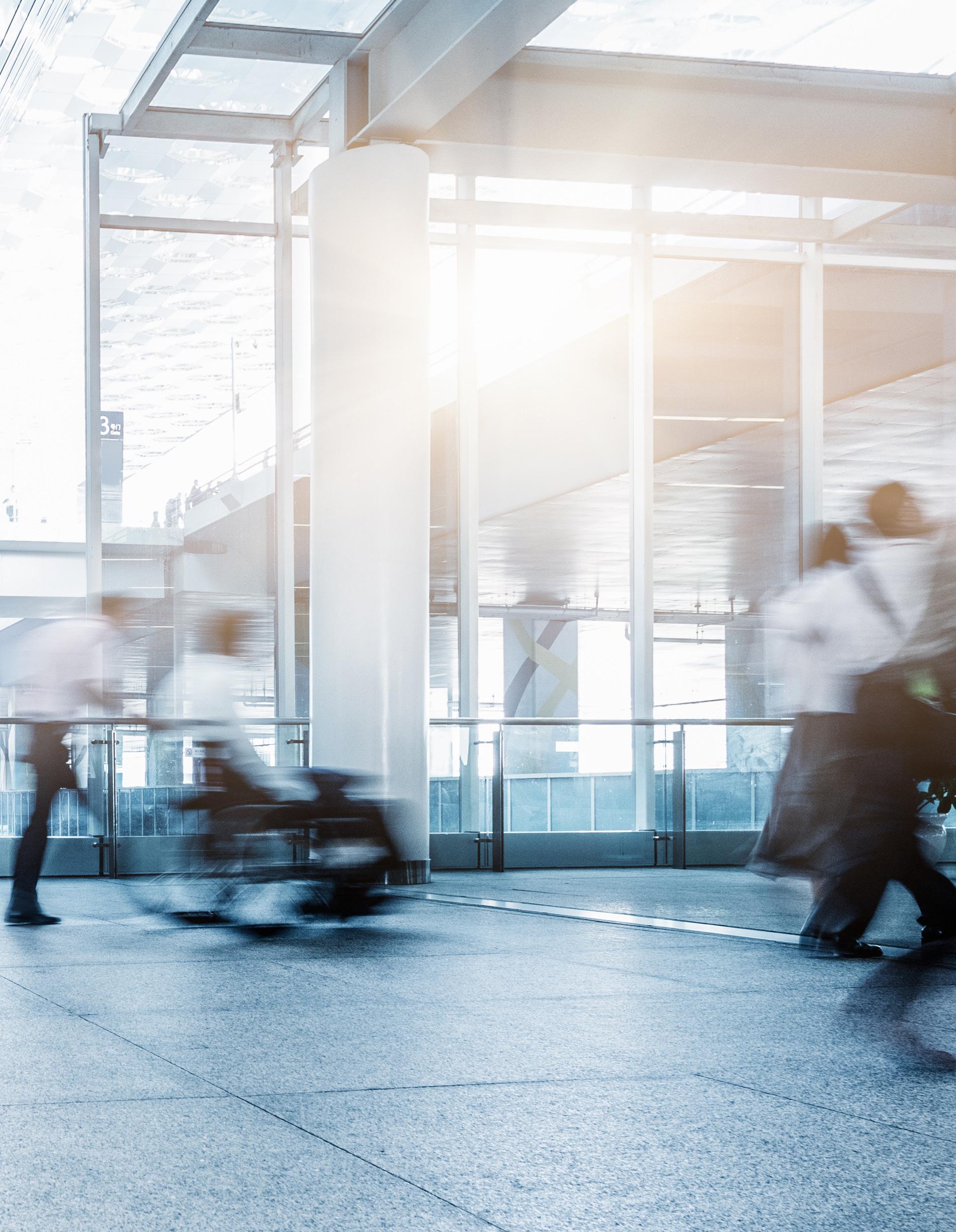
Aviation + Aerospace Design
CMTA Project Experience
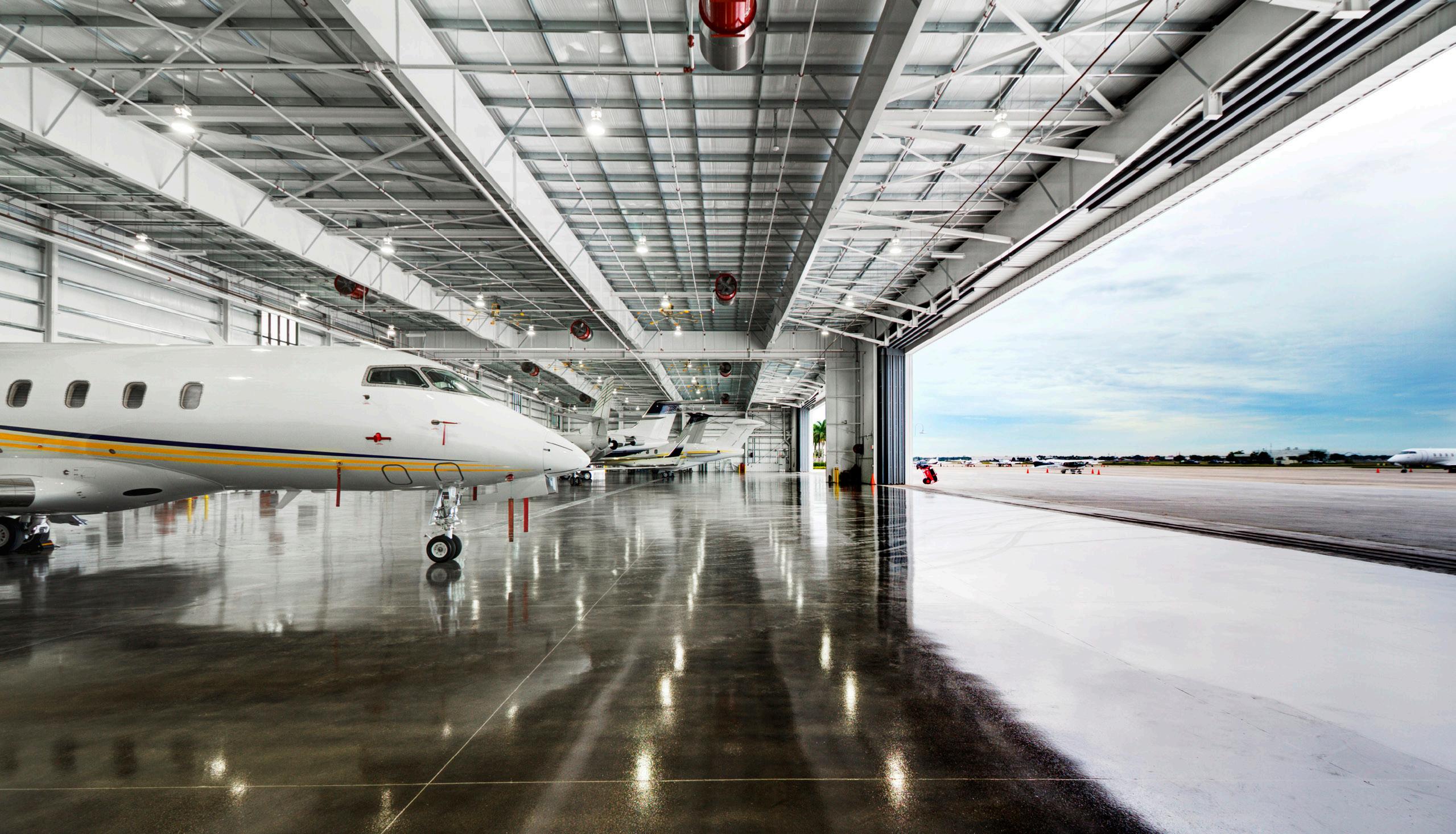
CMTA Project Experience
CMTA is a multi-specialty firm that focuses on building systems engineering – designing cost-effective, energy-efficient, high-performance buildings. We function as a trusted partner and guide for the owner and design team bringing energy reduction, decarbonization, and health and wellness goals to fruition. As CMTA strives to improve the built environment, we also invent products, set national goals, and work to transform the market to improve results for everyone. We define our innovative approach to engineering as — Building Science Leadership.
We are Data Driven, and Results Proven. Over the last 20 years, we have collected utility data on our projects, allowing us to continually improve our approach. This database means we design from verified information and not engineering theories, as well as understand how to make these buildings a reality without extra first costs.
– MEP Engineering
– Zero Energy/Carbon Engineering
– Renewable Energy & Sustainability Engineering
– LEED & WELL Building Certification Consulting
– Energy Modeling
Commissioning Services – Technology/Security Infrastructure Design – Performance Contracting – Construction Administration – Energy as a Service (EaaS)
1126+
We’ve completed airport/aviation design for clients around the nation using a holistic approach to address maintenance, reliability, and energy efficiency. We understand the importance of designing a space that supports state-of-the-art equipment and technology while focusing on safety and security. Whether designing a new terminal, a lounge renovation, hangar upgrades, or a flight operations facility, strategic collaboration among the design teams, owner, facilities staff, and code officials is key to project success. Due to the intricacies of these spaces, we encourage input from the owner and work directly with equipment suppliers to design systems specific to the owner’s needs.
