
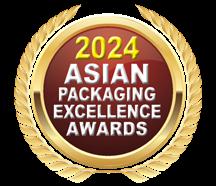
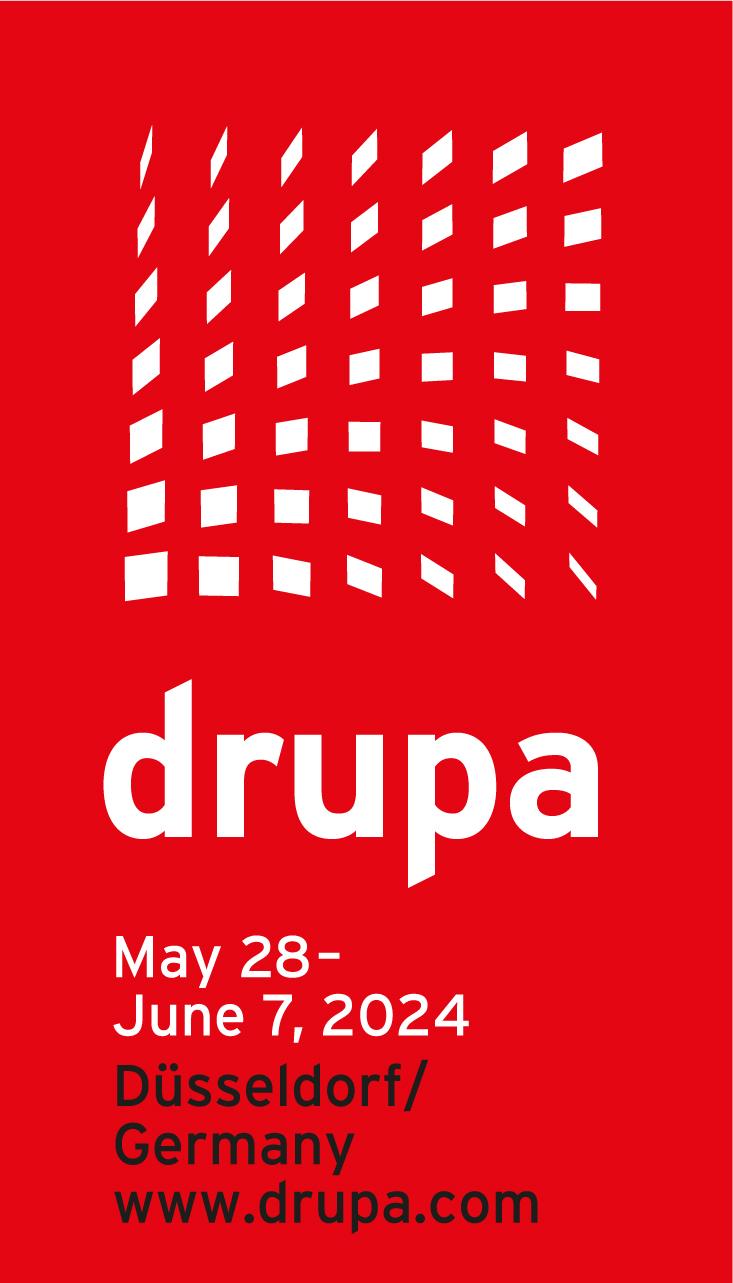
Our best-in-class inkjet and toner digital presses and imprinting solutions are built on the industry’s leading technologies.
So, from the smallest digital presses, to the largest integrated systems, you can trust Fujifilm to help transform your business.
Discover the difference at drupa 2024 Hall 8B, Stand A02
4 - 28 On these pages are the latest product news for drupa this month from durst - Komori
Koenig & Bauer - FUJIFILM
Kodak - Heidelberg
Hunkler - Scodix - HP
Landa - Epson - Highcon
Ricoh - KURZ - Xeikon
Screen - Glunz & Jensen - efi
CGS - Canon /OneVision
29 The 2024 ASIAN PRINT AWARDS ENTRY FORM
34 Modern Flexo Maximizes Returns in the Press Room
38 HEIDELBERG Asia Pacific ramp up packaging and label activities within the region and at drupa 2024.
42 IST has reinvented UV curing!
44 Digitalization, global dynamics, sustainability: The future of print
52 Unveiling the Big Brand Opportunity: Digital Print & Digitalization
55 The 2024 ASIAN PACKAGING EXCELLENCE AWARDS entry form
58 New and information from around the region and the world
2024
Issue 5 - 2024
Print - Packaging INNOVATION Asia Magazine
Published by
Asian Print Awards Management Pte Ltd
65 Chulia Street #46-23
OCBC Centre 049513
Singapore
Print Innovation Asia
Labels and Packaging Innovation Asia
Asian Print Awards
Packageing Excellence Awards
Label and Packaging Conferences
Publisher Paul Callaghan paul@printinnovationasia.com
Editorial Elizabeth Liew
elizabeth@printinnovationasia.com
Packaging Sales
Elizabeth Liew elizabeth@printinnovationasia.com
premedia/multichannel
postpress/converting/ technologies equipment/services/
prepress/print
premedia/multichannel
postpress/converting/ packaging future technologies materials equipment/services/ infrastructure
Gewichtung der Produktkategorien in den Hallen:
Emphasis on the product categories in the halls: hoch/high mittel/average wenig/low
PRINT& DIGITAL
Eingang/ Entrance CCD Süd
U-Bahnhof
Tram station
Merkur Spiel-Arena/ Messe Nord
8a
7a 70–2
6 61 5
4
3 1
Eingang Süd Entrance South
Eingang Süd Entrance South Nord/ North
Eingang/ Entrance
Durst Unleashing the boundaries of printing, discover the new KJet Durst are to unveil our latest innovation, the KJet hybrid machine, at this year's Drupa (Hall 16, Booth 41-1). The KJet represents the pinnacle of hybrid technology, offering operators a seamless experience with its user-friendly interface and ultra-short web path. This design not only minimizes waste but also reduces setup times, showcasing the advantages of digital printing. *
Lithrone GX/G advance EX Edition: New benchmarks for productivity and sustainability
Boasting world-class return on investment, the Lithrone GX/G advance Series is being introduced globally. Its ever-evolving productivity adapts to the times, addressing major challenges such as escalating energy costs and a shortage of operators that suppress the profits of printing companies.
To tackle these issues and achieve further productivity growth and sustainable management, Komori has developed the Lithrone GX/G advance Series equipped with revolutionary new functions. Leveraging the latest printing technology, this latest development from Komori reduces energy costs and enhances operator efficiency, propelling businesses to new heights.
Three essential developments achieve sustainable printing
Komori has pioneered an eco-friendly offset printing press designed to support printers while reducing greenhouse gas (GHG) emissions. By means of three ecoconscious functions, the press reduces power consumption by up to 18%* while printing and realizes stable feeder and delivery operation to cut wastepaper usage, thus both achieving reduced GHG emissions and high productivity.
*Effect of Smart Inking Flow and DC blower together
An optimized roller arrangement backed by state-of-the-art analysis, not only ensures enhanced print quality through stable density control but reduces
is its enhancement of sheet alignment during delivery.
Updated KID (Komori Information Display) - Improved operator efficiency through an improved interface - All necessary printing information is available on a single screen
The KID screen layout has been redesigned for enhanced operational efficiency. Now, all vital printing information is conveniently consolidated onto a single screen. Operators have visibility to inline quality inspections, density control, next job data, register, presets and more. There is no need to unnecessarily toggle between screens—our intuitive interface ensures that all essential data is easily accessible, optimizing operator workflow and productivity.
exhaust heat and energy consumption by alleviating the load on the rotary drive.
2. DC blower
Komori's DC blower achieves both economic and eco-friendly operation while maintaining the high-level airflow needed to properly stabilize the sheet. It significantly reduces power consumption through low-energy operation and minimal heat generation, all in a compact and lightweight design.
3. e-Mist
Komori's revolutionary micro-mist system directly controls the humidity of the paper to combat the effects of static electricity. By controlling the humidification time, power consumption and water usage, the system keeps energy usage to a minimum. An added advantage
- Operators on all levels can easily switch between jobs
All necessary data for a job including current job progress, estimated time remaining and timing of operator actions, can be visualized. Even inexperienced operators can easily and efficiently navigate between jobs.*
Durst unveils drupa line-ups with VariJET 106 a central focus
Koenig & Bauer Durst, a global market leader in folding carton and corrugated digital press systems and software services, will unveil the VariJET 106 in public for the first time with daily demonstrations
to take away will include applications for markets such as pharmaceuticals, health and beauty products, as well as food and beverage.
Koenig & Bauer Durst’s single-pass digital VariJET106 for folding carton markets press will be shown in a hybrid configuration linked to Koenig & Bauer’s industry-acclaimed Rapida offset press technology and workflow. The production story will also include latest die cutting and folding gluer technology.
The market-proven Delta SPC 130 used in corrugated markets – another family member in Koenig & Bauer Durst’s single pass digital sheet-fed press portfolio –will also be an important focus at drupa. A control station will be set up on the stand to demonstrate how the Delta SPC 130 works in a production environment utilising Durst Workflow and Durst Analytics.
Game-changing industry firsts such as the announcement of printing on mainly brown substrates with water-based digital white for primary food packagingannounced at the latest SPC Open House - will also be shown. Koenig & Bauer Durst is the first company in the world to offer digital white inks for primary food packaging. This creates new possibilities in packaging, for example printing on plain brown or lower grade white boards.
The SPC Open House at Durst Austria
in March was one of two pre-drupa customer-focused events hosted by Koenig & Bauer Durst, the other being the VariJET Open House in Radebeul, Germany, in April.
Daniel Velema, Managing Director of Koenig & Bauer Durst, said: “We can’t wait to show the VariJET 106, a monster of a machine, in full production flow at drupa. This combines the very best of conventional and digital printing. drupa will be a landmark in our journey within folding carton and corrugated markets. The tipping point is here. Corrugated and folding carton printers/converters who want to increase efficiency, flexibility and work even more closely with brands and retailers recognize that they need to digitize their production environments.
He added: “As a global leader in digital sheetfed, single pass press systems and software services for the folding carton and corrugated markets – and with the backing of two giants in the packaging and printing industry – we see huge opportunities to grow substantially over the coming years and continue to support and accelerate our customers’ digital journey.”
Koenig & Bauer Durst offers an unrivalled portfolio of digital printing machinery that, in addition to the Delta SPC and VariJET systems, also includes the CorruJET for corrugated markets. All presses use water-based food-safe inks &
coatings that comply with all regulatory requirements.
FUJIFILM to showcase the Jet Press 1160CFG, a high-speed inkjet continuous feed printer for commercial printing for the first time at drupa
Fujifilm Group began developing inkjet technology in the late 1970s and released the world’s first single-pass inkjet cutsheet printer, the Jet Press 720 in 2011. This was later followed by the Jet Press 750S, which with its high-resolution printing capability of 1200 dpi and exceptional quality, surpassing offset printing, has achieved significant global success, with over 300 printers sold to date.
In 2011, Fujifilm Group launched a continuous-feed inkjet printer for the transaction print market in Japan and Asia-Pacific. This was followed in 2019 with another press targeting the commercial printing market in Japan. In the transaction printing market, Fujifilm has achieved high-speed, highvolume, stable output of variable data using its own server technology, while in the commercial printing market, the company has achieved the high image quality demanded, using Fujifilm’s own pre-coatless ink. In Japan and AsiaPacific, with more than 150 printers sold, Fujifilm currently has the largest share of the market.
Fujifilm Group is pleased to announce that it’s now showcasing its new continuousfeed inkjet printer, the Jet Press 1160CFG at drupa 2024, combining the experience and technological capabilities cultivated over more than a decade. By adopting a newly developed water-based pigment ink, the new press is able to print beautifully on both coated and uncoated paper.
The innovative new press also adopts Fujifilm Group’s proprietary new technology “Paper Stabilizer*1“. Paper Stabilizer controls paper condition before printing, which solves production issues that customers of continuous-feed inkjet printers have often faced, such as ink adhesion on thick paper, waviness on thin paper, and quality fluctuations due to environmental and seasonal factors. The press can be used for a wide range of applications in commercial printing, including direct mail and brochures. At drupa 2024, Fujifilm will be demonstrating this new technology for the first time.
