
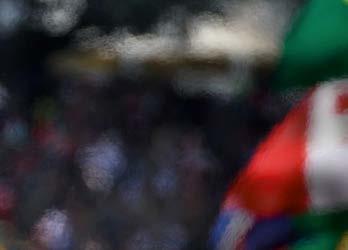
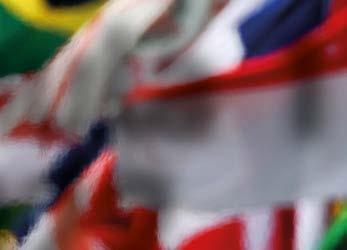
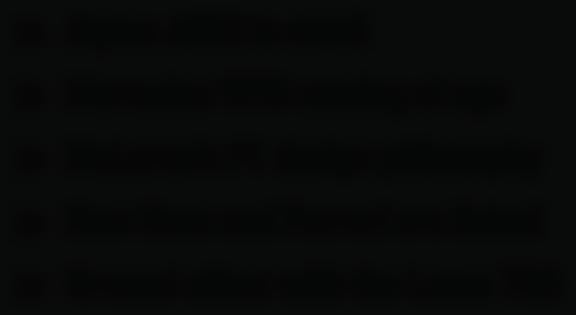
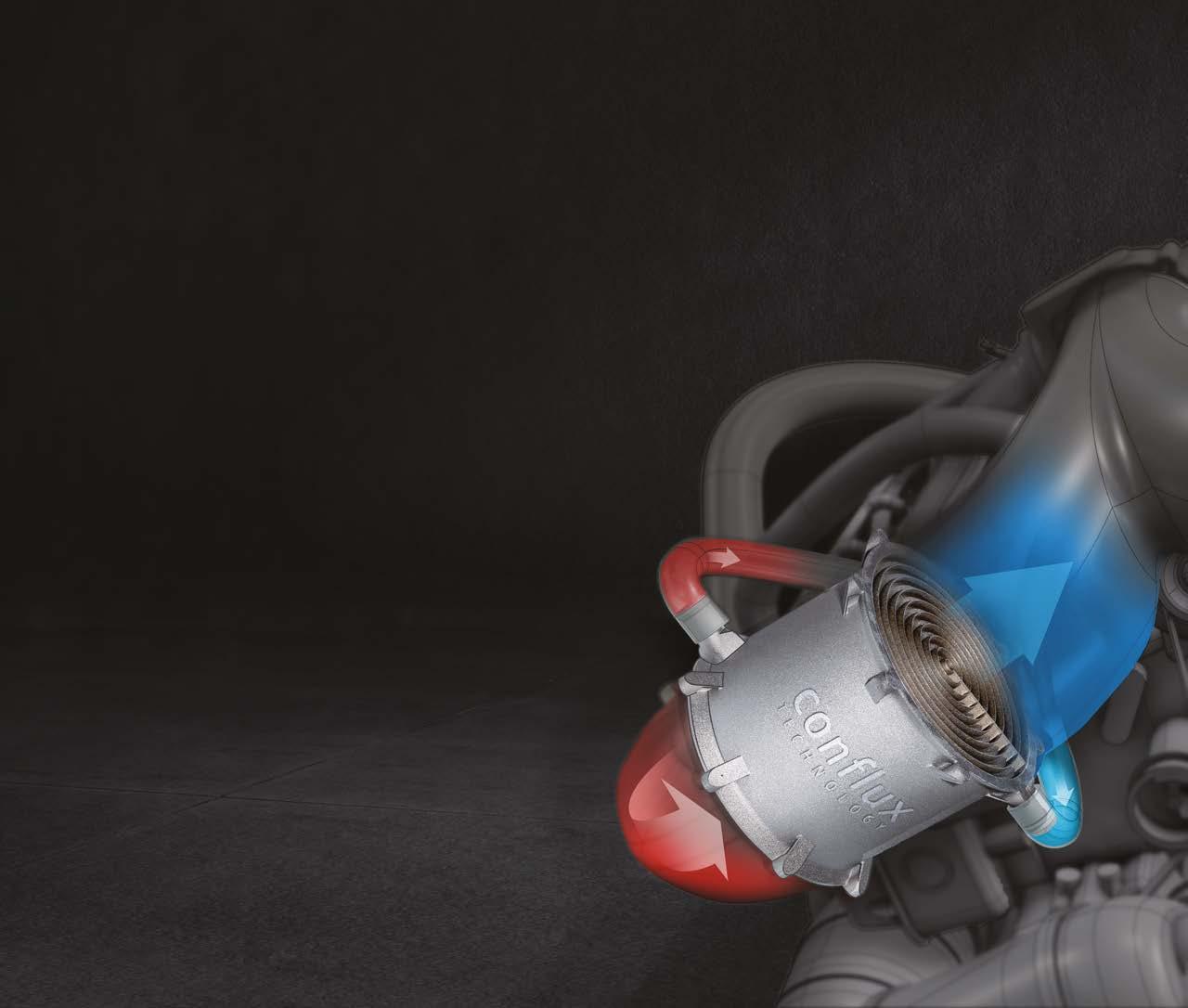

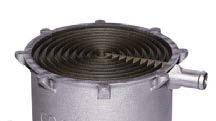
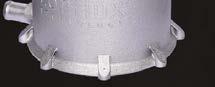
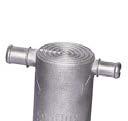
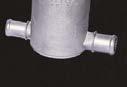
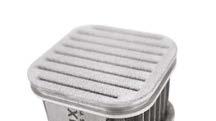
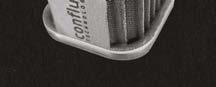
Formula 1 has been a rollercoaster for all the teams this year as they got to grips with the enormous changes to the technical regulations in one of the lengthiest and logistically complex Formula 1 seasons in history. With these changes, there has also been a mix-up in the field standings compared to the previous generation’s status quo.
Eight-time constructor champions Mercedes seemingly struggled to get to grips with the new instruments in the season’s early stages. At the same time, Ferrari started strong but began to lose position to its closest rivals as the season unfolded. Needless to say, the dominance of Red Bull has been akin to that of a Mercedes-esque manoeuvre coming into this new generation.
However, a dark cloud is hanging over the Red Bull Racing camp as it has been found to have breached the cost cap regulations for the 2021 season, the first year of its implementation.
Over the 2022 Mexican Grand Prix weekend, Formula 1 finally confirmed Red Bull’s penalty for breaking the budget cap in 2021; a $7 million fine and a 10% reduction of its aerodynamic testing allowance for the next 12 months.
The FIA adjusted the strength of the penalty given to Red Bull after its initial £1.8 million overspend was amended to just over £400,000 after a tax credit had been correctly applied.
The minor resulting penalty for the Milton Keynes outfit led many competitors to form the opinion that Red Bull has got away lightly, and that the integrity of Formula 1’s budget cap has been in jeopardy throughout this process. There are many critics of the outcome of Red Bull’s breach of the cost cap regulations, especially as a $7 million fine is minor for a company of Red Bull’s size. Moreover, it does not come out of its present or future cost cap; it must be settled separately. Reducing Red Bull’s budget cap in the future somehow wasn’t an option for the FIA under the terms of an accepted breach agreement.
The most significant damage to the team is in the aerodynamic testing element of the penalty, which has reduced the CFD and wind tunnel limit by 10%. This penalty is the equivalent of 1.5 finishing positions in the constructor’s championship associated with the diminishing testing scale as a function of the team’s place in the championship when wind tunnel allocations are determined.
Formula 1’s handicap system means successful teams have less aero testing than those that finished lower down. The team finishing last gets a 115% baseline allowance, dropping by 5% for each position until the winning constructor gets 70% of the nominal amount within their aerodynamic testing period, of which there are six per year, each lasting around eight weeks.
Because Red Bull has won the 2022 constructors championship, the development allowances would see them entitled to 70% of the baseline limit for 2023. This percentage amounts to 224 wind tunnel runs and 1400 CFD items per period. That is 16 fewer wind tunnel runs than the next highest-placed team and 32 fewer than the third. In CFD terms, it represents 100 fewer components versus the second and 200 fewer than the third. However, because Red Bull’s penalty for breaking the budget reduces this by 10% against what it was entitled to, it now has 63%. As such, this works out as a reduction of 22 wind tunnel runs and 140 CFD items per period, 38 fewer wind tunnel runs, and 240 fewer CFD runs during each period compared to the second-place team.
With the penalty added, second place is set to have around 15% more development than Red Bull, while third will have just over 20% more. Red Bull’s testing limitation is valid for 12 months from the execution of the accepted breach agreement, October 26 2022. The penalty will impact whatever development work Red Bull completes in the final part of 2022 and 2023 car development until the same date in October next year. Next year, it will have to balance wind tunnel and CFD allowance across the in-season development of next year’s car and 2024.
Red Bull indicates that the effect of the penalties on the team could be worth anywhere between 0.25 and 0.5 seconds of lap time. That’s not a game-changing amount, and other teams have voiced their desire for something much stricter for this breach. In light of the 2021 season being the drama that it was at the end of the season, the FIA and Formula 1 are not keen to start messing with the history books and this punishment is seen as fair in their eyes. Unlike many other sports where the boundaries are more precise, Formula 1 continues to prove to be one of the world’s most complex sports, business and technical exercises.
Stewart Mitchell, Deputy Editor, Racecar Engineering
Matt Harman, Technical Director at Alpine, details his team’s latest challenger, the A522 12 HAAS/FERRARI
Haas is contesting F1 in what it believes to be the most cost-effective manner. Here’s how its engineering is embedded with Ferrari 20
James key explains how his philosophy at McLaren hinges on the trackside operations
The most significant damage to the team is in the aerodynamic testing element of the
The Alpine F1 team is one of only a few complete ‘works’ constructors remaining in Formula 1 – meaning it produces both the chassis and power unit for its 2022 contender, the A522, as an official team of the car manufacturer, Alpine (Renault Group). Being a works team should mean less compromise on some design elements of the car and better systems integration of the power unit and the chassis. But how does it work in practice?
Matt Harman oversees Alpine’s technical group, and 2022 marks his first year in this role. Before becoming technical director, Harman spent half of his Formula 1 career to date designing power units and the other half developing chassis, making him well positioned to recognise the compromises and trade-offs needed to build a competitive car.
Racecar Engineering sat down with Harman at the British Grand Prix to find out a bit more about team operations and how the A522 was developed.
Harman says his philosophy as a technical director revolves around the harmony of systems, particularly in areas like powertrain integration.
‘In 2019, when we took the first pen to paper for the 2022 car, the initial intent of the project was to ensure we maintain maximum aerodynamic freedom’
Matt Harman, technical director at Alpine F1
‘Certain technical avenues on paper are faster because they improve the output in units of kilowatts but, once you’ve added up all the parasitic losses and considered driveability, we could end up with something that’s not actually quicker,’ he explains.
‘Over the years, I’ve taken responsibility for many different areas of the car and gained quite a lot of understanding of the car’s sensitivities. As a technical director, I think the most important thing is to be able to guide our talented engineers and make tough decisions on which sensitivities to focus on.’
Despite the deep technical understanding current F1 teams have of the physics at play on the track, the 2022 Formula 1 grid hadn’t seen the convergence some expected at the start of this era. In terms of chassis design and packaging, there are several schools of thought on show throughout the paddock, with no two cars following the same path.
