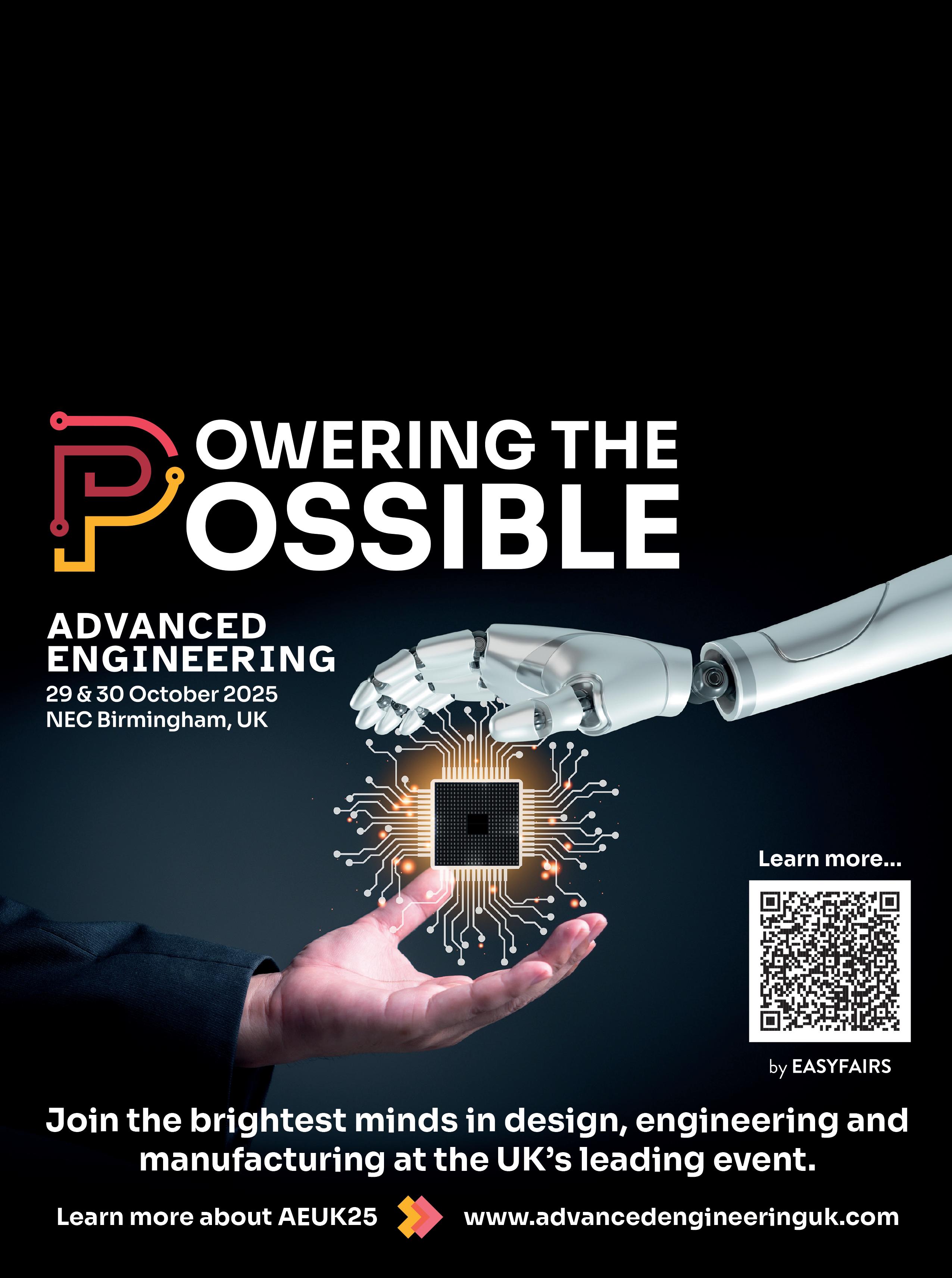
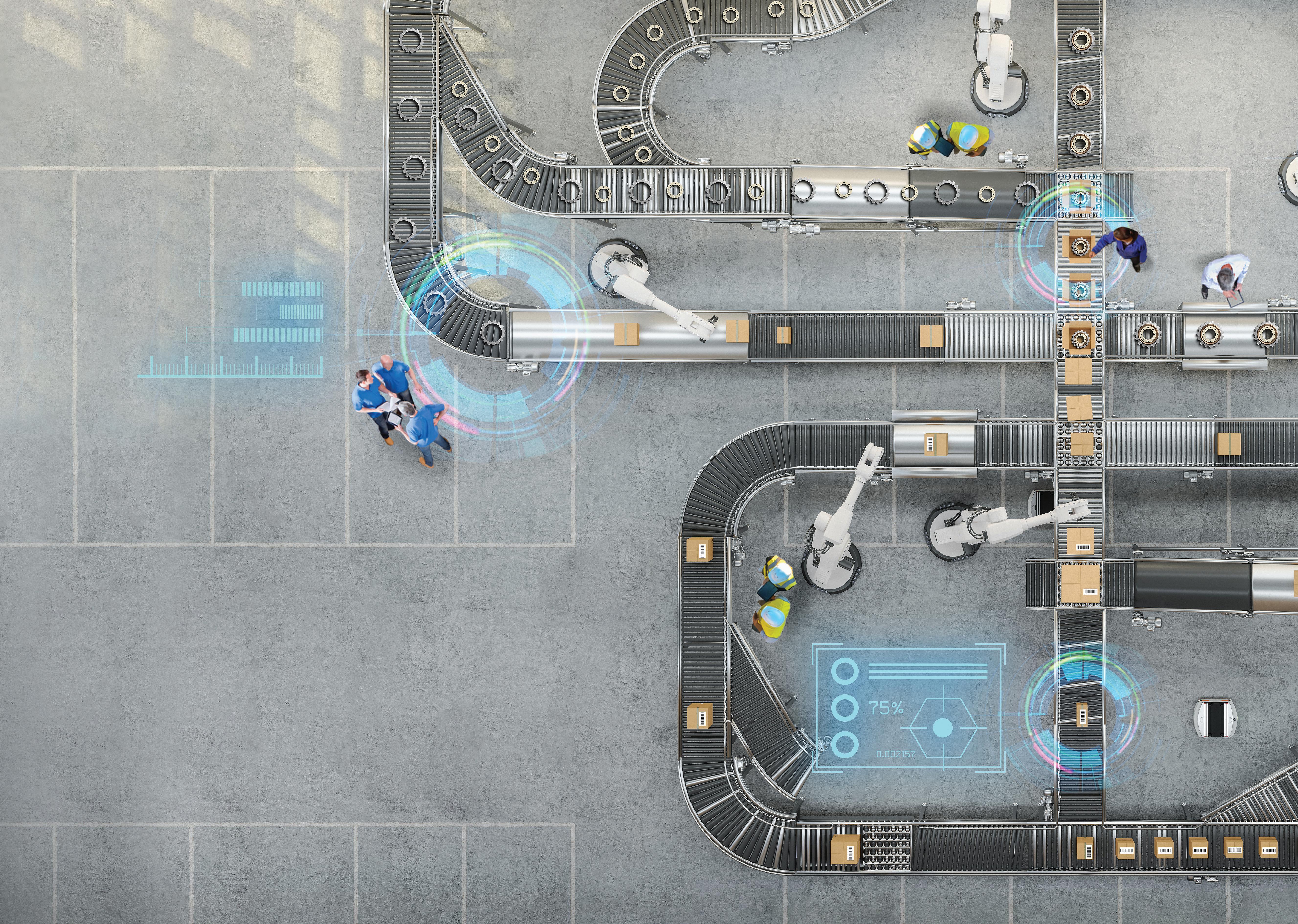
The Matrox Imaging solutions you know and trust just got better, and they are now available through Zebra.
More choices from the widest portfolio
More agility to scale and adapt in the moment
More interconnectivity via easier integration
More savings with streamlined solutions
Editor
Oliver Batt oliver@cimltd.co.uk
Publication Manager
James Burke jb@cimltd.co.uk 01795 509105
Account Manager
Jim Bearden jim@cimltd.co.uk 01795 509105
Design & Production Grant Waters grant@cimltd.co.uk
James Taylor james@cimltd.co.uk
Administration Manager
Natalie Woollin admin@cimltd.co.uk 01795 509103
Credit Facilities Manager
Gwen Lee creditcontrol@cimltd.co.uk 01795 509103
Head of Digital
Xhulio Bishtaja digital@cimltd.co.uk
Marketing Manager
Lucas Payne lucas@cimltd.co.uk
Sales Director
Tom Woollin tom@cimltd.co.uk
Chief Executive
John Denning
© 2025 Cogent Multimedia Limited,1st Floor, Saphir House, 5 Jubilee Way, Faversham, Kent, ME13 8GD. No part of this magazine may be reproduced or stored in a retrieval system or transmitted in any form – electronic, mechanical or physical – without express prior permission and written consent of the publisher. Contributions are invited and when not accepted will be returned only if accompanied by a fully stamped and addressed envelope. Manuscripts should be typewritten. No responsibility can be taken for drawings, photographs or literary contributions during transmission or in the editor’s hands. In the absence of an agreement the copyright of all contributions, literary, photographic or artistic, belongs to Cogent Multimedia Limited. The publisher accepts no responsibility in respect of advertisements appearing in the magazine and the opinions expressed do not necessarily represent the views of the publisher. The publisher cannot accept liability for any loss arising from the late appearance or non-publication of any advertisement.
elcome to the August issue of MEPCA magazine. I doubt I’m alone in wondering how we find ourselves past the mid-year point already, having enjoyed – or endured – several heatwaves. As jarring as this realisation is, it offers an opportunity to reflect on the year so far and plan for the months ahead, something that many business will be doing as we head into Q3.
I’ve noticed a renewed sense of positivity in the industry, which coincides with release of the UK’s Modern Industrial Strategy at the end June, the ambition and scope of which has been warmly welcomed by most.
At the centre of this issue is a focus on Business Operations, in which we look at range of topics and solutions that will assist manufacturers as they plan for the next half of the year. Supporting us in this, software expert Epicor, shares how companies can assess their digital readiness. Further into this section, Tork explains how a company’s approach to hygiene can affect employee productivity, while risk management company Gallagher shares its research on the biggest risks facing manufacturers in 2025.
Also within this section, I had the pleasure of interviewing Richard Rumbelow, Director of International Business, Make UK, for a better understanding of the impact of the US tariffs in practice.
In our Cover Story, Simon Farnfield, Director of Advanced Engineering UK, examines the AI skills gap, providing a more nuanced take on the typically polarising views.
Elsewhere in the issue, we reveal this month’s Manufacturing Champion, share industry insights from Bara and Lloyds, and provide a roundup of the industry shows so far in our Events Review section.
This issue is best enjoyed outside, perhaps in the shade of a pub garden.
Oliver Batt, Editor
ESI Technology Ltd has successfully achieved AS9100D certification, marking a significant milestone in its journey towards excellence and continuous improvement. This globally recognised standard is a testament to ESI’s unwavering commitment to quality, precision and customer satisfaction across all aspects of its operations.
AS9100D, developed by the International Aerospace Quality Group (IAQG), is the internationally recognised Quality Management System (QMS) standard specifically for the aerospace, defence, and aviation industries. It incorporates all the requirements of ISO 9001, with additional criteria designed to meet the rigorous demands and compliance obligations of these high-stakes sectors. Achieving this certification demonstrates that the company’s processes consistently meet both customer expectations and regulatory requirements with precision and reliability.
For ESI Technology, this certification
opens the door to exciting new possibilities across a wide range of critical and cuttingedge industries.
