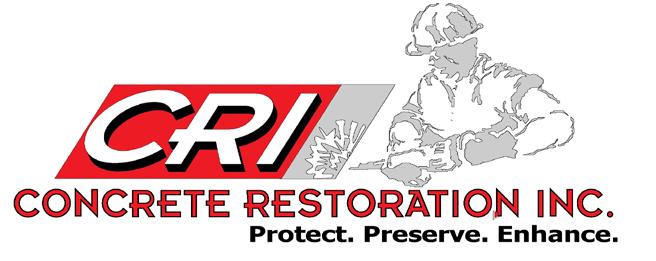
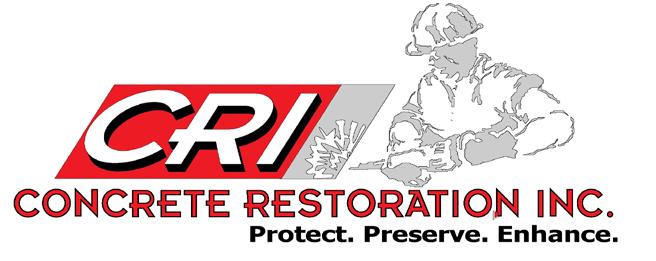
CRI Safety Manual
Welcome to the Concrete Restoration Team!
The safety of our team members and those we work with is of paramount importance. We are committed to the goal of seeing every job site injury eliminated. We believe this can be achieved through proper application of safe work practices and Team Member training.
All of us would like to wish you success as a Concrete Restoration Team Member. We are proud of our commitments to safety, teamwork, and professionalism. Of these commitments, safety is our highest priority. You should consider the health and well-being of yourself and your team members as your foremost duty while working with Concrete Restoration Inc. Please make a personal commitment to your future and always work safely.
Please read all the information contained in this handbook and make certain you understand it. Do not hesitate to ask questions of your supervisor.
Our company culture is based on honesty, respect, and professionalism. As an important part of our team, you will directly contribute to our success. We believe that open communication is the foundation of a successful company. Please feel free to call if you have any questions or comments. We look forward to hearing from you.
Sincerely,
Owner,
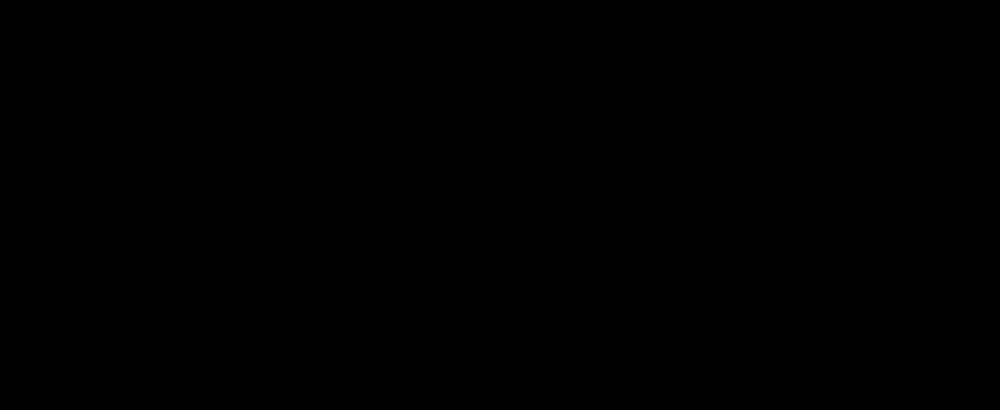
Shannon Ware
REVISED DATE: January 1, 2025
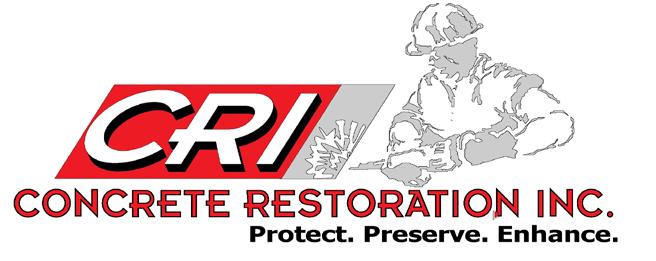
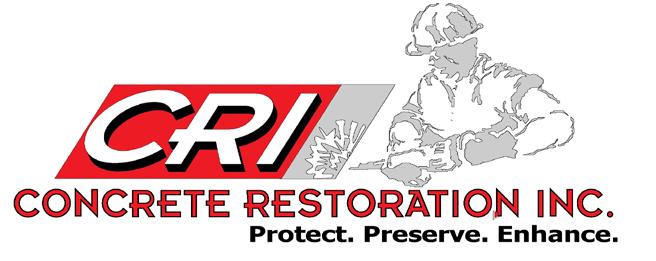
ACCIDENT/ INCIDENT ACTION PLAN
ACCIDENT/ INCIDENT ACTION PLAN
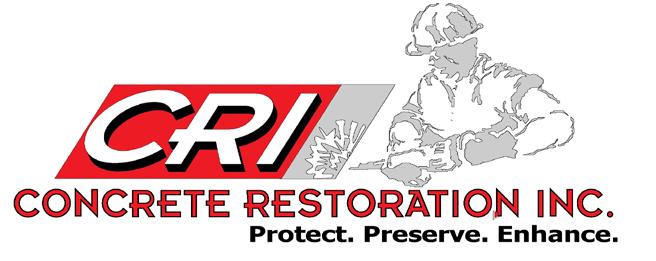
In the event of an accident/incident or emergency, contact the appropriate authorities. Each site shall maintain a listing of emergency phone numbers. It is important to always identify potential witnesses. Remember, a panicked person cannot aid in remediation of the situation, stay calm:
Chemical Spills:
In the case of a chemical spill, contact your supervisor immediately. Do not attempt to clean up a chemical spill with any other chemicals until the chemical is identified and proper clean-up procedures are found. If you are unsure of the chemical's properties, or it is spilled in massive quantities evacuate and isolate the area and call Chemical Response Center: 1800-424-8802, with as much information ready as possible.
• Type of Chemical
• Size of spill
• Date and time of spill
• Exact location of spill
Injured Persons:
In the event of an injury and the person is unconscious, not breathing, or has fallen from a height greater than that of their own height:
• Immediately call 911
• Get first aid/ CPR certified individual to the scene as soon as possible.
• If there is a possibility of a spinal injury: DO NOT MOVE THE VICTIM Stabilize them until authorities arrive.
• Try to stop all bleeding (take personal precautions and use PPE (i.e. gloves, and CPR mask).
ACCIDENT/ INCIDENT ACTION PLAN
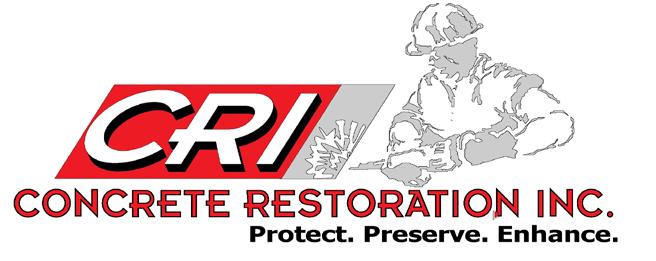
Fire:
In the event of a fire, call authorities immediately and evacuate the area. Firefighting efforts may begin with the first responders. Concrete Restoration Inc employees are instructed to maintain a safe distance from the fire. A fire extinguisher will be located on each site.
Violence:
In the event of violence in the workplace, the police should be notified immediately. It is imperative that our employees try to avoid confrontational situations and avoid acting as a mediator in a situation where violence could result.
When presented with a violent or potentially violent situation, employees are instructed to contact their' supervisor for help and contact authorities.
Intimidation is also considered workplace violence and will be punished according to the parameters of the Discipline Policy. Weapons are not allowed to be on company property or on company work sites. Concrete Restoration Inc encourages employees to bring disputes with co- workers and violence-related issues to the attention of a supervisor immediately.
Fatalities:
In the event of an occupational fatality, authorities must immediately be contacted. The Department of Labor and Industries will conduct an investigation.
Call 911, and then the main office. The main office will take responsibility for calling the Department of Labor and Industries and other necessary authorities.
REVISED DATE: January 1, 2025
ACCIDENT/INCIDENT INVESTIGATION POLICY
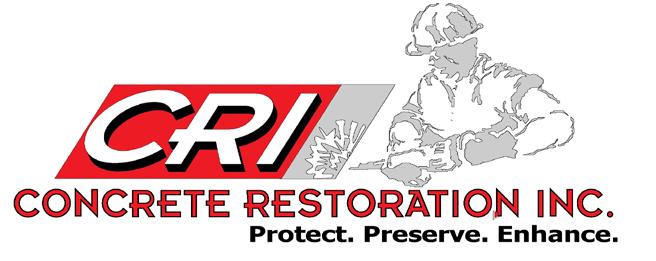
ACCIDENT/INCIDENT INVESTIGATION POLICY
Purpose
The purpose of the Incident Reporting and Investigation Policy is to make certain that incidents are investigated according to the injury, or injury potential of an event, in accordance with company policy and OH&S legislation. This will help to control further losses of human and material resources by identifying and correcting unsafe acts and conditions that lead to an incident.
This policy applies to all work-related incidents and close calls that affect company employees and others who are performing work for the company.
Policy
All staff and others working with the company are required to report all incidents and close calls, including ergonomic issues, soft tissue damage and any signs or symptoms of musculoskeletal (MSI) injury to their supervisor or company contact. All incidents will be reported and investigated following company and regulatory requirements.
Some incidents are immediately reportable to L&I WA. Incident sites should not be disturbed unless the safety of workers is at risk.
The company uses the word “incident” rather than “accident” because there is an inherent belief by many people that accidents just happen and cannot be prevented. We use the word incident because we believe that all incidents can be prevented. Belief that all incidents can be prevented will drive the level of investigation to determine causes that could otherwise be missed.
Incident reports will be reviewed by a supervisor and other management as appropriate to the severity or potential severity of the incident.
REVISED DATE: January 1, 2025
ACCIDENT/INCIDENT INVESTIGATION POLICY
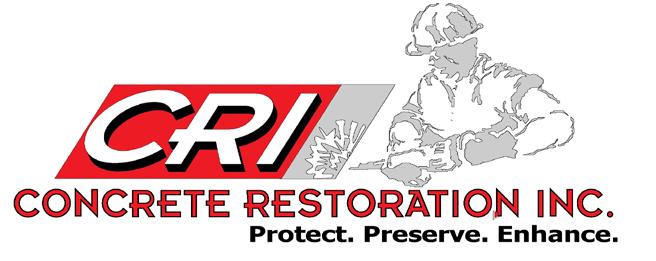
Action items from incidents will be documented and tracked for completion and a follow-up will occur in a timely manner. Implementation of action items will be monitored and reviewed by the Safety Manager. Work procedures will be reviewed by the Management Team after an incident to ensure that changes required by the investigation findings are implemented and that they meet or exceed jurisdictional requirements.
Injuries or incidents resulting from ergonomic hazards must be investigated.
Management
The Management team will investigate an incident reported by a direct report. A manager will participate in an investigation of an incident if the severity or potential severity requires action appropriate to the manager’s authority. All investigations requiring immediate notification to L&I WA will be attended by the appropriate management personnel. Copies of investigations required by L&I WA will be provided by the appropriate management personnel.
Management must advise new and returning workers of the requirement to report all incidents including close calls. An annual reminder to all employees to report incidents is recommended. Management must investigate incidents in a manner that is timely and appropriate to the circumstances and severity of the incident. Management incident review and signoff are a requirement.
Worker
A worker will report to the supervisor all incidents including close calls. A worker will attend the incident investigation unless unable to do so as a result of injury. Workers may choose to report a close call using the company’s form Incident Close Call Reporting or verbally to their supervisor, who will be responsible for completing the document.
REVISED DATE: January 1, 2025
ACCIDENT/INCIDENT INVESTIGATION POLICY
Procedure
Incident Reporting and Investigations
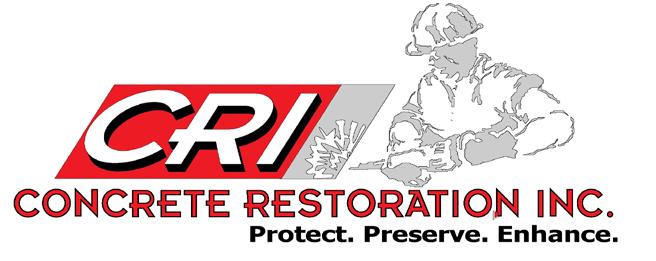
Concrete Restoration Inc has an obligation to make certain that all our employees, staff, contractors, volunteers and visitors are aware of the importance of and requirements for reporting and investigating close calls, near misses and other incidents. Investigations of close calls and near misses provide a learning and improvement opportunity to help prevent someone from being injured.
An investigation is held to prevent recurrence, not to place blame.
Definitions
Incident: An incident is any event that has resulted in or has the potential to result in an injury.
Incidents may include property damage, personal injury, death, close calls or near misses.
The Workers Compensation Act (Section 172 (1) requires the following regarding immediate notification of incidents:
An employer must immediately notify the Workers’ Compensation Board of the occurrence of any accident that:
• resulted in serious injury to or the death of a worker.
• Involved a major structural failure or collapse of a building, bridge, tower, crane, hoist, temporary construction support system or excavation
• Involved the major release of a hazardous substance
• Was an incident required by regulation to be reported
REVISED DATE: January 1, 2025
ACCIDENT/INCIDENT INVESTIGATION POLICY
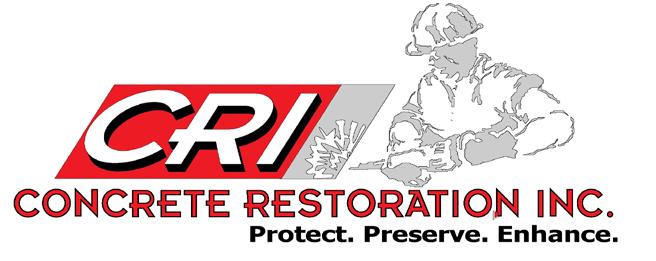
Incidents that are required to be investigated by the Workers Compensation Act:
• An employer must immediately undertake an investigation into the cause of any incident that:
o is required to be reported by Section 172
o resulted in injury to a worker requiring medical treatment.
o did not involve injury to a worker, or involved only minor injury not requiring medical treatment, but had a potential for causing serious injury to a worker.
o was an incident required by regulation to be investigated.
Responsibilities of Managers:
Supervisors, Workers Incident Reporting and Investigation Procedure:
• The incident is reported by a person to the company. (An incident involving an employee may be reported by others to the company.) The incident may be reported verbally or in writing.
• The incident site must be visited if possible and the site preserved until the investigation is complete, if safe to do so. Proper equipment to conduct investigations will be supplied. Photographs, sketches and other evidence collection should be undertaken promptly. Note: Incidents requiring immediate notification to L&I WA must be done within 8 hours and reported to facility within 24 hours.
• The Management team will organize and lead the investigation. The investigation must be carried out by those knowledgeable about the type of work involved.
• The investigation will follow the Incident Investigation Template format, which includes root cause analysis.
• The investigation must be held in a timely manner. A preliminary investigation may be necessary if required attendees are not able to attend due to injury or other reasons.
REVISED DATE: January 1, 2025
ACCIDENT/INCIDENT INVESTIGATION POLICY
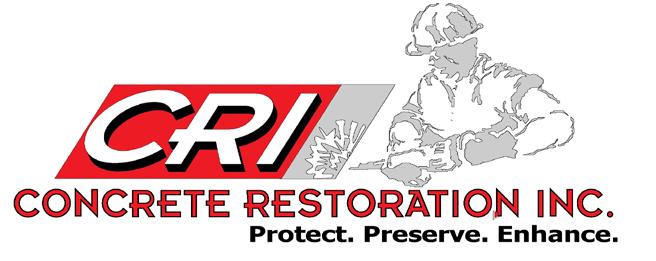
• Action required as the result of an investigation will be recorded and tracked for completion by the Management.
• Management will evaluate any future risks that recommendations or corrective actions could create.
• Management will monitor the effectiveness of any changes or implementations.
• Management will communicate the recommendations and corrective actions to all relevant parties.
• All investigation reports will be forwarded to the Safety/Training Manager. The Safety/Training Manager will review the reports for completeness and determine if additional investigation or distribution is required.
Training
Managers, supervisors and employees must be familiar with this policy and associated forms.
Training in the investigation process and the company’s specific policy and forms will be determined by company management and communicated to the employees.
The requirement to report and investigate close calls and other incidents will be covered during new employee orientation.
REVISED DATE: January 1, 2025
ACCIDENT/INCIDENT INVESTIGATION POLICY
Review
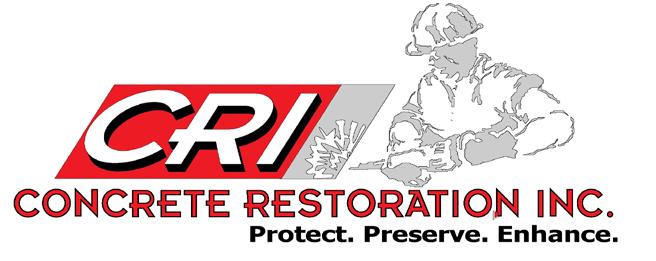
This policy should be reviewed at least annually, or when revision is required.
Incident investigation historical records should be reviewed annually by the Safety/Training manager in order to:
• Confirm that action required was implemented.
• Determine if the action was effective in prevention of recurrence.
• Identify trends.
• Determine areas for improvement.
Records
Copies of incident investigations will be electronically filed or kept in a secure filing area.
Incident Investigation Form
The main purpose of the process is to learn from the unfortunate circumstances that caused the incident to prevent future injuries. One of the best ways to reduce the likelihood of an incident recurring is to thoroughly understand why the incident happened in the first place. In other words, identifying the true responsible condition (root cause) and contributing factors will enable the organization to implement appropriate corrective actions.
Root causes generally stem from management, design, planning, organizational or operational oversight. A thorough and formal incident investigation process focused on fact-finding, not fault-finding, is paramount in enhancing an organization’s safety culture.
What defines an incident? An incident can mean an injury, illness or damage as well as near misses. A near miss is an unplanned event that did
REVISED DATE: January 1, 2025
ACCIDENT/INCIDENT INVESTIGATION POLICY
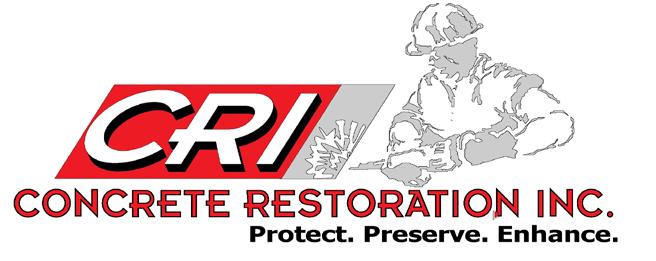
not result in an injury but had the potential to do so. Close calls (near misses) are just as important to report as they may prevent future incidents from happening.
Root Cause Analysis
WHO AND WHERE?
• Who was injured?
• Who saw the incident?
• Who was working with the employee?
• Who had instructed/assigned the employee?
• Who else was involved?
• Who else can help prevent recurrence?
• Where did the incident occur?
• Where was the employee at the time?
• Where was the supervisor at the time?
• Where were fellow workers at the time?
• Where were other people who were involved at the time?
• Where were the witnesses when incident occurred?
WHAT AND WHY?
• What was the incident?
• What was the injury?
• What was the employee doing?
• What had the employee been told to do?
• What tools was the employee using?
• What machine was involved?
• What operations was the employee performing?
• What instructions had the employee been given?
• What specific precautions were necessary?
• What specific precautions was the employee given?
• What protective equipment should have been used?
• What protective equipment was the employee using?
• What had other people done that contributed to the incident?
REVISED DATE: January 1, 2025
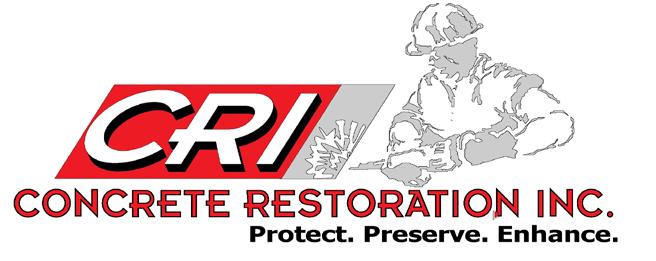
• What problems or questions did the employee encounter?
• What did the employee or witnesses do when the incident occurred?
• What extenuating circumstances were involved?
• What did the employee or witnesses see?
• What will be done to prevent recurrence?
• What safety rules were violated?
• What new rules are needed?
• Why was the employee injured?
• Why and what did the employee do?
• Why and what did the other person do?
• Why wasn’t protective equipment used?
• Where weren’t specific instructions given to the employee?
• Why was the employee in the positions?
• Why was the employee using the tools or machine?
• Why didn’t the employee check with the supervisor when the employee noted things weren’t as they should be?
• Why did the employee continue working under the circumstances?
• Why wasn’t the supervisor there at the time?
WHEN AND HOW?
• When did the incident occur?
• When did the employee start on that job?
• When was the employee assigned on the job?
• When were the hazards pointed out to the employee?
• When was the employee’s supervisor last check on the job progress?
• When did the employee first sense something was wrong?
• How did the employee get injured?
• How could the employee have avoided it?
• How could fellow workers have avoided it?
• How could supervisor have prevented it – could it be prevented?
REVISED DATE: January 1, 2025
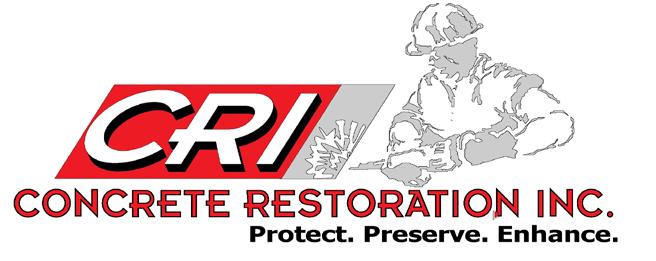
Step 1: Injured Employee (Complete for each injured employee)
Employee Name:
Sex: ■ Male
■ Female Age:
Department: Job title:
Parts of body affected:
Length of time employed:
On current job:
REVISED DATE: January 1, 2025
Nature of injury: This employee works:
■ Abrasion, scrapes ■ Regular full time
■ Amputation ■ Regular part time
■ Broken bone ■ Seasonal
■ Bruise ■ Temporary
■ Burn (heat)
■ Burn (chemical)
■ Concussion
■ Crushing injury
■ Cut, laceration, puncture
■ Hernia
■ Illness
■ Sprain or strain
■ Damage to a body system
■ Other ________________
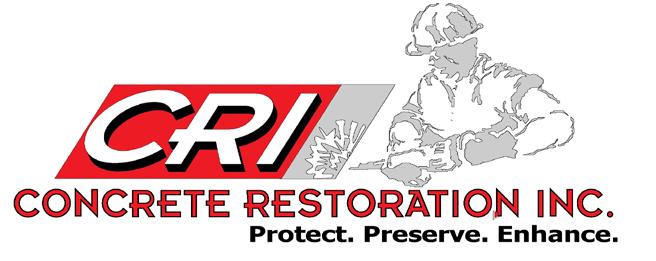
Step 2: Describe the Incident
Exact location:
Exact time:
What part of employee’s workday? ■ Entering or leaving work ■ During break ■ Doing normal work activities
Working overtime
During meal period
Other
Investigator:
Number of attachments: Written Witness Statements: Photographs: Maps / Drawings:
What Personal Protective Equipment was being used (if
any)?
Describe step-by-step the events that led up to the injury. Include names of any machines, parts, objects, tools, materials, and other important details.
PHOTOS:
REVISED DATE: January 1, 2025
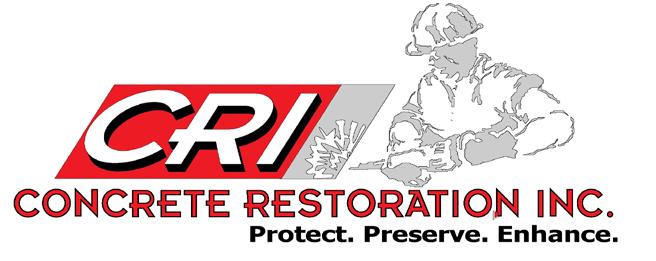
Step 3: Why did the incident happen?
Unsafe workplace conditions: (Highlight all that apply)
■ Inadequate guarding
■ Unguarded hazard
■ Safety device defective
■ Tool or equipment defective
■ Workstation layout hazardous
■ Unsafe lighting
■ Unsafe ventilation
■ Lack of needed personal protective equipment
■ Lack of appropriate equipment /tools
■ Unsafe clothing
■ No training or insufficient training
■ Other:
Unsafe acts: (Highlight all that apply)
■ Operating without permission
■ Operating at unsafe speed
■ Servicing equipment that has power to it
■ Making a safety device inoperative
■ Using defective equipment
■ Using equipment in an unapproved way
■ Unsafe lifting
■ Taking an unsafe position or posture
■ Distraction, teasing, horseplay
■ Failure to wear personal protective equipment
■ Failure to use the available equipment/tools
■ Other: Improper use of tool
• Why did the unsafe conditions exist?
• Why did the unsafe acts occur?
• Were unsafe acts or conditions reported prior to the incident?
• Have there been similar incidents or near misses prior to this one?
REVISED DATE: January 1, 2025
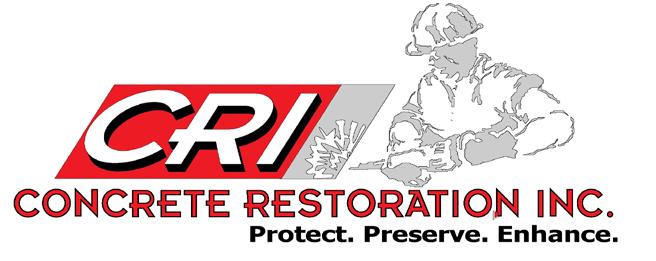
Step 4: How can future incidents be prevented?
What changes are suggested to prevent this incident from happening again? (Highlight)
• Stop this activity.
• Guard the hazard.
• Train the employees(s)
• Train the Foreman(s)
• Redesign task steps
• Redesign work area
• Write a new policy/rule.
• Enforce existing policy.
• Routinely inspect for hazards
• Personal protective equipment
• Other
What should be (or has been) done to carry out the suggestion(s) checked above?
Step 5: Who completed and reviewed this investigation?
Completed By:
Department:
LINK TO REPORT IN SMARTSHEETS
Title:
Date:
https://app.smartsheet.com/b/form/da760af5c89644d0b3a9999e0bd165d7
REVISED DATE: January 1, 2025
ACTIVITY HAZARD ANALYSIS
ACTIVITY HAZARD ANALYSIS
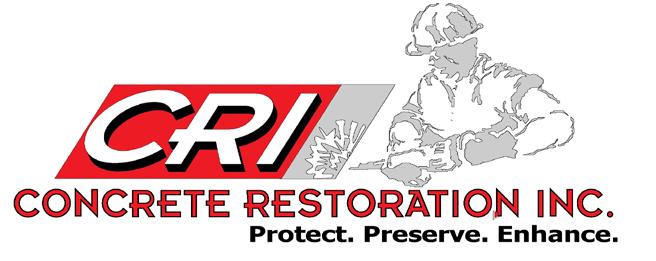
The site safety officer will conduct hazard analysis for each definable activity on this project follows. A list of required and recommended personal protective equipment is summarized in the following form.
Evaluated by:
REVISED DATE: January 1, 2025
Date:
AMMONIA POLICY
AMMONIA POLICY
Reference: 29 CFR 1910.111 OSHA/ WAC 296-826
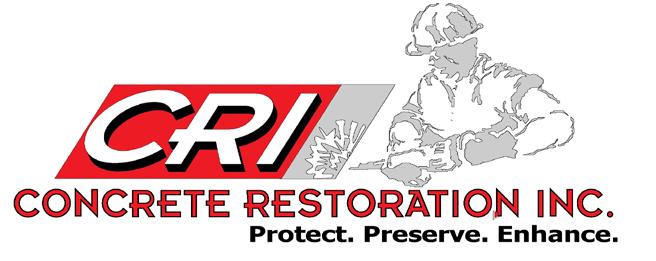
Purpose:
To establish awareness for employees who may be due to their job responsibilities come in contact with Ammonia.
Definition:
Ammonia (NH3) is one of the most produced industrial chemicals in the United States. It is used in industry and commerce and exists naturally in humans and in the environment.
Ammonia is essential for many biological processes and serves as a precursor for amino acid and nucleotide synthesis. In the environment, ammonia is part of the nitrogen cycle and is produced in soil from bacterial processes. Ammonia is also produced naturally from decomposition of organic matter, including plants, animals, and animal wastes.
Some chemical/physical properties of ammonia are:
• At room temperature, ammonia is a colorless, highly irritating gas with a pungent, suffocating odor.
• In pure form, it is known as anhydrous ammonia and is hygroscopic (readily absorbs moisture).
• Ammonia has alkaline properties and is corrosive.
• Ammonia gas dissolves easily in water to form ammonium hydroxide, a caustic solution and weak base.
• Ammonia gas is easily compressed and forms a clear liquid under pressure.
• Ammonia is usually shipped as a compressed liquid in steel containers.
REVISED DATE: January 1, 2025
AMMONIA POLICY
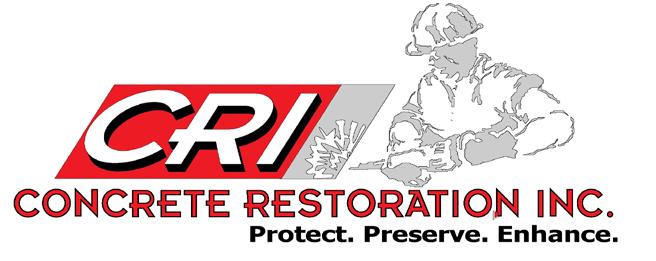
• Ammonia is not highly flammable, but containers of ammonia may explode when exposed to high heat.
Ammonia is widely used as refrigerant in industrial facilities such as:
• Meat, poultry, and fish processing facilities,
• Dairy and ice cream plants,
• Wineries and breweries,
• Fruit juice, vegetable juice, and soft drink processing facilities
• Cold storage warehouses,
• Seafood processing facilities aboard ships, and petrochemical facilities.
How can people be exposed to ammonia?
Most people are exposed to ammonia from breathing its gas or vapors. Since ammonia exists naturally and is also present in cleaning products, exposure may also occur from these sources.
Concrete Restoration Inc employees may specifically be exposed to ammonia while working on or near industrial refrigeration machinery rooms, equipment and piping.
How does ammonia act in the body?
When ammonia enters the body through breathing, swallowing or skin and eye contact, it reacts with water to produce ammonium hydroxide. This chemical is very corrosive and damages cells in the body on contact.
What
are the specific signs and symptoms of ammonia poisoning?
Ammonia is corrosive. The severity of health effects depends on the route of exposure, the dose, and the duration of exposure. Exposure to high concentrations of ammonia in air causes immediate burning of the eyes,
REVISED DATE: January 1, 2025
AMMONIA POLICY
nose, throat, and respiratory tract and can result in blindness, lung damage or death. Inhalation of lower concentrations can cause coughing, and nose and throat irritation.
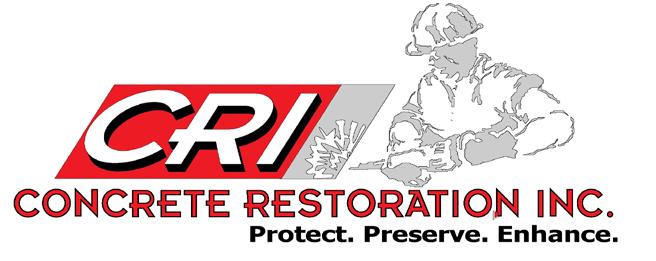
Swallowing ammonia can cause burns to the mouth, throat, and stomach. Skin or eye contact with concentrated ammonia can also cause irritation and burns.
How are employees protected from ammonia exposure?
Employees should be provided with and required to use impervious clothing, gloves, face shields and other appropriate protective clothing necessary to prevent any possibility of skin contact with liquid anhydrous ammonia or aqueous solutions of ammonia containing more than 10% by weight of ammonia. Similar precautions should be taken to prevent the skin from becoming frozen from contact with vessels containing liquid anhydrous ammonia.
What can you do if you think you may have been exposed to a large release of ammonia?
If you have been exposed to a large release of ammonia, take the following steps:
• Quickly move away from the area where you think you were exposed. If the release was indoors, go outside. If you are near a release of ammonia, emergency coordinators may tell you to either evacuate the area or to "shelter in place." To "shelter in place" means to remain indoors to avoid being exposed to the chemical. While indoors, shut and lock all doors and windows; turn off air.
• Quickly remove any clothing that may have ammonia on it. If possible, clothing that is normally removed over the head (like t-shirts and sweaters) should be cut off from the body to prevent additional contact with the agent.
• Place your clothing inside a plastic bag and seal the bag tightly.
REVISED DATE: January 1, 2025
AMMONIA POLICY
• Do not handle the plastic bag and wait for instructions on proper disposal.
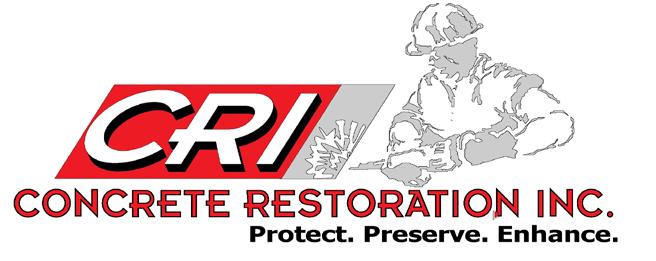
• Disposing of your clothing in a sealed bag helps protect you and other people from any additional exposure.
• Store the bagged clothing in a secure location away from people, especially children.
• Quickly wash any ammonia from your skin with large amounts of soap and water and flush your eyes with large amounts of water.
• Remove and dispose of contact lenses.
• Wash eyeglasses with soap and water before wearing.
• Do not use bleach to remove ammonia from your skin.
• If needed, seek medical attention right away
How is ammonia poisoning treated?
To reduce the effects from exposure to ammonia, it is important to wash your eyes and skin as quickly as possible with large amounts of water.
There is no antidote for ammonia poisoning, but ammonia's effects can be treated, and most victims recover. People who experience serious signs and symptoms (such as severe or constant coughing or burns in the throat) may need hospital care.
What if an employee is visiting Customer site?
Employees should be aware of clients' contingency plans and provisions. Employees must be informed where ammonia is used in the host facility and aware of additional plant safety rules
REVISED DATE: January 1, 2025
ARSENIC AWARENESS POLICY
ARSENIC AWARENESS POLICY
PURPOSE
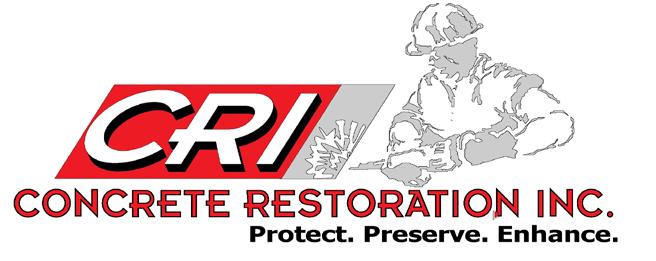
The purpose of this procedure is to identify the controls and actions necessary to prevent adverse health effects to employees from occupational exposure to arsenic, and to ensure that CRI arsenic exposure management practices meet regulatory requirements.
SCOPE
This procedure applies to all CRI operations where employees may be exposed to arsenic. When work is performed on a non-owned or operated site, the operator's program shall take precedence, however, this document covers CRI employees and contractors and shall be used on owned premises, or when an operator's program doesn't exist or is less stringent.
BACKGROUND
Arsenic exposure in the workplace occurs through inhalation, ingestion, dermal or eye contact. Chronic exposure to arsenic can lead to dermatitis, mild pigmentation keratosis of the skin, vasospasticity, gross pigmentation with hyperkeratinisation of exposed areas, wart formation, decreased nerve conduction velocity, and lung cancer. Acute exposures can cause lung distress and death.
RESPONSIBILITIES
Management
• In coordination with the Safety Manager, develop and implement written project/task specific arsenic exposure management procedures prior to the start of activities to reduce exposure to or below the permissible limits.
• Ensure personnel are aware of work that has the potential of exposure to arsenic.
REVISED DATE: January 1, 2025
ARSENIC AWARENESS POLICY
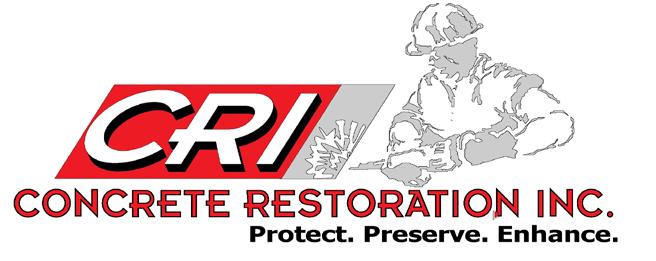
• Ensure individuals responsible for monitoring areas of exposure are properly trained.
• Ensure personnel receive documented medical surveillance if required.
• Ensure that all affected employees receive initial and annual arsenic required training.
• Ensure that training materials are readily available to all affected employees.
• Inform the Safety Manager of upcoming work involving arseniccontaining materials, allowing the Safety Manager to provide any necessary monitoring and training.
• Ensure employees have the appropriate personal protective equipment (PPE) and are properly trained in its use and care, including respiratory protection.
• Ensure employees comply with the arsenic compliance program.
Safety Manager shall:
• Implement a written arsenic compliance program when the PEL of 10 ug/m (3) is exceeded.
• Maintain the arsenic compliance program, notifying management of any regulatory changes and ensuring compliance with federal and state requirements.
Affected Employees shall:
• Comply with the arsenic compliance program, consulting with the supervisor or Safety Manager to ensure the proper PPE is used when required.
• Comply with the medical surveillance program.
REVISED DATE: January 1, 2025
ARSENIC AWARENESS POLICY
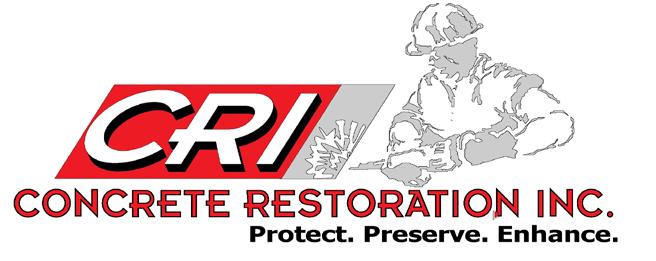
• Attend required training.
• Wear respiratory protection equipment and other specified PPE as required by the project/task specific control program.
• Maintain respiratory protection equipment in good working order, notifying the supervisor or Safety Manager of any problems prior to starting work.
• Review safety data sheets or consult with the supervisor to identify any container with arsenic containing material.
PROCEDURE
Written Arsenic Compliance Program
Each jobsite shall develop and implement a written arsenic compliance plan if arsenic poses any occupational exposure. The minimum criteria to be contained within the written plan shall include:
• A description of each operation where arsenic is omitted, machinery use, material processed, controls in place, crew size, employee job responsibilities and maintenance practices.
• A description of the specific means that will be employed to meet compliance.
The arsenic compliance program must be reviewed and updated annually or more often to reflect status of the program.
The arsenic compliance program must be provided for examination and copying upon request of affected employees or their representatives.
REVISED DATE: January 1, 2025
ARSENIC AWARENESS POLICY
EXPOSURE MONITORING
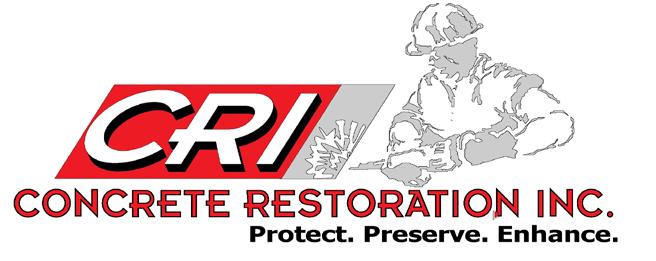
Determinations of airborne exposure levels shall be made from air samples that are representative of each employee's exposure to inorganic arsenic over an eight (8) hour period.
HOUSEKEEPING PLAN
A written housekeeping and maintenance plan shall be kept at each worksite and shall list appropriate frequencies for carrying out housekeeping operations and for cleaning and maintaining dust collection equipment.
SIGNAGE
Adequate signs shall be in place demarcating the regulated areas. If Concrete Restoration Inc is not the host employer, then Concrete Restoration Inc will verify proper signs are placed at the work location.
RESPIRATORY PROTECTION & PPE
Respiratory protection shall be provided in accordance with 29 CFR 1910.134 and WAC 296-842.
Respiratory protection will be used during the following circumstances required while working with arsenic:
• Periods necessary to install or implement feasible engineering or work-practice controls.
• Work operations, such as maintenance and repair activities, for which Concrete Restoration Inc establishes that engineering and workpractice controls are not feasible.
• Work operations for which engineering and work-practice controls are not yet sufficient to reduce employee exposures to or below the permissible exposure limit.
• Emergencies.
REVISED DATE: January 1, 2025
ARSENIC AWARENESS POLICY
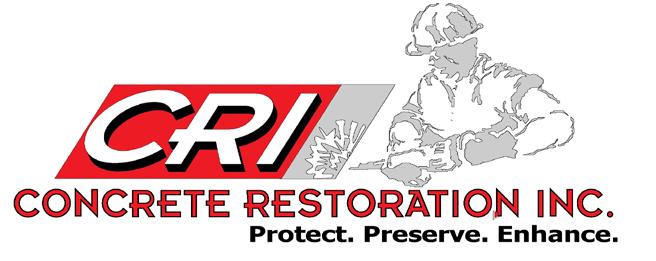
Where the possibility of skin or eye irritation from inorganic arsenic exists, and for all workers working in regulated areas, Concrete Restoration Inc shall provide at no cost to the employee and shall ensure that employees use appropriate and clean protective work clothing and equipment including, but not limited to, coveralls, gloves, shoes or coverlets, and face shields or vented goggles.
CHANGE ROOM AND SHOWERS:
Concrete Restoration Inc shall provide for employees working in regulated areas or subject to the possibility of skin or eye irritation from inorganic arsenic, clean change rooms equipped with storage facilities for street clothes and separate storage facilities for protective clothing and equipment. Concrete Restoration Inc shall assure that employees working in regulated areas or subject to the possibility of skin or eye irritation from inorganic arsenic shower at the end of the work shift.
MEDICAL SURVEILLANCE:
Concrete Restoration Inc shall establish and maintain an accurate record for each employee subject to medical surveillance.
TRAINING:
Training shall be conducted at or before initial assignment and annually thereafter for all employees who are potentially exposed to arsenic and CRI will ensure employee participation. Training materials must be readily available to all employees. All training shall be documented.
REVISED DATE: January 1, 2025
ASBESTOS AWARENESS POLICY
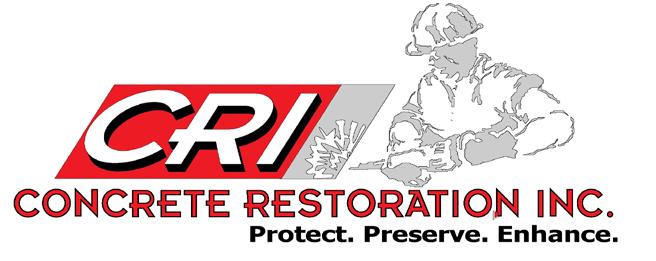
ASBESTOS AWARENESS POLICY
(Reference: OSHA 1910.1001/ 96-65 WAC standard.)
NOTE:
1. Concrete Restoration Inc., intentions are to never have our employees “knowingly” come in contact with asbestos during the functions of their daily job performance.
2. Employees will be trained in asbestos awareness and the contents of this informational policy prior to working in any area that contains or possibly contains asbestos. In multi-employer situations where class I removal is being performed – employees shall be removed from the area until such abatements have been completed.
3. If asbestos is discovered – employees will be immediately removed until an authorized abatement company has cleared the area and written “all clear” authorization is received. Employees will obey and adhere to all signs and warnings and labels and will not disturb Asbestos Containing Materials.
WHAT IS ASBESTOS?
Asbestos is a naturally occurring silicate mineral with long, thin fibrous crystals (normally found in rock form…see picture to the right) which are mined from the earth. The word asbestos (ἄσβεστος) is derived from a Greek adjective meaning inextinguishable. The Greeks termed asbestos the miracle mineral because of its soft and pliant properties, as well as its ability to withstand heat.
Asbestos is toxic. The inhalation of asbestos fibers can cause serious illnesses, including malignant

REVISED DATE: January 1, 2025
ASBESTOS AWARENESS POLICY
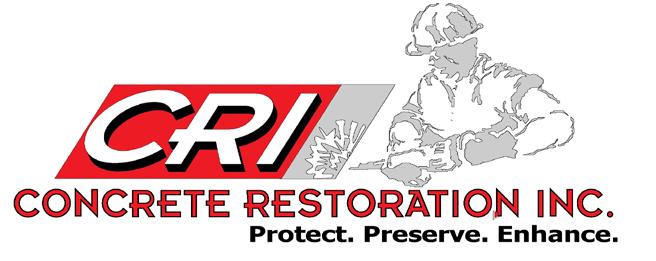
mesothelioma, lung cancer, and asbestosis (also called pneumoconiosis). Since the mid-1980s, many uses of asbestos have been banned in several countries.
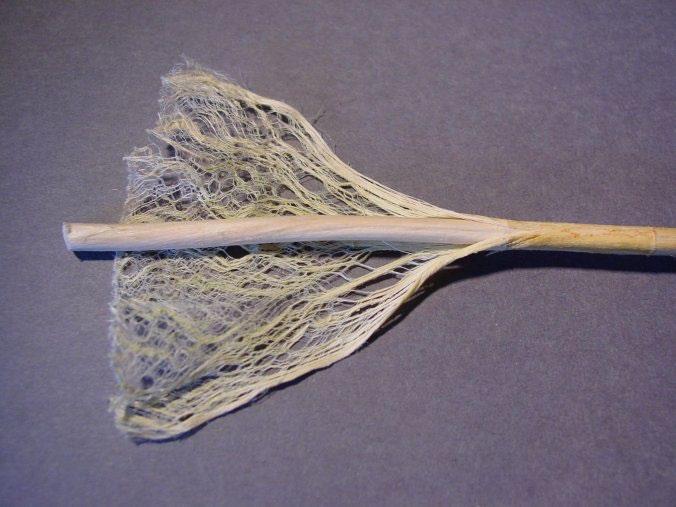
Asbestos became increasingly popular among manufacturers and builders in the late 19th century because of its resistance to heat, electricity and chemical damage, its sound absorption and tensile strength. When asbestos is used for its resistance to fire or heat, the fibers are often mixed with cement or woven into fabric or mats.
Asbestos was used in some products for its heat resistance, and in the past was used on electric oven and hotplate wiring (see picture to the left) for its electrical insulation at elevated temperature, and in buildings for its flame-retardant and insulating properties, tensile strength, flexibility, and resistance to chemicals.
The term asbestos refers to a specific group of naturally occurring fibrous minerals found in certain types of rock formations. Asbestos is mined in much the same way as other minerals, such as iron, lead, and copper.
In 2006, 2.3 million tons of asbestos was mined worldwide, in 11 or 12 countries. Russia was the largest producer with about 40% world share followed by China, Kazakhstan, and Canada (the last of which produces 10% of the world's asbestos). There are many varieties of asbestos but the three most common are chrysotile, amosite and crocidolite.
Asbestos is contained in more than 3,000 different building products.
These include thermal system insulation (pipe and boiler insulation), fireproofing, floor coverings, ceiling tile, cement pipe, and acoustical and decorative treatment for ceilings and walls. Asbestos fibers are mixed during processing with material which binds them together so they can be used in various applications. Asbestos became a very popular commercial product because it was a relatively inexpensive, virtually indestructible material with desirable physical properties including chemical resistance,
REVISED DATE: January 1, 2025
ASBESTOS AWARENESS POLICY
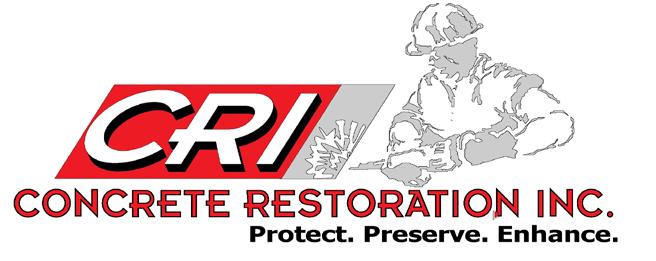
fire resistance, thermal insulating ability, electrical insulating ability, mechanical strength, flexibility and good friction and wear characteristics.
The number of asbestos fibers in these products varies widely from less than 1 percent to nearly 100 percent but any material with at least 1 percent asbestos is considered an asbestoscontaining material (ACM). While it is often possible to suspect that a product or material contains asbestos by experience and visual inspection, actual determinations can only be made by laboratory analysis. Until a material is tested, assume that it contains asbestos. (Notice the appearance of asbestos fibers in the photo to the right which have been magnified.)
HEALTH HAZARDS

Although asbestos is an excellent building material, it has the potential to cause serious health problems if it is inhaled. For asbestos fibers to be inhaled, they must first become airborne through some type of disturbance. Employees should be cautious of other contractors working with asbestos and the potential of unintended exposure. Employees working near other contractors can inadvertently inhale asbestos.
Concrete Restoration Inc employees subject to this exposure will be removed from that area by a supervisor until the potential for asbestos exposure has been abated. Intact, undisturbed material does not pose a significant health risk and can be safely managed in place.
The three illnesses most associated with asbestos exposure are asbestosis (non-cancerous scarring of lung tissue), lung cancer and mesothelioma (rare form of cancer which affects the lining of the lungs). These diseases do not develop immediately after inhalation but may take 15 to 40 years before symptoms appear. Most of these diseases have been diagnosed in workers who held jobs in industries such as shipbuilding, mining, milling, and fabricating, where employees were exposed to very high levels of asbestos on a routine basis. Regardless, appropriate measures should be taken to minimize exposure.
REVISED DATE: January 1, 2025
ASBESTOS AWARENESS POLICY
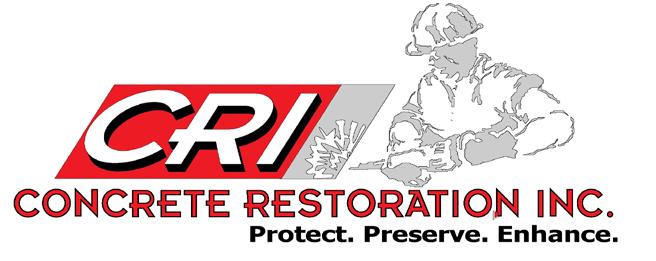
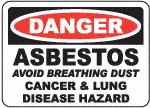
DEFENSE MECHANISMS
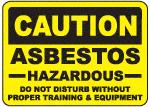
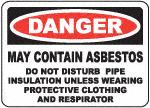
The body has natural defense mechanisms which help eliminate asbestos fibers and other foreign materials before they become lodged in the lung tissue. Many particles are stopped by the nose and mouth. The breathing passages are also lined with a sticky mucous layer that traps small particles. Lining the bronchial tubes are hair-like projections called cilia that continuously move the mucous layer towards the mouth for expectoration.
SMOKING
Although smoking alone is hazardous to your health, studies show that smokers who are also exposed to asbestos have an increased risk of lung cancer which is 50 to 55 times that of a non-exposed, non-smoker. Nonsmokers who are exposed to asbestos have a risk of 5 times that of non-exposed, nonsmokers. One explanation for this synergistic effect is that cigarette smoke greatly impairs the body's defense mechanism by paralyzing the cilia. This allows asbestos fibers and other contaminants to reach the lungs, and this is where they cause damage.
RECOGNITION OF DAMAGE
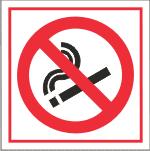
It is very important that you know how to recognize damaged asbestos containing material and then properly report it so it can be addressed in a timely manner and thus minimize risk of exposure to you and other
REVISED DATE: January 1, 2025
ASBESTOS AWARENESS POLICY
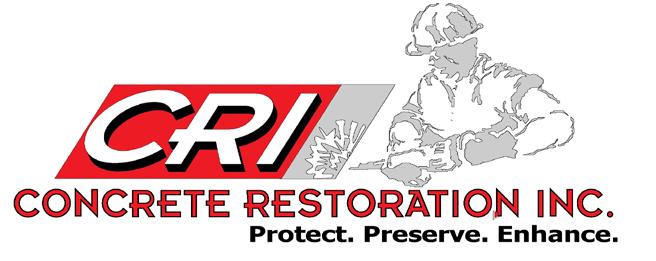
employees. The degree of friability will determine how easily a material can be damaged. Friability is the ease in which asbestos-containing material can be crumbled, pulverized, or reduced to powder by hand pressure. So, the more friable a material is, the more likely it is to become airborne. Ceiling material or fireproofing is friable as it can be easily damaged. Floor tiles, on the other hand, are non-friable as it would take quite a bit of effort to damage them. Damage can be in several forms including water damage (characteristic water ring), delamination (material has pulled away from the surface), general deterioration (aging) and physical damage (contact including gouge marks, etc.). You should immediately report any damaged material to your supervisor or the facility owner.
EMERGENCY PROCEDURES
If you encounter a major fiber release, you should take additional measures to protect yourself and other building occupants. A major fiber release of asbestos fibers is defined as a release of greater than 3 square feet of material and could result from water damaged ceilings, pipe rupture, or inadvertent disruption of material by contractors, staff or building occupants. If you encounter such a release:
• Stop work immediately and leave the area.
• Do not attempt to clean up debris.
• Secure the area by closing and locking the doors.
• Post a sign on all entry doors to inform other personnel of the hazard.
• Notify your supervisor and/or the facility owner.
• Do not reenter the area until the area has been decontaminated in the proper manner.
REGULATIONS

Concrete Restoration Inc Asbestos Program is in accordance with applicable rules and regulations including the OSHA Construction Industry Standard, the OSHA General Industry Standard, the Environmental Protection Agency National Emission Standards for Hazardous Air Pollutants, and the 296-65 WAC standard.
REVISED DATE: January 1, 2025
ASBESTOS AWARENESS POLICY
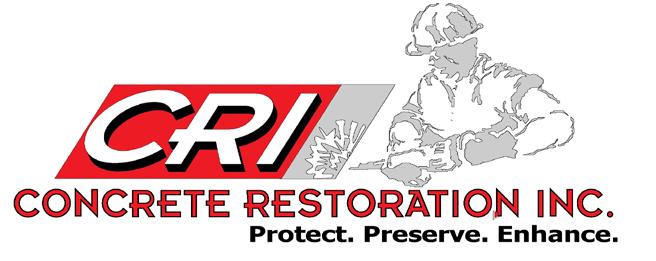
ASBESTOS MANAGEMENT
The Concrete Restoration Inc Asbestos Program emphasizes in-place management of asbestos-containing material because intact and undisturbed asbestos materials do not pose a significant health risk.
However, occasionally, jobsites must conduct small- or large-scale abatement, short duration maintenance, repair or minor renovation activities that may result in disturbance of asbestos-containing material.
These activities can only be performed by authorized personnel who have received appropriate training. Training will involve the employee attending a safety awareness class on asbestos and the related hazards. Records of this training will be kept on file for a minimum of 5 years. These activities are also limited by the amount of asbestos-containing material and the purpose of the activity.
Sometimes asbestos material must be abated because the condition of the material presents a significant health risk or the activity is beyond that of Concrete Restoration Inc personnel. These activities are conducted by an experienced and accredited asbestos abatement contractor with oversight by the facility owner. Asbestos abatement activities include removal, enclosure (airtight, impermeable, permanent barrier around asbestoscontaining materials to prevent the release of fibers) or encapsulation (treatment of asbestos-containing materials with a material that surrounds or embeds asbestos fibers in an adhesive matrix to prevent the release of fibers, as the encapsulant creates a membrane over the surface or penetrates the material and binds its components together).
All abatement activities must be performed in accordance with all applicable federal and state rules and regulations and can only be performed by personnel accredited by OSHA/L&I and the EPA.
Prior to any demolition, renovation or abatement project, the area must first be inspected to identify any asbestos-containing materials that may be disturbed during the project. If asbestos is identified, an accredited designer may be needed to design the abatement project to assure it complies with all health and safety rules and regulations. Permits must be obtained. An accredited contractor will be utilized to complete the project
REVISED DATE: January 1, 2025
ASBESTOS AWARENESS POLICY
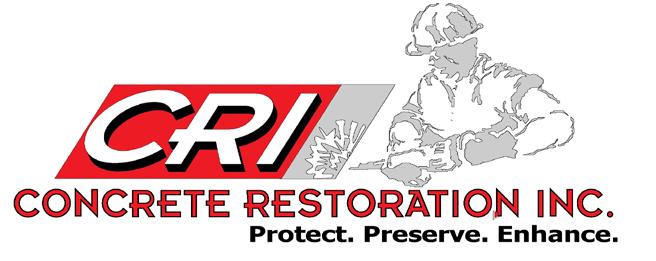
and they will use engineering controls to protect workers and building occupants. Abatement areas will be posted with warning signs and should not be entered except by authorized personnel and only if provided with appropriate personal protective equipment.
Air monitoring will be conducted throughout the project inside and outside the work area to assure concentrations are maintained below permissible limits.


REVISED DATE: January 1, 2025
ASSURED GROUNDING POLICY
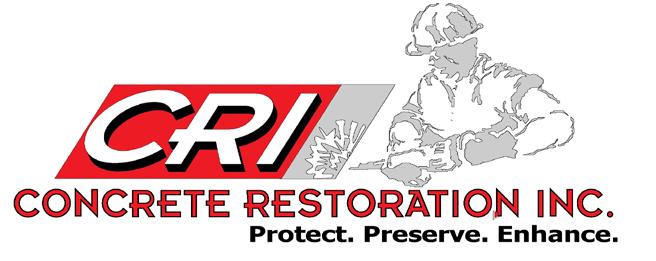
ASSURED GROUNDING POLICY
Reference: WAC 296-155-447/OSHA 1926.404
CRI’s assured equipment grounding conductor program on construction sites covering all cord sets, receptacles which are not a part of the building or structure, and equipment connected by cord and plug which are available for use or used by employees. In addition to the assured grounding program – CRI ALWAYS uses GFCI’s.
All Documents relating to this policy will be kept at the jobsite.
The Safety Manager and/or the Forman shall be the designated competent persons.
Each cord set, attachment cap, plug and receptacle of cord sets, and any equipment connected by cord and plug, except cord sets and receptacles which are fixed and not exposed to damage, shall be visually inspected before each day's use for external defects, such as deformed or missing pins or insulation damage, and for indications of possible internal damage. Equipment found damaged or defective shall be tagged and not be used until repaired.
The following tests shall be performed on all cord sets, receptacles which are not a part of the permanent wiring of the building or structure, and cordand plug-connected equipment required to be grounded:
• All equipment grounding conductors shall be tested for continuity and shall be electrically continuous.
• Each receptacle and attachment cap or plug shall be tested for correct attachment of the equipment-grounding conductor. The equipment-grounding conductor shall be connected to its proper terminal.
All tests shall be performed:
• Before first use
REVISED DATE: January 1, 2025
ASSURED GROUNDING POLICY
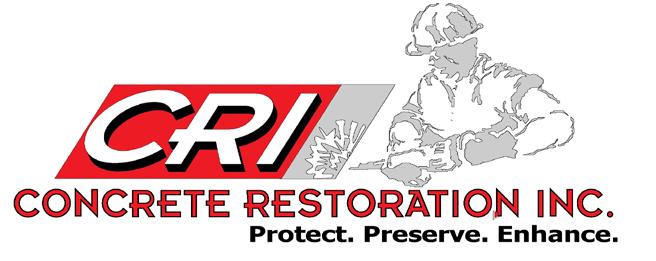
• Before equipment is returned to service following any repair;
• Before equipment is used after any incident which can be reasonably suspected to have caused damage (for example, when a cord set is run over)
• At intervals not to exceed 3 months, except that cord sets and receptacles which are fixed and not exposed to damage shall be tested at intervals not exceeding 6 months.
Tests performed shall be recorded. The test record shall identify each receptacle, cord set, and cord- and plug-connected equipment that passed the test and shall indicate the last date it was tested or the interval for which it was tested. This record shall be kept by means of logs. The record shall be made available on the jobsite for inspection.
Any equipment found not meeting the requirements will not be used until such time as it meets the requirements.
REVISED DATE: January 1, 2025
Auto Accident Report
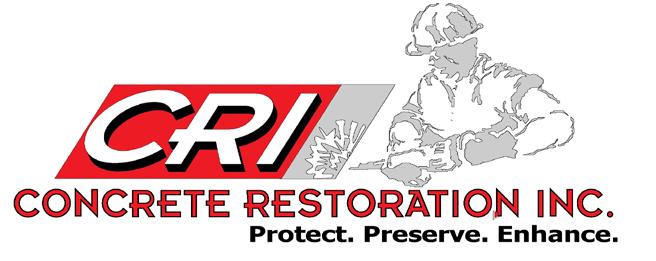
Auto Accident Report
ACCIDENT DETAILS
Date: ______________________
Time: ______________________
Weather/Road Conditions: ______________________________________
Location of Accident (city, state, intersection, etc.) ____________________
Accident Details (cause of accident, result, etc.) _____________________
Damage Descriptions
Your Vehicle: ________________________________________________
DATE: January 1, 2025
Auto Accident Report
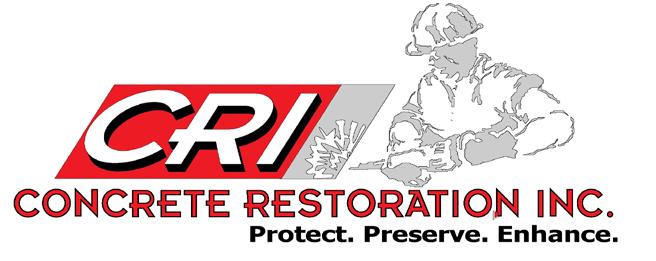
Other Vehicle: ________________________________________________
Towing Company (if any)
Name:______________________________________________________
Phone number: ______________________________
Driver/Vehicle Information:
Owners Name:________________________________________________
Owners Address: _____________________________________________ Phone Number:_______________________________
Vehicle Make: ________________________________________________
Vehicle Model & Year: _________________________________________
Vehicle Color: ________________________________________________
License Plate Number:_________________________________________
Insurance Company: ___________________________________________
Agent Name & Phone Number: __________________________________
Auto Accident Report
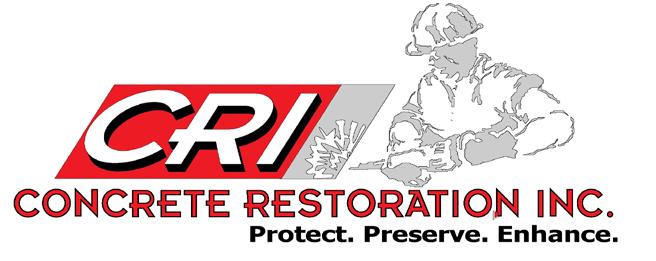
Passengers/Injuries
Your Vehicle: ________________________________________________
Other Vehicle: ________________________________________________
Police Information:
Officer Name: ________________________________________________
Department: _________________________________________________
Phone Number: _______________________________________________
Badge Number: _______________________________________________
Other Useful Information:________________________________________
DATE: January 1, 2025
Auto Accident Report
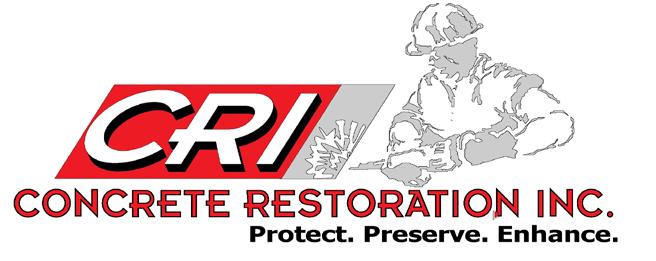
Witness Information
Witness Name: _______________________________________________
Phone Number: ______________________________________________
Address: ____________________________________________________
If able, sketch the accident scene below:
REVISED DATE: January 1, 2025
BENZYNE AWARENESS POLICY
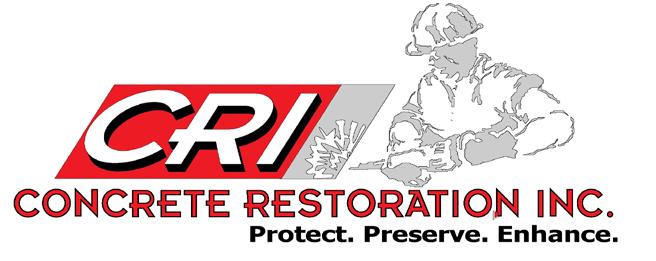
BENZYNE AWARENESS POLICY
Possible locations employees may be exposed to Benzene include, but are not limited by:
• Petroleum refining sites
• Tank Gauging (tanks at producing, pipeline & refining operations)
• Field maintenance
Employees will be made aware of Owner/Client contingency plan provisions. Employees will also be informed of where benzene is used in the host facility and aware of any additional plant safety rules.
• Part Number: 1910
• Part Title: Occupational Safety and Health Standards
• Subpart: Z
• Subpart Title: Toxic and Hazardous Substances
• Standard Number: 1910.1028 App A
• Title: Substance Safety Data Sheet
• WAC 296-849
Substance Identification
• Substance: Benzene
• Permissible Exposure: Except as to the use of gasoline, motor fuels and other fuels subsequent to discharge from bulk terminals and other exemptions specified in 1910.1028(a)(2):
o Airborne: The maximum time-weighted average (TWA) exposure limit is 1 part of benzene vapor per million parts of air (1 ppm) for an 8-hour workday and the maximum short-term exposure limit (STEL) is 5 ppm for any 15-minute period.
o Dermal: Eye contact shall be prevented and skin contact with liquid benzene shall be limited.
• Appearance and odor: Benzene is a clear, colorless liquid with a pleasant, sweet odor. The odor of benzene does not provide adequate warning of its hazard.
REVISED DATE: January 1, 2025
BENZYNE AWARENESS POLICY
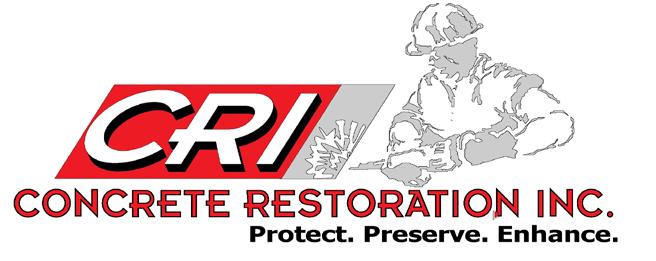
Health Hazard Data
• Ways in which benzene affects your health. Benzene can affect your health if you inhale it, or if it comes in contact with your skin or eyes. Benzene is also harmful if you happen to swallow it.
• Effects of overexposure.
1. Short-term (acute) overexposure: If you are overexposed to high concentrations of benzene, well above the levels where its odor is first recognizable, you may feel breathless, irritable, euphoric, or giddy; you may experience irritation in eyes, nose, and respiratory tract. You may develop a headache, feel dizzy, nauseated, or intoxicated. Severe exposures may lead to convulsions and loss of consciousness.
2. Long-term (chronic) exposure. Repeated or prolonged exposure to benzene, even at relatively low concentrations, may result in various blood disorders, ranging from anemia to leukemia, an irreversible, fatal disease. Many blood disorders associated with benzene exposure may occur without symptoms.
Protective Clothing and Equipment
• Respirators
Respirators are required for those operations in which engineering controls or work practice controls are not feasible to reduce exposure to the permissible level. However, if Concrete Restoration Inc can document that benzene is present in the workplace less than 30 days a year, respirators may be used in lieu of engineering controls. If respirators are worn, they must have joint Mine Safety and Health Administration and the National Institute for Occupational Safety and Health (NIOSH) seal of approval, and cartridge or canisters must be replaced before the end of their service life, or the end of the shift, whichever occurs first.
REVISED DATE: January 1, 2025
BENZYNE AWARENESS POLICY
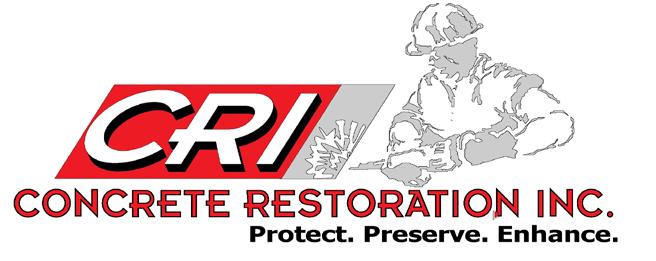
If employees experience difficulty breathing while wearing a respirator, they may request a positive pressure respirator. Employees will be thoroughly trained to use the assigned respirator, and the training will be provided by Concrete Restoration Inc at least annually.
• Protective Clothing
Employees must wear appropriate protective clothing (such as boots, gloves, sleeves, aprons, etc.) over any parts of their body that could be exposed to liquid benzene.
• Eye and Face Protection
Employees must wear splash-proof safety goggles if it is possible that benzene may get into their eyes. In addition, employees must wear a face shield if their face could be splashed with benzene liquid.
Emergency and First Aid Procedures
• Eye and face exposure. If benzene is splashed in an employee’s eyes, they are to wash it out immediately with large amounts of water or at an eye wash station if available. If irritation persists or vision appears to be affected employees will see a doctor as soon as possible.
• Skin exposure. If benzene is spilled on an employee’s clothing or skin, remove the contaminated clothing and wash the exposed skin with large amounts of water and soap immediately. Wash contaminated clothing before it is worn again.
• Breathing. If an employee or any other person breathes in large amounts of benzene, that person will be directed to fresh air at once. Apply artificial respiration if breathing has stopped. Call for medical assistance or a doctor as soon as possible. Never enter any vessel or confined space where the benzene concentration might be high without proper safety equipment and at least one other person present who will stay outside. A lifeline should be used.
REVISED DATE: January 1, 2025
BENZYNE AWARENESS POLICY
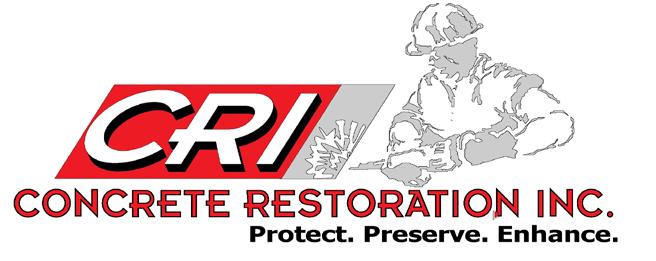
• Swallowing. If benzene has been swallowed and the patient is conscious, do not induce vomiting. Call for medical assistance or a doctor immediately.
Medical Requirements
If employees are exposed to benzene at a concentration at or above 0.5 ppm as an 8-hour time-weighted average or have been exposed at or above 10 ppm in the past while employed by Concrete Restoration Inc, then Concrete Restoration Inc is required to provide a medical examination and history and laboratory tests within 60 days of the effective date of this standard and annually thereafter. These tests will be provided without cost to the employee. In addition, if an employee is accidentally exposed to benzene (either by ingestion, inhalation, or skin/eye contact) under emergency conditions known or suspected to constitute toxic exposure to benzene, Concrete Restoration Inc will make special laboratory tests available to the employee.
Observation of Monitoring
Concrete Restoration Inc will perform measurements that are representative of employee exposure to benzene. Employees and their designated representative are entitled to observe the monitoring procedure. Employees are entitled to observe the steps taken in the measurement procedure, and to record the results obtained. When the monitoring procedure is taking place in an area where respirators or personal protective clothing and equipment are required to be worn, employees and their representative must also be provided with, and must wear the protective clothing and equipment.
Access to Records
Employees and their representative are entitled to see the records of measurements of their exposure to benzene upon written request to Concrete Restoration Inc. Employee medical examination records can be furnished to the employee, employee’s physician or designated representative upon request by the employee or Concrete Restoration Inc.
REVISED DATE: January 1, 2025
BENZYNE AWARENESS POLICY
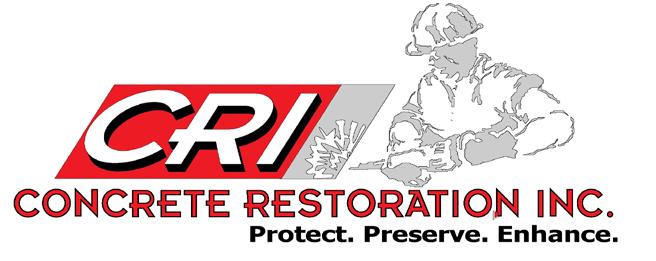
Precautions for Safe Use, Handling and Storage
Benzene liquid is highly flammable. It should be stored in tightly closed containers in a cool, well-ventilated area. Benzene vapor may form explosive mixtures in air. All sources of ignition must be controlled. Use non-parking tools when opening or closing benzene containers. Fire extinguishers, where provided, must be readily available. Know where they are located and how to operate them. Smoking is prohibited in areas where benzene is used or stored. Employees should ask their supervisors where benzene is used in their area and for additional plant safety rules.
• Part Number: 1910
• Part Title: Occupational Safety and Health Standards
• Subpart: Z
• Subpart Title: Toxic and Hazardous Substances
• Standard Number: 1910.1028 App B
• Title: Substance Technical Guidelines, Benzene
Physical and Chemical Data
• Substance identification.
o Synonyms: Benzol, benzole, coal naphtha, cyclohexatriene, phene, phenyl hydride, pyrobenzol. (Benzin, petroleum benzin and Benzine do not contain benzene).
o Formula: C(6)H(6) (CAS Registry Number: 71-43-2)
• Physical data.
o Boiling Point (760 mm Hg); 80.1 deg. C (176 deg. F)
o Specific Gravity (water = 1): 0.879
o Vapor Density (air = 1): 2.7
o Melting Point: 5.5 deg. C (42 deg. F)
o Vapor Pressure at 20 deg. C (68 deg. F): 75 mm Hg
o Solubility in Water: .06%
o Evaporation Rate (ether = 1): 2.8
o Appearance and Odor: Clear, colorless liquid with a distinctive sweet odor.
Fire, Explosion, and Reactivity Hazard Data
REVISED DATE: January 1, 2025
BENZYNE AWARENESS POLICY
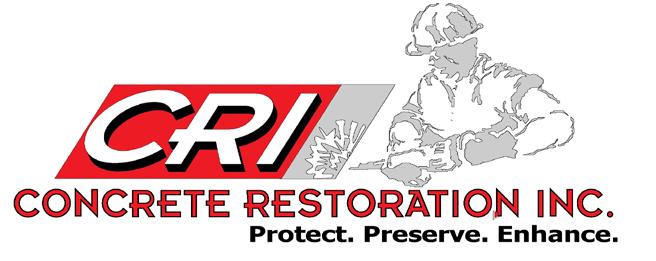
• Fire.
o Flash Point (closed cup): - 11 deg. C (12 deg. F)
o Autoignition Temperature: 580 deg. C (1076 deg. F)
o Flammable limits in Air. % by Volume: Lower: 1.3%, Upper: 7.5%
o Extinguishing Media: Carbon dioxide, dry chemical, or foam.
o Special Fire-Fighting procedures: Do not use solid stream of water, since stream will scatter and spread fire. Fine water spray can be used to keep fire-exposed containers cool.
o Unusual fire and explosion hazards: Benzene is a flammable liquid. Its vapors can form explosive mixtures. All ignition sources must be controlled when benzene is used, handled, or stored. Where liquid or vapor may be released, such areas shall be considered as hazardous locations. Benzene vapors are heavier than air; thus the vapors may travel along the ground and be ignited by open flames or sparks at locations remote from the site at which benzene is handled.
o Benzene is classified as a 1 B flammable liquid for the purpose of conforming to the requirements of 29 CFR 1910.106. A concentration exceeding 3,250 ppm is considered a potential fire explosion hazard. Locations where benzene may be present in quantities sufficient to produce explosive or ignitable mixtures are considered Class I Group D for the purposes of conforming to the requirements of 29 CFR 1910.309.
• Reactivity.
o Conditions contributing to instability: Heat.
o Incompatibility: Heat and oxidizing materials.
o Hazardous decomposition products: Toxic gases and vapors (such as carbon monoxide).
Spill and Leak Procedures
• Steps to be taken if the material is released or spilled. As much benzene as possible should be absorbed with suitable materials, such as dry sand or earth. That remaining must be flushed with large amounts of water. Do not flush benzene into a confined space, such as a sewer, because of explosion danger. Remove all ignition sources. Ventilate enclosed places.
REVISED DATE: January 1, 2025
BENZYNE AWARENESS POLICY
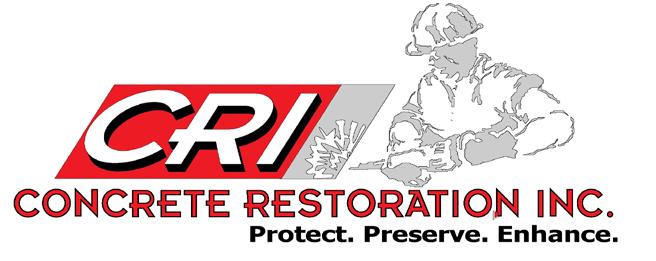
• Waste disposal method. Disposal methods must conform to other jurisdictional regulations. If allowed, benzene may be disposed of: (a) By absorbing it in dry sand or earth and disposing in a sanitary landfill; (b) if small quantities, by removing it to a safe location from buildings or other combustible sources, pouring it in dry sand or earth and cautiously igniting it; and (c) if large quantities, by atomizing it in a suitable combustion chamber.
Miscellaneous Precautions
• High exposure to benzene can occur when transferring the liquid from one container to another. Such operations should be well ventilated and good work practices must be established to avoid spills.
• Use non-sparking tools to open benzene containers which are effectively grounded and bonded prior to opening and pouring.
Concrete Restoration Inc will advise employees of all plant areas and operations where exposure to benzene could occur.
REVISED DATE: January 1, 2025
BLOODBORNE PATHOGENS
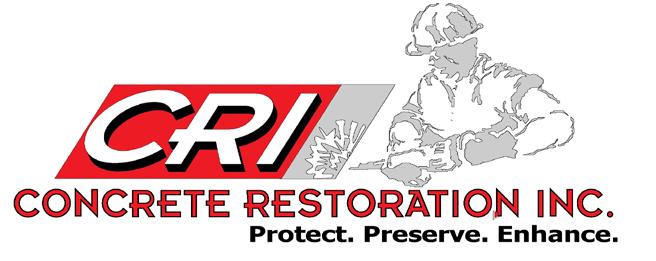
BLOODBORNE PATHOGENS POLICY
Reference: WAC 296-823/OSHA 29 CFR 1910.1030
Purpose
To protect exposed employees from hazards associated with bloodborne pathogens, in particular HIV and Hepatitis B Virus. To prevent employees who are administering first aid resulting from an accident, such as, a serious laceration from work tools.
Definitions:
• Blood: Human blood, human blood components, and products made from human blood.
• Bloodborne Pathogens: Pathogenic microorganisms that are present in the human blood and can cause disease in humans.
• Contaminated: The presence or the unreasonably anticipated presence of blood or other potentially infectious materials on an item or surface
• Occupational Exposure: reasonably anticipated skin, eye, mucous membrane, or potential contact with blood or other potentially infectious materials that may result from the performance of an employee's duty.
• Potential: Piercing mucous membranes, or the skin barrier through such events as needle sticks, human bites, cuts, or abrasions.
Exposure Determination
Concrete Restoration Inc employees have very little risk in being exposed to bloodborne pathogens, unless in close proximity of an occupational accident or when designated to administer first aid practices. Employees administering first aid are the affected employees who are considered exposed or will be potentially exposed, to blood and/ or other potentially infectious materials.
REVISED DATE: January 1, 2025
BLOODBORNE PATHOGENS
POLICY
Exposure Control
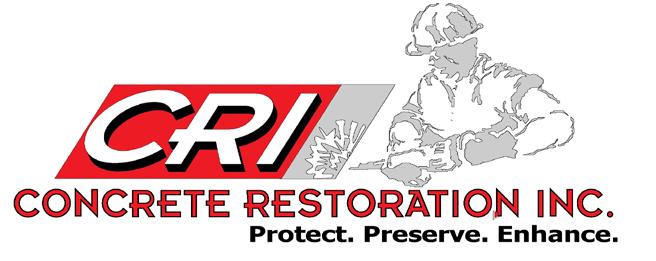
• Universal precautions must be observed to prevent contact with blood or other potentially infectious materials.
• When at all possible, victims of minor injury shall perform first aid to themselves under the supervision of a certified first aid individual.
• When first aid assistance is needed first aid trained employee must wear the appropriate Personal Protective Equipment
• Disposable rubber or vinyl gloves.
• Pocket masks or mouth pieces for CPR.
• All employees exposed to blood or other potentially infectious materials must wash and clean exposed areas of their bodies before returning to work.
• All work areas, materials and equipment must be cleaned after contact with blood or other possibly infectious material.
• •All contaminated materials must be properly collected, sealed in a plastic container for proper disposal.
Engineering Controls:
• Concrete Restoration Inc will provide hand washing facilities where possible. In case hand-washing facilities are impractical, First Aid Kits will provide antiseptic cleansers or towelettes.
• Proper PPE will be provided: gloves, face shields for CPR, eye protection.
• Orientation of employees to first aid supplies and PPE.
Post Exposure Evaluation and Follow up.
• Immediately available after an exposure incident the employee will be provided a confidential medical evaluation and follow up including:
• Documentation of the route of exposure, and the circumstances of the exposure incident.
• Identification and documentation of the source individual.
• Medical evaluations, testing and post exposure treatments will be made available to exposed employees.
REVISED DATE: January 1, 2025
BLOODBORNE PATHOGENS
POLICY
Information and Training
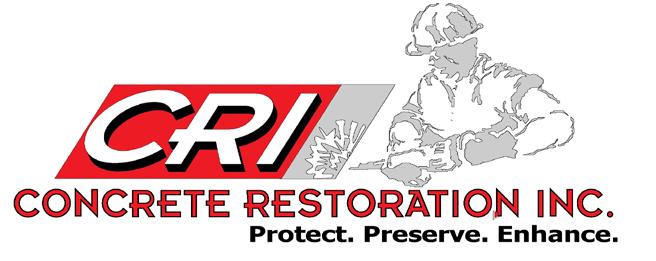
Concrete Restoration Inc will ensure that all employees participate in a training program which must be provided at no cost to the employee and during working hours.
Training will be provided as follows:
1. At the time of initial assignment to tasks where occupational exposure may take place.
2. Within 90 days after the effective date of the standard; and
3. At least annually thereafter.
For employees who have received training on bloodborne pathogens in the year preceding the effective date of the standard, only training with respect to the provisions of the standard which were not included need be provided.
Annual training for all employees will be provided within one year of their previous training.
Concrete Restoration Inc will provide additional training when changes such as modification of tasks or procedures or institution of new tasks or procedures affect the employee's occupational exposure. The additional training may be limited to addressing the new exposures created.
Material appropriate in content and vocabulary to educational level, literacy, and language of employees will be used.
The training program will contain at a minimum the following elements:
1. An accessible copy of the regulatory text of this standard and an explanation of its contents.
2. A general explanation of the epidemiology and symptoms of blood borne diseases.
3. An explanation of the modes of transmission of blood borne pathogens.
4. An explanation of Concrete Restoration Inc exposure control plan and how the employee can obtain a copy of the written plan.
REVISED DATE: January 1, 2025
BLOODBORNE PATHOGENS
POLICY
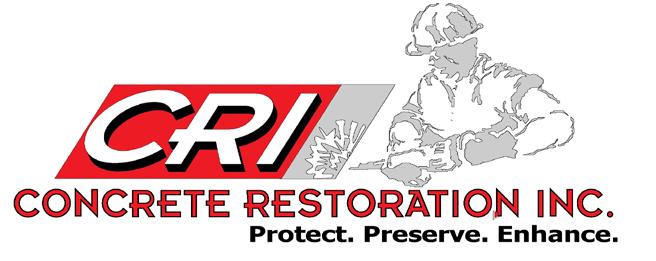
5. An explanation of the appropriate methods for recognizing tasks and other activities that may involve exposure to blood and other potentially infectious materials.
6. An explanation of the use and limitations of methods that will prevent or reduce exposure including appropriate engineering controls, work practices, and personal protective equipment.
7. Information on the types, proper use, location, removal, handling, decontamination, and disposal of personal protective equipment.
8. An explanation of the basis for the selection of personal protective equipment.
9. Information on the appropriate actions to take and people to contact in an emergency involving blood or other potentially infectious materials.
10. An explanation of the procedure to follow if an exposure incident occurs, including the method of reporting the incident and the medical follow-up that will be made available.
11. Information on the post-exposure evaluation and follow-up that Concrete Restoration Inc is required to provide for the employee following an exposure incident.
Recordkeeping –
Medical Records.
Concrete Restoration Inc will establish and maintain an accurate record for each employee with occupational exposure, in accordance with WAC 296823
This record will include:
1. The name and social security number of the employee.
2. A copy of all results of examinations, medical testing, and follow-up procedures
3. Concrete Restoration Inc’s copy of the healthcare professional's written opinion
4. A copy of the information provided to the healthcare professional
Confidentiality
REVISED DATE: January 1, 2025
BLOODBORNE PATHOGENS
POLICY
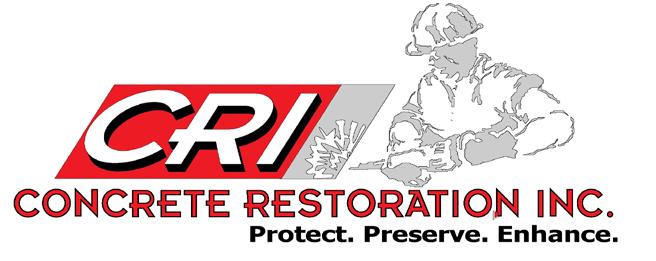
Concrete Restoration Inc will ensure that employee medical records are:
1. Kept confidential
2. Not disclosed or reported without the employee's express written consent to any person within or outside the workplace except as required by law.
Training Records.
Training records will include the following information:
1. The dates of the training sessions.
2. The contents or a summary of the training sessions.
3. The names and qualifications of persons conducting the training; and
4. The names and job titles of all people attending the training sessions. Training records will be maintained for 3 years from the date on which the training occurred.
REVISED DATE: January 1, 2025
COLD RELATED ILLNESS
COLD RELATED ILLNESS
Reference: WAC 296-305-05004
Objectives
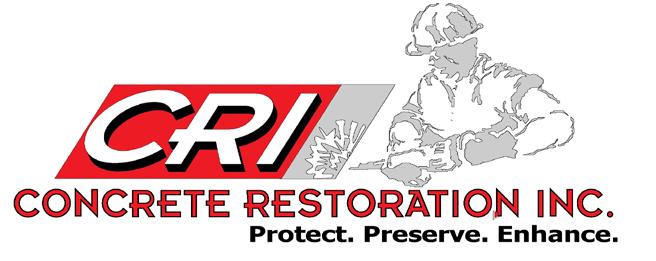
To explain the potential health hazards of exposure to cold, the symptoms, and ways to protect against and treat cold-related health problems. The result should be greater attention to cold hazards and fewer resulting problems.
Introduction/Overview
Very cold temperatures, like very hot ones, can be hazardous to an employee’s health even deadly. Employees can be exposed to hazards from the cold when they’re inside as well as out. It’s very cold, for instance, in food storage areas. Most of the problems associated with cold climates can be prevented by proper dress and the use of sensible practices. Knowing the symptoms of danger and how to treat them can keep problems that do occur from becoming disasters. Jobs that place workers at risk for cold exposures will be identified prior to employees working in those conditions using hazard assessments and training.
General Hazards
The most common hazard associated with cold is frostbite. When the body doesn’t get enough heat and the body tissues freeze. Body parts most often affected by frostbite are the nose, ears, cheeks, fingers, and toes. In very bad cases, frostbite can cause permanent tissue damage and loss of movement in the affected body parts. In the worst cases, the person could become unconscious and stop breathing.
Another cold hazard is hypothermia. That is what it’s called when someone is exposed to the cold for so long that their body temperature gets dangerously low. Like frostbite, the worst-case results are unconsciousness and death. With both cold hazards, employees are more at risk if they’re older, overweight or have allergies or poor circulation. Other factors that raise the risk are smoking, drinking, and taking medications such as sedatives.
REVISED DATE: January 1, 2025
COLD RELATED ILLNESS
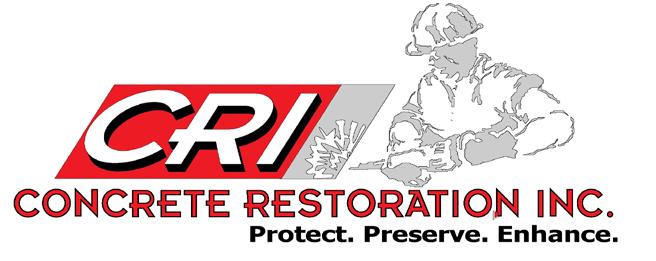
Situational awareness should also be observed. Employees should always be aware of their surroundings and notice if ice has formed in or around their work area. Regularly traveled walkways or work areas will be sanded, salted or cleared by other means of any snow or ice.
During training, Concrete Restoration Inc covers many safety issues concerning working in cold conditions. Another key hazard that is discussed is using caution when working around unstable snow and ice buildups. Employees can become crushed by unstable snow piles or impaled by sharp icicles from roof tops. These hazards can be avoided by staying clear of snow piles and remembering to check for cold climate hazards before beginning work.
Identifying Hazards
Prior to beginning work, Concrete Restoration Inc will perform a risk assessment which will consider all possible risk associated with completing that task, including cold climate. Any areas identified as cold hazard areas will require employees working in those areas to take special precautions. Employees working in those areas will receive training about cold climate hazards and methods for prevention. Identification of the symptoms of cold related hazards such as frostbite, hypothermia and trench foot are a very important part of the training. Employees who continually work in areas where cold conditions exist will receive initial training, and on an annual basis thereafter.
FROSTBITE
Frostbite can occur from being in a cold area or from touching an object whose temperature is below freezing. In many cases, people don’t have any idea that it’s happening. That’s why employees must be familiar with the symptoms. Frostbite victims usually start by feeling uncomfortably cold, then numb. Sometimes they also get a tingling or aching feeling or a brief pain.
A frostbite victim’s skin goes from white or grayish yellow to reddish violet to black. It may also blister.
REVISED DATE: January 1, 2025
COLD RELATED ILLNESS
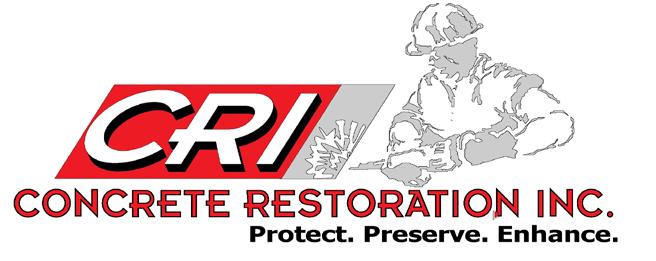
If frostbite occurs, immediate action must be taken to avoid or minimize permanent damage from occurring.
DO NOT rub affected areas.
DO NOT break any forming blisters.
DO NOT give stimulants such as alcohol etc.
DO NOT immerse in HOT water.
Move the person to a warm area and place affected body parts in warm water until skin becomes flushed. (Water should be 1000 F to 1050 F.)
After warming, keep affected fingers and toes separated by gauze, etc. Administer warm fluids to person and seek medical attention. For obvious reasons, no one should want to experience all the symptoms of frostbite, so if an employee feels numbness, they are required to take action.
HYPOTHERMIA
Hypothermia can also take an employee by surprise because it can begin to set in even when the temperatures are above freezing. Windy conditions, physical exhaustion, and wet clothing can all make an employee more prone to hypothermia. With hypothermia, the first feeling is cold, then pain in the extremities. Next, the person will begin to shiver, which is how the body tries to raise its temperature.
