbance of the soil on the site. As such, the house is designed to be nestled in a forest setting, with the speed of the prefabrication assembly process of the CLT limiting the impact on the land, and the vertical reach of the A-frame embracing the surrounding timber landscape.
200k
180k
140k
120k 100k 80k
-20k
-40k
-60k
-80k
-120k
-140k
40k 20k -160k
-180k
-200k
160k 60k -220k
220k -240k
Trees take decades to grow. Responsibly managed forests are critical to wood's overall carbon impact.
Each of the primary CLT panels are nearly identical, minimally tooled, 10’x50’ rectangular panels.
The floor panel is set on helical piles, lifted above the ground, and protected by a vapor barrier and insulation. The stair core is also erected, forming a structural and programmatic anchor for the project.
Subsequent panels are tilted into place, and various sleeping lofts, lounges, and work spaces are created as extensions of the stair.
CLT, wood fiber and siding, and metal connections can be disassembled and reused in other projects. Reused biogenic materials continue to sequester carbon.
The remaining panels are tilted up, enclosing the main living space, and supported by a stepped roof terrace made from a CLT panel, offering views of the landscape beyond.
Wood fiber insulation and wood siding wrap the exterior of the CLT panels, while the interior sides are left uncovered, treated with a natural finish.
Roof Deck
Sleeping Loft Work Area
Sleeping Loft/Lounge
Bathroom
Wood Fascia Board Wood Furring
Double Pane Glass
Wood Window Trim
Wood Flooring Wood Furring
CLT
Clay Plaster
Jumbo Straw Bale
Clay Plaster
This house joins two contrasting biogenic material systems, crosslaminated timber and straw-bale, leveraging their respective performative and spatial characteristics to create a tectonic symbiosis. Situated on a typical suburban lot in a seasonably variable climate, a cubic volume of jumbo bales, 4 bales square by 12 bales high, forms a thickened perimeter around a central, top-lit void that comprises the main collective area of the house. The straw volume is intersected by a series of five stacked and linked mass timber boxes that create a spiral of ascending rooms subtracted from the modular geometry of the bales.
The CLT boxes are open at two ends, framing large, operable windows to the exterior on one side and overlooking the central living space on the other. The boxes contain entry, bath, kitchen/dining, bedroom, and study sequentially and are linked by a torquing staircase that winds upward through the house to culminate in a roof deck overlooking the site. Partly prefabricated and then transported to the site, the timber boxes are scaled to fit the dimensional parameters of the straw bales, allowing rapid integration between systems. In addition, each of the CLT modules incorporates built-in equipment and ergonomic elements, oscillating between inhabitable furniture, structure, and room.
While straw’s thickness provides thermal insulation and supportive mass, the CLT boxes provide structural rigidity, accommodate the primary program, and link to the mass timber stress-skin roof. The roof, punctured by a large skylight equipped with a retractable wooden louver over the house’s central void, extends outward to provide summer shade and shelter a backyard deck. The roof’s cantilever also shields the outer straw-bale walls. The exterior walls are rendered in clay-based plaster with erosion checks to mitigate the effects of wind and rain. In this house, the intertwining of straw-bale and CLT creates a productive reciprocity, with the opposing qualities of each material system augmenting the other to produce a hybrid constructional and spatial logic.
14.6k emittedglass steel clay plaster
stone
hardwood
stored
200k
180k
140k
120k 100k 80k
0
-20k
-40k
-60k
-80k
-100k
-120k
-140k
40k 20k -160k
-200k
160k 60k -220k
220k -240k
Trees take decades to grow. Responsibly managed forests are critical to wood's overall carbon impact.
Biogenic materials can be composted and used to grow more raw materials.
This design works from the standard
of a CLT panel, 10'x50',
is derived from the press size.
Stone, timber and CLT can be disassembled and reused in other projects. Reused biogenic materials continue to sequester carbon.
design derives its efficiency from the use of jumbo straw-bales as the building unit to speed erection and set the formal organization of the interior.
growth cycle of straw is less
a year, and straw is a
product of the food grains
produce.
Stone foundations with a vapor barrier and wood joists serve as an alternative to concrete slab on grade. Straw-bales are thus lifted off the ground and protected from moisture penetration.
jumbo straw-bales set the construction module, are load bearing, and speed the assembly of the house.
Built off-site, these modules integrate all the systems of the house, including mechanical, electrical and plumbing lines.
Alternating spans of CLT panels, combined with structural timber beams create a stress skin roof that supports the cantilever that extends beyond walls to help protect the straw.
The prefabricated CLT modules knit into the straw-bale walls. These modules help stabilize the bales, and provide all the systems of the house.
To protect the straw wall even with clay plaster, the roof is designed to shield the walls from most direct rain fall and excessive moisture. The weight of the roof acts as further ballast to compress the straw.
