Clara Bucar Fit Construction LP 1666 Callowhill St Philadelphia, PA Master of Science in Construction Management Thomas Jefferson University MCM 901 Masters Project Summer 2018 Instructor: Professor Bennett Colesberry Advisor: Tony Maras Clara Bucar Fit Construction LP 1666 Callowhill St Philadelphia, PA Master of Science in Construction Management Thomas Jefferson University MCM 901 Masters Project Summer 2018 Instructor: Professor Bennett Colesberry Advisor: Tony Maras

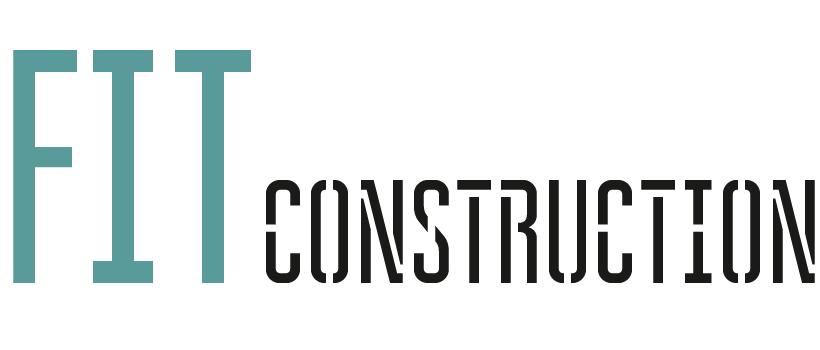
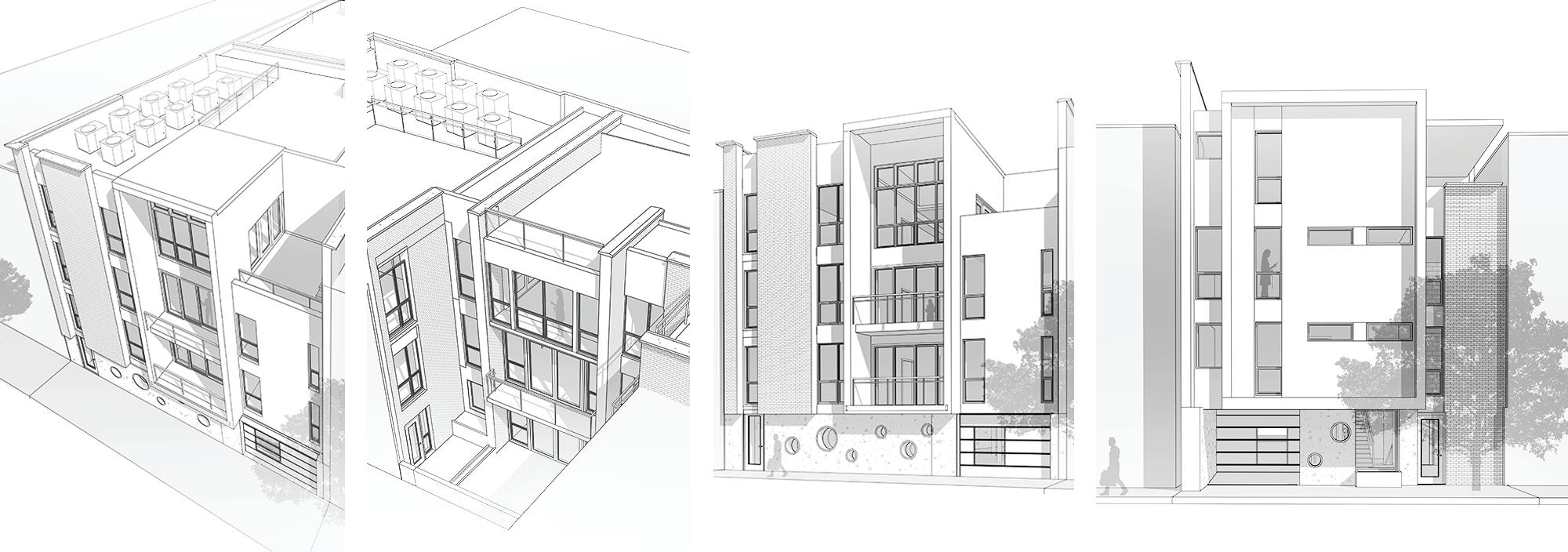
For the 620 N 3rd St project, we are aiming to transform issues into opportunities for improvement. Two aspects were identified as this project’s major challenges: the site location and layout and the incomplete design. First, the building will occupy the entire lot, leaving no space for construction staging, while also being located in a very densely populated residential area with no possibility for storage close by. This scenario forces strong communication and coordination between team members, as well as efficiency in material delivery and handling, cutting back waste in the form of time, material and effort, an ideal situation for LEAN implementation.
Fit Construction will provide in this manual, information about itemized budget, detailed schedule, construction risk administration divided into risk management, environmental, quality and safety, the demonstration of the BIM model to be updated and utilized all throughout the project, explanations on our management means, methods and processes, our layout for site logistics, suggestions for LEED Silver certification and more. This manual allows for a deep understanding of how Fit Construction will, by using a continual learning strategy, successfully manage the 620 N 3rd St project into completion on time, on budget, safely while upholding the highest quality standards.
All of these factors allows us to do what we do best: planning. This manual represents the consolidation of years of documented information and analysis of past projects applied to the reality of the 620 N 3rd St project, with a hint of creativity to foresee and prepare for potential future challenges.
This manual concerns the full planning of the 620 N 3rd St project, a five story multifamily residential building to be constructed in the Northern Liberties neighborhood in Philadelphia, PA. Close to Center City, this area has become one of Philadelphia’s hottest spots for real estate developers and families looking forward to buying or renting a home. This project, estimated at $3,016,360, will encompass 28,536 square feet distributed in nine residential units and made up of high end finishes and materials. Two of these units will have private roof decks. The building also has nine parking spots, an elevator and a shared roof deck. The structure is basically composed of a concrete and steel structure basement and first floor, wood structure and framing from the second floor up to the roof. Our company, Fit Construction, feels strongly about technology, relationships and people. We invest on BIM, Lean and LEED as ways of improving the quality of the service we provide our clients. Our bonds are tight with our employees and subcontractors, the core of our business.
08/01/2018MCM 901 Page 1 of 224 Master Thesis: 620 N 3rd St Clara Bucar INTRODUCTION
Considering the scenario, Fit Construction, PRDC, and the Owner, decided on a form of light IPD with the maintenance of the traditional Design-Bid-Build contractual relationships. The delivery method counts on monthly revisions to the scope to foresee and plan for upcoming changes while keeping full cost transparency on a cost plus a fee basis with an incentives program. An audacious plan that could, in the future, guide the way for more efficient processes.
Second, the agile decision to move forward with the plan to accelerate the construction schedule to start in 2018, despite of the incompleteness and inaccuracy identified in the set of construction drawings, drives for a flexible delivery method that’s able to quickly accommodate changes.
08/01/2018MCM 901 Page 2 of 224 Master Thesis: 620 N 3rd St Clara Bucar SECTION ONE - Company Information 1.1. Company Overview - Page 12 1.2 Company Organizational Chart - Page 15 1.3. Interaction Between Home Office and Field - Page 16 SECTION TWO - Project Information 2.1. Project Overview - Page 18 2.2. Project Organizational Chart - Page 19 2.3. Project Management Team Responsibilities Matrix - Page 20 2.4. Project Delivery Method Analysis - Page 22 2.5. Construction Administration / Communication - Page 23 2.6 Construction Risk Administration - Page 24 SECTION THREE - BIM Model 3.1. Floor Plans - Page 26 3.2. Building and Wall Sections - Page 32 3.3. Elevations - Page 37 3.4. Aerial Perspectives - Page 40 3.5. Renderings - Page 42 3.6. Cross Sections - Page 43 SECTION FOUR - WBS, Estimates, Schedules, Cash Flow 4.1. Work Breakdown Structure - Page 47 4.2. Basis of the Estimate - Page 64 4.3. Estimate Summary - Page 65 4.4. Division 01 - General Requirements - Page 66 4.5. Detailed Estimate Backup - Page 68 4.6. Masonry Detailed Back-up (Self Performed) - Page 73 TABLE OF CONTENTS
08/01/2018MCM 901 Page 3 of 224 Master Thesis: 620 N 3rd St Clara Bucar 4.7. Estimate Summary - LEED Option - Page 74 4.8. Detailed Estimate Backup - LEED Option - Page 75 4.9. Design and Preconstruction Schedule - Page 81 4.10. Procurement and Buy Out Log - Page 84 4.11. Submittal Schedule - Page 87 4.12. Schedule Summary with Milestones - Page 88 4.13. Construction Schedule with Critical Path - Page 89 4.14 Cash Flow - Page 113 4.15. Cash Flow Graphics - Page 114 SECTION FIVE - Site Layout and Logistics Plan 5.1. The Project, the Surrounding Community and Local Street Access - Page 116 5.2. Access to the Site - Page 117 5.3. Typical Working Hours and Days - Page 117 5.4. Safety for Pedestrians and Traffic Management - Page 117 5.5. Construction Staging and Parking Areas - Page 117 5.6. Material Delivery and Storage - Page 119 5.7. Mobilization Phasing - Page 119 5.8. Pre-Shell Phasing - Page 120 5.9. Post-Shell Phasing - Page 121 5.10. Waste Management - Page 122 5.11. Construction Impact Control And Community Relationship - Page 122 5.12. Clean-Up, Final Clean And Closeout - Page 122 5.13. Snow Removal - Page 122 5.14. Illustrated Construction Sequence - Page 123 SECTION SIX - Management Means, Methods and Controls 6.1. Preconstruction - Page 126 6.1.1. Delivery Method, Constructability And Value Engineering - Page 126
08/01/2018MCM 901 Page 4 of 224 Master Thesis: 620 N 3rd St Clara Bucar 6.1.2. Incentives Program - Page 126 6.1.3. Procurement - Page 127 6.1.4. Bonds and Insurance - Page 127 6.1.5. Mobilization - Page 127 6.1.6. Project Organization - Page 127 6.2. Construction - Page 128 6.2.1. Work Hours - Page 128 6.2.2. On Site Supervision And Home Office Support - Page 128 6.2.3. Subcontractors And Vendors - Page 129 6.2.4. Payment - Page 129 6.2.5. Organization Of The Site - Page 129 6.2.6. Safety And Health - Page 129 6.2.6. Quality Assurance - Page 130 6.2.7. Equipment - Page 130 6.2.8. Masonry (Self-Performed) - Page 130 6.2.9. Change Orders - Page 130 6.3. Communications - Page 130 6.3.1. Documentation - Page 131 6.3.2. Rfp: Request For Proposal - Page 131 6.3.3. Rfc: Request For Clarification - Page 131 6.3.4. Rfi: Request For Information - Page 131 6.3.5. Submittals And Transmittals - Page 131 6.3.6. Weekly Progress Reports - Page 132 6.3.7. Meetings - Page 132 6.4. Closeout - Page 132 SECTION SEVEN - Project Risk Management Analysis 7.1. Site Specific Risk Breakdown Structure - Page 135 7.2. Risk Register - Page 136
08/01/2018MCM 901 Page 5 of 224 Master Thesis: 620 N 3rd St Clara Bucar 7.3. Project Team Risk Responsibility Matrix - Page 138 7.4. Management Plans for the ‘Top Five’ Risks 7.4.1. Material Delivery And Storage Difficulty - Impact To Schedule - Page 139 7.4.2. Need For Highly Efficient Coordination - Page 139 7.4.3. Incomplete/Inaccurate Construction Documents - Page 140 7.4.4. Scarcity Of Qualified Subcontractors Due To High Season - Page 140 7.4.5. Disputes Over Budget Due To Delivery System (IDP) - Page 141 SECTION EIGHT - Site Specific Safety Plan 8.1. Site Specific Safety Management System - Page 143 8.2. Site Specific Safety Hazard Analysis - Page 145 8.3. Management Plans for the ‘Top Five’ Safety Hazards 8.3.1. Falls - Page 147 8.3.2. Electrocution - Page 148 8.3.3. Impalement - Page 149 8.3.4. Structure Collapsing - Page 149 8.3.5. Toxic Fume Inhaling - Page 150 SECTION NINE - Site Specific Environmental Plan 9.1. Site Specific Environmental Management System - Page 153 9.2. Site Specific Environmental Impacts - Page 154 9.3. Management Plans for the ‘Top Five’ Environmental Aspects 9.3.1. Air Pollution - Page 155 9.3.2. Waste Pollution - Page 156 9.3.3. Noise Pollution And Vibration - Page 156 9.3.4.Traffic Issues - Page 157 9.3.5. Pedestrian Experience Risk - Page 158
08/01/2018MCM 901 Page 6 of 224 Master Thesis: 620 N 3rd St Clara Bucar SECTION TEN - Site Specific QA/QC Plan 10.1. Site Specific Quality Management System - Page 160 10.2. Contract Quality Requirements - Page 161 10.3. Management Plans for the ‘Top Five’ Quality Issues 10.3.1. Concrete - Page 163 10.3.2. Steel - Page 163 10.3.3. Wood Framing - Page 164 10.3.4. Plumbing - Page 164 10.3.5. Mechanical - Page 165 SECTION ELEVEN - LEED Silver Credentials 11.1. Minimum Program Requirements (MPRs) 11.1.1. Location and Transportation - Page 167 11.1.2. Sustainable Sites - Page 167 11.1.3. Water Efficiency - Page 167 11.1.4. Energy and Atmosphere - Page 168 11.1.5. Materials and Resources - Page 168 11.1.6. Indoor Environmental Quality - Page 169 11.1.7. Innovation - Page 169 11.2. LEED v4 Scorecard - Page 170 REFERENCES - Page 171 APPENDIX Table of Contents - Page 173 A. Original Drawings and Specifications - Page 175 B. Management Means and Methods Referenced Documents and Forms - Page 180 C. LEED v4 - Requirements and Specs - Page 186 D. Agreement and Contracts - Page 216
08/01/2018MCM 901 Page 7 of 224 Master Thesis: 620 N 3rd St Clara Bucar Section One: Company Information FIGURE 01: The beach house, 2012: Fortaleza, Brazil - Page 13 FIGURE 02: Fortaleza Art Museum, 2015: Fortaleza, Brazil - Page 13 FIGURE 03: Sapiranga Social Housing Complex, 2016: Fortaleza, Brazil - Page 14 FIGURE 04: United Nations New Canopies, 2016: New York City, NY - Page 14 FIGURE 05: Company Organizational Chart - Page 15 Section Two: Project Information FIGURE 06: Project Location - Page 118 FIGURE 07: Project Organizational Chart - Page 119 Section Three: BIM Model FIGURE 08: Floor Plan - Basement - Page 26 FIGURE 09: Floor Plan - 1st Floor - Page 27 FIGURE 10: Floor Plan - 2nd Floor - Page 28 FIGURE 11: Floor Plan - 3rd Floor - Page 29 FIGURE 12: Floor Plan - 4th Floor - Page 30 FIGURE 13: Floor Plan - Roof - Page 31 FIGURE 14: Section AA - Page 32 FIGURE 15: Section BB - Page 33 FIGURE 16: Section Cc - Page 33 FIGURE 17: Section Dd - Page 34 FIGURE 18: Section Ee - Page 35 FIGURE 19: Section Through Southeast Wall - Page 36 FIGURE 20: East Elevation - Page 37 FIGURE 21: West Elevation - Page 37 FIGURE 22: South Elevation - Page 38 FIGURE 23: North Elevation - Page 39 LIST OF FIGURES
08/01/2018MCM 901 Page 8 of 224 Master Thesis: 620 N 3rd St Clara Bucar FIGURE 24: Aerial Perspective - Page 40 FIGURE 25: Aerial Perspective - Page 41 FIGURE 26: Renderings - Page 42 FIGURE 27: Renderings - Page 42 FIGURE 28: Cross Section - Page 43 FIGURE 29: Cross Section - Page 44 FIGURE 30: Cross Section - Page 44 FIGURE 31: Cross Section - Page 45 Section Five: Site Layout and Logistics Plan FIGURE 32: Google Maps. North 3rd Street view - Page 115 FIGURE 33: Google Maps. North Galloway Street view - Page 116 FIGURE 34: Regional Plan - Page 118 FIGURE 35: Mobilization Logistics - Page 119 FIGURE 36: Pre-Shell Logistics - Page 120 FIGURE 37: Post Shell Logistics - Page 121 FIGURE 38: Illustrated Construction Sequence (1) - Page 123 FIGURE 39: Illustrated Construction Sequence (2) - Page 123 FIGURE 40: Illustrated Construction Sequence (3) - Page 123 FIGURE 41: Illustrated Construction Sequence (4) - Page 123 FIGURE 42: Illustrated Construction Sequence (5) - Page 124 FIGURE 43: Illustrated Construction Sequence (6) - Page 124 FIGURE 43: Illustrated Construction Sequence (7) - Page 124 Section Seven: Project Risk Management Analysis FIGURE 44: Site Specific Risk Breakdown Structure - Page 135
08/01/2018MCM 901 Page 9 of 224 Master Thesis: 620 N 3rd St Clara Bucar Section Two: Project Information TABLE 01: Project Management Team Responsibilities Matrix - Pages 20 to 21 Section Four: WBS, Estimates, Schedules and Cashflow TABLE 02: Estimate: Basis of the Estimate - Page 64 TABLE 03: Estimate Summary - Page 65 TABLE 04: Division 01 - General Requirements - Pages 66 to 67 TABLE 05: Detailed estimate back-up - Pages 68 to 72 TABLE 06: Masonry Detailed Back-up (Self Performed) - Page 73 TABLE 07: Estimate Summary - LEED - Page 74 TABLE 08: Detailed Estimate Backup - LEED - Pages 75 to 80 TABLE 09: Design and Preconstruction Schedule - Pages 81 to 83 TABLE 10: Procurement and Buy Out Log - Pages 84 to 86 TABLE 11: Submittal Calculator - Page 87 TABLE 12: Schedule Summary with Milestones - Page 88 TABLE 13: Construction Schedule with Critical Path - Pages 89 to 112 TABLE 14: Cash Flow - Page 113 TABLE 15: Cash Flow Graphics - Page 114 Section Seven: Project Risk Management Analysis TABLE 16: Risk Register - Pages 136 to 137 TABLE 17: Project Team Risk Responsibility Matrix - Page 138 Section Eight: Site Specific Safety Plan TABLE 18: Description - Page 144 TABLE 19: Hazard Matrix - Page 144 TABLE 20: Site Specific Safety Hazard Analysis - Pages 145 to 146 LIST OF TABLES
08/01/2018MCM 901 Page 10 of 224 Master Thesis: 620 N 3rd St Clara Bucar Section Nine: Site Specific Environmental Plan TABLE 21: Site Specific Environmental Impacts - Page 154 Section Ten: Site Specific QA/QC Plan TABLE 22: Contract Quality Requirements - Pages 161 to 162 Section Eleven: LEED TABLE 23: LEED v4 Scorecard - Page 170
Section One will describe Fit Construction, its trajectory, past projects, strengths, values and communications. For that, a company’s written description can be found, as well as images and legends of successful projects. A diagram displaying how the company is organized can provide valuable information as to its processes and hierarchy. Lastly, this section aims to inform how the staff at the construction site maintains efficient communications with the home office, given that the project management happens in both worlds at the same time.
SECTION ONE COMPANY INFORMATION
08/01/2018MCM 901 Page 11 of 224 Master Thesis: 620 N 3rd St Clara Bucar
Currently, Fit Construction has over two hundred direct employees and several hundred people working as subcontractors, having reached a revenue of $85mi in 2017. Please see some of our completed projects within the next pages.
We love construction and believe there is no such thing as a perfect project, there is always room for improvement. That is what we work for!
08/01/2018MCM 901 Page 12 of 224 Master Thesis: 620 N 3rd St Clara Bucar 1.2. Company overview and data sheets
Fit Construction was founded by Clara Bucar in 2012. Initially, the company worked with small commercial and residential fit outs, providing design and construction, often on a Design-Build delivery method basis. Since then, the company has grown to perform a variety of small and mid size new construction and fit outs, as well as providing specific consulting services, such as LEAN and TechnologyLEED.isafocus point for Fit Construction. We invest in technologies such as Procore and BIM to provide excellence in management and quality. We invest even higher in the continued education for our employees, looking forward to making them feel valued and invested on as a way of maintaining our talents. Our people are our greatest strength.
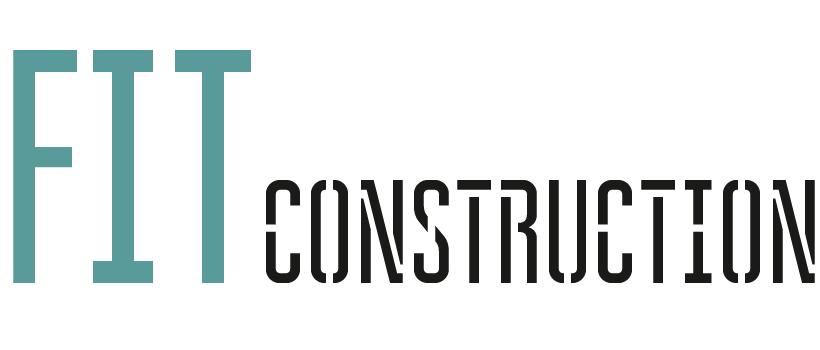
08/01/2018MCM 901 Page 13 of 224 Master Thesis: 620 N 3rd St Clara Bucar 01 02 Fortaleza Art Museum, 2015: Fortaleza, Brazil. Budget: $10mi. Design Build. The beach house, 2012: Build.$500,000.Brazil.Fortaleza,Budget:Design
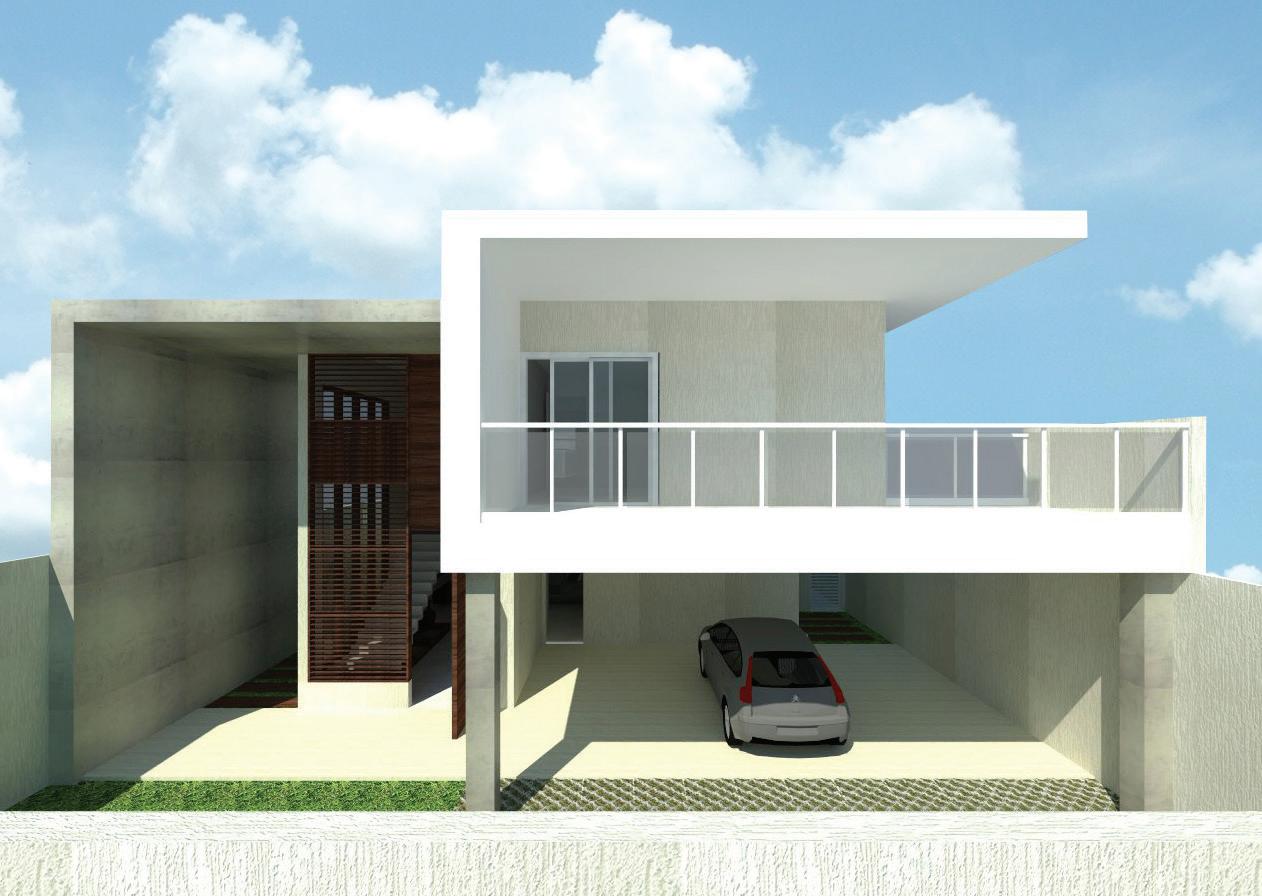
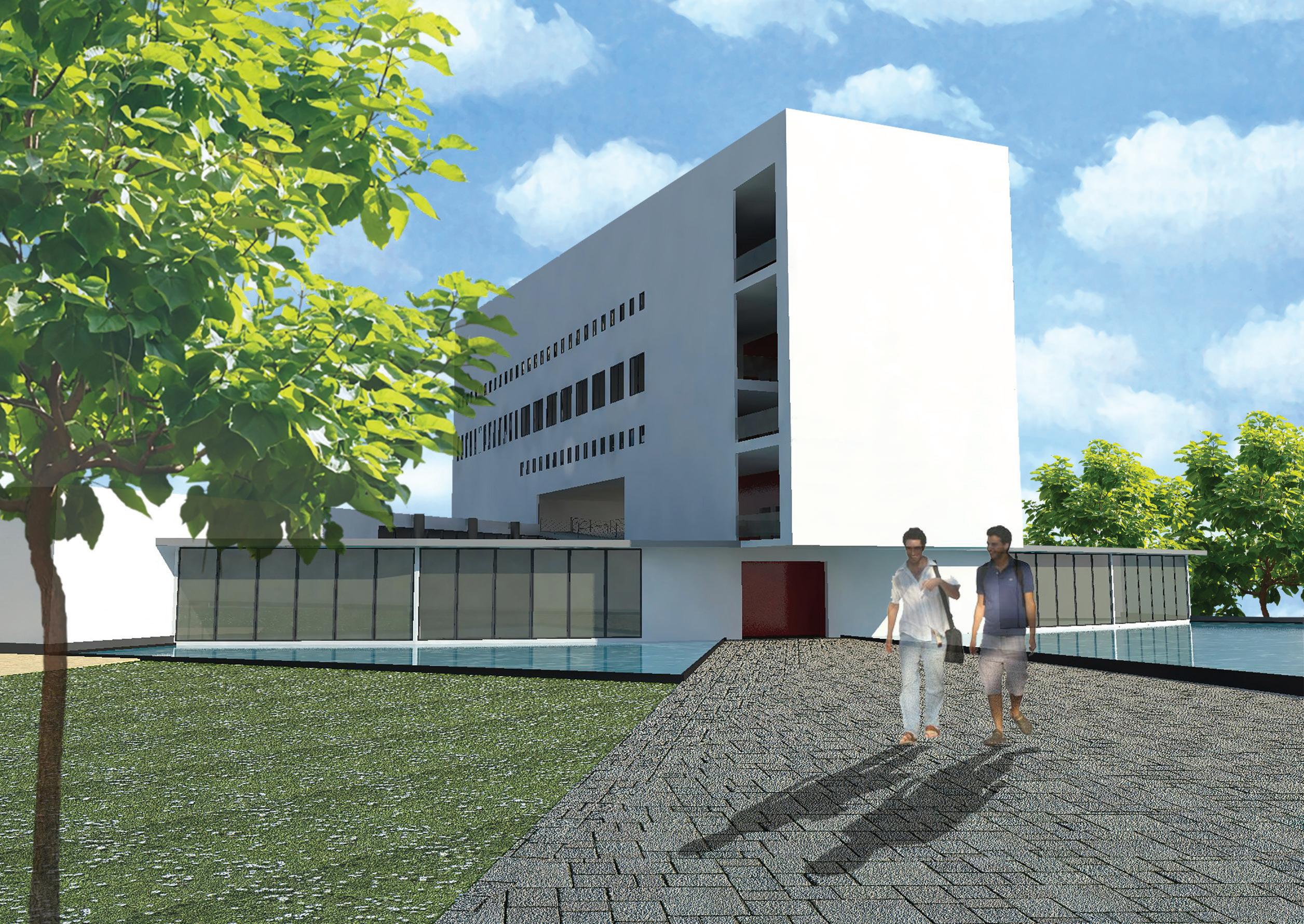
08/01/2018MCM 901 Page 14 of 224 Master Thesis: 620 N 3rd St Clara Bucar03 Sapiranga Social Housing Complex, 2016: Fortaleza, Brazil. Budget: $25mi. Design Build. United Nations New Canopies, 2016: New York City, NY. Budget: $4mi. 03 North Canopy
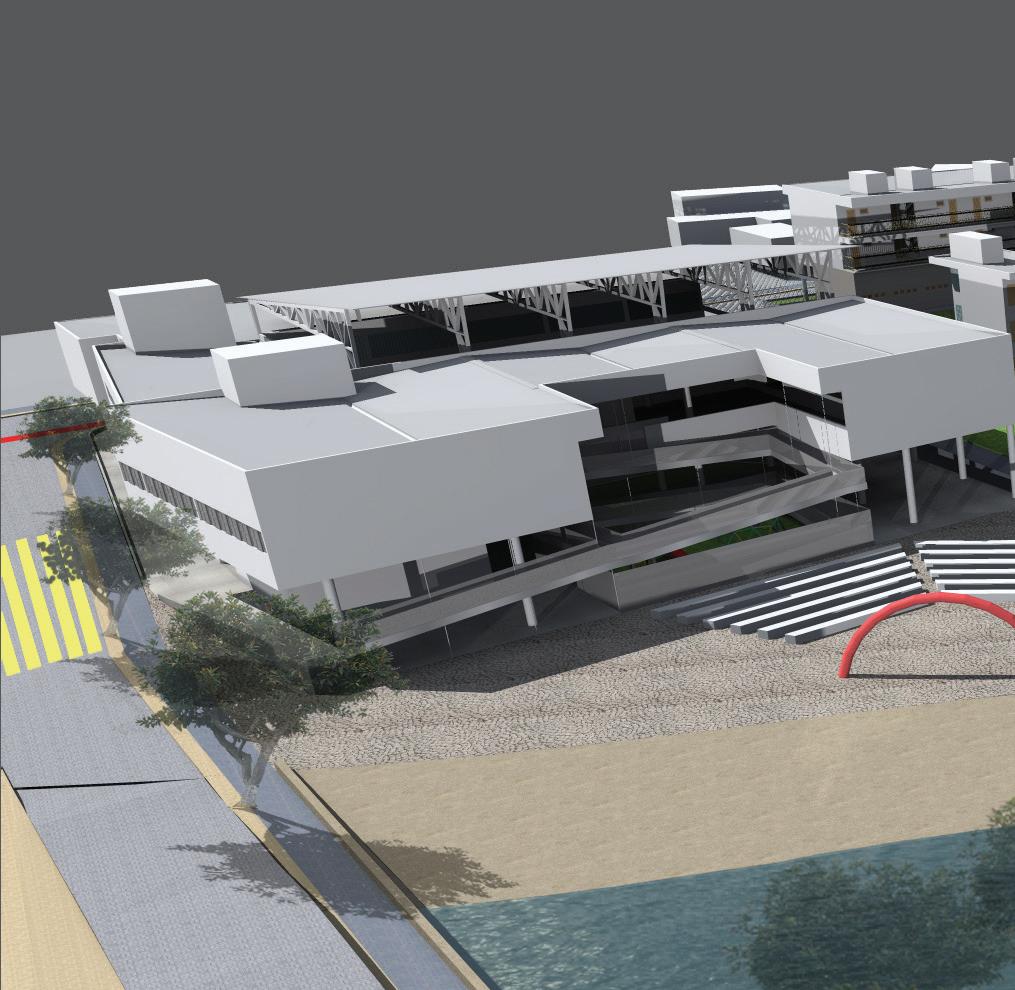


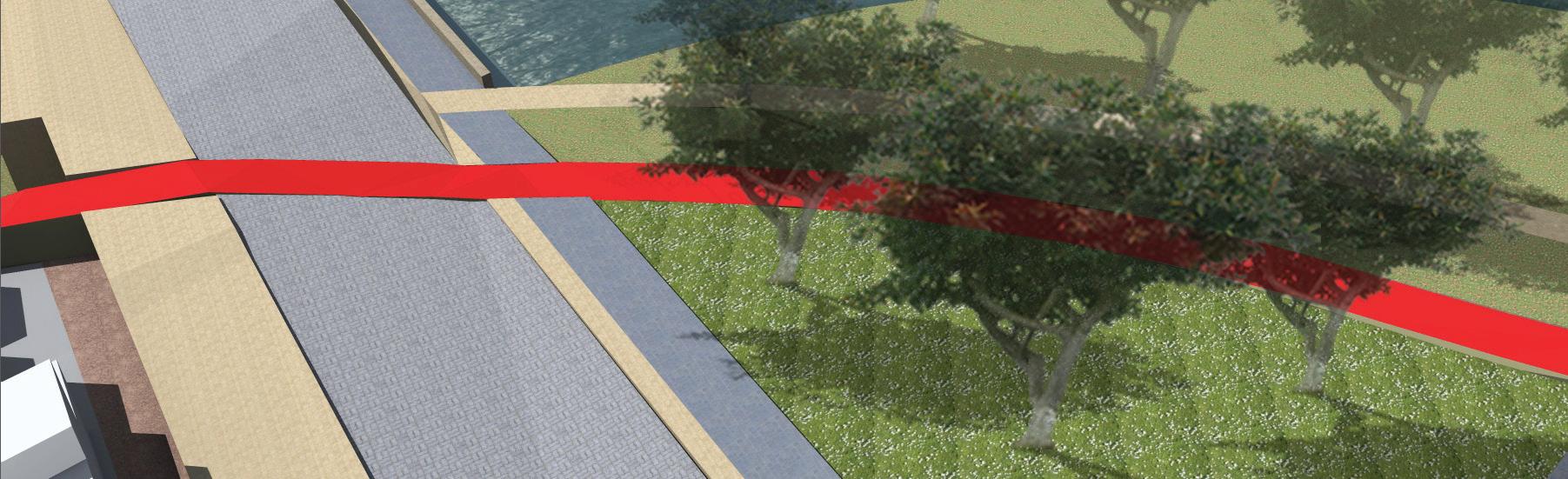
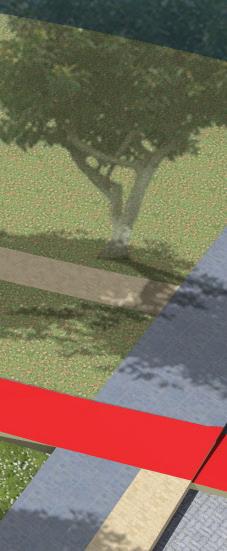

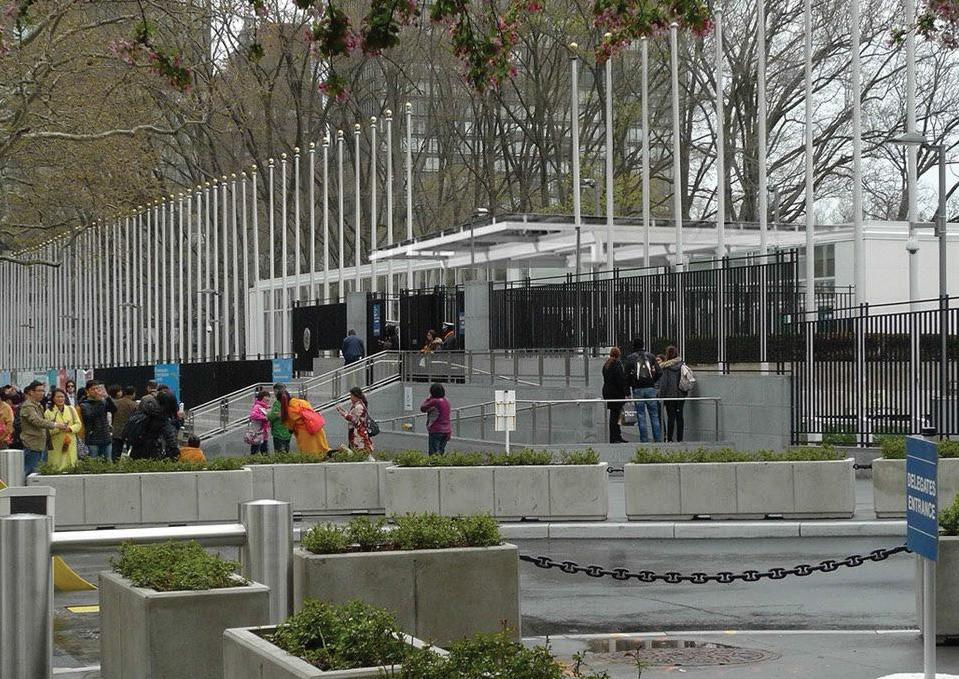
08/01/2018MCM 901 Page 15 of 224 Master Thesis: 620 N 3rd St Clara Bucar Fit Construction Board of PresidentDirectors (VManagementicepresident of construction) (OperationsOperationsDirector) HR (HR Director) SuperintendantGeneralSuperintendant (EstimatingEstimatingDirector) Senior AssistantManagerManagerProjectProjectPM Field Engineer PersonnelInsuranceManagerOffice EstimatorEstimatorSenior (MarketingMarketingDirector)(ProcurementProcurementDirector) EngineerProject DevelopmentMarketingSpecialistBusinessMaterialsProcurementManagerandNecessities (FinancialFinancesDirector)AccountantControllerCostEngineer EnvironmentalManagerSafetyQualityManagerManager BIM(BIMDepartmentManager)BIMEngineer 1.2. Company Organizational Chart
Every week, the Project Manager, the Owner, the Designer and other relevant project participants do a walk through the site with the Site Superintendent and the Field Engineer to identify results and challenges. This is another important strategy to keep communications effective: making the subjects concrete, instead of just an abstract subject line on an email.
In addition, the Site Superintendent participates on biweekly meetings with the General Superintendent and other superintendents to discuss each project. These meetings are held at the office and are useful to share strategies and results all across Fit Construction’s projects.
08/01/2018MCM 901 Page 16 of 224 Master Thesis: 620 N 3rd St Clara Bucar 1.3. Interaction between home office and field
The interactions between home office and field happen in different ways. All projects participants, especially those from Fit Construction, are connected at all time through the construction software, Procore. With Procore, all project communications, including emails, occur through the software and are automatically documented on the cloud. One of the Field Engineer’s primary responsibilities is to compose a daily report of the construction. This daily report is submitted to the Project Manager and all other relevant project participants.
Lastly, Fit Construction, being based in Philadelphia, allows for a direct line of communication with our staff, the 620 N 3rd St and the owner. All project participants are welcome to reach out to us at our office with any questions or concerns.
08/01/2018MCM 901 Page 17 of 224 Master Thesis: 620 N 3rd St Clara Bucar
SECTION TWO PROJECT INFORMATION
Section Two will demonstrate project specific, variate pieces of information. It starts with a description of the project, it’s main components, structure and spaces. Then, a diagram showing the interactions between the project participants is displayed, providing useful information on the project’s hierarchy and communication dynamics, which can provide clarification on team communication. These same project participants are then listed under a responsibility matrix which describes their roles in each project task and phase. Another part of Section Two concerns the description of the delivery method approach. In the 620 N 3rd St project, an unconventional delivery method system was defined, composing an important part of the project. Lastly, this section provides information on how Fit Construction will handle construction communication, as well as a description of the risk administration method utilized to analyze and plan around management, safety, quality and environmental issues.
08/01/2018MCM 901 Page 18 of 224 Master Thesis: 620 N 3rd St Clara Bucar 2.1. Project Overview
A new basement, to host storage units and mechanical/electrical rooms, will be excavated and will occupy roughly half of the property. The first floor will have a garage with nine parking spaces, as well as access lobbies and a trash room. The second, third and fourth floor will each have three residential units, totaling nine apartments in the entire building. The roof will host a mechanical area, two separate private decks, as well as a shared deck and planters dividing the spaces. The structure of the building will be diversified. The basement and the on-grade portion of the first floor will be composed of concrete slabs and columns, in addition to structural steel columns and beams. The other portion of the first floor and the second floor are structural steel with metal decking and poured concrete. From the second floor “floor” and up, the structure is all wood, including the roof and the exterior walls, with few exceptions.
The 620 N 3rd St project consists of a residential, multifamily building located at 620 N 3rd St, Northern Liberties, Philadelphia - PA (highlighted on the map below). It’s composed of basement, ground level, 3 floors of residential units and a deck on the roof. The site, which can be accessed from both N 3rd St and N Galloway St, will be completely occupied with construction.
The vertical circulations are two stairs, one on each side of the building, and one elevator. The elevator shaft structure is masonry. Further details will be demonstrated throughout this manual. Floor plans, elevations and sections Image: Bing.
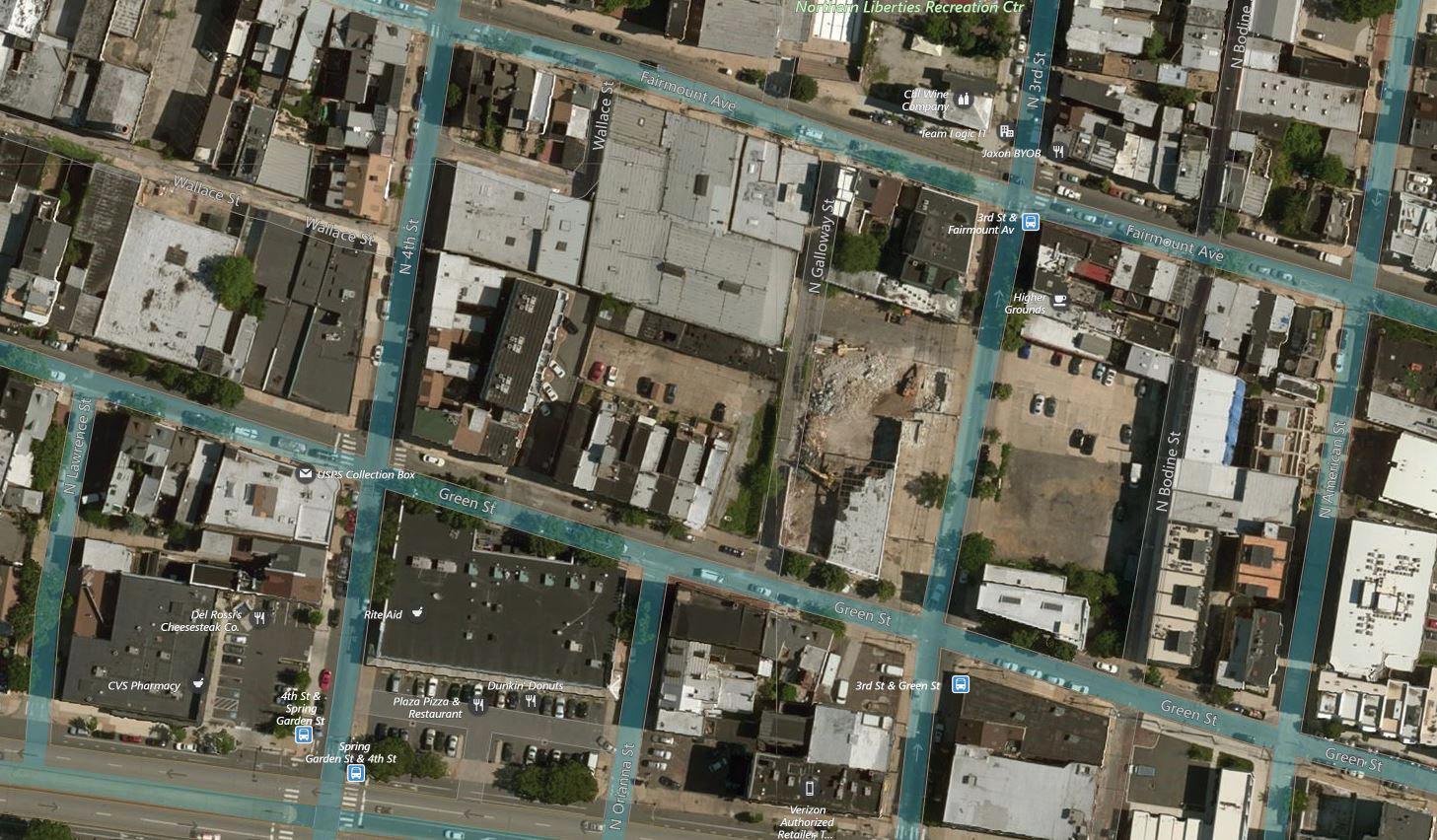
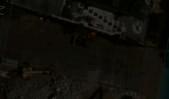
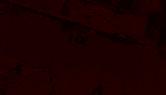
On the upper right side, the Fit Construction home office staff which work closely with the 620 N 3rd St project are listed. These employees work mainly from the office but may perform frequent visits to the site to assure that specific parts of the project are running accordingly, such as Quality, Safety, etc. Others are not required to visit the site, but still deal with the project on a daily basis, such as the Accounting Lastly,Department.onthe lower right quadrant the construction site based participants are showed. Its important to highlight that the masonry scope of the project will be self-performed. The foreman and the crew at the site are coordinated by the Site Superintendent. At the site, the Site Superintendent is the main authority and contact point to the subcontractors. The Project Manager is, overall, the main line of communication for the project, this person is the contact for the Designer and the Owner and has the responsibility of translating decisions to the subcontractors’ Project Managers and the Site Superintendent.
Construction (Field) EnvironmentalManagerSafetyQualityManagerManager Preconstruction DevelopmentBusinessEstimatorProcurementManager Field Engineer (Masonry)Labor Office support Operations Director Senior Project Manager Fit Construction Project Manager Accountant Owner Designer Accounts (Subcontractors/payableVendors) Superintendant Subcontractors/Vendors receivableAccounts(Owner) superintendantGeneral BIM Engineer
The Project Organizational Chart displayed in this manual is a diagram that shows the main interactions between the project participants. On the upper left quadrant, the contractual relationships are highlighted in yellow arrows, while the white arrow represents the close yet non-contractual relation between Fit Construction and the Designer.
On the lower left side, the main departments involved with preconstruction are listed. These departments work on attracting clients and providing the Project Manager with essential information for the bid and the client communications.
08/01/2018MCM 901 Page 19 of 224 Master Thesis: 620 N 3rd St Clara Bucar 2.2. Project Organizational Chart
08/01/2018MCM 901 Page 20 of 224 Master Thesis: 620 N 3rd St Clara Bucar 2.3. Project Management Team Responsibilities Matrix ResponsibilityResponsibilityDeliverableP-PrimaryA-Approval Authority S - Support or ConsultingI-Informed Owner ExecutiveProject ManagerProject EngineerField SuperintendentGeneral Superintendent Accounting SuperintendentCraft ManagerQuality ManagerEnvironmental/Safety EngineerBim Estimator managerProcurement ForemenCraft Architect ConsultantsArchitect's Subcontractors/Vendors Preconstruction DocumentsDesign/Construction A S S I I I I I I I I I I I P P I Permitting S S S I S S I S I I I I I I P P I Project Delivery System P P A I I I I I I I I I I I I I I Estimating I S S I S S I I I I S P S I I I I Contracts P A S I I I S I I I I I S I A I I Procurement / Buyout Qualifications based A P P I I I S I I I S S P I I I S Award A P P I I I S I I I S S A I I I S Preplanning Mobilization I S S P P P I P I I I I I I I I P Construction Management I P P S A A I S I I I I I I I I S Equipment I A A S A A I A I I I I I P I I P Labor I A A S A A I A I I I I I P I I P Material I A A S A A I A I I I I I P I I P Cost Control A A A S A A P S I I I I I S I S S Payments A A A I S S P S I I I I I S I I I Change Orders
08/01/2018MCM 901 Page 21 of 224 Master Thesis: 620 N 3rd St Clara Bucar ResponsibilityResponsibilityDeliverableP-PrimaryA-Approval Authority S - Support or ConsultingI-Informed Owner ExecutiveProject ManagerProject EngineerField SuperintendentGeneral Superintendent Accounting SuperintendentCraft ManagerQuality ManagerEnvironmental/Safety EngineerBim Estimator managerProcurement ForemenCraft Architect ConsultantsArchitect's Subcontractors/Vendors Risk Management Risk Management Plan S P P S S S I I I I I S S I I I I Risk ImplementationManagement S P P S A A I I I I I S S I I I I Safety & Environmental Safety Plan I S S A A S I A I P I I I I I I I Safety Implementation I I I A A S I A I P I I I I I I I Quality Quality Control I S S P S S I S P I S I I S A A S Quality Assurance I P P S S S I A P I S I I S I I S Communications Documentation A P P P P P P S P P P P P S S S S RFIs I A P S P P I S I I S S S S P P S Submittals A A P S P P I S S I S S S S P P S Weekly Progress Reports I A P S P P I S S S S I I S S S S Closeout closeoutPunchlist/Punchlist A A P S P P I S P I I I I I S S S Owner training P A A P P P I S S I I I I S S S S Warranties/O&M Manual P A A P P P I S S I I I I S S S S Financial resolution P P P I S S P S I I I I S I I I I Demobilization I A A P P P I P I S I I I P I I I Final payment P P P I S S P S I I I I I I I I I
An unconventional method was established for the 620 N 3rd Project due to the specific circumstances. First, the Owner, PRDC Properties, is a real estate development company, which implies the assumption that, in this case, the client has experience with construction. Second, the plot of land has already been purchased through an expected deal and the loan payback is scheduled to start in 2020. This scenario tells that, unless this project happens as scheduled, starting in 2018 and ending 2020, financial losses due to underutilized resources will start to incur. It’s important to note that, for higher efficiency during construction, the beginning of Spring and all of Summer is the ideal time to develop the work.
The Designers, due to the unexpected nature of the deal on the plot, were hired on an urgency basis to develop the project. Consequently, the incompleteness of the construction drawings was made evident during the bid, closed to pre-qualified contractors, including Fit Construction. Given the scenario, a complicated construction process could be foreseen with too many change orders, delays and relationship issues. To help solve this puzzle, Fit Construction came up with a strategy to help avoid these risks while transforming those into opportunities. The method is composed of two parts:
08/01/2018MCM 901 Page 22 of 224 Master Thesis: 620 N 3rd St Clara Bucar 2.4. Project Delivery Method Analysis
2) Preconstruction, construction and closeout: As stated previously, the incompleteness of the construction documents was made evident during the bid. Fit Construction and PRDC had previously worked with a multi residential building in Philadelphia and, therefore, had a pre-established relationship which influenced the contracting company selection. After winning the bid, Fit Construction approached PRDC to discuss the work. In that meeting, the complex variables were listed and the decision for an integrated project delivery was made. The contractual relationships were maintained as traditionally, between the Owner and Contractor, and Owner and Designer separately. Likewise, all the subcontractors are contractually obligated to Fit Construction, not PRDC. The lump sum number established during the bid was set as a baseline on a cost plus a fee basis but Fit and PRDC agreed that many project changes were inevitable, and that flexibility was essential. For that, a monthly meeting with Owner, Contractor, Designer and main subcontractors was established. In these meetings, the project team would bring issues regarding the following months’ worth of work and discuss what changes could provide value engineering to the work. These changes, once approved by all relevant project participants including the Owner, would then be incorporated to the project. To ease the weight of a changing budget, Fit Construction agreed to work with open books, on a cost plus a fee basis with PRDC, who would have full transparency and control over the project. Additionally, an Incentives Program was laid to stimulate results. Further details of the 620 N 3rd St delivery methods are explained under Section Six of this manual.
1) Bid and award: Before and during the bid process, a traditional Design-Bid-Build with a lump sum was utilized. Fit Construction received the set of construction documents, estimated the costs and submitted the bid to PRDC Properties, having won the job.
Naturally for an integrated delivery method project, communication is encouraged between all project participants as much as possible. From a process point of view, the Project Manager is in the center of the major communications. This person is the Owner’s main contact point, as well as the Designer’s. The Project Manager translates the information circulated between Owner and Designer and makes decisions regarding the subcontractors and the construction site. The Project Manager communicates these decisions to the Site Superintendent, who is then responsible for implementing these directions at the site. Conversely, the subcontractors and Site Superintendent gather questions and concerns at the construction site and inform the Project Manager, who is then assigned to discuss it with Owner and Designer. The project specific communications are further explained under Section Six of this manual.
The 620 N 3rd St project was studied and analyzed holistically by Fit Construction. Work packages were established with portions of the project, which were then awarded to prequalified subcontractors. A Master Schedule was established and weekly reports, including updates on the real progress of the schedule, are to be submitted. Fit Construction will bill PRDC monthly on the work performed. The subcontractors also bill Fit Construction monthly and agree to a paywhen-paid contract. The work is to be tracked utilizing a percentage completion strategy and communicated to the Owner every week.
08/01/2018MCM 901 Page 23 of 224 Master Thesis: 620 N 3rd St Clara Bucar 2.5. Construction Administration / Communication
08/01/2018MCM 901 Page 24 of 224 Master Thesis: 620 N 3rd St Clara Bucar 2.6.
Construction Risk Administration
Essentially, a risk is a potential occurrence with a possible negative effect. Considering the singularity and customization of each project, to understand risks and opportunities before they happen are challenges faced even by the most experienced managers. At the same time, the success of the project is highly dependent of the risk evaluation process during early stages of construction. That makes Risk Administration a pivotal component of the construction industry and a keyconcern of Fit Construction. In compliance with the ISO-9001 approach, Fit Construction adopts the cyclical process of Planning - Doing - Checking - Acting - Reviewing to gather and analyze project data. The mentioned strategy provides accurate data to be applied into future projects, contributing to its success rates and the growth of Fit Construction. It also offers the opportunity to allow a comprehensive yet realistic brainstorming of scenarios with tangible outcomes for potentially complex situations.
Likewise, other project’s previously gathered and tested information was applied on the development of the 620 N 3rd St project as a part of its preconstruction process of risk assessment. In addition, Fit Construction workers’ experience is a key factor to look ahead and anticipate opportunities, empowering the project overall.
Construction Risk Administration will be divided into Risk Management, Safety, Environmental and Quality. For each of these, the process will encompass the following steps: 1) determining the project specific context; 2) recognizing risks; 3) examining probability and severity of registered ; 4) assessing and classifying the priority risks; 5) establishing strategies to approach the priority risks, 6) keeping track of the recognized outcomes of plans put in action; 7) assessment of the mentioned outcomes to provide continuity and 8) effective documentation to make information available for company members and future projects.
08/01/2018MCM 901 Page 25 of 224 Master Thesis: 620 N 3rd St Clara Bucar
Building Information Modeling (BIM) is a one of Fit Construction’s highest bets. The company strongly believes that technology can improve construction in different ways and provide efficiency. In Section Three, the BIM model built for the 620 N 3rd St project is demonstrated in floor plans, sections, elevations and rendered perspectives for a holistic understanding of the construction work. The referred BIM model is an important part of this project. It will be detailed weekly and utilized as a tool to provide deeper information on coordination issues, missing or faulty design, boundaries of each sub’s scope of work, precise take-offs for waste reduction and identification of construction issues before they happen. Section Three provides visual content on how the modeled information can be seen and analyzed.
SECTION THREE BIM MODEL
08/01/2018MCM 901 Page 26 of 224 Master Thesis: 620 N 3rd St Clara Bucar UP ND NE NF NO E1E2E3E5E6 SF SE SD SC SB SA W1 W3 SG SH 071 091 101081 082 Unit Storage 1 Pump Room 3 Peco Vault 4 Scale Project number DrawnDate Checkedbybywww.autodesk.com/revit 1" = 10'-0" PM3:03:216/10/201806 basementProject NumberProjectOwner Name Issue CheckerAuthorDate No. Description Date 3.1. Floor Plan - Basement
08/01/2018MCM 901 Page 27 of 224 Master Thesis: 620 N 3rd St Clara Bucar UP DN UP ND NE NF NO E1E2E3E5E6 SF SE SD SC SB SA W1 W3 SG SH 071 091 101081 082 Garage 5 Lobby 6 Scale Project number DrawnDate Checkedbybywww.autodesk.com/revit 1" = 10'-0" PM3:05:026/10/201801 1st fl Project NumberProjectOwner Name Issue CheckerAuthorDate No. Description Date 3.1. Floor Plan - 1st Floor
08/01/2018MCM 901 Page 28 of 224 Master Thesis: 620 N 3rd St Clara Bucar DNUP DN ND NE NF NO E1E2E3E5E6 SF SE SD SC SB SA W1 W3 SG SH 071 091 101081 082 Bedroom 7 UNIT #2C Living, Dining, Kitchen 8 Bedroom 9 Bedroom 10 Bedroom 11 Lobby 12 Bedroom 13 Bedroom 14 UNIT #2A Living, Dining, Kitchen 15 Bedroom 16 UNIT #2B Living, Dining, Kitchen 17 Shared Deck 19 Scale Project number DrawnDate Checkedbybywww.autodesk.com/revit 1" = 10'-0" PM3:12:086/10/201802 2nd floor Project NumberProjectOwner Name Issue CheckerAuthorDate No. Description Date 1" = 10'-0"1 2nd Fl 3.1. Floor Plan - 2nd Floor
08/01/2018MCM 901 Page 29 of 224 Master Thesis: 620 N 3rd St Clara Bucar DN ND NE NF NO E1E2E3E5E6 SF SE SD SC SB SA W1 W3 SG SH 071 091 101081 082 Bedroom 20 UNIT #3C Living, Dining, Kitchen 21 Bedroom 22 Bedroom 23 Bedroom 24 UNIT #3B Living, Dining, Kitchen 25 Lobby 26 Bedroom 27 Bedroom 28 UNIT #3A Living, Dining, Kitchen 29 Bedroom 30 Scale Project number DrawnDate Checkedbybywww.autodesk.com/revit 1" = 10'-0" PM3:14:106/10/201803 3rd fl Project NumberProjectOwner Name Issue CheckerAuthorDate No. Description Date 3.1. Floor Plan - 3rd Floor
08/01/2018MCM 901 Page 30 of 224 Master Thesis: 620 N 3rd St Clara Bucar UP ND NE NF NO E1E2E3E5E6 SF SE SD SC SB SA W1 W3 SG SH 071 091 101081 082 UNIT #4C Living, Dining, Kitchen 31 Bedroom 32 Bedroom 33 Bedroom 34 Lobby 35 UNIT #4B Living, Dining, Kitchen 36 Bedroom 37 UNIT #4A Living, Dining, Kitchen 38 Bedroom 39 Deck 40 Deck 41 Scale Project number DrawnDate Checkedbybywww.autodesk.com/revit 1" = 10'-0" PM3:17:566/10/201804 4th fl Project NumberProjectOwner Name Issue CheckerAuthorDate No. Description Date 3.1. Floor Plan - 4th Floor
08/01/2018 Master Thesis: 620 N 3rd St Clara Bucar ND NE NF NO E1E2E3E5E6 SF SE SD SC SB SA W1 W3 SG SH 071 091 101081 082 Scale Project number DrawnDate Checkedbybywww.autodesk.com/revit 1" = 10'-0" PM3:21:496/10/201805 roof plan Project NumberProjectOwner Name Issue CheckerAuthorDate No. Description Date 3.1. Floor Plan - Roof





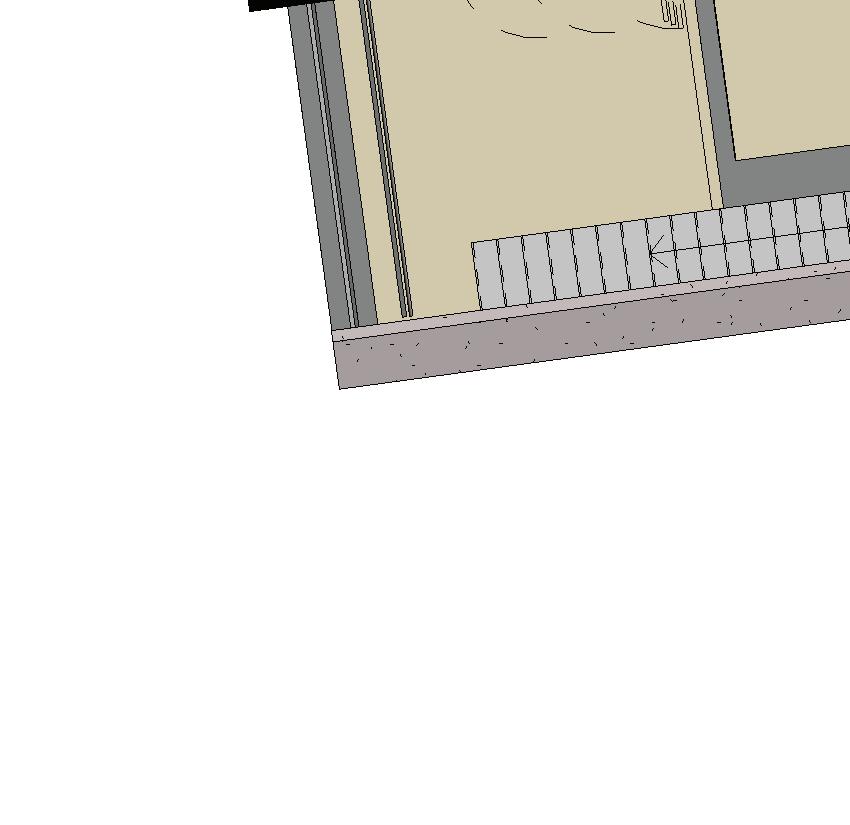
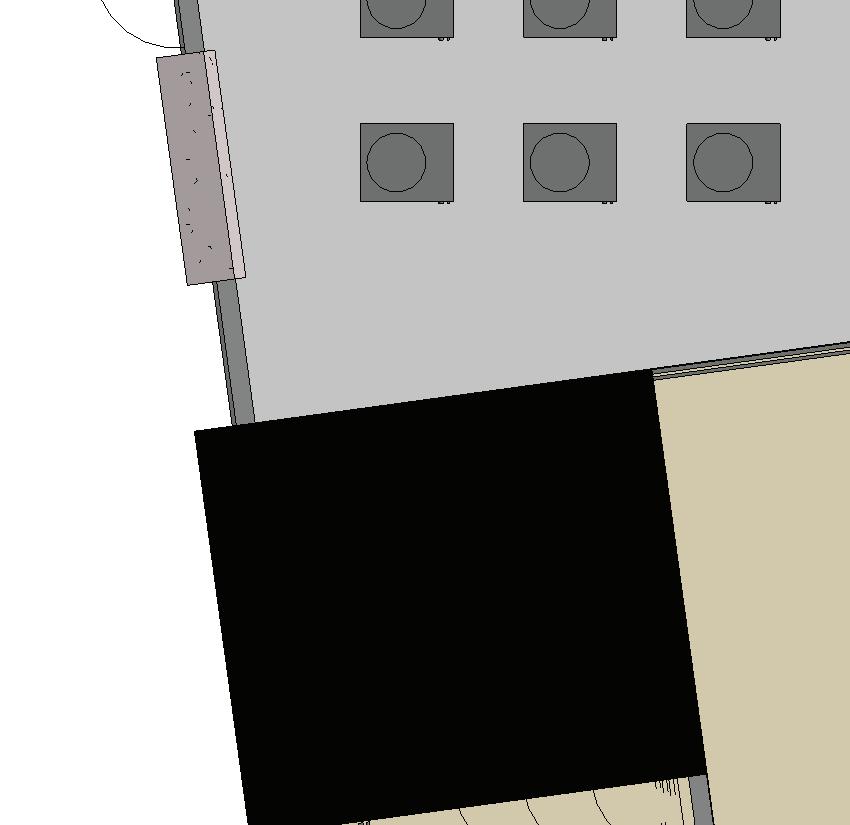
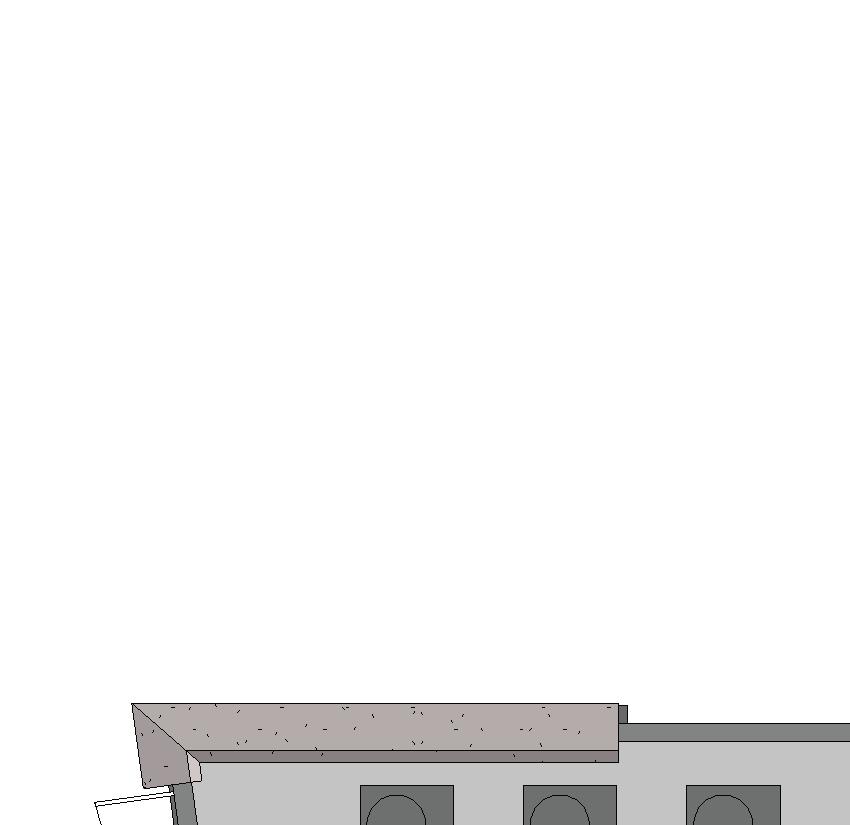

