
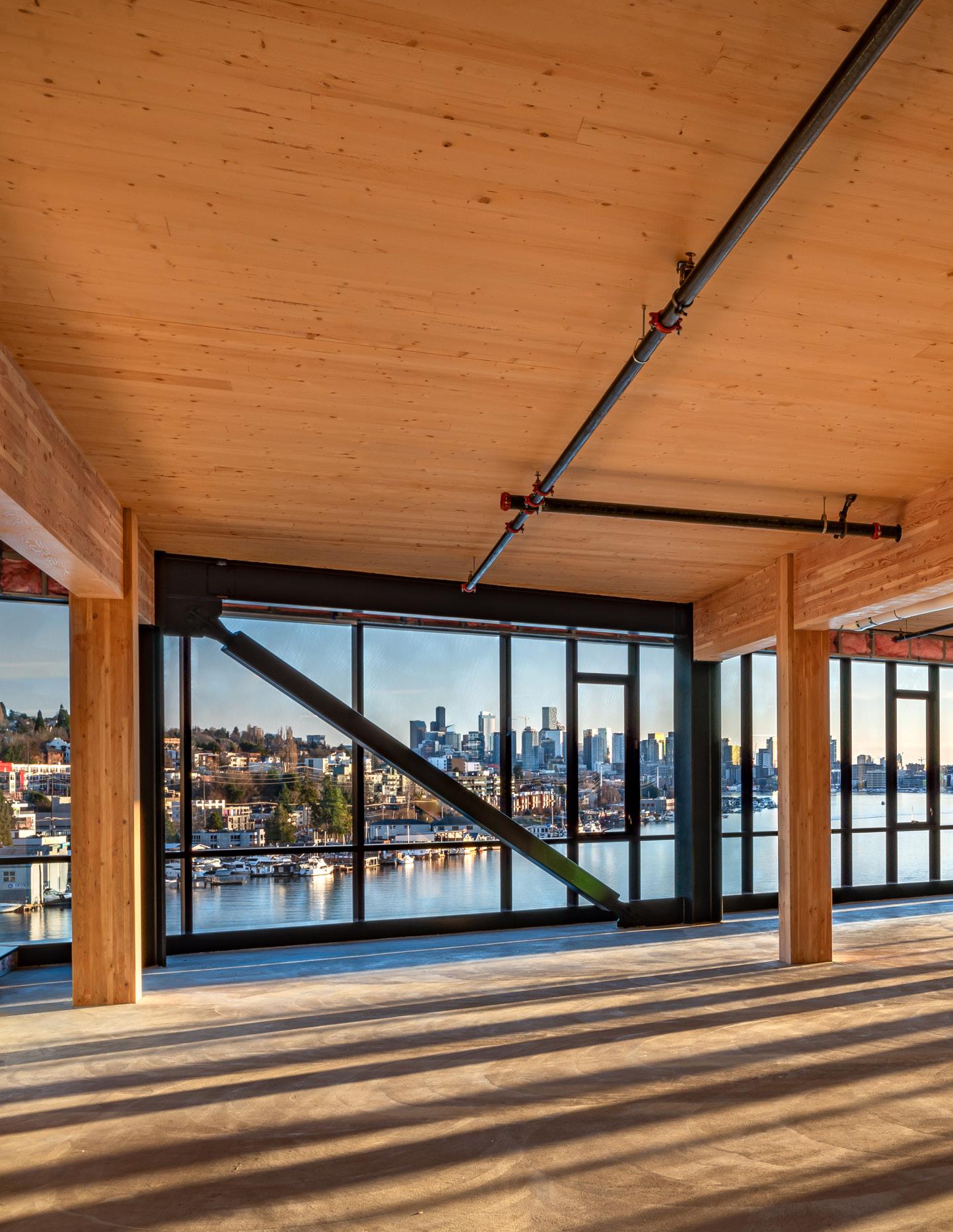
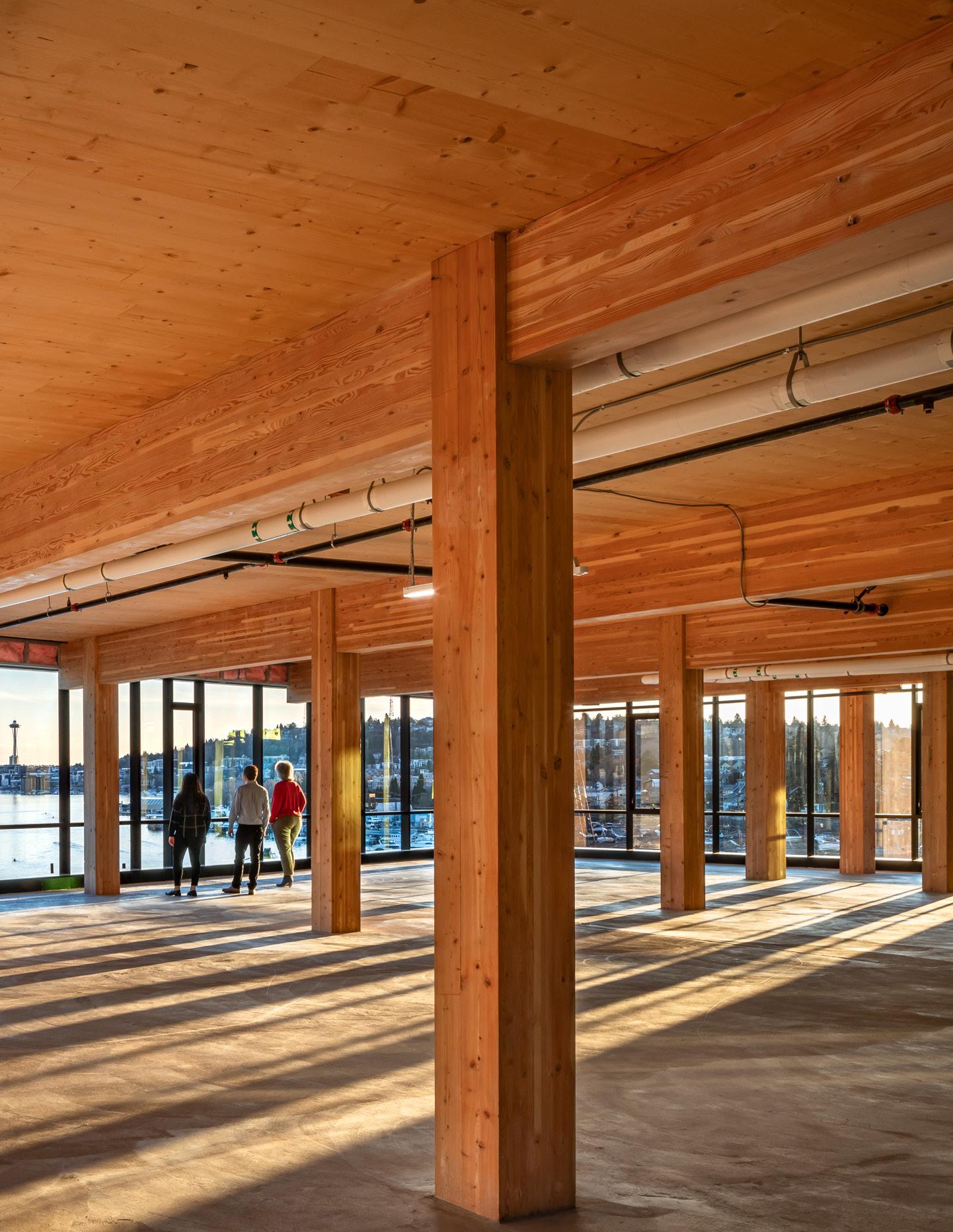
TABLE OF CONTENTS
SECTION I Firm Profile
SECTION II P roject Experience
SECTION III Meet the Team
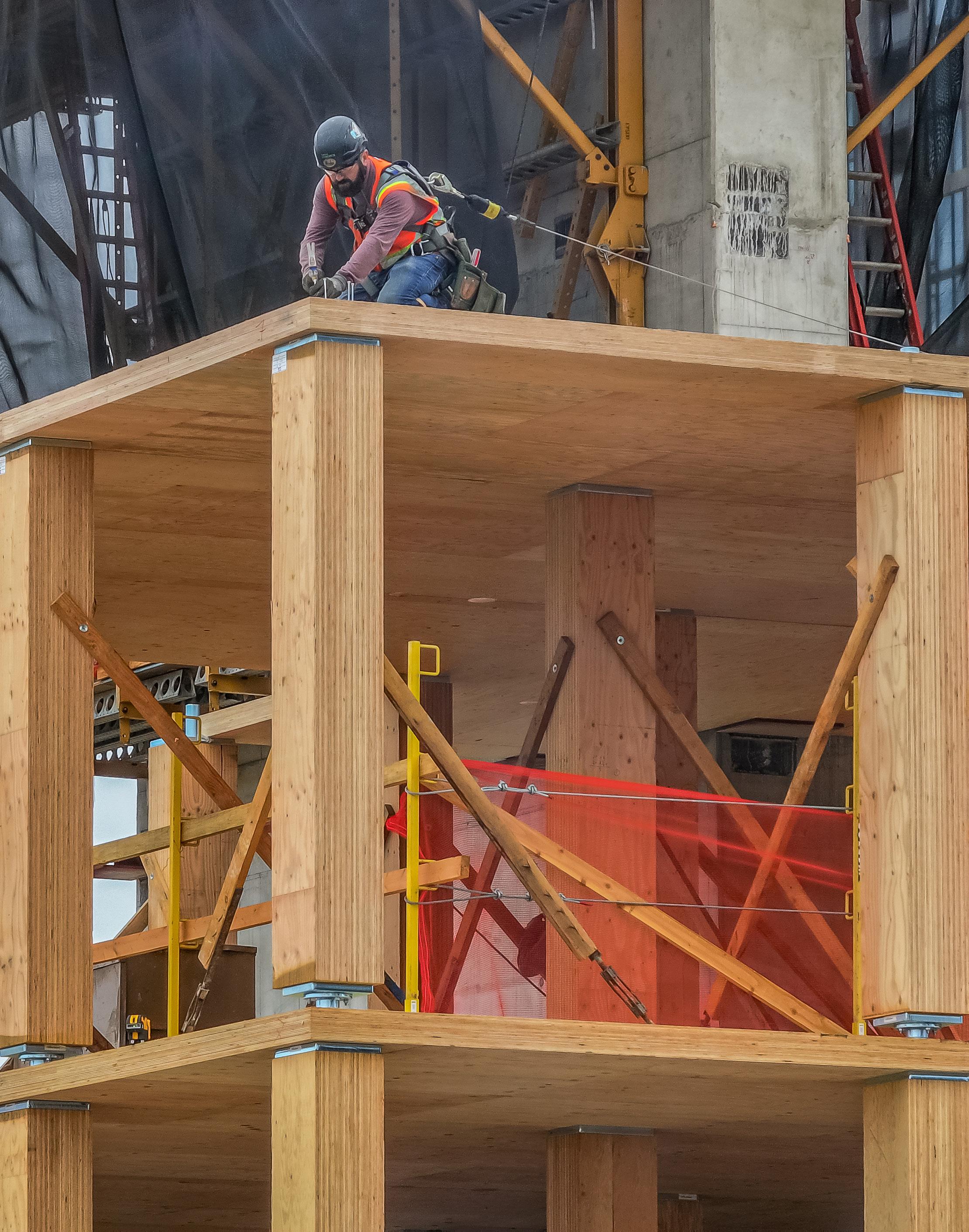
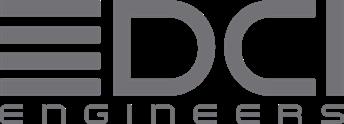

TABLE OF CONTENTS
SECTION I Firm Profile
SECTION II P roject Experience
SECTION III Meet the Team
are at the foundation of everything we do.
We build for it and strive to do better by it - whether it's through design, volunteer time or commitment to a greener future.
Means adapting to change and saying "yes" when others say "no." It's a willingness to give up the ego and truly listen.
is exploring new technologies and learning from past experiences to always improve. It's about efficiency over flash.
The secret sauce to successful relationships. We sharpen our pencils for our clients' toughest challenges.
you've got to earn it, and in the end, it's what we're ultimately providing our project partners.
DCI Engineers is a full service structural & civil design firm with office locations across the country – from Alaska to the East Coast. We employ over 350 of the most dedicated engineers and technical support staff in the industry and are licensed in all 50 states and many Canadian provinces. Since our founding in 1988, DCI has been on the forefront of emerging and innovative markets including mass timber.
We’re leaders in this sustainable construction method and have provided solutions for several milestone projects across the country
Bullitt Center, First Living Building Challenge and greenest office project in the U.S.
