Currently 50million tonnes of excess fly ash in landfill sites being managed as a waste material, with the remaining Coal-Fired Power Stations planned for complete closure by 2025
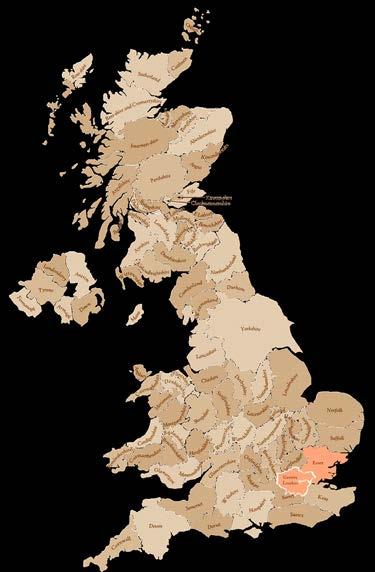
It creates opportunities to easily integrate a post and beam mass timber system into Nu-Build Modular system, to create more adaptable and open space for a range of uses, whilst eliminating the need for a concrete/steel frame ground floor within the system. With a maximum Story Height of the Nu Living developments on top of the Piles will be 5 storeys due to load bearing tolerances.
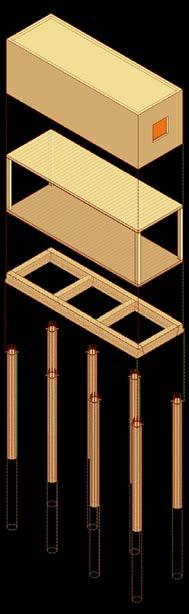
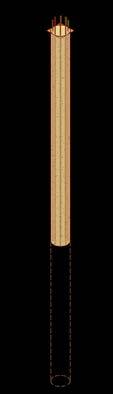
Using existing industries that create fine plastic waste as a by product of manufacture that would otherwise go to landfill as well as those materials already sitting on landfill sites
Using a relatively small mobile rig, The Auger is drilled down into the soil to a depth that corresponds to the prescribed column length. Powdered quicklime (CaO) is forced into the soil with compressed air through a hole located just below the horizontal blade of the auger, and the lime is mixed thoroughly with the soil.
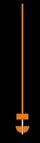
Utilising the soil conditions within the boundaries of where Nu Living are able to build, Lime Stabilised Soil Columns allow for a method of piling that replaces a large amount of concrete with the already existing soil on site and a mixture of quicklime, otherwise known as Calcium Oxide.
Coal-FiredStationsPower PlasticPlantsRecycling Lime Quarry Source Locally Reduce Reuse Recycle Lime Stabilised Soil IntegratingNu-BuildWith LimeConcreteStabilised
Project 01 PLUG-IN ELIMINATINGADDENDUM:CITY CEMENT Team Jack ClintonGabrielHardingPeckOlajide Supervisor Dave Lomax, Associate Lecturer Master of Architecture ARB/RIBA Part 2 UCA DesignCARC61022020/21SchoolCanterburyofArchitectureTechnologyEliminatingCement
Cement is the source of approx. 8% of world’stheCO2emissions
Concrete is the most widely used man-made material in existence. It is second only to water as the most-consumed resource on the planet
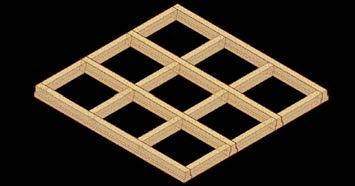
Eliminating cement from the design and replacing it with lime will reduce carbon emissions from the creation process by 20%. Where lime also absorbs CO2 within its dying and hardening process. Some of this lime can then further be replaced with recycled fly ash this will reduce further. Plastic aggregates that are common by-products of many industrial processes allows for a replacement of sand.
Lime Fly Ash AggregatesPlastic Fly Ash (9%) + Lime (9%) + Polyethylene terephthalate (30%) + Large Aggregate (45%) + water (7%)
A Pre cast Lime & Fly Ash concrete ring Beam allows for a greater reduction in Carbon dioxide, the use of waste materials Like Pulverised Fly Ash and Polyethylene terephthalate and precise tolerances for Mass timber to be attached to. This Plug-in looks to maximise the use of factory built and ready modules in both new mixed use residential developments and renovations by Nu-living, aiming to further improve the sustainability of the Nu-Build system.
Cement free Concrete Mix Ratio
Master of Architecture ARB/RIBA Part 2 UCA 2020/21SchoolCanterburyofArchitecture Project 01 PLUG-IN ELIMINATINGADDENDUM:CITY CEMENT Team Jack ClintonGabrielHardingPeckOlajide Table of Contents Phase 01 // Studying The Systems 02 Phase 02 // Identifying A Need 17 Phase 03 // Making a Proposal 26 Phase 04 // Refining & Disseminating // Addendum 45 // Poster 54 Bibliography 56 Supervisor Dave Lomax, Associate Lecturer DesignCARC6102Technology
Phase 01
Studying The Systems
NU Build Modular Design Guide 03 Published 2019 Swan Housing Association Text © Waugh Thistleton Architects, NU living and Ramboll Photographs and illustrations © Waugh Thistleton Architects Cover design by Fuel All rights reserved No part of this publication may be reproduced without the written permission of the publisher or the copyright owner. Printed in the UK
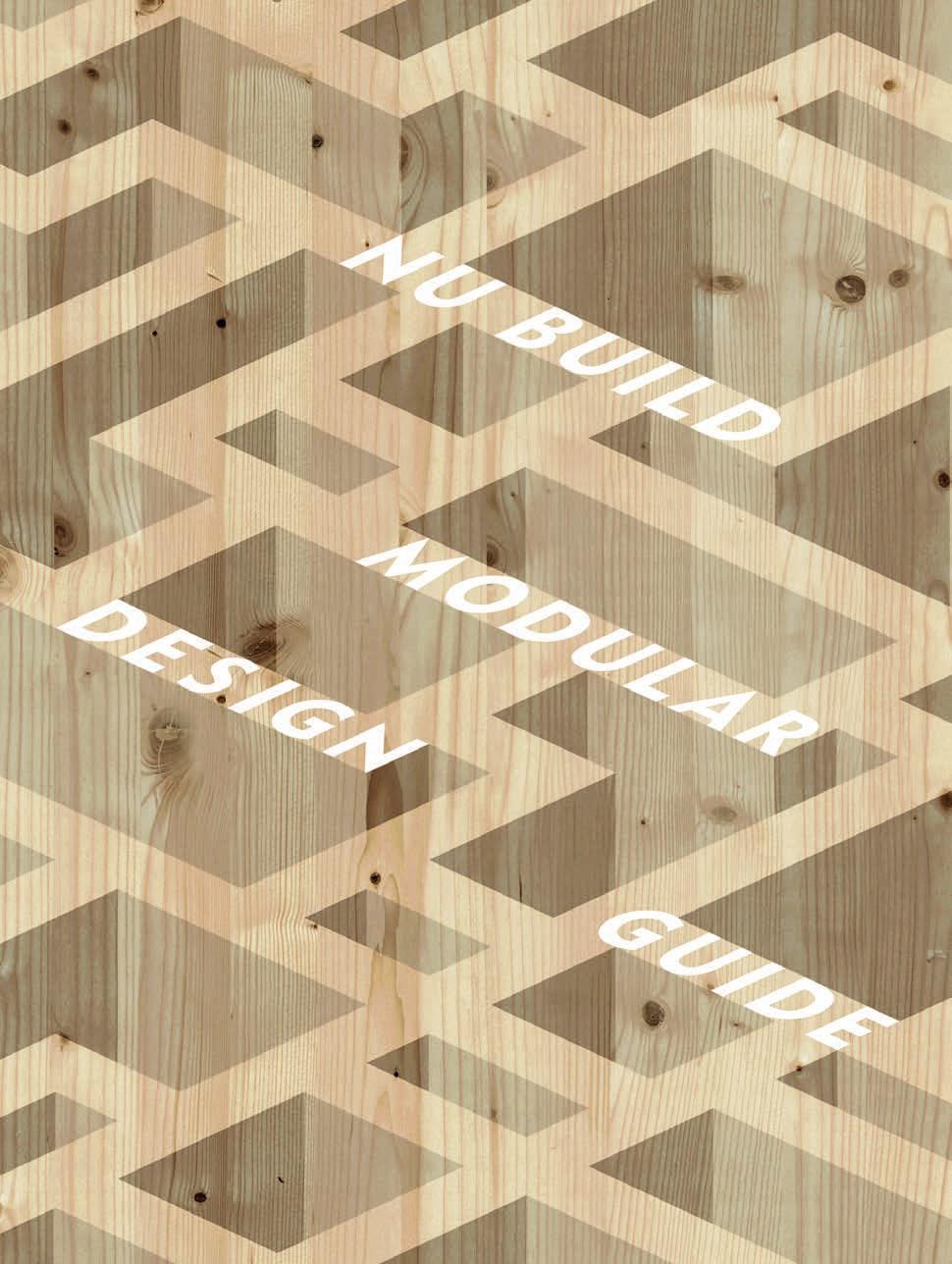
04
- For connection design, a low density value should be used
• Standard panel sizes determine floor to ceiling heights and lengths of modules. - Platform or ballroom construction?
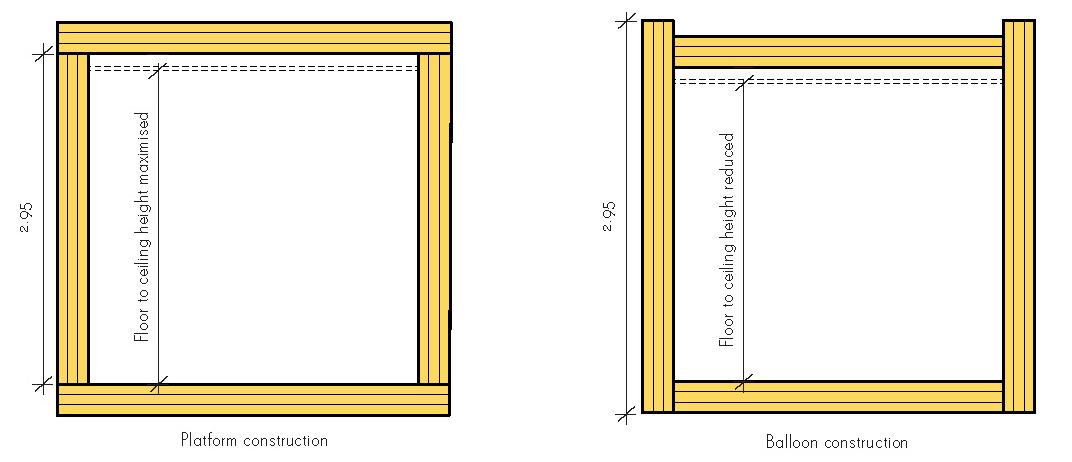
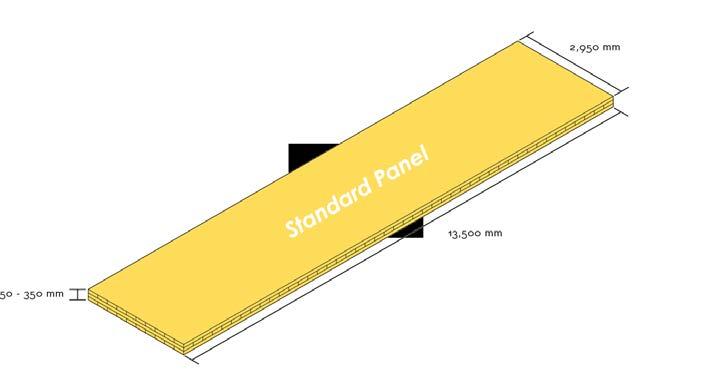
For lifting, a high density value should be used
• The standard panel size must be set out to maximise efficiency of cutting, limiting offcuts and wastage. - Jointing smaller panels together can be more efficient Waste offcuts will be used in factory biomass boiler.
• Structural design calculations must reflect the varying assumed densities of timber.
• Visual quality of CLT must be decided.
• The proposed panel size needs to be determined at the earliest opportunity.
• Information for manufacture needs to be fully coordinated at the point at which production begins. - Changes after this point will have high cost & time implications.
- Non visible (C) Visible industry quality (BC) Visible residential quality (AB).
• Developments are situated within a limited geographic area. - East London & Essex Limiting distances between fatory & site Limiting transport cost and emissions - Maximising familiarity with routes.
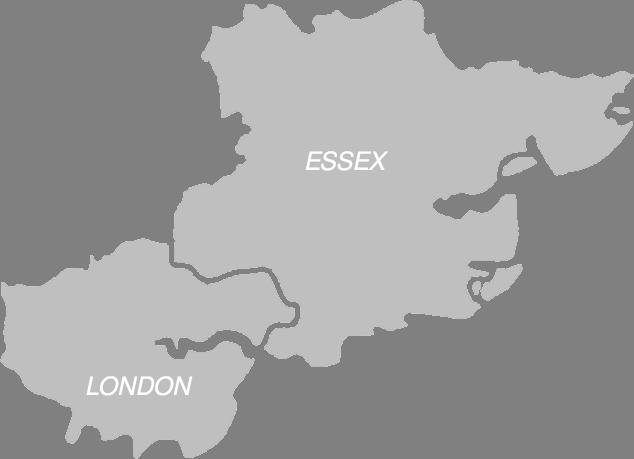
The mean density should be used when considering the requirements of the modules in their final built form.
Wider loads will require special interventions and special type vehicles Cost & time implications
• Module dimensions are determined by the size of the lorry and restrictions associated with route. - Load width of +/- 2.89m is optimum
Catalogue of Rules
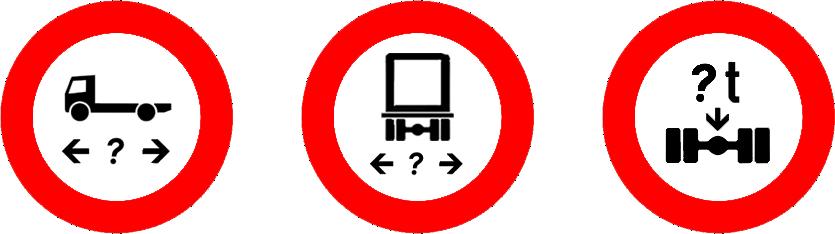
- Modular ground floor (preferred) Concrete or steel frame podium ground floor - Modules on basement foundation.
- Repeatable details and standardised processes - Pre-fabrication of certain elements Dry trades where possible.
• Housing is considered to be an arrangement of three by three modules, and multistorey greater than this.
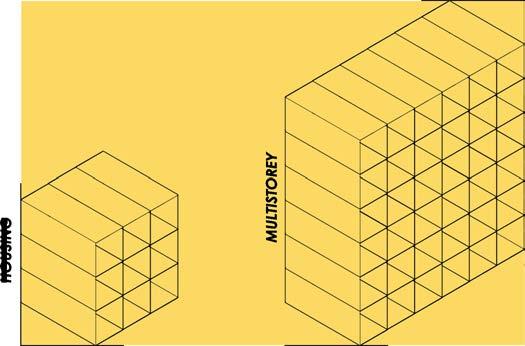
• Waterproofing must be considered inside the modules during transportation and assembly, as well as when the building is in use.
- Above five storys it is advised that CLT core walls will provide additional stability Beyond eight storeys further stability may be needed, which could be provided by a concrete core.
- Use of breathable wall build ups is encouraged Dew point analysis is required with all U-value calculations Kitchens & bathrooms should be lined with a wet room tanking membrane - The end grain of CLT must be protected by applying end grain sealer
All joints in CLT should be taped with waterproofing/air tightness tape.
• Connection design is critical. - CLT to ConnectionsCLT between modules.
• Fire strategy should be established in early stages and continually re-examined and readdressed.
• On site finishes should be efficient and maintain high quality.
- Protection methods: - Non-encapsulated - Partial encapsulation - Fully encapsulated. 05
• Cladding materials must be decided early - rainscreen or load bearing.
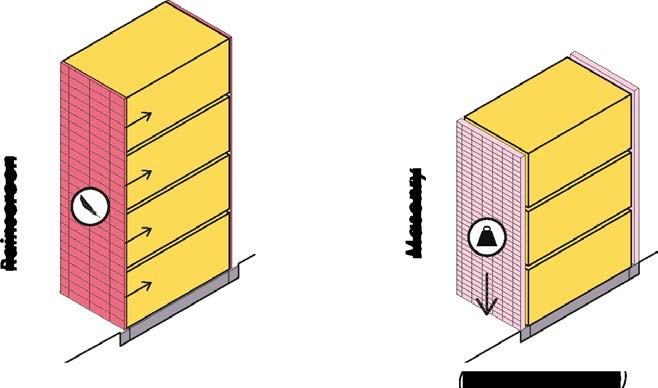
• Geometry and type of roof must take into account maximum module size and transport considerations.Flat roofs should be laid to 1:40 fall in order to achieve 1:80 fall Standing water & ponding is not acceptable Pitched roofs as trussed rafters or CLT panels?
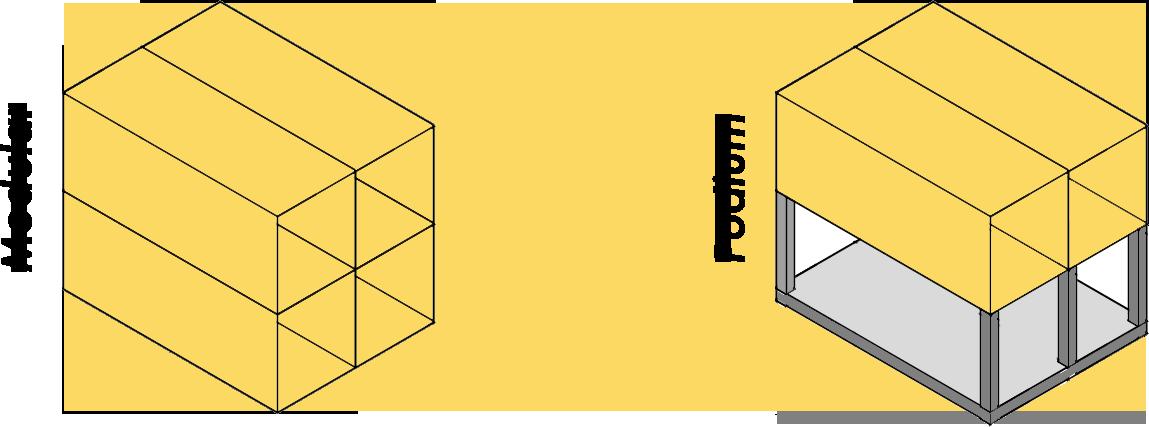
• Ground floor use and construction type needs to be determined early to inform rest of construction.
- Load bearing only applicable in buildings less than three storys Building movement and settlement must be considered in cladding.
• The long side panels of modules need to be continuous with the floor and ceiling panels spanning between. - Position of half-laps need to consider the diaphragm action.
• The wall build up must allow the timber structure to breath.
- The acceptable moisture content is around 12%
- Services should be rationalised to the entrance side of a module Service zones should be grouped together to reduce the amount of connections and Penetrationspenetrationsshould avoid module corners and areas above doors & windows - ‘Plug & Play’ services shoule be employed wherever possible Correct shaped service = Correct shaped whole.
- BIM execution plan required Common data environment Common data exchange formats Room data sheets
- Intumescent Encapsulatingcoatinginafire resistant material
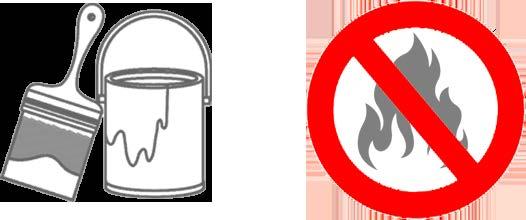
• MEP Engineer must be appointed early.
Do floors need to be acoustically floated? Acoustic ceiling considerations Acoustic sealing of service penetrations.
- Employers requirements Local council regulations.
- If the moisture content of the CLT exceeds 20% for long periods it will be susceptible to rot and mould damage.
- Reusable types Module types should be consistent between floors Consider variation of CLT dimensions.
Technical housing standards
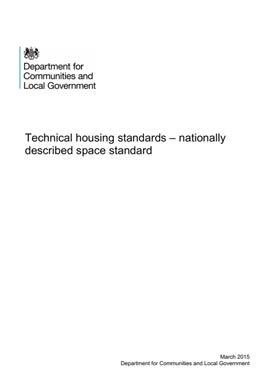
- Building regulations
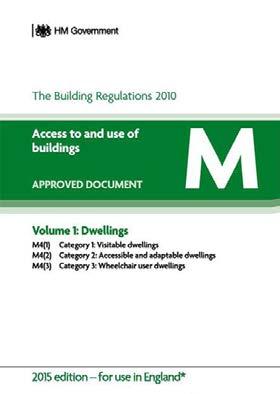
Extra care taken on cold bridges to steel connections.
• Modules should be set out to brick dimensions and/or cladding dimensions. 06
• BIM must be used to assist the delivery of the project at all design stages.
Breathable insulation must be used (avoid PUR & PIR insulations)
• Fewer module types allow for a quicker and simpler manufacturing process.
• Internal layouts have to conform to local and national guidance and regulations.
• Connections must be protected from fire.
• Thermal line should always be on the outside of the CLT.

• Acoustic seperation is provided by a wall build up that consists of materials with a variety of densities. CLT, airspace, wall lining material
• Wheelchair accessible dwellings are required in every development. - Locations
The Mayor of Londons Housing Supplimentary Planning Guidance
- The London Plan

07
01 - The NU build Modular Design Stages Pros • Capable of being manufactured to a fine tolerance. • Structural stability. • Environmentally sustainable model than alternative modular systems (steel frame). • Ability for high levels of air tightness. • Positive results for acoustic and thermal properties. System Pros & Cons Panelised CLT Modular Mass Timber System Cons • Limited geographic delivery region. • Turning circle restrictions. • Low bridges and obstacles e.g. trees, telegraph wires etc. • Road closures that might be required. • Bridge and power line height considerations. • Time and size constraints imposed by the relevant highways authority.
• Possible Police Escorts (Oversized Modules).

• Requires sufficient space around the building to allow cross ventilation under the modules, which might not be possible on constrained sites.
• Timber cladding. Exterior Finishes // Load Bearing System • Masonry (up to three storeys)
• Connections to, from and between timber panels are typically fabricated from steel (for ease of construction and speed), but they reduce in capacity with increasing temperatures.
Foundations Insulation // Finishes
04 - Illustrations of typical foundation used within the Modular system
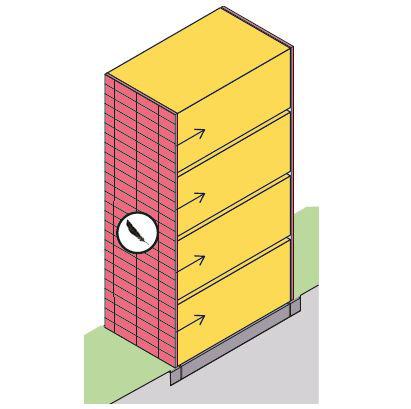
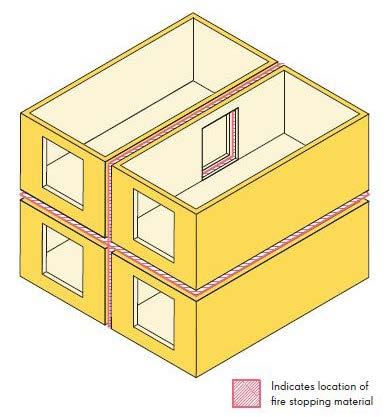
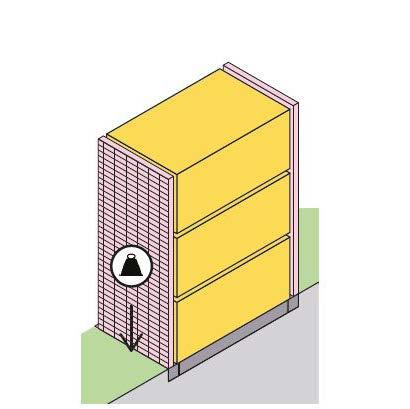

