spring 2025
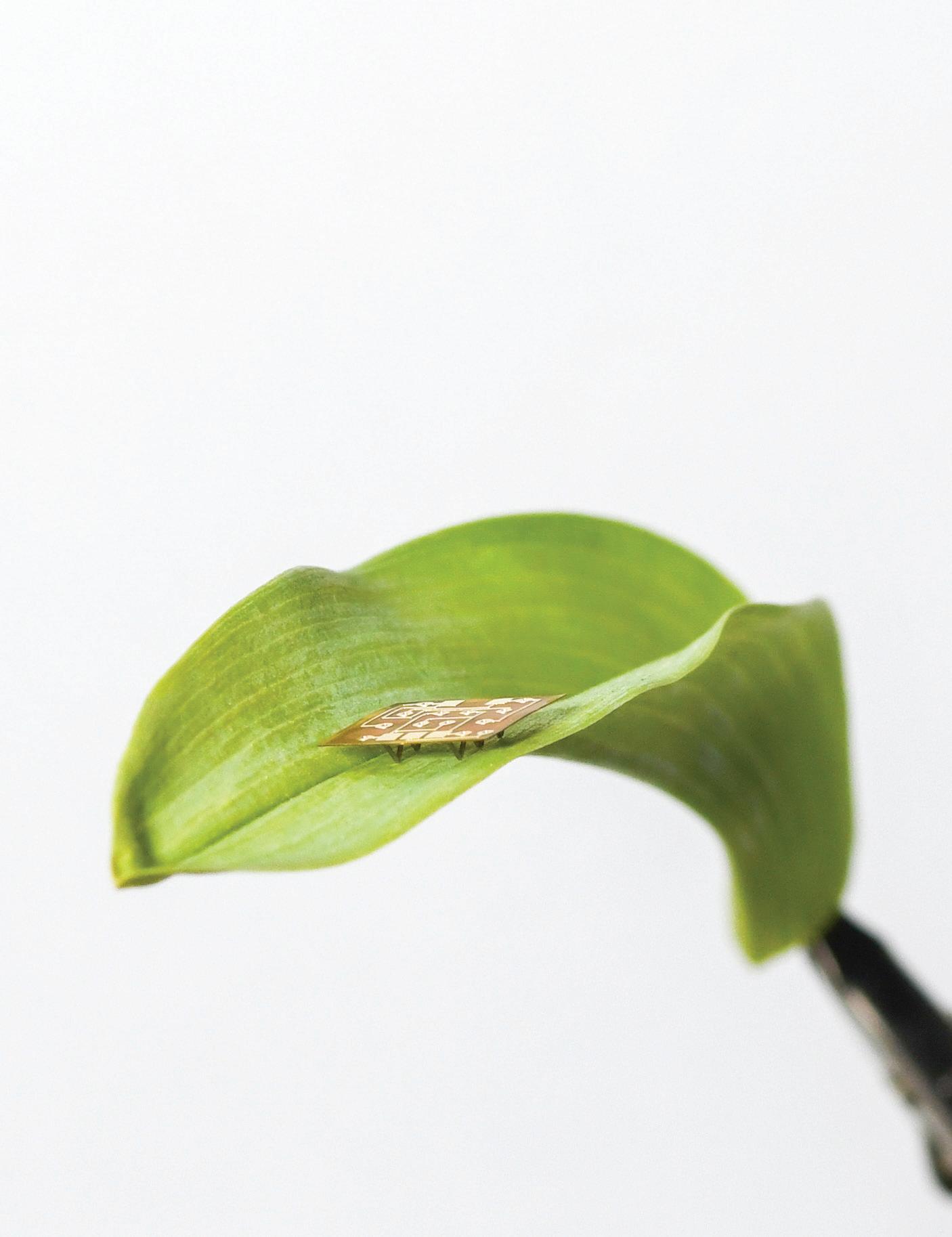
Dear Alumni, Students, Parents, and Friends,
It’s hard to believe that we’ve been settled into the “new” Scaife Hall for over a year - and what a year it has been!
We’ve welcomed two new faculty members- Liwei Wang and Burak Aksak, our undergraduate program jumped up in US News and World Report rankings to the number 5 spot, and we have had fun drawing inspiration from the world around us.
In this issue you’ll read about robots inspired by insects and dinosaurs, and classes influenced by video games. You’ll see first hand how our students spend their summer making an impact at internships across the country, and even selling wontons at local farmers markets.
Our researchers had a busy year collaborating across industry, government, and academia to bring cutting-edge technology to life.
In these pages, for example, you’ll learn how Ding Zhao is working with The City of Pittsburgh to make our streets safer, and Burak Ozdoganlar, with $42 million from ARPA-H, will develop bioelectronic devices to deliver patient-specific hypo-and hyperthyroidism therapy in real time.
As always, there’s too much good news to share and not enough magazine space to print on. I encourage you to stay up to date with our department at meche.engineering.cmu.edu, and on LinkedIn (@ CMUMeche) and Instagram (@CMUMeche)
Thank you for your continued support and involvement in our department.
Sincerely,
PUBLISHER Department of Mechanical Engineering
EDITOR
Kaitlyn Landram, Communications Manager
WRITERS
Andy Cummings, Kaitlyn Landram, Sara Pecchia, Kelly Rembold, Giordana Verrengia
DESIGN
Debra Vieira, Senior Multimedia Designer, College of Engineering
CMU, Meta announce research collaboration aimed at making computerbased tasks and gaming accessible to people with different motor abilities via wearable sensing technology
Engineering research center to improve robot dexterity selected to receive up to $52 million
Carnegie Mellon lands ARPA-H award for implantable bioelectric medicine project
Alumni
Embracing play - alumna uses toys to teach kids about engineering
What the Eyes Can’t See
Inspiration is all around us:
For plants, cleaning the air, providing food and medicines, and preserving our ecosystem is just another day’s work. In the Department of Mechanical Engineering at Carnegie Mellon University, however, plants are being studied in new ways to inspire future biohybrid Softbotic designs.
“Plants are a system much like planes, trains, and automobiles,” explained Phil LeDuc, Professor of Mechanical Engineering. “We want to understand plants’ mechanical systems, especially their sensing and signaling behavior, to potentially integrate them into biohybrid systems.”
Mimosa pudica, the subject of the study recently published in Advanced Science, rapidly closes its leaves when exposed to touch, wind, temperature and various other stimuli. Researchers theorize that this response is potentially an evolutionary advantage to protect against predators.