1 De Haro, First CLT building in San Francisco and First CLT project delivered by rail in the U.S. significantly reducing carbon footprint; and first multi-story mass timber building in California.
Project One, First Mass Plywood Panel (MPP) project in the U.S.
First United Bank Buildings, First Southern Yellow Pine CLT projects in the U.S.; First mass timber buildings in Oklahoma and Texas.
Heartwood, First Tall mass timber work force housing in Seattle; First Type IV-C in Seattle (residential).
Bush School, First Mass Plywood Panel (MPP) school in the U.S.
1510 Webster, First MPP point supported building in the world and first Type IV-A in North America at 19-stories.
DCI’s mass timber consultation services include cost-effective solutions for fire-rated member and connection detailing, composite wood and concrete systems, among other types of hybrid structural systems. This understanding of materials involves integration into whole building design, along with MEP/F systems, acoustic design, cladding compatibility, fiber optimization, and vibrational analyses.
Learn more about our commitment to Service, Innovation & Value at dci-engineers.com/markets/mass-timber.
DCI’s engineering teams have completed over 180+ projects utilizing mass timber in the United States. We participate in regional conferences and exchange ideas with mass timber industry leaders in order to pioneer the successful adoption of mass timber through several prominent North American projects.
We draw upon our engineers’ collective knowledge of the industry and mass timber’s various products and applications to serve as a resource for the design team, contractor, and owner as we move from conceptual-level studies, through the development of construction drawings, and into construction administration. We have experience employing mass timber in many different structural assemblies to optimize either cost, performance, or enhance aesthetic qualities—often with mass timber, we are able to exceed expectations on multiple fronts.
Mass timber is best suited for a range of projects types --from office, to retail, multi-family, K-12, higher-education, and single-family—and DCI Engineers has experience working with each of those types, in addition to most others. We are well-versed in the use of CLT for floor and roof applications, lateral force resisting systems, hybrid and/or composite wood and concrete structures, and we understand the importance of properly detailed connections. Our experience includes using glulam or steel frame to support different types of mass timber floor plates including CLT, NLT, and DLT. DCI completed the first of its kind testing of mass plywood panels (MPP) and is helping lead university research for point supported analyses of MPP to increase the product’s acceptability to building officials. This testing led the way for the two tallest MPP residential towers in the world. By having projects across America using all of the latest timber technologies, DCI is able to help provide our clients with the most cost-conducive solution while the project still reaps the benefits of sustainability, biophilia and aesthetics.
We are actively engaged in the development and promotion of Mass Timber through various conferences, community research organizations and technical educational commitments with employees engaged in the following sample areas:
• NEES’s Cross Laminated Timber Practitioners’ Advisory Committee
• ANSI/APA PRG 320 Committee (Develops standards for cross laminated timber)
• SEAO Mass Timber Committee
• NCSEA Tall Wood Committee
• ASCE Sub Task Group on CLT Shear Walls
• NEES Engineered Timber Structural Systems for Seismically Resilient Tall Buildings Consultant
• AWC Wind & Seismic Task Force
• CALBO / SEAOC CLT Policy Paper
• Associated Builders and Contractors (ABC), Framer’s Council
• “Mass Timber, Why Wood You?” Educational Presentation, 2016, 2017, 2018, 2019
• Mass Timber Conference Presented by Woodworks, Portland, OR , 2015, 2016, 2017, 2018, 2019
• North America Mass Timber Research Workshop, 2018, 2019
• International METSA Wood Design Competition - Futuristic Building Selection, October, 2016
• Council For Tall Buildings and Urban Habitat (CTBUH), Tall Timber Working Group
Last year, DCI Engineers started penciling out projects in 862 cities in North America! That's thousands of moments of forward momentum spanning various markets and materials.
DCI’s services include cost-effective solutions for fire-rated member and connection detailing, composite wood and concrete systems, steel and timber systems and other types of hybrid structural systems. This understanding of materials involves integration into whole building design, along with MEP/F systems, acoustic design, cladding compatibility, fiber optimization, and vibrational analyses.
DCI Engineers has designed low-rise, mid-rise, and high-rise (following the new Type IV construction types) projects with a multitude of occupancies.
DCI collaborates with a number of entities, both private and public, to explore innovative approaches and address whole-picture solutions for mass timber design and constructability.
