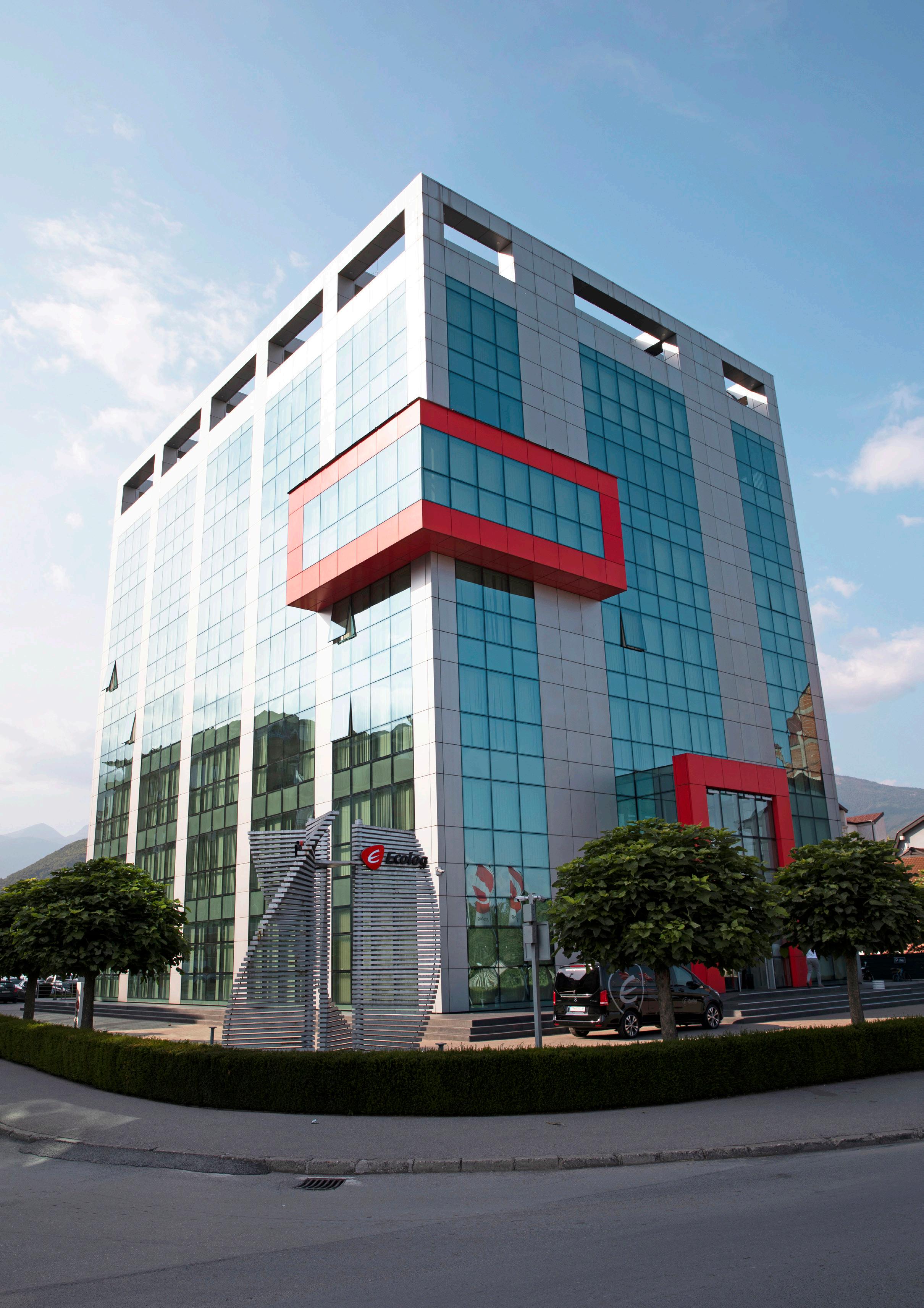
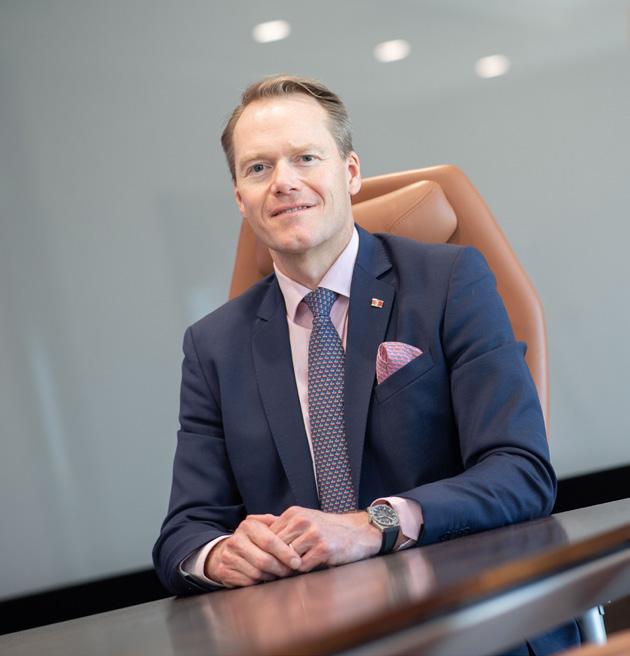
MARK BAILEY m.bailey@ceomediagroup.com
ANDREW BOURKE a.bourke@ceomediagroup.com
DEAN BROWN d.brown@ceomediagroup.com
CHRIS CONWAY c.conway@ceomediagroup.com
DAVID GARNER d.garner@ceomediagroup.com
TIMOTHY GARWOOD t.garwood@ceomediagroup.com
DAVID HAYVIS d.hayvis@ceomediagroup.com
JOHN HOLLIMAN j.holliman@ceomediagroup.com
HARRISON MITCHELL h.mitchell@ceomediagroup.com
ROBERT NAPIER SMITH r.smith@ceomediagroup.com
LIAM PYWELL l.pywell@ceomediagroup.com
JAMIE SIVYER j.sivyer@ceomediagroup.com
DAVID TAVERNOR d.tavernor@ceomediagroup.com
HAYDEN TURNER h.turner@ceomediagroup.com
RASH UDDIN r.uddin@ceomediagroup.com
ALICE YOUNG a.young@ceomediagroup.com
DESIGN
SCOTT ANDREWS design@ceomediagroup.com
ADRIANA STROIA artwork@ceomediagroup.com
ACCOUNTS
MIKE ASHER
PRODUCTION
KAMILA KAJTOCH
EDITORIAL
CHRIS FARNELL
SALES & MARKETING DIRECTOR
TREVOR GRETSINGER
SUBSCRIPTIONS, PRESS RELEASES AND GENERAL ENQUIRIES:
Business Focus Magazine profiles a wide array of companies across every industry sector, and while the challenges and opportunities vary wildly, there are sometimes recurring themes. One such theme that has come up again & again since the pandemic is the new challenges arising in recruitment.
The pandemic lockdown led to people spending more time with their families, learning how much they can get done working from home, and reassessing their priorities and their lifestyle. Employers have responded by offering more options in terms of flexitime and remote working where possible, but it is not always.
In this issue, we have investigated the challenges facing the hospitality sector in terms of recruitment and retention, and how the industry is responding to those challenges. We also profile businesses operating across the hospitality sector, including the hotel grounds Leonardo Hotels and Serena Hotels, as well as MITEC, the Malaysian International Trade & Exhibition Centre.
As well as recurring challenges, our conversations with business leaders will also often find they hit upon the same solutions. For instance, in terms of talent retention, skills development, particularly around new technology and the digital sector have been seen to be a common priority among employees. This issue contains profiles of both K2 Data Centres, and Caseware International, covering their applications of the latest cloudbased and digital solutions.
Another comment we keep hearing about the latest generation of employees is that more than
their predecessors, ethics, and particularly environmental issues are particularly close to their hearts. Companies which are playing a constructive role in the energy transition are a particular draw for new talent, such as Alexander Battery Technologies and LBC Tank Terminals, both profiled in this issue. Companies that have a social benefit, such as Afrigen’s efforts to create a homegrown pan-African vaccine infrastructure, are also seen as appealing employers.
Whether it is through skills development, environmental or social benefits, what it comes down to is we spend most of our days at work, and so we want to feel like what we are doing is worthwhile.
Ecolog International
Go to page 70
Strategically taking place before COP27, ADIPEC is the global platform for leaders to reinforce commitments that will drive the industry towards reducing emissions, meeting decarbonisation goals, and providing a realistic view on short- and long-term energy outlooks.
More than 150,000 energy professionals from 113 countries worldwide will come together to explore market trends, source solutions and conduct business across the industry’s full value chain.
ADIPEC 2022 is where the world’s energy ecosystem – including 2,200 exhibiting companies, 54 NOCs, IOCs, NECs and IECs and 28 international exhibiting country pavilions –will come together between 31 October to 3 November, to explore market trends, source solutions and conduct business across the industry’s full value chain.
Alongside the exhibition, ADIPEC 2022 will host the Offshore & Marine Exhibition
and Conference, Digitalisation In Energy Exhibition and Smart Manufacturing Exhibition and Conference. These dedicated exhibition and conferences will enable the global energy industry to strengthen existing business partnerships and form new models of crosssector collaboration to unlock and maximise value across businesses and drive future growth. www.adipec.com
Today, Internet is in our pockets; our virtual and real worlds are coming together. LTE offers you great potential to deliver a superior mobile broadband experience to your customers, but the stakes are high. Success in LTE means getting to market quickly, with services that offer subscribers more than what they have today, as cost efficiently as possible. With 60 live commercial LTE networks on all continents and about 50% of all smartphone traffic on LTE running through our networks, we have what it takes to support you.
ericsson.com/unplug
No matter whether in real estate construction, tunnel ling, bridge building, exploration and evaluation of raw material deposits of any kind, further development of your mining operations or unveiling geothermal po tential, precise and reliable knowledge of the nature of the subsoil always plays a decisive role.
Just call DMT. We know the world and its ground like no one else and offer profound insights based on 282 years of practical experience and foresight.
The broad range of services, innovative techniques, flexibility and solution orientation – all from one source –supports you to make the best out of your project.
We call this Engineering Performance
We are approaching the third anniversary of the outbreak of the Covid-19 pandemic, and yet many industries are still coming to terms with the impact of the crisis. Few industries were as affected by the pandemic as the hospitality sector. With everyone locked down and at home, hotels were forced to either close or were reduced to providing emergency accommodation for people who needed to travel.
Since lockdown restrictions were lifted, the industry has worked hard to welcome people back to hotels and make them feel comfortable and safe there. The efforts have largely been rewarded as well; customers who have spent over a year stranded at home are eager to start travelling again.
However, there is another group it has been harder to lure back into hotels. Workers.
Hospitality is not the only industry to have seen this phenomenon.
“Working from home during lockdown caused people to look at their lifestyle and what they want to do,” says Greg Kingham, CEO of manufacturing firm Camvac, profiled in this magazine. “That has attracted people into other roles. We
have lost a few people from Camvac, and finding good quality people, with the right skill set, that’s also a challenge. We are making progress. It is changed our outlook slightly on things, and we are looking proactively at future strategic recruitment strategies.”
Other industries a responding in a range of ways, from establishing in-house recruitment and HR departments, to allowing for great flexitime and remote working opportunities. But while remote working is a great solution for office work, it is not a solution that works for making beds or serving in restaurants, and flexitime is more of a challenge when you have to balance shift work to ensure your hotel is always staffed appropriately.
“This generation is looking for jobs that are more flexible or allow for more virtual work, which you can’t do as a server, but backof-house work can be done from home, with more flexible hours,” says Ronen Nissenbaum, CEO of the Fattal Hotel Group in Western Europe. “Pay levels for most employees have increased but money is only one element. How do you treat them? Do we give them a purpose? Do we meet their needs for a good work-life balance?”
We discuss the recruitment challenges facing the hospitality sector in this issue’s interview with Nissenbaum.
“All the industries are facing shortfalls in recruitment, especially in the more linelevel employee areas such as receptionists, cooks, servers, and housekeepers,” Nissenbaum acknowledges.
“The market has forced us to adjust the way we hire, be flexible and considerate to the requirements people are looking for in the workplace.”
The fact is that in a postCovid environment, the pool of potential talent is coming to the table with a different set of expectations from the prepandemic workforce.
But as well as having more demands than pre-pandemic workers, potential recruits are also facing greater challenges than their pre-2019 counterparts.
While hotels face escalating energy costs and a supply chain slowdown, so are their employees and potential employees.
“We’re all grappling with how difficult it is for team members,” Nissenbaum says. “In the same breath, you can talk about inflation, utility costs are surging, buying bread and milk,
chicken, and other essentials, all are increasing dramatically. One of our biggest challenges is attracting talent- but also the additional costs that come with running hotels.”
While the new generation of workers has problems of their own to contend with, they are also more concerned about wider issues in the environmental and ethical spheres.
“We’ve recognised that doing the right thing, not only by your employees but as a company, is essential,” Nissenbaum says.
“It relates to whom we hire. They want to know what we are doing, that we are a company with a conscience. The younger generation, more than any other generation, are asking about what we are doing to make their world better and more sustainable.”