Industries such as aerospace, defence, space, and advanced aviation systems can now place even greater confidence in ESI solutions. Applications ranging from aircraft engine monitoring and flight control systems to military-grade instrumentation stand to benefit from its enhanced capabilities and proven quality assurance.
ESI’s customers and partners can be assured that every product manufactured at ESI Technology adheres to the highest standards, not just in functionality and performance, but also in documentation,
traceability and risk management—crucial pillars of AS9100D.
Looking forward, ESI are excited about the new partnerships, projects and innovations this certification will bring. Whether it is developing bespoke sensor technology for next-generation aircraft or supporting critical infrastructure in space exploration, ESI Technology is now even better equipped to deliver excellence where it matters most.
With AS9100D certification in hand, ESI Technology is poised to reach new heights. Find out more on the company’s website. esi-tec.com
Plans in the Industrial Strategy to drastically cut electricity costs by 2027 may be too late for some under-pressure manufacturers battling to remain competitive.
The new British Industrial Competitiveness Scheme was announced in June and promises to reduce electricity costs by £3540/MWh.
Energy specialist Joe Collison, managing director of CES, which works with manufacturers to develop renewable systems, says manufacturers need support with rising costs now.
“The full effect of this announcement won’t be felt until 2027 – this may be too late for many manufacturers.
“For energy-intensive businesses, there’s somewhat earlier relief coming through the enhanced Network Charging Compensation scheme, which will increase from 60% to
90% starting in 2026.
“But this means most manufacturers will need to navigate high energy costs for at least another 12-18 months before seeing substantial relief.
“While the £1 billion Clean Energy Supply Chain Fund should help build domestic capacity in renewables relatively quickly, the direct impact on electricity bills will take longer to materialise.
CES designs and installs renewable solutions that can power energy-hungry operations during peak times, provide backup during outages, and help schedule production to match optimal energy generation periods.
Joe added: “At CES, we’ve seen firsthand how supply chain constraints have hindered deployment and increased costs across renewable projects.
“This targeted investment should help build domestic manufacturing capability,
reduce our reliance on imports, and ultimately bring down the cost of the clean energy transition.”
Joe added that the strategy also addressed grid connection delays through the new Connections Accelerator Service.
“This has been a major bottleneck for many of our clients, with some projects facing decade-long waits for grid capacity,” he concluded.
poweredbyces.co.uk
Discover how Tork high-capacity dispensers can save your cleaners valuable time by making refilling quicker, easier and less frequent. Better hygiene for better business torkglobal.com/gb/en or tork.ie
As with any capital expenditure purchase, risk must be carefully managed when investing in automation. Here, Oliver Selby, BARA Chairperson and Head of Sales at FANUC UK, examines four key risk areas to ensure an automation project stands the best chance of success.
While risk is dependent on the size, complexity and expected lifetime of the equipment, careful planning can support the business case for automation and help to de-risk investment.
This presents itself in two ways: firstly, the internal risk of capital outlay for the business; and secondly, the risk of working within supply chains generally formed of SMEs. Capital outlay risk can take the form of either depletion of cash reserves or cash flow. This can be managed by weighing up expenditure and analysing the best form of finance for the project. More firms are moving away from fully financing a project themselves and are instead focusing on lease arrangements, thereby making automation an operational cost. This can certainly lower risk, offering a fall back option should the project not meet expectations, or for shorter-term customer contracts.
Supply chain risk can be managed through contractual terms, e.g., staged payments, for when a supplier hits certain performance metric such as design, procurement, build, or acceptance testing. Additional methods include liquidated damages and bank guarantees.
This is this easiest risk area to mitigate, as process risks are generally covered by the integration partner or process solution provider.
Most system integration partners will provide upfront proof of concept support for anything that:
a) sits outside of normal known process risks
b) represents a new process c) constitutes a combination of processes
that rely on each other.
Once the process risks are removed, a full URS (User Requirement Specification) is normally issued, which enables the integration partners to provide a quote. At this point, potential suppliers may simulate the process to prove cycle time and throughput, allowing some confidence in future (Overall Equipment Effectiveness) calculations. The final chosen solution partner should also demonstrate capacity and competence in the solution.
Anything external to your or your supplier’s ability to deliver the project on time and to the quoted price should be reviewed prior to commitment. Currently, the geopolitical challenges impacting tariffs and global supply chains have caused a few headaches, as have domestic changes to UK Government policy, such as National Insurance payments. These all affect decision making, and should be considered from both a short and long term perspective.
Managing employee risk can be critical to an automation project’s overall success and may also improve buy-in from the workforce in the longer term. Getting support from suppliers, trade associations and other manufacturers can help firms to introduce automation in a manageable way. Early education and involvement of key stakeholders within the organisation around the ‘why’ and ‘how’ surrounding an automation project can also help to minimise future challenges. Remember, no
one knows your processes or products like those currently making them. Make use of that knowledge!
The most influential area when it comes to mitigating automation risk is communication. Talk internally with key stakeholders to define the financial risks, technical risks, external risks and human risks that will undoubtedly present themselves as part of the decisionmaking process. Talk externally to suppliers, trade associations and other firms who have automated. Finally, consider talking to third party consultants, who can bring experience and expertise to your automation investment plan.
Talk to Automate UK about how they can point you in the right direction with accredited suppliers and consultants to reduce your investment risk.
Automate-uk.com
David Atkinson, UK Head of Manufacturing SME & Mid Corporates at Lloyds, considers the impact of food & drink manufacturers, and their extraordinary potential.
The UK’s food & drink manufacturers are often the unsung heroes of the economy. By some distance, food & drink is Britain’s biggest manufacturing sector; bigger than automotive and aerospace put together. Indeed, food & drink manufacturers account for almost a quarter of all UK manufacturing turnover, contributing £37 billion to the UK economy and employing more than 486,500 people.
We’re home to more than 12,000 UK food & drink manufacturers, from household names like Warburtons and McVities’ to countless micro businesses producing artisan specialities. And the number of food & drink manufacturers grows on a daily basis, inspired by new food trends, emerging technologies, home-grown produce, global cuisines and more.
These food & drink manufacturers are at the forefront of innovation, launching thousands of new products every year. What’s more, they remain an exporting powerhouse, despite the complexities that producers face when selling their products overseas.
Like so many manufacturing sectors, food & drink has an opportunity to invest in automation, digitisation and sustainability. A recent report by the Food & Drink Federation found that manufacturers could unlock up to £14 billion of extra value by boosting productivity to the levels seen in other advanced manufacturing sectors, including automotive and aerospace.
However, food & drink firms are sometimes reticent to borrow and invest in their operations, often because listings in larger retailers are relatively short term in general, particularly for new businesses and
products. That creates uncertainty and can make it more difficult to plan investments.
Still, the sector has proved to be a fantastic incubator for an incredible diversity of entrepreneurs. SMEs account for 99% of businesses in food & drink manufacturing, and there are some great examples of firms producing distinctive products and scaling up on their own terms.
Like Cavan Bakery, which has expanded from three locations to 15 shops across South London and Surrey after Lloyds supported its investment in a purposebuilt site and new machinery to improve productivity and efficiency.
The new bakery meant Cavan could double production, providing a platform to accelerate its growth.
Then there’s Riddim, a finalist in the Birmingham Black Business Show’s
Founder Jared Spencer has worked for some big brands in the food & drink industry, and now he has created a business producing a range of plant-based and allergen friendly snacks inspired by the Caribbean, from popcorn to plantain chips.
It just goes to show that Britain’s food & drink sector has the recipe for success, showcasing an incredible diversity of established brands and emerging entrepreneurs, who are creating new markets at home and abroad.
Against this backdrop, the sector should take confidence in its achievements and accelerate its ambitions to invest and automate.
To read about more manufacturers succeeding with Lloyds’ support, visit: lloydsbank.com/manufacturing
Introducing, Eleanor Baker, Women Entrepreneur Lead at Lloyds, our Manufacturing Champion for August. Eleanor leads Lloyds’ initiative to support women-owned businesses. In our Q&A, she discusses how to accelerate gender parity and highlights the importance of inclusive hiring.
Eleanor has worked at Lloyds Banking Group for over 12 years, in a range of roles, supporting businesses across multiple sectors, helping them to achieve their strategic ambitions. In Eleanor’s role leading Lloyds’ initiative to support women-owned businesses, her focus has been on regional impact and supporting sectors such as manufacturing.
Throughout her career, Eleanor has helped to highlight the global gender gap and has championed women in roles where biases persist and female representation is lacking. The Global Gender Report 20251 revealed the closing of the global gender gap to be 68.8%. While a slight improvement on 2024 (68.5%), at the current trajectory, it could take 123 years. Eleanor shares her insights on the subject:
Given that it may take 123 years to achieve gender parity, what steps must we take to accelerate this?
I think intentional change is needed. 123 years is based on current trends so if we just keep going at the same pace, or worse, hit setbacks, it could take even longer. Gender parity isn’t a ‘women’s issue’; it’s a societal one. Diverse teams consistently perform better. They make smarter, more profitable decisions, so this is about building better businesses.
However, to get there, we have to ask ourselves some tough questions. Like, do we want our daughters to grow up with the same opportunities as our sons? And, do we want our sons to be free from the confines of outdated gender roles? If the answer is yes, we have to take bold, sustained action, such as education, challenging stereotypes, inclusive hiring, supporting work life balance and investment.
What can individual manufacturers do to reverse biases and create fairer career opportunities for women?
I hear myself saying this a lot, but imagery and visibility really matters. Review your imagery. Help the next generation of manufacturers see that the industry is for them – all of them. Representation sends a powerful message.
But it’s not just about the visuals. Companies should make sure that they look at how they hire and support people. That means using inclusive language in job descriptions, considering flexible working options, and making sure there’s a clear path for career growth to support attraction and retention. This also means reviewing who is responsible for recruitment in your team, who makes the shortlist and how you build your pipeline of talent by making your business the place where people want to work and thrive.
What advice do you have for women considering careers in manufacturing?
I’d say go for it! There’s so much more to
manufacturing than people think.
Naturally, people think of factories (and modern factories are a great place to work) but there is engineering, design, supply chain, robotics and sustainability and more! It’s a broad, exciting field with lots of different paths – explore your opportunities!
Build your network; I have met so many amazing people in the industry and they are all there to support, give advice, guidance and open doors for you. Problemsolving, collaboration, attention to detail, leadership… all these skills are in-demand, and manufacturers who want to attract talent are realising that they have a larger talent pool to draw from if they focus on inclusive hiring.
Keep learning – whether it’s through an apprenticeship, a course, or just picking up a new skill on the job, there’s no age limit on learning. The more you invest in yourself, the more doors you’ll open.
lloydsbank.com/womenbusinesses
1. www.weforum.org/publications/global-gender-gapreport-2025/
The conversation around AI in engineering often drifts into extremes: that it will either take over jobs, or magically improve processes. The reality is somewhere in between. It’s not just about the technology itself, but how it’s applied and who’s applying it explains Simon Farnfield, event director for Advanced Engineering UK, returning to the NEC, Birmingham, 29-30 October 2025.
Much like the early conversations around Industry 4.0, there’s still a sense that many companies aren’t entirely sure what AI is or how it can benefit them. That’s concerning, because in engineering and manufacturing, AI is no longer a distant prospect, it’s already here.
From predictive maintenance to real-time optimisation and supply chain analytics, AI is driving smarter, faster and more autonomous operations. In fact, 91 per cent of companies are planning1 to increase their investment in AI over the next two years.
Although investment is ramping up, there’s a growing concern that the skilled people needed to manage and scale these systems aren’t entering the workforce fast enough. Part of the problem is a lingering misconception that AI is something you can simply buy off the shelf. In reality, AI is a tool that only delivers value when it’s supported by the right strategy, quality data and skilled talent.