Louisville Muhammad Ali International Airport — KY
Cincinnati/Northern Kentucky International Airport — KY
Memphis International Airport — TN
Hector International Airport — Fargo, ND
Dayton International Airport — Dayton, OH
John F. Kennedy International Airport — Queens, NY
Baltimore-Washington International Airport — Baltimore, MD
Portland International Jetport — Portland, ME
Wolf Point Airport — Wolf Pointe, MT
Columbia Metropolitan Airport — Columbia, SC
Charlotte Douglas International Airport — Charlotte, NC
Elizabeth City State University Aviation School Hangar — Currituck, NC
Fargo Jet Center — Fargo, ND
The Boeing Company — Charleston, NC
Boone National Guard Army Aviation — Frankfort, KY
Blue Grass Airport — Lexington, KY
Monaco Air — Duluth, MN
Dulles International Airport — Dulles, VA
Bill and Hilary Clinton National Airport — Little Rock, AR
Ronald Reagan Washington National Airport — Washington, DC
TSA - Transportation Security Administration
Norman Y. Mineta San Jose International Airport — San Jose, CA
In 2021, the Louisville Regional Airport Authority (LRAA) selected CMTA to execute design and manage construction of terminal improvement projects at their facilities, including the Louisville Muhammad Ali International Airport (LMAIA). As Construction Manager at Risk (CMaR), CMTA is responsible for the design, acquisition, installation, and overall execution of current and future planned improvement projects, including architectural upgrades, energy management, energy conservation measures, and construction reporting services.
LRAA selected CMTA for this important project due to our commitment to cost savings and pricing transparency, and our
track record of proven results in Louisville and throughout the US.
The approach to this multi-phased project was developed to enable the execution of currently designed and owner approved projects, while additional terminal improvement plans are developed and analyzed by LRAA with future work being approved as local and Federal funding allows. The total project cost with all planned work phases is estimated to be between $60M to $100M.
This has involved the following scope of services:
– Developed, reviewed and approved a comprehensive LMAIA MEP and Terminal Improvement (MEP/TI) phasing/task order plan
– Developed phase 1 true guaranteed maximum price (GMP) contract that includes 100% local contractor participation. In addition, current phase anticipates ~22% labor and material disadvantaged business enterprise (DBE) participation which is 120% higher than LRRA’s typical DBE project utilization goal.
– Developed multi phased implementation plan that is currently on schedule.
– Central Generator Plant / Microgrid
– Terminal Tenant Office Renovations
– Terminal Tunnel Renovation
– Terminal Electrical Upgrades
– Terminal K5 and PR Gate Replacement
Continued
Louisville Muhammad Ali International Airport Renovations
Louisville Regional Airport Authority (LRRA) | Louisville, Kentucky
– Terminal Bag Belt Upgrades
– Terminal Security Checkpoint Addition and Renovation
– Terminal Graphics Addition
– Terminal Customs Office
– Terminal Retail Space Renovation
– Terminal Security Upgrades
– Replacement Bag Belt System
– Runway Lighting Upgrades
– Runway Lighting Assessment
– Roadway Signage Lighting Assessment
– Quick-Turn-Around Rental Car Facility and Parking Modifications
– Rental Car Renovation
– New Observation Waiting Parking Lot
– Airport Operations Center
Geothermal System
As part of this renovation effort, the team designed a geothermal system - the largest of any airport in the US. It includes 648 vertical wells each drilled 500 feet deep
into the earth. The system saves massive amounts of energy by using the earth’s natural temperature to heat in the winter and cool in the summer replacing the need for additional equipment. The HVAC system will increase the amount of outside air that is brought into the terminals and other spaces, which contributes to a healthier and more comfortable environment for travelers and airport staff.
With the geothermal system in place, old systems that require large, loud cooling towers and boilers will be removed, making space for needed future terminal expansion.
The geothermal project will cut carbon emissions by more than 80% and cut heating and cooling operating costs by nearly $400,000 per year. It will use 40% less energy than traditional heating and cooling systems and will require less maintenance over the course of system life. Geothermal systems have a much longer
life expectancy than traditional systems and contribute to a more resilient terminal overall.
Projects at a Glance
Various projects have stemmed from this contract as noted above. Ranges of these task orders are as follows:
Construction Cost: $1M-$400M
Design Cost: $12,000 - $2M
Project Type: Renovations
Completion: Ongoing
80% Carbon Reduction
40%
Energy Reduction vs. Traditional Systems
The airport terminal building at LMAIA currently has insufficient generator capacity to operate safely in the event of a complete utility outage. This project will improve the resiliency of the terminal building by providing a centralized generator plant that will allow the entire terminal building to remain operational in the event of complete utility power failure.
The new generator plant has been sized to accommodate current and projected airport loads based on the airport improvement program currently underway. Provisions have been included for additional generation capacity to be added in the future as it becomes necessary. The new generator plant has been designed with resiliency in mind, including resistance to severe storms as common for the region. Lastly, airport
sustainability has also been considered, including photovoltaic (solar) generation, battery energy storage, and microgrid controls.