Operable
Overhang
Bedroom
Kitchen/Dining
Bath
Polycarbonate Sheathing
Bamboo Lateral
Laminated Bamboo Canopy Slat
Bamboo Column
Bracing Dowel Clay Plaster
Bamboo Roof Truss HempLime Insulation
Bamboo Siding HempLime Insulation
Bamboo Interior
Located within a mature bamboo grove in a semi-tropic climate, the design of this house explores the diverse ways this fast growing grass can serve as renewable and regenerative building materials. Bamboo cleared to make the space for the house and its courtyards is used to build the house. A large rectangular shade canopy made from the bamboo, cut and compressed into parallel stranded timbers, defines the formal territory of the site above. The canopy is held aloft by large bamboo culms which merge the house into the clearing within the grove. Smaller bamboo members tie the parallel boards together and provide lateral stiffness to the overhead canopy. While mostly open to the air to allow for the continued growth of the grove, selected portions of the rectangular canopy are clad in translucent bio-based polycarbonate to shed rain while allowing daylight and starlight.
The enclosed walls and ceiling of the house are built from prefabricated panels made from an outer structural layer of bamboo that doubles as formwork for the hemp-lime insulation worked into the inner core. These cassettes are made off site and designed to be clipped into place, enabling future disassembly. Moreover, the notoriously slow dry time of site-cast hemp-lime insulation can be built into the prefabrication schedule, thus ensuring the speed of onsite installation. The modular nature of the cassettes allows for a diversity of plan configurations and future house growth to meet different living and social groupings. To ensure daylight inside, short bamboo culms located in the cassettes and covered with insulated glass double as skylights to the interior allowing views to the sky through the hollowed out center of the bamboo stalk.
When grouped, the panels create rectangular volumes that define the inner domestic areas of the house and walls that extend space out toward clearings made within the bamboo grove. Pivoting panels made from the bamboo and hemp-lime assembly ensure the interplay between fully enclosed and semi-conditioned spaces under the large canopy. Gathering areas, places of rest, and zones of recreation located within the bamboo grove expand the living space. Earthen floors compressed over insulating pumice further blur the boundary between what is inside, what is under cover, and what is within the grove. As the house ages, the fast growth of the bamboo grove serves as the source for future replacement, expansion and repair material. At the end of life, the house can be fully disassembled and parts either reused, or returned to a virtuous regenerative cycle.
stone clay plaster
rammed earth glass
polycarbonate bamboo plywood hemplime bamboo
4.6k emitted
200k
180k
-27.1k net -31.7k stored
140k
120k 100k 80k
-40k
-60k
-80k
-100k
-120k
-140k
40k 20k -160k
-180k
-200k
160k 60k -220k
220k -240k
Bamboo growth is prolific, achieving a usable size in years. Bamboo grows in a diversity of climates and can flourish in degraded land.
Hemp plants grow quickly and can reach a height of 6 to 15 ft in a year. They sequester a significant amount of carbon and replenish the soil. For this project, lime is added to hemp hurd with water to create a durable, rot resistant, flame-resistant, and highly insulating material.
Select bamboo culms are harvested, creating spaces serving as courtyards. Harvested culms are used toward the house’s construction.
Bamboo and bamboo assemblies can be reused in other building products. Hemp and lime materials can be reground and reused with the same performance capacities in another construction.
An expansive canopy covering the house and the immediate surroundings is built of slatted bamboo plywood beams and held up by bamboo culm columns.
BAMBOO CULMSPrefabricated cassettes are made with an outer structural layer of bamboo which doubles as the formwork containing a hemp-lime insulated core.
Adjacent panels are attached to one another with fasteners, to facilitate change and disassembly for future use.
The laminated bamboo canopy slats affixed to slotted bamboo culm columns.
Under the cover provided by the canopy, the primary walls are erected as prefabricated panels of bamboo and hemp-lime.
By expanding the overhead canopy, different house plans can be placed underneath, creating a complex of units, each built using the same prefabricated panels.
BAMBOO PRODUCTS Bedroom Slatted Canopy (Shade and Selective Rainwater Protection) Bathroom Kitchen/Living BedroomPrinceton School of Architecture October 6, 2022 - January 13, 2023
Exhibition Design: LTL Architects: Paul Lewis, Marc Tsurumaki, David J. Lewis, Celia Chaussabel, and Kyle Reich Exhibition Manager: Kira McDonald Exhibition Assistants: Tengku Sharil Bin Tengku Abdul Kadir, Danial Mahfoud, Olivia Ahmadi, Katharine Solien, Zhuofan Ma, Hongming Bruce Liang, and Elaine Qin Wang Five Biogenic House Designs: LTL Architects: Paul Lewis, Marc Tsurumaki, David J. Lewis, Celia Chaussabel, Kyle Reich, Tengku Sharil Bin Tengku Abdul Kadir, and Danial Mahfoud. Thanks to the students in Arc560a S’22 Building and Embodied Carbon Design Seminar for advancing ideas about biogenic wall sections that informed these designs: Melinda Denn, Jasen Domanico, Tessa Flanagan, Julian Gonzalez, Daniel Hall, Jonathan Hanna, Kaleb Houston, Rinna Jiang, Austin Madrigale, Danial Mahfoud, John Mikesh, Adrian Mitchell, and Ian Ting Material Donations: 475 High Performance Building Supply, The Donghia Healthier Materials Library at Parsons School of Constructed Environments
Special thanks to Dean Monica Ponce de Leon and the School of Architecture staff.