Mercedes opted for a narrow-body solution, while Ferrari went for a larger, flat-sided body car. On the other hand, Red Bull, Alfa Romeo, Aston Martin, AlphaTauri and Haas all have a deep, sculpted lower sidepod, while Williams and McLaren went in another direction.
The Alpine A522 is different again, entering at the start of the season with a body design unlike any of its colleagues.
‘In 2019, when we took the first pen to paper for the 2022 car, the initial intent of the project was to ensure we maintain maximum aerodynamic freedom,’ says Harman. ‘This was for two reasons: to maintain scope for
The beam wing has a strong influence on the diffuser. The rear wing, beam wing and diffuser are only powerful in the current aerodynamic regime when they work in harmony
our aerodynamicists to manipulate the car to be more performant in some ways for some tracks, and cost optimisation.
‘If you need to re-layout your car every time you want to change the bodywork, that’s a costly and risky thing to do in a racecar. So at the moment, we’ve got an excellent mechanical package, which allows us to change the body and go to any extreme without needing to change the position of any underlying systems.
‘Through the season so far, we’ve changed very little under the bodywork, which facilitates us making quite big changes to the car quickly and getting them to a circuit.’
Indeed, Alpine brought a massive body upgrade to the British GP, a significant departure from the one it raced in the season’s first half.
To enable such dramatic change, homologated elements such as the side impact structure position needed to be designed to accommodate the different bodies the car might adopt as it evolves, while at the same time not leaving the team vulnerable to having a non-optimised car.
‘The lower side impact structure is an area we often discuss when designing a racecar from scratch,’ says Harman. ‘It sets a reference point for an awful lot of development, and we’ve got a particular innovation on our car that allows us to manage that quite nicely, which I won’t go into too much detail on. That’s an area of the car we’ve worked incredibly hard to ensure we positioned it correctly.
‘There was a great collaboration with our aerodynamicists and mechanical teams
because it’s always a discussion around the chassis structure, the mass and the aerodynamic gain. In this particular car, we challenged the structural people because we needed to make sure the aerodynamicists had the freedom they require.’
Alpine heavily explored the stiffness of various chassis and floor sections during the car’s development as it is a characteristic that hugely influences the behaviour of parts throughout the operating range.
‘It has been part of the discussion that in some cars cause porpoising,’ highlights Harman. ‘It’s understood that there’s not a set-up option for most cars to eliminate the porpoising phenomena, so it needs to be structurally and aerodynamically approached.
‘Early in running the A522, we decided to focus on stiffness in specific areas. This is for several reasons, one being the
‘At the moment, we’ve got an excellent mechanical package, which allows us to change the body and go to any extreme without needing to change the position of any underlying systems’
risk of porpoising, and another due to correlation. We want to ensure a good correlation between our CFD, the wind tunnel and the live car on the circuit.
‘We maintain that, and we’ve got to a point now where we understand stiffness for the features that can cause porpoising issues, and understand where to run our car optimally to stay away from it.
‘Porpoising is now such a minor issue that it’s not something we even talk about too much in our engineering discussions. Our discussions are more about ground
clearance and heave movement [so-called bouncing] and ensuring we run the car in a performant manner. I think we’ve understood porpoising, and we will continue to develop stiffness locally where it’s needed to put it into the most performant condition. In the areas where we can be less stiff, we will dial it in to take weight out.’
The 2022 regulations see a much higher performance weighting on the car’s ground effect floor, which changes the wings’ reliance
and role. Alpine’s front wing, in particular, has a flow conditioning role in ordering the flow field towards the front floor, which was not part of the previous generation’s wing.
‘It’s fair to say the front wing isn’t the dominant force it used to be,’ says Harman. ‘Once you’ve got a good one, it’s not an area where we spend huge amounts on development. You will notice throughout the paddock that teams are not sending new front wings to every other race, or every three races, like maybe we would have done in the past.’
The rear wing, however, is a different story. ‘We need several rear wings for different configurations of racetrack through the year, but also different wings that change the interaction with the beam wing. You’ll notice we went for a biplane-style design beam wing, and we have a number of those that complement the main rear wing elements and the interaction with the diffuser.
‘The beam wing is a massive player in how we position our diffuser’s performance. The rear wing, the beam wing and the diffuser are only powerful together. There’s always a lot of discussion around the aero level configuration of each across the operating range because we can only have a finite number of options for them, so we need to be very careful about what we do here. It’s made us more mindful with our engineering discussions and car development in this region.’
In 2022, the minimum weight of a Formula 1 car is 798kg. This is the car’s mass with the driver, fitted with dry-weather tyres but without fuel.
The limit for car plus driver increased from 752kg in 2021 to reflect the change to 18in wheels and the introduction of new safety features in the chassis.
However, despite the increase, teams found it hard to get down to the limit, even after an increase was implemented to make it less important for them to devote additional funds to weight saving programmes.
‘The first thing to point out is that the original weight limit was a guess on the effect the changes to the chassis and the new wheels would mean on the scales,’ says Harman. ‘Several technical people consulted on the number at first, and we made an initial guess.
‘I think where we’ve ended up is in a position where, realistically, with the changes to the safety regulations and some of the homologated equipment we have to put on the car, that it needed to evolve as we move through the project.
‘The more we understood the difficulties of creating those structures, the more we needed to increase our weight. As time goes on, that weight limit will be able to return to where it was in the previous generation, or even go lower.
‘We are rapidly approaching the limit today, so I think we’ll see that lower limit reached up and down the grid by the end of the season.’
Formula 1 brought in the hybrid power unit regime to generate a much more efficient racecar. Initially, the regulations did not stipulate the minimum fuel load, and teams developed internal combustion engines to use the least amount of fuel to start the race with the lightest car.
However, this has since changed, and a mandated 110kg of fuel is now onboard every car on the starting grid. Some teams in the paddock felt this was a backwards step for the efficiency drive, but it did bring more competitiveness throughout the field for those without the resources to exploit the potential of that regime.
‘Without a minimum fuel load, it drove us to work on some particular elements to chase efficiencies within the engine and the surrounding systems you run it with,’ explains Harman. ‘Parasitic losses in a racecar are something we always try to minimise but, when you run a fixed fuel load, the emphasis on that is much greater. We’ve focused on heat rejection, parasitic losses of heat rejection and things like friction within the engine and round-trip losses.
‘With the drive for very high percentage internal combustion engine efficiency, you also need to minimise the losses you achieve on the energy storage system in terms of round-trip efficiency.
‘The round-trip efficiencies of this equipment have increased greatly over this era, and the regime we’re in now drives that. We’ve understood fluid technologies and we’ve understood particular inefficiencies and heat rejection capabilities and how you lay them out in the car. They all have an influence.’
When the energy-limited formula came into place in 2014 and research into the fuel started, Formula 1 fuel manufacturers discovered that some fuel molecules produce significantly more energy than others.
‘Without a minimum fuel load, it drove us to work on some particular elements to chase efficiencies within the engine and the surrounding systems you run it with’
Because the fuel flow and load are prescribed in kilogrammes, there is scope for developing the calorific value of the fuel.
The development targets are how engineers can apply as much energy into one kilogramme of fuel and generate the proper pressure and motion for the direct-injected petrol engine. The research octane number (RON), which ranks how close to the most efficient moment the spark plug can ignite the fuel, is a primary driver in the combustion development of the high-efficiency fuel.
Formula 1 introduced new E10 fuel regulations for 2022 (petrol, with a 10 per cent ethanol content). The construction of the ethanol molecule means it carries a lower quantity of joules per kilogramme as a combustible vapour than the equivalent volume of race fuel.
Regarding the effect this had on the Renault E-Tech RE22 (the Alpine A522’s PU), Harman notes: ‘Thanks to the work by BP Castrol, we haven’t allowed the lower calorific value of the ethanol to impact us. We have done a great deal of development in this area and adjusted the power unit to suit the particular E10 fuel. I can honestly say the actual difference from that fuel is unmeasurable.’
As per all alcohol-based compounds, ethanol’s evaporation characteristics mean it will extract temperature out of the combustion chamber during the intake and compression strokes and initial stages of combustion.
A522 features pushrod
The square sidepod intake was an in-season upgrade to make more of the scope of this entry. Previously, it had a curved outer surface
The lower vapour pressure and temperature can also take away some of the heat rejection requirements of the engine.
‘However we’re not seeing much of that heat rejection benefit because we push the fuel to the limit,’ says Harman. ‘The main difficulty we have had with the E10 fuel is the ability to pump it at temperature. We have to do some management of that, though it’s what we do in a racecar anyway because, even if we had a different vapour pressure, we’d still have it on the limit.’
The ethanol lets the mapping engineers lower the ignition advance, taking it closer to TDC and initiating better timed combustion. The design engineers can adjust several follow-on configuration parameters from
‘Thanks to the work by BP Castrol, we haven’t allowed the lower calorific value of the ethanol to impact us. We have done a great deal of development in this area and adjusted the power unit to suit the particular E10 fuel’
The
suspension on the front, pull rod at the rear, in line with the car’s aerodynamic philosophy
these characteristics, such as the compression ratio (if under the 18:1 limit within the rules), which could increase combustion efficiency.
Moreover, ethanol molecules contain oxygen so, instead of solely relying on the oxygen ingested into the engine through the intake, further oxygenation of the working fluids in the combustion chamber occurs. It’s also allowed engineers to optimise the enthalpy loop through the turbine because it will no longer have the same target of kilogrammes per hour of oxygen from ingested air.
‘The internal combustion engine still leaves the most opportunity for power unit development in the current
regime,’ highlights Harman. ‘There’s still a lot more efficiency to be had from these IC units from the thermodynamics side, but also some of the basics we can exploit – friction and things like that.
‘As we’ve amassed more and more knowledge into the engines, we can take a step forward in those areas, too. There’s still a great deal to be learned in the energy recovery system, particularly in battery technology, which is moving forward quickly. Although that area is broadly homologated, how you manage those batteries in terms of energy strategy and thermal management is still a huge development area in these power units.
Renault’s F1 power units have seen various different battery types, capacities and configurations over the years, but more recently the technologies of those that can supply the power densities needed for a Formula 1 racecar have converged throughout the paddock.
‘We’ve converged to the optimum for us in terms of configuration,’ says Harman. ‘We’re pretty happy with the configuration we have, though you’ve got to make sure you can thermally manage it in all different racing scenarios as that’s critical to its performance, power output and durability.’
The Renault E-Tech RE22 battery uses cylindrical-type cells that can be discharged and charged quickly and cooled efficiently, thanks to their architecture.
‘The cells we’ve selected demonstrate a very high power-to-weight ratio and power density,’ highlights Harman. ‘Being cylindrical, they are much easier to cool and a much easier mechanical solution to package when compared to pouch or prism cells. This is why batteries in the F1 space have this form factor.’
The Alpine F1 team and its A522 challenger are obviously doing something right. The car has proven to be a force to be reckoned with in the 2022 Formula 1 season and it has provided a good basis for the team’s 2023 design.
The Haas F1 Team is a truly global operation, with its HQ in North Carolina, the Design Office in Maranello, staff based at Dallara’s facility in Varano de Melegari, Italy and in Banbury, UK. Head count is currently around 350, but the team is looking to increase that to 400 for 2023
You have to hand it to Gene Haas and Guenther Steiner. Between them, they played Formula 1’s constructor regulations to perfection, so much so that without an in-house design office, or a fully-equipped factory, they have mounted a credible world championship campaign and, at the close of the European grand prix season, Haas lay seventh, ahead of Aston Martin, AlphaTauri and Williams – all teams with comprehensive facilities at their disposal.
