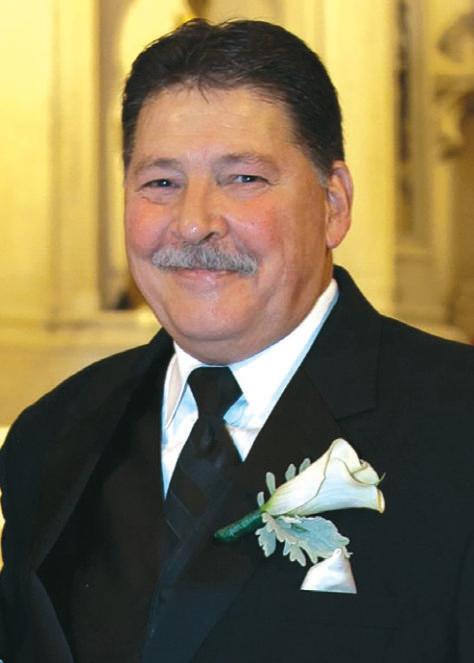
18 minute read
INDUSTRY VETERAN MICHAEL ‘MIKEY’ J. TULISH PASSES AWAY
Widely Respected Industry Veteran Michael ‘Mikey’ J. Tulish Passes Away
Jeff Tulish
Stephenson Equipment Inc.
Michael J. Tulish, 68, of Telford, Pa., passed away at his residence July 27, 2022.
Originally from Conshohocken, Pa., he was the son of the late Joseph and Rose (Dayoc) Tulish and was the husband of Deborah (Martin) Tulish for 38 years.
Mr. Tulish was a member of the Local #542 International Union of Operating Engineers for more than 45 years and worked primarily for Penn Jersey Machinery. Mr. Tulish was widely known and respected as an extremely hard worker and loved providing for his family. He especially loved spending time with his eight grandchildren.
Known to his customers and coworkers as “Mikey,” he started his career in the heavy equipment industry in 1970 with L.B. Smith Inc. at its Gravers Road location in Plymouth Meeting, Pa. At 16 years old, he lied on his application about having a driver’s license to obtain the part-time parts delivery position. After graduating high school in 1972, Mr. Tulish moved into a full-time warehouse associate position at L.B. Smith, eventually finishing the last decade of his career as the field service manager until his retirement.
Aside from a brief stint as an equipment operator during the layoffs caused by the 1981-1982 recession, Mr. Tulish worked solely for L.B. Smith Inc. (which later became Penn Jersey Machinery) for almost 50 years until his retirement in 2018.
Mr. Tulish’s true passion in the equipment industry was his love for customer service, according to his son, Jeff Tulish, vice president of Stephenson Equipment Inc., based in Prospect Park, Pa. In an age now where it seems hard to get someone to even answer a phone, said Jeff, he had a reputation with his technicians and customers for doing whatever it took to keep you going. Off hours or on, night or weekend, it didn’t matter; if your machine was down, he would work to do whatever it took to get you back up and running.
According to Jeff Tulish, in 1997, his father asked him to meet him for lunch.
“I was about to graduate high school and was just a kid with good amount of potential but no real direction,” said Jeff. “He pitched me on a career working in the heavy equipment industry, with the vision of operating and playing with big equipment, which was every little boy’s dream. I started on the steam rack, cleaning equipment. With the work ethic and customer service focus that my father instilled, along with some great opportunities, I am now vice president of Stephenson Equipment Inc. I also volunteer time outside of the workday to workforce development as vice chair of the AED workforce development committee and advisory committee member for Delaware County Technical High Schools, attempting to provide career opportunities to students and draw them to the heavy equipment industry. It’s my version of paying it forward.
“My father had a work ethic that was unmatchable,” Jeff added. “He took an extreme amount pride in whatever he did, whether it was keeping the cleanest floor of any stock room or running the most profitable service division in his company. It wasn’t worth doing if you weren’t trying to be the best at it.”
“Mikey always had your back, no question about it,” said John Bainbridge, retired field service technician of L.B. Smith/Penn Jersey Machinery. “If you ever needed anything, you could count on him.”
“He was a pleasure to work with,” said John “Herb” Herbut of James J. Anderson Construction Company Inc. “Mikey was always there for you when you needed him most, willing to jump right in and figure out a solution.”