Fujifilm Group aims to enhance the value and streamline the operations of customer businesses through the provision of high quality products, helping them to grow into the future. Visit the Fujifilm drupa stand to learn more.
*1: Newly developed technology for controlling paper condition.
also to showcase the world's first B2 full colour dry toner digital press, Revoria Press GC12500 at drupa 2024
Fujifilm Group has sold over 300 of its B2 sheet-fed digital presses - the Jet Press 750S, which boasts industry-leading image quality and printing speeds.
The addition of the newly released Revoria Press GC12500 to Fujifilm’s Revoria range means that customers now have a dry toner B2 size printing option, in addition to A3. This product offers high production efficiency, user-friendly operation, and media versatility.
The GC12500 supports the largest size available in the current digital B2 printer market, B2XL size*1 (750 mm x 662 mm) paper. It can print up to six A4-sizes in a sheet, delivering high productivity of 250 ppm with A4. The press is capable of printing on small sized applications and large-format applications, such as posters. Additionally, consolidating the paper feeder/stacker and machine control panel in one place significantly improves the daily work efficiency and productivity for printing operators.
The printer was developed to enable B2 printing on demand without the need for specialised operators. Furthermore, Fujifilm has improved maintenance capabilities and optimised routine operations to minimise downtime.
Printing on B2 paper with dry toner has its challenges, but Fujifilm has incorporated proprietary new technology to overcome this. By developing new mechanisms for the fuser unit and developing unit, the stress on the paper during the printing process is reduced, improving image quality.
With this new technology, the maximum paper size can be expanded to B2XL while also enabling automatic duplex printing on paper weights ranging from
64 gsm to 450 gsm. Combined with the wide media versatility*2 inherent to dry toner, a broad range of applications can be produced.
Fujifilm Group will exhibit at drupa 2024 where its Revoria PressTM GC12500 will be showcased alongside Fujifilm’s comprehensive product portfolio.
Kodak at drupa 2024:
groundbreaking solutions for inkjet and traditional offset
The revolutionary Kodak PROSPER ULTRA 520 Press, powered by Kodak ULTRASTREAM Continuous Inkjet Technology, will take center stage at Kodak’s booth A02-2 in Hall 5. Driven by the KODAK 900 Print Manager and integrated with the Kodak PRINERGY Workflow Platform, the high-speed press will be demonstrated with newly launched versatile KODAK manufactured pre and post finishing solutions.
During drupa, the PROSPER ULTRA 520 Press, which uses KODACHROME Inks, will be printing various high-quality applications at full production speeds of up to 152 mpm (500 fpm) on a range of substrates live every day.
Debuting at drupa 2024 will be the powerful new wide-width Kodak PROSPER imprinting solutions for hybrid packaging and commercial print applications. This inkjet innovation can be integrated into offset, flexo and gravure presses as well as postpress and converting systems for highly flexible, high-quality digital imprinting of custom packaging, security, and commercial print applications.
Kodak’s high-performance imprinting technology enables printers to enhance their existing analog equipment with flexible digital capabilities and offer value-added services to their customers.
Kodak PRINERGY Platform – smart integration of digital and traditional print The Kodak PRINERGY Platform will
How will megatrends such as sustainability and digitization impact on processes, products, business models, and the future of the industry? In Düsseldorf, you will find out how the printing and packaging community is shaping the future.
May 28 – June 7, 2024
Düsseldorf/ Germany
www.drupa.com
#drupa2024
blog.drupa.com
mdrep@mda.com.sg
http://mda.messe-dusseldorf.com/
play an important role at Kodak’s booth as it provides a single, integrated and future-proof workflow solution that consolidates production across digital and analog printing processes. The PRINERGY Platform is compatible with virtually all third-party software and equipment and connects with the broadest range of digital presses.
It can act as the central hub of a smart print factory enabling centralized management of jobs using an intuitive interface to create, submit, manage and quality control jobs. Show attendees will be able to learn more about the new PRINERGY version 11.0, which has just been announced.
Visitors to Kodak’s booth can also experience Kodak PRINERGY Business Solutions, a fully integrated MIS/ERP, e-commerce and collaboration software solution that is seamlessly compatible with any workflow solution. Powered by PRINERGY and backed by Microsoft Azure, Kodak has combined printspecific software applications into a single integrated solution.
Additionally, the Kodak team will showcase the cloud-based Kodak PRINERGY Access content management solution which combines PRINERGY’s high-performance automation and customer portal tools with the versatility of connectivity to any digital press and any on-premise workflow.
Innovating traditional offset Kodak is also committed to driving continued innovation in offset printing. This year, the company is celebrating the 20th anniversary of its industry-leading line of Kodak SONORA Process Free Plates. SONORA Plates can reduce costs
in both prepress and the pressroom and improve sustainability without compromising quality or productivity.
Industry partner Koenig & Bauer (Hall 16/A31-1 – A31-5) will be using Kodak SONORA Process Free Plates for printing a wide range of applications on its Rapida Presses during the show. At Koenig & Bauer, a Kodak MAGNUS Q800 Platesetter with T-Speed Plus (up to 84 B1 plates per hour) and a Multi-Pallet Loader will image SONORA Plates. The MAGNUS Q800, which is the industry’s fastest 8-up CTP system, will be driven by PRINERGY Workflow Software.
Up to 20 percent increase in overall productivity thanks to Peak Performance technology
“The new Peak Performance Speedmaster XL 106 cuts print production costs significantly, which makes our customers in the commercial, packaging, and label printing sectors more competitive,” says Dr. Ludwin Monz, CEO of HEIDELBERG. “Compared to the previous generation, we expect users who produce packaging in the 70 x 100 cm
format to achieve an increase in overall productivity of up to 20 percent.”
Costs down – competitiveness up: HEIDELBERG has the solution to this in the form of more speed and automation. The new Peak Performance generation of the Speedmaster XL 106 can print up to 21,000 sheets per hour. With this new generation, autonomous printing is now also possible in packaging production, thanks to the enhanced Push to Stop concept.
This means complex production parameters can now be configured completely automatically in packaging and label printing, too. “We anticipate that a high-volume packaging producer
or wet-glue label manufacturer will very soon achieve a benchmark of 100 million sheets per year. This figure represents a 20 percent increase on the 85 million sheets currently being produced by today’s industry leaders,” says Markus Leichtle, Senior Manager Industrial Packaging at HEIDELBERG.
With further improvements to the HEIDELBERG User Experience (UX) and a new ergonomic design, the new Peak Performance Speedmaster XL 106 is setting high standards. The new PowderStar XL (Duo) reduces powder consumption by up to 15 percent and powder emissions by up to 45 percent.
What’s more, strain on personnel capacity is eased, because use of production clusters means that fewer staff can operate the same number of presses efficiently. When fully automatic Plate to Unit printing plate logistics is incorporated, it is possible to save on one assistant entirely, while also handling up to 150 printing plates per hour automatically.
Sustainability – new DryStar Combination Eco energy-saving dryer:
Featuring insulation in the delivery, a cross-flow heat exchanger, and an improved dryer-cassette design, the new DryStar Combination Eco dryer uses up to 30 percent less energy for drying. This investment is of particular interest to companies operating in markets with high energy prices. Customers paying European industrial electricity prices will find an investment in this innovative dryer will pay off within around two years.
What’s more, the complete press uses less energy per 1,000 sheets when the production speed is faster – for example, when the printing speed is increased from 18,000 to 21,000 sheets per hour, energy consumption drops by around 4.5 percent.
Hunkeler World Premiere at drupa 2024
Hunkeler presents a world first. The new fully automated Starbook Sheetfolder solution. This produces glued book blocks from the sheet for further processing in perfect binders. The solution is designed for nearline or inline production on digital high-performance sheetfed printing systems and represents a further new development in Hunkeler’s Starbook family of “Digital Sheet Finishing”.
Hunkeler is presenting a world first at drupa, the leading trade fair for the graphic arts industry in Düsseldorf. From May 28 to June 7, 2024, it will be demonstrated several times a day at the Müller Martini partner stand in Hall 1, booth B50.
The new fully automatic Hunkeler Starbook Sheetfolder book solution enables the highly economical production of digitally printed books from run lengths of 1. Highly variable page counts, variable spine lengths from book to book and fully automatic retooling guarantee a high degree of format flexibility for short to medium runs. The system produces 4-sided, glued book blocks from single sheets and feeds them to the Vareo Pro perfect binder from Muller Martini.
The excellent book block quality with perfectly straight and flat book blocks makes the system the ideal solution for the production of soft and hardcover books. The simple operation, low maintenance requirements, media flexibility and the ability to deliver individual book blocks at a speed of up to 1000 deliveries (stacks or individual books) per hour in perfect FIFO (First In - First Out) order set new standards in digital book production from the sheet.
With the Sheetfolder SF8, printed sheets up to B3 format can be turned, halved and folded, depending on the desired end product. The sheets are measured at the module input and aligned at the exact angle for processing. When changing to a new format, positioning takes place fully automatically during ongoing production - on the fly.
In the Book Delivery BD8, the signatures are aligned and then pressed into glued book blocks, collected and output. The first-class, flat-lying book blocks leave the module either individually or stacked and are transferred to the Muller Martini Vareo Pro perfect binder.
Scodix - Two new presses, two new technologies and six new enhancement applications to debut
Scodix, the leading provider of digital embellishment solutions, gears up for a triumphant display at drupa as it announces today that two new presses will be launched at the show, the Scodix Ultra 2500 SHD and the Scodix Ultra 6500 SHD. In addition to Scodix SHD (Smart High Definition) technology, the two new presses also see the debut of Scodix MLE (Multi-layer Enhancement) and Scodix AI, an automated embellishment creator tool.
Scodix MLE opens a whole new dimension for embellishments on uncoated paper, favored for sustainability and affordability. The key to Scodix MLE is the ability to apply multiple Scodix layers in a single pass. For uncoated paper, the first layer acts as a selective micro coating primer before Scodix Foil™ or Scodix Sense™. With the flexibility to add layering, braille and crystal effects become more economical.
Made possible with Scodix SHD technology, now integrated into the new presses, and the introduction of Scodix MLE, Scodix is adding six new applications to the current ten, making Scodix the only solution with 16 embellishment options available.
These include: Scodix Uncoated, Scodix Sculpture, Scodix Matte, Scodix Security, Scodix Reflective, and by incorporating Scodix Art embellishing on transparent media with Scodix Transparent is now available on the Scodix Ultra 2500 SHD and the Scodix Ultra 6500 SHD presses.
In addition, both presses deliver new levels of automation and reduce the costper-page for incorporating value-added enhancement into printed products. The new product introductions signify the continued innovation Scodix brings to the world of enhancement, bridging the gap between traditional and digital technologies.
Elevating capabilities for enhancing print even further, Scodix is the first to introduce AI technology for automating embellishment additions. Drawing from databases of Scodix-enhanced pages, it suggests intelligent, proven design options, whilst also providing data on cost-per-page so print buyers can create embellished designs quickly and intelligently.
The new Scodix technologies, Scodix MLE and Scodix AI, join four existing Scodix technologies: Scodix SHD –for the finest enhancement quality experience yet, Scodix VDE (Variable Data Enhancement), Scodix PAS and Scodix RSP to bring the widest choice of Scodix embellishment applications available on a single press.
The primary distinction between the new presses lies in their formats: the Scodix Ultra 2500, Powered by SHD is available in a B2 (28-inch) size whilst the Ultra 6000 is in a B1 (41-inch format). Both presses, however, can be managed by a single operator, boosting the ease of use for print providers.
Eli Grinberg, Scodix CEO and CoFounder, asserts, “With over 400 successful installs across the globe, we stand as the most proven enhancement
technology in the market. However, we refuse to settle in that position, we are committed to elevating digital enhancement and driving the success of our customers even further. With these new products and technologies, we’re not just leading the pack – we’re setting the pace for the future of embellishment. And we are delighted to showcase all this at drupa!”
Join the excitement on stand E11 in Hall 5 at drupa from May 28th to June 7th, 2024, and witness firsthand the unmatched power of Scodix’ new enhancement technology.