Expressed differently, Haas F1 Team was about the only entrant able to file its budget cap reports on time, as required by the FIA’s financial regulations, without fear of breaching 2021’s $145m limit.
The history of the team, which took its first start in the 2016 Australian Grand Prix (finishing sixth, before going one better next time out in Bahrain) harks back to Steiner’s 2001-’03 tenure as Jaguar Racing’s technical director, but in real terms it was the aborted 2009 USF1 project that sparked Haas F1.
‘It would not be fair to say I learned what not to do from those teams,’ Steiner, who harks from Italy’s South Tyrol Germanspeaking area, told this author with a smile in 2015, ‘but there were lessons to take aboard.’
Between those two time points, he established Red Bull’s NASCAR operation and founded a carbon fibre business in Charlotte, USA – home to North America’s heavy metal series – where he came into machine tool magnate, Gene Haas’, orbit. The two had been approached for assistance by USF1, Steiner on composites, Haas supplying machine tools, and kept in contact after the project’s (predictable) demise.
At Jaguar, Steiner, who joined from a similar role at parent company Ford’s rally team, scoured F1’s technical and sporting regulations, particularly the Concorde Agreement, learning what to do and, perhaps more crucially, what not to do.
They say the most important thing in any category of motorsport is to read the rules. But few can claim to have read the rules quite as cleverly as those behind Haas F1 Team
Provided a team holds the intellectual property rights to ‘listed parts’, as per Concorde, they are deemed a constructor, regardless of who designed or produced the components
Key to funding the whole operation is Haas’ desire to expand its CNC tool business into markets outside the US, crucially those that are either on, or are about to be on, the F1 circuit
As a naturalised American, his ambition to be team boss of a US Formula 1 outfit burned deep, so he approached Ferrari about running a third car for an American driver.
The concept was embraced by the Scuderia, but rejected by the FIA. So, he investigated a Ferrari customer operation instead. Again, thumbed down by the governing body (and the other teams), so instead he turned to F1’s technical regulations, quickly learning that F1 constructors need not be constructors.
Explanation: provided a team holds the intellectual property rights to ‘listed parts’, as per the Concorde agreement, they are deemed a constructor, regardless of who designed or produced the components. Back then, listed parts were effectively ‘wetted parts’ ie those that got rained on, so front / rear wings, outer profile and body parts, crash / rollover structures and floor / diffuser.
All the rest could be bought in, so Steiner called then Fiat / Ferrari boss, Luca di Montezemolo. The two already knew each other from Italian rallying via Steiner’s stint with the privateer Jolly Club team, and then later from third / customer car proposals.
‘Would Ferrari be prepared to supply unlisted parts?’ he asked the Roman nobleman, who replied in the affirmative,
provided Steiner provide the relevant guarantees. Crucially, this meant Steiner had access to Ferrari powertrains, as long as someone paid for them.
Next stop was Dallara, to enquire whether the world’s largest customer car constructor would design and build all non-listed parts
required to fit the Ferrari Meccano set, and be prepared to cede IP rights to Steiner’s project on the basis that these were bespoke parts for specific use. Same reply: ‘If costs are covered, sure, why not…’
Enter Haas, then seeking to expand his eponymous machine tool business beyond
Racecar was granted exclusive access to the Haas F1 Team Design Office, situated within Ferrari’s Gestione Sportiva complex in Maranello, Italy
the USA and into auto manufacturing regions such as Brazil, China, Malaysia and Mexico –all countries on the F1 calendar, or about to join. If Steiner obtained FIA approval for the ‘constructor-without-constructing’ concept, he agreed to fund it. The FIA, seeking to fill F1 grids, agreed.
This was in 2014 / ’15 and, by 2016, the US-entered team was on the grid for its first season and shading Sauber and Renault with eighth place. That championship result was repeated the following year before improving to fifth in 2018. Not bad for a team whose ‘factory’ consists of a one metre square filing cabinet containing Ferrari, Dallara and F1 contracts, and whose wind tunnel is situated in Maranello.
Add in that Haas’ Kannapolis complex, situated beside the Stewart-Haas NASCAR outfit, acts as global headquarters for the F1 operation and fabricates tooling, jig and fixtures for the team, and a case could be made that Haas’ F1 entrant’s licence should be issued by the United Nations, what with staff based in the UK (race operations), Italy (Ferrari and Dallara) and USA. Around 30 nationalities in total are represented.
By now, there were rumblings of imminent budget caps. Liberty Media had acquired F1’s commercial rights in early 2017, and sought
Not bad for a team whose ‘factory’ consists of a one metre square filing cabinet containing Ferrari, Dallara and F1 contracts, and whose wind tunnel is situated in Maranello…
ways of paying teams less as it follows that the less they spend, the less their imperative for billion dollar prize funds. If the ‘new era’ cars were to be cheaper to design, build and race, an inherent part of the 2021-on regulations was a revamp of parts categories (see sidebar).
Crucially, though, the cap meant swingeing head count cuts for major teams. Where the Big Three numbered over 1000 in their performance departments, the right size was projected at 650. Mercedes consequently diversified into applied sciences with yachting and cycling projects, and ramped up in-house work for parent company, Daimler. Red Bull, meanwhile, embarked on the Aston Martin Valkyrie and its RB17 Hypercar, plus shifted staff to sister team, AlphaTauri.
By contrast, Ferrari opened a ‘customer technical services division’ to offer contract engineering services to Haas – therefore replacing Dallara, then ramping up on road car projects anyway – subject to FIA approval. The governing body considered the facts and insisted upon separate premises and systems in order to prevent ‘coffee-time chats’, during which secrets may be whispered, plus the right to make unannounced spot checks, which it has duly done.
Which brings us neatly to the first visit by a publication to the (contracted) Haas Design Office, situated within Ferrari’s Gestione Sportiva complex at the end of Via Ascari, overlooking Fiorano circuit. Haas’ offices are self-contained, with access by coded card
only and, significantly, our invitation was extended by Haas, not Ferrari.
How complex was it to set up what is effectively a team within another team’s building, while conforming to FIA’s requirements, particularly when competitor teams keep politicking about Haas’ structure? After all, engineering staff are effectively now Haas employees, albeit paid by Ferrari to maintain company benefits and perks, and work out of the same building as previously. Time spent is now ‘booked’ to Haas.
‘It wasn’t too difficult, because in 2020 / ’21 we came down [in technical head count due to Covid],’ admits Steiner in his trademark accented staccato style, ‘and it helped that the people were mainly working for Dallara, so it was pretty easy [for us] to reduce [numbers].
‘We were also helped by circumstances, because the budget cap came in and Ferrari had people available. I spoke to Mattia [Binotto, Ferrari team principal] and told him I need to ramp up.
‘He said, “maybe we can work together on some of the people [who] we need to move to other departments. Tell me what you need.”
Where until the end of 2021, F1’s components were categorised on a binary basis, either listed (own IP) or unlisted (free sourcing), under the ‘new era’ regulations there are now four umbrella groups, making Haas’ operation simultaneously easier and more complex, depending upon the specific component.
The four current categories and some examples of each are outlined below.
• Listed Team Components (LTC) are those whose design, manufacture and IP is owned and / or controlled by a single team or its agents on an exclusive basis. Examples are survival cell and primary roll structures, front impact structures and the fuel bladder.
These items must be unique, and Haas must hold the IP rights to them, whether designed and / or supplied by Ferrari’s ‘customer division’, Dallara or any other entity. Around 10 per cent of parts groups within categories are LTC, but many are major items.
• Standard Supply Components (SSC) are those whose design and manufacture is carried out by a supplier appointed by the FIA, to be supplied on an identical technical and commercial basis to each competitor team. Effectively, these items are mandated, and teams have no choice but to source them from the official supplier. Examples are (BBS) wheel rims, tyre pressure and clutch torque sensors, (Pirelli) tyres, primer pumps, flexible pipes / hoses and fuel flow sensors.
These are items required for FIA monitoring or mandated for costs reasons. Around 20 per cent of parts groups within categories are SSC.
• Transferable Components (TRC) are components whose design, manufacture and IP rests with a team or supplier but can be freely supplied to another team without limitation. Haas may avail itself of all these parts provided their notional value (see Financial regulations box out on p??) is equal to, or better, than it could produce or outsource such parts for itself. Examples are gearbox carrier and cassette, rear impact structure (fits gearbox), full front / rear suspension assemblies and non-LTC and SSC fuel system items. Around 30 per cent of parts groups within categories are TRC.
• Open Source Components (OSC) are components whose design specification and IP is available to all teams through the mechanisms defined in the regulations. Examples are pedal assemblies, wheel retention systems, brake systems, master cylinders and fuel system hydraulics. Around 40 per cent of parts groups within categories are OSC but these are standardised, non-performance items.
Access to the Haas F1 Design Office is by key card only, keeping it separate from Ferrari’s, housed in the same building
Whilst Haas F1 now has a greater choice of sources, it still has to evaluate all open components to ensure it obtains the best prices, crucial under a budget cap.
Much of the main hardware for the F1 cars comes from Ferrari, other parts are mandated by the FIA and the rest are sourced from whichever supplier is deemed the most operationally efficient
So, when I say it wasn’t too difficult, and didn’t give me sleepless nights, it’s because we found a good solution.
‘Simone [Resta, formerly Ferrari’s chief designer, now Haas technical director] was drafted in in December 2020 to set it up. The first question was where do we put the offices? So we started looking around Maranello, and then there were offices planned by Ferrari for expansions that they no longer needed [due to budget caps].’
Resta, like most of Haas’ Maranello staff, is on Ferrari’s payroll and acts as our guide for the day, explaining that around 100 staff operate from here, with the figure varying according to workload. It roughly works out at 30 in the Design Office and 70 aero staff working from offices situated alongside Ferrari’s wind tunnel.
‘Basically, what we have here in Maranello is a group of designers, aerodynamicists, test engineers, structural engineers, all the development group, plus some people involved with simulations,’ he says, adding, ‘while the model makers, they’re coming in mostly from Dallara.
‘There’s a nice group of people based at [Dallara’s base in] Varano de Melegari, say
50-70, and then there are more people at the operational base in Banbury, say 120 or 130.’
Add in folk in the USA and the number quickly spirals over 350, with additional hands required during pre-season car build. Indeed, the team is planning for 400 heads for next year and foresees 500 in the medium term. A new title sponsor was added in October, MoneyGram, which will enable them to increase spend in non-regulated areas.
‘We are now within five or 10 million [dollars] of the budget cap,’ smiled Steiner ahead of the announcement.
How does Resta decide which parts to design and build? The main hardware is easy. The complete ‘rear end’ consists of Ferrari’s latest specification power unit, gearbox and electronics / hydraulics, the latter plugging into the team’s own systems. Taking the rear suspension and crash structures is a nobrainer given they bolt onto the gearbox. For the rest, the design team picks and chooses from what is legally available.
‘Normally, we try to maximise in the way our business model has been defined. We try to maximise our opportunities wherever possible, showing what we can take where. There is always a chance you can carry over components. It’s a group effort but, ultimately, I’m accountable for things.’
He has a counterpart in Ferrari he meets regularly, and between them they decide the ‘menu’, within established processes.
‘There’s a process that involves regular discussion,’ confirms Resta. ‘It is all documented, with details where they can exchange in advance the areas where we are able to buy. Then they exchange [computer] models so we can keep up to date.’