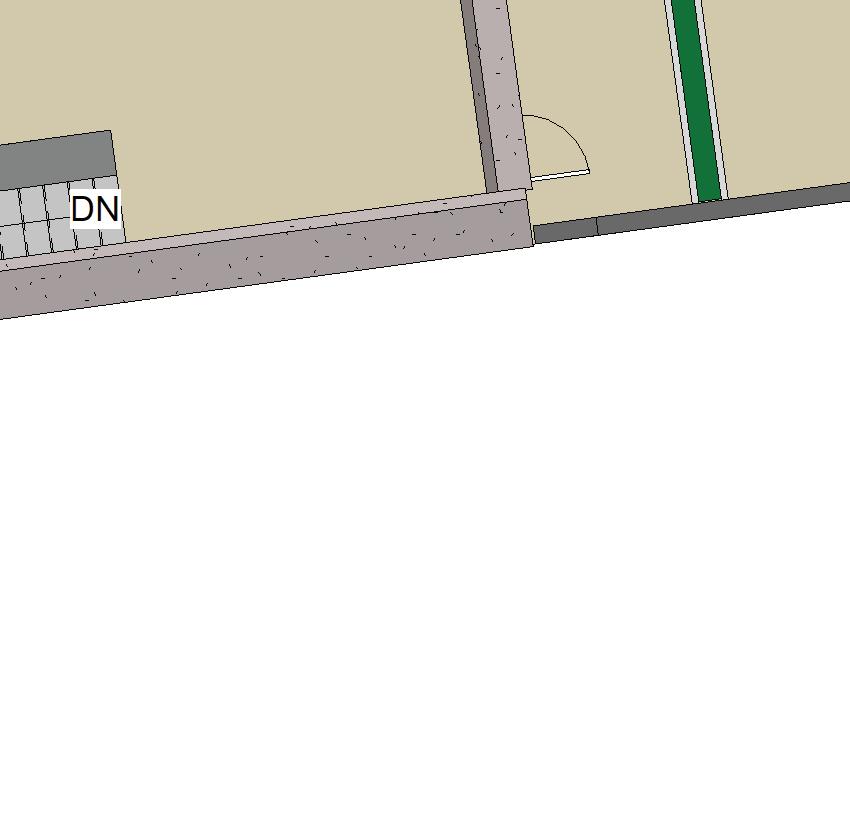




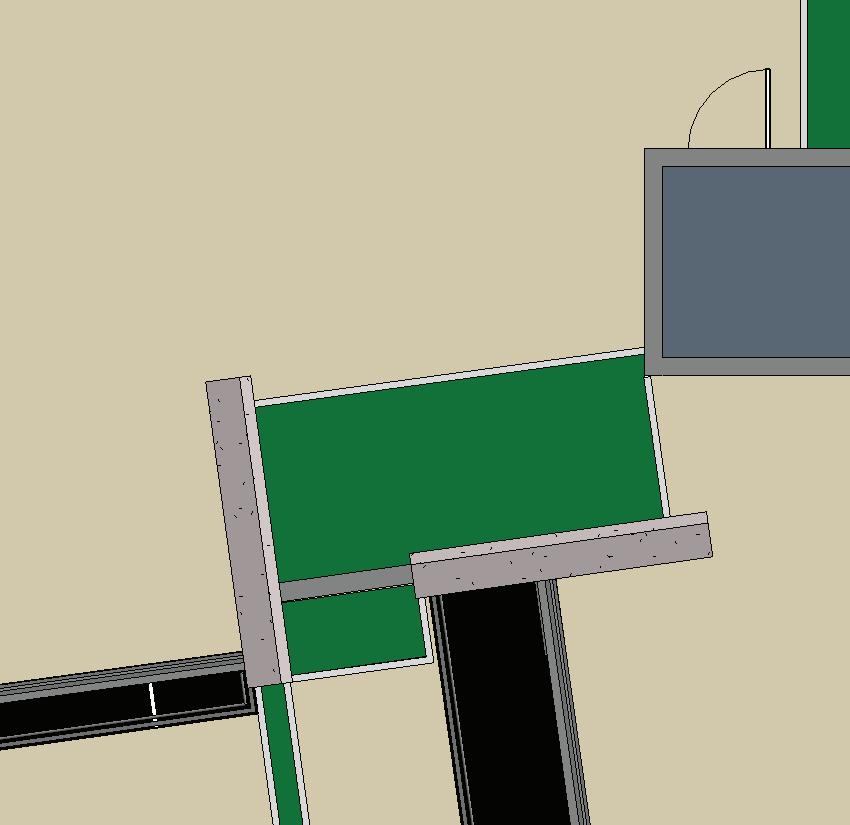



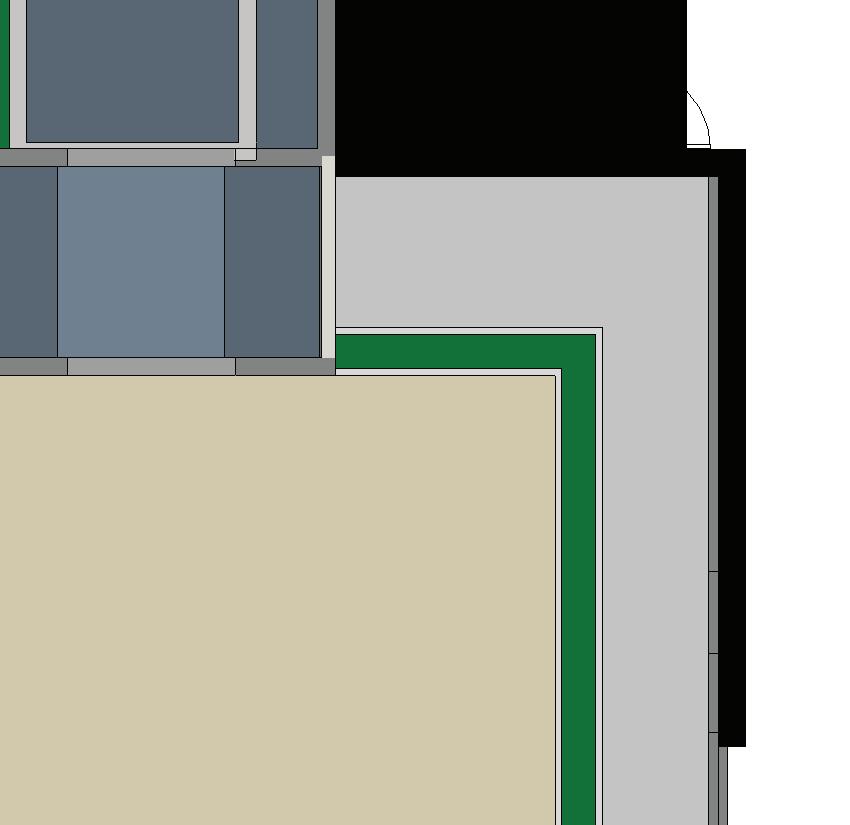





08/01/2018MCM 901 Page 32 of 224 Master Thesis: 620 N 3rd St Clara Bucar 3.2. Section AA ND NE NF SNO G SH 1st Fl Fin Flr 0' B0" .O. Footing2 2' 2 1/2" Utility Bas em ent - 9' - 11 B1/2" .O. Footing1 11' 10" B.O. Footing 17 1" T.O. Concrete W all 13' 9" 2nd Fl 9' 11 1/2" 3rd Fl 20' 4 1/2" 4th Fl 30' 9 1/2" T.O. Flat Roof 41' 2 1/2" T.O. Pilothous e Roof 50' 2 1/2" ND NE NF SNO G SH 1st Fl Fin Flr 0' B0" .O. Footing2 2' 2 1/2" Utility Bas em ent - 9' - 11 B1/2" .O. Footing1 11' 10" B.O. Footing 17' 1" T.O. Concrete W all 13' 9" 2nd Fl 9' 11 1/2" 3rd Fl 20 4 1/2" 4th Fl 30 9 1/2" T.O. Flat Roof 41' 2 1/2" T.O. Pilothous e Roof 50 2 1/2"
08/01/2018MCM 901 Page 33 of 224 Master Thesis: 620 N 3rd St Clara Bucar EE1E3 6 E5 E2 W 1 W 3 1st Fl Fin Flr 0' B0" .O. Footing2 2' 2 1/2" Utility Bas em ent 9' 11 B1/2" .O. Footing1 11' 10" B.O. Footing 17' 1" T.O. Concrete W all 13' 9" 2nd Fl 9' 11 1/2" 3rd Fl 20' 4 1/2" 4th Fl 30' - 9 1/2" T.O. Flat Roof 41' 2 1/2" T.O. Pilothous e Roof 50' 2 1/2" 1st Fl Fin Flr 0' B0" .O. Footing2 2' 2 1/2" Utility Bas em ent 9' 11 B1/2" .O. Footing1 11' 10" B.O. Footing 17' 1" T.O. Concrete W all 13' 9" 2nd Fl 9' 11 1/2" 3rd Fl 20' 4 1/2" 4th Fl 30' - 9 1/2" T.O. Flat Roof 41' 2 1/2" T.O. Pilothous e Roof 50' 2 1/2" 3.2. Section BB 3.2. Section CC EE1E3 6 E5 E2 W 1 W 3 1st Fl Fin Flr 0' B0" .O. Footing2 2' 2 1/2" Utility Bas em ent 9' 11 B1/2" .O. Footing1 11 10" B.O. Footing 17' 1" T.O. Concrete W all 13' 9" 2nd Fl 9' 11 1/2" 3rd Fl 20' 4 1/2" 4th Fl 30' - 9 1/2" T.O. Flat Roof 41' 2 1/2" T.O. Pilothous e Roof 50' 2 1/2" 1st Fl Fin Flr 0' B0" .O. Footing2 2' 2 1/2" Utility Bas em ent 9' 11 B1/2" .O. Footing1 11' 10" B.O. Footing 17' 1" T.O. Concrete W all 13' 9" 2nd Fl 9' 11 1/2" 3rd Fl 20' 4 1/2" 4th Fl 30' - 9 1/2" T.O. Flat Roof 41 2 1/2" T.O. Pilothous e Roof 50 2 1/2"
08/01/2018MCM 901 Page 34 of 224 Master Thesis: 620 N 3rd St Clara Bucar 3.2. Section DD 1st Fl Fin Flr 0' B0" .O. Footing2 2' 2 1/2" Utility Bas em ent 9' 11 B1/2" .O. Footing1 11' 10" B.O. Footing 17 1" T.O. Concrete W all 13' 9" 2nd Fl 9' 11 1/2" 3rd Fl 20' 4 1/2" 4th Fl 30' 9 1/2" T.O. Flat Roof 41' 2 1/2" T.O. Pilothous e Roof 50' 2 1/2" 1st Fl Fin Flr 0' B0" .O. Footing2 2' 2 1/2" Utility Bas em ent 9' 11 B1/2" .O. Footing1 11' 10" B.O. Footing 17' 1" T.O. Concrete W all 13' 9" 2nd Fl 9' 11 1/2" 3rd Fl 20 4 1/2" 4th Fl 30 9 1/2" T.O. Flat Roof 41 2 1/2" T.O. Pilothous e Roof 50 2 1/2"
08/01/2018MCM 901 Master Thesis: 620 N 3rd St Clara Bucar 3.2. Section EE T.O. Flat Roof 41' - 2 1/2" T.O. Pilothouse Roof 50' - 2 1/2" 1st Fl Fin Flr 0' B0" .O. Footing2 2' 2 1/2" Utility Bas em ent 9' 11 B1/2" .O. Footing1 11' 10" B.O. Footing 17 1" T.O. Concrete W all 13' 9" 2nd Fl 9' 11 1/2" 3rd Fl 20' 4 1/2" 4th Fl 30' 9 1/2" T.O. Flat Roof 41' 2 1/2" T.O. Pilothous e Roof 50' 2 1/2"
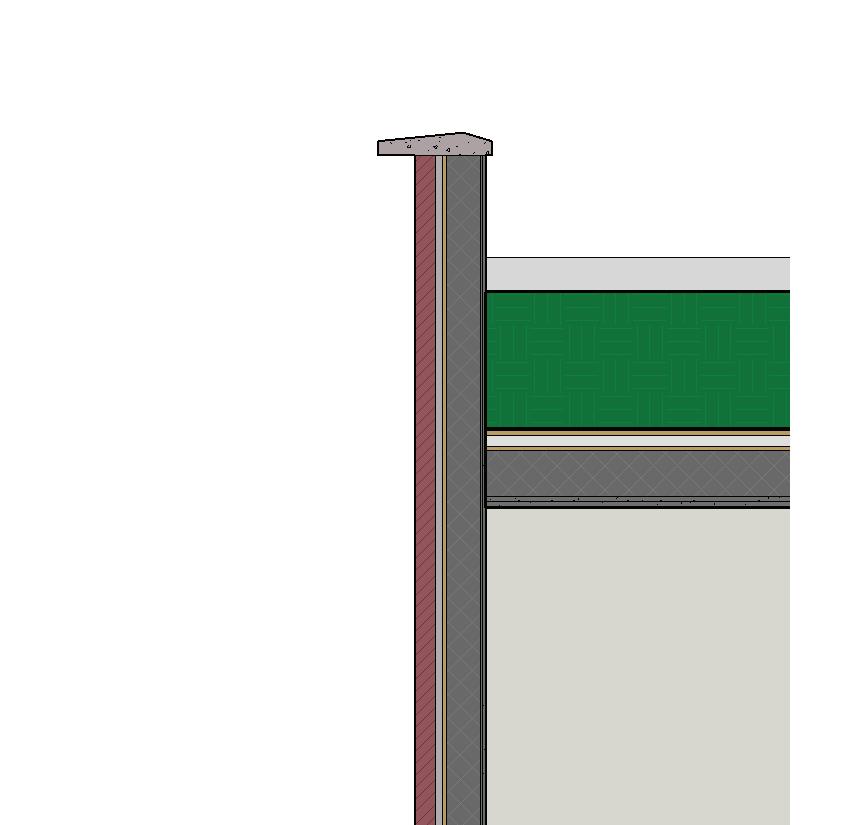
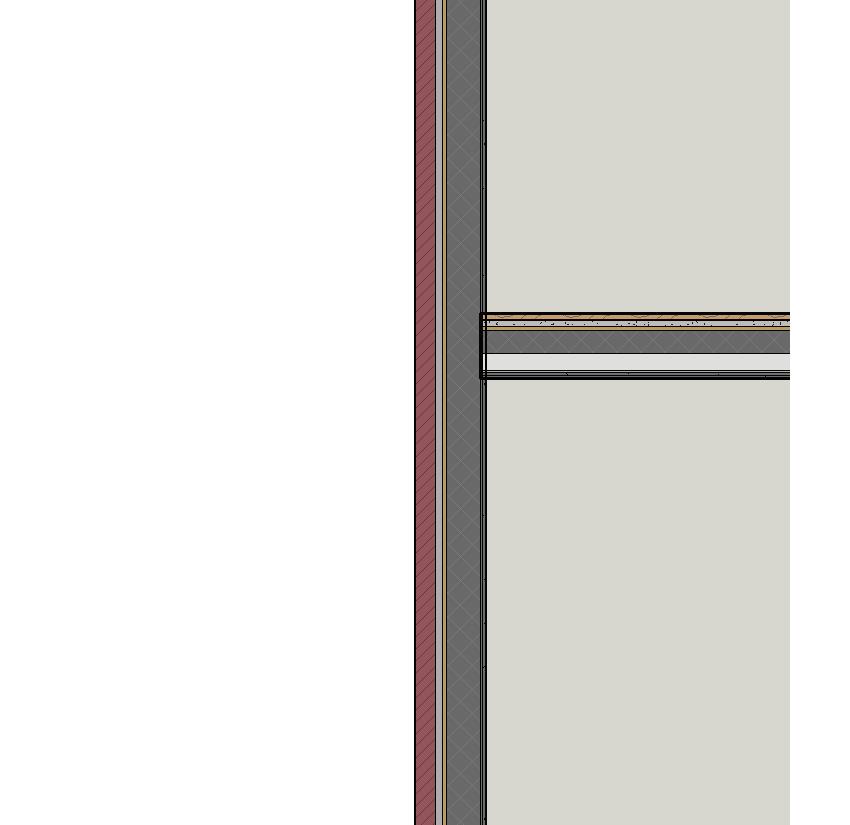
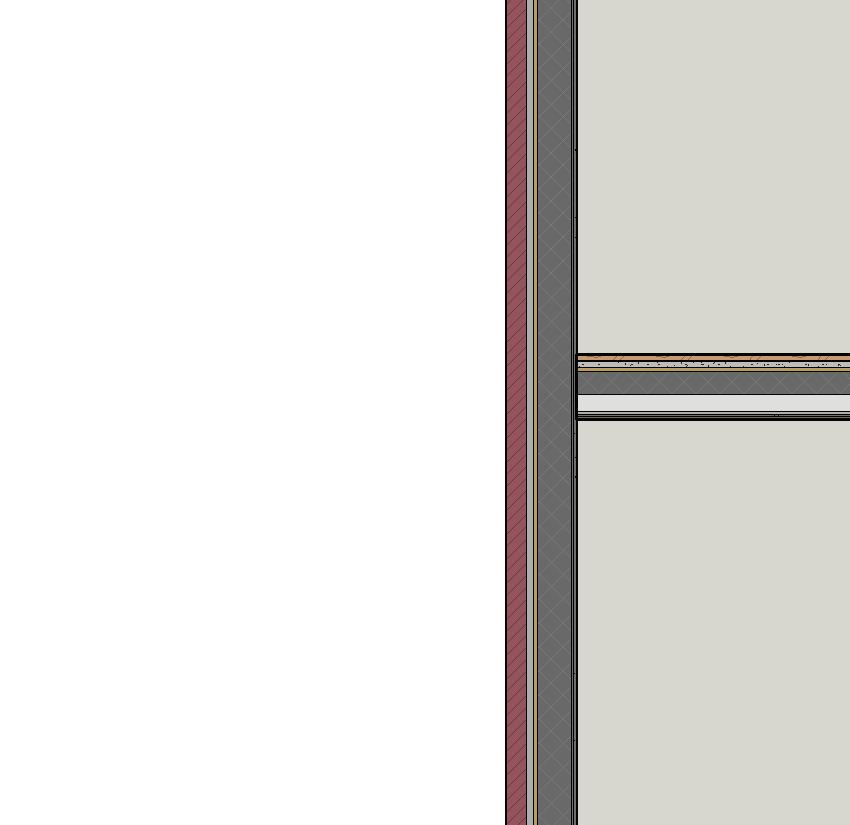
Master Thesis: 620 N 3rd St Clara Bucar 13' - 9" T.O. Flat Roof 41' - 2 1/2" T.O. Concrete Wall T.O. Flat Roof 41' - 2 1/2" 1st Fl Fin Flr Project number Drawn CheckedbybyUnnamed 3rd Fl 20' - 44th1/2"Fl30' - 9 1/2" B.O. -11'Footing1-10" T.O. Concrete13'Wall-9" ProjectOwner Name No. Description 1st Fl Fin Flr B.O.-2'Footing2-21/2" www.autodesk.com/revit ProjectOwner Name 1/2" = 1'-0"1 Section 1 1st Fl Fin Flr 0' - 0" B.O.-2'Footing2-21/2" Utility-9'Basement-111/2" 1st Fl Fin Flr B.O.-2'Footing2-21/2" UtilityB.O.-9'Basement-111/2"Footing1-11'-10" T.O. Concrete13'Wall-9"2ndFl 9' - 11 1/2" T.O. Concrete13'Wall-9"2ndFl 9' - 114th1/2"Fl30' - 9 Scale1/2"Project number DrawnDate Checkedbybywww.autodesk.com/revit 1/2" = 1'-0" PM8:56:357/7/201821 UnnamedProject NumberProjectOwner Name Issue CheckerAuthorDate No. Description Date 1/2" = 1'-0"1 Section 1 T.O. Concrete13'Wall-9"3rdFl20' - 44th1/2"Fl30' - 9 1/2" T.O. Flat Roof 41' - 2 1/2" www.autodesk.com/revit ProjectOwner Name A A B C B C D D E F E F
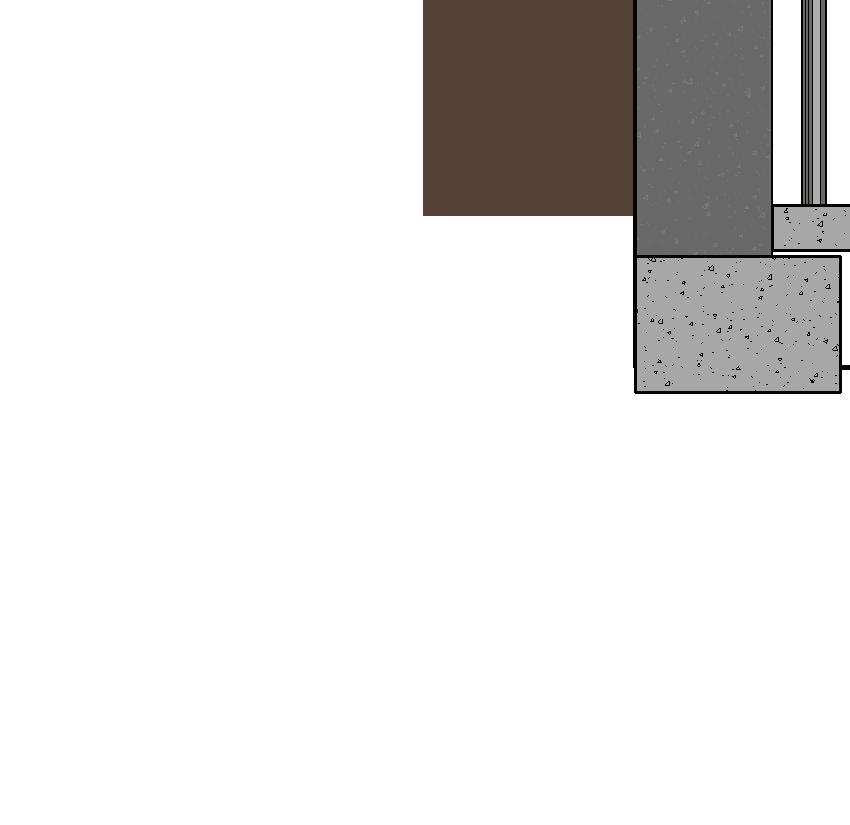
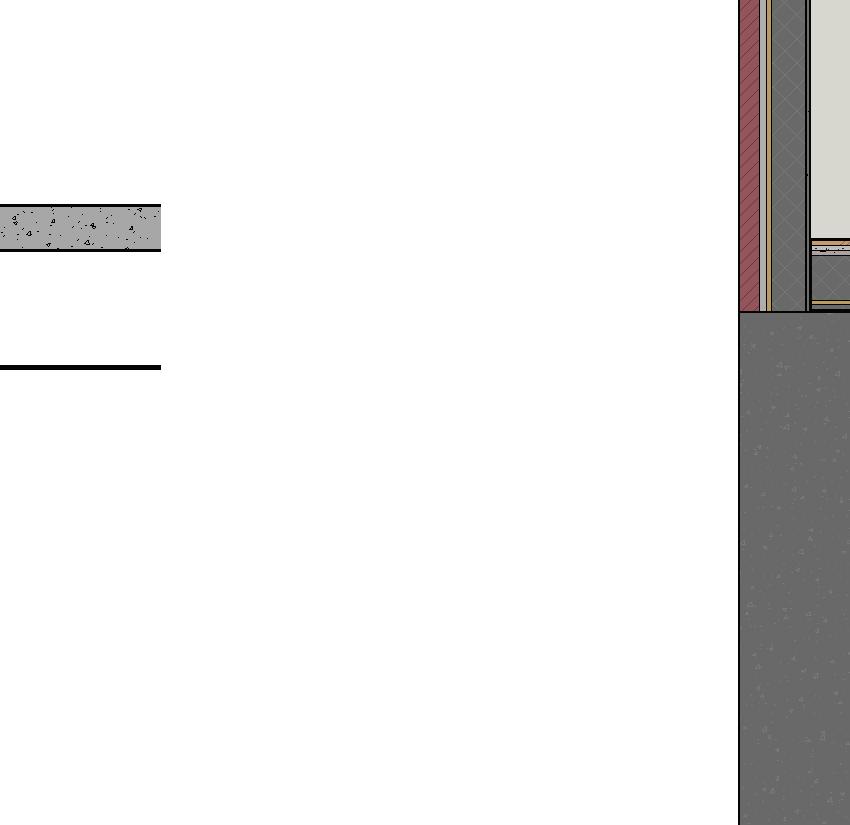
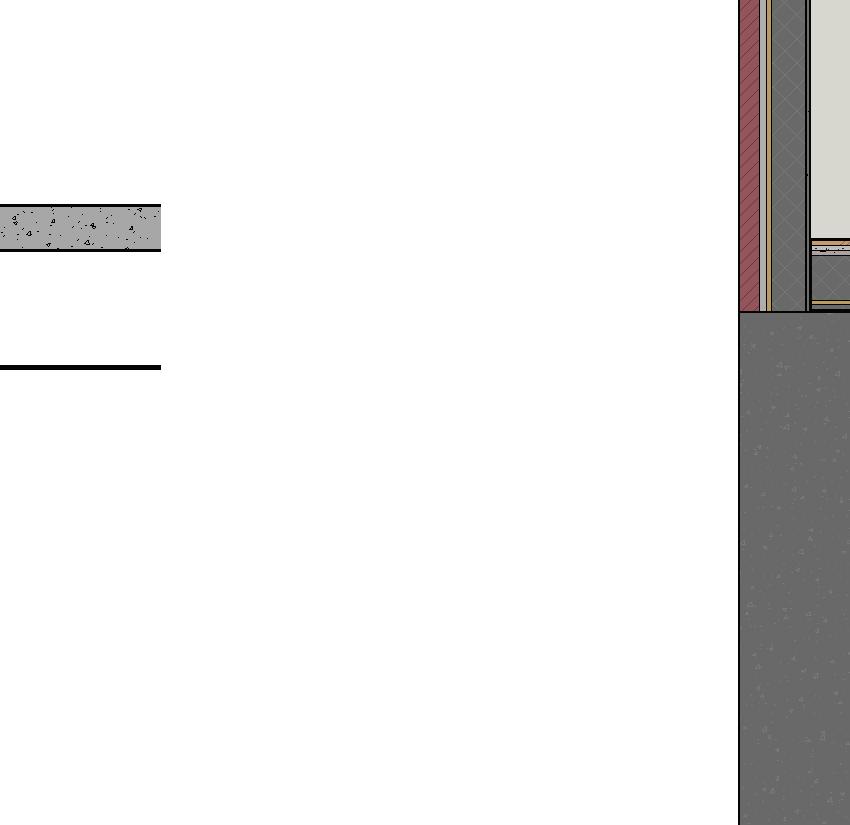
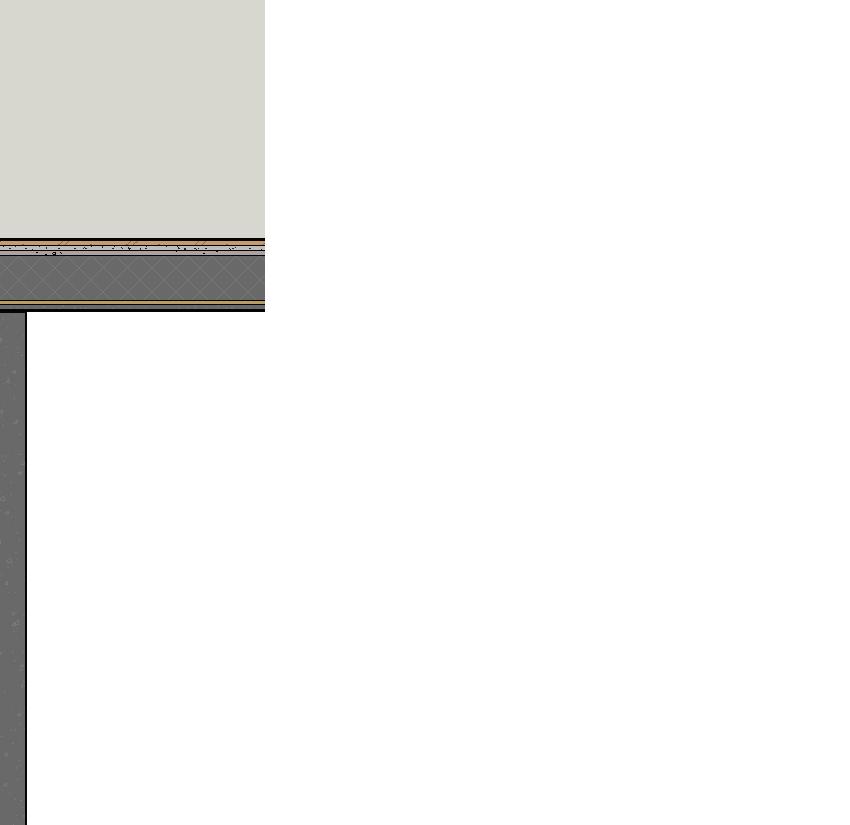
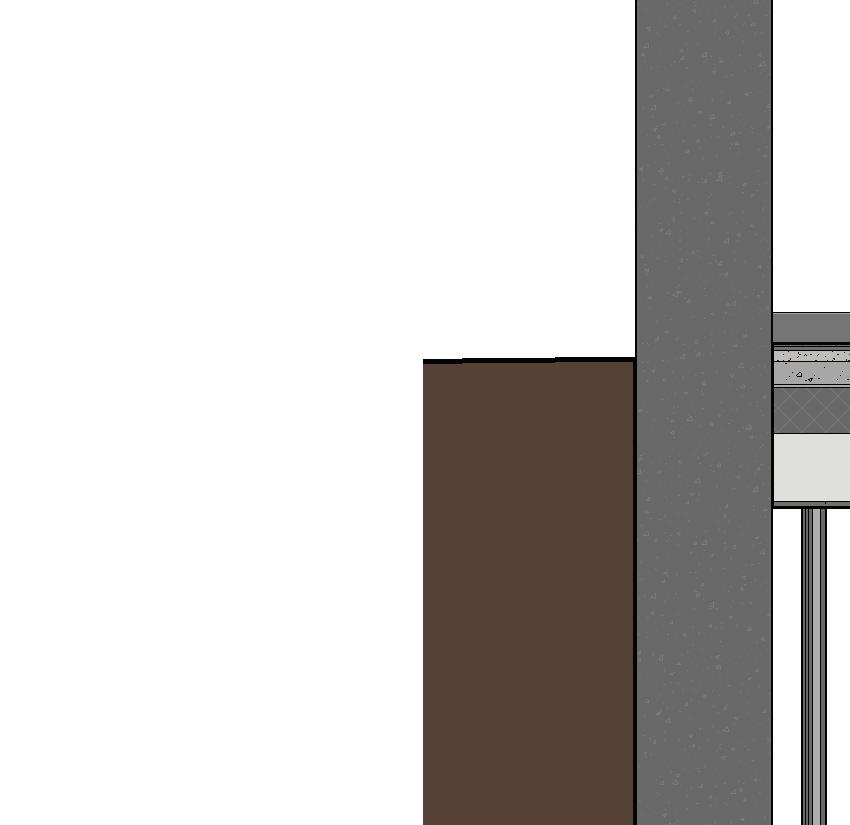
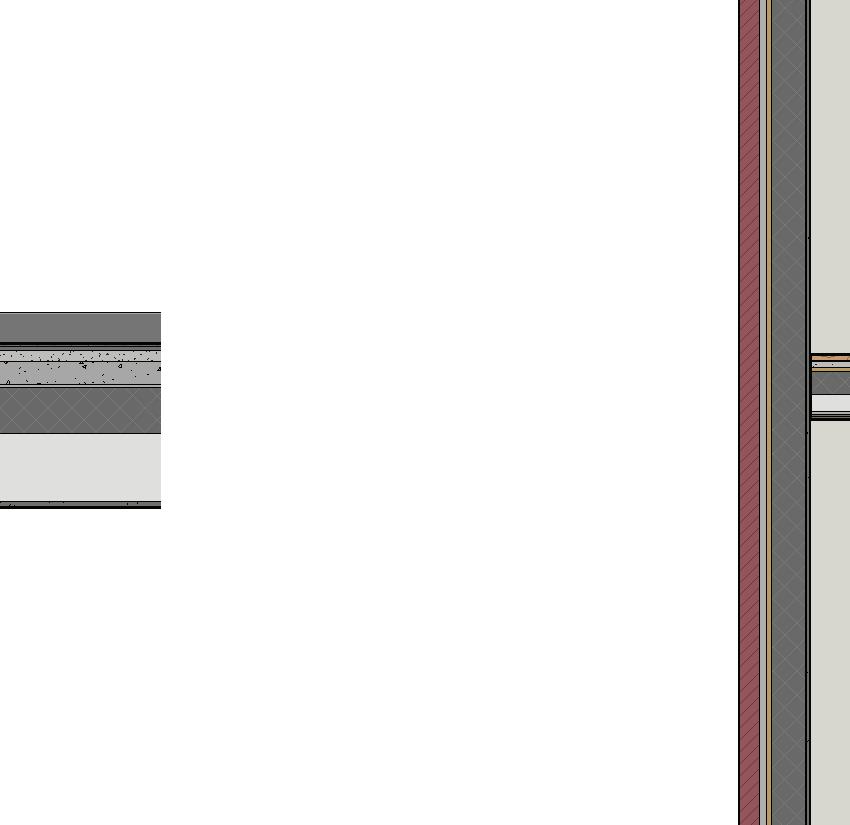
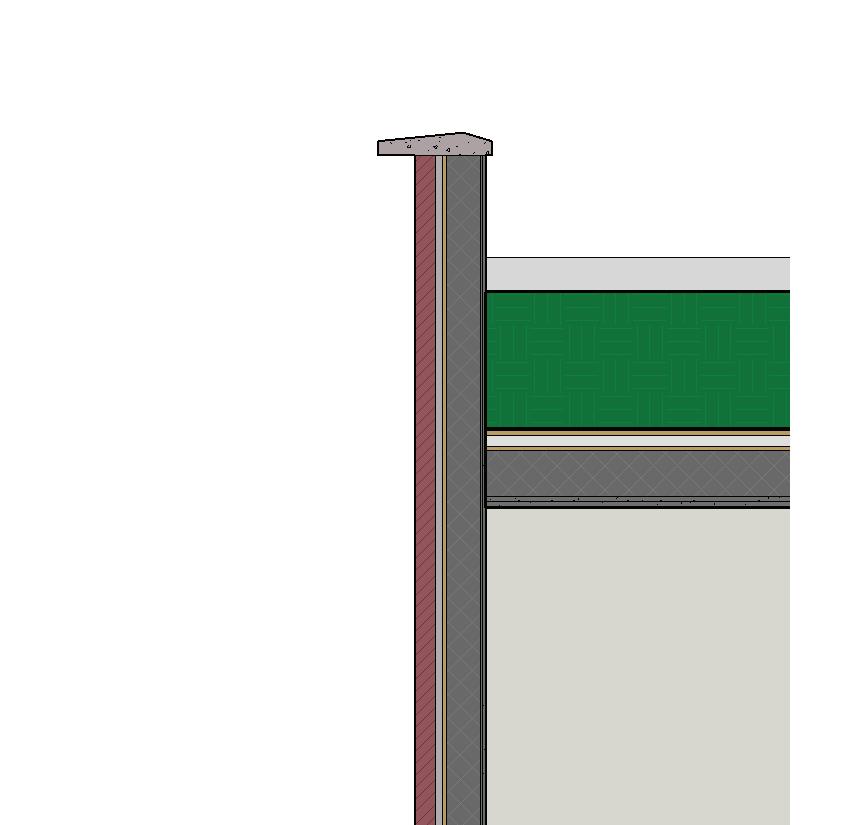
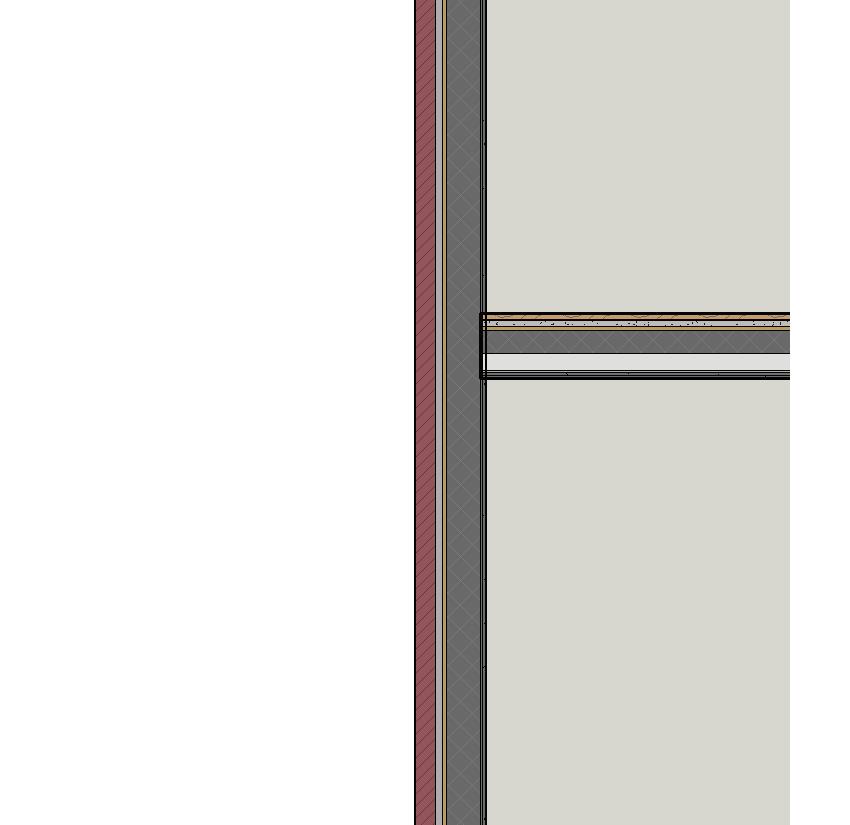
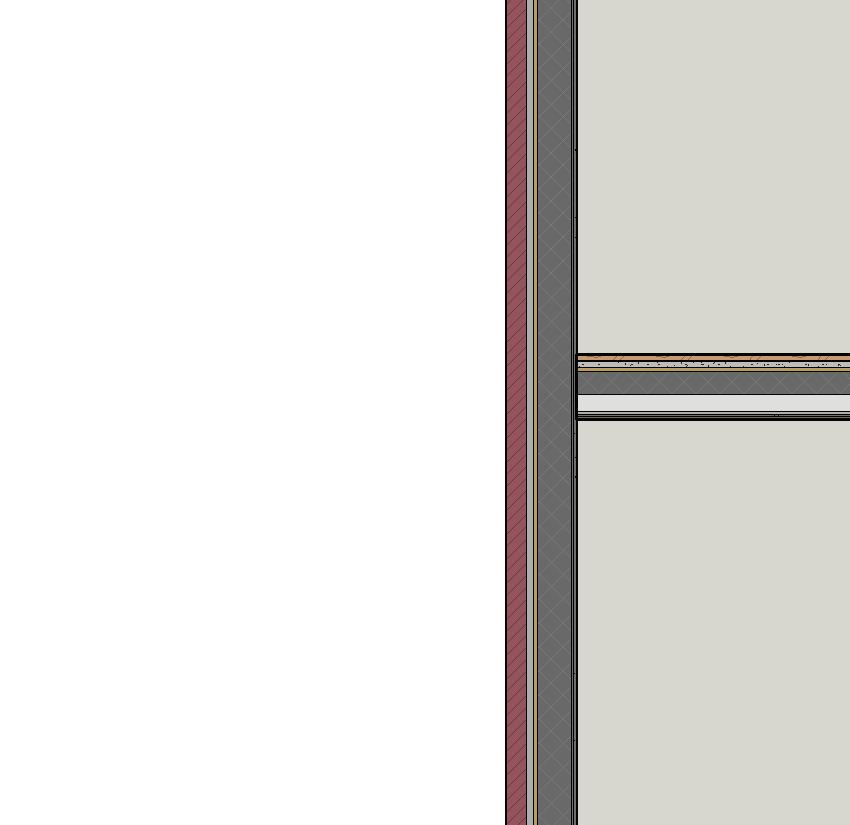
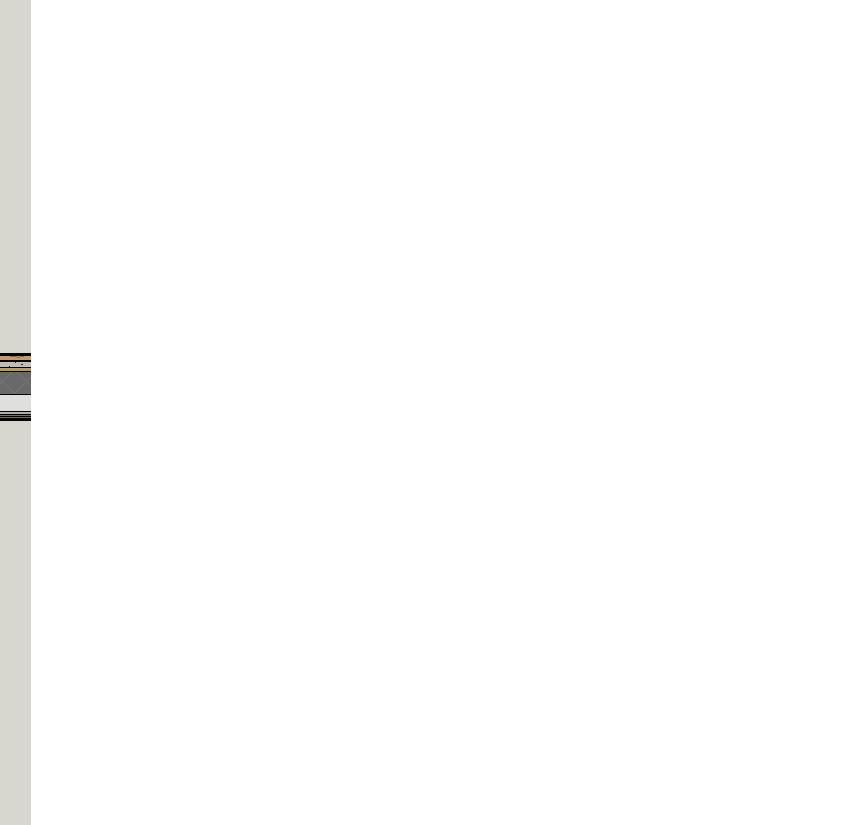
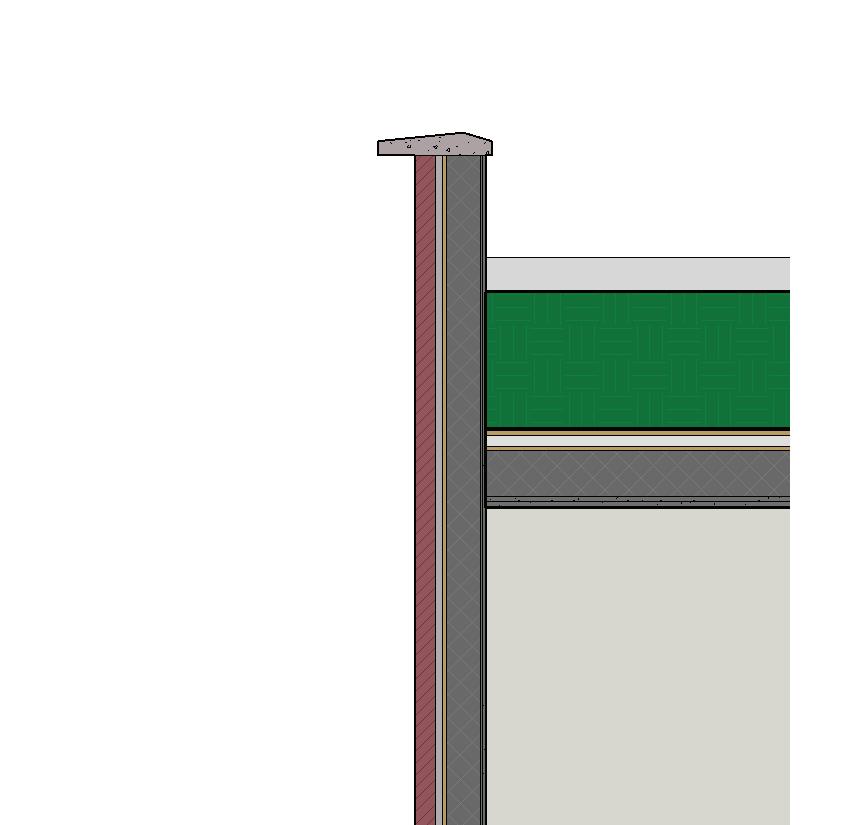
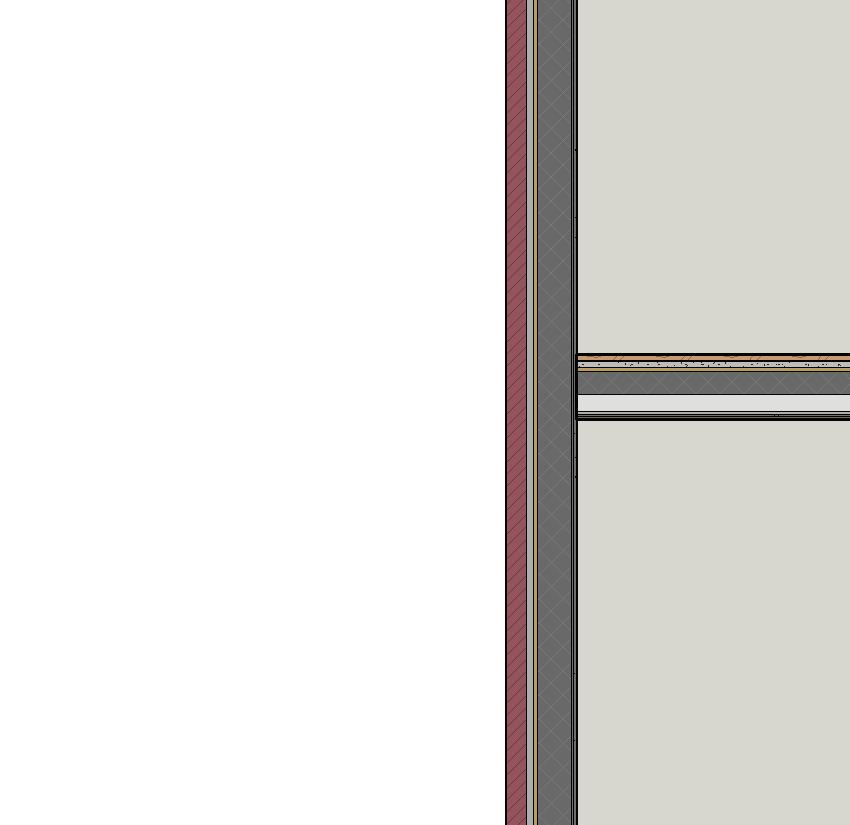
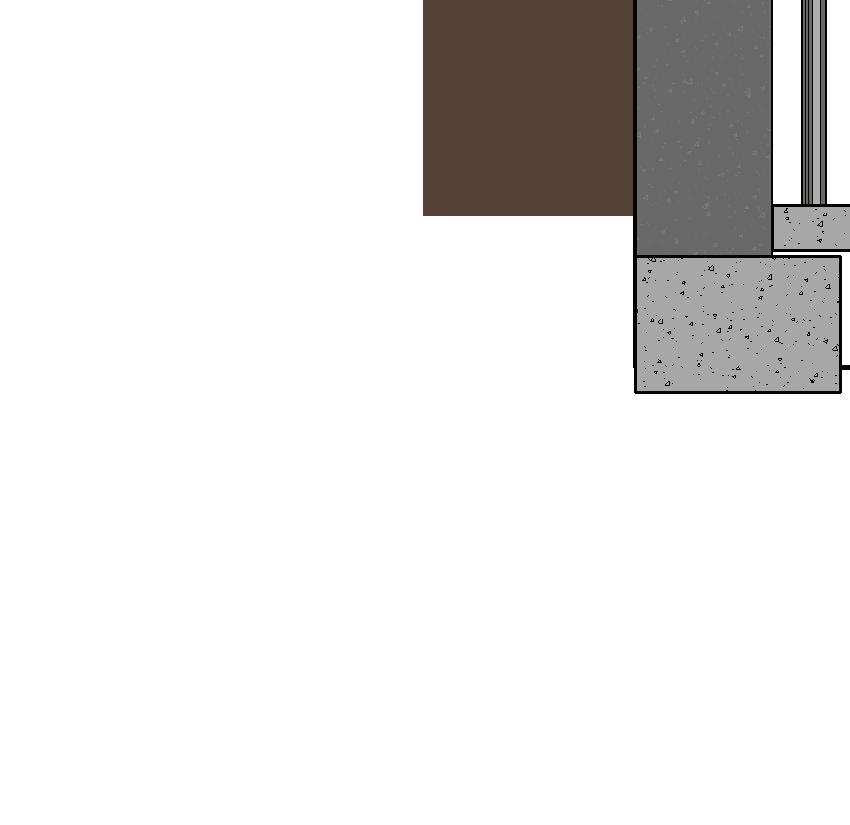
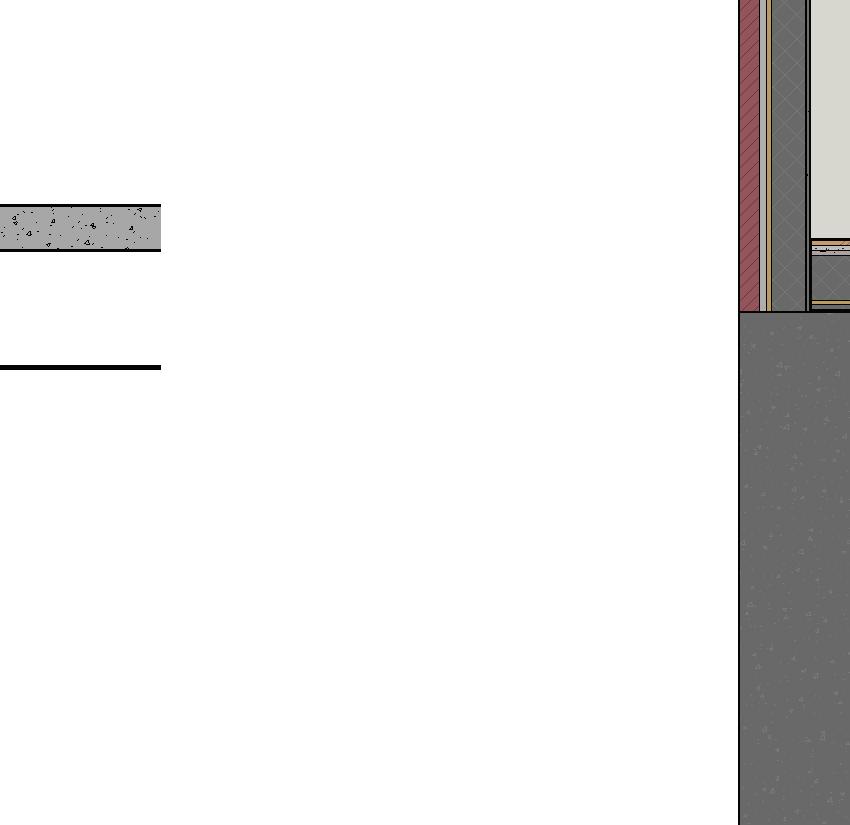
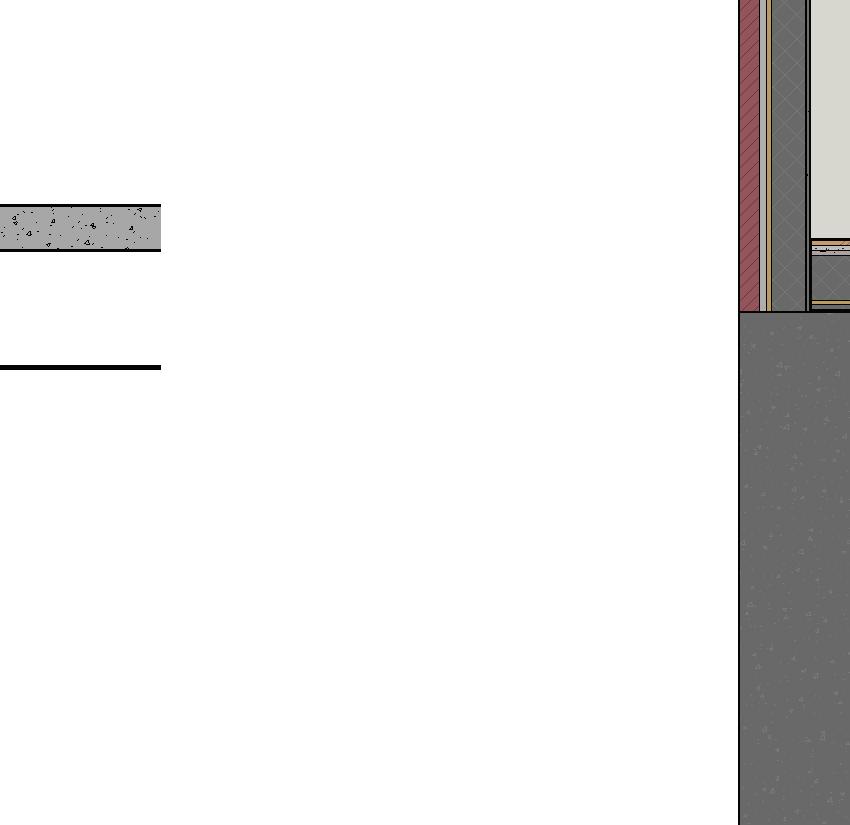
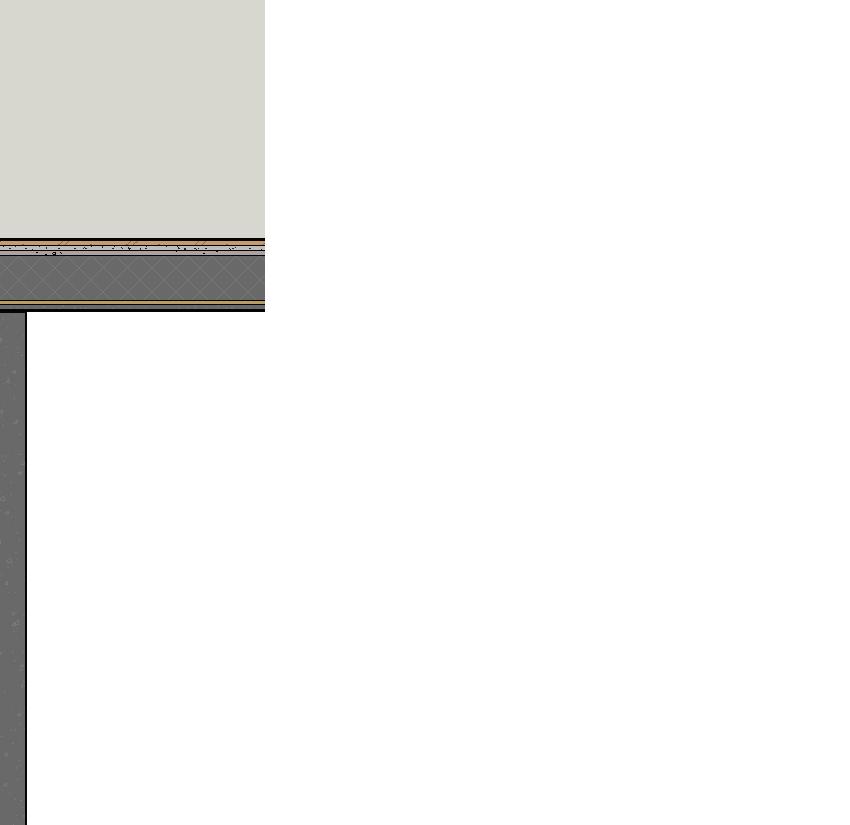
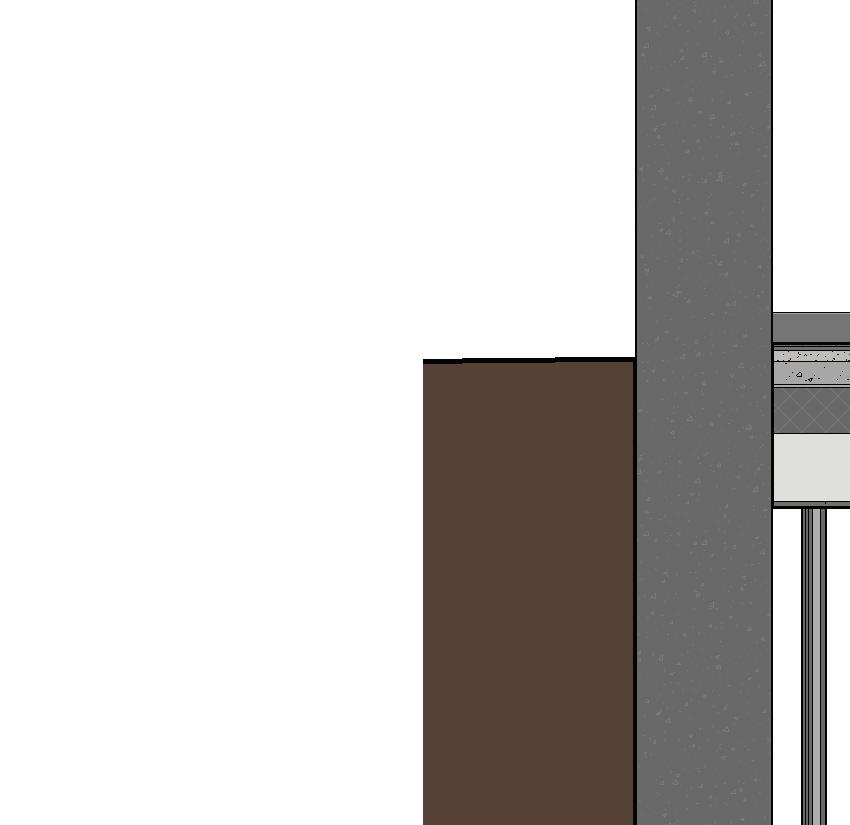
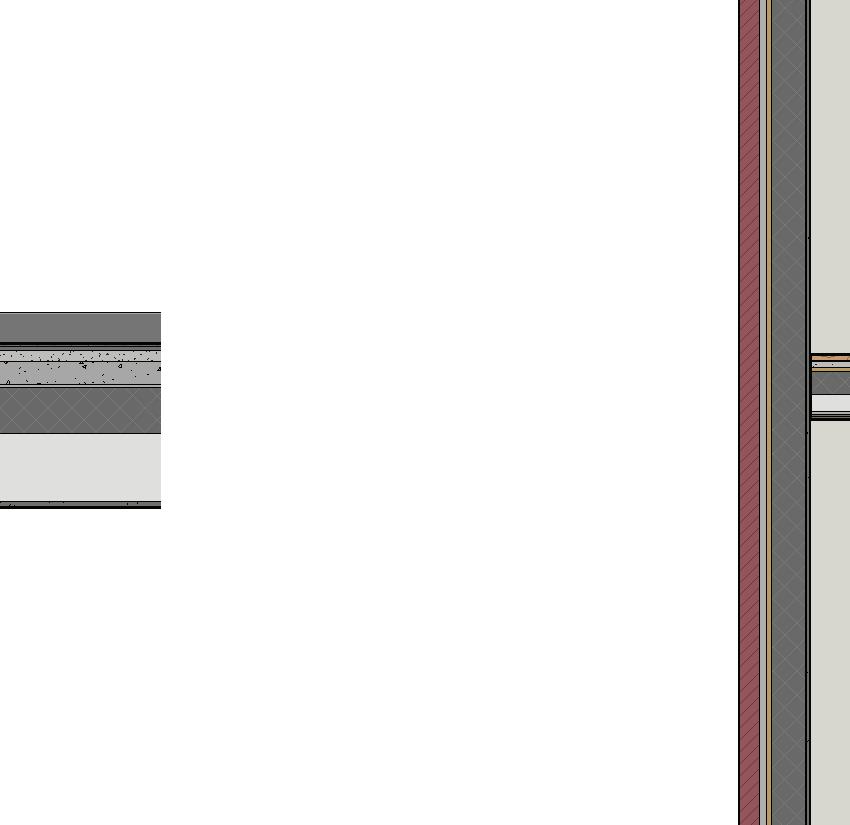
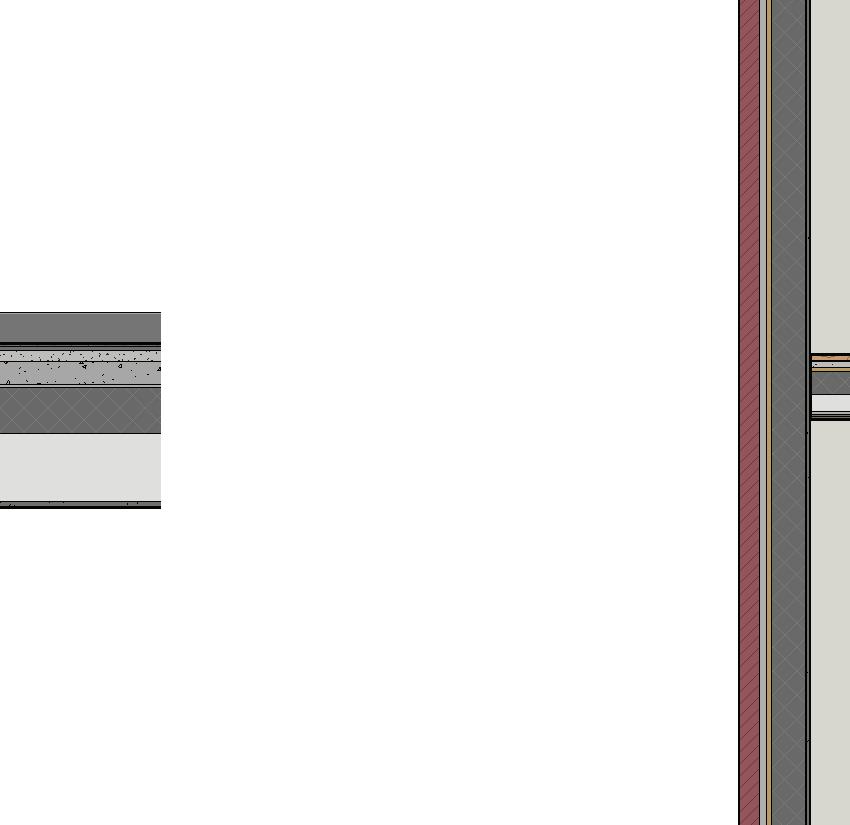
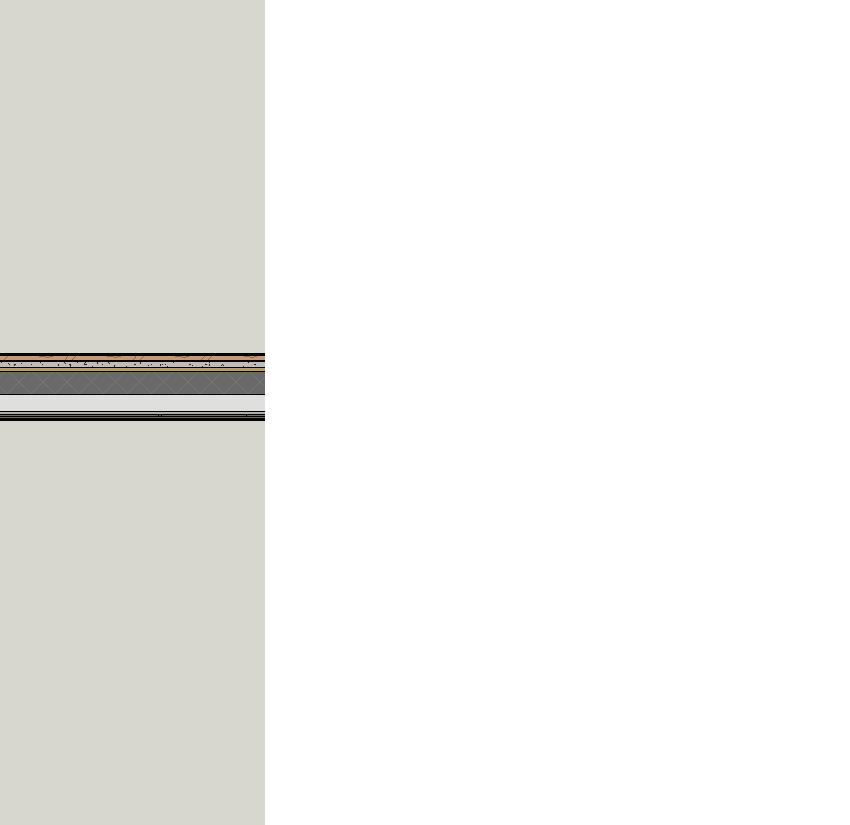
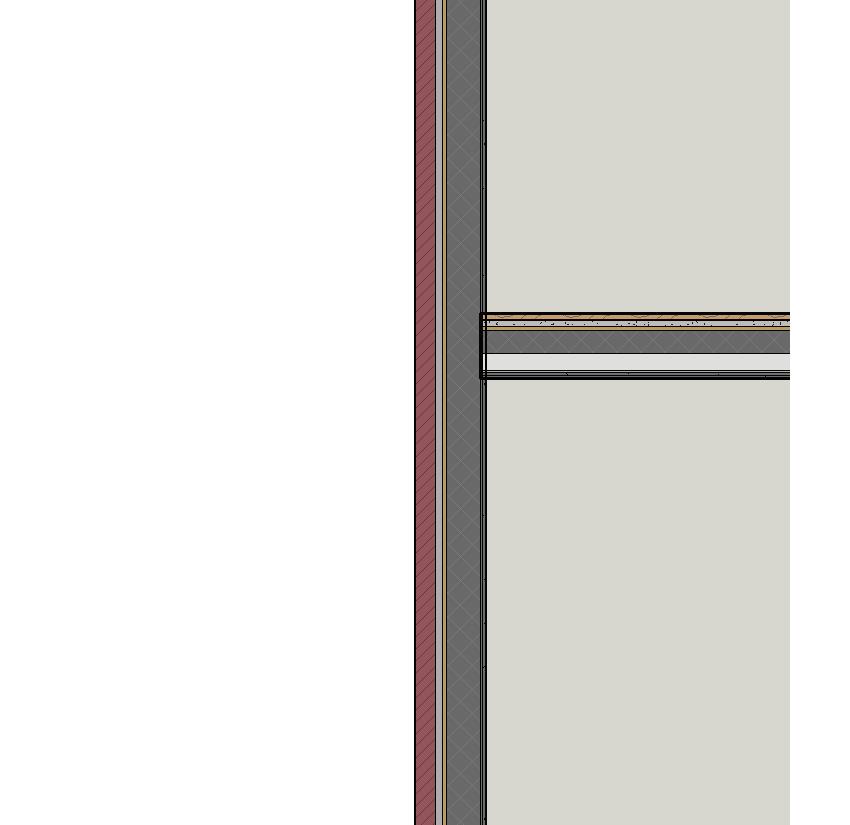
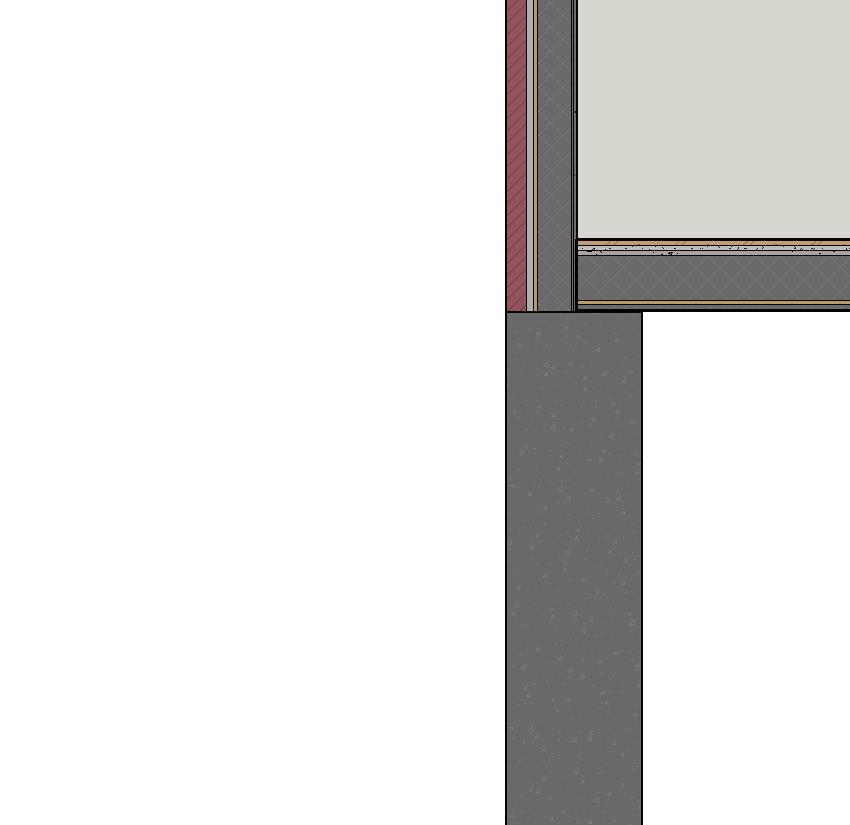
Master Thesis: 620 N 3rd St Clara Bucar W W1 3 9 11 B1/2 O Footing1 1st Fl Fin Flr 0' B0" .O. Footing2 2' 2 1/2" Utility Bas em ent 9' 11 B1/2" .O. Footing1 11' 10" B.O. Footing 17' 1" T.O. Concrete W all 13' 9" 2nd Fl 9' 11 1/2" 3rd Fl 20' 4 1/2" 4th Fl 30' - 9 1/2" T.O. Flat Roof 41' 2 1/2" T.O. Pilothous e Roof 50' 2 1/2" W W1 3 E1 E3 EE6E5 2 1st Fl Fin Flr 0' B0" .O. Footing2 2' 2 1/2" Utility Bas em ent 9' 11 B1/2" .O. Footing1 11' 10" B.O. Footing 17' 1" T.O. Concrete W all 13' 9" 2nd Fl 9' 11 1/2" 3rd Fl 20 4 1/2" 4th Fl 30 9 1/2" T.O. Flat Roof 41 2 1/2" T.O. Pilothous e Roof 50 2 1/2" 1st Fl Fin Flr 0' B0" .O. Footing2 2' 2 1/2" Utility Bas em ent 9' 11 B1/2" .O. Footing1 11' 10" B.O. Footing 17' 1" T.O. Concrete W all 13' 9" 2nd Fl 9' 11 1/2" 3rd Fl 20' 4 1/2" 4th Fl 30' 9 1/2" T.O. Flat Roof 41' 2 1/2" T.O. Pilothous e Roof 50' 2 1/2"
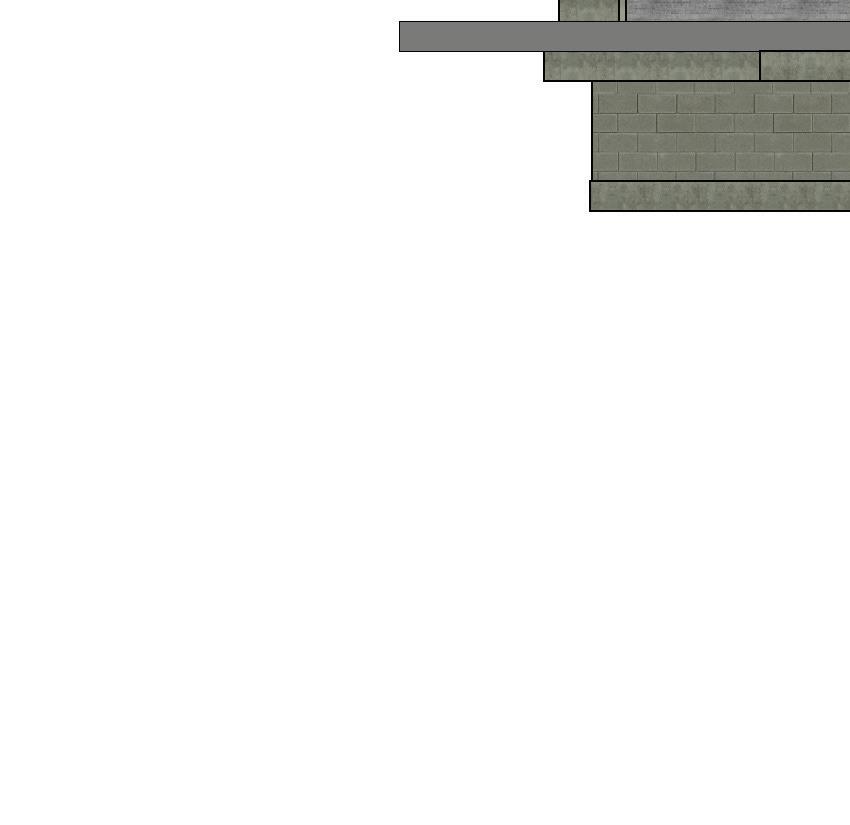
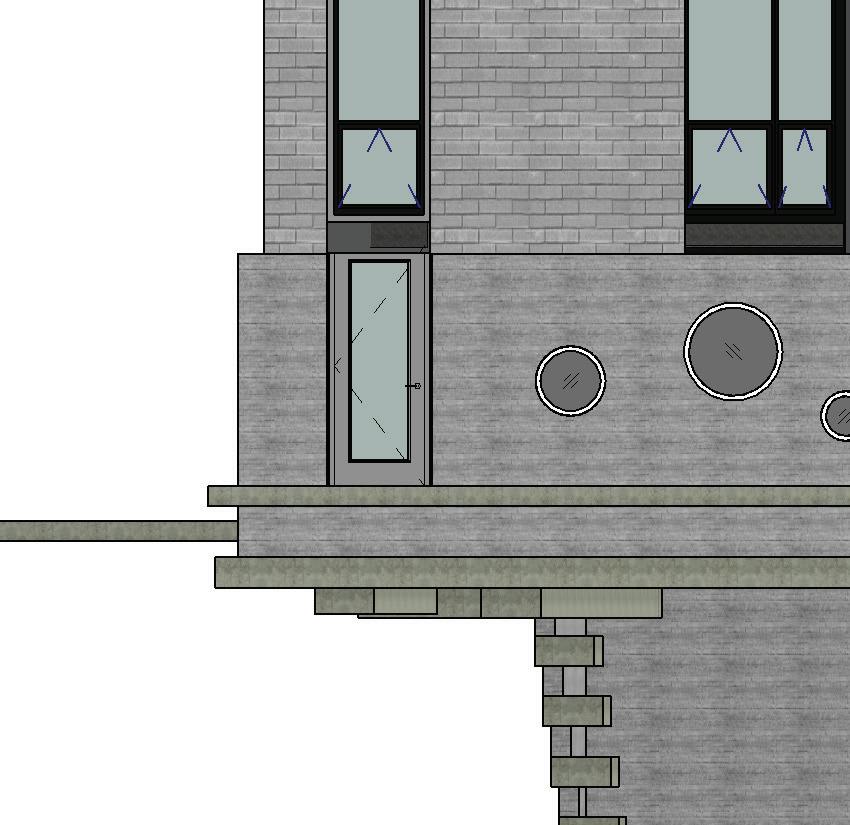
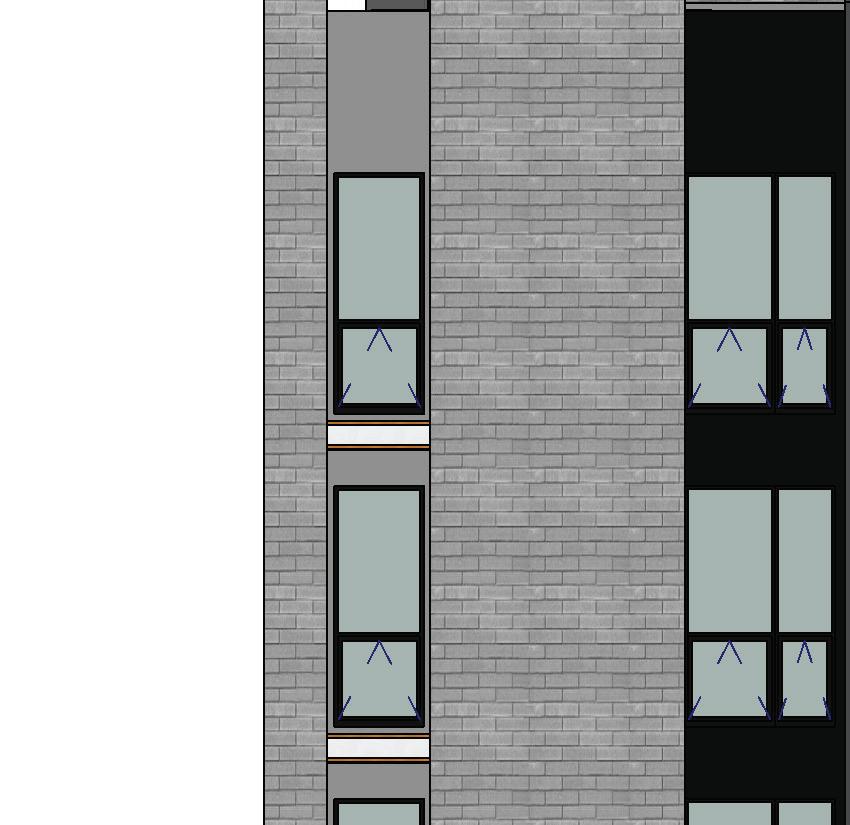
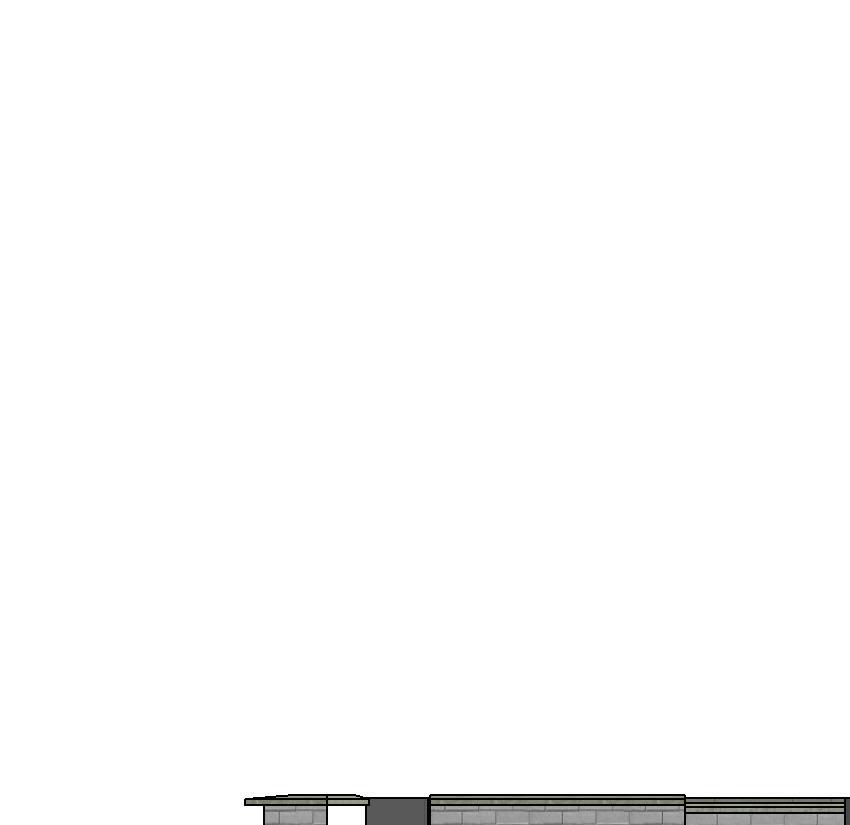

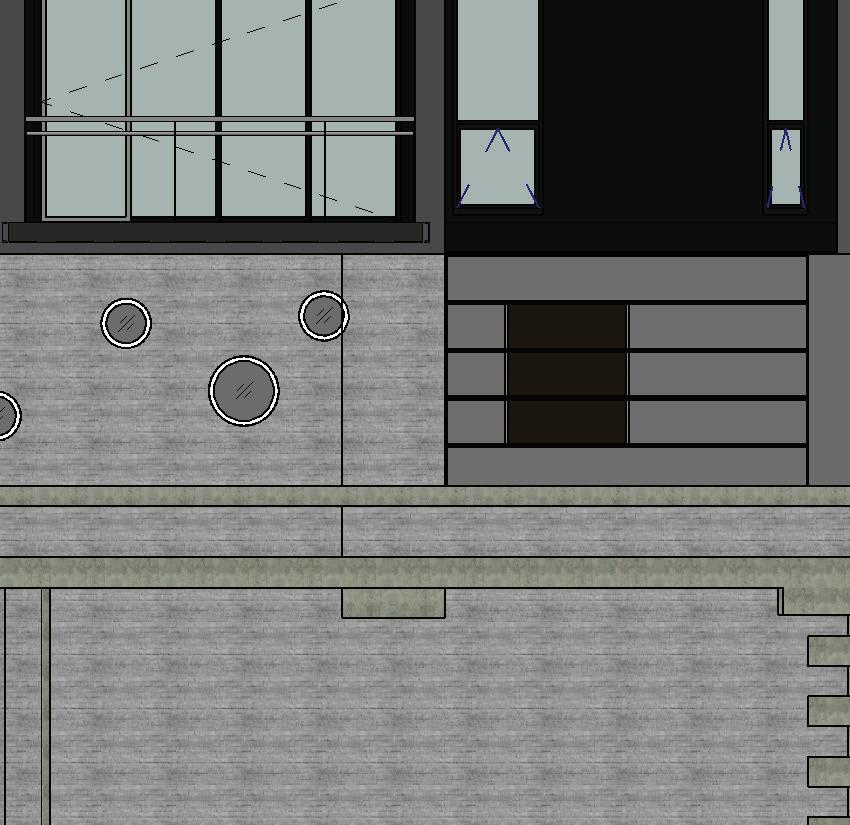

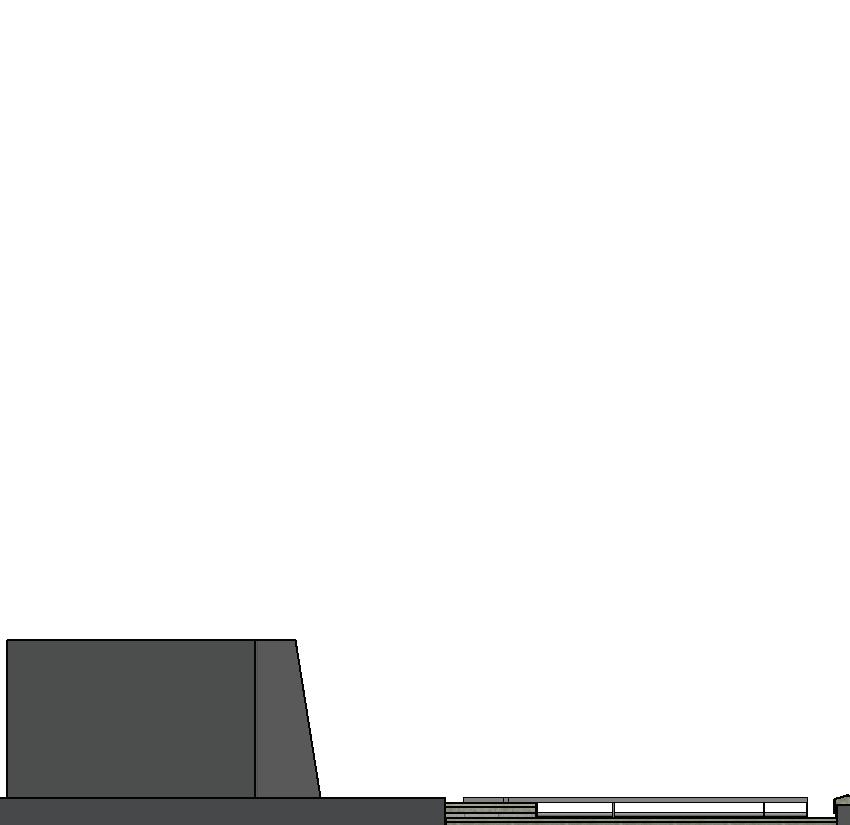
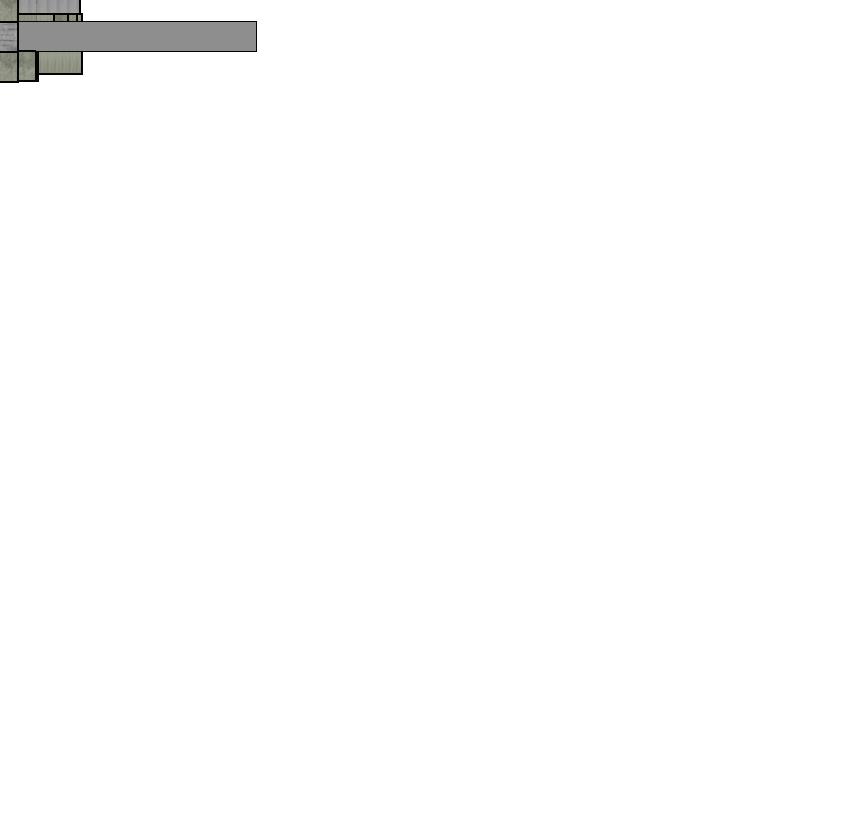
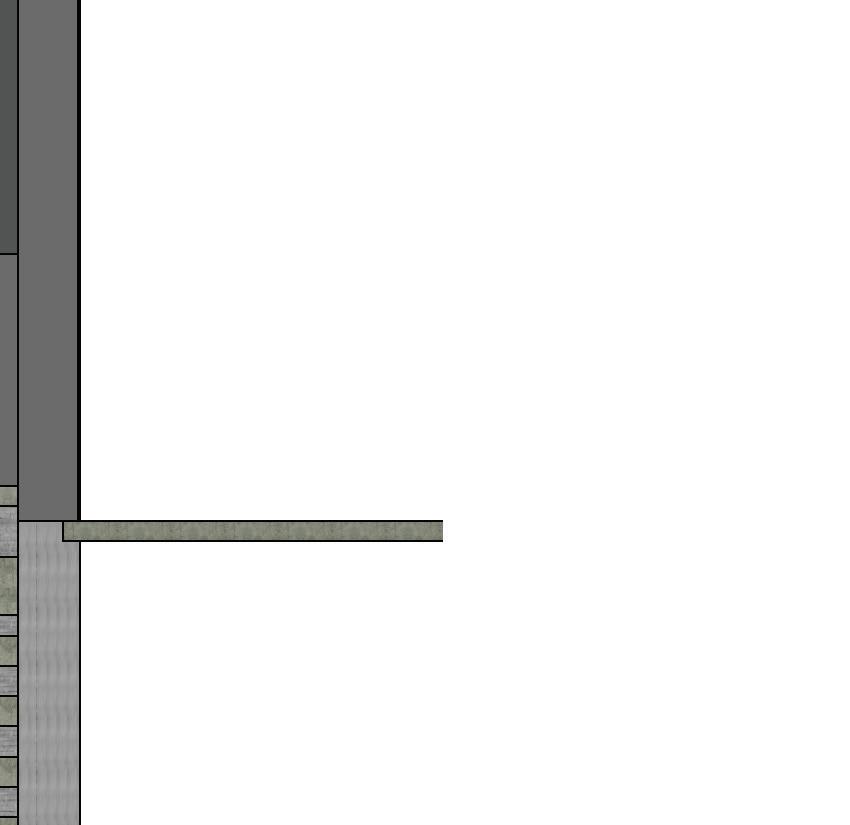

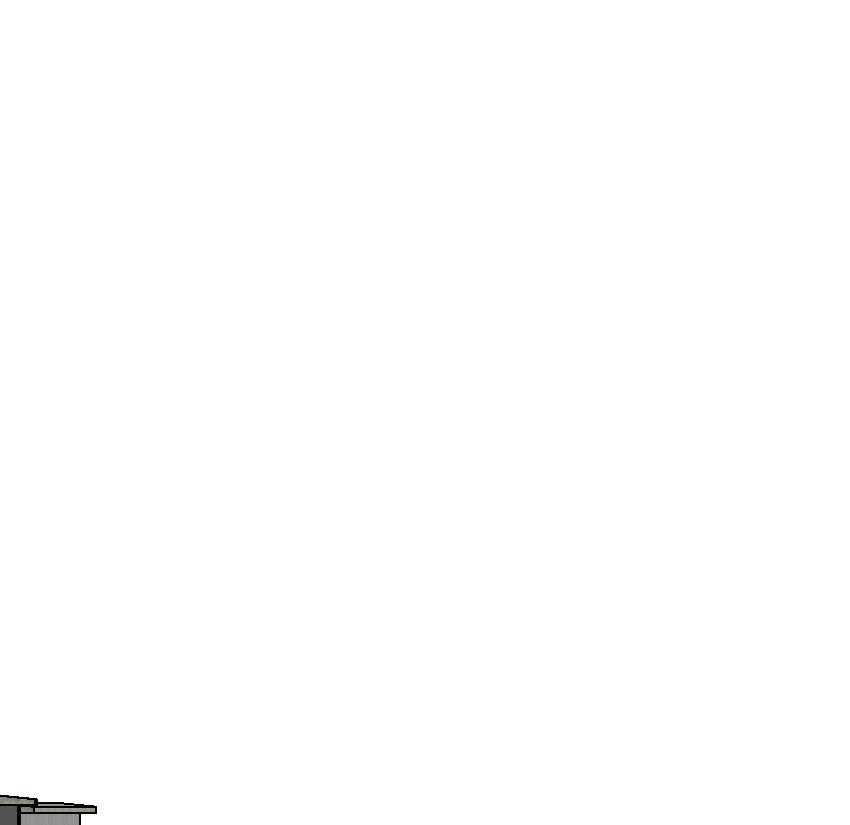

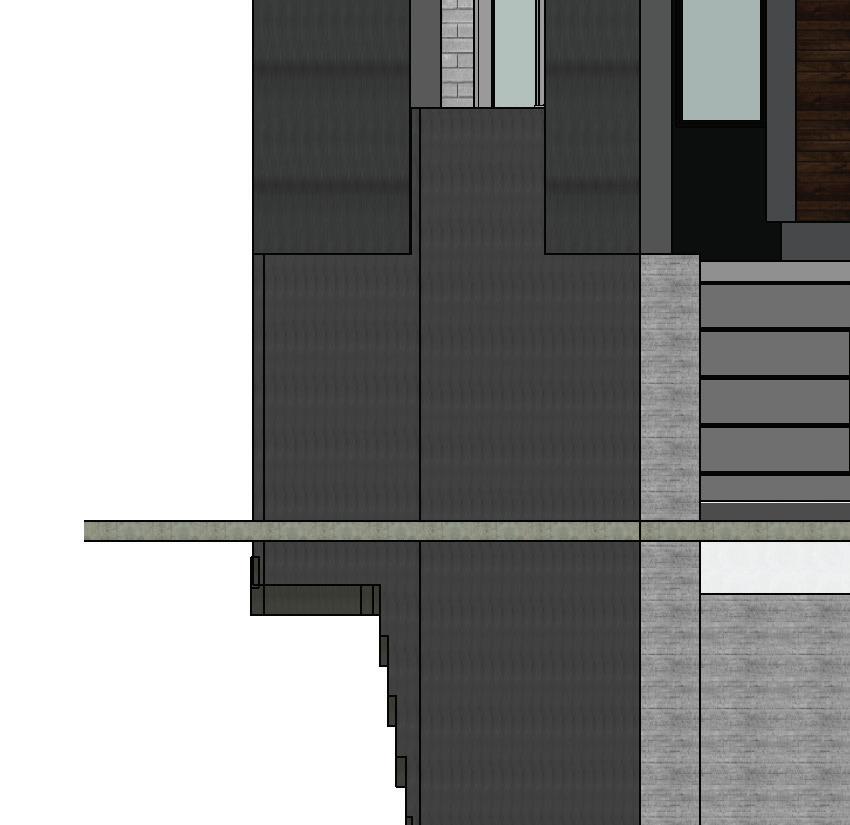
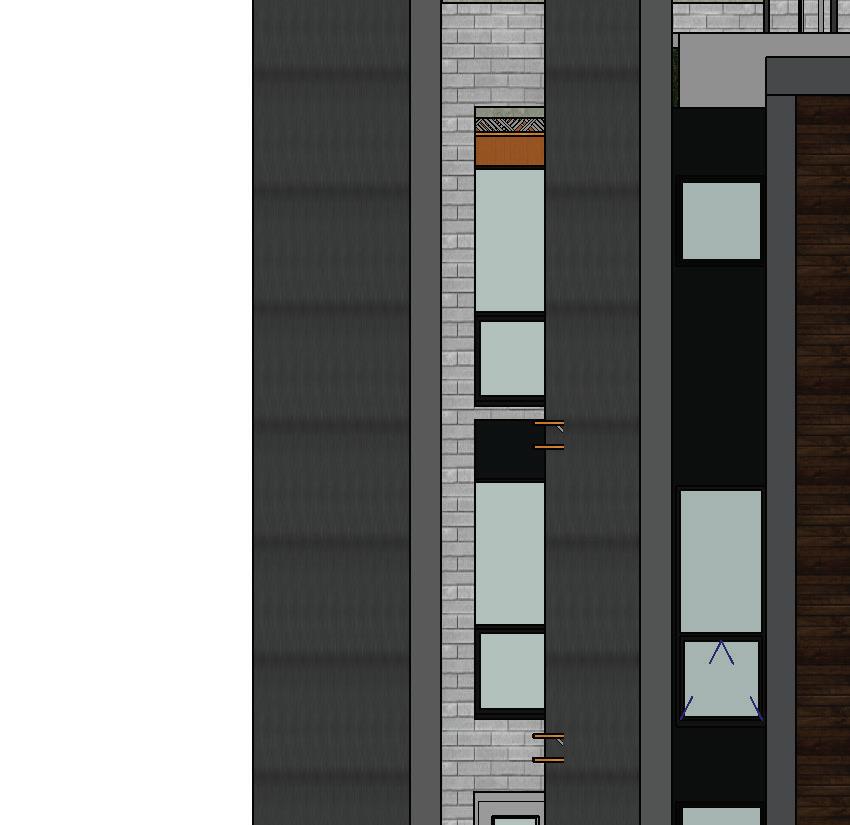
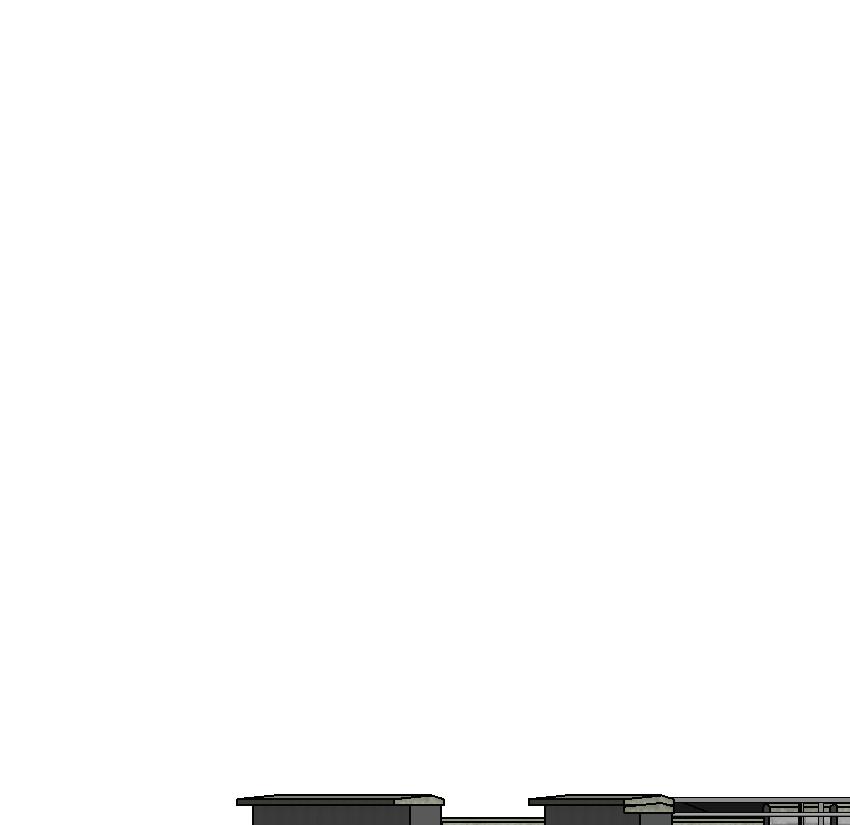
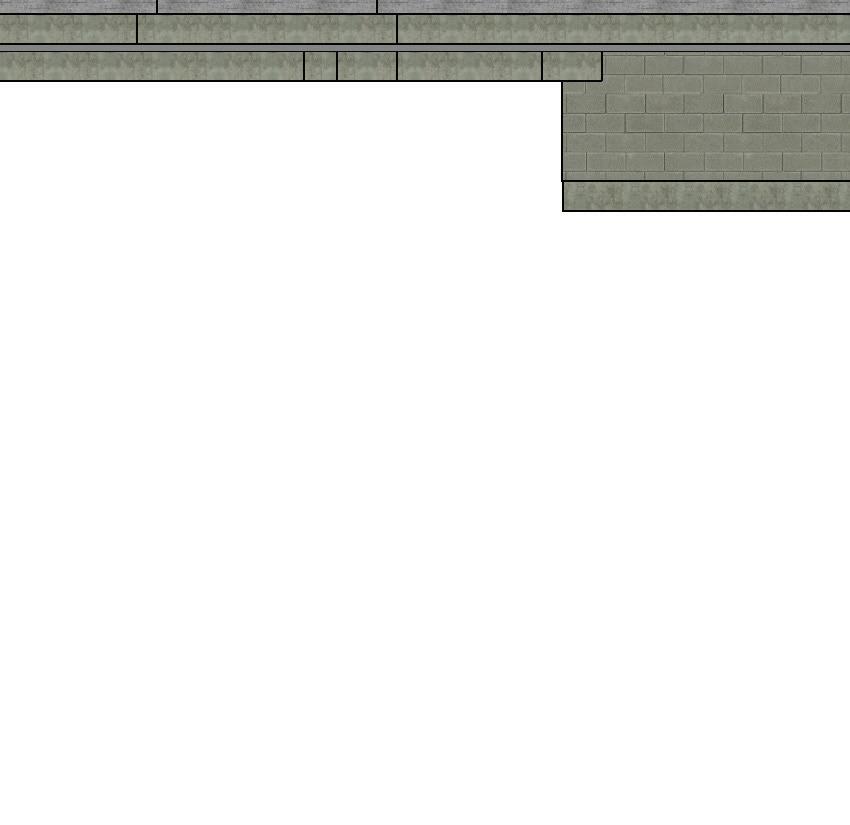

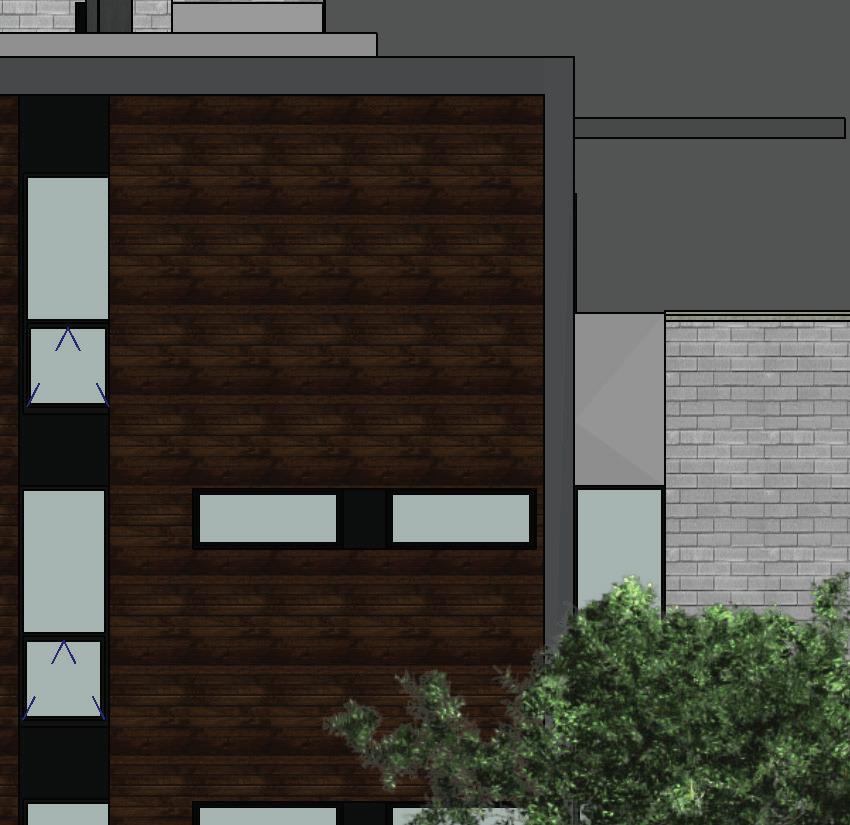
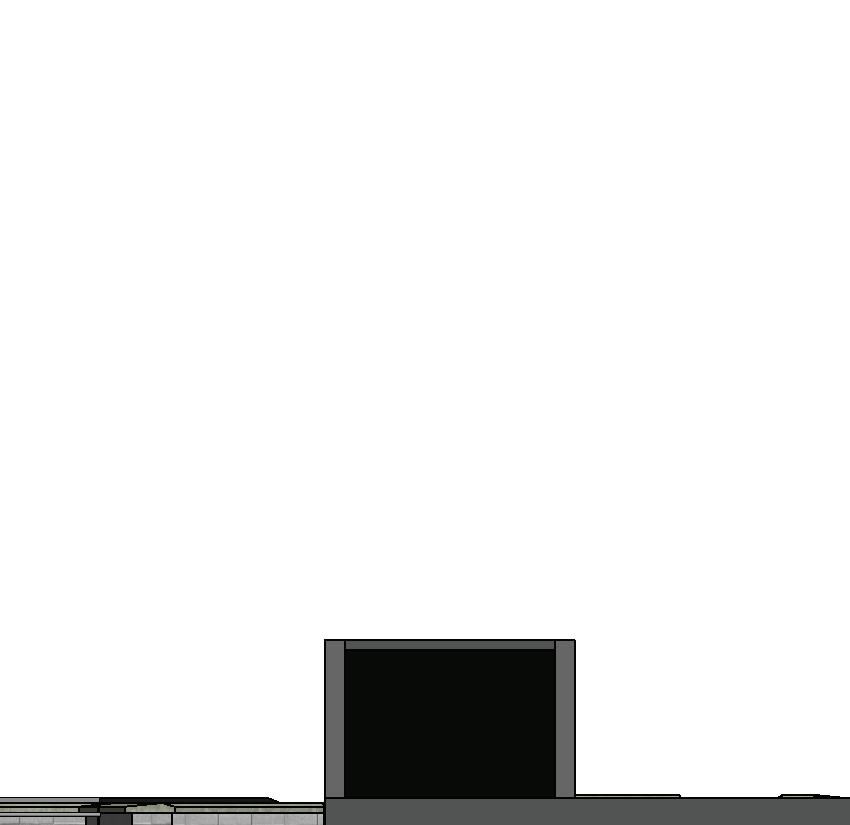
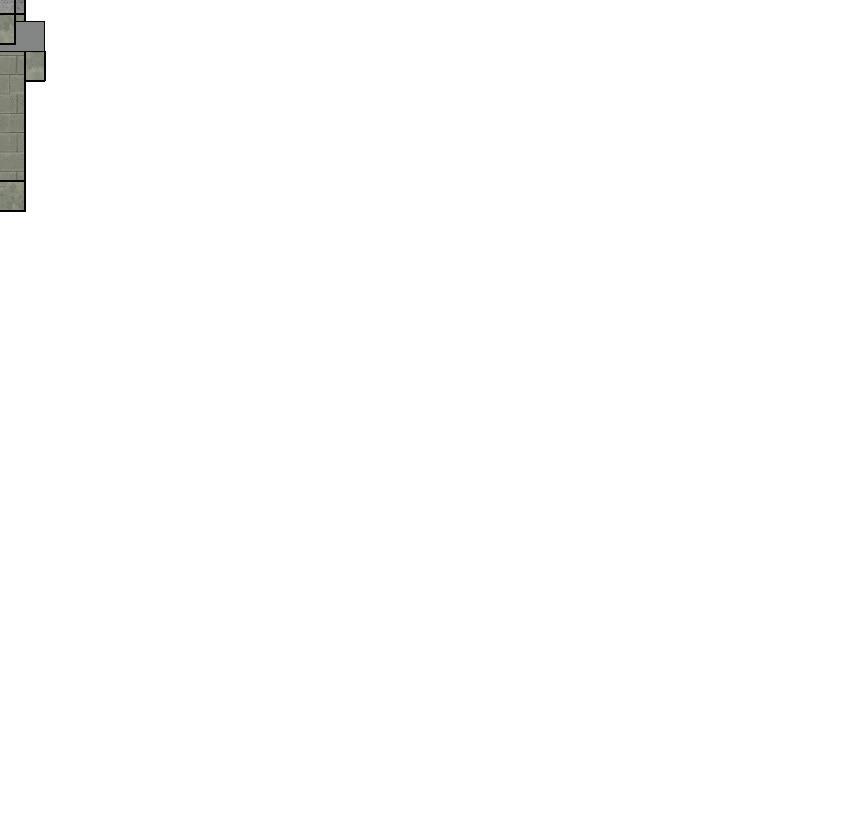
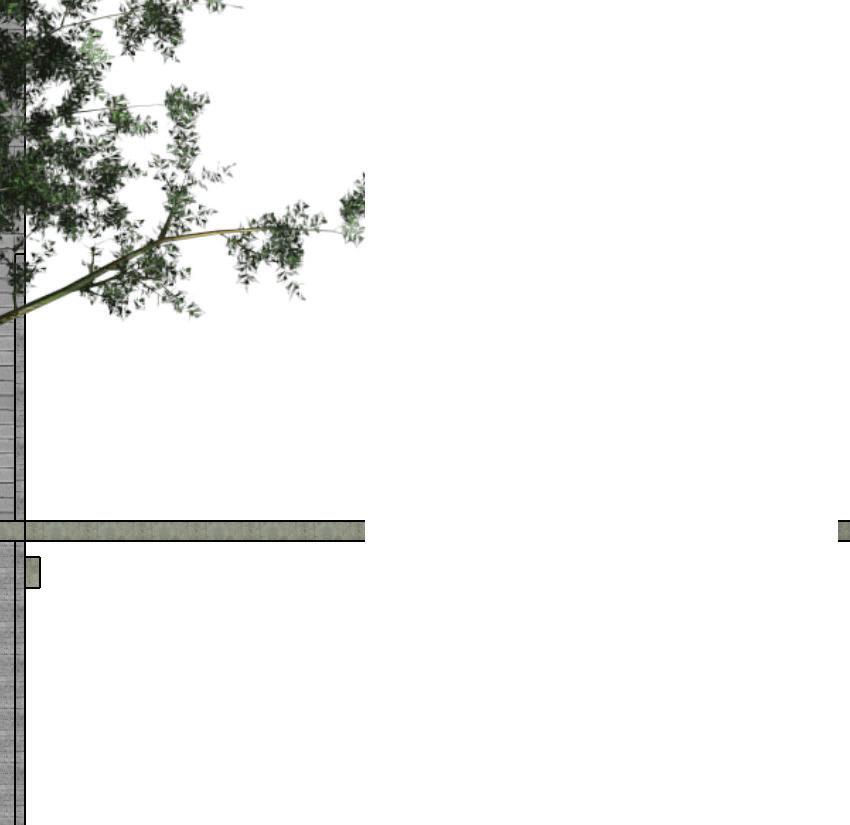
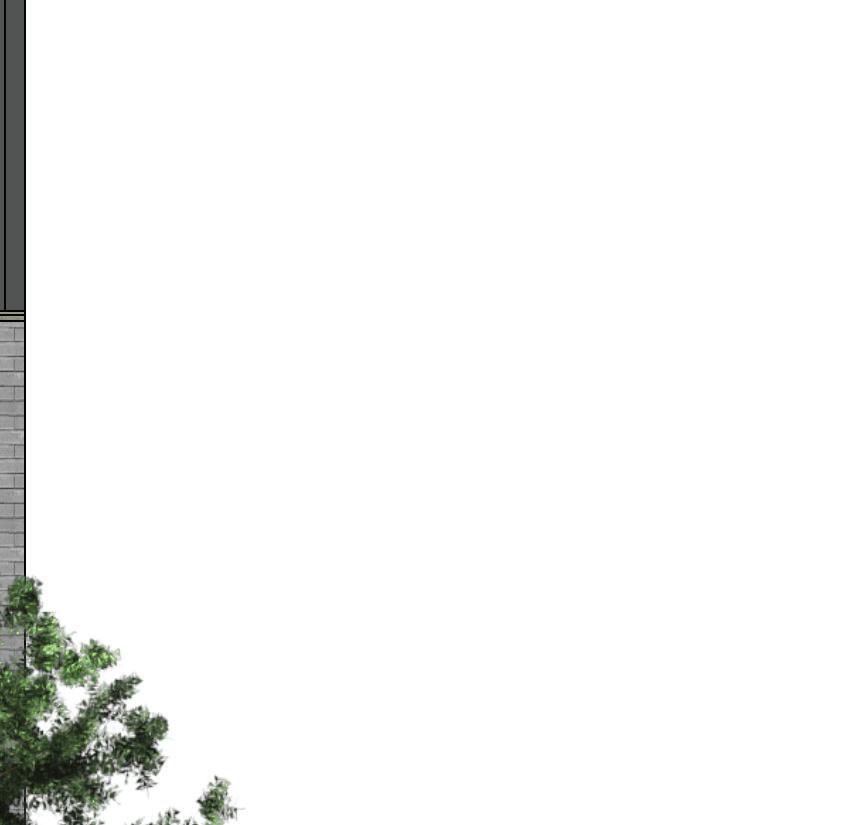

Master Thesis: 620 N 3rd St Clara Bucar 3.3. South Elevation ND NE NF SNO G SH 1st Fl Fin Flr 0' B0" .O. Footing2 2' 2 1/2" Utility Bas em ent 9' 11 B1/2" .O. Footing1 11' 10" B.O. Footing 17' 1" T.O. Concrete W all 13' 9" 2nd Fl 9' 11 1/2" 3rd Fl 20' 4 1/2" 4th Fl 30' 9 1/2" T.O. Flat Roof 41' 2 1/2" T.O. Pilothous e Roof 50' 2 1/2"

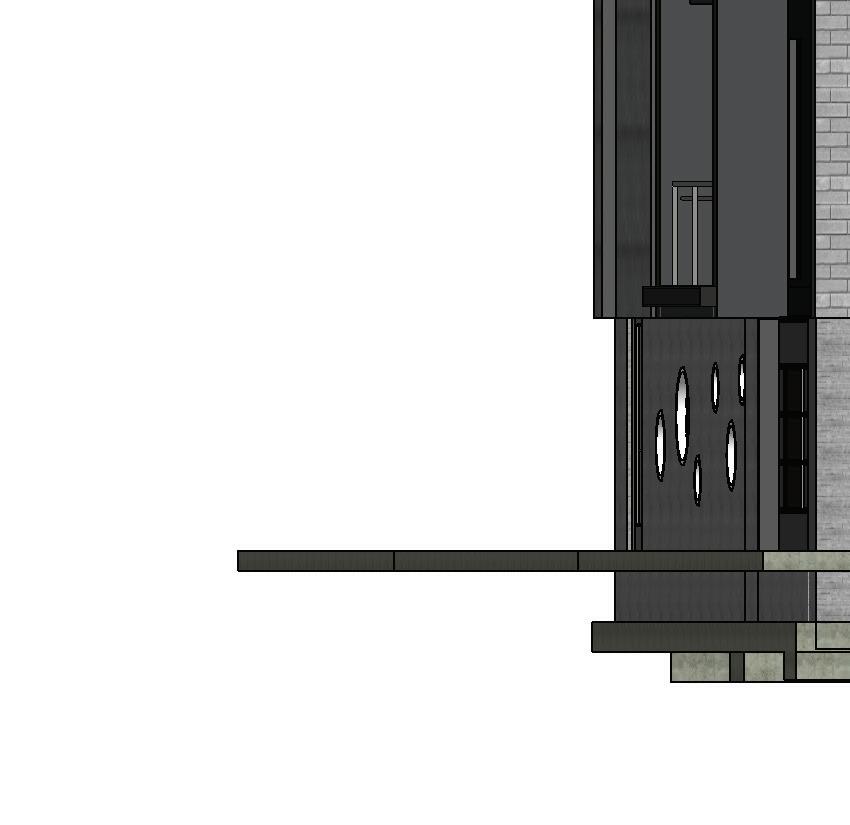
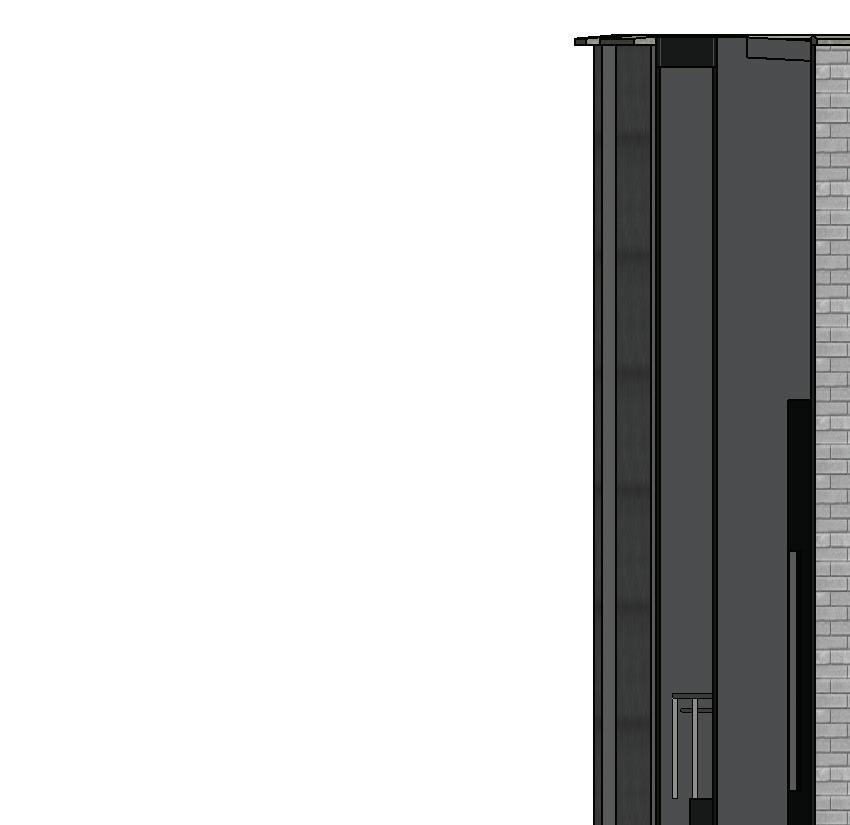


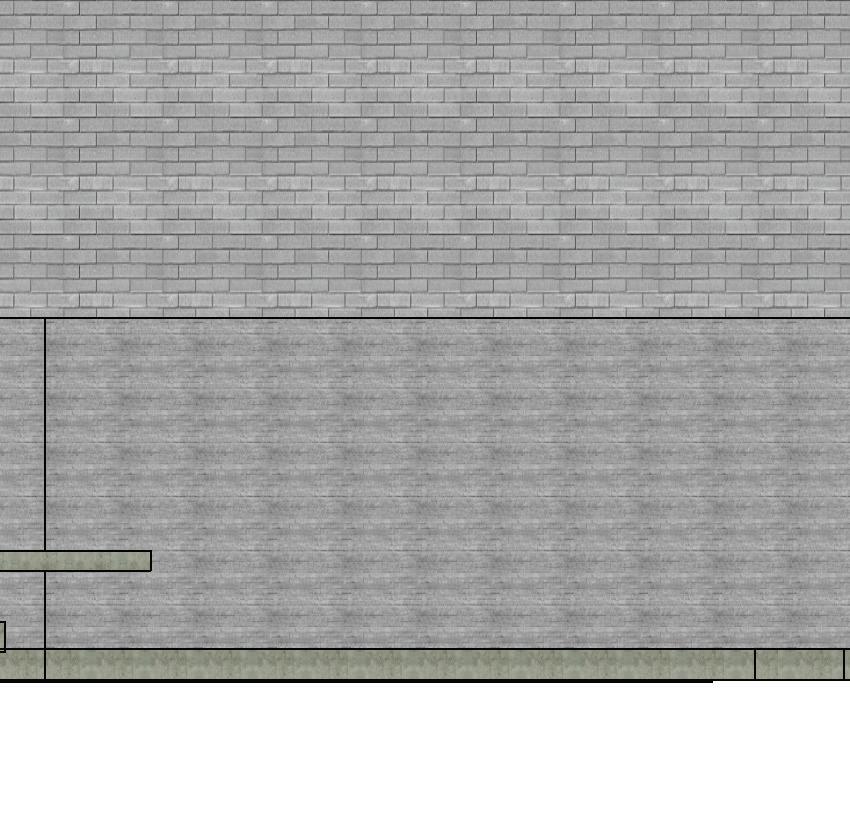
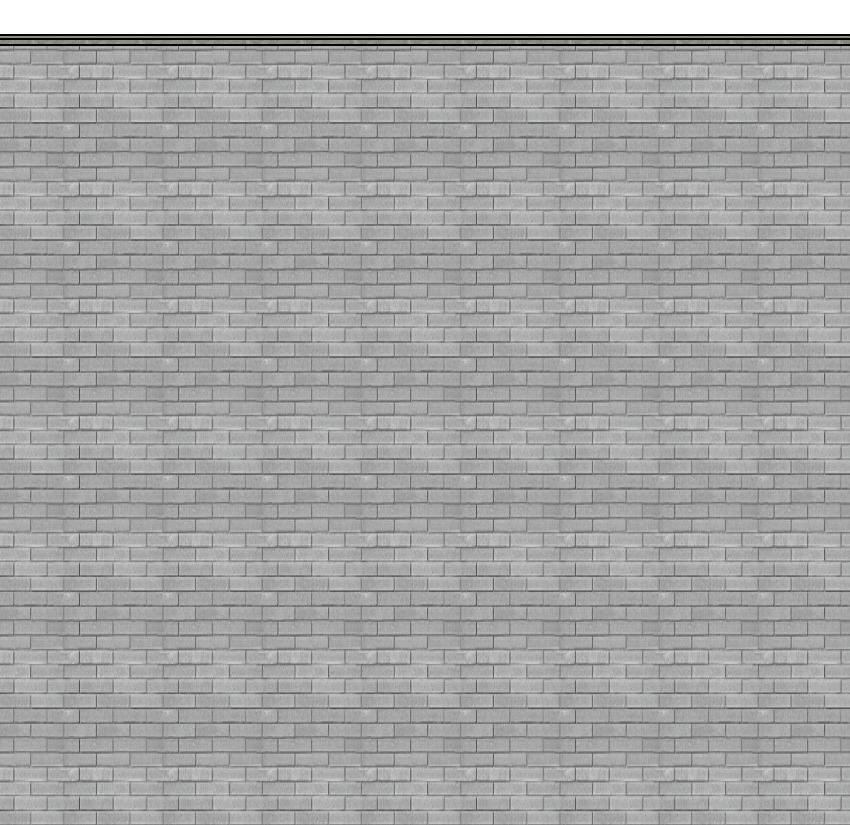

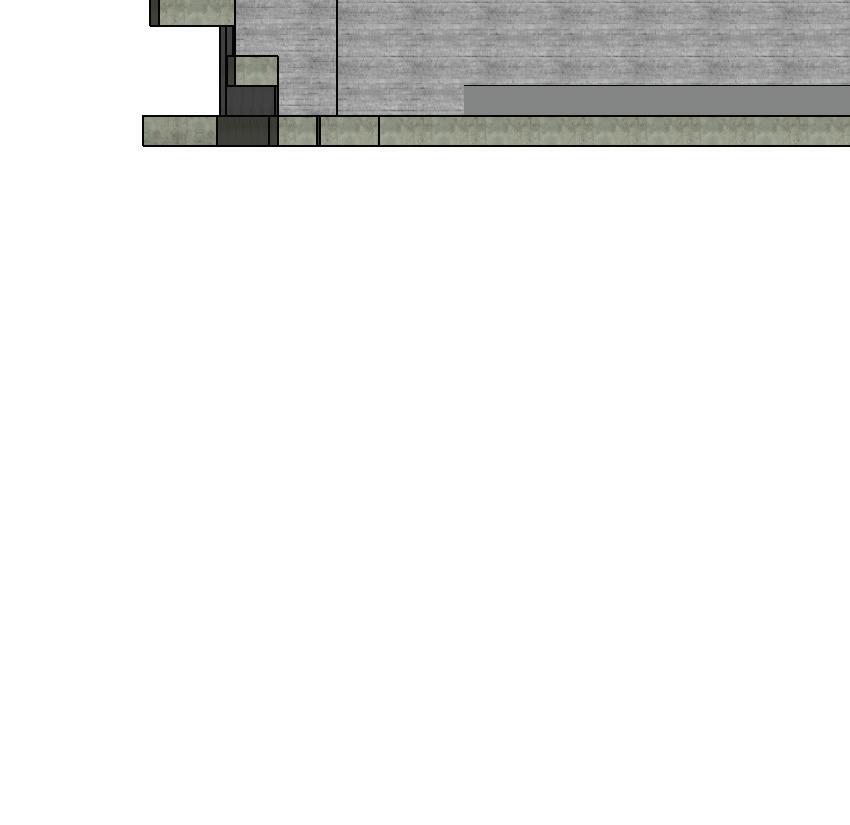
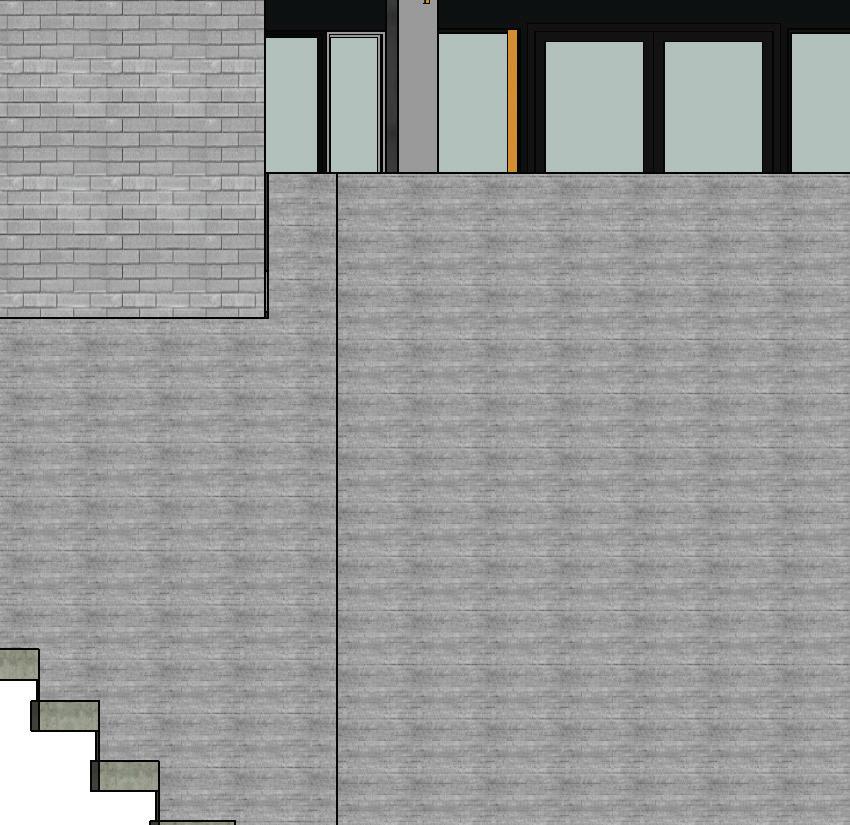
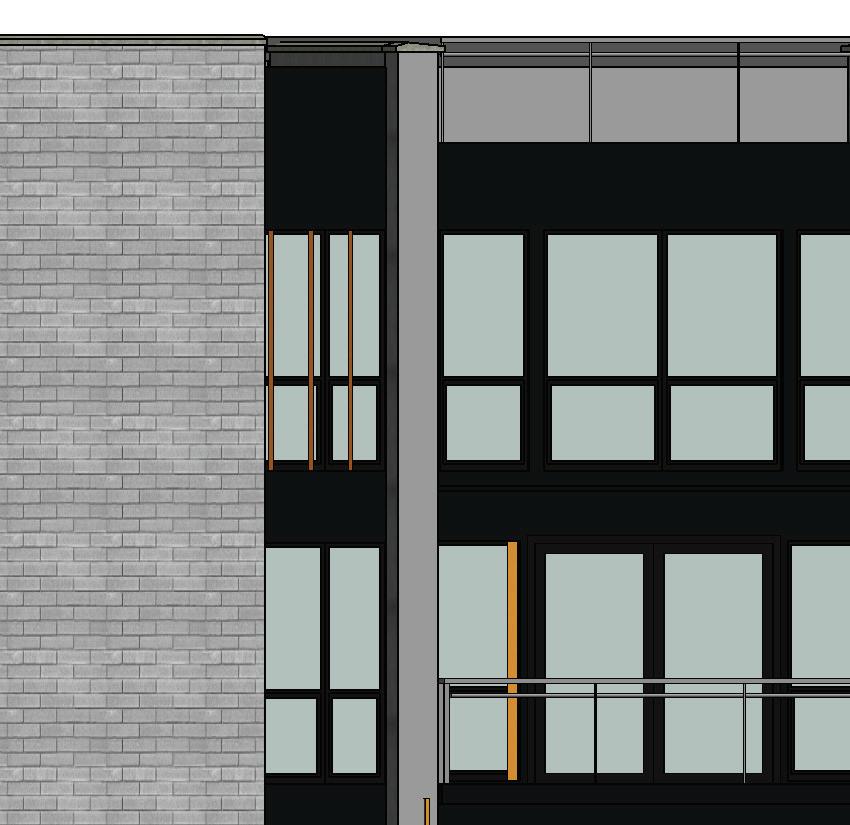