In addition to his wife, Deborah, Mr. Tulish is survived by his sons, Michael Tulish (Megan), Jeffrey Tulish (Kelly), Jason Tulish, Kevin Tulish and Brian Tulish; grandchildren, Alazaya, Zoe, Riley, Carter, Emily, Audrey, Julian and Rowan; siblings Alan Tulish and JoAnn Losew. He was predeceased by his sister, Carolyn Shirk.
Memorial Contributions may be made to St. Jude’s Children’s Hospital, 262 Danny Thomas Place, Memphis, TN 38105.
Photo courtesy of Jeff Tulish Michael J. Tulish, 68, of Telford, Pa., passed away at his residence July 27, 2022. 72 Everett Road Albany, NY 12205 518-438-4444 abeletractor.com
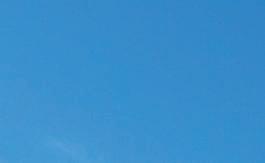

460 Main Street Spencer, MA 01562 508-885-7085 10 West Road Hudson, NH 03051 603-324-1164 ahearnequipment.com
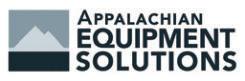
1750 Hackers Creek Road Jane Lew, WV 26378 304-786-9587 aesolutionswv.com
70 Upper Main Street Essex Junction, VT 05452 802-872-2666 ccrsalesvt.com
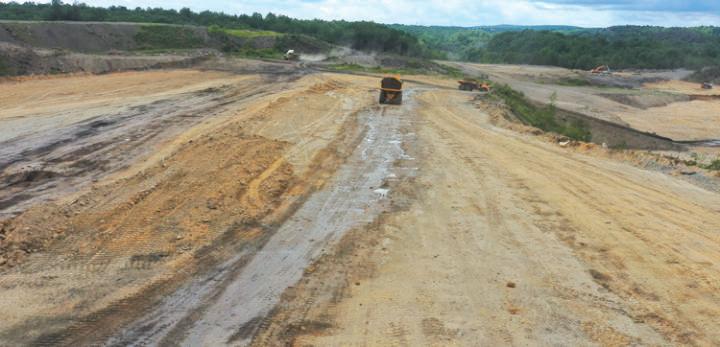
The current work also is taking place entirely within the original cut. A total of 345 acres of the Hazleton Creek site is to be graded level over the next five years, with everything to be re-used, as well as trucking in more fill.
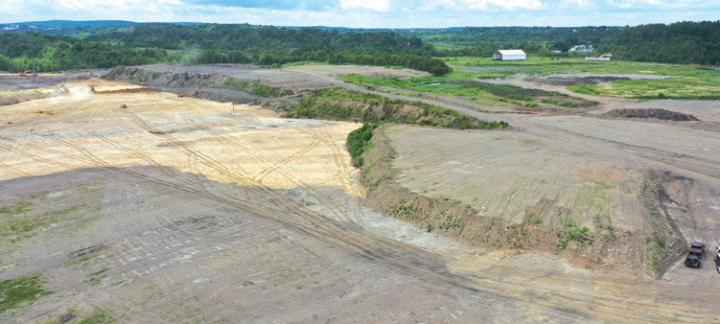
SCHLOUCH from page 36
“Our up time is just as important to him as it is to us,” he said about Foley’s Vice President of Machine Sales Jeff Merle, “We know that at any time anywhere we can pick up the phone and someone from his group will be here to assist us.”
The 207,000-lb. Cat 395 only came into Schlouch’s possession, though, after both Cat and Foley met with the contractor to answer questions about the machine and present the data on how well the excavator has performed.
“When the folks at Schlouch were in the decision-making process of which brand manufacturer to purchase, Cat excavator product specialists met with them, along with Cat district representatives and Foley’s executive leadership and sales reps, to discuss the contractor’s questions, concerns, product features and benefits,” said Sales Consultant Marty Lindmeier of Foley Inc.
Cat 395Ês Productivity
Exceeds Expectations
With 16 pieces of iron equipment on the project, to date including excavators, haul trucks, loaders and dozers, Schlouch and its group of equipment decision makers concluded that the big Hazleton project required a big machine and the 542-hp Cat 395 fits the bill at the Hazleton job site.