It’s true that AI will replace some repetitive tasks, but that doesn’t necessarily mean jobs will disappear. Instead, it’s changing what those jobs look like. As lower-value tasks are automated, people will be freed up to focus on higher-level decision-making and creative thinking.
That’s where the opportunity lies, but only if the workforce is equipped to make the most of it. Before we get into the technical skills required, soft skills like communication and leadership are often overlooked in this discussion, but they’re more important
“While AI can crunch numbers or generate solutions, it can’t negotiate, lead a team or build trust with stakeholders.”
Simon Farnfield, event director for Advanced Engineering UK.
than ever. While AI can crunch numbers or generate solutions, it can’t negotiate, lead a team or build trust with stakeholders.
These are still distinctly human skills, and they’re critical, especially at senior levels. Leaders in engineering don’t need to become coders, but they do need to understand how AI works, what its limitations are and how to ask the right questions when making strategic decisions.
This is where blind adoption becomes a huge part of the equation. AI systems are built on data, and that data is often
biased — sometimes subtly, other times significantly. There’s bias in how data is collected and in the algorithms themselves.
Without that layer of human oversight, there’s a risk that AI could lead us down the wrong path — and faster. This is important as we move into the next phase of AI, called agentic AI, which McKinsey names as the “next frontier2.”
These aren’t just systems that follow instructions, they’re designed to act
independently, make decisions in real time and respond to complex environments without waiting for human input. Built on large language models (LLM) and advanced contextual understanding, agentic AI introduces a new level of autonomy.
Agentic AI has potential, but like any tool, its value is only realised when it’s used thoughtfully and with the right checks and balances in place.
To meet this challenge, industries will need people who understand data. Programming and machine learning will be crucial, not just in developing AI tools but also in maintaining and improving them.
An emerging area of focus is prompt engineering, a skill that’s quickly becoming essential as companies explore the potential of generative AI. At its core, prompt engineering is about understanding how to communicate with AI systems effectively, using the right language, structure and context to get useful and accurate responses.
Closely linked to this is natural language processing (NLP), another fast-growing field. NLP allows machines to interpret, understand and respond to human language — whether that’s written commands, spoken queries or even messy, unstructured data.
As a result, data scientists, machine learning specialists and NLP engineers are quickly becoming core to manufacturing and engineering teams. However, systematically there are a few gaps, and one of them is in the form of education.
There’s often a lag between what companies need and what schools, colleges and universities are teaching. Coding and data science need to be embedded much earlier in the curriculum. That’s not just at university level, but in secondary schools, T Levels and vocational training programmes too. These aren’t just nice-to-have skills, they’re becoming on par with literacy and numeracy in a world increasingly driven by digital systems.
When it comes to policies, the picture is slightly more complicated. The UK’s AI Action Plan3 set out a framework, but it’s not always clear how the proposed investment will be delivered. There’s often a disconnect between big ideas, like the
Industrial Strategy4, and the practical support engineering companies actually need.
What’s missing is a voice at the top. Someone in government who understands engineering and manufacturing from firsthand experience and can speak to the real issues facing the sector. Funding and programmes are available today, but they’re not always clear, and with AI evolving so rapidly, there’s a real risk of falling behind while the government catches up.
In the meantime, companies must take responsibility for building their own future workforce. That starts with understanding which data matters most to their operations. Small-scale pilot projects are an effective way to begin, trialling AI on a specific process or production line to learn what works and where internal gaps exist. These early experiments not only help know how AI can help, but also identify the specific skills needed to scale AI successfully.
Support from organisations, like Made Smarter, is proving valuable in this regard. Although access can vary regionally, Made Smarter offers training, online courses and funding for pilot projects that help companies begin their AI journey in a manageable way. For manufacturers, especially SMEs, partnerships like these provide essential guidance.
Initiatives, such as Advanced Engineering UK’s ongoing #MINDTHEskillsGAP5, are also helping to tackle the skills gap in the industry. The campaign calls for closer collaboration between industry leaders and policymakers to develop solutions that will secure the next generation of engineering talent, especially in high-tech areas like AI and automation.
In addition, the show recently announced its ‘Unsung Heroes in Manufacturing’ initiative to support the efforts of this campaign. As part of the initiative, a searchable online library of industry experts has been created to provide easier access to the real-world voices, not only reflecting the full spectrum of manufacturing and engineering expertise but also enabling the connection between upcoming engineers and industry experts.
These efforts matter because AI’s true value comes from learning how it’s best applied, rather than being just about the technology itself. It’s a tool that only works if you understand the problem you’re trying to solve. That’s why the companies that succeed in the next phase of AI adoption won’t be the ones with the smartest machines, it’ll be the ones that understand the data they value, with the right people guiding how it’s used.
There is no place better to experience the innovation that the UK’s engineering and manufacturing industry has to offer. To book your stand, visit www. advancedengineeringuk.com and make an enquiry — but don’t hesitate as space is selling out fast. To attend, register now via the QR code.
advancedengineeringuk.com
1. http://bit.ly/40bm9jE
2. http://bit.ly/3I0E0ne
3. http://bit.ly/4nc3RsM
4. http://bit.ly/3ZEjJtT
5. http://bit.ly/4kNqrq0
Sponsored by
P16-17. Epicor explains how manufacturers can assess their digital readiness
Most UK manufacturers believe that digitisation is crucial to enhancing productivity, and yet there remains an industry-wide reluctance to implementing digital technologies. Epicor examines the cultural, financial and operational barriers separating belief from action, before sharing 7 ways businesses can assess their readiness for digitisation.
Digitisation in the UK manufacturing sector appears to be at a pivotal moment. According to the 2024 Make UK survey, while an overwhelming 71% of firms agree that digital technologies are key to enhancing productivity, only 12.5% have made digital technology central to their business strategy. This gap between belief and action highlights a sector caught between recognising the potential of digital transformation and the reality of implementing it.
Many UK manufacturers, particularly small and medium-sized enterprises (SMEs), continue to rely on legacy systems. This reliance is driven by a mix of cultural,
financial and operational factors. At the core is a deep-seated comfort with the status quo. These businesses have often used the same systems and processes for decades, and those systems have proven reliable. The idea of replacing them with unfamiliar digital tools can feel risky, especially when the current setup still “gets the job done.”
This sense of comfort is reinforced by the perception that digitisation is inherently disruptive. Manufacturers worry that introducing new technologies could lead to downtime, production delays, or even system failures. In industries where margins are tight and customer deadlines are critical, even a brief disruption can have serious consequences. As a result, many firms
adopt a “mend and make do” mentality, preferring to patch existing systems rather than overhaul them.
Financial concerns present another significant barrier. Digitisation often requires substantial upfront investment—not only in hardware and software but also in training, integration, and ongoing support. For SMEs with limited budgets, these costs can seem prohibitive. Even when funding is available, the return on investment may not be immediately visible, making it difficult to justify the expense to stakeholders.
The challenge is further compounded by a lack of digital skills within the workforce. Many manufacturers lack employees with the technical expertise to evaluate,
implement, or maintain digital systems. Hiring new talent is costly, and training existing staff takes time and resources. This skills gap often leads to a reliance on external consultants, which can increase both complexity and cost.
Integration issues also play a role. Legacy systems are often deeply embedded in a company’s operations and replacing or upgrading them can be technically challenging. New digital tools may not be compatible with older infrastructure, requiring custom solutions or even complete overhauls—adding to the perceived risk and cost.
Short-term thinking is another obstacle. Many manufacturers are focused on meeting immediate production targets and customer demands. Strategic planning for long-term digital transformation often takes a back seat to day-to-day operations. Without a clear digital roadmap, companies may struggle to prioritise or coordinate their efforts, leading to fragmented or stalled initiatives.
Regulatory and compliance concerns can also discourage change. Legacy systems may already be aligned with industry-specific regulations, and manufacturers may fear that new digital tools could introduce compliance risks or data security vulnerabilities. This is particularly true in highly regulated sectors such as aerospace, pharmaceuticals, and food production.
Leadership mindset is a final, but crucial, factor. In many traditional manufacturing firms, decision-makers may be older and
less familiar with digital technologies. This generational gap can lead to a more conservative approach to innovation. Without strong leadership advocating for change, digital transformation efforts often lose momentum or fail to launch altogether.
So
The first step is to evaluate their current level of digital maturity. This involves understanding what technologies are already in use, how automated their processes are, and whether data is being collected and used effectively. Tools like the Made Smarter Digital Maturity Assessment can help benchmark progress.
Next, manufacturers should assess their workforce. This means determining whether employees have the digital skills needed to work with new technologies and whether the company culture supports innovation and change. If the workforce is resistant or lacks training, that’s a clear area to address.
IT infrastructure is another critical factor. Companies should examine whether their current systems are modern, secure and capable of integrating with new digital tools. Reliable internet connectivity and strong cybersecurity measures are also essential. Data readiness is equally important. Manufacturers need to ensure they are
collecting data consistently, storing it in accessible formats, and using analytics tools to gain insights. Without good data practices, digitisation efforts may fall short.
Strategic alignment is key. Digitisation should support the company’s broader business goals. This means having a clear digital strategy or roadmap and ensuring that leadership is committed to driving transformation. If digital initiatives aren’t tied to measurable outcomes, they’re less likely to succeed.
Financial readiness must also be considered. Companies need to understand whether they have the budget to invest in new technologies, and whether they’re aware of funding opportunities such as grants or tax relief.
Finally, manufacturers should evaluate their ability to manage change and risk This includes having processes in place to handle the risks associated with digital projects and a plan to support staff through transitions.
In summary, while the UK manufacturing sector recognises the value of digitisation, many firms remain hesitant to act. By addressing the cultural, financial and operational barriers, and by assessing their readiness across key areas, manufacturers can begin to close the gap between digital ambition and digital action.
To discuss any of these areas in more detail, book time with Epicor’s advisors via its website. epicor.com
As artificial intelligence (AI) continues to reshape industries, manufacturers are uniquely positioned to benefit from its transformative potential. Here are the top five considerations manufacturers should keep in mind when exploring how to utilise AI in their operations.
From predictive maintenance to intelligent supply chain management, AI can unlock new levels of efficiency, agility and innovation. However, successful adoption requires more than just plugging in new technology; it demands strategic foresight and alignment with business goals.
Before diving into AI, manufacturers must define what they want to achieve. Whether it’s reducing downtime, improving quality control, or enhancing forecasting accuracy, AI initiatives should be tied to specific, measurable business outcomes. Epicor’s approach to AI emphasises practical, people-centric applications that solve real world problems, like automating repetitive tasks or optimising production schedules. By aligning AI efforts with strategic goals, manufacturers can ensure a higher return on investment and avoid the trap of adopting technology for its own sake.
AI thrives on data, and an ERP system is a goldmine. Epicor’s AI-infused Kinetic
ERP solution is designed to harness the vast amounts of operational data already flowing through a business. These types of platforms enable predictive modelling, realtime analytics, and intelligent automation, all within a familiar interface. By building AI capabilities on top of a robust ERP foundation, manufacturers can accelerate deployment and reduce integration complexity.
One of the most powerful aspects of AI is its ability to augment human decision making. Rather than replacing workers, AI should empower them, providing insights, automating mundane tasks, and freeing up time for higher-value activities. Epicor’s AI tools are designed with this philosophy in mind, offering intuitive user experiences that don’t require deep technical knowledge. For example, AI can assist with quoting by analysing historical data and predicting material costs, helping sales teams respond faster and more accurately.