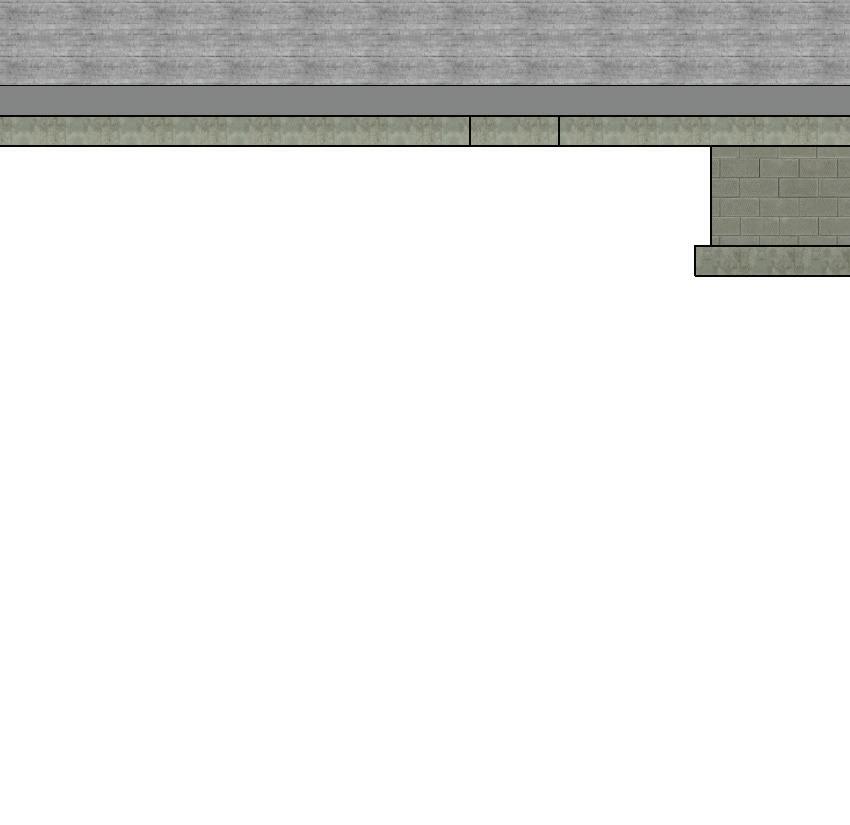
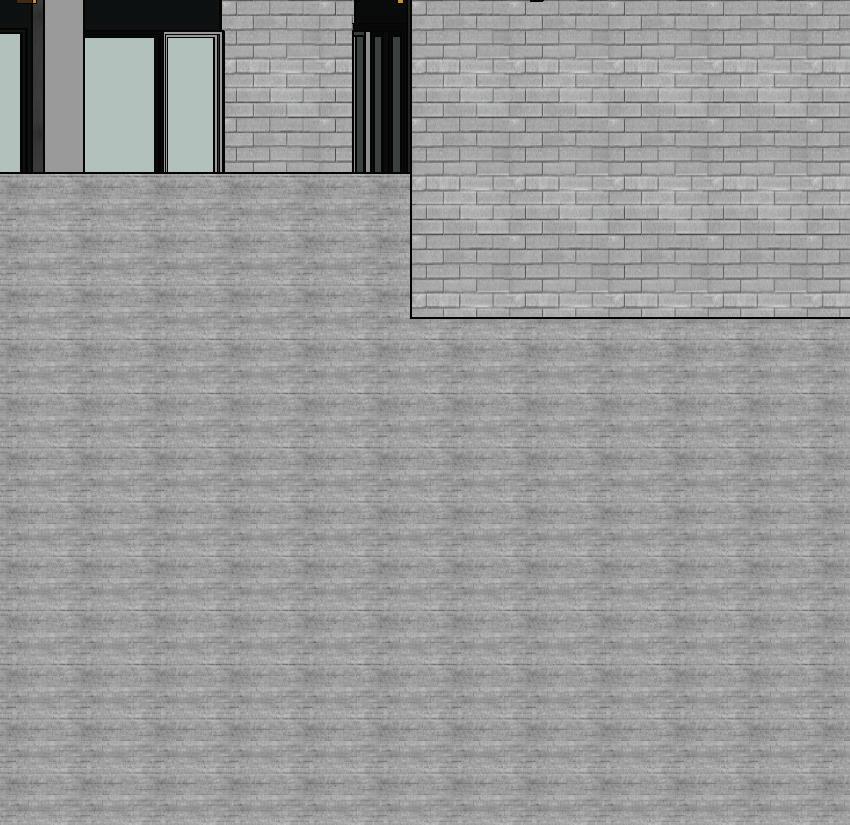
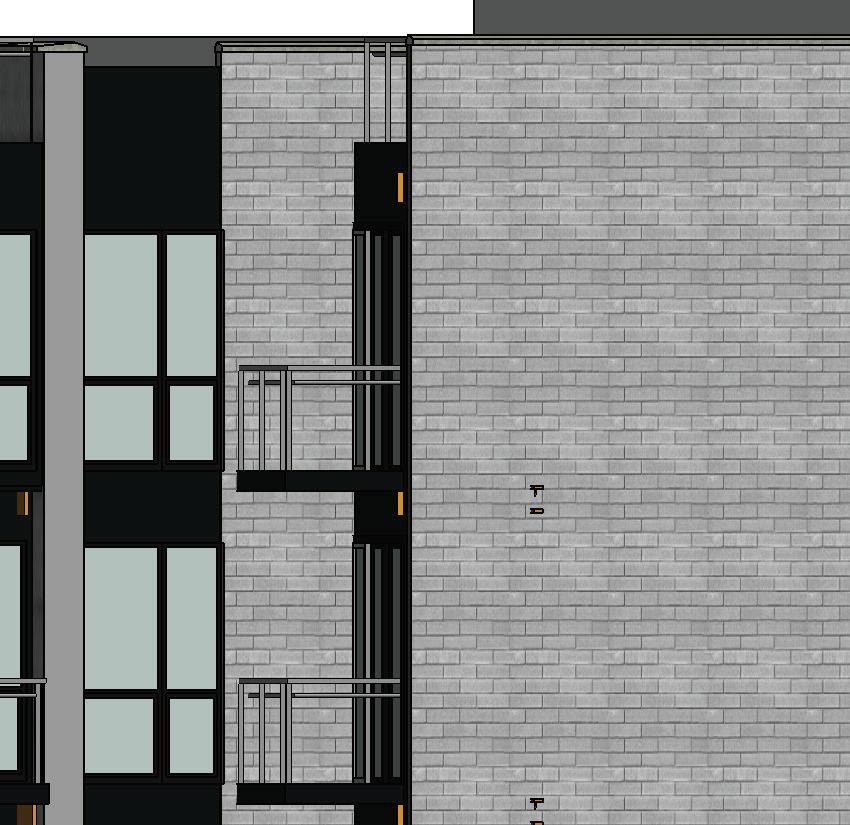
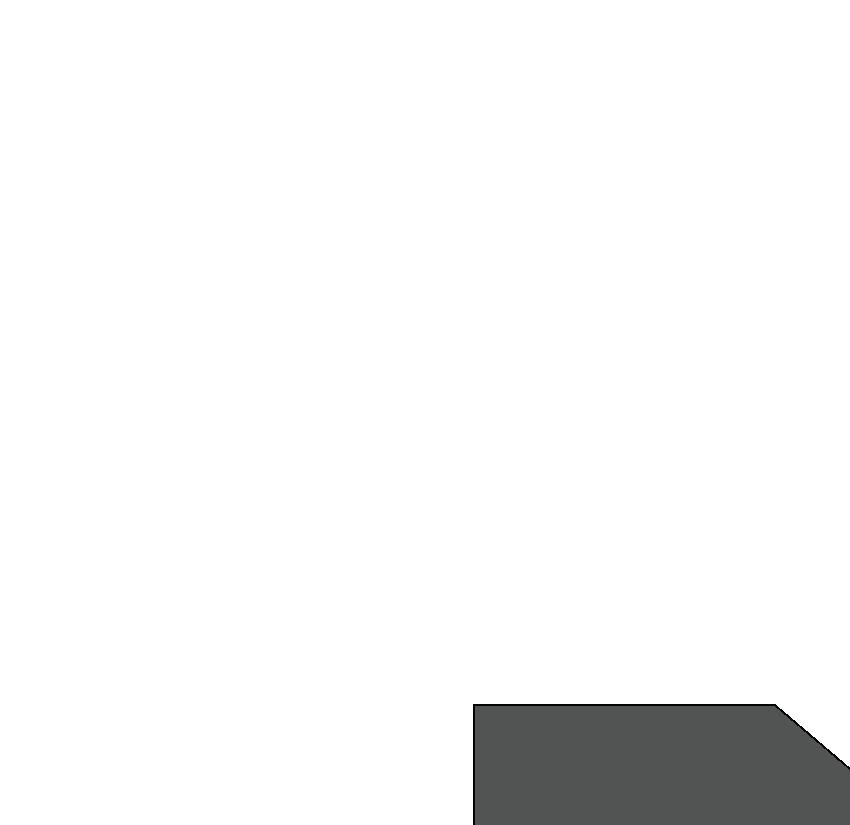
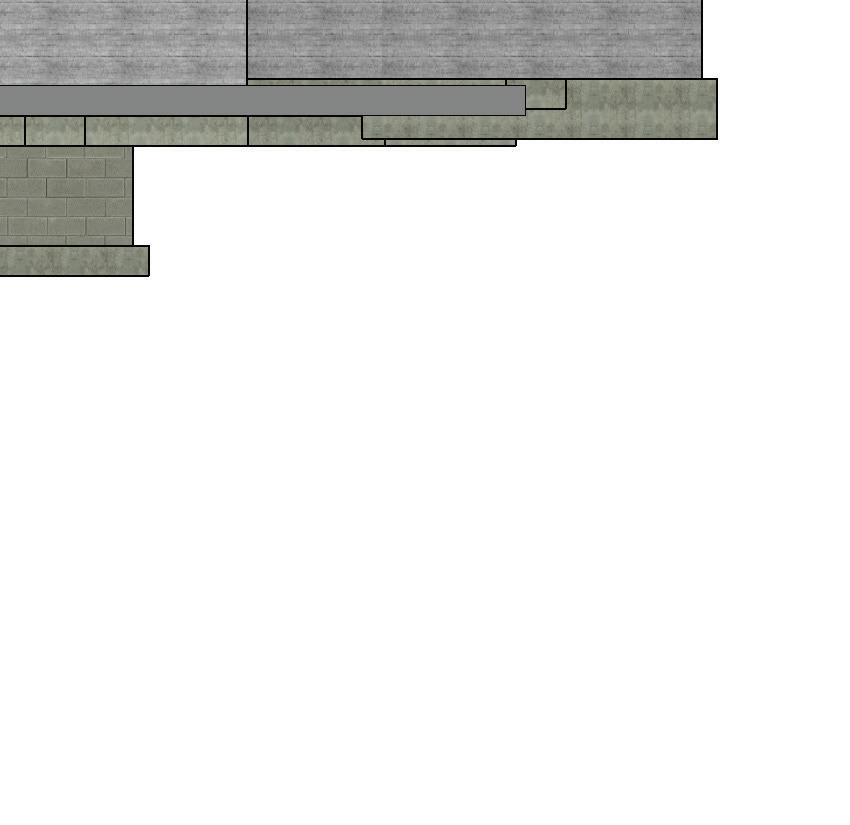
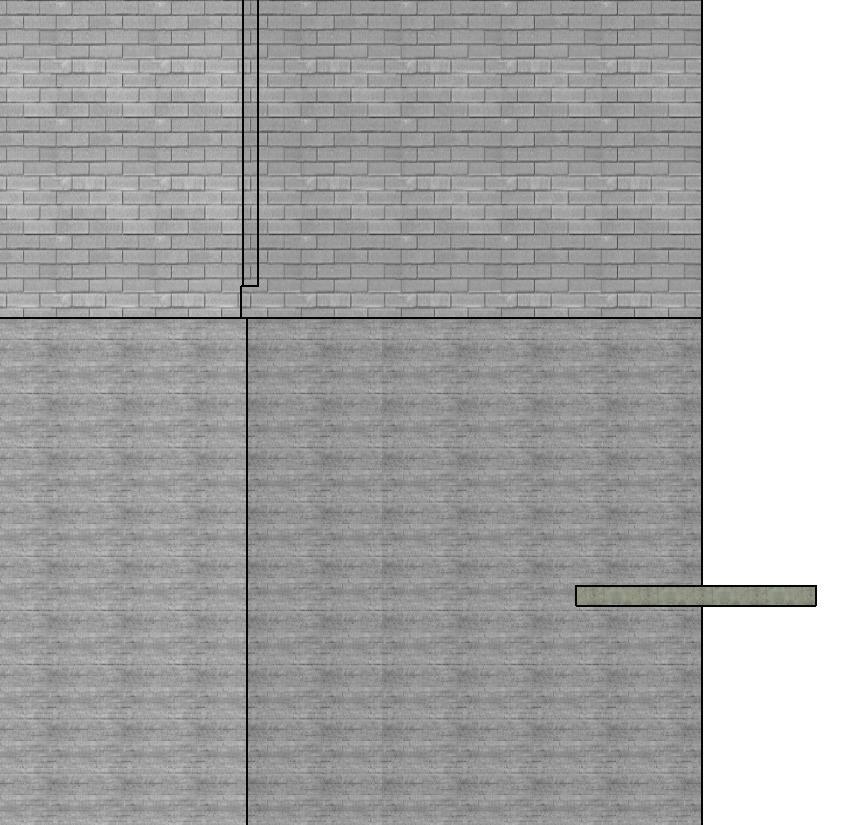
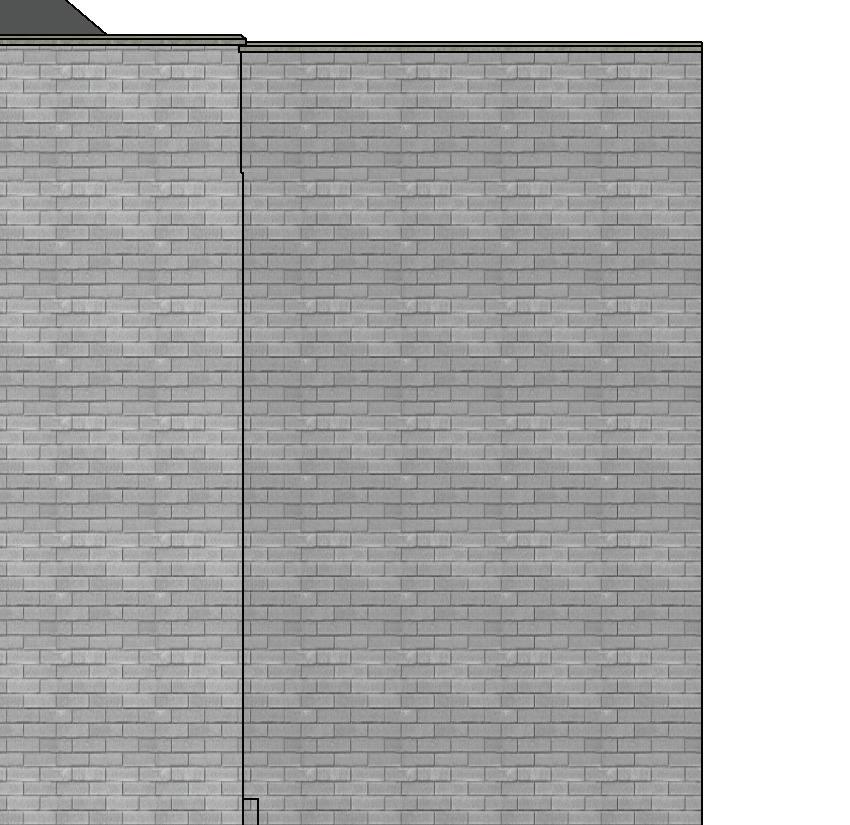
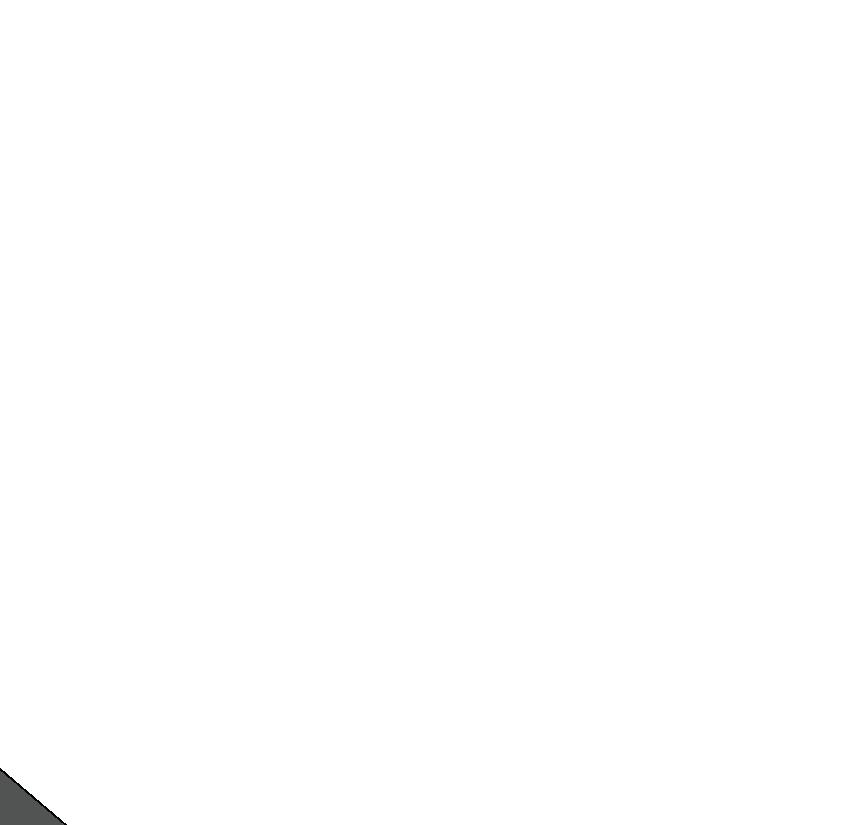




Master Thesis: 620 N 3rd St Clara Bucar 3.3. North Elevation NNDNENF O SSG H 1st Fl Fin Flr 0' B0" .O. Footing2 2' 2 1/2" Utility Bas em ent 9' 11 B1/2" .O. Footing1 11' 10" B.O. Footing 17 1" T.O. Concrete W all 13' 9" 2nd Fl 9' 11 1/2" 3rd Fl 20' 4 1/2" 4th Fl 30' 9 1/2" T.O. Flat Roof 41' 2 1/2" T.O. Pilothous e Roof 50' 2 1/2"


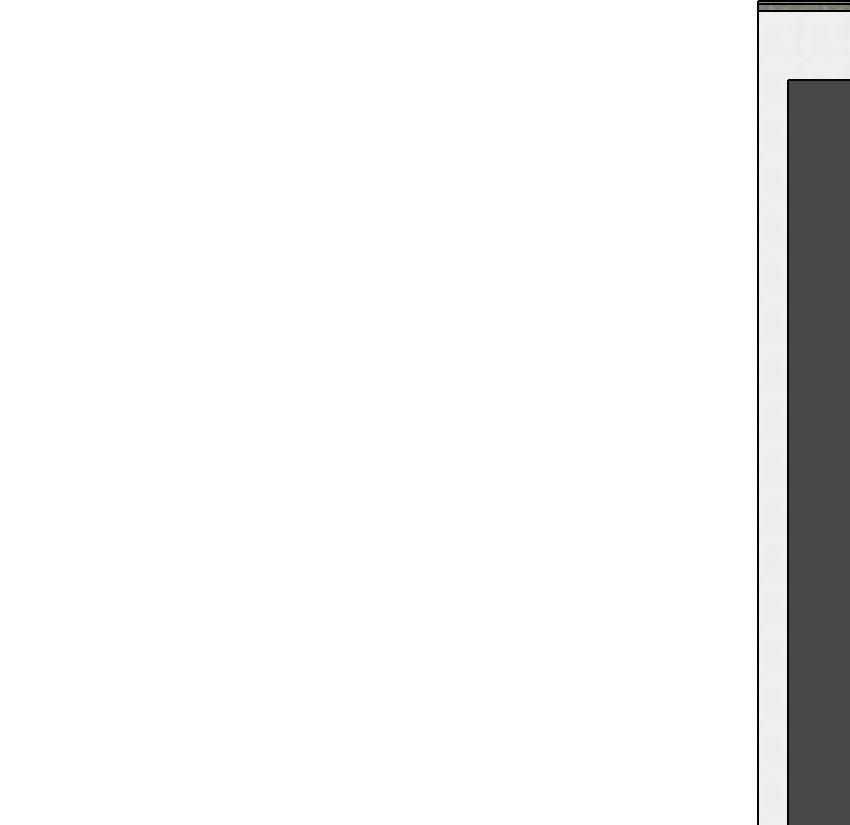


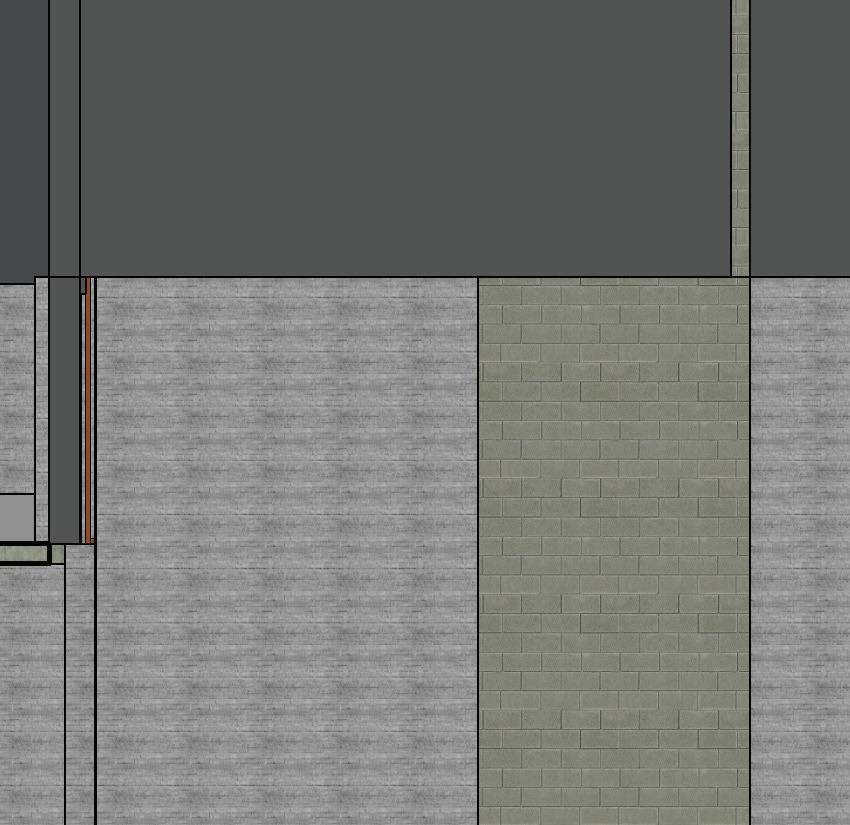
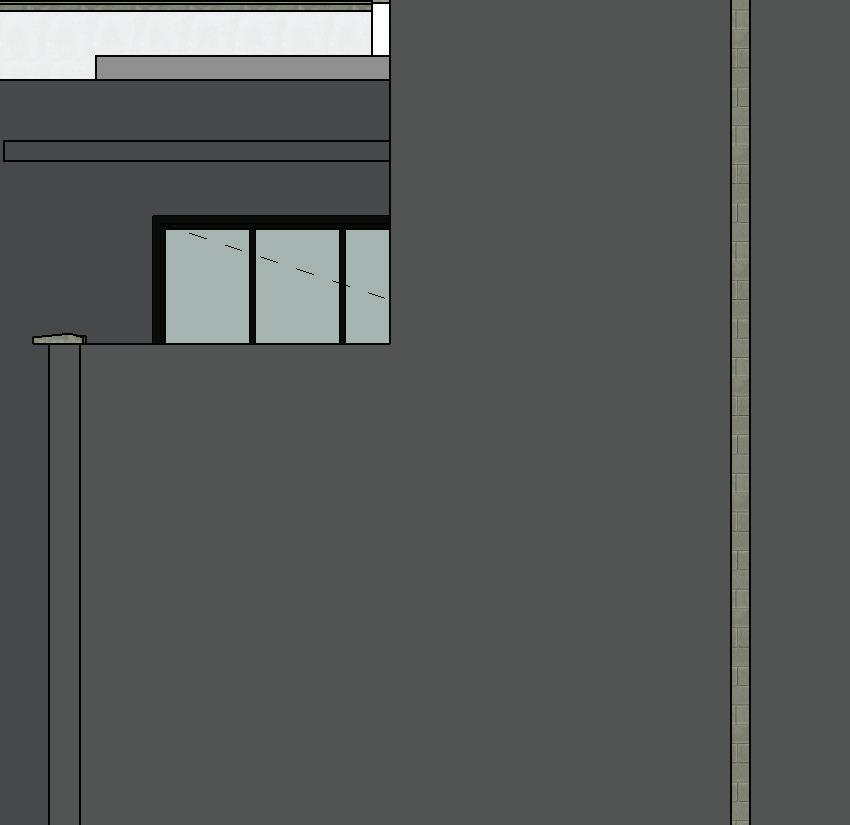


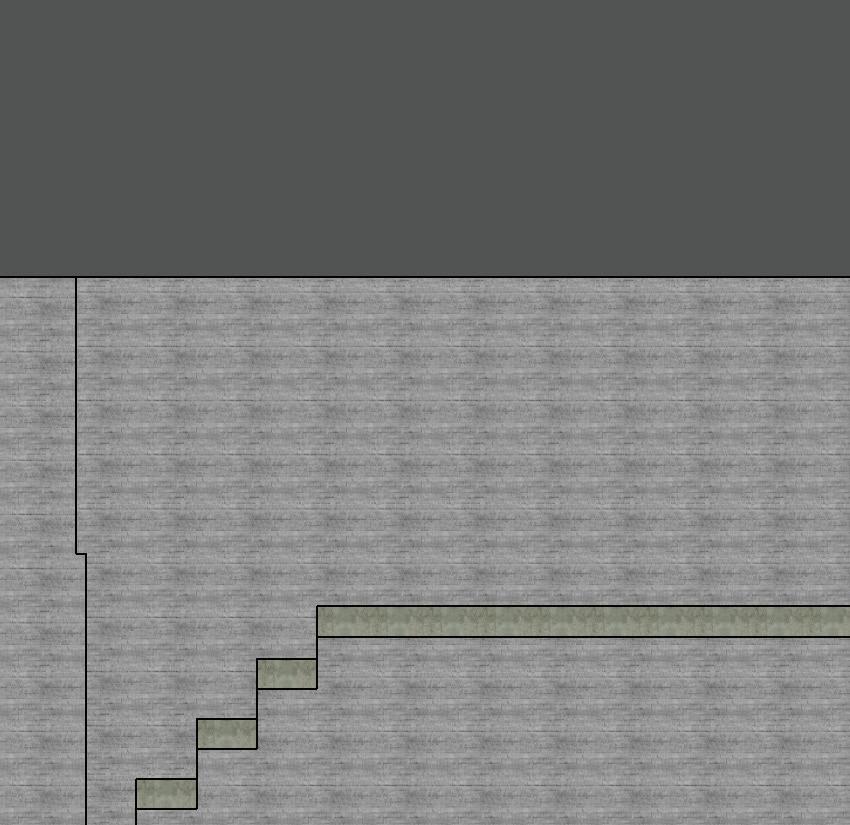
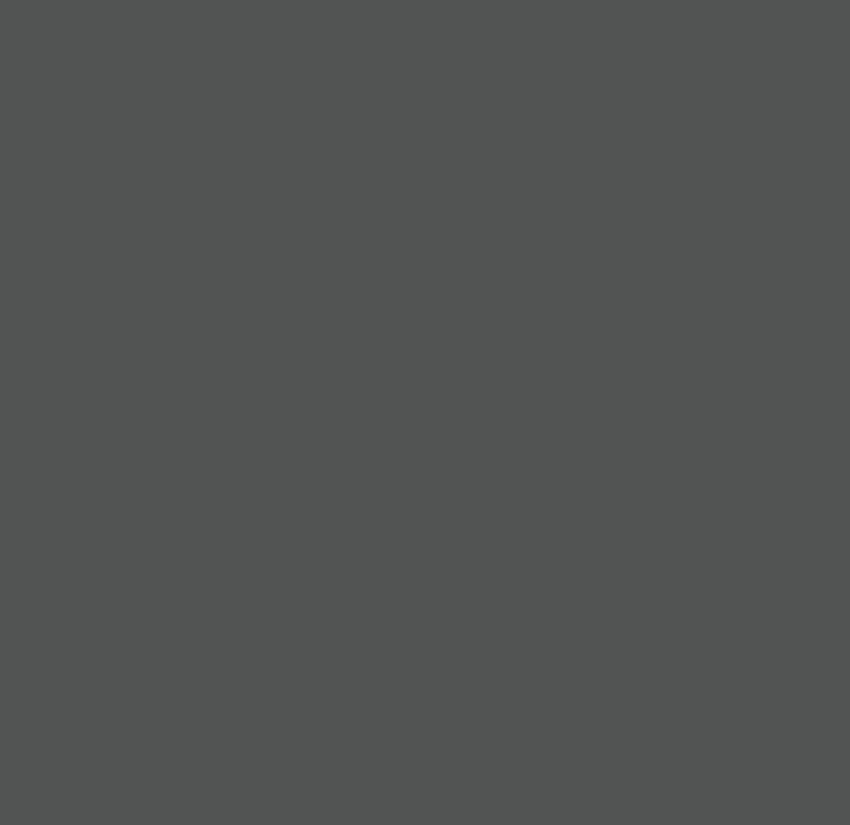

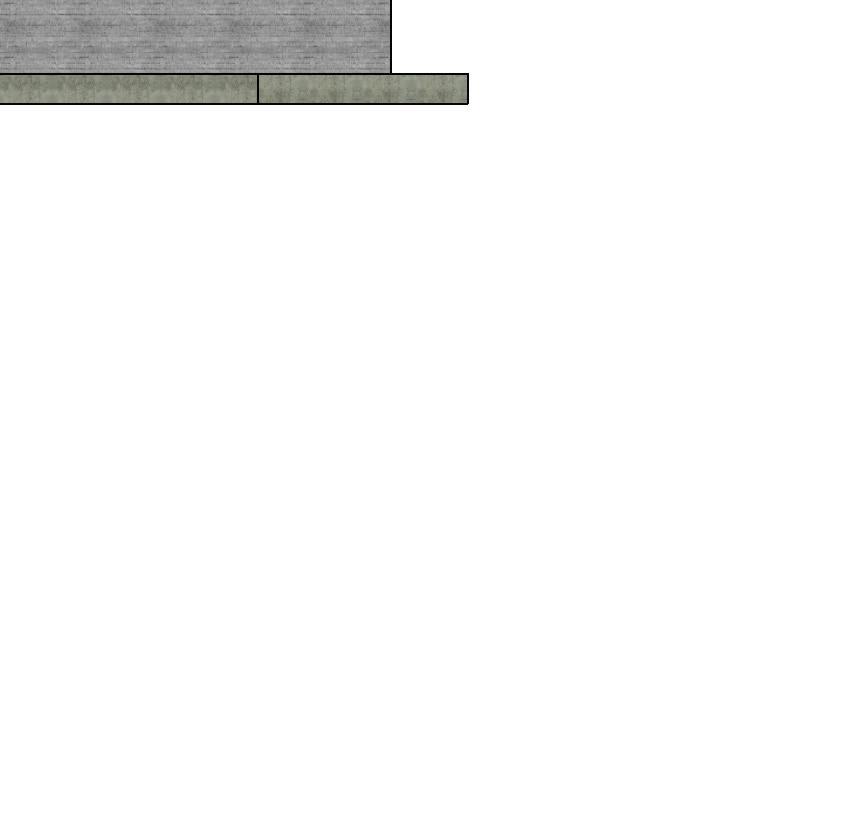
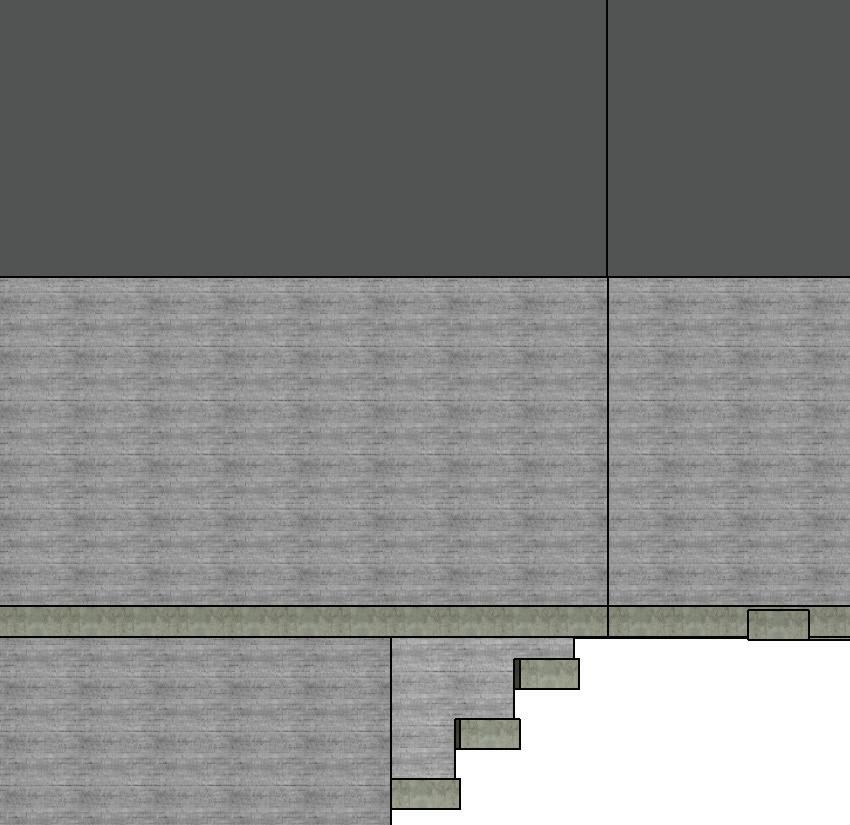
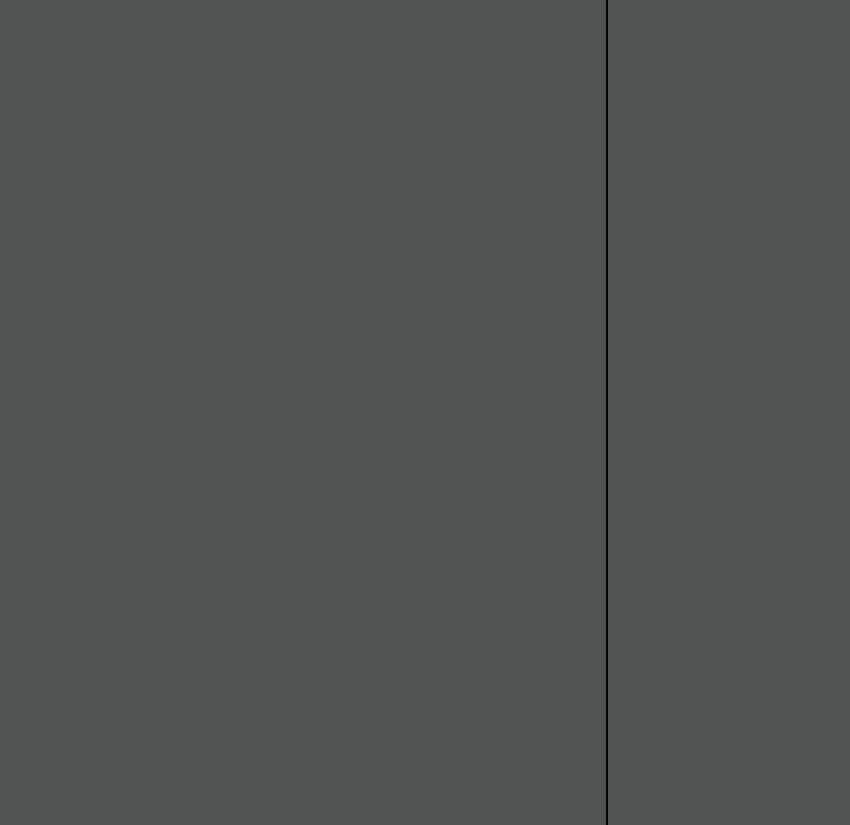
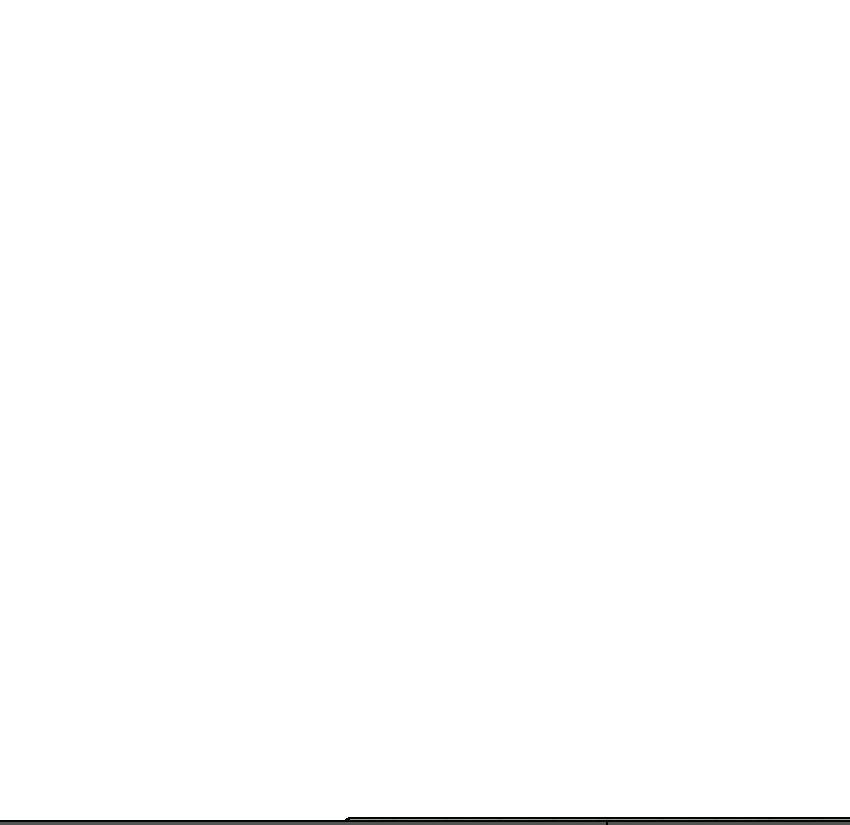

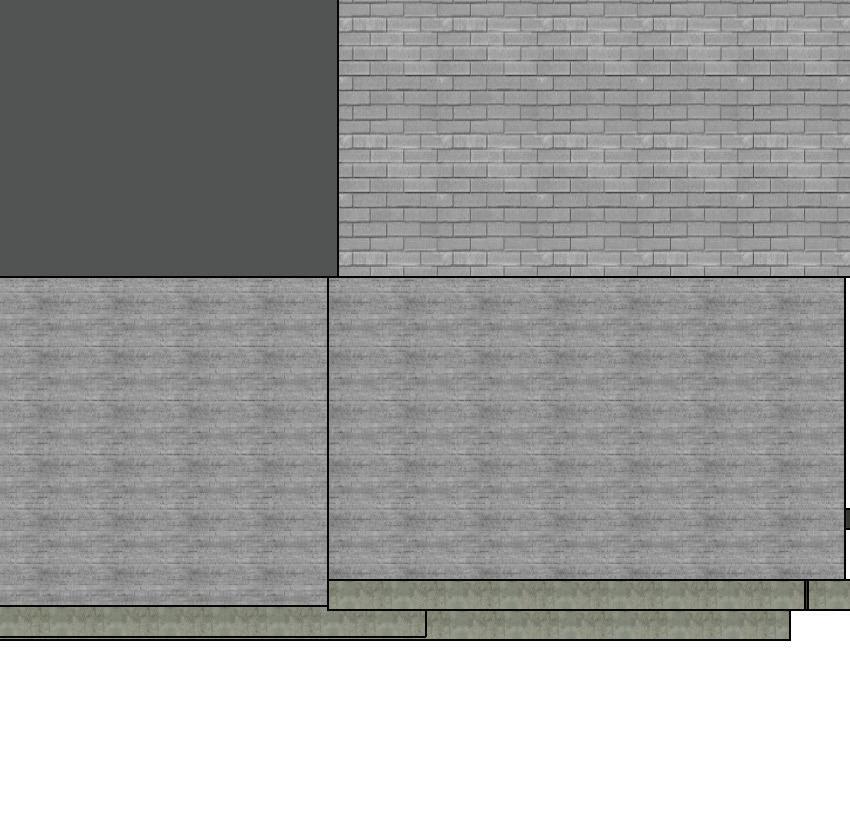
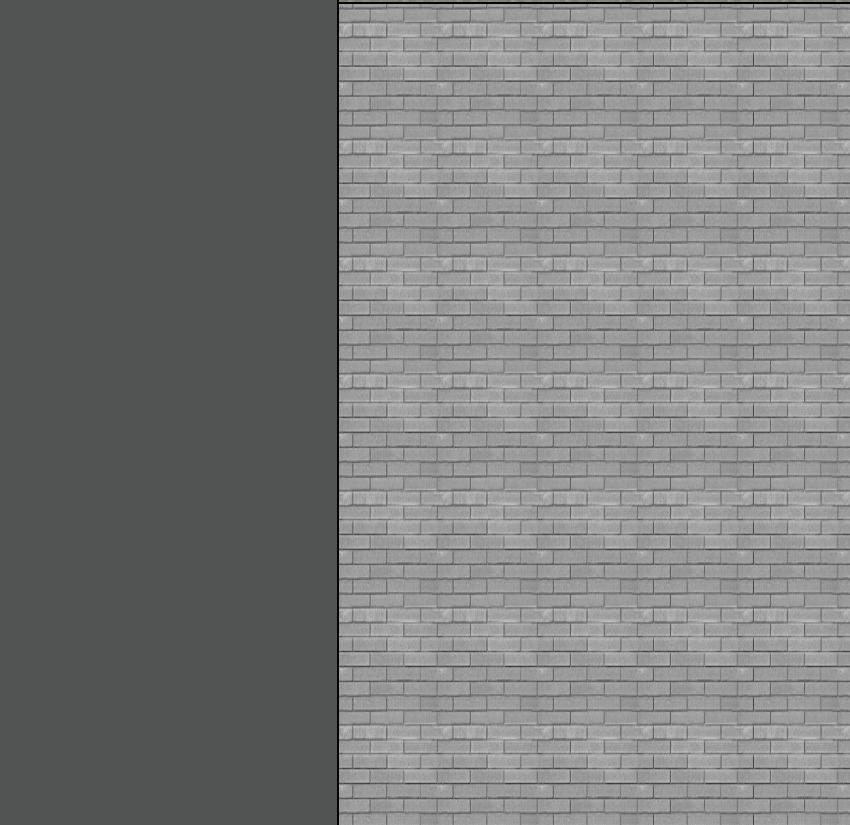
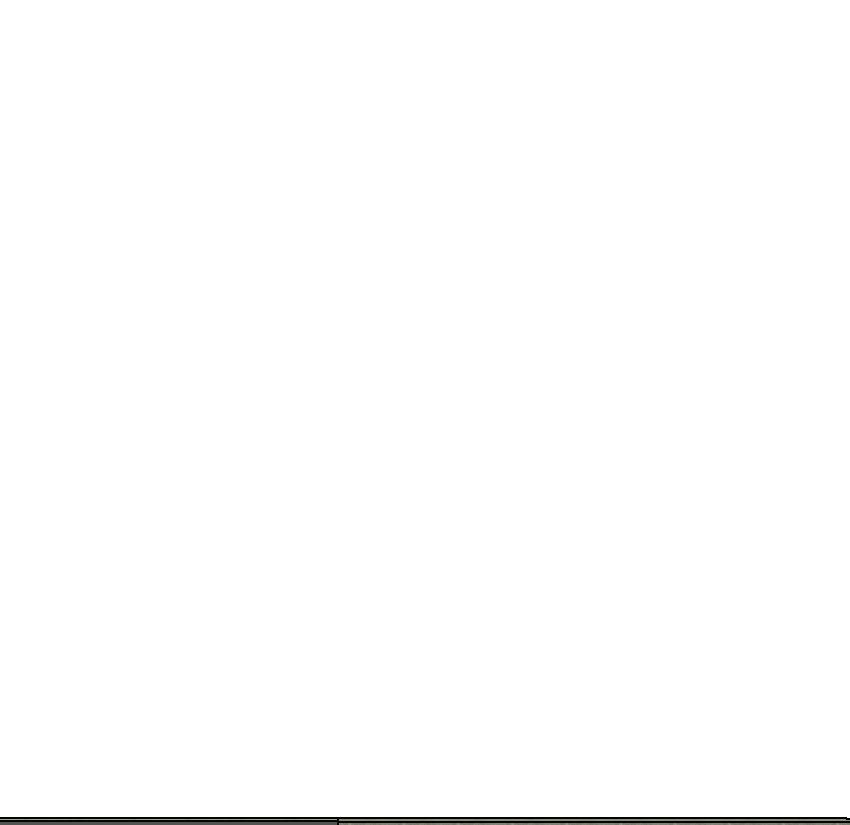

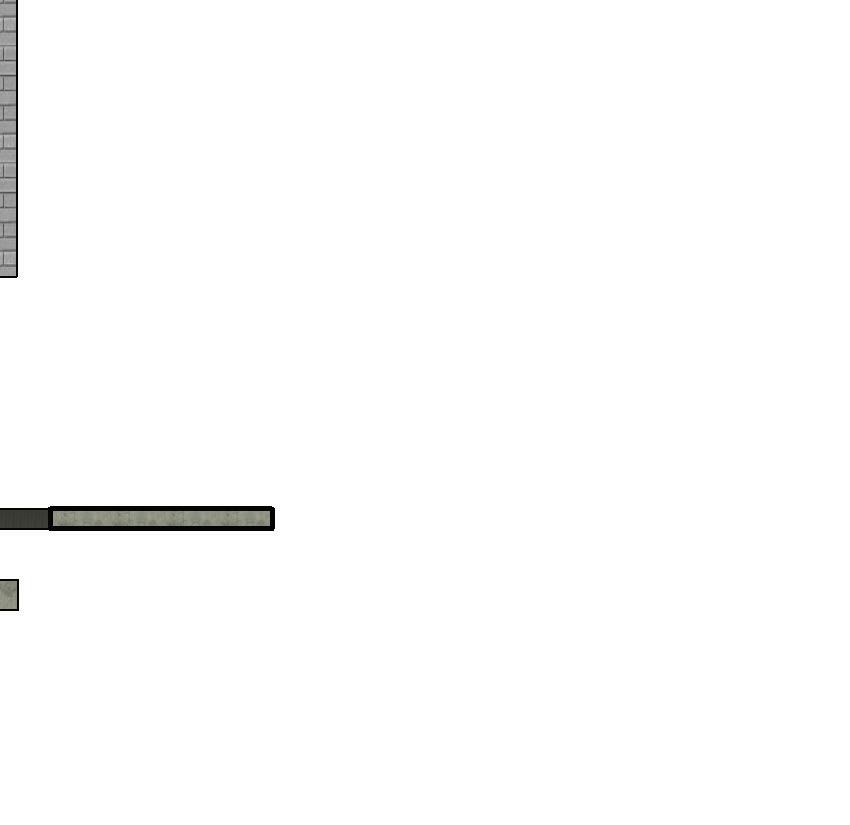

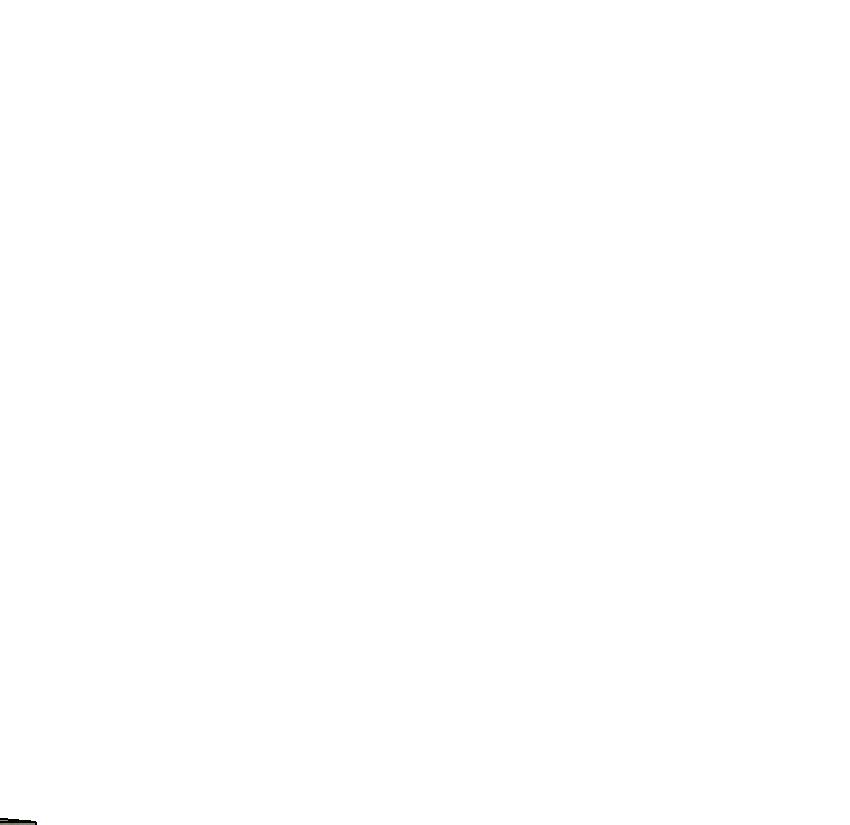
08/01/2018MCM 901 Page 40 of 224 Master Thesis: 620 N 3rd St Clara Bucar 3.4. Aerial Perspective
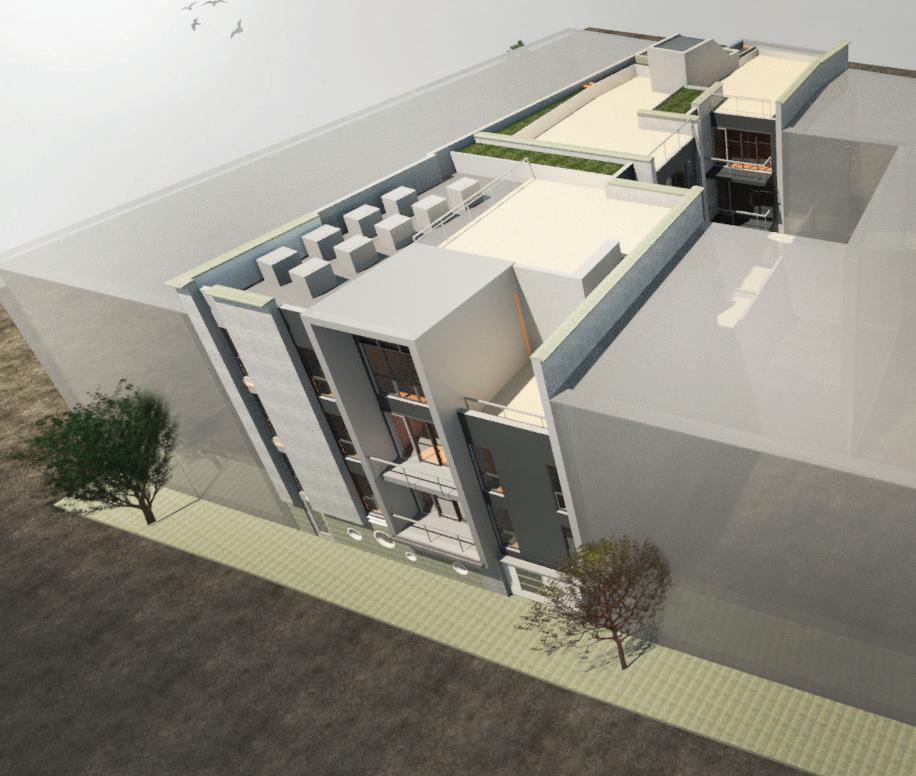
08/01/2018MCM 901 Page 41 of 224 Master Thesis: 620 N 3rd St Clara Bucar 3.4. Aerial Perspective
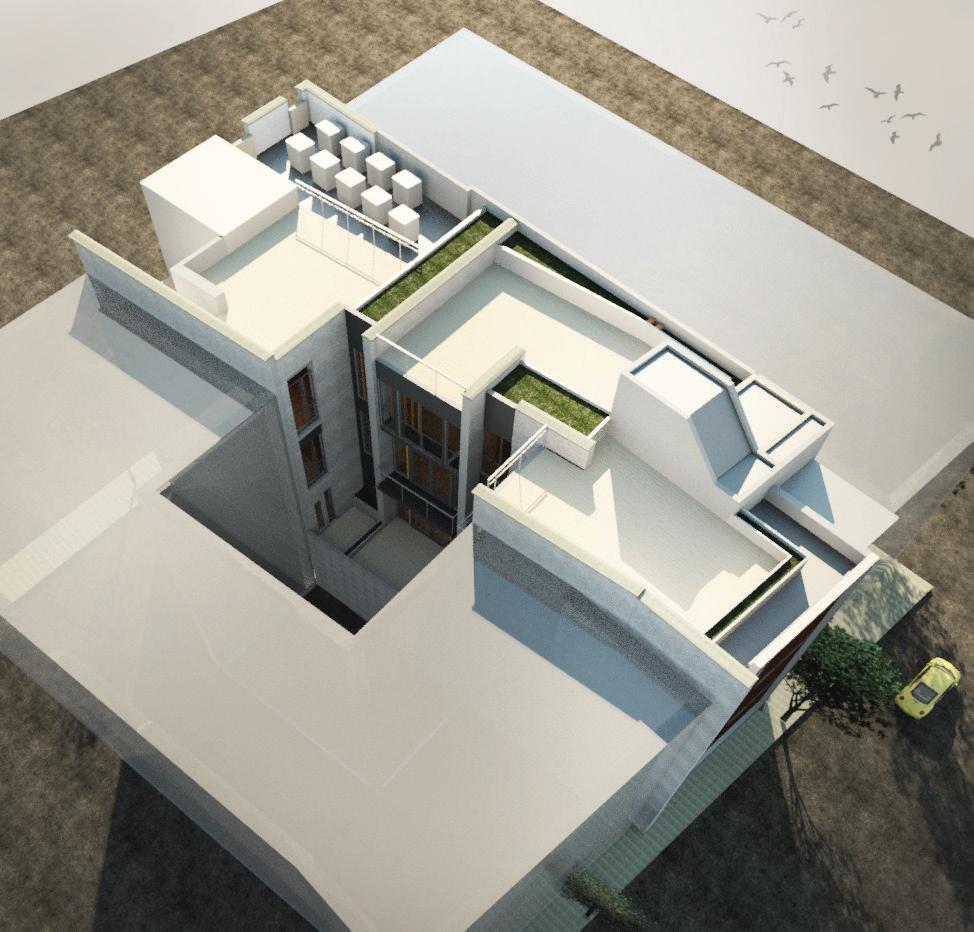
08/01/2018MCM 901 Page 42 of 224 Master Thesis: 620 N 3rd St Clara Bucar 3.5. Renderings
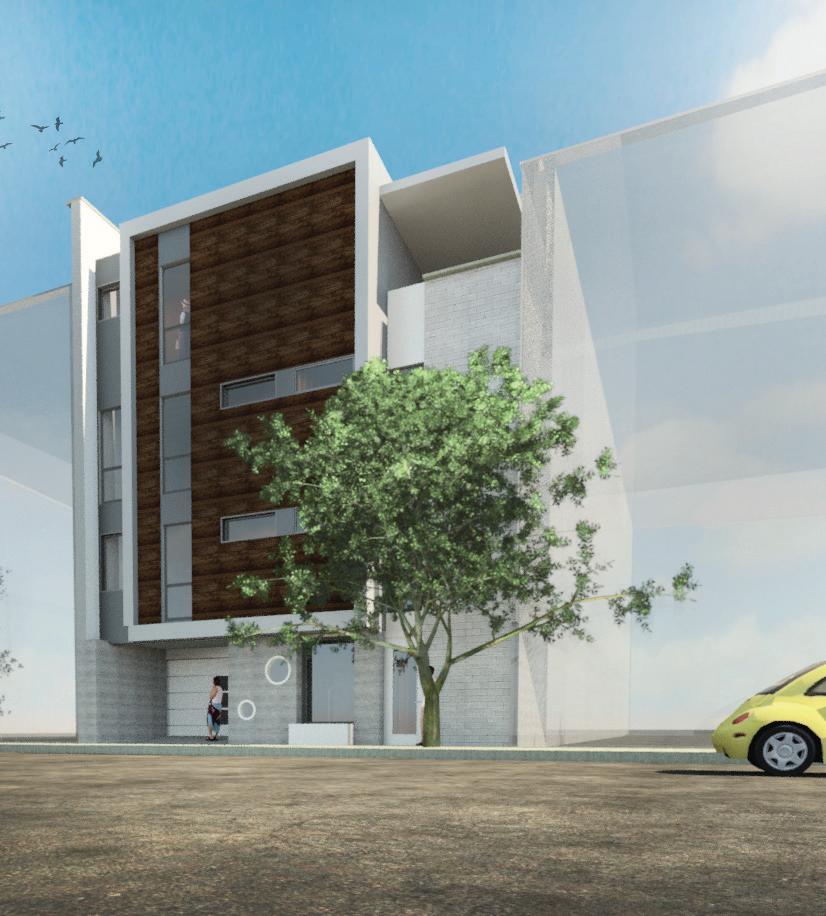

08/01/2018MCM 901 Page 43 of 224 Master Thesis: 620 N 3rd St Clara Bucar 3.6. Cross Section
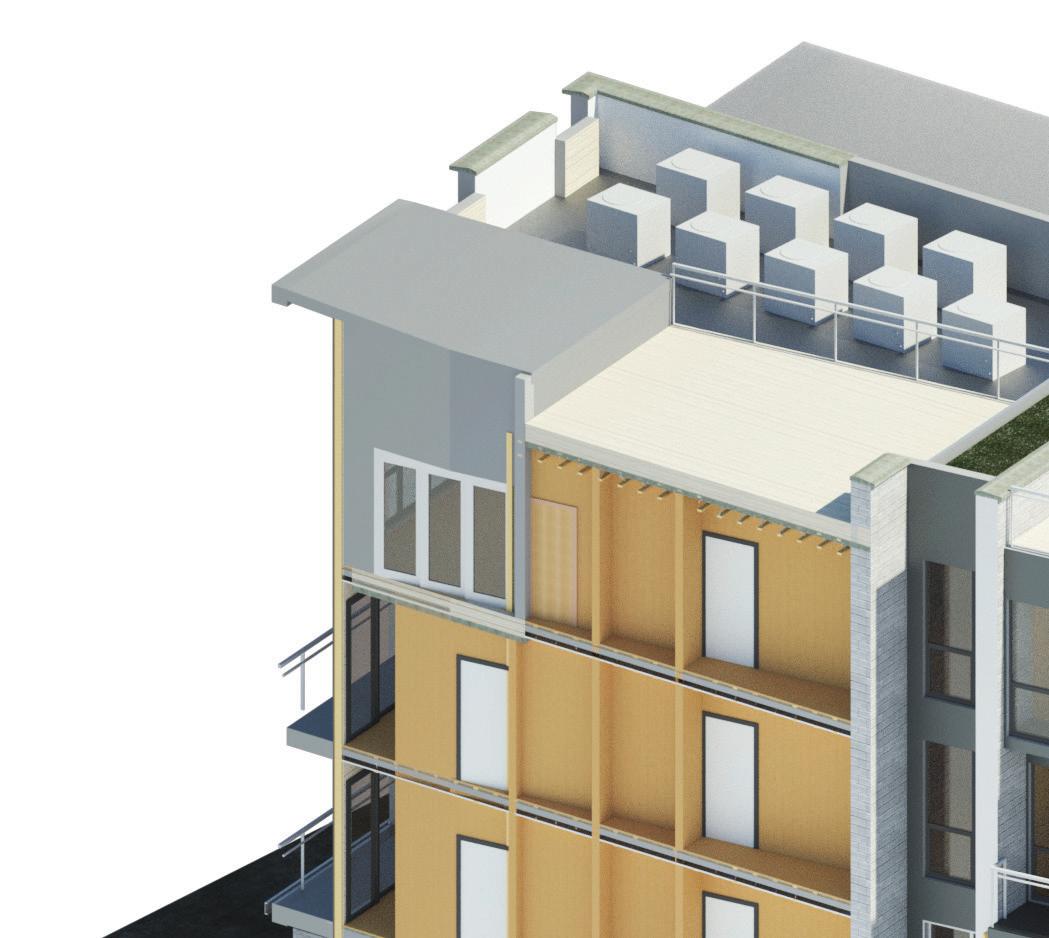
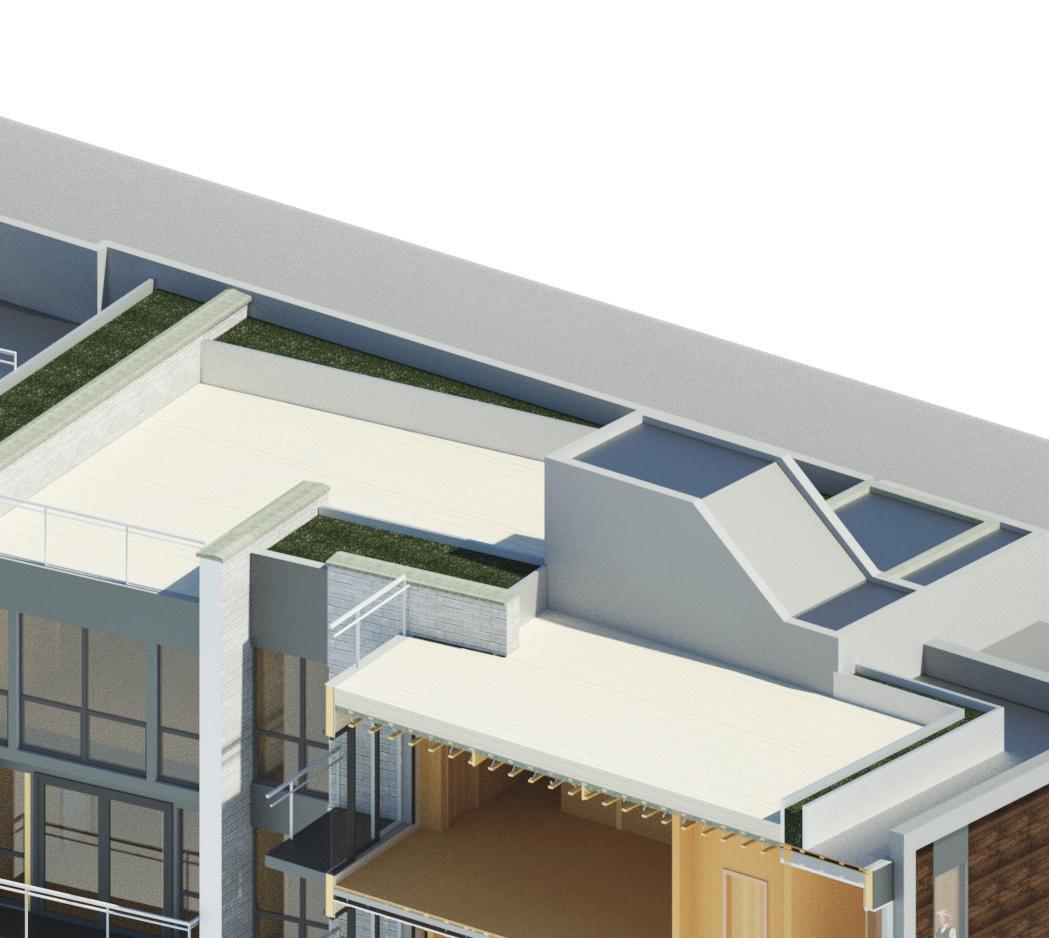
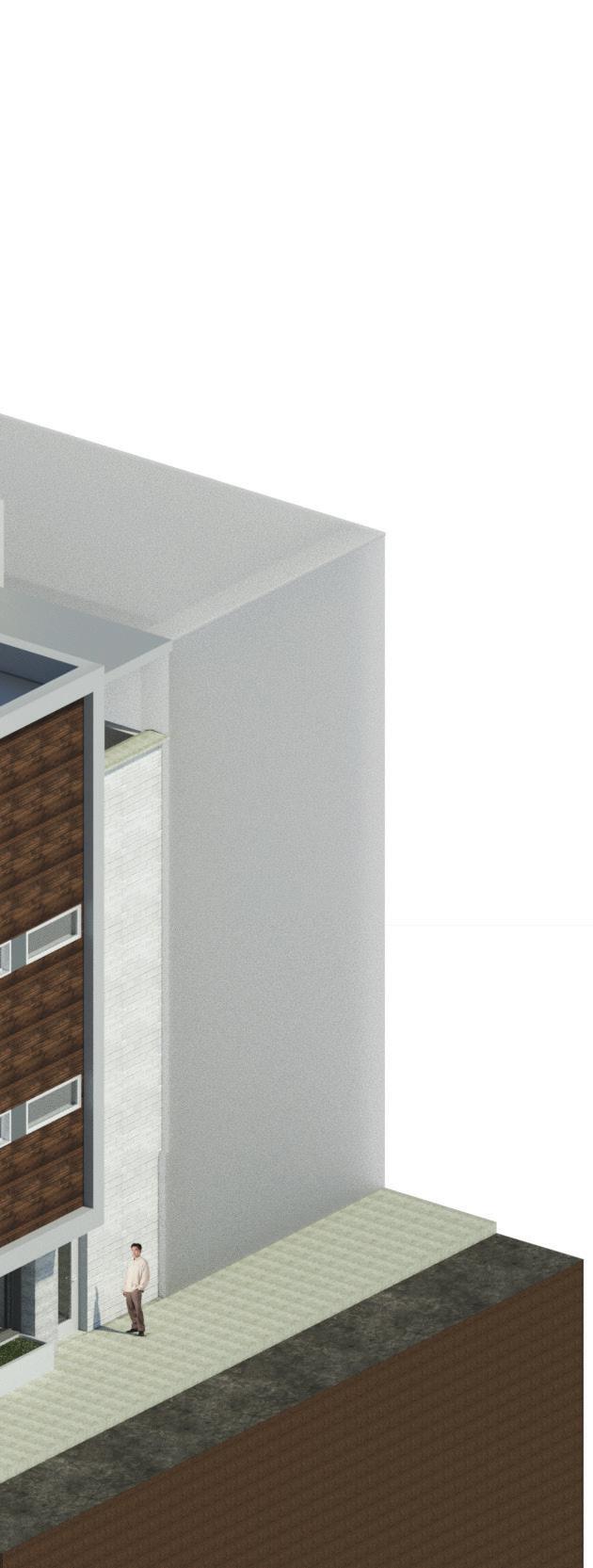
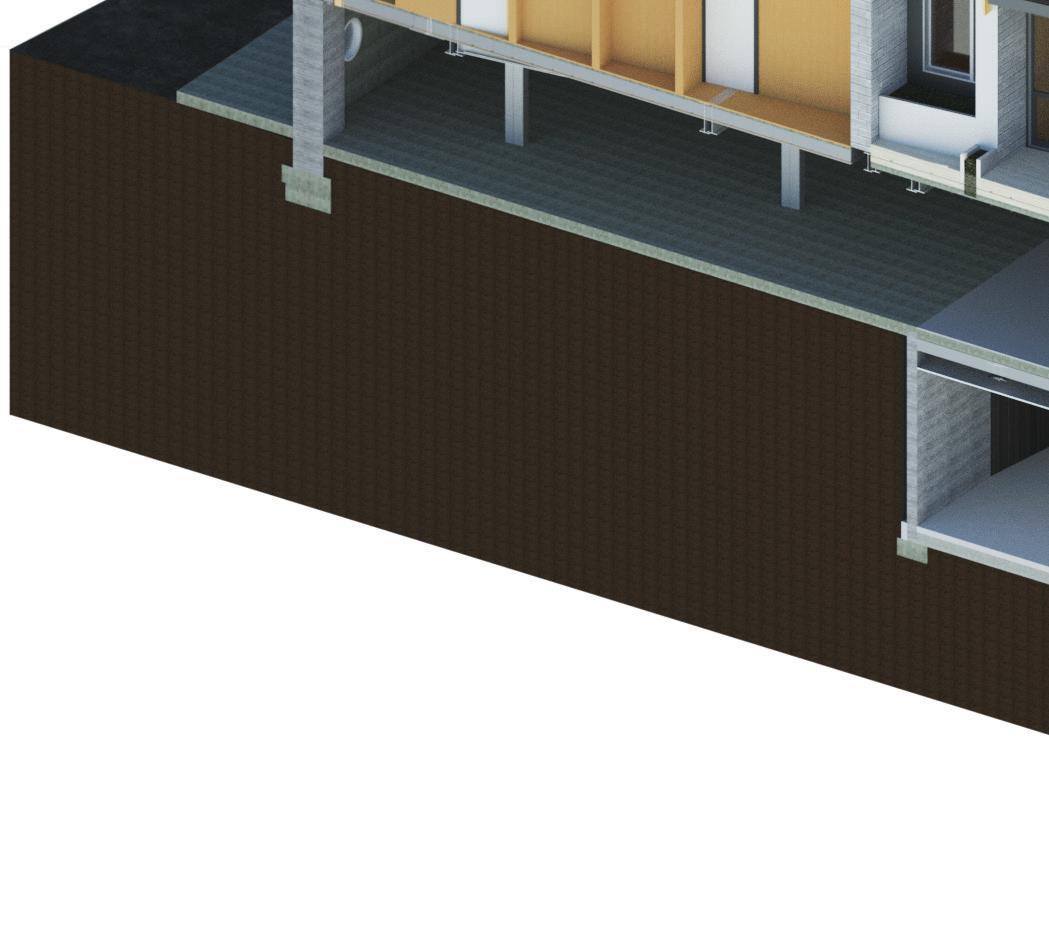
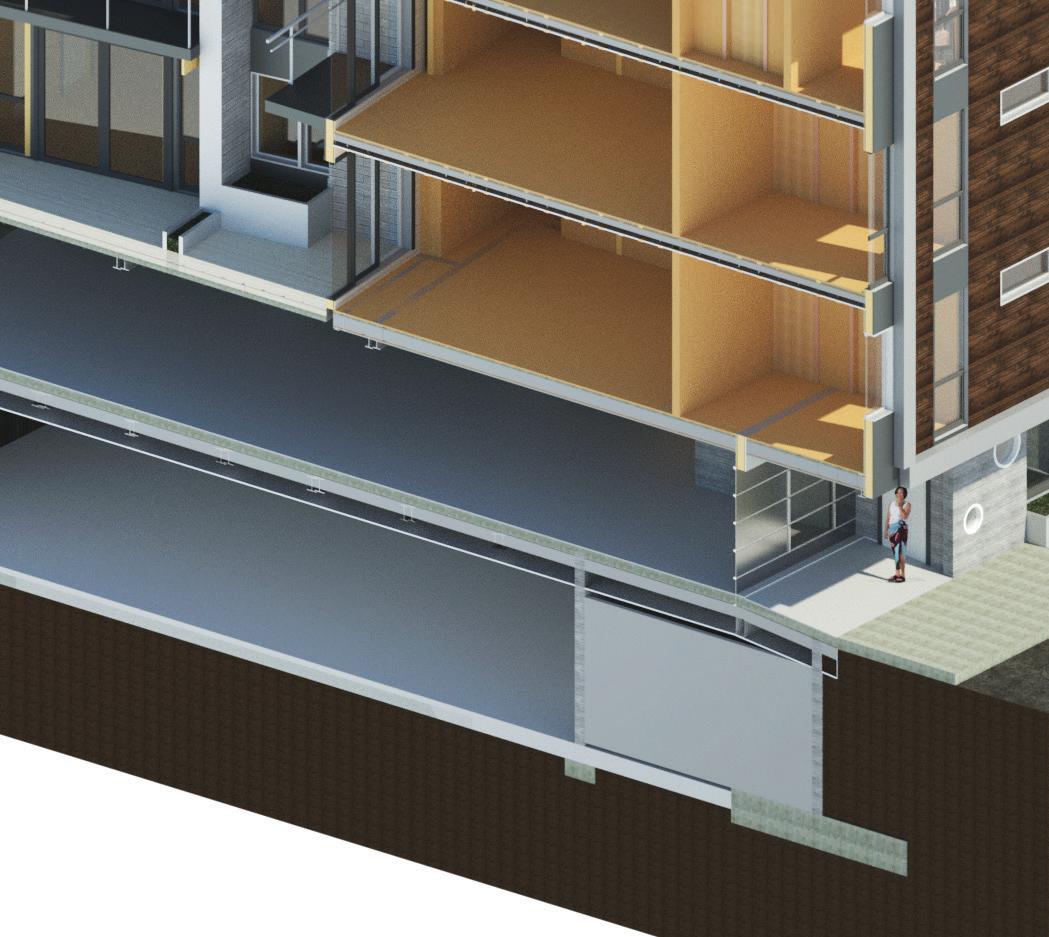
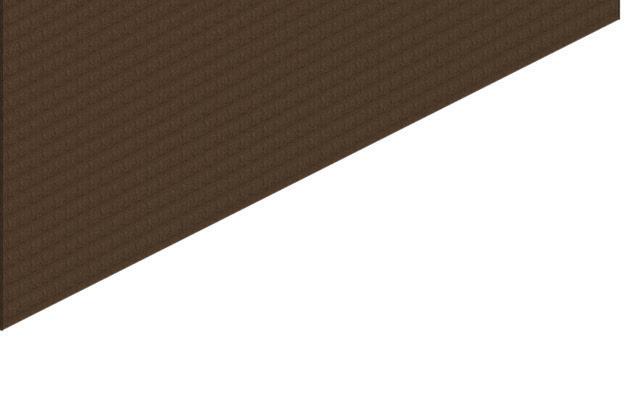
08/01/2018MCM 901 Page 44 of 224 Master Thesis: 620 N 3rd St Clara Bucar 3.6. Cross Section
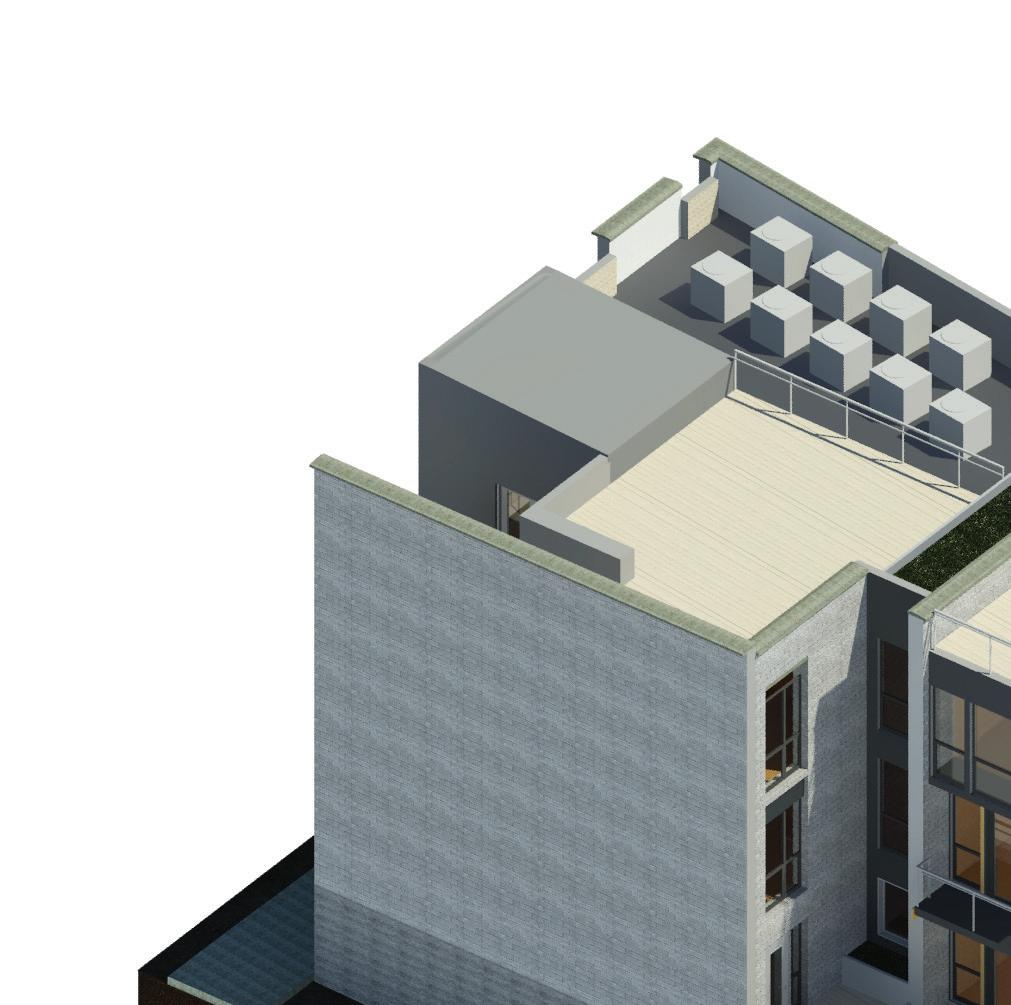
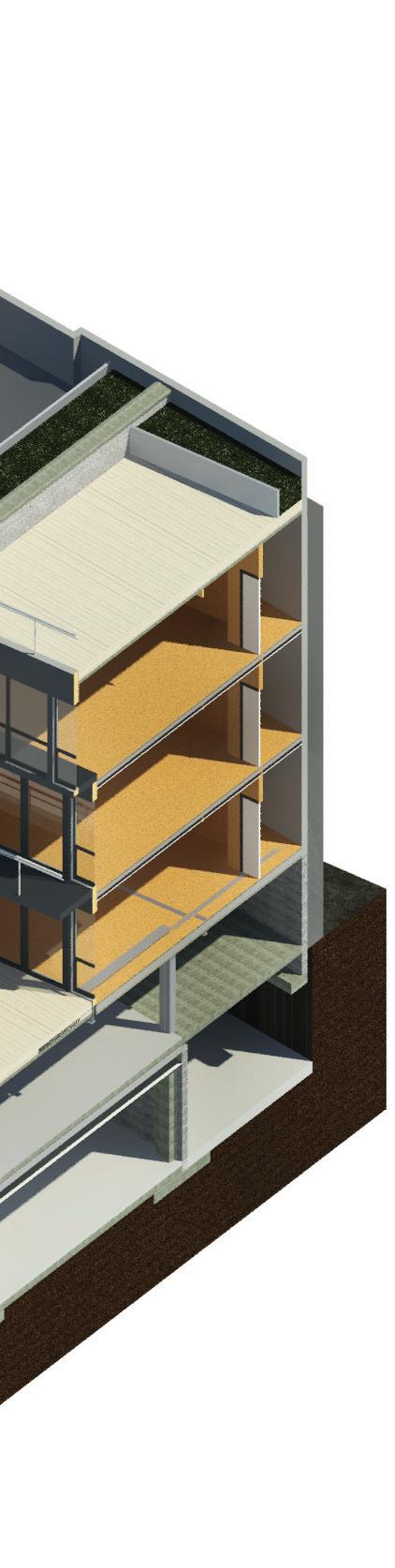
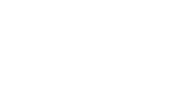
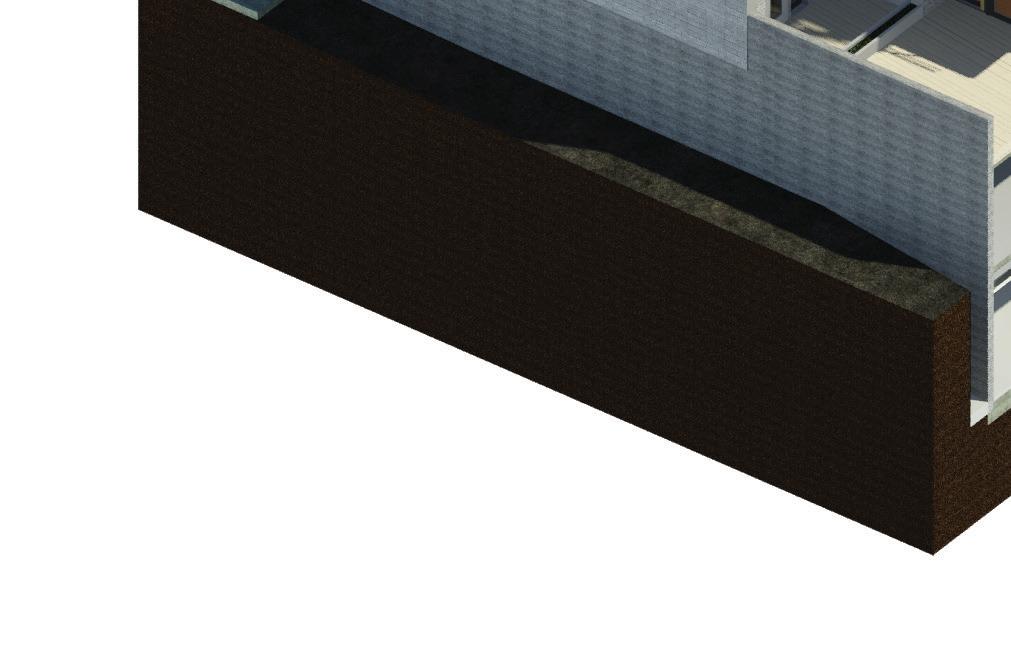
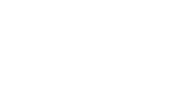
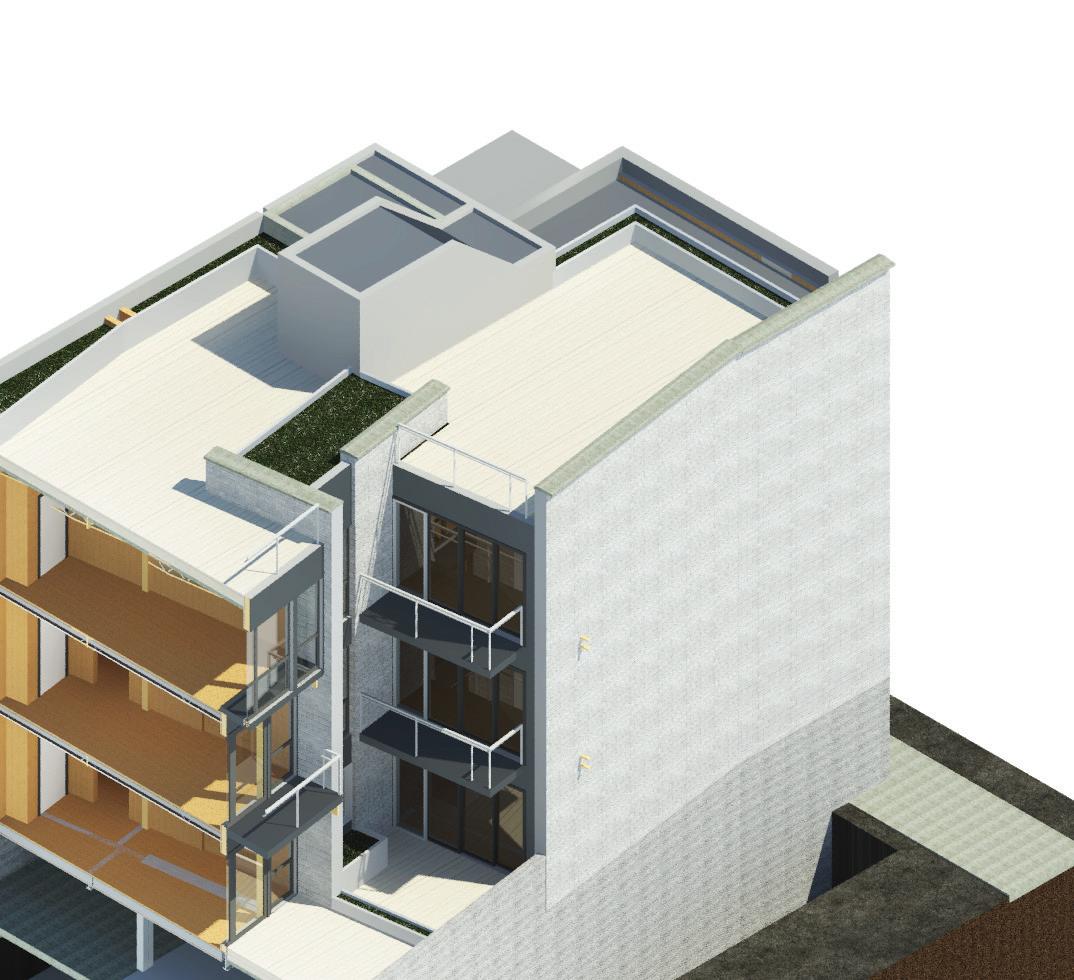
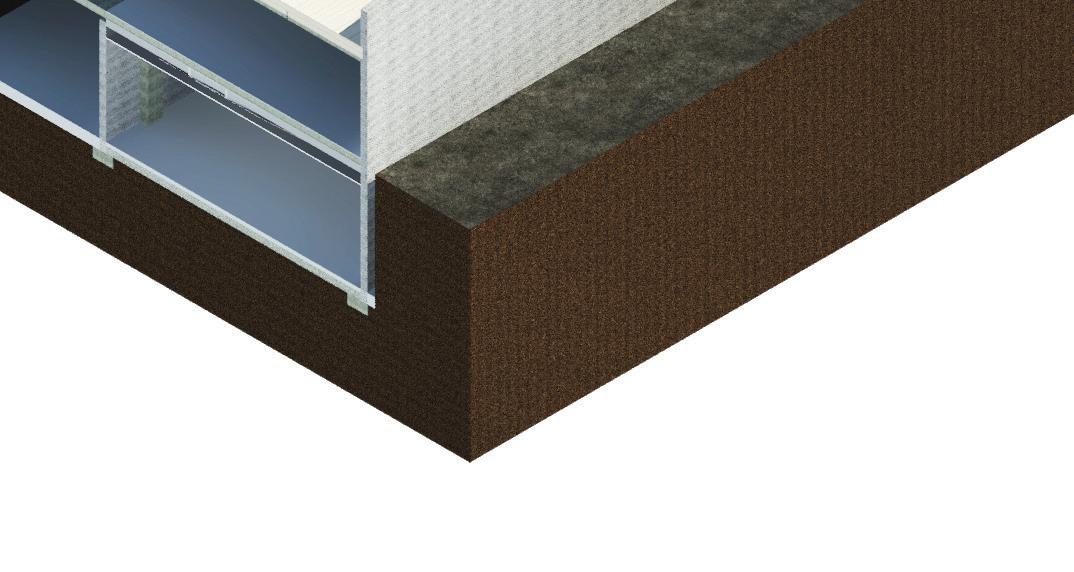

MCM 901 Page 45 of 224 Master Thesis: 620 N 3rd St Clara Bucar 3.6. Cross Section
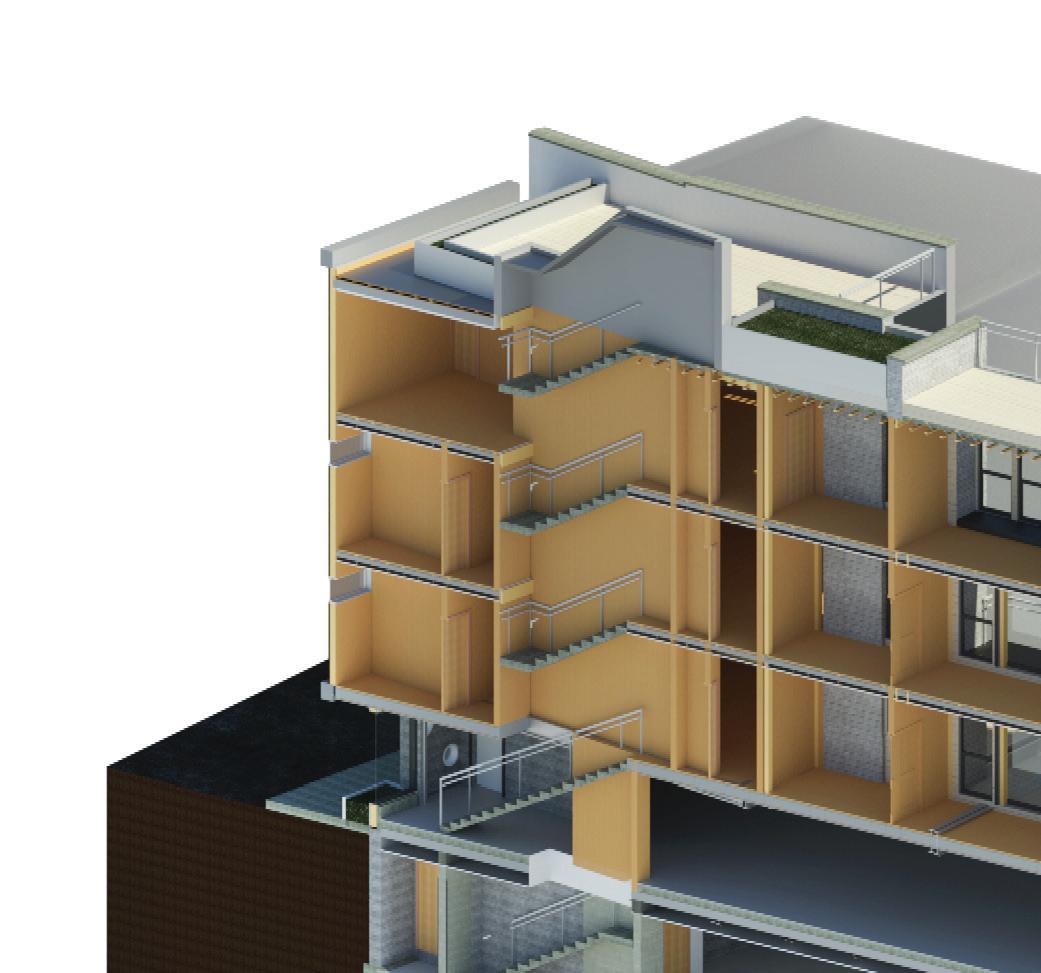
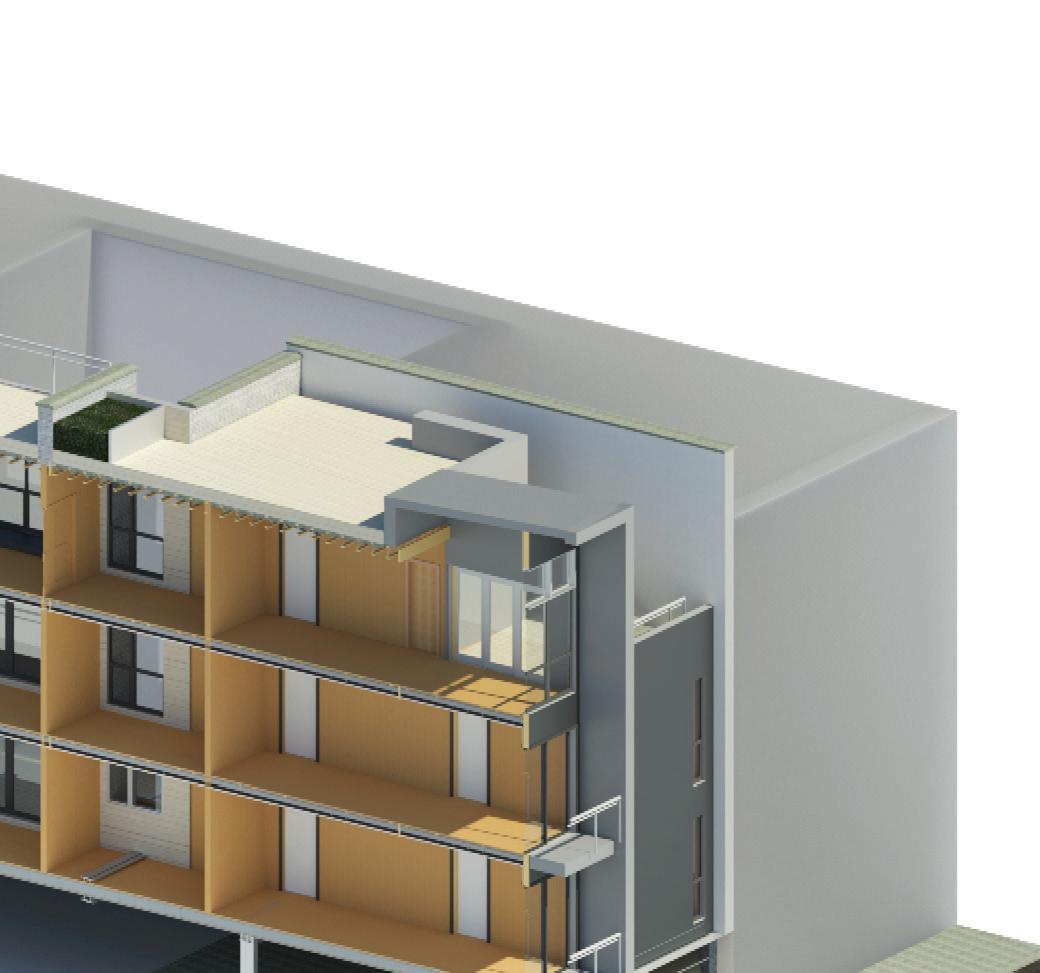


