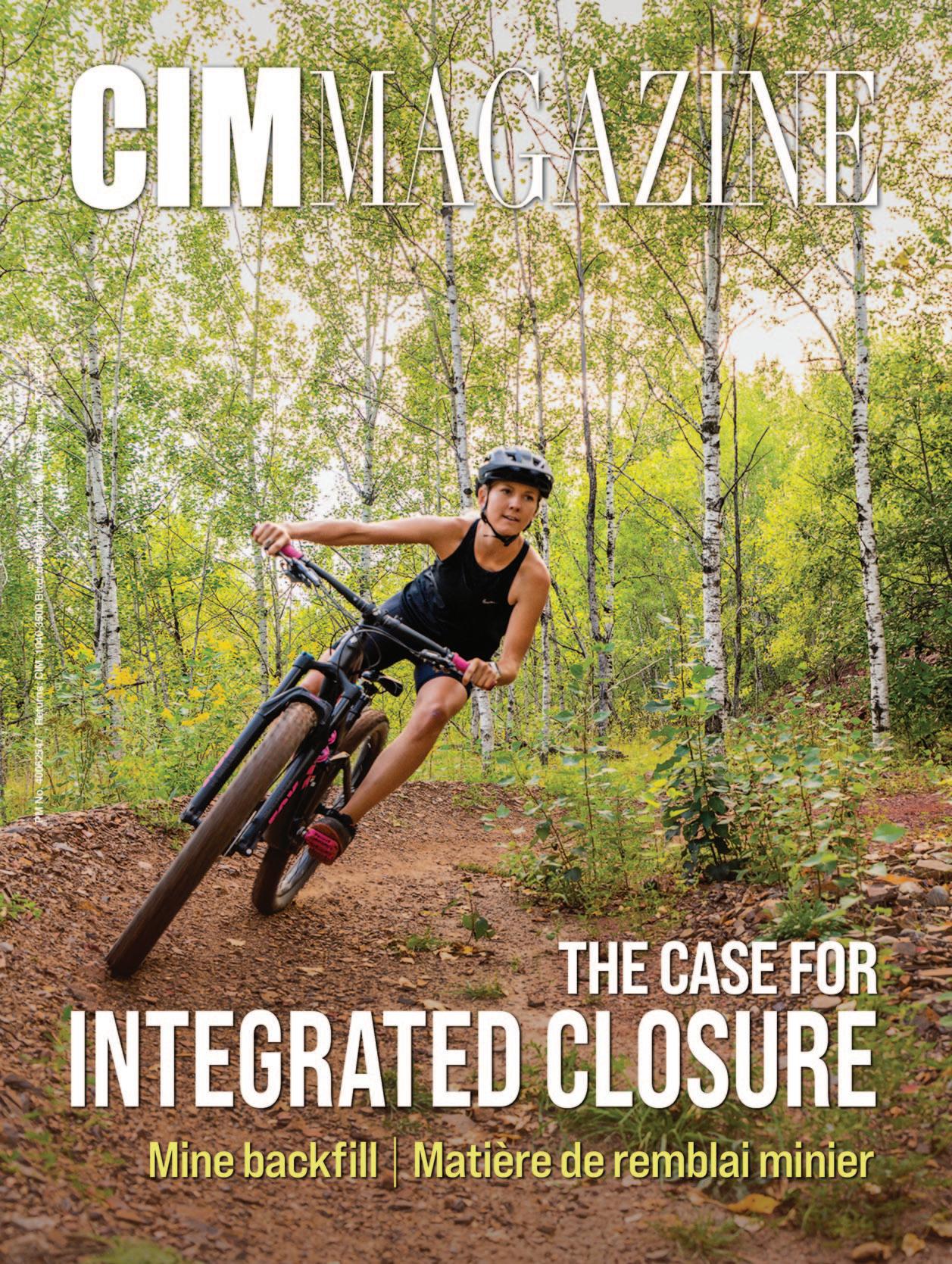
MARCH/APRIL 2024
• MARS/AVRIL 2024
MAGAZINE.CIM.ORG


MARCH/APRIL 2024
• MARS/AVRIL 2024
MAGAZINE.CIM.ORG
The GrizzlyDrive® Drum Motor, designed for harsh, abrasive, and demanding belt conveyor applications, provides 80,000 hours of continuous operation before maintenance, reducing operational and maintenance costs while increasing throughput.
ELIMINATE external drive components
REDUCE energy consumption
INCREASE workforce safety
The innovative Belt Cleaner is a VDG Drum Motor that has a replaceable spiral brush mounted on the drum and effectively cleans the conveyor belt without wear or damage to the belt.
ELIMINATE belt wear and damage
EXTEND the life of the belt
REDUCE belt maintenance
Tap into your resources with SiteConnect, the mobile app that provides remote visibility from any mobile device. The sensors that are already in your pumping systems can help you increase the reliability, lower the production cost per ton and significantly reduce the carbon emissions of your mineral processing operation. In addition, SiteConnect opens the door for FLSmidth product experts to provide regular reports and optimization recommendations.
■ Optimize all pumping systems to lower power and reduce downtime
■ Improve equipment performance visibility
■ Increase expert support
Mining and Mental Health
An employee-led initiative at Agnico Eagle’s Detour Lake mine encourages workers to open up about mental health
By Mackenzie PattersonIntegrated approaches to mine planning that include sustainable closure and reclamation plans and consider the potential for shared value for various stakeholders are becoming increasingly important
By Alexandra Lopez-PachecoMining at the McClean Lake uranium mine in Saskatchewan, which has been suspended since 2009, will restart in 2025 using technology developed to extract high-grade ore from small ore bodies
By Trish SaywellAs equipment manufacturers embrace automation and data-driven decisionmaking, development drilling at underground mines is becoming safer, greener and more efficient
By Nathan Munn21 A watershed moment for Indigenous financial independence
By Ashley Fish-RobertsonColumns
33 Moving away from controlsbased cybersecurity
By Rob Labbé36 Adding a new comparables section to the NI 43-101 framework could boost investor confidence in project studies
Advancements in mine backfill
42 Backfill specialists are turning the challenging conditions of mining in the Arctic into opportunities for innovation By Sarah St-Pierre
46 Lowering the carbon footprint of cemented paste backfill can contribute to lower CO2 emissions from underground mining operations
By Lynn Greiner48 Paterson & Cooke’s Maureen McGuinness discusses the evolution of backfill and the key role it has to play in mine planning
By Ailbhe GoodbodyCIM news
63 Outgoing CMP representative on CIM Council Stuart McTavish is ready to pass the torch
By Ashley Fish-Robertson63 Upcoming CIM Community events
Compiled by Michele Beacom
Mining the archives
72 The development of Sudbury as a Canadian nickel hub, which later became an example of how pollutionimpacted lands can be reclaimed successfully
By Ailbhe GoodbodyContenu francophone
68 Les immigrants sont sousreprésentés dans l’industrie minière
Par Silvia Pikal
Les progrès en matière de remblai minier
70 Réduire le bilan carbone du remblai en pâte cimenté permettra de diminuer les émissions de CO2 des exploitations minières souterraines
Par Lynn Greiner L’actualité
Axioscan 7 Geo multi-polarization slide scanner. Olivine gabbro with plane polarization (PPOL), circular polarization (CPOL), cross-polarization (XPOL)
Digitize your thin sections with Axioscan 7 – the reliable, reproducible way to create high quality, digitized petrography data in transmitted and re昀 ected light. Uniquely designed for petrographic analysis, ZEISS Axioscan 7 Geo combines unique motorized polarization acquisition modes with unprecedented speed and a rich software ecosystem for visualization, analysis, and collaboration.
• Ultra-fast high-resolution transmitted, re昀 ected, plain and cross-polarized image acquisition
• Fast throughput for up to 100 thin sections at a time
• Enabling remote collaboration and AI analysis
Scan for whitepapers and more zeiss.ly/424-cim
At last year’s Society for Mining, Metallurgy and Exploration (SME) annual conference MINEXCHANGE in Denver, Colorado, the panel of speakers at the big opening day session engaged with the topics of our times: environmental, social and governance (ESG) and decarbonization. While a speaker on the panel representing a mine operator noted the constraints miners must deal with when trying to reduce their use of fossil fuels, no one rejected the premise that doing so was a worthwhile goal. The response to a question from the audience about the growing number of Republican party-governed states enacting anti-ESG legislation dismissed such obstruction as short-sighted.
This year’s edition of our sister society’s flagship meeting in Phoenix, Arizona, had a very different tone, as CIM Magazine editor Silvia Pikal reported in her coverage of the event “SME panelists debate net-zero goals” (see p. 30). The event organizers gave the responsibility of framing the flagship panel discussion to a writer and commentator who has made a career for himself as a contrarian, touting the moral imperative of unfettered fossil fuel use. His argument: fossil fuels have made modern life in the developed world possible and only fossil fuels can offer something close to that quality of life to the vast majority of people on earth who can only dream of the comforts we take for granted. In his opinion, the risks of cutting out fossil fuels are far greater than the risks of continuing to use them unabated.
This message on the stage of a major mining conference comes as investors, particularly U.S. investors, continue to pull their money out of ESG-oriented funds, which take cutting carbon emissions as a fundamental goal. I have heard some celebrate this fact as confirmation that the trend of ESG investing was nothing more than marketing.
Editor-in-chief Ryan Bergen, rbergen@cim.org
Yes, there are certainly plenty of examples of greenwashing as companies, responding to the hot market, misled investors about their commitment to sustainable practices. And the great mass of sustainability rating agencies and indices that have blossomed to provide guidance have created more noise than clarity.
Accepting the argument, however, that was presented at MINEXCHANGE—that we are foolish to try to do better than we currently do—will not serve the mining industry very well. At its core, it suggests that human ingenuity won’t get us much farther. I am ready to take the other side of that bet. But, more specific to this industry, it ignores the reality that if investors and proponents discount the environmental and social risks inherent in mining—particularly in Canada and the United States—it means their projects don’t get built.
I am happy to report the discussions being planned for the CIM Connect Conference in May in Vancouver under the theme “Brand Canada: Our Critical Advantage” will engage with this reality.
Ryan Bergen, Editor-in-chief editor@cim.org @Ryan_CIM_Mag
Managing editor Michele Beacom, mbeacom@cim.org
Senior editor Ailbhe Goodbody, agoodbody@cim.org
Section editor Silvia Pikal, spikal@cim.org
Editorial intern Ashley Fish-Robertson, afrobertson@cim.org
Contributors Lynn Greiner, Dan Kappes, Rob Labbé, Alexandra Lopez-Pacheco, Tijana Mitrovic, Nathan Munn, Mackenzie Patterson, Trish Saywell, Sarah St-Pierre
Editorial advisory board Mohammad Babaei Khorzhoughi, Vic Pakalnis, Steve Rusk, Nathan Stubina Translations Karen Rolland, karen.g.rolland@gmail.com
Layout and design Clò Communications Inc., communications.clo@gmail.com
Advertising sales
Dovetail Communications Inc.
Tel.: 905.886.6640; Fax: 905.886.6615; www.dvtail.com
Senior Account Executives
Leesa Nacht, lnacht@dvtail.com, 905.886.6640 ext 321
Dinah Quattrin, dquattrin@dvtail.com, 905.886.6640 ext 308
Subscriptions
Online version included in CIM Membership ($197/yr). Print version for institutions or agencies – Canada: $275/yr (AB, BC, MB, NT, NU, SK, YT add 5% GST; ON add 13% HST; QC add 5% GST + 9.975% PST; NB, NL, NS, PE add 15% HST).
Print version for institutions or agencies – USA/International: US$325/yr. Online access to single copy: $50.
Copyright©2024. All rights reserved.
ISSN 1718-4177. Publications Mail No. 09786.
Postage paid at CPA Saint-Laurent, QC.
Dépôt légal:
The year is still young, but the 2024 mining event calendar is already well under way. We’ve had AME Roundup in Vancouver and PDAC in Toronto, where the best and brightest of the exploration companies gathered and showcased their prospects. It’s not easy—and hasn’t been for quite some time—being an exploration-stage company, so let’s applaud their tenacity and remember that exploration is the lifeblood of our industry. I’m lucky enough to work at a company that has grown its way into the senior producer ranks. But B2Gold was an exploration-stage company as recently as 2007, and in our shop, we remember that. Hats off to all the companies who are doing it. Keep it coming.
Another keystone industry event was CIM’s Canadian Mineral Processors (CMP)’s 56th annual conference, held in Ottawa in mid-January. Hats off again to the dedicated CMP executive team and volunteers who make this conference such a success every year. Special mention, too, to Stuart McTavish (see p. 63). Nobody is quite sure how old Stuart is—we may have to check some geological records to establish that—but everyone believes that Stuart was there at the start of the CMP. He has been a stalwart member of that technical society, and also of
CIM Council, over many years. Thank you, Stuart, for your service and dedication.
The final panel session of the CMP conference focused on renewable energy sources. Thanks to Scott Martin for moderating such a great discussion. I left feeling optimistic. Focusing our attention on making power sources more greenhouse gas (GHG)emission friendly is something all mining companies must make a priority. All of the panelists agreed that a continued focus on innovation and collaboration between all stakeholders is needed if companies are to achieve their GHG-emissions goals. But sharing information, new technologies and best practices with each other requires an ongoing venue. What better forum than the CIM Connect conference to continue that conversation, both this year and into the future? Just sayin’.
I’m also feeling very optimistic about the direction CIM is headed. As an organization, I think CIM has come a long way in the last couple of years, putting in the IT and other infrastructure needed to support all of its constituents, increasing its number of individual and corporate members and putting together and sharing a much better picture of what we are doing at all of our branch, society and national events.
This is my last President’s note to appear in the magazine before Ian Pearce steps in as 2024-25 President in May. Thanks, everyone, for the opportunity to act as President this year. It has been wonderful meeting so many of you during my travels and learning about all of the great things you do as part of our OneCIM community. Keep up the good work.
Englo’s line of de-dusters for underground mining and tunnelling work to provide cleaner air while trapping dust particles. The company’s Dry De-duster, which can be powered either by diesel or electricity via a motor-fan combination, uses easy-to-replace filters. The product was created for environments where the usage of a Wet De-duster may not be suitable. According to Englo, the Dry De-duster’s filters efficiently collect up to 99.99 per cent of particles, while its Wet De-duster collects up to 99.9 per cent of particles and is recommended for the collection of hazardous or combustible material. The Wet De-duster is self-cleaning, has low water consumption and, thanks to the product’s scrubber box, can reduce static loss. Its compactness makes it a suitable option for smaller spaces.
ABB’s Ability Ventilation Optimizer is a ventilation-ondemand system used in underground mining operations. The environmental and flow sensors, which are attached to mining vehicles, signal when fresh air is needed, and trigger fans to run for several minutes following a vehicle’s departure from an area to ensure that residual gases and exhaust from diesel vehicles and blasting have been cleared underground. Data gleaned from the system’s sensors can then be monitored through mobile devices, ensuring that fans throughout the mine are well coordinated. According to the company, the use of this system can extend the life of a mine’s ventilation system, result in energy savings of up to 50 per cent and provide workers with a healthier working environment that is free from dust, CO2 emissions and high humidity levels. The system has been developed for ease of maintenance and to be scalable due to standardized components.
HyperWATCH, a new digital service developed by Stantec, relies on the highest-resolution satellite-based hyperspectral imagery (HSI) available to delineate important data points that can aid in the exploration of valuable mineral deposits, track tailings storage facilities for toxicity, and more. According to Stantec, HSI is more detailed than traditional imagery systems, as traditional systems rely on just a few wide portions of the electromagnetic (EM) spectrum. HyperWATCH uses HSI information that is comprised of dozens to hundreds of individual, narrow channels from across the full EM spectrum, resulting in hundreds of detailed data points. The increased number of points drastically increases image fidelity and spectral precision. HyperWATCH generates targeted signatures of minerals, chemicals and vegetation health across an entire project area.
JENNMAR designs and manufactures a wide range of dependable ground control products, from bolts and beams to channels and trusses, resin, rebar, and more. We’re proud to make products that make the mining, tunneling, civil, and construction industries safer and more efficient.
Because we understand the ever-changing and demanding conditions above and below ground we have built the richest portfolio of diverse and complementary brands. JENNMAR sets the bar in every industry we serve and as we continue to grow, our focus will always be on the customer.
We feel it is essential to develop a close working relationship with every customer so we can understand their unique challenges and ensure superior customer service. Our commitment to the customer is guided by three words: SAFETY, SERVICE, and INNOVATION
It’s these words that form the foundation of our business. It’s who we are.
Compiled by Silvia Pikal
Winsome Resources announced that it will update its mineral resource estimate at its Adina lithium project in the Eeyou Istchee James Bay region of Quebec in the first half of 2024. It stated in a March press release that the core
(continued on page 15)
from its five drill rigs have delivered “strong assay results” and it is simultaneously conducting development and environmental studies for the project. In
its maiden inferred mineral resource estimate released last year, it declared 59 million tonnes at 1.12 per cent lithium at Adina, and that the estimate places it in
one of the top five largest lithium resources in North America. Initial project studies are anticipated to be published in the latter half of this year. CIM
Phase one of the strategy is a promising start but is missing key fiscal support, mining associations say
By Tijana MitrovicWhen B.C. Premier David Eby spoke at the opening keynote on Jan. 22 at the Association for Mineral Exploration (AME) Roundup conference, he made a strong statement after unveiling the first phase of the province’s new critical minerals strategy.
“The world needs a stable, free, democratic, high-standard producer of the metals and minerals needed to battle climate change,” Eby told the crowd. “That gives B.C. a generational opportunity to seize, one where we can be prosperous and protect the planet for our kids at the same time.”
As a mining jurisdiction that has reserves of, or produces, 16 of Canada’s 31 critical minerals, and is Canada’s largest copper producer, the province stated that phase one of the critical minerals strategy is its attempt to take advantage of the clean energy transition.
The first phase includes 11 action points, such as the creation of a B.C. critical minerals atlas to provide “world-class geoscience data,” and an alignment of the provincial strategy and the First Nations Energy and Mining Council’s critical minerals strategy, which was released on March 4 of this year. In addition, it includes continuing a commitment to engage with First Nations across the province and also to ensure what it calls “the highest” environmental, social and governance (ESG) standards. The strategy comes after the provinces of Quebec, Ontario, Saskatchewan and Manitoba— as well as the federal government—have all launched respective critical minerals strategies over the past few years.
In a Jan. 22 news release, Josie Osborne, the B.C. energy minister, said that securing critical minerals will help “drive growth
and create new jobs for people across the entire value chain of critical minerals.” The steps outlined in phase one go beyond development to also focus on growing downstream opportunities, such as processing, manufacturing and battery recycling, which will recycle mined materials and reintegrate them into the supply chain. No further details on these initiatives have been released so far.
While phase one of the strategy emphasizes the province’s commitment to First Nations on critical minerals development through partnerships and engagement, it stated that the next steps of the strategy will include specific actions such as support for First Nations’ capacity building to develop and refine policy actions, and ensure that the strategy aligns with the UN Declaration on the Rights of Indigenous Peoples. This is particularly important
following the ongoing legal developments regarding the province’s mineral staking system and Indigenous consultations.
But miners have raised concerns about phase one of the strategy, and feel that it does not do enough to ensure the province’s critical minerals supply is competitive. Keerit Jutla, president and chief executive officer of AME, told CIM Magazine in an interview that the provincial government must recognize that B.C. is competing not only with mining jurisdictions outside of Canada but within the country’s borders as well.
“We’re competing internally with Quebec, Ontario and other jurisdictions, so it’s essential that we get a critical minerals fund that matches that type of investment, if not exceeds it,” he said. “We’ve heard domestically and internationally that countries [in Europe and Asia] are looking
to Canada for the critical minerals supply chain. So we need to ensure that we have those key drivers there to ensure that we remain competitive on the world stage.”
Much of this concern from the B.C. mining industry has been around the lack of regulatory and financial incentives included in phase one of the strategy. Some want to see a clear focus on fiscal measures from the provincial government to deliver on a robust strategy.
“In 2023, B.C.’s contribution to the national mineral exploration expenditure decreased by 33 per cent for a total contribution lagging at 17 per cent, [compared to] Ontario and Quebec at 24 per cent and 23 per cent, respectively,” Jutla said. “We believe an investment of at least $50 million over three years is required to sufficiently fund and implement a strategy that’s at the same level as our provincial peers. We see what’s working in other jurisdictions here in Canada and we need to take note and apply those best practices.”
The Mining Association of B.C. (MABC) has similar concerns and noted that the government needs to put a competitive fiscal policy in place, which it said phase one of the strategy fails to
address. MABC president and CEO Michael Goehring expressed concerns about the province’s current fiscal policies, specifically its new output-based carbon pricing system (OBPS), which is slated to come into effect in April. In a Jan. 22 statement from the MABC, Goehring pointed out that while B.C. currently pays the highest carbon tax in Canada and also globally “while having the lowest GHG emissions globally,” the technology needed to help reach decarbonization goals—zero-emission haul trucks—will not be available until the end of the decade at the earliest.
“Changes to B.C.’s tax regime over the past 10 years have significantly increased operating costs across the sector,” Goehring stated. “It’s imperative existing and prospective critical mineral mines in B.C. pay a carbon tax that is competitive with Ontario and Quebec. If not, the OBPS will negatively impact investment decisions in B.C. and undermine the goals of the provincial government’s critical minerals strategy.”
Mining industry associations believe that improving fiscal competitiveness could not only bolster the province’s
In case you missed it, here’s some notable news since the last issue of CIM Magazine, which is just a sample of the news you’ll find in our weekly recap emailed to our newsletter subscribers.
