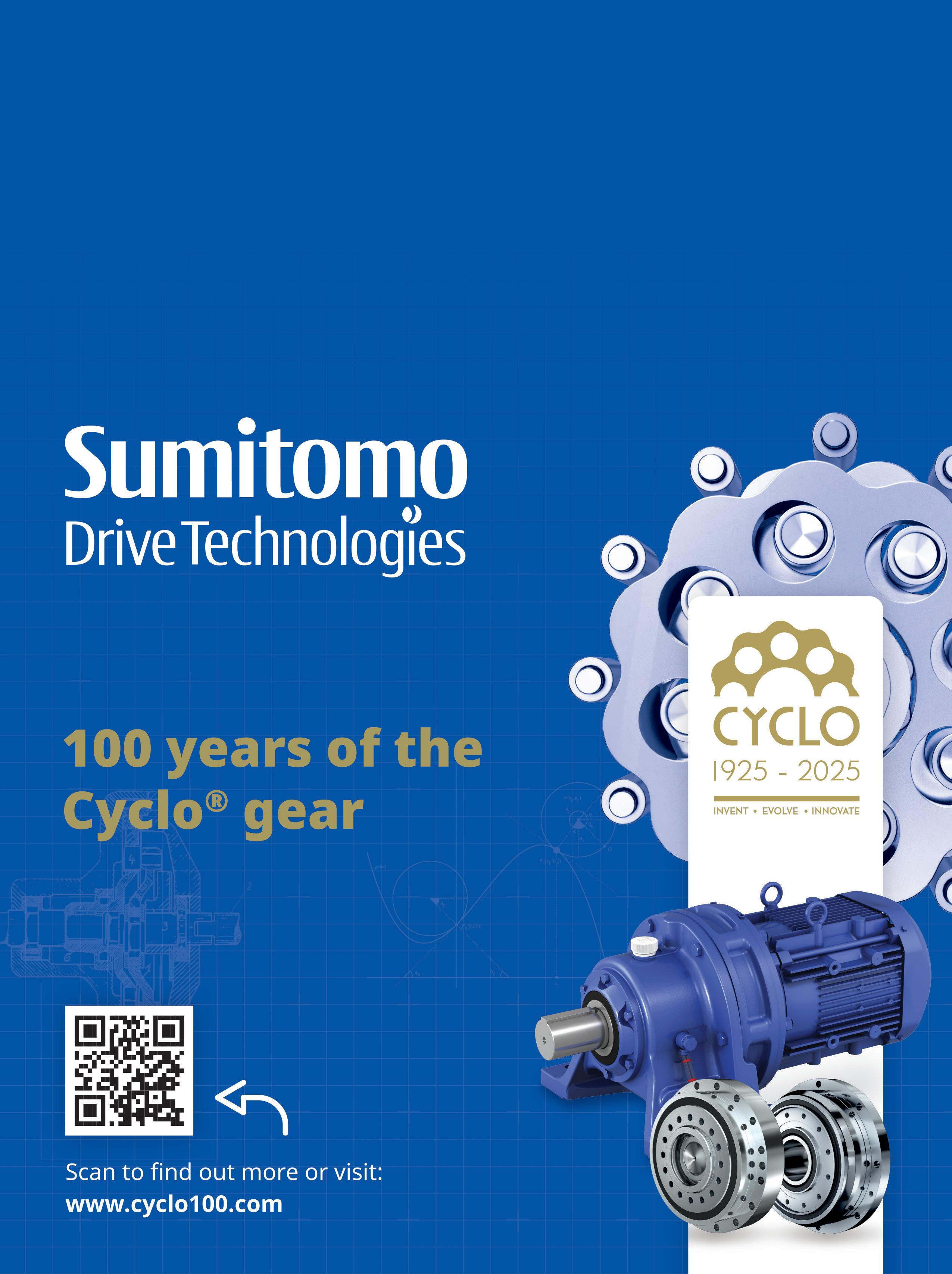
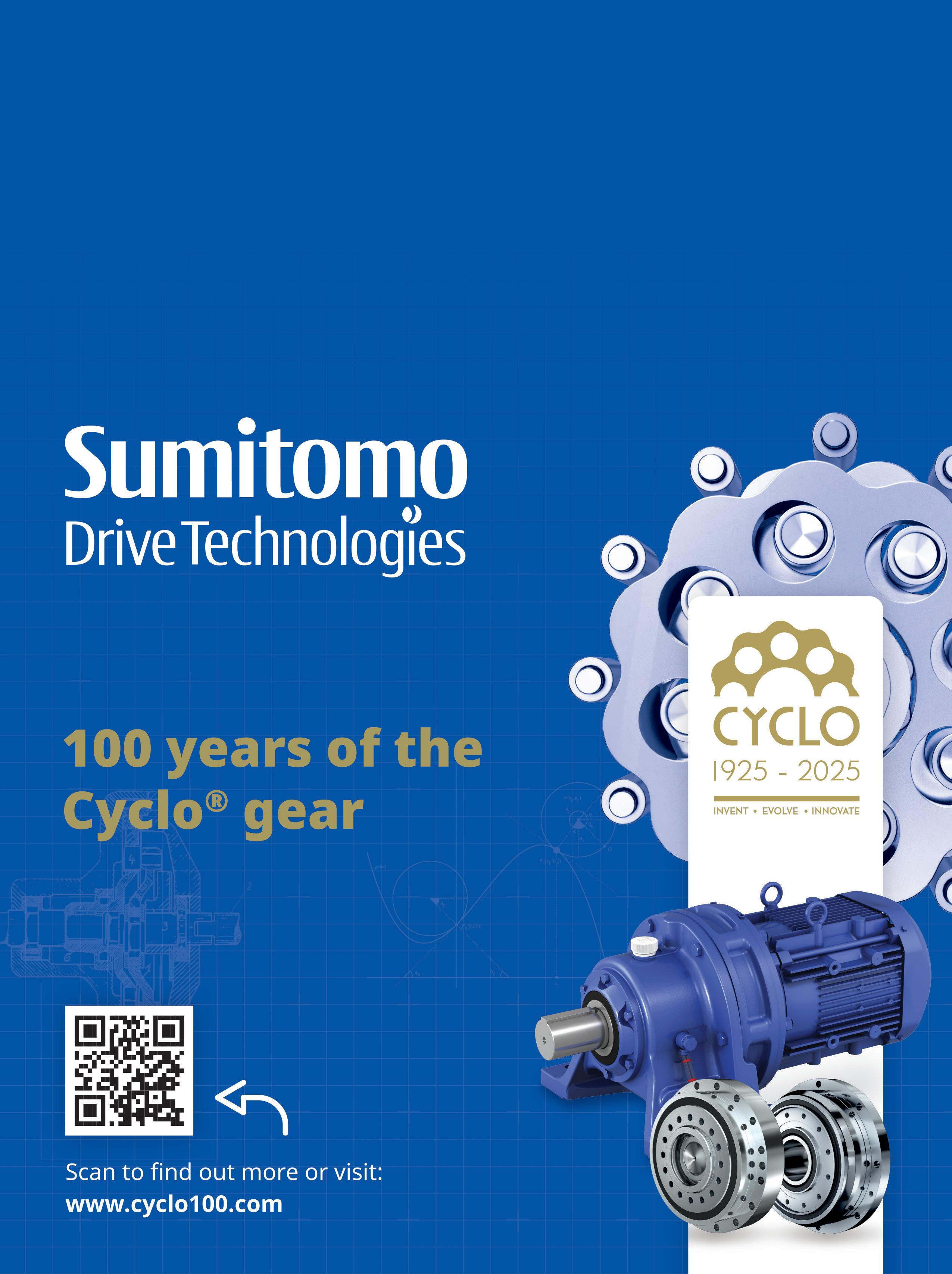
Geared Motors
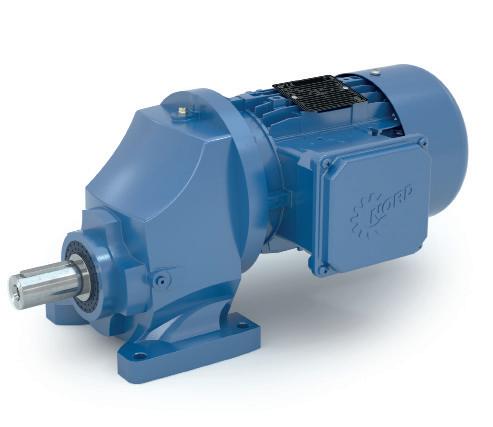
Inline Helical
Power Range 0.12 - 160kW
Ratio Range 1.07 - 14,340:1
Torque Range up to 26,000Nm
Available in Foot, B14 Face or B5 Flange mounted design
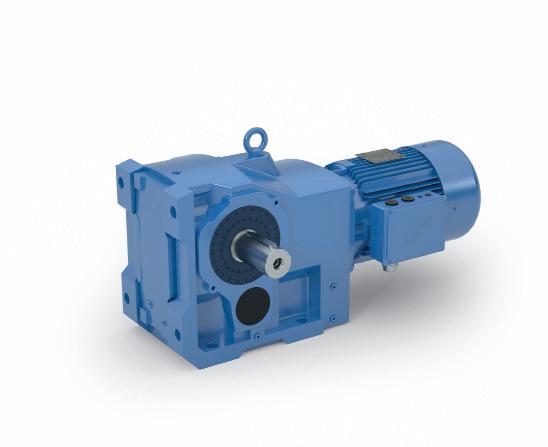
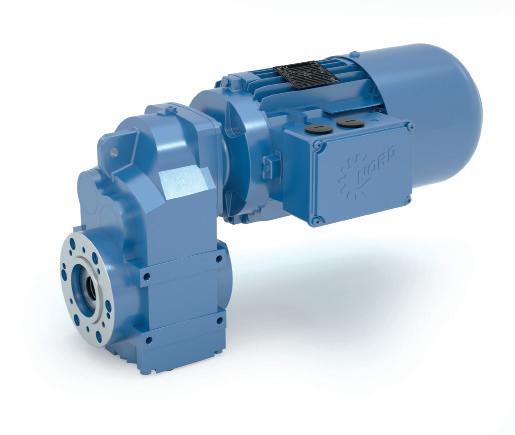
Parallel Helical
Power Range 0.12 - 200kW
Ratio Range 4.04 - 13,295:1
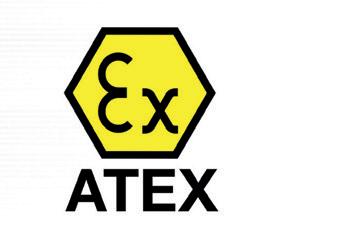
Dust zone 21 cat 2D and zone 22 cat 3D
Gas zone 1 cat 2G and zone 2 cat 3G
IEC Ex, EAC Ex, CCC Ex, UKEX and specifications for North American market NORD #1 for ATEX
Right Angle Helical-Bevel
Power Range 0.12 - 200kW
Ratio Range 3.03 - 13,432:1
Torque Range up to 50,000Nm
Available in Foot, B14 Face or B5 Flange mounted design
Solid or Hollow output shaft with keyed connection, shrink disc, splined or GRIPMAXX keyless friction locking system
Torque Range up to 100,000Nm
Available in Foot, B14 Face or B5 Flange mounted design
Solid or Hollow output shaft with keyed connection, shrink disc, splined or GRIPMAXX keyless friction locking system
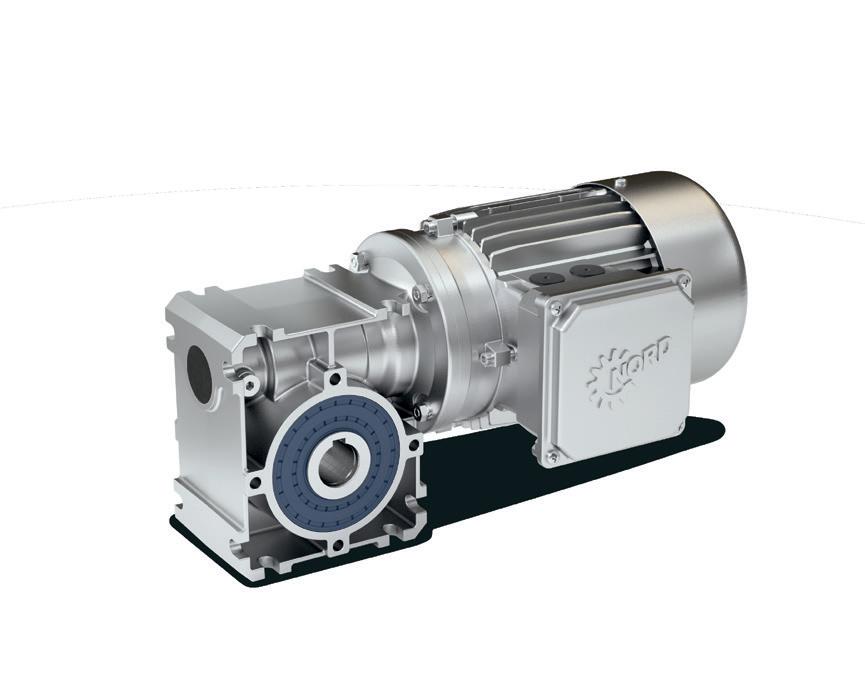
Industrial Gear Units


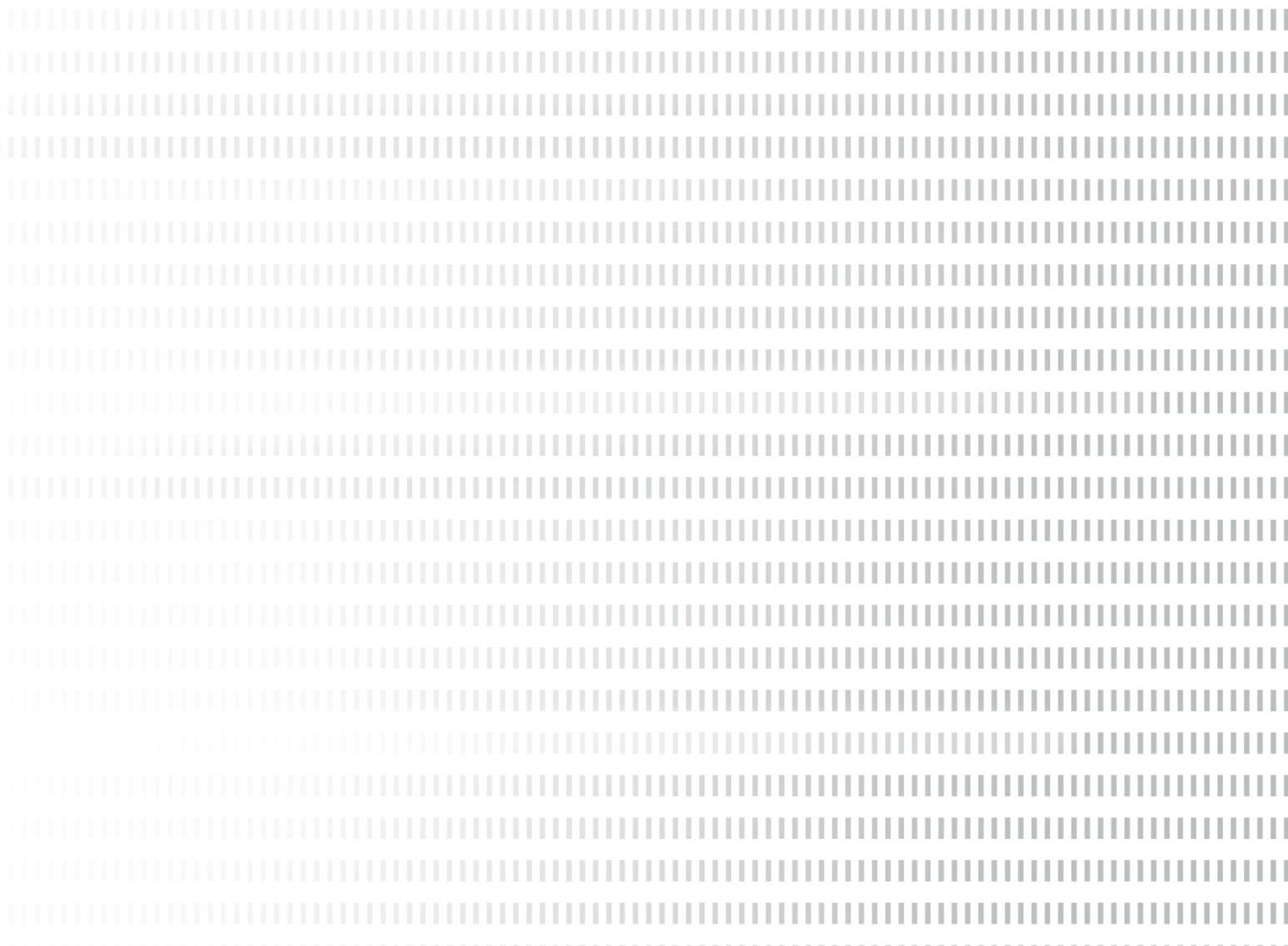
Right Angle Worm and Helical Worm
Power Range 0.12 - 15kW
Ratio Range 5 - 7,095:1
Torque Range up to 3,058Nm
Available in Foot, B14 Face or B5 Flange mounted design
Solid or Hollow output shaft with keyed connection
MAXXDRIVE Right Angle and Parallel
Power Range 1.5 - 6,000kW
Ratio Range 5.54 - 395.26:1
Torque Range up to 282,000Nm
Available in Foot, B14 Face or B5 Flange mounted design
Solid or Hollow output shaft with keyed connection
Modular design permitting tailoring to your application
Bedplate solutions with fluid coupling, motor, brake, etc.
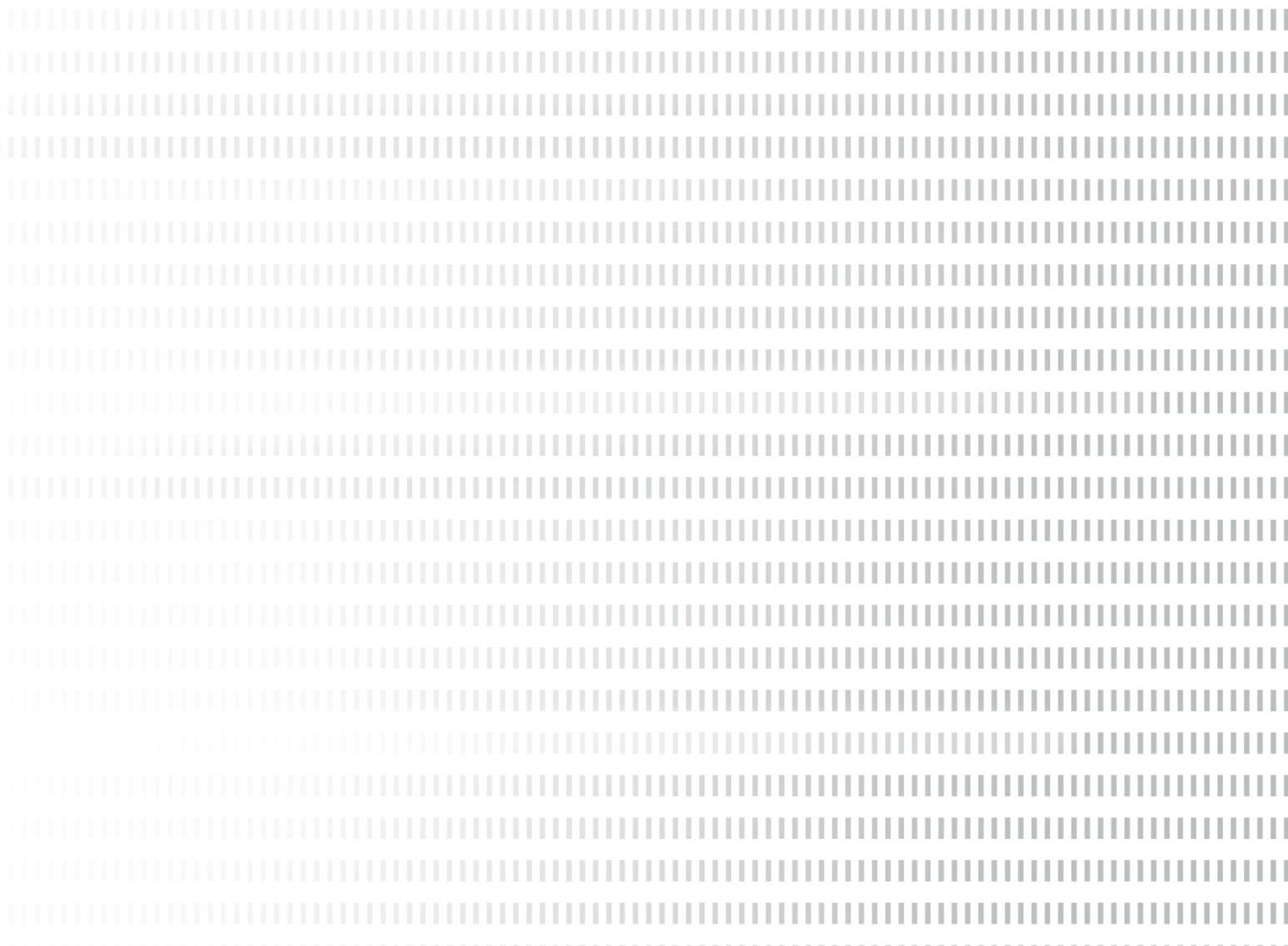
Motors

Frequency Inverters
NORDAC Frequency Inverters
Power Range 0.25 - 160kW
IP20 Control Cabinet or IP69 Decentralised or Motor mount
Open or closed loop operation with POSICON position control included
High overload capacity for dynamic performance
IEC61131 PLC included in firmware
Multi-protocol Ethernet interface with parameter selectable ProfiNet, EtherCat, Powerlink or Ethernet IP SmartPhone intergration - Parameterise, diagnose, store setup and email integration
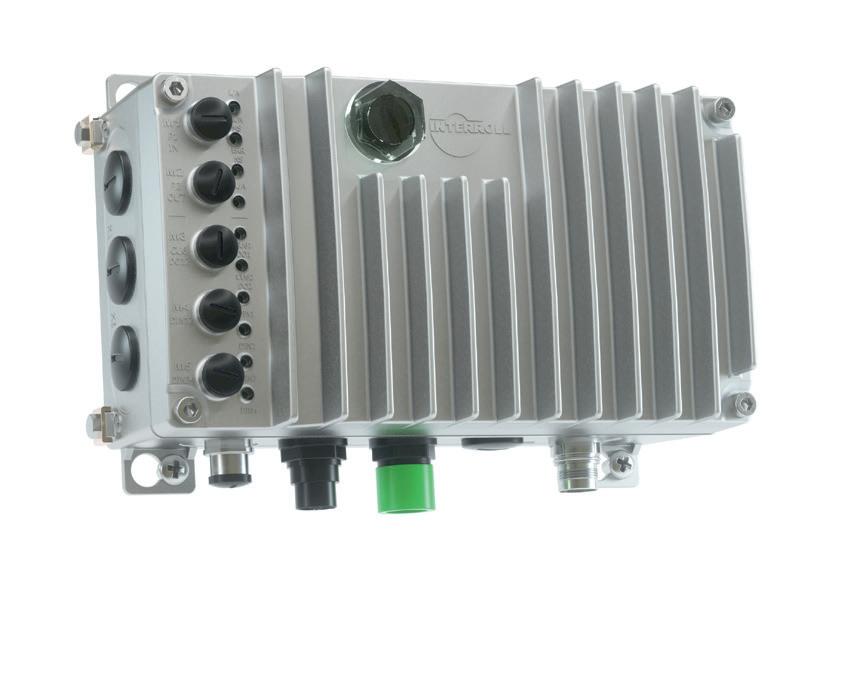
Power Range 0.12 - 200kW
Available in Foot, B14 Face or B5 Flange mounted design
Asynchronous motor efficiency level IE3 or IE4
Synchronous motor efficiency level IE5+, IE7 and IE8
All options like, encoder, brake, heaters, force cooling, etc. are available
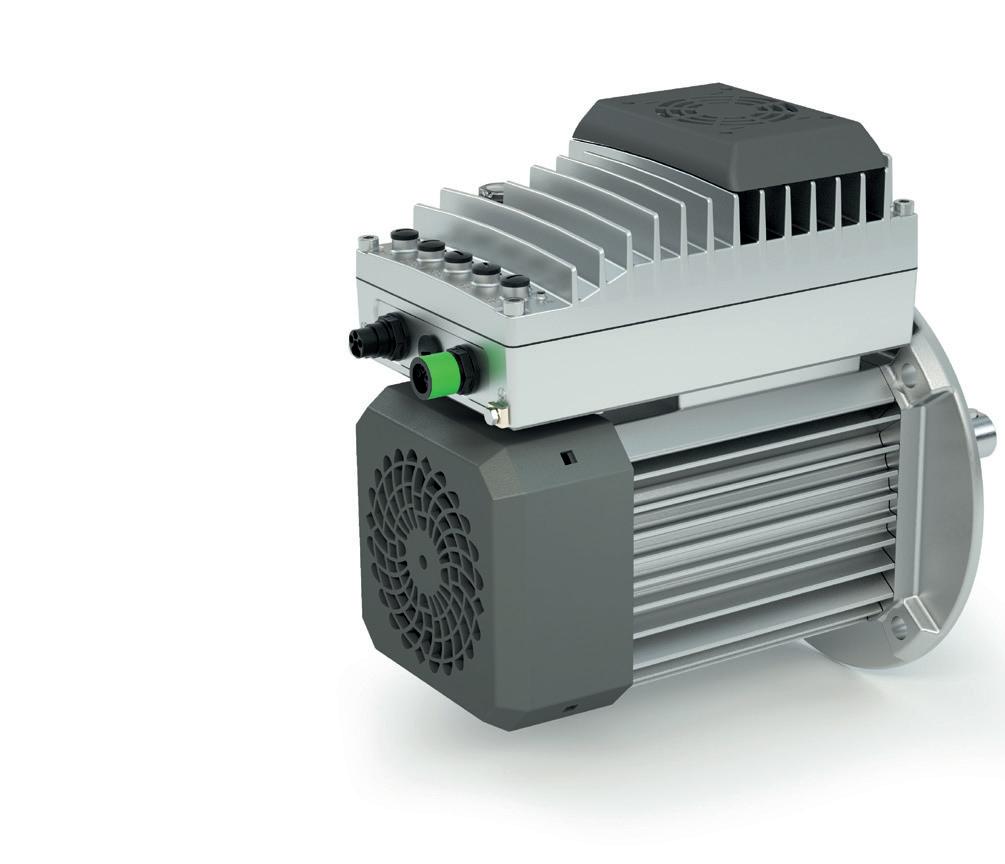
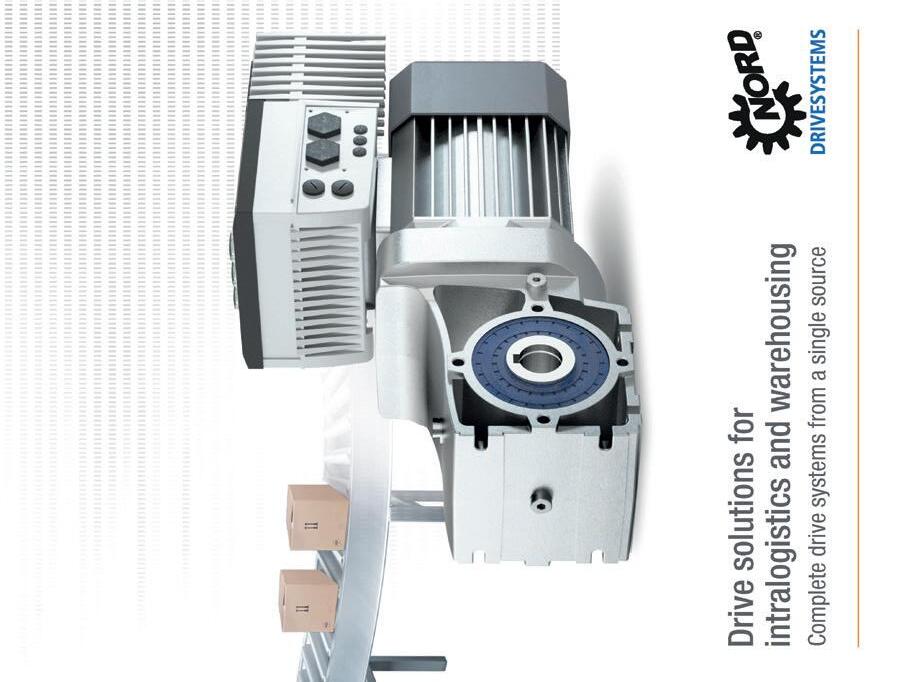
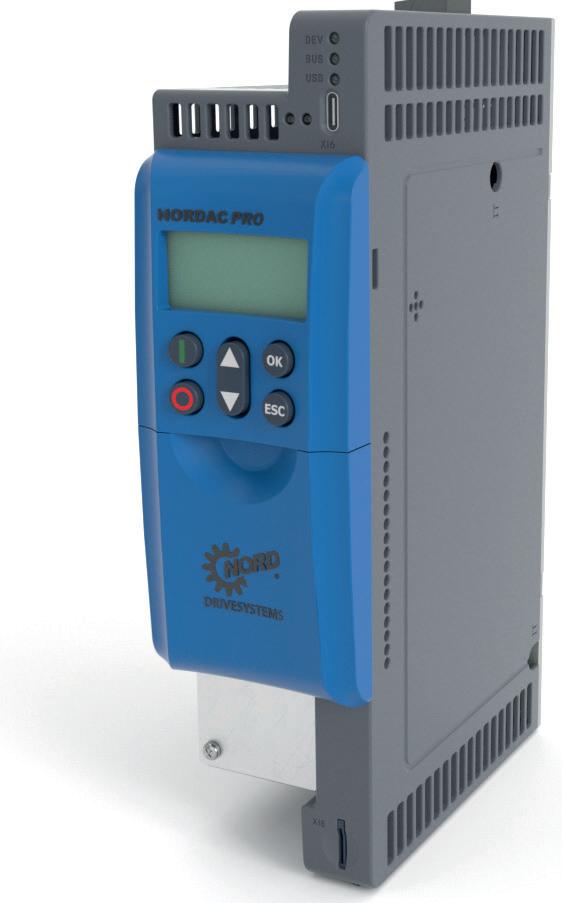
Application Specific Drives
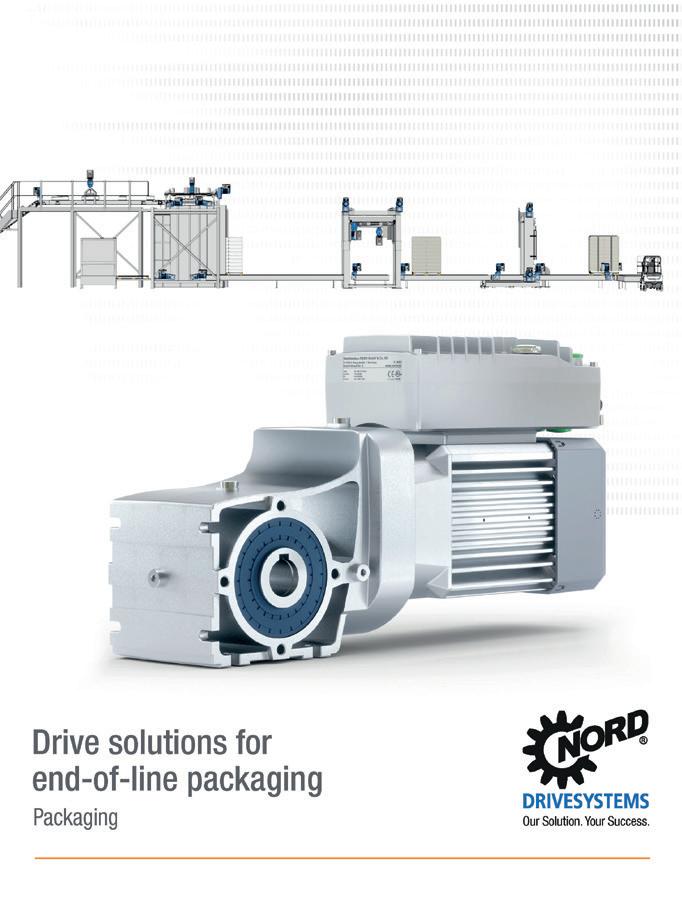
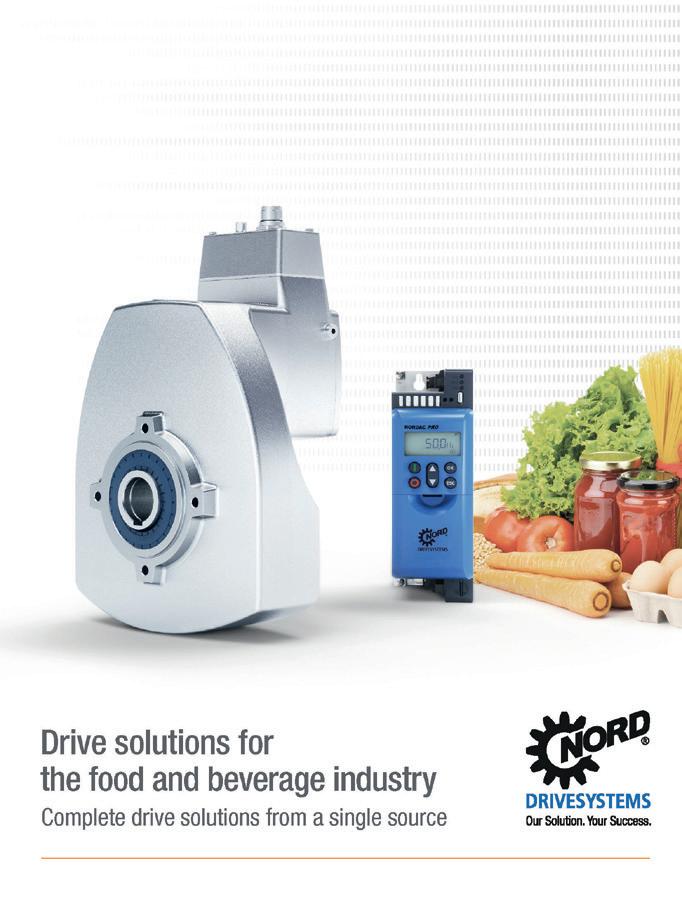
Assembled in our purpose built, ATEX approved UK assembly plant providing same day build and delivery.
Editor
Oliver Batt oliver@cimltd.co.uk
Publication Manager
James Burke jb@cimltd.co.uk 01795 509105
Account Manager
Jim Bearden jim@cimltd.co.uk 01795 509105
Design & Production
Grant Waters grant@cimltd.co.uk
James Taylor james@cimltd.co.uk
Administration Manager
Natalie Woollin admin@cimltd.co.uk 01795 509103
Credit Facilities Manager
Gwen Lee creditcontrol@cimltd.co.uk 01795 509103
Marketing Manager
Lucas Payne lucas@cimltd.co.uk
Sales Director
Tom Woollin tom@cimltd.co.uk
Chief Executive
John Denning
© 2025 Cogent Multimedia Limited,1st Floor, Saphir House, 5 Jubilee Way, Faversham, Kent, ME13 8GD. No part of this magazine may be reproduced or stored in a retrieval system or transmitted in any form – electronic, mechanical or physical – without express prior permission and written consent of the publisher. Contributions are invited and when not accepted will be returned only if accompanied by a fully stamped and addressed envelope. Manuscripts should be typewritten. No responsibility can be taken for drawings, photographs or literary contributions during transmission or in the editor’s hands. In the absence of an agreement the copyright of all contributions, literary, photographic or artistic, belongs to Cogent Multimedia Limited. The publisher accepts no responsibility in respect of advertisements appearing in the magazine and the opinions expressed do not necessarily represent the views of the publisher. The publisher cannot accept liability for any loss arising from the late appearance or non-publication of any advertisement.

June 2025
Welcome to the June issue of MEPCA magazine.
This month, our Focus is on Sustainability. Hidden amongst the current cynicism around net zero is an understandable fear of de-industrialisation and the impact this may have on the UK’s less-than-rosy economic situation. However, as demonstrated by the wealth of content received from our editorial call on sustainability, actions on sustainability are worth more than words, featuring solutions from ABB, Hunter Selection, Camozzi Automation, REO UK, Emerson, and many, many more.
Assisting our deep-dive into sustainability is the team at Waste Mission, who share how businesses can benefit from more sustainable waste management and provide advice to companies seeking to make their operations more sustainable. Following this, MEPCA addresses the practice of greenwashing and looks at how manufacturers can safely navigate it when sharing their ESG activities.

Our cover story this month will please coffee enthusiasts: Invertek takes us on a journey into coffee production and explains how a technological collaboration is improving coffee bean roasting.
Elsewhere in the issue, we reveal our Manufacturing Champion of the Month, while our Opinions section features Europump and GAMBICA.
I hope you enjoy this issue.
To subscribe to MEPCA visit our website www.mepca-engineering.com or scan the QR code. @Mepca-magazine
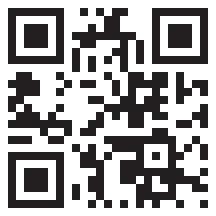
Oliver Batt, Editor
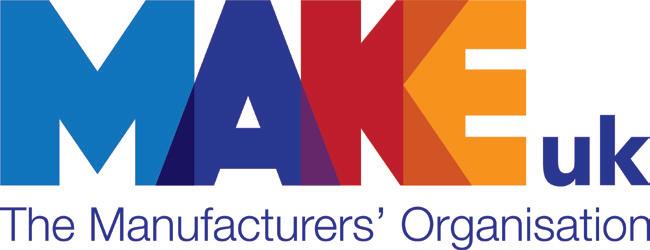
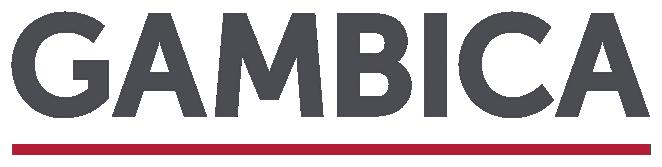
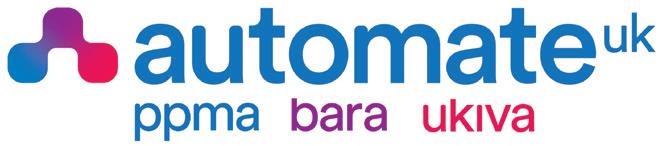
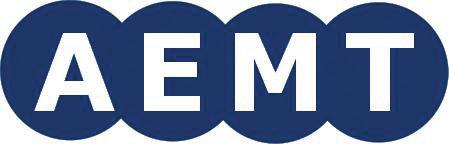
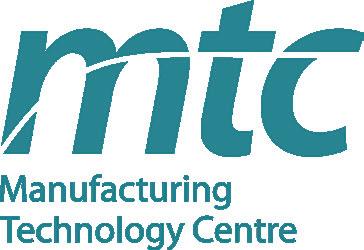
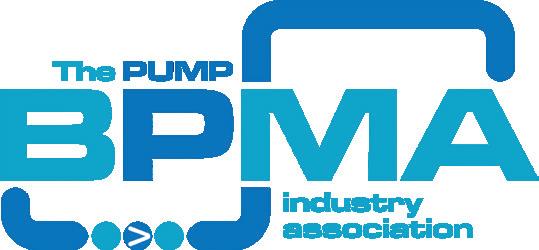
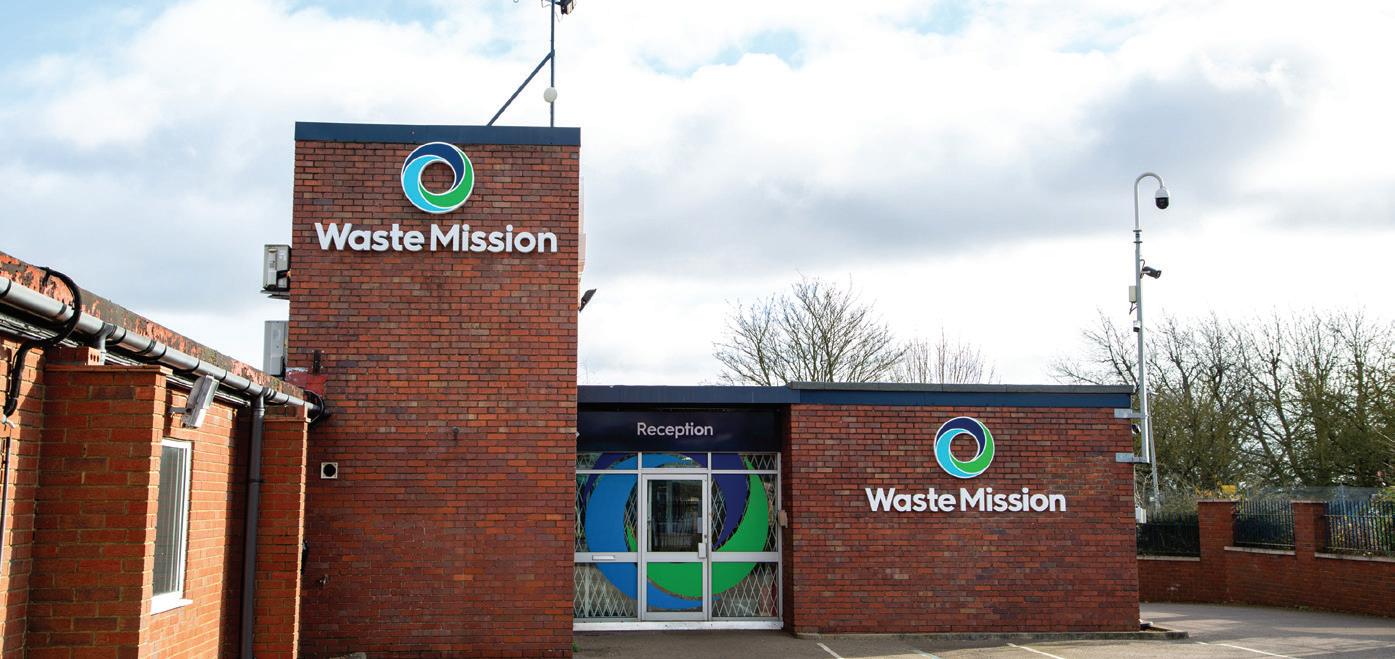
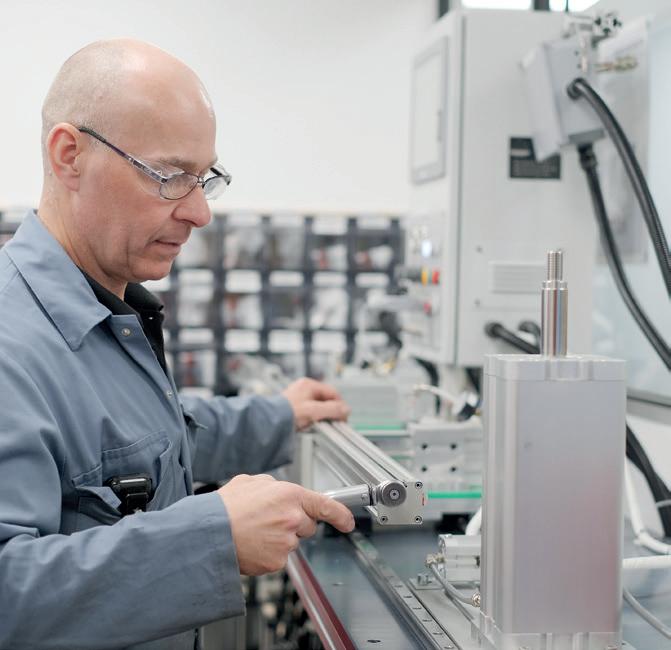
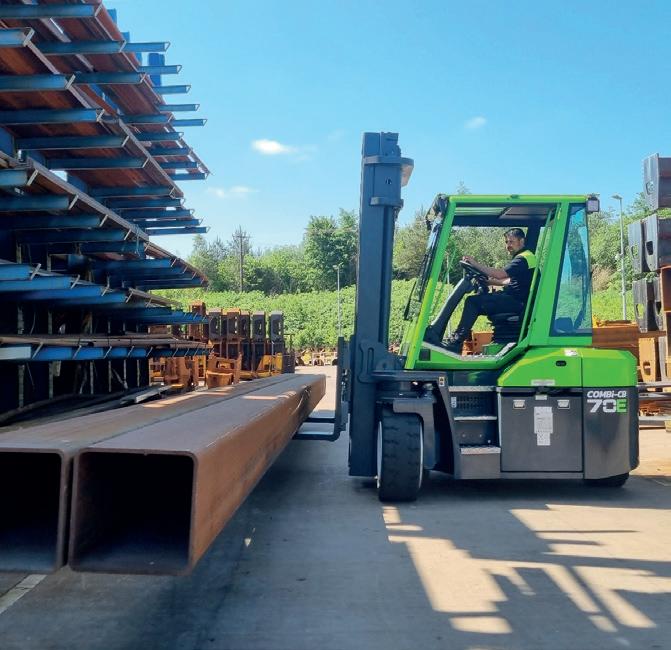
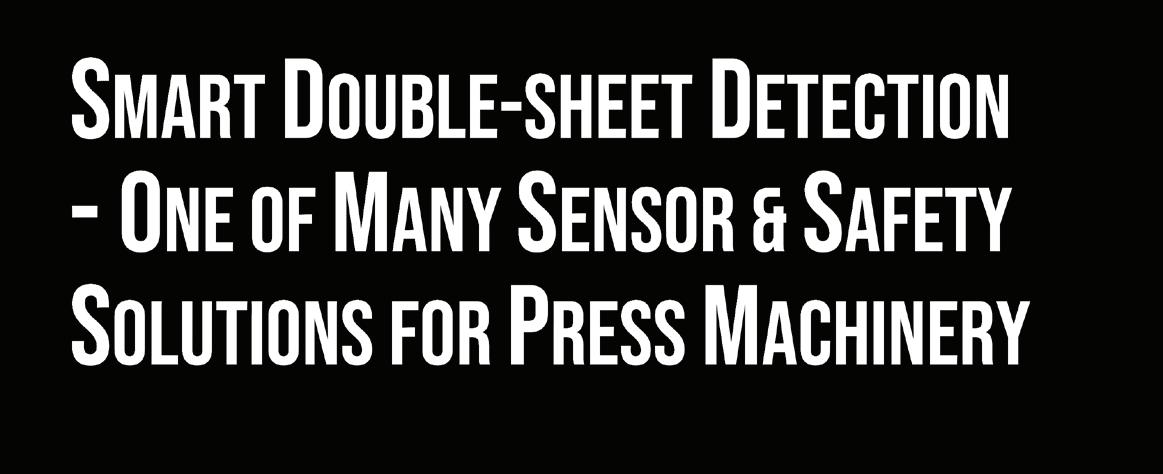