Other symptoms include numbness, stiffness (especially in the neck, arms, and legs) poor coordination, drowsiness, slow or irregular breathing and heart rate, slurred speech, cool skin, and puffiness in the face. A hypothermia victim may also seem confused and disoriented. It’s not unusual for the person to seem apathetic about getting out of the cold. If hypothermia occurs, it is very important to immediately minimize heat loss and add heat to the person’s body.
DO NOT use HOT water to warm victim…Warm water only.
DO NOT give hot liquids, alcohol, or anything by mouth.
DO NOT allow the victim to move.
DO NOT rub or manipulate body parts.
NOTE that this person may fall into unconsciousness, which requires verification of breathing and pulse.
REVISED DATE: January 1, 2025
COLD RELATED ILLNESS
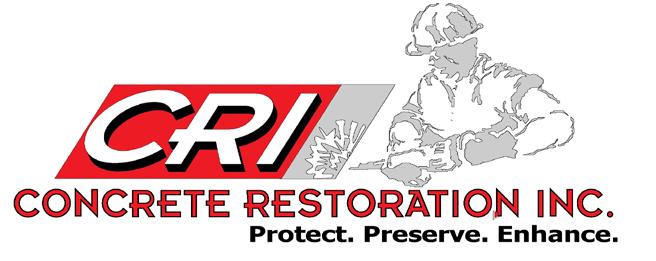
As you can see, many of these symptoms are not unusual and could mean different things. But if you’re exposed to very cold conditions, take them seriously and take steps to relieve them.
TRENCH FOOT
Trench foot is a medical condition caused by prolonged exposure of the feet to damp, unsanitary and cold conditions. It is one of many immersion foot syndromes. The use of the word "trench" in the name of this condition is a reference to trench warfare during World War I
Infected feet may become numb, affected by erythroses (turning red) or cyanosis (turning blue) as a result of poor vascular supply, and feet may begin to have a decaying odor due to the possibility of the early stages of necrosis setting in. As the condition worsens, feet may also begin to swell. Advanced trench foot often involves blisters and open sores, which lead to fungal infections. If left untreated, trench foot usually results in gangrene, which can cause the need for amputation. If trench foot is treated properly, complete recovery is normal, though it is marked by severe short-term pain when feeling returns. As with other cold-related injuries, trench foot leaves sufferers more susceptible in the future.
Unlike frostbite, trench foot does not require freezing temperatures and can occur in temperatures up to 60° Fahrenheit. The condition can occur with as little as eleven hours' exposure. The mechanism of tissue damage is not fully understood. Excessive sweating or hyperhidrosis has long been regarded as a contributory cause.
Trench foot is easily prevented by keeping the feet warm and dry, and changing socks frequently when the feet cannot be kept dry. Soldiers often wrote home about their daily lives living in the trenches, but also asked and pleaded for more socks, to help prevent things like trench foot.
REVISED DATE: January 1, 2025
COLD RELATED ILLNESS
Protection Against Hazards
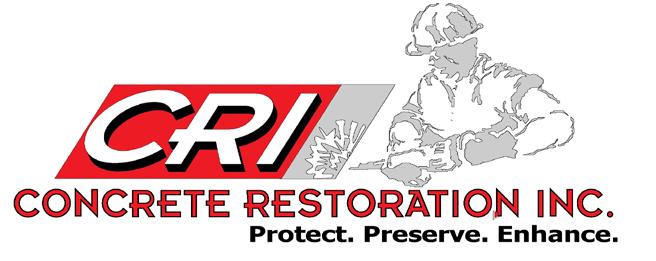
The best way to deal with cold problems is to prevent them in the first place. The most sensible approach is to limit exposure to cold, especially in windy and wet conditions. If an employee is going to be in cold conditions, they should not bathe, smoke, or drink alcohol just before going out. Anyone working in cold conditions must follow these rules:
• Dress for the conditions in layers of loose, dry clothes. The most effective mix is cotton or wool underneath, with something waterproof on top.
• Get dried or changed immediately if your clothes become wet.
• Be sure to cover your hands, feet, face, and head. A ski cap, toboggan or beanie is critical because you can lose up to 40 percent of your body heat if your head isn’t covered.
• Keep moving when you’re in the cold. Constant movement keeps blood flowing and increased circulation cuts down on experience one of the cold hazards discussed earlier.
• Wear insulated boots or other insulated footwear.
• Take regular breaks in warm areas and go where it’s warm any time you start to feel very cold or numb. Drink something warm, if it doesn’t contain alcohol or caffeine.
• When working in cold conditions employees should never work alone. Use of the “buddy system” is encouraged to help employees observe each other.
Cold weather supplies provided by Concrete Restoration Inc will be regularly inspected and restocked as necessary. If any article of clothing or personal protective equipment is found to be defective it will be promptly replaced.
REVISED DATE: January 1, 2025
COLD RELATED ILLNESS
Safety Procedures
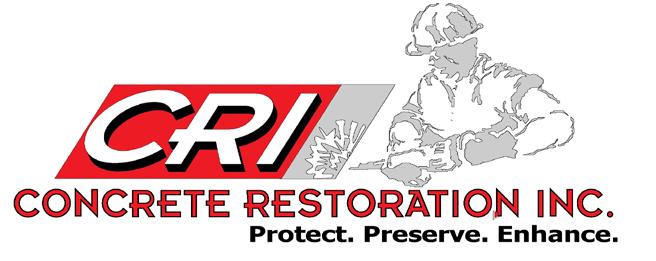
Prevention is the best countermeasure to combat cold conditions, but sometimes that is not enough. This is why it is very important to know what to do if someone shows symptoms of the cold hazards discussed earlier. Concrete Restoration Inc will ensure that all employees working in areas where cold conditions are present have proper training in first aid treatment for cold-induced injuries and illnesses.
When/if an employee shows signs of overexposure to cold the first thing to do is to get where it’s warm. Employees will remove any frozen, wet, or tight clothes and replace them with warm clothes or blankets. Employees will be encouraged to drink something warm, decaffeinated, and nonalcoholic.
For hypothermia, call for medical help and keep the employee covered with blankets or something similar. Don’t use hot baths, electric blankets, or hotwater bottles. Give artificial respiration if necessary and try to keep the employee awake and dry.
For frostbite, first be aware of the don’ts:
• Don’t rub the body part or apply a heat lamp or hot water bottle.
• Don’t go near a hot stove.
• Don’t break any blisters.
• Don’t drink caffeine.
Do warm the frozen body part quickly with sheets and blankets or warm (not hot) water.
Once the body part is warm, exercise it—with one exception: Don’t walk on frostbitten feet.
If in doubt, get medical attention, it’s a good idea to elevate the frozen body part and cover it with sterile cloths before travel.
REVISED DATE: January 1, 2025
COMPRESSED AIR POLICY
COMPRESSED AIR POLICY
Reference: WAC 269-36/OSHA 1926.803
Purpose
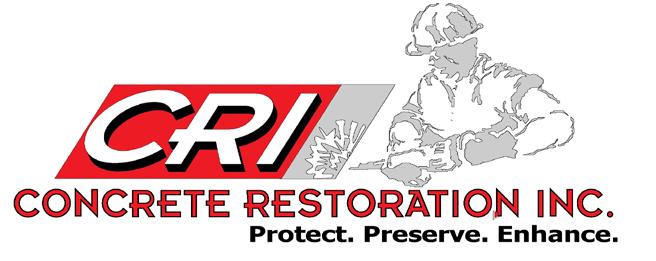
The purpose of this safety policy and procedure is to establish procedures for the protection of Concrete Restoration Inc employees working with or on compressed air equipment.
Background
Air compressors are used for a variety of applications in Concrete Restoration Inc. Air compressor storage tanks store excess air that is generated from the compressor, providing a convenient and readily accessible air source. Because of the air pressure within these storage tanks, potential dangers can develop if certain practices and precautions are not followed. This safety policy and program provides guidelines for the safe use of air compressor storage tanks. It lists training requirements, guidelines for locating drains and traps, and requirements for gauges and valves.
Responsibilities
Management
• Ensure adequate funds are available for the purchase and repair of air compressor storage tanks. Identifying and list employees affected by this safety policy and procedure.
• Provide training for affected employees
• Ensure proper use and maintenance of air compressor storage tanks and equipment.
REVISED DATE: January 1, 2025
COMPRESSED AIR POLICY
Supervisors
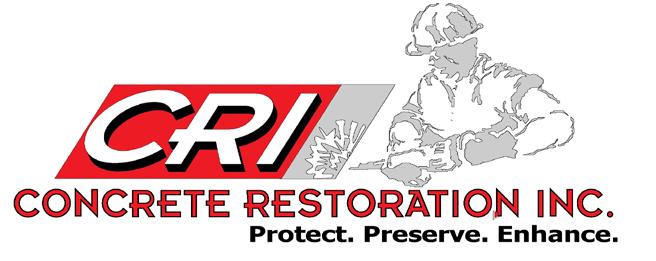
• Ensure that only those employees who have been trained to work with air compressor storage tanks are allowed to operate such equipment.
• Ensure that equipment needed is available and is in good working condition.
• Ensure damaged equipment is removed from service until repaired and tested Ensure that air compressor storage tanks are inspected every six months.
• Provide employees with Personal Protective Equipment (PPE) necessary for their job.
Employees
• Inspect air compressor storage tanks prior to use and note any damage or defects Inspect all hoses and equipment before connecting to any compressed air system Immediately report any damages or defects to their supervisors.
• Empty manual drains and taps on a regularly scheduled basis
Safety Manager
• Provide prompt assistance to managers, supervisors, or others on any matter concerning this safety policy and procedure.
• Assist in developing required training.
• Coordinate with Purchasing to ensure that all newly purchased air compressor storage tanks comply with current safety regulations.
• Provide consultative service and audit assistance to ensure effective implementation of this safety policy and procedure.
REVISED DATE: January 1, 2025
COMPRESSED AIR POLICY
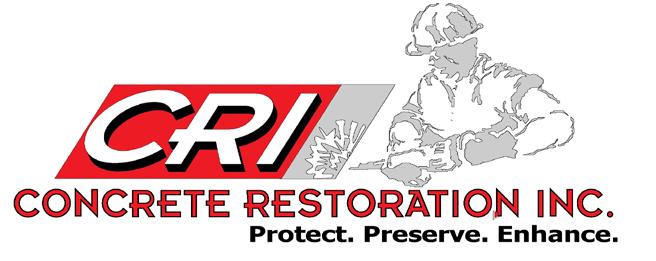
Definitions
Air Compressor Storage Tank - Pressurized vessel that stores air generated from an air compressor
Drain Valve - A valve that is installed at the lowest point of an air compressor storage tank to provide for the removal of accumulated oil and water.
Trap - A device which uses venting head pressure to purge the tank from condensed water.
Training
• All affected employees will be trained in:
• The purpose of air compressor storage tanks.
• The basic operation of air compressor storage tanks
• Maintenance requirements of drains and traps
• Reading gauges and operating valves
This training must be performed upon initial employment and/or job reassignment. Periodic refresher training shall also be conducted at the discretion of the supervisor or Safety Department.
Equipment
Drain valves are installed at the lowest point of an air compressor storage tank to provide for the removal of accumulated oil and water. Drain valves must be opened once a week to purge water build-up unless they are automatically operated traps.
Drain Traps are devices, installed on the lowest point of a storage tank, which use venting head pressure to automatically purge the tank from condensed water.
REVISED DATE: January 1, 2025
COMPRESSED AIR POLICY
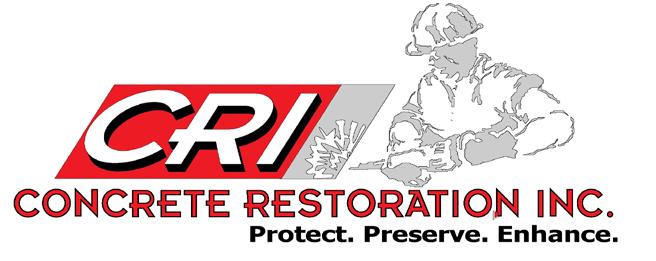
Gauges and Valves - All air compressor storage tanks must be equipped with a least one safety valve and pressure gauge. Gauges and safety valves will be tested at least every six months to ensure proper operation. No valve of any type shall be placed between the air receiver and its safety valve.
Accessibility - Air compressor storage tanks must be installed such that all drains, handholes, and manholes are easily accessible. Air compressor storage tanks shall never be buried underground or located in an inaccessible place.
Air Powered Equipment
• Equipment and tools that use compressed air must be inspected before each use. This includes all hoses and connections.
• Only approved snap type connectors are permitted on hoses. Use of hose clamps to connect fittings to hoses is not permitted.
• All hoses must be connected only to approved supply valve locations.
• Air power equipment must not be connected to any air supply unless the design pressure of the equipment meets or exceeds the supply air pressure.
• Temporary reducers may not be installed in any compressed air supply system without approval by the Safety Department.
• All air-lance/wand equipment must have an automatic hand closure valve that is positioned such that the employee holds the valve open while using the lance/wand.
• Goggles are required during air cleaning of facilities or equipment.
• Other PPE may be required based on the task and tools used.
REVISED DATE: January 1, 2025
COMPRESSED AIR POLICY
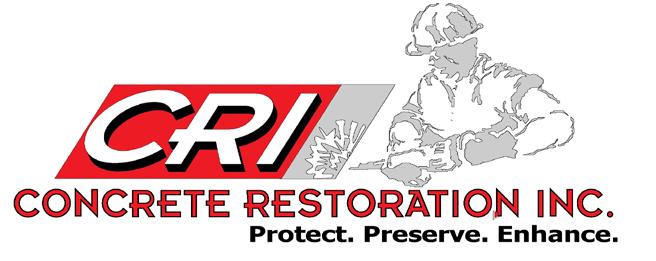
• All air receivers will be properly equipped with an indicating air pressure gauge.
Storage Tank Safety Checks
• All drains, handles, and manholes easily accessible
• Drainpipe and valve is installed on the lowest point of the air compressor storage tank.
• Drain valve is opened and frequently drained to prevent the accumulation of excessive amounts of liquids.
• Air compressor storage tanks have a pressure gauge.
• Safety valves operate to prevent the internal tank pressure from exceeding 10% above the maximum allowable working pressure of the air compressor tank.
REVISED DATE: January 1, 2025
Confined Space Policy
Confined Space Policy
I. Purpose, Scope, and Responsibility
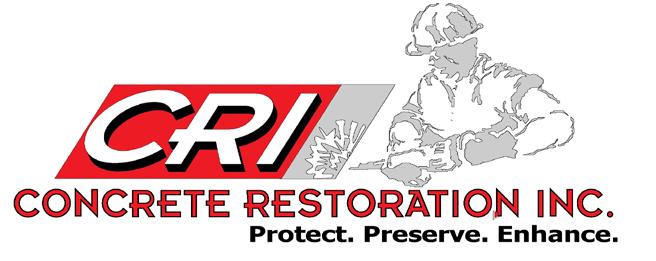
This procedure defines the requirements for safe entry into confined spaces by CRI personnel. Contract personnel performing confined space entries should be properly trained by their employers and will follow the CRI Confined Space Entry Procedure.
II. Environmental and Safety
OSHA has developed guidelines to protect workers who may be required to enter workspaces that have limited means of entry or exit and may contain a hazardous atmosphere. OSHA broadly defines confined spaces in two categories: confined space entries that require a permit to enter and those which do not have, or will not have the potential for, a hazardous atmosphere.
III. Overview
This procedure outlines the requirements for performing permit required confined space entries. Confined spaces can only be designated as nonpermit required confined spaces by the Safety Manager of Concrete Restoration Inc.
IV. Procedure Guidelines
1. Definitions
Confined Space - A space that is large enough and configured so that an employee can bodily enter and perform assigned work; and has limited or restricted means for entry or exit such as tanks, vessels silos, storage bins, hoppers and pits; and is not designated for continuous employee occupancy; or any space having limited means of egress, that is subject to accumulation of toxic or flammable contaminants or has a oxygen deficient atmosphere. This includes storage tanks, process vessels, bins, boilers, ventilation ducts, sewers, underground utility vaults, pipelines, and open spaces more than 4 feet in depth such as pits or vessels.
REVISED DATE: January 1, 2025
Confined Space Policy
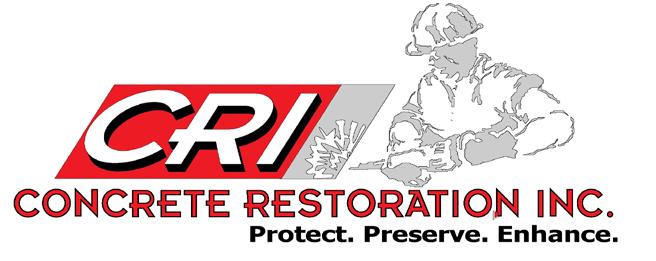
Permit-Required Confined Space – has one or more of the following characteristics: contains or has the potential to contain a hazardous atmosphere; contains a material that has the potential for engulfing the person entering the confined space; has an internal configuration that could causes the person entering the confined space to be trapped or asphyxiated; contains any other serious safety or health hazard
Non-Permit Required Confined Space – a confined space that does not contain or, with respect to atmospheric hazards, have the potential to contain any hazards capable of causing death or serious physical harm.
Authorized entrant – An employee who is authorized by the employer to enter a permit required space. Only employees who are trained as an entrant and have obtained a permit signed by the entry supervisor will be allowed to enter a permit required confined space. The entrant is the employee who will be performing work in the permitted confined space.
Attendant – An individual who is stationed outside the permit required space and who monitors authorized entrants. At least one individual must be stationed outside the permit required confined space.
Entry Supervisor – The entry supervisor is CRI’s lead foreman or supervisor responsible for determining if acceptable entry conditions are present at a permit space where entry is planned, for authorizing entry, for overseeing entry, and for terminating entry.
Isolation – In respect to confined spaces, the process of removing from service and completely protecting against the release of energy and material into the space by such means as blanking and blinding, double block and bleed, or physical disconnection of incoming lines or energy sources.
Annual review – A review of the safety policies outlined in a safety program, performed within a 12 month period. This program is reviewed at lease annually and revised as needed. Cancelled permits are used to make additions to the protocols outlined in this confined space policy.
REVISED DATE: January 1, 2025
Confined Space Policy
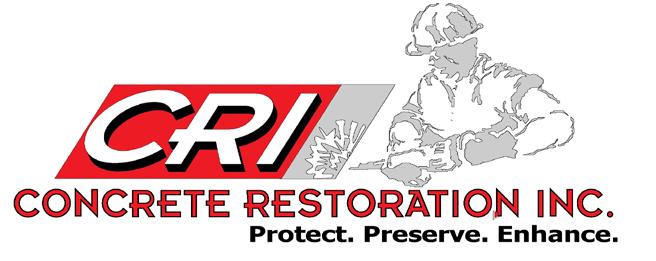
2. Preparing For A Permitted Confined Space Entry
a. Obtain the clients “Confined Space Entry” form for the confined space, and follow the procedure listed. The form will contain the following information specific to the space:
b. All provisions of the Lockout-Tagout procedure shall be followed where applicable.
c. A constant source of fresh air that is capable of providing adequate air exchange may be used in some enclosed confined spaces.
d. Provisions for possible confined space rescue will be made prior to entry.
e. All employees involved with the permitted confined space will attend a toolbox talk prior to work being completed. This toolbox talk is a reminder of important safety topics such as; procedures for a confined space rescue, preventing unauthorized personnel in/around the confined space, first aid & CPR, and the importance of constant contact between attendant and entrant.
f. When a ladder is required to enter the confined space, the ladder must be secured at the top and will not be removed while someone is in the confined space.
g. Procedures for cancelling the entry permit will be developed at this time.
3. Atmospheric Testing
a. All permitted confined space atmospheres shall be tested for oxygen content and flammable vapors prior to entry. The following test results must be achieved:
• Oxygen content 19.5 % – 21.5%
• Flammable vapors 0%
b. If applicable, the confined space will be tested for toxicity when a toxic material has been present, or may be expected to be present.
c. Atmospheric testing will be performed by trained personnel only.
REVISED DATE: January 1, 2025
Confined Space Policy
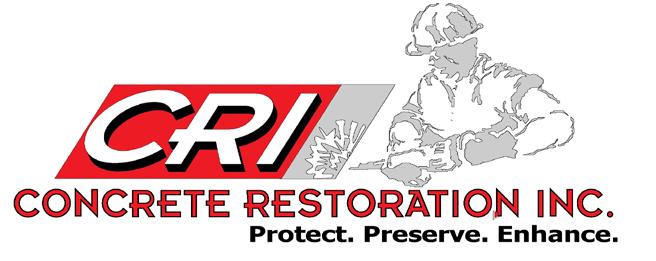
d. All employees have access to atmospheric testing results. Results from testing are posted in the break room.
e. Any employee has the right to request additional air monitoring if that employee feels their safety is at risk.
4. Confined Space Entry Permits
a. A confined space entry permit becomes void if:
The job is interrupted for more than sixty (60) minutes.
An employee working in the confined space becomes ill or injured.
Conditions occur where ventilation equipment, alarm systems, telephone or radio communications are inoperable.
Severe weather conditions occur or are imminent.
An emergency occurs on the plant site.
b. Each confined space entry permit is valid for a single work shift ONLY. On jobs requiring entries that extend beyond a normal work shift, special arrangements shall be made.
c. The permit shall be displayed at the job site.
5. Permitted Confined Space Entry
a. No person(s) are to enter any permitted confined space without the execution of a confined space entry permit.
b. The atmosphere in the confined space must be monitored.
c. All electrical equipment used in confined spaces shall be properly guarded, grounded, and protected by a ground fault interrupter.
d. Entrants working in confined spaces must be under constant observation and/or communications by an attendant outside the confined space.
e. If an entrant in a confined space exhibits any sign of irrational behavior or fatigue, they are to be removed from the confined space immediately. Re-entry is authorized only after the entrant is evaluated and is physically fit to re-enter the confined space.
REVISED DATE: January 1, 2025
Confined Space Policy
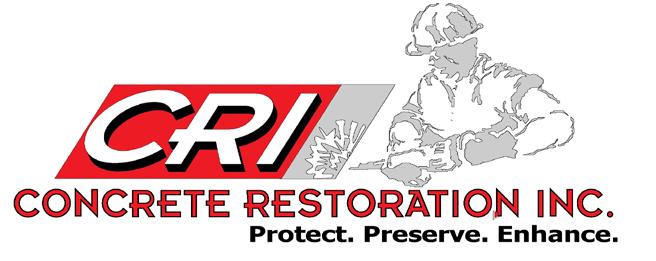
f. The following rules apply to the use of welding or burning equipment in confined spaces:
• A hot work permit shall be issued in addition to the confined space entry permit.
• Welding and burning equipment other than torches, hoses, cables, and electrodes must be stationed outside the confined space (i.e. gas cylinders, regulators, welding machines, etc.)
• The attendant must be able to shut off all welding and burning equipment used inside a confined space.
g. Barriers must be used to direct pedestrian or vehicular traffic away from the entrance to a confined space when the entrance cannot be secured by other means. Reflective traffic vests, flags and signs must also be used to protect both workers and passersby.
h. When covers of manholes or vaults are removed, the opening will be promptly guarded by a railing, temporary cover, or other suitable temporary barrier which is appropriate to prevent an accidental fall through the opening.
i. In the event that more than one contractor needs to perform work in/around a confined space, communication between contractors will be essential.
6. Terminating Entry/Canceling a Permit
The entry supervisor has the authority to terminate entry when a condition that is not allowed under the entry permit arises in or near the permit space, and/or to cancel the entry permit when the entry operations covered by the entry permit have been completed. The entry supervisor is responsible to ensure all employees are out of the confined space by checking the entrant sign in/out sheet. A final walk through will be performed by the supervisor to ensure all tools, cords, monitors, PPE, and anything that was not intended to stay in the confined space are accounted for. CRI will retain each canceled entry permit for at least 1 year to facilitate the review of the permit-required confined space program. Any problems encountered during an entry operation will be noted on the permit so that appropriate revisions to the permitted confined space program can be made.
REVISED DATE: January 1, 2025
Confined Space Policy
7. Provisions for Rescue
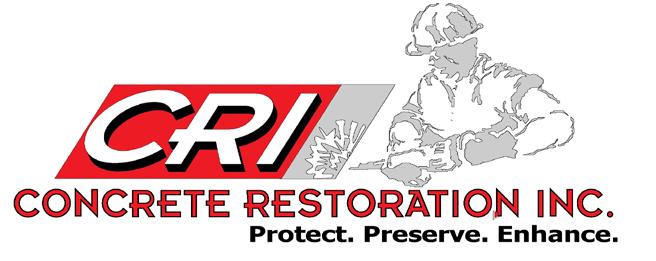
For every permitted entry into a confined space, this policy includes a plan for rescuing the entrants. The adequacy of the rescue plan must be verified before entry into the space. The decision to provide employee rescue or contract though outside services will be made during the “preparing for permitted confined space” portion of CRI safety talks. The selected rescue service’s response time and rescue capability should be evaluated. Any one of the following three rescue procedures, generally in order of preference, is adequate:
Rescue
Without Entry - CRI has made provisions for rescuing entrants without entry by rescue team members, whenever possible. In order to accomplish such a rescue without entry, entrants must wear a full body harness attached to a lifeline. The other end of the lifeline will be attached to a hoisting device to permit the attendant to begin rescue immediately if a prohibited condition arises in the space. If the full body harness presents a greater hazard, other rescue provisions must be used in absence of a full body harness.
Employee Rescue - A designated group of employees trained and equipped to enter the confined space to rescue an incapacitated entrant. The designated rescue team will have practiced rescue from the space entered (or a similar space) within the last year. Before entry, the confined space entry supervisor must verify that an adequate number of rescue team members are available to make a timely response to an emergency, and will verify that the rescue team members have current training. The procedure for summoning the response has been established and the attendant has the knowledge of when to issue the summons.
Outside Rescue Service – If required by the owner/client or when working in a confined space defined as an IDLH (immediately dangerous to life and health) a commercial ambulance service or local fire department will be present to perform a rescue from a confined space. Reliance on a general emergency
phone number available to the general public is not an adequate means of outside rescue service. It is the responsibility of the entry supervisor to
REVISED DATE: January 1, 2025
Confined Space Policy
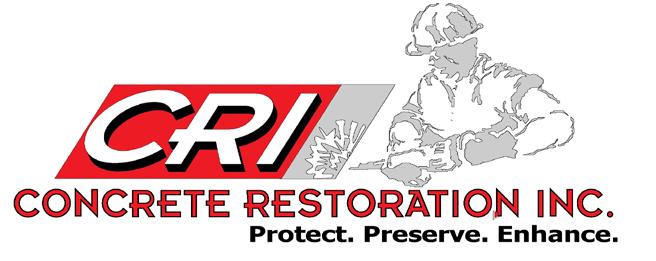
verify that the selected rescue service team is qualified to perform a rescue, has current training, and is available at the time of the entry. The adequacy of the response time must be considered in selecting an outside rescue service. If the rescue service cannot make a timely response to a summons, they may be required to standby in the area of the access to the confined space. The attendant will have the means and be trained in the procedure for summoning the outside rescue squad.
8. Entrant Duties
a. Know the hazards that may be faced during entry, including information on the mode, signs or symptoms, and consequences of the exposure.
b. Properly use equipment
c. Communicate with the attendant as necessary to enable the attendant to monitor entrant status and to enable the attendant to alert entrants of the need to evacuate the space as required by paragraph (i)(6) of this section.
d. Alert the attendant whenever:
• The entrant recognizes any warning sign or symptom of exposure to a dangerous situation, or
• The entrant detects a prohibited condition; and
• Exit from the permit space as quickly as possible whenever an order to evacuate is given by the attendant or the entry supervisor.
• The entrant recognizes any warning sign or symptom of exposure to a dangerous situation.
• The entrant detects a prohibited condition, or
• An evacuation alarm is activated.
9. Attendants Duties
a. The attendant is to remain at the confined space entrance and in contact at all times when entrant(s) are in the confined space.
b. The attendant must understand the hazards of the confined space and the requirements of the confined space entry permit.
REVISED DATE: January 1, 2025
Confined Space Policy
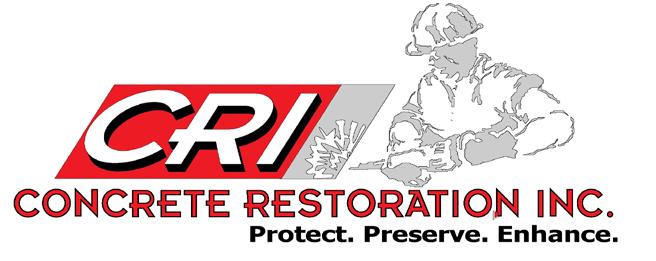
c. The attendant must be trained to activate emergency procedures in the event an emergency situation occurs in the confined space.
d. The attendant should monitor conditions outside the confined space that may affect the safety of the confined space.
e. The attendant must complete the attendant’s checklist prior to any entrants entering the confined space.
f. The attendant is not allowed to enter the confined space for any reason.
g. Each confined space will have its own attendant. Attendants are prohibited from monitoring more than one confined space at a time.
10. Entry Supervisor
a. Knows the hazards that may be faced during entry, including information on the mode, signs or symptoms, and consequences of the exposure.
b. Verifies, by checking that the appropriate entries have been made on the permit, that all tests specified by the permit have been conducted and that all procedures and equipment specified by the permit are in place before endorsing the permit and allowing entry to begin.
c. Terminates the entry and cancels the permit as required by paragraph (e)(5) of the OSHA Standard 1910.146.
d. Verifies that rescue services are available and that the means for summoning them are operable;
e. Removes unauthorized individuals who enter or who attempt to enter the permit space during entry operations; and
f. Determines, whenever responsibility for a permit space entry operation is transferred and at intervals dictated by the hazards and operations performed within the space, that entry operations remain consistent with terms of the entry permit
REVISED DATE: January 1, 2025
Confined Space Policy
11. Training
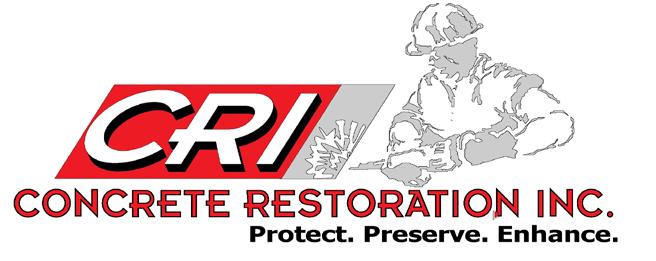
a. Each employee intending to make a confined space entry will be properly trained in all aspects of this procedure. This training will authorize the employee to perform confined space entries.
b. Re-training for affected employees will take place if there is a change to the procedure or if a new hazard becomes prevalent.
c. Contract employees are to be trained by their company in confined space entry and be familiar with CRI procedures for confined space entry.
d. Employees authorized to use atmospheric testing equipment should be properly trained in the use of the equipment prior to use.
e. Attendants will have proper training in attendant’s duties before being assigned to attendant duties.
f. Each employee will be informed on proper PPE required for the job, and have a working knowledge of how to use the PPE correctly and consistently.
g. Each employee that receives training will confirm their knowledge obtained by passing a written test. These tests, along with a safety roster will be documented and kept on file at CRI main office.
REVISED DATE: January 1, 2025
Confined Space Policy
ATTENDANT MUST:
Confined Space Permit Form
Understands the hazards of the confined space and the conditions of the confined space permit.
Remain at the entrance of the confined space at all times when personnel are in the confined space. Remain in contact with the entrants at all times. Be aware of possible behavioral effects of hazard exposure. Understand how to activate the emergency alarm system to summons help if needed.
Understand that the attendant cannot enter the confined space for any reason.
Understand that no duties can be performed that interfere with the attendant’s primary duty as a confined space attendant. Knows how to perform a non-entry rescue, if applicable. Stops unauthorized entries into the confined space. Monitors conditions outside the confined space that may affect the safety of the entrants
Maintain an accurate count of authorized entrants in the confined space. Has read and understands the Company Name Here Confined Space Entry procedures
ATTENDANT’S SIGNATURE:
DATE: ____/______/_______
REVISED DATE: January 1, 2025
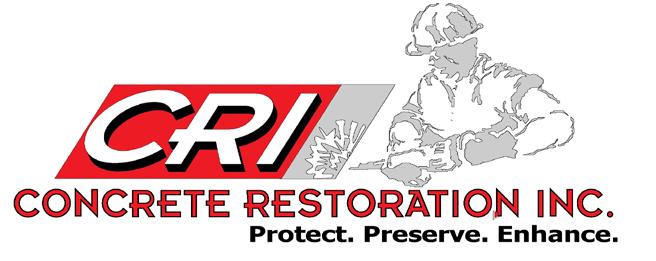
ATTENDANT’S INITIALS
CRANE POLICY
CRANE POLICY
Reference: WAC 296- 155 Part L/OSHA 1910.179
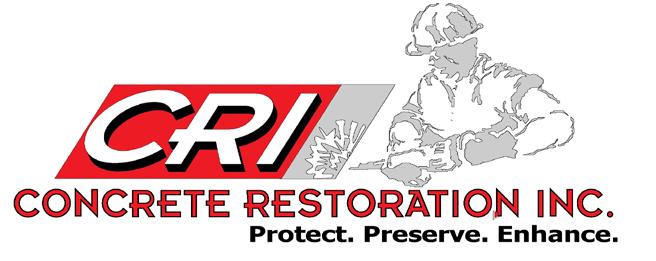
Concrete Restoration, Inc. (CRI) has developed these written guidelines for safe crane operation practices. These guidelines are drawn from WAC 296155 Part L and are not all encompassing. If there are any questions, concerns or comments, please consult WAC 296- 155 for the full details or a company Supervisor.
Areas of Responsibility
While organizational structure of various construction activities may differ, the following are areas of responsibility for crane operations. A single individual may perform on or more of these responsibilities concurrently. Complete "Crane Operations Checklist" and retain at site.
• Crane Owner -Concrete Restoration, inc. has custodial control of a crane by virtue of lease or ownership. (WAC 296-155-53401(3)) In some situations, the Crane Owner and the Crane User may be the same person or entity.
• Provide a certified crane that meets the specific job requirements defined by the Crane User.
• Provide a crane and all necessary components specified by the manufacturer, that meets the Crane User's requested configuration and capacity.
• Provide all applicable load/capacity chart(s) and diagrams
• Provide additional technical information when requested by the Crane User.
• Provide field assembly, disassembly, operation, and maintenance information.
REVISED DATE: January 1, 2025
CRANE POLICY
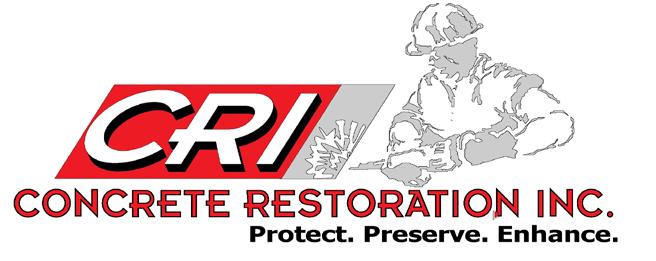
• Establish inspection, testing, and maintenance program.
• Using qualified personnel for maintenance, inspection, repair, transport, dis/assembly, etc.
Crane User
Concrete Restoration Inc arranges the crane's presence on a work site and controls its use there. (WAC 296-155- 53401(4))
• Comply with regulations and manufacturer information.
• Using qualified people as supervisors for crane activities.
• Ensuring the crane is in proper operating condition prior to initial use at work site.
• Verifying that the Crane Owner has provided crane certification.
• Verifying that crane inspections have been performed.
• Verifying the crane has the necessary lifting capacity to perform the proposed lifting operations in the planned configuration.
• Using certified operators, qualified riggers, qualified signal persons and a competent and/or qualified person for inspections, maintenance, repair, transport, assembly and disassembly.
• Ensuring the operator is made aware of adjustments or repairs that have not yet been completed.
• Ensure all personnel involved are aware of their responsibilities, assigned duties, and the associated hazards.
• Ensure the inspection, testing and maintenance programs specified by the crane owner are followed.
REVISED DATE: January 1, 2025
CRANE POLICY
Site Supervision
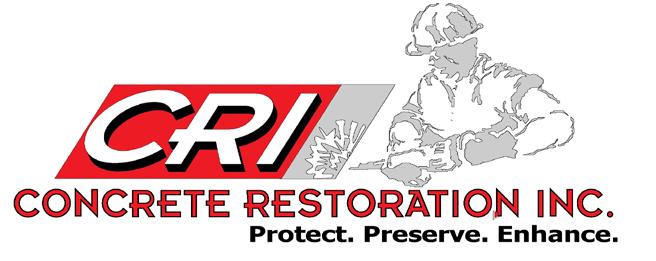
Concrete Restoration Inc exercises supervisory control over the work site on which a crane is being used and over the work that is being performed on that site. (WAC 296-155-53401(5))
• Ensuring the crane is certified prior to initial site usage.
• Determining if additional regulations are applicable to crane operations.
• Ensuring that a qualified person is designated as the Lift Director.
• Ensuring that crane operations are coordinated with other jobsite activities that will be affected by or will affect the lifts.
• Ensuring the area for the crane is prepared:
1. Access roads
2. Sufficient room for assembly/disassembly
3. Operating area that is suitable for the crane with respect to levelness, surface conditions, support capability, proximity to power lines, excavations, etc.
4. Traffic control is in place to restrict unauthorized access to the crane's working area.
• Ensuring that conditions which may adversely affect crane operations are addressed, such as:
1. Poor soil conditions;
2. Wind velocity or gusting winds; iii. Heavy rain;
3. Fog;
REVISED DATE: January 1, 2025
CRANE POLICY
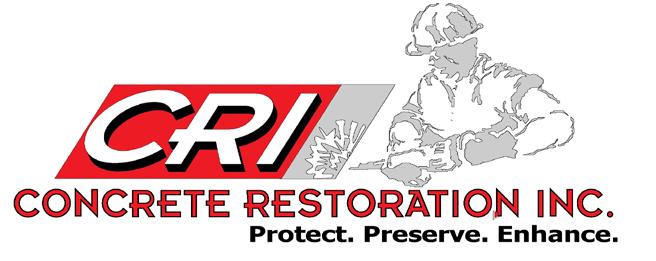
4. Extreme cold;
5. Artificial lighting.
• Allowing crane operation near electric power lines only when the requirements the power line section of this policy have been met.
• Permitting special lifting operations and/or critical lifts only when equipment and procedures required by regulation, the crane manufacturer, or a qualified person are employed such as:
1. Multiple crane lifts
2. Multiple load line lifts
3. Lifting personnel
4. Pick and carry operations
5. Mobile/articulating cranes operating on barges
6. Ensuring the crane is inspected and maintained.
7. Ensuring crane operators are certified.
8. Ensuring the rigging crew is supervised by a qualified person.
9. Ensuring that work involving the assembly and disassembly of a crane is supervised by an assembly/disassembly director.
10. Ensuring crane maintenance is performed by a designee.
Lift Director
Concrete Restoration Inc directly oversees the work being performed by a crane and the associated rigging crew. (WAC 296-155- 53401(6))
• Being present at the job site during lifting operations and overseeing the lifting operations.
REVISED DATE: January 1, 2025
CRANE POLICY
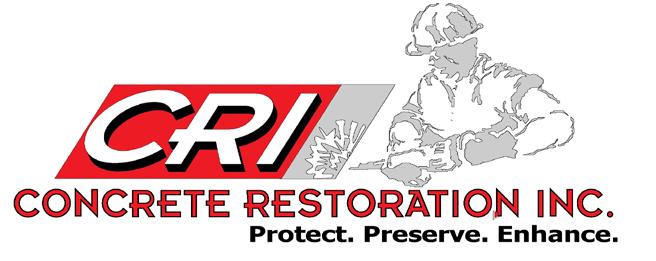
• Ensuring the area needed for crane operations has been prepared before operations commence.
• Ensuring necessary traffic controls are in place to restrict unauthorized access to the crane's work area.
• Ensuring personnel involved understand their responsibilities, assigned duties, and associated hazards.
• Addressing safety concerns and deciding if it is necessary to overrule those concerns and directs crane operations to continue. In all cases, the manufacturer's criteria for safe operation and the requirements of this chapter and any other applicable safety and health standards must be adhered to.
• Appointing the signal person(s). ensuring they are qualified, and conveying that information to the crane operator.
• Ensuring compliance when working near power lines or lifting personnel.
• Ensuring the load is properly rigged by a qualified rigger.
• Ensuring precautions are implemented in special lifting operations and/or critical lifts.
• Informing the crane operator of the weight of loads to be lifted, as well as the lifting, moving, and placing locations for these loads.
• Obtaining the crane operator's verification that this weight does not exceed the crane's rated capacity.
Crane Operator
• Reviewing the requirements for the crane with the Lift Director before operations.
REVISED DATE: January 1, 2025
CRANE POLICY
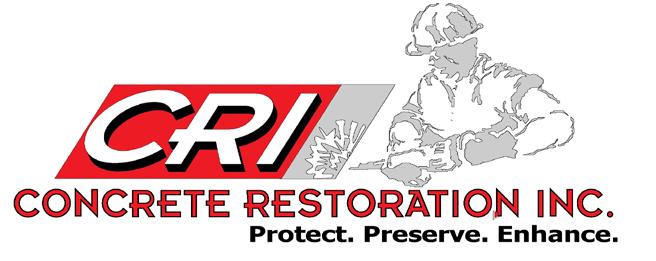
• Knowing what types of site conditions could adversely affect the operation of the crane and consulting with the Lift Director concerning the possible presence of those conditions.
• Understanding and applying the information contained in the crane manufacturer's operating manual.
• Understanding the crane functions and limitations as well as its particular operating characteristics.
• Using the crane's load/capacity chart(s) and diagrams and applying all notes and warnings related to the charts to confirm the correct crane configuration to suit the load, site, and lift conditions.
• Refusing to operate the crane when any portions of the load or crane would enter the prohibited zone of energized power lines except as defined in the power line section of this policy.
• Performing daily inspection as specified by the Crane Owner, Crane Manufacturer, applicable Regulations and Industry Standards.
• Promptly reporting the need for any adjustments or repairs to the appropriate person
• Following applicable lockout/tagout procedures.
• Not operating the crane when physically or mentally unfit.
• Ensuring that all controls are in the off or neutral position and that all personnel are in the clear before energizing the crane or starting the engine.
• Not engaging in any practice that will divert their attention while actually operating the crane controls.
• Testing the crane function controls that will be used and operating the crane only if those function controls respond properly.
REVISED DATE: January 1, 2025
CRANE POLICY
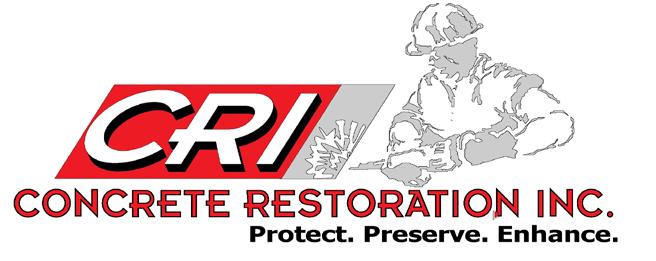
• Operating the crane's functions, under normal operating conditions, in a smooth and controlled manner.
• Knowing and following the procedures specified by the manufacturer or approved by a qualified person,for assembly, disassembly, setting up, and reeving the crane.
• Knowing how to travel the crane.
• Observing each outrigger during extension, setting, and retraction or using a signal person to observe each outrigger during extension, setting, or retraction.
• Ensuring that the load and rigging weight(s) have been provided.
• Calculating or determining the net capacity for all configurations that will be used and verifying, using the load/capacity chart(s), that the crane has sufficient net capacity for the proposed lift.
• Considering all factors known that might affect the crane capacity and informing the lift director of the need to make appropriate adjustments.
• Knowing the standard and special signals and responding to such signals from the person who is directing the lift or a qualified signal person.
Crane Crew Member Requirements
Crane Operator (WAC 296-155-53300)
• NCCCO certification or equivalent
1. Written exam by crane type
2. Practical exam by crane type
3. Maximum of 5-year qualification period.
REVISED DATE: January 1, 2025
CRANE POLICY
• Experience
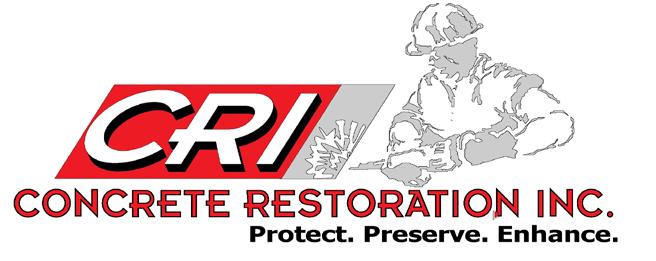
1. Number of hours of Crane Related Experience equal to or greater than the amounts identified in "Table 3" under WAC 296-155-53300. Documented through declaration or log.
2. Number of hours of Actual Crane Operating Experience equal to or greater than the amounts identified in "Table 3" under WAC 296-155- 53300. Documented through declaration or log.
3. Successfully passing a substance abuse test.
Signal Person (WAC 296-155-53302)
A qualified Signal Person is required whenever:
1. The point of operation is not in full view of operator.
2. View of direction of travel is obstructed
3. Site specific safety concerns where the Operator, Lift Director, or Rigger determines it is necessary.
4. Third Party Qualified Evaluator or Employer's Qualified Evaluator
5. Oral or written test and a practical test is required by signal type
6. Maximum of 5 year qualification period.
7. Documentation must be available at job site and denote qualified signal types.
Rigger (WAC 296-155-53306)
1. A qualified Rigger is required whenever workers are within the fall zone, hooking, unhooking, or guiding a load, or doing
REVISED DATE: January 1, 2025
CRANE POLICY
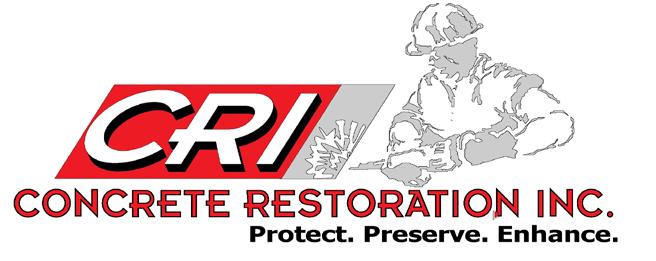
performing the initial connection of a load to a component or structure.
2. Third Party Qualified Evaluator or Employer's Qualified Evaluator
3. Written test and practical test is required by rigging type
4. Maximum of 5-year qualification period.
5. Documentation must be available at job site and denote qualified rigging types.
Assembly/Disassembly Director (WAC 296-155-53402)
• Competent and Qualified Person.
Crane repair, inspection, and maintenance employees (WAC 296-15553304)
• Maintenance and repair personnel must meet the definition of a Qualified Person with respect to the crane/derrick and maintenance/repair tasks performed.
• Allowed to operate the crane I derrick only where:
1. Operation is limited to those functions necessary to perform maintenance, inspect or verify the performance of the crane/derrick.
2. The personnel operate the crane/derrick under the direct supervision of a certified operator.
REVISED DATE: January 1, 2025
CRANE POLICY
Crane Inspection and Certification
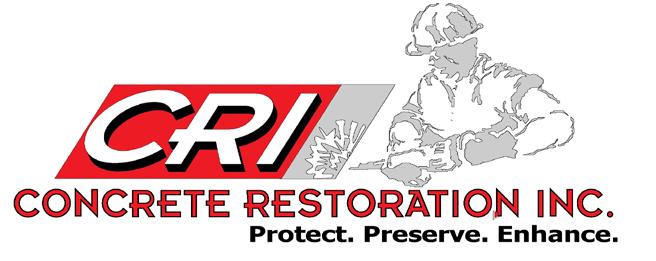
Crane Inspection Requirements (WAC 296-155-53405)
• Post – Assembly
- Performed by Qualified Person (Assembly/Disassembly Director)
- Inspection form must be kept on crane while on site
• Shift
- Performed by Competent Person (Crane Operator)
• Monthly
- Performed by Competent Person
- Inspection forms must be kept for at least three months.
• Annual
- Performed by Accredited Crane Certifier ii. Documentation must be kept on crane.
• Repaired or Adjusted
- Performed by Qualified Person
• Modified
- Performed by Accredited Crane Certifier
- Documentation must be kept on crane.
• Cranes not in regular use (idle for 3 months or more)
- Qualified person
Crane Certification (WAC 296-155-53144 through 296-155-53214)
REVISED DATE: January 1, 2025
CRANE POLICY
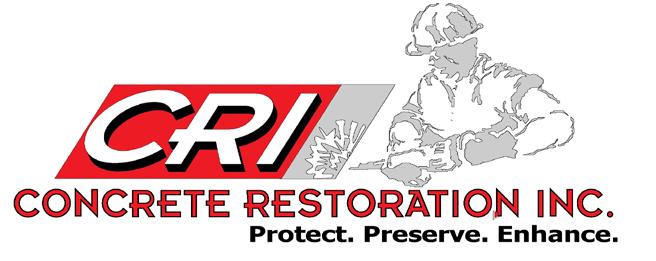
• Must be performed by an accredited crane certifier
- Temporary certificate of operation is issued by the crane certifier and valid until crane certification is received from DOSH.
• The accredited crane certifier will review the monthly and annual inspection documentation.
• The accredited crane certifier will perform a visual an inspection of the crane.
• The accredited crane certifier will observe operational tests of the crane.
• Proof Load Tests:
- Includes a proof load test on all hoist lines and needs to be at least 100% but not to exceed 110% as configured.
- If the crane is to be utilized in an ''on rubber" configuration, a free rated load test is also required.
• If any of the following occur, the crane is decertified and must be inspected by an accredited crane certifier and DOSH's crane certification section needs to be notified:
- Contact with an energized power line
- Any overload other than proof load testing or one that has been approved in writing in advance by the crane manufacturer or RPE
- Any significant modifications or significant repairs of a load sustaining/bearing part that affects the safe operations of the crane/derrick.
REVISED DATE: January 1, 2025
CRANE POLICY
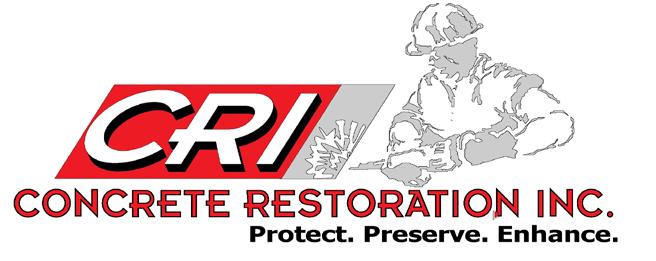
- Any deficiency that affects the safe operation of the crane or derrick that that has been identified by a qualified person
Tower Cranes additional certification items (WAC 296-155-53206)
• Parts must be inspected by an accredited crane certifier prior to assembly, following erection of the tower crane, after each climbing operation, or reconfiguring the boom, jib, or counter-jib before placing the crane in service.
• The accredited crane certifier must verify a registered professional structural engineer has certified that the crane foundations/structural supports and underlying soil are adequate support.
• Nonstandard tower crane bases must be reviewed and acknowledged as acceptable by an independent registered professional structural engineer.
Safety Devices (WAC 296-155-53410) and Operator Aids (WAC 296155-53412)
Safety Devices
• In the event safety devices are not properly functioning, operation must not begin.
• In the event a device stops working properly during operation, the operator must safely stop operations.
• Alternative measures are not penmitted to be used:
Safety Devices:
• Crane level indicator (can be either built in or available on the crane)
REVISED DATE: January 1, 2025
CRANE POLICY
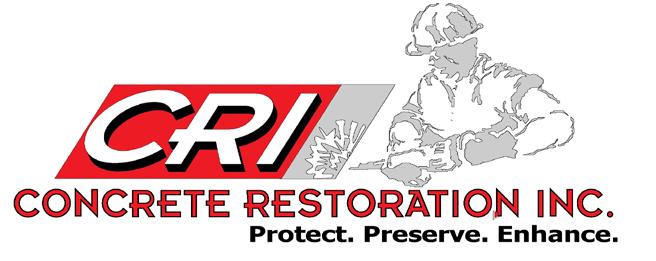
• Boom stops (exceptfor derricks and hydraulic booms)
• Jib stops (If a jib is attached - except for derricks
• Cranes with foot pedal brakes must have locks (except for portal cranes and floating cranes)
• Hydraulic outrigger jacks and hydraulic stabilizer jacks must have an integral holding device/check valve
• Horn (must be either built in or a portable horn available to the operator)
In the event operational aids are inoperative or malfunctioning, the crane and/or device manufacturer's recommendations for continued operations or shutdown of the crane must be followed until the problems are corrected. Without such recommendations and any prohibitions from the manufacturer against further operation, the following requirements apply:
• Recalibration or repair of the operational aid must be accomplished as soon as is reasonably possible, as determined by a qualified person.
• Temporary alternative measures must be in force and effect.
Assembly/Disassembly (WAC 296-155-534021)
• Assembly/disassembly must be directed by a qualified and competent Assembly/Disassembly Director.
• Assembly/disassembly must comply with all applicable manufacturer prohibitions and either manufacturer assembly/disassembly procedures or employer procedures developed by a qualified person.
REVISED DATE: January 1, 2025
CRANE POLICY
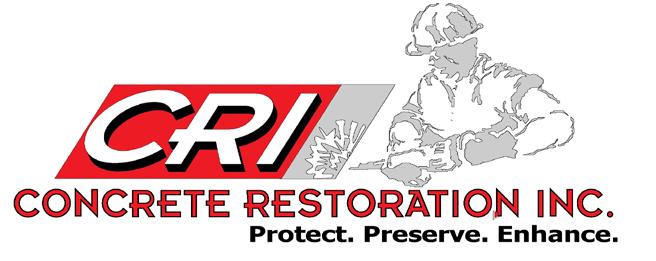
• The Assembly/Disassembly Director must visually inspect the components and attachments to ensure that they meet manufacturer's recommendations.
• A pre-assembly/disassembly safety meeting will be held by the Assembly/Disassembly Director and shall include all crew members.
• The safety meeting shall address the crew members tasks, hazards associated with their tasks, and hazardous positions/locations that need to be avoided.
• In the event any crew member takes on a different task or new personnel are added, the safety shall be reconvened.
• The Assembly/Disassembly director shall perform a post assembly inspection, document the results of the inspection and put the inspection record in the crane.
Power line safety (WAC 296-155-53408)
Identify work zone which is either:
• Marked lifting area and counterweight tail swing boundaries and prohibit operation past boundaries; or
• 360 degrees from crane's center of rotation to the crane's maximum working radius.
• Determine if any part of the equipment, load (including rigging) or load line could get closer than 20' (<350KV) or 50' (>350KV) to a power line.
• If outside of these limitations, crane operations are allowed.
• If inside of these limitations:
REVISED DATE: January 1, 2025
CRANE POLICY
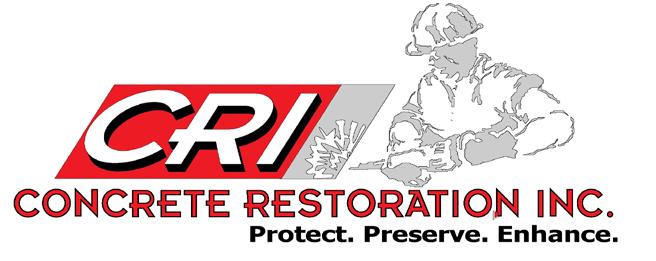
- Option 1- De-energize and ground the power line.
- Option 2 -Maintain a 20' clearance.
- Option 3-Ask Utility for voltage and use "Table A".
Option 2 or 3 require Encroachment Prevention Measures:
1. Planning Meeting
2. Non-conductive taglines (if used)
3. Elevated warning lines, barricade or line of signs.
4. Plus (Choose 1) -Spotter, proximity alarm, warning device, or range limiter.
If inside limitations established by "Table 4":
- Must demonstrate and document that staying outside of the zone is infeasible.
- Must demonstrate and document that it is infeasible to de-energize and ground.
All of the following items are required as a minimum:
• Power line owner sets minimum approach distance.
• Planning meeting I Pre-lift meeting
• Dedicated spotter
• Elevated warning line or barricade
• Insulating link I device
REVISED DATE: January 1, 2025
CRANE POLICY
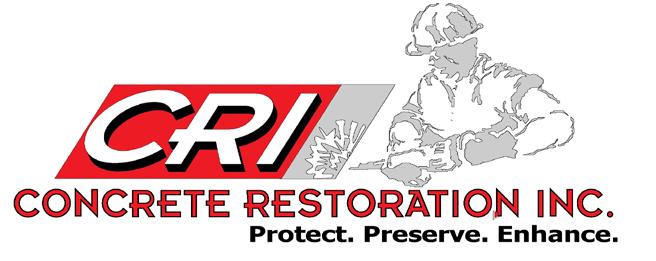
• Non-conductive rigging
• Range limiter (if equipped)
• Non-conductive tag line (if used)
• Barricades - 10' from equipment
• Limit access to essential workers
• Properly ground crane
General Requirements (WAC 296-155-53400)
• Cranes must be certified annually by an accredited certifier.
• All crane operators must be certified.
• Cranes must meet the requirements for design, construction, installation and testing as prescribed in the applicable ASME standard at the time the crane or derrick was manufactured.
• Warning decals and placards must be installed and legible.
• The operators manual and load rating chart, written in the English language with customary grammar and punctuation, must be in the operators cab or station when the crane is in operation.
• All manufacturer procedures applicable to the operational functions of cranes/derricks, including its use with attachments must be complied with.
• A portable fire extinguisher with a basic minimum rating of 10BC must be installed in the cab or at the machinery housing.
• Personal belonging must be stored in such a manner as to not interfere with access or operation of the crane.
REVISED DATE: January 1, 2025
CRANE POLICY
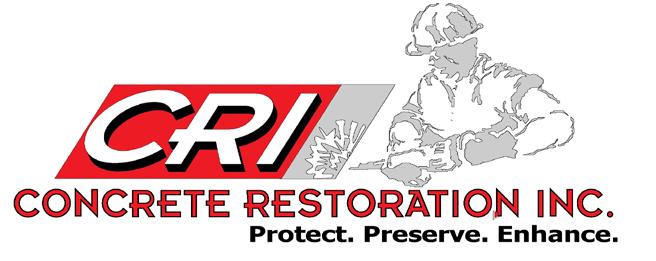
• Rigging gear, tools, oil cans, waste, and other articles must be stored in the toolbox or another appropriate location and must not be permitted to lie loose in or about the cab or operator's workstation.
• Operating controls must be properly marked to indicate the function of the controls in each position.
• Before starting the engine, the operator must verify that all controls are in the proper starting position and that all personnel are in the clear.
• While in operation, reciprocating, rotating or moving parts or equipment must be guarded if such parts are exposed to contact by employees or otherwise create a hazard.
• Neither the load nor the boom is allowed to be lowered below the point where less than two full wraps of rope remain on their respective drums.
• All exhaust pipes, turbochargers, and charge air coolers must be guarded or insulated in areas where contact by employees is possible in the performance of normal duties and are discharged in a direction away from the operator.
• Friction mechanisms must be of a size and thermal capacity to sufficiently control all rated loads with the minimum recommended reeving.
• Hydraulic drums must have an integrally mounted holding device or internal static brake to prevent load hoist movement in the event of hydraulic failure.
• Whenever internal combustion engine powered crane/derrick exhausts in enclosed spaces, tests must be made and recorded to see that employees are not exposed to unsafe concentrations of gases or oxygen deficient atmospheres.
REVISED DATE: January 1, 2025
CRANE POLICY
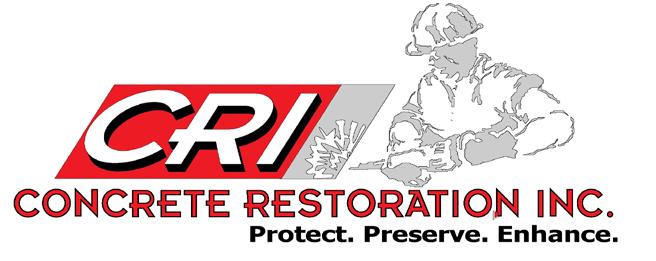
• If access to the cab roof is necessary, a ladder or steps must be provided to give access to a cab roof.
• Guardrails, handholds, and steps must be provided on cranes for easy access to the cab in accordance with Parts C-1 and J of 296155.
• Platforms and walkways must have antiskid surfaces.
• Fuel tank filler pipe must be located in such a position, or protected in such a manner, as to not allow spill or overflow to run onto the engine, exhaust, or electrical equipment.
• All crane hook ball assemblies and load blocks must be labeled with their rated capacity and their weight.
• Crane hooks must be equipped with latches or self-locking devices.
• Replacement parts must be at least equal to the original manufacturer's specifications.
• Erect and maintain control lines, warning lines, railings or similar barriers to mark the boundaries of swing radius hazard areas.
• Where available, hoisting routes that minimize the exposure of employees to hoisted loads must be used.
• Cranes with boom free fall (live boom) are prohibited from being used when:
- An employee is in the fall zone of the boom or load.
- An employee is being hoisted.
- The load or boom is directly over a power line or over any part of the area listed in Table 4
REVISED DATE: January 1, 2025
CRANE POLICY
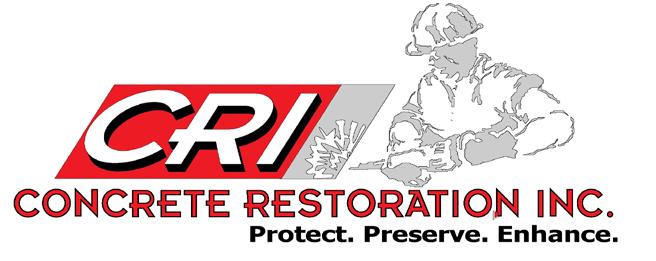
- The load is over a shaft that contains employees.
- The load is over a cofferdam, except where there are no employees in the fall zone.
- Lifting operations taking place in a refinery or tank farm.
- Crane was manufactured after November 1, 1984.
• Employees must not be allowed to ride on the hook or load.
• The hoist rope must not be wrapped around the load.
• All loads must be attached to the hook by means of suitable slings or other devices of sufficient lifting capacity.
• When moving a load it must be well secured and balanced in the sling of lifting device before it is lifted more than a few inches.
• The operator must not leave the controls while the load is suspended, except where all of the following are met:
- The operator remains adjacent to the crane and is not engaged in any other duties.
- The load is to be held suspended for a period of time exceeding normal lifting operations.
- Measures are implemented to restrain the boom hoist, telescoping, load, swing, and outrigger or stabilizer functions.
- Barricades or caution lines and notices are erected to prevent all employees from entering the fall zone.
• While moving the load the lift and swing path must be clear of obstructions.
REVISED DATE: January 1, 2025
CRANE POLICY
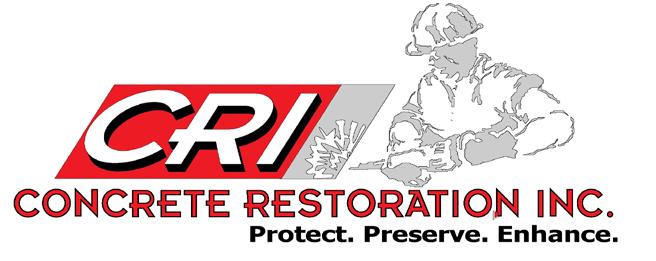
• Before starting to lift the following conditions must be met:
- The hoist rope must not be kinked.
- Multiple-part lines must not be twisted around each other.
- The hook must be brought over the load in such a manner as to minimize swinging.
- If there is a slack rope condition, it must be determined that the rope is seated on the drum and in the sheaves as the slack is removed.
- The effect of wind, ice, and snow on equipment stability and rated capacity must be addressed.
- If possible, the load must be free to be lifted.
• During lifting operations, care must be taken that there is no sudden acceleration or deceleration of the moving load and that the boom or other parts of the crane do not contact any obstruction.
• Any time the load is 90% or more of the maximum line pull, the operator must test the brakes by lifting the load a few inches and applying the brakes.
• No modifications or additions which affect the capacity or safe operation of the crane can be made without the manufacturers' written approval.
• Except for proof load testing, no crane is permitted to be loaded beyond the specifications of the load rating chart, unless authorized by the crane manufacturer.
• Tag lines or restraint lines must be used when rotation or swinging of the load is hazardous or if the load needs guidance.
REVISED DATE: January 1, 2025
CRANE POLICY
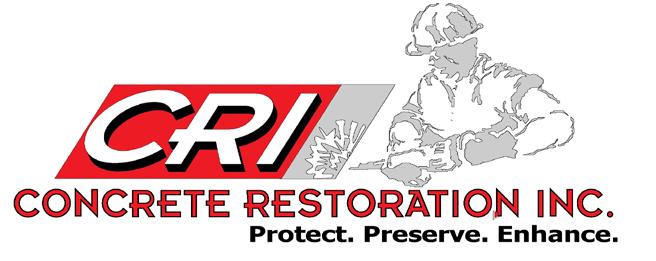
• Safety devices and/or operational aids must not be used as a substitute for the exercise of professional judgment by the operator.
• When a local storm warning has been issued, the crane operator must determine whether it is necessary to implement manufacturer recommendations for securing the crane.
• Whenever there is a concern as to safety, the operator has the authority to stop and refuse to handle loads until a qualified person has determined that safety has been assured.
• Where the crane has been taken our of service, a tag must be placed in the cab or at the operator station stating that the equipment is out of service and is not to be used.
• If adjustments or repairs are necessary, the operator must, inwriting, promptly inform the person designated by the employer to receive such information and, where there are successive shifts, to the next operator.
• A preventative maintenance program must be established based on the recommendation of the crane/derrick manufacturer.
Mobile Cranes- Operations (WAC 296-155-537151)
• All manual brakes must be tested prior to operation.
• Boom hoists that have manual brakes must also have mechanical locking devices that can be engaged to prevent inadvertent lowering of the boom.
• On wheel-mounted cranes, loads must only be lifted in areas permitted by the crane manufacturer.
• Cranes utilizing rolling outriggers must use load charts from the crane manufacturer or and RPE that specifically address this configuration. If the crane manufacturer does not address the use of rolling
REVISED DATE: January 1, 2025
CRANE POLICY
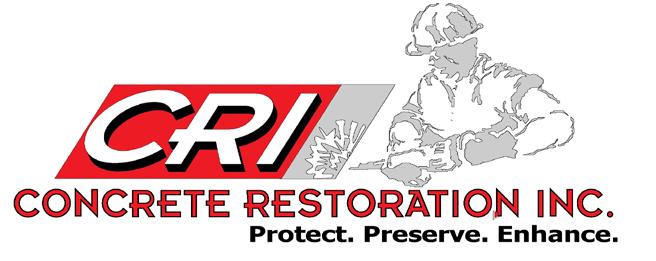
outriggers while some of the crane's weight is on its wheels, then the "on rubber'' chart must be used.
• While in transit, the boom should be carried in tine with the direction of motion and the superstructure must be secured against rotation except when negotiating turns when there is an operator in the cab or the boom is supported on a dolly.
• A crane with or without a load must be traveled in the configuration recommended by the crane manufacturer.
• When rotating the crane, sudden starts and stops must be avoided. Rotational speed must be such that the load does not swing out beyond the radius at which it can be controlled.
• A tag or restraint line must be used when rotation of the load is hazardous.
• Cranes must not be operated without the ballast or counterweight being in place as specified by the manufacturer.
• The crane must be leveled per the crane manufacturer's recommendation.
REVISED DATE: January 1, 2025
DRIVER SAFETY POLICY
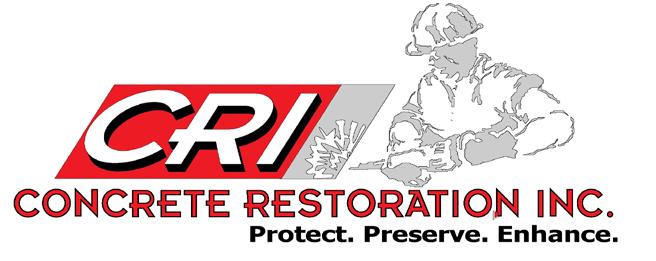
DRIVER SAFETY POLICY
Purpose
This program is written to be in compliance with local regulatory requirements and provide directives to managers, supervisors, and employees about their responsibilities in the operations and management of vehicle safety.
Key Responsibilities
Safety/Training Manager
The designated Safety Manager is responsible for developing and maintaining the program and related procedures. These procedures are located in Concrete Restoration Inc safety manual.
Shop Manager
Responsible for the implementation and maintenance of the program and ensuring all assets are made available for compliance with the plan.
Employees
All shall be familiar with this procedure and the local workplace vehicle safety program.
Follow all requirements, report unsafe conditions, and follow all posted requirements.
Vehicle and Transportation Related
Driving Safety
Operators of Concrete Restoration Inc vehicles, will be qualified by possession of a valid, current Washington state driver’s license for the type of vehicle being driven.
REVISED DATE: January 1, 2025
DRIVER SAFETY POLICY
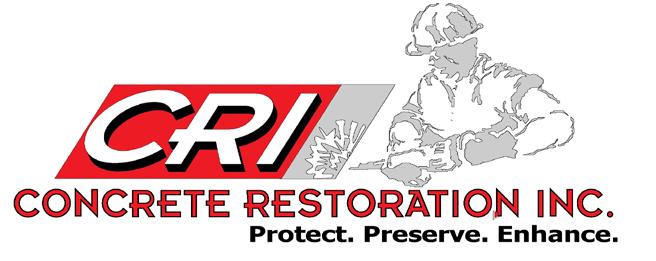
Only authorized employees will drive a motor vehicle in the course and scope of work or operate a concrete Restoration Inc owned vehicle. Drivers shall have 3 years of driving experience on the vehicle he/she is licensed to drive & regularly drives.
Drivers will be appropriately assessed, licensed and trained to operate the vehicle they have been authorized to operate.
No passengers shall be on trucks used to deliver goods.
Backing is prohibited whenever practicable. Where backing is required, drivers, when parking, should make every effort to park the vehicle in a manner that allows the first move when leaving the parking space to be forward.
Drivers must have either a reversing alarm, use a spotter or walk around the truck/trailer prior to backing.
Vehicles (light vehicles, heavy vehicles and trailers) may not be modified without the endorsement of the manufacturer.
Signs, stickers or labels are to be fitted in such a manner that they do not obstruct the driver's vision or impede the driver's use of any controls.
Employees driving vehicles are required to follow safe driving practices:
• Obey all federal and local driving laws or regulations as well as requirements of clients.
• Immediately report any citation, warning, traffic violation, collision, vehicle damage or near miss associated with company or client vehicle operation or while driving on company duties to the supervisor.
• Immediately report any restriction or change to their driving privileges to the supervisor.
REVISED DATE: January 1, 2025
DRIVER SAFETY POLICY
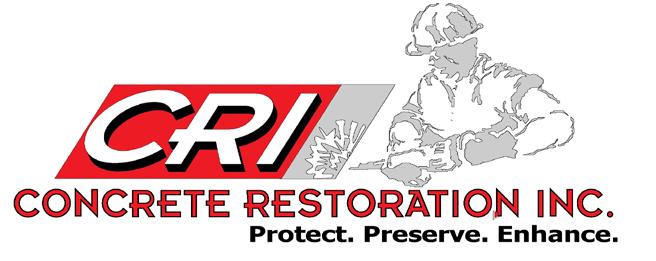
• Seat belts shall always be worn by all occupants whenever the vehicle is in motion; All vehicles capable of more than 10 mph/15 kph shall have seat belts installed.
• Defensive drivers continually assess conditions and hazards and remain prepared for any challenge that may approach them.
• When speaking with a passenger, always keep your eyes on the road.
• Both hands on the wheel
• No use of cell phones, radios or other electronic devices while driving any vehicle - vehicle must be safely parked prior to using a mobile phone or 2-way radio.
• Slow down around construction, large vehicles, wildlife, fog, rain, snow, or anything else that adds a hazard to your driving.
• Drive for conditions, not just the speed limit.
• Alcohol or illegal drugs are not allowed to be in a company, client or leased vehicle at any time
• Drivers shall not operate a motor vehicle while under the influence of alcohol, illegal drugs, or prescription or over-the counter medications that might impair their driving skills.
Drivers are to be prepared before leaving:
• Perform 360 vehicle inspection – report new damage.
• Check windshield for cracks that could interfere with vision.
• Make sure dirt or snow is removed from lights on all sides of the vehicle.
REVISED DATE: January 1, 2025
DRIVER SAFETY POLICY
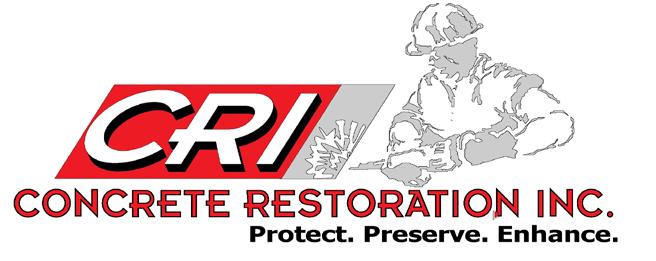
• Brush or clean off snow or ice on all windows to ensure complete vision.
• Check fuel level to be certain the destination can be reached.
• Check to ensure the license plates and inspection tag on vehicle are current
• Ensure that there is a first aid kit and inspected fire extinguisher in the company vehicle
• Ensure driver is rested and alert for driving.
• Employees are not to perform repairs or maintenance other than routine fluid additions.
Vehicle Requirements
• All vehicles shall be fit for the purpose and shall be maintained in safe working order.
• Tires, including spares if full size, are to be of same type, profile and tread pattern, except when the vehicle or tire Manufacturer recommends a different type for certain axles.
• Tire type and pattern is to be recommended by the vehicle or tire manufacturer for use on the vehicle in the area of operation.
• Vehicles are to be fitted with a spare wheel and changing equipment to safely change a wheel, or a suitable alternative.
• Vehicles longer than 20 feet or with restricted rear view (i.e. pickup trucks that are fully loaded) are to be fitted with an audible reversing alarm.
• All seats are to be fitted with headrests.
REVISED DATE: January 1, 2025
DRIVER SAFETY POLICY
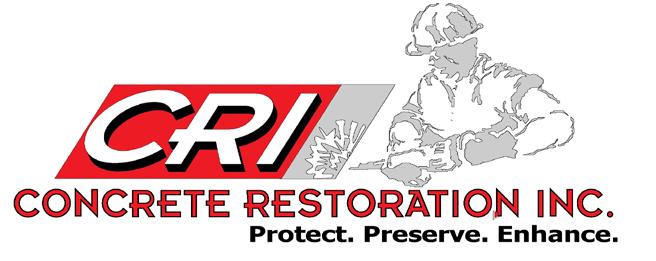
• All vehicles are to be equipped with an adjustable left, right and central rear-view mirrors.
• Loads shall be secure and shall not exceed the manufacturer’s specifications and legal limits for the vehicle.
• All vehicles are to be equipped with a multipurpose fire extinguisher with a capacity of at least 2 lb. The fire extinguisher shall be securely mounted on a bracket and located so that it is easily accessible in an emergency without becoming a hazard in case of an incident.
• All light vehicles shall be equipped with a securely stowed first aid kit.
Transportation
If workers are required to travel in a worker transportation vehicle, it must be ensured that reasonable measures are taken to evaluate road, weather and traffic conditions to ensure the safe transit of the workers.
The operator of a worker transportation vehicle must ensure that the worker transportation vehicle has been inspected by a qualified person before first use on a work shift.
Seated workers must wear seat belts while being transported in a vehicle equipped with seat belts.
Materials, goods, tools or equipment carried in a portion or compartment of a vehicle in which workers are riding must be located and secured to prevent injury to the operator or workers.
Any enclosed portion or compartment of a vehicle in which workers are transported must have:
• Effective ventilation, independent of doors, providing clean air,
• Adequate lighting and means for heating and cooling,
• Effective means of communication between the operator and passengers, and
REVISED DATE: January 1, 2025
DRIVER SAFETY POLICY
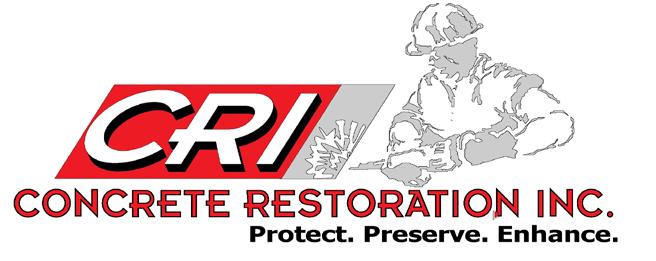
• More than one means of exit.
Traffic Control
There shall be developed, in writing, and implemented, a traffic protection plan for its workers at a worksite if any of them may be exposed to a hazard from vehicular or pedestrian traffic that may endanger the safety of any worker. It shall include the following control measures:
• Effective means of traffic control shall be provided whenever the unregulated movement of vehicular traffic constitutes a hazard to workers.
• Traffic control shall include barricades and cones as the primary control and, where required, signs, flagmen or other techniques and devices made necessary by the prevailing circumstances.
• Operations or equipment, encroaching on the traveled way, shall be protected by barricades and cones as the primary control and, where required other effective devices.
• Workers must be trained in traffic control safe work procedures.
• Designated flag person(s) must be trained in the safe work procedures for the safe control of traffic operations and wears the appropriate high visibility outer clothing and/or equipment, before working as a flag person.
• If a worker at a project on a highway may be endangered by vehicular traffic unrelated to the project, the project shall make use of as many measures as necessary to adequately protect the worker.
REVISED DATE: January 1, 2025
DRIVER SAFETY POLICY
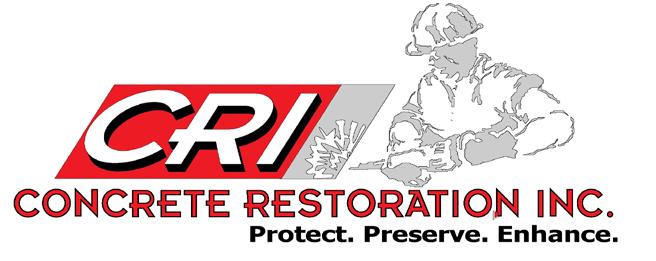
• A worker who is required to set up or remove traffic control measures on a roadway or a shoulder of a roadway shall be a competent worker, shall be equipped with the appropriate high visibility apparel, shall not perform any other work while setting up or removing the measures and shall be given adequate written and oral instructions in a language that he or she understands, with respect to setting up or removing the measures.
REVISED DATE: January 1, 2025
Drug and Alcohol Policy
Drug and Alcohol Policy
Reference: WAC 296-800-11025
INTRODUCTION:
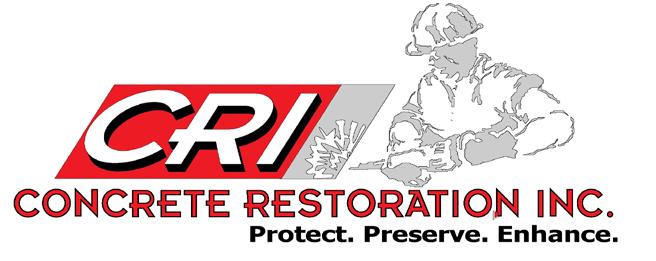
Concrete Restoration, Inc. has a policy of prohibiting the use and/or possession of drugs and alcohol in Concrete Restoration Inc vehicles or premises. The Company recognizes that the use of drugs and alcohol pose significant safety and health threats. In addition, a drug or alcohol user's efficiency and productivity are greatly diminished.
With the recent passage of various laws designed to curb the use of drugs and alcohol in the workplace, additional requirements have been imposed on both Concrete Restoration Inc and its employees. This Drug and Alcohol Policy incorporates both Concrete Restoration Inc policies as well as the requirements of the new legislation and implementing regulations.
Concrete Restoration Inc is committed to providing a safe, drug-free work environment for all its employees. While Concrete Restoration Inc has legitimate interests to minimize substance abuse and its workplace effects, every attempt has been made in this Policy to balance Concrete Restoration Inc workplace goals with legitimate employee privacy interests.
Each employee will be given a copy of this Policy and will acknowledge receipt of it. As a condition of employment, all employees will abide by all terms of this Policy.
LEGAL AUTHORITY:
This Drug and Alcohol Policy has been developed and implemented by Concrete Restoration Inc to maintain a drug- free workplace, promote safety and efficiency in its vehicles, and on its premises and to ensure compliance with various legislation, including, but not limited to, the DrugFree Workplace Act of 1988, regulations promulgated by the U.S. Coast Guard, the Federal Highway Administration, the Department of Defense, and the U.S. Customs Service, and the National Policy commonly referred to as "Zero Tolerance."
REVISED DATE: January 1, 2025
Drug and Alcohol Policy
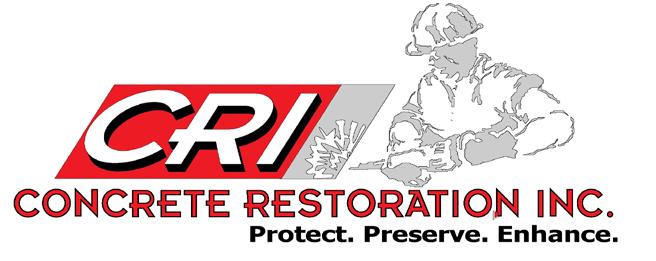
These laws and regulations require, among other things, that vessel and vehicle owners take measures to ensure that their vessels are free of drugs and alcohol and that employees are subject to testing for drugs and alcohol in certain circumstances.
PROHIBITIONS:
Drugs and Alcohol Prohibited: The use, possession, distribution, dispensation, or manufacture, or any activity likely to lead to the use, possession, distribution, dispensation, or manufacture of any drugs, paraphernalia, or alcohol is prohibited aboard in any Concrete Restoration Inc vehicle, or on any Concrete Restoration Inc premises.
The term "drugs" includes any substance, lawful or unlawful, which will impair the motor senses, judgment, behavior, actions, reactions, mood, pain threshold, or thinking process of an individual. The term "drugs" specifically includes a narcotic drug, controlled substance, and marijuana (as defined in section 102 of the Comprehensive Drug Abuse Prevention and Control Act of 1970).
The term "paraphernalia" includes any material or device which is commonly used, has been used, or is intended to be used in connection with the administration or other use of drugs.
Concrete Restoration Inc reserves the right to possess and service alcohol to guests at Concrete Restoration Inc events and or on Concrete Restoration Inc premises under the supervision of a Company official
The terms "impairment" and "impaired" mean that an employee is under any influence of a substance such that the employee's motor senses (e.g., sight, hearing, balance, reaction, reflex, etc.), judgment, behavior, actions, reactions, mood, pain threshold, or thinking process is, or may reasonably be presumed to be, affected. In addition, the terms "impairment" and "impaired" mean the presence of any detectable amount of drugs in the employee's system.
REVISED DATE: January 1, 2025
Drug and Alcohol Policy
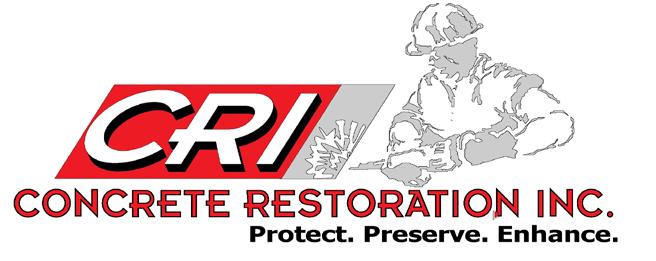
NOTIFICATION CONVICTIONS:
All employees must notify Concrete Restoration Inc of a criminal drug statute convictions for a violation occurring in the workplace no later than five (5) days after such conviction.
SANCTIONS FOR VIOLATION OF POLICY:
Any employee found in violation of any part of this Drug and Alcohol Policy shall be subject to disciplinary action, including possible termination of employment. Concrete Restoration Inc also require satisfactory participation in a drug or alcohol abuse assistance or rehabilitation program as a condition of continued employment.
INSPECTIONS:
For purposes of compliance with this Drug and Alcohol Policy, all employees, vendors, contractors, and visitors are subject to inspection. All areas of Concrete Restoration Inc vehicles, and premises, including, but not limited to, offices, work areas, common areas, and living quarters are subject to inspection.
In addition, personal effects (including, but not limited to work areas, common areas) are subject to inspection. In addition, personal effects (including, but not limited to, luggage, clothing, equipment, tools, and packages) delivered to or brought onto Concrete Restoration Inc premises, vehicles, or premises and personal vehicles brought onto Company premises may be inspected. Such inspections may be made by any means deemed appropriate.
Concrete Restoration Inc may conduct surveillance of all areas subject to inspection by video equipment, security personnel, or otherwise.
DRUG AND ALCOHOL TESTING PROGRAM:
REVISED DATE: January 1, 2025
Drug and Alcohol Policy
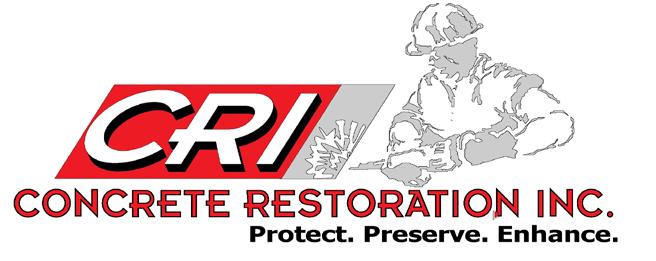
Employees to be tested: Applicants for employment with Concrete Restoration Inc, regardless of their job classifications, may be subject subject to pre-employment testing. All employees, regardless of their classifications, are subject to reasonable cause testing. All marine employees and vehicle drivers are subject to all aspects of the testing program.
DEFINITIONS:
"Chemical test" means a scientifically recognized test which analyzes an individual's breath, blood, urine, saliva, bodily fluids, or tissues for evidence of dangerous drug or alcohol use.
"Dangerous Drug" means narcotic drug, controlled substance, and marijuana (as defined in section 102 of the Comprehensive Drug Abuse Prevention and Control Act of 1970).
"Fails a chemical test for dangerous drugs" means the test result is reported as positive for the presence of drugs or drug metabolites in an individual's system after a Medical Review Officer's review conducted in accordance with applicable regulations.
"Intoxicant" means any form of alcohol, dangerous drug, or combination thereof.
"Medical Review Officer" means an individual designed by Concrete Restoration Inc to carry out the duties specified in applicable regulations.
"Vehicle driver" means an employee operating a Concrete Restoration Inc vehicle.
Collection of Specimens: Unless otherwise required by regulation, chemical testing will normally be performed on urine specimens. Procedures for collecting urine specimens shall allow for individual privacy unless there is reason to believe that a particular individual may alter or substitute the specimen.
REVISED DATE: January 1, 2025
Drug and Alcohol Policy
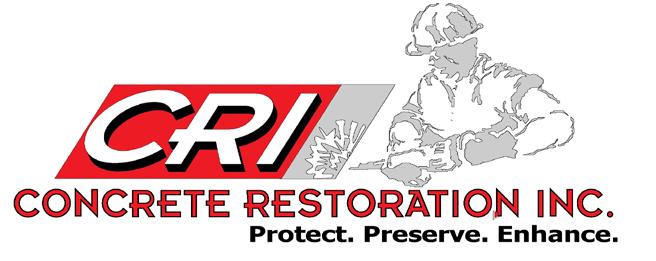
Reasonable Cause Testing: Concrete Restoration Inc will require any employee reasonably suspected of using dangerous drugs and/or alcohol to be tested for dangerous drugs and alcohol. Anyone tested because of "reasonable cause" shall be removed from further duties until the test results are received.
Concrete Restoration Inc decision to test must be based on a reasonable and articulable belief that the individual has used a dangerous drug or alcohol based on direct observation of specific, contemporaneous physical, behavioral, or performance indicators of probable use. Where practicable, this belief should be based on the observation of two people in supervisory positions.
When Concrete Restoration Inc requires the testing of an individual under the provisions of this section, the individual must be informed of the fact and directed to provide a urine specimen as soon as practicable.
In the case of a vehicle driver, the driver's conduct must be documented and signed by the witnesses within 24 hours or before the test results are released, whichever is earlier.
Periodic Testing: Certain employees are subject to periodic testing in accordance with applicable regulations.
Vehicle drivers shall be tested once for the use of controlled substances during the first medical examination of the vehicle driver after implementation of the periodic testing program.
Random Testing: Concrete Restoration Inc shall provide for the selection of employees for chemical testing for dangerous drugs on a random basis. Random selection of such employees means that every member of a given population has a substantially equal chance of selection on a scientifically valid basis.
Post Serious Incident and Vehicle Accident Testing: Concrete Restoration Inc reserves the right to subject persons directly involved in a serious incident or reportable vehicle accidents are chemically tested for dangerous drugs and alcohol in accordance with applicable regulation.
REVISED DATE: January 1, 2025
Drug and Alcohol Policy
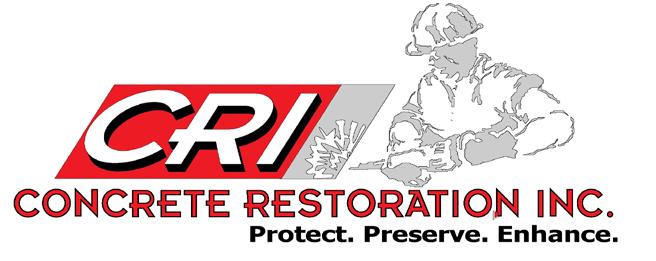
LABORATORY:
All chemical tests for dangerous drugs, controlled substances, or alcohol shall be conducted only by a laboratory certified by the Department of Health and Human Services. The following laboratory shall be utilized for all testing where practicable:
Concentra Urgent Care
200 Andover Park E Suite 8, Tukwila, WA 98188
Telephone (206) 575-3136
Each specimen shall be analyzed for marijuana, cocaine, opiates, phencyclidine (PCP), amphetamines, and, where requested, alcohol. A specimen which indicates the presence of a dangerous drug at a level equal to or exceeding the levels established in 49 CFR 40.24 or alcohol at a level equal to or exceeding the levels established in 33 CFR 95.020(b) shall be reported to the Medical Review Officer as positive. Positive reports are only reported to Concrete Restoration Inc after verification by the Medical Review Officer. The laboratory reports to Concrete Restoration Inc as negative all specimens which are negative on the initial test or negative on the confirmation test.
Medical Review Officer:
The Company shall designate a Medical Review Officer ("MRO") meeting the qualifications of 49 CFR 40.27. The MRO designated by the Company is:
Concentra Urgent Care
200 Andover Park E Suite 8, Tukwila, WA 98188
Telephone (206) 575-3136
REVISED DATE: January 1, 2025
Drug and Alcohol Policy
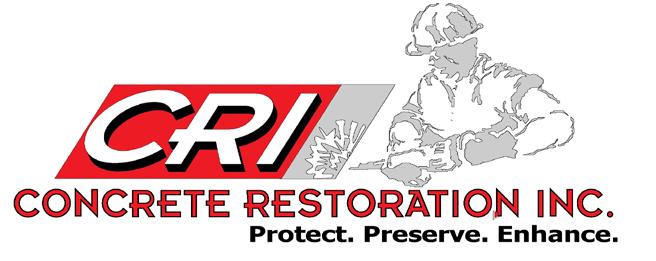
The MRO shall review and interpret each confirmed positive test result in accordance with 49 CFR 40.27. The MRO shall give the employee affected an opportunity to discuss and explain any positive test result. If the MRO verifies a laboratory confirmed positive report, the MRO shall report the positive test result to the Company by contacting Tim Coots, Concrete Restoration.
RELEASE OF INFORMATION:
Except where required by regulation to be reported, Concrete Restoration Inc shall not release individual test results or other related information. Individual results from drug tests may be released if the individual tested signs a specific authorization for the release of the results to an identified person.
MAINTENANCE OF RECORDS:
Concrete Restoration Inc shall maintain records of chemical tests which the MRO reports as "positive" for a period of five (5) years and shall make these records available to regulatory agencies as required.
Records of tests reported as "negative" shall be retained for one (1) year. The records shall be sufficient to confirm that individuals have complied with pre-employment test or random test requirements. In addition, the records shall identify the total number of individuals chemically tested annually for dangerous drugs in each of the categories set forth in this Drug and Alcohol Policy by job classification, including the annual number of individuals failing chemical tests and the number and types of drugs for which individuals tested positive.