The OEM bills the next-generation excavator as offering more production, more durability and less maintenance — traits that certainly drew the interest of Schlouch’s Equipment Triangle. In addition, the 395 model has more swing torque and stick force, boasts a stronger structure than similar-sized models and has a max digging depth of almost 32 ft.
“For Cat customers stepping up to a 100ton class excavator from smaller excavator classes, with the larger machine having a different life and maintenance cycles as well as different expectations — is almost like using a model from Cat’s mining group,” said Merle. “The intervals are longer, the life cycle is longer, there is more predictable uptime, so if you ever get to that point where you want to sell a 395, it is easier because it has great resale value.”
Kelchner quickly became an advocate for the Cat 395 and believes the bigger, more powerful excavator will open new doors for Schlouch because it will be more competitive in its region when up for large mass earthmoving projects.
“With the new 395 model, we can move a lot of earth and save time,” said Kelchner, who qualifies as an expert on the subject after having accrued more than 20,000 hours in the seat of big excavators. “We can handle projects of a larger magnitude with the group of guys we have now, not be tight against our resources and deliver on schedule. By bringing that Cat machine in, we can shrink down that schedule and do it safely. It is a different environment up here and a machine that size can handle all we can throw at it and remain reliable.”
Much of the Cat 395’s value, he said, comes from its size and the technologies it has that end up saving money over the long haul.
“First of all, having a GPS system on it was a must because it allows operators to know where they are at all times and it eliminates the need for an additional support machine for grading, meaning there is less congestion in the cut and a lower daily operations cost,” said Kelchner.
He added that the Cat’s automatic lubrication system, a new feature that increases the excavator’s run time, keeps its downtime low and greases the machine’s bearings and pins throughout the working day to prolong its life while also reducing wear on the 395, again, leading to lower operating costs.
This pair of advances in equipment design, Kelchner contended, are the biggest contributors to a grading contractor’s ability to fully utilize every minute of every daily shift.
“We are seeing challenging schedules on these large projects, and they are getting more complex,” King added. “With the schedules being tighter, one way to meet them and help our customers succeed is to be able to have that bigger machine that can do more or can accelerate the [the pace of work]. We now have the capability to do that on these larger, more complex warehouses.”
Schlouch used to run double shifts, Kelchner said, but added that after dark, “operators are just not going to be able to see as well doing that. The 395, though, is a huge safety machine, so instead of dealing with a nighttime safety issue, you just eliminate it.”
The operator assigned to run the Cat 395 loves the machine, Kelchner noted, particularly its size and ease of use. Phil Hobel is a bright young man who is a graduate of a vocational tech school and, so far, is not fazed by learning to work such a large excavator, said Kelchner.
“With a machine that size, and haul trucks to serve it, when you start to add the number of cycles with four or five trucks dumping 100 loads per day, that’s a lot of movement in that cut.”
Hazleton Work Site Brings Plenty of Challenges
Grading more than 5 million cu. yds. of dirt would be a massive enough project for any contractor. Schlouch, however, has been doing it for more than four months and, in the process, has added to its reputation for being able to find solutions to demanding projects.
The current work also is taking place entirely within the original cut. A substantial amount of blasting will take place in the Building 5 area and on the high side of the job at Building 4.
“This was one of the largest coal strip mines in the state back in the 1950s,” Bainbridge said. “Hazleton City Hall used to sit on the property, but they moved it to another location to get to the coal. The mine was later abandoned in the 1990s.”
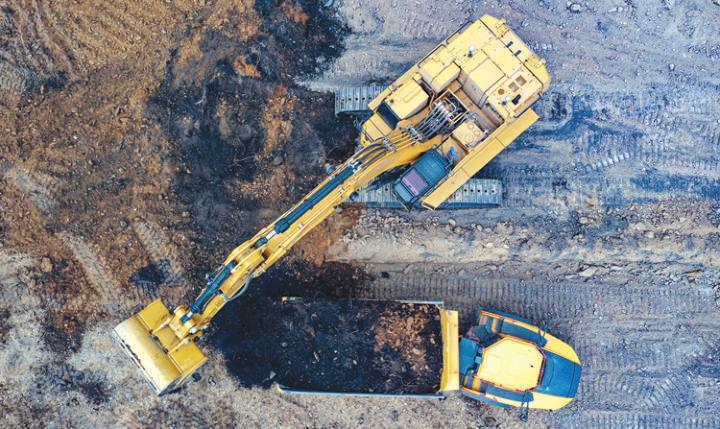
The big project required a big machine and the 542-hp Cat 395 fits the bill at the Hazleton job site.
