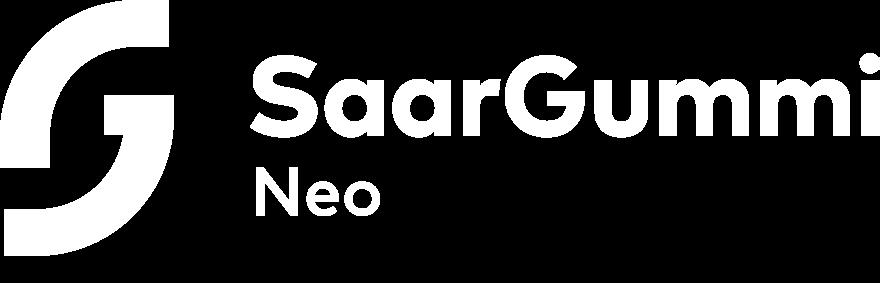
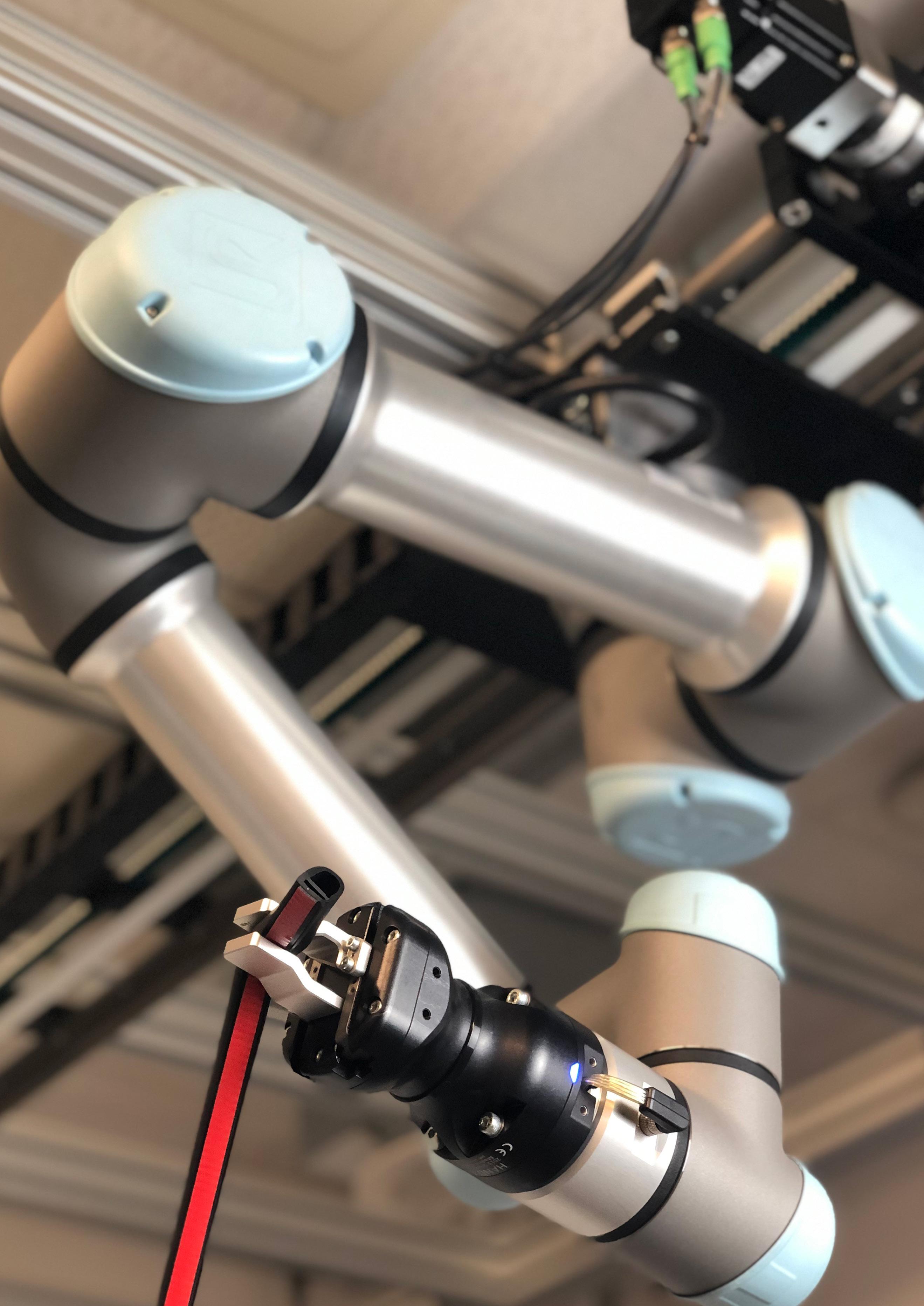
Sven Müller, Director of Innovation at the SaarGummi Group and Managing Director of SaarGummi Neo, on tapping into new ideas and fresh approaches, without losing sight of established principles or quality, when supplying high-performance rubber to the automotive industry worldwide.