Indonesia’s approach to nickel production (pictured) has given it a major market advantage at a steep environmental cost. Today, nearly half of the world’s nickel operations are struggling to make a profit due to a
price slump resulting from Indonesia flooding the market with low-cost nickel. It is in this market that Fortescue’s chairman and founder Andrew Forrest is urging the London Metal Exchange to distinguish “clean” nickel contracts from “dirty” ones to carve out a niche for “clean” nickel producers.
The Canadian government announced in February that it plans to reduce the amount of time it takes to construct new critical minerals mines by almost a decade thanks to what it promises will be a faster permitting process. The government intends to do this
standing among Canadian jurisdictions, it could also help unlock billions of potential revenue in new mining developments.
This comes on the heels of a new study by the MABC that estimated that 14 proposed critical minerals mines, along with two proposed mine extensions, could generate nearly $800 billion over several decades. According to the study, the proposed critical minerals mines represent $36.5 billion in near-term investment in development and construction, $10.9 billion in tax revenues and more.
Mining industry associations are already looking ahead to phase two of the strategy, with the hopes that it will address some of the perceived gaps. The province has not released a timeline for phase two.
“I think all of us are looking at the phase one announcement as a good first step and a good demonstration of intent to provide strong support for the critical minerals industry here in B.C.,” Jutla explained. “But that is really hinging on the expectation of a solid delivery: [that] will be key to honour and to validate [that] optimism. Now that’s back in the government’s court and we hope they’ll deliver something strong for B.C.” CIM
by boosting funding to the regulatory agency to help remove paperwork backlogs and by simultaneously running permitting and environmental assessment processes.
At least nine people were trapped when the wall of a heap leach pad failed and sent an estimated 10 million cubic metres of material flowing down slope at the Çöpler gold mine in Turkey on Feb. 13. The TSX-listed miner SSR Mining has an 80 per cent stake in the mine. Rescuers searched for the workers through the cyanide-soaked soil of the mine, and there are concerns the cyanide could contaminate the watershed. The Union of Chambers of Turkish Engineers and Architects said that it had previously issued warnings about a potential disaster that ultimately went ignored. The mine has had its environmental permit rescinded and is not operating.
Energy and Natural Resources Minister
Jonathan Wilkinson announced at the PDAC convention that took place from March 3 to 6 that Canada will be allocating $15 million in funding for projects to aid the country’s growth of its critical minerals industry, along with projects to boost Indigenous involvement in mining. Prior to the convention, he expressed unease about market manipulation and dumping practices of
As part of Fasken’s 2024 Global Mining Group Seminar Series, a recent episode held on Feb. 29 titled “Indigenous Community Engagement in the Changing World” explored the importance of effective engagement between mining companies and Indigenous community rights holders, and discussed how thoughtful engagement can lead to a deeper understanding of Indigenous traditions and knowledge and promote healthier relations between mining companies and communities. The session, led by Peter Mantas, co-managing partner at Orion Legal Group, featured three speakers from different parts of the world, including Canada.
Chief Nkandu Beltz, the founding director of Beltz Mining Limited, a copper exploration company with locations in Australia and Zambia, explained that Indigenous engagement is crucial prior
critical minerals in a conversation with The Globe and Mail. The minister suggested investigating an alternative pricing model to decrease Canada’s reliance on China when it comes to obtaining the key metals needed to advance the energy transition. Wilkinson has also suggested that Canada and other Western countries think about implementing tariffs against Indonesia and China as a way to target market manipulation stemming from an oversupply of low-cost nickel.
Canada and Australia announced on March 5 that the two countries will work together with the goal of improving transparency within global critical minerals supply chains and will also advocate for the importance of having firm environmental, social and governance (ESG) standards in place. The non-legally binding partnership is being led by Canada’s Natural Resources Ministry and Australia’s Critical Minerals Office and will look into prospects pertaining to the research and development of critical minerals.
First Quantum Minerals is aiming to secure US$20 billion through international arbitration after losing over half of its market value following Panama’s order to shut down its Cobre Panama copper mine. The mine has been closed since late last year after Panama’s Supreme Court ruled that First Quantum Minerals’ contract with the government was
to commencing a mining project, especially because it could prevent miningrelated destruction inflicted on historical sites. “Those are sacred grounds for us, so it is painful,” she said. “When such things happen…it creates distrust among traditional owners of the land. I think with continued positive engagement, we can create a win-win scenario for investors, lenders and the local people.”
Beltz said that when mining companies enter a new community, they should be considering the knowledge that locals can offer. “When companies come in, it’s just a matter of sitting down and explaining who you are, creating that bond and also seeing if there’s anybody in that community that can add value to what you’re doing,” she said. Beltz added that locals can also learn more about modern technologies and education related to mining, ultimately advancing mining knowledge within a given community.
The conversation turned over to Sheldon M. Wuttunee, president and CEO of the Saskatchewan First Nations Natural Resource Centre of Excellence, which supports and collaborates with Indigenous
unconstitutional, a move that followed months-long nationwide protests against the massive copper mine.
Canada has risen to the top of the fourth edition of energy research organization BloombergNEF’s recent global lithium-ion battery supply chain ranking, which is the first time China has not topped the list. The ranking examines 30 countries’ potential to develop a secure, reliable and sustainable supply chain for the production of lithium-ion batteries, using 46 different metrics across five categories to guide the rankings. BNEF said that Canada’s rise to first place was due to its consistent manufacturing and production advances, as well as its ESG credentials.
Stay up to date on the latest mining developments with our weekly news recap, where we catch you up on the most relevant and topical mining news from CIM Magazine and elsewhere you might have missed.
One of the seminar’s panelists, Sheldon M. Wuttunee, shared his experiences as former chief of Saskatchewan’s Red Pheasant Cree Nation (pictured), offering advice on how stronger connections between companies and communities can be forged.
communities to generate opportunities for innovative and environmentally sustainable development of natural resources located on Indigenous land.
As former chief of Saskatchewan’s Red Pheasant Cree Nation, Wuttunee expanded on Beltz’s beliefs about the importance of appreciating local knowledge, sharing how valuable the knowledge he has gained from elders within his community has been when it comes to improving engagement between mining companies and local communities in Red Pheasant, as well as better communicating the importance of spiritual context in natural resource development.
He encouraged mining companies to better educate themselves, not only by consulting policies relating to Indigenous lands, but to also make an honest effort to engage firsthand with the locals, learning more about their traditional beliefs tied to the natural environment, and to first build a relationship with locals before jumping straight into business.
“[Having these conversations] is the only way you’re going to…be able to develop that strong relationship with the community and to better understand what their needs are,” he said. “Then I think at some point, once there’s…a better understanding of environmental impacts, spiritual impacts and so forth, then perhaps there’s an opportunity to start to talk about the economic opportunities associated with a project.”
Rafael Vergara, partner of Carey, a Chile-based law firm, and co-head of the firm’s natural resources and environment group, reiterated Wuttunee’s sentiments around the importance of mining
companies taking the time to cultivate a relationship to better understand the connections that local communities have with their environments, while also being mindful of how a new mining project may impact their lands.
“What I have experienced is that sometimes Indigenous communities do not know how the mining project can affect them,” he said. “So, the first issue here is to approach the communities to know what their concerns are.”
He added that ongoing discussions regarding undeveloped projects with locals are imperative, so that they can get a better sense of what to expect, while also being able to voice potential concerns. “You have to discuss and plan as carefully as possible,” he said. “Create places of communication…constant, permanent communication. You have to go there… bi-weekly or once a month [to] have open discussions with the people.”
Wuttunee emphasized the importance of mining companies preparing to have what he considers to be “difficult conversations” with Indigenous communities. He said that in order to better integrate into a new community, companies need to recognize that these communities have a deep spiritual relationship with the lands they inhabit, and that this connection often gets overlooked.
“We have our natural laws and cultural laws and cultural protocols that we all need to adhere to,” he said. “As you go into a community, it’s extremely fundamental to understand that it’s not only an economic opportunity, [but] there’s a whole spiritual component.”
– Ashley Fish-RobertsonThe second episode of the Mission Critical webinar series from CIM Magazine and SGS Natural Resources took place on Feb. 22 and zoned in on the development of Canada’s store of critical minerals. Cohosted by Ryan Bergen, editor-in-chief of CIM Magazine, and David Anonychuk, global vice-president of metallurgy and consulting at SGS, the latest episode engaged several panelists in discussions surrounding the background and outlook for the battery recycling market, particularly in North America.
Anonychuk kicked off the episode by highlighting why battery recycling is such an important area of focus in the mining industry. “In order to meet the long-term battery raw materials supply challenge, and to meet those net-zero goals we think about for the long term, mining is not going to bring enough units to the market,” he explained.
Anonychuk turned the attention to Electra Battery Materials as a prime example of how black mass is being recycled within Canada, noting that the company is constructing North America’s sole cobalt-sulfate refinery.
Mark Trevisiol, vice-president of project development at Electra Battery Materials, explained that the company’s decision to shift to battery recycling came about when the company was putting together the proposal for its cobalt-sulfate plant. During presentations delivered before automotive manufacturers, such as Ford and General Motors, Trevisiol noticed that senior level management employees were posing questions about how the company would use recycled materials in its final product.
“There was that push, and we were also sitting on an asset that was operated as a hydrometallurgical site that produced cobalt and nickel products through hydrometallurgical processes,” he said. “There was the opportunity there to utilize some of the existing system processes
in place to start taking things like black mass and see if we could profitably put the metals through processing.”
So far, Electra Battery Materials has processed approximately 40 to 50 tonnes of black mass and made its first customer shipment of nickel-cobalt produced from recycled battery material in 2023.
As for hurdles related to battery recycling within Canada and North America in general, Trevisiol outlined overseas shipments of black mass material as being one of the biggest current challenges in the market.
“[Right now], there is nothing preventing people who recycle and make a black mass product from shipping that product overseas to be refined,” he said, adding that this was a sort of paradox considering that “our [federal] government is pumping billions into critical metal supply and encouraging investment in mines and processing facilities…and then on the recycling side, some of that [black mass material] is going overseas and ending up in China because there’s no regulatory framework to prevent that from happening.”
Sean De Vries, executive director at the Battery Metals Association of Canada, who has a background in electronics recycling, shared that when the country began introducing electronics recycling programs 25 years ago, Canada’s recycling market did have some existing recycling
infrastructure in place, but it was still considered to be at a nascent stage. “I think electronics recycling and those programs came about as a result of some of the regulatory push, so that helped to really spark the boom of the industry and processing technologies,” he said.
De Vries offered an example of when electronic products would be recovered through smelters during these early days, and the challenges companies had to face when complex products were being sent into these smelters. “A whole TV can’t necessarily be recovered through one single process, so we have to divide the process up…and get [the products] to the right smelter so that you can recover the copper and the lead,” he explained. “You see this need to have specific recovery technology.”
Niels Verbaan, director of technical services (hydrometallurgy) at SGS, expanded further on the need for specific recycling technology, noting that there needs to be a key distinction made between scrap and end-of-life material.
“It is important to know that scrap recycling involves the reprocessing of
materials that were produced now, today, or yesterday. It is today’s chemistry,” he said. In comparison, end-of-life material deals with chemistries that were produced a decade prior, which can result in feed material quite different from scrap. Verbaan noted that an argument could be made that scrap material is easier to reprocess than end-of-life material. “If you want to process that back into the current battery chemical producers, that means you’re going to have to separate these into their individual components, and that leads to an additional degree of difficulty.”
Trevisiol underpinned the important role that the Canadian government plays in the country’s battery recycling processing, noting that there needs to be more regulations set in place to address materials being shipped offshore. “Otherwise, it’s a paradox,” he said. “You’re pumping money into extracting these critical minerals and then they’re being sent [to be processed] elsewhere.”
He referred to the U.S.’s Inflation Reduction Act as an example of how Canada can improve its recycling regulations, explaining that the Act requires
North American electric vehicle (EV) manufacturers to have most of their battery components processed, refined and manufactured within the continent.
A recording of the webinar can be found on CIM’s YouTube channel.
– Ashley Fish-Robertson
David Francis Lyon, founder and president of engineering company Zero Nexus, spoke about the gaps in specialized training needed to prepare the mining workforce for electrification at the Battery Electric Vehicle Safety in Mines Symposium in Sudbury on Feb. 15.
“Canada is by far the leader in [battery electric vehicle] adoption, but there’s still a long way to go,” Lyon said.
The one-day event, hosted by Workplace Safety North (WSN), was attended by hundreds of people at Cambrian College and virtually through live streaming.
In Lyon’s presentation titled, “Plugged In and Prepared: Understanding Training
Needs for Electric Mobile Mining Equipment,” he outlined the results of a Zero Nexus qualitative research project that involved more than 100 virtual and onsite interviews with battery electric vehicle (BEV) machine operators, shift managers, mine planners and other industry stakeholders at operating mines in Canada that are trialling BEV equipment.
“We were really looking for information, both good and bad, to help us assess the needs,” he said.
Lyon said the research showed that there is a need to develop a collective base of knowledge on best practices for operationalizing BEVs. Some of the training opportunities identified included general BEV safety, as well as charging and maintenance safety.
In a follow-up statement to CIM Magazine, Lyon wrote that while visiting mine sites to conduct the research, the Zero Nexus team found that a mining company trialling BEV equipment is usually forced to develop its own training program for its workers, which is a process that takes several years; BEVs are not generally a plug-and-play solution.
“Despite best efforts to coordinate between mining companies, each operation ended up making their own version of site-specific training,” Lyon wrote. “We see this as a hurdle for miners at early stages since this data collection activity for finding best practices is lengthy.”
As part of its research, Zero Nexus also
“There’s no playbook that exists right now in the industry for how to operate [BEV] machines as a fleet.”
– David Francis Lyon, Zero Nexus
CIM Convention and Expo and CIM’s Maintenance, Engineering and Reliability/Mine Operators Conference (MEMO 2023) to gather feedback from mine operators, OEMs and other service providers currently using BEVs or interested in adopting BEVs. Lyon stated that a recurring theme from participants was a desire to learn more about battery chemistry and the full life cycle analysis of BEVs from a third-party, unbiased source.
“The other thing that we heard a lot was that people are looking for more applications and case studies as BEVs grow in popularity,” he said. “A big one was that there’s no rule of thumb. There’s no playbook that exists right now in the industry for how to operate [BEV] machines as a fleet.”
Lyon’s presentation emphasized that the different roles within mining operations involved in adopting BEV equipment also require job-specific training, from operators that are responsible for battery user-interface and charging, to electricians that must service BEV-specific highvoltage electric equipment.
He said that while there are some institutions in Canada that offer training programs, they tend to focus on skilled trades or are part of engineering programs that focus on the development of BEVs.
•
•
•
•
•
•
•
•
•
•
•
“There exists a gap in addressing the planning stages for BEVs,” he said. “By planning stages, I mean, everyone who isn’t an operator. I think that gap exists globally. Just understanding the nuances of the technology and the terminology, that’s very important. From the operator’s side, it felt like [text-book based and online] training may not be as critical; hands-on experience tends to be the most effective and addresses challenges more effectively than anything in a book. And on the mine maintenance side, there’s a steep learning curve…it necessitates a much more comprehensive training approach.”
Zero Nexus is currently working on designing and developing courses that cover battery technology fundamentals, safety principles, fleet management and the broader landscape of BEV integration in mining for CIM Academy.
“How to use EVs is the gap we hope we can help fill,” Lyon wrote.
The workforce research is segmented into mine maintenance, operations and planning, and mine management, and Zero Nexus will soon release a white paper publicly sharing the results of the research.
– Silvia Pikal
David Francis Lyon presented new research on BEV training opportunities at the Battery Electric Vehicle Safety in Mines Symposium.Once formed, Nations Royalty will be Canada’s largest majority Indigenous-owned public company
By Ashley Fish-RobertsonAn agreement inked on Feb. 1 between B.C.’s Nisga’a Nation and Vega Mining Inc. will see Canada’s largest majority Indigenous-owned public company form over the coming months. Vega Mining, which will be majority owned by the Nisga’a Nation and will eventually be renamed as Nations Royalty Corp., will acquire the rights to five annual benefit payment entitlements stemming from projects located in B.C.’s Golden Triangle region in
exchange for common shares in Vega Mining’s capital.
The five projects involved in the Nations Royalty holdings are Ascot Resources’ Premier gold project and Red Mountain project, Newmont’s Brucejack mine, Seabridge Gold’s KSM project and New Moly LLC’s Kitsault project.
“One of the [significant] things with this agreement is that since it’s the first Indigenous-owned royalty company in Canada, it allows us to be a bigger player
in the mining industry; it gives us the ability to build a lot of capital through what we’re doing with this company,” said Charles Morven, secretary-treasurer of Nisga’a Lisims Government, in an interview with CIM Magazine.
Morven explained that the Nisga’a Nation already has an existing alliance with the province of B.C. and several mining companies within the province— including Skeena Resources and FPX Nickel Corp—known as the B.C. Regional
Mining Alliance (BCRMA). The BCRMA represents a partnership between the province’s Indigenous groups and industry and provincial government representatives. The BCRMA currently makes it a priority to draw in international investment to the province through its partnerships, especially in the Golden Triangle region, and Morven foresees that Nations Royalty will be able to bring in further investment.
Over the last two years, the Nisga’a Nation and its partners were occupied with signing numerous agreements, as well as locating a company that would agree to house Nations Royalty. “We also had to communicate with mining companies that we had benefit agreements
with and had to get their permission to be able to include them in the royalty company,” he added.
Morven explained that the genesis of the company began with a discussion between the Nisga’a Nation and mining financier and CEO of Fiore Group, Frank Giustra, who asked about the aspirations of the Nisga’a Nation in mining. “One of the things that we wanted to do was to be more knowledgeable of the whole mining industry, especially mining operations, and how we could begin to have a bigger say by investing [into mining operations] ourselves,” Morven said.
Morven considers the formation of Nations Royalty to be a big step towards the Nisga’a Nation’s ability to become completely self-governing, emphasizing how a reduced reliance on current funding agreements would ultimately lead to greater economic independence for B.C.’s Indigenous communities.
Robert McLeod, who is serving as Nations Royalty’s interim chief executive officer (CEO), considers the new company to be a significant step in the right direction towards granting B.C.’s Indigenous communities financial independence.
When McLeod was CEO of IDM Mining Ltd., which was later acquired by Ascot Resources, the company employed many members from the Nisga’a Nation
In the opening commodity outlook keynote on March 3 at the annual Prospectors and Developers Association of Canada (PDAC) 2024 conference in Toronto, Rio Tinto CEO Jakob Stausholm highlighted how the need to produce metals sustainably is becoming more critical as the world shifts towards renewable energy, which presents opportunities for mining companies as core markets grow and new trends emerge.
The theme of the keynote was “In a world in transition, metals matter,” and Stausholm noted that political, social, economic and energy transitions are all affecting the global mining industry. “We are seeing heightened international tensions and risks to global security… We are also seeing a greater influence from
for its Red Mountain project. McLeod stayed in contact with Eva Clayton, president of Nisga’a Lisims Government, and recounted initially discussing the idea of Nations Royalty with her, along with Morven, and Brian Tait, the Nisga’a Lisims Government executive chairperson.
“We thought, wouldn’t it be a cool story if First Nations [across] Canada pooled their royalties together to crystalize that value and you would have one of the largest royalty companies in Canada,” McLeod said.
The Nation soon engaged with finance committees and held community meetings to discuss the idea, along with further nurturing the relationship it had with its key partner, Giustra, who is now an advisor to Nations Royalty.
Trading is set to happen on the Toronto Stock Exchange in the spring. Once the company is set up, both McLeod and Morven hope to see it expand to include Indigenous nations across Canada, and potentially even expand into different countries across the globe.
“Hopefully [Nations Royalty] can set the example that Indigenous people all over can access the public markets, and that Canada has a wonderful system of venture capital out there that can support many ideas,” said McLeod. CIM
carbon in industrial policy, particularly around energy and supply chain security,” he said. “We are in economic transition— I am optimistic we are moving away from a period of high inflation, and I believe costs will stabilize this year, but the global economic outlook remains uncertain and commodity prices have been volatile.”
Stausholm highlighted that “decades of extraordinary globalization” have left the world with a serious dislocation between geology, processing, manufacturing and consumption, and many governments are now seeking to close this gap. “In the last two years, we have entered a new era of industrial policy characterized by government intervention, subsidies and policy support,” he said. “This is aimed towards de-risking supply chains and supporting the energy transition. It means industrial and climate policies are increasingly influencing commodity prices, premiums and project economics.”
Stausholm noted that to avoid supply bottlenecks, governments are also promoting the development of new mining
and processing projects via financing and regulatory support. “This creates new growth opportunities for existing producers,” he said. “It also incentivizes competition that could result in risks such as trade barriers and resource nationalism as value chains adjust. Considering these trends, we anticipate robust growth in world demand for key commodities of around 3.7 per cent a year until 2035 in copper equivalent terms.”
He added that society’s expectations of how the mining industry will provide the materials needed for the renewable energy transition are evolving. “Decarbonization and the journey to net zero are a huge opportunity, but also a deeply physical and complex challenge,” he said. “We estimate [that] China’s renewable electrification and uptake of EVs will require four megatonnes in annual copper demand by 2035. As other countries work towards their own decarbonization goals, another 10 megatonnes of annual copper demand could be added.”
He pointed out that customers are increasingly expecting sustainable, traceable materials with security of supply.
“They want us to help them decarbonize by providing low-carbon materials, and they want support in decarbonizing their own processes and reducing Scope 3 emissions,” he said.
Stausholm stated that Rio Tinto’s operations in North America are a prime example of how the company is positioning itself to capture these opportunities. For example, he pointed to the full transition to renewable diesel that the company achieved in 2023 at its mine in Boron, California, and its plans to fully transition the Kennecott mine in Utah to renewable diesel starting in 2024.
