

A pluggable system solution for control cabinet-free automation: The MX-System
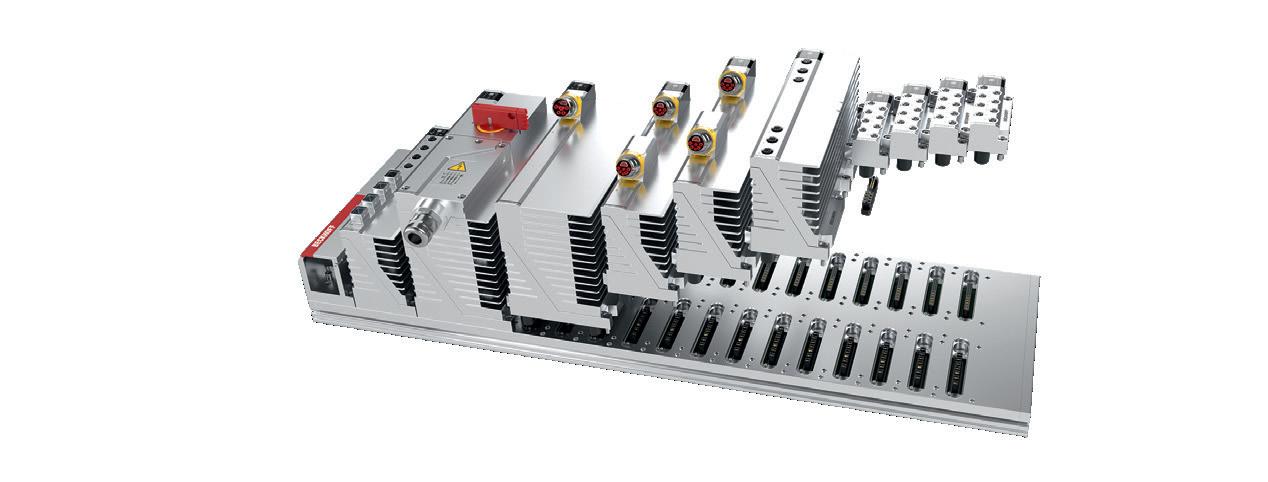
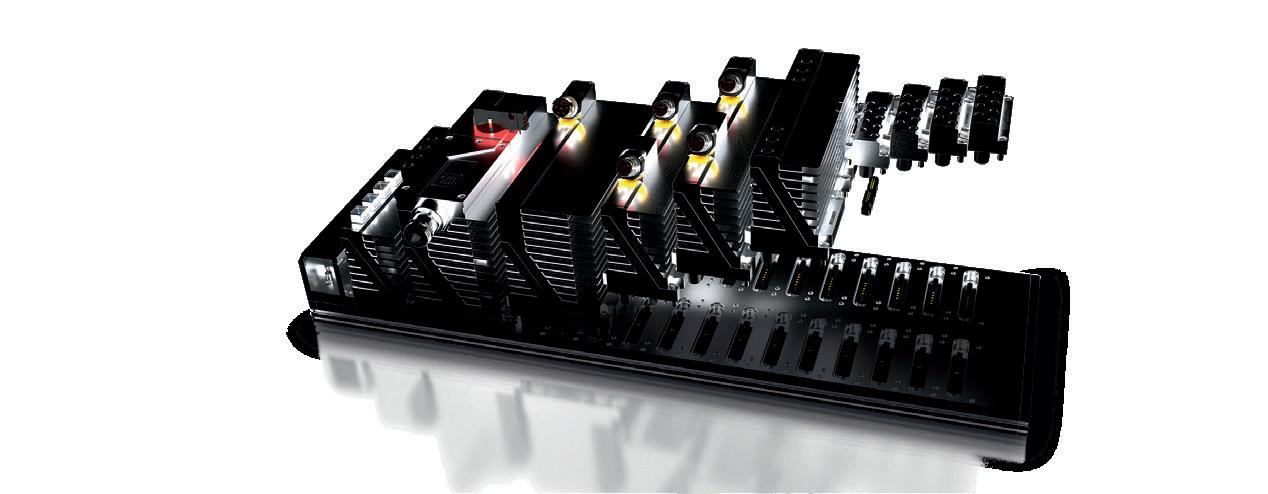
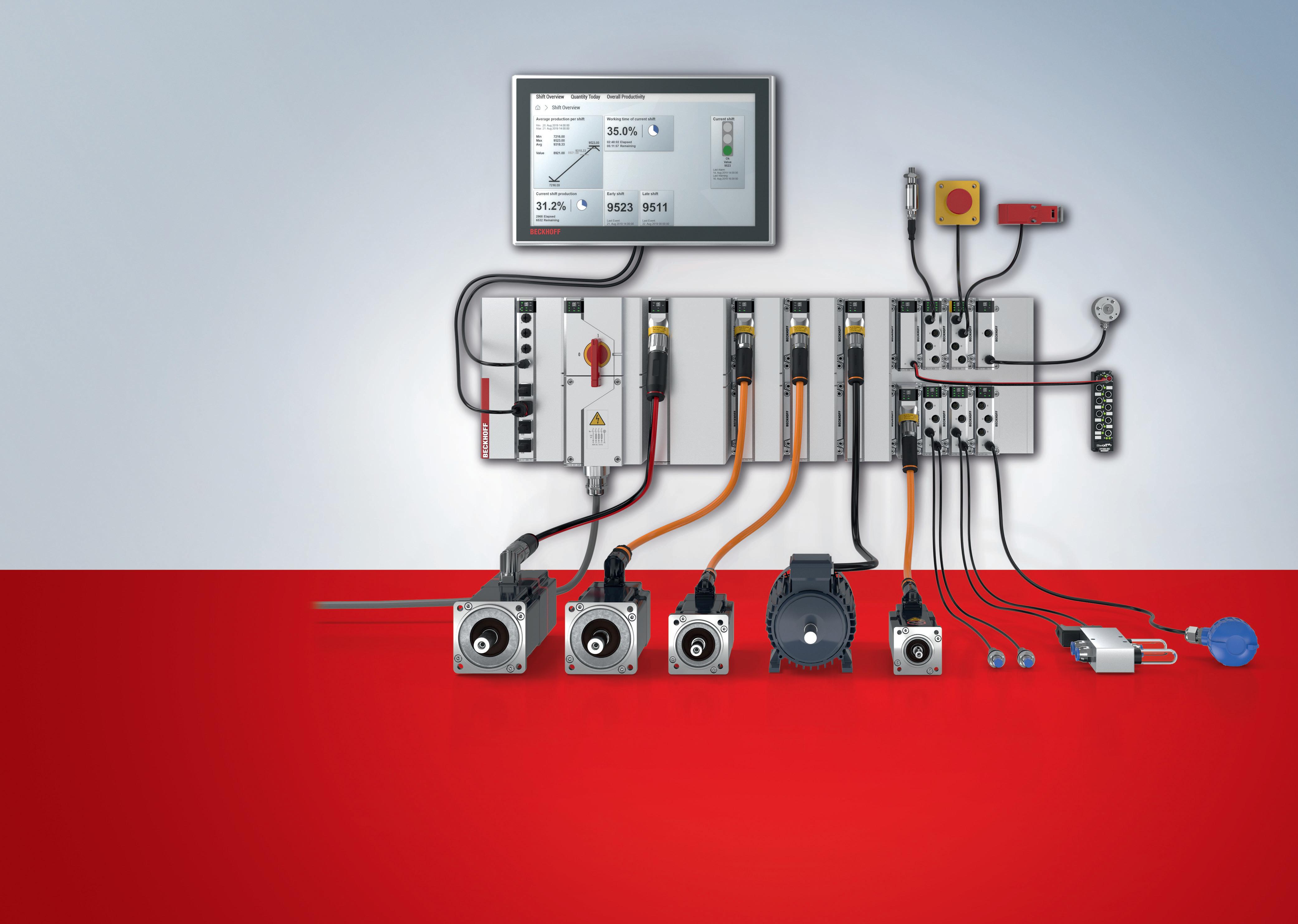
a highly flexible control cabinet-free automation solution robust, water- and dust-proof design (IP67 protection rating) plug-and-play with pluggable function modules for IPC, coupler, I/O, drive, relay and system standardized connectors for transmission of data and power EtherCAT communication tried-and-tested connector for the field level reduces engineering work high time and cost savings integrated diagnostic functions
Find out about
world of control-cabinet free automation!

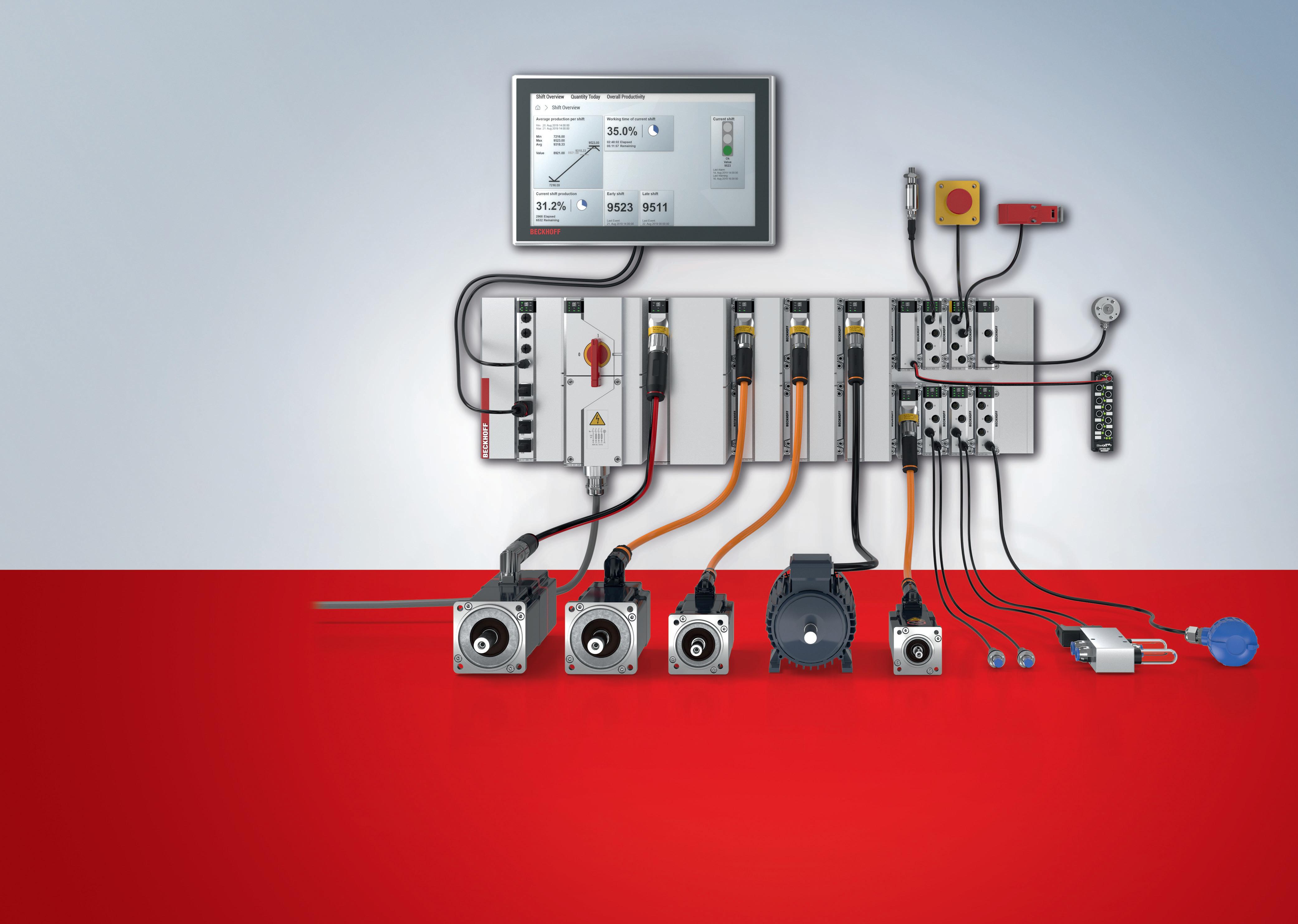
Editor
Chris Callander chrisc@cimltd.co.uk
Publication Manager
James Davies jamesd@cimltd.co.uk 01795 509105
Account Manager
Hannah Moody hannah@cimltd.co.uk 01795 509115
James Burke jb@cimltd.co.uk 01795 509115
Design & Production
Grant Waters grant@cimltd.co.uk
James Taylor james@cimltd.co.uk
Administration Manager
Natalie Murray admin@cimltd.co.uk 01795 509103
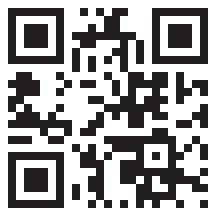
Credit Facilities Manager
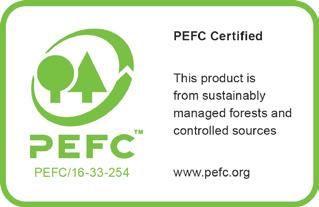
Gwen Lee creditcontrol@cimltd.co.uk 01795 509103
Marketing Manager
Lucas Payne lucas@cimltd.co.uk
Sales Director
Tom Woollin tom@cimltd.co.uk
Chief Executive
John Denning
© 2023 TGM Publishing Limited,1st Floor, Saphir House, 5 Jubilee Way, Faversham, Kent, ME13 8GD. No part of this magazine may be reproduced or stored in a retrieval system or transmitted in any form – electronic, mechanical or physical – without express prior permission and written consent of the publisher. Contributions are invited and when not accepted will be returned only if accompanied by a fully stamped and addressed envelope. Manuscripts should be typewritten. No responsibility can be taken for drawings, photographs or literary contributions during transmission or in the editor’s hands. In the absence of an agreement the copyright of all contributions, literary, photographic or artistic, belongs to TGM Publishing Limited. The publisher accepts no responsibility in respect of advertisements appearing in the magazine and the opinions expressed do not necessarily represent the views of the publisher. The publisher cannot accept liability for any loss arising from the late appearance or non-publication of any advertisement.
In this issue of MEPCA, Kuka explores the benefits of automating for small and medium-sized businesses. There are wide-ranging benefits, but with the term automation often evoking images of large, high-tech factories, it can look like a distant dream for many smaller manufacturers. It is important, then, to recognise that automation doesn’t have to be an all-or-nothing game. The key is to start small and focus on areas that offer immediate benefits.
Identify a single process that is labour-intensive or error-prone, such as packaging. Automating this one area can yield quick wins by improving efficiency and reducing costs almost instantly.
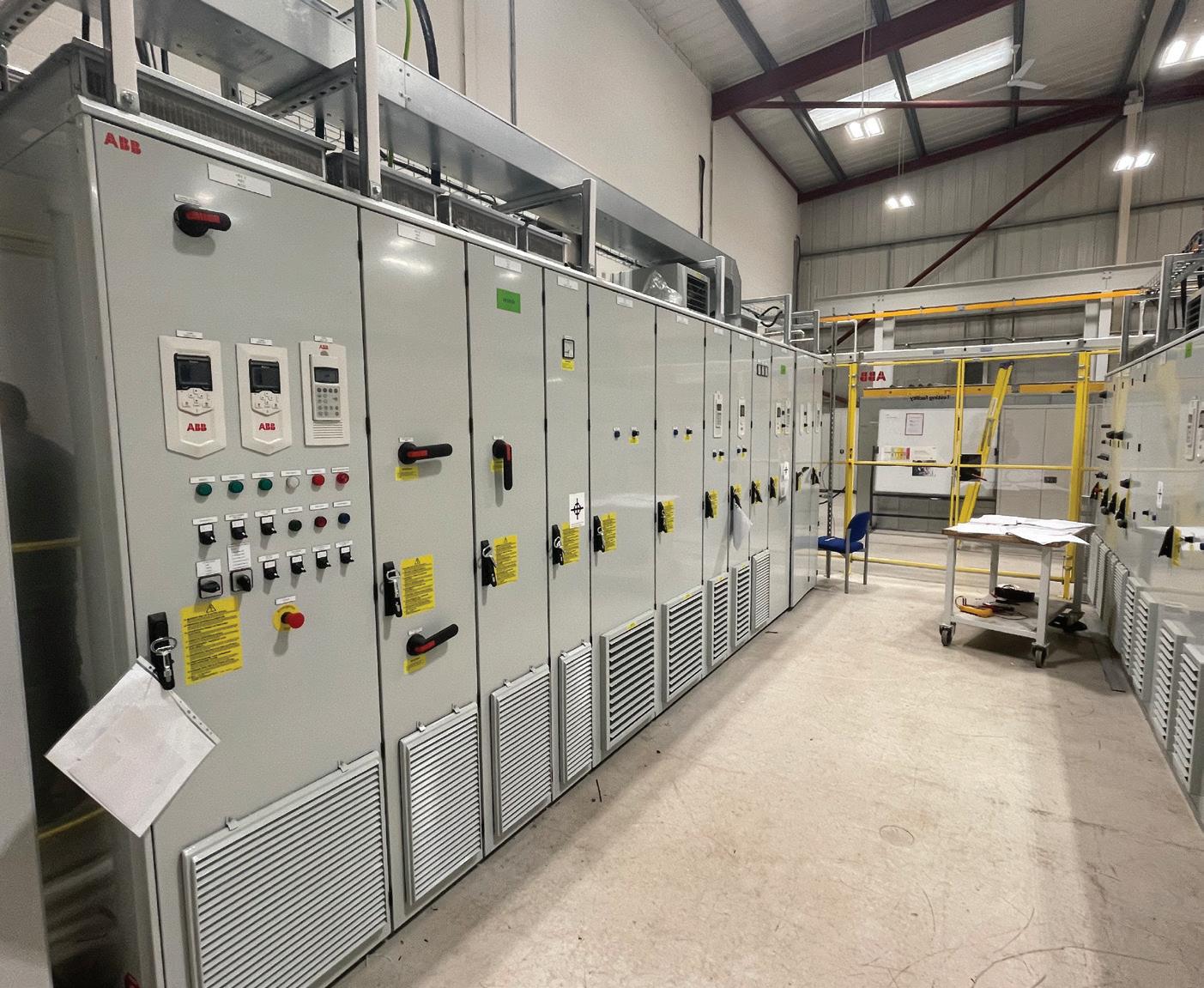
Smaller manufacturers should always consider the return on investment (ROI) when choosing where to start. Even a small project with a high ROI can justify the initial costs and pave the way for future automation.
Modern automation technology is also scalable. As experience is gained, it’s possible to gradually expand automation efforts to other areas, adding modules as needed.
For smaller manufacturers, automation is a journey, not a destination and starts with a single step. By focusing on immediate needs and high-ROI projects, even modest operations can begin to unlock the benefits of automation.
So maybe now is the time to take that first step towards a more efficient and profitable future.
Chris Callander, Editor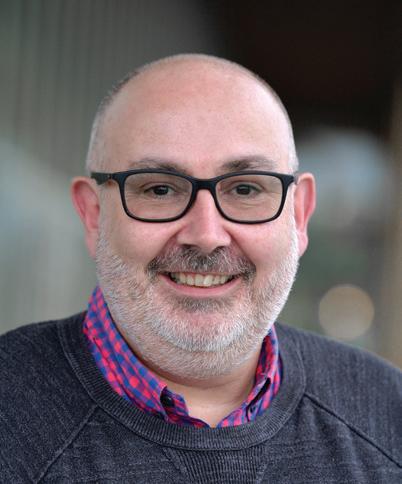
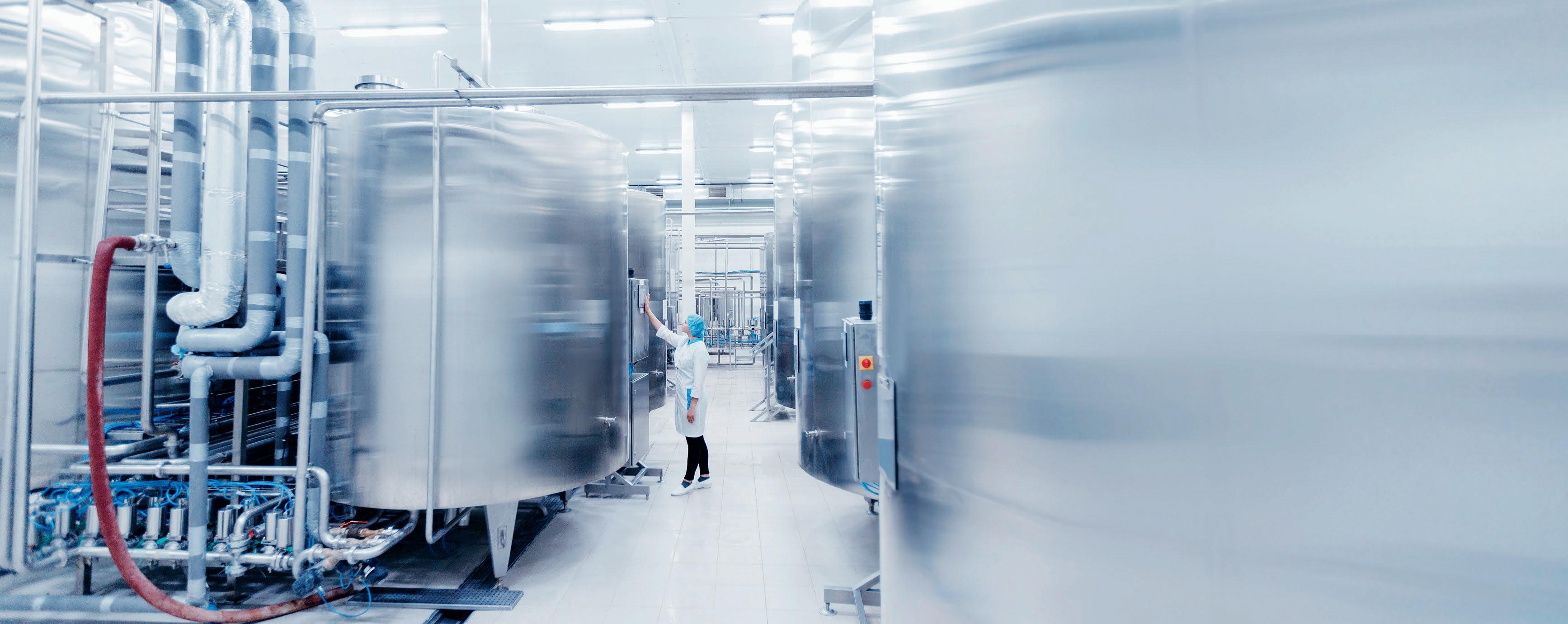

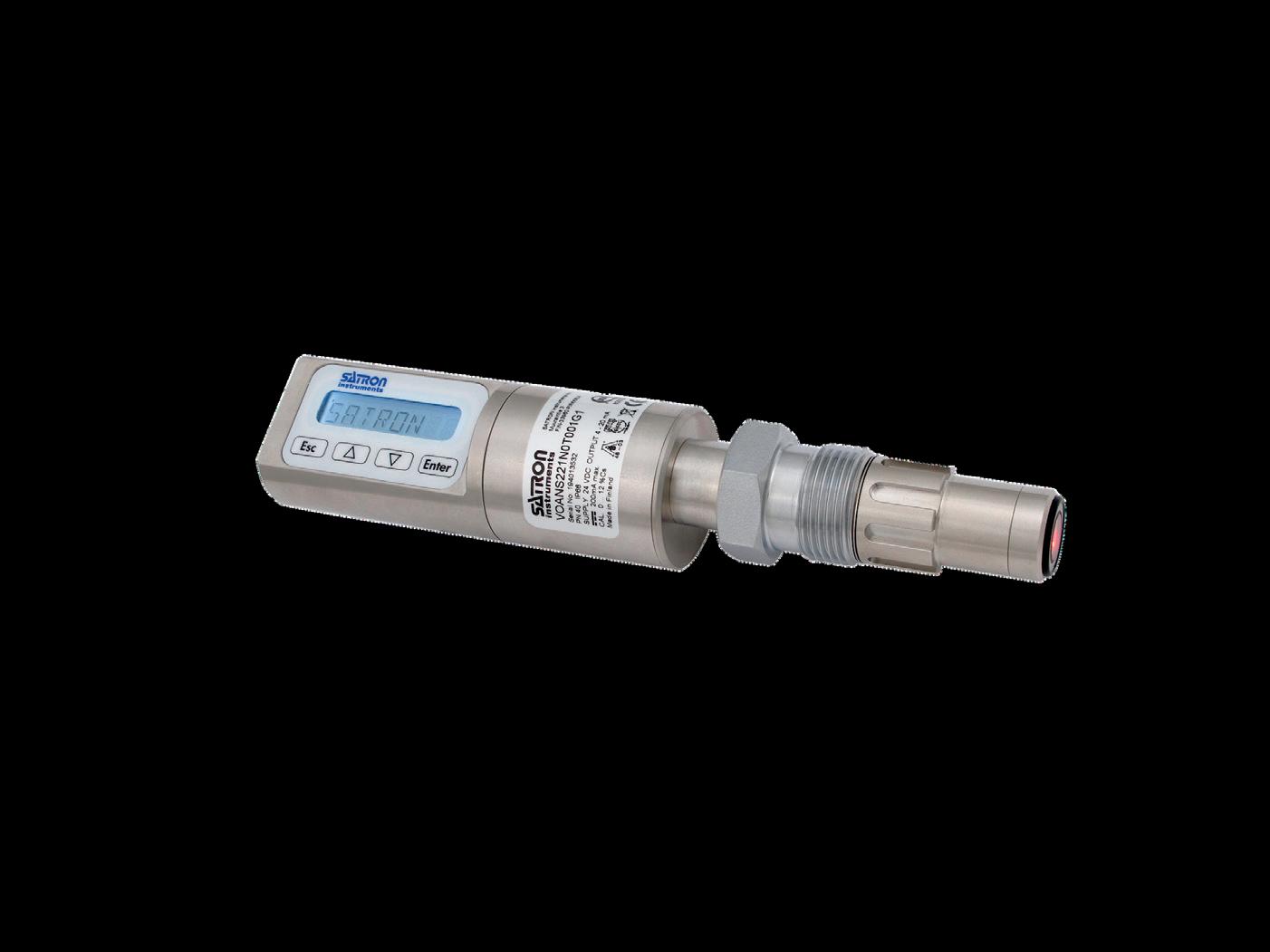
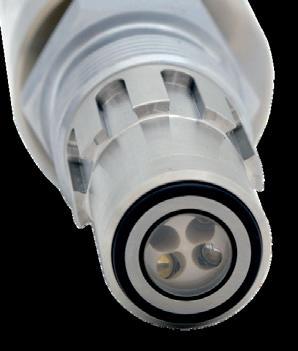


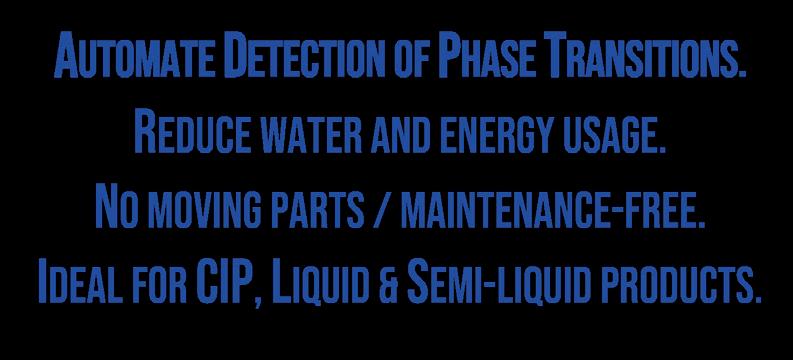
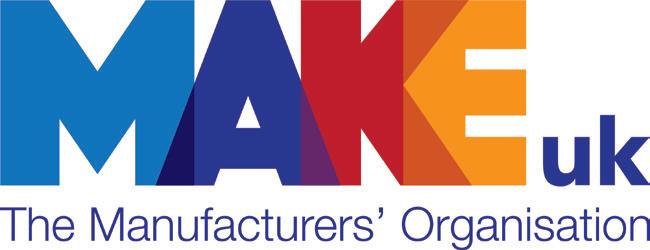
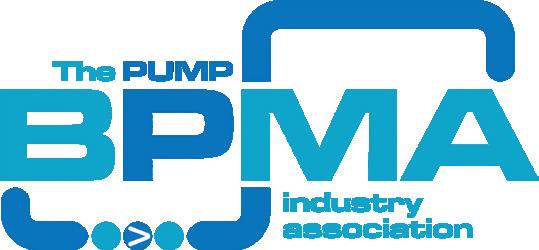
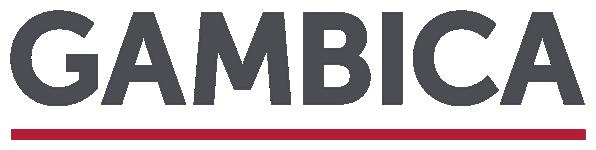
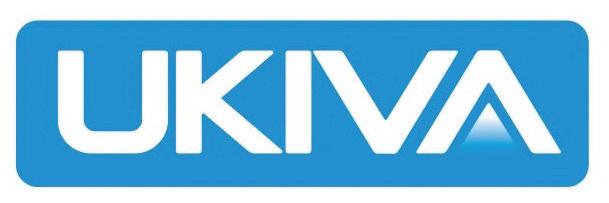