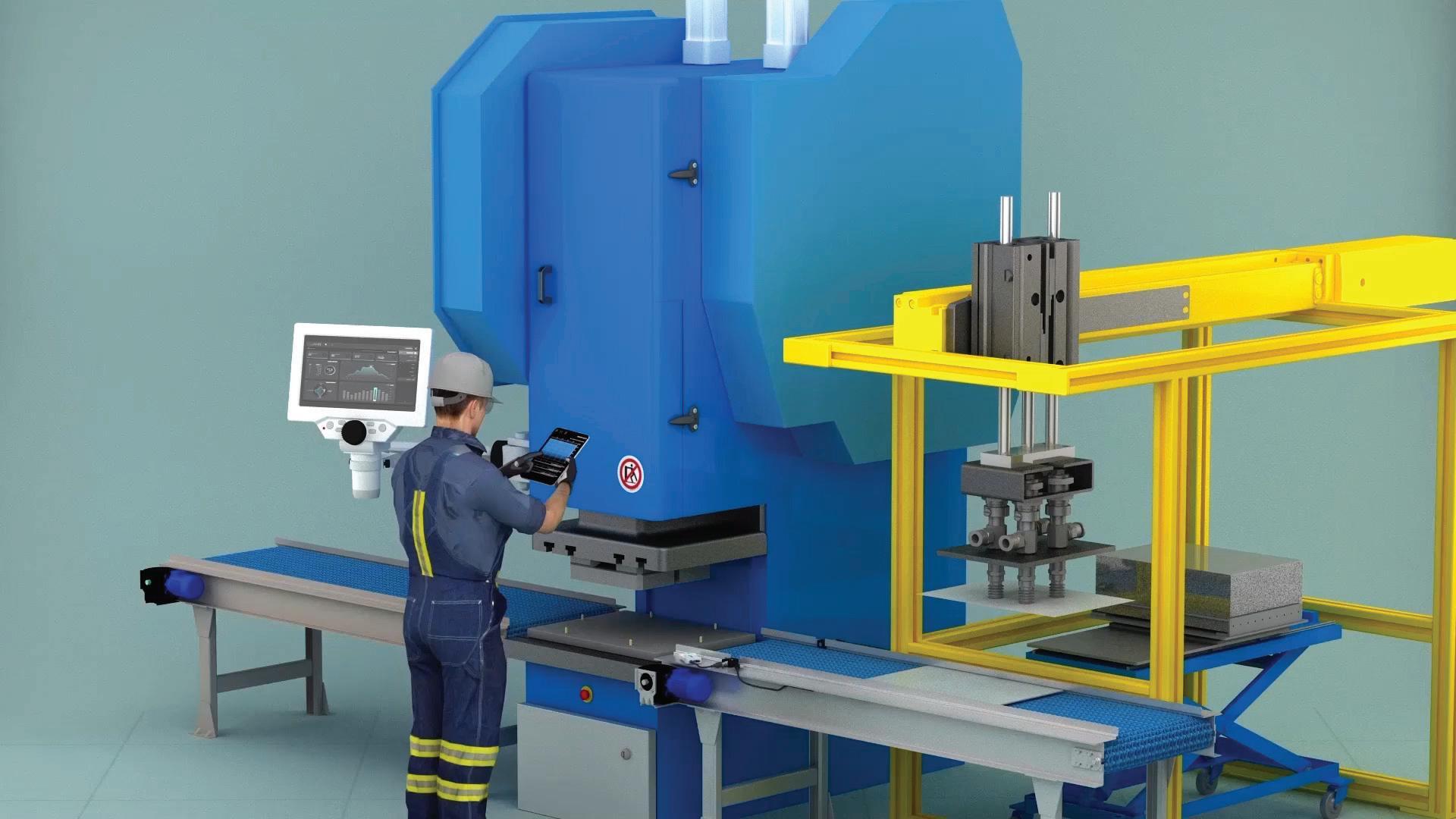


Ready, RE-Action!
This June, Relec Electronics is powering up for Smart Manufacturing Week 2025— and this year, the company is not just bringing products… it’s bringing RE-Action.
Attendees will find Relec at Stand 5/G52, where it will be showcasing the very best of its power supplies, display technology, and its industrial computing range. Built for the rigours of modern manufacturing environments, Relec’s industrial computing solutions combine reliability with the flexibility and performance design engineers need to keep operations running smarter, longer and leaner.
As ever, Relec’s expert team will be on hand to talk through the technical details behind their AC-DC & DC-DC power supplies and rugged TFT displays, with options tailored for automotive, rail, industrial and beyond. Whether looking for a lowprofile PSU or a sunlight-readable panel PC, Relec have it on display—and its team will be ready to jump into the details that matter.
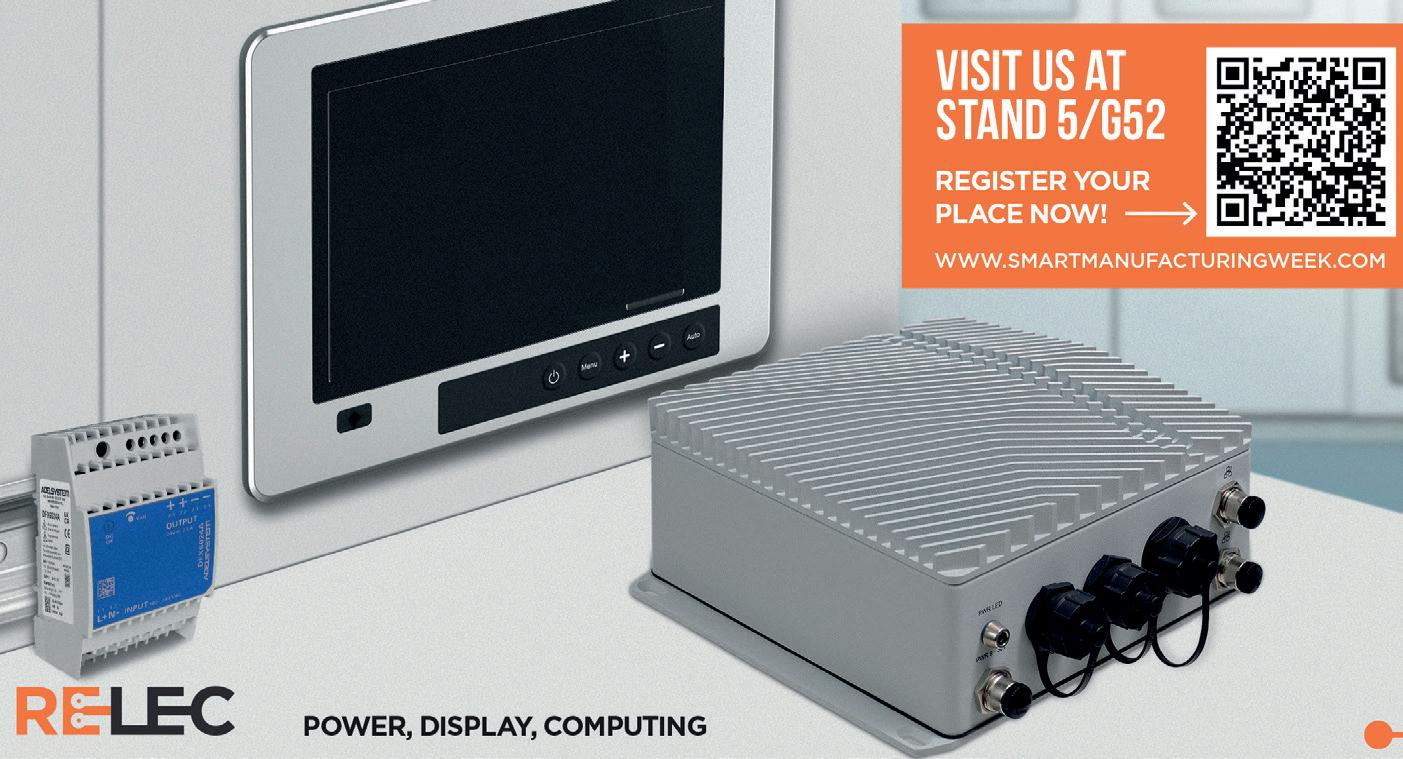
But don’t just come for the supplies. Come for the challenge. This year, Relec are launching RE-Action, an interactive game designed to test attendees’ reflexes, precision, and maybe their competitive streak. The highest score of the show taking home a £250 Red Letter Days Voucher— and the eternal glory of beating your peers at their own game (literally).
Attendees should mark their calendars and make a beeline for Stand 5/G52. Whether on the hunt the next embedded solution, wanting to chat standards and specs, or just fancy setting the benchmark on the RE-Action leaderboard – Relec will be there. Come for the kit. Stay for the challenge. relec.co.uk
Vision Engineering Introduces New
‘HALO’ 4K Digital Inspection Microscope
Vision Engineering, a UK based manufacturer of ergonomic microscopy and digital 3D visualisation technology unveils the EVO Cam HALO, a new 4K digital microscope that redefines the standard for clarity, precision and consistency in inspection and measurement tasks.
Suitable for a wide range of inspection applications, EVO Cam HALO combines stunning 4K image quality with advanced, adaptive illumination, and new intelligent software, empowering users to capture the most challenging details with unparalleled accuracy.
HALO’s key features include 4K resolution, which reveals previously obscured details with remarkable clarity, ensuring nothing escapes the user’s view. A Super-Wide Dynamic Range ensures the user captures images with exceptional brightness and contrast, even in challenging lighting
conditions. Additionally available with HALO is a new enhanced Illumination package, including a quadrant light, panel light, and white/UV light, to optimise illumination for a variety of inspection needs.
New intelligent hardware and software automatically detects lenses and adjusts magnification settings, ensuring seamless workflow and accurate results. Real-time insights are available providing intuitive image capture, measurement, and analysis tools, enabling faster and more informed decisionmaking. Vision Engineering’s popular 360 Direct/Oblique Viewer also works with HALO, enabling users to inspect details from different angles, revealing hidden features that would otherwise be inaccessible.
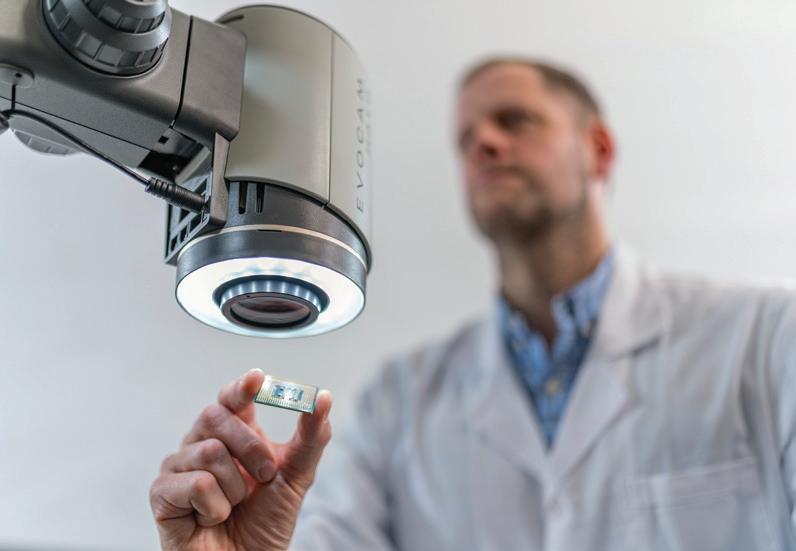
HALO cam improves the examination of Petri dishes with translucent samples, enhancing contrast and clarity for detailed analysis, and in Industrial Manufacturing, intricate assemblies, solder joints, and other components are inspected with much improved precision and efficiency.
HALO is effective at capturing fine details on small, reflective metal parts for precise inspection and quality control – perfect for Micro Mechanics. In the laboratory,
For more information, visiting Vision Engineering’s website. visioneng.com
Leveraging Generative AI for Carbon Capture
MEPCA’s editor donned a lab coat to tour Imperial College London for a first-hand demonstration of ABB’s latest development in measurement technology at work in the college’s famed carbon capture plant.
Nestled in the Imperial College London (ICL) in a university building like any other is a remarkable facility: the first and only fully operational carbon capture pilot plant of its kind.
Situated at the centre of the Chemical Engineering Department and stretching over four floors, the extensive facility offers a hands-on experience to researchers and students, allowing ‘real-world’ scenarios to be tested under the guidance of the university’s experienced professors, postgraduate students and on-site engineers.
Importantly, as a fully operational carbon capture plant, it plays a vital role in the fight against climate change by demonstrating how CO2 can be removed from the atmosphere and captured, safely, inspiring organisations to replicate this in industry, at scale, and enabling the training of a future net-zero workforce.
It is here, at the Chemical Engineering Department of ICL, that the ongoing collaboration between ABB and the University has reached new levels of automation, with the piloting of the next generation of digital measuring systems, My Measurement Assistant+ (MMA+), which leverages artificial intelligence (GenAI), cloud computing and Augmented Reality (AR) for advanced maintenance and troubleshooting.
The collaboration between ABB and ICL has to date provided the university with the most advanced sensors and control systems available. With the volume of sensors and instruments in place throughout the facility to measure and relay operational data, maintenance and troubleshooting is a highly complex undertaking, requiring a high-level expertise.
Omar Matar, the department head of chemical engineering at ICL: “We have
more than 250 devices installed in the carbon capture plant here, including the distribution control system for ABB 800XA, which is one of the leading control systems in the world.”
Omar went on to explain that the startling rate at which technology evolves, particularly with increased digitalisation, and their commitment to ensuring students are using the most advanced technology available has led to the embracing of AI at the facility.
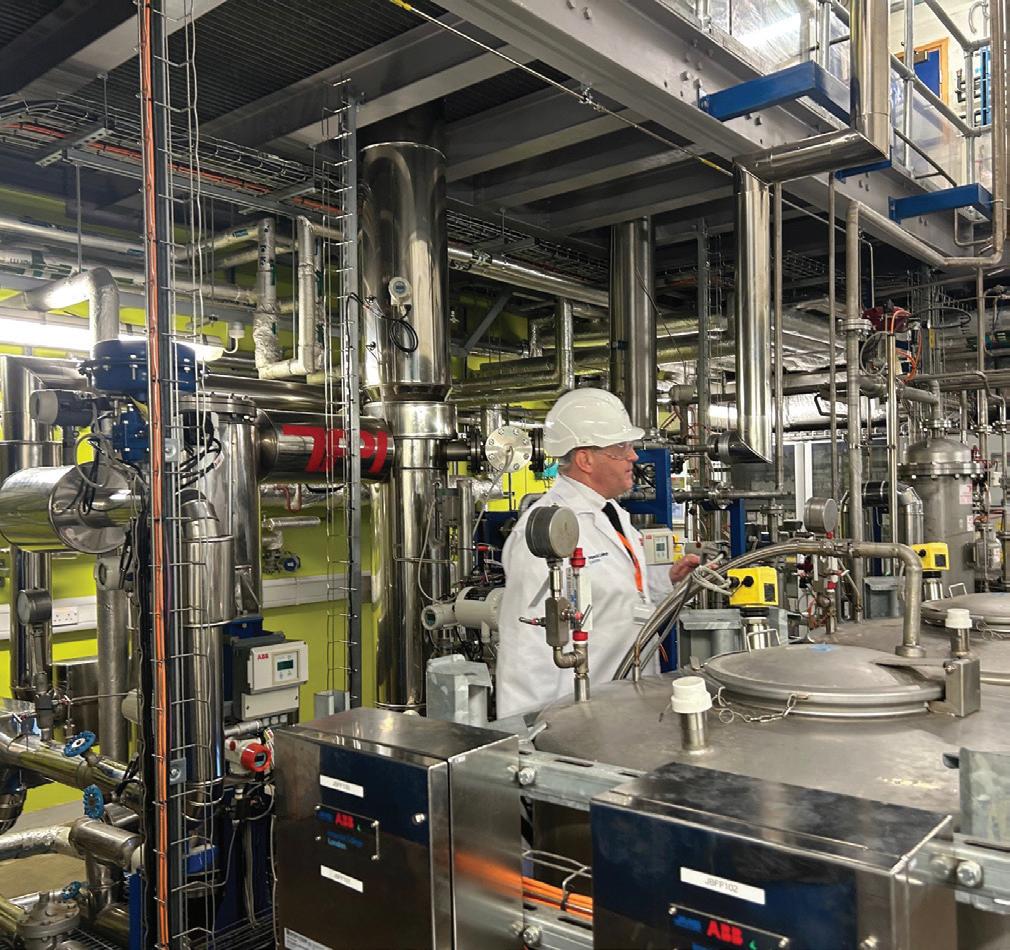
David Lincoln, Global Digital Lead, ABB Measurement & Analytics highlighted the issue: “When we looked in our technical support data, we recognised that a striking 80 % of the calls we were receiving, the information was available within the documentation itself.”
What started as a website that connected trouble shooting information and videos became a comprehensive and advanced maintenance and trouble-shooting system.
MMA+ is integrated with ABB Ability™
Genix Copilot, a GenAI solution developed by ABB in collaboration with Microsoft to provide an advanced maintenance package, widening the range of maintenance issues the system can respond to.
Before beginning the tour of the facility, we had to put on protective gear, a reminder that we were entering a working industrial facility.
Visitors witnessed how the use of
dynamic QR code capabilities, developed with Microsoft, allows engineers to simply point their tablets or smart phones at the QR codes present on every instrument in the facility to gain immediate access to a detailed report on its status.
As well as providing videos, manuals and the ability to contact support staff anywhere in the world, generative AI offers solutions based on the data available. Importantly, to avoid “hallucinations”, the phenomenon where AI provides false responses, the system parameters are weighted so that it will not provide an answer if there is any doubt at the accuracy.
David Lincoln: “We believe this tool can help resolve technical support issues in minutes and improve first time fix rates by up to 50%.”
In 2023, ABB and ICL signed a 10-year contract to continue this highly successful partnership. global.abb/group/en
Pumps: the Hidden Sustainability Heroes
In this article, Europump President Luboš Michlík highlights the vital role of pumps in powering the drive for a sustainable future.
As the global push for improved energy efficiency and sustainability intensifies across manufacturing, commerce, transportation, housing, and public services, pumps remain the unsung heroes at the heart of these transformations. Today, Europump, the European Pump Association, shines a spotlight on the critical yet often overlooked role that pumps play in shaping a more sustainable, energy-efficient world.
The backbone of energy efficiency in manufacturing and industry
In the manufacturing sector, where energy efficiency is a growing imperative, pumps are quietly driving progress. They facilitate vital processes such as cooling, heating, fluid transport, and circulation, all while consuming a sizeable portion of industrial energy. Yet, innovations in pump technology are helping industries cut down energy usage, reduce operational costs, and minimize their carbon footprint.
“Industrial pumps represent a key opportunity for energy savings, given that they account for up to 20% of global electricity consumption. By embracing more efficient pump systems, manufacturers can drastically reduce energy consumption, making a major contribution to global sustainability efforts.”
Driving innovation in renewable energy
Pumps are also key players in the renewable energy revolution. Whether it is through circulating fluids in geothermal systems, powering hydraulic mechanisms in wind turbines, or managing cooling in solar power plants, pumps are crucial to the smooth operation and efficiency of renewable energy technologies.
“The future of clean energy depends on the efficiency of every component, and pumps are no exception. They are essential to scaling up renewable energy solutions and achieving Europe’s net-zero carbon targets.”
A hidden hero in every household
Beyond industry and public services, pumps impact our daily lives in more personal ways. Every time we turn on the tap for fresh water, adjust the thermostat, or rely on modern appliances, pumps are working behind the scenes to make these conveniences possible. In residential homes, pumps ensure the efficient delivery of water, heating, and cooling—keeping households comfortable, safe, and sustainable.
“From individual homes to massive industrial plants, pumps are an often unseen yet essential part of daily life. They are indispensable to modern living and key to the sustainable, energy-efficient world we are working to build.”
Europump: leading the way towards a greener future
Europump and its members are at the forefront of promoting high-efficiency pump technologies and advocating for policies that support sustainability and innovation. Through collaboration with industries, regulators, and other stakeholders, Europump is committed to driving the adoption of innovative solutions that reduce energy consumption and environmental impact.
Ecopump is its flagship project, embodying the organisations energy reduction commitment. In 2004 the Europump Council endorsed the Ecopump initiative as the very cornerstone of the European pump sector’s energy and
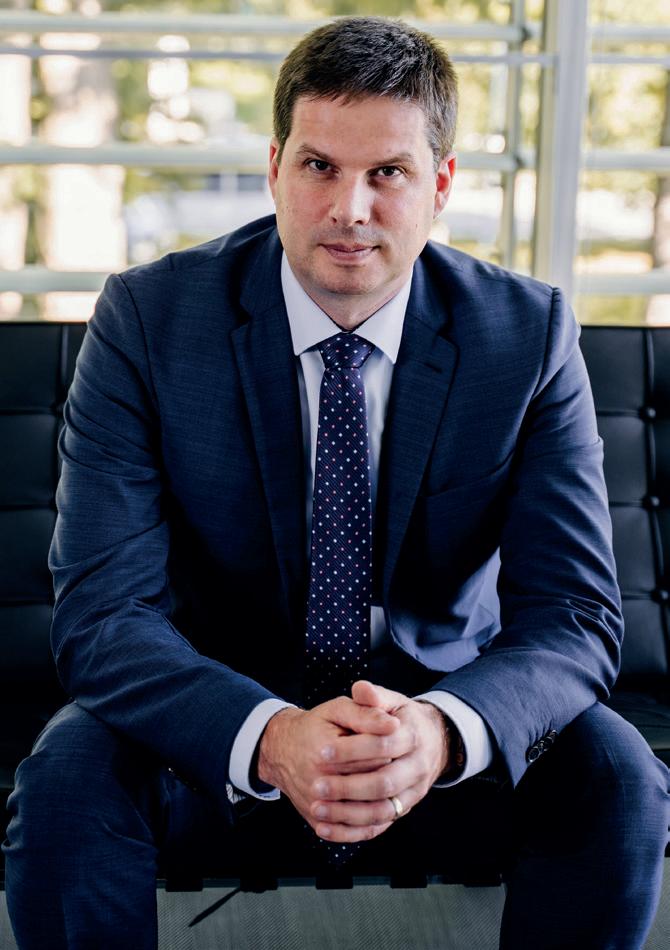
environmental policy. The Europump website now carries a dashboard that provides a real time illustration of the energy savings.
Since 2016, these endeavours have resulted in the saving of 233 million MWh of electricity and a reduction of 163 million tons of CO2 emissions. Additionally, the incorporation of the Extended Product Approach into the upcoming revision of EU Regulation 547/2012 for water pumps could unlock a further 35 TWh in energy savings.
“In a world increasingly focused on sustainability, it is crucial that pumps—often the unseen workhorses—are recognised for their potential to deliver significant energy savings and environmental benefits. Together, we can ensure that pumps continue to be a driving force behind the green transition in every sector.”
For more information about Europump and the work it undertakes on behalf of the European pump sector, please visit the association’s website.
europump.net
University and Industry Collaboration
Addressing the chronic skills gap, Nikesh Mystery, Section Head of Industrial Automation at GAMBICA, calls for greater collaboration between academia and industry to change outdated perceptions and put the next generation of talent on an industrial career path.
We must ensure our future workforce has the skills, ability and drive to want to succeed within industry. This has been a recurring topic of conversation amongst our membership over the past few years. 10 years ago, many of the current jobs in industry didn’t even exist, yet today we are constantly seeking ways in which we can use technology to create more jobs. However, one thing we must not forget is those who will be doing those jobs. Our future workforce. They require the same level, if not more attention than we are giving to digital transformation.
Of course, one of the best ways to do this is to reach out to directly to universities, colleges, schools and students at even younger ages, who haven’t yet decided where they would like their careers to unfold. For it is that generation that will be sure to shape the future of our industry. We need drastic changes in how engineering and STEM subjects are perceived. Not only in the media, but within the institutions mentioned above. It is so common for younger generations to believe an engineer will be stuck in a hard hat in a loud/messy environment all day, and that most certainly isn’t the case anymore. We need to educate the educated on being able to challenge these negative perceptions of STEM subjects.
One of the ways GAMBICA is acting to help on this journey has been by our University and Industry collaboration group (GUIC). We created this group 3 years ago now, with the aim to explore how industry and academia can collaborate in industrial member engagement with schools and 6th form colleges, and on collaborative research and policy. GAMBICA developed this group
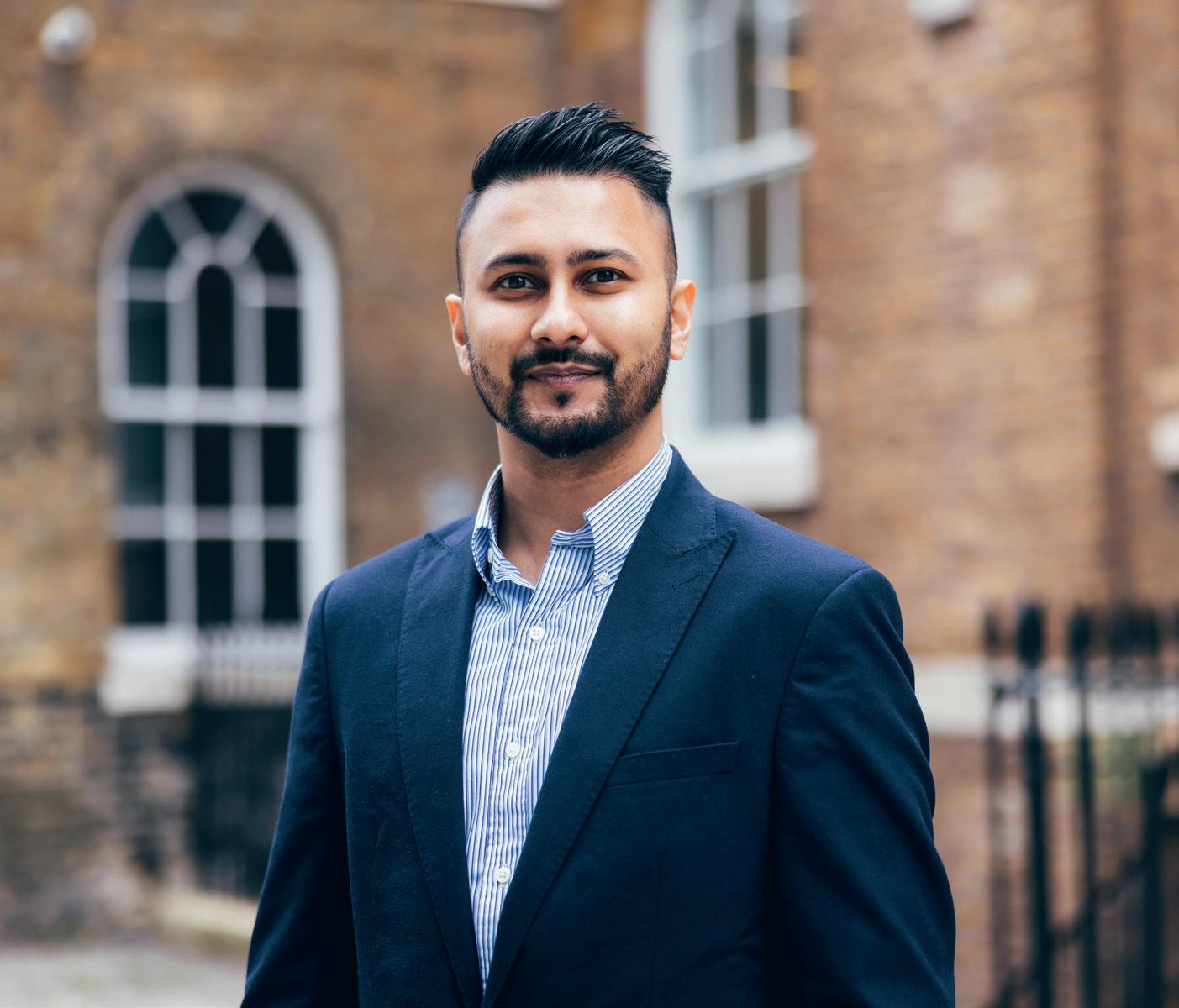
to explore the methods and practices that we could use to deliver value to students, university staff and industry members, and to augment teaching materials and equipment, as well as to offer relevant work placements, focus research, access industrial technology & data, and ultimately to retain talent in our industry.
GAMBICA can utilise our pool of experts to bridge this gap and fix the separation that has always been there. It is too often that we hear the dreaded circle, “I can’t find a job because I have no experience, but I can’t get experience because I can’t find a job”. This is a common issue and it STEM’s (if you’ll pardon my pun) directly from the miscommunication and lack of transparency between academia and industry. We are not
too late to connect this gap. The same way there is a skills gap between IT and OT in industry, all we need is the push in the right direction.
The GUIC has been developing case studies within its working groups, and each year we host a “Collaborate” event where our members showcase the work that the group has been achieving. The GUIC council consist of a combination of both industry and academic members from all GAMBICA sectors.
To find out how you can be involved in this University and Industry Collaboration group or to find out more about the upcoming event, get in touch on our website: gambica.org.uk
Manufacturing Champion of the Month
Introducing Kirsty Davies-Chinnock, MD of Professional Polishing Services Ltd and CEO of Woman With Metal, and our Manufacturing Champion for June. Kirsty discusses how far Woman With Metal has come since its inaugural event in 2023, and the importance of diversity and adaptability.
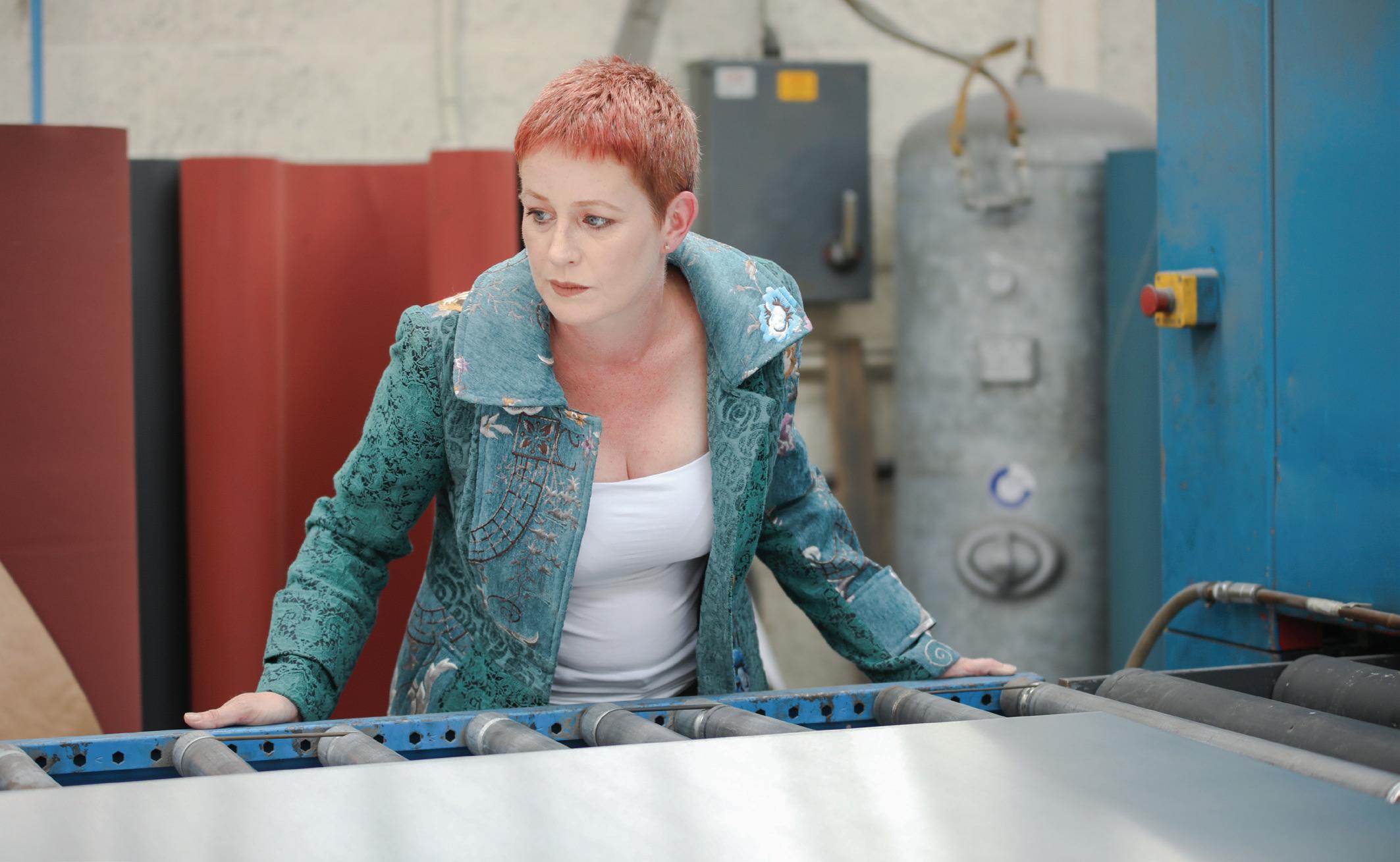
Alongside managing Smethwick-based Professional Polishing Services, which provides bespoke metal treatments to the UK and worldwide, Kirsty DaviesChinnock also hosts the Women in Industry podcast, is the director of the British Stainless Steel Association, a non-executive director of ART Business Loans, and an ambassador for ACORN’s Children’s Hospice.
As she explained to MEPCA, “I nearly always have two or three non-exec roles
at time. I am an international consultant for the use of polished stainless steel and other non-ferrous metals. And one of the jobs I consulted on was the Vessel in Hudson Yard in New York.”
More recently, Kirsty founded Women With Metal, an annual conference dedicated to connecting women and allies working within the metal sector, and which MEPCA was surprised to learn originated by accident in 2023.
Setting the scene, Kirsty explained that in a rare turn of events she had finished work early after a meeting in Birmingham and was
relaxing with a cigarette and glass of wine when she received a call from a contact of 20 years from a recruitment business within the metal sector. He was calling because more and more companies were seeking a 50-50 gender split in candidates, which got him thinking that, while his company hold event days for golf, clay pigeon shooting and five-a-side football, there was nothing aimed at female candidates. As a prominent figure in industry, he asked Kirsty do something for women, suggesting afternoon tea … Luckily, she took it in the spirit it was intended, and Women With Metal was born.
“I tell everybody this story; he absolutely hates it, which is why I don’t name him. That [phone call] was the Wednesday afternoon, and by the Friday I’d booked the Park Regis Hotel and five speakers. I thought there’d be about 30 people there. But we sold out at 100 and then we grew about 35-40% for last year, which we held at the ICC.”
Despite the unconventional origins of the conference, Women With Metal is quickly gaining traction and helping to increase the visibility of woman in the metal industry and beyond.
“In the sector as a whole, when we’re looking at diversity, obviously gender is only one small part of that. But we need new people; we need new ways of thinking.”
Expanding on this, Kirsty addresses the common misconception that this driven by a negativity towards cis-men: “There’s no ‘bashing’ here at all. But the more we can bring in different ways of thinking, diversity of thought, the more we try things, the more we’re going to innovate. Not only our own businesses, but the sector as a whole. And we’re going to attract, and more importantly, retain new people coming into the industry.”
It is Kirsty’s view that diversity is connected to innovation and adaptability. “The world changes faster than we can comprehend. In 2025, just the last six weeks, just on the tariffs, on the trade war. That in itself is something that 12 months ago we wouldn’t have considered. So we need to be able to be flexible and adapt.”
When asked about her own experiences as a woman in the industry, Kirsty said that she always finds this difficult to answer, as her personal experience has been a positive one, overall. She was well aware, however, that this has not been the case for many woman and other minorities in the industry. Having experienced the industry in the 80s and early 90s, Kirsty knows how far it has come already, but she has seen plenty of examples of the old attitude towards diversity.
“On one board, I was the only woman, there were three men on the board called Dave. So, the Dave’s outnumbered the women three to one. That board, I will say, now has four women in it and only one David. So, you know, we made progress.”
She clarified that this was an organic change: they didn’t kick any Daves off the board. Reiterating a point made earlier, Kirsty joked that this wasn’t about culling Daves, instead she sees the changing face of the industry as a positive step that will usher in
MANUFACTURING CHAMPION
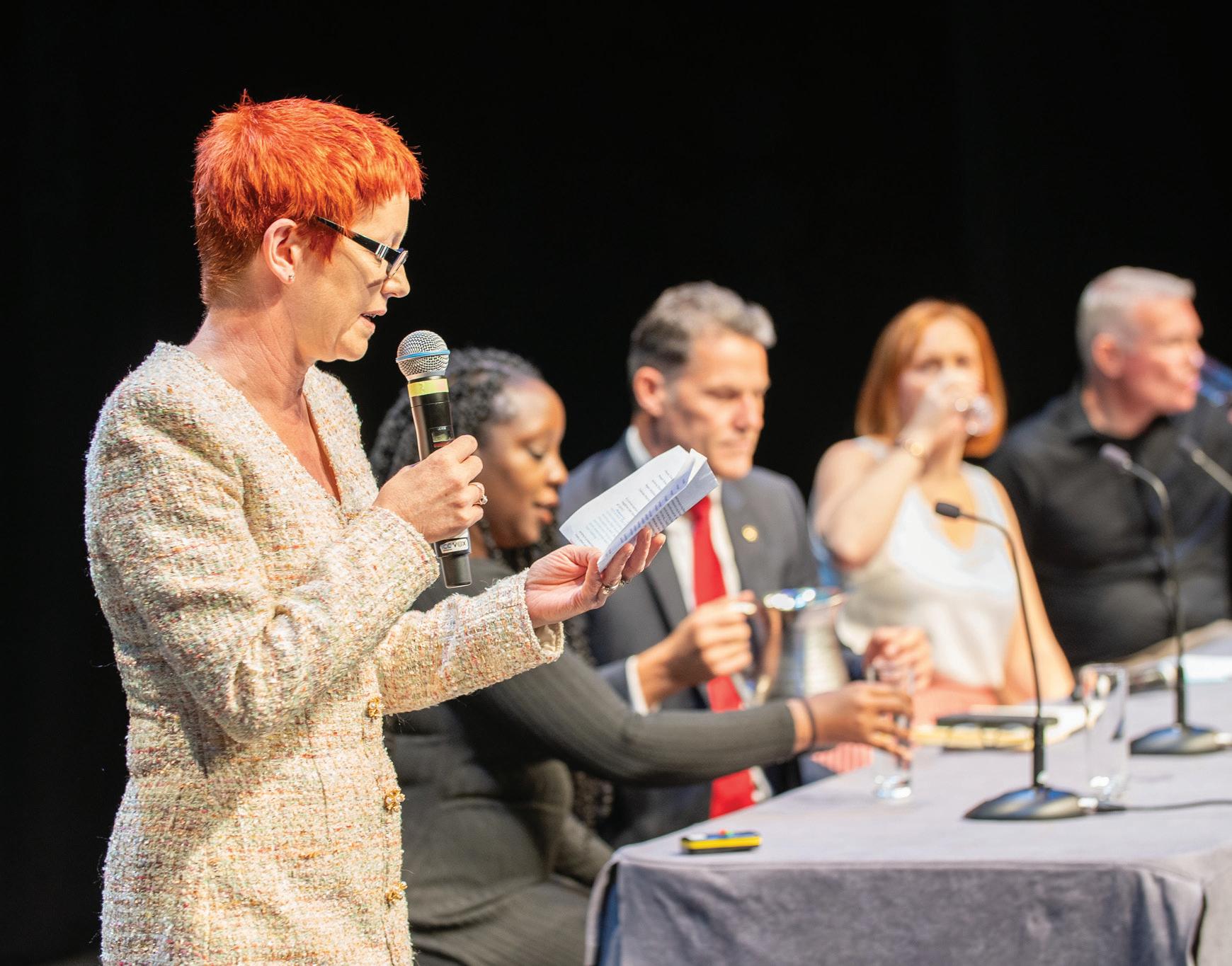
innovation and new ways of working.
An attitude she won’t accept is that bad work experiences are part of earning your ‘stripes’ at work; that because you went through something, the next generation must also do so, or else be considered less worthy of respect. “I’m not here to punish people for having a different experience to me,” she said, “I’m here to make sure that any negative experiences I had, they [employees] are not going to experience it 30 years later, because we’ve learned nothing otherwise.”
For this reason, she is excited to see Gen Z coming into management roles, particularly the changes they will usher in, such as more flexible working or improved work-life balance.
The next generation of talent is looking for a work-life-balance that suits them. To accommodate this, Kirsty believes that it’s ever more important to try new ways of working, including 4-day-weeks, or experimenting with shift patterns, rather than enforcing traditional working patterns. Unfortunately, the typical roles that allow more flexible working can be very limiting.
“One of the things I’ve seen in a lot of round tables where it’s been, oh, let’s get more women in manufacturing. Tell them it’s flexible; they can work from home. But you are only recruiting for this thin little layer of maybe sales, customer service, finance, nothing to do with production or quality or even HR because you’ve got to be on site.”
Elaborating on this, Kirsty explain that this
creates a “them and us” scenario, where “30% of the workforce are women, but only 5% work on site, the other 25% work from home. That’s adding barriers. And we need to stop doing that. And when it comes to retention, the main reason that women come out of manufacturing is because they’ve got a family.”
To illustrate how businesses can introduce flexibility without these pitfalls, Kirsty used the unusual shift pattern offered by a Scottish manufacturer of jams and jellies. In addition to having a day shift and a night shift, the company introduced a twilight shift, circa 5:30 to 8:30, with a production team consisting of 85% women, who are the primary caregivers during the day but need a second source of income. Kirsty pointed out that this won’t work for every business, but it worked well for this company and their demographic.
“All of these are great ideas for specific companies, their team, their customer base and their community. And the longer we go on developing these different flexible ideas and the more we listen to the flexible needs that the team bring to you, and try them on for size and see which works, every company will end up with a unique way of doing that.”
The Woman With Metal conference will take place 8 October 2025, at The ICC Birmingham. To register, visit the website below.
womenwithmetal.com
Roasting Up the Perfect Coffee Bean
Discover how a technological collaboration combining Optidrive variable frequency drives (VFDs) and gearmotor technology is elevating coffee production.
Sumitomo Drive Technologies is a globally recognised leader in industrial drivetrain technology, offering a wide range of high-performance motors, gearboxes and industrial automation solutions.
During 2019, it acquired Invertek Drives, a manufacturer of VFDs, specialising in innovative, high-performance and energyefficient solutions for a wide range of industries. Together, they now offer worldclass drive solutions for a wide range of industries and applications as described below.
In the heart of the world’s fourth-largest coffee bean producer, a technological collaboration is brewing perfection between three manufacturers of variable frequency drives, direct drive motors, and coffee roasteries.
As a result, coffee beans are being roasted with such precision and control that every batch achieves the desired flavour consistently, roast after roast.
Pratter, a coffee roastery branded range made by PT Patmanunggal Reka Abadi, use Invertek Drives Optidrive E3 VFDs to provide accurate control of Sumitomo Drive Technologies direct drive motors from SM Cyclo Indonesia, enabling consistent and high-quality coffee roasting across cafes, roasteries, and industrial settings.
The success of any coffee roast hinges on meticulous control of temperature and airflow.
VFDs step in to provide just that. By precisely controlling the speed of the motors powering the rotating bean drum, motor blower and cooling agitator, they ensure each batch achieves the desired roast profile with consistency. This creates exceptional drink quality, ensuring Pratter’s reputation for excellence.
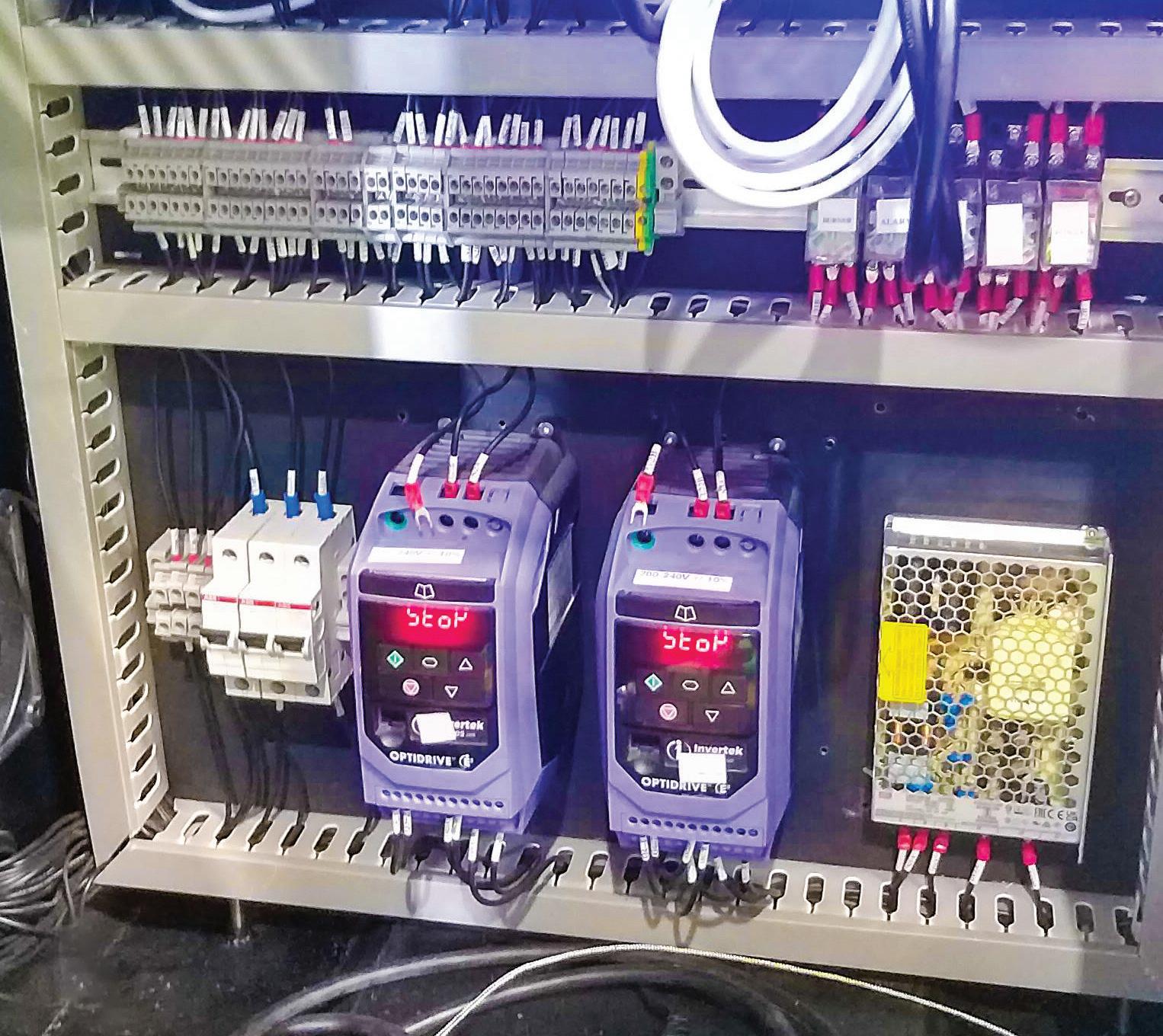
When testing and trialling the products in 2018, Sumitomo Drive Technologies had used another VFD manufacturer’s drive. It was when SM-Cyclo Indonesia worked with them, combining the Optidrive E3 in its place with Hyponic and Astero direct drive motors, that it saw the benefits.
Each roastery includes two Optidrive E3s, a Hyponic gearmotor and an Astero gearmotor.
Pratter’s range boasts an array of models designed to meet diverse needs. At the heart of its operation lies the rotating bean drum, meticulously controlled by the VFD. This cast iron drum gently agitates the coffee beans as heat envelops them, coaxing out their flavours and aromas. The VFD ensures precise temperature control, preventing
scorching and achieving the desired roast profile with unwavering consistency.
The motor blower accurately regulates airflow, ensuring even heat distribution and preventing unwanted hotspots. Meanwhile, the cooling agitator quenches the roasted beans, locking in their new flavours and preventing over-roasting. This intricate mix of heat, air, and cooling, controlled by the VFD, transforms green coffee beans into aromatic beans, ready to be brewed and enjoyed.
“The Optidrive E3 has been instrumental in streamlining our production process,” said Indrawan Samuels of PT Patmanunggal Reka Abadi. “The durability of the VFDs allows me to provide assurance the performance stability of the Pratter products in every use.
“The user-friendly setup allows for quick integration and adjustment, ensuring our roasters are up and running efficiently. Importantly, the reliable performance and precise control have significantly elevated our brand image, showcasing our commitment to quality and consistency.”
The success story extends beyond the VFD itself; the Optidrive E3 seamlessly integrates with direct drive motors from Sumitomo Drive Technologies, distributed in Indonesia by SM-Cyclo Indonesia and backed up with product and technical support.
This powerful combination delivers exceptional energy efficiency, unmatched reliability and unparalleled motor control, ideal for the demanding world of coffee roasting.
“The synergy between Invertek’s innovative VFD technology and the highperformance motors creates an unbeatable solution for Pratter,” said Carwyn Jones, Asia Pacific Technical Sales Manager for Invertek. “Together, they provide the precise control and unwavering reliability needed for exceptional coffee experiences.”
Bambang Suharyadi, of SM-Cyclo Indonesia, said: “The combination of drives and motors offers the perfect balance of power, precision and efficiency. We are proud to play a part in Pratter’s success story.”
This collaboration holds even greater significance considering the context of Indonesia’s coffee industry. As the world’s
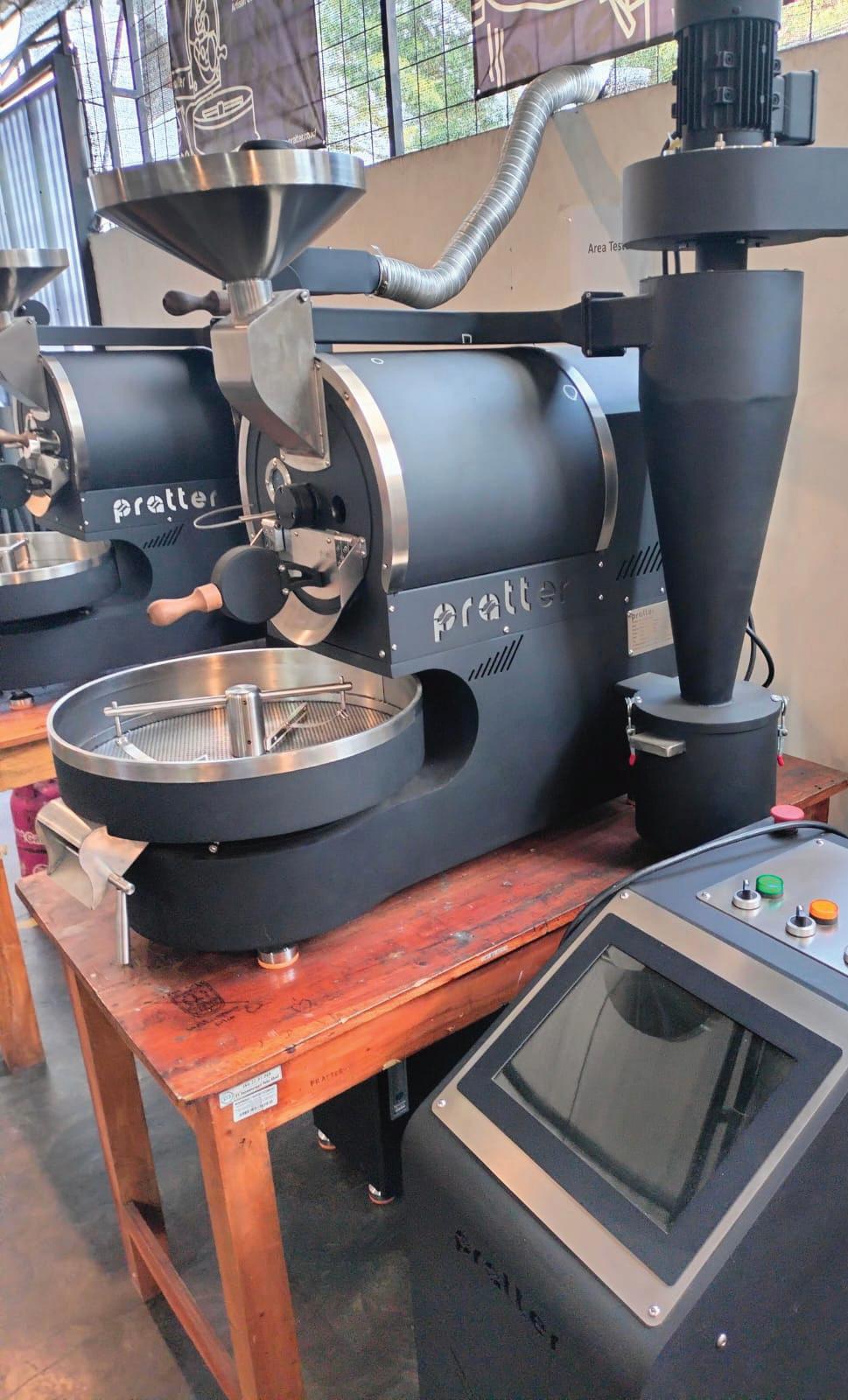
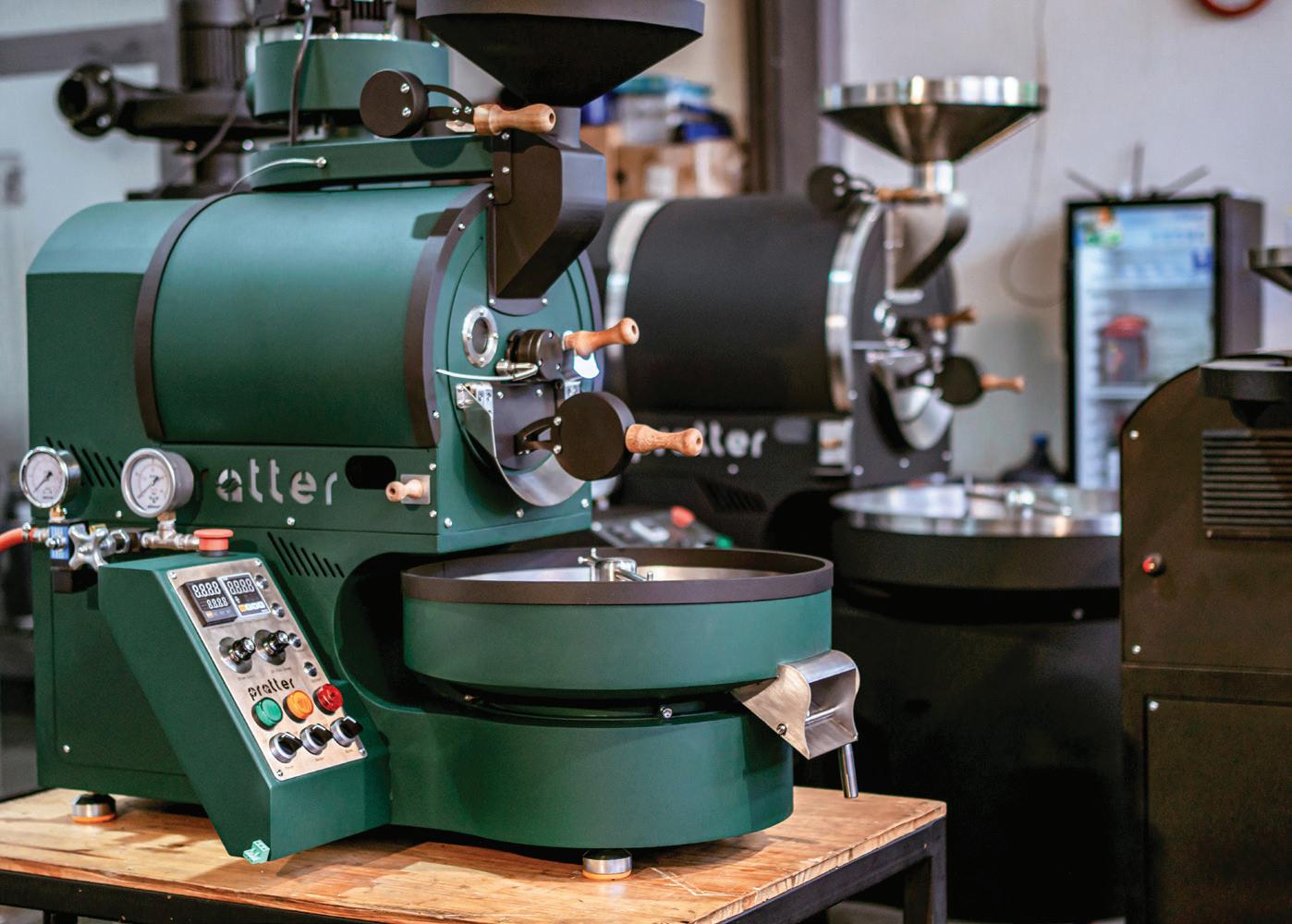
fourth-largest coffee bean producer, Indonesia boasts a rich coffee culture and a rapidly growing speciality coffee market.
Pratter, with its commitment to quality and innovation, perfectly supports this growth. The roasteries cater to coffee connoisseurs across various settings, from cafes to roasteries to industrial-scale coffee production. The technical specifications of the Optidrive E3s used are 0.37kW, 1PH and 0.75kW, 1PH.
Looking to the future: sustainability and social contribution
Today, Sumitomo Drive Technologies unites all activities in the field of drive technology under a recognised brand.
With recent acquisitions, such as the Lafert Group and Invertek Drives, Sumitomo Drive Technologies has evolved from a component manufacturer to a complete provider of motion control solutions. The portfolio consists of precision gears, industrial gears, centrifuges, actuators, motors, variable frequency drives and connected solutions for Industry 4.0.
Sumitomo Drive Technologies sees innovation as the key to a sustainable future. The integration of the latest technologies not only enables more efficient industrial processes, but also makes a positive contribution to society and the environment. The corporate culture, characterised by a passion for technology and a strong team spirit, offers room for continuous development. The needs of customers always remain in focus – with customised
solutions for the challenges of modern industry.
From the vision of a German engineer to global drive technology
Sumitomo Drive Technologies celebrates 100 years of cycloidal gears and thus a century of German engineering that continues to significantly influence the world of drive technology today.
Since the invention of the Cyclo® principle by Lorenz Braren in 1925, this technology has stood for precision, reliability and efficiency – qualities that have not only revolutionised industrial automation but also had a lasting impact on robotics.
There are groundbreaking technologies like the automobile, the steam engine, the printing press, or even the telephone and the internet, which everyone knows and which have had a lasting impact on society. The Cyclo® principle, also known as cycloidal gears, is less visible but has revolutionised the industrial world in the background and is now an indispensable part of modern drive solutions.
The cycloidal gear, the centerpiece of Sumitomo Drive Technologies’ product portfolio, has changed drive technology with its unique design. Unlike conventional gears, the Cyclo® principle distributes the load evenly over several pins and discs. This construction minimises wear, increases load capacity and significantly reduces maintenance effort. Invertekdrives.com