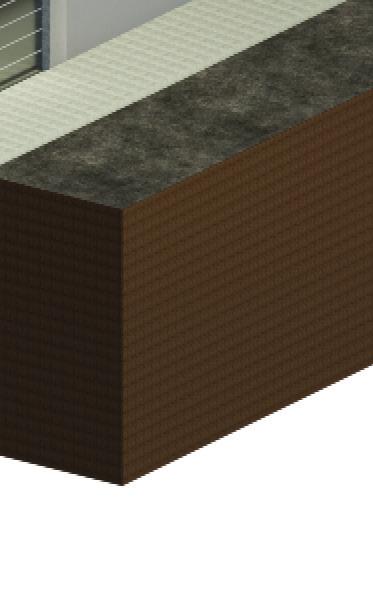

08/01/2018MCM 901 Page 46 of 224 Master Thesis: 620 N 3rd St Clara Bucar SECTION FOUR WBS, ESTIMATES, SCHEDULES AND CASH FLOW
Section Four provides the must-see pieces of information for the 620 N 3rd St project: the detailed and summarized descriptions of the project’s baseline budget, schedule and cash flow. The general conditions subsection lists all the costs related to the project that are not subcontracted work related, but rather the conditions through which Fit Construction enables the subcontractors to perform the work packages. The work packages are each subcontractor’s specific contract pertaining their scope of work, this information can be found under the “Procurement and Buy-Out Log” subsection. As provided on Section Two under the “Project Delivery Method Analysis” subsection, the cash flow commits to show PRDC transparent cost information month by month.
Additionally, Fit Construction provides an alternative estimate for LEED Silver certification. PRDC has the opportunity to review the base and the alternate estimate and make an educated decision whether to pursue the certification or not.
The schedule is another critical portion of Section Four. A milestone report, the most important dates for the project, is provided under this section. Lastly, it contains the master scheduled with a detailed plan for the 620 N 3rd St project, as well as the critical path.
08/01/2018MCM 901 Page 47 of 224 Master Thesis: 620 N 3rd St Clara Bucar 0.1.ProjectPreconstruction1.1.Estimate 1.1.1.1.1.1.1.Take-offsSite work 1.1.1.2. Concrete 1.1.1.3. Steel 1.1.1.4. Framing 1.1.1.5. Masonry (self performed) 1.1.1.6. Interior finishes 1.1.1.7. Exterior finishes 1.1.1.8. Mechanical 1.1.1.9. Electrical 1.1.1.10. Plumbing 1.1.1.11. Elevator 1.1.1.12. Roofing 1.2. Schedule 1.3. Risk Management 1.4. Safety Plan 1.5. Environmental Plan 1.6. Subcontractor pre qualification 1.7. Bid and award 1.8. Site survey 1.9. Procurement 1.10. QA/QC Plan 1.11. Site logistics 1.12. Permits 1.13. Constructability Review 1.14. Notice to proceed 1.15. Mobilization 1.15.1. General conditions 1.15.1.1. Signage 1.15.1.2. Construction fence/Gates 1.15.1.3. Sheltered walkway protection 1.15.1.4. PECO aerial lines protection 1.15.1.5. Dumpsters 4.1. Work Breakdown Structure
08/01/2018MCM 901 Page 48 of 224 Master Thesis: 620 N 3rd St Clara Bucar 1.15.1.6. Trailer 1.15.1.7. Portable toilets 1.15.1.8. Parking passes 1.15.1.9. Temporary water 1.15.1.10. Temporary power 1.15.1.11. Security system - cameras 1.15.1.12. Osha posters 1.15.1.13. Walkie talkies 2. 2.1.ConstructionSiteWork 2.1.1. Excavation 2.1.2. Dirt storage for backfill 2.1.3. Dirt removal 2.1.4. Compaction 2.1.5. Backfill 2.1.6. Sidewalks: sidewalk topping and curbing 2.1.6.1. Sidewalk topping and curbing 2.1.6.2. Landscaping 2.2. Utilities 2.2.1. Water main lines 2.2.2. Sewage main lines 2.2.3. Stormwater main lines 2.2.4. Gas 2.2.5. Electric 2.3. 2.3.1.ConcreteUnderpinning 2.3.1.1. Excavation 2.3.1.2. Pour concrete 2.3.1.3. Tie backs 2.3.1.4. Dry pack with non-shrink grout 2.3.1.5. Backfill 2.3.2. Footings 2.3.2.1. Excavation 2.3.2.2. Compaction
08/01/2018MCM 901 Page 49 of 224 Master Thesis: 620 N 3rd St Clara Bucar 2.3.2.3. Formwork 2.3.2.4. Rebar 2.3.2.5. Pour concrete 2.3.2.6. Cure concrete 2.3.2.7. Remove formwork 2.3.3. Foundations 2.3.3.1. Excavation 2.3.3.2. Compaction 2.3.3.3. Formwork 2.3.3.4. Rebar 2.3.3.5. Pour concrete 2.3.3.6. Cure concrete 2.3.3.7. Remove formwork 2.3.4. Concrete walls - board form concrete 2.3.4.1. Board form 2.3.4.2. Rebar 2.3.4.3. Pour concrete 2.3.4.4. Cure concrete 2.3.4.5. Remove board form 2.3.5. F1: Slab on grade (new basement and portion of 1st floor) 2.3.5.1. Excavation 2.3.5.2. Removal of dirt 2.3.5.3. Compaction 2.3.5.4. Vapor barrier 2.3.5.5. 4” PADOT No. 2B stone 2.3.5.6. Formwork 2.3.5.7. Rebar 2.3.5.8. Pour concrete 2.3.5.9. Cure concrete 2.3.5.10. Remove formwork 2.3.6. Concrete piers 2.3.6.1. Formwork 2.3.6.2. Rebar 2.3.6.3. Pour concrete 2.3.6.4. Cure concrete 2.3.6.5. Remove formwork 2.3.7. Concrete slabs 2.3.7.1. FF3: Typical floor assembly - 2hr fire separation 2.3.7.1.1. 2” synthetic fiber traffic wear layer
08/01/2018MCM 901 Page 50 of 224 Master Thesis: 620 N 3rd St Clara Bucar 2.3.7.1.2. Control joint @ 4’ O.C. (parking) 2.3.7.1.3. ⅜” protect/drainage layer, miradrain 9000 (parking) 2.3.7.1.4. Liquid applied waterproofing membrane (parking) 2.3.7.1.5. 0”-4” lightweight concrete to achieve slope 2.3.7.1.6. 4” poured in place concrete slab on 1 ½” composite decking 2.3.7.1.6.1. 4” concrete 2.3.7.1.6.2. 1 ½” decking 2.3.7.1.7. Welded wire fabric 2.3.7.1.8. Closed cell sprayed-in-insulation R-30 2.3.7.2. FF3.B: Typical floor assembly - 2hr fire separation 2.3.7.2.1. 0”-4” lightweight concrete to achieve slope 2.3.7.2.2. 4” poured in place concrete slab on 1 ½” composite decking 2.3.7.2.2.1. 4” concrete 2.3.7.2.2.2. 1 ½” decking 2.3.7.2.3. Welded wire fabric 2.3.7.2.4. Closed cell sprayed-in-insulation R-30 2.3.7.3. FF4: Typical floor assembly - 3hr fire separation 2.3.7.3.1. 2” synthetic fiber traffic wear layer 2.3.7.3.2. Control joint @ 4’ O.C. (parking) 2.3.7.3.3. ⅜” protect/drainage layer, miradrain 9000 (parking) 2.3.7.3.4. Liquid applied waterproofing membrane (parking) 2.3.7.3.5. 4 ½” poured in place concrete slab on 2” composite decking 2.3.7.3.5.1. 4 ½” concrete 2.3.7.3.5.2. 2” decking 2.3.7.3.6. Insulation 2.3.7.3.7. (3) 1” mineral wool batts @ beams 2.3.7.3.8. 1” mineral wool batts @deck 2.4. 2.4.1.Steel Steel columns 2.4.2. Steel beams 2.4.3. Structural channel shaped steel joist 2.4.3.1. FF2: Typical floor assembly above parking 2.4.3.1.1. 1” poured floor underlayment - usg levelrock 2.4.3.1.2. ¼” sound reduction mat - usg levelrock srm-25 2.4.3.1.3. (2) Vapor barrier
08/01/2018MCM 901 Page 51 of 224 Master Thesis: 620 N 3rd St Clara Bucar 2.4.3.1.4. ¾” structural concrete floor panels 2.4.3.1.5. R-30 fiberglass batt insulation 2.4.3.1.6. Structural channel shaped steel joist @ 16” O. C. 2.4.3.1.7. Resilient channels @ 16” O.C. 2.4.3.1.8. ¾” fire rated exterior sheathing 2.4.3.1.9. Air barrier 2.4.3.1.10. Stucco finish 2.4.3.1.10.1. 3 coat stucco finish 2.4.3.1.10.2. Wire lath 2.4.3.2. R2: Typical floor assembly above parking 2.4.3.2.1. Wood deck on sleepers 2.4.3.2.2. Roofing membrane 2.4.3.2.3. ¾” T&G Plywood 2.4.3.2.4. Wood sleepers for slope 2.4.3.2.5. Pressure treated wood blocking 6”x6” 2.4.3.2.6. ¾” structural concrete floor panels 2.4.3.2.7. Rubber padding 2.4.3.2.8. R-30 fiberglass batt insulation 2.4.3.2.9. Vapor barrier 2.4.3.2.10. Structural channel shaped steel joist 2.4.3.2.11. Resilient channels 2.4.3.2.12. ¾” fire rated exterior sheathing 2.4.3.2.13. Stucco finish 2.4.3.2.13.1. 3 coat stucco finish 2.4.3.2.13.2. Wire lath 2.4.3.3. RD2: Balcony Typical 2.4.3.3.1. Wood joists beyond 2.4.3.3.2. Steel channel 2.4.3.3.3. Cont. metal drip 2.4.3.4. RD3: Balcony @ West 2.4.3.4.1. Wood deck on sleepers 2.4.3.4.2. Roofing membrane 2.4.3.4.3. ¾” T&G Plywood 2.4.3.4.4. Wood sleepers for slope 2.4.3.4.5. Steel channel 2.4.4. Walls and partitions 2.4.4.1. WF3.b: 2hr steel stud exterior wall 2.4.4.1.1. Brick ties 2.4.4.1.2. Brick veneer
08/01/2018MCM 901 Page 52 of 224 Master Thesis: 620 N 3rd St Clara Bucar 2.4.4.1.3. 1” air space 2.4.4.1.4. Weather barrier 2.4.4.1.5. ½” cement board 2.4.4.1.6. (3) ⅝” Gypsum board fire rated 2.4.4.1.7. R-19 fiberglass insulation 2.4.4.1.8. 6” steel studs @ 16: O. C. 2.4.4.1.9. Vapor barrier 2.4.5. Header 2.4.5.1.1. ⅗” stl 2.5. 2.5.1.MasonryMasonry walls 2.5.1.1. Lintel precast 2.5.1.1.1. Max span 4’-0” 2.5.1.1.2. Max span 6’-0” 2.5.1.2. WF6: 2HR rated interior concrete masonry wall 2.5.1.2.1.2.5.1.2.1.1.Material8” nominal concrete block wall 2.5.1.2.1.2. Reinforcing 2.5.1.2.1.3. 1 ½” furring channels 2.5.1.2.1.4. 1 ½” rigid insulation 2.5.1.2.1.5. ⅝” gypsum wall board 2.5.1.2.2. Labor 2.5.1.3. WF7: 1hr rated exterior wall at elevator shaft 2.5.1.3.1. 8” nominal concrete block wall 2.5.1.3.2. Reinforcing 2.5.1.3.3. 3” rigid insulation R-19 minimum 2.5.1.3.4. 2x4 wood studs @ 16 O. C. 2.5.1.3.5. ¾” exterior grade plywood sheathing 2.5.1.3.6. Weather barrier 2.5.1.3.7. 3 coat cement stucco finish (where there is no adjacent building) 2.5.1.4. Stone coping 2.6. Wood structure 2.6.1. Floor joists 2.6.1.1. FF1: Typical floor assembly B/T residential stories 2.6.1.1.1. 1” poured floor underlayment - usg levelrock 2.6.1.1.2. ¼” sound reduction mat - usg levelrock srm-25
08/01/2018MCM 901 Page 53 of 224 Master Thesis: 620 N 3rd St Clara Bucar 2.6.1.1.3. Vapor barrier: 0.010” 2.6.1.1.4. ¾” T&G Subfloor sheathing glued and screwed 2.6.1.1.5. 3 ½” batt insulation 2.6.1.1.6. Vapor barrier 2.6.1.1.7. Engineered wood joist 2.6.1.1.8. Resilient channels @ 16” O.C. 2.6.1.1.9. (2) ½” gypsum board fire rated 2.6.1.2. F2: Typical non-rated floor assembly 2.6.1.2.1. ¾” nailed down hardwood flooring 2.6.1.2.2. ¾” T&G plywood 2.6.1.2.3. Floor joists 2.6.1.2.4. Resilient channels 2.6.1.2.5. ⅝” gypsum board 2.6.1.3. F3: Typical floor @ bay 2.6.1.3.1. ¾” nailed down hardwood flooring 2.6.1.3.2. ¾” T&G plywood 2.6.1.3.3. Vapor barrier 2.6.1.3.4. R-30 batt insulation 2.6.1.3.5. ¾” exterior grade sheathing 2.6.1.3.6. Floor joists 2.6.1.3.7. Weather barier 2.6.1.3.8. Furring or shim 2.6.1.3.9. ⅝” architectural panel 2.6.1.3.9.1. Aluminum 2.6.1.3.9.2. Stone 2.6.1.3.9.3. Stucco finish 2.6.1.4. R1: Typical hot-roof assembly 2.6.1.4.1. Wood deck on sleepers 2.6.1.4.2. Roofing membrane 2.6.1.4.3. ¾” T&G plywood 2.6.1.4.4. Wood sleepers for slope 2.6.1.4.5. Pressure treated wood blocking 6”x6” 2.6.1.4.6. Rubber padding 2.6.1.4.7. Floor joists 2.6.1.4.8. Closed cell sprayed-in-insulation 2.6.1.4.9. (2) ½” fire rated gypsum board 2.6.1.4.10. River stone 2.6.1.4.11. Perforated stainless steel “L” angle 2.6.2. Walls and partitions
08/01/2018MCM 901 Page 54 of 224 Master Thesis: 620 N 3rd St Clara Bucar 2.6.2.1. W1: Wood frame exterior wall with brick/stone veneer 2.6.2.1.1. 3 ¾” brick/stone veneer 2.6.2.1.2. Reinforcement 2.6.2.1.3. 1” air cavity 2.6.2.1.4. ¾” exterior grade plywood 2.6.2.1.5. R-19 fiberglass batt insulation 2.6.2.1.6. 2x6” wood studs @ 16” O.C. 2.6.2.1.7. Vapor barrier 2.6.2.1.8. ⅝” Gypsum board 2.6.2.2. W2: Wood framed exterior wall @ stucco and rainscreen 2.6.2.2.1.2.6.2.2.1.1.MaterialWeather barrier 2.6.2.2.1.2. ¾” exterior plywood sheathing 2.6.2.2.1.3. 2x6 wood studs @ 16” O. C. 2.6.2.2.1.4. R-19 fiberglass insulation 2.6.2.2.1.5. Vapor barrier 2.6.2.2.1.6. ⅝” Gypsum board 2.6.2.2.1.7. Exterior finish 2.6.2.2.1.7.1.2.6.2.2.1.7.1.1.Stucco 3 coat cement stucco 2.6.2.2.1.7.1.2. Wire lath 2.6.2.2.1.7.2. Architectural panels 2.6.2.2.1.7.2.1.2.6.2.2.1.7.2.1.1.Aluminum1”vented air layer 2.6.2.2.1.7.2.1.2. Aluminum rainscreen bearing system 2.6.2.2.1.7.2.2.2.6.2.2.1.7.2.2.1.Stone 1” vented air layer 2.6.2.2.1.7.2.2.2. Facade cladding panels 2.6.2.2.1.7.2.3. Wood slat rainscreen 2.6.2.2.1.7.2.3.1. 1” vented air layer 2.6.2.2.1.7.2.3.2. Heat treated poplar wood strips 2.6.2.2.1.7.2.3.3. Galvanized metal bar system 2.6.2.3. WF1: 1hr wood frame wall @ property line 2.6.2.3.1. Stucco finish (where there is no adjacent building) 2.6.2.3.1.1. 2 layers of stucco finish 2.6.2.3.1.2. Wire lath 2.6.2.3.2. Weather barrier
08/01/2018MCM 901 Page 55 of 224 Master Thesis: 620 N 3rd St Clara Bucar 2.6.2.3.3. ¾” exterior plywood sheathing 2.6.2.3.4. R-19 fiberglass insulation 2.6.2.3.5. 2x6 wood studs @ 16” 2.6.2.3.6. Vapor barrier 2.6.2.3.7. ⅝” Gypsum board fire rated 2.6.3. Posts 2.6.3.1. 2”x6” 2.6.3.2. 6”x6” 2.6.3.3. 5 ¼” x 5 ¼” PSL 2.6.4. Headers 2.6.4.1. 2”x8” 2.6.4.2. 2”x10” 2.6.4.3. 2”x12” 2.6.4.4. 1 ¾” x 11 ⅞” LVL 2.7. Interior partitions 2.7.1. Chain link partitions 8’ high (unit storage) 2.7.1.1. Partitions 2.7.1.2. Gates 3’ wide 2.7.2. P1: Typical interior partitions 2.7.2.1. Wood studs 2.7.2.1.1. 2x4 wood studs 2.7.2.1.2. 2x6 wood studs 2.7.2.2. Wood wall plates 2.7.2.2.1. 2x4 wall plates 2.7.2.2.2. 2x6 wall plates 2.7.2.3. Batt insulation 2.7.2.4. Nail heads 2.7.2.5. Wallboard joints covered with tape and joint compound 2.7.2.6.2.7.2.6.1.Wallboards ⅝” Gypsum board 2.7.2.6.2. ½” Dens-shield tile backer board (tile backer at tile and wet locations) 2.7.3. Perforations on fire rated walls 2.7.3.1. Seal sleeve with expanding concrete grout 2.7.3.2. Pipe sleeve schedule 40 galvanized 2.7.3.3. Seal: 3M wrapstrap firestop 2.7.4. WF2: 1h wood frame wall between units 2.7.4.1. (2) ⅝” fire rated gypsum wall board
08/01/2018MCM 901 Page 56 of 224 Master Thesis: 620 N 3rd St Clara Bucar 2.7.4.2. 2x6 wood studs @24” O.C. 2.7.4.3. 3” fiberglass batt insulation 2.7.4.4. Resilient furring channel 2.7.5. WF2.B: 1hr wood frame bearing wall 2.7.5.1. (2) ⅝” fire rated gypsum wall board 2.7.5.2. 2x6 wood studs @ 16” O.C. 2.7.5.3. R-19 fiberglass insulation 2.7.6. WF3: 2hr wood frame interior wall 2.7.6.1. (4) ⅝” fire rated gypsum wall board 2.7.6.2. 2x6 wood studs @16” O.C. 2.7.6.3. R-19 fiberglass insulation 2.7.6.4. Resilient furring channel 2.7.7. WF3.A: 2hr steel stud interior wall 2.7.7.1. (4) ⅝” fire rated gypsum wall board 2.7.7.2. 3 ⅝” steel studs @ 16” O. C. 2.7.7.3. 2” fiberglass batt insulation 2.7.8. WF8: 3hr shaft wall 2.7.8.1. (3) ⅝” fire rated gypsum wall board 2.7.8.2. 1” gypsum shaft liner 2.7.8.3. 2 ½” wide and 1 ½” deep C-H stud min 25 gauge steel @ 24” O.C. 2.7.9. WF5: Insulation and finish on concrete walls 2.7.9.1. WF5 with rigid insulation 2.7.9.1.1. ⅝” Gypsum board 2.7.9.1.2. 2” polyiso insulation 2.7.9.1.3. 2” Z-furring @ 16” O. C. 2.7.9.2. WF5 with batt insulation 2.7.9.2.1. Airgap 2.7.9.2.2. 2x4 wood studs @ 16” O.C. 2.7.9.2.3. R-19 batt insulation 2.7.9.2.4. ⅝” Gypsum board 2.8. Interior finishes 2.8.1. Walls 2.8.1.1. Gypsum board 2.8.1.1.1. Prime 2.8.1.1.2. Painting 2.8.1.2. Ceramic tiles - bathrooms 2.8.1.3. Ceramic tiles - kitchens 2.8.2. Ceiling
08/01/2018MCM 901 Page 57 of 224 Master Thesis: 620 N 3rd St Clara Bucar 2.8.2.1. Gypsum board 2.8.2.1.1. Paint 2.8.3. Floor 2.8.3.1. Concrete polishing 2.8.3.2. Baseboard 2.9. 2.9.1.OpeningsExterior openings 2.9.1.1.2.9.1.1.1.WindowsOperable windows 2.9.1.1.2. Fixed windows 2.9.1.1.3. Double panel operable and fixed 2.9.1.1.4. Circular glazing 2.9.1.2. Sliding doors 2.9.1.2.1. 2 panels 2.9.1.2.2. 3 panels 2.9.1.2.3. 4 panels 2.9.1.3. Entry doors 2.9.1.4. Garage doors 2.9.1.4.1. N 3rd St garage door 2.9.1.4.2. N Galloway St garage door 2.9.1.5. Peco access grating protection 2.9.2. Interior openings 2.9.2.1.2.9.2.1.1.Doors Insulated metal with aluminum frame 2.9.2.1.2. Wood core door 2.9.2.1.3. Interior solid wood door 2.9.2.1.4. Primed wood frame 2.10. Stairs 2.10.1. East staircase 2.10.2. West staircase 2.10.3. Exterior stairs - Unit 4C 2.11. Elevator 2.11.1. Structure 2.11.2. Elevator car
08/01/2018MCM 901 Page 58 of 224 Master Thesis: 620 N 3rd St Clara Bucar 2.12. Electric 2.12.1.2.12.1.1.Rough Wires 2.12.1.2. Receptacles 2.12.1.3. Junction boxes 2.12.1.4. Electrical panels 2.12.1.4.1. General panel (at basement) 2.12.1.4.2. Single panels (at floors, one per apartment) 2.12.2. Devices/Lighting 2.12.2.1. Light switches 2.12.2.2. Outlets 2.12.2.3. Interior lighting fixtures 2.12.2.4. Exterior lighting fixtures 2.12.2.5. Timers 2.12.2.6. Dimmers 2.12.2.7. Emergency exit signs 2.12.2.8. Motion detector 2.12.2.9. Owner appliances 2.12.2.9.1. Fridge 2.12.2.9.2. Stove 2.12.2.9.3. Oven 2.12.2.9.4. Microwave 2.12.2.9.5. Dishwasher 2.12.2.9.6. Washing machine 2.12.2.9.7. Dryer 2.12.3. Low voltage 2.12.3.1.2.12.3.1.1.Rough Automated shade wiring 2.12.3.1.2. Automated garage door wiring 2.12.3.1.3. Data wiring (CAT) 2.12.3.1.4. Tv Wiring 2.12.3.1.5. Intercom wiring 2.12.3.2.2.12.3.2.1.Final Shade motor power 2.12.3.2.2. Garage door opener 2.12.3.2.3. Data receptacles 2.12.3.2.4. Tv receptacles 2.12.3.2.5. Intercom 2.12.4. Security system
08/01/2018MCM 901 Page 59 of 224 Master Thesis: 620 N 3rd St Clara Bucar 2.12.4.1.2.12.4.1.1.Rough Wiring 2.12.4.2.2.12.4.2.1.Final Security cameras 2.12.4.2.2. Alarm keypad 2.12.5. Fire protection 2.12.5.1.2.12.5.1.1.Rough Wiring 2.12.5.2.2.12.5.2.1.Final Smoke detector 2.12.5.2.2. Fire alarm control panel 2.12.5.2.3. Duct smoke detector 2.12.5.2.4. Combo smoke and carbon monoxide detector 2.12.5.2.5. Photoelectric smoke detector 2.12.5.2.6. Manual pull station 2.12.5.2.7. Tamper switch 2.12.5.2.8. Water floor switch 2.12.5.2.9. Strobe only 2.12.5.2.10. Fire alarm horn/strobe 2.12.5.2.11. Photoelectric heat detector 2.12.5.2.12. Fire smoke damper 2.12.5.2.13. Auto dialer to locally approved central station 2.13. 2.13.1.PlumbingSanitary 2.13.1.1.2.13.1.1.1.Rough Sanitary sewer piping 2.13.1.1.1.1. 3” 2.13.1.1.2. Soil stack 2.13.1.1.3. Vent stack 2.13.1.1.4. Branch vent 2.13.1.1.5. Vent piping (cast iron) 2.13.1.2.2.13.1.2.1.Final Bathroom sink 2.13.1.2.2. Toilet 2.13.1.2.3. Shower drain 2.13.1.2.4. Kitchen sink 2.13.1.2.5. Sump pump 2.13.2. Cold and water supply
08/01/2018MCM 901 Page 60 of 224 Master Thesis: 620 N 3rd St Clara Bucar 2.13.2.1.2.13.2.1.1.Rough Cold water piping 2.13.2.1.2. Hot water piping 2.13.2.1.3. Tempered water piping 2.13.2.2.2.13.2.2.1.Final Bathroom faucet 2.13.2.2.2. Toilet 2.13.2.2.3. Kitchen faucet 2.13.2.2.4. Shower head 2.13.2.2.5. Hose bib 2.13.2.2.6. Valve 2.13.2.2.7. Owner appliances 2.13.2.2.7.1. Dishwasher 2.13.2.2.7.2. Washing machine 2.13.2.2.7.3. Dryer 2.13.3. Gas supply 2.13.3.1.2.13.3.1.1.Rough Gas piping 2.13.3.2.2.13.3.2.1.Final Devices connection valve 2.13.4. Storm water 2.13.4.1.2.13.4.1.1.Rough Storm water pipe 2.13.4.1.1.1. 6” 2.13.4.1.1.2. 5” 2.13.4.1.2. Roof downpipe 2.13.4.2.2.13.4.2.1.Final Roof drain 2.13.4.2.2. Floor drain 2.13.4.2.3. Spouts 2.13.5. Fire protection 2.13.5.1.2.13.5.1.1.Rough Piping 2.13.5.2.2.13.5.2.1.Final Hydrant 2.14. HVAC 2.14.1. Rough
08/01/2018MCM 901 Page 61 of 224 Master Thesis: 620 N 3rd St Clara Bucar 2.14.1.1.2.14.1.1.1.Ductwork6” diameter duct 2.14.1.1.2. 8” diameter duct 2.14.1.1.3. 12”x10” duct 2.14.1.1.4. 10”x10” duct 2.14.1.1.5. 8”x10” duct 2.14.1.1.6. 8”x8” duct 2.14.1.1.7. 12”x4” duct 2.14.1.1.8. 12”x6” duct 2.14.1.1.9. 24”x8” duct 2.14.1.1.10. 24”x10” duct 2.14.1.1.11. 20”x12” duct 2.14.1.1.12. 22”x16” duct 2.14.1.1.13. 14”x10” duct 2.14.1.1.14. 18”x10” duct 2.14.2. Final 2.14.2.1. Exhaust fans (bathrooms ceiling) 2.14.2.2. AHU (ceiling cassette heat pump units for lobbies) 2.14.2.2.1. Vibration isolation pad for roof 2.14.2.3. Gas furnace/Air conditioning units (one for each apartment) 2.14.2.3.1. AC unit (inside each apartment) 2.14.2.3.2. Filter 2.14.2.3.3. Flex connection 2.14.2.3.4. Vibration isolation pad for roof 2.14.2.3.5. Vibration isolation pad for each apartment’s mech. closet 2.14.2.4. Ceiling hung electric heaters 2.14.2.5. Baseboard electric heater 2.14.2.6.2.14.2.6.1.Grilles Surface mounted, 4 way square diffuser w/ adjustable discharge louvers 14”x14” 2.14.2.6.2. Aluminum surface mounted, 4 way square diffuser with adjustable discharge louvers 8”x8” 2.14.2.6.3. Aluminum, exhaust air grille 6”x6” 2.14.2.6.4. Steel, sidewall return grille 2.14.2.6.5. Steel, transfer air grille 2.14.2.7. Dryer boost fan 2.14.2.8. Roof caps 2.14.2.9. Duct cap 2.14.2.10. 10” Kitchen hood exhaust duct
08/01/2018MCM 901 Page 62 of 224 Master Thesis: 620 N 3rd St Clara Bucar 2.14.2.11. Thermostat 2.15. Landscaping 2.15.1. GD2: Planter at grade 2.15.1.1. Stone coping 2.15.1.2. Flashing 2.15.1.3. Geo filter fabric 2.15.1.4. ¾ x 2 x 4 treated blkg 2.15.1.5. ½” drain hole 2.15.1.6. Stainless steel spaces (provide weep holes) 2.15.1.7. Dirt 2.15.1.8. Plants 2.15.2. Planters at roof 2.15.2.1. Structure 2.15.2.2. Dirt 2.15.2.3. Plants 2.15.3. River stone 2.16. Specialties 2.16.1.2.16.1.2.2.16.1.1.MillworkKitchenCommon areas 2.16.2. Curtains 2.16.3. Cage for utilities in basement 2.16.4. Railing for balconies 2.16.5. Kitchen accessories 2.16.5.1. Kitchen counters 2.16.6. Bathrooms accessories 2.16.6.1. Toilet paper holders 2.16.6.2. Towel holders 2.16.6.3. Medicine cabinets 2.16.6.4. Shower base 2.16.7. Mailboxes 2.16.8. Stripe painting in garage 2.16.9. Garage bumper precast 2.16.10.2.16.10.1.SignageFront facade number 2.16.10.2. Leasing office reference 2.16.10.3. Trash room
08/01/2018MCM 901 Page 63 of 224 Master Thesis: 620 N 3rd St Clara Bucar 3. Close out 3.1. Punchlist 3.2. RFI closeout 3.3. Change order closeout 3.4. CO Inspection 3.5. Substantial completion 3.6. Commissioning 3.6.1. T&B 3.7. Financial resolution 3.8. Turnover
08/01/2018MCM 901 Page 64 of 224 Master Thesis: 620 N 3rd St Clara Bucar 4.2. Estimate: Basis of the Estimate Basis of the Estimate 7/7/2018 Project: 620 N 3rd St Building Type: Residential Location: 620 N 3rd St, Philadelphia PA Brief Description: 4 stories + basement and roof deck, 9 units total residential Below Grade Levels: Area SF Type / Description 1 2117 2117 Basement (storage and MEP) 2 Total Below Grade 2117 Ground Floor: Area SF 1 4527 4527 Parking and lobby 2 Total Ground Floor 4527 Supported Levels: Area SF 21 4105 4105 3 residential units 3 4105 4105 3 residential units 4 4105 4105 3 residential units 5 2933 Deck 6 Total Floor Area 21892 Gross Floor Area 28536 Net Finished Area 13860.6 Roof Area SF Total Area: 479.75 Walls LF / Height SF Foundations: 4664.5 Interior: 29762 Exterior: 15171 Site Work Area SF Total Site Area: 0 Parking: 0 Access Roads: 0 Sidewalk: 797 Landscaping: 381
08/01/2018MCM 901 Page 65 of 224 Master Thesis: 620 N 3rd St Clara Bucar Estimate Summary Company: Fit Construction Company Project: 620 N 3rd St Gross SF 28536 Date: August 1st 2018 WBS/CSI # Description Amount $ / S.F. % of Total 01 GENERAL REQUIREMENTS ($ 384,458) ($ 13.47) 12.7% 03 CONCRETE ($ 232,859) ($ 8.16) 7.7% 04 MASONRY ($ 33,947) ($ 1.19) 1.1% 05 METALS ($ 142,111) ($ 4.98) 4.7% 06 WOOD, PLASTICS, AND COMPOSITES ($ 228,915) ($ 8.02) 7.6% 07 THERMAL AND MOISTURE PROTECTION ($ 120,084) ($ 4.21) 4.0% 08 OPENINGS ($ 128,961) ($ 4.52) 4.3% 09 FINISHES ($ 432,638) ($ 15.16) 14.3% 10 SPECIALITIES ($ 137,096) ($ 4.80) 4.5% 14 CONVEYING SYSTEMS ($ 150,000) ($ 5.26) 5.0% 21 FIRE SUPPRESSION ($ 76,600) ($ 2.68) 2.5% 22 PLUMBING ($ 217,604) ($ 7.63) 7.2% 23 HVAC ($ 123,772) ($ 4.34) 4.1% 25 INTEGRATED AUTOMATION ($ 10,000) ($ 0.35) 0.3% 26 ELECTRICAL ($ 118,489) ($ 4.15) 3.9% 27 COMMUNICATIONS ($ 45,000) ($ 1.58) 1.5% 28 ELECTRONIC SAFETY AND SECURITY ($ 20,000) ($ 0.70) 0.7% 31 EARTHWORK ($ 13,865) ($ 0.49) 0.5% 32 EXTERIOR IMPROVEMENTS ($ 10,579) ($ 0.37) 0.4% 33 UTILITIES ($ 30,000) ($ 1.05) 1.0% TOTAL DIRECT COSTS ($ 2,656,977) 93.11 88.1% Subtotal ($ 2,656,977) 93.11 88.1% GENERAL OVERHEAD 6.0% ($ 159,419) 5.59 5.3% Subtotal ($ 2,816,396) 98.70 93.4% CM FEE/PROFIT 5.0% ($ 140,820) 4.93 4.7% SUBTOTAL A ($ 2,957,215) 103.63 98.0% BONDS 1.0% ($ 29,572) 1.04 1.0% Subtotal ($ 2,986,787) 104.67 99.0% INSURANCE 1.0% ($ 29,572) 1.04 1.0% Subtotal ($ 3,016,360) 105.70 100.0% CONTINGENCY 10.0% ($ 295,722) 10.36 9.8% TOTAL ($ 3,016,360) 105.70 100.0% 4.3 Estimate Summary
08/01/2018MCM 901 Page 66 of 224 Master Thesis: 620 N 3rd St Clara Bucar ITEM Unit Cost Unit Q'ty Total ON-SITE SUPERVISION & ADMIN. $194,300 Project Manager $1,000 Month 3 $3,000 Project Engineer $5,000 Month 3 $15,000 Project Superintendent (On site) $7,000 Month 12 $84,000 Field Engineer (On site) $4,500 Month 12 $54,000 BIM Engineer $4,500 Month 3 $13,500 Project Estimator $8,000 Month 0.25 $2,000 Safety Engineer $6,500 Month 2.4 $15,600 Health Insurance-Salary Staff $300 Mon Per Person 24 $7,200 ENGINEERING & SURVEY $33,800 2 way radios $150) Each 4 $600 Print bid packages $300) Each 2 $600 Print drawings for staff $500) Set 2 $1,000 Construction drawing print/copy $3,000) Lump sum 1 $3,000 As-built printing $750) Set 2 $1,500 O&M manuals $500) Each 2 $1,000 Outside Consultants $5,000) Lump sum 1 $5,000 PERMITTING $6,100 Zoning permit $500) Lump sum 1 $500 Building permit $2,000) Lump sum 1 $2,000 Permit to block sidewalk $300) Each 6 $1,800 Permit to block roads $300) Each 6 $1,800 SAFETY $5,110 Safety Incentives $500) Each 6 $3,000 Employee training $1,500) Lump sum 1 $1,500 First aid supplies $250) Lump sum 1 $250 Fire extinguishers (1 per 5,000 SF) $60) Each 6 $360 4.4. Division 01 - General Requirements
08/01/2018MCM 901 Page 67 of 224 Master Thesis: 620 N 3rd St Clara Bucar ITEM Unit Cost Unit Q'ty Total TEMPORARY FACILITIES $64,589 Office trailer 24x60 $2,000) Month 10.5 $21,000 Setup & remove trailer $1,000) Each 2 $2,000 Janitorial service for trailers $225) Month 10.5 $2,363 Temp toilets $125) Each per Month 24 $3,000 Wash stations (1 station for each 2 toilets) $95) Each per Month 12 $1,140 Preconstruction photo survey $1,500) Lump sum 1 $1,500 Bulletin boards $500) Each 2 $1,000 Project Signage $1,000) Each 2 $2,000 Office supplies $200) Month 12 $2,400 Computers $300) Each 2 $600 Printers $500) Each 1 $500 Network/Wireless (wiring & data lines) $120) Month 12 $1,440 Office software $2,500) Lump sum 1 $2,500 Postage & shipping $450) Month 12 $5,400 Cell phone $75) Month / phone 24 $1,800 Temp Fencing $8) Linear Foot 87 $696 Drinking water/Coffee $200) Month 12 $2,400 Temp water usage $300) Month 12 $3,600 Temp power – Office usage $350) Month 3 $1,050 Street sweeper $650) Month 12 $7,800 Snow removal $100) Month 4 $400 BUILDING SERVICES $77,660 Sheltered walkway $3,000) Month 6 $18,000 Temporary pulley $300) Month 6 $1,800 Temporary trash chute $300) Month 6 $1,800 Weekly cleanup (2mandays/week) $120) Man Day 117 $14,040 Dumpster rental - 40 CUYD $450) Pull 58.5 $26,325 Final building cleaning (int & ext) $0.55) SF 28536 $15,695 TRANSPORTATION $9,000 Pickup $450) Month 12 $5,400 Vehicle Fuel $215) Month / Vehicle 12 $2,580 Vehicle Maintenance $85) Month / Vehicle 12 $1,020 TOTAL $384,458
08/01/2018MCM 901 Page 68 of 224 Master Thesis: 620 N 3rd St Clara Bucar Detailed Estimate WBS/ CSI Code Description Material and Labor Allowance SubcontractorQuote Total $/GSFQty Unit Unit Cost 02250 Concrete: Underpinning 0.00 0 ($ 15,000.00) ($ - ) ($ 15,000.00) ($ 1.08) 03310 Concrete: Footings 45.69 CY 305 ($ - ) ($ - ) ($ 13,935.34) ($ 1.01) 03310 Concrete: Foundations 284.07 CY 495 ($ - ) ($ - ) ($ 140,613.37) ($ 10.14) 03310 Concrete: Piers 1.29 CY 495 ($ - ) ($ - ) ($ 636.53) ($ 0.05) 033313 Concrete: Walls - board form concrete 365.00 CY 50 ($ - ) ($ - ) ($ 18,250.00) ($ 1.32) 033113 Concrete: Slab on grade 52.11 CY 228 ($ - ) ($ - ) ($ 11,881.33) ($ 0.86) 033116 Concrete: Lightweight Concrete 13.90 CY 200 ($ - ) ($ - ) ($ 2,779.26) ($ 0.20) 033113 Concrete: Slab poured in place 7.95 CY 210 ($ - ) ($ - ) ($ 1,669.31) ($ 0.12) 035113 Concrete: 3/4" Structural Concrete Floor Panels 4092.00 SF 2 ($ - ) ($ - ) ($ 8,184.00) ($ 0.59) 035116 Concrete: 1" poured underlayment 3620.00 SF 5.5 ($ - ) ($ - ) ($ 19,910.00) ($ 1.44) 051223 Metal: W-Wide flange steel beams 12.63 TON 4500 ($ - ) ($ - ) ($ 56,837.39) ($ 4.10) 051223 Metal: LL-Double Angle: 2L3-1/2X3X5/16LLBB 0.09 TON 4500 ($ - ) ($ - ) ($ 414.00) ($ 0.03) 051223 Metal: L-Angle: L3-1/2X3-1/2X5/16 0.22 TON 4500 ($ - ) ($ - ) ($ 1,000.80) ($ 0.07) 051223 Metal: C-Channel C8X11.5 0.15 TON 4500 ($ - ) ($ - ) ($ 654.64) ($ 0.05) 051223 Metal: W8X10 0.04 TON 4500 ($ - ) ($ - ) ($ 184.50) ($ 0.01) 051223 Metal: HSS Columns 2.01 TON $4,500.00 ($ - ) ($ - ) ($ 9,051.61) ($ 0.65) 052100 Metal: Structured channel shaped steel joist 6.35 TON $4,500.00 ($ - ) ($ - ) ($ 28,579.02) ($ 2.06) 053600 Metal: Composite decking 0.00 SF $0.00 ($ - ) ($ 13,489.00) ($ 13,489.00) ($ 0.97) 051223 Metal: Headers 8.92 LF $15.00 ($ - ) ($ - ) ($ 133.86) ($ 0.01) 051223 Metal: Lintel 0.00 LF $0.00 ($ - ) ($ 471.40) ($ 471.40) ($ 0.03) 054100 Metal: Framing 0.00 LF $0.00 ($ - ) ($ 13,052.88) ($ 13,052.88) ($ 0.94) 055000 Metal: Welded wire fabric 1862.00 SF $0.50 ($ - ) ($ - ) ($ 931.00) ($ 0.07) 055001 Metal: Resilient channels 3799.00 SF $1.50 ($ - ) ($ - ) ($ 5,698.50) ($ 0.41) 055002 Metal: Railing balconies 42" high 165.30 LF $40.00 ($ - ) ($ - ) ($ 6,612.00) ($ 0.48) 055003 Metal: Elevator ladder 0.00 EA $0.00 ($ 2,000.00) ($ - ) ($ 2,000.00) ($ 0.14) 055004 Metal: PECO grate 0.00 EA $0.00 ($ 3,000.00) ($ - ) ($ 3,000.00) ($ 0.22) 061733 Wood: Structual Wood Floor Joists 0.00 LF $0.00 ($ - ) ($ 57,685.76) ($ 57,685.76) ($ 4.16) 061000 Wood: Girders 0.00 LF $0.00 ($ - ) ($ 18,014.75) ($ 18,014.75) ($ 1.30) 061000 Wood: Posts 0.00 LF $0.00 ($ - ) ($ 15,448.44) ($ 15,448.44) ($ 1.11) 061000 Wood: Headers 0.00 LF $0.00 ($ - ) ($ 5,411.73) ($ 5,411.73) ($ 0.39) 061100 Wood: Framing 0.00 SF $0.00 ($ - ) ($ 52,339.20) ($ 52,339.20) ($ 3.78) 061200 Wood: Interior Stairs Wood Framing and Handrails 0.00 EA $0.00 ($ - ) ($ 8,000.00) ($ 8,000.00) ($ 0.58) 061600 Wood: Wood 3/4" subfloor sheathing 6969.00 SF $2.50 ($ - ) ($ - ) ($ 17,422.50) ($ 1.26) 061600 Wood: Exterior Plywood 0.00 SF $0.00 ($ - ) ($ 41,243.95) ($ 41,243.95) ($ 2.98) 06160 Wood: 3/4" fire rated exterior sheathing 0.00 SF $0.00 ($ - ) ($ 10,230.00) ($ 10,230.00) ($ 0.74) 061600 Wood: Sheer wall nailing 0.00 SF $0.00 ($ - ) ($ 3,118.92) ($ 3,118.92) ($ 0.23) 071800 Thermal and moisture: 3/8" protection layer 1477.00 SF $0.75 ($ - ) ($ - ) ($ 1,107.75) ($ 0.08) 4.5. Detailed estimate back-up
08/01/2018MCM 901 Page 69 of 224 Master Thesis: 620 N 3rd St Clara Bucar Detailed Estimate WBS/ CSI Code Description Material and Labor Allowance SubcontractorQuote Total $/GSFQty Unit Unit Cost 071801 Thermal and moisture: 2" Synthethic fiber traffic wear layer 1477.00 SF $2.00 ($ - ) ($ - ) ($ 2,954.00) ($ 0.21) 071400 Thermal and moisture: Liquid applied waterproofing membrane 1477.00 SF $0.75 ($ - ) ($ - ) ($ 1,107.75) ($ 0.08) 072100 Thermal and moisture: Closed cell sprayed-in insulation R-30 4098.00 SF $2.00 ($ - ) ($ - ) ($ 8,196.00) ($ 0.59) 070000 Thermal and moisture: 1/4" sound reduction mat 10589.00 SF $0.50 ($ - ) ($ - ) ($ 5,294.50) ($ 0.38) 072500 Thermal and moisture: Vapor barrier 26631.00 SF $0.25 ($ - ) ($ - ) ($ 6,657.75) ($ 0.48) 072100 Thermal and moisture: R-30 fiberglass batt insulation 4092.00 SF $1.00 ($ - ) ($ - ) ($ 4,092.00) ($ 0.30) 072100 Thermal and moisture: Batt insulation, 3 1/2" 6969.00 SF $1.25 ($ - ) ($ - ) ($ 8,711.25) ($ 0.63) 072100 Thermal and moisture: 1" mineral wool batts 546.00 SF $0.75 ($ - ) ($ - ) ($ 409.50) ($ 0.03) 072500 Thermal and moisture: 6 mil puncture resistant vapor barrier 4220.00 SF $0.50 ($ - ) ($ - ) ($ 2,110.00) ($ 0.15) 075000 Thermal and moisture: Roofing membrane 4561.00 SF $7.00 ($ - ) ($ - ) ($ 31,927.00) ($ 2.30) 072100 Thermal and moisture: Batt insulation (interior partitions) 4310.00 SF $0.25 ($ - ) ($ - ) ($ 1,077.50) ($ 0.08) 072100 Thermal and moisture: 1 1/2" rigid insulation 1230.00 SF $1.50 ($ - ) ($ - ) ($ 1,845.00) ($ 0.13) 072100 Thermal and moisture: Min 3" fiberglass batt 3799.00 SF $0.75 ($ - ) ($ - ) ($ 2,849.25) ($ 0.21) 072500 Thermal and moisture: Weather barrier 9545.00 SF $0.25 ($ - ) ($ - ) ($ 2,386.25) ($ 0.17) 072100 Thermal and moisture: R-19 Batt Insulation 16899.00 SF $0.75 ($ - ) ($ - ) ($ 12,674.25) ($ 0.91) 072100 Thermal and moisture: 2" min fiber glass Batt insulations 391.00 SF $0.50 ($ - ) ($ - ) ($ 195.50) ($ 0.01) 072100 Thermal and moisture: 1/2" cement board 2063.00 SF $0.75 ($ - ) ($ - ) ($ 1,547.25) ($ 0.11) 072100 Thermal and moisture: 2" polyiso insulation 147.00 SF $5.00 ($ - ) ($ - ) ($ 735.00) ($ 0.05) 072100 Thermal and moisture: 1" gypsum shaft liner 162.00 SF $3.00 ($ - ) ($ - ) ($ 486.00) ($ 0.04) 076000 Thermal and moisture: Metal flashing 465.00 SF $8.00 ($ - ) ($ - ) ($ 3,720.00) ($ 0.27) 078400 Thermal and moisture: Coating for metal fireproofing 0.00 $0.00 ($ 20,000.00) ($ - ) ($ 20,000.00) ($ 1.44) 085000 Openings: Exterior aluminum frame and glazing 1873.00 SF $37.00 ($ - ) ($ - ) ($ 69,301.00) ($ 5.00) 085001 Openings: Miscellaneous glazing 9.00 SF $250.00 ($ - ) ($ - ) ($ 2,250.00) ($ 0.16) 083000 Openings: Louvers for trash room 1.00 EA $1,500.00 ($ - ) ($ - ) ($ 1,500.00) ($ 0.11) 083001 Openings: Overhead garage door 2.00 EA $5,000.00 ($ - ) ($ - ) ($ 10,000.00) ($ 0.72) 083002 Openings: Interior Woods Doors 0.00 EA $0.00 ($ - ) ($ 21,110.00) ($ 21,110.00) ($ 1.52) 081001 Openings: Specialty Doors 0.00 EA $0.00 ($ - ) ($ 24,800.00) ($ 24,800.00) ($ 1.79) 093013 Finishes: Ceramic for walls 5782.15 SF $5.50 ($ - ) ($ - ) ($ 31,801.81) ($ 2.29) 099123 Finishes: Gypsum board walls - Prime and paint 44285.87 SF $0.50 ($ - ) ($ - ) ($ 22,142.93) ($ 1.60) 096400 Finishes: Baseboard trims 4254.17 LF $4.00 ($ - ) ($ - ) ($ 17,016.66) ($ 1.23) 092900 Finishes: 5/8" gypsum board for walls 29857.00 SF $1.00 ($ - ) ($ - ) ($ 29,857.00) ($ 2.15) 092900 Finishes: 5/8" fire rated gypsum board for walls 19534.00 SF $1.25 ($ - ) ($ - ) ($ 24,417.50) ($ 1.76) 093013 Finishes: Ceramic for floor 872.17 SF $10.00 ($ - ) ($ - ) ($ 8,721.70) ($ 0.63) 096400 Finishes: Hardwood flooring 8307.00 SF $10.00 ($ - ) ($ - ) ($ 83,070.00) ($ 5.99) 092900 Finishes: 5/8" gypsum board for ceiling 15705.00 SF $1.00 ($ - ) ($ - ) ($ 15,705.00) ($ 1.13) 092900 Finishes: 1/2" fire rated gypsum board for ceiling 8307.00 SF $1.50 ($ - ) ($ - ) ($ 12,460.50) ($ 0.90)
08/01/2018MCM 901 Page 70 of 224 Master Thesis: 620 N 3rd St Clara Bucar Detailed Estimate WBS/ CSI Code Description Material and Labor Allowance SubcontractorQuote Total $/GSFQty Unit Unit Cost 099123 Finishes: Paint gypsum board ceiling 7398.00 SF $1.00 ($ - ) ($ - ) ($ 7,398.00) ($ 0.53) 095100 Finishes: Hung ceiling system 1275.00 SF $7.00 ($ - ) ($ - ) ($ 8,925.00) ($ 0.64) 096000 Finishes: Lobby and hallways flooring 1066.00 SF $14.00 ($ - ) ($ - ) ($ 14,924.00) ($ 1.08) 096000 Finishes: Stairs flooring 2.00 EA $7,000.00 ($ - ) ($ - ) ($ 14,000.00) ($ 1.01) 096400 Finishes: Wood decking 2709.15 SF $12.00 ($ - ) ($ - ) ($ 32,509.80) ($ 2.35) 099400 Finishes: Stucco, 3 layers 623.47 SF $5.00 ($ - ) ($ - ) ($ 3,117.36) ($ 0.22) 074600 Finishes: Architectural aluminum panel color A w/ bearing system 2383.07 SF $18.00 ($ - ) ($ - ) ($ 42,895.25) ($ 3.09) 074601 Finishes: Architectural aluminum panel color B w/ bearing system 89.14 SF $18.00 ($ - ) ($ - ) ($ 1,604.50) ($ 0.12) 093100 Finishes: 3 3/4" brick veneer 1693.98 SF $30.00 ($ - ) ($ - ) ($ 50,819.37) ($ 3.67) 097413 Finishes: Wood slat rainscreen 521.69 SF $20.00 ($ - ) ($ - ) ($ 10,433.75) ($ 0.75) 097500 Finishes: Stone coping 54.50 LF $15.00 ($ - ) ($ - ) ($ 817.50) ($ 0.06) 102200 Specialties: Chain link partitions 8' high 1298.40 SF $5.00 ($ - ) ($ - ) ($ 6,492.00) ($ 0.47) 102200 Specialties: Chain link gates 3' wide 9.00 EA $200.00 ($ - ) ($ - ) ($ 1,800.00) ($ 0.13) 102200 Specialties: Planters Walls 4294.00 SF $2.50 ($ - ) ($ - ) ($ 10,735.00) ($ 0.77) 10000 Specialties: Pre-manufactured wheel stops 9.00 EA $100.00 ($ - ) ($ - ) ($ 900.00) ($ 0.06) 101400 Specialties: Parking stripe painting 284.60 LF $2.00 ($ - ) ($ - ) ($ 569.20) ($ 0.04) 10000 Specialties: Kitchen millwork 9.00 EA $6,500.00 ($ - ) ($ - ) ($ 58,500.00) ($ 4.22) 10000 Specialties: Kitchen counters 9.00 EA $2,300.00 ($ - ) ($ - ) ($ 20,700.00) ($ 1.49) 102819 Specialties: Shower doors 19.00 EA $1,000.00 ($ - ) ($ - ) ($ 19,000.00) ($ 1.37) 102813 Specialties: Bathroom accessories kit 19.00 EA $600.00 ($ - ) ($ - ) ($ 11,400.00) ($ 0.82) 101400 Specialties: Signage exterior 1.00 EA $2,500.00 ($ - ) ($ - ) ($ 2,500.00) ($ 0.18) 101400 Specialties: Signage interior 12.00 EA $225.00 ($ - ) ($ - ) ($ 2,700.00) ($ 0.19) 105500 Specialties: Mailboxes 9.00 EA $200.00 ($ - ) ($ - ) ($ 1,800.00) ($ 0.13) 142000 Conveying Systems: Elevator 1.00 EA $150,000.00 ($ - ) ($ - ) ($ 150,000.00) ($ 10.82) 210000 Fire supression: Combo smoke and carbon monoxide detector 36.00 EA $150.00 ($ - ) ($ - ) ($ 5,400.00) ($ 0.39) 210000 Fire supression: Fire Alarm Horn/Strobe 64.00 EA $200.00 ($ - ) ($ - ) ($ 12,800.00) ($ 0.92) 210000 Fire supression: Manual Pull Station 14.00 EA $50.00 ($ - ) ($ - ) ($ 700.00) ($ 0.05) 210000 Fire supression: Photoelectric heat detector 1.00 EA $100.00 ($ - ) ($ 100.00) ($ 0.01) 210000 Fire supression: Rough wiring 1.00 $0.00 ($ - ) ($ 7,600.00) ($ 7,600.00) ($ 0.55) 211000 Fire supression: Sprinkler system, rough and final 0.00 $0.00 ($ 50,000.00) ($ - ) ($ 50,000.00) ($ 3.61) 221100 Plumbing: Water supply connections 0.00 EA $0.00 ($ - ) ($ 11,400.00) ($ 11,400.00) ($ 0.82) 221300 Plumbing: Sewage connections 0.00 EA $0.00 ($ - ) ($ 3,000.00) ($ 3,000.00) ($ 0.22) 221300 Plumbing: Sanitary pipping 0.00 LF $0.00 ($ - ) ($ 37,586.27) ($ 37,586.27) ($ 2.71) 224100 Plumbing: Toilets (final) 19.00 EA $600.00 ($ - ) ($ - ) ($ 11,400.00) ($ 0.82) 224100 Plumbing: Bathroom sink and counters (final) 28.00 EA $800.00 ($ - ) ($ - ) ($ 22,400.00) ($ 1.62) 224100 Plumbing: Showers (final) 19.00 EA $300.00 ($ - ) ($ - ) ($ 5,700.00) ($ 0.41)
08/01/2018MCM 901 Page 71 of 224 Master Thesis: 620 N 3rd St Clara Bucar Detailed Estimate WBS/ CSI Code Description Material and Labor Allowance SubcontractorQuote Total $/GSFQty Unit Unit Cost 224100 Plumbing: Kitchen Sink (final) 9.00 EA $1,200.00 ($ - ) ($ - ) ($ 10,800.00) ($ 0.78) 224100 Plumbing: Mop sink (final) 1.00 EA $300.00 ($ - ) ($ - ) ($ 300.00) ($ 0.02) 224100 Plumbing: Bath tubs (final) 5.00 EA $3,000.00 ($ - ) ($ - ) ($ 15,000.00) ($ 1.08) 224100 Plumbing: Floor drains (final) 12.00 EA $300.00 ($ - ) ($ - ) ($ 3,600.00) ($ 0.26) 221300 Plumbing: Waste water connections 0.00 EA $0.00 ($ - ) ($ 9,000.00) ($ 9,000.00) ($ 0.65) 221100 Plumbing: Water supply pipping 0.00 LF $0.00 ($ - ) ($ 48,831.80) ($ 48,831.80) ($ 3.52) 220000 Plumbing: Gas supply pipping 0.00 LF $0.00 ($ - ) ($ 38,585.50) ($ 38,585.50) ($ 2.78) 270000 Mechanical: Thermostats (final) 19.00 EA $100.00 ($ - ) ($ - ) ($ 1,900.00) ($ 0.14) 270000 Mechanical: Electric heater baseboard (final) 9.00 EA $1,200.00 ($ - ) ($ - ) ($ 10,800.00) ($ 0.78) 270000 Mechanical: Electric heater ceiling hung (final) 9.00 EA $3,500.00 ($ - ) ($ - ) ($ 31,500.00) ($ 2.27) 270000 Mechanical: Exhaust fan (final) 20.00 EA $75.00 ($ - ) ($ - ) ($ 1,500.00) ($ 0.11) 270000 Mechanical: Ceiling difussers (final) 59.00 EA $30.00 ($ - ) ($ - ) ($ 1,770.00) ($ 0.13) 270000 Mechanical: Anti vibration pads at roof (final) 9.00 EA $100.00 ($ - ) ($ - ) ($ 900.00) ($ 0.06) 270000 Mechanical: Air handling units (final) 3.00 EA $4,000.00 ($ - ) ($ - ) ($ 12,000.00) ($ 0.87) 273700 Mechanical: Suppliers (final) 9.00 EA $30.00 ($ - ) ($ - ) ($ 270.00) ($ 0.02) 273700 Mechanical: Returns (final) 18.00 EA $30.00 ($ - ) ($ - ) ($ 540.00) ($ 0.04) 232200 Mechanical: HVAC rough 0.00 LF $0.00 ($ - ) ($ 62,592.21) ($ 62,592.21) ($ 4.52) 250000 Integrated automation: Curtain system 0.00 $0.00 ($ 5,000.00) ($ - ) ($ 5,000.00) ($ 0.36) 250000 Integrated automation: Garage doors opening 0.00 $0.00 ($ 5,000.00) ($ - ) ($ 5,000.00) ($ 0.36) 265100 Electrical lighting: T5 Single Tube Economy Tube 21.00 EA $40.00 ($ - ) ($ - ) ($ 840.00) ($ 0.06) 265100 Electrical lighting: 5" Recessed Light Fixture 99.00 EA $60.00 ($ - ) ($ - ) ($ 5,940.00) ($ 0.43) 265100 Electrical lighting: PAR-20 50W Line Voltage 4" recessed Light Fixture 170.00 EA $60.00 ($ - ) ($ - ) ($ 10,200.00) ($ 0.74) 265100 Electrical lighting: Ceiling Box for Light fixture 34.00 EA $25.00 ($ - ) ($ - ) ($ 850.00) ($ 0.06) 265100 Electrical lighting: Wall sconces 84.00 EA $100.00 ($ - ) ($ - ) ($ 8,400.00) ($ 0.61) 265100 Electrical lighting: Deck light fixture 24.00 EA $120.00 ($ - ) ($ - ) ($ 2,880.00) ($ 0.21) 265100 Electrical lighting: Weather proof 4" light fixture 2.00 EA $120.00 ($ - ) ($ - ) ($ 240.00) ($ 0.02) 265100 Electrical lighting: Low voltage LED with remote transformer 9.00 EA $150.00 ($ - ) ($ - ) ($ 1,350.00) ($ 0.10) 260000 Electrical power: Outlets 0.00 EA $0.00 ($ - ) ($ 18,275.00) ($ 18,275.00) ($ 1.32) 260000 Electrical power: Panels 10.00 EA $150.00 ($ - ) ($ - ) ($ 1,500.00) ($ 0.11) 260000 Electrical: Smoke/carbon monoxide detector 39.00 EA $120.00 ($ - ) ($ - ) ($ 4,680.00) ($ 0.34) 260000 Electrical: Vent Fans 20.00 EA $200.00 ($ - ) ($ - ) ($ 4,000.00) ($ 0.29) 260000 Electrical: Ceiling fan boxes 28.00 EA $200.00 ($ - ) ($ - ) ($ 5,600.00) ($ 0.40) 260000 Electrical: Exit signs 14.00 EA $120.00 ($ - ) ($ - ) ($ 1,680.00) ($ 0.12) 260000 Electrical: Fire extinguisher Cabinet 12.00 EA $100.00 ($ - ) ($ - ) ($ 1,200.00) ($ 0.09) 261200 Electrical: Transformer 0.00 $0.00 ($ 10,000.00) ($ - ) ($ 10,000.00) ($ 0.72)
08/01/2018MCM 901 Page 72 of 224 Master Thesis: 620 N 3rd St Clara Bucar Detailed Estimate WBS/ CSI Code Description Material and Labor Allowance SubcontractorQuote Total $/GSFQty Unit Unit Cost 260000 Electrical: Main distribution panel 1.00 EA $5,000.00 ($ - ) ($ - ) ($ 5,000.00) ($ 0.36) 260000 Electrical: Temporary power 1.00 EA $2,000.00 ($ - ) ($ - ) ($ 2,000.00) ($ 0.14) 260000 Electrical: Rough wiring 0.00 $0.00 ($ - ) ($ 33,854.00) ($ 33,854.00) ($ 2.44) 270000 Communications: Sound system 0.00 $0.00 ($ 15,000.00) ($ - ) ($ 15,000.00) ($ 1.08) 270000 Communications: Intercom system 0.00 $0.00 ($ 15,000.00) ($ - ) ($ 15,000.00) ($ 1.08) 270000 Communications: Data wiring and final 0.00 $0.00 ($ 15,000.00) ($ - ) ($ 15,000.00) ($ 1.08) 280000 Electronic Safety and Security: Security system 0.00 $0.00 ($ 20,000.00) ($ - ) ($ 20,000.00) ($ 1.44) 312300 Earthwork: Excavation 1837.85 CY $5.00 ($ - ) ($ - ) ($ 9,189.26) ($ 0.66) 312300 Earthwork: Backfill 664.37 CY $2.00 ($ - ) ($ - ) ($ 1,328.74) ($ 0.10) 312300 Earthwork: Dirt removal 1173.48 CY $2.00 ($ - ) ($ - ) ($ 2,346.96) ($ 0.17) 310000 Earthwork: Survey 0.00 $0.00 ($ 1,000.00) ($ - ) ($ 1,000.00) ($ 0.07) 321300 Exterior improvements: Sidewalk curbing and finishing 797.00 SF $7.00 ($ - ) ($ - ) ($ 5,579.00) ($ 0.40) 329000 Exterior improvements: Planters 0.00 $0.00 ($ 2,500.00) ($ - ) ($ 2,500.00) ($ 0.18) 321600 Exterior improvements: Gutter 0.00 $0.00 ($ 2,500.00) ($ - ) ($ 2,500.00) ($ 0.18) 333000 Utilities: Sewage connection 1.00 EA $5,000.00 ($ - ) ($ - ) ($ 5,000.00) ($ 0.36) 331400 Utilities: Water supply connection 1.00 EA $5,000.00 ($ - ) ($ - ) ($ 5,000.00) ($ 0.36) 334000 Utilities: Stormwater connection 1.00 EA $5,000.00 ($ - ) ($ - ) ($ 5,000.00) ($ 0.36) 335000 Utilities: Gas connection 1.00 EA $5,000.00 ($ - ) ($ - ) ($ 5,000.00) ($ 0.36) 337000 Utilities: Electrical connection 1.00 EA $5,000.00 ($ - ) ($ - ) ($ 5,000.00) ($ 0.36) 330000 Utilities: Meters 0.00 $0.00 ($ 5,000.00) ($ - ) ($ 5,000.00) ($ 0.36) 0.00 $0.00 ($ - ) ($ - ) ($ - ) #DIV/0! Total ($ 186,000.00) ($ 555,140.81) ($ 2,238,572.06) ($ 161.51) TOTAL ($ 2,238,572.06) Project Square Footage-Net SF 13860.6
08/01/2018MCM 901 Page 73 of 224 Master Thesis: 620 N 3rd St Clara Bucar 4.6. Masonry Detailed Back-up (Self Performed) Company: Fit Construction Name:Project 620 N 3rd St Date: August 1st 2018 Material and Labor Labor Equipment (Rate Includes Operator U.N.O.) WBS/CSICode Description Qty Unit UnitCost MaterialTotal LaborHours Rate/HRLabor Rate/HourLaborXHours LaborTotal EquipUnit EquipHours EquipTotal Allowance Total $/GSF 42200 Generic - 8" Masonry. reinforced, 3500 psi 1793 CF 1.5 $2,689.50) 20 $25.00) $500.00) $500.00) ($ 30.00) 32 ($ 960.00) ($ - ) ($ 4,149.50) ($ 0.30) 42200 Generic - 12" Masonry. High Strengh, 5000 psi 410 CF 1.75 $717.50) 6 $25.00) $150.00) $150.00) ($ 30.00) 32 ($ 960.00) ($ - ) ($ 1,827.50) ($ 0.13) 42200 5 1/2" Masonry. reinforced, 3500 psi 305 CF 1.25 $381.25) 6 $25.00) $150.00) $150.00) ($ 30.00) 32 ($ 960.00) ($ - ) ($ 1,491.25) ($ 0.11) 40520 Rebar #4 @ 48" ASTM A615, Grade 60 1200 LF 11 $13,200.00) 10 $25.00) $250.00) $250.00) ($ 30.00) 32 ($ 960.00) ($ - ) ($ 14,410.00) ($ 1.04) 40520 Horizontal joint reinforcement ASTM A82 320 LF 10 $3,200.00) 10 $25.00) $250.00) $250.00) 0 ($ - ) ($ - ) ($ 3,450.00) ($ 0.25) 40510 Grout ASTM C476 20 CF 60 $1,200.00) 16 $25.00) $400.00) $400.00) 0 ($ - ) ($ - ) ($ 1,600.00) ($ 0.12) 40510 Mortar ASTM C270 Type S 30 CF 40 $1,200.00) 16 $25.00) $400.00) $400.00) 0 ($ - ) ($ - ) ($ 1,600.00) ($ 0.12) 40520 Galvanized dovetail anchors at 16" centers 150 EA 5.32 $798.00) 2 $25.00) $50.00) $50.00) 0 ($ - ) ($ - ) ($ 848.00) ($ 0.06) 40520 Continuous bond beam with 2 #5 at top of walls 160 LF 12 $1,920.00) 10 $25.00) $250.00) $250.00) 0 ($ - ) ($ - ) ($ 2,170.00) ($ 0.16) 40520 Continuous bond beam with 2 #4 at top of walls 160 LF 11 $1,760.00) 10 $25.00) $250.00) $250.00) 0 ($ - ) ($ - ) ($ 2,010.00) ($ 0.15) 42200 Control joints 80 LF 4.25 $340.00) 2 $25.00) $50.00) $50.00) 0 ($ - ) ($ - ) ($ 390.00) ($ 0.03) Total ($ 27,406.25) ($ 2,700.00) Totals ($ 3,840.00) ($ - ) ($ 33,946.25) ($ 2.45) ($ 33,946.58) Project Square Footage-Net SF 13860.6
08/01/2018MCM 901 Page 74 of 224 Master Thesis: 620 N 3rd St Clara Bucar 4.7 Estimate Summary - LEED Estimate Summary Company: Fit Construction Company Project: 620 N 3rd St Gross SF 28536 Date: August 1st 2018 WBS/CSI # Description Amount $ / S.F. % of Total 01 *GENERAL REQUIREMENTS ($ 404,458) ($ 14.17) 12.6% 03 CONCRETE ($ 232,859) ($ 8.16) 7.3% 04 MASONRY ($ 33,947) ($ 1.19) 1.1% 05 METALS ($ 142,111) ($ 4.98) 4.4% 06 *WOOD, PLASTICS, AND COMPOSITES ($ 274,698) ($ 9.63) 8.6% 07 *THERMAL AND MOISTURE PROTECTION ($ 141,294) ($ 4.95) 4.4% 08 *OPENINGS ($ 139,226) ($ 4.88) 4.3% 09 FINISHES ($ 432,638) ($ 15.16) 13.5% 10 *SPECIALITIES ($ 142,096) ($ 4.98) 4.4% 14 CONVEYING SYSTEMS ($ 150,000) ($ 5.26) 4.7% 21 FIRE SUPPRESSION ($ 76,600) ($ 2.68) 2.4% 22 *PLUMBING ($ 244,403) ($ 8.56) 7.6% 23 *HVAC ($ 147,473) ($ 5.17) 4.6% 25 INTEGRATED AUTOMATION ($ 10,000) ($ 0.35) 0.3% 26 *ELECTRICAL ($ 129,024) ($ 4.52) 4.0% 27 COMMUNICATIONS ($ 45,000) ($ 1.58) 1.4% 28 ELECTRONIC SAFETY AND SECURITY ($ 20,000) ($ 0.70) 0.6% 31 EARTHWORK ($ 13,865) ($ 0.49) 0.4% 32 *EXTERIOR IMPROVEMENTS ($ 12,079) ($ 0.42) 0.4% 33 UTILITIES ($ 30,000) ($ 1.05) 0.9% TOTAL DIRECT COSTS ($ 2,821,770) 98.88 88.1% Subtotal ($ 2,821,770) 98.88 88.1% GENERAL OVERHEAD 6.0% ($ 169,306) 5.93 5.3% Subtotal ($ 2,991,077) 104.82 93.4% CM FEE/PROFIT 5.0% ($ 149,554) 5.24 4.7% SUBTOTAL A ($ 3,140,630) 110.06 98.0% BONDS 1.0% ($ 31,406) 1.10 1.0% Subtotal ($ 3,172,037) 111.16 99.0% INSURANCE 1.0% ($ 31,406) 1.10 1.0% Subtotal ($ 3,203,443) 112.26 100.0% CONTINGENCY 10.0% ($ 314,063) 11.01 9.8% TOTAL ($ 3,203,443) 112.26 100.0% *LEED OPTION INCLUDED IN TRADE ESTIMATE
08/01/2018MCM 901 Page 75 of 224 Master Thesis: 620 N 3rd St Clara Bucar 4.8. Detailed Estimate Backup - LEED WBS/ CSI Code Description Material and Labor Allowance SubcontractorQuote Total $/GSFQty Unit Unit Cost 017000 *Waste Management 1.00 EA $0.00 ($ 12,000.00) ($ - ) ($ 12,000.00) ($ 0.87) 019100 *Enhanced Commissioning 1.00 EA $0.00 ($ 8,000.00) ($ - ) ($ 8,000.00) ($ 0.58) 02250 Concrete: Underpinning 0.00 0 ($ 15,000.00) ($ - ) ($ 15,000.00) ($ 1.08) 03310 Concrete: Footings 45.69 CY 305 ($ - ) ($ - ) ($ 13,935.34) ($ 1.01) 03310 Concrete: Foundations 284.07 CY 495 ($ - ) ($ - ) ($ 140,613.37) ($ 10.14) 03310 Concrete: Piers 1.29 CY 495 ($ - ) ($ - ) ($ 636.53) ($ 0.05) 033313 Concrete: Walls - board form concrete 365.00 CY 50 ($ - ) ($ - ) ($ 18,250.00) ($ 1.32) 033113 Concrete: Slab on grade 52.11 CY 228 ($ - ) ($ - ) ($ 11,881.33) ($ 0.86) 033116 Concrete: Lightweight Concrete 13.90 CY 200 ($ - ) ($ - ) ($ 2,779.26) ($ 0.20) 033113 Concrete: Slab poured in place 7.95 CY 210 ($ - ) ($ - ) ($ 1,669.31) ($ 0.12) 035113 Concrete: 3/4" Structural Concrete Floor Panels 4092.00 SF 2 ($ - ) ($ - ) ($ 8,184.00) ($ 0.59) 035116 Concrete: 1" poured underlayment 3620.00 SF 5.5 ($ - ) ($ - ) ($ 19,910.00) ($ 1.44) 051223 Metal: W-Wide flange steel beams 12.63 TON 4500 ($ - ) ($ - ) ($ 56,837.39) ($ 4.10) 051223 Metal: LL-Double Angle: 2L3-1/2X3X5/16LLBB 0.09 TON 4500 ($ - ) ($ - ) ($ 414.00) ($ 0.03) 051223 Metal: L-Angle: L3-1/2X3-1/2X5/16 0.22 TON 4500 ($ - ) ($ - ) ($ 1,000.80) ($ 0.07) 051223 Metal: C-Channel C8X11.5 0.15 TON 4500 ($ - ) ($ - ) ($ 654.64) ($ 0.05) 051223 Metal: W8X10 0.04 TON 4500 ($ - ) ($ - ) ($ 184.50) ($ 0.01) 051223 Metal: HSS Columns 2.01 TON $4,500.00 ($ - ) ($ - ) ($ 9,051.61) ($ 0.65) 052100 Metal: Structured channel shaped steel joist 6.35 TON $4,500.00 ($ - ) ($ - ) ($ 28,579.02) ($ 2.06) 053600 Metal: Composite decking 0.00 SF $0.00 ($ - ) ($ 13,489.00) ($ 13,489.00) ($ 0.97) 051223 Metal: Headers 8.92 LF $15.00 ($ - ) ($ - ) ($ 133.86) ($ 0.01) 051223 Metal: Lintel 0.00 LF $0.00 ($ - ) ($ 471.40) ($ 471.40) ($ 0.03) 054100 Metal: Framing 0.00 LF $0.00 ($ - ) ($ 13,052.88) ($ 13,052.88) ($ 0.94) 055000 Metal: Welded wire fabric 1862.00 SF $0.50 ($ - ) ($ - ) ($ 931.00) ($ 0.07) 055001 Metal: Resilient channels 3799.00 SF $1.50 ($ - ) ($ - ) ($ 5,698.50) ($ 0.41) 055002 Metal: Railing balconies 42" high 165.30 LF $40.00 ($ - ) ($ - ) ($ 6,612.00) ($ 0.48) 055003 Metal: Elevator ladder 0.00 EA $0.00 ($ 2,000.00) ($ - ) ($ 2,000.00) ($ 0.14) 055004 Metal: PECO grate 0.00 EA $0.00 ($ 3,000.00) ($ - ) ($ 3,000.00) ($ 0.22) 061733 *Wood: Structual Wood Floor Joists (CSRs verified vendor and certified by the Forest Stewardship Council) 0.00 LF $0.00 ($ - ) ($ 69,222.91) ($ 69,222.91) ($ 4.99) 061000 *Wood: Girders (CSRs verified vendor and certified by the Forest Stewardship Council) 0.00 LF $0.00 ($ - ) ($ 21,617.70) ($ 21,617.70) ($ 1.56) 061000 *Wood: Posts (CSRs verified vendor and certified by the Forest Stewardship Council) 0.00 LF $0.00 ($ - ) ($ 18,538.13) ($ 18,538.13) ($ 1.34) 061000 *Wood: Headers (CSRs verified vendor and certified by the Forest Stewardship Council) 0.00 LF $0.00 ($ - ) ($ 6,494.08) ($ 6,494.08) ($ 0.47) 061100 *Wood: Framing (CSRs verified vendor and certified by the Forest Stewardship Council) 0.00 SF $0.00 ($ - ) ($ 62,807.04) ($ 62,807.04) ($ 4.53) *LEED OPTION INCLUDED IN TRADE ESTIMATE
08/01/2018MCM 901 Page 76 of 224 Master Thesis: 620 N 3rd St Clara Bucar WBS/ CSI Code Description Material and Labor Allowance SubcontractorQuote Total $/GSFQty Unit Unit Cost 061200 *Wood: Interior Stairs Wood Framing and Handrails (CSRs verified vendor and certified by the Forest Stewardship Council) 0.00 EA $0.00 ($ - ) ($ 9,600.00) ($ 9,600.00) ($ 0.69) 061600 *Wood: Wood 3/4" subfloor sheathing (CSRs verified vendor and certified by the Forest Stewardship Council) 6969.00 SF $3.00 ($ - ) ($ - ) ($ 20,907.00) ($ 1.51) 061600 *Wood: Exterior Plywood (CSRs verified vendor and certified by the Forest Stewardship Council) 0.00 SF $0.00 ($ - ) ($ 49,492.74) ($ 49,492.74) ($ 3.57) 06160 *Wood: 3/4" fire rated exterior sheathing (CSRs verified vendor and certified by the Forest Stewardship Council) 0.00 SF $0.00 ($ - ) ($ 12,276.00) ($ 12,276.00) ($ 0.89) 061600 *Wood: Sheer wall nailing (CSRs verified vendor and certified by the Forest Stewardship Council) 0.00 SF $0.00 ($ - ) ($ 3,742.70) ($ 3,742.70) ($ 0.27) 071800 Thermal and moisture: 3/8" protection layer 1477.00 SF $0.75 ($ - ) ($ - ) ($ 1,107.75) ($ 0.08) 071801 Thermal and moisture: 2" Synthethic fiber traffic wear layer 1477.00 SF $2.00 ($ - ) ($ - ) ($ 2,954.00) ($ 0.21) 071400 Thermal and moisture: Liquid applied waterproofing membrane 1477.00 SF $0.75 ($ - ) ($ - ) ($ 1,107.75) ($ 0.08) 072100 Thermal and moisture: Closed cell sprayed-in insulation R-30 4098.00 SF $2.00 ($ - ) ($ - ) ($ 8,196.00) ($ 0.59) 070000 Thermal and moisture: 1/4" sound reduction mat 10589.00 SF $0.50 ($ - ) ($ - ) ($ 5,294.50) ($ 0.38) 072500 Thermal and moisture: Vapor barrier 26631.00 SF $0.25 ($ - ) ($ - ) ($ 6,657.75) ($ 0.48) 072100 *Thermal and moisture: Recycled cotton insulation as required for R-30 - Bonded's Logic's UltraTouch 0.00 EA $0.00 ($ 10,000.00) ($ - ) ($ 10,000.00) ($ 0.72) 072100 *Thermal and moisture: Recycled cotton insulation as requiredBonded's Logic's UltraTouch 0.00 EA $0.00 ($ 13,000.00) ($ - ) ($ 13,000.00) ($ 0.94) 072100 Thermal and moisture: 1" mineral wool batts 546.00 SF $0.75 ($ - ) ($ - ) ($ 409.50) ($ 0.03) 072500 Thermal and moisture: 6 mil puncture resistant vapor barrier 4220.00 SF $0.50 ($ - ) ($ - ) ($ 2,110.00) ($ 0.15) 075000 Thermal and moisture: Roofing membrane 4561.00 SF $7.00 ($ - ) ($ - ) ($ 31,927.00) ($ 2.30) 072100 *Thermal and moisture: Recycled cotton insulation - Bonded's Logic's UltraTouch (interior partitions) 4310.00 SF $1.00 ($ - ) ($ - ) ($ 4,310.00) ($ 0.31) 072100 Thermal and moisture: 1 1/2" rigid insulation 1230.00 SF $1.50 ($ - ) ($ - ) ($ 1,845.00) ($ 0.13) 072100 *Thermal and moisture: Recycled cotton insulation as requiredBonded's Logic's UltraTouch 0.00 EA $0.00 ($ 5,000.00) ($ - ) ($ 5,000.00) ($ 0.36) 072500 Thermal and moisture: Weather barrier 9545.00 SF $0.25 ($ - ) ($ - ) ($ 2,386.25) ($ 0.17) 072100 *Thermal and moisture: Recycled cotton insulation as required for R-19 - Bonded's Logic's UltraTouch 0.00 EA $0.00 ($ 18,000.00) ($ - ) ($ 18,000.00) ($ 1.30) 072100 *Thermal and moisture: Recycled cotton insulation as requiredBonded's Logic's UltraTouch 0.00 EA $0.00 ($ 500.00) ($ - ) ($ 500.00) ($ 0.04) 072100 Thermal and moisture: 1/2" cement board 2063.00 SF $0.75 ($ - ) ($ - ) ($ 1,547.25) ($ 0.11) 072100 Thermal and moisture: 2" polyiso insulation 147.00 SF $5.00 ($ - ) ($ - ) ($ 735.00) ($ 0.05) 072100 Thermal and moisture: 1" gypsum shaft liner 162.00 SF $3.00 ($ - ) ($ - ) ($ 486.00) ($ 0.04) 076000 Thermal and moisture: Metal flashing 465.00 SF $8.00 ($ - ) ($ - ) ($ 3,720.00) ($ 0.27) 078400 Thermal and moisture: Coating for metal fireproofing 0.00 $0.00 ($ 20,000.00) ($ - ) ($ 20,000.00) ($ 1.44) *LEED OPTION INCLUDED IN TRADE ESTIMATE
08/01/2018MCM 901 Page 77 of 224 Master Thesis: 620 N 3rd St Clara Bucar WBS/ CSI Code Description Material and Labor Allowance SubcontractorQuote Total $/GSFQty Unit Unit Cost 085000 *Openings: Exterior aluminum frame and SunGuard glazing 1873.00 SF $42.00 ($ - ) ($ - ) ($ 78,666.00) ($ 5.68) 085001 *Openings: Miscellaneous glazing (SunGuard glazing) 9.00 SF $350.00 ($ - ) ($ - ) ($ 3,150.00) ($ 0.23) 083000 Openings: Louvers for trash room 1.00 EA $1,500.00 ($ - ) ($ - ) ($ 1,500.00) ($ 0.11) 083001 Openings: Overhead garage door 2.00 EA $5,000.00 ($ - ) ($ - ) ($ 10,000.00) ($ 0.72) 083002 Openings: Interior Woods Doors 0.00 EA $0.00 ($ - ) ($ 21,110.00) ($ 21,110.00) ($ 1.52) 081001 Openings: Specialty Doors 0.00 EA $0.00 ($ - ) ($ 24,800.00) ($ 24,800.00) ($ 1.79) 093013 Finishes: Ceramic for walls 5782.15 SF $5.50 ($ - ) ($ - ) ($ 31,801.81) ($ 2.29) 099123 Finishes: Gypsum board walls - Prime and paint 44285.87 SF $0.50 ($ - ) ($ - ) ($ 22,142.93) ($ 1.60) 096400 Finishes: Baseboard trims 4254.17 LF $4.00 ($ - ) ($ - ) ($ 17,016.66) ($ 1.23) 092900 Finishes: 5/8" gypsum board for walls 29857.00 SF $1.00 ($ - ) ($ - ) ($ 29,857.00) ($ 2.15) 092900 Finishes: 5/8" fire rated gypsum board for walls 19534.00 SF $1.25 ($ - ) ($ - ) ($ 24,417.50) ($ 1.76) 093013 Finishes: Ceramic for floor 872.17 SF $10.00 ($ - ) ($ - ) ($ 8,721.70) ($ 0.63) 096400 Finishes: Hardwood flooring 8307.00 SF $10.00 ($ - ) ($ - ) ($ 83,070.00) ($ 5.99) 092900 Finishes: 5/8" gypsum board for ceiling 15705.00 SF $1.00 ($ - ) ($ - ) ($ 15,705.00) ($ 1.13) 092900 Finishes: 1/2" fire rated gypsum board for ceiling 8307.00 SF $1.50 ($ - ) ($ - ) ($ 12,460.50) ($ 0.90) 099123 Finishes: Paint gypsum board ceiling 7398.00 SF $1.00 ($ - ) ($ - ) ($ 7,398.00) ($ 0.53) 095100 Finishes: Hung ceiling system 1275.00 SF $7.00 ($ - ) ($ - ) ($ 8,925.00) ($ 0.64) 096000 Finishes: Lobby and hallways flooring 1066.00 SF $14.00 ($ - ) ($ - ) ($ 14,924.00) ($ 1.08) 096000 Finishes: Stairs flooring 2.00 EA $7,000.00 ($ - ) ($ - ) ($ 14,000.00) ($ 1.01) 096400 Finishes: Wood decking 2709.15 SF $12.00 ($ - ) ($ - ) ($ 32,509.80) ($ 2.35) 099400 Finishes: Stucco, 3 layers 623.47 SF $5.00 ($ - ) ($ - ) ($ 3,117.36) ($ 0.22) 074600 Finishes: Architectural aluminum panel color A w/ bearing system 2383.07 SF $18.00 ($ - ) ($ - ) ($ 42,895.25) ($ 3.09) 074601 Finishes: Architectural aluminum panel color B w/ bearing system 89.14 SF $18.00 ($ - ) ($ - ) ($ 1,604.50) ($ 0.12) 093100 Finishes: 3 3/4" brick veneer 1693.98 SF $30.00 ($ - ) ($ - ) ($ 50,819.37) ($ 3.67) 097413 Finishes: Wood slat rainscreen 521.69 SF $20.00 ($ - ) ($ - ) ($ 10,433.75) ($ 0.75) 097500 Finishes: Stone coping 54.50 LF $15.00 ($ - ) ($ - ) ($ 817.50) ($ 0.06) 102200 Specialties: Chain link partitions 8' high 1298.40 SF $5.00 ($ - ) ($ - ) ($ 6,492.00) ($ 0.47) 102200 Specialties: Chain link gates 3' wide 9.00 EA $200.00 ($ - ) ($ - ) ($ 1,800.00) ($ 0.13) 102200 Specialties: Planters Walls 4294.00 SF $2.50 ($ - ) ($ - ) ($ 10,735.00) ($ 0.77) 10000 Specialties: Pre-manufactured wheel stops 9.00 EA $100.00 ($ - ) ($ - ) ($ 900.00) ($ 0.06) 101400 Specialties: Parking stripe painting 284.60 LF $2.00 ($ - ) ($ - ) ($ 569.20) ($ 0.04) 10000 Specialties: Kitchen millwork 9.00 EA $6,500.00 ($ - ) ($ - ) ($ 58,500.00) ($ 4.22) 10000 Specialties: Kitchen counters 9.00 EA $2,300.00 ($ - ) ($ - ) ($ 20,700.00) ($ 1.49) 102819 Specialties: Shower doors 19.00 EA $1,000.00 ($ - ) ($ - ) ($ 19,000.00) ($ 1.37) 102813 Specialties: Bathroom accessories kit 19.00 EA $600.00 ($ - ) ($ - ) ($ 11,400.00) ($ 0.82) 101400 Specialties: Signage exterior 1.00 EA $2,500.00 ($ - ) ($ - ) ($ 2,500.00) ($ 0.18) *LEED OPTION INCLUDED IN TRADE ESTIMATE
08/01/2018MCM 901 Page 78 of 224 Master Thesis: 620 N 3rd St Clara Bucar WBS/ CSI Code Description Material and Labor Allowance SubcontractorQuote Total $/GSFQty Unit Unit Cost 101400 Specialties: Signage interior 12.00 EA $225.00 ($ - ) ($ - ) ($ 2,700.00) ($ 0.19) 105500 Specialties: Mailboxes 9.00 EA $200.00 ($ - ) ($ - ) ($ 1,800.00) ($ 0.13) 10000 *Specialties: Irrigation system for planters 1.00 EA $0.00 ($ 5,000.00) ($ - ) ($ 5,000.00) ($ 0.36) 142000 Conveying Systems: Elevator 1.00 EA $150,000.00 ($ - ) ($ - ) ($ 150,000.00) ($ 10.82) 210000 Fire supression: Combo smoke and carbon monoxide detector 36.00 EA $150.00 ($ - ) ($ - ) ($ 5,400.00) ($ 0.39) 210000 Fire supression: Fire Alarm Horn/Strobe 64.00 EA $200.00 ($ - ) ($ - ) ($ 12,800.00) ($ 0.92) 210000 Fire supression: Manual Pull Station 14.00 EA $50.00 ($ - ) ($ - ) ($ 700.00) ($ 0.05) 210000 Fire supression: Photoelectric heat detector 1.00 EA $100.00 ($ - ) ($ 100.00) ($ 0.01) 210000 Fire supression: Rough wiring 1.00 $0.00 ($ - ) ($ 7,600.00) ($ 7,600.00) ($ 0.55) 211000 Fire supression: Sprinkler system, rough and final 0.00 $0.00 ($ 50,000.00) ($ - ) ($ 50,000.00) ($ 3.61) 221100 Plumbing: Water supply connections 0.00 EA $0.00 ($ - ) ($ 11,400.00) ($ 11,400.00) ($ 0.82) 221300 Plumbing: Sewage connections 0.00 EA $0.00 ($ - ) ($ 3,000.00) ($ 3,000.00) ($ 0.22) 221300 Plumbing: Sanitary pipping 0.00 LF $0.00 ($ - ) ($ 37,586.27) ($ 37,586.27) ($ 2.71) 224100 *Plumbing: Low flush toilets 1.6 gpf (final) 19.00 EA $800.00 ($ - ) ($ - ) ($ 15,200.00) ($ 1.10) 224100 *Plumbing: Low flow bathroom sink and counters 1.5 GPM (final) 28.00 EA $1,000.00 ($ - ) ($ - ) ($ 28,000.00) ($ 2.02) 224100 *Plumbing: Low flow shower heads 1.5 GPM (final) 19.00 EA $400.00 ($ - ) ($ - ) ($ 7,600.00) ($ 0.55) 224100 *Plumbing: Low flow kitchen faucets and sink 1.5 GPM (final) 9.00 EA $1,400.00 ($ - ) ($ - ) ($ 12,600.00) ($ 0.91) 224100 *Plumbing: Low flow mop sink and faucet 1.5 GPM (final) 1.00 EA $500.00 ($ - ) ($ - ) ($ 500.00) ($ 0.04) 224100 *Plumbing: Low flow bath tubs and spouts 1.5 GPM (final) 5.00 EA $3,400.00 ($ - ) ($ - ) ($ 17,000.00) ($ 1.23) 224100 Plumbing: Floor drains (final) 12.00 EA $300.00 ($ - ) ($ - ) ($ 3,600.00) ($ 0.26) 221300 Plumbing: Waste water connections 0.00 EA $0.00 ($ - ) ($ 9,000.00) ($ 9,000.00) ($ 0.65) 221100 Plumbing: Water supply pipping 0.00 LF $0.00 ($ - ) ($ 48,831.80) ($ 48,831.80) ($ 3.52) 220000 Plumbing: Gas supply pipping 0.00 LF $0.00 ($ - ) ($ 38,585.50) ($ 38,585.50) ($ 2.78) 220000 *Plumbing: Extra pipping for downspout disconnection 1.00 EA $0.00 ($ 1,000.00) ($ - ) ($ 1,000.00) ($ 0.07) 220000 *Plumbing: Downspout 2.00 EA $250.00 ($ - ) ($ - ) ($ 500.00) ($ 0.04) 220000 *Plumbing: Extra pipping for cistern (capture and supply) 1.00 EA $0.00 ($ 3,000.00) ($ - ) ($ 3,000.00) ($ 0.22) 220000 *Plumbing: Extra pipping for planters irrigation system 1.00 EA $0.00 ($ 2,000.00) ($ - ) ($ 2,000.00) ($ 0.14) 220000 *Plumbing: Water reservoir (cistern) 1.00 EA $0.00 ($ 5,000.00) ($ - ) ($ 5,000.00) ($ 0.36) 270000 *Mechanical: Pump for cistern 1.00 EA $0.00 ($ 5,000.00) ($ - ) ($ 5,000.00) ($ 0.36) 270000 Mechanical: Thermostats (final) 19.00 EA $100.00 ($ - ) ($ - ) ($ 1,900.00) ($ 0.14) 270000 *Mechanical: Electric heater baseboard (final) 9.00 EA $1,500.00 ($ - ) ($ - ) ($ 13,500.00) ($ 0.97) 270000 *Mechanical: Electric heater ceiling hung (final) 9.00 EA $4,500.00 ($ - ) ($ - ) ($ 40,500.00) ($ 2.92) 270000 *Mechanical: Exhaust fan (final) 20.00 EA $125.00 ($ - ) ($ - ) ($ 2,500.00) ($ 0.18) 270000 Mechanical: Ceiling difussers (final) 59.00 EA $30.00 ($ - ) ($ - ) ($ 1,770.00) ($ 0.13) 270000 Mechanical: Anti vibration pads at roof (final) 9.00 EA $100.00 ($ - ) ($ - ) ($ 900.00) ($ 0.06) 270000 *Mechanical: Air handling units (final) 3.00 EA $6,000.00 ($ - ) ($ - ) ($ 18,000.00) ($ 1.30) *LEED OPTION INCLUDED IN TRADE ESTIMATE
08/01/2018MCM 901 Page 79 of 224 Master Thesis: 620 N 3rd St Clara Bucar WBS/ CSI Code Description Material and Labor Allowance SubcontractorQuote Total $/GSFQty Unit Unit Cost 273700 Mechanical: Suppliers (final) 9.00 EA $30.00 ($ - ) ($ - ) ($ 270.00) ($ 0.02) 273700 Mechanical: Returns (final) 18.00 EA $30.00 ($ - ) ($ - ) ($ 540.00) ($ 0.04) 232200 Mechanical: HVAC rough 0.00 LF $0.00 ($ - ) ($ 62,592.21) ($ 62,592.21) ($ 4.52) 250000 Integrated automation: Curtain system 0.00 $0.00 ($ 5,000.00) ($ - ) ($ 5,000.00) ($ 0.36) 250000 Integrated automation: Garage doors opening 0.00 $0.00 ($ 5,000.00) ($ - ) ($ 5,000.00) ($ 0.36) 265100 *Electrical lighting: Philips LED InstantFit Lamps 24T5 LED 21.00 EA $100.00 ($ - ) ($ - ) ($ 2,100.00) ($ 0.15) 265100 *Electrical lighting: Designers Fountain 4" White easy-up LED Down Light 99.00 EA $85.00 ($ - ) ($ - ) ($ 8,415.00) ($ 0.61) 265100 *Electrical lighting: TCP Elite Designer PAR Series LED 170.00 EA $100.00 ($ - ) ($ - ) ($ 17,000.00) ($ 1.23) 265100 Electrical lighting: Ceiling Box for Light fixture 34.00 EA $25.00 ($ - ) ($ - ) ($ 850.00) ($ 0.06) 265100 Electrical lighting: Wall sconces 84.00 EA $100.00 ($ - ) ($ - ) ($ 8,400.00) ($ 0.61) 265100 Electrical lighting: Deck light fixture 24.00 EA $120.00 ($ - ) ($ - ) ($ 2,880.00) ($ 0.21) 265100 Electrical lighting: Weather proof 4" light fixture 2.00 EA $120.00 ($ - ) ($ - ) ($ 240.00) ($ 0.02) 265100 Electrical lighting: Low voltage LED with remote transformer 9.00 EA $150.00 ($ - ) ($ - ) ($ 1,350.00) ($ 0.10) 260000 Electrical power: Outlets 0.00 EA $0.00 ($ - ) ($ 18,275.00) ($ 18,275.00) ($ 1.32) 260000 Electrical power: Panels 10.00 EA $150.00 ($ - ) ($ - ) ($ 1,500.00) ($ 0.11) 260000 Electrical: Smoke/carbon monoxide detector 39.00 EA $120.00 ($ - ) ($ - ) ($ 4,680.00) ($ 0.34) 260000 Electrical: Vent Fans 20.00 EA $200.00 ($ - ) ($ - ) ($ 4,000.00) ($ 0.29) 260000 Electrical: Ceiling fan boxes 28.00 EA $200.00 ($ - ) ($ - ) ($ 5,600.00) ($ 0.40) 260000 Electrical: Exit signs 14.00 EA $120.00 ($ - ) ($ - ) ($ 1,680.00) ($ 0.12) 260000 Electrical: Fire extinguisher Cabinet 12.00 EA $100.00 ($ - ) ($ - ) ($ 1,200.00) ($ 0.09) 261200 Electrical: Transformer 0.00 $0.00 ($ 10,000.00) ($ - ) ($ 10,000.00) ($ 0.72) 260000 Electrical: Main distribution panel 1.00 EA $5,000.00 ($ - ) ($ - ) ($ 5,000.00) ($ 0.36) 260000 Electrical: Temporary power 1.00 EA $2,000.00 ($ - ) ($ - ) ($ 2,000.00) ($ 0.14) 260000 Electrical: Rough wiring 0.00 $0.00 ($ - ) ($ 33,854.00) ($ 33,854.00) ($ 2.44) 270000 Communications: Sound system 0.00 $0.00 ($ 15,000.00) ($ - ) ($ 15,000.00) ($ 1.08) 270000 Communications: Intercom system 0.00 $0.00 ($ 15,000.00) ($ - ) ($ 15,000.00) ($ 1.08) 270000 Communications: Data wiring and final 0.00 $0.00 ($ 15,000.00) ($ - ) ($ 15,000.00) ($ 1.08) 280000 Electronic Safety and Security: Security system 0.00 $0.00 ($ 20,000.00) ($ - ) ($ 20,000.00) ($ 1.44) 312300 Earthwork: Excavation 1837.85 CY $5.00 ($ - ) ($ - ) ($ 9,189.26) ($ 0.66) 312300 Earthwork: Backfill 664.37 CY $2.00 ($ - ) ($ - ) ($ 1,328.74) ($ 0.10) 312300 Earthwork: Dirt removal 1173.48 CY $2.00 ($ - ) ($ - ) ($ 2,346.96) ($ 0.17) 310000 Earthwork: Survey 0.00 $0.00 ($ 1,000.00) ($ - ) ($ 1,000.00) ($ 0.07) 321300 Exterior improvements: Sidewalk curbing and finishing 797.00 SF $7.00 ($ - ) ($ - ) ($ 5,579.00) ($ 0.40) 329000 Exterior improvements: Planters 0.00 $0.00 ($ 2,500.00) ($ - ) ($ 2,500.00) ($ 0.18) 329000 *Exterior improvements: Specific plants purchase 1.00 EA $0.00 ($ 1,500.00) ($ - ) ($ 1,500.00) ($ 0.11) *LEED OPTION INCLUDED IN TRADE ESTIMATE
08/01/2018MCM 901 Page 80 of 224 Master Thesis: 620 N 3rd St Clara Bucar WBS/ CSI Code Description Material and Labor Allowance SubcontractorQuote Total $/GSFQty Unit Unit Cost 321600 Exterior improvements: Gutter 0.00 $0.00 ($ 2,500.00) ($ - ) ($ 2,500.00) ($ 0.18) 333000 Utilities: Sewage connection 1.00 EA $5,000.00 ($ - ) ($ - ) ($ 5,000.00) ($ 0.36) 331400 Utilities: Water supply connection 1.00 EA $5,000.00 ($ - ) ($ - ) ($ 5,000.00) ($ 0.36) 334000 Utilities: Stormwater connection 1.00 EA $5,000.00 ($ - ) ($ - ) ($ 5,000.00) ($ 0.36) 335000 Utilities: Gas connection 1.00 EA $5,000.00 ($ - ) ($ - ) ($ 5,000.00) ($ 0.36) 337000 Utilities: Electrical connection 1.00 EA $5,000.00 ($ - ) ($ - ) ($ 5,000.00) ($ 0.36) 330000 Utilities: Meters 0.00 $0.00 ($ 5,000.00) ($ - ) ($ 5,000.00) ($ 0.36) 0.00 $0.00 ($ - ) ($ - ) ($ - ) #DIV/0! Total ($ 255,000.00) ($ 597,439.36) ($ 2,383,365.36) ($ 173.40) TOTAL ($ 2,403,365.36) Project Square Footage-Net SF 13860.6
08/01/2018MCM 901 Page 81 of 224 Master Thesis: 620 N 3rd St Clara Bucar 4.9. Design and Preconstruction Schedule ID Task Name Duration Start Finish PredecessorsCost 1 Preconstruction 77 days 10/1/18Mon 1/16/19Wed $1,000.00 2 Schematic Design and DevelopmentDesign 22 days 10/1/18Mon 10/31/18Wed $0.00 3 Zoning permit 10 days 10/31/18Wed 11/14/18Wed 2 $0.00 4 conditionssubsurfaceSurveying 5 days 11/14/18Wed 11/21/18Wed 3 $1,000.00 5 DocumentsConstruction 25 days 11/14/18Wed 12/19/18Wed 3 $0.00 6 Invitation to bid 0 days 12/12/18Wed 12/12/18Wed 5FS-5 days $0.00 7 Estimate 5 days 12/19/18Wed 12/26/18Wed 5,6 $0.00 8 Schedule 5 days 12/19/18Wed 12/26/18Wed 5 $0.00 9 prequalificationSub 5 days 12/26/18Wed Wed 1/2/19 7 $0.00 10 Bid 1 day Mon 1/7/19 Tue 1/8/19 days9FS+3 $0.00 11 Award 1 day Tue 1/15/19 1/16/19Wed days10FS+5 $0.00 12 Procurement days285 1/16/19Wed 2/19/20Wed 11 $0.00 13 reinforcingMasonry 67 days 1/16/19Wed Fri 4/19/19 124SF $0.00 14 Unit masonry 67 days Thu 1/17/19 4/22/19Mon 125SF $0.00 15 Structural steel 97 days 1/16/19Wed Fri 5/31/19 161SF $0.00 16 Steel deck 97 days 1/23/19Wed Fri 6/7/19 170SF $0.00 17 Steel joists 97 days Tue 2/5/19 Thu 6/20/19 175SF $0.00 18 Rough carpentry 67 days Mon 4/1/19 Wed 7/3/19 182SF $0.00 19 TPO membrane 72 days Wed 5/8/19 Fri 8/16/19 210SF $0.00 20 Flashing and sheet metal 67 days Wed 5/8/19 Fri 8/9/19 205SF $0.00 21 Carpentry 67 days Fri 5/10/19 Tue 8/13/19 208SF $0.00 10/1 1/16 Preconstruction 10/1 10/31 Schematic Design and Design Development 10/31 11/14 Zoning11/14permit 11/21 Surveying subsurface conditions (stake-out) 11/14 12/19 ConstructionInvitationDocuments12/12tobid12/1912/19Estimate12/2612/26Schedule12/261/2Subprequalification1/71/8Bid1/151/16Award1/16 Procurement 1/16 4/19 Masonry reinforcing 1/17 4/22 Unit masonry 1/16 5/31 Structural steel 1/23 6/7 Steel deck 2/5 6/20 Steel joists 4/1 7/3 Rough carpentry 5/8 TPO membrane 5/8 Flashing and sheet metal 5/10 Carpentry 9/23 10/7 10/21 11/4 11/18 12/2 12/16 12/30 1/13 1/27 2/10 2/24 3/10 3/24 4/7 4/21 5/5 5/19 6/2 6/16 6/30 7/14 September 1 October 1 November 1 December 1 January 1 February 1 March 1 April 1 May 1 June 1 July 1
08/01/2018MCM 901 Page 82 of 224 Master Thesis: 620 N 3rd St Clara Bucar ID Task Name Duration Start Finish PredecessorsCost 22 Elevator days136 Fri 5/10/19 11/18/19Mon 305SF $0.00 23 Garage doors 97 days 5/27/19Mon 10/9/19Wed 253SF $0.00 24 Cold formed metal framing 67 days 6/10/19Mon 9/11/19Wed 228SF $0.00 25 Custom made glazing 86 days Tue 6/11/19 10/9/19Wed 249SF $0.00 26 Fire sprinklerextinguishingsystems 76 days Fri 6/14/19 9/30/19Mon 276SF $0.00 27 Firestoping 67 days 6/19/19Wed Fri 9/20/19 263SF $0.00 28 Exterior doors 77 days 6/24/19Mon 10/9/19Wed 249SF $0.00 29 windowsAluminum 76 days Tue 6/25/19 10/9/19Wed 249SF $0.00 30 Louvers: Trash room 70 days Wed 7/3/19 10/9/19Wed 255SF $0.00 31 Caulking and sealants 67 days Mon 7/8/19 10/9/19Wed 257SF $0.00 32 Trees, plants and ground covers 67 days 8/12/19Mon 11/13/19Wed 321SF $0.00 33 Gypsum board 67 days Thu 8/15/19 11/18/19Mon 337SF $0.00 34 Mineral fiber blanket insulationthermal 67 days Thu 8/15/19 11/18/19Mon 344SF $0.00 35 Board and block thermal insulation 67 days Thu 8/15/19 11/18/19Mon 344SF $0.00 36 Millwork 93 days 8/12/19Mon 12/19/19Thu 420SF $0.00 37 Specialty doors 78 days 8/28/19Wed 12/16/19Mon 435SF $0.00 38 Ceramic tiles 70 days 8/28/19Wed 12/4/19Wed 396SF $0.00 39 Steel doors and frames 77 days Thu 8/29/19 12/16/19Mon 435SF $0.00 40 Flush wood doors 77 days Thu 8/29/19 12/16/19Mon 435SF $0.00 41 Plumbing pipping systems 76 days Mon 9/9/19 12/24/19Tue 451SF $0.00 42 Fire extinguishers and Cabinets 76 days Thu 9/12/19 Fri 12/27/19 448SF $0.00 5/10 11/18 Elevator 5/27 10/9 Garage doors 6/10 9/11 Cold formed metal framing 6/11 10/9 Custom made glazing 6/14 9/30 Fire extinguishing sprinkler systems 6/19 9/20 Firestoping 6/24 10/9 Exterior doors 6/25 10/9 Aluminum windows 7/3 10/9 Louvers: Trash room 7/8 10/9 Caulking and sealants 8/12 11/13 Trees, plants and ground covers 8/15 11/18 Gypsum board 8/15 11/18 Mineral fiber blanket thermal insulation 8/15 11/18 Board and block thermal insulation 8/12 12/19 Millwork 8/28 12/16 Specialty doors 8/28 12/4 Ceramic tiles 8/29 12/16 Steel doors and frames 8/29 12/16 Flush wood doors 9/9 12/24 Plumbing pipping systems 9/12 12/27 Fire extinguishers and Cabinets 4/21 5/5 5/19 6/2 6/16 6/30 7/14 7/28 8/11 8/25 9/8 9/22 10/6 10/20 11/3 11/17 12/1 12/15 12/29 1/12 1/26 2/9 April 1 May 1 June 1 July 1 August 1 September 1 October 1 November 1 December 1 January 1 February 1
08/01/2018MCM 901 Page 83 of 224 Master Thesis: 620 N 3rd St Clara Bucar ID Task Name Duration Start Finish PredecessorsCost 43 Acoustical ceiling systems 70 days Thu 9/12/19 12/19/19Thu 414SF $0.00 44 systemsMechanical 75 days 9/18/19Wed Wed 1/1/20 465SF $0.00 45 Chain Link fences 67 days 9/18/19Wed Fri 12/20/19 416SF $0.00 46 Fire alarm systems 71 days Thu 9/19/19 Fri 12/27/19 448SF $0.00 47 Electrical systems 71 days Fri 9/27/19 Mon 1/6/20 473SF $0.00 48 Interior lighting 66 days Fri 10/4/19 Mon 1/6/20 474SF $0.00 49 Painting 66 days 10/9/19Wed Thu 1/9/20 499SF $0.00 50 Toilet and accessoriesbath 66 days 11/4/19Mon Tue 2/4/20 472SF $0.00 51 Exterior signage 76 days Tue 11/5/19 2/19/20Wed 497SF $0.00 52 Building permit 0 days 1/30/19Wed 1/30/19Wed days5FS+30 $0.00 53 Building permit: City comments and review 10 days 1/30/19Wed 2/13/19Wed 52 $0.00 54 Notice to proceed 0 days 2/13/19Wed 2/13/19Wed 53 $0.00 55 Mobilization days?263 2/13/19Wed 2/17/20Mon 54 $0.00 56 Trailer 1 day 2/13/19Wed Thu 2/14/19 $0.00 57 Fencing/Gates 2 days 2/13/19Wed Fri 2/15/19 $0.00 58 signageConstruction 1 day? 2/13/19Wed Thu 2/14/19 $0.00 59 Dumpsters 1 day 2/13/19Wed Thu 2/14/19 $0.00 60 Portable toilets 1 day? 2/13/19Wed Thu 2/14/19 $0.00 61 Temp water 2 days 2/13/19Wed Fri 2/15/19 $0.00 62 Temp power 2 days 2/13/19Wed Fri 2/15/19 $0.00 63 Security system install 3 days 2/13/19Wed 2/18/19Mon $0.00 9/12 Acoustical 9/18 Mechanical 9/18 Chain 9/19 Fire 9/2710/410/9 1/30 Building permit 1/30 2/13 Building permit: City comments and review 2/13 Notice to proceed 2/13 Mobilization 2/13 ConstructionFencing/Gates2/13Trailer2/142/152/132/14signage2/132/14Dumpsters2/132/14Portabletoilets2/132/15Tempwater2/132/15Temppower2/132/18Securitysysteminstall 12/16 12/30 1/13 1/27 2/10 2/24 3/10 3/24 4/7 4/21 5/5 5/19 6/2 6/16 6/30 7/14 7/28 8/11 8/25 9/8 9/22 10/6 December 1 January 1 February 1 March 1 April 1 May 1 June 1 July 1 August 1 September 1 October 1PredecessorsCost 414SF $0.00 465SF $0.00 416SF $0.00 448SF $0.00 473SF $0.00 474SF $0.00 499SF $0.00 472SF $0.00 497SF $0.00 days5FS+30 $0.00$0.00$0.00 $0.00 $0.00$0.00$0.00$0.00$0.00$0.00$0.00$0.00 9/12 12/19 Acoustical ceiling systems 9/18 1/1 Mechanical systems 9/18 12/20 Chain Link fences 9/19 12/27 Fire alarm systems 9/27 1/6 Electrical systems 10/4 1/6 Interior lighting 10/9 1/9 Painting 11/4 2/4 Toilet and bath accessories 11/5 2/19 Exterior signage 1/30 Building permit 1/30 2/13 Building permit: City comments and review 2/13 Notice to proceed 2/13 2/17 Mobilization 2/13 ConstructionFencing/Gates2/13Trailer2/142/152/132/14signage2/132/14Dumpsters2/132/14Portabletoilets2/132/15Tempwater2/132/15Temppower2/132/18Securitysysteminstall 12/16 12/30 1/13 1/27 2/10 2/24 3/10 3/24 4/7 4/21 5/5 5/19 6/2 6/16 6/30 7/14 7/28 8/11 8/25 9/8 9/22 10/6 10/20 11/3 11/17 12/1 12/15 12/29 1/12 1/26 2/9 2/23 3/8 3/22 December 1 January 1 February 1 March 1 April 1 May 1 June 1 July 1 August 1 September 1 October 1 November 1 December 1 January 1 February 1 March 1