• Requires Drainage to prevent rising ground water reaching the underside of CLT modules.
• Sheet cladding (cementious boards or fibre cement).
Connections
Connections // Installation System Key Elements Breathable Wall Insulation
• Connections between the modules.
Concrete or Steel Frame Podium Ground Floor
• Connectors are treated with appropriate method of fire protection, e.g. Intumescent (substance that swells) coating or encapsulation in fire resistant material. Installation
• Modular construction can produce more cavities than traditional construction, therefore Cavity protection strategies needed.
Modular Ground Floor on Concrete Slabs
• Reduces the amount of internal condensation.
• Cold bridging created by steel connections penetrating the timber must be addressed to minimise the risk of condensation forming on the timber. Exterior Finishes // Rainscreen System • Tiles (clay tiles or terracotta tile).
• Minimises fluctuations in internal humidity.
• CLT modules are raised above the ground, with no timber at ground floor level to reduce the risk from ground water ingress
02- Typical Fixings For joining components 03- Illustration of locations where cavities protection might be needed.
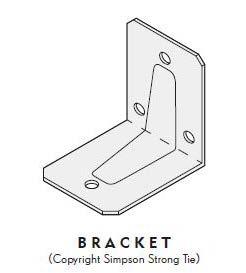
• Installing a frame at ground floor level allows flexibility in the design of the ground floor spaces.
• Allows moisture to migrate to the external surface.
• Reduces the risk of ground water rising up to underside of module. • Increases the risk of moisture building up at the perimeter.
• Requires periodic maintenance once the building is in use.
• CLT to CLT.
06 - Illustrations of 2 main facade systems used 08
Modular Ground Floor on Concrete perimeter upstands and crossbeams
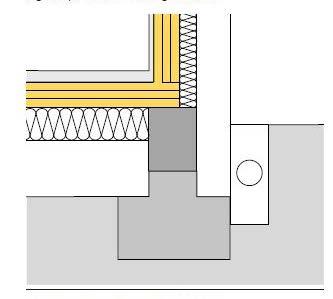
Building Concepts by Stora Enso Office buildings Stora Enso Buildling Concepts 09
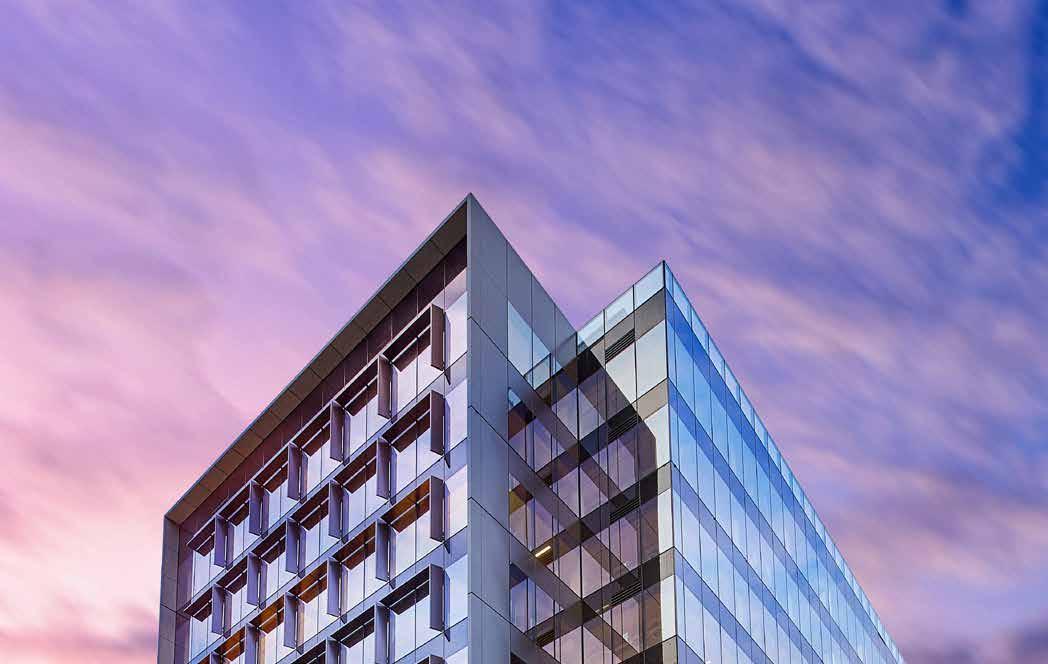
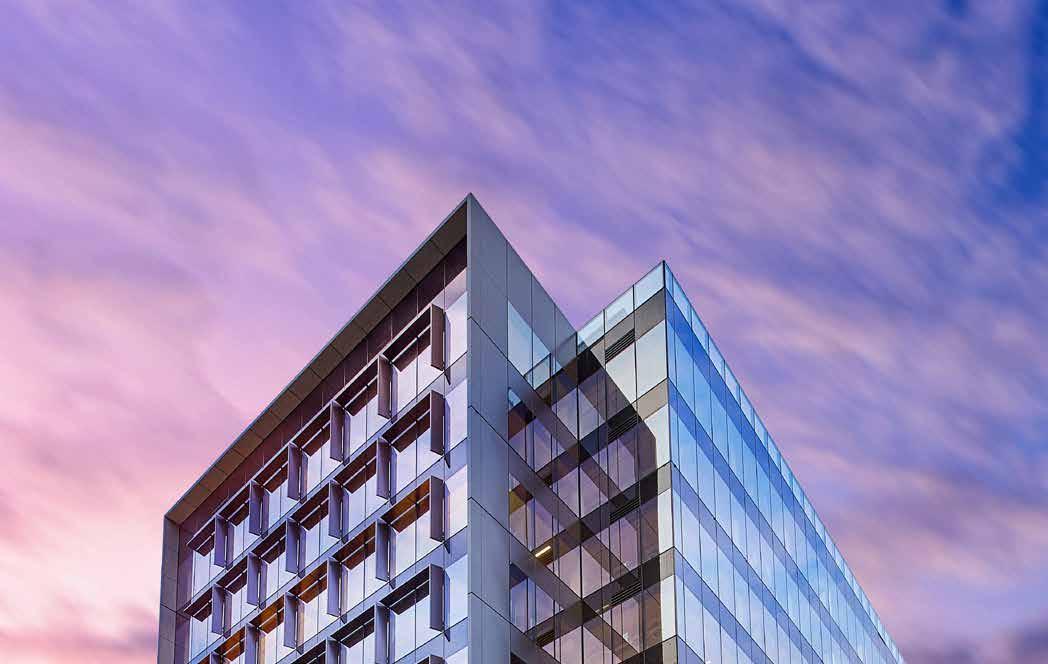
• Glued laminated timber (Glulam) - Posts & beams High strength & stiffness - High quality visible surfaces Use for long span designs.
Symmetrical layout with central core will optimise load bearing and bracing.
• Office buildings made from massive wood products. - Cross laminated timber (CLT) Laminated veneer lumber (LVL) Glued laminated timber (Glulam) - Rib panels.
• Rib panels - Use for long-span floor and roof structure Good for spans upwards 6m High load bearing capacity at low weight Made ready to install from CLT, LVL, Glulam.
Use for long spanning floors or roofs
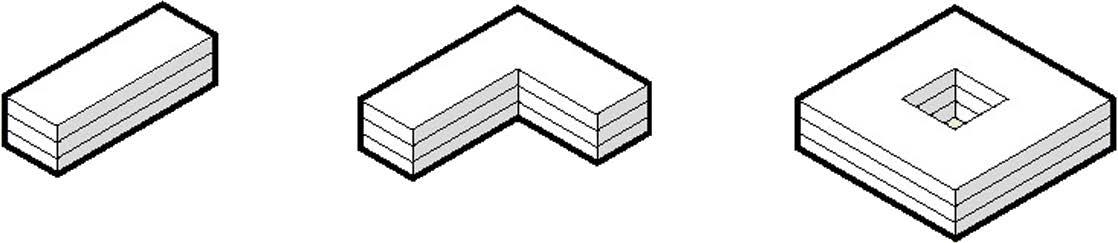
10
• Cross laminated timber (CLT) - Pre-cut Differentpanelspanel thicknesses - Structural.
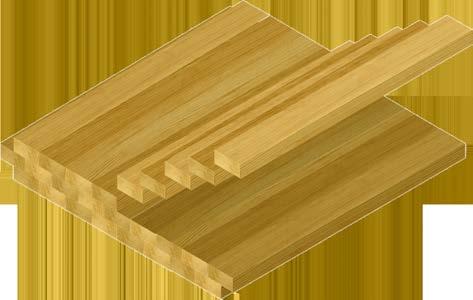
Catalogue of Rules
• Services should be integrated into structural zone. - Reduction of floor to floor height Less external cladding required.
3mm thick rotary peeled veneers bonded together under heat and pressure Max billet size of 24m x 2.5m.
• Building form will be achieved by repetition of chosen grid. - This can be adapted at borders to fit site and shape requirements.
• Urban scale of project must be defined early. - SiteVolumesand surroundings.
• Laminated veneer lumber (LVL) - Posts, beams, panels - High strength & stiffness Use for highly loaded structural elements
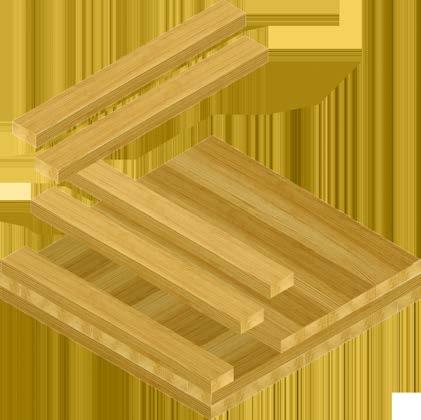
• Building form must be defined early. - Vertical access core requirements
• Simple miminal column grid with regular spans will be employed.
• Connections will varying depending on situation. - Beam toProprietycolumn: connections pre-installed in factory Column to column: - Fabricated spigot connection bolted together on site StabilityFabricatedconnections:steel plate & dowel connections. 11
- Floors can bear directly on to beams.
• Primary grid options are in increments of 1.5m - A services zone should be incorporated within grid spacing. 6m x 9m works well with UK standard. 7.5m x 7.5m allows for services distribution and works well for standard airconditioned offices.
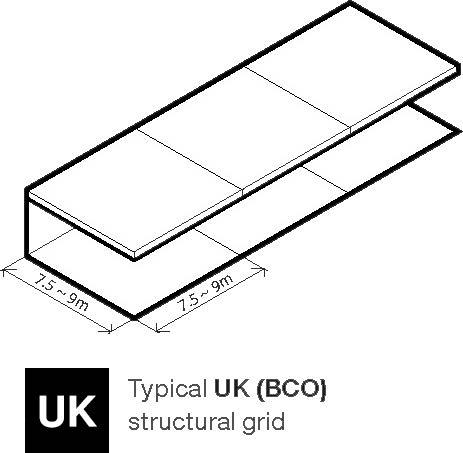
• HVAC systems must be considered. - Reduced span services zone is created in the grid spacing for HVAC systems Services can be coordinated within the services zone, preventing the need to penetrate the structure.
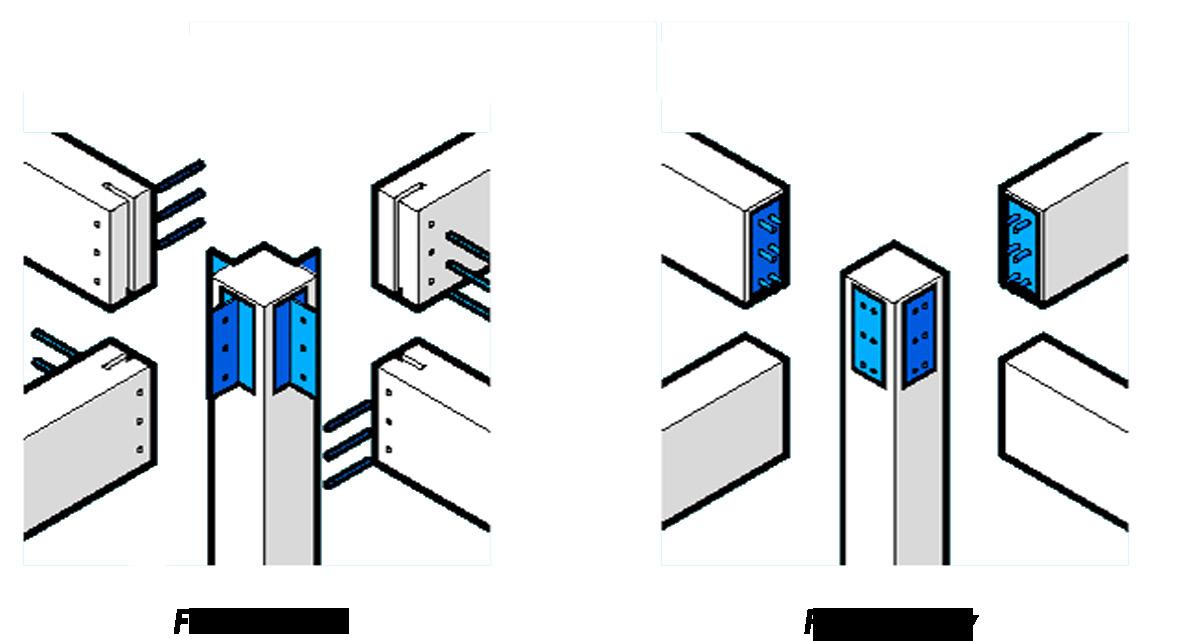
- Determined by: - Structural size - Aesthetic appeal.
• Bracing may be required. - Less than 5 CLT/LVLstorys:shear walls 6 to 9 -storeys:Braced bays Glulam or LVL More than 9 storeys: - Concrete core.
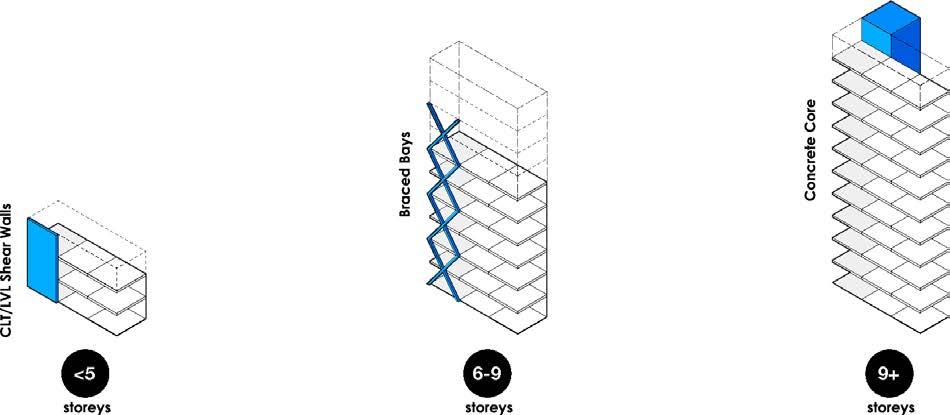
• Down-stand beams can support CLT or Rib panel floors.
• Structural framing can be formed from either Glulam or LVL columns and beams.
• Most non-load bearing facade cladding systems can be adapted to suit.
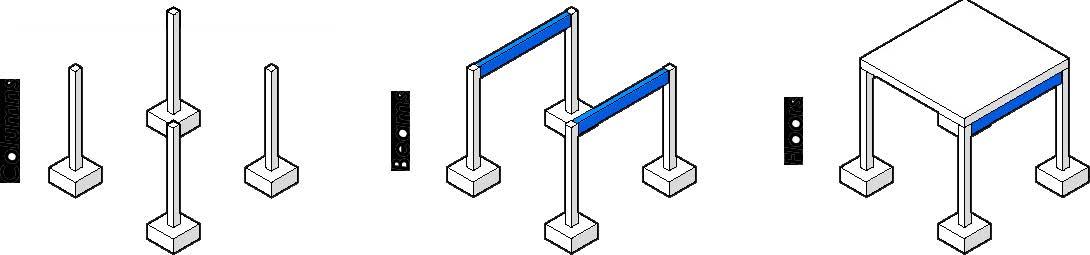
- Low Raised access floor on approx 100mm CLT Raised access floor on LVL casette with 25mm mineral wool - MediumRaised access floor on 25mm dense board on approx 100mm CLT Raised access floor on LVL casette with 75mm mineral wool - High Raised access floor on 2 x 25mm dense board on approx 100mm CLT with acoustic ceiling below Raised access floor on 25mm dense board on LVL casette with 75mm mineral wool.
• Sound insulation strategy must be defined early.
• Fire resistance must be considered.
• Ventilation strategy must be decided early.
12
- NaturalMaximum floor to ceiling heights - Mechanical-Fancoil system within service zone - DisplacementFancoil system within raised access floor.
- Passive protection - UseCharingoflining boards - Fire-seperating structures Active protection - Smoke ventilation - Sprinkler systems - Alarm systems Fire Sealingstopsof penetrations.
01 - Country Specific Grids Pros • Enables large open spaces • A simple, minimal column grid with regular spans • Decent floor to ceiling heights • Clean, efficient floor plates • Net-to-gross efficiencies in excess of 86% • Modern elegant facades, cores and reception spaces System Pros & Cons Post & Beam Mass Timber System Cons • More on site fixing required • Large beams can obstruct services • Low bridges and obstacles e.g. trees, telegraph wires etc • Road closures that might be required • Bridge and power line height considerations • Time and size constraints imposed by the relevant highways authority • Possible Police Escorts (Oversized Modules) 13
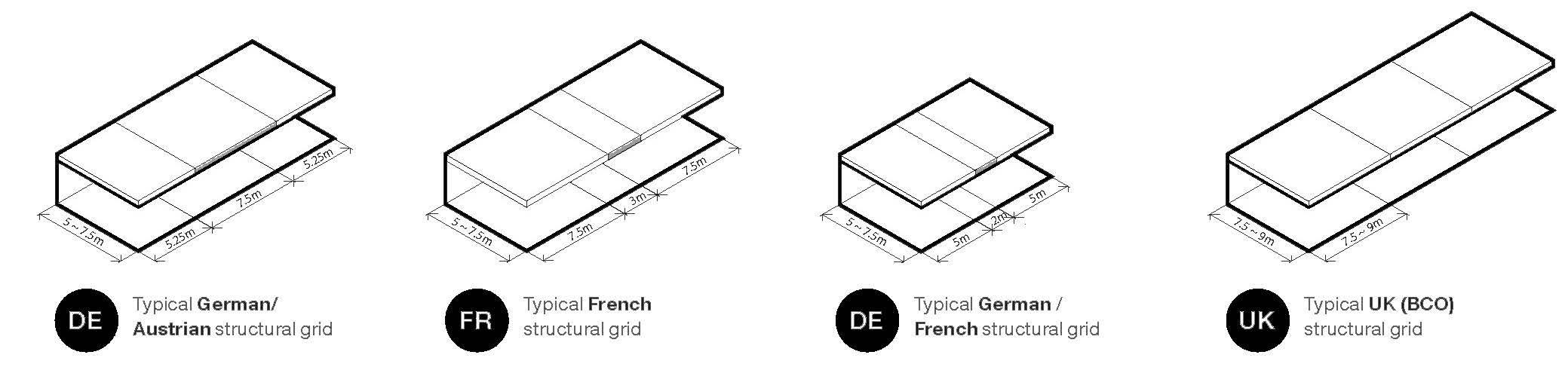
04 - Illustrations of typical foundation used within the Modular system
• Tailor made for lightweight cladding systems i.e rainscreen systems that can easily graft onto the frame work and panelised modules.
Uptate maximol oriam, sequas cus corpore sequaturit
• Fabricated connections (Preferred Option) - focussing on precut beams and posts for future installation of steel.
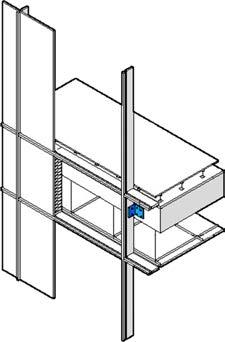
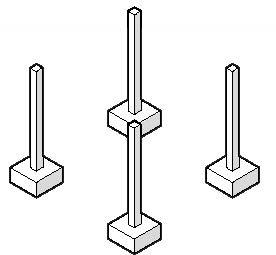
Connections // Installation System Key Elements
Uptate maximol oriam, sequas cus corpore sequaturit
• Predominantly uses perimeter up-stands and cross beams.
Foundations Insulation // Finishes
• The more common use of glazed curtain walling in the StoraEnso system, but this difference only occurs due to the use of the building.
Uptate maximol oriam, sequas cus corpore sequaturit
02- Typical Fixings For joining components
06 - Illustrations of 2 main facade systems used 14
• Proprietary connections - Sits pre-embed within the beams and post.
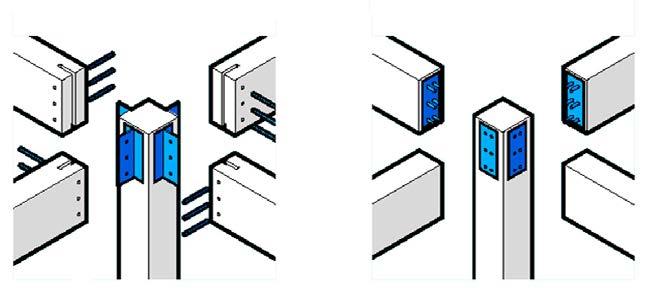
Assembled mostly off site Stora - Adaptable spaces for the use of offices and factories Flexible and attractive layouts For spans upwards of about 6 metres Range for components to assembly on site
Capability of being manufactured to a fine tolerance
Whist StoraEnso’s system predominantly uses perimeter up-stands and cross beams, it can also be used in the Nu Build Systems
Both seem to be tailor made for lightweight cladding systems i.e rainscreen systems that can easily graft onto the frame work and panelised
Bothmoduleshighlight
NU - Positive results for acoustic and thermal properties
Both take advantage of small scale steel connections to assemble and join components and modules
opportunities for the load bearing facade systems with Masonry walls but with a limit of the height these can be used
Proprietary connections - Sits pre-embed within the beams and post Nu - Primarily Brackets and screw use at on-site assembly
NU Living vs Stora Enso Comparison 15
Although it seems like Nu Build do focused more on the use of Concrete slab foundations, to reduces the risk of ground water rising up to underside of module, and future continued maintenance
Differences
The more common use of glazed curtain walling in the StoraEnso system, but this difference only occurs due to the use of the building.
Overall FinishesConnectionsFoundationsSystem&Installation
Structural Environmentallystabilitysustainable model than alternative modular systems (steel Abilityframe)forhigh levels of air tightness
Stora - Fabricated connections (Preferred Option) - focussing on precut beams and posts for future installation of steel
Restrictions and more logistical transportation strategies
Similarities
For strength, stability and high load-bearing capacity at a low weight.
16
Other Types of Mass Timber
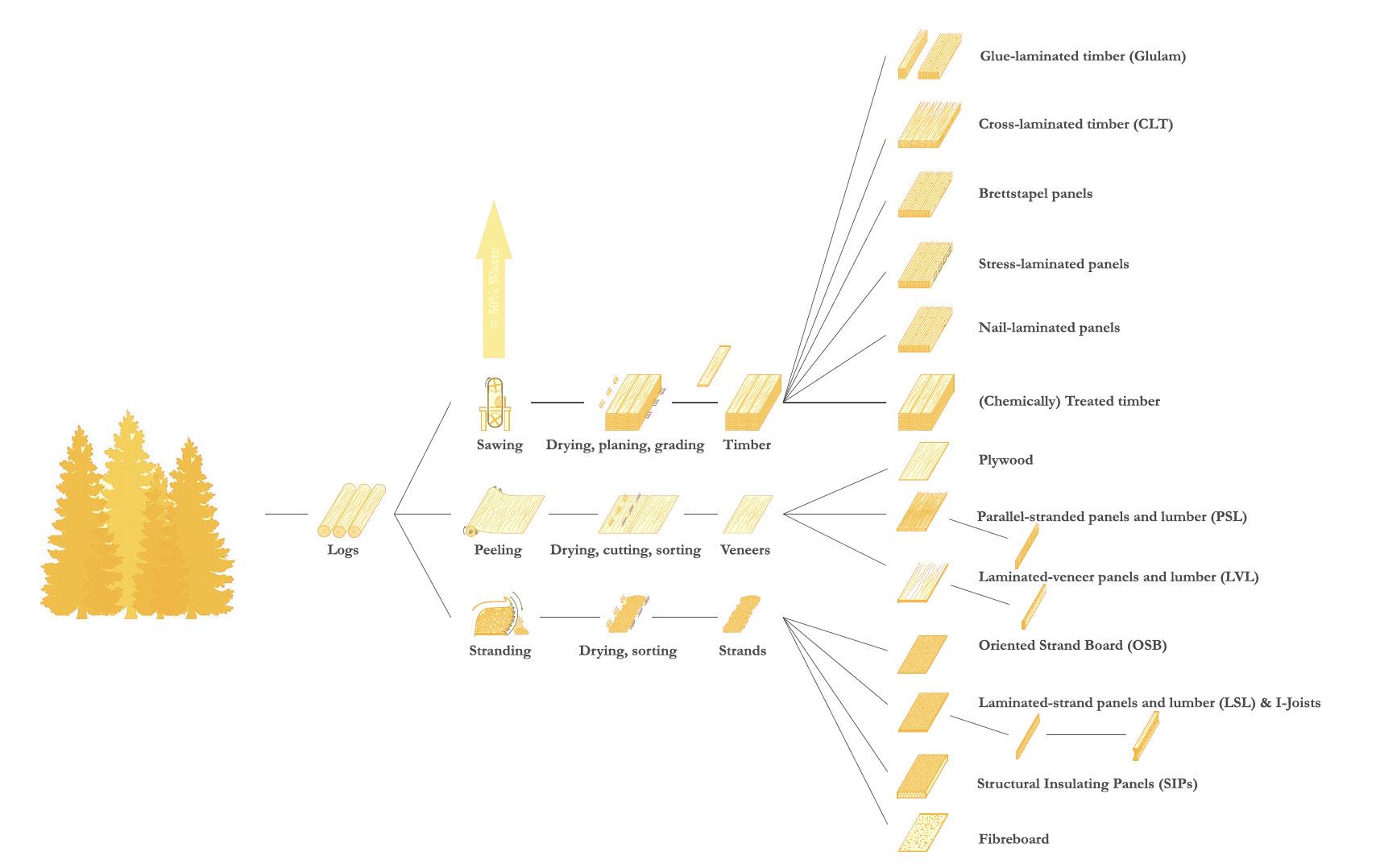
Phase 02 Identifying A Need
- Ground floor cannot be volumetric and fitted out in the factory
- The provision of adequate drainage to the perimeter
- Installation of a concrete or steel frame could restrict access to the rest of the site
•
Modular ground floor and Podium ground floor are the main 2 considerations for ground floor construction within the Nu Build System
• Is the crane or delivery vehicle required to drive over the foundations?
• Modular Ground Floor - Preferred method of construction as it remains consistent with the whole buildings.
- Retains quality of finish throughout the project, - Minimised on site labour and - Maximise the efficiency of the modular system
• Podium Ground Floor - This is the installation of either concrete or steel framework at ground floor level
- For the achievement of a level threshold for disabled accessible units
• Modular Ground Floor- The relationship between the base of the timber and the external drainage level
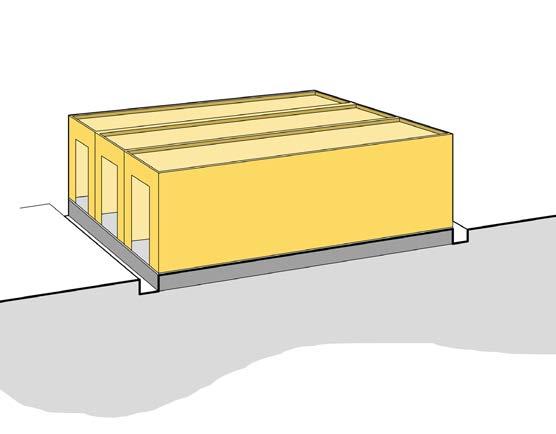
- The differences between the level thresholds and external landscaping
- Key considerations between point loads and line loads in module to slab connection • Podium ground floor -
- Even support required on all for walls of modules ground floor to avoid differential movement
• In both approaches, CLT modules are raised above the ground, with no timber at ground floor level to reduce the risk from ground water ingress, using either concrete slab or ventilated slab foundations.
• Ground Floor Uses- Communal spaces - Stores - Service cupboards - Substations - Disabled Accessible Accommodations
- Allows for flexibility in the design of the ground floor spaces to create commercial areas
- Efficacy of build reduced with further coordination with trades on site for the fit out
Modular Ground Floor Illustration Crane loading IllustrationPodium Ground Floor Illustration 18
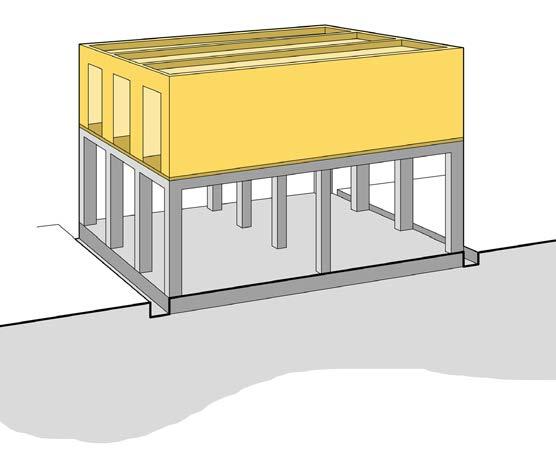
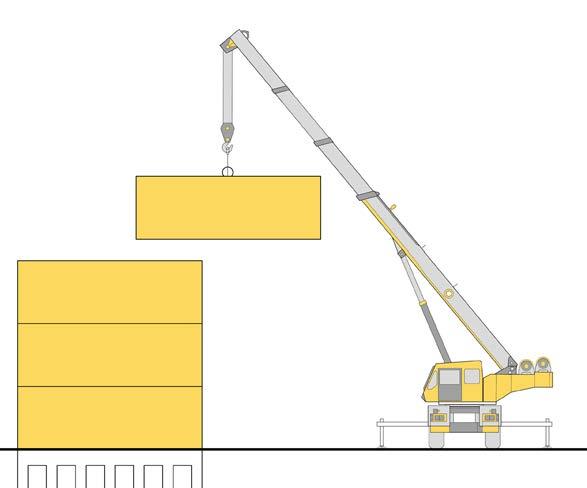
• Can the route of the crane avoid the foundations?
Identifying The Intervention Ground Floor Construction // Nu Living Use x Rationale
• Can the foundations bear the load of a crane and a module together?
• Can the foundations for the whole site be constructed in one go prior to the modules being delivered to site?
Opportunities and Constraints
• Glulam, LVL, CLT products are typically out sourced from Europe, the low numbers of manufactures in the UK can make it more expensive.
• The require relatively less energy to extract and harvest than other commonly used resources
• Once the timber has been harvested, residues can be burned for energy, which releases less carbon than other commonly used resources
• CLT - Typically ranging in thickness between 20mm and 45mm - As panels span to lengths of up to 7m - As Ribs span to lengths of more than 10m • LVL - Sheets/billets are usually manufactured to thicknesses of 35mm to 63mm, to lengths of up to 12m - Or as columns of appox. 300mm to 500mm for spans up to 7.5m or heights of 9m
Identifying The Intervention Use x Rationale
Beams
Opportunities and Constraints
• Although Ill-practice in the management use of forests/mass plantation of a singular species of desired timber leads to destruction and degradation in the forest ecology.
• In there production there is potential to generate no waste.
• Glulam - Columns of appox. 300mm to 650mm for up to for spans up to 7.5m or heights of 9m
19
• These systems are typically made utilising softwoods like spruce, pine, fir or larch.
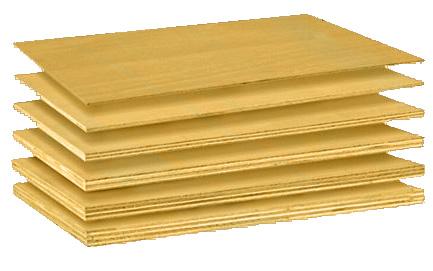
• Wood chips, leaves and pine needles can be used for compost and spreading on fields, for agricultural and cultivation purpose
• Logistical constraints, the main difficulty is in the transportation of systems to site
• Stora Enso’s main raw material is renewable wood from sustainably-managed forests
Lintels -
• Glulam is made from individual laminates of construction timber, joined to produce long lengths and then bonded (GLUED) together to create the desired dimension
• UsesPurlins - Floors Timber Layering for the CLT System Timber Layering for the Glulam SystemSheets Layering for the Laminated Veneer Lumber System
- Framwork
CLT, LVL and Gulam Production // StoraEnso
• Lvl (Laminated veneer Lumber) is made from rotary peeled or sliced thin wood veneers, bonded (GLUED) together and machine pressed under heat to create the desired thicknesses, then sawn to the desired dimensions
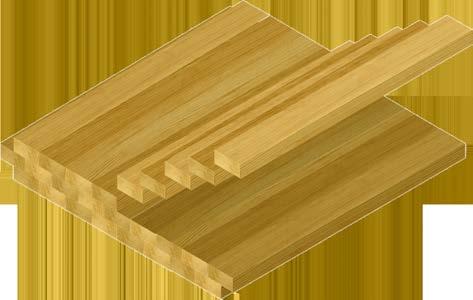
• CLT is made in panels of odd numbers of softwood plank layers laid on top of each other at right angles and glued together under pressure
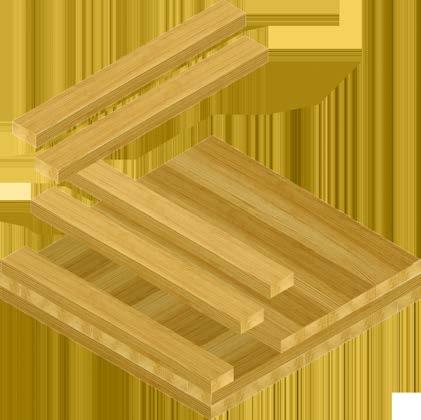
Doweled Connections Choked Cavity CLT Multi Species Boards
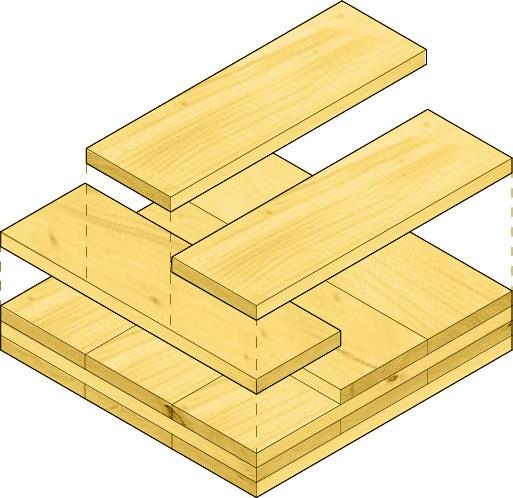
By calibrating cavity dimensions, convective forces can be “choked” - Warmside upward boundary layer air flow impeded by cold side downward boundary layer air flow - thereby reducing overall heat transfer in the wood panel. Currently the majority of fixings within mass timber assembly are steel brackets that are then treated in a fire retardant coating. This is done for efficiency and cost. What opportunities are there in the design process that allow to maximise the use of the Cross laminated timber to further reduce the amount of steel in the construction process but also speed up the installation? How can the panels be assembled in such a way that they can be fixed in place by dowels?
Combining multiple different species of wood into panel construction - allows for a building system that incorporates otherwise overlooked timber in regional forestry with a practical application in an all-wood system.
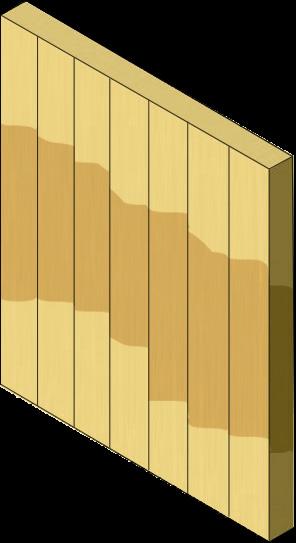
By being in discussion with regional foresters the panels/systems can respond to the shifts in forest dynamics by making use of undesirable species that are in overproduction.
20
System Plug-In Exploring Initial Ideas
Based on aspects of Salmaan Craig’s research, the introduction of air cavities in CLT wood panels, in the form of choked convection cavity cells, reveals significant increases in the thermal performance specific to the slowing of heat transfer while reducing the overall material volume.
The difference in properties, appearance and workability of different species creates a space that can allow to maximise the benefits from differences compared to being a single species panel/system.
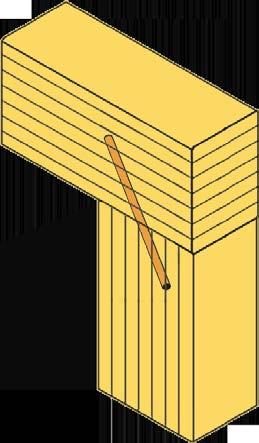
Lacaton and Vassal - Transformation of 530 dwellings 21
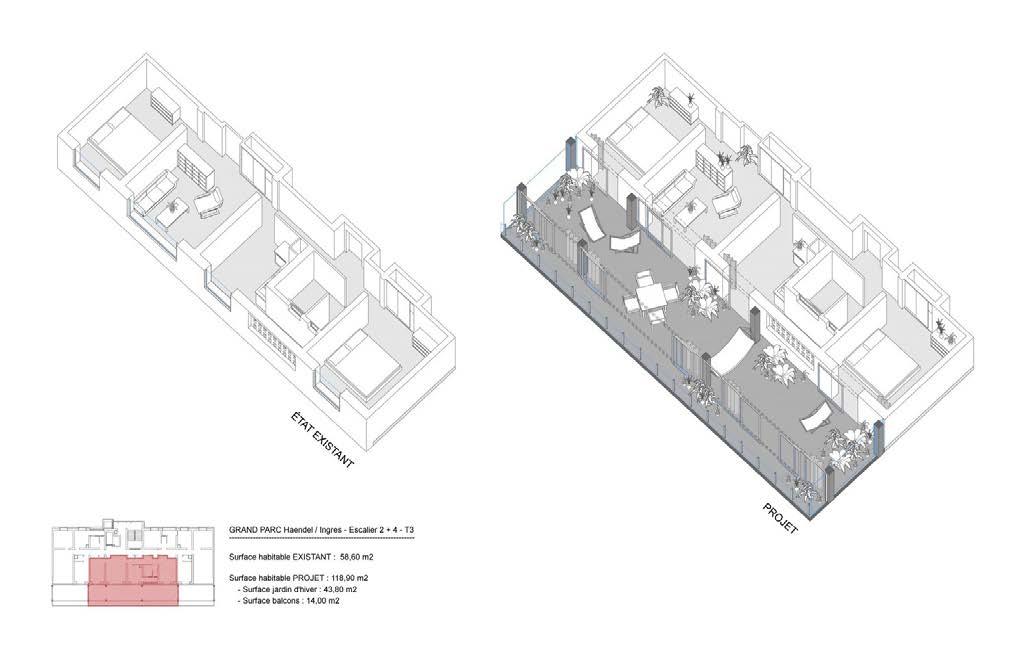
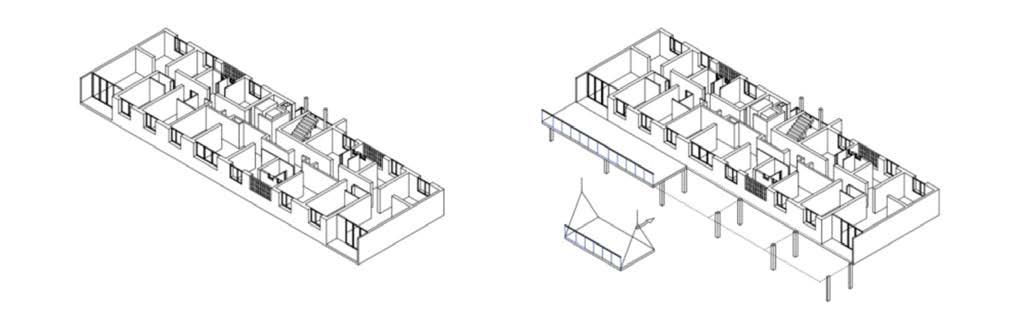
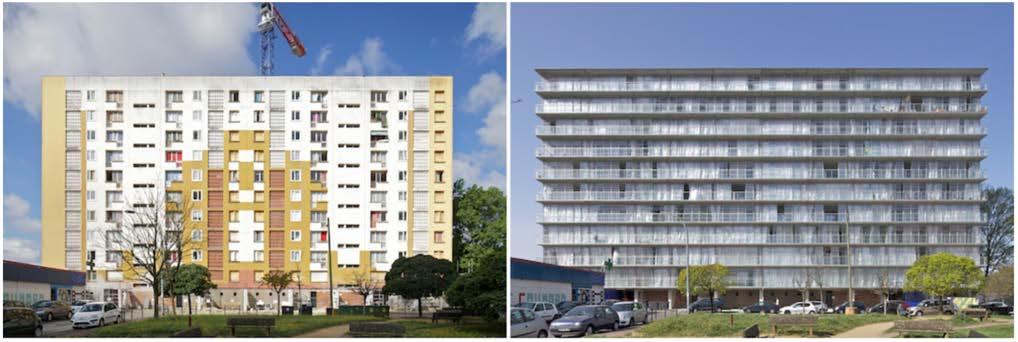
System Plug-In Exploring Initial Ideas
-Increased Thermal Performance. -Increased light. -Cheaper than Demolition and rebuilding. -Embodied carbon of existing building is saved.
-Increases space, provides winter gardens.
The project consists in the transformation of 3 modernist social housing’s buildings, fully occupied. It is part of the renovation program of the ‘Cité du Grand Parc’ in Bordeaux. Built from the early ‘60s, this modernist district counts more than 4000 dwellings. The 3 buildings G, H and I, 10 to 15 floors high, gather 530 dwellings and needed a renovation after the question of their demolition has been ruled out. By their location and their layout, these buildings give a capacity of transforming into beautiful dwellings with qualities and comfort. -Allows for residents to stay in their homes throughout construction - only having to leave for 1 day whilst they cut through existing exterior wall.
System Plug-In Exploring Initial Ideas
NU Stora+LivingEnso 22
NU Living Stora Enso
Ground Floor Construction // Combining Systems
- To achieve open ground floor spaces for retail/commercial uses the NU Living modules ordinarily require a concrete or steel podium to be installed. The modules can then be stacked onto this podium enabling smaller residential living above an open ground floor.
Can a concrete/steel podium be avoided when an open space is required at ground floor by a combination of the two systems?
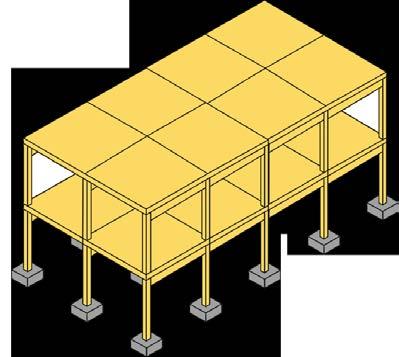
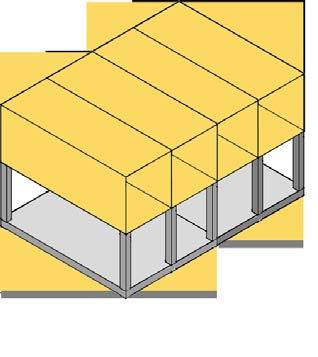
- The Stora Enso post & beam system can be employed on the ground floor as it can on the floors above due to larger spans being available.