Focus On: Sustainability
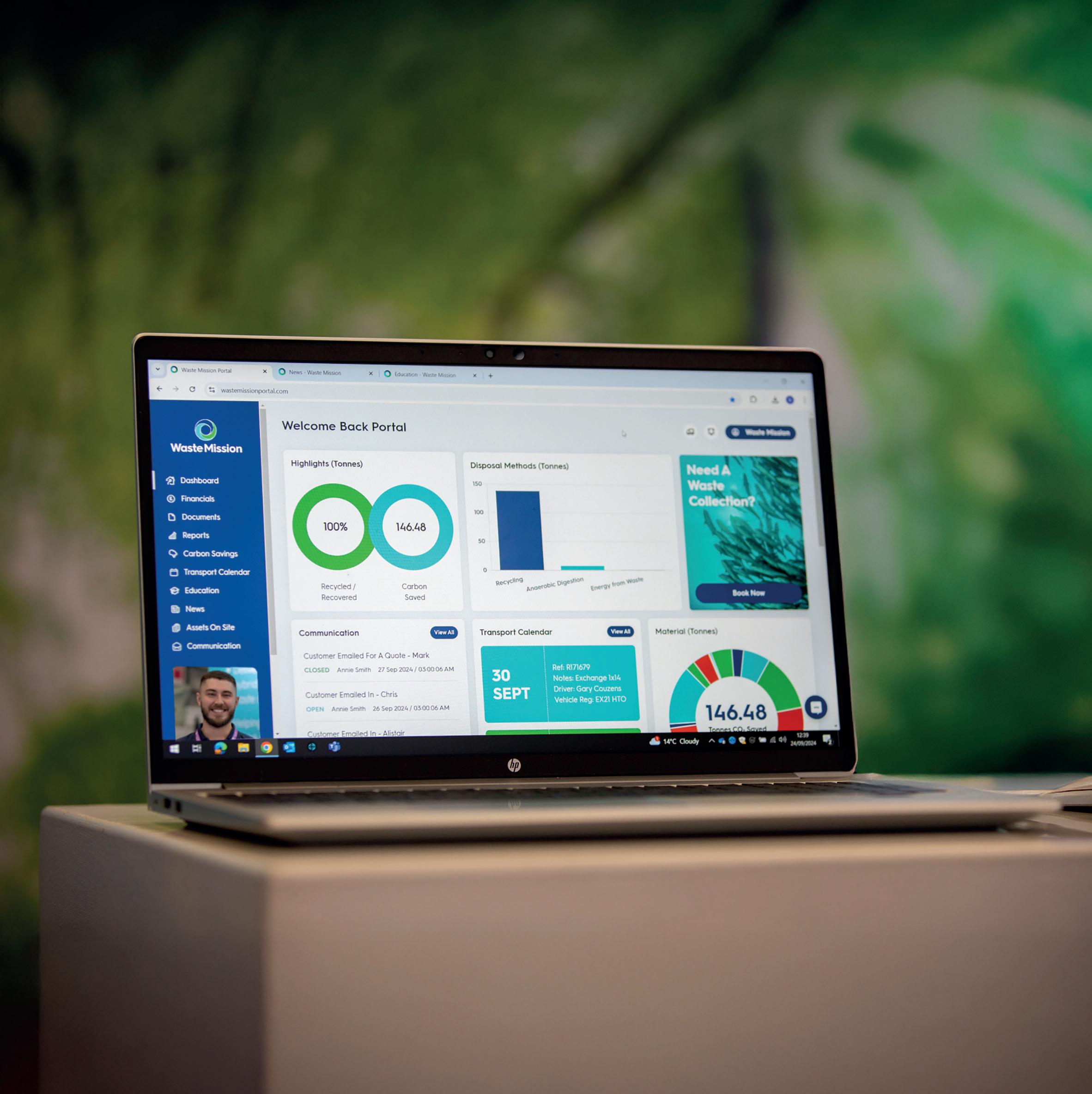
Sponsored by
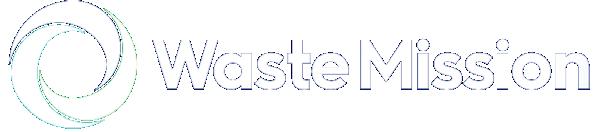
P16-17. Waste Mission shares how businesses can benefit from more sustainable waste management.
From Waste to Resource: a Case Study
Overhauling outdated waste management practices are an important step in achieving corporate sustainability goals, but with rising landfill costs there are many other benefits, as the following case study from Waste Mission demonstrates.
The UK’s agricultural sector is under increasing pressure to improve waste management practices. Rising landfill taxes, with the standard rate having increased to £126.15 per tonne since 1 April 2025, stricter environmental policies, and corporate sustainability goals are compelling businesses to rethink outdated waste practices. However, progress isn’t always easy. Many agricultural and manufacturing companies still face significant challenges, including excessive general waste, inefficient site traffic due to multiple waste containers, and a heavy reliance on landfill. These inefficiencies not only drive up costs but also hinder sustainability efforts.
Introduction to Trouw Nutrition
Trouw Nutrition is a global leader in animal nutrition, providing high-quality feed products, services, and solutions for livestock, aquaculture and pets. With a strong focus on innovation, Trouw Nutrition works closely with farmers and partners to drive progress in sustainable food production worldwide.
Operating in over 90 countries, the company is committed to creating innovative solutions across the feed-to-food value chain. Its product portfolio includes premixes, feed additives, health products, consulting services, and digital solutions that enhance animal health, productivity, and sustainability.
Sustainability is highly prized to their operation, yet the team found themselves grappling with the common issues in regards to their waste management. With multiple roll-on roll-off containers creating site congestion and a waste system misaligned with their sustainability targets, and there

was an opportunity to create a smarter, more efficient approach.
Trouw Nutrition’s experience reflects a wider challenge across the sector: how can businesses transition to more sustainable waste management without disrupting operations or increasing costs?
Why sustainable waste management was important
As part of Trouw’s quest to be a leading example of sustainable practices, they sought a waste partner who prioritised sustainability as much as they did. After a thorough procurement process, Waste Mission was selected to work with them to develop a high standard of sustainable
waste management practices across their sites in the UK.
Trouw Nutrition Regional Operations Manager, Alex Phillips, says, “Sustainability is central to our mission. Our goal is to improve the health, productivity, and sustainability of animals in the agricultural food supply chain, helping farmers and producers enhance the quality and efficiency of food production while minimising environmental impact.
“Partnering with Waste Mission was a natural fit as we work toward building a greener, more sustainable future for our industry and the planet.”
The challenge
The team behind Trouw Nutrition had a strong desire to align its waste management
practices with its sustainability goals, the company were keen to divert their waste streams from landfills, and increase opportunities for recycling and financial returns.
Trouw Nutrition had an ambitious zeroto-landfill target, and they needed to evolve their processes fast to reduce their carbon footprint. Priorities included managing hazardous powder waste, inefficiencies in waste segregation, and avoiding potential waste contamination.
The challenges faced by Trouw Nutrition were fourfold:
Hazardous powder waste management
The company generated significant volumes of powder waste, known as “Filter Waste,” during its production processes. Nonhazardous powder was sent to landfills, while hazardous powder waste remained on-site due to handling limitations from a previous provider. This created logistical challenges and required a more sustainable, compliant solution.
Improving waste segregation and contamination control
Waste segregation processes needed refinement to prevent contamination and optimise recycling. Limited signage and inconsistent sorting practices resulted in recyclable materials mixed with general waste, meaning there was an opportunity to increase efficiency.
Optimising financial efficiency
Ineffective segregation and contamination reduced opportunities to secure financial returns from recyclable materials, such as cardboard and plastics.
Logistical streamlining
Inefficient and untimely hazardous waste movement schedules further emphasised the need for a provider capable of delivering innovative, landfill-free solutions.
The solution: a partnership with Waste Mission
Within six months of partnering with Waste Mission, Trouw Nutrition achieved 100% waste diversion from landfills. This milestone reflects the effectiveness of a strategic, collaborative approach to waste management.

“Partnering with Waste Mission was a natural fit as we work toward building a greener, more sustainable future for our industry and the planet,”
Alex Phillips, Trouw Nutrition Regional Operations Manager.
Key initiatives implemented by Waste Mission included segregation improvements; through clearer signage, colour-coded containers, and dedicated waste operatives ensured that recyclable materials were properly sorted, stored and processed. For contamination control, the team implemented enhanced sorting practices significantly reduced the mixing of waste streams, enabling more materials to be recycled efficiently.
To address hazardous waste recycling, Waste Mission developed a sustainable, landfill-free solution for hazardous and non-hazardous powder waste, aligning with Trouw Nutrition’s long-term environmental goals. Improving waste handling and reducing contamination drastically decreased the frequency of general waste collections, leading to cost savings and, ultimately, greater operational efficiency.
Results and impact
The partnership has transformed Trouw Nutrition’s waste management approach, delivering substantial environmental and financial benefits. Among these, the company has achieved 100% landfill diversion, as all waste streams are now recycled or repurposed, eliminating the need for landfill disposal. In addition, clearer guidelines and improved segregation has led to a reduction in contamination, making
recycling processes more effective and sustainable.
The optimisation of waste collection schedules has reduced general waste movement from three times a week to once every fortnight, achieving substantial financial savings. What’s more, Trouw Nutrition has established a reliable, environmentally friendly system for managing hazardous powder waste, demonstrating its commitment to sustainability.
Nicola Guest, Group Marketing & Procurement Manager for Waste Mission, states, “Trouw Nutrition’s commitment to sustainability is evident in the progress we’ve achieved together. Their leadership in adopting innovative waste management practices has set a benchmark for others in the industry.”
Looking ahead
Trouw Nutrition’s sustainable waste management journey reflects the value of strategic partnerships in driving sustainability and operational excellence. By aligning its waste management practices with its broader environmental goals, the company continues to lead by example in building a more sustainable future.
To book a Waste Mission review, visit the company’s website.
wastemission.com
Top 5 Tips for Sustainability
Nicola Guest, Marketing and Procurement Manager, Waste Mission, shares five ways manufacturers can reap the benefits of embracing sustainable practices.
Nicola says: “Sustainability isn’t just a corporate buzzword — it’s a business priority. For manufacturers, it’s about cutting waste, improving efficiency and staying ahead of regulation. We work closely with manufacturers across the UK to turn waste challenges into opportunities and new revenue streams.”
Here are five practical ways your business can stay on track.
1. Circular economy adoption
The old linear economy model of ‘takemake-use-discard’ is being phased out. In its place is a circular economy approach where materials are reduced, reused, or recycled. Manufacturers that adopt this model reduce reliance on raw materials, cut costs and improve resource efficiency.
The Simpler Recycling legislation, applying to organisations with 10 or more employees, reinforces this shift. Since April 2025, businesses must separate recyclable materials at source, helping to keep valuable resources in use for longer.
Tip: audit your processes to identify materials that can be recovered, reused, or returned to your supply chain. What you’re throwing away today could become tomorrow’s resource.
2. Supply chain management
Sustainability doesn’t stop at your factory gate. Manufacturers are under growing pressure to manage the environmental impact of their entire supply chain, from raw material sourcing to end-of-life disposal.
This can be improved by working closely with suppliers that share your environmental goals and choosing production partners who prioritise low-impact materials, operate
transparent waste practices, and can demonstrate their own commitment to sustainable production.
Tip: ask suppliers for data on their waste outputs and recycling processes, and share yours in return. Collaboration across the supply chain leads to smarter, greener decisions.
3. Carbon reduction and net zero commitments

Net zero is no longer optional. Manufacturers are expected to measure, reduce and report emissions, especially Scope 3, which includes waste management and downstream distribution. Using cleaner production methods, upgrading to energyefficient machinery, and sourcing low-carbon materials are all part of the journey.
Your waste strategy also plays a key role. Recycling reduces emissions compared to disposal, and choosing local waste partners helps cut transport miles.
Tip: review how waste is collected and processed. A streamlined, low-carbon collection strategy is often a quick win on the road to net zero. For great examples of this, read the Trouw Nutrition case study in this section of the magazine.
4. Waste management hierarchy
Not all waste is equal. The waste management hierarchy sets out a clear order of preference: prevention, reuse, recycling, recovery, and disposal as a last resort.
Increasingly, manufacturers are expected to show they’ve considered this hierarchy in how they handle waste. That means rethinking product design, packaging, and production methods to avoid waste from the outset, and proving it to regulators and customers.
Tip: start with prevention, it’s the most
cost-effective and sustainable option. Even small tweaks in design or process can significantly reduce waste volumes over time.
5. Reliable data and reporting
Data is the foundation of any successful sustainability strategy. With mandatory digital waste tracking likely to take effect in April 2026, it’s vital to understand exactly where your waste goes, how it’s handled, and what its carbon footprint is.
Waste Mission’s customer portal provides detailed insights into your waste streams, recycling rates and emissions data, helping you to stay compliant, transparent and informed. It’s all part of our commitment to smarter, simpler waste management.
Tip: don’t wait for the legislation to land. Start tracking now so you’re prepared, instead of scrambling when the rules change.
Final word
Sustainability in manufacturing isn’t just about doing the right thing, it’s about future-proofing your business. By taking small, practical steps today, you’ll be better placed to meet customer expectations, stay compliant, and reduce costs in the long run. wastemission.com
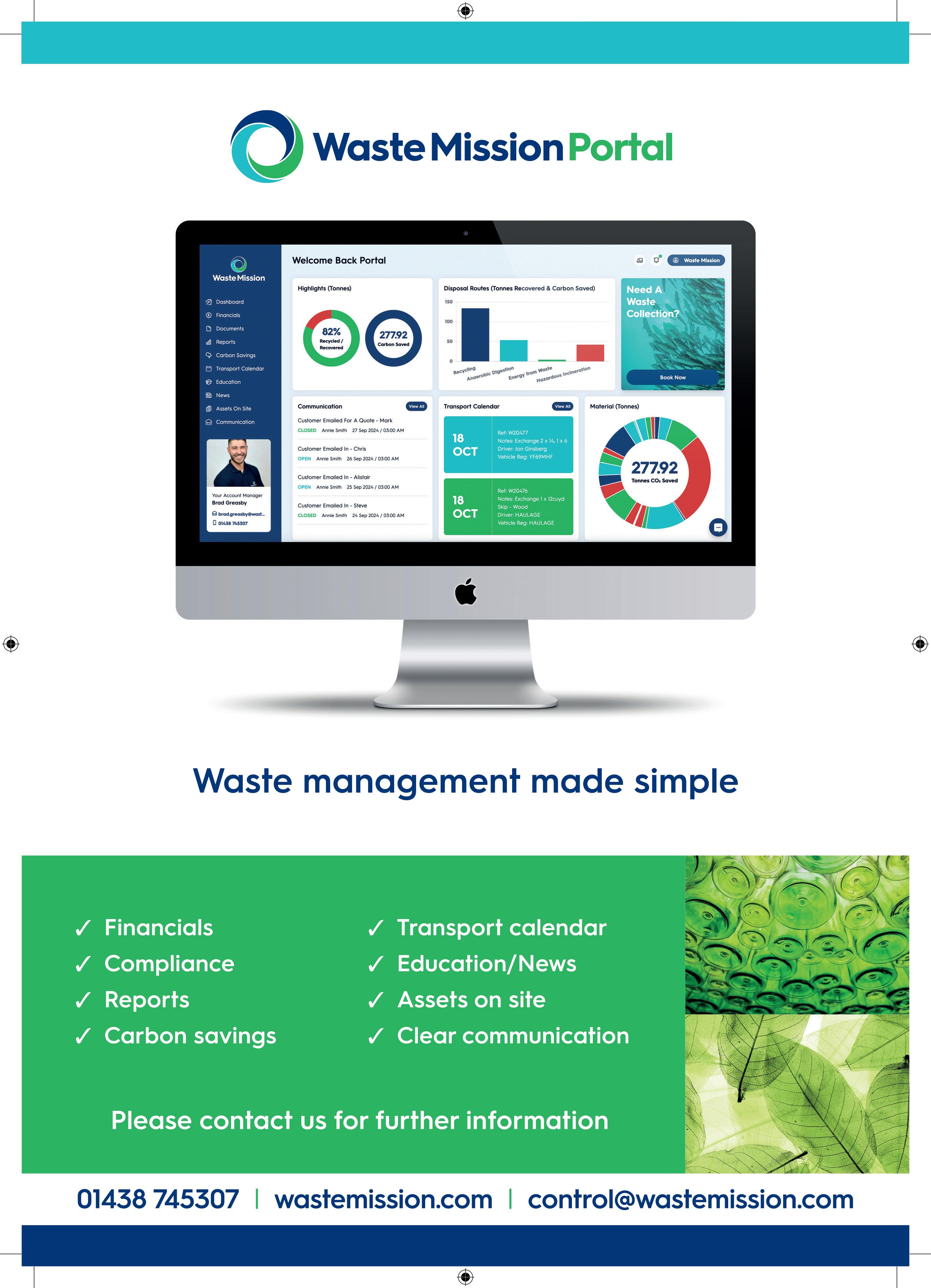
Greenwashing: a Consumer Red Flag
Increasingly eco-conscious consumers are seeking brands that are committed to helping the environment. This has led to a rise in businesses making unsubstantiated claims about corporate sustainability, resulting in greater scrutiny. MEPCA looks at how honest, eco-minded manufacturers can navigate the pitfalls of greenwashing.
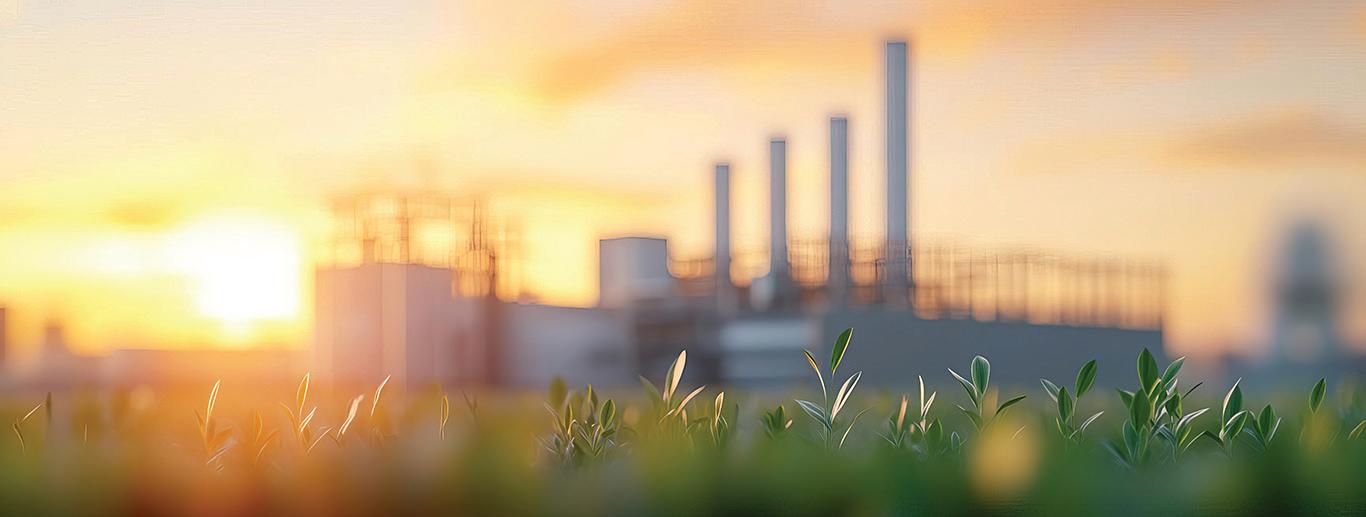
With the current focus industry is placing on corporate sustainability, it is fully understandable that companies implementing Environmental, Social, and Governance (ESG) policies would want to shout about it. It is the job of PR companies and marketing teams to leverage any positive messages about a company that appeal to consumers. The problem is when this goes too far, when hyperbole and spin far overshoot the actual impact the company is making. This is how otherwise well-meaning companies can fall afoul of “greenwashing.”
Greenwashing
While similar to “whitewashing”, which is the biased representation of information about a business or organisation that purposely avoids or glosses over certain unflattering facts to present it in a better light, greenwashing is essentially the same
practice but when promoting environmental friendliness.
Simply put, greenwashing is the act of providing deceptive information on the environmentally friendliness of an organisation. This includes making vague claims about how environmentally friendly a company’s products or services are.
In some extreme instances, environmental claims are simply a cynical marketing spin with no reality behind them whatsoever. In 2015, automotive manufacturer Volkswagen was involved in the biggest greenwashing scandal of all time when it was discovered that it was using software to manipulate emissions tests. The ‘defeat device’ software was able to detect when emissions tests were being undertaken and change the cars performance to improve results. Naturally, the cars were backed by a major campaign focused on the cars low emissions.
However, a business doesn’t have to set out to deceive their customers or lie about its achievements to be in danger of
greenwashing. Indeed there are many ways an otherwise reputable company could find itself under the green spot-light if it is not careful. Often, greenwashing happens on the fringes of branding communication with careless wording. It can also happen with the best intentions when a business undertakes ambitious long-term ESG targets, such as becoming carbon neutral by a set date, which it then struggles to meet, despite it already becoming part of its branding.
Why it matters
Putting aside the obvious moral implications of greenwashing, until recently, negative publicity was the main thing at stake. For many, the threat of reputational damage would serve as enough of a deterrent, which could be disastrous in a competitive market – but negative publicity alone has proved to be insufficient. When you consider some of the most high profile cases of green washing have included world-leading automotive
manufacturers and global oil and gas companies, a little bad press appears to be taken in stride
This has now changed dramatically. In the UK, as of April this year, Competition and Markets Authority (CMA), has been granted the power to directly fine companies for breaches of consumer protection. Under this regulation, those found guilty of greenwashing could face a substantial fine: up to 10% of their global turnover.1
How to avoid the pit falls of greenwashing
Firstly, and most importantly, manufacturers should avoid making any environmental claims that they cannot substantiate.
To ensure this, manufacturers should work with reputable environmental organisations that know exactly what to look for. In addition, manufacturers may wish to seek third-party certification, such as B Corp. This accreditation is assessed by B Lab, a not-for profit group, dedicated to making businesses a force for good. Not only is this a way for manufacturers to ensure they are avoiding greenwashing, once certified, manufacturers can display this in their advertising and branding, showing consumers, investors and employees that their corporate sustainability claims are accurate.
Careful consideration should also be given to how a business communicates its environmental claims, particularly in terms of the language it uses for PR and marketing purposes. As well avoiding hyperbole, companies should avoid vague, green sounding language, such as labelling a product “natural”, “green” or adding “eco” as a prefix, or suggesting that something is “better” for the environment or more ‘”natural” when there is no explanation of what it is better than.
This extends to non-verbal communication too. Businesses should avoid packaging featuring imagery that would suggest a product is sustainable, when in reality it isn’t. For example, it would be considered greenwashing for eggs produced by battery hens to be packaged in a box that depicts free-roaming hens in an idyllic setting – this imagery does not reflect the product within. While the threat of greenwashing is real and the effort of substantiating green credentials may seem intimidating, it should not stop companies from embarking on these important sustainability initiatives. As well as there being a wealth of support
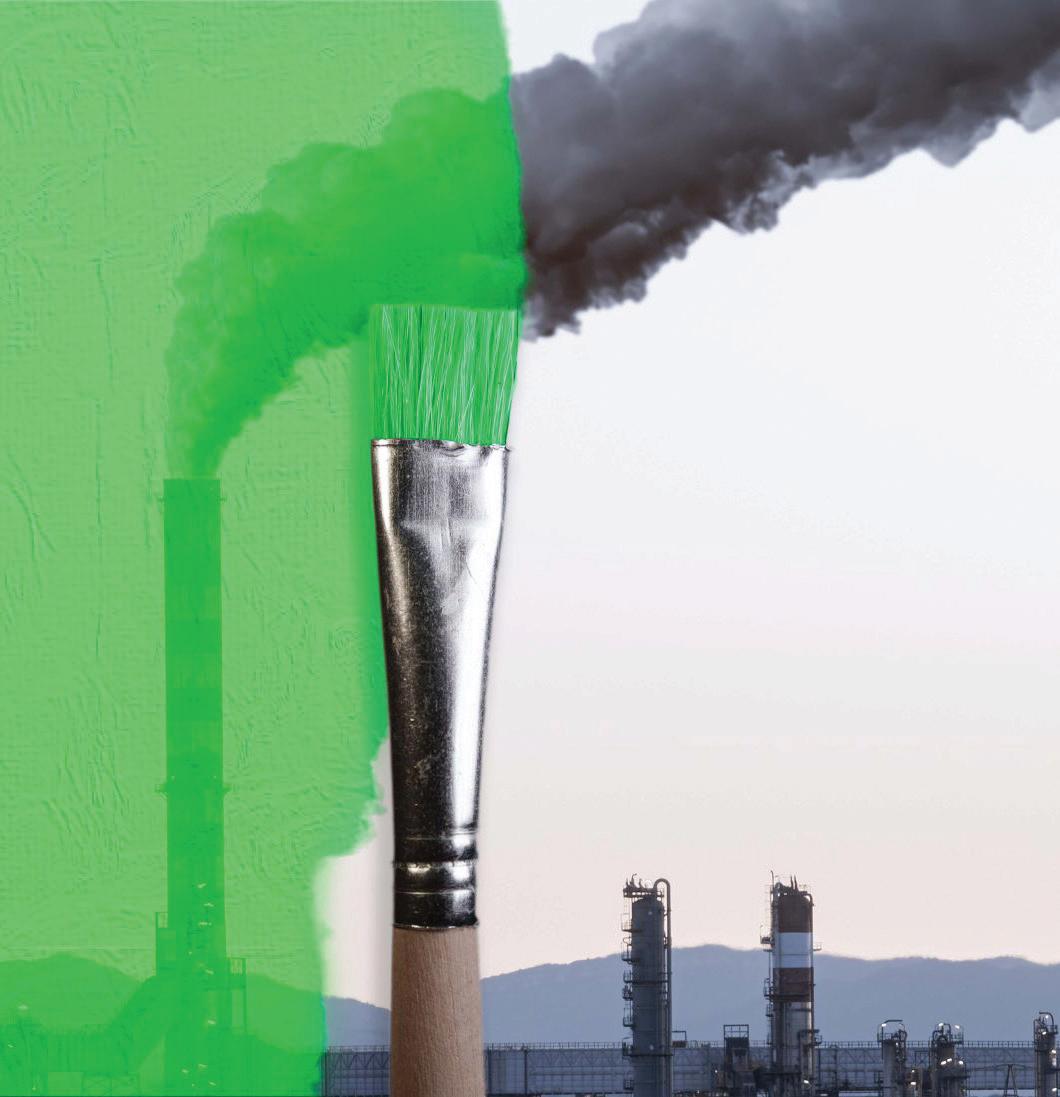
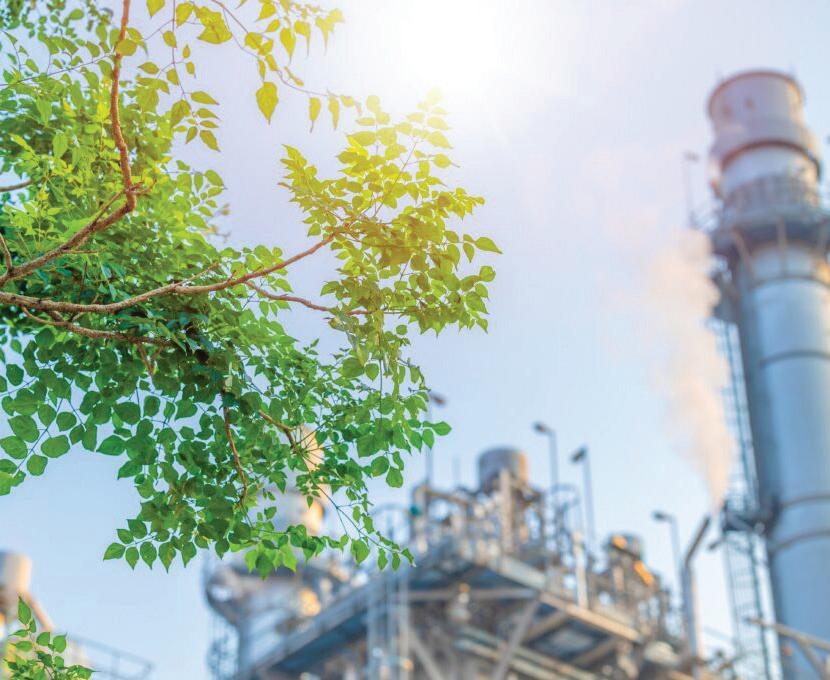
available, it is worth remembering that the reputational, and therefore commercial, benefits of corporate sustainability are also very real, and that’s without considering the cost savings of reducing energy
consumption or waste disposal as a result of the green actions themselves. bcorporation.net/en-us/ 1 www.businessgreen.com/news/4411916/reenwashing-cmagranted-power-fine-companies-cent-global-turnover
Aligning Efficiency with Sustainability
Most companies want to decarbonise and operate more sustainably, but need to make the business case for investment. Voltage Optimisation can help manufacturers improve efficiency and lower energy spend. James Hampshire, Business Development Engineer at Powerstar, explains how.
In their latest Manufacturing Outlook for Quarter 1 2025, Make UK and BDO consider where manufacturers should focus for financial resilience. For their first recommendation, “Regularly reviewing and controlling costs is essential. This includes everything from raw materials to overheads. Identifying areas where costs can be reduced without compromising quality is key.”1
Voltage Optimisation (VO) can play an important role – lowering energy bills without impacting product quality – especially for companies looking for a cost-effective first step on their own Net Zero journey.
Reducing wasted energy and equipment damage
VO is a transformer-based technology designed to ensure that the energy supply from the Grid matches on-site equipment demands. There is a disconnect between the standard 220V operating voltage of most electrical equipment in the UK and Grid supply, which is typically around 248V. Overvoltage means on-site equipment wastes energy, creating unnecessary expenditure and avoidable carbon emissions.
The stress caused by overvoltage can mean unnecessary maintenance costs due to significant wear and tear. It can potentially lead to equipment failure, with disruption to production, expensive downtime and the need to replace machines earlier than necessary – impacting cashflow and investment plans. VO stabilises incoming voltage on-site, ensuring consistent and optimum voltage levels. For any company looking to decarbonise and reduce overheads, eliminating energy wastage is an obvious first step.
Modern, dynamic VO for greater efficiencies
Although manufacturers might already include Voltage Optimisation (VO) in their energy management mix, upgrading legacy systems can offer immediate gains. Traditional VO typically uses a fixed autotransformer, stepping down the entire supply voltage and incurring energy losses. By contrast, modern, dynamic VO can offer real-time voltage management, with robust protection mechanisms to ensure reliable performance and longevity for VO applications.
Transparent data
Where companies need to justify investment – demonstrable evidence of the efficiency of the proposed technology – modern, dynamic VO solutions can offer remote monitoring where site consumption is logged, alongside harmonics, power factors and voltage, providing real-time performance data on voltage management and asset performance.
Measurable returns
Powerstar have designed and manufactured patented dynamic VO solutions for manufacturing customers across the UK, and the headline stats for ROI are compelling at between 6% and 9% reduction in annual consumption, with average ROI between 12 and 30 months.
For example, a precision industrial parts manufacturer invested in new specialised machines and processes, which led them to review their energy infrastructure – to maximise ROI and protect highly sensitive new manufacturing equipment. Powerstar’s comprehensive site survey identified a fluctuating incoming voltage, between
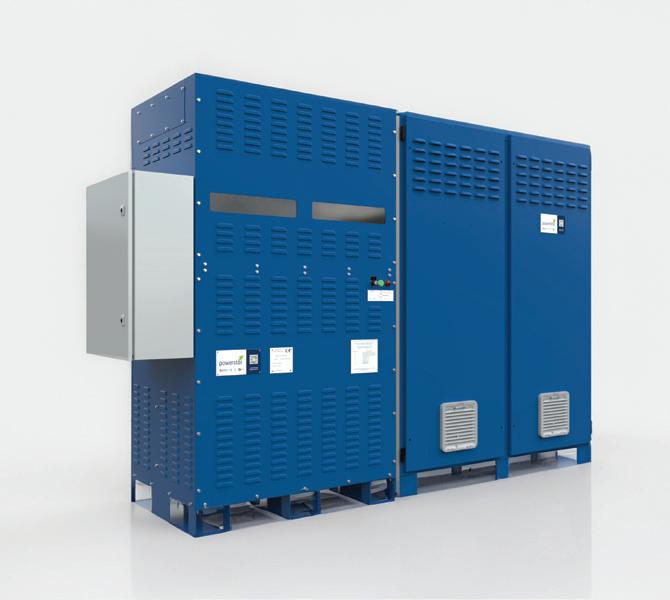
242V and 250V. The installation of VO has led to on-site consumption savings of 7%, eliminating 85.4 tonnes of carbon equivalent from net emissions, annually.
For another client, VO installation has led to 8,000kWh decrease in energy usage despite their production volume increasing by almost 10%, equating to 52.8kWh less per tonne of product. Further manufacturing client case studies demonstrate energy savings of more than 10% when VO is installed.
VO represents a win-win energy investment for any site where overvoltage is an issue. Cost savings and payback time can be identified from the outset, making the case for investment and signalling a company’s commitment to a sustainable future.
To find out more about voltage optimisation and Powerstar’s complementary range of energy management technologies, visit the company’s website.
powerstar.com 1 www.makeuk.org/insights/reports/manufacturing-outlook2025-q1
Voltage Optimisation System