Kilmoyley Construction Performs Long List of Projects for UMass, Local Towns
KILMOYLEY from page 20 starting each project in a timely manner and finishing the project on time and on spec. In fact, most projects are completed ahead of time.
“There are several reasons we are able to complete our projects ahead of schedule, including a hard-working, experienced crew and our fleet of JCB construction equipment,” said Sheehy.
Kilmoyley Construction’s fleet of equipment includes two JCB 427ZX wheel loaders, one JCB Hydradig 110W wheeled excavator and two Avant 640 compact articulated wheel loaders, all purchased from Alta Equipment Company.
The purchase of the JCB Hydradig involved matching the purchase of a piece of equipment to some of the unique circumstances that Kilmoyley faces at UMass, as well as other utility repair projects.
“UMass has a massive, sprawling campus, and our projects will jump from one end of the university to another, sometimes in the same day,” Sheehy said. “The JCB Hydradig is a wheeled excavator that travels over the road at about 25 mph. We can drive it straight down the roads of the campus doing no damage whatsoever to the road surface and saving ourselves the time and bother of loading the machine up on a trailer and hauling it from point A to point B.
“We have equipped the Hydradig with several attachments that have dramatically improved the flexibility of the machine, including several different buckets for a variety of digging applications, a 12-inch auger and a flail mower for cutting back trees and bushes.
“The Hydradig also gives us tremendous maneuverability because of its crab steer and four-way steering. You can position it just about anywhere turning on a dime. The Hydradig is also engineered with a very low center of gravity, which gives it a larger lifting capacity and additional stability. It would be extremely difficult to tip this machine and the visibility is amazing.
“The Hydradig is also amazingly easy to maintain. Everything you need to access you can do from the ground, including changing all of the filters.”
Sheehy is equally impressed with his JCB 427ZX wheel loaders.
“Initially, the 427s were purchased for work at UMass. We needed wheel loaders that would offer maneuverability, speed and visibility. Maneuverability is important because of vehicles and obstacles you deal with when doing snow removal, particularly with a 14-foot snow pusher attached; visibility is very important when you factor in thousands of students to the formula. No matter how heavy a snowfall we receive, pushing snow in some massive parking lots, the JCB 427ZX machines are hands down the best machines we have had.
“These machines are so comfortable my employees will

Kilmoyley Construction’s crew works at improving an entertainment area and installing new sidewalks at UMass. Kilmoyley Construction’s Avant loader is equipped with everything from forks and salt spreaders to buckets, plows and mowers. scrap over who gets to operate them. The loader is easy to get into, the seat is extremely comfortable and the cab stays toasty warm even during the coldest winter days.” For smaller demands, Kilmoyley Construction owns two Avant 640 compact articulated wheel loaders, along with a large variety of attachments, including salt spreaders, forks, mowers and a large variety of buckets. “These are very diverse machines. The wheels are designed in a way that we can run across the grass or even mow with them. They do a great job of salting or even snow removal on sidewalks. “The visibility is great; they are quite fast and very maneuverable. The Avant is also a very stable machine. We can deal with some very steep terrains without concerns of tipping over. It is a very safe and very comfortable machine to operate.” Alta Equipment Company is Kilmoyley Construction’s primary equipment supplier and it’s not just the quality of the equipment, it’s the support that comes along with doing business with Alta Equipment Company. “Kevin Swartz, our rep with Alta Equipment Company, has been amazing to work with. He goes above and beyond on anything we have asked of him. He answers the phone right away and comes out to our jobs when we need him, even on weekends. When needed, he will run to Alta Equipment, pick up a part and deliver it to us personally. We would recommend Alta Equipment Company, JCB and Avant to anyone who would ask.” CEG (All photos courtesy of Alta Equipment) ANDERSON EQUIPMENT CO.