‘Basically, what we have here in Maranello is a group of designers, aerodynamicists, test engineers, structural engineers, all the development group, plus some people involved with simulations’
Simone Resta, technical director at Haas F1
Resta admits that being a customer is not ideal, due to potentially being a step behind, but says, ‘You try your best to follow what’s going on, within limits. In the end, there’s not much room for frustration, you just get on with it, do the best you can and try to maximise your [return on investment].’
Once designed, build of parts is handed over to sub-contractors – mainly Dallara, but whoever offers a good deal within quality, quantity and delivery parameters. Dallara also steps in with engineering services during peak periods, as and when required.
‘Dallara is like an expansion tank for us during [new car] engineering time in November, December and January,’ explains Steiner. ‘They also manufacture all the structural parts, so those you need to do an FIA test, things like that. Ferrari only make those parts we buy direct, [as] they don’t have capacity for us [for other parts]. The rest is from anywhere, but only from good suppliers.’
Dallara then builds the cars, in conjunction with the Haas race crew.
‘Assembly of the car is normally at Dallara in January, because everything is there and, if something is missing, it can be made,’ confirms Steiner. ‘Normally, we send people there from England. It takes about a month, six weeks maybe, and then the cars don’t see Dallara again [as] they return to Banbury after each [European] race and between long hauls.’
How, then, does a naturalised American, German-speaking Italian based in North Carolina keep track of a trans-Atlantic, 400-strong team based across three countries to enable them to compete respectably in the upper echelons of global motorsport in order to sell machine tools?
Haas F1 Team is obviously required to adhere to budget cap requirements, which imposed a $145m limit 2021 performance spend, reducing at the rate of $5m per annum for 2022 / ’23. However, due to the varying nature of teams’ business models – ranging from Ferrari’s in-house operation at one extreme through Red Bull’s two-team supply set up to Haas at the other – various checks and balances on spend are included.
The regulations therefore define ‘fair value’, also known as ‘notional value’, as the price that could reasonably be charged for a component, including all its design, development and production costs, as though it were a unique component for a single team. So, when Ferrari sells a part to Haas, or Mercedes to Aston Martin, it is transacted at ‘fair value’, with FIA inspectors empowered to check every such item.
Equally, staff salaries and benefits are booked at fair value, so there is no chance of under charging. However, if an engineer spends, say, 50 per cent of their month on F1 design, and the balance on yachting projects, only the F1 portion of time is booked.
Equally, regulations provide for marketing, administration, heritage activities and travel / accommodation costs to be excluded.
Steiner believes that fair value calculations add around 20 per cent to Haas’ overall component bill, but that his team scores by having lower overheads and payrolls.
‘It is about equal, I estimate,’ he says. ‘As a company, we are pretty straightforward because we don’t have subsidiaries or anything like that, but the notional values of parts is clear. We are not involved in deciding how they are reached, that is done between the FIA and the suppliers, Mercedes or Ferrari etc.
‘They decide on notional values between them, and we get the numbers and have to make it work. Like everybody else, we need to report what we’re doing. Obviously, [the budget cap] is a big job, but it’s a big job for everybody.’
‘By video conferencing,’ he says, before breaking into a chuckle. ‘You know, it’s funny. When Covid came along, everybody started talking about this thing called video conferencing, but I laughed because we had been doing that for years already. When we set up the team, we built a movie theatre in Charlotte so we could stay in touch using a programme called Lifesize. So when Covid came, we were well ahead.’
Clearly, the unique business model he devised demands a punishing schedule. ‘I see the team on video all the time, but I am there
physically very little. I mean, the last time I was in Banbury was during Silverstone in early July [note, this interview was conducted at the end of September].
‘I went to Europe after the Canadian Grand Prix, and I stayed there the whole summer, based in my place in Italy. I even speak to my family via video…’
Still, a combination of filing cabinets, satellite offices, outsourced staff, facilities and componentry, pioneering use of video conferencing technology and the tightest of Formula 1 budgets has not only enabled Haas and Steiner to found a cost-effective, point-scoring team in under two years, but to keep it on the grid – and maintain a competitive position – in what is an extremely harsh and unforgiving commercial and sporting environment.
The wonder really then is that in a sport that copies so shamelessly, no-one else has thought to follow suit.
‘When we set up the team, we built a movie theatre in Charlotte so we could stay in touch using a programme called Lifesize’
Guenther Steiner, team principal at Haas F1Having offices around the world are no barrier for team communication. As well as on-site meetings, the team also relies heavily on digital conferencing
ezzo echnolo ie e i n e oke hi h e o m nce mic ot e he t e ch n e o tomotive moto o t e o ce e ence n o e ene tion ecto . he com ny i e chin o ine evelo ment n e ith n en inee in ck o n to e e o o l ck e o i e v iety o o ect n el te ine evelo ment ctivitie . he cce l c n i te ho l e o icient in comme ci l n technic l cto lie to the ine o he t e ch n e n ill e o t to the hie e tion ice n i ecto o n inee in .
he ole i in ho e t the com ny ton o e n e i e t vel to client n o ect o l i e. he l y n com en tion ck e e com etitive n e en ent on e e ience n e o m nce. yo e inte e te in le nin mo e o t thi c ee o o t nity o lyin i ectly to the ole cont ct in the et il elo . om eve yone in the ezzo echnolo ie te m e look o to he in om yo
Kevin W. elly e i ent
Mezzo Technologies
10246 Mammoth Avenue, Baton Rouge, LA 70814 m il kevin.kelly@mezzotech.com hone
In July 1984, a 12-year-old English lad was so enthralled as he watched Niki Lauda win the 1984 British Grand Prix in the McLaren-TAG MP4/2 that he vowed to not only work in Formula 1 as an engineer but, ultimately, to do so by joining McLaren.
Via a somewhat circuitous route that saw him take up an apprenticeship with Lotus before graduating as a mechanical engineer, he realised his ambition in 2019.
XPB The design of the 2022 car was helped by modelling data from the FIA that meant teams were not starting from a blank sheet of paper. The MCL36 Mercedes scored its first podium at Imola
I want to encourage people who want to go into engineering
That youngster was James Key, now technical director at McLaren, who led the design of the 2021 MCL35M (M for Mercedes), an evolution of the Renault-powered MCL35. In September last year, the MCL35M scored a one-two in Monza, a momentous day for Key and vindication for his chosen career path, although the now 50-year old modestly credits his entire team. It was he, though, that set the design direction.
In this interview for Racecar Engineering, Key provides valuable pointers for budding engineers and technical directors. The conversation may be liberally sprinkled with words such as ‘luck’ and ‘fortune’, but, as this interviews underscores, ‘luck’ can be created…
RE: How did you get into Formula 1?
JK: When I was very young, my father, a very successful engineer and car enthusiast, would open the bonnet of his car and I’d be fascinated by all these boxes and wires and pipes and stuff. He influenced me by explaining how things work and sharing his enthusiasm and passion for how important engineering is. It changes the way we live. It doesn’t come out of the brown of a tree.
I believe we don’t talk enough about it, but how the way we lead our lives, and how societies live, is heavily influenced by innovations out of science and engineering.
In a convoluted series of events, Jordan became Midland became Spyker (briefly), and eventually settled as Force India. It was a turbulent period but Key says it taught him some valuable lessons
Formula 1 I picked up when I was about 12, and was immediately hooked, not least by the wonderful commentary by Murray Walker and James Hunt, who made the world of Formula 1 sound like a magical thing. I decided that’s what I’ll do if I’m lucky enough to get the opportunity.
I was fortunate to have a plan at a young age, and left school and home at 16 to go and pursue it. I know drivers do that, but not many engineers do. I joined Lotus Engineering, who were not very well known at the time. It was mainly road car stuff, but they had some big clients with big projects like active suspension. I got into chassis simulation – incredibly important at the time – and we did a Le Mans project.
The way we lead our lives, and how societies live, is heavily influenced by innovations out of science and engineering
Key remembers his time spent at Sauber, and then Toro Rosso fondly, not least because it gave him the opportunity to work overseas with a number of very talented European engineers
Plus, Team Lotus [F1] was situated just down the road, which was very exciting.
Lotus [Engineering] sponsored me through university, and I tuned my degree to topics that were relevant to motor racing. I said to my professors, ‘This is what I want to do, how can you help me achieve it?’
And not just for my CV, but to learn the topics I needed to know, such as fluid dynamics, mechanics and vehicle dynamics. I was also able to work for them during the vacations and afterwards.
So, three years out [of university] I found myself in F1 with Jordan Grand Prix.
RE: What university did you attend, and what did you study?
JK: University of Nottingham, studying a Bachelor of Engineering degree,
mainly mechanical, which comprised a whole range of engineering disciplines, including mechanics.
My third-year project was to design, build and test a performance acquisition system for competition cars, which was really tuned to what F1 was doing at the time. I’ve since set up a scholarship at that university (see sidebar on p29).
Then I went back to Lotus for two years, and started at Jordan just before the 1998 season as a data engineer; what is now called a performance engineer. We were about five people doing the job of what is about 45 now.
It was at the transition of going from when you’d have someone who basically designed the car and had some help, to the sort of structure we’ve got now, where you’ve got a huge number of specialists all over the place who coalesce to design a car because it’s so complex nowadays. I was lucky I caught that transition.
RE: Within Jordan, which variously changed identities, you became technical director in 2005. At 33, you were amongst the youngest to hold that position in the sport.
JK: I was there for 12 years. I saw [the team] through the period going from Jordan to Midland, which is when I became the technical director of the team, just before the Midland buyout, which was the same time really.
Then the team became Spyker for a year, so it was a bit of a turbulent period with ownership changes and budgets and so on. It was quite a tough time. Then it became Force India [in October 2007] and everything began to settle down again.
I was incredibly lucky to be surrounded by some very good people at Jordan. It was a team that punched well above its weight, having some successful years.
I suppose the biggest thing it taught me was how a small team – it wasn’t really a small team, but it wasn’t as big as McLaren or Ferrari – can operate very successfully. The way in which that happens, the efficiencies involved in it, the sacrifices you have to make to make up for the fact you haven’t got so many people doing your job. Above all, how much difference people could make.
I learned so much from Gary [Anderson, former technical director], a huge amount from [colleague] Sam Michael and aerodynamicist Dino Toso, who so sadly passed away some time ago. All of these characters were just brilliant, and I was lucky [that word again…] to learn from them.
RE: Then in 2010 you joined Sauber in Switzerland, with all the challenges of moving countries.
JK: Sauber was another really good team, very similar to the way the Jordan
It was at the transition of going from when you’d have someone who basically designed the car and had some help, to the sort of structure we’ve got now
operated, with lots of experienced, good people. So it felt very familiar.
You’d have a group of four who did a whole suspension system, seven to do all the composites. It was impressive how much throughput there was. Everyone would quietly beaver away, and it was a really good, very efficient place to work.
But it was clearly going to be short of money, and because I joined just as BMW pulled out, there’d been such an awful period of uncertainty. It was also nice going in there to grab the bull by the horns and try and get away from that sort of difficult period.
RE: Then you had an offer from Toro Rosso. JK: That came out of the blue, to a certain extent, but what was attractive was that they had more stability, really strong ownership. It also meant that I worked in another country that’s got a Formula 1 team, so I did the rounds in Europe a little bit!
Toro Rosso was also fantastic to work in. I signed off [drawings] in a Portacabin next to the old Minardi factory, and the team was growing all the time. New facilities were being built – we needed a much bigger aero department, we needed a bigger, more structured design group. We had a really strong design team, we just needed more boots on the ground.