08/01/2018MCM 901 Page 84 of 224 Master Thesis: 620 N 3rd St Clara Bucar 4.10. Procurement and Buy Out Log Procurement - Buy-Out Log Procurement - Buyout Log WBS/CSICode Description SubcontractorVendor Prequal Bid Price RequiredDate AwardedDate 2250 Concrete underpinning, footings, foundations, piers, slab on grade Pours Inc. Y ($ 180,067) 2/27/2019 1/27/2019 33313 Concrete Walls - Board formed Purple Concrete Inc Y ($ 18,250) 5/30/2019 03/40/2019 33116 Concrete lightweight, slab, 3/4", 1" IncConstructionMcMaster Y ($ 32,543) 6/7/2019 5/7/2019 51223 Metal Structure Erector IncConstructionSet Y ($ 106,816) 5/31/2019 04/31/2019 54100 Metal framing, welded, resilient Alfred's Welds LP Y ($ 19,682) 8/7/2019 7/7/2019 55002 Metal Railing, elevator, PECO grate We Lift You Up LP Y ($ 11,612) 7/10/2019 5/10/2019 61733 Wood structural, girders, posts, headers, sheer Jenga LP Y ($ 99,680) 7/4/2019 6/4/2019 61100 Wood framing interior, 3/4" Chris Cross Inc Y ($ 77,762) 8/7/2019 7/7/2019 61600 Wood Exterior, 3/4" fire Phatcher Inc Y ($ 51,474) 8/5/2019 7/5/2019 71800 Thermal: traffic layer Insulate Inc Y ($ 7,280) 12/12/2019 11/12/2019 72100 Thermal: sprayied insulation Warm and Cozy LLC Y ($ 8,196) 11/18/2019 10/18/2019 70000 Thermal 1/4", vapor, 1.5", weather, R-19m, 1/2", 2", 1" Thermopolis LP Y ($ 31,626) 11/18/2019 10/18/2019 72100 Thermal: Batt insulation Hot and Cold Inc Y ($ 17,140) 12/18/19 11/18/2019 75000 Thermal roofing membrane Roof Mem Inc Y ($ 31,927) 8/16/19 7/16/2019 76000 Thermal Metal Flashing Flash Gordon Inc Y ($ 3,720) 10/7/2019 9/7/2019 78400 Thermal Coating, Overhead Coating Tech Inc Y ($ 30,000) 11/18/2019 10/18/2019 85000 Openings exterior, misc Gateways Inc. Inc Y ($ 71,551) 10/9/2019 9/9/2019 83000 Openings Louvers Lovers Louvers LP Y ($ 1,500) 10/9/2019 9/9/2019 83002 Openings interior, speciality doors, baseboard Doorways to Heaven Inc Y ($ 62,927) 10/9/2019 9/9/2019 92900 Finishes Gypsum GypsumGetsum Inc Y ($ 82,240) 11/18/2019 10/18/2019 99123 Finishes Paint Serial Paintists Inc Y ($ 29,541) 1/9/2020 12/9/2019 93013 Finishes Ceramic Claymation Inc Y ($ 40,524) 12/4/2019 11/4/2019
08/01/2018MCM 901 Page 85 of 224 Master Thesis: 620 N 3rd St Clara BucarProcurement - Buy-Out Log Procurement - Buyout Log WBS/CSICode Description SubcontractorVendor Prequal Bid Price RequiredDate AwardedDate 95100 Finishes Hung Ceiling You Spin Me Right Round Inc Y ($ 8,925) 12/19/2019 11/19/2019 96000 Finishes Hardwood, Lobby, Stairs Grand Finale Inc Y ($ 111,994) 11/18/2019 10/18/2019 96400 Finishes Wood Decking Decking Inc Y ($ 32,510) 10/25/2019 9/25/2019 99400 Exterior Finishes Maria's Inc Y ($ 109,088) 9/20/2019 8/20/2019 102200 Specialties: Chain link partitions and gate Machu Inc Y ($ 8,292) 12/20/2019 11/20/2019 102200 Specialties: Planters Walls Greenlife Inc Y ($ 10,735) 10/25/2019 9/25/2019 10000 Specialties: manufacturedPre-wheel stops Prestuff Inc Y ($ 900) 12/12/2019 11/12/2019 101400 Specialties: Parking stripe painting Lines and Stuff LP Y ($ 569) 12/12/2019 11/12/2019 10000 Specialties: Kitchen millwork Madonna LP Y ($ 58,500) 12/24/2019 11/24/2019 10000 Specialties: Kitchen counters Granarble Inc Y ($ 20,700) 12/12/2019 11/12/2019 102819 Specialties: Shower doors Real DoorsShowerLP Y ($ 19,000) 1/27/2020 12/15/2019 102813 Specialties: Bathroom accessories kit Bath in a Box Inc Y ($ 11,400) 1/27/2020 12/15/2019 105500 Specialties: Mailboxes You've got Mail Inc Y ($ 1,800) 1/27/2020 12/15/2019 101400 Specialties Signage Mini Billboards LP Y ($ 5,200) 2/19/2020 1/19/2020 142000 Conveying Systems: Elevator We Move You LP Y ($ 150,000) 11/18/2019 10/18019 210000 Fire Supression Fire Police LP Y ($ 76,600) 9/30/2019 8/30/2019 221300 Plumbing Rough and Utilities Sewer Snakes Inc Y ($ 168,400) 9/20/2019 8/20/2019 224100 Plumbing Final Waste Away Inc Y ($ 69,200) 9/20/2019 8/20/2019 270000 Mechanical Final Air Dancer Inc Y ($ 61,180) 10/30/19 9/30/19 232200 Mechanical HVAC rough Wind Walker Inc Y ($ 69,591) 10/30/19 9/30/19 250000 Integrated Automation DirectAutomationInc Y ($ 10,000) 1/3/2020 12/3/2019 265100 Eletrical Lighting, low voltage and utilities StarBright Inc Y ($ 35,700) 10/10/2019 9/10/2019 260000 Electrical Power, Fire Protection, Wiring Voltron Inc Y $ 87,789 10/10/2019 9/10/2019
08/01/2018MCM 901 Page 86 of 224 Master Thesis: 620 N 3rd St Clara BucarProcurement - Buy-Out Log Procurement - Buyout Log WBS/CSICode Description SubcontractorVendor Prequal Bid Price RequiredDate AwardedDate 270000 Communications Say What LP Y ($ 45,000) 11/8/2019 10/8/2019 280000 Electronic safety NoShock Inc Y ($ 20,000) 12/19/2019 11/19/2019 312300 Earth Work: Excavation Earth Movers Inc Y ($ 12,865) 2/18/2019 1/18/2019 310000 Earth work: Survey Earth Watchers Inc Y ($ 1,000) 11/14/2018 10/14/2018 321300 Exterior finishingSidewalkimprovements:curbingand Don't Tread on Me Inc Y ($ 5,579) 5/24/2019 4/24/2019 329000 Exterior improvements: Planters Greenlife Inc Y ($ 2,500) 11/13/2019 10/13/2019 321600 Exterior improvements: Gutter Guts & Sons LP Y ($ 2,500) 5/24/2019 4/24/2019 330000 Utilities Meters Imperial Inc Y ($ 5,000) 10/18/2019 9/18/2019
08/01/2018MCM 901 Page 87 of 224 Master Thesis: 620 N 3rd St Clara Bucar Submittal Schedule Calculator SPEC # DESCRIPTION DESIGNREQDATE BID AND DURATIONAWARD(weeks) CONTRACTSIGNEDDATE LEADSUBMITFOR(weeks) DUE DATE TO ARCH DUETODATESUB DURATIONFAB/DEL(weeks) DELIVERYON-SITEDATE STARTSCHEDULEPERDATE 02831 Chain Link Fences 09/19/19 3 10/10/19 4 11/07/19 11/28/19 2 12/12/19 12/19/19 02930 Trees, Plants, and Ground Covers 08/13/19 3 09/03/19 4 10/01/19 10/22/19 2 11/05/19 11/12/19 04200 Unit Masonry 01/20/19 3 02/10/19 4 03/10/19 03/31/19 2 04/14/19 04/21/19 04230 Masonry Reinforcing 01/17/19 3 02/07/19 4 03/07/19 03/28/19 2 04/11/19 04/18/19 05120 Structural Steel 01/17/19 3 02/07/19 4 03/07/19 03/28/19 8 05/23/19 05/30/19 05210 Steel Joists 02/06/19 3 02/27/19 4 03/27/19 04/17/19 8 06/12/19 06/19/19 05310 Steel Deck 01/24/19 3 02/14/19 4 03/14/19 04/04/19 8 05/30/19 06/06/19 05400 Cold-Formed Metal Framing 06/11/19 3 07/02/19 4 07/30/19 08/20/19 2 09/03/19 09/10/19 06100 Rough Carpentry 04/02/19 3 04/23/19 4 05/21/19 06/11/19 2 06/25/19 07/02/19 06200 Carpentry 05/13/19 3 06/03/19 4 07/01/19 07/22/19 2 08/05/19 08/12/19 06400 Millwork 08/07/19 3 08/28/19 4 09/25/19 10/16/19 8 12/11/19 12/18/19 07540 TPO membrane 05/09/19 3 05/30/19 4 06/27/19 07/18/19 3 08/08/19 08/15/19 07212 Mineral Fiber Blanket Thermal Insulation 08/18/19 3 09/08/19 4 10/06/19 10/27/19 2 11/10/19 11/17/19 07214 Board and Block Thermal Insulation 08/18/19 3 09/08/19 4 10/06/19 10/27/19 2 11/10/19 11/17/19 07270 Firestopping 06/20/19 3 07/11/19 4 08/08/19 08/29/19 2 09/12/19 09/19/19 07600 Flashing and Sheet Metal 05/09/19 3 05/30/19 4 06/27/19 07/18/19 2 08/01/19 08/08/19 07920 Caulking and Sealants 07/09/19 3 07/30/19 4 08/27/19 09/17/19 2 10/01/19 10/08/19 08110 Steel Doors & Frames 09/01/19 3 09/22/19 4 10/20/19 11/10/19 4 12/08/19 12/15/19 08210 Flush Wood Doors 09/01/19 3 09/22/19 4 10/20/19 11/10/19 4 12/08/19 12/15/19 08520 Aluminum Windows 06/25/19 3 07/16/19 4 08/13/19 09/03/19 4 10/01/19 10/08/19 08400 Exterior doors 06/25/19 3 07/16/19 4 08/13/19 09/03/19 4 10/01/19 10/08/19 08300 Specialty doors 09/01/19 3 09/22/19 4 10/20/19 11/10/19 4 12/08/19 12/15/19 08360 Garage doors 05/28/19 3 06/18/19 4 07/16/19 08/06/19 8 10/01/19 10/08/19 08810 Custom made glazing 06/11/19 3 07/02/19 4 07/30/19 08/20/19 6 10/01/19 10/08/19 09250 Gypsum Board 08/18/19 3 09/08/19 4 10/06/19 10/27/19 2 11/10/19 11/17/19 09310 Ceramic Tile 08/27/19 3 09/17/19 4 10/15/19 11/05/19 3 11/26/19 12/03/19 09500 Acoustical Ceilings 09/11/19 3 10/02/19 4 10/30/19 11/20/19 3 12/11/19 12/18/19 09900 Painting 10/09/19 3 10/30/19 4 11/27/19 12/18/19 2 01/01/20 01/08/20 10440 Exterior signage 11/05/19 3 11/26/19 4 12/24/19 01/14/20 4 02/11/20 02/18/20 12510 Louvers 07/06/18 3 07/27/18 4 08/24/18 09/14/18 4 10/12/18 10/08/19 15010 Mechanical Systems 09/17/19 3 10/08/19 4 11/05/19 11/26/19 4 12/24/19 12/31/19 15330 Fire Extinguishing Sprinkler Systems 06/16/19 3 07/07/19 4 08/04/19 08/25/19 4 09/22/19 09/29/19 15410 Plumbing Piping Systems 09/09/19 3 09/30/19 4 10/28/19 11/18/19 4 12/16/19 12/23/19 16011 Electrical Systems 09/29/19 3 10/20/19 4 11/17/19 12/08/19 3 12/29/19 01/05/20 16722 Fire Alarm System 09/19/19 3 10/10/19 4 11/07/19 11/28/19 3 12/19/19 12/26/19 14240 Elevator 05/12/19 3 06/02/19 4 06/30/19 07/21/19 16 11/10/19 11/17/19 10522 Fire Extinguishers and Cabinets 09/12/19 3 10/03/19 4 10/31/19 11/21/19 4 12/19/19 12/26/19 10800 Toilet and Bath Accessories 11/04/19 3 11/25/19 4 12/23/19 01/13/20 2 01/27/20 02/03/20 26500 Interior lighting 10/06/19 3 10/27/19 4 11/24/19 12/15/19 2 12/29/19 01/05/20 4.11. Submittal calculator
Plumbing rough inspectionThu
Substantial completion Fri
Core and shell completedThu
Turnover Mon
Final Payment Wed
Demobilization
Mech rough inspection Wed
Demobilization Fri
Functioning elevator Mon
Certificate of occupancyWed
Final Payment Wed
Sprinkler rough inspectionTue
T&B Report Thu 2/20/20 Fri 2/7/20
Substantial completion Fri 2/14/20 Fri 2/14/20 2/17/20 2/19/20 3/18/20 10/31/19 10/31/19 10/24/19 10/22/19 10/30/19 11/4/19 11/25/19 12/9/19 12/19/19 2/5/20 2/3/20 2/20/20 2/7/20 2/14/20 2/14/20 2/17/20 2/19/20 3/18/20
Remove trailer from job site. Transfer office, power generator, dumpsters and portable toilets to interior of the building Thu 10/31/19 Remove sheltered walkwayThu
Elevator inspection Mon
Startup of systems Mon
Rough electrical inspectionMon
Insulation completed Thu
Punchlist
Turnover Mon
Certificate of occupancyWed
T&B Report Thu
Punchlist Fri
Final Inspection Wed
08/01/2018MCM 901 Page 88 of 224 Master Thesis: 620 N 3rd St Clara Bucar 4.12. Schedule Summary with Milestones MILESTONE REPORT Name Start Invitation to bid Wed 12/12/18 Building permit Wed 1/30/19 Notice to proceed Wed 2/13/19 Construction starts Mon 2/18/19 Subsurface work completedThu 4/11/19 Footings inspection Thu 3/28/19 Major concrete work completed Thu 5/30/19 Install sheltered walkwayThu 5/30/19 Steel erection completedFri 6/7/19 Remove trailer from job site. Transfer office, power generator, dumpsters and portable toilets to interior of the building Thu 10/31/19 Remove sheltered walkwayThu 10/31/19 Core and shell completedThu 10/31/19 Plumbing rough inspectionThu 10/24/19 Sprinkler rough inspectionTue 10/22/19 Mech rough inspection Wed 10/30/19 Rough electrical inspectionMon 11/4/19 Elevator inspection Mon 11/25/19 Functioning elevator Mon 12/9/19 Insulation completed Thu 12/19/19 Final Inspection Wed 2/5/20 Startup of systems Mon 2/3/20 T&B Report Thu 2/20/20 Punchlist Fri 2/7/20 Substantial completion Fri 2/14/20 Demobilization Fri 2/14/20 Turnover Mon 2/17/20 Certificate of occupancyWed 2/19/20 Final Payment Wed 3/18/20 MILESTONE REPORT Name Start Invitation to bid Wed 12/12/18 Building permit Wed 1/30/19 Notice to proceed Wed 2/13/19 Construction starts Mon 2/18/19 Subsurface work completedThu 4/11/19 Footings inspection Thu 3/28/19 Major concrete work completed Thu 5/30/19 Install sheltered walkwayThu 5/30/19 Steel erection completedFri 6/7/19 Remove trailer from job site. Transfer office, power generator, dumpsters and portable toilets to interior of the building Thu 10/31/19 Remove sheltered walkwayThu 10/31/19 Core and shell completedThu 10/31/19 Plumbing rough inspectionThu 10/24/19 Sprinkler rough inspectionTue 10/22/19 Mech rough inspection Wed 10/30/19 Rough electrical inspectionMon 11/4/19 Elevator inspection Mon 11/25/19 Functioning elevator Mon 12/9/19 Insulation completed Thu 12/19/19 Final Inspection Wed 2/5/20 Startup of systems Mon 2/3/20
08/01/2018MCM 901 Page 89 of 224 Master Thesis: 620 N 3rd St Clara Bucar 4.13. Construction Schedule with Critical Path Milestone CriticalSubtaskTaskpath00000000 LEGEND 2/19/20 52 Building permit 0 days 1/30/19Wed 1/30/19Wed days5FS+30 $0.00 53 Building permit: City comments and review 10 days 1/30/19Wed 2/13/19Wed 52 $0.00 54 Notice to proceed 0 days 2/13/19Wed 2/13/19Wed 53 $0.00 55 Mobilization days?263 2/13/19Wed 2/17/20Mon 54 $0.00 56 Trailer 1 day 2/13/19Wed Thu 2/14/19 $0.00 57 Fencing/Gates 2 days 2/13/19Wed Fri 2/15/19 $0.00 58 signageConstruction 1 day? 2/13/19Wed Thu 2/14/19 $0.00 59 Dumpsters 1 day 2/13/19Wed Thu 2/14/19 $0.00 60 Portable toilets 1 day? 2/13/19Wed Thu 2/14/19 $0.00 61 Temp water 2 days 2/13/19Wed Fri 2/15/19 $0.00 62 Temp power 2 days 2/13/19Wed Fri 2/15/19 $0.00 63 Security system install 3 days 2/13/19Wed 2/18/19Mon $0.00 1/30 Building permit 1/30 2/13 Building permit: City comments and review 2/13 Notice to proceed 2/13 Mobilization 2/13 ConstructionFencing/Gates2/13Trailer2/142/152/132/14signage2/132/14Dumpsters2/132/14Portabletoilets2/132/15Tempwater2/132/15Temppower2/132/18Securitysysteminstall days5FS+30 $0.00$0.00$0.00 $0.00 $0.00$0.00$0.00$0.00$0.00$0.00$0.00$0.00 11/5 2/19 Exterior signage 1/30 Building permit 1/30 2/13 Building permit: City comments and review 2/13 Notice to proceed 2/13 2/17 Mobilization 2/13 ConstructionFencing/Gates2/13Trailer2/142/152/132/14signage2/132/14Dumpsters2/132/14Portabletoilets2/132/15Tempwater2/132/15Temppower2/132/18Securitysysteminstall
08/01/2018MCM 901 Page 90 of 224 Master Thesis: 620 N 3rd St Clara Bucar ID Task Name Duration Start Finish PredecessorsCost 64 Demobilization 1 day? Fri 2/14/20 2/17/20Mon 514 $0.00 65 Construction starts 0 days 2/18/19Mon 2/18/19Mon days53FS+3 $0.00 66 Site work 7 days 2/18/19Mon 2/27/19Wed 65 $1,000.00 67 Excavation 4 days 2/18/19Mon Fri 2/22/19 $1,000.00 68 Store dirt for backfill 1 day Fri 2/22/19 2/25/19Mon 67 $0.00 69 Removal of dirt 1 day 2/25/19Mon Tue 2/26/19 68 $0.00 70 Compaction 1 day Tue 2/26/19 2/27/19Wed 69 $0.00 71 Underpinning 21 days 2/27/19Wed Thu 3/28/19 66 $15,000.00 72 Excavate part I 2 days 2/27/19Wed Fri 3/1/19 $1,000.00 73 Tie backs part I 0.5 days Fri 3/1/19 Fri 3/1/19 72 $1,000.00 74 Formwork part I 0.5 days Mon 3/4/19 Mon 3/4/19 73 $1,000.00 75 Pour concrete part I 0.5 days Mon 3/4/19 Mon 3/4/19 74 $1,000.00 76 Cure concrete part I 5 days Tue 3/5/19 3/11/19Mon 75 $1,000.00 77 Dry pack partnon-shrinkwithgroutI 0.5 days Tue 3/12/19 Tue 3/12/19 76 $1,000.00 78 Excavate part II 2 days Thu 3/7/19 Fri 3/8/19 days76FS-3 $1,000.00 79 Tie backs part II 0.5 days 3/11/19Mon 3/11/19Mon 78 $1,000.00 80 Formwork part II 0.5 days 3/11/19Mon 3/11/19Mon 79 $1,000.00 81 Pour concrete part II 0.5 days Tue 3/12/19 Tue 3/12/19 80 $1,000.00 82 Cure concrete part II 5 days Tue 3/12/19 Tue 3/19/19 81 $500.00 83 Dry pack partnon-shrinkwithgroutII 0.5 days Tue 3/19/19 Tue 3/19/19 82 $500.00 84 Excavate part III 2 days Thu 3/14/19 3/18/19Mon days82FS-3 $500.00 Construction2/18starts2/182/27Sitework2/182/22Excavation2/222/25Storedirtforbackfill2/252/26Removalofdirt2/262/27Compaction2/27 3/28 Underpinning 2/27 3/1 Excavate part I 3/1 3/1 Tie backs part I 3/4 Formwork3/4part I 3/4 3/4 Pour concrete part I 3/5 3/11 Cure concrete part I 3/12 3/12 Dry pack with non-shrink grout part I 3/7 3/8 Excavate part II 3/11 3/11 Tie backs part II 3/11 Formwork3/11part II 3/12 3/12 Pour concrete part II 3/12 3/19 Cure concrete part II 3/19 3/19 Dry pack with non-shrink grout part II 3/14 3/18 Excavate part III 12/2 12/16 12/30 1/13 1/27 2/10 2/24 3/10 3/24 4/7 4/21 5/5 5/19 6/2 6/16 6/30 7/14 7/28 8/11 8/25 9/8 9/22 10/6 December 1 January 1 February 1 March 1 April 1 May 1 June 1 July 1 August 1 September 1 October
08/01/2018MCM 901 Page 91 of 224 Master Thesis: 620 N 3rd St Clara Bucar ID Task Name Duration Start Finish PredecessorsCost 85 Tie backs part III 0.5 days 3/18/19Mon 3/18/19Mon 84 $500.00 86 Formwork part III 0.5 days Tue 3/19/19 Tue 3/19/19 85 $500.00 87 Pour concrete part III 0.5 days Tue 3/19/19 Tue 3/19/19 86 $500.00 88 Cure concrete part III 5 days 3/20/19Wed Tue 3/26/19 87 $500.00 89 Dry pack partnon-shrinkwithgroutIII 0.5 days 3/27/19Wed 3/27/19Wed 88 $500.00 90 Backfill 1 day Tue 3/26/19 3/27/19Wed 89FS-1 day $500.00 91 Compaction 1 day 3/27/19Wed Thu 3/28/19 90 $500.00 92 Excavate basement 3 days 3/25/19Mon Thu 3/28/19 days71FS-3 $12,536.22 93 Excavate 2 days 3/25/19Mon 3/27/19Wed $3,000.00 94 Store dirt for backfill 1 day 3/27/19Wed Thu 3/28/19 93 $3,000.00 95 Removal of dirt 1 day 3/27/19Wed Thu 3/28/19 93 $2,346.96 96 Compaction 1 day 3/27/19Wed Thu 3/28/19 93 $4,189.26 97 Utilities 10 days Thu 3/28/19 Thu 4/11/19 92 $25,000.00 98 Water main line 2 days Thu 3/28/19 Mon 4/1/19 $5,000.00 99 Sewage main line 3 days Fri 3/29/19 Wed 4/3/19 98FS-1 day $5,000.00 100 Gas 3 days Tue 4/2/19 Fri 4/5/19 99FS-1 day $5,000.00 101 Electric 3 days Thu 4/4/19 Tue 4/9/19 day100FS-1 $5,000.00 102 Stormwater main line 3 days Mon 4/8/19 Thu 4/11/19 day101FS-1 $5,000.00 103 Subsurface work completed 0 days Thu 4/11/19 Thu 4/11/19 97 $0.00 104 Backfill 1 day Thu 4/11/19 Fri 4/12/19 103 $1,328.74 105 Compaction 2 days Fri 4/12/19 Tue 4/16/19 104 $0.00 3/18 3/18 Tie backs part III 3/19 Formwork3/19part III 3/19 3/19 Pour concrete part III 3/20 3/26 Cure concrete part III 3/27 3/27 Dry pack with non-shrink grout part III 3/26 StoreExcavate3/253/27Backfill3/273/28Compaction3/28basement3/253/27Excavate3/273/28dirtforbackfill3/273/28Removalofdirt3/273/28Compaction3/284/11Utilities3/284/1Watermainline3/294/3Sewagemainline4/24/5Gas4/44/9Electric4/84/11Stormwatermainline4/11Subsurfaceworkcompleted4/114/12Backfill4/124/16Compaction 12/2 12/16 12/30 1/13 1/27 2/10 2/24 3/10 3/24 4/7 4/21 5/5 5/19 6/2 6/16 6/30 7/14 7/28 8/11 8/25 9/8 9/22 10/6 December 1 January 1 February 1 March 1 April 1 May 1 June 1 July 1 August 1 September 1 October
08/01/2018MCM 901 Page 92 of 224 Master Thesis: 620 N 3rd St Clara Bucar ID Task Name Duration Start Finish PredecessorsCost 106 Footings 13 days Thu 3/28/19 Tue 4/16/19 92 $13,935.34 107 Formwork 1 day Thu 3/28/19 Fri 3/29/19 $2,000.00 108 Rebar 1 day Fri 3/29/19 Mon 4/1/19 107 $2,000.00 109 inspectionFootings 0 days Thu 3/28/19 Thu 3/28/19 $2,000.00 110 Pour concrete 2 days Thu 4/4/19 Mon 4/8/19 days109FS+5 $2,000.00 111 Cure concrete 5 days Mon 4/8/19 4/15/19Mon 110 $2,000.00 112 Remove formwork 0.5 days 4/15/19Mon 4/15/19Mon 111 $2,000.00 113 Backfill 0.5 days Tue 4/16/19 Tue 4/16/19 112 $1,935.34 114 Foundations 11 days 4/15/19Mon Tue 4/30/19 day106FS-1 $140,613.37 115 Formwork 1 day 4/15/19Mon Tue 4/16/19 $20,000.00 116 Rebar 2 days Tue 4/16/19 Thu 4/18/19 115 $20,000.00 117 Pour concrete 1 day Thu 4/18/19 Fri 4/19/19 116 $20,000.00 118 Cure concrete 5 days Fri 4/19/19 Fri 4/26/19 117 $20,000.00 119 Remove formwork 0.5 days Fri 4/26/19 Fri 4/26/19 118 $20,000.00 120 Drainage layer 0.5 days 4/29/19Mon 4/29/19Mon 119 $20,000.00 121 membraneWaterproofing 0.5 days 4/29/19Mon 4/29/19Mon 120 $10,000.00 122 Backfill 0.5 days Tue 4/30/19 Tue 4/30/19 121 $10,613.37 123 CMU: Elevator shaft 8 days Thu 4/18/19 Tue 4/30/19 days114FS-8 $33,946.58 124 Place rebar 4 days Thu 4/18/19 4/24/19Wed $10,000.00 125 Place CMU 4 days 4/22/19Mon Fri 4/26/19 days124FS-2 $10,000.00 126 Grout 4 days 4/24/19Wed Tue 4/30/19 days125FS-2 $13,946.58 3/28 4/16 Footings 3/28 Footings3/29Formwork3/294/1Rebar3/28inspection4/44/8Pourconcrete4/84/15Cureconcrete4/154/15Removeformwork4/164/16Backfill4/15 Waterproofing4/15Foundations4/304/16Formwork4/164/18Rebar4/184/19Pourconcrete4/194/26Cureconcrete4/264/26Removeformwork4/294/29Drainagelayer4/294/29membrane4/304/30Backfill4/184/30CMU:Elevatorshaft4/184/24Placerebar4/224/26PlaceCMU4/244/30Grout 12/2 12/16 12/30 1/13 1/27 2/10 2/24 3/10 3/24 4/7 4/21 5/5 5/19 6/2 6/16 6/30 7/14 7/28 8/11 8/25 9/8 9/22 10/6 December 1 January 1 February 1 March 1 April 1 May 1 June 1 July 1 August 1 September 1 October
08/01/2018MCM 901 Page 93 of 224 Master Thesis: 620 N 3rd St Clara Bucar ID Task Name Duration Start Finish PredecessorsCost 127 Basement slab on grade 14 days Tue 4/23/19 5/13/19Mon days123FS-5 $8,381.33 128 4" 2B Stone 1 day Tue 4/23/19 4/24/19Wed $800.00 129 Vapor barrier 1 day 4/24/19Wed Thu 4/25/19 128 $2,300.00 130 Formwork 2 days Thu 4/25/19 4/29/19Mon 129 $800.00 131 Rebar 2 days 4/29/19Mon Wed 5/1/19 130 $800.00 132 Pour concrete 2 days Wed 5/1/19 Fri 5/3/19 131 $800.00 133 Cure concrete 5 days Fri 5/3/19 Fri 5/10/19 132 $800.00 134 formworkRemove 1 day Fri 5/10/19 5/13/19Mon 133 $2,081.33 135 Concrete piers 9 days Mon 5/6/19 Fri 5/17/19 days127FS-5 $636.53 136 Formwork 1 day Mon 5/6/19 Tue 5/7/19 $236.53 137 Rebar 1 day Tue 5/7/19 Wed 5/8/19 136 $100.00 138 Pour concrete 1 day Wed 5/8/19 Thu 5/9/19 137 $100.00 139 Cure concrete 5 days Thu 5/9/19 Thu 5/16/19 138 $100.00 140 Remove formwork 1 day Thu 5/16/19 Fri 5/17/19 139 $100.00 141 1st Floor slab on grade 11 days Tue 4/30/19 5/15/19Wed days132FS-3 $5,000.00 142 Formwork 1 day Tue 4/30/19 Wed 5/1/19 $1,000.00 143 Rebar 2 days Wed 5/1/19 Fri 5/3/19 142 $1,000.00 144 Pour concrete 2 days Fri 5/3/19 Tue 5/7/19 143 $1,000.00 145 Cure concrete 5 days Tue 5/7/19 Tue 5/14/19 144 $1,000.00 146 Remove formwork 1 day Tue 5/14/19 5/15/19Wed 145 $1,000.00 147 Concrete (board-formedwalls in place) 11 days 5/15/19Wed Thu 5/30/19 141 $18,250.00 4/23 5/13 Basement slab on grade 4/23 4/24 4" 2B Stone 4/24 4/25 Vapor barrier 4/25 Concrete1st4/304/29Formwork4/295/1Rebar5/15/3Pourconcrete5/35/10Cureconcrete5/105/13Removeformwork5/65/17Concretepiers5/65/7Formwork5/75/8Rebar5/85/9Pourconcrete5/95/16Cureconcrete5/165/17Removeformwork5/15Floorslabongrade4/305/1Formwork5/15/3Rebar5/35/7Pourconcrete5/75/14Cureconcrete5/145/15Removeformwork5/155/30walls(board-formed in place) 12/2 12/16 12/30 1/13 1/27 2/10 2/24 3/10 3/24 4/7 4/21 5/5 5/19 6/2 6/16 6/30 7/14 7/28 8/11 8/25 9/8 9/22 December 1 January 1 February 1 March 1 April 1 May 1 June 1 July 1 August 1 September 1 October
08/01/2018MCM 901 Page 94 of 224 Master Thesis: 620 N 3rd St Clara Bucar ID Task Name Duration Start Finish PredecessorsCost 148 Board form install 2 days 5/15/19Wed Fri 5/17/19 $3,000.00 149 Bracing 1 day Fri 5/17/19 5/20/19Mon 148 $3,000.00 150 Rebar 1 day 5/20/19Mon Tue 5/21/19 149 $3,000.00 151 Pour concrete 1 day Tue 5/21/19 5/22/19Wed 150 $3,000.00 152 Cure concrete 5 days 5/22/19Wed 5/29/19Wed 151 $3,000.00 153 Remove board form 1 day 5/29/19Wed Thu 5/30/19 152 $3,250.00 154 Sidewalks and gutter 4 days Fri 5/24/19 Thu 5/30/19 days147FS-4 $4,500.00 155 Sidewalk curbing 2 days Fri 5/24/19 Tue 5/28/19 $1,000.00 156 Sidewalk topping 2 days Tue 5/28/19 Thu 5/30/19 155 $1,000.00 157 improvementGutter 2 days Fri 5/24/19 Tue 5/28/19 $2,500.00 158 Major concrete work completed 0 days Thu 5/30/19 Thu 5/30/19 154 $0.00 159 Install walkwaysheltered 0 days Thu 5/30/19 Thu 5/30/19 154 $0.00 160 Bring crane to job site 1 day Thu 5/30/19 Fri 5/31/19 159 $0.00 161 Steel basementStructure 3 days Fri 5/31/19 Wed 6/5/19 160 $35,523.01 162 Install columnssteel 1.5 days Fri 5/31/19 Mon 6/3/19 $5,051.61 163 Install steel beams 1.5 days Tue 6/4/19 Wed 6/5/19 162 $30,471.40 164 PECO aereal lines protection 1 day? Fri 6/7/19 6/10/19Mon 165 $0.00 165 Steel Structure 1st Floor 5 days Fri 5/31/19 Fri 6/7/19 160 $33,225.18 166 Install columnssteel 2 days Fri 5/31/19 Tue 6/4/19 $4,133.86 167 Install steel beams 3 days Tue 6/4/19 Fri 6/7/19 166 $29,091.32 168 Fireproof all steel 2 days Fri 6/7/19 Tue 6/11/19 165 $20,000.00 5/15 5/17 Board form install 5/17 MajorGutterSidewalksPour5/20Bracing5/205/21Rebar5/215/22concrete5/225/29Cureconcrete5/295/30Removeboardform5/245/30andgutter5/245/28Sidewalkcurbing5/285/30Sidewalktopping5/245/28improvement5/30concreteworkcompleted5/30Installshelteredwalkway5/305/31Bringcranetojobsite5/316/5SteelStructurebasement5/316/3Installsteelcolumns6/46/5Installsteelbeams6/76/10PECOaereallinesprotection5/316/7SteelStructure1stFloor5/316/4Installsteelcolumns6/46/7Installsteelbeams6/76/11Fireproofallsteel 12/2 12/16 12/30 1/13 1/27 2/10 2/24 3/10 3/24 4/7 4/21 5/5 5/19 6/2 6/16 6/30 7/14 7/28 8/11 8/25 9/8 9/22 December 1 January 1 February 1 March 1 April 1 May 1 June 1 July 1 August 1 September 1 October
08/01/2018MCM 901 Page 95 of 224 Master Thesis: 620 N 3rd St Clara Bucar ID Task Name Duration Start Finish PredecessorsCost 169 Steel completederection 0 days Fri 6/7/19 Fri 6/7/19 165 $0.00 170 1st Floor slab: Poured in place concrete over metal deck 12 days Fri 6/7/19 Tue 6/25/19 165 $17,437.57 171 Place metal deck 2 days Fri 6/7/19 Tue 6/11/19 $10,000.00 172 Place welded wire fabric 1 day Tue 6/11/19 6/12/19Wed 171 $3,489.00 173 concretePour-in-placeand cure 5 days 6/12/19Wed 6/19/19Wed 172 $1,669.31 174 Pour concretelighweightandcure 4 days 6/19/19Wed Tue 6/25/19 173 $2,279.26 175 2nd Floor slab: Steel joist structure 9 days Thu 6/20/19 Wed 7/3/19 days170FS-3 $68,403.02 176 Place steelchannelstructuralshapedjoist 4 days Thu 6/20/19 6/26/19Wed $28,579.02 177 Place subflooring 3 days Thu 6/20/19 Tue 6/25/19 $10,230.00 178 Place concrete floor panels 1 day 6/26/19Wed Thu 6/27/19 176 $8,184.00 179 Place upper vapor barrier 1 day Thu 6/27/19 Fri 6/28/19 178 $1,500.00 180 Pour underlaymentfloor and cure 3 days Fri 6/28/19 Wed 7/3/19 179 $19,910.00 181 Bracing below 2nd floor deck to store wood 2 days Mon 7/1/19 Wed 7/3/19 days180FS-2 $0.00 182 Transport wood to deck area on 2nd floor 1 day? Wed 7/3/19 Thu 7/4/19 181 $0.00 183 Remove crane from job site 1 day? Thu 7/4/19 Fri 7/5/19 182 $0.00 184 3rd Floor: Wood structure 8 days Thu 7/4/19 Tue 7/16/19 182 $40,000.00 185 Place posts below 1 day Thu 7/4/19 Fri 7/5/19 $5,000.00 186 Place belowgirders 1 day Fri 7/5/19 Mon 7/8/19 185 $8,000.00 187 Place wood joists 4 days Mon 7/8/19 Fri 7/12/19 186 $19,000.00 188 Install subflooring 2 days Fri 7/12/19 Tue 7/16/19 187 $8,000.00 6/7 Steel erection completed 6/7 6/25 1st Floor slab: Poured in place concrete over metal deck 6/7 6/11 Place metal deck 6/11 6/12 Place welded wire fabric 6/12 6/19 Pour-in-place concrete and cure 6/19 6/25 Pour lighweight concrete and cure 6/20 7/3 2nd Floor slab: Steel joist structure 6/20 6/26 Place structural channel shaped steel joist 6/20 6/25 Place6/26subflooring6/27Place concrete floor panels 6/27 6/28 Place upper vapor barrier 6/28 7/3 Pour floor underlayment and cure 7/1 7/3 Bracing below 2nd floor deck to store wood 7/3 7/4 Transport wood to deck area on 2nd floor 7/4 7/5 Remove crane from job site 7/4 7/16 3rd Floor: Wood structure 7/4 7/5 Place posts below 7/5 7/8 Place girders below 7/8 7/12 Place wood joists 7/12 7/16 Install subflooring 12/2 12/16 12/30 1/13 1/27 2/10 2/24 3/10 3/24 4/7 4/21 5/5 5/19 6/2 6/16 6/30 7/14 7/28 8/11 8/25 9/8 9/22 December 1 January 1 February 1 March 1 April 1 May 1 June 1 July 1 August 1 September 1 October
08/01/2018MCM 901 Page 96 of 224 Master Thesis: 620 N 3rd St Clara Bucar ID Task Name Duration Start Finish PredecessorsCost 189 4th Floor: Wood structure 8 days Tue 7/16/19 Fri 7/26/19 184 $41,422.56 190 Place posts below 1 day Tue 7/16/19 7/17/19Wed $5,000.00 191 Place belowgirders 1 day 7/17/19Wed Thu 7/18/19 190 $8,000.00 192 Place wood joists 4 days Thu 7/18/19 7/24/19Wed 191 $19,000.00 193 Install subflooring 2 days 7/24/19Wed Fri 7/26/19 192 $9,422.56 194 Roof structure 10 days Fri 7/26/19 Fri 8/9/19 189 $50,862.85 195 Place posts below 1 day Fri 7/26/19 7/29/19Mon $5,448.44 196 Place belowgirders 1 day 7/29/19Mon Tue 7/30/19 195 $7,426.78 197 Place wood joists 4 days Tue 7/30/19 Mon 8/5/19 196 $19,185.76 198 Install plywood 2 days Mon 8/5/19 Wed 8/7/19 197 $17,719.96 199 Roof coring for penetrationspermanent 1 day Wed 8/7/19 Thu 8/8/19 198 $1,081.91 200 Temporary cap penetrationspermanent 1 day Thu 8/8/19 Fri 8/9/19 199 $0.00 201 Stairwells 10 days Fri 8/9/19 Fri 8/23/19 194 $4,000.00 202 Install chute in West stairwell 2 days Fri 8/9/19 Tue 8/13/19 $0.00 203 Install pulley in West stairwell 1 day Tue 8/13/19 8/14/19Wed 202 $0.00 204 Place East stairs 10 days Fri 8/9/19 Fri 8/23/19 $4,000.00 205 Temporary roof drainage 2 days Fri 8/9/19 Tue 8/13/19 194 $0.00 206 Install permanent roof drains 2 days Fri 8/9/19 Tue 8/13/19 $0.00 207 Install pippingstormwatertemporary 2 days Fri 8/9/19 Tue 8/13/19 $0.00 208 Waterproofing: roof 5 days Tue 8/13/19 Tue 8/20/19 205 $31,927.00 7/16 7/26 4th Floor: Wood structure 7/16 7/17 Place posts below 7/17 7/18 Place girders below 7/18 7/24 Place wood joists 7/24 7/26 Install7/26subflooring 8/9 Roof structure 7/26 7/29 Place posts below 7/29 7/30 Place girders below 7/30 8/5 Place wood joists 8/5 8/7 Install8/7plywood8/8Roof coring for permanent penetrations 8/8 8/9 Temporary cap permanent penetrations 8/9 8/238/9Stairwells8/13Install chute in West stairwell 8/13 8/14 Install pulley in West stairwell 8/9 8/23 Place East stairs 8/9 8/13 Temporary roof drainage 8/9 8/13 Install permanent roof drains 8/9 8/13 Install temporary stormwater pipping 8/13 Waterproofing:8/20roof 5/19 6/2 6/16 6/30 7/14 7/28 8/11 8/25 9/8 9/22 10/6 10/20 11/3 11/17 12/1 12/15 12/29 1/12 1/26 2/9 2/23 3/8 May 1 June 1 July 1 August 1 September 1 October 1 November 1 December 1 January 1 February 1 March 1
08/01/2018MCM 901 Page 97 of 224 Master Thesis: 620 N 3rd St Clara Bucar ID Task Name Duration Start Finish PredecessorsCost 209 Install sleeperswood 3 days Tue 8/13/19 Fri 8/16/19 $0.00 210 Install membraneroofing 2 days Fri 8/16/19 Tue 8/20/19 209 $31,927.00 211 2nd floor interior framing 5 days Wed 8/7/19 8/14/19Wed 198 $19,000.00 212 Lift wood to 2nd Fl (from outside of the building) 1 day Wed 8/7/19 Thu 8/8/19 $0.00 213 Wood framing 5 days Wed 8/7/19 8/14/19Wed $15,000.00 214 Furring and other framing 2 days Wed 8/7/19 Fri 8/9/19 $4,000.00 215 3rd floor interior framing 5 days 8/14/19Wed 8/21/19Wed 211 $19,000.00 216 Lift wood to 3rd Fl (from outside of the building) 1 day 8/14/19Wed Thu 8/15/19 $0.00 217 Wood framing 5 days 8/14/19Wed 8/21/19Wed $15,000.00 218 Furring and other framing 2 days 8/14/19Wed Fri 8/16/19 $4,000.00 219 4th floor interior framing 5 days 8/21/19Wed 8/28/19Wed 215 $19,562.38 220 Lift wood to 4th Fl (from outside of the building) 1 day 8/21/19Wed Thu 8/22/19 $0.00 221 Wood framing 5 days 8/21/19Wed 8/28/19Wed $15,000.00 222 Furring and other framing 2 days 8/21/19Wed Fri 8/23/19 $4,562.38 223 1st floor framing 2 days 8/26/19Mon 8/28/19Wed days219FS-2 $7,339.19 224 Basement framing 1 day Tue 8/27/19 8/28/19Wed day223FS-1 $0.00 225 Framing inspection 10 days 8/28/19Wed 9/11/19Wed 224 $0.00 226 Repair reinspectionand 10 days 8/28/19Wed 9/11/19Wed $0.00 227 Exterior walls 7 days 9/11/19Wed Fri 9/20/19 225 $33,783.26 228 Place steel stud framing (WF3-B) 2 days 9/11/19Wed Fri 9/13/19 $6,189.00 8/13 8/16 Install wood sleepers 8/16 8/20 Install roofing membrane 8/7 8/14 2nd floor interior framing 8/7 8/8 Lift wood to 2nd Fl (from outside of the building) 8/7 8/14 Wood framing 8/7 8/9 Furring and other framing 8/14 8/21 3rd floor interior framing 8/14 8/15 Lift wood to 3rd Fl (from outside of the building) 8/14 8/21 Wood framing 8/14 8/16 Furring and other framing 8/21 8/28 4th floor interior framing 8/21 8/22 Lift wood to 4th Fl (from outside of the building) 8/21 8/28 Wood framing 8/21 8/23 Furring and other framing 8/26 8/28 1st floor framing 8/27 8/28 Basement framing 8/28 9/11 Framing inspection 8/28 9/11 Repair and9/11reinspection9/20Exteriorwalls9/119/13Place steel stud framing (WF3-B) 5/19 6/2 6/16 6/30 7/14 7/28 8/11 8/25 9/8 9/22 10/6 10/20 11/3 11/17 12/1 12/15 12/29 1/12 1/26 2/9 2/23 3/8 May 1 June 1 July 1 August 1 September 1 October 1 November 1 December 1 January 1 February 1 March 1
08/01/2018MCM 901 Page 98 of 224 Master Thesis: 620 N 3rd St Clara Bucar ID Task Name Duration Start Finish PredecessorsCost 229 Place boardcement(WF3-B) 2 days Fri 9/13/19 Tue 9/17/19 228 $1,547.25 230 Place sheathingplywoodexterior(W1, 2 days Tue 9/17/19 Thu 9/19/19 229 $23,524.00 231 Install shaft wall in basement 1 day Thu 9/19/19 Fri 9/20/19 230 $2,523.01 232 Exterior finish 15 days Fri 9/20/19 Fri 10/11/19 227 $111,301.24 233 Brick 6 days Fri 9/20/19 9/30/19Mon $50,819.38 234 Anchoring 2 days Fri 9/20/19 Tue 9/24/19 $0.00 235 Reinforcement 2 days Tue 9/24/19 Thu 9/26/19 234 $0.00 236 Brick veneer 2 days Thu 9/26/19 9/30/19Mon 235 $50,819.38 237 Aluminum panel 3 days 9/30/19Mon Thu 10/3/19 233 $44,999.75 238 Weather barrier 1 day 9/30/19Mon Tue 10/1/19 $500.00 239 Cladding panels 3 days 9/30/19Mon Thu 10/3/19 $44,499.75 240 Stucco finish 3 days Thu 10/3/19 Tue 10/8/19 237 $4,548.36 241 Weather barrier 1 day Thu 10/3/19 Fri 10/4/19 $500.00 242 Wire lath 1 day Thu 10/3/19 Fri 10/4/19 $931.00 243 3 coat cement stucco 3 days Thu 10/3/19 Tue 10/8/19 $3,117.36 244 Wood rainscreenslat 3 days Tue 10/8/19 Fri 10/11/19 240 $10,933.75 245 Weather barrier 1 day Tue 10/8/19 10/9/19Wed $500.00 246 Poplar wood strips 3 days Tue 10/8/19 Fri 10/11/19 $10,433.75 247 Install stone coping 2 days Fri 10/11/19 10/15/19Tue 232 $817.50 248 Flashing all exterior openings 5 days 10/7/19Mon 10/14/19Mon days232FS-4 $3,720.00 249 Exterior openings 14 days 10/9/19Wed 10/29/19Tue days248FS-3 $86,051.00 9/13 9/17 Place cement board (WF3-B) 9/17 9/19 Place exterior plywood sheathing (W1, W2) 9/19 9/20 Install shaft wall in basement 9/20 10/11 Exterior finish 9/20 9/30 Brick 9/20ReinforcementAnchoring9/249/249/269/269/30Brickveneer9/3010/3Aluminumpanel9/3010/1Weatherbarrier9/3010/3Claddingpanels10/310/8Stuccofinish10/310/4Weatherbarrier10/310/4Wirelath10/310/83coatcementstucco10/810/11Woodslatrainscreen10/810/9Weatherbarrier10/810/11Poplarwoodstrips10/1110/15Installstonecoping10/710/14Flashingallexterioropenings10/910/29Exterioropenings 5/19 6/2 6/16 6/30 7/14 7/28 8/11 8/25 9/8 9/22 10/6 10/20 11/3 11/17 12/1 12/15 12/29 1/12 1/26 2/9 2/23 3/8 May 1 June 1 July 1 August 1 September 1 October 1 November 1 December 1 January 1 February 1 March 1
08/01/2018MCM 901 Page 99 of 224 Master Thesis: 620 N 3rd St Clara Bucar ID Task Name Duration Start Finish PredecessorsCost 250 Install West side openings 4 days 10/9/19Wed 10/15/19Tue $23,000.00 251 Install East side openings 4 days 10/15/19Tue 10/21/19Mon 250 $23,000.00 252 Install openingscourtyard 6 days 10/21/19Mon 10/29/19Tue 251 $25,551.00 253 Install N 3rd St garage door 1 day 10/9/19Wed 10/10/19Thu $5,000.00 254 Install Galloway St garage door 1 day 10/10/19Thu Fri 10/11/19 253 $5,000.00 255 Install PECO vault grate 1 day 10/9/19Wed 10/10/19Thu $3,000.00 256 Install trash room louvers 1 day 10/9/19Wed 10/10/19Thu $1,500.00 257 Caulk openings 5 days 10/9/19Wed 10/16/19Wed $0.00 258 Caulking inspection 1 day 10/16/19Wed 10/17/19Thu 257 $0.00 259 Caulking repair and reinspection 10 days 10/17/19Thu 10/31/19Thu 258 $0.00 260 Remove trailer from job site. Transfer office, portabledumpstersgenerator,powerandtoilets to interior of the 0 days 10/31/19Thu 10/31/19Thu 259 $0.00 261 Remove walkwaysheltered 0 days 10/31/19Thu 10/31/19Thu 259 $0.00 262 Core and completedshell 0 days 10/31/19Thu 10/31/19Thu 259 $0.00 263 Plumbing rough-in 24 days Fri 9/20/19 10/24/19Thu 227 $150,903.57 264 Plumbing rough-in roof 1 day Fri 9/20/19 9/23/19Mon $10,000.00 265 Plumbing rough-in 4th floor 5 days 9/23/19Mon 9/30/19Mon 264 $32,000.00 266 Plumbing rough-in 3rd floor 5 days 9/30/19Mon 10/7/19Mon 265 $32,000.00 267 Plumbing rough-in 2nd floor 5 days 10/7/19Mon 10/14/19Mon 266 $32,000.00 268 Plumbing rough-in 1st floor 2 days 10/14/19Mon 10/16/19Wed 267 $20,000.00 10/9 10/15 Install West side openings 10/15 10/21 Install East side openings 10/21 10/29 Install courtyard openings 10/9 10/10 Install N 3rd St garage door 10/10 10/11 Install Galloway St garage door 10/9 10/10 Install PECO vault grate 10/9 10/10 Install trash room louvers 10/9 10/16 Caulk CaulkingCaulking10/16openings10/17inspection10/1710/31repairandreinspection10/31Remove trailer from job site. Transfer office, power generator, dumpsters and portable toilets to interior of the building 10/31 Remove sheltered10/31walkwayCore and shell completed 9/20 10/24 Plumbing rough-in 9/20 9/23 Plumbing rough-in roof 9/23 9/30 Plumbing rough-in 4th floor 9/30 10/7 Plumbing rough-in 3rd floor 10/7 10/14 Plumbing rough-in 2nd floor 10/14 10/16 Plumbing rough-in 1st floor 5/19 6/2 6/16 6/30 7/14 7/28 8/11 8/25 9/8 9/22 10/6 10/20 11/3 11/17 12/1 12/15 12/29 1/12 1/26 2/9 2/23 3/8 May 1 June 1 July 1 August 1 September 1 October 1 November 1 December 1 January 1 February 1 March 1
08/01/2018MCM 901 Page 100 of 224 Master Thesis: 620 N 3rd St Clara Bucar ID Task Name Duration Start Finish PredecessorsCost 269 Plumbing basementrough-in 2 days 10/16/19Wed Fri 10/18/19 268 $15,000.00 270 Install water meter 1 day Fri 10/18/19 10/21/19Mon 269 $2,500.00 271 Tie-in from water main 1 day 10/21/19Mon 10/22/19Tue 270 $1,000.00 272 Tie-in sewagefrommain 1 day 10/22/19Tue 10/23/19Wed 271 $3,000.00 273 Tie-in stormwaterfrom main 1 day 10/23/19Wed 10/24/19Thu 272 $3,403.57 274 Plumbing inspectionrough 0 days 10/24/19Thu 10/24/19Thu 263 $0.00 275 Plumbing rough repair reinspectionand 10 days 10/24/19Thu Thu 11/7/19 274 $0.00 276 Sprinkler rough-in 16 days 9/30/19Mon 10/22/19Tue $25,000.00 277 Sprinkler rough-in 4th fl 3 days 9/30/19Mon Thu 10/3/19 265 $5,000.00 278 Sprinkler rough-in 3rd fl 3 days 10/7/19Mon 10/10/19Thu 266 $5,000.00 279 Sprinkler rough-in 2nd fl 3 days 10/14/19Mon 10/17/19Thu 267 $5,000.00 280 Sprinkler rough-in 1st fl 2 days 10/16/19Wed Fri 10/18/19 268 $5,000.00 281 Sprinkler basementrough-in 2 days Fri 10/18/19 10/22/19Tue 269 $5,000.00 282 Sprinkler inspectionrough 0 days 10/22/19Tue 10/22/19Tue 276 $0.00 283 Sprinkler rough repair reinspectionand 10 days 10/22/19Tue Tue 11/5/19 282 $0.00 284 Mechanical rough 21 days Tue 10/1/19 10/30/19Wed $62,592.21 285 Mech rough roof 2 days Tue 10/1/19 Thu 10/3/19 days286FS-7 $5,000.00 286 Mech rough 4th floor 5 days Thu 10/3/19 10/10/19Thu 277 $13,500.00 287 Mech rough 3rd floor 5 days 10/10/19Thu 10/17/19Thu 278 $13,500.00 288 Mech rough 2nd floor 5 days 10/17/19Thu 10/24/19Thu 279 $13,500.00 289 Mech rough 1st floor 2 days 10/24/19Thu 10/28/19Mon 288 $8,000.00 10/16 10/18 Plumbing rough-in basement 10/18 10/21 Install water meter 10/21 10/22 Tie-in from water main 10/22 10/23 Tie-in from sewage main 10/23 10/24 Tie-in from stormwater main 10/24 Plumbing rough inspection 10/24 11/7 Plumbing rough repair and reinspection 9/30 10/22 Sprinkler rough-in 9/30 10/3 Sprinkler rough-in 4th fl 10/7 10/10 Sprinkler rough-in 3rd fl 10/14 10/17 Sprinkler rough-in 2nd fl 10/16 10/18 Sprinkler rough-in 1st fl 10/18 10/22 Sprinkler rough-in10/22basementSprinkler rough inspection 10/22 11/5 Sprinkler rough repair and reinspection 10/1 10/30 Mechanical rough 10/1 10/3 Mech rough roof 10/3 10/10 Mech rough 4th floor 10/10 10/17 Mech rough 3rd floor 10/17 10/24 Mech rough 2nd floor 10/24 10/28 Mech rough 1st floor 5/19 6/2 6/16 6/30 7/14 7/28 8/11 8/25 9/8 9/22 10/6 10/20 11/3 11/17 12/1 12/15 12/29 1/12 1/26 2/9 2/23 3/8 May 1 June 1 July 1 August 1 September 1 October 1 November 1 December 1 January 1 February 1 March 1
08/01/2018MCM 901 Page 101 of 224 Master Thesis: 620 N 3rd St Clara Bucar ID Task Name Duration Start Finish PredecessorsCost 290 Mech basementrough 2 days 10/28/19Mon 10/30/19Wed 289 $9,092.21 291 Mech inspectionrough 0 days 10/30/19Wed 10/30/19Wed 284 $0.00 292 Mechanical rough repair reinspectionand 10 days 10/30/19Wed 11/13/19Wed 291 $0.00 293 Electrical rough-in 17 days 10/10/19Thu 11/4/19Mon $51,354.00 294 Rough-in electric 4th floor 5 days 10/10/19Thu 10/17/19Thu 286 $8,000.00 295 Rough-in electric 3rd floor 5 days 10/17/19Thu 10/24/19Thu 287 $8,000.00 296 Rough-in electric 2nd floor 5 days 10/24/19Thu 10/31/19Thu 288 $8,000.00 297 Rough-in electric 1st floor 2 days 10/28/19Mon 10/30/19Wed 289 $5,000.00 298 Rough-in basementelectric 2 days 10/30/19Wed Fri 11/1/19 290 $5,000.00 299 Install electric meter 1 day Fri 11/1/19 11/4/19Mon 298 $2,354.00 300 Connection from PECO 2 days 10/29/19Tue 10/31/19Thu 249 $0.00 301 Install transformer 1 day 10/31/19Thu Fri 11/1/19 300 $10,000.00 302 Install electric panel 1 day Fri 11/1/19 11/4/19Mon 301 $5,000.00 303 Rough inspectionelectrical 0 days 11/4/19Mon 11/4/19Mon 293 $0.00 304 Rough electrical repair reinspectionand 10 days 11/4/19Mon 11/18/19Mon 303 $0.00 305 Install elevator 5 days 11/18/19Mon 11/25/19Mon 304 $152,000.00 306 Install rails 5 days 11/18/19Mon 11/25/19Mon $75,000.00 307 Assemble cab 5 days 11/18/19Mon 11/25/19Mon $77,000.00 308 Elevator inspection 0 days 11/25/19Mon 11/25/19Mon 305 $0.00 309 Elevator repair and reinspection 10 days 11/25/19Mon 12/9/19Mon 308 $0.00 310 Functioning elevator 0 days 12/9/19Mon 12/9/19Mon 309 $0.00 10/28 10/30 Mech rough basement10/30Mech rough inspection 10/30 11/13 Mechanical rough repair and reinspection 10/10 11/4 Electrical rough-in 10/10 10/17 Rough-in electric 4th floor 10/17 10/24 Rough-in electric 3rd floor 10/24 10/31 Rough-in electric 2nd floor 10/28 10/30 Rough-in electric 1st floor 10/30 11/1 Rough-in electric basement 11/1 11/4 Install electric meter 10/29 10/31 Connection from PECO 10/31 11/1 Install RoughRoughInstall11/1transformer11/4electricpanel11/4electricalinspection11/411/18electricalrepairandreinspection11/1811/25Installelevator11/1811/25Installrails11/1811/25Assemblecab11/25Elevatorinspection11/2512/9Elevatorrepairandreinspection12/9Functioningelevator 5/19 6/2 6/16 6/30 7/14 7/28 8/11 8/25 9/8 9/22 10/6 10/20 11/3 11/17 12/1 12/15 12/29 1/12 1/26 2/9 2/23 3/8 May 1 June 1 July 1 August 1 September 1 October 1 November 1 December 1 January 1 February 1 March 1
08/01/2018MCM 901 Page 102 of 224 Master Thesis: 620 N 3rd St Clara Bucar ID Task Name Duration Start Finish PredecessorsCost 311 Security systems rough-in 5 days 10/31/19Thu Thu 11/7/19 262 $10,000.00 312 Fire rough-inprotection 5 days Tue 11/5/19 11/12/19Tue days262FS+3 $7,600.00 313 Audio, intercom, data rough-inmiscellaneousand 5 days Fri 11/8/19 Fri 11/15/19 days262FS+6 $15,000.00 314 Roof: landscaping 30 days 10/14/19Mon 11/25/19Mon 248 $50,244.80 315 Rubber padding 3 days 10/14/19Mon 10/17/19Thu $3,000.00 316 Pressure treated wood blocking 3 days 10/17/19Thu 10/22/19Tue 315 $3,000.00 317 Sleepers 3 days 10/22/19Tue Fri 10/25/19 316 $3,000.00 318 Wood deck over sleepers 5 days Fri 10/25/19 Fri 11/1/19 317 $20,509.80 319 Flash areas'decked 3 days Fri 11/1/19 11/6/19Wed 318 $3,000.00 320 Place river stone to parapet 5 days 11/6/19Wed 11/13/19Wed 319 $0.00 321 Planters 8 days 11/13/19Wed 11/25/19Mon 320 $17,735.00 322 Framing 3 days 11/13/19Wed 11/18/19Mon $2,400.00 323 proofingMoisture 1 day 11/18/19Mon 11/19/19Tue 322 $2,400.00 324 Install drain 1 day 11/19/19Tue 11/20/19Wed 323 $2,400.00 325 Install geo filter fabric 1 day 11/20/19Wed 11/21/19Thu 324 $2,400.00 326 Flashing upper edges 1 day 11/21/19Thu Fri 11/22/19 325 $2,400.00 327 Exterior aluminumfinish: 1 day Fri 11/22/19 11/25/19Mon 326 $5,735.00 328 Balconies 14 days 11/25/19Mon Fri 12/13/19 314 $3,000.00 329 Place floor drain 1 day 11/25/19Mon 11/26/19Tue $0.00 330 Install flashing 3 days 11/25/19Mon 11/28/19Thu $0.00 331 Place sleeperswood 3 days 11/28/19Thu Tue 12/3/19 330 $0.00 10/31 11/7 Security systems rough-in 11/5 11/12 Fire protection rough-in 11/8 11/15 Audio, intercom, data and miscellaneous rough-in 10/14 11/25 Roof: landscaping 10/14 10/17 Rubber padding 10/17 10/22 Pressure treated wood blocking 10/22 Wood10/25Sleepers10/2511/1deckoversleepers11/111/6Flashdeckedareas'11/611/13Placeriverstonetoparapet11/1311/25Planters11/1311/18Framing11/1811/19Moistureproofing11/1911/20Installdrain11/2011/21Installgeofilterfabric11/2111/22Flashingupperedges11/2211/25Exteriorfinish:aluminum11/2512/13Balconies11/2511/26Placefloordrain11/2511/28Installflashing11/2812/3Placewoodsleepers 5/19 6/2 6/16 6/30 7/14 7/28 8/11 8/25 9/8 9/22 10/6 10/20 11/3 11/17 12/1 12/15 12/29 1/12 1/26 2/9 2/23 3/8 May 1 June 1 July 1 August 1 September 1 October 1 November 1 December 1 January 1 February 1 March 1
08/01/2018MCM 901 Page 103 of 224 Master Thesis: 620 N 3rd St Clara Bucar ID Task Name Duration Start Finish PredecessorsCost 332 Place plywoodexterior 3 days Tue 12/3/19 Fri 12/6/19 331 $0.00 333 Place membraneroofing 2 days Fri 12/6/19 12/10/19Tue 332 $0.00 334 Place deckingwood 3 days 12/10/19Tue Fri 12/13/19 333 $0.00 335 Place guardrail 10 days 11/25/19Mon 12/9/19Mon $3,000.00 336 Place guardrailsother 10 days 12/9/19Mon 12/23/19Mon 335 $3,612.00 337 One-siding interior partitions 10 days 11/18/19Mon 12/2/19Mon 304,275 $18,000.00 338 basementOne-sidingand 1st floor 1 day 11/18/19Mon 11/19/19Tue $3,000.00 339 One-siding 2nd floor 3 days 11/19/19Tue Fri 11/22/19 338 $5,000.00 340 One-siding 3rd floor 3 days Fri 11/22/19 11/27/19Wed 339 $5,000.00 341 One-siding 4th floor 3 days 11/27/19Wed 12/2/19Mon 340 $5,000.00 342 Insulation: Roof 3 days 11/18/19Mon 11/21/19Thu 304,275 $8,196.00 343 Spray insulation 3 days 11/18/19Mon 11/21/19Thu $8,196.00 344 Insulation: Exterior walls days?10 11/18/19Mon 12/2/19Mon 304,275 $11,323.25 345 W1 2 days 11/18/19Mon 11/20/19Wed $4,500.00 346 Place barriervapor 1 day 11/18/19Mon 11/19/19Tue $1,500.00 347 Place insulationbatt 1 day 11/19/19Tue 11/20/19Wed 346 $3,000.00 348 W2 2 days 11/20/19Wed Fri 11/22/19 345 $4,092.00 349 Place barriervapor 1 day 11/20/19Wed 11/21/19Thu $0.00 350 Place insulationfiberglass 1 day 11/21/19Thu Fri 11/22/19 349 $4,092.00 351 WF7 2 days Fri 11/22/19 11/26/19Tue 348 $1,486.25 352 Place insulationrigid 1 day Fri 11/22/19 11/25/19Mon $600.00 12/3 12/6 Place exterior plywood 12/6 12/10 Place roofing membrane 12/10 12/13 Place wood decking 11/25 12/9 Place12/9guardrail 12/23 Place other guardrails 11/18 12/2 One-siding interior partitions 11/18 11/19 One-siding basement and 1st floor 11/19 11/22 One-siding 2nd floor 11/22 11/27 One-siding 3rd floor 11/27 12/2 One-siding 4th floor 11/18 11/21 Insulation: Roof 11/18 11/21 Spray insulation 11/18 12/2 Insulation: Exterior walls 11/18 11/20 W1 11/18 11/19 Place vapor barrier 11/19 11/20 Place batt insulation 11/20 11/22 W2 11/20 11/21 Place vapor barrier 11/21 11/22 Place fiberglass insulation 11/22 11/26 WF7 11/22 11/25 Place rigid insulation 5/19 6/2 6/16 6/30 7/14 7/28 8/11 8/25 9/8 9/22 10/6 10/20 11/3 11/17 12/1 12/15 12/29 1/12 1/26 2/9 2/23 3/8 May 1 June 1 July 1 August 1 September 1 October 1 November 1 December 1 January 1 February 1 March 1
08/01/2018MCM 901 Page 104 of 224 Master Thesis: 620 N 3rd St Clara Bucar ID Task Name Duration Start Finish PredecessorsCost 353 Place barrierweather 1 day 11/25/19Mon 11/26/19Tue 352 $886.25 354 WF6 2 days? 11/26/19Tue 11/28/19Thu 351 $600.00 355 Place insulationrigid over concrete 1 day? 11/26/19Tue 11/27/19Wed $600.00 356 Place channelsfurring 1 day 11/27/19Wed 11/28/19Thu 355 $0.00 357 G1 2 days 11/28/19Thu 12/2/19Mon 354 $645.00 358 Place insulationrigid 1 day 11/28/19Thu Fri 11/29/19 $645.00 359 Place z-furring 1 day Fri 11/29/19 12/2/19Mon 358 $0.00 360 Insulation: 4th Floor 2 days 12/2/19Mon 12/4/19Wed 344 $7,000.00 361 Flooring 2 days 12/2/19Mon 12/4/19Wed $3,000.00 362 Place barriervapor 1 day 12/2/19Mon Tue 12/3/19 $1,500.00 363 Place reductionsoundmat 1 day Tue 12/3/19 12/4/19Wed 362 $1,500.00 364 Interior partitions 1 day 12/2/19Mon Tue 12/3/19 $4,000.00 365 Batt insulation 1 day 12/2/19Mon Tue 12/3/19 $4,000.00 366 Insulation: 3rd Floor 2 days 12/4/19Wed Fri 12/6/19 360 $6,157.75 367 Flooring 2 days 12/4/19Wed Fri 12/6/19 $2,157.75 368 Place barriervapor 1 day 12/4/19Wed Thu 12/5/19 $657.75 369 Place reductionsoundmat 1 day Thu 12/5/19 Fri 12/6/19 368 $1,500.00 370 Interior partitions 1 day 12/4/19Wed Thu 12/5/19 $4,000.00 371 Batt insulation 1 day 12/4/19Wed Thu 12/5/19 $4,000.00 372 Insulation: 2nd Floor 4 days Fri 12/6/19 12/12/19Thu 366 $11,946.75 373 Flooring 4 days Fri 12/6/19 12/12/19Thu $7,294.50 11/25 11/26 Place weather barrier 11/26 11/2811/26WF611/27Place rigid insulation over concrete 11/27 11/28 Place furring channels 11/28 12/2 G1 11/28 11/29 Place rigid insulation 11/29 12/2 Place PlaceInsulation:12/2z-furring12/44thFloor12/212/4Flooring12/212/3Placevaporbarrier12/312/4soundreductionmat12/212/3Interiorpartitions12/212/3Battinsulation12/412/6Insulation:3rdFloor12/412/6Flooring12/412/5Placevaporbarrier12/512/6Placesoundreductionmat12/412/5Interiorpartitions12/412/5Battinsulation12/612/12Insulation:2ndFloor12/612/12Flooring 5/19 6/2 6/16 6/30 7/14 7/28 8/11 8/25 9/8 9/22 10/6 10/20 11/3 11/17 12/1 12/15 12/29 1/12 1/26 2/9 2/23 3/8 May 1 June 1 July 1 August 1 September 1 October 1 November 1 December 1 January 1 February 1 March 1
08/01/2018MCM 901 Page 105 of 224 Master Thesis: 620 N 3rd St Clara Bucar ID Task Name Duration Start Finish PredecessorsCost 374 Place reductionsoundmat 1 day Fri 12/6/19 12/9/19Mon $2,294.50 375 Install insulationbatt 1 day 12/9/19Mon 12/10/19Tue 374 $5,000.00 376 Place lower vapor barrier 1 day 12/10/19Tue 12/11/19Wed 375 $0.00 377 Place fire rated sheathing over exterior spaces 1 day 12/11/19Wed 12/12/19Thu 376 $0.00 378 Interior partitions 1 day Fri 12/6/19 12/9/19Mon $4,652.25 379 Batt insulation 1 day Fri 12/6/19 12/9/19Mon $4,652.25 380 Insulation: 1st Floor 4 days 12/12/19Thu 12/18/19Wed 372 $10,279.50 381 Flooring 4 days 12/12/19Thu 12/18/19Wed $7,279.50 382 membranewaterproofingPlace 1 day 12/12/19Thu Fri 12/13/19 $1,107.75 383 Place drainage layer 1 day Fri 12/13/19 12/16/19Mon 382 $1,107.75 384 Place layertrafficfiberwear 1 day 12/16/19Mon 12/17/19Tue 383 $2,954.00 385 Spray insulation 1 day 12/17/19Tue 12/18/19Wed 384 $2,110.00 386 Interior partitions 1 day 12/12/19Thu Fri 12/13/19 $3,000.00 387 Batt insulation 1 day 12/12/19Thu Fri 12/13/19 $3,000.00 388 basementInsulation: 1 day 12/18/19Wed 12/19/19Thu 380 $3,000.00 389 Interior partitions 1 day 12/18/19Wed 12/19/19Thu $3,000.00 390 Batt insulation 1 day 12/18/19Wed 12/19/19Thu $3,000.00 391 completedInsulation 0 days 12/19/19Thu 12/19/19Thu 388 $0.00 392 Finish: 4th floor 5 days 12/4/19Wed 12/11/19Wed 360 $60,165.50 393 Ceiling: install gypsum board and prime 5 days 12/4/19Wed 12/11/19Wed $10,165.50 394 Flooring: install finished flooring 5 days 12/4/19Wed 12/11/19Wed $27,000.00 12/6 12/9 Place sound reduction mat 12/9 12/10 Install batt insulation 12/10 12/11 Place lower vapor barrier 12/11 12/12 Place fire rated sheathing over exterior spaces 12/6 12/9 Interior partitions 12/6 12/9 BattInsulation:12/12insulation12/181stFloor12/1212/18Flooring12/1212/13Place waterproofing membrane 12/13 12/16 Place drainage layer 12/16 12/17 Place fiber traffic wear layer 12/17 12/18 Spray insulation 12/12 12/13 Interior partitions 12/12 12/13 Batt 12/4Insulation:12/18insulation12/19basement12/1812/19Interiorpartitions12/1812/19Battinsulation12/19Insulationcompleted12/11Finish:4thfloor12/412/11Ceiling: install gypsum board and prime 12/4 12/11 Flooring: install finished flooring 5/19 6/2 6/16 6/30 7/14 7/28 8/11 8/25 9/8 9/22 10/6 10/20 11/3 11/17 12/1 12/15 12/29 1/12 1/26 2/9 2/23 3/8 May 1 June 1 July 1 August 1 September 1 October 1 November 1 December 1 January 1 February 1 March 1
08/01/2018MCM 901 Page 106 of 224 Master Thesis: 620 N 3rd St Clara Bucar ID Task Name Duration Start Finish PredecessorsCost 395 Walls: Dry wall, tape and prime 5 days 12/4/19Wed 12/11/19Wed $10,000.00 396 Walls: ceramicinstalltiles 3 days 12/4/19Wed 12/9/19Mon $13,000.00 397 Finish: 3rd floor 5 days Fri 12/6/19 Fri 12/13/19 366 $59,000.00 398 Ceiling: install gypsum board and prime 5 days Fri 12/6/19 Fri 12/13/19 $9,000.00 399 Flooring: install finished flooring 5 days Fri 12/6/19 Fri 12/13/19 $27,000.00 400 Walls: Dry wall, tape and prime 5 days Fri 12/6/19 Fri 12/13/19 $10,000.00 401 Walls: ceramicinstalltiles 3 days Fri 12/6/19 12/11/19Wed $13,000.00 402 Finish: 2nd floor 5 days 12/12/19Thu 12/19/19Thu 372 $64,868.01 403 Ceiling: install gypsum board and prime 5 days 12/12/19Thu 12/19/19Thu $9,000.00 404 Flooring: install finished flooring 5 days 12/12/19Thu 12/19/19Thu $29,070.00 405 Walls: Dry wall, tape and prime 5 days 12/12/19Thu 12/19/19Thu $12,274.50 406 Walls: ceramicinstalltiles 3 days 12/12/19Thu 12/17/19Tue $14,523.51 407 Finish: 1st floor 1 day 12/18/19Wed 12/19/19Thu 380 $22,749.00 408 Ceiling: install gypsum board and hung system 1 day 12/18/19Wed 12/19/19Thu $4,925.00 409 Flooring: install finished flooring 1 day 12/18/19Wed 12/19/19Thu $14,924.00 410 Walls: Dry wall and tape 1 day 12/18/19Wed 12/19/19Thu $2,000.00 411 Install wheel stops 1 day 12/18/19Wed 12/19/19Thu $900.00 412 Install counterskitchenallfloors 5 days 12/12/19Thu 12/19/19Thu 372 $20,700.00 413 Finish: basement 4 days 12/19/19Thu 12/25/19Wed 388 $14,292.00 414 Ceiling: install hung systemceiling 1 day 12/19/19Thu Fri 12/20/19 $4,000.00 415 Walls: Dry wall and tape 1 day Fri 12/20/19 12/23/19Mon 414 $2,000.00 12/4 12/11 Walls: Dry wall, tape and prime 12/4 12/9 Walls: install ceramic tiles 12/6 12/13 Finish: 3rd floor 12/6 12/13 Ceiling: install gypsum board and prime 12/6 12/13 Flooring: install finished flooring 12/6 12/13 Walls: Dry wall, tape and prime 12/6 12/11 Walls: install ceramic tiles 12/12 12/19 Finish: 2nd floor 12/12 12/19 Ceiling: install gypsum board and prime 12/12 12/19 Flooring: install finished flooring 12/12 12/19 Walls: Dry wall, tape and prime 12/12 12/17 Walls: install ceramic tiles 12/18 12/19 Finish: 1st floor 12/18 12/19 Ceiling: install gypsum board and hung system 12/18 12/19 Flooring: install finished flooring 12/18 12/19 Walls: Dry wall and tape 12/18 12/19 Install wheel stops 12/12 12/19 Install kitchen counters all floors 12/19 12/25 Finish: basement 12/19 12/20 Ceiling: install hung ceiling system 12/20 12/23 Walls: Dry wall and tape 5/19 6/2 6/16 6/30 7/14 7/28 8/11 8/25 9/8 9/22 10/6 10/20 11/3 11/17 12/1 12/15 12/29 1/12 1/26 2/9 2/23 3/8 May 1 June 1 July 1 August 1 September 1 October 1 November 1 December 1 January 1 February 1 March 1
08/01/2018MCM 901 Page 107 of 224 Master Thesis: 620 N 3rd St Clara Bucar ID Task Name Duration Start Finish PredecessorsCost 416 Partitions: install chain (storagepartitionsarea) 3 days Fri 12/20/19 12/25/19Wed 414 $8,292.00 417 Carpentry: 4th floor 9 days 12/11/19Wed 12/24/19Tue 392 $30,000.00 418 Door frames 3 days 12/11/19Wed 12/16/19Mon $5,000.00 419 Baseboards 3 days 12/16/19Mon 12/19/19Thu 418 $5,000.00 420 Kitchen millwork 3 days 12/19/19Thu 12/24/19Tue 412 $20,000.00 421 Carpentry: 3rd floor 6 days 12/24/19Tue Wed 1/1/20 417 $30,000.00 422 Door frames 3 days 12/24/19Tue Fri 12/27/19 $5,000.00 423 Baseboards 3 days Fri 12/27/19 Wed 1/1/20 422 $5,000.00 424 Kitchen millwork 3 days 12/24/19Tue Fri 12/27/19 420 $20,000.00 425 Carpentry: 2nd floor 6 days Wed 1/1/20 Thu 1/9/20 421 $28,500.00 426 Door frames 3 days Wed 1/1/20 Mon 1/6/20 $5,000.00 427 Baseboards 3 days Mon 1/6/20 Thu 1/9/20 426 $5,000.00 428 Kitchen millwork 3 days Wed 1/1/20 Mon 1/6/20 424 $18,500.00 429 Carpentry: 1st floor 5 days Thu 1/9/20 Thu 1/16/20 425 $4,016.66 430 Door frames 1 day Thu 1/9/20 Fri 1/10/20 $2,000.00 431 Baseboards 1 day Fri 1/10/20 1/13/20Mon 430 $2,016.66 432 Lobby details 3 days 1/13/20Mon Thu 1/16/20 431 $0.00 433 Install basement door frames 2 days Thu 1/16/20 1/20/20Mon 429 $0.00 434 Install mailboxes 1 day Thu 1/16/20 Fri 1/17/20 432 $1,800.00 435 Interior doors 27 days 12/16/19Mon 1/22/20Wed $28,910.00 436 Interior doors 4th floor 5 days 12/16/19Mon 12/23/19Mon 418 $6,000.00 12/20 12/25 Partitions: install chain partitions (storage area) 12/11 12/24 Carpentry: 4th floor 12/11 12/16 Door 12/16frames12/19Baseboards12/1912/24Kitchenmillwork12/241/1Carpentry:3rdfloor12/2412/27Doorframes12/271/1Baseboards12/2412/27Kitchenmillwork1/11/9Carpentry:2ndfloor1/11/6Doorframes1/61/9Baseboards1/11/6Kitchenmillwork1/91/16Carpentry:1stfloor1/91/10Doorframes1/101/13Baseboards1/131/16Lobbydetails1/161/20Installbasementdoor frames 1/16 1/17 Install mailboxes 12/16 1/22 Interior doors 12/16 12/23 Interior doors 4th floor 5/19 6/2 6/16 6/30 7/14 7/28 8/11 8/25 9/8 9/22 10/6 10/20 11/3 11/17 12/1 12/15 12/29 1/12 1/26 2/9 2/23 3/8 May 1 June 1 July 1 August 1 September 1 October 1 November 1 December 1 January 1 February 1 March 1
08/01/2018MCM 901 Page 108 of 224 Master Thesis: 620 N 3rd St Clara Bucar ID Task Name Duration Start Finish PredecessorsCost 437 Interior doors 3rd floor 5 days Fri 12/27/19 Fri 1/3/20 422 $6,000.00 438 Interior doors 2nd floor 5 days Mon 1/6/20 1/13/20Mon 426 $6,000.00 439 Interior doors 1st floor 2 days Fri 1/10/20 Tue 1/14/20 430 $4,000.00 440 Interior basementdoors 2 days 1/20/20Mon 1/22/20Wed 433 $6,910.00 441 Install West stairs 9 days Fri 1/17/20 Thu 1/30/20 days435FS-3 $11,000.00 442 Remove chute and pulley 1 day Fri 1/17/20 1/20/20Mon $0.00 443 Install finishstructurestairsand 8 days 1/20/20Mon Thu 1/30/20 442 $11,000.00 444 Install exterior stairs 1 day? Thu 1/30/20 Fri 1/31/20 441 $0.00 445 Finish sidewalks 5 days 1/15/20Wed 1/22/20Wed days435FS-5 $3,579.00 446 Security cameras final 3 days 12/19/19Thu 12/24/19Tue 407 $10,000.00 447 Audio, intercom, data miscellaneousand final 3 days 12/24/19Tue Fri 12/27/19 446 $30,000.00 448 Fire protection final 5 days Fri 12/27/19 Fri 1/3/20 447 $36,160.00 449 Automation for garage doors 2 days Fri 1/3/20 Tue 1/7/20 448 $5,000.00 450 Curtain systems 5 days Tue 1/7/20 Tue 1/14/20 449 $5,000.00 451 Plumbing final 24 days 12/24/19Tue 1/27/20Mon $88,200.00 452 Plumbing final 4th floor 5 days 12/24/19Tue 12/31/19Tue 420 $26,000.00 453 Plumbing final 3rd floor 5 days Fri 12/27/19 Fri 1/3/20 424 $26,000.00 454 Plumbing final 2nd floor 5 days Mon 1/6/20 1/13/20Mon 428 $27,000.00 455 Plumbing final 1st floor 3 days 1/20/20Mon Thu 1/23/20 days454FS+5 $3,000.00 456 Plumbing basementfinal 1 day Thu 1/23/20 Fri 1/24/20 455 $3,000.00 457 Plumbing final roof 1 day Fri 1/24/20 1/27/20Mon 456 $3,200.00 12/27 1/3 Interior doors 3rd floor 1/6 1/13 Interior doors 2nd floor 1/10 1/14 Interior doors 1st floor 1/20 1/22 Interior doors basement 1/17 1/30 Install West stairs 1/17 1/20 Remove chute and pulley 1/20 1/30 Install stairs structure and finish 1/30 1/31 Install exterior stairs 1/15 1/22 Finish sidewalks 12/19 12/24 Security cameras final 12/24 12/27 Audio, intercom, data and miscellaneous final 12/27 1/3 Fire protection final 1/3 1/7 Automation for garage doors 1/7 1/14 Curtain systems 12/24 1/27 Plumbing final 12/24 12/31 Plumbing final 4th floor 12/27 1/3 Plumbing final 3rd floor 1/6 1/13 Plumbing final 2nd floor 1/20 1/23 Plumbing final 1st floor 1/23 1/24 Plumbing final basement 1/24 1/27 Plumbing final roof 8/11 8/25 9/8 9/22 10/6 10/20 11/3 11/17 12/1 12/15 12/29 1/12 1/26 2/9 2/23 3/8 3/22 4/5 4/19 5/3 5/17 5/31 August 1 September 1 October 1 November 1 December 1 January 1 February 1 March 1 April 1 May 1 June 1
08/01/2018MCM 901 Page 109 of 224 Master Thesis: 620 N 3rd St Clara Bucar ID Task Name Duration Start Finish PredecessorsCost 458 Install accessoriesbathroom 1 day 1/27/20Mon Tue 1/28/20 451 $11,400.00 459 Sprinkler final 18 days Fri 1/3/20 1/29/20Wed 452 $25,000.00 460 Sprinkler final 4th floor 2 days Fri 1/3/20 Tue 1/7/20 453 $5,000.00 461 Sprinkler final 3rd floor 2 days 1/13/20Mon 1/15/20Wed 454 $5,000.00 462 Sprinkler final 2nd floor 2 days Thu 1/23/20 1/27/20Mon 455 $5,000.00 463 Sprinkler final 1st floor 1 day 1/27/20Mon Tue 1/28/20 462 $5,000.00 464 Sprinkler basementfinal 1 day Tue 1/28/20 1/29/20Wed 463 $5,000.00 465 Mechanical final 25 days Wed 1/1/20 Wed 2/5/20 $61,180.00 466 Place vibration pads on roof 1 day Wed 1/1/20 Thu 1/2/20 days468FS-8 $900.00 467 Condensers and AHU placementunits 2 days Thu 1/2/20 Mon 1/6/20 466 $43,500.00 468 Mechanical final 4th floor 4 days Tue 1/7/20 1/13/20Mon 460 $4,000.00 469 Mechanical final 3rd floor 4 days 1/15/20Wed Tue 1/21/20 461 $4,000.00 470 Mechanical final 2nd floor 4 days 1/27/20Mon Fri 1/31/20 462 $4,000.00 471 Mechanical final 1st floor 2 days Fri 1/31/20 Tue 2/4/20 470 $3,000.00 472 Mechanical final basement 1 day Tue 2/4/20 Wed 2/5/20 471 $1,780.00 473 Electric final: 4th floor 5 days Mon 1/6/20 1/13/20Mon days468FS-5 $14,450.00 474 Lighting 3 days Mon 1/6/20 Thu 1/9/20 $9,000.00 475 Outlets and covers 2 days Thu 1/9/20 1/13/20Mon 474 $5,000.00 476 Water heater 1 day Mon 1/6/20 Tue 1/7/20 $0.00 477 Electric panel in unit 1 day Tue 1/7/20 Wed 1/8/20 476 $450.00 478 LV Boxes 1 day Wed 1/8/20 Thu 1/9/20 477 $0.00 1/27 1/28 Install bathroom accessories 1/3 1/29 Sprinkler final 1/3 1/7 Sprinkler final 4th floor 1/13 1/15 Sprinkler final 3rd floor 1/23 1/27 Sprinkler final 2nd floor 1/27 1/28 Sprinkler final 1st floor 1/28 1/29 Sprinkler final basement 1/1 2/5 Mechanical final 1/1 1/2 Place vibration pads on roof 1/2 1/6 Condensers and AHU units placement 1/7 1/13 Mechanical final 4th floor 1/15 1/21 Mechanical final 3rd floor 1/27 1/31 Mechanical final 2nd floor 1/31 2/4 Mechanical final 1st floor 2/4 2/5 Mechanical final basement 1/6 1/13 Electric final: 4th floor 1/6 ElectricOutletsLighting1/91/91/13andcovers1/61/7Waterheater1/71/8panelinunit1/81/9LVBoxes 8/11 8/25 9/8 9/22 10/6 10/20 11/3 11/17 12/1 12/15 12/29 1/12 1/26 2/9 2/23 3/8 3/22 4/5 4/19 5/3 5/17 5/31 August 1 September 1 October 1 November 1 December 1 January 1 February 1 March 1 April 1 May 1 June 1
08/01/2018MCM 901 Page 110 of 224 Master Thesis: 620 N 3rd St Clara Bucar ID Task Name Duration Start Finish PredecessorsCost 479 Electric final: 3rd floor 5 days Tue 1/14/20 Tue 1/21/20 days469FS-5 $14,450.00 480 Lighting 3 days Tue 1/14/20 Fri 1/17/20 $9,000.00 481 Outlets and covers 2 days Fri 1/17/20 Tue 1/21/20 480 $5,000.00 482 Water heater 1 day Tue 1/14/20 1/15/20Wed $0.00 483 Electric panel in unit 1 day 1/15/20Wed Thu 1/16/20 482 $450.00 484 LV Boxes 1 day Thu 1/16/20 Fri 1/17/20 483 $0.00 485 Electric final: 2nd floor 5 days Fri 1/24/20 Fri 1/31/20 days470FS-5 $15,150.00 486 Lighting 3 days Fri 1/24/20 1/29/20Wed $9,700.00 487 Outlets and covers 2 days 1/29/20Wed Fri 1/31/20 486 $5,000.00 488 Water heater 1 day Fri 1/24/20 1/27/20Mon $0.00 489 Electric panel in unit 1 day 1/27/20Mon Tue 1/28/20 488 $450.00 490 LV Boxes 1 day Tue 1/28/20 1/29/20Wed 489 $0.00 491 Electric basementfinal:and 1st floor 4 days Thu 1/30/20 Wed 2/5/20 days471FS-3 $6,425.00 492 Lighting 2 days Thu 1/30/20 Mon 2/3/20 $3,150.00 493 Outlets and covers 2 days Mon 2/3/20 Wed 2/5/20 492 $3,275.00 494 Finish East stairs 5 days 1/27/20Mon Mon 2/3/20 451 $7,000.00 495 Final Inspection 0 days Wed 2/5/20 Wed 2/5/20 491 $0.00 496 Final reinspectionrepairInspectionand 10 days Wed 2/5/20 2/19/20Wed 495 $0.00 497 Exterior signage install 2 days 2/19/20Wed Fri 2/21/20 496 $2,500.00 498 Interior signage install 2 days 2/19/20Wed Fri 2/21/20 496 $3,269.20 499 Final painting 21 days Thu 1/9/20 Fri 2/7/20 $26,040.93 1/14 1/21 Electric final: 3rd floor 1/14 ElectricOutlets1/17Lighting1/171/21andcovers1/141/15Waterheater1/151/16panelinunit1/161/17LVBoxes1/241/31Electricfinal:2ndfloor1/241/29Lighting1/291/31Outletsandcovers1/241/27Waterheater1/271/28Electricpanelinunit1/281/29LVBoxes1/302/5Electricfinal:basementand 1st floor 1/30 Finish1/27OutletsLighting2/32/32/5andcovers2/3Eaststairs2/5FinalInspection2/52/19Final Inspection repair and reinspection 2/19 2/21 Exterior signage install 2/19 2/21 Interior signage install 1/9 2/7 Final painting 8/11 8/25 9/8 9/22 10/6 10/20 11/3 11/17 12/1 12/15 12/29 1/12 1/26 2/9 2/23 3/8 3/22 4/5 4/19 5/3 5/17 5/31 August 1 September 1 October 1 November 1 December 1 January 1 February 1 March 1 April 1 May 1 June 1
08/01/2018MCM 901 Page 111 of 224 Master Thesis: 620 N 3rd St Clara Bucar ID Task Name Duration Start Finish PredecessorsCost 500 Painting 4th floor 4 days Thu 1/9/20 1/15/20Wed days473FS-2 $7,000.00 501 Painting 3rd floor 4 days Fri 1/17/20 Thu 1/23/20 days479FS-2 $7,000.00 502 Painting 2nd floor 4 days 1/29/20Wed Tue 2/4/20 days485FS-2 $7,000.00 503 Painting 1st floor 3 days Mon 2/3/20 Thu 2/6/20 days491FS-2 $3,000.00 504 Painting basement 1 day Thu 2/6/20 Fri 2/7/20 503 $2,040.93 505 meetingPre-closeout 1 day Fri 1/31/20 Mon 2/3/20 days499FS-5 $0.00 506 Final Cleaning 5 days Wed 2/5/20 2/12/20Wed days499FS-2 $0.00 507 Startup of systems 0 days Mon 2/3/20 Mon 2/3/20 days465FS-2 $0.00 508 Commissioning 5 days 2/10/20Mon 2/17/20Mon days465FS+3 $0.00 509 T&B Report 0 days Thu 2/20/20 Thu 2/20/20 days508FS+3 $0.00 510 Owner training 2 days 2/17/20Mon 2/19/20Wed 507,508 $0.00 511 Punchlist 0 days Fri 2/7/20 Fri 2/7/20 499 $0.00 512 Punchlist closeout 5 days Fri 2/7/20 Fri 2/14/20 511,495 $0.00 513 completionSubstantial 0 days Fri 2/14/20 Fri 2/14/20 512 $0.00 514 Demobilization 0 days Fri 2/14/20 Fri 2/14/20 512 $0.00 515 Turnover 0 days 2/17/20Mon 2/17/20Mon day512FS+1 $0.00 516 Warranties 5 days Fri 2/7/20 Fri 2/14/20 days513FS-5 $0.00 517 RFI Closeout 12 days 1/29/20Wed Fri 2/14/20 days499FS-7 $0.00 518 Change CloseoutOrder 12 days 1/29/20Wed Fri 2/14/20 days499FS-7 $0.00 519 Financial Resolution 9 days Fri 2/14/20 Thu 2/27/20 518 $0.00 520 Cost completioncontrol 9 days Thu 2/27/20 3/11/20Wed 519 $0.00 1/9 1/15 Painting 4th floor 1/17 1/23 Painting 3rd floor 1/29 2/4 Painting 2nd floor 2/3 2/6 Painting 1st floor 2/6 2/7 Painting basement 1/31 2/3 Pre-closeout meeting 2/5 2/12 Final Cleaning2/3Startup of Change1/291/29SubstantialPunchlist2/7PunchlistCommissioning2/10systems2/172/20T&BReport2/172/19Ownertraining2/72/14closeout2/14completion2/14Demobilization2/17Turnover2/72/14Warranties2/14RFICloseout2/14OrderCloseout2/142/27FinancialResolution2/27 3/11 Cost control completion 8/11 8/25 9/8 9/22 10/6 10/20 11/3 11/17 12/1 12/15 12/29 1/12 1/26 2/9 2/23 3/8 3/22 4/5 4/19 5/3 5/17 5/31 August 1 September 1 October 1 November 1 December 1 January 1 February 1 March 1 April 1 May 1 June 1
08/01/2018MCM 901 Page 112 of 224 Master Thesis: 620 N 3rd St Clara Bucar ID Task Name Duration Start Finish PredecessorsCost 521 O&M Manuals 12 days 1/29/20Wed Fri 2/14/20 days499FS-7 $0.00 522 communicationsMajor log 5 days Fri 1/31/20 Fri 2/7/20 days499FS-5 $0.00 523 Certificate of occupancy 0 days 2/19/20Wed 2/19/20Wed 496 $0.00 524 As Builts 15 days 1/29/20Wed 2/19/20Wed days499FS-7 $0.00 525 Final Payment 0 days 3/18/20Wed 3/18/20Wed days,524513,517,518,521,523FS+20$0.00 526 Affidavits of payment 1 day? 3/18/20Wed Thu 3/19/20 525 $0.00 527 Lien releases 1 day? 3/18/20Wed Thu 3/19/20 525 $0.00 528 Consent of surety 1 day? 3/18/20Wed Thu 3/19/20 525 $0.00 1/29 2/14 O&M Manuals 1/31 2/7 Major communications 2/19logCertificate of occupancy 1/29 2/19 As Builts 3/18 Final Affidavits3/18Payment3/19ofpayment3/183/19Lienreleases3/183/19Consentofsurety 8/11 8/25 9/8 9/22 10/6 10/20 11/3 11/17 12/1 12/15 12/29 1/12 1/26 2/9 2/23 3/8 3/22 4/5 4/19 5/3 5/17 5/31 August 1 September 1 October 1 November 1 December 1 January 1 February 1 March 1 April 1 May 1 June 1
08/01/2018MCM 901 Page 113 of 224 Master Thesis: 620 N 3rd St Clara Bucar 4.14. Cash FlowCash Flow Profit Margin 5% General Overhead 6% Retention Rate: 10% 10% 10% 10% 10% 10% 10% 10% 10% 10% 10% 10% 10% 10% 10% Month February 19 March 19 April 19 May 19 June 19 July 19 August 19 September 19 October 19 November 19 December 19 January 19 February 19 March 19 April 19 Gross Pay Request to Owner 0 393,119 49,955 210,598 34,544 155,544 118,285 131,845 138,538 402,759 258,465 452,268 312,086 62,333 295,722 Labor 0 10,011 1,496 6,307 1,035 4,658 3,543 3,949 4,149 12,062 7,741 13,545 9,347 1,867 0 Material 0 70,079 10,473 44,151 7,242 32,609 24,798 27,641 29,044 84,436 54,185 94,815 65,427 13,068 0 Subcontractor 0 246,944 36,904 155,578 25,519 114,907 87,382 97,400 102,344 297,536 190,939 334,110 230,552 46,048 0 Equipment 0 6,674 997 4,205 690 3,106 2,362 2,632 2,766 8,042 5,161 9,030 6,231 1,245 0 Total L,M,S,E Costs 0 333,708 49,870 210,241 34,485 155,280 118,084 131,622 138,303 402,075 258,026 451,501 311,556 62,228 0 Bonds (1%) 29,422 Insurance(1%) 29,422 General Overhead (6% L,M,S,E) 0 20,022 2,992 12,614 2,069 9,317 7,085 7,897 8,298 24,125 15,482 27,090 18,693 3,734 0 Profit Margin 0 17,687 2,643 11,143 1,828 8,230 6,258 6,976 7,330 21,310 13,675 23,930 16,512 3,298 0 Total receivable 371,417 55,505 233,998 38,382 172,826 131,428 146,495 153,931 447,509 287,183 502,520 346,762 69,259 Retainage 0 37,142 5,551 23,400 3,838 17,283 13,143 14,649 15,393 44,751 28,718 50,252 34,676 6,926 Retainage receivable 295,722 Receivables from Owner 0 0 393,119 49,955 210,598 34,544 155,544 118,285 131,845 138,538 402,759 258,465 452,268 312,086 358,055 Payments Labor 10,011 1,496 6,307 1,035 4,658 3,543 3,949 4,149 12,062 7,741 13,545 9,347 1,867 0 0 Material 70,079 10,473 44,151 7,242 32,609 24,798 27,641 29,044 84,436 54,185 94,815 65,427 13,068 0 0 Subcontractor 246,944 36,904 155,578 25,519 114,907 87,382 97,400 102,344 297,536 190,939 334,110 230,552 46,048 0 0 Equipment 6,674 997 4,205 690 3,106 2,362 2,632 2,766 8,042 5,161 9,030 6,231 1,245 0 0 Overhead 20,022 2,992 12,614 2,069 9,317 7,085 7,897 8,298 24,125 15,482 27,090 18,693 3,734 0 0 Bonds+Insurance 58,844 Total Payments 333,708 49,870 210,241 34,485 155,280 118,084 131,622 138,303 402,075 258,026 451,501 311,556 62,228 0 0 Profit Recognized 17,687 2,643 11,143 1,828 8,230 6,258 6,976 7,330 21,310 13,675 23,930 16,512 3,298 Payments Including Profit 351,395 52,513 221,383 36,313 163,510 124,343 138,597 145,633 423,385 271,701 475,430 328,069 65,526 0 0 Monthly Net Cash Flow -430,261 -55,505 159,121 11,573 37,772 -96,884 9,049 -35,646 -315,664 -148,645 -99,762 -88,298 383,009 312,086 358,055 Cumulative Cash Flow -430,261 -485,766 -326,645 -315,072 -277,300 -374,184 -365,135 -400,781 -716,445 -865,090 -964,852 -1,053,150 -670,141 -358,055 0
08/01/2018MCM 901 Page 114 of 224 Master Thesis: 620 N 3rd St Clara Bucar 4.15. Cash Flow Graphics
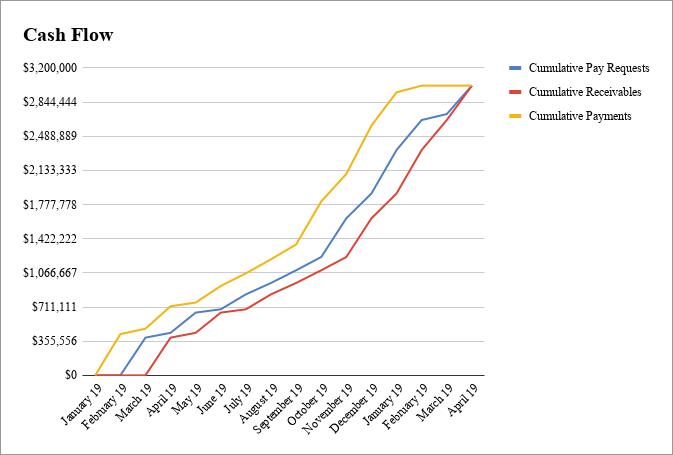
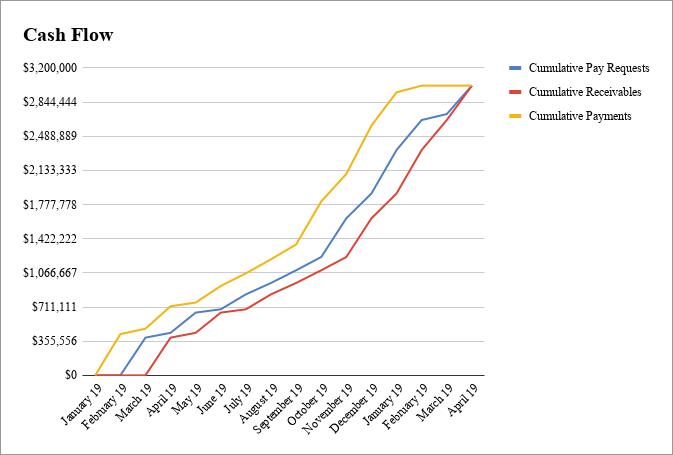
The Logistics Plan provides essential information for all project stakeholders in all phases of construction, starting with mobilization all throughout closeout. The Plan sets the stage for how the project will be coordinated at the site, foreseeing, for example, specific locations for waste management, safe spots, material delivery location including schedule and permitting aspects and areas to lay material.
Another major objective is setting the relationship with the nearby community. The Plan brings specific safety requirements such as sheltered walkways, community communication standards and strategies to lessen the pollution, noise and air quality impact brought by the construction project.
Image: Google Maps. North 3rd Street view. SITE North3rdStreet
08/01/2018MCM 901 Page 115 of 224 Master Thesis: 620 N 3rd St Clara Bucar SECTION FIVE SITE LAYOUT AND LOGISTICS PLAN
The Construction Site Logistics Plan section will demonstrate how the execution of the 620 N 3rd St project will occur, especially in regards of its interaction with the area where it is located. It will display images and written descriptions of the location of the site, main access routes, the neighborhood, essential mobilization items, in the different stages of construction, main safety measures for pedestrians in the surrounding community, the construction staging, parking areas, material delivery and storage, barricade locations for traffic management and other elements.
Lastly, the Logistics Plan helps avoiding critical delay and loss issues by providing depth to the construction schedule. It outlines specific, often illustrated strategies to make the execution of each phase smooth. For example, the Plan demonstrates specific dates to prepare for City permits in advance, avoiding wasted time, and also communicates to subcontractors exactly when they’ll be able to have material delivered to the site, without disturbing the community or risking lack of space for material lay.