The scope of work includes:
– Generator Building to be constructed South of existing Main Switchgear Building
– (3) 2.25 MW 15kV Tier 4 Diesel Generator Sets, plus space for (1) Future
– Fuel Tanks sized to provide 72 hours of runtime at 75% rated load
– Integrates new 15kW Generator Paralleling Switchgear with Existing 15kV Switchgear
– Clean Agent Fire Suppression Systems in 15kV switchgear and generator buildings
– Removal of existing generators at Operations Center, Landside, and Airside Terminals
– 500 kW / 1.5MwH Battery Energy Storage System for Demand Reduction
– 80kWDC Photovoltaic (PV) System on East Baggage Building Roof for Carbon Reduction
Project at a Glance
Completion: 2025 Estimated
Size: 6.75 MW (Expandable to 9 MW)
Power Generation
Cost: $18M Estimated
Project Type: New Construction
CMTA was proud to be part of the Elevate CVG campaign, a multi-year, $400M terminal redevelopment effort that will transform the Cincinnati/Northern Kentucky International Airport (CVG) into a modern, efficient hub for travelers.
As a subconsultant to Corgan and Pasley, our team contributed our expertise in mechanical, electrical, plumbing, fire protection, and technology to the project’s planning design documents, serving as a critical guide for the design-build teams in the upcoming phase of the redevelopment.
The Elevate CVG project is simple. It seeks to overhaul operational efficiency, enhance passenger experience, and modernize facilities that haven’t seen significant renovations in decades. The project will breathe
new life into the two existing concourses A and B, originally constructed in 1993, which had not undergone any major upgrades since 2012.
A key focus of the redevelopment is the modernization of the Welcome Pointe—the airport’s primary customer-facing area for arriving passengers. This redesign includes new security technology to streamline passenger flow and boost safety.
Additionally, CVG is aiming to create a more welcoming and regionally representative space with artwork and displays that celebrate the Greater Cincinnati area. This sense of place will be woven throughout the terminal, giving travelers a clear connection to the region as they arrive and depart.
To accommodate this bold change, major mechanical and electrical infrastructure will need to be relocated and expanded. With this, operational efficiencies and maintenance, along with energy efficiency are a primary focus throughout the project.
This ambitious modernization effort, funded through a combination of the airport’s capital budget, general airport revenue bonds, and passenger facility charges, will position CVG as a leader in the aviation industry.
Project at a Glance $400M Terminal Redevelopment
As part of the growing passenger and cargo aviation needs in Cincinnati and Northern Kentucky, CMTA was selected as the prime contract holder for the MEP on-call project at Cincinnati/Northern Kentucky International Airport (CVG) to implement a host of enabling and remediation jobs for the airport. This project is a key component of the Elevate CVG program, a multi-year redevelopment plan designed to modernize the airport’s infrastructure, boost operational efficiency, and enhance the passenger experience.
Our role as the lead on the MEP on-call project positions us at the heart of this transformation, where we will be responsible for developing the airport’s Utility Master Plan. This crucial master planning effort will inform and support the broader Elevate CVG program, ensuring that CVG’s utility infrastructure is optimized to meet the growing demands of travelers and airlines alike.
In collaboration with a powerful team of national consultants, including Gresham Smith, Prime Engineering, Arora Engineers, and Motz Consulting Engineers, CMTA is in the process of delivering cutting-edge mechanical, electrical, plumbing (MEP), civil, surveying and fueling design services.
Together, we will assess the current infrastructure, plan for future utility needs, and contribute to the modernization efforts that will reshape the airport’s main terminal and concourses.
Our work on this project will also lay the groundwork for several other significant initiatives at CVG, including upgrades to fire alarm and PA systems, the installation of emergency evacuation systems, enhancements to cooling towers and chillers, and the integration of EV charging stations to support sustainability goals.
Additionally, we will provide essential support for the $100M baggage system modernization, a cornerstone of Elevate CVG’s efforts to streamline operations and improve the overall passenger journey.
Being awarded this MEP on-call contract is a testament to our expertise and commitment to delivering innovative, future-forward solutions. We are honored to play such a vital role in shaping the next chapter of CVG’s history, working alongside a renowned team of national experts to ensure that this redevelopment will set a new standard for airports across the country.
Project at a Glance
MEP On-Call Services
Utility Master Plan Infrastructure Assessments Baggage System Modernization Alignment with Elevate CVG Program
Airports today are challenged to manage safety, operational costs and capacity, reduce environmental risks and liability, ensure employee and customer satisfaction, while demonstrating a commitment to the economic impact, health, and vitality of the communities they serve. As the aviation industry establishes goals for decarbonization, key stakeholders and investors have high expectations for how airports reduce environmental impacts.
To address this challenge, the CVG Airport Authority enlisted the services of Donovan and CMTA to develop an Energy and Sustainability Master Plan. The plan aligns ongoing efforts and models how the CVG
Airport Authority can adopt and adapt sustainable actions, innovative technologies and strategies.
This plan contains a comprehensive highlevel set of recommendations to achieve energy reduction, reduce carbon emissions, and water-use reduction, through enhanced land management, vehicle and equipment transitions, and sustainable design and construction practices.
Project at a Glance
Carbon Reduction Road Map
Sustainability Plan
Funding Plan
This project includes a new concourse at Washington Dulles International Airport to replace outdoor boarding areas currently used by regional flights, upgrade aircraft service facilities, and bring new conveniences and amenities to passengers. It will replace gates built in the 1990s at the eastern end of Concourse A, where many regional-flight passengers currently go.