Alex Naglich, a PhD candidate in the Department of Mechanical Engineering, observed Mimosa pudica’s responses to three different mechanical stimuli to gain a better understanding of its macroscopic behavior. To emulate a predator, Naglich cut a cluster of leaves from the plant and watched as nearby clusters folded together immediately in seemingly self defense. When Naglich prodded just one leaf on the plant to create a mild disturbance, like that an insect might cause,
only the affected leaf folded. After repeated poking, however, the leaves folded one after another the whole way down the plant. For the final test, Naglich used an air pulse to imitate wind and found that only the leaves directly affected by the pulse of air folded.
“When mimosa folds, it’s less efficient for photosynthesis, so it makes sense why it wouldn’t want to stay folded,” Naglich said. “If a light breeze is only hitting a couple of leaves, why hide the entire plant?”
While the “intelligent” plant’s small size, impressive power density, and high efficiency makes it a promising candidate to act as a biohybrid actuator, Naglich also believes its response system could be the foundation for improved agricultural health monitoring.
“If we can continue to explore this plant’s intelligence, its ability to distinguish against threats and respond accordingly, we could integrate it with electronics to create a biohyrbid sensor and place it among crops so that farmers can be notified in real time when there’s a disturbance in the field.”
Moving forward, the lab plans to explore how mimosa pudica’s physical structure plays a role in its behavior.
“When it comes to biohybrid robotic research, there are a lot of naturally occuring mechanisms that could advance the field and we just haven’t looked into them yet,” said LeDuc. “Plants are one of those complex and sophisticated systems that we need to be studying more.”
MIMOSA PUDICA RAPIDLY CLOSES ITS LEAVES WHEN EXPOSED TO TOUCH, WIND, TEMPERATURE,
It’s an ant… it’s a robot… it’s
Picture this: hundreds of ant-sized robots climb over rubble, under rocks, and between debris to inspect the damage of a fallen building before human rescuers explore
on-site.
Researchers in MechE have created the first legged robot of its size to run, turn, push loads and climb miniature stairs
Picture this: hundreds of ant-sized robots climb over rubble, under rocks and between debris to inspect the damage of a fallen building before human rescuers explore on-site.
Downscaling legged robots to the size of an insect enables access to small spaces that humans and large robots cannot reach. A swarm of small robots can even collaborate like their insect counterparts to haul objects and protect one another. Picotaur, a new robot from the labs of Sarah Bergbreiter and Aaron Johnson, is the first of its size able to run, turn, push loads and climb miniature stairs.
“This robot has legs that are driven by multiple actuators so it can achieve various locomotion capabilities,” said Sukjun Kim, a recent PhD graduate advised by Bergbreiter. “With multiple gait patterns it can walk like other hexapod robots, similar to how a cockroach moves, but it can also hop from the ground to overcome obstacles.”
The 7.9 mm robot was 3D-printed using twophoton polymerization, a process previously successful in building various small-scale robotic systems in the lab such as microbots, microgrippers, microswimmers, and microsensors.
“Using this process, we were able to miniaturize the two degree of freedom linkage mechanism
that allows Picotaur to clear step heights and easily alternate between walking and jumping,” said Bergbreiter, Professor of Mechanical Engineering.
Kim tested Picotaur’s ability to push loads by creating a miniature soccer field. He found that the robot has enough force to push the ball and then turn, reorient itself, and follow the ball into the net.
“Historically, microfabrication technology was limited in manufacturing microscale devices in two-dimensional spaces, like for the semiconductor industry,” said Kim. “But now we have this capability to expand the design space from 2D to 3D. We can apply this process to create other smallscale robotic systems for various applications, for example, microgrippers for grasping and delivering small objects for surgical applications and microscale manufacturing applications.”
Because microrobotics is still in early development there are challenges yet to overcome before we see fully integrated robots in the field. For example, the team hopes to explore adding solar cells to the top of the robot so that it can be powered without tethers.
“Now that we see and accept larger robotic systems in the world, I hope that with this work people can imagine small-scale robots working around us and understand that that future is not too far off,” Kim said. “We can start thinking about where micro-robots would be useful and even find applications we haven’t thought of yet.”
year-old
Humans have been walking the earth for roughly 300 thousand years, an unfathomable period of time that in the grand scheme of Earth’s history is relatively recent. In fact, our time on earth represents only 0.007% of both the planet’s history. Therefore, the modernday animal kingdom that influences our understanding of evolution and inspires todays’ mechanical systems is just a fraction of all creatures that have existed through history.
To broaden our perspective of animal design and movement, researchers in Carnegie Mellon University’s Department of Mechanical Engineering, in collaboration with paleontologists from Spain and Poland, are introducing Paleobionics - a field aimed at using Softbotics, robotics with flexible electronics and soft materials, to understand the biomechanical factors that drove evolution using extinct organisms.
“Our goal is to use Softbotics to bring biological systems back to life, in the sense that we can mimic them to understand how they operated,” said Phil LeDuc, professor of Mechanical Engineering.
Using computational simulations and soft robots, a research team led by LeDuc and Carmel Majidi have given pleurocystitid, a marine organism that existed nearly 450 million years ago, new life. Pleurocystitids, a member of the echinoderm
class which includes modern day star fish and sea urchins, were one of the first echinoderms capable of movement using a muscular stem. Despite the absence of a current-day analogue, pleurocystitids have been of interest to paleontologists due to their pivotal role in echinoderm evolution.
“Softbotics is another approach to inform science using soft materials to construct flexible robot limbs and appendages. A lot of fundamental principles of biology and nature can only fully be explained if we look back at the evolutionary timeline of how animals evolved. We are building robot analogues to study how locomotion has changed,” explained Carmel Majidi, senior author and Professor of Mechanical Engineering.
The team used fossil evidence to guide their design and a combination of 3D printed elements and polymers to mimic the flexible columnar structure of the moving appendage to build the robot. They demonstrated that pleurocystitids were likely able to move over the sea bottom with the aid of a stem that pushed the animal forward and determined that wide sweeping movements were likely the most effective motion. Increasing the length of the stem was also found to significantly increase the animals’ speed without forcing it to exert more energy.
“Researchers in the bio-inspired robotics
“We aren’t just looking at fossils in the ground; we are trying to better understand life through working with amazing paleontologists.”
-
Phil LeDuc, Professor, Mechanical Engineering
community need to pick and choose important features worth adopting from organisms over time,” said Richard Desatnik, PhD candidate and co-first author.
“Essentially, we have to decide on good locomotion strategies to get our robots moving. For example, would a starfish robot really need to use 5 limbs for locomotion or can we find a better strategy?” added Zach Patterson, CMU alumnus and co-first author.
One of the biggest remaining questions about pleurocystitids are how the type of surface they lived on affected how they moved, be that sand or mud. Now that the team has demonstrated that they can use Softbotics to engineer extinct organisms, they hope to explore other animals, like the first organism that could travel from sea to land - something that can’t be studied in the same way using conventional robot hardware.