• Launches new HP Indigo 120K Digital Press for best-in-class productivity1, 18K Digital Press handling the widest range of print applications ever produced with a single B2 digital press2.
• Unveils innovative approach to digital security printing with new HP Indigo 7K Secure Digital Press.
• Defines industry standard for endto-end automation using artificial intelligence and robotics.
• Introduces enhancements to the HP PageWide portfolio to solve production challenges and unlock growth opportunities for the printing industry.
Today’s printing businesses are navigating increasing production challenges. Supply chain disruption, energy supply concerns and worsening sector labor shortages reinforce the need for greater efficiency, speed and reliability across the production floor.
The HP Indigo 120K Digital Press announced today sets a new standard for high-volume production and automation, while enabling printers to move jobs from analog to digital more intuitively and economically to meet demanding customer needs. Optimizing production floors by combining analog and digital technologies, the HP Indigo 120K reduces human touchpoints and enables multi-press operation by a single operator.
The new press delivers offset-matching image quality, flexible job routing between offset and digital, and an ECO mode option that reduces the press’s
carbon footprint by 11%3, supporting sustainability goals.
The next-generation of the bestselling B2 sheet-fed digital press, today’s launch of the HP Indigo 18K Digital Press takes versatility, efficiency, and user-friendliness to new heights. As the commercial printing sector tackles significant competitive transformation, the need for presses and solutions that help printers enrich their offering and sustainably grow their business is critical.
The new HP Indigo 18K Digital Press handles the widest range of print applications ever produced with a single B2 digital press4 , accommodating diverse substrates and job types seamlessly. Advanced AI features like auto recovery and proactive alerts enhance productivity and simplify the entire production process, achieving up to 80% press availability5 within a single shift. Aligning with HP’s sustainability commitment, the Indigo 18K supports Enhanced Productivity Mode (EPM), delivering 24% energy savings per sheet6.
Today HP introduces the groundbreaking HP Indigo 7K Secure Digital Press, revolutionizing restricted digital security printing by executing security-focused
print jobs in a single pass. Collaborating with Jura JSP, this cutting-edge sheet-fed press enables workflows tailor-made for security production lines, so customers can diversify their offerings, cater to a comprehensive range of security needs, and acquire new customers to grow their business.
At drupa 2024 HP members of the global print community will be able to see firsthand eight automated production lines equipped with the latest innovation across HP Industrial, involving over 25 partner companies and incorporating more than 20 unique automation solutions.
Landa Digital Printing today announces that it is launching the next generation of its market leading B1 digital print technology, the Landa S11 and S11P Nanographic Printing® Presses. The new Landa models offer extreme production versatility while reaching 11,200 SPH print speed. The increased speed drives superior economics for customers looking to increase productivity while reducing job turnaround times.
Commercially available at Drupa 2024 and utilizing artificial intelligence
technology, the new Landa presses will also offer a new PrintAI module which enhances print quality even further. It ensures a perfect fit for even the most demanding folding cartons and commercial print applications requiring micro text and other brand protection features. PrintAI opens the door to additional profit generating opportunities for many businesses.
Gil Oron, CEO, Landa Digital Printing comments, “We’re delighted to announce the launch of the Landa S11 and S11P. Following the success of our customers with current Landa S10 and S10P models and based on deep understanding of the industry’s future needs, we are taking Nanography to its next level. The new Landa models enable printers and packaging converters to not only increase print quality, but also elevate productivity and profitability while further reducing job turnaround times.
“As a mature and proven technology platform, we’re proud that over 50 Landa presses are now at the heart of many businesses in 14 countries around the world - with more than 20% of our customers having placed a repeat order for a second or third press. Considered a critical growth engine for folding carton converters, commercial printers, and point of purchase specialists, we’ve entered a new era of print production with Nanography.
A time when previous technology limitations have been removed, and print buyers can finally have what they want, when they want it – beautiful print, with unlimited design potential produced economically, at market leading turnaround times, and with the environment always in mind.”
The new Landa S11 and S11P models include a new ink drying system that enables transfer of dry ink from the blanket to the media, at the higher speed of 11,200 SPH. Unlocking additional productivity and improving economic benefits, the new high-speed capability is key for printers and converters looking to produce more jobs, with shorter deadlines.
The new Landa S11 and S11P can be customized to the exact requirements
A T D R U P A 2 0 2 4 !
Discover our solutions! CGS ORIS offers a wide range of software solutions to tackle the specific needs of the packaging, proofing and decor markets. Find your perfect match! Visit us! Join us in hall 8A, booth A06 from May 28June 7 in Düsseldorf!
of every customer. This means that each new press comes with a choice of four or seven colors, a continuous printing capability, an optional in-line coating unit, and the opportunity to purchase the 11K Module elevating productivity to 11,200 SPH and/or the PrintAI module.
Gil Oron, concludes: “The new Landa modules provide a significant premium to customers. While much of the new S11 series is based on the same robust and proven S10 platform, with the additional capabilities launched today, customers can expand their service offering or break into profitable new markets. More widely, there’s no question that the B1 digital print revolution is underway, with Landa presses helping many print houses and converters to meet some of the industry’s biggest challenges - and take advantage of some of its biggest opportunities.”
Epson at drupa focus on personalisation and production ondemand
Global technology firm Epson is demonstrating the full capabilities of its commercial and industrial digital inkjet range at drupa in Düsseldorf this year –from large industrial label presses, wide format direct-to-fabric, dye-sublimation and signage machines to award-winning smaller, compact devices designed for high quality colour printing on a wide variety of materials and substates.
Epson Global President, Yasanori Ogawa, will attend drupa and give a keynote speech on the first day entitled ‘Up Close and Personal – Innovation in Digital Printing’.
Mr Ogawa will say how Epson has ‘reinvented itself’ moving away from old analogue towards a more sustainable digital inkjet future: “I will discuss the potential for digital in Commercial and Industrial printing, how this is more sustainable, less wasteful and meets a growing demand for personalised, more valued products.”
Mr Ogawa continues: “The pursuit of ever greater efficiency, compactness, and precision that Epson has embraced for many years goes well beyond just technology. ‘Efficient, compact, and precise’ (sho sho sei) encompasses an enduring philosophy of eliminating waste, reducing dimensions, and increasing precision. I believe that this approach
will enable us to create even greater social value.”
A major focus for Epson at drupa this year is how to meet the growing demand for localised on-demand production. As the industry moves away from analoguebased one-sized-all printing towards more personalised, bespoke products, the demand for high quality, compact and flexible printers for micro-production has never been greater.
At drupa theywill be showing a storefront of stunning products that illustrate how our printing technology encourages creativity and allows individuals the creative freedom to realise their dreams working with many colours on numerous materials and surfaces - from vivid, colourful custom-designed t-shirts, photos, phone cases and coasters, to golf balls, surf boards, deck chairs, towels, car wrappings and beautifully designed wallpapers and home furnishings.
New Epson products on display at drupa this year include:
The new 64-inch SureColor SC-P20500, displayed for the first time, for producers of high-quality fine art photography, posters and indoor signage.
The new ColorWorks C8000 on-demand digital colour label printer designed for high quality commercial label production. New direct-to-fabric Monna Lisa 13000, an affordable single-step digital textile
printer with smaller footprint that delivers in-line printing using sustainable pigment inks.
The SureColor F10000 with new optional jumbo roll, Epson’s most productive dye-sublimation printer to date. Also announcing the new SC-F11000H with added orange and violet inks and optional jumbo roll.
New additions to Epson’s personalisation and micro-production printer range that include the new hybrid DTG/ DTFilm SureColor F1000, the A4 UV flatbed SureColor V1000, the A3 UV flatbed SureColor V2000 and the microproduction DTG/DTFilm SureColor F2200.
Our complete range of mini-lab (D1000, D500) and smaller dye sublimation printers (SureColor F500 and F100) designed for micro-producers and creative designers working on all kinds of materials and substrates.
Epson’s latest industrial robust printhead, the D3000, designed for aqueous and UV ink applications, showing the flexibility of Epson’s high precision printhead technology. Epson at drupa 2024 (stand D20, Hall 5).
Announces New Digital Die Cutting Solutions with Advanced Features for Mainstream Folding Carton and Corrugated Production
Highcon announced a new portfolio lineup ahead of drupa 2024, addressing the fastest-growing segments of paperboard packaging. Responding to a global market with continuously growing demand for smaller production batch sizes, faster
delivery, increased sustainability and enhanced customer experience, the company’s new portfolio accelerates Highcon’s strategy of mainstreaming digital die cutting by focusing on productivity, efficiency and quality. The new portfolio line-up includes:
- For Folding Carton, the Highcon Beam 3 with optional new Beam Writer for offline writing of DART foils, will allow customers to produce around 50% more per shift than with Beam 2 - while delivering higher and more consistent quality .
- For Corrugated Packaging and Display: o The Vulcan1, a revolutionary nextgeneration system with 1.4 x 1.7 (55” x 66”) sheet size, still under development, will enable the full benefits of digital die cutting to mainstream corrugated production.
o An upgrade to the Highcon Beam 2C that delivers up to 50% enhanced productivity when paired with the optional Beam Writer and facilitates the expansion of Highcon’s footprint in the short- and medium-run corrugated market - especially for POS and web-topack.
New Highcon Beam 3
The new Highcon Beam 3 has been
developed to respond to the feedback of both customers and prospects over recent years. It is packed with innovations and enhancements that will allow customers to be more productive and address a broader range of applications. A converter will be able to run 10 jobs with an average run length of 1000 sheets every shift. This will typically drive an ROI for customers of less than two years in a two shift operation.
New Highcon Beam Writer
The new Highcon Beam Writer, compatible with all Highcon Beam systems already installed, enables customers to create creasing rules using Highcon’s proprietary DART system and 5th Generation Consumables offline. For every 100 jobs per month, Beam Writer can free up more than 16 hours of Beam capacity, or two full shifts, improving productivity and increasing capacity.
New Highcon Vulcan
The new Highcon Vulcan will enter mainstream corrugated production and address a painful gap in current solutions. It has a maximum sheet size of 1.4 x 1.7 meters (55” x 66”) and supports boards up to 5mm, including microflute, B-, C-, and EB-flutes. Like all Highcon systems, Vulcan will combine true physical creasing with laser cutting, and will have a maximum throughput of 3000 fullsize sheets per hour (up to7000 sqm/ hr or 75,000 sqft/hr). It will have a job changeover time of 5-10 minutes.
During the tough economic environment of 2023, Highcon slowed down the Vulcan development with the intention to resume the program fully before the end of 2024. During 2026, the first Vulcan unit is targeted to ship for Alpha testing at a customer site.
Highcon is offering thought-leading customers the option to secure a finite number of early delivery slots. These slots will only be converted into binding
Make the move to digital – and unbox your business with the flexibility to accommodate fast turns, versioning requests, last minute edits, and changing buying decisions.
With the new EFITM Nozomi 14000 LED digital press for corrugated packaging and POS, you can reduce process steps from weeks and days to hours and minutes. And personalize runs from one to infinity at higher margins and with lower costs – all in a single pass.
Let’s build your brilliant future. Together.
Scan to learn how corrugated converters and packaging printers are opening up new ways to say, “Yes!”
orders following a successful production demo.
Upgraded Highcon Beam 2C
Based on a running speed that is ~15% faster , the upgraded Highcon Beam 2C offers higher productivity for corrugated customers with faster sheet throughput. When used in conjunction with the new optional Beam Writer, it will offer corrugated customers approximately 50% higher productivity per shift for typical customer job baskets. It also includes the Digital die cutting Workflow Package (DWP) for smoother, more effective and automated integration into a site’s production workflow.
“Inspired by our amazing customers, their feedback and how they’re using our solutions today - as well as inputs that we’ve received over several yearsHighcon will be demonstrating how digital die cutting is becoming mainstream. The time to die cut digitally has arrived.”
Ricoh showcases latest innovations and technology with immersive experiences at drupa 2024 Ricoh announced it will feature an immersive booth experience at drupa 2024, Hall 8a, Messe Düsseldorf, Germany, May 28 to June 7. Based on HENKAKU, the Japanese term for transformational innovation, the exhibit
will allow visitors to visualise new ways Ricoh solutions can help expand their business and reduce total cost of ownership through greater automation and efficiency.