It is not enough for companies to attract new talent, however. For a company to succeed it needs to keep hold of the people it has. This is something that Frank Olsen, the CEO of Inchcape Shipping, was keen to highlight in our profile of the company in this issue.
“The most important task is retaining the good people we have in the company,” he says. “There is a lot of attrition right now. People are moving jobs and it is a tight labour market. So, it is important not to lose someone who might go to a competitor. We focus on providing a fair and attractive salary and remuneration, but also continuous learning, development, and career progression so that people feel they are developing while they are with us.”
Across every industry, the importance of skills development cannot be overstated. In this issue’s profile of MITEC, the Malaysian International Trade and Exhibition Centre’s CEO, Mala Dorasamy, explains, “Through our plethora of events, MITEC has become a training hub for
youth and students from the higher learning institutions through our MITEC Graduate program. We also provide job opportunities for parttimers who gain a great deal of exposure to the industry, better equipping them with knowledge and experience through culinary and event protocols from local and international events.”
Recent research from Virgin Media O2 Business revealed that a third of UK employees say they do not receive enough training in digital skills, while 55% of workers across the UK’s private and public sectors believe their employer suffers from a 55% shortage in digital skills. The study demonstrates that employees do not just want hybrid working policies and better remuneration, they also want their job to be an opportunity to upskill and advance along a career path.
Mike Smith, Large Enterprise & Public Sector Director at Virgin Media O2 Business, comments, “As UK employers grapple with the impact of the ‘Great Resignation’, our research shows that technology could be the tipping point for many. From concerns about digital skills shortages to outdated tech holding them back at work, the nation’s employees are ready to vote with their feet: and a decision to revert to pre-Covid technologies could see one in two leave their post in the next six months.”
Ultimately, an existing employee is worth more, in terms of expertise, team dynamics, and even financially, than a recruit.
“If someone is with us on a salary, the cost of replacing them is higher. So, retention is crucial,” Olsen tells us.
Stena Drilling was formed in 1996, managing four semi-submersible drilling units working predominantly in the North Sea. That North Sea focus has remained key for Stena Drilling, but in the late 90s the construction and acquisition of Stena’s first dynamically positioned drilling rig, Stena Tay, opened up deep water and subsequently ultra-deepwater basins, worldwide. This paved the way for the business to transition from being a regional contractor to becoming a worldwide contractor.
In 1999, we took delivery of our first deepwater drilling unit, Stena Tay. Based on the success of that, we then built a midwater unit in Germany, specifically for midwater Norwegian operations, Stena Don, delivered in 2002,” recalls Erik Ronsberg, Stena Drilling’s CEO. “Over the years since then, the business has increased in size. We have bought and sold rigs, but the biggest change for our business was in 2005 when we ordered our first drillship. A further three
followed, all from the Samsung Heavy Industry Shipyard in Korea. The first unit, Stena DrillMAX, was delivered on the 31st of December 2007. These are big ships, with capabilities to transit and operate globally. This transformed our business and led to us increasing our staff and support requirements significantly.”
Stena Drilling is privately owned, part of the Stena Sphere of companies. The parent, Stena AB is a family-owned business based in Gothenburg Sweden.
Erik Ronsberg, CEO, Stena Drilling.The Sphere [of companies] includes Stena RoRo, dealing in roll-on roll-off shipping; Stena Line, one of Europe’s largest ferry operators; Stena Bulk, which operates tankers worldwide; Stena Fastigheter, which owns and manages real estate worldwide; Stena Finance, which supports and manages the financial aspects of the group; and finally Stena Adactum, an investment business with a broad portfolio, from kitchen suppliers & windfarms to garden centres & florists. Stena Metall, a separate part of the wider Stena Group, is one of the largest metal recycling companies in the Nordics. All these Stena companies form an ecosystem of which Stena Drilling is a critical part.
Stena Don is a harsh environment semi-submersible unit; suitable for drilling, completion and workover operations.
“We’re a diverse group, with a very engaged owner who is keen to add value for our clients, maintain repeat business and protect the environment around us,” Ronsberg says.
“WE’RE A DIVERSE GROUP, WITH A VERY ENGAGED OWNER WHO IS KEEN TO ADD VALUE FOR OUR CLIENTS, MAINTAIN REPEAT BUSINESS AND PROTECT THE ENVIRONMENT AROUND US.”
While Stena Drilling has seen a great deal of growth, it is still relatively small compared to its peers. However, this also gives the business a great deal of versatility.
“We are privately owned and can make decisions quickly. We have high-value assets which we keep well-maintained, and we have a very can-do attitude regarding finding solutions to our clients’ challenges,” Ronsberg points out.
Engineers onboard the drilship ‘Stena Forth’, drilling off the coast of Peru.
Stena Drilling has been particularly successful in finding solutions following the fallout of both the market downturn in late 2014 and of course in 2020, when faced with the Coronavirus situation. When the market collapsed, many peer companies were forced into bankruptcy and subsequent restructuring, while Stena Drilling stayed whole and retained its talent.
“It has been difficult few years for us, navigating the downturn while keeping the group together,” says Ronsberg. “Of late, Covid created a massive drop in demand and contracts dried up. In order to remain intact, we had to look after our people and maintain our assets.
We managed to keep our strong culture and keep our drilling units ready to go back to work.”
Today, Stena Drilling is in a stronger position.
“We have six drilling units in operation at the moment. We are hoping to bring another into the market soon, although we have not exercised the option for purchase yet, for a small business we have a very wide reach,” Ronsberg says.
“We have just operated a unit off Eastern Canada, now on its way to Egypt; two working in the North Sea; one off Israel and two working off the coast of Guyana in South America. We have managed very well to get these contracts worldwide.”
Micron Eagle Hydraulics Ltd are a long-established hydraulic service and engineering company based in Aberdeen and are delighted to be allowed to support Stena Drilling Ltd in their drive to become the world’s foremost independent drilling contractor.
From individual component supply, fluid conditioning services, hydraulic equipment overhaul, including pumps, motors, and various mechanical equipment, as well as fluid power equipment rental, Micron Eagle’s expertise is available 24/7.
As an ‘Authorised Danfoss Power Solutions Distributor’ along with our renowned capability to identify and source components from all hydraulic manufacturers, Micron Eagle are ideally placed to assist Stena Drilling with most hydraulic equipment supply.
Eagle’s rental equipment fleet has assisted Stena Drilling Ltd on many occasions. Our extensive rental portfolio and our range of fluid conditioning systems are available on flexible terms to match requirements.
look forward to many more years of close collaboration with Stena Drilling Ltd and to further develop our ongoing relationship well into the foreseeable future.
For all your hydraulic requirements, be it motor, pump, gearbox, valve repairs, component supply, fluid conditioning including remote monitoring, contact us for assistance.
Mark Burnett - Business Development Director
Eagle Hydraulics Ltd
/ info@microneagle.com
owned
The world’s first dynamically positioned, dual mast ice-class drillship, ‘Stena IceMAX’.
Of course, the oil and gas sectors are reaching a key turning point right now, and everywhere you go people are using the word “transition.” But what Ronsberg wants to draw attention to is the key role oil and gas will play in that transition.
“We’re a great supporter of the transition to renewable energy, but it has to be done with care,” he says. “There has been a huge focus on
promoting green energy, which we support, with regards to wind and solar power. In fact, one of our sister companies is one of the biggest wind turbine owners in Sweden. But it is important to balance that with just now to provide the oil and gas we need for the transition.”
It is clear from speaking with Ronsberg that sustainability is a core part of Stena Drilling’s outlook moving forward.
“We have a big focus on sustainability and cutting waste. We received ISO 50001 energy management certification last year, which requires us to constantly look for better ways to reduce the fuel we use and reduce emissions at all times,” he explains. “We changed our lighting systems on rigs, installed more efficient equipment, use sophisticated digital solutions to reduce
fuel burn, and are optimising drilling technology to reduce the energy we need to run the units. We have also installed solar cells at our base office to reduce the electricity we require from the grid, which has also been very successful. The majority of these initiatives have spawned from innovations submitted by our people on and offshore.”
is “Care, Innovation and Performance,” which is a philosophy Ronsberg stands by.
“‘Care’ means care for resources, the environment, for people and the way we do business,” he says. “‘Innovation’ means we encourage our colleagues on and offshore to think ‘Could you do something better?’ They do not need to reinvent penicillin, but if there is a better way of doing something we want to hear it. Your crazy idea may not be so crazy when someone else sees it. And finally, there is ‘Performance.’ We need to deliver top performance at all times, to be working at our peak & keeping our clients satisfied.”
This philosophy sounds great on paper, but it is people that put that philosophy into action, and Stena Drilling draws people from all around the world.
“We have a multinational crew on all our rigs. We have reached that point from being a company founded in the northeast of Scotland, where our biggest contingent is from, but regardless of that we always try to give everyone an opportunity,” Ronsberg says.
Once people are part of Stena Drilling, Ronsberg encourages sincere and open communication across the group to strive to keep everyone on the same page.
“WE’RE A GREAT SUPPORTER OF THE TRANSITION TO RENEWABLE ENERGY, BUT IT HAS TO BE DONE WITH CARE.”
“I try to let people know how the business is doing by giving an overview of how the group is performing and what future work is going to be like,” he tells us. “I like to hear people’s views and encourage curiosity, so management can ensure positive stewardship. By promoting an open-door policy, I hope that everyone feels empowered.”
This means more than just coming to the boss if you have a good idea, it also means nobody should be embarrassed or feel apprehensive if there are things they are not sure about.
“Everyone has a job, and everyone has the right to put their hand up if they’re not clear what’s happening,” Ronsberg insists. “It is an approach that is paramount for safety, among other things. People can and should always stop the job if they do not understand the task at hand or if they feel there is a safety issue.”
“SOCIETY IS WAKING UP TO THE FACT WE WILL NEED HYDROCARBON ENERGY FOR SOME TIME YET. THAT IS NOT A REASON NOT TO INVEST IN RENEWABLES.”Crew change on Stena IceMAX.
As well as ensuring safety, it also engenders empowerment at every level within Stena Drilling.
“We have a culture that tries to empower people. I believe in the saying Together Everyone Achieves More (TEAM). I like to think that we are listening to our staff,” Ronsberg says. “Visible leadership is very important, and we try to do that as much as possible while empowering everyone throughout the business.”
It is also key for innovation within the business.
“We all need to pull in the same direction to be more sustainable. I am clear with our people - if you have any innovative ideas, please bring them forward and share them.
That is the ethos,” Ronsberg points out. “Innovation impacts everything we do. Good enough is not good enough. It can lead to complacency. Stay curious and keep learning!”
It is an outlook that is more important now than ever.
“Society is waking up to the fact we will need hydrocarbon energy for some time yet. That is not a reason not to invest in renewables, but we have a good future going forward providing we continue to deliver high value, sustainable forms of work which create value,” Ronsberg says. “Right now, there is much more focus on other locations to go forward with during our transition to cleaner fuels, which will hopefully lead to prices going down for consumers as
well, but this must be done in an environmentally astute manner. We are hoping to bring a seventh drilling unit into our fleet this year, and then looking forward with our clients.”
“WE ALL NEED TO PULL IN THE SAME DIRECTION TO BE MORE SUSTAINABLE. I AM CLEAR WITH OUR PEOPLE - IF YOU HAVE ANY INNOVATIVE IDEAS, PLEASE BRING THEM FORWARD AND SHARE THEM. THAT IS THE ETHOS.”
Caseware considers itself to be the technological leader in the audit and financial reporting solutions sector, providing robust solutions for businesses, corporations, and even governments.
We’ve had half a million customers in 130 countries, and have helped them work efficiently, collectively, and more productively to drive transformational change in the audit and assurance, financial reporting, tax space,” says David Osborne, CEO of Caseware. “We enable professionals to see not only what the data reveals in audits, but why it reveals it. Our customers, like our staff, are strategic thinkers and problem solvers, and we are helping them connect better with clients.”
Caseware was founded in Canada in 1988, quickly establishing a name for itself, but talking to Osborne today it is clear that the industry is evolving, and Osborne has a clear vision for the future.
“This isn’t an old boys club with desktop software billing clients as much as we want and moving
on,” Osborne says. “Right now, it is more open and inclusive, more accountable on factors like ESG, and more productive. Audit firms are saying ‘I do not want to spend this much money; you need to do more with less.’ For audit firms to be more productive they have to be strategic thinkers and problem solvers. They need to be more connected to their clients and appreciate the growing value of relationships. That is where the industry is moving.”
It is an approach that requires a bold new skillset from Caseware’s people, and fortunately, a new generation is providing just that.
“People in the industry enjoy solving problems. That was not always the case before. They are building trust. That was not always the case. And they truly believe their efforts help the economy and society,” Osborne
explains. “We are trying to drive this transformation by being robust, analytical, thoughtful, and designing collaborative tools. The industry before was functional, only talking about the quality of the software. We are now trying to be more experiential, global, and transformative.”
Caseware today is the only end-to-end technology company in the financial and auditing space that really is truly global, allowing multinational corporations to have partners around the world.
“Tax and auditing are very different in, say, Germany, versus Netherlands, or the UK, so we must think about how local compliance can change and created on top of our platform around the world. We want to always ensure multinationals can use one product globally for their office. They should have exactly what product they need when they need it.”