“Bringing a new life to something that existed nearly 500 million years ago is exciting in and of itself, but what really excites us about this breakthrough is how much we will be able to learn from it,” said LeDuc. “We aren’t just looking at fossils in the ground, we are trying to better understand life through working with amazing paleontologists.”
Normally, doing homework and playing video games are assumed to be at odds with each other. For students in Reeja Jayan’s upper-level course, Materials and Their Processing for Mechanical Engineers, they are one and the same. Over the past seven years, Jayan has continued to develop and refine a course syllabus that leverages Minecraft, the popular online game, as a way to give students a closer look at concepts in materials science and engineering with a digital venue to carry out experiments like chemical vapor deposition (CVD) polymerization so that they can simultaneously observe the process at an atomic level and learn how to operate such equipment in a lab.
“Minecraft was selected because it’s a game where people build using blocks, and in materials science we build entire objects using atoms. In the game, the
planned during the COVID pandemic thanks to the virtual environment.
Also, while access to labs may seem par for the course in an engineering curriculum, theory–based classes like Materials and Their Processing rarely have a lab component, and entering these facilities even once requires substantial preparation. Safety training is paramount, but it often takes several months to learn about handling toxic chemicals and equipment properly. This timeline isn’t practical for a semesterlong course.
With a virtual lab, students can practice with greater peace of mind because if they make mistakes, the results play out on a computer screen and do not risk physical harm.
blocks become surrogates for the atoms,” said Jayan, an associate professor of mechanical engineering
“I think this is the very first time such a class existed in higher education—it’s definitely the first engineering course of its kind.”
The perks of using Minecraft in the classroom range from matters of convenience to safety. For one thing, many aspects of the class were able to continue as
will turn pink, but if there’s a mistake, it crumbles like feta cheese.
While Jayan’s course is the first at CMU to use Minecraft, there’s less of a learning curve for students considering many of them grew up playing video games. Jayan takes a survey at the beginning of the semester to gauge how comfortable each group is with Minecraft and adjusts her lesson plans accordingly, adding or nixing tutorials based on feedback from students.
After fine-tuning the course over the last few years, Jayan has conducted her first case study (with researchers from the Eberly Center) to support the notion that Minecraft is not only an interesting pedagogical tool—it’s an effective one.
“We looked at student performance in exams,” Jayan said of the preliminary research. “We found statistically relevant improvements in student exam scores on topics requiring 3D spatial understanding and/or manipulation that is not possible on a two-dimensional book or paper or chalkboard.”
Jayan kick-started this project in 2016 with resources from the Donald L. and Rhonda Struminger Teaching Fellowship, which supports innovation in the classroom. When Jayan received the National Science Foundation’s (NSF) CAREER Award the following year, she turned her focus to developing virtual lab equipment. The interns who worked on the course were instrumental to this process, including Miguel Brandao, a College of Engineering alumnus and Takumi Natsume, a College of Fine Arts alumnus who designed the analogous lab. The most important
piece of equipment to include was the chemical vapor deposition machine.
“The actual tool sits in the basement of Scott Hall in the clean room housed within the Claire & John Bertucci Nanotechnology Laboratory,” explains Jayan. “It can create layers of atoms into thin films/coatings that you use for electronics and batteries. Students run the virtual machine to apply the chemistry and physics they learn in class.”
“The machine takes in a monomer gas, an initiator gas, and a carrier gas,” said Miguel Brandao, a mechanical engineering alumnus and former head teacher’s assistant for the course. “Once they flow in through the chamber, the machine heats the gasses. This causes the electrons in
the initiator molecules to break loose and attach to the monomer molecules, which then diffuse onto the surface of the object we are coating. This causes polymer chains to form.”
CVD is an essential part of manufacturing microchips for computers and mobile phones, and the process was meticulously recreated in Minecraft, allowing students to observe the process step-by-step. Even routine albeit essential rituals of lab protocol, like putting on bunny suits and shoe covers, have been incorporated into the virtual experience. When students conduct a polymer deposition experiment with the CVD machine, they know if it’s correct based on the color of the result. A properly grown nanolayered coating
Crystal structures, interatomic bonding, diffusion, and property anisotropy are some of the engineering concepts that translate well to a 3D and interactive format. According to the case study, students scored higher on concepts that were covered in a Minecraft module compared with topics that were not taught in Minecraft. Based on these results, Jayan would like to fortify the Minecraft server and establish a technical support team to accommodate a higher volume of users from across the university. Furthermore, Jayan hopes this data will inspire other schools at CMU to recognize the potential of Minecraft and other virtual tools for application in the classroom.
“This is still very legitimate, serious coursework that is supplemented by Minecraft—not the other way around.”
In recognition of this unique approach to teaching foundational engineering concepts, Jayan received the Teaching Innovation Award at CMU’s annual Celebration of Education Awards.
AI Coach for teams drives a profound change in results
Teams working with the AI Coach have shown:
• Quality of the project and design goes up significantly
• Improvements are optimized
• Unforeseen changes are responded to faster
• Team member learning and satisfaction goes up
Changing the way teams perform for better results.
Learn more at: engineering.cmu.edu/ai-coach.
For three weeks this summer, Chris McComb stepped away from his lab to explore AI in the aerospace industry as part of Boeing’s Visiting Professorship Program.
Embedded in the company’s commercial aircraft division, McComb worked closely with research and technology leadership to understand what type of AI would best aid Boeing’s product development and how it could be rolled out effectively.
In one project, McComb explored uncertainty quantification for large language models. His team studied ways to improve the usefulness of models across topics like career development, python programming, and composite wing structure designs.
“Uncertainty quantification of large language models is something that I would like to see become a benchmark in the industry,” said Ron Engelbeck, an associate technical fellow who started work with Boeing on the B-52 over four decades ago. “Engineers are going to want to understand how much the uncertainty of the prompts are influencing the model responses. This will probably be one of the criteria we would look at to decide which large language model Boeing engineers will want to utilize.”
McComb also worked with Allison Fisher to model AI uptake within the organization.
Leaning into past research that used AI to explore pathogen risk, the team used a mathematical models for disease spread to treat AI as a “pathogen” - studying the way that people new to AI adopt it (“become infected”) as well as how those who use AI share that knowledge with others (“spread the disease”).
“By utilizing this model, companies can effectively plan for the uptake and adoption of AI technology,” said Fisher, a technical lead at Boeing. “It can help with planning for future opportunities in human-AI teaming.”
McComb is eager to continue his collaboration with Boeing and bring students into the mix.