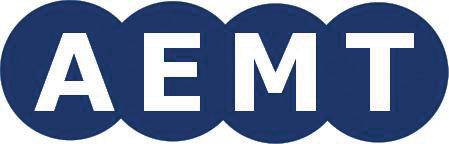



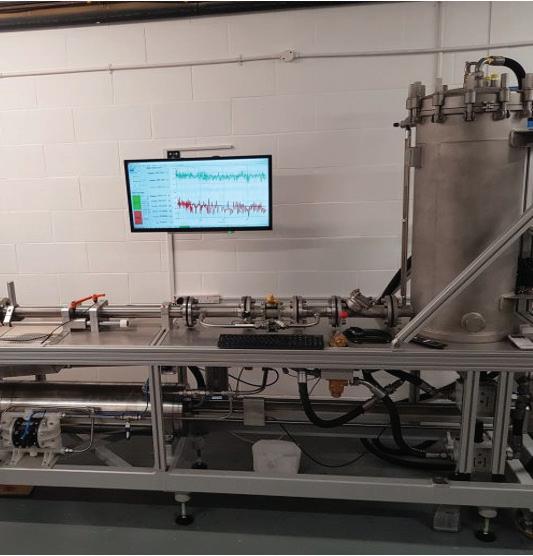
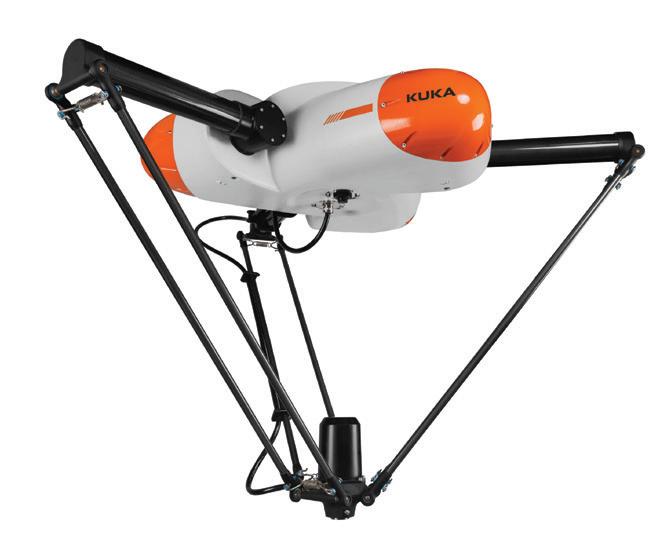
FANUC opens its doors
Demonstrating how automation can help manufacturers address the key challenges facing their business today –namely cost pressures, sustainability targets, and labour shortages – FANUC UK will bring together the country’s leading names from the world of robotics and automation for a three-day showcase event at its Coventry HQ this November. The event will feature over 30 exhibitors, 20+ speakers, 600+ visitors – PLUS the live final of the WorldSkills UK Industrial Robotics competition.
This year’s event (14-16 November 2023, Ansty Park, Coventry) will comprise a mix of live product demonstrations, engaging panel debates and hands-on robot training, enabling manufacturers to experience the latest automation innovations. Attendees will also learn from peers and colleagues about the difference that automation has made to their operation, such as increasing efficiency, cutting costs and alleviating staff shortages.
Leading names from the manufacturing, engineering and automation world will take to the stage across the three days, sharing their knowledge, experience and insight with hundreds of attendees. Influential thought leaders, including FANUC UK’s MD Tom Bouchier, Stuart Whitehead of the Jefferson
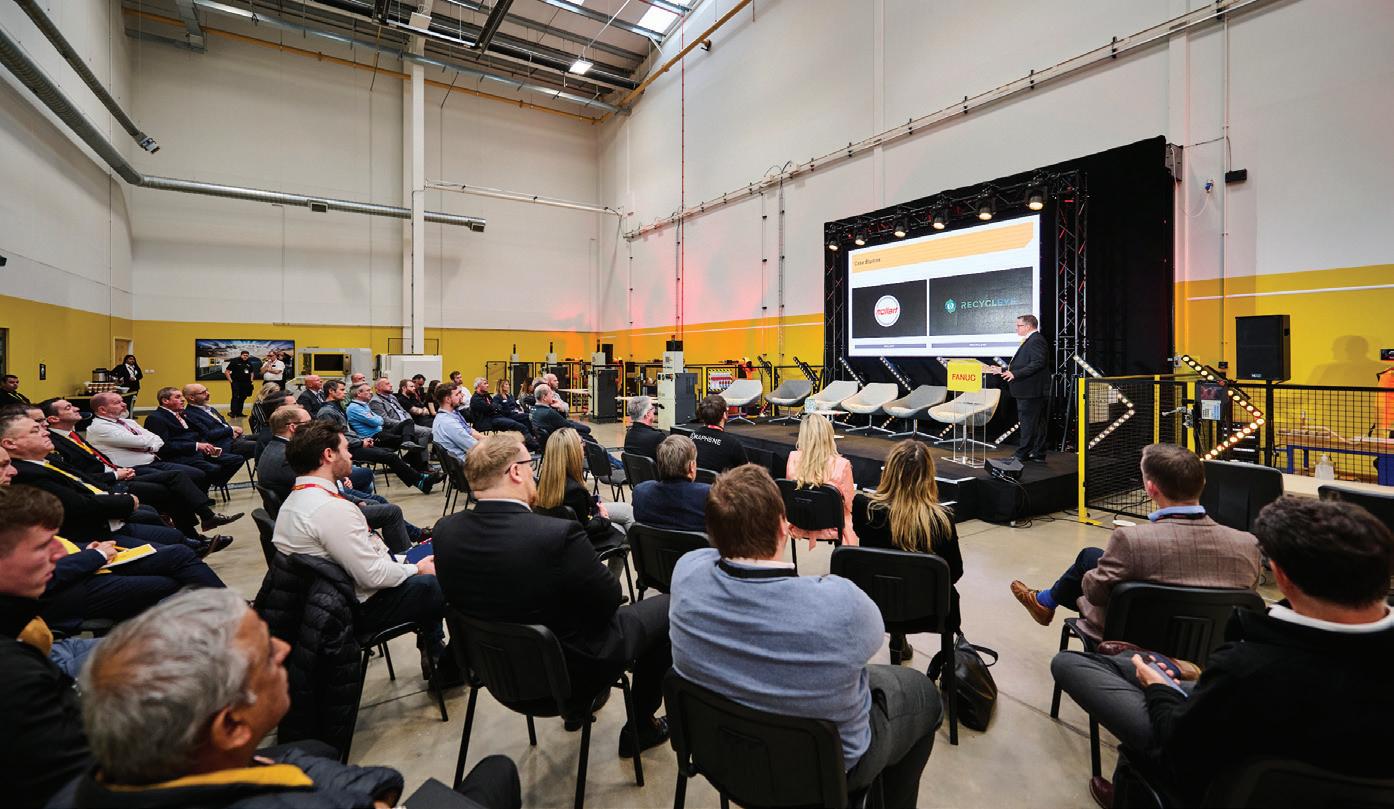
Group, new President & CEO of FANUC EU Marco Ghirardello and Phil Hadfield from Rockwell Automation, as well as leading UK manufacturers, will take part in a series of panel discussions, live debates and presentations on the industry’s most pressing topics.
The first day will focus on the future of UK manufacturing, looking at barriers to future growth, the role that robotics and automation can play in boosting productivity, and the latest technology to ease production and labour headaches.
The second day is devoted to sustainability, including ways to ease the
transition to net zero and innovations to encourage energy efficiency across all facets of the manufacturing supply chain.
On the third day, attention turns to education and ways to inspire the next generation of engineers. As well as the LIVE UK final of the WorldSkills Industrial Robotics competition, visitors can also hear first-hand testimonials from current apprentices about engineering as a career path.
More information, including the programme of each of the three days and details of how to book a place, can be found at the event websitehttps://ukopenhouse.fanuc.eu
Ultra-low voltage motors market worth $6.5bn by 2027
New research by market intelligence firm Interact Analysis shows that the ultra-low voltage motors market is experiencing a period of growth. By 2027, the market will be worth almost $6.5bn, driven by demand from battery-driven applications and a need for greater flexibility in manufacturing and logistics processes. The increased use of mobile robots is having a huge impact on the market for ultra-low voltage motors, and, as a result of this, the supplier landscape will change significantly.
One of the major trends that Interact Analysis has seen across the
manufacturing industry is the need for greater machine flexibility due to the increased number of product variations that automated machines need to handle. As a result of this, the number of small actuation points requiring an ultra-low voltage motor is greater. By 2027, the market for ultra-low voltage motors will be worth almost $6.5bn, growing at a CAGR of 12.6% between 2022 and 2027. Another trend that has been observed is the increasing demand for mobile and industrial robots, which is driving up revenues for the ultra-low voltage market due to their rapid proliferation across manufacturing and logistics.
Due to the impact that demand for mobile robots is having on the ultra-low voltage motors market, the supplier landscape is set to alter dramatically. Three main players, Maxon, Ametek and MinebeaMitsumi, currently dominate the market, but the landscape is highly fragmented. This means that the development of this landscape depends on what solutions suppliers decide to develop within many sectors of the market, particularly mobile robots. There is also an increasing trend towards integrated motors and drives, particularly within the mobile robotics segment, which presents opportunities for different vendors to emerge and gain market share.
New platform from IFR to help SMEs automate
The labour shortage has become one of the most pressing challenges for small and medium-sized enterprises (SMEs) in OECD countries. The manufacturing sector is hit especially hard by high job vacancy rates. Since robots are becoming easier to install, implement and operate, SMEs have greater access to automation. The new Go4Robotics (https://go4robotics.com/) online platform by the International Federation of Robotics (IFR) provides independent guidance for their automation journey.
“The lack of skilled labour is a strong driver for automation in many countries,” said Dr Susanne Bieller, IFR´s General Secretary. “In fact, statistics from the EU say that threequarters of all companies across the EU have a problem attracting workers with the required skills.”
Given a choice, many young people prefer to work in a company that uses future technology. If a robot is operating on the shop floor, the employer can advertise a job to
prospective employees as work that involves controlling a robot. This is often a game-changer. Since the robot takes on the four “Ds” of dull, dirty, dangerous and difficult work, their use is even more attractive. Employees have more time to up-skill for more interesting jobs.
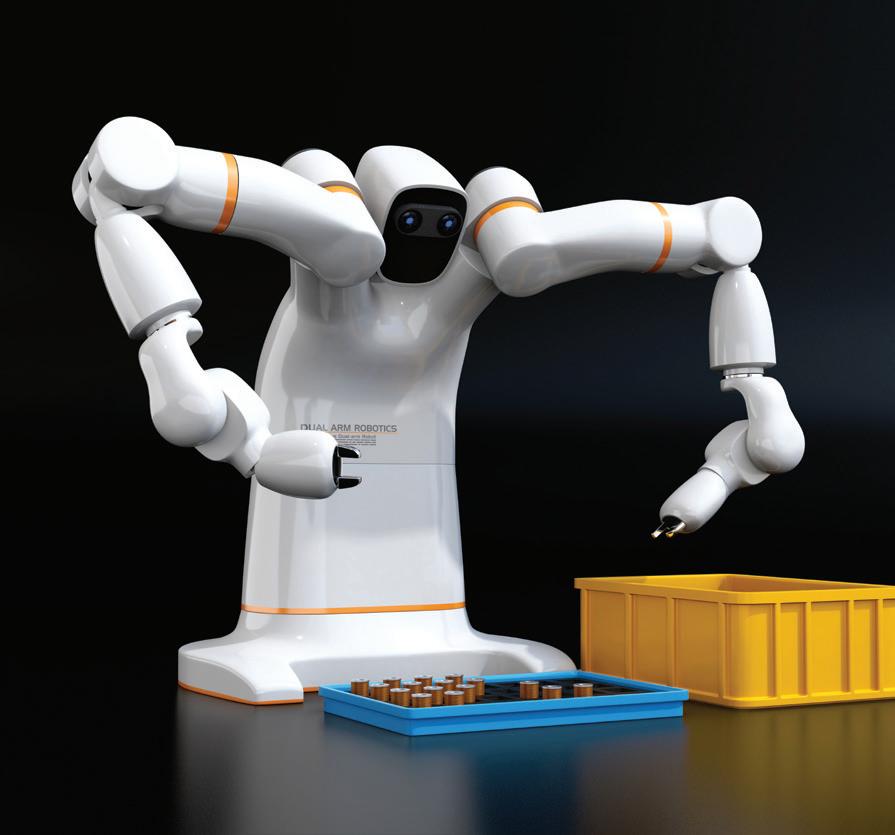
The new online platform Go4Robotics by the IFR raises awareness of the many advantages robotics provide. SMEs will find educational content that comes with a checklist. Experts are dispelling myths about segments that are relatively new to automation. Managers learn how to benefit from new trends like easy-to-program robots for non-experts.
As a non-profit organisation, the mission of The IFR is to promote the use of robotics to address societal challenges and improve the quality of life for all. Its vision is that robotics will revolutionise various industries
and create a better future for all. With almost 100 institutional members from over 20 countries representing over 3000 robotics organisations worldwide, the federation says it offers an all-round view of the world of robotics across industries and countries. Its Go4Robotics campaign aims to provide beginners with easily accessible and understandable information and experts with deeper insights into trends and innovations in the robotics industry.
Nottingham researchers receive share of £19 million committed to battery research
Research at the University of Nottingham into the development of new materials and technologies for nextgeneration batteries is one of four projects to receive additional funding from the Faraday Institution.
The Faraday Institution, the UK’s flagship institute for electrochemical energy storage research, has announced a £19 million investment in four key battery research projects aimed at delivering a beneficial impact for the UK. These existing projects in three research areas – next-generation cathode materials, electrode manufacturing and sodium-ion batteries – have been reshaped to focus on the areas with the greatest potential for success.
As part of this project refocusing and its ongoing efforts to drive impact in energy
storage research, the Faraday Institution recently issued an open call for short, costed proposals for new research topics with tightly defined scopes that strengthen the delivery of these core research projects. The round was highly competitive, with 40 proposals submitted.
Researchers from the University of Nottingham/s School of Chemistry have been awarded £230,000 as part of this project to drive innovation in energy storage technologies with its ‘FutureCat’ project that will transform the UK energy landscape from transportation to the grid.
The Nottingham FutureCat project is led by Dr Lee Johnson together with Professor Darren Walsh, Professor Pete License, and Dr Graham Newton, and is targeting the development of new electrolytes that will open up the use of next-generation cathodes.
The FutureCat project will run over the next two years and cover three key areas. The first is understanding novel redox processes as a route to stabilise both high capacity, high performance, nickel rich and emerging cathodes. The second area is scalable designer morphologies, which builds on the university’s success with doped-LNO in developing reliable, scalable routes to deliver longer lifetime, high energy/ power cathodes through the use of gradient morphologies, co-doped cathodes (with the aim of delivering reversible discharge capacities exceeding 220/mAh/g), single crystal particles and thin coatings. The final area is materials delivery, which is a scale-up of the high nickel W-LNO material previously developed by FutureCat being transferred to the Degradation project for testing in industry-relevant pouch cells.
Enhanced productivity with highperformance error diagnosis
The Schmersal Group is about to launch a new version of the SD Gateway for its SD bus. Users will be able to take advantage of the improved fault diagnostics offered by the new SDG Fieldbus Gateway. This, in turn, will help to increase machine and plant productivity by minimising downtime and simplifying commissioning and maintenance. The device is also user-friendly and easy to install.
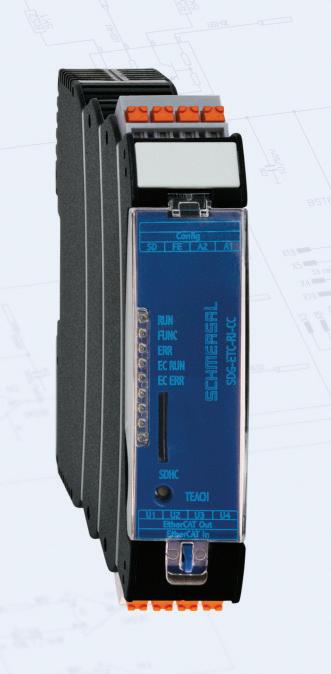
Electronic safety sensors and interlocks with the SD interface can transmit comprehensive status and diagnostic data to a higher-level machine control system. Data from the serially connected switchgear is sent via the SD bus to the SDG fieldbus gateway and then passed on via the fieldbus to the machine control unit – enabling the forwarding of error messages such as overtemperature warnings, faulty actuator warnings and invalid actuator combination messages.
The diagnostic information is transmitted separately from safety signals. Warning notifications enable controlled process shutdown and targeted maintenance so as to prevent process interruptions.
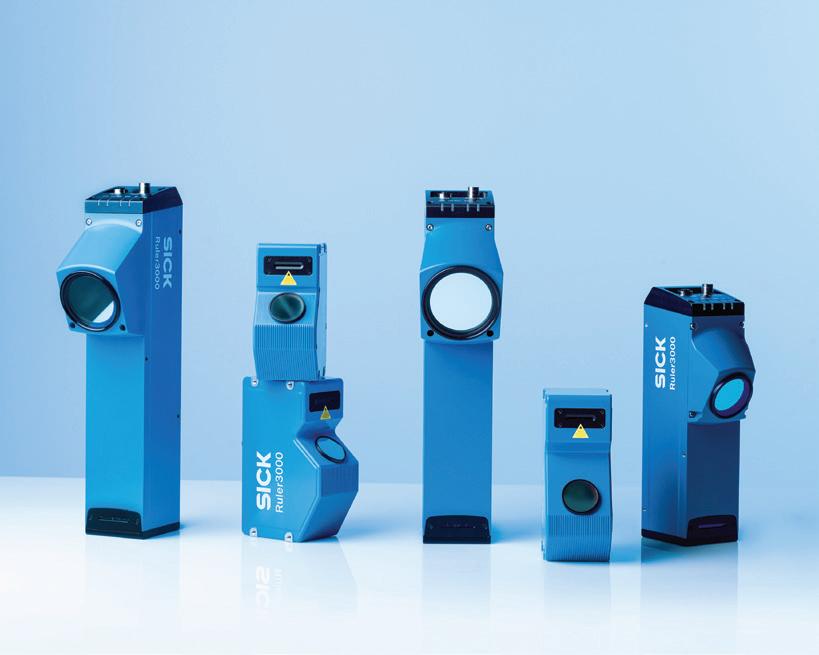
The new variant of the SD Gateway also offers a web server and has a microSD memory card. Event logs can be evaluated in real time via the web interface, and complete diagnostic data from all safety switchgear devices are displayed in plain text in the browser window. In addition, devices, such as interlocks and control panels, can be controlled directly via the web interface, while the microSD card allows event logs to be exported for evaluation and long-term storage. The configuration of the series connection is stored on the microSD card to enable
seamless device replacement in case of error.
An additional and significant benefit of the SD bus system is being retained in the new Gateway: by connecting sensors and interlocks with the SD bus in series (an SD Gateway can communicate with up to 31 safety switchgear devices), this safety solution enables extremely lean wiring and reduces costs without sacrificing Performance Level (series connection for applications up to PL e). Setup and commissioning of an SD installation have been designed to be as convenient and straightforward as possible, and all devices receive addresses from the Gateway automatically.
www.schmersal.co.uk
SICK’s extended Ruler3000 family focuses on the finest details
SICK has expanded its nextgeneration Ruler3000 family to focus the outstanding speed and precision of its top-flight 3D streaming cameras on the finest details of high-quality, high-resolution 3D inspection and measurement tasks. With the launch of three compact cameras, as well as an additional mid-range variant, the Ruler3000 cameras now span fields of view between 26.6mm and 1680mm, down to heights of 0.8 micrometers.
The SICK Ruler3000 has set a new standard by combining the outstanding image quality of SICK’s Ranger3 streaming camera with the convenience of a built-in laser, pre-selected optics and factorycalibrated fields of view. Since its launch two years ago, vision specialists all over the world have taken advantage of the Ruler3000’s unmatched processing speed and ease of integration. Already, it has solved challenging 3D applications as diverse as inspecting
railway tracks, windmill blades and tire walls, measuring and portioning meat products, and volume dimensioning of legal-for-trade freight.
Now, the SICK Ruler3002, 3004, and 3010 cameras open up the high performance of the Ruler3000 to guaranteed fields of view down to 26.6mm. The addition of a highpowered blue 3R laser gives the three smaller cameras the rapid exposure times necessary to capture the tiniest three-dimensional details at rapid production speeds. With more compact dimensions, these cameras, therefore, extend the capabilities of the Ruler3000 to the minutest details required to inspect electronics and consumer goods assemblies, printed circuit boards and semiconductors. The addition of the mid-range Ruler 3060, with a field of view of 740mm, is targeted at applications in the automotive and consumer goods industries.
The SICK Ruler3000 achieves outstanding repeatability on light, reflective and metal surfaces, and a new patent-pending Surface+ technology adds another image dimension that reveals even the tiniest scratch on smooth, shiny metal surfaces such as battery housings.
www.sick.co.uk
Mobile freedom with AGV’s Material transport in dynamic environments
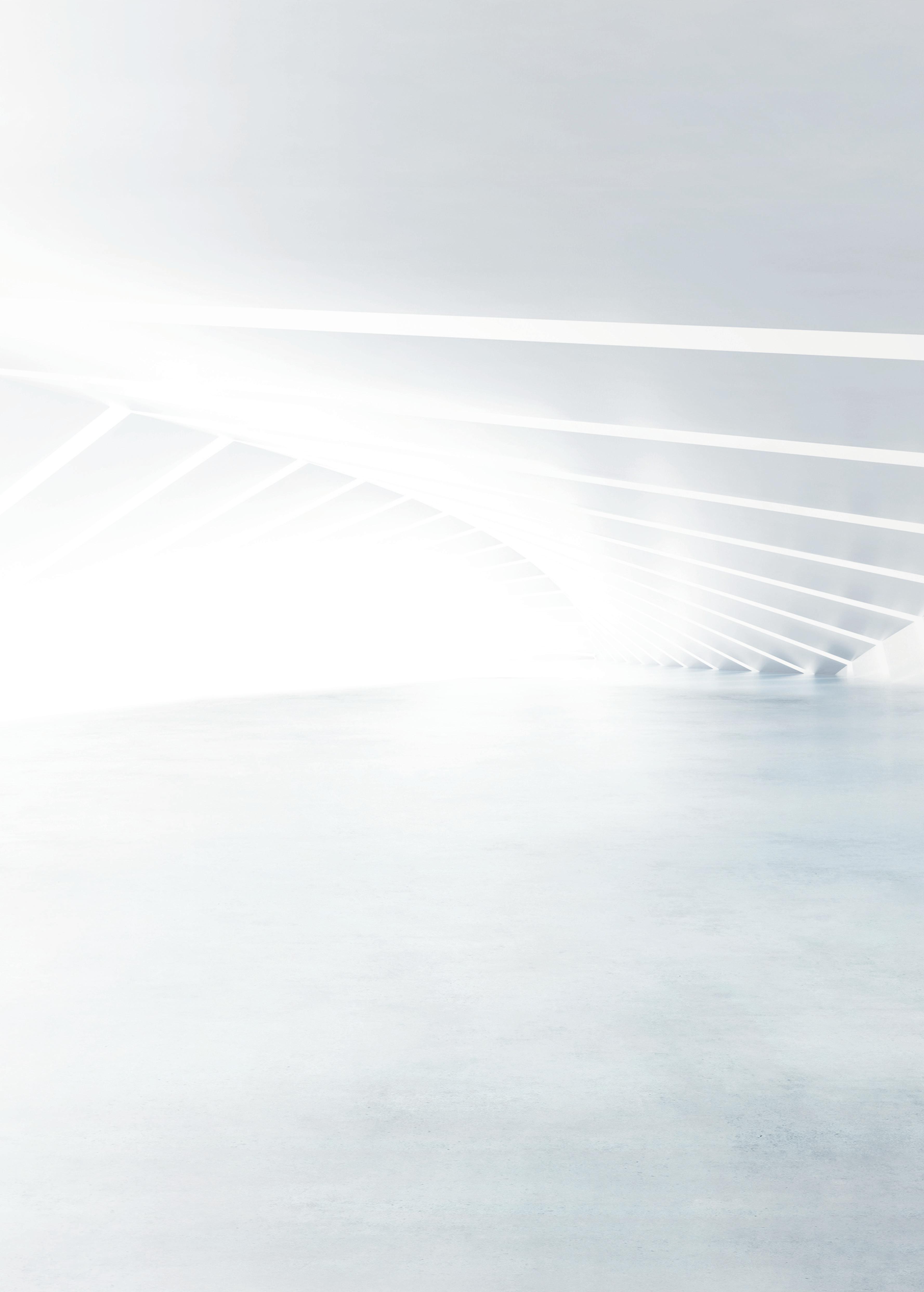
The KMP 600-S diffDrive mobile platform from KUKA opens up new avenues and provides greater flexibility for production intralogistics. The automated AGV has a payload of up to 600 kilograms, needs no safety fencing enabling maximum freedom of movement and laser scanners mounted at the front and rear provide maximum safety, allowing for high speeds in all directions of travel, when cycle times require it.
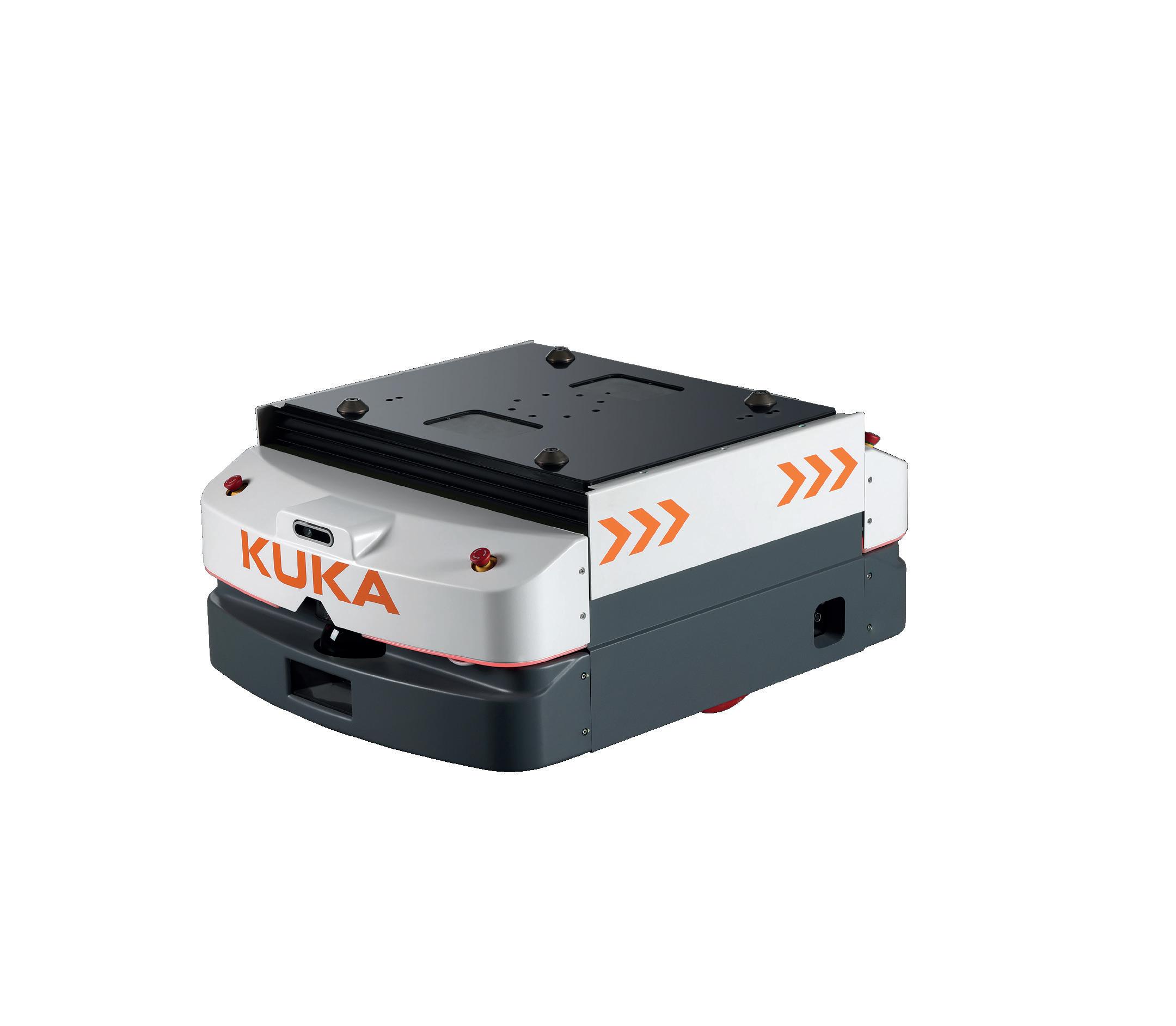
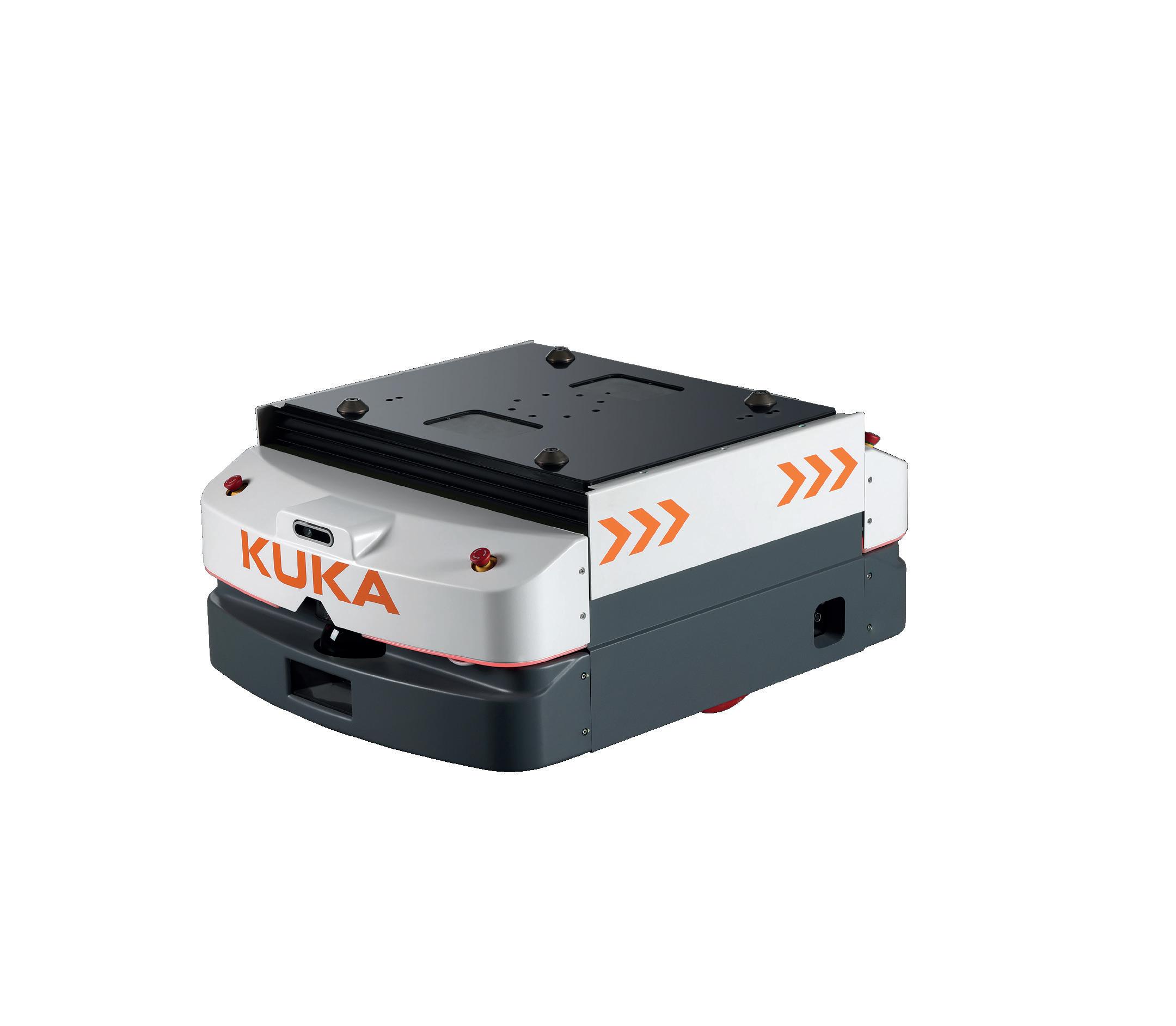
KUKA Robotics UK Ltd.
T: 0121 505 9970
E: sales.uk@kuka.com
Effective protection for submerged and shoreline pipelines

For over 50 years, SeaShield corrosion control systems have provided enduring protection on jetty piles and marine structures from the devastating effects of corrosion. The recent addition of the SeaShield 70/80 System is a response to the industry’s need for a robust, UV-stable, easyto-apply system designed specifically for submerged and shoreline pipelines situated in aggressive marine environments.
The SeaShield 70/80 System, from Winn & Coales (Denso) Ltd, was created by combining a water-displacing petrolatum tape and primer with a tough PVC-backed bitumen tape (the SeaShield 80 System) and a moisture-cured glass-fibre reinforced outer wrap (from the SeaShield 70 System). The resulting system provides exceptional mechanical and impact strength and is available in three variations to suit the level of protection required.
The flexibility offered by the SeaShield 70/80 System marked it as the ideal choice for a recently completed project on the West Sussex coast. Leith Hill Plant Ltd., on behalf of Arun District Council, applied the heavy-duty version of the system in stages, both off-site and in-situ, to protect newly laid pipe sections on two outfall pipes that had previously suffered
LITF series ignites new phase of din rail power
Relec Electronics has announced the availability of MORNSUN’s new LITF series, a range of high-quality 3-phase input DIN rail AC-DC power supplies. The series aims to realign industry standards with its high reliability and compact power density. Engineered for a wide variety of industrial applications, the LITF series boasts a wide input voltage of up to 600Vac and an impressive efficiency rate of up to 95.6%.
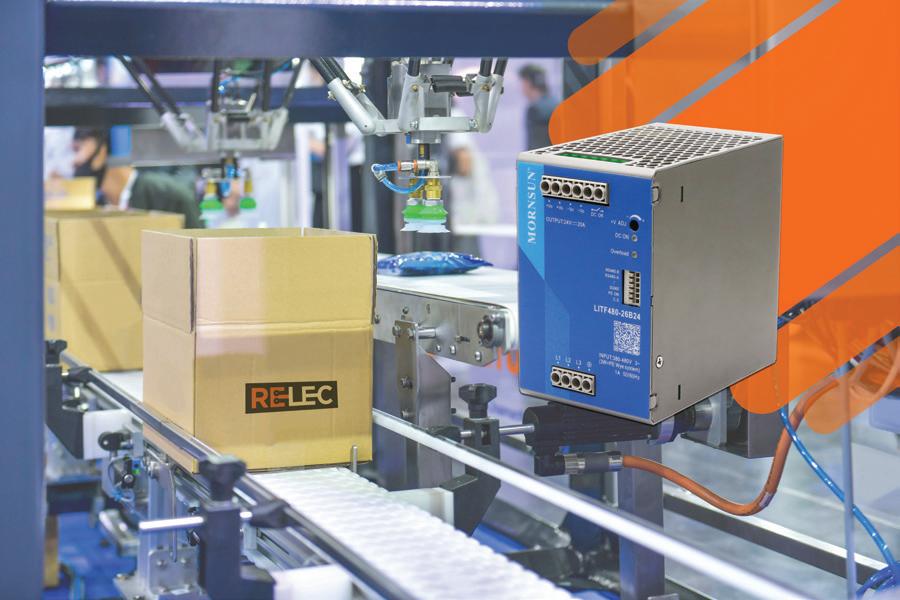
Active power factor correction, with PF>0.95, enhances the series’ energy efficiency and reduces harmonic distortion, complying with EN61000-3-2 standards.
Built for challenging conditions, the LITF power supplies operate effectively in temperatures between -30 and +60°C without performance degradation. They also come with a 150% peak load capability, making them suitable for motor and highly capacitive loads, allowing the units to handle sudden increases in load without sacrificing
performance.
The LITF series is certified according to several safety standards, including UL61010
Over Voltage Category level III, EN/UL/BSEN62368, and UL508 and ANSI/ISA71.042013 level G3 standard, making them suitable for use in polluted industrial settings. These certifications ensure that the power supplies meet stringent safety requirements, adding an extra layer of reassurance for users.
The series also features the RS485 communications protocol, enabling centralised control and monitoring of multiple power supply units. This adds to the system’s adaptability and integrability. Additionally, the LITF series supports parallel operation for applications requiring higher power levels or redundancy.
Overall, the LITF series is poised to redefine the landscape of 3-phase din-rail power supplies by combining advanced features and compliance with the latest safety standards, showcasing MORNSUN’s engineering skills and Relec Electronics’ dedication to bringing the most innovative products to the market.
www.relec.co.uk/LITF-series
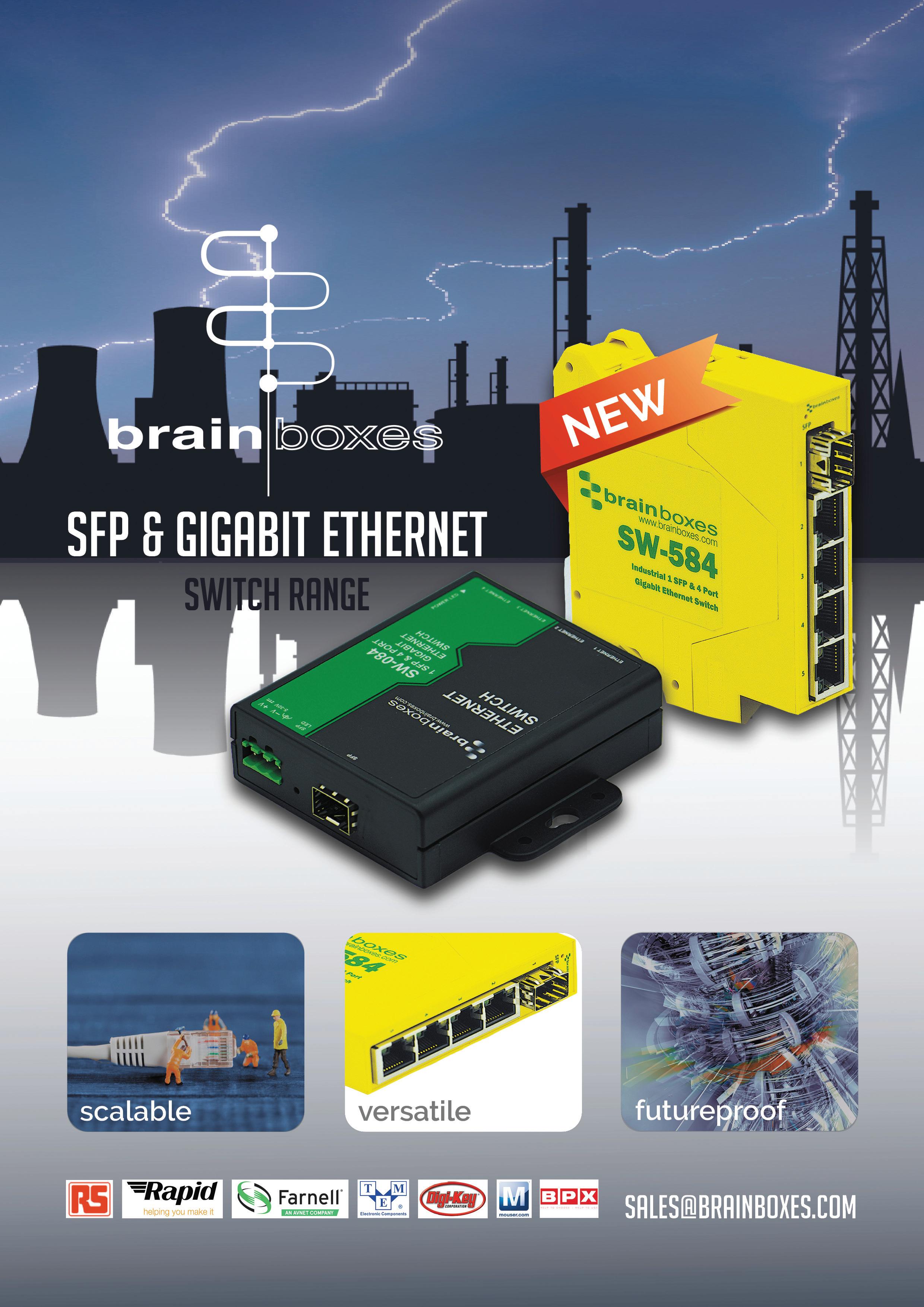
Keep a close eye on air and industrial gases
Sensors in the new SD range from ifm electronics have been developed specifically to allow users to accurately monitor the usage of compressed air and other industrial gases. This makes them an ideal choice for use in bottling and packaging machines in the food industry, and in welding, cutting, soldering and similar processes where protective gases are used.
All sensors in the SD range monitor volumetric flow rate and have an integrated totaliser function for measuring total flow. This makes it easy to allocate costs precisely in compressed air installations and in processes where costly gases such as argon, carbon dioxide, nitrogen and helium are used. Additionally, the sensors monitor gas temperature and pressure for corrected volume calculation, eliminating the expense and inconvenience of using separate sensors to measure these parameters.
SD sensors are available in versions to suit a range of gases. SDX5XX versions are designed for use with compressed air, while 4-in-1 SDX6XX versions have integrated characteristics for argon, carbon dioxide and nitrogen as well as air, and SDX8XX versions are optimised for use with helium. Depending on the sensor model, flow rates from just 0.05m3/hr up to 700m3/hr can be accurately measured. For all types of media, the temperature range is -10 to +60ºC and the maximum operating pressure is 16 bar.
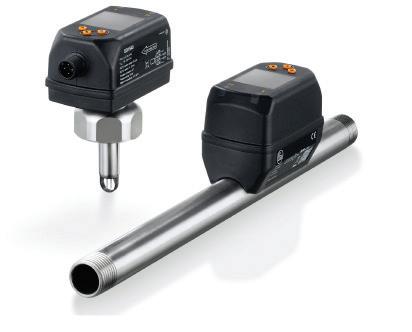
A built-in TFT display, which offers a choice of four user-selectable graphic layouts, makes it easy to see and interpret measurements made by the sensors, while the provision of both analogue, pulse and IO-Link outputs makes the devices easy to integrate into almost any type of control system. Flexible switching outputs related to
programmable setpoints are also provided.
As an aid to fast and convenient set-up, the SD sensors offer a simulation mode, which allows custom outputs and display settings to be checked before putting the sensor into service. A flash mode is also supported, which allows users to quickly identify sensors where measurements have reached or exceeded a setpoint.
www.ifm.com
More efficiency for simple motors
The drive specialist NORD DRIVESYSTEMS is known for its IE4 and IE5 motors but also offers reliable solutions for lower performance ranges. The company’s new single-phase asynchronous motor not only has a new design but also features an improved efficiency by one efficiency class.
For suppliers to the construction, food and agricultural industries as well as amusement park operators, the new singlephase asynchronous motor from NORD DRIVESYSTEMS is an attractive offer. The company has thoroughly revised its existing single-phase asynchronous motor.

The new single-phase asynchronous motor can be used in a power range from 0.12 to 1.5kW as before, but now corresponds to efficiency class IE2 according to the Ecodesign Regulation 2019/1781. A new electronic relay replaces the previous mechanical one. The design was also refreshed, and the capacitors are mounted in the terminal box. Therefore, the motor now also complies with protection class IP66 and is
protected against the entry of dust and water.
“For simple applications, for example, in mobile concrete mixers or pumps, our revised single-phase asynchronous motors are a cost-effective and efficient drive solution,” emphasised Jörg Niermann, Head of Marketing at NORD.
The motor is approved for use in many regions of the world thanks to certification according to the European CE mark, the Chinese CCC standard and the UKCA mark for Great Britain.
Up to 30% less assembly time during onsite installation enables efficient equipment changes.
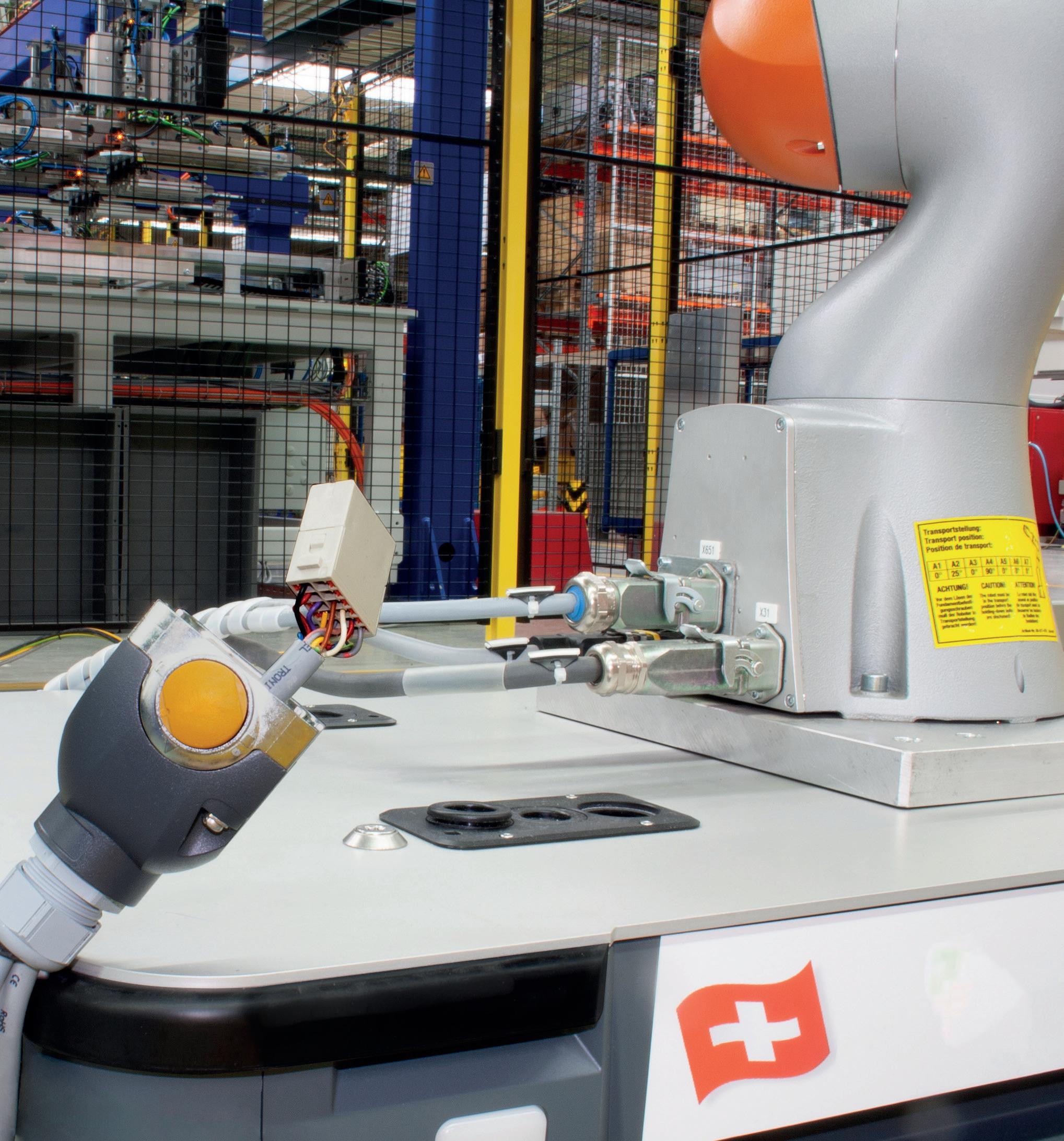
Han® Push-In expands the largest variety of termination technologies for industrial connectors.