“We are heavily invested in Canada, which plays a significant role in our global portfolio of aluminum, iron ore and minerals,” said Stausholm. He added that Canada’s incredible wealth of hydropower makes it a world leader in low-carbon aluminum; last year, Rio Tinto invested $1.4 billion to expand its low-carbon AP60 aluminum smelting technology in Saguenay–Lac-Saint-Jean, Quebec. “Our hold of [AP60 technology] is an essential bridge to meet our customers’ demand for lowcarbon materials,” said Stausholm.
“In this developing and opportunity-rich world, metals and the way we provide them to society really matters. At Rio Tinto, we are absolutely convinced that Canada is a vital part of how we would drive the energy transition and create a low-carbon future together.”
– Jakob Stausholm, Rio Tinto CEO
The company is working with Alcoa, Canada’s federal government and the government of Quebec to develop its ELYSIS technology, which aims to move towards zero-carbon aluminum smelting, and Stausholm said there were significant
Compiled by Ashley Fish-Robertson
In response to Sayona Mining Limited’s operational review of its North American Lithium project, Guy Belleau, chief executive officer of the company’s Quebec subsidiary, has stepped down from his position as of Jan. 24. Sylvain Collard, Sayona’s chief operating officer for Quebec, assumed direct management of Sayona’s Quebec operations following Belleau’s departure. Collard has 19 years of experience in the mining industry, which has included the management of copper and gold mine projects in Quebec, Ontario and the U.S.
François Vézina has been hired by Nion Nickel Inc. as COO of its undeveloped Dumont nickel project in Quebec. Vézina’s role involves guiding the company through Dumont’s next development phase, which is anticipated to lead to a construction decision in 2025. Vézina, who has more than 25 years of practical experience both in Canada and internationally, will bring extensive knowledge in mine construction and operations to the new role, having contributed to the engineering, construction and development of six mines, the majority of which are located in Quebec.
Fleet Space Technologies announced that it has formed a new experts-in-residence program, which relies on the expertise of an internal group of industry leading experts to offer support to the company and advise it on how to tailor its technology to global mineral exploration customers amidst the mining industry’s rapid transformation. The company’s first appointed advisor, Keenan Jennings, joined Fleet Space in February. Among his previous roles, Jennings held the position of vice-president of metals exploration at BHP.
Scott Monteith will be stepping into the role of CEO at Avalon Advanced Materials Inc. after serving in the interim role since May 2023. Monteith has guided Avalon through the acquisition of a site in Thunder Bay, Ontario, for its future lithium processing facility, as well as its joint venture with SCR-Sibelco NV.
Wesdome Gold Mines Ltd. has appointed Fernando Ragone as its new chief financial officer. Ragone brings with him nearly three decades of global experience in the mining industry. Prior to this new role, Ragone was the CFO for Bear Creek Mining Corp.
steps planned for this year in its development towards commercial maturity.
Stausholm also cited the BlueSmelting technology that Rio Tinto is developing in Sorel-Tracy, Quebec, including a demonstration plant that started last year. “[BlueSmelting] could enable the production of titanium dioxide, steel and metal powders with a significantly lower carbon footprint,” he said. “Since then, we have demonstrated that BlueSmelting works on an industrial scale, and that we can achieve the quality levels we’re looking for. The next step will be to incorporate hydrogen in the process.”
Stausholm said that as the world’s biggest iron ore producer, Rio Tinto has a key role to play in decarbonizing the entire steel value chain, which he called an industry-wide and global challenge. “By scaling our capabilities, we can accelerate our progress,” he said.
On Feb. 27, Canada’s federal government awarded $18.1 million to Rio Tinto’s Iron Ore Company of Canada (IOC) to help decarbonize iron ore processing at its Labrador West operations. In Australia, Rio Tinto recently announced a partnership with BHP and BlueScope Steel for an electric smelting furnace pilot (see article below), and the company is also developing a low-carbon ironmaking process called BioIron.
“I have no doubt that we can crack the code for green steel, [and] it will be the material that builds the future,” said Stausholm. “Still, it’s a huge challenge, and it will take years to progress the technology. We need to keep working in collaboration with our customers, peers and governments to accelerate lowcarbon pathways.”
He said that working in partnership with governments and getting help, particularly in subsidies for research and development, is very important. However, he added, “what really matters is to have a country and a government [that] has an overall mindset towards the future we are looking into. I travel around, and it is not very often that I see the clarity of thought that I see here in Canada.”
Stausholm told the audience that in his opinion, “there is not a single western country which is better placed than Canada [for decarbonizing the mining industry]. You are definitely a decade, if not more, ahead of the rest of the world because of your hydropower, [and] you will have a unique opportunity to electrify societies faster than other western coun-
tries. And we, Rio Tinto, would like to be part of that.”
Rio Tinto does not currently produce lithium, but last year the company signed agreements with other companies that own lithium properties in Canada. “Lithium is fascinating, and we are trying to build a lithium business,” Stausholm said, noting that Rio Tinto is following battery technology quite closely. “We have not gone into cobalt, not gone into nickel, but we have gone into lithium…because we believe that it is difficult to predict what batteries will win, but the likelihood is that the future will have lithium in it. Two thirds of the batteries produced in China are actually LFP [lithium ferrophosphate] batteries, so [they have] lithium but no nickel or cobalt.”
He added that it is clear that lithium is abundant, “therefore, you’ve seen very volatile and sometimes very high prices, and now the prices have come down somewhat,” he said. “How do we make sure that we only get into resources of sufficient scale where we can build a real tierone business that is low cost? I would love to be a lithium producer in Canada, but it has to be the right resource.”
Stausholm concluded his keynote presentation by saying that while we do not yet have all the necessary technology and infrastructure to achieve net-zero emissions in the mining industry, partnerships can help in the acceleration of decarbonization pathways. “In this developing and opportunity-rich world, metals and the way we provide them to society really matters,” he said. “At Rio Tinto, we are absolutely convinced that Canada is a vital part of how we would drive the energy transition and create a low-carbon future together.”
– Ailbhe GoodbodyMajor iron ore producers BHP and Rio Tinto have partnered up for the first time on a downstream project with BlueScope Steel, Australia’s largest steelmaker, with the intent of developing a green steel pilot project that could significantly reduce carbon emissions for global steelmakers relying on Australia for iron ore.
If constructed, the facility will be used to demonstrate how the production of molten iron from iron ore sourced from BHP and Rio Tinto’s mines in the Pilbara region of Western Australia is possible through the combined use of
renewable power and direct reduced iron (DRI) technology.
The first step of this project requires the two mining giants and BlueScope to produce a pre-feasibility study (PFS) centred on developing a pilot ironmaking electric smelting furnace (ESF). The PFS is planned to be completed by the end of this year. If constructed, this furnace would be the first of its kind in Australia, and if the project progresses, the pilot facility operations could start sometime in 2027.
Once running, the pilot plant will require several years of operation before it progresses to commercial production. Potential locations for the project are being assessed by the companies.
In a Feb. 9 joint statement, the companies stated that the ESF allows for greater flexibility when inputting raw materials, as other low CO2 emissionintensity production approaches—such as electric arc furnaces—rely on scrap steel and DRI produced from high-grade iron ores. Most of the iron ore currently produced in the Pilbara region is not of a high enough grade for DRI-based green steel production; howeve r, the ESF would enable the use of lower-grade iron ore. The companies stated that the ESF could address one of the key barriers to
wider adoption of low-carbon emissions technology for steel production.
“If we can crack it, it’s going to be a significant uptick for the mining industry for Australia in general and the globe,” said Tim Day, BHP’s incoming Western Australia iron ore asset president, at a Feb. 9 press conference announcing the project, as reported by Reuters.
The project will build on previous work done by Rio Tinto and BlueScope back in 2021, where the companies first began to zone in on how carbon emissions could be cut during an early phase of processing iron by using clean hydrogen for direct reduction instead of metallurgical coal. This then converts the iron ore to DRI.
The companies stated in the recent project announcement that DRI-ESF technology could replace the traditional blast furnace, which uses metallurgical coal as feedstock in the steel production process, which could reduce emissions by more than 80 per cent when processing Pilbara iron ore.
This would help to reduce the global carbon footprint for steelmaking, the companies said in the Feb. 9 joint statement.
“We need to ensure that iron ore from Australia is well-positioned for a green steel future,” said Simon Trott, Rio Tinto’s iron ore chief executive, during the press
“We know we can’t solve this issue alone, we need to partner with others to find a solution.”
– Simon Trott, Rio Tinto
conference. “We know we can’t solve this issue alone; we need to partner with others to find a solution.”
According to the World Economic Forum’s Net-Zero Industry Tracker, steelmaking production was responsible for eight per cent of global energy-related greenhouse gas emissions in 2023.
In response to the announcement, Simon Nicholas, lead analyst for the global steel sector at the Institute for Energy Economics and Financial Analysis (IEEFA), expressed in a Feb. 12 article that with the shift to using hydrogenbased DRI plants over coal-fed blast furnaces for low-carbon steelmaking, “it is becoming even clearer that CCUS [carbon capture, utilization and storage] will not play a meaningful role in steel decarbonization.” On the same day, Fortescue executive chairman Andrew Forrest voiced concerns around the ineffectiveness of CCUS in reducing global CO2 emissions from fossil fuels while speaking at the 50th anniversary meeting of the International Energy Agency.
In the Feb. 9 announcement, the companies stated that they would consolidate the work each party has completed to date in ESF technology.
– Ashley Fish-RobertsonNewmont Corporation has announced that Rob Atkinson will officially depart from the company as COO on May 2 and transition his remaining responsibilities to incoming COO Natascha Viljoen after a five-month handover period. Viljoen was previously the group head of processing at Anglo American.
Several changes to SSR Mining’s executive leadership team have taken place after the company was ordered to cover the clean-up costs following a massive leach pad landslide on Feb. 13 at its Çöpler mine in Turkey. Most notably, Michael J. Sparks, the company’s executive vice-president and chief legal and administrative officer, will be stepping into the role of CFO. Sparks is succeeding Alison White, who will step down from the role to explore other opportunities.
This year’s 34th edition of the Canadian Mining Games took place from March 7 to 10 at Sudbury’s Laurentian University and offered post-secondary mining engineering students from across Canada the opportunity to showcase a variety of skills through 24 unique theoretical and practical challenges related to mining.
The schools that participated in this year’s games included the University of British Columbia (UBC), the British Columbia Institute of Technology, the University of Alberta, the University of Saskatchewan, the University of Toronto, Queen’s University, Laurentian University, McGill University, Polytechnique Montréal, Université Laval and Dalhousie University.
Mining engineering students from UBC took first place in this year’s games, with the University of Alberta claiming second and McGill University claiming third. Each of the students who placed first were gifted with an all-expenses paid trip to Barrick and Newmont’s joint venture Nevada Gold Mines, where they will have the chance to tour the joint venture’s mine sites and operations.
Ian Berdusco, chair of the Canadian Mining Games, told CIM Magazine that in addition to the games’ cornerstone events such as the mine design and mine
rescue challenges, there were also new challenges introduced this year, which focused on innovation in mining and challenges related to sustainability in mining. For example, the tailings/closure management challenge required students to design a tailings management facility and develop a mine closure plan.
In addition, a livestream of the jackleg competition, in which students drill various patterns using a jackleg drill while being graded based on safety, technique, accuracy and speed, was made available to those who could not attend the games, a feature introduced this year.
All 24 events were sponsored by different mining companies that helped develop the challenges. Berdusco explained that some challenges were weighted more than others, such as the mine rescue challenge that lays out a simulation where students must respond to a hypothetical emergency, requiring participants to use first aid and firefighting skills.
“Mine rescue is a pretty intense fourhour competition with four people, so it should be worth something more than a competition that only requires one person,” Berdusco said.
This year, students had the chance to work with actual mine rescue equipment, which Berdusco said was not done with past editions. Students also had the chance to try out their rappelling skills and use specialized equipment during this essential mine safety skill.
Other components of the challenge included a task where students had to open a door using a pry-bar, ascend a rope and use air lifting bags to move a ball through a large-scale maze.
As a former Canadian Mining Games national champion himself, Berdusco recalled his experience as a student representing Laurentian University in 2012 and how beneficial it was for him at the time.
“You get to meet representatives from companies that you’ll likely bump into at different parts of your career, and you get to meet students from other schools,” he said. “This event has typically been a pretty good place for recruitment and, just in general, there’s some really good networking opportunities.”
At a time when enrolment in postsecondary mining programs has decreased significantly, posing a concern for many in the industry, the Canadian Mining Games stated on its website that it will continue to unite mining companies and suppliers with new talent, playing an important role in fueling the industry’s growth.
The 35th edition of the games is set to be hosted in Quebec City next year by Université Laval.
– Ashley Fish-RobertsonThe introduction of a new program focused on mineral exploration and development within B.C. was announced in late January by Geoscience BC. The program will involve a province-wide study that will zone in on possible concentrations of critical metals and minerals located in mine tailings and waste rock facilities around B.C.
Geoscience BC, a not-for-profit engaged in publicly available geoscience research, will bring together the provincial government, mining industry and other partners for its Critical Minerals and Metals in British Columbia Mine Tailings and Waste Rock program. The first phase of the program will see data
on both active and inactive mining sites being collected. The data will then be used to create a map of all the possible sites that could contain critical mineral and metal resources.
Potential sources of the resources that were once deemed irrecoverable or invaluable but may now prove useful will be identified by Geoscience BC. “After we put the data altogether on one map, we can then connect everything to it so we know what’s there—like the geology, what was produced at the site, how much was produced—and then we can tie it into infrastructure and anything else we can find,” explained Brady Clift, manager of minerals at Geoscience BC, in an interview with CIM Magazine.
Clift added that once the map is created, phase two of the program will involve matching potential projects to specific mining sites following data collection and the mapping of possible sites during the first phase. Some potential projects that Clift mentioned could include biological extraction techniques aimed at removing ore from a tailings pond, or projects aimed at treating water.
“The big thing about this program is that it hasn’t been done before,” said Clift. “We can use the data to try new research, innovate techniques and methods, and we’ll know where to apply them.”
In addition to this, when all the data is compiled, it will offer a list of exploration targets, which could include areas where environmental remediation may be considered, for example. “After talking with the abandoned mines groups, we know that there’s more than 2,800 sites that will be included [in the data] just from them, so each one of those could be an exploration target.”
Another reason that this program could greatly benefit the mining industry, Clift added, is the fact that the collected data will grant companies the opportunity to test out new ideas: “There’s lots of things that could happen in B.C. that we just don’t have a good sense of where we could apply them, but then everything we learn from phase two and beyond can then be applied across the world. So, we could be a leader in getting this going, and then other people can look at this model and use it for their own jurisdictions.”
Along with Geoscience BC, the program’s first phase research funders include Arca Climate Technologies Inc. and New Gold Inc., though Clift noted that there is still time for other miners to get involved in this groundbreaking program. The program will also receive support from the Abandoned Mines Branch of the
Ministry of Energy, Mines and Low Carbon Innovation, along with the Association for Mineral Exploration and the Mining Association of BC.
“We’re very proud to be involved in this program,” said Paul Needham, CEO of Arca, in an interview with CIM Magazine. Arca is a carbon mineralization company that is currently piloting its technology at BHP’s Nickel West mine in Western Australia. “I think this is part of a broader imperative to look very closely at mine waste and to find ways of capturing more value there.” Needham explained that for many mines, only one per cent of the target mineral is considered usable, leaving behind 99 per cent of what is mined in the waste. He considers it exciting to think that valuable minerals are just waiting to be discovered in these active and historic sites.
“A lot of work needs to be done in B.C. and then globally to map the legacy tailings, and I hope that by contributing to this study, we will get smarter about how to identify valuable minerals and how to map the resources,” he said.
It was later announced by Geoscience BC on Feb. 29 that research it conducted revealed potential locations and concentrations of lithium in northeast B.C. Its recent project, NEBC Lithium – Formation Water Database, examined brines located below the ground and found that extracting lithium alongside natural gas development in this area of B.C. could be economic. More analysis on the brine
samples is needed, but it considers the early results to be encouraging.
Any mining companies wanting to get involved in the initiative are encouraged to reach out to Geoscience BC at info@geosciencebc.com
– Ashley Fish-RobertsonHighly educated newcomers to Canada with transferable skills beneficial to mining employers still face multiple barriers to entering the workforce and require support with integration, according to a Jan. 25 webinar hosted by the CIM Diversity and Inclusion Advisory Committee.
Panelists from the Mining Industry Human Resources Council (MiHR) and the Immigrant Employment Council of B.C. provided an overview of the supports available to employers that could help boost employment of newcomers and help with the industry’s labour shortage.
The MiHR panelists drew from a new report from their organization called “Support for Newcomer Integration into Canada’s Mining Sector,” which provides an overview of challenges faced by newcomers and outlines the various resources, programs and supports available for employers looking to hire them.
Victoria Burnie, manager of equity, diversity and inclusion at MiHR, said that while the immigrant population in Canada is growing at a faster rate compared to the rest of the population, immigrants are still underrepresented in mining.
Using data compiled from a Statistics Canada labour force survey from January 2007 to September 2023, Burnie said that in 2023, immigrants represented only 13.3 per cent of the workforce in mining, while they represented 31.5 per cent of the workforce across all industries. She added that immigrant representation in all industries had grown in the time period that the data was collected, while in mining it remained relatively flat.
“Unlike women in mining, where we see some pockets of promise—such as in HR and finance—immigrants are underrepresented across the board when we look at specific occupations,” Burnie said.
As an example, in the professional and physical science category, immigrant representation in all industries is 42 per cent, compared to 23 per cent for mining.
“This means for immigrants that it is a mining industry problem,” she said. “Immigrants are just not choosing mining or mining isn’t choosing immigrants in the job market competition stage.”
Burnie described the multiple barriers that prevent newcomers from entering the workforce in Canada.
“Understanding and adapting to the local workplace culture can be challenging to newcomers,” she said. “For example, different countries might have distinct expectations regarding communication styles and professional norms.”
Additional challenges include building professional networks without local contacts, getting foreign credentials recognized in Canada, and a lack of familiarity with the local job market that can prevent newcomers from understanding job trends in Canada and knowing where to look for job openings.
Glencore Canada’s Nickel Rim South mine, part of its Sudbury Integrated Nickel Operations. The federal Rural and Northern Immigration Pilot aims to bring skilled foreign workers to communities like Sudbury that are experiencing labour shortages.
Furthermore, newcomers may have a limited knowledge of available support services, such as career counselling, mentorship programs and job placement services. They may also be unfamiliar with
local hiring practices and resumé formats while job hunting, and once they reach the interview stage, might face discrimination or bias based on race, ethnicity, cultural or linguistic differences.
Our approach to mine closure is simple – we partner with clients to develop and implement tailored solutions that streamline reclamation and meet project objectives – all while considering stakeholder needs. Stantec is a world leader in the closure of operating, inactive, historic, and abandoned mines.
stantec.com/mine-closure
“Immigrants are just not choosing mining or mining isn’t choosing immigrants in the job market competition stage.”
– Victoria Burnie, MiHR
Finally, newcomers with a limited proficiency in the local language would struggle with everything from job interviews to daily interactions with colleagues once they are in the workplace.
“Overcoming these challenges often requires a combination of cultural adaptation, language enhancement, networking efforts and access to support services,” Burnie said. “Employers and communities can play a crucial role in facilitating the integration of newcomers into the workforce by providing resources and creating inclusive environments.”
Leslie Woolcott, director of equity, diversity and inclusion at MiHR, said that there is no shortage of resources available to support employers with recruiting and hiring newcomers.
“Part of the problem or challenge relates to understanding this complex of programs and navigating through the different eligibility criteria for both employers and newcomers,” she said. “While a limited number of programs specifically target mining, most are available to the sector and have relevance for the sector.”
One of the examples she pointed to was the Express Entry immigration program, which offers a faster pathway to permanent resident status for immigrants and includes a skilled trades stream. Two other examples are the Atlantic Immigration Program and the Rural and Northern Immigration Pilot, both of which were launched in 2022 and create a path to permanent residence for skilled foreign workers who want to live and work in communities that have a need to attract more workers. Some of the communities eligible for the Rural and Northern Immigration Pilot, for example, are known to be hotbeds of mining activity, including Sudbury, Timmins and Thunder Bay in Ontario.
Patrick MacKenzie, chief executive officer of the Immigrant Employment
Council of B.C., said that Immigrant Employment Councils of Canada (IECC) has 12 partner organizations across the country that support employers in recruiting, hiring and retaining immigrants into jobs that make the best use of their skills. Some of the services they offer employers include curated strategies for recruiting immigrant workers, cultural competency training, mentorship programs and initiatives to enhance workplace diversity and inclusion.
“We know that resource industries, extractive industries, are really important to the Canadian economy,” he said. “And it’s an area where more newcomers need to be made aware of the opportunity that’s there.”
MiHR’s report is available on its website at mihr.ca/resources in English and French and the IECC offers employer resources online through iecc.network.
– Silvia PikalA theme that emerged from the Feb. 26 keynote session that kicked off MINEXCHANGE, the 2024 SME Annual Conference and Expo in Phoenix, Arizona, was the pressure that net-zero greenhouse gas emission goals are exerting on the global energy sector and whether it can meet ambitious energy transition targets without compromising on affordability and reliability.
Keynote speaker Alex Epstein, the author of books such as The Moral Case for Fossil Fuels and Fossil Future, argued that net-zero goals have not served to significantly reduce or eliminate the use of fossil fuels, but rather slowed down their growth, which he said is causing a global energy crisis. He referenced California’s power shortages in the last few years as an example, stating that solar and wind farms are not a reliable source of energy.
“The problem with net zero is that it ignores the unique and enormous benefits of fossil fuels,” he said. “The path forward is energy freedom, not preferences for fossil fuels or anything else, but the freedom of all sources of energy to be produced and consumed.”
He argued that fossil fuel use provides more than 80 per cent of the world’s energy and will continue to do so as fossil fuels are affordable, reliable, versatile
and scalable, and cannot be rapidly replaced by solar and wind power, or nuclear and geothermal energy.