“We are looking for projects that are both valuable for Boeing and are good learning and development experiences for master’s students interested in AI, manufacturing, and engineering design,” he said.
“We are at the stage now where the functionality of Generative AI can be applied to a multitude of places, so we want to find applications across a broad range of engineering problems.”
Beyond new research opportunities, McComb believes the experience will also help him to be a better advisor and advocate for his students that are interested in a career in the aerospace industry.
“I had a great experience with Boeing, and now I have a better understanding for how to prepare students for the aerospace industry and also drive industry-relevant research.”
An internship with NASA gives Scotty McGee a unique opportunity to bridge the gap between her academic research and industry application. The third year PhD student has been exploring applications of AI in academic team settings and with NASA, is now introducing the AI Coach to a unique industry setting.
“As an undergrad I was drawn to the design process and project based courses,” she explained. “This internship not only gives me the opportunity to work on an exciting NASA project with a great team of people, but gives me the chance to independently build an AI Coach to help their design process.”
McGee, advised by Chris McComb, Associate Professor of Mechanical Engineering, and Jon Cagan, Professor of Mechanical Engineering, has conducted multiple human subjects studies in design courses to validate her approach with students. At NASA, she has the opportunity to build an AI Coach tailored to a NASA team’s needs and study its use over time. This experience aligns closely with her PhD work, providing valuable feedback that will inform the next steps of her research and further refine the AI Coach for broader applications.
Until now, McGee has only studied how students use the AI Coach in very controlled settings so she believes she will gain valuable insight by observing design teams at work and collecting feedback.
As part of the Convergent Aeronautics Solutions (CAS) team, McGee also worked over the summer on the Aerial Aid project, which focuses on developing drones for emergency medical services. The project’s goal is to create drones that can automatically assess the scene of an accident, determine the number of patients and their conditions, and communicate this information to EMS personnel. This enables paramedics to arrive well-prepared, equipped with the resources they need, potentially saving time and lives “I’m grateful for the opportunities that the NASA CAS group is providing me to study how the AI Coach can be implemented outside of the university setting. The early stage projects in this group provide a strong platform to build from and I’m looking forward to seeing it evolve.”
Martha Baldwin, PhD candidate in the Design Research Collective lab, spent her summer in State College, Pennsylvania as a SOAR intern with Penn State University’s Applied Research Laboratory.
As part of the SOAR program, one of the most prestigious career development programs for student leaders in the country, Baldwin worked as a research and development engineering intern focused on making large-scale lattice structures manufacturable to address inherent limitations in large-scale additive manufacturing.
Lattices are a material structure made up of repeating patterns that are used to fill a 3D-space. They can help strengthen an additively manufactured product. As many industries look to adopt additive manufacturing methods to create more flexible, higher performance parts, being able to scale these structures is more important than ever before.
“My role focused on programming and validating a method to redesign lattices, ensuring compatibility with the constraints of large-scale additive manufacturing,” she explained.
Baldwin was particularly drawn to the SOAR program because of its unique combination of networking opportunities, professional development seminars, and specialized mentorship for students.
“Collaborating with a multidisciplinary research team was incredibly valuable. It highlighted how teamwork can significantly expand a project’s reach, contrasting with the narrower scope of individual PhD work. Additionally, I gained proficiency in nTop, a software essential for lattice design, thanks to support from team members who helped me master its advanced functionalities,” she said. “This experience has equipped me with practical skills and a new perspective on collaborative research, which I look forward to applying in my work at CMU.”
Baldwin published “Taking TPMS to the Limit: Developing a Novel Formulation to Control the Thickness of TPMS-based lattices for Additive Manufacturing” as a result of the internship.
1 Richard Desatnik and Nathan Zimmerer showcased three robots at the Robotics for a Better Tomorrow Robotics Showcase and Demo Day in Washington D.C.
2 Bailey O’Malley, Andrew McGovern Eyal Davidov and Alex Ivanov brought home the best prototype award at the 2024 TechSpark Design Expo for their FishTech SmartCast Fishing Reel. The reel automates casting and reeling operations for beginners and disabled fishers.
3 Hariharan Ramasubramanian’s paper, Impact of Static Disorder and Dynamic Disorder on the Thermal Conductivity of Sodium Superoxide (NaO2), was selected as a Featured Article in The Journal of Applied Physics. Its findings offer strategies for the design of thermal conductivity switches that are responsive to external stimuli.
4 Vismaya Walawalkar was selected as the best MechE TA for Spring 2024.
5 Sruti Bapatla, Sarah Jensen and Vic Nguyen were named Andrew Carnegie Scholars. They embody Carnegie Mellon’s high standards of academic excellence, volunteerism, leadership and involvement in student organizations, athletics or the arts.
6 Robert Coury was named a preseason All-American for the third consecutive time this football season.
7 Ellen Lee won the People’s Choice at the OSTEM conference in Portland, Oregon.
8 Vedant Puri, PhD student, and Aviral Prakash, Postdoctoral researcher, received the Best Poster Award in Computational Fluid Mechanics from the 16th World Congress on Computational Mechanics and 4th Pan American Congress on Computational Mechanics conference. The poster described a non-intrusive ML based reduced order model which speeds up numerical calculation of advection dominated PDE problems by up to 199x while maintaining high accuracy.
If engineers followed the ageold adage “If it ain’t broke, don’t fix it,” we wouldn’t have 95% of the technology that we can’t imagine our lives without. So when Erica Martelly was tasked with hosting a clinical trialsomething CMU has never done before - she didn’t bat an eye.
Martelly joined Kenji Shimada’s lab in 2018 to advance research on an existing project focused on developing comfortable, customizable sleep apnea masks. The team was developing a user-friendly software capable of generating custom mask designs via photogrammetry that could then be easily 3D printed.
“Our goal was to make something more comfortable than what is currently on the market, in a way that was simple enough for a technician to use without extensive training,” said Martelly.
Once the software was running, the team needed to conduct a clinical trial to test the efficiency and comfortability of the masks. But without a CMU medical school, Martelly couldn’t lean on existing processes.
“We collaborated with Allegheny General Hospital and the Allegheny Health Network, but because we don’t have a medical school the trial was sponsored by the university. We needed to obtain insurance and create a legal clinical trial agreement between the university and the hospital.”
After nearly four years of back and forth between the Institutional Review Board, the Food and Drug Administration, the hospital, and the university, the first patient was enrolled in the study during the fall of 2023.
Participants in the trial wore custom masks printed by Shimada’s lab in a sleep study so that researchers could analyze patients’ oxygen saturation levels, eye movement, brain activity, and more.
Despite success in the trials, Martelly said, “The coolest thing I’m taking away from this project is not the mask itself but that we got a clinical trial off the ground.