The new Tier-2 Concourse East will be a modern 14-gate facility with convenient access to the airport’s underground Aerotrain system and will include new shops, restaurants, and other customer services. Additionally, it will include the latest aircraft-servicing technologies to accommodate future needs.
The new concourse also meets additional criteria required by the FAA grant program, including:
– Improved convenience and
connectivity for travelers navigating the airport
– More space (410,000 square feet versus 110,000 square feet in the current facility) for larger seating areas, more concessions, airline lounges, ADA-compliant restrooms, and other amenities
– Larger operational areas for servicing aircraft, handling baggage and other airport and airline support functions
– Enhanced sustainability features, including electric vehicles to service aircraft and carry passengers, increased usage of the electric Aerotrain to move passengers to and from the new gates; energy-efficient construction featuring LED lighting, high R-value insulation and highefficiency climate control systems that will follow LEED Silver building standards.
The project included the implementation of displacement ventilation, a process
that delivers ventilation at the occupant level, as part of the 30% documents. CMTA went above and beyond to employ chiller control and pumping strategies, that were introduced to meet LEED standards, and resulted in effectively reducing the need for heat recovery and expensive heat exchangers.
Furthermore, CMTA identified a more efficient and better location for the heating hot water plant, which reduced pump sizes, centralized equipment, and saved construction costs.
Project at a Glance
Completion: 2026 Estimated
Size: 410,000 SF (300,000 SF addition)
Cost: $675M ($60M HVAC/Plumbing)
Project Type: Addition/Renovation Awards / Certifications:
– LEED Silver Targeted
The Airport is operated by the MemphisShelby County Airport Authority and is the headquarters for the FedEx cargo operation; an important destination for multiple airlines; and home of a state-of-the-art Air National Guard facility.
This multi-phased project focuses on updating the terminal buildings (A,B, and C)—which are nominally 60 years old—to accommodate future demand, improve ADA accessibility, increase energy efficiency, and improve life safety. Encompassing approximately 500,000 SF of terminal area, the renovated facility aims to provide modern amenities and meet the future needs of operations, various airlines, TSA, and other airport stakeholders.
The project scope will expand the face of the building, reconfigure vertical circulation,
reconfigure the ticket lobby, construct a Checked Baggage Inspection System (CBIS), expand the Security Screening Checkpoint (SSCP), construct an employee screening checkpoint, expand bag claim and prepare an area for a future new FIS. The team will focus on minimizing interruptions to operations and the traveler experience during this comprehensive phased renovation. In addition, the project will focus on reducing environmental impacts through sustainability measures.
The design team has collaborated to create a sustainable and energy efficient modernization plan for Memphis International Airport. The goal is to enhance the terminal’s usability, safety, and comfort while minimizing costs and environmental impact. Through an integrative design process, we have considered factors such as site design,
water use, energy use, material use, and environmental quality. The intent is to optimize energy consumption and minimize maintenance costs, all within the available budget.
As a result, we reduced the EUI from 193 kBTU/SF to 157 kBTU/SF. We are transitioning from steam to heating hot water to increase efficiency by 30%. Combined with the heat recovery chiller, we are targeting a 991-ton reduction in greenhouse gas emissions. The project is targeting LEED Silver certification.
Project at a Glance
Completion: 2027-2028 Estimated
Size: 1,000,000 SF
Cost: $950M
Project Type: Renovation
CMTA has worked with Hector International Airport for nearly 30 years. We’ve completed projects varying in size and scope – ranging from food service upgrades to boiler replacements and terminal renovations. The airport has faced a growing demand for travel, initiating their investment in $150M+ in substantial facility upgrades.
Currently, CMTA is providing MEP and fire protection design services for the main terminal expansion project. Many years in the making, the all-encompassing project expansion includes four additional gates (for a total of nine), a fourth security checkpoint, additional departure lounge spaces, and expanded accommodations for
travelers. Renovations include ticketing/ check-in areas, including self-service kiosks, baggage claim improvements, as well as overall aesthetic and operational efficiency upgrades.
In order to enhance the overall passenger experience, part of these upgrades include a parking ramp addition to increase the airport’s parking capacity.
The partially enclosed 4-story structure will be connected to the enhanced airport terminal via skyway. It will provide approximately 1,000 additional parking spaces, EV charging capabilities, and full generator backup. The ramp is scheduled for completion in Summer 2025.
Project at a Glance
Completion: 2027 (Terminal); 2025 (Parking) Terminal Size: 86,000 SF Addition; 113,000 SF Renovation
Parking Ramp Size: 400,000 SF
Cost: $150M Total
CMTA has been providing MEP/FP engineering on a continuous basis for this airport for over three decades. Projects range from small fit-ups to major terminal and concourse expansions and new parking decks.