■ Up to 30% less assembly time with direct insertion of the conductor into the contact chamber
■ Easy handling due to toolless termination
■ Cost savings compared to alternative termination technologies
■ Maximum flexibility - suitable for ferrules, stranded wires and solid conductors
■ Compatible with identical products with other termination technologies
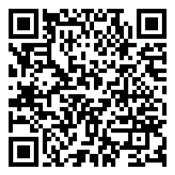
One Range. No Limits: www.HARTING.com/push-in
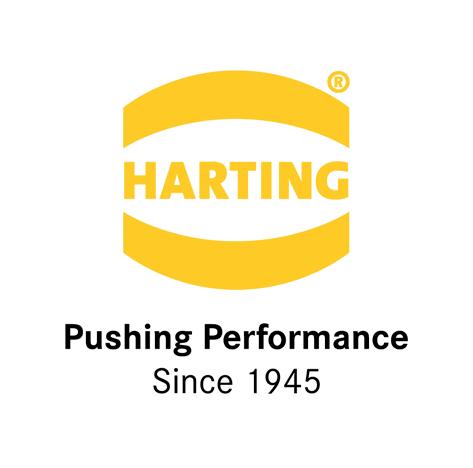
The skills gap: There’s more to do but help is at hand
GAMBICA’s Sector Head for Industrial Automation and Test and Measurement, Nikesh Mistry, believes there is still more manufacturers can do to help alleviate the skills gap, but explains they are not on their own in working to address the challenge.
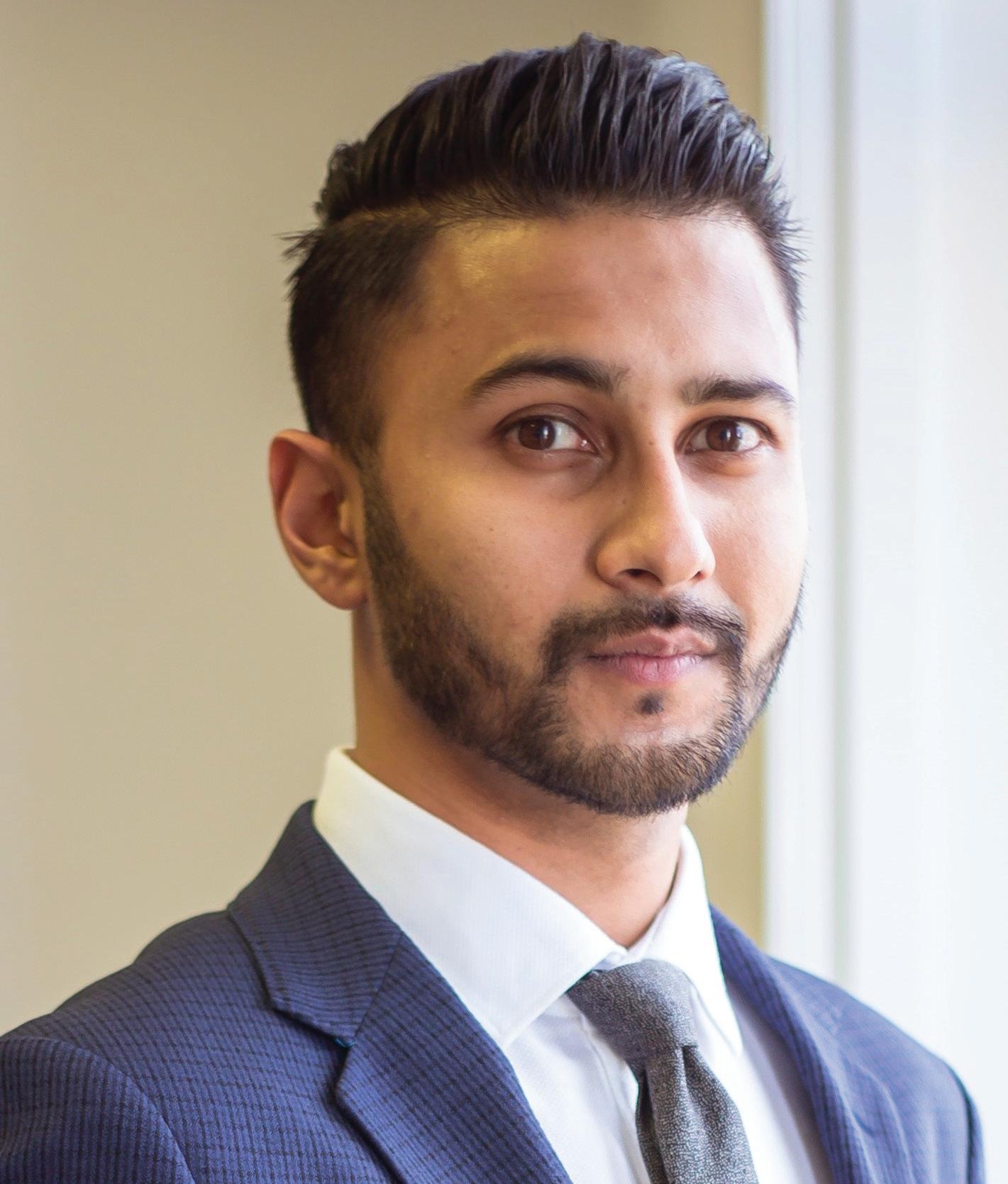
The manufacturing industry is facing a major skills gap. The demand for skilled workers is increasing as the industry becomes more automated and digitised. However, the supply of skilled workers is not keeping pace. This is a major challenge for the industry, as it could lead to a loss of competitiveness and innovation.
There are several reasons for the skills gap in manufacturing. One is that the industry is changing rapidly. New technologies are being introduced all the time, and workers need to be constantly upskilling to keep up. Another reason is that the manufacturing industry has never been advertised as the most attractive career for younger generations. The industry has a reputation for being dirty, dangerous, and low-paying. But most of us delving into the modern manufacturing world know that this isn’t always the case and that we need to start erasing these old-fashioned stereotypes in our industry.
There are a number of things that can be done to address the skills gap in manufacturing. One is to invest in training and education. Manufacturers have to provide their employees with the skills they need to use the latest technologies. They also need to work with schools and colleges to promote manufacturing as a career choice. It is the only way to increase the attractivity and widen the knowledge that the youth have of our industry.
A little also needs to be addressed regarding suitable working conditions postpandemic; manufacturers need to ensure that their factories are clean, safe, and wellpaying. They also need to offer flexible work arrangements and other benefits that appeal to young people.
By taking these steps, manufacturers can address the skills gap and ensure they have
the workforce they need to succeed.
If certain manufacturers were to partner with local schools and colleges to develop apprenticeship programs, this would allow students to learn the skills they need while in school. GAMBICA has begun to address this issue by forming our University and Industry Collaboration Group, in which our industry experts and academic members meet to work on policy, collaborative research, STEM and more.
Manufacturers can also offer on-the-job training and development programs. This will help employees to upskill and stay up-to-date on the latest technologies. This is another area that GAMBICA has begun focusing on to support the future workforce, by forming a ‘Young Council’ to work on STEM and also on sustainability and personal development. This new initiative targets employees from member companies in the first ten years of their industrial career to work together and decide where GAMBICA can assist them in their future progression.
By creating this culture of continuous learning and opportunities, future generations are encouraged to get more
involved, widen their understanding, and develop their future careers.
With digital technologies, we can use data analytics to identify skills gaps and focus on more heavily targeted areas. This will help manufacturers to refine their training and development efforts more effectively.
GAMBICA also aims to leverage ties with the government and other stakeholders to develop policies supporting the manufacturing industry. This could include providing funding for training and development or creating tax breaks for manufacturers that hire apprentices.
By taking these initial steps, we believe we can help manufacturers ensure that they have the workforce they need to compete in the global economy.

LiftEx 2023, a must visit for anyone in manufacturing
LiftEx 2023 is the unmissable global showcase for the Lifting Industry, taking place at the Exhibition Centre, Liverpool, on 21-22 November 2023. The annual flagship event of the LEEA (Lifting Equipment Engineers Association) is free to attend, and registration is open now at bit.ly/LiftEx23
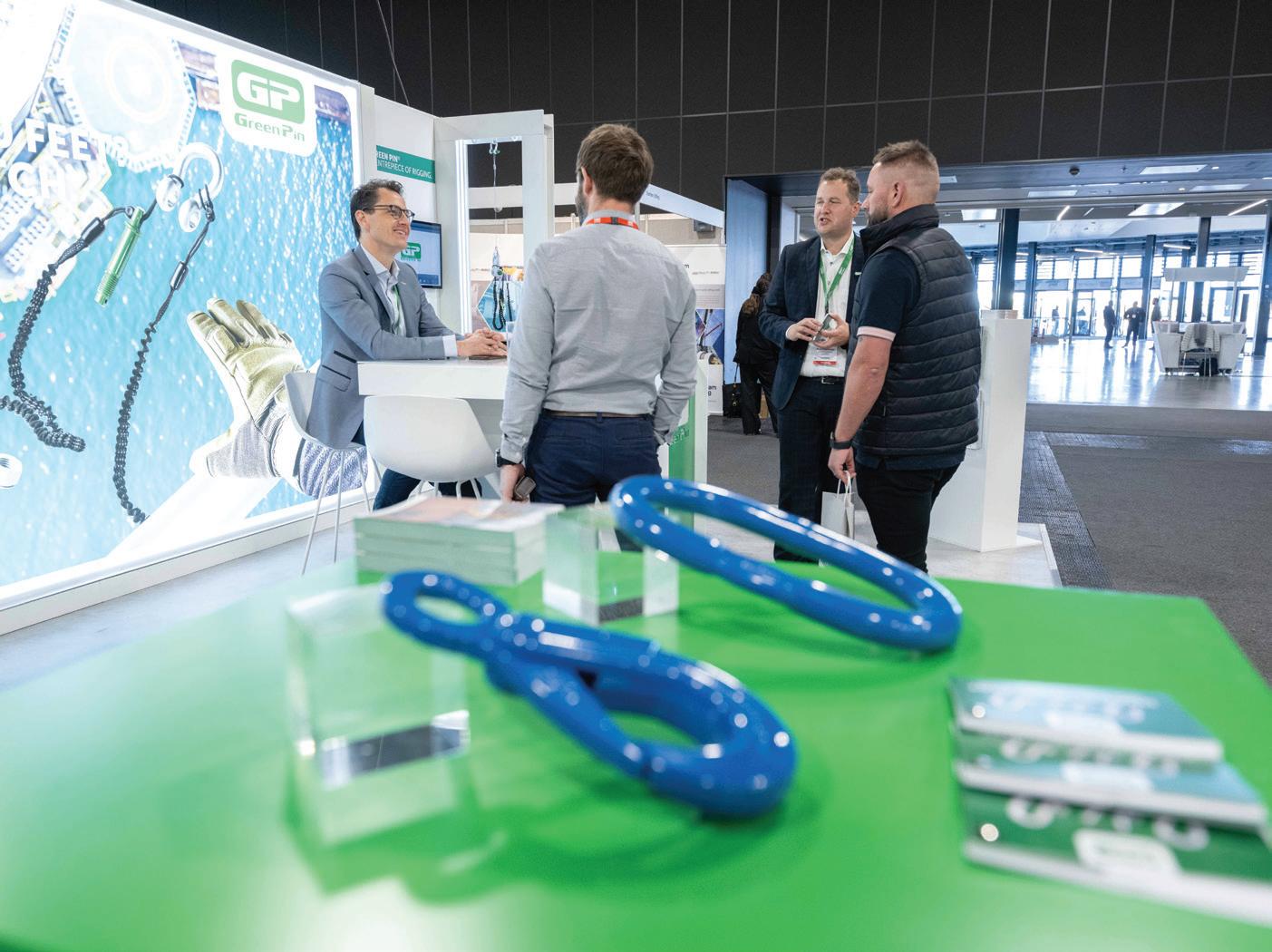
LiftEx 2023 is an essential event for the manufacturing sector.
Plants and factories use a wide variety of cranes, hoists, platforms, cradles and their associated chains, ropes, slings and other tackle to lift goods during production and lineside support.
Reliability leading to minimised downtime is the key to manufacturing efficiency, but it is safety that is paramount in any lifting operation. One of the best ways manufacturing and production operations can mitigate the risk of an inspection by health and safety authorities is to ensure that when procuring lifting equipment or supporting services, they look for the LEEA logo. This shows that the equipment or service provider is an association member and has, therefore, undergone a rigorous auditing process to uphold LEEA’s ‘gold standard’ and provide customers with the assurance of excellence.
LEEA members are driven by quality and commitment to the highest possible practices. The association is established across the globe as the leading representative body for all those involved in the lifting industry worldwide and contributes to the development and dissemination of legislation, regulation and ‘best practice’ guidance. Through its rigorous auditing scheme, the LEEA gives assurance that members’ equipment and procedures are both compliant and safe. Training is promoted, and LEEA assesses experience and qualifies by examination to indicate that people are competent to specify, maintain, inspect and take responsibility for the safe operation of lifting equipment of all kinds. Safety underpins everything the LEEA has
been doing throughout its almost 80-year history and will continue to do so going forward. Zero accidents and injuries from working at height is the association’s prime goal, with members around the world united in the desire to make industry safe.
Best practice abounds at LiftEx
Celebrating its 18th year in 2023, LiftEx offers the best opportunity to find the LEEA logo on a whole host of lifting equipment, products and services from its member companies. These companies operate in a forward-looking lifting industry that is always innovating, with constantly developing technologies – including AI, virtual reality simulation, condition and load monitoring, remote control and anti-collision systems –
spreading throughout the sector to reduce risk from working at height.
The dedicated event addresses many different challenges, solutions, regulations and best practice advice under one roof. This makes LiftEx the ideal venue for anyone involved with, or responsible for, lifting equipment in the manufacturing sector to join over 1,500 industry professionals in catching up with suppliers and exploring their latest innovations, viewing demonstrations and gaining valuable lifting knowledge across two days.
Expertise and industry insights will be shared through informative speaker sessions and speciality programmes designed to help visitors in their everyday roles and delivered by the LEEA team and industry experts. Topics on the agenda include the latest in
safety regulations, technology innovations, recruitment strategies and industry best practice. The event will also welcome careers advisors, teachers, universities, colleges and regional boards. They all make a vital contribution to the lifting equipment industry’s sustainability by engaging with the next generation of talent and attracting them into the lifting sector.
With CoreRFID, the provider of Lifting Inspection software and RFID technology, as the headline sponsor of the event, joining other sponsors, Rope and Sling Specialists, Green Pin and Delta, this year promises to be the best LiftEx yet. Among almost 100 exhibitors on the show floor, over 20% will be appearing at LiftEx for the first time.

A show full of lifting innovation
On display will be a broad array of lifting equipment solutions from companies such as Atlas Winch & Hoist Services, Cromax, Delta Hoisting Equipment, Foster Cranes, George Taylor Lifting Gear, Green Pin (Royal Van Beest), Hird, JD Neuhaus, Mipromet, Modulift, Nautilus Hooks, Pinpoint Manufacturing, Rope and Sling Specialists (RSS), TTC Lifting, Tusk Lifting and Worlifts. Visitors interested in materials handling equipment will find Davinder Technical Services, GGR Group, Lift Turn Move, Probst, Prolift Handling and Tracked Carriers. Chains, ropes and accessories will be featured by companies including Bridon Bekaert, Codipro, European Management & Marine (EMM Corp), Ferryl, Hendrik Veder Group, Latch and Batchelor, Lift Turn Move, Lift-Tex Heavy Lift Slings, RUD Chains, Sahm Splice, Talurit and William Hackett Chains. There will be slings and rigging from Aberdeen Web, Crosby, Dolezych, Hendrik Veder Group, Petersen Stainless Rigging, PMS Industrie and Suhbo Industrial Co. Exhibitors displaying height safety equipment include Guardian Fall, North Sea Lifting, RidgeGear, SafetyLiftinGear, Safehold, SpanSet, Tiger Lifting, Trans-Web and YOKE Industrial Corp. There will be load monitoring equipment from DLM, Load Monitoring Systems (LMS) and Red Rooster Lifting. A range of IT solutions will be shown from companies, including CoreRFID, Formability, Onix Work, RiConnect and Tele Radio UK.
Stands featuring load moving and transport include Liftket UK. Test machinery can be seen from Structure-flex, and there will be administrative services exhibited by IBS Industrial.
There will be organisations such as the Career Transition Partnership (CTP), the MoD’s official provider of Armed Forces Resettlement for over 13,000 skilled and experienced individuals who leave the military. The military trains and employs many personnel with direct experience in lifting engineering – think of swapping an engine out of an aircraft or a tank, or changing a propellor shaft on a ship. Many service personnel, therefore, have the qualities craved by the lifting industry. Through its Military Transition scheme, LEEA is connecting those transitioning from the armed forces into civilian life and their potential employers. Employers visiting LiftEx can find out how to access this pool of service leavers with a wide range of transferable skills.
MND Association, LEEA’s chosen charity for 2023, will have a stand as will LEIA Assessment, the sole end point assessment organisation for the Level 3 Lifting Equipment Technician apprenticeship available in England. Qualitrain will also be on hand to discuss training. LEEA itself will, of course, have its usual prominent stand for visitors to meet and engage with the association’s team.
A great networking experience
In addition to the traditional exhibition activities on offer, there will be plenty of time for members to socialise. For example, the night before the exhibition, there is a reception for LEEA members at Liverpool FC’s world-famous and legendary Anfield Stadium, with former players in attendance. On the middle evening of 21 November 2023, there will be the fifth annual LEEA Awards ceremony, a prestigious event exclusively for members, where LEEA recognises and celebrates excellence. There are ten awards: five for individuals and five for teams, spread across several categories such as innovation, safety, sustainability, training, and personal development. There will be around 300 guests at the Rum Warehouse for the ceremony, which is hosted by special guest Jason Manford, so it’s sure to be the best night out in Liverpool and the Lifting Industry’s party of the year.
For information, visit liftex.org/liftex-liverpool-2023
For a free ticket, visit bit.ly/LiftEx23
www.leeaint.com
Drive service workshop takes shape
ABB has spent the summer putting the finishing touches to its upgraded drive service workshop in Coalville, Leicestershire. MEPCA caught up with Neil Rayns, Drives Workshop Manager, to see how things are going ahead of September’s grand opening.
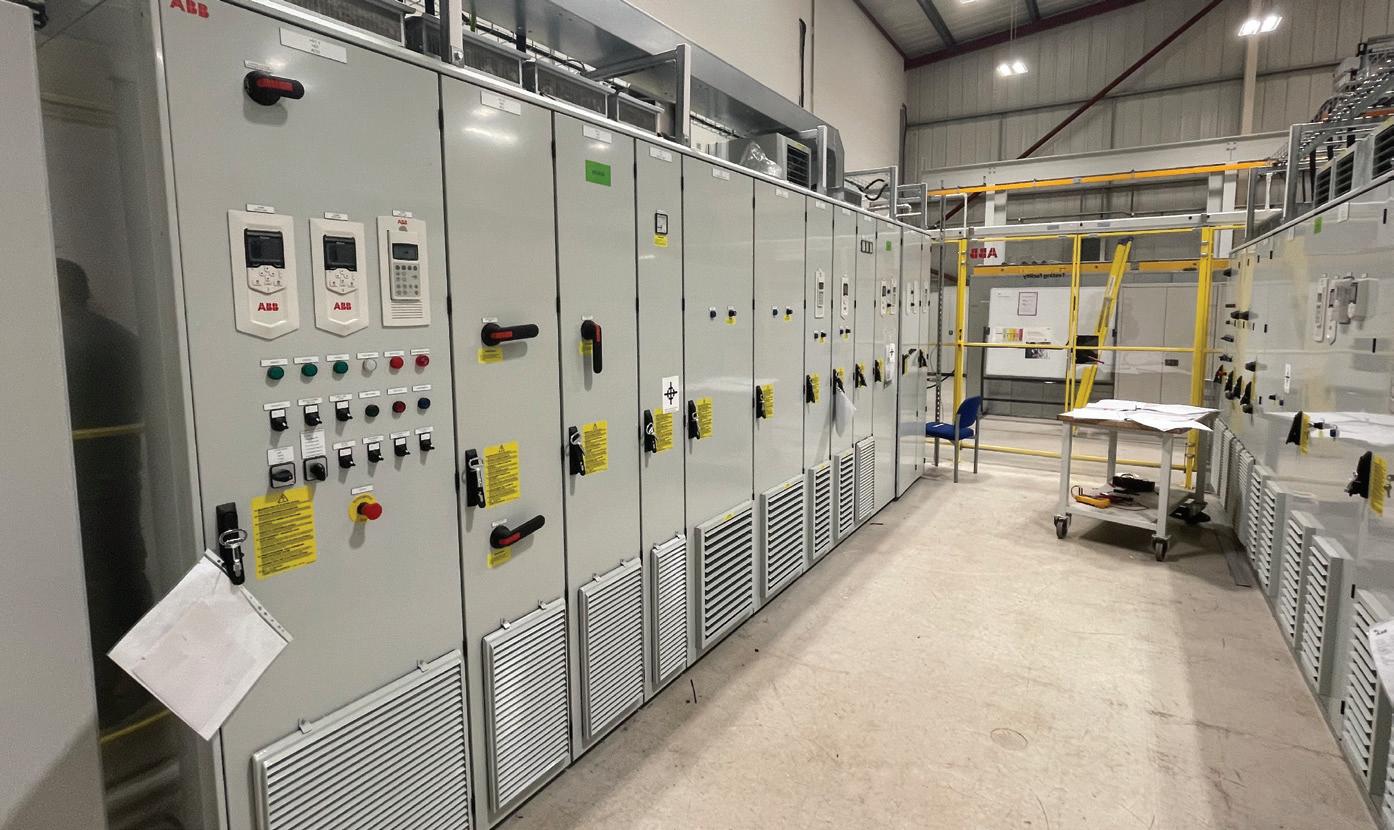
MEPCA: It sounds like you’ve had a busy summer –how are things going?
Neil Raynes: You’re right; it’s been hard work, but it’s been really good. In August, we received our accreditation as a certified ABB Drives Service Workshop. This had been some time in the making but it opens up exciting new possibilities for what we can do out of Coalville. It also puts us among only a handful of ABB workshops across the world that are factory accredited. In practical terms, accreditation means we have access to advanced diagnostic tools, processes and documentation that no other UK service facility has. It adds a level of prestige, and shows that ABB is serious about investing in the facilities and talent we have in the UK.
There’s a whole host of things we can do now that we couldn’t do before. We’ve invested in a range of six motors up to 160kW to provide a spinning load for Direct Torque Control (DTC) testing, along with a suite of inductive choke loads with condition variables, to enable us to fully load test the drives. This means we can now test under fully representative load conditions and really put drives through their paces, whereas previously, we could only carry out functional testing. As a result, drive owners and operators can have additional confidence that their drive will perform as expected once it’s been returned to them.
M: Describe a typical day at the workshop
NR: Our Motion Services offering is a 24/7 operation, so the team here is highly skilled, very experienced, and ready for any eventuality. We’ll typically have a pre-planned schedule of drives to maintain and repair at the workshop, and we also have a dedicated team ready to head out and help customers with emergency issues. Each ABB drive has its own suitcase containing all the parts and
documentation an engineer could need to service a drive, and so when our team arrives on-site, they’re always fully prepared.
M: What’s going particularly well at the moment?
NR: We have a packed schedule right now, which is always a good thing. Where previously a UK drive in need of comprehensive servicing would be sent back to ABB’s factory in Helsinki, the ABB workshop at Coalville now enables a wide range of maintenance activities to be carried out without the drive having to leave the country. This means that repairs can be turned around much faster and require less transportation to get to where they need to be, significantly reducing carbon footprint.
In addition, a Reconditioning or Premium Repair service here in Coalville uses 55-80% less carbon compared to buying a brand-new drive, and so we’re helping to extend the lifetime of customers’ assets while also making drives more sustainable generally.
M: What day-to-day challenges do you typically face?
NR: Like any workplace, no two days are alike,
so there are always interesting challenges to address and new opportunities to be found. Managing the unexpected alongside the routine is what makes my work so satisfying. We’re equipped to deliver the same level of service and quality, whether it’s a regular service or a business-critical turnaround, so while the circumstances might be different, the quality of the work is identical. Crucially, once we’ve serviced a drive, it stays serviced. After a drive leaves our workshop, it’s very rare that we’ll see it again until its next scheduled maintenance interval.
M: What does this mean for drive owners and operators?
NR: Everything we do here is geared towards safeguarding our customers’ investment and minimising the chance of unplanned downtime. We can now carry out more sophisticated repairs to factory standards, and turn drives around much quicker than before. Not only can we now get our customers back on track faster, but we’re also helping to extend the lifetime of their assets. bit.ly/ABBadms

Automation in mediumsized businesses pays off
Robotics specialist KUKA explains how automation offers benefits not just to industry giants but to small and medium-sized enterprises, too, fostering enhanced success, heightened productivity and increased employer appeal.
To remain competitive in an increasingly competitive market, small and mediumsized enterprises (SMEs) must enhance efficiency and productivity. One way to achieve this is through the implementation of robotics and automation in production processes. But how can SMEs efficiently optimise established processes by leveraging robotics and automation technologies, and what are the benefits?
Identify the opportunities
To effectively optimise production processes using robotics and automation, a thorough assessment of existing operations must take place – don’t automate for the sake of automating. SMEs must identify processes that can truly benefit from automation and deliver value across their process chains. These could include repetitive tasks, high-risk activities, or processes that may attract high labour costs. A comprehensive analysis can enable SMEs to pinpoint areas where automation can have the biggest impact.
Ensured quality control
Automation systems are extremely reliable and can maintain consistent product quality output. In SMEs, where resources might be limited, product consistency and quality are crucial for establishing and maintaining a strong reputation and building customer trust. Robots have been proven to perform tasks with both precision and repeatability, reducing manufacturing errors.
Enhanced efficiency
One of the primary reasons SMEs adopt automation is to enhance efficiency and productivity. By automating repetitive and time-consuming tasks, output can be increased without significantly impacting
labour. This allows SMEs to meet growing demand, reduce customer lead times, and improve their production efficiencies.
Improved safety
Automated production processes can lead to a safer working environment. Robots are able to safely handle dangerous materials or manage physically demanding tasks that can create risks for human workers.
Data-driven decisions
Modern automation systems can be equipped with sensors that enable data collection. SMEs can leverage this data to achieve valuable insights into their processes. By analysing the data generated by automated systems, SMEs can identify bottlenecks, address inefficiencies, and strive for continuous operational improvement. A data-driven approach allows SMEs to make informed decisions and continually optimise processes based on fact.
Scalability and adaptability
SMEs face fluctuating demand and constantly changing market dynamics. Robotics and automation can be scaled up or down to accommodate these changes. Scalability provides SMEs with the flexibility to adapt to such changes quickly, making them more resilient and competitive.
Competitive advantage
Robotics and automation can give an SME a significant competitive advantage by streamlining production processes. Costs are reduced, product quality is improved, and
response times can help SMEs compete with larger companies, as they can react to changing trends. Customers are also more likely to choose suppliers that can not only deliver high-quality products quickly and reliably but also demonstrate that they are innovative and looking to the future.
SMEs are currently grappling with significant challenges, including soaring energy costs, supply bottlenecks for essential production materials, and a challenging labour market characterised by a severe shortage of skilled workers. These hurdles are further compounded by the pressing need to swiftly and flexibly respond to evolving customer demands and changes within their own production processes. While it’s important to acknowledge that automation might not offer a one-size-fits-all solution to every challenge faced by SMEs, it undeniably holds the key to addressing many of them.
Investing in automation is worthwhile –that’s what those who have done so know. Because the risk is low, and the opportunities are huge. Robots perfectly complement well-established human teams and master their tasks reliably and precisely, whether it is palletising, loading and unloading machines, quality control or welding. They take over unergonomic, stressful, monotonous and time-consuming work. Employees are therefore physically relieved, and more highpro¬file activities can be undertaken.
The strategic utilisation of robotics and automation can have a transformative impact on SMEs’ production processes. By identifying opportunities for automation, selecting the right technology, and investing in integration and training, SMEs can enhance efficiency, reduce costs, improve product quality, and gain a competitive edge. The long-term benefits in terms of productivity, scalability, and adaptability make automation an essential tool for SMEs looking to thrive in today’s dynamic business environment.
As technology continues to evolve, SMEs that embrace automation will be well-positioned to meet the challenges and opportunities of the future.
www.kuka-robotics.com
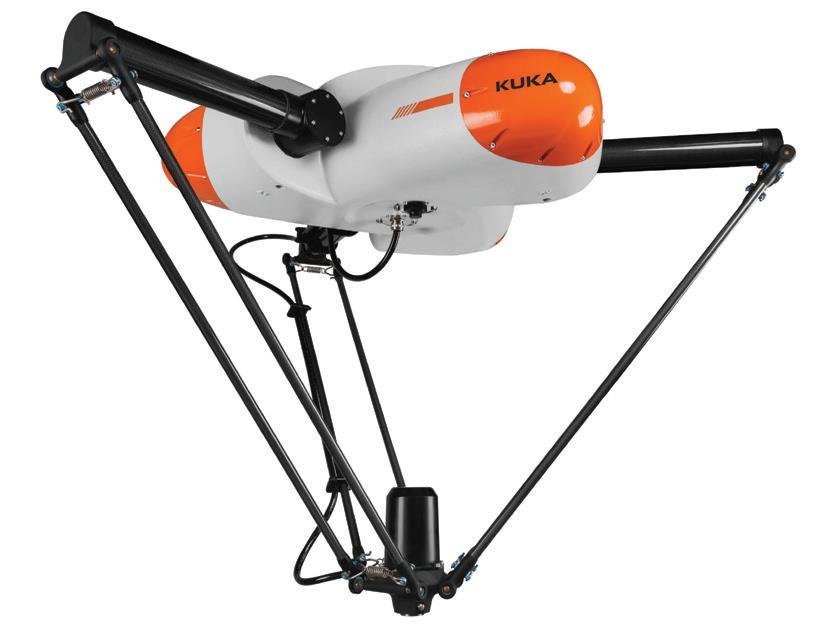
ESS ENTI ALS
ESS ENTI ALS
Now directly in the online shop order and receive quickly
Now directly in the online shop order and receive quickly
With the Connectivity Essentials, Murrelektronik offers a wide range of connectors that are immediately available. High performance, essential components – M8, M12, Valve and RJ45 connectors available now.
With the Connectivity Essentials, Murrelektronik offers a wide range of connectors that are immediately available. High performance, essential components – M8, M12, Valve and RJ45 connectors available now.
Choose the right servomotor solution
Planetary gearboxes are the ideal compact high-precision servomotor solution for mobile robots, with estimates showing that the vast majority of mobile robots employing precision gear products will have planetary gears (~95%) by 2026. It is of paramount importance that mobile robot manufacturers select the best precision planetary gearboxes for the specific needs of their robots and applications.
Here are seven key factors to consider when using planetary gearboxes in mobile robots in order to ensure optimal performance, reliability and efficiency:
Torque and power requirements
Torque and power requirements are specific to the intended applications and payloads. Manufacturers must carefully address the torque demands of each robot’s motors and actuators in order to select planetary gearboxes that can handle loads effectively. Ensuring adequate torque ratings for planetary gearboxes can help to prevent premature wear, overheating and potential system failure.
Efficiency and gear ratios
A crucial element of mobile robot design, planetary gearboxes generally offer higher efficiency than other types of gearboxes. Manufacturers should carefully evaluate the efficiency of gearboxes and consider the gear ratios that suit each mobile robot’s operational needs. The selection of proper gear ratios ensures optimal motor speed and torque output, which translates into better energy utilization and enhances overall performance.
Size and weight constraints
Compact autonomous systems such as mobile robots often have limited space and weight allowances. Planetary gearboxes are known for their compact and lightweight designs, making them the preferred choice for many manufacturers. Manufacturers must
give consideration to selecting gearboxes that fit within the space constraints and adhere to the weight limitations of their mobile robots without compromising performance.
Backlash and precision
Precision gearboxes are designed to have low or zero backlash, meaning the clearance between interlocking teeth is much smaller than in standard gearboxes. This improves the accuracy and repeatability of robot movements, which is particularly important in applications where fast, precise movement is required, such as industrial automation or medical robots. Choosing planetary gearboxes with minimal backlash helps to maintain positional accuracy and reduce errors.
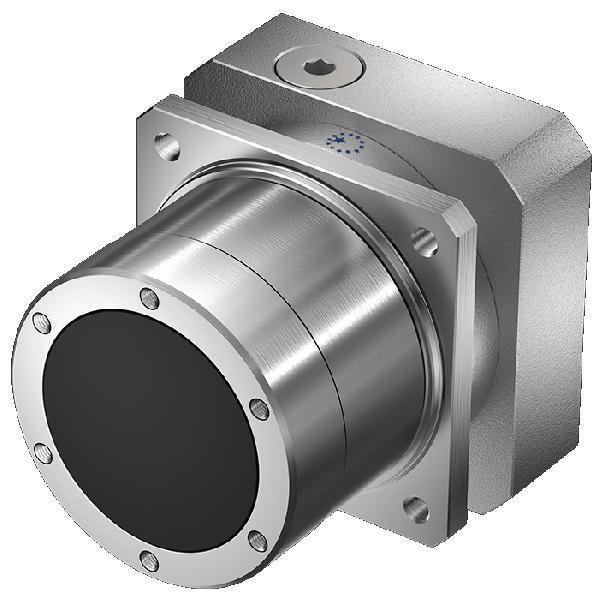
Lubrication and maintenance
Choosing the correct type of lubrication and understanding the maintenance needs of planetary gearboxes is vital to ensure the smooth and efficient operation of mobile robots. For example, sealed gearboxes or those with extended intervals between lubrication may be preferred by mobile robot manufacturers in order to reduce maintenance requirements and extend system uptime.
Durability and reliability
These factors are key to the overall longevity of mobile robot systems, with some robotic applications operating in or exploring harsh environments or carrying out heavy-duty material handling tasks. Mobile robots operate in a range of environmental conditions, including extreme temperatures and environments heavy on moisture and/or dust, with some even designed to operate in underwater environments.
Intense operating conditions make it crucial for mobile robot manufacturers to select gearboxes that are made from high-quality materials and that are precision manufactured to ensure they can withstand the rigours of
the application, with adequate protection against corrosion, ingress and environmental contaminants. For example, all Apex Dynamics UK gearboxes are made in a CE and ATEX-certified manufacturing facility and come with a five-year warranty.
Cost and availability
A further consideration for mobile robot manufacturers is the cost of the gearboxes they are selecting for their mobile robots and their availability on the market. It is important to strike the correct balance between required performance and budget constraints to ensure the project (and product) remains economically viable. Furthermore, good delivery times for planetary gearboxes are crucial to ensure products are ready to ship to customers. Apex guarantees delivery within three to four weeks.
With an array of possibilities to choose from when it comes to planetary gearboxes, there is the potential to find the right fit for each mobile robot and its potential applications. By considering the variables above, manufacturers can make informed decisions and help to ensure they develop robust, best-in-class products with high performance, low backlash, precision, durability, minimal downtime, and success in their respective applications. bit.ly/PlanGear
Mike Gulliford, Managing Director, Apex Dynamics UK, outlines seven things mobile robot manufacturers need to think about when choosing planetary gearboxes.
Reach new heights
The ELEVATE™ lifting column extends the range of your cobot palletiser, taking performance to new heights.
Matches the cycle time of your production line
• 100 mm/s - adjustable and independent of load up to 100 kg
• Column is fully extracted in less than 10 seconds