I don’t think researchers knew it was a possibility, but because we were pioneers I’m confident
other projects can move forward in their own clinical trials without partnering with a medical school.”
“If you’re looking to take a new path, whether that be a clinical trial or not, my advice would be to ask for help. Use your network and use the CMU community to your advantage.”
Carnegie Mellon Ph.D. students Darren Cheng, Chase McDonald, and Jenny Chang run a wonton stall, called Cup of Wontons, at the Squirrel Hill Farmers Market, where they serve traditional pork wontons with hot tea. They also serve special weekly wontons made with different ingredients like cumin lamb and black pepper chicken, and they sell custom locally printed t-shirts.
Cheng, a fifth-year Ph.D. student studying mechanical engineering, said his favorite part of running the stall is interacting with the Squirrel Hill community. As a Ph.D. student he spends a lot of time working in a lab, so getting out to make food for others is a welcome break.
“I couldn’t do it without Chase and Jenny,” said Cheng.
Cheng credits his passion for cooking to the trio’s annual Friendsgiving celebration, along with other “cooking parties.” He said socializing remains an important part of their kitchen dynamic, even while running a business.
“It’s nice to get really great feedback from the community,” said Cheng. “When we started back up this year, a lot of people said they were waiting for us and were so excited that we were back.
There are definitely people that I see every single weekend, and I know most of their names by now. Being part of the broader community outside of CMU is something that I’m really proud of.” Cheng, McDonald, and Chang all play integral roles at Cup of Wontons. The process begins on Thursday evenings in a rental kitchen at Eastminster Presbyterian Church where they prepare and freeze the food. On Sunday mornings, Cheng and Chang set up the stall at the market while Chase picks up the food from the church. Cup of Wontons is open from 9:00 a.m.–1:00 p.m., or until they sell out. Cheng typically takes orders while Chang cooks and McDonald garnishes.
“Being part of the broader community outside of CMU is something that I’m really proud of.”
Darren Cheng, Ph.D student, Mechanical Engineering
“During recipe development, we all mix a half-pound of pork and try throwing different ingredients in to try to improve things,” Cheng explained.
“We’re just eating and talking and hanging out at the same time.”
Cheng was inspired to create Cup of Wontons in the fall of 2023 after eating at his girlfriend’s aunt’s pho shop in Vietnam. It reminded him of his childhood when he would make and eat wontons with his family.
“Every morning we’d wake up and get pho. It was such a great way to start off the morning, and I kept thinking it would be really cool if we had something like this in Pittsburgh,” Cheng said.
Running Cup of Wontons provides valuable business experience, too. Cheng said learning how to do administrative tasks like obtaining an LLC is helpful if he starts an engineering company.
The future of Cup of Wontons is unclear after Cheng and McDonald graduate in May and leave Pittsburgh. But even with this uncertainty, Cheng is confident this experience will stay with him after leaving CMU.
“It sounds corny, but it will always be a part of me,” said Cheng.
Our AI powered robots mimic natural organisms and do not disturb sea life. They operate without motors and move and sense silently, without creating noise or acoustic traces to interfere with the environment.
Softbotic systems are ideal for tracking the health and quality of water and are used by national and international oceanographic agencies. They can also be made biodegradable to eliminate waste and protect the natural environment.
Bringing robotics into everyday life.
When we work together, we come up with better solutions more efficiently. In partnership with peer universities, corporations, and government agencies, MechE faculty are making real-world impact.
24 Safe AI for safer city streets for all
26 CMU, Meta announce research collaboration aimed at making computer-based tasks and gaming accessible to people with different motor abilities via wearable sensing technology
28 Engineering research center to improve robot dexterity selected to receive up to $52 million
30 Carnegie Mellon lands ARPA-H award for implantable bioelectric medicine project
IMAGE / Research map built by Associate Professor Chris McComb showcases the interdisciplinary nature of the Mechanical Engineering Department at Carnegie Mellon University and the many opportunities for collaboration. Each dot is representative of a faculty research paper while each color represents an individual faculty member. The dots are mapped according to research focus-areas.
In collaboration with THE CITY OF PITTSBURGH
Ding Zhao is teaming up with The City of Pittsburgh to improve road safety and eliminate traffic fatalities using AI.
Over 40,000 people have died on U.S. roads in each of the last three years. In an effort to eliminate these preventable accidents, The Department of Transportation has awarded The City of Pittsburgh, in partnership with Ding Zhao, $1.3 million to analyze Pittsburgh’s current transportation infrastructure and inform safety-first upgrades by the end of 2026.
As part of the Biden-Harris Administration’s Bipartisan Infrastructure Law for the Safe Streets and Roads for All (SS4A) program, the project will support a road safety audit, the development of a Vision Zero-focused streets design manual along with quick build projects and a Vision Zero ambassador program to eliminate traffic fatalities and increase equitable mobility.
Ding Zhao, director of the Safe AI Lab and Professor of Mechanical Engineering at Carnegie Mellon University will use large language models (LLMs) to analyze Pittsburgh’s streets, identify which intersections are the highest-risk for drivers and pedestrians, and work with city officials to test new street design improvements.
“Large language models offer a very scalable, very powerful way to collect data and run simulations,” explained Zhao. “By collecting more data, more efficiently, we can be inclusive of rare events and vulnerable users.”
The team will also use LLMs to analyze the results of their simulations, an approach Zhao says is novel to transportation and infrastructure.
“We have a clear goal for this project and by working with The City of Pittsburgh we are guaranteeing real world impact,” said Zhao. “I’m excited to see how my research will positively affect our neighborhoods. If we can save even one person, I’ll be very proud.”
“We’re excited to partner with the research teams at Carnegie Mellon University as we work toward our goal of zero traffic fatalities,” said Mayor Ed Gainey. “To make our streets safer, we need to break down silos and build strong
partnerships between the City of Pittsburgh and our private institutions. Together, we can drive the kind of innovation that makes a real difference in roadway safety.”
Zhao, who has been working to advance AI in self-driving cars for nearly a decade, is also eager to explore how enhanced infrastructure can make the roads safer for semi and fully autonomous vehicles.
The team will leverage on its inhouse tool
SafeBench (https://safebench.github.io/), an open-sourced platform designed to assess and improve the safety of AI models based on a highfidelity autonomous driving simulator. SafeBench provides a suite of standardized benchmarks and testing environments for evaluating how AI models perform in dynamic, safety-critical situations, such as autonomous driving or infrastructure planning. This tool can be integrated into projects like Pittsburgh’s transportation audit by offering a rigorous framework for analyzing AI-driven systems’ resilience under various conditions, including multimodal perturbations and rare events. By ensuring the safety and robustness of AI systems, SafeBench will help cities like Pittsburgh deploy cutting-edge AI technologies with confidence, minimizing risks and enhancing the overall safety of public infrastructure.