EDUCATION AND TRAINING:
Concrete Restoration Inc will provide an education program for all employees which includes the display and distribution of informational material and a community service hotline number for employee assistance. In addition, Concrete Restoration Inc will provide mandatory training for supervisors on the effects and consequences of drug and alcohol use on personal health, safety, and work environment. This training will also focus
REVISED DATE: January 1, 2025
Drug and Alcohol Policy
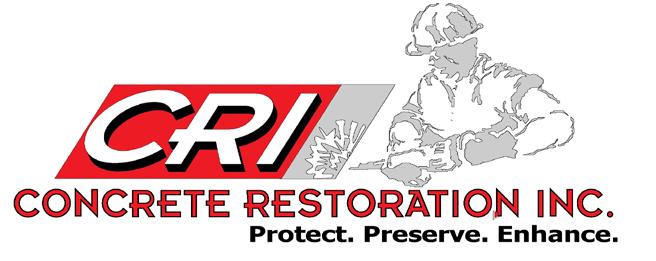
on the manifestations and behavioral cues that may indicate drug and alcohol use and abuse. Drug testing procedures and workplace inspections will be discussed.
CHANGES:
The Company reserves the right to interpret, change, rescind or depart from this Drug and Alcohol Policy, in whole or in part, without notice. Nothing in this Drug and Alcohol Policy alters an employee's employment status.
REVISED DATE: January 1, 2025
ELECTRICAL SAFETY POLICY
ELECTRICAL SAFETY POLICY
Reference: WAC 296-46B/OSHA 29 CFR 1910
Purpose and Scope
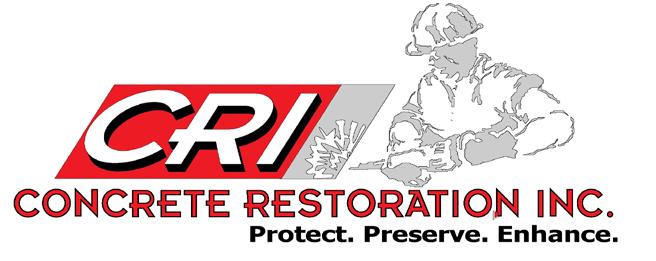
Concrete Restoration Inc is committed to providing a safe and healthy work environment and to protecting employees from injury or death caused by uncontrolled electrical hazards in the workplace. The purpose of Concrete Restoration Inc Electrical Safety Program is to establish work policies, practices, and procedures to train employees in basic electrical hazard recognition and safe work practices. This program applies to qualified and non-qualified employees who are exposed to electricity as part of their job.
Program Responsibilities
Management
Along with providing financial and leadership support, the management of Concrete Restoration Inc will assist the Safety/Training Manager, supervisors, and employees with complying with this policy.
Safety/Training Manager
The Safety/Training Manager is responsible for:
• Identifying work tasks that need to be performed by a qualified employee.
• Conducting electrical safety inspections
• Correcting electrical safety hazards as soon as possible
• Ensuring all new electrical equipment and components comply with this program.
• Reviewing this program annually and revising if necessary
• Maintaining a list of all qualified employees
• Conducting training for employees
Supervisors
REVISED DATE: January 1, 2025
ELECTRICAL SAFETY POLICY
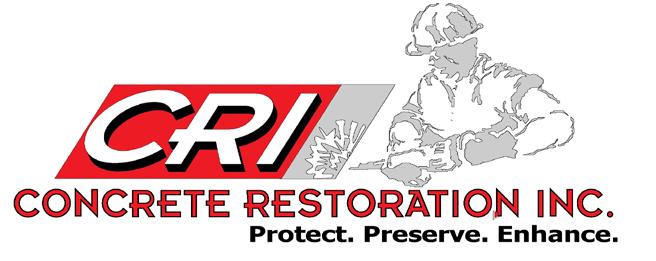
Supervisors are responsible for:
• Conducting periodic work inspections
• Ensuring employees are provided with and use the appropriate PPE.
• Ensuring employees comply with all aspects of the Electrical Safety Program
• Testing electrical hand tools every three months with an ohmmeter
Employees
An employee will only work on electrical equipment if he/she is a qualified worker, meaning he/she has been trained and authorized to perform work on deenergized electrical equipment and components. Employees are responsible for:
• Wearing the appropriate PPE when working with or around electrical equipment
• Reporting electrical safety hazards to their supervisor of the Program Administrator
• Following the safe work practices outlined in this program.
• Visually inspecting electrical equipment, tools, and cords before each use
• Completing all required training
Work Practices
All electrical equipment will have the manufacturer’s name, trademark or other descriptive marking which identifies the organization responsible for the product. The equipment will also have its operating voltage, current, wattage or other rating clearly marked on it. All exposed deenergized parts should be considered live when working on or around equipment.
Qualified employees will use lockout/tagout procedures on all electrical equipment while completing maintenance work. Lockout/tagout procedures are found in Concrete Restoration Inc Lockout/Tagout Program. If the equipment cannot be deenergized because it would introduce an additional or increased hazard, or it is infeasible due to the design or its operational
REVISED DATE: January 1, 2025
ELECTRICAL SAFETY POLICY
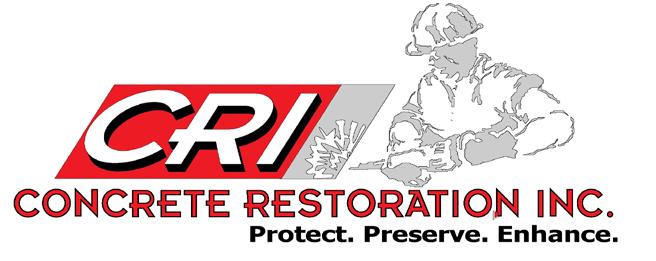
limitations (i.e., emergency alarm systems), Concrete Restoration Inc will hire a qualified electrical contractor to perform the work. No work will be performed on energized equipment by Concrete Restoration Inc employees.
Extension Cords and Power Strips
Employees must be aware of the hazards associated with the misuse of extension cords and power strips. All power strips must be UL listed and used according to the manufacture’s guidelines.
Choosing an Appropriate Extension Cord. Concrete Restoration Inc has a variety of extension cords available for employee use. Employees will select an extension cord that can handle the electricity requirement for any connected tools or equipment. All employees will adhere to the following guidelines when choosing an appropriate extension cord.
• Lights and fans (1-13 amperage rating). Employees may use a 25100-foot-long extension cord with 16-gauge wire, or a 150-foot cord with 14-gauge wire.
• Small electrical hand-held tools, such as drills and sanders (1415 amperage rating). May use a 25-100-foot-long extension cord with 14-gauge wire, or a 150-foot cord with 12-10-gauge wire.
• Large electrical tools such as shop vacuums, circular saws, table saw and space heaters (16-20 amperage rating). May use a 25-100-foot-long extension cord with 12-10-gauge wire. Do not use an extension cord longer than 100 feet with large electrical tools
* All extension cords used for construction or outdoor maintenance work will be equipped with, or connected to, a ground fault circuit interrupter (GFCI).
If an employee is unsure which size of extension cord, he/she should use, contact a Foreman or the Safety/Training Manager.
REVISED DATE: January 1, 2025
ELECTRICAL SAFETY POLICY
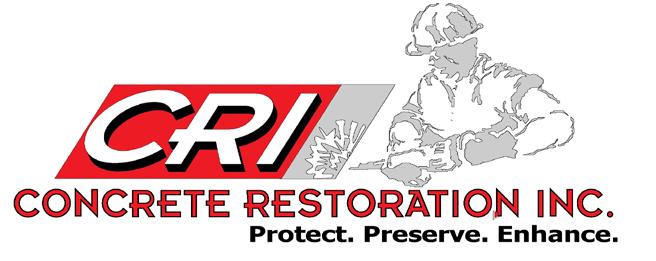
Safe Work Practices for Extension Cords and Power Strips.
The following safe work practices will be always followed by all employees when using an extension cord or power strip.
• No employee will plug in or unplug a power strip or extension cord with wet hands.
• Power strips will only be used in office settings.
• Grounding prongs will never be removed from the end of any extension cord or power strip. No strip or cord with a missing grounding prong shall be plugged into outlets.
• All extension cords and power strips will be inspected before use. If any defects are found, the cord or strip will be removed from service.
• All power strips and extension cords will be tested using an ohm meter every 3 months.
• When extension cords or power strips are used, they will not be:
o Run through holes in walls, ceilings, or floors.
o Run through doorways or windows without appropriate protection.
o Used in areas where vehicles, forklifts or other equipment could drive over the cord.
o Fastened with staples or hung in a way that could damage the insulation.
o Used for more than 30 days.
If it is necessary to run an extension cord through a doorway (for example, work completed outdoors with no outlet), the cord will be protected using high contrast tape or coverings and will not be left out overnight.
REVISED DATE: January 1, 2025
ELECTRICAL SAFETY POLICY
Repairing and Replacing Electrical Cords
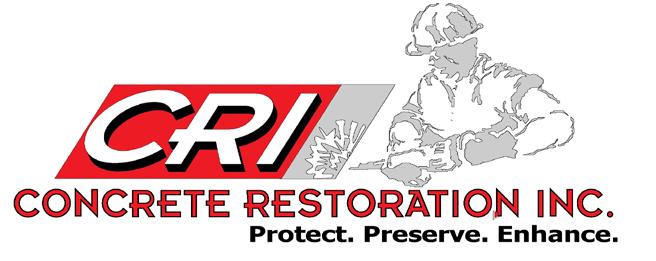
If a cord is damaged, the following guidelines will be followed:
• All repairs will be completed by Concrete Restoration Inc shop personnel.
• If there is a break in cord insulation and wires are exposed, then cord mush be replaced or cut down to eliminate exposure.
• After the repair, the cord must retain its original flexibility and integrity.
• If the inner insulation is damaged, the cord must be replaced. Damaged cords used in wet areas shall be immediately replaced.
Circuit Overload
To reduce the possibility of overloaded circuits, Concrete Restoration Inc employees will only plug in one device per outlet. Employees will not use splitters, multi-plug adapters, etc. without direct permission from the Safety/Training Manager. If you have a concern that a circuit may be overloaded, you are to contact your Foreman or the Safety/Training Manager
Tools
The following requirements shall be adhered to at all times:
• All electrical tools will be stored in a clean, dry place when not in use.
• Employees will not carry electrical tools by the cord or yank cords from the wall.
REVISED DATE: January 1, 2025
ELECTRICAL SAFETY POLICY
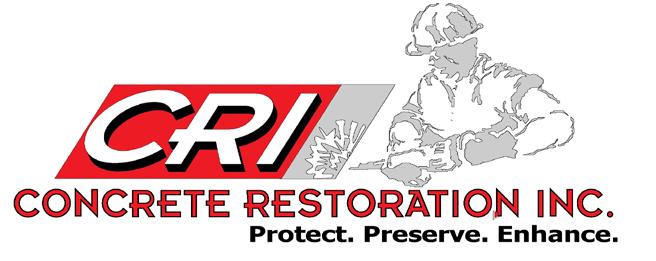
• If a tool is unintentionally deenergized due to a circuit breaker or GFCI, it must be removed from service until the cause of de energization is discovered.
• All electrical tools will be tested using an ohm meter every 3 months.
• All tools will have grounding prongs. Any tool without a grounding prong will be removed from service.
• All electrical tools will be inspected before use. If any defects are found, the tool will be removed from service until it can be repaired or replaced.
• Fiberglass ladders will be used when working around or on electrical equipment or wires.
Guarding
All electrical systems must be guarded to prevent contact with live conductors. The following requirements will be adhered to at all times:
• All electrical distribution panels, breakers, disconnects, switches and junction boxes will be completely enclosed.
• Live parts to electrical equipment operating at 50 volts or more must be guarded to prevent contact and prevent damage.
• All electrical receptacles and cover plates will be kept intact and in good condition.
• All electrical panels will be easily accessible at all times and a minimum of three feet of clearance shall be maintained on all sides.
REVISED DATE: January 1, 2025
ELECTRICAL SAFETY POLICY
High Voltage Electrical Rooms and Closets
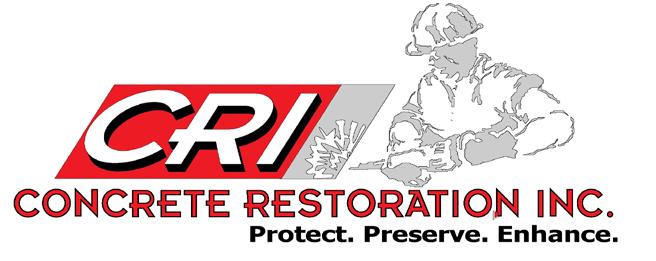
The following requirements for electrical rooms and closets shall be adhered to at all times:
• High voltage rooms and closets must be locked at all times.
• Only qualified employees are allowed into high voltage rooms and closets.
• No Concrete Restoration Inc employee will open or remove covers or access panels of high voltage electrical distribution panels or transformers.
• Nothing will be stored in rooms or closets designated for electrical equipment.
• Safety signs which warn employees about any electrical hazards shall be displayed prominently on the door of the room or closet.
Ground Fault Circuit Interrupters
Ground fault circuit interrupters (GFCIs) protect Concrete Restoration Inc employees who use electrically powered tools and equipment from electrical shocks, especially when working in wet environments. GFCIs are required for electrically powered equipment and tools in the following conditions:
• When used at locations where employees are likely to contact water or conductive liquids, such as outdoors, bathrooms, kitchens or any other area with potential exposure to water.
• When used at construction or renovation sites
• When used for portable lighting in wet or other conductive locations (such as inside boilers or tanks)
REVISED DATE: January 1, 2025
ELECTRICAL SAFETY POLICY
Working near Power Lines
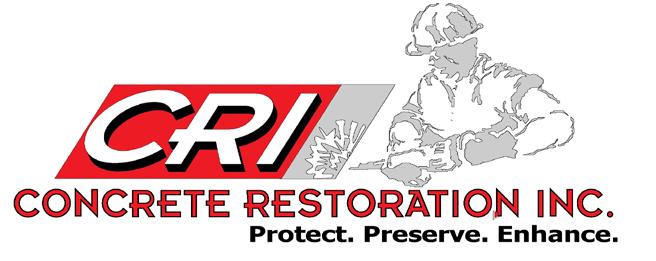
Both overhead and underground power lines present electrical hazards. The following procedures shall be adhered to when working near power lines.
• Remain at least 10 feet away from overhead power lines, this includes vehicles and equipment.
• If the voltage is greater than 50,000 volts, add 4 more inches of safe distance for each 10,000 volts beyond 50,000.
• When working around high voltage lines, ground all equipment that may become energized.
• Call WA state One Call Center 48 hours before any digging. Once underground power lines have been identified, add an additional 18-inch clearance on either side of the marking or flag. Do not dig in this clearance area. If it is required to dig within the clearance area Concrete Restoration Inc will use an outside contractor to perform the work.
Additional Safety Precautions
The following additional safety precautions shall be adhered to at all times.
• If a circuit breaker trips or blows a fuse more than once, it shall be investigated and corrected by a qualified employee or contractor before being cleared for continued use.
• All areas with electrical equipment shall be properly illuminated.
• Housekeeping duties will not be performed in an area if there is a possibility of contact with an electrical hazard unless there are protective shields, barriers or if insulated materials are used to protect the employee.
REVISED DATE: January 1, 2025
ELECTRICAL SAFETY POLICY
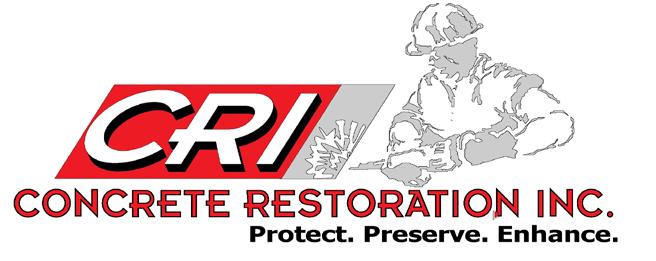
• Safety signs that warn employees about any electrical hazards shall be displayed prominently when a hazard is present.
Personal Protective Equipment (PPE)
Employees working in areas where electrical hazards are present will be provided with and shall use PPE that is designed for the specific part of the body to be protected and for the work being performed. Employees are required to adhere to the following procedures for PPE use:
• All PPE must be inspected prior to each day’s use and immediately following any incident.
• Non-conductive head protection will be worn if there is danger of electrical burns or shock from contact with electricity.
• When working on electrical equipment or wiring, employees will:
o Not wear conductive articles of clothing or jewelry
o Wear non-melting clothing such as cotton.
o Wear electrical-rated boots.
o Wear non-conductive gloves.
REVISED DATE: January 1, 2025
ELECTRICAL SAFETY POLICY
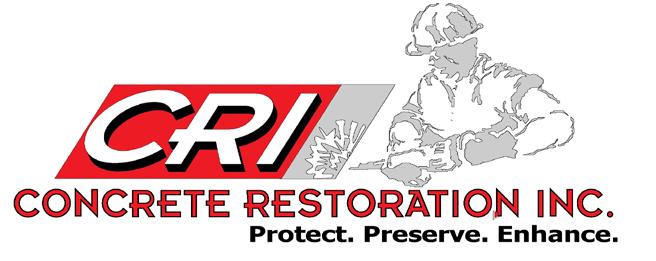
If there is a danger of:
Then use the following:
- head injury from electric shock, or Nonconductive head protection - Class II
- burns due to contact with exposed energized nonconductive hard hat parts
Injury to the eyes or face from: Protective equipment for the eyes and face - face
- electric arcs or flashes, or shield and safety glasses.
- flying objects resulting from electrical explosion
Shock to hands while handling energized wires Lineman's rubber insulated gloves rated for the voltage exposed to; leather over gloves may be needed if exposure to abrasive surfaces is possible
- shock while working in areas where high Non-conductive protective foot wear
voltage electrical systems or present, or
- shock when performing electrical repairs
Exposure to electric arcing or flash from: Protective coveralls made of Nomex or other
- opening or closing 2400-volt oil cutout suitable flash-proof material. switching devices;
- removing or installing links in high voltage
cable tap boxes; or
- Removing or installing fuses in high voltage circuits.
IF THEN
Energized parts are exposed
Use nonconductive ropes and handlines near the exposed energized part.
Working near exposed energized Use insulated tools or handling equipment
REVISED DATE: January 1, 2025
ELECTRICAL SAFETY POLICY
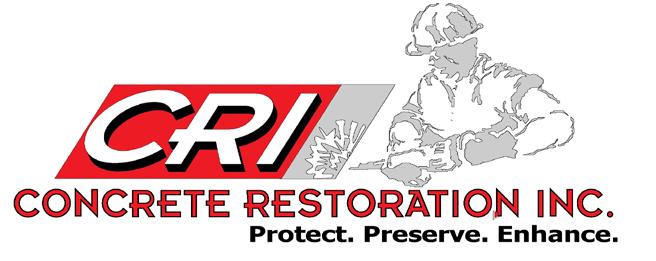
conductors or if the circuit parts tools or handling equipment might make contact with such conducts or parts. The insulating capability of insulated tools or Protect the insulating material. handling equipment is subject to damage
Removing or installing fuses when the fuse Use fuse-handling equipment, insulated for the terminals are energized circuit voltage. Working near exposed energized parts that might Use protective shields, protective barriers, or be accidentally contacted or where dangerous insulating materials to protect from shock, burns, electric heating or arcing might occur or other electrically related injuries. Normally enclosed live parts are exposed for Guard the parts to protect unqualified persons maintenance or repair from contact with the live parts.
Employee Training
Qualified Workers. At a minimum, qualified workers must be trained on the following:
• The hazards associated with electrical equipment.
• Electrical safety practices and procedures (lockout/tagout) for doing deenergized work.
• Safe work practices that must be followed when working around or with electrical tools or equipment.
• How to distinguish exposed live parts from other parts of electrical equipment
• How to properly inspect and use the appropriate PPE.
• The location of the electrical breaker panels and fuse boxes
REVISED DATE: January 1, 2025
ELECTRICAL SAFETY POLICY
Unqualified Workers
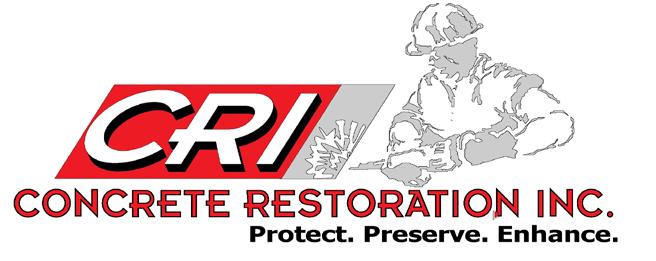
Unqualified workers will receive general electrical safety awareness training on how to recognize, evaluate and avoid electrical hazards and training on all Concrete Restoration Inc electrical safety practices.
Training will occur before an employee begins work in a new area and when an employee does not comply with safe work practices. Retraining will occur every year. Training will be documented.
Periodic Program Review
The Program Administrator will review the Electrical Safety Program and procedures annually. The review will be documented.
ELECTRICAL HAZARD CHECK SHEET
Location Inspected: ______________________________
Job No:
Date Inspected:
Name of Inspector:
REVISED DATE: January 1, 2025
ELECTRICAL SAFETY POLICY
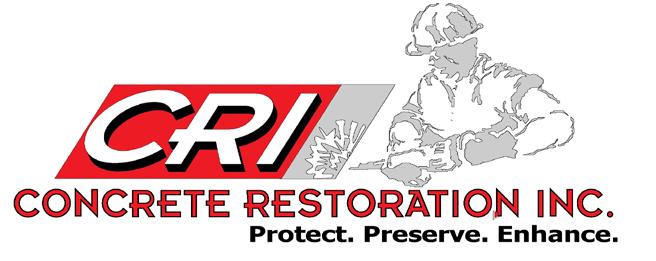
Electrical Equipment Markings
1. Disconnecting switches and circuit breakers are labeled to indicate their use or equipment served.
2. The necessary voltage, wattage, or current ratings are labeled.
3. Circuit breakers clearly indicate whether they are in the "on" or "off" position.
Electrical Grounding
4. Extension cords used have a grounding conductor (third plug).
5. GFCI's are installed as required.
6. Portable electrical tools and equipment are of the double insulated type.
7. Ground fault circuit interrupters open the circuit on a ground current of 5 milliamperes or greater and are equipped with an integral push button test circuit.
8. Ground fault circuit interrupters are installed in accordance with the manufacturer's instructions.
9. Ground fault circuit interrupters are tested prior to initial use and periodically thereafter.
10. Grounding rods are at least 5/8-inch diameter steel or iron rods, 1/2inch diameter copper clad steel, or 3/4-inch diameter galvanized pipe.
11. Grounding rods are in eight-foot lengths and driven to full depth.
12. The path from circuits, equipment, structures, and conduits or enclosures to ground are:
13. ♦ Permanent and continuous.
14. ♦ Have ample carrying capacity for the current likely to be imposed on it.
15. ♦ Have resistance sufficiently low to permit current flow to operate circuit breakers and similar overcurrent devices on the circuit.
REVISED DATE: January 1, 2025
ELECTRICAL SAFETY POLICY
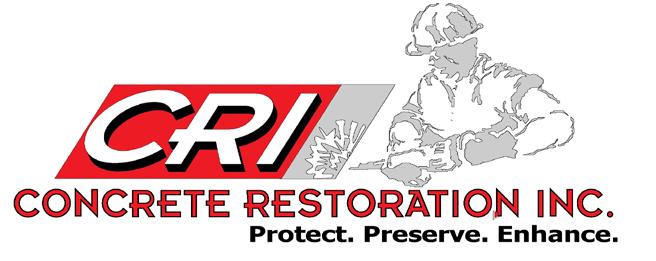
16. Driven ground rod electrodes have a resistance to ground not exceeding 25 ohms.
17. Upon installation of the driven ground rod electrode, the resistance was tested and recorded.
18. Conductors, used for bonding and grounding circuits, are of sufficient size to carry the anticipated current.
19. Grounds are not removed until all work is complete. Yes No
Electrical Guarding
20. Switches, receptacles, etc. are provided with tightfitting covers or plates.
21. All energized parts of electrical circuits and equipment are guarded against accidental contact by approved cabinets or enclosure
22. All unused openings (including conduit knockouts) in electrical enclosures and fittings are enclosed with appropriate covers, plugs or plates.
23. Ground-fault circuit interrupters are installed on each temporary 15 or 20 ampere, 120 volt AC circuit at locations where construction, demolition, modifications, alterations or excavations are being performed.
24. Electrical switches and breakers (rated 440 volts or greater) are provided with a means for locking them out in the OFF position.
Electrical Systems
25. Circuit breakers accessible to personnel are protected from physical damage, and located away from ignitable material.
26. Weatherproof cabinets or enclosures are used when switches, circuit breakers, fuse panels and motor controllers are in a wet or outside location.
27. A readily accessible, manually operated switch is provided for each incoming service or supply circuit rated less than 5 kilovolts.
REVISED DATE: January 1, 2025
ELECTRICAL SAFETY POLICY
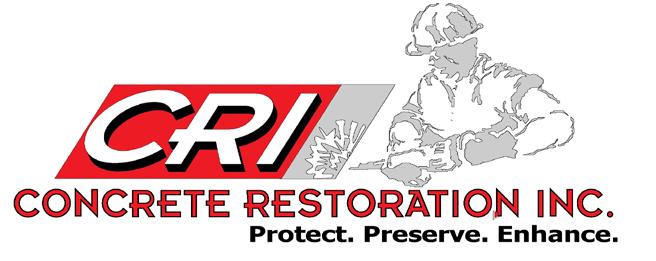
28. Electrical raceways and enclosures are securely fastened in place.
29. Overcurrent protection is provided for fuses or circuit breakers for each feeder and branch circuit.
30. Insulating fuse tongs or extractors are used when removing fuses from circuits rated 50-600 volts.
31. Fuse cabinets have close-fitting doors that can be locked.
Extension Cords
32. Clamps or other securing means are provided on flexible cords or cables at plug receptacles, tools, equipment, etc. and the cord jacket is securely held in place.
33. Flexible cords and cables are free of splices and taps.
34. Only 3-wire grounded type extension cords, designated for hard or extra hard service are used.
35. Extension cords are listed by Underwriters Laboratories, Inc.
36. Extension cords are checked for damage before use.
37. The rated load on extension cords is not exceeded.
38. Extension cords are not fastened with staples, hung by nails or suspended by wire.
Temporary Wiring
39. Temporary wiring is guarded, buried or isolated by elevation to preventaccidental contact by workers and equipment.
40. A vertical clearance above walkways for temporary wiring is not less than ten feet from circuits carrying 600 volts or less.
41. All exposed temporary wiring is supported on insulators.
42. Temporary wiring is protected from accidental damage.
Lighting Strings
REVISED DATE: January 1, 2025
ELECTRICAL SAFETY POLICY
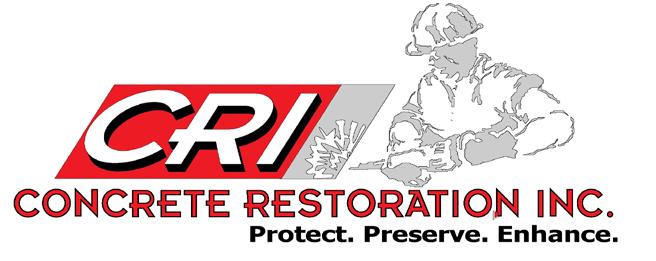
43. Nonconductive lamp sockets and connections are permanently molded to the conductor insulation on lighting strings.
44. Lighting strings have lamp guards.
45. Broken or defective bulbs are replaced promptly.
46. Lights are protected from accidental contact or breakage.
47. Wiring installed in conduit is equipped with bushings at outlets and terminals.
48. Receptacles are of the grounding type, and electrically connected to the equipment-grounding conductor.
Worker Practices
49. Personnel performing electrical repairs are properly trained and "qualified".
50. Workers de-energize, ground or guard electric circuits before working in close proximity.
51. Workers consider all electrical systems as hot, until verified de-energized and grounded.
52. Proper lockout tag-out procedures are used for deenergizing electric circuits.
Equipment
53. Only fiberglass or wood ladders are used when working near electrical hazards.
54. Insulation mats are placed on floors and on frames of equipment when working on energized equipment.
Personal Protective Equipment
55. Rubber matting, blankets, insulated sleeves, and rubber gloves are inspected before use.
56. Workers use safety glasses and face shields during work activities where there is a reasonable probability of eye injury.
Remarks:___________________________________________________
REVISED DATE: January 1, 2025
Emergency Action Plan
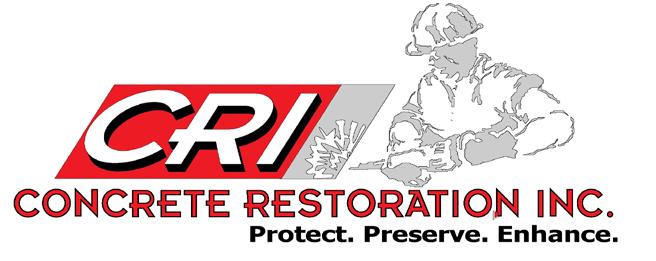
Emergency Action Plan
Reference: WAC 296-56-60010/OSHA 1910.38
OBJECTIVE
The objective of the Concrete Restoration Inc Emergency Action Plan is to comply with the WAC 296-56-60010 Emergency Action Plan Standard and to prepare employees for dealing with emergency situations. This plan is designed to minimize injury, loss of human life, and company resources by training employees, procuring, and maintaining necessary equipment, and assigning responsibilities. This plan applies to all emergencies that may reasonably be expected to occur at Concrete Restoration Inc and must be available for all employees to review.
ASSIGNMENT OF RESPONSIBILITY
Manager
Manager will manage the Emergency Action Plan for Concrete Restoration Inc. The Emergency Plan Manager will also maintain all training records pertaining to this plan. The plan manager is responsible for scheduling routine tests of the Concrete Restoration Inc emergency notification system with the appropriate authorities.
The Emergency Plan Manager will also coordinate with local public resources, such as the fire department and emergency medical personnel, to ensure that they are prepared to respond as detailed in this plan. This includes allowing emergency responders to perform a walkthrough of the facility to familiarize themselves with the layout of the structures, types, and volume of hazardous chemical storage, and other hazards they might encounter when responding to an emergency. Emergency-responder input will be incorporated into this Emergency Action Plan.
Management
Concrete Restoration Inc will provide adequate controls and equipment that, when used properly, will minimize, or eliminate risk of injury to employees and EMS in an emergency.
REVISED DATE: January 1, 2025
Emergency Action Plan
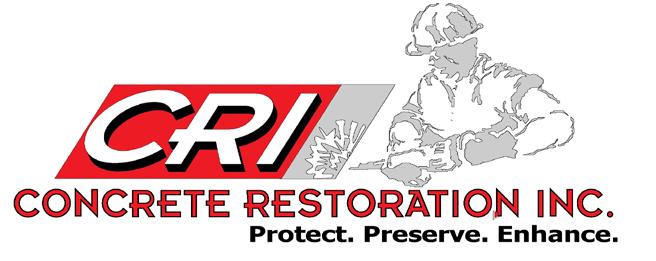
Concrete Restoration Inc management will review this plan regularly to ensure proper adherence.
Management Team
The management team will follow, and ensure that their employees are trained in, the procedure in this plan.
Employees
Employees are responsible for following the procedures in this plan.
Contractors
Contract employees are responsible for complying with this plan and will be given the training described in the plan by the Safety/Training Manager.
PLAN IMPLEMENTATION
Reporting Fire and Other Emergency Situations
All fires and other emergency situations will be reported as soon as possible to the Company President by one of the following means:
• Verbally, as soon as possible during normal work hours
• By telephone, after normal work hours or on weekends
To eliminate confusion and false alarms, the Company President is authorized to contact community emergency response personnel. Contact information for the emergency response personnel for Concrete Restoration Inc:
Type of Emergency Responder Person(s) Responsible
REVISED DATE: January 1, 2025
Emergency Action Plan
Police/Sheriff Shannon
Ambulance/EMS
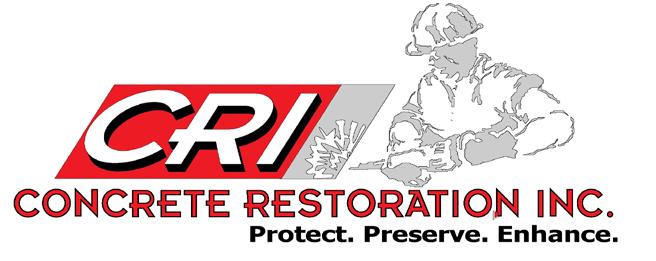
If the Company President cannot be reached, any individual with knowledge of a fire or other emergency situation may then contact emergency responders.
Under no circumstances will an employee attempt to fight a fire after it can no longer be put out with a fire extinguisher, nor will any employee attempt to enter a burning building to conduct search and rescue. These actions must be left to emergency services professionals (such as the fire department or emergency medical professionals) who have the necessary training, equipment, and experience to do so. Untrained people might endanger themselves or those they are trying to rescue.
Informing Concrete Restoration Inc Employees of Fires and Other Emergency Situations
In the event of a fire or other emergency, Manager will ensure that all employees are notified as soon as possible using the building alarm system (which includes audible and visual alarms, 24 hours a day).
If a fire or other emergency occurs after normal business hours, Operations Manager will contact all employees not on shift to provide future work status, depending on the nature of the situation.
Emergency Contact Information
The Controller/HR will maintain a list of all employees’ personal emergency contact information and will keep the list in office/cloud for easy access in an emergency.
Evacuation Routes
Emergency evacuation escape route plans are posted in shop area. In the event that a fire or emergency alarm is sounded or instructions for evacuation are given by a Manager, all employees must immediately exit
REVISED DATE: January 1, 2025
Emergency Action Plan
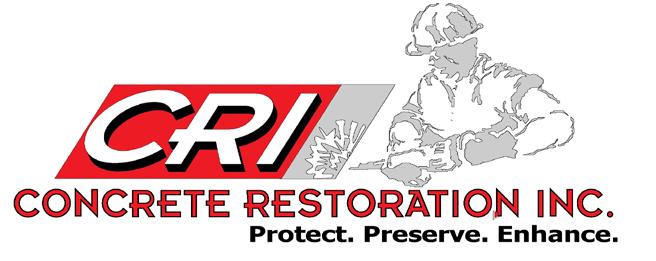
the building(s) at the nearest exits as shown in the escape route plans and must meet as soon as possible at the parking area.
Employees with offices must close the doors (unlocked) as they exit the area.
Mobility-impaired employees and their assigned assistants will gather at the shop within the building to ensure safe evacuation in the pre-determined fashion.
Securing Property and Equipment
If evacuation of the premises is necessary, some items may need to be secured to prevent further danger to the facility and personnel on hand (such as securing confidential or irreplaceable records or shutting down equipment to prevent release of hazardous materials). Only the following people may remain in the building for the prescribed amount of time to secure the property and equipment to which they have been assigned.
President
Safety & Training Manager
Operations Manager Controller
All people remaining behind to shut down critical systems or utilities must be capable of recognizing when to abandon the operation or task. Once the property or equipment has been secured, or the situation becomes too dangerous to remain, those who remained behind must exit the building by the nearest escape route as soon as possible and meet the remainder of the employees at the Parking Area.
Advanced Medical Care
Under no circumstances may an employee provide advanced medical care and treatment. These situations must be left to emergency services professionals, or Safety/Training personnel, who have the necessary training, equipment, and experience. Untrained people might endanger themselves or those they are trying to assist.
REVISED DATE: January 1, 2025
Emergency Action Plan
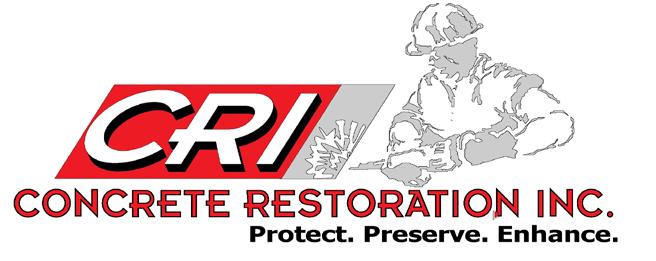
Accounting for Employees/Visitors After Evacuation
Once an evacuation has occurred, the Manager will account for each employee or visitor assigned to them at the parking area. Each employee is responsible for reporting to the Manager so an accurate head count can be made.
Re-entry
Once the building has been evacuated, no one may re-enter the building for any reason, except for designated and properly trained rescue personnel (such as fire department or emergency medical professionals). Untrained people might endanger themselves or those they are trying to rescue.
All employees must remain at the parking area until the fire department or other emergency response agency notifies the manager that either:
• The building is safe for re-entry, in which case personnel will return to their workstations; or
• The building or assembly area is not safe, in which case the Manager will instruct personnel how or when to vacate the premises.
Sheltering in Place
If chemical, biological, or radiological contaminants are released into the environment in such quantity or proximity to Concrete Restoration Inc, authorities and/or the Manager might determine that is safer to remain indoors rather than evacuate. The Manager will announce shelter-in-place status by public address system or other means of immediate notification available at worksite.
• will immediately close the business. If customers, clients, or visitors are in the building, they will be advised to stay in the building for their safety.
REVISED DATE: January 1, 2025
Emergency Action Plan
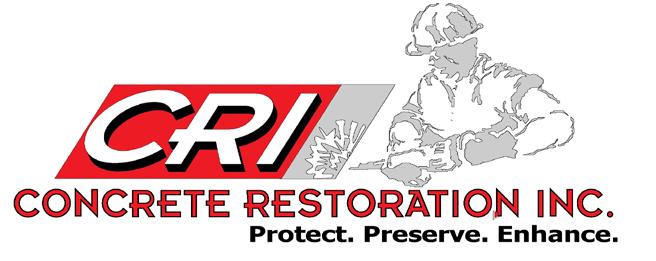
• Unless there is an imminent threat, employees, customers, clients, and visitors will call their emergency contacts to let them know where they are and that they are safe.
• Controller / HR will turn on call-forwarding or alternative telephone answering systems or services. The recording for voice mail or automated attendant will be changed to indicate that the business is closed, and that staff and visitors will be remaining in the building until authorities advise that it is safe to leave.
• The Manager will quickly lock exterior doors and close windows, air vents, and fireplace dampers. The Shop manager familiar with the building’s mechanical systems will turn off, seal, or disable all fans, heating and air conditioning systems, and clothes dryers, especially systems that automatically exchange inside air with outside air. If there is a danger of explosion, the Shop Manager must close window shades, blinds, or curtains.
• The Manager will gather essential disaster supplies (for example, nonperishable food, bottled water, battery-powered radios, first-aid supplies, flashlights, batteries, duct tape, plastic sheeting, and plastic garbage bags), which are stored at shop, and will take them to the shop area within the building.
• All employees, customers, and visitors will move immediately to the Shop Area within the building. The shop Manager will seal all windows, doors, and vents with plastic sheeting and duct tape.
• The Manager will write down the names of everyone in the room and will call 911 to report who is in the room, and their affiliations with Concrete Restoration Inc.
• The Manager will monitor telephone, radio, television and Internet reports for further instructions from authorities to determine when it is safe to leave the building.
A. Severe Weather
REVISED DATE: January 1, 2025
Emergency Action Plan
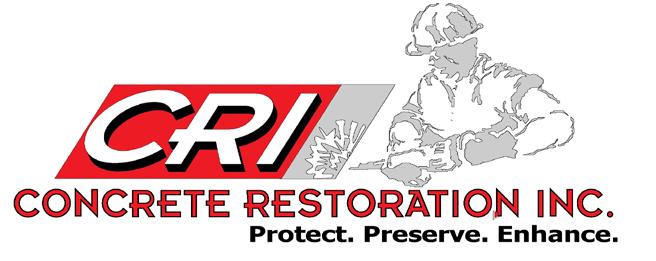
The Manager will announce severe weather alerts (such as tornados) by public address system or other means of immediate notification available at the worksite. All employees will immediately retreat to the Shop Area until the threat of severe weather has passed as communicated by the Manager.
TRAINING
Employee Training
All employees will receive instructions on this Emergency Action Plan as part of new-employee orientation. Additional training must be provided:
• When there are any changes to the plan or facility.
• When an employee’s responsibilities change; and
• Annually, as refresher training. Items for review during the training include:
• Proper housekeeping.
• Fire-prevention practices.
• Fire extinguisher locations, usage, and limitations.
• Threats, hazards, and protective actions
• Means of reporting fires and other emergencies.
• Names of Emergency Action Plan manager and coordinators
• Individual responsibilities
• Alarm systems
• Escape routes and procedures.
• Emergency shut-down procedures
• Procedures for accounting for employees and visitors.
• Closing doors
• Sheltering in place.
• Severe weather procedures, and
• Emergency Action Plan availability.
Fire/Evacuation Drills
Fire/evacuation drills must be conducted at least annually and in coordination with local police and fire departments. Additional drills will be
REVISED DATE: January 1, 2025
Emergency Action Plan
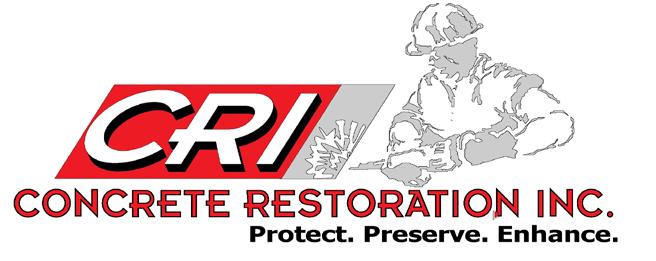
conducted if physical properties of the business change, processes change, or it is otherwise deemed necessary.
Training Records
Safety/Training Manager will document all training pertaining to this plan and will maintain records at the office.
PLAN EVALUATION
This Emergency Action Plan must be reviewed annually, or as needed if changes to the worksite are made, by the Safety/Training manager. Following each fire drill, The Safety/Training Manager will evaluate the drill’s effectiveness and any weaknesses or gaps in the plan and will implement improvements.
REVISED DATE: January 1, 2025
EMPLOYEE SAFETY CONCERNS
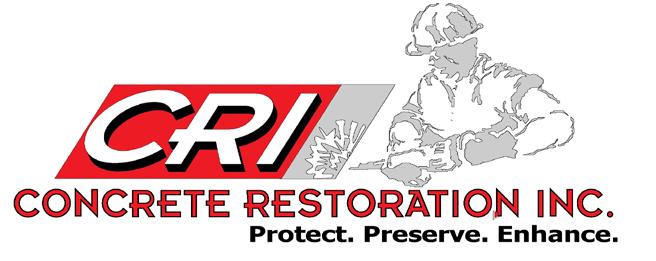
EMPLOYEE SAFETY CONCERNS STATEMENT
EMPLOYEE CONCERNS
It is Concrete Restoration lnc’s intent to have all employees Involved in safety. It is requested and Concrete Restoration, Inc. supports and encourages employees to report all incidents or situations which they believe or perceive could cause injury or illness.
Concerns may be reported in any of the following ways:
• Speak to job foreman
• Weekly safety meeting
• Completing a Near-Miss Report
• Safety Manager or safety team member
• Company Management team member
All concerns will be documented, and the foreman/management is responsible to report back to the employee any resolution of the concern.
REVISED DATE: January 1, 2025
EQUAL OPPORTUNITY
EMPLOYMENT STATEMENT
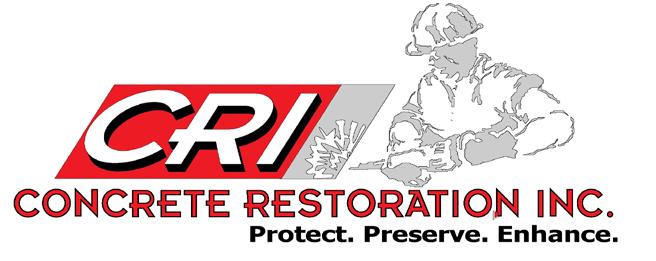
EQUAL OPPORTUNITY EMPLOYMENT STATEMENT
Statement of Policy Concrete Restoration, Inc.
This Organization Practices
Equal Employment Opportunity
We do not discriminate on the grounds of race, color, religion, sex, marital status, age, disability or national origin in the hiring, retention, or promotion of employees; nor in determining their rank, or the compensation or fringe benefits paid them.
This Organization Practices
Equal Treatment of Clients
We do not discriminate by reason of race, color, religion, sex, marital status, disability, age, or national origin in services or accommodations offered or provided to our employees, clients, or guests.
These policies and this notice comply with the regulations of the United States Government
Please report violations of this policy to:
Administrator Concrete Restoration Inc 9587 8th Avenue South Seattle, WA 98108
REVISED DATE: January 1, 2025
FALL PROTECTION WORK PLAN
FALL PROTECTION WORK PLAN
Job Number
Job Task
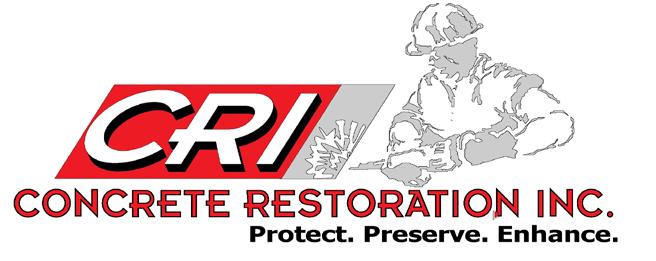
Fall Protection is required at 4 feet; however, a written plan is required at or above 10 feet
Site Location
Job Location/Description
Plan prepared by Date C
Workers must review and sign this Fall Protection Work Plan prior to starting work. Workers must understand this plan and be trained in fall protection and the systems and equipment that will be used.
This Fall Protection Work Plan must be posted at the worksite for the duration of work activities.
1. Identify potential fall hazards (check all that apply)
☐ Mobile elevating work platforms
☐ Excavations/trenches
☐ Floor openings
Stairways
Roof steep slope (greater than 4:12)
Roof low slope (4:12 or less) ☐ Wall openings
☐ Skylight openings
☐ Roof openings
☐ Elevator shaft
☐ Ladders (fixed or portable)
Swing fall
Hazardous process/equipment
Debris/objects falling to lower level
Sharp edges
Reinforcing steel installation ☐ Scaffold
2. Describe the fall hazard(s) details
Other:
3. Identify fall protection systems to be used ☐ Guardrail system
☐ Covers (holes and openings)
☐ Appropriate anchors for systems used
Aerial lift
Horizontal lifeline
Vertical lifeline and rope grab ☐ Personal fall arrest system
☐ Personal fall restraint system
Warning line
Safety monitor Name: ☐ Positioning device system
☐ Scaffold with guardrail
REVISED DATE: January 1, 2025
Safety watch Name:
Other:
FALL PROTECTION WORK PLAN
Scissor lift
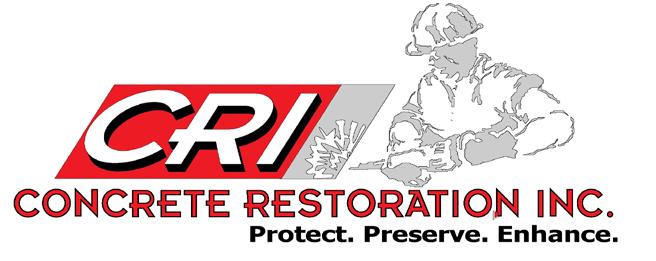
4. Describe procedures for assembly, maintenance, inspection, disassembly of fall protection system to be used
5. Describe procedures for handling, storage, securing tools and materials
6. Identify methods of overhead protection for workers who may be in, or pass through the area below worksite
Barricading
Hard hats required
Catch net
Warning signs
Tool belts
Tool lanyards
Toe boards/screens on scaffolds
Toe boards/covers on floor openings
Screens on guardrails
Secure large tools
7. Identify method for prompt, safe removal of injured workers CALL 9-1-1 IF FALL OCCURS
Written agreement with:
Site first aid
Self-rescue
employees
8. Identify method used to determine adequacy of anchorage points
Evaluation by professional engineer
Manufacturer’s data
9. Describe and identify locations of anchorage points
Existing engineering/design documents
10. Select system components
Full body harness
Vertical lifeline
Horizontal lifeline
Lanyard
Boatswains chair
Connecting devices (identify)
Other:
REVISED DATE: January 1, 2025
Choker
Carabiner
Rope grab
Personal shock absorber
Beamer
Anchorage points (identify)
FALL PROTECTION WORK PLAN
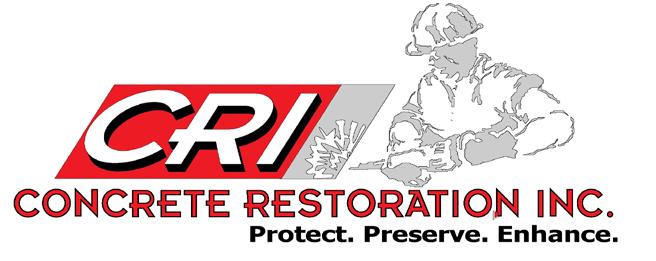
11. Distance from anchor to ground, lower level or obstruction (see page 4 chart)
12. Calculated minimum fall clearance (see page 4 chart)
13. Inspection Checklist
☐ Identification Tags
☐ Horizontal Lifeline Tension is Correct
☐ Integrity of stitching in Shock Absorber
☐ Integrity of stitching in Harness/ Lanyard
☐ Manufacturers assembly/ disassembly instructions
☐ Locking capability of retractable lanyards assured
☐ Locking capability of carabiners assured
☐ Locking capability of snap hooks assured
☐ Knots and other connection methods do not weaken lifeline
☐ Lifelines installed and protected from cuts or abrasions
☐ Rope (wear, fraying, damage, mildew)
☐ Lanyards (wear, fraying, damage, mildew)
☐ D-rings have adequate strength, are not cracked or deformed
☐ Guardrails are sound and of adequate strength
☐ Devices that are used to connect to horizontal lifelines lock in both directions
☐ Anchorage points provide adequate strength and are capable of meeting requirements
☐ Warning line meets strength and other requirements
☐ Safety Monitor is Competent Person, can see workers, is close enough to communicate, has no other duties
☐ Safety Watch is Competent Person, can see worker, is close enough to communicate, has no other duties
☐ Hole covers are secured, marked and capable of withstanding anticipated weight loads
☐ Other
☐ Other
14. Employee(s) trained to work under this plan
Name (print)
Name/title of Competent Person who provided training under this plan
15. Work plan approval(s)
Name of lead worker or supervisor
DATE: January 1, 2025
FALL PROTECTION WORK PLAN
Name of Competent Person (If engineered system: Name of Qualified Person)
If administrative controls: Name of department manager
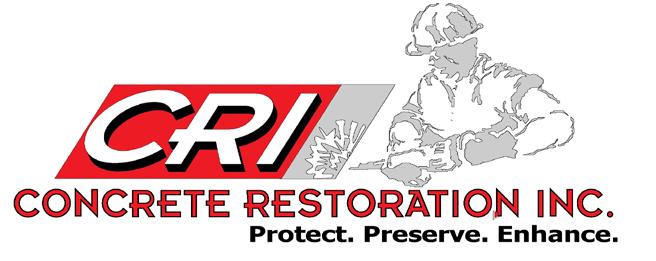
Fall clearance is the minimum vertical distance needed between the anchor point and a lower level (this can be the ground or lower obstruction) with a safety factor to prevent the worker from hitting the lower level in a fall.
What is the distance from the anchor point to the ground or lower level where a worker would fall?
If a worker falls, when wearing a fall protection system, what is the minimum fall clearance from the anchor point to the worker’s feet including a 3 ft. safety factor? (Calculate as shown below.)
The calculated minimum fall clearance of a specific fall protection system may never be equal or greater than the distance between the anchor point and the lower level.
Lanyard length or free fall distance for self-retracting lifeline
Maximum allowable deceleration distance 3 ½ ft. Workers height
Minimum fall clearance (sum of above)
Calculating Fall Clearance using a Shock-Absorbing Lanyard
Example:
•First, add the length of the shock-absorbing lanyard (6 ft.) to the maximum elongation of the shock absorber during deceleration (3 ½ ft.) to the average height of a worker (6 ft.)
•Then, add a safety factor of 3 ft. to allow for the possibility of an improperly fit harness, a taller than average worker and/or a miscalculation of distance.
•The total, 18 ½ ft. is the suggested safe fall clearance distance for this example.
• NOTE: Should the shock-absorbing lanyard be used in conjunction with a cross-arm anchorage connector or other, the additional length of the anchorage connector must be taken into consideration.
REVISED DATE: January 1, 2025
FALL PROTECTION WORK PLAN
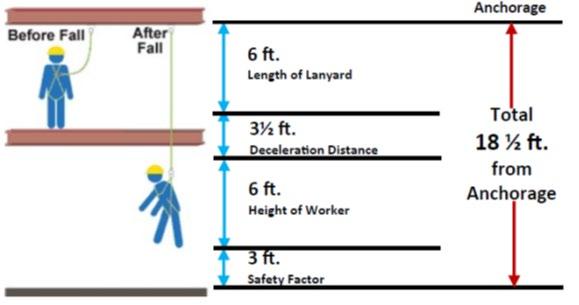
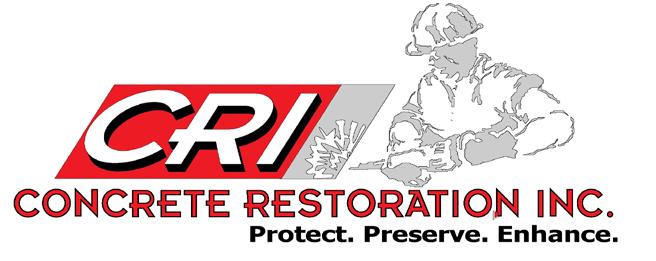
Calculating Fall Clearance using a Self-Retracting Lifeline
Example:
• First, add the maximum free fall distance (2 ft.) with a retractable lifeline to the maximum deceleration distance (3 ½ ft.) to the average height of a worker (6 ft.)
• Then, add a safety factor of 3 ft. to allow for the possibility of an improperly fit harness, a taller than average worker and/or a miscalculation of distance.
• The total, 14 ½ ft. is the suggested safe fall clearance distance for this example.
NOTE: When using a retractable lifeline, the distance is calculated from the point where the retractable attaches to the back D-ring of the worker’s
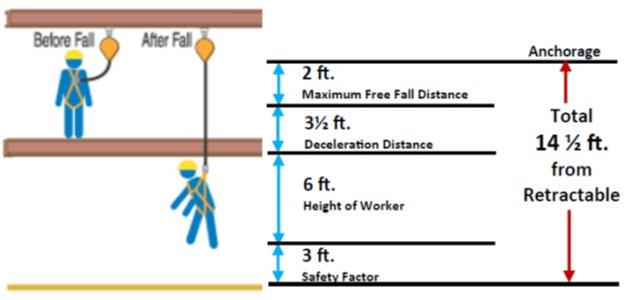
REVISED DATE: January 1, 2025
FALL PROTECTION POLICY
FALL PROTECTION POLICY
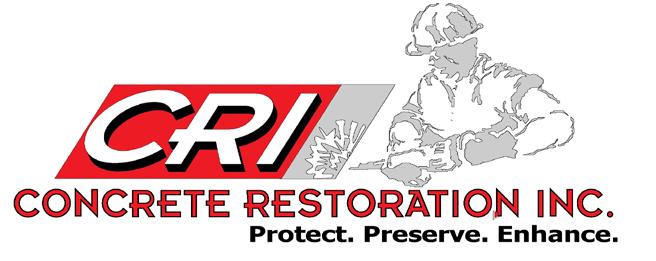
Purpose: All employees, supervisors, and members of management, understand the importance of fall protection; when to use it, how to use it, and how to prevent hazardous conditions that could result in slips, trips or falls.
Scope: Applicable to all Concrete Restoration Inc locations
WAC: Chapter 296-880 WAC Unified Safety Standards for F
OSHA:1926.501
Fall Protection
Note – any references made to paragraphs or sections are of the WAC standard itself; not of this policy.
DEFINITIONS:
Anchorage means a secure point of attachment for lifelines, lanyards or deceleration devices.
Body belt (safety belt) means a strap with means both for securing it about the waist and for attaching it to a lanyard, lifeline, or deceleration device.
Body harness means straps which may be secured about the employee in a manner that will distribute the fall arrest forces over at least the thighs, pelvis, waist, chest and shoulders with means for attaching it to other components of a personal fall arrest system.
Buckle means any device for holding the body belt or body harness closed around the employee's body.
Connector means a device which is used to couple (connect) parts of the personal fall arrest system and positioning device systems together. It may be an independent component of the system, such as a carabineer, or it may be an integral component of part of the system (such as a buckle or
REVISED DATE: January 1, 2025
FALL PROTECTION POLICY
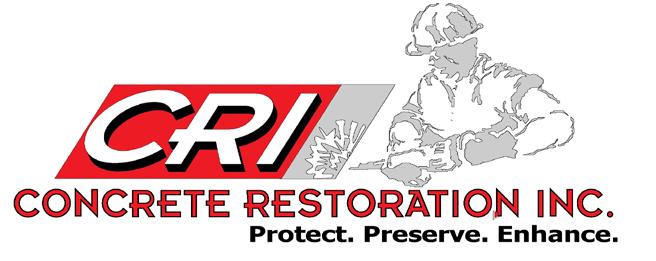
dee-ring sewn into a body belt or body harness, or a snap-hook spliced or sewn to a lanyard or self-retracting lanyard).
Dangerous equipment means equipment (such as pickling or galvanizing tanks, degreasing units, machinery, electrical equipment, and other units) which, because of form or function, may be hazardous to employees who fall onto or into such equipment.
Deceleration device means any mechanism, such as a rope grab, ripstitch lanyard, specially woven lanyard, tearing or deforming lanyards, automatic self-retracting lifelines/lanyards, etc., which serves to dissipate a substantial amount of energy during a fall arrest, or otherwise limit the energy imposed on an employee during fall arrest.
Deceleration distance means the additional vertical distance a falling employee travels, excluding lifeline elongation and free fall distance, before stopping, from the point at which the deceleration device begins to operate. It is measured as the distance between the location of an employee's body belt or body harness attachment point at the moment of activation (at the onset of fall arrest forces) of the deceleration device during a fall, and the location of that attachment point after the employee comes to a full stop.
Equivalent means alternative designs, materials, or methods to protect against a hazard which Concrete Restoration Inc can demonstrate will provide an equal or greater degree of safety for employees than the methods, materials or designs specified in the standard.
Failure means load refusal, breakage, or separation of component parts. Load refusal is the point where the ultimate strength is exceeded.
Free fall means the act of falling before a personal fall arrest system begins to apply force to arrest the fall.
Free fall distance means the vertical displacement of the fall arrest attachment point on the employee's body belt or body harness between onset of the fall and just before the system begins to apply force to arrest the fall. This distance excludes deceleration distance, and lifeline/lanyard elongation, but includes any deceleration device slide distance or self-
REVISED DATE: January 1, 2025
FALL PROTECTION POLICY
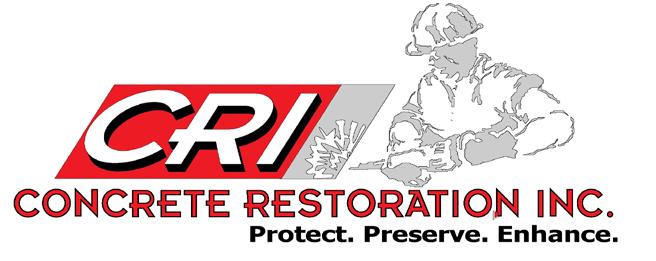
retracting lifeline/lanyard extension before they operate and fall arrest forces occur.
Guardrail system means a barrier erected to prevent employees from falling to lower levels.
Hole means a gap or void 2 inches (5.1 cm) or more in its least dimension, in a floor, roof, or other walking/working surface.
Infeasible means that it is impossible to perform the construction work using a conventional fall protection system (i.e., guardrail system, safety net system, or personal fall arrest system) or that it is technologically impossible to use any one of these systems to provide fall protection.
Lanyard means a flexible line of rope, wire rope, or strap which generally has a connector at each end for connecting the body belt or body harness to a deceleration device, lifeline, or anchorage.
Leading edge means the edge of a floor, roof, or formwork for a floor or other walking/working surface (such as the deck) which changes location as additional floor, roof, decking, or formwork sections are placed, formed, or constructed. A leading edge is considered to be an "unprotected side and edge" during periods when it is not actively and continuously under construction.
Lifeline means a component consisting of a flexible line for connection to an anchorage at one end to hang vertically (vertical lifeline), or for connection to anchorages at both ends to stretch horizontally (horizontal lifeline), and which serves as a means for connecting other components of a personal fall arrest system to the anchorage.
Low-slope roof means a roof having a slope less than or equal to 4 in 12 (vertical to horizontal).
Lower levels mean those areas or surfaces to which an employee can fall. Such areas or surfaces include, but are not limited to, ground levels, floors, platforms, ramps, runways, excavations, pits, tanks, material, water, equipment, structures or portions thereof.
REVISED DATE: January 1, 2025
FALL PROTECTION POLICY
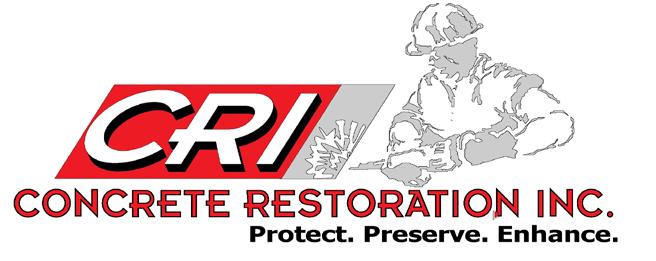
Mechanical equipment means all motor or human propelled wheeled equipment.
Openings means a gap or void 30 inches (76 cm) or higher and 18 inches (48 cm) or in width, in a wall or partition, or floor, through which employees can fall to a lower level.
Overhand bricklaying and related work means the process of laying bricks and masonry units such that the surface of the wall to be jointed is on the opposite side of the wall from the mason, requiring the mason to lean over
Personal fall arrest system means a system used to arrest an employee in a fall from a working level. It consists of an anchorage, connectors, a body belt or body harness and may include a lanyard, deceleration device, lifeline, or suitable combinations of these. As of January 1, 1998, the use of a body belt for fall arrest is prohibited.
Positioning device system means a body belt or body harness system rigged to allow an employee to be supported on an elevated vertical surface, such as a wall, and work with both hands free while leaning.
Rope grab means a deceleration device which travels on a lifeline and automatically, by friction, engages the lifeline and locks so as to arrest the fall of an employee. A rope grab usually employs the principle of inertial locking, cam/level locking, or both.
Roof means the exterior surface on the top of a building. This does not include floors or formwork which, because a building has not been completed, temporarily becomes the top surface of a building.
Roofing work means the hoisting, storage, application, and removal of roofing materials and equipment, including related insulation, sheet metal, and vapor barrier work, but not including the construction of the roof deck.
Safety-monitoring system means a safety system in which a competent person is responsible for recognizing and warning employees of fall hazards.
REVISED DATE: January 1, 2025
FALL PROTECTION POLICY
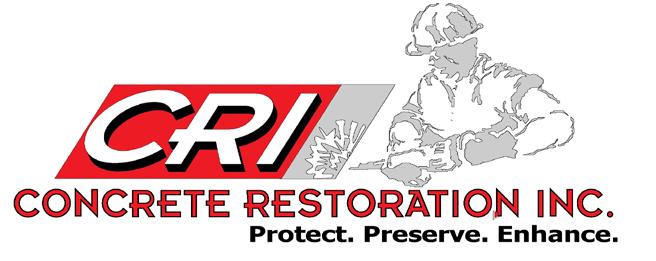
Self-retracting lifeline/lanyard means a deceleration device containing a drum-wound line which can be slowly extracted from, or retracted onto, the drum under slight tension during normal employee movement, and which, after onset of a fall, automatically locks the drum and arrests the fall.
Snap hook means a connector comprised of a hook-shaped member with a normally closed keeper, or similar arrangement, which may be opened to permit the hook to receive an object and, when released, automatically closes to retain the object. Snap hooks are generally one of two types:
The locking type with a self-closing, self-locking keeper which remains closed and locked until unlocked and pressed open for connection or disconnection; or
The non-locking type with a self-closing keeper which remains closed until pressed open for connection or disconnection. As of January 1, 1998, the use of a non-locking snap hook as part of personal fall arrest systems and positioning device systems is prohibited.
Steep roof means a roof having a slope greater than 4 in 12 (vertical to horizontal).
Toe board means a low protective barrier that will prevent the fall of materials and equipment to lower levels and provide protection from falls for personnel.
Unprotected sides and edges means any side or edge (except at entrances to points of access) of a walking/working surface, e.g., floor, roof, ramp, or runway where there is no wall or guardrail system at least 39 inches (1.0 m) high.
Walking/working surface means any surface, whether horizontal or vertical on which an employee walks or works, including, but not limited to, floors, roofs, ramps, bridges, runways, formwork and concrete reinforcing steel but not including ladders, vehicles, or trailers, on which employees must be located in order to perform their job duties.
REVISED DATE: January 1, 2025
FALL PROTECTION POLICY
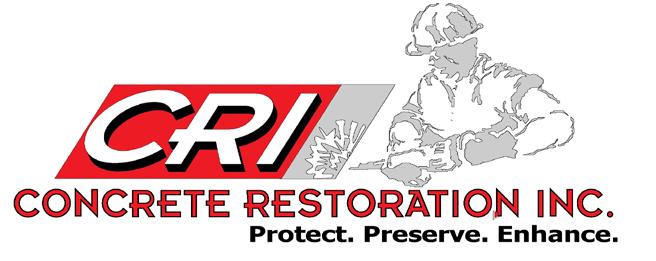
Warning line system means a barrier erected on a roof to warn employees that they are approaching an unprotected roof side or edge, and which designates an area in which roofing work may take place without the use of guardrail, body belt, or safety net systems to protect employees in the area.
Work area means that portion of a walking/working surface where job duties are being performed.
General
This section sets forth requirements for Concrete Restoration Inc to provide fall protection systems. All fall protection required by this section will conform to the criteria set forth in Chapter 296-880 WAC Unified Safety Standards for Fall Protection
Concrete Restoration Inc will determine if the walking/working surfaces on which its employees are to work have the strength and structural integrity to support employees safely. Employees will be allowed to work on those surfaces only when the surfaces have the requisite strength and structural integrity.
Unprotected Sides and Edges.
Each employee on a walking/working surface (horizontal and vertical surface) with an unprotected side or edge which is 4 feet or more above a lower level will be protected from falling by the use of guardrail systems, safety net systems, or personal fall arrest systems.
Leading Edges
Each employee who is constructing a leading edge 4 feet or more above lower levels will be protected from falling by guardrail systems, safety net systems, or personal fall arrest systems. Exception: When Concrete Restoration Inc can demonstrate that it is infeasible or creates a greater hazard to use these systems, Concrete Restoration Inc will develop and implement a fall protection plan
REVISED DATE: January 1, 2025
FALL PROTECTION POLICY
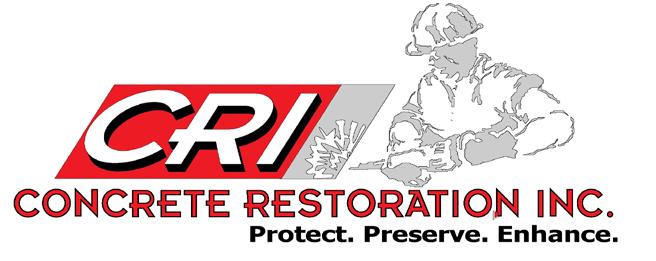
Each employee on a walking/working surface 4feet or more above a lower level where leading edges are under construction, but who is not engaged in the leading edge work, will be protected from falling by a guardrail system, safety net system, or personal fall arrest system. If a guardrail system is chosen to provide the fall protection, and a controlled access zone has already been established for leading edge work, the control line may be used in lieu of a guardrail along the edge that parallels the leading edge.
Hoist Areas
Each employee in a hoist area will be protected from falling 4 feet or more to lower levels by guardrail systems or personal fall arrest systems. If guardrail systems, [or chain, gate, or guardrail] or portions thereof, are removed to facilitate the hoisting operation (e.g., during landing of materials), and an employee must lean through the access opening or out over the edge of the access opening (to receive or guide equipment and materials, for example), that employee will be protected from fall hazards by a personal fall arrest system.
Holes
Each employee on walking/working surfaces will be protected from falling through holes (including skylights) more than 4 feet above lower levels, by personal fall arrest systems, covers, or guardrail systems erected around such holes.
Each employee on a walking/working surface will be protected from tripping in or stepping into or through holes (including skylights) by covers. Each employee on a walking/working surface will be protected from objects falling through holes (including skylights) by covers.
Formwork and Reinforcing Steel
Each employee on the face of formwork or reinforcing steel will be protected from falling 4 feet or more to lower levels by personal fall arrest systems, safety net systems, or positioning device systems.
REVISED DATE: January 1, 2025
FALL PROTECTION POLICY
Ramps, Runways, and Other Walkways
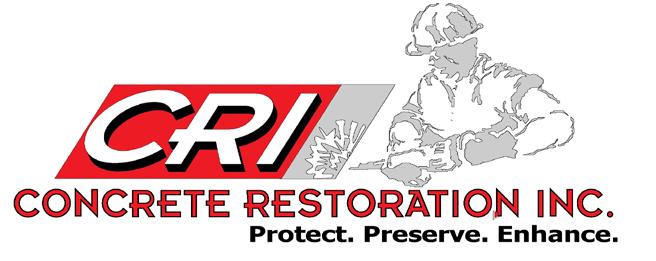
Each employee on ramps, runways, and other walkways will be protected from falling 4 or more to lower levels by guardrail systems.
Excavations
Each employee at the edge of an excavation 4 feet or more in depth will be protected from falling by guardrail systems, fences, or barricades when the excavations are not readily seen because of plant growth or other visual barrier.
Each employee at the edge of a well, pit, shaft, and similar excavation 4 feet or more in depth will be protected from falling by guardrail systems, fences, barricades, or covers.
Dangerous Equipment
Each employee less than 4 feet above dangerous equipment will be protected from falling into or onto the dangerous equipment by guardrail systems or by equipment guards.
Each employee 4 feet or more above dangerous equipment will be protected from fall hazards by guardrail systems, personal fall arrest systems, or safety net systems.
Roof Work on Low-Slope Roofs
Each employee engaged in roofing activities on low-slope roofs, with unprotected sides and edges 4 feet or more above lower levels will be protected from falling by guardrail systems, safety net systems, personal fall arrest systems, or a combination of warning line system and guardrail system, warning line system and safety net system, or warning line system and personal fall arrest system, or warning line system and safety monitoring system.
REVISED DATE: January 1, 2025
FALL PROTECTION POLICY
Steep Roofs
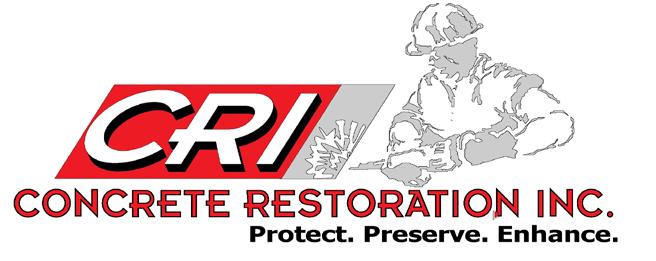
Each employee on a steep roof with unprotected sides and edges 4 feet or more above lower levels will be protected from falling by guardrail systems with toe boards, safety net systems, or personal fall arrest systems.
Precast Concrete Erection
Each employee engaged in the erection of precast concrete members (including, but not limited to the erection of wall panels, columns, beams, and floor and roof "tees") and related operations such as grouting of precast concrete members, who is 4 feet or more above lower levels will be protected from falling by guardrail systems, safety net systems, or personal fall arrest systems.
Residential construction
Each employee engaged in residential construction activities 4 feet or more above lower levels will be protected by guardrail systems, safety net system, or personal fall arrest.
Wall Openings
Each employee working on, at, above, or near wall openings (including those with chutes attached) where the outside bottom edge of the wall opening is 4 feet or more above lower levels and the inside bottom edge of the wall opening is less than 39 inches above the walking/working surface, will be protected from falling by the use of a guardrail system, a safety net system, or a personal fall arrest system.
Walking/Working Surfaces not otherwise addressed
Each employee on a walking/working surface 4 feet or more above lower levels will be protected from falling by a guardrail system, safety net system, or personal fall arrest system.
REVISED DATE: January 1, 2025
FALL PROTECTION POLICY
Protection from falling objects
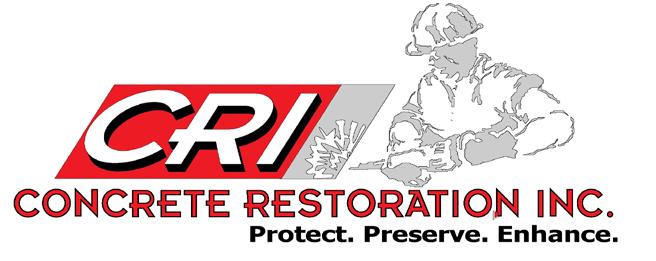
When an employee is exposed to falling objects, Concrete Restoration Inc will have each employee wear a hard hat and will implement one of the following measures:
Erect toe boards, screens, or guardrail systems to prevent objects from falling from higher levels; or,
Barricade the area to which objects could fall, prohibit employees from entering the barricaded area, and keep objects that may fall far enough away from the edge of a higher level so that those objects would not go over the edge if they were accidentally displaced.
General
Fall protection systems required by this part will comply with the applicable provisions of this section.
Concrete restoration Inc will provide and install all fall protection systems required by this subpart for an employee, and will comply with all other pertinent requirements of this subpart before that employee begins the work that necessitates the fall protection.
Guard rail systems
Guardrail systems and their use will comply with the following provisions:
Top edge height of top rails, or equivalent guardrail system members, will be 42 inches plus or minus 3 inches above the walking/working level. When conditions warrant, the height of the top edge may exceed the 45-inch height, provided the guardrail system meets all other criteria of this paragraph.
Note: When employees are using stilts, the top edge height of the top rail, or equivalent member, will be increased an amount equal to the height of the stilts.
REVISED DATE: January 1, 2025
FALL PROTECTION POLICY
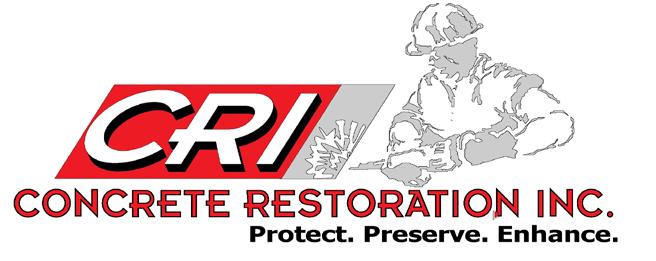
Mid rails, screens, mesh, intermediate vertical members, or equivalent intermediate structural members will be installed between the top edge of the guardrail system and the walking/working surface when there is no wall or parapet wall at least 21 inches high.
Mid rails, when used, will be installed at a height midway between the top edge of the guardrail system and the walking/working level.
Screens and mesh, when used, will extend from the top rail to the walking/working level and along the entire opening between top rail supports.
Intermediate members (such as balusters), when used between posts, will be not more than 19 inches apart.
Other structural members (such as additional midrails and architectural panels) will be installed such that there are no openings in the guardrail system that are more than 19 inches wide.
Guard rail systems will be capable of withstanding, without failure, a force of at least 200 pounds applied within 2 inches of the top edge, in any outward or downward direction, at any point along the top edge. When the 200 pound test load is applied in a downward direction, the top edge of the guardrail will not deflect to a height less than 39 inches above the walking/working level.
Mid rails, screens, mesh, intermediate vertical members, solid panels, and equivalent structural members will be capable of withstanding, without failure, a force of at least 150 pounds applied in any downward or outward direction at any point along the mid rail or other member.
Guardrail systems will be so surfaced as to prevent injury to an employee from punctures or lacerations, and to prevent snagging of clothing. The ends of all top rails and mid rails will not overhang the terminal posts, except where such overhang does not constitute a projection hazard.
Steel banding and plastic banding will not be used as top rails or mid rails. Top rails and mid rails will be at least one-quarter inch nominal diameter or thickness to prevent cuts and lacerations. If wire rope is used for top rails, it will be flagged at not more than 6-foot intervals with high-visibility material.
REVISED DATE: January 1, 2025
FALL PROTECTION POLICY
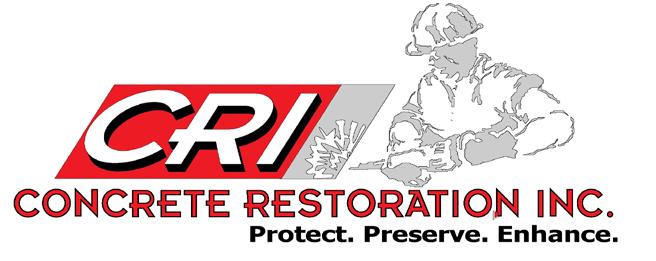
When guardrail systems are used at hoisting areas, a chain, gate or removable guardrail section will be placed across the access opening between guardrail sections when hoisting operations are not taking place.
When guardrail systems are used at holes, they will be erected on all unprotected sides or edges of the hole.
When guardrail systems are used around holes used for the passage of materials, the hole will have not more than two sides provided with removable guardrail sections to allow the passage of materials. When the hole is not in use, it will be closed over with a cover, or a guardrail system will be provided along all unprotected sides or edges.
When guardrail systems are used around holes which are used as points of access (such as ladderways), they will be provided with a gate, or be so offset that a person cannot walk directly into the hole.
Guardrail systems used on ramps and runways will be erected along each unprotected side or edge.
Manila, plastic or synthetic rope being used for top rails or mid rails will be inspected as frequently as necessary to ensure that it continues to meet the strength requirements.
Personal fall arrest systems
Personal fall arrest systems and their use will comply with the provisions set forth below. Effective January 1, 1998, body belts are not acceptable as part of a personal fall arrest system.
Connectors will be drop forged, pressed or formed steel, or made of equivalent materials.
Connectors will have a corrosion-resistant finish, and all surfaces and edges will be smooth to prevent damage to interfacing parts of the system.
Dee-rings and snap hooks will have a minimum tensile strength of 5,000 pounds.
REVISED DATE: January 1, 2025
FALL PROTECTION POLICY
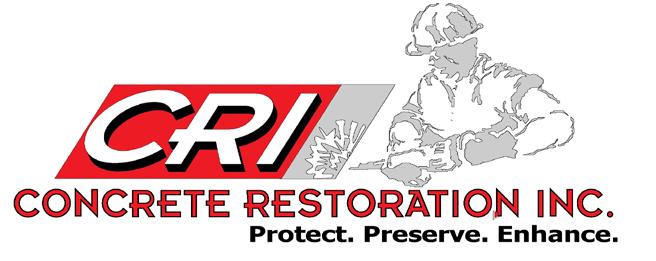
Dee-rings and snap hooks will be proof-tested to a minimum tensile load of 3,600 pounds without cracking, breaking, or taking permanent deformation.
Snap hooks will be sized to be compatible with the member to which they are connected to prevent unintentional disengagement of the snap hook by depression of the snap hook keeper by the connected member, or will be a locking type snap hook designed and used to prevent disengagement of the snap hook by the contact of the snap hook keeper by the connected member. Only locking type snap hooks will be used.
Unless the snap hook is a locking type and designed for the following connections, snap hooks will not be engaged:
1. Directly to webbing, rope or wire rope;
2. To each other;
3. To a Dee-ring to which another snap hook or other connector is attached;
4. To a horizontal lifeline; or
5. To any object which is incompatibly shaped or dimensioned in relation to the snap hook such that unintentional disengagement could occur by the connected object being able to depress the snap hook keeper and release itself.
On suspended scaffolds or similar work platforms with horizontal lifelines which may become vertical lifelines, the devices used to connect to a horizontal lifeline will be capable of locking in both directions on the lifeline.
Horizontal lifelines will be designed, installed, and used, under the supervision of a qualified person, as part of a complete personal fall arrest system, which maintains a safety factor of at least two.
Lanyards and vertical lifelines will have a minimum breaking strength of 5,000 pounds.
REVISED DATE: January 1, 2025
FALL PROTECTION POLICY
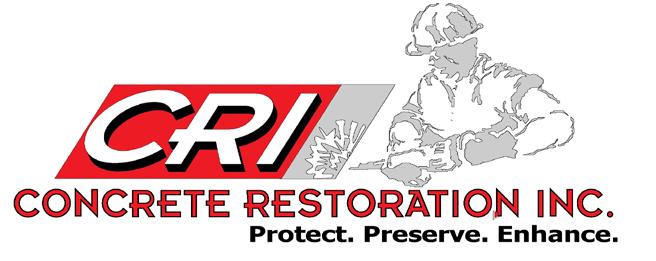
Lifelines will be protected against being cut or abraded.
Self-retracting lifelines and lanyards which automatically limit free fall distance to 2 feet or less will be capable of sustaining a minimum tensile load of 3,000 pounds applied to the device with the lifeline or lanyard in the fully extended position.
Self-retracting lifelines and lanyards which do not limit free fall distance to 2 feet or less, rip stitch lanyards, and tearing and deforming lanyards will be capable of sustaining a minimum tensile load of 5,000 pounds applied to the device with the lifeline or lanyard in the fully extended position.
Ropes and straps (webbing) used in lanyards, lifelines, and strength components of body harnesses will be made from synthetic fibers.
Anchorages used for attachment of personal fall arrest equipment will be independent of any anchorage being used to support or suspend platforms and capable of supporting at least 5,000 pounds per employee attached, or will be designed, installed, and used as follows:
1. As part of a complete personal fall arrest system which maintains a safety factor of at least two; and
2. under the supervision of a qualified person.
Personal fall arrest systems, when stopping a fall, will:
1. Limit maximum arresting force on an employee to 1,800 pounds when used with a body harness.
2. Be rigged such that an employee can neither free fall more than 6 feet (1.8 m), nor contact any lower level.
3. Bring an employee to a complete stop and limit maximum deceleration distance an employee travels to 3.5 feet (1.07 m); and,
REVISED DATE: January 1, 2025
FALL PROTECTION POLICY
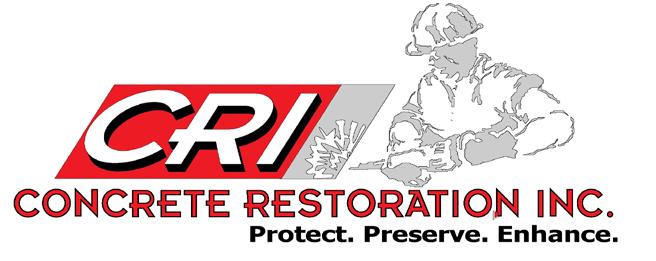
4. Have sufficient strength to withstand twice the potential impact energy of an employee free falling a distance of 6 feet, or the free fall distance permitted by the system, whichever is less.
The attachment point of the body harness will be located in the center of the wearer's back near shoulder level, or above the wearer's head.
Harnesses, and components will be used only for employee protection (as part of a personal fall arrest system or positioning device system) and not to hoist materials.
Personal fall arrest systems and components subjected to impact loading will be immediately removed from service and will not be used again for employee protection until inspected and determined by a competent person to be undamaged and suitable for reuse.
Concrete restoration Inc will provide prompt rescue of employees in the event of a fall or will assure that employees are able to rescue themselves.
Personal fall arrest systems will be inspected prior to each use for wear, damage and other deterioration, and defective components will be removed from service.
Personal fall arrest systems will not be attached to guardrail systems, nor will they be attached to hoists except as specified in other subparts of this Part.
When a personal fall arrest system is used at hoist areas, it will be rigged to allow the movement of the employee only as far as the edge of the walking/working surface.
Warning Line Systems
Warning line systems and their use will comply with the following provisions:
The warning line will be erected around all sides of the roof work area.
REVISED DATE: January 1, 2025
FALL PROTECTION POLICY
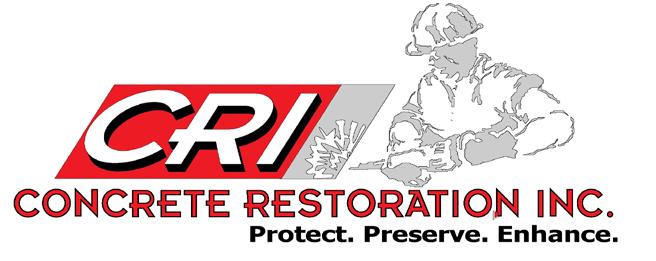
When mechanical equipment is not being used, the warning line will be erected not less than 6 feet from the roof edge.
When mechanical equipment is being used, the warning line will be erected not less than 6 feet from the roof edge which is parallel to the direction of mechanical equipment operation, and not less than 10 feet from the roof edge which is perpendicular to the direction of mechanical equipment operation.
Points of access, materials handling areas, storage areas, and hoisting areas will be connected to the work area by an access path formed by two warning lines.
When the path to a point of access is not in use, a rope, wire, chain, or other barricade, equivalent in strength and height to the warning line, will be placed across the path at the point where the path intersects the warning line erected around the work area, or the path will be offset such that a person cannot walk directly into the work area.
Warning lines will consist of ropes, wires, or chains and supporting stanchions erected as follows:
1. The rope, wire, or chain will be flagged at not more than 6-foot intervals with high-visibility material;
2. The rope, wire, or chain will be rigged and supported in such a way that its lowest point (including sag) is no less than 36 inches from the walking/working surface and its highest point is no more than 45 inches from the walking/working surface;
3. After being erected, with the rope, wire, or chain attached, stanchions will be capable of resisting, without tipping over, a force of at least 16 pounds applied horizontally against the stanchion, 30 inches above the walking/working surface, perpendicular to the warning line, and in the direction of the floor, roof, or platform edge;
4. The rope, wire, or chain will have a minimum tensile strength of 500 (lbs) pounds.
REVISED DATE: January 1, 2025
FALL PROTECTION POLICY
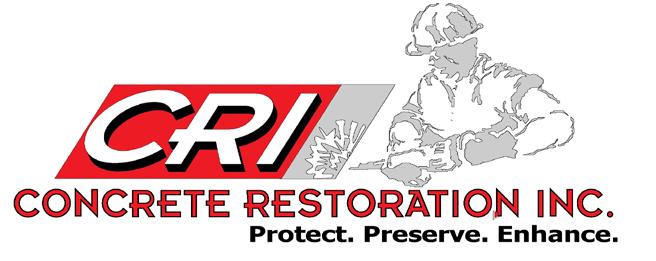
5. The line will be attached at each stanchion in such a way that pulling on one section of the line between stanchions will not result in slack being taken up in adjacent sections before the stanchion tips over.
No employee will be allowed in the area between a roof edge and a warning line unless the employee is performing roofing work in that area.
Mechanical equipment on roofs will be used or stored only in areas where employees are protected by a warning line system, guardrail system, or personal fall arrest system.
Safety Monitoring Systems
Safety monitoring and their use will comply with the following provisions:
Concrete Restoration Inc will designate a competent person to monitor the safety of other employees and Concrete Restoration Inc will ensure that the safety monitor complies with the following requirements:
The safety monitor will be competent to recognize fall hazards;
1. The safety monitor will warn the employee when it appears that the employee is unaware of a fall hazard or is acting in an unsafe manner;
2. The safety monitor will be on the same walking/working surface and within visual sighting distance of the employee being monitored;
3. The safety monitor will be close enough to communicate orally with the employee; and
4. The safety monitor will not have other responsibilities which could take the monitor's attention from the monitoring function.
Mechanical equipment will not be used or stored in areas where safety monitoring systems are being used to monitor employees engaged in roofing operations on low-slope roofs.
REVISED DATE: January 1, 2025
FALL PROTECTION POLICY
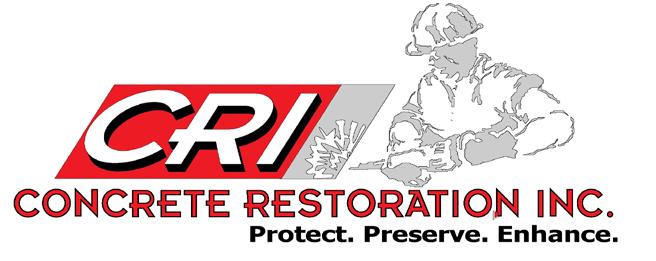
No employee, other than an employee engaged in roofing work [on lowsloped roofs] or an employee covered by a fall protection plan, will be allowed in an area where an employee is being protected by a safety monitoring system.
"Covers."
Covers for holes in floors, roofs, and other walking/working surfaces will meet the following requirements:
Covers located in roadways and vehicular aisles will be capable of supporting, without failure, at least twice the maximum axle load of the largest vehicle expected to cross over the cover.
All other covers will be capable of supporting, without failure, at least twice the weight of employees, equipment, and materials that may be imposed on the cover at any one time.
All covers will be secured when installed so as to prevent accidental displacement by the wind, equipment, or employees.
All covers will be color coded or they will be marked with the word "HOLE" or "COVER" to provide warning of the hazard.
Note: This provision does not apply to cast iron manhole covers or steel grates used on streets or roadways.
Protection from Falling Objects
Falling object protection will comply with the following provisions:
1. Toe boards, when used as falling object protection; will be erected along the edge of the overhead walking/working surface for a distance sufficient to protect employees below.
2. Toe boards will be capable of withstanding, without failure, a force of at least 50 pounds applied in any downward or outward direction at any point along the toe board.
REVISED DATE: January 1, 2025
FALL PROTECTION POLICY
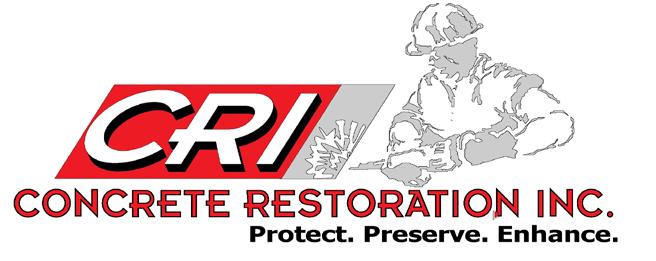
3. Toe boards will be a minimum of 3 1/2 inches in vertical height from their top edge to the level of the walking/working surface. They will have not more than 1/4-inch clearance above the walking/working surface. They will be solid or have openings not over 1 inch in greatest dimension.
Where tools, equipment, or materials are piled higher than the top edge of a toe board, paneling or screening will be erected from the walking/working surface or toe board to the top of a guardrail system's top rail or mid rail, for a distance sufficient to protect employees below.
Guardrail systems, when used as falling object protection, will have all openings small enough to prevent passage of potential falling objects.
Fall Protection Plan
The fall protection plan will be prepared by a qualified person and developed specifically for the site where work is to be performed.
Any changes to the fall protection plan will be approved by a qualified person.
A copy of the fall protection plan with all approved changes will be maintained at the job site.
The implementation of the fall protection plan will be under the supervision of a competent person.
Training Program
Concrete Restoration Inc will provide a training program for each employee who might be exposed to fall hazards. The program will enable each employee to recognize the hazards of falling and will train each employee in the procedures to be followed in order to minimize these hazards.
Concrete Restoration Inc will assure that each employee has been trained, as necessary, by a competent person qualified in the following areas:
1. The nature of fall hazards in the work area;
REVISED DATE: January 1, 2025
FALL PROTECTION POLICY
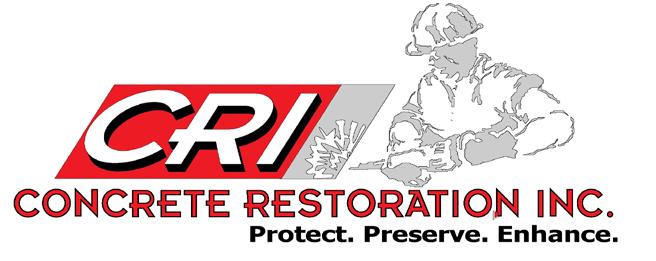
2. The correct procedures for erecting, maintaining, disassembling, and inspecting the fall protection systems to be used;
3. The use and operation of guardrail systems, personal fall arrest systems, safety net systems, warning line systems, safety monitoring systems, controlled access zones, and other protection to be used;
4. The role of each employee in the safety monitoring system when this system is used;
5. The limitations on the use of mechanical equipment during the performance of roofing work on low-sloped roofs;
6. The correct procedures for the handling and storage of equipment and materials and the erection of overhead protection; and
7. The role of employees in fall protection plans;
Certification of Training
Concrete Restoration Inc will prepare a written certification record. The written certification record will contain the name or other identity of the employee trained, the date(s) of the training
Retraining
When Concrete Restoration Inc has reason to believe that any affected employee who has already been trained does not have the understanding and skills required in this policy, Concrete Restoration Inc will retrain each such employee. Circumstances where retraining is required include, but are not limited to, situations where:
1. Changes in the workplace render previous training obsolete; or
2. Changes in the types of fall protection systems or equipment to be used render previous training obsolete; or
3. Inadequacies in an affected employee's knowledge or use of fall protection systems or equipment indicate that the employee has not retained the requisite understanding or skill.