An Inspired Partnership
In the following case study, a rubber compounds specialist, shares how it saved £180k and 32 tons of CO2 by engaging a sustainability consultant.
Clwyd Compounders is a manufacturer of custom rubber compounds based in North Wales. Its business is energy intensive, and as such, an increase in energy costs has a huge impact on production.
After Clwyd’s supplier withdrew from the market, the business looked to mitigate the impact of energy price rises and increase its efficiency measures.
Clwyd engaged Inspired PLC, an established sustainability consultant, to help achieve its goals, and to respond to both government targets and client expectations in regard to net-zero and sustainability.
The solution
Clwyd partnered with Inspired and placed technology, software and services at the centre of its energy and carbon strategy helping the business to address the following four challenges with Inspired’s Energy Manager as a Service (EMaaS) solution:
Cost
The Inspired team moved Clwyd onto a flexible energy supply contract with a new supplier, executing a risk management strategy that would deliver price protection whilst allowing the business to take advantage of falling prices.
In addition, Inspired’s Bill Validation service gave Clwyd’s team the peace of mind they were only paying for the exact energy they consumed.
Compliance
Inspired took over management of Clwyd’s Climate Change Agreement (CCA) scheme to maximise relief whilst ensuring it remained compliant. Inspired also provided performance reporting for benchmarking against targets and minimising the risk of penalties.
Consumption
Inspired deployed circuit-level sensors and water monitoring equipment on site so that Clwyd could better understand its
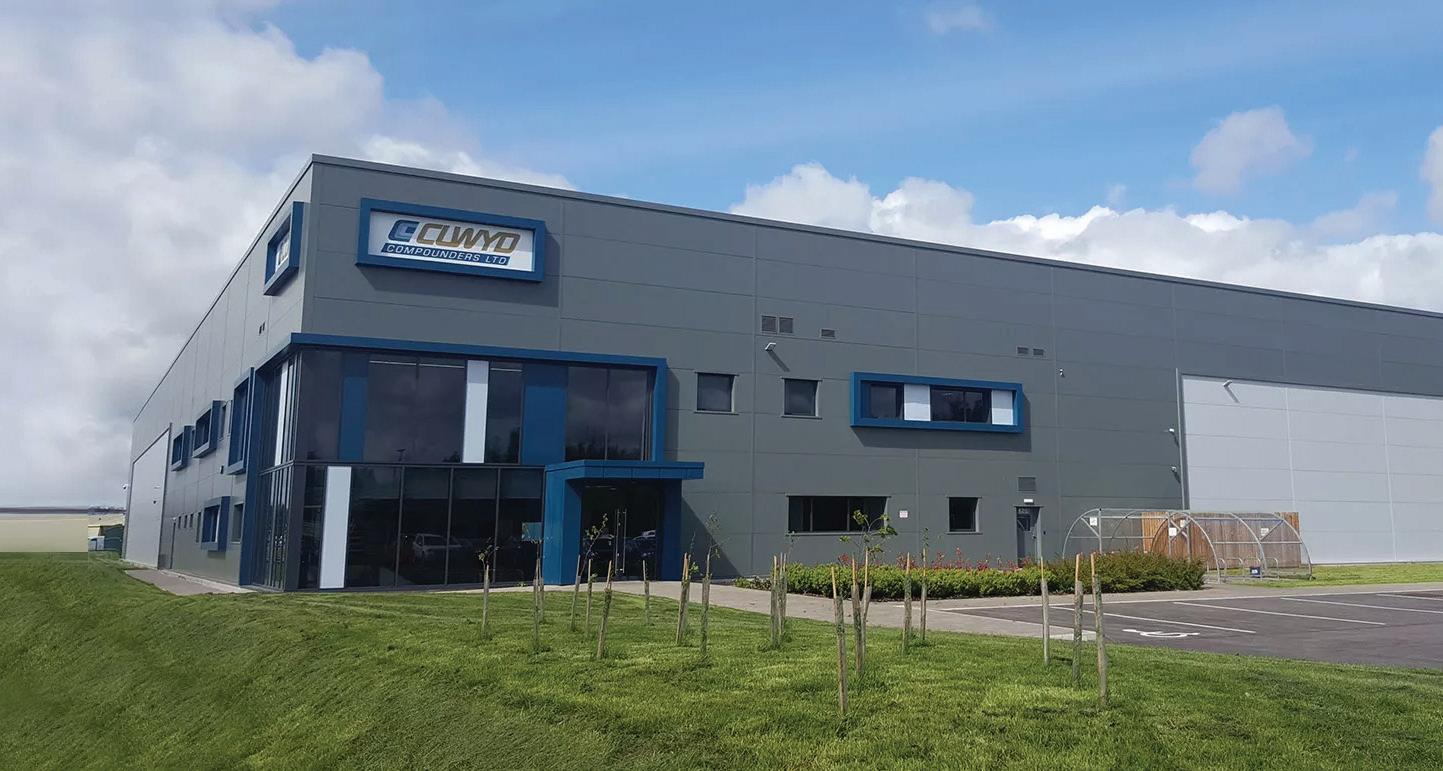
energy and water usage “behind the meter”. Through Inspired’s online portal, Clwyd was given access to real-time data-driven insights, allowing Clwyd’s team to make informed decisions about the company’s consumption.
Carbon
To assess Clwyd’s environmental impact, Inspired measured the manufacturer’s Scope 1, 2 and 3 emissions. This will lead to development of a net-zero strategy and target, which will, in turn, reduce Clwyd’s carbon footprint and ultimately benefit the business commercially.
The results
Following the implementation of circuitlevel sensors, Inspired were able to quickly identify opportunities to reduce consumption and increase efficiency, resulting in a saving of over £48,000 and 22 tons of CO2, meaning the client achieved an ROI and profit within the first quarter of service delivery. The water system findings also mounted to an additional £16,500 and 10 tonnes of CO2 savings
By providing Clwyd with access to risk managed strategies for energy procurement, Inspired managed to secure savings of £62,734 for this year’s energy contract and in-line with current trading, Clwyd can expect to see a further reduction of £53,679 for next year.
Inspired’s on-site feasibility study found that Clwyd’s Wrexham site was suitable for solar PV generation that – following install from the specialist team – generates over 290,000 kWh of renewable energy per year. Clwyd now generate its own renewable energy, reducing its exposure to the volatile wholesale market. The client’s payback on the current installation, which is on a 25-year warranty, is less than 2.5 years.
David O’Hare, Managing Director, Clwyd Compounders: “Prior to engaging with Inspired PLC, our energy management requirements were dealt with by a variety of energy advisors. This was fraught with headaches such as unreliable service, difficulties with contract and pricing management, and service levels, which were below an acceptable standard.
Since moving our energy management to Inspired, there is only one word to describe their service and that is ‘faultless’. We now have a system that is giving us unrivalled service in terms of scaled energy procurement, operating cost reductions and excellent visibility of future costs. Furthermore, the Inspired team are a pleasure to deal with, always listening carefully to customer requirements and ensuring first class customer service is delivered every time.”
This article was provided by Inspired PLC, the UK’s leading sustainability consultant. inspiredplc.co.uk
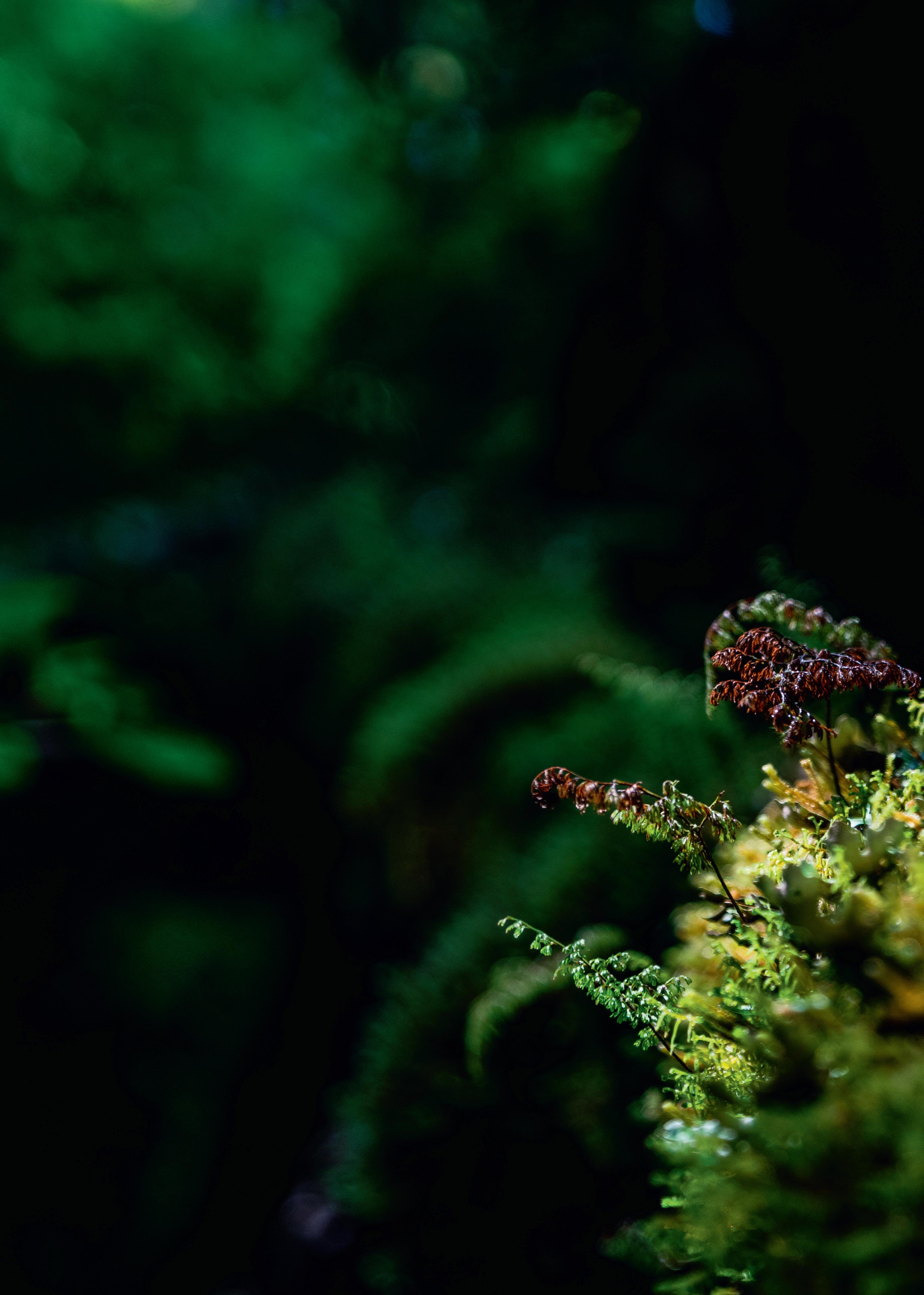
New Careers in Sustainability
The growing awareness of sustainability and environmental responsibility in manufacturing is creating a demand for green talent. Russell Smith, Founder and B Corp Certified Managing Director of Hunter Selection, explains why it matters and how businesses can benefit.
The United Kingdom’s manufacturing, process and production sector is undergoing a significant transformation, driven by the imperative to meet net-zero targets, comply with evolving environmental regulations, and respond to shifting consumer preferences. The UK’s commitment to a green industrial revolution is evident in the rising number of green job opportunities. In 2024, green job adverts increased by 9.2%, reaching 3.3% of all job postings, despite a 22.5% contraction in the overall job market. This surge indicates a robust demand for green skills across various sectors, including manufacturing and process.
To support the growth of green jobs, the UK government has established the Green Jobs Delivery Group, aiming to create up to 480,000 skilled green jobs by 2030. This initiative focuses on upskilling and training the workforce to meet the demands of the green economy across all industries.
This evolution is giving rise to a diverse array of new roles focused on sustainability and environmental responsibility.
Emerging sustainability roles in manufacturing
As manufacturers strive to integrate sustainable practices, several key positions have emerged: Sustainability Manager, Carbon Analyst, Environmental Policy Advisor, Renewable Energy and Efficiency Engineer, and Climate Change Analyst
Beyond the need for roles directly involved with environmental sustainability, there is a growing need to look at employment practises at large across the industry with sustainability in mind.
Sustainable recruitment in manufacturing is about creating long-term hiring practices
that not only meet the current talent needs of the industry but also support environmental, social and economic sustainability. In the manufacturing sector—where labour shortages, skills gaps and environmental concerns are ongoing challenges— sustainable recruitment helps companies build a resilient workforce while supporting broader ESG (Environmental, Social and Governance) goals.
How it works and why it matters
Sustainable recruitment means hiring with a focus on long-term workforce planning, upholding principals of Equity, Diversity and Inclusion, promoting environmental consciousness and community engagement, and it ultimately leads to greater economic stability for both employer and employee.
Why it matters in manufacturing
Firstly, manufacturing has an aging workforce; many experienced workers are retiring, and there is a shortage of younger talent to replace them. Related to this, is the growing skills gap, and technology adoption (e.g., automation, robotics) is changing the skills needed. In such an incredibly competitive market, reputation is crucial, and ESG-conscious hiring improves a company’s image and attracts socially aware employees. Sustainable practices also help reduce turnover and boost job satisfaction, improving employee retention.
Benefits for manufacturers in summary
• Reduced turnover and training costs
• Heightened appeal to discerning applicants
• Improved employer brand and community trust
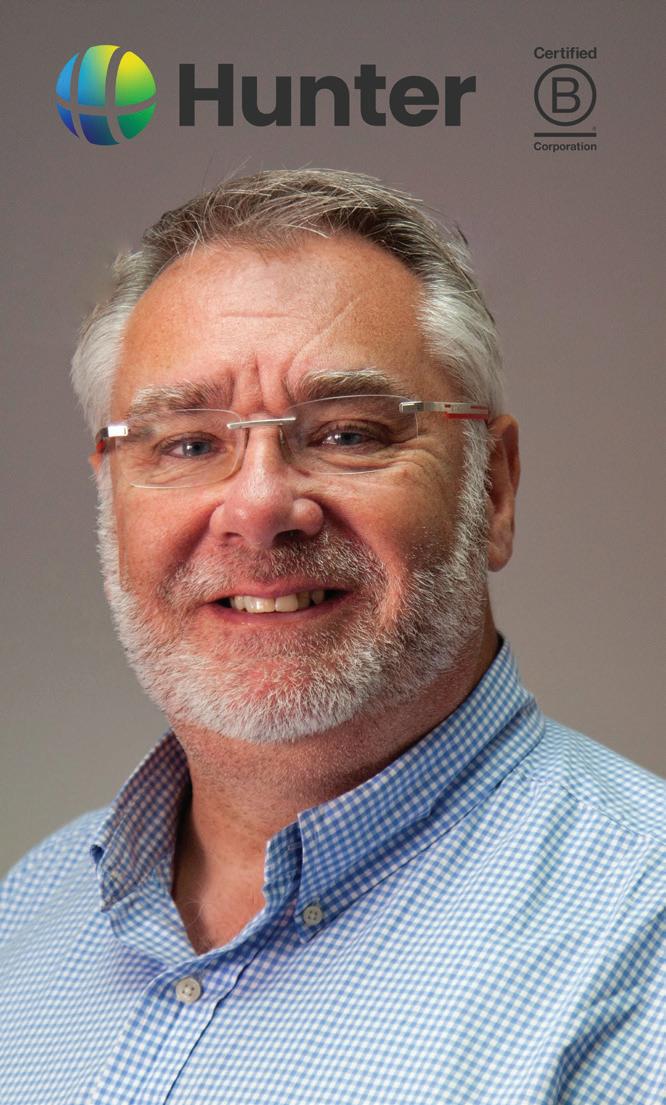
• Greater resilience in workforce planning
• Better alignment with ESG goals and regulatory standards
Partnering with a Recruiter that understands these demands and adds value to a businesses’ Sustainability proposition as a manufacturer and employer can create a genuine and strategic advantage in a competitive marketplace.
Hunter embeds sustainability in its culture, processes and behaviour. Confirmed as a B Corp organisation in 2024, the internationally recognised and audited standard for ethical business, Hunter knows that it offers exceptional recruitment solutions to the manufacturing, process and production sectors whilst achieving adding enormous value to its client’s Sustainable credentials.
To find out more go to Hunter’s website and take a look at its Impact Report. hunterselection.co.uk
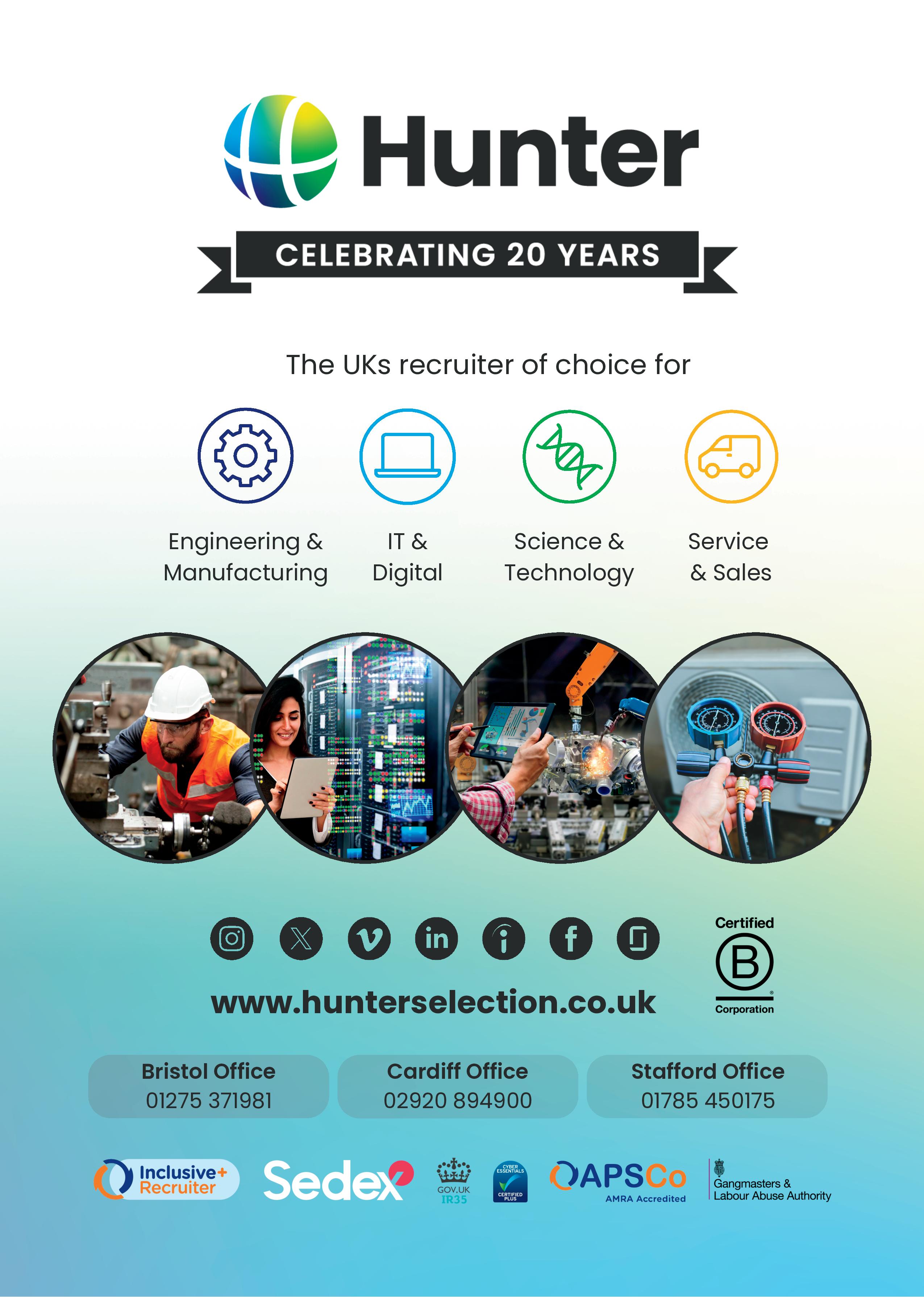
Emerson Improves Dust Collection
Smart technologies are optimising dust collector processes from floor to cloud. Here, Samuele Oliva, Product Marketing Manager at Emerson’s Discrete Automation, explains the energy efficiency and environmental benefits of improving dust collection practices.
Dust collector systems are critical for maintaining safe, efficient operations in facilities processing dry powdered products and bulk solids. These systems protect workers, ensure compliance with environmental regulations, and support consistent productivity. However, as companies face labour shortages and rising production demands, many dust collection systems are pushed beyond their original design capacity.
To address these evolving challenges, Emerson developed a comprehensive Dust Collector Monitoring and Control Solution. This pre-engineered system spans sensors to HMI and SCADA, enabling realtime monitoring and intelligent control for dust collectors of any size.
Digital transformation enhances dust collection
Digital transformation is revolutionising dust collection by offering real-time system visibility, predictive maintenance, and optimised cleaning processes. Many facilities currently lack detailed insight into dust collector performance, leading to premature filter failures, inefficient pulsing and costly emergency maintenance.
Emerson’s solution introduces digital sensors and edge devices that feed data into analytics software. This creates a live dashboard showing key metrics like particle levels, air temperature, and differential pressure between filter chambers.
The digital process follows a “see-decideact” framework:
• See: sensors detect system conditions such as pressure drops or particle build-up.
• Decide: edge gateways aggregate data and send it to software that visualises trends and diagnostics.
• Act: based on insights, the system triggers alerts or automated responses, such as recommending filter or valve replacements.
Smarter cleaning and energy efficiency
A key improvement area is pulse jet cleaning, where valves release compressed air to clean filters. In traditional systems, pulsing is often done on fixed schedules, regardless of actual dust build-up. This wastes energy and shortens valve and filter life.
Emerson’s intelligent system uses sensor data to initiate pulsing only when needed. This not only minimises air waste and energy costs but also extends the life of components—delivering both environmental and financial benefits.
Compressed air leaks are another common issue. Facilities often detect leaks only during scheduled maintenance, allowing waste to go unchecked. Emerson’s sensors continuously monitor airflow, identifying leaks early for prompt repair. This proactive approach saves energy and reduces unplanned maintenance.
Data-driven maintenance and optimisation
With data aggregated from across the system, operators gain insight into equipment performance, allowing for targeted interventions. Instead of manual inspections, maintenance teams receive alerts with clear, actionable information—like identifying faulty valves by row or tracking the condition of filter bags.
Predictive alerts also help streamline spare part ordering and scheduling, reducing downtime. By integrating edge computing and analytics, Emerson’s system supports smarter decisions and reduces manual workloads.
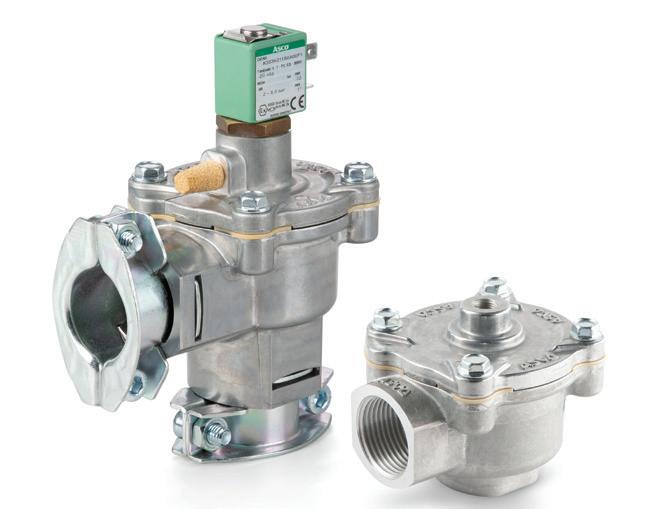
Though some may worry about the cost of digitisation, the return on investment is clear. Automating maintenance, reducing energy waste, and extending component life can significantly improve the bottom line.
Floor to cloud transformation
Emerson’s solution exemplifies a Floor to Cloud approach—starting with sensor upgrades on the plant floor and scaling up to cloud-based analytics across multiple facilities. This provides both local control and enterprise-wide visibility.
Operators benefit from dashboards that visualise conditions in real time, helping them respond to compressed air leaks or clogged filters faster. Over time, data from multiple plants can be analysed to establish best practices, enhance compliance, and support sustainability goals.
By embracing digital transformation, companies can ensure their dust collector systems are prepared to meet today’s operational, environmental and productivity demands. For more information visit the company’s website.
emerson.com
Emerson’s ASCOTM Series 353 Pulse Valves with patented quick-mount clamp connection feature high peak pressure and fast valve response time.
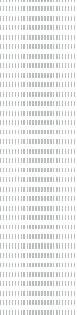
Fit and forget...
No more flaking paint, no more corrosion, no more contamination worries...
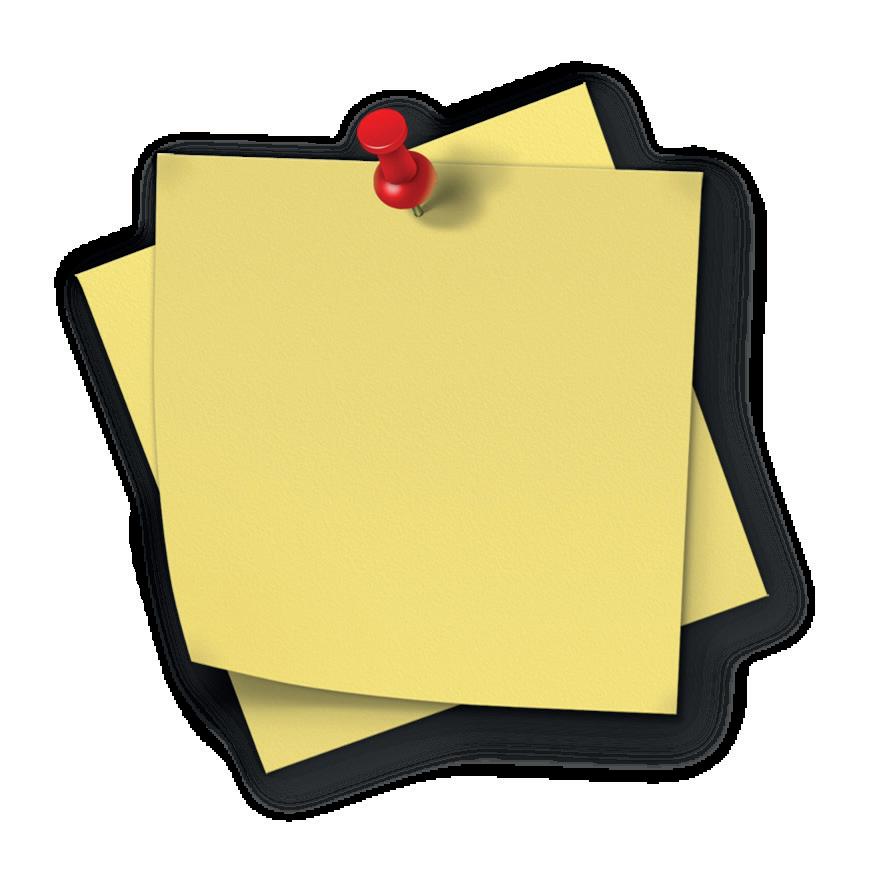
Smooth surface, hygiene friendly, easy to clean washdown design.
Resistant to acids and alkalis
No blistering, flaking or microcracks
Food-safe according to FDA and EU Regulation 1935/2004
Protection to IP69K possible
Motor efficiency levels from IE3 to IE8
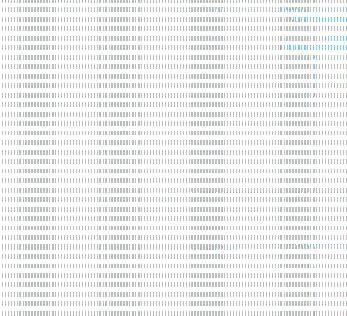
Drive Systems
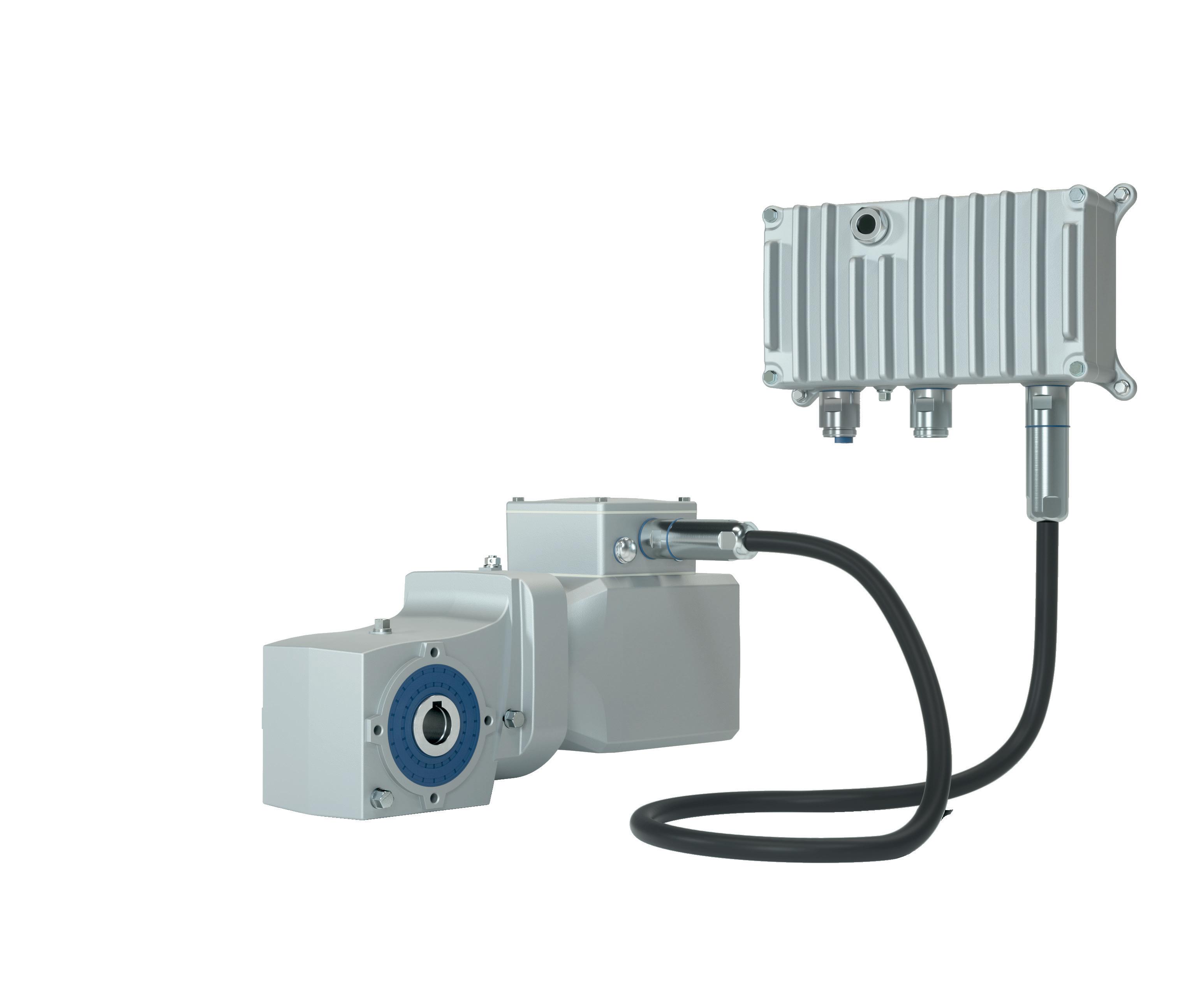
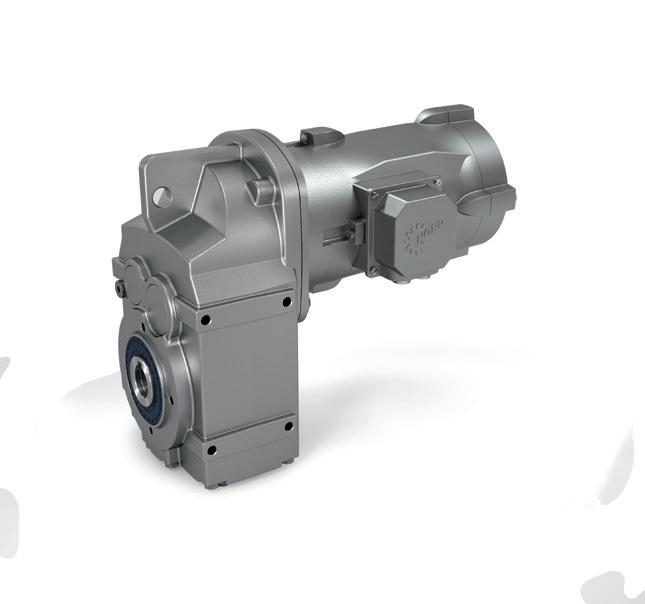
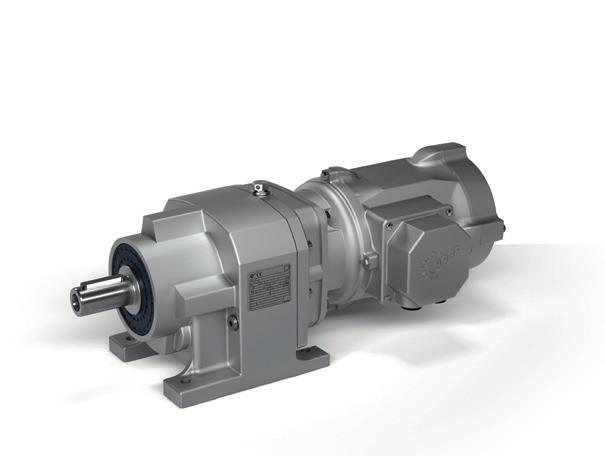

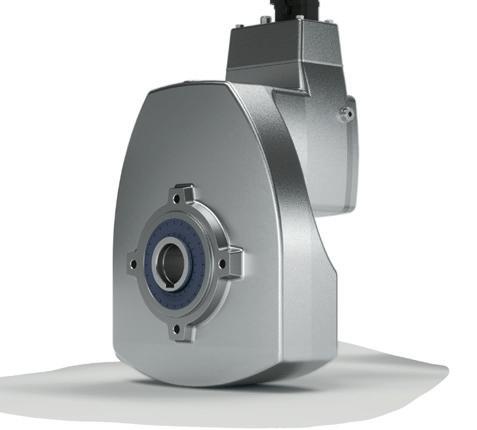
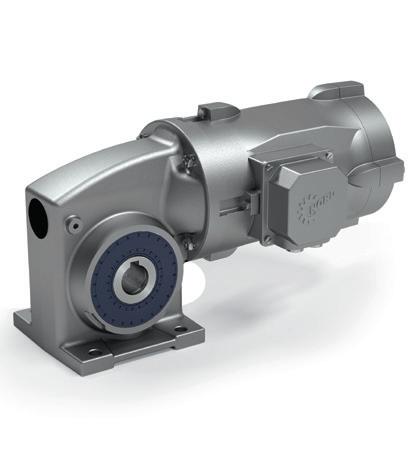
Food Safe - Washdown Drive Systems
Gearbox Motor Inverter
Driving Efficiency in Pneumatics
Compressed air waste is often overlooked when assessing energy efficiency, particularly in terms of sustainability, but as Camozzi Automation UK explains here, the cost and impact is considerable. Newly ISO 14001 accredited, the company shares the secret of more sustainable pneumatics.
Sustainability is no longer a ‘nice-to-have’—it’s a necessity. Businesses across the UK are facing increasing pressure to reduce their environmental impact whilst also seeking to reduce running costs. One of the most important yet often-overlooked areas for energy savings in manufacturing is compressed air systems (pneumatics), where inefficiencies can lead to significant waste.
Camozzi Automation UK is committed to helping businesses optimise their compressed air systems, reducing energy consumption while improving performance.
This year, the company has strengthened its sustainability efforts by achieving ISO 14001 environmental accreditation, reinforcing its focus on responsible resource management. But sustainability is more than just a certification—it’s a mindset that drives everything Camozzi Automation does.
The hidden cost of compressed air waste
Compressed air systems are integral to almost every manufacturing process, yet they are often one of the biggest energy drains on a facility. Shockingly, up to 35% of compressed air is wasted due to leaks, adding unnecessary costs and increasing a company’s carbon footprint. The old approach of prioritising performance over efficiency is no longer viable; the future of industrial automation lies in balancing power with sustainability.
This is where Camozzi Automation comes in. It supports manufacturers in numerous, including by providing technical guidance on optimising pneumatic efficiency and reducing air leaks; delivering smart solutions, such as energy-efficient components and intelligent monitoring systems; and assessing air usage
to identify improvements, whether through small adjustments or complete system overhauls.
Sustainability at the core of Camozzi
The company’s commitment to sustainability extends beyond its products; the Camozzi Group has made seismic changes across its global operations, embracing an ambitious green strategy. This includes investing in renewable energy sources, such as photovoltaic systems, and driving energy efficiency across all its operations. In addition, the company has embraced the circular economy – over 79% of total waste is recycled, ensuring a more sustainable production process.
Solutions for a greener future
Camozzi Automation UK offer a range of solutions designed to help manufacturers achieve greater efficiency and lower environmental impact. Some of its key products include:
• GRIPfit Pneumatic Connections – a new generation of quick-fit connectors, featuring bio-sourced materials and highperformance sealing to reduce leaks and improve durability.
• Air Filtration & Treatment – preventing energy waste by improving compressed air quality and system performance.
• Pressure Boosters & Flow Sensors –intelligent monitoring and control solutions that optimise air usage and cut operating costs.
Enhancing pneumatic expertise with Camozzi Training
Camozzi Automation UK believes that
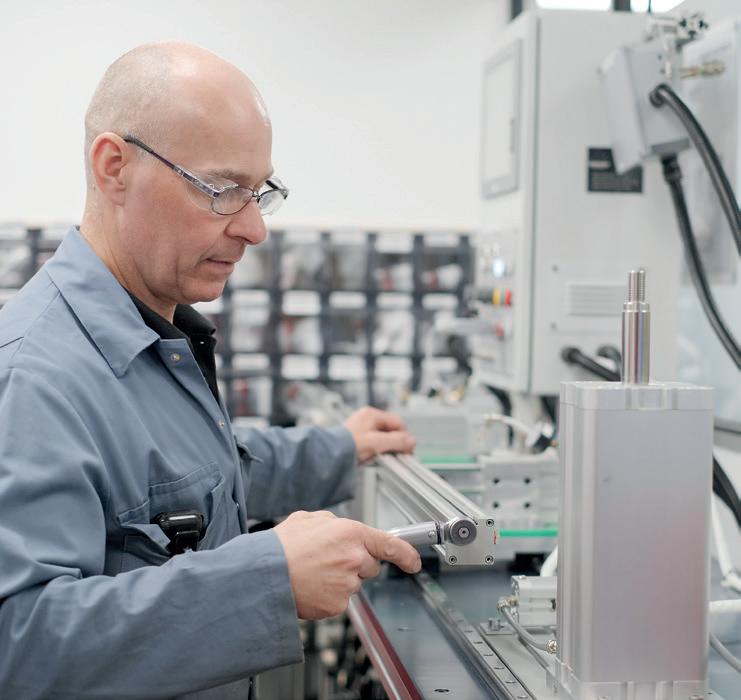
sustainability goes hand in hand with education and expertise. That’s why it offers specialist Pneumatic Training Courses, designed to help engineers, technicians, and industry professionals stay ahead in an evolving landscape.
Looking to master the art of pneumatics?
Camozzi’s 2025 Pneumatic Training Courses provide in-depth knowledge and practical skills to support professionals at every level.
Looking ahead: the future of sustainable pneumatics
The shift towards sustainable manufacturing is accelerating, and pneumatic efficiency is becoming a key area of focus. Camozzi Automation UK is at the forefront of this transformation, helping businesses bridge the gap between performance and sustainability.
The future is clear: energy efficiency and sustainability must go hand in hand. Camozzi Automation UK is proud to be driving this change—one pneumatic system at a time.
camozzi.co.uk
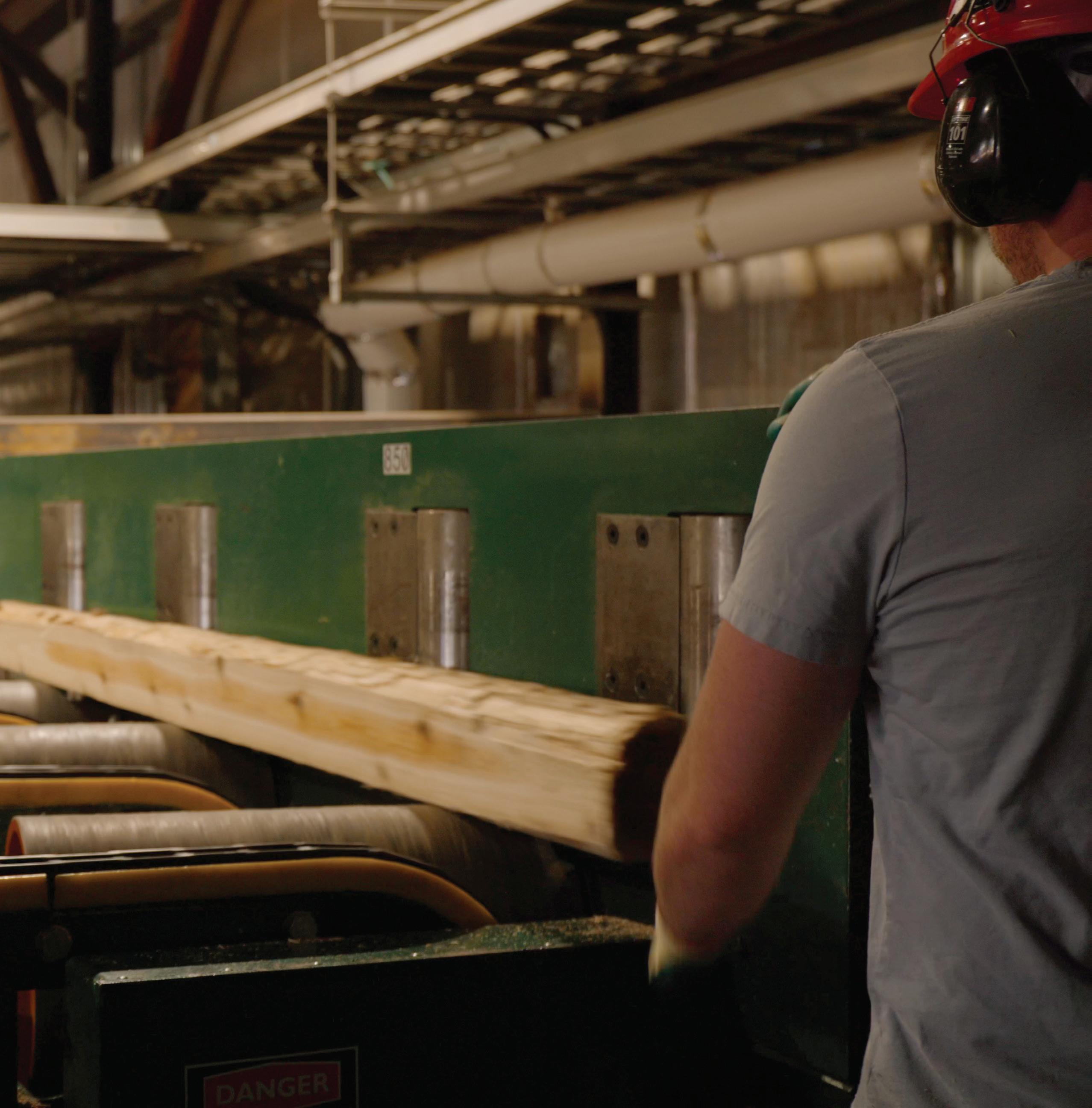
Engineered For Today. Responsible For Tomorrow.
Environmental sustainability drives every aspect of our smart 3D technologies—from 100% recyclable, biodegradable packaging to digital guides that cut paper use. Our ISO-certified processes and efficiencyfocused products reduce waste, rework, and environmental impact—reflecting our commitment to continuous improvement.
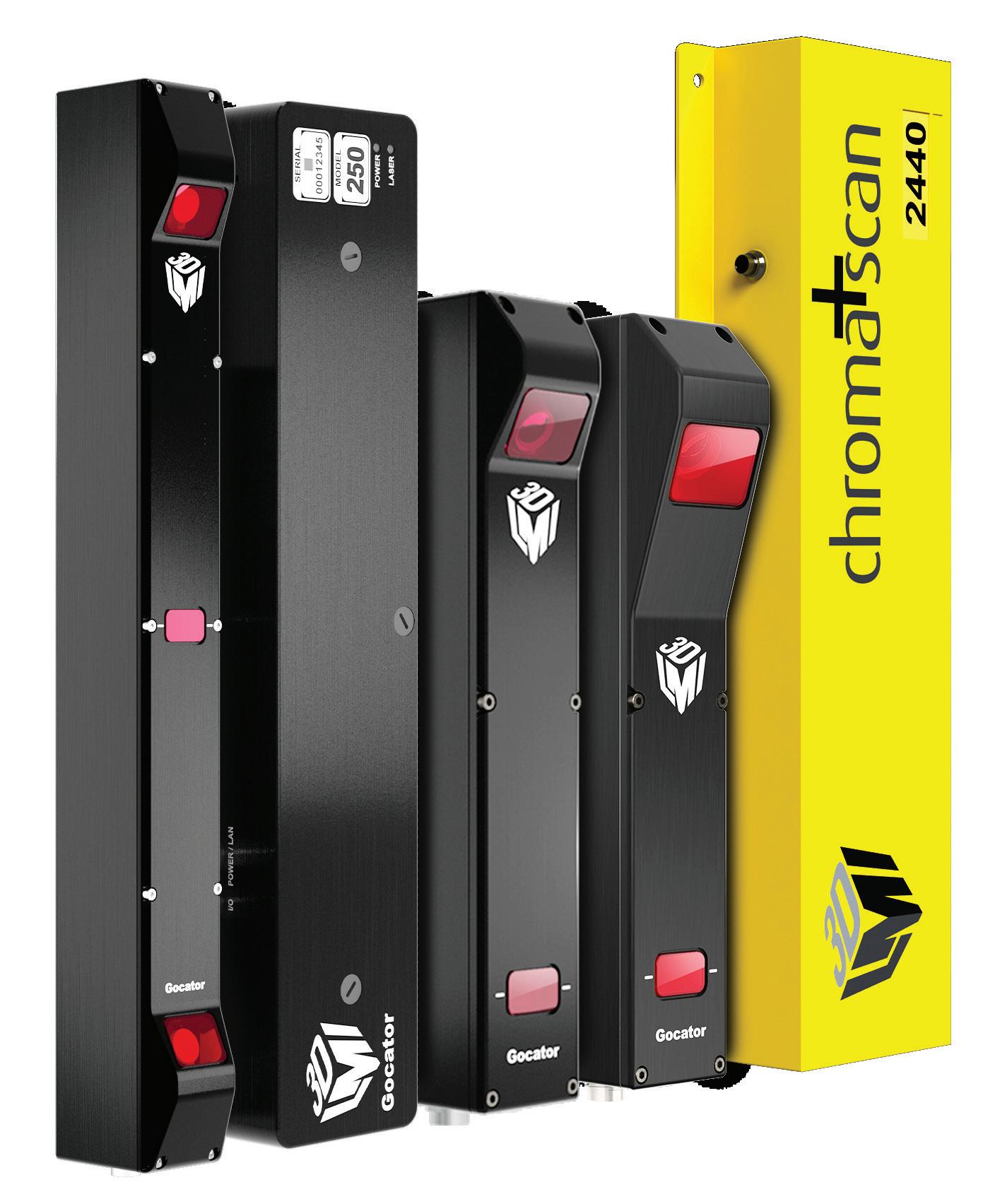
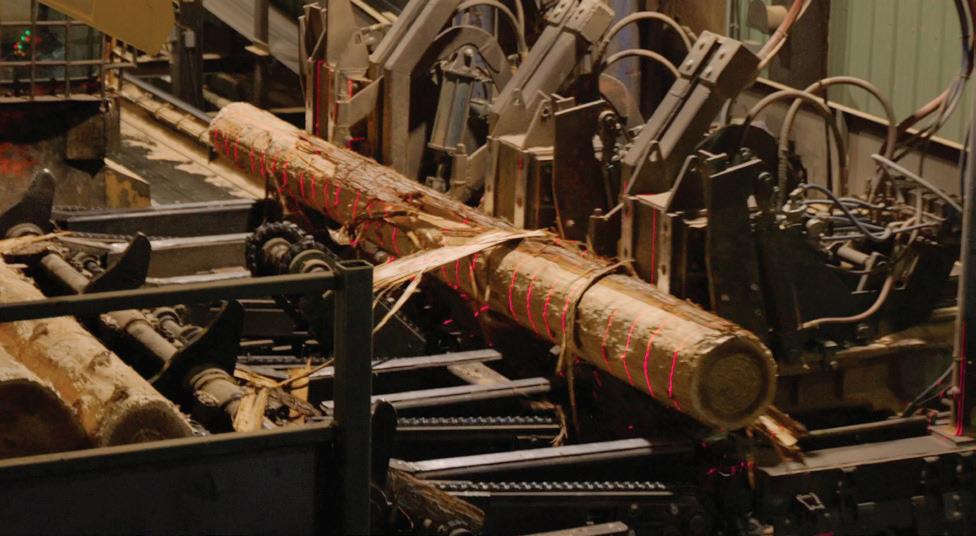
40+ YEARS Driving Sustainability
• Maximizing yield with precise 2D/3D scanning
• Reducing waste through optimized cutting
• Cutting energy use with automated inspection
• Powering data-driven, sustainable processing
Toroidal Transformers
Electronics manufacturers REO UK explains how toroidal transformers improve energy efficiency, lower CO2 emissions, and can save a business 40% on its electricity bill.
Global energy demand is rising rapidly, driven by economic growth, technological development, and evolving consumer behaviour. As countries continue to industrialise and populations expand, energy consumption is projected to increase significantly. According to the U.S. Energy Information Administration’s (EIA) International Energy Outlook 2017, global energy consumption is expected to grow by approximately 28% between 2015 and 2040.
While this growth supports progress and improved quality of life, it also brings serious challenges, chief among them being a corresponding increase in carbon emissions and environmental impact; the same report projected that fossil fuels would still account for 77% of global energy consumption in 2040.
As energy consumption grows, so too does the urgency to find solutions that reduce the associated carbon footprint. In response, governments and organisations worldwide are stepping up to the challenge. In the UK, the government has set an ambitious target of reaching net zero carbon emissions by 2050. Achieving this will require a multi-faceted approach, and one crucial component is improving the energy efficiency of electrical and electronic equipment across all sectors. Notably, through its Footprint Label scheme, the Carbon Trust is vital in helping consumers, businesses and manufacturers make informed choices about the energy and carbon impact of the products they use and purchase. Therefore, energy efficiency has become a focal point in today’s markets. Whether in industrial, commercial, or domestic settings, the importance of choosing efficient electrical equipment has never been greater. A significant part of many electrical systems is the transformer, which steps down mains voltage to a level suitable for the intended application. While many lowpower applications have moved to Switch
Mode Power Supplies (SMPS), particularly for mobile phones and computers, traditional transformers are still widely used in more demanding environments.
Despite their ongoing importance, not all transformers are the same, especially regarding efficiency. Many older systems still rely on conventional laminated core transformers, typically EI transformers. Although functional, these units often lag behind modern designs in terms of energy efficiency. They can contribute to significant energy loss, accumulating over the product’s operational lifetime and increasing running costs and carbon output.
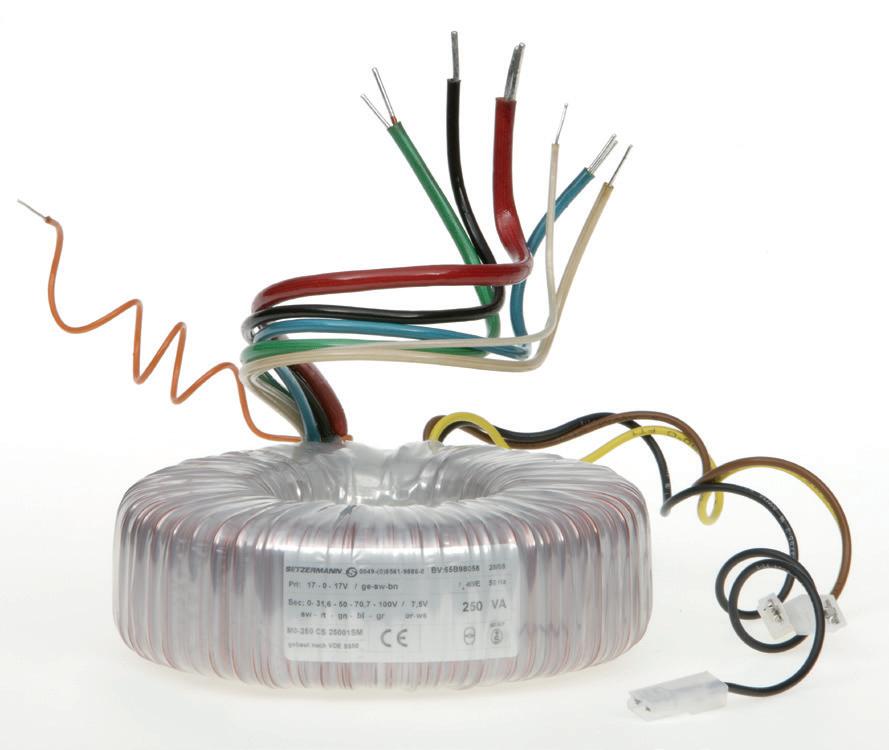
By comparison, modern toroidal transformers substantially improve performance and efficiency. A typical 1000 VA EI transformer can have operational losses of approximately 66 watts when running at full load. Over a year—and more so across several years—this translates into considerable wasted energy. In contrast, a similarly rated toroidal transformer, such as those manufactured by REO, can reduce these losses to around 40 watts – this represents a reduction of almost 40% in energy wastage.
To put this into perspective, over five years, the energy savings equate to approximately 21 kilograms of CO2 not being emitted into the atmosphere. That’s roughly the equivalent environmental benefit of driving 128 fewer kilometres in a petrolpowered car, without even factoring in the financial savings from reduced energy consumption.
In addition to improved efficiency, toroidal transformers offer several practical advantages. Their compact design and central fixing hole make them easy to install within control cabinets or enclosures, saving installation time and reducing labour
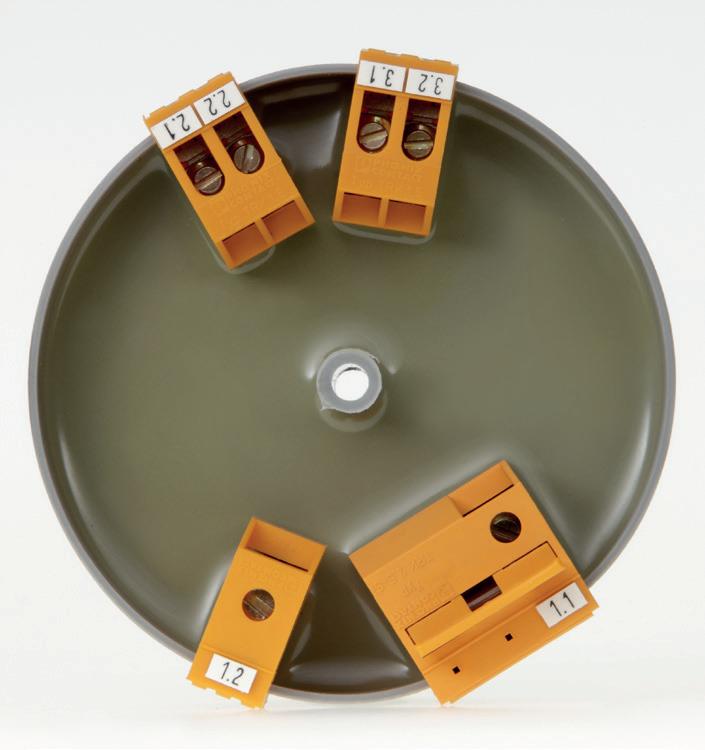
costs. They can also be encapsulated for protection against dust and moisture, with ingress protection ratings up to IP54. Products like REO’s toroidal transformers conform to strict standards such as IEC/EN 60601, making them ideal for use in safetycritical environments.
Ultimately, embracing newer technologies like toroidal transformers is a simple yet highly effective way for companies to reduce their energy consumption, lower carbon emissions, and align with long-term sustainability goals. As the pressure to act on climate change increases, upgrading outdated electrical infrastructure is no longer optional—it’s essential.
reo.co.uk
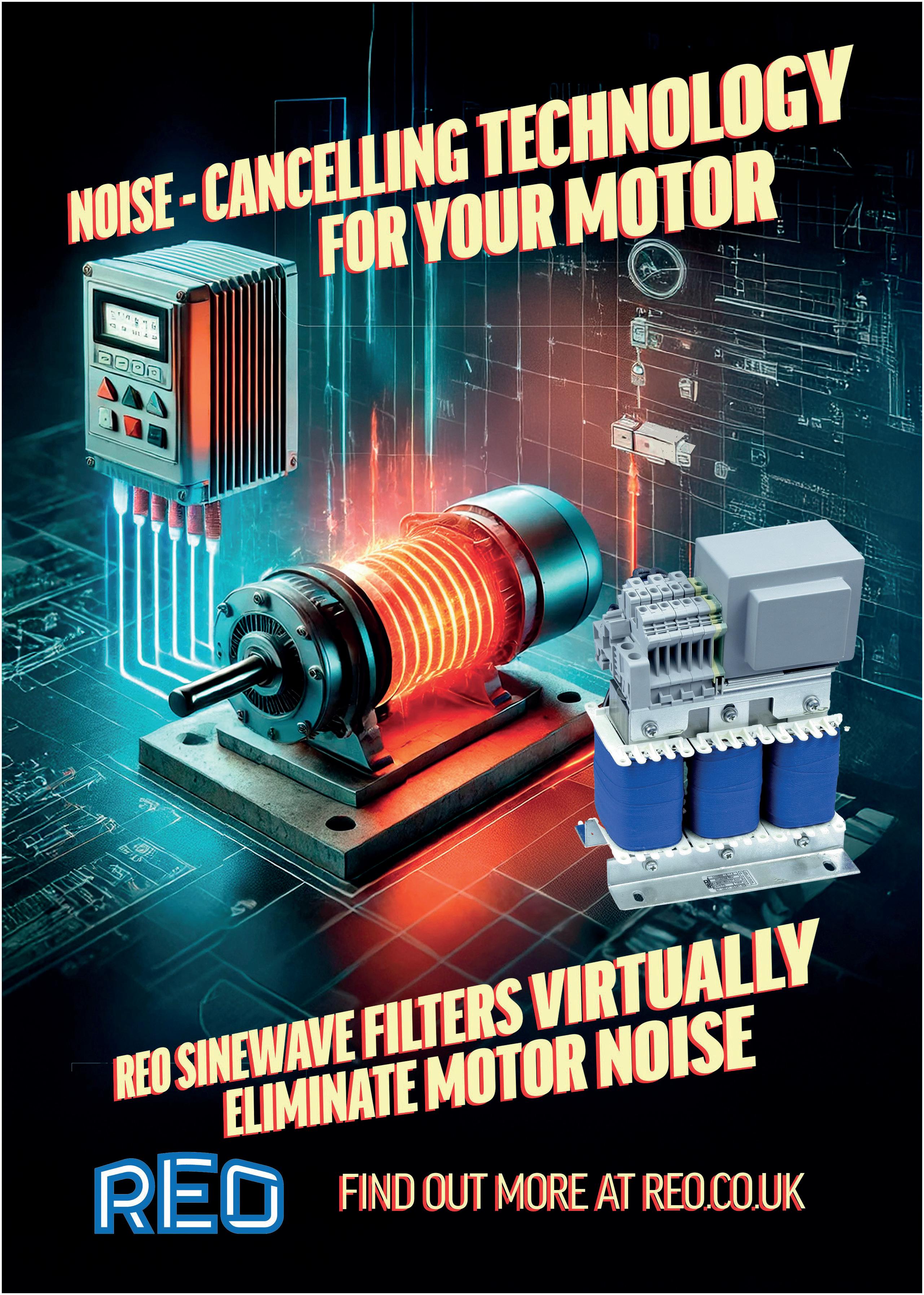
How Better Planning Helps Sustainability
While large-scale changes like switching to renewable energy or redesigning products may grab headlines, it is often the less visible improvements that deliver the most consistent and measurable results. Discover how better planning can help manufacturers reach sustainability goals.
Strategic planning can help manufacturers reduce waste, conserve resources and take meaningful steps toward their sustainability objectives. Here are five ways to improve planning.
1. Optimised resource usage
One of the most effective ways to cut waste is simply to prevent it from happening in the first place. Through accurate forecasting and production planning, manufacturers can better align their output with actual demand. This reduces overproduction, excess inventory, and the unnecessary use of raw materials—all of which carry environmental as well as financial costs. Better planning ensures that you only produce what’s needed, when it’s needed, leading to less storage, less waste and less money spent on inefficiencies.
2. Lower energy consumption
Running machines that don’t need to be running? Keeping facilities lit and heated during downtime? Poor planning often leads to unreliable and inefficient scheduling, which in turn drives up energy use. A carefully structured production plan allows manufacturers to optimise shift schedules, reduce machine idling, and consolidate operations to avoid fragmented or inefficient runs.
3. Inventory and supply chain efficiency
Excess inventory is often seen purely as a financial issue. It ties up working capital, takes up warehouse space, and can eventually lead to spoilage or obsolescence.
But it also has a less visible cost: its environmental impact. Storing surplus goods requires lighting, heating, cooling and physical infrastructure— all of which consume energy and resources. For perishable goods or temperature-sensitive items, the carbon footprint of storage can be especially high.
Better planning enables manufacturers to maintain optimal stock levels and reduce the likelihood of overstocking. This means less waste from expired or outdated inventory, fewer resources spent on storage, and results in a smoother, leaner operation overall.
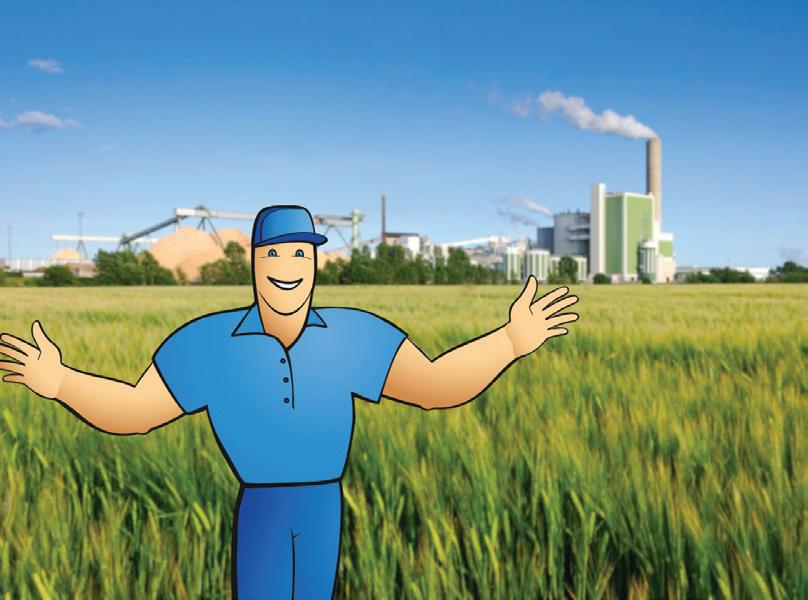
5. Continuous improvement
Stockouts are also more than just a logistical headache. When critical components or materials run out unexpectedly, manufacturers often resort to quick fixes that come with environmental penalties, like last-minute airfreight, long-distance shipping, or the use of higher-emission transport options to meet production deadlines. These emergency decisions, while sometimes necessary, are rarely sustainable.
4. Data-driven decision making
Modern planning tools give manufacturers access to valuable data: material usage patterns, waste statistics, downtime reports, and more. With this information, companies can set realistic sustainability targets, measure progress, and continuously refine their operations for better outcomes.
It’s not just about acting on gut feeling or best guesses—data allows for informed, proactive changes that deliver both environmental and business value.
Sustainability isn’t a one-time achievement— it’s an ongoing effort. Better planning supports a culture of continuous improvement by creating the visibility and structure needed to identify inefficiencies and respond to them quickly. Whether it’s reducing scrap rates, shortening lead times, or cutting down on idle machine hours, small incremental changes can lead to big cumulative gains over time. With the right systems in place, manufacturers can monitor performance in real time, benchmark against sustainability goals, and fine-tune processes with each production cycle.
Plan better with MRPeasy
Sustainability starts with control—and MRPeasy puts businesses in the driver’s seat. Slash waste, trim energy bills, and say goodbye to bloated inventories with smart, connected planning. With integrated tools for production planning and scheduling, inventory management, purchasing, sales, and real-time analytics, MRPeasy gives small manufacturers the control and visibility they need to operate leaner, meaner and greener. mrpeasy.com
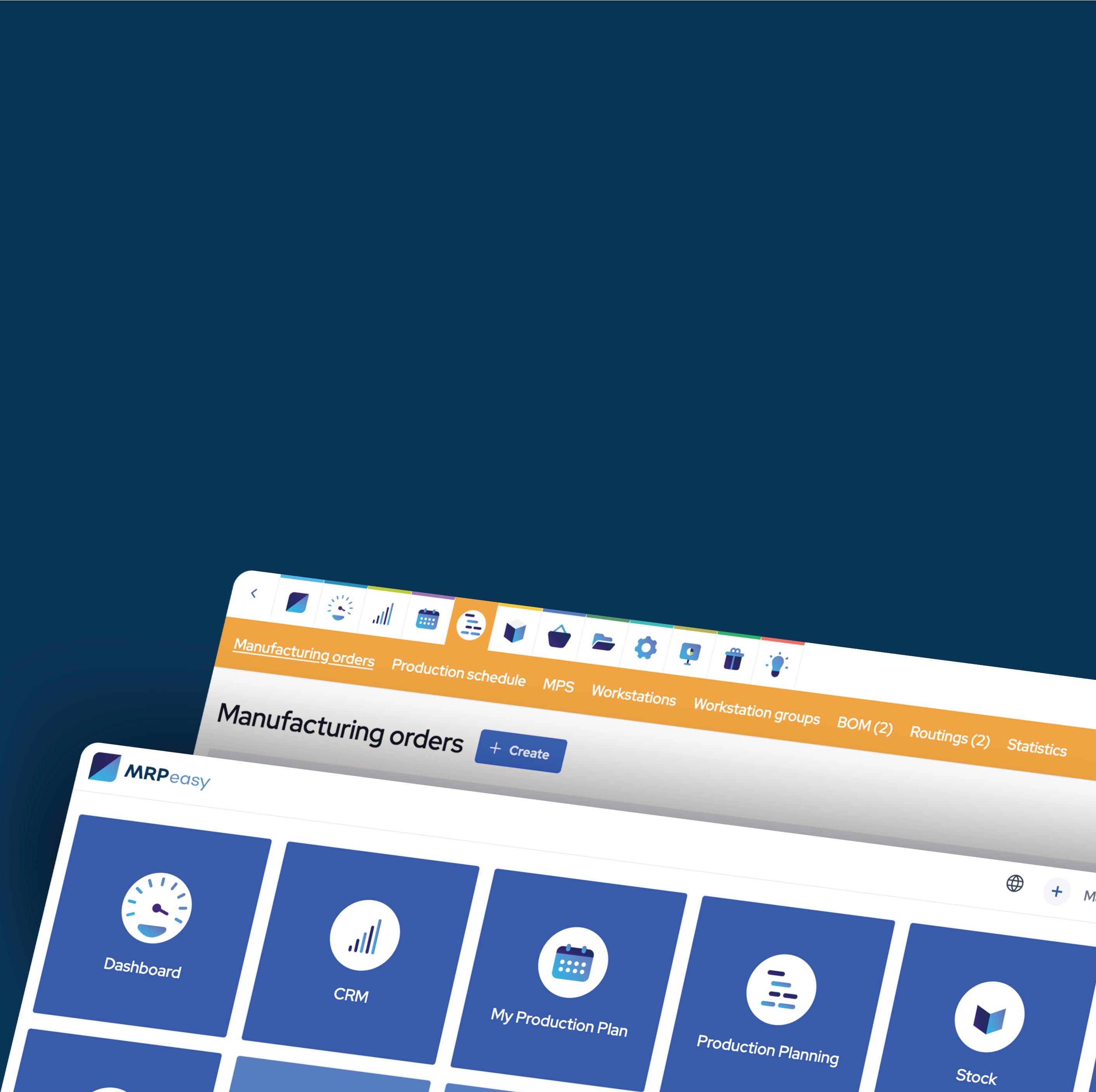
Striving Forward with Green Initiatives
Titan Enterprises shares how it drives innovation and sustainability with strategic green investments and supply chain resilience.
Reconciling environmental and economic objectives can be challenging. However, being green is no longer viewed as a cost of doing business, but a catalyst for innovation, new market opportunity, long-term cost-savings and company resilience.
“Establishing environmental priorities and goals that are compatible with our business strategy is not straightforward, and the ultimate benefits need to be viewed over a longer term,” says Kate Thomas, Titan’s Company & Finance Director. Expected bottom-line rewards and environmental payoffs won’t be achieved with any quick fixes but with strategic investments and planning.
Powering sustainability with solar energy
In December 2024, Titan installed two solar panel arrays at its manufacturing facility, a move expected to offset six tonnes of CO2 annually. This green energy initiative will power production processes, with surplus energy sold back to the National Grid. The solar panel installation was part funded by Low Carbon Dorset as part of the UK Government Shared Prosperity Fund. By reducing reliance on fossil fuels, Titan is cutting costs and its carbon footprint, demonstrating its commitment to a sustainable future.
Enhancing supply chain resilience
To safeguard growth in 2025, Titan has focused on strengthening its supply chain. Titan is proud to source its key suppliers from the UK, and by diversifying its network, Titan has been able to explore different materials, designs and moulding that have improved the technical performance of its flowmeters. With a stronger buying
power brings the capability to manage increasing costs of raw materials and components, maintain competitiveness and meet customer demands more effectively. Maintaining local suppliers and securing larger quantities of stock also reduces the overall environmental impact of transportation and mitigates the risk of supply disruption.
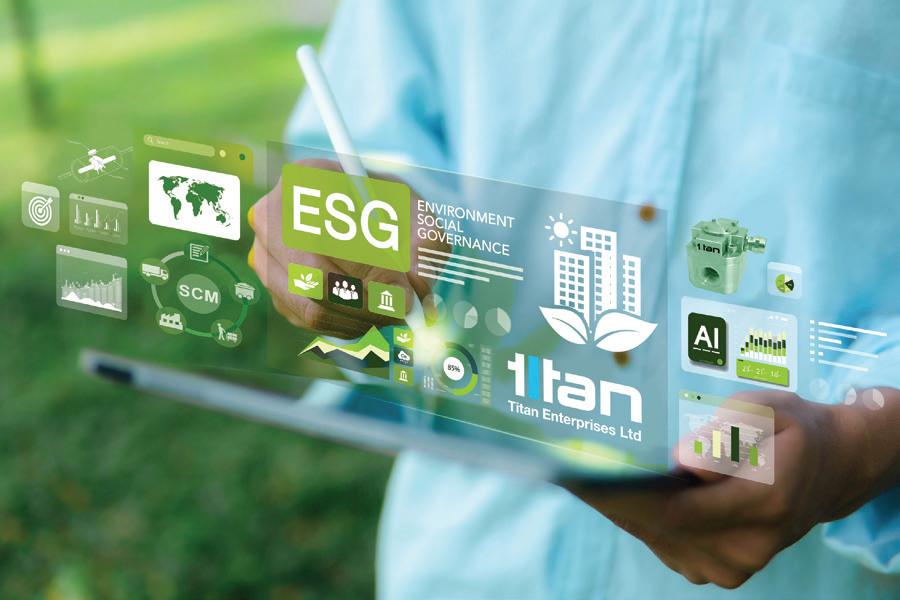
Recycling and efficiency through technology
Titan is rethinking its approach to recycling and has embraced innovative solutions, such as switching from printed technical documents to QR code systems, reducing paper use and waste. The company is also exploring ways to recycle old PCBs used in R&D or found faulty and rejected during production. Packaging material is an easy consideration when it comes to ‘going green’. Titan is moving away from traditional polystyrene packaging to recyclable cardboard and the use of biodegradable ‘worms’ as filler, showcasing its commitment to environmental responsibility.
Product redesign for environmental benefits
In a dedicated effort to use fewer environmentally harming or resourcedepleting raw materials, Titan’s R&D and production team redesign products where possible. While regulatory requirements in industries like medical, pharmaceutical and food production pose a challenge, Titan is determined to strike a balance between economic and environmental objectives and continues to explore evolving technologies.
“Investigating new technologies and materials and pushing the performance
boundaries to test what can be achieved is exciting,” states Neil Hannay, Titan’s Senior R&D Engineer. “Something that wasn’t feasible, say, 10 years ago, is now delivering results beyond our expectations because of new technology and materials available that have properties that perform differently.”
Facing challenges and looking ahead
Despite 2024 being a rollercoaster year shaped by an unsettled geopolitical landscape, Titan remains focused on delivering quality and expertise. Through thought leadership, technical articles, and targeted marketing, Titan builds trust and demonstrates its capabilities and resilience to a global audience.
“Through targeted investments and strategic initiatives, we are placing our commitment to sustainable practices firmly in our priorities alongside operational excellence,” says Kate Thomas. “These efforts are likely to result in a reduction of direct manufacturing costs and inventory savings, aligning our environmental stewardship with economic growth.”
Titan Enterprises’ commitment to sustainability and innovation is a long-term vision that will safeguard the company’s growth into 2025 and beyond. flowmeters.co.uk
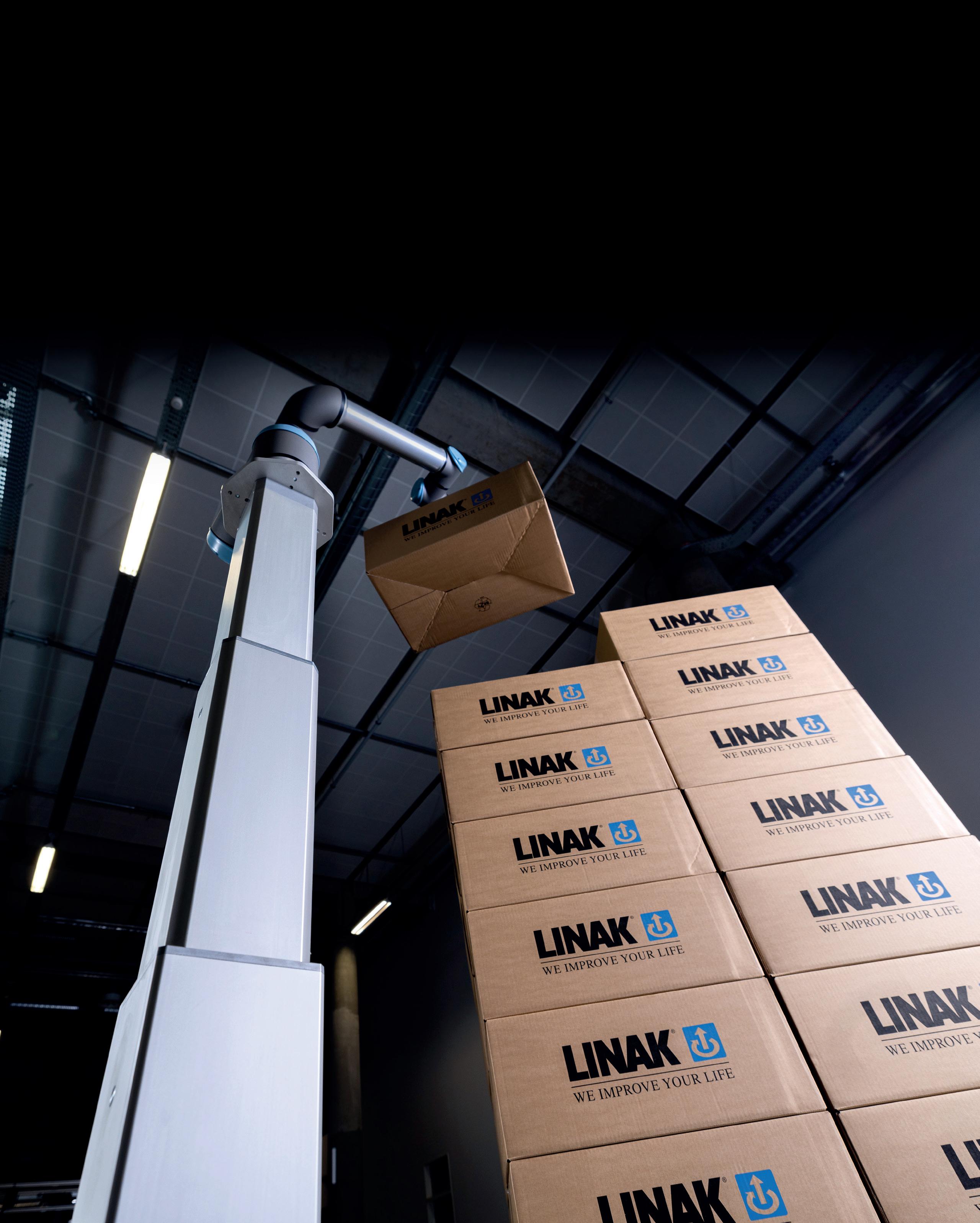
ELEVATE™ your cobot palletiser to the next level
The ELEVATE™ lifting column extends the range of your cobot palletiser, taking performance to new heights.
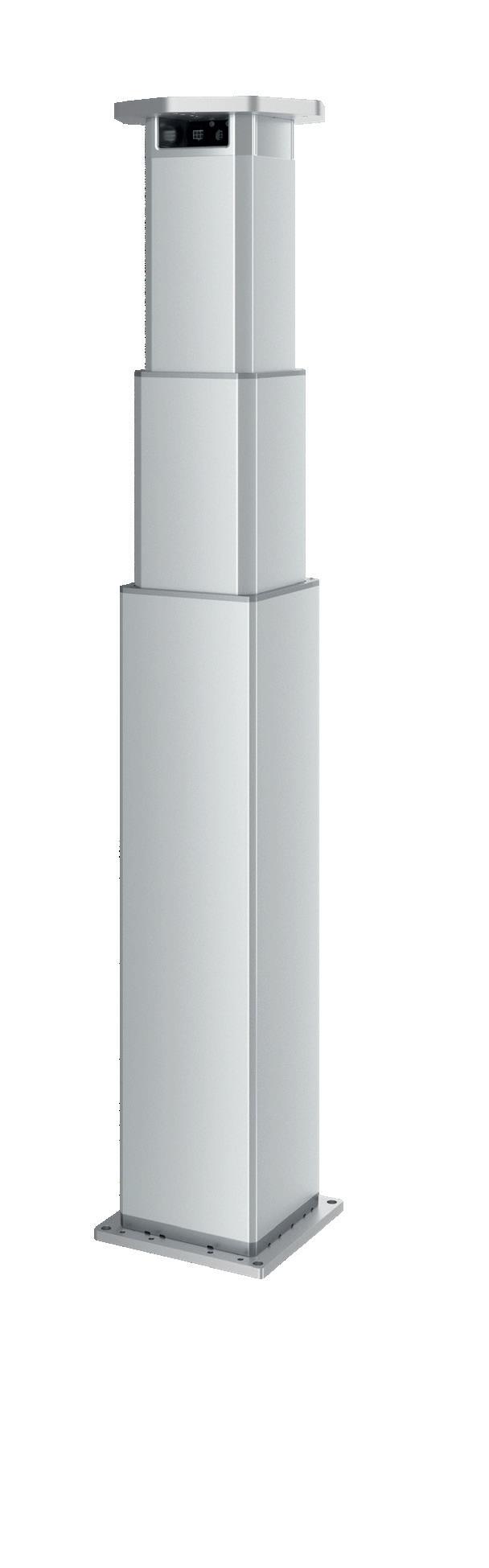
AERZEN Turbo –an Efficient Solution
In the following case study, AERZEN’s technology provides increased efficiency resulting in significantly lower OPEX for a wastewater treatment company, while also reducing CO2 emissions and waste, leading to greener wastewater treatment.
Operational efficiency, reliability should be priorities in wastewater treatment plants. Consequently, there has been a prominent focus on being more efficient and reducing carbon footprints. How can sewage treatment works contribute to helping the environment?
One way is by being energy efficient and reducing CO2 emissions. Owing to a collaboration between Air Technology, an independent energy adviser, and AERZEN, a specialist manufacturer of compressed air, gas and vacuum solutions, the sewage treatment plant in this case study did exactly that and more.
The site reduced its carbon footprint and became more cost and energy efficient, in line with the customer‘s missions. How did AERZEN help accomplish this?
The solution
The efficient, reliable, and innovative Turbo. Air Technology’s mission: to identify and propose measures to improve operating efficiency and productivity, therefore saving money, reducing pollution, and avoiding the wastage of the earth’s valuable, natural resources.
The end user is a company that treats wastewater for over eight million people. They entrusted Air Technology to find a suitable solution. AERZEN was contacted to look for a reliable and efficient solution tailored to suit the sewage treatment works.
AERZEN supplied 3 Turbo G5plus blowers (3 x AT150 0.8S DN250), which modernised the plant, as they replaced the competitor’s aging blowers that were consuming a lot of energy.
Whilst these works were going on, the client involved AERZEN Rental to avoid downtime, who supplied, the end user with 2 BVO 55000 skid-mounted assemblies.
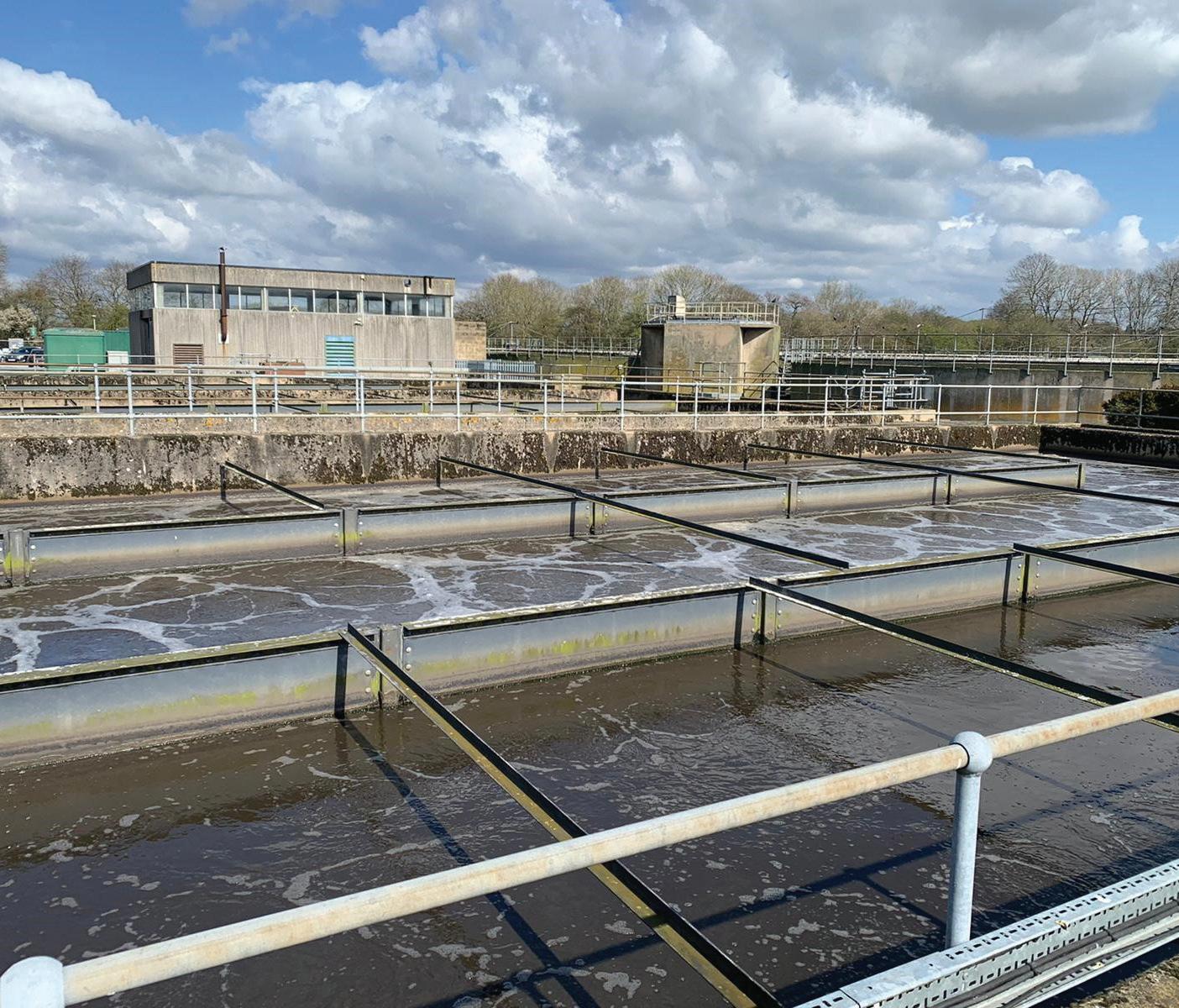
However, the site did not need to hire for long as AERZEN only had a lead time of 4 weeks.
The result
AERZEN’s customer successfully installed the quieter AERZEN Turbo G5plus blowers. The site is now 21% more energy efficient, and the pay back can be made in under 3 years. AERZEN received great feedback from Air Technology’s Technical Director, Ian Moore, “It’s looking like a really good installation, and it is quieter and more efficient than the old system”.
The AERZEN Turbo G5 plus is an innovative product that is reliable, energy efficient and low maintenance. AERZEN’s Turbo G5plus has an extremely compact design. Another outstanding feature is the
innovative AERZEN air foil bearings with double coating and the multilevel frequency converter technology, which reduces the heat loss in the motor to a minimum, improving the total efficiency significantly.
Summary
AERZEN’s Turbo G5 plus Blower has helped Air Technology accomplish its mission. The end user will be making savings of over £20,000 per year, helping them to continue to treat water for many communities. Optimisation was made affordable and climate-friendly wastewater treatment was achieved.
AERZEN provides tailor-made solutions. Visit the company’s website for more details.
aerzen.com
Performance³ - The new generation
The innovative Roots, Screw and Turbo Blowers
Up to 30 % efficiency increase
Up to 40 % CO2 reduction
Less than 2 years pay back
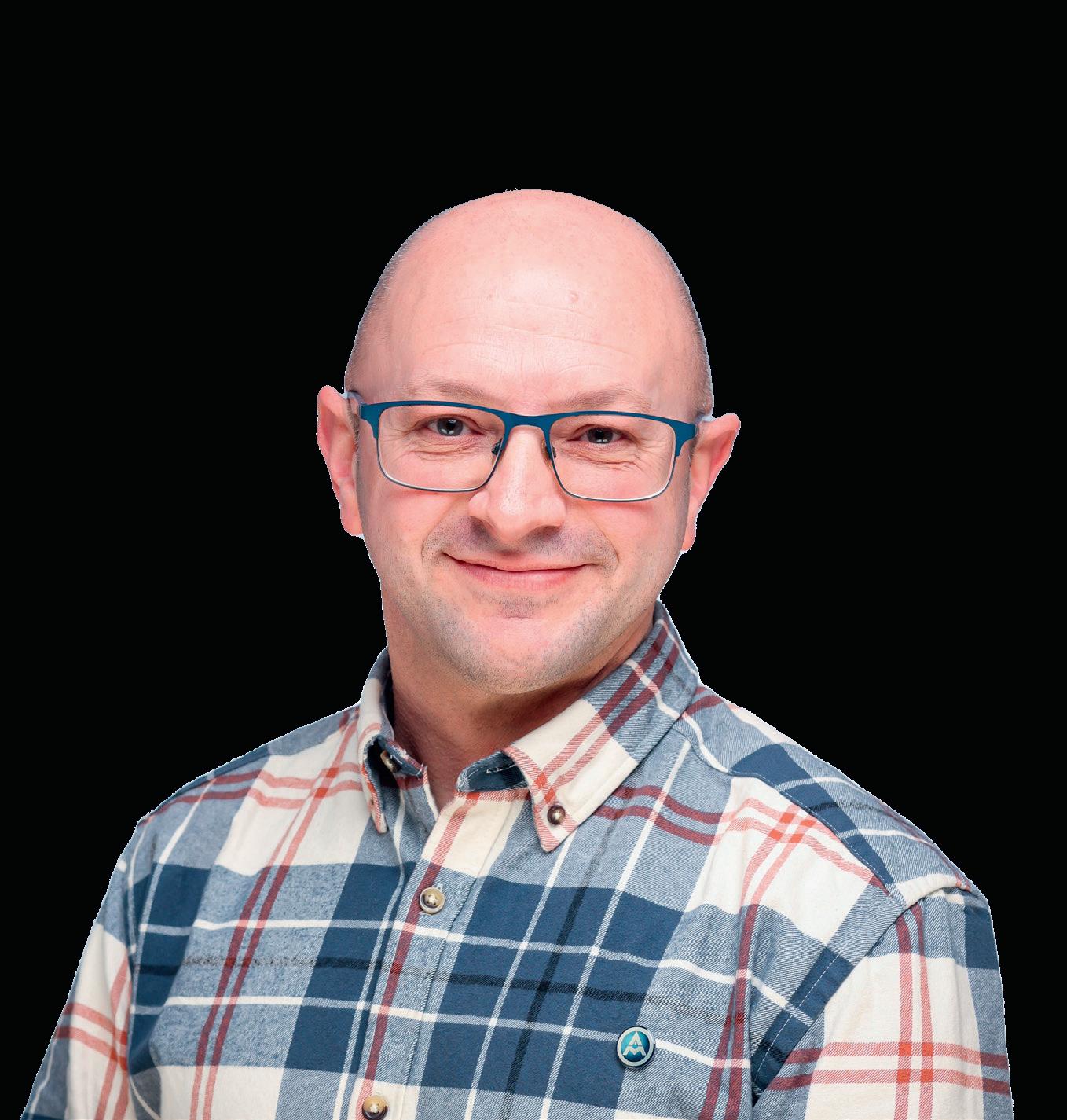
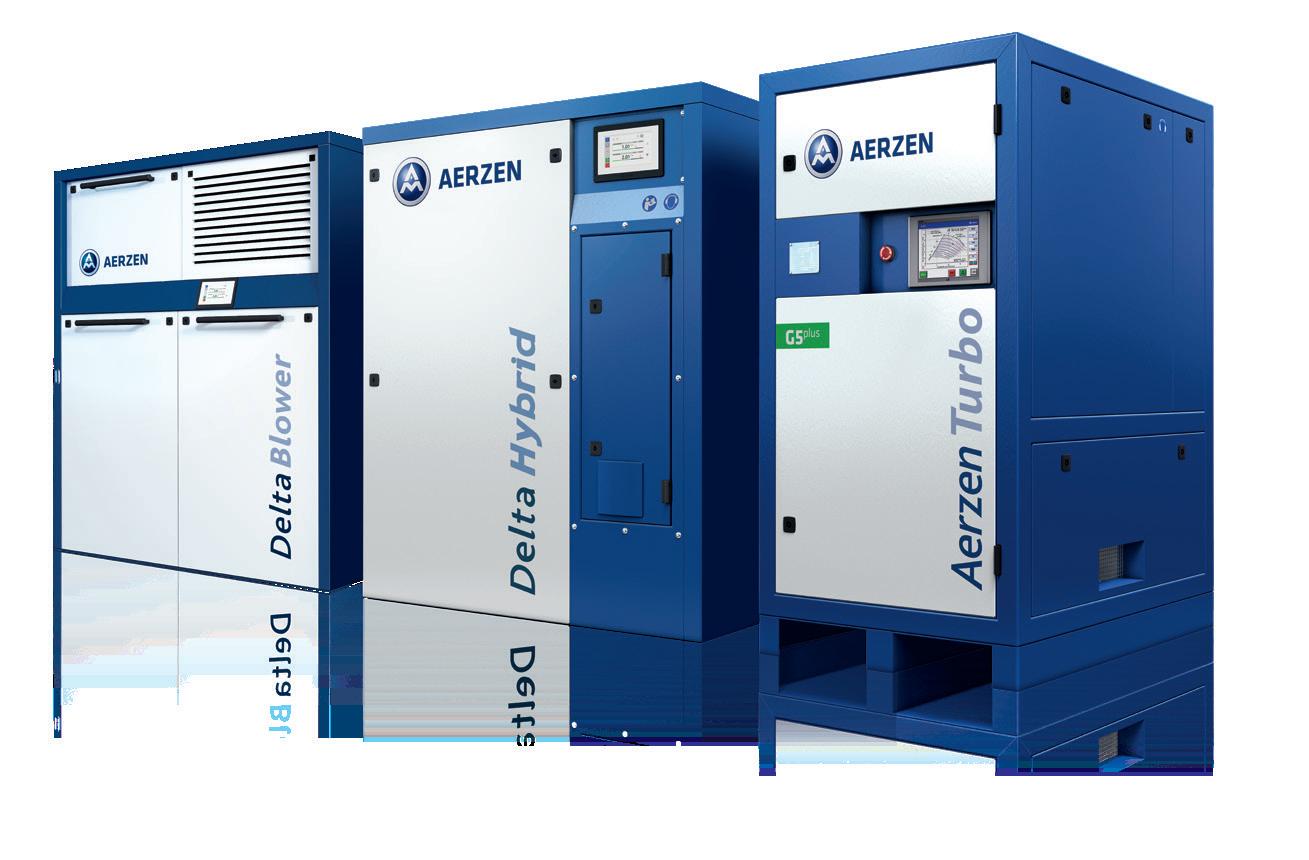
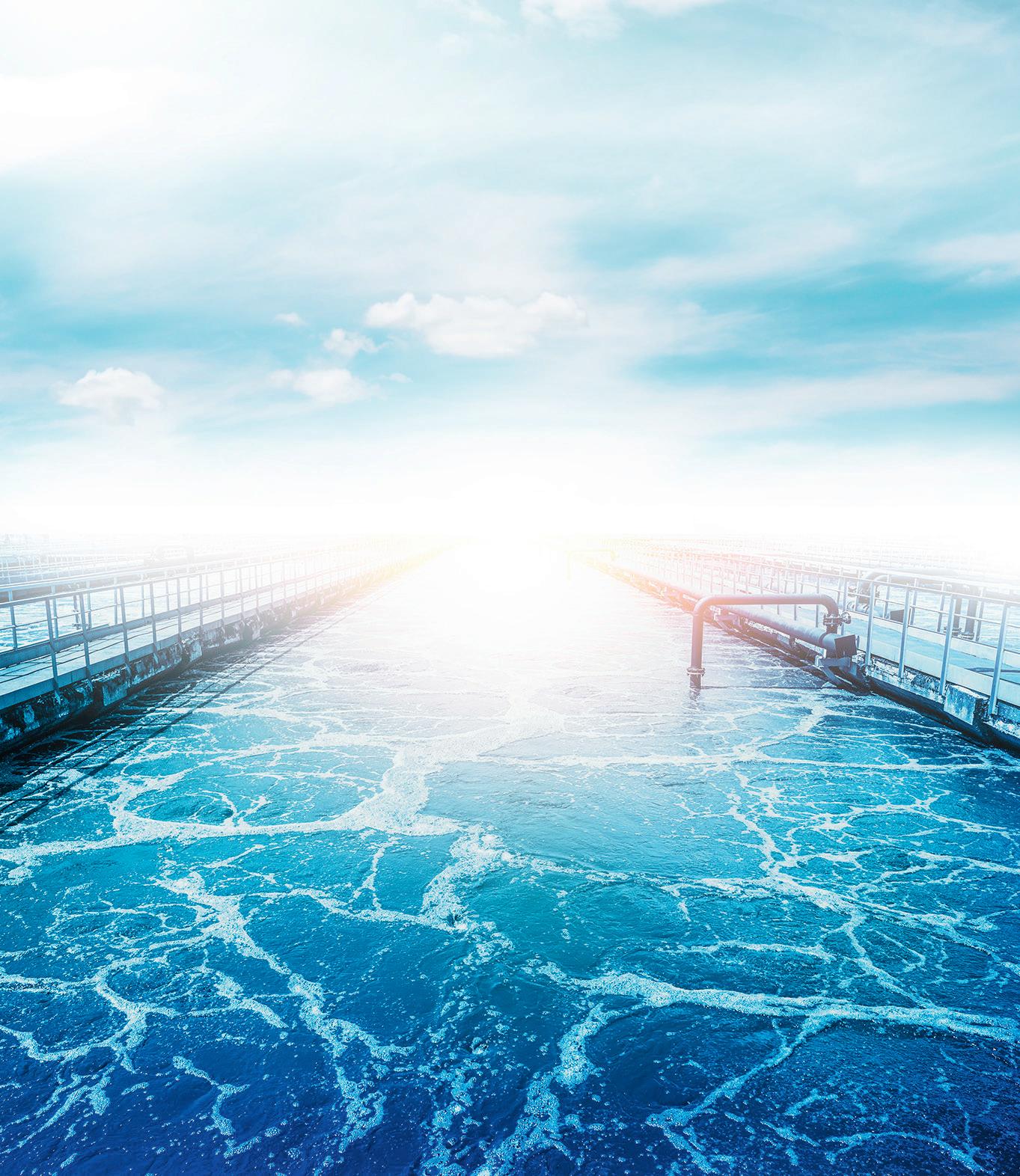