Originally founded in Germany more than 75 years ago, the SaarGummi Group is now a global powerhouse operating wherever you find the automotive industry.
t its core, the SaarGummi Group produces sealing and weatherstrip products made from rubber material (ethylene propylene diene terpolymer – EPDM) for the automotive industry. Its products include door sealing, trunk lid seals, sunroof or glass runs and much more besides. With 5,400 employees and 17 production sites worldwide, the organisation turns over roughly €650m per year in sales.
While the design of the products and manufacturing technologies have always been fine-tuned over the years, the fundamental principles of the company – such as reliability, the highest quality standards and working in close partnership with customers – have remained the same. This heritage creates trust among customers. Nevertheless, it sometimes presents a challenge when cultivating new ideas and introducing them to the customers.
Here to elaborate on how the SaarGummi Group and its sub-division SaarGummi Neo develop process, product and material innovations while embracing digitalisation and sustainability is Sven Müller, Director of Innovation at the SaarGummi Group and Managing Director of SaarGummi Neo.
“We are a traditional business in some regards,” begins Sven. “There have been some changes in the recipes of the rubber material alongside design changes over the years. But in general, it’s quite an established industry in terms of the process as well as from the product point of view. However, one of the dynamics which separates us from our competitors and similar businesses in other industries is we produce various rubber compounds ourselves, before embarking on the manufacturing phases.
“In terms of our innovation and sustainability, this control over our
processes is a crucial factor – helping us to lead the industry in terms of our practices because we have direct influence on them.
One of Sven's core responsibilities is to guide the innovation strategy for the SaarGummi Group and lead the SaarGummi Neo team as well as the company's global innovation centre, which is located in Germany.
“We officially started our innovation journey in 2016 with the founding of the SaarGummi Neo team, which I joined as Managing Director in 2018,” recalls Sven. “We are effectively the innovation department for the whole SaarGummi Group. But unlike many companies who declare themselves innovative just because they created an innovation department, we decided
to be deliberate and different by making ours its own legal entity. We did that on purpose, as I like to think of it, to build a speedboat rather than a big cruising ship which is slower and harder to turn. We wanted to be as agile as possible within the rules and procedures of the Group.
“But the big challenge is even though we are a separate entity, technically, we never wanted to be disconnected from the Group since this would undermine the very innovation we are trying to promote. We need to stay as close as possible to the rest of the organisation, while simultaneously existing as far away as possible from the daily operations of the business. In my dual role as Director of Innovation at the SaarGummi Group and Managing Director of SaarGummi
“One of our major tasks is to analyse the trends or technologies to see what might be a good fit for us, now or in the future”
Neo, it is my job to strike this balance. It is sometimes not an easy job, but it also fosters our strength in the Neo team.”
Sven explains there are four main categories of innovation at the SaarGummi Group: process, product, materials and digitalisation. But Sven reiterates these are not distinct silos since different categories often overlap within the same project or initiative.
So how is the SaarGummi Group approach injecting innovation into its operations within these four categories? Sven insists there are external and internal factors worth
noting when it comes to embracing innovation at the SaarGummi Group.
“In terms of external factors, there are megatrends which come along which we have to adapt to as a company,” says Sven. “You might be able to ignore them for a little while, but ultimately you have to react to these trends, or you’ll be left behind.
“For instance, digitalisation is a crucial megatrend for us which we had to incorporate. There have been a range of buzzwords flying around related to ‘digitalisation,’ but for us, it’s about asking how can
we actually use it? How should we adapt new technologies to meet our needs? Are we exploring this because there is a business case and it will generate profit, or are we being led by the hype? After careful consideration, we decided to explore digital twin technology in our journey towards building fully digitalised factories while weaving data analytics and algorithms into our processes. Also under the umbrella of digitalisation, we consider new technologies for use. For example, we are exploring how to integrate XR solutions (VR, AR, MR) in order to support employee training or communication between employees but also to have virtual 3D meetings where necessary.
“So besides our daily innovation projects, one of our major tasks is to analyse the trends or technologies to see what might be a good fit for us, now or in the future. We do that not only to be ready for new technologies but also to select the right projects for us. It doesn’t make sense to invest in innovation if it will become redundant in the near future – we have to keep the long-term goals of the Group in mind.”
When it comes to internal factors impacting the innovation strategy at the SaarGummi Group, Sven describes the need to consider the values and objectives of the organisation while also convincing internal stakeholders to see the merit in the projects. Here, he uses sustainability and process innovations as examples.