“Fossil fuels are uniquely cost effective, and that makes the earth a place that’s livable for billions of people, a place where human beings can flourish,” he said. “They can live lives that are long, healthy, opportunity filled. And without cost-effective energy, they can’t on a large scale. Without fossil fuels, we don’t have cost-effective energy.”
He stated that developing countries rely on fossil fuels, and since roughly a third of the world population uses wood and animal dung for heating and cooking, they present an opportunity for people to “flourish on this otherwise naturally inhospitable planet.”
After the keynote presentation, Epstein moderated a panel discussion with Bradford Crabtree, assistant secretary for the U.S. Department of Energy’s Office of Fossil Energy and Carbon Management, Jimmy Staton, the president and CEO of Santee Cooper and Jimmy Brock, the CEO of Consol Energy.
Epstein asked the panelists for their thoughts on the industry reaching netzero emissions by 2050, which he referred to as “the prevailing political goal guiding energy policy today.”
Crabtree disagreed with what he described as Epstein’s pessimistic view of net-zero goals, stating that the industry needs to embrace the challenge.
“First of all, it’s not a policy,” Crabtree said. “And it’s not just political as the question characterized. It’s a metric. And it’s a metric to which we can hold ourselves accountable.”
He added that while it will be difficult to reach net-zero emissions by 2050, it has not served the mining industry well in the past to challenge decarbonization and contend with the climate science behind it.
“We’re losing an entire generation [of workers]; in fact, we’ve lost two generations of young people around the world, by not embracing this challenge, being optimistic about the technologies,” he said.
He stated that while he does not disagree with earlier concerns raised by other panelists about energy reliability in a world rapidly transitioning away from fossil fuels, he believes that rejecting the net-zero framework means “we’re not willing to tackle the problem. I think you can be in favour of energy abundance,
MINEXCHANGE
“We’re losing an entire generation [of workers]; in fact, we’ve lost two generations of young people around the world, by not embracing this challenge.”
– Bradford Crabtree, U.S. Department of Energy
you can be optimistic about technology, and still get to net zero.”
Santee Cooper’s Staton expressed uncertainty about the ability for the company, which is South Carolina’s largest energy provider, to reach net zero by 2050, stating that while it is an aspirational and laudable goal, he does not currently see the path to reach it with existing technologies.
“What I do know is between now and 2035, Santee Cooper is going to reduce our emissions by 55 per cent. And after that, I’m uncertain,” Staton said. “What I’m afraid of, by setting it as a hard goal for any organization, [is] will you do anything to make it happen? Will you
sacrifice affordability? Will you sacrifice reliability?”
Brock, who heads up the coal producer and natural gas company Consol Energy, described net-zero goals as “somewhere in the middle to dangerous.”
He said that the U.S. has significantly shifted away from coal-fired generation in the last decade—in a 2023 report, the Institute for Energy Economics and Financial Analysis stated that the country is well on its way to closing half of its coalfired generation capacity by 2026—and that he is concerned about the timeline to net zero.
“The fast pace that we’re trying to do this—this is where I think it’s very dangerous,” he said. “We could very easily lose our competitive advantage.”
As an example, he pointed to China dominating the global supply of critical minerals and said that if the U.S. has an unreliable energy grid and is forced to increase the cost of electricity, it will give China another advantage over the country.
He added that net-zero goals do not allow time for the U.S. to supply the critical minerals needed for the energy transition, as it takes decades for new mines to open.
“Where this becomes dangerous is, what do we lose in the meantime?” he said. “If we lose 40 to 60 per cent of our
coal-fired generation here in the U.S., I do not see how the grid is going to function as it is today. And to me, it’s a real danger of moving too fast.”
Epstein concluded the keynote by stating that “global energy abundance” by 2050 should be the industry’s goal.
“That matters a hell of a lot more than how much CO2 is in the atmosphere,” he said. “Because with energy, you can deal with just about any amount of CO2 in the atmosphere. And without energy, it doesn’t matter how much CO2 is in the atmosphere, because life sucks. So instead of allowing it to be framed as, ‘When exactly do we get rid of CO2 emissions?’ let’s frame it as, ‘energy as the most important thing. Let’s bring it to everyone.’”
The U.S. government has committed to having all of its electricity needs coming from carbon pollution-free sources by 2030, with at least half coming from clean energy produced in the country.
The Canadian government has committed to reducing the country’s emissions by 40 to 45 per cent from 2005 levels by 2030, with the goal of reaching net zero by 2050. It pledged to phase out coalfired power by 2030, and Alberta will already reach this goal sometime this year, according to the province, which forced operating mines to close earlier than planned.
– Silvia PikalOnly Enduron® HPGR comes with a 10-year bearing warranty. Not that you’ll need it. After all, there hasn’t been one premature bearing failure to date. Enduron® HPGR delivers unmatched grinding efficiency, even when processing the hardest rocks, boosting mineral recovery. Expect ≥95% equipment availability, so operators can rest assured production targets
will be achieved whilst using the lowest possible resources. With lowest energy consumption and no water or grinding media required, typical operating costs for HPGR based circuits are over 20% lower compared to conventional SABC circuits whilst reducing comminution CO2 emissions by 30%. It’s no wonder we say Enduron® on and on and on.
n the last column, we started digging into the three components of cyber resilience with a discussion of how to build a cyber-resilient operation—one that can continue operations in the event of a technology outage—be it caused by error, failure or a cyber incident. In this column, I will discuss the building of a resilient cybersecurity program, regardless of the size and budget available to your organization.
A resilient cybersecurity program places the business and its employees at the centre of the program design and implements controls that protect the business and the users. This contrasts to a traditional, controls-based program that places controls and control frameworks at the centre of the design and deploys the controls based on those security frameworks to the users.
Controls-based cybersecurity is the model that we have used for over 25 years. To support controls-based security, the industry has developed several frameworks. And at first glance, there are a number of advantages that come from adherence to controls-based frameworks, such as their conceptual simplicity, ease of measurement and audit, and supportability by vendors. These advantages have given rise to a huge network of managed services providers, security software vendors, cybersecurity assessment organizations and consultants to help support the selection, deployment and maturity of control frameworks in organizations of all types.
Of course, IT and security teams love these frameworks. In addition to robust best practices and guidance for security controls, frameworks reduce the effort needed to assess and design security controls. They also make product and vendor selection easy since security vendors provide matrices showing the areas of these frameworks their products cover, and many services are available to rate security products and services against those frameworks. Adherence to a framework also allows the team and its leaders to easily set and measure goals, such as “increase security maturity to 4.6 in the next 12 months” or “be in the top quartile of mining organizations for security maturity.”
The challenge of the blind application of security frameworks is that they lack nuance and recognition of the context, the specific risks and the threat profile under which the business operates. Due to their intended purpose of applying security frameworks to all organizations and industries, they are designed to cover all risks and attacker techniques and behaviours. The base assumption is that all organizations can and should similarly deploy those controls to protect their organization.
Unfortunately, like most universal “best practices,” this lack of nuance becomes the fatal flaw. In practice, controls-based frameworks are most likely to either serve as a convenience function for the security team, making their jobs easier, or a method to transfer responsibility for an incident from the security team to the business.
To illustrate, most security frameworks will list multi-factor authentication as a critical control. To be sure, multi-factor authentication is a very useful control to protect against identity-based attacks; however, mining presents unique challenges. Typically, multi-factor authentication can be successfully deployed in the corporate business units and offices.
When the deployment moves to the operation, however, it falls flat. Obstacles such as a lack of mobile phone access due to a combination of no cell service at remote locations or health and safety rules that prohibit employees from carrying phones on-site mean phones are often not available to act as multifactor authentication devices, while legacy equipment prevents the use of USB-based multi-factor authentication devices. What is the result? The security team requires the business to sign some form of risk acceptance for the lack of multi-factor authentication at the site, absolving them of responsibility and leaving that part of the business vulnerable (conveniently not negatively affecting the maturity ranking reported as often the maturity ranking is net of signed risk acceptance).
Rather than starting from a control framework, resilient security programs look at the business and user context first, engineering security risk out of the business and then deploying controls that work with the needs of the company. Instead of seeing a signed risk acceptance as a necessary transfer of accountability, a resilient cybersecurity program will see that as a failure to recognize and adjust to the needs of the business.
To transition your cybersecurity program from controlsbased to a resilient program, the security team must build a deep understanding of how the business operates, the data flows and how its users work. In other words, “How do we do things around here?” From that point, an appropriate number of security or other controls can be deployed. Taking the example above, how would a resilient cybersecurity program deal with the multifactor authentication problem?
First off, a resilient cybersecurity program would not start with a need to deploy multi-factor authentication for all users in the offices and the operations; rather, thanks to good threat intelligence, it would recognize that misused identity is a major risk factor for the organization and has a high probability of being a vector of successful compromise. Armed with that knowledge, the team can utilize their existing knowledge of how the business functions to implement a mobile app-based multi-factor authentication for the most likely stolen accounts
— the corporate accounts that staff use to answer email and browse the web. For operational technology systems, rather than focusing on figuring out how to make multi-factor authentication work, the security team instead focuses on the goal of preventing stolen or misused credentials from being used in operational technology (OT) through separation of corporate accounts and operational ones. In doing so, it has identified that by not permitting corporate credentials to be used in sensitive OT systems and ensuring that stolen OT credentials, in turn, cannot be used on the accessible corporate network—in other words, implementing identity segmentation, supported by monitoring, brings the risk of OT network credential misuse down to an acceptable level.
With that minor adjustment in approach, the challenges around a failed control deployment are now avoided, the mess around risk acceptance is avoided, and we have a focus on risk mitigation that supports the operation rather than hinders it.
The organization needs a leader responsible for the new security program. This should not be a technical leader or technician but a business-focused cybersecurity leader or chief information security officer (CISO). For a smaller company, hiring a CISO may not make a lot of sense; however, fractional or virtual CISO capability is available, be it through a member-based organ-
ization such as MM-ISAC or from a security services vendor. It is critical that the CISO understands the industry, is positioned appropriately in the organization to have access to corporate business unit executives and operational general managers and that they are kept informed of company strategy, direction and key business decisions.
From there, industry threat intelligence, acquired through MM-ISAC or other sources, is combined with the business process knowledge to develop evidence-based ways to reduce cyber risk to an acceptable level for the organization.
In order to ensure the program that is developed helps to meet the objectives of the organization, the following success metrics should be implemented:
Cost: Most security programs measure costs based on the capital and operational costs of the program itself, as well as the costs of the tools and solutions purchased by the program. However, many forget the business impact costs of security controls.
The impact and costs on the rest of the business are missing from this analysis. Most planned or implemented controls will impact how employees do their work and may add time to tasks, require the vendors to work differently, add additional costs, and require more frequent hardware/software updates than can be supported by pure business use cases. Resilient cyber programs capture these costs even though they live outside the IT or security budget and actively work to manage them.
Residual risk: Most organizations report risk on a one-to-10 scale or some form of “High, Medium, Low” scale. The challenge with these measures is twofold: first, risk inflation causes all risks to slowly migrate towards “High,” and second, once many risks get there, it is difficult to prioritize, so many controls get deployed to address those risks.
In contrast, a resilient cyber program measures risk using a standard, supportable quantitative methodology, such as the factor analysis of information risk (FAIR) model. This exercise focuses the security program on activities that will limit the scope, impact or probability of an incident in your operational context. The security program should have defined targets for risk and be measured on their success in meeting them. Control effectiveness testing: In a controls-based program, often audits are done to establish the presence and maturity of a given control. In other words, is the control present, with all processes and procedures documented, and is a control test performed to ensure the control is working within the documented procedures?
Resilient security makes use of empirical testing of security controls, using automated tools combined with manual testing and tabletop exercises to actually simulate the attacker’s behaviours and measure the resultant effectiveness of your controls.
These measures are far more robust than a simple maturity score and give the board and executive team an easy-to-understand view not only of the strengths and opportunities of the security function but also of the impact those have on what is really important—the business of producing the key materials needed to support the company, our economies and the societal changes the world is counting on the mining industry to supply the materials for.
In the next issue, we will look at the final component of the cyber resilience triad—communications. CIM Building
MINE DEVELOPMENT
SHAFT SINKING
MASS EXCAVATION
PRODUCTION MINING
RAISEBORING
RAISE MINING
UNDERGROUND CONSTRUCTION
MECHANICAL EXCAVATION
ENGINEERING & TECHNICAL SERVICES
SPECIALTY SERVICES redpathmining.com
ore and more feasibility studies are showing numbers that simply cannot stand up to any comparison with reality. This problem, of course, is not new. Len Harris and Plato Malozemoff, very well-respected anchors of the early Newmont management team, wrote articles in the 1980s that pointed out that capital and operating costs in feasibility studies could never be achieved in practice. The problem seemed to get better for a while in the early 1990s but has recently been on a downhill slide. We all realize that this is not a good state of affairs.
Why does this happen? Corporate people get pushed by the financiers to show maximum ounces in a deposit. But often in order to do so, the ore grade must be reduced to submarginal
levels. What is a good feasibility study preparer to do? In order to get financing, they must then push to reduce capex and opex so the project shows a good internal rate of return.
The people who did the engineering and feasibility studies are prepared to explain why the study targets were not met. They will pin it on poor on-the-ground management, of course. This can go on for a long time, sufficient for the financiers to have reaped their rewards—and long enough for everybody else to have forgotten about the details of that old study. The problem builds on itself.
Our engineers here at Kappes, Cassiday & Associates get a lot of pushback from project managers who say our study costs are too high, but they compare our costs to costs in other studies, not to actual realized costs. Could it be that the Canadian regulatory industry has evolved to where it values consistency over reality? And if so, should something be done about it?
One thing to consider is that there might be a larger pool of investors if they felt that the data being presented was realistic. Another thing is that junior mining companies might actually generate significant, or at least predictable, cash flows if they had received realistic guidance during the study stages. Many junior mining companies are a bit demoralized by the fact that nobody seems to take them seriously anymore.
After Bre-X, Canadian securities regulators implemented the National Instrument 43-101 (NI 43-101) framework, ostensibly to keep everybody honest. In fact, it has done a reasonable job on the geology side to make sure the resource is actually there. But beyond that, it seems to be failing.
Here’s an idea to solve part of this problem: Add another numbered section to the 43-101 study format entitled “Capital and Operating Cost Comparables.” The first step must be that securities regulators make it mandatory for listed companies to publish on SEDAR the details of the annual all-in-sustaining cost (AISC) for each operation. This step should be mandatory for all operations that have been listed for at least two years. As AISC intends, these costs should be all-inclusive. Then, in the “Comparables” section of any new 43-101 report, the study lead author must compare the report costs with at least two similar operations that they pick from the SEDAR database and justify any low-side variance.
Since no two operations are exactly identical, implementing the above idea will not always lead to obvious or “clean” conclusions. But the process of making the comparisons will add a level of confidence to any study, which will make it much easier for the investment community to proceed with financing. CIM
Dan Kappes has over 50 years’ experience in mining and metallurgical engineering. He is a founder and the president of Kappes, Cassiday & Associates (KCA).
This article was first published in the January 2024 edition of Golden Opportunities, a newsletter of the Nevada Mineral Processors Chapter of the Society for Mining, Metallurgy and Exploration.
No matter how challenging your needs, BKT is with you offering a wide range of OTR tires specifically designed for the toughest operating conditions: from mining to construction sites.
Sturdy and resistant, reliable and safe, able to combine comfort and high performance. BKT is with you, even when work gets tough.
– Harness 40 years of Liebherr’s electric-drive excavator expertise and experience unmatched design,manufacturing, and maintenance
– Choose from the largest range of electric mining excavators to find the perfect fit for any application
– Reduce maintenance costs and extend component service life with fewer component changeouts than a standard diesel excavator
– Achieve the flexibility to work anywhere with multiple supply voltages and frequencies available
– Optimize safety and improve machine mobility with the fully autonomous Liebherr cable reeler
– Ensure peace of mind for operations as all Liebherr electric excavators comply with IEC or CAS/UL standards
An employee-led initiative at Agnico Eagle’s Detour Lake mine encourages workers to open up about mental health
By Mackenzie PattersonSome studies have suggested that in comparison to other industries, there is a greater prevalence of mental health issues in mining, with workers developing conditions such as depression, stress, anxiety and sleep disorders. A 2021 literature review by the journal Industrial Health found that several factors may contribute to this, including a high workload, risky working conditions, the demands of shift work and having to travel long distances away from home and families to work. A landmark 2019 study funded by Vale Canada found that 56 per cent of its mining workers in Ontario reported symptoms of mental health conditions such as depression or post-traumatic stress.
Dylan Loiselle is a mining worker who has first-hand experience of mental health struggles. After taking a short-term leave to recover, he came up with the idea of launching the Dig Deep program, an internal mental health and addictions initiative at Agnico Eagle’s Detour Lake gold operation in Ontario, where he currently works as a blaster helper with the drill and blast team.
“It had dawned on me that if I was struggling with these issues, there may be many others out there doing the same in silence,” Loiselle wrote in an email to CIM Magazine. “When I
presented the concept to mine leadership, I was extremely nervous, but it quickly changed to excitement when I received a standing ovation. The program launched a few months later.”
Primarily driven by employees, the Dig Deep initiative was designed to help everyone within the Detour Lake team gain a clearer understanding of the mental health challenges that many workers in the industry face every day. Through the program, participants challenge the mental health stigma by talking openly about topics such as mental illness and substance abuse.
“The role that all volunteers share is being a point of contact for anyone who may need an ear to listen,” Loiselle wrote. “We are not here to give advice, but rather to listen and guide you through the hurdles that come with reaching out for help if need be. A lot of the times, people just need someone to vent to, and our volunteers are their mental health support team.”
Dig Deep volunteers can take training sessions in peer support, as well as Applied Suicide Intervention Skills Training (ASIST), to help equip them with the skills and knowledge they may need to support their co-workers.
“We aim to be the voice for many who struggle in silence,” Loiselle wrote. “We also aim to end the stigma surrounding mental health and illness, while building a mentally strong workforce. We believe that with these tools in our tool belt, we can better understand one another and provide proper support.”
When the Dig Deep program was first introduced in 2021, it quickly attracted a team of 45 volunteers across 10 departments at Detour Lake who were eager to get involved. In 2024, Loiselle, who is the program leader, is still working on expanding the group and creating a solid support network for Detour Lake employees.
Kevin Watson, Agnico Eagle’s health and safety superintendent for the Ontario region, said that supporting the Dig Deep program is in line with the company’s objectives to ensure its employees are healthy and fit for duty.
“Our goal is ultimately to reduce harm and to ensure the safety of all employees at our mine sites,” he said.
When it comes to other initiatives the company offers to its employees across all operations, Watson said the company places a strong focus on education and awareness to help its global workforce understand mental health issues and support one another as needed. Initiatives vary depending on site location. At Detour Lake, initiatives include mental health awareness programs, mental health first aid training and ASIST, and the company employs a full-time psychotherapist on-site to ensure that employees who are experiencing symptoms of a mental health condition have easy access to the help of a mental health professional.
Norman Ladouceur, corporate manager of health and safety at Agnico Eagle, said the company places a strong focus on destigmatizing mental illness as part of its mental health strategy.
“Over the last few years, we’ve really emphasized removing the stigma and reminding people that if they’re being affected by mental health issues, they should be free to speak about it,” he said. “Maybe a good way to put it is that when a worker sustains an injury at work, there’s no shame in admitting that or going to the clinic to get help. Mental health should be no different.”
Loiselle believes that since its launch, the Dig Deep program has helped employees open up to one another about mental health challenges in a way they would not have in the past.
“The most tangible changes…are the ones happening behind the scenes, the ones where people are feeling more courage within themselves to take initiative and to seek the help they need to grow,” he wrote.
The Dig Deep team’s goal is to continue generating interest in the program and empowering volunteers to help other mining workers implement programs like these at their sites.
“As the saying goes, ‘when working amongst heavy equipment, if you don’t take time for preventive maintenance on your equipment, the equipment will do it for you,’” Loiselle wrote. “I believe that people need preventive maintenance as well.” CIM
Mining and Mental Health will run throughout 2024 and showcase the people, programs and initiatives that are prioritizing the mental health of mining workers. Each article will examine how to improve worker mental health, which is key to a safe and productive workplace. If you have a story tip, email editor@cim.org.
Real Progress is leading the mining industry through the energy transition.
Our holistic framework eMine™ is empowering the conversion of fossil fuel mines to all-electric. Combined with energy efficient technologies for deep vertical ore haulage and grinding, we are optimizing the use of power while reducing greennhouse gas emissions in real time. solutions.abb/realprogress
Be part of Real Progress.
Backfill specialists are turning the challenging conditions of mining in the Arctic into opportunities for innovation
By Sarah St-PierreThe mines Betty Lin visited as the global backfill specialist for Hatch often ended up being in areas where the mercury regularly drops below minus 50 degrees Celsius. The rising costs of general use cement—also known as ordinary portland cement (OPC)—and its transportation challenges are affecting backfilling operations at underground mines everywhere, but when permafrost and remote sites are added to the equation, unique challenges arise. The backfilling knowledge and experience acquired in mines located in warmer climates become somewhat obsolete.
Backfilling in underground mines disposes of potentially hazardous waste and reduces environmental impacts on surface. About half of Canada’s ground surface lies over permafrost, and many mines are in these regions. Advances in backfill technology, materials and additives are unlocking improved backfill properties for mines that operate in the extreme cold, ensuring that these sites remain stable, reduce risk of subsidence and see minimal ore dilution.
According to Lin, who is now the technical director and tailings practice lead for Hatch and is on the technical committee of the 14th International Symposium on Mining with Backfill (Minefill 2024) conference that will be held May 12 to 15 in Vancouver, B.C., the key to successfully backfilling at underground mines in the Arctic is to get the backfill recipe just right—that means striking the right ratio of solids, water and binder. The
solids are typically tailings, aggregate or waste rock, whereas the binder is usually general use cement. The ratio’s sweet spot is determined by the mining sequence and the strength of the host rock in the surrounding area. “In seven days, the mine might be blasting next to this backfill, so the backfill has to provide sufficient strength to blast next to it,” Lin said. The backfill design typically produces a range of mixtures to service the different parts and requirements of the mine.