Accident Investigation: All accidents and serious incidents (near misses) must be investigated, implementing changes to the fall protection plan as necessary.
REVISED DATE: January 1, 2025
First Aid Policy
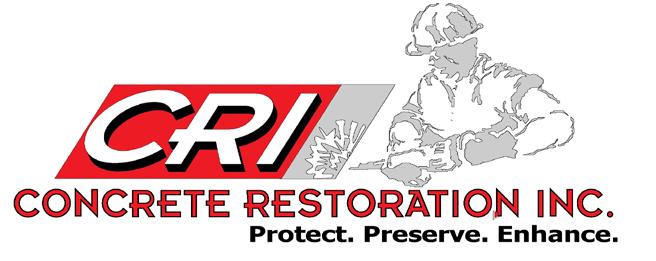
First Aid Policy
Reference: OSHA 29 CFR 1926.50 and WAC 296-800-150
Purpose
Ensure employees have a working knowledge of basic first aid procedures.
Scope
Applicable to Concrete Restoration Inc employees working on site.
It is the goal of Concrete Restoration Inc to have a safe work environment for employees, visitors, and those that are conducting business on any Concrete Restoration Inc sites. Emphasis is placed on the prevention of accidents, injuries, and illnesses through safe work practices. In the event of an accident, prompt and knowledgeable treatment of injured employees will, in many cases, prevent minor injuries from becoming major ones.
Concrete Restoration Inc will ensure personnel have been trained in basic first aid and Blood-Borne Pathogens exposure. These trained personnel will respond to medical problems or medical emergencies.
The job site Foreman are responsible for all tasks related to this policy.
Concrete Restoration Inc will ensure the availability of medical personnel for advice and consultation on matters of occupational health.
Provisions will be made prior to the commencement of the project for prompt medical attention in case of serious injury.
In the absence of an infirmary, clinic, or hospital in near proximity to the workplace and used for the treatment of injured employees, a person who has a valid certificate in first-aid training will be available at the worksite to render first aid.
In areas where 911 calls are not available, the telephone numbers of the physicians, hospitals, or ambulances will be conspicuously posted.
REVISED DATE: January 1, 2025
First Aid Policy
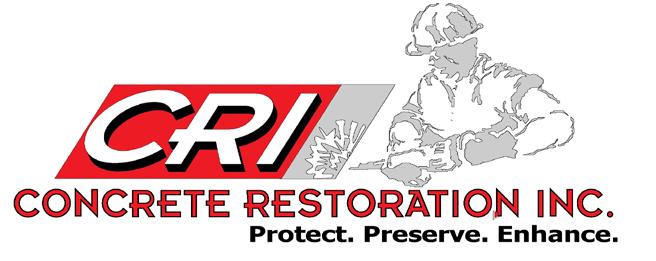
Where the eyes or body of any person may be exposed to injurious corrosive materials, suitable facilities for quick drenching or flushing of the eyes and body will be provided within the work area for immediate emergency use.
Proper equipment for prompt transportation of the injured person to a physician or hospital, or a communication system for contacting necessary ambulance service, will be provided.
There may be cases when injured employees who need professional medical attention can be transported to the hospital by car. There may be other cases, however, when injured employees should be transferred by ambulance to a hospital or medical center. If there is any doubt about the mode of transportation, an ambulance should be called. For example, the following conditions would definitely indicate ambulance service:
• Employee is unconscious or in shock
• Hemorrhaging
• Severe abdominal cramps and/or vomiting
• Any apparent fracture
Other symptoms of internal injury
All animal bites, because of the possibility of rabies, should receive prompt medical attention by a physician. If someone is bitten, every attempt should be made to confine the animal.
NOTE – It is imperative that medical supplies be easily accessible when required. Keep the kits and supplies in a place that can be easily accessed by all employees.
First Aid Kits – will include at a minimum:
The contents of the first aid kit will be placed in a weatherproof container with individual sealed packages for each type of item, and will be checked by the shop before being sent out on each job and at least weekly on each job to ensure that the expended items are replaced.
REVISED DATE: January 1, 2025
First Aid Policy
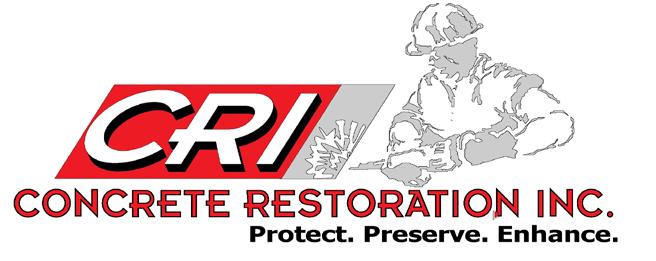
Components: 16 adhesive strips (1" x 3"), 1 surgical (5" x 9"), 2 rolls of adhesive tape (1/2" x 2-1/2 yds.), 4 sterile pads (3" x 3"), 1 triangular bandage unit, 6 burn treatment applications, 10 antiseptic applications and 2 pair vinyl exam gloves. Additional contents are as follows:
• (16) 3/4"x3" Adhesive plastic bandages
• (1) 2"x4" Elbow & knee plastic bandage
• (1) 1-3/4"x2" Small fingertip fabric bandage
• (4) 2"x2" Gauze dressing pads, (2) 2-pks
• (4) 3"x3" Gauze dressing pads, (2) 2-pks
• (2) 4"x4" Gauze dressing pads, (1) 2-pack
• (1) 5"x9" Trauma pad
• (1) 2"x4.1 yd Conforming gauze roll bandage
• (1) 3"x4.1 yd Conforming gauze roll bandage
• (1) Triangular sling/bandage
• (1) 6"x9" Instant cold compress
• (2) Exam quality gloves, 1 pair
• (1) Sterile eye pad
• (3) Triple antibiotic ointment packs
• (1) Burn relief pack, 3.5 gm
• (6) Alcohol cleansing pads
• (6) Antiseptic cleansing wipes (sting free)
• (1) 1"x5 yd. First aid tape roll
• (6) Aspirin tablets, (3) 2-pks
• (1) 4-1/2" Scissors, nickel plated
• (1) 4" Tweezers, plastic
• (1) First aid guide
REVISED DATE: January 1, 2025
HAZARDOUS CHEMICAL COMMUNICATION POLICY
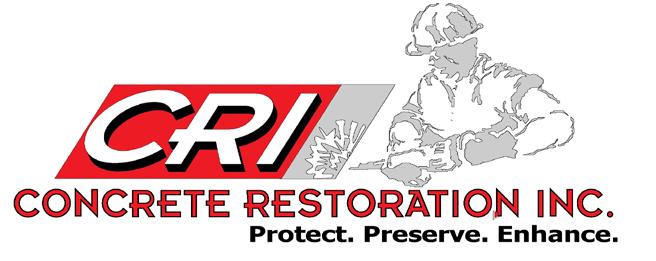
HAZARDOUS CHEMICAL COMMUNICATION POLICY
Reference: 29 CFR 1910 Subpart P/R/T/WAC WAC 296-155-350
Purpose
There are various types of tools and equipment used in the workplace for many different purposes. Examples include, but are not limited to, portable hand tools, power tools, pneumatic tools, and powder-actuated tools.
The purpose of this policy is to provide employees with appropriate knowledge relating to the care and use of tools and equipment and to protect employees from hazards associated with improper use of tools and equipment and defective and poorly maintained tools and equipment.
Policy
Only trained and/or experienced employees may use/operate tools or equipment. Tools and equipment shall not be modified and they are to be used only for their designed purpose.
It shall be the responsibility of the employee to inspect tools and equipment prior to use and to use all tools and equipment in a safe manner. Employees observed abusing, altering, modifying or misusing tools or equipment shall be subject to disciplinary action.
Employees shall wear all appropriate personal protective equipment while using tools and equipment. Additionally, if a tool or piece of equipment is found to be defective, the tool/equipment shall be red-tagged, taken out of service until it can be replaced or repaired by a qualified person.
It shall be the responsibility of the Project Manager or Management Team to designate a competent person who will be assigned to be responsible for testing/inspecting and repairing all tools and equipment. All periodic inspections, maintenance and repairs of tools or equipment shall be documented.
REVISED DATE: January 1, 2025
HAZARDOUS CHEMICAL COMMUNICATION POLICY
Procedure
General Tool Safety
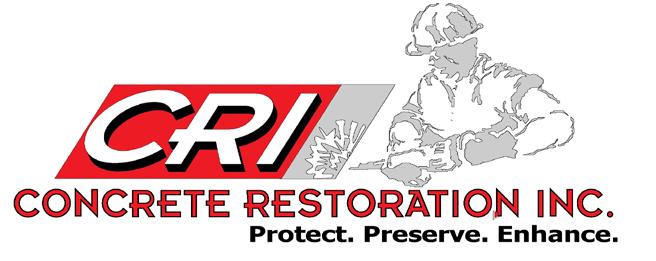
Many serious injuries have resulted from the improper use of tools and equipment. Many of these injuries could have been prevented if the following rules were followed:
Inspection and Maintenance:
• All tools shall be identified and inventoried either individually or by group.
• All tools in the inventory shall have a documented inspection at least once every six months. In addition to these periodic documented inspections all tools shall be inspected prior to issue and upon return by the tool room attendants and prior to each use by the user.
• All tools will be kept in good working condition with no modifications.
• All periodic inspections and all maintenance & repairs shall be documented
• Selection
Use the right tool for the task instead of trying to make the wrong one fit.
• Use Keep control of yourself, the tool, and the job. When applying force with a tool, remember that it may slip, break, or just suddenly do its job. Watch your hands and your balance (body mechanics) to avoid injury.
Vibration Absorbing Gloves are to be made available to workers using pneumatic impact guns or other vibrating equipment. These gloves are required PPE for worker’s operating heavy vibrating tools
REVISED DATE: January 1, 2025
HAZARDOUS CHEMICAL COMMUNICATION POLICY
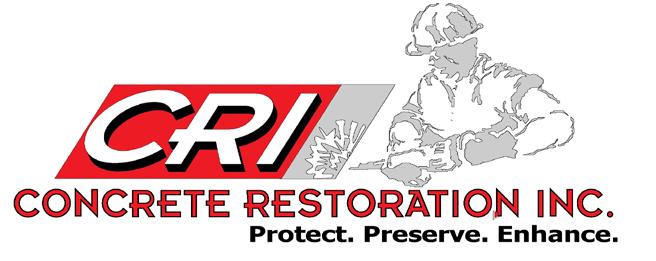
(i.e. jack hammers, 90 guns, impact guns etc.). The use of these gloves are designed to dampen vibration, dissipate impact and absorb shock, they can assist in the prevention of cumulative trauma injury often associated with operating this type of equipment. They only work if you use them.
Select the right protective equipment for the task and use it properly. Do not use tools and equipment that you have not been trained to use.
• Care
Take proper care of your tools and equipment. Keep them stored where they will not get damaged and will not present a hazard. Check your tools and equipment prior to use for defects, wear, or damage. Immediately remove from service and tag any defective tools. Damaged tools shall be turned into the tool room for repair or replacement.
• Supervision
Supervisors shall be responsible for ensuring that employees are trained before using a specific tool. Watch your employees at work. Ask them about their immediate assignment and take an interest in finding the safest way to do the job. Then follow up to insure that the tools and equipment in your area are being used safely.
Hand Tool Safety
Hand tools shall only be used for the purpose for which they are intended.
All appropriate PPE will be worn while using hand tools.
Wrenches, including adjustable, pipe and socket shall not be used when jaws are sprung to the point of slippage.
REVISED DATE: January 1, 2025
HAZARDOUS CHEMICAL COMMUNICATION POLICY
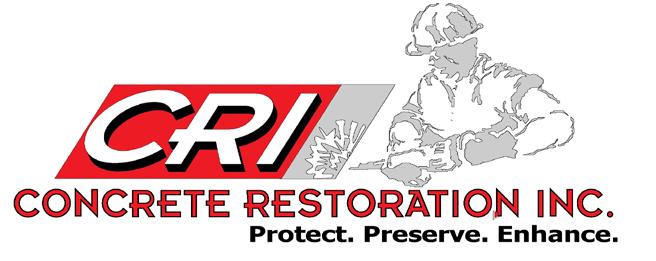
Pipe wrench parts (i.e., jaws) are not to be removed and used for anything other than the manufactured use.
The use of snipes and cheater bars or double wrenching to gain leverage is prohibited.
Always use tool holder while using hammer and knocker wrenches.
Hand tools shall be tagged and removed from service if any of the following defects are present:
• Impact tools, such as hammers, flange wedges chisels, drift pins, pin bars and knocker wrenches with visible signs of mushrooming, cracking or bending.
• Wooden handle tools, such as hammers, picks, shovels, and brooms with visible sign of cracking, loosening or splintering of the handle.
• Wrenches, such as adjustable, combo and pipe with visible signs of bending, cracking, defective handles or other defects that impair their strength.
Electrical Power Tool Safety
All appropriate PPE will be worn while using power tools.
Be sure that the proper permit has been obtained prior to use of electrical power tools.
GFCI’s are to be used with all portable electric equipment. GFCI’s are to be inspected and tested prior to each use.
Do not connect electrical power unless the operating switch is turned off.
Employee shall avoid loose fitting clothing when operating power tools.
REVISED DATE: January 1, 2025
HAZARDOUS CHEMICAL COMMUNICATION POLICY
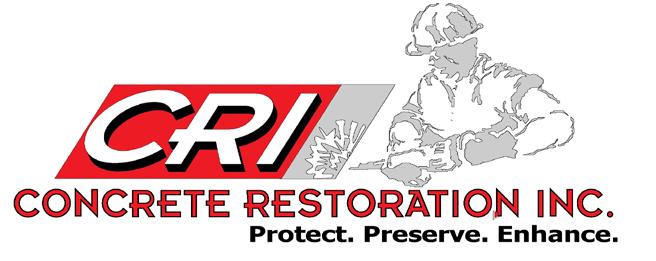
The power source on tools shall be physically disconnected prior to attempting any repairs or attachment replacement.
Protective guards on power tools shall not be removed, altered or modified.
All electrical tools and power cords must be inspected.
Electrical tools and power cords must display the current inspection color code for the current inspection period to it being placed in service.
Electrical tools shall not be hoisted or carried by their power cords.
Cords are tripping hazards. Route them so as to minimize interference in walkways. Overhead is preferred.
Electrical power tools shall be tagged and removed from service if any of the following defects are present:
• Electrical power tool cord does not have current inspection color code.
• Power cord is frayed, cut or damaged. The use of electrical tape to cover damage to cords is prohibited.
• Defective or faulty on/off switches.
• Loose or defective components
Air Power Tool Safety
All hoses exceeding 1/2” inside diameter shall have a safety device at the source of supply or branch line to reduce pressure in case of hose failure.
Chicago fittings shall be pinned.
Attachments on air tools shall be secured by retainer pins and rings.
REVISED DATE: January 1, 2025
HAZARDOUS CHEMICAL COMMUNICATION POLICY
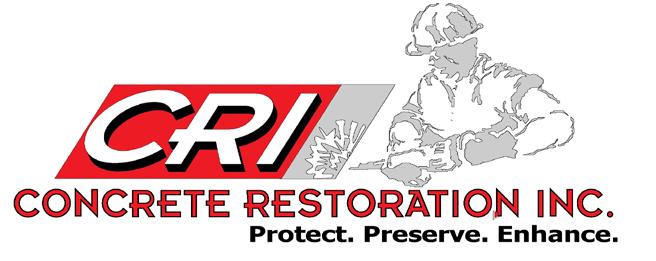
Do not connect air unless the operating switch is turned off.
Do not disconnect tool until air supply is shut off and air pressure is bled off.
Air power tools shall not be hoisted or carried by their hoses.
Hoses are tripping hazards. Route them so as to minimize interference in walkways. Overhead is preferred.
Air power tools shall be tagged and removed from service if any of the following defects are present:
• Air power tools, such as air power grinders, impact wrenches, German hacksaws with visible signs of deformities in the body of the tool, improperly functioning actuator, bent or deformed blades, or any signs of obvious damage to the air supply line fittings.
• Hoses must be visually inspected for cracking, signs of aging, worn or damaged connecting fittings, or any other obvious deformities, such as blistering or bulges.
Powder Actuated Tool Safety
Only employees who have received an approved training course and license for the particular tool to be used may operate powder-actuated tools.
Tool room personnel shall not issue powder-actuated tools unless the person requesting the tool can provide a current license for that tool.
Powder-actuated tools shall be tested prior to use to ensure all safeties are functioning.
The fastener shall not be loaded until ready for the shot. The tool shall not be left unattended unless it is unloaded.
Never point either an empty or loaded tool at any person.
REVISED DATE: January 1, 2025
HAZARDOUS CHEMICAL COMMUNICATION POLICY
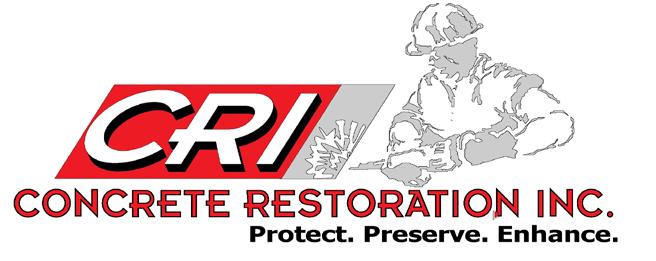
Keep both hands and feet clear of the open-end of the barrel.
In the event of a misfire, the operator shall hold the tool firmly against the work surface for a period of 30 seconds and then follow manufacturer’s instructions.
Personnel, other than the operator of the tool, must stay clear of the area where the tool is being used.
Operators of powder-actuated tools shall wear goggles for eye protection while operating these tools.
A sign at least 8 x 10 inches, using boldface type no less than 1 inch in height, shall be posted within 50 feet of the area where the tool is being used. The sign shall bear the following wording:
CAUTION
POWDER-ACTUATED TOOL IN USE
Powder-actuated tools shall be tagged and removed from service if any of the following defects are present:
• Tool has visible signs of worn or damaged parts.
• Missing or malfunctioning parts or accessories.
• Missing operator’s instruction manual or missing power load and fastener chart.
• Tool misfires more than once during use.
Abrasive Wheel Machinery
Abrasive wheels shall be used only on machines provided with safety guards as defined:
REVISED DATE: January 1, 2025
HAZARDOUS CHEMICAL COMMUNICATION POLICY
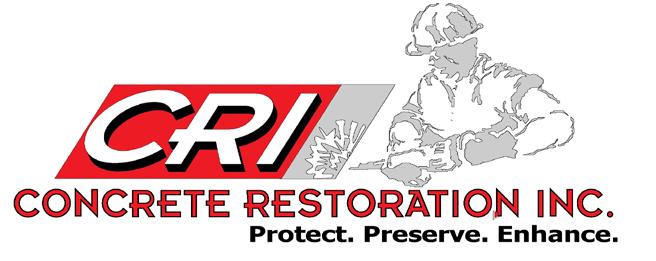
• The safety guard shall be mounted so as to maintain proper alignment with the wheel, and the strength of the fastenings shall exceed the strength of the guard.
• Grinding machines shall be equipped with flanges
• Abrasive wheel machinery guards shall meet the design specifications of the American National Standard Safety Code for the Use, Care, and Protection of Abrasive Wheels, ANSI B7.1-1970, which is incorporated by reference as specified in Sec. 1910.6.
• Never exceed the maximum wheel speed RPM. (every when is marked) Check the speed marked on the wheel and compare it to the speed on the grinder.
• When installing the wheel, check for cracks and defects. Ensure mounting flanges are clean and the mounting blotters are used. Do not over tighten the mounting nut.
Physical Risk Factors
Importance of Ergonomics
The application of ergonomics can:
• Improve health and safety through the reduction of ergonomics risk factors and resulting work-related injuries and disorders
• Improve comfort, morale, productivity, and job satisfaction.
• Reduce workers’ compensation costs and employee turnover.
Injuries – Musculoskeletal Disorders (MSD)
MSDs are a category of injuries and disorders that deal with the musculoskeletal system. These disorders are not usually caused by acute trauma but instead occur slowly over time due to wear and tear on soft tissues such as:
REVISED DATE: January 1, 2025
HAZARDOUS CHEMICAL COMMUNICATION POLICY
• Muscles
• Tendons
• Ligaments
• Cartilage
• Nerves
Work-related Musculoskeletal Disorders (WMSDs)
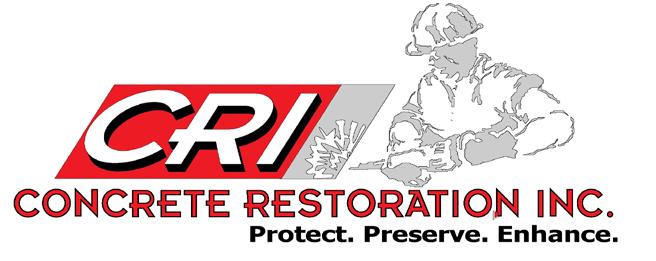
WMSDs are MSDs that are caused or aggravated by work practices and/or environments. WMSDs do not generally result from a single event or accident, but rather are disorders that have developed gradually from chronic workplace and occupational conditions causing repeated trauma. Common WMSDs include:
• Tendonitis
• Epicondylitis
• Bursitis
• Carpal Tunnel Syndrome
• Herniated Spinal Disc
Physical Risk Factors
Physical workplace risk factors can cause WMSDs to develop. The risk factors must occur in combination to present a risk of WMSDs and they typically magnify each other as a result. There are some common physical risk factors:
• Compression or Contact Stress
• Position or Posture
REVISED DATE: January 1, 2025
HAZARDOUS CHEMICAL COMMUNICATION POLICY
• Non-neutral
• Static
• Vibration
• Whole body
• Hand-Arm
• Force
• Repetition
• Duration
Compression or Contact Stress
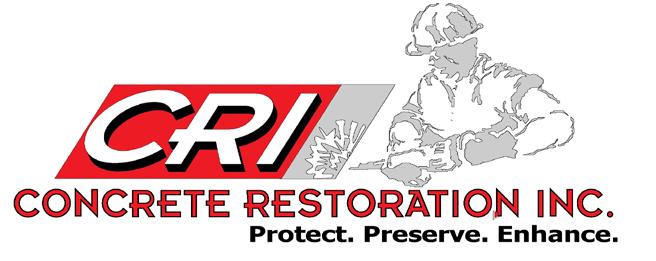
Compression occurs when an object presses on soft tissue. This concentration of force on small areas reduces blood flow and nerve transmission and can damage the soft tissue. Compression occurs from:
Leaning or pressing against hard edges, sharp surfaces, corners Supporting excessive weight Gripping tools
Neutral Posture vs. Non-neutral Posture
Posture or position dictates how hard the body works.
Neutral posture - a posture that maximizes strength, speed, endurance, and comfort while decreasing the risk of WMSDs.
Non-neutral posture - an awkward or unsupported position that stretches the physical limits and which can cause muscle fatigue, micro-trauma to tendons or ligaments, and compress or elongate soft tissues such as nerves.
REVISED DATE: January 1, 2025
HAZARDOUS CHEMICAL COMMUNICATION POLICY
Vibration
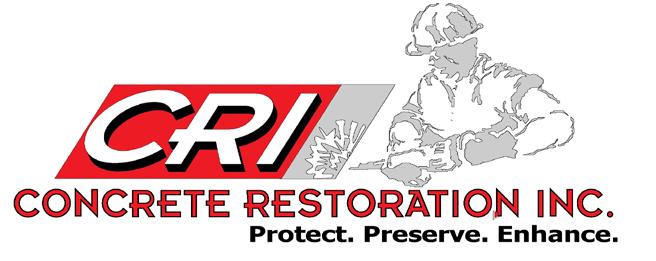
Vibration is another type of physical risk factor. A simple definition of vibration is rapid movement back and forth; however, vibration involves the exposure to movement against the body from all directions. Vibration occurs in two forms:
Whole body
Hand-Arm
Whole Body Vibration
Whole body vibration is caused by standing or sitting on vibrating surfaces, which in turn causes muscle contractions and fatigue. The vibration works its way through the body and results in muscle fatigue and contractions. High or prolonged exposure to whole body vibration can affect the skeletal muscles and digestive system and cause lower back disorders. An example of workers who experience this type of vibration are heavy vehicle operators who are exposed to whole body vibration when they drive.
Hand-Arm Vibration
Hand-arm vibration is usually caused when a worker holds a vibrating hand tool for a long period of time. This action causes reduced blood flow to the fingers and can lead to blanching of the fingers or Raynaud’s Syndrome. Cold weather is a contributing factor to vibration-related WMSDs. Some of the WMSDs associated with hand-arm vibration are:
Reynaud’s Syndrome
Vibration-induced white finger
Carpal Tunnel Syndrome
What are some examples of tools that contribute to hand-arm vibration? A chain saw, jack hammer, impact wrench, saws-all, needle gun, riveter, chipping hammers, soil compactor, pavement breaker, floor buffer are all
REVISED DATE: January 1, 2025
HAZARDOUS CHEMICAL COMMUNICATION POLICY
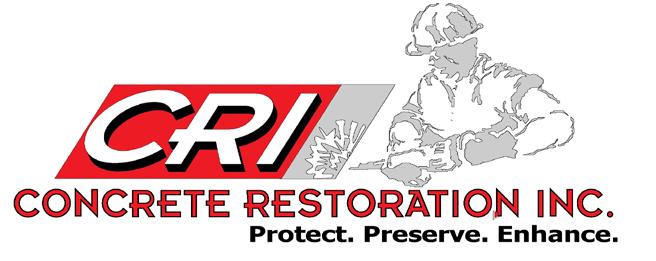
considered percussion types of tools which typically produce high levels of vibration. A jig saw, grinder, and sander usually cause moderate vibration.
Force
Force is the use of power or exertion to move, direct, or operate equipment. The less force required to operate equipment the less traumatic it is to the body. Excessive force exertion may cause the muscles to meet or exceed their maximum capability, resulting in possible fatigue or injury. Repeated muscle trauma can result in damage or injury.
High Force Examples
High force risk factors can occur while lifting, carrying, pushing, pinching and gripping. Posture and position are important in considering high force risks. The power zone for lifting with the greatest strength and lowest risk of injury is close to the body between thigh and shoulder height. And, it is important to note that lifting even a 20 lb weight one hundred times a day in a non-neutral posture may pose a high force risk.
Repetition
The physical risk factor repetition is defined as performing the same motion or group of motions excessively, for example:
• Repeating the same motion every few seconds
• Repeating a cycle of motions involving the same body parts/muscle groups
• Using a tool or device in a steady manner
Repetition usually occurs in conjunction with other risk factors. It is important to note that if you change the job but still use same muscle group you are not doing anything different.
Repetition is often seen in tasks such as assembly, typing, operating machinery, or loading and unloading a vehicle.
REVISED DATE: January 1, 2025
HAZARDOUS CHEMICAL COMMUNICATION POLICY
Duration
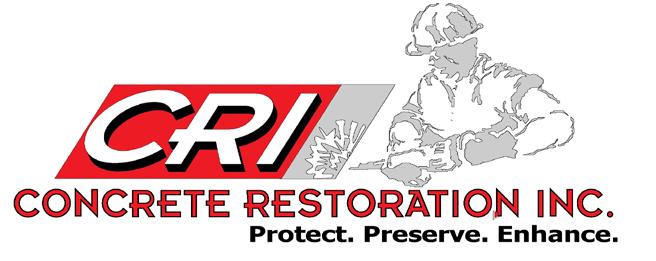
How long a task is performed or how frequently the same muscle groups are used in a day contributes to the risk factor known as duration. Duration is defined as the time period that an action continues or lasts. Continuous use does not allow muscles time to recover and in turn magnifies other risk factors. The key point to remember is that the longer the duration the greater the exposure and the greater the risk. Taking breaks, reducing the amount of time spent on similar tasks, and alternating between jobs that use different actions can help reduce duration exposure.
Company Policy:
It is the policy of Concrete Restoration, Inc. to maintain a work environment that prohibits the harassment of employees in any form by any other employee, vendor, customer, or other persons while the employee is engaged in company business, on premises or outside of the workplace.
General Principles:
It is the responsibility of every employee to recognize the rights of others. We expect our management team to respond promptly and confidently to all complaints of harassment.
If an employee becomes aware of harassment, whether it affects them or someone else, they should promptly tell management about it. Employees can contact any of the following Manager directly for this purpose: President, V.P. of Operations, Controller or Safety Manager.
Harassment can involve a wide range of unwanted behavior. There can be ethnic, racial, sexual, disability, age, marital status, veteran, and religious harassment, or harassment directed to members of other legally protected groups.
Harassment can result from the conduct of someone in management towards an employee, one employee towards another, or employee and non- employee towards each other. Harassment can apply to conduct at the workplace or conduct off the premises after hours. Among the many
REVISED DATE: January 1, 2025
HAZARDOUS CHEMICAL COMMUNICATION POLICY
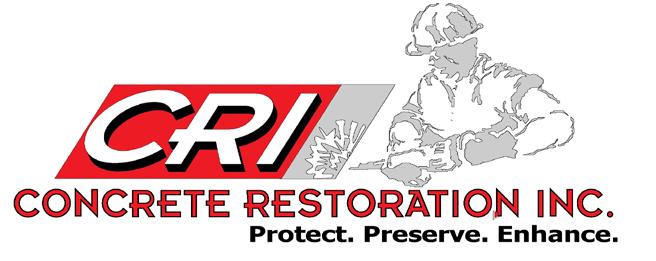
forms of harassment are verbal harassment (threats, derogatory comments, slurs, or epithets), physical harassment (assault, touching or interference), visual harassment (posters, cartoons, pictures, or drawings), and innuendos or rumors, just to name a few.
Sexual harassment can include unwelcome sexual advances, requests for sexual favors, sexually motivated physical contact, and other unwelcome conduct of sexual nature. Harassment results from these types of unwelcome conduct when:
submission to the conduct is made either explicitly or implicitly a term or condition of a person’s employment; or
submission to or rejection of the conduct is used as the basis for employment decisions affecting a person; or
The conduct has the purpose or effect or unreasonably interfering with someone’s work performance or creating an intimidating, hostile, or offensive working environment.
When any member of management receives a report of harassment, the matter must be referred to the Human Resources Department and a determination will be made on who will conduct the investigation. The results of the investigation will determine the response made.
Reports and investigations of harassment contain sensitive information. Our policy is to handle this information confidentially, subject to our responsibility to perform a proper investigation and take corrective action. All persons who act on behalf of the Company in processing or investigating harassment reports must observe this confidentiality.
Retaliation against a person who has made a harassment report or participated in a harassment investigation is prohibited. Employees who engage in harassment, retaliation, or other violations of this harassment policy are subject to appropriate corrective action up to and include termination of employment.
REVISED DATE: January 1, 2025
HAZARDOUS CHEMICAL COMMUNICATION POLICY
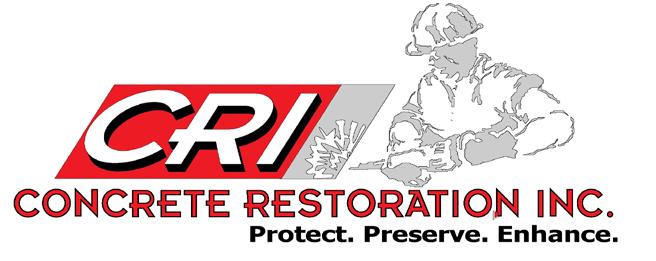
Any person involved in a harassment matter who feels that the issue has not been properly resolved may request a review of the situation by higher level management. Results of the review will be communicated to the person requesting it in a timely manner. If you have any questions about this policy, you should feel free to ask your Human Resource Department
Reference: OSHA 29 CFR 1910.1200/WAC 296-901
PURPOSE:
A. This policy is established to:
• Ensure the hazards of all chemicals produced or imported are classified, and that information concerning the classified hazards is transmitted to employers and employees.
• Be consistent with the provisions of the United Nations Globally Harmonized System of Classification and Labeling of Chemicals (GHS), Revision 3.
• Ensure compliance with the applicable state and federal standards.
• Safeguard the health and safety of Concrete Restoration Inc employees.
• Create guidelines to follow for implementation and maintenance of a hazard communication program.
SCOPE:
Concrete Restoration Inc intends to ensure the transmission of necessary information to employees regarding substances in the workplace, pursuant to the Federal Occupational Safety and Health Act.
INTRODUCTION AND GENERAL STATEMENT:
Almost every workplace contains some substances, which could pose potential health problems to employees if exposed to them in concentrations or in a manner not prescribed. Concrete Restoration Inc recognizes that its employees have the right and need to know
REVISED DATE: January 1, 2025
HAZARDOUS CHEMICAL COMMUNICATION POLICY
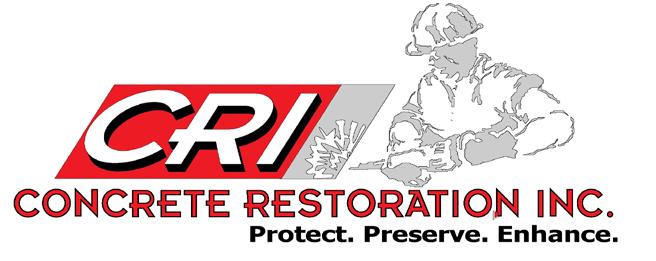
the properties and potential safety and health problems of substances to which they may be exposed. With this policy, Concrete Restoration Inc intends to ensure the transmission of necessary information to employees regarding substances in the workplace, pursuant to the Federal Occupational Safety and Health Act Hazard Communication Standard, 29 Code of Federal Regulations 1910.1200.
A. Chemical - any substance or mixture of substances
B. Hazardous chemical - any chemical that is classified as a physical hazard or a health hazard, a simple asphyxiant, combustible dust, pyrophoric gas, or hazard not otherwise classified.
C. Hazard category - the division of criteria within each hazard class, e.g., oral acute toxicity and flammable liquids include four hazard categories. These categories compare hazard severity within a hazard class and should not be taken as a comparison of hazard categories more generally.
D. Hazard class - the nature of the physical or health hazards, e.g., flammable solid, carcinogen, oral acute toxicity
E. Hazard not otherwise classified (HNOC) - an adverse physical or health effect identified through evaluation of scientific evidence during the classification process that does not meet the specified criteria for the physical and health hazard classes addressed in this section. This does not extend coverage to adverse physical and health effects for which there is a hazard class addressed in this section, but the effect either falls below the cut-off value/concentration limit of the hazard class or is under a GHS hazard category that has not been adopted by OSHA (e.g., acute toxicity Category 5).
F. Label - an appropriate group of written, printed or graphic information elements concerning a hazardous chemical that is affixed to, printed on, or attached to the immediate container of a hazardous chemical, or to the outside packaging.
REVISED DATE: January 1, 2025
HAZARDOUS CHEMICAL COMMUNICATION POLICY
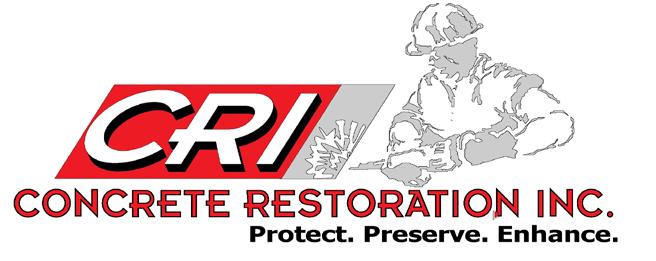
G. Label elements - the specified pictogram, hazard statement, signal word and precautionary statement for each hazard class and category.
H. Mixture - a combination or a solution composed of two or more substances in which they do not react.
I. Physical hazard - a chemical that is classified as posing one of the following hazardous effects: explosive; flammable (gases, aerosols, liquids, or solids); oxidizer (liquid, solid or gas); selfreactive; pyrophoric (liquid or solid); self-heating; organic peroxide; corrosive to metal; gas under pressure; or in contact with water emits flammable gas. See Appendix B to §1910.1200 -- Physical Hazard Criteria.
J. Pictogram - a composition that may include a symbol plus other graphic elements, such as a border, background pattern, or color, that is intended to convey specific information about the hazards of a chemical. Eight pictograms are designated under this standard for application to a hazard category.
K. Safety data sheet (SDS) - written or printed material concerning a hazardous chemical that is prepared in accordance with OSHA’s HCS 2012 guidelines found in the mandatory Appendix D
REQUIREMENT:
Concrete Restoration Inc will provide employees with information concerning the hazards associated with chemical substances in the work place in compliance with the requirements of the OSHA Hazard Communication Standard (29 CFR 1910.1200), updated 2012. The standard requires this written hazard communication program to provide information on container labeling, area safety signs, SDS sheets, and training on the hazards of specific workplace chemicals.
REVISED DATE: January 1, 2025
HAZARDOUS CHEMICAL COMMUNICATION POLICY
AVAILABILITY:
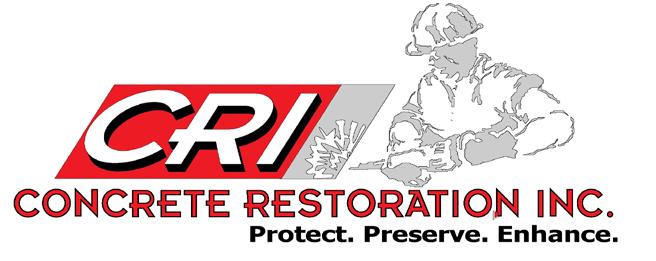
This written program is available for all interested employees and will be located at the main office. SDS will be uploaded in Smartsheet and available to all employees on jobsites.
RESPONSIBILITIES:
A. Supervisors
Supervisors are responsible for ensuring that all containers are properly labeled, the appropriate SDS’s are obtained, maintained and that training about these chemicals is provided.
All SDS’s for chemicals brought onto any Concrete Restoration Inc job will be kept in the SDS section of the Hazard Communication program, will be added to the list of hazardous chemicals on the site, and a copy will be forwarded to the Concrete Restoration Inc Safety Manager for addition to the central SDS chemical list. (The SDS’s for any new chemical or product brought onto a Company Name Here property or business is to be discussed with the affected employees and documented.)
B. Employees
Employees are responsible for identifying any potential hazard and reporting it to the appropriate supervisor. In addition, all employees should understand the hazards of the chemical being used and will wear all prescribed personal protective equipment. It is the employees’ further responsibility to seek assistance if there is any uncertainty about potential hazardous material from the supervisor.
HAZARDOUS CHEMICALS LIST:
The master chemical list is retained at the main office and will only be given out upon request. A copy of a job specific “Chemical List,” along with a copy of the written Hazard Communication Program, will be kept with each
REVISED DATE: January 1, 2025
HAZARDOUS CHEMICAL COMMUNICATION POLICY
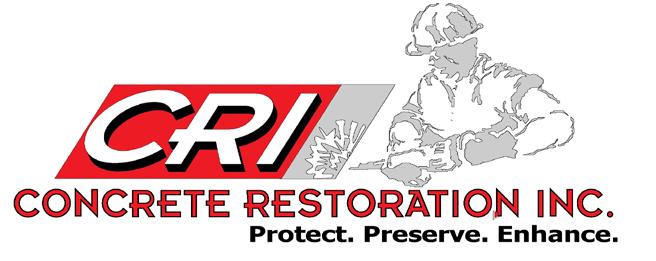
of the SDS books, which are located in the office of Concrete Restoration Inc. SDS are available to all employees under job number in Smartsheet.
LABELS AND OTHER FORMS OF WARNING:
A. Labels on shipped containers:
1. Chemical manufacturers, importers, and distributors are required to ensure that each container of hazardous chemicals is labeled leaving the workplace is labeled, tagged, or marked. The company management will ensure that containers of hazardous chemicals, which have been shipped to CRI, are properly labeled when received. Hazards not otherwise classified do not have to be addressed on the container. Where the chemical manufacturer or importer is required to label, tag or mark the following information shall be provided:
a. Product identifier.
b. Signal word
c. Hazard statement(s)
d. Pictogram(s)
e. Precautionary statement(s)
f. Name, address, and telephone number of the chemical manufacturer, importer, or other responsible party.
2. The chemical manufacturer, importer, or distributor shall ensure that the information provided in a. through f. is in accordance with Appendix C to §1910.1200, for each hazard class and associated hazard category for the hazardous chemical, prominently displayed, and in English (other languages may also be included if appropriate).
3. The chemical manufacturer, importer, or distributor shall ensure that the information provided b. through d. of this section is located together on the tag, label, or mark.
4. Attach an SDS to each shipped container. When this method is used, the following procedures must be followed:
REVISED DATE: January 1, 2025
HAZARDOUS CHEMICAL COMMUNICATION POLICY
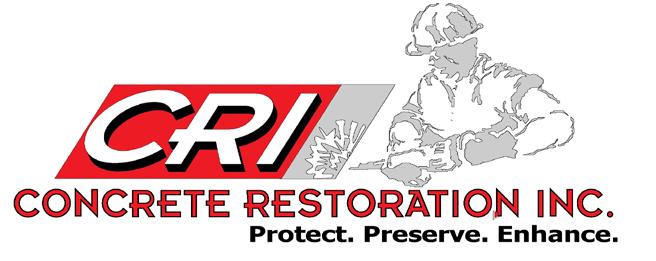
a. The SDS must be securely attached to each container.
b. The SDS must be properly protected from the weather so that it does not become detached or damaged while in shipment.
5. Each supervisor will be responsible for obtaining new and updated SDS’s on all incoming hazardous chemicals and updating his/her site SDS’s to the office to update the central file and chemical list.
6. These SDS’s will be forwarded to the Safety Manager, who will see that:
a. Copies of these sheets are placed in the central SDS manual.
b. The Hazardous Chemicals List is updated to include required information from all new and updated SDS’s.
c. A copy of each new SDS will be given to each supervisor so that he/she can relay the information to the effected employees and update the site-specific SDS manual.
7. Product identifier and words, pictures, symbols, or combination thereof, which provide at least general information regarding the hazards of the chemicals, and which, in conjunction with the other information immediately available to employees under the hazard communication program, will provide employees with the specific information regarding the physical and health hazards of the hazardous chemical.
8. Concrete Restoration Inc may use signs, placards, process sheets, batch tickets, operating procedures, or other such written materials in lieu of affixing labels to individual stationary process containers, as long as the alternative method identifies the containers to which it is applicable and conveys the information required by paragraph (f)(6) of this section to be on a label. Concrete Restoration Inc will ensure the written
REVISED DATE: January 1, 2025
HAZARDOUS CHEMICAL COMMUNICATION POLICY
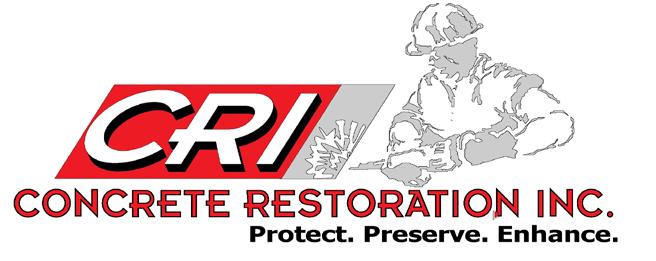
materials are readily accessible to employees in their work area throughout each work shift.
B. Portable container labeling: Concrete Restoration Inc is not required to label portable containers into which hazardous chemicals are transferred from labeled containers, and which are intended only for the immediate use of the employee who performs the transfer.
C. Concrete Restoration Inc shall not remove or deface existing labels on incoming containers of hazardous chemicals unless the container is immediately marked with the required information.
D. Concrete Restoration Inc will ensure that workplace labels or other forms of warning are legible, in English, and prominently displayed on the container, or readily available in the work area throughout each work shift. Employers having employees who speak other languages may add the information in their language to the material presented, as long as the information is presented in English as well.
REVISED DATE: January 1, 2025
HAZARDOUS CHEMICAL COMMUNICATION POLICY
PICTOGRAMS AND HAZARDS:
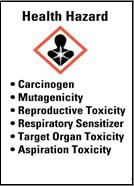
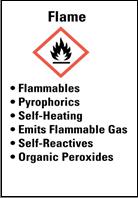
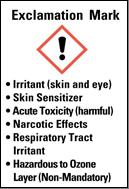
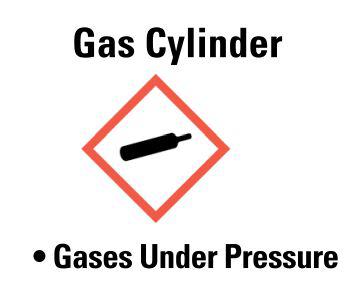
REVISED DATE: January 1, 2025
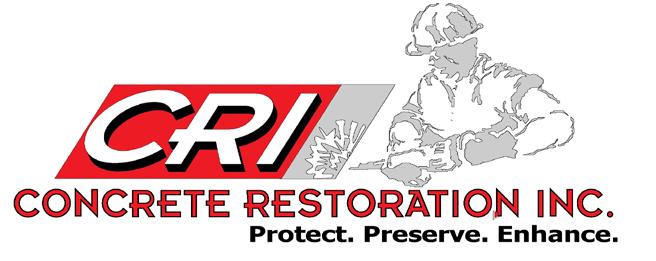
HAZARDOUS CHEMICAL COMMUNICATION POLICY
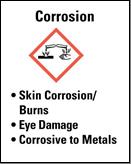
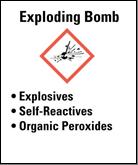
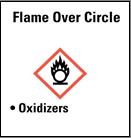
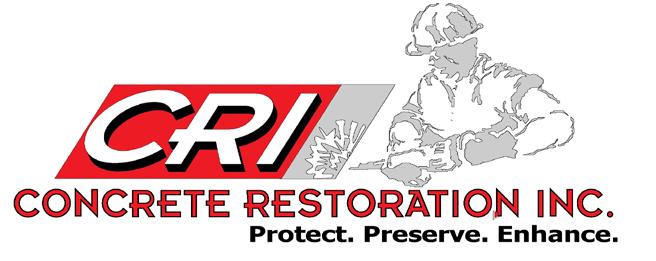
REVISED DATE: January 1, 2025

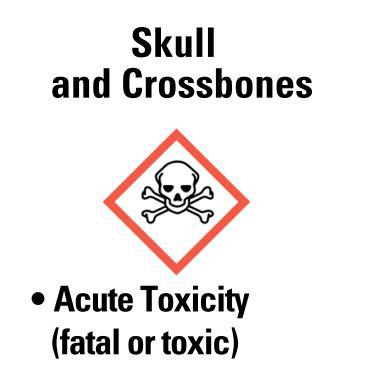
HAZARDOUS CHEMICAL COMMUNICATION POLICY
HAZARD REVIEW:
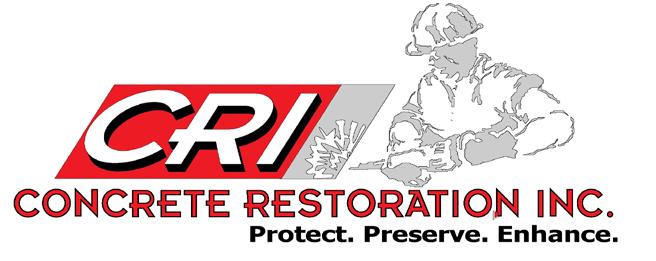
Concrete Restoration Inc management will review incoming SDS’s for new and significant physical and health hazard information that is applicable to local operations. They will see that any new applicable information is incorporated in the Information and Training Program so that it will be passed on to affected employees.
LOCATION OF SDS SHEETS:
Copies of SDS’s will be kept at the following locations:
A. Concrete Restoration Inc main office
B. Smart Sheets
The above-listed locations have been selected so that the SDS’s will be readily available to all employees in their work area(s) for reference and review during each work shift.
If SDS’s are not available, or if new chemicals are used which do not have SDS’s, immediately contact the Safety Manager located in the main office.
EMPLOYEE TRAINING AND INFORMATION:
Concrete Restoration Inc management is responsible for the employee training program and will ensure that all elements of training specified below are carried out.
A. Training
Information and training will be provided to all employees. Training will occur when:
1. Employees are assigned to a work area for the first time (i.e., a new hire or transfer to a new job.)
REVISED DATE: January 1, 2025
HAZARDOUS CHEMICAL COMMUNICATION POLICY
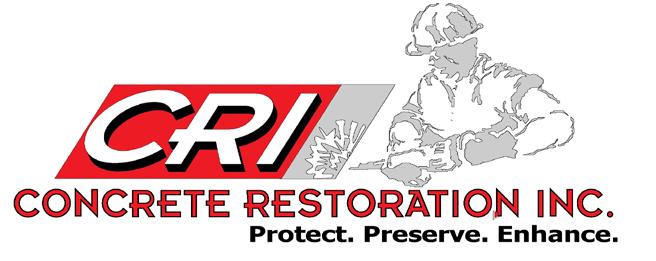
2. New chemical hazards are introduced into the work area.
3. New information becomes available (updated SDS, etc.)
B. Specific Training
Information and training provided to employees shall include an overview of the requirements contained in the OSHA Hazard Communications Standard in addition to the following:
1. Concrete Restoration Inc Hazard Communication Program will be reviewed in detail.
2. The location and availability of the Written Hazard Communication Program and the Hazardous Chemicals List
3. An explanation of the labeling procedures for:
a. Portable containers, and
b. Shipped containers – and how to interpret the information on the labels.
4. Safety Data Sheets (SDS’s)
a. How to use and understand SDS’s
b. Where SDS’s are located on the properties
c. How to read container labels, locate and review SDS’s to obtain and use appropriate information.
5. The identity of the physical and health hazards of the chemicals in the work area
6. Monitoring techniques that may be used to detect the presence or release of chemicals in the work area.
7. The physical, health, simple asphyxiation, combustible dust and pyrophoric gas hazards, as well as hazards not otherwise classified, of the chemicals in the work area.
REVISED DATE: January 1, 2025
HAZARDOUS CHEMICAL COMMUNICATION POLICY
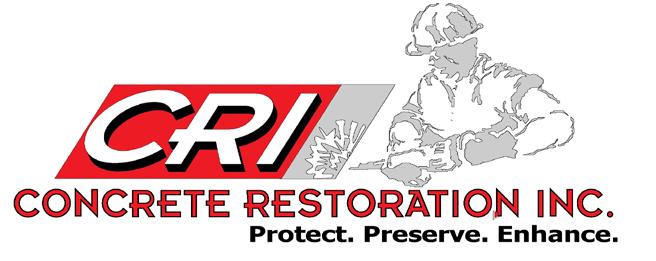
8. Prevention of exposure to hazardous chemicals through:
a. Appropriate work practices
b. Emergency procedures of each property
c. Use of personal protective equipment
d. Instructional procedures relating to tasks that involve chemicals.
9. Emergency Procedures
a. Emergency procedures are to be followed if employees are exposed to hazardous chemicals. (i.e., eyewash stations, safety showers, first aid kits and emergency phone numbers.)
10. The details of the hazard communication program developed by the employer, including an explanation of the labels received on shipped containers and the workplace labeling system used by their employer, the safety data sheet, including the order of information and how employees can obtain and use the appropriate hazard information.
C. Documentation of Training
All training provided to Concrete Restoration Inc employees will be documented.
Supervisors/trainers must ensure that employees sign documentation that describes the training he/she has received and will verify that the company’s policies on Hazard Communication were understood.
Training records will be maintained at Concrete Restoration Inc main office in compliance with the OSHA Hazard Communication Standard.
NON-ROUTINE TASKS:
There will be occasions when employees may be required to perform nonroutine tasks involving chemicals. Prior to starting work on such projects,
REVISED DATE: January 1, 2025
HAZARDOUS CHEMICAL COMMUNICATION POLICY
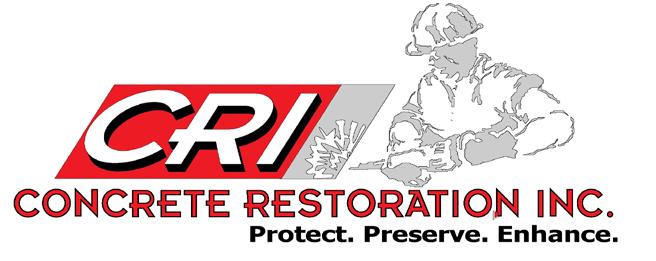
each affected employee will be instructed by his/her supervisor on the chemical hazards of the task, and the appropriate protective measures.
MULTI-EMPLOYER WORK SITES:
SDS and chemical listing will be provided upon request to any client company, sub-contractor, and or any trades working in proximity to the jobsite.
NON-ENGLISH-SPEAKING EMPLOYEES:
A fluent translator is to be provided on all jobs with any non-English speaking employees. The translator will communicate the elements of this program to the employees.
EACH WORK SITE:
Site-specific HAZCOM written plans will be generated.
SPECIFIC HAZARD WARNINGS:
Appropriate hazard warnings, or alternatively, words, pictures, symbols, or combination thereof, will provide employees with specific information regarding the physical and health hazards of the hazardous chemical(s)
REVISED DATE: January 1, 2025
HAZARDOUS TRANSPORT POLICY
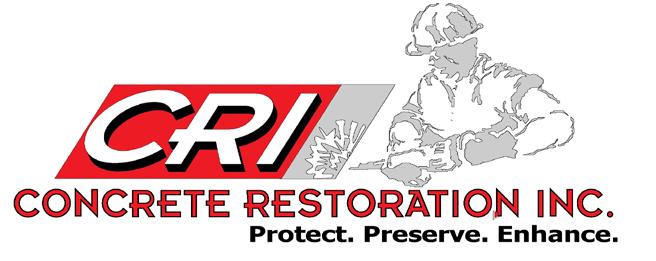
HAZARDOUS TRANSPORT POLICY
Reference: OSHA 1910.120,1910.1200 WAC 446-50-080
Purpose
This program is written to be in compliance with State and local regulatory requirements and provide directives to managers, supervisors, and employees about their responsibilities during the transportation of hazardous materials.
Emergency Response Information
Where an accidental release of hazardous materials in excess of a prescribed quantity or concentration occurs or is imminent from a means of containment being used to handle of transport dangerous goods, and person who at the time has the charge, management or control of the means of containment shall report the occurrence of the release. Every person required to make a report shall, as soon as possible in the circumstances, take all reasonable emergency measures to reduce or eliminate any danger to public safety that results or may reasonably be expected to result from release.
All hazardous material shipments (except those that do not require shipping papers) must have emergency response information on or accompanying the shipping paper. All emergency response information must legible and in English. The information on or accompanying the shipping paper must be in the form a safety data sheet, or any other form that provides all the following information:
The basic description and technical name of the hazardous material
• Immediate hazards to health.
• Risks of fire or explosion.
• Immediate precautions to be taken in the event of an accident or incident.
REVISED DATE: January 1, 2025
HAZARDOUS TRANSPORT POLICY
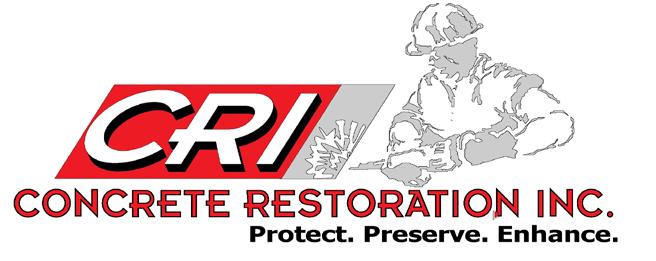
• Immediate methods for handling fires.
• Initial methods for handling spills or leaks in the absence of fire.
• Preliminary first aid measures.
Classification
Before allowing a carrier to take possession of hazardous materials for transport the consignor must determine the classification of the hazardous material. Under the Hazardous Materials Transportation Program, there are 11 hazard classes (nine numbered and two unnumbered) – classes 1 through 9, divisions plus the classes Combustible Liquids and Other Regulated Materials (ORM).
Each hazardous material is assigned to one of three packing groups (PG), based on tests for dropping, leakage, etc. Packing groups I, II and III indicate the degree of danger presented by the material great, medium or minor, respectively. If more than one packing group is indicated for an entry, the packing group for the hazardous material is determined using the criteria for assignment of packing groups specified for each class in 49 Code of Federal Regulations (CFR) 173 Subpart D. Class 2, Class 6.2, Class 7 and ORM-D materials, do not have packing groups. All packing groups are specified in column 5 of the 172.101 Hazardous Materials Table.
All markings on the outside of a hazardous material package must be durable, easy to read, in English and unobstructed by anything else on the package.
The outside of each non-bulk package and any inside containers of hazardous materials must be marked with the following information:
• Proper shipping name.
• Identification number (preceded by “UN” or “NA”, as appropriate)
REVISED DATE: January 1, 2025
HAZARDOUS TRANSPORT POLICY
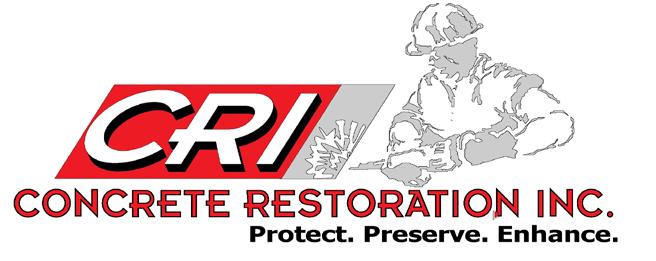
• Name and address of the consignee or the consignor (the consignee is the person to whom the package is sent. The consignor is the person who sends the package except when the package is transported by highway only and will not be transferred from one motor carrier to another; or part of a carload lot, truckload lot or freight container load, and the entire contents of the rail car, truck or freight container are shipped from one consignor to on consignee.
Identification numbers are not required on packages which contain only limited quantities or ORM-D materials.
When a non-bulk package contains inner containers of hazardous liquid materials, the inner containers must be packed with the caps/lids upright. In addition, it must be legibly marked with package orientation markings on two opposite vertical sides of the package with the arrows pointing in the correct upright direction. Arrows for purposes other than indicating proper package orientation may not be displayed on a package containing a liquid hazardous material.
For materials poisonous by inhalation, the package shall be marked “Inhalation Hazard” in association with the required labels or placards. Each non-bulk plastic outer packaging used as a single or composite packaging for materials meeting the definition of 6.1 shall be permanently marked, by embossment or other durable means, with the word “POISON” in letters at least 6.3 millimeters (0.25 inch) in height. The marking shall be located within 150 millimeters (6 inches) of the closure of the packaging.
If the package contains the reportable quantity of a hazardous substance, the letters “RQ” must be marked in association with the proper shipping name. Reportable quantity means the quantity specified in column 2 of the Hazardous Materials Table for any material identified in Column 1 of the table.
Table 2 of the Hazardous Materials Table lists materials which are considered to be Marine Pollutants or Severe Marine Pollutants. If a material is considered to be a Marine Pollutant or Severe Marine Pollutant the package must be marked accordingly.
REVISED DATE: January 1, 2025
HAZARDOUS TRANSPORT POLICY
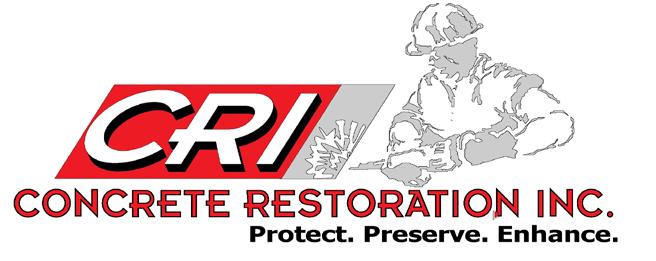
Bulk packages are required to display the proper shipping name on two opposite sides. The “UN” or “NA” identification number shall be displayed on each side and each end if the packaging has a capacity of 3,785 liters (1,000 gallons) or on two opposing sides if the packaging has a capacity of less than 3,785 liters (1,000 gallons).
For bulk packaging containing materials poisonous by inhalation, the package shall be marked “Inhalation Hazard” on two opposing sides in association with the required labels or placards.
Each package containing hazardous materials presented for transportation must be labeled with a hazard label(s) that corresponds to the hazard class of the material it contains. Hazard labels must be placed on the same side of the package as the proper shipping name and “UN” or “NA” identification number markings. These labels must be clearly visible and unobstructed by anything else on the package. Column 6 of Hazardous Materials Table indicates the required label for each material listed.
Hazard warning labels must meet strict Department of Transportation (DOT) guidelines regarding size, shape, color and content. Domestic labels will generally have words; however, labels used in international commerce may be wordless.
Documentation
All hazardous materials transported in commerce are required to be accompanied by shipping papers. Shippers may use bills of lading, manifests or waybills as long as these documents contain the required information. The shipping paper requirements do not apply to materials, other than hazardous wastes or hazardous substances, identified by the letter “A” or “W” in column 1 of the 172.101 – Hazardous Materials Table unless they are intended for transportation by air or water, and materials classed as ORM-D unless they are intended for transportation by air. Before allowing a carrier to take possession of hazardous materials for transport, the consignor must prepare and give to that carrier a shipping document or, if the carrier agrees, an electronic copy of the shipping document.
REVISED DATE: January 1, 2025
HAZARDOUS TRANSPORT POLICY
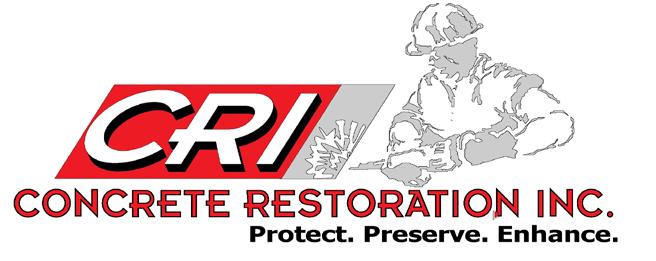
The shipping document must be legible and printed or typed in English. No unauthorized codes or abbreviations may be used. A shipping document may consist of more than one page, if each page is consecutively numbered and the first page bears a notation specifying the total number of pages included in the shipping document (for example, “Page 1 of 4 pages”).
The following five items must appear on shipping documents containing hazardous materials:
A basic description consisting of four elements in the following sequence:
• Proper shipping name
• Hazard class or division
• UN or NA identification number
• Packing group number
Total quantity except for empty packaging, cylinders for Class 2 (compressed gases) materials, and bulk packaging, the total quantity (by net or gross mass, capacity, or as otherwise appropriate), including the unit of measurement, of the hazardous material covered by the description (e.g., “800 lbs.” or “208 L”) must appear on the shipping paper. For cylinders of Class 2 (compressed gases) materials and bulk packaging, some indication of total quantity must be shown (e.g., “10 cylinders” or “1 cargo tank”);
• Emergency Number: A 24-hour emergency response telephone number is located on the Safety Data Sheet.
• Certification Statement: The shipper certifies that the materials listed on the shipping papers have been properly classified, described, packaged, marked and labeled, and are in proper condition for transport according to the regulations established by DOT.
REVISED DATE: January 1, 2025
HAZARDOUS TRANSPORT POLICY
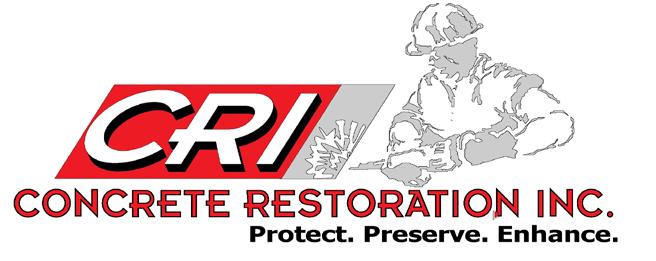
• Signature: The signature of the shipper or his agent signifies that the shipment is in compliance with all relevant regulations.
• When a description of a hazardous material is required to be included on a shipping document, that description must conform to the following requirements:
• When a hazardous material and a material not subject to the requirements of this section are described on the same shipping paper, the hazardous material description entries must be entered first.
• The hazardous material description entries must be entered in a color that clearly contrasts with any description on the shipping paper of a material not subject to the requirements of this section
• Except: A description on a reproduction of a shipping paper may be highlighted, rather than printed, in contrasting color, or must be identified by the entry of an “X” placed before the proper shipping name in a column captioned “HM”.
The basic description must be shown in sequence with no additional information interspersed. For example: “Gasoline, 3, UN 1203, PG II” (Shipping Name, Hazard Class, Identification Number, Packing Group).
Record Keeping
A consignor must be able to produce a copy of any shipping document containing the following information:
• Proper Shipping name
• Hazard class
• ID number
• Total quantity
• Shipper's certification
• Emergency Response telephone number
REVISED DATE: January 1, 2025
HAZARDOUS TRANSPORT POLICY
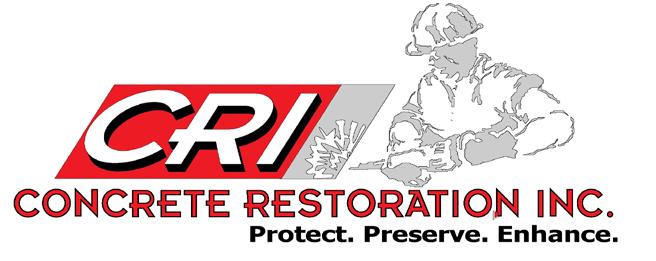
for two years after the date the shipping document or an electronic copy of it was prepared or given to a carrier by the consignor, for hazardous materials imported into the US, for two years after the date the consignor ensured that the carrier, on entry into the US, had a shipping document of was given an electronic copy of one, and within 15 days after the on which the consignor receives a written request from an inspector.
Placarding Motor Vehicles
Concrete Restoration Inc will not offer for transport, transport or import means of containment that contains hazardous materials unless each hazardous materials placard is displayed on it. 49 CFR 172.504 lists those hazard classes which require placards for motor vehicles no matter what amount of material is being hauled and hazard classes which require placards for motor vehicles carrying hazardous materials, but the amount of material being hauled will determine when placards are required.
Prohibited Placarding
Other signs or devices which by color, design, shape or content could be confused with required placards shall not be displayed or affixed on any motor vehicle transporting hazardous materials.
Subsidiary Hazards
A transport vehicle containing two or more categories of materials, requiring different placards specified in Table 2, may be placarded DANGEROUS in place of the separate placarding specified for each of the materials listed in Table 2. Refer to 49 CFR 172.504 for more information.
REVISED DATE: January 1, 2025
HAZARDOUS TRANSPORT POLICY
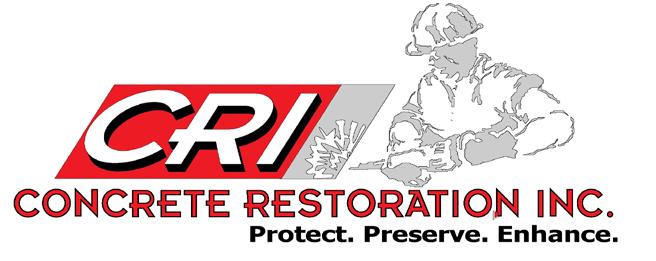
Visibility and Display of Placards
It is the responsibility of the shipper to offer the required placards to the carrier when the carrier loads the hazardous materials for transport. Refer to 49 CFR 172.504 for more information.
Loading and Unloading & Containment
Any tank, barrel, drum, cylinder, or other packaging, not permanently attached to a motor vehicle, which contains any Class 3 (flammable liquid), Class 2 (gases), Class 8 (corrosives), Division 6.1 (poisonous), or Class 7 (radioactive) material must be loaded in such a manner as to secure against movement within the vehicle during transportation.
A person must load and secure hazardous materials in a means of containment and must load and secure the means of containment on a means of transport in such a way as to prevent under normal conditions lf transport, damage to the means of containment of to the means of transport that could lead to an accidental release of the hazardous material.
The Hazardous Materials Regulations contain Segregation Tables 49 CFR 177.848 which indicates which hazardous materials may not be loaded, transported, or stored together. Concrete Restoration Inc will not handle, offer for transport or transport hazardous materials in a means of containment unless the means of containment is designed, constructed, filled, closed, secured, and maintained so that under normal conditions of transport, including handling, there will be no accidental release of hazardous materials that could endanger public safety. Materials which are in packages that require labels, in a compartment within a multicompartment cargo tank or in a portable tank are subject to the Segregation Tables. In addition, cyanides or cyanide mixtures may not be loaded or stored with acids.
REVISED DATE: January 1, 2025
HAZARDOUS TRANSPORT POLICY
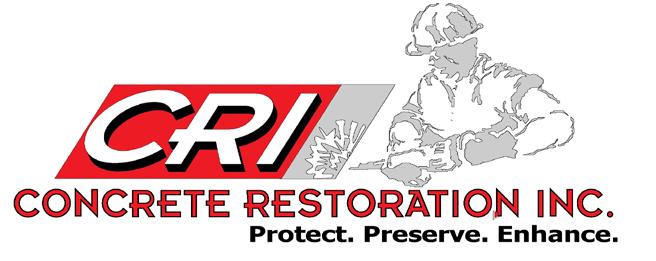
Hazmat Training
Concrete Restoration Inc requires employees that handle, offer for transport, or transport hazardous materials to receive hazardous materials training. All employees working with hazardous materials must be adequately trained and hold a certificate or Hazmat endorsement to preform those activities. Any employee that has not been through a hazardous material training must not handle hazardous materials unless those activities are performed in the presence and under the direct supervision of a person who is adequately trained and who holds a training certificate. The PHMSA requires any company that plans to transport hazardous materials to train its employees six months in advance of the transportation.
Environmental Health and Safety shall provide a training program for employees who during the course of employment directly affect hazardous materials transportation through one or more of the following activities:
• Loads, unloads, or handles hazardous materials.
• Tests, reconditions, repairs, modifies, marks, or otherwise represents containers, drums, or packaging as qualified for use in the transportation of hazardous materials.
• Prepares hazardous materials for transportation.
• Signs hazardous materials waste manifests.
• Operates a vehicle used to transport hazardous materials.
The training will be conducted within 90 days of employment for those employees whose job functions involve any of the aforementioned hazardous material tasks and once every two years thereafter. Exception: Additional training shall be provided within 90 days of any job change involving the use of hazardous materials.
REVISED DATE: January 1, 2025
HAZARDOUS TRANSPORT POLICY
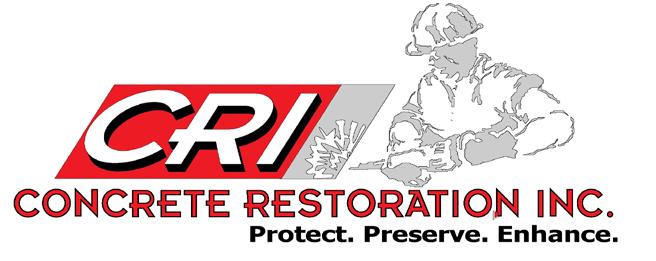
An employee may perform job functions prior to the completion of training provided the employee performs those functions under the supervision of a properly trained and knowledgeable employee.
A comprehensive training program shall include the following:
• General training to provide awareness and familiarization of the requirements of the Hazardous Materials Transportation Program and to enable the employee to recognize and identify hazardous materials consistent with the hazard communication standard.
• Function-specific training applicable to the functions the employee performs;
• Safety training pertaining to the following:
o Emergency response information.
o Measures to protect the employee from the hazards associated with hazardous materials to which they may be exposed in the workplace, including specific measures the employer has implemented to protect employees from exposure.
o Methods and procedures for avoiding accidents, such as the proper procedures for handling packages containing hazardous materials.
o Any additional department specific training (e.g., Pre-trip safety inspection or the use of vehicle controls and equipment, including the operation of emergency equipment).
All employees engaged in the act of shipping infectious substances shall be trained on doing so through additional, function-specific training requirements. Infectious materials are regulated under both IATA and DOT regulations if shipped by air. Contact Environmental Health and Safety at 773-702-9999 for assistance or for copies of the IATA regulations.
REVISED DATE: January 1, 2025
HAZARDOUS TRANSPORT POLICY
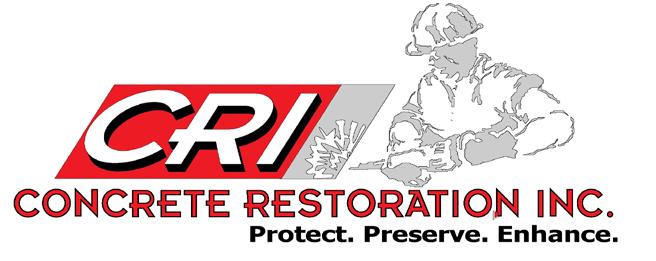
Training records shall be maintained by Environmental Health and Safety and include the following:
• The employee’s name.
• The most recent training date.
• A description, copy, or the location of the training materials used to meet the aforementioned training requirements.
• The name and address of the person providing the training
• Certification that the employee has been trained and tested as required.
• Results of the learning measurement exercise.
All employees attending training shall be required to demonstrate adequate knowledge retention as shown through a learning measurement exercise.
Immediate Release
Most incidents involving unintentional releases of hazardous materials in transportation must be reported to DOT. Detailed criteria concerning written reports are published in CFR, Title 49, Sections 171.15 and 171.16. In the event of an accidental release of hazardous material from a means of containment must make an immediate report of the accidental release to the appropriate authority if the accidental release consists of a quantity of hazardous materials or an emission of radiation that exceeds quantities set out for each class of hazardous material. The carrier who transports hazardous materials (including hazardous waste and hazardous substances) is responsible for reporting requirements.
REVISED DATE: January 1, 2025
HAZARDOUS WASTE POLICY
HAZARDOUS WASTE POLICY
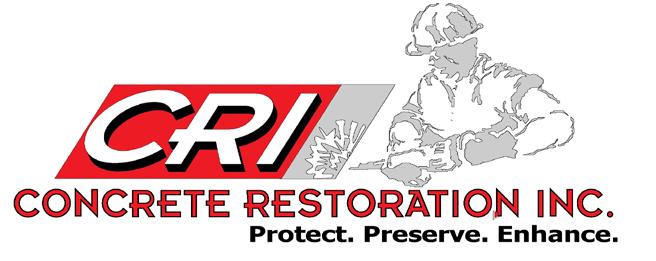
Reference: 1910 subpart E, H, I, J, L, Z 1926.65/WAC 173-303
Concrete Restoration, Inc. strives to have controls in place to properly dispose of created hazardous waste. This program applies to Concrete Restoration Inc., and its subcontractors.
Clean-up operations that are required by a governmental body, whether Federal, state local or other involving hazardous substances that are conducted at uncontrolled hazardous waste sites (including, but not limited to, the EPA's National Priority Site List (NPL), state priority site lists, sites recommended for the EPA NPL, and initial investigations of government identified sites which are conducted before the presence or absence of hazardous substances has been ascertained).
Operations involving hazardous waste that are created, stored, and disposed of by Concrete Restoration, Inc. are regulated by 173-303 WAC
Hazardous waste includes but is not limited to:
• Any substance defined under section 103(14) of the Comprehensive Environmental Response Compensation and Liability Act.
• Any biologic agent and other disease-causing agent.
• Any substance listed by the U.S. Department of Transportation as a hazardous material.
• Any combination of the above.
Any waste generated on a job site is to be brought to Concrete Restoration, Inc. headquarters located at 9587 8th Ave. S., Seattle, WA 98108. Drums, which are clearly marked per waste type, are to be used to store any hazardous waste. This waste is to be picked up by Emerald Services for disposal at least monthly, or more frequently if required.
REVISED DATE: January 1, 2025
HAZARDOUS WASTE POLICY
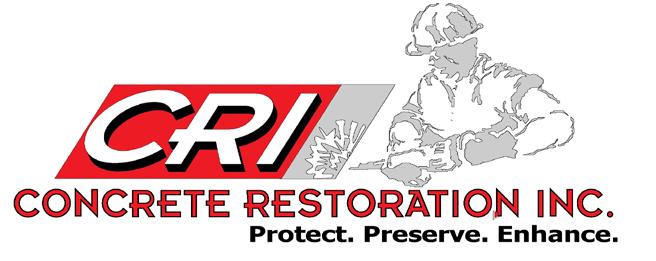
All PPE including, but not limited to: latex gloves, respirator, and safety glasses, should be used while transporting, storing, or disposing of hazardous waste.
Any time hazardous waste is in transport, stored, or disposed of, it is required that a spill skit is on site. The spill kit shall include absorbent rags, granular material, and a debris bag & bucket for waste.
In the event of a spill the following steps shall be taken:
• The employee shall ensure they are wearing all applicable PPE.
• Any drains shall be blocked off from hazardous waste using the granular material (sand).
• The employee should clean in a circular motion moving from the outside in, using rags to absorb the hazardous waste, unless circumstances call for different action.
REVISED DATE: January 1, 2025
HEARING CONSERVATION POLICY
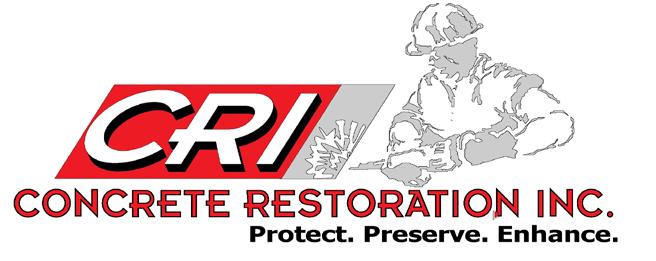
HEARING CONSERVATION POLICY
Reference: OSHA 1910.95/WAC 296-62-09015
Occupational Noise Exposure
• Noise, or unwanted noise, is one of the most pervasive occupational health problems. It is a by-product of many industrial and construction processes.
• Sound consists of pressure changes in the medium (usually air), caused by vibration or turbulence. These pressure changes produce waves emanating away from the turbulent or vibrating force. Exposure to high levels of noise causes hearing loss and may cause other harmful health effects as well. The extent of hearing damage depends primarily on the intensity of the noise and the duration of the exposure. Noise induced hearing loss can be temporary or permanent.
• Temporary hearing loss results from short – term exposure to noise, with normal hearing returning after a period of rest. Generally, prolonged exposure to high noise levels over a period of time gradually causes permanent damage.
• Our hearing conservation program has been designed to protect you, the worker on a CRI project site with significant occupational noise exposure, from suffering hearing impairment even of you were subject to such noise exposure continually over your working lifetime.
• Warnings shall be posted of the high area of noise levels (>115 Dba), areas where explosive – actuated tools are in use and as deemed necessary by the Foreman, Project Manager, or Safety manager.
REVISED DATE: January 1, 2025
HEARING CONSERVATION POLICY
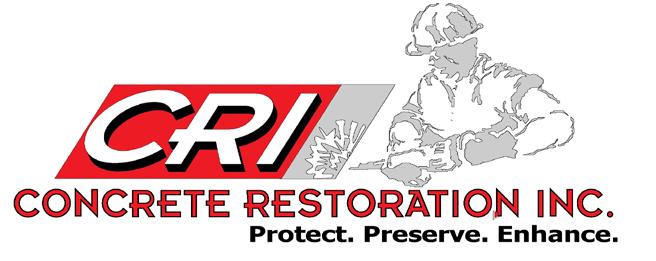
Monitoring
• The states regulations governing the hearing conservation program requires employers to monitor noise exposure levels in a manner that will accurately identify employees who are exposed to noise at or above 85 decibels (Db) averaged over 8 working hours or an 8-hour time weighted average (TWA). For those exceptionally noisy projects or project sites we shall contract with an outside professional testing laboratory to monitor several job positions that we assume will have the highest decibel levels. The results of this testing will be posted at the jobsite for your review. As a result of this testing we will determine what steps are needed to ensure that our workers are adequately protected from occupational hearing loss.
1. Audiometric Testing
• Concrete Restoration Inc requires all employees who are exposed to noise levels at or above 85 dB must be given audiometric testing as soon possible and annually thereafter. This testing is to be provided to the employee at no cost.
The basic elements in this type of audiometric testing program is the baseline audiogram, the annual audiogram’s, employees training, and proper use of required hearing protection.
• This type of audiometric testing program will not only determine the sharpness and acuity of your ears at the present time but will also allow for monitoring of any changes in hearing capability and the effectiveness of the hearing protection over time.
2. Baseline Audiograms
• The baseline audiogram is the reference audiogram against which the future audiograms are compared. Baseline audiograms must be provided within 6 months of an employee’s first exposure at or above an 8-hour TWA of 85 dB.
REVISED DATE: January 1, 2025
HEARING CONSERVATION POLICY
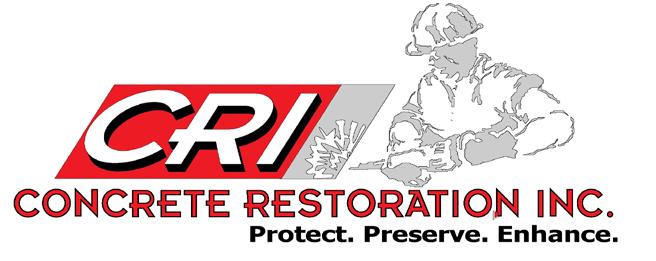
Employees, however, must be fitted with, issued, and required to wear hearing protection for any period exceeding 6 months after their first exposure until the baseline audiogram is obtained.
• Baseline Audiograms can also be a useful tool to demonstrate to an employee the necessity of wearing his or her hearing protection properly.
3. Annual Audiograms
• Annual audiograms must be conducted within one year of the baseline. It is important to test hearing on an annual basis to identify any deterioration in hearing ability so that the protection measures can be evaluated, and changes made to prevent further progression of hearing loss.
4. Hearing Protection
• Hearing protection must be available to all workers expected to be exposed to noise levels of 85 dB, in an 8-hour TWA, or above. This requirement is to ensure that employees have access to hearing protection before they experience any hearing loss.
• Hearing protection is recommended to be worn at all times on the project site.
• Hearing protection must be worn by:
1) Employees for any period exceeding 6 months from the time they are first exposed to 8 hour TWA noise levels of 85 dB or above or until they receive their baseline audiogram in situations where baseline audiograms are delayed.
2) Employees who have incurred standard threshold shifts since these workers have demonstrated that they are susceptible to noise.
REVISED DATE: January 1, 2025
HEARING CONSERVATION POLICY
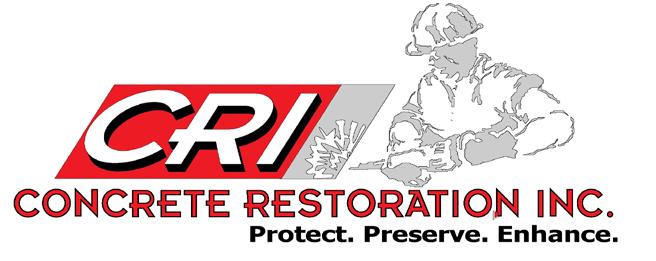
3) Employees exposed over the permissible exposure limited of 85dB over an 8 hour TWA.
Hearing protection shall be worn by all employees:
1) In posted areas
2) Operating heavy industrial and mechanized equipment
3) Operating portable and stationary power tools, all power saws, pneumatic hammers and chisels.
4) Mechanics and laborers working around heavy equipment and trucks.
• Earmuff hearing protection shall be worn by all operators of heavy industrial equipment, explosive actuated tools and as determined by site management.
• All employees in the above-mentioned work areas must also wear the authorized hearing protection
• Failure to comply with the hearing protection requirements shall result in disciplinary actions be taken, from an oral reprimand to dismissal from job site.
7. Training
• Employee training is very important. When workers understand the reason for hearing conservation programs, they will be better motivated to participate actively in the program and to cooperate by wearing their protection and procedure of audiometric testing.
• Employees exposed to 85 dB and above must be trained at least annually in the effects of noise, the purpose, advantages, and
REVISED DATE: January 1, 2025
HEARING CONSERVATION POLICY
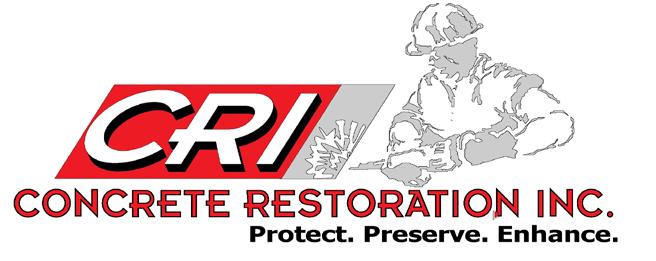
disadvantages of various types of hearing protectors; and the purpose and procedures of audiometric testing.
5. Record Keeping
o Noise exposure measure records must be kept for two years. Records of audiometric testing results must be maintained for the duration of employment of affected employee.
9. Regulations - WAC 296-62-09015
REVISED DATE: January 1, 2025
Heat Related Illness
Heat Related Illness
Reference: WAC 296-307-097
Purpose
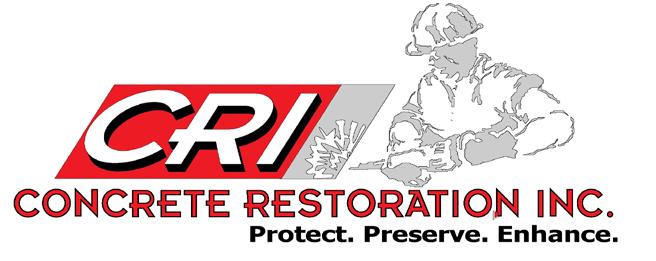
To provide a safe and healthful working environment and protect Concrete Restoration Inc employees who perform work in an outdoor environment. Concrete Restoration Inc will evaluate and reduce hazards if employees are exposed to temperature extremes.
Policy
It is the policy of Concrete Restoration Inc that all affected employees are required to comply with this Heat-Related Illness policy and are encouraged to actively participate in identifying ways to reduce the risk of experiencing heat-related illness in the workplace.
It is also the policy of Concrete Restoration Inc to check the workplace for unsafe conditions, monitor the health and safety of employees, and take prompt action in response to any identified heat-related illness hazards. (Definitions related to this content can be found at the end of this policy.)
Hazard Evaluation
Concrete Restoration Inc has evaluated the workplace and identified the following heat-related illness hazards:
• Reflected heat from pavement.
• Radiated heat from equipment, tar, torches.
• Heavy clothing and PPE’s
• Specific job duties like grinding, chipping, cutting concrete, demolition, etc
Employees exposed to temperatures at or above those listed in Table 1 (below) are subject to all provisions in this policy.
REVISED DATE: January 1, 2025
Heat Related Illness
Table 1
Type of clothing
All other clothing
Nonbreathable clothing including vapor barrier clothing or PPE such as chemical resistance suits
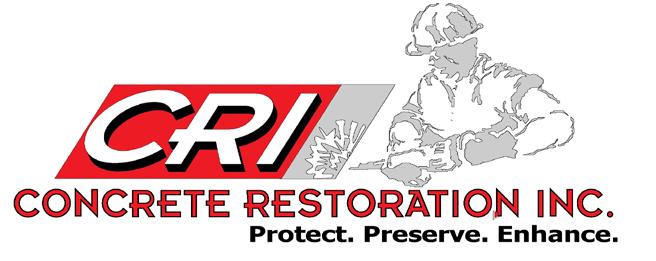
Work in direct sun
80◦ F
52◦ F
Note: There is no requirement to maintain temperature records. The temperatures in Table 1 were developed based on Washington State and are not applicable to other states.
Prevention, Controls, and Correction of Hazards
• Employees are responsible for monitoring their own personal factors for heat related illness, including consumption of water or other suitable beverages and taking preventative cool-down breaks.
• Provide adequate shade or other ways to reduce body temperature, including the location of such means and how employees can obtain them.
• Encourage and allow employees to take preventative cool-down breaks when they feel the need to do so in order to protect themselves from overheating.
• The preventive cool-down rest period must be paid for unless taken during a meal interval. If any employee displays signs and symptoms of heat-related illness during the cool-down rest period, the employer must comply with the requirements.
• Encourage employees to frequently consume water or other acceptable beverages to ensure hydration. One quart of suitably chilled water per employee per hour shall be made available and made easily accessible. (List specifically where water can be obtained on the job.)
• Close observation for signs of heat-related illness by; regular communication with employees such as by radio or cellular phone; Mandatory buddy system; or other effective means. Employees working in remote locations will be contacted periodically.
• Acclimatization methods and procedures
REVISED DATE: January 1, 2025
Heat Related Illness
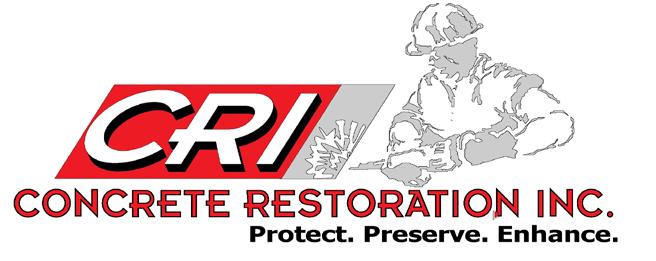
• Emergency response procedures for employees displaying symptoms or signs of heat-related illness.
• Night work or early start to reduce heat exposure
• Additional rest breaks will be provided during peak temperature times.
Acclimatization
For 14 days, employees must be closely monitored for signs and symptoms of heat-related illness any time they have been newly assigned to a role that is at or above the triggers in Table 1, have been absent from work for more that 7 days and returning to a role at or above Table 1 triggers, or during a heat wave. The appropriate options for observation are:
• Regular communication with employees working alone (radio or cellular phone)
• Mandatory buddy system
High Heat Procedures
When temperatures exceed 90 degrees Fahrenheit, unless engineering or administrative controls (such as air-conditioning or scheduling work at cooler times of the day) are used to lower employee exposure below 90degree Fahrenheit. Ensure that employees take at minimum the mandatory cool-down rest periods in Table 2. The cool-down rest periods must be provided in the shade or using other equally or more effective means to reduce body temperature. The mandatory cool-down rest period may be provided concurrently with any meal or rest period required under the requirements paid unless taken during a meal period.
Table 2
Air Temperature Mandatory cool-down rest periods
At or above 90◦ F 10 minutes/2 hours
REVISED DATE: January 1, 2025
Heat Related Illness
At or above 100◦ F
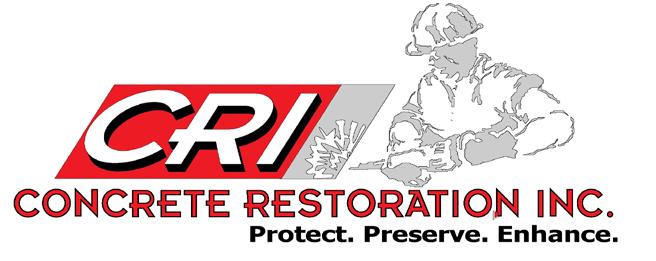
15 minutes/1 hour
Note: Employers may also consider implementing additional protective rest periods per NIOSH or ACGIH methods:
First Aid awareness and actions in the event of a heat-related illness
The following chart helps employees recognize the main types of heat related illnesses, signs, symptoms, and the appropriate treatment to reduce the effects of the heat related illness. This chart will be posted (list where chart will be posted such as safety board, near water, near first aid kit, break area, etc).