I caught it at a time when it wasn’t performing particularly well, so there was a lot of work to do. It was another
In March 2019, Key received an offer to work for McLaren, the team that had inspired him to forge a career in F1 as a child. With a new rule set and then Covid, it was in many ways a baptism of fire
great challenge. I’d been through it a bit with Jordan, so I thought there was some familiar ground, even though the team was unfamiliar, and the language was definitely unfamiliar, although they did a great job of speaking English.
In terms of the challenges, it was familiar, and I thoroughly enjoyed working with the Italian engineers. Very skilful guys and girls, and a pleasure to work with. That was a fantastic time.
RE: That came to an end when you received the McLaren offer, the realisation of a dream. You came in ahead of a regulation change that was pushed back a year due to Covid, which meant rolling over the MCL35 for a season and entailed a change of power unit from Renault to Mercedes. How did your team manage to dovetail the two?
JK: New regulations are always a great challenge for engineers. We like new regs – I certainly do – because it gives you an opportunity to step back and re-think everything, rather than just the detail of what you’re doing now.
RE: During your time in F1, you’ve worked with virtually every power unit supplier, and almost every configuration: V10, V8, with and without hybrid units, Ferrari, Renault, Ford, Cosworth, Mercedes…
JK: You can add Toyota to that list.
RE: What are the major differences in approach and modus operandi?
JK: They were all very different. Not only do they have different architectures and so on, but their facilities, the approach, that sort of thing. There wasn’t a set formula. It was all done differently, depending on the supplier you’re working with.
The way the data is formatted and presented is different, so are the details, the electrical installations and systems and voltages, their cooling systems… Everything is totally different.
When it came to installing another power unit in the car after a change, there was very little carryover, you really did have to start again.
One of the most difficult things with engines is heat rejection, to get your cooling correct. It’s a very difficult thing to measure and quantify as you don’t really have any references. So, you really do have to start from scratch when you’ve got to design and integrate a totally different cooling system.
In fact, you have seven cooling systems on these cars, and must invent a package to fit into a space that you want to try to reserve for it. They’re all very different, and they’ve all got their pros and cons.
New regulations are always a great challenge for engineers
Last year’s car regulations had been around for a while. It was maybe the fifth season of both [sporting and technical] sets of the regulations. With the new regs, we could look at an entire car in a very innovative, fresh way, particularly when they’re so different.
RE: What was the next step once you’d grasped the overall direction?
JK: You start off a set of projects based around relatively robust regulations that changed a lot, and they continue to do so. You have the bones of what a 2022 car should look like, then everything else is applied to that.
We also had this very good process of developing the regs, which meant we had [modelling data] from F1 and the FIA in terms of aero surfaces. So you weren’t really starting completely from scratch, there were reference points and aero data around from the white paper.
It was kind of a fuzzy beginning, because we weren’t picking up the regs
for the first time and reading them, they gradually introduced themselves.
RE: And the next step after that?
JK: It was a really a case of allocating resource and coming up with some ground rules on how you’re going to approach it. You don’t want to commit to things too early because there’s so much to learn, but you don’t want to be be sitting there waiting for things either. So we left our options open, assessed how much potential performance there was, because in some way we’ve got to know what sort of lap times makes a good 2022 car.
It’s a whole range of things. A lot of simulation, a lot of understanding of tyres, because these factors are balanced and the set of balances will govern what you do with your suspension design, your front wing and so on.
It’s an iterative process. We were constantly circling around all those things and gradually a direction and architecture emerges, which tries to complement
everything you’ve learned. Then you really start getting into the details of setting out your platform based around that architecture and hitting your CFD and wind tunnel with finer detail of things like suspension geometries, until finally you end up with something. Then you’re iterating a car around what you’ve established and fixed.
RE: How many decisions did you have to take almost on a daily basis, because obviously you’ve got all sorts of compromises to make that affect cooling, drag and so on?
JK: I couldn’t tell you on a daily basis because I took decisions all the time, but the big ones – I suppose once, or maybe twice, a week you’d end up with, what are we actually going to do about this or that major component?
What should we prioritise? Something that can change the direction totally.
It shouldn’t be just down to me, so I tend to discuss it, to look for data or simulations, the trade offs. So there’s
ways of making those decisions, which isn’t just an executive decision.
RE: The way F1 has developed, there is no longer such a thing as a ‘James Key car’, but how much concept input did you have into any of the cars that were designed under your leadership?
JK: That’s changed over time because teams have got bigger and bigger, and more and more complex, and the need to specialise has increased.
Nowadays, a technical director is spinning plates to ensure we’ve got all the enormous levels of resource within a team on the engineering side headed in the same direction, or at least in a few relevant directions, because all of them complement each other and join together down the line.
So, you’re kind of managing the process. I wouldn’t say it’s more managerial, or more technical, because it’s also about meeting heavy budgets, HR matters, and many other factors.
RE: You seem to have really enjoyed your
you’ve founded a scholarship
is under £35,000 (approx. $43,000)
JK: Yes, I had a brilliant time at university. It was a really special time in my life, although maybe it should have been weighted a bit more toward the academic side, rather than the 50 / 50 studies and enjoying myself it was!
I’ve since set up a scholarship there to help engineers from disadvantaged backgrounds to go through it, because it was a great place to be and I wanted to give something back.
I want to encourage people who want to go into engineering so, as well as the scholarship there, I’ve also provided support for their Formula Student team. I wish it had been there when I was at university because I love the concept.
I think a lot of [the job] nowadays is influencing the direction you’re going in. You’re outlining what the priorities are, then monitoring them, then discussing it, all the while making decisions as you go along.
You’ve got experts to then go away and really get into the details.
The 2006 Midland was the first car I did, but it’s all changed since.
RE: Do you own one of ‘your’ cars?
JK: No, but it would be nice to actually own one. I’ve got a special space put aside for one, should the opportunity arise…
Mercedes AMG has had a rude awakening in Formula 1 in 2022. Racecar talks to Mike Elliott, the team’s technical director, to find out how it has approached the problems
‘It’s easy to say we’re having a tough time when we’ve been through the last eight Formula 1 world championships, winning them all, and we’re not in that position this year,’ says Mike Elliott, technical director of Mercedes AMG Formula 1, on the team’s 2022 performance to date.
‘We’re bound to think it’s not brilliant. However, looking at a wider context, the 2022 regulations intended to mix up the field and improve the show. In that way, Formula 1 achieved those outcomes.’
At time of writing, with just one race remaining, Mercedes sat third in the Constructors’ Championship, behind the champions Red Bull but within reach of Ferrari in second. Mercedes’ change of
Unlike the previous generation of dominant Mercedes machinery, the W13 has had a somewhat bumpy coming of age
fortune since the introduction of the new era has been well documented. The AMG F1 W13 E Performance (the 13 referring to it being the 13th car produced by the Mercedes-AMG works team since re-entering F1 in 2010), is the product of a top to bottom re-design in line with this year’s Formula 1 regulations. The only carry-over element from its predecessor is the steering wheel.
Operating from a blank slate, with a steep development curve, the team’s Brackley and Brixworth engineering squads have had to push even harder than the previous generation of Formula 1, where they stole a march on the competition and carried it through to the end of the era. Unlike the prior dominance of Mercedes machinery, though, the W13 has had a bumpy coming of age.
For context, the 2022 rules have reduced the cars’ wake (turbulence caused by the car passing through the air) as a function of the new aerodynamic regime, allowing competitors to get closer to one another, particularly in the corners. The challenge of overtaking in the previous generation of F1 was primarily down to this wake. However, the lower wake means the corner gains are somewhat outweighed by the tow effect (slipstreaming) reduction on the straights.
Net, Elliott feels the cars’ resulting closeness and overall competitiveness over an individual lap have not changed much.
‘In terms of closing up the grid, it’s probably the same split as we’ve had before,’ he notes. ‘I guess we are the only ones that have seriously changed position this year, and that’s our problem to deal with. We’ve ended up with a poorly behaving car and an uncomfortable ride for the drivers, thanks to the direction we’ve taken with the new aerodynamic establishment.’
Thanks to the introduction of groundeffect aerodynamics, the 2022 rules reward running the car as close to the ground as possible. But if platform control isn’t sufficient, this low running can induce instability in underfloor flow fields and lead to so-called porpoising and bouncing. Mercedes suffered badly from flow field instability in various ways throughout the 2022 season, but has not been alone in this battle.
‘I don’t think any teams effectively spotted porpoising over the winter period between 2021 and 2022,’ says Elliott. ‘We did anticipate having to run the car very low under these full ground-effect regulations. However, the challenges of ground-effect aerodynamics are stronger on some cars than others. They are unique to the flow field structure under the car, its set-up scope and performance window.’
Cars have three modes in their suspension: roll, pitch and heave, which operate at different frequencies. In a porpoising scenario, the car ends up with a phase shift between its front and rear aerodynamics, which feeds into the pitch mode. With these cars, teams see predominantly heave, and some pitch, which depends on speed and the characteristics of the circuit.
‘It became apparent early, even without significant aerodynamic work, that these cars wanted to run very low to the ground. So we focused on designing the floor to survive in those conditions, and at the ride height that would be most performant,’ says Elliott. ‘We underestimated one problem and didn’t spot another, which is why we have the behavioural issues. One thing we can put our finger on is that it is a consequence of the aerodynamic changes in the regulations.’
Mercedes claimed to make good progress ironing out its issues regarding underfloor flow field instability that led to the porpoising
phenomenon seen so dramatically in the season’s early stages. However, the W13 continued to suffer from ‘bouncing’ – a heave motion response caused by the underfloor aerodynamic instability.
‘Bouncing issues are complex,’ notes Elliott. ‘The aerodynamics put energy in the vertical motion of the car due to a phase shift between the aerodynamic load and the car’s ride height position that gives a net energy input more than the dampers can deal with.
‘The fact we have to run these cars so low to the ground, with so much downforce on them to be performant, means they must run really stiff, and that’s a huge contributor to these significant consequences.’
As well as the changes to the aerodynamic regulations, the new-for-2022 18in wheel and tyre package has changed how teams approach car performance. ‘As per every era of Formula 1, there are significant amounts of
Mercedes ran a pushrod suspension design on the front of the W13 to free up space below the suspension to flow condition the air towards the front floor
‘The challenges of groundeffect aerodynamics are stronger on some cars than others. They are unique to the flow field structure under the car, its set-up scope and performance window’
Mike Elliott, technical director at Mercedes AMG Formula 1
lap time to be found by improving the car’s dynamic behaviour, and engineers can find some of this in setting up the car to get the tyres into their performance window,’ notes Elliott. ‘The new tyres want slightly different things to get them into the window that works when compared to the previous 13in ones. Though this isn’t the
way to solve the challenges we’ve been facing with car behaviour. You have to put it in perspective. The tyre is not particularly stiff, and then you’ve got stiff suspension springs and, in parallel with the suspension springs, you have the stiff dampers. In reality, these cars are inflexible, so it’s hard to dampen the motions and take a lot of energy out of the car’s movement.’
The chassis regulations also changed for 2022 and now include a more challenging side squeeze test, requiring a higher strength than the previous generation of cars. The aerodynamic regime has also driven teams to stiffen their cars in areas they otherwise wouldn’t have in the last regulation set. Even with good engineering design, these
elements add significant weight to the cars, which have gone up from 752kg to 798kg.