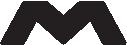
Unlock Efficiency with Magnetic Motors
Reliable and scalable magnetic motors play a vital role in driving innovation across multiple sectors. Gary Rodgers, CEO of Magnomatics, outlines the benefits of magnetic gear technology.
Efficient motor systems provide both economic and environmental advantages across different sectors by lowering energy consumption and reducing CO2 emissions.
Magnetic gears, in particular, outperform traditional geared systems in terms of energy efficiency. By imitating the attributes of a direct drive, they can deliver high torque at low speeds, surpassing the torque generation limits of traditional direct-drive electric motors. Additional efficiency gains come from having no mechanical friction and low electrical current; as heat output is limited, the need for energy-consuming cooling is minimised.
The absence of mechanical gears also reduces the overall mass of the magnetic motor – currently, magnetic motors are the smallest and lightest high-torque motors available. When used for propulsion, whether in rail, marine, aerospace or road applications, this reduces the vehicle’s mass and enables a more compact and lightweight design, resulting in further efficiencies.
In terms of manufacturing, these systems are inexpensive to produce and inherently more sustainable as they consist of fewer materials. Moreover, their compatibility with standard power electronics makes installation seamless and non-intrusive.
Magnetic gear systems also provide enhanced reliability and safety while requiring negligible maintenance, and the lack of mechanical gears means there is no physical wear, which cuts repair costs, prevents bottlenecks and reduces the risk of operational breakdowns.
They can be supplied with fault-tolerant windings (electrical, magnetic, mechanical and thermal isolation) between typically two 3-phase banks. Magnetically geared motors
can also maintain rated operation following a short-circuit fault and the loss of one phase bank, preventing fires, and limiting the impact of electrical failures elsewhere in the system.
Far-reaching applications
Magnetically geared thrusters provide the efficiency, reliability and sustainability needed for electric marine propulsion systems. Suitable for a wide range of vessels, including subsea, they deliver direct power transmission without convoluted gear systems, providing reliable and efficient propulsion that is more environmentally friendly and requires less maintenance.
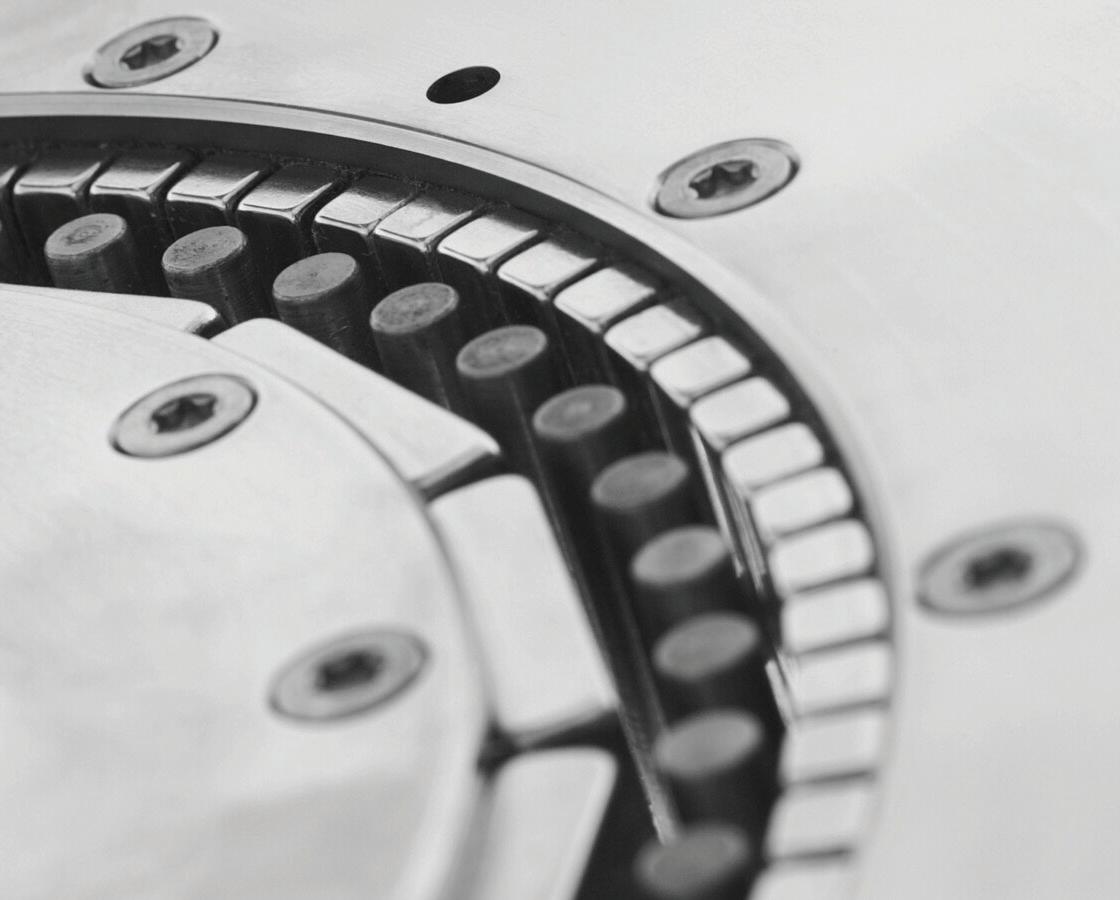
improved efficiency and reliability due to the lack of mechanical gears. Additionally, the motor can tolerate the shock loads of wheel hub applications and direct-drive locomotive axles, even within the limited space envelope.
They also offer huge potential for the aerospace industry, including for eVTOL and UAM applications. Besides being durable, efficient, low-maintenance and quiet, these systems offer enhanced safety measures, including redundancy and fault tolerance, non-contact power transmission and system isolation. Moreover, magnetic gears operate as a passively resettable torque fuse, eradicating the need for a clutch or shear pins in case of jamming.
Magnetically geared motor systems offer several advantages for e-mobility – they are more powerful and efficient than traditional motors, their simpler design minimises manufacturing costs and their low weight cuts energy consumption, increases range, and reduces the frequency of charging.
In rail applications, the system’s hightorque to low-size ratio offers increased flexibility to engine designers, as well as
The same goes for the renewable energy sector, where the superior efficiency of magnetic gears can reduce the cost of operating wind turbines, while their design reduces the costs of maintenance, installation and decommissioning. Their compactness, meanwhile, increases the hydrodynamic efficiency of tidal generators, minimising flow restriction while delivering low-cost, high-power output.
The low-speed, high-torque technology of magnetic gear systems, together with their low-mass, compact design, superior reliability and partial load efficiency, makes them an economic and environmentally sound choice for use across a range of applications in multiple key sectors.
For more information, visit the company’s website.
magnomatics.com

The Barriers to Decarbonising Industry
Collaboration is key to meeting the challenges faced by energy transition to decarbonisation, as Giampiero Frisio, President, ABB Electrification, explains here.
Electrification and the shift towards clean energy generation, distribution, and more efficient consumption are essential to combat climate change and secure a low-carbon future. It’s a topic at the top of the agenda at many companies across all industries as they can make great gains in reducing energy costs as well as reducing emissions, while also meeting legislation. Indeed, over 70% of respondents in a survey by ABB1 agreed that a key strategic objective in the next couple of years is transitioning to renewable energy sources.
However, the move away from fossilfuelled power sources to renewable energy is creating many challenges for organisations. Some of the key issues facing senior leaders include how to control operational costs, how to manage infrastructure investments effectively, securing a skilled workforce, and how to best implement new solutions such as energy storage.
More than 425 of the electrification purchase decision-makers surveyed across Europe, expressed reservations about their ability to mobilise adequate human and capital resources. Additionally, as leaders are navigating a digital world, with digital components and software solutions, the need to understand and mitigate cybersecurity risks is also a concern.
Embracing technology
Simply moving to renewable energy sources such as wind and solar from fossil fuels will not be enough to meet future power needs. Smarter approaches to electrification are needed, including leveraging technologies such as Battery Energy Storage Systems (BESS), decentralised energy systems and microgrids. And much of the technology (approximately 80%) that’s needed to achieve the energy transition already
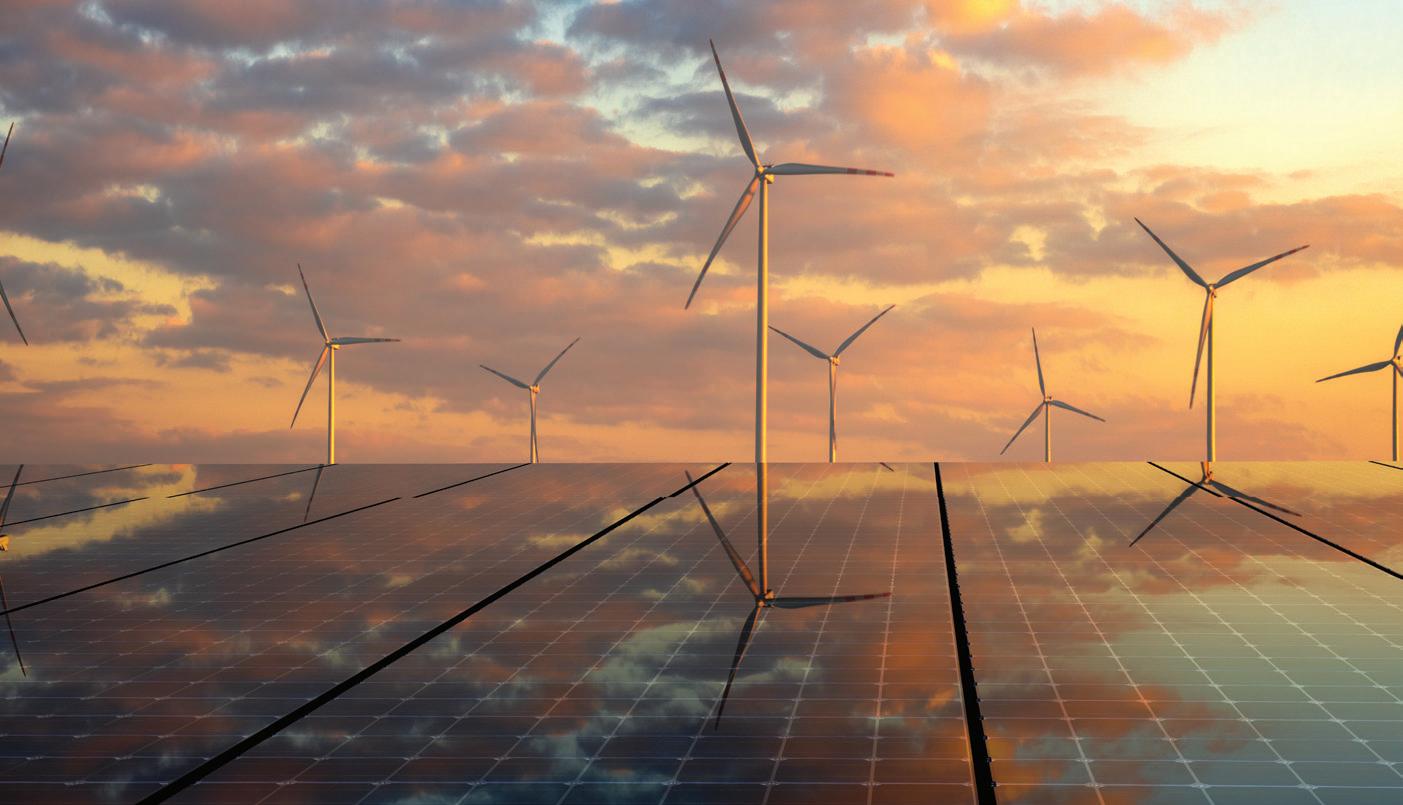
exists, including new methods for energy integration, storage and management.
Artificial Intelligence (AI) and Machine Learning (ML) is already powering data analytics and helping improve efficiencies within grid systems and security. Energy suppliers and infrastructure owners can better match supply demand from energy users. Electrical asset health and predictive maintenance practices will also be vastly improved thanks to AI and ML, increasing the lifetime of mission critical electrical equipment and systems.
There’s an additional benefit to AI too, as it can deliver financial benefits to a business. For example, it enables customers to sell renewable energy they have generated onsite back to the grid, thereby creating a new revenue stream. Furthermore, AI can help reduce energy bills through energy arbitrage and real-time energy pricing. The data insights from the digital tools monitoring a facility can help to build business cases and measure ROI, boosting confidence in long-term investment and helping to address any financial barriers to execution.
Working together
However, if we are to achieve net-zero by 2050, collaboration is essential. Only through discussion, can complexities of the energy transition be fully understood and issues addressed. By bringing customers, technology businesses, startups and academia together and opening up dialogue, we can accelerate the energy transition and discover new ways to tackle the global energy challenges. For example, innovation can flourish, and cleaner and more efficient energy systems can be designed and built through an open ecosystem.
At ABB we’re working closely with organizations of all sizes and across different industries, by not only simply providing the technology, but also sharing our expertise in addressing the world’s most pressing energy distribution and management challenges. Working together, business leaders can benefit from a partner with the resources and knowledge to harness the full potential of today’s proven electrification technologies and secure their energy efficient future. global.abb/group/en 1 new.abb.com/news/detail/120464/abb-survey-reveals-most-europeancompanies-want-to-shift-from-fossil-fuels-but-many-lack-resources
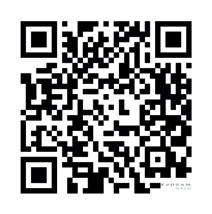
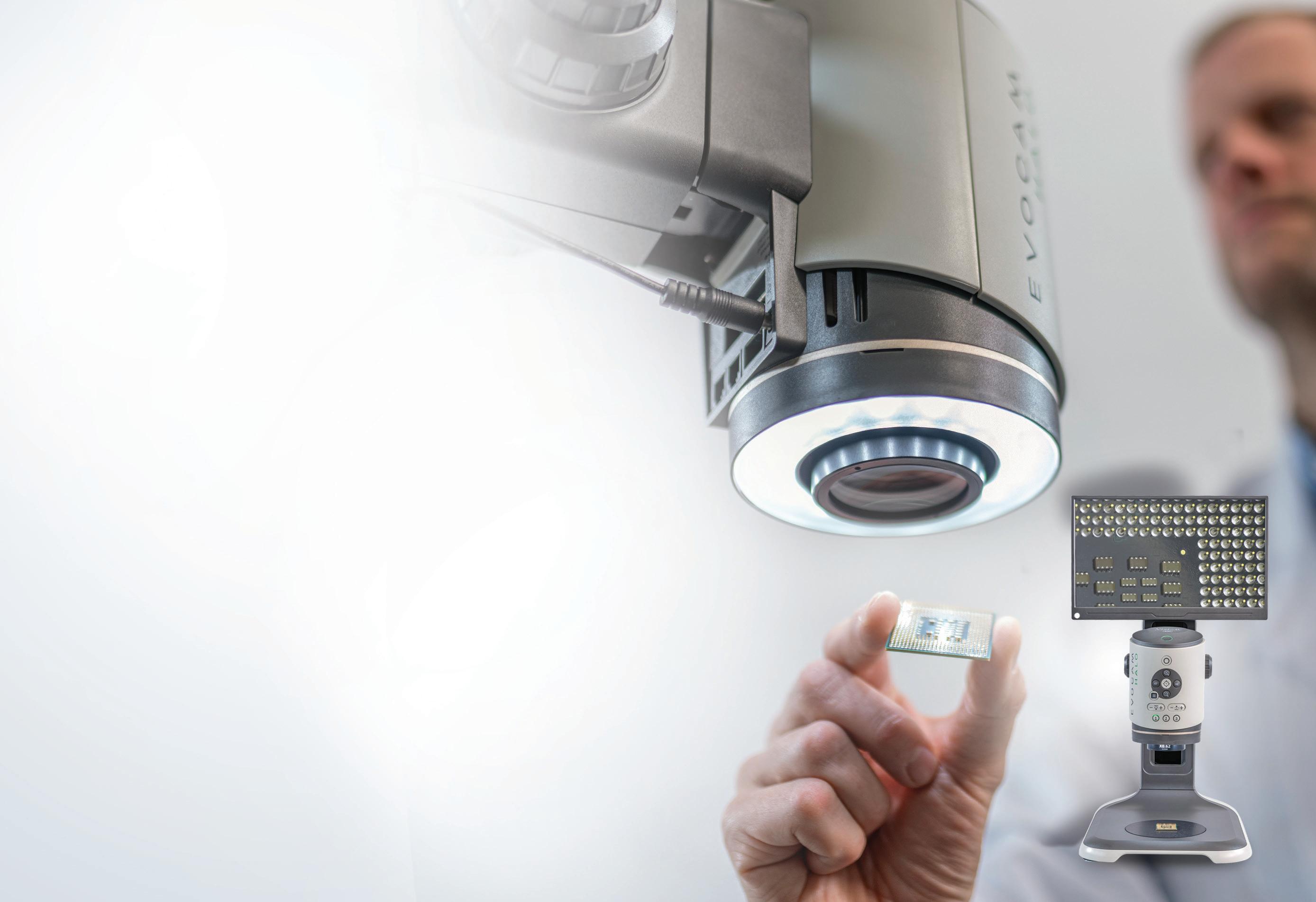
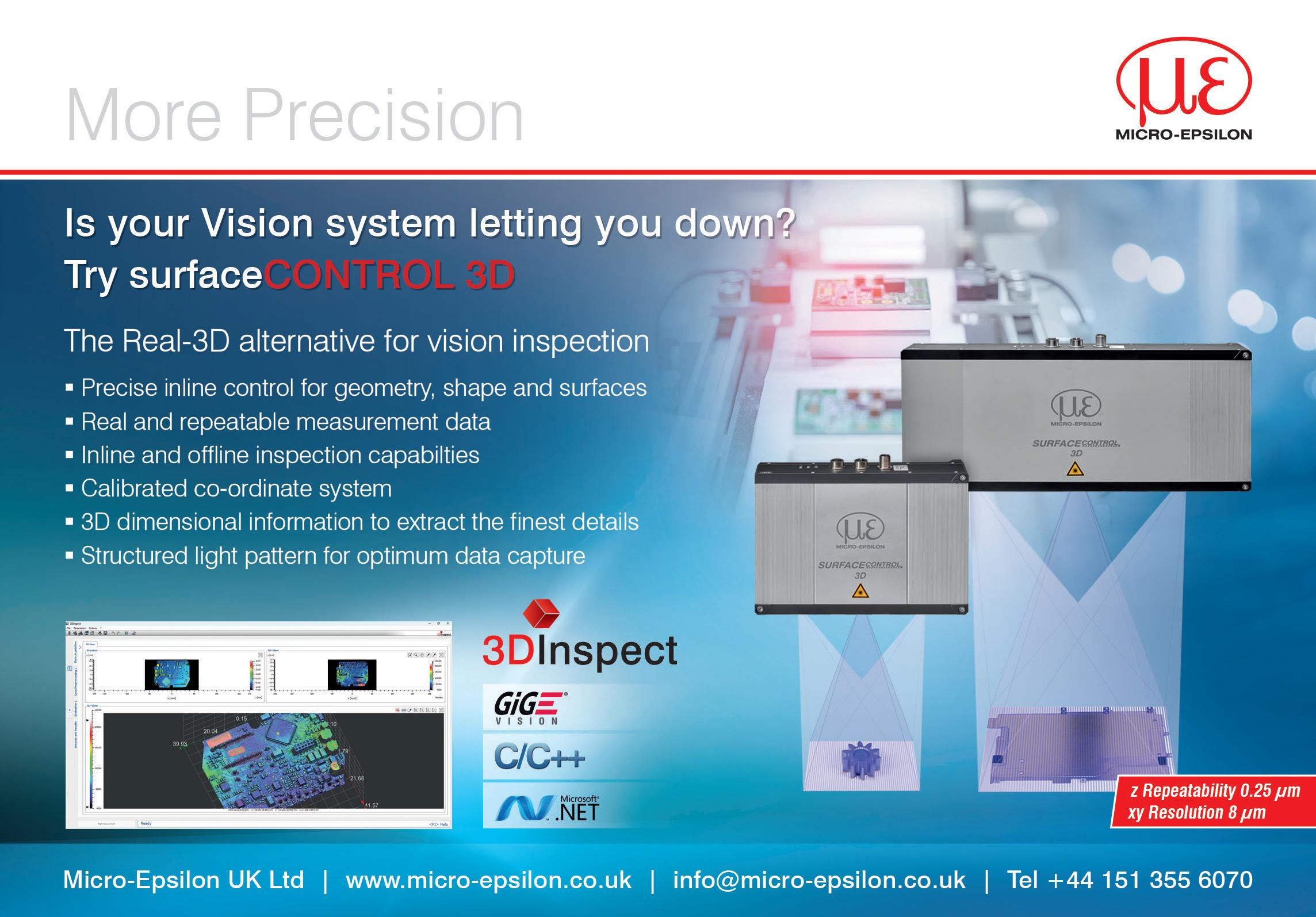
Green is More Than Just a Colour
From increased electrification to floor plan optimisation, Martin McVicar, Combilift’s CEO and Co-Founder, demonstrates the tangible benefits of green thinking in materials handling operations.
Sustainability is a term that is becoming increasingly important for most companies around the world. “Green” is no longer just a colour: it has now turned into a symbol of commitment to environmental friendliness.
Reducing a company’s carbon footprint benefits society and the environment, and transitioning to electric-powered equipment can ensure a more sustainable business model. Martin McVicar explains: “Sustainability is at our core – we’re highly focused on making our vehicles more environmentally friendly and helping our customers maximise their warehouse efficiency.”
The Irish material handling specialist is responding to the increasing demand for greener technologies, with 98% of its R&D dedicated to developing energy-efficient and electric-powered equipment. Recent product innovations, such as the Combi CB70E, Combi-Cube, and Combi-AGT, are fully electric models, exemplifying this commitment. Additionally, over 70% of its current production is electric.
Martin McVicar emphasises: “Almost every model in our extensive range of products is now available with electric power. The ever-increasing lift capacities will answer the demand for more powerful products, which at the same time help companies to achieve their aims for more sustainable operations”
As well as using electric power, optimising warehouse space also contributes to a sustainable supply chain. Maximising space use leads to lower energy consumption for utilities like heating and lighting. By narrowing aisles and using higher racking, a company can free up space to create more storage.
Martin McVicar emphasises this point: “We have always viewed Combilift as more than just a designer and manufacturer of

forklifts and other handling solutions. Space is one of the most valuable assets our customers possess, and if our trucks can help them improve storage density, then everyone benefits.”
As well as improving the efficiencies of customers, Combilift is also striving to become more sustainable in its own operations.
“We are strongly committed to reducing our own carbon footprint, which extends to optimising our resources and minimising waste. This encompasses everything from biomass fuel being used in our paint lines, to our lighting and use of renewable energy,” says McVicar.
30 per cent of the manufacturing plant’s
roof space is equipped with skylights, allowing staff to work in natural daylight. The facility also practices rainwater harvesting, which is utilised for jet washing and in employee restrooms and employs solar technology that generates 185 kW of energy, accounting for 10 per cent of its daily energy usage. In addition, Combilift has transitioned to using water-based paints for all the machines it manufactures, significantly reducing the Volatile Organic Compounds (VOCs) used, thereby helping to protect the environment.
Discover how Combilift can enhance the safety, productivity, and sustainability of your material handling operations: Combilift.com
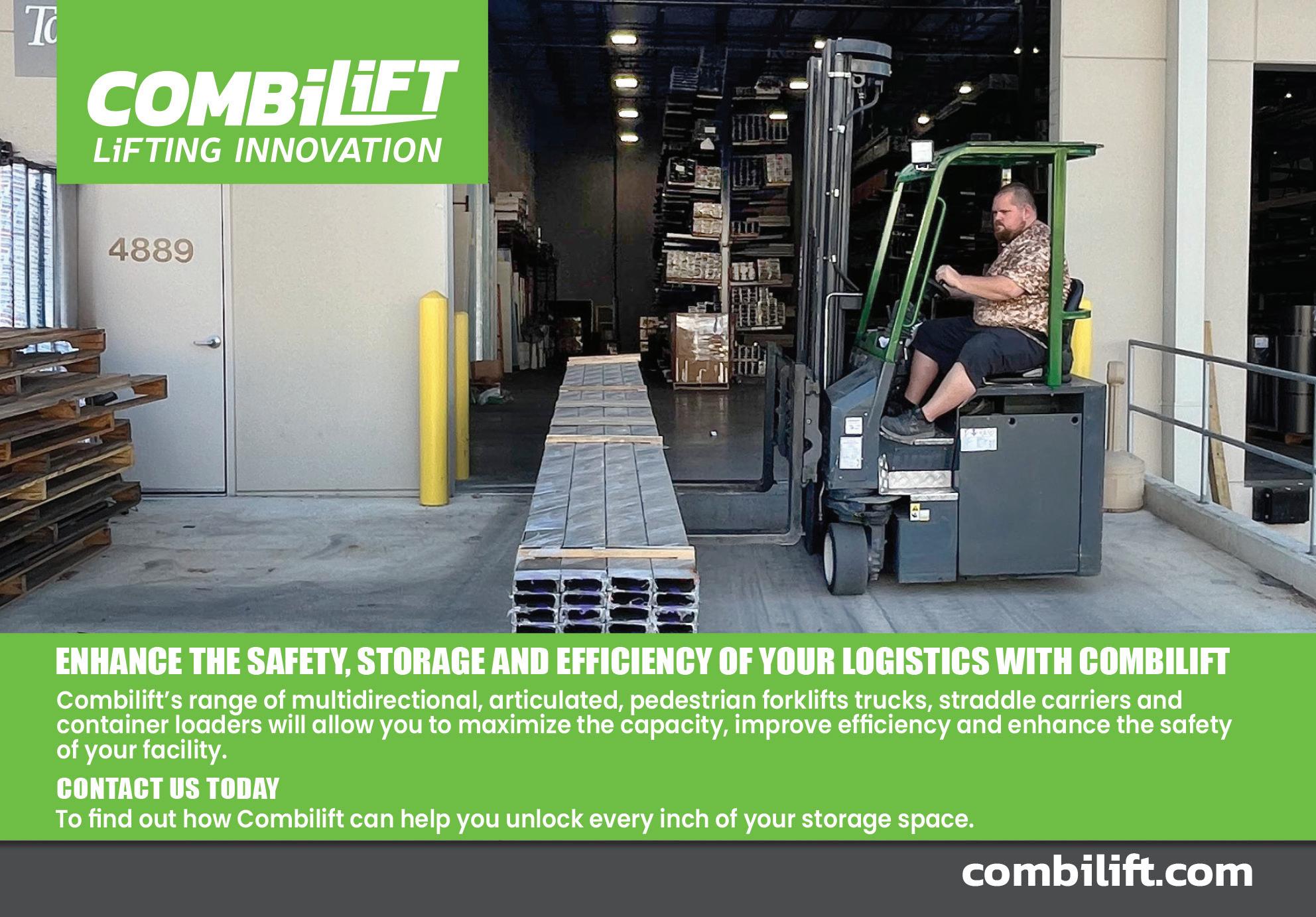
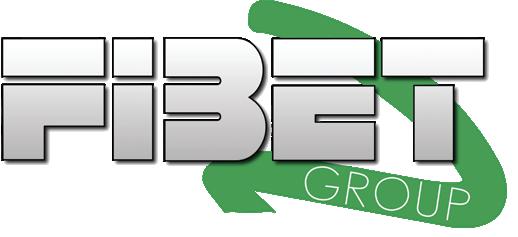

