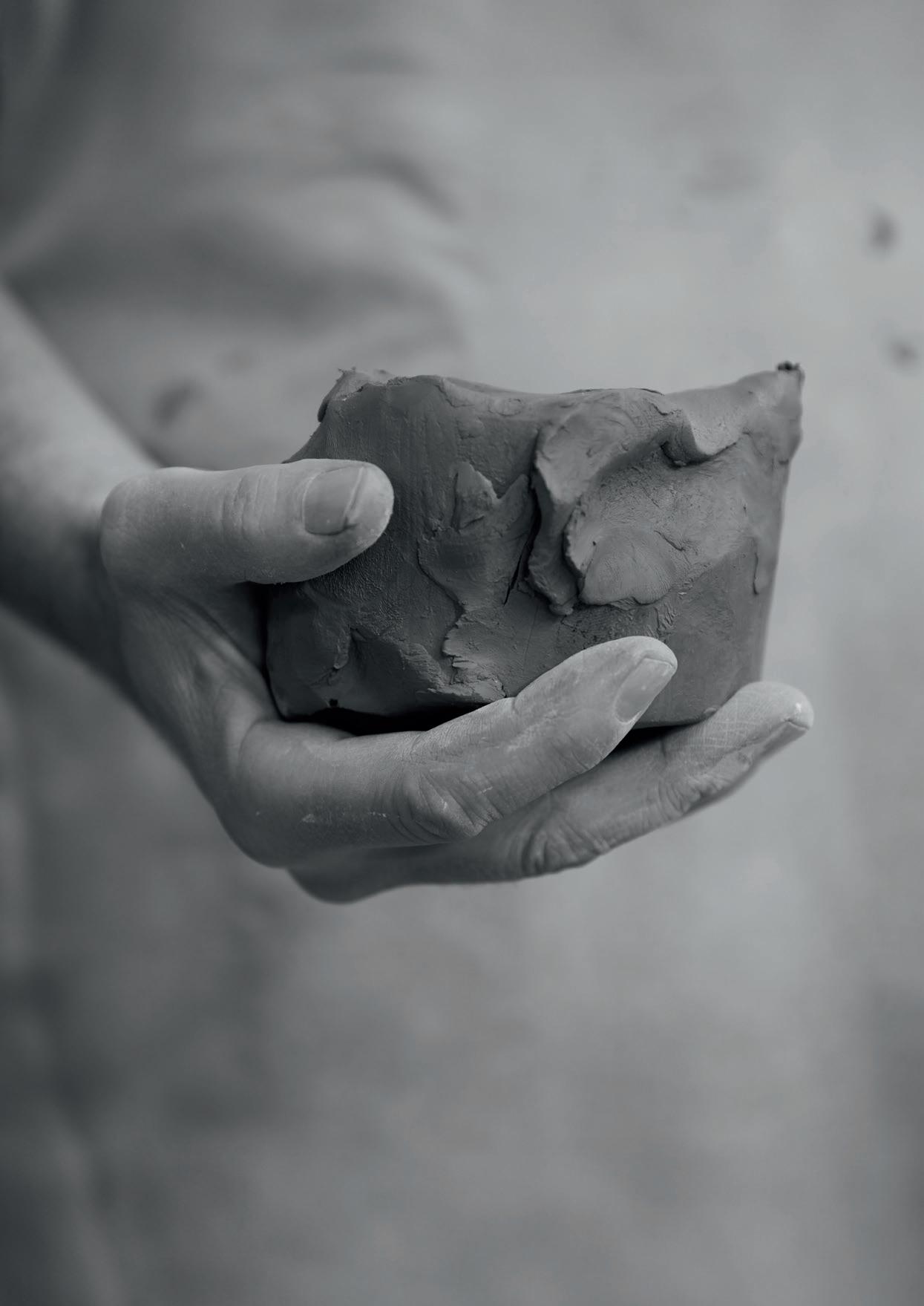
20 pairs of hands craft every piece...
20 pairs of hands craft every piece...
At Denby, ‘handcrafted’ is not a word we use lightly. For us the word reflects the care taken by the expert hands of our super-talented craftspeople, along with the amazing crafting techniques which sit behind every piece. For over 200 years, our passion for high quality, handcrafted British ceramics has never wavered.
Visitors to Denby sometimes comment that it’s like ‘being in the biggest studio pottery in the world’. We are not about endless volumes of plates dropping off the end of a faceless machine production line; at Denby, spouts are shaped, handles are attached, pots are dipped, glazes are sprayed, kilns are emptied - all by human hands.