Signs and Symptoms
Sunburn
Heat Rash
Heat cramps
• red, hot skin
• may blister
• red, itchy skin
• bumpy skin
• skin infection
• muscle spasms in legs or abdomen
• grasping the affected area
• abnormal body position
First Aid and Treatment
• move to shade, loosen clothing
• apply cool compresses or water
• apply cool water or compresses
• keep affected area dry
• control itching and infection with prescribed medication
• move person to a cooler location
• stretch or massage muscles for cramps
• get medical evaluation if cramps persist
• give cool water or electrolytecontaining fluid to drink
Heat exhaustion
• headaches
• clumsiness
• dizziness/lightheadedness/fainting
• weakness/exhaustion/fatigue
• heavy sweating/clammy/moist skin
• irritability/confusion
• nausea/vomiting
• paleness
• high pulse rate
DATE: January 1, 2025
• move person to a cooler place (do not leave alone)
• loosen and remove heavy clothing that restricts evaporative cooling
• if conscious, provide small amounts of cool water to drink
• fan person, spray with cool water, or apply a wet cloth to skin to increase evaporative cooling
• lay flat and elevate feet
• evaluate mental status (ask who, where, when questions)
• call 911 if not feeling better within a few minutes
Heat Related Illness
Heat stroke
• any of the above, but more severe
• sweating may or may not be present
• red or flushed, hot dry skin
• bizarre behavior
• mental confusion or losing consciousness
• panting/rapid breathing
• rapid, weak pulse
• seizures or fits
• can be fatal
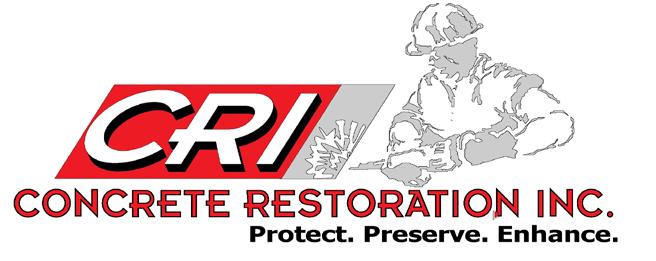
• call 911
• move person to a cooler place (do not leave alone)
• cool worker rapidly
• if conscious, provide small amounts of water to drink
• loosen and remove heavy clothing that restricts evaporative cooling
• fan person, spray with cool water, or apply a wet cloth to skin to increase evaporative cooling
• lay flat and elevate feet
• monitor airway and breathing, administer CPR if needed
In the event that medical treatment is needed beyond first aid and 911 must be called we crew member will call 911 from cell phone.
Directions to the worksite will be posted on job box or job board.
Employee training
Effective training in the following topics must be provided to all employees who may be exposed to a heat-related illness hazard:
• The environmental factors and other work conditions (i.e., workload, work duration, personal protective equipment, clothing) that contribute to the risk of heat-related illness.
• General awareness of personal factors that may increase susceptibility to heat illness including but not limited to, an individual’s age, physical fitness, degree of acclimatization, medical conditions, drinking water consumption, alcohol use, previous heat-related illness, pregnancy, and use of medications that affect the body’s response to heat.
• The importance of removing heat-retaining personal protective equipment and clothing such as nonbreathable chemical resistance clothing during all breaks.
REVISED DATE: January 1, 2025
Heat Related Illness
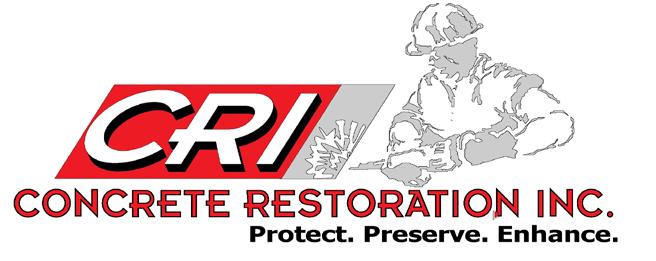
• The importance of frequent consumption of small quantities of water or other acceptable beverages
• The acclimatization, requirements under WAC 296-62-09545, the concept of acclimatization, and the importance of the following considerations.
• The importance of taking preventative cool-down rest periods when employees feel the need to do so in order to protect themselves from overheating.
• The mandatory cool-down rest periods under WAC 296-62-09547 when the outdoor temperature reaches or exceeds 90 degrees Fahrenheit.
• The procedures for providing shade or other sufficient means to reduce body temperature, including the location of such means and how employees can access them.
Supervisor training
Prior to assignment, supervisors must have training on the following topics:
• The information required to be provided in employee training above.
• The procedures the supervisor is to follow to implement the applicable provisions in this policy
• The procedures the supervisor is to follow when an employee exhibits signs or symptoms consistent with possible heat-related illness, including emergency response procedures;
• Procedures for moving employees to a place where they can be reached by an emergency medical service provider, if necessary; and
• How to provide clear and precise directions to the emergency medical provider who needs to find the work site.
REVISED DATE: January 1, 2025
Heat Related Illness
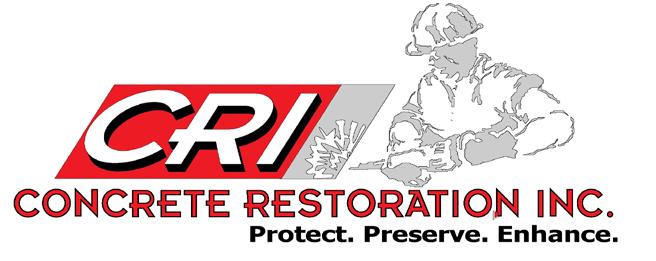
Definitions
Acclimatization –The body’s temporary adaptation to work in the heat that occurs as a person is exposed to it over a period of seven to 14 days depending on the amount of recent work in the heat and the individual factors. Acclimatization can be lost after seven consecutive days away from working in the heat.
Buddy System- A system where individuals are paired or teamed up into work groups so each employee can be observed by at least one other member of the group to monitor and report signs and symptoms of heatrelated illness.
Drinking Water-Potable water that is suitable to drink and suitably cool in temperature. Drinking water packaged as a consumer product and electrolyte-replenishing beverages (i.e., sports drinks) that do not contain caffeine are acceptable.
Engineering Controls- The use of devices to reduce exposure and aid cooling. Examples of engineering controls include fans, misting stations, air-conditioning, etc.
Heat-Related Illness (HRI) - A medical condition resulting from the body’s inability to cope with a particular heat load, and includes, but not limited to, heat cramps, heat rash, heat exhaustion, fainting), and heat stroke.
Heat Wave- any day in which the predicted high temperature for the day will be at least the temperatures listed in Table 1 of WAC 296-62-09530 and at least 10 degrees Fahrenheit higher than the average high daily temperature in the preceding five days.
Outdoor Environment – An environment where work activities are conducted outside. Work environments such as vehicle cabs, sheds, and tents, or other structures may be considered an outdoor environment if the environmental factors affecting temperature are not managed by engineering controls.
Risk Factors for Heat-Related Illness- Conditions that increase susceptibility for heat-related illness including:
REVISED DATE: January 1, 2025
Heat Related Illness
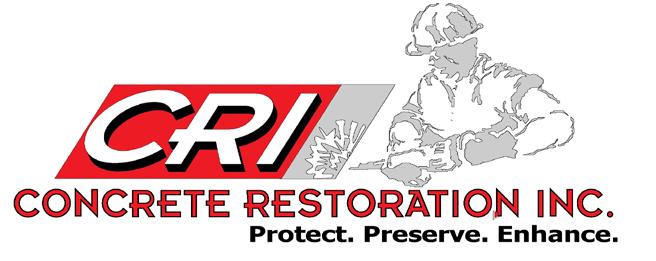
(a) Environmental factors such as air temperature, relative humidity, air movement, radiant heat from the sun and other sources, conductive heat sources such as the ground.
(b) Workload (light, moderate, or heavy) and work duration.
(c) Personal protective equipment and clothing worn by employees; and (d) Personal factors such as age, medication, physical fitness, and pregnancy
Shade- A blockage of direct sunlight. One indicator that blockage is sufficient is when objects do not cast a shadow in the area of blocked sunlight. Shade is not adequate when heat in the area of shade defeats the purpose of shade, which is to allow the body to cool. For example, a car sitting in the sun does not provide acceptable shade to a person inside it, unless the car is running with air conditioning. Shade may be provided by any natural or artificial means that does not expose employees to unsafe or unhealthy conditions and that does not deter or discourage access or use.
Vapor barrier clothing- Clothing that significantly inhibits or completely prevents sweat produced by the body from evaporating into the outside air. Such clothing includes encapsulating suits, various forms of chemical resistant suits used for PPE, and other forms of nonbreathable clothing.
REVISED DATE: January 1, 2025
HEAVY MOBILE EQUIPMENT
POLICY
HEAVY MOBILE EQUIPMENT POLICY
Reference: OSHA 1926.600/WAC 296-155-605
Purpose
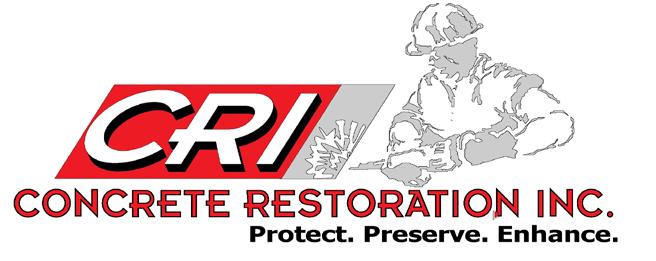
This program is intended to assist Concrete Restoration Inc employees in compliance with local regulatory requirements and Owner/Client rules and regulations. This program also provides directives to managers, foreman, and employees about their responsibilities in the operations and management of heavy mobile equipment.
Scope
This program applies to all Concrete Restoration Inc projects, operations, and locations.
Responsibilities
CRI Safety Manager
This person is responsible for developing and maintaining the safety program and related procedures. He/She also ensures these programs are implemented correctly and trains Foreman on key safety issues.
Foreman
This person is responsible for ensuring safety on the individual employee level. He/She will perform toolbox safety talks, assist employees in correct/safe procedures, and ensure employees comply with the safety program in place.
REVISED DATE: January 1, 2025
HEAVY MOBILE EQUIPMENT
POLICY
Employees
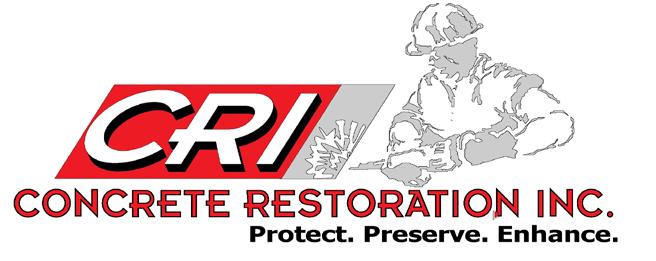
All should be familiar with procedures within their workplace. Employees are required to follow the rules of the safety program, report unsafe conditions, and abide by all posted requirements.
Heavy Mobile Equipment
Concrete Restoration Inc has developed and implemented safe work procedures for the use of powered mobile equipment in the workplace. Employees will and have been trained in proper safe work procedures for powered mobile equipment.
Equipment operators of mobile equipment are directly responsible for the safe operation of that equipment and will comply with all laws and regulations governing the operation of that equipment.
All heavy mobile equipment will be maintained in safe operating condition.
Any inspection, repair, maintenance or modification performed by a CRI employee will be carried out in accordance with manufacturer's instructions.
Maintenance records for any service, repair or modification which affects the safe performance of the equipment must be maintained and be readily available to the operator and maintenance personnel during work hours.
Servicing, maintenance, and repair of mobile equipment, should be done when the equipment is not in operation. Some equipment may be serviced during operation if the continued operation is essential to the process and a safe means is provided.
Only authorized employees are allowed to operate mobile equipment.
Employees must be qualified through appropriate training and practicum test before authorization to operate mobile equipment is issued. The employee must also possess an applicable operator's licence and airbrake
REVISED DATE: January 1, 2025
HEAVY MOBILE EQUIPMENT
POLICY
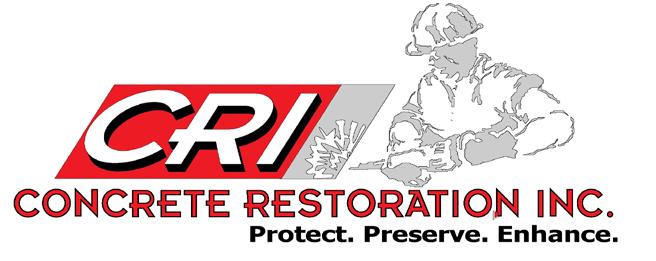
certificate where required and be familiar with the operating instructions pertaining to the equipment being operated. Authorization will be issued after these requirements are met.
Supervisors should not operate, or allow any employee to operate, mobile equipment that is in violation of any local or federal regulations or could create, an undue hazard to the health or safety of any person. To ensure a situation such as this does not occur, some of Concrete Restoration Inc guidelines for mobile equipment have been listed.
• Mobile equipment, in which the operator cannot directly, or by mirror, or other effective device see immediately behind the machine, must have an automatic audible warning device which activates
• All mobile equipment will be equipped with a working signal alarm for backing up. The operator will ensure this signal is operating prior to using equipment.
• Passengers are not allowed to ride on any equipment unless the equipment was manufactured to accommodate riders safely.
• Before each shift, the operator will perform an inspection of their assigned equipment. CRI provides electronic equipment inspection checklist with easy to follow step by step instructions for employees to use. This pre-operation checklist covers things such as; malfunction of the clutch or of the braking system, steering, lighting, audible horns, fire extinguisher, tires, fluid leaks, missing guards or warning labels, etc... If any item(s) on the equipment are not functioning properly the employee will write that on the checklist and report the malfunction immediately to his/her supervisor. The piece of equipment will be tagged “out of service” until repairs have been made.
• Before an employee starts any powered mobile equipment they are to make a complete 360 degree visual inspection of the equipment and the surrounding area to ensure that no worker, including the operator, is endangered by the start-up of the equipment.
REVISED DATE: January 1, 2025
HEAVY MOBILE EQUIPMENT
POLICY
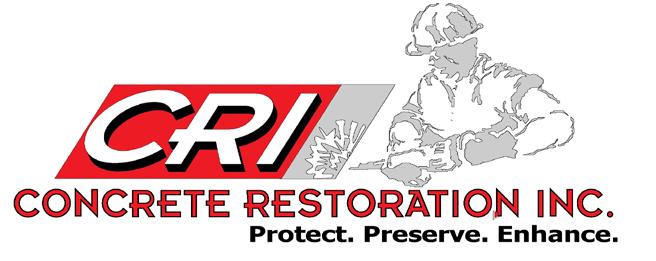
• The operator of mobile equipment must not leave the controls unattended unless the equipment has been secured against inadvertent movement such as by setting the parking brake, placing the transmission in the manufacturer's specified park position, or by chocking wheels where necessary.
• No operator will leave a suspended load unattended.
• Powered equipment shall not be left unattended unless forks, buckets, blades and similar parts are in the lowered position or solidly supported.
• The operator will use the access provided to get on or off of the equipment. Do not jump to the ground.
• All operators of mobile equipment are required to use some form of approved eye protection. Operators that use mobile equipment with an enclosed cab are not required to use additional eye protection.
CRI ensures their powered mobile equipment is inspected by a competent person for defects and unsafe conditions as often as is necessary to ensure that it is capable of safe operation. A written record of these inspections, repairs, and maintenance carried out, are kept in SmartSheets and made readily available to the operator of the equipment.
Safe Work Practices
Concrete Restoration Inc requires their mobile equipment to be equipped with a suitable and adequate cab, screen or guard when there is a danger to the operator of the equipment or any employee required to be in the area, from a falling object or projectile.
For all equipment that is equipped with a safety belt, Concrete Restoration Inc requires the employee operating that piece of equipment to wear their safety belt. Before starting the engine, the operator should fasten their safety belt and adjust if for a proper fit.
REVISED DATE: January 1, 2025
HEAVY MOBILE EQUIPMENT
POLICY
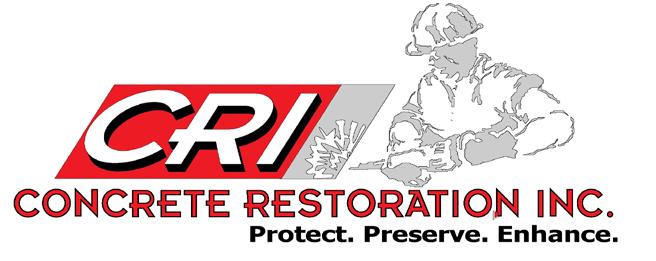
Each mobile equipment vehicle used for lifting must be provided with a durable and clearly legible load rating chart that is readily available to the operator. The operator is not to load the vehicle/equipment beyond the established load limits and will not move loads which have not been centered and secured for safe transportation. Any mobile equipment used for lifting or hoisting will have a permanently affixed notation stating the safe working load capacity of the equipment. The notation must be kept legible and clearly visible to the operator.
Operators will not use or attempt to use any vehicle/equipment in any manner or for any purpose other than what it was designed for. Employees who are unclear on these limitations should refer to the vehicle/equipment’s owner’s manual. The operator's manual for powered mobile equipment must be readily available to a worker who operates the equipment.
All mobile equipment should be equipped with (a) an audible warning signal; (b) a means of illuminating the path of travel at any time and tail lights when, because of insufficient light or unfavourable atmospheric conditions, (c) adequate illumination of the cab and instruments; and (d) a mirror providing the operator with an undistorted reflected view to the rear of the mobile equipment.
Operator of a gasoline or diesel vehicles/equipment will shut off the engine before filling the fuel tank and make sure that the nozzle of the filling hose rest securely in the neck of the tank. No employees are allowed on the vehicle during fuelling operations except as specifically required by design. There is absolutely no smoking or open flames within 50ft of fuelling operations.
When a worker is required to work beneath elevated parts of mobile equipment including trucks, the elevated parts are to be securely blocked.
Materials and equipment being transported shall be loaded and secured in a manner to prevent movement which could create a hazard to workers or another person. This includes keeping the cab, floor and deck of mobile equipment free of material, tools or other objects which could create a
REVISED DATE: January 1, 2025
HEAVY MOBILE EQUIPMENT
POLICY
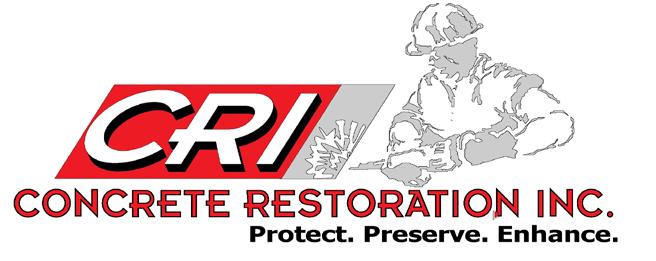
tripping hazard, interfere with the operation of controls or be a hazard to the operator or other occupants in the event of an accident.
Where a vehicle, crane, or similar equipment is operated near a live power line carrying electricity at more than 750 volts, every part of the equipment should be kept at least the minimum distance from the live power line for the particular voltage as required by local or federal law.
REVISED DATE: January 1, 2025
HEXAVALENT CHROMIUM POLICY
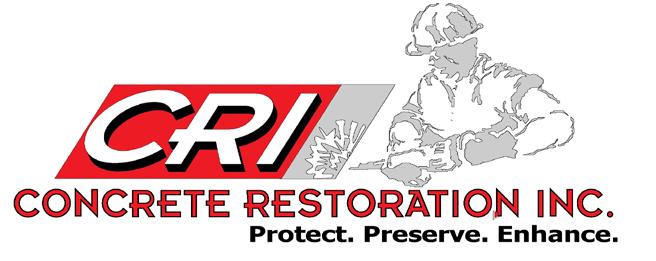
HEXAVALENT CHROMIUM POLICY
Reference: OSHA 1910.1026/WAC 296-62-08003
Uses and Occurrences
Chromium is a naturally occurring element in rocks, animals, plants, soil, and volcanic gases. Chromium occurs in the environment predominantly in one of two valence states:
• Trivalent (Cr III), which occurs naturally and is an essential nutrient, and
• Hexavalent chromium (Cr VI), which, along with the less common metallic chromium (Cr 0), is most commonly produced in plating processes.
The major industrial sources of Cr VI compounds are chromate pigments in dyes, paints, inks, and plastics; chromates added as anti-corrosive agents to paints, primer, and other surface coatings; chrome plating by depositing chromium metal onto an item’s surface using a solution of chromic acid; particles released during smelting of ferro-chromium ore, fumes from welding stainless steel or nonferrous chromium alloys; and as an impurity in Portland cement.
Physical Characteristics Appearance: Dark red flakes or powder
Odor: None
Flammable: Non-combustible, solid, but will accelerate the burning of combustible materials
Flash Point: None
Flammable Range: None
Specific Gravity: 2.7 for Cr VI
Stability: Stable
REVISED DATE: January 1, 2025
HEXAVALENT CHROMIUM POLICY
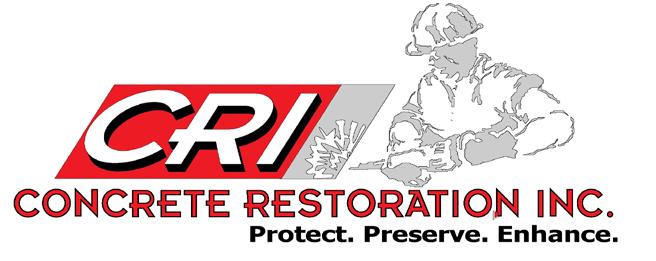
Incompatibilities: Reducing and oxidizing agents, acetic acid
Melting point: 1907°C or 3465°F for Cr
Boiling point: 2671°C or 4840°F for Cr
Signs and Symptoms of Exposure
Short term (Acute): Coughing, sneezing, chest pain, breathing difficulty, itching long term (Chronic): Allergic (asthma like symptoms) respiratory reaction, skin and eye irritation, nosebleeds, contact dermatitis, allergic like skin reaction, ulceration and perforation of the nasal septum
Modes of Exposure
Inhalation: Dusts and fumes Skin Absorption:
Liquid Ingestion: Dusts and liquids
Exposure Limits
Action level: 2.5 micrograms per cubic meter (μg/m³)
PEL: 5 μg/m³
STEL: None TLV: 5 μg/m³
PPE
Eye: Safety glasses
Skin: Chemical protective gloves and body protection
Respiratory: Air-purifying respirators and supplied-air respirators, depending on the exposure, and a PAPR if requested by the worker
First Aid
REVISED DATE: January 1, 2025
HEXAVALENT CHROMIUM POLICY
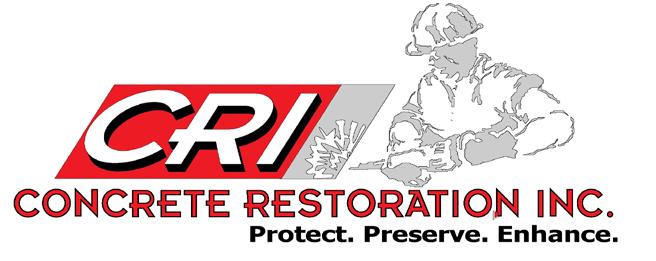
Inhalation: Move to fresh air; seek medical attention promptly
Skin: Quick drenching with water; wash skin with soap and water; seek medical attention promptly
Eyes: Flush with water for 15 minutes, lifting the lower and upper lids occasionally; seek medical attention promptly
Ingestion: Seek medical attention promptly
REGULATORY STANDARD: OSHA - 29 CFR 1910.1026 & 1926.1126
WAC 296-62-08003
Purpose: The purpose of this program outlines the requirements that Concrete Restoration Inc employees and subcontractors must comply with when implementing a program to evaluate and control worker exposure to hexavalent chromium (Cr VI).
The program provides information and the process to follow to recognize, evaluate, and control employee exposure to Cr VI at Concrete Restoration Inc project locations.
References:
Occupational Exposure to Hexavalent Chromium – Federal Register Number 71:10099-10385, U.S. Department of Labor, Final Rule, 29 CFR 1910.1026 and 29 CFR 1926.1126, Chromium VI
U.S. Department of Labor, Occupational Safety and Health Administration (OSHA), Final Rule, 29 CFR 1910.1026, and 29 CFR 1926.1126, Chromium VI
WAC 296-62-08003
REVISED DATE: January 1, 2025
HEXAVALENT CHROMIUM POLICY
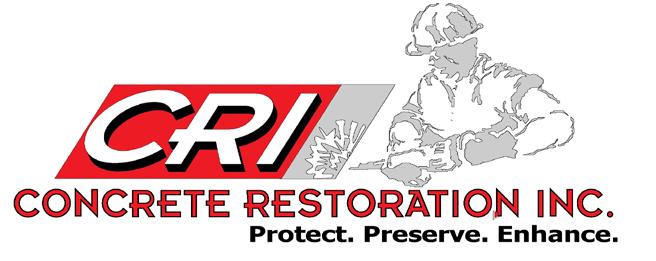
SCOPE AND APPLICATION
This program applies when employees may be exposed to Cr VI due to the following activities:
• Concrete Restoration Inc employees who may be exposed to Cr VI when performing hot work such as welding on stainless steel or Cr VI painted surfaces, traffic painting or paint removal containing Cr VI, refractory brick restoration, or soil disturbance activities such as drilling or from heavy equipment moving on soils containing Cr VI soils.
• Concrete Restoration Inc workers who may be exposed to Cr VI when working at project sites or in proximity to Cr VI related operations such as electroplating, painting, chromate pigment and chemical production, chromium dye and catalyst production, glass manufacturing, or plastic colorant production.
• Operations or tasks involving exposure to Cr VI in confined spaces
• Disposal of personal protective equipment (PPE) or other debris contaminated by chromium compounds.
• Demolition where materials containing Cr VI could become airborne and present a potential worker exposure.
DEFINITIONS
Action Level (AL)
The action level for implementation of this program is a concentration of airborne Cr VI of 2.5 micrograms per cubic meter (2.5μg/m³) of air calculated as an 8-hour time-weighted average (TWA).
Chromium VI or Hexavalent Chrome
Chromium with a valence of positive six, in any form and in any compound.
REVISED DATE: January 1, 2025
HEXAVALENT CHROMIUM POLICY
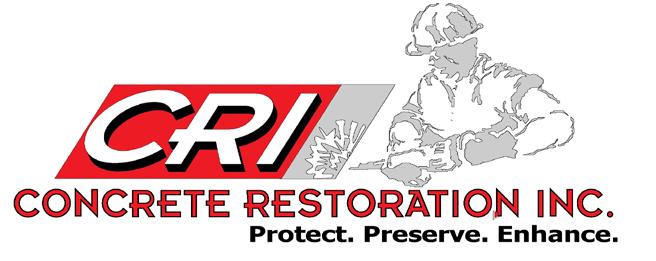
Emergency Release
Any activity that results or is likely to result in an uncontrolled release of Cr VI. If an incidental release of Cr VI (measured at or below the Permissible Exposure Limit) can be controlled at the time of release by workers in the immediate release area, it is not an emergency.
Worker Exposure
The exposure to airborne Cr VI that would occur if the worker was not using respiratory protection.
High-Efficiency Particulate (HEPA) Filter
Filter that is at least 99.97 percent (%) efficient in removing monodispersed particles of 0.3 micrometers (μg) in diameter or larger.
Objective Data
Information such as air monitoring data from industry-wide surveys or calculations based on the composition or chemical and physical properties of a substance demonstrating the worker exposure to Cr VI associated with a particular product or material or a specific process, operation, or activity. The data must reflect workplace conditions closely resembling the processes, types of material, control methods, work practices, and environmental conditions in the employer’s current operations.
Permissible Exposure Limit (PEL)
The level of worker exposure to an airborne concentration of Cr VI, without regard to the use of respirators, at 5 micrograms per cubic meter of air (5 μg/m³) calculated as an 8- hour time-weighted average (TWA) that cannot be exceeded.
ROLES AND RESPONSIBILITIES
The following sections outline the roles and responsibilities for individuals when applying this program.
REVISED DATE: January 1, 2025
HEXAVALENT CHROMIUM POLICY
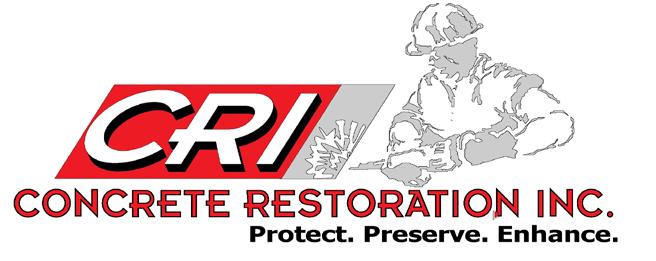
Foreman and Leads
Foreman and Leads are responsible for assisting Project Managers in implementing this program for all projects where there is a potential for worker exposure to Cr VI. The Foreman/Lead has the authority to approve deviations from this standard to accommodate additional domestic and international requirements.
Project Manager
Concrete Restoration Inc project manager (PM) is responsible for implementing this procedure and providing adequate resources for projectspecific implementation of the H&S management process on projects where there is a potential for worker exposure to Cr VI.
Safety Manager
The Safety/Training Manager is to provide health and safety technical guidance and support to the project. The Safety/Training Manager prepares and /or approves the Concrete Restoration Inc Project H&S plan and provides H&S support and guidance to the project.
Requirements
The following requirements outline the mandatory criteria that each Concrete Restoration Inc., employee must comply with when implementing this program using their policies, procedures, processes, training, and contracting documents.
REVISED DATE: January 1, 2025
HEXAVALENT CHROMIUM POLICY
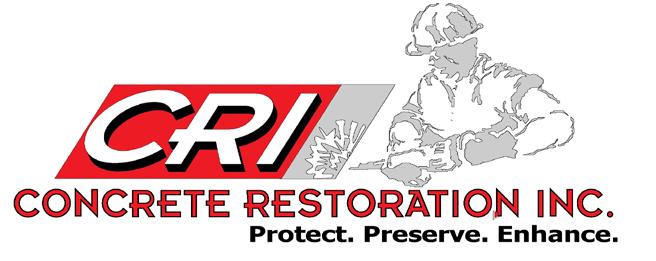
Exposure Determination
Initial exposure monitoring must be conducted to document worker breathing-zone exposures over the course of a full shift. A representative 8hour TWA sample shall be collected to determine employee exposure for each job classification in each work area.
• Exposure determinations must follow the current, accepted sampling and analytical method equivalent to that used by OSHA.
• Periodic monitoring of workers is required at least every 6 months when the initial monitoring indicates TWA results are equal to or greater than the Action Level (AL) but below the Permissible Exposure Limit (PEL).
• When initial monitoring results are greater than the PEL, additional periodic monitoring, at least quarterly, for each worker involved is required.
• When monitoring results fall below the AL, monitoring may be suspended.
• Additional monitoring is required when there has been a change in production process, control equipment, personnel, or work practices that may result in new or additional exposures.
• A performance-oriented option may be used to determine the initial 8hour TWA exposure for each worker on the basis of any combination of air monitoring data, historical monitoring data, or objective data sufficient to accurately characterize exposure to Cr VI.
• When the PEL has been exceeded, notification to the affected worker shall include the control measures utilized to reduce the exposure to below the PEL.
REVISED DATE: January 1, 2025
HEXAVALENT CHROMIUM POLICY
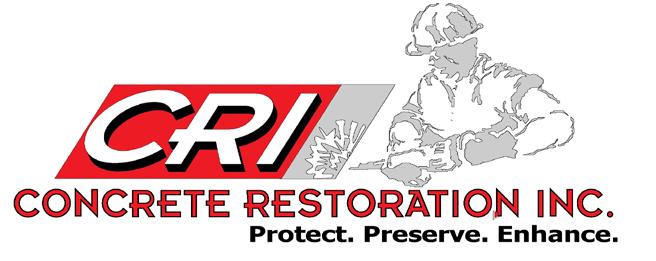
Demarcation of Regulated Areas
Work areas where worker exposure to Cr VI is or can reasonably be expected to exceed the OSHA PEL must be demarcated and access limited to only workers authorized to enter.
Methods of Compliance
Engineering and work practice controls must be applied to reduce the Cr VI worker exposure level to below the OSHA PEL unless it can be demonstrated that such controls are not feasible. Rotating employees to different jobs shall not be used to achieve compliance with the PEL. Methods of compliance in the hierarchy of controls include the following:
• Substitution – gas tungsten arc welding (GTAW) instead of shielded metal arc welding (SMAW) or flux cored arc welding (FCAW)
• Engineering controls – mechanical ventilation to remove fumes from the breathing Zone
• Administrative controls – safe work practices for the worker on proper positioning to minimize fume trail in their breathing zone, either through positioning upwind in an open area or in proper alignment with ventilation controls.
• Personal protective equipment (PPE) – use of respiratory protection as the last resort in reducing exposure or as an interim measure until substitution can be applied or engineering controls installed.
Respiratory Protection
Respiratory protection will be provided by the employer and worn by the worker sufficient to reduce the exposure to below the Cr VI action level.
The elements of the respiratory protection program must comply with the Concrete Restoration Inc Respiratory Protection Policy.
REVISED DATE: January 1, 2025
HEXAVALENT CHROMIUM POLICY
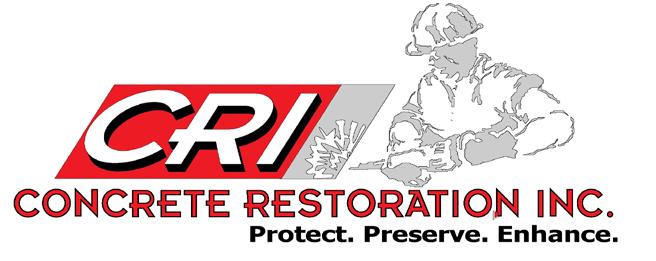
Key Elements
For an appropriate respiratory protection program include the following:
• Exposure assessment to determine the appropriate respiratory protection to be selected with the required protection factor and fit factor
• Medical surveillance for workers to determine their ability to wear respiratory Protection.
• Fit testing of workers to identify which model and type of respiratory protection can be worn.
• Training workers on the how to wear, use, clean and maintain their respiratory protection equipment.
• Respirator cartridge change-out guidelines for workers
• Periodic evaluation of the respiratory protection program by the Safety/Training Manager
Personal Protective Equipment (PPE) and Work Clothing
• Personal protective equipment and work clothing shall be provided to workers where an eye or skin hazard may exist to Cr VI.
• Key elements for an appropriate protective work clothing program include the following:
• Evaluation by the Safety/Training Manager of work tasks to identify the appropriate type of PPE and work clothing.
• Providing the appropriate PPE and work clothing in a variety of sizes and styles
REVISED DATE: January 1, 2025
HEXAVALENT CHROMIUM POLICY
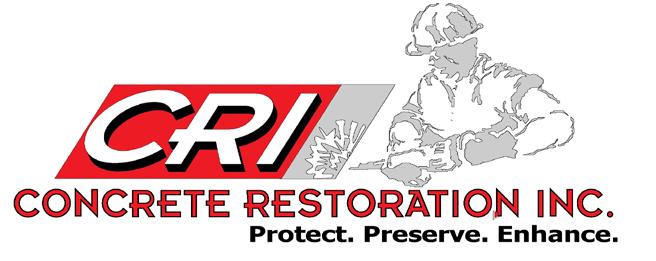
• Training workers on wearing, using, cleaning, and maintaining PPE and work Clothing.
• Ensuring that workers do not remove contaminated PPE or work clothing from the Worksite
• Repair or replace as needed.
Hygiene Areas and Practices
Where work clothing is required to be worn in place of street clothing to prevent skin exposure to Cr VI, change rooms and washing facilities must be provided. Change rooms must include separate storage facilities for work clothing and for street clothes. Washing facilities must be readily accessible to workers and must be used by them at the end of the work shift and prior to eating, drinking, smoking, chewing tobacco or gum, applying cosmetics, or using the toilet.
An area on the worksite must be designated to be free of Cr VI for workers to consume food or beverages.
General Work Practices and Housekeeping
Work areas or project sites where Cr VI can potentially expose workers must implement and follow work practices to maintain acceptable housekeeping conditions to minimize contact or exposure. General work practices and housekeeping must include the following:
• All surfaces must be maintained as clean as practicable to minimize accumulation of Cr VI containing substances, dust or particles
• All spills and releases of Cr VI containing material must be cleaned up promptly
• Surfaces contaminated with Cr VI must be cleaned with HEPA-filter vacuuming or equivalent methods or practices that minimize the potential for worker exposure
REVISED DATE: January 1, 2025
HEXAVALENT CHROMIUM POLICY
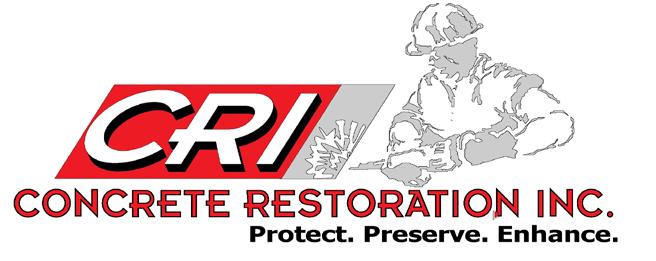
• Avoid using compressed-air, dry-shoveling, dry sweeping, or dry brushing, and use only when a HEPA-filter vacuum system or equivalent method has been tried and found to be not effective
• Collection of waste, scrap, debris, or other materials contaminated or containing Cr VI must be in impermeable containers or bags and labeled meeting hazard communication requirements described in Concrete Restoration Inc Hazard Communication
Medical Surveillance
Workers who are or will be potentially exposed to airborne Cr VI above the action level for at least 30 days per year, without regard to respirator use, will participate in their employer’s Cr VI medical surveillance program.
Further participation in periodic Cr VI medical surveillance will be based on exposure conditions (such as an emergency or when a worker shows signs or symptoms of exposure), annually, or within a specified frequency determined by the company consulting physician (or equivalent), and at termination of employment.
5.3 Communication of Hazards
Information concerning Cr VI hazards will be communicated according to the requirements of the OSHA Hazard Communications Standard and the OSHA Cr VI Standard including, but not limited to, the requirements concerning warning signs and labels, safety data sheets (SDSs), and employee information and training.
The entrance to regulated areas must be posted with signs that read “CHROMIUM VI REGULATED AREA – AUTHORIZED PERSONNEL ONLY”.
In addition to the posting requirements, owners, contractors, and other personnel working in the area must be notified.
All storage or shipping containers shall be labeled with the following “Danger – Contains Cr VI – Cancer Hazard – Harmful if Inhaled or
REVISED DATE: January 1, 2025
HEXAVALENT CHROMIUM POLICY
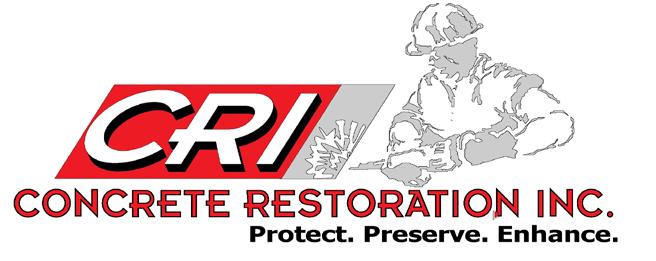
Swallowed – Use Only with Adequate Ventilation or Respiratory Protection”.
A copy of this program and the OSHA Cr VI Standards (General Industry and Construction) will be made available to all affected project workers.
TRAINING REQUIREMENTS
Workers who may be exposed to airborne Cr VI above the action level or anticipate working on projects where they could be exposed to airborne Cr VI above the action level, or to soil that contains elevated levels of Cr VI, must complete initial Cr VI exposure training. This training covers the following information:
• Where Cr VI is typically encountered at Concrete Restoration Inc projects
• The regulatory requirements, exposure limits, potential hazards including toxicity and physical characteristics, and medical monitoring requirements
• For site-specific Cr VI hazards, discussion on the location and tasks associated with potential exposure and associated control measures
• Information contained in the site-specific Health, Safety, and Environmental Protection Plan or Job Hazard Analysis created for the project
• Quantity, location, manner of use, storage, sources of exposure, and the specific nature of operations that could result in exposure to Cr VI, as well as any necessary protective steps
• Purpose, proper use, and limitation of respirators
• Purpose and a description of the medical surveillance program
• Engineering controls and work practices associated with the employee’s job assignment.
REVISED DATE: January 1, 2025
HEXAVALENT CHROMIUM POLICY
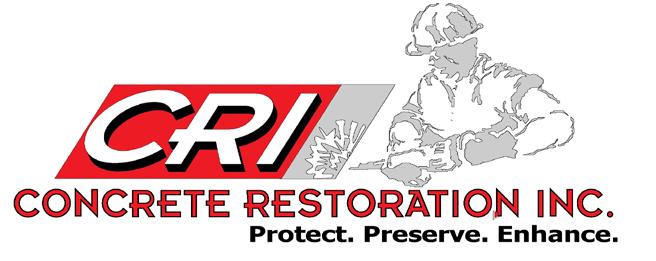
• A review of this program
• Each worker must be provided with a copy of the OSHA/WAC Chromium Standard (General Industry and/or Construction) and appendices if requested.
RECORDKEEPING
An accurate record of all workers personal air sampling and other air monitoring related to determining Cr VI exposure for Concrete Restoration Inc employees must be completed and maintained that includes the following:
• Industrial hygiene sampling surveys
• Specific information on the sample date, worker(s) sampled, job classification, process or task sampled, materials used, PPE worn, sample duration, air sampling, and analytical method.
REVISED DATE: January 1, 2025
HOT WORK POLICY
HOT WORK POLICY
Reference: OSHA 1917.152/WAC 296-56-60235
Purpose
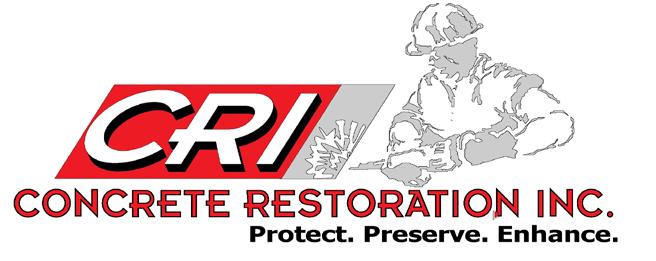
This Program to provide occupational safety guidelines for welding, cutting and brazing flame activities in order to comply with Occupational Safety and Health Administration (OSHA) and WAC 296-56-60235 regulations.
Scope
This Program applies to all welding, cutting, and brazing work activities performed by Concrete Restoration Inc employees.
PROGRAM ELEMENTS
Hazard Identification and Prevention
Welding, cutting, and similar processes produce molten metal, sparks, slag, and hot work surfaces that can cause fire or explosion if precautionary measures are not followed. Remove all combustible materials before starting hot work. Flying sparks are the main cause of fires and explosions in welding and cutting. If combustibles cannot be removed always use a shield or guard.
Hot Work Responsibilities
Persons initiating the hot work process are responsible for ensuring that the requirements of this program are understood and followed by all employees. Also, persons initiating the hot work process are responsible for contractors who will be performing hot work activities, as defined, must comply with the requirements of the Hot Work Program.
Never perform hot work if it is unsafe too. Hot work permit must be obtained before performing Hot work.
REVISED DATE: January 1, 2025
HOT WORK POLICY
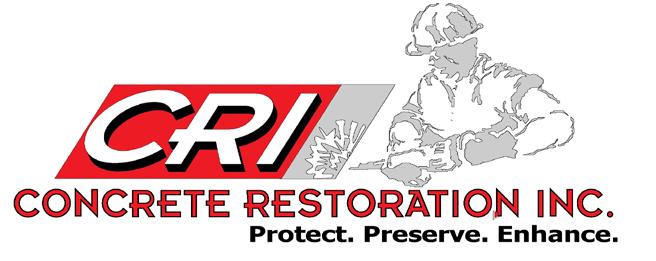
Hot Work Authorizer (Safety/Training Manager or Project Manager):
• Selecting suitable personnel that are trained in the safe operation of their equipment, the safe use of the process, and emergency procedures in the event of a fire.
• Contact Building Liaison and appropriate personnel responsible for the area in which hot work operations are to take place, inform them of the scope of work to be performed and determine if they have any specific concerns about the operations.
• Coordinating hot work activities to minimize fire hazards, authorizing hot work, and ensuring all parties involved have a copy of the hot work permit.
Hot Work Supervisor Responsibilities:
The Hot Work Supervisor is responsible for the safe operations of hot work activity under their supervision. These duties include:
Establish permissible areas for hot work.
• Ensure that Hot Work tools and equipment are in good condition. All defective hot work tools shall be removed.
• Ensure that all individuals involved in the hot work operations are familiar with Hot Work requirements.
• Ensure that all individuals involved in the hot work operations are trained in the safe operation of their equipment and the safe use of the process. These individuals must have an awareness of the risks involved and understand the emergency procedures in the event of a fire.
• Determine site-specific flammable materials, hazardous processes, or other potential fire hazards present or likely to be present in the work location.
• Ensure combustibles are protected from ignition.
REVISED DATE: January 1, 2025
HOT WORK POLICY
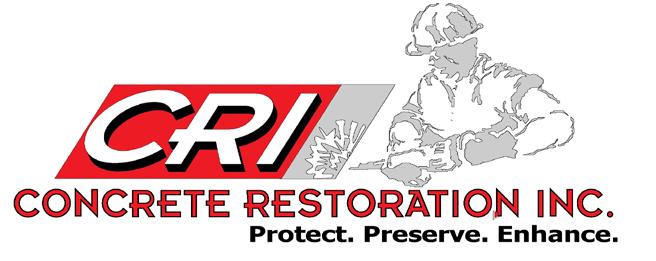
• Determine that fire protection and extinguishing equipment are properly located and readily available.
• Ensure sufficient local exhaust ventilation is provided to prevent accumulation of any smoke and fume.
• Ensure that a fire watch is posted on the work site and / or where hot work hazards exist.
Safety/Training Manager:
• Responsible for developing and maintaining this program to ensure compliance.
• Periodic and annual audits of hot work activities.
• Maintain completed hot work permits.
Fire Watch Responsibilities:
Fire watch shall be required whenever hot work or fire detection system impairment is not available. The fire watch shall be conducted by trained personnel but shall not be the actual employee who is performing the hot work operation.
Specific Responsibilities:
• Have a fire extinguisher readily available and be trained in its use and limitations.
• Be familiar with facilities and procedures for sounding an alarm in the event of a fire.
• Aware of inherent hazards of the work site and of any hot work taking place.
• Watch for fires in all exposed areas and try to extinguish them only when within the capacity of the equipment available.
REVISED DATE: January 1, 2025
HOT WORK POLICY
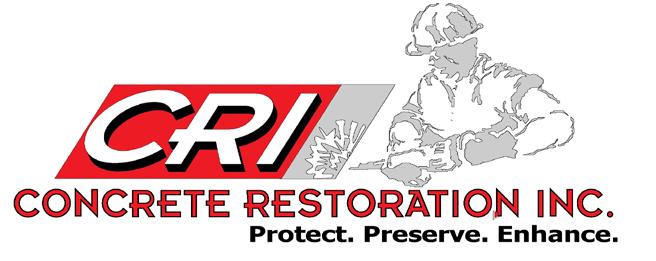
• Remain at the work area to monitor for smoldering fires while work is in progress and for at least 30 minutes following job completion. If the fire watch must leave the work site, all hot work activities must stop.
Hot Work Operator Responsibilities:
• The Operator shall be responsible for obtaining, completing, and returning the hot work permit.
• The operator shall be fully trained and qualified to perform the required hot work.
• The operator shall be responsible for using appropriate safety equipment (eye and face protection, hand protection, etc.) and verifying their equipment and tools are in good working condition.
• The operator shall be responsible for stopping hot work activities when conditions change from those established when the permit was issued.
Electrical Shock Hazards and Safety Precautions
Electric shock from electrical welding and cutting equipment can result in death or severe burns. Additionally, serious injury can occur if the welder falls as a result of the shock. This safety hazard is associated with operations that use electricity to generate heat, such as arc and resistance welding and cutting.
Employees shall use proper precautionary measures and recommended safe practices at all times to avoid electrical shocks. Personnel using electrical welding and cutting equipment must be trained in safe work practices and procedures before use of this equipment. Some measures to prevent electrical shock include:
• Never use a bare hand or wet glove to change electrodes.
REVISED DATE: January 1, 2025
HOT WORK POLICY
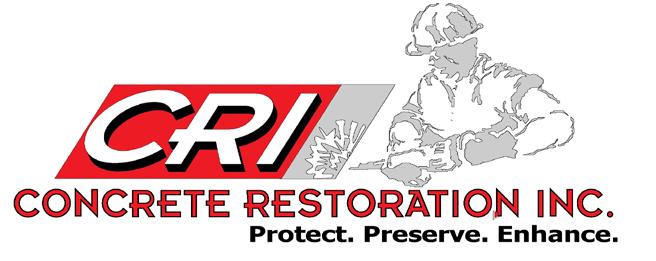
• Do not touch an energized electrode while you are in contact with the work circuit.
• Never stand on a wet or grounded surface when changing electrodes.
• Do not allow the electrode holder or electrode to come in contact with any other person or any grounded object.
• Ground the frames of welding units.
• Insulate yourself from the work piece and ground using dry insulating mats or covers big enough to prevent any physical contact with the work or ground, or wear properly designed and approved rubber-soled boots in good condition.
• If utilizing long lengths of cable, suspend them overhead whenever possible.
• If run along the floor, be sure they do not create a tripping hazard, become damaged, or tangled.
Fumes and Gases
When engaging in welding, cutting, or brazing activities, various fumes, gases, and vapors are generated from the metals, fluxes, and fillers being used in addition to coatings, paints, galvanizing and plating. To protect workers from these, appropriate personal protective equipment (PPE) in the form of a respirator and/or ventilation is recommended. Fume and gas hazards to be considered prior to conducting WCB are:
Fumes (metals) – Aluminum, Antimony, Arsenic, Beryllium, Cadmium, Chromium, Cobalt, Copper, Iron, Lead, Manganese, Molybdenum, Nickel, Silver, Tin, Titanium, Vanadium, and Zinc;
REVISED DATE: January 1, 2025
HOT WORK POLICY
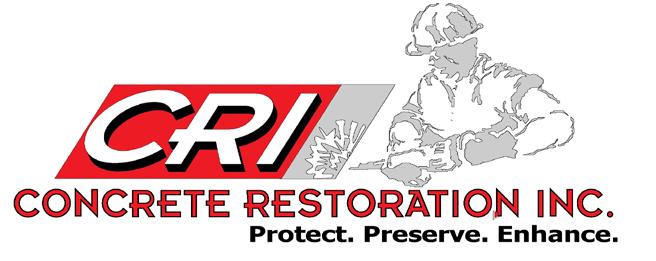
Shielding Gases – Argon, Helium, Nitrogen, Carbon Dioxide; and
Process Gasses – Nitric Oxide, Nitrogen Dioxide, Carbon Monoxide, Ozone, Phosgene, Hydrogen, Fluoride, and Carbon Dioxide.
Personal Protective Equipment (PPE)
Employees exposed to the hazards created by welding, cutting, or brazing operations shall be protected by PPE. Appropriate protective clothing required for any welding operation will vary with the size, nature, and location of the work to be performed. PPE must protect against hazards such as burns, sparks, spatter, electric shock, optical radiation, and inhalation hazards as identified below.
General Protective Equipment
The following are minimum requirement for proper personal protective equipment needed for welding activities:
• Eye and Face Protection
• Clothing with adequate body cover & leather boot protection.
• Hand protection.
• Additional personal protective equipment may include the use of respiratory protection.
Eye and Face Protection
All filter lenses and plates must meet the test for transmission of radiant energy prescribed in the ANSI standard Z87.2010, Personal Eye and Face Protection Devices.
REVISED DATE: January 1, 2025
HOT WORK POLICY
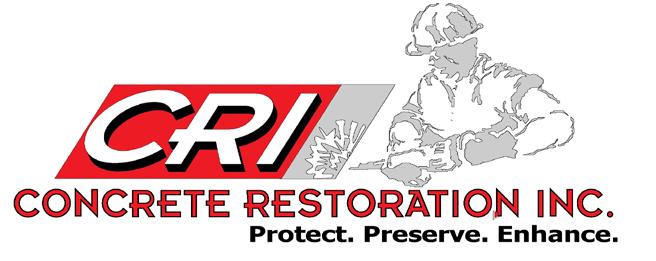
Helmets and hand shields shall protect the face, forehead, neck, and ears to a vertical line in back of the ears, from the arc’s direct radiant energy, and weld splatter.
Welding helmets with filter plates are intended to protect users from arc rays and from weld sparks and spatters which strike directly against the helmet. They are not intended to protect against slag chips, grinding fragments, wire wheel bristles, and similar hazards which can ricochet under the helmet. Spectacles, goggles, or other appropriate eye protection must also be worn to protect against these impact hazards.
OSHA/WAC WAC 296-56-60235 requires that when arc cutting and arc welding with open arcs, helmets or hand shields with filter lenses and cover plates shall be used by operators and nearby personnel viewing the arc also subject to wear proper protection. Spectacles with a shade 2 lens are recommended for general purpose protection for viewers. When resistance welding or brazing, operators of resistance welding must use face shields, spectacles, or goggles depending on the particular job to protect their faces and eyes from welding hazards.
Protective Clothing
Appropriate protective clothing for any welding and cutting operation will vary with the size, nature and location of the work to be performed. Clothing shall provide sufficient coverage and be made of suitable materials to minimize skin burns caused by sparks, spatter, or radiation. Covering all parts of the body is recommended to protect against ultraviolet and infrared ray flash burn.
Dark clothing works best to reduce reflection under the face shield. Heavier materials such as wool clothing, heavy cotton or leather are preferred as they resist deterioration. Materials that can melt or can cause severe burns due to sparks that may lodge in rolled- up sleeves, pockets of clothing or pant cuffs are not recommended.
Other protective clothing includes durable, flame-resistant aprons made of leather or other suitable materials to provide protection to the front of the body when additional protection against sparks and radiant energy is needed.
REVISED DATE: January 1, 2025
HOT WORK POLICY
Gloves
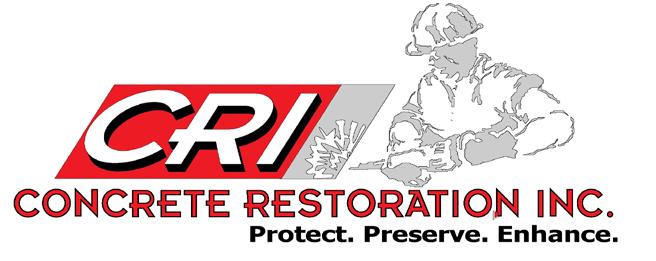
The standard requires all welders and cutters to wear protective flameresistant gloves, such as leather welder's gloves, which provide the heat resistance needed for welding. A gauntlet cuff offers additional arm protection, and insulated linings shall be used to protect areas exposed to high radiant energy.
Respiratory Protection
Respiratory protection is recommended for all welding, cutting, or brazing operations regardless of ventilation due to the variable nature of potential toxic exposure to fumes that are carcinogenic or toxic at very low levels as in the case of manganese or hexavalent chrome. It is precautionary to assume that fumes will be above the level of acceptable risk during all WCB activities.
Ventilation
Ventilation refers to changes of room air as often as necessary to prevent welders and other workers from breathing high levels of airborne contaminants. Ventilation is a means of providing adequate breathing air, and must be provided for all welding, cutting, brazing and related operations.
Adequate Ventilation - depends on the following factors:
• Volume and configuration of the space where the welding operations occur
• Number and type of operations that are generating contaminants
• Natural air flow rate where operations are taking place
REVISED DATE: January 1, 2025
HOT WORK POLICY
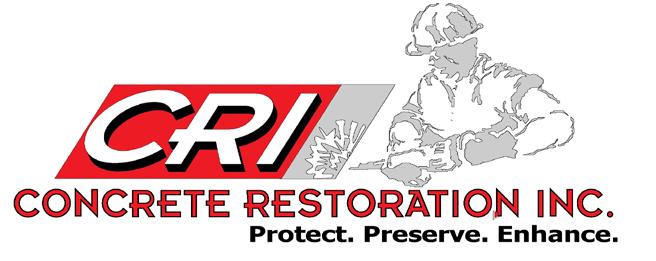
Locations of the welders' and other workers' breathing zones in relation to the contaminants or sources.
Welding in a confined space can be extremely dangerous. Without adequate ventilation, welding can transform an acceptable atmosphere into a toxic one very quickly. When welding in a confined space, atmospheric monitoring shall be conducted before anyone enters the space and periodically during the entry to ensure that the process of welding is not creating a hazardous atmosphere.
Compressed Gas Cylinders
Gas cylinders shall be stored in approved spaces and must be secured from falling. The control valves of cylinders not in use will be covered by protective caps.
Compressed gas cylinders shall be legibly marked to identify the gas contents.
Acetylene cylinders must be kept in an upright position to prevent acetone (solvent used to dissolve the acetylene) from spewing out with the gas.
All gas units must have antiflashback devices installed on them.
REVISED DATE: January 1, 2025
HOT WORK POLICY
Training and Record Keeping
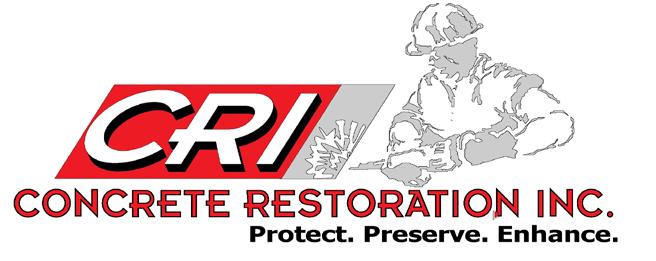
Training is required when employees are first hired and annually for refresher training. Welding, Cutting and Brazing Safety training includes the following topics:
• Proper equipment operation
• Handling and storage of welding materials
• Compressed gas cylinder safety
• Physical and chemical hazards
• Hazard control
• PPE selection and use
• Fire precautions
• Fire watch
• Hot work procedures, including how to obtain the written hot work permit.
• Confined space training is required when the work necessitates confined space entry.
Copies of training records are to be maintained and kept by company.
REVISED DATE: January 1, 2025
HYDROGEN SULFIDE POLICY
HYDROGEN SULFIDE PROGRAM
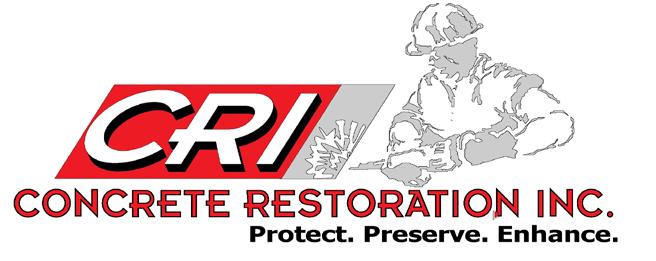
Reference: OSHA - 29 CFR 1910.1200 and 1926.55/WAC 296-841-20025
Purpose: The purpose of this program is to inform interested persons, including employees, that Concrete Restoration Inc is complying with OSHA's Gases, Vapors, Fumes, Dusts, and Mists standard, Title 29 Code of Federal Regulations 1926.55 and other OSHA rules as needed to ensure that no employee is exposed to inhalation, ingestion, skin absorption, or contact with any material or substance at a concentration above those specified in the standard
This program will address potential exposures to Hydrogen Sulfide.
To achieve compliance Concrete Restoration Inc must first implement all feasible administrative and engineering controls. However, when such controls are not feasible, employees will use protective equipment provided by Concrete Restoration Inc at no cost to the employee or other protective measures to keep the exposure of employees to air contaminants within the limits prescribed in Appendix A of 29 CFR 1926.55. All equipment and technical measures used to achieve compliance will first be approved for each particular use by a competent industrial hygienist or other technically qualified person.
Administrative Duties: This written safety program is for Concrete Restoration Inc employees. The Site Supervisor is the program coordinator/manager and is responsible for its implementation.
Scope: Concrete Restoration Inc. has chosen to establish a Hydrogen Sulfide Awareness Program for emergencies that could arise from exposure to Hydrogen Sulfide.
Physical and Chemical Characteristics
• Sulfur and Sulfur Compounds may be present in crude oil as hydrogen sulfide (H2S), as compounds (e g mercaptans, sulfides. disulfides, thiophenes, etc.), or as elemental sulfur. Each crude oil has different amounts and types of sulfur
REVISED DATE: January 1, 2025
HYDROGEN SULFIDE POLICY
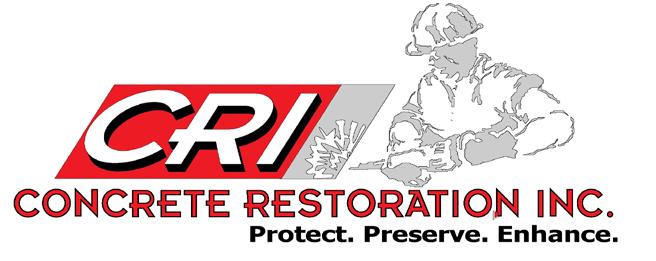
compounds, but as a rule the proportion stability and complexity of the compounds are greater in heavier crude-oil fractions.
• As part of the work of Concrete Restoration Inc our employees may be exposed to H2S especially when working in confined spaces or refineries. Hydrogen sulfide is a primary contributor to corrosion in refinery processing units and piping. Other corrosive substances are elemental sulfur and mercaptans. Moreover, the corrosive sulfur compounds have an obnoxious odor.
Health Effects
Inhalation, ingestion, and contact with are all methods by which H2S can affect the body. The effects may range from irritation of the eyes, nose, and throat; to temporary loss of smell. Headaches, dizziness, and upset stomach are more intense symptoms caused by higher concentrations.
However, inhalation of high concentrations of H2S may cause instant paralysis of the respiratory system causing loss of consciousness and death. In concentrations of H2S at 1000 to 2000 ppm even a single breath may cause coma and may be fatal. Because of its extremely serious and/ or fatal potential, any employee believed to be exposed to H2S shall immediately notify the Foreman or Safety Manager.
General Requirements. Concrete Restoration Inc will establish Hydrogen Sulfide operational procedures through the use of this document.
Permissible Exposure Levels (PEL)
While not definitive, H2S levels below 10 ppm appear to cause little short term effects. When H2S level is unknown, respirators shall be used.
Current OSHA standards are:
20 ppm Ceiling Level
50 ppm Maximum allowable peak for 10 minutes with no other exposure
REVISED DATE: January 1, 2025
HYDROGEN SULFIDE POLICY
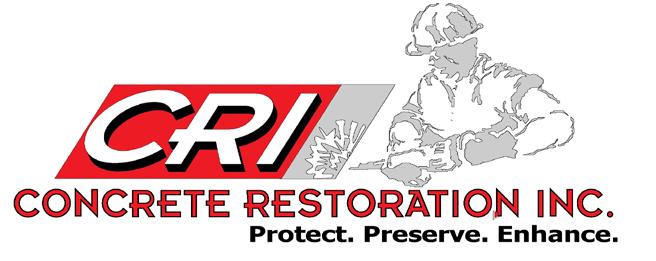
Exposure detection, assessment, and monitoring
• Concrete Restoration Inc Site Supervisor shall conduct personal or area sampling for hydrogen sulfide to measure worker exposures. Air sampling is needed to measure worker exposures and select appropriate engineering controls and respiratory protection. Where data is collected it must be retained to support negative
• exposure assessments. Concrete Restoration Inc conducts both initial and periodic air monitoring with Monitors that will alarm when exposure limits have been reached.
• Concrete Restoration Inc will further perform air monitoring as needed to measure the effectiveness of controls and as required under our written excavation procedures.
• Concrete Restoration Inc, Inc will utilize direct reading instruments (4 gas meter) and colorimetric tubes for quantification of exposures to Hydrogen Sulfide. Signs and symptoms of exposure are as follows:
o Short Term Effects:
o 0.13 ppm - Threshold of odor detection
o 0.77 ppm - Faint, but readily perceptible odor
o 4.6 ppm - Easily noticeable odor
o 10 ppm - Eye irritation, soreness, redness, burning 27 ppm Strong, unpleasant, but not intolerable odor
o 5 0 ppm - Irritation & dryness of nose, throat, and airways cough, shortness of breath, pneumonia
o 100 ppm - Immediate irritation of eyes and respiratory tract 150 ppm Sense of smell may be paralyzed
o 200 ppm - Headaches, dizziness, nausea
o 500 ppm - Unconsciousness and death within a few minutes may be no warning odor
o 1000 ppm - Immediate loss of consciousness and respiratory paralysis leading to Death
REVISED DATE: January 1, 2025
HYDROGEN SULFIDE POLICY
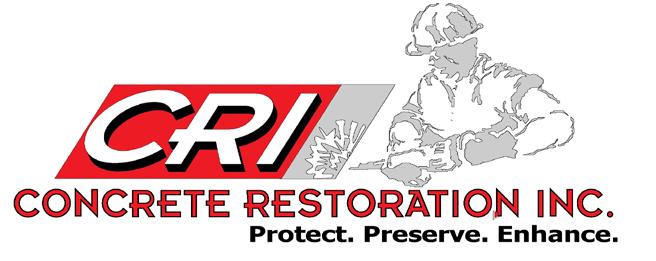
Employee Notification and Signage.
This employer shall post signs at entrances to regulated areas. The signs shall bear the following information:
DANGER HYDROGEN SULFIDE TOXIC
FLAMMABLE - NO SMOKING AUTHORIZED PERSONNEL ONLY
RESPIRATOR REQUIRED
Method of Compliance. Exposures to Hydrogen Sulfide (H2S) can generally be controlled through the use of engineering controls, work practices, and personal protective equipment. Engineering controls are hazard controls designed into equipment and workplaces. Work practices are procedures followed by employers and workers to control hazards. The following engineering Controls, work practices, and personal protective equipment should be used when dealing with H2S.
• Ventilate spaces to mitigate accumulation of hydrogen sulfide or other gases.
• Notify the Foreman upon detection of H2S
• If the potential for exposure exists and assessment of levels cannot be performed, assume the Permissible Exposure Limit is being exceeded, and wear a NIOSH approved supplied air respirator.
Training.
Concrete Restoration Inc will provide our employees workers with regulatory training that includes the requirements of the substance specific requirements. This will include health effects, background information, engineering controls, PPE, medical surveillance, communication of hazards, hygiene, and methods of compliance at a minimum.
Medical surveillance
REVISED DATE: January 1, 2025
HYDROGEN SULFIDE POLICY
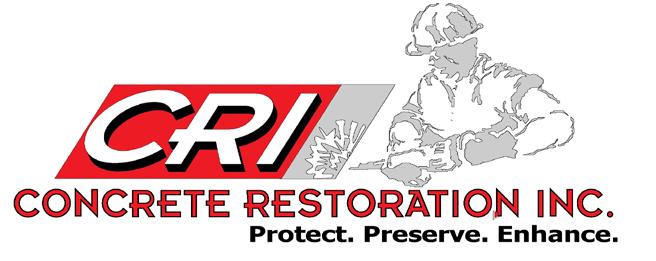
• Although Concrete Restoration Inc, Inc understands that medical examinations should always supplement effective gas, vapor, fume, dust, and mist monitoring and controls, and never substitute for them, we provide medical examinations for all workers who may be exposed to Hydrogen Sulfide at or above the respective PEL for greater than 30 days per year, found in 29 CFR 1926.55.
• These medical examinations are provided by professional healthcare
Emergency, Spill and Leak Procedures.
Concrete Restoration Inc should be aware of Owners contingency plan provisions. Employees must be informed of the plan of the host facility and aware of additional plant safety rules
REVISED DATE: January 1, 2025
LEAD AWARENESS POLICY
LEAD AWARENESS POLICY
Reference: OSHA 1910.1025/WAC 296-62-07521
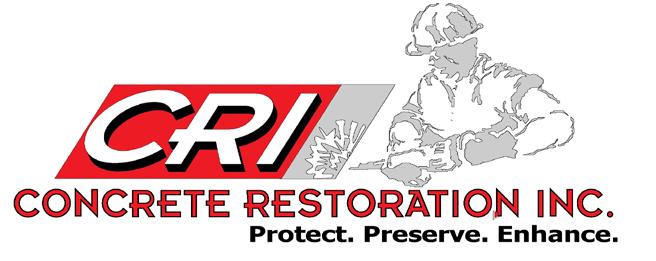
*NOTE – CONCRETE RESTORATION INC does not perform work in atmospheres that contain lead above the action level. No employee exposures will be contemplated.
*Any reference to “We” or “Our” is a reference to Concrete Restoration Inc
Lead Exposure Compliance Program for Construction
The purpose of this program is to inform interested persons, including employees, that CRI is complying with the WAC 296-62-07521 Standard by:
• Ensuring that no employee is exposed to lead at concentrations greater than 50 micrograms per cubic meter of air averaged over an eight-hour period.
• Ensuring that if an employee is exposed to lead for more than eight hours in any workday the employee's allowable exposure, as a time weighted average (TWA) for that day, must be reduced according to the following formula: Allowable employee exposure (in micrograms per cubic meter) = 400 divided by hours worked in the day.
• Knowing that when respirators are used to limit employee exposure, which is considered to be at the level provided by the protection factor of the respirator for those periods the respirator is worn. Those periods may be averaged with exposure levels during periods when respirators are not worn to determine the employee's daily TWA exposure.
REVISED DATE: January 1, 2025
LEAD AWARENESS POLICY
Administrative Duties
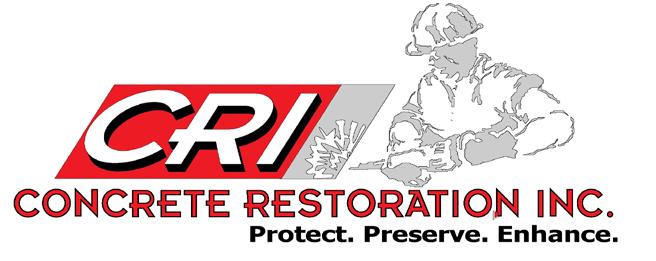
Tim Coots is the program coordinator/manager and is responsible for its implementation. Copies of the written program may be obtained at CRI’s office.
This written safety plan is for all locations worksite.
Exposure Assessment
Protection of Employees during Exposure Assessment
When tasks are presumed to generate lead exposures greater than the permissible exposure limit (PEL) of 50 micrograms per cubic meter of air averaged over an (8) eight-hour period, we treat affected employees as if they were exposed above the PEL and implement procedures to protect workers until we perform an employee exposure assessment and document that an employee's lead exposure is not above the PEL.
Tasks estimated to generate a TWA of 50 micrograms per cubic meter of air include:
• Manual demolition of structures (e.g., dry wall), manual scraping, manual sanding, heat gun applications, and power tool cleaning with dust collection systems where lead containing coatings or paint are present.
• Spray painting with lead paint. Tasks estimated to generate a TWA of 500 micrograms per cubic meter of air include:
• Using lead containing mortar or lead burning.
• Rivet busting, power tool cleaning without dust collection systems, cleanup activities where dry expendable abrasives are used, and abrasive blasting enclosure movement and removal where lead containing coatings or paint are present.
REVISED DATE: January 1, 2025
LEAD AWARENESS POLICY
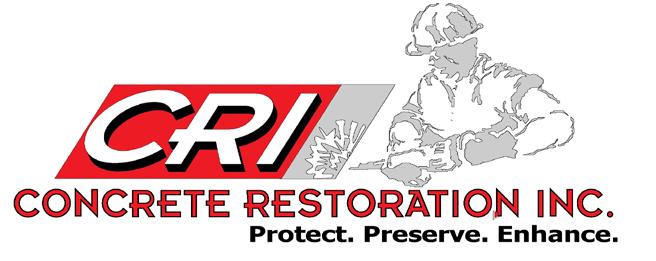
Our counter measures include:
• Appropriate respiratory protection (protection factor of 10, 25, or 50, depending on the tasks involved and the estimated exposures).
• Proper personal protective clothing and equipment.
• Change areas.
• Hand washing facilities.
• Biological monitoring.
• Training.
Initial Determination
We assess each new project to determine if employees may be exposed to lead at or above the action level of 30 micrograms per cubic meter of air as an eight-hour TWA. This initial determination can be based on:
• Employee exposure monitoring,
• Objective data demonstrating that under any expected conditions, specific processes, operations, or activities involving lead cannot result in employee exposure to lead at or above the action level.
• Previous monitoring for lead exposures within the past 12 months during work operations conducted under workplace conditions closely resembling the processes, types of materials, control methods, work practices, and environmental conditions used and prevailing in our operations.
We base initial determinations on employee exposure data. Our employee exposure monitoring data includes:
REVISED DATE: January 1, 2025
LEAD AWARENESS POLICY
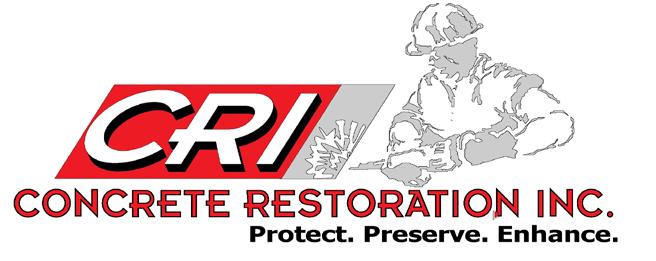
• Information, observations, or calculations that would indicate employee exposure to lead
• Previous measurements of airborne lead.
• Any employee complains of symptoms that may be attributable to exposure to lead.
• As part of our initial exposure assessment, we have historical measurements of airborne lead monitored at other construction sites substantially similar to the current job. This data:
• Was obtained within the past 12 months during work operations conducted under workplace conditions closely resembling the processes, type of material, control methods, work practices, and environmental conditions used and prevailing in our operations.
• Has accuracy (to a confidence level of 95 percent) of not less than plus or minus 25 percent for airborne concentrations of lead greater than or equal to 30 micrograms per cubic meter of air.
• Is recorded and maintained as relevant previous exposure data.
We base our initial determinations on objective data. Our objective data, described below, demonstrates that under any expected conditions of use a particular product or material containing lead or a specific process, operation or activity involving lead cannot result in employee exposure to lead at or above the action level during processing, use, or handling. None
We rely on this data to satisfy in part our requirements for initial exposure assessment and show that employees have no exposure to lead at or above the action level.
Positive Initial Determination
If initial monitoring or subsequent monitoring reveals employee exposure to be at or above the action level but below the permissible exposure limit our company will repeat monitoring at least every 6 months.
REVISED DATE: January 1, 2025
LEAD AWARENESS POLICY
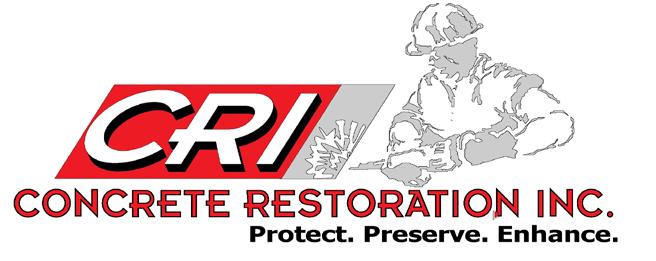
CRI will continue monitoring at the required frequency until at least two consecutive measurements, taken at least 7 days apart, are below the action level. A written record of this determination along with the corrective actions taken will be displayed in an appropriate area for employees to observe.
Negative Initial Determination
If initial monitoring reveals employee exposure to be below the action level, employees will be allowed to work in and around that area. A written record of this determination will be displayed in an appropriate area for employees to observe.
Additional Exposure Assessments
If changes in equipment, process, control, personnel, or tasks occur after our initial determination, we reevaluate to determine if employees are exposed to higher concentrations of lead. Our procedure for monitoring for change and initiating additional monitoring is: follow WAC standards
Employee Notification
Once CRI has received the results from air monitoring, we will inform our employees within five working days of those results. The results will be posted in a common area or break room and be accessible by all employees. Any employee that is directly affected will be notified individually.
Employees that participate in biological testing will be notified within five working days upon the receipt of biological monitoring results. CRI will notify in writing each employee whose blood lead level exceeds 40 ug/100g:
of (A) that employee's blood lead level and (B) that the standard requires temporary medical removal with Medical Removal Protection benefits when an employee's blood lead level exceeds the numerical criterion for medical removal under paragraph (k)(1)(i) of the standard.
REVISED DATE: January 1, 2025
LEAD AWARENESS POLICY
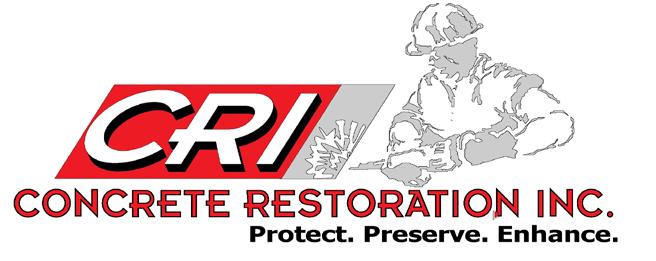
Our procedure for this notification process is delivering written information
Methods of Compliance
This lead exposure control program for this worksite is implemented when employee exposure exceeds the permissible exposure limit (PEL).
This program is our written strategy and schedule for protecting our workers from lead exposure. It incorporates all relevant information that relates to this goal, so that we determine whether we appropriately analyzed problems and solutions (including alternatives) relating to lead exposure.
This program is intended to reduce employee exposure to the PEL or below the PEL. When all feasible engineering and work practice controls that can be instituted are not sufficient to reduce employee exposure to acceptable levels, appropriate respiratory protection will be provided to supplement such controls.
The job site, materials, and equipment are regularly inspected. Concrete Restoration Inc reviews this program at least every six months to revise it as necessary.
To reduce and maintain employee exposure to lead at or below the PEL, we will utilize engineering and work practice controls.
Mechanical ventilation to control employee exposure to lead.
The technologies used to control employee exposure are documented and kept at the main office. Lists of these are available if requested.
The air monitoring data collected at each job site documents the source of lead emissions. The data is kept on site as well as the main office.
Included in our plan, is a detailed schedule for implementation of our program. This includes documentation such as copies of purchase orders for equipment and construction contracts.
REVISED DATE: January 1, 2025
LEAD AWARENESS POLICY
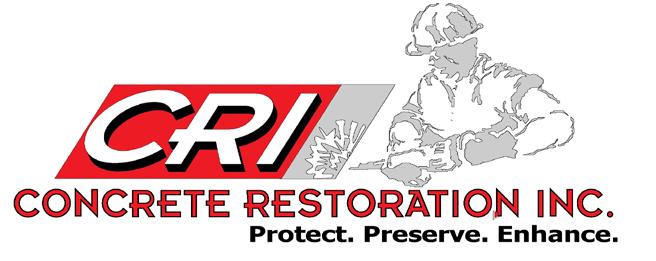
Work practice programs such as Protective Work Clothing and Equipment program, Housekeeping program, and a Hygiene Facilities and Practices program, are required by Federal regulations and are required to be a part of this document. We do have these work practice programs and they are included in this compliance program under their separate heading
Administrative controls, such as job rotation, are used at CRI to lower employee TWA exposure to lead.
If any of our employees are exposed to lead released from another contractor, work in that area will be discontinued and our employees will be removed. Employees will not return to that area until lead exposure assessments have shown lead levels to be below the action level.
As an employer we want to keep our employees fully informed of all aspects of this plan. Concrete Restoration Inc will make frequent and regular inspections of jobsites, materials, and equipment, and ensure a copy of this written plan is available at worksites. We review and update our written plan at least annually to reflect the current status of the program.
Respiratory Protection
When engineering and work practice controls are not sufficient to reduce exposures to the PEL or below the PEL Concrete Restoration Inc employees will be provided respirators.
During our exposure assessment to document that our employees are not exposed above the PEL, we treat employees performing certain operations as if they were exposed above the PEL. This means providing respiratory protection.
We provide respirators to employees who request them.
Protective Work Clothing and Equipment
We provide personal protective equipment as interim protection for employees during exposure assessment, since our employees may be
REVISED DATE: January 1, 2025
LEAD AWARENESS POLICY
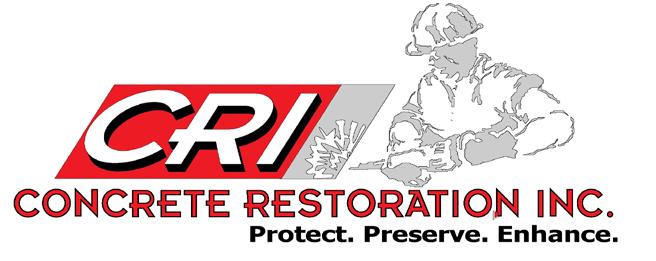
exposed to lead (1) above the PEL without regard to the use of respirators, or (2) to lead compounds which may cause skin or eye irritation. This outline of our Protective Work Clothing and Equipment policy is included as a part of the site plan when required. We provide protective clothing and equipment at no cost to our employees.
Work conditions with lead exposures over 200 micrograms per meter cubed of air as an (8) eight hour TWA without regard to use of a respirator require replacement of protective clothing.
Our procedure for cleaning, laundering, and disposing of protective clothing and equipment will be included in the Site-Specific Safety plan
Our policy for repairing or replacing damaged equipment, and procedures for accomplishing this task will be included in the Site-Specific Safety plan.
Housekeeping
Concrete Restoration Inc believes that a rigorous housekeeping program is necessary in jobs where there is lead exposure or the potential of lead exposure to keep airborne lead levels below permissible limits. This requires a regular housekeeping schedule adapted to exposure conditions on site.
For all jobsites, our procedure for housekeeping is:
• Keeping surfaces as lead-free as practicable.
• Vacuuming floors and other surfaces where lead accumulates to minimize the likelihood of lead becoming airborne.
• Shoveling or dry or wet sweeping (allowed only where vacuuming or other equally effective methods have been tried and found ineffective).
• Using HEPA filters on vacuums.
REVISED DATE: January 1, 2025
LEAD AWARENESS POLICY
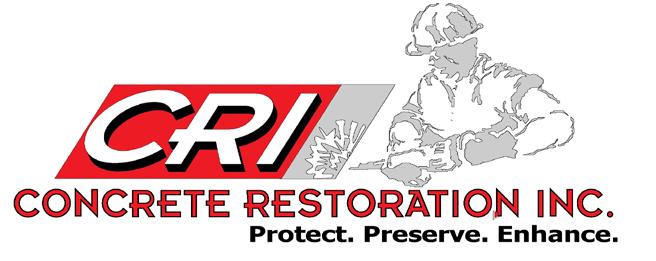
• Emptying vacuums so that lead is not reintroduced into the workplace.
Hygiene Facilities and Practices
We provide hygiene facilities for our workers who are exposed to lead above the PEL and ensure they follow good hygiene practices such as, washing their hands and face and keeping their PPE clean and functioning properly.
We prohibit smoking, eating, applying cosmetics, and the presence of tobacco products, foodstuffs, or cosmetics in all work areas where employees are exposed to lead above the PEL. Concrete Restoration Inc ensures all employees comply with these rules and regulations.
Medical Surveillance
Concrete Restoration Inc supports the practices necessary for early detection of lead exposure. The medical surveillance program supplements the primary goals of the lead exposure control program of preventing disease through elimination or reduction of airborne concentrations of lead, and sources of ingestion. The medical surveillance provisions incorporate both initial and ongoing medical surveillance.
We provide initial medical surveillance to employees who are occupationally exposed to airborne lead levels at or above the PEL. This monitoring consists of sampling blood and analyzing it for lead and zinc protoporphyrin levels. Where this initial biological monitoring indicates that an employee's blood lead level is at or above 40 micrograms per deciliter of whole blood, we provide biological monitoring at least every two months. This frequency continues until two consecutive blood samples and analyses indicate that the employee's blood lead level is below 400 micrograms per deciliter of whole blood.
All medical examinations and procedures are performed by an approved source.
REVISED DATE: January 1, 2025
LEAD AWARENESS POLICY
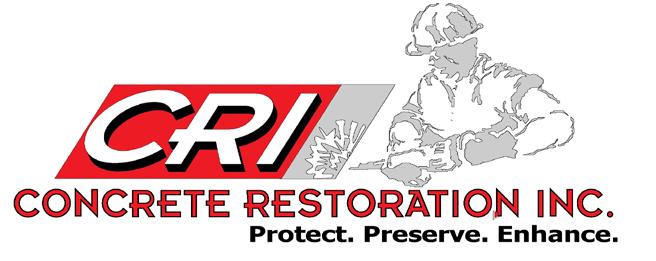
All blood lead level sampling and analysis are conducted by an approved source.
Medical Removal Protection
(During the medical removal period sampling will be performed at least monthly.)
We remove employees from work who have exposures to lead at or above the action level each time a periodic and a follow-up blood sample indicates that the blood lead levels are at or above 50 micrograms per deciliter of whole blood. We also remove employees from work who have exposures to lead at or above the action level when a health care professional determines that they have medical conditions which, when exposed to lead, places them at greater risk of health problems.
Medical Removal Benefits – Concrete Restoration Inc will comply with the standard as is attached:
Medical removal protection benefits –
Concrete Restoration Inc shall provide an employee up to eighteen (18) months of medical removal protection benefits on each occasion that an employee is removed from exposure to lead or otherwise limited pursuant to this section.
For the purposes of this section, the requirement that an employer provide medical removal protection benefits means that the employer shall maintain the earnings, seniority and other employment rights and benefits of an employee as though the employee had not been removed from normal exposure to lead or otherwise limited.
During the period that an employee is removed from normal exposure to lead or otherwise limited, Concrete Restoration Inc may condition the provision of medical removal protection benefits upon the employee's participation in follow-up medical surveillance made available pursuant to this section.
REVISED DATE: January 1, 2025
LEAD AWARENESS POLICY
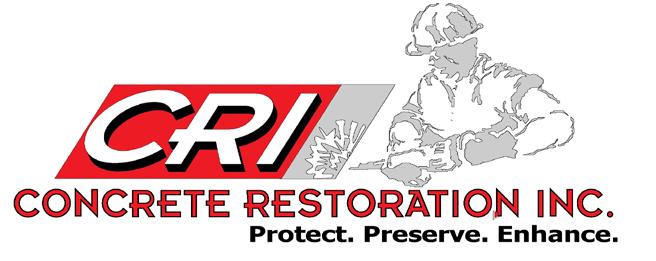
If a removed employee files a claim for workers' compensation payments for a lead-related disability, then Concrete Restoration Inc shall continue to provide medical removal protection benefits pending disposition of the claim. To the extent that an award is made to the employee for earnings lost during the period of removal, the employer's medical removal protection obligation shall be reduced by such amount. Concrete Restoration Inc shall receive no credit for workers' compensation payments received by the employee for treatment-related expenses.
Concrete Restoration Inc’s obligation to provide medical removal protection benefits to a removed employee shall be reduced to the extent that the employee receives compensation for earnings lost during the period of removal either from a publicly or employer-funded compensation program or receives income from employment with another employer made possible by virtue of the employee's removal.
Employees whose blood lead levels do not adequately decline within 18 months of removal. Concrete Restoration Inc shall take the following measures with respect to any employee removed from exposure to lead due to an elevated blood lead level whose blood lead level has not declined within the past eighteen (18) months of removal so that the employee has been returned to his or her former job status:
• Concrete Restoration Inc shall make available to the employee a medical examination pursuant to this section to obtain a final medical determination with respect to the employee;
• Concrete Restoration Inc shall assure that the final medical determination obtained indicates whether or not the employee may be returned to his or her former job status, and if not, what steps should be taken to protect the employee's health;
• Where the final medical determination has not yet been obtained, or once obtained indicates that the employee may not yet be returned to his or her former job status, Concrete Restoration Inc shall continue to provide medical removal protection benefits to the employee until either the employee is returned to former job status, or a final medical determination is made that the employee is incapable of ever safely returning to his or her former job status.
REVISED DATE: January 1, 2025
LEAD AWARENESS POLICY
Employee Information and Training
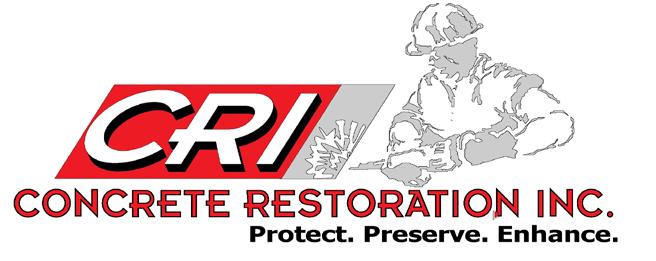
Employees can do much to protect themselves from the risks of occupational lead exposure if they know about them. In our training program we inform employees of the specific hazards associated with their work environment, protective measures that can be taken, and their rights under the standard. All affected employees will be trained prior to first assignment and annually thereafter. The entire contents of this plan should be covered in the training program.
All affected employees are required to attend training programs. This training will be provided prior to the time of initial job assignment or during orientation depending on the task that employee will be performing. Training will be provided at least annually to ensure employees remain aware of the dangers of lead.
During training the employees are informed on specific tasks and operations that could result in exposure to lead above the action level. Employees are informed of the purpose, proper selection, fitting, use, and limitation of respirators.
Employees are informed about engineering controls put in place to reduce lead exposure. Training also covers information on the purpose for, and a description of, the medical surveillance & medical removal programs and many health effects of lead.
Lead can affect the employee right away (acute) or later in life (chronic). Employees are informed of acute lead poisoning effects such as, stomach cramps, loss of appetite, nausea, vomiting, headaches and fatigue, as well as chronic effects such as; damage to the nervous system, reproductive system, and urinary system.
Because these symptoms are commonly confused with “normal” health problems, lead poisoning is often overlooked. Concrete Restoration Inc encourages all employees who work around lead and experience any of these symptoms to seek medical attention immediately.
REVISED DATE: January 1, 2025
LEAD AWARENESS POLICY
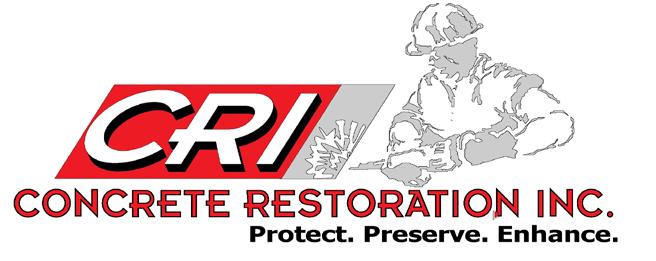
All training documents will be kept on file at our main office. These records are kept on file for a minimum of five years. All documents include the name of employee, date trained, subject trained, location, and name of instructor.
Signs
Because exposure to lead is a serious health hazard, Concrete Restoration Inc posts signs that warn employees of lead hazards and of the possible need to use respirators and other protective equipment in the area. Employees are also informed of lead hazards through training.
Recordkeeping
Concrete Restoration Inc maintains accurate biological and environmental monitoring records of employee exposure to potentially toxic materials, including lead. We allow employees access to their records.
We include the following exposure monitoring records:
• Exposure assessment.
• Medical surveillance results.
• Medical removals
• Objective data for exemption from requirement for initial monitoring
• Procedures for making records available.
• Procedures for transfer of records.
REVISED DATE: January 1, 2025
LEAD AWARENESS POLICY
Observation of Monitoring
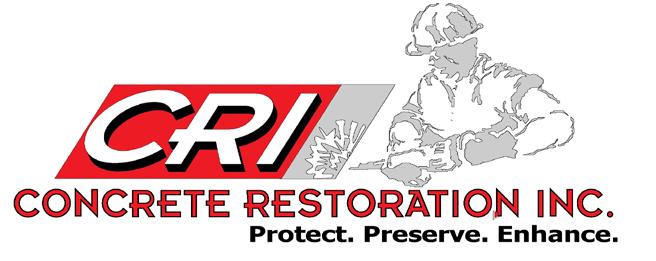
We provide our employees or their representatives the opportunity to observe exposure monitoring of toxic materials or harmful physical agents. Our procedure for allowing observation includes:
• Explaining the measurement procedure
• Allowing observation of all steps related to the measurement procedure
• Disseminating of the results when returned by the laboratory
• Providing an observer with proper personal protective devices
• Assuring that observers comply with all applicable safety and health procedures
REVISED DATE: January 1, 2025
LOCKOUT/TAGOUT POLICY
LEAD AWARENESS POLICY
Reference: OSHA 1910.147/WAC 296-803
PURPOSE
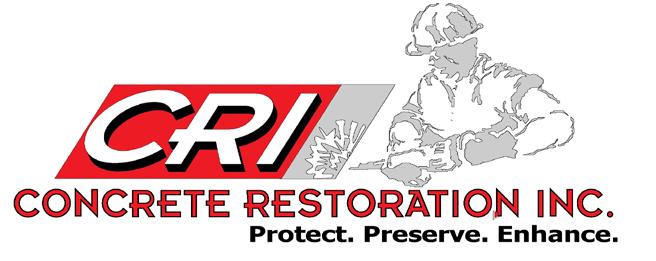
This procedure establishes the minimum requirements for the lockout of energy isolating devices whenever maintenance or servicing is done on machines or equipment. It shall be used to ensure that the machine or equipment is stopped, isolated from all potentially hazardous energy sources and locked out before employees perform any servicing or maintenance where the unexpected energizing or start-up of the machine or equipment or release of stored energy could cause injury.
POLICY
All employees are required to comply with the restrictions and limitations imposed upon them during the use of lockout. The authorized employees are required to perform the lockout in accordance with this procedure. All employees, upon observing a machine or piece of equipment which is locked out to perform servicing or maintenance shall not attempt to start, energize or use that machine or equipment. This policy shall be reviewed annually.
DEFINITIONS
Energized - Connected to an energy source or containing residual or stored energy.