Private Partners: include developers, architects, general contractors & timber suppliers to explore:
» Affordable housing
» Modular construction
» Moisture management
» Design-assist
» Builders risk insurance
» Proprietary connection development, seismic component development, and timber product development
Public Partners: include local & regional jurisdictions, industry and university organizations & the U.S. Forest Service to explore:
» Tall mass timber code adoption
» Performance-based design (PBD)
» Termite treatment
» Seismic systems
» Acoustics
» Point supported systems
» Fire ratings
» Detailing of fire rated connections
» Future tall mass timber design and analysis
We are committed to helping our project partners arrive at costeffective design solutions that employ sustainable design practices – whether aiming for specific certifications such as LEED® Design or the Living Building Pilot Program, or simply helping to make this planet a little bit greener… DCI is here for you.
Below are a few ways we help our clients achieve their sustainability goals:
• Structure & Enclosure Life Cycle Assessment
Our services include green building rating system documentation & coordination leading to more points to qualify including, but not limited to, LEED, ILFI, Green Globes, and AEGB.
• Schematic Structural Life Cycle Assessment
Our team explores environmental impacts for consideration during the structural system comparison and selection process.
• Structural Life Cycle Assessment Design Coordination
We can track & optimize environmental impacts throughout the structural design process, assist with reduced carbon material procurement and coordinate structural LCA results with the project’s sustainability consultant. We utilize OneClick LCA, Tally, and EC3 based on the phase of the project and desired outcome from the client.
• Embodied Carbon and Structural Sustainability Education
Contact DCI for our official AIA-approved sustainability presentations, tailored to audience levels of experience and interests including topics like comparative LCAs, performance specifications, CALGreen, Executive Order 14057, and CLF pursuits.
Our fees for Structure & Enclosure Life Cycle Assessments typically range from $10,000-$25,000 per unique building depending on the project’s complexity and sustainability goals. Contact sustainability@dci-engineers.com to inquire about the sustainability services and fees appropriate for your development!
ARROWHEAD PHARMACEUTICALS, Verona, Wisconsin
LEED v4.1 Silver - (3) Points for Building Life-Cycle Impact Reduction
This project is a new pharmaceutical office building consisting of approximately 129,200-GSF over 5 levels. The construction team procured low carbon concrete containing Type IL Portland Limestone Cement which demonstrated environmental impact reductions when compared to the North Central regional baseline. Global Warming Potential reduced by 12% or 587 metric tons of CO2e which equates to the GHG emissions associated with 130 gasoline-powered vehicles driven for one year.
WILMINGTON COLD STORAGE, Wilmington, North Carolina
LEED v4 Gold - (3) Points for Building Life-Cycle Impact Reduction
This development is a new two-story, 288,174-GSF cold storage and distribution center. The design team utilized insulated metal panels in lieu of traditional concrete tilt-up panels to demonstrate environmental impact reductions. Global Warming Potential reduced by 15% or 1,180 metric tons of CO2e which equates to the carbon sequestered by 1,400 acres of U.S. forests in one year.
CLACKAMAS COUNTY COURTHOUSE, Oregon City, Oregon
LEED v4.1 Gold - (3) Points for Building Life-Cycle Impact Reduction
This project is a 241,000-GSF, six-story courthouse building. Efforts to reduce environmental impacts include: rearranging the column grid to cantilever the slab along one edge to eliminate a row of columns; coordinating a simplified formwork solution to reduce slab thickness by 1" for approximately 75% of the floor plate; utilizing mass timber canopy at the main entrance of the building in lieu of concrete; implementing performance-based concrete specifications, EPD requirements & GWP limits. Global Warming Potential reduced by 24% or 2,440 metric tons of CO2e which equates to the GHG emissions associated with 540 gasoline-powered vehicles driven for one year.
LEED v4.1 Gold - (5) Points for Building Life-Cycle Impact Reduction
The JCI Engineering Center is a two-story, 103,736-GSF lab facility. Instead of pursuing entirely new construction, this renovation utilized the roofing, steel framing and foundations from the existing building to meet the needs of the expanded building program. Global Warming Potential reduced by 12% or 313 metric tons of CO2e which equates to the CO2 emissions from powering 60 homes electricity for one year.