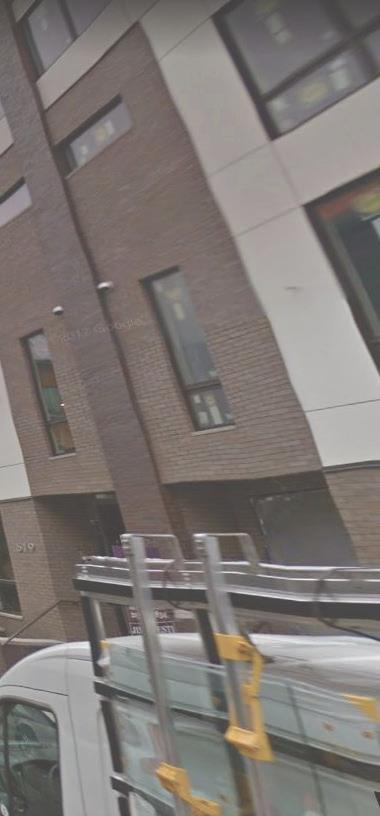


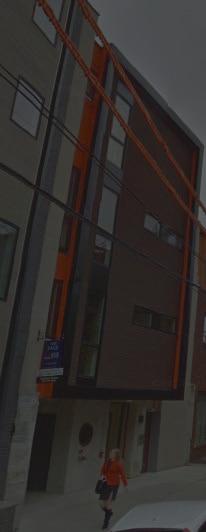

The project consists of the construction of a residential multi family building with a basement, a garage on the first floor, three floors with three residential units each and decks on the roof. The building has access to two different streets: North 3rd St, main access and a local high traffic for vehicles and pedestrians; and North Galloway St, a narrow alley and secondary access. The building will occupy the entire lot area, touching the neighbor buildings on both sides. It will also have garage doors opening to each street.
08/01/2018MCM 901 Page 116 of 224 Master Thesis: 620 N 3rd St Clara Bucar Image: Google Maps. North Galloway Street view. GallowayNorthStreet SITE
5.1. The project, the surrounding community and local street access
The Northern Liberties neighborhood, where the site is located, is currently one of the highest real estate speculation areas in Philadelphia. The entire area is populated with new construction projects that have been happening in an already densely occupied region. The neighborhoods proximity to Center City and easy access to main highways like 676 and the Benjamin Franklin Bridge have helped accelerate the occupation of the area. Northern Liberties is primarily residential, mostly low rise multi family, but also has an intense local commerce and restaurant scene with active night life. It’s common to see young families and their pets walking or biking around the neighborhood.
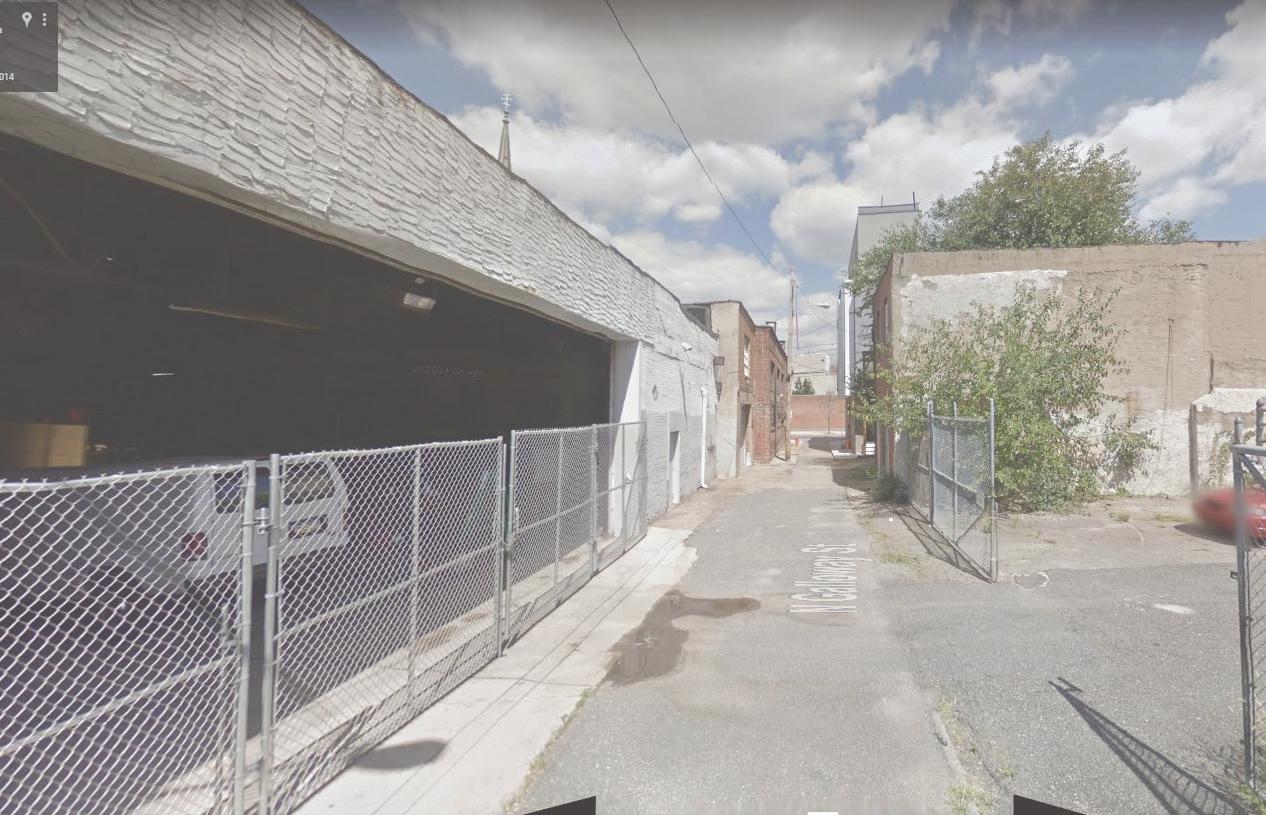
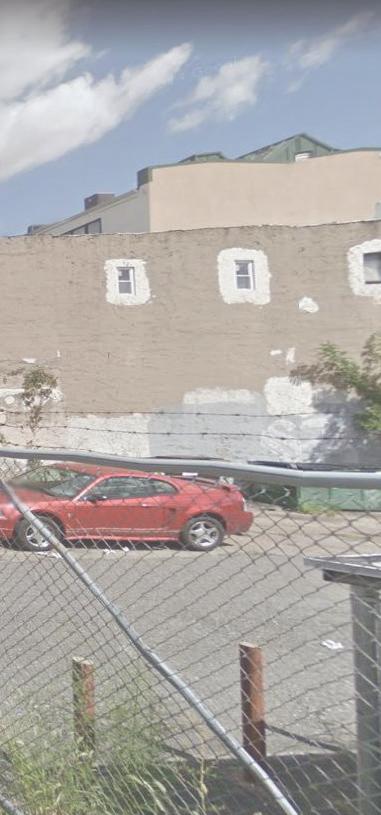




08/01/2018MCM 901 Page 117 of 224 Master Thesis: 620 N 3rd St Clara Bucar 5.2. Access to the site
5.5. Construction staging and parking areas
Per the local jurisdiction rule, the City of Philadelphia Bill No. 050749 defines as regular construction from 7 am to 8 pm, Monday through Friday, and from 8am to 8pm on weekends and legal, national or state holidays. All construction work is to be performed during the mentioned times. Work is to be mainly performed from 7am to 4pm Mondays through Fridays, unless otherwise specified.
Parking will be provided for the site superintendent and the project engineer, in additional to one vehicle per subcontractor and other vehicles providing equipment and materials. Parking will be granted through temporary city parking permits, specific for construction purposes, since there are no parking garages in the area.
5.4. Safety for pedestrians and traffic management
All throughout mobilization and pre-shell, the trailer and power generator will be located on N 3rd St and the portable toilets and dumpster on N Galloway St. For both of these, city permits will be necessary since these will be located on the street parking area/sidewalk. After the shell is completed, these items will be transfered to the interior of the building. Also, for the concrete walls construction the sidewalk will need to be blocked to allow for formwork bracing.
Safety will be accomplished by he combination of different, complimentary approaches. Starting with mobilization, no work will be performed before the 8’ high fence and gates are installed and the sidewalks will be treated to avoid slips and falls by both the construction crews and the Barricadescommunity.will close the sidewalks and the streets (partially or completely, per the plans) to keep people away from hazard areas and activities and there will be additional signage to warn the community about the work. When N 3rd street is blocked, a company employee will be at the road to assist with the traffic flow. In addition, sheltered walkways will be installed on each street for the period of time when work is being done on the building facades to protect pedestrians from falling objects.
As can be perceived in the Regional Plan, there are plenty main highways connecting the job site from every direction. The most important connecting roads are 676, North Broad St, the Delaware Expy and the Benjamin Franklin Bridge. Going in the neighborhood, however, the roads are narrow and mostly occupied by vehicles parked in parallel. It is also important to keep in mind that Northern Liberties is a residential neighborhood, therefore heavy equipment/vehicles traffic needs to be schedule accordingly.
5.3. Typical Working Hours and Days
08/01/2018MCM 901 Page 118 of 224 Master Thesis: 620 N 3rd St Clara Bucar Vine Express - 676 DelawareExpyNorthBroadSt Spring Garden St DelawareRiver PHILADELPHIA JERSEYNEW City Hall Logan Square CommonsSchmidt’s NorthernLiberties 620 N 3rd St PENNSYLVANIA REGIONAL PLAN Benjamin Franklin Bridge Image: Google Maps. Preferred route for truck deliveries and heavy equipment PropertyFencing DumpstersTrailer Gates Construction parking - Staff Portable BasementGeneratortoilets excavation Muster pointTGD*T Underpinning Wheeled excavator maximum radius PulleyMaterialStreetBarricadedirectionlaydown area Trash chute # walkwayProtected Lifting equipment Concrete washout LEGEND Project site: 620 N 3rd St Northern Liberties Philadelphia HillCherry-NJ Conshohocken Camden - NJ
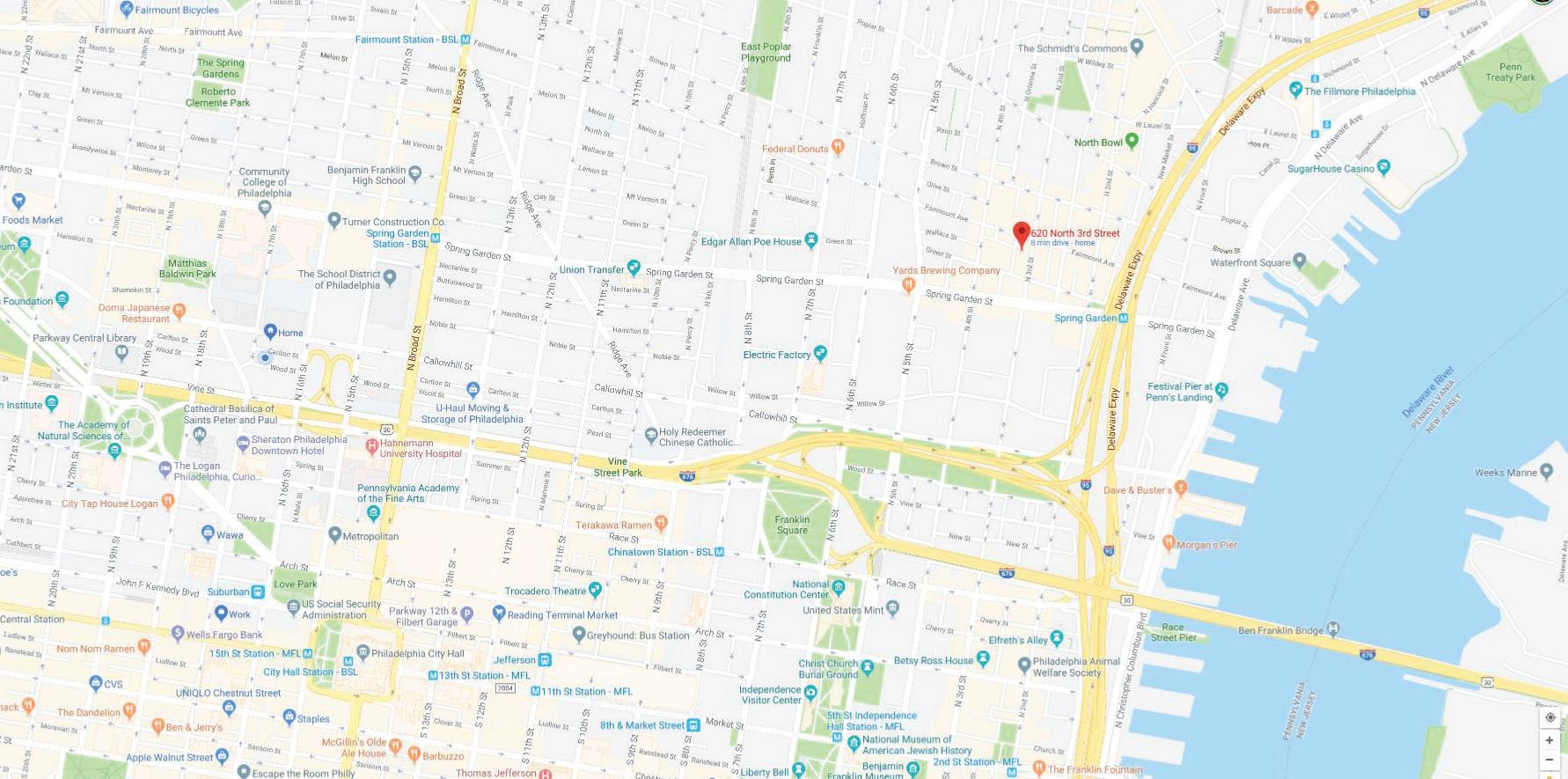
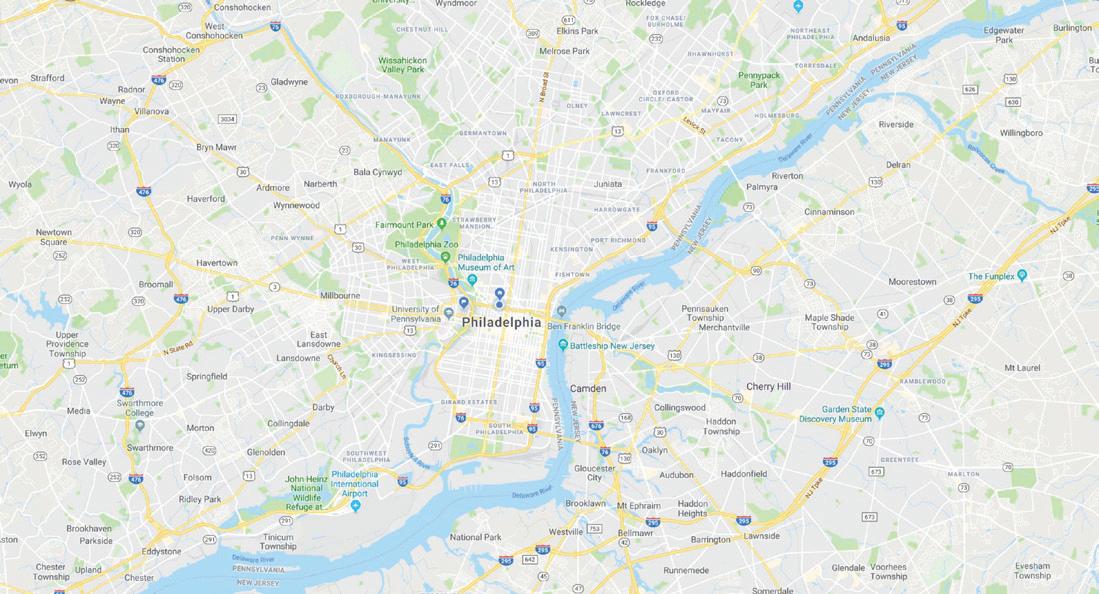
All material deliveries will be performed on N Galloway St due to its lighter traffic flow. For the same reason, all waste to be removed from the site will be taken from N Galloway St.. Due to the site’s limited space, materials will mostly need to be delivered to the proportion of install. Concrete will be mixed inside of trucks located at N Galloway St and poured in as needed, steel will be brought by trucks and erected with the use of a crane on the day the material is delivered to the site and the structural wood will be delivered in parts accordingly to the construction of each floor. The wood for interior framing will be delivered to the site and transported with a lift to the floor it’ll be used on. One area on the second floor will be assigned to receive necessary material. This area will be temporarily braced on the below floor to support the extra weight, see location for the plan. No materials should be stored at the site for periods longer than one week and each subcontractor is responsible for the safety of their own materials. A pulley will be installed to ease material transport to floors.
Dumpsters: 02/13/19 Portable toilets: 02/13/19 Temporary water: 02/13 - 02/15/19 Temporary electric: 02/13 - 02/15/19 Security system install: 02/13 - 02/18/19
5.6. Material delivery and storage
08/01/2018MCM 901 Page 119 of 224 Master Thesis: 620 N 3rd St Clara Bucar MOBILIZATION LOGISTICS Image: Bing Maps - Birds Eye. NorthGallowayStreet accessPedestrianonly pick-upsand * North3rdStreet D GT T Fairmount Avenue Trailer ongeneratorandparking andDumpsterportabletoiletonsidewalk Preferred route for truck deliveries and heavy equipment PropertyFencing DumpstersTrailer Gates Construction parking - Staff Portable BasementGeneratortoilets excavation Muster pointTGD*T Underpinning Wheeled excavator maximum radius PulleyMaterialStreetBarricadedirectionlaydown area Trash chute # walkwayProtected Lifting equipment Concrete washout LEGEND Project site
5.7. Mobilization Phasing Notice to proceed: 02/13/19
*Construction starts: 02/18/19
Trailer: Fencing/Gates:02/13/1902/13 - 02/15/19 Construction signage: 02/13/19
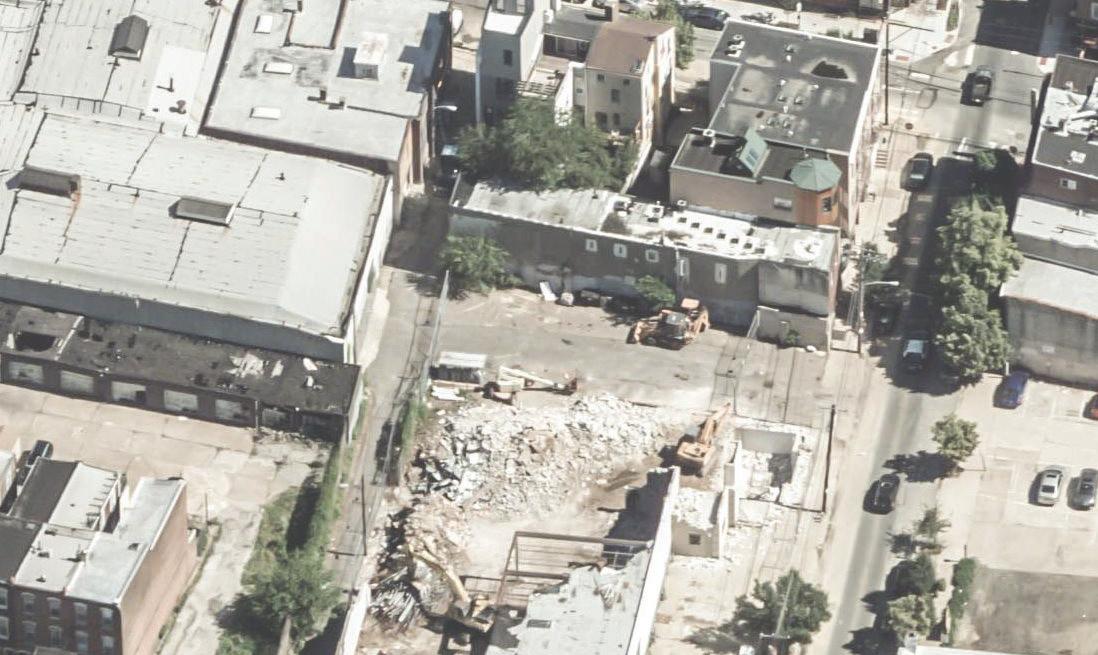




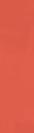



08/01/2018MCM 901 Page 120 of 224 Master Thesis: 620 N 3rd St Clara Bucar Image: Bing Maps - Birds Eye. NorthGallowayStreet * D GT T PRE-SHELL LOGISTICS Underpinning Fairmount Avenue New basement Fullblockage Partialbl. Preferred route for truck deliveries and heavy equipment PropertyFencing DumpstersTrailer Gates Construction parking - Staff Portable BasementGeneratortoilets excavation Muster pointTGD*T Underpinning Wheeled excavator maximum radius PulleyMaterialStreetBarricadedirectionlaydown area Trash chute # walkwayProtected Lifting equipment Concrete washout LEGEND Project site North3rdStreet 5.8. Pre-Shell Phasing Site work: 02/18 - 02/27/19 *Removal of dirt from excavation: 02/25/19 Underpinning: 02/27 - 03/28/19 Excavate basement: 03/25 - 03/28/19 Utilities: 03/28 - 04/11/19 *Subsurface work completed: 04/11/19 Footings and foundations: 03/28 - 04/30/19 CMU/Elevator shaft: 04/18 - 04/30/19 Slab on grade Basement: 04/23 - 05/13/19 Concrete piers: 05/06 - 05/17/19 Slab on grade 1st Fl: 04/30 - 05/15/19 Concrete walls: 05/15 - 05/30/19 Sidewalks: 05/24 - 05/30/19 *Major concrete work completed: 05/30/19 *Install sheltered walkway: 05/30/19 *Bring crane to job site (steel erection, joists, transport wood structure to 2nd fl): 05/30/19 *PECO aereal lines protection: 06/07/19 Steel structure: 05/31 - 07/03/19 Lay wood for 2nd fl structure on designated location (see post-shell plan): 07/03/19 *Remove crane from job site: 07/04/19 Wood structure: 07/04 - 08/09/19
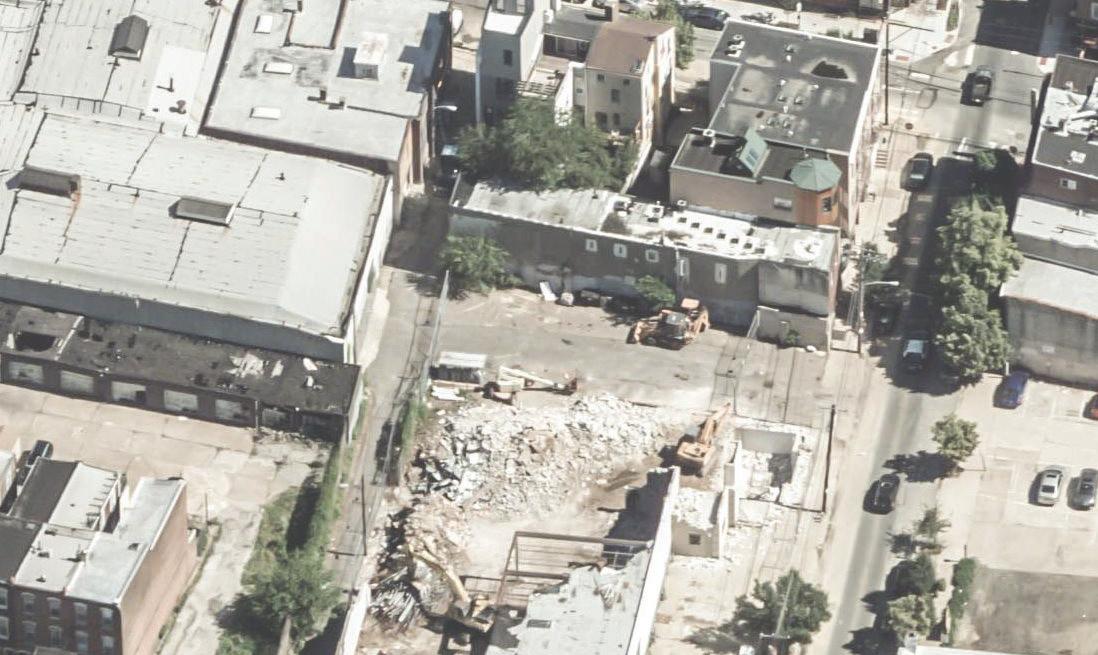
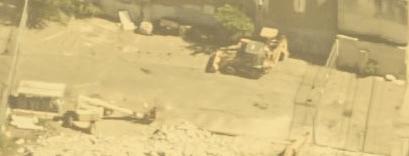

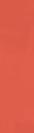
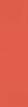




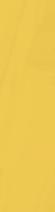


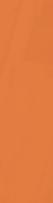
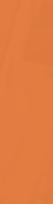
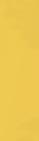
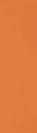
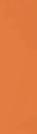

08/01/2018MCM 901 Page 121 of 224 Master Thesis: 620 N 3rd St Clara Bucar Image: Bing Maps - Birds Eye. NorthGallowayStreet * North3rdStreet Fullblockage Partialbl. POST SHELL LOGISTICS 2nd3rd4thRoofFlFlFl Trash chute and pulley from 1st to 4th fl Dumpster and toilets on 1st floor, close to back exit Office and generatorpower on 1st floor ##TD T Preferred route for truck deliveries and heavy equipment PropertyFencing DumpstersTrailer Gates Construction parking - Staff Portable BasementGeneratortoilets excavation Muster pointTGD*T Underpinning Wheeled excavator maximum radius PulleyMaterialStreetBarricadedirectionlaydown area Trash chute # walkwayProtected Lifting equipment Concrete washout LEGEND Project site 5.9. Post-Shell Phasing Install East stairs: 08/09 - 08/23/19 Install chute and pulley on West stairwell location: 08/09 - 08/14/19 Temporary roof drainage: 08/13 - 08/20/19 *Transport interior framing wood material to site; use a lift to place wood on each designated floor slipping the pieces through the exterior framing: 08/07/19; 08/14/19; Interior08/21/19framing: 08/07 - 08/28/19 Exterior walls, finishes and flashing: 09/11Install10/14/19exterior openings: 10/09 - 10/29/19 *Remove trailer from job site. Transfer office, power generator, dumpsters and portable toilets to 1st floor: 10/31/19 *Remove sheltered walkway: 10/31/19 MEP/Sprinkler rough-in: 09/20 - 11/04/19 Elevator install: 11/8 - 11/25/19 Low voltage rough-in: 10/31 - 11/15/19 Roof landscaping: 10/14 - 11/25/19 Balconies and guardrails: 11/25 - 12/23 Insulation: 11/18 - 12/19/19 Interior finishes: 12/04/19 - 02/07/20 *Remove trash chute and pulley and Install West stairs: 01/17 - 01/30/20 MEP/Sprinkler final: 12/24/19 - 02/05/20 Install signage: 02/19 - 02/21/20 Final cleaning: 02/05 - 02/12/20 Demobilization and turnover: 02/27/19
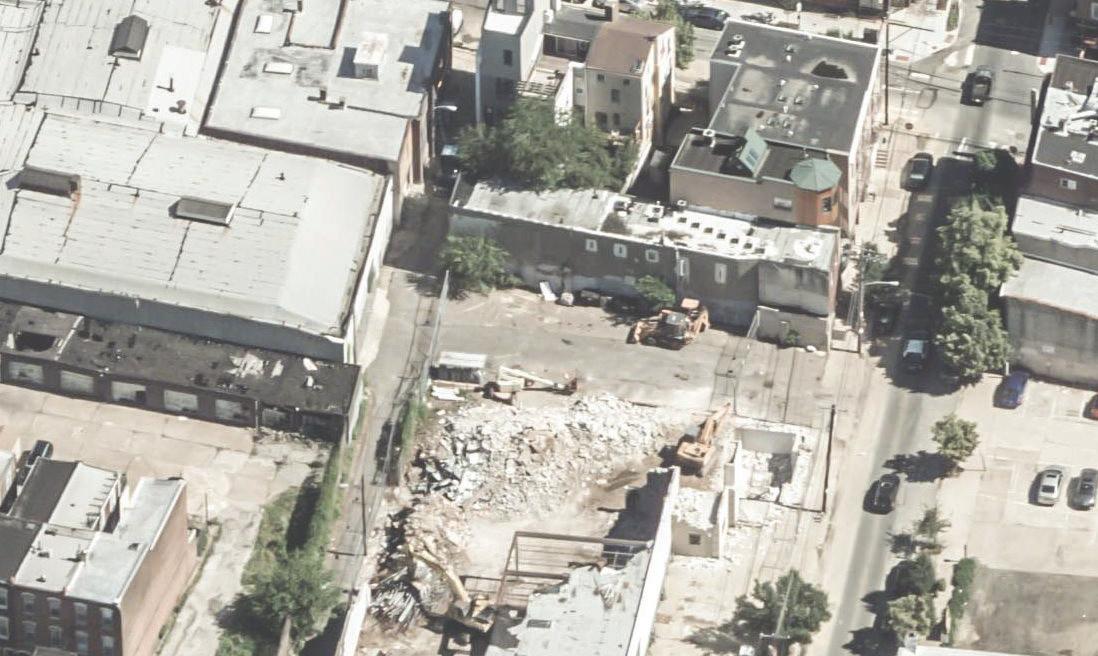
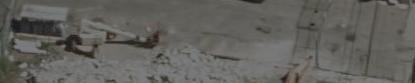



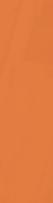
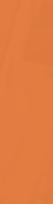
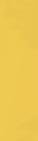
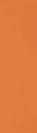
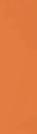

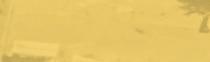
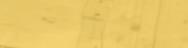

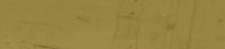





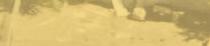
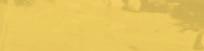















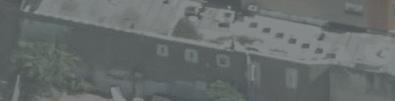
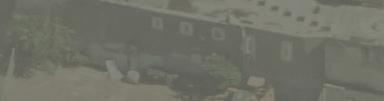
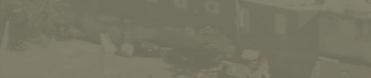
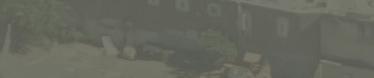

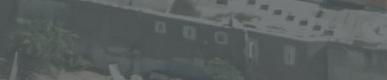
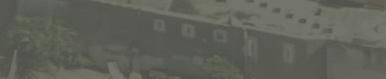
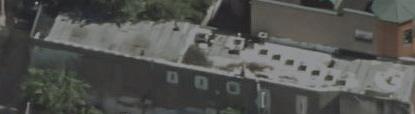




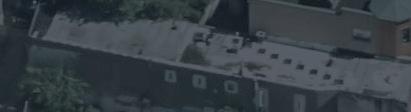






The contractor is responsible for snow removal from sidewalks after mobilization and before turnover. The contractor has considered (04) snow days included in the schedule.
All waste removal will occur on N Galloway St, where dumpsters will be located. A trash chute will be installed on the West stairwell, connecting all floors to the dumpster. Dirt from excavation will be removed from site through the N Galloway St. The (2) portable toilets provided for the construction project will be cleaned twice a week by the vendor providing the toilets, location per the plan. Any hazardous waste shall be immediately removed from site under respective subcontractor’s responsibility and penalty.
Various strategies to control the impacts imposed by the construction of this project will be implemented and further discussed in the Environmental Plan. Due to the fact that Northern Liberties is a very residential area, it’s essential that pollution and noise are controlled to admissible levels. As stated in this Logistics Plan, standard work hours are between 7pm and 4pm, Mondays through Fridays. All heavy noise work will be scheduled to happen between 9am and 4pm on week days in order to ease the noise. Specific equipment furnished with water sprays will be utilized to control the dust created by construction. Street and sidewalk blockage, major material deliveries and other tasks that can bring disturbance to the neighborhood will be previously scheduled and communicated to the Owner ’s associations of the nearby homes. The goal is to establish a community relationship based on communication and to maintain a reasonably good environment for the current people living in the neighborhood.
5.12. Clean-up, final clean and closeout
08/01/2018MCM 901 Page 122 of 224 Master Thesis: 620 N 3rd St Clara Bucar
5.10. Waste management
5.11. Construction impact control and community relationship
Each subcontractor is solely responsible of cleaning up their own work under penalty of backcharging. A janitorial services subcontractor will perform the final clean of the building before turnout. The dumpsters shall not be removed from site until final clean is completed. The window vendor is responsible for supply and install and is required, by contract, to deliver windows clean on the exterior. The office trailer will be cleaned twice a month by a subcontracted company. A specialized subcontractor will be hired to perform a power wash of the facades before turnover. The Contractor is not responsible for cleaning the interior or exterior of the building after turnover.
5.13. Snow Removal
08/01/2018MCM 901 Page 123 of 224 Master Thesis: 620 N 3rd St Clara Bucar 5.14. Illustrated Construction Sequence 1) Site excavated for new basement 3) Structuralsteelworkcompleted 4) woodStructuralframingcompleted 2)completedConcretework
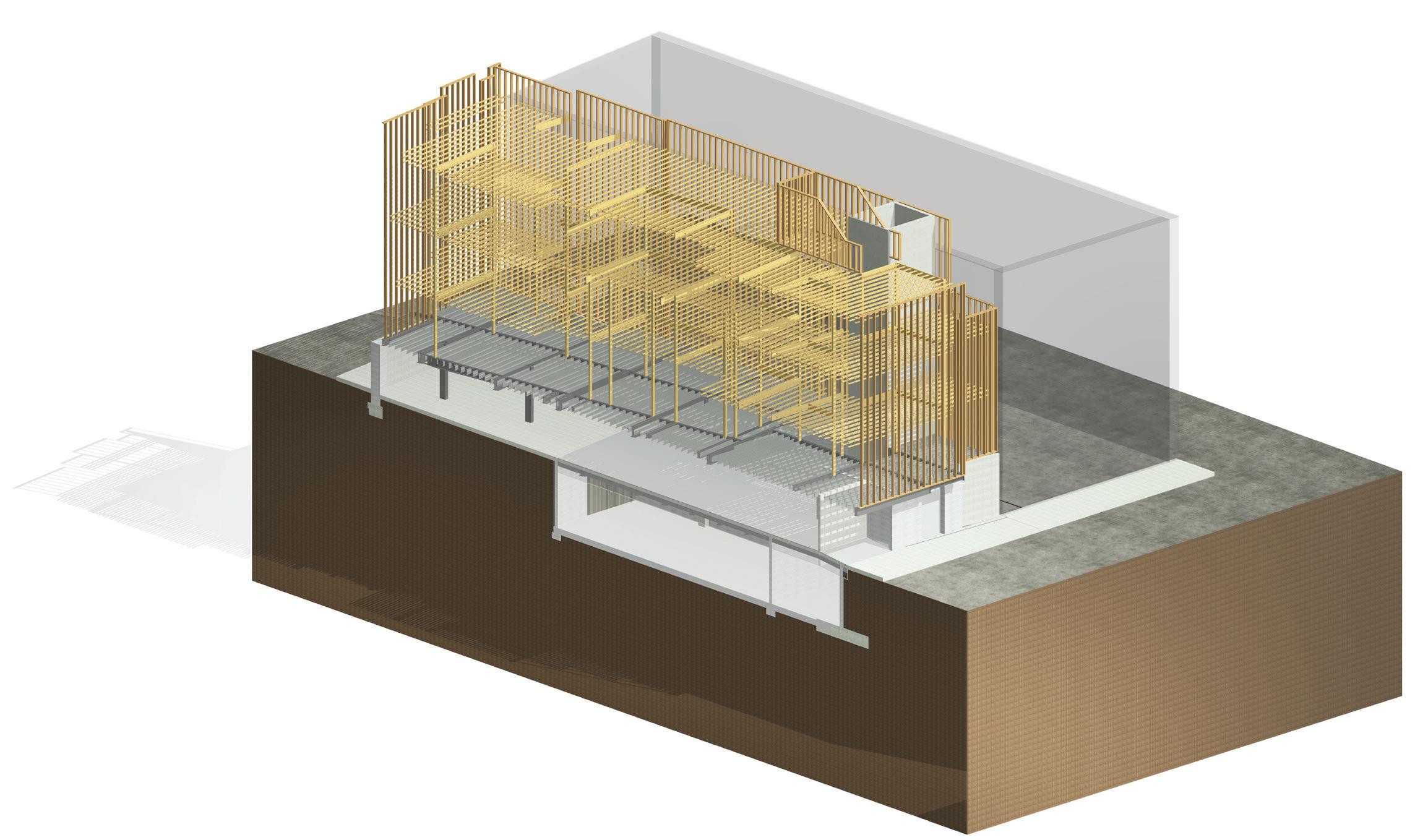


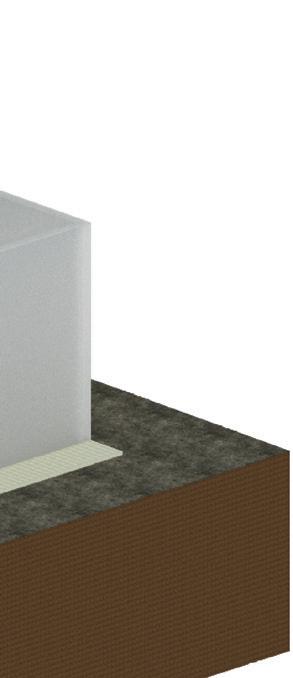
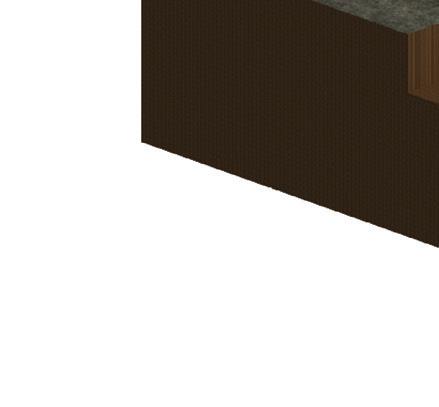