“SafeBench allows us to identify potential safety issues in the AI-empowered systems early on, which helps improve their reliability as they are integrated into real-world applications,” said Haohong Lin, a PhD student at Carnegie Mellon University working with Zhao.
“I have been working on self-driving cars for 17 years,” Zhao said. “This project opens a new door for us to explore how streets can be modified to provide a safer environment for us all both today and in the future when humans will share the road with AVs.”
As part of a larger commitment to developing equitable technology, Carnegie Mellon University and Meta announce a collaborative project to make computerbased tasks accessible to more people. This project focuses on using wearable sensing technology to enable people with different motor abilities to perform everyday tasks and enjoy gaming in digital and mixed reality environments.
Meta’s research in electromyography uses sensors placed on the skin to measure the electrical signals the user generates through muscles in their wrist, which are translated into input signals for various devices. While Meta has already demonstrated that this technology could replace keyboards and joysticks, the team continues to invest and support different projects to confirm that this technology can be used by a wide range of people.
physical motion and relying instead on muscle signals. If successful, this approach could make computers and other digital devices more accessible for people with physical disabilities,” said Weber.
Working with Meta, Weber’s team seeks to build upon their initial results to assess whether and to what extent people with spinal cord injury can interact with digital devices, such as computers and mixed reality systems, by using Meta’s surface electromyography (sEMG) research prototype and related software.
Wearing the electromyography wristband, a participant in the study who has been unable to move his fingers since 2005, was able to control a computer cursor and gamepad buttons.
Douglas Weber, a professor in the Department of Mechanical Engineering and the Neuroscience Institute at Carnegie Mellon University, has shown previously that people with complete hand paralysis retain the ability to control muscles in their forearm, even muscles that are too weak to produce movement. His team found that some individuals with spinal cord injury still exhibit unique muscle activity patterns when attempting to move specific fingers, which could be used for human computer interactions.
“This research evaluates bypassing
The project centers on interactive computing tasks. Approved by the Institutional Review Board, study participants begin by performing a series of adaptive mini games. Once their proficiency is benchmarked, the CMU team creates new games and other activities in mixed reality that are tailored to the abilities and interests of the participant.
“In the digital world, people with full or limited physical ability can be empowered to act virtually, using signals from their motor system,” explained Dailyn Despradel Rumaldo, PhD candidate at Carnegie Mellon University.
“In the case of mixed reality technology, we are creating simulated environments where users interact with objects and other users, regardless of motor abilities.”
The project comes as an ongoing research investment by Meta to support the development of equitable and accessible interfaces to help people do more, together.
Carmel Majidi will lead a research thrust in a new multi-institutional collaboration that has received $26 million from the National Science Foundation to launch an Engineering Research Center (ERC) dedicated to revolutionizing the ability of robots to amplify human labor.
Carnegie Mellon University will be a core partner in a new multi-institutional collaboration that has received $26 million from the National Science Foundation to launch an Engineering Research Center (ERC) dedicated to revolutionizing the ability of robots to amplify human labor.
Nine Carnegie Mellon University faculty members, with expertise ranging from Softbotics, engineering, and computer science to psychology, will help to develop highly dexterous robotic hands, userfriendly interfaces, and accessible training materials to empower diverse workforces to implement robotic solutions quickly and reliably.
The NSF grant will fund the new center across five years, with the ability to renew for another $26 million for an additional five years. It marks the first ERC led by Northwestern. Core partners include Carnegie Mellon University, Florida A&M and Texas A&M with additional faculty support from Syracuse University, the University of Wisconsin-Madison and the Massachusetts Institute of Technology.
Called Human AugmentatioN via Dexterity (HAND), the new ERC will build robot hands with the ability to assist humans with manufacturing, caregiving, handling precious or dangerous materials, and more. The center aims to build technological tools
that are versatile and easy-to-integrate, creating robots capable of intelligent and versatile grasping, fine motor skills, and hand-eye coordination.
An expert in Softbotics, Carmel Majidi, professor of mechanical engineering at Carnegie Mellon University, will lead the research thrust focused on developing robust, mass-manufacturable robot hands that achieve breakthrough capability via soft-yetdurable sensing skins, advanced actuators, and novel designs optimized for versatility and robustness.
“It’s an exciting time for Softbotics,” said Majidi. “We will be solving major challenges to build the artificial muscles, responsive skin-like material, and motor-powered tendons needed for user-friendly robots with dexterous capabilities to empower tomorrow’s workforce.”
This research is an extension of his 2020 moonshot project, Intelligent Symbiotic Systems, which pioneered new classes of intelligent programmable matter for transformative impacts on robotics and human-machine interactions.
“Our moonshot project was all about creating a new paradigm in bio-inspired engineering in which autonomous robotic functionality—with integrated sensing, actuation, learning, decision making, self-repair, and energy storage—is intrinsically achieved at the materials level with limited dependency on traditional motors or electronic hardware. These novel materials are critical to the development of lightweight yet mechanically robust and versatile robot hands,” said Majidi.
Other CMU collaborators include Alaine Allen and Gary Fedder from The College of Engineering; Roberta Klatzky from the Department of Psychology and Human
Computer Interaction Institute; Nancy Pollard, Oliver Kroemer, and Melisa Orta Martinez from the Robotics Institute; and Katharine Needham from the School of Computer Science.
The interdisciplinary team will work to ensure new robotic hands are inexpensive, easy to operate without expertise, robust, durable, and massmanufacturable. They will help to develop and prepare a diverse workforce for an entirely new field of study focused on dexterous robots and foster a culture that nourishes inclusivity and ensures equitable access to new technologies. Potential outcomes will include increased worker productivity, improved job opportunities, reshoring of manufacturing, reduced supply chain vulnerability, enhanced food safety, improved quality of life and democratization of the benefits of robotics.
Since its founding in 1985, the ERC program has supported convergent research, education, and technology translation at U.S. universities. Each ERC unites members from academia, industry, and government to produce transformational engineered systems along with engineering graduates who are adept at innovation and primed for leadership in the global economy.
“NSF’s Engineering Research Centers ask big questions in order to catalyze solutions with far-reaching impacts,” said NSF Director Sethuraman Panchanathan. “NSF Engineering Research Centers are powerhouses of discovery and innovation, bringing America’s great engineering minds to bear on our toughest challenges. By collaborating with industry and training the workforce of the future, ERCs create an innovation ecosystem that can accelerate engineering innovations, producing tremendous economic and societal benefits for the nation.”