AI is only as good as the data it learns from. Manufacturers must invest in data quality,
integration and governance to ensure AI models are accurate and reliable. This includes cleaning legacy data, standardising formats, and establishing clear ownership and access policies. Epicor’s solutions support this by centralising data within the ERP and offering tools to manage and visualise it effectively. Additionally, manufacturers should remain vigilant about AI “hallucinations” and validate outputs before acting on them.
Introducing AI into manufacturing workflows isn’t just a technical shift, it’s a cultural one. Employees need to understand how AI will impact their roles and how to work alongside it. Training, communication and change management are critical to building trust and adoption. By investing in upskilling and fostering a culture of innovation, manufacturers can ensure their workforce is ready to embrace AI.
AI offers immense potential for manufacturers, but realising that potential requires thoughtful planning and execution. By focusing on clear objectives, leveraging ERP data, augmenting human capabilities, ensuring data readiness, and preparing their workforce, manufacturers can turn AI from a buzzword into a business advantage. With Epicor’s industry focused solutions, manufacturers have a trusted partner to guide them on this journey, helping them work smarter, respond faster and grow stronger in the new age of intelligent manufacturing.
Visit Epicor’s website to learn more.
epicor.com
With the US tariffs in place and looking likely to remain, MEPCA explores the wider implications on the UK-US trade relationship, with expert opinion from Richard Rumbelow, Director of International Business, Make UK, helping manufacturers navigate the new trading landscape.
The shadow of the US tariffs has been hanging over the UK industry since January, evoking an atmosphere of uncertainty for manufacturers exporting to the US. With the 10% tariff on the majority UK goods entering the US now ratified, manufacturers can at least operate from an informed position. However, it is not quite ‘business as usual’ because this new trading landscape is littered with complexities.
Speaking from Geneva while attending the WTO trade negotiations, Richard Rumbelow, Director of International Business, Make UK, took time out of his busy schedule to discuss the tariff implications with MEPCA’s editor.
Richard’s role at Make UK has evolved over the last nine years. Initially, his focus was assessing and responding to the UK’s vote to leave the European Union in 2016. This then led to a more comprehensive international trade relationship role, but maturing the UK’s relationship with the EU continues to be a fundamental part of what he does. Wider trade policy is also a key focus for Richard, which involves closely
following the work of the UK government’s trade policy. Richard explained this element of his role encompasses three key areas: Firstly, he is helping to develop, renew, or set up for the first time, the UK’s global trade deals, of which here are around 70 plus at present. The second part of this is supporting companies, particularly SMEs. Richard explained, “We have a high propensity of SMEs in our economy. As we found out in the EU exit situation, many of them are unfamiliar with international trade and the legalities of it and the practicalities and the administration of it.”
“The third area, which will become more prominent, [is] related to the work of the Department of Business and Trade is the work of the Trade Remedies Authority. The Trade Remedies Authority is a quasi-agency of government. It is independent but reports into DBT. Its responsibility is to manage the UK’s trade defence arrangements from situations where the UK becomes a safe haven for products, which would have economic harm either to businesses or to consumers.
“And in the current circumstances, the
work and role of the TRA will become more important given the prospect of ongoing tariffs being applied by the US and potentially other countries.”
On the tariffs imposed by the US and the impact on the UK economy, Richard was quick to point out that, despite the US having previously been a top growth market for the UK, overall, the EU has been a greater focus:
“The EU has and will continue to be the most prominent geographical economic region for us and our members. And that goes back and is quite clearly linked to the 40 plus years of deep economic cooperation we had with the EU being an integral part of the EU in the development of that economic market.”
Of course, the US remains an important market for the UK, with the cultural and language connection making it attractive to UK businesses. However, the tariffs have contributed to it dropping from prominence as a growth market for UK industries. As Richard explained, “The assumption and also the expectation of our members at this stage is that the US has fallen from that top
three position into the top six, being replaced by other countries, other economic areas such as the Gulf [States] and Southeast Asia”
He continued, “I think at the moment, the US is probably on hold in terms of people’s desire to commit to new expansions into the US. They’re trying to manage current relationships with customers, clients, and supply chain in the US, which is uncertain in itself.”
Uncertainty is rarely good for business, and for many business in the UK, the US is a crucial market. What can individual companies do to mitigate the risks involved in trading with the US?
Richard advised that those companies should do their utmost to maintain relationships with their US customers. To protect those relationships, those companies must ensure they fully understand all customs administration requirements involved in getting their products into the US, including correct certifications and tariff codes, etc., and ensure that their customs submissions are accurate.
This would also be a good time for a company to assess and analyse the wider supply chain supporting its US exports. The reasons for this are twofold. Firstly, because the supply chain “has a bearing on how quickly and whether your goods are going to be subject to tariffs and in what way.” Secondly, because it may present opportunities for a company to adjust its supply chain to work with “countries which
may be less restrictive for goods going into the US”, therefore lessening the impact of the US tariffs on their products.
“It is also perhaps a time to look at other export markets,” he suggested, highlighting Mexico, Canada, the Gulf States and South East Asia, including Australia and New Zealand, as markets of great potential for the UK.
Finally, as well as firms being vigilant with customs administration and aware of supply chains, Richard strongly advises that they ensure the Incoterms (International Commercial Terms) are in their favour; “that customs duties and other administrative costs don’t fall on you, they fall on US customer.”
So far, the UK has remained level-headed in its negotiations with the US, no doubt contributing to the Economic Prosperity Deal with the US, which has afforded the UK exemptions in automotive and aerospace. But given that the US tariff situation is still unfolding, is it likely the UK will impose reciprocal tariffs in retaliation?
Richard thinks not: “My sense is the UK is not in a position and will not want to retaliate because of the adverse effects that it would have on the UK. I think retaliation against the US or applying reciprocal measures on the US at this stage is not within the review of the UK government, and I think that’s a position that will carry on for the conceivable future.”
However, if the EU chooses to apply retaliatory tariffs, this will add a further layer of complexity for UK exporters, particularly
those connected with Northern Ireland, which, due to the Windsor Framework, falls within some of the EU’s trade mechanism responsibilities.
As evidenced by the timeline so far, this remains a developing situation, which has taken many twists and turns to date, and could continue to do so as the year goes on. This volatility highlights just how crucial it is for the UK manufacturing sector to adapt and diversify into other global markets, and, just as crucially, build more robust, transparent supply chains.
As the US turns inwards, the UK must look outwards, committing to free trade, strengthening its relationship with the EU and developing relationships with other global markets. To keep apprised of the latest developments in tariffs, visit Make UK’s website. makeuk.org/tariffs
Many manufacturers are overlooking a valuable source of visual intelligence: security cameras. Here, Abraham Alvarez, Vice President of Product Management, Cameras at Verkada, examines how manufacturers are using video security cameras to supercharge factory operations.
Video security cameras today do far more than monitor entry points to a facility or find footage of a slip-and-fall event. Operational leaders are now leveraging video security cameras for visual intelligence to help them streamline and boost productivity – from optimising floor layouts for efficiency to improving quality control on an assembly line.
The layout of a manufacturing facility can significantly impact operational efficiency. Small delays and inefficiencies compound over time – and in turn, small time savings and efficiencies can also compound.
Carolina Ingredients, an industrial seasoning manufacturer and supplier, turned to its video security system to reevaluate and optimise its 23,000 square foot warehouse. Heatmaps generated from those security cameras gave Carolina Ingredients critical visibility into forklift movement and traffic patterns across its narrow aisles and 1,200 pallets.
After running several experiments with these heatmaps, Frank McKinney, COO and Plant Manager at Carolina Ingredients, discovered that his team was running about 17% of wasted time on three forklifts. The culprit? Low-usage items stored in highvolume aisles restricted traffic and caused delays because only one forklift could access an aisle at a time. This suboptimal layout didn’t just waste operational hours, it also cost the business thousands of dollars each week.
After redesigning and relocating materials based on the heatmap data, Carolina Ingredients has seen a drastic improvement in efficiency, making up well beyond the 17% it was losing before – and even netting 5% gains in the pounds per hour that its team moves via forklift each day.
Chips, dents and dings have long plagued
manufacturers. Video security cameras have opened up a new avenue to address the root causes and ultimately decrease spending on time- and cost-intensive reprocessing.
Operations teams can quickly investigate and identify exactly when a defect occurred on the line by integrating production machinery with video security systems. For example, one global auto manufacturer links its video security footage with its assembly line data to pinpoint issues like chips or dents quickly by using a vehicle’s VIN to source relevant video security footage. This enables teams to trace defects, verify the problem with visual evidence, and quickly take corrective action – all within a matter of hours, not days or weeks.
This kind of precision in quality control also extends to routine reporting and compliance investigations. One industrial manufacturer
was able to leverage License Plate Recognition (LPR) on video security cameras that overlook a weighbridge to verify the contents of an outbound delivery and run reports based on the aggregate information – time, weight, contents, vehicle, destination, and more.
As manufacturers work to stay competitive in the face of rising costs and tightening margins, the visual intelligence that they can leverage from video security cameras – which, in most cases, are already in operation – is emerging as a strategic asset for leading manufacturers. Increased visibility and interconnected data is ultimately the foundation for safer and smarter, data-driven operating environments.
verkada.com/uk/
Andy Price, Director Supply Chain & Sustainability at UK-based sheet metal fabrication manufacturer Mec Com, highlights the advantages of adopting new technologies into stocktaking processes and shares the benefits accurate stocktaking has had on the business.
Before digital tools helped to revolutionise and improve efficiency globally, manual stocktaking was time-consuming and often inefficient.
For Mec Com, the scale and complexity of counting millions of components –particularly small parts – made it challenging to maintain consistently accurate records, sometimes leading to discrepancies that impacted various areas of the business. From order fulfilment to financial reporting, the absence of a comprehensive stock auditing process introduced inefficiencies and delays, with potential financial losses.
As a manufacturer of small parts, relying on a manual stocktaking process for high-volume counts proved increasingly impractical. And, having not completed a full stocktake for several years, the decision was made to adopt a more digitally focused solution to help bring Mec Com into the 21st century and significantly reduce discrepancies across the stocktaking management process.
Automated systems like RFID scanners, barcode tracking and cloud-based inventory software provide real-time data, ensuring precise stock control and minimising downtime. By streamlining the process, a business can optimise resource allocation, prevent shortages and improve overall productivity.
Additionally, enhanced traceability helps maintain quality standards and regulatory compliance. As the industry moves towards smarter, technology-driven operations, embracing these innovations is crucial for businesses looking to improve inventory efficiency.
Bringing in more advanced stocktaking capabilities can also optimise workflows and increase productivity, freeing up staff for higher-value tasks and ultimately reducing employee downtime.
Beyond just the technology, Mec Com found that third-party providers can help reshape inventory management – something that is particularly useful when handling millions of components.
Recognising the need for a comprehensive and efficient stocktake, Mec Com enlisted the help of inventory management specialists, RGIS. With over seven million parts to count, RGIS provided the people and the technology to conduct a warehouse stocktake – across two sites – in just three days, ensuring precise inventory records and improving operational efficiency.
Using RGIS Vision – an optical character recognition (OCR) software – the experts were able to deliver a much faster and more accurate audit than traditional manual methods. This technology can scan part numbers, product codes and barcodes, enabling auditors to achieve faster and more accurate results than a manual in-house stock take.
The partnership enabled a full reconciliation of the company’s stock records, identifying discrepancies and rectifying errors that had built up over the years. The use of technology not only reduced the time required for stocktaking but also minimised the risk of human error, providing a clearer picture of actual stock levels in real-time.
In fact, the audit of 7,600,000 pieces of inventory resulted in a £10,000 stock gain, demonstrating a true financial benefit of accurate inventory management. With more
than 70 experts deployed by RGIS, Mec Com’s own team were able to continue with their day-to-day tasks, helping to reduce disruption across the business.