DCI’s comprehensive services include structural, civil, bridge and industrial work. While these services are distinct, they operate under our core values of Service, Innovation & Value. Woven throughout is an obligation for more sustainability-forward thinking—from the materials we use to the tools and technologies we can apply.
» Early Procurement Collaboration & Supplier Coordination
» Low Carbon Material-Focused Specifications
» Environmental Product Declaration (EPD) Evaluation & Tracking
» Green Building Rating System Assistance
This 19 story mixed-use high-rise building in Oakland consists of 182 apartments, retail, commercial spaces, and a covered public plaza. 1510 Webster Street became the first high-rise in the United States to utilize point-supported mass timber and mass plywood panels (MPP). Early involvement in the conceptual design phase allowed DCI to advocate for mass timber over traditional concrete framing which not only resulted in embodied carbon savings but provided cost and scheduling savings that helped the owners achieve affordable housing goals. The mass timber building’s structure & enclosure demonstrated 5% less embodied carbon than the all-concrete scenario and 49% less embodied carbon when considering anticipated biogenic carbon storage during the lifetime of the building.
The Artise will be a 25-story office tower in Bellevue’s central business district appealing to high-tech businesses and professionals. The 1,040,000-sf tower will consist of a steel framed gravity and lateral structure with buckling restrained mega braces and steel moment frames.
By utilizing an innovative lateral system along the perimeter, DCI saved an estimated 25% of steel tonnage in the structural frame. Additionally, because there were no traditional concrete cores or interior braced frames, the parking plans were optimized to eliminate an entire belowgrade level. By eliminating approximately a quarter of the steel framing required for a traditional steel-framed office layout, the project reduced its embodied carbon by an estimated 11% as well as substantial cost savings.
Oakland, California
1510 Webster Street is the tallest, masstimber building in California. The timely construction of 1510 Webster Street aligns with the updated California Building Code, allowing for taller mass timber than ever before. The 19-story multi-family residential building provides 182 units and 15,000-sf of office and retail space on the ground floor. A landscaped garden is situated on Level 7, while the high-rise rooftop provides a trendy rooftop lounge and amenity space.
1510 Webster Street is also the first high-rise in the United States to utilize point-supported mass timber and mass plywood panels (MPP). This unique system required custom, laboratory testing of the MPP to determine the punching shear capacity at the point supports, as well as validate the deflection and vibration performance. The MPP is less expensive than typical cross-laminated timber (CLT) and also provides greater strength and stiffness per equivalent thickness. In addition to designing the first ever mass timber high-rise in California, DCI Engineers also helped the team save significant cost on the foundation and temporary shoring system by repurposing the basement walls from the existing structure that was located on the site.
TEAM
oWow
1510 Webster LLC
SIZE
193,286-sf |19-Story
MATERIAL
Wood, concrete
TEAM
Perkins&Will/Pfau Long Architecture, Hathaway Dinwiddie Construction, SKS Investments
SIZE
170,000-sf | 5-Story
MATERIAL
Mass timber, concrete
This 170,000-sf office building is the first of its kind in San Francisco. With three levels of Type IV framing over two stories of Type I framing, the building features approximately 100,000-sf of Type IV heavy timber framing, including cross laminated timber (CLT), glulam beams and columns and a timber concrete composite floor. The building utilizes a mixed construction method (Type IV over Type I) in order for the client to maximize the assembly area at the roof for tenants.
The project went through an extensive pricing exercise that spanned almost a year where DCI worked closely alongside the contractor to price concrete, steel and mass timber options. In the end, the mass timber option was agreed upon by the design team for its savings in both schedule and structure, along with its sustainability aspects. By selecting a mass timber building, the design team was able to save 40% in the number of piles required at the foundations for the project.
Oakland, California
Part of Oakland’s Jack London Square waterfront, Channel House is an eight-story, mixed-use, multi-family complex with 333 living units, 2,400-sf of ground level retail space, landscaped courtyards, communal gathering areas, outdoor terraces, and fitness center. The development includes five stories of Type III wood-framing over three stories of Type 1 concrete with posttensioned concrete slabs supported by a combination of concrete columns and shear walls. DCI’s use of a straight wall system for the Type 1 portion minimized construction costs while accommodating architectural layout, specifically for the 10-inch thick walls in the living units, which limits projections and maximizes floor area.