A Carnegie Mellon University-led team has secured an award of up to $42 million from the Advanced Research Projects Agency for Health to accelerate the development of implantable, cell-based bioelectronic devices that deliver patient-specific therapy and monitor disease status, for conditions like hypo- and hyperthyroidism, in real time. This award is part of the ARPA-H REACT program, which supports the advancement of implantable bioelectronic devices to improve patient management of chronic diseases.
Ginkgo Bioworks and Velentium, are also integral parts of the consortium.
During the six-year project term, the team will develop and test two multi-part, pacemaker-sized system platforms that will be implanted in a patient’s chest cavity through an outpatient procedure and offer realtime, adjustable, low-cost therapy and disease monitoring for up to 12 months.
Following a “living pharmacy” concept, one of the systems will use human cells to produce and release the necessary dose of a hormone or other therapeutic
Burak Ozdoganlar, professor of mechanical engineering at Carnegie Mellon University, will head the Biointegrated Implantable Systems for Cell-based Sensing and Therapy (BIO-INSYNC) project as the primary investigator. This effort is part of the ongoing Bioelectric Medicine Initiative at Carnegie Mellon University. In addition to Carnegie Mellon researchers, the multidisciplinary project team includes members from the University of Pittsburgh/UPMC, University of Florida, and University of California - Santa Cruz. Two companies,
adults. BIO-INSYNC devices will provide a significant advantage to patients who will be able to continuously monitor key hormones and deliver the right therapeutic dose as needed, eliminating current management protocols like daily medications and regular blood testing. Notably, the project will conduct a first-in-human clinical trial for patients facing thyroid conditions.
“The thyroid gland controls so many integral processes within the body, and thyroid hormone imbalances can lead to weight gain or loss, mental health
“The aim is to improve patients’ quality of life by improving thyroid treatments while bridging disparities in healthcare to attain equitable care for all.”
-Burak Ozdoganlar, professor, mechanical engineering
molecules on demand. Utilizing a “living sentinel” concept, the second system will use cells that measure critical biomarkers to monitor the patient’s disease status continuously in real time. Both will feature remote interfaces to communicate key information and measurements with the patient via smart devices or directly to their healthcare provider.
While this technology can be used to treat various diseases and conditions, the collaborative team will specifically focus on its application to thyroid disorders, which impact an estimated 12% of Americans, including children and
issues, fertility problems, and even heart diseases,” explained Ozdoganlar.
“It’s important also to note that thyroid disorders disproportionately impact vulnerable populations. Our bioelectronic system offers an innovative avenue for patients to self-manage their thyroid hormone levels at a fraction of the cost.
The aim is to improve patients’ quality of life by improving thyroid treatments while bridging disparities in healthcare to attain equitable care for all.”
It wasn’t until after Natha (Bam) Singhasaneh, MechE ‘18, spent a few years at startup companies, explored teaching, pursued a master’s, and joined a BattleBots team that she found her place at the intersection of all of the above. Today, Singhasaneh is a product designer at Crunch Labs where she designs toys that inspire kids to become creative problem solvers by evoking their curiosity in science and engineering. “I’ve always felt that being interdisciplinary minded made all the difference in my pursuits,” she said. “I am far from being an expert in everything, but being able to look at problems from different perspectives allows me to come up with creative and unique solutions.”
As an undergraduate in The Department of Mechanical Engineering at CMU, Singhassaneh was a researcher in Aaron Johnson’s Robomechanics Lab. There
she drew inspiration from mountain goat hooves to study the underlying principles behind optimal surface grip and compliance for legged robots to improve their ability to maneuver steep and uneven surfaces. With minors in robotics and business, and a special interest in entrepreneurship, Singhasaneh went on to work in consumer product development at two different startups.
“Working in a startup environment was a good learning experience because I had the opportunity to do not just engineering, but also user research, marketing, business planning, and more,” she said. “I learned that being able to view a product in a holistic way is critical towards success. For example, it doesn’t matter how well you hone in on your product, if it doesn’t address a real need no one will buy it. And as an engineer, it’s very easy to be focused on asking
‘how’. But sometimes, it’s also important to take a step back and ask ‘why.’”
Like many during the Covid-19 pandemic, Singhasaneh was furloughed, but it didn’t slow her down.
“There was a math school across the street from my apartment, and I went up to their door and asked if they needed teachers. That job made me fall in love with working with kids.”
Singhasaneh explained that when working with students as young as six years old you have to challenge your assumptions of what they know and empathize with them.
“Their mental model of the world is completely different from our own,” she said. “Although teaching wasn’t always easy, receiving a message from a student at the end of class expressing his or her love for math made it all worthwhile.”
With a new found appreciation for
interdisciplinary thinking, Singhasaneh enrolled in MIT’s Integrated Design and Management program where she practiced human-centered design and had her first experience designing toys.
“We didn’t start out the project knowing that we were going to design a toy. Instead, we found through research that a toy was the right solution to the problem we were trying to solve. This was when I started seeing toys as a medium that has great potential to communicate and bring about mindset and behavioral change.”
She dove deeper into her passion for creating meaningful experiences for children in her master’s thesis titled Climate Change Conversations with Children: Making Sustainability Meaningful, Tangible, and Actionable. Utilizing human-centered design, she engaged various stakeholders to develop a framework for communicating sustainability to young children.
“When it comes to toys and play, the best kind is when you’re just having so much fun that you don’t even know you’re learning,” she said.
“We called this ‘Sneaky Learning.’”
After designing a toy called the RumbleBug for a class project, Singhasaneh spent a summer in San Francisco interning at IDEO’s Play Lab as a toy inventor where she further gained exposure to the toy industry.
“The toy space is a really fun space to be creative in,” she said. “Empathy is at the heart of it because you have to put yourself in the kids’ shoes. However, you also have to be mindful about what parents want their kids to gain from playing with the toys. Parents don’t want just another piece of ‘plastic glitter’, they want to see value in it.”
It was around this same time that a friend talked her into joining a BattleBots team where she learned a
lot about hands-on engineering, design iteration, and the value of failure.
“It’s also rewarding to see many young kids get excited watching robots fight and grow curious about engineering. At her current role as a product designer at CrunchLabs, Singhasaneh is using toys to inspire and teach kids about science and engineering. One toy she designed allows kids to build their own treasure chest with a unique combination code that can only be opened with a corresponding key.
“To me, to play means to explore without a purpose, and to engage in activities without fear of failure –even an expectation of it. And play is not just for kids! We shouldn’t be afraid to play and explore because it’s by doing that that we garner new perspectives, fail in unexpected ways, and are propelled to create change and bring new things to the world.”