Glulam post with tapered end and steel cap driven into ground to form pile foundation, steel connection at ground plane to attach ground floor glulam posts. Steel ground screw driven into ground to form foundation, connected to glulam post at ground plane.
10° 23
Foundations Without Concrete // Piles
Ground Plane Common connection of glulam post to concrete pile foundation. Glulam post with tapered end and steel cap driven into ground to form pile foundation, extending from ground plane to form ground floor frame. Can piles be driven in at slight angle to provide bracing?



System Plug-In Exploring Initial Ideas

Composite Piles
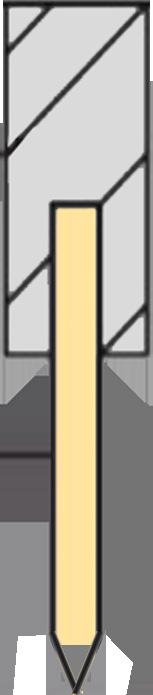
Concrete Cap >> Glulam Pile >> Depth of Water Table Glulam Post >> Steel Connector >>
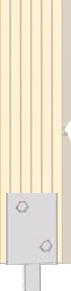
Glulam post with tapered end and steel cap driven into ground to form pile foundation, capped with concrete cap to protect timber from water table. Common steel connection from concrete cap to glulam post forming ground floor frame. Ground Plane Steel Shoe Cap
System Plug-In Exploring Initial Ideas
>> 24
System Plug-In Concept Eliminating Cement Lime Stabilised Soil (clay) Columns >> Fly Ash/Lime Concrete Ground Slab >> Glulam Post & Beam Ground Floor Timber Frame >> CLT Modular Floors Above Ground >>
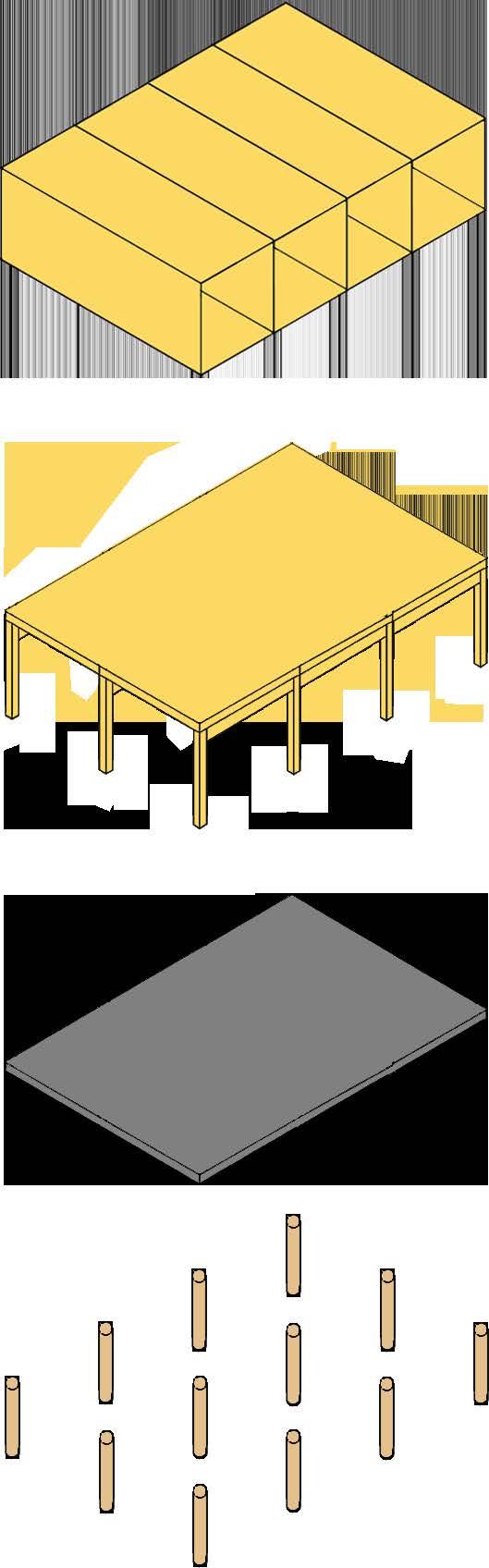
Phase 03 Making a Proposal
System Plug-In Business Case 1) Project Title Inasinglesentence,whatisyouridea?
2) ‘Elevator Pitch’
• The complete elimination of cementitious concrete from the design, whilst maintaining the ability to create large open ground floor spaces.
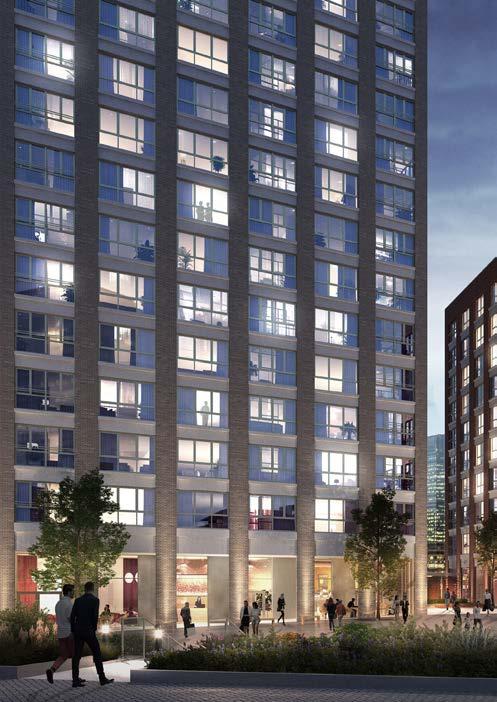
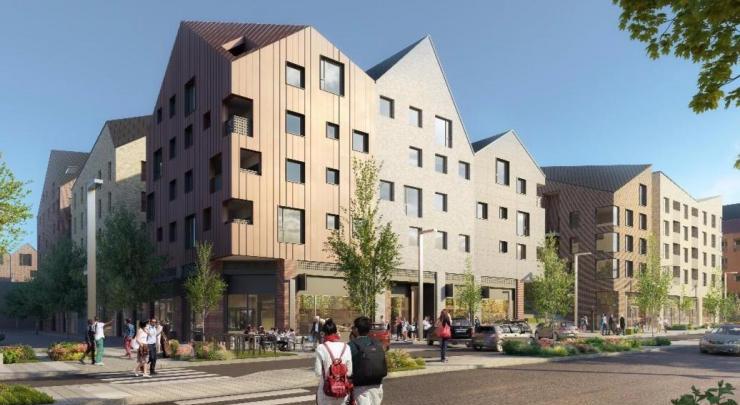
3) Target Market Howwideornarrowisthemarketforyourproduct? Insimpleterms,howmanymighta factoryproduceeachyearbasedonhowmanypurchasersonemightexpecttheretobe?Yourtargetmarketshouldbenarrowenoughforyourproducttobemassproducedwithinstandardisedconstraints,butwideenoughtobeviableformassproduction.Areyouabletogiverealfigurestobackthisup?Whoisyourideafor,andwhoisitnotfor?Trytobeasspecific(andconcise)asyoucan.waytoameeting,howwouldyouexplainwhatyourproposalcando,whydoingthatisimportantoruseful,andwhytheymightconsiderinvestinginit.•Ourplug-inlookstomaximisetheuseoffactorybuiltandreadymodulesinbothnewmixeduseresidentialdevelopmentsandrenovationsbyNu-livingforSwansHousingAssociationanditsdevelopmentpartners•SwanHousingAssociationcurrentlyownandmanageoverappox.11,500homesinEssexandEastLondon.Seeingincreasesofover300unitsbetween2019and2020,withsomeownershipstretchingbackto1994.(SwanHousingAssociation-AnnualReportandFinancialStatements2019-2020)•In2019/20SwanandNu-Livingcompleted466homesacrossarangeofprojectswithafurther230homeinconstruction.CurrentlySwanhasappox.11projectsunderwayandweeseeourpluginbeingeffectiveinaroundhalfoftheircurrentregenerationprojectsbasedaroundmajortowncentrese.g.BlackwallReachinTowerHamlet,BlackHorseYardinWalthamForest,LaindonPlaceandPurfleet-on-ThamesinEssex.
wayIfyoumettheCEOoftheNu-BuildorStoraEnso,orapotentialinvestorintheliftonthetoameeting,howwouldyouexplainwhatyourproposalcando,whydoingthatisimportantoruseful,andwhytheymightconsiderinvestinginit.•Ourproposalisaddressingthelastpartofbothsystemsthatisnotalignedtothesustainablebuildingapproachpursued,duetopracticalreasonsofeaseandaccessibilityatpresent.Eliminatingcementfromthedesignandreplacingitwithlimewillreducecarbonemissionsfromthecreationprocessby20%;ifsomeofthislimecanthenfurtherbereplacedwithrecycledflyashthiswillreducefurther.Theultimategoalisaproductasgoodasconcretethatdoesnotcreatetheemissionsgeneratedthroughhightemperatureproduction;limecolumnpilesandslabsareafirststeptowardsthis.
27
Inwhatwaysisitcompatiblewiththeexistingproductswehavestudiedandwiththeexistingfactoryprocessesandmaterialstheyaremadefrom?•Ourplug-inlookstobuilduponNu-LivingandSwanethosofbeinginnovativeandsolution
focus with out emphasis on how to improve the sustainability of their building across the variety of sectors their buildings currently look to provide for.
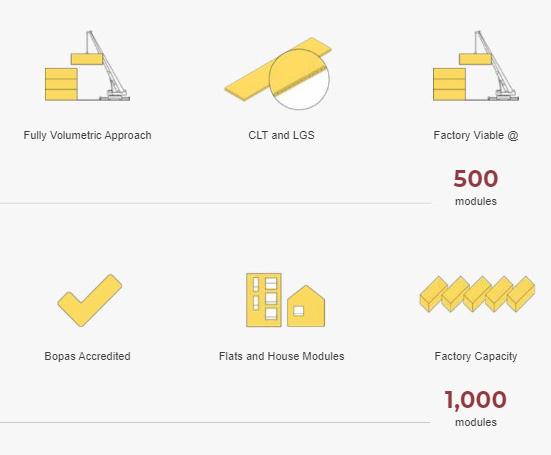

5) Don’t forget…
• By developing a process that looks to further reduce the use of concrete and steel within the buildings, and looking at ways in which the factory can develop structural and flexible units for the spaces range of uses i.e. building services, retail and commercial uses.
Isthereonemoreimportantthingweshouldknowabouthowexcitingyourideais?•Itcouldbeusedasacasestudyforanancienttechnologyrecentlybeinglooked
System Plug-In Business Case 4) Compatibility
at being employed in mass production techniques as the world looks to reduce global emissions; especially those related to construction of which cement contributes 8% overall. 28
Eliminating Cement Lime Stabilised Soil (clay) Columns >> Fly Ash/Lime Concrete Ring Beam Grid >> Ground Floor Build Up >> Air gap Insulation in grid voids Waterproofing membrane CLT floor panels Glulam Post & Beam Ground Floor Timber Frame >>