“The market is evolving at a rapid pace. Innovation is increasingly becoming
Our success story is based on the reliable business relationships we create. We understand your business and craft solutions to meet your goals. In this digital era, we use technology to modernize and digitize all aspects of your business.
Our solutions acknowledged and highlighted us among top development agencies by Clutch.co.
Our partnership with Caseware is such a powerful example.
We worked closely to deliver a solution that eficientise their entire internal processes and enables end users and other businesses, in the accounting and audit market, to access a solution that helps them grow, being more productive and effective.
Synergo optimized Caseware’s development environment and ultimately their business application.
“Synergo quickly became an extension to our existing development team, seamlessly integrating across multiple agile squads to collaborate on driving major improvements to the way we test our software. Their deep knowledge and expertise in modern testing frameworks proved invaluable in increasing the efficiency of our development lifecycle and training our internal teams on how to build on top of the new foundation” – Ricardo Navarrete, Software Development Manager, Caseware.
To read the entire story check out our website’s case study.
We are based in Toronto, Canada, with cross-functional teams in the US, U.K., Denmark, Germany, Romania and The Netherlands.
LET’S SYNERGIZE AND BUILD YOU AN AWARD WINNING APPLICATION!
Cristi Beres, Founder Synergo Group +1 (647) 560-4412 | info@synergogroup.net | www.synergogroup.net
essential to both businesses and customers, who demand and deserve more than ever before.”
“We invest heavily in Research & Development, as we’re building better, more expansive cloud solutions all the time. Historically, auditing software was desktop-based, but now, it’s all moving to the cloud.”
“A big part of our innovation strategy is being nimble and adaptive. We’ve acquired several companies this year, have hired more than 250 people and have an ambitious product roadmap. We’re listening to our global customers and innovating as quickly as possible to meet their needs in through best-inclass products that make their jobs and lives easier.”
Osborne says. “We’re private equity backed, which means we are still fairly nimble and can adapt quicker.”
As Osborne points out, the industry is going through a period of transformation.
“I think these are unprecedented times, and our industry is changing dramatically. 30, 20, even 10 years ago, the people and the processes were vastly different than they are today. The needs of clients are changing. Our clients need to do more with less, and we need to help them do that,” Osborne observes.
As the industry undergoes this transformation, the biggest challenge becomes finding fresh talent that can meet the demands of the modern industry as it evolves.
“Our industry is at an inflection point, as we’re on the brink of transformation. At the same time, between the great resignation and a competitive job market, it’s a war for talent. Finding exceptional talent is always challenging, but today more than ever.
We have many different programs to help recruit and retain employees. Hiring people early in their careers with great potential is something for which I’m extremely passionate, as I’ve been fortunate to be in stretch roles for myself and was grateful for the opportunity; I’ve also hired many people over the years and watched them grow and succeed. For more junior to midlevel roles, we offer a bootcamptype experience where you’re immersed into Caseware and also have a great comradery with your colleagues hired at similar
times. We spend a great deal of time onboarding, training and launching their careers.”
Solutions providers like Caseware cannot respond to the changing industry by simply charging audit firms more money, so they need to work smarter, not harder, finding greater efficiencies through innovation.
“We also make sure to tap into young, early-in career talent from all the great schools. We were the number one hirer from the University of Toronto a couple of years ago. We are having a University Day soon inviting students from across Ontario. We are hiring earlier in career talent & investing heavily in not just our industry but technology as well.”
While Osborne tells us about changes in attitude and approach around Caseware’s
work, a lot of these changes originate with one simple shifttaking auditing software from a single, desktop computerbased location, to a widely accessible and flexible cloudbased solution.
“There is a way of viewing our work as functional,” Osborne says. “That means talking about quality, efficiency, reliability, and simplicity. I am tired of the industry talking like that because those are table stakes. They should be a given. Of course, it has to be good quality software, but there are other components.”
The first of these other criteria is the experiential criteria. Good software needs to be accompanied by training, knowledge, customer support, and a global reach. This is where Caseware excels. But from there, Caseware is working to truly transform the industry.
“That means professional empowerment, strategic collaboration, examining the
economic and social impact of the way we do business,” Osborne explains.
Cloud technology provides the leverage to make that happen.
“It allows clients to be more transformational and do more with less. You have to have an analytical platform,” Osborne says. “Cloud is about collaboration and having better collaborative tools allows for better relationships. That is what we are trying to accomplish.”
To accomplish that transformation, Osborne’s plans include organic growth and acquisition, shifting the company from an indirect route to market relying on distributors, towards acquiring those distributors to give Caseware a direct relationship with its customers.
“The industry is changing. It is transforming and we are at the heart of helping to drive that transformation. We not only offer fast and responsive software
but a new perspective, better insights, and better questions. We are working more productively, leaving our clients feeling more fulfilled,” Osborne says. “That is what we are trying to accomplish. We are driving that change and nobody else is doing it.”
“THE INDUSTRY IS CHANGING. IT IS TRANSFORMING AND WE ARE AT THE HEART OF HELPING TO DRIVE THAT TRANSFORMATION. WE NOT ONLY OFFER FAST AND RESPONSIVE SOFTWARE BUT A NEW PERSPECTIVE, BETTER INSIGHTS, AND BETTER QUESTIONS.”
K2’S
As online retail, digitalisation and the Internet of Things become ever more in demand, so grows the need for robust, large-scale data infrastructure to support it. K2 Data Centres was founded in 2017 as a subsidiary of Singapore’s Kuok Group to meet that need as an international developer, owner, and operator of hyper-scale digital infrastructure assets.
The company has become a specialist in providing the critical digital infrastructure to leading technology companies, laying the foundations for the internet, cloud services and even as-yet undeveloped digital solutions.
It has built a proven track record of world-leading levels of service, and is equipped to act as a technically focused, longterm partner to its customers, providing peace of mind to those investing in significant physical network, storage, and computing resources to serve millions of users of online and digital tools.
“We are serving hyperscale customers who may not be able to act as quickly as we do because they cannot move forward without a lot of
approvals on internal issues, but we are a privately-owned company,” explains Dr Fred Ho, Chief Technical Officer of K2. “We can make decisions quickly. When we receive the signal from our user we can act on it immediately.”
That ability to act quickly is more important than ever at a time when demand for data centres is rapidly on the increase.
“The most important challenge is the demand on the data centre,” Ho tells us. “Power needs have gone from 4kw to 12kw. We’ve introduced liquidcooled solutions. The density of the data centre is increasing dramatically as we design data centres that can fulfil customer requirements.”
Sustainable, Simplified, Autonomous Driving, Reliable
Huawei Digital Power focuses on clean power generation, energy digitalization, green ICT power infrastructure, and transportation electrification.
For Data Center industry, Huawei Digital Power adheres to the "modular + intelligent" design concept and reshapes the architecture, cooling, O&M, and power supply to build next-generation data centers.
The features of the next-generation data center facilities can be summarized as Sustainable, Simplified, Autonomous-driving and Reliable.
K2 has the vision of not only developing its own modular infrastructure to support customer requirements, but also leveraging the products for modular construction.
As a long-term partner of K2, Huawei has applied cutting-edge technologies and design of the Next-Generation Data Center Facility to the K2 Ireland Data Center project, and helped K2 push through the limitations of existing designs, creating a more sustainable, simplified and reliable data center.
Green Power: The data center uses roofmounted photovoltaic panels to offset the cooling electrical loads. This translates to up to a 19.5% reduction in energy usage to cool the IT equipment, reducing the overall PUE.
Free Cooling: The data center makes full use of natural cooling resources, with an annual PUE as low as 1.15. It is expected to save over 14 million kWh of electricity per year & reduce carbon emissions by 66,000 tons over 10 years.
Simplified Modular Architecture: By adopting Huawei’s Modular Infrastructure approach, K2 was able to integrate the racks, cooling, power supply, etc. into one module, and realized fast deployment. Compared to traditional construction projects, modular infrastructure construction projects save up to 30% deployment time.
Simplified Power Supply: Thanks to a full-chain converged power supply system, combined with a 10-year replacement-free intelligent lithium-ion system, the upgraded supply and distribution system saves nearly 50% of the coverage area, allowing more space to deploy IT racks. Such a system also reduces the deployment time from 2 months to 2 weeks.
Simplified cooling: The cooling system is an indirect evaporative cooling system that integrates several components into one intelligent module to achieve “one module, one system”, reducing the delivery time from 6 months to 2 months. Meanwhile, natural cooling
is used to reduce multiple heat exchanges to one, shortening the cooling flows to improve the cooling exchange efficiency.
Reliable
Proactive security and secure architecture ensure high quality and sustainable development of data centers in component, device and system levels to ensure safe and reliable next-generation data centers.
At the component level: For critical subsystems like power supply and cooling, key components that adopt modular design are hot-swappable to quickly recover from faults.
At the device layer: The full redundancy design enables seamless switching to redundant modules within 0 ms delay after a single point of failure (SPOF), ensuring that the devices run without any interruption.
At the system level: An end-to-end (E2E) visualizable, manageable, and management platform enables the system’s high availability.
Technological innovation is a crucial force in ensuring sustainable development of nextgeneration data centers. Looking ahead, Huawei will keep making breakthroughs in product design and technologies through continuous investment in R&D and with the allaround cooperation with customers, ecosystem partners, and industry organizations. Together, we jointly usher in a new era of data center development.
Prefabricated Modular DC | Smart Modular DC Smart power supply solutions | Smart Cooling
As demand for data infrastructure skyrockets, so does the need to build and implement it rapidly. A common solution to this challenge is modular construction. As Ho explains it, “They put the equipment in a box, bring it on-site and put the data centre together like Lego, dividing up the construction process between the building and the data infrastructure itself.”
While this method of building certainly creates efficiencies, even here a great deal of the construction process has to take place on-site, and completing that construction while commissioning and connecting the data infrastructure requires a huge amount of labour.
K2’s approach is different. “We’re not just doing modular construction, but modular infrastructure,” Ho tells us. “Our ‘Lego pieces’, which we call Power Pods, are prefabricated structures with the complete infrastructure already installed. It is almost plug-and-play to put together, saving time in construction and commissioning.”
While traditional modular construction still requires the building and its power generation capabilities to be constructed and commissioned, K2’s modular infrastructure approach means its standalone
“WE CAN MAKE DECISIONS QUICKLY. WHEN WE RECEIVE THE SIGNAL FROM OUR USER WE CAN ACT ON IT IMMEDIATELY.”
power pod solutions can be assembled and commissioned in parallel with any construction work.
“We can run the infrastructure project outside the building, completely in island mode, and fully test it while waiting for the power shell and construction project to be completed,” Ho says. “It means we can construct a hyper-scale project within one year and have it fully operational.”
Ho has two decades of consultancy experience behind him, and so has an intuitive grasp of how mission-critical people are to any data centre project.
“We created our own design and IP for our power pod,” Ho says. “We used consultants to change details of the design to suit different countries but based on our own standard design and IP.”
Kirby Group Engineering has been working with K2 since 2016 on a range of data centre projects. K2 is currently focusing much of their project activity in Ireland and Kirby is proud to have forged such a strong partnership with them.
The success of this working relationship is due in part to the two companies’ shared values. Kirby has been committed to its core values of People, Safety, Quality, Delivery and Value for decades, and it is evident that K2 shares highly similar priorities.
Kirby also started out as, and still is, a family business, like the Kuok Group, of which K2 is a wholly owned subsidiary.
Brothers Tom and Michael Kirby established their company in Thomondgate, Limerick in 1964. It now employs over 1300 people at sites across Europe and recorded a turnover of over €400 million in 2021.
Kirby is proud to be a market leader in Power Transmission and Distribution and it provides HV/MV design & build services on AIS and GIS systems, up to 400kV to DNOs, TSOs, the renewables sector and large industry facilities requiring high-capacity power.
The company’s in-house team of professional engineers, construction and commissioning teams deliver first-rate services to its valued clients.
Kirby’s scope of work focuses on electrical and civil Balance of Plant contracts. Over decades of experience, the company has developed indepth expertise and experience in the design & build of new contestable and non-contestable substations, as well as the refurbishment of existing substations in live environments.
In recent years, the Limerick-headquartered company has successfully delivered contestable HV/MV substation projects for high-profile clients including ESB Networks, EirGrid, Scottish Power and other large industry facilities and wind developers. The company has connected over 2GW of renewable energy to the grid in Ireland and the UK.
John Davitt is Kirby’s Associate Director of the Transmission & Distribution Business Unit. He says, K2’s focus on innovation matches his team’s determination to find new and better ways to deliver first-class results for clients: “Working with K2 has provided fantastic opportunities for our team to work on cutting-edge projects in the data centre industry. This is a rapidly evolving area of technological innovation, of which we are proud to be playing our part. We value their approach to working with Kirby, from the clarity around construction deliverables that’s established from the get-go to the flexibility that’s assured on addressing areas like engineering options and tech queries”.
Group MD at Kirby, Mark Flanagan is looking forward to building on the foundations of the existing relationship with K2: “K2 sets extremely high standards for its contractors. They want flexible, solutions-driven partners, willing to go the extra mile, who prioritise safety and bring local expertise to their projects. When we began working with K2, we were confident that we would bring all of these qualities to the table, and more. We are constantly learning, through our own programmes and project experience. We are determined to utilise this combination to keep our place at the cutting edge of this sector”.