The craft begins by carefully observing real lives and designing products for the way we live. And this care continues through the design process, in the magic of the glaze reactions, in the unique iron-rich Derbyshire clay used, in the scores of intriguingly-named pottery techniques we use (items can be ‘fettled’, ‘jolleyed’, ‘sponged’, ‘turned’ and ‘dipped’!), in the journey into the high temperature kilns and right through to the rigorous final inspection which happens to every piece before it gets the Denby backstamp of approval.
So let’s go behind the scenes in our pottery to see where at least 20 pairs of hands craft every piece and discover the true meaning of the word handcrafted, from start to finish.
All of our stoneware clay is processed here at Denby from a large clay pile stored at the back of the pottery. The unique iron-rich clay needed for that day is taken by a digger to the Cylinder House where it is moved into cylinder mills to remove the impurities, and mixed with Quartz and Feldspar.
The processed clay is in the form of a liquid and then requires ‘pressing’ to remove most of the moisture. During pressing, a series of clay slabs are formed between the various sections of the press and each slab needs to be separated from the press cloth by hand, as it has been for hundreds of years.
When the clay is needed, it is manually moved to the various departments and placed by hand on to the machines that shape the clay using a mould.
Once shaped, most items are removed by hand from the mould.
Most items are then sponged down by hand to make them smooth for the first firing.
Items are then placed by hand onto a dottie (like a trolley) and taken to the kiln area for their first firing.
The items are placed by hand onto a kiln trolley and biscuit fired for 18 hours.
The items are then unloaded carefully by hand after the first firing.
Larger items are taken to be fettled and made smooth by hand before colour and decoration are applied.
Items are then placed again onto a dottie and taken to be decorated.
We have various ways of decorating and every item has an element of hand decorating - we hand spray, hand dip, hand band, hand paint or apply transfers by hand.
Some flatter items can be glazed by machine like plates or pasta bowls, though our craftspeople must still feed this ‘auto-sprayer’, remove the piece to ‘wipe back’ the foot of the item then place it back by hand to spray the other side.
Items are then ‘tidied’ by wiping away any excess glaze and making the foot smooth.
At this stage. items are then carefully handled onto a trolley and taken to the kiln areas for a second firing.
Once there, items are placed on a kiln trolley to go through the glost firing for 12 - 18 hours which sets the glaze firm to the pot and creates the stunning Denby effects.
Items are removed by hand after their glost firing.
All items are then placed onto a trolley to go to final inspection.
When in final inspection, items are ‘ring’ tested where trained ears listen out for a clear ‘ting’ when struck with a small metal implement. A clear ting means the item is good as is passed, whereas a dull thud means an item has as internal crack for example and this item is rejected and sent for recycling.
All items are foot polished to ensure the feet are smooth and won’t scratch surfaces in use, and are then back stamped to confirm they have passed all of Denby’s rigorous quality checks.
Small branding labels with our logo and our proudly made in England stamp, alongside the barcode are then applied.
Some items are gift-packaged by hand into recycleable boxes.
All items get carefully hand-packed into trays and transferred to our warehouse facility.
Orders are then hand-picked and packed to send out to our customers around the UK and around the world.
The various steps in our ‘20 pairs of hands’ process represent what it takes to make a simpler item such as a rice bowl. We have many items that go through many more processes. The handles on our Mugs for example are hand applied, adding at least 3 further hand processes (the handle is cast by hand-pouring liquid clay slip into into a handle ring mould to set which is then taken out of the mould and skillfully hand-applied to the body of the mug).
The spout of the cafetière is shaped by a finger gently padding and moulding into shape. Cast items, like teapots, are handled much more too and have multiple pieces (bases, lids, handles, spouts) so when combined can involve over 30 pairs of hands. Items which have a ‘transfer’ decoration applied can go through the kiln 3 times with hand-crafting and expertise happening at every step of the way. Not forgetting items such as large vases which are fully hand-thrown on a potter’s wheel!
We make all the glaze recipes we use on our pots in-house and these are mixed and stirred by hand periodically to keep them fresh. It’s real people who ensure we have zero process waste going to landfill; glazes which get recycled are removed by hand and clay ribbon ‘off-cuts’ are transported by hand. We make the moulds which shape our products in our workshop by hand and even when we use semi-mechanised processes to decorate or mould items, they are handled on and off and checked by hand to ensure the quality is what you would expect from Denby.
So we definitely mean it when we say handcrafted, and it’s easy to see why we get called ‘the biggest studio pottery in the world’! This means each piece of Denby is made with purpose and soul, crafted by skilled hands and techniques which have been in our pottery for over 200 years, to ensure that you can enjoy the quality and beauty of Denby, every time you find it in your hands too...
The Denby Pottery Company Ltd. Denby, Derbyshire
DE5 8NX
denbypottery.com
Telephone: +44(0) 1773 74 0 899