Systems producing a wide range of high quality vibrant and versatile applications live on stand will include the new:
• RICOH ProTM Z75 B2 sheetfed digital inkjet press
The Dragon has landed, and the first B2 perfecting (auto-duplexing) sheetfed inkjet platform using aqueous ink accelerates the shift from offset to digital with higher print quality, faster turnaround times, and fewer demands on staff.
• RICOH Pro™ VC80000 digital colour high speed inkjet webfed press
This newest addition to Ricoh’s technology rich portfolio enables commercial, book, and direct mail printers to enjoy efficient operation and application agility with its enhanced automated production, closed loop quality control and advanced production floor integration.
• RICOH Pro™ C9500 digital colour sheetfed press
This next generation 135ppm press, known as the Jaguar, will be showcased at drupa. It empowers commercial printers to expand revenue streams and enhance
operational efficiency with its laboursaving automation.
• RICOH Pro™ C7500 digital colour sheetfed press
Commercial printers can elevate their creative and versatile print production capabilities by achieving richer and more accurate colour with this next generation five colour digital sheetfed press. The newest Jaguar of all.
Visitors will be able to see first hand how Ricoh’s brand-agnostic software solutions can unleash the power of information and transformation by delivering datadriven insights, driving operation-wide productivity and supporting opportunities to grow revenue. Some of the solutions demonstrated will be the new RICOH TotalFlow™ Producer, a SaaS solution that automates the submission and consolidation of incoming jobs from multiple sources into a web-based dashboard for operation-wide production visibility.
The award winning, trailblazing RICOH Auto Color Adjuster which provides precise colour management and matching capability without the need for a colour specialist, RICOH ProcessDirector™ the leading automated end to end workflow management solution that delivers piecelevel integrity, and FusionPro® that handles all personalised communication
as well as RICOH Supervisor™ which collects and interprets operational data sourced from connected production print devices and software, and its BI (Business Intelligence) engine creates web-based dashboard views to optimise device utilisation and throughput.
“Ricoh is set to showcase, with our broad range of market defining technologies, how we can partner with print production specialists and empower them to enhance their offering and drive growth,” says Koji Miyao, President of the Ricoh Graphic Communications (RGC) Business Unit, Ricoh Company, Ltd.
“Our flagship high speed inkjet and sheetfed toner presses will demonstrate their versatile and agile application production capabilities alongside the much-anticipated Ricoh Pro Z75 - the world’s first B2 aqueous inkjet sheetfed press – and the brand new Ricoh Pro VC80000. Our fast growing portfolio will present an array of revenue-generating applications supported by our owndeveloped printhead technology.
Our intelligent vendor agnostic software solutions will provide ways visitors can ensure efficient and resource-saving operations in their own production environments. These technologies will help PSPs unleash the spirit of Coinnovation today. Co-innovation is the shared journey to value generation with Ricoh as the partner to future proof their business for tomorrow.”
unveils the latest technologies at drupa 2024. The future of digital print embellishment With the aim of redefining digital print embellishment, LEONHARD KURZ will offer visitors to drupa a comprehensive experience with live demonstrations, expert insights, and interactive exhibits from May 28 to June 7, 2024. At booth E71 in hall 3, the DMMAXLINER 3D, DM-MAXLINER 2D and DM-SMARTLINER machines will be presented as special highlights.
As a pioneer in the field of thin-film technology and digital finishing machines, KURZ will be showcasing perfectly coordinated machines and consumables. Antonie Reinhart, Marketing Manager at LEONHARD KURZ, explains: “At drupa 2024, customers and interested visitors can experience the industryleading production speed and efficiency of our machines live and learn first-hand how they can benefit from our decades of technical expertise and broad portfolio of equipment. We are also delighted to be back as a Platinum Partner and look forward to continuing our strong collaboration with drupa.”
Revolution in print embellishment with ‘3D Inkjet on Substrate’ technology
The DM-MAXLINER 3D uses the innovative ‘3D Inkjet on Substrate’ technology for a particularly high-quality digital 3D embellishment. This enables high-precision application of digital
metallization and UV spot and relief coatings, creating amazing tactile effects with a brilliant gloss. Production speeds of up to 5,100 sheets/hour (B2) and 4,000 sheets/hour (B1) enable printers to outpace the competition with industryleading performance. From packaging and commercial printing to web-to-print, this press offers unparalleled singlepass efficiency and industrial high-speed performance. “This combination of efficiency, innovation and quality makes the DM-MAXLINER 3D the first truly industrial solution in the digital finishing industry,” says Antonie Reinhart.
Another machine is celebrating its world premiere at drupa and will be presented to the trade audience for the first time:
The DM-MAXLINER 2D. Alongside the DM-MAXLINER 3D, KURZ is presenting another highly innovative highlight for sheet-fed printing from KURZ Digital Embellishment Solutions that will redefine the landscape of digital embellishment.
‘Transfer on Toner’ technology impresses with outstanding user-friendliness
The DM-SMARTLINER also sets new standards in the digital embellishment market. Its innovative and easy-touse ‘Transfer on Toner’ technology is responsible for this. This enables unparalleled user-friendliness and opens up new dimensions in digital metallization. With the DM-SMARTLINER, users can carry out high-quality digital metallization without having to rely on complex processes or specialist knowledge. The application process is divided into three simple steps, consisting of printing the design, metallization with the DM-SMARTLINER, and optional overprinting.
Trade fair appearance with strong partners KURZ’s presence at the trade fair impressively demonstrates the Group’s in-depth expertise in machine manufacturing. An excellent example is the DM-MAXLINER 3D, which was developed by Steinemann DPE. With over 50 years of experience in the design and construction of machines for the printing and packaging industry, the KURZ subsidiary has earned a reputation for supplying machines that will work reliably for years to come.
In addition to presenting the leading technologies in digital embellishment, KURZ subsidiary MPRINT will also be demonstrating its expertise. There will be a world premiere at drupa: MPRINT will be presenting a completely new machine design for ultra-compact 4C digital printing, which can be used flexibly in sheet-fed and narrow-web printing. The turnkey solution, which can be integrated into new or existing press systems, improves productivity and efficiency. Finally, it produces less waste than conventional solutions.
The KURZ subsidiary Hinderer + Mühlich (H+M) will be presenting the latest developments in the field of embossing tools. H+M will be presenting various samples that have been specially created for drupa and show the fascination of tactile effects in hot stamping, blind embossing, and pressuresupported embossing. In addition, new effects in micro and nano embossing will be presented. . Besides outstanding tactile and visual results, the show will also demonstrate how customers can realize efficiency gains in production with H+M embossing tools. With the H+M EasyFix plate, for example, the set-up time can be reduced by up to 50%.
Xeikon unveils new 1200 dpi inkjet press for high-end label segment
Xeikon has announced details of the next evolution Panther inkjet technology as the leading press manufacturer prepares for the world premiere of the Xeikon PX3300HD, a new 1200 dpi digital press that will be launched at drupa 2024. Developed for high quality labels, the five-color machine offers a 330mm printing width and speeds up to 70 m/ min, even when printing with high opacity white. In addition, Xeikon PX3300HD utilizes a newly developed ink series, PXCure LED HD, to ensure perfect curing, while supporting sustainability targets for converters.
“As inkjet technology continues to mature, there’s a clear need to update Xeikon’s Panther portfolio with a higher resolution option to meet specific customer requests. Consequently, we’re now introducing a 1200 dpi engine to complement the existing 600 dpi product range,” states Jeroen Van Bauwel, Director Solution Design. “The new Xeikon PX3300HD will extend the capabilities for printers by giving them the tools to reach excellent quality at even higher productivity levels in a TCO-friendly way (Total Cost of Ownership).”
A small footprint machine, Xeikon PX3300HD excels at producing high durability, full-color labels for diverse markets, covering up to 88% of Pantone colors within Delta E 2 (rising to 94% within Delta E 3). To meet the specific requirements of the higher resolution engine, Xeikon has developed new PX-Cure LED HD inks. The new inks match the sustainability benefits of the recently introduced PantherCure UV LED series for Xeikon 600-dpi inkjet presses, including significant savings in energy consumption, instant warm up for more agile operation, and 10 times longer lamp life compared to traditional UV arc lamps, resulting in lower waste.
Combining superior image quality and resolution with remarkable productivity, the new press leverages Xerox W-Series industrial inkjet printheads with dedicated waveforms and screening software developed by Xeikon. Furthermore, PX3300HD is fully prepared for hybrid printing to increase productivity, with the option to add Xeikon’s modular inline LCUs (Label Converting Units) and a
large unwinder for longer uninterrupted production runs.
The highly efficient print workflow presented by Xeikon PX3300HD is driven by the powerful Xeikon X-800 DFE (Digital Front End), supplying faster job turnaround and just-in-time delivery. Color management is an integral part of the software: every X-800 comes with a Pantone license so customers can easily convert all the latest Pantone colors for their press and substrates. In addition, the basic press configuration offers efficient operational support with an inline camera for quality inspection included by default.
Adjusting registration, stitching and compensation for missing nozzles, all measured and corrected in a fully automated way, this feature also helps to alleviate ongoing issues with finding skilled staff to run the press, while extending the lifetime of the printheads and ensuring consistent high quality.
Van Bauwel concludes, “This extension of Xeikon’s inkjet capabilities is an incredibly exciting development for customers. It offers them a very cost-effective and highly competitive opportunity to scale their businesses, so they can supply profitable luxury market segments with exceptional productivity and quality. We are currently well underway with customer trials and will start sales at drupa.
I’d like to encourage all attendees to make their way to Hall 11, booth A01, to experience the PX3300HD 1200 dpi press running live and discuss their future path in inkjet for labels and packaging with Xeikon.”
adopts “Creating a Future in Print – Tech x Irodori” as its theme for drupa 2024
In today’s highly uncertain world, the printing industry faces constant change, demanding new forms of value creation at an unprecedented pace. Over the past 80 years, SCREEN has been a leader in the prepress and printing field, creating a wide variety of innovative products and working closely with its customers to make the world a more colourful place through printing.
In 2024, SCREEN is poised to elevate its collaboration with customers, integrating offset and digital presses at an unprecedented level to deliver a new future for printing. At drupa 2024, the company has chosen a theme of “Creating a Future in Print – Tech x Irodori” where visitors to our booth will gain valuable insights into the transformative impact of industry cooperation on the future of printing.
For the publishing and commercial printing markets, SCREEN is set to unveil
the Truepress JET 560HDX—a totally new high-productivity, roll-fed digital inkjet press that stands as a revolutionary platform, pushing the boundaries of innovation in the printing landscape. The system includes remarkable new inkjet technology that delivers significantly improved definition when used with SCREEN’s brand-new Truepress ink SC2. This new range of high-density inks enables printing directly onto offset coated papers without surface processing.
The Truepress JET 560HDX also features a high-efficiency dryer unit with support for 560 mm paper and print widths, providing a major improvement in productivity. Attendees will have the opportunity to look at print samples that demonstrate the Truepress JET 560HDX’s ability to achieve commercial print quality.
The Truepress JET 560HDX is also equipped with SCREEN’s newest digital front end and comprehensive workflow software system that incorporates the many market-proven technologies to drive front end efficiency as well as fast, repeatable file handling to reduce the need for manual operator intervention. Visitors to drupa should ensure they make time to see this cutting-edge digital inkjet press. (Hall 8A, Stand A03).
Step into the Future of Flexography with the new Flex-Pose LED 420 Plate Exposure Unit!
Unveiling a paradigm shift in the plate industry, Glunz & Jensen A/S proudly presents the Flex-Pose LED 420 Plate Exposure Unit –a masterpiece driven by the power of technology.
Are you ready to revolutionize your operations and embrace a new era of efficiency and sustainability? Do you desire a greener approach to your production processes?
The Flex-Pose LED 420 is your answer, combining top-tier performance with environmentally friendly LED, paving the way for a more sustainable.
Stay ahead of the curve and futureproof your operations with our mercury tube-free. Avoid being caught off guard by upcoming regulations and make the switch to our cutting-edge LED-driven unit for peace of mind.