Energy Source - Any source of electrical, mechanical, hydraulic, pneumatic, chemical, thermal, or other energy, including gravity.
Lockout - The placement of a lockout device on an energy isolating device, in accordance with an established procedure, ensuring that the energy isolating device and the equipment being controlled cannot be operated until the lockout device is removed.
REVISED DATE: January 1, 2025
LOCKOUT/TAGOUT POLICY
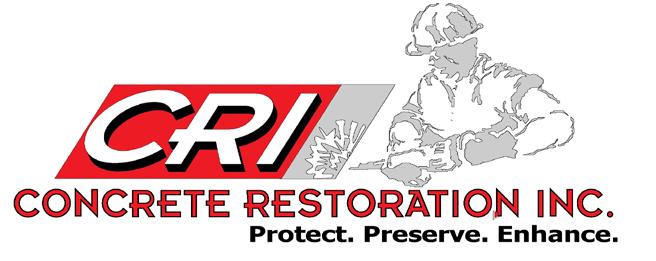
Lockout Device - A device that utilizes a positive means such as a lock, either key or combination type, to hold an energy isolating device in the safe position and prevents the energizing of a machine or equipment.
Tagout - The placement of a tagout device on an energy isolating device, in accordance with an established procedure, to indicate that the energy isolating device and the equipment being controlled may not be operated until the tagout device is removed.
Energy Isolating Device - A mechanical device that physically prevents the transmission or release of energy, including but not limited to the following: A manually operated electrical circuit breaker, a disconnect switch, a manually operated switch by which the conductors of a circuit can be disconnected from all ungrounded supply conductors and, in addition, no pole can be operated independently, a line valve, a block, and any similar device use to block or isolate energy. Push buttons, selector switches, and other control circuit type devices are not energy isolating devices.
PROCEDURE
Application
These procedures are required for all activities in which the unexpected release or transmission of energy or a material could cause injury to employees or damage to equipment. This policy applies to energy sources such as electrical, mechanical, hydraulic, pneumatic, radiation, thermal, compressed air, energy stored in springs, and potential energy from suspended parts (gravity).
Before beginning work on the machine or equipment, notify all affected employees that servicing or maintenance is required and that the machine or equipment must be shut down and locked out to perform the servicing or maintenance.
The authorized employee shall refer to the company procedure to identify the type and magnitude of the energy that the machine or equipment
REVISED DATE: January 1, 2025
LOCKOUT/TAGOUT POLICY
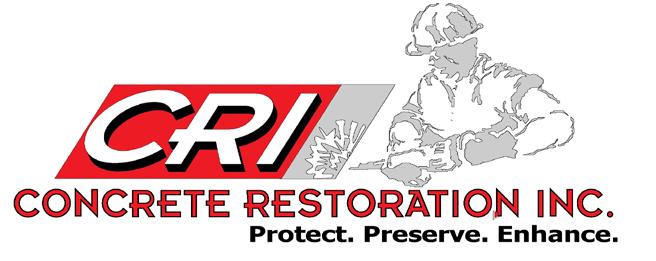
utilizes, shall understand the hazards of the energy, and shall know the methods to control the energy.
Before de-energizing any equipment, machinery, or electrical equipment and applying a Lockout / Tagout procedure, written permission will be obtained from an authorized owner / client representative specifying the date, inclusive items of lockout, and specific equipment to be locked out. An authorized signature, date, and phone number are required prior to commencing the Lockout / Tagout procedure.
After Lockout/Tagout procedure has been implemented, all stored energy must be released, and isolation/zero energy must be verified.
Locks
All persons having the need to enter a locked out area or system will be issued as many locks as necessary to perform the expected tasks of the job. Lockout locks will be identified with the individual’s lock number and name. One key will be issued with each lock. The remaining keys will be forwarded to the Safety Office.
Identification of Lockout Points
Lock out points will be identified by a qualified person, operator, or supervisor who understands how to effectively control the equipment/ process through application of hazard isolating devices.
1. Placement of Locks
• The owner/ client must be notified and have given approval to lockout the system or equipment before attaching the locks to the isolating devices. A stop button or electrical interlock must never be used as a substitute for lockout.
• It is the responsibility of each person working within the lockout area to place his/her own lock on all lockout points. Use of another person’s lock (i.e. working in the area under the security of another person’s lock) is STRICTLY FORBIDDEN.
REVISED DATE: January 1, 2025
LOCKOUT/TAGOUT POLICY
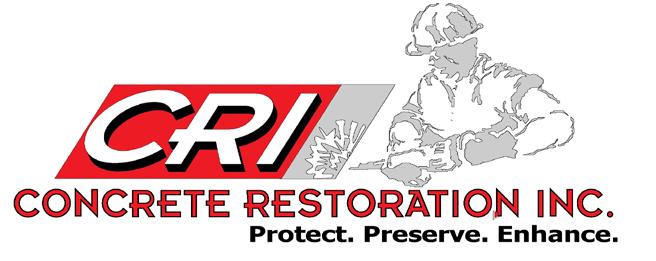
• When more than one employee is required to lockout the same system or equipment, one lock with a tag identifying all employees on the crew shall be used. The crew foreman shall sign the tag and be responsible for accounting for all crew members prior to removing locks and re-energizing the system. Crew members entering the area shall initial the lockout tag and, prior to removing the tag, shall re-initial the lockout tag.
• If a job extends over a change in shifts, the person coming on the job shall put his/her lock on all the lockout points and the person leaving shall remove his/her locks.
Removal of Locks/Restoring Equipment to Service
• When the servicing or maintenance is completed and the machine or equipment is ready to return to normal operation condition, the following steps shall be taken.
• Check the machine or equipment and the immediate area around the machine or equipment to ensure that nonessential items have been removed and that the machine or equipment components are operationally intact.
• Check the work area to ensure that all employees have been safely positioned or removed from the area.
• Verify that the controls are neutral.
• Remove the lockout devices and re-energize the machine or equipment.
• Notify affected employees that the servicing or maintenance is completed, and the machine or equipment is ready for use.
If an employee who has finished a job leaves the work site without removing his/her lock, a Foreman or Concrete Restoration Inc Management memebr or, in their absence, the Safety/Training manager may remove the lock using the following steps in the order shown
REVISED DATE: January 1, 2025
LOCKOUT/TAGOUT POLICY
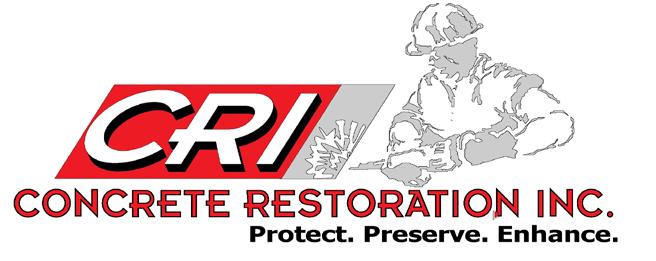
Determine whether the employee whose lock remains on the equipment has left the work site by checking ExactTime. If the employee has not left the site, he/she will be called back to complete the job and/or remove the lock.
If the employee has left the site, a reasonable attempt to reach him/her will be made to verify why the lock was not removed. The employee will be requested to return to the work site to remove his/her lock.
If the employee cannot be reached, a reasonable attempt to contact his/her Foreman will be made to verify why the lock was not removed.
If the Foreman cannot be contacted or does not know if the employee has finished the job, the equipment or system must be thoroughly inspected and determined to be safe for operation. This must be verified by an authorized owner/client representative. The lock may then be removed and the equipment or systems tested for operation. If the test is normal, the equipment will be turned over to regular operation.
The locks removed by a supervisor will be retained and sent to the Safety/Training Manager, along with a brief report explaining why the removal was necessary, the time removed, and by whom.
If the equipment or system is of such a size that the operator cannot see all potential hazard points, personnel shall be stationed at the points of access which are not visible to assure that no one enters an exposed area during start up.
TRAINING
• All employees will be trained at on boarding Process, and annually on this procedure.
• All training on this process will be documented
REVISED DATE: January 1, 2025
LOCKOUT/TAGOUT POLICY
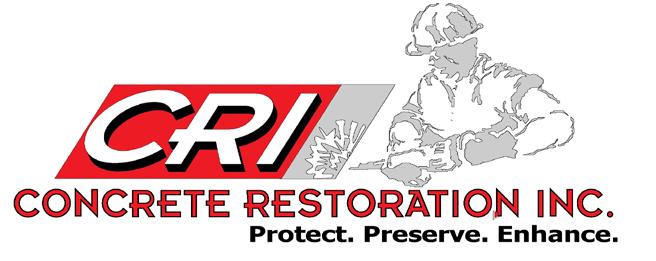
PLEASE
SEE
FOLLOWING PAGE FOR ENERGY CONTROL PLAN
Process/equipment:
Equipment ID #:
Energy sources:
(electrical, mechanical, hydraulic, pneumatic, chemical, gravity, thermal, or others)
Location of energy control sources:
(Disconnect switches, breakers, valves, block, or others)
Authorized employees:
Energy Control Plan
Date:
Shut down procedures: (How to turn off all equipment)
Machine/equipment isolation: (Energy sources shut off dissipated to isolate the source)
Apply lockout devices: (Affixed to ensure the energy source will not be activated)
Verification of isolation: (Try to start the machine to ensure all energy sources are identified and properly locked out.)
REVISED DATE: January 1, 2025
LOCKOUT/TAGOUT POLICY
Perform work:
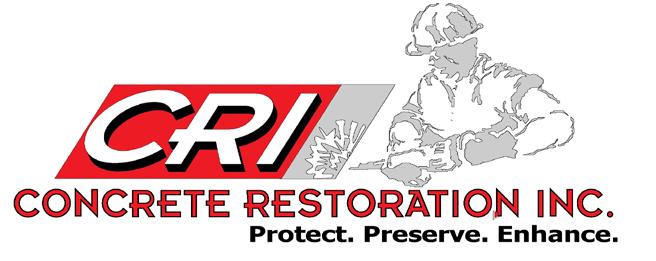
Removal of lockout devices: (Make sure all tools are removed from the work area and all guards placed back on equipment prior to restarting equipment.)
Restore energy: (Advise all affected employees that machine will be restarted.)
Verification by:
REVISED DATE: January 1, 2025
MANUAL MATERIAL HANDLING POLICY
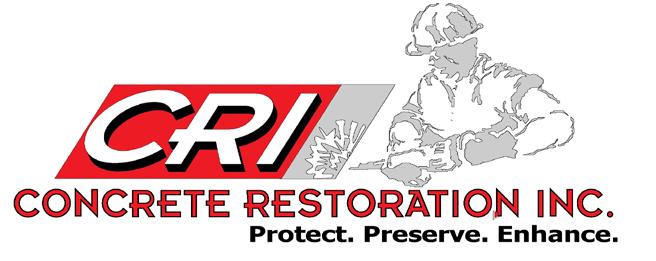
MANUAL MATERIAL HANDLING POLICY
Reference: OSHA 1910.176/WAC 296-24-215
Overview
The purpose of the Concrete Restoration Inc Manual Material Handling Program is to apply ergonomic principles and sound decision-making to the workplace in an effort to reduce the number of manual lifts thus decreasing workplace injuries and, where possible, increasing productivity, quality and efficiency. A proactive material handling approach focuses on making changes when risk factors have been identified, as well as incorporating automated material handling whenever possible.
All employees are required to follow the minimum procedures outlined in this program. Any deviations from this program must be immediately brought to the attention of Management.
Scope
Concrete Restoration Inc strives to provide all employees with a safe and healthy workplace. This Manual Material Handling Program is integrated into our company’s written safety manual and is a collaborative effort that includes all employees. The Safety/Training Manager is responsible for the program’s implementation, management, and recordkeeping requirements.
Program Responsibilities
Safety/Training Manager: All evaluations, controls and training will be coordinated under the direction of the Safety/Training Manager. The Safety/Training Manager will monitor the results of the program and Investigate injuries to determine additional areas of focus as needed. The Safety/Training manager will also:
• Ensure that those performing worksite evaluations and training are properly trained.
REVISED DATE: January 1, 2025
MANUAL MATERIAL HANDLING
POLICY
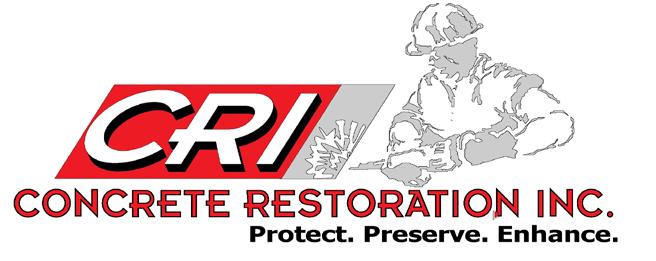
• Ensure that control measures are implemented in a timely manner.
• Schedule supervisor and employee training and maintain records to include date, name of instructor, topic and materials used
• Follow-up with any material handling strategy and/or solutions
• Monitor the program on an annual basis and provide an annual review.
• Assist in selection of appropriate material handling equipment and tools.
Foreman: Foreman/Leads of Concrete Restoration Inc will:
• Remain accountable for the health and safety of all employees through the active support of this program.
• Attend material handling training on the recognition and control of work-related material handling risk factors.
• Ensure that safe material handling practices and principles are considered daily and when conducting worksite evaluations.
• Ensure that recommended controls are implemented and/or used appropriately through active follow-up.
• Provide employees with and ensure the proper use of appropriate tools, equipment, parts and materials.
• Maintain clear communication with managers and employees.
• Make assistance available to employees who manually handle or lift items weighing 50 pounds or greater.
REVISED DATE: January 1, 2025
MANUAL MATERIAL HANDLING POLICY
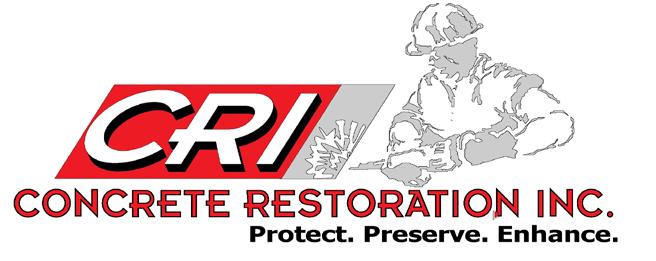
Employees: Every employee of Concrete Restoration Inc is responsible for conducting himself/herself in accordance with this policy and program. All employees will:
• Use two-wheeled trucks, four-wheeled carts, pallet jacks, or any other material handling equipment in the manner established by managers and supervisors.
• Ensure that equipment is properly maintained in good condition and when not, report it immediately.
• Provide feedback to managers and Foreman regarding the effectiveness of design changes, new tools or equipment.
• Attend training as required and apply the knowledge and skills acquired during training to their jobs, tasks, processes, and work activities.
• Use proper lifting and material handling techniques as outlined in this policy.
• Limit manual lifting or handling tasks to objects less than 50 pounds.
• Get assistance whenever manually handling or lifting materials that are 50 pounds or greater.
• Report injuries within 24 hours of their occurrence
Manual Material Handling Risks
Material Handling Equipment. Additional tools and equipment are required when lifting or handling material weighing over 50 pounds. Manual material handling equipment should be used only for its designed task and maintained in good condition. The manual material handling equipment available at Concrete Restoration Inc includes
REVISED DATE: January 1, 2025
MANUAL MATERIAL HANDLING
POLICY
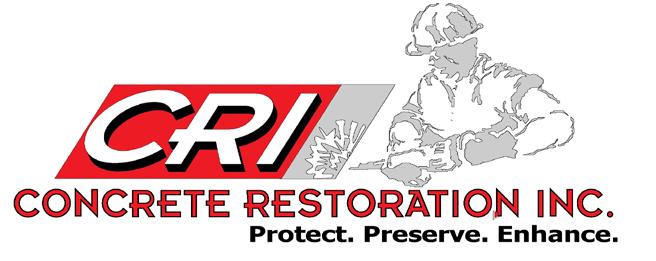
• Two-Wheel Trucks: Do not overload these trucks; load a maximum of 200 pounds. Make sure hand trucks are stored in a vertical position when not in use.
• Four-Wheel Carts: Load material evenly on carts to prevent tipping and view obstruction. Push rather than pull carts, unless specially designed to be pulled.
• Pallet Jacks (manual or powered): Use a jack properly rated for the load. Place the jack on a level, stable, and clean surface. Avoid metal-to-metal contact (jack to surface being lifted) by using wooden shims.
Housekeeping. Material handling and storage areas must be kept free of excess materials that create hazards (i.e. fire, explosions, slips, trips.)
Aisles and Passageways. Where mechanical handling equipment is used, 6-foot safe clearances shall be allowed for aisles, at loading docks, through doorways, and wherever turns or passage must be made. Aisles and passageways shall be kept clear and in good repair, with no obstruction across or in aisles that could create a hazard.
Employee Training
Training is intended to enhance the ability of managers, Forman, and employees to recognize work-related material handling risk factors and to understand and apply appropriate control strategies. Training in the recognition and control of these risk factors will be given as follows:
• To all new employees during orientation
• To all employees assuming a new job assignment requiring manual material handling
REVISED DATE: January 1, 2025
MANUAL MATERIAL HANDLING
POLICY
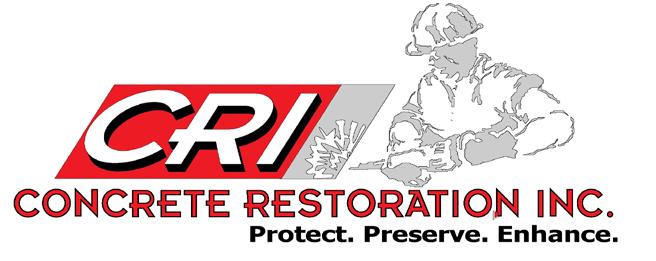
• When new jobs, tasks, tools, equipment, machinery, workstations or processes are introduced
• When high exposure risk factors have been identified.
The minimum training requirements for all managers, supervisors and employees will include the following elements:
• An explanation of Concrete Restoration Inc material handling program and their role in the program
• Knowledge of job tasks that require manual material handling
• An understanding of the basics of ergonomics
The methods used by Concrete Restoration Inc to minimize work-related risk factors. Training should include the following topics:
• Mechanical aids for carrying or moving loads are to be used whenever possible to minimize manual material handling. These mechanical aids include hand trucks, carts, dollies, wheelbarrows, etc. When designing or modifying storage areas, store heavy items on shelves between knee and shoulder level and avoid storing items on the floor. Also, lighter items should be stored on top shelves. Whenever possible, decrease the object container size, change container shape and/or add handles to aid in handling.
Even when mechanical aids are used to move materials, some lifting cannot be avoided. Before you lift, remember the following:
• Use manual material handling devices (hand dollies, carts, lift tables, forklifts) where defined by the company and wherever possible in all other situations.
• Wear supportive shoes.
REVISED DATE: January 1, 2025
MANUAL MATERIAL HANDLING
POLICY
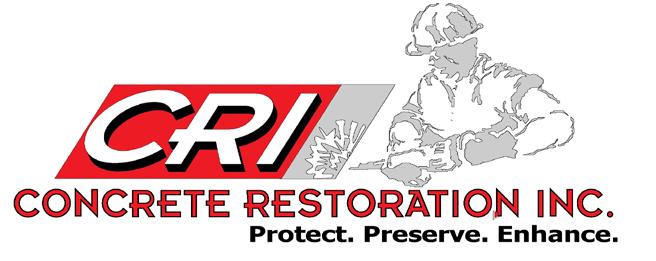
• When possible, push and pull rather than lift and lower.
• Reduce the size of the material to keep it light, compact and easy to grasp.
• Try to have most workplace deliveries placed at hip height.
• Always keep objects in the comfort zone (between hip and shoulder height)
• Keep all loads close to and in front of the body.
• Keep the back aligned while lifting.
• Keep elbows near 90 degrees.
• Avoid slopes.
• Avoid uneven floors
• Maintain the center of balance.
• Let the legs do the actual lifting.
• Decide on the route to take.
• Check the route for any problems or obstacles such as slippery or cluttered floors.
• Always perform a Job Hazard Analysis
Unloading objects should be done the same way as loading objects, but in the reverse order as follows:
• Slowly bend your knees to lower the load.
REVISED DATE: January 1, 2025
MANUAL MATERIAL HANDLING
POLICY
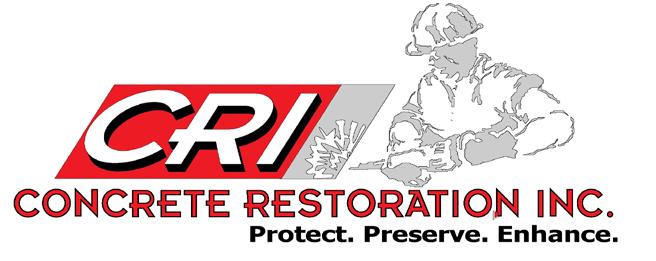
• Keep your back straight and the weight close to the center of your body
• Allow enough room for fingers and toes when the load is set down.
• Place the load on a bench or table by resting it on the edge and pushing it forward with your arms and body
• Secure the load to ensure that it will not fall, tip over, roll or block someone’s way.
One-arm loads are used when carrying items such as pails or buckets. Lifting and carrying one- arm loads should be performed as follows:
• Bend at the knees and waist, keeping your back straight.
• Reach for the load.
• Grasp the handle of the load firmly
• Lift with your legs, not your shoulders and upper back.
• Keep your shoulders level while switching hands regularly to reduce overexerting one side of the body
Team lifts are used when objects are too heavy, too large or too awkward for one person to lift. Team lifts should be performed as follows:
• Work with someone of similar build and height, if possible.
• Choose one person to direct the lift (e.g., “lift on the count of three”)
• Lift with your legs and raise the load to the desired level at the same time.
REVISED DATE: January 1, 2025
MANUAL MATERIAL HANDLING
POLICY
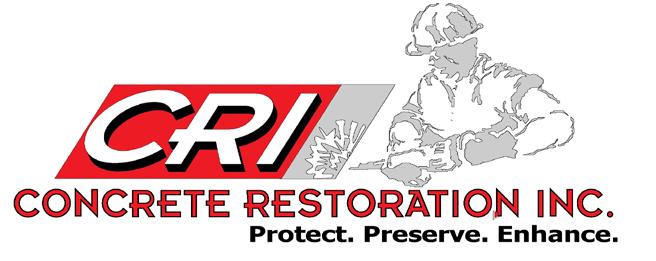
• Always keep the load at the same level while carrying.
• Move smoothly and in unison.
• Set the load down together.
Overhead loads should be eliminated, if possible, but, if necessary, should be conducted as follows:
• When lifting or lowering objects from above the shoulders, lighten the load whenever possible.
• Stand on something sturdy such as a step stool or platform to decrease the vertical distance.
• When lowering objects from above the shoulders, grasp the object firmly, bring the load as close to your body as possible, slide it down slowly and proceed with your move.
Review
The Manual Material Handling Program will be reviewed annually.
REVISED DATE: January 1, 2025
MOBILE ELEVATED WORK PLATFORM POLICY
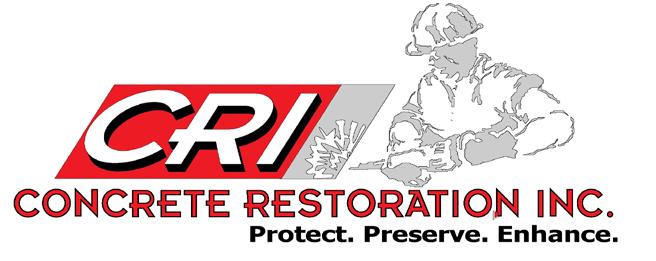
MOBILE ELEVATED WORK PLATFORM POLICY
Reference: OSHA 1910.67/WAC 296-869
Introduction
Mobile Elevating Work Platforms (MEWPs) are types of aerial devices or equipment that can be used to conduct work at an elevated position by raising people from ground/floor level. MEWPs can pose a serious safety hazard if not used properly. It is the policy of Concrete Restoration Inc to train employees on the hazards of operating MEWPs and to ensure such equipment is safely operated and maintained.
Purpose
The purpose of this program is to comply with Occupational Safety and Health Administration (OSHA) Powered Platforms, Manlifts and VehicleMounted Work Platforms standard – 29 CFR 1910.67, Aerial Lifts – 29 CFR 1926.453 and WAC 296-869 compliance regulations.
Scope
This program applies to all Concrete Restoration Inc owned or rented MEWPs designed to elevate personnel on a platform that is propelled by a powered lifting device. It applies to all Concrete Restoration Inc employees and subcontractors who operate them.
Program Responsibilities
Executive Management
Concrete Restoration Inc has legal responsibility for compliance with the occupational safety and health and WAC standards.
Program Administrator
The Safety/Training Manager is responsible for:
REVISED DATE: January 1, 2025
MOBILE ELEVATED WORK PLATFORM POLICY
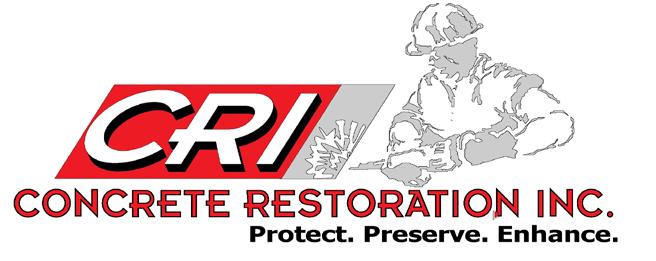
• Planning and recommending programs that adhere to all applicable federal, state, and local laws and regulations pertaining to environmental health and safety.
• Assisting Foreman with implementing environmental health and safety plans
• Curtailing or stopping work that poses a clear and imminent danger to health or safety.
• Periodically reviewing the program and updating it as needed to ensure compliance with all applicable federal and state regulations.
Employees
Every Concrete Restoration Inc employee is responsible for conducting himself/herself in accordance with this program. All employees shall:
• Adhere to all safety programs, procedures, and practices while performing his/her duties in a safe manner.
• Notifying your immediate supervisor of unsafe working conditions, potential hazards, and accidents as soon as possible.
Contractors
Contractors are required to develop their Mobile Elevated Work Platform compliance program and adhere to compliance regulations.
Authorized Mobile Elevating Work Platform (MEWP) Operation
• Designation by your Forman or Safety Manager.
• Completion of the required training course prior to operating a MEWP.
• Performing MEWP pre-use inspections.
REVISED DATE: January 1, 2025
MOBILE ELEVATED WORK PLATFORM POLICY
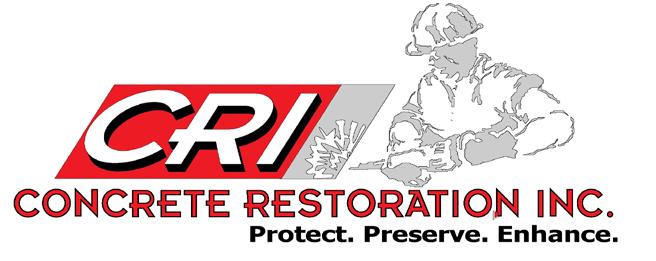
• Review Site Specific Safety plan, and conduct an inspection prior to use.
• Reporting all MEWP maintenance issues to their foreman and removing the equipment from service if necessary.
• Operating and maintaining equipment in a safe manner at all times.
• Adhere to the manufacturer’s operating manual and all provisions in this program. Consult with your Foreman and/or Safety Manager regarding any unusual hazards.
General Requirements
• Only designated and trained operators shall operate a MEWP.
• Operators shall follow safe work practices when operating a MEWP.
• MEWPs are operated at a safe speed. Speeds are adjusted to compensate for surface conditions, visibility, load weight, vehicle or pedestrian traffic or any other circumstances affecting safe operation.
• Accidents shall be reported immediately to the Foreman and the Safety Manager
• Maintenance or repair activities are to be performed by a qualified service technician. Maintenance shall be conducted according to the manufacturers’ recommendations.
• Horseplay or unsafe driving is not tolerated.
• Smoking, open flames or spark producing activities are prohibited in designated refueling or battery charging areas or while operating the vehicle.
REVISED DATE: January 1, 2025
MOBILE ELEVATED WORK PLATFORM POLICY
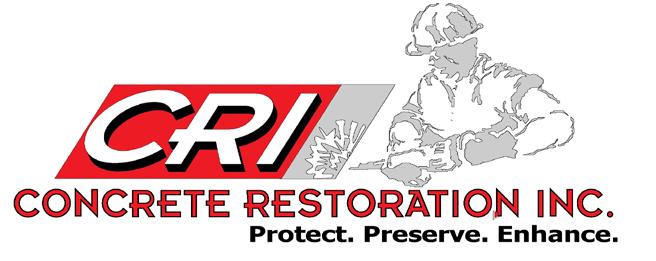
• Battery charging or replacement is not performed in locations that obstruct access to exits.
• Materials on the work platform floor shall be secured and not pose a hazard.
• Never carry loads that exceed the rated capacity listed on the nameplate of the MEWP.
• Check the rated capacity of the MEWP before use to ensure that it can support the combined weight of the MEWP, its occupants and additional tools.
• Use of mobile technology devices (i.e., cell phone, in-ear headphones, tablets) is prohibited while operating a MEWP, except in an emergency.
• The MEWP cannot be altered in any manner, unless written approval has been received by the manufacturer.
• The MEWP shall not be operated on grades, slopes, ramps, or cambers exceeding those for which the MEWP is rated by the manufacturer.
• The operator and occupant(s) on the MEWP shall use fall protection and fall protection anchors, if applicable.
Management shall:
• Review and ensure understanding of this program and its applicability to your project.
• Attend and adhere to all required training.
• Observe the MEWP operators who are operating the equipment
• Ensure employees receive training appropriate to their assigned tasks
REVISED DATE: January 1, 2025
MOBILE ELEVATED WORK PLATFORM POLICY
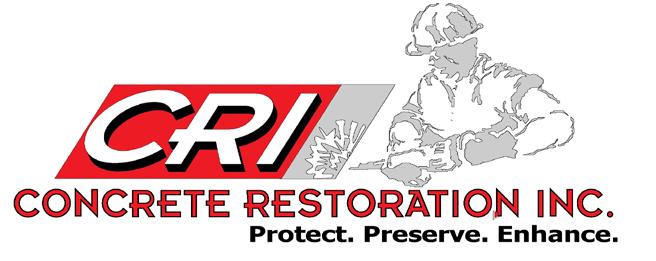
• Ensure employees are provided with and use appropriate personal protective equipment (PPE).
• Take prompt action including disciplinary action when unsafe conditions or acts are observed.
• Investigate MEWP usage injuries and damage.
• Ensure periodic maintenance is performed on the lift.
• Complete a Site Specific Safety plan that includes the MEWP selected for the job task and the risks associated with the equipment and the work to be performed.
Operators shall:
Review and follow the manufacturers’ operating manual.
Attend and adhere to all required training.
Immediately report any unsafe acts or conditions to the supervisor, including equipment defects. Discontinue operations when unsafe conditions exist.
Ensure the worksite is barricaded.
Complete pre-use and worksite inspections and consult with supervisor and/or EHS regarding any unusual hazards.
Ensure all occupants can work safely. Explain to the occupant(s) how to use the MEWP controls prior to use, in the event they need to operate the MEWP in an emergency. This instruction does not give the occupant authorization to operate the controls at any time except in an emergency.
Understand the limitations of the equipment.
Occupants shall:
REVISED DATE: January 1, 2025
MOBILE ELEVATED WORK PLATFORM
POLICY
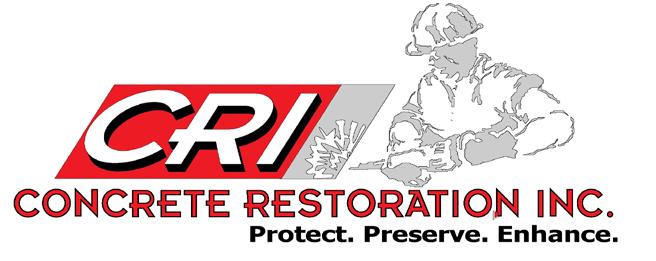
Understand the hazards related to the task at hand and their avoidance (risk assessment) and how their action could affect stability.
Have general knowledge of the intended purpose and function of MEWP controls, emergency shut-down and lowering procedures, and safety-related items specified by the manufacturer.
Understand that in a Rescue situation they will contact Concrete Restoration Management immediately.
Frequent and Annual Inspection
Frequent inspection shall be performed when MEWP has been out of service for a period longer than three (3) months, or if environmental conditions require a shorter period. The inspection shall be performed by a person qualified to inspect the specific make and model of the MEWP. The frequent inspection shall include all items specified by the manufacturer for a frequent inspection and manufacturer’s bulletins.
If damage is observed or a malfunction occurs during the inspection, remove the key from the MEWP and place a sign over the controls that indicates the MEWP is tagged out of service. The MEWP shall not be placed back into service until all malfunctions and problems identified in the inspection have been corrected and/or repaired by an authorized and trained maintenance technician.
Annual inspections of the MEWPs shall be performed no later than thirteen (13) months from the date of the prior annual inspection by a person qualified to inspect the specific make and model of MEWP. The inspection shall include items specified by the manufacturer and shall verify that the MEWP is registered with the MEWP manufacturer, and any open safety-related bulletins are addressed at that time. If damage is observed or a malfunction occurs during the inspection, remove the key from the MEWP and place a sign over the controls that indicates the MEWP is tagged out of service. The MEWP shall not be placed back into service until all malfunctions and problems identified in the inspection have been
REVISED DATE: January 1, 2025
MOBILE ELEVATED WORK PLATFORM POLICY
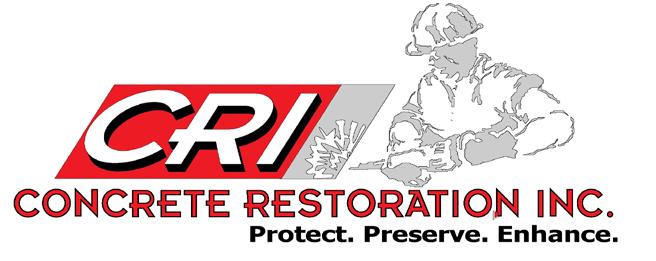
corrected and/or repaired by an authorized and trained maintenance technician.
Pre-Use Inspection
A pre-use inspection of the MEWP must take place before each daily use to assist in preventing incidents that are caused by faulty or worn out equipment. MEWPs that are not in good operating condition shall be removed from service until the proper repairs have been made by an authorized and trained maintenance technician. The pre-use inspection shall cover the following:
• Operators shall verify that the manufacturers operator’s manual is located on the MEWP.
• Operators shall verify that all brakes, controls, gauges, audible and visual alarms and beacons, tires and wheels, emergency controls, electrical cables, stabilizers/outriggers and extendable and oscillating axles and routine operational features are in proper working order. Defects when found shall be immediately reported and corrected before use continues.
• Operators shall verify that structural items such as extending structure and stabilizers/outriggers, extendable and oscillating axles, and pins, pin securing device and damage to the means of the support of the work platform and extendable structure are not damaged, missing or broken. Defects when found shall be immediately reported and corrected before use continues.
• Operators shall verify that MEWPs have a nameplate listing lift category, maximum weight capacity, maximum platform height, and rated work load. Defects when found shall be immediately reported and corrected before use continues.
• Operators shall check for air, hydraulic and fuel system leaks before starting the MEWP. Report deficiencies to the Foreman and tag out of service until repairs have been made.
REVISED DATE: January 1, 2025
MOBILE ELEVATED WORK PLATFORM
POLICY
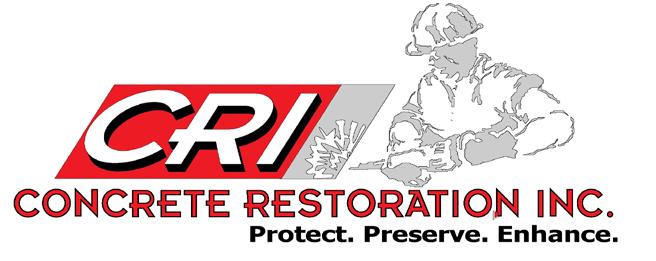
• Operators shall verify that personal protective devices that will be worn or used while operating/occupying the MEWP have been inspected for damage and deterioration. Defects when found shall be immediately reported and corrected before use continues.
• Operators shall remove the MEWP from service any time it is found to need repair, is defective or in any way unsafe. The MEWP will be taken out of service until it has been restored to safe operating condition.
• Operators shall inspect the work site for the following hazards:
• Drop-offs, slope, or holes, including those concealed by water, ice, mud, etc.
• Bumps, floor obstructions, electric cables, and/or other debris.
• Overhead obstructions, including electrical conductors.
• Hazardous atmospheres and/or hazardous locations.
• If damage is observed or a malfunction occurs during the inspection, remove the key from the MEWP and place a sign over the controls that indicates the MEWP is tagged out of service. In the event that a MEWP has been out of service for a period longer than three (3) months, or if environmental conditions require a shorter period, a Frequent Inspection of the MEWP is required. This inspection is to be completed by an authorized and trained maintenance technician. The MEWP shall not be placed back into service until all malfunctions and problems identified in the inspection have been corrected and /or repaired by an authorized and trained maintenance technician.
REVISED DATE: January 1, 2025
Personal Protective Equipment
MOBILE ELEVATED WORK PLATFORM POLICY
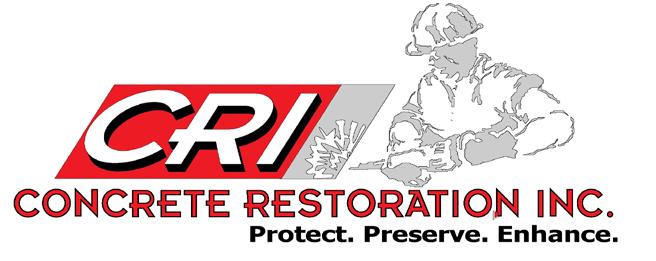
Fall protection equipment must be used as follows when operating Mobile Elevating Work Platforms (MEWPs):
• Operators and occupants shall be secured to the anchor point provided by the equipment manufacturer by either a self-retracting lanyard or by a lanyard short enough to prevent the employee from being ejected.
• Operators and occupants must follow manufacturer’s recommendations as to which fall protection system to use.
• Personal Protective Equipment shall be inspected prior to use.
• Check personal protective devices (harnesses and lanyards) that will be worn while operating / occupying the MEWP.
• Check the work platform, including guardrail system for structural integrity.
• For scissor lifts and one-man lifts, the guardrail system provides fall protection. If the manufacturer has installed an anchorage point, a fall protection system (restrain, positioning, personal fall arrest system) as designated by the manufacturer’s instructions must be utilized.
• Tying a lanyard off to an adjacent pole, structure, or equipment while working from an aerial lift shall not be permitted.
• Other types of personal protective equipment (PPE) such as hard hats, safety glasses, safety gloves, shall be worn according to the task specific PPE hazard assessment.
Training
Mobile Elevating Work Platform (MEWP) Training is required for all employees designated by their Foreman to operate a MEWP. The training must be specific to the type of MEWP being used. Both Foreman and MEWP operators must be trained.
REVISED DATE: January 1, 2025
MOBILE ELEVATED WORK PLATFORM
POLICY
Initial Training:
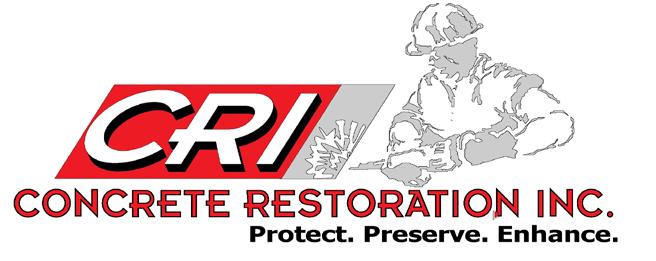
The training course will consist of formal instruction and practical hands-on familiarization. The hands-on practical familiarization must be specific to the type of MEWP that the employee will operate, and the supervisor will supervise. The formal instruction will include manufacturer’s manual instructions, warnings, limitations, precautions and the MEWP program requirements. The hands-on practical familiarization will include operation of the MEWP in a safe environment. Operators must demonstrate proficiency in the actual operation of the MEWP.
Re-training:
Re-training shall include both formal instruction and practical evaluation, and may be necessary due to certain circumstances as follows:
The operator is observed operating the MEWP in an unsafe manner.
The operator is involved in an accident or near-miss incident.
The operator receives an evaluation revealing unsafe practices. There is a change in workplace conditions affecting the safe operation of a MEWP.
The operator is assigned to drive a different type of MEWP.
Maintenance
Periodic (depending on activity, severity of service and environment) maintenance shall be performed by the manufacturer or authorized representative. The items listed in the manufacturer’s manual shall be tested, evaluated and, if applicable, corrected by authorized service technician before the MEWP is returned to service. MEWPs shall not be operated if they are out of compliance with manufacturer specifications. Disabling of safety devices, such as warning beepers, guards or interlocks is prohibited. Moreover,
REVISED DATE: January 1, 2025
MOBILE ELEVATED WORK
PLATFORM POLICY
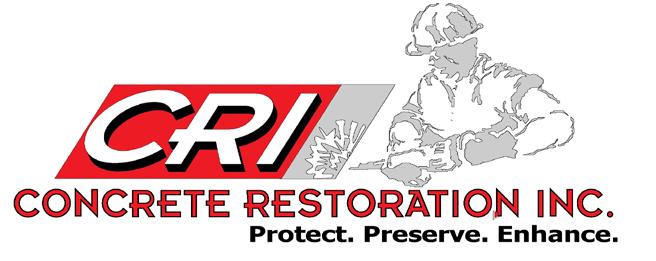
Any MEWP found not safe for operation must be immediately removed from service.
Maintenance to be conducted on any MEWP shall not be performed in a hazardous location.
All repairs shall be made by an authorized service technician and all replacement parts should be equivalent to the original MEWP part.
MEWPs shall be deemed safe for operation following all maintenance activities.
Recordkeeping
The safety office will maintain training records for all designated operators who have successfully completed the MEWP program training requirements.
REVISED DATE: January 1, 2025
MEWP Inspection Form
MOBILE ELEVATED WORK
PLATFORM POLICY
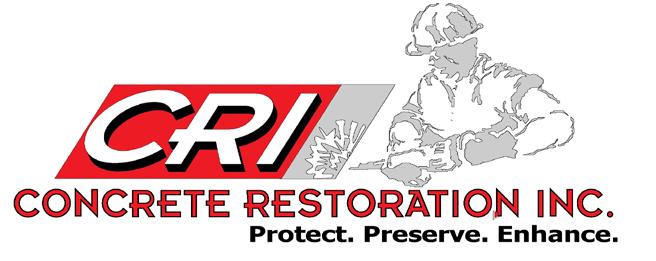
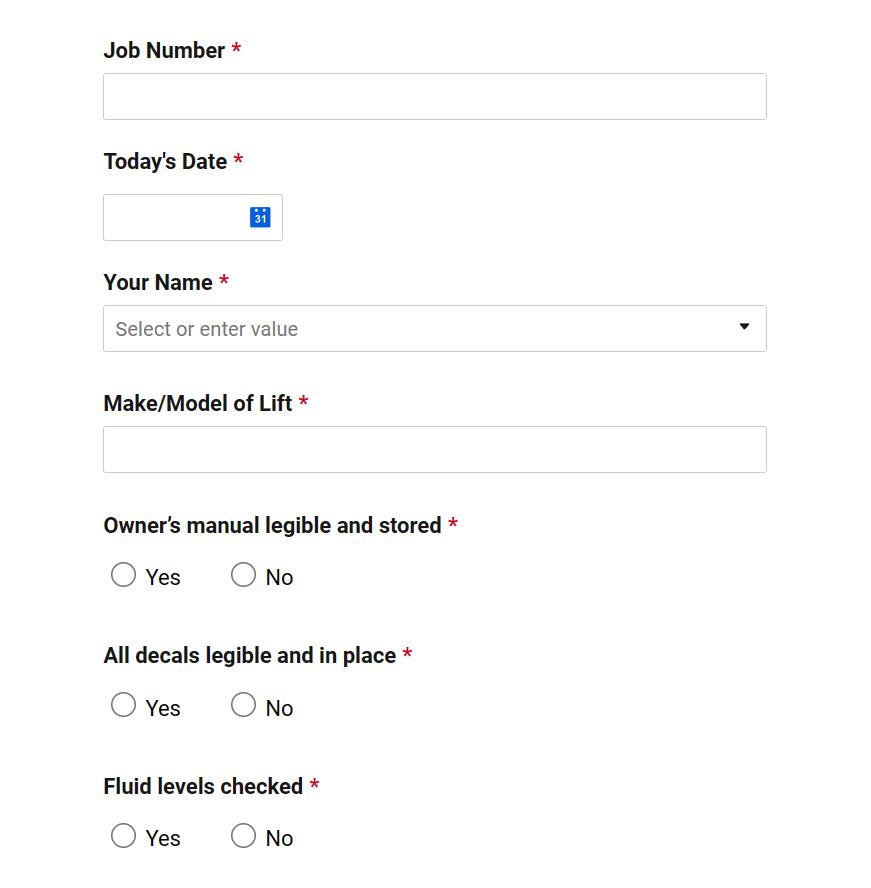
REVISED DATE: January 1, 2025
MOBILE ELEVATED WORK PLATFORM
POLICY
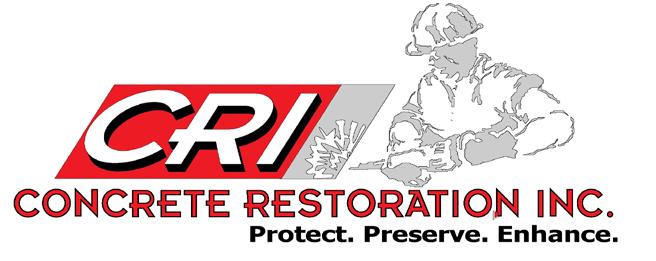

REVISED DATE: January 1, 2025
MOBILE ELEVATED WORK
PLATFORM POLICY
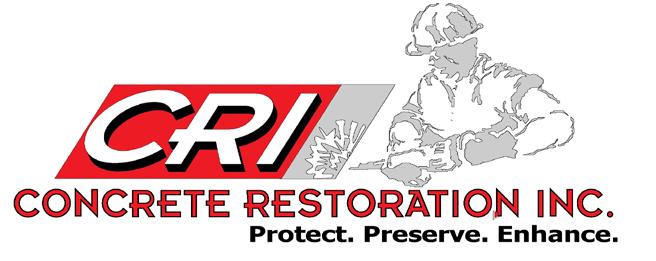
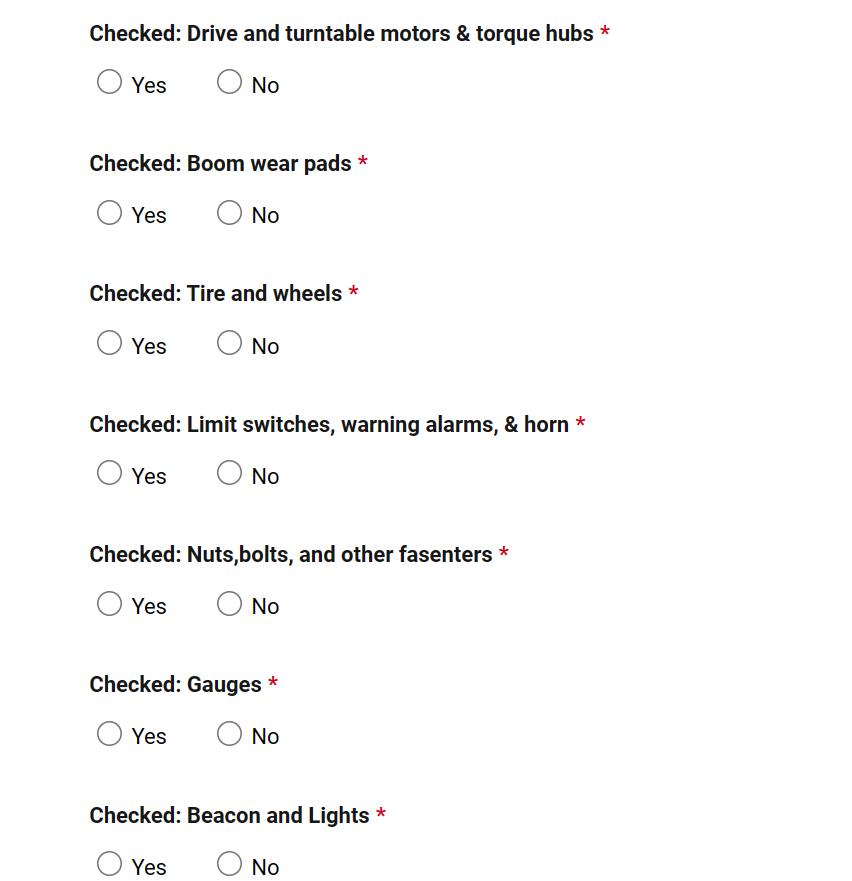
REVISED DATE: January 1, 2025
MOBILE ELEVATED WORK PLATFORM
POLICY
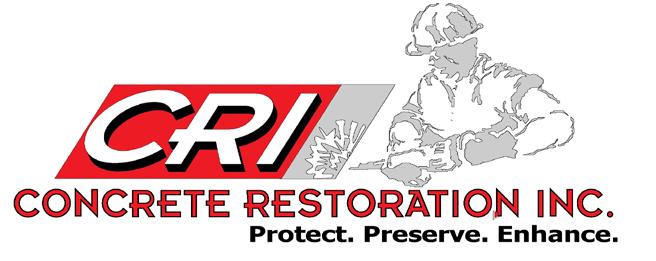
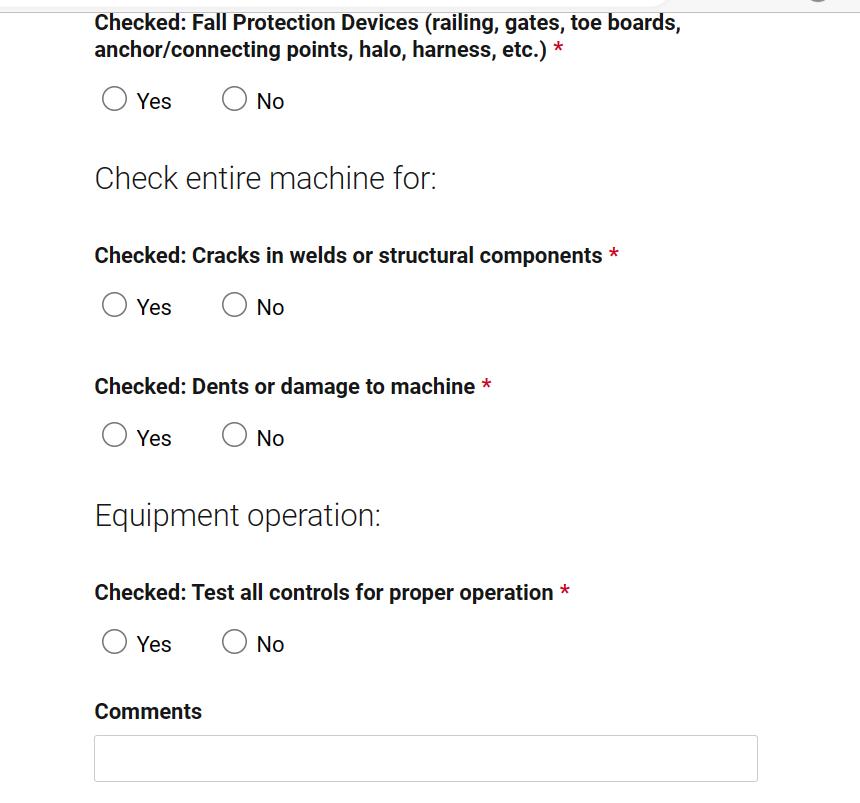
REVISED DATE: January 1, 2025
PANDEMIC RESPONSE PLAN
PANDEMIC RESPONSE PLAN
Purpose
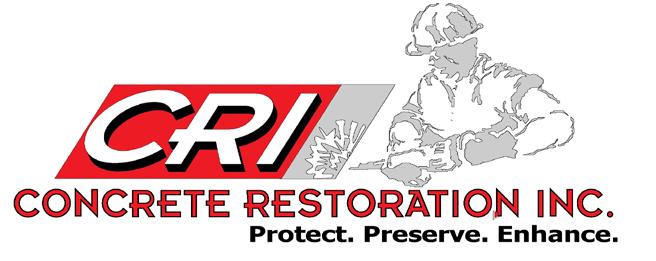
Business continuity means ensuring that essential business functions can survive a natural disaster, technological failure, human error, or other disruption. Many existing business continuity plans anticipate disruptions such as fires, earthquakes, and floods. These events are restricted to certain geographic areas and the time frames are fairly well defined and limited. Pandemic disease, however, demands a different set of continuity assumptions since it will be widely dispersed geographically and potentially arrives in waves that could last several months at a time.
A pandemic disease plan or disease containment plan will be developed for Concrete Restoration Inc and a coordinator appointed. There will be a workplace coordinator who will be responsible for dealing with disease issues and their impact at the workplace. This may include contacting local health department and health care providers in advance and developing and implementing protocols for response to ill individuals.
Assumptions
A pandemic disease will spread rapidly and easily from person to person, affecting all businesses due to absenteeism. Businesses that are relied upon by other businesses will be facing the same massive absentee rates and will be unable to provide essential components to maintain the daily operations.
Risk assessments to identify the essential/critical components of our business operation need to be conducted. Recognize that a pandemic includes:
• Healthcare services not being available (they are already full at present with the usual ailments).
• Schools, churches and other public places not being open.
• Borders are partially or fully closed, especially airports, leaving people (our families, employees, business partners, customers and suppliers) “stranded”.
REVISED DATE: January 1, 2025
PANDEMIC RESPONSE PLAN
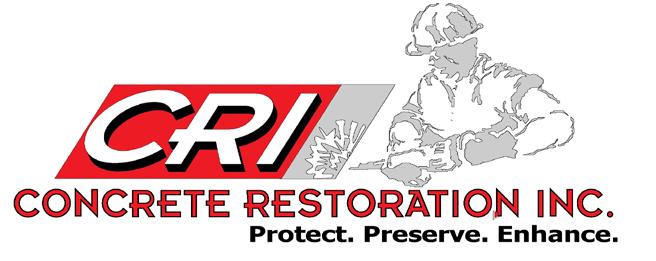
• Essential materials and supplies may be limited due to distribution chains that are affected by the travel restrictions or absentee workers supporting those transportation means.
• Essential services around utilities, food distribution/access and banking systems may not be at “normal levels”; access to cash flow could be tight.
• People may not be willing to or able to come to work.
Communications
Communications during a pandemic involves both internal communications and external communications. Internal communication will be provided to employees to educate them about pandemic diseases and measures they can take to be prepared.
Key contacts, a chain of communications and contact numbers for employees and processes for tracking business and employee’s status have been developed as described in this section.
Risk communication is critical to inform employees regarding changes in the pandemic status. The following is one method for providing such information.
Alert: conveys the highest level of importance; warrants immediate action or attention.
Advisory: provides key information for a specific incident or situation; might not require immediate action.
Update: provides updated information regarding an incident or situation; unlikely to require immediate action.
Provide continuous updates through internal & external communications when a pandemic is imminent:
• Notification to employees of operational changes
• Provide frequent updates about the pandemic status
• Provide advisories and alerts as conditions change
• Ensure vendors and suppliers have available a dedicated communications contact
• Monitor local, state, and federal pandemic updates
REVISED DATE: January 1, 2025
PANDEMIC RESPONSE PLAN
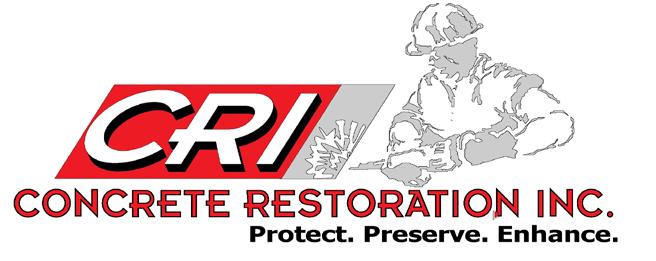
We will notify key contacts including both customers and suppliers in the event an outbreak has impacted Concrete Restoration Inc’s ability to perform services. This procedure also includes notification to customers and suppliers when operations resume.
We will use our phone systems to send notifications and messages about alerts. The use of Concrete Restoration Inc website also will serve as a portal for sharing information with employees and vendors.
Business Continuity Planning
During an emergency, employees look to management to provide leadership for the Concrete Restoration Inc. If a large percentage of personnel become ill our business continuity plans will be initiated so that if significant absenteeism or changes in business practices are required business operations can be effectively maintained.
Command Staff:
Incident Commander (President/CEO)
Office Manager (Media/Public Relations)
Liaison Officer (Vice President)
Safety Officer (Safety Manager)
Finance Section: Controller (Purchasing/Accounting Manager)
Organizes and directs all aspects of the incident response
Creates and releases upon approval from the incident commander all information to the staff, media and public.
Establishes and maintains relationships with outside organizations
Ensures the safety of all persons involved with the pandemic
Monitors all expenditures and ensures fiscal resource availability during the pandemic
Pandemic Response by Pandemic Phase
Currently the World Health Organization (WHO) has created various phases for a pandemic but does not always relate to events locally.
REVISED DATE: January 1, 2025
PANDEMIC RESPONSE PLAN
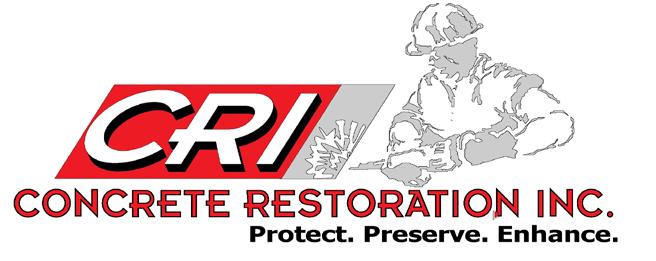
Level 0 (WHO Phase 3)- Novel virus alert- not human-to-human transmission
Level 1 (WHO Phase 4)- Confirmed cases of human-to-human transmission of novel disease virus.
Level 2 (WHO Phase 5)- Suspected/confirmed cases in the Mobile area.
Level 3 (WHO Phase 5)- Numerous suspected/confirmed cases in the Mobile area.
Work At Home Considerations
There is a work-at-home and stay-at-home policy when employees are ill or are caring for others. Flexible work policies will be developed as much as possible. Employees are encouraged to stay at home when ill, when having to care for ill family members or when caring for children when schools close, without fear of reprisal. Tele-commuting or other work-at-home strategies will be considered.
Infection Control Measures
Guidelines for infection control are important to clarify the routes of transmission and the ways to interrupt transmission through measures of hygiene. Infection control is an essential component of pandemic management and a component of public health measures. Essential measures include:
• Hand washing and use of hand sanitizers shall be encouraged by CRI supervision. Hand washing facilities, hand sanitizers, tissues, no touch trash cans, hand soap and disposable towels shall be provided by CRI.
• Workers are encouraged to obtain appropriate immunizations to help avoid disease. Granting time off work to obtain the vaccine is considered when vaccines become available in the community.
• Social distancing including increasing the space between employee work areas and decreasing the possibility of contact by limiting large or close contact gatherings will be considered.
REVISED DATE: January 1, 2025
PANDEMIC RESPONSE PLAN
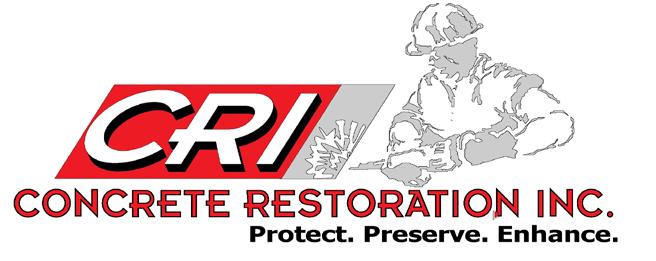
• We will clean all areas that are likely to have frequent hand contact (like doorknobs, faucets, handrails) routinely and when visibly soiled. Work surfaces will also be cleaned frequently using normal cleaning products.
Additional examples of infection control measures include:
• Stay at home when you are sick. If possible, stay away from work, school and from running errands. You will help others from catching your illness.
• Cover your coughs and sneeze into tissue, or cough into your shirt sleeve.
• Enhance existing housekeeping service by wiping down and disinfecting work areas (i.e. keyboards, telephones, desks, etc.) frequently.
• Enhance housekeeping services for general public use areas several times throughout the work period.
• Use personal protective equipment where appropriate to minimize exposure (i.e. gloves- for handling money, masks- for ill employees)
Implementation, Testing, and Revision of the Plan
The plan and emergency communication strategies will be periodically tested (at least annually) to ensure it is effective and workable.
Testing the plan will be accomplished by conducting exercises. Exercises range from low stress to full-scale, hands-on drills. A tabletop exercise is the easiest way to begin testing the plan. This type of exercise involves having discussions regarding a scenario that challenges the plan and the decision makers during an emergency. Functional exercises take on an additional level of complexity, in that they actually require participants to conduct functional components of the plan. This usually involves planning specific scenarios, creating pretend data and present issues that target an area within the plan to be tested.
REVISED DATE: January 1, 2025
PANDEMIC RESPONSE PLAN
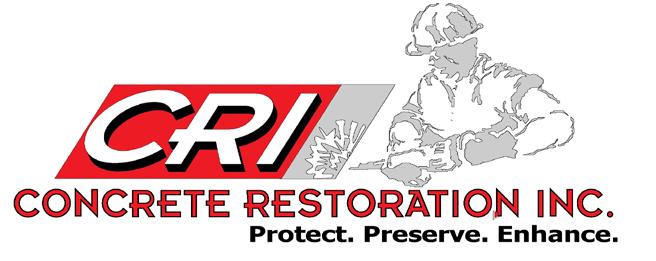
Each of these methods of testing the plan requires extensive planning for the exercise and the evaluation. The evaluation is critical to revising the plan, by capturing actual responses during the exercise or drill objectively. Once this data is captured, an after-action report with recommendations to revising the plan should be completed within a few weeks of the exercise.
Training
Employees will be trained in health issues of the pertinent disease to include prevention of illness, initial disease symptoms, preventing the spread of the disease and when it is appropriate to return to work after illness. Disease containment plans and expectations should be shared with employees. Communicating information with non-English speaking employees or those with disabilities must be considered.
Documentation of all training is required.
REVISED DATE: January 1, 2025
PERSONAL
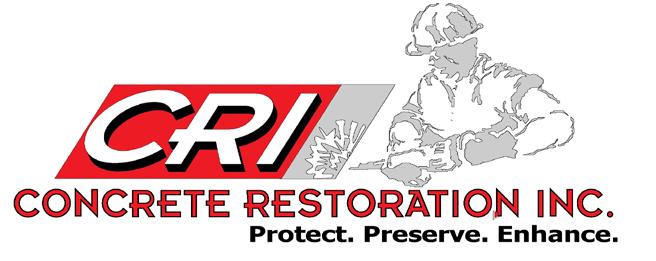
PERSONAL PROTECTIV EQUIPMENT PROGRAM
Reference: OSHA 1910 Subpart G, H, I, J, Q, Z/WAC 296-800-160
Purpose
To provide guidance in the specification, selection, use, training and care of personal protective equipment.
Scope
Applicable to Concrete Restoration Inc employees who work in areas containing hazards or potential hazards.
Comments
These personal protective equipment procedures will apply to all areas suspected of hazards or potential hazards.
Definitions
PPE – Personal Protective Equipment refers to any manufactured piece of equipment that helps protect a person’s extremities from a hazard after engineering controls have failed.
Safety Manager – The individual at Concrete Restoration Inc with the assigned responsibility to develop safety procedures and audit their use.
Workplace – Areas occupied by Concrete Restoration Inc employees while performing their job.
General Requirements
REVISED DATE: January 1, 2025
PERSONAL PROTECTIVE EQUIPMENT PROGRAM
Application
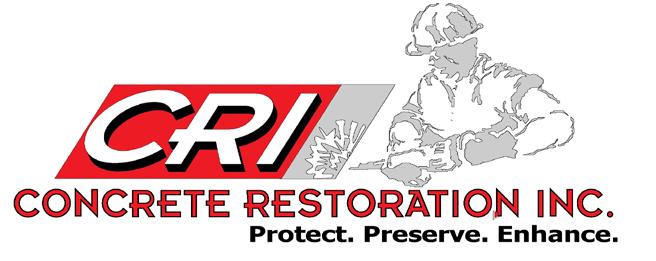
• Protective equipment, including personal protective equipment for eyes, face, head, hands, and feet, as well as, protective clothing, respiratory devices, and fall protection, will be provided, used, and maintained in a sanitary and reliable condition. Rules and guidelines are set forth for employees to follow in regard to maintenance, storage, use, and inspection of their PPE.
• Requirements for each site will be established for the wearing of appropriate PPE in all operations where there is an exposure to hazardous conditions or where there is the need for using such equipment to reduce the hazards to the employees.
• All personal protective equipment will be of safe design and constructed for the work to be performed.
PPE Hazard Assessment and Equipment Selection
A written copy of the personal protective program is available to all employees and located at Concrete Restoration Inc main office and in the Company Safety Manual. The program contains the following elements:
• An assessment of each workplace area to determine if hazards are present, or likely to be present, necessitates the use of personal protective equipment. This assessment is performed by the Safety Manager and included in the Site-Specific Safety Plan.
• If hazards requiring PPE are present, or likely to be present, each site will:
o Select the appropriate PPE.
o Ensure each affected employee uses the type(s) of PPE that will protect the affected employee.
o Communicate selection decisions to each affected employee.
o Ensure the PPE selected properly fits each affected employee. The Safety Manager will verify and certify in writing that a workplace PPE hazard assessment has been performed and included in Site Specific Safety plan. The certification will include at a minimum:
REVISED DATE: January 1, 2025
PERSONAL PROTECTIVE EQUIPMENT PROGRAM
• An identification of the workplace area evaluated.
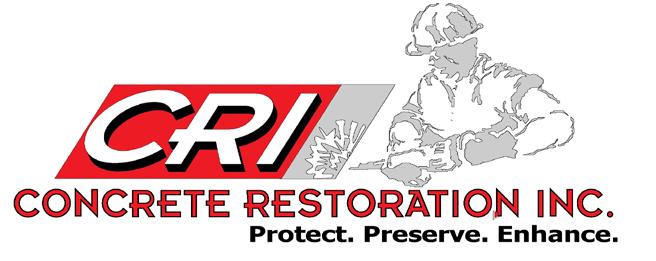
• Name and title of the person certifying the evaluation.
• The date(s) of the hazard assessment.
• A list of hazards addressed.
• Certification of hazard assessment must be documented.
Care
At no time will defective, unsanitary, unreliable, or damaged personal protective equipment be used. Employees are trained to inspect their PPE every time prior to use. Concrete Restoration Inc encourages their employees to practice good hygiene while using PPE and teaches proper ways to clean and reuse PPE. A personal protective equipment inspection program is conducted at least once a year.
Training
Training will be provided to each employee who is required by the hazard assessment to use PPE. Training will be specific to the type of personal protection used and the hazard assessed. Each affected employee will be trained to know at least the following:
• When PPE is necessary
• What PPE is necessary for the job
• The correct ways to don, doff, adjust and wear PPE
• Any limitations of required PPE
• The proper care, maintenance, and useful life and disposal of the PPE
• The relationship between the PPE and the hazards described
REVISED DATE: January 1, 2025
PERSONAL
EQUIPMENT PROGRAM
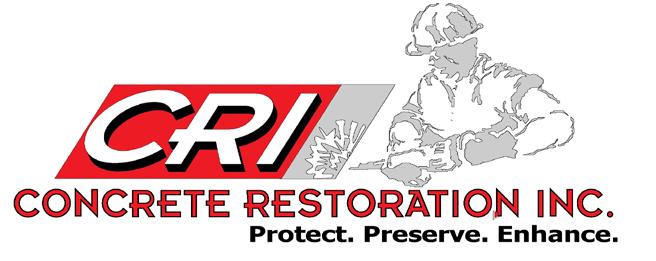
When there is reason to believe that any affected employee who has already been trained and does not have the proper understanding and skill required, the employee will be retrained. Circumstances requiring retraining include, but are not limited to, the following situations:
• Changes in the workplace are rendering the previous training obsolete.
• A change in the nature of the hazards, or potential hazards.
• Changes in the types of PPE or introduction of new PPE, thus rendering previous training obsolete.
• Inadequacies in an affected employee’s knowledge or use of assigned PPE indicating that the employee has not retained the requisite understanding of skill.
Training is documented and records of training are kept at the main office. The training roster includes the names of employees trained, the date trained, subject taught, and name of instructor.
Equipment Selection & Use
Eye and Face Protection
General Requirements
• Concrete Restoration Inc will ensure that each affected employee uses appropriate eye or face protection when exposed to eye or face hazards, such as flying particles, molten metal, liquid chemicals, acids or caustic liquids, chemical gases or vapors.
• Concrete Restoration Inc will ensure affected employees use eye protection that also provides side protection when there is a hazard from flying objects. Detachable side protectors (e.g. clip-on or slide-on side shields) are acceptable if they meet the appropriate ANSI standard.
REVISED DATE: January 1, 2025
PERSONAL PROTECTIVE EQUIPMENT PROGRAM
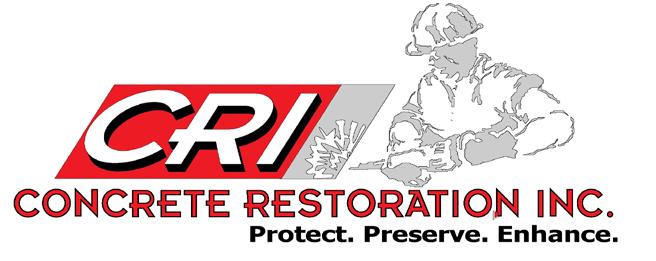
• Each affected employee who wears prescription lenses while engaged in operations that involve eye hazards shall wear eye protection that incorporates the prescription in its design, or shall wear eye protection that can be worn over the prescription lenses without disturbing the proper position of the prescription lenses or the protective lenses.
• Eye and face PPE must be distinctly marked to facilitate identification of the manufacturer.
Criteria for protective eye and face devices.
Protective eye and face devices must comply with any of the following consensus standards:
• ANSI/ISEA Z87.1-2010, Occupational and Educational Personal Eye and Face Protection Devices, incorporated by reference in § 1910.6;
• ANSI Z87.1-2003, Occupational and Educational Personal Eye and Face Protection Devices, incorporated by reference in § 1910.6; or
• ANSI Z87.1-1989 (R-1998), Practice for Occupational and Educational Eye and Face Protection, incorporated by reference in § 1910.6;
Respiratory Protection
See our Respiratory Protection Policy
Head Protection
Criteria for protective helmets (hard hats)
Head protection must comply with any of the following consensus standards:
REVISED DATE: January 1, 2025
PERSONAL
PROGRAM
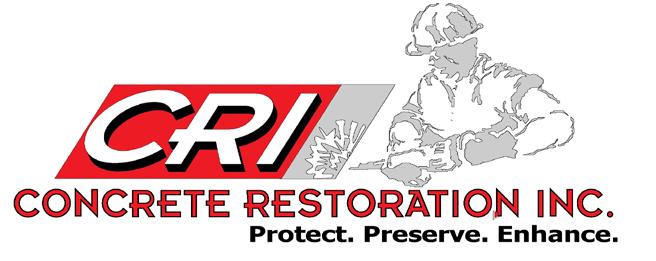
• American National Standards Institute (ANSI) Z89.1-2009, "American National Standard for Industrial Head Protection," incorporated by reference in Sec. 1910.6;
• American National Standards Institute (ANSI) Z89.1-2003, "American National Standard for Industrial Head Protection," incorporated by reference in Sec. 1910.6; or
• American National Standards Institute (ANSI) Z89.1-1997, "American National Standard for Personnel Protection--Protective Headwear for Industrial Workers Requirements," incorporated by reference in Sec. 1910.6.
• Hard hats will not be altered. No holes will be punched to attach adornments.
Electrical protective equipment
Where the requirements of 29 CFR 1910.137 apply, Concrete Restoration Inc will supply affected employees with appropriate PPE to ensure safety and compliance.
Hand Protection
General Requirements
Concrete Restoration Inc will select and require employees to use appropriate hand protection when employees' hands are exposed to hazards such as those from skin absorption of harmful substances; cuts or lacerations; abrasions; punctures; burns; and harmful temperature extremes.
REVISED DATE: January 1, 2025
PERSONAL PROTECTIVE EQUIPMENT PROGRAM
Selection
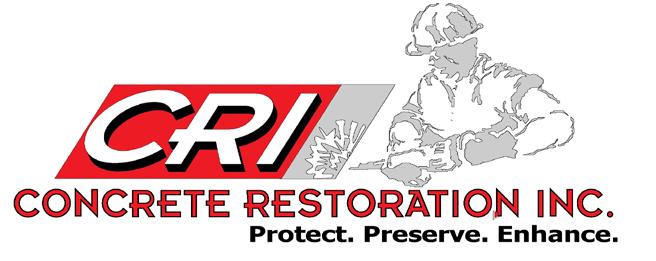
• Concrete Restoration Inc will select the appropriate hand protection based on an evaluation of the performance characteristics of the hand protection relative to the task(s) to be performed, conditions present, duration of use, and the hazards and potential hazards identified.
Fitting
• Employees are shown the correct way to don and doff their PPE as well as how to ensure good fit during training. Employees are expected to practice these teaching in the field and on the job site. Employees will ensure their PPE is properly fitted to address each hazard.
Employee-owned Equipment
• Concrete Restoration Inc provides employees with required personal protection equipment. If an employee chooses to use employee owned equipment, that equipment will be in good working order, per the requirements in this policy. Before any employee is allowed to use such equipment the supervisor will inspect the equipment for adequacy, maintenance, and sanitation.
REVISED DATE: January 1, 2025
POWERD INDUSTRIAL TRUCK/ FORKLIFT
POLICY
Overview
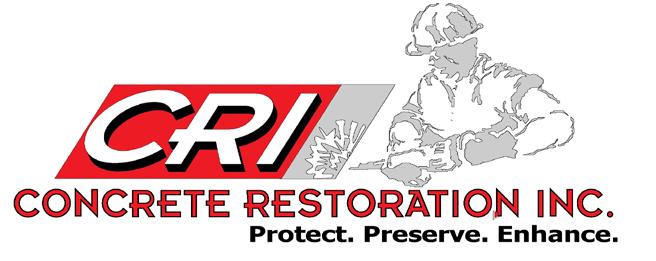
Material handling is a significant safety concern. During the movement of products and materials, there are numerous opportunities for injuries and property damage. Powered industrial trucks, better known as forklifts, pallet jacks and stand-up riding reach trucks are essential tools in handling materials. This document has been created to minimize the risk of injury to operators, bystanders, and to avoid damaging Concrete Restoration Inc property.
Concrete Restoration Inc will utilize this program to increase operator awareness of recognized safety standards. Qualified trainers will be used to provide all training activities.
Policy
Concrete Restoration Inc operators must comply with all aspects of this safety program. All employees must successfully complete this training program and have documented completion forms. Contractors operating powered industrial trucks are expected to meet or exceed the requirements found in this program and comply with all applicable statues and regulations governing the use of powered industrial trucks as listed in Section 3.0 of this document.
Requirements
OSHA Standard 29CFR 1910.178 (Powered Industrial Trucks)
ANSI/ISTDF B56.1 – 2017 (Safety Standard for Low Lift and High Lift Trucks)
WAC 296-863
Valid driver’s license and a good driving record
REVISED DATE: January 1, 2025
POWERD INDUSTRIAL TRUCK/ FORKLIFT POLICY
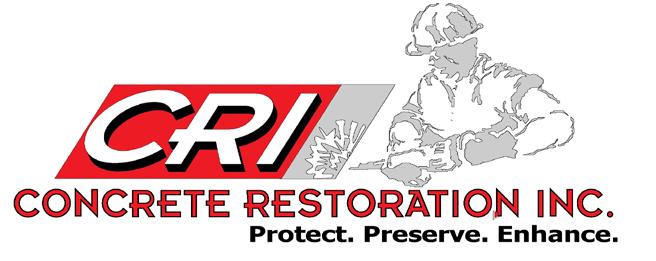
Purpose
This program has been developed to reduce the risk of physical injury or property damage in areas where powered industrial trucks are in operation. It also brings Concrete Restoration Inc into compliance with federal, state, and local law.
Scope
This program applies to the operation of all powered industrial trucks, forklifts, tractors, platform lift trucks, motorized hand trucks, and other specialized industrial trucks powered by electric motors or internal combustion engines by employees and contractors, engaged in company projects.
Pre-Use Inspection
• Prior to the operation of any powered industrial truck a Pre-Use Inspection must be performed. This applies at the beginning of every work period, and whenever a new equipment operator takes control of the powered industrial truck.
• Any safety defects (such as hydraulic fluid leaks; defective brakes, steering, lights, or horn; and/or missing fire extinguisher, lights, seat belt, or back-up alarm) must be reported for immediate repair. They must also be locked and tagged and taken out of service.
Operation
• Operators must wear seat belts at all times.
• Operators must sound the horn and use extreme caution when meeting pedestrians making turns, and cornering.
• Passengers are not allowed to ride on an industrial truck, unless the truck has an extra seat that allows the passenger to buckle-up while riding.
REVISED DATE: January 1, 2025
POWERD INDUSTRIAL TRUCK/ FORKLIFT
POLICY
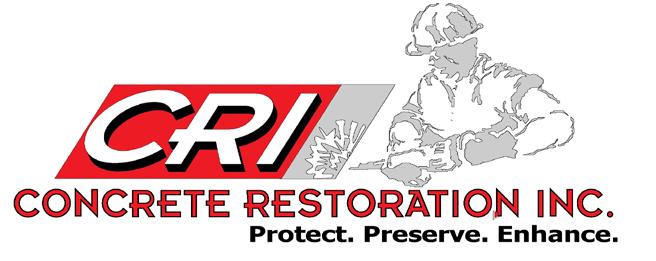
• Arms or legs may not be placed between the uprights of the mast or outside the running lines of the truck.
• People are not allowed to stand or pass under any elevated portion of a truck.
• Travel-ways must be maintained free from obstructions, aisles must be marked, and wide enough (six-foot minimum) for vehicle operation.
• Maintain sufficient headroom under overhead installations such as: lights, pipes, sprinkler systems, etc.
• An overhead guard must be used as protection against falling objects.
• Lift capacity must be marked on all powered industrial trucks. Operators must ensure the load does not exceed rated weight limits.

• When a powered industrial truck is left unattended (more than 25ft. away or out of sight), load engaging means must be fully lowered, controls neutralized, power shut off, and brakes set. Wheels must be blocked if the truck is parked on an incline.
• All modifications must be approved by the manufacturer, and new rated load capacities determined and posted on the truck. Written approval is required.

• Operators must report all accidents, regardless of fault and severity, to their Foreman.
Loading
• Only handle loads within the rated capacity of the truck.
REVISED DATE: January 1, 2025
POWERD INDUSTRIAL TRUCK/ FORKLIFT POLICY
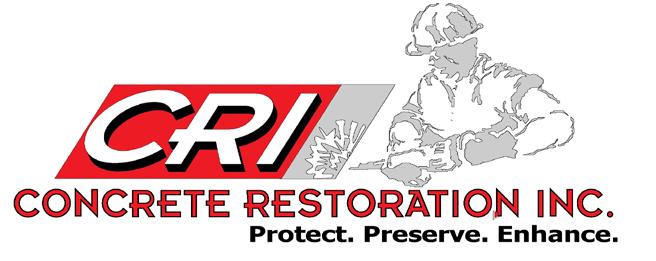
• Loads should be safely arranged, stable, and centered – always use caution when handling loads. Adjust long or high (including multipletiered) loads that may affect capacity.
• Trucks equipped with attachments must be operated as partially loaded trucks even when not handling a load
• A load engaging means must be placed under the load as far as possible. The mast must be carefully tilted backward to stabilize the load.
• Use extreme care when tilting the load forward or backward, particularly when high tiering. Tilting forward with load engaging means elevated is prohibited except to pick up a load. An elevated load may not be tilted forward except when the load is in a deposit position. When stacking or tiering, use only enough backward tilt to stabilize the load.
Traveling
• The driver must slow down and sound the horn at cross aisles and other locations where vision is obstructed.
• If the load being carried obstructs forward view, the driver must travel with the load trailing.
• Loads must be tilted back and carried no more than four inches above the ground.
• The driver must look in the direction of and keep a clear view of the path of travel.
• Grades must be ascended and descended slowly. Position the load uphill relative to the operator when ascending or descending grades.
• Stunt driving and horseplay are prohibited.
REVISED DATE: January 1, 2025
POWERD INDUSTRIAL TRUCK/ FORKLIFT POLICY
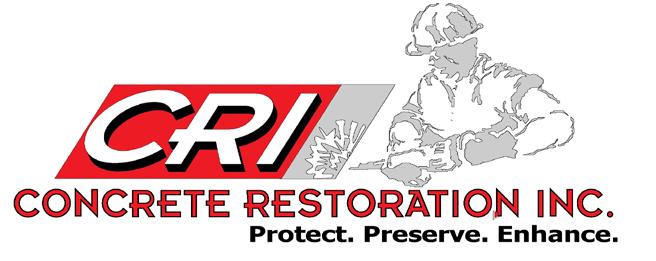
• While negotiating turns, reduce speed and turn the hand steering wheel in a smooth, sweeping motion.
• Operators must verify trailer chalks, supports, and deck plates prior to loading.
Changing and Charging Batteries
• Battery charging installations must be located in areas designated for that purpose.
• Facilities must provided for: flushing and neutralizing spilled electrolyte, fire protection, protection of charging apparatus from damage by trucks, adequate ventilation for dispersal of fumes from gassing batteries.
• Precautions must be taken to prevent open flames, sparks, or electric arcs in battery charging areas.
• Employees charging and changing batteries shall be authorized to do the work, trained in the proper handling, and required to wear protective clothing, including face shields, long sleeves, rubber boots, aprons, and gloves.
Maintenance
• Any power-operated industrial truck not in safe operating condition must be removed from service. Authorized personnel must make all repairs.
• Repairs to the fuel and ignition systems of industrial trucks that involve fire hazards must be conducted only in locations designated for such repairs.
• Trucks in need of repairs to the electrical system must have the battery disconnected before such repairs.
REVISED DATE: January 1, 2025
POWERD INDUSTRIAL TRUCK/ FORKLIFT POLICY
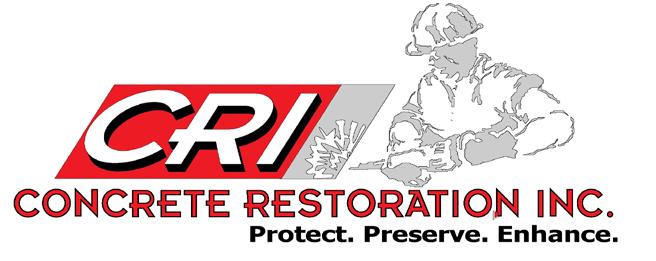
• Only use replacement parts that are currently recommended by the manufacturer.
Responsibilities
Persons Utilizing Powered Industrial Trucks
• Must implement and administer the Powered Industrial Truck program.
• Review the Powered Industrial Truck program annually for compliance and effectiveness.
• Verify that all employees who operate or work near powered industrial trucks are properly trained and certified.
• Maintain written records of operator training of a Powered Industrial Truck and the name of the trainer.
• Maintain written records of the frequent and annual inspections performed by the Powered Industrial Truck owner, including the date any problems found, the date when fixed, and the name of the person performing the repairs.
• Make recommendations for revisions if necessary.
Operators
• Complete the Forklift Safety Program.
• Complete the Daily Pre-Use Inspection Checklist before operating any powered industrial truck.
• At least annually review the procedures outlined in this policy.
REVISED DATE: January 1, 2025
POWERD INDUSTRIAL TRUCK/ FORKLIFT
POLICY
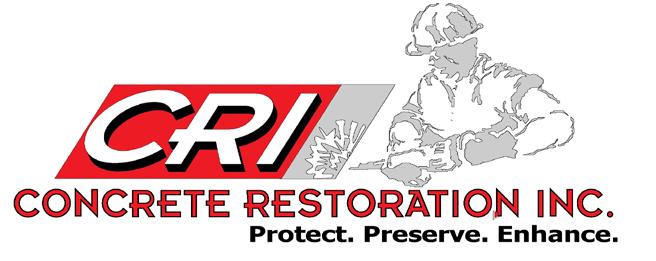
• Observe the operation of powered industrial trucks in your department and report unsafe practices to your supervisor.
Training Requirements
Employees who are authorized to operate powered industrial trucks must receive training prior to engaging in their duties, and at least every three (3) years thereafter. The training is to ensure that the Forklift Safety Program is understood. The Trainer will also ensure that authorized powered industrial truck operators have acquired the necessary practical skills required for safe operation.
Company trainers will be selected by management. Company trainers must be experienced operators who have the knowledge, training, and skills necessary to evaluate the competence of trainees. Operational training will consist of a combination of general safety instruction, practical/operational training (demonstrations performed by the trainer, and practical exercises performed by the trainee), and evaluation of the operator's performance in the workplace. All operational training must be conducted under close supervision.
Initial Training
• Receive instruction on the intended purpose and function of each control.
• Prior to operating any Powered Industrial Truck the trainee will read and understand the manufacturer's operating instruction(s) and user's safety rules, or receive training by a qualified person on the contents of the manufacturer's operating instruction(s) and users safety rules.
REVISED DATE: January 1, 2025
POWERD INDUSTRIAL TRUCK/ FORKLIFT
POLICY
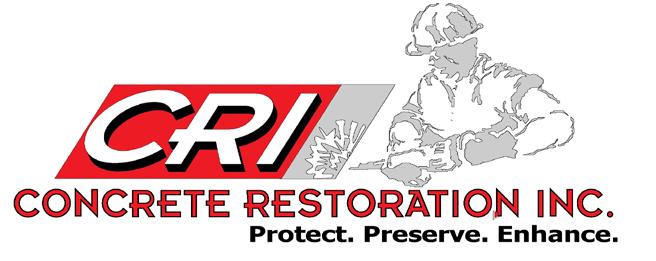
• Be informed of the Powered Industrial Truck operating limitations and restrictions as defined by the manufacturer.
• Understand by reading or having a qualified person explain all decals, warnings, and instructions displayed on the Powered Industrial Truck.
• During operational training, trainees may operate a powered industrial truck only under the direct supervision of authorized trainers, and where such operation does not endanger the trainee or other employees.
• All training and evaluation must be completed before an operator is permitted to use a powered industrial truck without continual and close supervision.
Annual Training – must include at least the following:
• Updated information on new equipment.
• Review of company written program.
Training Records
Company must maintain a record of all individual training, including:
• Subject of training.
• Date of training.
• Name of individual trained.
Program Evaluation
The forklift program shall be evaluated on an annual basis.
REVISED DATE: January 1, 2025
RESPIRABLE CRYSTALLINE SILCA
POLICY
RESPIRABLE CRYSTALLINE SILCA POLICY
Reference: OSHA 1910.1053/WAC 296-840
PURPOSE
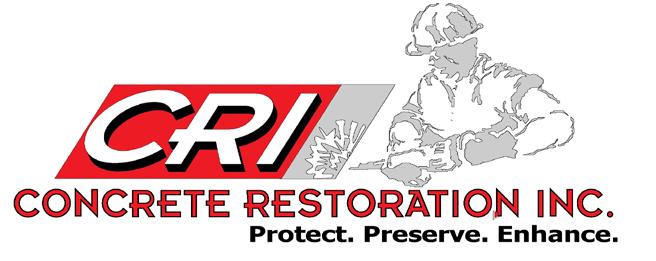
This Respirable Crystalline Silica Program was developed to prevent employee exposure to hazardous levels of Respirable Crystalline Silica that could result through construction activities or nearby construction activities occurring on worksites. Respirable Crystalline Silica exposure at hazardous levels can lead to lung cancer, silicosis, chronic obstructive pulmonary disease, and kidney disease. It is intended to meet the requirements of the Respirable Crystalline Silica WAC 296-840 Silica Standard
All work involving chipping, cutting, drilling, grinding, or similar activities on materials containing Crystalline Silica can lead to the release of respirablesized particles of Crystalline Silica (i.e. Respirable Crystalline Silica). Crystalline Silica is a basic component of soil, sand, granite and many other minerals. Quartz is the most common form of Crystalline Silica. Many materials found on constructions sites include Crystalline Silica; including but not limited to – cement, concrete, asphalt, pre-formed structures (inlets, pipe, etc.) and others. Consequently, this program has been developed to address and control these potential exposures to prevent our employees from experiencing the effects of occupational illnesses related to Respirable Crystalline Silica exposure.
SCOPE
This Respirable Crystalline Silica Program applies to all employees who have the potential to be exposed to Respirable Crystalline Silica when covered by the WAC 296-840 Silica Standard. The Respirable Crystalline Silica Construction Standard applies to all occupational exposures to Respirable Crystalline Silica in construction work, except where employee exposure will remain below 25 micrograms of Respirable Crystalline Silica per cubic meter of air (25 μg/m3) as an 8-hour time-weighted average (TWA) under any foreseeable conditions.
REVISED DATE: January 1, 2025
RESPIRABLE CRYSTALLINE SILCA POLICY
RESPONSIBILITIES
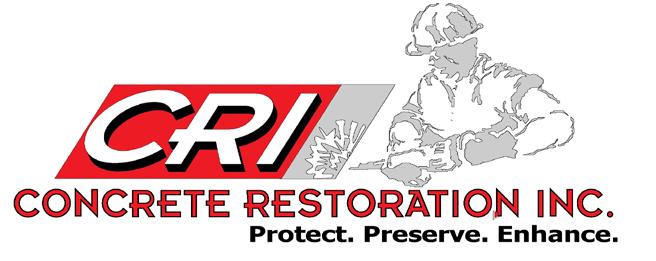
CRI firmly believes protecting the health and safety of our employees is everyone’s responsibility. This responsibility begins with upper management providing the necessary support to properly implement this program. However, all levels of the organization assume some level of responsibility for this program including the following positions.
Upper Management:
• Conduct job site assessments for Silica containing materials and perform employee Respirable Crystalline Silica hazard assessments in order to determine if an employee’s exposure will be above 25 μg/m3 as an 8-hour TWA under any foreseeable conditions
• Select and implement into the project’s ECP the appropriate control measures in accordance with the Construction Tasks identified in OSHA’s Construction Standard Table 1; and potentially including (but not limited to) - a written Exposure Control Plan (ECP), exposure monitoring, Hazard Communication training, medical surveillance, housekeeping and others.
NOTE: OSHA’s Construction Standard Table 1 is a list of 18 common construction tasks along with acceptable exposure control methods and work practices that limit exposure for those tasks.
• Ensure that the materials, tools, equipment, personal protective equipment (PPE), and other resources (such as worker training) required to fully implement and maintain this Respirable Crystalline Silica Program are in place and readily available if needed.
• Ensure that Project Managers, Competent Persons, and employees are educated in the hazards of Silica exposure and trained to work safely with Silica in accordance with WAC 296-840 Silica Standard and Hazard Communication Standard. Managers and Competent Persons may receive more advanced training than other employees.
REVISED DATE: January 1, 2025
RESPIRABLE CRYSTALLINE SILCA POLICY
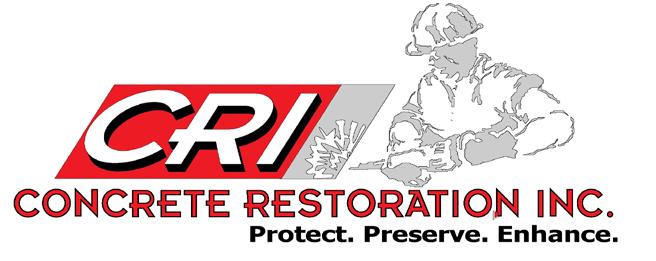
• Maintain written records of training (for example, proper use of respirators), ECPs, inspections (for equipment, PPE, and work methods/practices), medical surveillance (under lock and key), respirator medical clearances (under lock and key) and fit-test results.
• Conduct an annual review (or more often if conditions change) of the effectiveness of this program and any active project ECP’s that extend beyond a year. This includes a review of available dust control technologies to ensure these are selected and used when practical.
• Coordinate work with other employers and contractors to ensure a safe work environment relative to Silica exposure.