Teams throughout the grid have not pushed to meet the minimum weight, instead choosing to maximise more lap time performant opportunities that were perceived as more rewarding than just having the lightest car possible by regulation.
‘We were overweight at the beginning of the season, though we have done a lot of work to bring it down towards the minimum,’ explains Elliot. ‘However, weight is an interesting equation in this era of Formula 1. Although it’s one of the key performance drivers, it is also limited by regulations. Because of that, car development differs from what one might think.
‘We are always targeting a lower lap time, and reducing the weight to the minimum amount gains a certain amount of lap time performance, but we’ve found that a heavier car with a more sophisticated aerodynamic package actually generates much more performance on the track.
‘Because we have so many tools to develop a more performant car, lowering the weight to the minimum isn’t as dramatic a driver as it once was in Formula 1. Additionally, we’ll take a weight penalty for a more reliable car, as a DNF or grid penalty from replacing components that have failed, or run over the maximum unit allocation for the season, carries a high burden in the championship standings.’
The position of the homologated side impact structure is defined in the regulations, but early in the design phase for the W13, Mercedes spotted an opportunity to design a wing around the upper side impact structure to add downwashing flow in that area.
‘We spent a lot of the winter figuring out how best to work this loophole, and wondering if there was any part of the wording that would see the other teams trying to get it stopped,’ says Elliott of the wings that sit either side of the driver’s cell. ‘We went for it at a certain point in the development, and it performs well and suits our overall aero regime for the car.’
Others are yet to follow suit, instead using the space Mercedes carved away for this structure to house components.
It became apparent early on, even without significant aerodynamic work, that the current generation of F1 cars want to run very low to the ground. Mercedes focused on designing the floor to survive in such harsh conditions and at a ride height that would be most performant
The teams’ aerodynamic philosophies dictate the direction they go in terms of the weight of each component that affects aerodynamic performance. Once a philosophy is settled on, much of the design concept then comes from that, and forces you down a particular route to effectively deploy it. Interestingly, there is a variety of concepts seen across the 2022 grid. Mercedes has gone with a very narrow packaging concept, while much of the rest of the grid has chosen a wider body
‘In reality, these cars are inflexible, so it’s hard to dampen the motions and take a lot of energy out of the car’s movement’Mercedes saw an opportunity in the rules to design a wing around the side impact structure to add downwashing flow in that area
to suit their philosophies. Elliott doesn’t think there’s a big difference in the potential of any one philosophy because the detail is where it counts, much of which is under the floor.
‘When you look at a Formula 1 car as an aerodynamicist, you immediately see that the dominant features are the front wheels. These generate a tremendous amount of wake, and how you deal with that is the key to performance. In the past, we would counter the effect of front tyre wake by implementing complex structures behind the wheels in the form of bargeboards and other wake control devices. But in 2022, we can’t do that. So, our philosophy for the W13 was to bring the bodywork in the central chassis of the car as tight as possible to the driver cell and the PU to have a minimal effect from front tyre wake.’
The W13’s aggressive sidepod packaging is partly thanks to the compact design of the M13 power unit, which features volume dense systems such as water-to-air intercooling. On its creation, Elliott says the team have built up a lot of power unit systems modelling capability over the last few years, enabling them to do a superior job at predicting where the heat capacity and flow rates need to be in order to be as efficient as possible.
‘We do a lot of work to optimise airflow through the car and work out the pressure losses around radiators,’ he says. ‘Charge air cooling is based on water-to-air heat exchange because we see a massive benefit in that in terms of the entire design philosophy of the car. Its role cannot be underestimated.’
The underfloor aerodynamic regime only slightly changes the packaging of the cars. However, Elliott notes that, in every era, Formula 1 teams always try to push the limits when it comes to packaging
‘One significant change for us was the limited wheelbase regulations this season. We had the longest car in the previous regime,
‘Our philosophy for the W13 was to bring the bodywork in the central chassis of the car as tight as possible to the driver cell and the power unit to have a minimal effect from front tyre wake’Mercedes’ charge air cooling is based on water-to-air heat exchange and coincides with the design philosophy of the car. This allows the car to run fewer cooling louvres in the body than many of its competitors The W13 floor has an exit flow condition positioned midway down. This rejects airflow under the car that isn’t in the tunnel flow. Slots further back on the floor edge re-ingest some of the exit flow to work the diffuser and control rear tyre jets Unlike the rest of the grid, Mercedes chose to go with a very narrow packaging concept for this car, wrapping the bodywork extremely tightly around the driver cell and power unit
giving us some freedom. We certainly had a lot more packaging work to do in 2022.
‘The cost cap also drives this because you don’t want to reinvent every bit of the car every year. So, much of our thinking over the winter was about how we could develop a car where much of the architecture and critical systems could carry over from year to year. That drove more work on packaging than the aerodynamic regime.’
‘We’ve come through the 2022 season so far with a huge amount of humility,’ says Elliott of the learning journey into this new era to date. ‘We have looked at all the other car solutions on the grid, investigated how other teams have arrived at their solutions and wondered if any of them are better than ours.
It’ll be interesting to see how the cars turn out next year with all the lessons of the first season of this regulation set behind us.
‘The most significant thing we have learnt in 2022 is how to go about adapting to a new rule regime, and figuring out how best to find a performant compromise in adverse circumstances. We’ve learnt how to find the right operations approach to finding performance in a very different type of Formula 1. Without giving too much away about what we did wrong in the first place, we’ve learnt and adapted to this new F1.’
Earlier this year, the World Motor Sport Council confirmed there would be alterations to the 2023 technical regulations, citing driver safety as the main reason for the adjustments. These changes include raising the floor edges by 15mm and raising the diffuser throat height. The diffuser edge’s stiffness will also increase, and there will be a mandated sensor to monitor porpoising more effectively.
As to how the rule changes for 2023 will affect Mercedes’ performance, Elliott says; ‘the raised floor edges are probably the main thing that will affect the car aerodynamically, and this will influence performance. I think that’s going to keep the floor edges off the ground in the high-speed sections, and I think that, generally, it will be helpful for most teams running the car really low.
‘On the flip side, to recover the lost performance from that, we’ll have to see which way drives us, whether to run the car lower or see a re-design. Running the
car lower could end up back in the same order with the same problem, but we will investigate that. 15mm is not a huge move.
‘We’re still going to have ground-effect cars, and they’re still prone to underfloor flow field instability. If you’re not careful with how you deal with that aerodynamically, you’ll still have the same problems.’
The 2023 car, Elliott admits, will see a different design to the current W13, succeeding Mercedes’ investigations into the aerodynamic concepts of the other teams lined up on the grid.
‘Normally, in a set of rule changes, as the rules get fixed – and they’re fixed for longer and longer these days – the teams tend to converge. I think the intention of the new rules and the cost cap was to try and constrain the grid, though the front three teams are as far ahead as they have ever been. Whether that will change in time, we will just have to wait and see.
‘If you look at Ferrari, Red Bull and Mercedes, the three quickest teams, they all look very different. The logical thing is to copy the quickest one, which, unfortunately, is Red Bull. But you can’t just photocopy a car and suddenly jump to the front of the grid. It doesn’t work like that. It’s more about trying to understand what people are thinking and their approach, which will converge a bit and maybe the teams will move together, but I don’t think it’ll be next year we see parity. I think it will take a few years.’
‘The most significant thing we have learnt in 2022 is how to go about adapting to a new rule regime, and figuring out how best to find a performant compromise in adverse circumstances’The Mercedes W13 ran a dual beam wing and pullrod rear suspension to leave as much space as possible to make the most of the car’s rear-end aerodynamics. This could all change for 2023 though
Many involved in motorsport will be familiar with the name Rob Schirle. For quite a while he was a very capable driver, competing successfully in karting and then excelling in one-make championships in the UK in the early 1990s, before graduating to international GT racing and Le Mans. He was also a well-known team boss, his Cirtek outfit at the forefront of GT competition for a number of years.
These days, though, you will not see his name so often in the motor racing press, yet Schirle is probably more involved in motorsport now than he’s ever been.
Name any top-line motorsport discipline and the chances are Schirle’s Protec fuel systems concern has some involvement in it. Indeed, its products are found in WRC, NASCAR, IndyCar, WEC, F2, F3 and Formula 1 (where they are chiefly employed in pumping the fuel from the cars), while the company equips the majority of fuel cell / system manufacturers.
It also supplies numerous manufacturer motorsport departments, including Porsche, VAG, Hyundai and Subaru. And then there’s the high-performance road cars, supercars and hypercars, not to mention powerboats, drag bikes and even tractor pulling machines.
Before he became a market leader in fuel pump technology, Rob Schirle was a successful racer, seen here sharing this Lister Storm with Ian Donaldson and Gregor Fisken at the 2004 Spa 24 Hours
To put it another way, Protec is pretty much involved in everything to do with motorsport.
But how does someone go from being a team boss to a businessman and engineer, developing and marketing fuel pumps and systems?
‘Running the team meant I had plenty of contacts within the industry, and also plenty of experience working and running systems,’ says Schirle. ‘I think that was a really good grounding for some of the stuff I’m doing now.
‘But how Protec came about was that I lost my father [Hans Schirle] and so took a year out and thought about what I was going to do. So it was a clean sheet of paper. What did I think could be done better, looking back on all my experience with the team? I literally started from the front of the car and worked back to the rear, and I seemed to keep coming back to the fuel system, especially the fuel pump.
‘I also asked myself at that time, what hasn’t changed on a racecar for many years?
‘I also asked Adrian Newey, because Adrian and I were both racing in historics then, and he said the same thing – the fuel pump.
‘The Bosch 044 pump had been around for a long time, and nobody had improved on it. I thought, well, I’m onto something here. At the time I didn’t really understand how the pump worked, and I didn’t understand how to design a pump, I just thought we had to be able to make something better if it hadn’t been improved in all that time.
‘So, that was my first task, and it proved to be quite an interesting experience.’
Fuel pumps have become quite a talking point in motorsport recently, because of the issues that hit Red Bull in the Bahrain Grand Prix. This highlighted not only their importance, but also their complexity, though that should not be surprising, given the work they are asked to do.
In essence, this is taking the fuel from the cell and sending it to the fuel metering system. But it must be delivered at exactly the right pressure for the whole range of engine speeds and loadings, while the car’s attitudes while it is cornering, accelerating and braking also need to be considered. It must do this without leaks in the system and without allowing air in, while always keeping the fuel at the required temperature.
Designing and manufacturing a fuel pump, or fuel system, is quite a challenge then.
And it has become even more so in recent times, with the introduction of biofuels, such as ethanol, which have created a range of new problems for fuel system manufacturers to address. For example, ethanol can eat
away at the metal parts of a fuel pump’s motor, eventually causing them to fail. With an increased use of biofuels in motorsport looming on the horizon when Schirle was setting up the company in 2010, it was clear that addressing this issue was a priority.
‘I started to look into the change of fuels, and the demands the use of EFI and everything else were requiring, and I saw there was a massive hole in the market,’ recalls Schirle. ‘I could see the gradual movement towards ethanol-based fuels, and an increase in toluene and benzene coming into fuels, so we concentrated on brushless motor technology to begin with, as this is a way to counter the issues the newer fuels can cause.
‘Brushless motors have other advantages, too. They are more efficient, they are lighter, and you generally get more bang for your buck. You’ve also got no brushes to wear out.’
The company’s first work was with NASCAR, during the series’ switch from carburettors to fuel injection. Schirle helped design the new system, alongside NHRA fuel pump guru, Sid Waterman, and after that it launched its 340 pump into the wider market.