But while everyone is working from the same blueprint, Ho encourages innovation across the board.
“Innovation is important for me, and we work differently from traditional data centre companies.
K2 Data Centres under my leadership is about innovation. We introduce any efficiencies we can find to bring down the total power consumption,” Ho points out.
One such centre for innovation is K2 Renewable Energy, investing in green energy sources to power K2’s data infrastructure.
“We connect our data centres up to our renewable centres to make them greener and more sustainable for our hyper-scale customers,” Ho says.
This focus on innovation has proven to be a valuable draw for new talent.
AVK are the leading provider of Critical Power Systems, specialising in all aspects of the design, planning, implementation and continuing maintenance for Data Centre applications.
For over 30 years we’ve been providing Critical Power Solutions for mission critical services and systems. We are trusted by many of the world’s largest Blue-Chip companies to design, install and maintain 100% power integrity to guarantee their operations when mains power fails. Since our founding in 1989, AVK have enjoyed steady and consistent growth, not only in size, but also in our reputation.
With offices across the UK, Ireland and Europe, AVK supply standby Critical Power and protection to all major market sectors; in both the private and public sectors, from standard configurations to special applications, with a particular specialism in the Data Centre market.
It’s always our aim to provide maximum support to our clients coupled with reliable, high-quality products delivered on time and within budget, working closely with high-profile clients such as K2 Data Centres to ensure an efficient and effective system design. But our offering doesn’t simply end at handover…
We also offer the most competitive and bespoke proactive critical power service and maintenance plans based around our clients’ requirements. With a dedicated service division and an extensive network of technical engineers and support staff on call across the UK, Ireland and Europe, AVK also guarantees the very best in critical power maintenance.
In a society increasingly dependent on the internet and connectivity, fast, safe storage and processing of data is a top priority – and downtime is not an option. As experts in the field of data centre power protection, AVK understand the considerations Data Centre owners and operators face from:
• Increasing pressures on processing and power density
• Sustainability and efficiency drives
• Managing risks to reputation, reliability and security
• Restrictions on location of power equipment & availability of supply
We’ve worked closely with operators such as K2 Data Centres for a number of years, supporting their traditional critical power requirements, and more recently, exploring off grid and renewable solutions to overcome grid restraints and power usage restrictions.
In an ever-growing market, where demand is increasing and capacity is limited, AVK and K2 Data Centres share a vision of off grid, sustainable power generation, and are leading the way in achieving our net-zero goals.
For more information about how AVK can deliver and support your critical power application, contact us today on sales@avk-seg.com or call us on +44 (0)1628 503900.
“Because of our innovation requirement, a lot of the younger generation want to work with K2. We have developed a team, driven by our K2 modular infrastructure vision. For a lot of the young generation and traditional consultant engineers that is attractive,” Ho points out. “Combined with how well we treat our staff, it makes an appealing prospect for prospective hires.”
It is an innovation-led approach that led to the development of K2’s original power pods. That design has been improved. The capacity of one of the current generation of power pods is equivalent to four of the original power pods combined.
“The power density becomes higher and higher while the power pod becomes smaller and smaller. We improve our cooling technology, and we squeeze more power into a smaller footprint,” Ho says.
K2 is driving innovation in the cross-section of renewable energy and data infrastructure, recently winning the DCS award for data centre innovation ability of the year thanks to its power pod design and its modular infrastructure.
It is an approach K2 is taking worldwide, and when we speak to Ho, he is looking to expand the firm’s operations.
“In the future, we want to develop more data centres in Ireland, in Europe,” Ho tells us. “We want to explore potential business in Indonesia, and Malaysia, and also we will continue to see the opportunities in Singapore, Hong Kong and China.”
Dublin in Ireland, in particular, is an exciting market for K2, as a rapidly growing data hub for the whole of Europe.
“15% of the whole island’s power consumption is for data centres. Data centres need a lot of power consumption & making that sustainable is a charge for everyone on the market,” Ho insists. “What we want to do next is minimise the cooling capacity required using renewable energy to cool the data centres. The total cost of ownership needs to be lower.”
The market’s demand for data facilities, particularly at the hyperscale, is only set to grow. K2 is ensuring that demand can be met quickly, efficiently & sustainably.
“WE CONNECT OUR DATA CENTRES UP TO OUR RENEWABLE CENTRES TO MAKE THEM GREENER & MORE SUSTAINABLE FOR OUR HYPER-SCALE CUSTOMERS.”
ROC Equipment draws on 30 years of industry experience in providing new and used speciality foundation drilling equipment, such as drilling rigs, oscillators, rotators, crawler cranes and grabs, customizable to fit individual customers’ needs.
The company is a womanowned and operated business – Vanessa Lucido, the daughter of the founder, took the business over in 2012 at the age of 25 when her father was killed in an industry-related accident. Having started a professional relationship with BUMA CE, a leading manufacturer and supplier of foundation equipment, in high school, and being around her father’s business since childhood, she took up the challenge and has moved the business forward.
In 2022, ROC celebrates its’ 15th anniversary. Vanessa Lucido describes the beginnings of the business: “My father had a drilling contracting company
that he founded in 1979 and eventually he wanted to design equipment for his company. That is how ROC came to life – from 2007 to 2012, we only made equipment for our own projects. Then my father sold his drilling company, and this opened the doors for ROC to offer its services to the public.”
ROC today is the sole distributor of BUMA foundation drilling equipment, taking care of all North America and South America, and assisting in Europe and Australia. “We rent and sell and consult for large foundation projects for highways, bridges, secant walls, buttress shafts, in other words, high infrastructure and civil work, as well as some private work.”
CZM has been the leader in the foundation drilling industry since 1976, offering a comprehensive line of machines engineered for every foundation application, including CFA, Drilled Shaft, Low Over Head, displacement piles, Micropiles, Hydraulic hammer pile driving, Segmented Casing and more. Our team of skilled engineers offers intelligent solutions for development and improvement of the finest and broadest product line made in the USA.
Our North American headquarters is located outside of Savannah, Georgia, with factories in Italy and Brazil. Our footprint has continued to expand with a branch in Texas and service centers in California and Pennsylvania, allowing us to reach our customers throughout the United States and Canada.
We offer the best after sales service in the market, with a huge inventory of parts, a skilled team of field technicians, and a group of technical support specialists ready to help you troubleshoot any issues 24/7.
Our expansive rental fleet is configured for many applications and is spread throughout the country making CZM drill rigs more available than ever.
In 2023, CZM will continue its growth with a 33,000 square foot expansion of its North American headquarters, adding two additional assembly lines and a new warehouse. This additional space will allow CZM to bring the production of their forthcoming Micropile line to the US.
CZM has been a family operated company for almost 5 decades under the direction of three generations of the Clo family and will continue to be the leader in foundation drilling technology for years to come.
“You don’t see much of our work, because we’re doing foundations,” Vanessa points out. “However, what makes me proud is the knowledge that, over the years, my Dad’s subcontracting company put the foundations under almost every casino in Las Vegas. Similarly, many hotels, bridges, and important structures across the country rest on our foundations.”
Designing equipment is still one of the company’s core competencies. “ROC works very closely with BUMA, a partnership that stretches back 20 years, even before ROC was established. I approached BUMA when I was 17 with my Dad, to start designing the equipment, and only then did we formalise the companies and the partnership. We design the equipment, they manufacture it.”
The fruits of the partnership are plentiful. For example, in 2022, the ROC and BUMA partnership completed the design and fabrication of their C4268H Oscillator, currently the largest oscillator in the world. The unit was finalised and tested in BUMA’s factory in South Korea and will be brought to the US in October to be deployed in a large project in California.
Vanessa adds that in addition to BUMA, ROC works closely with several other drill manufacturers and has cultivated a particularly strong relationship with CZM, another major foundation drilling equipment supplier. “ROC’s equipment works in conjunction with a drill rig or crane, and CZM provides an impressive range of drill rigs that are compatible with ROC’s equipment. Above the quality of their equipment are the outstanding individuals who make up the CZM team.”
“We are thankful for the 15 years in the industry, partnering with great companies. The latest results of our cooperation will be showcased at Conexpo in 2023, the largest construction expo in the United States, to be held in Las Vegas in March of 2023, where ROC and BUMA, alongside other manufacturers including CZM, will be presenting their equipment.”
Speaking of the last two years, she admits that while the pandemic brought challenges, it also brought opportunities that the company has utilised well. The business has grown three times in size over the last three years and this year has been its biggest year ever.
Still, for Vanessa, continuing her father’s legacy is not only about financial performance and increased profits. The company bears a strong social responsibility as well. “I always knew on the personal end that once my profit was healthy, I wanted a non-profit. I very much believe in giving back. ROC is connected to several charities and organisations.”
These include the Ron McBride Foundation which helps underprivileged youths all over the US and AZ Coalition
which helps abused women and children. In 2020, Vanessa established her own charitable organization, ROC Rescue Ranch, which helps rescue horses, cats, and dogs, and either rehome them or retire them.
What contributed to this new endeavour was the company’s participation in one of the programmes on the History
Channel - The Curse of Oak Island, a multi-season reality television series that chronicles an eclectic team of treasure hunters and their search for legendary treasure on Oak Island, off the shore of Nova Scotia, Canada.
“Our equipment and crew were used to assist the Oak team to solve a 220- year-old
mystery,” explains Vanessa. “The program is shown in 65 countries with 35 million viewers. People were calling and emailing, asking for ROC gear. I thought as ROC Equipment does not need that money, why not use this to support a good cause, and help the animals. That’s how ROC Rescue Ranch came to life.”
Vanessa can rightfully be proud of what ROC has achieved under her management. Reflecting on the past decade, she says: “The beginning was extremely challenging. My father’s passing was obviously unexpected, and I was thrown into the company management overnight, as the youngest of the team. Now, looking back 10 years, I am amazed by what we have done.”
ROC’s achievements and success over the last 10 years speak for themselves. The company’s equipment was used to drill the largest foundation shaft in the world two years ago in Hawaii, and ROC has designed some ground-breaking equipment that can be remotely operated.
“Having lost my father in an industry-related accident, safety is of paramount importance to me. Our partner BUMA has designed a drilling rig that can be run by remote control, nearly taking away any safety issues as it would eliminate having an individual in the cab.”
“We have also designed safety rails and safety arms for other machines. All our oscillators can be operated from a good 30 to 50 feet away from the machine. We have put in a lot of safety components to ensure that whoever is on that job site, gets home that night.”
And prospects are positive. The company is set to participate in future projects such as the New York Airport, California High-Speed Rail and more, continuing its growth trajectory and literally expanding its footing.
“WE HAVE PUT IN A LOT OF SAFETY COMPONENTS TO ENSURE THAT WHOEVER IS ON THAT JOB SITE, GETS HOME THAT NIGHT.”
WE LEARN HOW SCRIBANTE CONSTRUCTION AND ITS SISTER COMPANIES ARE AN INVALUABLE ASSET TO THE INDUSTRY.
Scribante Construction is a thirdgeneration family-owned company, founded by the current ownership’s grandfather, Aldo Scribante. It remains today, one of the largest private family-owned companies in South African civil construction.
It is part of a triumvirate of related family-owned businesses, including Scribante Concrete, and SupaCrush.
Together the companies control facilities across South Africa, including quarries and two batching plants at Port Elizabeth, four plants in Johannesburg, and another two
plants in Zimbabwe. Today the companies employ a combined workforce of over 1,000 people.
The company works across three areas. The first of these is concrete. Scribante’s concrete business has been running for 25 years, with a focus on supplying ready mix cement. The construction side of the business
works in the road construction, aggregate and asphalt laying sectors, including a blockyard facility for manufacturing bricks, and a civil engineering business run by this generation’s Aldo Scribante. His brother, Silvio, is a qualified civil engineer who has worked at every level of the company and is now Managing Director of Scribante Concrete.
Finally, the third company of the group is SupaCrush, a mobile, high-volume, aggregate-crushing business, with state-of-the-art equipment deployed across South Africa.
Across all three businesses, Scribante Construction remains the keystone, founded in 1938
by Aldo Scribante when he sailed to South Africa from Italy to join his brother, Franco Scribante. The company was founded as a joint family venture, and it would remain as such, building an impressive portfolio of successful achievements. Throughout all of those achievements, the company has been guided by the belief that success can only be achieved through a combination of hard work and sound financial practice. It is a recipe that has contributed to Scribante’s continual growth and the success it has reaped to this day.
That hard work is the result of the people Scribante employs, and as a family concern, the company recognises that these people reflect the business as a whole.
Scribante Construction stands today as one of the oldest family-owned construction companies in South Africa. It can compete on equal terms with any of the competitors on the market, across any region of the country.
The firm owns a plant-for-hire and offers a wide selection of machinery, equipment, and tool rentals.
A more recent addition to the construction firm has been Scribante Asphalt, which has already been used in the completion of several projects around the Port Elizabeth area.
Across all of Scribante Construction’s activities, there remains one key priority – the preservation, & improvement upon Scribante’s excellent safety record.
ISO 18001, with a safety system that works according to the latest standards and new OHSA Regulations.
Scribante Construction’s sister company, Scribante Concrete, is a far young company, founded in only 1999. However, it has still grown rapidly to become one of the largest family-owned ready mix concrete suppliers in South Africa, and on March 18th, 2019, the firm was recognised as a Level 1 Contributor.