While stocktaking may often be perceived as a burdensome task, the benefits of investing in modern technology and expert inventory management solutions far outweigh the costs.
For businesses looking to improve their stock control, adopting stocktaking solutions such as those provided by RGIS can be a game-changer. By leveraging technology, Mec Com achieved greater accuracy, efficiency and financial stability – all of which are crucial in today’s competitive market.
Mec Com’s journey from outdated stock records to streamlined, high-accuracy inventory management serves as a valuable lesson for manufacturers and businesses of all sizes that investing in professional stocktaking solutions can lead to long-term operational success.
mec-com.co.uk rgis.co.uk
Before investing in a Computerised Maintenance Management System (CMMS), an organisation should familiarise itself with the concept of maintenance maturity. Customer-centric software company Elecosoft explains why.
Choosing a CMMS is a major decision. It’s not just about selecting software that works today, it’s about finding a solution and a provider that can grow with an organisation as its maintenance practices evolve. This is where the concept of maintenance maturity comes in.
Maintenance maturity refers to the stages an organisation passes through as it improves and refines its maintenance practices. Companies with a low level of maintenance maturity are generally only performing maintenance when equipment breaks down, or typically no more than an 60% vs 40% ratio between reactive and planned maintenance. This leads to high costs, unplanned downtime, and operational inefficiency.
Over time, organisations often aim to move towards planned, preventive, and ultimately predictive or condition-based maintenance approaches, usually powered through IoT and AI integration. The maintenance maturity journey isn’t linear, or the same for every organisation. Different sectors, asset types and operational pressures all influence how maintenance practices develop.
A well-chosen CMMS helps organisations progress along their maintenance maturity journey. At first, CMMS software might only need to log work orders, record asset data, and track reactive work. As maintenance practices become more mature, it may need to support preventive maintenance, cost tracking, data analysis, and more advanced strategies like condition monitoring or predictive analytics.
This is where the choice of CMMS really matters. ShireSystem, for example, is
designed to support organisations of all sizes and at every stage of their maintenance maturity journey.
Many organisations start with ShireSystem Essential, delivering core maintenance management functionality and mobile access. As needs evolve, they can move to ShireSystem Professional for advanced planning, stock control and BI integration. Moving on further, ShireSystem Advanced adds features including multisite management, system integration, and compliance tools like Permit-to-Work. Finally, ShireSystem Expert provides full CMMS customisation, integrated procurement, and custom branding. By this time, maintenance teams will typically be undertaking 80%+ planned maintenance.
Such scalable and flexible CMMS software ensures maximum cost efficiency and consistency as organisations move up the maintenance maturity scale.
By partnering with a trusted and future ready CMMS provider, businesses avoid the risk of technology obsolescence along with potentially costly and cumbersome CMMS migrations.
As organisations become more proactive in their maintenance efforts, their data requirements often increase. Maintenance teams may now require detailed asset histories, cost tracking, stock control, and integration with other business systems. The right provider will adopt a partnership approach, continually working with an organisation to seamlessly upgrade, configure and scale its CMMS as the organisations priorities change, such as adding new features, linking with IoT sensors, or using data to inform strategic decisions.
Maintenance maturity is an ongoing process. By choosing a CMMS provider that can support it at every stage of the journey, an organisation sets itself up for long-term success. The right partner will help make the most of a CMMS investment, not just today, but long into the company’s future as its maintenance requirements and ambitions evolve.
For more information visit: elecosoft.com/shiresystem
Drive Return on Investment at Every Stage of Your Maintenance Maturity Journey with our Scalable, AI-Ready CMMS
Smarter maintenance powered by your asset data.
From reactive to predictive, we’re with you.
Simple to set up. Easy to use. Built for results.
Where are You on Your Maintenance Maturity Journey?
If you’re ready to take the next step, why not book a personalised demo to see how ShireSystem can support your maintenance transformation
From the rising cost of raw materials and the threat of cyberattacks to concerns surrounding tariffs, trusted insurance and risk management firm Gallagher shares its latest research into the biggest risks facing manufacturers in 2025.
The manufacturing industry has experienced a turbulent time over recent years as firms overcome major changes in market conditions and an unstable economy. Over 100 leaders in the manufacturing sector recently took part in research aimed to lift the lid on how they feel about trading conditions and what keeps them up at night.
The research, conducted by insurance and risk management firm Gallagher, which specialises in manufacturing risks, asked leaders to identify the major concerns that might hamper their successful trading. The cost of materials topped the list with nearly half of all managers saying this was the biggest issue, followed by supply chain problems, cyber-crime, salaries and the impact of tariffs.
Inflation was cited as the root cause for the problems around the cost of materials, with the issue not only impacting materials but also the value of assets. Steve Fletcher, who specialises in the manufacturing sector at Gallagher, said, “The pace of change of inflation is impacting across the board. Materials have increased hugely in the last few years and this doesn’t look like changing anytime soon. Developing contingency plans such as diversifying supply chains can help mitigate price fluctuations as well as looking at ways to increase efficiencies. But firms should also bear in mind that inflation impacts asset values – which can be overlooked – so it’s important to ensure correct valuations of equipment are done. I’d recommend a valuation exercise at least every 12 months to avoid finding assets are underinsured if something goes wrong.”
Cyber-crime continues to be a significant theme, and the manufacturing industry is a prime target for cyberattacks, experiencing a significant increase in incidents in recent
years. In fact, in 2024 the sector faced more than a quarter of all detected cyberattacks globally. Ransomware attacks are particularly prevalent and can cause substantial financial losses. Steve said, “There’s much greater awareness now that risk doesn’t just mean machinery or physical damage. Cyber and in particular ransomware attacks that shut down operations are a huge risk and with criminals becoming ever sophisticated, manufacturing businesses need to take steps to mitigate the chance of falling foul to a cyber-attack – clearly it’s important to have insurance cover in place but risk management can help prevent the issue in the first place. Easy steps including training employees, making sure applications are up
to date with new versions and thinking about your supply chain and vulnerabilities and how a criminal could intercept this way.”
The impact of tariffs was the only new risk to enter the top five for manufacturers in 2025 with the current uncertainty giving cause for concern. Steve said, “It’s particularly hard for businesses to plan with only short-term tariff agreements in place, so it is no wonder this has crept into the top five concerns for manufacturers. Forward planning is important here – thinking about where else you could source raw materials from and at the other end, which markets you may want to diversify into to help mitigate the risk.”
ajg.com
Discover how Tork exelCLEAN® Cleaning Cloths can save your business time by cleaning 32% faster than rags.* And Tork Performance® Dispensers can be placed exactly where needed to decrease interruptions and reduce motion waste.
Better hygiene for better productivity
tork.co.uk or tork.ie
Tork, an Essity brand
*Panel test conducted by Swerea Research Institute (Sweden, 2014)
When businesses take steps to improve operations, hygiene is rarely considered, yet it can have a profound impact on employee performance. Tork, from leading hygiene and health company, Essity, explains how clean washrooms present an easy win for better productivity.
Market volatility is causing inconsistency in manufacturing supply chain deadlines. More efficient methods are continuously being developed to enable complex machinery manufacturing to be agile and adapt. With this overhead pressure, it can be easy to overlook the more straightforward efficiencies that can be implemented to maximise productivity in day-to-day workplace operations.
While it may seem a minor detail, the state and accessibility of workplace washrooms can have a profound impact on employee wellbeing, satisfaction, and ultimately, productivity.
Research from Tork has found that 38% of people have limited the amount they eat or drink to avoid going to a washroom, and 1 in 6 have left their job because of poor washrooms. The reasons that people avoid the washroom in the first place are varied, but factors include the perception that the toilets were unhygienic as well as being poorly stocked with soap and toilet paper, the presence of unpleasant odours and the washrooms being out of order.
This avoidance behaviour can in time lead to long-term health conditions due to dehydration and discomfort, impacting employee performance and engagement.
The most obvious benefit lies in the cleanliness of washrooms as poorly maintained facilities foster germs, creating a health hazard. The COVID-19 pandemic has left in its wake a public more aware and concerned with good hygiene practices and employees expect higher standards. With cleanliness in the spotlight, workers increasingly prioritise adequate supplies of
chemical-free soap, user-friendly paper towel dispensers and touch-free amenities.
Clean washrooms reduce the risk of illness, which in turn minimises sick days and keeps teams operating at full strength. Moreover, a visibly clean environment reassures staff, reducing anxiety and allowing them to focus on their work.
Besides the psychological benefits to personnel, businesses in the UK have a legal requirement to provide suitable and sufficient facilities to employees. The Workplace (Health, Safety and Welfare) Regulations 1992 state that toilets must be kept clean, ventilated, well lit and stocked with ample hygiene supplies.
These regulations also stipulate that any broken fixtures must be fixed promptly, and that all facilities must be readily accessible and suitable for all employees.
However, provisioning appropriate facilities are more than a compliance tick-box exercise. Clean, well-maintained washrooms are an entitlement for everyone and poor facilities can undermine morale and drive talent away. Avoiding the washroom at work can erode concentration over time as employees fixate on their own discomfort and potential distress. Ignoring these needs can result in higher turnover, as employees seek workplaces that prioritise their comfort and dignity.
This is particularly true for employees managing health conditions that require frequent washroom visits, such as diabetes or Crohn’s disease. If facilities are inadequate, these employees may feel compelled to limit their intake of food or drink, or even avoid using the washroom altogether, behaviours that are detrimental to both health and productivity.
Similarly, accessible washrooms are not just for those with visible disabilities. Temporary injuries, pregnancy, and agerelated mobility issues can affect anyone. By designing facilities that are truly accessible, organisations demonstrate a commitment to all employees. This fosters a sense of belonging and a duty of care, which are key drivers of engagement and productivity.
In some workplaces, the washroom can be the only respite for an employee during a busy day. A private space where employees
can gather thoughts, manage personal needs and refresh before returning to work. If the toilets are unhygienic or unsuitable for employees’ needs, motivation levels amongst the workforce can fall and general abstention from work is likely to increase.
Absenteeism due to illness costs UK businesses billions annually. While not all of this can be attributed to poor hygiene, the role of shared facilities in spreading germs is well documented.
With the rise of working from home, employees that feel uncomfortable using workplace toilets are more likely to work from home and avoid the workplace. While this isn’t as common in manufacturing, the alternative is that employees will take more sick days to avoid having to deal with the washrooms at work.
Consulting with staff is also crucial. Needs and expectations will vary, and a one-sizefits-all approach is unlikely to succeed. Regular feedback mechanisms, such as anonymous surveys, can help identify issues before they become problems. Employees
that feel unvalued are likely to seek other job opportunities and generally lack the motivation at work.
Productivity efficiencies in the workplace can be difficult to measure tangibly, but prioritising workers health and wellbeing is a quick win for employers that results in more comfortable, productive workers.
The immediate business benefit lies in the reduction of absenteeism, a financial and operational burden on employers that costs them billions every year.
The psychological benefit, while harder to measure, undeniably creates a more motivated and productive workforce as employees feel comfortable, cared for and valued.
Ultimately, investing in suitable washroom facilities is a strategic decision that pays dividends in employee satisfaction, operational resilience, and long-term business success. tork.co.uk
Implementing an ERP solution can drastically improve a business’ operations. Here, a precision engineering firm based in Kent shares how it leveraged software to transform its processes.
Precision engineering company Intake Engineering introduced control and tracking into the operation, making every piece of vital information easily accessible. “Everything is just a click away and I can access it anywhere. It’s a godsend,” says Lee Brien, Director.
Intake Engineering is a precision engineering company from Whitstable, England, that specialises in CNC turning and milling, with a particular focus on sliding head work. While the business has been active for about four years, its predecessor, Woodfields, had been in business for approximately 50 years before the takeover.