‘That was our first big break,’ says Schirle. ‘We designed the 340 as a replacement for the Walbro 255, and we’ve now sold around 100,000 of these pumps. It was one of the biggest sellers that [fuel system provider]
Aeromotive have ever had. And it’s still a core product now. It basically just completely changed the marketplace within a year.
I asked myself at that time, what hasn’t changed on a racecar for many years?
‘That put us on the map, and gave us funds to develop the brushless range. And, within the market at least, we became well known.’
From there, the company has gone from strength to strength but, despite all its high-level success, is no smoked glass atrium packed with art installations sort of concern. Rather, it’s run from a nondescript unit on an industrial estate in Burton-onTrent, UK, usefully close to Donington Park.
What’s more, there are no production lines, just a clean room-type space that seems more laboratory than factory, where the pumps and pump assemblies are expertly built by a key member of staff, Mark Heaton, the assembly builder. Before coming to Protec, Heaton worked at Premier Fuel Systems, with which the firm works closely, for around 20 years. He pieces together components made offsite by trusted suppliers with some now 3D printed in-house, assembling pump systems that will typically include a power source, level sensor, filter and regulator, all designed to fit snugly into a fuel cell.
Other members of the team at Protec include Andy Green, who designs the products on CAD, and Liza Wong, who runs the office and the shipping operation. There are a couple of other people involved in day-to-day activities, as well as motorsport engineering students, currently including Green’s brother, Kris, who will often help with the testing. Schirle’s wife, Mandy, is an integral part of the business, too.
It’s a small team, but Schirle would have it no other way. ‘It’s almost fighting expansion, in a way,’ he says. ‘We don’t want to expand, we want to stay niche and focused.’
This is partly down to keeping a firm grip on quality control, but Schirle also feels
comfortable with the size of the business, its location, and the sector he is working in.
‘I think this is what Great Britain does best. And motorsport in particular. We have a huge pool of small firms like this. It is very much a specialist industry, that’s for sure.’
It’s also very much a specialist product, as Schirle readily admits, though he insists there is much more to fuel pumps than people sometimes realise.
‘What I find strange is, when you say, “I do fuel pumps”, people think it’s quite a boring little thing. But when you get into it, it’s not boring at all, and with some of the stuff we’re doing here we’re
really pushing the boundaries of what’s possible, and we always want to do that.’
The main way Protec is doing that right now is by embracing some game-changing technology, which has partly arisen from the groundbreaking approach the firm took from the start, which is to supply individual components when required, rather than just complete replacement fuel pumps. Now, with the onset of additive manufacturing, this has gone a step further.
‘We’re the first to launch commercially, 3D printing into the fuel market,’ says Schirle.
‘We’ve partnered with Spanish company, BCN3D, to do it, and one of the reasons for partnering up with a printer manufacturer is because for these parts, the G code [the commands for the printer], the slicing and the material must be 100 per cent right.
‘We’ve also partnered with Italian firm, Filoalfa, which supplies the filament [the printing material].’
Now, in the corner of the workshop there sits an Epsilon W27, one of three 3D printing machines in which Protec has invested.
‘It means we’ve got the ability to just print what we want for a specific application, and it is also changing the way we look at the design of fuel systems,’ says Schirle. ‘I think what we’re doing on the 3D printing side could get quite big quite quickly. What I envisage is that we have people signed up to the system, and we then make it easy, and make it repeatable, for them.
‘It’s a massive benefit to us, and to our customers. Instead of having to send off for what can be quite a bulky item, customers can just stock the pumps, and then they can print the rest themselves. All they’ve got to do is buy the machine from the manufacturer [which, at around £6000 (approx. $7350), is relatively cheap] – and they can also use that machine for anything else they want to do –and then we send them the G code and they can print out the part anywhere in the world.’
Manufacturing products this way can work out much cheaper, too.
‘Whereas it used to cost us x amount to make an aluminium bush, for example, we can now do it in house and it costs a fraction of what the aluminium did, but it still does exactly the same job. And you’re only printing the material you use, so there’s no waste.’
However, there are limitations, as Schirle explains. ‘It’s that understanding of what you can print, because you can’t print everything. Safety is obviously paramount to us, and at the moment I don’t see having 3D printing on the pressure side of this, but maybe that will come in the future. I think
injection moulding for an aluminium part is currently better there. But again, the design advantages of this means we can, for instance, print things out just to get proof of concept, and that’s a good thing. We may print something, and then think actually, it’s good, but we’re going to make it in billet.’
But the principles behind designing a fuel pump remain the same, even with 3D printing to help.
‘It’s about efficiency,’ notes Schirle. ‘Reducing the heat to make the system efficient. Often, the first thing we talk through with a customer is the pressures. Because pressures vs flow, there’s a massive difference. As the pressure goes up, the flow will come down. And in some instances, you’ll get pressures up to 10 and 11bar, which is really quite high.
‘I think that’s where our pumps score. In fact, we’re confident our brushless Cobra pumps give the most amount of output for flow with the least amount of amperage, for higher pressures.’
It’s also important to remember that, however good the pump is, it will only be as good as the system it is part of. ‘You can put the best pump in the world into a bad system and, if the filter isn’t rated accordingly, or the regulator, you can create massive problems. Some of these pumps flow so much fuel that if you haven’t got a filter, or regulator, strong enough to bypass, or to flow, then all you’re going to do is create a lot of amp draw, the pump head pressure will go up dramatically and the rest of the system can’t cope with it. It’s that overall understanding of the flow and volumes involved that is vitally important.’
Of equal importance to Protec is quality control. All pumps are tested on the company’s array of flow rigs using Flowrite fluid (made by leading fuel injector supplier, ASNU, another company Protec works closely with).
‘Flowrite gives us the same specific gravity as fuel, but without the flammability,’ explains Schirle. ‘And every single pump we make gets tested here before it leaves the factory. That’s something we’re very rigid with.’
There are quality checks on product aesthetics, too. Even if a part is destined to spend its life tucked away in a fuel cell, neat engineering intricacies and smart finishes are at the core of all Protec’s products.
‘I want people, when they pick something up of ours, whatever that product may be, to think that somebody has really thought about that, how it looks. I think that’s really important,’ says Schirle.
This approach probably comes from all those years running racecars but, even before he reached the car stage of his racing career, Schirle believes he learnt many things that are still put to good use today.
Things I learned when I was building kart engines, those fundamental basics, are still applied here todayEpsilon W27 3D printing machine. Additive manufacturing technology is revolutionising the way Protec can service its customers and design its products
‘It’s amazing, but things I learned when I was building kart engines, those fundamental basics, are still applied here today. When balancing the motors that go in the Cobra pumps, I still use a knife edge, and we do still balance the motors, because we understand the benefits. If you balance a motor really finely, it will run smoother, and those basic facts are core to everything we design.’
Yet for all the motorsport background, and the undoubted benefits it brings, much of the development at Protec is about seeing what’s currently available in OEM, and then adapting it for motorsport and performance applications. A great example of this is the syphon jet Protec has developed.
To explain, one of the toughest tasks a fuel system faces is dealing with surge – the fuel sloshing around in the cell during hard cornering, acceleration or braking – which can move it away from the pick-up, meaning the pump will potentially just suck in air. Scavenge pumps are often used to counter this, but Protec’s syphon technology, which works a little like a drinking straw, albeit with much more advanced fluid dynamics, has proved it is possible to do away with the need for lots of scavenge pumps.
‘Basically, we’ve taken the best OEM system, and made it useable for motorsport,’ says Schirle. ‘It collects fuel from one side of the cell, or from a corner, and moves it to the collector area. It’s a very efficient way of making sure the fuel is always where you want it, and that’s key in a fuel system. It means there’s not such a need for additional lift pumps, while it also doesn’t need electric power, as it pulls the fuel without power [300 litres per hour, in fact].
‘It’s very simple and very clever, with the fuel passing through a Bernoulli system that creates a negative pressure, which then sucks more fuel in.’
Fuel pump assemblies incorporating syphon jets are just one product among many supplied by Protec. The company also sells full fuel systems, fuel cells and all the components associated with fuel, from filter socks through brackets, valves and couplings. But pumps remain the focus.
‘The number of pumps we make each year just seems to increase all the time,’ says Schirle. ‘We supply a lot of different companies, but we’re pulling back a little bit from having other company names on our product now. We don’t want to do so much customer-branded stuff now Protec is a stronger brand, so a lot of our product has the Protec name on it.’
New technology that might bear that brand name soon includes, ‘controllers that are CAN bus, so fully integrated, and will accept PWM [pulse width modulation, which helps keep the amperage low in brushless motors]. They’ve got diagnostics built in. That’s something that will be coming out next year. So, it’s just staying ahead, and just watching for little changes.’
But what about the big changes? What will a fuel pump company do in a world of electric cars and electric racing?
‘They still need to cool the battery packs,’ says Schirle. ‘And, when you think about it, we’ve got a pump that would only draw about one and a half to two amps. With an electric vehicle, if you’ve got a heavy amperage motor, or pump, or heater, or anything, it’s taking from that core source of energy. So, if you’ve got a pump that can move the coolant around but only use one and a half amps, it’s a better solution than a pump that uses five or 10 amps.
‘There are always ways for us to supply our technology because our brushless motors don’t care what they drive. It could be an impeller for a water pump, it could be an impeller for a dyno pump, or for a 1000bhp car. If it uses less power, it’s better. It’s more efficient.’
Of course, the future is not just electric, and it seems likely synthetic fuels will also play a large part, especially in motorsport.
‘That’s something we keep at the forefront of our minds,’ Schirle says. ‘In fact, we’re in discussions with synthetic fuel companies now. We know who’s developing it, and we want to be able to test it, and do material tests, both for our own benefit with the pump, but also with Premier Fuel Systems. They want to test the material for the bladders, because it has a knock-on effect for not just the pump, but everything you use in a fuel system: the hose, the regulators, the diaphragms, everything can be affected by a new type of fuel.’
Fuel pump design and manufacture is clearly far from ‘boring’. It’s about keeping ahead of the competition, and abreast of technology. Which, when you think about it, is exactly what Rob Schirle was doing when he was a race driver and a team boss. Maybe some things don’t change so very much, after all?
If it uses less power, it’s better. It’s more efficientThe evolution of an in-tank fuel collector, from cardboard prototype through iterations of 3D printed versions to the final design on the right Typical fuel pump modules. Note the flexible tubes: one system has a single syphon jet pick up (left), while the other has two
Intercomp’s RFX® HubScale360™ Wireless Scale System is the Industry’s first vehicle alignment system with selfcontained wireless scales. Bluetooth® Technology is included with all RFX® Wireless Scale Systems and securely displays live weight data from the indicator to the user’s Bluetooth ®-enabled mobile device with the Intercomp iRaceWeigh™ app installed.
Mario Andretti finished a creditable third at the wheel of the Cosworth V8-powered Lotus 80 in the 1979 Spanish Grand Prix at Jarama, but the car had yet to show its nasty side
Following the first 2022 F1 test at Barcelona in March, the paddock was forced to dig into the archive and produce a term that has been gathering dust for over 40 years, ‘porpoising’.
In the late 1970s, Team Lotus was deeply into the development of ground effect: T78, the original, skirted ground-effect car had lots of downforce, good; T79, more downforce, better still; T80, even more downforce, yet almost undriveable…
As Lewis Hamilton has commented with reference to his Mercedes W13; ‘whatever we do makes no difference.’