CMTA provided the mechanical, electrical, and fire protection engineering design for the renovation and expansion of the existing U.S. Customs FIS facility and an expansion of the connector area between concourses C and D. The project comprises the renovation of the existing concourse D ticketing level and baggage level. Work
in the baggage level includes relocating, renovating, and adding the required custom and border protection spaces, restrooms, baggage claim devices, and altering the overall passenger flow. The ticketing level work includes new hold rooms, restrooms and corridors. The total area for this expansion/renovation effort is approximately 225,630 SF.
Project at a Glance
Completion: 2023 Estimated Size: 225,630 SF
Project Type: Addition/Renovation
CMTA provided the plumbing, mechanical, fire protection, and electrical engineering for this combined project of the Charlotte Douglas International Airport (CLT) new 30,000 SF customer service facility and an adjoining 7-story, 3,500,000 SF parking deck.
CLT serves over 50 million passengers per year and is on a track for rapid growth. Airport officials wanted each of the parking decks to extend beyond the bounds of conventional design while focusing on user experience and accommodating future growth. Innovative materials and sophisticated design resulted in unique solutions that addressed the owner’s function, safety, and maintenance needs while preserving the architect’s aesthetic vision.
Project at a Glance Completion: 2017
Size: 30,000 SF Customer Service Center / 3,500,000 SF Parking Deck
Construction Cost: $71M
Project Type: New Facility
The Monaco Air Fixed-Base Operation (FBO) facility caters to private aircraft, crew, and passengers. The facility underwent an expansion and renovation to accommodate increased occupants and provide a more modern, sophisticated, and comfortable space. The first-class business atmosphere reflects the service-oriented nature of Monaco Air. The project also consisted of transforming the existing space into U.S. Customs quarters.
The facility has three seating areas for passengers from multiple flights, an upper
crew lounge, a catering kitchen, conference rooms, a fitness room, and an abundance of windows for natural light. In addition, the building’s various design materials, including bluestone and reclaimed wood, reflect the region’s natural environment.
Project at a Glance
Completion: 2016
Size: 10,000 SF
Project Type: Addition & Renovation
Located at Miami’s Opa Locka Executive Airport (OPF), the Orion Jet Center is one of the largest independent Fixed Base Operators (FBO) in the nation. The 123,000 SF facility features state-ofthe-art amenities, as well as cutting-edge security and technology. CMTA, designed the mechanical, electrical, plumbing, fire protection, and low voltage systems for the phased project that included a new Fixed Base Operator (FBO) Terminal and two Aircraft Maintenance, Repair & Overhaul (MRO) hangars.
The new, 25,000 SF terminal includes a large lobby, a lounge, planning and leisure space for VIP pilots, offices for crew and facility employees, conference rooms, a café, and a rooftop garden. An additional 20,000 SF is dedicated to tenant shops, offices, and a garage.
The two MRO hangars, strategically situated alongside other hangars, provide essential additional space for the airport and contain the equipment necessary to handle every type of aircraft. Each aircraft hangar is equipped with a unique fire suppression system that quickly dispatches high-expansion foam to extinguish flames and prevent reignition—a critical feature for protecting high-value assets within the hangars.
Project at a Glance
Size: 123,000 SF
Cost: $25M
CMTA partnered with the Louisville Regional Airport Authority to design and commission the new state-of-the-art Operations Center and Data Center at Louisville Muhammad Ali International Airport. The Operations Center is the most critical location on the airport’s campus, enabling the operations department to administer airfield and facility activity – ensuring the safety of all cargo, its airline partners and the traveling public.
The Command Operations Center is a 24/7 facility that uses various technologies to monitor and control airport access control, parking, flight information, weather, property work orders, airfield status, radio communications, airport public safety, operations, maintenance, and aircraft radio traffic. Resiliency features include:
downtime minimalization, implementation of energy efficiency, and staff safety. The electrical and mechanical system design allow it to be isolated from the rest of the terminal building and remain operational under emergency conditions.
Unique circadian lighting design strategies were implemented to increase alertness of operations center employees throughout the day and night. The centralized Building Automation System monitors all HVAC, lighting, fire alarm, fire suppression, and plumbing systems. If any issue arises, staff are automatically notified immediately for a quicker response time to correct any situation. Intercom technology allows staff to be alerted throughout all locations of the space.
Project at a Glance
Completion: 2021
Size: 6,500 SF
Construction Cost: $18.5M
Project Type: New Construction
This new 16,000 SF state-of-the-art facility houses fire services staff 24 hours a day and includes offices, living quarters, fitness facility, decontamination and storage space, gear wash/dry, kitchen/day room, locker room, showers, storage and a multi-vehicle drive through apparatus bays.
Commercial aircraft landing at Daytona Beach International Airport requires at least 126-feet in length but no more than 159-feet in length. This means the personnel at Station 17 must protect the lives of up to 250 passengers in the event of an emergency on-board a commercial aircraft arriving or departing Daytona Beach.
International Airport Station 17’s personnel are also required by the FAA (Federal Aviation Administration) to be in place on the runway for a declared aircraft emergency within three minutes of notification.