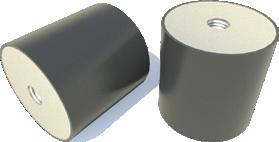
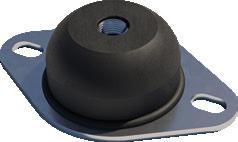
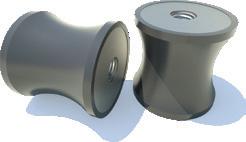

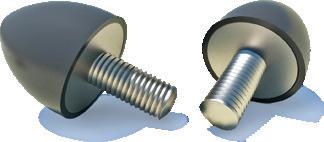
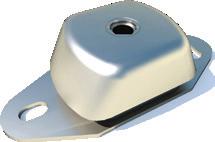
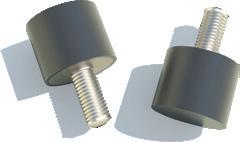
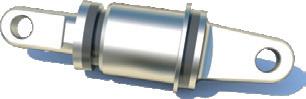
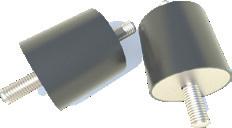
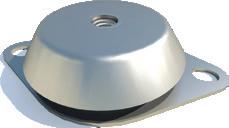
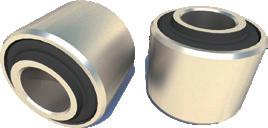
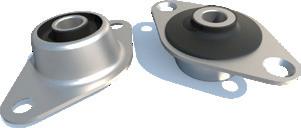
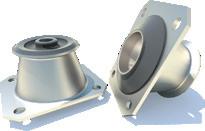
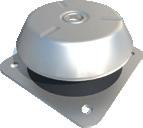
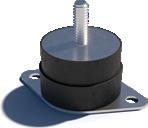
Smarter Process Water Cooling
Process water cooling is typically an energy intensive activity. In this article, Summit Systems demonstrates how smarter process water cooling can drive sustainability by reducing the reliance on outdated refrigerants and improving energy efficiency.
As industries face mounting pressure to cut carbon emissions and tighten energy use, the role of process water cooling has quietly become central to sustainable manufacturing.
Summit Process Cooling, a division of Summit Systems, is at the forefront of this transformation, offering innovative solutions that help industries achieve their sustainability goals while enhancing productivity.
Process water cooling is essential across various sectors, including manufacturing, food and beverage, pharmaceuticals, and plastics. Traditional cooling methods often involve significant energy use and environmental concerns, particularly when relying on outdated refrigerants with high Global Warming Potential (GWP). Summit Process Cooling addresses these challenges by providing advanced cooling technologies that prioritise energy efficiency and environmental responsibility.
• Low GWP Chillers: utilising eco-friendly refrigerants such as R454B, R464B, and R32, these chillers deliver high performance and energy efficiency. They ensure precise temperature control across various applications while significantly reducing greenhouse gas emissions.
• Free Cooling Chillers: these systems leverage ambient air temperatures to cool water, significantly reducing energy consumption during cooler periods and lowering operational costs.
• Chillers with Natural Refrigerants: a full range of chillers are available with CO2 and Propane to reduce the GWP to zero or as close to zero.
Additionally, Summit’s range includes energy-efficient free cooling systems, which can be retrofitted to existing chiller plants, heat pumps, and adiabatic coolers,
all designed to offer maximum efficiency and reliability while helping to reduce environmental footprints.
Recognising that no two operations are the same, Summit Process Cooling works closely with customers to design, install, and optimise cooling systems that meet the precise needs of their production environments. Summit’s in-house design, installation and project management team ensures seamless integration of cooling systems, delivering consistency and continuous improvement throughout the project lifecycle.
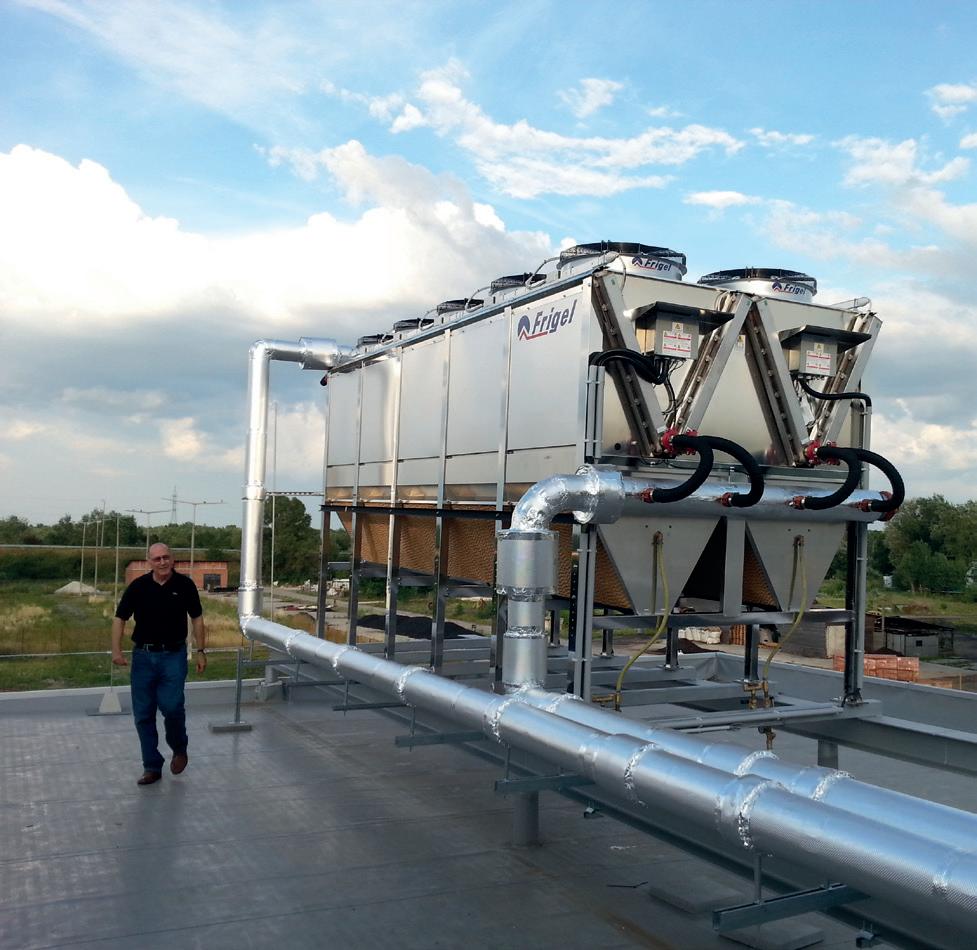
payback period of under 12 months for the units.
With over 30 years of experience in the process cooling industry, Summit has a proven track record of solving complex cooling challenges across various sectors. The company’s commitment to quality service and ongoing investment in engineering expertise ensures that clients receive innovative and effective cooling solutions.
A testament to Summit’s capabilities is its recent collaboration with Carclo, a global leader in precision manufacturing. Aiming to optimise its injection moulding processes, Carclo partnered with Summit to trial Frigel Microgel units—compact, high-performance temperature control systems. The results were impressive: a cycle time reduction of 0.6 seconds, bringing the cycle time below 9 seconds, and an average cycle time reduction of 9% across four manufacturing lines. This enhancement not only boosted efficiency and output but also projected a
Summit Process Cooling’s dedication to sustainability extends beyond product offerings. It provides comprehensive after-sales support, including preventative maintenance visits, emergency assistance, and commissioning services, ensuring longterm performance and reliability of cooling systems.
By integrating advanced technologies with expert support, Summit empowers industries to achieve their sustainability objectives, reduce operational costs, and enhance productivity. Summit’s holistic approach to process water cooling positions it as a trusted partner in the journey towards a more sustainable industrial future.
To discover how Summit Process Cooling can tailor sustainable solutions to suit specific operations, visit the company’s website.
summitprocesscooling.co.uk
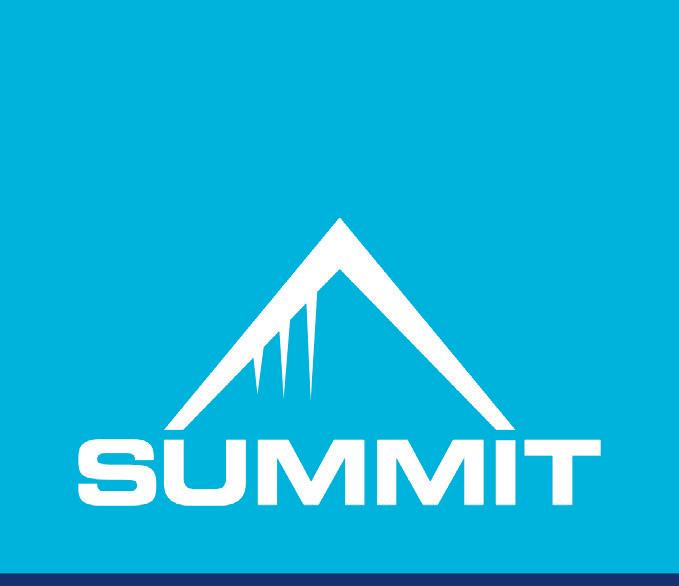

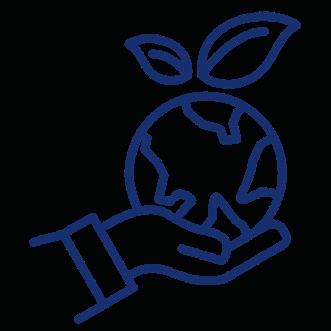
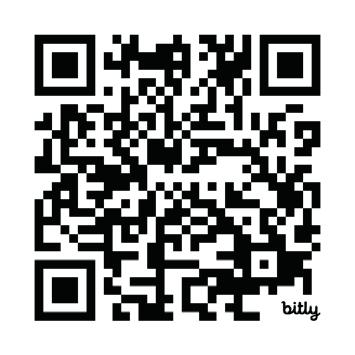
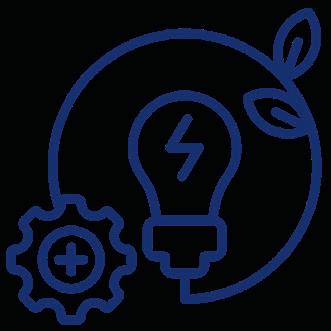
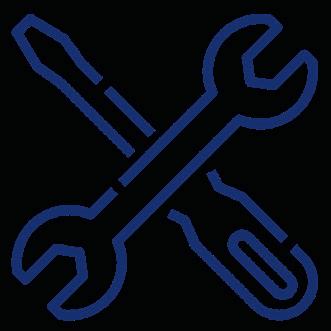
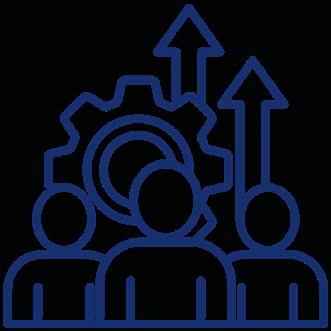
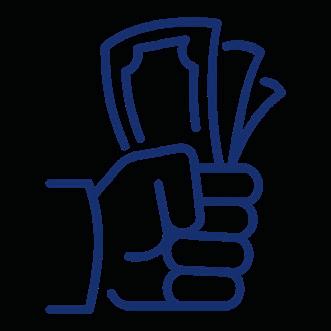
Verciti Joins CESPA
A new collective that is promising to accelerate the development of clean energy systems has welcomed a new member in what is being viewed as a major skills boost for the emerging sector.
Anew collective that is promising to accelerate the development of clean energy systems has welcomed a new member in what is being viewed as a major skills boost for the emerging sector.
The Clean Energy Systems Partner Alliance (CESPA), which has been created to deliver a single source solution for innovators and developers of green tech technology, has increased its ranks to seven specialists with the arrival of Verciti.
A leader in the delivery of immersive Net Zero training, the company believes it can help bridge the widening skills gap for industry by providing access to virtual reality and augmented reality courses covering hydrogen production (plus use and storage), power electronics, machines and drives and hazardous voltage.
“CESPA embodies the same spirit of clarity and collaboration that we value highly, so it was a natural decision to join the alliance in a bid to collectively advance the UK’s clean energy sector,” explained Tony Smith, Technical Training Manager at Verciti.
“Today, 62% of businesses are reporting skills shortages, with manufacturing badly affected. Worse still, 20% of the UK workforce is projected to be significantly under skilled for their actual jobs by 2030. This is a major issue and is going to hold us back – there’s no doubt about that.”
He continued: “What we can bring to the mix is access, access to courses that have been developed with both academic and industry input and, importantly, will appeal to both experienced professionals and new entrants to green technology.
“The idea is that we can join forces with other CESPA members to open up our existing training to current clients, as well as factoring it into future tenders where we can promise to deliver even more solutions.”
Manchester-based Verciti was born out of The Blair Project – a brilliant social enterprise that gets young people building and racing electric go-karts as a way into STEM.
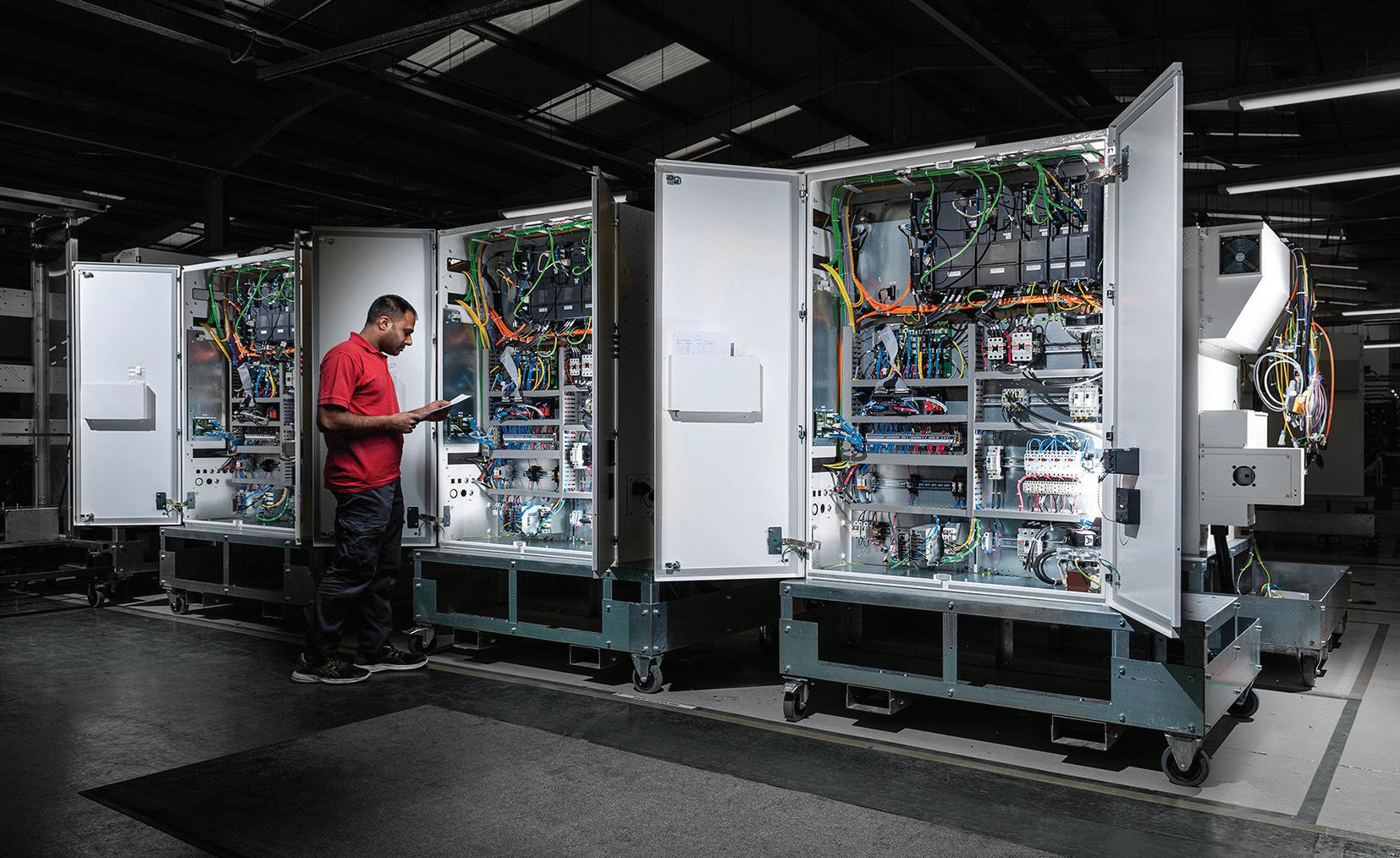
As that work grew, it noticed something bigger going on.
Universities were losing their way - too slow, too expensive, too broad, whereas employers were crying out for fast, focused technical training that reflected the pace of innovation.
And, worryingly, too many people still felt like STEM ‘wasn’t for them’ - that it was for brainiacs, or people who ‘looked the part.’
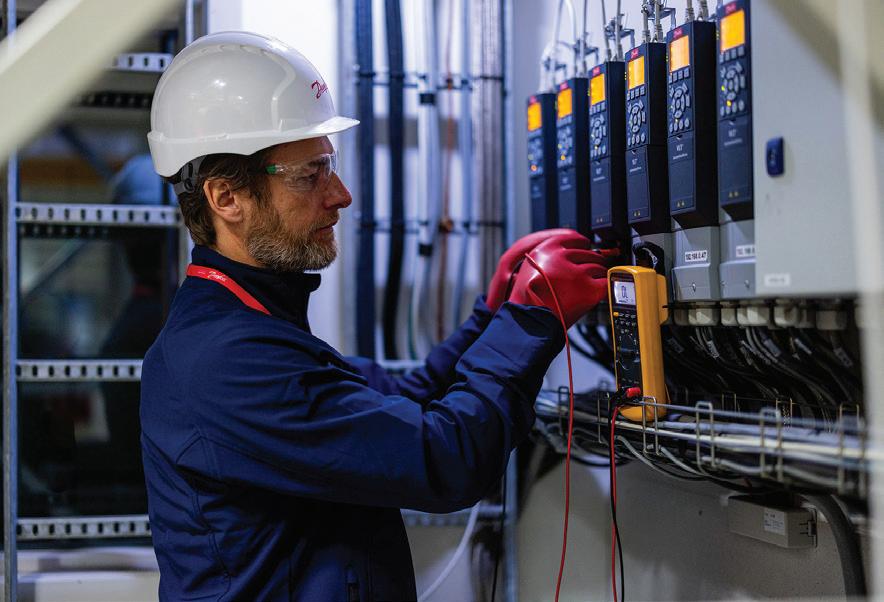
“That just didn’t sit right with us,” added Tony. “We want to provide access to opportunity, understanding and work that builds a better, greener future that will deliver new jobs and economic value.
“There needs to be a solution to scalingup volume delivery of Net Zero skills training to power the clean tech economy and, working with this alliance, I think we can be part of the answer.”
The introduction to CESPA came through a networking event at the Ignite Hydrogen Labs Programme. There were immediate synergies between the alliance and Verciti, especially the organisation’s AR EdTech project that is pioneering the delivery of training and upskilling in the hydrogen industry.
Richard Spears, Marketing Manager at PP Control & Automation and one of the key drivers behind the collaboration, added his support: “What Verciti’s inclusion means is that we can help the very businesses we’re trying to target with the skills needed to bridge the hydrogen and green skills gap. The other really important aspect of the collaboration is that CESPA members can tap into developing in-house certified training programmes with their support.”
He concluded: “The Clean Energy Systems Partner Alliance can now address the skills needed, as well as the capabilities required to maximise the potential of green and clean.”
cespa.org.uk
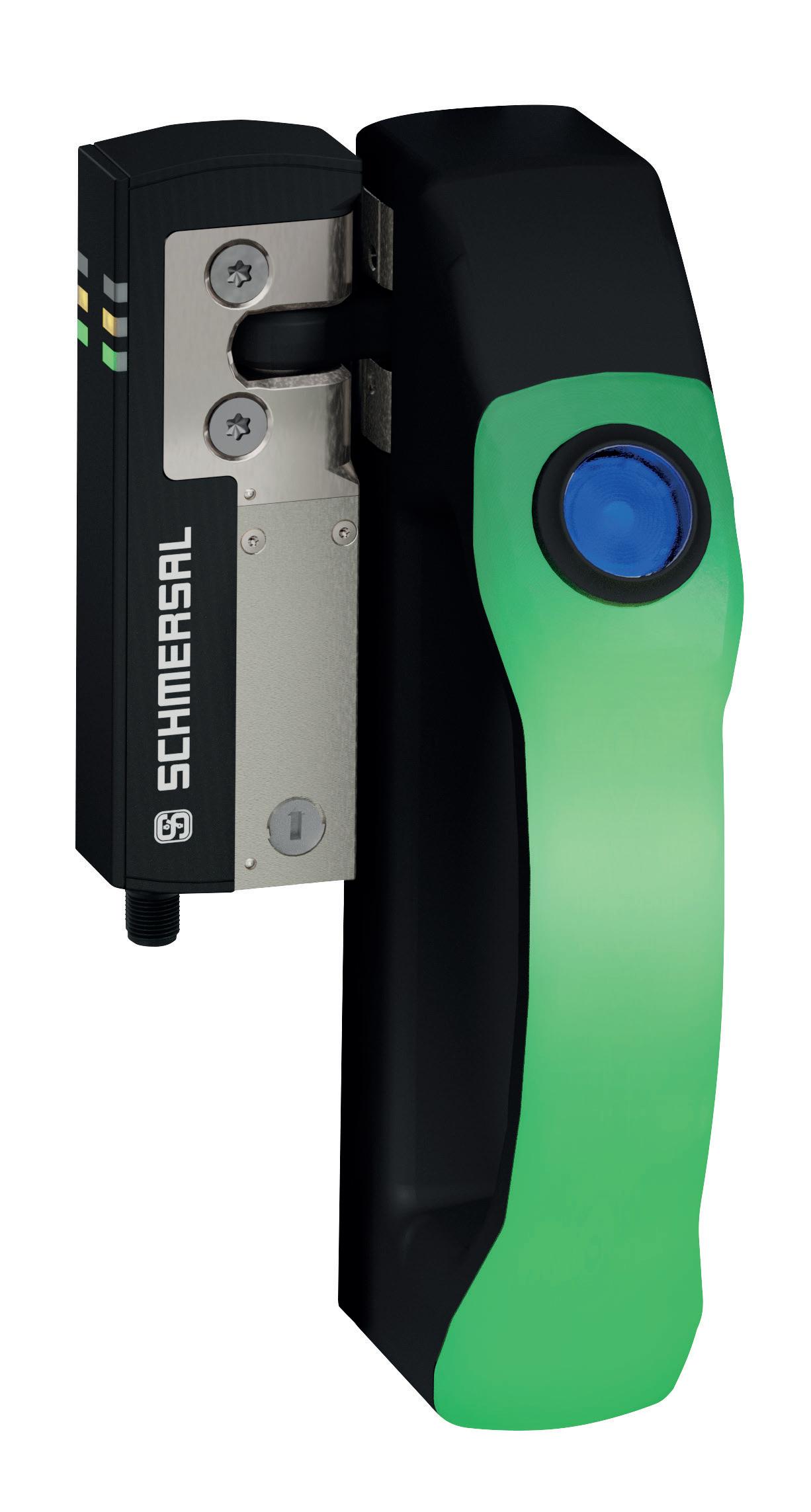
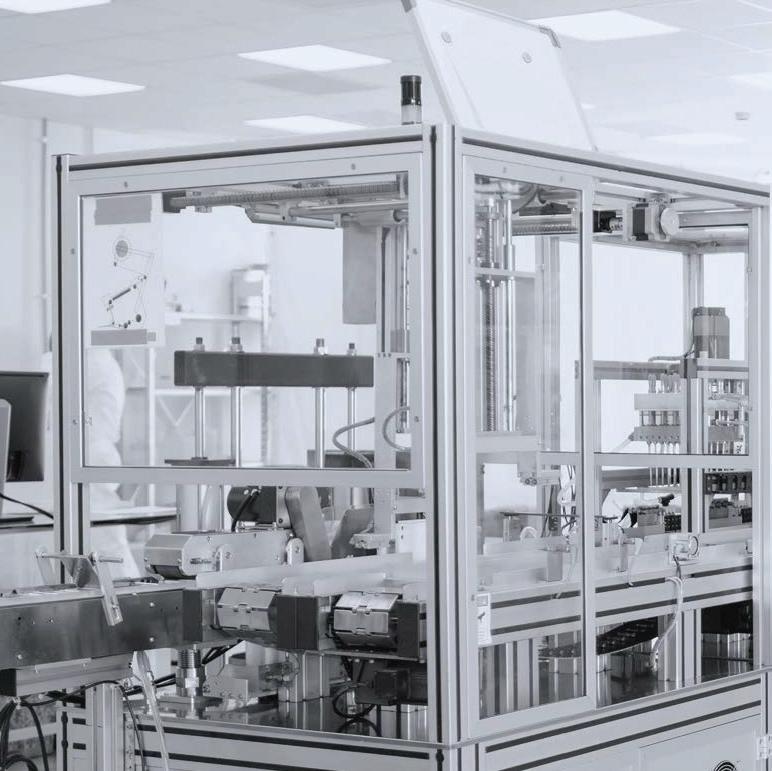
DHS DOOR HANDLE SYSTEM: ENHANCE YOUR PRODUCTIVITY WITH VISIBLE MACHINE STATUS
Schmersal’s innovative DHS door handle system combines the functions of a robust door handle with the signalling of machine status via illuminated handle or push-button.
The door handle system is designed for use with the AZM40 solenoid interlock or with safety sensors from the RSS36 and RSS260 series or as a stand-alone solution. The illuminating handle signals various machine conditions over its area using seven different colours, enabling the user to control the colours individually to signal the machine status.
In addition, a push button is available, which can be individually adapted to customer requirements using the coloured push button caps. The pushbutton can be used for tasks such as a reset function or a request to open the guard door.
SCHMERSAL | Enigma Business Park
Malvern, Worcestershire, WR14 1GL
www.schmersal.co.uk
uksupport@schmersal.com
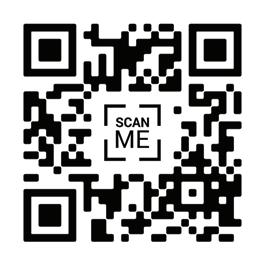
Introducing Musketeers Capital’s Robots
BS Handling Systems proudly announces its partnership with Musketeers Capital, a collaboration that will bring next-generation automation to businesses across the UK.
It is an exciting time to be a part of the retail and logistics sectors. Revenues are generally on the up, and with innovation snowballing at a staggering rate, operations across the world are coming to terms with technologies that utterly transform the ways in which they work.
BS Handling Systems is doing its best to temper its enthusiasm for this progress with a healthy amount of caution. After all, new developments in materials handling must be handled correctly (so to speak) to avoid the pitfalls of drastic change.
Yet the company has heard the industry’s demands loud and clear: businesses require operational agility, accuracy, and scalability like never before. And that’s why BS Handling Systems have partnered with Musketeers Capital – a bold new force in the world of warehousing.
The temptation here is to focus solely on their cutting-edge robotics, but what truly sets Musketeers apart, and what gives the most confidence in this change-making partnership, is how the company supports its clients’ transition to automation. They come for the robots… but they stay for the service.
Two Musketeers
Though Musketeers Capital is a relatively young business, established less than two years ago, its leadership team brings decades of hands-on experience in warehouse automation. Specialising in advanced robotics, intelligent sorting, and material handling solutions, Musketeers is already transforming the way warehouses operate.
Together, BS Handling Systems and Musketeers Capital are making nextgeneration automation accessible to businesses across the UK – offering scalable, cost-effective solutions.
Built for the modern warehouse
Musketeers Capital is a UK-based system integrator with a strong focus on robotic automation. Their core expertise spans autonomous mobile robots (AMRs), intelligent sortation systems, good-to-person technologies, and packaging automation. With a consultative approach and a flexible business model, it helps customers deploy high-performance systems quickly, without the complexity and delays often associated with larger integrators.
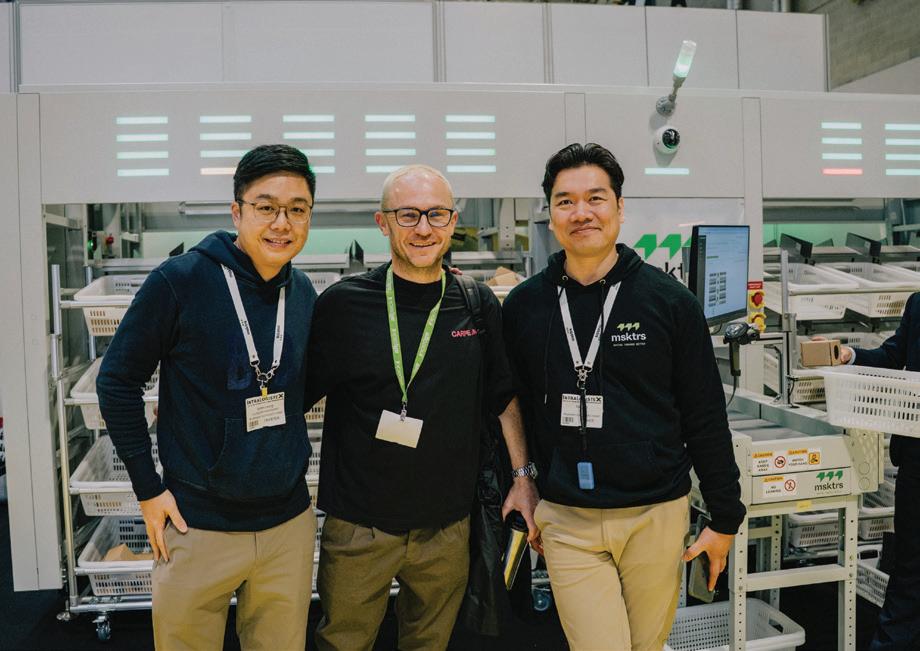
The company serves a broad range of sectors, including retail (apparel, grocery, and high-street), food and beverage, electronics, spare parts, and third-party logistics.
Unique in the market
What sets Musketeers apart is a combination of agility, independence and global reach. Unlike some integrators, the company is not tied to any single technology provider. This allows it to select best-fit solutions based on each customer’s unique operational needs. By working closely with innovative partners – especially those from Asia – Musketeers is able to bring advanced technologies to the UK market at speed and scale.
Designed for tomorrow
One of the key strengths of Musketeers’ offering is future proofing. Its systems are designed to grow with a customers business, thanks to modular hardware and intelligent software. As customer demand shifts or product ranges expand, the technology evolves, keeping performance high without costly overhauls.
Musketeer’s roadmap for 2025 reflects this focus on continuous innovation. New features include AI-powered system analytics, dynamic routing for AMRs, and an enhanced Warehouse Execution System (WES) known as “Automation Hub” tailored to the UK logistics landscape. The company are also exploring automation-as-a-service models to support SMEs and smaller operations, shifting automation from a capital investment to an operating expense.
Why this partnership matters
Musketeers’ fresh thinking, fast deployment capabilities, and access to global technologies complement BS Handling Systems’ decades of experience, trusted customer relationships, and UK market presence. As the demand for flexible, scalable automation continues to grow, this partnership enables BS Handling Systems to deliver automation to a wider audience.
For more information about this partnership or to learn how BS Handling Systems and Musketeers Capital can support your business’ operational needs, please visit the website below.
bshandlingsystems.com
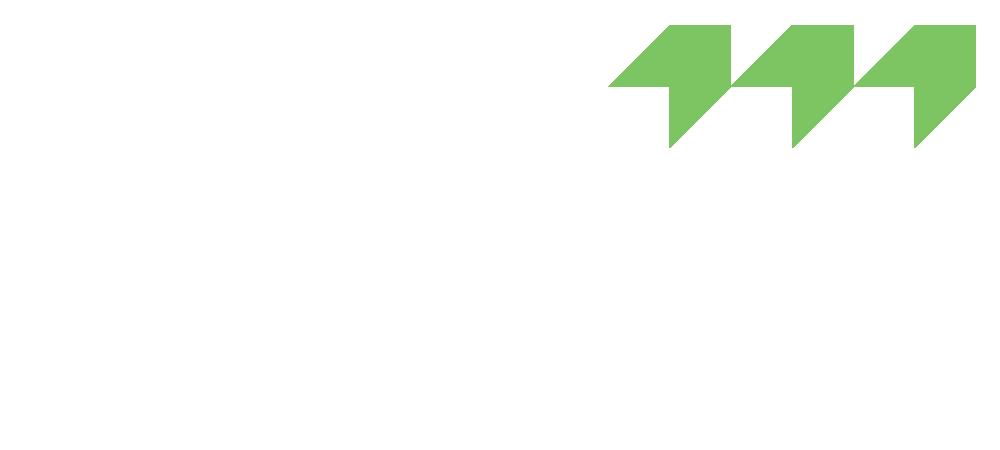
Robot Revolution.
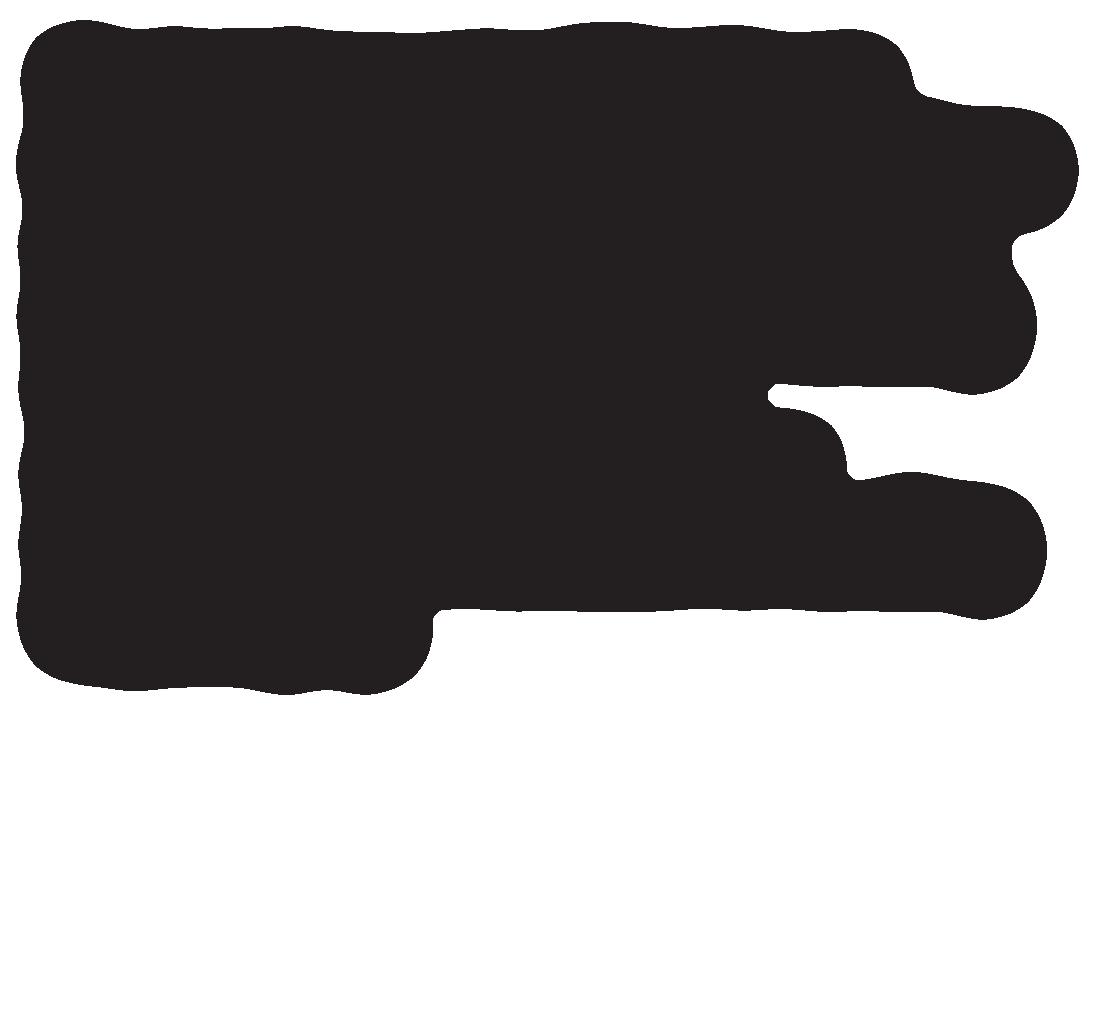
The bots have arrived! But it’s not frightening like it is in the movies. These machines, engineered by Musketeers Capital and integrated by BS Handling Systems, are simply here to automate every aspect of your warehouse, from sortation to handling to packaging.
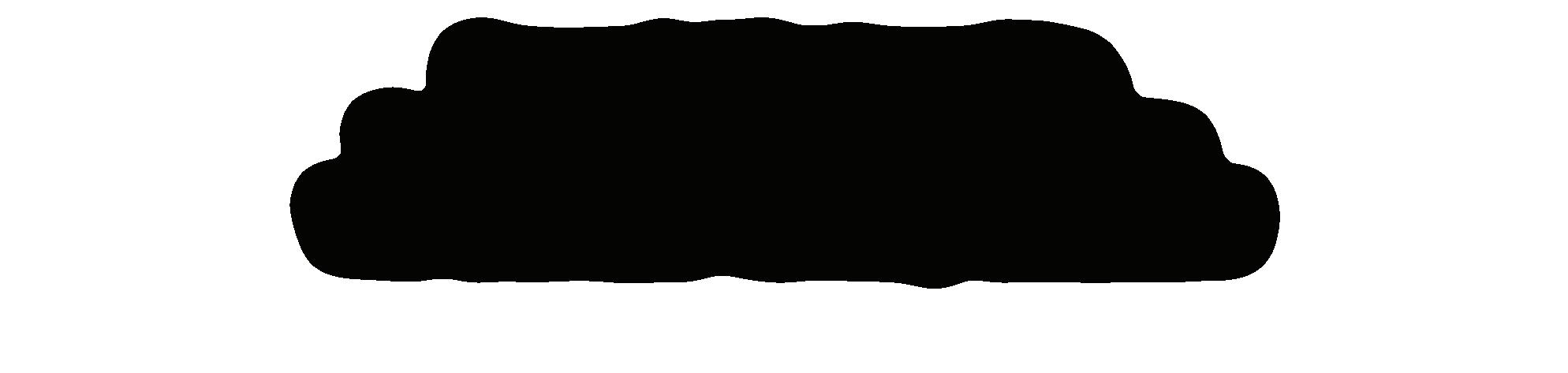
Silverson Videos Show Mixer Versatility
In the latest additions to its ‘how to’ video series, Silverson Machines covers manufacturing ice cream mixes and mixing carrageenan, demonstrating the versatility of its high shear mixers.
In over 75 years of business, Silverson Machines has sold mixers to thousands of customers around the world working in the food and beverage industries. One of the first applications for Silverson high shear mixers was the manufacture of ice cream mixes. Now, going back to its roots, Silverson has added a ‘how to’ video on this application to its already extensive library, along with another recently released video on mixing carrageenan.
Whilst these applications require many different mixing processes to be accomplished – deagglomerating, emulsifying, homogenising and powder/ liquid mixing to name a few – a single Silverson mixer is able to perform all of these mixing tasks. With the exceptionally rapid mixing action of a Silverson high shear mixer, process times are substantially reduced compared to a conventional mixing equipment, whilst achieving a high quality end product.
How to manufacture ice cream mixes
In this video, Silverson demonstrates how to manufacture ice cream mixes and how a typical premix would be made.
Formulations vary widely, but ingredients usually include milk, cream, skimmed milk powder, fat including dairy fat such as butter or vegetable fat, sugars, flavours, colouring, and emulsifiers. Other ingredients, such as hydrocolloids can be used as stabilisers, so it is essential that the mixing equipment is able to incorporate these ingredients into the mix.
Mixing powders into liquids is one of the most difficult mixing operations. This part of the process can cause issues in production, especially when using conventional mixing equipment such as agitators or stirrers. Many manufacturers
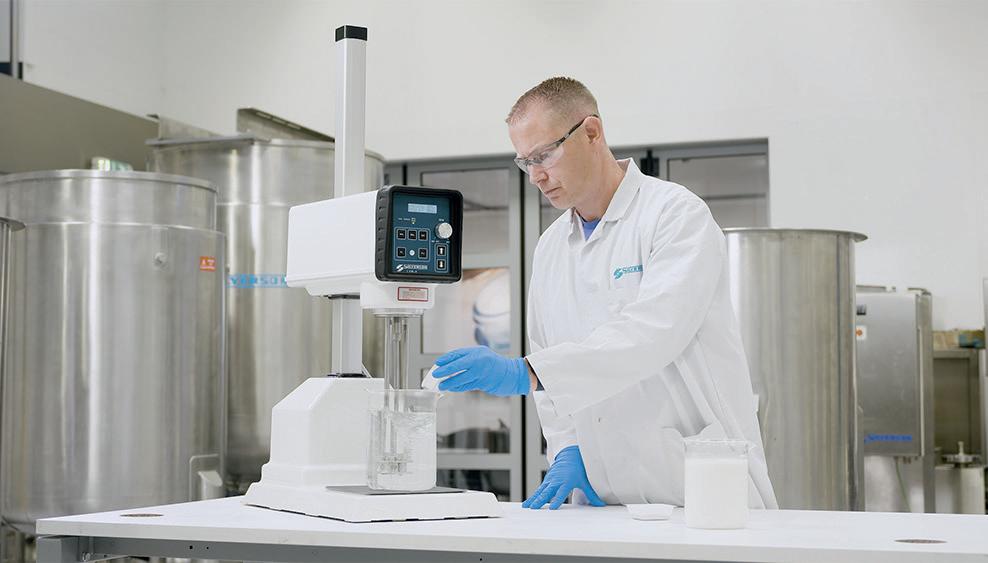
using this type of equipment increase their process time and costs by premixing the powders to try to reduce the formation of agglomerates. But, even when premixing the powders, conventional systems do not provide sufficient shear to break down any agglomerates that form.
The action of the high shear mixer disperses any powders without the formation of agglomerates and ensures that the fat and aqueous phase ingredients are emulsified and reduced to a uniform and fine droplet size, which gives the product the desired stability.
Depending on the scale of manufacturing and recipe, the premix may be subjected to further processing with a high-pressure homogeniser to obtain the smallest possible droplet size. With this process, using a Silverson mixer to create a uniform premix offers considerable reductions in process time.
How to mix carrageenan
In this video, viewers can see how Silverson high shear mixers are able to overcome the common problems associated with mixing different types of Carrageenan and create
an agglomerate-free dispersion. In particular, the video shows how a Silverson in-tank batch mixer is able to disperse carrageenan as quickly as it is added to the vessel. The high speed, high shear mixing action will rapidly draw the powder and liquid into the workhead, where any agglomerates are broken down as they pass through the precision gap between the rotor and stator. This process is completed as rapidly as possible, cutting mixing times by up to 90%.
Processing times can be further reduced with a Silverson high shear mixer as premixing of gum with other powders or non-aqueous phase ingredients is not required – this also simplifies the process.
Other advantages of using high shear mixing technology include obtaining the maximum yield from raw ingredients. As all the agglomerates in the mix are broken down by the high shear action of the mixer, there is no wastage, allowing the manufacturer to reduce the gum content and their raw material costs.
Find the entire series of ‘how to’ videos on the Silverson YouTube channel. silverson.co.uk youtube.com/user/silversonmixers
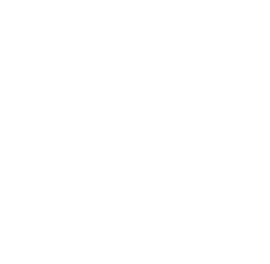
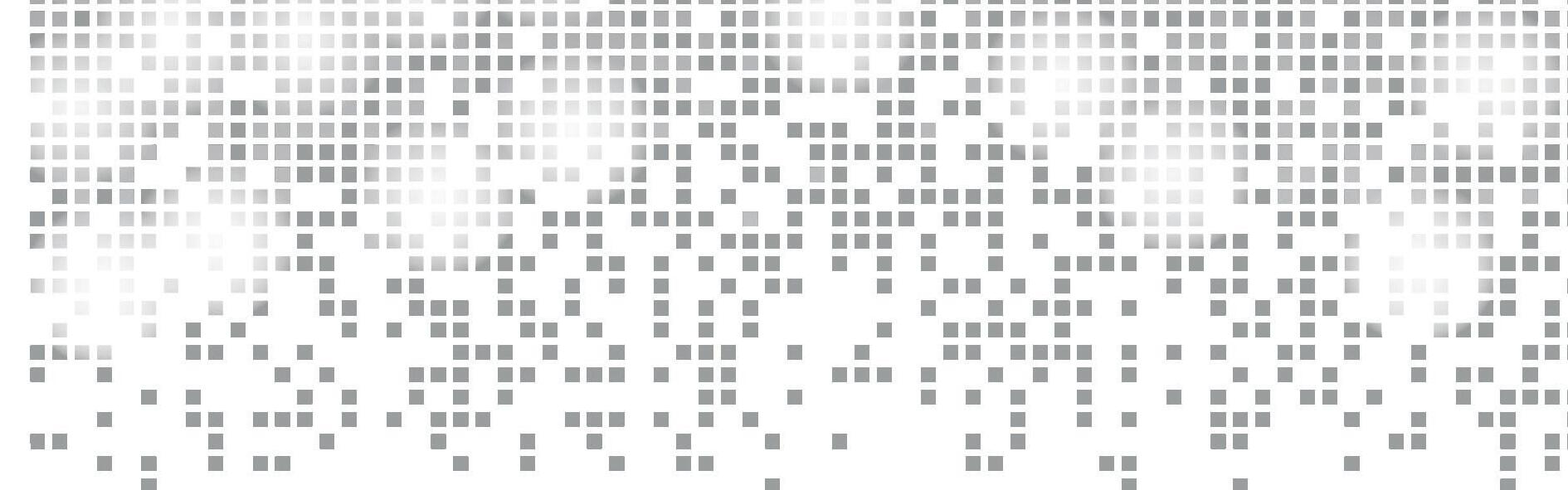
TPL VISION
EXPERTS IN LED LIGHTING FOR THE MACHINE VISION INDUSTRY
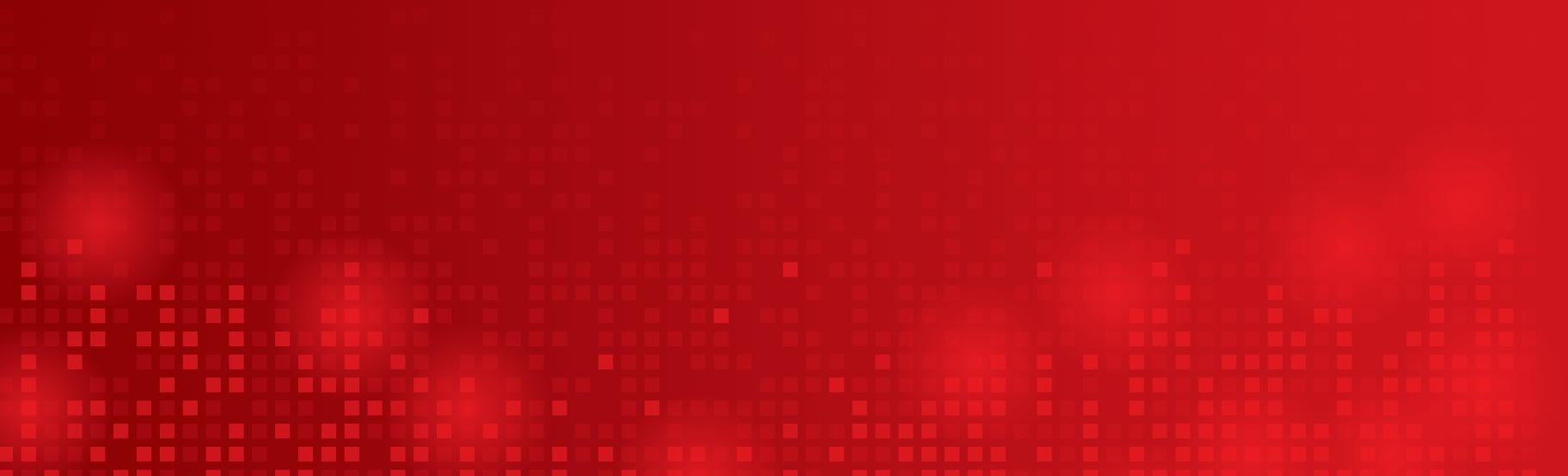
100s POSSIBILITIES WITH JUST A FEW PRODUCTS.
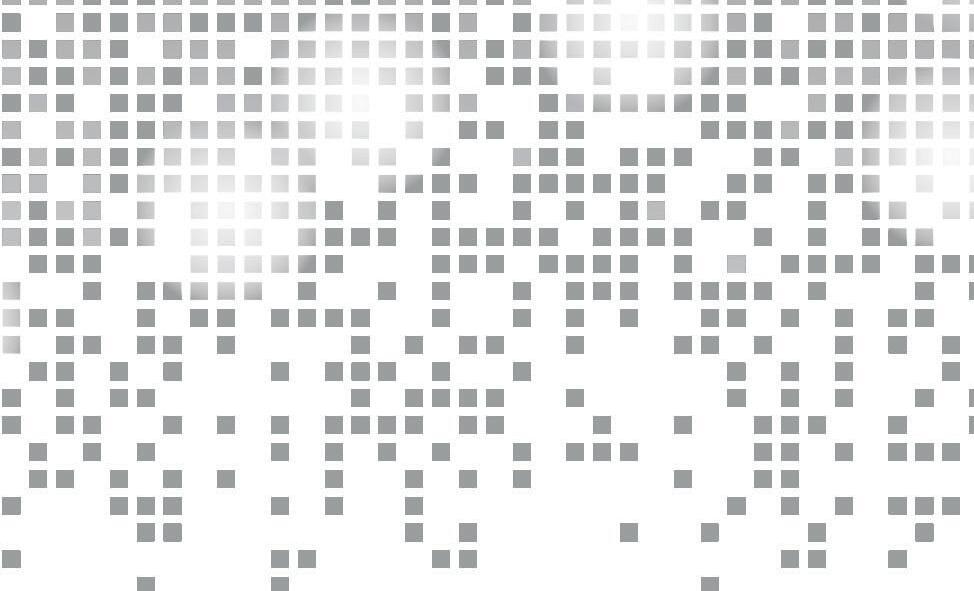
RING LIGHTS FOR EVERY APPLICATION!
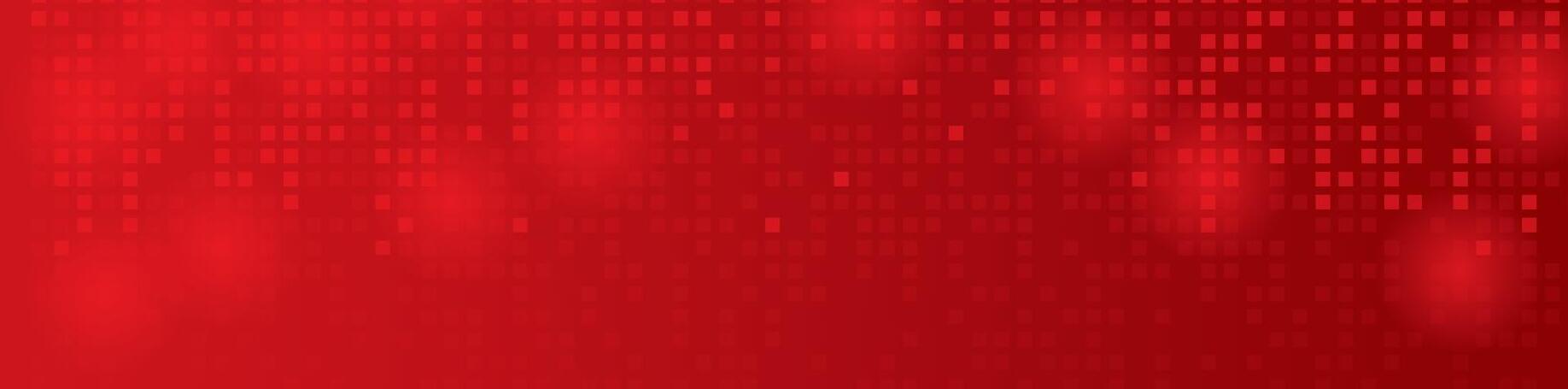
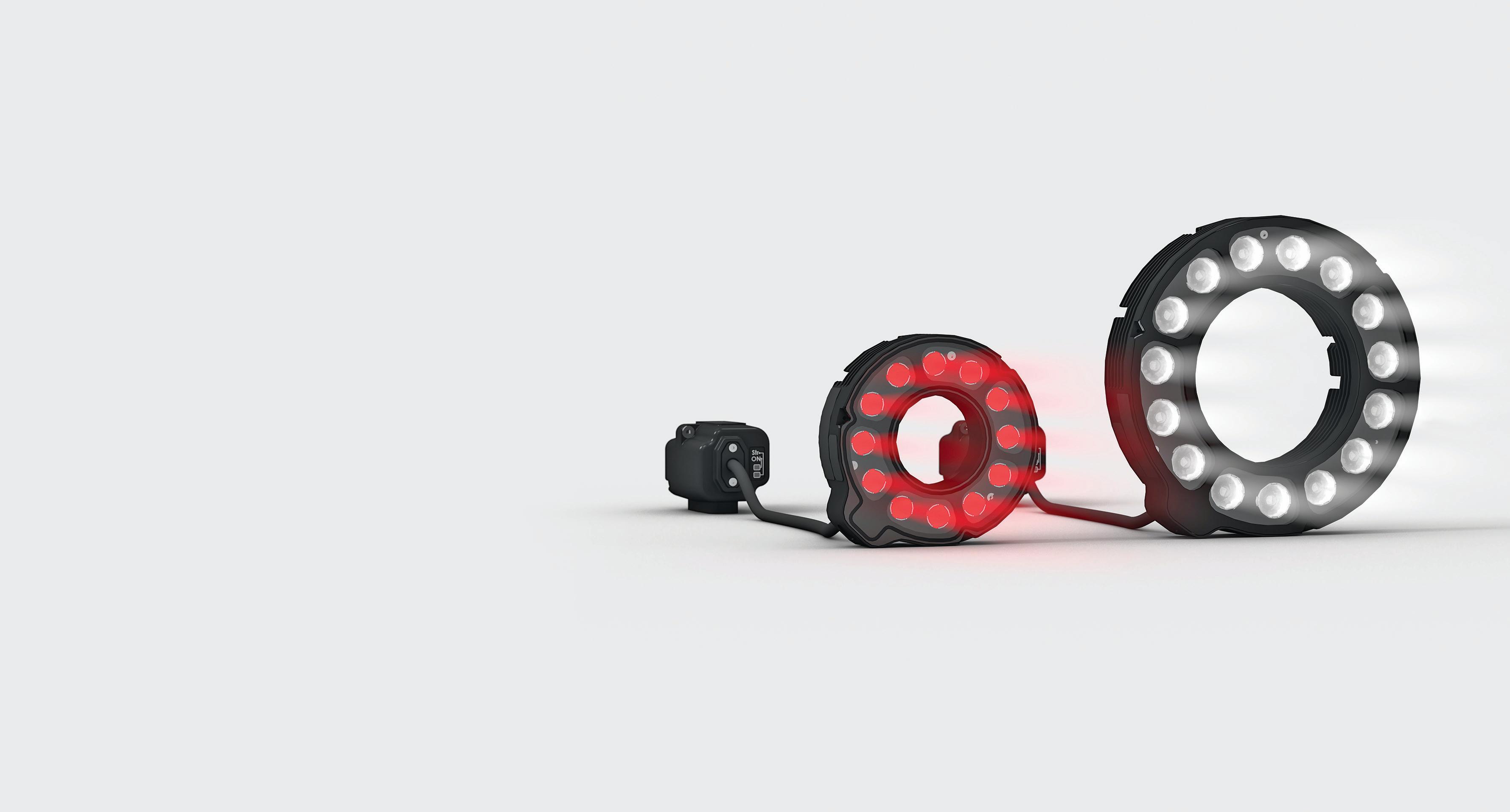
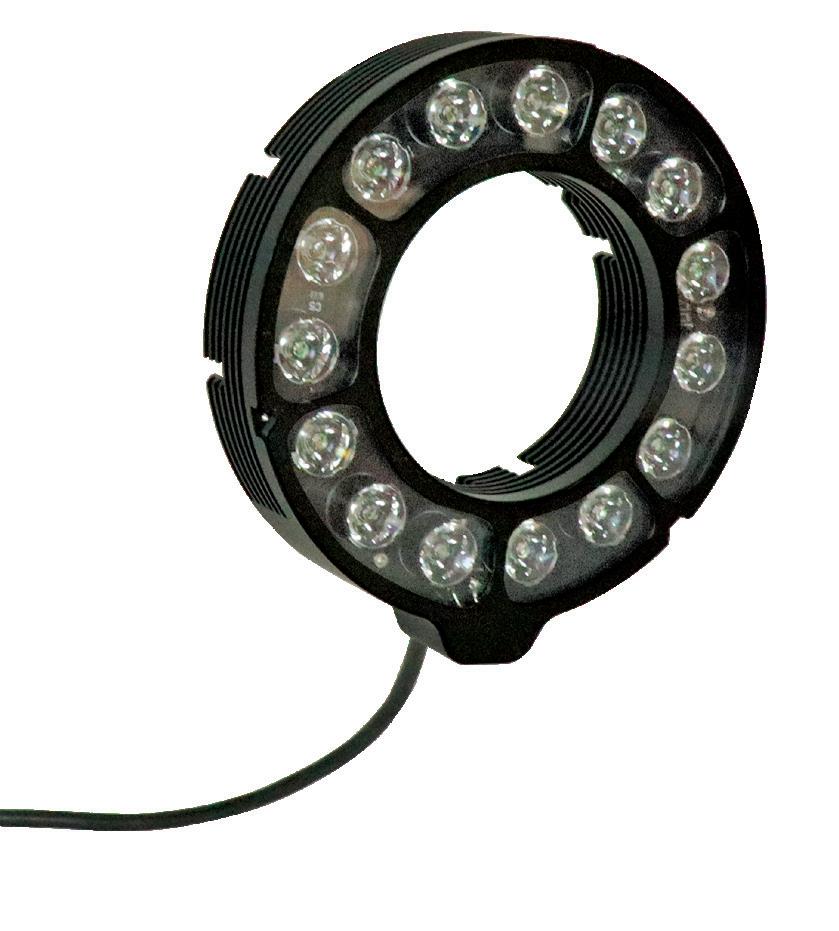
/ High-power 76 mm ring, / CW and Strobe OverDrive, / Transparent or opaque diffuser.
Compatible with 8 different Angle Changers, including the Convergent version.
CONFINED ENVIRONMENTS
/ Compact 37 mm ring, / Angle Changer compatible, / Transparent or opaque diffuser.
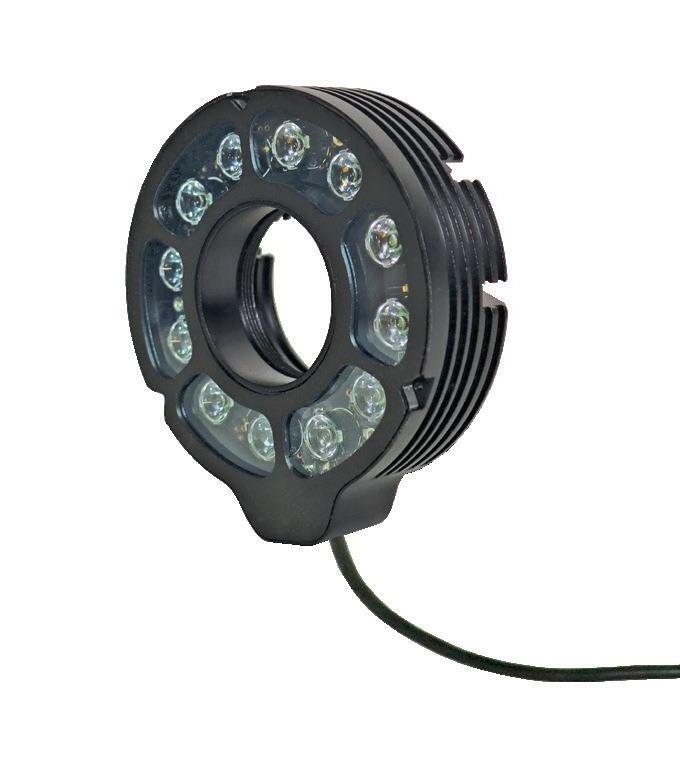
VERSATILE RING LIGHT POWERFUL RING LIGHT
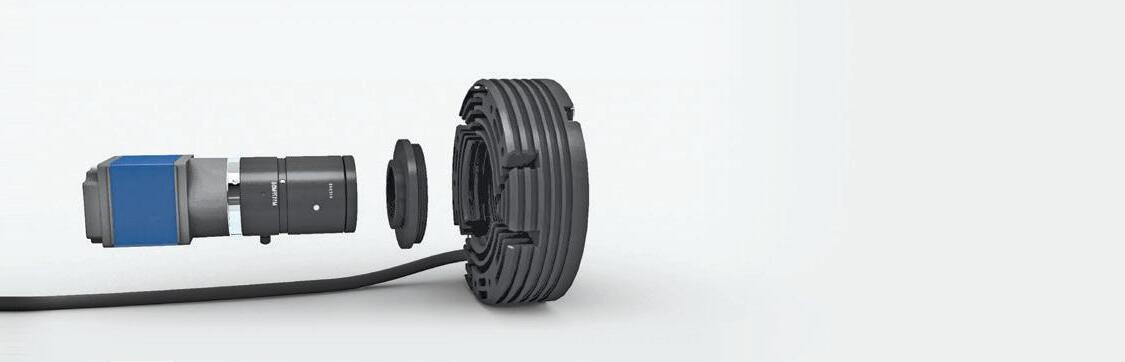
Direct attachment to C-MOUNT lenses.
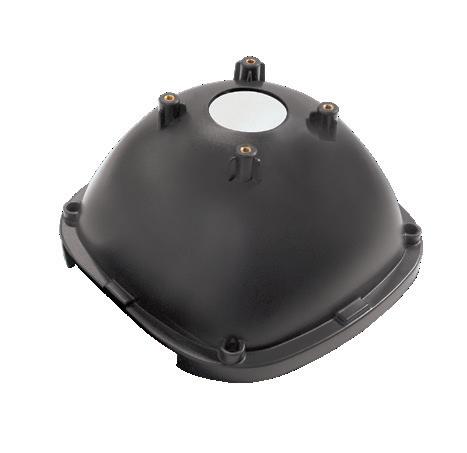
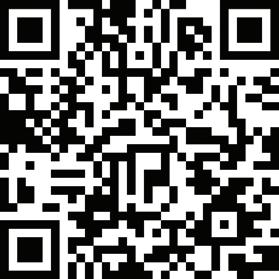
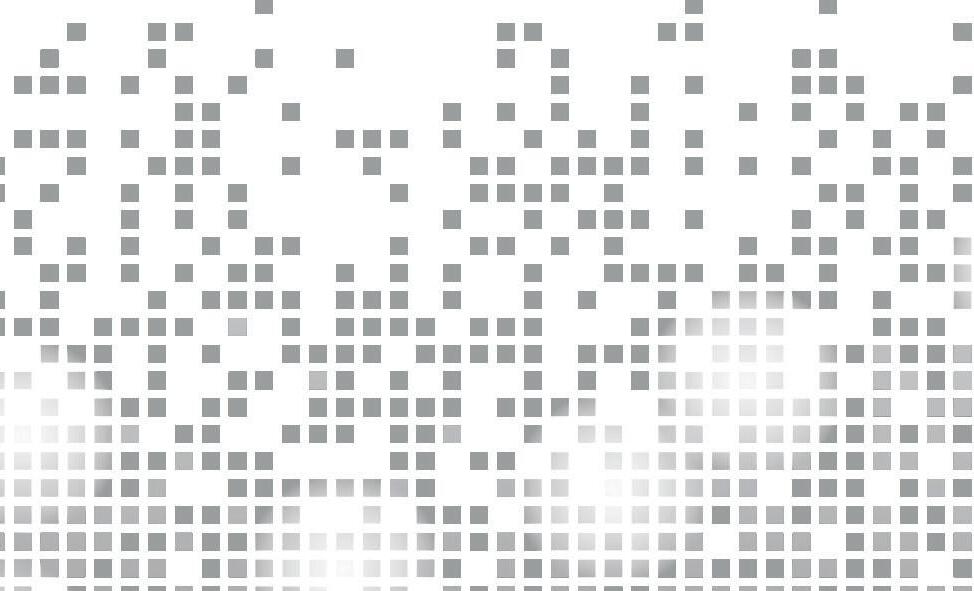
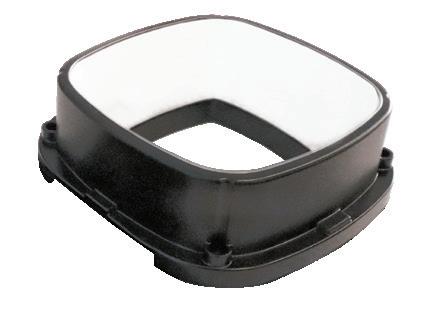
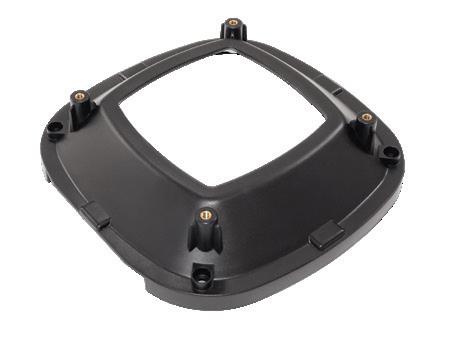
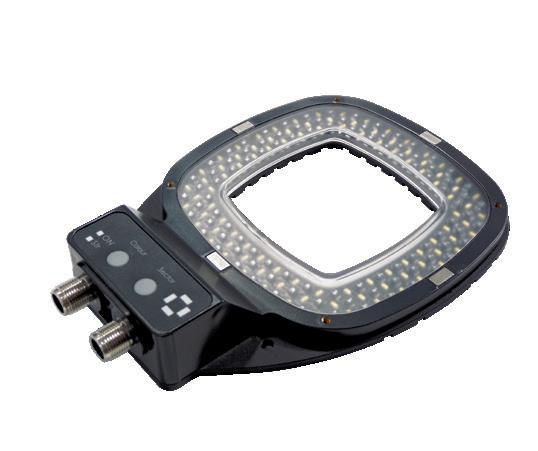
/ Bicolour Modular ring light, / Available in 2 dimensions, / Full control of the 4 sectors / OverDrive embedded, / 3 accessories: Dome, Dark Field & Low Angle, / IP65 as standard.