Project Manager:
• Ensure all applicable elements of this Respirable Crystalline Silica Program are implemented on the project including the selection of a Competent Person.
• Assist the Safety Department in conduct job site assessments for Silica containing materials and perform employee Respirable Crystalline Silica hazard assessments in order to determine if an ECP, exposure monitoring, and medical surveillance is necessary.
• Assist in the selection and implementation of the appropriate control measures in accordance with the Construction Tasks identified in OSHA’s Construction Standard Table 1; and potentially including (but not limited to) - a written Exposure Control Plan (ECP), exposure monitoring, Hazard Communication training, medical surveillance, housekeeping and others.
• Ensure that employees using respirators have been properly trained, medically cleared, and fit-tested in accordance with the company’s Respiratory Protection Program. This process will be documented.
• Ensure that work is conducted in a manner that minimizes and adequately controls the risk to workers and others. This includes
REVISED DATE: January 1, 2025
RESPIRABLE CRYSTALLINE SILCA
POLICY
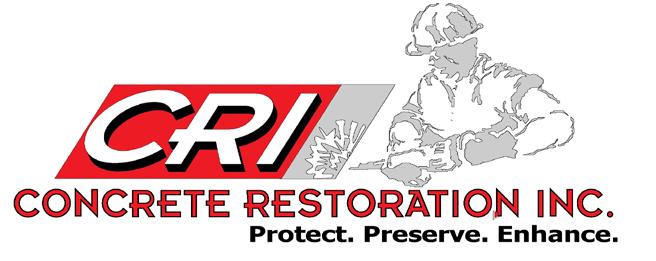
ensuring that workers use appropriate engineering controls, work practices, and wear the necessary PPE.
• Where there is risk of exposure to Silica dust, verify employees are properly trained on the applicable contents of this program, the project specific ECP, and the applicable WAC Standards (such as Hazard Communication). Ensure employees are provided appropriate PPE when conducting such work.
Competent
Person and/or (Superintendent, Foreman, etc.)
• Make frequent and regular inspections of job sites, materials, and equipment to implement the written ECP.
• Identify existing and foreseeable Respirable Crystalline Silica hazards in the workplace and take prompt corrective measures to eliminate or minimize them.
• Notify the Project Manager and/or Safety Department of any deficiencies identified during inspections in order to coordinate and facilitate prompt corrective action.
• Assist the Project Manager and Safety Department in conducting job site assessments for Silica containing materials and perform employee Respirable Crystalline Silica hazard assessments in order to determine if an ECP, exposure monitoring, and medical surveillance is necessary.
Employees:
• Follow recognized work procedures (such as the Construction Tasks identified in OSHA’s Construction Standard Table 1) as established in the project’s ECP and this program.
• Use the assigned PPE in an effective and safe manner.
• Participate in Respirable Crystalline Silica exposure monitoring and the medical surveillance program when necessary.
REVISED DATE: January 1, 2025
RESPIRABLE CRYSTALLINE
SILCA POLICY
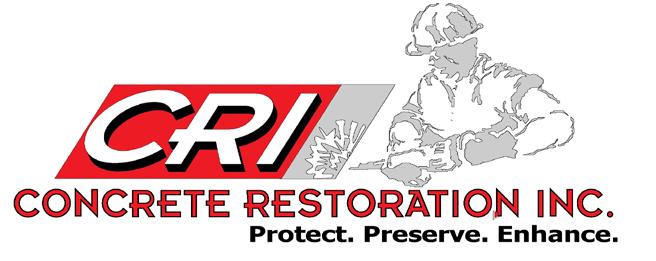
• Report any unsafe conditions or acts to the Foreman and/or Competent Person.
• Report any exposure incidents or any signs or symptoms of Silica illness.
DEFINITIONS
If a definition is not listed in this section, please contact your supervisor. If your supervisor is unaware of what the term means, please contact the Competent Person or your Safety Department.
• Action Level means a concentration of airborne Respirable Crystalline Silica of 25 μg/m3, calculated as an 8-hour TWA.
• Competent Person means an individual who is capable of identifying existing and foreseeable Respirable Crystalline Silica hazards in the workplace and who has authorization to take prompt corrective measures to eliminate or minimize them.
• Employee Exposure means the exposure to airborne Respirable Crystalline Silica that would occur if the employee were not using a respirator.
• High-Efficiency Particulate Air (HEPA) Filter means a filter that is at least 99.97 percent efficient in removing monodispersed particles of 0.3 micrometers in diameter.
• Objective Data means information, such as air monitoring data from industry-wide surveys or calculations based on the composition of a substance, demonstrating employee exposure to Respirable Crystalline Silica associated with a particular product or material or a specific process, task, or activity. The data must reflect workplace conditions closely resembling or with a higher exposure potential than the processes, types of material, control methods, work practices, and environmental conditions in the employer's current operations.
REVISED DATE: January 1, 2025
RESPIRABLE CRYSTALLINE SILCA POLICY
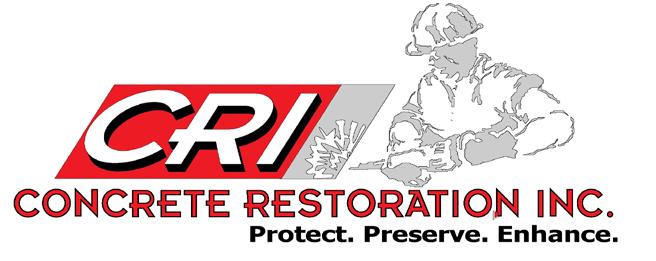
• Permissible Exposure Limit (PEL) means the employer shall ensure that no employee is exposed to an airborne concentration of Respirable Crystalline Silica in excess of 50 μg/m3, calculated as an 8-hour TWA.
• Physician or Other Licensed Health Care Professional (PLHCP) means an individual whose legally permitted scope of practice (i.e., license, registration, or certification) allows him or her to independently provide or be delegated the responsibility to provide some or all of the particular health care services required by the Medical Surveillance Section of the OSHA Respirable Crystalline Silica Standard.
• Respirable Crystalline Silica means Quartz, Cristobalite, and/or Tridymite contained in airborne particles that are determined to be respirable by a sampling device designed to meet the characteristics for respirable-particle size- selective samplers specified in the International Organization for Standardization (ISO) 7708:1995: Air Quality-Particle Size Fraction Definitions for Health-Related Sampling.
• Specialist means an American Board Certified Specialist in Pulmonary Disease or an American Board Certified Specialist in Occupational Medicine.
REQUIREMENTS
Specified Exposure Control Methods
When possible and applicable, CRI will conduct activities with potential Silica exposure to be consistent with OSHA’s Construction Standard Table
1. Supervisors will ensure each employee under their supervision and engaged in a task identified on OSHA’s Construction Standard Table 1 have fully and properly implemented the engineering controls, work practices, and respiratory protection specified for the task on Table 1 (unless CRI has assessed and limited the exposure of the employee to
REVISED DATE: January 1, 2025
RESPIRABLE CRYSTALLINE SILCA
POLICY
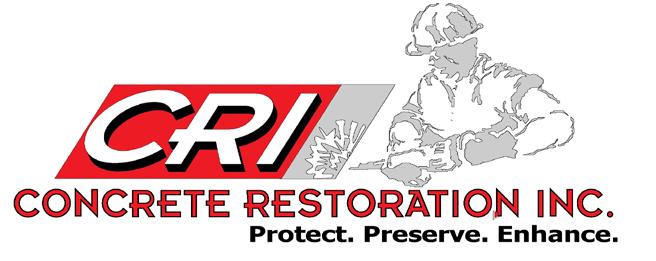
Respirable Crystalline Silica in accordance with the Alternative Exposure Control Methods Section of this program).
The task(s) being performed by CRI identified on OSHA’s Construction Standard Table 1 is/are:
Table 1: Specified Exposure Control Methods When Working With Materials Containing Crystalline Silica
Construction
1 Stationary masonry saws
• Use saw equipped with integrated water delivery system that continuously feeds water to the blade.
• Operate and maintain tool in accordance with manufacturer's instructions to minimize dust emissions.
None None
2a Handheld power saws (any blade diameter) when used outdoors
2b Handheld power saws (any blade diameter) when used indoors or in an enclosed area
• Use saw equipped with integrated water delivery system that continuously feeds water to the blade.
• Operate and maintain tool in accordance with manufacturer's instructions to minimize dust emissions. None APF 10
• Use saw equipped with integrated water delivery system that continuously feeds water to the blade.
• Operate and maintain tool in accordance with manufacturer's instructions to minimize dust emissions. APF 10 APF 10
REVISED DATE: January 1, 2025
RESPIRABLE CRYSTALLINE SILCA
POLICY
Construction Task or Equipment
Operation
3
Handheld power saws for cutting fiber-cement board (with blade diameter of 8 inches or less) for tasks performed outdoors only
• Use saw equipped with commercially available dust collection system.
• Operate and maintain tool in accordance with manufacturer's instructions to minimize dust emissions.
• Dust collector must provide the air flow recommended by the tool manufacturer, or greater, and have a filter with 99% or greater efficiency.
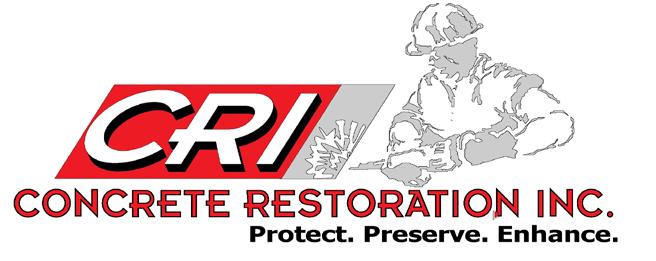
4a
Walk-behind saws when used outdoors
• Use saw equipped with integrated water delivery system that continuously feeds water to the blade.
• Operate and maintain tool in accordance with manufacturer's instructions to minimize dust emissions.
None
None
None
None
4b Walk-behind saws when used indoors or in an enclosed area
5 Handheld and standmounted drills
• Use saw equipped with integrated water delivery system that continuously feeds water to the blade.
• Operate and maintain tool in accordance with manufacturer's instructions to minimize dust emissions. APF 10 APF 10
• Use drill equipped with commercially available shroud or cowling with dust
REVISED DATE: January 1, 2025
None
None
RESPIRABLE CRYSTALLINE SILCA POLICY
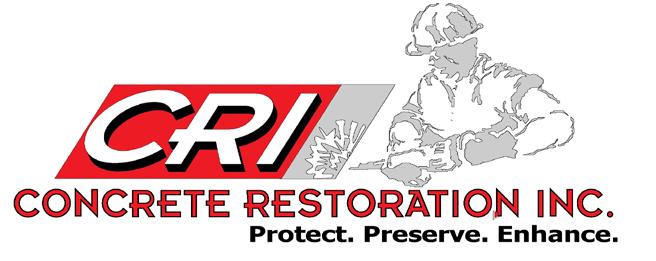
Construction Task or Equipment
Operation
Engineering and Work Practice Control Methods
hift (including impact and rotary hammer drills) collection system.
• Operate and maintain tool in accordance with manufacturer's instructions to minimize dust emissions.
• Dust collector must provide the air flow recommended by the tool manufacturer, or greater, and have a filter with 99% or greater efficiency and a filtercleaning mechanism.
• Use a HEPA-filtered vacuum when cleaning holes.
6a
Jackhammers and handheld powered chipping tools when used outdoors
6b Jackhammers and handheld powered chipping tools when used indoors or in an enclosed area
6c
• Use tool with water delivery system that supplies a continuous stream or spray of water at the point of impact. None APF 10
• Use tool with water delivery system that supplies a continuous stream or spray of water at the point of impact.
10
Jackhammers and handheld powered
• Use tool equipped with commercially available shroud and dust collection
REVISED DATE: January 1, 2025
10
RESPIRABLE CRYSTALLINE SILCA
POLICY
Construction Task or Equipment
Operation
Engineering and Work Practice Control Methods
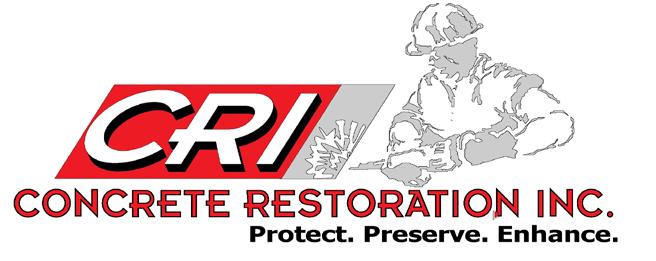
hours/s hift chipping tools when used outdoors system.
• Operate and maintain tool in accordance with manufacturer's instructions to minimize dust emissions.
• Dust collector must provide the air flow recommended by the tool manufacturer, or greater, and have a filter with 99% or greater efficiency and a filtercleaning mechanism.
hift
6d Jackhammers and handheld powered chipping tools when used indoors or in an enclosed area
• Use tool equipped with commercially available shroud and dust collection system.
• Operate and maintain tool in accordance with manufacturer's instructions to minimize dust emissions.
• Dust collector must provide the air flow recommended by the tool manufacturer, or greater, and have a filter with 99% or greater efficiency and a filtercleaning mechanism.
7 Handheld grinders for mortar removal (i.e., tuckpointing)
• Use grinder equipped with commercially available shroud and dust collection system.
• Operate and maintain tool
REVISED DATE: January 1, 2025
RESPIRABLE CRYSTALLINE SILCA
POLICY
Construction Task or Equipment
Operation Engineering and Work Practice Control Methods
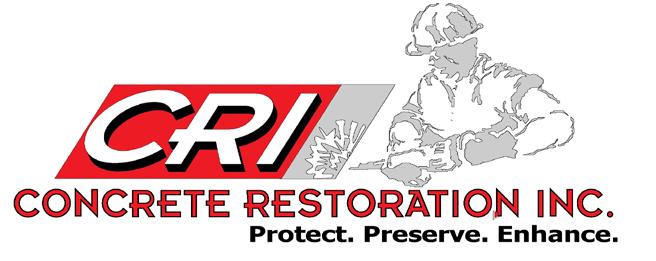
≤ 4 hours/s hift >4 hours/s hift
8a Handheld grinders for uses other than mortar removal for tasks performed outdoors only
in accordance with manufacturer's instructions to minimize dust emissions.
• Dust collector must provide 25 cubic feet per minute (cfm) or greater of airflow per inch of wheel diameter and have a filter with 99% or greater efficiency and a cyclonic pre-separator or filter-cleaning mechanism.
• Use grinder equipped with integrated water delivery system that continuously feeds water to the grinding surface.
• Operate and maintain tool in accordance with manufacturer's instructions to minimize dust emissions.
None None
8b Handheld grinders for uses other than mortar removal when used outdoors
• Use grinder equipped with commercially available shroud and dust collection system.
• Operate and maintain tool in accordance with manufacturer's instructions to minimize dust emissions.
• Dust collector must provide
REVISED DATE: January 1, 2025
None None
RESPIRABLE CRYSTALLINE SILCA
POLICY
Construction Task or Equipment
Operation Engineering and Work Practice Control Methods
25 cubic feet per minute (cfm) or greater of airflow per inch of wheel diameter and have a filter with 99% or greater efficiency and a cyclonic pre-separator or filter-cleaning mechanism.
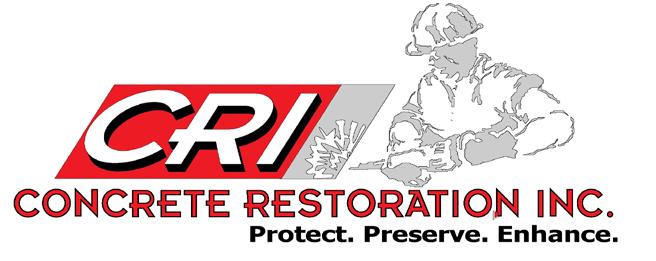
≤ 4 hours/s hift >4 hours/s hift
8c
Handheld grinders for uses other than mortar removal when used indoors or in an enclosed area
• Use grinder equipped with commercially available shroud and dust collection system.
• Operate and maintain tool in accordance with manufacturer's instructions to minimize dust emissions.
• Dust collector must provide 25 cubic feet per minute (cfm) or greater of airflow per inch of wheel diameter and have a filter with 99% or greater efficiency and a cyclonic pre-separator or filter-cleaning mechanism.
9a Walk-behind milling machines and floor grinders
• Use machine equipped with integrated water delivery system that continuously feeds water to the cutting surface.
• Operate and maintain tool in accordance with
REVISED DATE: January 1, 2025
None None
RESPIRABLE CRYSTALLINE SILCA
POLICY
Construction Task or Equipment
Operation Engineering and Work Practice Control Methods
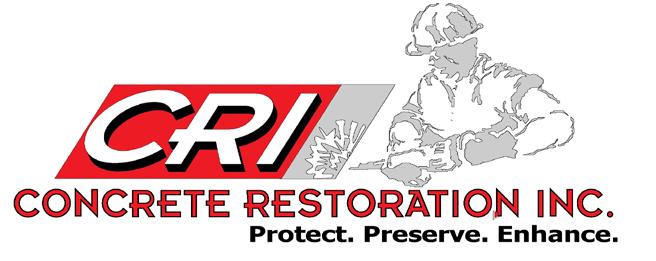
hours/s hift
9b Walk-behind milling machines and floor grinders
manufacturer's instructions to minimize dust emissions.
• Use machine equipped with dust collection system recommended by the manufacturer.
• Operate and maintain tool in accordance with manufacturer's instructions to minimize dust emissions.
• Dust collector must provide the air flow recommended by the manufacturer, or greater, and have a filter with 99% or greater efficiency and a filtercleaning mechanism.
• When used indoors or in an enclosed area, use a HEPA-filtered vacuum to remove loose dust in between passes.
None None
10a Heavy equipment and utility vehicles used to abrade or fracture silicacontaining materials (e.g., hoeramming,
• Operate equipment from within an enclosed cab.
REVISED DATE: January 1, 2025
None None
RESPIRABLE CRYSTALLINE SILCA
POLICY
Construction Task or Equipment
Operation Engineering and Work Practice Control Methods
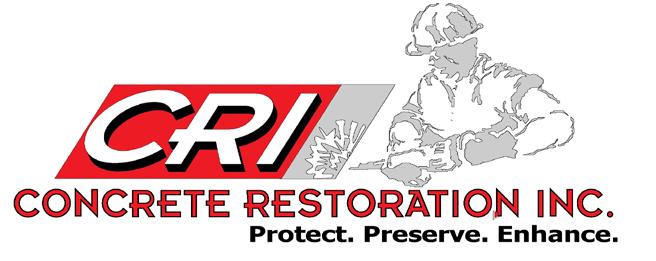
hours/s hift rock ripping) or used during demolition activities involving silicacontaining materials
10b Heavy equipment and utility vehicles used to abrade or fracture silicacontaining materials (e.g., hoeramming, rock ripping) or used during demolition activities involving silicacontaining materials
11a Heavy equipment and utility vehicles for
• When employees outside of the cab are engaged in the task, apply water and/or dust suppressants as necessary to minimize dust emissions.
hift
None
None
• Apply water and/or dust suppressants as necessary to minimize dust emissions.
REVISED DATE: January 1, 2025
None
None
RESPIRABLE CRYSTALLINE SILCA
POLICY
Construction Task or Equipment
Operation Engineering and Work Practice Control Methods
tasks such as grading and excavating but not including demolishing, abrading, or fracturing silicacontaining materials
11b
Heavy equipment and utility vehicles for tasks such as grading and excavating but not including demolishing, abrading, or fracturing silicacontaining materials
• When the equipment operator is the only employee engaged in the task, operate equipment from within an enclosed cab.
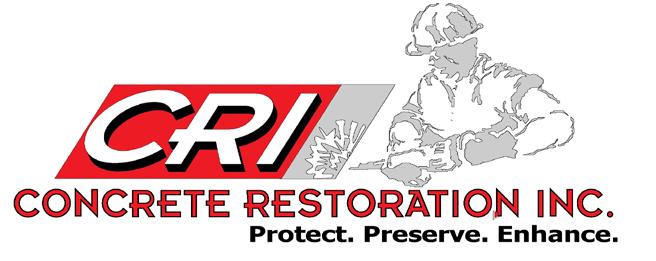
hift
hours/s hift
None
None
When implementing the control measures specified in Table 1, CRI shall:
REVISED DATE: January 1, 2025
RESPIRABLE CRYSTALLINE SILCA POLICY
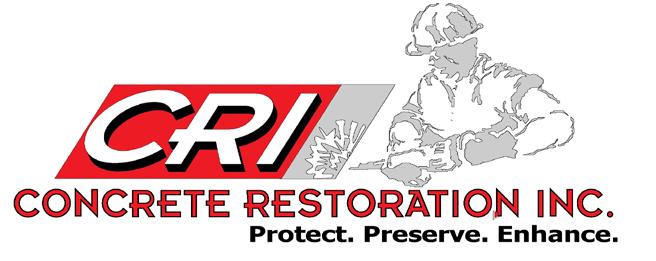
• For tasks performed indoors or in enclosed areas, provide a means of exhaust as needed to minimize the accumulation of visible airborne dust;
• For tasks performed using wet methods, apply water at flow rates sufficient to minimize release of visible dust;
• For measures implemented that include an enclosed cab or booth, ensure that the enclosed cab or booth:
o Is maintained as free as practicable from settled dust;
o Has door seals and closing mechanisms that work properly;
o Has gaskets and seals that are in good condition and working properly;
o Is under positive pressure maintained through continuous delivery of fresh air;
o Has intake air that is filtered through a filter that is 95% efficient in the 0.3-10.0 μm range (e.g., MERV-16 or better); and
o Has heating and cooling capabilities.
• Where an employee performs more than one task included on OSHA’s Construction Standard Table 1 during the course of a shift, and the total duration of all tasks combined is more than four hours, the required respiratory protection for each task is the respiratory protection specified for more than four hours per shift. If the total duration of all tasks on Table 1 combined is less than four hours, the required respiratory protection for each task is the respiratory protection specified for less than four hours per shift.
Alternative Exposure Control Methods
REVISED DATE: January 1, 2025
RESPIRABLE CRYSTALLINE SILCA POLICY
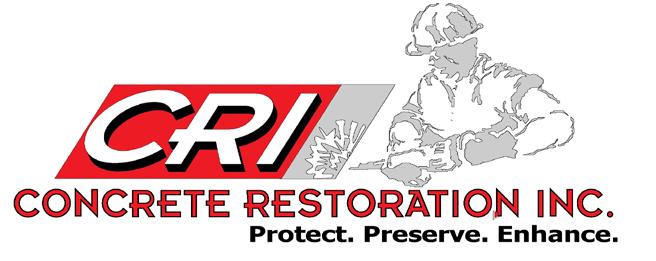
Alternative Exposure Control Methods apply for tasks not listed in OSHA’s Construction Standard Table 1, or where CRI cannot not fully and properly implement the engineering controls, work practices, and respiratory protection described in Table 1.
First, CRI will assess the exposure of each employee who is or may reasonably be expected to be exposed to Respirable Crystalline Silica at or above the Action Level in accordance with either the Performance Option or the Scheduled Monitoring Option.
• Performance Option – CRI will assess the 8-hour TWA exposure for each employee on the basis of any combination of air monitoring data or objective data sufficient to accurately characterize employee exposures to Respirable Crystalline Silica.
• Scheduled Monitoring Option:
o CRI will perform initial monitoring to assess the 8-hour TWA exposure for each employee on the basis of one or more personal breathing zone air samples that reflect the exposures of employees on each shift, for each job classification, and in each work area. Where several employees perform the same tasks on the same shift and in the same work area, CRI will plan to monitor a representative fraction of these employees. When using representative monitoring, CRI will sample the employee(s) who are expected to have the highest exposure to Respirable Crystalline Silica.
o If initial monitoring indicates that employee exposures are below the Action Level, CRI will make a determination if further monitoring is required as to those employees whose exposures are represented by such monitoring.
o Where the most recent exposure monitoring indicates that employee exposures are at or above the Action Level but at or below the PEL, CRI will repeat such monitoring within six months of the most recent monitoring.
REVISED DATE: January 1, 2025
RESPIRABLE CRYSTALLINE SILCA POLICY
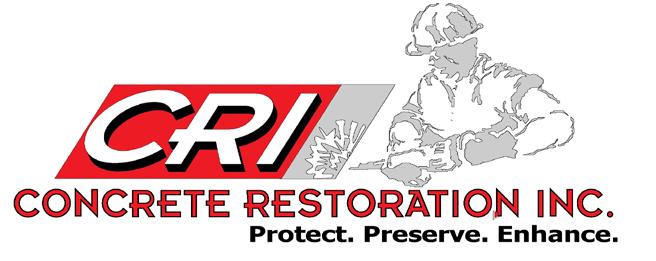
o Where the most recent exposure monitoring indicates that employee exposures are above the PEL, CRI will repeat such monitoring within three months of the most recent monitoring.
o Where the most recent (non-initial) exposure monitoring indicates that employee exposures are below the Action Level, CRI will repeat such monitoring within six months of the most recent monitoring until two consecutive measurements, taken seven or more days apart, are below the Action Level, at which time CRI will make a determination if further monitoring is necessary for those employees whose exposures are represented by such monitoring, except when a reassessment is required. CRI will reassess exposures whenever a change in the production, process, control equipment, personnel, or work practices may reasonably be expected to result in new or additional exposures at or above the Action Level, or when CRI has any reason to believe that new or additional exposures at or above the Action Level have occurred.
CRI will ensure that all Respirable Crystalline Silica samples taken to satisfy the monitoring requirements of this program and OSHA are collected by a qualified individual (i.e. a Certified Industrial Hygienist) and the samples are evaluated by a qualified laboratory (i.e. accredited to ANS/ISO/IEC Standard 17025:2005 with respect to Crystalline Silica analyses by a body that is compliant with ISO/IEC Standard 17011:2004 for implementation of quality assessment programs).
Within five working days after completing an exposure assessment, CRI will individually notify each affected employee in writing of the results of that assessment or post the results in an appropriate location accessible to all affected employees.
Whenever an exposure assessment indicates that employee exposure is above the PEL, CRI will describe in the written notification the corrective action being taken to reduce employee exposure to or below the PEL.
Where air monitoring is performed, CRI will provide affected employees or their designated representatives an opportunity to observe any monitoring of employee exposure to Respirable Crystalline Silica.
REVISED DATE: January 1, 2025
RESPIRABLE CRYSTALLINE SILCA POLICY
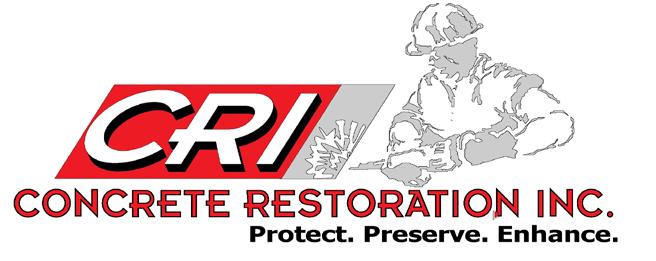
Once air monitoring has been performed, CRI will determine its method of compliance based on the monitoring data and the hierarchy of controls. CRI will use engineering and work practice controls to reduce and maintain employee exposure to Respirable Crystalline Silica to or below the PEL, unless CRI can demonstrate that such controls are not feasible. Wherever such feasible engineering and work practice controls are not sufficient to reduce employee exposure to or below the PEL, CRI will nonetheless use them to reduce employee exposure to the lowest feasible level and shall supplement them with the use of respiratory protection.
In addition to the requirements of this program, CRI will comply with other programs and OSHA standards (such as 29 CFR 1926.57 [Ventilation]), when applicable where abrasive blasting is conducted using Crystalline Silica-containing blasting agents, or where abrasive blasting is conducted on substrates that contain Crystalline Silica.
CRI will provide control methods that are either consistent with Table 1 or otherwise minimize worker exposures to Silica. These exposure control methods can include engineering controls, work practices, and respiratory protection.
Project:
Description of Work:
Competent Persons:
Date:
Stationary masonry saws
Use saw equipped with integrated water delivery system that continuously feeds water to the
and/or Operate and maintain tool in accordance with manufacturer's instructions to None None
REVISED DATE: January 1, 2025
RESPIRABLE CRYSTALLINE
SILCA POLICY
MARK BOX WITH X TASK OR EQUIPM ENT
Handheld power saws (any blade diameter) when used outdoors
Handheld power saws (any blade diameter) when used indoors or in an enclosed area
Handheld power saws for cutting fiber-cement board (with blade diameter of 8 inches or less) for tasks performed outdoors only
Walk-behind saws when used outdoors
Engineering and Work Practice Control Methods
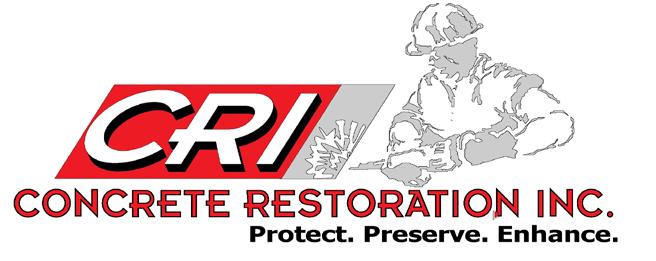
Required Respiratory Protection ≤ 4 hours/sh ift >4 hours/shift minimize dust emissions.
Use saw equipped with integrated water delivery system that continuously feeds water to the blade and/or Operate and maintain tool in accordance with manufacturer's instructions to minimize dust emissions.
None APF 10
Use saw equipped with integrated water delivery system that continuously feeds water to the blade and/or Operate and maintain tool in accordance with manufacturer's instructions to minimize dust emissions. APF 10 APF 10
Use saw equipped with commercially available dust collection system and/or Operate and maintain tool in accordance with manufacturer's instructions to minimize dust emissions. Dust collector must provide the air flow recommended by the tool manufacturer, or greater, and have a filter with 99% or greater efficiency.
Use saw equipped with integrated water delivery system that continuously feeds water to the blade and/or
REVISED DATE: January 1, 2025
None
None
None
None
RESPIRABLE CRYSTALLINE
SILCA POLICY
MARK BOX WITH X TASK OR EQUIPM ENT
Walk-behind saws when used indoors or in an enclosed area
Engineering and Work Practice Control Methods
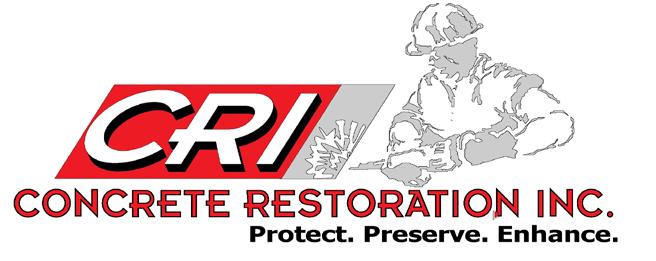
Required Respiratory Protection ≤ 4 hours/sh ift >4 hours/shift
Handheld and standmounted drills (including impact and rotary hammer drills)
Operate and maintain tool in accordance with manufacturer's instructions to minimize dust emissions.
Use saw equipped with integrated water delivery system that continuously feeds water to the blade and/or Operate and maintain tool in accordance with manufacturer's instructions to minimize dust emissions.
Use drill equipped with commercially available shroud or cowling with dust collection system.
Operate and maintain tool in accordance with manufacturer's instructions to minimize dust emissions. Dust collector must provide the air flow recommended by the tool manufacturer, or greater, and have a filter with 99% or greater efficiency and a filter-cleaning mechanism. Use a HEPA-filtered vacuum when cleaning holes.
10
10
None None
Jackhammers and handheld powered chipping tools when used
Use tool with water delivery system that supplies a continuous stream or spray of water at the point of impact.
REVISED DATE: January 1, 2025
None APF 10
RESPIRABLE CRYSTALLINE
SILCA POLICY
MARK BOX WITH X TASK OR EQUIPM ENT
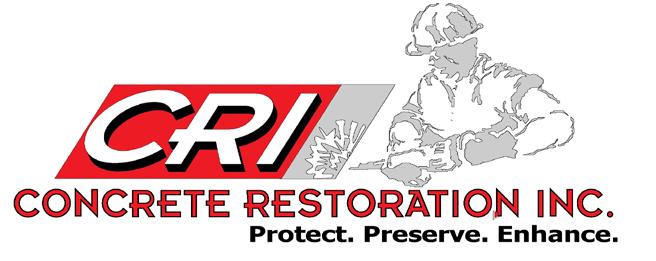
Required Respiratory Protection ≤ 4 hours/sh ift >4 hours/shift outdoors
Jackhammers and handheld powered chipping tools when used indoors or in an enclosed area
Engineering and Work Practice Control Methods
Jackhammers and handheld powered chipping tools when used outdoors
Use tool with water delivery system that supplies a continuous stream or spray of water at the point of impact. APF 10 APF 10
Jackhammers and handheld powered chipping tools when used indoors or in an enclosed area
Use tool equipped with commercially available shroud and dust collection system. Operate and maintain tool in accordance with manufacturer's instructions to minimize dust emissions. Dust collector must provide the air flow recommended by the tool manufacturer, or greater, and have a filter with 99% or greater efficiency and a filter-cleaning mechanism. None APF 10
Use tool equipped with commercially available shroud and dust collection system. Operate and maintain tool in accordance with manufacturer's instructions to minimize dust emissions. Dust collector must provide the air flow recommended by the tool manufacturer, or greater, and have a filter with
REVISED DATE: January 1, 2025
10
10
RESPIRABLE CRYSTALLINE SILCA
POLICY
MARK BOX WITH X TASK OR EQUIPM ENT
Handheld grinders for mortar removal (i.e., tuckpointing)
Engineering and Work Practice Control Methods
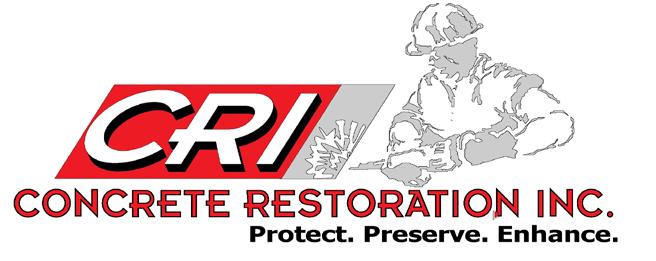
Required Respiratory Protection ≤ 4 hours/sh ift >4 hours/shift
Handheld grinders for uses other than mortar removal for tasks performed outdoors only
Handheld grinders for uses other than mortar removal when used outdoors
99% or greater efficiency and a filter-cleaning mechanism.
Use grinder equipped with commercially available shroud and dust collection system. Operate and maintain tool in accordance with manufacturer's instructions to minimize dust emissions. Dust collector must provide 25 cubic feet per minute (cfm) or greater of airflow per inch of wheel diameter and have a filter with 99% or greater efficiency and a cyclonic preseparator or filter-cleaning mechanism. APF 10 APF 25
Use grinder equipped with integrated water delivery system that continuously feeds water to the grinding surface. Operate and maintain tool in accordance with manufacturer's instructions to minimize dust emissions. None None
Use grinder equipped with commercially available shroud and dust collection system. Operate and maintain tool in accordance with None None
REVISED DATE: January 1, 2025
RESPIRABLE CRYSTALLINE
SILCA POLICY
MARK BOX WITH X TASK OR EQUIPM ENT
Handheld grinders for uses other than mortar removal when used indoors or in an enclosed area
Engineering and Work Practice Control Methods
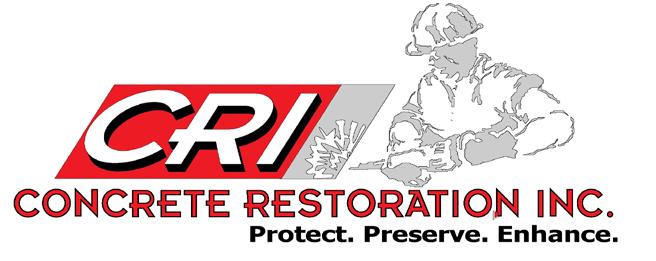
Required Respiratory Protection ≤ 4 hours/sh ift >4 hours/shift
Walk-behind milling machines and floor grinders
manufacturer's instructions to minimize dust emissions.
Dust collector must provide 25 cubic feet per minute (cfm) or greater of airflow per inch of wheel diameter and have a filter with 99% or greater efficiency and a cyclonic preseparator or filter-cleaning mechanism.
Use grinder equipped with commercially available shroud and dust collection system. Operate and maintain tool in accordance with manufacturer's instructions to minimize dust emissions.
Dust collector must provide 25 cubic feet per minute (cfm) or greater of airflow per inch of wheel diameter and have a filter with 99% or greater efficiency and a cyclonic preseparator or filter-cleaning mechanism.
Use machine equipped with integrated water delivery system that continuously feeds water to the cutting surface. Operate and maintain tool in accordance with
REVISED DATE: January 1, 2025
None APF 10
None
None
RESPIRABLE CRYSTALLINE
SILCA POLICY
MARK BOX WITH X TASK OR EQUIPM ENT
Walk-behind milling machines and floor grinders
Engineering and Work Practice Control Methods
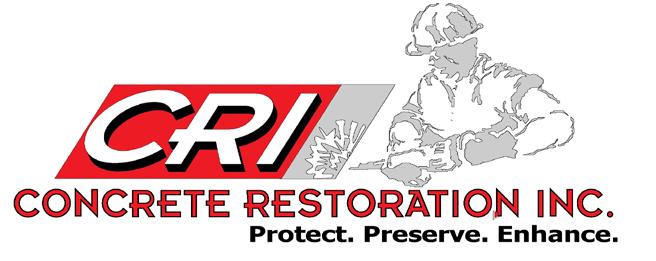
Required Respiratory Protection ≤ 4 hours/sh ift >4 hours/shift
Heavy equipment and utility vehicles used to abrade or fracture silicacontaining materials (e.g., hoeramming, rock ripping) or used during
manufacturer's instructions to minimize dust emissions.
Use machine equipped with dust collection system recommended by the manufacturer.
Operate and maintain tool in accordance with manufacturer's instructions to minimize dust emissions. Dust collector must provide the air flow recommended by the manufacturer, or greater, and have a filter with 99% or greater efficiency and a filtercleaning mechanism. When used indoors or in an enclosed area, use a HEPAfiltered vacuum to remove loose dust in between passes.
Operate equipment from within an enclosed cab.
None None
REVISED DATE: January 1, 2025
None None
RESPIRABLE CRYSTALLINE
SILCA POLICY
MARK BOX WITH X TASK OR EQUIPM ENT
demolition activities involving silicacontaining materials
Heavy equipment and utility vehicles used to abrade or fracture silicacontaining materials (e.g., hoeramming, rock ripping) or used during demolition activities involving silicacontaining materials
Heavy equipment and utility vehicles for tasks such as grading and excavating but not
Engineering and Work Practice Control Methods
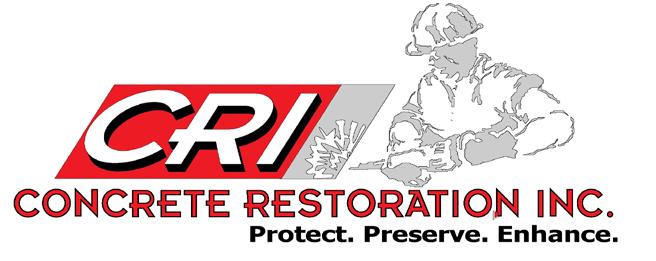
Required Respiratory Protection ≤ 4 hours/sh ift >4 hours/shift
When employees outside of the cab are engaged in the task, apply water and/or dust suppressants as necessary to minimize dust emissions.
None None
Apply water and/or dust suppressants as necessary to minimize dust emissions.
REVISED DATE: January 1, 2025
None None
RESPIRABLE CRYSTALLINE
SILCA POLICY
MARK BOX WITH X TASK OR EQUIPM ENT
Engineering and Work Practice Control Methods
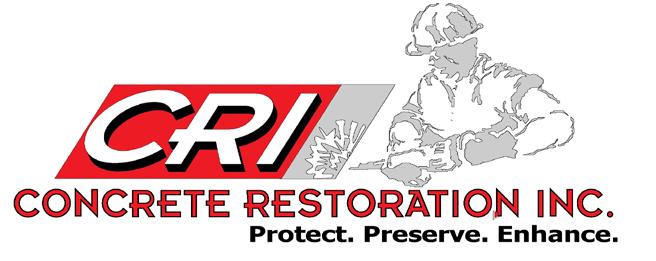
Required Respiratory Protection ≤ 4 hours/sh ift >4 hours/shift including demolishing, abrading, or fracturing silicacontaining materials
Heavy equipment and utility vehicles for tasks such as grading and excavating but not including demolishing, abrading, or fracturing silicacontaining materials
OTHER
When the equipment operator is the only employee engaged in the task, operate equipment from within an enclosed cab.
None
None
Respiratory Protection
Where respiratory protection is required by this program, CRI will provide each employee an appropriate respirator that complies with the
REVISED DATE: January 1, 2025
RESPIRABLE CRYSTALLINE SILCA
POLICY
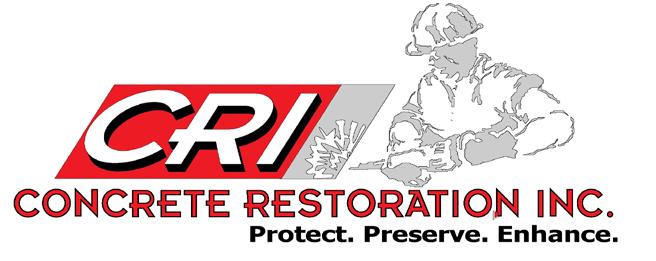
requirements of the company’s Respiratory Protection Program and the WAC Chapter 296-842 Standard
Respiratory protection is required where specified by the OSHA Construction Standard Table 1, for tasks not listed in Table 1, or where the company has not fully and properly implemented the engineering controls, work practices, and respiratory protection described in Table 1. Situations requiring respiratory protection include:
• Where exposures exceed the PEL during periods necessary to install or implement feasible engineering and work practice controls;
• Where exposures exceed the PEL during tasks, such as certain maintenance and repair tasks, for which engineering and work practice controls are not feasible; and
• During tasks for which an employer has implemented all feasible engineering and work practice controls and such controls are not sufficient to reduce exposures to or below the PEL.
Housekeeping
CRI does not allow dry sweeping or dry brushing where such activity could contribute to employee exposure to Respirable Crystalline Silica.
CRI does not allow compressed air to be used to clean clothing or surfaces where such activity could contribute to employee exposure to Respirable Crystalline Silica unless:
• The compressed air is used in conjunction with a ventilation system that effectively captures the dust cloud created by the compressed air; or
• No alternative method is feasible.
Written Exposure Control Plan
REVISED DATE: January 1, 2025
RESPIRABLE CRYSTALLINE SILCA POLICY
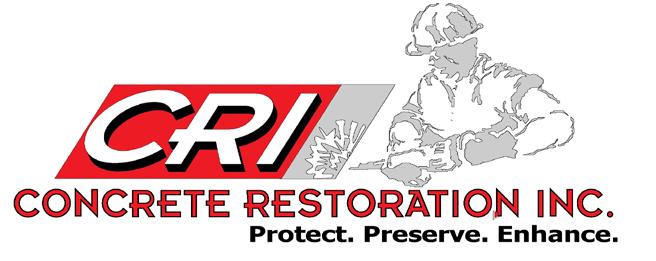
When employee exposure on a construction project is expected to be at or above the Action Level, a Written Exposure Control Plan (ECP) will be established and implemented. This ECP will contain at least the following elements:
• A description of the tasks in the workplace that involve exposure to Respirable Crystalline Silica;
• A description of the engineering controls, work practices, and respiratory protection used to limit employee exposure to Respirable Crystalline Silica for each task;
• A description of the housekeeping measures used to limit employee exposure to Respirable Crystalline Silica; and
• A description of the procedures used to restrict access to work areas, when necessary, to minimize the number of employees exposed to Respirable Crystalline Silica and their level of exposure, including exposures generated by other employers or sole proprietors.
The written ECP will designate a Competent Person to make frequent and regular inspections of job sites, materials, and equipment to ensure the ECP is implemented.
The written ECP will be reviewed at least annually to evaluate the effectiveness of it and update it as necessary. Having said this, ECP’s are project specific and most project durations do not exceed a year. The written ECP will be readily available for examination and copying, upon request, to each employee covered by this program and/or ECP, their designated representatives, and OSHA.
Medical Surveillance
Medical surveillance will be made available for each employee who will be required to use a respirator for 30 or more days per year due to their Respirable Crystalline Silica exposure. Medical surveillance (i.e. medical examinations and procedures) will be performed by a PLHCP and provided at no cost to the employee at a reasonable time and place.
REVISED DATE: January 1, 2025
RESPIRABLE CRYSTALLINE SILCA POLICY
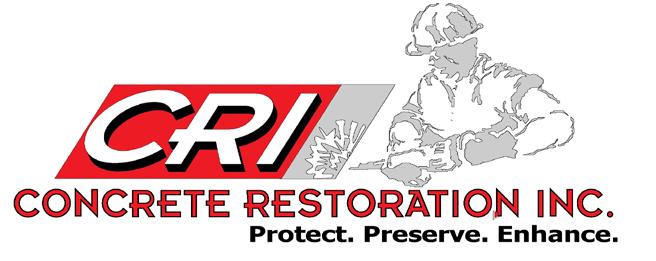
CRI will make available an initial (baseline) medical examination within 30 days after initial assignment, unless the employee has received a medical examination that meets the requirements of the WAC Chapter 296-842 Standard within the last three years. The examination shall consist of:
• A medical and work history, with emphasis on past, present, and anticipated exposure to Respirable Crystalline Silica, dust, and other agents affecting the respiratory system in addition to any history of respiratory system dysfunction, including signs and symptoms of respiratory disease (e.g., shortness of breath, cough, wheezing), history of tuberculosis, and smoking status and history;
• A physical examination with special emphasis on the respiratory system;
• A chest X-ray (a single postero-anterior radiographic projection or radiograph of the chest at full inspiration recorded on either film [no less than 14 x 17 inches and no more than 16 x 17 inches] or digital radiography systems) interpreted and classified according to the International Labour Office (ILO) International Classification of Radiographs of Pneumoconiosis by a NIOSH-certified B Reader;
• A pulmonary function test to include forced vital capacity (FVC) and forced expiratory volume in one second (FEV1) and FEV1/FVC ratio, administered by a spirometry technician with a current certificate from a NIOSH-approved spirometry course;
• Testing for latent tuberculosis infection; and
• Any other tests deemed appropriate by the PLHCP.
CRI will make available medical examinations that include the aforementioned procedures (except testing for latent tuberculosis infection) at least every three years. If recommended by the PLHCP, periodic examinations can be more frequently than every three years.
REVISED DATE: January 1, 2025
RESPIRABLE CRYSTALLINE SILCA POLICY
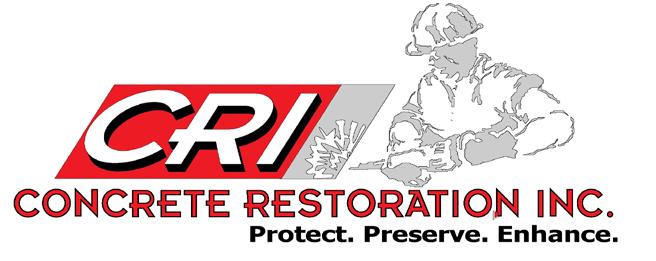
CRI will ensure that the examining PLHCP has a copy of the WAC Chapter 296-842 Standard, this program, and the following information:
• A description of the employee's former, current, and anticipated duties as they relate to the employee's occupational exposure to Respirable Crystalline Silica;
• The employee's former, current, and anticipated levels of occupational exposure to Respirable Crystalline Silica;
• A description of any personal protective equipment (PPE) used or to be used by the employee, including when and for how long the employee has used or will use that equipment; and
• Information from records of employment-related medical examinations previously provided to the employee and currently within the control of CRI.
CRI will ensure that the PLHCP explains to the employee the results of the medical examination and provides each employee with a written medical report within 30 days of each medical examination performed. The written report shall contain:
• A statement indicating the results of the medical examination, including any medical condition(s) that would place the employee at increased risk of material impairment to health from exposure to Respirable Crystalline Silica and any medical conditions that require further evaluation or treatment;
• Any recommended limitations on the employee's use of respirators;
• Any recommended limitations on the employee's exposure to Respirable Crystalline Silica; and;
• A statement that the employee should be examined by a Specialist if the chest X-ray is classified as 1/0 or higher by the B Reader, or if
REVISED DATE: January 1, 2025
RESPIRABLE CRYSTALLINE
SILCA POLICY
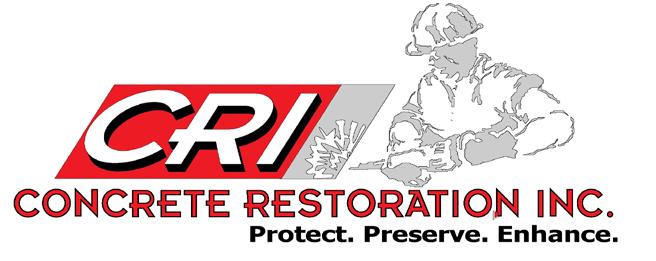
referral to a Specialist is otherwise deemed appropriate by the PLHCP.
CRI will also obtain a written medical opinion from the PLHCP within 30 days of the medical examination. The written opinion shall contain only the following in order to protect the employee’s privacy:
• The date of the examination;
• A statement that the examination has met the requirements of the OSHA Respirable Crystalline Silica Construction Standard; and
• Any recommended limitations on the employee's use of respirators.
If the employee provides written authorization, the written opinion shall also contain either or both of the following:
• Any recommended limitations on the employee's exposure to Respirable Crystalline Silica; and/or
• A statement that the employee should be examined by a Specialist if the chest X-ray is classified as 1/0 or higher by the B Reader, or if referral to a Specialist is otherwise deemed appropriate by the PLHCP.
If the PLHCP's written medical opinion indicates that an employee should be examined by a Specialist, CRI will make available a medical examination by a Specialist within 30 days after receiving the PLHCP's written opinion. CRI will ensure that the examining Specialist is provided with all of the information that the employer is obligated to provide to the PLHCP.
CRI will ensure that the Specialist explains to the employee the results of the medical examination and provides each employee with a written medical report within 30 days of the examination. The written report will contain:
REVISED DATE: January 1, 2025
RESPIRABLE CRYSTALLINE SILCA
POLICY
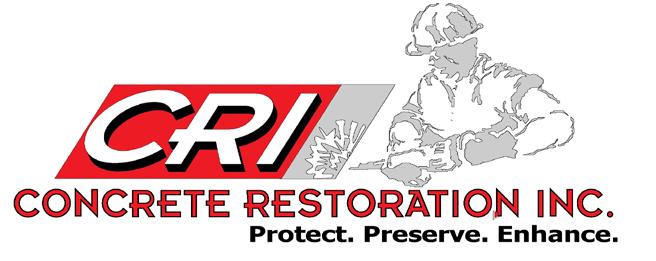
• A statement indicating the results of the medical examination, including any medical condition(s) that would place the employee at increased risk of material impairment to health from exposure to Respirable Crystalline Silica and any medical conditions that require further evaluation or treatment;
• Any recommended limitations on the employee's use of respirators; and
• Any recommended limitations on the employee's exposure to respirable crystalline Silica.
In addition, CRI will obtain a written opinion from the Specialist within 30 days of the medical examination. The written opinion shall contain the following:
• The date of the examination;
• Any recommended limitations on the employee's use of respirators; and
• If the employee provides written authorization, the written opinion shall also contain any recommended limitations on the employee's exposure to Respirable Crystalline Silica.
Hazard Communication
CRI will include Respirable Crystalline Silica in the company’s Hazard Communication Program established to comply with the OSHA Hazard Communication Standard (29 CFR 1910.1200).
CRI will ensure that each employee has access to labels on containers of Crystalline Silica and those containers respective Safety Data Sheets (SDS’s).
All employees will be trained in accordance with the provisions of the OSHA Hazard Communication Standard and the Training Section of this
REVISED DATE: January 1, 2025
RESPIRABLE CRYSTALLINE SILCA
POLICY
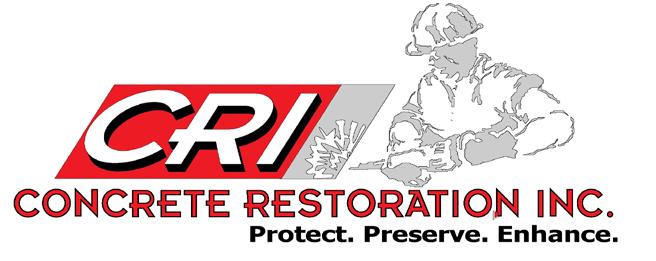
program. This training will cover concerns relating to cancer, lung effects, immune system effects, and kidney effects.
CRI will ensure that each employee with the potential to be exposed at or above the Action Level for Respirable Crystalline Silica can demonstrate knowledge and understanding of at least the following:
• The health hazards associated with exposure to Respirable Crystalline Silica;
• Specific tasks in the workplace that could result in exposure to Respirable Crystalline Silica;
• Specific measures CRI has implemented to protect employees from exposure to Respirable Crystalline Silica, including engineering controls, work practices, and respirators to be used;
• The contents of the WAC Chapter 296-842 Silica Construction Standard;
• The identity of the Competent Person designated by CRI; and
• The purpose and a description of the company’s Medical Surveillance Program.
CRI will make a copy of the OSHA Respirable Crystalline Silica Construction Standard readily available without cost to any employee who requests it.
Recordkeeping
CRI will make and maintain an accurate record of all exposure measurements taken to assess employee exposure to Respirable Crystalline Silica. This record will include at least the following information:
• The date of measurement for each sample taken;
• The task monitored;
REVISED DATE: January 1, 2025
RESPIRABLE CRYSTALLINE SILCA POLICY
• Sampling and analytical methods used;
• Number, duration, and results of samples taken;
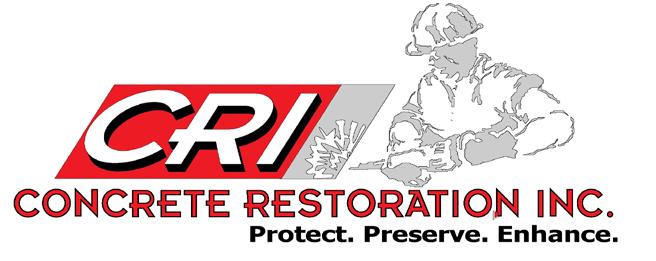
• Identity of the laboratory that performed the analysis;
• Type of personal protective equipment (PPE), such as respirators, worn by the employees monitored; and
• Name, social security number, and job classification of all employees represented by the monitoring, indicating which employees were actually monitored.
CRI will ensure that exposure records are maintained and made available in accordance with 29 CFR 1910.1020. Exposure records will be kept for at least 30 years.
The employer shall make and maintain an accurate record of all objective data relied upon to comply with the requirements of the OSHA Respirable Crystalline Silica Construction Standard. This record shall include at least the following information:
• The Crystalline Silica-containing material in question;
• The source of the objective data;
• The testing protocol and results of testing;
• A description of the process, task, or activity on which the objective data were based; and
• Other data relevant to the process, task, activity, material, or exposures on which the objective data were based.
CRI will ensure that objective data are maintained and made available. Objective data records will be kept for at least 30 years.
REVISED DATE: January 1, 2025
RESPIRABLE CRYSTALLINE SILCA POLICY
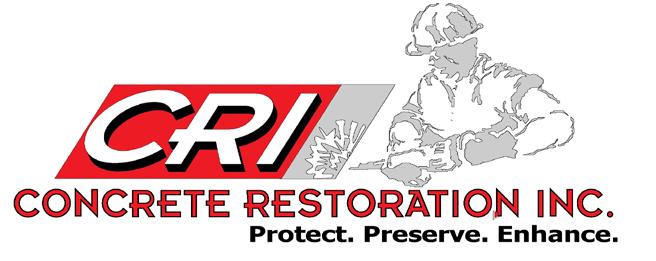
CRI will make and maintain an accurate record for each employee enrolled in the Medical Surveillance portion of this program. The record shall include the following information about the employee:
• Name and social security number;
• A copy of the PLHCPs' and/or Specialists' written medical opinions; and
• A copy of the information provided to the PLHCPs and Specialists.
Medical records will be kept under lock and key for at least the duration of employment plus 30 years. It is necessary to keep these records for extended periods because Silica-related diseases such as cancer often cannot be detected until several decades after exposure. However, if an employee works for an employer for less than one year, the employer does not have to keep the medical records after employment ends, as long as the employer gives those records to the employee.
PROGRAM EVALUATION
This program will be reviewed and evaluated on an annual basis by the Safety Manager unless changes to operations, the WAC Chapter 296-842 Standard or another applicable OSHA Standard require an immediate revalidation of this program.
Employee Information and Training
Employees can do much to protect themselves from the risks of occupational silica exposure if they know about them. In our training program we inform employees of the specific hazards associated with their work environment, protective measures that can be taken, and their rights under the standard. All affected employees will be trained prior to first assignment and annual thereafter. The entire contents of this plan shall be covered in the training program.
All affected employees are required to attend training programs. The training will be provided prior to the time of initial job assignment. Training
REVISED DATE: January 1, 2025
RESPIRABLE CRYSTALLINE SILCA
POLICY
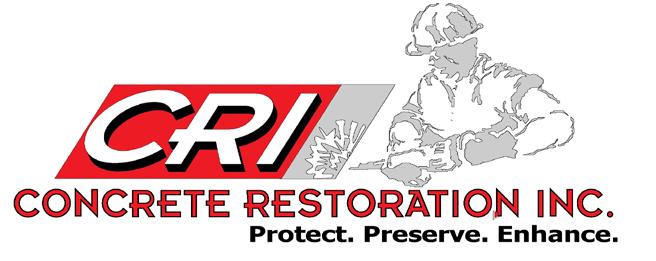
should be provided at least annually and refresher training as needed. During training the employees are informed on specific task and operations that could result in exposure to silica above the action level. Employees are informed of the purpose, proper selection, fitting, use, and limitation of respirators. Employees are informed on engineering controls put in place to reduce silica exposure. Training also covers information on the purpose for, and a description of, the medical surveillance & medical removal programs and how silica can cause adverse effects on respiratory systems.
REVISED DATE: January 1, 2025
RESPIRATORY PROTECTION POLICY
RESPIRATORY PROTECTION POLICY
Reference: OSHA 1910.134/WAC 296-842
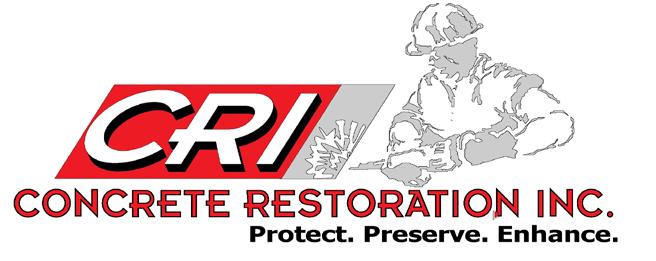
How to Evaluate your Workplace for Employee Exposure to Chemicals
Respirators are required when employees are exposed (can inhale) chemicals or dust in the air that are at harmful levels. These can include vapors from handling solvents, spray-painting, dust from grinding or sanding, or welding fumes. If you manage a small business, you are probably quite familiar with each employee’s job, what chemicals they use or how much welding, spray painting, grinding or sanding they do. Your employees may have told you that the chemical odors or dust bothered them or that they were worried about their chemical exposure. You may have switched to less hazardous chemicals. Or you may have no alternative but to use more hazardous chemicals to do the job or make your product. But without some knowledge of the amount of chemical or dust in the air in the workplace, you cannot know whether your employees are exposed to harmful amounts of chemicals they use.
Just about every chemical has its toxic amount or level that will make person sick. Even too much table salt can be harmful. On the other hand, highly toxic chemicals can be used without harm to employees if handled properly. Most commonly used chemicals have safe limits or “permissible exposure limits” in the air that if exceeded will cause harm.
If these limits are exceeded, you are required to take steps to protect your employees from that air exposure. If the levels cannot be reduced below the permissible exposure limits by ventilation, changes in the process or reduction in the length of time of exposure, then you must provide respirators to exposed employees.
The best way to accurately determine the levels of chemicals or dust in the air is to do some type of air sampling. There are a variety of instruments and devices for measuring air contaminants. Some are simple and inexpensive, most are quite expensive. The methods for doing the air
REVISED DATE: January 1, 2025
RESPIRATORY PROTECTION POLICY
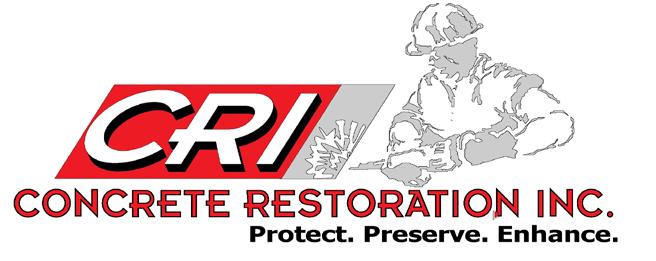
sampling accurately are usually fairly complicated and should not be done by a layperson. Air sampling can be done by WISHA industrial hygiene consultants at your request. This is a free service and will not result in a citation or penalty or a report to WISHA safety inspectors. To request this service, contact the nearest Department of Labor & Industries Office near you
You can also have a private industrial hygiene consultant conduct air sampling. They can be found under “industrial hygiene services” in the Yellow Pages.
If you belong to a trade association or industry group, that organization may have information on common chemical hazards and methods of controls. The safety data sheets for products used also provide information about the hazards of the chemicals, permissible exposure limits, methods of controls and recommended respirators.
Our respirator program administrator is Tim Coots
Our administrator’s duties are to oversee the development of the respiratory program and, make sure it is carried out at the workplace. The administrator will also evaluate the program regularly to make sure procedures are followed, respirator use is monitored and respirators continue to provide adequate protection when job conditions change.
Selection of Respirators
The Safety Department, with the help of supervisors, will identify the proper respirator for specific jobs based on the hazards workers face. Respirators will be used against harmful vapors. Respirators will be provided to affected employees at no additional cost to the employee.
Medical Evaluations
Every employee of this company who must wear a respirator will be provided with a medical evaluation before they are allowed to use the respirator. Our first step is to give the attached medical questionnaire to
REVISED DATE: January 1, 2025
RESPIRATORY PROTECTION POLICY
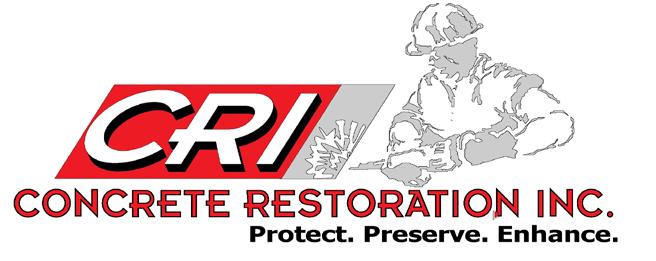
those employees. Employees are required to fill out the questionnaire in private and send or give them to Concentra Urgent Care, 3223 1st Ave S Seattle, WA (206) 624-3651. Completed questionnaires are confidential and will be sent directly to the medical provider without review by management.
If the medical questionnaire indicates to our medical provider that a further medical exam is required, this will be provided at no cost to our employees by Concentra Urgent Care , 3223 1st Ave S. Seattle, WA (206) 624-3651. We will get a recommendation from this medical provider on whether or not the employee is medically able to wear a respirator.
Respirator Fit-testing
All employees who wear tight -fitting respirators will be fit-tested before using their respirator or given a new one. Fit-testing will be repeated annually. Fit testing will also be done when a different respirator face piece is chosen, when there is a physical change in an employee’s face that would affect fit, or when our employees or medical provider notify us that the fit is unacceptable. No beards are allowed on wearers of tight-fitting respirators. Respirators are chosen for fit-testing following procedures in the WISHA Respirators Rule (Table 11). Fit-testing is not required for loose -fitting, positive pressure (supplied air helmet or hood style) respirators. We do fit-testing using one or more of the following fit-testing protocols or quantitative fit-testing instrument: Fit Test method and Irritant smoke protocol.
The quantitative fit-testing instrument we use is: Irritant smoke protocol
Documentation of our fit-testing results is kept at the following location: Concrete Restoration, Inc. (Main office) 9587 8th Avenue S. Seattle, WA 98108.
Our respirators will be checked for proper sealing by the user whenever the respirator is first put on, using seal check procedures (attached). Click here for seal check procedures.
Respirator storage, cleaning, maintenance
REVISED DATE: January 1, 2025
RESPIRATORY PROTECTION POLICY
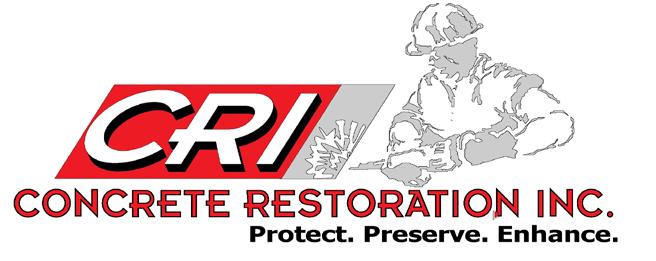
Our respirators will be stored a zip lock bag or sealed container at the end of the work shift and in an area that the respirator will not be squeezed.
Respirators will be cleaned and sanitized every other day using sanitizer pads and will be thoroughly cleaned using water and mild soap weekly or whenever they are visibly dirty. Respirators will be cleaned according to the attached instructions weekly (either the manufacturer’s instructions or the Respirators Rule cleaning procedures.)
All respirators will be inspected before and after every use and during cleaning. In addition, emergency respirators and self-contained tank-type supplied air respirators in storage will be inspected monthly.
Respirators will be inspected for damage, deterioration or improper functioning and repaired or replaced as needed. We don’t do respirator repairs.
Respirator Use
The Program Administrator will monitor the work area in order to be aware of changing conditions where employees are using respirators.
Employees will not be allowed to wear respirators with tight-fitting facepieces if they have facial hair (e.g., stubble, bangs) absence of normally worn dentures, facial deformities (e.g., scars, deep skin creases, prominent cheekbones), or other facial features that interfere with the facepiece seal or valve function. Jewelry or headgear that projects under the facepiece seal is also not allowed.
If corrective glasses or other personal protective equipment is worn, it will not interfere with the seal of the facepiece to the face. A seal check will be performed every time a tight-fitting respirator is put on. The program administrator will make sure that the NIOSH labels and color-coding on respirator filters and cartridges remain readable and intact during use.
Employees will leave the area where respirators are required for any of the following reasons:
o to replace filters or cartridges,
REVISED DATE: January 1, 2025
RESPIRATORY PROTECTION POLICY
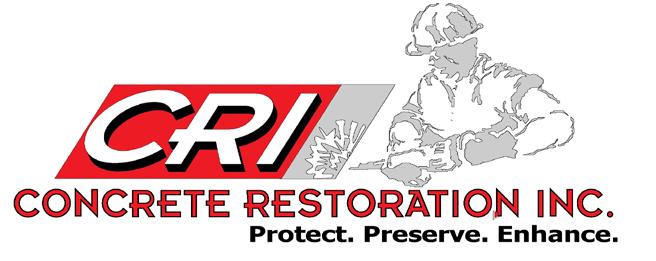
o when they smell or taste a chemical inside the respirator,
o when they notice a change in breathing resistance
o to adjust their respirator,
o to wash their faces or respirator,
o if they become ill,
o if they experience dizziness, nausea, weakness, breathing difficulty, coughing, sneezing vomiting, fever or chills.
Respirator Training
Training is done by Tim Coots before employees wear their respirators and annually thereafter as long as they wear respirators. Our supervisors or foreman who wear respirators or supervise employees who do will also be trained on the same schedule.
Additional training will also be done when an employee uses a different type of respirator or workplace conditions affecting respiratory hazards or respirator use have changed. Training will cover the following topics:
o Why the respirator is necessary,
o The respirator’s capabilities and limitations,
o How improper fit, use or maintenance can make the respirator ineffective,
o How to properly inspect, put on, seal check, use, and remove the respirator,
o How to clean, repair and store the respirator or get it done by someone else,
o How to use a respirator in an emergency situation or when it fails,
o Medical symptoms that may limit or prevent respirator use,
o Our obligations under the Respirators Rule.
Respiratory Program Evaluation
We evaluate our respiratory program for effectiveness by doing the following steps:
1. Checking results of fit-test results and health provider evaluations.
REVISED DATE: January 1, 2025
RESPIRATORY PROTECTION
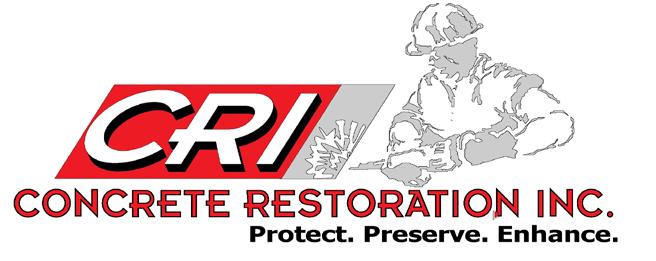
2. Talking with employees who wear respirators about their respirators –how they fit, do they feel they are adequately protecting them, do they notice any difficulties in breathing while wearing them, do they notice any odors while wearing them, etc.
3. Periodically checking employee job duties for changes in chemical exposure.
4. Periodically checking maintenance and storage of respirators.
5. Periodically checking how employees use their respirators.
6. Other
Recordkeeping
The following records will be kept:
o A copy of this completed respirator program
o Employees’ latest fit-testing results
o Employee training records
o Written recommendations from our medical provider
o The records will be kept at the following location: CRI Main Office & onsite job trailer.
o Employees will have access to these records.
PLEASE SEE FOLLOWING PAGES FOR RESPIRATOR FIT TEST AND RESPIRATOR TRAINING SAMPLES
REVISED DATE: January 1, 2025
RESPIRATORY PROTECTION
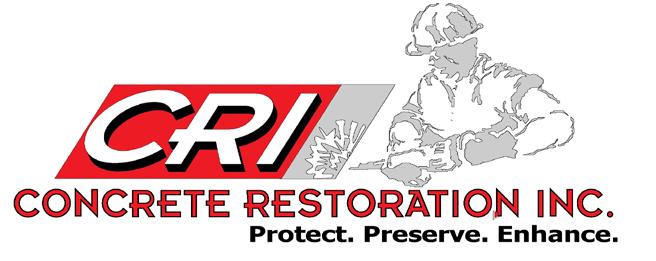
Respirator Fit Test Record Sample
Name: Initials:
Type of qualitative/quantitative fit test used:
Name of test operator: Initials:
Date:
Respirator Mfr./Model/Aproval no.
Size Pass/Fail or Fit Factor
Note: “Fit factor” is numerical result of quantitative fit test from instrument reading
Clean Shaven? Yes No (Fit-test cannot be done unless clean-shaven)
Medical Evaluation Completed? Yes____ No
NOTES:
REVISED DATE: January 1, 2025
RESPIRATORY PROTECTION POLICY
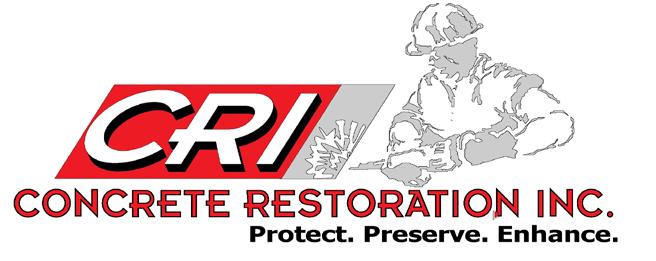
This record indicates that you have passed or failed a qualitative or quantitative fit test as shown above for the particular respirator(s) shown. Other types will not be used until fit tested.
Respirator Training Record Sample
Employee Name (printed)
I certify that I have been trained in the use of the following respirator(s):
This training included the inspection procedures, fitting, maintenance and limitations of the above respirator(s). I understand how the respirator operates and provides protection. I further certify that I have heard the explanation of the respirator(s) as described above and I understand the instructions relevant to use, cleaning, disinfecting and the limitations of the respirator(s).
Employee Signature
Instructor Signature
Date
REVISED DATE: January 1, 2025
RESPIRATORY PROTECTION
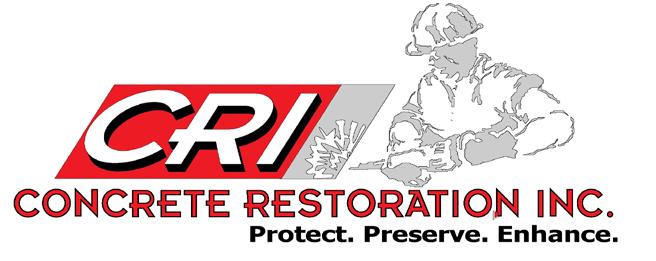
Respirator Cleaning Procedures (from Respirators Rule)
1. Remove filters, cartridges, canisters, speaking diaphragms, demand and pressure valve assemblies, hoses, or any components recommended by the manufacturer. Discard or repair any defective parts.
2. Wash components in warm (43°C [110°F] maximum) water with a mild detergent or with a cleaner recommended by the manufacturer.
• A stiff bristle (not wire) brush may be used to help remove the dirt.
• If the detergent or cleaner doesn't contain a disinfecting agent, respirator components should be immersed for 2 minutes in one of the following:
o A bleach solution (concentration of 50 parts per million of chlorine). Make this by adding approximately one milliliter of laundry bleach to one liter of water at 43°C (110°F)
o A solution of iodine (50 parts per million iodine). Make this in 2 steps:
o First, make a tincture of iodine by adding 6-8 grams of solid ammonium iodide and/or potassium iodide to 100 cc of 45% alcohol approximately.
o Second, add 0.8 milliliters of the tincture to one liter of water at 43°C (110°F) to get the final solution.
• Other commercially available cleansers of equivalent disinfectant quality when used as directed, if their use is recommended or approved by the respirator manufacturer
3. Rinse components thoroughly in clean, warm (43°C [110°F] maximum), preferably, running water.
REVISED DATE: January 1, 2025
RESPIRATORY PROTECTION
POLICY
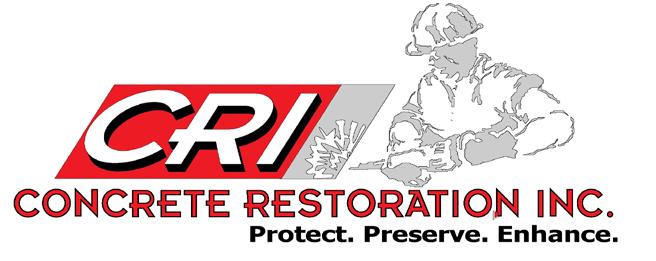
Note:
The importance of thorough rinsing can't be overemphasized. Detergents or disinfectants that dry on facepieces could cause dermatitis. In addition, some disinfectants may cause deterioration of rubber or corrosion of metal parts, if not completely removed.
4. Drain components.
5. Air-dry components or hand dry components with a clean, lint-free cloth.
6. Reassemble the facepiece components and replace filters, cartridges, and canisters if necessary.
7. Test the respirator to make sure all components work properly
Seal Check Procedures (from Respirators Rule)
Important Information for Employees:
You need to conduct a seal check each time you put your respirator on before you enter the respirator use area. The purpose of a seal check is to make sure your respirator (which has been previously fit tested by your employer) is properly positioned on your face to prevent leakage during use and to detect functional problems.
The procedure below has 2 parts; a positive pressure check and a negative pressure check. You must complete both parts each time. It should only take a few seconds to perform, once you learn it.
If you can't pass both parts, your respirator is not functioning properly, see your supervisor for further instructions.
REVISED DATE: January 1, 2025
RESPIRATORY PROTECTION
POLICY
Positive Pressure Check:
• Remove exhalation valve cover, if removable.
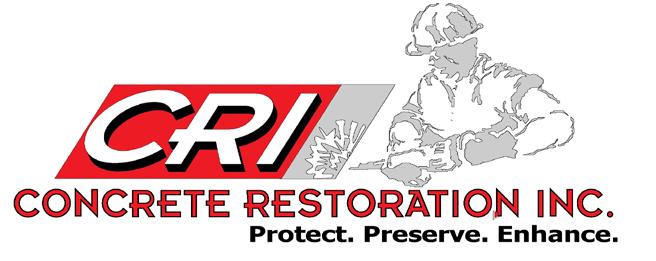
• Cover the exhalation valve completely with the palm of your hand while exhaling gently to inflate the facepiece slightly.
• The respirator facepiece should remain inflated (indicating a build-up of positive pressure and no outward leakage).
• If you detect no leakage, replace the exhalation valve cover (if removed), and proceed to conduct the negative pressure check.
• If you detect evidence of leakage, reposition the respirator (after removing and inspecting it), and try the positive pressure check again.
Negative Pressure Check:
• Completely cover the inhalation opening(s) on the cartridges or canister with the palm(s) of your hands while inhaling gently to collapse the facepiece slightly.
• If you can't use the palm(s) of your hands to effectively cover the inhalation openings on cartridges or canisters, you may use:
Filter seal(s) (if available) or
Thin rubber gloves
• Once the facepiece is collapsed, hold your breath for 10 seconds while keeping the inhalation openings covered.
• The facepiece should remain slightly collapsed (indicating negative pressure and no inward leakage).
REVISED DATE: January 1, 2025
RESPIRATORY PROTECTION
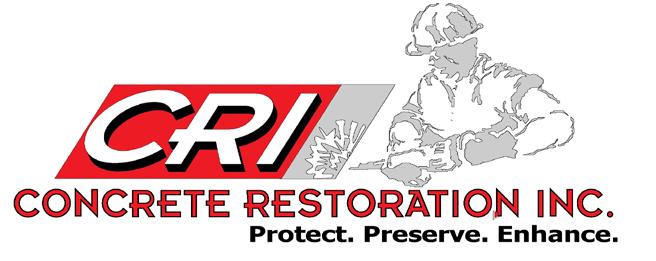
How to Select the Correct Respirator
The type and brands of respirators vary widely ranging from simple dust masks to supplied air respirators like the kind firemen wear. Following is description of the main types of respirators.
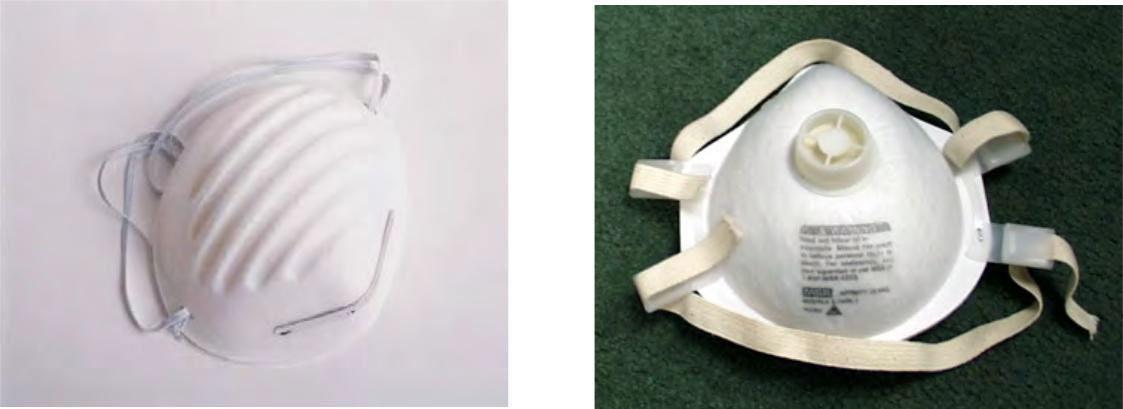
Dust Masks (filtering facepieces)
These simple, two-strap disposable dust masks are designed only for dusts. They are not as protective as other respirators, but do an adequate job in many cases, unless the dust is really toxic or copious. Don’t confuse these two-strap masks with the less protective one-strap dust mask designed only for pollen or non-toxic dust.
REVISED DATE: January 1, 2025
RESPIRATORY PROTECTION
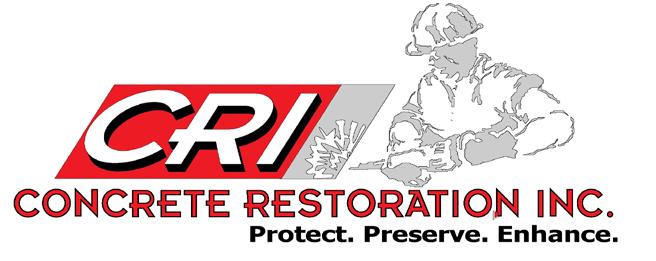
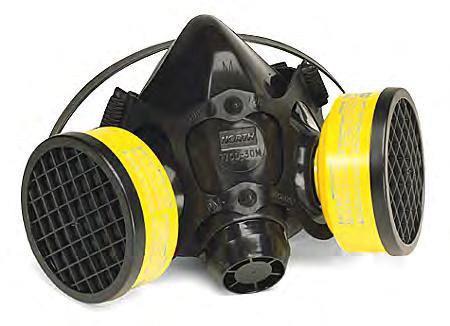
Half-Face Air-Purifying Respirator
These respirators are sometimes called “half-face” or “half-mask” respirators since they cover just the nose and mouth. They have removable cartridges that filter out either dust, chemicals or both. Selecting the correct cartridges is essential since they are designed for particular types of chemicals or dust. A reputable respirator vendor can assist you in selecting the correct cartridges.
These cartridges are typically removable and sometimes interchangeable. Cartridges are available for solvents, ammonia, chlorine, acids and other chemicals. The cartridges must be changed out or replaced periodically, especially for chemicals, since they can absorb only so much contaminant before breakthrough occurs. A few cartridges are equipped with end-ofservice indicators that show when a cartridge should be replaced. Most cartridges don’t have this indicator and you must develop a change-out schedule to prevent breakthrough. The change -out schedule is based on the chemical concentration, physical work effort, temperature and humidity. Many respirator manufacturers have cartridge change schedule calculators available on the Internet.
REVISED DATE: January 1, 2025
RESPIRATORY PROTECTION

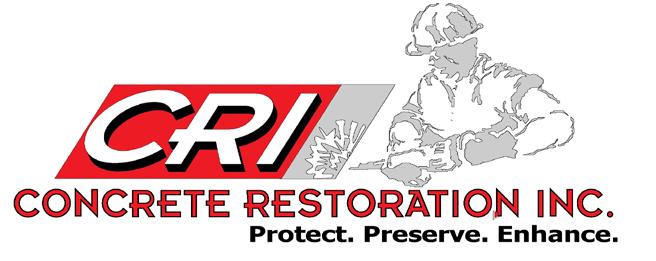
Full-Face Air-Purifying Respirator
In some situations, you may need or want to use full-face respirators. This type of respirator is used when the air contaminant irritates the eyes. They also provide somewhat higher protection to the lungs since they tend to fit tighter and are less prone to leaking. These respirators also have replaceable cartridges that must be changed on a regular basis as described above for half-face respirators.
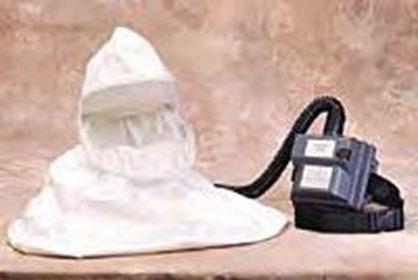
Powered Air Purifying Respirator (PAPR)
Powered Air Purifying Respirators have a battery pack that draws air through replaceable cartridges and blows into a full facepiece, helmet or
REVISED DATE: January 1, 2025
RESPIRATORY PROTECTION POLICY
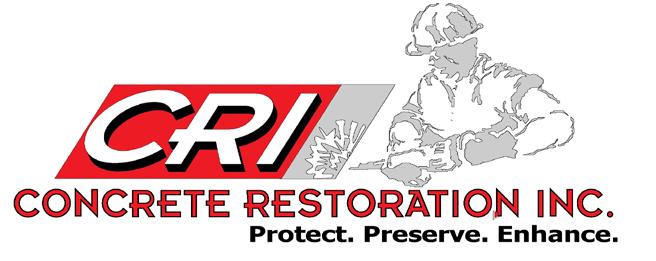
hood. These respirators are often more comfortable in hot weather and some can provide more protection, depending on the type. The cartridges must be changed regularily as describe for half-face respirators above.
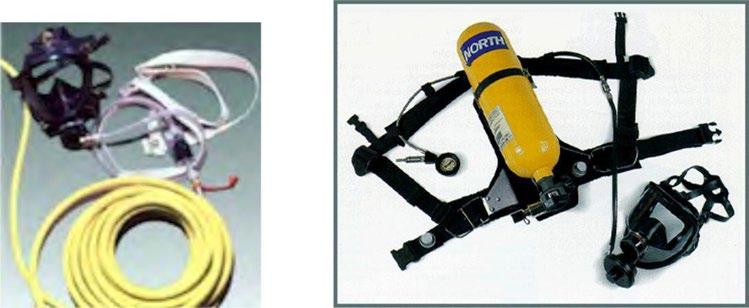
Supplied Air Respirators and Self-Contained Breathing Apparatus (SCBA)
In a few situations, you may need to provide a supplied air respirator to your employees. These situations include large chemical spills or leaks, entering a confined space where there is lack of oxygen or high levels of air contaminants, or working around extremely toxic chemicals. They may also be necessary working at hazardous waste sites, during sandblasting or in some spray-painting operations. “Supplied air,” means that clean air is provided by means of an air hose from a compressor or a pressurized air tank.
Supplied air respirators are required when a respiratory hazard is considered “immediately dangerous to life or health” (also called “IDLH”). Respiratory hazards are classified as IDLH as follows:
• There is a lack of oxygen (less than 19.5% oxygen)
• There is too much oxygen (more than 23.5% - a fire hazard)
• You know there are toxic chemicals in the air, but you don’t know how much
REVISED DATE: January 1, 2025
RESPIRATORY PROTECTION POLICY
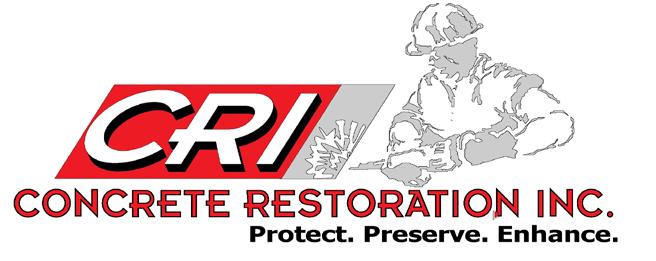
• The amount of chemical in the air is known or expected to be above the IDLH level for that chemical. See the NIOSH Pocket Guide to Chemical Hazards for chemical IDLH levels.
Levels of chemicals above IDLH can occur in confined spaces, or enclosed spaces where there is little or no ventilation.
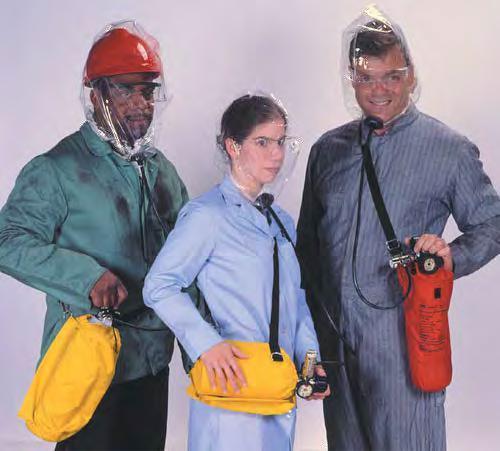
Emergency Escape Respirators
Emergency escape respirators, as the name implies, can only be used for one thing – to escape or exit from a room or building in an emergency, usually a large chemical release, leak or spill, or when a supplied air respirator fails or runs out of air. An escape respirator is typically a small bottle or tank of air connected to a facepiece that supplies 5-10 minutes of air. Some supplied air respirators will have an auxiliary bottle of air for escape that connects to the existing facepiece.
How do you decide which type of respirator to select? First, it must be the correct type for the air contaminant. Second, it must fit properly. Third, it must provide adequate protection for the amount of chemical in the air. The more toxic or more concentrated the chemical is in the air, the higher the level of protection the respirator must provide.
Different respirators provide different protection. Depending on the amount of chemical in the air, you may need to use a respirator that provides more protection. Respirators are rated by their “assigned protection factor” (APF)
REVISED DATE: January 1, 2025
RESPIRATORY PROTECTION POLICY
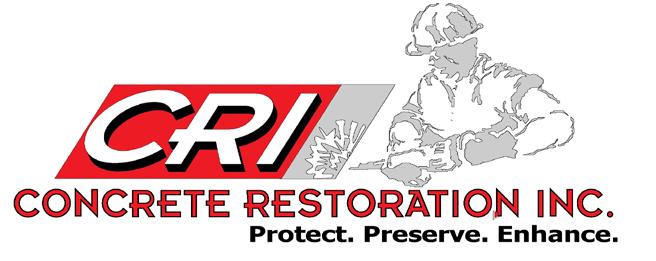
which is a number between 10 and 10,000. The higher the number, the greater the protection. A respirator with a protection factor of 10 will provide adequate protection to levels of the chemical in the air 10 times the safe limit of that chemical.
Type of Respirator and Cartridges for Concrete Restoration Inc Employees
CRI employees are permitted and fit tested annually for the North 7700 Half Mask
o Full masks can be purchased at the employee’s expense.
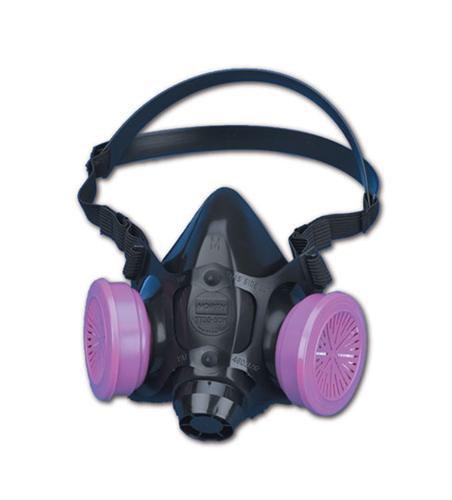
Cartridge Use
There are three main types of cartridges for the North 7700 half mask:
REVISED DATE: January 1, 2025
RESPIRATORY PROTECTION
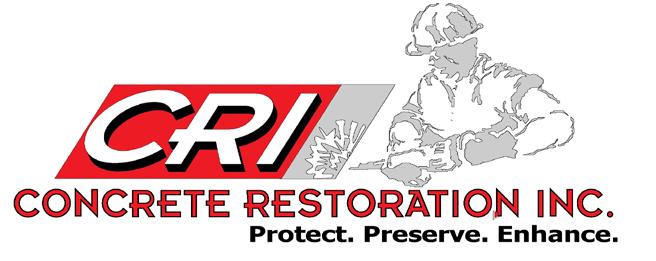
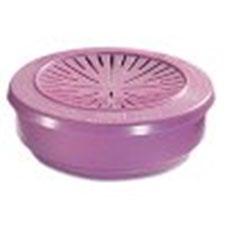
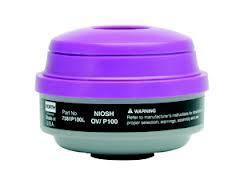
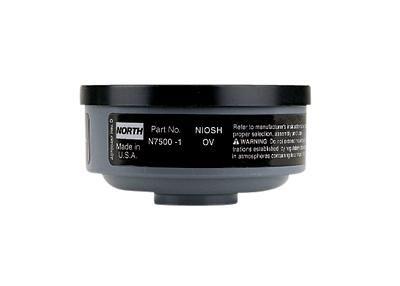
REVISED DATE: January 1, 2025
P100 Dust – Meant for airborne dust particles
P100 Dual – Meant for airborne dust particles and organic vapors
N7500 – Meant for organic vapors
RETURN TO WORK POLICY
RETURN TO WORK POLICY
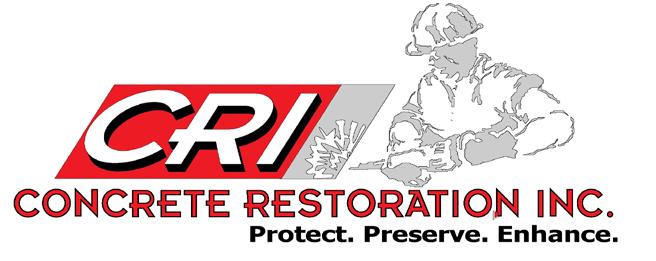
Concrete Restoration, Inc. values the safety, health, and wellbeing of all employees. Our company policy is to provide safe and healthful working conditions in all operations and to follow all safety and health laws and regulations.