The construction company has achieved as much as 1 million LTI free hours on one of its recent contracts, thanks to strict adherence to international standards of ISO 14001, and
The firm is a full-service, ready-mix concrete producer with experience that spans the commercial, industrial, renewable, civil, residential, and agricultural construction sectors. The company boasts a fleet of over 140 trucks, giving it the versatility needed to relocate to the project locations that require it.
Much like Scribante Construction, from the beginning Scribante Concrete set itself a mission, grounded in the understanding that great service is defined by personal attention to each and every order, and each and every customer.
Working with everyone from the largest companies to small contractors and homeowners, Scribante Concrete treats all of its customers with the same courtesy and attention to detail. All of the firm’s work is underpinned by the belief that its combined efforts will allow it to become a stronger, more efficient company, and it is confident that this change will only strengthen the firm’s ability to provide consistent quality products and services to valued customers.
Scribante Concrete’s vision is to insist on the high highest standards, deliver results, and build open and
“SCRIBANTE CONSTRUCTION STANDS TODAY AS ONE OF THE OLDEST FAMILYOWNED CONSTRUCTION COMPANIES IN SOUTH AFRICA.”
honest relationships through communication. The firm works to build a positive team and family spirit and do more with less while remaining passionate and determined, yet humble. Scribante Construction’s sister company pursues growth and learning by embracing and driving change.
The most recent member of the Scribante business family is SupaCrush (Pty) Ltd, which was founded in 2007 by its owners, M.D. Pledger and the Scribante Family trust. The company works across several divisions, including SupaCrush Mobile which focuses on contract crushing, supplying large volumes of aggregate with very short turnaround times. SupaCrush Mobile was the firm responsible for delivering over 1 million tonnes for the expansion of Coega Harbour. The company can achieve this thanks to its fleet of “state of the art” mobile crushing units, which operate throughout Southern Africa.
The company retains full ownership of its own equipment, including jaw and cone crushers, primary and secondary screens, tipper trucks, loaders, excavators and LDVs. SupaCrush’s own experienced service technicians maintain their equipment to ensure quality, efficient production, and timely delivery of its products. The workforce
boasts a wealth of accumulated industry experience, motivation, and sound training, which means that SupaCrush can operate effectively anywhere in the region.
Like Scribante Construction and Scribante Concrete, SupaCrush’s staff work in a family-based environment where every employee is a valued and recognised member of the family. The company
strives for excellence through its culture of responsibility, accountability and visibly felt leadership. No employee goes unnoticed.
With this workforce on its side, SupaCrush, Scribante Concrete and Scribante Construction will be leading companies in South Africa, able to always put the needs of its clients first by delivering a quality product at a competitive cost.
“THE COMPANY BOASTS A FLEET OF OVER 140 TRUCKS, GIVING IT THE VERSATILITY NEEDED TO RELOCATE TO THE PROJECT LOCATIONS THAT REQUIRE IT.”
Alexander Battery Technologies is a custom battery and charger manufacturer serving a wide range of OEMs in different industries. The firm’s products are being put to use in medical devices, test & measurement equipment, communications, specialised tools, military and robotic applications.
We’re very flexible and customers approach us to support them in all markets. We’re a one-stopshop,” says Mark Rutherford, Alexander Battery Technologies’ Managing Director. “We design the battery from the spec, put it through regulatory submission, manufacture it and ship it to the customer.”
The battery sector is a rapidly growing one, but what puts Alexander Battery Technologies ahead of the competition is its entirely bespoke development approach.
“Everything we do is customised - no two batteries are the same,” Rutherford says. “With every customer, we start from scratch and give them a customised solution. We evaluate what our customer needs and offer rapid time-tomarket solutions, with a robust NPI process that has been
recognised by automotive and military standard customers. We have a very responsive supply chain, and we have a lot of inventory on the shelf to allow our customers that flexibility.”
This is vital in a sector where components can have lead times ranging from 52 to 90 weeks. That is why Alexander Battery Technologies identifies and keeps in stock the parts necessary to get new products through to the prototype stage.
“We take time, effort and energy to be proactive in our approach,” says Rutherford. “In the end, you have to have a carefully manufactured product that will be robust enough for the markets we are active in.”
Alexander Battery Technologies has been in increasing demand of late. Over the course of the pandemic, the firm’s revenue
increased tenfold within its work for the medical sector. Its revenue rose from £15 million to £45 million over a period of only three to four months. It was an exciting growth trajectory, but one that brought challenges with it.
“This was a real challenge, it meant bringing in staff, upgrading facilities and negotiating supply chain issues,” Rutherford recalls
Even at the vanguard of the sector, Rutherford is still capable of being surprised by the new applications reaching the market.
Rutherford tells us. “Electric Vehicles are an exciting new area. Obviously, it’s a competitive market but we’ve found an interesting niche where there’s a requirement for high-powered batteries, but at a low-to-mid range volume that most high-volume EV manufacturers aren’t interested in.”
Rutherford is intrigued by the possibilities of producing a lowvolume, niche battery product in the EV sector, and it is a
possibility the company is able to explore thanks to the flexible strategy he has instilled in the company throughout its growth.
“Whatever happens we can react to it and provide a good quality service,” Rutherford says. “We’ve recently invested £2 million in a new R&D facility. That facility was going to bring some of our external supply chain in-house, but we’re holding off on that while we evaluate this new market. We’re evaluating putting highpowered manufacturing in there. Once we’ve seen that grow, we’d love to expand into Europe. It’s very exciting.”
Of course, an essential element in that growth is the people that make it happen, and Alexander Battery Technologies has forged a strong relationship with a local recruitment company, capable of bringing over 40 people every fortnight to put through its training programme. Rutherford is particularly proud that the company is bringing jobs to the Northeast of England.
“When it came to hiring engineers, we were lucky that we could take people from the automotive and rail industry, bringing that experience with them,” Rutherford says. “We use RGA processes (Roles, Goals, and Achievements) to lay out with our employees and their direct line manager what we need them to do for the whole business to be successful. It is not just about what the business wants but what the employee wants as well. We lay out soft
skills and training requirements, so the idea is to keep staff focused on their goals and achievements and how they can get to that while making the company successful as well. We develop people internally so that if they outgrow their role, we can offer them more.”
To keep that talent pipeline going, Alexander Battery Technologies has implemented an apprenticeship scheme, adding two or three apprentices in each sector of the business every September and January, backfilling more advanced roles as they go. But crucially, everyone in the company knows the plan.
“I believe if everyone knows where they stand, the business will be successful. I want to develop local talent and have people proud to work in the
Northeast,” Rutherford says. “We don’t need to lose our talent to the South. The Northeast is a good place to manufacture, and big companies are recognising that. I want to be part of that, creating high-skilled jobs and growth.”
Growth is Rutherford’s watchword, but that does not mean unplanned growth. As the company grows, its needs change, and it is Rutherford’s job to make sure it adapts to that.
“The biggest challenge when you try to grow is managing the change. Everyone’s afraid of change, but how we counteract that is by having a strategic plan,” Rutherford says. “We’re focused on the next five years, then distributing that vision through the company.”
“WE DON’T NEED TO LOSE OUR TALENT TO THE SOUTH. THE NORTHEAST IS A GOOD PLACE TO MANUFACTURE, AND BIG COMPANIES ARE RECOGNISING THAT. I WANT TO BE PART OF THAT, CREATING HIGHSKILLED JOBS AND GROWTH.”
It is a different approach from what Rutherford has seen with other companies.
“Other businesses I’ve seen can be secretive- the plan isn’t shared with everyone. We make sure everyone knows what the plan is and how they are contributing to it,” he insists.
“We have seen huge success because everyone knows what they’re contributing and why changes happen when they come along, allowing for growth.”
And there is more growth coming. The company has a world-class facility, and the plan is to fill that with manufacturing capabilities for more OEM customers. The company has invested £2 million into buying a nearby facility in preparation to break into bigger battery pack markets. If that is successful, Rutherford can see the company branching out into Europe to support customers with supply chain problems.
“If they are manufacturing in Eastern Europe, we want a factory there to support them more easily while keeping our main hub in the UK and the Northeast,” Rutherford says.
“We want to grow our sales team with a sales office in Germany by the end of the year, then grow across other markets as we add to our revenue.”
ESTABLISHED IN 1998 BY GERMAN ENTREPRENEUR NAZIF DESTANI TO SUPPORT THE PEACEKEEPING MISSION IN THE BALKANS, ECOLOG STARTED OPERATING INTERNATIONALLY IN 2002 AND HAS BECOME A MAJOR PROVIDER OF MISSION-CRITICAL SUPPLY CHAIN AND SUPPORT SERVICES ON A GLOBAL SCALE.
Ecolog International is a leading provider of integrated services and sustainable solutions. Its portfolio of services includes supply chain management, life support, construction and engineering, facility management, as well as healthcare and environmental services. For over two decades, Ecolog has been a trusted partner for many governments, international organizations, including the UN, NGOs, and leading commercial companies in the energy, oil, gas, and mining sectors.
Be it serving food in a conflict-ridden area, an urgent response to the COVID pandemic in Europe or a construction project in a middle of a desert, Ecolog enables clients to focus on their operations by taking care of their needs. Celebrating its 20th anniversary this year, Ecolog International has completed over 1,000 projects in over 40 countries, even in some of the world’s most remote or challenging locations.
“Our corporate culture is based on being ready anywhere, anytime, at very short notice,” says company CEO Andy Vargoczky. “These two decades of continuous success are about being fearless, responsive, and
of course, entrepreneurial. Ecolog is nimble and agile, which is unique for the size of international company we are.”
Responsiveness is one of the key factors driving the company’s growth. Ecolog’s ability to evolve swiftly in line with current needs was clearly demonstrated during the global pandemic.
“Our unique and extensive experience in providing urgent response solutions, managing crisis logistics, as well as the mission and lifecritical operations was crucial in providing a quick, reliable, and effective solution to help European governments fight the pandemic,” says Mr Vargoczky.
Since May 2020, EcoCare has become one of the leading providers of testing and vaccination facilities in Western Europe and is currently expanding its operations in Africa. Today, Ecolog is looking toward the future in a postpandemic world. EcoCare is evolving, and preparing new customized healthcare solutions around the world.
In 2022, Ecolog defined a new Corporate Social Responsibility Policy that clearly states the aim of creating value not only for its staff and clients but also fostering social-economic development of the local communities in the areas of operations and minimising any impact on the environment. This is going to be achieved by its hardworking and dedicated employees, solid business ethics, innovations, and consistent service values.
As a global group, Ecolog employs 10,000 people of different nationalities and Mr Vargoczky affirms that managing such a diverse workforce is not a challenge but an enriching experience.
“We are able to mobilize at a quick pace across complex environments and geographies. As a projectbased organisation, we address the variety of our workforce with three recruitment streams. First, we have a permanent pool of professionals who provide the core logistics services and the strategic commercial, operational and administration tasks at the core of our business.”
Ecolog has a proven track record in the construction of both civilian and governmental facilities and infrastructure.
He explains that the company has implemented a rotation programme across all its international offices, giving opportunities to its team members to gain new skills and to better understand cultural diversity, thus enabling them to provide an even higher level of customer interface.
“Then we have professionals who are on standby, having worked for Ecolog in the past. We source colleagues either from local communities or we deploy them from their home base. We are proud to develop a workforce that ultimately benefits local communities and then supports the country’s economic growth,” he states, adding that depending on the project requirements,
Ecolog can also mobilise a large workforce from multiple geographies, the third recruitment stream.
“Many of our colleagues have been with us from the very beginning, which is a testament to the leadership and management of the organisation. However, as an organisation, we remain humble. The outstanding contribution of our people, who
deliver exceptional service to meet the strong demand for our services, has been a vital factor in our accomplishments.”
Mr Vargoczky says that the company is always on the lookout to enhance its service offering in order to meet the changing needs of its clients.
But more importantly, the company is making a huge shift toward sustainability by implementing new technologies and smart solutions to reduce waste and energy consumption.
“WE ARE ABLE TO MOBILIZE AT A QUICK PACE ACROSS COMPLEX ENVIRONMENTS AND GEOGRAPHIES.Transportation by air, sea, land and rail end-to-end with a single point of contact under a single contract.
Ecolog’s water supply operations cover the entire water cycle from purification to the delivery of potable or bottled water.
Ecolog is now complementing its core business with renewable energy solutions by introducing Water-as-a-Service and Energyas-a-Service offers.
“In 2020, we partnered with Desolenator, a Netherlandsbased solar desalination technology company, in order to scale up and deliver a gamechanging solution that harnesses the world’s two most abundant resources – sunshine and seawater – and purify even the toughest water types without the need for filters, chemicals or polluting fossil fuels.”
He explains that the company has invested in renewable technology that converts, with zero emissions, brackish and saltwater into hospitalgrade drinking water, through solar panel technology, without the need to use heavy energy consumption units. This technology has been deployed in water-scarce areas,
particularly in the Middle East and Africa. Similarly, Ecolog is looking at technologies to harness solar power.
“A second major pillar of our strategy focuses on inorganic diversification with new services, solutions, partnership opportunities, and revolutionary technologies that bolt on to the Ecolog of the past. We are also expanding in mature and prominent markets such as North America and parts of Europe, where we have a proven track record in our service offerings.”