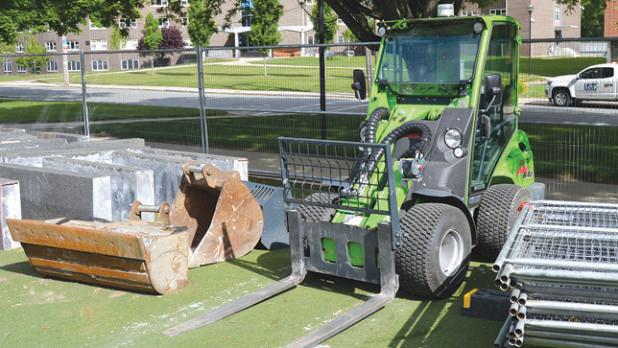
1000 Washington Pike, Bridgeville, PA 15017 412-343-2300 Pleasant Valley, WV 304-366-3075 South Charleston, WV 304-756-2800 www.andersonequip.com
TRACEY ROAD EQUIPMENT
East Syracuse, NY 315-437-1471 Kirkwood, NY 607-775-5010 Henrietta, NY 585-334-5120 Adams Center, NY 315-788-0200 Utica, NY 315-765-8746 • 800-872-2390 www.traceyroad.com
HIGHWAY EQUIPMENT COMPANY
Zelienople, PA 724-452-7800 Dubois, PA 814-371-3600 McKean, PA 814-476-7755 Millstone Township, NJ 732-446-7600 www.highway-equipment.com

MARSHALL MACHINERY, INC.
South Abington Twp., PA 570-489-3642 Tannersville, PA 570-895-4884 marshall-machinery.com
MINOTAUR from page 40 machine control solutions from any of the big three providers of precision construction solutions — Leica Geosystems, Topcon and Trimble. This allows equipment owners to add the machine to their fleet with the confidence it can be integrated directly into preferred/existing machine control ecosystems. It also provides rental fleets the ability to easily switch between machine control brands, which allows for excellent rental flexibility based on customer preference.
Powerful Site Loader, Attachment Beast
In its loader configuration, the Case Minotaur DL550 features a 5,500-lb. rated operating capacity (50 percent of tipping load) with 12,907 lb. of breakout force. It features a vertical lift pattern and operates in the ISO control pattern. It also features advanced electro-hydraulic control capabilities where operators can easily dial in total machine responsiveness to low, moderate or aggressive; or independently set tilt, lift and drive speed, as well as loader arm and drive control to best meet the demands of the work.
Case builds the machine standard from the factory with enhanced high-flow auxiliary hydraulics for running the most demanding and high-powered attachments — such as mulching heads and cold planers. Minotaur’s enhanced high-flow hydraulics can deliver up to 41.6 gpm at 4,100 psi via hydraulic quick couplers.
The machine also allows operators to harness all that power with “Hydraulics on Demand”, where the operator can easily select the percentage of auxiliary hydraulic flow to the attachment via the machine’s multi-function display. This allows the operator to dial in attachment performance to their preference or the recommendation of the attachment manufacturer — ensuring both effective and proper operation of the attachment.
“The front coupler featured on this machine is the same as you will find on most compact loaders — this opens the machine up to be used with hundreds of attachments,” said Jacobsmeyer. “We’ve given operators the ability to turn this compact dozer loader into one of the industry’s most versatile and powerful compact machines, and deliver on the awesome capabilities that other manufacturers tried to emulate after the original concepts were announced.”