• Optional simultaneous run with the cobot
Fits into multiple palletiser designs
• Integrated controller for compact size and reduced complexity
• Digital and analogue I/O options or Ethernet Modbus TCP/IP for the level of control and feedback a specific task requires
• Feedback data for easy troubleshooting, diagnostics, and optimisation of performance
• Compatible with a wide range of cobot brands and models
• Works with cobot palletising programs and simulation software
Accurate palletising at its finest
• Low deflection by high bending moment
• BLDC motor for high position accuracy
• Minimised vibration by soft start and stop
Faster than ever
Flexibility meets simplicity
For more information - please contact me:
Craig Tromans
- TECHLINE® E-mail: craigt@linak.co.uk
Zebra and Matrox Imaging Are One
The Matrox Imaging solutions you know and trust just got better, and they are now available through Zebra.
More choices from the widest portfolio
More agility to scale and adapt in the moment
More interconnectivity via easier integration
More savings with streamlined solutions
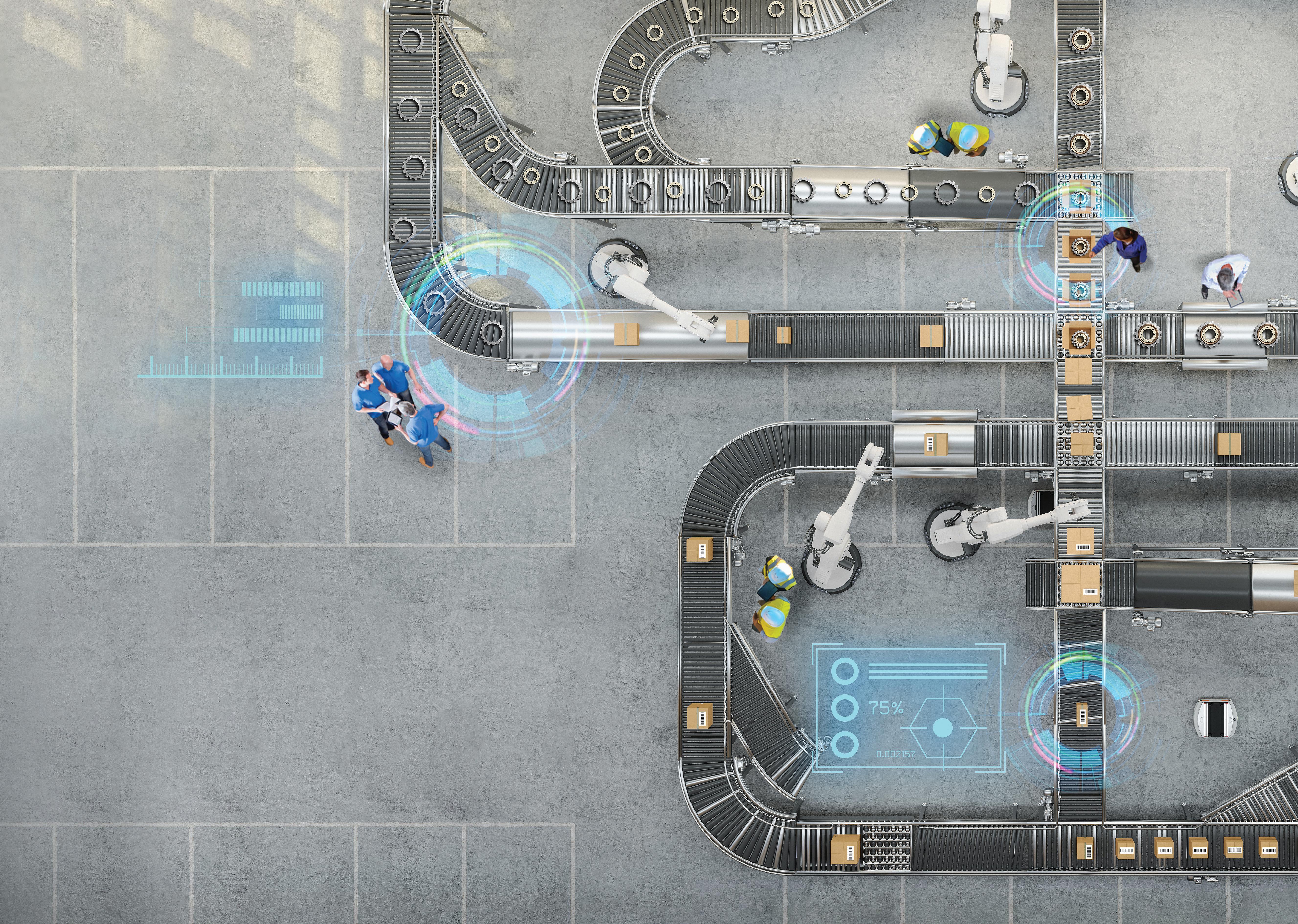
Get more from your vision solutions and stay informed
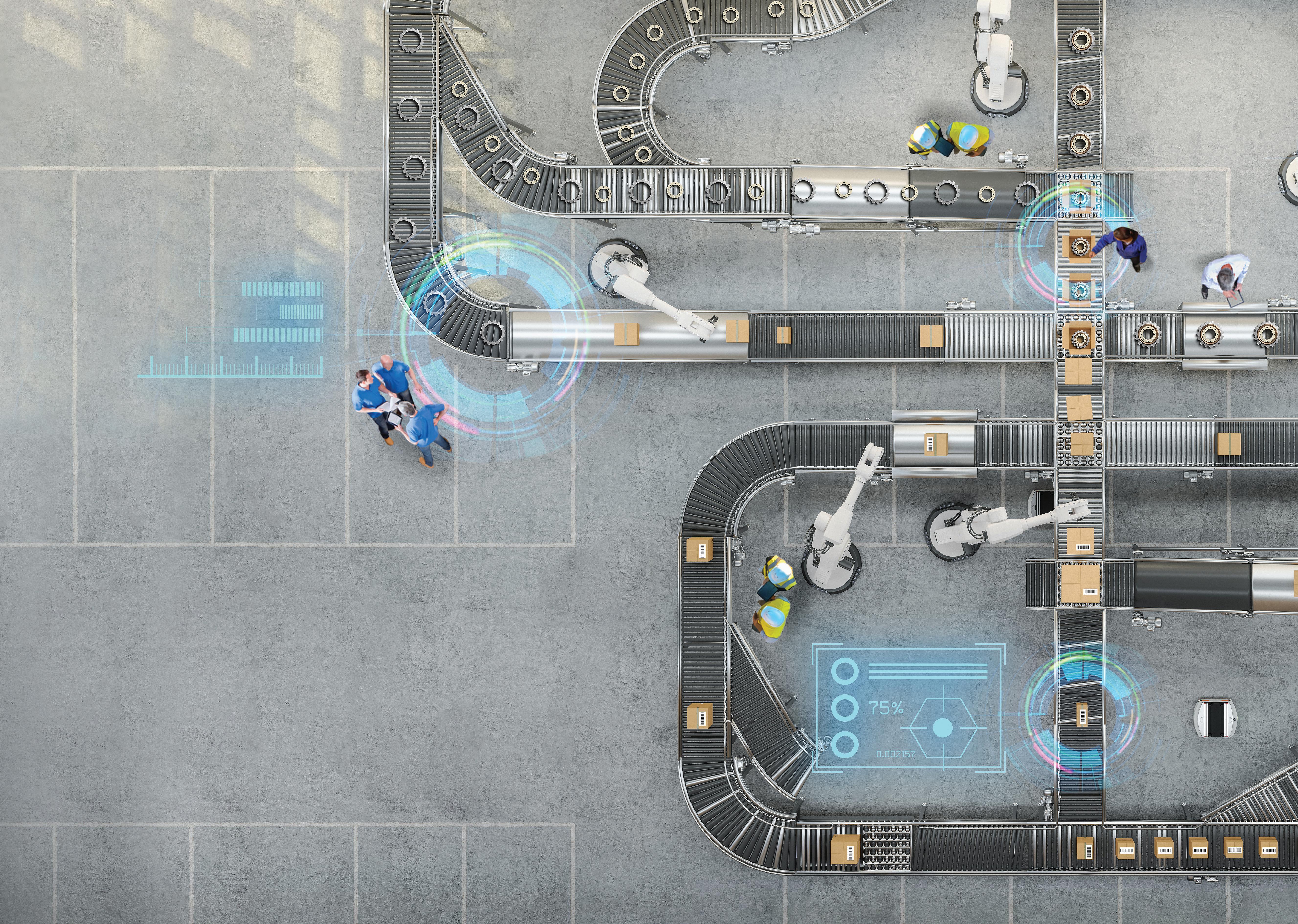
New termination technologies
HARTING shares details of its new range of push-in
HARTING solutions are characterised by an efficient plug-and-play system, which eliminates errors by ensuring plug-in security with the help of coding. They offer the largest variety of termination technologies on the market and have now expanded this portfolio with the new Han Push-In range.
The connection technology behind the Han Push-In represents a refinement of the cage connection method, which is particularly well suited to field termination thanks to its speed and ease of use. It also expands the flexibility of Han industrial connectors by providing an additional field connection method, allowing fast and uncomplicated assembly of connectors whilst ensuring consistent quality and robustness. As a result, assembly times in the field are reduced by up to 30%.
With Push-In technology, the stranded wire for the connection can be inserted directly into the contact chambers. An internal clamp spring ensures a high-strength contact. If ferrules are used, the connection can be established without tools. In the case of stripped stranded wires, all you need for installation is a screwdriver.
Han Push-In allows you to assemble several conductor variations, ranging from stranded conductors to conductors with ferrules (insulated and uninsulated) and solid conductors. Combined with a wide selection of inserts from the Han portfolio, this new range offers customers a selection of connectivity solutions.
The connection technology behind the Han Push-In is particularly well suited to field termination thanks to its speed and ease of use. As part of the Han-Modular range, it allows users to configure customised connectors which are exactly tailored to their design requirements. Power, signal, data or compressed air can now be combined in one module, reducing the total number of interfaces required.
As the connection technology is smaller and more lightweight, users can now fit more modules and module types than before into
connectors.
one connector. As a result, assembly areas which are difficult to reach can be equipped more efficiently or even opened up for assembly in the first place. There are now over 250 modules to choose from and many thousands of potential combinations available, increasing design flexibility.
The new technology simplifies the handling of components during maintenance work in
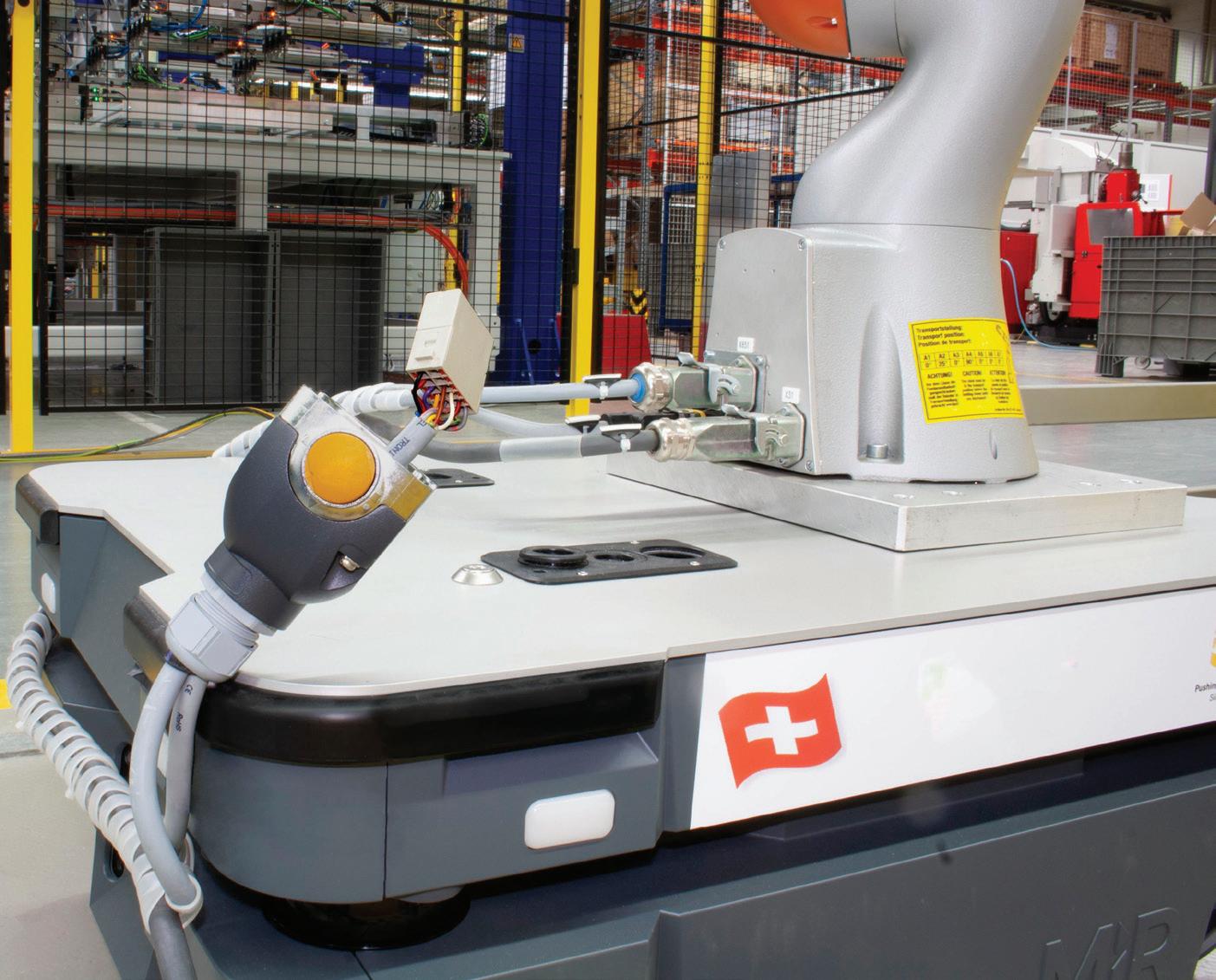
If you’re looking to stay up to date with the latest HARTING products and technological solutions, there are now two new innovations available.
Firstly, users can discover the latest in connectivity and cabling with a HARTING Tech Day. Available digitally or in-person, HARTING’s field engineers will demonstrate and explain the latest technology, helping users to plan out current or future projects.
This is a great opportunity to get engineering and design teams involved and for them to ask any questions. The Tech
environments with limited room for manoeuvre, such as in wind turbines or interior fittings in trains. It is particularly well suited to applications where a high degree of flexibility is required, such as when changing tools on machines. Thanks to Han Push-In, this can be done simply, quickly and without the need for tools.
www.harting.com
Day will be tailored to ensure users get the most value out of the time. bit.ly/HTechDay
In addition, HARTING has also launched the newly updated User’s Guide Termination Technologies manual.
It contains a wealth of information to help users select components, install connectors and contacts and choose the right termination techniques for their applications. Readers of the guide will also learn more about the latest technical innovations and standards.
bit.ly/TermTech
Series D is the new valve island from Camozzi Automation, able to ensure optimum productivity and flexibility for use in many industrial automation systems.
MULTIPOLE
DIAGNOSTICS AND VALVE COMMUNICATION LED
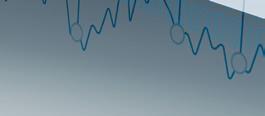
MANUAL OVERRIDES
MODULARITY 1 SUB-BASES WITH INTERCHANGEABLE CARTRIDGES
BENEFITS
Compact design
Individual, modular sub-bases in technopolymer
Flexibility in connecting different I/O modules
Integrated diagnostics and predictivity
Available protocols: PROFIBUS-DP, CANopen, EtherNet/IP, PROFINET, EtherCAT, IO-Link

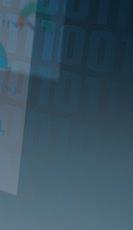
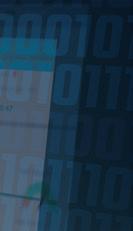
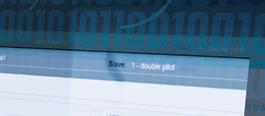
FIELDBUS
HIGH NUMBER OF MODULES
CAN BE CONNECTED WITH THE MAIN FIELDBUS PROTOCOLS
FLEXIBILITY IN CONNECTING DIFFERENT I/O MODULES
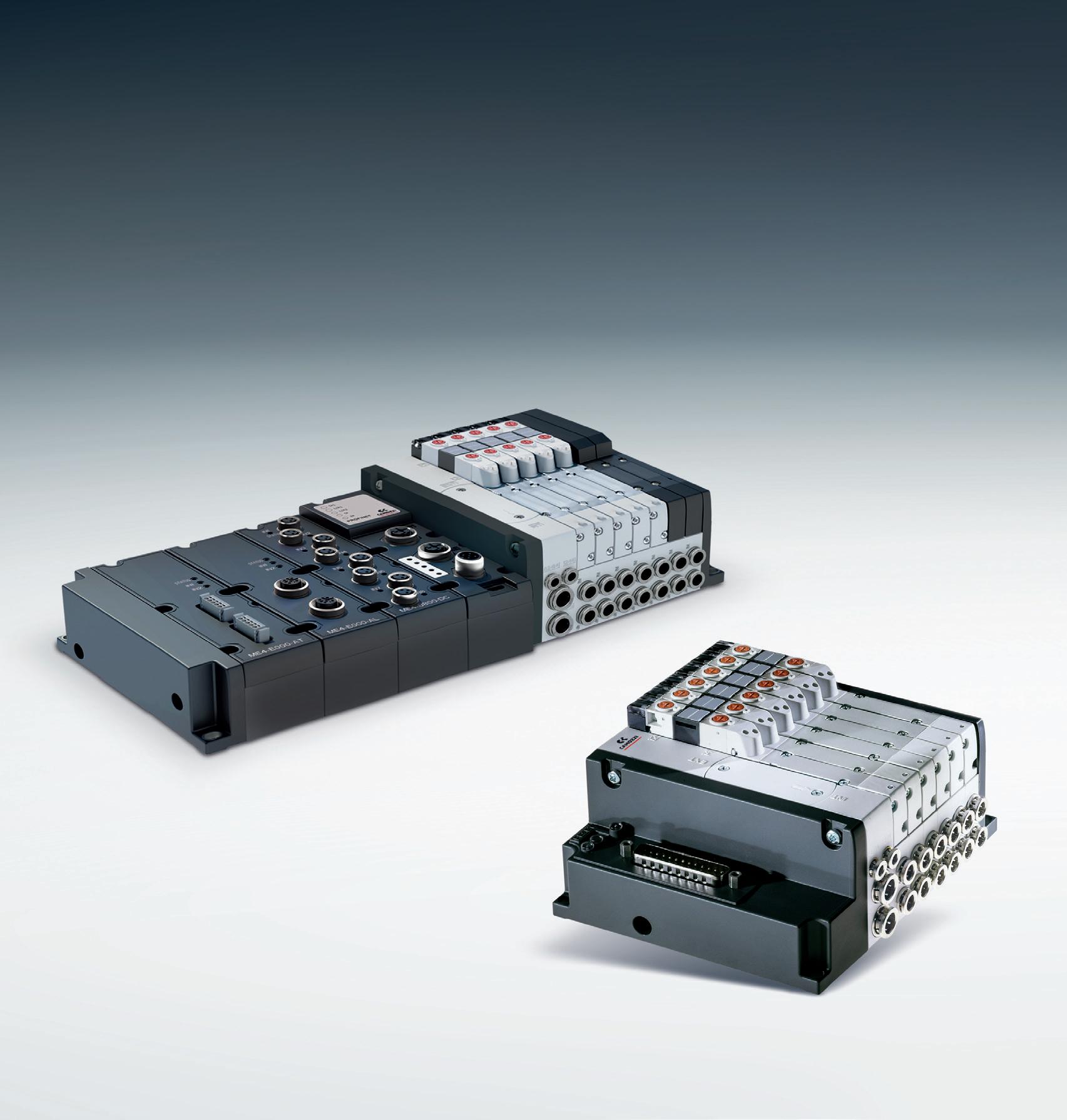
4.0 READY
SERIES D VALVE ISLAND INCREASE EFFICIENCY, REDUCE DOWNTIME MAKE YOUR OPERATIONS SEAMLESS WITH SERIES D
PREDICTIVE MAINTENANCE
The Series D valve island is equipped with CoilVision® technology which can monitor and predict the wear and efficiency of parts of the solenoid valves.
Camozzi Automation Ltd 024 7637 4114
askus@camozzi.co.uk www.camozzi.co.uk store.camozzi.co.uk
DIGITAL MONITORING AND ANALYSIS
ON/OFF status of each valve
Health status
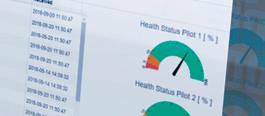



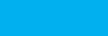



Power consumption
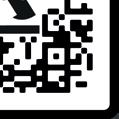
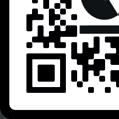

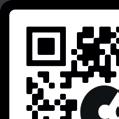

DIGITAL MONITORING AND ANALYSIS



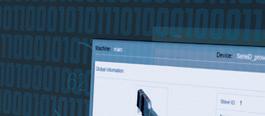
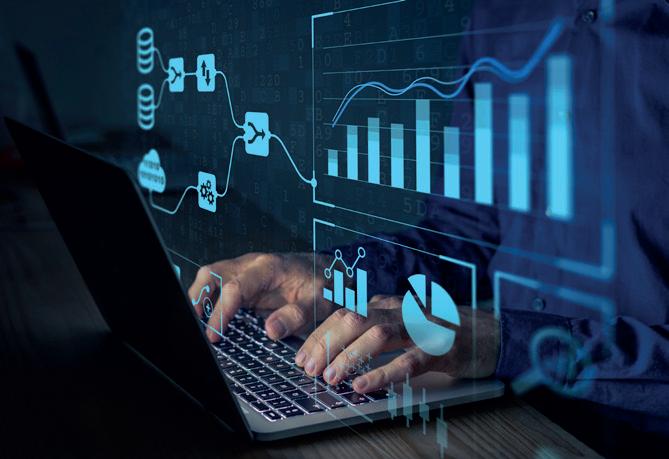
24HR EMERGENCY VALVE ISLAND BUILDS
Within 24 hours, we can assemble and test Series D Valve Islands, creating an unbeatable turn around for valve islands in the UK. If you need valve islands fast, get in touch with our team today.
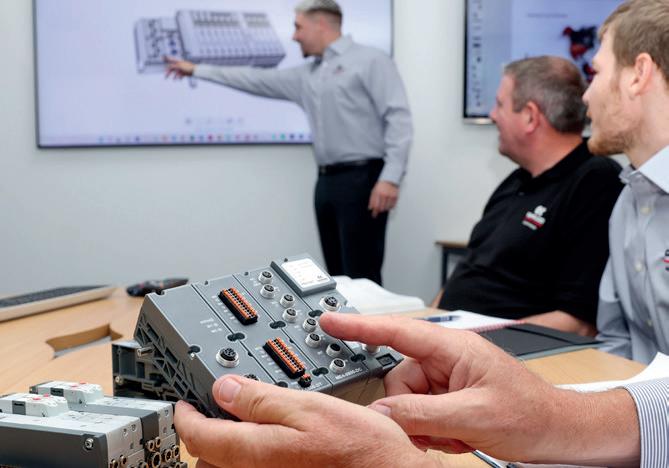
LEARN MORE ABOUT SERIES D
https://qrco.de/seriesd
Power for outdoors
Outdoor applications such as agricultural machinery or process plants require highly robust connection technology that can withstand extreme conditions such as submersion and highpressure cleaning. HECs from binder are also resistant to chemicals, corrosion and UV light. In addition to power supply, in hybrid design, they can also ensure the signal connectivity of machine and plant components.
Industrial circular connectors supplier binder has launched the 696-series Harsh-Environment Connector (HEC) for outdoor use in extreme weather, dust, humidity, contact with liquids, extreme temperatures, or vibrations. The power connector was engineered for versatile power supply in both the low- and high-voltage segments under particularly harsh conditions. Its compact design supports the supply of equipment or assemblies, such as drive units, in confined spaces. In addition, the bayonet quicklocking mechanism, which can be closed or opened simply by pushing and turning, saves installation time. In hybrid design, power and simultaneous signal coupling is possible in a particularly efficient manner with one single mating.
The HEC’s target applications are plants in process industries, including chemical and non-contact food technology, conveyor systems, and machines in agriculture, construction, or mining and surface mining. To withstand the mechanical, chemical, and climatic impacts typical there, components of the 696 series – cable connectors and square
panel mount parts – are also available with protective fittings. Thus, at the connector, the power interface meets the requirements of protection degree IP68 – and IP69K when mated. Thanks to the integrated sealing function, all wires placed in the protective fitting are protected according to IP67.
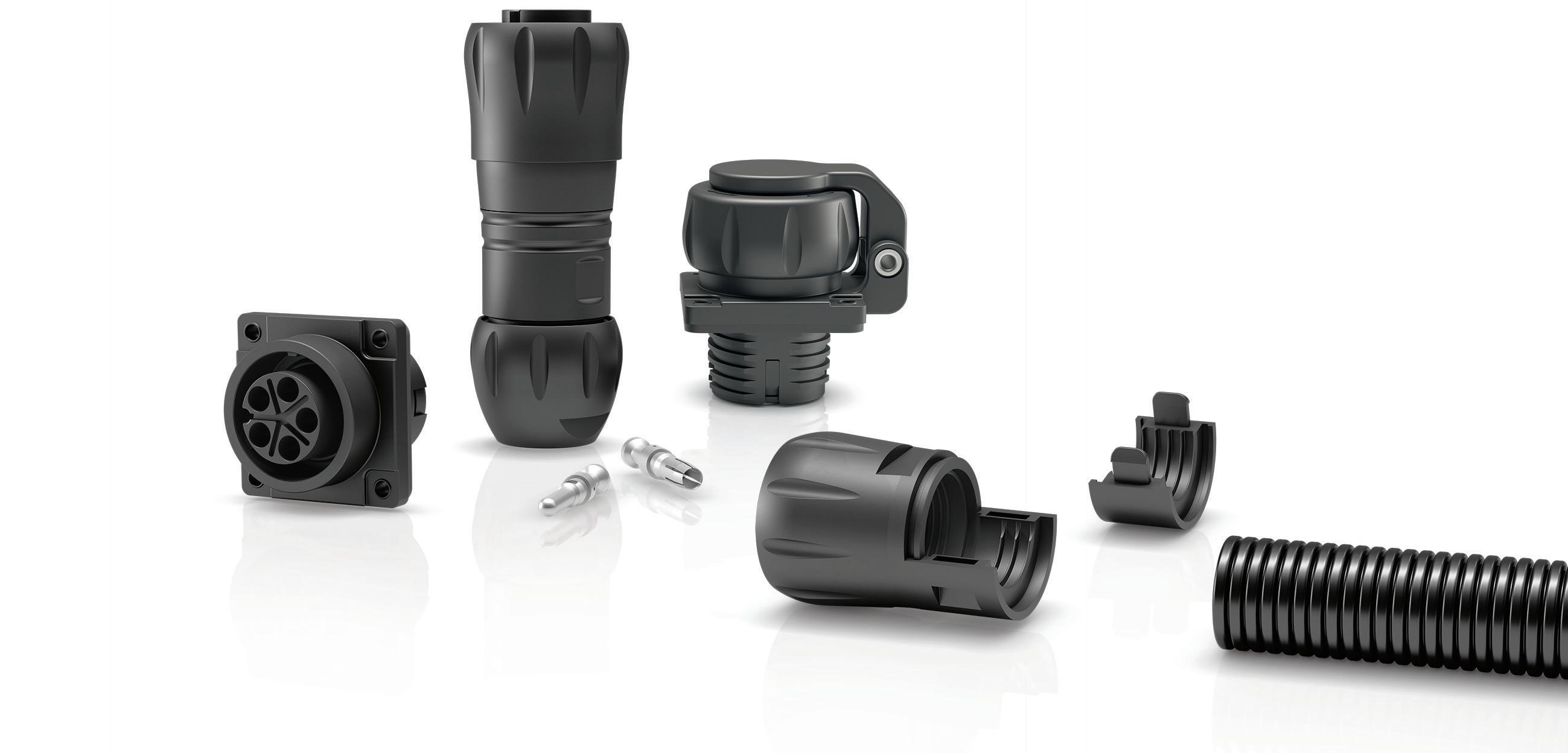
Protection degrees
According to the DIN EN 60529 and ISO 20653 standards, so-called IP codes (International Protection) indicate the resistance of connectors to environmental influences, which include, in particular, contact and the ingress of foreign particles and water. The protection degree of a connector is specified in terms of these IP codes, with the first digit referring to the ingress of solid particles such as dust and the second defining the protection degree against humidity and water.
The IP67 protection degree, as for the wires in the HEC’s protective fitting, represents protection against temporary submersion. IP69K indicates that the power connector itself is protected against exposure to water under high pressure. It
is important to know that the protection degrees specified in connector data sheets generally apply only when the connector is mated.
Extraordinarily resilient
The 5- to 12-pin connectors are designed for rated voltages from 60 to 600V and rated currents from 3 to 32A. They work reliably at operating temperatures from -40 to +100°C, are UV-, oil- and fuel-resistant, as well as vibration-proof thanks to crimp connection. This non-detachable, solderless mechanical connection technology ensures a particularly tight fit of the wire to the terminating part of the contact.
Cable parts measure 36mm in diameter, and panel mount parts are 40mm x 40mm. The 696-series components are both VDE-approved and UL-approved. Their mechanical strength is clearly reflected in the lifespan of the connectors, which reaches more than 1000 mating cycles in cases of the 5- and 8-pin connectors and more than 500 mating cycles with the 12-pin parts. www.binder-connector.com/uk
BESPOKE AUTOMATION SOLUTIONS
Designing, developing and producing innovative special purpose and bespoke automated machinery for manufacturing industries.
Committed to learning and at the forefront of technological developments, our team has diverse experience in specialist technologies such as mechatronics, production automation, vision inspection, robotics, control systems engineering, and so much more, including:
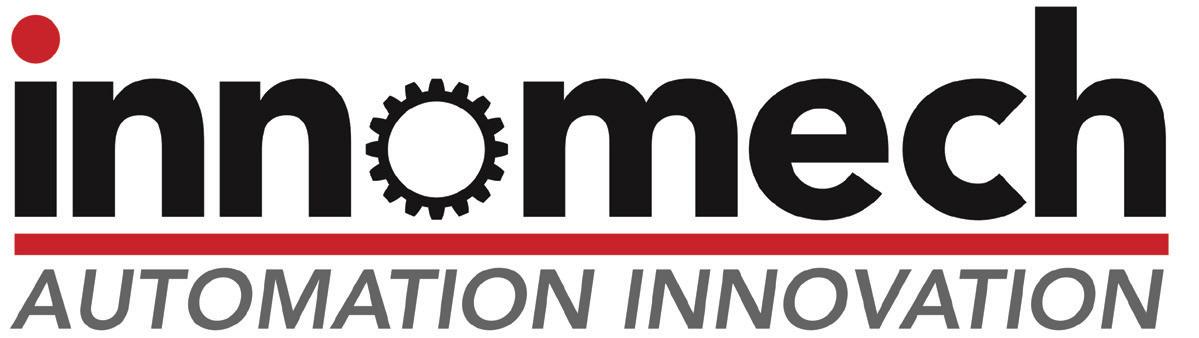
• Creating more productive and sustainable businesses through green technology solutions.
• Designing manufacturing automation equipment for medical device product assembly and testing.

• Bespoke special purpose-built machinery.
• At the forefront of technology advances with best-in-class performance solutions in laboratory automation.
Our multi-disciplinary team are highly experienced in:
• Delivering solutions in regulated industries.
• Mechanical, Software and Electronic Engineering.
• Expertise in a broad range of advanced manufacturing technologies.

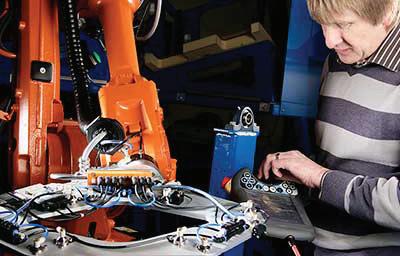
+44 1353 667394
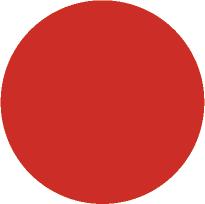
Evolution in electrical component supply
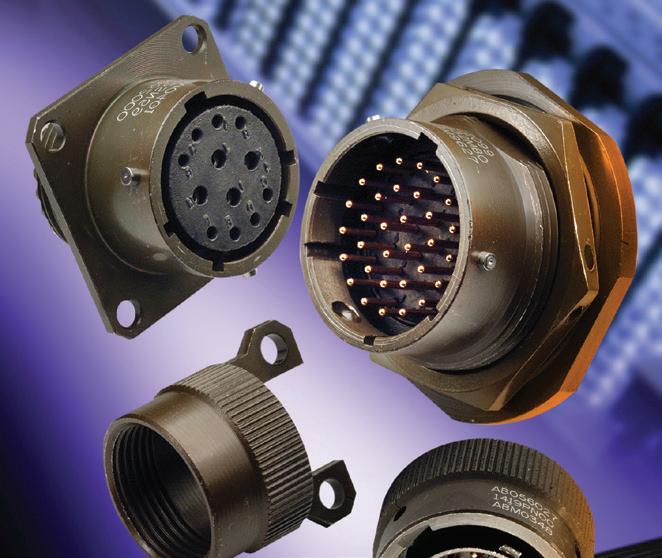
In the 60-plus years since specialist supplier and distributor Aerco was formed a lot has changed in the electrical component market. MEPCA found out how the company has evolved over that time and how it plans to support its customers going forward.
MEPCA: A lot has changed in Aerco’s 60-plus years of supplying electrical components. How, and why, was the company formed?
Aerco: While the giant US-owned distribution businesses made their beginnings in the 1930s in the UK after the Second World War, the UK-based manufacturers of electrical components still sought to maintain control of their customers through direct supply. Smaller geography and a weakened manufacturing base made this just about possible.
Bill Laughton, founder of Aerco, created a business to service the radio requirements of commercial aircraft in 1956. But as the growth of manufacturing accelerated during the 1960s, he saw that component manufacturers were failing to deliver the small quantities of connectors, switches and lighting components needed by service businesses such as his own, and he set about filling that void.
Aerco’s first distribution agreement was with Plessey, under which Aerco began to stock and sell their electrical connectors. The business environment was slower then. Orders arrived by post, but they still could usually be fulfilled from stock, and the connectors would arrive to the customer within a week or so.
M: How have those requirements evolved in the years, and how has Aerco’s offer adapted to meet those requirements?
A: Since those early days, Aerco has extended the range of types of components supplied, and the distribution agreements have broadened to formal franchise agreements with over 30 principles. Further, Aerco’s customer list has developed, and the company now supplies these components to major national and international manufacturers in defence, aerospace, transportation, medical and industrial markets.
M: Has Aerco driven any of the trends and practices we see as common today?
A: Proof of traceability and product origin have now become bywords in all areas of manufacturing, but that hasn’t always been the case. Back in the 1950s, it was just expected that component suppliers would be supplying legitimate products. Because of Aerco’s background in civil aviation, it has always been essential to maintain traceability and the ability to identify a product’s source and manage recall has become ingrained in our business. As times have changed and the need for certification has grown, Aerco has constantly been able to adapt and adopt these needs. For example, we were one the first distribution companies in the UK to gain UL approval to respool cable while retaining the UL approval for the product.
M: What are the prominent trends today, and how is Aerco meeting them?
A: Long lead times, unreliable delivery promises and escalating prices are creating a perfect storm for supply chain professionals. With growing economic volatility, we have seen prices increase very frequently and variable lead times from manufacturers, causing delays to projects and line stops in manufacturing. Customers need stability and consistency in their supply chain to be able to operate efficiently and reliably. We developed our CallOff order service to counter these customer concerns. We are able to hold larger quantities of stock for them, and they are able to CallOff as required throughout the year. This gives them the reassurance of having the stock available to them at short notice but with the reassurance that the price is fixed for a year. Being privately owned and in financially robust health, along with having such a close relationship with many of our suppliers, means we are able to support our customers with initiatives like this.
M: Finally, what emerging trends are you seeing that will affect Aerco’s offer in the future, and how does the business plan to adapt to meet them?
A: Lots of component manufacturers are looking to reduce their overheads and cut back on non-core activities, which have seen them reduce sales team numbers and, on some occasions, reduce technical support to end-users, too. This leaves a void of support, especially for small and mid-size engineering firms that still require the technical expertise of the component manufacturer to aid with the designing process.
At Aerco we see the need to support our customers with our in-house technical support and have developed our Aerco Academy to help grow the knowledge of new staff but also harness the experience and expertise of our longer-standing team members. Aerco Academy is our repository for training and knowledge on the products that we supply to the market. All online and available to all staff, Aerco Academy is a key investment the company is making to ensure that we deliver on our mission to customers to deliver technical expertise. With our technical support, we can help with the component selection and evaluation activities in our customers’ design process. www.aerco.co.uk
The RGC Series guarantees error free operation over a ver y large number of cycles.
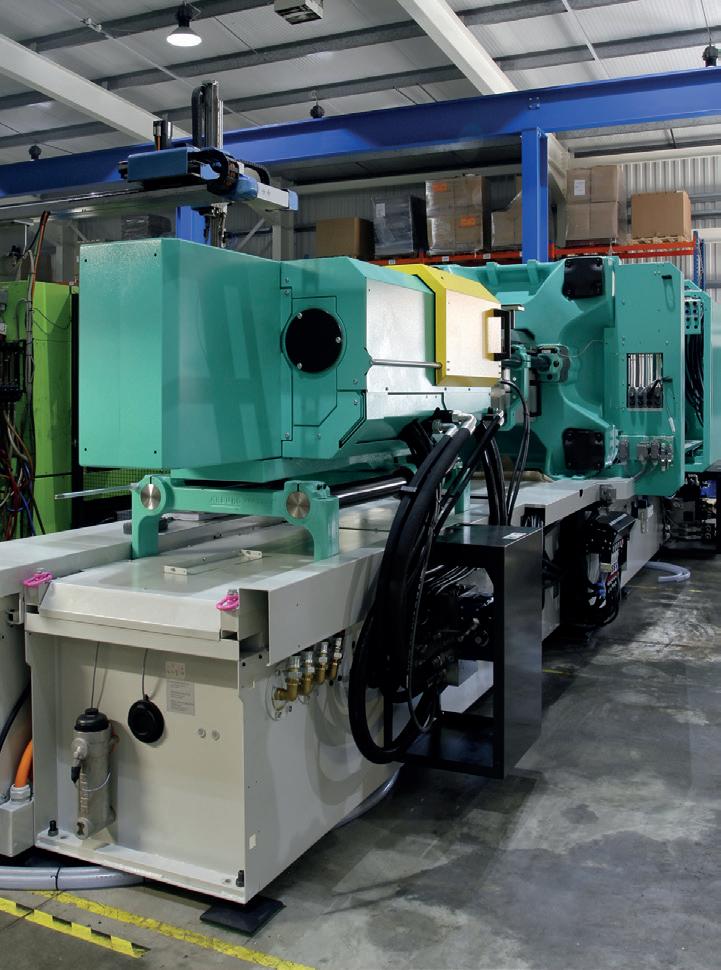
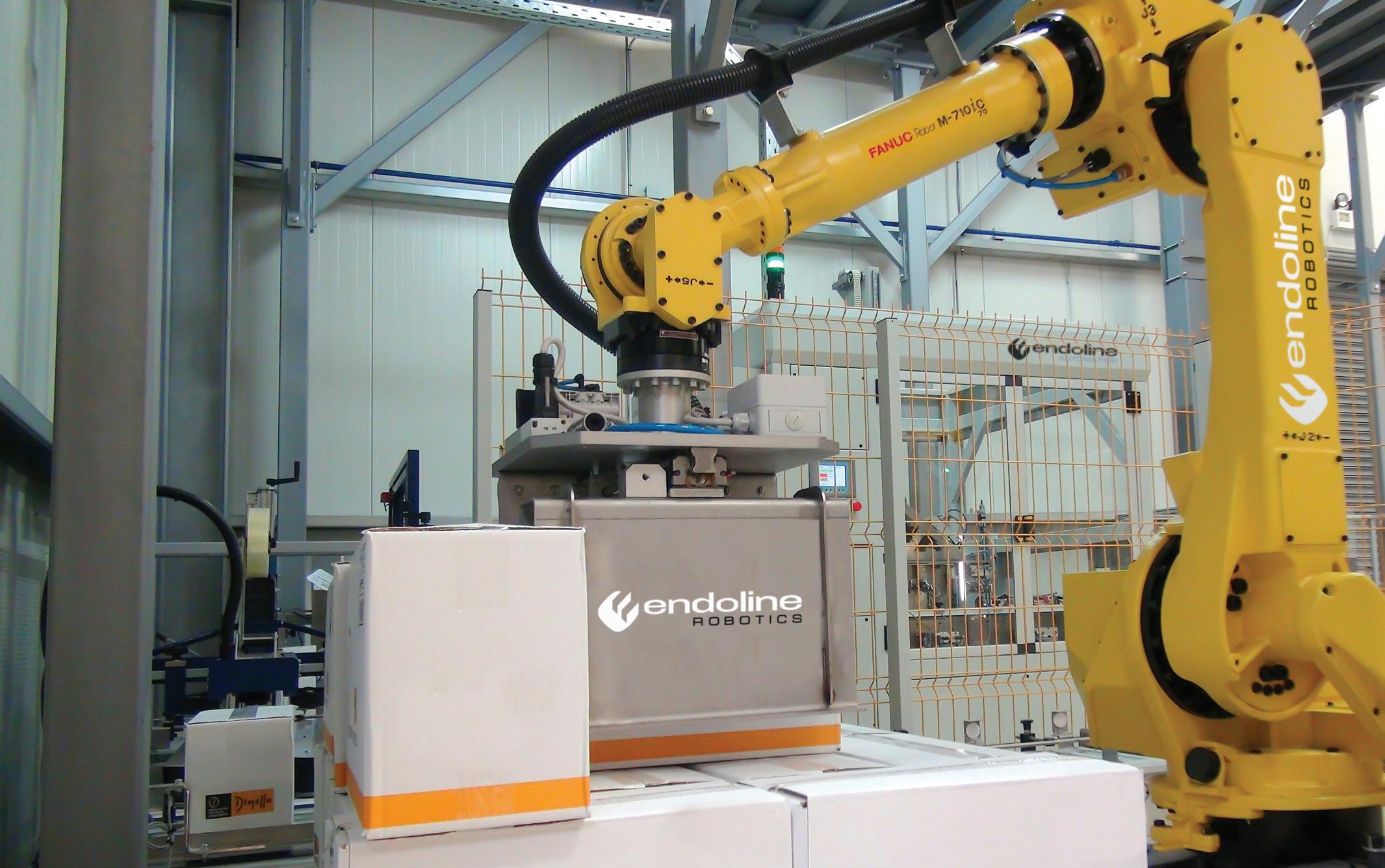
The RGC Series provides a slim single phase switching solid state contactor, at a mere 17.5mm width and is rated at 25AAC @ 40°C (104°F).
RGC1A Series: 1-phase switching solid state contactors up to 85 AAC
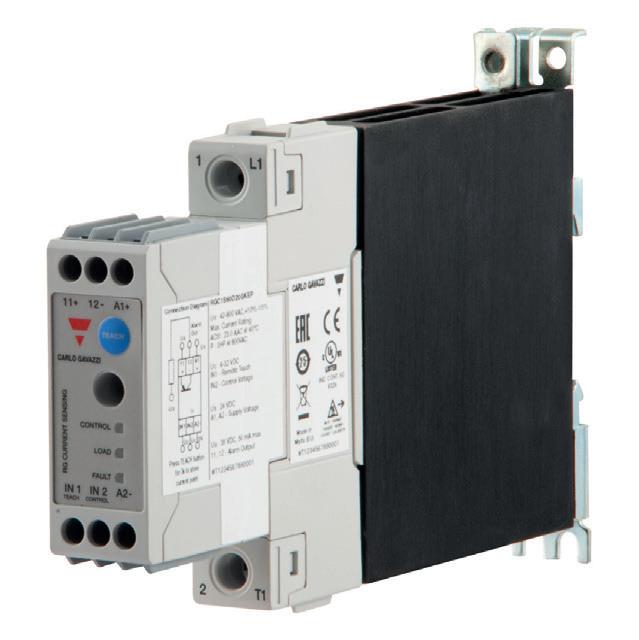
• Ratings up to 600VAC, 85AAC @ 40°C (104°F)
• Suitable for resistive and motor loads

• Integrated over voltage protection
• UL listed with 100kArms short circuit current rating
Current sensing models include:
• Integrated current measurement
• Partial load failure (teach) and load failure alarm
• Overheat protection
RFID made simple
The new all-in-one, F191 UHF RFID read/write device from Pepperl+Fuchs covers a wide range of applications cost-effectively, enabling users to seamlessly identify and track parts and goods according to the track and trace principle, establish transparency throughout the entire manufacturing process and create the information basis for implementing Industry 4.0 concepts, as MEPCA discovered.
Pepperl+Fuchs now offers a practical solution for users looking for an easy entry into the world of RFID with all its possibilities. The new F191 RFID read/write device combines the advantages of sophisticated industrial UHF technology with a standardised interface for IO-Link communication –and is, therefore, a cost-effective enabler component for a wide range of standard applications in areas such as intralogistics, automotive, and material handling.
A strong combination
The IO-Link masters from Pepperl+Fuchs support the simple connection of the new UHF RFID read/write devices.