With a team of 10 employees, the company serves customers mainly in the oil and gas, aircraft, and electrical sectors, with a large part of their revenue coming from repeat business from a few large clients.
Before Director Lee Brien joined the company in October 2024, the business was run on multiple separate systems, mainly different spreadsheets. “They were putting in jobs on one system, making a stock list on another, and so forth,” he says.
The lack of integration and efficiency of the management system prompted the company to implement a manufacturing ERP solution. The owner of Intake Engineering had frequently visited Lee’s previous employer, where Lee and his team used MRPeasy to run the operation. Impressed with the software’s usability, he decided to implement it in his business as well.
“The price of the system played a big role as well,” Lee maintains. “We haven’t found
another package that does what MRPeasy does. This price range with such breadth of functionality, an open API, and a large variety of native integrations is practically unbeatable.”
When Lee was hired as the Director, however, he found that the software was not being used to its full potential, with many of the business’s functions still being performed within spreadsheets. His first order of business was to get MRPeasy properly implemented. He started by setting up the bills of materials, production routings and inventory tracking, which he believes to be the basis for successful adoption.
“I personally think that with concentrated effort, you could sit down and implement MRPeasy within a weekend,” he suggests.
According to Lee, the re-implementation has introduced a large degree of discipline and control to the company. In a company that used to put purchase orders in verbally, every action is now logged, every item tracked.
“Now it’s all completely set up so I can manage the business even on my phone at home,” he says. “I can look at the jobs, see where the material is, see what’s coming in, see progress on the shop floor, and so forth. It’s fantastic!”
For Lee, one of the most significant benefits of the system is the seamless communication it enables with his clients. Within just moments, he can find the customer order in question, see when production is due, send out an invoice and ship out the order.
“Everything is just a click away and I can access it anywhere,” he says. “Invoicing is fantastic now. It doesn’t tie you up as much as before, and the shipment side of things is great. It’s a godsend really.”
As a final recommendation to other small manufacturers like himself, Lee suggests that everyone try out a manufacturing ERP system.
“Just try it, it’s so-so easy,” he says. “I’ve used other MRP systems, and nothing measures up to MRPeasy.”
mrpeasy.com
In today’s demanding industrial environments, staying connected to process instruments should be simple. Whether in a quiet office, a noisy control room, or a dust-filled production plant, VEGA’s digital tools ensure that users can easily configure, monitor and maintain sensors.
VEGA’s trio of digital tools – myVEGA, the VEGA Tools App, and PACTware – work seamlessly together to simplify every stage of instrument operation and support. These platforms are designed to help users overcome everyday challenges on-site, such as inaccessible instruments, harsh working conditions, or a lack of clear data visibility.
myVEGA is the central cloud platform that houses everything related to VEGA devices. From ordering and re-ordering to storing test certificates, PINs, inspection records and sensor back-ups, it offers a single place to access, share and manage instrument data across the business. It connects directly with VEGA Tools and PACTware to allow data to flow effortlessly between field and office.
VEGA Tools App, available for iOS and Android, is tailored for on-site users. With encrypted Bluetooth communication, users can adjust, back up or restore sensor settings in dusty or high-noise environments where cables and laptops are impractical. This app enables engineers to get fast, secure access to their devices from a phone or tablet – even if the sensor is in a hard-toreach or hazardous spot.
PACTware is the PC-based solution for those who prefer a laptop interface or need to work within control cabinets via HART. From October 2023, VEGA made the full version of the DTM Collection – which includes PACTware, VEGA DataViewer and more, previously a paid upgrade –completely free for all users. This move gives everyone access to powerful features like diagnostic tools, advanced vessel
geometry setup, and integration with VEGA’s DataViewer software for analysing echo curves, event data and parameter trends.
These tools are transforming the way customers interact with their instrumentation.
With VEGA Tools App’s cloud-based Backup & Restore function, users can confidently save and restore sensor settings to the cloud in seconds – reducing downtime and simplifying maintenance. The DataViewer tool, part of the DTM Collection, lets users archive and review field data in detail, and even share it directly with VEGA’s technical support team for quicker troubleshooting.
It’s not just about device configuration either. Sales teams can check live delivery times and prices directly through myVEGA. Spares and repeat orders can be placed instantly. Certain teams who process payments in different departments can collaborate with shared access to sensor settings, reports and documentation – regardless of where they’re based.
Security is built in from the start. Bluetooth communication uses 64-bit encryption, and all data stored in myVEGA is protected in the cloud. With over 200,000 registered users worldwide and Bluetooth compatibility on virtually every level device since 2002, VEGA’s digital suite is trusted across industries and applications.
Most importantly, everything is free – no licences, no subscriptions. Whether a user is just getting started with VEGA or managing a fleet of hundreds of instruments, these tools are ready to support them.
By combining mobile flexibility, PC-level diagnostics and secure cloud infrastructure, VEGA’s digital ecosystem helps users get more from their sensors – faster. From commissioning and troubleshooting to procurement and long-term support, VEGA keeps industrial operations connected, streamlined and simple.
To learn more about VEGA’s tools for the digital future, visit the company’s website. bit.ly/464jPir
Tom Parker Ltd, distributor of high-performance fluid power solutions, introduces CEJN Smartflow and explains why dry break couplings are transforming fluid transfer across UK industries.
In industries where precision, safety and efficiency are non-negotiable, CEJN Smartflow dry break couplings are setting a new standard.
Distributed in the UK by Tom Parker Ltd, CEJN’s trusted partner for over 50 years, Smartflow delivers spill-free, highperformance fluid transfer solutions tailored to demanding applications.
From oil and gas to food and beverage, Smartflow couplings excel in safety-critical and aggressive environments. Their innovative design eliminates spillage during connection and disconnection, reducing downtime, cutting costs, and protecting both operators and the environment. With a 25-bar working pressure and a 5x safety factor, Smartflow’s lightweight aluminium fittings offer a cost-effective alternative to stainless steel without compromising strength.
Smartflow’s universal compatibility, adhering to TEAM SPEC and STANAG 3756, ensures seamless integration with existing dry break systems. For food and beverage applications, FDA-approved O-ring seals meet stringent hygiene standards, making Smartflow a trusted choice across diverse sectors, including petrochemicals, marine, aviation, road and rail.
Smartflow couplings redefine efficiency with an innovative, integrated poppet system that makes connecting and disconnecting faster and easier than ever. Effortlessly fit the female hose unit onto the
male tank adaptor and twist clockwise by just 1/3 of a turn to secure it in place. This simple action opens the poppets in both units, releasing the flow. When it’s time to disconnect, a simple anticlockwise twist unlocks the coupling, shutting off the flow immediately with near-zero spillage.
Smartflow’s spill-free technology not only boosts productivity but also prioritises health, safety and environmental sustainability. By eliminating fluid
waste, businesses can enhance profitability while safeguarding their workforce and surroundings.
For industries seeking reliable, highperformance fluid transfer solutions, Smartflow is the clear choice.
Visit Tom Parker Ltd’s website to explore the Smartflow range.
tom-parker.co.uk
When every drop counts, choose Smartflow dry break couplings – the trusted solution for precision fluid transfer in thermal management and chemical handling environments.
• Spill-free connections
• No additional valves required
• Minimal moving parts for maximum reliability
Engineered for aggressive, safety-critical environments, Smartflow couplings deliver safe, clean, and efficient fluid transfer – reducing downtime, cutting waste, and improving workplace safety.
• Chemical dosing & transfer systems
• Thermal control units (TCUs) & cooling loops
• AdBlue & DEF distribution
• IBC filling & tanker loading/unloading
www.tom-parker.co.uk
A Power Supply Unit (PSU) is one of the most overlooked areas in electronics product development, but it is also one of the most important. Ideal Power, design-in PSU supplier, explains why it is optimal to establish a suitable PSU for the product design early on.
Without a suitable designed-in power supply, newly designed electronic products could suffer from reliability and incompatibility issues from the start – the PSU is a critical component needed for an electronic system to operate at its best and be reliable, efficient and compliant.
Choosing the right PSU at the right time, with help from a bespoke/design-in PSU supplier, reduces delays, simplifies the process, and provides an engineering team with more information to make an informed decision.
Many teams focus on processors, interfaces, or enclosures first – leaving the power supply to the final stage. It seems logical: get the ‘core’ designed, then bolt on the PSU. But this creates serious problems:
• The PSU might be too large for the space left in the product.
• It may lack the correct certifications.
• Long lead times slows product launch and create supply chain issues.
• Incorrect optimisation leads to over-spec’d or underperforming part.
These issues cost time and money. They can be problematic within an organisation and generate stress and unnecessary delays, with engineering, procurement, and production all scrambling to fix a late-stage problem. Getting the PSU locked in early avoids this entirely.
This isn’t about sending over a part number and hoping for the best. As a design-in PSU supplier, Ideal Power works closely with
the engineering team from the first stage of product development.
That means helping to match a product to the specific application; reviewing layout constraints and offering suggestions for better integration, assisting with compliance to avoid redesigning at the last minute; and guiding on thermal, electrical and mechanical limits constraints from the start.
Whether a project requires standard options or minor modifications, Ideal Power supports engineering teams with a technical clarity and responsiveness that general suppliers can’t match.
Every market has its regulations. CE, UKCA, TUV, RoHS, REACH, EN 62368— it’s a minefield if a non-compliant PSU is chosen too late. Ideal Power only offers fully certified units. Its datasheets are accurate, the support it provides is fast, and its experts can walk the engineering team through documentation, product advice and required declarations.
The product design may be perfect – but without the right supply plan, the production line won’t move. Once a PSU is selected and designed in, Ideal Power help lock-in availability.
This is ideal for teams managing rolling
production, tight inventory control, JIT, Kanban or multi-phase product builds. It’s also one less thing for the procurement team to worry about.
Late-stage changes to a PSU spec can push the entire schedule back. That means missed go-live dates, lost customer confidence, and increased pressure across a business.
Working with a design-in PSU supplier from the start reduces that risk, locking in technical stability, sourcing certainty, and predictable deliveries.
Ideal Power believes sourcing a power supply should be simple, not stressful. That’s why it works with businesses from day one, offering expert advice, proactive support, and flexible fulfilment. Ideal Power offer a vast range of products available to provide the best option, ensuring its customers don’t get caught out with an unsuitable part too far down the line.
Need help choosing the right PSU? Contact Ideal Power’s technical team today.
Idealpower.co.uk
Work with Ideal Power from the start of your project to get the right PSU first time.
Our expert-led support, bespoke products, and flexible call-off service help you avoid delays, reduce risk, and stay in control. Visit our Website
Automation and electrification are crucial components in tackling the environmental impact of offshore gas processing. Rotork, manufacturer of industrial flow control equipment, supplies actuators for an automated, ‘Next Generation’ fully electrified offshore gas platform.
Rotork has supplied over 200 actuators to ONE-Dyas for the N05-A upstream gas processing platform, located in the Dutch North Sea.
The Skilmatic SI intelligent self-contained electro-hydraulic actuators, IQT3 Pro intelligent part-turn electric actuators and CVA continuous unrestricted modulating actuators will support the electrification and automation of the platform.
HSM Offshore was contracted to build N05-A – which will turn upstream wet natural gas into dry natural gas for pipeline export – by Dutch exploration and production company ONE-Dyas.
The next generation platform, scheduled for production in the winter of 2024/2025, is expected to reach ‘near zero’ operational emissions (Scope 1 and 2) and will be the North Sea’s first fully electrified gas production platform. Electrification is central to ONE-Dyas’ near-zero strategy, with power primarily supplied by a nearby German offshore wind farm, Riffgat.