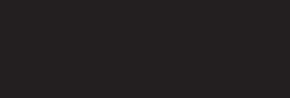
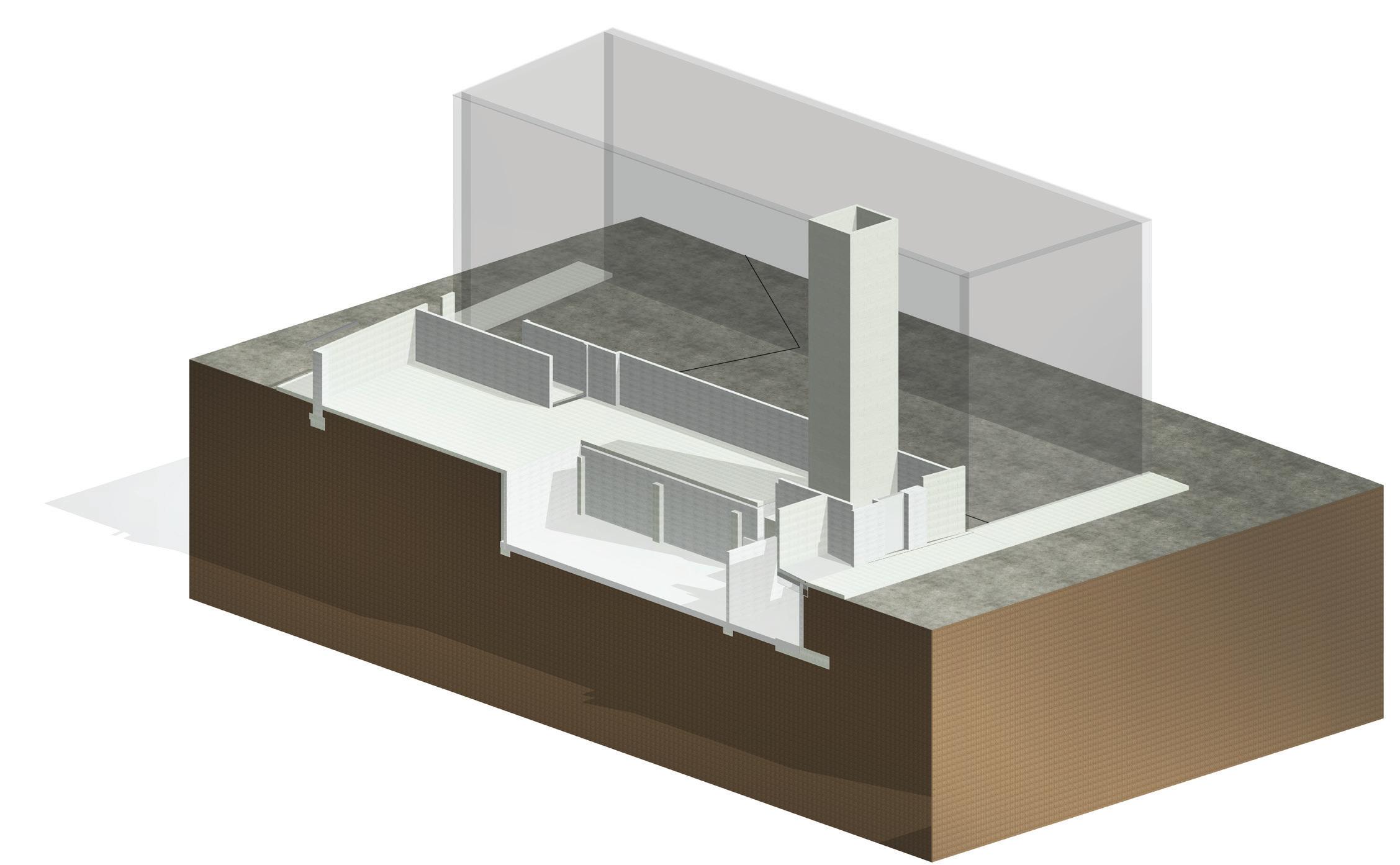
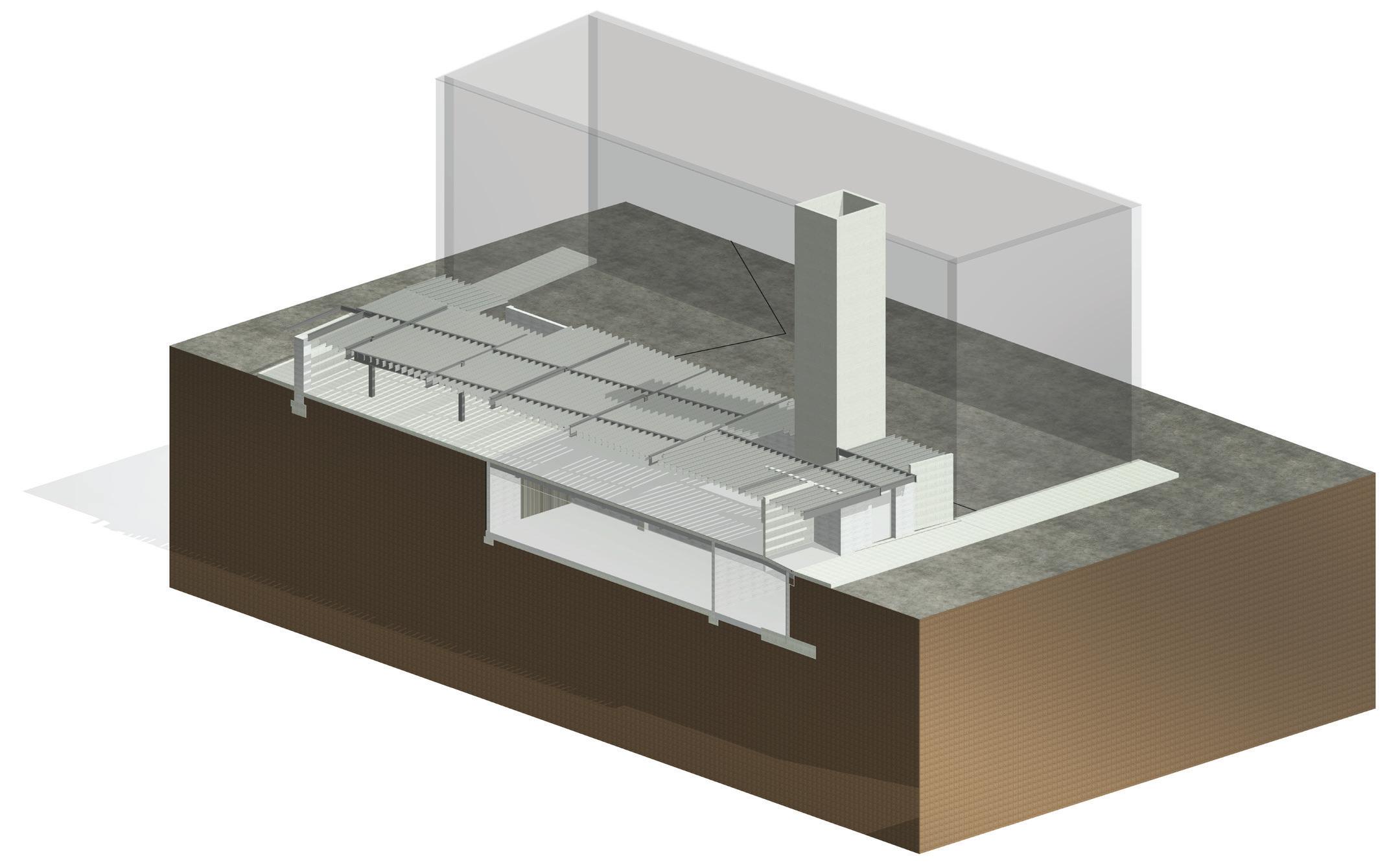
08/01/2018MCM 901 Page 124 of 224 Master Thesis: 620 N 3rd St Clara Bucar 5) Woodinteriorcomplete,framingandexterior 6) Building shell fully enclosed with plywood, no insulation, openings or finishes 7) completeBuilding
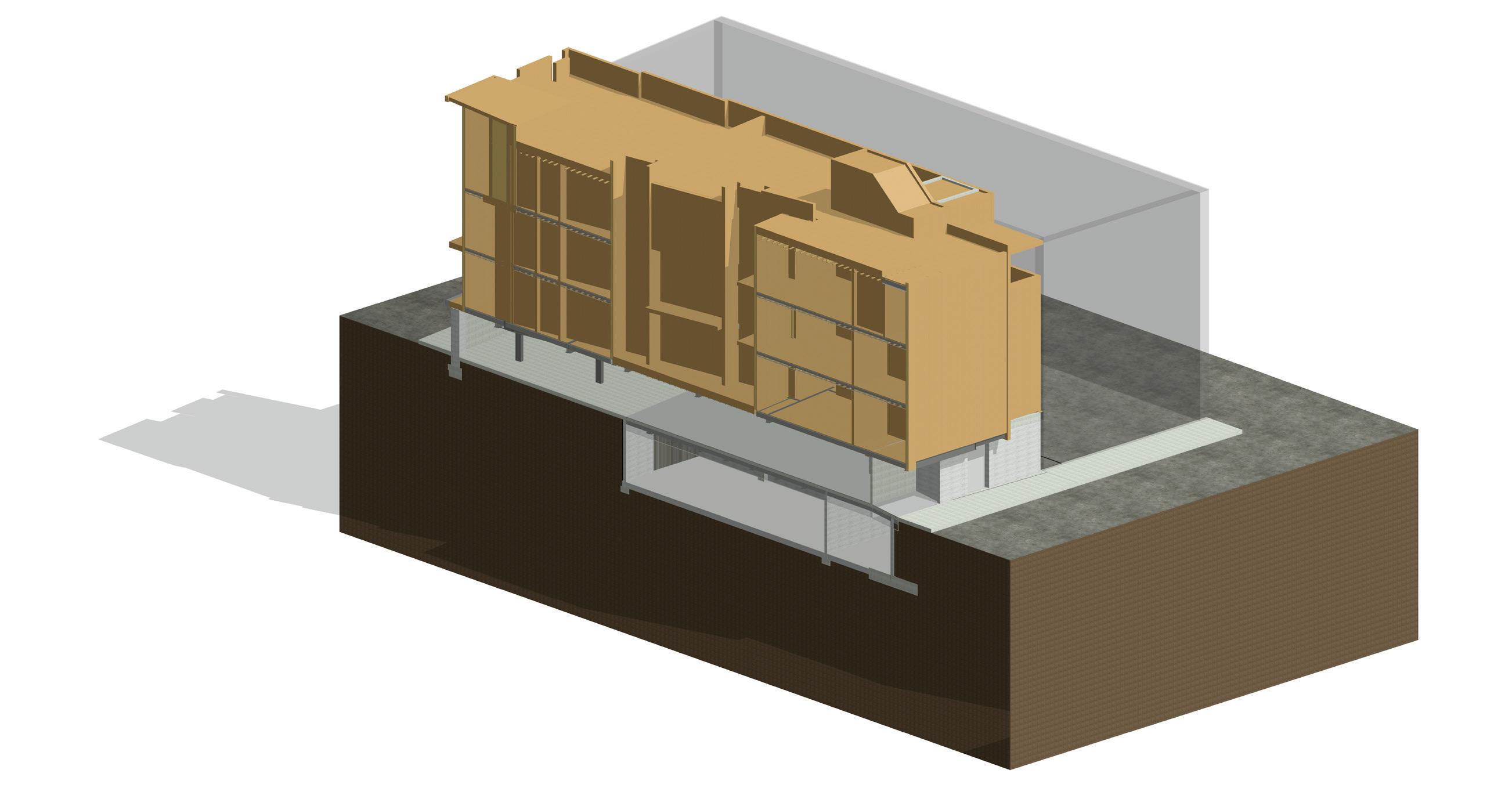
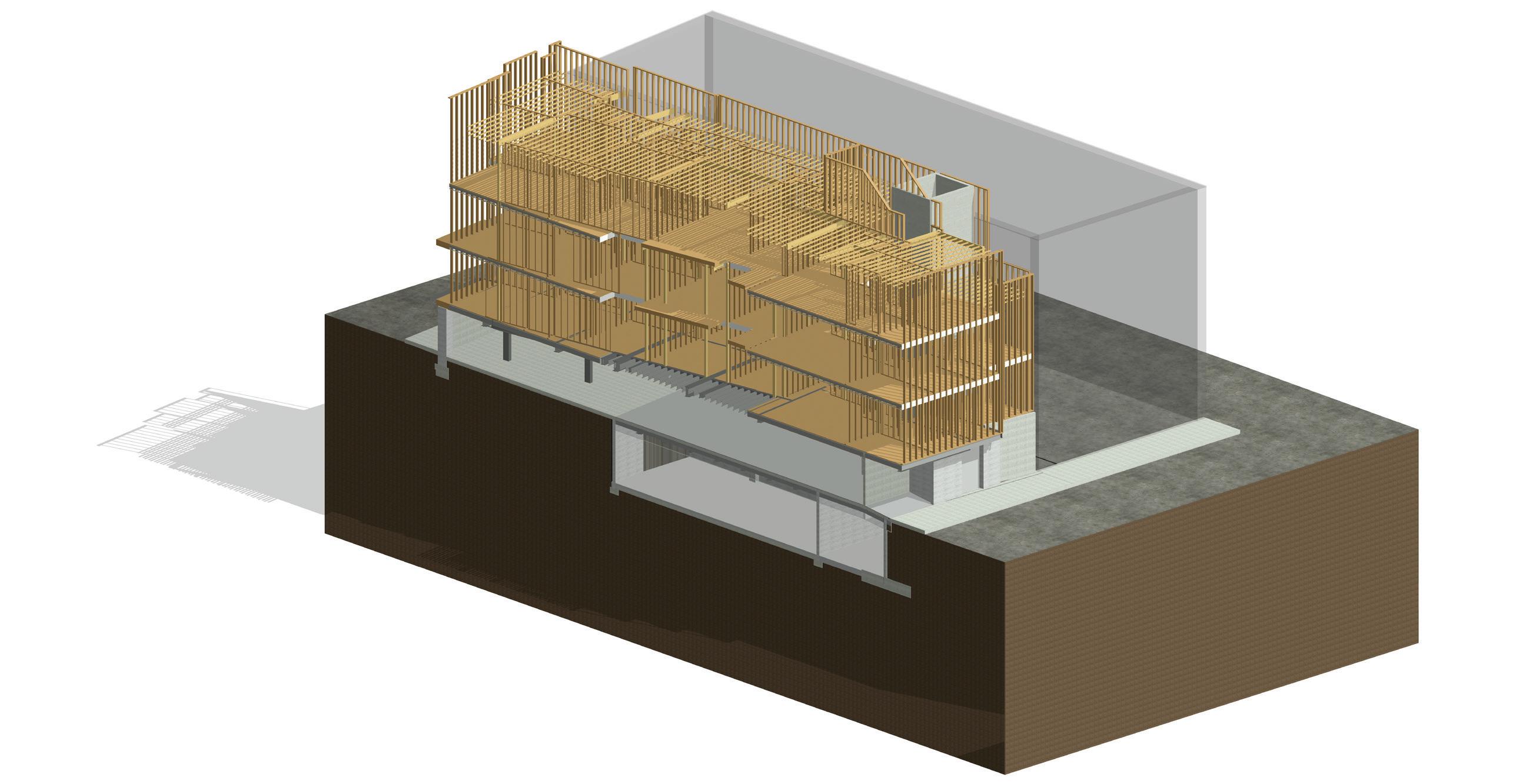
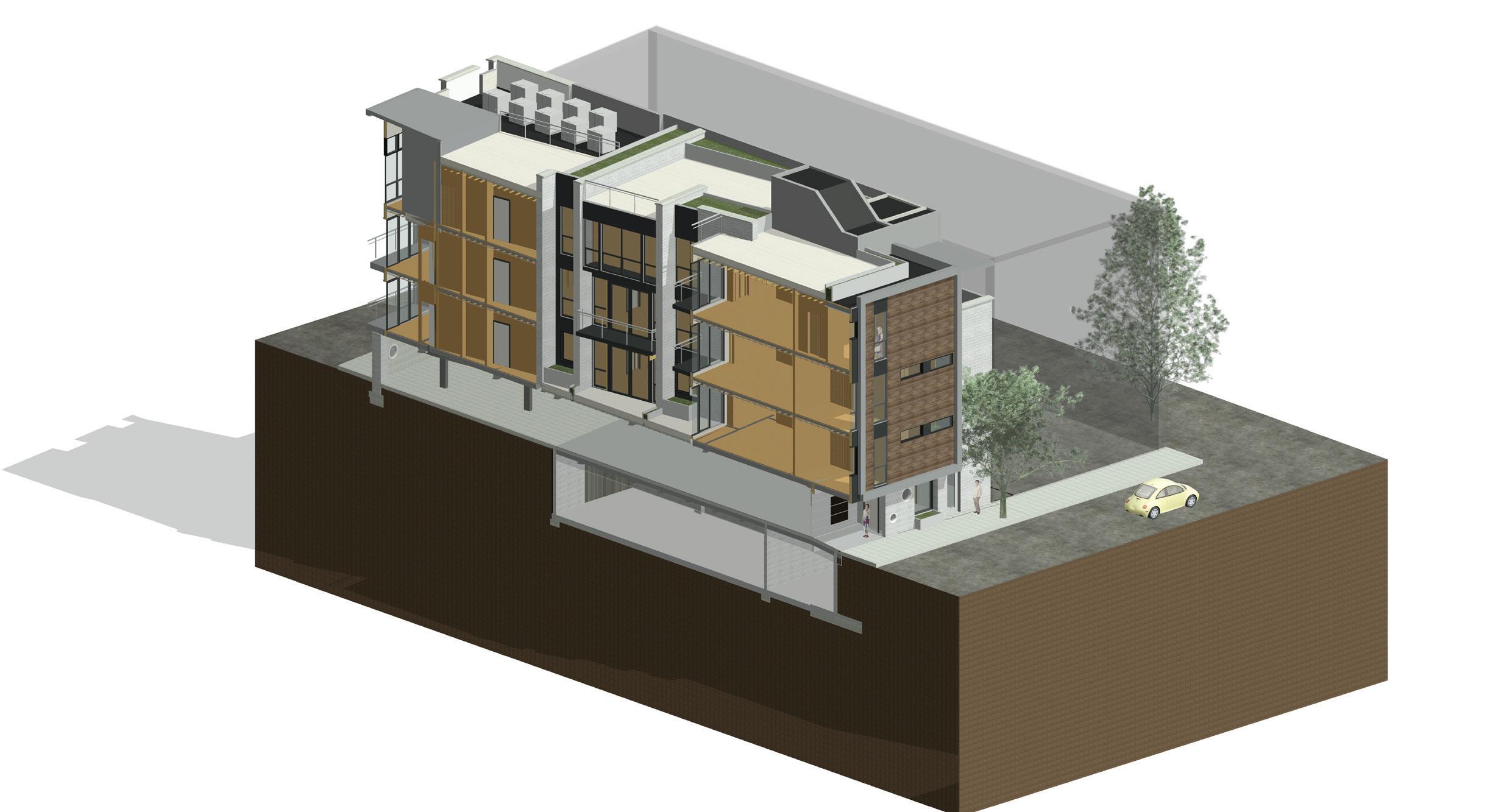
Section Six demonstrates the managerial aspect of the 620 N 3rd St project. It describes the processes and the mechanisms through which construction will happen. Channels of communication between team members, standard documents, templates to be utilized for documentation and many other construction standard practices can be found in this section.
In addition, within the next pages a thorough description of the unconventional delivery method chosen for this project can be found, as well as the set of meetings and other processes utilized to allow for the delivery method to function. Fit Construction believes strongly that foreseeing and being ready for the circumstances is the best management practice. With that in mind, the company developed the hybrid delivery method composed of an Integrated Project Delivery on a cost-plus-a-fee basis with full cost transparency and an Incentives Program.
08/01/2018MCM 901 Page 125 of 224 Master Thesis: 620 N 3rd St Clara Bucar SECTION SIX MANAGEMENT MEANS, METHODS AND CONTROLS
6.1.2.
Incentives program
6.1.1. Delivery method, constructibility and value engineering
08/01/2018MCM 901 Page 126 of 224 Master Thesis: 620 N 3rd St Clara Bucar 6.1. PRECONSTRUCTION
Another IPD element utilized in this project is the Incentives program. After the revision of the permit set and the update to the budget, the goal of 2.5% over the overall budget is set for the Incentives program. That means that, if the final budget is no higher than 3% over the first revised budget, an extra 15% on top of the original fee will be granted to the GC and the Designer. Following the same logic, if the final budget exceeds 5% over the revised budget, the GC and the Designer agree to have their fees cut by 15% from the original value. Fit Construction reserves the right to negotiate its own incentives program with its subcontractors.
The delivery method adopted by the 620 N 3rd St project is a hybrid of cost plus a fee lump sum and IPD (Integrated Project Delivery). The revision to the construction documents showed that the set lacks a large portion of specifications and details, which reveals that a traditional delivery system would result in serious budget disputes and delays. For that reason, the adopted delivery system foresees an initial budget composed by a cost plus a fee lump sum, traditional of a Design-Bid-Build, but allowing flexibility for changes offered by an IPD system. The first estimate will occur per the bid set. During that period of time, Fit construction will build a complete BIM model that will help identify items that need to be procured as soon as the job is awarded. These are long lead items such as the elevator, doors and windows, and also items that can be value engineered or that could present constructibility issues. When award happens, a set of three meetings will occur with the participation of all major stakeholders to discuss and decide the mentioned specs. These decisions will then be incorporated into an updated budget and a revised set of drawings which will allow for procurement and mobilization. After that, the BIM model will continue to be updated by Fit on a weekly basis with a combination of as built of the previous work and the detailing of the work to follow, contributing to identifying mistakes and coordination issues before they happen. Monthly meetings will be held with the purpose of revising and aligning the scope for the next month’s worth of work. These meetings’ resolutions will have the authority to update budget while aiming to keep the schedule unchanged. In other words, this project will utilize IPD methods of cooperation between team members to improve results on a fast tracking basis, while construction is happening. Fit Construction believes this strategy will allow for a continuous constructibility review and value engineering while helping to eliminate long waiting times between the issuance of change orders and the required approvals, which often causes exponentially growing financial losses combined between budget and schedule.
08/01/2018MCM 901 Page 127 of 224 Master Thesis: 620 N 3rd St Clara Bucar 6.1.3. Procurement
The 620 N 3rd St project will work traditionally regarding the contractual relationships. The Owner will hold two separate, independent contracts with the Designer and Fit Construction. Fit Construction will not be contractually connected to the Designer. All the construction subcontractors and vendors will be contractually connected to Fit Construction, not with the Owner. Loose furniture, appliances and decorative architectural details are not included in the scope of work provided by Fit Construction. Therefore, this portion of the work will work directly with the Owner.
Fit Construction has a steady relationship with the subcontractors selected to bid the 620 N 3rd St project. These companies were prequalified through a process that involves an analysis of past projects and outcomes, work safety accidents and casualty rates, main partner companies, economic growth over time and many other aspects. Fit Construction commits to bid work packages with at least three subcontracting companies in order to verify best value, but reserves the right to veto any subcontractor, recommended by the Owner. The subcontractor choice must include their scope, quality, commitment and reputation in addition to the price.
6.1.6. Project Organization
All the subcontractors selected for the job must provide a detailed estimate and schedule of the work to Fit Construction, in addition of their insurance certificates and the resumes for all the staff participating in the project. The subcontractor award will occur 5 business days after the budget commitment from the Owner.
A Payment Bond is included in the 620 N 3rd St budget. Fit Construction is covered by a $3,000,000.00 Commercial General Liability insurance with an additional $2,000,000.00 provided by an Umbrella Liability Coverage. Fit Construction is also covered by a $1,500,000.00 Builder’s Risk insurance.
Fencing, gates and construction signage shall be the first three items installed at the site to assure site enclosure previous to any work and, therefore, community safety.
6.1.4. Bonds and Insurance
6.1.5. Mobilization Mobilization efforts will start right after Notice to proceed. Fit Construction will be responsible for providing the Office trailer, fencing and gates, portable toilets and lavatories, construction signage and the necessary permitting with the exception of the Building Permit, which is the Designer’s responsibility and should be readily available with the original hard copy at the site on the first day of mobilization. Fit Construction is also responsible for coordinating its subcontractor’s mobilization and start of work activities.
08/01/2018MCM 901 Page 128 of 224 Master Thesis: 620 N 3rd St Clara Bucar
The Project Manager will actively work from the office to centralize all the information between the Site Superintendent, the vendors and subcontractors and the Owner, as well as to control the schedule and the budget. The Project Manager will also perform weekly visits to the site or as required. The Estimator will work with the initial and the revised budget, as well as the updates to the budget provided by the Monthly Revisions explained under “Delivery method, constructibility and value engineering”. All major meetings will happen either at the site or at the Fit Construction office.
Specific work hours are established in the Logistics Plan. All vendors and subcontractors need to inform and coordinate work outside of these regular hours with Fit Construction. Given the project is located in a residential area, only silent night work will be allowed and weekend work will be limited.
Although not contractually bonded, Fit Construction will work closely with the Designer to provide the best possible project result. The Project Manager will communicate on a regular basis with the Designers to clarify information, send submittals and approve specs. The Designer will be required to participate on all project meetings detailed under the subsection “Meetings”.
6.2.2. On site supervision and home office support
The Owner has the power to veto specs and scopes of work, as long as these are not required by code or by security and safety standards.
The Site Superintendent and the Field Engineer will be on site full time to coordinate, supervise and document all the performed work, including the access and maintenance of the site. A Safety Engineer will develop the Safety Plan and will visit the site on a weekly basis or as required.
The Project Manager will also be responsible for communicating management decisions to the Site Superintendent, which will then reflect these decisions at the construction site. A Field Engineer will assist the Site Super and both of them will perform the tasks of subcontractor coordination, supervision and quality assurance. The subcontractors at the site report to the Superintendent, while the subcontractors’ Project Managers negotiate items such as change orders directly with the contractor Project Manager. A portion of the materials will be procured directly by Fit Construction and installed by subcontractors, but other portion will be fully the subcontractor’s responsibility, leaving the Site Superintendent with the tasks to verify the accuracy of the specs and the quality of the work.
6.2.1.CONSTRUCTIONWorkhours
6.2.
The Owner will also be required to participate and provide input on a number of project decisions, especially those involving costs. The Project Manager will act as the center of the information, communication and negotiations. A Project Engineer will assist the Project Manager and participate actively in the meetings taking notes, sending reports and working with the documentation of the project.
All subcontractors are required to follow the Fit Construction Safety Standards program. See more information about safety on the Safety Plan section. This program, developed utilizing the OSHA standards as a base, provides essential guidelines to help keep the construction site a safe place for all project participants and the community. All visitors to the site need to utilize PPE as required and be accompanied by the Site Superintendent or the Field Engineer at all times.
Items such as Designer’s fee, Building permit, appliances furnishing and install, loose furniture and interior architecture decorative details are not included in the bid.
All material deliveries and waste pick up will happen on the N Galloway entrance and have to be coordinated with the Site Superintendent, see Logistics Plan for further information. The Office trailer will act as a support spot for subcontractors, vendors and consultants but spare desks will not be provided on a regular basis. The portable toilets and lavatories will be provided for all the staff involved with the project. Subcontractors are responsible for the meals of their own staff off site during Pre-Shell. During Post-Shell, the office, the portable toilets, lavatories and dumpsters will be transferred to the interior of the building. At that point, a meal area will also be assigned for subcontractors. Temporary power and water will be provided by Fit Construction.
6.2.6. Safety and health
08/01/2018MCM 901 Page 129 of 224 Master Thesis: 620 N 3rd St Clara Bucar 6.2.3. Subcontractors and vendors
6.2.4. Payment
Fit Construction commits to providing a 100% transparent budget to the Owner, reserving the right to manage the Incentives program with its own subcontractors. Fit Construction will bill the Owner monthly regarding the performed work, which shall be paid no longer than 30 consecutive days after billing. Fit Construction will pay its subcontractors no longer than 3 business days after receiving the payment from the Owner. Fit Construction reserves itself and its subcontractors’ the right to stop work if payment from the Owner is not accomplished 10 business days after billing, considering no disputes over performance.
6.2.5. Organization of the Site Parking will be provided for 1 representative of each major subcontractor, consultant and vendor, with the addition of parking for large vehicles carrying materials and equipment. The assigned parking will be provided through special city permits for street parking. The areas will include selected streets close to the job site and will be determined upon receit of the parking permits.
All construction work is subcontracted, with the exception of Masonry, which will be self performed. The masonry work refers to the construction of the elevator shaft and stair enclosure in the basement, including material and labor.
6.2.6. Quality assurance
6.2.8. Masonry (self-performed) Masonry will be self performed at the 620 N 3rd St project. Fit Construction will directly procure all required materials and provide labor to perform the work. This scope of work is limited to the construction of the elevator shaft, composed by CMU blocks, rebar reinforcement and grout, and the staircase enclosure in the basement. The crew at the site will respond to the Site Superintendent, who will have the authority and responsibility to coordinate the work. The price provided for the Masonry work package includes only material, equipment and labor. The profit margin is included in the project’s lump sum. The price breakdown will be provided along with the cost control reports submitted to the Owner.
All efforts are being made to avoid time consuming change orders. When the changes to the scope are not caught by the monthly revisions, a change order can be issued. The change order can be originated by the Designer, the contractor, a subcontractor or vendor. Small subcontractor change orders - less than $3,000.00 - only need to be approved by Fit Construction. Designer, Fit Construction relevant change orders, however, need to be reviewed and approved by the Owner.
In addition to the thorough subcontractor prequalification described under “Procurement”, biweekly job walk throughs will be performed to help identify incomplete, inaccurate or inadequate work early in the process. The Site Superintendent and the Field Engineer will be on site at all times to closely follow up with the work being performed, including verifications of specs and quality standards.
The party issuing the change order need to provide sufficient evidence of the necessity of the change and quotes and/or receipts to attest the new price. Change orders will aim to be processed as soon as possible, since they can hold the schedule back and harm other areas of the project.
08/01/2018MCM 901 Page 130 of 224 Master Thesis: 620 N 3rd St Clara Bucar
6.2.9. Change orders
6.2.7. Equipment Rule of thumb, subcontractors are responsible for their own equipment, which should be properly insured and maintained. Fit Construction reserves the right to require the subcontractors to utilize low noise equipment to avoid community disturbance.
Requests for clarification are issued from Fit Construction and other subcontractors and vendors to the Designers during preconstruction. It’s an official, contractual form of communication to clarify questions regarding the set of drawings and the project overall before construction.
A software called Procore will be utilized for documentation purposes. All RFIs, RFCs, Submittals, Transmittals, Weekly progress reports, important emails and other official or relevant documents will be uploaded to the system and automatically saved to the cloud, safe from hardware issues and other unforeseen circumstances. An additional backup to the company’s server will be made weekly. The software allows the other party to answer directly, recording the date and time of answers as well as the content. Procore will also be utilized to track budget and schedule, comparing weekly progress with the baseline. All project participants should be aware that the input on the software is official and can be utilized for legal purposes. The documents regarding 620 N 3rd St will be maintained for a total of 5 years, unless otherwise requested by the Owner.
During construction, questions about the design arise. A request for information is another type of official, contractual form of communication to clarify questions during construction.
6.3.4. RFI: Request for information
08/01/2018MCM 901 Page 131 of 224 Master Thesis: 620 N 3rd St Clara Bucar
6.3.2. RFP: Request for proposal Requests for proposals are issued before bid by the Owner to contractors and by the contractor to the subcontractors. It’s an official form of communication, an invitation to bid.
6.3.3. RFC: Request for clarification
Submittals are a form of official communication between project team members. It’s applicable for the approval of a material specification and/or material sample. It’s issued by Fit Construction and may require approval from the Designers and the Owner, depending on the nature of the spec. When a spec is approved by the Designer, it becomes their responsibility.
6.3.5. Submittals and Transmittals
6.3. 6.3.1.COMMUNICATIONSDocumentation
08/01/2018MCM 901 Page 132 of 224 Master Thesis: 620 N 3rd St Clara Bucar Transmittals are also official documents that confirm the transmission of relevant construction documents between project team parties or members.
A punchlist meeting will be performed as a walk through with all project participants including the Owner to verify remaining items which require completion. If, by the end of the project, unresolved change orders are a threat to the project participants relationship, cost dispute meetings will be held as required.
6.3.6. Weekly progress reports
A kick-off meeting will be held prior to mobilization. Weekly conference calls will be held to provide quick updates on the progress of the work, followed by the issuance of the Weekly report, emailed to all major project participants including the Owner. A biweekly job walk involving the value engineering team performing the monthly revisions will take place to contribute to the early recognition of potential issues.
6.3.7. Meetings
6.4. CLOSEOUT
Project closeout starts before the near completion. For 620 N 3rd St, closeout starts in the beginning of the project, with the collection of documentation and production of As-Builts on a regular basis as the work is completed. The goal is to reduce change order as much as possible and to resolve them as soon as possible, when they occur, to help avoiding financial disputes. After all the work is done with the exception of painting, a final inspection by the Building Department will occur. Ten business days are allowed in the schedule to accommodate any repairs necessary to the satisfaction of the Building Department in order to achieve the Certificate of Occupancy, to be issued, by schedule, two days after Turnover. The final cleaning will start before the painting is over and the Punchlist. The Startup of the
On Mondays at 2pm, a weekly report will be issued by the Project Manager from Fit Construction containing updated photos, percent completion for each portion of work in progress, baselines for budget and schedule, main issues, items at risk and an outline of the upcoming work week.
The first meeting will occur once the job is awarded. As explained under “Delivery method, constructibility and value engineering”, a set of three meetings involving all major project participants will take place to discuss long lead times and value engineering items. After that, a monthly meeting will be scheduled with the purpose of revising and planning the work for the following month. During these monthly meetings construction items can continue to be value engineered as long as the changes don’t harm the schedule.
The closeout process carries on after turn over with the completion of the Change orders, RFIs, As Builts, HVAC reports such as the ones mentioned above, Cost control, Communications Log, Warranties, O&M Manuals and Financial Resolution if required. Once all these items are closed to the satisfaction of the Owner, the Owner issues the Final Payment with the condition of the issuance of Affidavits of Payment, Lien Releases and Consent of Surety.
08/01/2018MCM 901 Page 133 of 224 Master Thesis: 620 N 3rd St Clara Bucar systems, Commissioning and T&B Reports will occur before Substantial Completion. After the Punchlist, Fit Construction will allow for seven consecutive days to perform outstanding items. When Punchlist items are completed, Substantial Completion will be issued by the Designer. In that occasion, Demobilization will occur and the building will be turned over to the Owner.
The descriptive portion of this section dedicates to the five top identified risks. These were explained in depth regarding the nature of the risk as well the impact. Additionally, the consequences, triggers and risk responses are also demonstrated for each of the five risks.
Fit Construction believes the continuous process of application and revision of these practices provides the information necessary to the full absorption of experience, therefore improving future projects.
SECTION SEVEN
Fit Construction produces a Project Risk Management Analysis for all of our projects. This is a practice derived from the Plan - Do - Check - Act - Review approach which applies also to our Safety, Environmental and Quality plans to be demonstrated in the next sections.
08/01/2018MCM 901 Page 134 of 224 Master Thesis: 620 N 3rd St Clara Bucar
PROJECT RISK MANAGEMENT ANALYSIS
Section Seven brings relevant information on the main management potential issues to be encounter during the preconstruction and construction of the 620 N 3rd St project. The fifteen most important recognized risks were categorized under technical, project management, construction, internal or external tags. After that, these fifteen risks were analyzed and ranked under a combination of risk probability and impact to cost and schedule. A responsibility matrix shows how the project members relate to each risk.
08/01/2018MCM 901 Page 135 of 224 Master Thesis: 620 N 3rd St Clara Bucar 7.1. Site Specific Risk Breakdown Structure RISK CATEGORY Technical Incomplete/ inaccurate construction documents Need for highly efficient coordination small, urban property Analysis Unkown subsurface conditions, especially regarding underpinning Machinery in small property phasing risk Project Management Construction External Scarcity of qualified subcontractors due to high season Disputes over budget due to delivery system Permits obtention: variety of different permits Difficulty with inspections/ inspectors Material delivery and storage difficulty impact to schedule Union strikes Internal Board form concrete poured on site limited space for tiltup Community relationship risk: blocking of streets and sidewalks Communication between parties IPD as a challenging delivery system Long lead items/material scarcity Project's low priority for the company staff issues
08/01/2018MCM 901 Page 136 of 224 Master Thesis: 620 N 3rd St Clara Bucar 7.2. Risk Register Risk Rank & ID Risk Statement & Category Risk Analysis Matrix Risk Response Strategy & Response Planning RankRisk UniqueID# Risk Statement Risk Category ProbabilityRisk Risk Impact ScheduleScore ScoreCost ScoreFinal Quantitative Risk Impact Trigger ResponseRiskStrategy Risk Response Action Plan Category Risk Owner Schedule Cost ScheduleImpact(Days) Cost ($)Impact 13 RM1 Permitsdifferentvarietyobtention:ofpermits ManagementProject Architect/CM 2 5 2 10 4 14 20 $2,000.00 Identification of required permits during Schedule and Logistics Plan Transfer Contractually tie Architect responsible for part of the permits. Hire an expeditor company to take care of the CM related permits. 11 RM2 Difficulty inspections/inspecwithtors ManagementProject CM/Subs 3 3 2 9 6 15 15 $2,000.00 Longtime/Failurewaiting Accept Thoroughly prepare for the inspections, allow time for repair and reinspection on schedule without harm to critical path 1 RM3 Material delivery anddifficultystorage-impacttoschedule Construction CM/Subs 5 4 3 20 15 35 15 $8,000.00 Identification of issues LogisticsduringPlan Mitigate Extra detailed Logistics Plan elaboration, with the input of major subcontractors 3 RM4 Incomplete/inaccurateconstructiondocuments Technical Designers 5 3 3 15 15 30 10 $10,000.00 Identification of issues ConstructabilityduringReview Mitigate Require shop drawings from all subcontractors 4 RM5 Scarcity subcontractorsqualifiedofduetohighseason ManagementProject CM 3 5 3 15 9 24 25 $15,000.00 Low quantity of subs bidding the job Accept Perform a market pre research, identify critical trades and include contigencies 11 RM6 Project's low priority for the company - staff issues Internal CM 3 3 2 9 6 15 15 $3,000.00 Busy backlog Avoid Plan for project's staff in advance 1 RM7 Need for coordinationefficienthighly-small,urbanproperty Technical CM 5 4 3 20 15 35 18 $15,000.00 Identification of issues subsmeetingsduringwithandduringLogisticsPlan Mitigate Extra detailed Logistics Plan elaboration, with the input of major vendors and subcontractors 14 RM8 Union strikes External CM 3 2 2 6 6 12 5 $3,000.00 Union posters on walls/wordpropertyon the street Mitigate Identify open shop trades, their latest behavior and allow for extra days in the schedule
08/01/2018MCM 901 Page 137 of 224 Master Thesis: 620 N 3rd St Clara Bucar Risk Rank & ID Risk Statement & Category Risk Analysis Matrix Risk Response Strategy & Response Planning RankRisk UniqueID# Risk Statement Risk Category ProbabilityRisk Risk Impact ScheduleScore ScoreCost ScoreFinal Quantitative Risk Impact Trigger ResponseRiskStrategy Risk Response Action PlanCategory Risk Owner Schedule Cost ScheduleImpact(Days) Cost ($)Impact 14 RM9 underpinningconditions,subsurfaceUnkownespeciallyregarding Technical Site work sub 3 2 2 6 6 12 5 $2,500.00 Post excavationsurvey Transfer Contractually tie Site work subcontractor to be responsible to the fullest in regard of unkown subsurface conditions 9 RM10 blockingrelationshipCommunityrisk:ofstreetsandsidewalks ManagementProject CM 4 2 2 8 8 16 5 $4,000.00 Streets and sidewalk blocking cars oftenpedestriansandmorethanonceaweek Mitigate Schedule big material deliveries for off-rush hours 9 RM11 Machinery in small propertyphasing risk Technical CM 4 2 2 8 8 16 5 $3,000.00 Identification of issues LogisticsduringPlan Transfer Work with equipment vendor to identify early in the process what type of machinery would be suitable for the site conditions and coordinate that with subcontractors 6 RM12 betweenCommunicationparties-IPDasachallengingdeliverysystem ManagementProject All parties 4 3 2 12 8 20 10 $5,000.00 Miscommunicationsigns Avoid Set effective communication matrix with responsible partitipants of each part of the project, issue weekly reports visible to all team members, set on site weekly meetings to plan ahead 5 RM13 Disputes over budget due to delivery system ManagementProject All parties 3 4 3 12 9 21 15 $20,000.00 Discussions about scope Accept Set effective responsibilities matrix, write complete scopes of work, build BIM model to foresee issues like MEP coordinatioin, set allowances and contigencies for identifyable complex parts of the project 8 RM14 Long items/materialleadscarcity ManagementProject CM/Subs 2 5 4 10 8 18 20 $20,000.00 Marketresearchpre Mitigate Effective constructability review, market pre research, contingencies and strategic alternates for the project 6 RM15 Board form concrete poured on site - limited space for tilt-up Technical Concrete sub 4 3 2 12 8 20 10 $10,000.00 Sub shopcontractordrawings Accept Specific portion of the Site Logistics Plan; if tilt-up reveals to be unfeasable, change strategy for concrete wall, such as smaller portions of tilt-up, pre fabricated or poured in place
08/01/2018MCM 901 Page 138 of 224 Master Thesis: 620 N 3rd St Clara Bucar 7.3. Project Team Risk Responsibility Matrix No. Risk Responsibility P - Primary Responsibility A - Approval Authority S - Support or Consulting I - Informed RankRisk Owner ExecutiveProject ManagerProject EngineerProject EngineerField SuperintendentGeneral Superintendent ManagerSafety/Environmental ManagerQuality ForemanCraft Architect ConsultantsArchitect's Technical RM4 Incomplete/inaccurate construction documents 3 A A A S S A A I S S P P RM7 Need for highly efficient coordinationsmall, urban property 1 I P P S S S S I I S I I RM9 Unkown subsurface conditions, especially regarding underpinning 14 A A A I I A A A I P I I RM11 Machinery in small property - phasing risk 9 I A A S S A A I I P I I RM15 Board form concrete poured on sitelimited space for tilt-up 6 A S S S S P P I A A A A External RM8 Union strikes 14 I P P S S S S S I I I I Internal / Organizationnal RM6 Project's low priority for the companystaff issues 11 A P P I I A A I I I I I Project Management RM1 Permits obtention: variety of different permits 13 I A A S S P P I A S P P RM2 Difficulty with inspections/inspectors 11 I A A S S P P S A P S S RM5 Scarcity of qualified subcontractors due to high season 4 I P P S S A A I I I I I RM10 Community relationship risk: blocking of streets and sidewalks 9 I A A S S P P P I S I I RM12 Communication between parties - IPD as a challenging delivery system 6 A P P S S A A S S S A A RM13 Disputes over budget due to delivery system 5 A P P S S S S S S A A A RM14 Long lead items/material scarcity 8 I P P S S A A I I P A A Construction RM3 Material delivery and storage difficulty - impact to schedule 1 I P P S S P P A S A I I
08/01/2018MCM 901 Page 139 of 224 Master Thesis: 620 N 3rd St Clara Bucar 7.4. Management Plans for the ‘Top Five’ Risks
Trigger: Identification of issues during Logistics Plan
7.4.1. Material delivery and storage difficulty - impact to schedule
Category: Technical Risk Owner: CM Trigger: Identification of issues during meetings with subs and during Logistics Plan
Risk Statement: The limited space inside of the construction site will need to be shared between construction work, GC staff, mobilization items such as portable toilets and dumpsters and also multiple subcontractor’s teams performing different tasks. Such high density workload can potentially causes serious schedule and cost problems, in addition of safety related issues.
Risk response: Mitigate. The subcontractor’s tasks, if coordinated properly, can provide for the share of resources and auxiliary action. That can boost construction productivity by decreasing the work time and reducing waste, improving the budget and overall project results.
Risk Statement: Due to the site’s location and project layout, logistics will be challenging in different ways. Risk response: Mitigate. The access to the site itself will be restricted, since it is situated in a densely populated residential area, with plenty other construction sites around. Material deliveries will have to be done in restricted hours of the day, week days planned ahead and often communicated or negotiated with the community to avoid disturbance. Material storage will also require a lot of planning, as the entire property area corresponds to the construction area. Specific issues can be identified during the layout of the Logistics Plan and therefore can be efficiently approached. A detailed schedule will be developed with the input of the subcontractors on the material quantity/volume and the equipment required to perform their work. The schedule will foresee specific dates and locations where each subcontractor will lay their materials before installation. Coordination between subcontractors is also essential, as the following top 5 risk will demonstrate.
Category: Construction Risk Owner: CM/Subs
7.4.2. Need for highly efficient coordination
Again, a highly detailed schedule, with the addition of illustrative phasing plans showing each subcontractor’s area of work and durations can provide for the required coordination. On top of that, the CM will gather subcontractors for an “all staff” action plan revision on early morning, before shift starts, as required per each phase, possibly multiple times in one week. It’s crucial that the subcontractor’s learn to communicate with each other, even when the responsibility and final word comes from the CM team.
Risk response: Mitigate. In addition to the above mentioned measures, two other measures will be taken. The first consists in a part of the weekly meetings being dedicated to review and plan ahead the work to be performed three weeks in advance, including all major participants such as important subcontractors and vendors. The second measure will be the development of a realistic and complete BIM model to help identify clashes, design gaps and conflicting information.
Category: Project Management Risk Owner: CM Trigger: Low quantity of subs bidding the job
Risk response: Mitigate. The response strategy, in that case, consists of addressing both sides of the situation from two different perspective. The first is to plan early, perform a market research to identify critical trader and prequalify enough bidders to open the possibilities as much as possible. The second perspective is to play with allowances and contingencies in the original project budget to foresee a complicated situation and try to contain damage on only the financial side This is important since, as stated before, the delay of the award can delay the entire work and potentially cause further loss than one overpriced subcontractor.
Risk Statement: The construction market is booming and it’s a possibility that there might be more work than workers. Several GCs and CMs are facing difficulties in contracting with a full set of reliable, well known subcontractors. The risks involved directly impact schedule and budget. The work could be severely delayed, harming logistics, sequencing and coordination with other trades. At the same time, the lack of competition is recognized to drive the prices up high.
7.4.3. Incomplete/inaccurate construction documents
Trigger: Identification of issues during Constructibility Review
7.4.4. Scarcity of qualified subcontractors due to high season
Risk Statement: Prior to the bid, during the estimating phase, several information gaps and conflicting information between design parties were identified. Multiple RFIs were issued, but that fact yells the necessity of a thorough Constructibility Review, to be followed by a value engineering analysis, prioritizing critical items. All efforts must be made to prevent scope surprises and to protect schedule, budget and relationships.
08/01/2018MCM 901 Page 140 of 224 Master Thesis: 620 N 3rd St Clara Bucar
Category: Technical Risk Owner: Designers
08/01/2018MCM 901 Page 141 of 224 Master Thesis: 620 N 3rd St Clara Bucar 7.4.5. Disputes over budget due to delivery system (IDP) Category: Project Management Risk Owner: All parties Trigger: Frequent discussions about scope
Risk response: Accept. These disputes, being the “intended result”, must still be closely tracked, analyzed and controlled. In addition to the detailed weekly meetings, when budget is also discussed, the production of the BIM model will be developed with the input and participation of each major subcontractor, who then has the ability to view, in 3D, the almost exact scope they should include in their base prices. The original contracts might include a written description of the scope and images of the 3D model to further illustrate and define the boundaries of the contracted work. That approach would help arise deeper questions, which then would become solid answers with the capability of decreasing disputes.
Risk Statement: The decision to perform an IDP hybrid delivery system comes from an intention to remedy incomplete set of drawings. With the fast tracking of the project, decisions can be made on-the-go and the project budget is not completely restricted to the bid. This flexibility is intended to improve final schedule and quality results, as changes in scope can be approached as something simpler than a change order. The same scenario, due to its unpredictable and risky nature, could likely set the stage for disputes over scope.
08/01/2018MCM 901 Page 142 of 224 Master Thesis: 620 N 3rd St Clara Bucar
The greatest objective of the Site Specific Safety Plan is the elimination of serious accidents at Fit Construction’s sites through the documentation and analysis of the information and results achieved by each project.
SECTION EIGHT SITE SPECIFIC SAFETY PLAN
Section Eight identifies potential hazards during construction. These hazards are specific to the 620 n 3rd St project and categorized by their probability and severity calculated through the Boston Square. For each of the top five hazards, descriptive information is provided on the nature of the risk, the Safety Plan’s main goal, the legal requirements, the monitoring methods, the responsibility structure, the training requirements, the emergency response and the documenting process.
As mentioned in the summary of Section Seven, Fit Construction produces a Project Risk Management Analysis, a Safety, an Environmental and a Quality plan for all of our projects deriving from the Plan - Do - Check - Act - Review approach.
The Site Specific Safety Management System is structured to have the OSHA standards as a minimum. This Safety System does not replace, it rather complements OSHA directions. It is composed by three parts:
1) Fit Construction Safety Guidelines, a complete publication with all the company’s safety preferred methods that will guide subcontractors as how to act in the company’s job sites and also demonstrate to Owners how we address the subject; 2) The identification of the main hazards in the 620 N 3rd St project specifically with the listing of the controls and hazard ranking before and after them; 3) The detailed description of plans to address the top 5 identified hazards.
A Safety Engineer works exclusively on the identification of hazards, application of controls and collection of data on Fit Construction projects, including 620 N 3rd St. This employee will periodically visit the site and perform reports which will then be analyzed and applied as controls during construction.
In the field, the Site Superintendent and the Field Engineer have the authority to monitor safety at all times and to stop the work if an unsafe activity is identified. They are the main contact points on site to address all subjects related to safety, including emergencies. They will also provide specific directions to subcontractors when required. However, all people working or visiting the site are strongly encouraged to watch out for each other’s work and to point out if they see something which isn’t correct or safe.
The Fit Construction Safety Guidelines is a document which has been carefully tailored by years of experience in the construction field. This publication is also periodically updated in accordance with the latest trends presented in the projects. Fit Construction utilizes the Plan - Do - Check - Act - Review approach when it comes to safety and believes that this process provides continuous learning and improvement.
08/01/2018MCM 901 Page 143 of 224 Master Thesis: 620 N 3rd St Clara Bucar 8.1. Site Specific Safety Management System
Fit Construction collects and documents data from all projects and combines it into a comprehensive system which then allows us to process that information and foresee the main activities that need to be closely tracked, as well as the subcontractors that are a better fit with our safety culture.
08/01/2018MCM 901 Page 144 of 224 Master Thesis: 620 N 3rd St Clara Bucar Severity InjuryIllness Essential Equipment Damage Project Damage Financial Cost Catastropic Fatality Fatality PermanentorDisability PermanentLoss LossDisastrousofTimetoRepair >20%IncreaseCost Major Lost GreaterTimethan2Weeks Lost GreaterTimethan2Weeks Loss of > 1 month Major Loss of Time Repairto >10%IncreaseCost Moderate Lost Time Less thab 2 Weeks Lost Time Less thab 2 Weeks Loss of < 1 month 1-3 months to Repair >5%IncreaseCost Minor TreatmentMedicalBasic TreatmentMedicalBasic RepairableonSite<Week < 1 Month to Repair < 5% IncreaseCost Insignificant MinorAidFirst Headache / Nausea etc. onRepairableSiteinaDay DisruptionNo Little or No Cost Description Catastropic5510152025 Major448121620 Moderate33691215 Minor2246810 Insignificant112345 12345 RareUnlikelyPossibleLikelyCertain Moderate High Extreme SeverityHazardMatrix RatingLikelihoodRating Catastropic5510152025 Major448121620 Moderate33691215 Minor2246810 Insignificant112345 12345 RareUnlikelyPossibleLikelyCertain Moderate High Extreme SeverityHazardMatrix RatingLikelihoodRating
08/01/2018MCM 901 Page 145 of 224 Master Thesis: 620 N 3rd St Clara Bucar 8.2. Site Specific Safety Hazard Analysis Work Package / Activity # Work Package / Activity Description Hazards RiskInherentRatingBeforeControls Controls ResidualRiskRatingAfterControls 184, 189, 194Rough carpentryFalls 20Tie-in PPE10 184, 189, 194Rough carpentry injuryMuscular 10 Training on lifting 3 184, 189, 194Rough carpentryOverheating5Shorter shifts3 161, 165, 175Steel erectionOverheating5Shorter shifts3 161, 165, 175Steel erectionFalls 12Tie-in PPE10 161, 165, 175Steel erection Injury materialby drop 15 Steel PPEadequateboots, 5 161, 165, 175Steel erectionBurns 5 protectionPPE,Adequatefire 3 106, 114, 127, 135, 141 Concrete Overheating5Shorter shifts3 106, 114, 135Concrete Empallement15 Tie-in PPE, rebar caps 10 106, 114, 127, 135, 141 Concrete silicaRespirable 12 maskBreathingPPE 5 293 Electrical rough-inElectrocution20 ofdisconnectionsupervision,PPE,Adequatesystems 10 101 Utilities - ElectricalElectrocution20 ofdisconnectionsupervision,PPE,Adequatesystems 10 71 Underpinning collapsingStructure 12 Survey, work per plansstructural 10 66, 92, 93Excavation collapsingStructure 5 equipmentadequateSurvey, 4 499 Painting Toxic inhalingfume 10 maskBreathingPPE 6 114, ofdisconnectionsupervision,PPE,Adequatesystems
08/01/2018MCM 901 Page 146 of 224 Master Thesis: 620 N 3rd St Clara Bucar Work Package / Activity # Work Package / Activity Description Hazards RiskInherentRatingBeforeControls Controls ResidualRiskRatingAfterControls 184, 189, 194Rough carpentryFalls 20Tie-in PPE10 184, 189, 194Rough carpentry injuryMuscular 10 Training on lifting 3 184, 189, 194Rough carpentryOverheating5Shorter shifts3 392, 397, 402, 407 Gypsum board (prime) Toxic inhalingfume 10 maskBreathingPPE 6 247, 248, 257 Install windows)openingsexterior(façade Electrocution12 protectionaerealsupervision,PPE,Adequateline 8 232 Exterior finishes (façade) Electrocution12 protectionaerealsupervision,PPE,Adequateline 8 247, 248, 257 Install windows)openingsexterior(façade Falls 20 Tie-in (lift)equipmentadequatePPE, 10 232 Exterior finishes (façade) Falls 20 Tie-in (lift)equipmentadequatePPE, 10 382 Roofing Falls 20Tie-in PPE10 343, 344Insulation Toxic inhalingfume 8 maskBreathingPPE 4 465 Mechanical final Injury materialby drop 8 Steel PPEadequateboots, 5 473, 479, 485, 491 Electrical final Injury materialby drop 8 Steel PPEadequateboots, 5 412 Kitchen countertops Injury materialby drop 8 Steel PPEadequateboots, 5 457 Plumbing final - RoofFalls 20Tie-in PPE10 508 CommissioningElectrocution20 ofdisconnectionsupervision,PPE,Adequatesystems 10 457 Plumbing - 20Tie-in PPE10 508 CommissioningElectrocution20 10 Falls (lift)equipmentadequatePPE, (façade) Tie-in (lift)equipmentadequatePPE, 382 Falls 20Tie-in PPE10
Responsibilities: All people on site have the duty and authority to check on one another. The Site Superintendent is the responsible contact point on site full time for safety, followed by the Field Engineer. The Safety Engineer visits the site on a periodic basis and has the authority to provide the safety plans and reports.
Description of the hazard or risk: Falls are statistically among the number one cause of serious accidents in construction. In 620 N 3rd St project it’s no different. A number of work packages will include height exposure and therefore the possibility of falls. These work packages are rough carpentry, steel erection, install of exterior openings and finishes, roofing and other activities to occur on the roof like final plumbing. In this project, falls can occur when vertical elements are being installed or connected to horizontal ones, such as welded connections between columns and beams, from facade work or from activities on the roof.
Objective or goal: The objective of this item of the Safety Analysis is to prevent falls from happening.
Training Requirements: All workers on site on a regular basis should be OSHA-30 certified. All site visitors, with the exclusion of the Owner and authorities, should be OSHA-10 certified.
Monitoring Methods: All people at the site have the duty and authority to verify if an employee performing work in a high level is doing so securely. The infraction should be called out immediately and the work should be stopped until the safety rules are followed.
Emergency Response: In case a fall does occur, the employee should be kept immobile and an ambulance should be called.
List of Resource Requirements: For heights up to 6 feet, metal, sturdy ladders should be utilized for the work. These ladders should be maintained and checked for safety every week. When working above 6’ high, the employee should utilize tie-in PPE and a scaffolding should be utilized. The scaffolding should have a 42” high handrail all around. When working in heights over 10 feet, the scaffolding should also include a kickplate all around. When working on a roof, a temporary support structure should be built in order to allow the employees to connect their tie-in equipment. If working anywhere less than 6 feet from the edge of the building, employees are required to be tied-in. When working on the facade, a lift with 42” double guardrail and a kickplate is required.
Documents and Records: A record of infractions will be kept by the Site Superintendent even if it doesn’t become an OSHA violation. These records will contribute to the subcontractor qualification in future projects, as well as to assessments of the work in general.
08/01/2018MCM 901 Page 147 of 224 Master Thesis: 620 N 3rd St Clara Bucar 8.3. Management Plans for the ‘Top Five’ Safety Hazards 8.3.1. Falls
Legal and other requirements: Generally, by the minimum OSHA standard, an employee needs fall protection when working from 6 feet high above the floor. The full OSHA rules on fall protection is extensive and consists of the 29 CFR 1926 regulation.
08/01/2018MCM 901 Page 148 of 224 Master Thesis: 620 N 3rd St Clara Bucar 8.3.2. Electrocution
Emergency Response: In case of emergency, other people around the victim need to be extremely careful to avoid also being electrocuted. A highly insulating material, like rubber or wood needs
The Site Superintendent is in charge of imposing safety rules to the subcontractors, including the verification of their equipment’s maintenance on a regular basis. Anyone at the job site can and should point out when an unsafe practice is taking place.
Responsibilities:
Monitoringrequired.Methods:
List of Resource Requirements: The most common electrical hazards arise from unsafe equipment, environment or bad practices. To reduce and eliminate these hazards we will invest on periodic equipment maintenance and utilize strategies including insulation, electrical protective devices, guarding and safe work practices. The insulation should be in accordance with the type of work being performed, like voltage, presence of oil or other easily burning material and weather conditions. Electrical protective devices consists of a mechanism that automatically shuts the circuits down in case of higher than regular electrical discharges. Guarding means to protect high voltage equipment by installing guardrails all around it to prevent people from coming to close. Safe work practices include training, the use of proper PPE, equipment maintenance and the de-energizing of equipment during activities to which it isn’t
It’s important to note that low voltage doesn’t imply low risk, and that electricity hazards have a high fatality rate, therefore should be treated with the required attention. Electrocution is a constant hazard in this project and can happen during the entire construction period. Starting with the utilities connection, then electrical rough work, electrical final, low voltage and ending with commissioning, all electrical work includes a risk. In addition to that, the proximity of the building’s facade with PECO aerial cabling imposes one more serious hazard.
Description of the hazard or risk: Another frequent safety hazard in construction sites is electricity. In the 620 N 3rd St project, the high density of power outlets, low voltage items and lighting, due to the residential nature of the building, cause the work to be electricity intensive.
Objective or goal: To eliminate the occurrence of serious electrocutions during the construction of the 620 N 3rd St project.
Training Requirements:
Legal and other requirements: When employees are working with exterior openings and finishes, they’ll be very close to the electrical lines. PECO requires by law that owners apply to require aerial line protection when these conditions occur. PECO installs their own protection equipment on the lines for the period of time determined by the project. That dramatically reduces electrocution hazard from this scenario, but employees are still required to take the same measures designated for other types of electrical hazard exposure
All workers on site on a regular basis should be OSHA-30 certified. All site visitors, with the exclusion of the Owner and authorities, should be OSHA-10 certified.
All people on site have the duty and authority to check on one another. The Site Superintendent is the responsible contact point on site full time for safety, followed by the Field Engineer. The Safety Engineer visits the site on a periodic basis and has the authority to provide the safety plans and reports.
Objective or goal: To dramatically reduce the risk of impalement from the construction work.
List of Resource Requirements: Utilization of rebar caps, as well as investing in falls protection further described under 8.3.1.
Description of the hazard or risk: The impalement hazard can be closely related to falls, described under item one of this section. Consists of the risk of an employee’s body being perforated by a construction element. This hazard is often connected to unprotected sharp protruding structures incorporated in structure and masonry partitions. In the 620N 3rd project, the entire first floor exterior walls are concrete reinforced with rebar. Due to the fact that the schedule foresees the install of structural steel concomitant with the construction of the concrete walls and the CMU elevator shaft, falls risk includes impalement hazard.
Documents and Records: The same documenting process used for falls described under the previous item should be used to track the job’s safety conditions.
Legal and other requirements: By OSHA’s 29 CFR 1926.701(b) requirement, “all protruding reinforcing steel, onto and into which employees could fall, shall be guarded to eliminate the hazard of impalement”.
8.3.3. Impalement
Documents and Records: The same documenting process used for falls described under the previous item should be used to track the job’s safety conditions.
Responsibilities: All people on site have the duty and authority to check on one another. The Site Superintendent is the responsible contact point on site full time for safety, followed by the Field Engineer. The Safety Engineer visits the site on a periodic basis and has the authority to provide the safety plans and reports.
Training Requirements: All workers on site on a regular basis should be OSHA-30 certified. All site visitors, with the exclusion of the Owner and authorities, should be OSHA-10 certified.
Emergency Response: If impaled by a foreign object, the object should not be removed and medical attention should be provided immediately.
At the 620 N 3rd St project, one entire side of the building, which extends the length from one
620 N 3rd St Clara Bucar to be utilized to disconnect the person being electrocuted from the electricity source and an ambulance should be immediately called.
08/01/2018MCM 901 Page 149 of 224 Master Thesis:
Monitoring Methods: The Site Superintendent is in charge of imposing safety rules to the subcontractors, including the verification of their equipment’s maintenance on a regular basis. Anyone at the job site can and should point out when an unsafe practice is taking place.
8.3.4. Structure collapsing Description of the hazard or risk: The collapsing of structures is a critical hazard during excavation and especially underpinning, but also a possibility during the pour of the foundations.
08/01/2018MCM 901 Page 150 of 224 Master Thesis:
620 N 3rd St Clara Bucar street to another, will need to be excavated and underpinning in order to provide the existing neighbor building structural support previously provided by the ground. That process exposes structures and has to be done in portions, in a way that only these portions are treated at once.
The first measure taken to prevent this hazard is the design in itself. An underground specific survey is performed during preconstruction to identify the existing structure. The design is made accordingly, but subsurface unknown conditions are a constant in construction, making underpinning a risky activity. The second measure would be to follow the design meticulously and not underpin larger portions than what is provided in the drawings. Lastly, the neighbor building should be braced, a minimum amount of staff should be at the site while underpinning is happening, the sidewalks should be closed and the neighbor building should be advised that underpinning is occurring. Ideally, the building should be empty during excavation. A clear emergency exit path has to be defined previously to the start of the work and all staff members should be made aware of it.
Training Requirements: All workers on site on a regular basis should be OSHA-30 certified. All site visitors, with the exclusion of the Owner and authorities, should be OSHA-10 certified. The subcontractors should be specialized in performing this type of work (underpinning), so no special training is required.
Responsibilities: All people on site have the duty and authority to check on one another. The Site Superintendent is the responsible contact point on site full time for safety, followed by the Field Engineer. The Safety Engineer visits the site on a periodic basis and has the authority to provide the safety plans and reports. The Site Superintendent has the authority to stop the work if he/she finds the circumstances to be unsafe.
Documents and Records: The same documenting process used for falls described under the previous item should be used to track the job’s safety conditions.
8.3.5. Toxic fume inhaling
Legal and other requirements: OSHA’s 1926.651 regulation provides the minimum standards for specific excavation requirements.
Objective or goal: To reduce the likelihood and consequences of a collapsing structure accident.
List of Resource Requirements:
Emergency Response: If the structures start to crack, shift or present any kind of change whatsoever, the entire area, especially the building, need to be evacuated immediately.
Description of the hazard or risk: Inhaling toxic fumes can be identified in a number of different activities, the two main ones being painting and gypsum board priming. This is a hazard that can be easily underestimated and frequently neglected by employees, but that could cause serious health damages. In the 620 N 3rd St project, large areas of gypsum board partitions will
Monitoring Methods: The Site Superintendent is in charge of imposing safety rules to the subcontractors. Anyone at the job site can and should point out when an unsafe practice is taking place, that should then be informed to the Site Superintendent. The Safety Engineer is responsible for compiling this information into a comprehensive report.
Monitoring Methods: The Site Superintendent is in charge of imposing safety rules to the subcontractors. Anyone at the job site can and should point out when an unsafe practice is taking place, that should then be informed to the Site Superintendent. The Safety Engineer is responsible for compiling this information into a comprehensive report.
Documents and Records: The same documenting process used for falls described under the previous item should be used to track the job’s safety conditions. All these internal infractions will be documented and kept in Fit Construction’s records. These will later be utilized to assess subcontractor’s performance, likelihood of future bidding and also bonuses provided by the Incentives Program.
620 N 3rd St Clara Bucar be primed and painted in an enclosed, dense space, amplifying this hazard’s impact. Sprayed insulation can also release fumes.
Responsibilities:
All workers on site on a regular basis should be OSHA-30 certified. All site visitors, with the exclusion of the Owner and authorities, should be OSHA-10 certified. The subcontractors should be specialized in performing this type of work (priming, painting and insulating), so no special training is required.
Objective or goal: To protect all project participants from inhaling harmful toxic fumes and therefore prevent long term consequences.
All people on site have the duty and authority to check on one another. The Site Superintendent is the responsible contact point on site full time for safety, followed by the Field Engineer. The Safety Engineer visits the site on a periodic basis and has the authority to provide the safety plans and reports. The Site Superintendent and the Field Engineer have the authority to command subcontractors to utilize the required PPE and, if they don’t, to stop the work. In addition, other subcontractors can also help supervise each other and contact the Site Superintendent if they see something wrong.
Legal and other requirements: OSHA’s 1910.134 regulation provides the minimum standards for respiratory protection.
08/01/2018MCM 901 Page 151 of 224 Master Thesis:
Training Requirements:
List of Resource Requirements: As ways to prevent it, firstly, the areas where toxic fumes could be being spread should be isolated with plastic and the entrance should be controlled. Only people wearing the require mask as PPE should be allowed inside of these areas during these activities. Subcontractors who are exposed during full shifts or considerable amounts of time are required to provide their own respiratory protection in accordance to OSHA, at a minimum. Fit Construction will provide its own staff’s PPE, as well as three extra sets for visitors available at the trailer or site office, which should be used only for quick visits.
Emergency Response: If anyone enters an area where toxic fumes are being released (these areas will be isolated), that person should be immediately removed from the isolated perimeter. If large amounts of fume are inhaled, immediate medical assistance is required.
Fit Construction believes that this exercise allows for learning and improvement in a continuous process to be built project after project.
08/01/2018MCM 901 Page 152 of 224 Master Thesis: 620 N 3rd St Clara Bucar SECTION NINE SITE SPECIFIC ENVIRONMENTAL PLAN
Section Nine dedicates to identify and prepare for potential environmental risks to be faced during the 620 N 3rd St project. The main risks are listed and categorized by severity and probability through the Boston Square. After that, the five top environmental risks are studied in depth. Each one of these five risks are analyzed in their nature and impact potential, the organizational controls to be utilized to respond to these events, the list of the required resources in order to prevent and control the risks, monitoring methods, the responsibility structure demonstrating which project members own the risk, training requirements and emergency responses.
08/01/2018MCM 901 Page 153 of 224 Master Thesis: 620 N 3rd St Clara Bucar 9.1. Site Specific Environmental Management System
The Environmental Plan will list the major risks regarding 1) the identification of areas potentially affected by construction; 2) the mapping of the involved community; 3) the monitoring and assessment of the air quality, noise and soil conditions before, during and after construction.
The environmental risk evaluation is pivotal to the maintenance of comfort levels to the nearby community, the future tenants and to construction itself. The data provided will help protect budget and schedule, protecting not only the construction work, but everyone directly or indirectly involved with it as well. Fit Construction’s management will closely observe and allocate the required resources in order to prevent undesirable events, reversing the crisis management mentality and investing in prevention.
Before the 620 N 3rd St Environmental Management System is developed, Fit Construction’s top management engages and establishes the overall policies that guide all the company’s work. Only after that, the actual plan is composed and then implemented. In accordance with ISO-9001, the process then moves on to comparison and evaluation of the foreseen results versus the actual achieved ones. The last step is the revision of the system according to the processed data. This information is documented at Fit Construction, helping to improve the initial overall policies and becoming available to the following projects.
Periodic air monitoring; special equipment; isolation of critical areas; water sprays; adequate PPE 2.1; 2.3; 2.4; 2.5; 2.6; 2.7; 2.8 Waste pollution
2.1; 2.3; 2.4; 2.5; 2.6; 2.7; 2.8
AspectEnvironmentalDescription EnvironmentalDescriptionImpact
Selective collection and sorting of waste to be performed previously to the removal from the site. Each type of material to be addressed to appropriate recycling facility.
Noise pollution and vibration
Site Superintendent will inspect sidewalks periodically for potential hazards and coordinate repairs; additional signage indicating reroutes; additional sensorial warning signs for visually disabled people 2.2; 2.3; 2.13 Discharge of waste water
The site was previously occupied by a factory. Therefore, the sanitary main line and other utilities could be old and hard to connect to, potentially provoking leaks
L
Opaque fencing and temporary gates; daily clean up of sidewalk from debri and constructiontocommunicationwaste;withcommunityinformscheduleandenddate
08/01/2018MCM 901 Page 154 of 224 Master Thesis: 620 N 3rd St Clara Bucar 9.2. Site Specific Environmental Impacts WBS #
Env.(RatingRiskH,M,L)
Site work, concrete and masonry will release high levels of dust in the air, causing distress and potential health issues to the community H
Street storm inletrisk of flash floods Waste and debri from construction could block nearby gutters and provoke flash floods during rainy seasons
Limit loud noise activities to business hours with no exceptions; adequate equipment with periodic maintenance asConstructionawhole Traffic issues
2.1; 2.3; 2.5Air pollution
Several different activities will produce high levels of noise and vibration, causing distress to the community H
L
Roads will need to be blocked for different activities, parking spots will be occupied with construction related personnel, delivery and pick up trucks will circulate in the area, affecting the traffic H Traffic control staff on site at rush hours when street blockage is occuring; additional signage indicating construction areas and reroutes; scheduledcommunicationcommunityregardingwork asConstructionawhole experiencePedestrian risk Sidewalks will need to be blocked for different activities, affecting the circulation of pedestrians. Construction work could damage sidewalks and produce hazards. Sheltered walkways are a necessary M
2.3; 2.4 Material source and waste Renewability- risk Large amounts of natural resources (wood and steel) utilized in the project
Plumber subcontractor should perform a survey previously to utility connection and repairs should be made as required asConstructionawhole
Environmental Controls
Site Superintendent will instruct subcontractors to leave exterior of the site free from waste and debri at all times
L Should be well planned ahead to avoid waste and purchased from sustainability certified
All activitiesexterior Visual pollution
Construction will possibly cause aggressive visuals to nearby community L
Construction activities produce large amounts of waste, some of them non degradable H
Operational Controls: When possible, activities that could release high levels of particles into the air should be isolated. Water sprays should be utilized as considered required by the Site Superintendent. The air should be periodically tested and the subcontractor’s equipment should be properly maintained.
Documents and Records: All negative occurrences should be informed to the Site Superintendent, who gathers the details and sends the information to the Environmental Engineer The Environmental Engineer then provides the appropriate documentation for Fit Construction’s purposes.
08/01/2018MCM 901 Page 155 of 224 Master Thesis: 620 N 3rd St Clara Bucar 9.3. Management Plans for the ‘Top Five’ Environmental Aspects 9.3.1. Air Pollution
Monitoring Methods: The level of air pollution will be periodically tested. During the most critical activities, the air should be tested as considered required by the Site Superintendent. The subcontractor’s equipment should be periodically checked for performance.
Emergency Response: If air pollution levels become critical, the work should be stopped until the Environmental Engineer issues a new plan and considers the conditions safe again.
Responsibilities: Each subcontractor is responsible for the maintenance of their own equipment. The Site Superintendent is in charge of the environmental risk controls on site full time and has the authority to direct subcontractors and to supervise their equipment and work. The Environmental Engineer performs periodical site visits, provides the main guidelines of what should be done in order to control environmental hazards, collects information from the Site Superintendent, documents and generates reports for improvement of the plans.
List of Resource Requirements: Fit Construction will provide water spray equipment to contribute with dust control inside the premises. In addition, the company will provide masks for their own staff and for visitors. There will be an equipment to measure air pollution levels on site during the entire pre-shell phase.
Description of the Environmental Aspect & Impact: The release of dust in the air is the most common environmental hazard during construction activities. In the 620 N 3rd St project, the three activities that are the most concerning when it comes to air pollution are site work, concrete and masonry. The particles released in the air provoke pollution and cause not only discomfort, but also potential health issues, especially for the construction workers who are the closest to the critical areas. There is a tolerance for temporary air pollution levels, but controlling this environmental risk is critical for a healthy community.
Training Requirements: The Site Superintendent should receive specific training on how to measure air pollution levels.
List of Resource Requirements: Fit Construction will provide signage to be hung on gates to provide information of scheduled loud work activities. An equipment to measure sound intensity will be provided and kept at the site all throughout the construction project.
List of Resource Requirements: A third party company will run the educational workshop about construction waste management on site. Fit Construction will provide the required separate dumpsters to allow for the appropriate process.
Operational Controls: Selective waste management with the objective of encouraging recycling to the fullest extent.
Responsibilities:
Each subcontractor is responsible for the proper selective collection of their own waste. The Site Superintendent is in charge of supervising the subcontractors waste management outcome. Subcontractors are obligated by contract to perform the required waste sort to the penalty of backcharge.
08/01/2018MCM 901 Page 156 of 224 Master Thesis: 620 N 3rd St Clara Bucar 9.3.2. Waste pollution
Description of the Environmental Aspect & Impact: This hazard concerns pollution on a scale larger then the construction project, but the measures to be taken start on site.
Description of the Environmental Aspect & Impact: As air pollution, noise and vibration are very common construction environmental hazards. Long exposure to loud noise can cause hearing problems to construction workers in the long run. Construction noise and vibration are often motives for community discomfort and consequent disputes.
Documents and Records: All negative occurrences should be informed to the Site Superintendent, who gathers the details and sends the information to the Environmental Engineer The Environmental Engineer then provides the appropriate documentation for Fit Construction’s purposes. 9.3.3. Noise Pollution and Vibration
Monitoring Methods: The Site Superintendent will perform sound intensity measurement as required, as well as the periodic checking of the subcontractor’s equipment maintenance proof.
Monitoring Methods: Selective dumpsters will be verified at the end of each day.
Operational Controls: Considering Northern Liberties as a densely populated residential area, Fit Construction determines that high noise activities will be strictly restricted to business hours, no exceptions. The loudest activities will be mapped and scheduled in advance and the community will be previously communicated of it. Additionally, subcontractors are required to utilize low noise and vibration equipment, which should be properly maintained.
Training Requirements: Fit Construction’s staff and subcontractors will participate on a workshop on site to learn how to properly sort construction waste.
Emergency Response: Not applicable.
Responsibilities: Each subcontractor is responsible for the maintenance of their own equipment.
08/01/2018MCM 901 Page 157 of 224 Master Thesis: 620 N 3rd St Clara Bucar
Operational Controls: All work blockages have to be previously scheduled and a specific permit needs to be issued, allowing the work. In that occasion, Fit Construction will notify the community of the upcoming blockage and, during these activities, a traffic controller will work at the site to help orient the traffic. Additional temporary traffic signage will be placed to provide safe directions.
The Environmental Engineer then provides the appropriate documentation for Fit Construction’s purposes. 9.3.4.Traffic Issues
Emergency Response: If construction activities exceed the maximum allowed for that time and day, the work should be stopped.
Monitoring Methods: The Site Superintendent will coordinate the traffic controller and stay in touch for updates.
List of Resource Requirements: Fit Construction will provide one staff members to control traffic during the hours when road blockage will happen. Additional traffic signage will be provided. Specific permits will be gathered.
Responsibilities:
Description of the Environmental Aspect & Impact:
Training Requirements: No specific training is required.
Training Requirements: No specific training is required.
The main access to the site is the N 3rd St, a local, fairly busy street which provides access to many residential units nearby. Even though material deliveries and waste pick-ups will occur on N Galloway St, it is undeniable that the 620 N 3rd St project will increase vehicle flow and provoke disruptions in the area, especially when the streets will need to be partially or fully blocked for certain construction activities. That scenario will likely cause traffic and disturbance to the nearby community
Emergency Response: Not applicable.
Each subcontractor is responsible for the maintenance of their own equipment. The Site Superintendent is in charge of the environmental risk controls on site full time and has the authority to direct subcontractors and to supervise their equipment and work. The Environmental Engineer performs periodical site visits, provides the main guidelines of what should be done in order to control environmental hazards, collects information from the Site Superintendent, documents and generates reports for improvement of the plans.
The Site Superintendent is in charge of the environmental risk controls on site full time and has the authority to direct subcontractors and to supervise their equipment and work. The Environmental Engineer performs periodical site visits, provides the main guidelines of what should be done in order to control environmental hazards, collects information from the Site Superintendent, documents and generates reports for improvement of the plans.
Documents and Records: All negative occurrences should be informed to the Site Superintendent, who gathers the details and sends the information to the Environmental Engineer
Emergency Response: If the sidewalk presents serious hazards, it should be immediately blocked and urgently repaired. If a pedestrian suffers an accident arisen from unsafe sidewalk conditions, the authorities, Fit Construction insurance and medical assistance should be contacted as Documentsrequired.
The Environmental Engineer then provides the appropriate documentation for Fit Construction’s purposes.
Operational Controls: Additional signage, sheltered walkaway, specific tactile floor as a warning sign for visually disabled people.
Monitoring Methods: The Field Engineer will personally verify sidewalk conditions periodically.
Responsibilities: Fit Construction is responsible for the maintenance of the sidewalks. If a subcontractor is responsible for sidewalk damages, they will be backcharged for the repair but the work will be provided by Fit Construction. The Site Superintendent is in charge of the environmental risk controls on site full time and has the authority to direct subcontractors and to supervise their equipment and work. The Environmental Engineer performs periodical site visits, provides the main guidelines of what should be done in order to control environmental hazards, collects information from the Site Superintendent, documents and generates reports for improvement of the plans.
The Environmental Engineer then provides the appropriate documentation for Fit Construction’s purposes. 9.3.5.
08/01/2018MCM 901 Page 158 of 224 Master Thesis: 620 N 3rd St Clara Bucar
Pedestrian Experience Risk
Documents and Records: All negative occurrences should be informed to the Site Superintendent, who gathers the details and sends the information to the Environmental Engineer
Training Requirements: No specific training is required.
and Records: All negative occurrences should be informed to the Site Superintendent, who gathers the details and sends the information to the Environmental Engineer
Description of the Environmental Aspect & Impact: During the construction project, the sidewalks adjacent to the site on both N 3rd St and N Galloway St will be exposed to damage due to material and equipment transportation, working in the surrounding areas, etc. Additionally, these sidewalks will need to be blocked to allow for specific construction activities, disturbing pedestrian circulation.
List of Resource Requirements: Additional signage, sheltered walkaway, tactile floor.
Section Ten is dedicated to the Site Specific Quality Control and Quality Assurance Plan.
According to ISO-9000, Quality Control relates to the nature of the final product achieved. Quality Assurance, however, relates to the processes which are utilized to orient the final product towards what it should be.
SECTION TEN SITE SPECIFIC QA/QC PLAN
Through the monitoring of the process of planning for these issues, implementing a plan, placing the plan in action and then analyzing the results Fit Construction is able to provide valuable insight for the next projects, accumulating experience exponentially.
08/01/2018MCM 901 Page 159 of 224 Master Thesis: 620 N 3rd St Clara Bucar
The QA/QC plan lists the 620 N 3rd St main specs and their specific requirements, actions, rating and environmental controls. Then, the top five quality risks are deeper demonstrated. The standards for the description of each of the five risks are: the description of the issue, their operational controls, the list of the required resources, the monitoring methods, the responsibility ownership, the training requirements and the documentation process.
08/01/2018MCM 901 Page 160 of 224 Master Thesis: 620 N 3rd St Clara Bucar 10.1. Site Specific Quality Management System
This Quality’s Plan main goal is to plan and prepare for the upcoming work by providing further clarification and direction on specific work packages. Fit Construction utilizes the ISO 9001 approach of Plan - Do - Check - Act - Revise to provide continuous learning and increasing efficiency in our risk predictions. The data utilized to develop this Quality Plan was achieved partially by the specific conditions of the 620 N 3rd St project, by Fit Construction’s database and by our staff’s skills and experience. By adopting this strategy, we believe to be working with the best possible available information.
The 620 N 3rd St Quality Plan dedicates to provide a comprehensive list of quality requirements included in the construction documents and other information derived from these, summarized in accordance with their respective CSI divisions and main action required. The five top quality risks identified in this first analysis are then described under their resource requirements, operational controls, monitoring methods, specific responsibilities, training requirements and documentation.
As mentioned, Quality Control and Quality Assurance are not the same, but are rather complementary approaches regarding quality. In construction, large amounts of resources are wasted on rework caused by ineffective quality assurance methods.
5. DeckComposite Comply with latest editions of Steel Deck Institute "Design Manual for Floor Decks and Roof Decks" and American Iron and Steel Institute "Specification for the Design of Cold Formed Steel Structural Members" Report M
5. Cold Form Steel Framing Comply with latest edition of American Iron and Steel Institute "Specification for the Design of Cold Formed Steel Structural Members" Report H
23. Mechanical
6. FramingWood Comply with 2009 IBC Chapter 23 or National Design Specification for Wood Construction (NDS), latest edition Report H
26. Electrical
QA: Subcontractors are contractually obligated to submit documentation atesting all work is in compliance with requirements. QC: Superintendent on site will inspect work.
22. Plumbing
QA: Subcontractors are contractually obligated to submit documentation atesting all work is in compliance with requirements. QC: Superintendent on site will inspect work. deternmined standard proctor test ASTM D698 Inspection M
QA: Subcontractors are contractually obligated to submit documentation atesting all work is in compliance with requirements. QC: Superintendent on site will inspect work.
All construction work shall be performed in accordance with the state construction code and other national and state codes, including the "National Fire Protection Association" (NFPA) Report H
All construction work shall be performed in accordance with the state construction code and other national and state codes, including the 2011 "National Electric Code" (NEC) Report M
QA: Subcontractors shall submit shop drawings to Designers for approval. QC: Superintendent on site will inspect work.
QA: Subcontractors are contractually obligated to submit documentation atesting all work is in compliance with requirements. Subcontractors shall submit shop drawings to Designers for approval. QC: Superintendent on site will inspect work.
QA: Subcontractors are contractually obligated to submit documentation atesting all work is in compliance with requirements. QC: Superintendent on site will inspect work.
Comply with latest edtitions of American Concrete Institute ACI 530 "Building Code Requirements for Masonry Structures" and ACI 530.1 "Specifications for Masonry Structures" Report L
QA: Subcontractors are contractually obligated to submit documentation atesting all work is in compliance with requirements. QC: Superintendent on site will inspect work. Masonry
QA: Subcontractors are contractually obligated to submit documentation atesting all work is in compliance with requirements. Subcontractors shall submit shop drawings to Designers for approval. QC: Superintendent on site will inspect work.
QA: Subcontractors are contractually obligated to submit documentation atesting all work is in compliance with requirements. QC: Superintendent on site will inspect work.
QA: Subcontractors are contractually obligated to submit documentation atesting all work is in compliance with requirements. Subcontractors shall submit shop drawings to Designers for approval. QC: Superintendent on site will inspect work.
by
3. (Foundations)Concrete Compact to 95% maximum dry density as
5. Steel Comply with latest editions of American Institute of Steel Construction "AISC Specification for the Design, Fabrication and Erection of Structural Steel for Buildings" and "AISC Code of Standard Practice" Report H
4.
QA: Subcontractors are contractually obligated to submit documentation atesting all work is in compliance with requirements. QC: Superintendent on site will inspect work.
8.1. Doors Provide doors that comply with AWI tolerance requirements for hinge, hardware and frame openings Submittal L
8.1. Doors
QA: Subcontractors are contractually obligated to submit documentation atesting all work is in compliance with requirements. Subcontractors shall submit shop drawings to Designers for approval. QC: Superintendent on site will inspect work.
Comply with latest editions of American Concrete Institute ACI 301 'Specification for Structural Concrete for Buildings", ACI 318 "Building Code Requirements for Structural Concrete", ACI 305 "Hot Weather Concreting" and ACI 306 "Cold Weather Concreting" Report H
All construction work shall be performed in accordance with the state construction code and other national and state codes, including the "National Fire Protection Association" (NFPA) Report H
Solid-core finish grade flush wood doors shall comply with NWWDA Industry Standard for Flush wood doors Submittal L
3. Concrete
QA: Subcontractors shall submit shop drawings to Designers for approval. QC: Superintendent on site will inspect work.
08/01/2018MCM 901 Page 161 of 224 Master Thesis: 620 N 3rd St Clara Bucar 10.2. Contract Quality Requirements Spec Section / Paragraph QA / QC Requirement Action Description Quality Risk Rating (H,M,L) QA / QC Controls 3. (Foundations)Concrete Backfill excavations and areas requiring structural fill with clean ML or better borrow per ASTM D2487 Inspection M
QA: Subcontractors shall submit shop drawings to Designers for approval. QC: Superintendent on site will inspect work.
11. Equipment Energy rating: Provide Energy Guide labels with energy cost analysis and efficiency information as required by the Federal Trade Commission. -UL Standards: Provide Residential Equipment with AUL Labels. Submittal M QA: Subcontractors are contractually obligated to submit documentation atesting all work is in compliance with requirements. QC: Superintendent on site will inspect work.
QA: Subcontractors shall submit shop drawings to Designers for approval. QC: Superintendent on site will inspect work.
9.3. Painting A level 5 paint finish shall be provided as described by the Drywall Finishing Council, Inc Inspection L QA: Subcontractors are contractually obligated to comply with requirements. QC: Superintendent on site will inspect work.
9.1. AssembliesBoardGypsum Install steel framing members to comply with ASTM C754 and C645 requirements that apply to framing installation. Install as recommended in the Gypsum Construction Handbook published by USG. Submittal M QA: Subcontractors shall submit shop drawings to Designers for approval. QC: Superintendent on site will inspect work.
8.2. Glass and Glazing
9.1. AssembliesBoardGypsum Gypsum wallboard shall be finished with a Level 5 finish as described by the Gypsum Association, AWCI, Painting and Decorating Contractors of America, and CISCA's recommendation GA-214-96 Inspection L QA: Subcontractors are contractually obligated to comply with requirements. QC: Superintendent on site will inspect work.
Where safety glass in required, provide tempered glass cerified by the Safety Glazing Certification Council (SCCC) Submittal L
08/01/2018MCM 901 Page 162 of 224 Master Thesis: 620 N 3rd St Clara Bucar Spec Section / Paragraph QA / QC Requirement Action Description Quality Risk Rating (H,M,L) QA / QC Controls
8.2. Glass and Glazing Comply with the recommendations of the Flat Glass Marketing Association (FGMA)Glazing Manual and Sealant Manual except where more stringent requirements are indicated. Submittal L
QA: Subcontractors shall submit shop drawings to Designers for approval. QC: Superintendent on site will inspect work.
8.1. Doors Where fire-rated door assemblies are required, provide fire-rated door and frame assemblies that comply with NFPA80 Standard for Fire Doors and Windows and have been tested, listed and labeled in accordance with ASTME 152 Standard Methods of Fire Testes of Door Assemblies. Submittal M
08/01/2018MCM 901 Page 163 of 224 Master Thesis: 620 N 3rd St Clara Bucar 10.3. Management Plans for the ‘Top Five’ Quality Issues
Training Requirements: Subcontractors are specialists, no training required. Specific past experience is required and verified during prequalification.
Operational Controls: Subcontractors to submit legally binding report of how the work to be performed in is compliance with requirements. The “AISC Specification for the Design, Fabrication and Erection of Structural Steel for Buildings” confirms that, while the publication is accurate, specifications and approval from the responsible licensed professional is imperative.
Operational Controls: Subcontractors to submit legally binding report of how the work to be performed in is compliance with requirements. The ACI 301 Standard doesn’t include specific required strength of concrete and types and grades of reinforcing steel and other supplemental requirements, to be defined by Designer. For hot weather and cold weather concreting, per ACI 305 and ACI 306, subcontractors are required to submit production procedures for the Designer’s approval previously to the start of the work.
Responsibilities: Subcontractors are contractually obligated to perform work per the drawings and specs, to the penalty of backcharge, and to provide related warranty.
10.3.1. Concrete
Documents and Records: Quality Engineer to develop report on work completed, document it to Fit Construction’s records and continual learning process. These records will contribute to shape better quality solutions and to evaluate subcontractor’s performance, influencing future bids. 10.3.2. Steel Description of the QA / QC Issue: Structural steel must comply with latest editions of American Institute of Steel Construction “AISC Specification for the Design, Fabrication and Erection of Structural Steel for Buildings” and “AISC Code of Standard Practice”.
Description of the QA / QC Issue: Concrete work must comply with latest editions of American Concrete Institute ACI 301 ‘Specification for Structural Concrete for Buildings”, ACI 318 “Building Code Requirements for Structural Concrete”, ACI 305 “Hot Weather Concreting” and ACI 306 “Cold Weather Concreting”.
List of Resource Requirements: Designers to include in specs the required strength of concrete and types and grades of reinforcing steel (ACI 301) and revise subcontractor ’s shop drawings.
Monitoring Methods: Quality Engineer and Site Superintendent to perform inspections of work completed. Fit Construction to perform additional revising of shop drawings.
List of Resource Requirements: Designers to include in specs all required information on structural work to be performed and responsibly revise and approve shop drawings. Subcontractors to submit shop drawings. Fit Construction to perform additional revising of shop drawings.
Responsibilities: Subcontractors are contractually obligated to perform work per the drawings and specs, to the penalty of backcharge, and to provide related warranty.
Training Requirements: Subcontractors are specialists, no training required. Specific past experience is required and verified during prequalification.
08/01/2018MCM 901 Page 164 of 224 Master Thesis: 620 N 3rd St Clara Bucar
Training Requirements: Subcontractors are specialists, no training required. Specific past experience is required and verified during prequalification.
Responsibilities: Subcontractors are contractually obligated to perform work per the drawings and specs, to the penalty of backcharge, and to provide related warranty.
Documents and Records: Quality Engineer to develop report on work completed, document it to Fit Construction’s records and continual learning process. These records will contribute to shape better quality solutions and to evaluate subcontractor’s performance, influencing future bids.
Description of the QA / QC Issue: Wood framing must comply with 2009 IBC Chapter 23 or National Design Specification for Wood Construction (NDS), latest edition.
Monitoring Methods: Quality Engineer and Site Superintendent to perform inspections of work completed. Fit Construction to perform additional revising of shop drawings.
Operational Controls: According to NFPA, the state of Pennsylvania requires compliance with the International Mechanical Code (IMC), the International Building Code (IBC) and the
10.3.4. Plumbing
Monitoring Methods: Quality Engineer and Site Superintendent to perform inspections of work completed. Fit Construction to perform additional revising of shop drawings.
10.3.3. Wood Framing
Documents and Records: Quality Engineer to develop report on work completed, document it to Fit Construction’s records and continual learning process. These records will contribute to shape better quality solutions and to evaluate subcontractor’s performance, influencing future bids.
List of Resource Requirements: Subcontractor to provide shop drawings and report in accordance with 2009 IBC Chapter 23, Designer to review and approve. Fit Construction to perform additional revising of shop drawings.
Description of the QA / QC Issue: Plumbing work shall be performed in accordance with the state construction code and other national and state codes, including the “National Fire Protection Association” (NFPA).
Operational Controls: Designer to develop wood framing design in accordance to National Design Specification for Wood Construction (NDS), under penalty of professional liability. Subcontractors to submit legally binding report of how the work to be performed in is compliance with the requirements included in 2009 IBC Chapter 23.
List of Resource Requirements: Designer to submit construction drawings in compliance with the above mentioned requirements, subcontractors to provide shop drawings and Designer to approve them. Fit Construction to perform additional revising of shop drawings.
Documents and Records: Quality Engineer to develop report on work completed, document it to Fit Construction’s records and continual learning process. These records will contribute to shape better quality solutions and to evaluate subcontractor’s performance, influencing future bids.
List of Resource Requirements: Designer to submit construction drawings in compliance with the above mentioned requirements, subcontractors to provide shop drawings and Designer to approve them. Fit Construction to perform additional revising of shop drawings.
Documents and Records: Documents and Records: Quality Engineer to develop report on work completed, document it to Fit Construction’s records and continual learning process. These records will contribute to shape better quality solutions and to evaluate subcontractor ’s performance, influencing future bids.
Training Requirements: Subcontractors are specialists, no training required. Specific past experience is required and verified during prequalification.
10.3.5. Mechanical Description of the QA / QC Issue: Mechanical work shall be performed in accordance with the state construction code and other national and state codes, including the “National Fire Protection Association” (NFPA).
Responsibilities: Subcontractors are contractually obligated to perform work per the drawings and specs, to the penalty of backcharge, and to provide related warranty.
Training Requirements: Subcontractors are specialists, no training required. Specific past experience is required and verified during prequalification.
Operational Controls: According to NFPA, the state of Pennsylvania requires compliance with the International Mechanical Code (IMC), the International Building Code (IBC) and the International Fuel Gas Code (IFGC), all provided by the International Code Council (ICC), in addition of the local codes. Subcontractors to submit legally binding report of how the work to be performed in is compliance with requirements.
Monitoring Methods: Quality Engineer and Site Superintendent to perform inspections of work completed. Fit Construction to perform additional revising of shop drawings.
08/01/2018MCM 901 Page 165 of 224 Master Thesis: 620 N 3rd St Clara Bucar International Fuel Gas Code (IFGC), all provided by the International Code Council (ICC), in addition of the local codes. Subcontractors to submit legally binding report of how the work to be performed in is compliance with requirements.
Monitoring Methods: Quality Engineer and Site Superintendent to perform inspections of work completed. Fit Construction to perform additional revising of shop drawings.
Responsibilities:
Subcontractors are contractually obligated to perform work per the drawings and specs, to the penalty of backcharge, and to provide related warranty.
Section Eleven’s objective is to provide PRDC with an insight on how and what can be achieve through a LEED Silver certification. It consists of the LEED scorecard with the options considered by Fit Construction. For each of these options, there is a written description of the minimum requirements and the project specific solutions suggested to 620 N 3rd St. The information under this section correlates with the LEED estimate option shown in Section Four for a better holistic understanding of the pros and cons of pursuing a LEED Silver certification.
08/01/2018MCM 901 Page 166 of 224 Master Thesis: 620 N 3rd St Clara Bucar SECTIONLEEDELEVEN
• Access to Quality Transit (5 points): This items refers to the accessibility to multi-modal transportation options from the site, especially those that are non motorized. Being close to Center City, Northern Liberties has abundant access to public transportation, including buses and subway. In addition, it offers bike lanes and mostly decent sidewalks for those who prefer to walk or bike to and from work.
11.1.3. Water Efficiency
• Bicycle Facilities (1 point): The original project already includes a storage space on the basement, ideal to store bicycles. Every residential unit has it’s own storage and inside of it both residents’ and visitors’ bikes can be stored. In addition to that, Philadelphia’s shared bicycle system has several stations located close by to the 620 N 3rd St site.
11.1.2. Sustainable Sites
• Rainwater Management (3 points): This item refers to the commitment of replicating the natural site hydrology process by managing at least 95% of the rainfall poured on the site by using green infrastructure or low impact development. We will address this item by implementing rainwater harvesting, which will consist of a cistern located in the basement that’s used to captured rain water to be later used for gardening purposes. In addition, we will utilize downspout disconnections, which basically consists of a downspout on the building facade that connects the stormwater pipe coming from the roof and flows the water adjacently to a street gutter, where the water can then directly drain into the main stormwater system without running off the streets and collecting pollution. This will only occur on the N Galloway St facade and if approved by the Building Department.
• Surrounding Density and Diverse Uses (5 points): This item refers to the residential and nonresidential separate or combined density values regarding the one quarter of a mile radius concerning the site. Northern Liberties is a highly dense neighborhood with a strong commercial scene, which guarantees that people can move less and utilizing non-motorized means to get to places.
11.1.1. Location and Transportation
• Reduced Parking Footprint (1 point): This item consists of not exceeding the minimum local code requirements for parking capacity. Despite of the fact that the 620 N 3rd St has nine parking spaces on the first floor, these slots do not belong to the home owners automatically. Rather, they can be purchased additionally to the homes, which indicates that parking is not offered as included with the residential units.
• Outdoor Water Use Reduction ((2 points): This item concerns the reduction or elimination of the necessity for irrigation in outdoor facilities such as planters and lawns. In the 620 N 3Rd
08/01/2018MCM 901 Page 167 of 224 Master Thesis: 620 N 3rd St Clara Bucar 11.1. Minimum Program Requirements (MPRs)
• Indoor Water Use Reduction (6 points): This item concerns the reduction of the indoor water consumption. To address this, we have specified high efficiency plumbing fixtures in accordance with the LEED requirement, which can be seen in full in the Appendix of this manual. As an example, we are specifying toilets (water closets) with a maximum of 6 liters per flush and shower heads that use 9.5 liters per minute. See specs in the Appendix.
08/01/2018MCM 901 Page 168 of 224 Master Thesis: 620 N 3rd St Clara Bucar St project, the water utilized to irrigate the planters will be provided by the cistern filled with rainwater, demonstrated under “Rainwater Management” above. Philadelphia is a location where rain is abundant all throughout the year, making this plan actually feasible. In addition to that, highly resilient, low water necessity plants will be placed in the planters in order to assure the cistern will supply enough water for this use. The goal is to eliminate the need for an irrigation system that is connected to the main water supply lines.
• Enhanced Commissioning (6 points): This item addresses the requirement for a specialized commissioning party which could be an independent consultant, an employee of the owner or a subcontractor. This entity has to have proved experience in commissioning buildings of the same type. The enhanced commissioning consists of 1) reviewing contractor’s submittals; 2) verifying if construction documents have manual requirements and their respective updates and delivery; 3) verifying if construction documents have operator and occupant training guidelines, as well as their effectiveness; 4) verifying periodic testing; 5) reviewing buildings operations after ten months of turnover; 6) establishing a continuous commissioning plan to assure the system’s best performance throughout the time. Fit Construction will hire a specialized third party company to perform these services.
• Optimize Energy Performance (10 points): This item addresses the reduction of energy consumption, beyond the minimum ASHRAE standard requirements, to try to minimize the environmental impact imposed by energy production. We will address this item by adopting several different approaches. Energy Star appliances will be furnished by the Owner. The electrical and mechanical devices such as the Air Handling Units, chillers and water heaters will be highly energy efficient, which, in addition to the Enhanced Commissioning, will provide an optimized system. The building itself will exceed the minimum requirements of insulation, including SunGuard Advanced Architectural Glass glazing, compliant with ASHRAE Advanced Energy Design Guide, ANSI and IESNA standards, reducing the necessity for artificial heating and cooling. Daylighting strategies and high efficiency artificial lighting will be further described under the “Indoor Environmental Quality” section. Please see specs on this manual’s Appendix.
11.1.5. Materials and Resources • Building Product Disclosure and Optimization - Sourcing of Raw Materials (2 points): This item concerns the rewarding of the choice for raw materials due to the fact that their life cycles are limited and recognizable. In the 620 N 3rd St project, the entire upper structure and interior
11.1.4. Energy and Atmosphere
11.1.7. Innovation • Brownfield redevelopment (5 points): The innovation subsection regards items that are not listed on the scorecard but are related to sustainability. The 620 N 3rd St site, previously a part of an industrious facility which left the soil contaminated, is now redeveloped into housing and returned to community usage.
• LEED Accredited Professional: All of Fit Construction’s Project Managers are LEED AP.
• Acoustic Performance (1 point): This item has the goal to ensure comfort through acoustic performance, using as a minimum standard the ASHARAE 2011 Applications Handbook. In the 620 N 3rd St project, all walls between units are acoustically insulated, as well as the floors. The floors also received sound reduction mat layers, in order to minimize sound and vibration travel between residential units.
620 N 3rd St Clara Bucar
• Construction and Demolition Waste Management (2 points): This item regards the reduction of construction waste, as well as the recycling of that waste. We will address this item by diverting at least 75% of the total construction waste and separating this waste into at least four material categories and send it to recycling. A third party, specialized company will be subcontracted to perform this work. In addition to the recycling, LEAN methods will be incorporated to the construction practices at the 620 N 3rd St to reduce the amount of produced waste overall.
• Daylight (2 points): This item regards both human comfort and energy efficiency by the utilization of daylighting to promote biophilia by connecting the occupant with the exterior, while reducing the need for electricity to light the interior of the building. Daylighting efficiency was thought throughout the design process and was addressed from the beginning by the presence of large windows on all high occupancy rooms in the building. In addition to that, the glass specified (see specs in Appendix) offers high visual transmittance while still providing efficient insulation.
11.1.6. Indoor Environmental Quality • Interior Lighting (2 points): This item addresses the use of artificial lighting to promote human comfort for occupants, while still achieving low energy consumption in order to do so. For that, we will utilize only LED, high efficiency lighting with a luminance of less than 2,500cd/m2 distributed between different work planes such as the ceiling and walls. Specs for these lighting fixtures and bulbs are attached on the Appendix of this manual.
framing is primarily wood and wood based. To achieve this requirement, we will purchase the materials from five different accredited manufacturers who have released verified Corporate Sustainability Reports (CSRs) regarding their raw material supply and production. These manufacturers are also directly responsible for replenishing the resources utilized for their production. Lastly, all wood materials must be certified by the Forest Stewardship Council.
08/01/2018MCM 901 Page 169 of 224 Master Thesis:
08/01/2018MCM 901 Page 170 of 224 Master Thesis: 620 N 3rd St Clara Bucar LEED v4 for BD+C: New Construction and Major Renovation Project Checklist Project Name: 620 N 3rd St Date: Augus 1st 2018 Y?N Credit 1 1200 16400 13 Credit 16 Y Prereq Required Credit 1Y Prereq Required Credit 2 Credit 5 5 Credit 5 Credit 2 5 Credit 52 Credit 2 1 Credit 1 Credit Building Product Disclosure and Optimization - Material Ingredients 2 1 Credit 12 Credit 2 Credit Green Vehicles 1 600Indoor Environmental Quality 16 300 10 Y Prereq Required Y Prereq RequiredY Prereq Required Credit 1 Credit 2 Credit 2 Credit 3 Credit 1 Credit Construction Indoor Air Quality Management Plan 1 3 Credit 3 Credit 2 Credit 2 Credit 1 Credit 12 Credit 2 3 Credit 3 800 11 Credit 1 Y Prereq Required1 Credit 1 Y Prereq Required Y Prereq Building-Level Water Metering Required 600Innovation 6 2 Credit 25 Credit 5 6 Credit 61 Credit 1 Credit 2 Credit Water Metering 1 000Regional Priority 4 Credit Regional Priority: Specific Credit 1 1600 33 Credit Regional Priority: Specific Credit 1 Y Prereq Required Credit Regional Priority: Specific Credit 1 Y Prereq Required Credit Regional Priority: Specific Credit 1 Y Prereq Required Y Prereq Required 55 0 0 TOTALS Possible Points: 110 6 Credit 6 10 Credit 18 Credit 1 Credit 2 Credit 3 Credit 1 Credit 2 Acoustic Performance Quality EnhancedViewsIndoor Air Quality Strategies Low-Emitting Materials Indoor Air Quality Assessment Thermal Comfort Certified: 40 to 49 points, Silver: 50 to 59 points, Gold: 60 to 79 points, Platinum: 80 to 110 Access to Quality Transit Reduced Parking Footprint Open Space Site Assessment Interior LEEDDaylightLightingAccredited Professional Brownfield redevelopment Rainwater Management Light Pollution Reduction Environmental Tobacco Smoke Control Energy and Atmosphere Minimum Energy Performance Fundamental Refrigerant Management Cooling Tower Water Use Green Power and Carbon Offsets Heat Island Reduction Outdoor Water Use Reduction Indoor Water Use Reduction Outdoor Water Use Reduction Indoor Water Use Reduction Enhanced Building-LevelCommissioningEnergyMetering Water Efficiency Fundamental Commissioning and Verification Demand RenewableResponseEnergy Production Enhanced Refrigerant Management Optimize Energy Performance Advanced Energy Metering Construction Activity Pollution Prevention High Priority Site Surrounding Density and Diverse Uses Sustainable Sites Building Life-Cycle Impact Reduction Site Development - Protect or Restore Habitat Building Product Disclosure and Optimization - Sourcing of Raw Materials Location and Transportation Sensitive Land Protection LEED for Neighborhood Development Location Bicycle Facilities Construction and Demolition Waste Management Planning Materials and Resources Storage and Collection of Recyclables Construction and Demolition Waste Management Minimum Indoor Air Quality Performance Building Product Disclosure and Optimization - Environmental Product Declarations Integrative Process 11.2. LEED v4 Scorecard

Heating, cooling, lighting: design methods for architects (3th ed.). Hoboken, NJ: John Wiley & Sons. Occupational Safety and Health Administration [OSHA]. (August 1994a). Safety and Health Regulations for Construction: Excavations. Retrieved June 12, 2018, Occupationalid=10778https://www.osha.gov/pls/oshaweb/owadisp.show_document?p_table=STANDARDS&p_fromSafetyandHealthAdministration[OSHA].(August1994b). Safety and Health Regulations for Construction: Concrete and Masonry Construction Retrieved June 12, 2018, Occupationalid=10778https://www.osha.gov/pls/oshaweb/owadisp.show_document?p_table=STANDARDS&p_fromSafetyandHealthAdministration[OSHA].(June2011). Occupational Safety and Health Standards: Personal Protective Equipment. Retrieved June 12, 2018, id=12716https://www.osha.gov/pls/oshaweb/owadisp.show_document?p_table=STANDARDS&p_from
Retrieved July 15, 2018, from https://inhabitat.com/lets-talk-about-insulation-baby/ Gould, F. E. (2011). Managing the construction process: estimating, scheduling, and project control (4th ed.). Upper Saddle River, NJ: Prentice Hall. Halpin, D. W., & Senior, B. A. (2009). Financial management and accounting fundamentals for construction. Hoboken, NJ: John Wiley & Sons. ISO 9000 family – Quality management. (n.d.). Retrieved July 21, 2018, from https://www.iso.org/iso-9001-quality-management.html.
08/01/2018MCM 901 Page 171 of 224 Master Thesis: 620 N 3rd St Clara Bucar REFERENCES
Ab Rahman, N. N. N., & Esa, N. (2014). Managing Construction Development Risks to the Environment. In Sustainable Living with Environmental Risks (pp. 193-202). Springer, Tokyo. Bill No. 050749. (2006). Retrieved June 11, 2018, Fehrenbacher,https://www.phila.gov/health/pdfs/air/Noise_Bill_050749.pdffromJ.(2006).
MasterFormat Numbers & Titles. (April 2016). Retrieved June 13, 2018, from Norbert,https://www.edmca.com/media/35207/masterformat-2016.pdfL.,&Heating,C.(2008).
New ideas for green insulation.
Estimating in building construction (8th ed.). London, UK: Pearson. Pieplow, B. (June 2012). Project Risk Management Handbook: A Scalable Approach. Risk. Quality Management Principles. (2015). Retrieved July 19, 2018, Stromme,https://www.iso.org/files/live/sites/isoorg/files/archive/pdf/en/pub100080.pdffromM.H.(2010).ClearingUptheConfusionSurroundingFallProtection.RetrievedJune10,2018,fromhttps://www.ehstoday.com/construction/news/clearing-confusion-surrounding-fall-protection-0510
UltraTouch Denim Insulation. (n.d.). Retrieved July 10, 2018, from http://www.bondedlogic.com/ultratouch-denim-insulation/ United States Environmental Protection Agency [EPA]. (n.d.). Stormwater Management and Green Infrastructure Research. Retrieved July 12, 2018, https://www.epa.gov/water-research/stormwater-management-and-green-infrastructure-from research U.S. Green Building Council [USGBC]. (January 2017). LEED v4 for BUILDING DESIGN AND CONSTRUCTION. Retrieved July 20, 2018, from Waier,LEEDv4forBuildingDesignandConstructionBallotVersion.pdfhttp://greenguard.org/uploads/images/P.R.(September2011).
08/01/2018MCM 901 Page 172 of 224 Master Thesis: 620 N 3rd St Clara Bucar Perritano, J. (n.d.). Top 5 Green Insulation Options. Retrieved July 10, 2018,
RSMeans: Building Construction Cost Data 2012 (70th ed.). Norwell, MA: RSMeans. American Concrete Institute [OCI]. (March 2007). Specification for Hot Weather Concreting: An ACI Standard. Retrived July 29th, 2018, Americanfor%20Hot%20Weather%20Cncreting.pdfhttp://www.arquitectosrp.com/archivo/download/ACI%20305.1-06%20Specification%20fromInstituteofSteelConstruction[AISC].(July2016). Specification for Structural Steel Buildings. Retrieved July, 2018, commentary.pdfhttps://www.aisc.org/globalassets/aisc/publications/standards/a360-16-spec-and-from
Peterson,insulation-options6.htmhttps://home.howstuffworks.com/home-improvement/construction/green/5-green-fromS.,&Dagostino,F.R.(2015).
08/01/2018MCM 901 Page 173 of 224 Master Thesis: 620 N 3rd St Clara Bucar APPENDIX A. Original Drawings and Specifications Key Plans - Page 175 Second Floor Plan - Page 176 Front and Rear Elevations - Page 177 Building Sections - Page 178 Typical Assemblies - Page 179 APPENDIX B. Management Means and Methods Referenced Documents and Forms Punchlist - Page 180 Transmittal - Page 181 RFI - Request for Information - Page 182 T&B - Test and Balance Report (Commissioning) - Pages 183 to 185 APPENDIX C. LEED v4 - Requirements and Specs Scorecard requirements: Acoustic Performance - Page 186 Scorecard requirements: Daylight - Page 187 Scorecard requirements: Interior Lighting - Pages 188 to 189 Scorecard requirements: Building Product Disclosure and OptimizationSourcing of Raw Materials - Page 190 Scorecard requirements: Optimize Energy Performance - Pages 191 to 192 Scorecard requirements: Enhanced Commissioning - Page 193 Scorecard requirements: Indoor Water Use Reduction - Page 194 Scorecard requirements: Outdoor Water Use Reduction - Page 195 Scorecard requirements: Rainwater Management - Page 196 Scorecard requirements: Bicycle Facilities - Page 197 Scorecard requirements: Reduced Parking Footprint - Page 198 Scorecard requirements: Access to Quality Transit - Page 199 TABLEAPPENDIXOFCONTENTS
08/01/2018MCM 901 Page 174 of 224 Master Thesis: 620 N 3rd St Clara Bucar Scorecard requirements: Surrounding Density and Diverse Uses - Page 200 Recycled Cotton Insulation Spec Sheet: Bonded’s Logic’s UltraTouch - Pages 201 to 202 LED Lighting Spec Sheets - Pages 203 to 207 Plumbing Fixture Spec Sheets - Pages 208 to 211 Energy Efficient Device Spec Sheets - Pages 212 to 213 Glass Selection Spec Sheet - Pages 214 to 215 APPENDIX D. Agreement and Contracts AIA A134 - 2009 Standard Form of Agreement Between Owner and Construction Manager as Constructor where the basis of the payment if the Cost of the Work Plus a Fee without a Guaranteed Maximum Price - Page 216 AIA A401 - 2007 Standard Form of Agreement Between Contractor and Subcontractor - Pages 217 to 221 AIA A201 - 2007 General Conditions of the Contract for Construction - Pages 222 to 224
08/01/2018MCM 901 Page 175 of 224 Master Thesis: 620 N 3rd St Clara Bucar APPENDIX A: Key Plans rium D e s g n G o u p C 215-768-8225 T 215-923-1028 F 215-923-1029 0 N 3 d S e 2 P A 9 3 A m D e g G u p c m DATE ISSUE STREET3RDN620 19123PAPHILADELPHIA, PROPERTIESPRDC 19106PAPhiladelphia,501,SuiteStreet,Sansom740 T 267-519-3652 E david@prdcproperties.com OWNER: SOSOCSOOSGSHTDRAWNNTBEAEDFRDMENN OOOGSHTDRAWNANDALLNFRMATNCNTANEDHERENS OOOOOOHTUARZEDFRUSENLYBYTHEPARTYFRWHMTHEWRKWAS OOOCNTRACTEDTHISDRAWNGMAYNTBECPIEDREUSED OOOOOOSDTRBUTEDRRELEDUPNFRANYTHERPURPSEWTHUTTHE OOOCNETTRWNSENTFATRUMDESGNGRUPLLC SSGRLLAHTREERVED F m e n s e N A X PLANSKEY SCALE: BASEMENT3/32"=1'PLAN1 SCALE: 3/32"=1' FIRST FLOOR PLAN2 SCALE: 3/32"=1' SECOND FLOOR PLAN3 SCALE: 3/32"=1' PILOT HOUSE PLAN6SCALE: 3/32"=1' FOURTH FLOOR PLAN5 SCALE: 3/32"=1' THIRD FLOOR PLAN4 A0.010.16.15BLDGPERMIT01.13.1680%CD
08/01/2018MCM 901 Page 176 of 224 Master Thesis: 620 N 3rd St Clara Bucar APPENDIX A: Second Floor Plan rium D e s g n G o u p C 215-923-1029215-923-1028215-768-8225 2 d S S e 2 1 P P 9 3 A u m D e g G u p c o m DATE ISSUE STREET3RDN620 19123PAPHILADELPHIA, PROPERTIESPRDC 19106PAPhiladelphia,501,SuiteStreet,Sansom740 T 267-519-3652 E david@prdcproperties.com OWNER: SOSOCSOOSGSHDRAWNNTBEALEDFRDMENN OOOGSHTDRAWNANDALLNFRMATINCNTANEDHERENS OOOOOOHTUARZEDFRUSENLYBYTHEPARTYFRWHMTHEWRKWAS OOOCNTRACTEDTHSDRAWNGMAYNTBECPEDREUSED OOOOOOSDTRBUTEDRRELEDUPNFRANYTHERPURPSEWTHUTTHE OOOCNETTRWNSENTFATRUMDESGNGRUPLLC SSGRLLAHTREERVED F m c e n s e N A PLANFLOORSECONDSCALE: 1/4"=1' SECOND FLOOR PLAN1 A1.2 1 10.16.15 BLDG PERMIT 01.13.16 80% CD
08/01/2018MCM 901 Page 177 of 224 Master Thesis: 620 N 3rd St Clara Bucar APPENDIX A: Front and Rear Elevations rium D e s g n G o u p C 215-923-1029215-923-1028215-768-8225 2 N d S 2 h A 1 3 A u m D e g G o u p c o m DATE ISSUE STREET3RDN620 19123PAPHILADELPHIA, PROPERTIESPRDC 19106PAPhiladelphia,501,SuiteStreet,Sansom740 T 267-519-3652 E david@prdcproperties.com OWNER: OOOOOOSUUUSU OOOCNETTRWNSENTFATRUMDESGNGRUPLLC SSG F m L c e n s e N A X ELEVATIONSREARANDFRONTSCALE: 1/4"=1' N. 3RD ST (FRONT) ELEVATION1 SCALE: 1/4"=1' GALLOWAY ST. (REAR) ELEVATION2 A2.1 1 10.16.15 BLDG PERMIT 2 01.13.16 80% CD
08/01/2018MCM 901 Page 178 of 224 Master Thesis: 620 N 3rd St Clara Bucar APPENDIX A: Building Sections rium D e s g n G o u p C 215-923-1029215-923-1028215-768-8225 2 N 3 S e 1 Ph A 9 2 A m D e g n G o p c o m DATE ISSUE STREET3RDN620 19123PAPHILADELPHIA, PROPERTIESPRDC 19106PAPhiladelphia,501,SuiteStreet,Sansom740 T 267-519-3652 E david@prdcproperties.com OWNER: SOSOCSOOSGSHTDRAWNNTBEALEDFRDMENN OOOGSHTDRAWNANDALLNFRMATNCNTANEDHERENS OOOOOOHTUARZEDFRUSENLYBYTHEPARTYFRWHMTHEWRKWAS OOOCNTRACTEDTHSDRAWNGMAYNTBECPEDREUSED OOOOOOSDTRIBUTEDRRELEDUPNFRANYTHERPURPSEWTHUTTHE OOOCNETTRWNSENTFATRUMDESIGNGRUPLLC SSGRLLAHTREERVED F m L c e n s e N o A X 1 1 4 0 SECTIONSBUILDINGSCALE: 1/4"=1' NORTH FACING SECTION5 A3.4 1 01.13.16 80% CD
08/01/2018MCM 901 Page 179 of 224 Master Thesis: 620 N 3rd St Clara Bucar APPENDIX A: Typical Assemblies rium D e s g n G o u p C 215-923-1029215-923-1028215-768-8225 2 d S 2 h A 3 A u m D e g G o u p c o m DATE ISSUE STREET3RDN620 19123PAPHILADELPHIA, PROPERTIESPRDC 19106PAPhiladelphia,501,SuiteStreet,Sansom740 T 267-519-3652 E david@prdcproperties.com OWNER: OOOOOOSUUUSU OOOCNETTRWNSENTFATRUMDESGNGRUPLLC SSG F m L c e n s e N A X ASSEMBLIESTYPICAL A5.10110.16.15BLDGPERMIT201.13.1680%CD
08/01/2018MCM 901 Page 180 of 224 Master Thesis: 620 N 3rd St Clara Bucar Punchlist - Sign-off Sheet Project Information Project Resources Schedule Information Project Name ON.5309.VILLAGECOLON.MINS.2018 Senior PM Anabell Felix Construction Start 22-Apr-18 REPS Project ID 0000133416 Project Analyst Richard Viray Substantial Completion Store Number 5309 CPM Sean Christopher Store Turnover To Ops Brand Old Navy General Contractor Freshco Retail Maintenance Inc. Store Effective Date 13-May-18 Punchlist Item Location Root Cause Driving Results Est Completion No open punchlist items Additional Items 1. The below signature indicates that all outstanding work has been captured on the punch list. GM or DM Signature: _____________________________________________ Name & Title (please print): ____________________________________ Date: ____________________________________ 2. The below signature indicates that all punch work has been completed to satisfaction. GM or DM Signature: _____________________________________________ Name & Title (please print): ____________________________________ Date: ____________________________________ Punchlist - Sign-off Sheet Project Information Project Resources Schedule Information Project Name ON.5309.VILLAGECOLON.MINS.2018 Senior PM Anabell Felix Construction Start 22-Apr-18 REPS Project ID 0000133416 Project Analyst Richard Viray Substantial Completion Store Number 5309 CPM Sean Christopher Store Turnover To Ops Brand Old Navy General Contractor Freshco Retail Maintenance Inc. Store Effective Date 13-May-18 Punchlist Item Location Root Cause Driving Results Est Completion No open punchlist items Additional Items 1. The below signature indicates that all outstanding work has been captured on the punch list. GM or DM Signature: _____________________________________________ Name & Title (please print): ____________________________________ Date: ____________________________________ 2. The below signature indicates that all punch work has been completed to satisfaction. GM or DM Signature: _____________________________________________ Name & Title (please print): ____________________________________ Date: ____________________________________ APPENDIX B: Punchlist
08/01/2018MCM 901 Page 181 of 224 Master Thesis: 620 N 3rd St Clara Bucar Transmittal 311 Elm Street Suite 600, Cincinnati, OH 45202 PROJECT: WSI WS Highland Village 035384.000 DATE: 6/25/2018 SUBJECT: WS Highland Village Plan Check TRANSMITTAL ID: 00003 PURPOSE: For your use VIA: Info Exchange FROM NAME COMPANY EMAIL PHONE Nicole Gorla 311 Elm Street Suite 600 Cincinnati OH 45202 United States FRCH Design Worldwide ngorla@frch.com 513-241-3000 TO NAME COMPANY EMAIL PHONE mresneck@wsgc.com mresneck@wsgc.com TJHannig@wsgc.com TJHannig@wsgc.com YZHONG@WSGC.com YZHONG@WSGC.com Jbarrett@wsgc.com Jbarrett@wsgc.com KNemeth@wsgc.com KNemeth@wsgc.com SBrogan@wsgc.com SBrogan@wsgc.com EFlynn@wsgc.com EFlynn@wsgc.com EDuarte2@wsgc.com EDuarte2@wsgc.com JReifenberger@wsgc.co m JReifenberger@wsgc.com nthompson@wsgc.com nthompson@wsgc.com jneumann@wsgc.com jneumann@wsgc.com ITDataNetworkCircuitOrd ers@wsgc.com ITDataNetworkCircuitOrders @wsgc.com LPConstruction@wsgc.c om LPConstruction@wsgc.com JHGuerrero@wsgc.com JHGuerrero@wsgc.com sodion@wsgc.com sodion@wsgc.com cmcnealley@wsgc.com cmcnealley@wsgc.com ahaas@wsgc.com ahaas@wsgc.com josephfarais@aol.com josephfarais@aol.com cthornton@glwdetroit.co m cthornton@glwdetroit.com tgatliff@glwdetroit.com tgatliff@glwdetroit.com jmilliken@ferraricolor.co m jmilliken@ferraricolor.com APPENDIX B: Transmittal
08/01/2018MCM 901 Page 182 of 224 Master Thesis: 620 N 3rd St Clara Bucar REQUEST FOR CLARIFICATION - RFI PAGE 1 PROJECT #0000 PHILADELPHIA, PA RFI 14 TO: COMPANY FROM: XXXXXX PHONE: 000000000000 PHONE: XXXXXX FAX: # FAX: XXXXXX ATTN: XXXXX BY: XXXXXX PROJECT#: 0000 DATE: 7/5/2018 SUBJECT: XXXXX SUB: XXXXX SPEC. REF. <Specification Reference> TRADE: XXXXX DWG.REF. XXXX JOB NO. XXXXX PLEASE PROVIDE THE FOLLOWING INFORMATION/CLARIFICATION: Provide dimension at XXXX BY: XXXXXX DUE DATE: 1/11/2011 RESPONSE: <type response here> BY: <Responding Individual> RESPONSE DATE: <Enter Date of Response> ATTACHMENTS: See below DISTRIBUTION: WSI Project Manager ☐ VIATechnik General Contractor ☐ Shrader & Martinez Engineers ☐ EEA Consulting Engineers Architect ☐ Chrome Architecture APPENDIX B: RFI - Request for Information
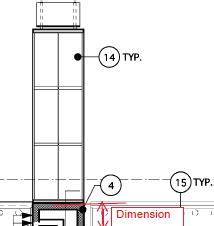
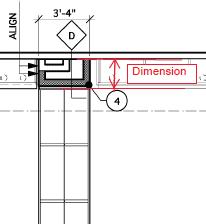
08/01/2018MCM 901 Page 183 of 224 Master Thesis: 620 N 3rd St Clara Bucar APPENDIX B: T&B - Test and Balance Report (Commissioning)