In concluding, he affirms that on many fronts the past twenty years have been both exciting and rewarding. “The acceleration of technology and innovations enable us to find smarter and more sustainable ways to deliver our services. I am even more excited about our future and where we are headed.”
Afrigen is a young biotech start-up company founded in 2014, with the mandate to localise the manufacturing of tuberculosis vaccines to South Africa.
The core of its strategy is the localisation of vaccine production to the continent,” explains
Professor Petro Terblanche.
“We started as a Research and Development company, with a small team of five PhDs and an administrator establishing a platform for the formulation of essential elements of this vaccine.”
From these humble origins, the company became fully operational by 2020, when Africa had an urgent need for localised vaccine development. While the Covid pandemic was in full swing, Afrigen was bringing its facilities into production and getting manufacturing processes started. Using technology licensed from a US partner, Afrigen created the first ever adjuvant formulation
Agribiomed Africa (ABM), a 100% held subsidiary of Agriobiomed Global (AGL), has secured an exclusive license for Afrigen Biologics & Vaccines proprietary encapsulation technology for Cannabidiol (CBD) oil in the EU, UK and EEC. The process makes CBD water soluble, resulting in more rapid absorption and a faster onset of action than regular CBD oil. This has the benefit of offering greater bioavailability and thus enhanced therapeutic effect.
A supplementary clinical study using the Afrigen technology is currently underway at an accredited EU clinical trial facility with the results thereof due for release in Q3 2022. ABM’s Chief Medical Director has been acting in a consultant role for the study.
Morama Holdings, an AGL facility, is licensed to cultivate cannabis in Lesotho.
Africa, specifically Lesotho, is expected to dominate the global medical cannabis market due to its favorable agricultural conditions and local expertise.
Morama is a Lesotho registered company which holds a full cannabinoid and hemp cultivation, manufacturing and export sales license granted in terms of section 12 of the Drugs Act, 2008. Morama is the registered owner of a 14 hectare site of pristine agricultural land which is situated in the picturesque Berea Valley in the Maluti foothills in Lesotho. It is located approximately 30 minutes from the capital, Maseru, and 45 minutes from the international airport.
Over 50 people from the local community are employed by Morama, which is 20% owned by local partners. As well as the district council and its stakeholders, we have built strong relationships with the local community and traditional leaders.
A number of skills transfer programmes have already been implemented at Morama for the community employees, and this will continue until the workforce is sufficiently skilled to conduct operations independently.
• Lesotho was the first African country to issue licenses that allow for full-scale cultivation, distribution, export, import and R&D of all cannabinoid species.
• Lesotho has received the highest INCB quota for the export of Tetrahydrocannabinol (THC) in Africa.
centre on the continent with the capability to produce a cGMP grade library of the latest adjuvants. Adjuvants are used in many vaccines to help create a stronger immune response.
Afrigen has already achieved a lot, but it is still early days.
“We are still in the prerevenue status of our life cycle. We started with two shareholders, a development finance company, IDC, and a non-profit, the Infectious Diseases Research Institute,” Professor Terblanche tells us. “That’s quite unusual, but in 2018 the non-profit exited and the majority shareholder is now Avacare Health, a pan-African healthcare company started in 1994 which is now backwards integrating into manufacturing and R&D.”
Afrigen itself now boasts the capability to carry out vaccine innovation and manufacturing, not only establishing its own RNA platform but also acting as an RNA technology transfer hub for the continent and other low-middle income countries (LMICs).
“Our company entered the market with the capacity to allow vaccine development from the design of the vaccine right through to clinical trials and further development. It is a unique capability for low-income countries,” Terblanche says. “Our purpose is to offer a combination of discovery, research, right through to market relevance and the production of GMP grade material and a microbial base for RNA. We operate in the One Health sphere, for human health and animal health, developing products with the same platform suitable for both applications. That is quite unique.”
This is the short version of the story, but it begs the question, how has Afrigen gone from being a start-up in a lab with
a handful of people to being a critical part of the continent’s vaccine infrastructure?
In the beginning, like most start-ups, the first challenge Afrigen faced was raising capital. It is particularly difficult to source capital in Africa, where there is not a venture capital market, so the firm had to rely on development finance corporations or bank loans, which required collateral.
“We’ve learned that the number one reason for failure is to not have enough working capital, taking into account the long lead times before products
reach the market,” Terblanche points out. “So, our earliest challenges were access to years of working capital to develop the technologies we needed. We found a shareholder, and one of their unique components was their willingness to take risks and fund working capital.”
With its immediate future assured, Afrigen finally came to prominence in 2020, when it was announced that mRNA vaccines would receive emergency market authorisation. Afrigen responded by strategically building a facility for mRNA vaccines, aligned with the Afrigen formulation capabilities to formulate lipid nanoparticle formulations for mRNA vaccines.
“We had a strategic view that if we could prove our platform was suitable for rapid response vaccine development, that would be a strategically valuable capability to have, particularly in Africa,” Terblanche recalls. “So, we built it and looked for a technology partner to licence the latest mRNA vaccine technology to us.”
Afrigen would play a crucial role here, not just bringing the technology into the continent to develop themselves but building a network of partnerships that will contribute to vaccine innovation and manufacturing on the African continent to Africa’s entire pharmaceutical industry.
The WHO mRNA programme is a ‘hub and spoke’ model. We were busy building the infrastructure for our facility when the Covax Initiative put out a global call for companies to become global mRNA hubs to receive technology, develop vaccines and transfer that technology to other ‘spokes’,” Terblanche says.
To do this, Afrigen partnered with other key organisations.
“Early on we realised we would be operating at development scale and would be able to make clinical material, but our capacity would be 50 million doses and we needed much more,” Terblanche says. “So, we partnered with the Biovac Institute which had capacity for 200-300 million doses, a foremost vaccine manufacturer and supplier in the country.”
While the mRNA platform was established the SAMRC is working with Afrigen and partners to build a network for vaccine R&D and start researching a pipeline of products, which Terblanche knew would be essential for long-term sustainability in Afrigen’s tech hub role.
“We couldn’t establish a platform on a single product, we needed a pipeline of products,” she tells us. “We hit the ground running because the call was for pandemic response and there was an urgency to fasttrack vaccine production in low-middle income countries.
The South African proposal had three strategic partners, the tech transfer and development entity (Afrigen), the first
commercial spoke (Biovac), and the Medical Research Council for leading novel mRNA vaccine research.”
Following due diligence and many discussions, WHO and other partners selected Afrigen as the global mRNA tech transfer hub and secured non-dilutive funding to fasttrack the establishment of the hub, fundamentally changing the company’s growth speed and strategy. In 16 months, the company went from 22 people
to 34, with the company recently hitting a workforce of 70 people, with more growth promised for the near future. Afrigen has expanded its facilities with an additional 2,000 square metres of high-tech facilities, including cryogenics, sequencing facilities, and creating plasmids right through to finished drug product for clinical trial materials - creating a complete value chain.
Of course, to fuel that growth, Afrigen needs the right people.
“Our challenge now is to get access to the necessary skilled and experienced workforce. We are building a unique sector in Africa, drug substance production. Few companies in Africa can do that,” Terblanche explains. “We are taking on the entire sector, end-to-end. The challenge is finding manufacturing personnel at the supervisory level with relevant industry experience. We have to bring in people from university well trained in an academic knowledge base but
without experience in the vaccine manufacturing space, so that is our biggest challenge now.”
The key is creating a space where people want to work.
“We recruit through word-ofmouth, it’s a small community,” Terblanche says. “We create an exciting work environment that is stimulating, conducive for personal growth, and enjoyable. We run facilities where people can excel and grow.”
When we speak with Terblanche, she is preparing the company to achieve its most stringent technology licence yet, with the goal of eventually making Afrigen a CDMO operating under a contract development organisation model.
“In the short term we are incredibly focused now on developing the first mRNA vaccine on the African continent and taking it through to clinical trials,” Terblanche reports.
Longer term, Afrigen has much bigger plans as it readies its Covid-19 vaccine for the market.
“We are part of the biggest tech transfer project in the history of vaccines, a multilateral transfer to create capacity and capability for low-middle income countries and companies to develop mRNA vaccines for pandemic preparedness and vertically integrated, decentralised vaccine development,” Terblanche tells us. “Our primary focus is on unmet needs, and with our shareholder who has massive distribution networks extending into all continents, we will take our products to market.
Five years from now I see us becoming fully integrated with at least two vaccines in development and one in the market and a portfolio of 15 unique applications for human and animal health.”
THE HOTEL INDUSTRY HAS SEEN TOUGH TIMES RECENTLY, BUT AS THE MARKET PICKS UP ONCE MORE, LEONARDO HOTELS IS ADAPTING QUICKLY TO THE NEW NORMAL.
Leonardo Hotels was founded in 1998, with just one hotel in Israel, quickly becoming the main brand of the Fattal Hotel Group. Over the last 24 years, the Group has grown to include 240 hotels under the Leonardo brand, as well as the Royal Leonardo brand for high-end establishments.
Afew years ago, the Group added 35 Jurys Inn hotels, giving Leonardo Hotels a strong market presence across the UK and Ireland.
“The majority of our hotels in the UK and Ireland are Jurys Inn but by the first quarter of next year they will all be under our main brand, Leonardo” explains Ronen Nissenbaum, CEO of the Fattal Hotel Group for Western Europe. “We also have an additional high-end lifestyle brand called “NYX”. The first hotel under this brand was built in Israel. It is a boutique, more artistic, whimsical high-end hotel. We opened one in London, in Holborn, and we’re building one in Dublin and one in Edinburgh. It is younger, hipper, with outlets like a rooftop bar where possible. NYX will complement our existing brands.”
In its home country of Israel, the Group has 50 hotels, often seven or eight in a city like Eilat or the Dead Sea area, alongside 85 hotels across Germany and Eastern Europe, and another 85 across Western Europe.
The Group also owns a selection of unique properties, including a waterpark resort in Israel. As Nissenbaum explains, the key to the company’s growth is the success of our existing portfolio of hotels.
“We have great locations in each city where we’re present,” Nissenbaum says. “We prefer to cluster a few hotels and brands in a location so that we’re available at various levels for different customers with differentiated experiential needs. We have three in Manchester, 7 in greater London, several in Brighton, Southampton, Edinburgh, Glasgow, Dublin and Aberdeen,
Fusion is a leading customer experience management and digital transformation solution provider with a presence in 28 locations in 14 countries. We cater to the travel, tourism, and transportation industry’s multiple customer communication and outsourcing needs with the power of human connect. Across the globe, travel, tourism, and transportation businesses strive to keep up with the changing customer expectations. Besides, they face challenges like changing travel regulations, rapid digitalization, and the mounting cost of operations. To surmount these challenges, many travel, tourism, and transportation businesses opt for customer-centric travel and transportation outsourcing partner.
With 30+ years of experience in the outsourcing industry, Fusion has carved its niche as a customer-centric outsourcing solution provider for the travel, tourism, and transportation industry. Our end-to-end outsourcing solutions for the industry are designed keeping customer engagement and satisfaction in mind. As an omnichannel outsourcing partner with multilingual capabilities, we can support all types of customer communication needs of a business in over 40 languages.
Our travel and hospitality services include reservations and sales, customer service, chat assistance, hotel navigation, social listening and engagement, guest surveys, and voice of customer analytics. We also manage L1 & L2 escalation desk, case management, hotel content and inventory, commission reconciliation, audits, back office, and digital marketing for our travel clients. Our other offerings include social media support, website development and online content management, chatbot and AI, and rate loading.
a globally recognized digital transformation solution provider, we offer Travel and tourism industry-specific automation solutions, including hotel analytics services, AI and ML-enabled chatbot solutions, quality assurance
software solutions, and other robotic process automation. When incorporated into our clients’ existing systems, these solutions can help get actionable customer insights, improve customer experience and satisfaction, boost overall operational efficiency and enhance cost-efficiency.
To drive exceptional customer experience at each touchpoint throughout a customer’s journey, we emphasize first call resolution, the voice of customer analysis, and customer value management.
Focusing on these areas allows us to know the customers better and offer them a highly-personalized, compliant and comprehensive solution that fosters first contact resolution, improves customer satisfaction, and boosts customer loyalty and market share through continuous improvement and best practices. We also have an automated quality assurance process that allows us to audit 100% of the calls on the same day for compliance and behavioral errors, offer timely feedback on human errors, and improve customer experience.
As a leading outsourcing partner for travel tourism and transportation, we have earned the trust of many industry leaders. We are the outsourcing partner of a reputed hotel group operating across the UK, Ireland, and the Czech Republic.
As our client, we have one of the world’s fastest-growing companies recognized among the world’s largest chains of operated hotels, homes, managed living, and workspaces. We have touched 157,000+ Hotels & Homes in 35 Countries for our three Hospitality Industry Clients.
and we’re building a second in Liverpool and a third in Dublin. It is about putting the right product in the right city and location. Our brands are very accessible and very friendly. These are not intended to be a Ritz or Dorchester; our hotels are not pretentious. They are affordable, friendly, with excellent team members and service, with great value for money and did I mention, in great locations.”
It is an approach that has earned Leonardo Hotels a reputation, and its international footprint means it is often seen as a familiar friend in foreign climes.