CMU alumnus Pete Manautou invents sensor to detect harmful airborne pathogens before they spread
Carnegie Mellon University alumnus Pete Manautou had two goals when starting his company: fulfill a promise he made to his son and make a difference in people’s lives.
Pete is the founder of Scanit Technologies, which currently helps agricultural growers maximize yield and minimize crop loss through autonomous airborne pathogen detection. The company’s platform uses its patented SporeCam, a multi-modal miniaturized optical microscopic sensor, to capture, inspect and classify particles in the air, and then alert growers of the presence of harmful pathogen spores that can lead to disease.
“We have an ability to tell farmers and growers, both indoor and outdoor, that disease is coming their way,” Pete, a 1999 graduate of the College of Engineering, says. “We can see it two to three weeks before the human eye and current postinfection technologies can detect it.”
The data collected by the optical sensors empowers growers to mitigate disease before it’s too late. In the future, Pete hopes to expand the technology to other industries where early detection could make a difference.
“Having access to that data, that amount of information early on, can equip the end user with the information they need to make better decisions,” he says.
“That’s what we’re doing at Scanit — improving quality of life.”
Keeping his Promise
Scanit’s vision — to dramatically improve quality of life by knowing what’s in the air — is personal to Pete. He founded the company in 2015 after his then 2 1/2-yearold son, Christian, died following a year-long battle with cancer.
When first diagnosed with cancer at 18 months old, Christian spent four straight weeks in the hospital undergoing treatment that compromised his immune system. When he was discharged, the doctors issued a warning to Pete and his wife.
“They said ‘Keep him away from things that will make him sick,’” Pete says. “So my wife and I had a discussion with the doctors. We said, ‘How do we know what’s going to make him sick?’ And they’re like,
‘Definitely anything with fungus. If you think there’s black fungus in your home, which you would usually see around windows with high condensation or humidity, there’s probably some fungus out there.’”
Pete and his wife began looking for something they could use to instantly identify fungus or other harmful particles in their home. When they couldn’t find a solution, he decided to invent one.
“I was surprised we could not find anything,” Pete says. “So I told her, ‘I think I can build something based on what know that can tell me what the actual particle is. Not only that there is a particle, or the size of the particle. I want to
classify that particle we are breathing and being exposed to. I want to know if the particle is friendly or if it’s a foe that is going to make me sick.’”
A few months after Christian’s death, Pete quit his full-time job to focus on Scanit Technologies. It was an easy decision, because it meant fulfilling a promise he made to Christian on the day he was discharged from the hospital.
“It was just me and him and the EMTs [riding home] in an ambulance,” Pete says. “I was holding him the entire ride, knowing this would be
experience necessary to make it work.
During his third year at CMU, Pete received a Small Undergraduate Research Grant to test cyclic fatigue of spinning rods.
“I had to use a lot of the knowledge from different disciplines that I took courses on,” says Pete, referring to various electrical and mechanical engineering subjects. “There were so many things that came into play.”
His research led to two internships at Aristech, the former U.S. Steel’s chemicals division, which manufactured chemicals
devices. The experience gave him the confidence he needed to start Scanit and develop a detection device of his own.
Creating a Legacy
Pete credits Carnegie Mellon for the success he’s achieved in his career.
“I wonder, had I not gotten that SURG grant, where would I be today?” he says.
“Because that led to the two internships, then my first job from those internship experiences, then where I’m at now. It propelled my career. Being able to connect so many skillsets to solve
“We have an ability to tell farmers and growers, both indoor and outdoor, that disease is coming their way. We can see it two to three weeks before the human eye and current post-infection technologies can detect it.”
-CMU alumnus
Pete Manautou
his last going home. And I told him that I’m going to do something that will hopefully make a difference in people’s lives. And that was it.”
Building a Blueprint
Pete faced a major challenge when he started Scanit. He wasn’t adapting technology that already existed — he was inventing something completely new.
“If a technology already exists in the market and somebody already went through all the kinks and twists and troubles of figuring it out, you have a blueprint to do something better,” he says. “In our case, there was nothing that could tell us what’s in the air. Specifically, classifying the actual particle that’s in the air. And when you’re first at doing something that the world hasn’t seen, it’s going to take some time to figure out all the science and the engineering behind it.”
Still, he felt he had the background, from his Carnegie Mellon education, and
used across multiple industries, and then a full-time job at DaimlerChrysler doing design work on autonomous rail systems. He worked there for about a year before deciding to switch careers.
“With autonomous trains, you’re working with a lot of government agencies and you’re super busy at times and then not so busy sometimes,”
Pete says. “I wanted to do something a little more active and exciting.”
He contacted the CMU Alumni Association, which helped him set up interviews and land a job in the semiconductor inspection and process control industry in San Jose, California.
“That’s what catapulted me into learning so much about so many different disciplines,” Pete says.
He stayed in the industry for more than 15 years, focusing on defect detection, process control and metrology, and sensor development, which involves studying the physical, chemical, material and electrical properties of semiconductor
problems, not just to learn the theory behind them, but to solve problems, is an incredible experience. I don’t think I would be here without that, honestly.”
In 2014, he and his wife established the Christian J. Manautou Andrew Carnegie Society Legacy Scholarship in honor of their son. Through the scholarship, they are able to assist a student enrolled in a designated school or college. The gift immediately benefits the student, much like the SURG grant benefited Pete. It also honors Christian’s life in a touching way.
“He didn’t get to see the world,” Pete says. “And feel that if I can make a difference in someone’s life through that scholarship, there’s a little piece of Christian in them out in the world, and hopefully they will make an impact on someone’s life as well.
“I feel that if I make a difference, there’s a little piece of Christian out there doing the same.”
received the International Association for Computational Mechanics (IACM) Fellows Award.
was named faculty director of the Center for Faculty Success.
was awarded the Outstanding Academic Award by the Construction Industry Institute.
received the Dean’s Early Career Fellowship.
participated in the 2024 Grainger Foundation Frontiers of Engineering Symposium, a signature activity of the National Academy of Engineering (NAE).
was awarded the Denice Denton Mentorship Award from the Transducers Research Foundation at the Hilton Head Workshop.
was named a Fellow in the American Association for the Advancement of Science for 2023 due to his research in the mechanics of cellular and molecular systems.
Jon Malen
was named the Raymond J. Lane Distinguished Professor of Mechanical Engineering.
Levent Burak Kara
received the Clarence H. Adamson Professorship in Mechanical Engineering.
Chris McComb
was named the Gerard G. Elia Associate Professor of Mechanical Engineering.
Amir Barati Farimani
received the George Tallman Ladd and Florence Barrett Ladd Professorship in Mechanical Engineering. was named the Russell V. Trader Associate Professor of Mechanical Engineering.