08/01/2018MCM 901 Page 184 of 224
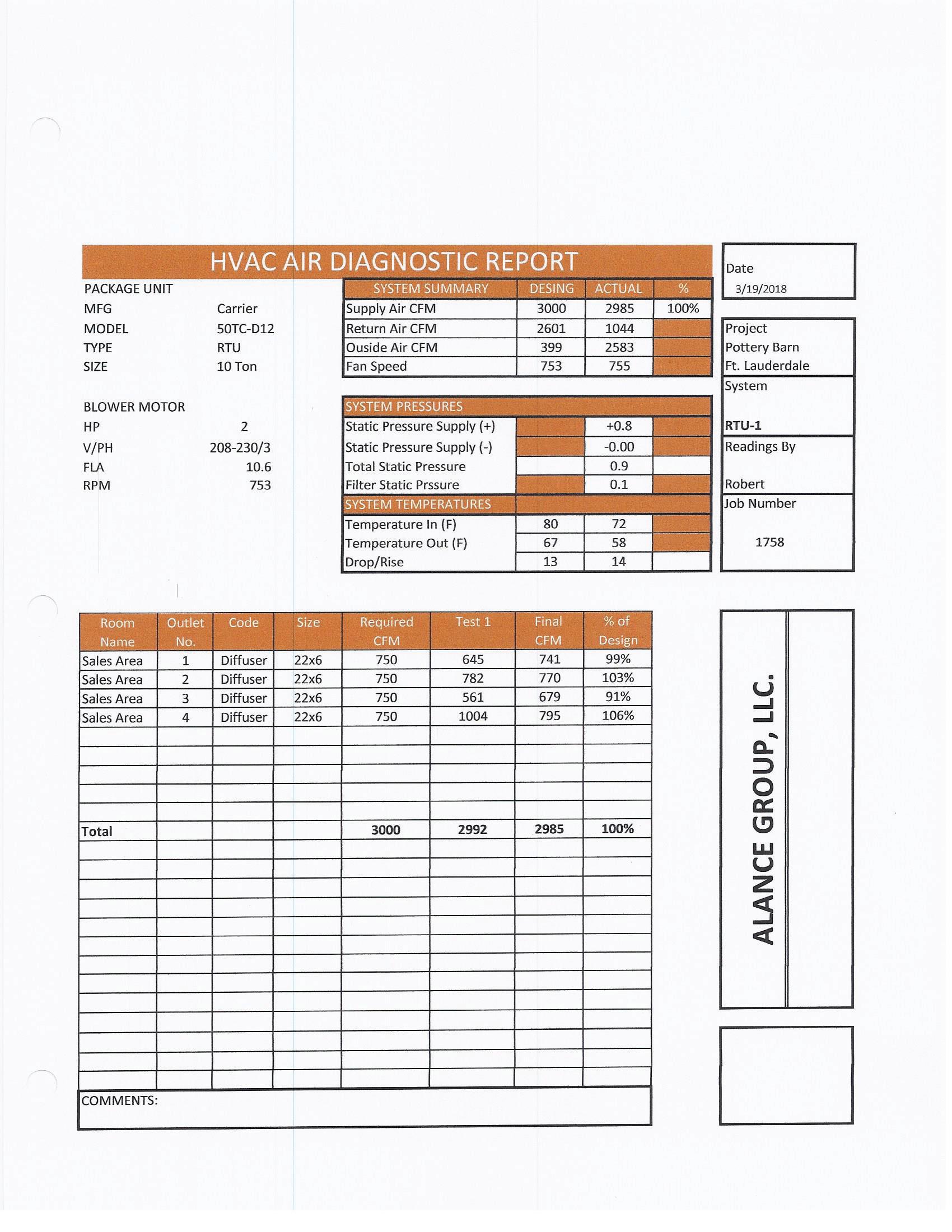
08/01/2018MCM 901 Page 185 of 224
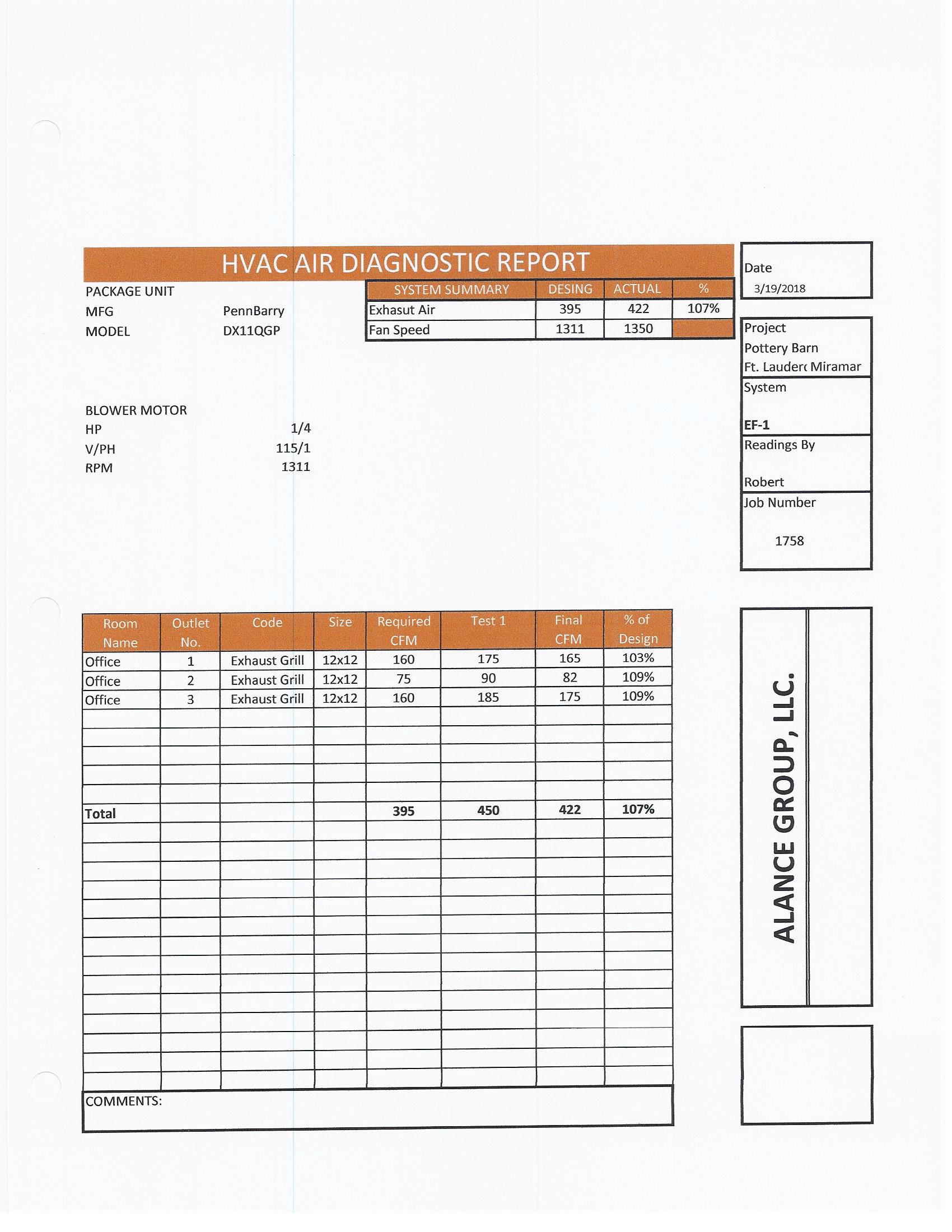
08/01/2018MCM 901 Page 186 of 224 Master Thesis: 620 N 3rd St Clara Bucar APPENDIX C: Scorecard requirements - Acoustic Performance 135 EQ CREDIT : ACOUSTIC P ERFORMANCE BD&C 1 2 points This credit applies to New Construction (1 point) Schools (1 point) Data Centers (1 point) Warehouses & Distribution Centers (1 point) Hospitality (1 point) Healthcare (1 2 points) Intent To provide workspaces and classrooms that promote occupants’ well being, productivity, and communications through effective acoustic design. NC,RequirementsDATACENTERS, WAREHOUSES & DISTRIBUTION CENTERS, HOSPITALITY For all occupied spaces, meet the following requirements, as applicable, for HVAC background noise, sound isolation, reverberation time, and sound reinforcement and masking. HVAC Background Noise Achieve maximum background noise levels from heating, ventilating, and air conditioning (HVAC) systems per 2011 ASHRAE Handbook, HVAC Applications, Chapter 48, Table 1; AHRI Standard 885 2008, Table 15; or a local equivalent. Calculate or measure sound levels. For measurements, use a sound level meter that conforms to ANSI S1.4 for type 1 (precision) or type 2 (general purpose) sound measurement instrumentation, or a local equivalent. Comply with design criteria for HVAC noise levels resulting from the sound transmission path s listed in ASHRAE 2011 Applications Handbook, Table 6; or a local equivalent. Sound Transmission Meet the composite sound transmission class (STC C) ratings listed in Table 1, or local building code, whichever is more stringent.. Table 1. Maximum composite sound transmission class ratings for adjacent spaces Adjacency combinations STCC Residence (within a multifamily residence), hotel or motel room Residence, hotel or motel room 55 Residence, hotel or motel room Common hallway, stairway 50 Residence, hotel or motel room Retail 60 Retail Retail 50 Standard office Standard office 45 Executive office Executive office 50 Conference room Conference room 50 Office, conference room Hallway, stairway 50 Mechanical equipment room Occupied area 60 Reverberation Time
08/01/2018MCM 901 Page 187 of 224 Master Thesis: 620 N 3rd St Clara Bucar APPENDIX C: Scorecard requirements - Daylight 130 EQ CREDIT : D AYLIGHT BD&C 1 3 points This credit applies to New Construction (1 3 points) Core & Shell (1 3 points) Schools (1 3 points) Retail (1 3 points) Data Centers (1 3 points) Warehouses & Distribution Centers (1 3 points) Hospitality (1 3 points) Healthcare (1 2 points) Intent To connect building occupants with the outdoors, reinforce circadian rhythms, and reduce the use of electrical lighting by introducing daylight into the space. NC,RequirementsCS,SCHOOLS, RETAIL, DATA CENTERS, WAREHOUSES & DISTRIBUTION CENTERS, HOSPITALITY, HEALTHCARE Provide manual or automatic (with manual override) glare control devices for all regularly occupied Selectspaces.one of the following three options. Option 1. Simulation: Spatial Daylight Autonomy and Ann ual Sunlight Exposure (2 –3 points, 1-2 points Healthcare) Demonstrate through annual computer simulations that spatial daylight autonomy300/50% (sDA300/50%) of at least 55%, 75%, or 90% is achieved. Use regularly occupied floor area. Healthcare projects should use the perimeter area determined under EQ Credit Quality Views. Points are awarded according to Table 1. Table 1. Points for daylit floor area: Spatial daylight autonomy NC, CS, Schools, Retail, Data Centers, Warehouses & Distribution Centers, Hospitality Healthcare sDA (for regularly occupied floor area) Points sDA (for perimeter floor area) Points 55% 2 75% 1 75% 3 90% 2 DemonstrateAND through annual computer simulations that annual sunlight exposure 1000,250 (ASE1000,250) of no more than 10% is achieved. Use the regularly occupied floor area that is daylit per the sDA 300/50% simulations.ThesDAand ASE calculation grids should be no more than 2 feet (60 0 millimeters) square and laid out across the regularly occupied area at a work plane height of 30 inches (76 millimeters) above finished floor (unless otherwise defined). Use an hourly time step analysis based on typical meteorological year data, or an equivalent, for the nearest available weather station. Include any permanent interior obstructions. Moveable furniture and partitions may be excluded.
08/01/2018MCM 901 Page 188 of 224 Master Thesis: 620 N 3rd St Clara Bucar APPENDIX C: Scorecard requirements - Interior Lighting 128 EQ CREDIT : I NTERIOR LIGHTING BD&C 1 2 points This credit applies to New Construction (1 2 points) Schools (1 2 points) Retail (2 points) Data Centers (1 2 points) Warehouses & Distributio n Centers (1 2 points) Hospitality (1 2 points) Healthcare (1 point) Intent To promote occupants’ productivity, comfort, and well being by providing high quality lighting. NC,RequirementsSCHOOLS,DATA
Lighting for any presentation or projection wall must be sep arately controlled. Switches or manual controls must be located in the same space as the controlled luminaires. A person operating the controls must have a direct line of sight to the controlled luminaires.
Option 2. Lighting Quality (1 point) Choose four of the following strategies.
CENTERS, WAREHOUSES & DISTRIBUTION CENTERS, HOSPITALITY
For all shared multioccupant spaces, meet all of the following requireme nts.
A. For all regularly occupied spaces, use light fixtures with a luminance of less than 2,500cd/m 2 between 45 and 90 degrees from nadir. Exceptions include wallwash fixtures properly aimed at walls, as specified by manufacturer’s data, indirect uplighting fixtures, provided there is no view down into these uplights from a regularly occupied space above, and any other specific applications (i.e. adjustable fixtures).
Have in place multizone control systems that enable occupants to adjust the lighting to meet group needs and preferences, with at least three lighting levels or scenes (on, off, midlevel).
For at least 90% of individual occupant spaces, provide individual lighting controls that enable occupants to adjust the lighting to suit their individual tasks and preferences, with at least three lighting levels or scenes (on, off, midlevel). Midlevel is 30% to 70% of the maximum illumination level (not including daylight contributions)
C. For at least 75% of the total connected lighting load, use light sources that have a rated life (or L70 for LED sources) of at least 24,000 hours (at 3 hour per start, if applicable).
Select one or both of the following two options.
B. For the entire project, use light sources with a CRI of 80 or higher. Exceptions include lamps or fixtures specifically designed to provide colored lighting for effect , site lighting, or other special use
Option 1. Lighting Control (1 point)
Hospitality only Guest rooms are assumed to provide adequate lighting controls and are therefore not included in the credit AND/ORcalculations.
Recycle and/or salvage nonhazardous construction and demolition mat erials. Calculations can be by weight or volume but must be consistent throughout.
08/01/2018MCM 901 Page 189 of 224 Master Thesis: 620 N 3rd St Clara Bucar APPENDIX C: Scorecard requirements - Interior Lighting 105 MR CREDIT : CONSTRUCTION AND DEMOLITION W ASTE M ANAGEMENT BD&C 1 2 points This credit applies to New Construction (1 2 points) Core & Shell (1 2 points) Schools (1 2 points) Retail (1 2 points) Data Centers (1 2 points) Warehouses & Distribution Centers (1 2 points) Hospitality (1 2 points) Healthcare (1 2 points) Intent To reduce construction and demolition waste disposed of in landfills and inci neration facilities by recovering, reusing, and recycling materials. NC,RequirementsCS,SCHOOLS, RETAIL NC, DATA CENTERS, WAREHOUSES & DISTRIBUTION CENTERS, HOSPITALITY NC, HEALTHCARE
Exclude excavated soil, land clearing debris, and alternative daily cover (ADC). Include wood waste converted to fuel (biofuel) in the calculations; other types of waste to energy are not considered diversion for this that cannot meet credit requirements using reuse and recycling methods, waste to energy systems may be considered waste diversion if the European Commission Waste Framework Directive 2008/98/EC and Waste Incineration Directive 2000/76/EC are followed and Waste to Energy facilities meet applicable European Committee for Standardization (CEN) EN 303 standards.
Path 1. Divert 50% and Three Material Streams (1 point) Divert at least 50% of the total construction and demolition material; diverted materials must include at least three material streams. OR Path 2. Divert 75% and Four Material Streams (2 points) Divert at least 75% of the total construction and demolition material; diverted materials must include at least four material streams.
OR Option 2. Reduction of Total Waste Material (2 points) Do not generate more than 2.5 pounds of construction waste per square foot (12.2 kilograms of wast e per square meter) of the building’s floor area.
However,credit.forprojects
Option 1. Diversion (1–2 points)
08/01/2018MCM 901 Page 190 of 224 Master Thesis: 620 N 3rd St Clara Bucar APPENDIX C: Scorecard requirements - Building Product Disclosure and OptimizationSourcing of Raw Materials 94 MR CREDIT : BUILDING P RODUCT DISCLOSUR E AND O PTIMIZATION –S OURCING OF R AW M ATERIALS BD&C 1–2 points This credit applies to New Construction (1 2 points) Core & Shell (1 2 points) Schools (1 2 points) Retail (1 2 points) Data Centers (1 2 points) Warehouses & Distribution Centers (1 2 points) Hospitality (1 2 points) Healthcare (1 2 points) Intent To encourage the use of products and materials for which life cycle information is available and that have environmentally, economically, and socially preferable life cycle impacts. To reward proj ect teams for selecting products verified to have been extracted or sourced in a responsible manner. NC,RequirementsCS,SCHOOLS, RETAIL NC, DATA CENTERS, WAREHOUSES & DISTRIBUTION CENTERS, HOSPITALITY NC, HEALTHCAREOption1.Raw Material Source and Extraction Reporting (1 point) Use at least 20 different permanently installed products from at least five different manufacturers that have publicly released a report from their raw material suppliers which include raw material supplier extraction locations, a commitment to long term ecologically responsible land use , a commitment to reducing environmental harms from extraction and/or manufacturing processes , and a commitment to meeting applicable standards or programs voluntarily that address responsible s ourcing criteria
o Global Reporting Initiative (GRI) Sustainability Report
o U.N. Global Compact: Communication of Progress o ISO 26000: 2010 Guidance on Social Responsibility o USGBC approved program: Other USGBC approved programs meeting the CSR criteria.
Option 2. Leadership Extraction Practices (1 point) Use products that meet at least one of the responsible extraction criteria below for at least 25%, by cost, of the total value of permanently installed building products in the project.
Products sourced from manufacturers with self declared reports are valued as one half (1/2) of a product for credit achievement. Third party verified corporate sustainability reports (CSR) which include environmental impacts of extraction operations and activities associated with the manufacturer’s product and the product’s supply chain, are valued as one whole product for credit achievement calculation. Acceptable CSR frameworks include the following:
o Organisation for Economic Co-operation and Develoment (OECD) Guidelines for Multinational Enterprises
Extended producer responsibility. Products purchased from a manufacturer (producer) that participates in an extended producer responsibility program or is directly responsible for extended
Table 1. Points for percentage improvement in energy performance
08/01/2018MCM 901 Page 191 of 224 Master Thesis: 620 N 3rd St Clara Bucar APPENDIX C: Scorecard requirements - Optimize Energy Performance 73 EA CREDIT : O PTIMIZE E NERGY P ERFORMANCE BD&C 1 20 points This credit applies to New Construction (1 18 points) Core & Shell (1 18 points) Schools (1 16 points) Retail (1 18 points) Data Centers (1 18 points) Warehouses & Distribution Centers (1 18 points) Hospitality (1 18 points) Healthcare (1 20 points) Intent To achieve increasing levels of energy performance beyond the prerequisite standard to reduce environmental and economic harms associated with excessive energy use. NC,RequirementsCS,SCHOOLS, RETAIL, W AREHOUSES & DISTRIBUTION CENTERS, HOSPITALITY, HEALTHCARE
Project teams pursuing the Integrative Process credit must complete the basic energ y analysis for that credit before conducting the energy simulation. Follow the criteria in EA Prerequisite Minimum Energy Performance to demonstrate a percentage improvement in the proposed building performance rating compared with the baseline. Points a re awarded according to Table 1.
Establish an energy performance target no later than the schematic design phase. The target must be established as kBtu per square foot year (kW per square meter year) of source energy use. Choose one of the options below.
ConstructionNew Major Renovation Core and Shell Healthcare)Schools,(exceptPoints HealthcarePoints Points Schools 6% 4% 3% 1 3 1
Option 1. Whole-Building Energy Simulation (1–18 points except Schools and Healthcare, 1–16 points Schools, 1 20 points Healthcare) Analyze efficiency measures during the design process and account for the results in design decision making. Use energy simulation of efficiency opportunities, past energy simulation analyses for similar buildings, or published data (e.g., Advanced Energy Design Guides) from analyses for similar buildings. Analyze efficiency measures, focusing on load reduction and HVAC related strategies (passive measures are acceptable) appropriate for the facility. Project potential energy savings and holistic project cost implications related to all affected systems.
08/01/2018MCM 901 Page 192 of 224 Master Thesis: 620 N 3rd St Clara Bucar APPENDIX C: Scorecard requirements - Optimize Energy Performance 74 8% 6% 5% 2 4 2 10% 8% 7% 3 5 3 12% 10% 9% 4 6 4 14% 12% 11% 5 7 5 16% 14% 13% 6 8 6 18% 16% 15% 7 9 7 20% 18% 17% 8 10 8 22% 20% 19% 9 11 9 24% 22% 21% 10 12 10 26% 24% 23% 11 13 11 29% 27% 26% 12 14 12 32% 30% 29% 13 15 13 35% 33% 32% 14 16 14 38% 36% 35% 15 17 15 42% 40% 39% 16 18 16 46% 44% 43% 17 19 50% 48% 47% 18 20 Retail only For all process loads, define a clear baseline for comparison with the proposed improvements. The baselines in Appendix 3, Tables 1 4, represent industry standards and may be used without additional documentation. Calculate the baseline and design as follows: Appliances and equipment. For appliances and equipment not covered in Tables 1 4, indicate hourly energy use for proposed and budget equipment, along with estimated d aily use hours. Use the total estimated appliance/equipment energy use in the energy simulation model as a plug load. Reduced use time (schedule change) is not a category of energy improvement in this credit. ENERGY STAR ratings and evaluations are a valid basis for performing this calculation. Display lighting. For display lighting, use the space-by-space method of determining allowed lighting power under ANSI/ASHRAE/IESNA Standard 90.1 2010, with errata (or a USGBC approved equivalent standard for projects outside the U.S.), to determine the appropriate baseline for both the general building space and the display lighting. Refrigeration. For hard wired refrigeration loads, model the effect of energy performance improvements with a simulation program designed to account for refrigeration equipment. OR Option 2. Prescriptive Compliance: ASHRAE Advanced Energy Design Guide (1 6 points) To be eligible for Option 2, projects must use Option 2 in EA Prerequisite Minimum Energy Performance. Implement and document compliance with the applicable recommendations and standards in Chapter 4, Design Strategies and Recommendations by Climate Zone, for the appropriate ASHRAE 50% Advanced
Commissioning Authority
Implement, or have in place a contract to implement, the following commissioning process activities in addition to those required under EA Prerequisite Fundamental Commissioning and Verification.
08/01/2018MCM 901 Page 193 of 224 Master Thesis: 620 N 3rd St Clara Bucar APPENDIX C: Scorecard requirements - Enhanced Commissioning 70 EA CREDIT : E NHANCED COMMISSIONING BD&C 2-6 points This credit applies to New Construction (2 6 points) Core & Shell (2 6 points) Schools (2 6 points) Retail (2 6 points) Data Centers (2 6 points) Warehouses & Distribution Centers (2-6 points) Hospitality (2-6 points) Healthcare (2 6 points) Intent To further support the design, construction, and eventual operation of a project that meets the owner’s project requirements for energy, water, indoor environmental quality, and durability. NC,RequirementsCS,SCHOOLS, RETAIL, DATA CENTERS, WAREHOUSES & DISTRIBUTION CENTERS, HOSPITALITY, HEALTHCARE
The CxA must have documented commissioning process experience on at least two building projects with a similar scope of work. The experience must extend from early design phase through at least 10 months of occupancy; The CxA may be a qualified employee of the owner, an independent consultant, or a disinterested subcontractor of the design team.
Option 1. Enhanced Systems Commissioning (3-4 points) Path 1: Enhanced Commissioning (3 points) Complete the following commissioning process (CxP) activities for mechanical, electrical, plumbing, and renewable energy systems and assemblies in accordance with ASHRAE Guideline 0 2005 and ASHRAE Guideline 1.1 2007 for HVAC&R systems, as they relate to energy, water, indoor environmental quality, and durability.Thecommissioning
authority must do the following: Review contractor submittals. Verify inclusion of systems manual r equirements in construction documents. Verify inclusion of operator and occupant training requirements in construction documents. Verify systems manual updates and delivery. Verify operator and occupant training delivery and effectiveness. Verify seasonal testing. Review building operations 10 months after substantial completion. Develop an on going commissioning plan. Include all enhanced commissioning tasks in the OPR and BOD.
08/01/2018MCM 901 Page 194 of 224 Master Thesis: 620 N 3rd St Clara Bucar APPENDIX C: Scorecard requirements - Indoor Water Use Reduction 56 WE CREDIT : I NDOOR W ATER USE REDUCTION BD&C 1 7 points This credit applies to New Construction (1 6 points) Core & Shell (1 6 points) Schools (1 7 points) Retail (1 7 points) Data Centers (1 6 points) Warehouses & Distribution Centers (1 6 points) Hospitality (1 6 points) Healthcare (1 7 points) Intent To reduce indoor water consumption. NC,RequirementsCS,SCHOOLS, NC RETAIL, DATA CENTERS, WAREHOUSES & DISTRIBUTION CENTERS, NC HOSPITALITY, HEALTHCARE Further reduce fixture and fitting water use from the calculated baseline in WE Prerequisite Indoor Water Use Reduction. Additional potable water savings can be earned above the prerequisite level using alternative water sources. Include fixtures and fittings necessary to meet the needs of the occupants. Some of these fittings and fixtures may be outside the tenant space (for Commercial Interiors) or project boundary (for New Construction). Points are awarded according to Table 1. Table 1. Points for reducing water use Percentagereduction (BD&C)Points Healthcare)Hospitality,(Schools,PointsRetail, 25% 1 1 30% 2 2 35% 3 3 40% 4 4 45% 5 5 50% 6 Schools, Retail, Hospitality, and Healthcare only Meet the percentage reduction requirements above. AND
08/01/2018MCM 901 Page 195 of 224 Master Thesis: 620 N 3rd St Clara Bucar APPENDIX C: Scorecard requirements - Outdoor Water Use Reduction 55 WE CREDIT : O UTDOOR W ATER USE REDUCTION BD&C 1 2 points This credit applies to New Construction (1 2 points) Core & Shell (1 2 points) Schools (1 2 points) Retail (1 2 points) Data Centers (1 2 points) Warehouses & Distribution Centers (1 2 points) Hospitality (1 2 points) Healthcare (1 point) Intent To reduce outdoor water consumption. Requirements NC, CS, SCHOOLS, RETAIL, DATA CENTERS, WAREHOUSES & DISTRIBUTION CENTERS, HOSPITALITY, HEALTHCARE
OR
Option 1. No Irrigation Required (2 points except Healthcare, 1 point Healthcare) Show that the landscape does not require a permanent irrigation system beyond a maximum two year establishment period. Option 2. Reduced Irrigation (2 points except Healthcare, 1 point Healthcare) Reduce the project’s landscape water requirement (LWR) by at least 50% from the calculated baseline for the site’s peak watering month. Reductions must first be achieved through plant species selection and irrigation system efficiency as calculated in the Environmental Protection Agency (EPA) WaterSense Water Budget Tool. Additional reductions beyond 30% may be achieved using any combination of efficiency, alternative water sources, and smart scheduling technolo gies.
Table 1. Points for reducing irrigation water Percentage reduction from baseline Points Healthcare)(except (Healthcare)Points 50% 1 100% 2
1
Reduce outdoor water use through one of the following options. Nonvegetated surfaces, such as permeable or pavement, should be excluded from landscape area calculations. Athletic fields and playgrounds (if vegetated) and food gardens may be included or excluded at the project team’s discretion.
impermeable
08/01/2018MCM 901 Page 196 of 224 Master Thesis: 620 N 3rd St Clara Bucar APPENDIX C: Scorecard requirements - Rainwater Management 36 SS CREDIT : R AINWATER M ANAGEMENT BD&C 1 3 points This credit applies to New Construction (1 3 points) Core & Shell (1 3 points) Schools (1 3 points) Retail (1 3 points) Data Centers (1 3 points) Warehouses & Distribution Centers (1 3 points) Hospitality (1 3 points) Healthcare (1 2 points) Intent To reduce runoff volume and improve water quality by replicating the natural hydrology and water balance of the site, based on historical conditions and undeveloped ecosystems in the region. NC,RequirementsCS,SCHOOLS,
Path 1. 95th Percentile (2 points except Healthcare, 1 point Healthcare) In a manner best replicating natural site hydrology processes, manage on site the runoff from the developed site for the 95th percentile of regional or local rainfall events using low impact development (LID) and green infrastructure Use daily rainfall data and the methodology in the U.S. Environmental Protection Agency (EPA) Technical Guidance on Implementing the Stormwater Runoff Requirements for Federal Projects under Section 438 of the Energy Independence and Security Act to determine the 95th percentile amount.
OR Path 2. 98th Percentile (3 points except Healthcare, 2 points Healthcare) Achieve Path 1 but for the 98th percentile of regional or local rainfall events, using LID and green ORinfrastructure.
Path 3. Zero Lot Line projects only – 85th Percentile (3 points except Healthcare, 2 points Healthcare)
The following requirement applies to zero lot line projects in urban areas with a minimum density of 1.5 FAR. In a manner best replicating natural site hydrology processes, manage on site the runoff from the developed site for the 85th percentile of regional or local rainfall events, using LID and green ORinfrastructure.
Option 2. Natural Land Cover Conditions (3 points except Healthcare, 2 points Healt hcare) Manage on site the annual increase in runoff volume from the natural land cover condition to the postdeveloped condition.
RETAIL, DATA CENTERS, WAREHOUSES & DISTRIBUTION CENTERS, HOSPITALITY, HEALTHCAREOption1.Percentile of Rainfall Events
To promote bicycling and transportat ion efficiency and reduce vehicle distance traveled.
Planned bicycle trails or lanes may be counted if they are fully funded by the date of the certificate of occupancy and are scheduled for completion within one year of that date.
NC,RequirementsCS,DATACENTERS, WAREHOUSES & DISTRIBUTION CENTERS, HOSPITALITY
Design or locate the project such that a functional entry or bicycle storage is within a 200 yard (180 meter) walking distance or bicycling distance from a bicycle network that connects to at least one of the following:at least 10 diverse uses (see Appendix 1); a school or employment center, if the project total floor area is 50% or more residential; or a bus rapid transit stop, light or heavy rail station, commuter rail station, or ferry terminal. All destinations must be within a 3 mile (4800 meter) bicycling distance of the project boundary.
Intent To
Bicycle Network
08/01/2018MCM 901 Page 197 of 224 Master Thesis: 620 N 3rd St Clara Bucar APPENDIX C: Scorecard requirements - Bicycle Facilities 21 LT CREDIT : BICYCLE F ACILITIES BD&C 1 point This credit applies to New Construction (1 point) Core & Shell (1 point) Schools (1 point) Data Centers (1 point) Warehouses & Distribution Centers (1 point) Hospitality (1 point) Retail (1 Healthcarepoint)(1point)
Provide long term bicycle storage for at least 30% of all regular building occupants, but no less than one storage space per residential unit.
Provide short term bicycle storage for at least 2.5% of all peak visitors, but no fewer than four storage spaces per building.
Bicycle Storage and Shower Rooms
Provide long term bicycle storage for at least 5% of all regular building occupants, but no fe wer than four storage spaces per building in addition to the short term bicycle storage spaces. Provide at least one on site shower with changing facility for the first 100 regular building occupants and one additional shower for every 150 regular building occupants thereafter.
Case 1. Commercial or Institutional Projects
improve public health by encouraging utilitarian and recreational physical activity.
Case 2. Residential Projects
Provide short term bicycle storage for at least 2.5% of all peak visitors but no fewer than four storage spaces per building.
For All Projects
The credit calculations must include all existing and new off street parking spaces that are leased or owned by the project, including parking that is outside the project boundary but is used by the project. On street parking in public rights of way is excluded from these calculations.
08/01/2018MCM 901 Page 198 of 224 Master Thesis: 620 N 3rd St Clara Bucar APPENDIX C: Scorecard requirements - Reduced Parking Footprint 25 LT CREDIT : REDUCED P ARKING FOOTPRINT BD&C 1 point This credit applies to New Construction (1 points) Core & Shell (1 points) Schools (1 points) Data Centers (1 points) Warehouses & Distribution Centers (1 points) Hospitality (1 points) Retail (1 Healthcarepoints)(1point) Intent To minimize the environmental harms associated with parking facilities, including automobile dependence, land consumption, and rainwater runoff. NC,RequirementsCS,RETAIL, SCHOOLS, DATA CENTERS, WAREHOUSES & DISTRIBUTION CENTERS, HOSPITALITY, HEALTHCARE Do not exceed the minimum local code requirements for parking capacity. Provide parking capacity that is a percentage reduction below the base ratios recommended by the Parking Consultants Council, as shown in the Institute of Transportation Engineers’ Transportation Planning Handbook, 3rd edition, Tables 18 2 through 18 4. Case 1. Baseline Location Projects that have not earned points under LT Credit Surrounding Density and Diverse Uses or LT Credit Access to Quality Transit must achieve a 20% (1 point) or 40% (2 points ID&C) reduction from the base ratios. Case 2. Dense and/or Transit-Served Location Projects earning 1 or more points under either LT Credit Surrounding Density and Diverse Uses or LT Credit Access to Quality Transit much achieve a 40% (1 point) or 60% (2 points) reduction from the base ratios.
For projects that use pooled parking, calculate compliance using the project’s share of the pooled parking.Provide preferred parking for carpools for 5% of the total parking spaces after reductions are made from the base ratios. Preferred parking is not required if no off street parking is provided.
tripsWeekday tripsWeekend Points and(exceptBD&CCoreShell) Points BD&C (Core and shell 72 40 1 1 144 108 3 3 360 216 5 6 Table 2. Minimum daily transit service for projects with commuter rail or ferry service only Weekday trips Weekend trips Points projects)(all 24 6 1 40 8 2
08/01/2018MCM 901 Page 199 of 224 Master Thesis: 620 N 3rd St Clara Bucar APPENDIX C: Scorecard requirements - Access to Quality Transit 18 LT CREDIT : ACCESS TO Q UALITY TRANSIT BD&C 1 6 points This credit applies to New Construction (1 5 points) Core & Shell (1 6 points) Schools (1 4 points) Data Centers (1 5 points) Warehouses & Distribution Centers (1 5 points) Hospitality (1 5 points) Retail (1 5 points) Healthcare (1 2 points) Intent To encourage development in locations shown to have multimodal transportation choices or otherwise reduced motor vehicle use, thereby reducing greenhouse gas emissions, air pollution, and other environmental and public health harms associated with motor vehicle use . NC,RequirementsCS,DATACENTERS, WAREHOUSES & DISTRIBUTION CENTERS, HOSPITALITY
Locate any functional entry of the project within a ¼ mile (400 meter) walking distance of existing or planned bus, streetcar, or rideshare stops, or within a ½ mile (800 meter) walking distance of existing or planned bus rapid transit stops, light or heavy rail stations, commuter rail stations, or commuter ferry terminals. The transit service at those stops and stations in aggregate must meet the minimums listed in Tables 1 and 2. Planned stops and stations may count if they are sited, funded, and under construction by the date of the certificate of occupancy and are complete within 24 months of that date. Both weekday and weekend trip minimums must be met.
Qualifying transit routes must have paired route service (service in opposite directions). For each qualifying transit route, only trips in one direction are counted towards the threshold If a qualifying transit route has multiple stops within the required walking distance , only trips from one stop are counted towards the threshold. or ferry)
Table 1. Minimum daily transit service for projects with multiple transit types (bus, streetcar, rail,
08/01/2018MCM 901 Page 200 of 224 Master Thesis: 620 N 3rd St Clara Bucar APPENDIX C: Scorecard requirements - Surrounding Density and Diverse Uses 15 LT CREDIT : S URROUNDING DENSITY AND D IVERSE USES BD&C 1 6 points This credit applies to New Construction (1 5 points) Core & Shell (1 6 points) Schools (1 5 points) Retail (1 5 points) Data Centers (1 5 points) Warehouses & Distribution Centers (1 5 points) Hospitality (1 5 points) Healthcare (1 points) Intent To conserve land and protect farmland and wildlife habitat by encouraging development in areas with existing infrastructure. To promote walkability, and transportation efficiency and reduc e vehicle distance traveled. To improve public health by encouraging daily physical activity. NC,RequirementsCS,SCHOOLS, RETAIL, DATA CENTERS, HOSPITALITY Option 1. Surrounding Density (2–3 points BD&C except Core and Shell , 2-4 points Core and Shell) Locate on a site whose surrounding existing density within a ¼ mile (400 meter) radius of the project boundary meets the values in Table 1. Use either the “separate residential and nonresidential densities” or the “combined density” values. Table 1a. Points for average density within 1/4 mile of project (imperial units) densityCombined Separate residential and nonresidential densities Shell)andCore(exceptBD&CPoints Shell)and(CoreBD&CPoints Square feet per acre of buildable land densityResidential(DU/acre) densityNonresidential(FAR) 22,000 7 0.5 2 2 35,000 12 0.8 3 4 Table 1b. Points for average density within 400 meters of project (metric units) densityCombined Separate residential and nonresidential densities Core(exceptBD&CPoints and(CoreBD&CPoints
08/01/2018MCM 901 Page 201 of 224 Master Thesis: 620 N 3rd St Clara Bucar APPENDIX C: Recycled Cotton Insulation Spec Sheet - Bonded’s Logic’s UltraTouch
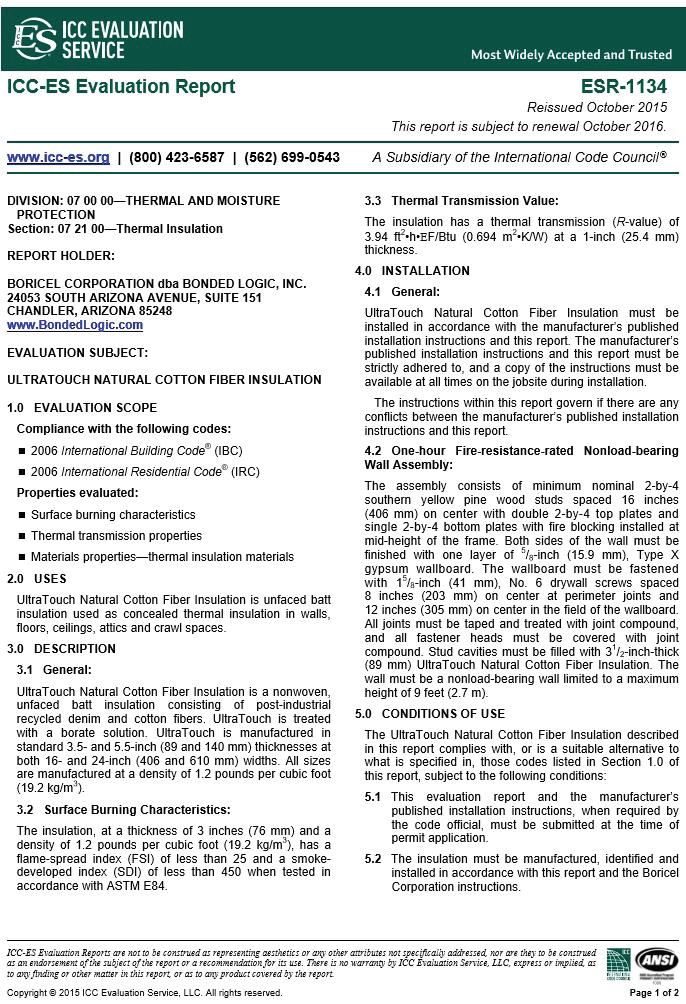
08/01/2018MCM 901 Page 202 of 224 Master Thesis: 620 N 3rd St Clara Bucar APPENDIX C: Recycled Cotton Insulation Spec Sheet - Bonded’s Logic’s UltraTouch

08/01/2018MCM 901 Page 203 of 224 Master Thesis: 620 N 3rd St Clara Bucar APPENDIX C: LED Lighting Spec Sheet 5 Year Warranty Direct 60W Incandescent Replacement No Housing Required!!! Energy Savings of up to 80% Lumen Maintenance over 70% @ 50,000+ Hours Compatible w/Most Triac Phase Control Dimmers No UV/IR Radiation, No Toxic Mercury Die Cast Aluminum Housing OPTICS Magnetic Interchangeable Trim Rings Available Frosted White Lens Regressed Reflector APPLICATIONS Ceiling Installations for General Ambient Lighting in Homes, Offices & Public Facilities Retail Store Lighting Museums, Galleries, Showrooms Hotels, Hospitality Areas Hospitals, Clinics, Workrooms Corridors, Lobbies, Stairways CERTIFICATIONS cETLus Listed Energy Star Listed for Rebate and Tax Incentive Programs California Title 24 Compliant Rated for Wet Locations / Airtight Rated 4” Easy Up MODEL EV407941WH50EV407941WH40EV407941WH35EV407941WH30EV407941WH27NUMBER KELVIN5000K4000K3500K3000K2700K(CCT) WATTS11.4811.7011.5311.7911.72 LUMENS701724746742789 CRI9193939293 TRIM COLOR WHITE MAGNETIC WHITE MAGNETIC WHITE MAGNETIC WHITE MAGNETIC WHITE MAGNETIC TRIM ORDERING OPTIONSWSPECIFICATIONSFEATURESarranty 5 yrs Expected Life 50,000 hrs Max Ambient Temp: 45°C Min Ambient Temp: 18°C R9 Value: 50 Power Factor: >0.9 Beam Angle: 103° THD: <20% EV407941WHxx 20101 South Santa Fe Avenue Rancho Dominguez, CA 90221 Specifications subject to change without notice © Copyright JIMWAY, INC., 2016 Catalog #: Project: Date: Prepared Commentsby: EV407941WHxx 4” WHITE EASY-UP LED DOWN LIGHT Designers Fountain Main (310) 886 5143 | email@designersftn.com

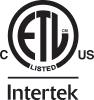



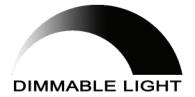
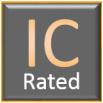

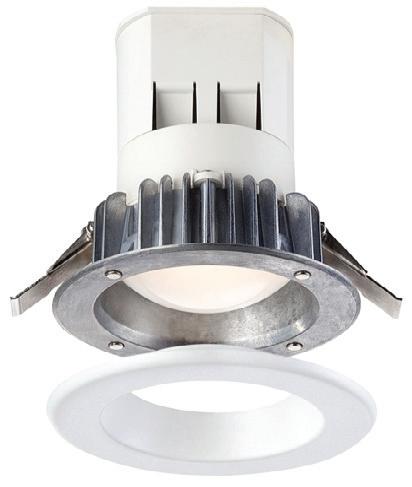
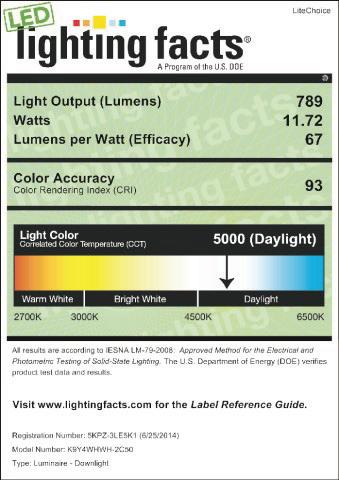
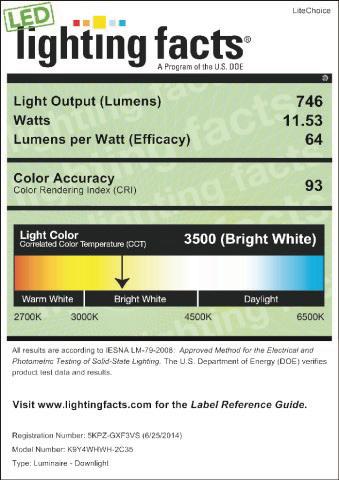
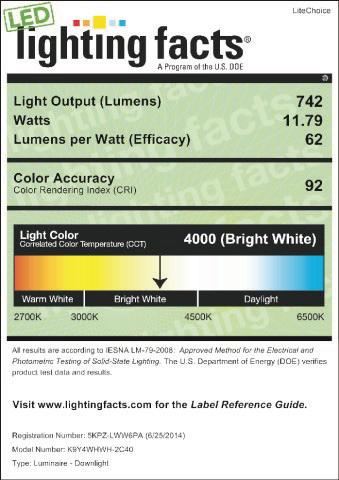
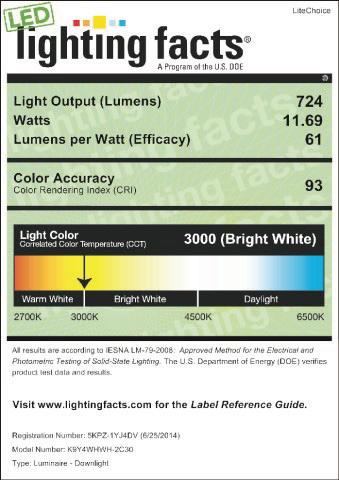
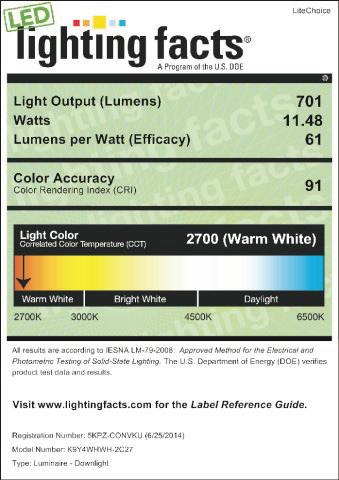

08/01/2018MCM 901 Page 204 of 224 Master Thesis: 620 N 3rd St Clara Bucar APPENDIX C: LED Lighting Spec Sheet LED RecessedLK5GDownlighting 5" Gimbal LED Recessed Kit IC/Non-IC New & Remodel Construction FEATURES & SPECIFICATIONS INTENDED USE — Recessed LED kits include housing, trim, and wire connectors in one package. The LED kit is the most economical means to create a well lit environment with exceptional energy efficiency and near zero maintenance. The LED kit maintains at least 70% light output for 35,000 hours. CONSTRUCTION — Steel housing with 3 remodel clips and 3 wire nuts for installation in existing plaster, sheet rock or mechanical ceiling. Heavy-gauge galvanized steel raceway arm. Durable, powder coat paint prevents rust. Easily converts to new construction application using accessories (sold separately). Galvanized steel junction box with three 7/8" knockouts with slots for pryout. Not suitable for pulling wires. Hook & hang snap-on J-box doors for easy access. Rated for 90°C. Ground wire provided. Available in 3000 K or 5000 K color temperature LEDs. OPTICS — White gimbal recesses optical system into the ceiling to prevent glare and provide a traditional look. Diffused lens provides even illumination throughout the space. ELECTRICAL — High-efficiency driver mounted on the module. Primary power disconnect provided for simple connection to a dedicated LED connector in the housing. Dimming down to 15%. See page 2 for recommended triac dimmers. Standard input wattage is 10.6W, 67 lumens per watt (3000 K), 10.2W, 84 lumens per watt (5000 K); equivalent to 50 watt PAR20. LISTINGS — CSA certified for use in the US and Canadian safety standards. California T24 compliant. ENERGY STAR® qualified. WSEC ASTM E283 for Air-Tight. Damp location listed. WARRANTY — 3-year limited warranty. Complete warranty terms located at: www.acuitybrands.com/CustomerResources/Terms_and_conditions.aspx Note: Actual performance may differ as a result of end-user environment and application. All values are design or typical values, measured under laboratory conditions at 25 °C. Specifications subject to change without notice. LK5GMW LED Series Reflector Finish Lamps Color temp/CRI/Watts/Lumens Voltage LK5 5" LED recessed kit G Gimbal MW Matte white LED (blank) 3000 K/93CRI/10.6W/720L 50K 5000 K/95CRI/10.2W/856L (blank) 120V Accessories: Order as separate catalog number. LKA5P 5" new construction pan LKABH Hanger bars for conversion to new construction ORDERING INFORMATION For shortest lead times, configure products using bolded options Example: LK5GMW LED DIMMABLE HangerLKABHbarsLKA5P New construction pan DOWNLIGHTING LK5G-LED_(GEN4) All dimensions are inches (centimeters) unless otherwise indicated. 5 (12.7) 9 (22.9) 6 (15.2) 6-1/4 (15.9) Specifications Aperture: 5 (12.7) Ceiling opening: 5-1/2 (14) Overlap trim: 6-1/4 (15.9) Height: 6 (15.2) Length: 9 (22.9) TypeNotesNumberCatalog
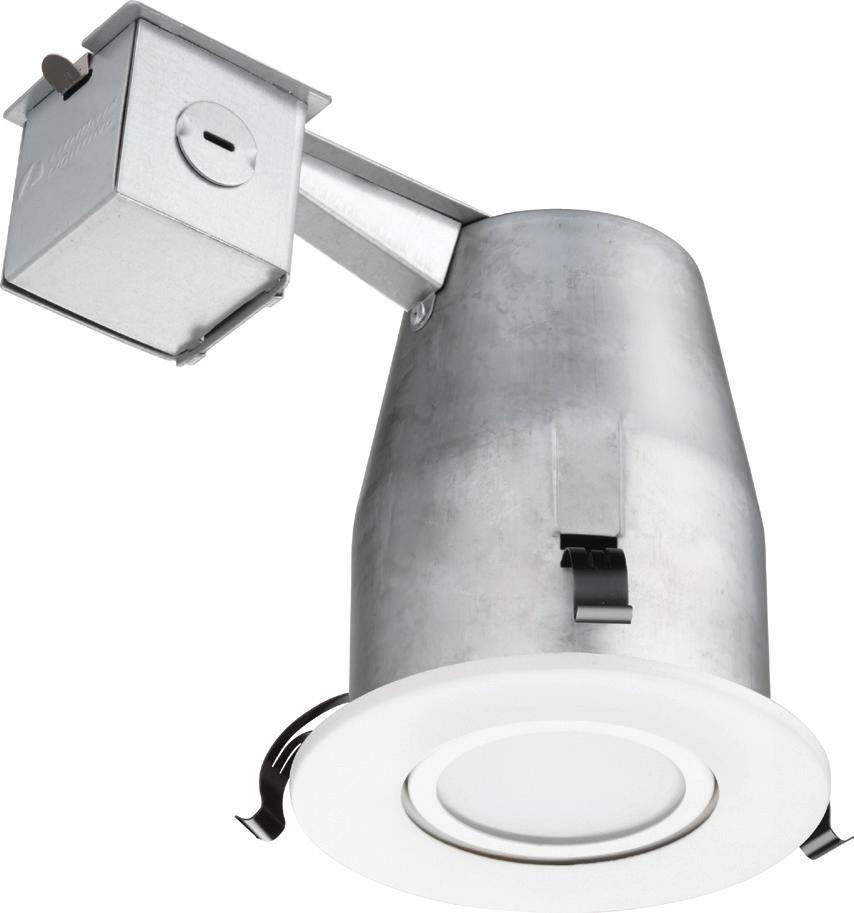
08/01/2018MCM 901 Page 205 of 224 Master Thesis: 620 N 3rd St Clara Bucar APPENDIX C: LED Lighting Spec Sheet L E D I n s t a n t F i t L a m p s 24T5 LED/HO/48-5000 IF 10/1 Philips LED T5 InstantFit Lamps are an ideal energy saving choice for existing linear fluorescent fixtures. Product data General Information Cap Base G5 [ G5] Nominal Lifetime (Nom) 50000 h Switch ng Cyc e 50000X B50L70 50000 h Light Technical Color Code 850 [ CCT of 5000K (2)] Init al lumen (Nom) 3500 lm Luminous Flux (Rated) (Nom) 3500 lm Correlated Color Temperature (Nom) 5000 K Color Consistency <5 Color Rendering Index (Nom) 82 LLMF At End Of Nominal Lifetime (Nom) 70 % Operating and Electrical Input Frequency 40000-80000 Hz Power (Rated) (Nom) 24 W Lamp Current (Max) 600 mA Lamp Current (Min) 400 mA Starting Time (Nom) 0.5 s Warm Up Time To 60% Light (Nom) 0.5 s Power Factor (Nom) 0.9 Voltage (Nom) 39-64 V TTemperatureAmbient(Max) 45 °C T Ambient (Min) -20 °C T Storage (Max) 65 °C T Storage (Min) -40 °C Controls and Dimming Dimmable No Mechanical and Housing Product Length 1100 mm Approval and Application DesignL ghts Consortium Qua ified Product List DesignLights Consortium Qualified Product List Energy Sav ng Product Yes Approbation Marks UL certificate RoHS compliance Product Data Order product name 24T5 LED/HO/48-5000 IF 10/1 EAN/UPC Product 046677467159 Order code 467159 Numerator Quantity Per Pack 1 Datasheet, 2017, February 17 data subject to change Lighting
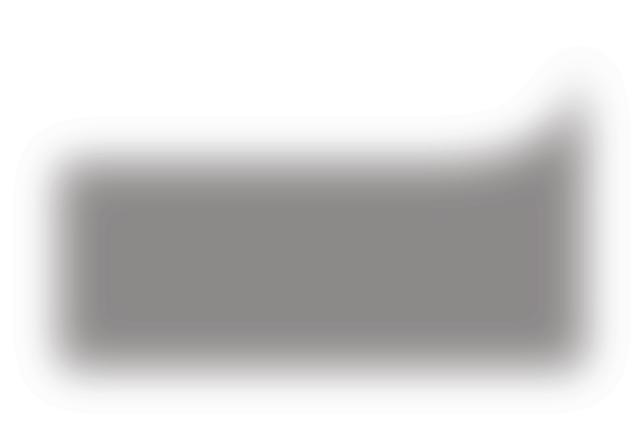
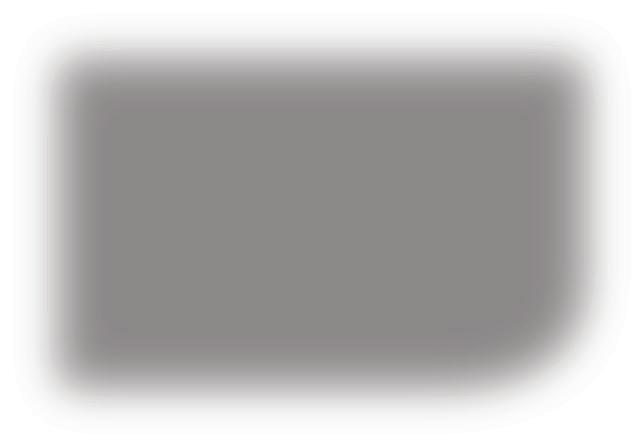
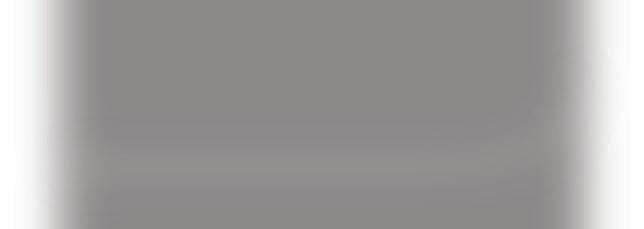

08/01/2018MCM 901 Page 206 of 224 Master Thesis: 620 N 3rd St Clara Bucar APPENDIX C: LED Lighting Spec Sheet TCPs award winning PARs have just got better. With over 500 options, TCP’s new PAR series combines traditional beauty with top-notch technology. • Energy Efficient: Up to 85% less energy than halogen replacements. • Smooth, uniform dimming; also available as non-dimming. • Long Life: 25,000 hours • 120W, 90W, 75W, 60W and 50W replacements. • NEW smooth outer housing. • Excellent color consistency and high color rendering (CRI). • Available in 2400K, 2700K, 3000K, 3500K and 4100K. we know light.™ Elite Designer PAR Series 325 Campus Dr. | Aurora, Ohio 44202 | P: 800-324-1496 | tcpi.com ©TCP, Inc. JUNE 2013/50709 TCP, Inc. Great features and benefits: PAR38 PAR30LN PAR30SN PAR20 Limitless options for the following applications: • Track Lights • Recessed Downlights • Display Lights • Outdoor Fixtures that Protect Lamps from the Elements PAR30PAR30LNPAR3

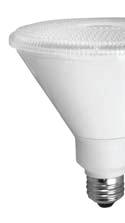

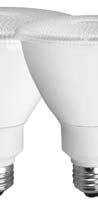
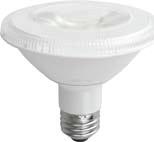
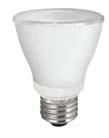

08/01/2018MCM 901 Page 207 of 224 Master Thesis: 620 N 3rd St Clara Bucar APPENDIX C: LED Lighting Spec Sheet
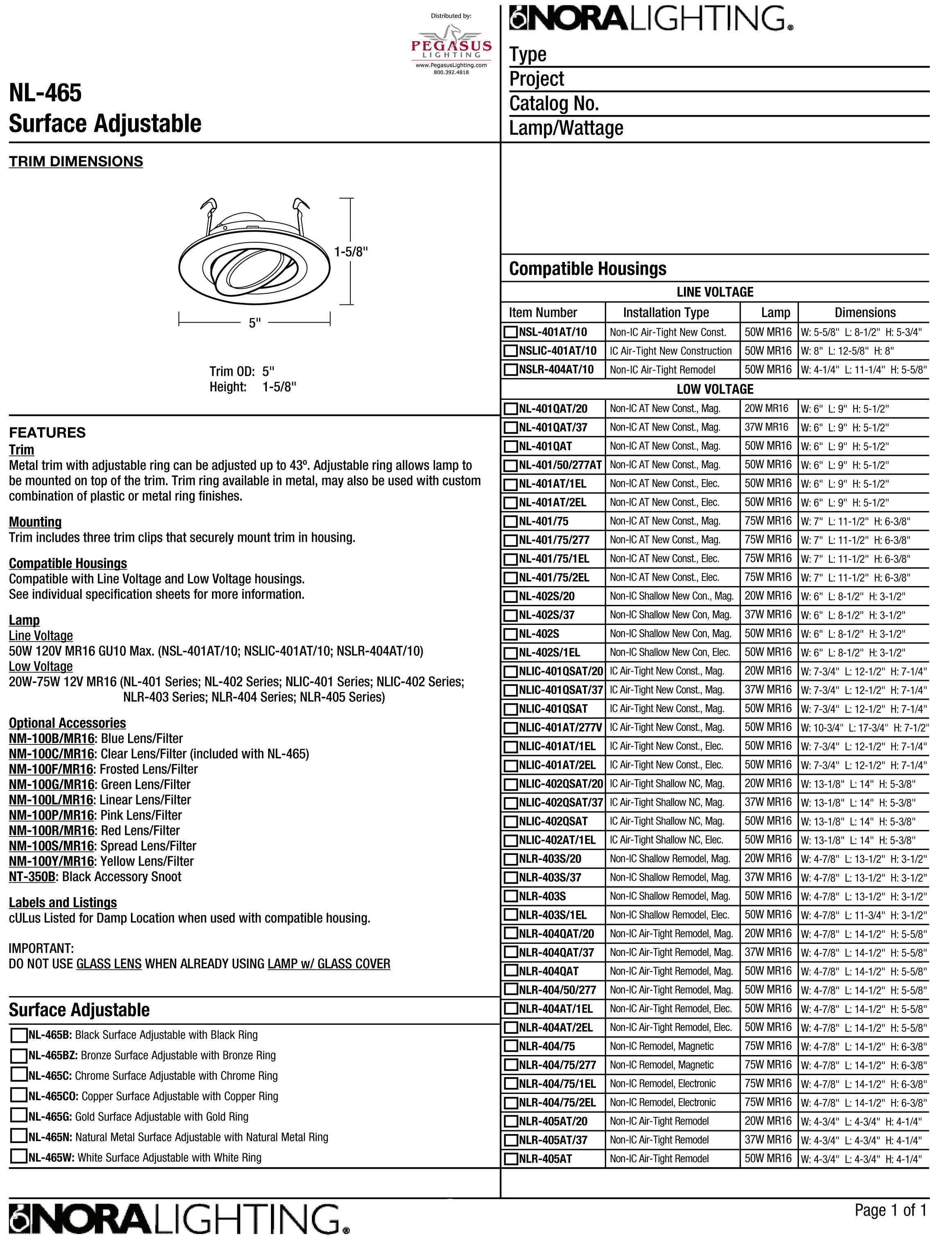
PRODUCT FEATURES: UniversalVALVE: Inlets / Outlets: 1/2" NOM Copper Sweat or 1/2" NPT. Cast Brass Valve Body: Durable. Ideal material for prolonged contact with water. Ceramic Disc Valve Cartridge: Assures a lifetime of drip-free performance. Allows easy control over both water temperature and volume. Pressure Balancing Valve Cartridge: Maintains constant output temperature in response to changes in relative hot and cold supply pressure. Diaphragm system with integrated check valves engineered to eliminate cross flow. Avoids failure due to mineral deposits - ideal for use in hard water. Back-to-Back Capability: Hot and cold can be reversed quickly and easily. Adjustable Hot Limit Safety Stop: Limits the amount of hot water allowed to mix with cold. Reduces the risk of accidental scalding. Exclusive Plaster Guard: Plaster guard is designed to protect valve during installation and serve as a mounting plate for thin-wall installations. Two-piece design allows valve to be tested prior to trim installation.
FLOW RATE MINUTEPERGALLONS INLET PRESSURE
SUGGESTED SPECIFICATION Shower system shall feature a wall supply with 1/2" NPT female inlets and 1/2" NPSM male outlet, 59" metal hose, vacuum breaker, 1.5 gpm/5.7 L/min. 3-function water saving personal shower with pause feature, 2-way diverter valve, FloWise ® showerhead and a 36" slide-grab bar. Pressure Balance valve shall feature a cast brass body. Shall feature ceramic disc valve cartridge which controls water temperature and volume. Shall also feature hot limit safety stop. Fitting shall be American Standard Model # 1662SG.213.002. (PSI) 10080604020
PERSONAL SHOWER: Water Saving: Saves 40% in water usage. ADA-Compliant: Non-positive shut-off button on handle reduces flow to a trickle.
SLIDE-GRAB BAR: Stronger Than Standard Slide Bars: 1-1/2" diameter stainless steel bar meets ANSI standard 250 lb. pull test. Chrome-plated hand shower holder with ADA compliant lever handle.
3210
08/01/2018MCM 901 Page 208 of 224 Master Thesis: 620 N 3rd St Clara Bucar APPENDIX C: Plumbing Fixture Spec Sheet © 2018 AS America Inc. FloWise ® COMMERCIAL SHOWER SYSTEMS 1.5 GPM SHOWER SYSTEM KIT WITH SLIDE-GRAB BAR, HAND SHOWER & FloWise ® SHOWERHEAD Revised 1/18 MODEL NUMBER: ❏ 1662SG.213 Commercial Shower System Kit Includes: • Universal pressure balance Shower R121SS Valve with screwdriver stops • Colony Soft Shower Only Trim T675.507.002 • 3-Function Hand Shower 1660.766.002 with FloWise ® Showerhead • In-Line Vacuum Breaker 1660.400.002 • Metal Hose 8888.035.002 • Wall Supply 8888.037.002 • 36" Slide Bar 1660.236.002 • 2-Way Diverter Valve R422 • Heritage Diverter Handle T342.430 GENERAL DESCRIPTION: Complete commercial shower system includes: an R121SS pressure balance valve and trim, a wall supply with 1/2" NPT female inlet and 1/2" NPSM male outlet, a 59" (1500 mm) metal shower hose, vacuum breaker, a 3-function water-saving personal shower with pause feature, 2-way diverter valve, and a 36" slide-grab bar. Valve features a cast brass body, washerless 47 mm ceramic disc valve cartridge with volume and temperature control, back-to-back capability, integrated check valves and hot limit safety stop. Pressure balancing cartridge maintains constant output temperature in response to changes in relative hot and cold supply pressure. Universal inlets/outlets. With screwdriver stops. Rough-in plaster guard designed for use as thin wall mounting adapter. Durable metal handle. 3-function water saving hand shower with pause feature and 1.5 gpm/5.7 Lmin. flow restrictor. Slide bar features an adjustable hand shower holder which can be set at any height or position along the bar and angle up to 45˚.
08/01/2018MCM 901 Page 209 of 224 Master Thesis: 620 N 3rd St Clara Bucar APPENDIX C: Plumbing Fixture Spec Sheet L25 © 2016 AS America Inc. MONTERREY® SINGLE CONTROL CENTERSET FAUCET PRODUCT FEATURES: Pressure Compensating Outlet: Provides a constant water flow throughout the pressure range Durable Cast Brass Body: Perfect for high-use commercial installations Ceramic Disc Valve Cartridge: Assures a lifetime of drip-free, maintenance-free performance Adjustable Hot Limit Safety Stop: Limits the amount of hot water allowed to mix with cold. Reduces the risk of accidental scalding Lead Free: Faucet contains ≤ 0.25% total lead content by weighted average SUGGESTED SPECIFICATION: Single control centerset lavatory fitting shall feature a cast brass body with metal handle Shall feature 1/2" male threaded brass inlet shanks with quick spin nuts Shall also feature washerless ceramic disc valve car tridge with integral hot limit safet y stop Faucet shall be American Standard Model # 6114.11__.002. GENERAL DESCRIPTION: Cast brass centerset body with metal handle 1/2" male threaded brass inlet shanks with quick spin nuts Washerless ceramic disc valve car tridge with integral hot limit safet y stop Metal pop-up drain with 1-1/4" (32mm) tailpiece Choice of flow outlet. Fitting mounts on 4" centers. 25mm(1")MIN.WALL 1/2"(5-11102mm(4")47mm3/16")NPSM MOUNTING(129mm-1/8")HOLES SURFMOUNTINGACE MOUNTINGSURFACE (15-1/8"30mm) 1-1/2"(38mm)MAX 4-5/8(14-5/8"17mm)"MAX.(117mm) 32mm OD (1-1/4" OD) (60mm)2-3/8" (48mm)1-7/8" 6114.110.0 02 Monterrey Single Control Centerset Cast brass body. Metal pop-up drain. 1.5 gpm pressure compensating aerator 6114.111.0 02 Monterrey Single Control Centerset Cast brass body. Less pop-up drain, rod & hole. 1.5 gpm pressure compensating aerator 6114.113.0 02 Monterrey Single Control Centerset Cast brass body. Metal pop-up drain. 0.35 gpm vandalresistant, pressure compensating multi-laminar spray 6114.114.0 02 Monterrey Single Control Centerset Cast brass body. Less pop-up drain, rod & hole. 0.35 gpm vandal-resistant, pressure compensating multi-laminar spray 6114.115.0 02 Monterrey Single Control Centerset Cast brass body. Metal pop-up drain. 0.5 gpm vandal resistant, pressure compensating multi-laminar spray 6114.116.0 02 Monterrey Single Control Centerset Cast brass body. Less pop-up drain, rod & hole. 0.5 gpm vandal-resistant, pressure compensating multi-laminar spray MODEL NUMBER: Revised 4/16
SUGGESTED SPECIFICATION: Single control kitchen fitting shall feature a brass body with metal handle and brass field convertible rigid /swivel gooseneck spout. Shall also feature washerless ceramic disc valve cartridge with integral hot limit safety stop. Fitting shall be American Standard Model #6114.30_.002. (6-1/2")164mm (1-3/4")43mm (1-1/4")32mmMAX. 3/8" COMPRESSION SUPPLIES (4-3/4")120mm (2")51mmMAX. (10-1/4")261mm (20-1/2")547mm 51.5mm203mm(8")(2") 55.3mm(2-1/8")54mm(2-3/16")MAX.(5-1/8")130mm (5-1/4")134mm 35 to DIA.(1-3/838mm"to1-1/2")MOUNTING HOLES Revised 8/13© 2013 AS America Inc.
PRODUCT FEATURES: Pressure Compensating Aerator: Provides a constant water flow of 1.5 gpm throughout the pressure range. Solid Brass Construction: Durable. Excellent in high use applications. Ideal for prolonged contact with water. Ceramic Disc Valve Cartridge: Assures a lifetime of drip-free performance. Adjustable Hot Limit Safety Stop: Limits the amount of hot water allowed to mix with cold. Reduces the risk of accidental scalding. Field-Convertible Rigid / Swivel Gooseneck Spout Lead Free: Faucet contains ≤ 0.25% total lead content by weighted average. 6114.301 Shown NUMBER: 6114.301 Single Control Faucet with Remote Valve Field-convertible rigid / swivel gooseneck spout. Metal lever handle with red/blue index. 1.5 gpm pressure compensating aerator. With color matched spray. 6114.300 Single Control Faucet with Remote Valve Field-convertible rigid / swivel gooseneck spout. Metal lever handle with red/blue index. 1.5 gpm pressure compensating aerator. Less spray.
08/01/2018MCM 901 Page 210 of 224 Master Thesis: 620 N 3rd St Clara Bucar APPENDIX C: Plumbing Fixture Spec Sheet L123 MONTERREY ™ SINGLE CONTROL KITCHEN FAUCET WITH BRASS GOOSENECK SPOUT GENERAL DESCRIPTION: Durable cast brass construction. Field-convertible rigid-swivel gooseneck spout. Ceramic disc valve cartridge with integral hot limit safety stop. 20" long S.S. flex inlet hoses with 3/8" compression fittings. Metal lever handle with red/blue index. 1.5 gpm/5.7L/min. maximum flow rate.
MODEL
08/01/2018MCM 901 Page 211 of 224 Master Thesis: 620 N 3rd St Clara Bucar APPENDIX C: Plumbing Fixture Spec Sheet M54 © 2010 AS America Inc. Revised 2/10 CADET ELONGATED PRESSURE-ASSISTED TOILET 1.6 gpf / 6.0 Lpf VITREOUS CHINA CADET PRESSURE-ASSISTEDELONGATED TOILET 1.6 gpf/ 6.0 Lpf ❏ 2462.016 • Vitreous china • Low-consumption (1.6 gpf/6.0 Lpf) • EverClean ® surface inhibits the growth of stain- and odor-causing bacteria, mold, and mildew on the surface • Elongated bowl • Pressure-assisted siphon jet flush action • Fully-glazed 2-1/8" trapway • 10 x 12" water surface area • Metal chrome trip lever • Close-coupled flushometer tank* • Speed Connect ® tank/bowl coupling system • 2 bolt caps • 100% factory flush tested • 12" Rough-in ❏ 3481.016 Bowl with two bolt caps ❏ 3481.001 Same as above, Universal Bowl ❏ 4142.016 Tank complete with coupling components Nominal Dimensions: 768 x 521 x 743mm (30-1/4" x 20-1/2" x 29-1/4") Fixture only, seat and supply by others Recommended working pressure range 25 psi - 80 psi Alternate Configurations Available: ❏ 4142.600 Tank and tank cover only with tank cover locking device ❏ 4142.800 Tank and tank cover only with right hand trip lever ❏ 4142.900 Tank complete with right hand trip lever and tank cover locking device Compliance CertificationsMeets or Exceeds the Following Specifications: • ASME A112.19.2-2008 / CSA B45.1-08 for Vitreous China Fixtures NOTES: THIS COMBINATION IS DESIGNED TO ROUGH-IN AT A MINIMUM DIMENSION OF 305MM (12") FROM FINISHED WALL TO C/L OF OUTLET. * DIMENSION SHOWN FOR LOCATION OF SUPPLY IS SUGGESTED. SUPPLY NOT INCLUDED WITH FIXTURE AND MUST BE ORDERED FORSEPARATELY.ADDITIONAL INFORMATION REFER TO INSTALLATION INSTRUCTIONS SUPPLIED. IMPORTANT: Dimensions of fixtures are nominal and may vary within the range of tolerances established by ASME A112.19.2-2008 / CSH B45.1-08. These measurements are subject to change or cancellation. No responsibility is assumed for use of superseded or voided pages. (305mm)12" (768mm)30-1/4"C/LOF OUTLET FINISHED WALL9"(226mm)(27mm)1" 15" ( 381mm) 18-1/2" ( 470mm) C/L OF SEAT POST HOLE S 5-1/2" (140mm CENTERS) (347mm)13-3/4"(150mm)6" FLOORFINISHED (742mm)29-1/4"(516mm)(238mm)9-1/2"20-1/2"14"(356mm)(16mm)5/8" * SUPPLY(152mm)6"*8"(203mm)ASREQ'D3" (76mm) To Be Specified: ❏ Color: ❏ White ❏ Bone ❏ Linen ❏ Black ❏ Seat: American Standard #5324.019 “Rise and Shine” (with easy to clean lift-off hinge system) solid plastic closed front seat with cover. ❏ American Standard #5321.110 EverClean ® seat with Slow Close snap-off hinges. ❏ Alternate Seat: ❏ Supply with Stop:
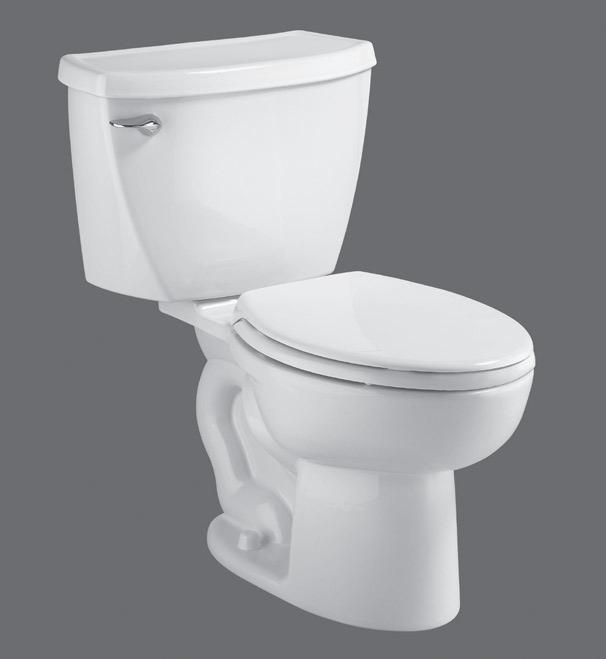
08/01/2018MCM 901 Page 212 of 224 Master Thesis: 620 N 3rd St Clara Bucar The Voltex Hybrid Electric heat pump water heater from A. O. Smith is the most cost effective energy-efficient option available for consumers who want to save money on their utility bills. Voltex can reduce water heating costs up to 73% and provide payback in 2-3 years. With annual savings of $305 or more, there is no better way to go green than Voltex. © May 2017 A. O. Smith Corporation. All Rights Reserved www.hotwater.com | 800-527-1953 Toll-Free USA | A. O. Smith Corporation | 500 Tennessee Waltz Parkway | Ashland City, TN 37015 INCREASED ENERGY EFFICIENCY • Improved efficiency designed in, to ensure available hot water at the lowest possible cost. Up to a 3.52 Uniform Energy Factor (UEF) Rating conserves energy and meets ENERGY STAR® qualifications CHOICE OF OPERATING MODES • Select from Efficiency, Hybrid, or Electric modes to match heating requirements to environmental conditions. • Hybrid mode automatically adjusts between compressor and element, depending upon heat requirements. • Vacation mode reduces operating costs and provides freeze protection during extended absence BACKUP ELECTRIC ELEMENTS • Long-lasting backup heating elements help heat water according to environmental conditions, demand, and the chosen operating mode COREGARD™ ANODE ROD • Our anode rods have a stainless steel core that extends the life of the anode rod allowing superior tank protection far longer than standard anode rods • 66 and 80 gallon models have dual anodes for added protection. DRY FIRE PROTECTION • Control system checks to ensure the tank is full of water during start up to prevent dry firing the heating elements ELECTRONIC USER INTERFACE • User-friendly electronic interface allows easy control of temperature setting, operating mode, and communicates diagnostics • Easy to read temperature display (see back) shows temperature in °F or °C • Advanced diagnostics convey error messages for service purposes. The last four error messages are saved in the control system memory. OTHER FEATURES • Ideal for basements or garage installations; the compressor transfers heat to the water while dehumidifying and cooling the ambient air • Washable air filter is easily removed for routine cleaning OPTIONAL AIR DUCT ADAPTER KIT • Permits installation in confined spaces TEN YEAR LIMITED WARRANTY • For complete information, consult written warranty or go to hotwater.com Page 1 of 2 AOSXE50007 VOLTEX® HYBRID ELECTRIC HEAT PUMP WATER HEATER HOW DO THEY WORK? Absorb ambient heat from the surrounding air to heat water using a compressor and “Environmentally-Friendly” R134a refrigerant • Self-contained heat pump unit is integrated into the top of the tank • Multiple operating modes to maximize efficiency and performance QUALIFIES FOR MANY STATE AND LOCAL UTILITY REBATESCHECK WWW.DSIREUSA.ORG COMMERCIAL-GRADE RESIDENTIAL ELECTRIC WATER HEATERS APPENDIX C: Energy Efficient Device Spec Sheet


• K TV DI M E le ct ro n ic co n t ro l p a n e l wit h d isp la y, f o r se mi re ce sse d wa ll in st a lla t io n , in clu d in g O N/ O FF b u t t o n , MO DE , 3 S p e e d s+A UTO , S E TP O I NT ch a n g e ; a u xilia ry co n t a ct s t o co n t ro l O N/ O FF va lve in 2 p ip e a n d 4 p ip e syst e ms; su mme r/ win t e r swit ch in g ; ma n u a l/ a u t o ma t ic/ f ro m co n t a ct ; co n t in u o u s/ t h e rmo st a t ve n t ila t io n ; co n f ig u ra b le d ig it a l in p u t s (S CR, E CO , S I C, A L A RM), we e kly t ime b a n d s ma n a g e me n t , co mp le t e wit h RS 4 8 5 re sid e n t se ria l in t e rf a ce (Mo d b u s RTU p ro t o co l)
• K RCA 1 E le ct ro n ic co n t ro l p a n e l wit h d isp la y, f o r se mi re ce sse d wa ll in st a lla t io n , in clu d in g O N/ O FF b u t t o n , MO DE , 2 S p e e d s, S E TP O I NT ch a n g e ; su mme r/ win t e r swit ch in g wit h b u t t o n o r re mo t e d ig it a l in p u t ;
Ac c e s s o ry mo d u le s P MA I n t a ke / o u t le t p le n u m wit h p re cu t sid e o u t le t s S I L P le n u m wit h a b so rb e n t ca rt rid g e sile n ce r t o b e p la ce d o n d e live ry o r in t a ke MUV P RV P le n u m wit h st e a m h u mid if ie r a n d e xt e rn a l e le ct ric g e n e ra t o r • B E A d d it io n a l e le ct rica l co il f o r co n n e ct io n t o ch a n n e l ct o ry f it t e d a cce sso rie s S G O p t io n a l p o lyp ro p yle n e d ro p se p a ra t o r a t lo w lo a d lo sse s TA G O p t io n a l a n t if re e ze t h e rmo st a t
•
•
Fa
•
• K P TZ Ro t a t in g p o t e n t io me t e r f o r wa ll mo u n t in g in st a lla t io n , d e d ica t e d t o ma n u a l f a n sp e e d co n t ro l Th e sp e e d o f d e live ry a n d re t u rn f a n s is ca lib ra t e d wit h a sin g le p o t e n t io me t e r
08/01/2018MCM 901 Page 213 of 224 Master Thesis: 620 N 3rd St Clara Bucar APPENDIX C: Energy Efficient Device Spec Sheet T ermin al u n it U TN A Plat inum 013÷120 C o o l i n g ca p a ci ty: 6 4 ÷7 0 kW H e a ti n g ca p a ci ty: 4 9 ÷7 8 kW √ Co mp lia n t wit h ErP 2 0 1 8 NRVU √ BRUSHL ESS EC f a n √ F 7 h ig h e f f ic ie n c y f ilt e rs We b c ode : U TA P1 Modula r duc ta ble a ir ha ndling te r m ina l units Co n s t ru c t io n f e a t u re s • Te rmin a l a ir h a n d lin g u n it : wit h mo d u le s f o r h o rizo n t a l o r ve rt ica l in st a lla t io n (0 1 3 0 5 0 ) wit h o r wit h o u t d u ct in g • S t ru ct u re wit h d o u b le wa ll sa n d wich t yp e f re e st a n d in g p a n e llin g , 3 0 mm t h ick wit h clo se d ce ll p o lyu re t h a n e f o a m in su la t io n wit h h ig h so u n d p ro o f in g a n d t h e rma l in su la t io n ca p a cit y • Ro u t in e ma ch in e ma in t e n a n ce f ro m t h e b o t t o m (f o r t h e h o rizo n t a l ve rsio n wit h in st a lla t io n in f a lse ce ilin g o r h a n g in g f ro m ce ilin g ) o r f ro n t a lly (f o r t h e ve rt ica l ve rsio n ) wit h re mo va b le p a n e ls • B A co il mo d u le (h o rizo n t a l) / B A V co il mo d u le (ve rt ica l u p t o size 0 5 0 ) co mp le t e wit h : G 4 st a n d a rd f ilt e r, o p t io n a l f in e F7 f ilt e r A ll f ilt e rs a re su p p lie d co mp le t e wit h d if f e re n t ia l p re ssu re swit ch t o sig n a l f ilt e r clo g g in g co n d it io n in co mp lia n ce wit h E u ro p e a n re g u la t io n n o 1 2 5 3 / 2 0 1 4 Fin n e d co il h e a t e xch a n g e r, wit h co p p e r p ip e s a n d 2 ro ws o f a lu min iu m f in s f o r h e a t in g o r re h e a t in g o n ly a n d 4 6 ro ws f o r co o lin g a n d / o r h e a t in g wit h rig h t o r le f t co n n e ct io n s t o b e se le ct e d wit h o rd e r Co n d e n sa t e d ra in p a n in a lu min iu m b o t h f o r h o rizo n t a l B A 4 R a n d B A 6 R ve rsio n s a n d ve rt ica l B A V 4 R a n d B A V 6 R ve rsio n s • S V f a n mo d u le co mp le t e wit h E C B ru sh le ss ce n t rif u g a l p le n u m f a n wit h sin g le in t a ke d ire ct ly co u p le d t o e le ct ric mo t o r S t a t ic a n d d yn a mic b a la n cin g o f t h e e n t ire a sse mb ly, b u ilt in a cco rd a n ce wit h st a n d a rd DI N I S O 1 9 4 0 G 6 3 b a la n cin g g ra d e S t a n d a rd co n t ro l o f t h e ro t a t io n sp e e d via sp e cia l 0 1 0 V a n a lo g u e in p u t E le ct rica l co n n e ct io n p a n e l f it t e d a s st a n d a rd co mp le t e wit h d isco n n e ct swit ch , p ro t e ct io n f u se s a n d co n n e ct in g t e rmin a l b lo ck
•
•
•
•
•
•
Se p a ra t e ly s u p p lie d a c c e s s o rie s K S G P o lyp ro p yle n e d ro p se p a ra t o r a t lo w lo a d lo sse s (o n ly f o r B A ) K TA G A n t if re e ze t h e rmo st a t (o n ly f o r B A ) K S E R K it in co mb in a t io n wit h P MA co n sist in g o f : d a mp e r wit h a lu min iu m b la d e s a n d f ra me , f it t e d wit h se a l g a ske t , ce rt if ie d cla ss 2 a cco rd in g t o E n 1 7 5 1 f o r f re sh a ir (ma x 3 0 %) o r re circu la t e d a ir a n d a f a st e n in g p a n e l t o P MA mo d u le Th e d a mp e r is size d f o r t re a t in g u p t o 1 0 0 % o f t h e UTNA a ir ca p a cit y a n d ma y b e p o sit io n e d a t t h e f ro n t , t o p o r b o t t o m o f t h e P MA K MS Ma n u a l co n t ro l f o r K S E R d a mp e r K B 2 R S e p a ra t e ly su p p lie d a d d it io n a l re h e a t co il Co n t ro ls
•






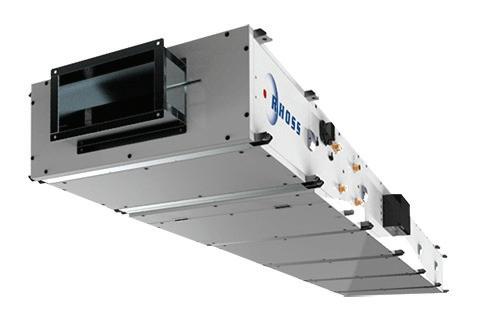
t here are two versions of L eed currently in effect: v3-L eed 2009 and the new L eed v4. d esign professionals can choose to register new projects under either version until o ctober 31, 2016. at that time, all new project registrations must use v4. Projects registered with L eed 2009 may continue to provide submittals for certification until June 6, 2021, when this rating system closes.
LEED pOINTS Certified 40-49 Si Lver 50-59 Go L d 60-79 P L atin UM 80+ 4
p
08/01/2018MCM 901 Page 214 of 224 Master Thesis: 620 N 3rd St Clara Bucar APPENDIX C: Glass Selection Spec Sheet
Guardian Glass Sustainability Calculator. a lthough L eed does not certify specific products, using SunGuard advanced a rchitectural Glass may help your project earn L eed points. Guardian Glass offers design professionals our Sustainability Calculator online to help evaluate and document environmental performance during the project design phase. Go to SunGuardGlass.com to find a SunGuard advanced a rchitectural Glass product, and other Guardian glass products, to help your project achieve L eed certification. t he charts on the following pages further illustrate L eed categories and credits, in addition to SunGuard solutions for complying with L eed standards. v EL OF C OM LIANCE
e arning L eed points in six categories.
L eed for n ew Construction is a voluntary standard for developing high-performance sustainable buildings. Using SunGuard glass can boost your L eed score in up to six categories. Some are very apparent; others you may not think of at first. Ultimately, SunGuard advanced a rchitectural Glass can help you maximize your building’s appearance without compromising its energy performance.
t he L eed scoring system. to qualify as L eed -certified, a building must score at least 40 of 110 possible points. h igher levels of compliance are possible, indicating higher levels of energy efficiency and environmental sustainability.
L E
SUStaina BL e S iteS SSpc55: Bird Collision d eterrence. 1 point. reduce bird injury and mortality from in-flight collisions with buildings. d reflectionsandmakeevelop
Mrc4: Building Product disclosure and optimization - Material ingredients. Up to 2 points. to encourage the use of products and materials for which life-cycle information is available and that have environmentally, economically and socially preferable life-cycle impacts; and are verified to minimize the use and generation of harmful substances. o thetotaloptimizationproductsoproductdemonstrateleastptionption
baseline.percentagerelatedsavingsfenergysimulationwocus
SSc5: h eat i sland reduction. Up to 2 points. to minimize effects on microclimates and human and wildlife habitats by reducing heat islands.
inte G rative P ro C eSS i Pc1: i ntegrative Process. 1 point. t o support interrelationshipsthroughcost–effectivehigh-performance,projectoutcomeanearlyanalysisoftheamongsystems. d basicsuchreduceenergyiscovery;
0.33athavestructuresmeasurestogetherroof
ener Gy and at M o SP here eac2: o ptimize e nergy Performance. Up to 20 points. t o achieve increasing levels of energy performance beyond the prerequisite standard to reduce environmental and economic harms associated with excessive energy use.
M ateria LS and reS o U r C eS M rc2: Building Product d isclosure and o ptimizatione nvironmental Product d eclarations. Up to 2 points. to encourage the use of products and materials from manufacturers who have verified improved environmental, economic and socially preferable life-cycle impacts. e nvironmental ( declaration.productso M rc3: Building Product d isclosure and o ptimization - Sourcing of r aw Material. Up to 2 points. to encourage the use of products and materials for which life-cycle information is available and are verified to have been extracted or sourced in a responsible manner. extraction25%Sourcing
9 - LEED v4: Scoring and Solutions
eed
v4
08/01/2018MCM 901 Page 215 of 224 Master Thesis: 620 N 3rd St Clara Bucar APPENDIX C: Glass Selection Spec Sheet
L Cate G ory L eed Credit L eed PointS the intent
08/01/2018MCM 901 Page 216 of 224 Master Thesis: 620 N 3rd St Clara Bucar APPENDIX D: AIA A134 - 2009 Standard Form of Agreement Between Owner and Construction Manager as Constructor where the basis of the payment if the Cost of the Work Plus a Fee without a Guaranteed Maximum Price
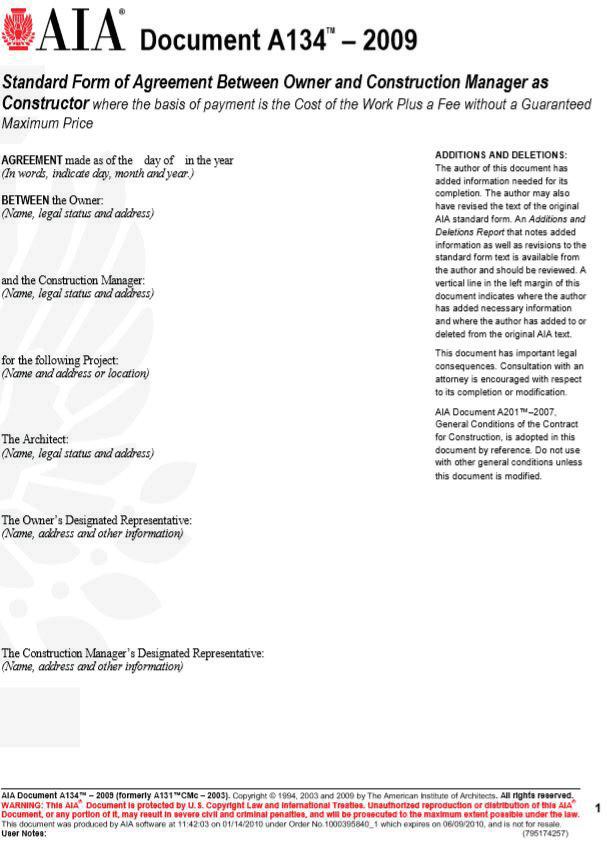
08/01/2018MCM 901 Page 217 of 224 Master Thesis: 620 N 3rd St Clara Bucar APPENDIX D: AIA A134 - 2009 Standard Form of Agreement Between Owner and Construction Manager as Constructor where the basis of the payment if the Cost of the Work Plus a Fee without a Guaranteed Maximum Price
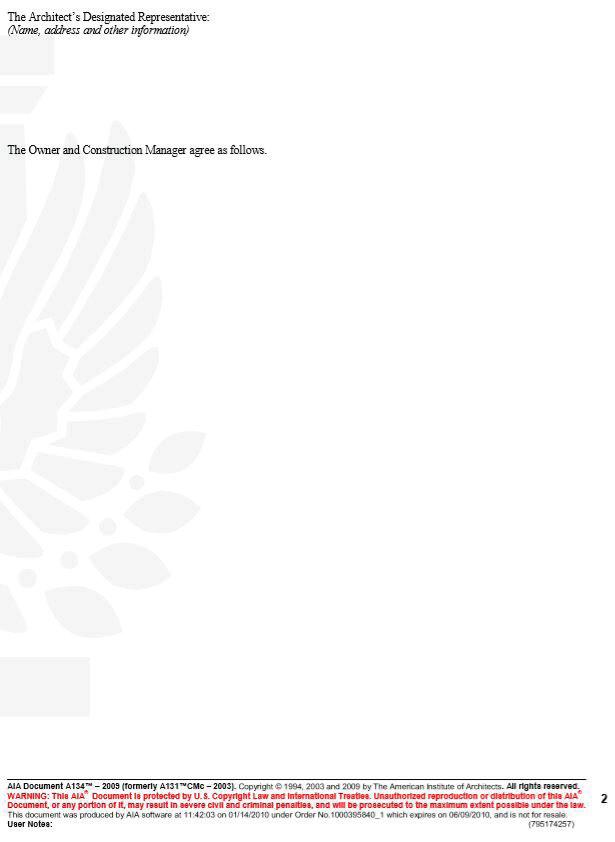
08/01/2018MCM 901 Page 218 of 224 Master Thesis: 620 N 3rd St Clara Bucar APPENDIX D: AIA A134 - 2009 Standard Form of Agreement Between Owner and Construction Manager as Constructor where the basis of the payment if the Cost of the Work Plus a Fee without a Guaranteed Maximum Price
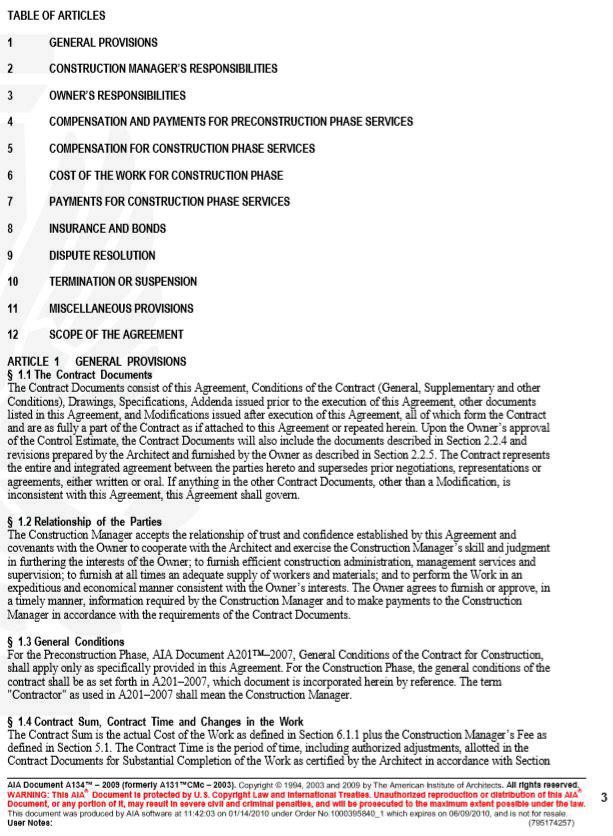
08/01/2018MCM 901 Page 219 of 224 Master Thesis: 620 N 3rd St Clara Bucar APPENDIX D: AIA A401 - 2007 Standard Form of Agreement Between Contractor and Subcontractor
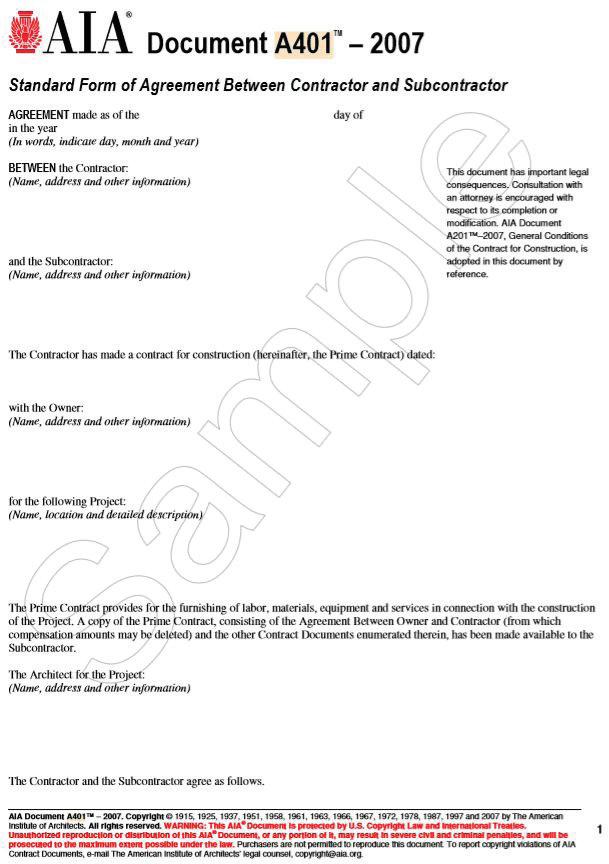
08/01/2018MCM 901 Page 220 of 224 Master Thesis: 620 N 3rd St Clara Bucar APPENDIX D: AIA A401 - 2007 Standard Form of Agreement Between Contractor and Subcontractor
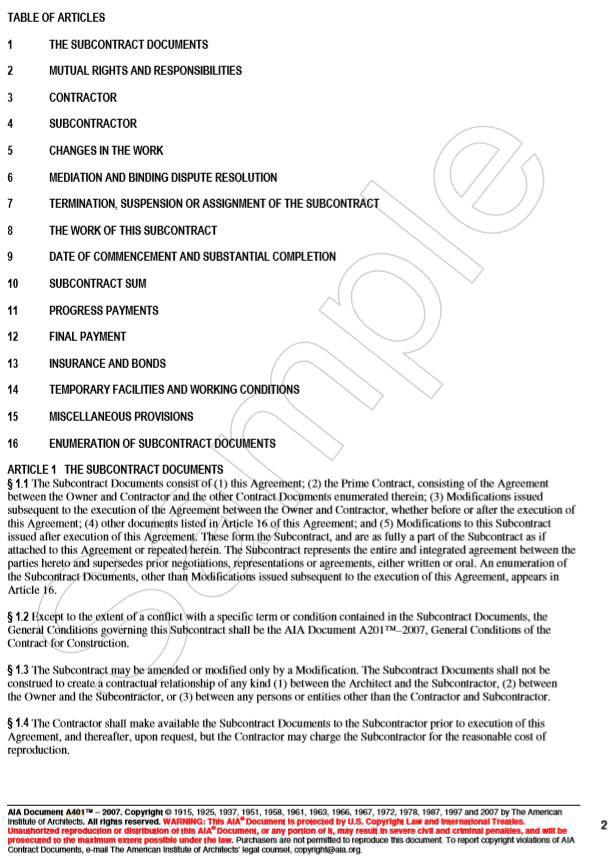
08/01/2018MCM 901 Page 221 of 224 Master Thesis: 620 N 3rd St Clara Bucar APPENDIX D: AIA A401 - 2007 Standard Form of Agreement Between Contractor and Subcontractor
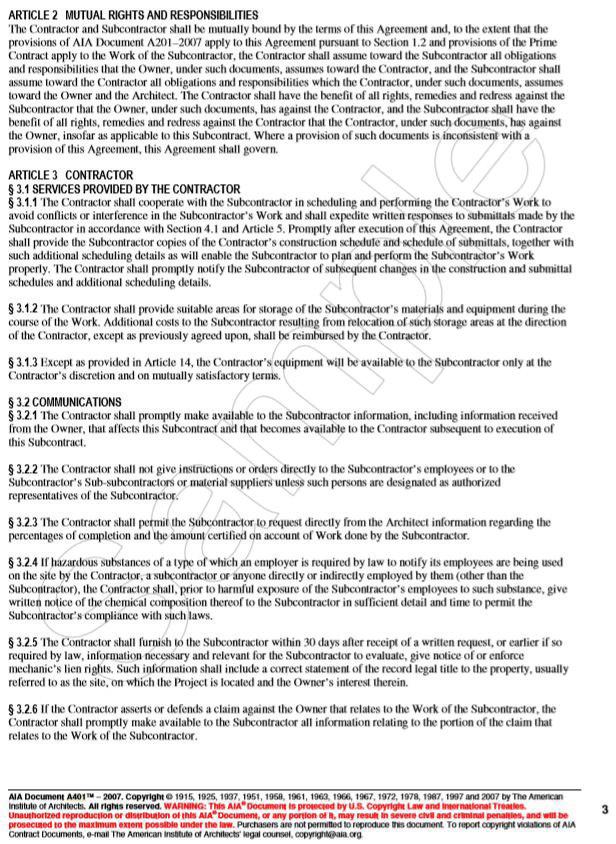
08/01/2018MCM 901 Page 222 of 224 Master Thesis: 620 N 3rd St Clara Bucar APPENDIX D: AIA A201 - 2007 General Conditions of the Contract for Construction

08/01/2018MCM 901 Page 223 of 224 Master Thesis: 620 N 3rd St Clara Bucar APPENDIX D: AIA A201 - 2007 General Conditions of the Contract for Construction
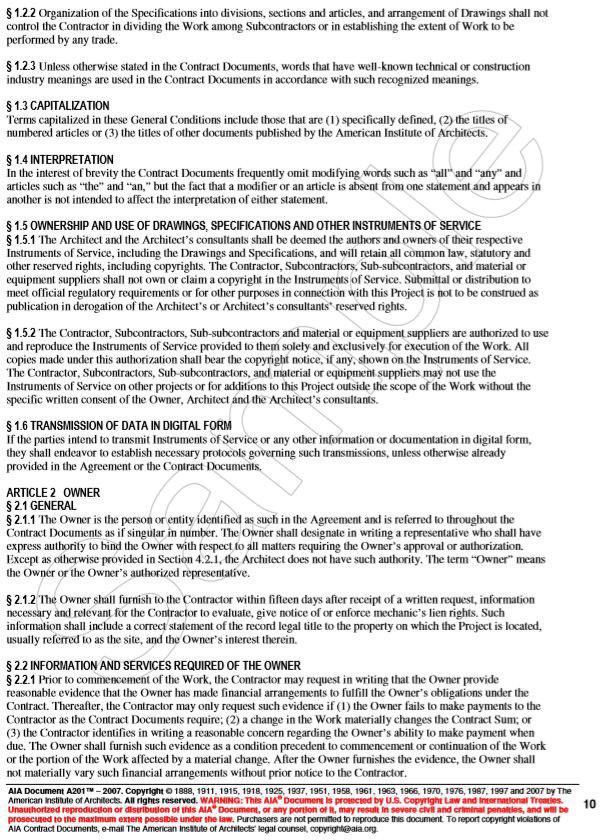
08/01/2018MCM 901 Page 224 of 224 Master Thesis: 620 N 3rd St Clara Bucar APPENDIX D: AIA A201 - 2007 General Conditions of the Contract for Construction
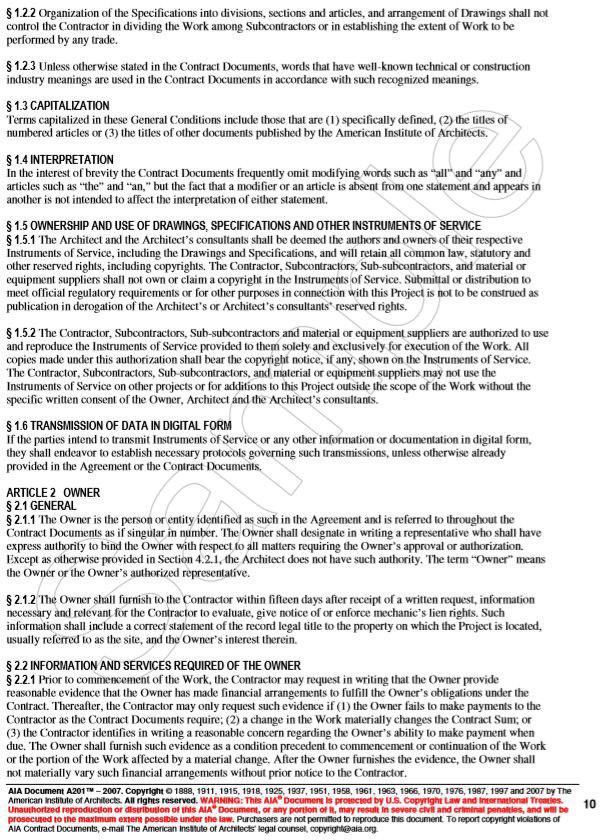