Columns
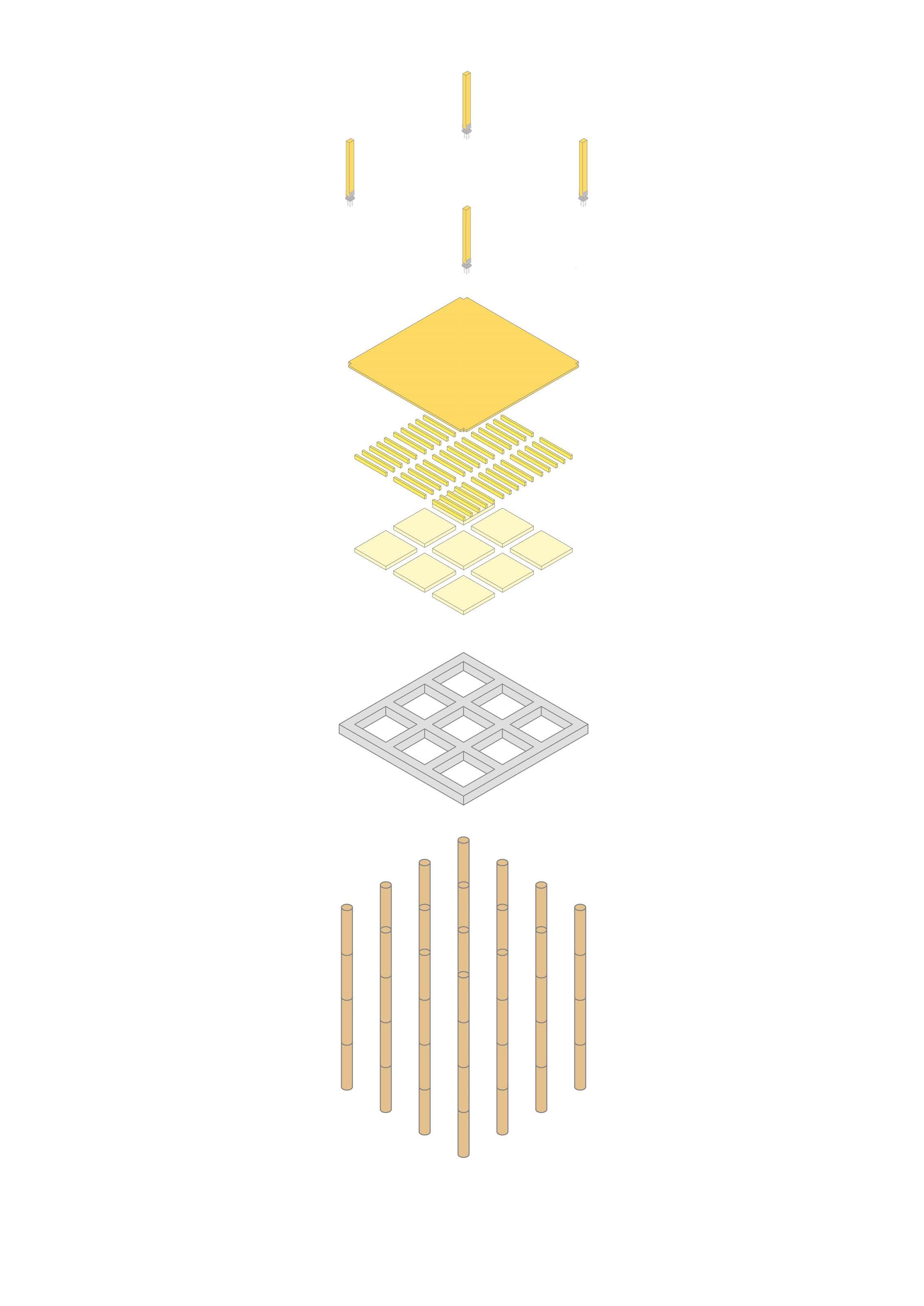
Large diameter boreholes filled with lime stabilised clay soil - Lime requires lower temperature to create - 20% less CO2 emissions when creating lime rather than cement
LimeFoundationsStabilisedSoil(clay)
30
- Additional CO2 absorbed during lime hardening process - Lime can be produced locally possibly reducing transport costs - Working with the NU living limited geographic proximity already in place, a large portion of that area is clay soil - Can be drilled and inserted with relatively small mobile rig - Does not create any soil spoil as soil is not removed.
Columns
31
LimeFoundationsStabilisedSoil(clay)
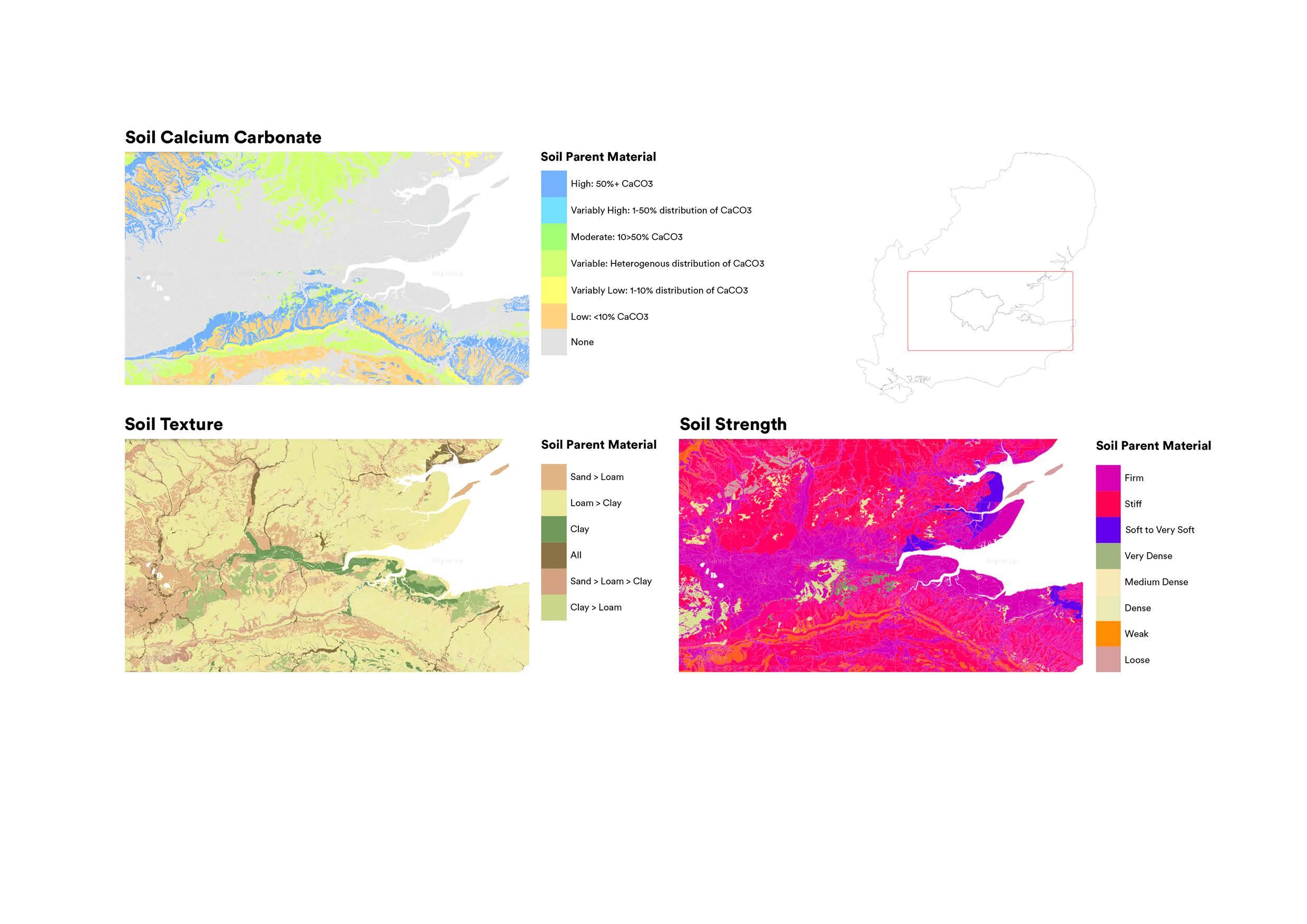
Columns
LimeFoundationsStabilisedSoil(clay)
32
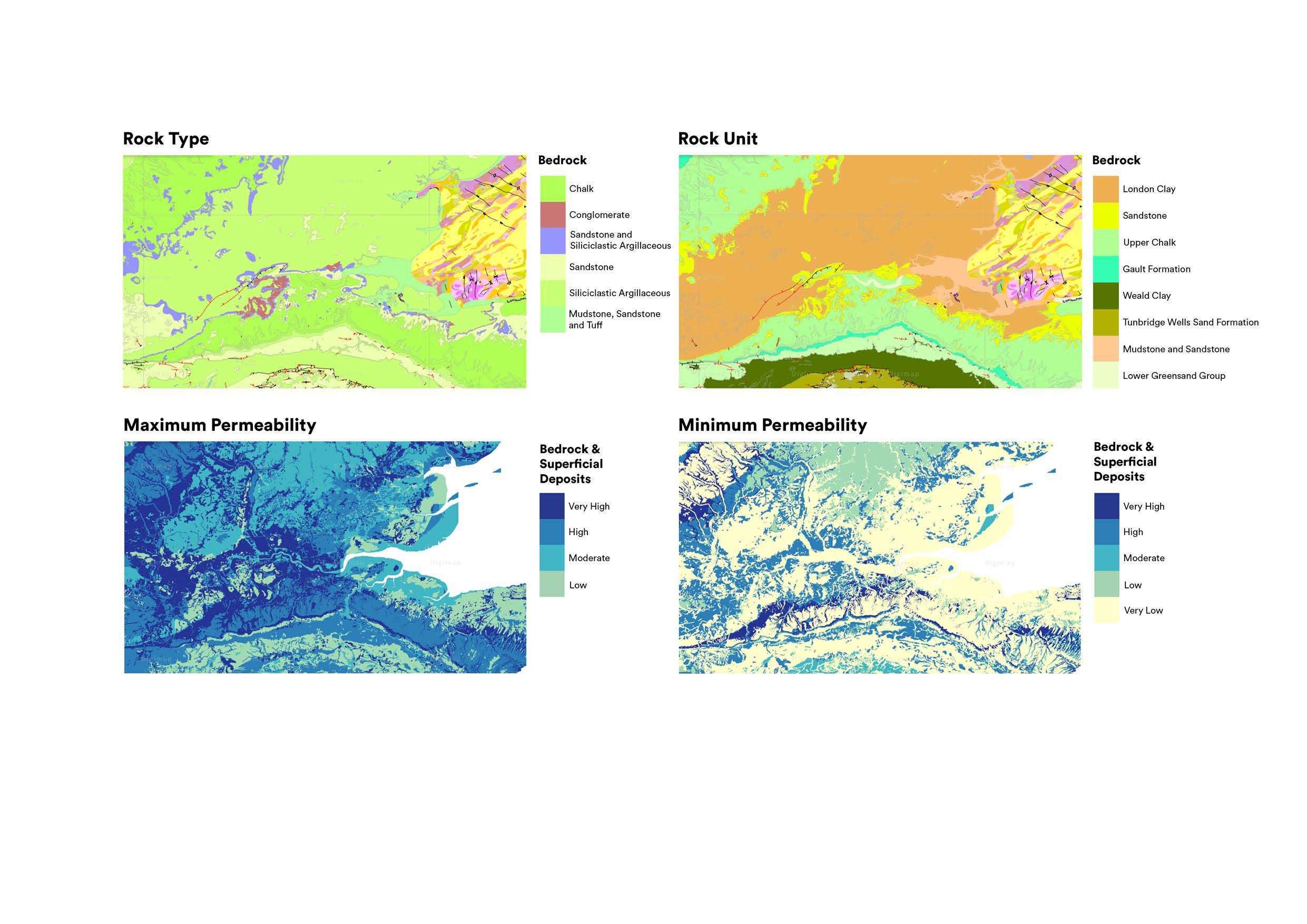
Making Concrete BINDING AGENT + WATER & AIR + SMALL AGGREGATES + LARGE AGGREGATES (10%) (20%) (30%) (40%) Typical Materials CEMENT + WATER & AIR + SAND + GRAVEL Alternative MaterialsLIME& CEMENT + WATER & AIR + SAND + GRAVEL FLY ASH & CEMENT + WATER & AIR + SAND + GRAVEL CEMENT + WATER & AIR + RECYCLED PLASTIC AGGREGATES EliminatingLIMECement&FLYASH + WATER & AIR + RECYCLED PLASTIC AGGREGATES 33
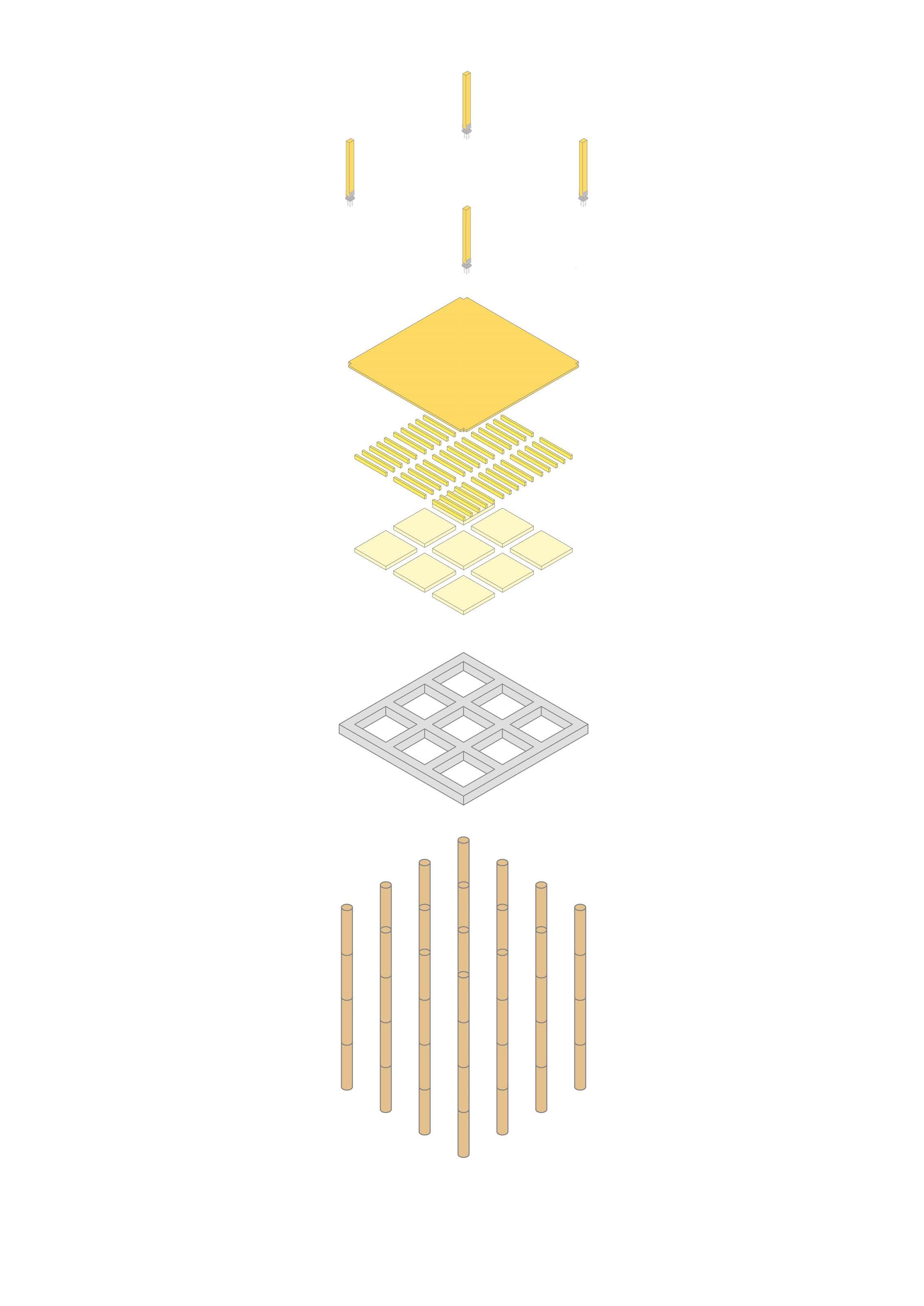
Ring Beam Structure 34

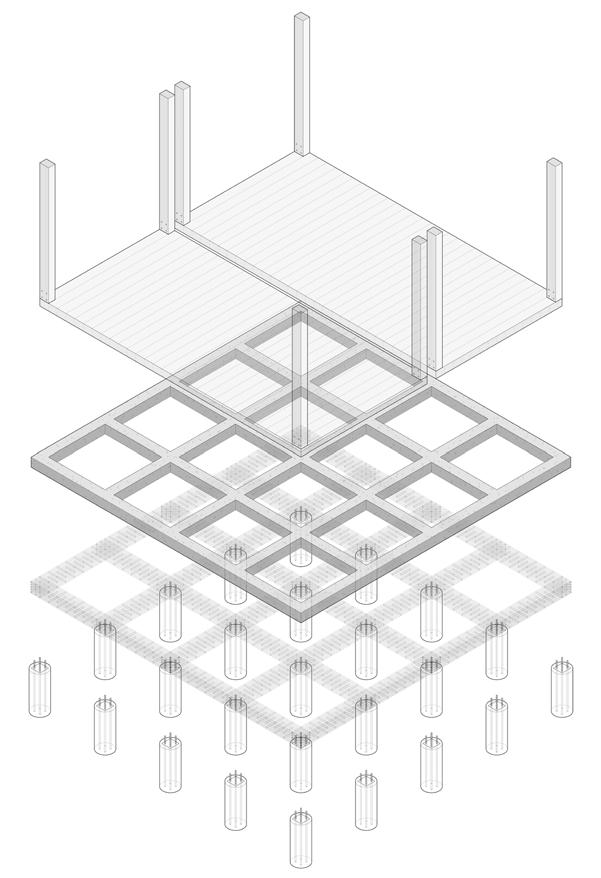
Cast In-situ Concrete Cement-Free Ground Beams Pros - Quicker and relatively easier installation - Can be designed to incorporate notches, end details and sloping faces to create seamless interfaces with load.
Ground beams are beams designed to span between pad foundations, piles and so on, as an alternative to traditional foundations. They are structural elements that transfer loads imposed along their length to their end points where the loads are transferred from the floor and columns to foundations. They support the wall, joist and other structures, especially in places where the soil is not sturdy enough to support the Groundstructurebeams are typically constructed from concrete, and for low-rise buildings are commonly constructed in situ. They can be relatively time-consuming method, the use of pre-cast concrete ground beams has become more common to mitigate this.
Pre Cast Concrete Cement-Free Ground Beams
- Secondary beams can also be easily connected to the ground beam system to form a beam and block ground floor. - Can be installed where the existing ground levels are uneven or the landscape is slopping in any direction - Can also be raised or lowered to prevent the costly exercise of diverting or removing live underground services Cons - Can be time-consuming for the overall project due to the length of time concrete sets
Pros - Quicker and relatively easier installation - Can be designed to incorporate notches, end details and sloping faces to create seamless interfaces with load.
- Secondary beams can also be easily connected to the ground beam system to form a beam and block ground floor.
- Can be installed where the existing ground levels are uneven or the landscape is slopping in any direction - Can also be raised or lowered to prevent the costly exercise of diverting or removing live underground services - Off site production to accurate measurements in relation to pile foundation.
Ring Beam Structure Sourcing Materials FLY DirectASHSources >> Coal Fired Power Stations >> Nottinghamshire (until 2024) >> Nottinghamshire (until 2022) >> County Atrim (until 2023) Indirect Sources >> Landfill Sites >> Currently 50million tonnes of excess fly ash in landfill sites being managed as a waste material >> Often adjacent to power station sites >> This can be repurposed SourcesLIME >> Lime Producers >> Lhoist - Buxton >> Tarmac - Buxton >> Singleton Birch - Lancashire RECYCLED PLASTIC AGGREGATES Direct Sources >> Industry >> Industries that create fine plastic waste as a by product of manufacture that would otherwise go to landfill >> Plastic optical lenses for glasses - for example Indirect Sources >> Plastic Recycler Services >> Rubber & Plastic Collection Services LTD - Berkshire >> Axion Polymers - Salford >> Chase Plastics - Suffolk 35
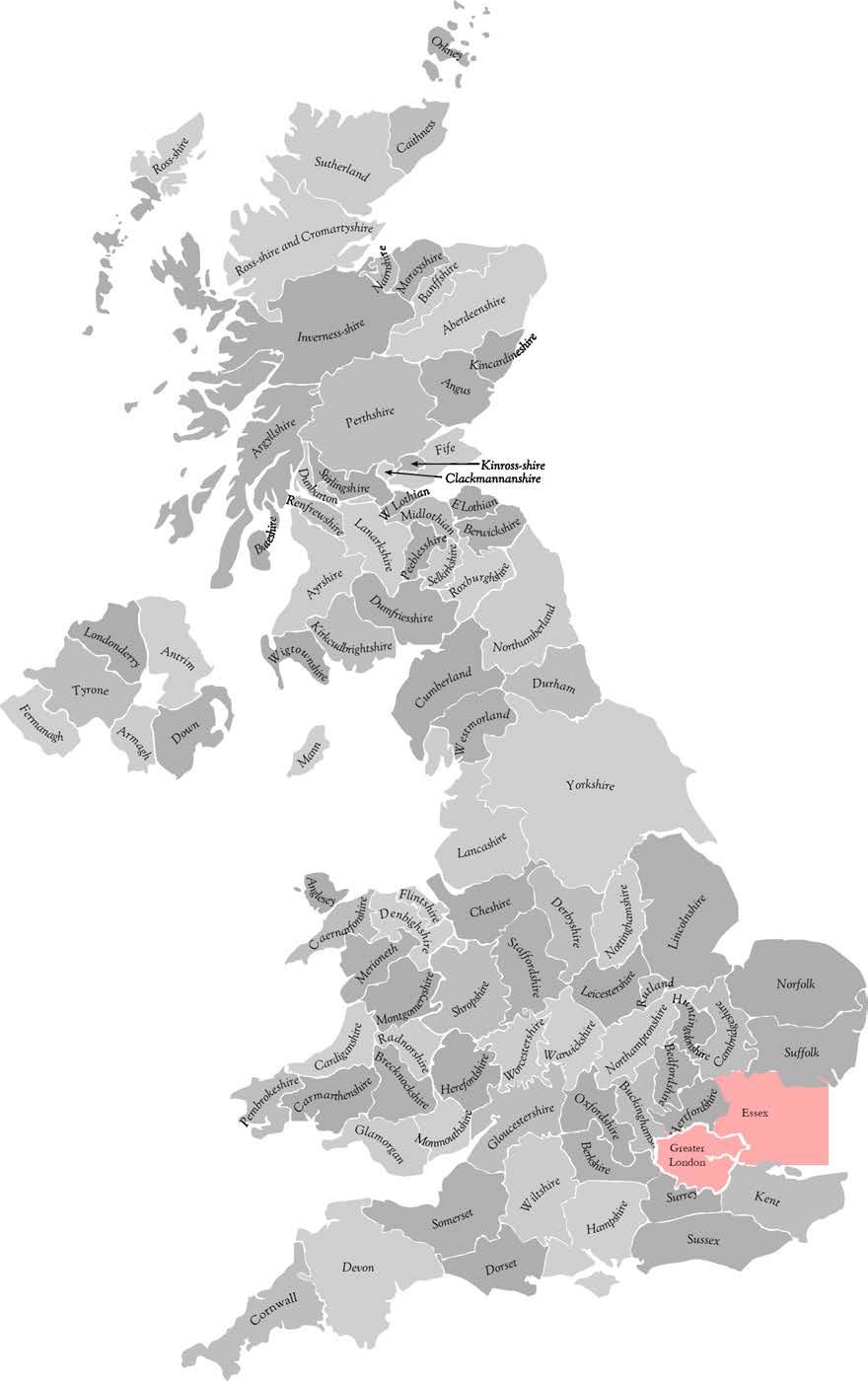
36