Looking to cut costs without sacrificing The Flex-Pose LED 420 is engineered for efficiency, helping you save on operational expenses while upholding the highest standards of performance.
Energize your workflow with enhanced energy efficiency. Say goodbye to wasteful practices and hello to a more sustainable operation with the energy-efficient FlexPose LED 420.
Efficiency is the heartbeat of and the Flex-Pose LED 420 embodies just that. Experience a seamless workflow, improved productivity, and streamlined processes that redefine what efficiency truly means.
Seeking versatility and options tailored to your needs?
The Flex-Pose LED 420 offers a customizable solution for your unique requirements, ensuring adaptability in a fast-paced
Witness the future of flexographic technology firsthand at our stand in Hall 3 A91 at drupa 2024 in Duesseldorf, Germany.
Immerse yourself in innovation as the Flex-Pose LED 420 dazzles with its groundbreaking features alongside our other cutting-edge inventions.
Mark your calendars as we prepare for the first shipments later in 2024 following an extensive beta regime. Get ready to elevate your flexographic plate production with and the game-changing Flex-Pose LED 420 Plate Exposure Unit.
EFI at drupa in Hall 9/A20-1 for what’s new and what’s next in inkjet innovations for the display graphics market.
Like the DISRUPTIVE innovation of the super-high-speed, high-quality production capabilities of the EFINozomi 14000 SD printer. This 1.4-metre-wide platform adds capacity and significantly improves your speed to market as you profitably produce short runs, longer runs, and personalised jobs. Boost your hashtag#growth and profitability with:
- Maximum productivity that assures more profits
- Premium print quality that wins more jobs
- Digital technology that drives production savings
- Superior sustainability that meets customer demands
- EFI Professional Services focused on your success every step of the way
As we get ready for drupa, we thought we’d share a glimpse of what we’re bringing to the table:
Decor Market: Elevate your decor printing with our solutions. Our Decor Print Software ensures a flawless replication of surface textures, colors, and gloss levels, mirroring the final product like never before.
- Packaging Market: Revolutionize your packaging proofs with us. Utilize our FLEX PACK Software for substrate proofs directly on materials like shrink film, cardboard, or metal. Experience proofs that seamlessly match final prints.
- Complete Solution System: Our offerings extend individual markets. From proof and mock-up to production and color communication, we’ve got you covered! Plus, not only do we offer exceptional software, but the right
hardware and media to go hand in hand with it.
Join us at DRUPA in Hall 8A, Stand A06, from May 28th to June 7th and explore our solutions! Let’s discover how we can help you create better proofs, every step of the way.
Together with technology partner
Canon, software manufacturer
OneVision presents a holistic workflow solution for individual print products at drupa
Automation becomes a success when systems work together seamlessly and different processes run smoothly. Printing systems and solutions manufacturer Canon and automation expert OneVision Software AG, together with other partners, are demonstrating how this works in live demos at the Canon. booth B41 in hall 8A.
Perfect interaction between hardware and software
Cutting-edge sheet fed and roll fed
digital printing systems for commercial, book, wide format, packaging and label printing – used for example to produce visual communication including direct mailings and POS, labels, interiors and more – unleash their full power when supplied with perfectly prepared print files and integrated into a fully connected production ecosystem.
To make this possible for print service providers, OneVision and Canon are working closely together. “In today’s world, which is characterised by enormous margin pressure and a lack of skilled workers, it is very important for companies to invest in holistic solutions. The partnership between Canon and OneVision serves exactly this purpose: to enable our partners on the customer side to react to the constantly changing challenges and to work profitably today and in the future with a complete solution for print production”, explains Stephan Reiter, Sales Director Indirect Channels, EMEA at OneVision Software AG.
Holistic production workflow at drupa
In live showcases, drupa visitors can experience the automated production process of various small and large format printing applications. From incoming orders in the web shop, customized packaging design and automated file preparation through printing, finishing and production control, print jobs run efficiently through the production process.
Modular software for automated production processes
As middleware, OneVision’s automation software is easily integrated into existing system environments to speed up production processes. The creation of barcodes, e.g. for job control, enables job tracking and provides greater transparency.
In addition, state-of-the-art technologies for dynamic and automated print form creation (imposition, nesting, ganging) ensure greater sustainability in terms of substrate usage. OneVision and Canon will be represented at drupa 2024 in Hall 8A.
SINGAPORE 28-29th OCTOBER 24
Deadline for submission - 24th September by 5pm Awards Dinner in Singapore on the 29th October 2024 at Marina Bay Sands We are 23 this year
Recognising PRINT excellence across the Asian region
The annual Asian Print Awards was founded to recognise outstanding achievement in the print and packaging industries across Asia. With more than half the world’s population represented in this fast growing area, communication in the form of printed matter links Asia’s diverse cultures. It is imperative that such print achievements do not go unrecognised, especially among the population base that Asia enjoys.
The Awards are judged on a wholly quality-oriented set of criteria to ensure that fair play is enacted at all times.
The Independent Judging Panel comprises highly qualified personnel from within Asia and around the world. The independent judging panel has no knowledge of the actual entrants details. ALL ENTRIES ARE NUMBER-CODED. Entries must be commercially produced work.
The Asian Print Awards is the only regional print quality competition of its kind in Asia. Supported by leading industry-supply companies, any progressive quality print house should enter and prove that they are the best - by winning the Gold, Silver or Bronze award. Proving pride in quality awareness is what customers love to see. It’s not just empty words, you can prove it.
Categories 1-8 : Offset Printing Only
1. Calendars – any format
2. Sheetfed Magazines
3. Book printing – less than 4 colours
4. Book printing – 4 or more colours
5. Limited Editions & Artwork Reproductions (under 1000 print run)
6. Web Offset – Coated stock 70gsm and above
7. Web Offset –LWC (light weight coated) 65gsm or less
8. Offset Packaging products
Categories 9 - 21 : Digital Printing Only
9. Book Printing
10. Calendars
11. Personalised photo books – any format.
12. Posters 13. Showcards & Point-of-Sale material 14. Digital Magazines
15. Gold, Silver and Special colours 16. Restaurant Menus
17. Limited Editions & Artwork reproductions (under 500 print run)
18. Digital Proofing (must supply the digital proof and the prinnted product)
19. Digital Packaging
20. Digital Labels
21 Digital - Outdoor Billboard
22. Digital Embellishment
Categories 22-27 : Specialty Categories
22. Multi–Piece Productions and Campaigns
Any substrate or print process: Multi–piece Production must be 3 or more items such as folder, leaflets, ring binders, inserts, envelopes including their contents. Campaigns must be 3 or more items with a consistent theme produced during the year by the same printer for the same client.
23. Embellishment
Any substrate – any combination - for example: embossing – diecutting – foil stamping –laminatingcoating.
24. Innovation / Specialty Printing / New technology
The entry must exhibit any innovative and/ special application of machinery, process, substrate or finishing. A short description must be provided for the judges, detailing reasons for entry into this category.
25. Company Self Promotion
Any item printed to promote a product or company involved in the graphic arts industry. Self promotion cannot be entered into any other Category.
26. Judges Special Award (A job that catches all the Judges’ attention)
27. Design and layout. We look at the impact and visual effect.
28. Security applications
Send your entries by 24th September 2024 - by 5pm to: Asian Print Awards
c/o Print & Media Association of Singapore 627A Aljunied Road, Biztech Centre, #04-07 Singapore, 389842 Tel +61 422 869 728
INNOVATION PRINT AWARDS
Deadline for Entries Submission: 24th September 2024, 5pm
Remember to submit 2 copies of each job! Why? - Just in case one is damaged.
If you win an Award, YOU MUST attend the Award Dinner in Person. This is part of the competition rules!
SECTION A (This will not be shown to judges). Please fill the form in capital letters.
Entered by (company name): ______________________________________________________________________________________
Contact Person: ________________________________________________ Email______________________________________________
Address: ___________________________________________________________________________________________________________
Telephone: __________________________________ Country____________________________________________________
Category entered: ___________________________________________________________ (Example Cat 4 Book printing)
Title of entry (ie: " Paul's Ice Cream" ): ________________________________________________________________________________
Printed by (Printers name): ________________________________________________________________________________________
Client name: _______________________________________________________________________________________________________
Designer Pre Press House: ___________________________________________________________________________________________
Brand of Printing Machine used: _____________________________________________________________________________________
Stock supplied by (Merchant’s name): ______________________________________________________________________________
Ink used to produce the entry : ____________________________________________________________________________
By signing here you accept the rules and conditions of the Asian Print Awards
Signature over printed name_____________________________ Name_____________________________________________________
SECTION B Production information to be shown to judges ( tape this securely to the back of your entries)
Category entered (Same as above): __________ Entry number (Administrative use only]
Title of entry (ie: " Paul's Ice Cream" )__________________________________________Print method: _______________________
Number of ink colours (4-6-8 etc) ________ Any Embellishment (foil stamping etc) __________________________________
Quantity produced (Print run copies): ___________ Other technical details (finishing processes etc) ________________________
The Awards Dinner will be held in October on the 9th November in Singapore Send all entries to - Asian Print Awards c/o Print & Media Association of Singapore 627A Aljunied Road, Biztech Centre, #04-07 Singapore, 389842 email:Paul@printinnovationasia.com Tel. +61 422 869728 Additional entry forms can be downloaded online at www.printinnovationasia.com All entries are non-returnable unless a prepaid self addressed courier pack can be provided
The 2024 Asian Print Awards Checklist!
1. Have you submitted your best work to be judged?
2. Have you checked the work to make sure its 1st class?
3. Check it one more time!
4. Are their 2 copies of each entry ?
5. Is it packed correctly for shipment with 2 copies of each entry ?
6. Have you left enough time for shipment24th September 2024 5pm is the Deadline
7. Check the address you have written - it should be
Asian Print Awards 2024
c/o Print & Media Association of Singapore
627A Aljunied Road, Biztech Centre, #04-07
Singapore, 389842
Tel +61 422 869 728
Good luck and may the regions BEST Printing Companies WIN!
Packaging printers and prepress specialists today are looking to get more out of their flexo production. New technologies and techniques are driving flexo to a higher standard for packaging printing, transitioning flexo from craft-based to a more standardized, sustainable manufacturing process.
In the last 4 years, the packaging printing industry has been through constant change due to various pressures including Covid, supply chain crisis and inflation. While these pressures have begun to stabilize, brands continue to focus on continuity of supply, driving more efficient SKUs, as well as prioritizing sustainability to protect the environment, which is driven by the consumer. The needs of the brands are creating increasing requirements for printers to be more efficient and sustainable in their production.
Fortunately, at the same time, new technologies and techniques are driving flexo to a higher standard for packaging printing. Flexo is evolving from its ‘traditional’ capabilities, practices and processes to a new era of what we at Miraclon call modern flexo that is a
standardized, sustainable manufacturing process. The lack of skills in the industry, combined with the pressures on printers to increase yields and implement sustainability improvements necessitates less ‘craft’, and more efficient, intervention-free printing that can cope with the full range of client demands.
Modern Flexo — standardized and sustainable manufacturing Modern flexo describes a production state where
• Flexo can achieve visual parity with gravure, offset and digital.
• Results are consistent and predictable enough to enable printing by numbers.
• Jobs are printed with as few colors as possible (more process, less spots)
• Print conditions offer wide print latitude and facilitate clean printing.
• Outcomes can be optimized in more challenging environments, including — crucially — with more sustainable materials.
As a result, printers that implement modern flexo benefit from increased uptime, less troubleshooting, reduced waste, and more efficient job scheduling. They are positioned to commercialize more sustainable offerings and compete for work traditionally printed with other print processes.
The plate is the catalyst
While implementing modern flexo practices requires collaborative effort between the printer and their key suppliers — press, ink and anilox manufacturers
Simply consistent
Decrease waste and setup with predictable plates
Simply efficient
Increase on-press performance with a robust plate
Simply sustainable
Support sustainable inks and substrates all with the same plate
Simply better
Address your most demanding brand and quality requirements
From prepress to on-press, deliver the efficiencies and productivity needed from your plates to maximize your bottom line.
and prepress providers have all innovated steadily over the last decade and a half — it is the flexo plate that sits at the center of the flexographic print process. The plate brings together substrates, inks, tape and anilox, influencing press capability and results, and is the key enabler of best-in-class flexo printing that is highly consistent in the press room.