The F191 RFID read/write devices are commissioned without time-consuming programming via the future-proof, integrated IO-Link interface. In easy mode the devices transfer their data to the higher-level system in accordance with the plug-and-play principle without integrating complex function blocks. It doesn’t matter whether this is an IoT-centric or PLCcentric architecture – Pepperl+Fuchs offers the appropriate IO-Link masters for connecting the RFID read/write devices from a single source for both applications. This means that up to eight RFID read/write devices can be operated cost-effectively on just one IO-Link master. The multi-protocol capability of the IO-Link master module ensures compatibility with almost any bus or control system.
Rugged UHF technology
When the F191 RFID read/write devices are in operation, they enable reliable detection of various UHF tag types in a sensing range of up to 1m by means of transmit power of up to 100mW ERP (adjustable). A wide range of application-specific tags
from the Pepperl+Fuchs product selection is available. UHF technology makes it possible to simultaneously detect bulk data from multiple tags in one read operation. With a rugged IP67 housing, integrated antenna, and a wide temperature range of -25 to +70°C (or -25 to +60°C in continuous operation), the F191 RFID read/ write devices are also designed for use under adverse ambient conditions.
In the Pepperl+Fuchs UHF RFID portfolio, the F191 read/write device joins the F190 and F192 versions already established on the market. Compared to the new F191, these support advanced setting options for the continuous solution of more complex special applications or a significantly increased sensing range (F192 up to 6m). Combined with the broad experience gained over 30 years of RFID development and other LF and HF frequency range solutions, a wide variety of applications can be covered by the
identification experts at Pepperl+Fuchs.
The F191 UHF read/write device with IO-Link is therefore an economical, highperformance identification solution with IOLink interface, which is simple to operate thanks to its Easy Mode with plug-and-play connectivity and no programming required. Low channel costs can be achieved for maximum efficiency by connecting multiple read/write devices to an IO-Link master. The device offers flexible system integration with connection via IO-Link master to almost all bus systems and controllers with an optimal read range of up to 1 m for a wide range of applications. Multi-tag reading of numerous tags is possible delivering maximum efficiency and maximum process reliability is possible thanks to a high degree of protection, an extended temperature range, and adjustable transmitter-radiated power
www.pepperl-fuchs.com
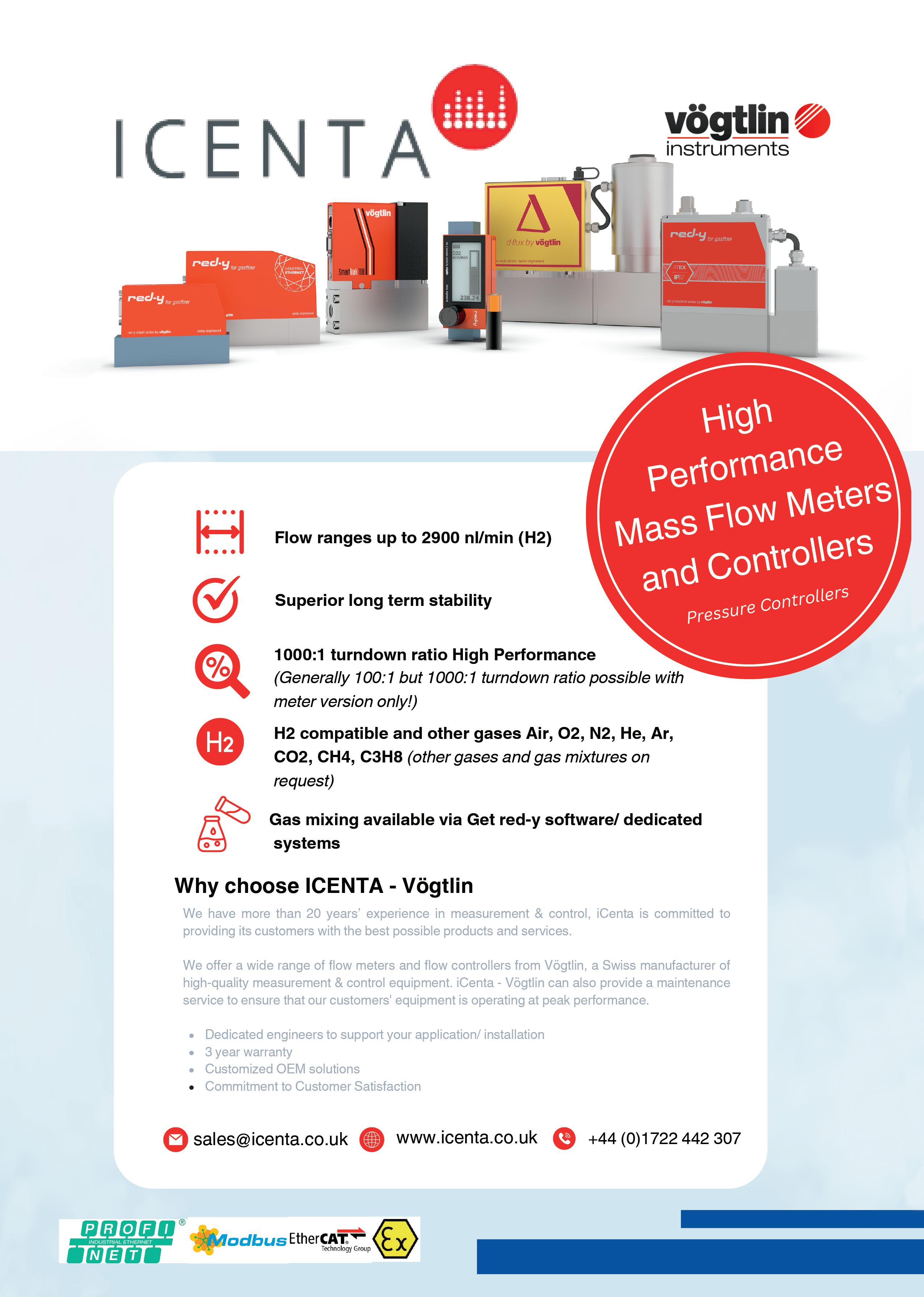
Not just for pressure
Paired with the newly enhanced, award-winning ESI-USB software, users can now measure, analyse and record any analogue output, making it a cost-effective solution to expand sensor connectivity without the need for costly I/O interface boards.
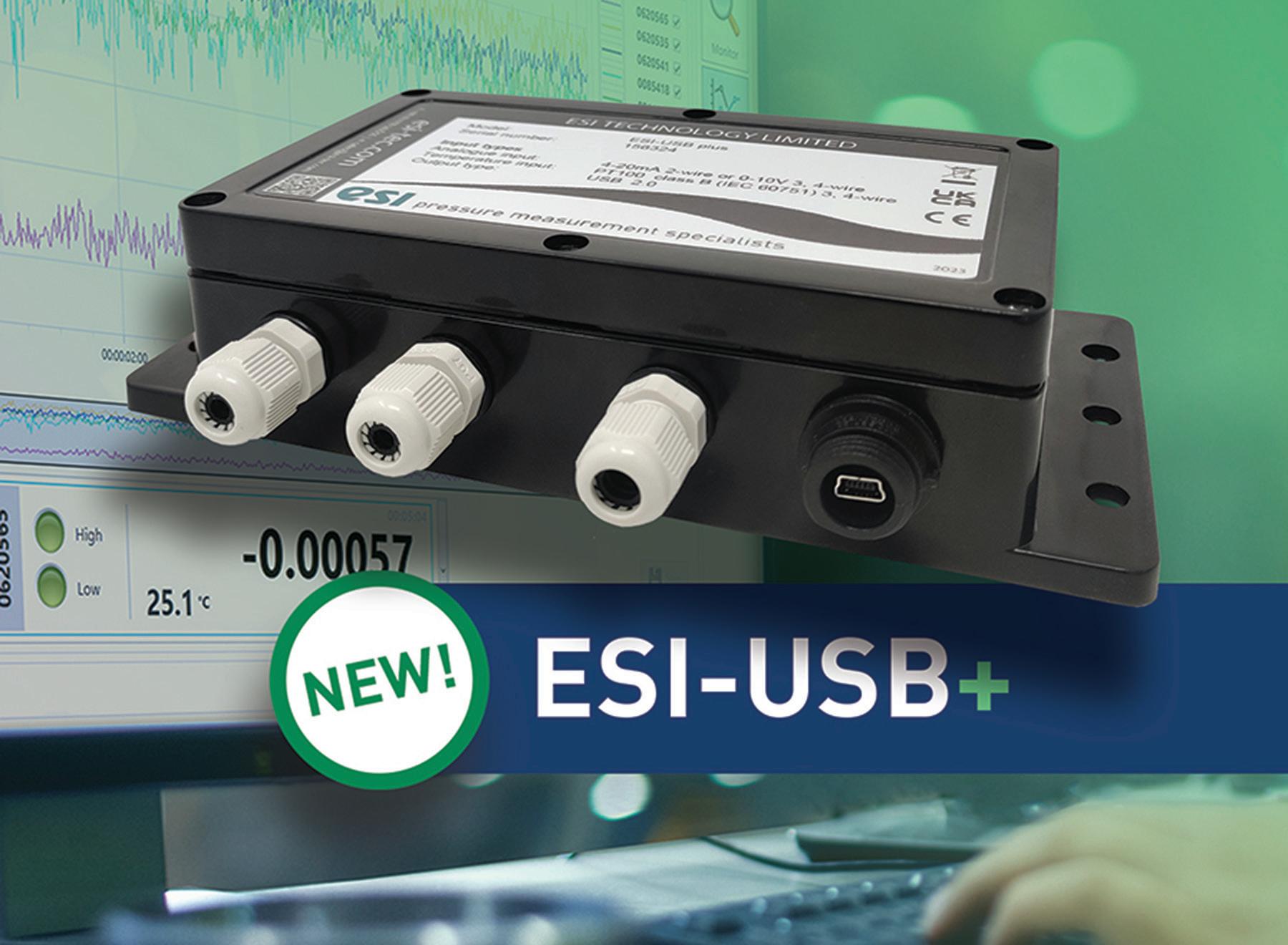
Just like the popular GD4200-USB pressure transmitter, the new ESI-USB+ has been designed to be plug & play. It includes a dedicated input for precise temperature measurement via a PT1000 RTD, and two further inputs suitable for connecting any type of transmitter with a 4-20mA or 0-10V output.
In identifying the needs of the customer, the natural course of the products development was to enable the user to measure multiple inputs all at once,
instantaneously. Having to use multiple computers and endless connections is time consuming and inefficient. With the ESI-USB+ you can use up to 16 different inputs and have them all at your fingertips on the one screen.
The new device connects to the computer’s USB port and data from a user’s chosen input is then presented onscreen via the ESI-USB fully configurable Windows Interface software, which is free to download from the ESI website.
With instant connection and autodetection, the software will automatically configure with desktops, laptops, or Windows tablets via USB protocol.
Compatible with USB 2.0/3.x type A ports, the ESI-USB software runs on Windows 8, 10 and 11. Data can be displayed in graphical or tabular form,
with a choice of pressure units and fully adjustable scales.
Other useful features include certificate generation, customisable certificate templates, leak testing, the ability to measure, record and view up to 16 sensors at the same time, virtual differential pressure measurement, set automatic test start and stop times, alarm levels for each individual sensor and auto-updates for new software versions. Data can be saved to a file or exported to Excel/PDF.
Whatever needs to be measured ¬such as pressure, temperature or flow, the ESI-USB+ will do the job with excellent accuracy and a range of data analysis and reporting features.
The ESI-USB+ is the new, versatile product in the company’s digital measurement range.
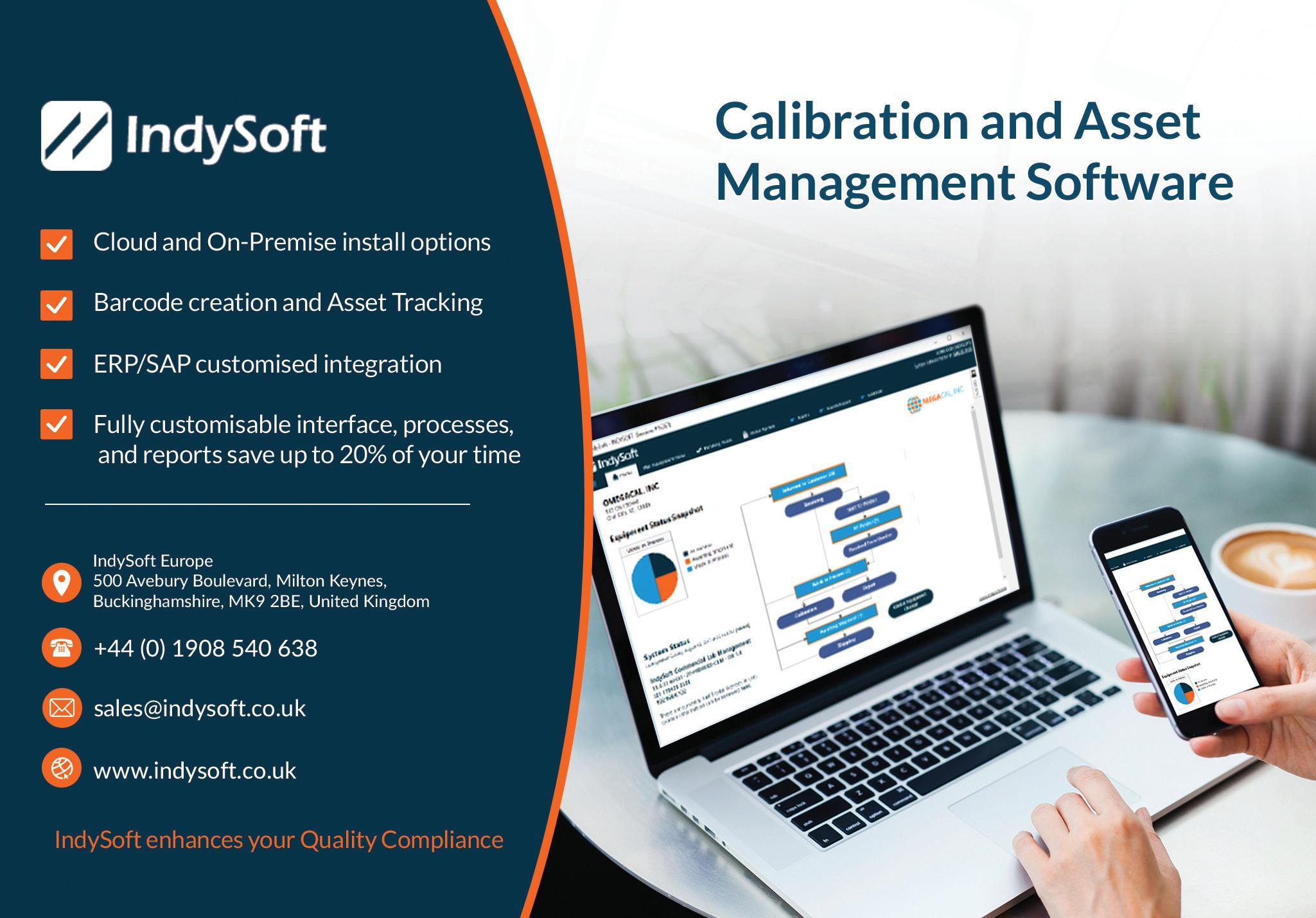
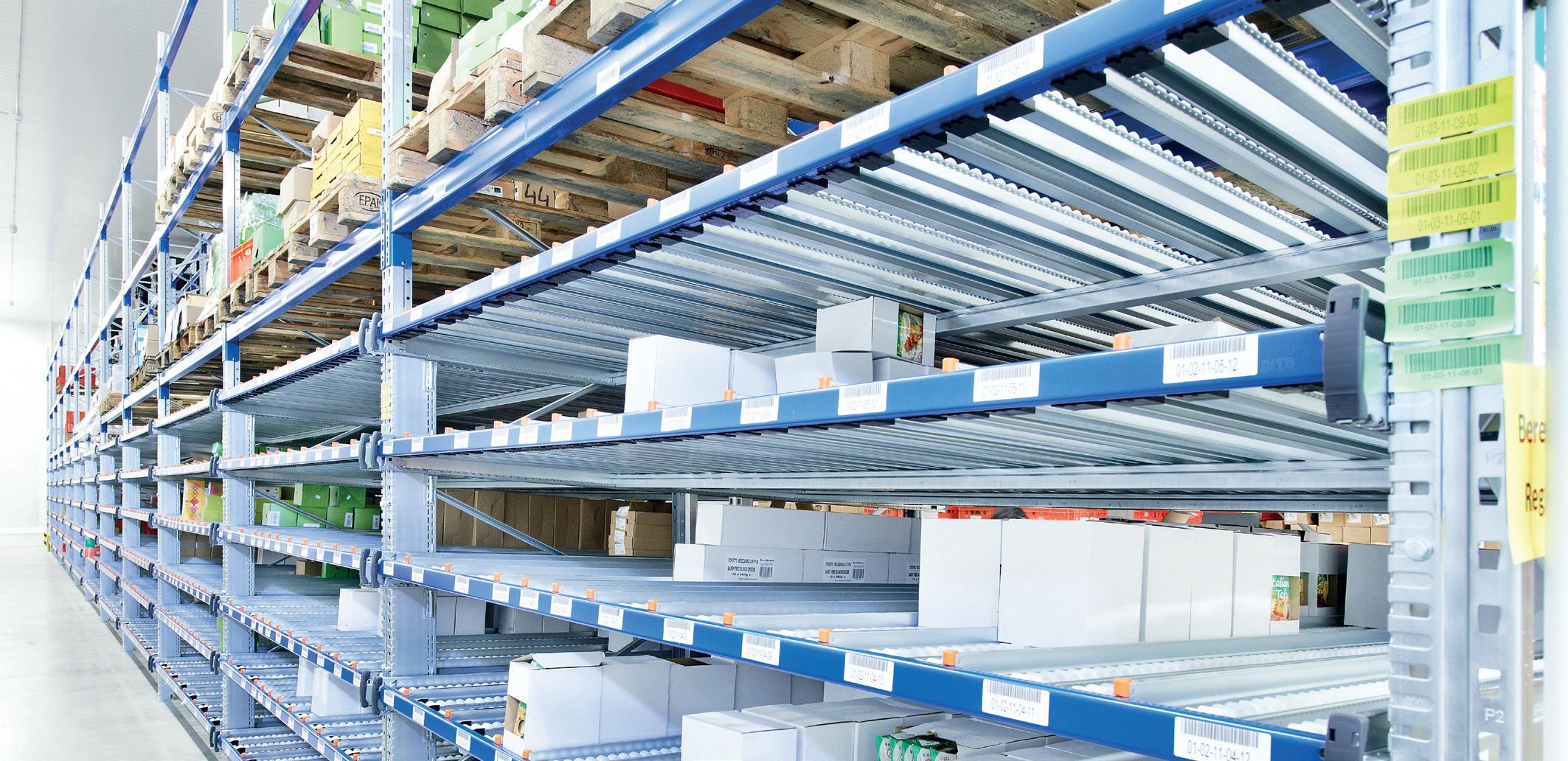
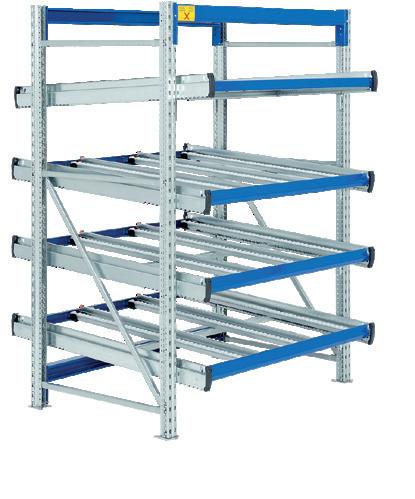
Versatile ultrasonic flowmeter with ASCII flow streaming
As a specialist liquid flow meter manufacturer, Titan Enterprises’ patented ultrasonic technology has led to an expanding line of ultrasonic flowmeters and patents ranging from signal processing methodology to novel mechanical design, as MEPCA discovered.
Titan’s most versatile Atrato line of ultrasonic inline flowmeters now has ASCII flow streaming capability via USB and is reverse flow enabled, enhancing its capacity to be optimised for the user’s application, in addition to its datalogging and diagnostic features.
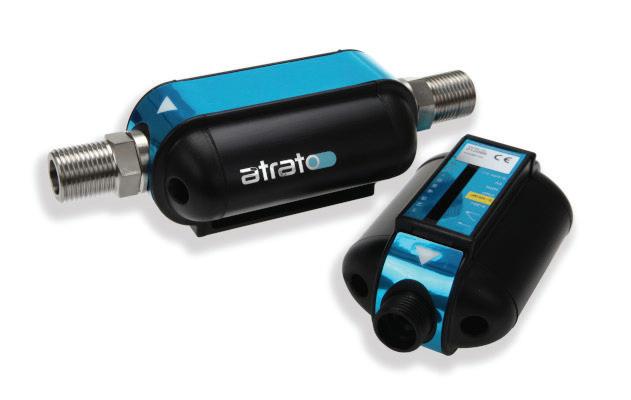
The sophistication of the Atrato’s ultrasonic technology, together with the proprietary embedded signal processing software developed by Titan Enterprises, allows both viscous and non-viscous liquids to be routinely measured precisely.
Neil Hannay, Senior R&D Engineer with Titan Enterprises, said: “The device’s USB connection gives the Atrato flowmeter computer interface capability, enabling the user to directly monitor the flow rate being measured and alter the operating parameters using a laptop PC. ASCII flow streaming capability has been a logical next step in the advancement of these ultrasonic flowmeters.”
The additional ASCII flow streaming means the measured liquid flow is output at 10-20 times per second in human-readable text form (ASCII encoded). This stream of data can then be interpreted and processed by software running on the USB host.
The advantages of ASCII streaming for the user are three-fold:
• The flow measurements are streamed directly over the USB connection to the PC.
• No additional pulse counting or analogue interface devices are required.
• Flow measurements are configured directly to the user’s software system, such as LabVIEW.
Titan’s Atrato ultrasonic flow devices are
ideal for low-flow applications and precision process control, laboratory processes and chemical dosing. Ultrasonic flow meters are also becoming an important flow metering sensor within petrochemical process applications; about 40% of ultrasonic flowmeter sales fall into the oil & gas industry, refining and chemical.
Using Titan’s patented ‘time-of-flight’ ultrasonic technology, the Atrato flow meters operate with unmatched accuracy over a flow range of 2ml/min to 20l/min. The superior non-intrusive design and electronics, coupled with Titan’s unique algorithms, make the Atrato an advanced
signal processing flow measurement system with no moving parts, virtually eliminating mechanical wear, critical for long life and repeatability.
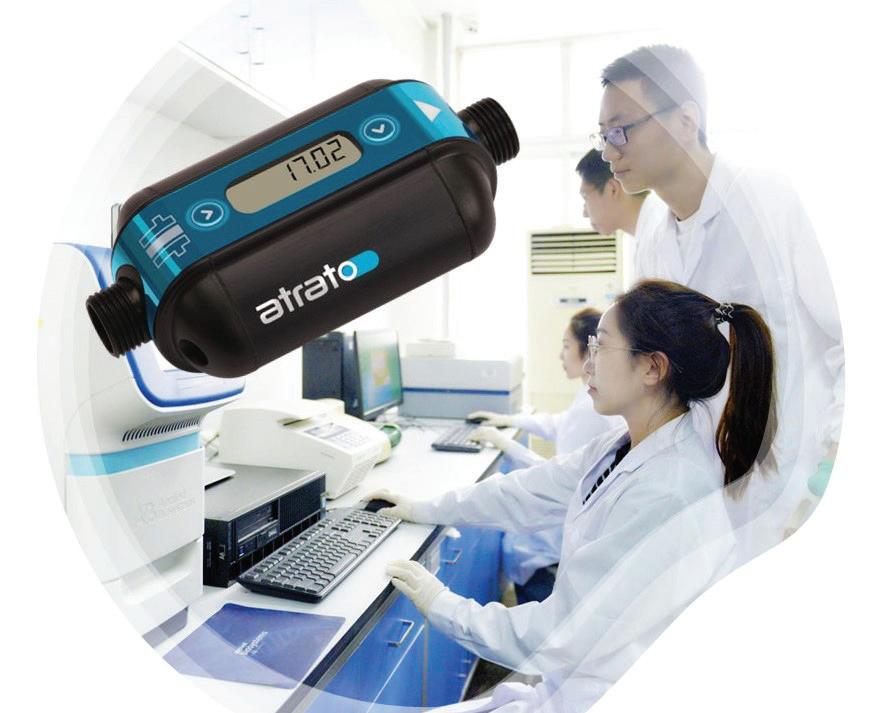
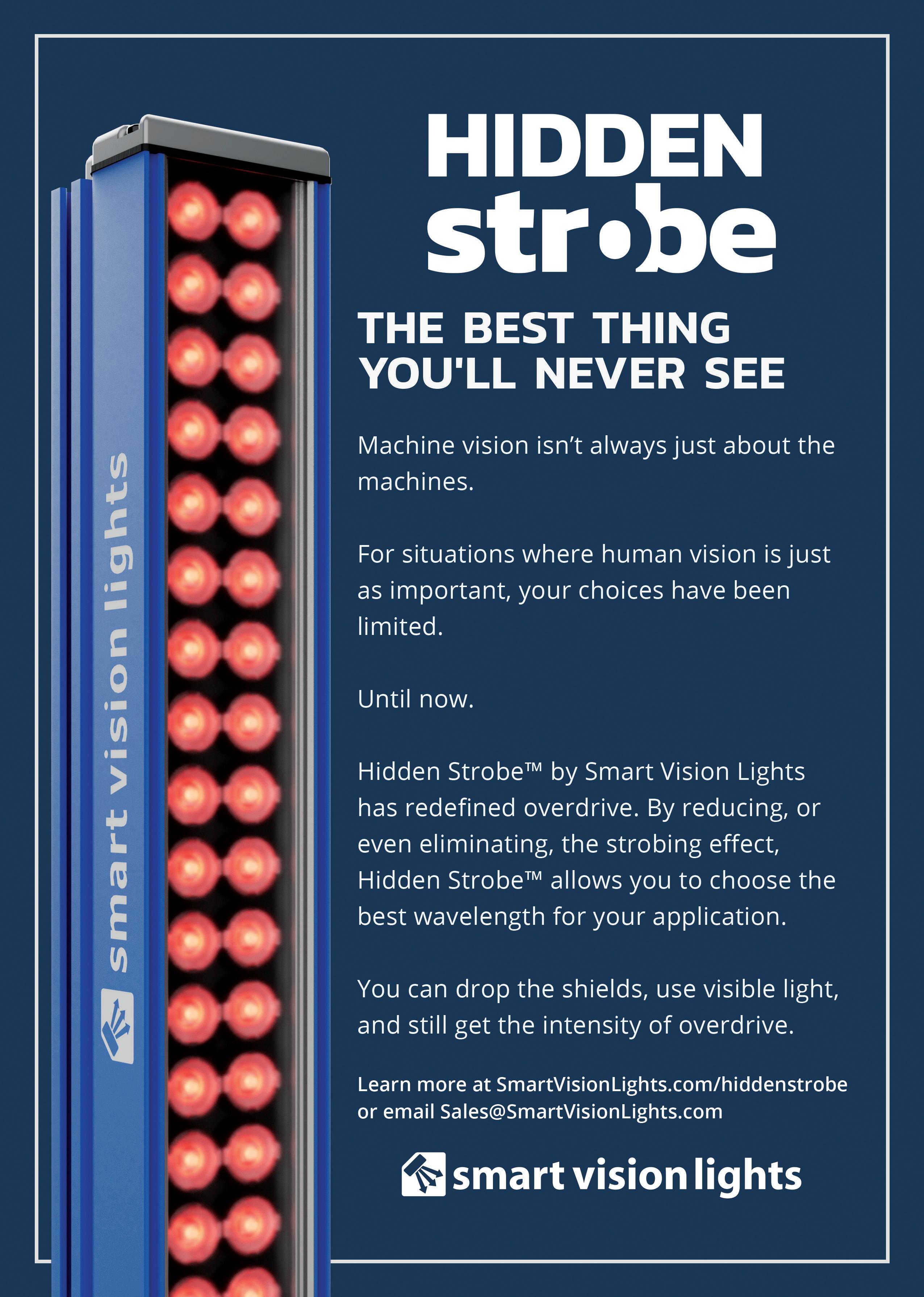
Monte Carlo or bust
ICENTA Controls has adopted the Monte Carlo method to establish its high-performance flow calibration systems’ uncertainty. As a manufacturer and supplier of flow meters, the method used to calibrate meters is of the utmost importance to ICENTA. This uncertainty methodology is critical to establish, maintain and improve product performance and long-term repeatability.
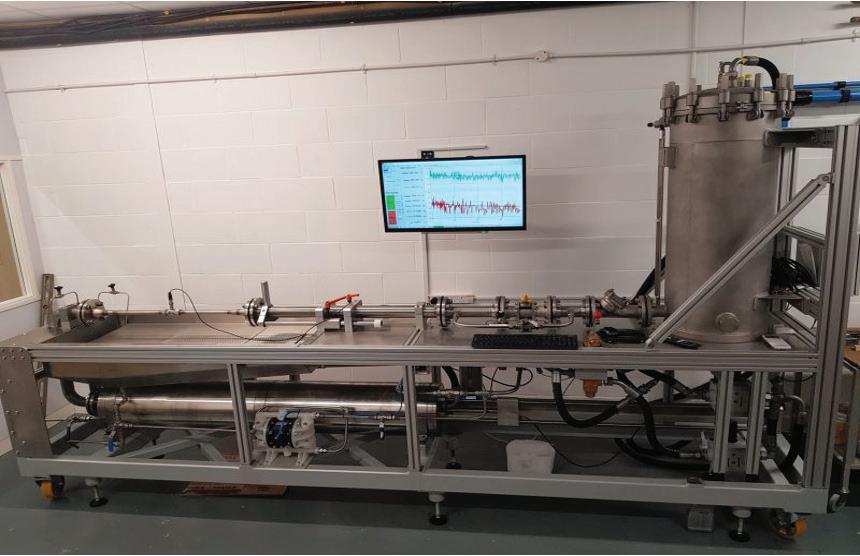
The Monte Carlo method is a powerful statistical technique that can also be used to estimate the uncertainty of a measurement. It works by repeatedly simulating the measurement process and considering each input parameter’s uncertainty. This allows ICENTA to calculate the probability of obtaining different measurement results and to estimate the range of possible values for the measurement.
The Monte Carlo method is often used in engineering and scientific applications where the measurement process is complex or where there is uncertainty about the input parameter values. It is also used in finance to estimate the risk of investments.
In the context of piston proving, the Monte Carlo method can be used to estimate the uncertainty of the volume measurement. This is done by repeatedly simulating the measurement process, allowing for variation in the dimensions of the cylinder due to manufacture and changes due to variations in temperature and pressure. The results of the simulations are then used to calculate the probability distribution of the measurement results. The Monte Carlo method has several advantages over traditional methods for estimating measurement uncertainty.
First, it can be used to estimate the uncertainty of measurements that are too complex or expensive to be measured directly.
Second, it can be used to estimate the uncertainty of measurements where there is uncertainty about the input parameter values.
Third, it can be used to estimate the uncertainty of measurements that are affected by random errors.
The Monte Carlo method is a probabilistic method. This means that it uses random numbers to generate the simulated measurement results. The number of simulations needed to obtain accurate results depends on the complexity of the measurement process and the amount of uncertainty in the input parameters. The Monte Carlo method can estimate the uncertainty of any type of measurement, including length, volume, mass, force, and temperature. It is a relatively computationally expensive method. However, the cost of the simulations can be reduced by using a statistical software package. Ultimately, it is a valuable tool for engineers and scientists who need to estimate the uncertainty of their measurements and is a versatile technique that can be used in a wide variety of applications.
The Monte Carlo method is a powerful tool that can be used to solve various problems. It is a versatile technique that can be used in a variety of disciplines. For example, in addition to its use in this calibration application, the Monte Carlo
method can be used to estimate the risk of investments by simulating the possible returns of an investment over a period of time. It can also be used to estimate the uncertainty of clinical trials by simulating the possible outcomes.
In environmental modelling, the Monte Carlo method can be used to model the behaviour of environmental systems, such as the spread of pollution or the effects of climate change. While in manufacturing, the method can optimise manufacturing processes by simulating the possible outcomes of different process parameters.
As you would expect, the name derives from the Monte Carlo Casino in Monaco, famed for its games of chance, randomness, or skill.
And on a topical note, with the recent release of the film Oppenheimer, the Monte Carlo Method was likely conceived and developed by Stanislaw Ulam and John von Neumann, mathematicians working on the Manhattan Project.
www.icenta.co.uk
NCC
8-pole bayonet locking
> 5000 mating cycles
Panel mount parts unplugged IP67