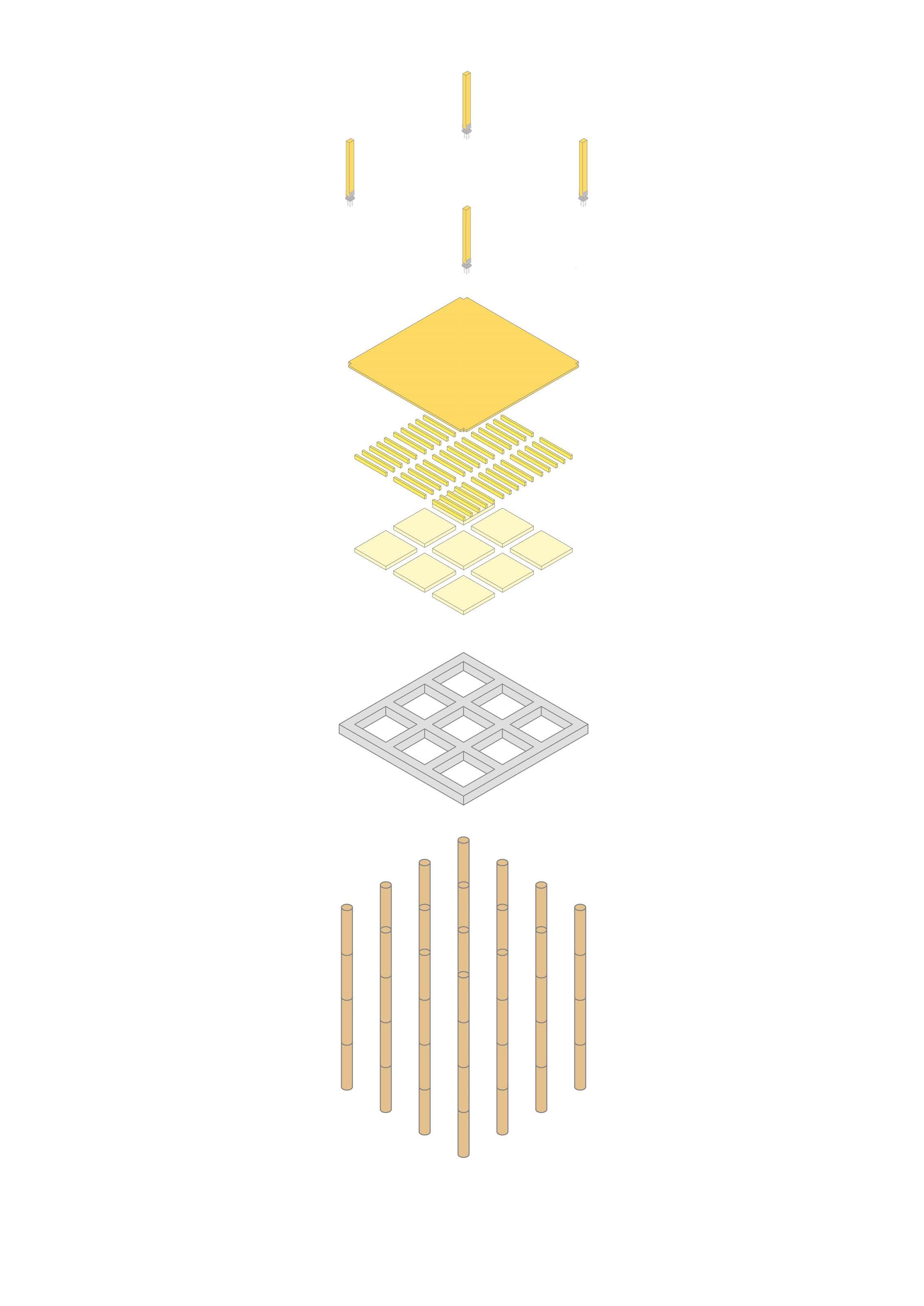
Ground Floor Frame Glulam Post & Beam Ground Floor Timber Frame (Connections)
Nailed Plates - Nailed sheet metal for fixed support, normally on the column’s narrow sides.
Pole Shoe - Suitable solution to prevent water ingress through the column’s end grain.
-sheetMoisture protection required Angled Steel Fastenters - Angular steel is tightly screwed in the concrete construction with expander screws. - Reduces the risk of wrong placing, creating opportunities for thorough and more precise measurements. - Moisture protection required Key : 1. Glulam Posts 2. CLT Floor Build Up 3. Knife Plate Connector 4. Bolts 5. Adjustable Anchoring Rods 6. Cement free Concrete Pile Foundation 1 3 4 2 37
65
- End grain surfaces should be moisture protected against concrete and other moisture absorbing material and preferably be.
- The fitting can either be molded into concrete structures or welded to an embedded fixed metal sheet. Force transfer occurs with anchor nails or with screws.
- The lower part of the anchoring rod is often moulded into the concrete structure, but the rod can also be welded to an embedded fixed metal sheet. - Provides opportunities for adjustable standard fittings for more accurate grd floor levels.
Flat Rolled Steel - Fixed support on the column’s narrow sides - The flat rolled steel is moulded into the concrete construction or is welded to an embedded fixed metal
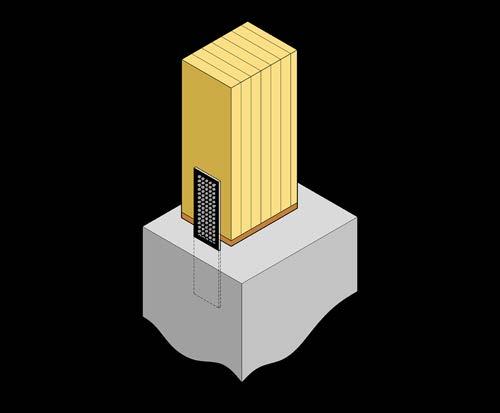
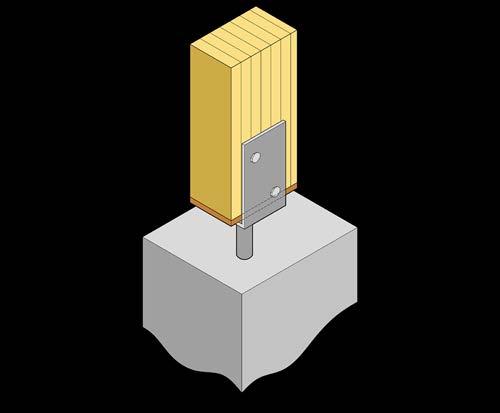
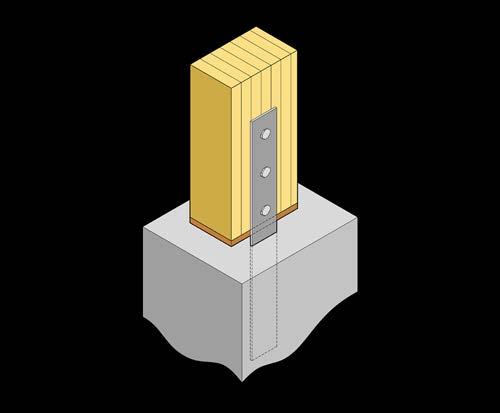
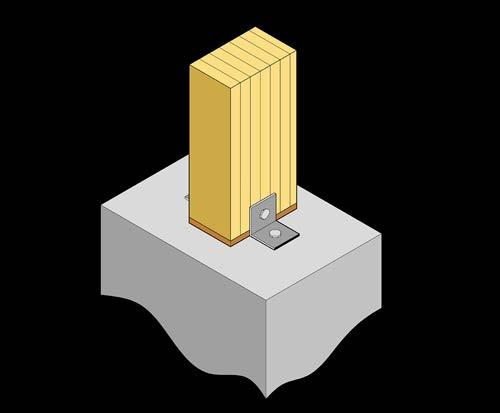
- Interface between Stora Enso ground floor frame
- The steel dowels can be counter sunk in the beam and covered with wooden plugs, where completely hidden fittings provide greater fire protection
CLT Modules - Utilising current NU Living CLT modular system
- The transference of force between the beam and column occurs as a rule with the aid of the throughgoing screw, nut and washer.
Recessed Steel - Pinned connections with steel sheet and steel dowels slotted into posts and beams
- Flat rolled steel, type flat rod or universal rods, are suitable for both small and large forces.
Glulam Post & Beam Frame Connections to Modular Units
Above Ground Floor 38
- Counter sunk beams are often used for corner columns in order to transfer the column’s horizontal forces to the beam.
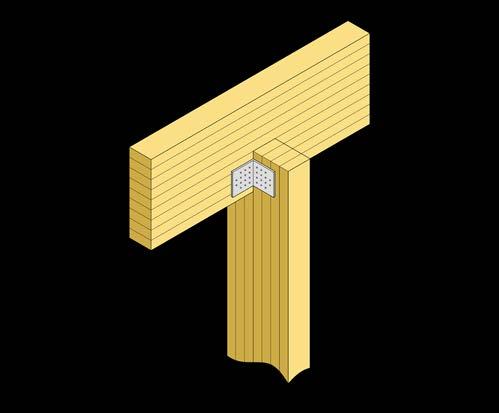
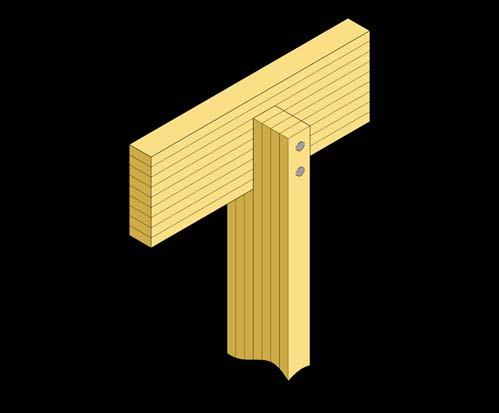
Flat Rolled Steel
- Special measures for fire protection required
- The groove in the column is often made as big as the width of the beam.
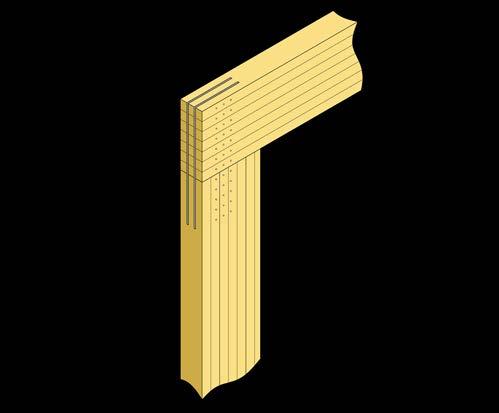
Counter Sunk Beams
- The upper hole in the beam should be oval due to moisture movements.
- Pinned connections on either side of the section column’s - Simple and effective.
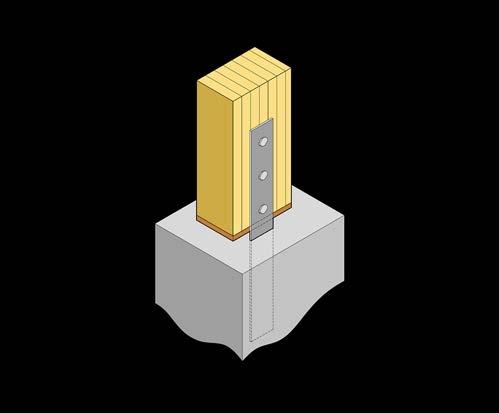
- Can ground floor ceiling beams be eliminated by utilising inherent strength of CLT modules to span between posts below and provide bracing?
- For small horizontal and vertical (lift) forces attachments with the aid of metal sheet angles or axial-loading screws or even coach screws
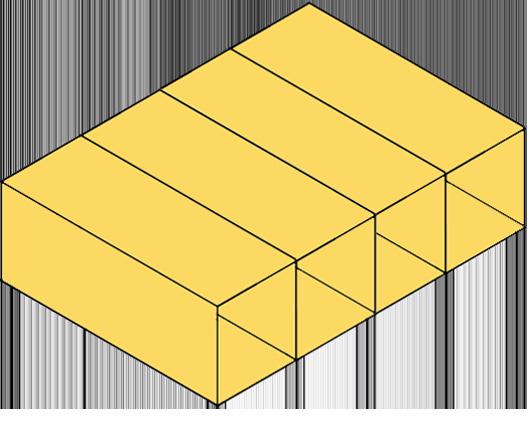
Pros - Quicker and relatively easier installation - Secondary beams can also be easily connected to the ground beam system to form a beam and block ground floor.
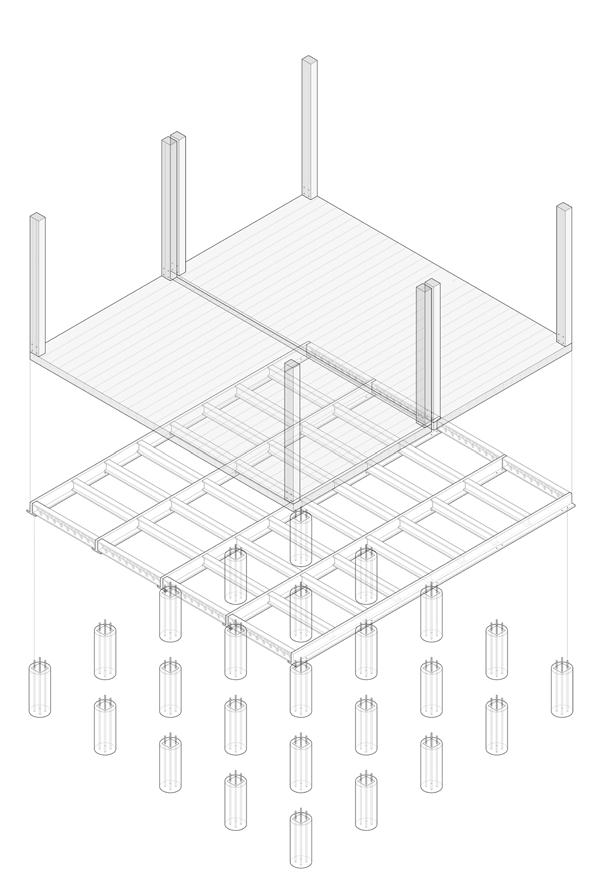
Beams with CLT Modules
Ring Beam Alternative MethodSteel Ring BeamSteelOptionGround
Steel
- Can be installed where the existing ground levels are uneven or the landscape is slopping in any direction - Can also be raised or lowered to prevent the costly exercise of diverting or removing live underground services
Steel Ground Beams with Steel Frame Ground Floor System
Pros - Quicker and relatively easier installation - Secondary beams can also be easily connected to the ground beam system to form a beam and block ground floor. - Can be installed where the existing ground levels are uneven or the landscape is slopping in any direction - Can also be raised or lowered to prevent the costly exercise of diverting or removing live underground services 39

steelframedbuilding”
Main Disadvantage : framed buildings have no more, and arguably slightly less, embodied CO2 than a
Graph02-Embodiedcarbonbreakdownbyelement(kgCO2e/m2) {CundallReport:ClardD;BradleyD,2013,P10)
Graph03-EmbodiedcarbonresultsfromEaton&Amatostudy{CundallReport:ClardD;BradleyD,2013,P7)
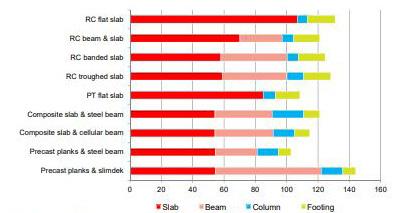
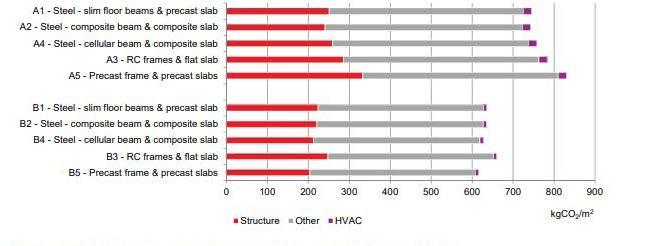
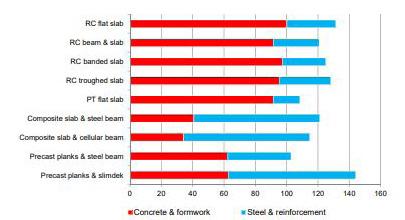
40
Rebar Basement ConcreteScreed
This was found in a study carried out by Arup (a multidisciplinary engineering and architectural design firm base in the UK) on behalf of The Concrete Centre in 2010, they investigated the embodied carbon within structural frames of non residential. Using models of a range of material compositions, they found and concluded that for typical medium rise office, hospital and school buildings. These findings are illustrated in Graphs 1 ,2 & 3 as part of a case study analysis undertaken by Cundall in 2013, scrutinising Arup‘s claims in relation to other similar investigations that occurred between 1998 and 2013, analysing the breakdown of embodied carbon in structural elements and materials. Structural Steel Steel
Graph01-Embodiedcarbonbreakdownbymaterial(kgCO2e/m2) {CundallReport:ClardD;BradleyD,2013,P10)
Ring Beam Alternative Method - Steel Steel Ring Beam Option
ConcreteConcreteDesk(6,000PSI)(4,000PSI)SteelRebar SuperstructureRebarFoundationRebarFoundationConcreteSuperstructureConcreteSuperstructureSteel SubstructureShell
“Concrete
The diagram above is a Sankey diagram of suggested available reductions in embodied carbon, based on supply chains. This diagramwasdrawnfromaEmbodiedCarboninConstructionCalculatordevelopedbytheCarbonLeadershipForumtoinvestigatetheimpactofmaterialselectionforbothretrofitandnewconstructionprojects.{ArchitectMagazine:ShapiroG,2020}
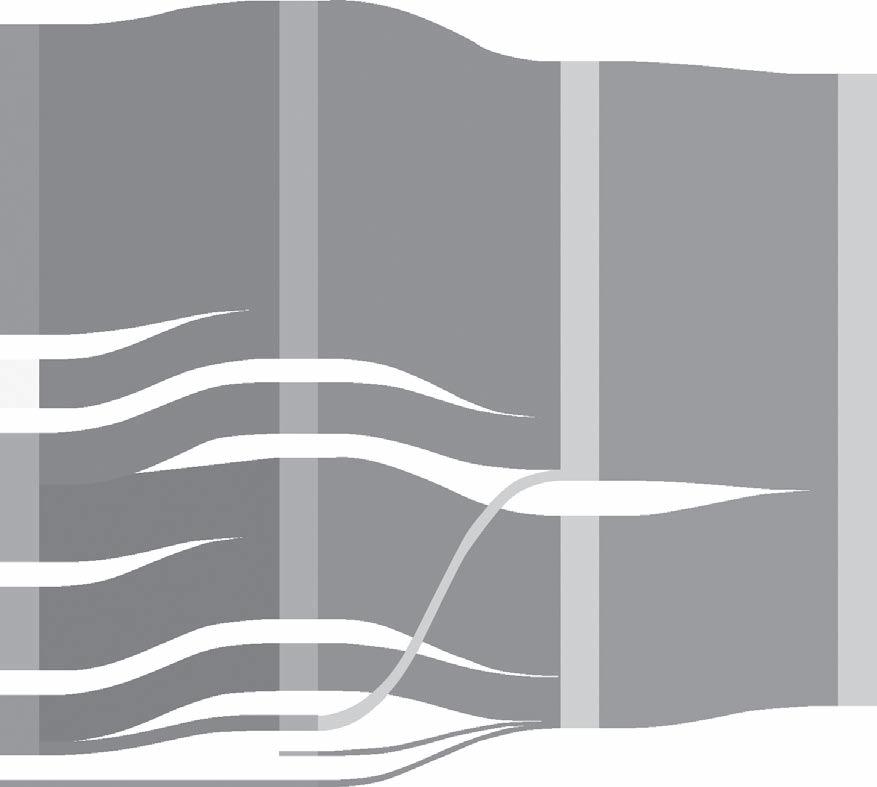
Basement
CarbonAchievableConservativeNet-ZeroEmbodiedCarbonEmbodiedCarbonBaselineEmbodiedTarget(-25%)
Constraints - The maximum Story Height of the Nu Living developments on top of the Piles will be 5 stories due to load bearing tolerances. Ave Depth 6000mm
450mm
41
Eliminating Cement - Lime Stabilised Soil (clay) Column Foundations
Finalised Plug In Design Elements








Installation - Using a relatively small Mobile Rig, the auger is drilled down into the soil to a depth that corresponds to the prescribed column length. Powdered quicklime (CaO) is forced into the soil with compressed air through a hole located just below the horizontal blade of the auger, and the lime is mixed thoroughly with the soil. The withdrawal rate of the tool is about one-fifth of that when the auger was initially drilled down into the soil.
Utilising the soil conditions within the boundaries of where Nu Living are able to build, Lime Stabilised Soil Columns allow for a method of piling that replaces a large amount of concrete with the already existing soil on site and quicklime, otherwise known as Calcium Oxide. This both reduces the amount of waste on site in terms of excavated soil spoil and reduces the carbon dioxide emitted by 20%. The drying process of the lime also absorbs carbon in the process. The lime can be sourced from between 190-250 miles allowing for a reduction in the transport distances for the primary materials.
Production and Transportation - Being produced in a factory setting allows for precise and regulated ring beams at a mass scale. Assembled in components allows for a far greater number to be transported to site reducing the overall transport times and costs and allows for a quick and dry assembly once on site compared to traditional forms of concrete foundation construction. Fly Ash (9%) + Lime (9%) + Polyethylene terephthalate (30% + Large Aggregate (45% + water (7%
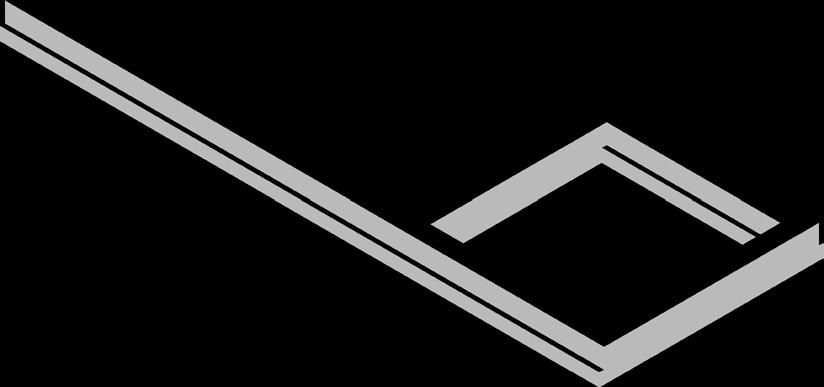
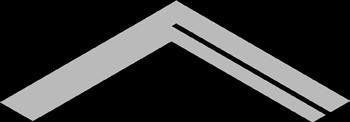
A Pre cast Lime & Fly Ash concrete ring Beam allows for a greater reduction in Carbon dioxide, the use of waste materials Like Pulverised Fly Ash and Polyethylene terephthalate and precise tolerances for Mass timber to be attached to.
)
Material -Pulverized fly ash (PFA) is a a by-product of coal fire power stations that would otherwise go to landfill. Currently all coal power plants will be decommisioned by 2024 but there are some 50 million tons of Fly ash in landfill that are in close proximity to the site at which they were produced with the possibilty of being reused. Ash also allows for better strength and less permeability to water and chemicals when compared to cement.Limeas well as being a core material in the creation of the soil column foundations will also be used in the production of the ring beams. Lime is already an element in a large number of cement mixes but the main benefit of using just lime is the lower temperatures required to produce it and a reduction in carbon dioxide of 20%.Plastic aggregate allows for a replacement of sand. Fine plastic aggregate is a common by-product of many industrial processes and is easy to source throughout the uk. Polyethylene terephthalate (PET) is a byproduct from plastic recycling plants that still requires to be sent to landfill. PET can replace sand as fine aggregate. Using plastic aggregate replacement does mean for a slight reduction in compression strength compared to traditional concrete whilst maintaining similar tensile strengths.
)
Eliminating Cement - Lime & Fly Ash Pre Cast Concrete Ring Beam
) 2950mm 2550mm 9200mm 450mm 500mm 300mm 42
Finalised Plug In Design Elements
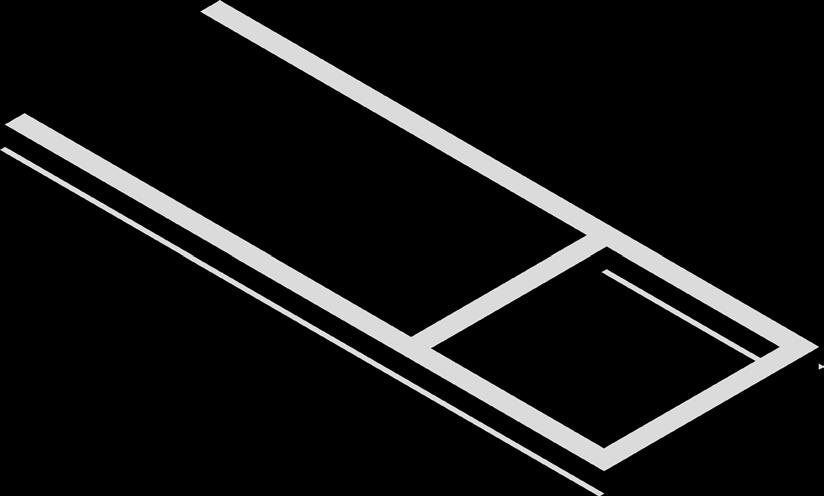
To maximise the use of factory built and ready modules in both new mixed use residential developments and renovations by Nu-living, and to further improve the sustainability of the Nu-Build system, we propose an integration of existing mass timber systems like that of StoraEnso’s Post and beam system on the ground floor. Suitable for circumstances where larger open-span spaces are required in New Living developments. Our proposal explores how a post and beam system can be easily integrated into NuBuild Modular system. Where we illustrate the continued compatibility that can be attained with our Pre-Cast Ring Beam system.
43Finalised Plug In Design Elements Eliminating Cement - Above Ground 2550mm 500mm 2950mm 2950mm 8850mm Proposed Modular ArrangementAxo-1:100@A3 Ground Floor ConnectionAxoDetail-NTS Ground Floor Modular & Ring Beam SystemAxo-NTS Glulam Posts CLT Floor Build-Up Gap for Fire StoppingExistingMaterial Nu-Build CLT BracketsModules and Screw Fixings Pre Cast Lime and Ash Concrete Ring Beams Reinforced In-situ Lime and Ash Concrete Piles Reinforcement is for added strengthandrigidity
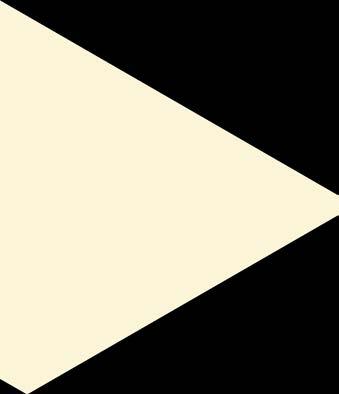
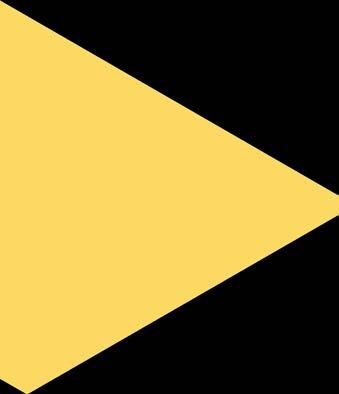

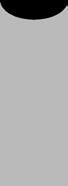

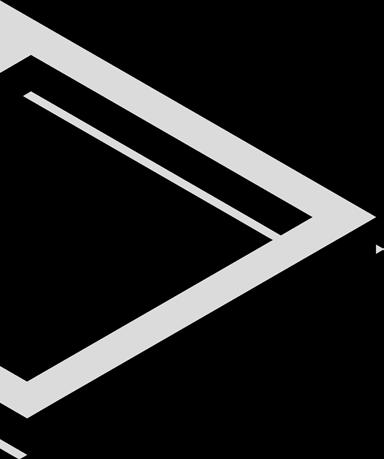
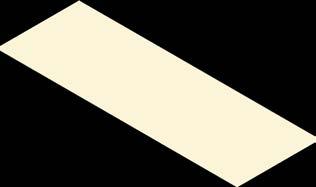
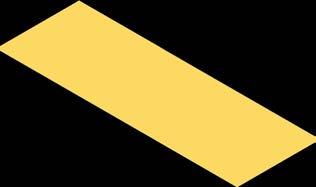
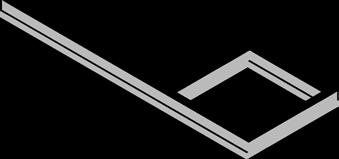