Miraclon is a key enabler of Modern Flexo, through our innovative and differentiated FLEXCEL NX Technology and applications expertise.
Our proprietary FLEXCEL NX technology makes possible the ultimate control of ink transfer on which modern flexo is founded, and which is enabled by advanced plate surface patterning. The surface of a FLEXCEL NX plate incorporates digitally imaged surface
channels that enable the ink to flow. The channels are just 4-6 microns wide — there are 6 channels in the width of a human hair — and can be modified for different applications and different combinations of presses, substrates, inks and aniloxes. Advanced plate surface patterning can only be achieved through Miraclon’s unique imaging and plate making technology that eliminates variables from the plate making process.
Over the years successive iterations of our plate surface patterning technology have brought new levels of control in ink transfer, improving the quality, predictability and consistency of flexo printing. The scanning electron microscope (SEM) images in the illustration below clearly show the progression.
The most recent iteration — brought to market as PureFlexo™ Printing — specifically tackles unwanted ink spread, which puts pressure on the production process, often leading to lower press speeds, more frequent unscheduled stoppages to clean plates, and a general reduction in press setup latitude. Wide print latitude is key to profitable production: less latitude, and the more likely that a small change in printing conditions will affect quality and result in reduced productivity, increased time and material waste.
The best way to understand the impact of modern flexo is to see it in action. Miraclon is a key enabler of the transformation to modern flexo, and at drupa we’ll be highlighting 12 case studies of printers that have made that transformation. Each of them has used FLEXCEL NX technology to change the way they print and realize significant financial and sustainability benefits. The benefits are quantified, and the case studies cover a range of packaging applications and challenges from around the world. We invite printers to visit the Miraclon stand to learn how implementing modern flexo can help them meet their efficiency, sustainability and quality goals.
At drupa 2024 in Dusseldorf, under the banner of “Unfold Your Potential” HEIDELBERG will display equipment and workflow covering the full end to end production for the packaging and label segment.
The global printing industry faces several hurdles which includes - the rising cost of materials, a shortage of skilled labour, the challenge with implementation of a true digitalization strategy within the entire print production chain and finally the increasing requirements for compliance to meet global sustainability targets.
With an array of equipment and software solutions Heidelberg aims to address these growing mega trends within the industry through increased competitiveness, promoting the workforce, improving sustainability and digitalization of the print production chain.
One of the highlights at drupa will be the 2024 Generation Speedmaster XL 106 in a specialized packaging configuration and the digital label press Gallus One amongst many other highlights, along with partner company MK Masterwork who will complement Heidelberg with a complete packaging postpress equipment and workflow aimed to achieve higher overall production efficiency.
The Speedmaster presses at the Heidelberg booth will all be complemented with the Prinect Production manager controlling all aspect of the print workflow from
prepress design, Scheduling, MIS, Print and Postpress production finally through to invoicing. Heidelberg will also launch the highly anticipated Heidelberg customer portal platform which will be the interface for Heidelberg users to the Heidelberg digital ecosystem.
At drupa 2024 in Dusseldorf, Heidelberg will also showcase together with partner IST Metz, the Speedmaster CX 104-6+L UV with a focus on special applications and value-added print production.
The CX 104 is the primary choice for high-end packaging applications within the Asia Pacific region. The CX 104
platform is fully scalable with wide range of models and specifications for each individual customer requirements.
Recently the highly successful packaging printer Zhanjiang Cigarette Packaging Materials Printing Co., Ltd. Installed a further two specialized configuration 16 units CX 104 presses at their state-ofthe-art factory located in Guangdong. This outlines the companies trust in Heidelberg and our world leading CX 104.
The machines are producing the high-end packaging requirements for the Chinese and international markets with a focus
concept on “customer first, service first” The top priority for Zhanjiang Cigarette Packaging is product research and development, technological innovation they have an R & D center covering professional design, process research and development Additionally the state-ofthe-art factory has a technology center which continues to improve, excellence, and all-round customer service.
The company pays attention to lean production, implements quality control management of the whole life cycle of products, and does not let a piece of waste flow out of the door of Zhanjiang cigarette prints, so that customers can be fully rest assured in receiving quality products,
World premier -The new 2024 Generation of the Speedmaster XL 106 - the success continues. The highlight for many visitors at drupa 2024 will be the unveiling of the next generation Speedmaster XL 106 with new technologies aimed to benefit the folding carton and Label segment.
A number of new technological innovations will be showcased for the
first time at the world premier launch. Amongst many new groundbreaking technologies, the focus at drupa for the Speedmaster XL 106 will be toward, improved operating systems with the Heidelberg UX - User Experience, higher Overall Equipment Effectiveness - OEE, increasing performance and the reduction of waste materials, energy and makeready times, improving the overall ecological footprint of a users production environment.
Heidelberg Partnership in packaging segment solutions with MK Masterwork continues to grow rapidly.
Established in 2020 as one of the flagship divisions of PT Mega Grafindo Indonesia, a renowned cosmetic company, has specialized in producing high-quality packaging for various lines of MS Glow cosmetic products. Located in Tabanan, 30 km from Denpasar, Bali, PT Mega Grafindo Indonesia has rapidly evolved into a printing company catering to printing needs ranging from packaging for MSMEs, hotels, and restaurants in 2023. "Initially, we operated as a division supporting the packaging needs of cosmetic manufacturers in Bali, and
to enhance efficiency, we established a printing unit in Bali," said Mr. Victor Humardhani, Operational Manager of PT Mega Grafindo Indonesia.
With the growth of MSMEs, hotels, and restaurant industries in Bali steadily increasing, the demand for packaging printing is also on the rise. Recognizing this opportunity, PT Mega Grafindo began accepting orders from outside the cosmetic manufacturing sector. The choice of the Easymatrix 106 FC machine as a solution for die-cutting and hot foil stamping needs with the best quality is a crucial decision.
This machine can perform die-cutting at an output of approximately 6,500 sph (sheets per hour) and hot foil stamping at an output of 5,000 sph (sheets per hour) to produce high-quality packaging in line with market demands, especially in the cosmetics segment. "We aspire to be pioneers in producing packaging of the highest quality in Bali and Eastern Indonesia, which is why we choose machines with the best technology and perfect after-sales service like Heidelberg products. Based on our experience, Heidelberg machines have excellent durability and cutting-edge technology that facilitate operations," added Mr. Victor.
With the configuration of state-of-theart machines, including the Speedmaster SX 74-4, Easymatrix 106 FC, Diana Go 85, Polar 115 PF, and CtP Suprasetter A 75 equipped with Prinect Production Manager, PT Mega Grafindo Indonesia has developed into a leading solution provider offering various high-quality packaging prints. Practically, the range of Heidelberg machines in PT Mega Grafindo Indonesia simplifies and enhances the efficiency of the production process. From pre-press, press to postpress, everything can be monitored efficiently, ensuring that the quality of the packaging products meets market demands.
Heidelberg continues Expansion of digital activity with the Gallus One.
Another Gallus digital installation with Gallus One is coming – Dragon Printing, a leading label company in Australia, reports about their experiences on the digital label printing press from Gallus. An improved technology and perfectly fit for right jobs mix are the positive conclusion by Dragon Printing, in Sydney Australia on further investment into digital with Gallus.
The reasons for the Gallus One was, as we continue to grow, primarily an expansion of capacity, explains Paul McCullum, Managing Director at Dragon Printing; we wanted to do this as cost-effectively as possible. He explained compared to his existing Gallus Labelfire; Gallus One has
a faster output speed with digital white and improved technology improvement with ultra sonic cleaning at the ink jet print heads.
He also could see the benefits of having the Labelfire for high quality high embellished goods and utilizing the Gallus One for the simpler “day-to-day” jobs; making it perfectly fit for the various job mix with diverse job applications. Mr McCullum expressed his satisfaction and confidence on the reliability and professionalism of Heidelberg Australia service support team.
Dragon Printing is an Australian owned and a leading label printing company manufacturing coming from Sydney NSW. Company expansions have combined to create innovative and high-quality solutions for their clients’ products, continuously keeping the company vision alive.
Heidelberg to showcase the new Boardmaster at drupa.
One of the big drupa attractions at Heidelbergs Wiesloch event will be the official fist public viewing of the new Boardmaster.
The Boardmaster is a flexographic web printing system with a machine uptime availability of up to 90 percent and a maximum printing speed of 600 meters per minute.
It delivers double the productivity and thus dramatically reduces the total cost of ownership in industrial packaging production. As the global demand for packaged goods continues to grow, packaging and label printing is experiencing structural growth, making it an important core segment for Heidelberg.
The new Boardmaster is especially suited to the food and beverage sector’s folding carton applications, which are becoming increasingly popular worldwide due to a growing global demand for packaged products.
In combination with the Intellimatch scanner, the Boardmaster completely automates job setup and achieves a print quality previously unattainable in flexographic printing.
At a printing speed of 600 meters per minute, it moves from one job to the next. This means non-stop production with zero changeover times for long runs of folding cartons, lottery tickets, and packaging for beverages and food.
“With the world premiere of our Boardmaster, we are responding to key customer challenges in the packaging market – cost pressure, the skills shortage, and the need to optimize productivity and sustainability,” says CEO Dr. Ludwin Monz. „At the same time, we underline our innovative capability and technological leadership in packaging printing“.
Heidelberg Asia Pacific with our branch operations and dealer network in 17 countries within the region provides the most comprehensive after sales and service support with the Apac region.
We look forward to personally welcoming you to our booth located at Hall 1 in Dusseldorf during drupa.
A whole host of new innovations addressing current market dynamics, new business ideas, applications, digitalization, consultancy and training will be available both at drupa and at the Heidelberg Wiesloch days in Heidelberg. Furthermore, we hope that we can welcome later this year at our Print media center in Shanghai and also our technology center in Tokyo Japan where we will bring drupa 2024 to you our customers in the region.
IST METZ, a leading innovator in UV technology, will be presenting its latest developments in UV curing at drupa in Hall 1, Stand A24. In response to the increasing demand for efficient and customised solutions, the company has developed pioneering technologies that take the performance and versatility of UV curing to a new level. Come by and get to know our company and curing solutions.
IST have been living the motto "more than UV" with passion for half a century. Over the past 45 years, we have always managed to catch on the trends of the time and still see ourselves as a modern family business with visions. Because, with a view to a sustainable future, we think long-term and our UV solutions are not just a trend for us, but pave the way for the next generation of light curing.
We are working on this together with enthusiasm and are convinced that our experience and philosophy of always going that little bit further will enable us to write the next chapter of technology together, which will undoubtedly bring with it a paradigm shift and challenges. In the spirit of digitalisation and sustainability, for a safe and green future for us all.
Nothing is more fitting to this idea than our tried and tested motto “more than UV” - which is why we have given our corporate image a new appearance that wonderfully transports our company philosophy into the future. As the saying
goes, a picture is worth a thousand words, be curious to see what this looks like at IST.
With this in mind, we look forward to presenting our latest breakthroughs in UV drying technology at drupa this year - come along and take yet a look at the future of UV.
LED-UV: At a time when the international market for LED-UV systems seems oversaturated, we are certain that our LED solutions make a small but significant difference. Because we don’t just focus on the short-term effect, but look at sustainability from all perspectives. We believe that the different applications also require special curing solutions, which is why we have developed specific and market-orientated LED solutions for the respective printing applications. The full energy-saving potential of an LED can only be utilised if experienced personnel and all the features on the printing press are used. In our experience, this is often not the case in practice. At this point, namely
determining the most energy-saving setting on site, we have started to ask ourselves how we can flatten this hurdle for the user in a simple and flexible way. The answer is:
SMARTcure: SMARTcure is our innovative AI-supported curing assistant that determines the optimum principle instead of the maximum applicationspecific principle and optimally controls the dryer based on the parameters from the pre-press stage - for a revolutionary UV curing process.