The challenge of optimizing the backfill recipe does not typically have such high stakes outside of permafrost areas, where the heat from the cement’s chemical reaction with water, known as hydration, is enough to achieve the temperature for backfill to set on its own over time. In extremely cold climate areas, though, the strength of the backfill could be undermined by flash freezing of its outer shell, so mimicking underground conditions as closely as possible during testing becomes crucial to understand how the cold temperature will affect the placed backfill.
As the highest operating cost associated with backfilling tends to be cement, optimization of the cement ratio in the backfill also has important financial repercussions. “The key is to minimize the cement or binder content and still maximize strength,” Lin explained.
“The other challenge in underground backfill is getting this material that flows like a toothpaste to the desired area, without having it cure in the pipe during transport,” Lin said. This issue comes up with cemented paste backfill (CPB), which combines tailings, cement and sometimes additives to produce a
low-strength concrete. If this CPB sets prematurely, it leaves a block of concrete in the pipes that then needs to be removed, causing downtime. To avoid this situation, pipes need to be monitored for pressure to detect blockages early, and designed to include rupture spools and pressure release systems.
As climate change forecasts thaws of permafrost, shifting temperatures also need to be factored into backfill design, according to Lin. Thawing in the permafrost regions can affect the strength of the backfill, meaning that the backfill recipe will need to be designed for increased strength to account for potential changes in the region’s climate in the future.
From 1948 to 2004, the Giant mine near Yellowknife produced 7.6 million ounces of gold. The processing of gold resulted in the production of approximately 237,000 tonnes of arsenic trioxide dust, currently stored in 15 chambers underground. As part of an initiative led by the federal government of Canada, the primary remediation challenge at this site is to safely secure the arsenic trioxide dust. The preferred approach for managing the arsenic trioxide dust is by using ground freezing to prevent the release of the arsenic into the surrounding environment, followed by filling the chambers with paste made from cement and surface tailings to immobilize the arsenic.
Lin worked on the first phase of the underground stabilization project at the Giant mine from 2014 to 2016, and spent three months in a makeshift laboratory experimenting with different types of cement. She provided specialist guidelines for remediating the contaminated land abandoned by previous operators by utilizing existing surface tailings to make paste backfill that is delivered underground to seal the stopes—some containing arsenic trioxide. Lin explained that “extensive testwork and planning was completed prior to commissioning in order to optimize paste recipes to meet paste quality requirements, in terms of strength and flowability of the paste.”
The production of paste for the backfill took place over the spring and summer of 2015, where a total of 60,000 cubic metres of paste was used to seal the six stopes.
Lin successfully completed trial batching and innovative application of slag cement during this first phase of the project; prior to that, only OPC was used and permitted at site. Slag cement was chosen for several reasons by Lin. “Trial batching showed that when using slag cement, a lower cement content (half) was required to achieve the target 28-day strength,” she said. “It also produced a paste product with favourable flow properties to fill the odd-shaped chambers.”
Slag cement has a slower curing rate, which was beneficial in managing the heat and forming a monolithic structure. Furthermore, the slag cement produced a higher 28-day strength when compared to OPC, Lin said. This meant less cement was required for the project, reducing the stress on the logistics of supply and cost for the project. The use of this type of cement ended up saving the project millions of dollars.
Transportation is another deciding factor in settling on a backfill strategy. Many mines in the Arctic are remote, which complicates logistics as well as increasing costs of transporting materials to site. A Mining Association of Canada 2023 report highlights that transportation costs by both rail and road have
increased by over 50 per cent over the past five years, particularly since the end of 2020.
Once paired together, the rising costs of both cement and its transportation can really add up. “In the Arctic, it’s even harder for us,” said Louis-Philippe Gélinas, geotechnical subject matter expert at Agnico Eagle Mines. Cement gets shipped by boat and trucked in at Agnico Eagle’s Meliadine mine in Nunavut, inflating the cost of the material. “[For] each and every percentage and every kilogram [of material] you’re using, you want to make sure you’re not using it for nothing,” Gélinas said.
His work involves pinpointing the exact temperature and curing conditions for backfill that uses the optimal and necessary amount of binder to provide the required stability for Agnico Eagle’s Meliadine and Amaruq gold mines in Nunavut. He started working on the question back in 2018, when Meliadine was being built and Amaruq was still only a satellite underground project at the Meadowbank mining complex.
A mix of CPB and cemented rockfill is used for backfilling at the Meliadine mine, whereas only cemented rockfill is used at the Amaruq mine due to its distance from Meadowbank’s mill. “When we were planning for these mines, early on, we wanted to make sure that backfilling would not be an issue,” he said.
Through experimentation, Gélinas and his team decided high early (HE) cement would be the best choice as a binder for backfilling at these mines, over the general use cement or fly ash cement generally used at mines farther south. “It’s just a cement that is crushed finer; so by being finer, it’s going to hydrate faster,” he explained.
Compared to general use cement that would take a week to set in the same conditions, HE cement needs only three days to set. Because it is finer and hydrates more quickly, it can be more complex to utilize in backfilling, but a faster reaction time is key in the Arctic because the cold temperature eventually halts the hydration process. “We were able to beat the cold, basically,” he said.
There also turned out to be a financial advantage to using HE cement as a binder. In low curing temperatures, the team found that they needed to use much less HE cement compared to other cement types in terms of percentage in the paste. Therefore, even though HE cement is more expensive per tonne, using it over other types could save Agnico Eagle several tens of thousands of dollars over a single year, according to Gélinas.
Another conclusion his team came to was that the recycled water from mining in the Arctic, which typically contains a lot of brine, was particularly suited to backfilling purposes. Adding the right amount of salt to the backfill hastened the cement hydration process and slowed freezing. “It’s like when you put salt on your roads, when you put salt in your backfill,” Gélinas explained. The discovery also had an environmental advantage. “This water, we were kind of stuck with it and had to store and treat it,” he said. “And now we could use it in backfill.”
Gélinas and his team also found that proper mixing of the cement was key in Arctic conditions. Whereas in a warmer climate, the demands of a backfill recipe are looser, at Amaruq, the temperature and the mixing are closely monitored to make sure that every kilogram of cement is used as efficiently as possible.
Backfilling traditionally involves using cement as a binder. However, the logistics of using it become even more complicated for De Beers’s Chidliak diamond project on Baffin Island, Nunavut. “Transportation would be very difficult and [is] usually by air, because there are no roads,” said Fatemeh Tavanaei Sereshgi, a PhD candidate in mining engineering at McGill University. She works with Prof. Ferri Hassani, who is conducting research for De Beers on the backfill aspects and processes of the project.
The combined costs of cement and its transportation to the site spurred De Beers to seek out alternative methods for backfilling. As a result, the team has removed cement from the equation entirely.
Enter frozen backfill. It removes the need for cement as a binder, substituting it for water that freezes in the stopes. This will fit the new mining technique—bore and fill from surface.
At Chidliak, the plan is to fill vertical drop shafts, which are bored from the surface, with tailings and water from melted snow and nearby water bodies, which then freezes after being placed in the shafts. According to Tavanaei Sereshgi, this will have minimal effects on the chemical composition of the area’s environment, including groundwater, and will also help to stabilize the permafrost equilibrium after mining. Tests conducted at the site indicated that the ground temperature would be suited to frozen backfill up to 450 metres below the surface, because the permafrost extends to that depth. Uniaxial compressive strength testing also indicated that the frozen backfill would provide sufficient strength.
The method also accounts for temporary rises in temperature. The vertical stopes stem from a novel boring technique that is designed to make sure that any thaw in the ice will be too slow to compromise stability before it freezes again. “So even if the weather gets [warmer], nothing is going to happen,” Hassani said.
However, the method is not without challenges. For the planned size of the stopes at the mine, it may take three to four months for backfill to fully freeze. To account for this, careful calculations have to go into the sequencing of the mine shafts (stopes) and the scheduling of operations, according to Tavanaei Sereshgi.
As planning for the Chidliak mine strives to achieve the lowest possible carbon footprint, replacing emissions-heavy cement with frozen water and eliminating the need for the transportation of an additional material becomes doubly strategic.
“Up north, because our environment is so fragile, backfilling becomes very important,” Hassani said. “Instead of dumping the tailings on the surface, you’re basically burying it where you got it from.” CIM
Innovative solutions. Positive transformation.
You need a partner that can meet your needs and embrace the future. One with new solutions for a changing world. Together, we can work toward a better future. komatsu.com/hardrock
The looming climate change crisis and consequent increase in environmental concerns is driving every industry, including mining, to reduce its carbon footprint. One area where there is a significant opportunity to reduce overall carbon dioxide (CO2) emissions in underground mines is cemented paste backfill (CPB).
“Cemented paste backfill is a combination of mine tailings that you mix with water and cement to create a paste that is pumpable and that, after being placed, will harden and generate structural strength,” explained Sara Arcila Gut, business development for mining at Sika Canada, a creator of specialty products and chemicals for industrial applications, including mining. “The component of cemented paste backfill that really emits [the high] carbon footprint is your [general use] cement.”
The resulting paste is pumped into the underground voids created by mining excavation and solidifies, supporting the surrounding rock and mitigating the risk of surface subsidence. Anything from between two to 10 per cent of CPB comprises cement, she noted, and around 30 mines in Canada use it—so that represents a lot of cement.
Cement production is responsible for between five and eight per cent of worldwide CO2 emissions due to the chemical and thermal combustion processes needed to produce it, according to Neea Heino, a researcher and project manager at the Geological Survey of Finland. Heino is part of the SETELIT project that is investigating ways to bind tailings in paste backfill via carbonneutral methods.
Consequently, by reducing the amount of cement used, or replacing it with other binder materials, mines using CPB can reduce their carbon footprint in a meaningful way, she said.
That reduction can be significant and can help mining companies with underground operations to accomplish their commitments to achieving net-zero greenhouse gas emissions. Paul Deram, technical services engineer at building solutions provider Lafarge Canada, said that a mining operation that uses 200,000 tonnes of backfill material per year can reduce its emissions by 7,000 tonnes of CO2 by switching from general use cement to an alternative cementitious product.
“Considering the substantial carbon footprint of cement production, coupled with the complexities of the supply chain to reach mine sites, it’s evident that cemented backfill tends to be a carbon-intensive process,” he noted, observing that the Canadian average Environmental Product Declaration (EPD) for CPB shows a total global warming potential (GWP) of 850 kilograms of CO2 equivalent per tonne.
“While both the mining and cement sectors have independent aggressive CO2 reduction ambitions and take tangible steps towards achieving them, the potential for effective accelerated progress is great if we work together.”
– Paul Deram, Lafarge Canada
One effective strategy for reducing the carbon footprint associated with cement usage in CPB is to utilize alternative binders made from waste materials sourced from other industries. These may include slag from steel plants or fly ash from coalfired power plants. Sika’s Arcila Gut pointed out that these lower-footprint cements allow the mine to reduce the related CO2 emissions from the purchased cement, which is reported in the Scope 3 emissions—the indirect emissions that occur across the value chain and are outside of the mine’s direct control. However, she noted, the increasing demand for these alternative binders from numerous mines exceed the local available supplies of these waste materials.
Some cement manufacturers are also replacing 10 to 15 per cent of the cement with limestone filler, which, Arcila Gut said, sometimes seems to affect some CPB properties such as set time, and can potentially lead to a reduction in uniaxial compressive strength (UCS).
Alternatively, admixtures in CPB—additives that modify the properties of the paste—can allow mines to cut back on the amount of cement used. This has several benefits: reducing the CO2 emissions from their cement consumption; increasing the amount of tailings placed underground, which reduces the environmental effect of storing the tailings aboveground; accelerating the placement process, reducing the time required to fill the voids; and reducing the mine’s water consumption.
“By using admixtures, it is possible to reduce up to 26 per cent of the mine’s cement consumption. For me, this is a way of saying the key to sustainable CPB is trying to optimize the use of a cement [that] emits the lowest emissions,” Arcila Gut said.
But how can admixtures reduce the carbon footprint of CPB so much? “By adding a small dosage of additive—0.5 to 2 per cent by weight of cement—into the CPB mixture, the paste becomes much more flowable. This allows [mines] to cut back a certain amount of the water and increase the solid content until it brings the paste to its original flowable consistency. With the admixture, the paste behaves similarly, but due to the lower water content, it is much stronger. So, this approach allows us to progressively reduce the cement content until we achieve the originally required compressive strength,” explained Arcila Gut.
Heino added that there are also aboveground positive effects to using lower-carbon CPB in underground mines, which supports the circular economy and sustainable mining. “Without
backfilling, the tailings are disposed as waste in the tailings area, which is typically a large area. If the tailings can be utilized as CPB that hardens in underground structures, the aboveground environmental and landscape effects [of the mine] will be smaller,” she explained.
“Reduced land use is a better option for biodiversity. Tailings areas can also cause resistance in the community because the dammed tailings are often seen as a safety risk to the environment and the community. Without competent management of extractive waste, it can really pose a risk to its environment. As a result of smaller environmental and landscape impacts [from the use of CPB] and the safe handling of tailings, the social acceptability of mining can increase.”
Deram said that Lafarge is already collaborating with several mining customers to identify the best products to use in their specific situations, keeping in mind not only the carbon footprint, but logistical considerations, operational efficiency and costs. Many, he said, have already transitioned to products that have carbon footprints of up to 85 per cent less than general use cement.
The cement industry is on board with reducing cement’s carbon footprint as well, in self-defence if nothing else. The World Cement Association (WCA), an independent not-for-profit organization based in England, is also working to reduce the carbon footprint of its members’ products; its website says, “WCA supports a sustainable cement industry and encourages technical development and other steps to achieve full decarbonization.”
After the 2023 UN Climate Change Conference (COP28) in Dubai at the end of 2023, the WCA president issued a statement endorsing the agreement to advance low-carbon cement and concrete production that was signed at the conference, saying, “As the need to address climate change has become more urgent, many industries around the world recognize lowcarbon transition is the way forward. [With cement] accounting for seven per cent of global emissions, carbon emissions reduction and capture is a major challenge the cement industry must face head-on if it is to make progress towards achieving green and sustainable development.”
Deram noted that suppliers need to be proactive in reducing the carbon footprint of the cement industry. “Offering low-CO2 products isn’t just a commitment to their sustainability but also a direct contribution to the environmental goals of end-users,” he said. “I believe that making the carbon footprint of the products a decision factor in the purchasing process can help drive this change. This shift is gradually gaining momentum across several industries.”
To speed that shift, he suggested that dialogue could be the answer. “I believe there needs to be a bigger conversation between our industries,” he said. “While both the mining and cement sectors have independent aggressive CO2 reduction ambitions and take tangible steps towards achieving them, the potential for effective accelerated progress is great if we work together.”
But improved technology is not the entire answer, Heino pointed out. “The solutions for a more sustainable future also require a cultural change, to work differently than you are used to working,” she said. “In order for a change in operating methods to occur, people’s attitudes and ways of thinking must also change. Each of us is therefore responsible for our own actions and together we can bring about change.” CIM
Paterson & Cooke’s Maureen McGuinness discusses the evolution of backfill and the key role it has to play in mine planning
By Ailbhe GoodbodyMaureen McGuinness is a director in Paterson & Cooke Canada Inc. in the Sudbury, Ontario, practice. She has more than 30 years of experience working in mining and milling, and specifically in paste backfill design and operations. Her expertise includes backfill operation, backfill management planning, dry tailings plant-feed operations, hydraulic modelling of distribution systems, startup and commissioning of backfill operations and training of staff.
McGuinness is co-chair of the 14th International Symposium on Mining with Backfill (Minefill 2024) conference that will be held May 12 to 15 in Vancouver, B.C. This year’s conference theme is “Full Circle: Supporting a holistic mining cycle.” CIM Magazine spoke to McGuinness to find out more about this key aspect of mining that is sometimes undervalued in mine design and operation.
CIM: What role does backfill play in the mining cycle, and where are the opportunities for mining companies to optimize this?
McGuinness: The role of backfill is to help manage the stress in the mine and aid in local regional ground stability; it doesn’t hold up the mine, but it helps with that whole process. The increased stability allows mining companies to get more out of their mine, for example they can work safer, faster, extract more or have better cycle times, all with the goal of getting more ore out of every deposit.
While the main role of backfill is stress management, the resulting benefit is that we can recover more ore and it helps provide different mining options to a mine site. Backfill is at the end of the mining cycle, so it is often thought of as a necessary
evil, but there is an opportunity to see it as an extra tool in the mine design toolkit that can push the limits of the mine being developed or designed.
There are also opportunities to look at the waste management of the site as a whole, to see what materials from the surface can be used as backfill and how that can help in other ways. Using backfill allows a mine to maximize how much of a mine’s waste products can be put back underground, minimizing surface impact.
The other part is safety; having a fill that you can rely on allows the designers to be more confident when they’re looking at taking out different stopes. Backfill should be a planned, engineered process with results that can be foreseen.
CIM: What key aspects do mines need to consider when designing and operating mine backfill systems?
McGuinness: One of the first things is to look at what material is available for the fill and to get a good sense of what the mining process will produce in terms of fill potential—it could be waste rock or tailings, or depending on the situation of the mine, there may not be tailings or backfill components close by. If the mine is sending the ore off site, then a key consideration will be what can be used as backfill.
It is also important to size the backfill system appropriately, and make sure that it will meet the needs of the mine in the short and long term. The backfill system can help a mine to catch up if there have been delays throughout the different processes, and having it sized appropriately and robustly allows you to bring that mine cycle back on track if it can fill fast.
Understanding the strength requirements of the fill is important, including short-, medium- and long-term strength
requirements. You may need to understand how strong it needs to be very early on, even after one or two days, to meet the requirements of the filling process. For a cemented backfill, it could be how quickly, or how far in the future, you want to expose the adjacent stope, depending on the mining sequence.
Sometimes these are components that we figure out later, but they should be done upfront with mine design. By understanding what the requirements need to be, then we can dial in the recipes and make sure that we can meet a complex profile of strengths.
Then of course the other key aspect, which makes backfilling unique, is that we’ve got plants on surface and then the whole distribution system underground. We need to make sure that those two systems are working in sync, and that one is not developed in a silo compared to the other. For a successful backfill system, it is very important that the plant matches the underground distribution system, and that the operation is configured or managed with that whole entity in mind.
CIM: Is this an area that is sometimes undervalued in mine design?
McGuinness: Definitely. Backfill is the last part of the mining cycle and tends to get less attention than other parts of the mine design, especially in earlier stages of studies. Often, these studies will have quite a detailed look at how the ore will be extracted and processed, and then there’s one line that says, “and it will be backfilled.”
But if we plan backfill at an early stage, then we can identify opportunities to match the backfill with tailings storage, which can help alleviate some of the pressures of the surface disposal. It also helps if we can have fewer surprises going forward. If everybody knows what it means to backfill, and its requirements in terms of costs, footprint and effort, then they won’t try to squeeze it into a predetermined design.
I would like to show people that we need to plan for backfill so that it can work more efficiently. Our end goal with backfill would be—if you don’t hear about it, it’s going well. But if that doesn’t happen and you’ve let things go, then everything will be in an emergency state. Reacting to a problem usually works out more expensive in the long run, versus planning backfill properly.
We find that backfill is a little undervalued in operations as well. Often, mine sites have no dedicated people working on backfill, so you see people managing the backfill as a secondary part of their job.
CIM: Would the Canadian mining industry be considered to be a leader in backfill?
McGuinness: Canada is definitely a leader in pastefill, which had its origins right here in Sudbury, and Canadian mines were early adopters of paste backfill. We also have extensive backfill research being done in Canadian universities, including some very new studies about how backfill behaves in situ. While the industry has been backfilling for a long time, actually understanding how it works and how the strength develops is relatively new, and Canada has been a great provider of that information. There is a hub of engineering companies, too, in Canada that are really specialized in backfill, which I think indicates where we are in the field.
And then of course, there are a lot of Canadian mining companies that have this background and expectation of backfill,
and as they are going out worldwide and starting up different mining operations, they are bringing that expertise with them.
CIM: What changes have you seen in this area of the mining industry over the course of your career?
McGuinness: There has been a shift, especially recently with the new guidelines on how to manage tailings storage, including the benefits of filtered tailings disposal as opposed to wet tailings. There are a lot of synergies because if you’re going to filter these tailings, then that sets you up for synergies with tailingsbased backfill. We are seeing a lot of companies diverting filtered tailings as much as possible to pastefill, and disposing of the rest on the tailings stack. That’s probably one of the most recent changes that we’ve seen.
I started working in backfill in the early 2000s, and I was starting up one of the new paste systems that were coming in. At that time, the industry was focused on the fundamentals of backfill and how to distribute it, in terms of pastefill in particular, as that was a newer technology that was becoming more mainstream. We did not have that full understanding yet of the theory behind how the hydraulics work or how the rheology or flow properties of the material affect how we place it underground. This meant that startups were difficult, and there were a lot of places where it didn’t run smoothly. But once they got running properly, then sites immediately saw the benefits of it. As an industry, we have learned about the best methods of delivering the paste underground, and looking at what did and didn’t work in the plant as it became more popular in Canada.
For example, the mining industry used to just take a mixer from the concrete industry, but now it has adjusted these and made them specific for pastefill. It is the same with binders— general use cement used to be the main ingredient for the binder, but now slags and other additions are being used in mining. What works as a specialized admixture in the concrete industry isn’t really feasible at the mining scale, so the mining industry is now developing admixtures specifically for backfill.