These firefighters must have knowledge regarding the types of aircraft arriving/ departing, maximum number of passengers possibly inside, location of emergency exits on the aircraft, and location of critical systems on the aircraft which could increase the danger to passengers exiting the aircraft if it was on fire. As the thin walled aluminum exterior of a large commercial aircraft burns so hot and quickly, all lives on board can be lost in less than five minutes making immediacy of response critical.
Project at a Glance
Completion: 2014
Size: 16,000 SF
Cost: $5.7M
CMTA’s team designed the HVAC system with a packaged rooftop heat pump system. This system provides conditioned air to the executive terminal and the office spaces located in the hangars. A building automation system (BAS) interface operates the HVAC system and allows for automated and remote control of the building systems.
Certain hangars were also equipped with high-velocity low-speed fans within the large volume space. All hangars are designed with rooftop exhaust fans to provide a set amount of ventilation that varies based on air quality conditions within the space.
The project included six 33,000 SF hangars designed with a combination of automatic sprinkler protection and automatic low-level high-expansion foam system with AFF foam hand hose stations. This hangar is fitted with two 700-gallon foam storage tanks.
The seventh hangar totals 69,000 SF to accommodate the Boeing 767 aircraft. Group II hangars are designed with a closed head foam water sprinkler system with AFF foam hand hose stations and two 300-gallon foam storage tanks.
A 40,000-gallon underground tank was provided for emergency direct disposal of water and flammable liquids in case
of fire emergencies or system activation. The executive airport terminal’s fire protection design has a full automatic wet fire sprinkler system. The airport complex also has a fuel garden designed with two 515-gallon diesel tanks fitted with flexible fuel connections.
Project at a Glance
Size: 270,000 SF
Cost: $82M
CMTA, along with a joint venture between Woolpert and KZF, designed the Air Force Special Operations Command (AFSOC) Osprey Campus at Yokota Air Base. The USACE Japan Engineering District (JED) is the design and construction agent that managed and executed this project.
The Simulator Facility is designed according to the requirements set forth in the Facility Requirements Specification for a Flight Safety Design Simulator with Motion System, as prepared by the Flight Safety International Simulation Systems Division, September 2013 release.
CMTA design services for the 9,100 SF Flight Simulator Facility supporting the crew members of the Osprey aircraft to conduct required training for both annual
and semi-annual events, to support crew upgrade training, and to conduct specific mission rehearsals. A high-bay room is required to support a full-motion simulator. Additional space is required to support the large communications and the uninterrupted power supply (UPS) system dedicated to the simulator.
Other spaces within this facility include maintenance and system storage, office space for both government and contractor personnel, briefing/debriefing room, and a training classroom.
CMTA was the designer of record for Mechanical, Electrical, Lighting, Communication, Audio-visual, Security, and Technology services. All systems were developed according to DoD Unified
Facilities Criteria (UFC) such as the General Building Requirements per UFC 1-200-01, seismic design due to location per UFC 3-310-04, and DoD antiterrorism/force protection requirements per UFC 4-101-01. In addition, the designs adhered to the Osprey Facility Requirements Specification and AFSOC Facilities Requirements Specification.
Project at a Glance
Completion: 2023
Size: 9,100 SF
Cost: $7.9M
Project Type: New Construction
The Boone National Guard Aviation Support Facility is the most energy efficient aviation hangar in the world, operating at 15 kBtu/ sf/yr. The project is Net Zero Ready, and easily achieved LEED Gold, by achieving all 19 points for EA Credit 1 – Energy Optimization, including an exemplary point and regional priority credit for a total of 21 points. The project bid under budget, and the Kentucky National Guard was able to install an 80 kW monocrystalline photovoltaic system. The 80 kW photovoltaic system will offset 20% of the total building energy usage. The building infrastructure is in place to increase the photovoltaic system and allow for 100% energy offset.
A radiant slab heating system was used in the maintenance bays, with ground source
heat pump water heaters for hot water generation. The 90°F hot water heating temperature increased the heat pump efficiency by 20%, operating at a COP of 5.4. High volume, low velocity fans were used for summer time ventilation. The two story administration and operation space is conditioned using an enhanced geothermal HVAC system with dedicated outdoor air unit with energy recovery.
All LED lighting was used in the administration space, and high efficiency linear fluorescents in the maintenance bay. A building pressurization test was included in the project requirements, and the maintenance bays passed at an air leakage of 0.19 cfm per square feet of building envelope.
Project at a Glance
Completion: 2015 Size: 122,000 SF
Project Type: New Construction Awards / Certifications: – LEED Gold
Wright-Patterson Air Force Base (WPAFB) operates centralized heat and hot water systems that utilize both natural gas-fired and coal-fired boilers to serve both areas (Area A and B) of the base. These centralized heat plants are located at base facilities 20770, 31240 and 34019. Facility 31240 serves part of Area A through three distribution lines (A, C and D).