The required data transfer between the plant and the cloud creates a system that can provide operating data for maintenance in addition to an assistance function - all with the aim of establishing modern and environmentally friendly work processes. In this way, precise specifications for the power settings per dryer are determined and implemented in an energy-saving manner. The resulting reduction in power consumption and operating temperature has a positive effect on the service life of LED systems. The user can evaluate the drying quality via a feedback option. Feedback and
setting changes are processed directly in the cloud. Other measuring systems and analyses can also be used here, such as the UV Analyzer, measurement of the double-bond conversion, solvent resistance or simply a thumb test. The SMARTcure system thus learns continuously and enables a simple and customer-friendly optimisation process for modern drying applications.
This is where the future is being created: we have laid the foundation for this in Nürtingen, namely in our stateof-the-art application centre, the UV Technology Campus. Over the last two years, a new top-class research laboratory has been created, where the ideas of tomorrow are already being developed in the “original Swabian sense”. The centrepiece of the new laboratory is not only test facilities, but also a hightech analytical laboratory. Here, at the birthplace of SMARTcure technology so to speak, the ink and coating
series are measured and the data prepared for the SMARTcure Cloud. SMARTcure combines the data from the UVTC with the data from prepress and creates a
recommendation for the printer/press - the printer does not have to intervene manually in the process - it can accept the recommendation and thus produce the job under optimised conditions with maximum energy savings.
You can find out what this looks like in practice at our exhibition stand. Come and see us and discover the smartest way to save energy.
IST’s UV lamp systems are already fit to make the changeover uncomplicated: They are either “LED prepared” or equipped with the direct change option “HotSwap”. These features make it possible to switch without having to change the entire periphery of the unit. So- called hybrid systems, in which a mix of UV lamps and UV LED systems are installed inline on a machine, are also becoming increasingly popular.
We rise to the challenges: IST has revolutionised and further developed lamp technology from the Swabian town of Nürtingen and thus also found an answer to the new printing ink regulation: The patented FREEcure system, which
minimises the use of photoinitiators or even helps to eliminate them altogether thanks to an extremely high proportion of UVC. This is particularly important and of great benefit in the production of sensitive products and packaging using low-migration inks. However, the extremely powerful system fundamentally improves the curing result and promotes energy savings - because the number of dryers can be reduced in many cases by using FREEcure.
In concrete terms, this means - using here an example from the wood sector - possible energy savings of up to 75%, several tonnes of CO2 savings depending on the production site, a significantly smaller space requirement and amortisation times of 1.5 to 2.5 years. And last but not least: the low photoinitiator content, which means that the FREEcure system is also becoming increasingly important in other areas of UV curing.
Another development in the field of light control is flexible shutter positioning. Thanks to the infinitely variable control of the shutters, the dose and heat input on the substrate, for example, can be optimally controlled or fully automated using the new SMARTcure technology. A reliable and predictable process is extremely important for every production - IST has developed a measuring system for quality assurance that is suitable for both UV LED and UV lamp solutions: the UV-Analzyer. The combination of UV app (compatible for Android and iOS), measuring strips and analyser stick offers a handy tool for quality assurance and documentation of common UV and LED systems.
And finally, our company history has led us to a very special anniversary: We are delighted to be handing over the 100,000th special light source to the german company Wiesendanger from Murnau this year. We will of course be celebrating this directly at the trade fair stand - visitors can look forward to it.
The printing and packaging industry is facing a number of challenges driven by new technologies, global market dynamics and increased environmental requirements. In this environment, it is crucial to ally with strong partners who lead the way through innovation, commitment to quality and sustainability.
An industry in transition: Digitalization and technological innovations are advancing
The printing and packaging industry is undergoing a continuous transformation process that is being driven to a large extent by digitalization and the use of new technologies. This rapid development presents companies in the industry with challenges. At the same time, however, it is essential for manufacturers and print service providers to keep their finger on the pulse and fully exploit the potential offered by technological innovations. After all, technological advances open up new business opportunities and markets. They make it possible to offer more individual and innovative products that meet today's ecological and social requirements.
Opportunities through the successful implementation of innovations
This development not only offers new opportunities to increase efficiency and reduce costs, but also paves the way for personalized and flexible printing solutions that meet the changing demands of the market. Digital printing in particular has proven to be a revolutionary force, enabling shorter run jobs, personalized print products, and packaging that can be produced on-demand without compromising on quality. This flexibility is crucial in order to be able to react promptly to individual customer requests and market trends.
New technologies also contribute to more environmentally friendly
production. Digital techniques and innovative finishing processes reduce the consumption of water, energy, and chemicals. These technologies also make it possible to use materials more efficiently and minimize waste, which makes a decisive contribution to the sustainability of the industry.
Global merging creates the need for a worldwide presence
In an increasingly interconnected global economy, the printing and packaging industry is experiencing a wave of consolidation, with larger companies acquiring or merging with smaller competitors to strengthen their market position. This development has farreaching implications both for the companies involved and for the market as a whole. Consolidation through mergers and acquisitions offers companies the opportunity to pool their resources, exploit synergies and increase their efficiency. For larger companies, this often means improved access to new markets and technologies as well as a stronger negotiating position with suppliers and customers.
However, this can also lead to reduced diversity in the market and restrict competition, which poses major challenges for smaller companies in particular. They are increasingly confronted with the pressure of competing in a market dominated by a few large players. This makes a global orientation all the more important - even for smaller companies. This enables them
to benefit from economies of scale, diversify their risk and gain access to new growth opportunities.
for a successful global orientation
Successful companies in the printing and packaging industry use strategic partnerships to expand their global presence and gain local market knowledge. Digitalization also plays a decisive role here by making it possible to decentralize production processes and serve customers worldwide more efficiently. In addition, flexible adaptation to local market conditions and customer requirements is essential for global success. To survive in this dynamic environment, companies must find a balance between global expansion and preserving their unique values and qualities.
Accelerated market dynamics and scarcity of resources are keeping the industry busy
Our industry is under increasing pressure to adapt quickly to changing market requirements, while at the same time facing rising production costs and increasingly scarce raw materials.
The cost of raw materials, energy and transportation has risen in many parts of the world, which has a direct impact on production costs in the printing and packaging industry. At the same time, the scarcity of certain raw materials creates challenges in the supply chain and requires strategic planning and diversification of sourcing channels. Companies need
to increase their resource efficiency, use alternative materials, and turn to technologies that are more cost-efficient and sustainable.
In a market characterized by constant change, the ability to develop products quickly and bring them to market is crucial. Customers expect not only high-quality products, but also rapid realization of their individual wishes, including small series and limited editions. This requires companies to be highly flexible in production and to work closely with suppliers in order to shorten the time to market. This also includes the implementation of digital printing technologies that enable high variability and personalization while keeping setup costs low.
Strategies for efficiency and flexibility
It takes a successful combination of technological innovation and agile
production methods to survive in the market. By introducing automation, advanced planning tools and real-time data analysis, companies can optimize their production processes and react more quickly to changes in the market. In addition, investment in research and development enables the creation of new materials and production processes that are both environmentally sustainable and cost-efficient. The ability to respond quickly and efficiently to the ever-changing needs of the market, while controlling costs and improving sustainability, can provide a significant competitive advantage in the printing and packaging industry. Having technology partners who can provide end-to-end solutions from a single source can be critical to speeding up production and shortening coordination paths.
Global supply chains and the evolution of marketing
Optimizing global supply chains and adapting to changing marketing demands are critical for companies in the printing and packaging industry to succeed in today's fast-paced and information overloaded world. A well-organized, global supply chain is essential to respond
is becoming increasingly difficult to attract and retain the attention of the target group. Customers increasingly value honesty and authenticity in communication. They are looking for brands that reflect their values and interact with them in a transparent and credible way. Companies must therefore develop innovative marketing strategies that go beyond traditional advertising measures and create real added value for the customer.
To be successful in this new marketing environment, companies need to build and maintain an authentic brand identity. Storytelling, content marketing and social media offer excellent platforms for telling stories that resonate with the target group and build an emotional connection to the brand. At the same time, it is important to be transparent in all communication and
to the dynamic changes in the market. Companies must be able to rely on a network of suppliers and partners that enables them to procure and distribute materials and products quickly, reliably, and cost-effectively. Digitalization plays a key role here by ensuring transparency and efficiency in the supply chain and enabling companies to identify and resolve bottlenecks at an early stage.
At the same time, in a world in which consumers are confronted with a flood of advertising messages every day, it
product presentation, especially in terms of production processes, material sources and sustainability efforts.
Given the growing importance of sustainability and social responsibility for consumer decisions, it is essential for companies to integrate these aspects into their brand strategy. This includes not only the use of environmentally friendly materials and production processes, but also open communication about the company's efforts to achieve a positive social and environmental impact.
Sustainability in the printing and packaging industry
The growing awareness of environmental issues and the need for sustainable business practices have led to a fundamental rethink in our industry. Companies are faced with the challenge of rethinking their business practices and implementing sustainable solutions that go beyond mere lip service and greenwashing. True sustainability requires a comprehensive view of the entire value chain - from the procurement of raw materials through production to recycling or disposal of the end products. It is about minimizing environmental impact, using resources efficiently and taking social responsibility seriously. Companies that pursue this approach recognize that sustainable management is not only an ethical obligation, but also an opportunity for innovation and the creation of competitive advantages.
- Use of sustainable materials: The use of recycled or renewable materials helps to reduce the consumption of natural resources and the ecological footprint of products
- Increasing efficiency in production: By using modern technologies and production processes, companies can save energy and raw materials, reduce waste and improve overall efficiency
- Circular economy and recycling: Promoting the circular economy, in which materials and products are designed in such a way that they can be reused, recycled or composted, is a key aspect of sustainable business
to print MDO-PE
Highest quality with best register
Connected to RUBY to digitize the value chain ... and many more!
Windmöller & Hölscher KG
Lengerich / Germany
Phone + 49 5481 14 - 0 · info@wuh-group.com www.wh.group/int/en/
Best profitability at printing speeds up to 600 m/min. and fast job changes
- Transparent communication: Honesty and transparency regarding environmental efforts are crucial to building trust with customers and partners and avoiding greenwashing. Companies should disclose the steps they are taking to become more sustainable and the goals they have set themselves
Sustainability does not necessarily mean doing without but can also lead to improved products and processes through innovation and efficient design. Companies that implement sustainable practices often discover new business opportunities, increase their brand appeal, and meet the growing demands of consumers and business partners for environmentally friendly products and services.
Is print still relevant in an increasingly digital world?
There is a clear answer to this question: Yes! Because despite the increasing digitalization of all areas of life, print
retains its important role and significance. In the printing and packaging industry, the importance of print is particularly evident in its ability to highlight products through creative and appealing design and thus differentiate them at the point of sale (POS). Print media offers a sensory experience that digital media cannot replicate.
The feel of paper, the quality of a stylishly finished printed image and even the smell of freshly printed material create an emotional connection that can reinforce the perception and memory of a brand or product. In a world where consumers are inundated with digital content on a daily basis, print offers a soothing break and the opportunity to engage with content on a deeper, more personal level.
At the POS, countless products compete for the attention of shoppers. This is where print can make a decisive difference. Innovative packaging designs, high-quality printing processes and special finishes can make products stand out visually from the competition and positively influence the purchasing decision. Attractive packaging not only appeals to the senses but can also increase the perception of the quality and value of the product.
The printing industry has made significant progress towards sustainability and environmental responsibility. By using environmentally friendly materials, recycled papers, and energy-efficient printing processes, print media is helping to reduce the ecological footprint. Innovations such as biodegradable inks and recyclable packaging underline print's
potential to adapt to the demands of an environmentally conscious society.
How does LEONHARD KURZ meet the challenges of the market?
In an era of change and transformation for the printing and packaging industry, at LEONHARD KURZ we have made it our goal to continuously develop our holistic solutions and services. We believe that a strong commitment to quality, innovation, and sustainability pays off in the long run, helping both us and our customers to establish and grow in a highly competitive market.
We are aware that market requirements are changing rapidly. Not only must packaging and labels be real eye-catchers these days to make products stand out from the crowd, but they must also reflect the major trends.
From shiny metallic effects and tactile textures to impressive holographic designs, we therefore enhance products with a visual and tactile quality that will be remembered. In our view, it is also essential to develop holistic solutions, including complete machine systems, perfectly coordinated product sets and individual solutions. In this way, we create smooth, reliable processes for our customers and ensure that all customer requirements are implemented precisely and efficiently.