“I asked our managing director in the Netherlands how they achieved their results during the Covid times. He reiterated that since we rebranded the hotels to Leonardo, we’ve had a tremendous influx of German guests,” Nissenbaum tells us. “We have been in Germany for the last 20 years. Our brand is now well-recognised and appreciated. In addition to the Dutch local business, we do incredibly well because the German market recognises our brand and prefers to stay with us.”
Leonardo Hotels has achieved a level of recognition in the UK too, but the rebranding of its Jurys Inn assets will “put that recognition on steroids” according to Nissenbaum.
“That’s why we focused on growing in Europe, making our brand recognisable while growing sustainably,” Nissenbaum says.
“We’re taking that approach to other markets including the Americas soon. Now that we have a strong foothold in Europe and Israel, we are ready for further expansion.”
Even now, Leonardo Hotels is one of the five biggest hotel brands in the UK, a small brand but with serious plans to continue its growth. The Group has just opened a third hotel in Manchester, next to the Piccadilly Train Station, but the growth strategy goes beyond simply buying hotels. We develop and build them too. When we speak with Nissenbaum the Group has a significant development underway in Edinburgh, next to its Jurys Inn hotel, and near Edinburgh Castle, the company is building an NYX hotel, as well as another one in Portobello, Dublin, the third in the city.
“What’s unique about us is that we are very much a onestop shop. Some of the larger hotel companies are more
Decotel
firmly believe in our core principal of ‘Delivering Excellence in Hotels and Hospitality’. Since opening our doors in 1947 we have built up a reputation as a leading supplier of Guest room and Housekeeping products across the UK, Europe and the Middle East. Our long standing relationships and synergy with hotel owner/operators such as Jury’s Leonardo are a testament to the way in which we operate not only as a supplier, but a partner. Operating from our offices in Loughborough and Valencia, our experienced and dedicated team of hospitality specialists are always on hand to discuss your needs. We’ll work with you towards finding the best solutions for your business, whether it’s housekeeping, room service, linen or in room amenities, we are here for you. So, no matter if you’re looking for a simple product replacement, planning a full refurbishment, or anything in between, we’re here to help.
Decotel has been providing innovative products designed to the meet highest standards and the rigors of daily use in the hotel and hospitality sector for over 70 years.
Our products are manufactured to our own meticulous specifications and regularly checked against our proactive customer engagement programme. This allows us to design and develop new products as the demands of the industry grow and develop.
Along with our own range of high quality products we also partner with other well established manufacturers including Brabantia, Caddie, Numatic and GHD to make sure we have the right products for you.
www.decotel.com
franchisers and managers on behalf of owners. They are marketing organisations, where we own hotels, lease hotels, and manage our own hotels. All our hotels carry our family of brands, and they are managed by us,” Nissenbaum says. “We’re unique in our geographic expansion. We’re publicly traded, and the majority owner is Mr Fattal. As company CEO and Chairman he is intricately involved, especially in development. There are three regional CEOs that report to Mr Fattal, myself and my counterparts in Germany and Israel.”
Leonardo Hotels’ growth has been rapid, but it has also faced its challenges, including the impact of the Covid-19
pandemic. The hospitality market has largely recovered from the lockdown and its aftereffects, but in its aftermath, there are new challenges.
“All the industries are facing shortfalls in recruitment, especially in the more linelevel employee areas such as receptionists, cooks, servers, and housekeepers,” Nissenbaum acknowledges. “The market has forced us to adjust the way we hire, be flexible and considerate to the requirements people are looking for in the workplace.”
In the post-Covid world, potential recruits have a different set of expectations from those of job hunters before the pandemic.
“This generation is looking for jobs that are more flexible or allow for more virtual work, which you can’t do as a server,
but back-of-house work can be done from home, with more flexible hours,” Nissenbaum says. “Pay levels for most employees have increased but money is only one element. How do you treat them? Do we give them a purpose? Do we meet their needs for a good work-life balance?”
Staff shortages are only one of a mesh of interconnected new challenges, however. This industry, like others, is experiencing escalating energy costs, a supply chain slowdown, and an increasingly urgent focus on corporate, environmental, and social responsibilities. These issues
don’t just affect the business, but its team members and their personal life too.
“We’re all grappling with how difficult it is for team members.
In the same breath, you can talk about inflation, utility costs are surging, buying bread and milk, chicken, and other essentials, all are increasing dramatically,” Nissenbaum points out. “One of our biggest challenges is attracting talent- but also the additional costs that come with running hotels.”
The newest generation of workers also holds their employers to higher standards when it comes to environmental issues.
“We’ve recognised that doing the right thing, not only by your employees but as a company, is essential,” Nissenbaum says. “It relates to whom we hire. They want to know what we’re doing, that we’re a company with a conscience. The younger generation, more than any other generation, are asking about what we are doing to make their world better and more sustainable.”
The current business levels are reaching pre-Covid levels and Leonardo Hotels is using its decentralised leadership structure to meet these challenges.
“You can’t have a topdown ‘this worked in the US, it will work in Paris’ attitude,” Nissenbaum says.
But while having that handson insight is invaluable, Nissenbaum speaks highly of the guiding vision of Fattal Hotel Group’s founder.
“David Fattal is a relatively young entrepreneur in his midsixties and has achieved this incredible result of 240 hotels in less than 25 years. He has always been able to attract great people that remain loyal for many years. It is a testament to his natural character; How easily he connects with all levels of the organization, internal and external. His drive to grow the company is palpable,” Nissenbaum says. “I can sense it when I’m sitting with him, this motivation to grow the company is inspiring”. “At the current development rate, within the next five years, we could hit the 300 hotels mark, but it is not a numbers game, it’s a commitment to developing, growing, and understanding that the larger and more substantial the company is, the more geographical coverage we achieve, the more it strengthens our existing legacy hotels.”
Spread across 75 and a half acres of the KL Metropolis, the Malaysia International Trade and Exhibition Centre (MITEC) is an integrated development within Kuala Lumpur’s International Trade and Exhibition District. The facility has been positioned as an economic catalyst, as well as a gateway to Southeast Asia. MITEC is not only the largest MICE (Meetings, Incentives, Conferences, and Exhibitions) venue in Malaysia, but also the fourth largest in the Southeast Asia region, and the largest trade and exhibition centre in Malaysia with over 51,000 square metres of exhibition space and triple volume exhibition halls with infinite possibilities.
As Malaysia opens up its economy and its borders
MITEC is busy and excited to welcome back national and international events as they return to the venue.
“To us, the journey from start to end matters. The key is to remain agile and keep a real-time pulse on changing customer preferences and rapidly innovating to redesign journeys that matter in the MICE industry,” says Mala Dorasamy, Chief Executive Officer at MITEC. “We are constantly looking at various touch points like efficiency levels, convenience, consistency, friendliness, and the main connecting factor, the human touch.”
There is no denying it has been a tough few years for companies that rely on live events. The
entire sector ground to a halt in the face of the Covid-19 pandemic, and MITEC was not spared either. However, Dorasamy views it as a learning experience.
“The pandemic taught us to be resilient, transform the way we do business, continually evolve to remain innovative, and most importantly continue to touch lives with our passion to serve,” she says.
Indeed, during the pandemic MITEC took the initiative to play a crucial role in the Malaysian government’s immunisation plan, operating as one of the first mega vaccination delivery centres (PPV) for senior citizens in the country.
“We served mainly the elderly and disabled people besides providing services to corporate organisations,” Dorasamy recalls. “In keeping with MITEC’s standards, we provided five-star treatment to the attendees who came by to get vaccinated. Our staff served their purpose with passion. Little things that matter such as ensuring the process was seamless and completed in the shortest time, helping push wheelchairs, providing an umbrella service from the drop-off zone during rainy days, helping senior citizens with the MySejahtera App, and preparing wholesome food and beverages for the volunteers who spent long hours daily at Mitec.”
Today, however, the face-toface events are recovering, and while it is seeing a dramatic resurgence, nobody is under
any illusions that things have gone back to “business as usual”. MITEC has undergone stringent inspection and auditing from Bureau Veritas, the worldrenowned certification body, to become a certified Safe Business Events Venue. The certification falls under its Public Buildings Inspection category, specifically Convention Centre Certification Guideline.
Businesses and organisations looking to host events at MITEC will benefit from an astonishingly well-equipped facility, including a massive loading bay on each floor to allow for easy loading and unloading of exhibition materials, large, flexible, pillar-less mega exhibition halls for banquets, concerts, sports events and conferences, ranging from 50 to 50,000 people a day. The venue is the first of its kind in Malaysia.
focus on the sales & service
full color display, offering turn-key solutions for medium & high-end indoor & outdoor.
operate an in-house service department to keep your installation in full working order throughout its lifetime
we will be responsible for repairing any defective parts to our customers.
MITEC has also evolved to meet the demands of a greener, more environmentally conscious customer base with its #myWorld program, obtaining the Green Building Index certification from the GBI Accreditation Panel in 2020. The venue has been evaluated across a range of eleven winning practices, including the use of recycled material during construction, the installation of 70% UV repellent glass, and a timed garden watering system, among others. The centre preserves water through a rainwater harvesting system. The system will use rainwater collected on the rooftop for irrigation purposes, resulting in a reduction in potable water consumption.
But MITEC has more to offer than an expansive and well-equipped space. Host an event here, and your guests will also have a gastronomical experience with the highly experienced world-class Chef’s and staff that are passionate about service.
“In 2022 we started a herb garden linked to our Garden Court Café,” Dorasamy tells us. “We have a tree planting program in our gardens during major events and encourage the delegates, staff, and community of KL Metropolis to walk or jog the tracks surrounding the MITEC building, including the use of our amphitheatres for daily exercise.”
MITEC’s very own inhouse culinary team is highly experienced, catering to various cuisines and sensory guest experiences. MITEC offers menus that include a selection of Malay, Chinese, Indian and innovative fusion dishes with a modern international touch, as well as a gastronomic western experience. The gracious Garden
Court Café situated at the north entrance dishes up both local and international delights.
“Our creative and dedicated culinary team is ready to assist in designing the catering solution for every event imaginable,” Dorasamy says proudly.
Live events are not the only area to have been affected by the pandemic, and with many companies taking a new approach to flexible and remote working, MITEC’s Smart Trade Zone allows for a premium and flexible co-working space, and a smart solution for entrepreneurs and small businesses.
The zone is accompanied by the Smart Partners Programme, encouraging businesses to ally with each other and use the
platform to collaborate create opportunities and facilitate data and resource sharing.
But MITEC is still not all business.
“Tourism is a key contributing factor to the country’s overall economy as the third largest after Manufacturing and
Commodities,” Dorasamy points out. “MITEC is a catalyst to the key economic sectors by hosting business events and thus driving trade, investment, research, and development as well as ensuring job creation.”
While everyone is very keen to get back to-face-face events, two years of Zoom meetings, Webinars, and virtual events have had an impact, and MITEC now brings a host of networked and online tools to the table to enhance its hybrid events.
This includes Qualtrics, an online guest experience survey form that measures MITEC stakeholders’ satisfaction.
“The moment customers think of MITEC, they are reminded of MITEC’s customer experience journey, seamless services and the employees who assist them to make the events successful and memorable,” Dorasamy says.
MITEC is also launching the Ungerboeck Exhibitor portal this month, to ensure exhibitors have a seamless online ordering system and payment gateway. This is combined with the MITEC App, allowing users to obtain information about MITEC and upcoming events, as well as access MITEC’s e-commerce platforms. Those platforms include the Garden Court Café and Smart Trade Zone, letting customers pre-order the meals and beverages, book space at
MITEC’s co-working space or purchase merchandise.
But while these online tools are a valuable enhancement to MITEC’s service offering, talking to Dorasamy, it is clear she believes that people are at the heart of MITEC’s culture.
“The team at MITEC is not just a group of people who work together but rather a group of passionate people who trust, support, respect, and help each other,” she says. “At MITEC, we look for commitment, great people skills, exceptional attention to detail, innovation, leadership, teamwork skills, and contagious enthusiasm and attitude.”
By employing like-minded staff, MITEC can build a
seamless, #Justdifferent preferred experience for customers, from start to finish.
“Through our plethora of events, MITEC has become a training hub for youth and students from the higher learning institutions through our MITEC Graduate program,” Dorasamy says. “We also provide job opportunities for part-timers who gain a great deal of exposure to the industry, better equipping them with knowledge and experience through culinary and event protocols from local and international events.”
MITEC is the Gateway to South East Asia. Let MITEC be the canvas to your imagination for your next event!
Serena Hotels maintains a portfolio of 36 luxury resorts across Africa and Asia, providing the peak of service and quality across all its properties with the help of a team of 1,700 employees in Pakistan alone.
Even in the face of the Covid-19 pandemic, Serena Hotels has stood strong, adjusting its strategy to the changing circumstances to avoid losing a single member of staff due to the pandemic. While the hotel industry as a whole was in shut down, Serena Hotels used that time to refurbish, clean and upgrade its establishments while finding ways to be more innovative, creative and outside the box in its thinking, even going on to add two new hotels to its portfolio.
Over the last year, Serena Hotels has been building back better, achieving its prepandemic footfall levels in June 2021, just in time for the firm to celebrate the 20th anniversary of the foundation of the Islamabad Serena Hotel.