There has been a refinement of understanding, too, of the material components that can be used in backfill. Instead of taking what’s available, people are refining it in terms of particle size or mineralogy, or choosing to split up types of tailings so that more problematic materials are either selectively removed from the backfill, or put into the backfill because it is an opportunity to get it in an isolated condition underground. I think these have all been really interesting developments over the last 25 years.
CIM: What do you think is the future of mine backfill?
McGuinness: Pastefill is coming into maturity now. We have largely figured out the mechanics, although there is always more to be done on that side. We are seeing a lot more clients wanting to know about the processes they need in place to make sure their backfill system is sustainable, reliable and high quality all the time. Once the fill becomes reliable, the mine can react accordingly and reap even more benefits.
I think we’re going to see a lot more instrumentation being used. The digitalization of mining has benefitted backfill because before, there wasn’t really a way to get a lot of real-time information. We are seeing a lot more equipment like cameras, automatic valves and widespread use of pressure transmitters; now there is more connectivity between the systems and ondemand information. Even simple things like measuring the
height of the backfill in the stope as you’re pouring, which sometimes is very difficult—those are the types of challenges that we’re going to see get solved.
We are seeing a rethink of binders too. One of the main costs of backfill is the cementitious materials used as binders, and as a global industry, we’re looking for ways to use less cement, or to further bring out every ounce of strength we can get from the materials that we put in.
Backfill already has a key role in mine waste disposal, and I think we’ll see that expanding as mines go deeper, and as more mines are opened in remote areas like northern Canada. Anything you can do to lower the amount of material that you have to ship onto site is important; or at least if you do use it, to make sure that you’re using it to its maximum capacity.
CIM: What is the typical path to a backfill career?
McGuinness: In the mining and mineral processing programs at universities, backfill isn’t highlighted too much as a career. People usually get into this specialization through either a mineral processing or mining type of role, and all of us have learned this on the job.
When I was studying, I knew nothing about backfill as a career. I had chosen mineral processing as a specialty and became a mill metallurgist, and it was by luck that I was the one told to go over to run this paste plant. I went on to specialize in backfill because I just loved it.
Backfill is a unique career that I wish we could get people to consider more often. It’s very dynamic because of the link between the processing plant and underground operations— you’ve got some mining, and there is a large mineral processing component to it with filtration and thickening. There is a chemistry element as well, for example with cement hydration. Then there is the distribution of this new engineered material that you’ve created, how it flows underground and how you make sure it flows to where you want it, so you need to understand pipeline design and hydraulics. And then of course you’re putting it underground, so you need to know about support underground and how to get the physical distribution system installed. Then you’re placing it in the stope, so there are requirements to keep this fill in place and make it set, which has elements of geomechanics. It requires quite extensive knowledge, and there is a range of engineers and scientists that have an affinity for this field, like mining, process, chemical, mechanical and geotechnical specialists.
I feel it is a fun package for someone who likes a lot of different things, and yet it is a very niche specialty. This is a field that someone could go into as a career and be very challenged and happy. There is also a shortage of people with this expertise; we always get asked if we know any pastefill engineers.
I would like to see more of a formalization of backfill engineers, the way we have blasting engineers and things like that. As an industry, I would like us to find a way to identify that and bring that out as a career. CIM
INSTRUCTORS Kristopher J. Shelswell, SRK Consulting, Canada • PLACE Montreal, QC • DATE September 18 - 20, 2024
INSTRUCTORS Roussos Dimitrakopoulos, McGill University, Canada, and Luis Montiel Petro, Vale, Canada • PLACE Montreal, QC • DATE September 25 – 27, 2024
INSTRUCTORS David F. Machuca, SRK Consulting, Canada, and Roussos Dimitrakopoulos, McGill University, Canada
• PLACE Montreal, QC • DATE September 30 to October 4, 2024
INSTRUCTOR Mustafa Kumral, McGill University, Canada • PLACE Montreal, QC • DATE October 9 to 11, 2024
Sleipner E Series dollies bring the wheeled advantage your mining operation has been looking for. More working hours, longer undercarriage life, and fewer on-site repairs – the Sleipner E Series dollies will elevate your operation with higher productivity and sustainability.
Reduce equipment travel time up to 85% and increase excavator productivity by up to 12-20%.
Save on excavator undercarriage maintenance by up to 50%.
Reduce life cycle costs by up to 10–18% with fewer spare parts for maintenance and lower fuel consumption.
brandt.ca
1-888-227-2638
Integrated approaches to mine planning that include sustainable closure and reclamation plans and consider the potential for shared value for various stakeholders are becoming increasingly important
By Alexandra Lopez-PachecoThe next major revolution for the mining industry might not lie in leading-edge technologies such as artificial intelligence, automation or even the electrification of operations or the industry morphing into a leading player in the energy sector. Instead, it very likely will come from an approach to mine closure, reclamation and post-mining socio-economic transition that has emerged in the last decade.
Some experts believe this revolution has already started. It is led by members of the industry in the form of integrated mine planning—and the development of industry standards to help mining companies solve many of their challenges by working backwards from closure and post-closure when starting a new project.
Forty years ago, when Dirk van Zyl, professor emeritus and chair of mining and the environment at the University of British Columbia, began his mining career, “People who managed mines—when the time for closure arrived—would move on to start a new mine,” he said. “One of them actually told me, ‘There is no glory in closing a mine. The glory is in starting a new one.’”
The mining industry is still coping with the negative reputation and challenges in gaining a social licence to operate from communities as a result of the short-term, fragmented thinking that prevailed in much of the 20th century—as well as numerous ingloriously abandoned mines that still need remediation.
Today, increasingly, mining experts are recognizing there is indeed glory in closing a mine successfully, which van Zyl called “a full circle.”
Van Zyl, who ignored his colleague’s advice and went on to build a successful career in sustainable mine development and tailings and rock waste management, was the convenor for the International Organization for Standardization (ISO) to develop an international standard for mine closure and reclamation planning that was released in October 2021. It took five years for the working group, which consisted of representatives of 13 countries and who in turn brought in multidisciplinary teams, to develop the comprehensive best-practices-based document, called ISO standard (ISO 21795) Mine Closure and Reclamation Planning.
“The hope in developing the standard was that it could move governments and mining companies alike towards the kind of consistency and quality in planning for mine closure and reclamation globally that can bolster sustainability, environmental protection and local economies and communities that depend on mining,” said van Zyl.
Michael Nahir, director of mining for engineering firm Parsons Corporation, served as the project manager for ISO 21795. “The whole premise of the document, frankly, is early, highquality planning so that there’s not a lot of mystery by the time you’re actually doing the physical work of closing,” said Nahir. “It’s not prescriptive; it’s very objective-based and would support the whole mining life cycle for all aspects of the mine. Whereas other standards look at the specific parts, this standard takes a holistic approach and covers all the ESG [environmental, social and governance].”
The standard also covers the importance of integrating that early planning—including post-closure socio-economic transition—into mine planning.
The reality is that not all mining projects are planning early for closure, let alone reclamation and post-closure socio-economic transition. In late 2019 and early 2020, the Intergovernmental Forum on Mining, Minerals, Metals and Sustainable Development (IGF) surveyed its 84 country members to assess their readiness for mine closure. It found that only 76 per cent of countries have a formal legal requirement for industry to submit a mine closure plan as part of mine development. Among these, the rigour and scrutiny required in the closure plans varies largely.
Mine closure planning is still treated as a separate process from mining operations. In Canada, mine closure plans are typically prepared by consultants who specialize in mine closure and remediation. These plans are then updated every five years and are reviewed by the regulator for approval until the mine reaches its end-of-life phase.
When it comes to socio-economic transition, the inconsistencies are even more pronounced. The IGF found that 41 per cent of jurisdictions it surveyed have no requirements at all for planning and consideration of social transition and community impacts. Even in Canada, when it comes to post-closure social or economic impacts, regulations across the provinces and territories remain vague.
“Today, [mining companies] do need to actually think about what [their] responsibilities and liabilities are post-closure, and come up with some plans around that,” said Arn Keeling, who heads Memorial University’s department of geography and whose research focuses on the historical and contemporary encounters of Indigenous communities in Northern Canada with large-scale resource developments.
But, he said, most of the regulatory guidelines and requirements in Canada for socio-economic transition are inadequate and full of gaps. “There are still questions over whose responsibility it is,” he said. “There’s some level of responsibility on the company and probably risk. There are definitely responsibilities on governments, at different levels, ranging from municipalities right up to provincial and territorial governments to initiate and deal with some of that planning. Post-closure socio-economic impact considerations lag behind the kind of technical advances in reclamation and restoration we’ve seen in the industry.”
However, ESG issues keep many mining executives up at night. A global survey of 150 mining executives by EY in October 2023 found that most respondents ranked ESG as the biggest risk to their business. The report that accompanied the survey results attributed this to increased scrutiny from all stakeholders, particularly investors.
Research by global sustainability consultancy ERM backed up the executives’ concern. “ESG is critical,” said Nicola Lower, the company’s lead for North America’s mining and metals division. “With the need for critical minerals for the energy transition, now more than ever, the business case is becoming a lot clearer for folks. We’re conducting research looking at the cause of delay for critical minerals projects; so far, our research has shown that globally between 2017 and 2023, almost 60 per cent of projects reported pre-production delays ranging from a few months to several years.”
The ERM research found that the biggest cause of delay to critical minerals projects was permitting issues at the development stage, caused primarily by stakeholder opposition and concerns
around the projects’ environmental impacts. “If you translate that into the financial impacts, our research has shown that a mining project with capital expenditure of between US$3 billion to US$5 billion will suffer at roughly US$20 million per week in terms of net present value from delayed production,” said Lower. “Essentially, there is a cost to not doing the right thing.”
Today, some mining companies might be more focused on getting buy-in for a new project and even building a leadingedge sustainable operation than closing a mine, but the reputational risk of treating closure as an afterthought is more significant than ever.
“If you’ve just left a particularly dirty mine, the local community is not going to want to work with you ever again,” said Tom Rogers, associate director of professional services company Turner & Townsend Canada. “Your reputation has been harmed in their eyes. And with globalization and globalized press, suddenly, it’s very quick and very easy for your company’s reputation to be damaged globally. That will impact you getting future rights to a strike, [and] investor groups might be less interested in working with you.”
As global awareness of social and environmental impacts continues to grow, governments are likely to face mounting pressure to implement stricter ESG and closure regulations. That means that companies embarking on a new mining project need to “understand upfront that at the time of closure, there could be a regulatory expectation that you [would] use very high design parameters with very strict criteria to look at the longterm impacts,” said van Zyl. “That really puts you on notice that you should design and operate so that you can actually reach those high expectations for the closure period.”
As it is, experts such as van Zyl and Nahir said closure costs are notorious for spiralling out of control.
“Ultimately, if you look at what it can cost to close a big mine, it is in the billions,” said van Zyl. “If people talk about closing a big mine for less than a billion dollars, then they’re going to be very surprised because that doesn’t happen.”
However, by planning upfront for closure, mining projects can mitigate those risks.
Integrated mine planning, which emerged about a decade ago, is the next step in the mining industry’s evolution towards sustainability. “It is important to realize that a mining project is really a temporary land use,” said Denise Chapman, vice-president of Canada-headquartered Okane Consultants, a company specialized in integrated mine closure and relinquishment solutions.
“The objective of integrated closure planning is to take that recognition, and combine it with expertise and strategic mine planning, and then work together to identify some solutions to make sure that we’re providing adequate designs, and that the designs and the plans that we’re proposing are not underfunded in the long term. It is integrated mine planning and closure planning using interdisciplinary teams that work towards one fully integrated life-of-mine plan.”
That vision, said Scott Laberge, a Calgary-based geo-environmental engineer with Barr Engineering and Environmental Science Canada Ltd., needs to incorporate the site’s postreclamation physical and chemical stability and aim for any project component that remains after closure to not require long-term active care, as this tends to be a liability.
“What’s challenging is that those can sometimes be in conflict with each other,” said Laberge. “Something that will allow chemical stability might challenge the objective for physical stability. As well, every single closure project is entirely unique. There are learnings we take from different places, but every site is different because of the communities impacted, the geography, the regulations, the processing method and the mining type. All of this influences what might be required for closure.”
For this reason, the multidisciplinary teams working on an integrated mine plan will differ from project to project. The teams may include not just conventional mining expertise but also a wide array of subject-matter expertise including biodiversity experts, social performance experts, human rights experts and supply chain experts. “Really, you need to think about the whole value chain, not just the raw materials and how we extract them,” said Lower.
One area that has been overlooked in conventional mine closure planning is professional logistics expertise, according to Rogers, who thinks that the mining industry would particularly benefit from professionals with military logistics training. “The nice thing about military logistics is there’s an awful lot of doctrine and supporting information to help the practitioner, whereas less of that exists in the mine closure space,” he explained. “The earlier that you can bring in professional logistics, and you start to plan for professional logistics, the more benefits you will reap.”
The key reason integrated mine planning for closure, reclamation and post-closure is gaining traction in the mining industry is because it is pro-active and iterative—which means it opens up opportunities to improve and demonstrate an operation’s ESG performance throughout the mine’s life cycle. For
example, by identifying opportunities for progressive reclamation—which involves reclaiming disturbed areas in phases as mining progresses—an operation can not just reduce its footprint on an ongoing basis, but also build trust with the local community by giving it concrete examples of the company’s commitment to sustainability.
Integrating the socio-economic benefits and well-being for communities and workers “is the next frontier,” said Keeling, who was on the advisory panel for a report published by the Canadian Standards Association in 2022 called “SocioEconomic Transition for Mine Closure in Canada—Investigating Standards-based Solutions.”
Among the report’s key findings was that currently, “socioeconomic transition is not considered early enough in the minelife planning cycle to allow for the time needed to plan, fund and build capacity or a community to transition to another economic sector or otherwise prepare for the social impacts of closure.”
It also pointed to a tendency among mining operations to lean on community relations teams to plan the socio-economic transition. With an integrated approach, the socio-economic plans bring together the perspectives of all stakeholders, including workers and communities, with professionals such as workforce transition experts and regional economic or community planners.
“The first step is developing a clear vision with stakeholders, Indigenous rights holders and operations of what the future could look like at the end of a mine’s operating life,” said Chapman. “Creating that vision for the future will help determine the starting point on the roadmap of how to get there.”
Community perspectives throughout the mine planning can also add value to the future vision for the land and socioeconomic plans for the community.
“I think we’ve evolved from just socio-economic benefits to what does [creating] a new shared value look like?” said Lower. “Are there more effective ownership models, even through
[mine] development, but particularly into post-closure? Because mining often has a finite life cycle and lifespan, so what does the shared value look like when you consider post-closure and not just returning land to vegetation? What does it look like for opportunities for rights holders or for the local communities to repurpose these assets under new ownership?”
There are many benefits to including the perspectives of all stakeholders from day one to minimize the negative socioeconomic impacts and maximize the positive ones throughout the mine and post-closure—or in the case of a downturn in the mining cycle that leads to a project being put in care and maintenance. It builds trust and flexibility, according to Keeling. “It is increasingly widely recognized that the earlier you think about the back end, the more you’re ready for it,” he said. “The back end can come at you pretty quickly. This gives you an adaptive management plan.”
Professionals working in the field of closure and integrated mine planning express excitement for a future of mining in which communities and the public will think of the many successful closed projects instead of the abandoned mines and failed tailings storage facilities.
“The reality is that mining is a business, and mining provides essential materials that benefit the economy in the local region as well as the wider one,” said Laberge. “It is really hard to quantify the gains [of] a social licence to operate in terms of something on a spreadsheet. What it really means is trust in the community and the potential ability to open other mine sites.
“If an operator can go to a local community, to a regulator and to governments and show ‘this is what we are doing at sites already,’ it just builds your credibility and builds that trust so that they’re more likely to want you to be in the community to open the mine and do so responsibly.” CIM
Mining at the McClean Lake uranium mine in Saskatchewan, which has been suspended since 2009, will restart in 2025 using technology developed to extract high-grade ore from small ore bodies
By Trish SaywellAfter spending 15 years and more than $100 million on research and development, partners Orano Canada Inc. and Denison Mines have built mining equipment that is deployed from surface to extract high-grade uranium ore. They plan to use it to restart mining operations at their McClean Lake property in northern Saskatchewan; Orano owns a 77.5 per cent stake and is the operator of the McClean Lake Joint Venture (MLJV), while Denison owns 22.5 per cent.
Restarting uranium production at McClean Lake is a major milestone. Mining operations at the site began in 1995
and the MLJV extracted ore from five open pits, producing approximately 50 million pounds on a 100 per cent basis, before operations were suspended in 2009 due to low uranium prices.
The McClean Lake mill shut down in 2010 after milling the remains of the stockpiled ore. However, when the Cigar Lake uranium mine—located 69 kilometres southwest of McClean Lake— came into production in 2014, the mill restarted operating as a toll miller of Cigar Lake feed. Orano has a 40.45 per cent participating interest in the Cigar Lake joint venture, with 54.55 per
cent owned by Cameco Corporation and the remaining five per cent stake owned by Tepco Resources Inc.
The new technology, called Surface Access Borehole Resource Extraction (SABRE), uses a high-pressure water jet placed at the bottom of a drill hole to excavate mining cavities. The cuttings are then airlifted to the surface, separated and stockpiled.
SABRE will give Orano and Denison access to relatively small high-grade ore bodies that are either not big enough or too deep to be conventionally mined economically.
“In the Athabasca Basin, you have a few monster ore bodies —Cigar Lake, McArthur River, Arrow—but you also have a significant number of high-grade deposits that become stranded assets because they are small,” Jim Corman, president and CEO of Orano Canada, told CIM Magazine
“At around 10 to 40 million pounds, they’re not insignificant, but the cost of developing them in northern Saskatchewan means to mine them conventionally as open pits or as underground mines is very costly.”
Consequently, these deposits remain in the ground until market conditions are good enough to support their development, “and even then,” Corman explained, “it’s often difficult to justify the expenditures and the environmental footprint associated with them.”
With SABRE, Denison and Orano are targeting production of about 800,000 pounds of uranium oxide (U3O8) at the McClean North deposit in 2025. They have also identified potential additional production of approximately three million pounds U3O8 from a combination of the McClean North and Caribou deposits from 2026 to 2030.
“The beauty of SABRE is you don’t need a 50 million pound deposit,” Corman said. “You can go after the smaller high-grade deposits of less than five million pounds, and we have lots of hits like that on the MLJV property where you can scale out a couple million pounds in a very small footprint and surgically extract the high-value ore one cavity at a time.”
The MLJV will start drilling some of the development holes at the McClean North deposit this summer, as part of a 2024 program with a budget of approximately $7 million, and plans to begin mining the first eight mining cavities next year.
“Orano had the vision to invest in a technology at a time when the uranium price was low and with that long-term view, we’ve come out now with a technology that can access ore bodies that aren’t the biggest or the best out there,” David Cates, Denison’s president and CEO, told CIM Magazine. “We are grateful to be partners with an industry leader like Orano, which has such a positive long-term view and a willingness to be innovative to make a difference for its business. We are now able to respond to higher prices in a much more nimble way and come back into production.”
The concept for SABRE started to evolve in early 2004 when Orano and Denison were re-thinking how to mine additional ore bodies on their MLJV property.
The root of the idea emerged long before, however, through problem solving by Cameco and Orano in the 1990s about how best to mine Cigar Lake. Mineral reserve grades at the site are over 100 times the world average for uranium deposits, but the sandstone host rock is water saturated, making water inflows and radiation exposures a significant challenge.
To deal with the poor ground conditions at Cigar Lake and radiation risk to workers from the high ore grade, the joint venture co-developed a ground freezing plan and a non-entry jet boring mining system. The method involved cutting ore cavities out with a high-pressure water jet. The jets were inserted from boreholes drilled upwards from production crosscuts located in competent ground below the ore body. The ore-bearing slurry was then contained and sent off to the plant for processing.
Orano and Denison believed they could flip the concept around at McClean Lake—instead of developing all the typical underground mine infrastructure, they would use the same jet boring concept to selectively mine, but from surface. Drills would need to be adapted and modified, and cuttings from the ore excavation brought to surface using a high-pressure airlift system.
“We ran a series of small-scale tests to advance our understanding of the technical challenges,” Corman said. “Encouraged by the success we saw with the start of jet boring at Cigar Lake in 2014, we redesigned our system and scaled up the water pressures and volumes needed to perform better at McClean Lake.”
Several design iterations of the technology followed, with the R&D project concluding in a multi-year test mining program that was completed in September 2021. The final stage of the test involved mining four cavities at McClean Lake and producing about 1,500 tonnes of ore ranging in grade from four to 11 per cent U3O8.
“It’s high-pressure water jetting and airlift so the concept is not unique, but the design of the mining pipe was quite complicated. To get all of these various functions to happen with one mining tool, and the pressures and volumes, you need to run in the sweet spot for productivity rates,” said Corman. “Those are all the things we’ve learned over the decades of testing to this point—the nuances and pressures and details. That took a lot of effort and time to develop.”
Although high-grade uranium ore is very dense, tests of SABRE so far have shown the equipment can excavate and lift ore-bearing slurry from a depth of 200 metres, and Corman believes that with more fine-tuning and modification, they could go deeper.
SABRE currently involves using two rigs—one to gain access with a larger diameter drill, and then a second rig, which supports the introduction of the mining tool that does the actual mining. The mining tool has a number of internal conductors that supply high-pressure water for jet boring, as well as an air injection line that changes the density of the water in the mined cavity that lifts the ore-bearing slurry to surface through an internal slurry return line.
Once at surface, liquid-solid separation takes place to separate the ore from the water, and then the water is recycled back into the ground to cut more ore.
“Once a cavity is mined out, it is filled with concrete, effectively decommissioning it as we go,” Corman said. There are no legacy waste rock piles, open excavations or impacts on groundwater.