Reduced maintenance visits and limited
unplanned helicopter flights also form part of the near-zero initiative. The platform will be fully automated and normally unmanned, with all plant equipment controlled autonomously. Reliability is also key to reducing unplanned visits to the platform, and digital solutions further support the reliability and availability of assets.
The energy efficiency of Rotork’s actuators will further support the near-zero emissions target. Electric actuators only consume power when in operation, unlike pneumatic actuators and controls, which need a constant supply of either gas or locally produced compressed air.
Rotork performed a factory fit of the Skilmatic SIs with free issued valves for the N05-A project, which were fitted and calibrated at Rotork’s Rotterdam Service Centre then shipped to the HSM Offshore yard.
Rotork is a market-leading global provider of mission-critical flow control and instrumentation solutions for oil and gas, water and wastewater, power, chemical, process and industrial applications. It helps customers around the world to improve efficiency, reduce emissions, minimise their environmental impact and assure safety.
rotork.com/en
Martin Preece, Head of UK Subsidiary for STOBER, introduces the company’s advanced right-angle servo gearbox. Discover how the technology improves on prior versions to achieve a higher output speed, greater durability, and more.
STOBER has further developed its KS right-angle servo gearbox. Delivering ‘power without compromise’, it is now offered not only in two- and three-stage versions, but also in a one-stage version. The new series features robust bearing technology and high-quality gearing.
Compared to other variants, the new one-stage version enables a higher output speed. The gear ratio range has been extended on both the low and high ends for all variants, so customers benefit from receive precise, low-backlash and maintenance-free solutions for highly dynamic requirements.
“Compared to multi-stage variants, onestage right-angle servo gearboxes are not only more compact, but they are also more robust thanks to the reduced number of components. And since there is only one gear ratio stage, this has a positive effect on energy efficiency,” explains Martin Preece, Head of UK Subsidiary for STOBER.
With their robust bearings and highquality gearing, KS gearboxes are
extremely durable making them suitable for continuous operation, even at high speeds. This series also features very high torsional stiffness. The new one-stage version is available in ratios 2 and 4.
Continues Martin: “By combining the KS right-angle servo gearbox with compact STOBER planetary gearboxes, it can be further expanded into multi-stage gearboxes with ratios from 6 to 400. This more than doubles the previous gear ratio range we have been able to offer so it covers an even wider range of applications.
“The new solution is also robust, rigid and low backlash making it suitable for dynamic requirements. We have also standardised the type of designation and adapted the design of the right-angle servo gearbox to the new, round shape of our planetary gearboxes.”
“Just as with the two- and three-stage versions, designers can choose between three shaft designs,” adds Martin. Thanks to these customised output geometries, KS gearboxes can be used for a variety of applications. The two- and three-stage gearboxes can be combined with various STOBER motors via direct attachment. The space-saving drive ensures operators benefit from less weight in addition to high torque and the resulting increased power density. Because the mass moment of inertia of the gearbox is lower due to the absence of the motor adapter, users can take advantage of the full dynamics of the drive.
Director of Research & Development
Mechatronics at STOBER, Artur Wagner, is responsible for the new generation. Having studied mechanical engineering,
he began his career with STOBER in Pforzheim, Germany as a computational engineer more than 30 years ago. Today, he is responsible for design and development in the mechatronics department. Outlines Artur: “We are supporting the consistent optimisation of our very broad product portfolio – which also includes the KS rightangle servo gearbox. Thanks to low-friction bearings in the input, higher speeds can be realised, whilst most competitors rely on preloaded tapered roller bearings, which are less efficient.
“We have increased the nominal torques by up to 20 percent and increased the permissible input speed. Together with the smaller gear ratios, the customer can realise significantly higher output speeds – a clear advantage in the market.”
Concludes Artur: “Another highlight is the modular design throughout. By adding planetary gearboxes, multi-stage variants can be implemented flexibly – according to the customer’s exact – according to the customer’s exact requirements. Successful lateral thinking in action!” stober.co.uk
As additive manufacturing reaches a tipping point in its transition from prototyping to production, 3D Midlands warns that traditional service bureaus risk being left high and dry if they can’t scale.
Midlands-based 3D print specialist Midlands 3D has seen rapid growth over the past few years, establishing itself as one of the UK’s leading additive manufacturing service providers. While the 3D printing sector has long been associated with prototyping, this growth signals a broader shift in how the technology is being used – moving from experimental to essential in low-to-mid volume production.
As new capabilities in printing and postprocessing continue to mature, the industry is witnessing a sharp rise in demand for batch manufacturing. For service bureaus, the message is clear: evolve or risk being left behind.
According to Midlands 3D, the pivotal moment came in the third quarter of 2024. With capable and affordable desktop 3D printers becoming widely accessible, many customers began bringing prototyping in-house. In response, Midlands 3D refocused its business around scalable manufacturing support, doubling down on what it could offer that desktop setups could not: consistent, high-volume output and a comprehensive suite of production services.
The company believes the era of the traditional print bureau is fading. Future success will depend on whether providers can operate as true manufacturing partners offering scale, quality, and strategic value beyond printing.
Scaling for production means more than just owning more machines. It requires physical space, throughput capability, and a commitment to quality control.
To meet rising demand, Midlands 3D has relocated to a new headquarters offering four times the previous floor space. It has also expanded its finishing facilities and embraced automation—becoming one of the first UK-based additive manufacturers to implement automated workflows across multiple platforms. The company now claims to be one of the most automated AM providers in the country.
Customers increasingly require more than parts. They need complete manufacturing support. Midlands 3D has responded by investing in value-added services including 3D scanning, reverse engineering, assembly, PPAP inspection, bag-and-tag delivery, and the integration of threaded inserts. The company emphasises that these services are now baseline expectations, particularly when supplying into production environments.
Close collaboration with customers is also proving key. Midlands 3D reports that early engagement in the design process often leads to improved performance, reduced material use, and lower overall costs, particularly when optimising for Design for Additive Manufacturing (DfAM).
The shift to batch production is also transforming procurement models. Midlands 3D is seeing increased demand for longerterm agreements, schedule alignment, and support for leaner stockholding, all areas where a collaborative supplier relationship can unlock value.
As AM becomes embedded in critical supply chains, standards matter more than ever. Midlands 3D holds ISO 9001 certification and Cyber Essentials accreditation and sees such compliance as essential for working with manufacturers at scale.
With the sector evolving quickly, Midlands 3D believes a market shakeout is underway. Only those investing in automation, value-added capabilities, and long-term partnerships are likely to thrive.
As AM crosses its tipping point, the message from the Midlands is clear: for those ready to scale, a new era of manufacturing opportunity has arrived.
midlands3d.com
Discover how a new robotics solution engineered by Musketeers Capital and integrated by BS Handling Systems has been designed for the practical optimisation of materials handling.
The pressure is building in UK warehousing. Material handling businesses are compelled to process an ever-increasing amount of orders, faster, all while grappling with labour shortages and rising operational costs. It has the makings of a perfect storm.
But there is shelter to be found in the form of turnkey automated solutions provided by BS Handling Systems. For businesses that need scalable, intelligent sorting without the complexity of traditional systems, a new solution has entered the market with serious momentum: the Omnisort, a high-speed modular robotic sorting system, engineered by Musketeers Capital and integrated by BS Handling Systems.
The Omnisort boasts an intelligent, threedimensional design. Designed specifically to meet the needs of fast-moving retail, e-commerce, and logistics environments, it enables seamless handling of parcels, fashion items, returns and small goods – all in a compact footprint. With a capacity to sort 1,800+ items per hour and support for over 100 destination chutes, it’s both powerful and adaptable.
The system follows an “orders-to-person” working principle and supports both order sorting and batch sorting, allowing operations to maximise efficiency based on their fulfilment strategy. Integration with the OmniStorage Pro system enables even more advanced workflows, supporting complex picking, secondary sorting, and rapid returns processing.
From the outset, Omnisort has been engineered with operational realities in mind. Its modular architecture supports a variety of layouts and this makes it a smart choice
for both space-constrained warehouses and larger fulfilment centres looking to scale. Quick installation means minimal disruption to existing operations, and integration via API allows the system to connect seamlessly with existing WMS/ ERP platforms.
“It’s a true plug-and-play solution,” says Robert BrandSmith, Managing Director at BS Handling Systems. “The Omnisort brings smart sortation within reach of mid-sized operations, not just the top-tier players. And because it’s modular, it grows with you, so it’s ideal for scaling businesses.”
For many, the appeal goes beyond performance metrics. The simplicity of the system – from setup to operation – makes it easier to adopt, operate and scale. That’s particularly important for companies facing fast-changing customer expectations and ever tighter delivery windows.
As part of their broader roadmap,
Musketeers Capital and BS Handling Systems are focused on making automation more accessible across the board. Their vision is clear: combine speed, flexibility and intelligence in a way that delivers lasting value – not just to tier-one logistics giants, but to ambitious regional operations, 3PLs, and retailers across the UK.
To learn more about Omnisort, or how BS Handling Systems and Musketeers Capital can support materials handling businesses, visit the website below.
bshandlingsystems.com
.... to a fresh and innovative approach to turnkey solutions
Smart Manufacturing Week 2025 has officially cemented its position as the UK’s largest event for advanced manufacturing and engineering, welcoming 13,319 attendees across two action-packed days at the NEC.
Held on the 4th and 5th June, the event combined impressive technology with an extensive educational programme and a vibrant show floor. Adding extra flair were celebrity look-a-likes, movie robots and live music, creating a dynamic atmosphere that celebrated innovation and industry.
This year’s strong turnout reinforces the event’s vital role in the UK’s industrial calendar. With 456 exhibitors on the show floor, attendees explored hundreds of cutting-edge products and innovative solutions driving the future of industry.
Exhibitors enjoyed strong footfall across both days, with a steady buzz of conversation and energy resonating throughout the show floor. The atmosphere reflected a high level of engagement from visitors, keen to explore new technologies and forge meaningful connections.
Alongside the bustling exhibition floor, the Solutions Theatres delivered over 170 free-to-attend educational sessions led by experts in manufacturing and technology. Covering key themes such as Industrial Data & AI, IIoT & Connectivity, Digital Transformation, and Leadership and Strategy, the programme offered valuable insights for professionals at every level. Attendees also benefited from practical workshops hosted by the Institute for Manufacturing and explored the latest advancements showcased in the everpopular Innovation Alley.
A brand-new feature for 2025, Smart Tank took place on Day 1. Exhibitors from Innovation Alley pitched their business ideas and solutions to a panel of industry leaders, who scored entries based on criteria ranging from innovation to market size to business readiness. Two sessions ran, with a winner crowned from each. Uie impressed
the judges with the simple ingenuity of its batteryless heat sensor for electrical condition monitoring applications, while Logidot stood out for taking the idea of GPS vehicle tracking software, moving it inside the factory and then expanding its capability to create a unified seamless system.
In the Solutions Theatres, a standout session on Day 1 came from Professor Henrik von Scheel, whose headline keynote drew significant attention, while Former Team Principal of the Haas Formula 1 Team Guenther Steiner captivated visitors on Day 2 with a keynote that offered rare insight into the high-stakes world of elite motorsport.
The festival atmosphere was genuine with music upon entry, Elton John, Dolly Parton, Stormzy, Lady Ga-Ga and Ed Sheeran looka-likes walking the floor and a piano busking spot. The Guitar Legends Competition, a much-loved feature of Smart Manufacturing Week, gave engineering guitarists a chance
their
A winner was crowned on each day of the event, with both taking home a custom 3D-printed guitar. Day 1’s winner also joined live band The Shadow Monkeys on stage, adding to the energy and entertainment of the evening drinks reception.