It is important that employees injured in the course of employment return to work with our company as early as it is medically safe to do so. For on-thejob injuries, we will stay in contact with employees and their medical provider to stay current on medical recovery progress. Employees will report any job-related injury or illness to their supervisor and seek medical care immediately.
Our company will create light duty assignments for employees who are unable to return to their normal duties while recovering from an on-the-job injury. We will solicit input from employees about their physical ability to perform a job. We will also provide the attending doctor with information about work the employee is to perform and obtain the attending doctor’s approval for the employee’s ability to perform any work offered by the company.
Employees will be expected to always follow the advice of their attending doctor. Any problems with an employee’s physical ability to perform a job assignment should be reported to the supervisor immediately and the difficulties should also be reported to the attending doctor as soon as possible to address the possibility of modifications to the work assignment.
It is the company’s policy to strive for safe performance of job assignments within the company. We actively ask for suggestions from employees and encourage reporting of near miss safety concerns.
It is the company policy to provide a safe work environment and create a safety culture- no job is so important that it cannot be done safely.
Shannon Ware, President
REVISED DATE: January 1, 2025
Rigging Policy
Rigging Policy
Reference: OSHA 1926.251/WAC 296-155-55600
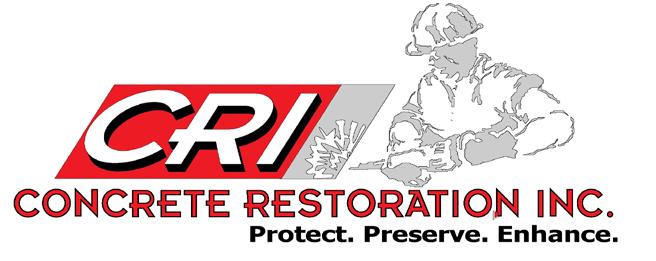
Properly rated rigging is essential for moving materials and equipment to keep the load safe and under control at all times.
When on the jobsite, the rigging of the loads is the responsibility of the customer unless other arrangements have been made.
Rigging Responsibilities
• Employees shall familiarize themselves with the proper methods for hooking and slinging required to make a safe lift.
• Only qualified riggers and signal persons shall direct lifting or craning operations, using hand, voice, or audible signals established by the industry.
• Only one person in the rigging crew shall direct the operator with the standard signals. If more than one person is directing the operator with hand signals, the operator shall cease all craning operations until it is determined which one person in the rigging crew is responsible for directing the craning operation.
• Operators and employees assigned to the rigging crews shall have a full understanding of the proper procedures used to determine the weight. Concrete Restoration, Inc. employees will use these procedures prior to making any lifts.
Rigging Guidelines
Rigging shall be inspected for suitability, wear, and damage. This includes all hooks, hoist chains, wire ropes, and nylon slings. This inspection will be documented on our inspection form and includes the date, name of the person doing the inspection, and the ID number of each device. This documentation will be available in the office for review. Rigging shall be
REVISED DATE: January 1, 2025
Rigging Policy
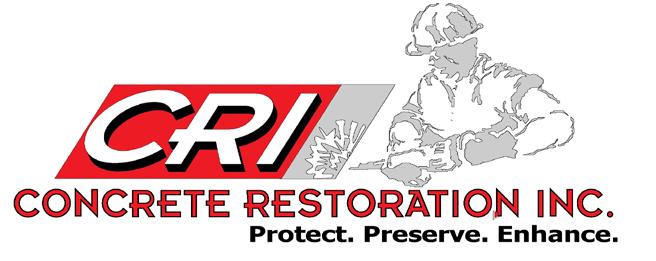
inspected prior to use on each shift, and as necessary during its use to assure that it is safe to use. Defective rigging equipment shall be removed from service.
• Tie down chains shall not be used by Concrete Restoration, Inc. for rigging.
• Wire rope slings used for material handling shall have a safety factor of at least five.
• Wire rope slings shall not be used if they do not meet inspection criteria.
• Shackles must have a safety factor of at least five.
• Hooks shall not be modified by welding or drilling unless written approval by the manufacturer has been received.
• Wire rope slings shall be frequently inspected.
• Protective pads shall be used where cables are wrapped around sharp objects or comers. Corner pads or wood blocks shall be used to prevent cable kinks.
• Slings shall be placed on the load at safe lifting angles.
• Rigging shall not be overloaded. Rated capacities of each lifting device shall be checked. Loads shall be checked just off the ground for balance and stability before hoisting.
• When applying U bolts (Crosby clips) to cables, a sufficient number shall be used (refer to rigging chart) and the U bolt shall press against the dead end of the rope.
REVISED DATE: January 1, 2025
Rigging Policy
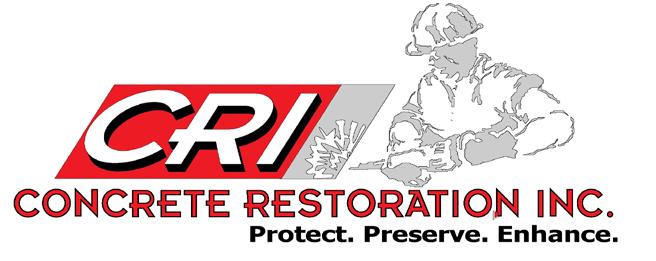
• Complicated rigging and crane picks shall be discussed and planned with the supervisor and all of the parties involved, prior to making the lift.
• Where necessary for rigging or servicing purposes, a ladder or steps shall be provided to give access to a cab roof.
• Tilt-up blocks and rigging should be inspected before and after each job. Frayed or cut wires on any running lines must be replaced immediately. Tilt-up blocks should be cleaned and free of dirt and be greased regularly. Do not rely on others to help you rig the bars correctly. You supervise them, but always check their work.
Sling Practices
This section applies to wire rope slings used in conjunction with other material handling equipment for the movement of material hoisting.
Sling Responsibilities
• Slings that are damaged or defective shall not be used.
• Slings shall not be shortened with knots, bolts, or other makeshift devices.
• Sling legs shall not be kinked.
• Slings shall not be loaded in excess of the rated capacities. They shall have a safety factor of at least five.
• Slings used in a basket hitch shall have the loads balanced to prevent slippage.
• Slings shall be securely attached to their loads.
• Slings shall be padded or protected from the sharp edges of their loads.
DATE: January 1, 2025
Rigging Policy
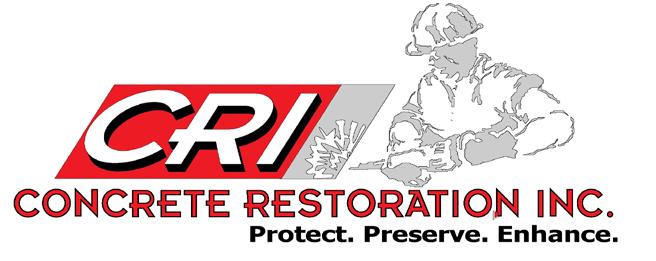
• Running ropes shall be removed from service when they do not meet inspection criteria.
• Standing ropes shall be removed from service when they do not meet inspection criteria.
• Wire rope safety factors shall be as follows:
For supporting rated loads, including boom suspensions:
A. Live and running ropes that wind on drums or pass over sheaves: not less than 3.5.
B. Boom pendants or standing ropes: not less than 3.0.
For supporting the boom and working attachments at recommended travel or transition positions and boom lengths:
A. Live and running lines: not less than 3.5.
B. Boom and pendants and standing lines: not less than 3.0.
For supporting the boom under recommended boom erection conditions:
A. Live and running lines: not less than 3.0.
B. Boom pendants and running lines: not less than 2.5.
• Hand or fingers shall not be placed between the sling and its load while the sling is being tightened around the load.
• Shock loading shall be prohibited.
• A sling shall not be pulled under a load when the load is resting on the sling.
• Cribbing shall always be used when landing a load, if proper footing is unacceptable.
REVISED DATE: January 1, 2025
SAFETY DISCIPLINARY POLICY
SAFETY DISCIPLINARY POLICY
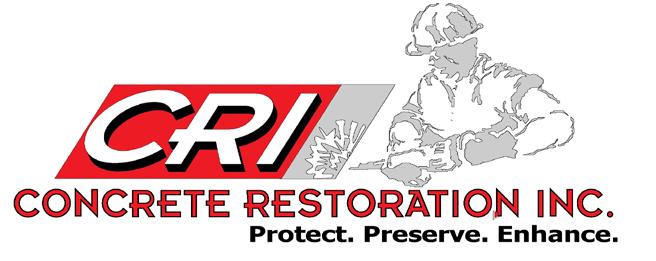
The Safety Department, Management and Foreman are responsible to enforce the disciplinary action program.
The following constitute violations of the policies of Concrete Restoration Inc:
General Rules
All employees have a responsibility to themselves for their own safety. They also have a responsibility to their families, their fellow employees and to their employer, Concrete Restoration Inc, to work safely. The following list contains general rules for safety and is not all inclusive.
• Safety procedures, policies and regulations will be followed.
• Employees will become familiar with and comply with all company safety policies, rules and procedures applicable to their job duties. Compliance with the safety policies and procedures is mandatory and is considered a requirement for employment.
• Before beginning a job, the employee will make sure that the task(s) can be performed without injury. If in doubt for any reason, the employee should call this to the attention of the Foreman.
• No person will be allowed to work until he has satisfied the Foreman that he/she is competent to perform his/her duties in a safe manner.
• Follow Foreman instructions.
• All necessary personal protective equipment must be properly used for the task(s) being performed.
• Horseplay and fighting on the job is very dangerous and will not be tolerated.
REVISED DATE: January 1, 2025
SAFETY DISCIPLINARY POLICY
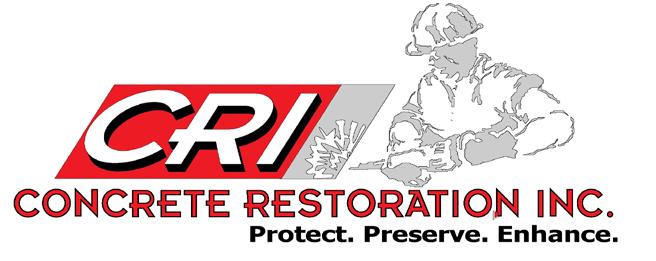
• Possession of firearms, weapons, explosives or stolen property on the job site is prohibited and is subject to disciplinary action and/or immediate dismissal.
• Possession, use of, or under the influence of illegal drugs or alcohol is prohibited and will not be tolerated and is reason for immediate dismissal.
• Employees should observe and obey all caution and danger signs, barricades and warning tags that are placed on equipment, materials, or other areas of the job site.
• Good housekeeping is always necessary in order to prevent accidents. Waste materials will be disposed of properly and will not be allowed to accumulate in work areas.
• Gasoline, kerosene or diesel should not be used for cleaning purposes. Contact the Safety Manager for an approved cleaning solution.
• All accidents and/or injuries, no matter how minor, should be reported immediately to the employee's Foreman.
• Employees will know where to go for first aid and go there for first aid treatment.
• Employees should know where fire extinguishers are located and know how to use them.
• Employees should practice fire prevention on the job by obeying the “No Smoking” signs, keeping their work areas free from trash and being aware of the potential for a fire, such as a frayed cord or a bad plug on equipment.
• Employees will attend all required safety meetings.
• Unsafe conditions, equipment and unsafe acts, regardless of the department in which the condition exists, must be reported to the Foreman immediately.
REVISED DATE: January 1, 2025
SAFETY DISCIPLINARY POLICY
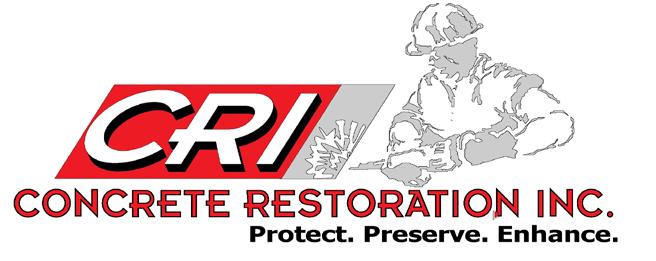
• Use all guards or devices provided for machinery, equipment, tools and processes. No guard should be removed from any machine or equipment except to perform maintenance. Only qualified personnel will perform maintenance.
• Maintenance personnel should evaluate each job to ensure that the source of energy for machines or equipment has been eliminated, and the equipment locked out and tagged out before employees perform any servicing or maintenance activities.
• Employees should cooperate with their Foreman when accident investigations are conducted so that accident causes can be determined and corrective action taken.
• Employees should follow all manufacturers’ instructions and guidelines for the safe operation of equipment.
• Employees should follow all manufacturers’ instructions and guidelines, including SDS’s for the safe handling of chemicals.
• Employees should follow safe lifting practices and lift objects the right way bending knees, keeping back erect, and getting help for loads.
• Failure to follow these rules will result in disciplinary action up to and including termination of employment.
Employees will be met with to discuss any non-compliance activities and a course of action will be decided on at that time. The course of action depends on the gravity and/or frequency of policy violation(s).
1. A first violation will be discussed orally between Concrete Restoration Inc Management and the employee.
2. A second time offence will be administered in a written form and a copy will be placed in the employee’s file
3. A third violation will result in possible time off or termination depending on the seriousness of the violation.
Management is responsible for being committed to this policy
REVISED DATE: January 1, 2025
SITE SPECIC SAFETY PLAN
SITE SPECIC SAFETY PLAN
Project:
Subcontractor: Concrete Restoration Inc.
Sub Superintendent:
Sub Safety Representative:
Sub First Aid Trained Individuals:
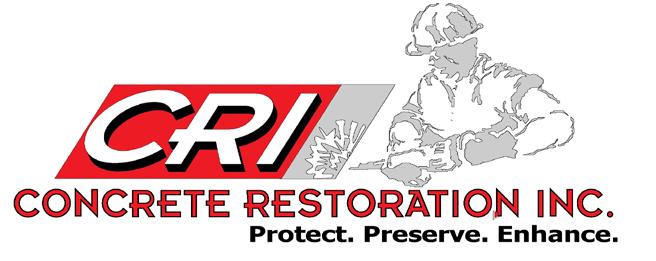
Date:
Day/time of weekly safety meetings:
Tasks with Potential Potential Hazard
Specific Abatement Method – Action, Engineering Hazards Control, Equipment, etc.
Briefly describe work to be performed.
List tools and equipment to be used for performance of work.
Indicate the PPE your employees are required to wear for your specific scope of work.
REVISED DATE: January 1, 2025
SUBCONTRACTOR MANAGEMENT POLICY
SUBCONTRACTOR MANAGEMENT POLICY
Purpose
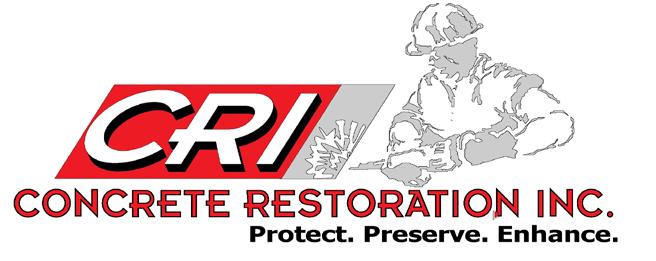
The purpose of this program is to ensure that Concrete Restoration Inc continues to improve subcontractor health, safety and environmental performance and to establish a standard for pre-qualification, evaluation/selection and development of our subcontractors.
Scope
This program applies to all subcontractors on all Concrete Restoration Inc worksites.
General Information
• All Concrete Restoration Inc subcontractors are to be managed in accordance with this program.
• The use of subcontractors must be pre-approved by Concrete Restoration In Management. Approval requirements for subcontractors include:
• A formal safety review of the subcontractor, performed by Concrete Restoration Inc safety department.
• The scope of the review is proportionate with the hazards and risk exposure.
• Subcontractor has been/will be oriented to the safety policies, expectations and requirements of Concrete Restoration Inc.
• The subcontractor agrees to abide by our Drug and Alcohol policy and onsite safety rules throughout the duration of the work being performed.
• Any subcontractor that has a “Non-Approved” safety status will not be used on any Concrete Restoration Inc worksite.
REVISED DATE: January 1, 2025
SUBCONTRACTOR MANAGEMENT POLICY
Procedure
Pre-Qualification of Subcontractors
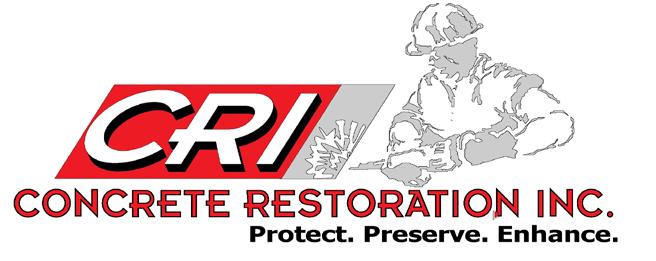
Subcontractors will be pre-qualified by CRI’s safety department reviewing their safety programs, safety training documents and safety statistics.
Evaluation Safety Metrics
Acceptable safety metrics will be used as criteria for prequalifying and selecting subcontractors. The safety metrics and scoring will consider:
• Subcontractor safety programs that outline different types of work the subcontractor performs and safety procedures for each type
• Subcontractor safety training records review.
Subcontractor Involvement
Contractors are required to follow or implement the work practices and systems described below while performing work on CRI worksites:
• Attend a safety orientation, pre-job meeting or kick-off meeting provided by Concrete Restoration Inc prior to beginning work
• Monitor employees for substance abuse and report nonconformities to Concrete Restoration Inc.
• Ensure personnel have the required training and competency to perform their work safely.
• Participate in Concrete Restoration Inc tailgate safety meetings, job safety analysis, hazard assessments, and on the job safety inspections.
• Perform a pre-job safety inspection that includes equipment.
REVISED DATE: January 1, 2025
SUBCONTRACTOR MANAGEMENT POLICY
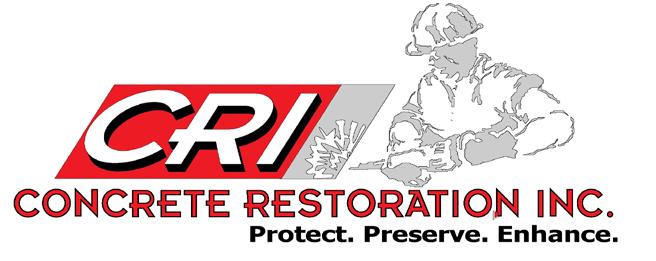
• Participate in the behavior-based safety hazard reporting system.
• Report all injuries, spills, property damage incidents and near misses.
• Comply with onsite and Owner Client safety rules.
• Implement Concrete Restoration Inc safety practices and processes as applicable.
• Clean up and restore the worksite after the job is over.
• Ensure compliance with regulations at all times.
• Complete post job safety performance reviews with subcontractors and Concrete Restoration Inc representatives.
REVISED DATE: January 1, 2025
SUPERVISORS ACCIDENT
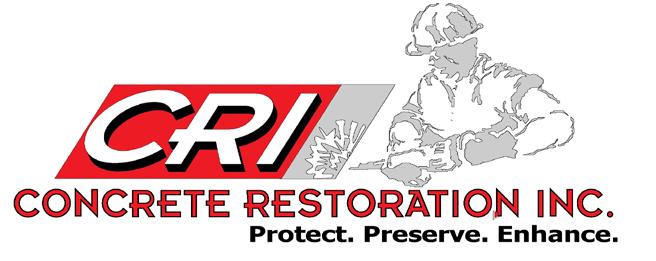

REVISED DATE: January 1, 2025
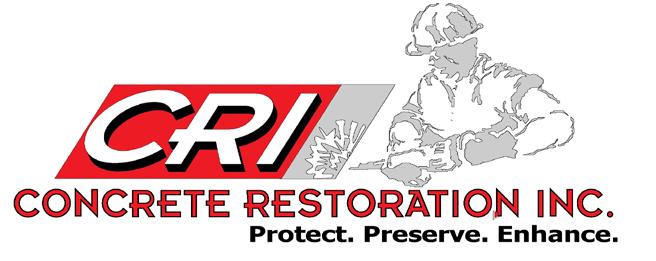


TRENCHING AND EXCAVATION
POLICY
TRENCHING AND EXCAVATION POLICY
Reference: OSHA 1926.651/WAC 296-155
PURPOSE
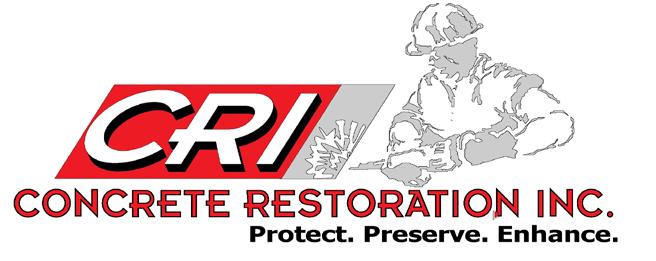
This program outlines procedures and guidelines for the protection of employees working in and around excavations and trenches. This program requires compliance with OSHA Standards described in Subpart P (CFR 1926.650) for the construction industry and WAC 296-155-650 Part N
Compliance is mandatory to ensure employee protection when working in or around excavations. The programs in this manual on confined space, hazard communication, lock-out/tag-out, respiratory protection, and any other safety programs or procedures deemed essential for employee protection, are to be used in conjunction with this program.
SCOPE
This program pertains to all Concrete Restoration Inc projects that require any excavations or trenches.
RESPONSIBILITIES
It is the responsibility of all Concrete Restoration Inc foreman and Management to implement and maintain the procedures and steps set forth in this program. Each employee involved with excavation and trenching work is responsible to comply with all applicable safety procedures and requirements of this program.
DEFINITIONS
BENCHING - A method of protecting employees from cave-ins by excavating the sides of an excavation to form one or a series of horizontal levels or steps, usually with vertical or near vertical surfaces between levels.
CAVE-IN - The separation of a mass of soil or rock material from the side of an excavation, or the loss of soil from under a trench shield or support
REVISED DATE: January 1, 2025
TRENCHING AND EXCAVATION
POLICY
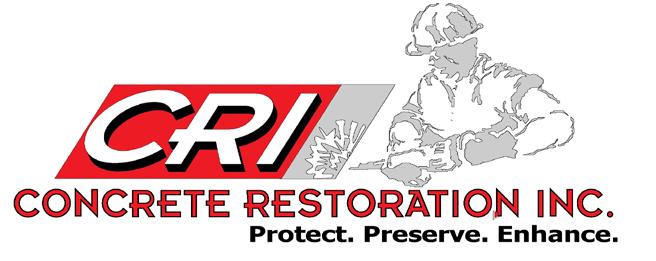
system, and its sudden movement into the excavation, either by failing or sliding, in sufficient quantity so that it could entrap, bury, or otherwise injure and immobilize a person.
COMPETENT PERSON - One who is capable of identifying existing and predictable hazards in the surroundings or working conditions, which are unsanitary, hazardous, or dangerous to employees, and who has authorization to take prompt corrective measures to eliminate them.
DURATION OF EXPOSURE - The longer an excavation is open, the longer the other factors have to work on causing it to collapse.
EXCAVATION - Any man-made cut, trench, or depression in an earth surface, formed by earth removal.
HAZARDOUS ATMOSPHERE - An atmosphere which by reason of being explosive, flammable, poisonous, corrosive, oxidizing, irritating, oxygen deficient, toxic, or otherwise harmful, may cause death, illness, or injury.
PROTECTIVE SYSTEM - A method of protecting employees from cave-ins, from material that could fall or roll, from an excavation, or from the collapse of adjacent structures. Protective systems include support systems, sloping and benching systems, shield systems, and other systems that provide necessary protection.
SHIELD - A structure that is capable of withstanding the forces imposed on it by a cave-in and thereby protects employees within the structure. Shields can be permanent structures or can be designed to be portable and moved along as work progresses. All shields must be in accordance with 29 CFR 1926.652(c)3 or (c)4 and WAC 296-155-650 Part N
SLOPING - A method of protecting workers from cave-ins by excavating to form sides of an excavation that are inclined away from the excavation to prevent cave-ins. The angle of incline required to prevent a cave-in varies with differences such as soil type, length of exposure, and application of surcharge loads.
REVISED DATE: January 1, 2025
TRENCHING AND EXCAVATION
POLICY
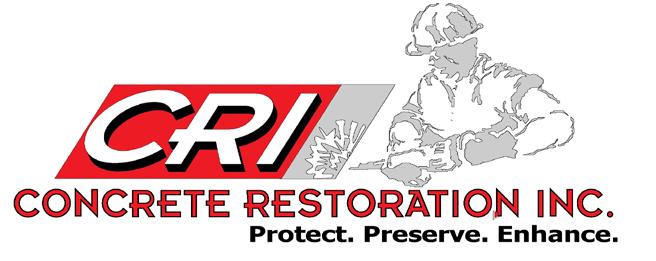
SURCHARGE LOADS - Generated by the weight of anything in proximity to the excavation, push starts for a cave-in (anything up top pushing down). Common surcharge loads:
• Weight of spoil pile
• Weight of nearby buildings, poles, pavement, or other structural objects.
• Weight of material and equipment
TRENCH - A narrow excavation below the surface of the ground, less than 15 feet wide, with a depth no greater than the width.
UNDERMINING - Undermining can be caused by such things as leaking, leaching, caving or over-digging. Undermined walls can be very dangerous.
VIBRATION - A force that is present on construction sites and must be considered. The vibrations caused by backhoes, dump trucks, compactors and traffic on job sites can be substantial.
GENERAL REQUIREMENTS
Before any work is performed and before any employees enter the excavation, a number of items must be checked and insured:
• Before any excavation, underground installations must be determined. This can be accomplished by either contacting the local utility companies or the local "one-call' center for the area. All underground utility locations must be documented on the proper forms. All overhead hazards (surface encumbrances) that create a hazard to employees must be removed or supported to eliminate the hazard.
• No employee should perform work under, or in the vicinity of, digging equipment where there is the potential for falling loads.
• If the excavation is to be over 20 feet deep, it must be designed by a registered professional engineer who is registered in the state where work will be performed.
REVISED DATE: January 1, 2025
TRENCHING AND EXCAVATION
POLICY
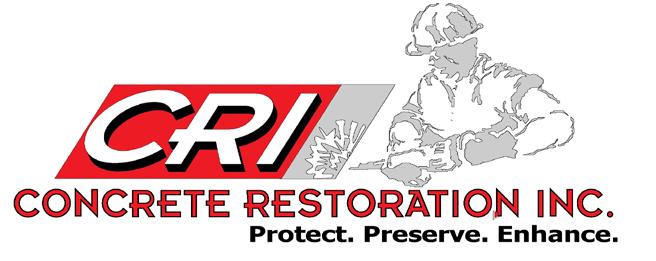
• Adequate protective systems will be utilized to protect employees. This can be accomplished through sloping, shoring, or shielding.
• The worksite must be analyzed in order to design adequate protection systems and prevent cave-ins. There must also be an excavation safety plan developed to protect employees.
• Concrete Restoration Inc employees will be supplied with and required to wear personal protective equipment deemed necessary to assure their protection.
• All spoil piles will be stored a minimum of four (4) feet from the sides of the excavation. The spoil pile must not block the safe means of egress.
• If a trench or excavation is 4 feet or deeper, stairways, ramps, or ladders will be used as a safe means of access and egress. For trenches, the employee must not have to travel any more than 25 feet of lateral travel to reach the stairway, ramp, or ladder.
• If a trench or excavation site requires a walkway over the trench, guardrails will be installed to protect employees from falling. These guard rails will have a top rail, mid rail, and a toe board if required.
• No employee will work in an excavation where water is accumulating unless adequate measures are used to protect the employees.
• A competent person will inspect all excavations and trenches daily, prior to employee exposure or entry, and after any rainfall, soil change, or any other time needed during the shift. The competent person must take prompt measures to eliminate any and all hazards.
• Excavations and trenches 4 feet or deeper that have the potential for toxic substances or hazardous atmospheres (O2, flammable, etc…) will be tested at least daily. If the atmosphere is inadequate, protective systems will be utilized (including ventilation, etc…)
REVISED DATE: January 1, 2025
TRENCHING AND EXCAVATION
POLICY
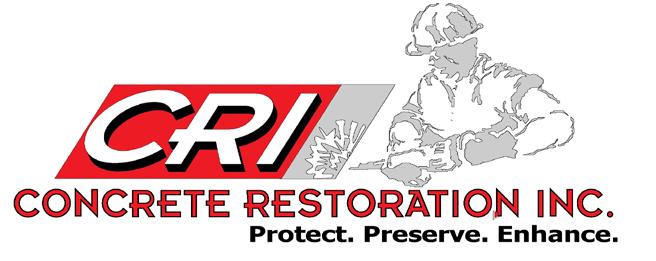
• If work is in or around traffic, employees will be supplied with and wear high vise vests. Signs and barricades must be utilized to ensure the safety of employees, vehicular traffic, and pedestrians. These will help protect pedestrians and workers, whether on crosswalks or pathways.
COMPETENT PERSON RESPONSIBILITIES
The OSHA/WAC Standards require that the competent person must be capable of identifying existing and predictable hazards in the surroundings, or working conditions which are unsanitary, hazardous, or dangerous to employees, and have authorization to take prompt corrective measures to eliminate them and, if necessary, to stop the work. These shall be foreman.
A competent person is required to:
• Have a complete understanding of the applicable safety standards and any other data provided.
• Assure the proper locations of underground installations or utilities, and that the proper utility companies have been contacted.
• Conduct soil classification tests and reclassify soil after any condition changes.
• Determine adequate protective systems (sloping, shoring, or shielding systems) for employee protection.
• Conduct all air monitoring for potential hazardous atmospheres.
• Conduct daily and periodic inspections of excavations and trenches.
• Approve design of structural ramps, if used.
EXCAVATION SAFETY PLAN
REVISED DATE: January 1, 2025
TRENCHING AND EXCAVATION
POLICY
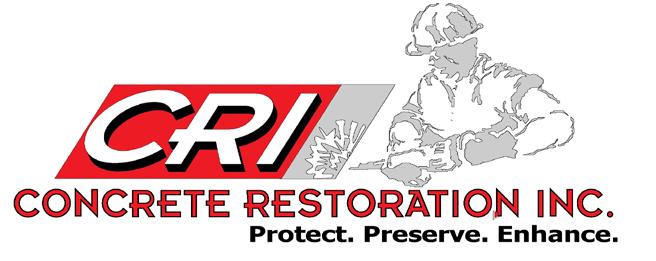
An excavation safety plan is required in written form. This plan is to be developed to the level necessary to insure complete compliance with the OSHA/WAC Excavation Safety Standard.
Excavation safety plan factors:
• Utilization of the local one-call system
• Determination of locations of all underground utilities
• Consideration of confined space atmosphere potential
• Proper soil protection systems and personal protective equipment and clothing
• Determination of soil composition and classification
• Determination of surface and subsurface water
• Depth of excavation and length of time it will remain open
• Proper adherence to all OSHA//WAC Standards, this excavation and trenching safety program, and any other coinciding safety programs.
SOIL CLASSIFICATION AND IDENTIFICATION
The OSHA Standards define soil classifications within the Simplified Soil Classification Systems, which consist of four categories: Stable rock, Type A, Type B, and Type C. Stability is greatest in stable rock and decreases through Type A and B to Type C, which is the least stable. Appendix A of the Standard provides soil mechanics terms and types of field tests used to determine soil classifications.
Stable rock is defined as natural solid mineral matter that can be excavated with vertical sides and remain intact while exposed.
REVISED DATE: January 1, 2025
TRENCHING AND EXCAVATION
POLICY
Type A soil is defined as:
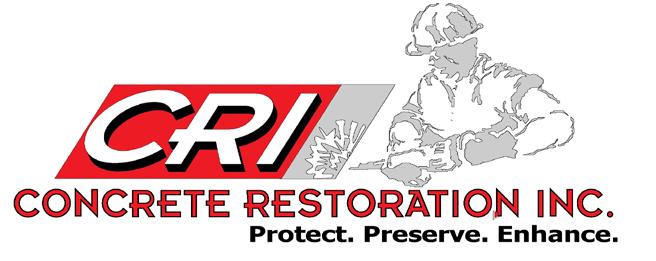
• Cohesive soils with an unconfined compressive strength of 1.5 tons per square foot (TSF) or greater.
• Cemented soils like caliche and hardpan are considered Type A.
Soil is NOT Type A if:
• It is fissured.
• The soil is subject to vibration from heavy traffic, pile driving or similar effects.
• The soil has been previously disturbed.
• The material is subject to other factors that would require it to be classified as a less stable material.
• The exclusions for Type A most generally eliminate it from most construction situations.
Type B soil is defined as:
• Cohesive soil with an unconfined compressive strength greater than .5 TSF, but less than 1.5 TSF.
• Granular cohesion less soil including angular gravel, silt, silt loam, and sandy loam.
• The soil has been previously disturbed except that soil classified as Type C soil.
• Soil that meets the unconfined compressive strength requirements of Type A soil but is fissured or subject to vibration.
REVISED DATE: January 1, 2025
TRENCHING AND EXCAVATION
POLICY
• Dry rock that is unstable.
Type C soil is defined as:
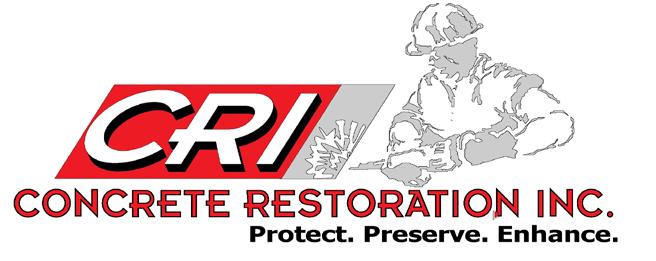
• Cohesive soil with an unconfined compressive strength of .5 TSF or less.
• Granular soils including gravel, sand and loamy sand.
• Submerged soil or soil from which water is freely seeping.
• Submerged rock that is not stable.
Soil Test & Identification
The competent person will classify the soil type in accordance with the definitions in Appendix A on the basis of at least one visual and one manual analysis. These tests should be run on freshly excavated samples from the excavation and are designed to determine stability based on a number of criteria: the cohesiveness, the presence of fissures, the presence and amount of water, the unconfined compressive strength, the duration of exposure, undermining, and the presence of layering, prior excavation and vibration.
The cohesion tests are based on methods to determine the presence of clay. Clay, silt, and sand are size classifications, with clay being the smallest sized particles, silt intermediate and sand the largest. Clay minerals exhibit good cohesion and plasticity (can be molded). Sand exhibits no elasticity and virtually no cohesion unless surface wetting is present. The degree of cohesiveness and plasticity depend on the amounts of all three types and water.
When examining the soil, three questions must be asked: Is the sample granular or cohesive? Fissured or non-fissured? What is the unconfined compressive strength measured in TSF?
Methods of testing soils:
REVISED DATE: January 1, 2025
TRENCHING AND EXCAVATION
POLICY
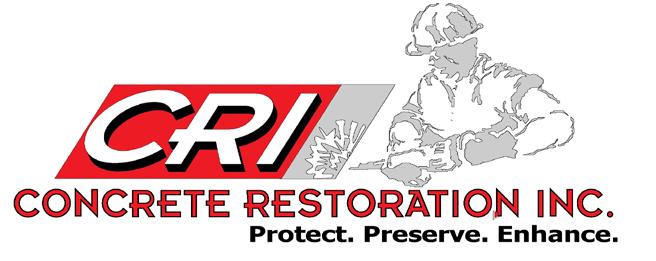
• Visual test: If the excavated soil is in clumps, it is cohesive. If it breaks up easily, not staying in clumps, it is granular.
• Wet manual test: Wet your fingers and work the soil between them. Clay is a slick paste when wet, meaning it is cohesive. If the clump falls apart in grains, it is granular.
• Dry strength test: Try to crumble the sample in your hands with your fingers. If it crumbles into grains, it is granular. Clay will not crumble into grains, only into smaller chunks.
• Pocket penetrometer test: This instrument is most accurate when soil is nearly saturated. This instrument will give unconfined compressive strength in tons per square foot. The spring-operated device uses a piston that is pushed into a coil up to a calibration groove. An indicator sleeve marks and retains the reading until it is read. The reading is calibrated in tons per square foot (TSF) or kilograms per cubic centimeter.
• Thumb penetration teal: The competent person attempts to penetrate a fresh sample with thumb pressure. If the sample can be dented, but penetrated only with great effort, it is Type A. If it can be penetrated several inches and molded by light pressure, it is Type C. Type B can be penetrated with effort and molded.
• Shearvane: Measures the approximate shear strength of saturated cohesive soils. The blades of the vane are pressed into a flat section of undisturbed soil, and the knob is turned slowly until soil failure. The dial is read directly when using the standard vane. The results will be in tons per square foot or kilograms per cubic centimeter.
The competent person will perform several tests of the excavation to obtain consistent, supporting data along its depth and length. The soil is subject to change several times within the scope of an excavation and the moisture content will vary with weather and job conditions. The competent person must also determine the level of protection based on what conditions exist at the time of the test and allow for changing conditions.
REVISED DATE: January 1, 2025
TRENCHING AND EXCAVATION
POLICY
EXCAVATION PROTECTION SYSTEMS
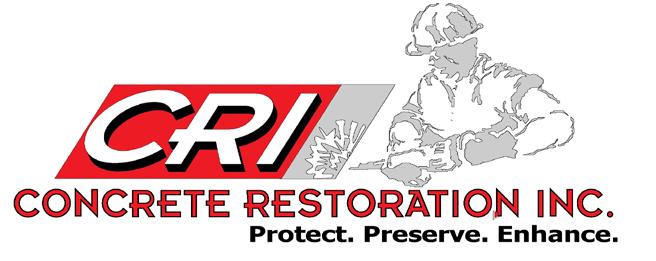
The three basic protective systems for excavations and trenches are sloping and benching systems, shoring, and shields.
The protective systems shall have the capacity to resist without failure all loads that are intended or could reasonably be expected to be applied to or transmitted to the system. Every employee in an excavation shall be protected from cave-ins by an adequate protective system.
Exceptions to using protective system:
• Excavations are made entirely in stable rock
• Excavations are less than 4 feet deep and declared safe by a competent person.
SLOPING AND BENCHING SYSTEMS
There are four options for sloping:
• Slope to the angle required by the Standard for Type C, which is the most unstable soil type.
• The table provided in Appendix B of the Standard may be used to determine the maximum allowable angle (after determining the soil type).
• Tabulated data prepared by a registered professional engineer can be utilized.
• A registered professional engineer can design a sloping plan for a specific job.
Sloping and benching systems for excavations five (4) to twenty (20) feet in depth must be constructed under the instruction of a designated competent person.
REVISED DATE: January 1, 2025
TRENCHING AND EXCAVATION
POLICY
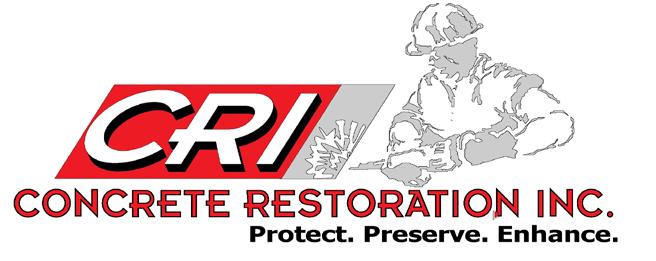
Sloping and benching systems for excavations greater than twenty (20) feet must be designed and stamped by a registered professional engineer.
Sloping and benching specifications can be found in Appendix B of the OSHA Standard (Subpart P) or WAC 296-155-66403
SHORING SYSTEMS
Shoring is another protective system or support system. Shoring utilizes a framework of vertical members (uprights), horizontal members (whales), and cross braces to support the sides of the excavation to prevent a cavein. Metal hydraulic, mechanical or timber shoring is common examples.
The different examples of shoring are found in the OSHA Standard under these appendices:
APPENDIX C - Timber Shoring for Trenches
APPENDIX D - Aluminum Hydraulic Shoring for Trenches
APPENDIX E - Alternatives to Timber Shoring And in WAC 296-155-6645
SHIELD SYSTEMS (Trench Boxes)
Shielding is the third method of providing a safe workplace. Unlike sloping and shoring, shielding does not prevent a cave-in. Shields are designed to withstand the soil forces caused by a cave-in and protect the employees inside the structure. Most shields consist of two flat, parallel metal walls that are held apart by metal cross braces.
Shielding design and construction is not covered in the OSHA Standards. Shields must be certified in design by a registered professional engineer and must have either a registration plate on the shield or registration papers from the manufacturer on file at the jobsite office. ANY REPAIRS OR MODIFICATIONS MUST BE APPROVED BY THE MANUFACTURER.
SAFETY PRECAUTIONS FOR SHIELD SYSTEMS
• Shields must not have any lateral movement when installed.
REVISED DATE: January 1, 2025
TRENCHING AND EXCAVATION
POLICY
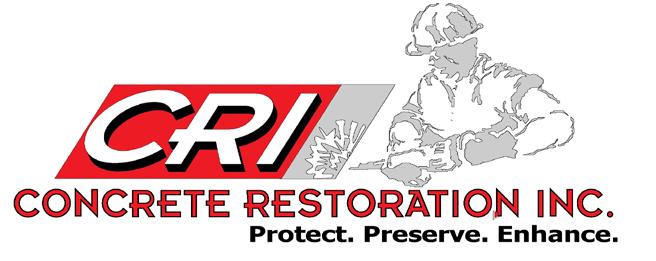
• Employees will be protected from cave-ins when entering and exiting the shield (examples - ladder within the shield or a properly sloped ramp at the end).
• Employees are not allowed in the shield during installation, removal, or during any vertical movement.
• Shields can be 2 ft. above the bottom of an excavation if they are designed to resist loads at the full depth and if there are no indications of caving under or behind the shield.
• The shield must extend at least 18 inches above the point where proper sloping begins (the height of the shield must be greater than the depth of the excavation).
• The open end of the shield must be protected from the exposed excavation wall. The wall must be sloped, shored, or shielded. Engineer designed end plates can be mounted on the ends of the shield to prevent cave-ins.
PERSONAL PROTECTIVE EQUIPMENT
It is Concrete restoration Inc policy to wear a hard hat, safety glasses, gloves, and work boots on the jobsite. Because of the hazards involved with excavations, other personal protective equipment may be necessary, depending on the potential hazards present (examples -goggles, and respiratory equipment).
INSPECTIONS
Daily inspection of excavations, the adjacent areas and protective systems will be made by the competent person for evidence of a situation that could result in a cave-in, indications of failure of protective systems, hazardous atmospheres or other hazardous conditions.
• All inspections are to be conducted by the competent person prior to the start of work and as needed throughout the shift.
REVISED DATE: January 1, 2025
TRENCHING AND EXCAVATION
POLICY
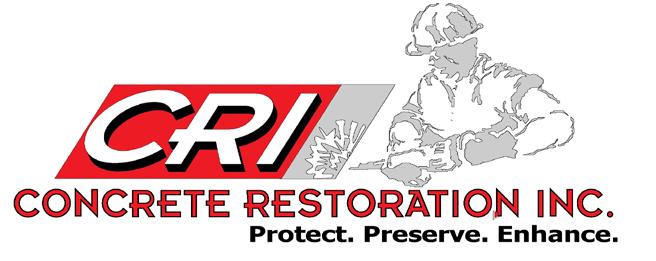
• Inspections will be made after every rainstorm or any other increasing hazard.
TRAINING
The competent person(s) must be trained in accordance with the OSHA/WAC Excavation Standard, and all other programs that may apply (examples Hazard Communication, Confined Space, and Respiratory Protection), and must demonstrate a thorough understanding and knowledge of the programs and the hazards associated.
All other employees working in and around the excavation must be trained in the recognition of hazards associated with trenching and excavating.
REVISED DATE: January 1, 2025
VEHICLE SAFETY INSPECTION
VEHICLE SAFETY INSPECTION
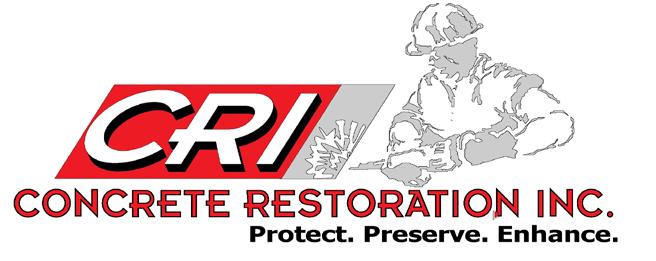
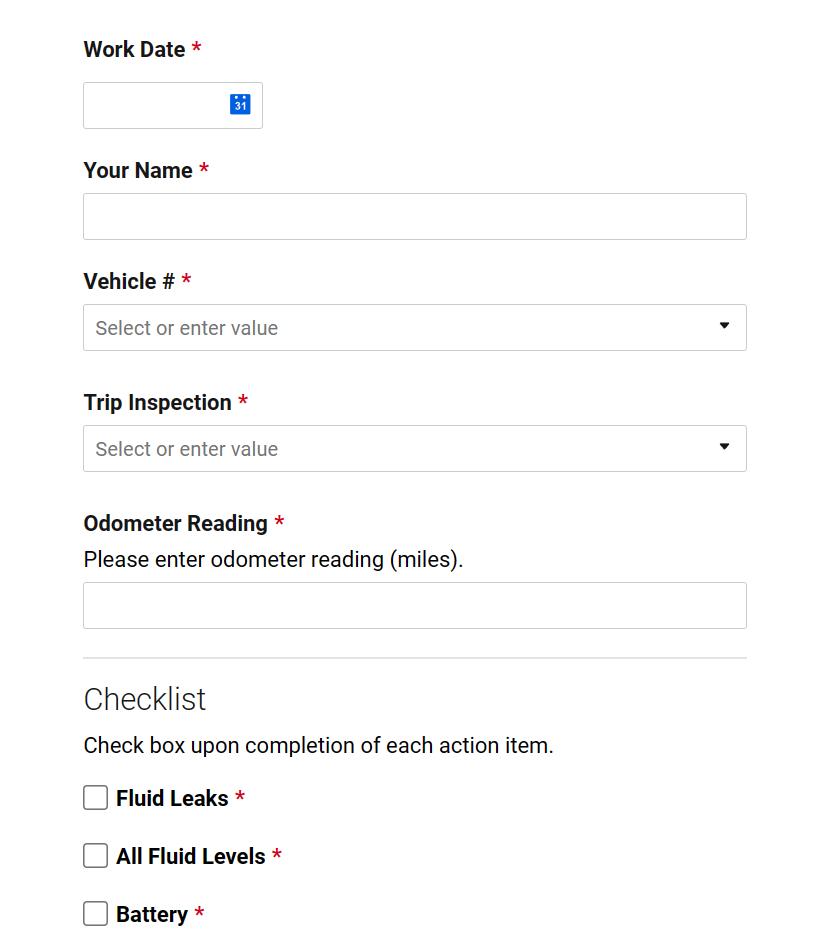
REVISED DATE: August 2025
VEHICLE SAFETY INSPECTION

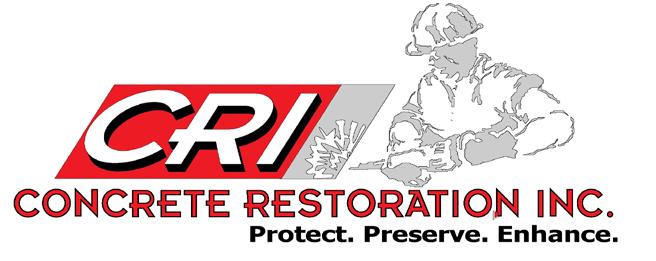
REVISED DATE: August 2025
VEHICLE SAFETY INSPECTION
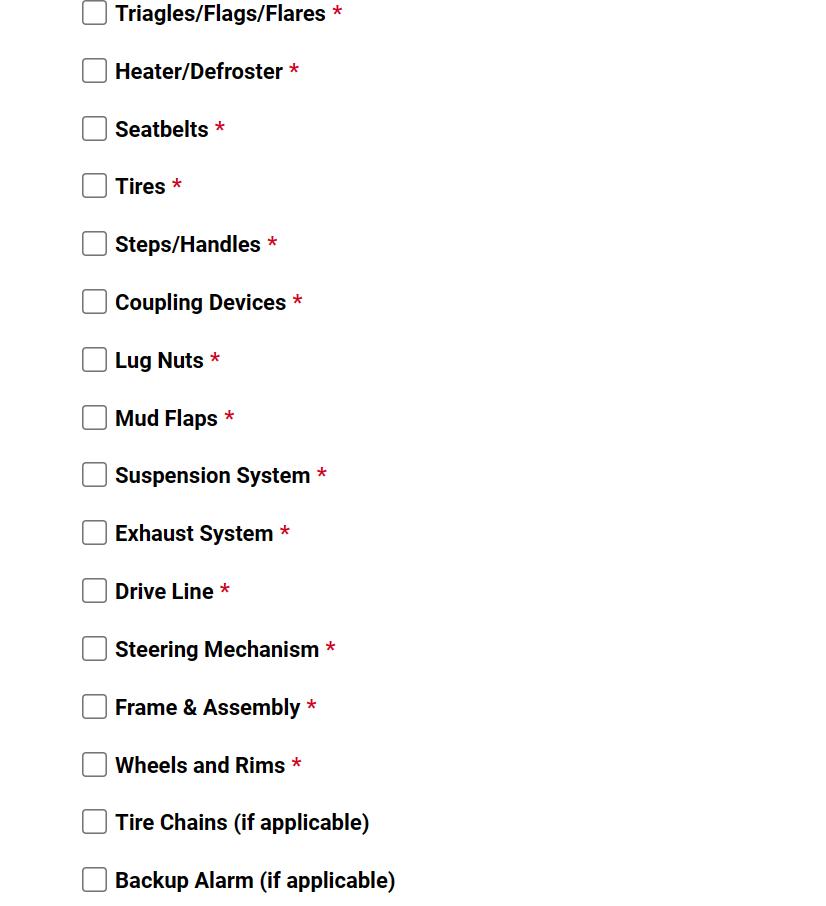
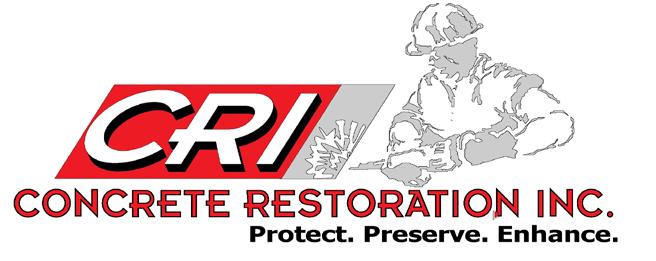
REVISED DATE: August 2025
VEHICLE SAFETY INSPECTION
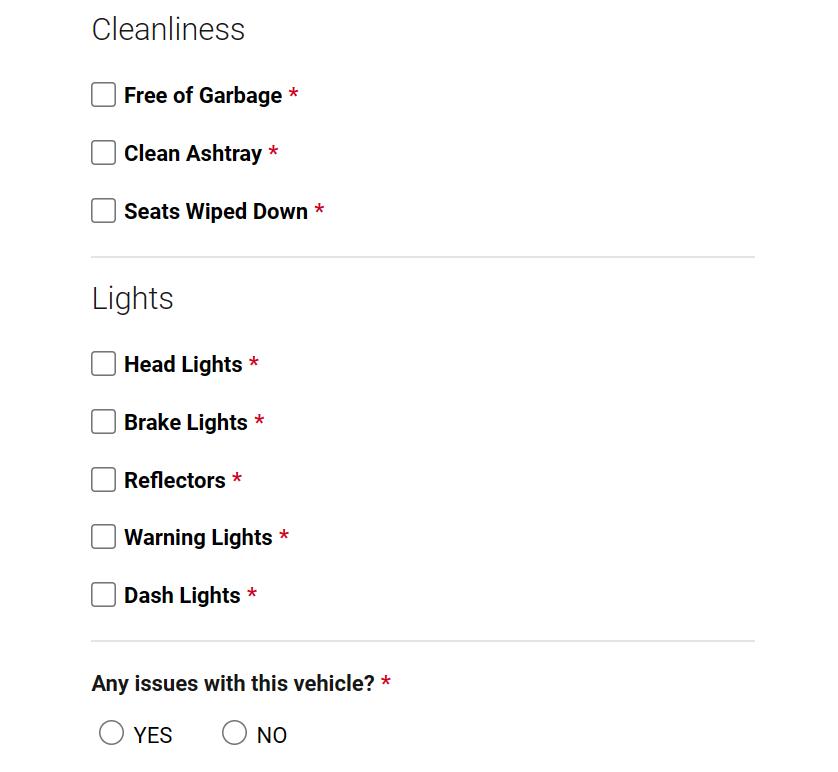
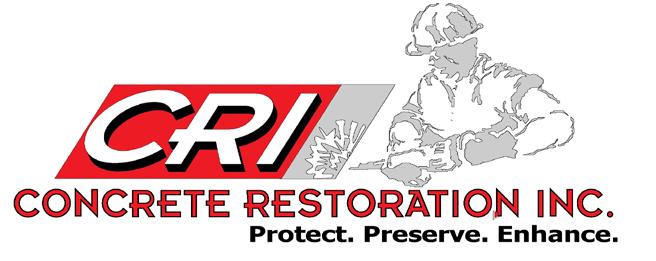
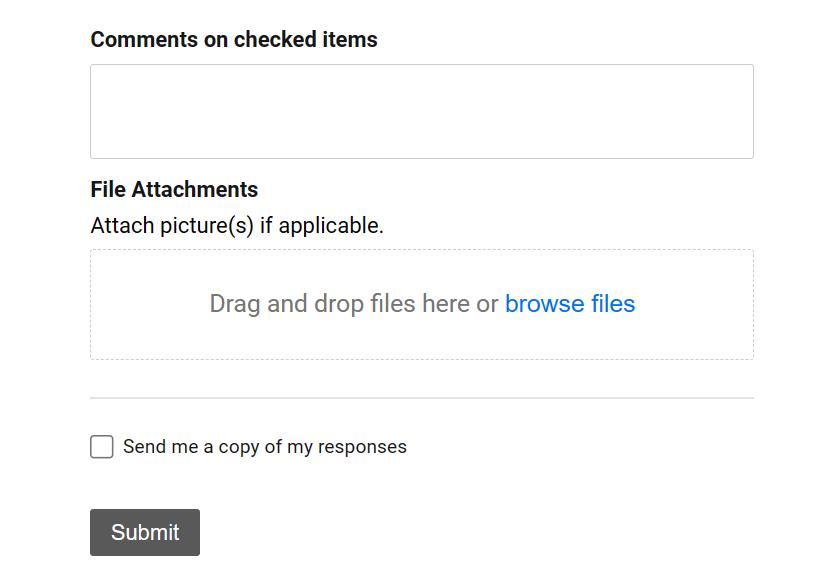
REVISED DATE: August 2025
WILDFIRE SMOKE POLICY
WILDFIRE SMOKE REPONSE PLAN
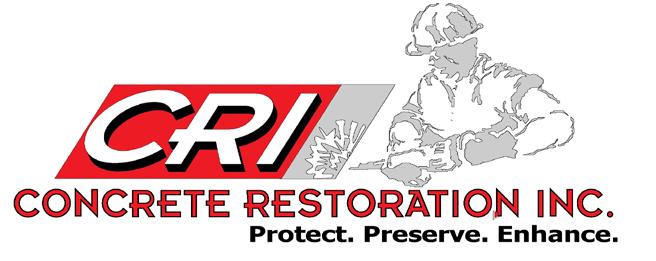
Employees who work outdoors when there is a heightened level of exposure to wildfire smoke and the AQI for PM2.5 exceeds 69 are at risk of experiencing negative health effects from breathing in hazardous chemicals.
It is the policy of the Concrete Restoration Inc to reduce employee exposure to harmful respiratory hazards when wildfire smoke causes unhealthy air quality by developing employee and supervisor awareness of the health effects of wildfire smoke and proper response. All employees who work outdoors when AQI for PM2.5 exceeds 151 are expected to comply with the procedures in this program.
This policy is based on the Washington Administrative Code (WAC) 296-820 Wildfire Smoke.
The following workplaces and operations are exempt from this rule:
• Enclosed buildings or structures in which the employer ensures that windows, doors, bays, and other exterior openings are kept closed, except when it is necessary to open doors to enter and exit.
• Enclosed vehicles in which the air is filtered by a cabin air filter and the employer ensures that windows, doors, and other openings are kept closed except when it is necessary to open doors to enter or exit.
• Work within the scope of Chapter 296-305 WAC, Safety Standards for firefighters.
• Workers performing prescribed burns.
Definitions.
Adverse Symptoms requiring medical attention. Adverse symptoms to wildfire smoke exposure requiring medical attention include, but are not limited to: Difficulty breathing or shortness of breath, particularly when accompanied by greater use of accessory muscles; chest pain; nausea; or dizziness.
REVISED DATE: August 2025
WILDFIRE SMOKE POLICY
Air Quality Index (AQI). A unitless index used by the U.S. Environmental Protection Agency (EPA) to communicate air quality for several pollutants, including PM2.5.
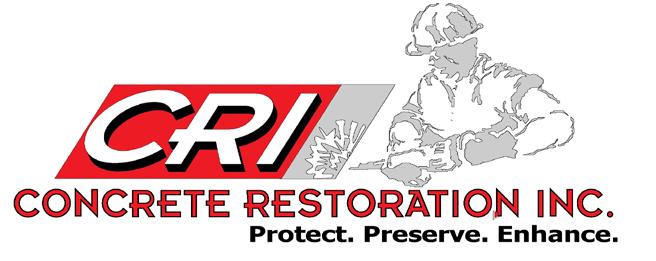
Current PM2.5. The concentration of PM2.5 for the most current hour available, calculated using an hourly average of PM2.5 data.
Emergency Response. Rescue, evacuation, utilities, communications, transportation, and medical operations; when such operations are directly aiding firefighting; protecting public health and safety; or actively protecting, restoring, or maintaining the safe and reliable operation of critical infrastructure at risk.
High-efficiency particulate air (HEPA) filter. A filter capable of trapping and retaining at least 99.97 percent of all monodispersed particles of 0.3 micrometers mean aerodynamic diameter or larger.
NIOSH. The National Institute for Occupational Safety and Health of the U.S. Centers for Disease Control and Prevention. NIOSH tests and approves respirators for use in the workplace.
NowCast Air Quality Index (AQI). The method used by the U.S. Environmental Protection Agency (EPA) to communicate air quality using color-coded categories. It shows the air quality for the most current hour available by using a calculation that involves multiple hours of past data using the NowCast. The NowCast uses longer averages during periods of stable air quality and shorter averages when air quality is changing rapidly, such as during a wildfire. The NowCast is generally updated every hour.
NowCast Washington air quality advisory (WAQA). The method used by the Washington state department of ecology to communicate air quality using color-coded categories. It shows the air quality for the most current hour available by using a calculation that involves multiple hours of past data using the NowCast. The NowCast uses longer averages during periods of stable air quality and shorter averages when air quality is changing rapidly, such as during a wildfire. The NowCast is generally updated every hour.
REVISED DATE: August 2025
WILDFIRE SMOKE POLICY
PM2.5. Solid particles and liquid droplets suspended in air, known as particulate matter, with an aerodynamic diameter of 2.5 micrometers or smaller. Measured in micrograms per cubic meter (μg/m3).
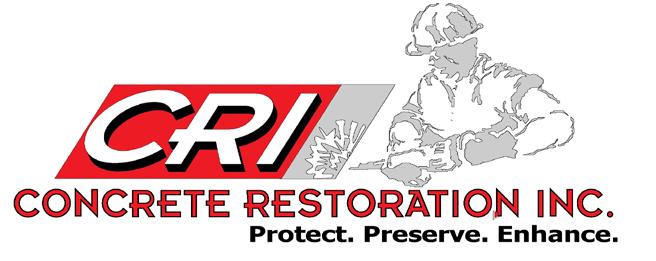
Wildfire smoke. Emissions from fires in wildlands or in adjacent developed areas. Wildfire smoke contains a complex mixture of gasses and particulates. Fine particulates such as PM2.5 are the primary pollutant in wildfire smoke.
Wildlands. Sparsely populated geographical areas covered primarily by grass, brush, trees, crops, or combination thereof.
Air Quality Monitoring and Communication
The Safety/Training manager will determine the air quality for exposure to PM2.5 before each shift by checking the PM2.5 from any of the following:
• (a) Washington Department of Ecology website;
• (b) Air Quality WA mobile app;
• (c) Washington smoke information website;
• (d) U.S. EPA AirNow Fire and Smoke Map;
• (e) U.S. EPA AirNow website;
• (f) U.S. EPA AirNow mobile app;
• (g) U.S. Forest Service AirFire website; or
• (h) Local clean air agency website.
The Safety/Training manager will also review the forecast to anticipate conditions that may require further actions.
The Safety/Training manager will communicate wildfire smoke hazards of PM2.5 is 20.5 µg/m3 (WAQA 101, AQI 69) or more, as needed via tool box talks, signage or email. Employees are encouraged to inform their supervisor, site supervision, or safety professional when air quality is worsening, or adverse symptoms are noticed that could be related to wildfire smoke exposure, without fear of reprisal.
REVISED DATE: August 2025
WILDFIRE SMOKE POLICY
Training
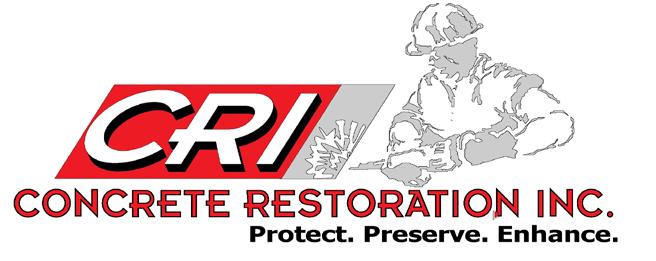
The Safety/Training manager will train all employees regarding the health effects (including those in sensitive groups), action limits, controls, and accepted measurement/ reporting of wildfire smoke concentrations. Employees will be trained in their rights to seek medical treatment for wildfire smoke exposure, the requirements of WAC 296-820-805 through WAC 296-820-860. This training will also detail the company plan for tracking and mitigating wildfire smoke exposure, including respirator use and limitations.
Foreman/Leads will be given additional training prior to supervising employees performing work that exposes the worker to PM2.5 levels that are 20.5 µg/m3 (AQI 69) or more,
• Company procedures for implementation of this policy
• Employee adverse symptom response and monitoring,
• Procedures for moving or transporting employees to an emergency medical service provider, if necessary
• How to get medical help for employees in the event of adverse reactions.
• The procedures the supervisor must follow if an employee exhibits adverse symptoms of wildfire smoke exposure, including appropriate emergency response procedures.
Controls
Where the PM2.5 is 20.5 µg/m3 (WAQA 101, AQI 69) or more, the employer is encouraged to implement exposure controls. Where the NowCast PM2.5 is 55.5 µg/m3 (WAQA 173, AQI 101) or more, the employer must implement exposure controls whenever feasible.
Controls include:
• providing enclosed buildings, structures or vehicles
• providing portable HEPA filters in enclosed areas
• relocating work to a safer air quality location
• changing work schedules
• reducing work intensity
• providing additional rest periods
REVISED DATE: August 2025
WILDFIRE SMOKE POLICY
Respiratory Protection
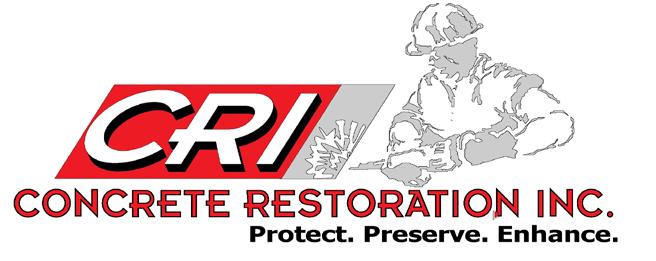
N95 masks are available for employee voluntary use and can be obtained from Safety/Training manager.
At an AQI above 100, Concrete Restoration Inc will provide access to respirators at no cost.
At an AQI above 300, Concrete Restoration Inc will distribute N95 filtering facepiece respirators and encourage their use and implement exposure controls, where feasible.
At an AQI above 500, Concrete Restoration Inc will enroll employees in a full respiratory protection program and workers will wear N95 filtering face piece respirator.
Where the air quality exceeds the AGI (PM2.5 555 µg/m3) Concrete Restoration Inc will require employees to wear one of the following respirators with an APF of 25 or more equipped with P100 filters:
• Loose-fitting powered air purifying respirator;
• Full-facepiece air purifying respirator;
• Full-facepiece powered air purifying respirator; or
• Other respirators with an assigned protection factor of 25 or more.
Training for use of respirators shall be provided in a manner and language readily understood by the worker, following WAC 296-820-840 and include:
1. The health effects of wildfire smoke
2. Importance of notifying the employer of any adverse symptoms
3. The right to obtain medical treatment without fear of reprisal
4. How to obtain the NowCast PM 2.5
5. Resources to obtain the air quality data
6. Requirements of WAC 296-820-840 through WAC 296-820-850
7. The company’s wildfire smoke response plan
8. The importance, limitations, and benefits of using a respirator when exposed to wildfire smoke
9. The risks and limitations of using an unfitted respirator
10. How to properly use and care for respirator
REVISED DATE: August 2025
WORK ALONE POLICY
WORK ALONE POLICY
Reference: OSHA 1915.84/WAC 296-79-020
Purpose
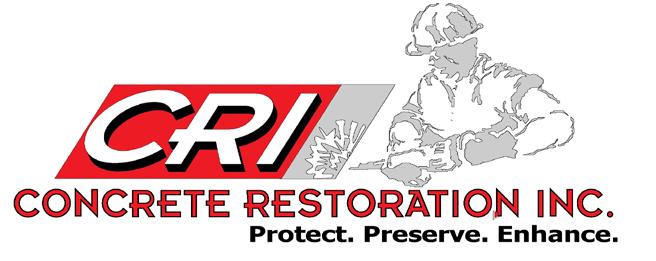
To establish a safe working environment for concrete Restoration Inc employees who must work alone.
Scope
Applicable to all CRI employees
Introduction/Overview
The practice of employees working alone in isolated areas, out of sight or normal audible range or co-workers, should be avoided whenever possible. Concrete Restoration Inc recognizes that at times, working alone may be unavoidable and wants to ensure that any employee working in an isolated area is able to instantly notify a co-worker that they require emergency assistance.
Responsibilities
Foreman - This person is responsible for ensuring safety on the individual employee level. He/She will perform tool box safety talks, assist employees in correct/safe procedures, and ensure employees comply with the safety program in place. Before any employee is allowed to work alone, the Foreman will conduct a hazard assessment on the activities the individual employee is about to conduct, including the risks of working alone. The Foreman will ensure that he/she communicates the results of the hazard assessment and the necessary corrective actions that address each hazard.
Employees – All employees must be aware of the potential hazards they may be exposed to in their workplace, as well as the safety rules and procedures that address these hazards. They must know how to address job circumstances that are new, unusual or beyond the scope of training –when to stop work and seek advice from a Foreman. Employees who must
REVISED DATE: January 1, 2025
WORK ALONE POLICY
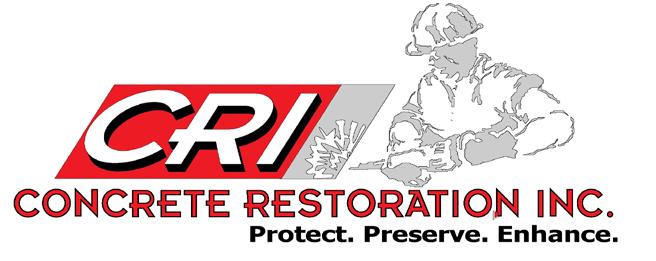
work alone are strictly required to adhere to this policy in that this act presents unique conditions and potential exposures.
Safe Work Practices
• Request for emergency assistance can be accomplished in any number of different manners. Employees must be allowed to utilize hand-held radios, "medical alert" systems, cellular phones or other electronic devices that will permit them to summon assistance when necessary.
o When any type of electronic system is utilized, the system must be checked for proper operation from the isolated area prior to each usage.
• The Foreman or his/her designee will make regular, informal visits to monitor the safety of lone workers. If it is not feasible for the Foreman or his/her designee to complete this activity, the employee will contact him/her at intervals pre-determined when the hazard assessment is completed.
• There must be a secondary communication system to back up any primary electronic device. This may be a second electronic communication device, air horn, etc.
• When an employee does not respond or check in at the expected time, the Foreman or his/her designee will physically travel to the working location to assess the condition of the employee. If the employee is not present, the nearest appropriate emergency personnel will be contacted immediately.
• The following guidelines will direct when an employee search is necessary:
o After checking the surrounding work area;
o After interviewing any nearby workers or personnel;
o After checking the nearest restrooms, lavatories and/or break rooms;
o After checking adjacent work areas in all directions;
o After meeting with and establishing a specific search plan
REVISED DATE: January 1, 2025
WORKERS ACCIDENT REPORT
WORKERS ACCIDENT REPORT
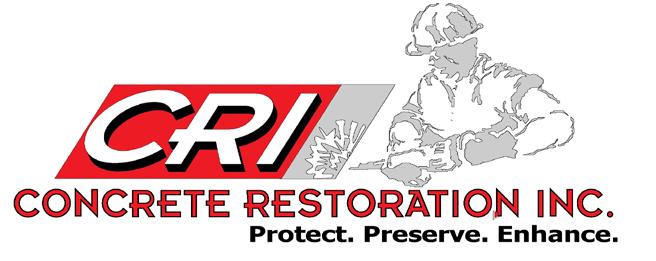
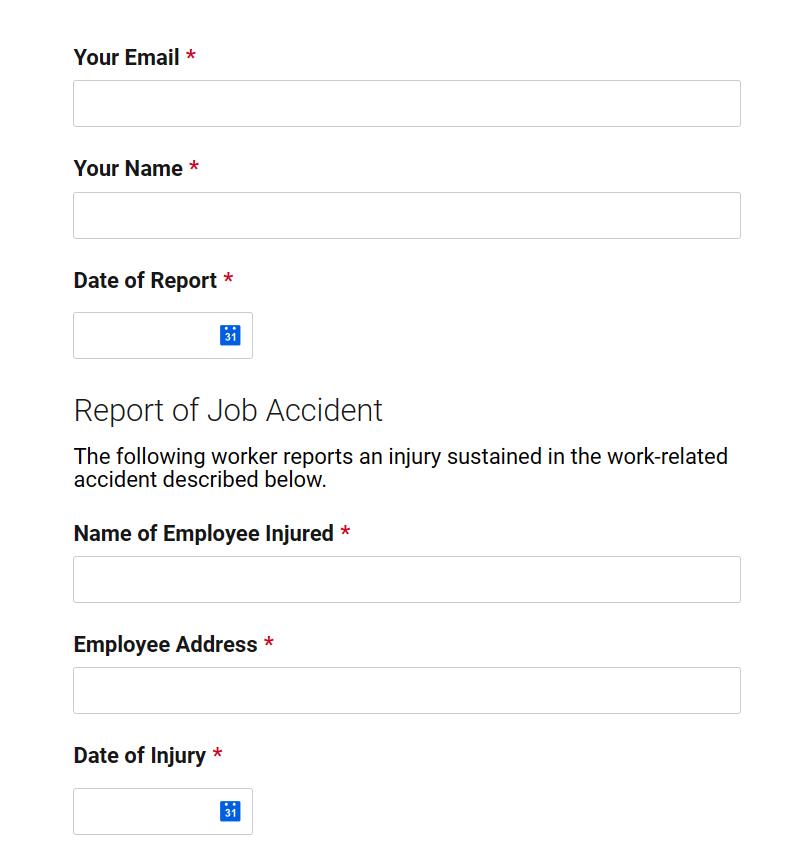
REVISED DATE: January 1, 2025
WORKERS ACCIDENT REPORT
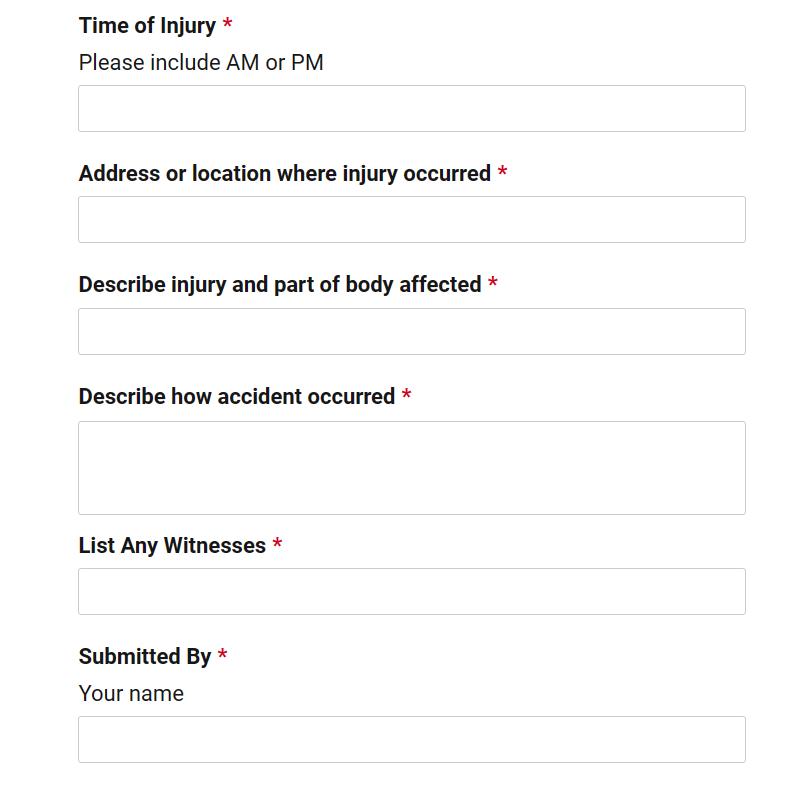
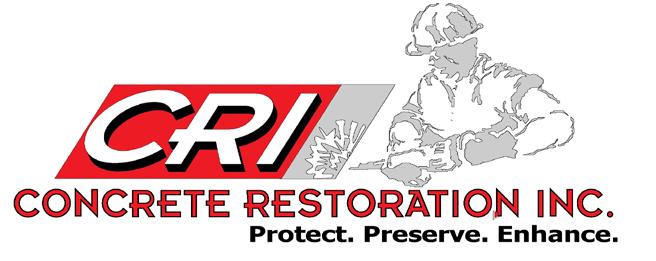
REVISED DATE: January 1, 2025
WORKERS
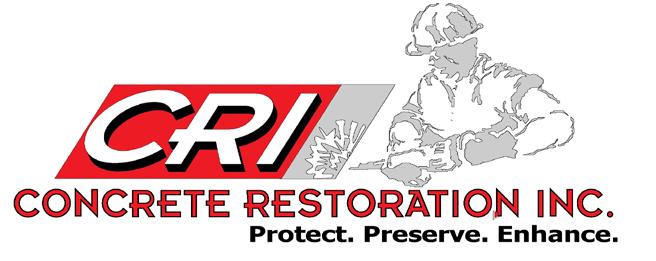
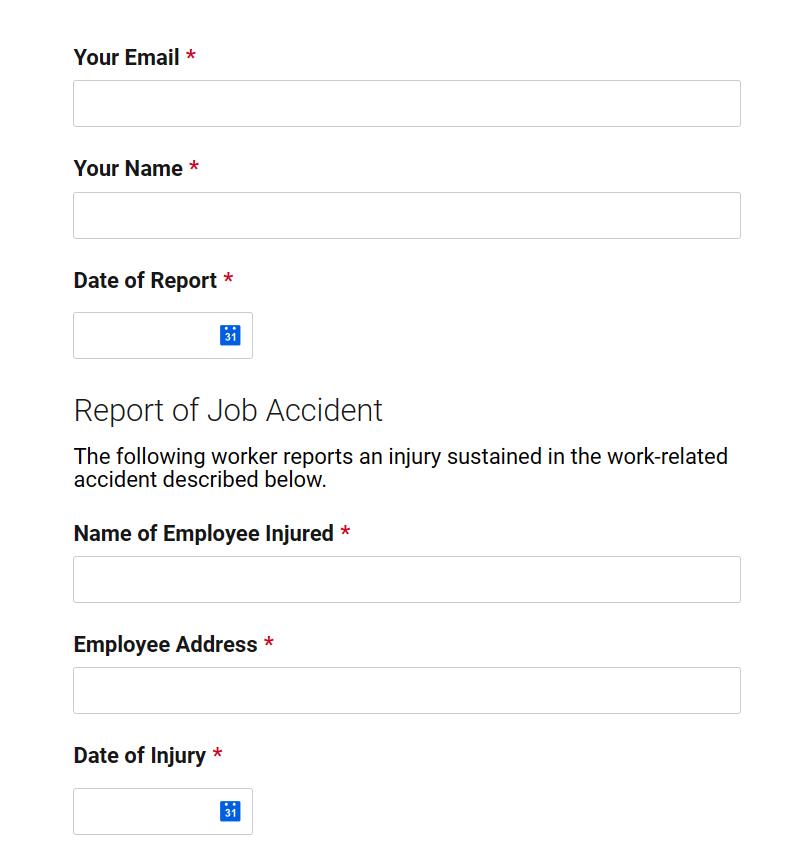
REVISED DATE: January 1, 2025
WORKERS
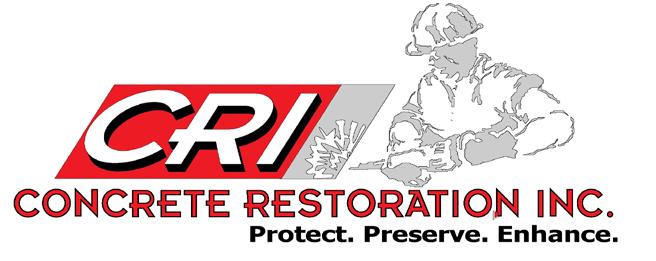
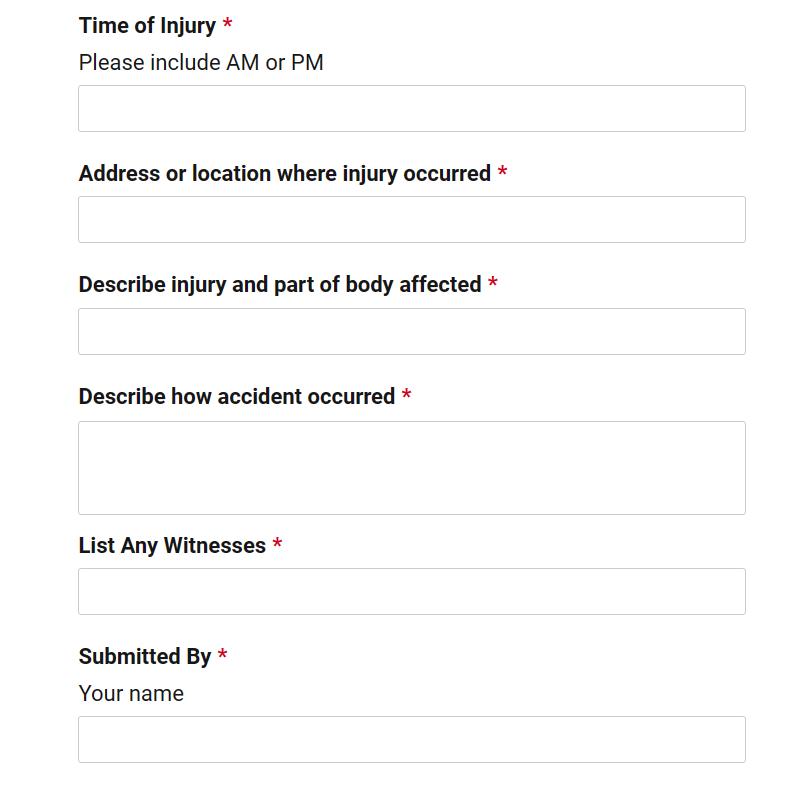
WORKPLACE VIOLENCE PREVENTION
Workplace Violence Prevention
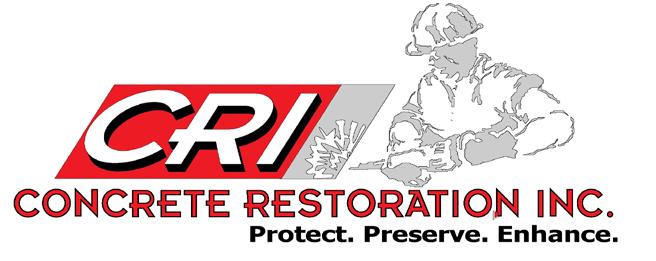
Concrete Restoration Inc. is committed to preventing workplace violence and to maintaining a safe work environment. Given the increasing violence of society in general, Concrete Restoration Inc. has adopted the following guidelines to deal with intimidation, harassment, or other threats of (or actual) violence that may occur during business hours or on its premises.
All employees, including supervisors and temporary employees, should be treated with courtesy and respect at all times. Employees are expected to refrain from fighting, horseplay, or other conduct that may be dangerous to others.
Conduct that threatens, intimidates, or coerces another employee, a customer, or a member of the public at any time, including off duty periods, will not be tolerated. This prohibition includes all acts of harassment, including harassment that is based on an individual’s sex, race, age, or any characteristic protected by federal, state, or local law.
All threats of (or actual) violence, both direct and indirect, should be reported as soon as possible to your immediate supervisor or any other member of management. This includes threats by employees, as well as threats by customers, vendors, solicitors, or other members of the public. When reporting a threat of violence, you should be as specific and detailed as possible.
All suspicious individuals or activities should also be reported as soon as possible to a supervisor. Do not place yourself in peril. If you see or hear a commotion or disturbance near you workstation, do not try to intercede or see what is happening.
Concrete Restoration Inc will promptly and thoroughly investigate all reports of threats of (or actual) violence and of suspicious individuals or activities. The identity of the individual making a report will be protected as much as is practical. In order to maintain workplace safety and the integrity of its investigation, Concrete Restoration Inc may suspend employees, either with or without pay, pending investigation. Anyone determined to be responsible for threats of (or actual) violence or other conduct that is in
REVISED DATE: January 1, 2025
WORKPLACE VIOLENCE PREVENTION
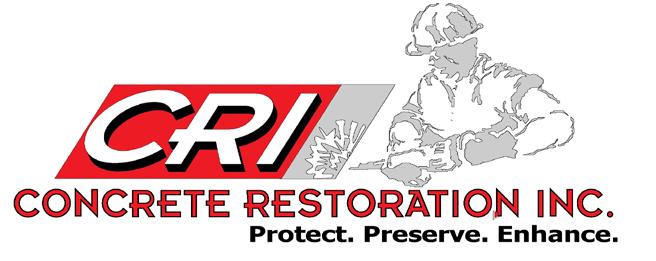
violation of these guidelines will be subject to prompt disciplinary action up to and including termination of employment.
Concrete Restoration Inc encourages employees to bring their disputes or differences with other employees to the attention of their supervisor or the Human Resources Manager before the situation escalates into potential violence. Concrete Restoration Inc is eager to assist in the resolution of employee disputes and will not discipline employees for raising such concerns.
PURPOSE
To define the policy of this company that all employees have the right to work in an environment free from physical violence, threats, and intimidation.
The Concrete Restoration Inc position is that violence is a form of serious misconduct that undermines the integrity of the employment relationship. No employee should be subject to unsolicited and physical violence, threats, or intimidation. Such behavior may result in disciplinary action up to and including dismissal.
POLICY
Concrete Restoration Inc has a strong commitment to its employees to provide a safe, healthy, and secure work environment. Concrete Restoration Inc also expects its employees to maintain a high level of productivity and efficiency. The presence of weapons and the occurrence of violence in the workplace during working hours or otherwise are inconsistent with these objectives.
While Concrete Restoration Inc has no intention of intruding into the private lives of its present or potential employees, it expects all employees to report on the work site without possessing weapons and to perform their job without violence towards any other individual. Concrete Restoration Inc expects all of its employees to work in a manner so that they can perform their duties in a safe and productive manner.
REVISED DATE: January 1, 2025
WORKPLACE VIOLENCE
PREVENTION
COVERAGE
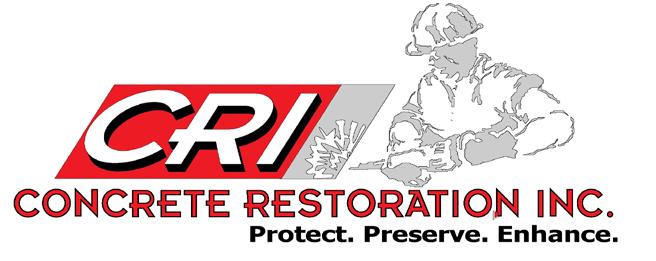
All applicants considered for employment with Concrete Restoration Inc will be required to sign an acknowledgement that they have received this policy and understand its contents and intent. All current employees will be required to sign an acknowledgement that they have received this policy and understand its contents and intent. Any applicant or employee who refuses to sign the acknowledgement will be subject to termination.
POLICY IMPLEMENTATION
It is the responsibility of Concrete Restoration Inc management to ensure that all employees are informed of and aware of this policy and legal guidelines.
Employees who are victims of or witnesses to violent incidents should immediately report such conduct to their supervisors or the Human Resources Manager.
DEFINITIONS
A. Crime of Violence
Includes any degree of murder, voluntary manslaughter, rape, mayhem, robbery, burglary, aggravated assault, and physical or verbal threats.
B. Weapon
Includes an explosive or an explosive weapon, a device principally designed, made or adapted for delivering or shooting an explosive weapon, a machine gun, a short barrel rifle or shotgun, a handgun, a firearm silencer, a switchblade knife or metal knuckles, or any other implement for infliction of bodily injury, serious bodily injury or death which has no common lawful purpose.
C. On the work site
Includes all property owned or occupied by (including company job sites) or in a company vehicle.
REVISED DATE: January 1, 2025
WORKPLACE VIOLENCE PREVENTION
D. Possession
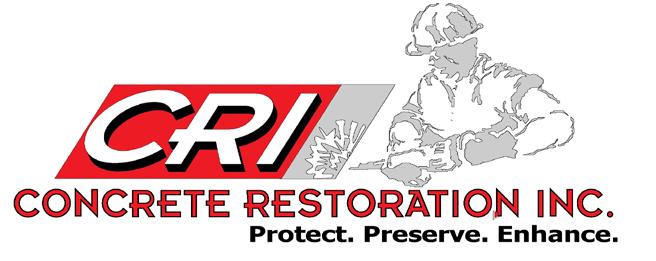
Includes, but is not limited to, the presence of weapon on the employee, in his/her motor vehicle, lunch box, locker, tool kit, bag, purse, cabinets, office, etc.
PROHIBITED ACTIVITIES
Concrete Restoration Inc. specifically prohibits the following and will routinely discipline an employee up to and including discharge for any of the following:
PROHIBITED ACTIVITIES
Concrete Restoration Inc. specifically prohibits the following and will routinely discipline an employee up to and including discharge for any of the following:
• Use, possession, or sale of any weapon as described above.
• Storing any weapon in a locker, desk, vehicles, lunch box, tool kit, bag, purse or other repository on the work site or other company premises.
• Illegal possession, use, or sale of a weapon off company property that adversely affects his/her own or other’s safety at work or indicates a propensity for same.
• Refusing to submit to an inspection for the presence of a weapon that is requested by the company.
• Refusing to sign a statement to comply with the Company’s Policy on Workplace Violence.
• Refusing to participate in an investigation pertaining to allegations or suspicion that violence has or is likely to occur, or an investigation pertaining to the carrying of a weapon by the employee or a coemployee
• Verbal or physical threats, threatening gestures, or statements.
• Fighting.
REVISED DATE: January 1, 2025
WORKPLACE VIOLENCE PREVENTION
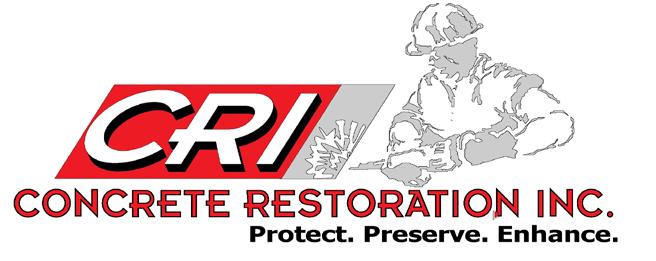
Concrete Restoration Inc in its discretion may from time to time modify this policy. In the event that this Workplace Violence Policy is revised, a copy of the revised policy will be provided to each employee. To the extent that the employee acknowledgement form of the policy may need to be updated or revised, each employee will be required to sign an updated version.
REPORTING
An employee who witnesses an incident of violence or threatening language or conduct must report the incident to his or her supervisor or Human Resources promptly.
Concrete Restoration Inc. has No Tolerance for retaliation for those who witness, report or take part in an investigation.
DICIPLINE
An employee who violates this policy by engaging in violent conduct or bringing a weapon into the work place is subject to discipline up to and including immediate termination.
An employee who violates this policy by bringing onto the work site a weapon and whose employment is not terminated by the company will be subject to searches from time to time, for an indefinite period of time not to exceed one (1) year from the date of the violation.
An employee’s consent to submit to a search is required as a condition of employment and the employee’s refusal to consent may result in disciplinary action, including discharge, for a first refusal or any subsequent refusal.
MISCELLANEOUS
The Company has the right to search any areas on Concrete Restoration Inc premises for weapons including, but not limited to, lockers, furniture, containers, drawers, equipment or other facilities, lunch boxes, briefcases, personal bags, personal toolboxes or tool kits, parking lots, company vehicles and personal vehicles parked on company premises.
If an employee is injured while participating in a fight or after instigating a fight, then entitlement to workers compensation benefits may be denied.
REVISED DATE: January 1, 2025
WORKPLACE VIOLENCE
PREVENTION
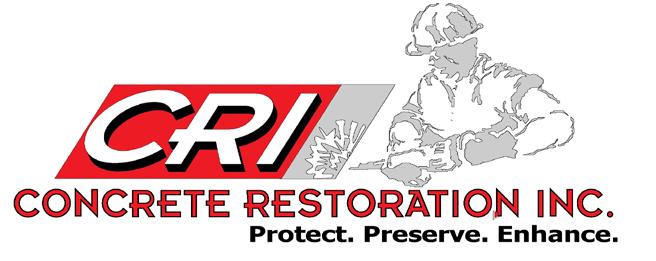
No part of this policy or any procedure therein, is intended to affect the Company’s right to manage or control its workforce, or be construed as a guarantee or contract of employment or continued employment.
NON-RETALIATION
This policy also prohibits retaliation against employees who report incidents of threats, physical violence, intimidation conduct, or weapons possession. Any employee bringing a harassment complaint or assisting in the investigation of such a complaint will not be adversely affected in terms and conditions of employment, nor discriminated against or discharged because of the complaint.
EXCEPTIONS
Exceptions to this policy must be approved by Shannon Ware.
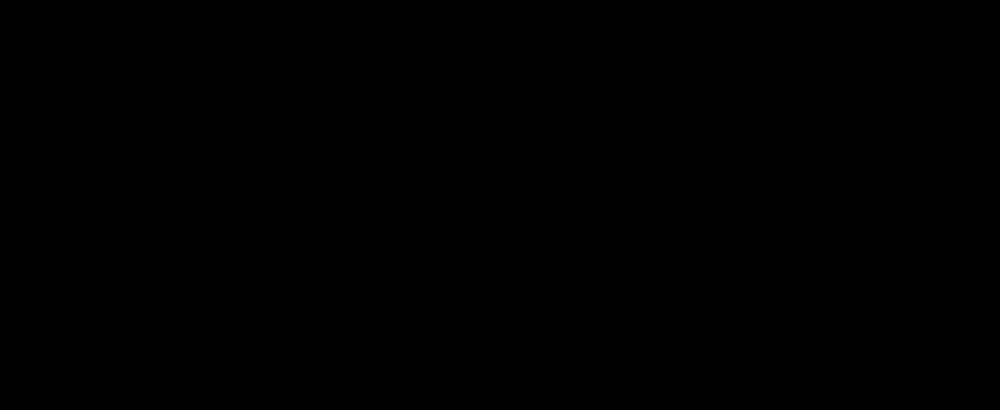
Shannon Ware, President Concrete Restoration Inc.
REVISED DATE: January 1, 2025
01/01/2025
Date:________________