CMTA teamed with Woolpert to design a comprehensive solution to reduce energy loss study by converting the existing distribution systems to natural gas fired condensing boilers and steam generating boilers provided locally at each of the facility groups. The final designs were delivered on an aggressive schedule and within the budget.
The existing distribution Line C provides heating to 14 facilities that support the missions of Headquarters Air Force Materiel Command (HQ AFMC), National Air and Space Intelligence Center (NASIC), Visiting Officer Quarters (VOQ) and 88th AB Wing (88 ABW).
The existing distribution Line D provides heating to 24 facilities that support the critical missions at Wright Patterson AFB. The Line D project has scope challenges due to current funding and programming budgets do not align with the scope of the project. The current targeted construction cost limitation is $6,460,000 which is less than Line C although this project impacts more
facilities. Woolpert & CMTA continue to work through these challenges to develop an optimum combination of solutions to meet the needs of the end user.
Line C at a Glance Completion: 2020
Cost: $12.3M
Line D at a Glance Completion: 2020/2021
Cost: $6.5M
USACE, Ft. Worth District
This new facility replaces the original B Wing of Building 499. The total construction budget for this two-story, 68,000 SF project is $32,864,000. The project will provide new administrative space for an Air Force Personnel Center and was managed by USACE Ft Worth District.
CMTA was engineer of record for Mechanical, Electrical, Plumbing, Lighting, Communication, Audio-visual, and Technology. All systems have been designed to exceed the requirements of the high performance UFC 1-200-02.
CMTA leveraged our building science leadership to help the team find optimization opportunities. The results of this effort found significant structural improvements that greatly improved the envelope while also reducing costs. The team continued to optimize the design to find additional savings opportunities; this allowed the team to design a zero energy facility within budget. This will be the first zero energy building on Randolph AFB.
Project at a Glance
Completion: 2024 Estimated
Size: 68,000 SF
Cost: $32.6M
Project Type: New Construction
CMTA has performed services for many renowned aerospace and aviation companies, both public and private. The following includes a brief overview of this experience, which ranges from carbon reduction strategies to full MEP design services.
Confidential Aerospace Client Various Locations, Florida & Texas
Hanger Launch Support Facility
Multiple Rocket Factories
Manufacturing Facility Core/Shell
Manufacturing Facility Office Fit-Up
Manufacturing Facility PCB Fit-Up
Manufacturing Facility Tool Fit-Up
Fortune 50 Aerospace Manufacturing Company, Carbon Reduction & Sustainability Plan U.S. & International
Ball Aerospace, Various Renovations Boulder, Colorado
Peterson Space Force Base Renovations Colorado Springs, Colorado
Northrop Grumman at Grand Sky
Grand Forks Air Force Base, North Dakota
Redwire Aerospace New Corporate Office Edwardsville, Indiana
CMTA, in partnership with Donovan Energy, has embarked on a multi-year evaluation of a global company’s domestic and international sites in the US, Italy, Singapore, Brazil, Europe, and India. The confidential company’s goal is to identify at least a 70% reduction in emissions across all the aviation division’s sites, which will encompass more than 10 million square feet. The reduction strategy will include infrastructure efficiency improvements and renewable energy procurement, ultimately aligning the company to their commitment to be carbon neutral by 2030.
At each site, the team will establish benchmarking by evaluating energy usage and utilizing baseline data. This will involve both
on-site walkthroughs and remote audits of select manufacturing sites and testing facilities. Infrastructure efficiencies that have the highest impact on carbon reduction will be identified along with the associated supporting cost estimates and a return on investment. The assessment and resulting report will also include potential renewable energy systems, with local market and regulatory requirements, procurement, PPAs, etc. in mind.
The overall strategic roadmap developed will consider timeline, procurement and progress milestones as well as opportunities to leverage federal, state and local incentives.
Project at a Glance
20 Domestic and International Sites
Carbon Reduction Roadmap
Sustainability Plan
120,000 MTCO2e
Annual savings potential identified through efficiency improvements and electrification opportunities
26,000 Cars
Equivalent to 26,000 gas-powered cars driven for one year
Northrop Grumman opened a facility on the Grand Sky business and aviation park located at Grand Forks Air Force Base near Grand Forks, ND. The first phase included the office support area dedicated to fostering autonomous systems associated with Unmanned Aerial Systems.
The building features several individual office spaces as well as larger open office space environments which also include several conference rooms and break rooms for the support staff. The facility is a two story building with the main lobby/reception area open to the story above. Server rooms are spread throughout the facility to provide the computational service requirements for the program of the building.
The first phase was completed with an overall square footage of 36,000 square feet having an overall construction cost of $1,620,000 and there is currently an addition under design for the hangar and subsequent aviation support spaces. The first phase is a LEED Certified project and the second phase is striving for LEED Silver. Fire protection, plumbing, and HVAC design and construction administration services were provided for the project.
Project at a Glance
Completion: 2018
Size: 36,000 SF
Cost: $1.62M
Project Type: New Construction Awards / Certifications: – LEED-Certified
Let’s Talk.