Event Director, Grace Gilling said, “It’s been incredible to feel the buzz throughout Smart Manufacturing Week 2025. We knew this year would be special, but the response has truly exceeded expectations. From the moment doors opened to the final moments, the floor was alive with innovation, collaboration and a real sense of excitement for the future of manufacturing.”
The dates for next year’s Smart Manufacturing Week exhibitions have been confirmed as 3-4 June 2026. For more information, visit the website.
smartmanufacturingweek.com
With dimensions of just 119.5 x 40 x 20 mm, the AZM40 is the smallest electronic solenoid interlock in the world. This makes it especially suitable for small safety doors and flaps. Despite its compact size it has an amazing 2000 newton interlocking force and 25 Newton latching force.
Thanks to the 180° angle flexibility of the actuator, it can approach the AZM40 on a stepless basis, making the interlock also suitable for flaps which do not close at 90° or those that open upwards to a 45° angle. This means the angle flexibility helps the interlock easily fit into compact spaces and difficult to access areas.
In the event of a power cut, the AZM40 retains the current position. This ensures safe operation, whatever the status of the machine. Even if there are hazardous run-on movements, the safety door remains locked in the event of a power failure. Another advantage of the bistable principle is the consistently low energy consumption, as the interlock only requires power when the door is to be locked or unlocked.
SCHMERSAL | Enigma Business Park Malvern, Worcestershire, WR14 1GL
www.schmersal.co.uk
uksupport@schmersal.com
On the 4-5 June 2025, TCT 3Sixty welcomed over 6,000 professionals and around 150 exhibitors, reaffirming its status as the UK’s premier additive manufacturing event. Here is a roundup of the event’s highlights.
This year’s TCT 3Sixty focused sharply on industrial-grade 3D printing, presenting complete end-to-end workflows – from concept to post-processing – with breadth and depth rarely seen under one roof.
The event hosted a strong lineup of speakers, including representatives from the UK Ministry of Defence, Leonardo, GKN Aerospace, and the Natural History Museum. A standout moment came from Wing Commander Jon McMahon, who outlined the MoD’s “factory-to-foxhole” initiative. With projected savings of £118 million, the programme highlights how agile, battlefield-ready AM supply chains are reshaping defence logistics.
Innovation dominated the show floor. Notable launches included:
• UltiMaker’s S6, offering a fourfold speed increase.
• Pollen AM’s fastest-ever 3D printer.
• WAAM3D’s full-scale rocket stage demonstrator.
• AMS’s “Powder Pro” software, which debuted with real-time traceability, lifecycle tracking, and predictive reuse insights. These products impressed not just for technical advancement, but also for their clear readiness for industrial deployment.
The event fostered active networking, aided by AI-driven matchmaking through the official TCT app. Its co-location with Med-Tech Innovation Expo, Subcon,
Automechanika, and Smart Manufacturing
Week added value and broader context across industries.
Held on 4 June, the black-tie TCT Awards celebrated innovation across eleven categories. Neil Hopkinson and Jonné Messer were inducted into the Hall of Fame, while award-winning applications ranged from BMW’s WAAM-produced suspension strut tower to a Lithoz ceramic jaw implant. It was a fitting tribute to additive manufacturing’s growing real-world impact.
Manchester Metropolitan University hosted hands-on student challenges, encouraging emerging talent to engage directly with the technology. These live competitions added energy to the show floor and emphasised AM’s educational pipeline.
Alongside the main exhibition, the annual TCT User Group event provided a valuable forum for open, peer-to-peer knowledge exchange, where users shared candid insights, practical lessons and operational challenges in additive manufacturing implementation. Meanwhile, the Project TAMPA meeting offered a focused platform for defence and government stakeholders to explore how AM technologies are enabling more responsive, decentralised supply chains, particularly in forward-deployed and mission-critical environments. These side events reinforced TCT 3Sixty’s role not just as a showcase, but also as a strategic hub for dialogue, collaboration and applied innovation.
TCT 3Sixty 2025 delivered a well-rounded snapshot of where additive manufacturing stands today – covering everything from hardware and software to real-world
applications, education and strategy. Whether attendees were experienced in AM or just exploring its potential, the event offered practical insights and useful connections. Its strong focus on industrial adoption and implementation made it a worthwhile stop for anyone serious about keeping pace with the sector.
Building on its continued growth and strategic partnerships, TCT 3Sixty will return 3-4 June 2026 co-located with Interplas and the Med-Tech Innovation Expo – creating the UK’s largest cross-sector showcase for advanced manufacturing, plastics and medical technology. This convergence of events promises even greater opportunities for knowledge exchange, collaboration, and innovation across aligned industries. Attendees will benefit from access to expanded show floors, joint conference tracks, and a broader spectrum of cuttingedge solutions, from polymer processing and biocompatible materials to smart factory integration and regulatory insights.
tct3sixty.com/newfront
Subcon 2025 has officially drawn to a close, leaving behind two days of innovation, networking and industry inspiration at the NEC Birmingham. Read on for highlights from the highly successful event including the winners of the Manufacturing Solutions Awards.
This year’s event exceeded all expectations, welcoming thousands of manufacturing professionals, subcontractors and supply chain specialists from across the UK. With a packed programme of content and exhibitors, Subcon 2025 once again proved itself to be the UK’s premier subcontract manufacturing supply chain show for the aerospace, defence and security, automotive, and medical industries.
The show also featured a fantastic line-up of speakers, who delivered insightpacked sessions covering everything from advanced manufacturing technologies and sustainable production methods to the future of automation and supply chain resilience.
Networking was elevated to new heights with the debut of the Pubcon networking area, a vibrant, relaxed hub where meaningful connections were forged over a game of pool. The informal setting allowed for conversations to flow and collaborations to spark in a way that’s uniquely Subcon.
One standout highlight of the twoday event was the second year of the Manufacturing Solutions Awards Recognising outstanding achievements in the manufacturing industry.
“This year’s Manufacturing Solutions Show Awards – the second year of the programme – saw numerous high-quality entries, covering everything from leading UK and international manufacturers to innovative products addressing key challenges in the manufacturing sector and individuals who have an illustrated an unwavering advocacy for UK manufacturing. The winners really do showcase the best-of-the-best in this cutting-edge industry,” said Ben Watkins, Sales Manager, Subcon, host of the Manufacturing Solutions Show Awards.
A panel of judges selected from across the industry reviewed the shortlist, agonised over the decision and now very pleased to announce the winners:
• Start-up of the Year – Buckingham Magnetics
• UK Manufacturing Partner of the Year –Sertec
• International Partner of the Year – Sahasa Electronics
• Product Innovation of the Year – xGenBi
UXLI Limited
• Outstanding Industry Contribution
– Andrea Wilson, Director at Hone-All Precision Limited
“I’m truly honoured and humbled to be recognised by Subcon and my industry peers as everything I do is with one simple
goal – to give UK manufacturing the profile, platform and processes it needs to succeed. I am simply the Managing Director of an SME machining business in Leighton Buzzard – if my little personal crusade for UK manufacturing can have this much impact, and be recognised by so many, imagine what we could achieve if each of us did a little more to get the message across to those who need to listen,” Andrea Wilson, Director at HoneAll Precision Limited
Planning is already underway for an even bigger and better event in 2026. Please sign up on Subcon’s website to be the first to hear about next year’s show.
subconshow.co.uk
No more flaking paint, no more corrosion, no more contamination worries...
Smooth surface, hygiene friendly, easy to clean washdown design.
Resistant to acids and alkalis
No blistering, flaking or microcracks
Food-safe according to FDA and EU Regulation 1935/2004
Protection to IP69K possible
Motor efficiency levels from IE3 to IE8
The UK’s biggest processing and packaging machinery, robotics and industrial vision event, the PPMA Total Show®, is set to return to the NEC, Birmingham in September, with the show offering a host of opportunities and brand-new features for attendees. Read on for what to expect from the event.
The PPMA Total Show® 2025 will take place from 23-25 September, bringing together industry professionals from across the entire manufacturing spectrum offering networking opportunities, live equipment demonstrations, and valuable insight into innovative technologies.
The PPMA Show 2024 has been shortlisted as a finalist in the Best UK Trade Show category at The AEO Excellence Awards 2025. Organisers Automate UK have pledged to deliver a show that exceeds expectations this year, with an itinerary of expert speakers, a networking reception and a series of live demos to showcase the latest technology solutions.
The PPMA Show® 2024 was a resounding success, with more than 80% of visitors reporting that they discovered new solutions to enhance and support their businesses as a direct result of their attendance.
The 2025 show is now set to be bigger and better, with more than 350 exhibitors and 1,500 brands in attendance.
Scott McKenna, Chief Operating Officer, said: “The PPMA Show® 2024 was a great success, and this year’s show will build on that, giving attendees access to cuttingedge technology and solutions to optimise performance, reduce costs, and future-proof their businesses.
“This year, we’re offering visitors to chance
to benefit and learn from expert-led seminars with relevant topics including sustainability, smart manufacturing, and operational efficiency, as well as dedicated networking opportunities throughout the course of the show.
“One of the standout successes of The PPMA Show® 2024 was Innovations Eleven – a brand-new live demo theatre, in which 11 selected exhibitors launched new technology directly to attendees, and we’re enhancing that experience this year.
“The PPMA Total Show® 2025 live demo theatre will be broadcast in real-time via PPMA Show TV, whilst expert-led daily innovation tours will be hosted for visitors to expand on the technology being showcased and its suitability for their business needs,” he added.
Attendance for The PPMA Total Show® 2025 is free, with registration now open. To register, visit the website below.
ppmashow.co.uk
Midlands 3D Printing
T: 01785 594389
E: sales@midlands3d.com
W: www.midlands3d.com
Fibet Rubber Bonding (UK) Ltd
T: 01282 878200
E: sales@fibet.co.uk
W: www.fibet.co.uk
CEMBRE Ltd
T: 01675 470 440
E: sales@cembre.co.uk
W: www.cembre.com/en
Ideal Power
T: 01733 309865
E: salessupport@idealpower.co.uk
W: www.idealpower.co.uk
Nord
T: 01235 534404
E: GB-sales@nord.com
W: www.nord.com
Axair Fans UK Limited
T: 01782 349 430
E: sales@axair-fans.co.uk
W: www.axair-fans.co.uk
Schmersal UK Ltd
T: 01684 571980
E: uksupport@schmersal.com
W: www.schmersal.co.uk
T-Mark
T: 0330 153 8320
E: sales@t-mark.co.uk
W: www.t-mark.co.uk
ESI Technology Ltd
T: +44 (0)1978262255
E: sales@esi-tec.com
W: www.esi-tec.com
Robotics & Automation
KUKA Robotics UK Ltd
T: 0121 505 9970
E: sales.uk@kuka.com
W: www.kuka.com
Titan Enterprises Ltd
T: +44 (0)1935 812790
E: sales@flowmeters.co.uk
W: www.flowmeters.co.uk
Silverson Machines Ltd
T: +44 (0)1494 786331
E: sales@silverson.co.uk
W: www.silverson.co.uk
Brainboxes
T: + 44 (0) 151 220 2500
E: sales@brainboxes.com
W: www.brainboxes.com
Intoware
T: 0115 977 8969
E: hello@intoware.com
W: www.intoware.com
IFM Electronic
T: 020 8213-0000
E: enquiry.gb@ifm.com
W: www.ifm.com
PLUS Automation Ltd
T: 0121 58 222 58
E: Sales@PLUSAutomation.co.uk
W: www.PLUSAutomation.co.uk
BITO Storage Systems Ltd.
T: 02476 388 852
E: Info.uk@bito.com
W: www.bito.com
AMETEK Land (Land Instruments International)
T: +44 1246 417691
E: land.enquiry@ametek.com
W: www.ametek-land.com