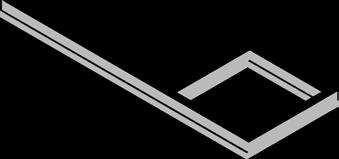
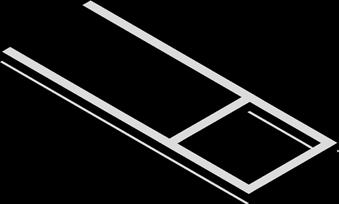
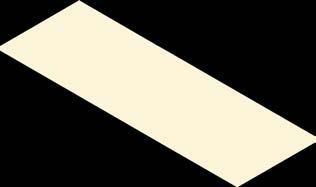
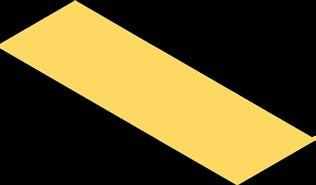
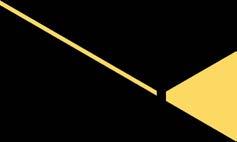


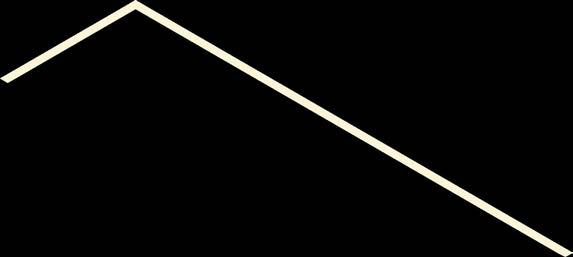
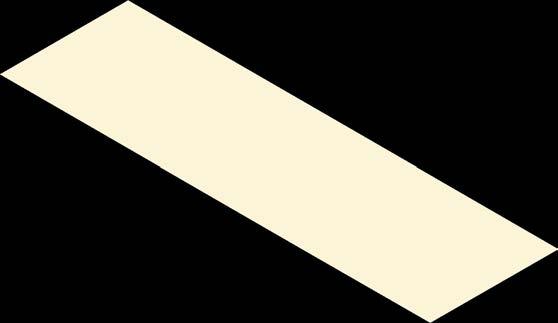
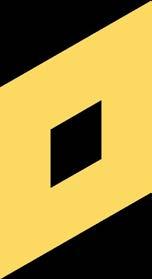
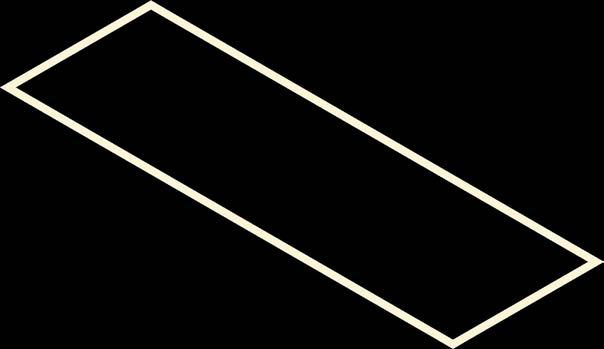
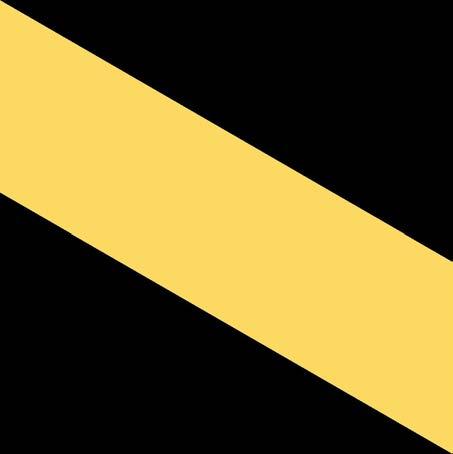
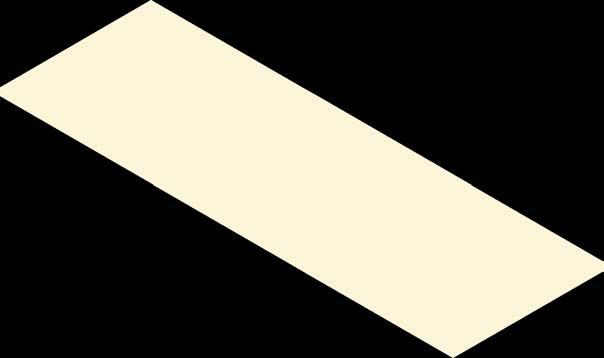
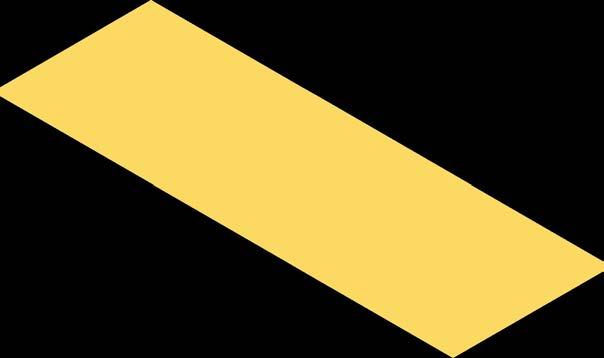


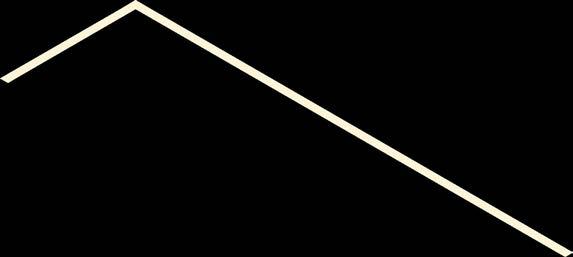
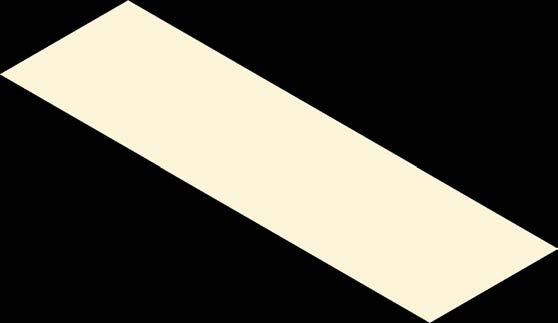
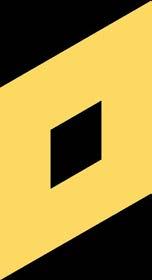
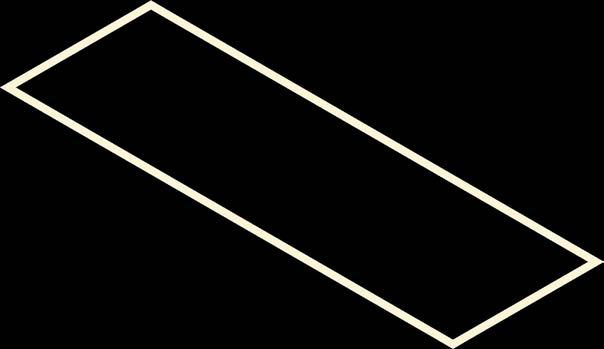
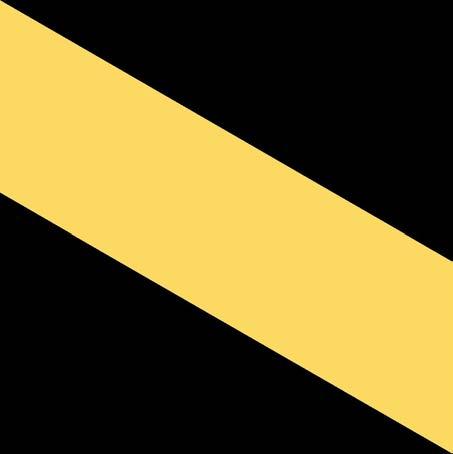
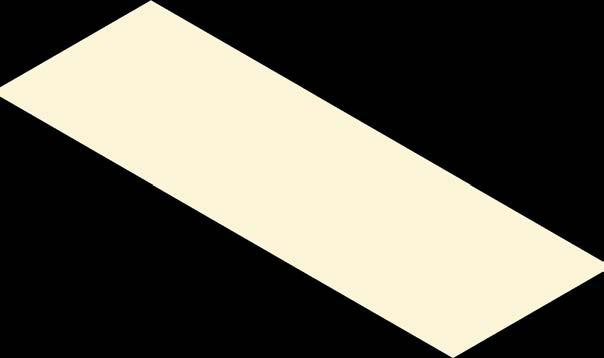
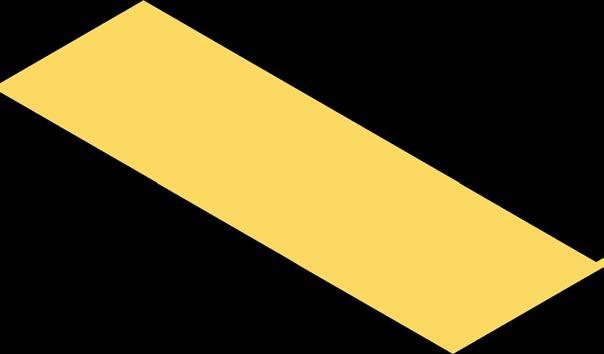



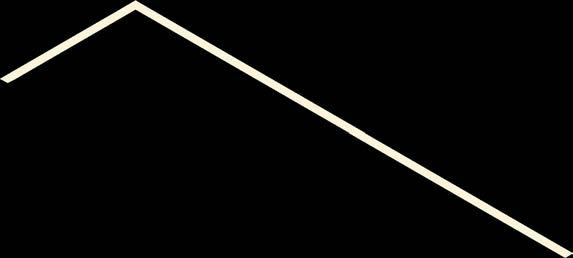
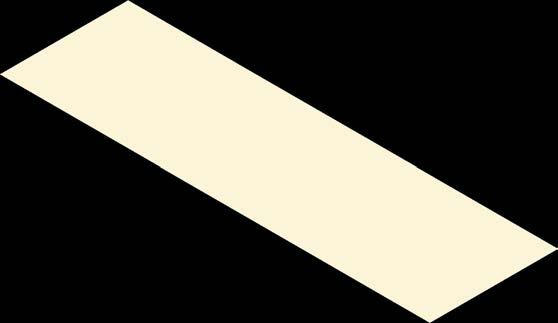
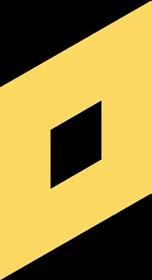




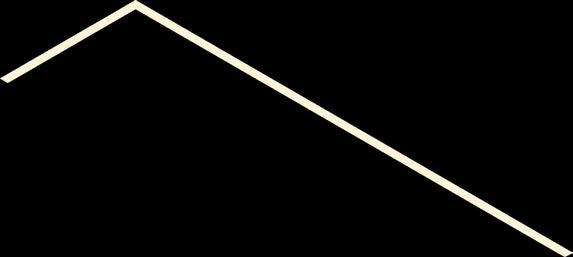
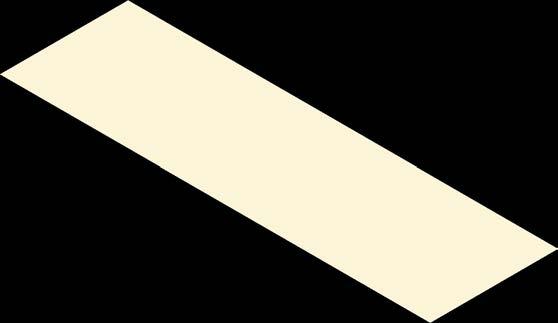
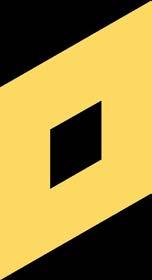
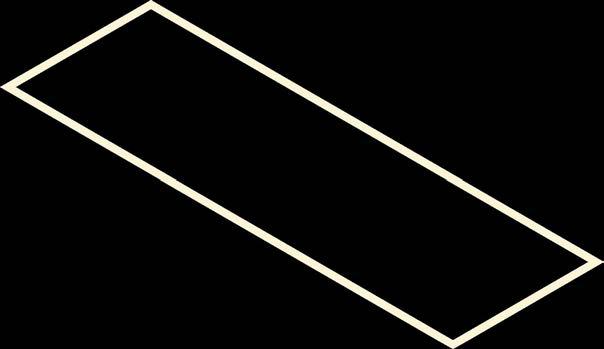
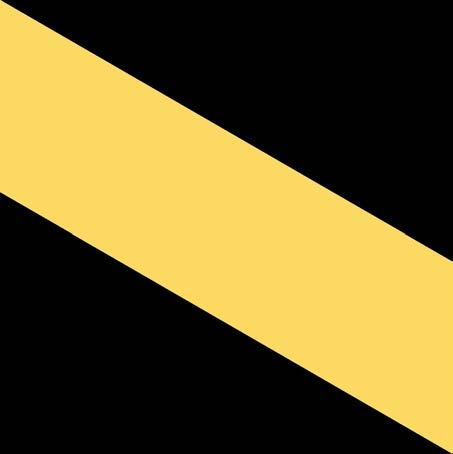
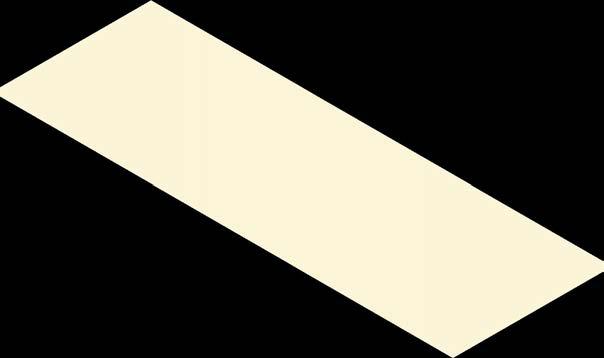
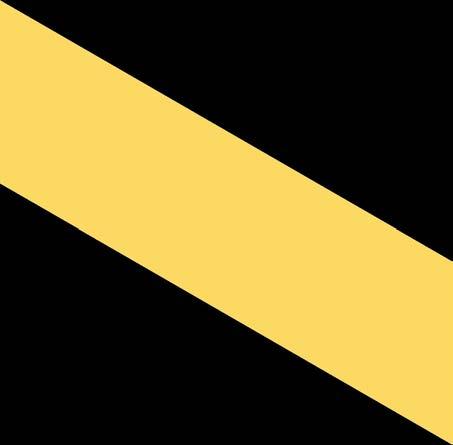
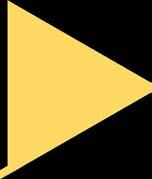
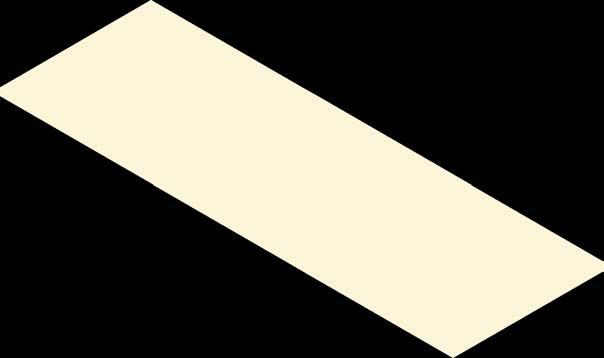
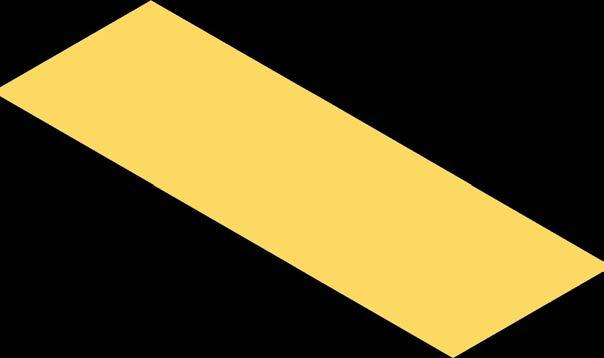
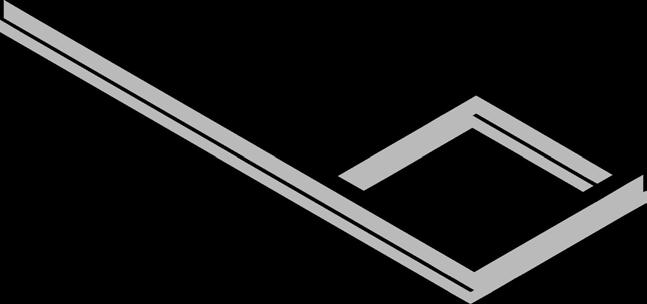
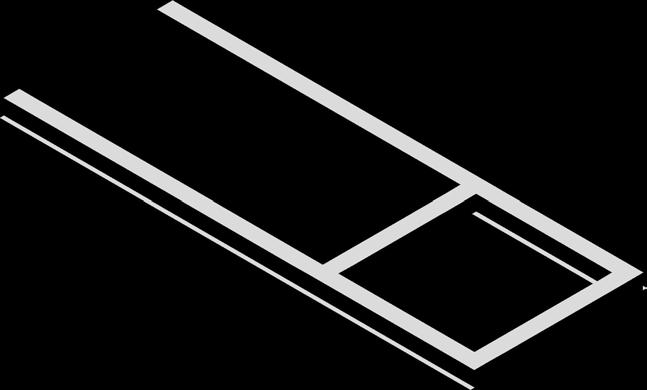
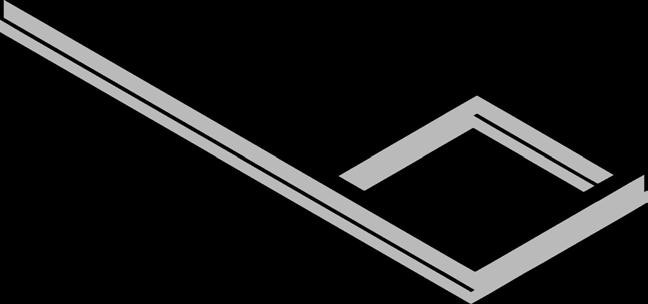
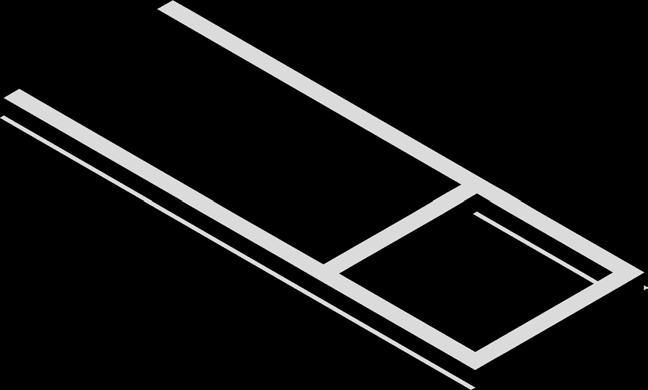
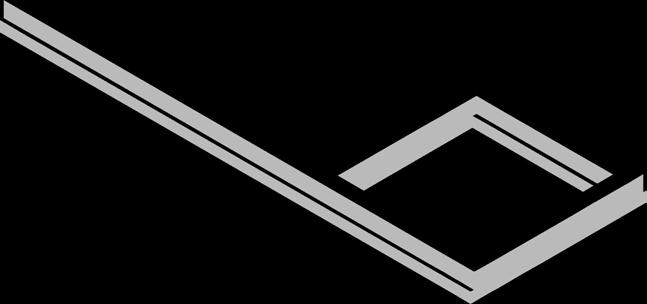
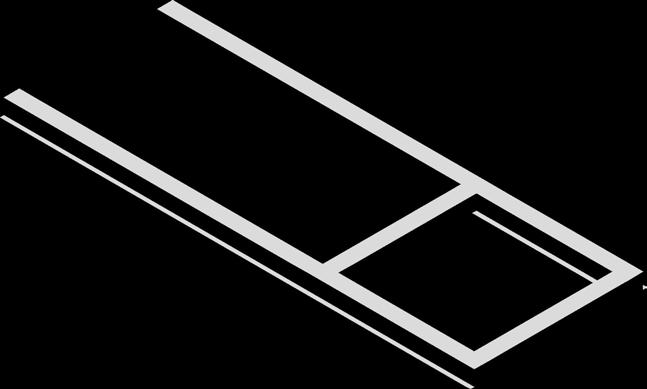