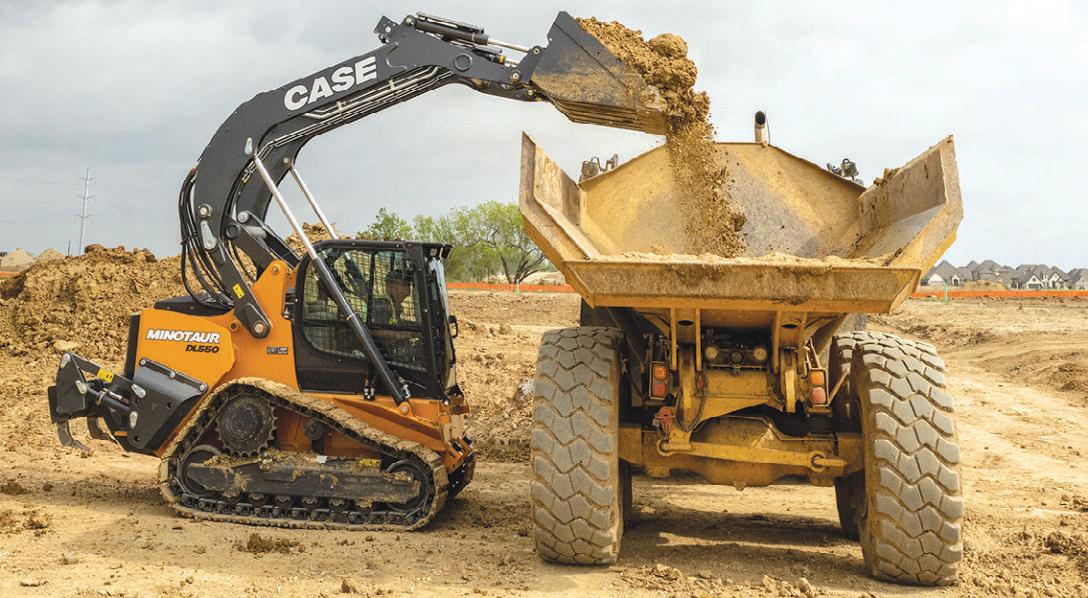
The Case Minotaur DL550 compact dozer loader has pushed through more than 10,000 hours of field tests, in addition to countless customer clinics and typical lab and engineering testing.
Module — a powerful device that improves the volume, flow and integration of data to the Case SiteWatch telematics platform for real-time monitoring and management of maintenance and service intervals, as well as the analysis of equipment utilization and performance.
It’s also the foundation from which Case has made the collaborative fleet management and remote diagnostics of compact equipment a reality. This enhanced connectivity allows the machine owner to share — with permission — real-time machine information with their Case dealer and the Case Uptime Center in Racine, Wis.
“With both Case and the local Case dealer monitoring machine performance, we’re able to be proactive and anticipate potential equipment needs to maximize uptime,” said Jacobsmeyer. “The goal of these advances is rooted in customer need for maximum uptime, and the Case Minotaur DL550 compact dozer loader delivers that — including the ability to remotely diagnose machine events and drastically shorten response times when service is needed.”
Case achieves these remote service capabilities through the Case SiteManager App (iOS and Android). This app pairs the operator’s phone or device to the machine to enable remote analysis by a certified Case technician, which allows them to diagnose the health of each connected machine through various parameter readings and fault codes. The technician decides as to whether the issue can be addressed remotely — such as clearing codes or updating software — or if it requires a trip to the machine.
“Reducing trips to the field, showing up with the needed parts on the first visit, and the ability to avoid field visits all together by remotely clearing basic codes all drive major savings in time and resources, both for the equipment owner and the dealer service department,” said Jacobsmeyer. “This type of collaborative fleet management has the ability to drive major gains for fleets of all sizes and ensure optimal uptime.”
And in the case of a service need, the Case Minotaur DL550 is built for ease of service with groundline access to grouped service points and checks like every machine in the Case lineup. Service intervals and machine operating information are easily accessed in the machine’s eight-inch LCD display in the cab.
Proudly Manufactured in Wichita, Kan.
The Case Minotaur DL550 compact dozer loader is manufactured in Wichita, Kan., on a dedicated line purpose-built for this one-of-a-kind, industry-first machine. It represents more than six years of development and collaboration between numerous Case plants, personnel, testing facilities and departments.
“The Case Minotaur DL550 embodies our dedication to practical innovation — real world, customer-driven solutions,” said Jacobsmeyer. “Through this, we created a whole new equipment category and we’re delivering the integrated technologies that drive improvements for operators in the field and for business owners at their bottom line.”
New Rockstar Machine Tours North America
In its 180th year in business, Case has proven to be a company on the move — and the development of the Case Minotaur DL550 compact dozer loader is proof of that in both iron and technology. To celebrate the launch of this first-of-its-kind machine, Case is launching a tour of the United States and Canada with more than 30 stops where the machine will be showcased at Case dealer locations.
“We are bringing the excitement of this industry-changing launch to every corner of North America,” said Terry Dolan, vice president — North America, Case Construction Equipment.