Solder and dip solder contacts
www.binder-connector.co.uk
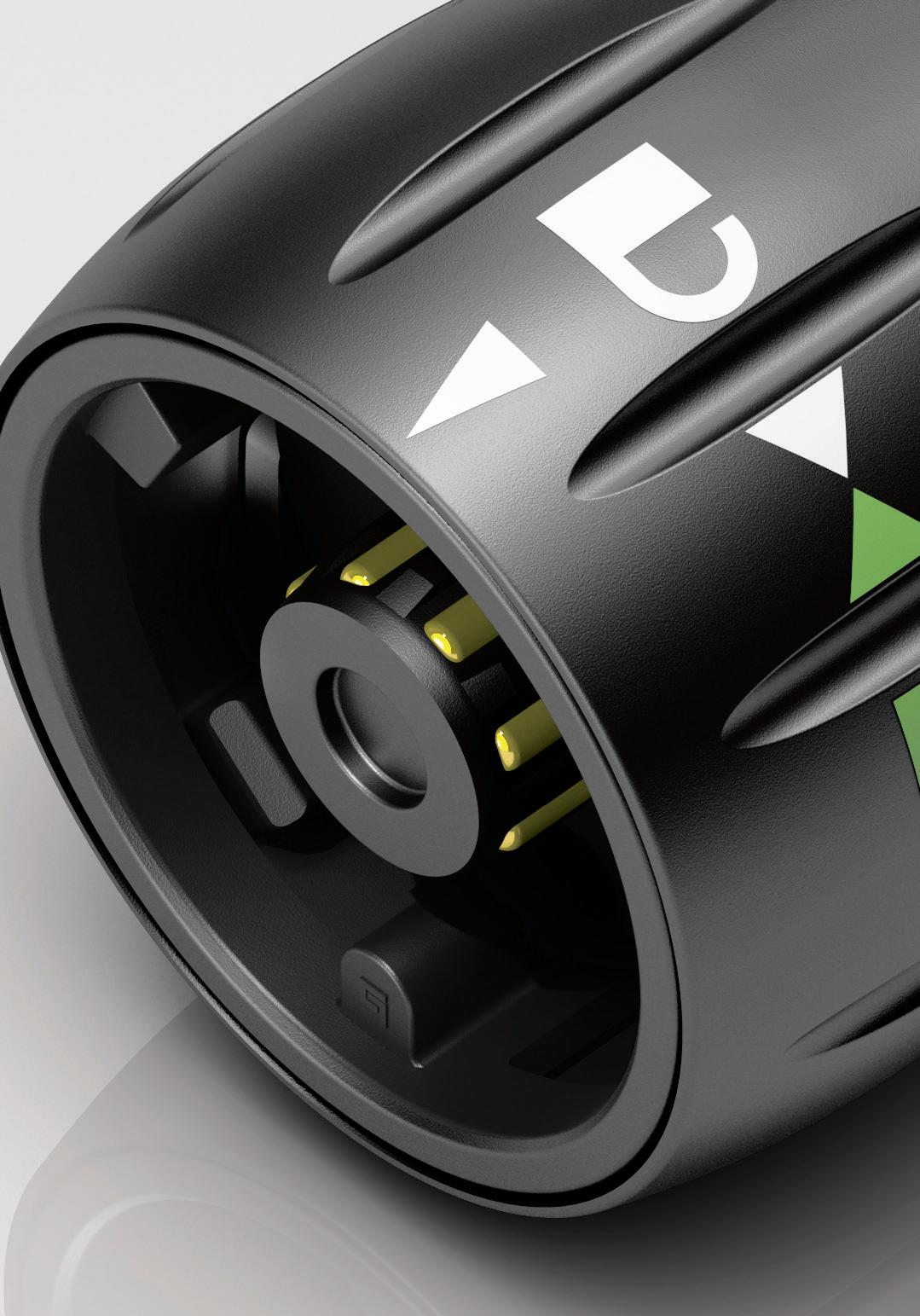
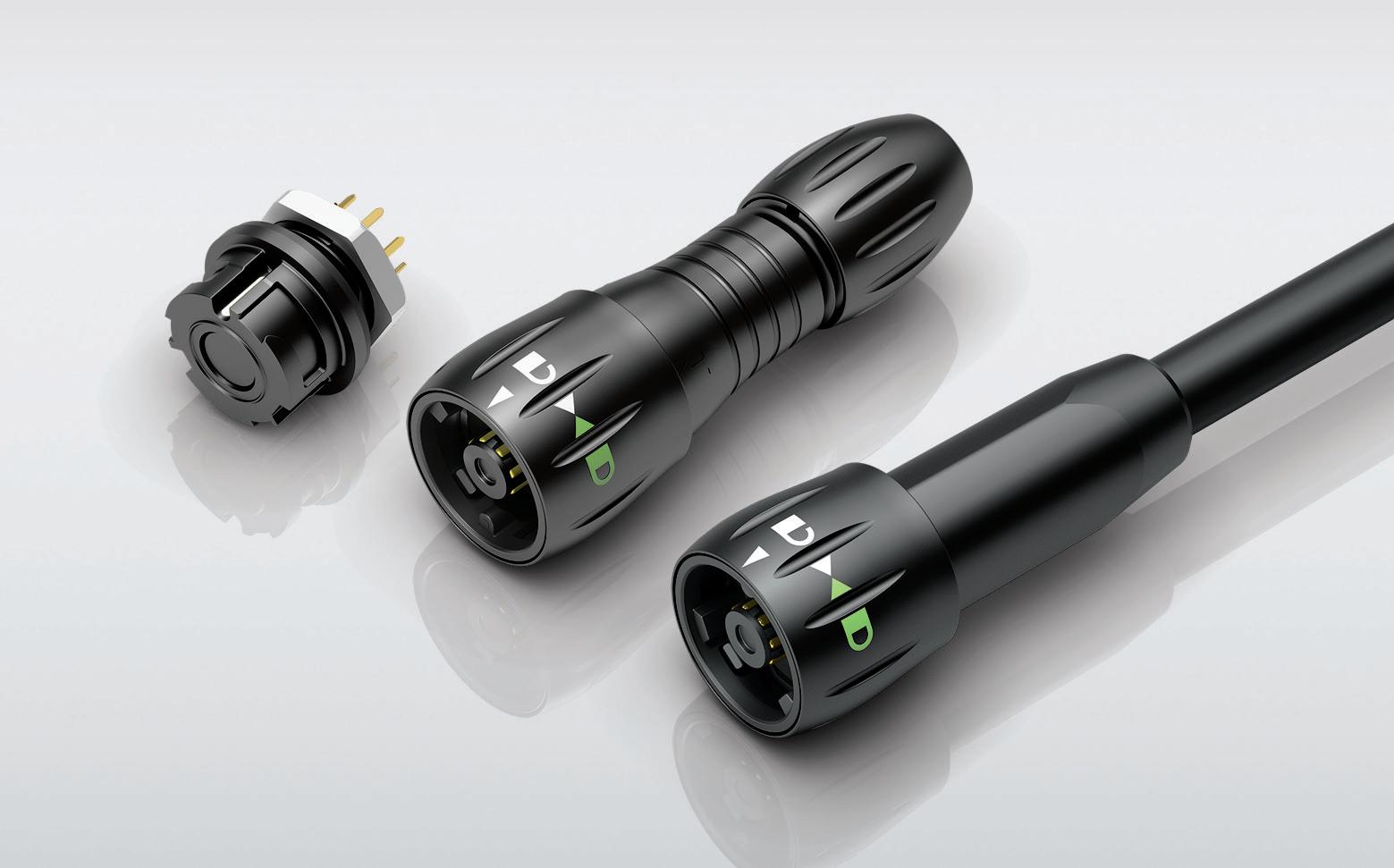
Ensure your pumps are compatible
Castle Pumps outlines some of the factors that need to be considered when selecting a pump for a specific application.
When it comes to needing a new pump for your process, “What fluid are you handling?” is one of the first questions you will be asked. Everyone understands that ensuring the wetted parts are in materials compatible with your fluid is vital, as failing to do so can cause the impellers, seals and other components to swell, become brittle, erode or even melt.
Castle Pumps often hears customers saying, “Oh, EPDM is fine for my fluid”, which is a great starting point. But did you know that the concentration and temperature of a chemical can also impact material selection? For example, Hastelloy C is compatible with Hydrochloric acid at 10% concentration at 20°C. However, at 40°C, it has limited resistance.
Not everyone realises that a supplier asking about your fluid is not solely down to material selection but also pump selection. So, what else should you be ready to tell your supplier about your fluid when you have a process requiring a pump?
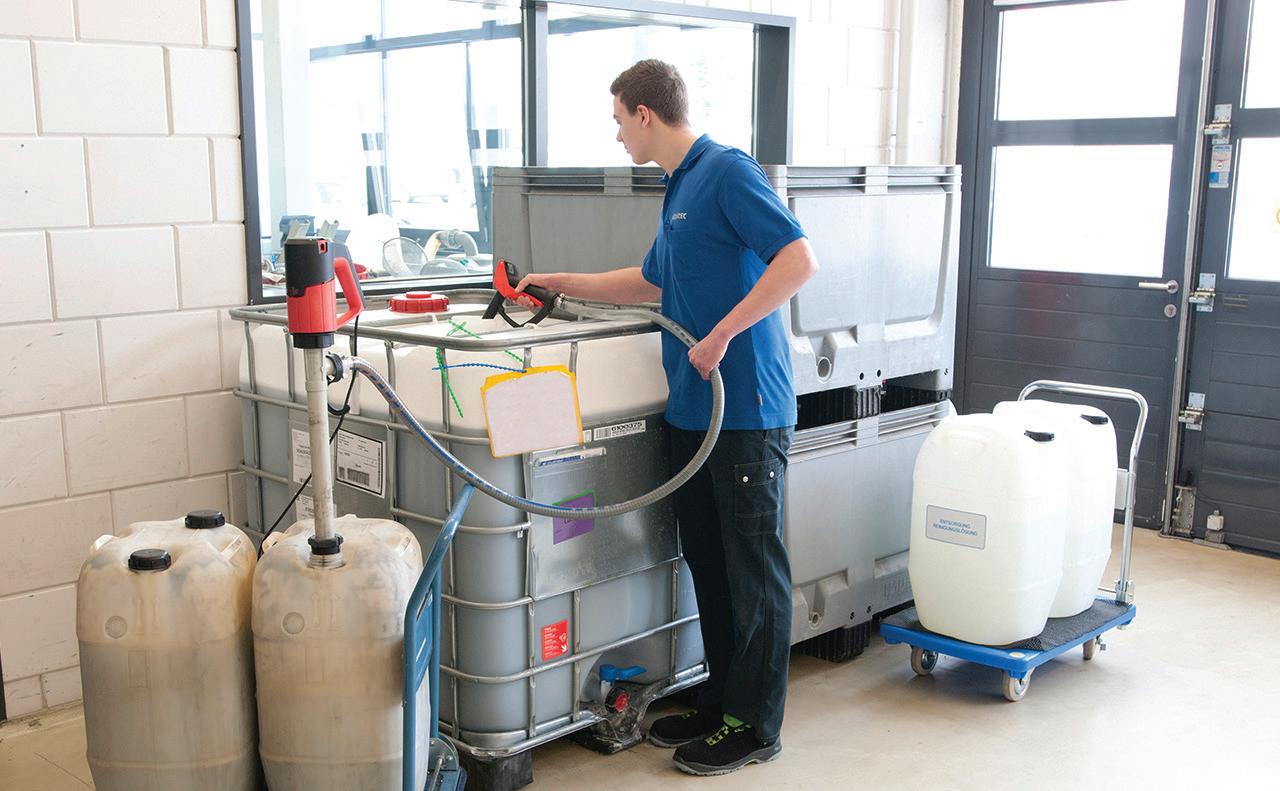
Presence of solids in the liquid
Certain pumping technologies are not suitable for handling even the smallest of particles. Due to the tight tolerances between the casing and the moving parts, vane, gear, and side channel pumps will jam when attempting to pass solids, causing immediate wear. On the other hand, peristaltic and diaphragm pumps can handle solids up to the size of their inlet/outlet. For that reason, sometimes a larger pump than is needed duty-wise is specified to handle the solid size but run at a lower speed.
It’s also important to consider whether the solids are hard and abrasive or soft and malleable. Are they thin and stringy, susceptible to clogging?
Peristaltic pumps have no moving parts that encounter the fluid and, therefore, have no valves, seals or impellers to clog or erode. Whereas other pumping technologies could find stringy solids such as fruit juice pulp wrapping around their impellers. For softer solids, flexible impeller pumps are often a lower cost solution, thanks to their supple rubber impellers being able to bend around them.
Viscosity of the fluid
Certain designs, such as centrifugal pumps, which are excellent for thin, water-based chemicals, can struggle with thicker fluids due to frictional losses inside the pump, causing flow rates to decline rapidly, whereas many positive displacement pumps excel. Knowing the viscosity of your fluid is therefore very important to pump specification, but also be aware that this can change with temperature. A pump may be able to handle gear oil at 10°C, but at -10°C, it becomes too thick.
As well as this, the presence of solids within a thin liquid such as sand in water is much more abrasive than larger solids in a higher viscosity, lubricating fluid such as oil. The continuous cavities between the rotor and stator of the progressive cavity design and the slight flexibility of the stator means that large solids in think liquids can be easily handled. However, when an abrasive water-based liquid is pumped, wear can occur more prematurely than a peristaltic pump with limited internal components.
Is the fluid shear sensitive?
Shear-sensitive fluids are those that, under force, can be damaged or altered, like
cream being whipped, shampoo frothing or solids being crushed like fruit pieces in a yoghurt. Being aware of your fluid’s delicate nature can impact the specified pump type. While centrifugal pumps apply high shear in operation, shear-sensitive pump designs such as progressive cavity, flexible impeller, and peristaltic pumps can keep such fluids intact due to their low internal velocity and the wider tolerances between their pump casing and internal components.
www.castlepumps.com
Castle Pumps’ top tips
• Give full disclosure of the fluid and specify all fluids for which you plan to use the pump.
• Where available, providing an MSDS sheet is the most accurate way of ensuring compatibility.
• When it comes to fuel and oils, always specify any additives that may get added afterwards.
• Confirm temperature and concentration if it’s a chemical, as this can impact material selection.
• If you aren’t sure about the exact viscosity of your fluid, liken it to a more well-known liquid.
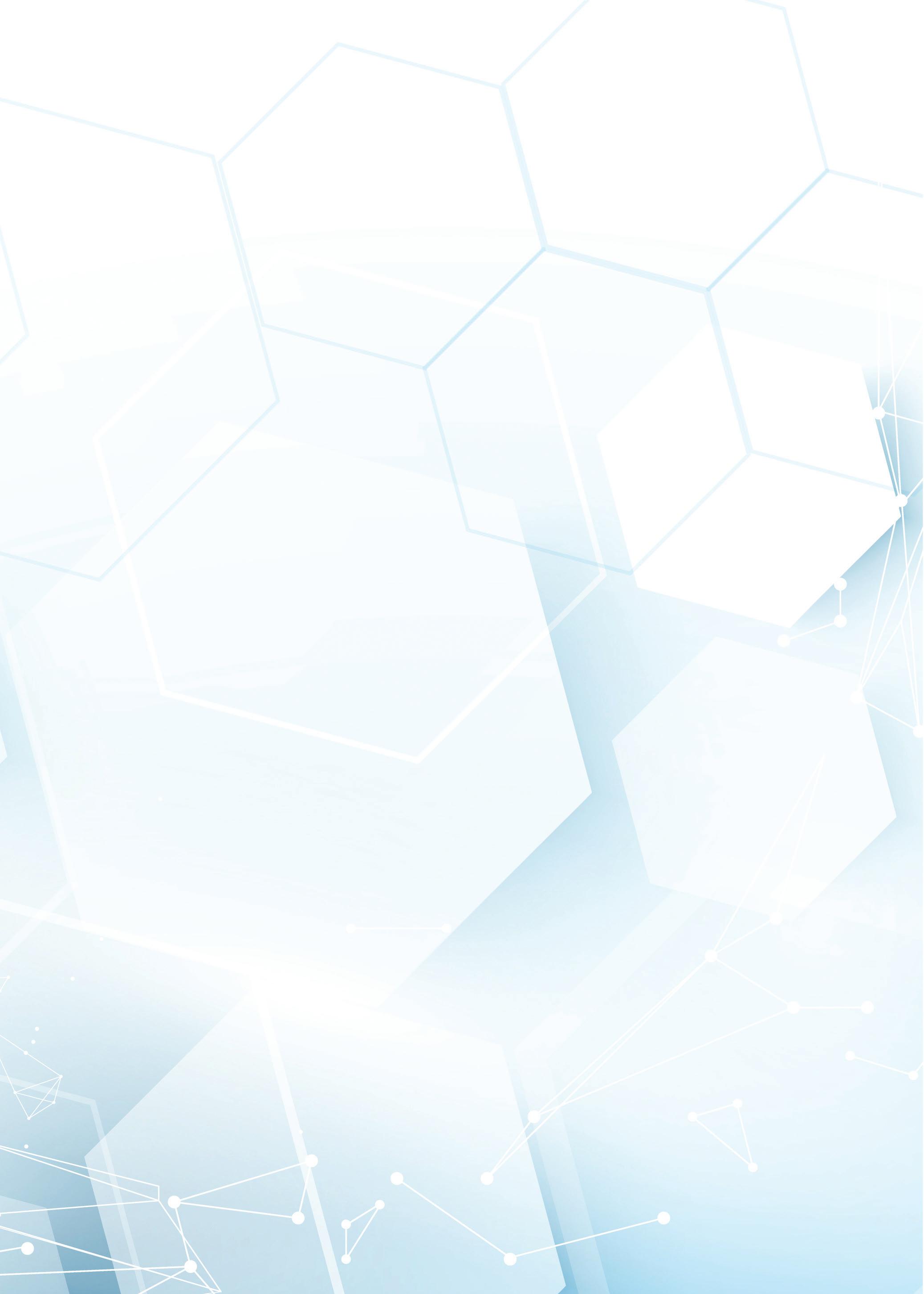
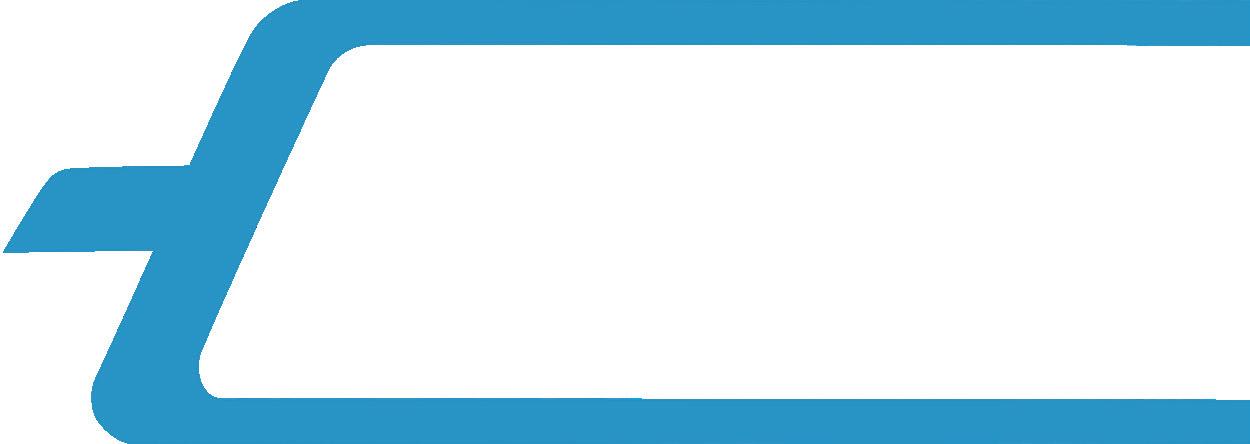
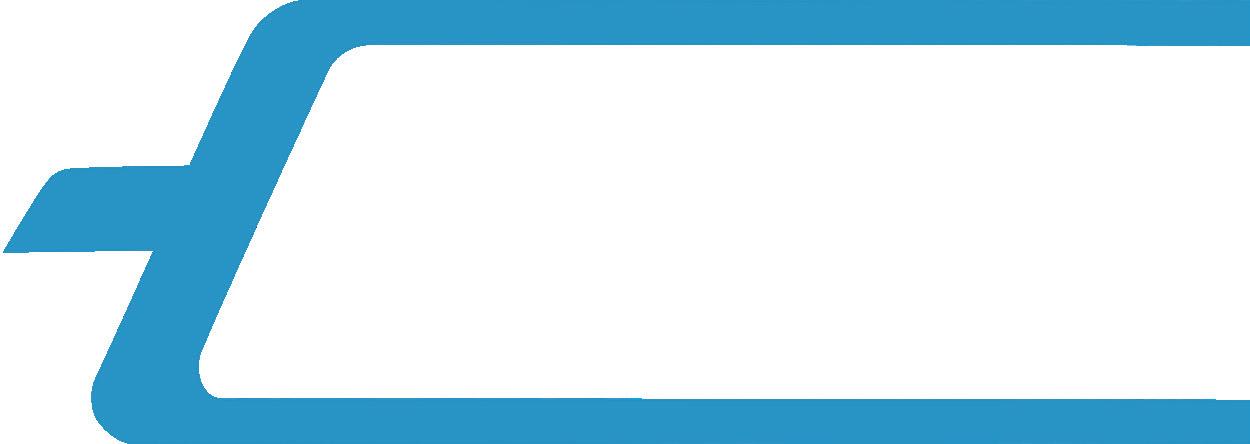
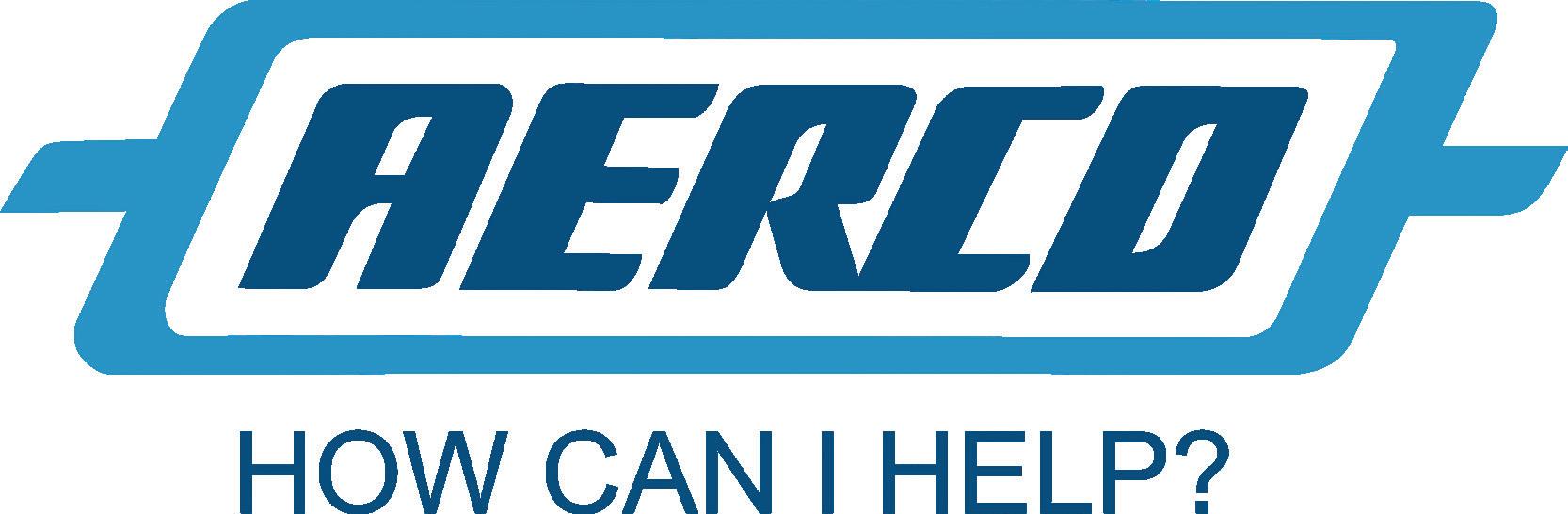
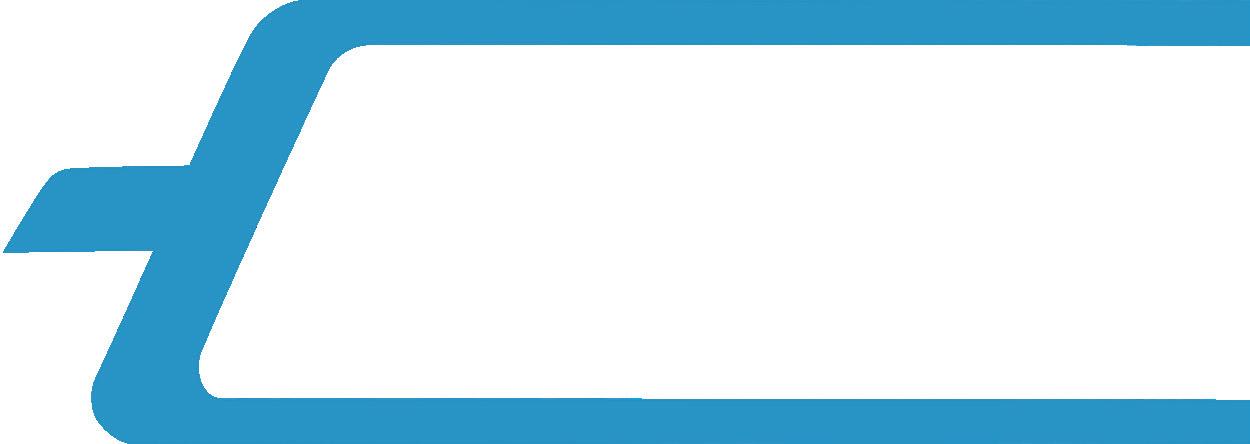
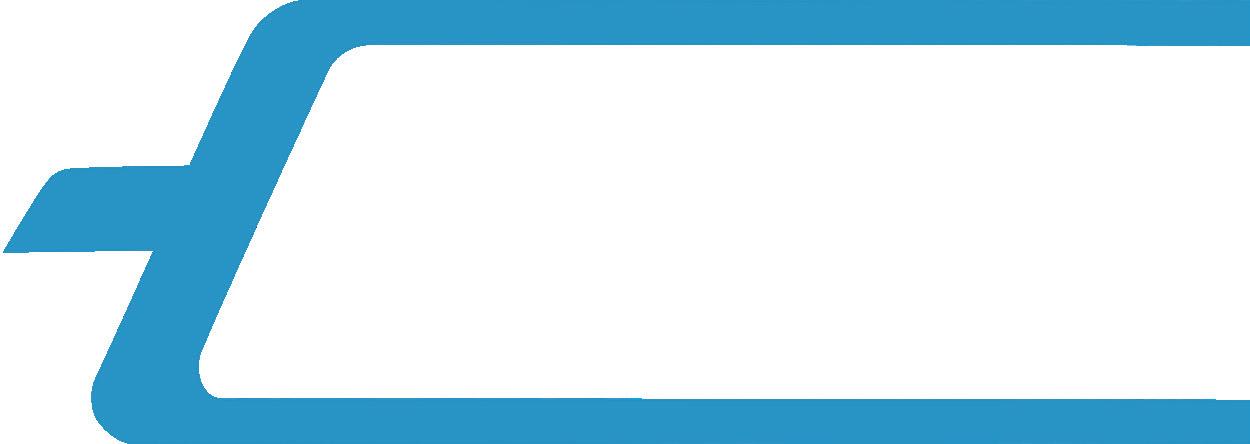
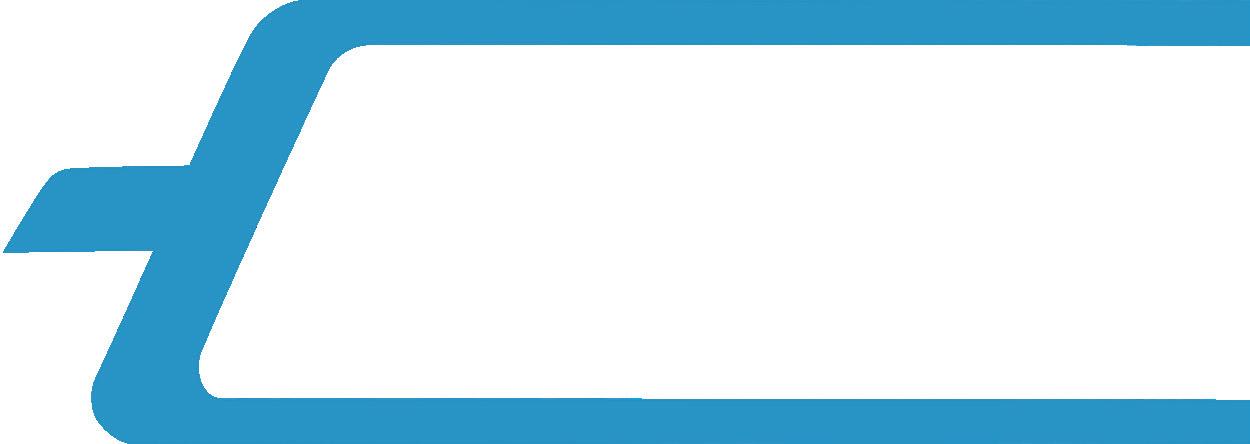
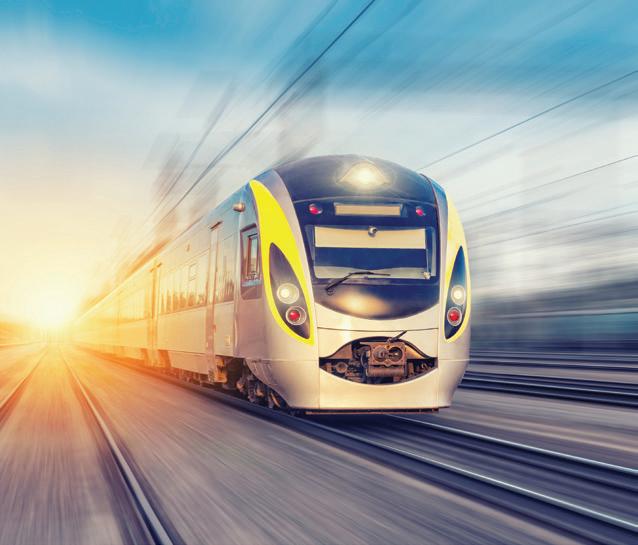

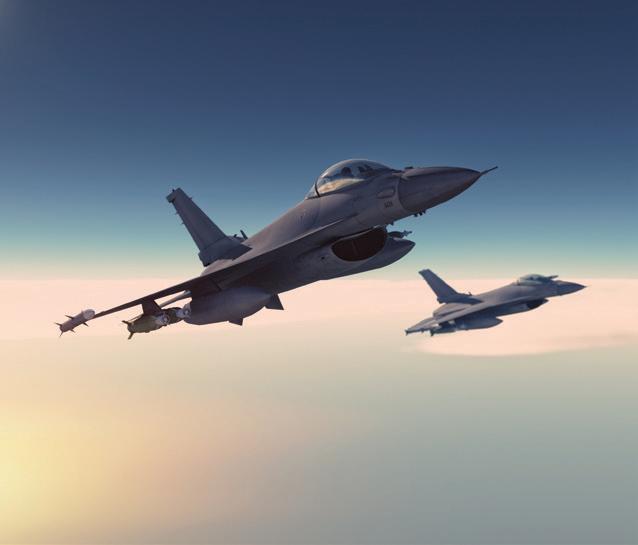

Innovative pump solutions power sustainable sludge treatment
Progressive cavity pumps specialist, SEEPEX, has reduced downtime and delivered cost savings for one of Thames Water’s sewage treatment works.
Thames Water owns and operates Basingstoke Sewage Treatment Works. This regional sludge treatment centre processes sludge from various locations in either liquid or cake form. The Basingstoke Sludge Treatment Centre (STC) houses advanced facilities, including thermal hydrolysis and anaerobic digestion plants, capable of processing 53tDS/day of sludge from Basingstoke, Farnham, Fleet, Guilford, and Newbury. The site now generates enough energy from waste to power itself and export to the national grid.
Problematic pulper feed pumps
The pulper feed pumps from another supplier were experiencing stator failures every four months, which caused breaks in the processing of the sludge, leading to reduced energy production and timeconsuming, costly repairs. Thames Water approached SEEPEX with the task to offer a more reliable pump, capable of efficiently transferring up to 30m3/hr of 6-10%DS high-temperature sludge.
Following detailed discussions with the on-site process engineers and maintenance manager, SEEPEX selected its BNM pump – fitted with smart maintenance solutions, and also incorporated its advanced digital monitoring package.
Simple maintenance
The SEEPEX BNM maintain-in-place pump range is designed to make maintenance for large and challenging-to-maintain pumps simple. By leveraging innovative design features, maintenance time is significantly reduced, up to 80%. Fast and straightforward maintenance of pump components ensures streamlined
preventative inspections and improves operational reliability and service life, effectively eliminating unscheduled downtime.
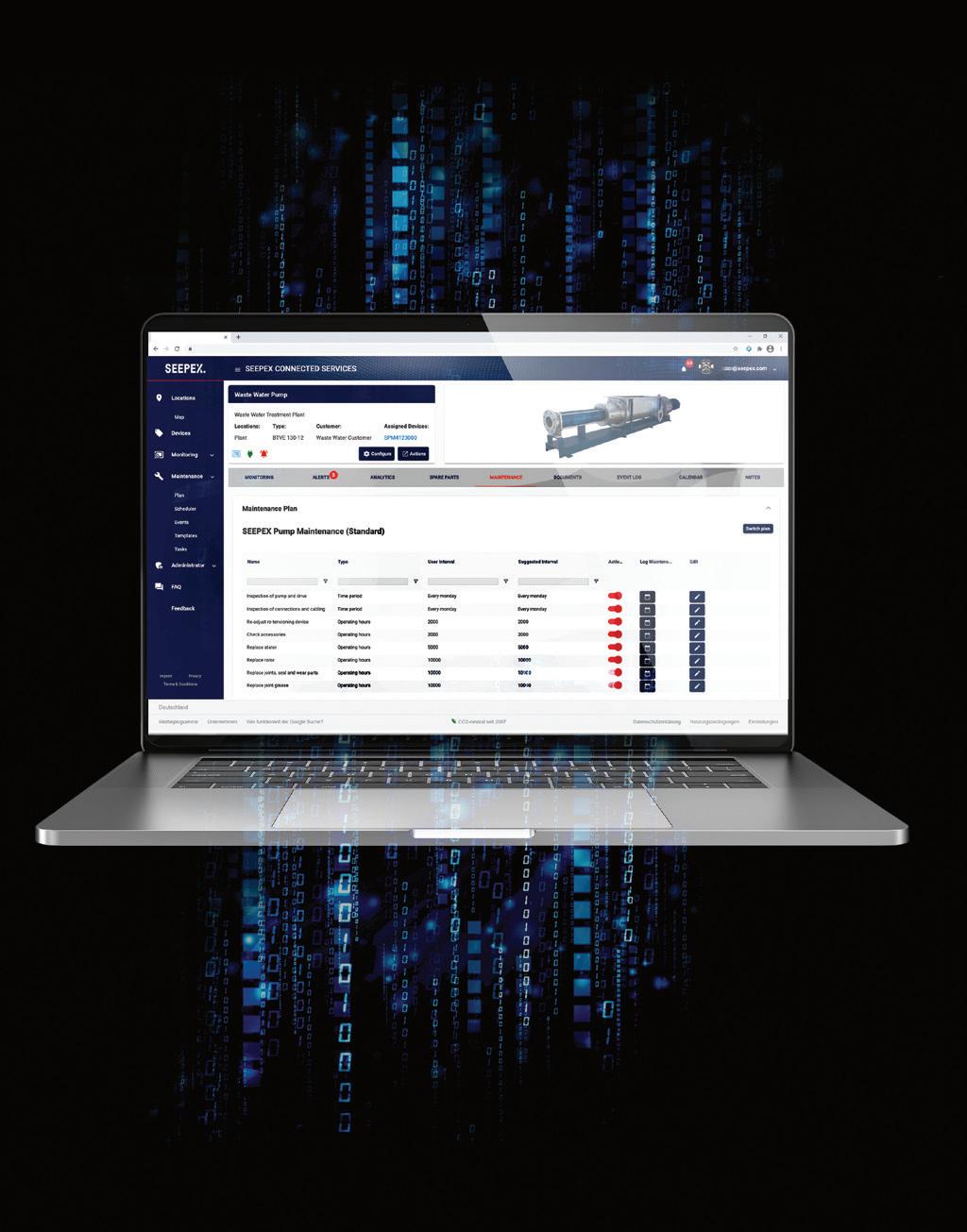
Invaluable insights
Since its installation, the BNM pump with integrated pump monitoring, has been operating 24/7 without requiring any service intervention. Real-time data collected through the monitoring sensors has allowed SEEPEX to provide the site with invaluable, real-time information on the pump’s performance. Any deviation from the pump’s design parameters triggered an investigation. This proactive approach highlighted fluctuations in the sludge temperature and the time of day these fluctuations occurred. Analysis of the data by SEEPEX enabled the correct rotor/stator combination to be selected which will again reduce the downtime of this asset even more.
Adapting innovation empowers efficiency
The incorporation of SEEPEX’s innovative pump solution with monitoring capabilities has enabled Thames Water’s Basingstoke to benefit from reduced downtime and cost savings. The elimination of frequent
stator failures and prompt detection of potential issues drastically increased uptime, maximising operational efficiency while the streamlined maintenance process has reduced spend on costly spares, ensuring cost-effectiveness and improved overall financial performance.
As the Basingstoke Sewage Treatment Works continues to set new benchmarks in sustainability and efficiency, the collaboration between Thames Water and SEEPEX serves as a glowing example of how cutting-edge technology and expertise can drive positive change in the wastewater industry.
Improved asset management for Anglian Water
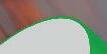



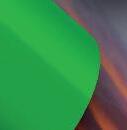


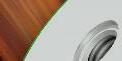
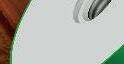













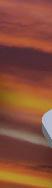



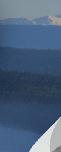

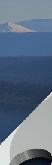

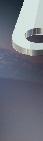







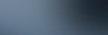

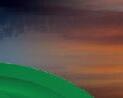

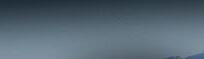
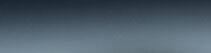

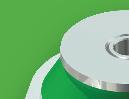

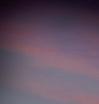
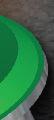
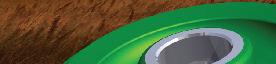
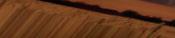



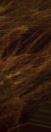

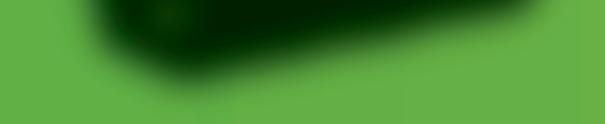
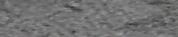










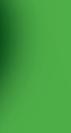




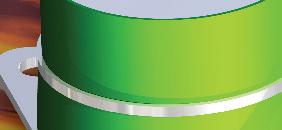
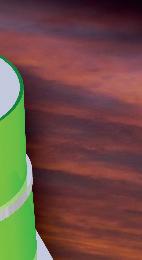
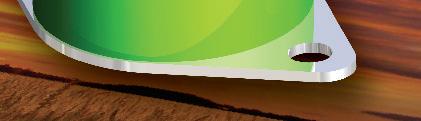





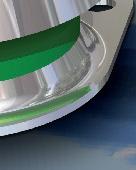

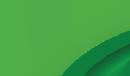




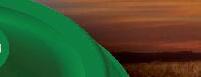
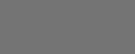

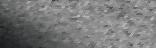
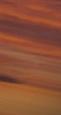
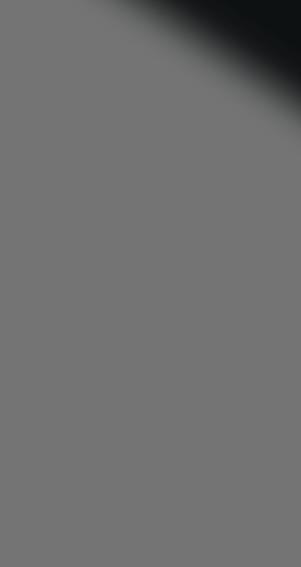
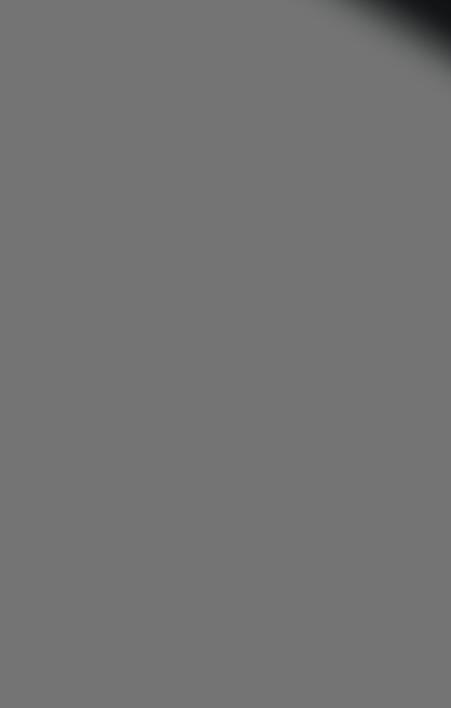


Anglian Water has revolutionised its Brockley pump station operations by integrating SEEPEX pump monitoring and connected services. This cutting-edge technology enables remote monitoring, providing Anglian Water with numerous benefits. It helps with compliance and consent flows, avoids pipework rupture caused by excessive pressure, and will support Anglian Water to efficiently implement planned maintenance work.
The Brockley sewage pump station was using SEEPEX macerators alongside obsolete pumps from a different supplier resulting in frequent engineer attendance to address performance, which placed a significant burden on resources.
The need to spend a considerable amount of maintenance time on the older pumps prompted Anglian Water to explore the latest maintain-in-place technologies. As they

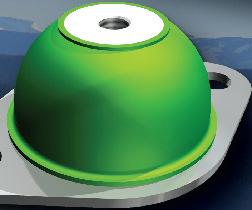
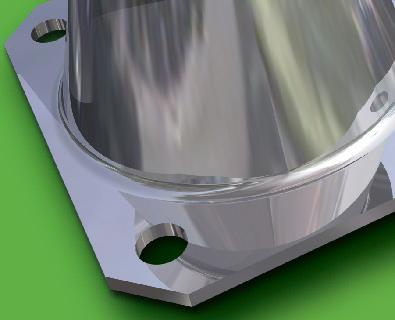
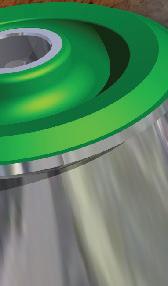
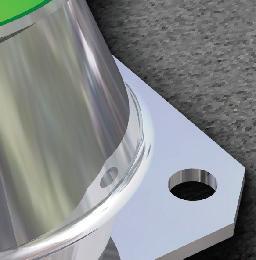
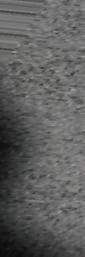
sought a solution to replace both the macerators and pumps, Anglian Water turned to SEEPEX, its trusted framework partner.
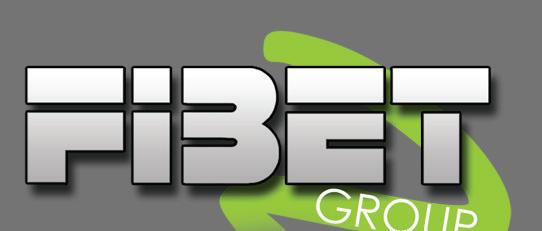
SEEPEX provided Anglian Water with new replacement macerators and progressive cavity (PC) pumps fitted with Smart Conveying Technology (SCT) and pump monitoring with advanced analytics. SCT enables the adjustment of the pumping elements, restoring pump efficiency and extending the life of wearing parts. Additionally, it allows for easy dismantling, changing of parts, and reassembly without the need to remove suction or discharge pipework, reducing on-site maintenance time.
Anglian Water can remotely monitor Brockley through SEEPEX pump monitoring, gaining insight into operating conditions and performance before visiting the station. By implementing planned maintenance and spare parts availability, Anglian Water achieves a ‘first-time’ fix approach, sending the right
person with the right skills at the right time, resulting in improved efficiency and reduced downtime.
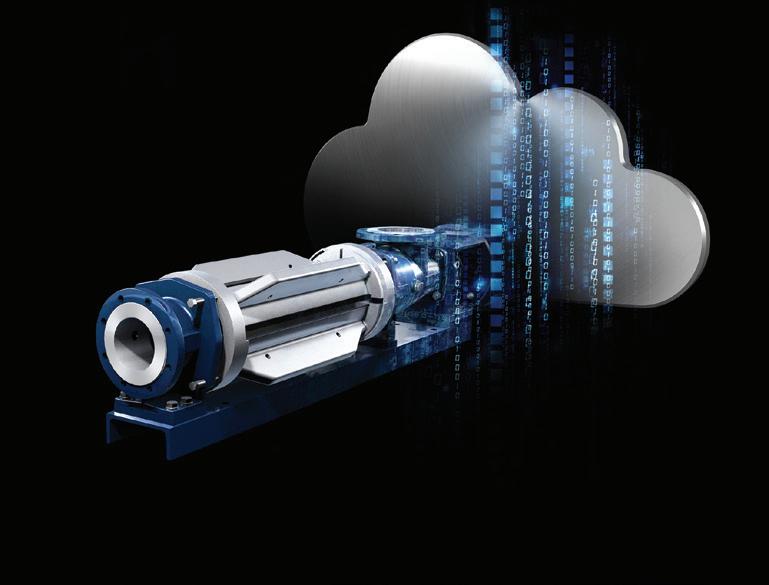

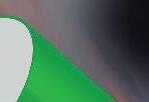

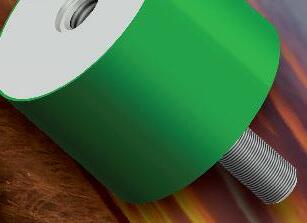










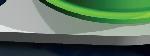
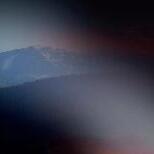
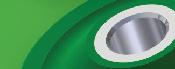
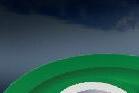
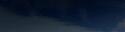
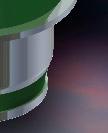