Corman noted that the environmental footprint of SABRE is a fraction of conventional mining. Greenhouse gas emissions are orders of magnitude less than open-pit mining that has diesel emissions from shovels, loaders and trucks, he said, and are also far less than conventional underground mining,
because it can be done with small, all-electric equipment with no need for underground heating and ventilation burning large amounts of propane.
“We expect that it can be a fairly straightforward, shorter environmental impact assessment process,” Corman said. “You don’t need all the development work underground or pre-stripping of a pit, so time and capital expenditures to first production are a fraction of what a conventional mine would take.”
The capital outlay is also quite small in comparison, he added, noting that the MLJV is continuously doing trade-off assessments with underground and open-pit mining. “On a cost per pound basis, it’s very competitive and—in many cases— lower than conventional mines,” said Corman. “When you add in the environmental benefits and the speed with which we can move from a conceptual project to a producing operation, it’s all a bit of a game-changer for us.”
Mining with SABRE will also provide more feed to the McClean Lake mill, which has a capacity of 24 million pounds a year and is currently processing about 18 million pounds a year by toll milling feed from Cigar Lake.
The SABRE methodology also will not require large crews and is more of a drilling challenge than a mining challenge, Corman said. “We will need drilling expertise, and skilled drillers which are in high demand, so we have to do our work to attract and maintain the workforce,” he said, noting using SABRE might require hiring about 40 additional positions, many of them from local northern communities.
Nuclear energy is at an inflection point
The urgent need to slow climate change with carbon-free sources of electricity is driving a renaissance in nuclear energy and the uranium industry. At the recent United Nations Climate Change Conference (COP28) that was held in Dubai in late 2023, 22 countries pledged to triple their current nuclear energy output by 2050.
“We’ve been through cycles in the past where there were spikes [of uranium demand], but they were driven by different fundamentals than what we see now,” Corman said. “Today we see an enduring, sustainable demand and a growing gap between production and demand. We have estimates that there could be up to two billion pounds of uncovered demand over the course of the next 20 years.”
In February 2024, spot uranium prices hit US$102.25 per pound, which is about double the price of a year earlier. Spot uranium averaged US$100.25 per pound in January of this year, up from the January 2023 average of US$50.63 per pound, according to statistics published by Cameco. The last time prices were higher was in June 2007 when uranium hit a record of US$136 per pound.
“The change in the uranium market since 2021 has been fairly dramatic and it has made us that much more convinced to get going with the SABRE methodology,” Corman said. “SABRE really gives us the opportunity to augment the feed to the plant with other sources that will make a lot of sense in the current market conditions.” CIM
As equipment manufacturers embrace automation and data-driven decisionmaking, development drilling at underground mines is becoming safer, greener and more efficient
By Nathan MunnToday, automation is fundamentally transforming nearly every aspect of resource extraction, and development drilling is no exception. Artificial intelligence (AI), software automation and an increase in the use of machine-assisted human operations are rapidly changing the way underground mining projects are scoped, launched and completed, all with an eye to improving safety and increasing efficiency.
Unsurprisingly, major drilling equipment manufacturers are at the forefront of this real-time revolution. By embracing increased automation and other technologies—including fully electric battery-powered heavy equipment and digital training simulators, among other innovations—leading manufacturers are pushing the science of development drilling forward at a rapid pace.
Sweden-based Epiroc has incorporated automation into its Boomer series of smart development drills. “The Boomer M20 S and Boomer E20 S are Epiroc’s new generation of smart development rigs, designed to meet the evolving needs of our customers,” said Ann-Sofie Andersson, global manager for brand and communications at Epiroc. “With a high focus on safety and productivity, these rigs are the enabler for our customers’ automation journey.”
To support development activities, Boomer rigs are equipped with features including digital drill plans, auto-levelling and setup assist, which help to simplify the rig positioning process for operators. The Boomer M20 S and Boomer E20 S are compatible with Epiroc scanner technology, allowing for efficient rig navigation and the generation of detailed mine scans for
progress and quality monitoring. The Boomer M20 SG and Boomer E20 SG rig models are also equipped with a batterypowered electric driveline.
In addition, the Boomer rigs feature a comfortable working area for operators. “The cab is designed with operator work environment as top priority, and to help keep the operator alert throughout the shift with an ergonomic and modern operator panel,” Andersson explained. “No hydraulics are connected to the cab, resulting in a low sound level of 65 decibels.”
Epiroc’s Boomer series of rigs are equipped with automation features; its Boomer M20 S and Boomer E20 S models include Epiroc’s proprietary autonomous drilling functionality ABC (Advanced Boom Control) Total, and can be operated teleremotely with high resolution PTZ (pan-tilt-zoom) cameras.
“The Boomer M20 S features the BUT M Pro boom, [which is] a robust boom with very high precision,” Andersson explained. “However, the unique feature is the internal hydraulics. There are no external hydraulic hoses on the boom telescope. This lack of external hoses maximizes rig availability and uptime.”
In the design of the Boomer M20 S, the hydraulics are routed to the front end of the boom and rock drill through four telescopic hydraulic pipes inside the boom telescope cylinder. This feature ensures time is spent drilling, not changing hydraulic hoses.
Epiroc has also invested significantly in digital simulation for development drilling, specifically in the creation of digital models of mines to move development activities forward quickly. “Together with Boliden, Örebro University and Algoryx, we are working on how to build digital twins to speed up development,” said Andersson. “AI and machine
learning is utilized to support the operator in adapting drill plans, to navigate the rig and to improve the ability of the autonomous drilling.”
Global engineering firm Sandvik, which is also headquartered in Sweden, is also integrating automation across its product line. A major innovation is the AutoMine Concept Underground Drill, a fully autonomous, twin-boom development rig capable of drilling without human interaction, which the company unveiled at a customer event in September 2022. Operating without a cabin, this battery-electric drill can “plan and execute an entire drilling cycle from tramming to the face, setting up for drilling, drilling the pattern and returning to base to recharge for the next cycle,” said Emily Neil, marketing manager for underground drilling at Sandvik.
Sandvik also offers scalable automation packages to enable 24/7 development drilling for select jumbo rigs, providing flexibility for customers to choose which automation features to incorporate with their operations. The company has long been developing battery-powered solutions for the sector; Sandvik said that the battery-powered electric DD422iE, which it launched at MINExpo 2016, was the first battery electric underground drill from any manufacturer in the industry.
“The DD422iE rig is designed to remove emissions while tramming,” said Neil. “It reduces noise, thermal load and requirements for ventilation capacity, making the underground working environment safer for the teams in operation.”
Sandvik also supports enhanced drill and blast planning with iSURE, an application that generates detailed data about the
mining process, and the Sandvik DrillConnect app. Together, these two programs provide customers with data and process guidance to help them optimize the drilling and blasting cycle.
The company has also released advanced controls for specific drill rigs in recent years. “The introduction of the Dual Controls package for Sandvik rig models DD422i and DD422iE has been a popular option in Australia and Canada, particularly for mining contractors, offering a more advanced and multipurpose solution for boring, bolting and meshing,” Neil said.
In addition, Sandvik is committed to the use of digital simulation in development drilling. This includes using a digital simulation platform for training, where the company’s Digital Driller simulator allows operators to be trained and the entire drilling cycle optimized from a single digital environment, which the company said optimizes their transition to operating real equipment. According to Sandvik, Digital Driller behaves exactly like a real drill rig, using authentic controls and the same control system software that is installed on Sandvik equipment.
Other manufacturers are pursuing automation and digital optimization in several areas of development drilling. Heavy vehicle manufacturer Komatsu offers a full suite of smart mining solutions, including high-precision navigational guidance systems, tele-remote drilling operations, drill automation and
in-depth data analytics. Together, Komatsu said that these features support the company’s mission to improve efficiency and safety during development drilling, while laying the foundation for greater environmental sustainability during mineral extraction.
Training and workforce development solutions provider Immersive Technologies is also playing a role in the advancement of simulation technology with its mining equipment simulators. Immersive Technologies works closely with mining operations and equipment manufacturers to solve real-world problems to improve safety, increase productivity and support the training and deployment of skilled personnel.
ThoroughTec Simulation is also a major player in underground drill rig simulators. The company’s CYBERMINE underground drill rig simulator range simulates the use of heavy equipment from major development drill manufacturers, including Epiroc and Sandvik.
Considering the investment major equipment manufacturers and other industry pioneers are placing in automation technologies, there is no doubt that automation in all its forms will continue to play an outsized role in the future of development drilling. As mining operators increasingly embrace advanced equipment, mineral extraction projects are positioned to deliver better outcomes across a range of indicators, including operator safety, process efficiency and sustainability. CIM
Outgoing CMP representative on CIM Council Stuart McTavish is ready to pass the torch
By Ashley Fish-RobertsonStuart McTavish, a longtime member of CIM and the Canadian Mineral Processors Society (CMP), has announced that he will be stepping down from his role as CMP Society CIM Council representative. McTavish, president of SF McTavish Consulting Inc., is a graduate of Queen’s University’s Engineering (BSc) in metallurgy and mineral processing. He first entered the mining industry after graduating in 1971, when he found work at Wabush Mines in Labrador.
In 1972, McTavish became involved with CIM. He credits several people and companies for urging him to join the institute and make use of its many opportunities. “The companies [I worked for] and my bosses were strongly encouraging me to get involved in the CIM, which I think is something we need to really encourage,” he said.
He named three influential figures who inspired him to join CIM. The first one being Tim Ebee, a colleague from Wabush Mines who was the mill superintendent at the time. “He was a strong supporter of CIM, so he tried to get as many people involved as possible,” McTavish recalled.
The second person was the late Klaus Konigsmann, who passed away in 2018. McTavish met Konigsmann when the two worked at Noranda’s Mattagami Lake mine. “Noranda as a company was a very strong supporter of CIM and CMP,” he said, reminiscing how Konigsmann would encourage McTavish to attend plenty of mining conferences and write papers to be considered for publication.
“The third person was my wife, who started paying my membership fees and didn’t let it lapse,” he chuckled. “That’s how I got to be a life member.”
Upon returning to his home of Waterloo in 2004, he officially joined CMP, where he later became involved with the society’s Southern Ontario (Toronto) Region branch, becoming the branch chair in 2005. Following this, he stayed on the CMP board, working as regional coordinator and director at large before he took on the most recent role of CIM Council repre-
sentative. He also provided mentoring services, and helped students form valuable connections within the industry.
He emphasized that Canada’s mining industry is relatively small and explained that if companies want people to get involved with the mining industry, they need to continue to encourage people to attend conferences and other events that promote learning, as well as networking within the mining community.
“There’s a lot of benefits. If you had to present a paper, you’d learn how to do it. If you went to the conferences, you’d get to know a lot of people and you would get a lot of knowledge out of it.”
McTavish remains involved with the CMP as a mentor and also represents CIM in the Global Action on Tailings, an initiative aimed at finding ways to reduce the amount of tailings produced.
“Stuart’s presence at CIM Council will definitely be missed,” said Angela Hamlyn, chief executive officer of CIM. “His enduring commitment, sharp eye and curious mind were invaluable in the work that our institute does.” CIM
CIM Toronto hosts
Student mine tour
May 3-10, 2024
Northeastern Ontario
Become a sponsor!
toronto-sponsorship@cim.org
May 12-15, 2024
Vancouver, BC
May 12-15, 2024
Vancouver, BC
CIM Vancouver hosts
CIM Luncheon
May 16, 2024
Vancouver, BC
May 22-25, 2024
Edmonton, AB
See our Calendar of Events:
L’actualité
Les progrès en matière de remblai minier
Lors de la conférence annuelle MINEXCHANGE de la Society for Mining, Metallurgy and Exploration (SME, la société des mines, de la métallurgie et de l’exploration), qui s’est tenue l’année dernière à Denver, dans le Colorado, les experts ont dialogué lors de la grande session de la journée d’ouverture sur des thèmes d’actualité, à savoir les principes environnementaux, sociaux et de gouvernance (ESG) et la décarbonation. Si l’un des conférenciers, qui représentait un exploitant minier, évoquait les contraintes que rencontrent les sociétés minières lorsqu’elles tentent de s’éloigner des combustibles fossiles, personne n’a réfuté l’argument selon lequel cet objectif était louable. La réponse à une question du public concernant le nombre grandissant d’États gouvernés par le parti républicain promulguant des lois anti-ESG accusait cette obstruction de manquer de perspicacité.
Comme le faisait remarquer Silvia Pikal, cheffe de rubrique du CIM Magazine, dans son article SME panelists debate net-zero goals (voir p. 30, uniquement en anglais) couvrant l’événement, l’édition de cette année de la rencontre phare de notre filiale à Phoenix, en Arizona, adoptait un tout autre ton. Les organisateurs de l’événement avaient confié l’encadrement du débat d’experts à un auteur et commentateur ayant bâti sa carrière sur une réputation d’anticonformiste vantant l’obligation morale d’un usage non restrictif des combustibles fossiles. Ce dernier soutenait que les combustibles fossiles sont à l’origine de la vie moderne dans le monde développé. Seuls les combustibles fossiles peuvent offrir une qualité de vie proche de celle à laquelle aspire la majorité des habitants de la planète, lesquels ne peuvent que rêver du mode de vie confortable que nous tenons pour acquis. Selon lui, les risques liés à l’élimination des combustibles fossiles sont bien supérieurs aux risques de continuer à les utiliser sans relâche.
Ce message, relayé sur la scène d’une grande conférence du secteur minier, arrive à un moment où les investisseurs, et particulièrement les investisseurs américains, continuent de puiser leur argent dans des fonds axés sur les principes ESG, dont l’objectif fondamental est de réduire les émissions de CO2. J’ai entendu certaines personnes porter ces affirmations aux nues comme une confirmation que l’investissement dans les principes ESG n’était rien d’autre que du marketing.
Certes, les exemples d’écoblanchiment ne manquent pas dans un contexte où les sociétés, qui cherchent à s’adapter à un marché très tendu, ont trompé les investisseurs concernant leur engagement vis-à-vis des pratiques durables. La grande majorité des agences de notation et des indices de durabilité qui ont vu le jour pour prodiguer des conseils ont généré plus de bruit qu’ils n’ont apporté de clarté.
Toutefois, accepter l’argument présenté à MINEXCHANGE, selon lequel il est ridicule d’essayer d’améliorer nos pratiques, ne servira pas l’intérêt de l’industrie minière. Fondamentalement, il suggère que l’ingéniosité humaine ne nous mènera pas bien loin. Je suis prêt à prendre parti pour l’autre face de ce pari. Toutefois, plus spécifique à cette industrie, cet argument fait fi de la réalité : si les investisseurs et les promoteurs de projets ne tiennent pas compte des risques environnementaux et sociaux inhérents à l’industrie minière, notamment au Canada et aux États-Unis, cela veut dire que leurs projets ne verront pas le jour.
Je suis ravi de vous annoncer que les débats prévus dans le cadre du congrès CIM Connect, qui se tiendra en mai à Vancouver sur le thème La marque canadienne : un avantage décisif, s’intéresseront à cette réalité.
Ryan Bergen, Rédacteur en chef editor@cim.orgL’année vient à peine de commencer, mais le calendrier des événements du secteur minier pour 2024 est déjà bien entamé. L’AME BC Roundup (le tour d’horizon sur l’exploration minière de l’association minière du Canada) a déjà eu lieu à Vancouver, de même que le congrès de la Prospectors and Developers Association of Canada (PDAC, l’association canadienne des prospecteurs et entrepreneurs) à Toronto, où les sociétés d’exploration les plus reconnues et les plus brillantes se sont réunies et ont présenté leurs projets en perspective. Ce n’est pas simple d’être une société en phase de prospection. Cela fait d’ailleurs un moment que c’est compliqué, c’est pourquoi j’applaudis leur ténacité. N’oublions pas que l’exploration est le moteur de notre industrie. J’ai la chance de travailler dans une société qui s’est propulsée aux rangs des grands producteurs. Pourtant, en 2007 (et ce n’est pas si vieux), B2Gold était une société en phase de prospection. Nous ne l’oublions pas. Chapeau à toutes les sociétés qui ne baissent pas les bras. Poursuivez vos efforts.
La 56e conférence annuelle des Minéralurgistes du Canada, qui s’est tenue à Ottawa à la mi-janvier, était un autre événement important pour l’industrie. De nouveau, je félicite l’équipe de direction dévouée de la société canadienne du traitement des minerais (SCTM) ainsi que les bénévoles, qui font de cette conférence un tel succès chaque année. Stuart McTavish mérite une mention spéciale (voir p. 63, uniquement
en anglais). Personne ne connaît son âge exact, et il nous faudrait sans doute consulter des registres géologiques pour en être certains. Toutefois, tout le monde croit que Stuart était présent au tout début du CMP. C’est un membre loyal de cette société technique ainsi que du conseil de l’ICM, depuis de longues années. Merci, M. McTavish, pour votre service et votre dévouement.
La dernière réunion d’experts de la conférence CMP portait sur les sources d’énergie renouvelables. Nous remercions Scott Martin d’avoir présidé ce débat exceptionnel. Je suis parti rempli d’optimisme. Toutes les sociétés minières doivent axer leurs priorités sur les sources d’énergie qu’elles utilisent pour que leurs activités émettent moins de gaz à effet de serre (GES). Tous les conférenciers étaient d’accord sur un point : si les sociétés veulent atteindre leurs objectifs en matière d’émissions de GES, elles devront accorder une attention continue à l’innovation et à la collaboration entre les parties prenantes. Toutefois, le partage d’informations, de nouvelles technologies et de pratiques exemplaires exige des rencontres suivies. Quelle meilleure plateforme que le congrès CIM Connect pour poursuivre la conversation, cette année et dans les années à venir ? Vous voyez où je veux en venir.
Je suis aussi très optimiste quant à la direction que prend l’ICM. En tant qu’organisation, l’ICM a beaucoup évolué ces dernières années. L’institut s’est doté des capacités informatiques et de l’infrastructure nécessaires pour soutenir ses membres, le nombre de membres individuels et corporatifs a augmenté. En outre, il a créé et partagé une image bien plus positive des actions menées dans le cadre des événements de nos sections, de nos sociétés et du bureau national.
Cette note du président sera ma dernière à paraître dans le CIM Magazine, avant qu’Ian Pearce ne prenne le relais en mai en tant que président de l’ICM pour l’année 2024-2025. Je tiens à vous remercier, toutes et tous, de m’avoir donné la possibilité d’être votre président cette année. J’ai été très heureux de rencontrer nombre d’entre vous lors de mes déplacements, et d’en apprendre davantage sur toutes les actions exceptionnelles que vous menez dans le cadre de la communauté Un ICM pour tous. Poursuivez l’excellent travail que vous faites.
Un séminaire web organisé le 25 janvier dernier par le comité consultatif pour la diversité et l’inclusion (CCDI) de l’ICM, au Canada, indiquait que les nouveaux arrivants hautement qualifiés et possédant des compétences polyvalentes intéressantes pour les employeurs du secteur minier se heurtent toujours à de nombreux obstacles pour pénétrer le marché du travail, et ont besoin d’aide pour s’intégrer.
Des experts du conseil des ressources humaines de l’industrie minière (RHiM) et de l’Immigrant Employment Council of British Columbia (IECBC, le conseil de l’emploi des immigrants de la ColombieBritannique) ont donné un aperçu des aides dont peuvent bénéficier les employeurs. Elles pourraient contribuer à stimuler l’embauche de nouveaux arrivants et à faire face à la pénurie de maind’œuvre dans l’industrie.
La représentation des immigrants dans le secteur minier
Les experts du RHiM se sont appuyés sur un nouveau rapport de leur organisation, intitulé « Soutien à l’intégration des nouveaux arrivants dans le secteur minier canadien : une analyse contextuelle ». Ce dernier offre un aperçu des difficultés auxquelles sont confrontés les nouveaux arrivants et présente les différents programmes, ressources et aides à disposition des employeurs qui cherchent à les embaucher.
D’après Victoria Burnie, gestionnaire du département Équité, diversité et inclusion au RHiM, si la population d’immigrants au Canada augmente plus rapidement que le reste de la population, les immigrants restent sous-représentés dans le secteur minier.
En s’appuyant sur des données recueillies à partir d’une enquête sur la population active réalisée par Statistique Canada entre janvier 2007 et septembre 2023, Mme Burnie indiquait qu’en 2023, les immigrants représentaient seulement 13,3 % de la main-d’œuvre dans le secteur minier, alors qu’ils représentaient 31,5 % de la main-d’œuvre tous
La mine de Nickel Rim South de Glencore Canada, qui fait partie du complexe Sudbury Integrated Nickel Operations. Le programme pilote d’immigration dans les communautés rurales et du Nord, une initiative fédérale, vise à faire venir des travailleurs étrangers dans des communautés telles que Sudbury qui sont sujettes aux pénuries de main-d’œuvre.
secteurs confondus. La représentation des immigrants dans tous les secteurs a augmenté durant la période où les données ont été collectées, alors qu’elle est restée relativement inchangée dans le secteur minier, ajoutait-elle.
« Contrairement aux femmes dans le secteur minier, où l’on observe quelques éléments prometteurs, notamment dans les domaines des ressources humaines et de la finance, les immigrants sont globalement sous-représentés lorsque l’on s’intéresse à des professions particulières », indiquait-elle.
À titre d’exemple, dans la catégorie des professionnels des sciences physiques, la représentation des immigrants tous secteurs confondus est de 42 %, par rapport au secteur minier où ils ne sont que 23 %.
« Pour les immigrants, il s’agit d’un problème lié à l’industrie minière », indiquait-elle. « Les immigrants ne choisissent pas le secteur minier, ou c’est le secteur minier qui ne choisit pas les immigrants durant la phase de concurrence sur le marché du travail. »
Les difficultés pour les nouveaux arrivants
Mme Burnie décrivait les nombreux obstacles qui empêchent les nouveaux arrivants d’intégrer le marché du travail au Canada.