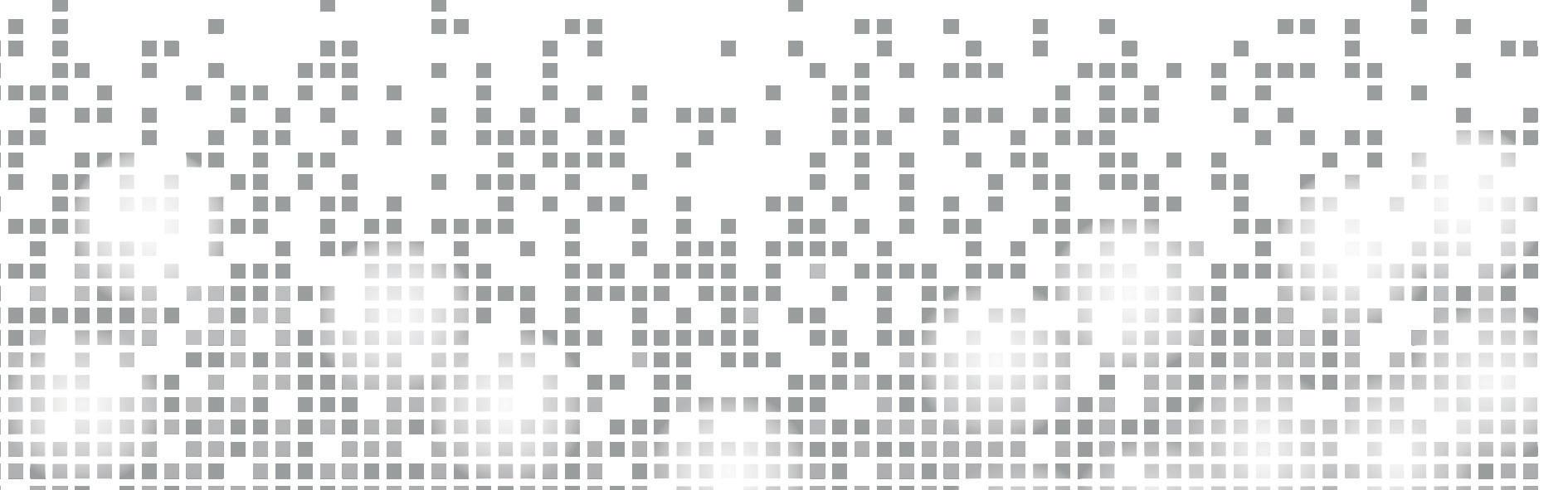

Transforming Detection and Analysis
Quantum Design UK and Ireland Introduces IXRF, designer and manufacturer of world-class scientific measurement instruments. Here, IXRF explains the wide applicability of microXRF systems, from QA in manufacturing to determining the material composition of artefacts on archaeological sites.
Led by a team of experienced scientists and engineers, IXRF has distinguished itself as an innovator in the field of high-end X-ray microanalysis instruments. Here, IXRF’s experts satisfy our curiosity about the many fascinating applications of their leading microanalysis technology.
1. How are IXRF’s microXRF systems commonly applied in the processing industry?
IXRF’s microXRF systems are widely used across the processing industry for rapid, non-destructive elemental analysis. They are essential for quality control, measuring coating thickness, detecting contamination, and verifying raw materials. Industries such as metal processing, petrochemical production, electronics, and ceramics rely on IXRF’s systems to ensure product consistency and compliance with strict material specifications. Our microXRF technology enables the analysis of a wide range of sample types, including bulk materials, thin films, powders, and even irregular surfaces, providing a flexible and efficient solution for industrial process monitoring.
2. In addition to its range of innovative products, how else does IXRF support its customers?
At IXRF, we believe that innovation should be matched with exceptional support. Our team offers comprehensive services including expert application development, personalised training, on-site installations, and dedicated technical support. We
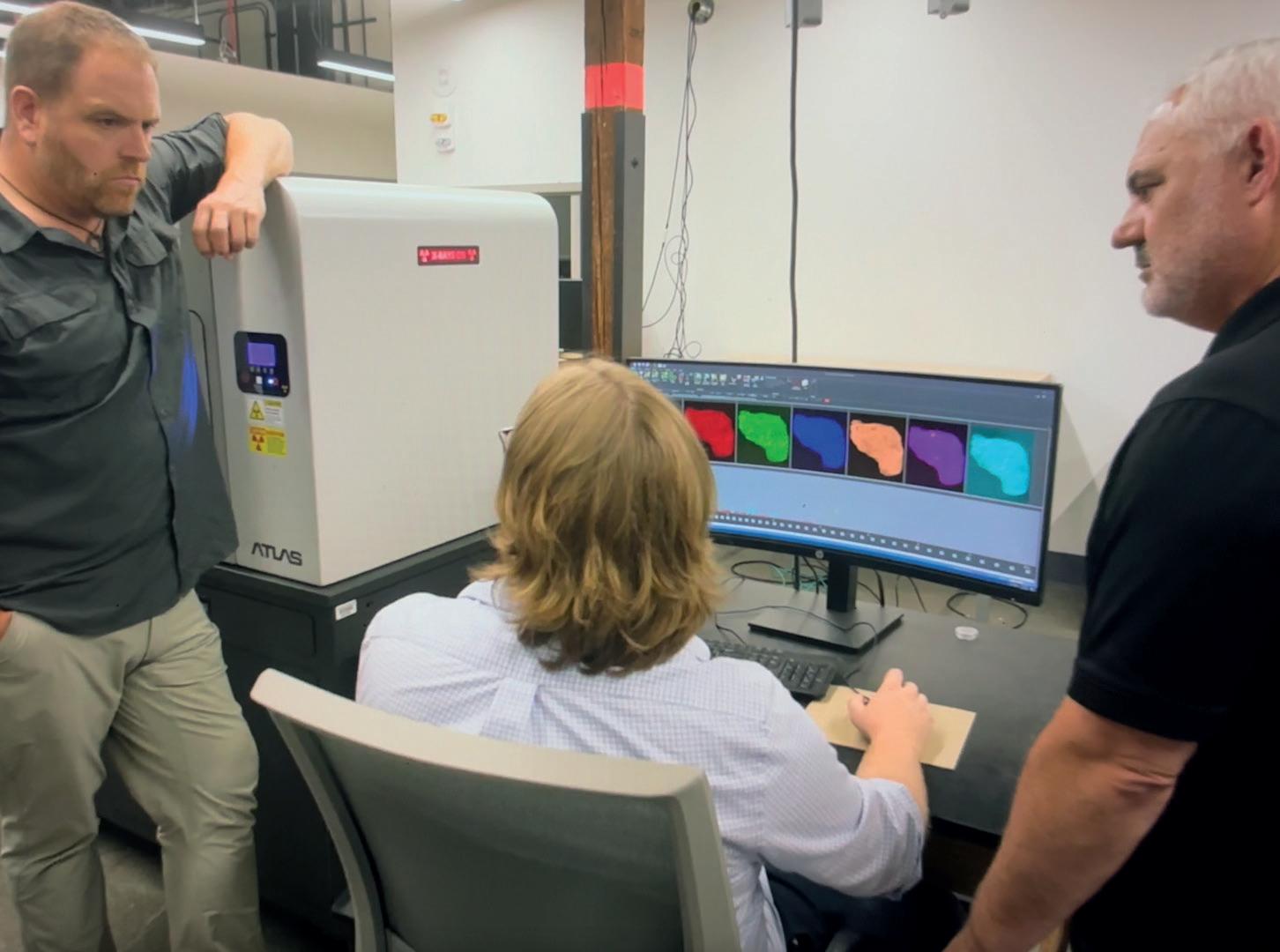
work closely with customers to tailor solutions to their specific needs and provide ongoing consultation to optimise performance. Additionally, we offer free software upgrades for life, ensuring that users always have access to the latest capabilities. Our commitment to partnership ensures that customers are supported at every stage—from initial consultation to long-term system optimisation.
3. How are IXRF’s microXRF solutions applied to the recycling and waste industries?
IXRF’s microXRF technology plays a crucial role in the recycling and waste industries by enabling rapid, non-destructive elemental analysis of complex, heterogeneous materials. A growing application is the recycling of used solar panels, where our systems are used to identify and quantify valuable elements such as silicon, silver, and lead. By providing precise compositional data, microXRF helps recyclers efficiently recover materials that can be reused in the manufacturing of products such as glass bottles, electronic components, and even new photovoltaic devices. Our solutions enhance material recovery rates, reduce environmental impact, and ensure compliance with regulatory standards—all
while handling the challenging variability found in post-consumer waste streams.
4. To date, what is the most interesting or unusual custom application of IXRF microXRF analysis?
One of the most fascinating custom applications involved analysing ancient artefacts recovered from archaeological sites. Our microXRF system was used to determine the elemental composition of rare coins, ceramics, and pigments without damaging the priceless materials. This allowed researchers to uncover historical trade routes, manufacturing techniques, and even authenticate artefacts—all while preserving their integrity. It’s a testament to the versatility of IXRF technology: from cutting-edge industrial quality control to unravelling the mysteries of history, our instruments empower users across a stunning range of fields. qd-uki.co.uk
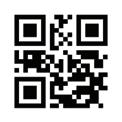
Micro-XRF systems
The 5 micron advantage
The ATLAS M is the bench-top micro-XRF tool of choice for sample characterisation using micro X-ray fluorescence (micro-XRF) hyperspectral imaging microscopy for information on composition (phase) and elemental distribution. With the smallest X-ray spot in the industry at 5 µm, this unique XRF microscope is optimised for analysis speed without compromising accuracy.
The instrument can measure a wide range of sample types, whether small or large, even or irregularly shaped. Equipped with a large high-speed stage, it supports 2D analysis of virtually any kind of sample: solids, liquids, powders, thin-films and particles. Its large vacuum chamber delivers superior light element (low-Z) sensitivity.
• Largest sample chamber in the industry
• Spot size down to 5 microns with anti-halo optic
• SDD detectors w/ active area up to 150 mm2
• Edge-to-edge mapping of 300 mm wafers
• 50 kV / 50 W polycapillary optic micro X-ray source
• Multi-point/multi-area automation & mapping
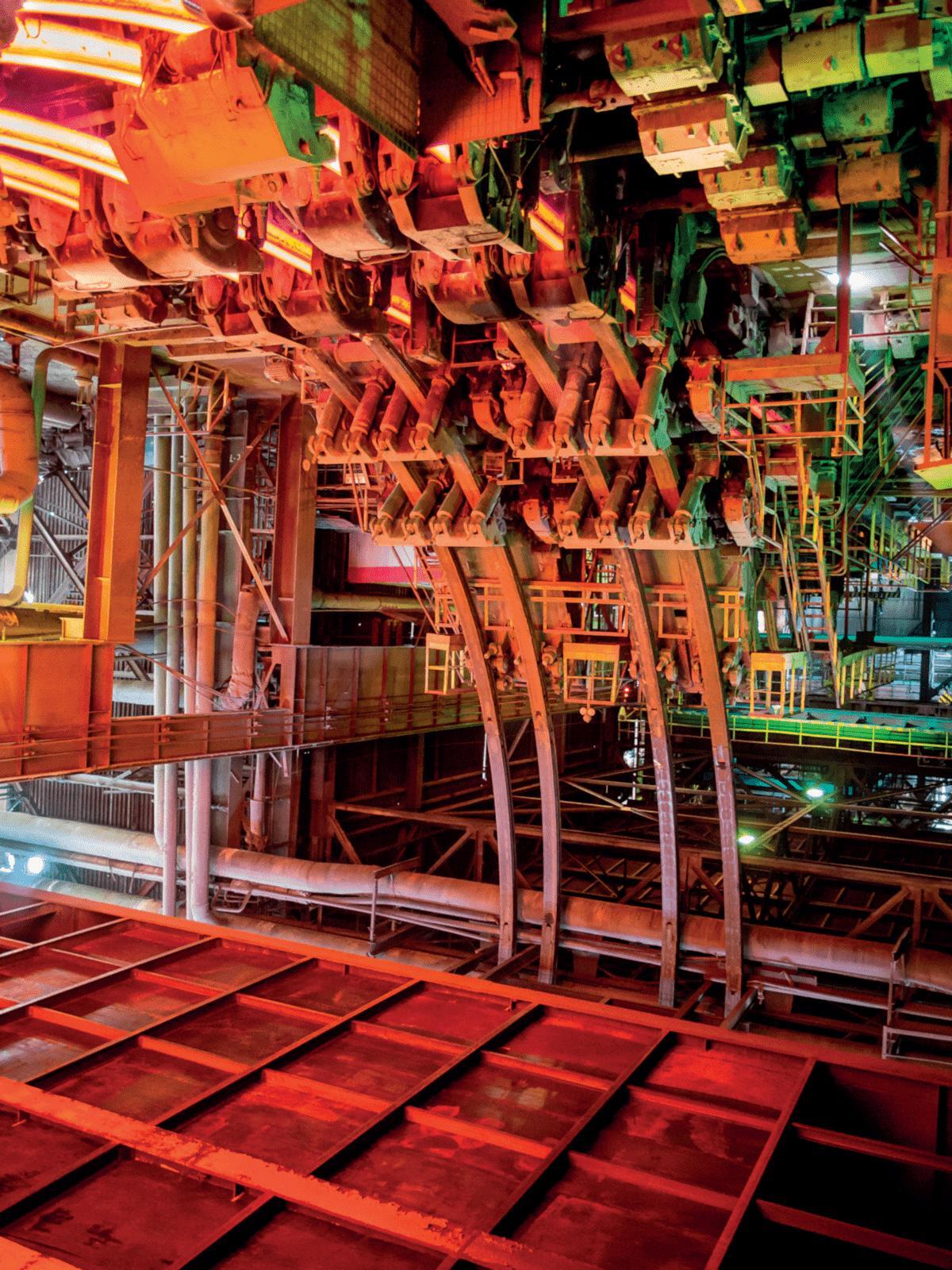