One of the architectural features of the project is a double height lounge area space located on the southwest corner of Level 4. In order to economically achieve this design feature, DCI evaluated mass timber, steel, and concrete options. Through coordination with the architects, the team determined a steel framed option combined with a CLT floor plate above the amenity areas provided a cost effective solution.
©Photos Courtesy of Bruce Damonte
TEAM
Solomon Cordwell Buenz Architects CIM Group
Suffolk Construction
SIZE
330,100-sf |8-Story
MATERIAL
Type III mass timber (CLT) over Type 1 concrete podium
AWARDS
2022 Golden Nugget Awards - Multi-Family Community of the Year, 100 du/acre or more
TEAM
Gensler
Plyler Construction
SIZE
37,000-sf |2-Story
MATERIAL
Wood, steel, concrete
The First United Bank in Sherman, Texas is a newly constructed two-story commercial building totaling 37,000-sf. The bank includes drive-thru teller features, a vault, offices, and a reclaim water system for irrigation purposes. The mass timber, steel, and concrete framing system provides an open floor plan, natural lighting, and exposed wood architectural elements.
DCI was the primary structural engineer of record and designed the prefabricated roof panel system supported by long-span glulam beams and columns; CLT shear walls and supplemental wood sheathed shear walls to resist lateral loads, cold-form steel framing for non-load bearing walls; and coordinated concealed connections via pre-engineered timber hangars and connector products. Extra attention was devoted for the exposed connections and column splices throughout the design and construction.
Seattle, Washington
Cedar Speedster is a newly constructed, mixed-use commercial building comprised of mass timber material. The timber structure honors the neighborhood’s historic industrial and lumber business influence once rife in Fremont. The three-story building includes 5,000-sf of retail, 10,000-sf of below-grade parking, and above-grade office levels. Prefabricated glulam columns and steel knife-plate connections were installed to accommodate uninterrupted columns from the ground floor to the roof level. This configuration of continuous columns minimizes timber shrinkage. DCI Engineers designed the custom beam and column connections for timber, concrete, steel, masonry, and foundation details.
DCI and the architect determined the strategic positioning of glulam girders for HVAC systems and utility piping to run tightly along the ceiling to preserve views and daylighting below the structures, which enhance the tenant’s overhead space. The engineers opted for a concrete shear wall core that allowed the architect to open up the perimeter of the storefront area.
TEAM
Revelution LLC
Weber Thompson
Turner Construction Company
SIZE
39,345-sf | 3-Story
MATERIAL
Mass timber, concrete
AWARDS
WoodWorks 2021 U.S. Wood Design Awards - Award of Regional Excellence
Portland, Oregon
TEAM
Ankrom Moisan Architects
Gerding Edlen Development
Andersen Construction
SIZE
111,657-sf | 6-Story
MATERIAL
Wood, steel, concrete
KEY FEATURES
LEED® Gold status
DCI provided structural design services for 38 Davis, a six-story, mixed-use building located in Portland’s Old Town Historic District. The L-shaped, wood-framed building is comprised of heavy timber construction over onestory concrete podium slab, which is a post-tensioned flat slab supported on concrete columns with concrete shear walls. Commercial retail/office spaces are located on the ground floor.
Levels two through four, which are dedicated to commercial/office space, are framed with glulam beams and columns, and offer an open office design. The upper two levels of residential units, which include affordable housing options, are framed with TJIs over glulam beams and columns. Concrete topping over levels two through six act as a diaphragm and mass to achieve the acoustic rating.
The building’s design was approved by the Historic Landmarks Commission in December 2014 and has earned LEED® Gold status. One of its most notable features includes gray water reclamation, which uses shower water runoff from the apartments to flush toilets in the office spaces.
©Photos Courtesy of Ankrom Moisan Architects
Oak Grove, Oregon
North Clackamas School District built a new two-story facility with 23 classrooms for the New Urban High School and renovated a separate, existing gymnasium. The new two-story building has a light-filled commons area, media center, art room, and technical education classroom. The building features ADA accessibility, a missing component in the original school constructed during the 1950s.
DCI Engineers provided both structural and civil engineering services for the project. The structural team proposed seismic improvements for the main building and gymnasium. For the new building, they designed the foundation, framing, stud and shear wall configuration, and structural details. For the gym, the team designed new shear walls; strengthened the trusses with post tension cable; and added fasteners to interconnect the roof walls and foundation.