Those words brought memories flooding back of the desperate days of Mario Andretti trying to tame the porpoising T80, to no avail. I recall well that test day at Silverstone where we equipped him with a tape recorder to give us a running commentary, and when we played it back, his strained voice noted, ‘I can see daylight under the front wheels!’ as he ran down Hangar Straight at speed.
Initially, the car had flattered when Mario finished third at the Spanish GP in Jarama with its short straights and many slow corners. But by mid-season, the car was abandoned in favour of the older T79s.
Racecar examines the Lotus T80 of 1979, the first Formula 1 car to exhibit the supposedly ‘new’ phenomenon of porpoisingXPB XPB The term porpoising is everywhere in contemporary F1, and some teams are struggling more than others to deal with it, yet it was a well-known phenomenon in 1979…
Akin to flutter on an aircraft; the dynamic instability of a structure associated with the interaction of aerodynamic, elastic and inertial forces
The T80 was designed to exploit the underneath of an F1 car to the maximum. From the radiator intakes to the extreme rear of the car was shaped as a venturi, terminated by a large flap. No rear wing was fitted. The under surface of the wide nose was another venturi, and no front wings were planned. Both the nose and main undertray were fitted with sliding skirts, the main skirts being curved to pass between the rear wheels.
Quite early on, front and rear wings were added to generate a contribution to downforce that was independent of the car’s attitude relative to the ground, and which was unaffected by skirt performance.
The previous T79 was designed with allenclosing sidepods housing the radiators and exhausts, and forming the venturi and diffusers. The skirts were mounted to the outer edges and the cars suffered overheating of the exhausts, which then cracked. The drivers lost power, but still won.
The following year, Williams built its first ground-effect car, and made the sidepods in a simpler way with the skirt boxes forming the sides, supported on frames, with top and bottom skins. These could not only be quickly removed for access, but easily re-designed as aerodynamic development progressed.
The T80, by coincidence, followed the same design philosophy based on the experience with the T79. The car
was launched with fabricated titanium suspension, which was quickly changed to steel following cracking in early testing.
Before too many parallels are drawn between the porpoising T80 and the current porpoising F1 cars, it should be noted that the cars in the late 1970s were fully skirted, and the tyres were Goodyear crossplys that grew in diameter with speed, raising the car. Also, suspension rates were of the order of 300lb/ in ie 50+N/mm – way down on today’s rates. Finally, top speed was significantly lower at under 300km/h compared to 350km/h today.
To help develop the T78 and T79, Team Lotus commissioned a chassis data system from Cranfield’s flight instrumentation department. Based on a system developed for a Neil Williams aerobatic aircraft, it stored data on a cassette tape, sometimes. We knew we needed such data to enable correlation between track and wind tunnel, and to monitor the performance of the skirts, in particular the effects of wear.
By the time the T80 came along, it had become routine to fit the data system for tests, although the mechanics didn’t really like the wires and sensors all over their cars. David Williams, head of the flight instrumentation department, brought his aeronautical experience to bear on the T80’s problem and advised that the phenomenon was akin to flutter on an aircraft: the dynamic instability of a structure associated with the interaction of aerodynamic, elastic and inertial forces. In other words, an aeroelastic issue.
Flutter affects aircraft structures, especially wings, but also bridges and tall chimneys, and often results in structural failure. The T80 was heaving and pitching on its springs and tyres, excited by changing aerodynamic forces as it moved relative to the ground. At higher speeds this caused resonance in a mode involving both heave and pitch.
On aircraft, this is limited by imposing a VNE (velocity never exceed), but that’s clearly not a suitable solution for a racecar!
So, at the end of 1979, we took a T80 to Ricard for a winter test, and Stephen South drove the car with some extreme modifications to see if we could better understand it. The amazing thing about working for Colin Chapman was that if something failed to work as expected, he didn’t just dump it; he could recognise a technical barrier and wanted to overcome it to hopefully achieve technical supremacy. There were not many like Chapman.
The T80 was heaving and pitching on its springs, excited by changing aerodynamic forces as it moved relative to the groundColin Chapman and Team Lotus recognised the answer to the porpoising problem was to separate the two main functions of a racecar suspension, giving each its own set of characteristics Classic Team Lotus
Once we had initiated Stephen with a porpoising T80, we fitted it with the stiffest springs we could, some three times the normal rates. Ricard is pretty smooth and Stephen reported that the car was not porpoising, was pretty nice to drive and had plenty of grip, but he had trouble keeping his feet on the pedals. That set us thinking.
What the car’s aerodynamics wanted was the minimum attitude change relative to the road, but what the main masses of the car wanted was isolation from road disturbances. In technical terms, the two main functions of a racecar suspension needed separating, each given its own set of characteristics.
The forces due to inertia – cornering, acceleration, braking – along with aerodynamic downforce and fuel mass changes should be reacted according to the vehicle dynamic needs, and the road disturbances minimised in terms of sprung and unsprung mass modes. To do this completely requires an active suspension, where the different inputs to the suspension are sensed using accelerometers, load cells, displacement transducers, air speed etc, and the hydraulic suspension reacts according to algorithms and control loop gains.
This was more than Team Lotus was capable of in 1980, though work started on such a system in 1981. In the meantime, a car with two chassis and two suspension systems was developed: the T86 mule car, which was then followed by the T88.
The approach taken with the T88 was to give the body its own suspension system, such that the aerodynamic downforce it and the wings generated was reacted by its own suspension, attached to the wheel hubs.
As speed increased, the body lowered until it was virtually directly connected to the wheels. As speed reduced below that of racing speeds, the body slowly rose (high rebound damping) to a legal height, as measured with the car stationary.
The T86 ran successfully in testing in the autumn of 1980, in great secrecy. Ferrari, however, got wind of it and stimulated a rule change that banned cars with no suspension. That rule still survives today!
At around the same time, the FIA decided to ban sliding skirts, and we realised we had a concept that was perfect for this new regulation, so proceeded to the T88.
When it appeared at Long Beach, our competitors realised what we had done and made sure it was never allowed to run in anger. Would it have worked? We never had the chance to find out, but it didn’t porpoise!
While Chapman licked his wounds, he okay’d a move to plan b – active suspension.
T80 was
during use
This completed the job of separating the functions of the suspension, and also proved a solution to porpoising, but was also banned at the end of 1993.
So how come, 30 years later, porpoising has become a buzzword in F1 and has brought World Champions, Mercedes, temporarily, and unexpectedly, almost to its knees?
Since 1983, Formula 1 cars have been mandated with flat-bottom undertrays with a short diffuser. The aerodynamics that control the flow under the car evolved to the amazingly complex detail of bargeboards, vanes and vortex control devices that culminated in the 2021 cars.
To control the way the cars move relative to the road, sophisticated front and rear suspensions have been developed, banned, and re-developed, incorporating ride height control systems and inertial dampers.
As a result, the cars remained stable and did not porpoise. But for 2022, with the good intent of reducing the wake of the cars to facilitate overtaking, the regulations defining bodywork were re-written following major CFD and wind tunnel programmes by FOM. Each team then took the new regulations and performed their own safety and wind tunnel development programmes to find out how to get the most out of these regulations.
Part of the new concept was to reintroduce a degree of venturi shaping to the underside of the cars, ‘powered’ by a large diffuser. Why, then, did the threat of porpoising not make itself apparent during all these hours of wind tunnel testing and teraflops of CFD analysis? Or did it?
Compounding the problem of the whole vehicle becoming unstable in heave and pitch are some other changes to the regulations: 18in wheels and low profile tyres, and a ban on all forms of ‘tricky’ suspensions, including ride height control devices and inertial dampers.
Both wind tunnels and CFD generally assess static or quasi-static characteristics.
For 2022, with the good intent of reducing the wake of the cars to facilitate overtaking, the regulations defining bodywork were re-written
To assess how these characteristics interact with the inertias of the sprung and unsprung masses, and all the springs and dampers in the suspension and tyres, requires extremely complex dynamic modelling.
To just model heave and pitch requires a fourdegree of freedom model. But add bodywork and wing flexibility and the number of degrees of freedom goes up. Then add nonlinear and dynamic aerodynamics, and even the best model will only be as good as the input of aero and tyre data.
Once a model with all the above characteristics and inputs that influence porpoising is developed, it requires validating. This can be done by comparing the model outputs with data from sensors mounted on the car during testing, but is only possible once the car is available.
Alternatively, a seven-post shaker rig could be introduced. For this, a previous year car could be used as only the inertias, suspension and tyres need be representative, and the proposed aerodynamic characteristics are input to the two aero force and moment ‘posts’. Most seven posters apply aero, downforce and pitching moment loads by two low-rate springs, the preloads of which are controlled by actuators. However these actuators are usually slow response, simply used to set the aero loads for a given test.
To validate the dynamic changes to the aero load as the car moves in heave and pitch requires high response actuators with load feedback. Such a facility may not be available.
Given all this, it can be better understood why porpoising was perhaps not anticipated in 2022, unless a senior and suitably experienced engineer foresaw it. It is
interesting to note that Red Bull with Adrian Newey, and Ferrari with Rory Byrne, seem to suffer less from porpoising, and also display the most performance.
In F1 racing terms, the T80 can only be described as a failure. In spite of its one podium finish in the hands of Mario Andretti, it was stood down from Team Lotus’ championship challenge mid-season. And yet it was an essential part of the intense aerodynamic development that started in the 1960s, gained momentum with ground effect in the 1970s, and continues to this day.
Having found out how to exploit ground effect, Team Lotus reached the limits of how much conventional suspension systems could control it. The T80 showed the target was no longer simply more downforce, but an integrated vehicle that generated downforce and managed it throughout the speed range. At the same time, the FIA set out to limit the magnitude of available downforce, firstly banning moveable skirts, then setting a minimum gap to the edge of the body, and finally, in 1983, mandating flat bottoms.
What emerged from all this was an aero configuration that didn’t generate so much downforce that there were safety issues, nor did the cars porpoise, but where the flat bottom was critical to the attitude relative to the road, resulting in the need for very stiff suspension. This incentivised the development of full active suspension (Team Lotus) and semi-active suspension (Williams).
If Peter Warr, team principle of Team Lotus following Chapman’s death in 1982, had continued to fund the team’s development of active suspension beyond the first races of ’83, it could have been way ahead of the field.
Instead, by the time Gerard Ducarouge and Ayrton Senna requested it for the T99T in 1987, Williams had commenced work on its own semi-active system based on Automotive Products’ road car suspension.
Peter Warr again dropped the Team Lotus system for 1988, while Williams continued to develop its system to dominate in 1993, after which the FIA banned it.
The basis on which all active suspensions were banned was they influenced aerodynamics. The next decade saw some very clever passive suspension systems that served everything from the high-rake Red Bull to the low-rake Mercedes. All banned for 2022, just as a new aerodynamic configuration was introduce that really needed these sophisticated systems.
Surely now would be a good time to consider allowing a limited form of active suspension. It could be semi-active, and have both physical and algorithm limitations. With hydraulic systems already fitted to F1 cars, cost could be kept under control, and the issues that have re-emerged eliminated.
The T80 will never go down in history as a successful Formula 1 car, but its influence on the sport was far from insignificant.
The T80 showed the target was no longer simply more downforce, but an integrated vehicle that… managed it throughout the speed rangeXPB The Adrian Newey-designed Williams FW15C had semi-active suspension and dominated in 1993. It is perhaps no coincidence then that Red Bull appear to better understand the porpoising issue