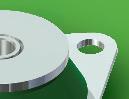



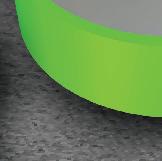


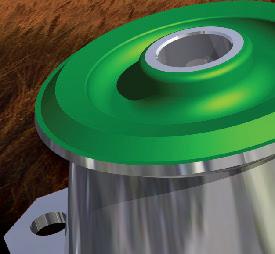

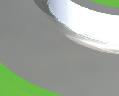





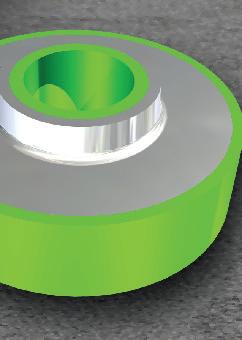





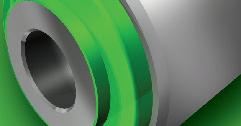


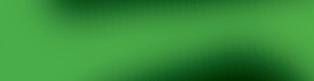
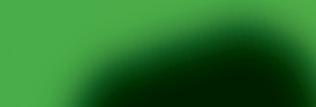
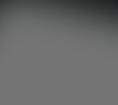
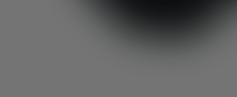





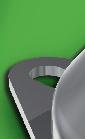



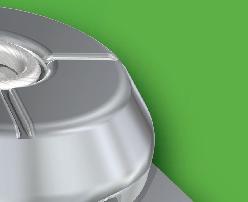
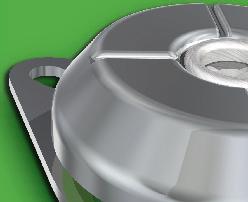
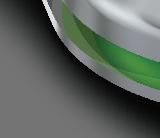
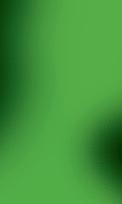
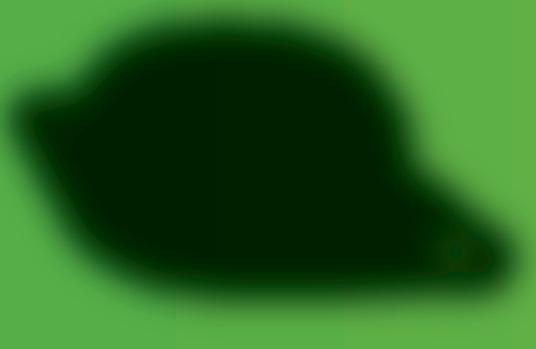
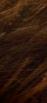
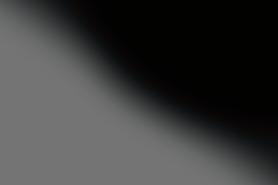
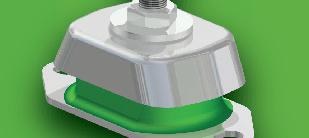

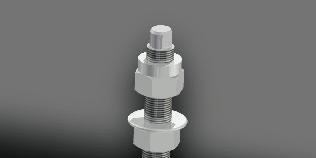


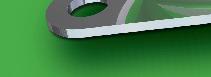
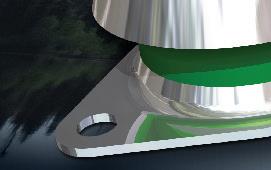

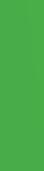

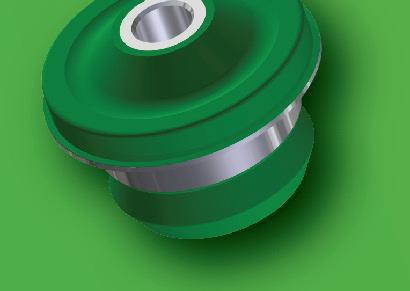



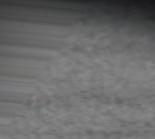
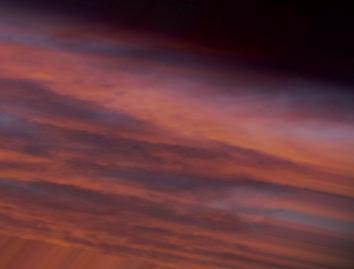
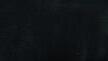




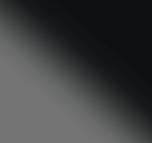
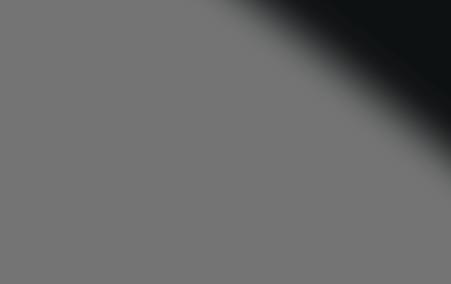
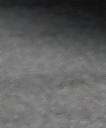



The newly optimised pump station now benefits from totally remote monitoring with advanced analytics of pump station assets, flow verification which ensures compliance and forward planned maintenance. First-time fixes are possible with issue detection before arrival for skill-based attendance, preventive maintenance avoids pump station outages and there are reduced maintenance costs thanks to the SCT pumps.
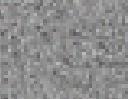
Saving time and space with Kanban storage
Standard container storage systems that do not properly support Kanban because of their size or nature will waste space and time, denting the efficiency of production processes, warns Edward Hutchison, Managing Director of BITO Storage Systems.
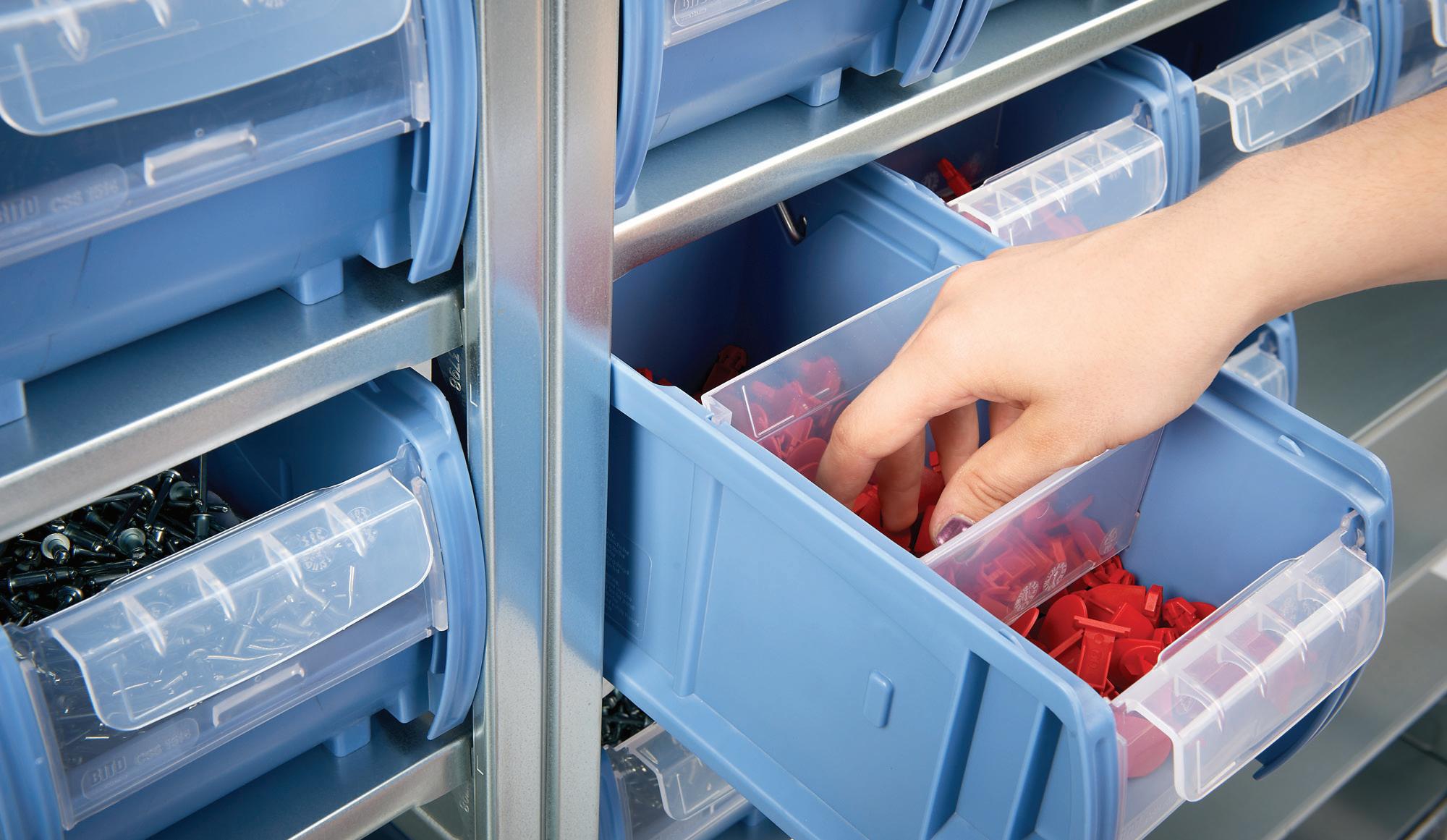
Manufacturers require small components such as nuts, bolts, fasteners and screws in their thousands, relying on these ‘C-parts’ to keep the lines flowing just as much as large components. Naturally enough, they will be kept in the highest quantity, and it is not uncommon to hold tens of thousands of these parts – often in bins on racking to make them available for picking.
Many of these manufacturers will also be operating a Kanban system to provide efficient control of production processes. Kanban is a method of self-regulating production using the pull or fetch principle in which data cards – called Kanban in Japanese – or the more advanced option of RFID tags are used to trigger individual production processes and logistics processes. It fits best with a high proportion of identical parts that have a small number of variants.
An operator working to Kanban decides how many of the necessary small parts, such as screws and nuts, they need and when. In doing so, they are guided exclusively by their own requirement. This reduces long-term stockholding and, at the same time, guarantees a continuous supply to the workstations and assembly points. The advantages of this method are decentralised control, lean warehousing and just-in-time (JIT) logistics of parts needed in production.
Individually, C-Parts have a low value, but ordering a part valued at a pound or less generates exactly the same process costs as ordering a £10,000 A-part. The potential savings with C-parts lie less with the price and rather with the ordering procedures and the associated process costs. With Kanban, the purchase order is automatically initiated as required for replenishment. There is a further cost saving with the Kanban principle due to it requiring less space for storage in valuable shop floor areas.
Making the best use of storage space
However, it is not uncommon for companies to use standard container storage systems that do not properly support Kanban because of their size or nature. Such systems will waste space. BITO, however, has developed special, torsionally rigid Kanban racking that takes up little space. CTB container racking allows 25% more C-part bins to be stored than on other shelves, thanks to an exceptionally thin base that doesn’t compromise on stability. The shelves of the CTB container rack are a mere 25mm thick, which allows storage of a significantly higher number of items, including C-parts.
There are also CTB parts containers for storing C-parts. These have sliding front windows, allowing easy retrieval of parts without having to remove entire containers from shelves. This is particularly useful when picking parts in production environments, where speed is key. The container dimensions are perfectly matched to the shelf dimensions preferred in the Kanban process.
These bins can be used in a ‘two-bin Kanban system’, which keeps reserve stock
in one of the bins and provides a calculated number of parts to the workstation. The first crate is extracted from the shelf after the last part has been removed. The picker removes the card, or RFID tag, from the back of the box, triggering the ordering process. Then, the second box is pulled into the front position. The ordered box with the supply parts is then pushed in from behind, producing a FIFO flow of parts.
‘One-bin Kanban’ can also be used for parts that are either very small or are only used in small quantities. The Kanban bin must be divided into two for this purpose with a transparent transverse divider. When the stock in the front compartment has been used, the operator removes the divider and allows the material to slide from the reserve stock to the picking position. The divider is then replaced.
Having a complete Kanban system, which saves space and ensures operators can be supplied with those essential C-parts parts as required, continuously and efficiently, will be a major contributor to boosting manufacturing efficiency.
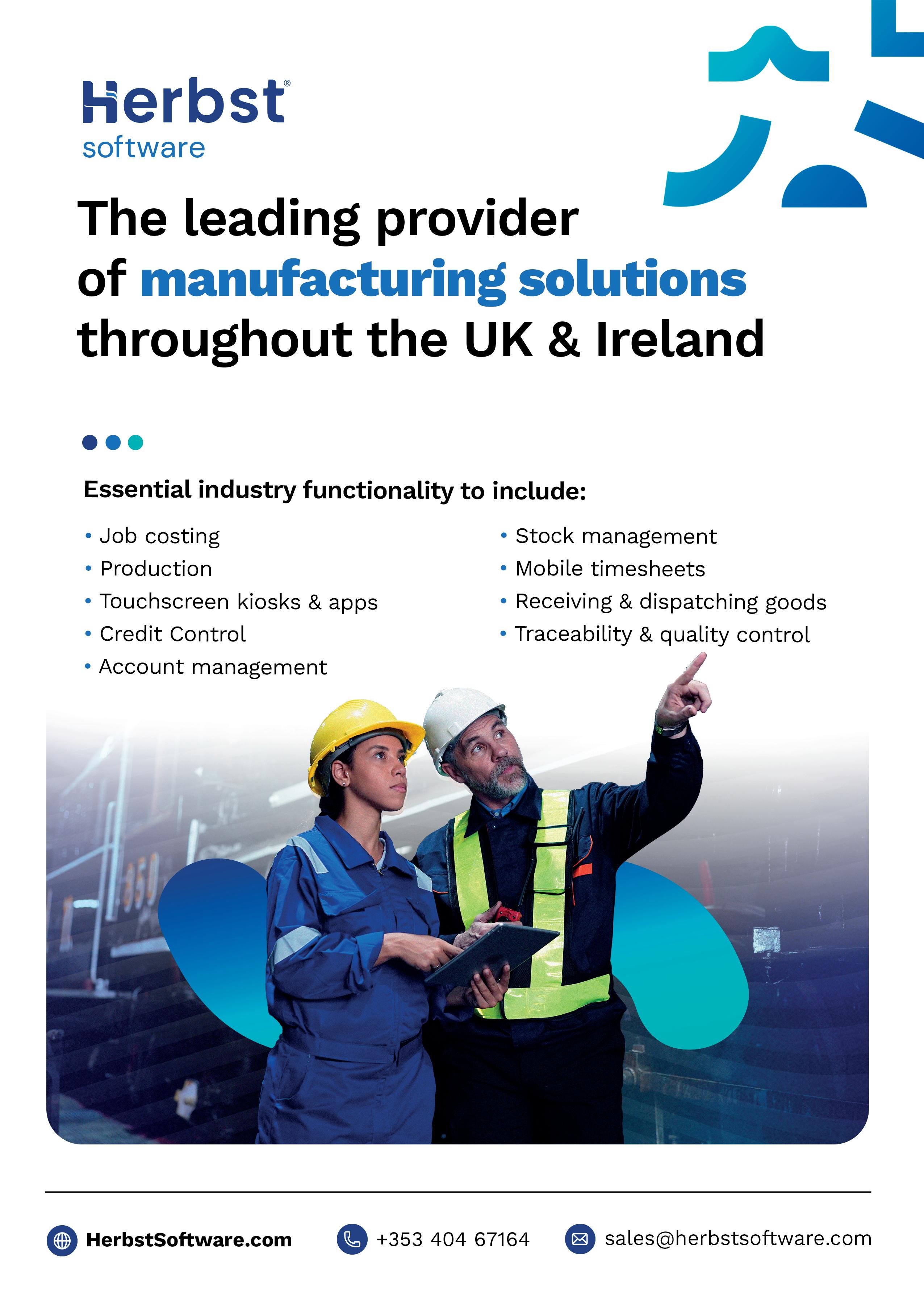
IO-Link: Fast becoming a safety interface
David Dearden of Euchner – one of the world’s first machinery safety specialists to adopt the common IO-Link platform and launch a range of compatible devices – looks at its growing popularity, especially within the machinery safety industry, and how its adoption can help machine builders and end-users protect personnel and equipment, at the same time maintaining efficient processes and preventative maintenance programmes.
IO-Link is a standardised IO technology for transmitting pointto-point data to different fieldbus systems or PLCs. It readily lets you control and operate devices, communicate diagnostic data and present parameter settings to and from field devices, including safety interlocks, using vendor-agnostic communication standards.

Functional safety communications over fieldbus technology has been around for over 20 years, but it is only recently that the widespread adoption of safety over communications channels has become a go-to. The recent increased adoption rate has been supported by the growth in the popularity of the safety PLC and associated components. Generally, the safety fieldbus connects remote and decentralised safety I/O with the local(ish) devices then hard-wired into these local points. With IO-Link, this becomes even easier and creates a host of valuable data in the process.
Even for products that do not contain an embedded IO-Link connection, there are solutions for retrofitting. For example, Euchner’s IO-Link Gateways (the GWY-CB and ESM-CB) can be added to any of their BR-type devices and serve as the interface between the safety interlock and the IOLink master on the PLC or Fieldbus.
An Euchner IO-Link Gateway and up to 20 safety devices using them can transmit both cyclical (process) data, which the system continuously supplies to the IO-Link master, and acyclical (device/event) data, which can be polled specifically as needed. Process data includes door position status, actuator limit range, safety outputs state, general error messages, guard locking
state, locking element state, and escape release state, with device/event data including sensor version/order number, number of devices in a chain, current/stored diagnostic code, code of current/ blocked/taught-in actuator, voltage, temperature, number of switching cycles and LOG files.
But with the push towards Industry 4.0, which both produces and requires significant amounts of data, one question being asked is what the retrieved data is being used for and how to analyse that data.
As mentioned above, by using IO-Link compatible devices or gateways, end users can learn exactly what every device on a processing line is doing at all times. But additionally, by using the device data, for example, users can see when parameters change or predict when a unit is coming towards the end of its useful life, therefore affording engineers the time to schedule planned maintenance or, with the version/ order number to hand in the data, simply remove the ageing device and install in a new one.
Putting process efficiencies to one side, more importantly, there’s personnel safety to consider, especially as we see IO-Link technology being adopted into our safety solutions. In traditional safety systems, devices would often be wired in series, so when one switch was opened, it would drop out a safety relay at the end of the chain, and everything would
appear acceptable. However, determining which safety switch was open or closed was more difficult and often resulted in additional wiring going back to individual inputs on the PLC. And while the safety relays would themselves do some monitoring and fault finding, it was very easy for faults to be masked or the systems to be manipulated, e.g. the removal of a device from a series chain or opening downstream devices to remove faults on upstream devices. By using Euchner’s BR series-wiring technology with an IOLink interface, it becomes very easy to bring all this information back to the control system and give real-time alarms when issues do occur.
With manipulation in mind, data including the number of devices in the chain, the taught-in switch/actuator codes, the codes of blocked actuators, etc., can also be retrieved, all of which can, if using IO-Link, be incorporated in the machine control system to protect the operator.
Now, with standards such as EN ISO 14119:2013 being the driving force for minimising the defeating of safety interlocks, the prevention of fault masking is very much a priority. This means those still operating older-style, safety-related control systems on their machines or designing-in series-connected switches may want to reflect on the new technology and latest standards.
www.euchner.co.uk

Businesses net zero plans blown off track
According to research published by Schneider Electric, a specialist in the digital transformation of energy management and automation, 82% of UK business leaders say the energy crisis will impact their organisation’s ability to meet emissions reduction plans.
Of the businesses which are reporting impacts to their emissions reduction plans, around half say they are delaying planned investment in sustainability and net zero plans (49%). Just over one-third of the same organisations (34%) say they now have more immediate business challenges to meet. More than a quarter of these organisations claim that taking practical action to meet targets is difficult (27%).
Given the direct link between lower energy use and decreased emissions, organisations that maintain efforts to meet their emissions targets will also reduce energy use as a result. This, in turn, will lower their overall energy costs and provide a useful boost to the bottom line in a challenging economic climate.
Crucially, the survey of more than 1,200 large organisations reveals that business leaders still recognise the importance of working toward emissions reduction targets, as 39% believe that climate change and net zero ambitions will become more of a priority over the next three years. Only a small minority (12%) believe that national net zero commitments will be diluted in that time.
“Business leaders tell us that the energy crisis should be seen alongside the many other challenges they have faced over the last twelve months, including economic pressures, cyber security and skills shortages. Yet our research suggests that some of the UK and Ireland’s largest organisations are ‘kicking the carbon emissions can down the road’ as a result of the energy crisis,” said Kelly Becker, Zone President, Schneider Electric UK and Ireland.
“As fears grow about progress against global commitments made under the Paris Agreement, and the UK’s Climate Change Committee warns of a lack of progress on
emissions cuts, the UK and Ireland need businesses and organisations in the public sector to play their part and stick to their net zero and emissions reduction targets,” added Kelly.
The survey also reveals that only around one in five (21%) of those surveyed believe that energy prices will fall over the next three years, while over two-thirds (69%) think their organisation will still be addressing the energy crisis in 12 months’ time.
Presenting the survey findings, Kelly Becker urged business leaders to re-engage with their emissions reduction ambitions: “It’s not all doom and gloom: as our research shows, business leaders still believe in their climate change ambitions – they simply need to push the subject back up the corporate agenda.
“The technology required to help
businesses decarbonise is already available – and the return on investment for these solutions has never been more attractive, with payback periods measured in months rather than years. Organisations still have time to meet their net zero commitments by understanding and addressing energy use, investing in renewable energy and energy-saving technology, and embedding sustainability and carbon reduction targets in their business plans,” she continued.
“What’s more, those that invest in green skills and green jobs will reap the rewards of a diverse workforce for decades to come. At Schneider, we’ve seen this for ourselves through our apprenticeship and graduate programmes.” www.se.com
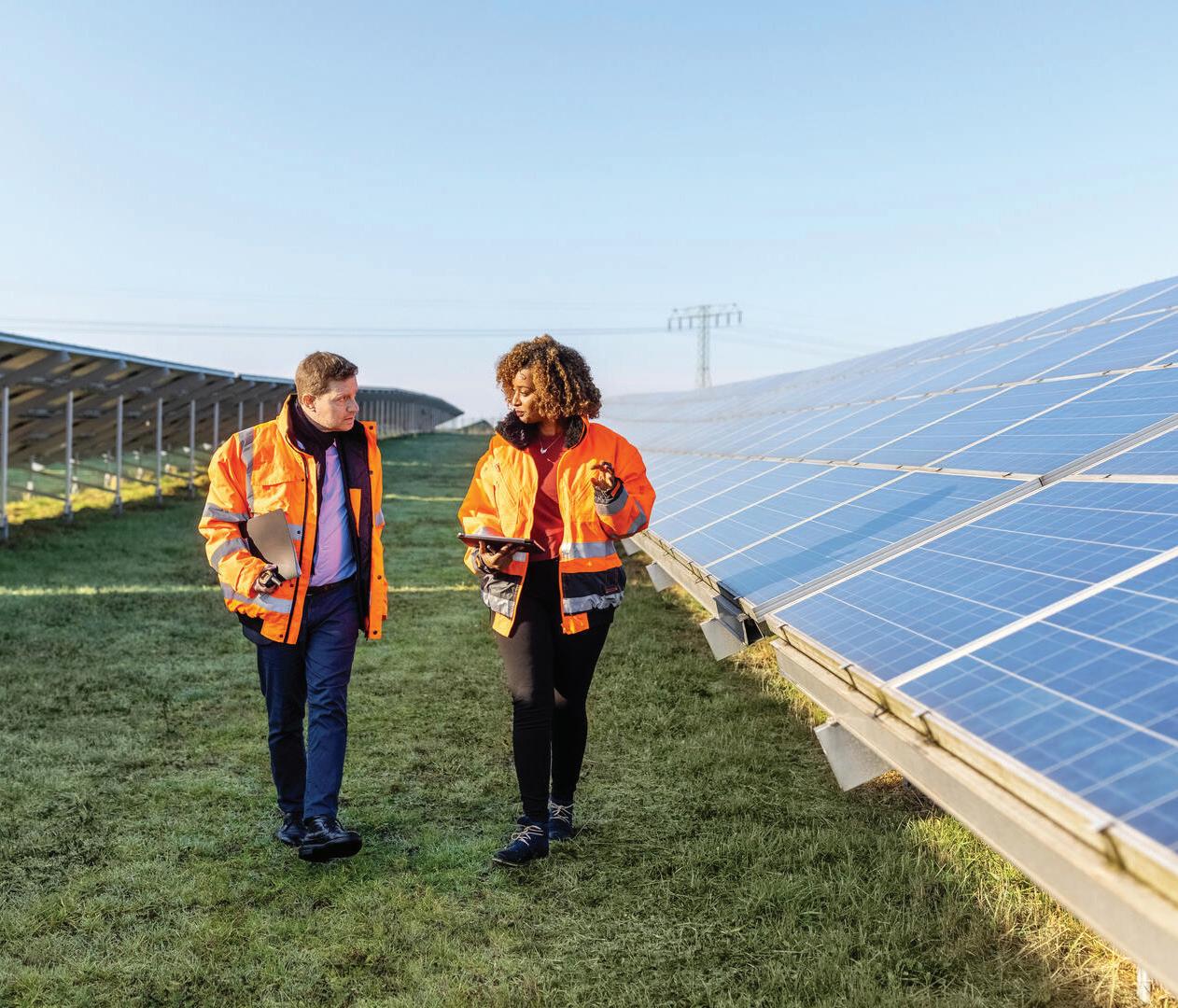
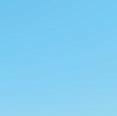
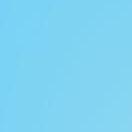
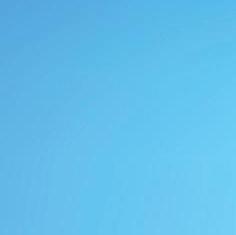

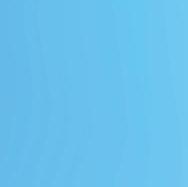
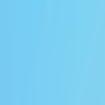





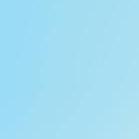






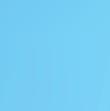


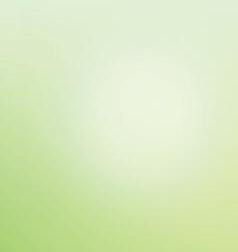


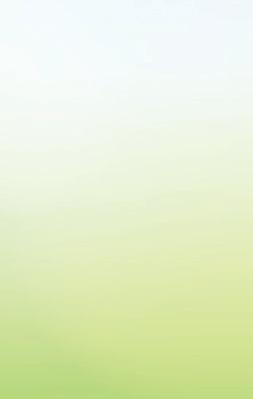
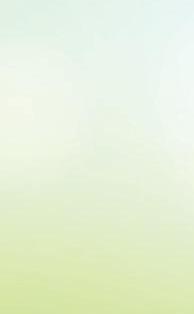
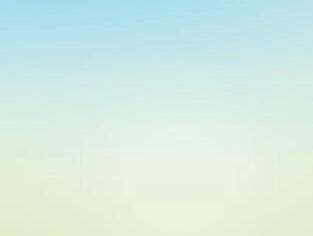

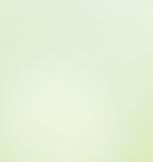
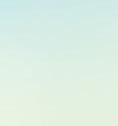
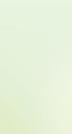
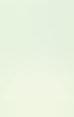


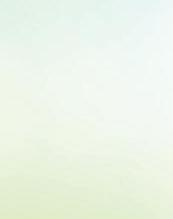

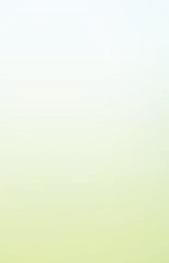
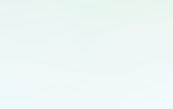
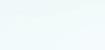


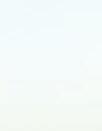


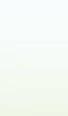




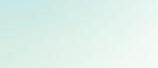

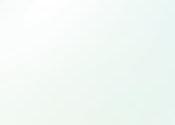



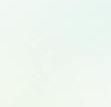
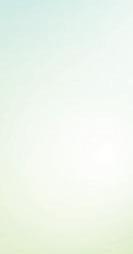

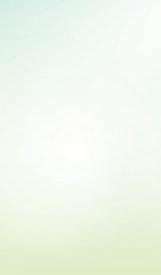

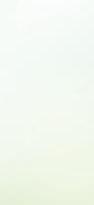




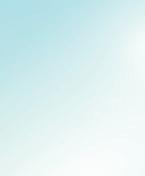
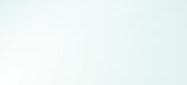






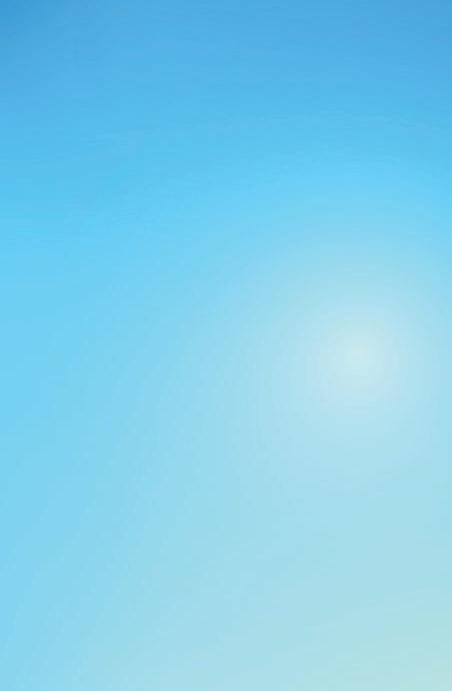
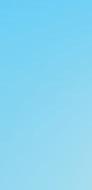
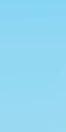



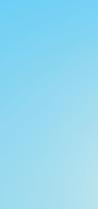


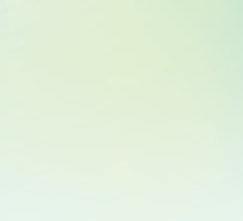


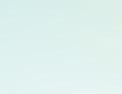
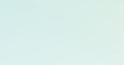









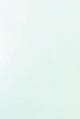
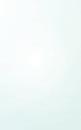


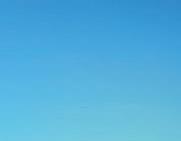
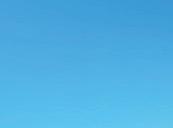
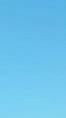
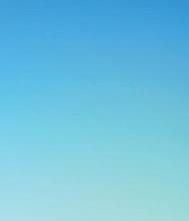

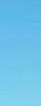
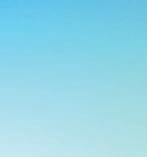
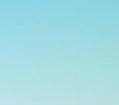


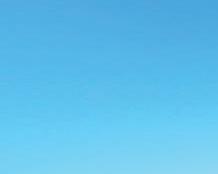

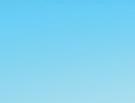




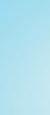
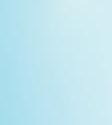




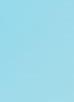

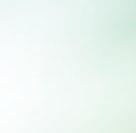




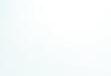



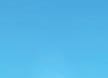


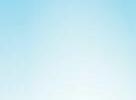




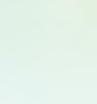


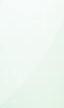







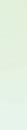







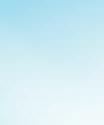






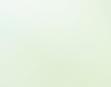
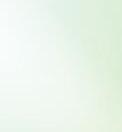







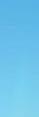







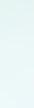





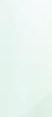










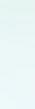























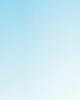

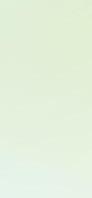


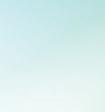


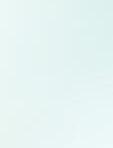













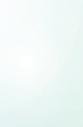












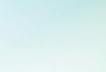






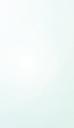








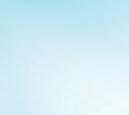
















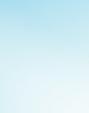










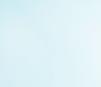

















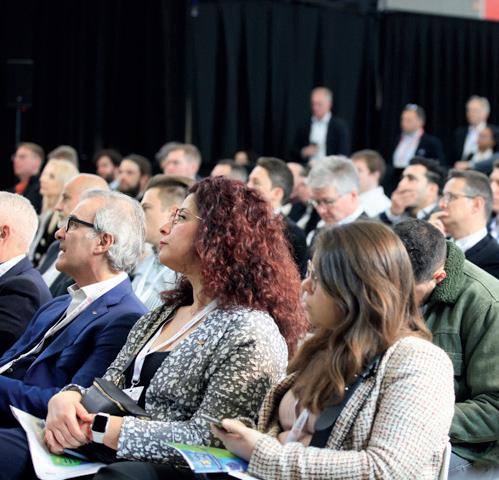
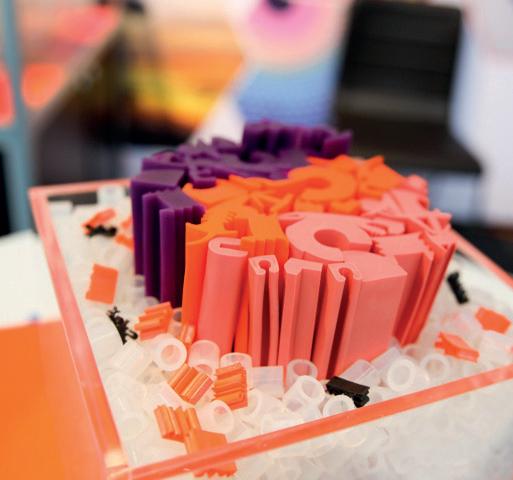
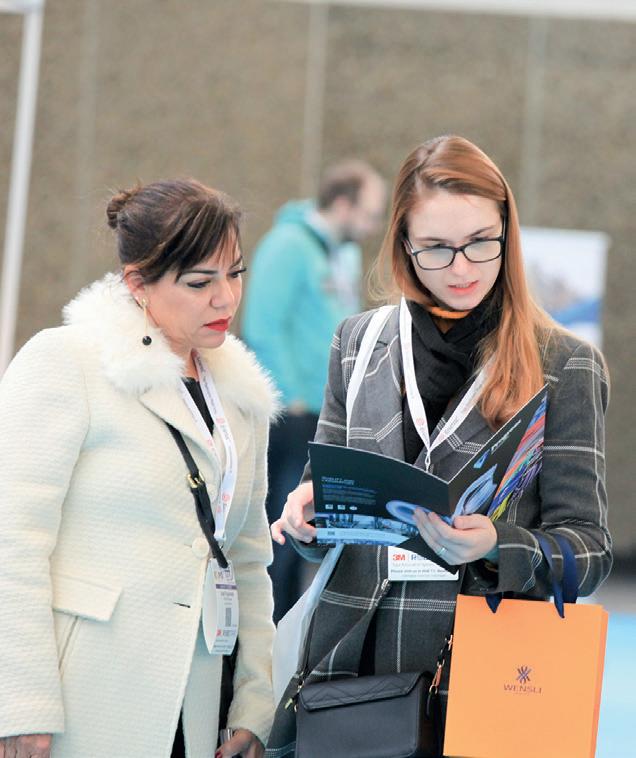