“You could see sustainability as an external factor if you consider the rising regulations and legal requirements at play,” says Sven. “But we see it as an internal priority since we have a duty as a company to make our products and processes more sustainable. We also want to be carbon-neutral in the coming years. It is then a case of presenting sustainability innovation to internal stakeholders in terms of these values or objectives. Or, if we consider process innovations it is again a question of presenting the projects or initiatives as vehicles for improving production speeds, lowering scrap rates, increasing practicality or helping towards KPIs.
“For us, sustainability is more than just a phrase. There is a high impact on our
“We are certainly creative in our approach, with an array of experts who have diverse knowledge in different areas”
footprint coming from the material side of the organisation. The big challenge in our business is that the vulcanised rubber material we use cannot easily be recycled. Compared with metal or plastics which can be re-melted, our finished material is vulcanised which is a non-reversible process. In the last few years, there have certainly been steps forward
Install an automated entry system to reduce backlog.
Utilise live occupancy data for immediate truck navigation.
Use parking data analyses to detect and reduce process-disrupting downtimes.
Apply historical occupancy data to plan management of pick-ups and deliveries.
Integrate live data into yard management systems to enhance logistic insights.
but it remains a challenge. Therefore we are working actively, especially on the material side, towards more sustainable ingredients and recycling or re-using methods. We also incorporate our sustainability agenda into innovation projects with promising overlap, for instance within our digitalisation strategy.”
However, Sven relays how SaarGummi Neo does not monopolise innovation for the SaarGummi Group – regardless of whether the inspiration for it arises externally or internally.
“We implemented our Innovation Committee Meeting which meets bimonthly,” says Sven. “Here, the C-level board of SaarGummi Group
join dedicated representatives from across the organisation in different departments to hear me present on the status of our innovation projects, but also discuss strategic topics and the other members of the meeting can offer feedback. What is new? Where do we want to go? Are projects succeeding or do we need to put them on hold? We come together and judge what is most beneficial for the organisation and take things from there.”
While the innovation strategy is deeply embedded into the SaarGummi Group and SaarGummi Neo, Sven explains it is not undertaken in isolation. External collaboration and strategic partnerships are crucial as well.
“Innovation is not created in thin air,” says Sven. “We are certainly creative
in our approach, with an array of experts who have diverse knowledge in different areas. Nevertheless, we also need input from the outside. For us, this is generated in several ways. We work with universities or institutes when it comes to the scientific developments and research side of things. We also collaborate with startups or emerging companies that are interesting to us as an organisation due to their products, processes or digitalisation offerings.
“One such example is our partnership with Smart City System, which offers a clever way for getting a live overview of logistics movements on site. They provide sensors for recognising if a loading point is blocked or free for the next truck. All information is provided in a customised software where
additional functionalities can be added. We made a pilot project with them not only for this ‘daily business’ solution, but also to get a better understanding of sensors, data exchange, and the integration of different parties to come to a digital twin of the factory in the long term as part of our digitalisation strategy.
“If we look at our digitalisation strategy, we are always striving for ways to improve our processes. We have about 150 process parameters which can be complex and challenging, so we need the right data analytics and solutions in place to make them efficient and effective – whether this is in loading sensors, capacity analysis, production lines or digital twin technology.
“Our pilot project with Smart City System is a piece in the puzzle, the starting point for ultimately working towards a fully digitalised factory system. We gain so much from these types of projects because both sides learn so much in the process. Working with companies like Smart City System is a terrific example of the collaborative partner approach to innovation.”
Looking ahead to the future and the role of technology in promoting innovation at the SaarGummi Group, Sven wraps up our discussion by focusing on additive manufacturing.
“For several years, we have made a lot of progress on integrating additive
manufacturing methods into our business,” says Sven. “There is an uncountable amount of potential use cases which have been identified either in plastics or metal printing. Additive manufacturing has huge potential as a technology to transform the traditional processes in our industry.
“At one level it can lower costs because it is cheaper to print products in certain cases than it is to take the traditional manufacturing approach. But if you look closer at the new technology of additive manufacturing, it is a real game changer because it allows us a completely new kind of freedom when it comes to the design of objects.
“I think there will be a lot of changes and progress in the future with additive manufacturing in the background. It allows you to build different styles of support tools and offers a greater level of customisation for specific parts that require it.
“Fortunately, we already realised the potential of additive manufacturing several years ago, and since then we have implemented it very successfully in the Group and look forward to realising even more of its potential in the coming years.”
For further information about the SaarGummi Group and SaarGummi Neo, visit their websites: saargummi.com and neo.saargummi.com.
When he isn’t at work, Sven prioritises spending quality time with his wife and two children. But if he gets a bit of spare time, Sven likes to experiment and play with the 3D plastics printer he has at home – for his own curiosity and creativity, but also to have fun with his kids and make them objects to play with.
Sven takes great pride in SaarGummi Neo’s recent recognition as one of the top 100 innovators in Germany as a testament to the hard work and collaboration among his team and the entire organisation.
Connect with Sven