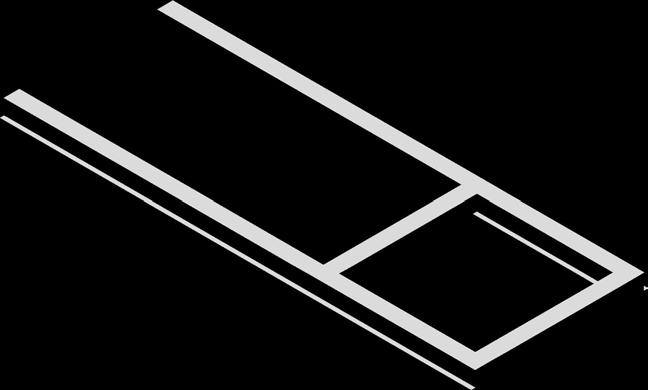
Plantation
Choked Convection Cavity Based on aspects of Salmaan Craig’s research, the introduction of air cavities in CLT wood panels, in the form of choked convection cavity cells, reveals significant increases in the thermal per formance specific to the slowing of heat transfer while reducing the overall ma terial volume. By calibrating cavity dimensions, convective forces can be “choked” - Warm side upward boundary layer air flow impeded by cold side downward boundary layer air flow - thereby reducing overall heat transfer in the wood panel.
RefersShelterwoodtotheprogression of forest cuttings leading to the establishment of a new generation of seedlings of a particular species or group of species without planting. This silvicultural system is normally implemented in forests that are considered mature, often after several thinnings.
Mass Timber Panels - Glue mass timber construction (GLULAM) Glue laminated timber - (CLT) Cross-Laminated timber (SCL) Structural composite Lumber (LVL) Laminated Veneer Lumber (LSL) Laminated Strand Lumber (OSL) Oriented Strand Lumber (PSL) Parallel Strand Lumber - Non-Glue mass timber construction (NLT) Nail-Laminated Timber (DLT) Dowel-Laminated Timber - (CNLT) Cross Nail-Laminated Timber - (ICLT) Interlocking Cross Nail-Laminated Timber (PTLT) Post Tensioned Laminated Timber Multi Species Panel Combining multiple different species of wood into panel construction - allows for a building system that incorporates otherwise overlooked timber in regional forestry with a practical application in an all-wood system.
Glossary 44
- Group Selection Under this system, a number of ‘groups’, or small openings created by the removal of several adjacent trees, are created in complement to the harvest of scattered individual -trees.Single
Tree Cutting Strategies - Clear ForestryCuttingpractice in which most or all trees in an area are uniformly cut down.
Aberations Aberatoins are wood features typically seen as flaws that include rot, “pecky”, wormy, bur ly, knotten, reaction and curved wood. “Pecky” material is rot that doesn’t immediated kill the tree but rather gradually eats away at the heartwood.
A plantation is a large-scale estate for farming that specializes in cash crops. The crops that are grown include cotton, coffee, tea, cocoa, sugar cane, sisal, oil seeds, oil palms, fruits, rubber trees and forest trees. Species Flow Species flow is the assisted movement of plants to other suitable climates intentionally extending their evolutionary migration further and faster. One example of this is the relocation of the tree species pinus radiata, also known as Monterey Pine, a native to temperate coastal California and mexico. Because of its versatility as both timber and fiber, it has been transplanted across similar climatic regions throughout the world. In addition to its versatility, the species is hardy and fast growing, making it ideal for tree plantation. It is now grown in Spain, Chile, Australia and New Zealand.
Tree Selection Under the single tree system of forest harvest/regeneration, individual trees are marked and cut. The objective of the method is to maintain a self-sustaining forest of multiple age/ size classes. Woodshed The “woodshed” is estimation of the amount of standing timber per hectare in relation to the amount of raw wood required for building construction.
Phase 04 Refining & Disseminating
The Eliminating Cement addendum presents our plug in as a more sustainable alternative to the current cementitious concrete options employed and how these alternatives would integrate with existing principles & processes employed by NU Build.
NU Build Modular Design Guide - Addendum: Eliminating Cement
The dissemination of our plug-in takes the form of an addendum to the current NU Build Modular Design Guide
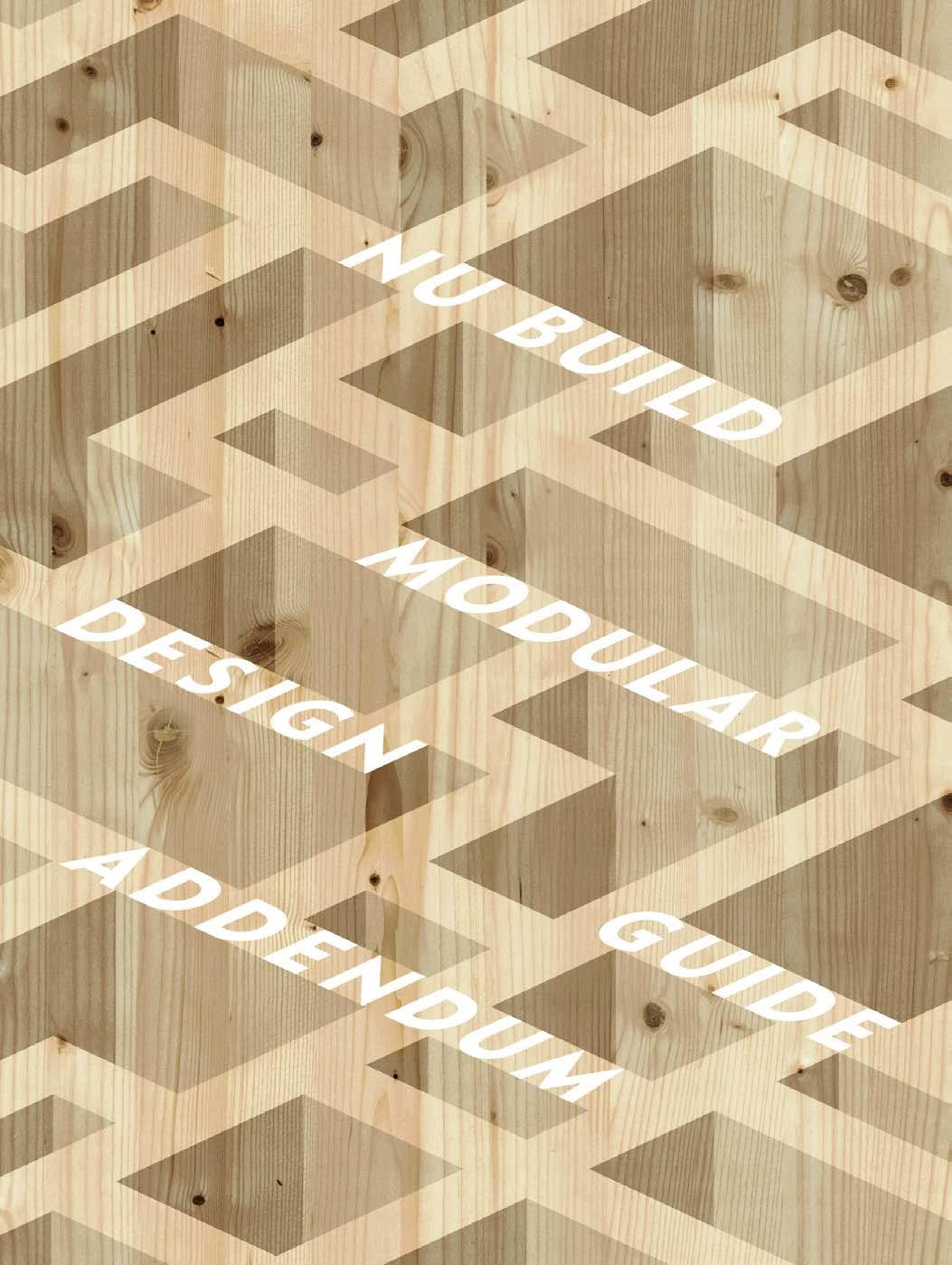
1CONTENTSINTRODUCTION 7 1.1 How to use this guide 9 1.2 Swan and NU living 10 1.3 Modular benefits 12 1.4 Sustainability 14 2 MODULAR PROCESSES 19 2.1 Factory process 20 2.2 Design and assembly process 22 3 MODULAR PRINCIPLES 35 3.1 Transportation 36 3.2 Site considerations 42 3.3 CLT panels 48 3.4 Structural principles 52 3.5 Ground floor construction 58 3.6 Waterproofing 64 3.7 On site finishes 68 3.8 Roofs 3.9 Communal stair cores 3.10 Fire design principles 3.11 Thermal principles 3.12 Acoustic principles 4 INTERNAL PRINCIPLES 4.1 Internal layout of modules 4.2 Servicing principles 5 INFORMATION FOR MANUFACTURE 5.1 Using BIM and 4D 5.2 Drawing for manufacture 5.3 Room data sheets 5.4 Module types 6 APPENDIX 6.1 Checklist 6.2 Glossary 7 ADDENDUM: ELIMINATING CEMENT 7 . 1 Ground floor construction currently 7 . 2 Foundation alternative 7 . 3 Ground slab alternative 7 . 4 Ground floor frame 7 . 5 CLT flooring options 7 . 6 Emissions comparison 7 . 7 Integrating disciplines 7 . 8 Future possibilities 1 INTRODUCTION 7 1.1 How to use this guide 9 1.2 Swan and NU living 10 1.3 Modular benefits 12 1.4 Sustainability 14 2 MODULAR PROCESSES 19 2.1 Factory process 20 2.2 Design and assembly process 22 3 MODULAR PRINCIPLES 35 3.1 Transportation 36 3.2 Site considerations 42 3.3 CLT panels 48 3.4 Structural principles 52 3.5 Ground floor construction 58 3.6 Waterproofing 64 On site finishes 68 1CONTENTSINTRODUCTION 7 1.1 How to use this guide 9 1.2 Swan and NU living 10 1.3 Modular benefits 12 1.4 Sustainability 14 2 MODULAR PROCESSES 19 2.1 Factory process 20 2.2 Design and assembly process 22 3 MODULAR PRINCIPLES 35 3.1 Transportation 36 3.2 Site considerations 42 3.3 CLT panels 48 3.4 Structural principles 52 3.5 Ground floor construction 58 3.6 Waterproofing 64 3.7 On site finishes 68 3.8 Roofs 72 3.9 Communal stair cores 76 3.10 Fire design principles 80 3.11 Thermal principles 84 3.12 Acoustic principles 88 4 INTERNAL PRINCIPLES 93 4.1 Internal layout of modules 94 4.2 Servicing principles 100
1CONTENTSINTRODUCTION 7 1.1 How to use this guide 9 1.2 Swan and NU living 10 1.3 Modular benefits 12 1.4 Sustainability 14 2 MODULAR PROCESSES 19 2.1 Factory process 20 2.2 Design and assembly process 22 3 MODULAR PRINCIPLES 35 3.1 Transportation 36 3.2 Site considerations 42 3.3 CLT panels 48 3.4 Structural principles 52 3.5 Ground floor construction 58 3.6 Waterproofing 64 3.7 On site finishes 68 3.8 Roofs 72 3.9 Communal stair cores 76 3.10 Fire design principles 80 3.11 Thermal principles 84 3.12 Acoustic principles 88 4 INTERNAL PRINCIPLES 93 4.1 Internal layout of modules 94 4.2 Servicing principles 100 5 INFORMATION FOR MANUFACTURE 107 5.1 Using BIM and 4D 108 5.2 Drawing for manufacture 112 5.3 Room data sheets 116 5.4 Module types 120 6 APPENDIX 125 6.1 Checklist 126 6.2 Glossary 136 7 ADDENDUM: ELIMINATING CEMENT 7 . 1 Ground floor construction currently 7 . 2 Foundation alternative 7 . 3 Ground slab alternative 7 . 4 Ground floor frame 7 . 5 CLT flooring options 7 . 6 Emissions comparison 7 . 7 Integrating disciplines 7 . 8 Future possibilities 1 INTRODUCTION 7 1.1 How to use this guide 9 1.2 Swan and NU living 10 1.3 Modular benefits 12 1.4 Sustainability 14 2 MODULAR PROCESSES 19 2.1 Factory process 20 2.2 Design and assembly process 22 3 MODULAR PRINCIPLES 35 3.1 Transportation 36 3.2 Site considerations 42 3.3 CLT panels 48 3.4 Structural principles 52 3.5 Ground floor construction 58 Waterproofing 64 On site finishes 68 7 1.1 How to use this guide 9 1.2 Swan and NU living 10 1.3 Modular benefits 12 1.4 Sustainability 14 2 MODULAR PROCESSES 19 2.1 Factory process 20 2.2 Design and assembly process 22 3 MODULAR PRINCIPLES 35 3.1 Transportation 36 3.2 Site considerations 42 3.3 CLT panels 48 3.4 Structural principles 52 3.5 Ground floor construction 58 3.6 Waterproofing 64 3.7 On site finishes 68 3.8 Roofs 72 3.9 Communal stair cores 76 3.10 Fire design principles 80 3.11 Thermal principles 84 3.12 Acoustic principles 88 4 INTERNAL PRINCIPLES 93 4.1 Internal layout of modules 94 4.2 Servicing principles 100 47
1CONTENTSINTRODUCTION
7 . 1 GROUND CONSTRUCTIONFLOOR CURRENTLY
The design of the ground floor also depends on the strategy for transferring the loads from the upper floors to the foundations. Two ground floor details should be investigated: a concrete slab or ventilated void foundation under the module. Both have their advantages and disadvantages, which should be analysed and understood when determining the appropriate strategy.
It is preferable for the whole building to be made from modules. This ensures the quality of finish is maintained throughout the project, on site labour is minimised and the efficiency of the modular system is maximised. Care needs to be taken to ensure the CLT module is kept dry. The relationship between the base of the timber and the external drainage level and the provision of adequate drainage to the perimeter are key considerations which may have implications on level thresholds and external landscaping.
59 Ground floor construction Figure 47 Module at ground floor
It is important that all four walls of the module are evenly supported to avoid differential movement. The strategy to achieve this is dependent on whether the module to slab connection is via point loads, line loads or a combination of the two.
In section 3.5, GroundFloorConstruction,it is stated that, ‘it is preferable for the whole building to be made from modules. This ensures the quality of finish is maintained throughout the project, on site labour is minimised and the efficiency of the modular system is maximised.’ However, if a large open space is required on ground floor this is not always possible with modules. In this case the current solution is to employ either a steel or concrete ground floor frame. A modular ground floor solution is preferable where the functions at ground floor can be accommodated within the constraints of the defined modular space Careavailable.needs to be taken to ensure the CLT module is kept dry. The design of the ground floor also depends on the strategy for transferring the loads from the upper floors to the foundations.
7.1.1 Modular ground floor
Two ground floor details should be investigated: a concrete slab or ventilated void foundation under the module. Both have their advantages and disadvantages, which should be analysed and understood when determining the appropriate strategy. 01 Module at ground floor

Figure
CEMENTELIMINATINGADDENDUM:7
3.5.3 Modular ground floor
Figure 50 Overview of concrete or steel frame ground floor
Ground floor construction currently
Another draw back is access - installation of a concrete or steel frame could restrict access to the rest of the site and needs to be considered in the context of the module assembly strategy. 3.5.8 Concrete or steel frame ground floor (podium)
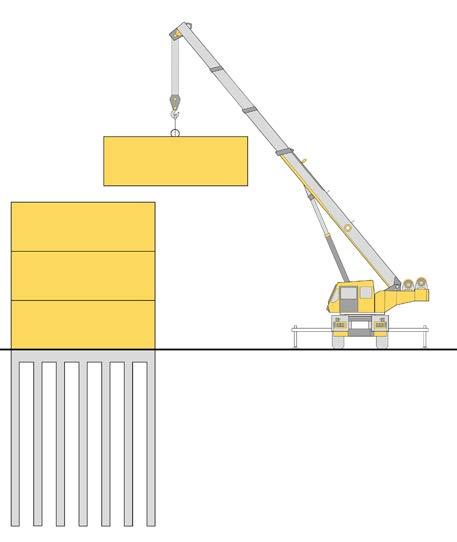
The CLT modules are raised above the ground and there is no timber at ground floor level thereby reducing the risk from ground water ingress. A metal deck or concrete slab supports the module at first floor level. Installing a frame at ground floor level allows flexibility in the design of the ground floor spaces. It is easy to achieve a level threshold for disabled accessible units.
The CLT modules are raised above the ground and there is no timber at ground floor level thereby reducing the risk from ground water ingress. A metal deck or concrete slab supports the module at first floor level. Installing a frame at ground floor level allows flexibility in the design of the ground floor spaces. It is easy to achieve a level threshold for disabled accessible units. However the ground floor cannot be volumetric and fitted out in the factory so NU living have to coordinate trades on site for the fit out.
61 Ground floor construction However the ground floor cannot be volumetric and fitted out in the factory so NU living have to coordinate trades on site for the fit out. This is not as efficient as building entirely out of modules.
Metal and concrete both have drawbacks when it comes to the large carbon emissions they generate through high temperature production of their constituent elements, when compared with the relatively low carbon emissions generated by the majority timber NU build modular system. This is accentuated by the use of non-renewable resources in the production of steel and concrete elements compared to the sustainably sourced timber from certified appropriately managed forests used in the modular system.
Concrete foundations Foundations are another area of the design which rely predominately on the use of concrete. The NU build modular system, whilst not specifically focusing on foundation design, would ordinarily employ a concrete pile or raft system in the ground. The lightweight nature of the CLT modules when compared to an alternative entire concrete frame design allows for the traditional foundation coverage to be decreased due to reduced loads placed upon it.
7.1.2 Concrete or steel frame ground floor (podium)
The element within the concrete which contributes most to carbon emissions is cement. Cement requires very high temperature production which releases harmful gases into the atmosphere. The almost universal use of majority cementitious concrete mixes within the construction industry has to be curved in order to reduce emissions. An alternative to the cementitious concrete usually used within the foundations and ground floor slab & frame of the NU build modular system can be incorporated into the system to achieve an even more holistic approach to sustainability than is currently the case.
Figure 03 Pile foundations beneath CLT modules
Ground floor construction currently 7.1.3
However, the foundations are still a contributing source of the carbon emissions generated by a NU build modular system building, due to the methods of concrete production already discussed.
Figure 02 Overview of concrete or steel frame ground floor
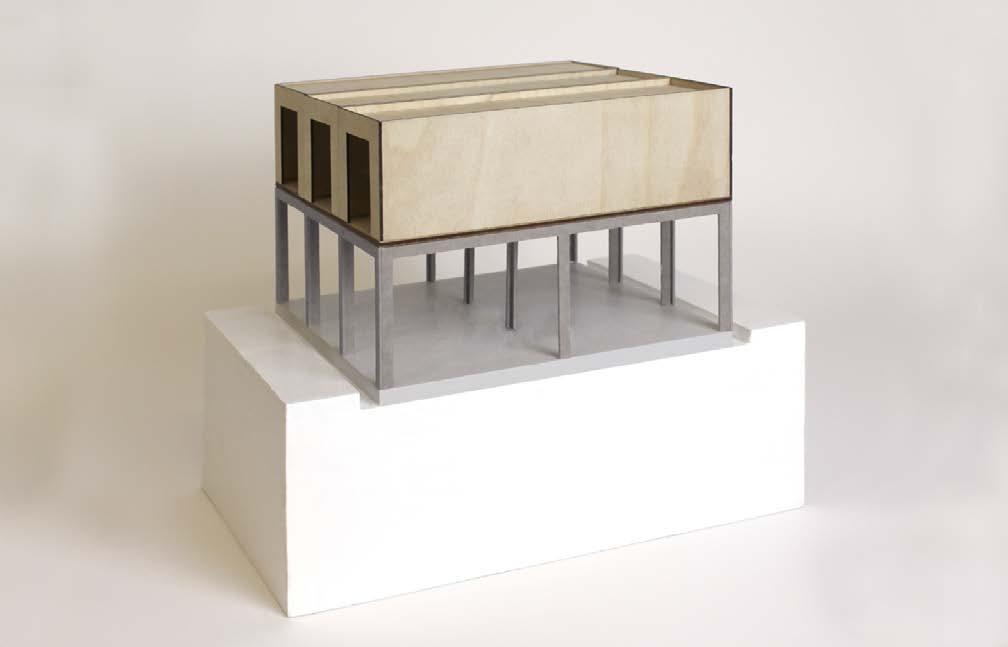
Lime stabilised soil columns Eliminating cement from the design starts with the foundations. Cementitious concrete has long been the industry standard foundation material as if it is mixed in the correct ratios, laid in the appropriate conditions and given time to set it can provide a fantastic base for the building above. Other options have been considered but after investigation it is clear that concrete is used because it is the best material for the job. The alternative provided maintains the performance of concrete foundations but substitutes the cement element. Lime stabilised soil column foundations are an alternative to cementitious concrete pile foundations that eliminate cement from this design element. They are commonly utilised in areas in Japan and Scandinavia where lightweight construction and appropriate soil conditions allow for their use. They have also been employed in limited cases in the US and UK, usually as a method to stabilise road embankments. This alternative would be appropriate for use with the current NU build system up to 5 storeys, as is also defined as the point at which a core would be required in the NU build modular system. Beyond this point further additives than those discussed here would be required to provide adequate stability. Also, this method is appropriate below 5 storeys due to the lightweight nature of the CLT modules when compared to traditional construction techniques. With increasing storeys of modules comes increased weight and so when 8 storeys or more is reached further investigation would be required as to whether lime stabilised soil columns would have the sufficient load bearing capacity, even with additional strengthening additives incorporated. Clay soil is required for lime stabilised soil columns to perform and function most efficiently. Working with the defined NU build geographic proximity of London & Essex provides an area with a high majority coverage of clay soil, and so it is appropriate for employing this as an alternative method to cementitious concrete foundations. When the stage is reached that a specific site is identified further soil analysis will be required to determine the suitability of certain areas. This can be achieved by core samples of soil being collected and tested for clay content, water permeability and other elements present in the soil.
2.1
2.1.2 Factory operation style
Use of lime Lime is an alternative binder to the cement traditionally used in foundations. Lime’s main advantage over cement is that it does not require as high a temperature to produce. When making lime there is 20% less carbon emissions created than when making cement. Lime also absorbs additional CO process. There is also the opportunity for lime to be produced locally at a smaller scale, due to the lower temperature requirements, which could allow for transport emissions to be reduced.
7.2.1
2.1.1 Geographic region
Existing industrial scale lime producers are: Lhoist Buxton, Tarmac, Buxton Singleton Birch Lancashire ALTERNATIVE
The installation of lime stabilised soil columns can be carried out by a small mobile rig. This rig is made up of a drilling post equip with an injection unit containing the lime and any other additives. The soil is drilled down to a predetermined depth and injected on removal. This method creates a series of columns of clay soil that have been individually strengthened.
Another benefit of this method is that it does not create any soil spoil. The clay soil is not removed and replaced with concrete as is usually the case. The soil itself stays in place and is strengthened by the lime injection. This then eliminates the need to find alternative places to store soil spoil, which often requires transportation by 7.2.4 Figure 06 Lime stabilised soil column foundations
The NU build system uses a continuous flow production model. This is where modules move through a series Figure 10 Current geographic region of the NU build factory 20 km NU build factory Modular sites 0
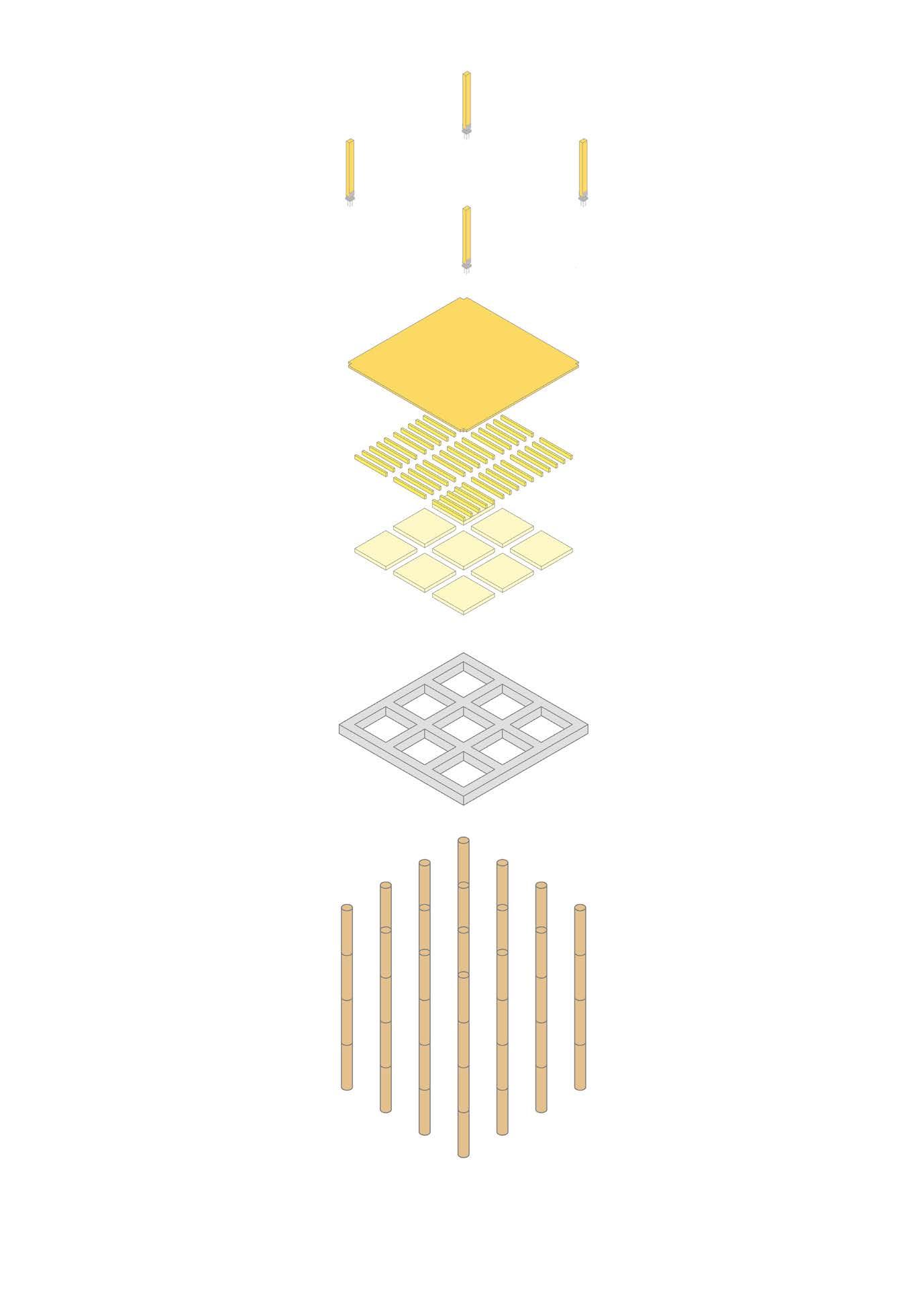
In order to successfully design for modular construction, the designer should have an understanding of the way in which the NU living factory operates This will allow elements of the design to be adapted to compliment the manufacturing process, creating an efficient and easily assembled modular design.
7 . 2 FOUNDATION
Installation
NU living’s state of the art factory is located in Prologis Park, Basildon and comprises a 7000 sq m facility which includes the manufacturing plant, staff and office areas and an Innovation Centre that is used to host events and as a creative space for the Swan Group. The building is sustainably designed, with performance measured through environmental certification, reduced operational carbon emissions and mitigated embodied carbon emissions. Waste from CLT panels is used to make wood chips that are used to heat the factory. Swan’s modular developments are situated within a limited geographic region. The factory’s location in Basildon allows for good connections to the M25, providing easy access to Essex and east London, reducing the distances between the factory and site. 7.2.3
FACTORY PROCESS
Figure 04 NU build geographic proximity 7.2.2 Soil requirements
MakingEliminatingAlternativematerialsmaterialscementconcrete weather conditions in order to lay in situ concrete. The pre cast elements will be connected to the pile foundations below and to each other through reinforcing steel rods being exposed at junctions and subsequently connected, boxed and filled with concrete mix. The voids between the grid can be filled with insulation and CLT as part of a bespoke CLT floor build up panel.
As well as the cement in concrete being an issue due to carbon emissions, sand is also in huge demand by the construction industry. Being a finite resource the reduction of sand within concrete is also an issue the industry needs to address in the current and near Asfuture.with fly ash replacing some of the cement in concrete, plastic can be used to replace some of the sand in concrete. As a way to reduce the amount of discarded plastic going to landfill, including a plastic aggregate in the ring beam could help achieve this goal if it were adopted as standard by the industry.
LIME & FLY ASH + WATER & AIR + RECYCLED PLASTIC AGGREGATES CEMENT + WATER & AIR + SAND + GRAVEL
CEMENT + WATER & AIR + RECYCLED PLASTIC AGGREGATES
7 . 3 GROUND SLAB ALTERNATIVE
LIME & CEMENT + WATER & AIR + SAND + GRAVEL
Ring beam grid structure required quality of fly ash to be an appropriate concrete UKadditive.coalfire power stations closing dates: Nottinghamshire - 2024 Nottinghamshire - 2022 County Atrim 2023 Fly ash landfills are often located adjacent to current and previous UK coal fired power stations, with it currently being managed as a waste material.
7.3.4
Pulverized fly ash (PFA) is an additive than can be used to reduce the percentage of cement required in concrete. It is currently used in areas in the construction industry but not on a massive scale. The main benefit of fly ash is that it is a by-product of coal fire power stations that would otherwise go to landfill. With the current generation of UK coal fire power stations due to all be converted or decommissioned by 2024 the by product will not be available for use indefinitely. However, every year previously only a small percentage of the total amount of fly ash produced has been repurposed. There are currently ‘stockpiles’ of 50 million tonnes of fly ash in landfill and stored in pools around the country. This fly ash can be dehydrated and refined to make the 7.3.3
A ring beam grid structure, rather than a solid floor slab, reduces the amount of concrete used in the design. The grid sits atop the lime stabilised soil column foundations below. Traditionally concrete ground slabs would be cast in situ on site. This approach can be taken with the ground slab alternative or a pre cast option is available. The pre cast option would involve a concrete element cast in factory conditions to a size no larger than the NU build CLT modules currently used. This will enable the same transportation to be used for the ground slab as well as the modules. With the ground slabs being a maximum of 500mm thick, this would enable several to be stacked on a singular lorry to keep transport emissions to a minimum. This method will reduce the number of wet trades on site and eliminate the need to wait for the appropriate 7.3.5
Cementitious concrete ground slabs are traditionally employed in the majority of buildings where a concrete frame is utilised. Similarly, this is also the case for the NU build modular system where a steel or concrete frame is being employed at ground level. The alternative presented greatly reduces, with the intention to get to zero over time, the amount of cement used in the ground floor plane. Rather than a full slab, a ring beam and grid structure is employed to connect the lime stabilised soil columns below. Several alternatives to cement, and also sand aggregates, can be explored.
BINDING AGENT + WATER & AIR + SMALL AGGREGATES + LARGE AGGREGATES (10%) (20%) (30%) (40%) Typical
Ground slab alternative Figure 08 Eliminating cement process
The same lime used in the foundation alternative can also be used in the ground floor ring beam grid. Lime’s main advantage over cement is that it does not require as high a temperature to produce. When making lime there is 20% less carbon emissions created than when making cement. Lime also absorbs additional CO2 during the hardening process. There is also the opportunity for lime to be produced locally at a smaller scale, due to the lower temperature requirements, which could allow for transport emissions to be reduced.
Figure 07 Ring beam grid structure
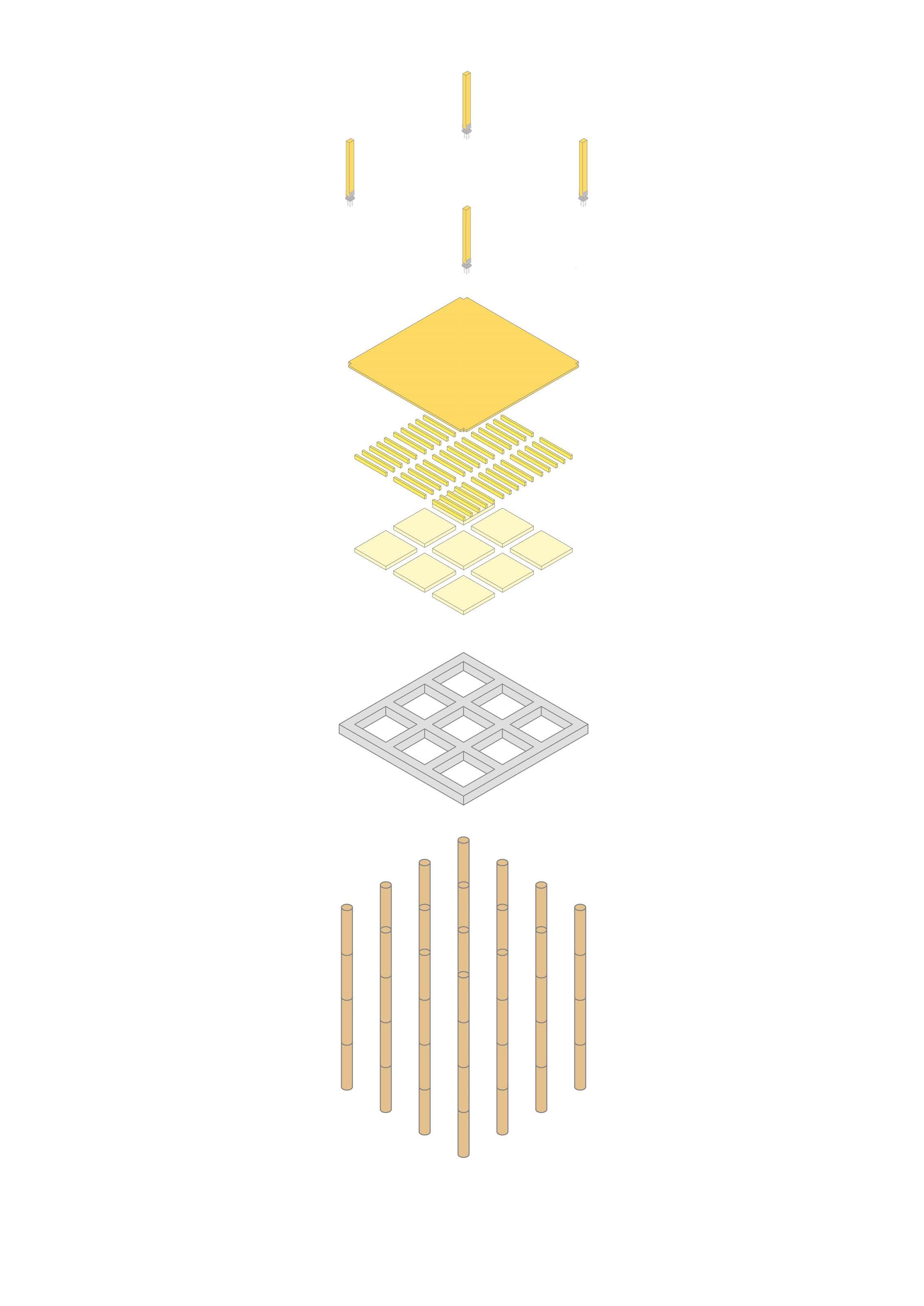
FLY ASH & CEMENT + WATER & AIR + SAND + GRAVEL
Eliminating cement process
Use of plastic aggregates
7.3.1 Use of lime
7.3.2 Use of fly ash
The interface between glulam posts and beams at high level on ground floor are well detailed within the Figure 11 Glulam post interface details Above ground floor Above ground floor the NU living modules can be placed onto the glulam frame and fixed with steel brackets. They can then be stacked up to the height restraints previously discussed using the methods outlined in the NU living modular design guide. Figure 12 Ground floor build up
3 65 4 2 7 .
Ground Floor Frame Glulam Post & Beam Ground Floor Timber Frame (Connections)
Nailed sheet metal for fixed support, normally on the The fitting can either be molded into concrete structures or welded to an embedded fixed metal sheet. Force transfer occurs with anchor nails or with screws. End grain surfaces should be moisture protected against concrete and other moisture absorbing material and
Interface details In order to achieve an open ground floor space NU living ordinarily employ a steel or concrete frame. An alternative to this that avoids the use of these materials is a glulam post and beam system. These elements could be incorporated into the NU living manufacturing process over time, but for current projects the Stora Enso catalogue offers a range of options. Constructing a glulam post and beam system on ground floor out of Stora Enso or similar products would allow for large open spaces to be created whilst avoiding the use of steel & concrete. The same sustainability and sourcing criteria for the NU living timber modules can be sort for the Stora Enso timber posts and beams. There are a number of standard interface details between the glulam post and alternative concrete ring beam at ground level that can be employed. This decision can be taken at the design stage as to how loads from the posts are to be distributed to the ground and foundations below. Below is a possible detail for an integrated CLT flooring panel to sit within the ring bean grid voids and provide an optional finished internal ground floor material. It can also be designed to incorporate insulation below sitting in the ring beam voids and provide possible raised floor access for piping and electricals.
Pole Shoe - Suitable solution to prevent water ingress through the column’s end grain. - The lower part of the anchoring rod is often moulded into the concrete structure, but the rod can also be welded to an embedded fixed metal sheet. - Provides opportunities for adjustable standard fittings for more accurate grd floor levels.
The flat rolled steel is moulded into the concrete construction or is welded to an embedded fixed metal
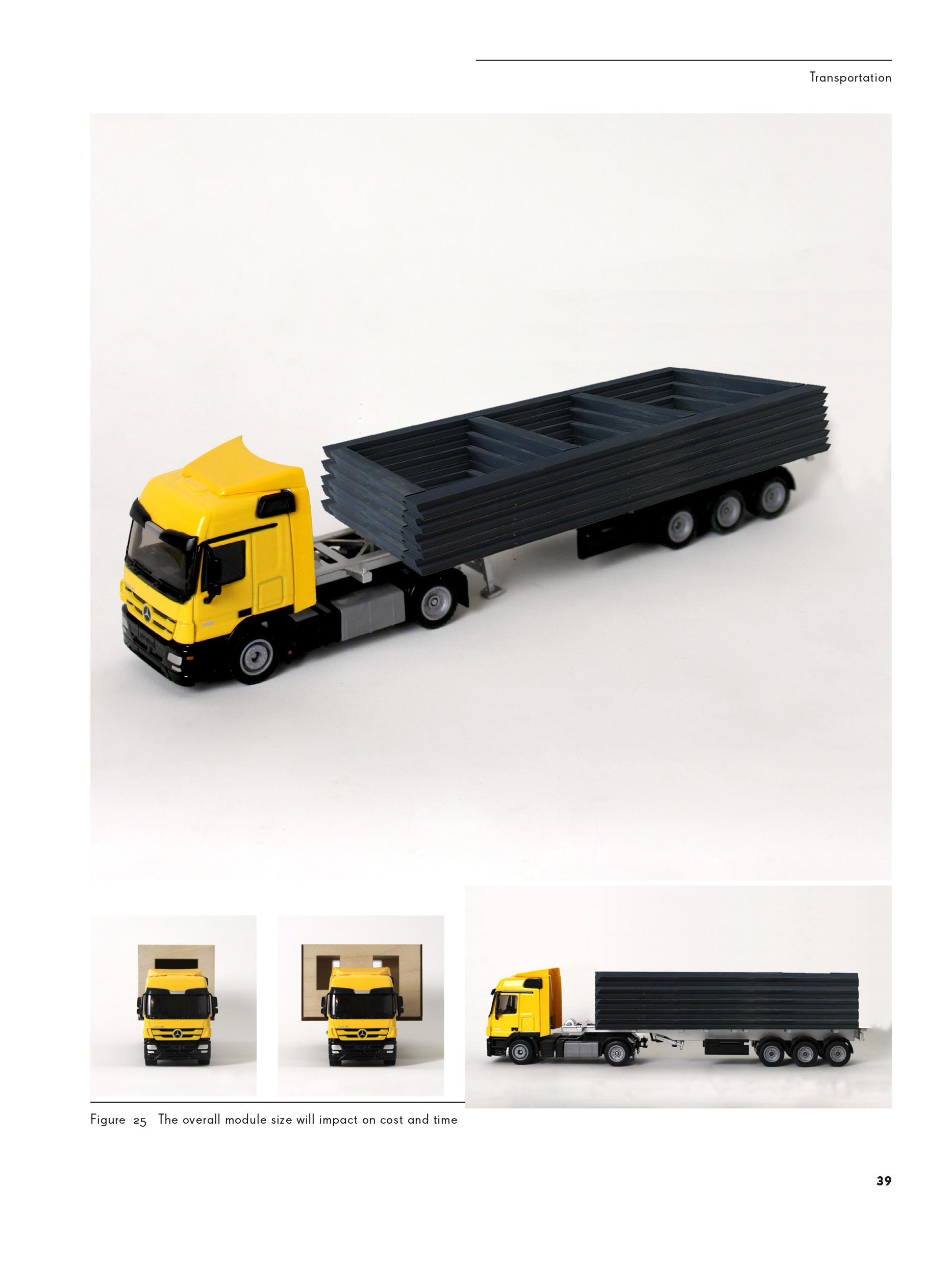
Angled Steel Fastenters - Angular steel is tightly screwed in the concrete construction with expander screws. - Reduces the risk of wrong placing, creating opportunities for thorough and more precise measurements. - Moisture protection required Key 1. Glulam Posts 2. CLT Floor Build Up 3. Knife Plate Connector 4. Bolts 5. Adjustable Anchoring Rods 6. Cement free Concrete Pile Foundation 1
4 GROUND FLOOR FRAME
7.4.3 Ground floor CLT build up
Fixed support on the column’s narrow sides
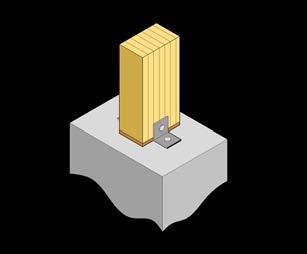
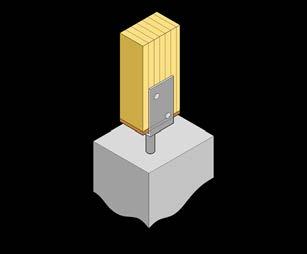
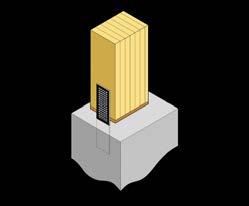
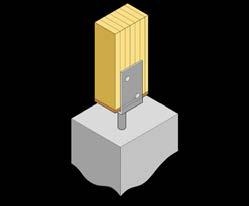
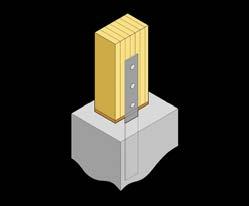
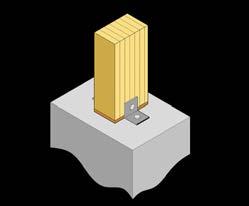
Poster
Currently 50million tonnes of excess fly ash in landfill sites being managed as a waste material, with the remaining Coal-Fired Power Stations planned for complete closure by 2025 Utilising the soil conditions within the boundaries of where Nu Living are able to build, Lime Stabilised Soil Columns allow for a method of piling that replaces a large amount of concrete with the already existing soil on site and a mixture of quicklime, otherwise known as Calcium Oxide. A Pre cast Lime & Fly Ash concrete ring Beam allows for a greater reduction in Carbon dioxide, the use of waste materials Like Pulverised Fly Ash and Polyethylene terephthalate and precise tolerances for Mass timber to be attached to.
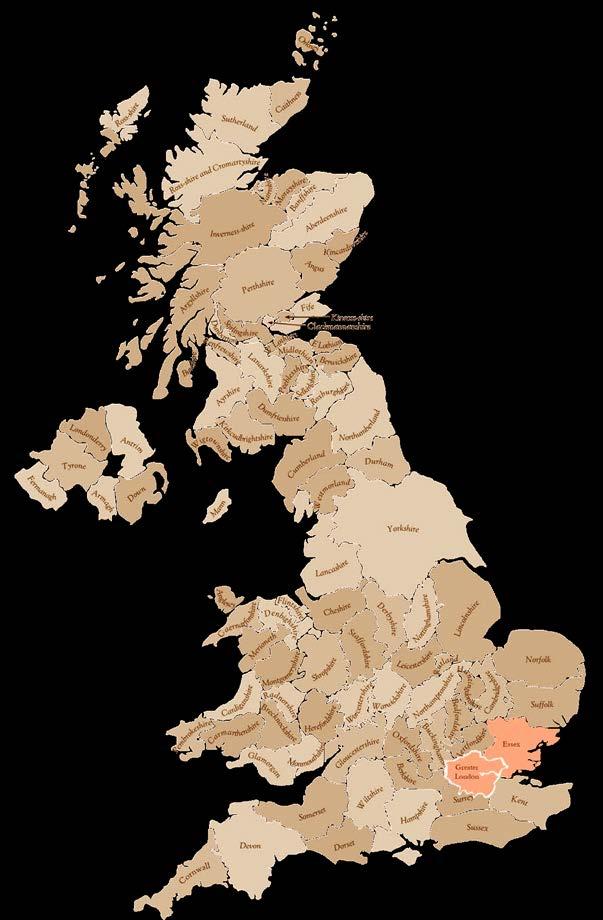
Lime Stabilised Soil IntegratingNu-BuildWith LimeConcreteStabilised
This Plug-in looks to maximise the use of factory built and ready modules in both new mixed use residential developments and renovations by Nu-living, aiming to further improve the sustainability of the Nu-Build system. It creates opportunities to easily integrate a post and beam mass timber system into Nu-Build Modular system, to create more adaptable and open space for a range of uses, whilst eliminating the need for a concrete/steel frame ground floor within the system. With a maximum Story Height of the Nu Living developments on top of the Piles will be 5 storeys due to load bearing tolerances.
Coal-FiredStationsPower PlasticPlantsRecycling Lime Quarry Reduce Reuse Recycle