Sustainability is at the heart of LEONHARD KURZ’s philosophy. We strive to offer the industry’s most environmentally friendly finishing solutions without compromising quality or aesthetics. With processes that optimize material and energy consumption and reduce waste, we are making a significant contribution to a more sustainable industry.
Our long-term goal is to establish a true circular economy in our industry, and all our developments contribute to this goal. In doing so, we not only act as a strong global partner for print service providers and converters, offering a decisive competitive advantage, but also represent a deep understanding of the industry and an unwavering commitment to sustainability.
We meet our customers‘ needs by exploring nature
Uncover the growing demand for tape solutions in the packaging industry, as the need for sustainable options continues to soar. Strike the perfect balance between reducing material thickness and ensuring the utmost strength and protection for your packaged goods. Experience the power of an exceptional unboxing moment, leaving a lasting impression on your customers. Seamlessly glide through the package opening process with our reliable and smooth tape, delivering an unmatched user experience. Embrace the tape revolution and make your mark in the ever-evolving world of packaging.
For more information: Please visit www.tesa.com/en-sg for more information.
tesa® 51345 paper-based reinforcement tape tesa® 51344 design tape for corrugated board productionIn the dynamic landscape of modern business, where innovation is the heartbeat of success, the convergence of digital print - or our own Nanography™ - and digitalization offers an unprecedented opportunity for big brands to reimagine their strategies, engage consumers on a deeper level, and unlock new avenues for growth.
As we delve into this transformative synergy, it becomes evident that the fusion of these two forces isn't merely a trend but a strategic imperative for those aiming to thrive in the digital age.
The Rise of Digital Print: Redefining Traditional Paradigms
Since the early 1990’s when Benny Landa launched Indigo and changed the print
landscape, digital print has emerged as a disruptive force - challenging conventional paradigms and offering unparalleled flexibility, customization, and speed-tomarket.
With further advancements in technology, brands can now create print materials with stunning visual fidelity, intricate personalization, and cost-effectiveness
previously unattainable with traditional methods. This democratization of printing empowers brands of all sizes to deliver targeted, impactful campaigns that resonate with their audience on a profound level.
Moreover, digital print transcends the limitations of static content, enabling brands to craft dynamic, interactive
experiences that captivate and inspire. From augmented reality-enhanced packaging to personalized direct mail campaigns, the possibilities are endless, limited only by imagination. By harnessing the power of digital print, brands can amplify their storytelling capabilities, forge emotional connections with consumers and differentiate themselves in a crowded marketplace.
The Digitalization Imperative: Driving Innovation and Efficiency
Simultaneously, the pervasive influence of digitalization is reshaping every facet of business operations, from supply chain management to customer engagement –indeed, at Drupa 2024, we’ll no doubt hear how many manufacturers are integrating AI and machine learning into their portfolios. Landa has too.
But embracing digitalization isn't merely about adopting new technologies; it's about fostering a culture of innovation, agility, and data-driven decision-making. By leveraging analytics, automation, and artificial intelligence, brands can glean actionable insights, streamline processes, and anticipate market trends with unprecedented accuracy. In today’s market, with part supply issues, skilled labor shortages and other macro-economic trends challenging the operational success of many print businesses, the advantages of digitization are essential to the road to sustained profitability.
Furthermore, digitalization empowers brands to cultivate deeper, more meaningful relationships with consumers across multiple touchpoints. Through omnichannel marketing strategies,
brands can deliver cohesive, personalized experiences that seamlessly transition from the digital realm to the physical world via digital print. Whether through social media engagement, mobile applications, or immersive in-store experiences, brands can create immersive journeys that resonate with consumers throughout their decision-making process.
And for GenZ and GenX who live in a digital world and consume information differently from previous generations, this is key to ensuring their engagement and increasing sales.
The Synergy Unveiled: Transforming Possibilities into Realities When digital print and digitalization converge, the result is a potent synergy that transcends the sum of its parts. By
The UV Analyzer is a app-based UV radiation measuering device. The measuring is quite easy. Put the strip on your substrate, irradiate it with UV and measure the strip with the stick. The app will show you the measured dose in mJ/cm². This dose value can be compared with your reference value to determine aging.
Scope of delivery:
UV Analyzer Stick and reference white, charging cable, lanyard, measuring strips
integrating digital printing technologies with digitalization initiatives, brands can unlock a myriad of opportunities to drive innovation, enhance agility, and maximize ROI. Imagine a world where brands can dynamically adjust packaging designs based on real-time consumer feedback, personalize product offerings at scale, and optimize marketing campaigns in response to shifting market dynamics.
And it’s exactly this type of production agility that Nanography was designed to support – full personalization, at high speed, with high quality print for short to medium runs. Crucially, this unlocks very fast ‘time to market’ services – a gamechanger for brands.
Moreover, the marriage of digital print and digitalization enables brands to embrace sustainability in a meaningful way. We’ve seen it ourselves here at Landa - by leveraging on-demand printing capabilities and digital workflows, brands can minimize waste, reduce carbon footprint, and align with evolving consumer preferences for eco-conscious practices. This commitment to sustainability isn't just a moral imperative, it's a strategic advantage that resonates with environmentally conscious consumers and fosters long-term brand loyalty.
The Road Ahead: Navigating the Digital Frontier with Confidence
As we stand on the precipice of a digital revolution, the big brand opportunity beckons with promise and possibility.
By embracing the transformative power of digital print and digitalization, brands can embark on a journey of reinvention, innovation, and sustainable growth. However, success in this new paradigm requires more than just technological prowess—it demands a willingness to challenge the status quo, embrace change, and continuously adapt to the evolving needs and expectations of consumers.
In conclusion, the convergence of digital print and digitalization isn't merely a
fleeting trend but a seismic shift that will redefine the very essence of brandcustomer relationships. The opportunity is ripe, the possibilities boundless—now is the time to seize the moment and embark on a journey of limitless potential. In the famous words of our Chairman, Benny Landa: ‘What can become digital will become digital, and print is no exception’. I think it’s fair to say that Benny’s prediction is becoming a reality.
The Asian Packaging Excellence Awards is the only regional Independent Packaging Print competition. Since 2001, awarding Gold Silver and Bronze for packaging printers who have excelled in producing world class quality. The judges are non-supplier but are retired educators or production professionals and come from all over Asia/Europe/Australia.
* We MUST have 2 consecutive samples for each job in ALL catergories you enter (If 1 is damaged)
* ONLY 3 jobs allowed for each catergory that you enter.
1. Narrow Web Flexo (up to 500mm width only)
1a Paper/Board
1.b Film
2. Mid Web Flexo (501mm to 914mm width only)
2a .Paper/Bpard
2b Film
3. Wide Web Flexo (915mm and over)
3a . Paper/Board
3b Film
4.Carton & Cups
5.Post Print for Corrugated
6.Pre Print for Corrugated
1. Flexo
2. Letterpress
3. Offset Labels
4. Gravure Labels
5. Combination Printing (Many different processes)
6. Non Pressure Sensitive material
7.Digital Labels
7a. Up to 4 colours
7b. 4 to 5 colours
7c. 5 to 6 colours
7d. 7 + Colours
1. Paper/Board
2. Metallised Paper/ Aluminium Foil Surface Print
3. Film
3a.. Surface Print
3b. Reversive Print
4.Speciality Gravure (Must provide written explanation)
6. Embellishment
Mockup/Sample
Digital Packaging
Hybrid Printing
Offset Packaging
PLEASE READ: Asian Packaging Excellence Awards are open to all packaging compnaies across Asia. It is free to enter and winners will be presented Gold Silver Bronze awards live on stage in Vietnam 8th November 2024. If you do not attend, we will not send awards to you. Jobs must have been produced from November 2023 till September 20th 2024.
Catergory Entered for this job (See catergories opposite page)
Company Name_____________________________Contact Person________________________
Compnay Address________________________________________________________________ Country________________Contact Number _______________e-mail ______________________
Name of Entry_____________________________Printing
Please send your entries to: Send your best work to: ATT Asian Packaging Excellence Awards c/o PRINT & MEDIA ASSOCIATION OF SINGAPORE 627A Aljunied Road, Biztech Centre, #04-07, Singapore, 389842 Telephone: +65 6336 4227 THIS IS YOU FREE ENTRY FORM. PLEASE WRITE CLEARLY SO WE CAN READ IT
SECTION B - CUT AND TAPE THIS TO THE BACK OF THE JOB ENRTY - *fill out each process
Catergory Entered_____________Print Method_______________Number of colours__________
*Brand of Machine
*Plate Supplier
*Ink Supplier
*Tape Supplier
*Pre Press by *Printed Quanity
*Paper/Board/Film/Label supplier
*Web Width ___________________Other detials_______________________________________
If you would like to supply more information, please attach this to Section A above
THE SHIFT 24 Conference will be held in Ho Chi Minh Vietnam on the 7th and 8th November 2024 and the Asian Packaging Excellence Awards dinner will be the 8th after the SHIFT Conference
The SHIFT 24 conference (now in its 21st year) is designed to give Packaging companies, no matter what area of production they are involved in, a view on the trends and technologies that effect business today.
Supported by the leading manufacturers and suppliers, the event offers you the chance to hear from world leading speakers on a whole range of industry topics. Also meet and network with other companies like yours at this intensive one-day event.
More detailed information will be available in the coming weeks so mark this date in your calendar, 7-8th November 24, Ho Chi Minh - Vietnam..
And if you enter the Asian Packaging Excellence Awards, we hope to see you on stage receiving your Awards for excellence in packaging live on stage. See you then!
Hard photopolymer flexo plate with inherent flat top dots
LED optimized plate formulation
Developed for the high end flexible packaging market
Smooth plate surface is able to hold all customized surface screening patterns (e.g. Pixel+ and Woodpecker
+ Highest ink transfer and excellent highlights out of the box
+ Robust and consistent on press, simple to process, already includes flat top dots and a surface screening pattern
+ Optimal for short (quick to color) and long clean print runs (anti ink-filling)
+ Known in the market as THE digital plate for high quality Flexible Packaging Print
+ Excellent print results even under challenging printing conditions
+ Very good for long clean print jobs (anti-ink filling)
XSYS unveils Catena ProServX for real-time equipment monitoring, alerting and reporting
XSYS is proud to introduce Catena ProServX, a cloud-based, real-time equipment monitoring tool for proactive maintenance and superior quality control. By precisely measuring equipment performance, energy consumption, and consumable usage, ProServX empowers customers with unparalleled insights into their operations. With this data, decisionmakers can make informed, data-driven choices to optimize OEE and ensure the highest quality standards, while minimizing waste for sustainable plate making.
“Catena ProServX, the latest innovation from XSYS, represents a significant leap forward in digitalizing equipment management and KPI reporting. It is a connected, cloud-based solution that delivers immediate data about asset performance and consumable usage according to industry 4.0 principles,” said Bert Eeckhout. “This new software development, provides a unique access to plate processing data which until today was not available. Now, with the launch of ProServX customers can access and use this data to optimize their operations, and make fact based decisions.”
ProServX provides in-depth production reports at regular intervals detailing
the number of plates produced during the specified period, along with the materials consumed. Alerts are sent out if any abnormal activity is registered, such as excessive solvent usage or a malfunctioning lamp, enabling customers to engage in proactive error management and predictive maintenance actions.
Another standout feature of ProServX is its ability to generate individual reports for each job with detailed insights into every aspect, from laser exposure to plate finishing. With this level of traceability, platemakers can ensure 100% quality control, promptly identify and resolve issues, and optimize resource allocation for enhanced efficiency and productivity.
The data provided by ProServX accelerates remote service capabilities to new heights and reduces unnecessary travel for technicians. “Catena ProServX represents a holistic approach to remote equipment management by offering advanced statistics, comprehensive reporting, and unparalleled support. It is not just a software solution but a real catalyst for improving production performance, and achieving sustainable business success in today’s dynamic landscape,” concludes Bert Eeckhout.
Discover new speeds and continuous feeds. Accelerate your business with the Jet Press 1160 CF’s unrivalled productivity and reliability
Find out more