• Air, vacuum, helium for solids, liquids, and powders
• Iridium Ultra software running on Windows™ 10 OS
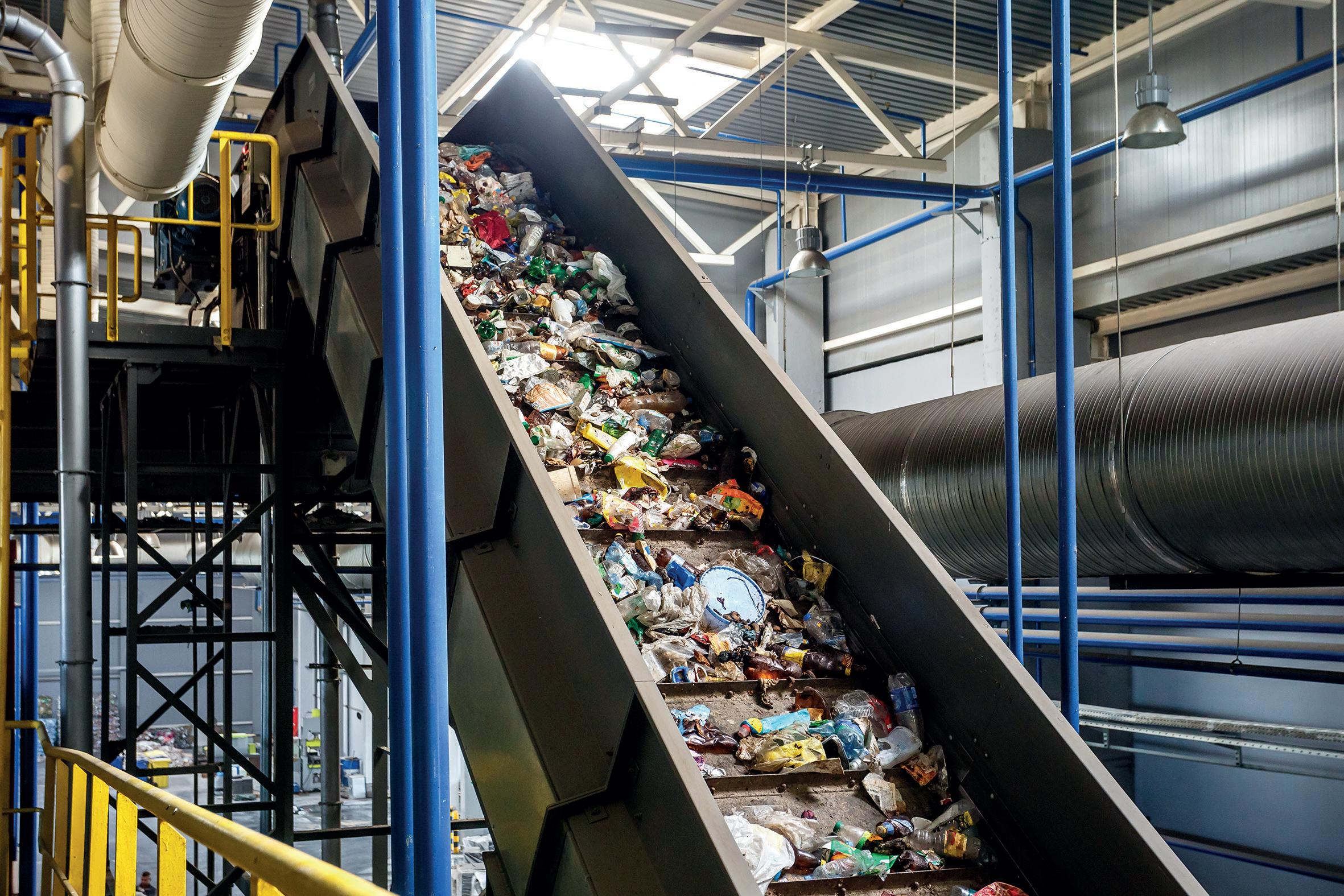
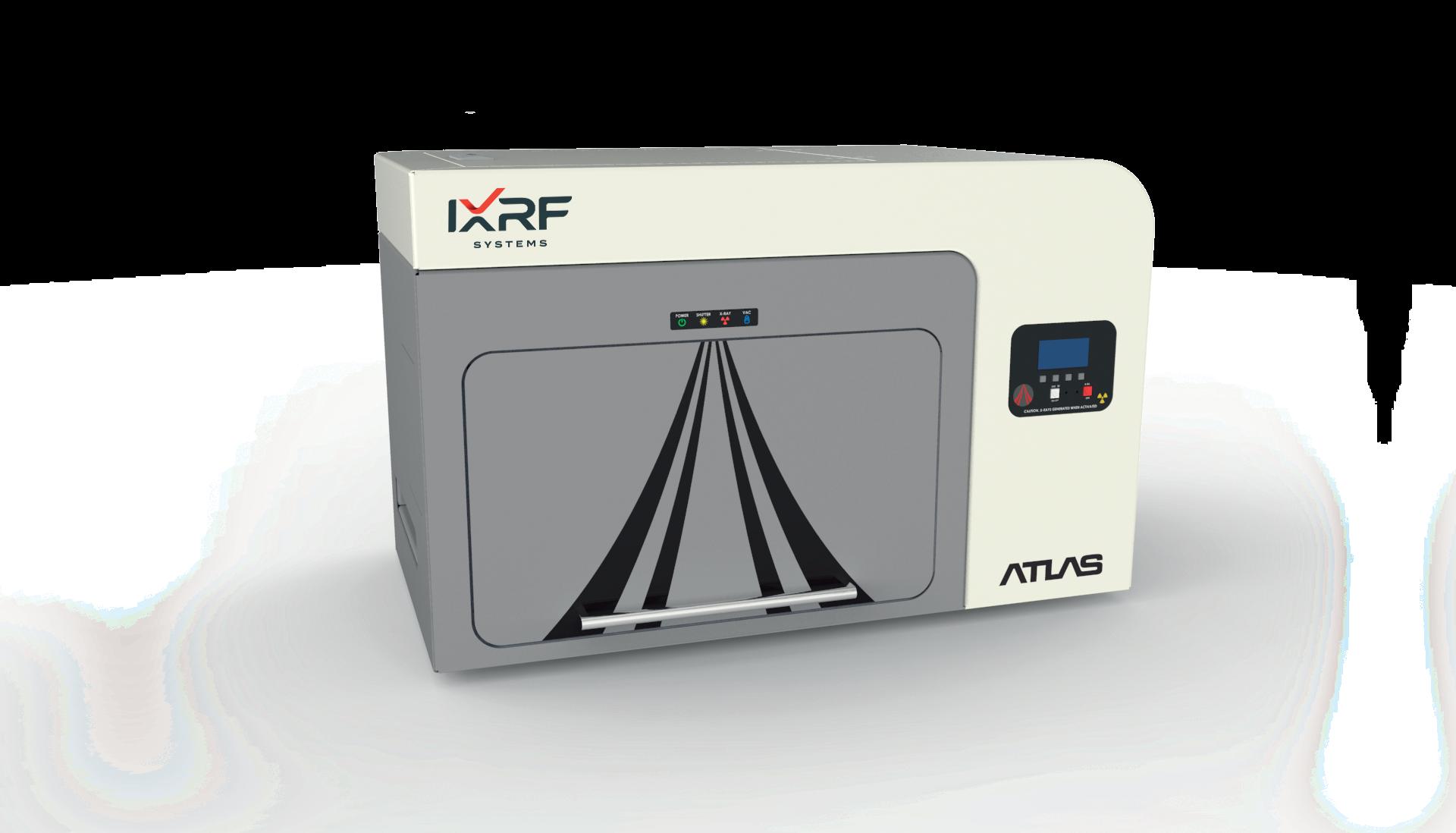
Tel: 01372 378822
Email: info@qd-uki.co.uk
Advanced Automation Confocal Controllers
Precision sensor supplier Micro-Epsilon has extended its confocalDT range of confocal chromatic measurement systems with two new confocal controllers. Compact in size, they enable even higher precision for non-contact distance and thickness measurements in industrial environments on almost all surfaces.
Confocal Chromatic sensor technology has become the preferred technology when laser sensors cannot achieve the measurement requirement. They offer significant advantages over laser sensors including the use of a white LED light source, not laser, which is much more stable and has lower noise on reflective surfaces. They measure in direct axis and not in triangulation, so can measure against very shiny or even mirrored surfaces and because of this, confocal sensors do not suffer from shadowing when scanning over a surface or object. Furthermore, confocal chromatic sensors are able to measure on transparent and liquid surfaces without problems.
The new confocalDT IFC2411 and 2416 confocal controllers are compatible with all confocal sensors in the Micro-Epsilon portfolio, while setting new standards in precision and speed. Modern interfaces enable rapid integration into industrial machines and control systems.
Fastest controller in its class
The new confocalDT IFC2416 controller is the fastest in its class with a measuring rate of up to 25 kHz, achieved through a greater LED light intensity. This enables precise, stable measurements at high speed, even on challenging materials and surfaces. Its compact design makes it ideal for high resolution (up to 2 nm) distance and thickness measurements in almost all industrial sectors – from the production line to semiconductor machines. Due to the multipeak measurement function, even multi-layer thickness measurements (up to five layers) can be carried out on transparent objects.
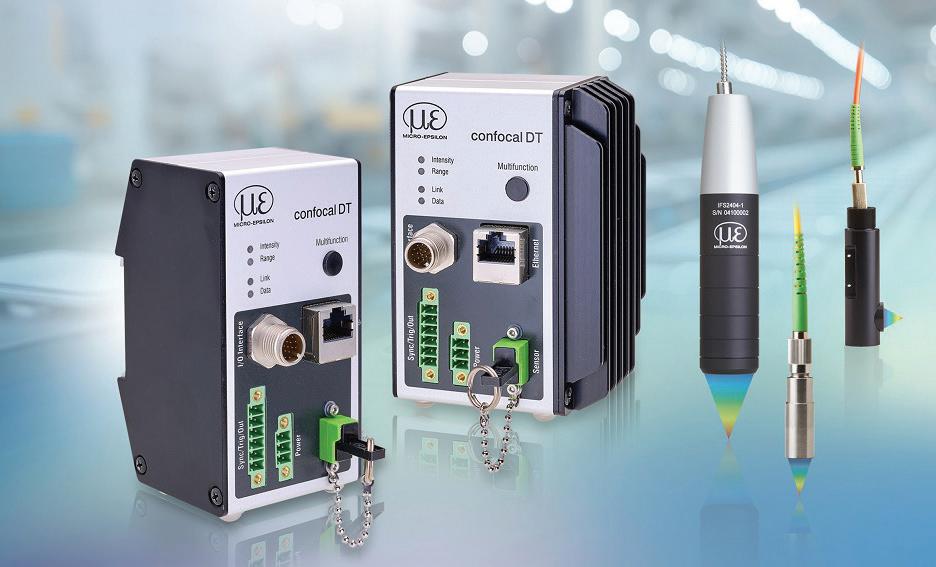
The IFC2416 controller is also versatile: it is compatible with all Micro-Epsilon confocal sensors, so that the measuring range, base distance and special sensor properties such as vacuum suitability, measuring angle or beam path can be chosen as required. Due to its extremely small, unique design, the controller requires hardly any space and fits into even the smallest of control cabinets. At just 460 g, the controller is also extremely light, enabling fast, easy installation on a DIN rail. The entire configuration of the controller and sensors is carried out via an easy-touse web interface (accessed via an Ethernet connection) without requiring any additional software. A material database is available to store thickness parameters, which can be expanded as required.
World’s smallest controller
The confocalDT IFC2411 controller delivers high precision measurements at a resolution of 2 nm and has an adjustable measuring rate of up to 8 kHz. Due to a wide range of interfaces, including a new Ethernet connection, the controller offers maximum flexibility for integration into machines and systems. The housing is up to 300% smaller than comparable controllers and weighs just 335 g, enabling it to be mounted on a DIN rail in the smallest of control cabinets.
The introduction of the direct Ethernet interface completes an impressive lineup of interface options available for the IFC2411 controller family. This includes fieldbus versions for EtherCAT, ProfiNET and Ethernet/IP, an RS422 serial interface, as well as analogue output. Further integration possibilities include direct encoder input channels and trigger input options.
The confocalDT IFC2411 and 2416 controllers are compatible with all confocalDT sensors from Micro-Epsilon, covering measuring ranges from 0.1 to 30 mm. The introduction of these new compact controllers complements the existing confocal portfolio and offers customers even greater flexibility when it comes to selection for their control system environment and advanced automation setups.
For more information on the confocalDT IFC241x range of controllers, please visit Micro-Epsilon’s website. micro-epsilon.co.uk
The confocalDT IFC2411 and 2416 confocal controllers are compact and robust, while setting new standards in precision and speed.
HGM-S: MAKING A WELCOME CONTRIBUTION TO ENERGY TRANSITION.
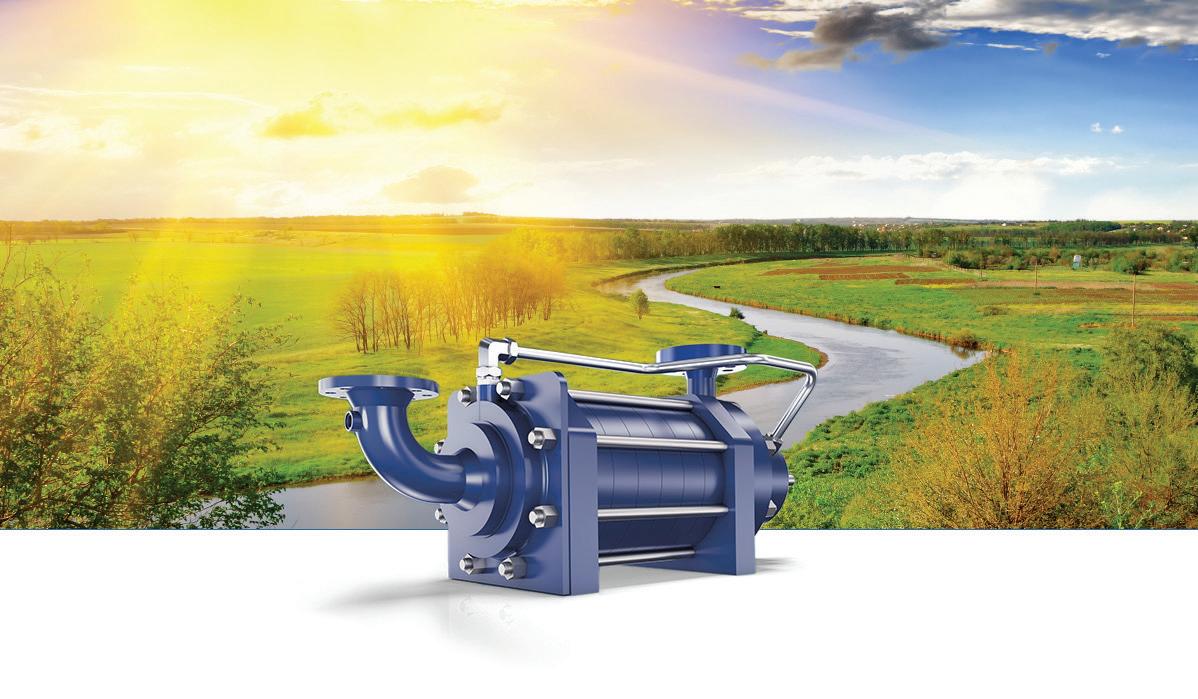
The future belongs to energy generation from renewable sources, and KSB drives this progress. With highly efficient and reliable products that are perfectly prepared for the aggressive environmental conditions they may encounter. The HGM-S has been specially developed for use in regenerative power plants, such as waste-toenergy plants, biomass power plants and industrial boilers.
www.ksb.co.uk - 01509 231872 - sales@ksb.com
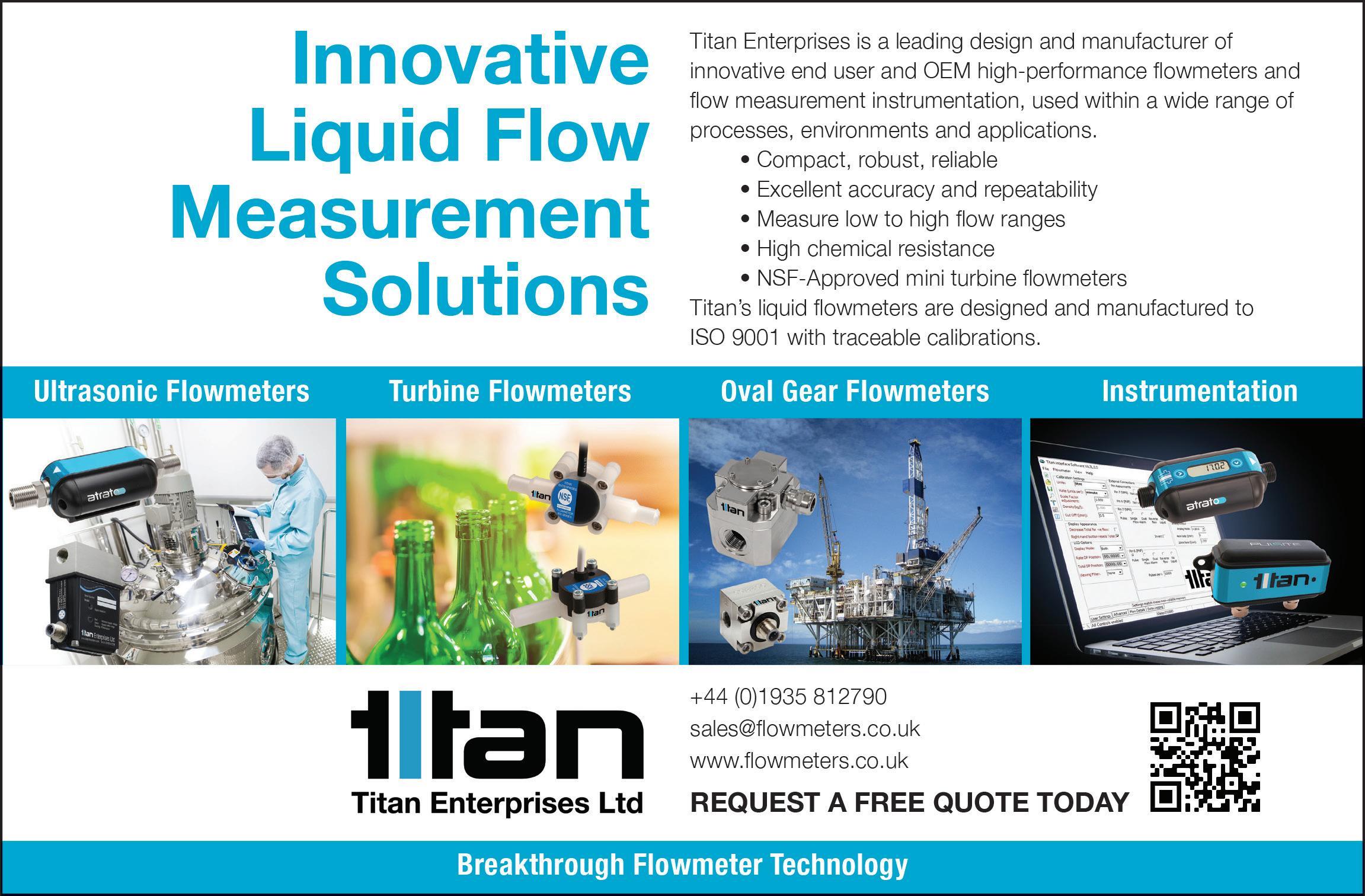
Precise Thermocouple Connectors
Thermocouple connectors are vital components in temperature measurement systems, ensuring accurate and reliable connections between thermocouples and instrumentation. The engineering behind these products is key to their precision and reliability, as temperature and control specialist Labfacility demonstrates.
The role of thermocouple connectors
Thermocouple connectors act as the interface between thermocouple wires and the measuring device, ensuring that the thermoelectric signal generated by the thermocouple remains intact during transmission. A high-quality connector minimises signal loss, preserves measurement accuracy, and ensures stable operation in challenging environments.
As a trusted name in temperature sensing and control, Labfacility offers a comprehensive range of thermocouple connectors designed to meet the demands of various industries, from manufacturing and process control to research laboratories.
Available in a wide range of configurations, Labfacility’s connectors are suitable for both standard and miniature applications and are compatible with a variety of thermocouple types, including K, J, T, N, and more.
Key features of Labfacility thermocouple connectors
Robust materials: Labfacility’s thermocouple connectors are manufactured from high-quality materials such as durable thermoplastics for the body and precisionengineered alloys for the contact pins. This ensures excellent performance even in harsh conditions, including extreme temperatures, high humidity, and exposure to corrosive substances.
Colour coding and compliance: to simplify installation and reduce the risk of wiring errors, Labfacility’s connectors are colour-coded according to international thermocouple standards, such as IEC, ANSI & JIS. This ensures compatibility and ease of use in global applications.
Ease of assembly: with user-friendly
designs, Labfacility connectors enable quick and secure assembly. Features like captive screws and clearly labelled polarity markings make installation straightforward, saving time during setup and maintenance.
Versatile mounting options: whether the requirement is for in-line, panel-mount, or quick-wire connectors, Labfacility offers a versatile selection to suit an application’s specific requirements. This adaptability ensures seamless integration into existing systems.
Applications and benefits
Thermocouple connectors are used across diverse industries, including aerospace, automotive, pharmaceuticals, food processing, and energy. They are particularly valued in critical processes where temperature accuracy and reliability are paramount. The engineering behind these connectors reduces measurement uncertainties, enhances system reliability and minimises downtime, all of which contribute to operational efficiency and cost savings.
Labfacility
Labfacility’s connectors undergo rigorous quality control to ensure consistent performance. This commitment to excellence has made them a preferred choice for professionals worldwide. With over 50 years of expertise in temperature measurement and control, Labfacility is a trusted partner for high-quality thermocouple connectors.
Labfacility’s partnerships with Digikey and Farnell, provides multiple convenient options to access our high-quality temperature measurement products. Both Digikey and Farnell stock an extensive selection of our products, including thermocouples, RTDs,
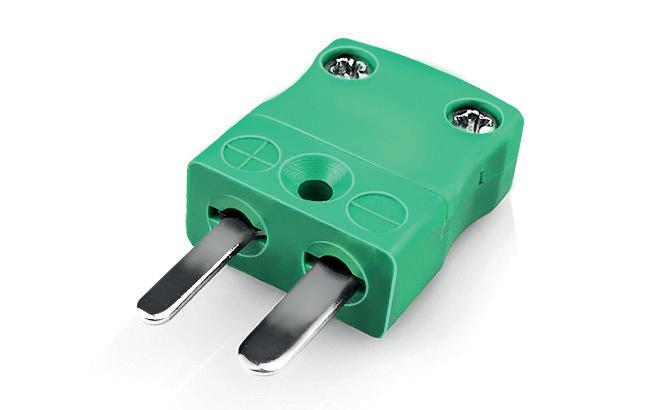
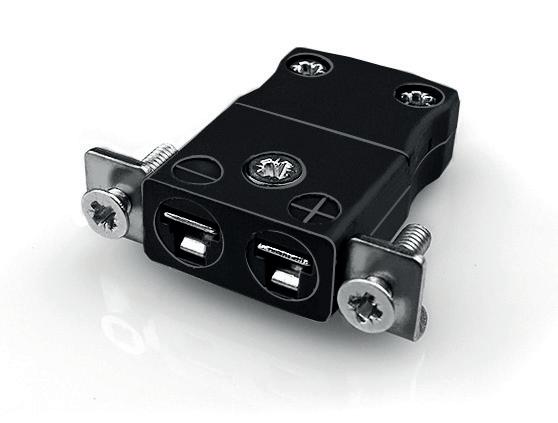
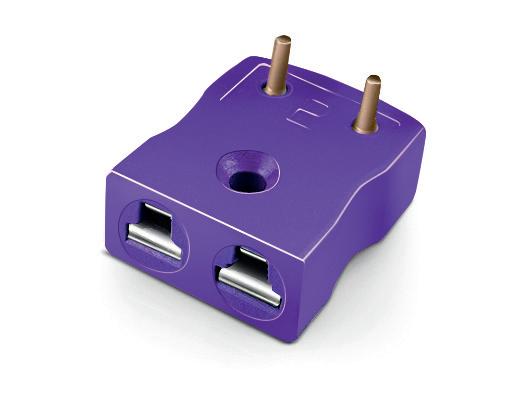
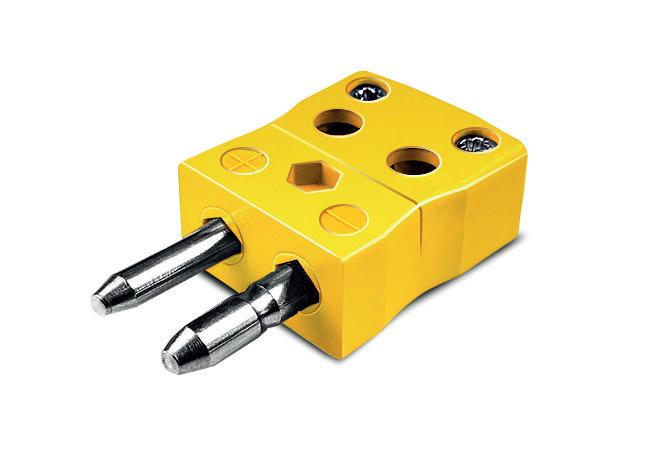
and Connectors, ensuring buyers can quickly find the specific product needed for a given application. labfacility.com
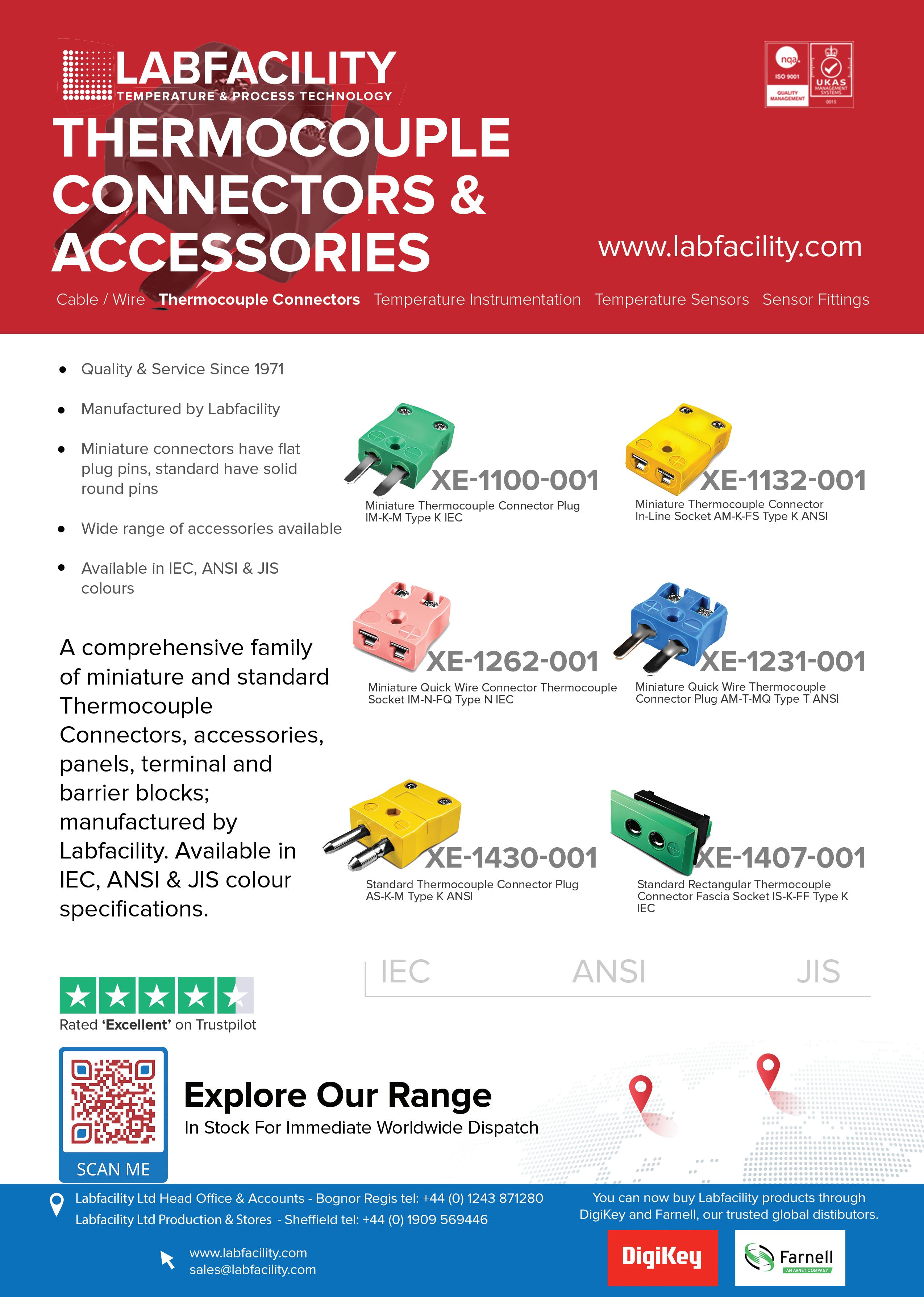
A New Chapter in Quality & Opportunity
Wrexham-based manufacturer of pressure transducers and transmitters ESI Technology is thrilled to share news of its latest accreditation with MEPCA’s readers.
ESI Technology is delighted to announce that it has successfully achieved AS9100D certification, marking a significant milestone in its ongoing commitment to excellence, innovation and continuous improvement. This globally recognised standard affirms its dedication to the highest levels of quality, precision and customer satisfaction in every aspect of the company’s operations.
AS9100D is more than just a badge of honour—it is a comprehensive and rigorous Quality Management System (QMS) standard developed by the International Aerospace Quality Group (IAQG). Specifically tailored for the aerospace, aviation, and defence industries, AS9100D builds upon the foundation of ISO 9001 and adds additional layers of control, traceability, risk management, and regulatory compliance required for these high-risk, highperformance sectors.
This achievement is a clear demonstration that ESI Technology’s systems, procedures and culture of quality meet or exceed the stringent expectations of global industry leaders. Every process—from initial design through production, testing, and final delivery—has been thoroughly assessed and aligned with internationally accepted best practices. The certification reflects the company’s ability to consistently provide products and services that meet both customer and regulatory requirements with a high degree of reliability.
For ESI Technology, AS9100D certification is not just a milestone—it’s a gateway to exciting new opportunities. With this recognition, the company are now even better positioned to serve the critical and demanding sectors of aerospace, defence, and space exploration. Its advanced pressure measurement solutions can be
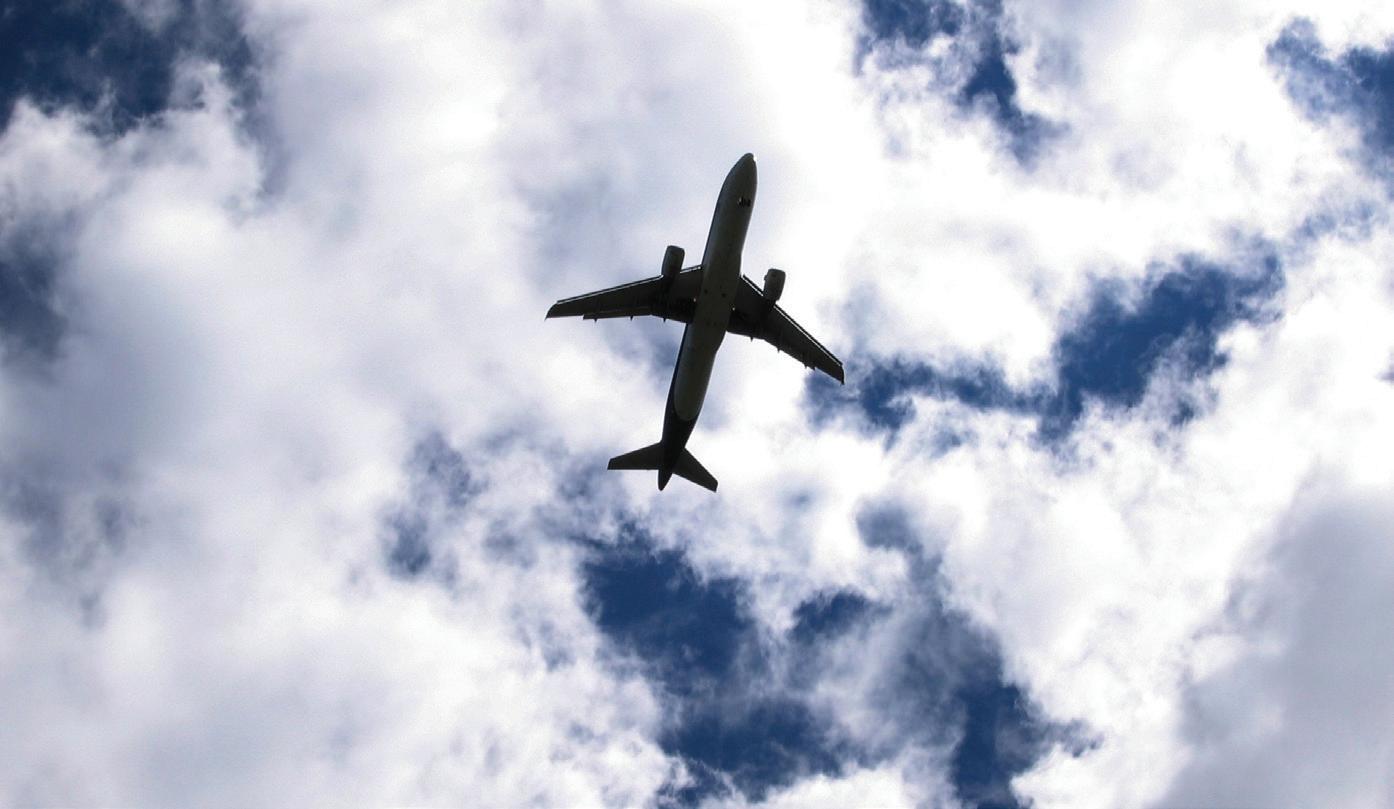
confidently integrated into systems where reliability, safety, and performance are absolutely vital.
Whether it’s monitoring critical components in jet engines, supporting avionics systems, or providing instrumentation for military vehicles and spacecraft, our technology is now validated to operate at the highest standards required in these mission-critical environments. This opens the door to collaborative projects with OEMs, Tier 1 suppliers, and government agencies that rely on partners with proven, audited capabilities.
Moreover, AS9100D enhances our internal practices as well. By implementing and maintaining the standard, we ensure that quality is built into every stage of our operations—from engineering and procurement to manufacturing and support. Customers benefit not only from high-performing products but also from comprehensive documentation, robust supply chain control, and consistent communication—all of which are essential components of modern aerospace supply chains.
Achieving this certification would not
have been possible without the incredible dedication and hard work of the company’s entire team. Every department—from engineering and production to quality assurance and customer service—played an integral role in reaching this achievement. It was a truly collaborative effort that reflects the passion and professionalism that define ESI Technology.
Looking ahead, the company are excited about the new partnerships, projects, and innovations this certification will foster. Whether this is creating custom sensor solutions for next-generation aircraft, developing instruments for space-bound missions, or supporting complex defence applications, ESI Technology are now even more equipped to deliver excellence where it matters most.
ESI Technology team extends their heartfelt thanks to their customers, partners and suppliers for their ongoing trust and support. With AS9100D certification now in place, ESI Technology is poised to soar to new heights and help shape the future of aerospace and defence through precision engineering and uncompromising quality. esi-tec.com
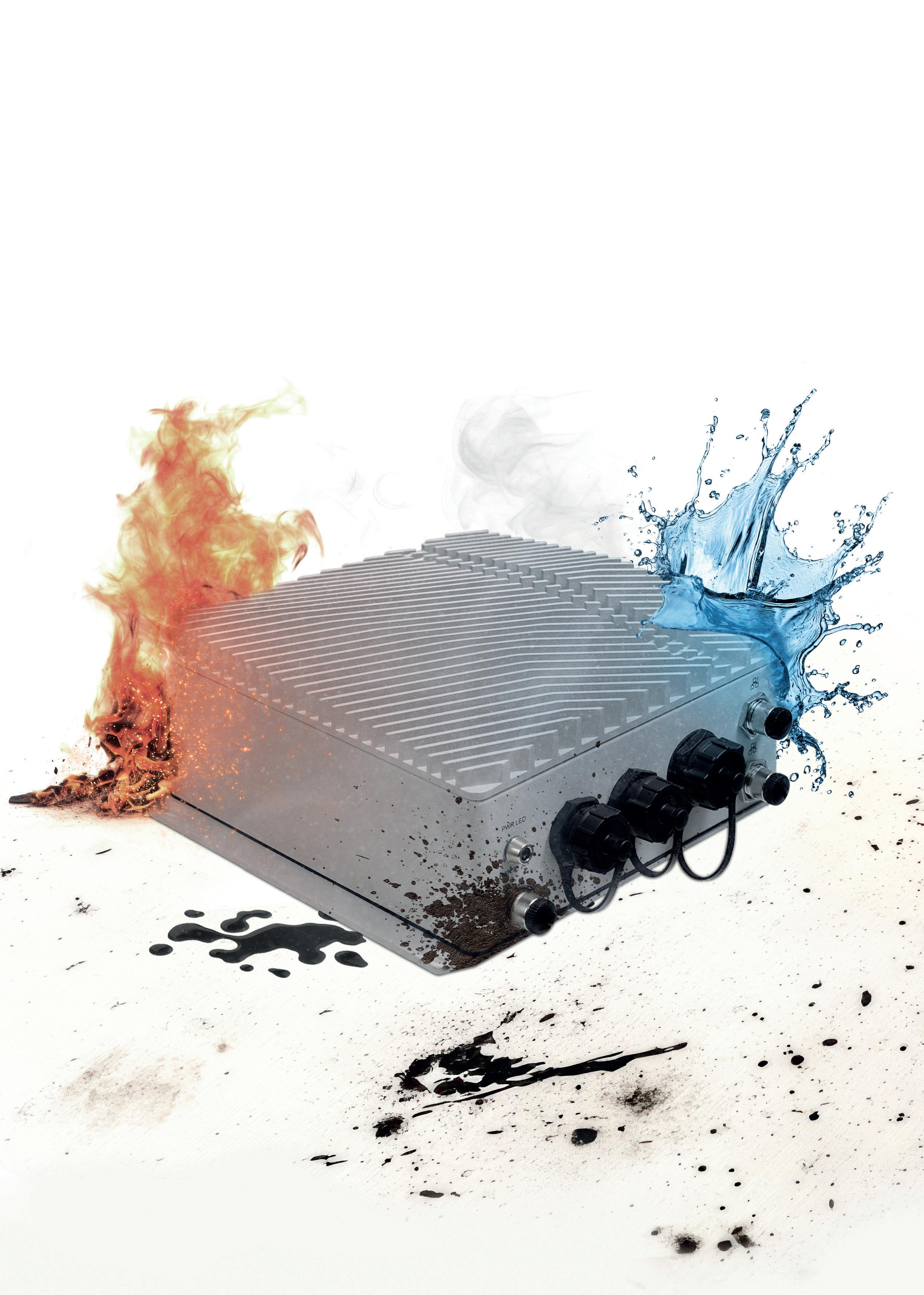
BUILT For the extremes trusted everywhere
Smart-Source Assets to Reduce Downtime
The swift replacement of broken equipment is crucial for avoiding downtime. Unfortunately, lead times for new machinery can be lengthy. Here, Industrial Auctions, the online machine auction specialist, shares how manufacturers can cut costs and lead times.
In today’s world, efficiency is key, however, challenges arise when it comes to acquiring new machinery. Lead times for new food and beverage equipment can still stretch from several months to a year or longer. This can be problematic if a machine breaks down unexpectedly, as companies need replacement equipment quickly to avoid production delays and losses.
Industrial Auctions has found the solution to these challenges. Specialising in the food and beverage industry, Industrial Auctions is an online auctioneer with a wealth of experience organising auctions across Europe. The company has facilitated the sale of thousands of machines, ranging from individual units to entire production lines and factories. Its key advantage? Availability. With Industrial Auctions, businesses can acquire second-hand food and beverage machines that are ready to be picked up in just a week after the auction closes—dramatically reducing the waiting period compared to new equipment purchases.
The convenience of Industrial Auctions’ online platform is another major benefit. Buyers can participate from anywhere in the world, eliminating the need to travel and saving valuable time. For companies looking to streamline their operations, Industrial Auctions also offers complete production lines, allowing buyers to secure an entire line with a single bid. This combination of speed, accessibility, and comprehensive offerings makes Industrial Auctions an essential partner for food and beverage companies seeking fast, efficient machinery solutions. By facilitating machinery auctions, Industrial Auctions contributes to the circular economy and helps companies reduce their carbon footprint. The reuse of existing equipment reduces the demand for new production, resulting in less raw material

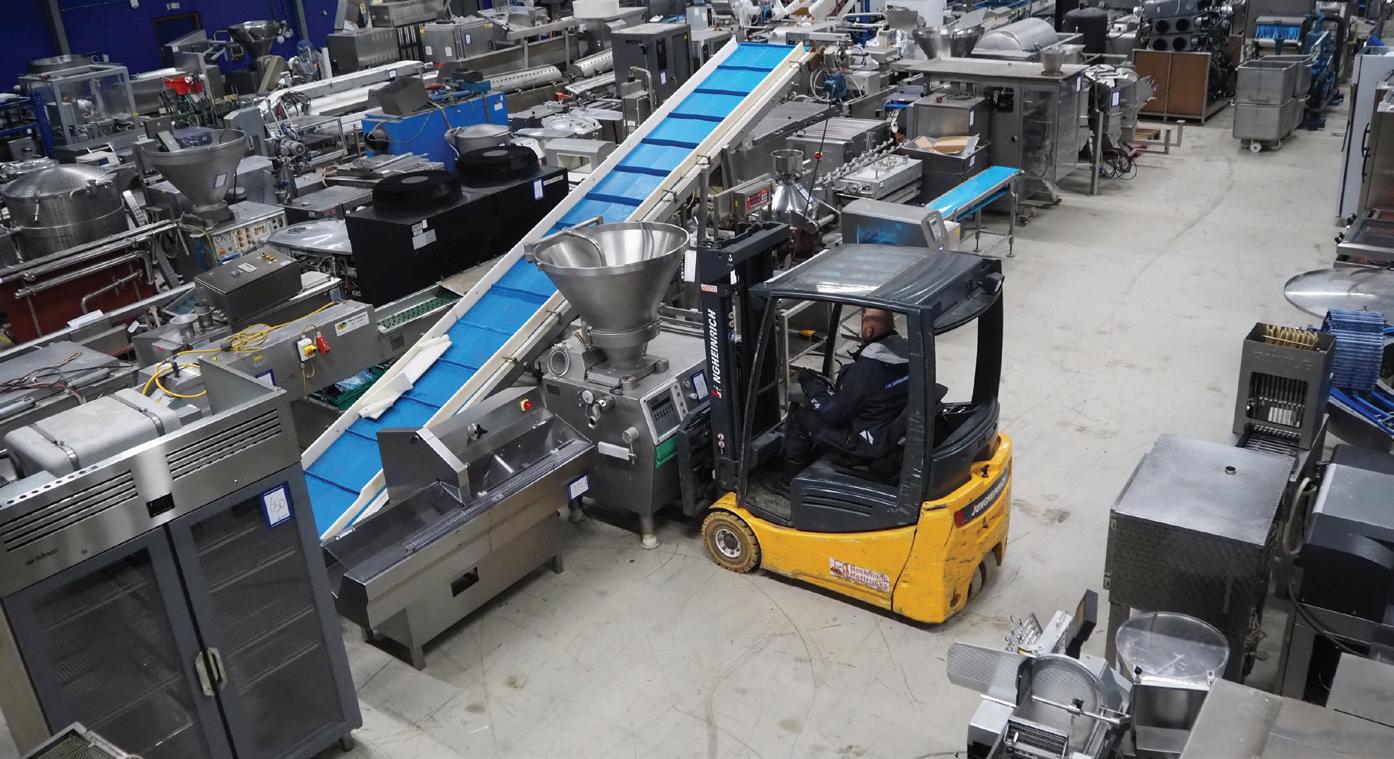
use and energy consumption. Moreover, it allows companies to invest in high-quality equipment in a cost-efficient way, without the environmental impact of newly produced machinery.
The auctioneer weekly adds new auctions to their platform, offering machinery for all segments in the food and beverage industry, including transport systems, cooling, freezing, heating and water treatment systems, tanks and silos, product and liquid pumps. On offer are also various
kinds of packaging solutions. Think about thermoformers, packaging robots, vacuum machines, traysealers, vertical forming, filling and sealing machines, flow wrappers, bottling and filling machines, carton erectors, labelling machines, checkweighers and metal detector systems from brands such as Multivac, GEA, Ishida, Krones, Mettler Toledo, Ulma and Bosch.
View the entire offer on Industrial Auctions’ website.
Industrial-Auctions.com
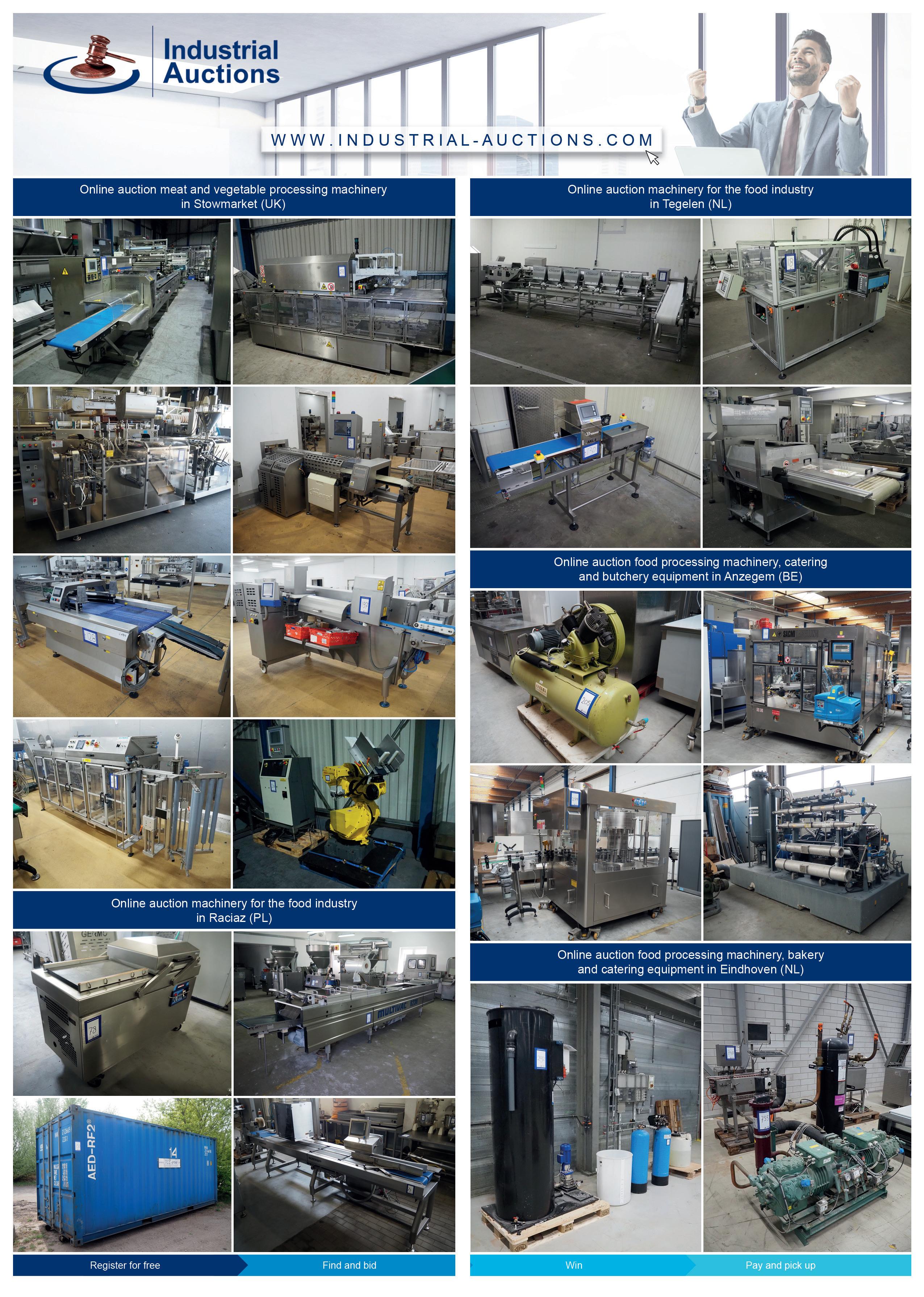
MEPCA Invites Readers to Subcon 2025
Subcon is back at The NEC, Birmingham, from the 4-5 June, bringing together over 170 exhibitors and thousands of manufacturing professionals.
This premier event is where manufacturers and buyers across aerospace, automotive, defence, medical and more connect to redefine the supply chain with cutting-edge innovations. Expect UK and International solution providers, hands-on product demos, CPD-accredited workshops, and thought-provoking keynote presentations tackling the industry’s hottest trends.
Event highlights
Subcon will feature 180+ exhibitors – 10% bigger show floor compared to 2024 – while the new and improved forum and workshop programme boasts key speakers Airbus, Jaguar Land Rover, Kraft Heinz, NHS Supply Chain, Rolls Royce, and more.
The free networking drinks from 16:30 on Day 1 are open to all visitors. On Day 2, The Manufacturing Solutions Show Awards provides celebrate the best and brightest in the industry.
Attendees will have the opportunity to go head-to-head with a real motorsport legend Michael O’Brien – one of the most successful drivers in modern McLaren motorsport history – on the motorsportgrade simulators. The fastest driver will win a track day experience at Bedford Autodrome.
The event’s vibrant new networking hub, PUB-CON, is perfect for reconnecting with old friends and meeting new contacts. Enjoy refreshing drinks and classic ‘pub’ games for a relaxed, fun atmosphere.
Open to senior manufacturers, the VIP Buyers Programmes offers exclusive networking opportunities and other perks including free parking, complimentary refreshments and an invitation to an exhibitor breakfast.
Conference programme
From Human-Robot collaboration and sustainable practices to clean mobility and breaking silos, this programme tackles the hottest topics shaping the industry. Explore challenges like manufacturing security, IP management, and global trading, plus game-changing insights on PLM, composites, and connecting the shop floor to the top floor. Here’s a sneak peek at to expect:
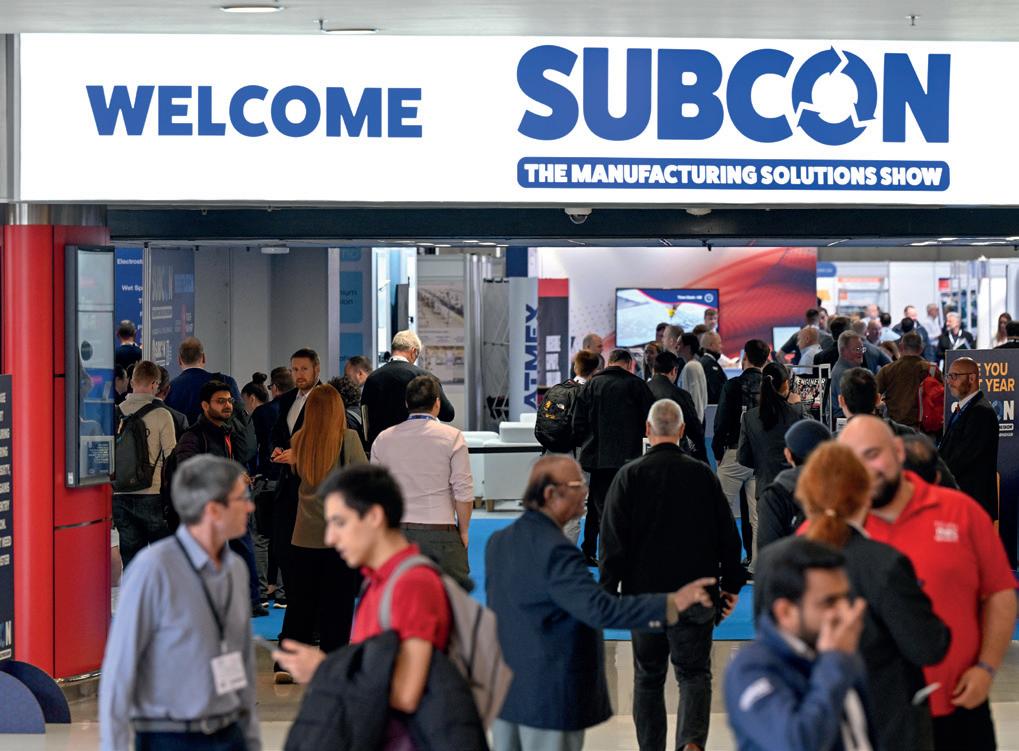
metrology solutions, frictionless bearings and cables and controls.
Matthew Atkinson, Lead Research Engineer, Jaguar Land Rover– Composite Cross Car Beam: A Case Study in Sustainable Design (14:00 - 14:30 – 4 June).
Speakers from Rolls Royce SMR, NHS Supply Chain, University of Warwick, Hexagon Consultants Limited and Digital Catapult – Manufacturing Supply Chains Under Geopolitical Uncertainties (12:4513:30 – 4 June).
Speakers from Airbus Commercial Aircraft, Cranfield University, Fanuc UK and Automate UK – Human Robot Collaboration in Manufacturing, the Future or Just Hype? (14:15 - 15:00 – 5 June).
Be sure to check out the full conference agenda for more details on session times and speakers!
Exhibitors
Over 170+ exhibitors will be attending the trade show. Innovations and solutions will be showcased ranging from CNC machining, metal fabrication, electronics and component parts. Other solutions on show include additive manufacturing and
Sponsors and partners include Allstar, serving businesses with the UK’s largest fuel and electric charging network; Smiths Metal Centres, global supplier of engineering alloys & plastics; leading trade and investment promotion organisation EEPC India; Qimtek, connecting manufacturing buyers with UK-based subcontract supplier; along with UK trade associations The MTA (Manufacturing Technologies Association), and The BTMA (British Turned Parts Manufacturing Association).
Dates, location, tickets
• 4 June 2025 - 09.30 - 17.00 (networking drinks party from 16:30 onwards)
• 5 June 2025 – 09 30 - 17.00
• Hall 3A, NEC, Birmingham Subcon is free to attend for all manufacturing professionals. Registering for Subcon also gives access to co-located events running at the NEC on the same dates –Automechanika Birmingham, Med-Tech Innovation Expo, Smart Manufacturing Week, and TCT 3Sixty. subconshow.co.uk
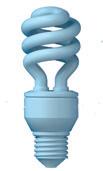

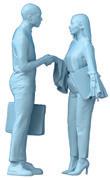
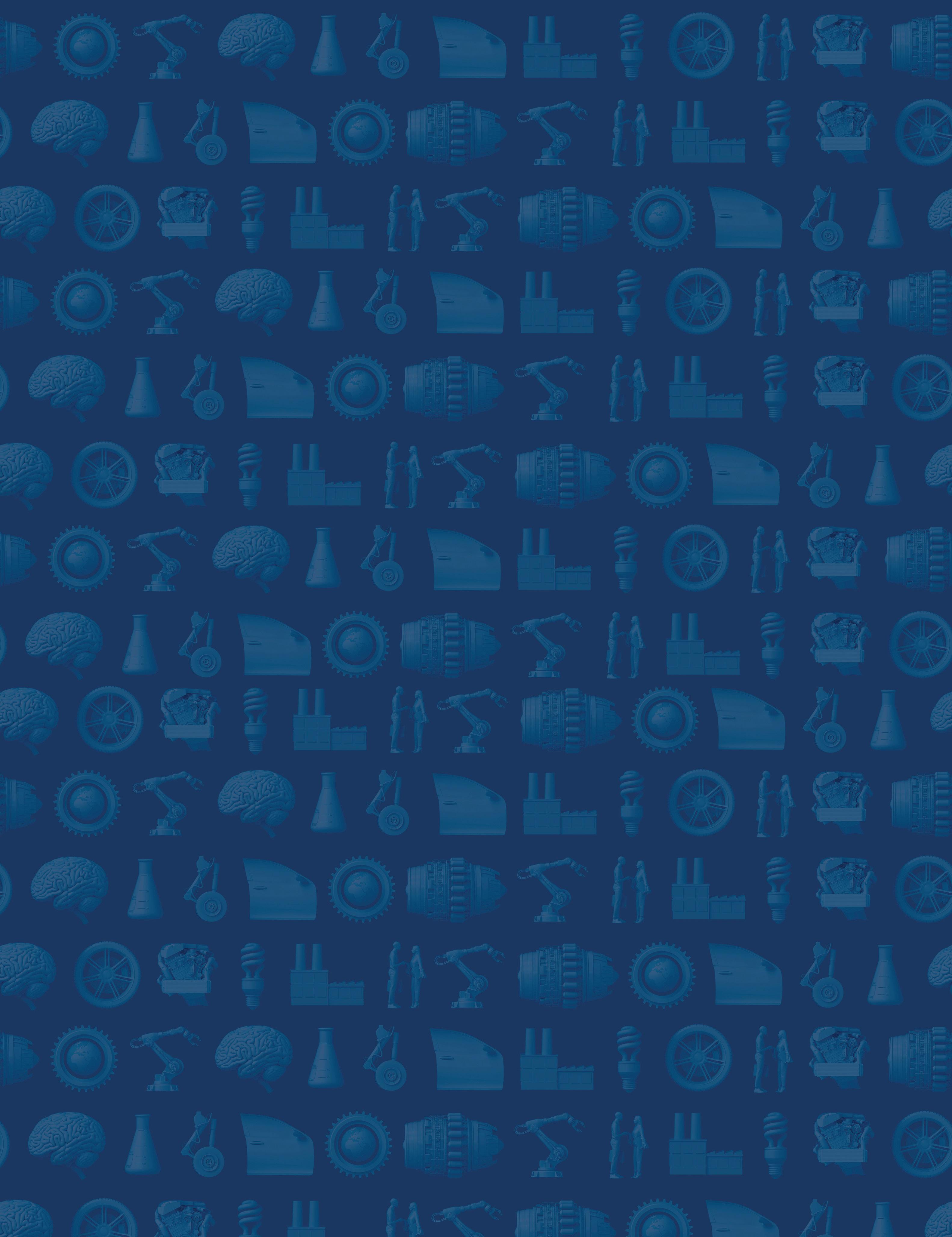
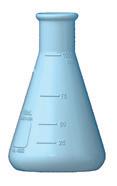
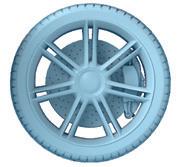

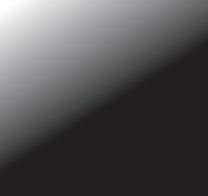
3D Print Manufacturing
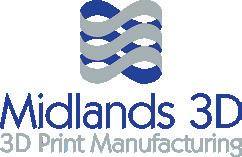
Midlands 3D Printing
T: 01785 594389
E: sales@midlands3d.com
W: www.midlands3d.com
Anti Vibration Products, Mounts & Bushes
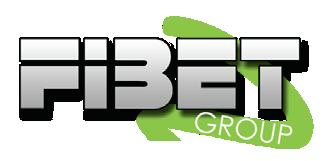
Fibet Rubber Bonding (UK) Ltd
T: 01282 878200
E: sales@fibet.co.uk
W: www.fibet.co.uk
Connectors & Cabling Solutions
CEMBRE Ltd
T: 01675 470 440
E: sales@cembre.co.uk
W: www.cembre.com/en
Design-In Power Supply Solutions
Ideal Power
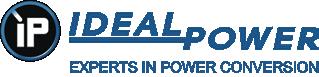
T: 01733 309865
E: salessupport@idealpower.co.uk
W: www.idealpower.co.uk
Drives, Motors & Gears
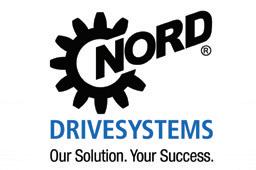
Flow Meters
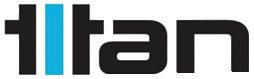
Nord
T: 01235 534404
E: GB-sales@nord.com
W: www.nord.com
Industrial Fans
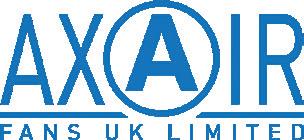
Axair Fans UK Limited
T: 01782 349 430
E: sales@axair-fans.co.uk
W: www.axair-fans.co.uk
Machine Safety
Schmersal UK Ltd
T: 01684 571980
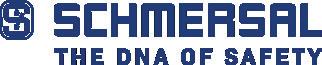
E: uksupport@schmersal.com
W: www.schmersal.co.uk
Marking Solutions
T-Mark
T: 0330 153 8320
E: sales@t-mark.co.uk
W: www.t-mark.co.uk
Pressure Measurement Specialists
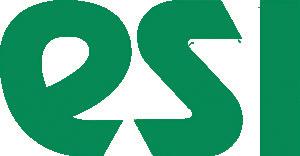
ESI Technology Ltd
T: +44 (0)1978262255
E: sales@esi-tec.com
W: www.esi-tec.com
Robotics & Automation
KUKA Robotics UK Ltd

T: 0121 505 9970
E: sales.uk@kuka.com
W: www.kuka.com
Sensors
Titan Enterprises Ltd
T: +44 (0)1935 812790
E: sales@flowmeters.co.uk
W: www.flowmeters.co.uk
High Shear Mixing Equipment
Silverson Machines Ltd

T: +44 (0)1494 786331
E: sales@silverson.co.uk
W: www.silverson.co.uk
Industrial Communications
Brainboxes

T: + 44 (0) 151 220 2500
E: sales@brainboxes.com
W: www.brainboxes.com
Intoware
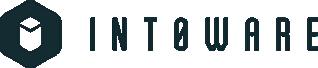
T: 0115 977 8969
E: hello@intoware.com
W: www.intoware.com
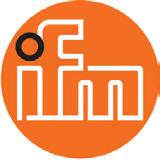
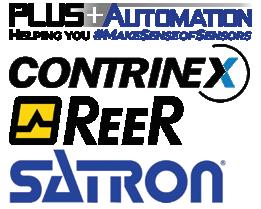
IFM Electronic
T: 020 8213-0000
E: enquiry.gb@ifm.com
W: www.ifm.com
PLUS Automation Ltd
T: 0121 58 222 58
E: Sales@PLUSAutomation.co.uk
W: www.PLUSAutomation.co.uk
Storage Solutions
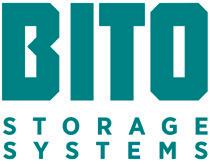
BITO Storage Systems Ltd.
T: 02476 388 852
E: Info.uk@bito.com
W: www.bito.com
Test & Inspection
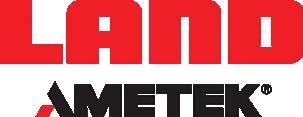
AMETEK Land (Land Instruments International)
T: +44 1246 417691
E: land.enquiry@ametek.com
W: www.ametek-land.com
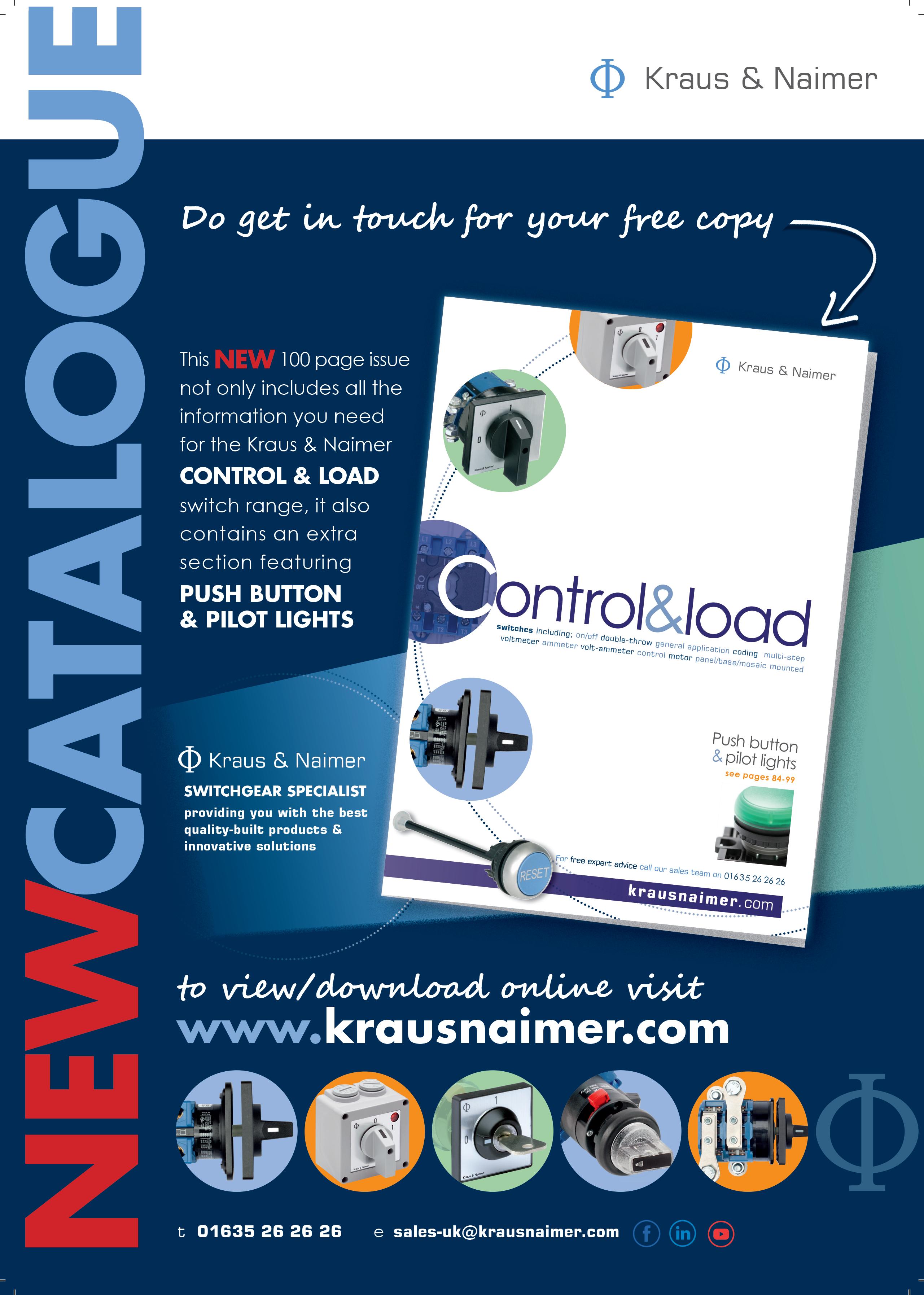
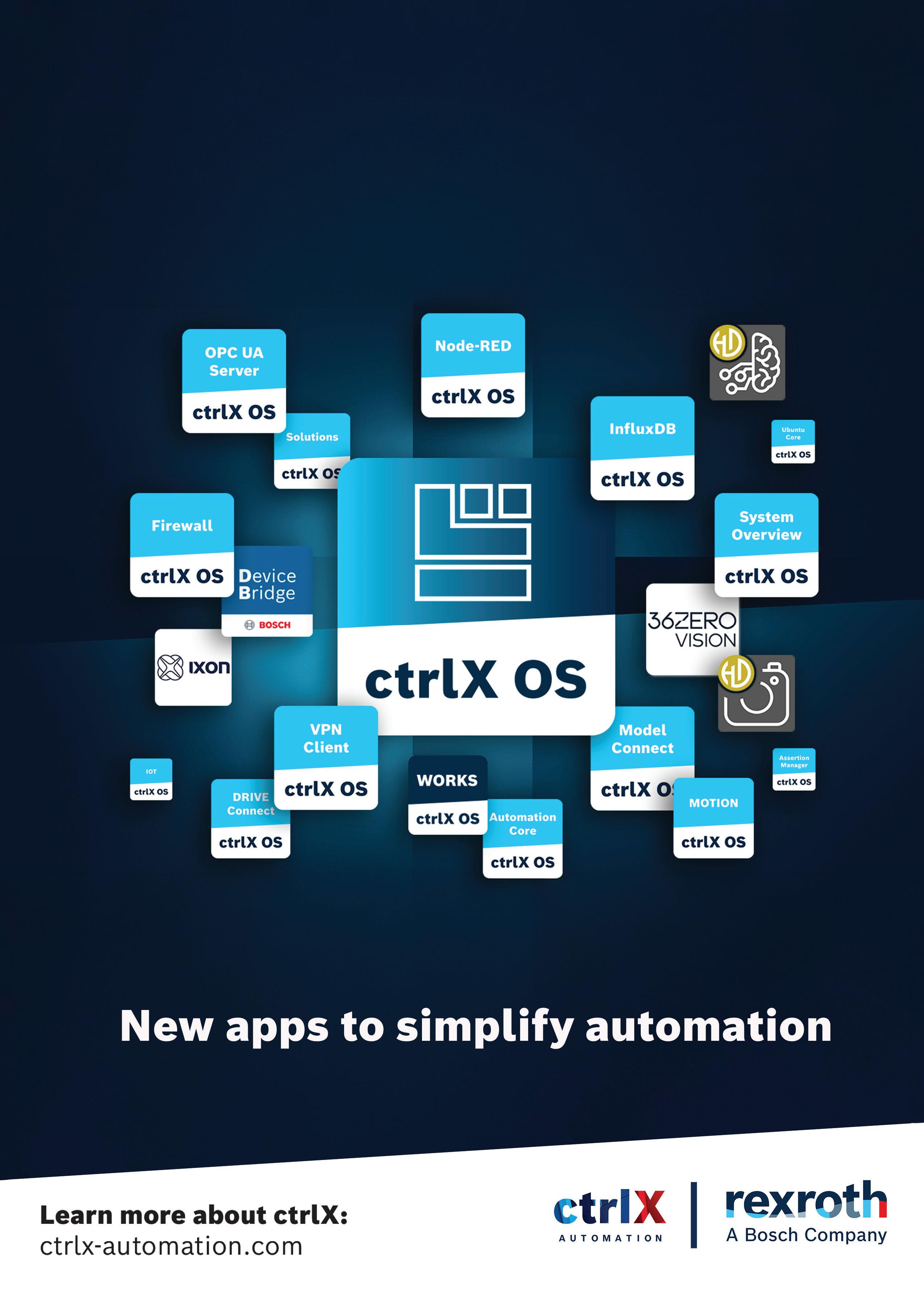