Source Locally
Using a relatively small mobile rig, The Auger is drilled down into the soil to a depth that corresponds to the prescribed column length. Powdered quicklime (CaO) is forced into the soil with compressed air through a hole located just below the horizontal blade of the auger, and the lime is mixed thoroughly with the soil.

Using existing industries that create fine plastic waste as a by product of manufacture that would otherwise go to landfill as well as those materials already sitting on landfill sites
Eliminating cement from the design and replacing it with lime will reduce carbon emissions from the creation process by 20%. Lime also absorbs CO2 within its drying and hardening process. Some of this lime can then further be replaced with recycled fly ash this will reduce further. Plastic aggregates that are common by-products of many industrial processes allows for a replacement of sand.
Cement free Concrete Mix Ratio : Cement is the source of approx. 8% of world’stheCO2emissions
Concrete is the most widely used man-made material in existence. It is second only to water as the most-consumed resource on the planet Lime Fly Ash AggregatesPlastic Fly Ash (9%) + Lime (9%) + Polyethylene terephthalate (30%) + Large Aggregate (45%) + water (7%)
EliminatingCement

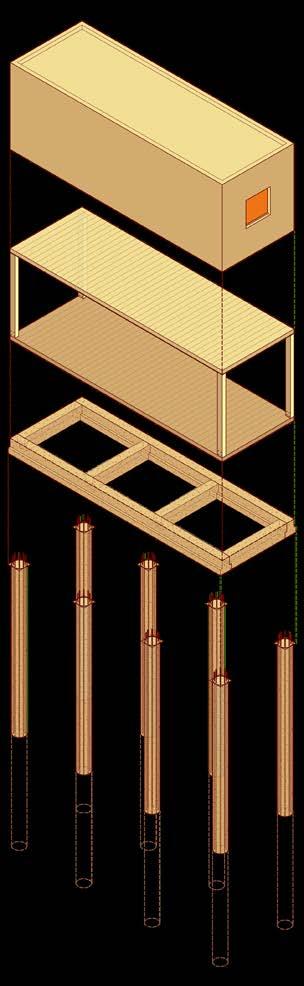
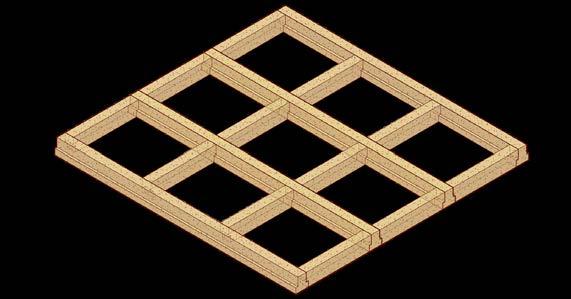
Bibliography
• Brookes, A. H. et al. (1997) Laboratory Trial Mixes for Lime-stabilised Soil Columns and Lime Piles. (s.l.): Thomas Telford.
• GLU_HAND_VOLUME-1.pdf (s.d.) At: uploads/2019/05/GLU_HAND_VOLUME-1.pdfhttps://www.woodcampus.co.uk/wp-content/
• Fly Ash Concrete - Green Education Foundation (s.d.) At: fly-ash-concrete.htmlgreeneducationfoundation.org/green-building-program-sub/learn-about-green-building/1229-http://www.(Accessed03/05/2021).
• Brown, D. (2017) Parametric Timber Connections for Revit - Dylan Brown Designs. At: http:// dylanbrowndesigns.com/resources/parametric-timber-connections-for-revit/ (Accessed 03/05/2021).
• As fly ash supplies dwindle what should the construction industry do? (2018) At: 03/05/2021).ice.org.uk/news-and-insight/the-civil-engineer/may-2018/fly-ash-supplied-dwindlehttps://www.(Accessed
• Breathable-Insulated-Lime-Floors.pdf (s.d.) At: uploads/2015/04/Breathable-Insulated-Lime-Floors.pdfhttps://www.telling.co.uk/wp-content/
• British Lime Association (BLA) part of the Mineral Products Association (MPA) (s.d.) At: https:// britishlime.org/technical/soil_stabilisation.php (Accessed 03/05/2021a).
• Driving Piles in Grand Isle, vulcan hammer (2013) At: https://www.youtube.com/ watch?v=xzs6hw5tNeY (Accessed 03/05/2021).
• Lime Mortar, Render and the Environment (s.d.) At: https://www.greenspec.co.uk/buildingdesign/lime-mortar-render/ (Accessed 03/05/2021).
• Lutenegger, A. J. (s.d.) ‘Hist Historical Application of Scrorical Application of Screw-Piles and Screw-Piles and Screw-Cylinder ew-Cylinder Foundations for 19th Centur Foundations for 19th Century Ocean Piers y Ocean Piers’ At: students_ucreative_ac_uk/Documents/Microsoft%20Teams%20Chat%20Files/229075376.pdfhttps://ucreative-my.sharepoint.com/personal/gpeck1_
• Guthrie, S. (2018) Concrete without cement developed. At: https://www.khl.com/news/ Concrete-without-cement-developed/1135617.article (Accessed 03/05/2021).
55
• Carder, G. W. A. D. (s.d.) ‘Review of lime piles and lime-stabilised soil columns - Transport research laboratory’ At: http://trl.demo.varistha.co.uk/uploads/trl/documents/TRL305.pdf
• El-Reedy, M. A. (2012) Geotechnical Data and Pile Design. In: Offshore Structures. Directed by El-Reedy, M.A. (s.l.). pp.213–292. At: http://dx.doi.org/10.1016/b978-0-12-385475-9.00004-3
• Almeshal, I. et al. (2020) ‘Eco-friendly concrete containing recycled plastic as partial replacement for sand’ In: Journal of Materials Research and Technology 9 (3) pp.4631–4643.
• Cross Laminated Timber Construction (2020) At: https://www.thinkwood.com/mass-timber/clt (Accessed 03/05/2021).
• Gutschick, B. Y. K. A. (s.d.) ‘LIME STABILIZES POOR SOILS’
• Broms, B. B. and Boman+, P. (s.d.) Stabilisation of soil with lime coulmns. At: (Accessedca.emap.com/wp-content/uploads/sites/13/1979/05/1979-05_Pages_23_25-26_-29-30_32.pdfhttps://cdn.03/05/2021).
• Guardian staff reporter (2007) ‘Lime is a much greener option than cement’ In: The Guardian 22/10/2007 At: http://www.theguardian.com/commentisfree/2007/oct/23/comment.comment (Accessed 03/05/2021).
• Kaye, L. (2011) ‘Less is more if we want to be sustainable with concrete’ In: The Guardian 19/10/2011 At: http://www.theguardian.com/sustainable-business/sustainable-green-buildingsconcrete (Accessed 03/05/2021).
• Design Solutions (s.d.) At: https://www.setragroup.com/en/glulam/design-solutions/ (Accessed 03/05/2021).
• Khan, M. et al. (2016) ‘A Comparative Study of Ground Improvement by Lime and Granular Columns’ In: 8th International Civil Engineering Congress (ICEC-2016) ‘Ensuring Technological Advancement through Innovation Based Knowledge Corridor’. unknown. At: http://dx.doi.org/ (Accessed 03/05/2021).
• Enso, S. (s.d.) Building Concepts by Stora Enso (Office). (s.l.): (s.n.). • Fly Ash (s.d.) At: https://www.cemex.co.uk/fly-ash.aspx (Accessed 03/05/2021).
• London energy transformative initiative (s.d.) ‘LETI Climate Emergency Design Guide’ At: Files/252d09_3b0f2acf2bb24c019f5ed9173fc5d9f4.pdfstudents_ucreative_ac_uk/Documents/Microsoft%20Teams%20Chat%20https://ucreative-my.sharepoint.com/personal/iolajidejr_
• British Lime Association (BLA) part of the Mineral Products Association (MPA) (s.d.) At: https:// britishlime.org/education/how_lime_is_made.php (Accessed 03/05/2021b).
• INGENIERÍA DE DETALLE – VIVIENDA EN MAR DEL PLATA (2015) At: https://consulsteel.com/ ingenieria-de-detalle-vivienda-en-mar-del-plata/ (Accessed 03/05/2021).
• British Lime Association (BLA) part of the Mineral Products Association (MPA) (s.d.) At: https:// britishlime.org/technical/lime_in_mortars.php (Accessed 03/05/2021c).
• Bradley, D. C. &. (2013) ‘Embodied carbon of steel vs concrete buildings’ At: concrete%20buildings.pdfTeams%20Chat%20Files/IP-31%20-%20Embodied%20carbon%20versus%20steel%20v%20my.sharepoint.com/personal/iolajidejr_students_ucreative_ac_uk/Documents/Microsoft%20https://ucreative-
• circlet (s.d.) Piling Begins at Conisford Court. At: https://circlethomes.co.uk/?p=520 (Accessed 03/05/2021).
• 2020 James Templeton Kelley Prize: Anna Goga’s ‘Porch House + 300 Panels, 400 Cuts, 400 Bandages’ - Harvard Graduate School of Design (2020) At: 400-bandages/project/2020-james-templeton-kelley-prize-anna-gogas-porch-house-300-panels-400-cuts-https://www.gsd.harvard.edu/(Accessed03/05/2021).
• Wade, A. (2018) UK study shows waste plastic can replace sand in concrete. At: https://www. theengineer.co.uk/uk-waste-plastic-sand-concrete/ (Accessed 03/05/2021).
Wood Poles & Pilings, Structural Timber Products & Building Materials (2017) At: https:// www.americanpoleandtimber.com/wood-timber-products/poles-pilings-posts/ (Accessed 03/05/2021).
• What are Micropiles? (2015) At: https://www.youtube.com/watch?v=8q3e6DmJAe4 (Accessed 03/05/2021).
• Countdown to 2025: Tracking the UK coal phase out (2016) At: https://www.carbonbrief.org/ countdown-to-2025-tracking-the-uk-coal-phase-out (Accessed 10/05/2021). 56
• Waugh Thistleton Architects (2018) Think-Wood-Publication-100-Projects-UK-CLT. (s.l.): (s.n.).
• Potential Advantages and Limitations of Screw-Piles and Helical Anchors (s.d.) At: http:// helicalfoundations.org/faqs-2/advantages-and-limitations-of-screws/ (Accessed 03/05/2021).
• What is glulam (2014) At: http://glulambeams.co.uk/about-glulam/what-is-glulam (Accessed 03/05/2021).
• Wood Pilings Options (2013) At: https://www.youtube.com/watch?v=KNqKvygzdt0 (Accessed 03/05/2021). •
• Vroom Funderingstechnieken Wooden piles with concrete pile caps (2014) At: https://www. youtube.com/watch?v=CFyR5ddUsTI (Accessed 03/05/2021).
• Plastic Waste Recycling UK - Post-Industrial Plastic Recycling - RPCS (2018) At: https://rpcsltd. co.uk/about-plastic-waste-recycling/ (Accessed 03/05/2021).
• Swan Housing Association (2019) NU Build Modular Design Guide. (s.l.): (s.n.).
• Pavements (s.d.) At: https://www.fhwa.dot.gov/pavement/recycling/fach01.cfm (Accessed 03/05/2021).
• Muhedin, D. et al. (2016) ‘Sustainable Concrete by Using Fly ash as a Cement Replacement’
• The Construction Index (2015) A phoenix from the ashes. At: https://www.theconstructionindex. co.uk/news/view/a-phoenix-from-the-ashes (Accessed 03/05/2021).
• Rogers, C. D. F. and Glendinning, S. (1997) ‘Improvement of clay soils in situ using lime piles in the UK’ In: Engineering Geology 47 (3) pp.243–257.
• Mass Timber Institute – UofT Daniels Faculty (s.d.) At: https://academic.daniels.utoronto.ca/ masstimberinstitute/ (Accessed 03/05/2021).
• PARFECT (2017) Treatment of soft soil foundation by cement soil mixing method - PARFECT. At: http://www.parfect.net/treatment-soft-soil-foundation-cement-soil-mixing-method/ (Accessed 03/05/2021).
In: Second International Engineering Conference On Developments in Civil & Computer Engineering Applications 2016. unknown. At: http://dx.doi.org/ (Accessed 03/05/2021).
• Namita (2017) GROUND TREATMENT WITH LIME COLUMNS & CEMENT COLUMNS. At: https://civildigital.com/lime-cement-columns/ (Accessed 03/05/2021).
• Pullen, T. (2020) What is Limecrete?. At: https://www.homebuilding.co.uk/advice/what-islimecrete (Accessed 03/05/2021).