« Comprendre et s’adapter à la culture du marché du travail local peut s’avérer difficile pour les nouveaux arrivants », expliquait-elle. « Par exemple, les attentes en matière de modes de communication et de normes professionnelles peuvent varier d’un pays à l’autre. »
Parmi les autres difficultés qu’ils peuvent rencontrer, citons la création de réseaux professionnels sans points de contact locaux, la reconnaissance des diplômes étrangers au Canada, ainsi que le manque de connaissances du marché du travail local qui pourrait rendre difficile pour les nouveaux arrivants de comprendre les tendances de l’emploi au Canada et de savoir où chercher des offres d’emploi.
De plus, les nouveaux arrivants peuvent avoir une connaissance limitée des
services d’aide disponibles, tels que l’orientation professionnelle, les programmes de mentorat et les services de placement. Ils peuvent également ne pas
« Les immigrants ne choisissent pas le secteur minier, ou c’est le secteur minier qui ne choisit pas les immigrants durant la phase de concurrence sur le marché du travail. »
– Victoria Burnie, RHiM
avoir connaissance des pratiques d’embauche locales et du format attendu des curriculum vitæ lorsqu’ils cherchent un emploi. Arrivés à l’étape de l’entretien, ils peuvent être confrontés à une discrimination ou à des préjugés raciaux, sur leur appartenance ethnique ou encore sur les différences culturelles ou linguistiques.
Enfin, les nouveaux arrivants dont la maîtrise de la langue locale est limitée éprouveront des difficultés à tous les niveaux, des entretiens d’embauche aux interactions quotidiennes avec les collègues une fois qu’ils sont au travail.
« Pour surmonter ces difficultés, il est souvent nécessaire de combiner l’adaptation culturelle, l’amélioration de la langue, les efforts de mise en réseau et l’accès aux services de soutien », expliquait Mme Burnie. « Les employeurs et les communautés jouent un rôle essentiel pour faciliter l’intégration des nouveaux arrivants sur le marché du travail en leur fournissant des ressources et en créant des environnements inclusifs ».
Les aides à disposition des employeurs
Leslie Woolcott, directrice du département Équité, diversité et inclusion au RHiM, déclarait qu’il existe une multitude de ressources destinées à aider les employeurs pour le recrutement et l’embauche des nouveaux arrivants.
« Une partie du problème ou de la difficulté consiste à comprendre cet ensemble de programmes et à naviguer à travers les différents critères d’éligibilité, aussi bien pour les employeurs que pour les nouveaux arrivants », indiquaitelle. « Si peu de programmes ciblent spécifiquement l’industrie minière, la plupart des autres programmes peuvent
s’appliquer au secteur minier et sont pertinents. »
Elle citait notamment en exemple le programme d’immigration Entrée Express, qui propose une voie d’accès plus rapide à la résidence permanente pour les immigrants et qui inclut un volet destiné aux travailleurs qualifiés dans un métier spécialisé. Il existe également deux autres programmes, le programme d’immigration au Canada atlantique et le programme pilote d’immigration dans les communautés rurales et du Nord. Tous deux lancés en 2022, ils proposent un accès à la résidence permanente aux travailleurs étrangers qualifiés souhaitant vivre et travailler dans des communautés qui ont besoin d’attirer davantage de main-d’œuvre. Certaines des communautés éligibles au programme pilote d’immigration dans les communautés rurales et du Nord sont connues pour être des foyers d’activité minière. C’est notamment le cas de Sudbury, de Timmins et de la baie Thunder en Ontario.
Patrick MacKenzie, directeur général de l’IECBC, indiquait que les Immigrant
Employement Councils of Canada (IECC, les conseils pour l’emploi des immigrants du Canada) comptaient 12 organisations partenaires dans l’ensemble du pays qui aident les employeurs à recruter, à embaucher et à garder les immigrants dans des emplois qui valorisent au mieux leurs compétences. Parmi les services qu’ils proposent aux employeurs figurent des stratégies adaptées pour recruter des travailleurs immigrés, des formations en compétence culturelle, des programmes de mentorat et des initiatives visant à améliorer la diversité et l’inclusion sur le lieu de travail.
« Nous connaissons l’importance du secteur primaire et des industries extractives pour l’économie canadienne », déclarait-il. « Il faut sensibiliser davantage de nouveaux arrivants aux possibilités que leur offrent ces secteurs. »
Le rapport du RHiM est disponible sur le site mihr.ca/resources en anglais et en français. Les ressources en ligne proposées par l’IECC pour les employeurs sont disponibles sur le site iecc.network. ICM
DORIS HIAM-GALVEZ Conseillère principale, Hatch
GARY POXLEITNER Consultant principal (exploitation minière), SRK
HANI MITRI Professeur du département de génie minier, Université McGill
MUSTAFA KUMRAL Professeur agrégé du département du génie des mines et des matériaux, Université McGill
NANCY WILK Spécialiste de l’environnement, de la santé et sécurité (ESS), WSP Canada Inc.
PRITI WANJARA Chercheuse principale, Conseil national de recherches du Canada (CNRC)
ROY SLACK Directeur, Cementation Americas
Les mines souterraines qui utilisent un remblai en pâte cimenté pourraient réduire leur empreinte carbone en diminuant la quantité de ciment utilisée ou en la remplaçant par d’autres liants.
Réduire le bilan carbone du remblai en pâte cimenté permettra de diminuer les émissions de CO2 des exploitations minières souterraines
Par Lynn GreinerLa crise climatique menaçante et les fortes préoccupations environnementales qui en découlent incitent toutes les industries, secteur minier y compris, à réduire leur bilan carbone. Le remblai en pâte cimenté (RPC) est l’un des domaines dans lequel il est possible de considérablement réduire les émissions de dioxyde de carbone (CO2) dans les mines souterraines.
« Le remblai en pâte cimenté est un mélange de résidus miniers associé à de l’eau et du ciment en vue de créer une pâte qui sera aspirée, puis qui durcira et générera une force structurelle après avoir été déposée », expliquait Sara Arcila Gut, responsable du développement de l’entreprise à Sika Canada, une société créatrice de produits et substances chimiques spécialisés pour des applications industrielles, dont l’exploitation minière. « La composante du remblai en pâte cimenté réellement responsable du bilan carbone [élevé] est le ciment [tout usage]. »
La pâte ainsi formée est aspirée par une pompe dans les vides souterrains créés par l’excavation minière. Elle se solidifie et soutient donc la roche environnante tout en réduisant le risque d’affaissement de surface. Entre 2 % et 10 % du RPC contient du ciment tout usage, indiquait-elle. Environ 30 mines au Canada l’utilisent, cela représente donc une quantité considérable de ciment.
D’après Neea Heino, chercheuse et directrice de projet à la Geological Survey of Finland (GTK, la commission géologique de Finlande), la production de ciment est responsable de 5 % à 8 % des émissions mondiales de CO2 en raison des procédés de combustion chimique et thermique nécessaires. Mme Heino fait par-
tie du projet SETELIT qui étudie les manières de lier les résidus dans le remblai en pâte par le biais de méthodes neutres en carbone.
Par conséquent, en réduisant la quantité de ciment utilisée, ou en la remplaçant par d’autres agglomérants, les mines qui utilisent le RPC peuvent réduire leur bilan carbone.
Manières de réduire l’utilisation de ciment
Cette réduction peut être considérable et aider les sociétés minières ayant des exploitations souterraines à respecter leur engagement à éliminer leurs émissions de gaz à effet de serre (GES). Paul Deram, ingénieur des services techniques chez le prestataire de solutions en construction Lafarge Canada, indiquait qu’une exploitation minière qui utilise 200 000 tonnes de matériaux de remblai par an peut réduire de 7 000 tonnes ses émissions de CO2 en passant du ciment tout usage à un produit cimentaire (semblable au ciment) de substitution.
« Compte tenu du bilan carbone très élevé de la production de ciment, ainsi que des complexités de la chaîne d’approvisionnement pour atteindre les sites miniers, il est évident que le remblai en pâte cimenté est un processus à haute teneur en carbone », faisait-il remarquer. Il faisait par ailleurs remarquer que la déclaration environnementale de produits (DEP) moyenne au Canada pour le RPC indique un potentiel de réchauffement planétaire (PRP) de 850 kilogrammes d’équivalent CO2 par tonne.
Une stratégie efficace pour réduire le bilan carbone associé à l’utilisation de ciment dans le RPC consiste à utiliser d’autres
liants faits à partir de déchets provenant d’autres industries. Ils peuvent inclure des scories d’usines d’acier ou des cendres volantes de centrales à charbon. Mme Arcila Gut de Sika faisait remarquer que les ciments à plus faible bilan carbone permettent à la mine de réduire les émissions de CO2 connexes du ciment acheté, qui est déclaré dans les émissions de champ d’application 3 (les émissions indirectes qui interviennent dans la chaîne de valeur et qui échappent à l’autorité directe de la mine).
Toutefois, faisait-elle remarquer, la demande croissance de ces liants de substitution de la part de nombreuses mines dépasse l’offre disponible de ce déchet.
Certains fabricants de ciment remplacent aussi 10 % à 15 % du ciment par des fines calcaires. Selon Mme Arcila Gut, cela semble parfois avoir une incidence sur les propriétés du RPC, par exemple sur le temps de prise, et peut potentiellement mener à une réduction de la résistance à la compression uniaxiale (UCS, de l’anglais uniaxial compressive strength).
Des adjuvants du béton dans le RPC (des additifs qui modifient les propriétés de la pâte) peuvent sinon aider les mines à réduire la quantité de ciment qu’elles utilisent. Ceci présente plusieurs avantages : réduire les émissions de CO2 émanant de la consommation de ciment, augmenter la quantité de résidus entreposés sous terre, ce qui réduit l’effet sur l’environnement du stockage des résidus à la surface, accélérer le processus de coulage du béton, ce qui diminue le délai nécessaire pour combler les trous, et réduire la consommation d’eau des mines.
« En utilisant des adjuvants du béton, on peut réduire de 26 % la consommation de ciment de la mine. Pour moi, c’est une manière de dire que, pour obtenir un RPC durable, il faut optimiser l’utilisation du ciment [qui] émet les émissions les plus faibles », indiquait Mme Arcila Gut.
Toutefois, comment les adjuvants du béton peuvent-ils autant réduire le bilan carbone du RPC ? « En ajoutant une petite dose d’additifs, de 0,5 % à 2 % du poids du ciment, dans le mélange du RPC, la pâte devient bien plus fluidifiable. Ceci permet aux [mines] de réduire la quantité d’eau nécessaire et d’augmenter le contenu solide jusqu’à ce que la pâte arrive à sa consistance originelle fluidifiable. Avec l’adjuvant du béton, la pâte se comporte de la même manière. Toutefois, en raison de sa teneur en eau plus faible, elle est bien plus résistante. Cette approche nous permet donc de réduire progressivement la teneur en ciment jusqu’à ce que nous atteignions la résistance à la compression requise dès le début », expliquait Mme Arcila Gut.
Mme Heino ajoutait que l’utilisation du RPC à plus faible émission de carbone dans des mines souterraines a aussi des effets positifs à la surface, ce qui est en faveur de l’économie circulaire et de l’exploitation minière durable. « Sans remblai, les résidus sont éliminés en tant que déchets dans la zone réservée aux résidus, généralement une grande superficie. Si les résidus sont utilisés comme RPC qui se solidifie dans les structures souterraines, les effets pour l’environnement et le paysage à la surface [de la mine] sont moindres », expliquait-elle.
« Réduire l’utilisation des terres constitue une meilleure option pour la biodiversité. Les zones de stockage des résidus peuvent aussi créer une certaine résistance de la part des communautés, car les résidus endigués sont souvent considérés comme un risque de sécurité pour l’environnement et la communauté. Sans gestion compétente des déchets issus de l’extraction, ces zones peuvent réellement poser un risque à l’environnement. La diminution des incidences sur l’environne-
ment et le paysage [en utilisant le RPC] ainsi que la manipulation sans risques des résidus renforcera l’acceptabilité de l’exploitation minière. »
M. Deram indiquait que Lafarge collabore déjà avec plusieurs clients miniers pour identifier les meilleurs produits à utiliser dans leurs situations spécifiques, en gardant à l’esprit le bilan carbone, mais aussi les considérations logistiques, l’efficacité opérationnelle et les coûts. Nombreux sont ceux qui ont déjà adopté des produits affichant des bilans carbone inférieurs de 85 % au ciment tout usage.
L’industrie du ciment est également en faveur de la réduction du bilan carbone du ciment, à tout le moins en position de légitime défense. La World Cement Association (WCA, l’association internationale du ciment), un organisme indépendant à but non lucratif basé en Angleterre, s’efforce aussi de réduire le bilan carbone des produits de ses membres. On peut lire sur son site Internet que « la WCA est en faveur d’une industrie du ciment durable et encourage le développement technique et d’autres étapes pour atteindre la décarbonation totale. »
Après la Conférence des Nations unies sur le changement climatique de 2023 (COP28), qui s’est tenue à Dubaï fin 2023, le président de la WCA a publié une déclaration approuvant l’accord visant à promouvoir la production de ciment et de béton à faible émission de carbone signée lors de la conférence. « Il est devenu impératif de réagir face aux effets du changement climatique, aussi de nombreuses industries dans le monde reconnaissent que la transition vers une économie faible en carbone est la seule voie possible pour l’avenir », ajoutait-il. Les émissions de CO2 représentent 7 % des émissions mondiales. Ainsi, la réduction des émissions de dioxyde de carbone et le captage du CO2 constituent un enjeu majeur que l’industrie du ciment doit attaquer de front si elle envisage d’embrasser un développement écologique et durable.
M. Deram ajoutait que les fournisseurs doivent faire preuve d’initiative pour réduire le bilan carbone de l’industrie du ciment. « Proposer des produits à faible émission de CO2 n’est pas un simple engagement vis-à-vis de leur durabilité. C’est aussi une contribution directe aux objectifs environnementaux des utilisateurs finaux », indiquait-il. « Selon moi, c’est en introduisant le bilan carbone de ces produits comme facteur de décision dans le processus d’achat que l’on encouragera le changement. Cette évolution s’impose peu à peu dans beaucoup d’industries. »
Pour accélérer cette transition, le dialogue serait, selon lui, la réponse. « Nos industries doivent renforcer leurs échanges sur ce sujet », indiquait-il. « Si les industries minière et du ciment ont des ambitions agressives indépendantes de réduction du CO2 et prennent des mesures concrètes pour les réaliser, la possibilité de progrès effectifs accélérés est réellement importante si nous collaborons. »
Toutefois, l’amélioration de la technologie ne fait pas tout, faisait remarquer Mme Heino. « Les solutions pour un avenir plus durable requièrent également un changement culturel. Elles impliquent de changer nos habitudes de travail », indiquait-elle. « Pour qu’un changement s’opère dans les méthodes d’exploitation, les attitudes et la manière de penser des personnes doivent aussi évoluer. Chacun et chacune de nous est donc responsable de ses propres actions. Ensemble, nous pouvons provoquer le changement. » ICM
The origin stories of our industry are contained within the digital archives of the CIM Bulletin, the predecessor to CIM Magazine. In this issue, we examine the development of Sudbury as a Canadian nickel hub, which later became an example of how pollution-impacted lands can be reclaimed successfully
By Ailbhe GoodbodyThe Sudbury Basin was formed by a meteorite impact approximately 1.85 billion years ago, which made mineral-rich magmas rise from deeper in the earth to create the valuable mineral resource deposits in the region.
Robert C. Stanley [CIM Bulletin, July 1927] stated that the first authentic discovery of nickel in the Sudbury district was recorded about 1856. “Sudbury was at that time the terminus of the Canadian Pacific Railway, from which point construction was being pushed westward,” he said. “In the course of this work, a cutting was made which passed through an outcrop of copper ore that was later to be the Murray mine. Prospectors after copper immediately flocked into the surrounding country, and a very large number of claims were staked.”
H.F. Zurbrigg [CIM Bulletin, June 1948] pointed out that many of the conditions of the development of mining geology in the Sudbury district were unique. “The initial ore discovery was accidental. All the major mines were staked for copper,” he said. “Discovery of the nickel content was made in the metallurgical treatment, where it created difficulties, and for that reason and lack of a market, it was for a time regarded as a liability rather than an asset.”
E. Ozberk, W.G. Davenport and N. Gibson [CIM Bulletin, September 1983] stated that by the 1950s, “Canada produced more than ninety-five per cent of the noncommunist world’s nickel and achieved dominance in terms of production, technology and pricing policies.”
However, there were some negative environmental effects from Sudbury’s nickel boom. It is commonly said that the landscape around Sudbury half a century ago was comparable to the Moon’s landscape; this idea seems to date from the early 1970s, as crewmembers from NASA’s Apollo 16 and 17 missions underwent training in Sudbury.
However, Sudbury was chosen due to its meteorite crater, rather than its vegetation, and the astronauts’ geological training included the study of the area’s impact structures, breccia and shatter cones, which are similar to those found on the Moon.
Nevertheless, sulfur dioxide (SO2) emissions from smelting processes resulted in highly acidic soil and water in large areas around Sudbury. “No advance in process technology should ever again be put into practice without built-in environmental control,” said J. McCreedy [CIM Bulletin, July 1971]. “The mining industry is keenly aware of its responsibility, and I believe that environmental protection—pollution control, if you will—is going to be as critical a concern as cost in process planning and plant design. New mines and plants will have full provision for eliminating, treating or containing pollutants that affect plant and animal life, air, soil and water.”
Some of the early steps towards environmental improvement in the region included efforts to reduce air pollution from SO2 emissions. A.L. McKague, G.E. Norman
and J.F. Jackson [CIM Bulletin, June 1980] described the treatment of nickel-copper concentrate in a new smelter at Falconbridge Nickel Mines that was constructed in 1978. “The objective of the new process was to reduce the emission of SO2 and particulates to the atmosphere and to improve the working environment while maintaining smelter production levels and metal recoveries,” they said.
They noted that smelters throughout the world were visited to examine the various new technologies and equipment applications. “As a result of numerous studies, the best process to meet our objectives was concluded to comprise fluid-bed roasters, with the calcine treated in electric furnaces and the sulfur in the roaster gas fixed in an acid plant,” they explained.
M.C. Bell, J.A. Blanco, H. Davies and P. Garritsen [CIM Bulletin, January 1990] outlined the development of Inco’s SO2 Abatement Program. “By 1994, Inco Limited will lower sulfur dioxide emissions from the Copper Cliff smelter by 60 per cent to 265,000 tonnes/year, primarily through implementing two key process changes,” they wrote.
“The program in the mills will consolidate Inco’s three Sudbury area mills into one, while providing facilities for rejecting 67 per cent of the sulfur in the ore. In the smelter, this bold new program of flash smelting of bulk concentrate will implement the most energy efficient smelting process, and deliver 70 per cent of the remaining sulfur as very high strength SO2 gas uniquely suited to economic fixation. On completion, 90 per cent of the sulfur in the ore mined will be fixed. The acid plant has been oversized to provide for further decreases in emissions in the years ahead.”
As well as reducing environmental contaminants, reclamation work was already under way in the Sudbury region. T. H. Peters [CIM Bulletin, December 1978] summarized the Inco Metals Reclamation Program up to that point, which he said dated from the first phase of construction of Nickel Park at Copper Cliff in 1917. Some of the contemporary practices he discussed included growing vegetation on stressed areas, improving the aesthetic appearance of company properties and improving the workplace for employees.
“There is no doubt that the greatest impact of this work is in the public relations sector,” said Peters. “To those tourists and travellers programmed to the moonscape idea of Sudbury by the national media, the green sward which greets their eyes as they drive along the Trans-Canada Highway through the improvement area must bring them to question whether the reporters were objective in their observations.”
Peters explained that while trees were re-established in the area due to reforestation efforts in the 1960s and 1970s, other natural flora and fauna moved in too. “Various insects, grasshoppers, spittle bugs, ants and small
mammals (deer mice and voles) became the basis on which a new ecosystem for the area started to develop. Meadow birds attracted by the small insects became residents, and sparrow hawks, owls and marsh hawks, along with foxes, began to supply the predatory control of small mammals. Waterfowl and shorebirds began making stops during their spring and fall migrations and some even began to raise their broods in the area. This activity started a new line of thought in the development of a possible end use for this area,” he said.
In 1974, Inco decided to develop the tailings near Copper Cliff and the adjacent area as a Wildlife Management Area, and hired a wildlife biologist to design a development plan. “This is a long-term project, but I do feel that the Wildlife Management Area concept is the proper end use for this particular area,” said Peters.
In 1973, the City of Greater Sudbury established the Technical Tree Planting Committee, which consisted of volunteer members including representatives from Laurentian University, Inco, Falconbridge, the Ministry of Natural Resources and the Nickel District Conservation Authority. After five years of research and site-specific trials, the committee was renamed as the Vegetation Enhancement Technical Advisory Committee (VETAC) and its program of reclaiming industrially disturbed lands around Sudbury commenced in 1978.
The City of Greater Sudbury has received several awards for its regreening efforts, including the United Nations Local Government Honors Award at the 1992 Earth Summit in Rio de Janeiro, Brazil, and the United States Chevron Conservation Award in the same year. In 2022, Greater Sudbury marked the planting of the 10 millionth tree since the start of its regreening program in 1978. CIM
Throughout 2024, we will be looking back through the CIM archives for contemporary coverage of the discovery and development of major mineral deposits in Canada.
United. Inspired.
Boost productivity, enhance safety and cut emissions – all while lowering your total cost of operation.
NewLeopardTM DI650i down-the-holesurfacedrillrig offers long-termproductivityand superiorstability withrobustand reliablemain components – seamlessly integrated withstate-of -the-art technicalsolutions.Scalable automation, easymaintenance andoutstandingmovabilityarethefeatures that make LeopardTM DI650i apremiumproduct,which isan honortoown.
Leaveyour pawprintand enjoy thesmooth, efficientride.