The civil team evaluated the existing site conditions and developed the site demolition, erosion control, grading, stormwater, and utility plans. They coordinated documents to relocate parking; to replace the gravity storm line with new vegetated water quality and detention facilities; and to devise on-site and off-site improvements.
©Photos Courtesy of Opsis Architecture
TEAM
Opsis Architecture
North Clackamas School District
Corp Inc Construction
SIZE
49,350-sf main building | 7,000-sf gymnasium |2-Story
MATERIAL
Concrete, steel, wood, masonry
TEAM
Weber Thompson, Dunn Lumber, Hess Callahan Grey Group, Spear Street Capital, 3800 Latona Owner, LLC, Swinerton, Timberlab
SIZE
173,000-sf | 5-Story
MATERIAL
Wood
CERTIFICATIONS
Pursuing Leed CS Gold and Fitwel
Seattle, Washington
Northlake Commons is a two-tower, five-story life science-ready office building with connecting floor spaces. The mass timber office building is supported on three levels of below-grade parking; 9,500-sf of retail space; 27,000-sf of warehouse space; and 64,500-sf of outdoor space.
DCI designed the concrete parking levels and the timber framing to support future office and life science requirements; configuring column and girder layouts to optimize the balance of future requirements and market needs with current construction variables. The lower two levels are currently lab-ready and have been designed to meet anticipated floor load and vibration requirements. The upper floors are designed for office floor loading and can be upgraded during tenant improvement work for higher load and vibration requirements where needed.
Bellingham, Washington
Situated on a sloping site, the new Bellingham Public School Administration Building provides upgraded administrative, conference room and support facilities within a beautiful mass timber structure. The project capitalized on Type V-B construction, using light-frame exterior walls and shear walls with a glulam post and beam interior framing system that allows for maximum future flexibility, along with an exposed CLT floor plate and roof plate system. One end of the building is also designed as non-load bearing in its entirety for a possible future expansion of the structure.
DCI pursued a “use the materials where they make sense” approach. For example, the long span conference spaces use steel beams as a more efficient use of material. The team also utilized concrete shear walls to limit the length of shear walls needed to maximize the future flexibility of the spaces.
The building is oriented around the Community Space, the heart of the new development. A grand ‘feature stair’ encourages movement and provides a welcoming pathway to staff and visitors alike. This central space is bordered by various public program elements, including a cafe, informal meeting areas and an Early Learning Center.
TEAM
RMC Architects
Bellingham School District
Dawson Construction
SIZE
53,000-sf | 3-Story
MATERIAL
Mass timber, steel, concrete
CERTIFICATIONS
Washington Sustainable Schools Protocol (WSSP) Fitwel
JEFF BRINK, PE, SE Principal | CEO San Francisco, CA
DANIELLE JACOBS, PE, SE Principal Seattle, WA
WILSON, PE, SE Principal Austin, TX
ROGER HEERINGA, PE, SE Principal Seattle, WA
STEVEN KRUMENACKER, PE Principal Wayne, PA
THOMAS HOLMAN, PE, SE Principal Cottonwood, ID
MICHAEL BAUER, PE Senior Project Manager San Francisco, CA
GREG GILDA, PE, SE Principal Seattle, WA
KRISTOPHER SWANSON, PE, SE Principal Austin, TX
ERIC POPE, PE, SE Associate Principal Seattle, WA
HARRY RODIN III, PE Senior Project Manager Seattle, WA
JESSICA MARTINEZ, PE, LEED AP BD+C Structural Sustainability Specialist Seattle, WA
CHALUPA, PE, SE Principal Portland, OR
JONGEWARD, PE, SE Principal Portland, OR
COLLINS, PE Associate Wilmington, DE
KEVIN MILLER, PE Project Manager Portland, OR
ARIZONA DABRUSIN, PE Structural Sustainability Engineer Austin, TX
contact
Adam Jongeward, PE, SE Principal
921 SW Washington Street, Suite 560 Portland, OR 97205 (503) 850-9817
ajongeward@dci-engineers.com
Danielle Jacobs, PE, SE Principal 728 134th Street, Suite 220 Everett, WA 98204 (206) 787-8916
djacobs@dci-engineers.com
Jessica Martinez, PE, LEED AP BD+C Structural Sustainability Specialist 818 Stewart Street, Suite 1000 Seattle, Washington 98101 (512) 982-6459
jmartinez@dci-engineers.com