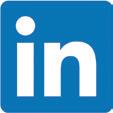
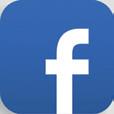
What’s on at Advanced Engineering 2023?
Registration is open for Advanced Engineering, the UK’s largest annual gathering of engineering and manufacturing professionals, held at the NEC, Birmingham, on November 1 and 2.
Now in its 14th year, this year’s show comes with a fresh and future-focused rebrand, removing the previous show zones from its exhibition floor and introducing a main stage for the event’s well-attended forums. This year, the long-established composite zone will remain, but the automotive, aerospace, and connected manufacturing zones will be removed. However, these sectors will still have a strong presence at the event, with the industry-specific forums remaining. There will also be a main, central stage on this year’s floor plan where discussions about key challenges in the industry will be discussed.
To ensure that visitors and exhibitors can still easily find relevant contacts, Advanced Engineering exhibitors will now be categorised by the services, products and solutions offered. They will have the opportunity to highlight all of the sectors they work in, removing any limitations created by the specific show zones.
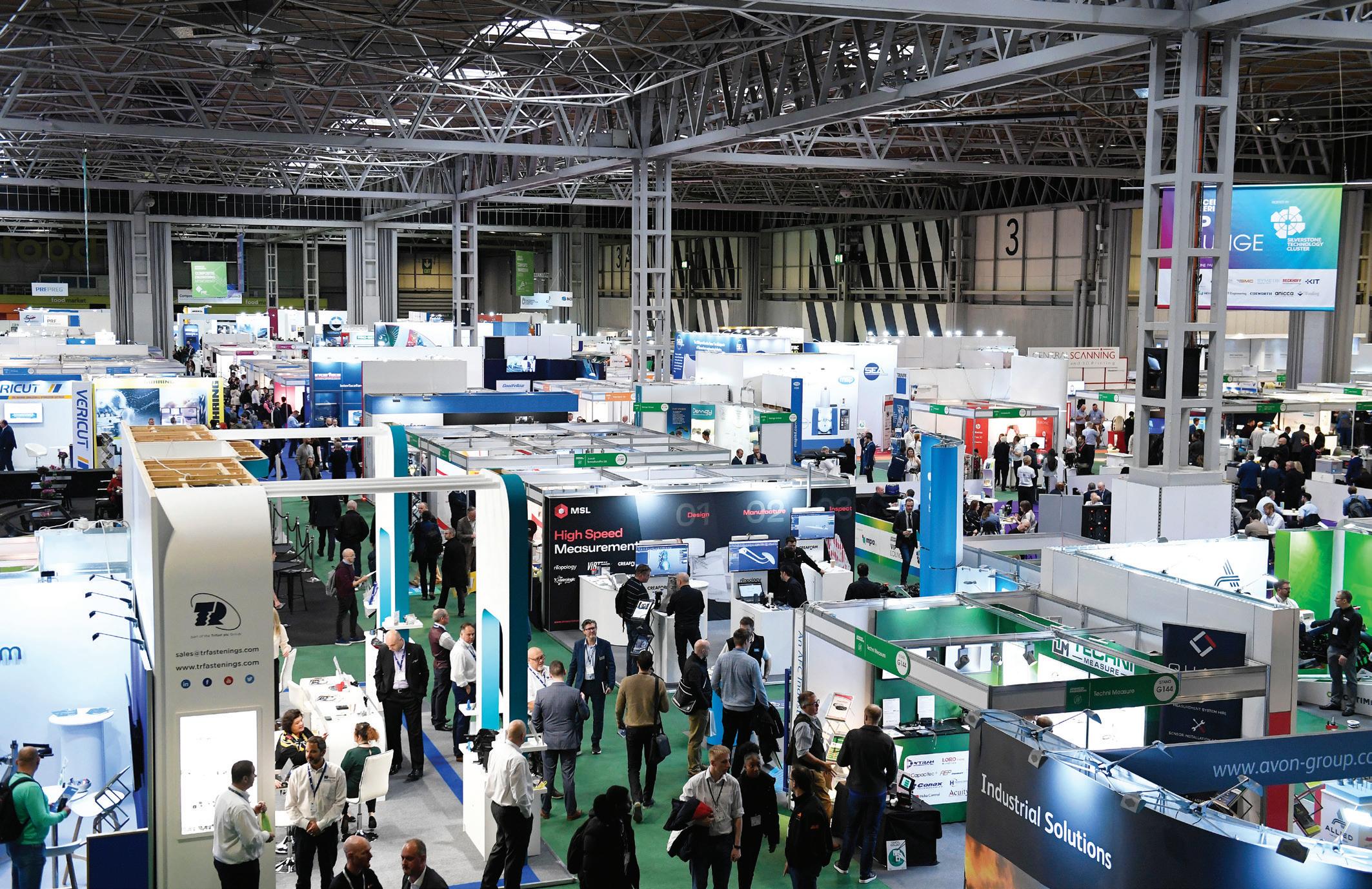
“This year, we’ve made a big change to our floor plan by removing the different show zones that have been present in previous years and expanding it over a wider area,” explained Alison Willis, director of Easyfairs, the organiser of Advanced Engineering. “We felt like this was important since cross-industry working is one of the things that attendees value the most, so we want
them to feel like they aren’t segregated to a particular area because of their industry sector.
In 2023, Advanced Engineering will welcome back a full speaker programme with representatives from some of the leading companies in UK manufacturing. Last year, attendees were treated to talks from leading industry figures from companies like Siemens, Ford, Jaguar Land Rover, Make UK, Rolls-Royce and Airbus.
To secure a visitor pass, see a current exhibitor list and check out the growing list of confirmed speakers, visit the Advanced Engineering website.
advancedengineeringuk.com
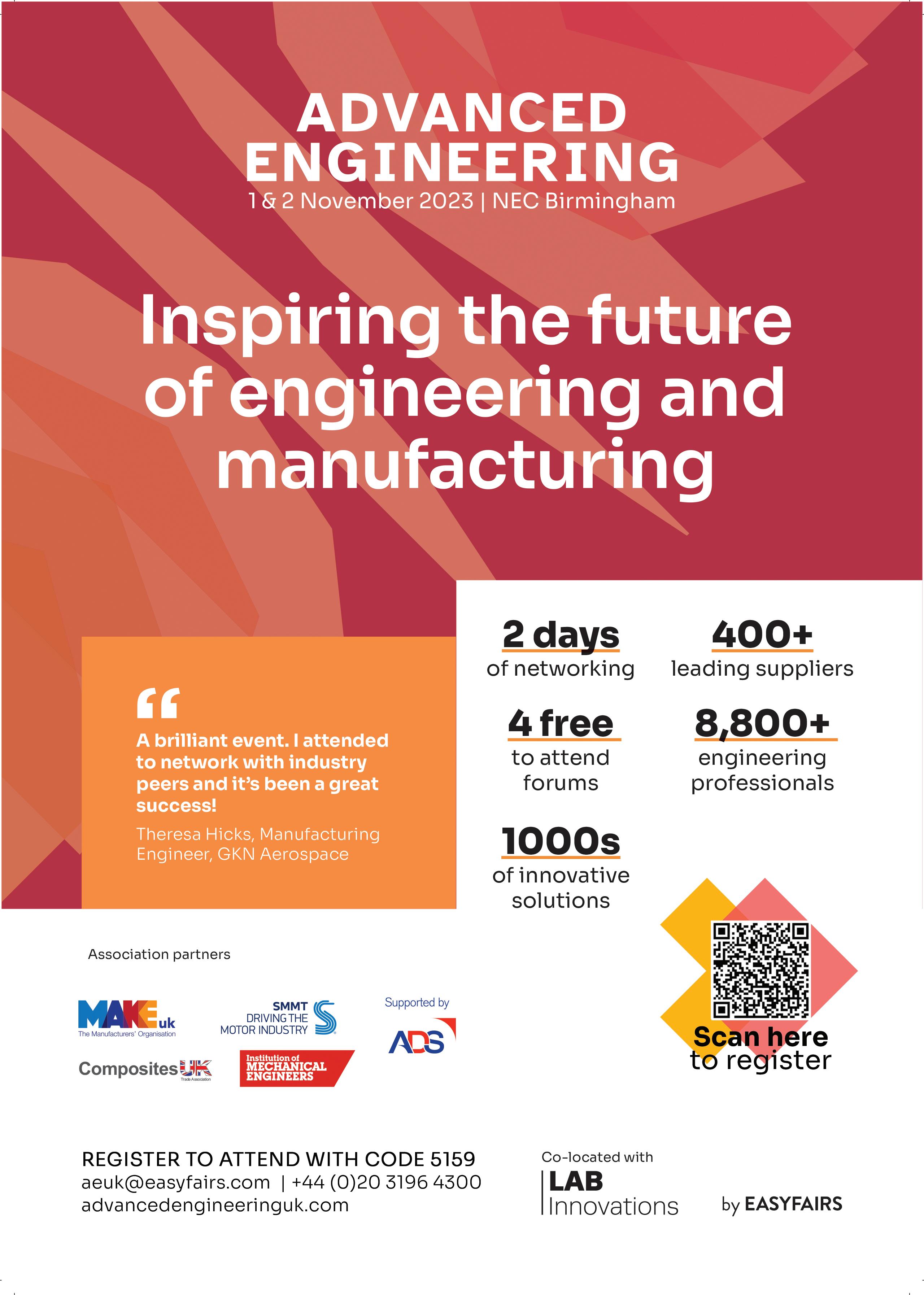
Solid state relay range extended
Keep a close eye on air and industrial gases
The new SD sensor range from ifm electronics has been developed to allow users to accurately monitor the usage of compressed air and other industrial gases.
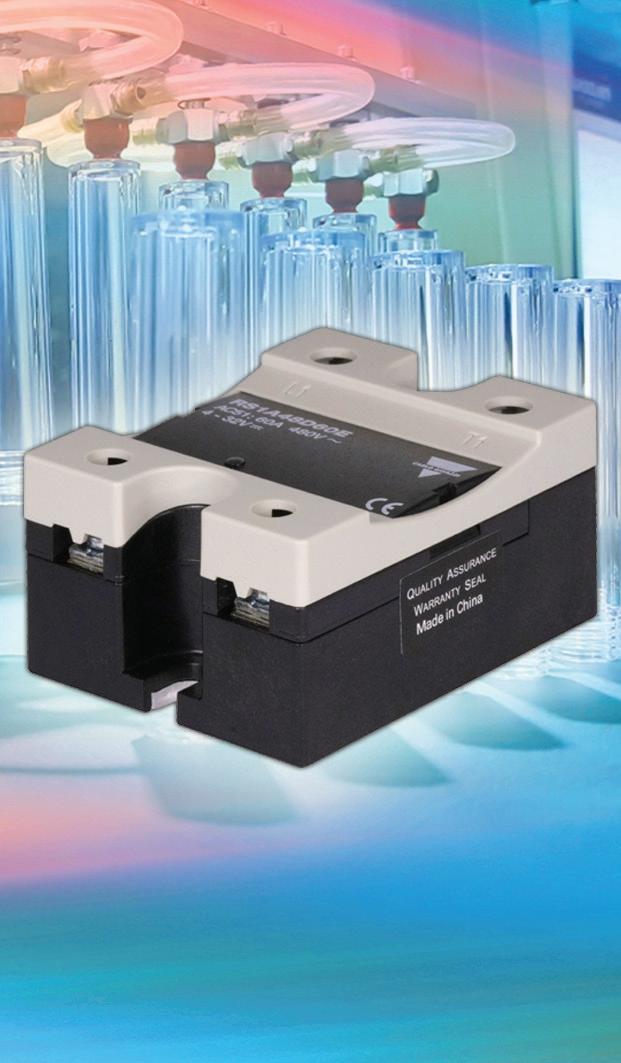
All sensors in the range monitor volumetric flow rate and have an integrated totaliser function for measuring total flow.
SD sensors are available in versions to suit a range of gases, including argon, carbon dioxide, helium and nitrogen, as well as air, with flow rates from just 0.05 to 700m3/hr, media temperatures from -10 to +60ºC and a maximum operating pressure of 16 bar.
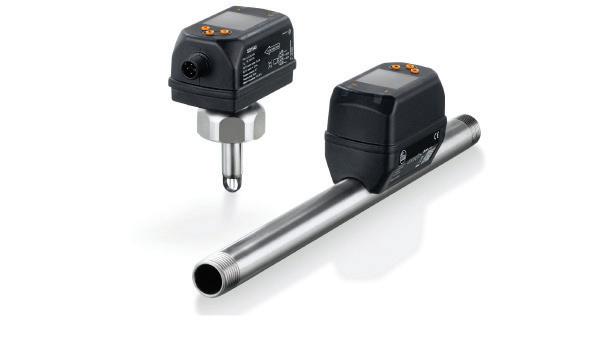
www.ifm.com
The key to industry compliance
Intoware, a company specialising in workflow automation software, has unveiled its latest industry e-book, providing guidance to companies looking for ways to better manage risk and regulatory compliance through digitalisation.
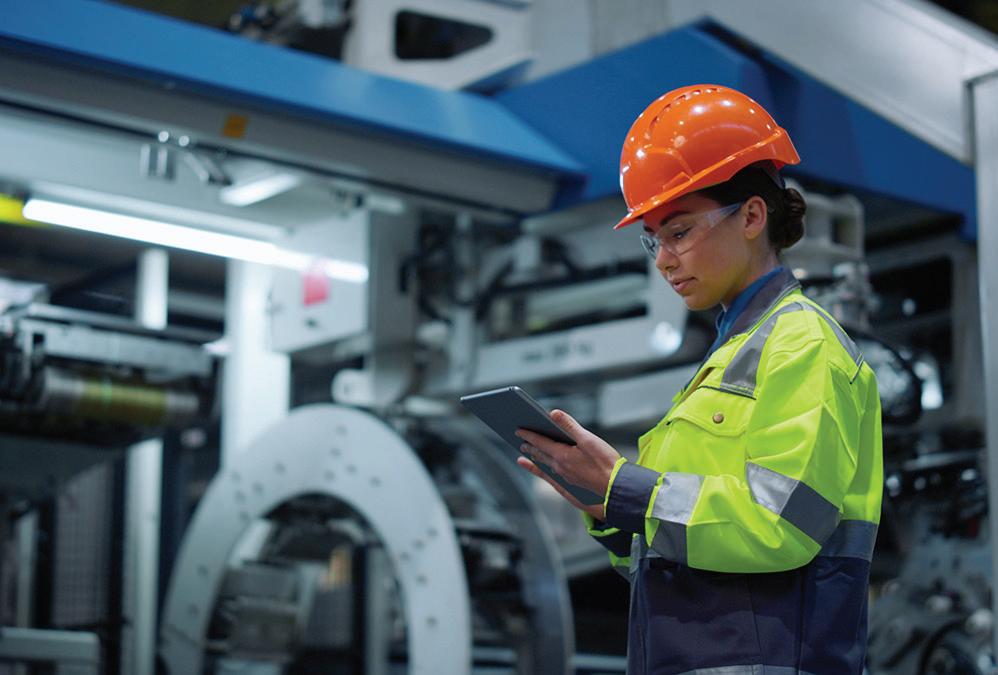
The publication, titled ‘Digitalisation: The Key to Compliance’, outlines the role of digitalisation when it comes to compliance and risk management, and highlights the ways digital transformation can improve transparency, reduce protocol errors and notify the workforce of changes in regulatory requirements.
Carlo Gavazzi has expanded its popular RS_E range of solidstate relays up to 100AAC, a cost-effective solution for resistive loads, providing reliable operation and excellent longevity.
The RS_E is a 1-pole zero cross switching relay offering a rated current of 25, 40, 60, 80 and 100AAC. Each version is available in 400VAC and 480VAC ratings. The 60 and 80AAC versions also feature triac output, whilst the 100 AAC versions feature back-toback thyristor output with both AC and DC versions available.
Since the RS_E is a fully solid-state solution, it can perform millions of switching cycles without failure. Fast response time guarantees stable temperatures in critical processes where temperature overshoots can create quality issues in the final product. An additional feature of the RS_E is the integrated overvoltage protection on the output, which prevents damage to the solidstate relay from uncontrolled voltage surges that may occur on the supply lines. This minimises unplanned production stops.
The RS-E range is CE, UKCA, EAC, and cURus (only for 25 AAC and 40 AAC versions) certified.
www.carlogavazzi.co.uk
Keith Tilley, CEO of Intoware, said: “Compliance is at the top of the agenda for many organisations right now. Outdated paper-based systems still exist as a way of managing compliance requirements within many organisations, but they carry the risk of information going missing and increase the chances of workers deviating from established protocols, especially when updates are issued, or new requirements come into effect.
“Moving to digitalised systems can feel daunting, but when implemented correctly, the benefits are enormous. Accountability, traceability and transparency increase, audit trails are much easier managed and maintained, and reporting capabilities are transformed at the touch of a button.” bit.ly/TKtC
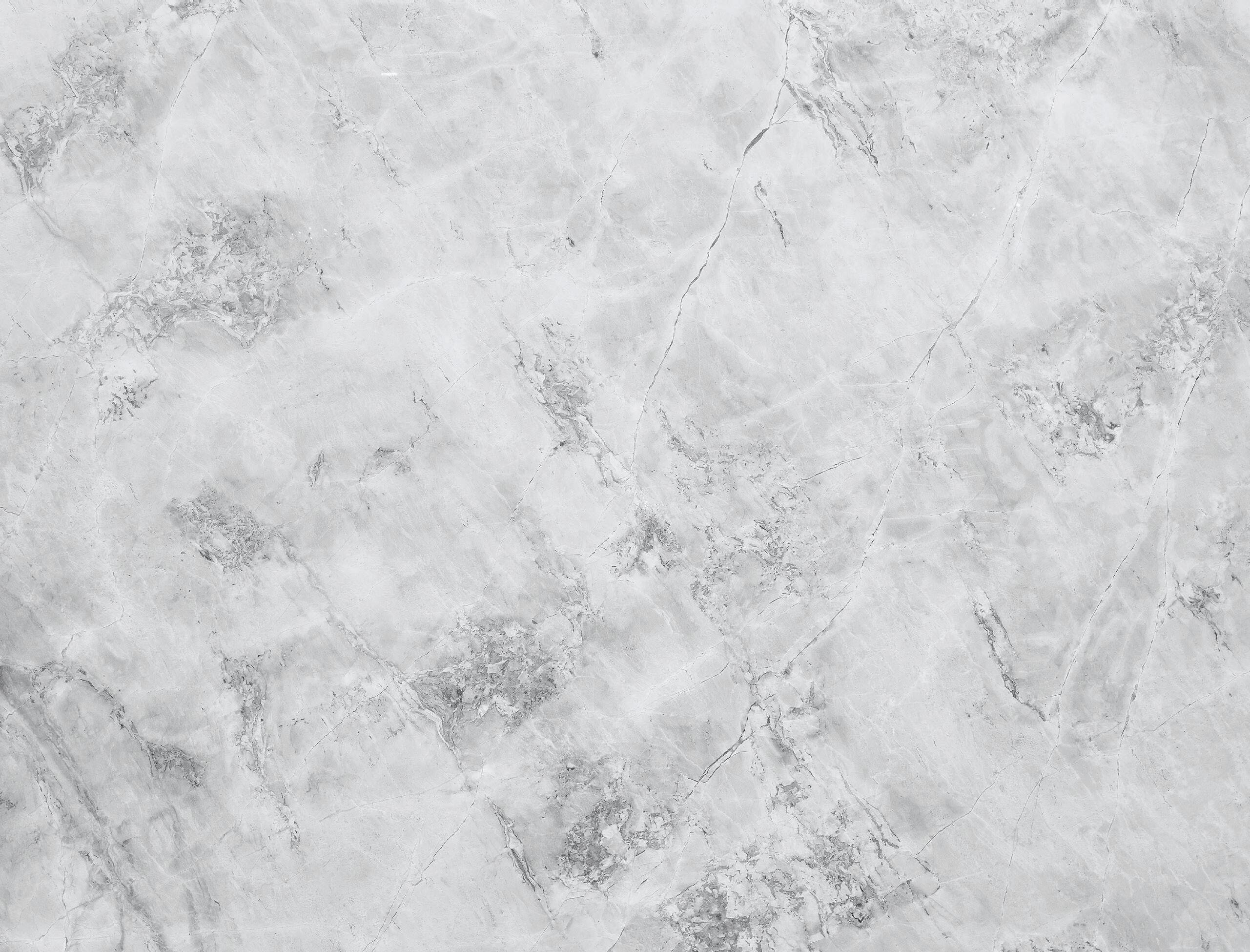

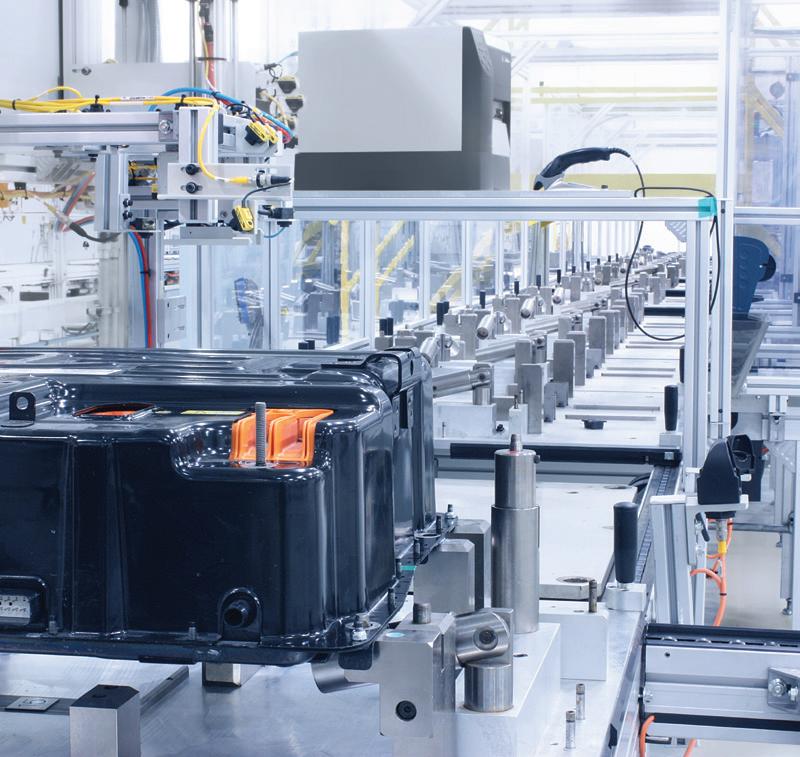
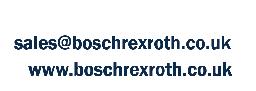
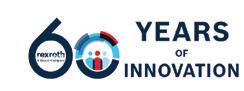
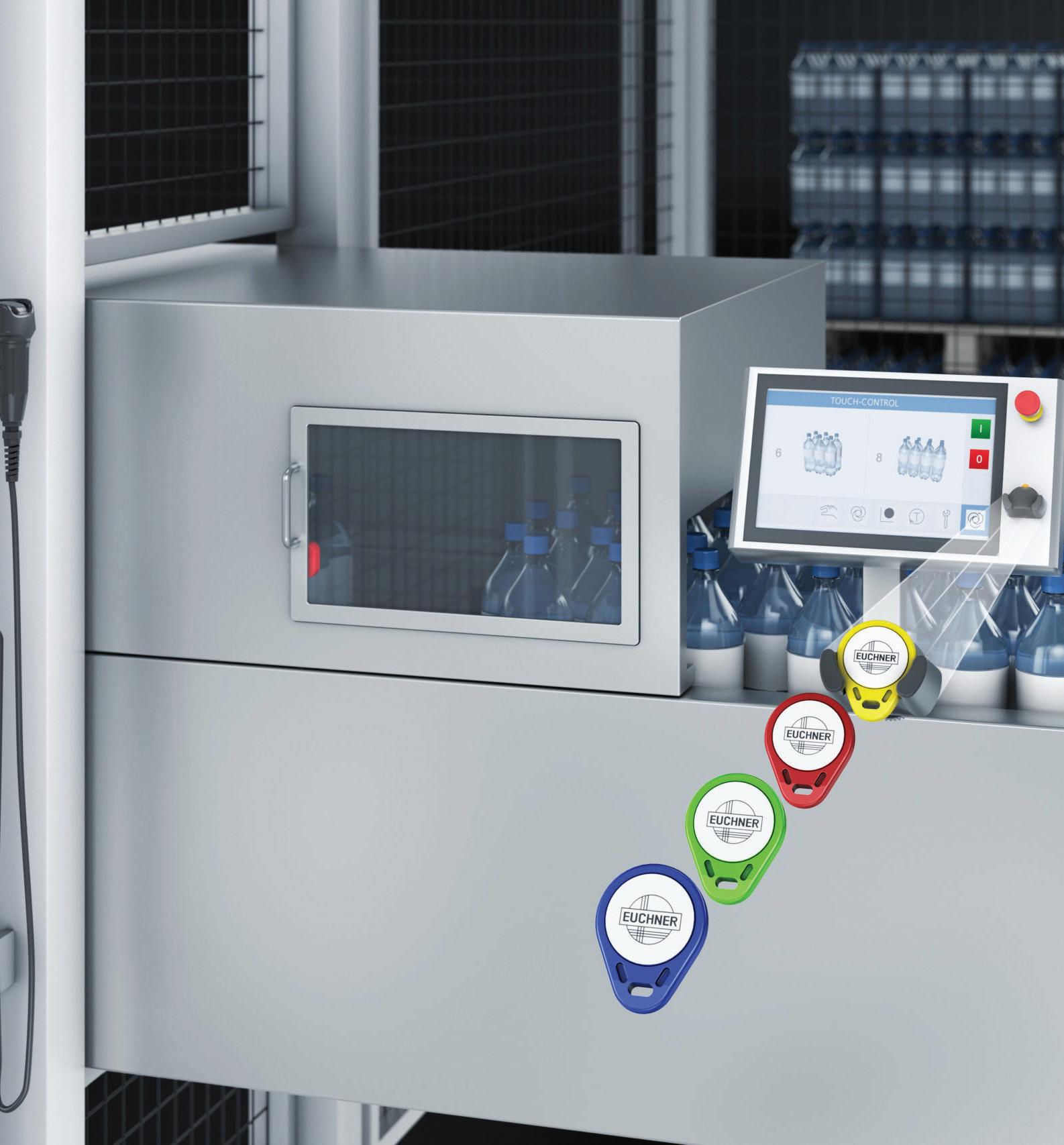
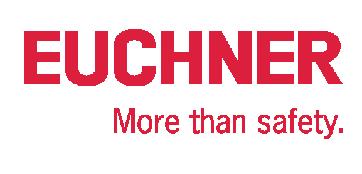
CONNECTIONS
3D Print Manufacturing
Midlands 3D Printing
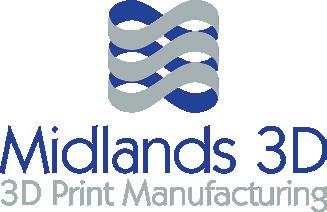
Units 6-7 Emerald Way, Stone Business Park, Stone, Staffordshire, ST15 0SR
T: 01785 594389
E: sales@midlands3d.com
W: www.midlands3d.com
Anti Vibration Products, Mounts & Bushes
Fibet Rubber Bonding (UK) Ltd

Unit 9 Dale Mill, Hallam Road, Nelson, Lancashire, BB9 8AN
T: 01282 878200
E: sales@fibet.co.uk
W: www.fibet.co.uk
Control Systems
Beckhoff Automation Ltd
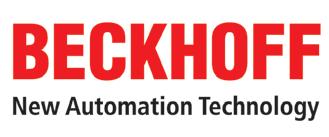
The Boathouse, Station Road
Henley-on-Thames, Oxon RG9 1AZ
T:+ 44 (0)1491 410539
E: info@beckhoff.co.uk
W: www.beckhoff.co.uk
Dust & Fume Solutions
Impact Technical Services
3 Kingsley Street, Leicester, LE2 6DY
T: 0116 244 8855
E: enquiries@impactts.co.uk
W: www.impacttechnicalservices.co.uk
Flow Meters
Titan Enterprises Ltd Unit 2, 5A Cold Harbour Business Park, Sherborne, Dorset, DT9 4JW
T: +44 (0)1935 812790
E: sales@flowmeters.co.uk
W: www.flowmeters.co.uk
High Shear Mixing Equipment
Silverson Machines Ltd

Waterside, Chesham, Buckinghamshire, HP5 1PQ
T: +44 (0)1494 786331
E: sales@silverson.co.uk
W: www.silverson.co.uk
Industrial Communications
Brainboxes
T: + 44 (0) 151 220 2500
E: sales@brainboxes.com

W: www.brainboxes.com
Industrial Fans
Axair Fans UK Limited
Lowfield Drive, Wolstanton, Newcastle-under-Lyme, ST5 0UU
T: 01782 349 430
E: aj@axair-fans.co.uk
W: www.axair-fans.co.uk
Machine Safety
Schmersal UK Ltd
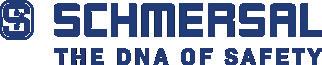
Sparrowhawk Close, Malvern, Worcestershire, WR14 1GL
T: 01684 571980
E: uksupport@schmersal.com
W: www.schmersal.co.uk
Pipework Systems

Jacob UK Ltd
Laundry Bank, Church Stretton, SY6 6PH
T: 01694 722841
E: sales@jacob-uk.com
W: www.jacob-group.com/uk
Robotics & Automation
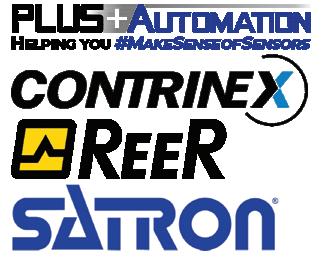
KUKA Robotics UK Ltd

Great Western Street, Wednesbury, West Midlands, WS10 7LL
T: 0121 505 9970
E: sales.uk@kuka.com
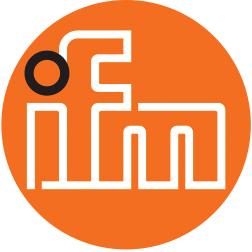

W: www.kuka.com
Rotation Monitoring Equipment
Rotech Systems

Unit 57, Canal Bridge Centre, Ellesmere Port, Cheshire, England, CH65 4EH
T: +44 (0)151 356 2322
E: sales@rotechsystems.co.uk
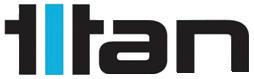
W: www.rotechsystems.co.uk
Sensors
Carlo Gavazzi UK Ltd
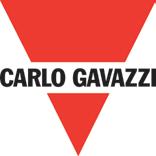
4.4 Frimley Business Park, Frimley, GU16 7SG
T: 01276 854110
W: www.carlogavazzi.co.uk
IFM Electronic
Efector House, Kingsway Business Park, Oldfield Road, Hampton, Middlesex, TW12 2HD
T: 020 8213-0000
E: enquiry.gb@ifm.com
W: www.ifm.com
PLUS Automation Ltd
Lyth Farm, Lyth Lane, Ombersley, Droitwich, Worcestershire, WR9 0LG
T: 0121 58 222 58
E: Sales@PLUSAutomation.co.uk
W: www.PLUSAutomation.co.uk
Test & Inspection
Cupio Services Ltd
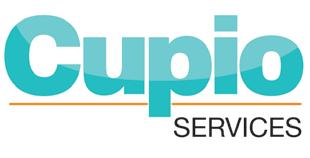
T: 01256 262800
E: info@cupioservices.co.uk
W: www.cupioservices.co.uk
Giving sight to robots
3D vision sensor for plug and play integration into gripper applications from Universal Robots
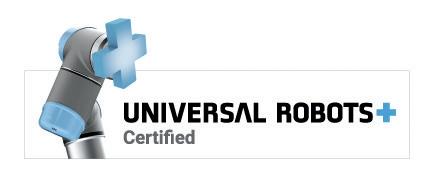
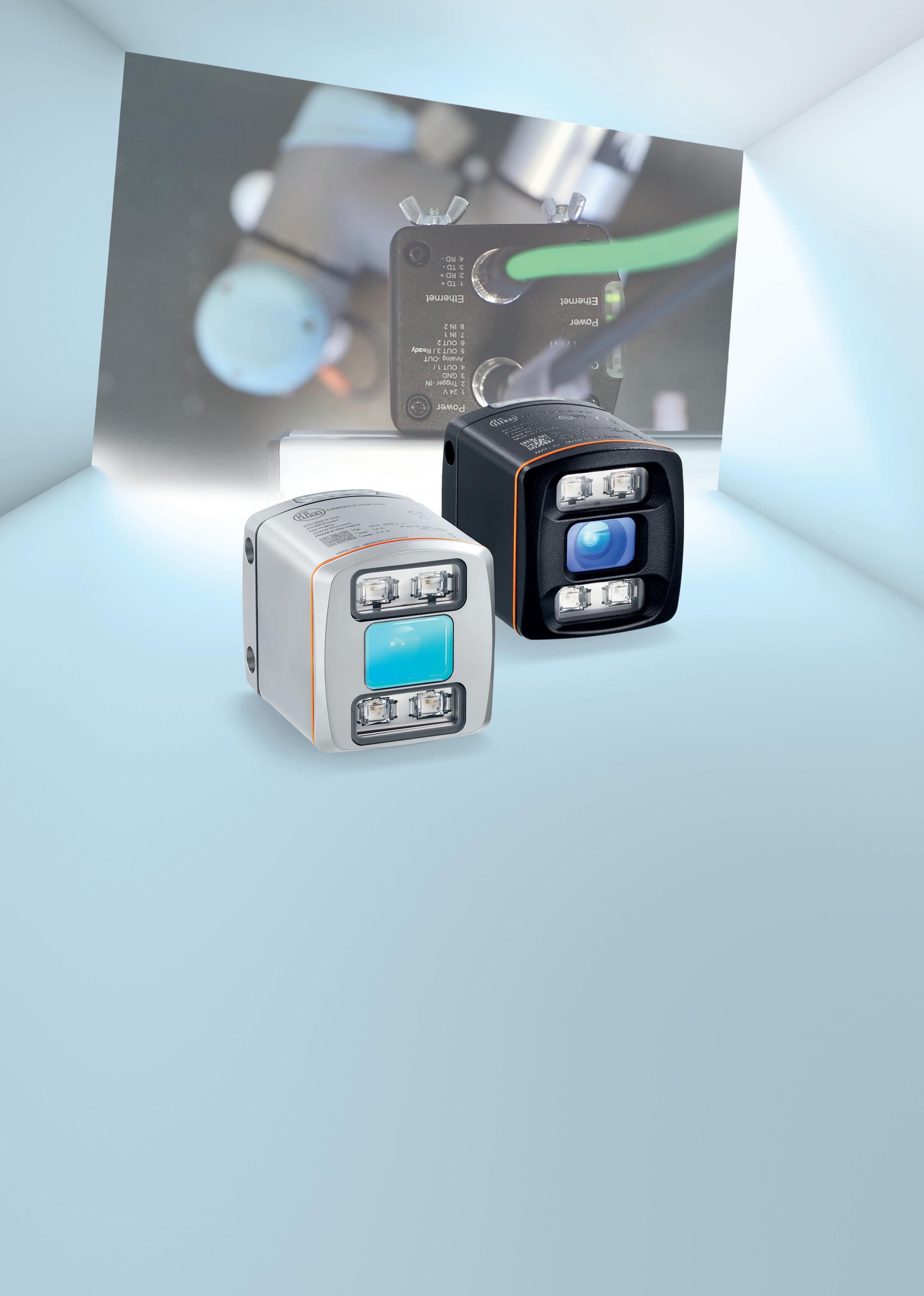
The perfect combination of powerful hardware and easy - to - use software makes it possible to easily implement vision sensors in gripper applications from Universal Robots.
The core element of the ifm vision sensor is a 3D camera chip. It creates a 3D image using PMD technology and time of flight measurement.
The UR+ plugin ensures smooth and quick integration of the sensor. It detects any object, even moving ones, and transmits its exact position and dimensions to the robot control. Never before was gripper navigation so easy! ifm – close to you!
Go ifmonline Go ifmonline

: Levitating, contactless, intelligent!
Free 2D product movement with up to 6 degrees of freedom
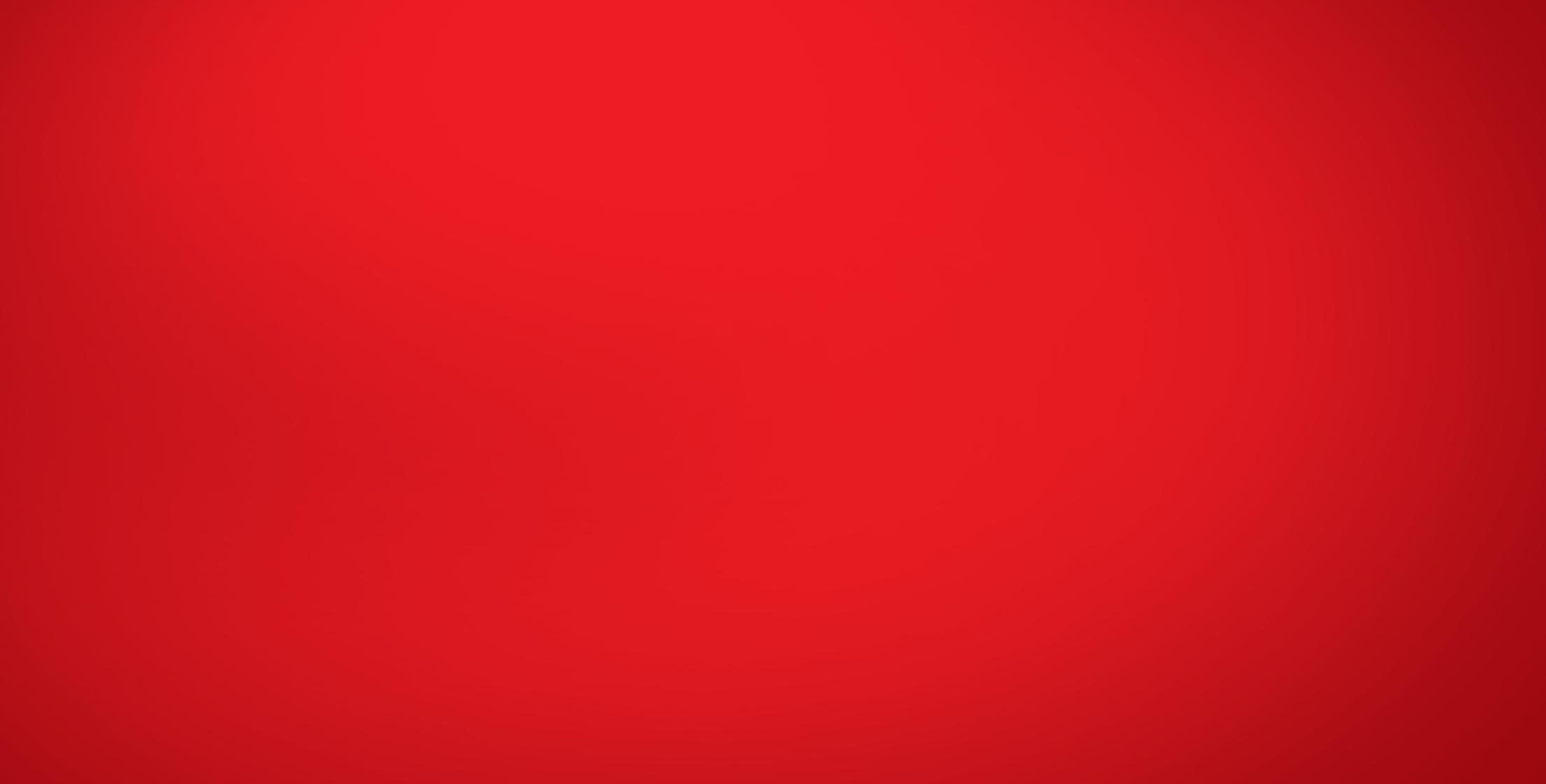
www.beckhoff.com/xplanar
XPlanar enables new degrees of freedom in product handling: Levitating planar movers float over individually arranged planar tiles on freely programmable tracks.
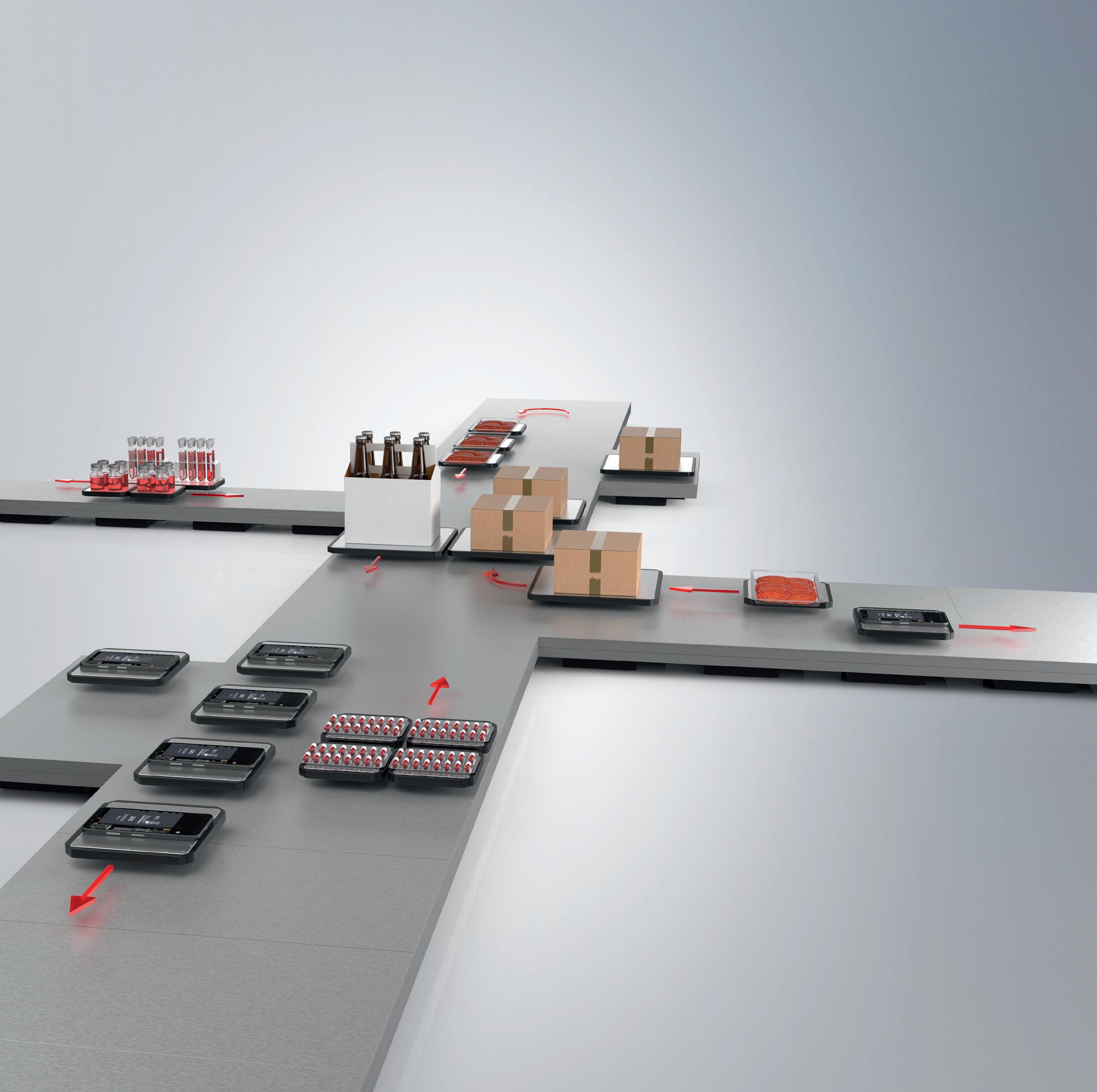
Individual 2D transport at up to 2 m/s
Processing with up to 6 degrees of freedom
Transport and processing in one system
Wear-free, hygienic and easy to clean
Free arrangement of planar tiles enabling customized machine layout
Multi-mover control allowing parallel and individual product handling
Fully integrated into the powerful PC-based Beckhoff control system
(TwinCAT, PLC IEC 61131, Motion, Measurement, Machine Learning, Vision, Communication, HMI)
For use across all industries: assembly, food, pharma, laboratory, entertainment, …