“We have more than 180 years of experience in the field, but we’re making moves like a startup, dedicating more time and resources to the field, and spending more time where it counts — with the men and women who run businesses and operate this equipment every day. We can’t wait to see you on tour.”
For more information, visit CaseCE.com/Minotaur.
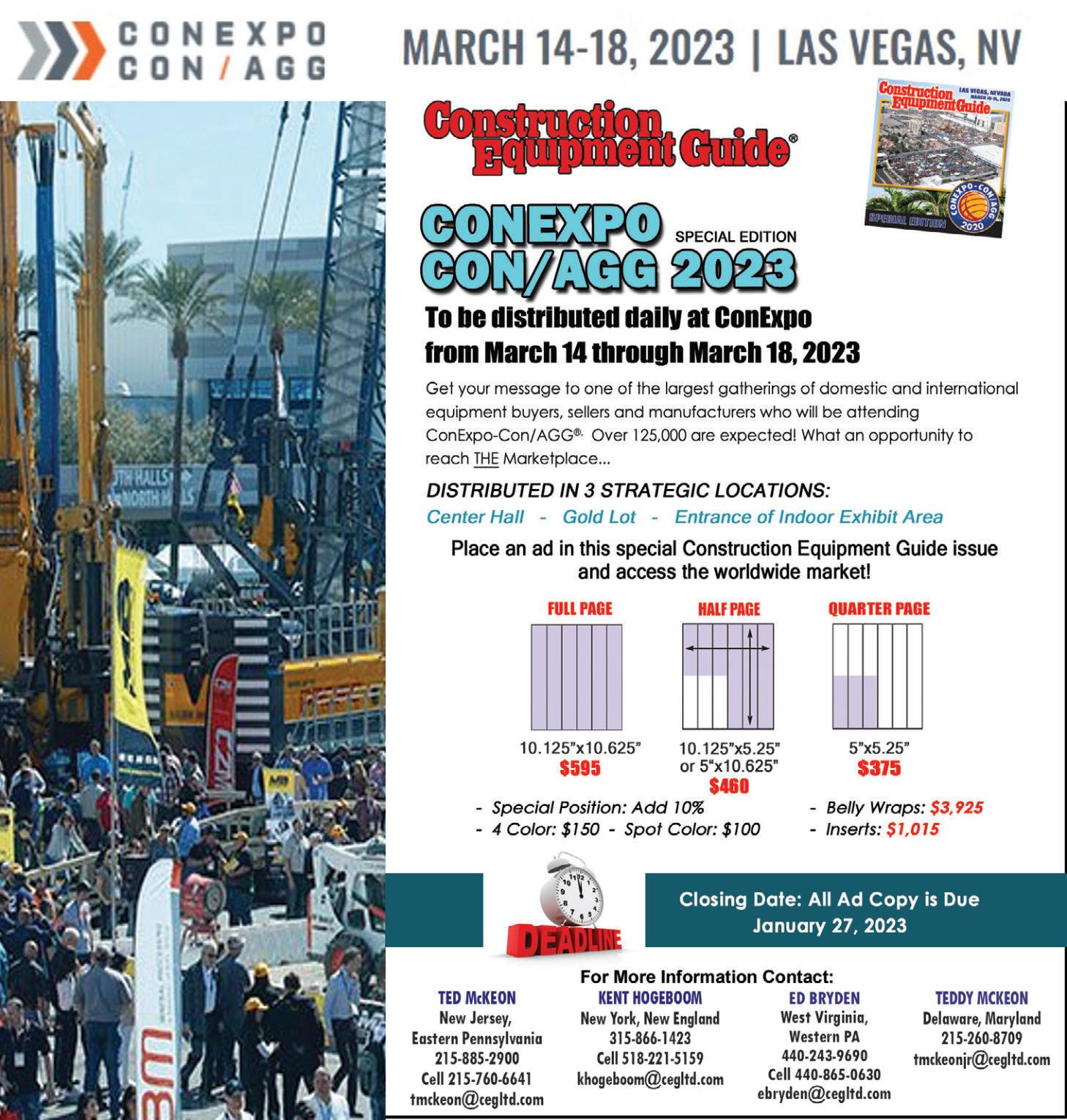