The anniversary celebrations culminated this summer in a Jashn-i-Qawwali, a musical event featuring Sufi melodies and a lavish sehri, hosted by legendary Qawwal Imran Aziz Mian.
As Aziz Boolani, CEO of Serena Hotels, said at the event, “We must promote our culture otherwise our young generation will never become familiar with our immensely rich heritage. Moreover, without encouragement, through platforms and by the audience, this talent will not flourish. Like the performers and artists, the audience also matters.”
This respect for the cultures and art that Serena Hotels works within and alongside is a crucial part of the brand’s identity.
Serena Hotels has always given priority to the communities which live around the hotelier’s areas of operation, ensuring economic independence that will allow those communities to navigate uncertain times and build a sustainable livelihood for the future.
Serena Hotels are many things, including fantastic accommodation for leisure and business trips, but they are also an opportunity for the local community to build their
AS THE COMPANY CELEBRATES ITS 20TH ANNIVERSARY AS ONE OF ITS PROUDEST ESTABLISHMENTS, WE TAKE A LOOK AT SERENA HOTELS, AND HOW MUCH THE HOTELIER HAS ACHIEVED.
own businesses providing fresh foodstuffs, selling artefacts and handicrafts through Serena Hotels’ on-site gift shops, and developing their skills and finding employment through the company’s work-training opportunities that provide the youth with marketable skills that lead to meaningful work.
Serena Hotels invests in its local communities as part of a business-wide attitude to sustainability and environmentalism that informs everything they do. When Serena Hotels was founded over 40 years ago, operating under the company name Tourism Promotion Services, it pioneered a brand new way of running a tourism business.
From the beginning, the company’s outlook was that very few locations are not actually suitable for tourism, and with local knowledge and strategic choices a hotelier can combine developmental objectives with real economic sustainability and profitability for stakeholders within and adjacent to the business.
Ever since, Serena Hotels has strived to deliver the best practices in social, cultural, environmental, and economic development to locations that might be remote, even deprived, but which possess a fragile allure that can be nurtured in careful hands.
Serena Hotels has focused on developing properties in areas of the world that have been relatively excluded from globalisation, but it has done this working within a strong ethical framework with in-depth risk and environmental analyses backed up by a policy of constant innovation.
Working within this framework has allowed Serena Hotels to contribute toward communities’ economic growth, developing a thriving tourism industry and a range of ancillary services while growing the provision of local human resources and investing in the conservation of cultural and natural heritage with the minimum possible ecological footprint.
The company has always remained sensitive towards ways of improving and preserving its
environment. This means that its operations have included the responsible management of resources since the construction of its first hotel over 40 years ago. During the enormous amounts of expansion that have occurred since then, Serena Hotels’ developments and operations have always been guided by a dynamic ecological policy which focuses on actions and projects that relate to climate change, water and energy conservation, air emissions, conserving biodiversity, restore natural habitats and reducing and recycling waste while respecting local tradition, culture, and heritage.
Using a carefully selected regime of programs, driven by internal innovation, Serena Hotels responds to the needs of
the economy, local communities and the environment following the fundamental tenets of sustainability. Its programs have been aligned toward achieving the Sustainable Development Goals set out by the United Nations Development Programme (UNDP). In this way, the Company’s sustainable development agenda is directed in such a way that inspires its stakeholders to take a wider view of their work that encompasses the long-term in its business decisions.
Through its three key focus areas, Responsible Business, Environment, and Community Engagement, Serena Hotels integrates its initiatives under the definition of “sustainability”.
The company carries this philosophy forward in its two latest Gold Level Eco-Certified properties, Lake Elmenteita Serena Camp and Amboseli Serena Safari Lodge. These destinations won two awards under the “Social Impact” category in the 2019 Gala Dinner of the Eco-Warrior Awards. The Eco-Warrior Award is an annual fete hosted by Eco-Tourism Kenya to recognise tourism industry players’ that embrace sustainable business practices in their day-to-day operations.
These plaudits join previous recognition from the World Travel Awards, the Best Luxury Hotel category at the World Luxury Spa Awards in 2013, the Best Corporate Hotel in Tanzania according to the Tanzania Society of Travel Agents and the “Best Africa Hotel Chain” according to the Africa Travel Awards.
Serena Hotels is look set to continue to grow driven by its philosophy of sustainability and investment in local communities, which is great news for the hotel group, its neighbours, and visitors alike.
“SERENA HOTELS HAS STRIVED TO DELIVER THE BEST PRACTICES IN SOCIAL, CULTURAL, ENVIRONMENTAL, AND ECONOMIC DEVELOPMENT TO LOCATIONS THAT MIGHT BE REMOTE, EVEN DEPRIVED, BUT WHICH POSSESS A FRAGILE ALLURE THAT CAN BE NURTURED IN CAREFUL HANDS.”
Sisram Medical is a global consumer wellness group deeply rooted in the global medical aesthetics industry for over two decades, specialising in harnessing natural energy sources for the treatment of aesthetics as well as medical clinical indications.
Sisram Medical is led by Chief Executive Officer Lior Dayan, with global operations led by Chief Operations Officer, Ran Ezioni. The company and its subsidiaries form an ecosystem, bound through various synergies with their joint parent company, the Chinese firm, Fuson Pharma.
That eco-system consists of the Alma brand, a global leader in the Medical Aesthetics Industry with EBD (Energy Based Device) treatments and products with a wide-ranging global footprint. Alma’s products make use of five energy sources- laser, light, ultrasound, radiofrequency and plasma, and the company has made over 30,000 installations. Alma is joined by Sisram’s new personal care division with its “Home Use Device” or HUD, called LMNT. This product has
been just recently launched in mainland China and Italy. At the same time, Sisram is pioneering a new Aesthetics and Digital Dentistry division with two leading brands Copulla and Foshion Dental, as well as moving into injectables.
The company boasts digitalised entities which allow for a strong synergy between the different units of the business. It enables the use of a combination of different databases to grow each individual business unit nonorganically. Sisram Medical is a one-stop-shop which offers the full range of solutions for medical professionals through a strong, established brand. Its offering covers a wide range of well-being aspects across the board – from aesthetics to sexual wellness, dentistry, and more.
With over two decades in the global medical aesthetics industry, Alma Lasers and Sisram Medical are well placed to meet this demand, specializing in harnessing natural energy sources for the treatment of aesthetics as well as medical clinical indications. Sisram’s products and services are featured in the leading surgical, medical and beauty clinics around the world, treating dozens of millions of consumers worldwide.
As Ezioni points out, “Our vast products and treatments portfolio is constantly expanding, ranging from hair removal, skin rejuvenation, acne and acne scars, body & face contouring, pigmentation & skin resurfacing, fat grafting, dermal facial fillers, skin tissue remodelling, injectables, personal care, aesthetics, digital dentistry and more.”
With over 800 employees, nine direct channels and over 100 global distributors, Sisram Medical’s well-diversified and balanced geographic sales coverage has led to revenues
The applications for laser technologies have exploded in recent years with new solution paths in scientific discovery, automotive safety, security and defense, and healthcare. Leonardo delivers into all these segments. With their continued progress in laser diode technology, they advance performance levels with increasingly compact, lightweight footprints to enable laser systems that replace traditional technologies with more precise, efficient, and effective solutions.
The healthcare industry is ever more embracing the benefits of lasers. Innovations in diode technology and packaging have improved medical laser usability for a broadening patient base, while reductions in weight and size ensure comfort for the practitioner.
Leonardo Electronics US Inc. is a global leader in diode lasers and is the top producer of aesthetic lasers. Their commitment to a collaborative partnership to develop custom solutions has helped their customers command markets with significant competitive advantages. Leonardo worked with an industry leader in the aesthetic laser market to develop the world’s first all-diode-based 3-wavelength laser hair removal device resulting in unprecedented compactness and flexibility in the market.
From component design to prototyping and volume production, the right partnership model can create long-term success. But in a time of supply chain challenges and ever-present time to market pressures, how can companies build such win-win partnerships?
Transparency is critical to strategic supplier alignment. Leonardo’s business development model focuses on matching the product requirements with the technology landscape, creating the right solution for each customer. By selecting best-fit, strategic projects, they can dedicate the time and engineering resources necessary to meet the customer’s product performance objectives and establish a path to commercialization.
Access to engineering expertise without the layers of go-betweens allows for effective, collaborative innovation. In the medical and aesthetic laser market, this engineering collaboration led to the development of a unique medical device handpiece that can be used across the full range of skin and hair types, adding to the system’s versatility and improved procedure outcome.
Working together and thinking beyond components to include packaging, environmental conditions, integration, power, and data management allows for innovative commercial products. Systems thinking requires transparency, consideration of interdependencies, a willingness to experiment, iterate together and share test results.
Leonardo Electronics US Inc. enables next-generation technologies in medical, defense, security, and industrial segments and is a subsidiary of Leonardo. Their research, development, and service provide nimble product development, program support, and vertically integrated production of laser and electronic components and systems. With vertically integrated diode laser fabrication in Tucson, AZ, and locations worldwide, Leonardo can provide full design, customization, production, service, and support. Their expertise in a broad range of engineering disciplines supports system integrators from design through high volume production to meet performance, environmental, and cost demands.
Learn more at: www.leonardo.us
of $294.3 million in 2021, with impressive 81.4% growth yearon-year. That includes an overall net profit of $32.5 million, with 121% year-on-year growth from 2020. This is all thanks to the unique ecosystem Sisram provides. During H1’2022 Sisram Medical presented revenue growth of 39.3% vs H1’2021 with significant growth in all geographical regions, and adjusted net profit for H1’2022 was $24.9 million, increased by 27.5% as compared to H1’2021.
“We have a strong combination with our ecosystem, our strong background in clinical research, patents, FDA clearances and global regulation,” Ezioni tells us. “We adhere to all the required regulations, from a quality point of view and a customer point of view, which is also a barrier that low-cost companies cannot meet, especially these days as regulations become more robust. We offer not only the system but clinical training and service.”
With a strong combination of customer-focused company and innovative technology developer, Sisram Medical is a global leading company with robust academic and clinical research knowledge. Sisram itself boasts 51 technological patents.
But across Sisram Medical, Ezioni’s top priority remains the company’s people.
“‘People first’ is one of our top values,” Ezioni tells us. “It is not just a phrase. It is in our DNA to have open, transparent communication with our manager level, the production team, and team leaders on the ground.”
And the company’s services are more in need than ever. In the aftermath of the Covid pandemic, as remote-working, Teams meetings and Zoom calls continue to be the norm, we are all spending more time than ever before looking at our own faces.
“Post-covid, when everyone is sitting in front of screens, you see the wrinkles, you see some spots, and now there’s good technology available to improve that,” Ezioni tells us.
As demand increases, Sisram Medical has deployed an agile operational organization to perform a massive production ramp-up, even as global supply chains are often behind plan.
“We are ramping up during the toughest time in global supply chain management,” says Ezioni. “We are asking how we can mitigate that to satisfy the customer.”
With ongoing supply chain interruption since 2020, raw material lead times are growing rapidly, especially in the electronic components segment of the industry.
“We’re talking about a system with a lot of electronics hardware, software, mechanical, cooling system, optics, lasers and multi-disciplinary technologies,” Ezioni emphasises. “As an assembly company, you need all of them to make one system. It’s commonly known that ‘It takes thousands of parts to build a car,
But only one not to’ - it’s the same for complicated medical devices.”
To achieve the necessary ramp-up, Ezioni is taking a wide approach to expanding production capacity in-house and through subcontractors. Such a massive ramp-up drives additional LEAN manufacturing projects.
Two years ago, Alma moved into a new modern Campus to support capacity extension as well as process improvements and operational efficiency.
Ezioni is also Six Sigma blackbelt certified, which is a strong quality and process orientated background from the ASQ, American Society for Quality. “With that record and the lean manufacturing methods we are applying we can open more bottlenecks in our production to improve capacity,” Ezioni says.
Among the measures taken, vendors must verify they have material ahead of time, which is not always easy.
“Too often I face last meeting de-commit alerts from vendors that failed to meet the required delivery plan, but having a professional and experienced staff on board allows our operations the required flexibility to mitigate unexpected supply chain disruptions,” Ezioni says.
The company has established a cross-functional task force
“Being a global leader in the premium medical aesthetic device market, we set the highest bar for quality assurance,” Ezioni reminds us.
A fundamental ingredient in Sisram’s offering has always been its cutting-edge research and development programs, even during the pandemic.
“Keeping our innovative Research and Development projects on track during Covid-19, and successfully launching new technologies and products, has been a major challenge,” Ezioni says. “We kept production and deliveries running even during toughest times of lockdown, as a medical provider.”
Despite the global challenges of Covid, a strategic decision was taken to keep the company’s innovative projects up and running as expected of a leading company in aesthetic global markets. The company accomplished new product introduction programs and has launched two high-end applications and products, the Alma Hybrid and Alma PrimeX.
It is a track record Ezioni has every intention to build on. Sisram Medical will continue to launch new innovative services, medical applications, and premium products to meet its customers’ expectations, with more systems ready to be implemented over the coming years.
Camvac was established in the early 1950s as a manufacturer of vacuum coating equipment. In 1955, the firm moved to Thetford, Norfolk, a site that Camvac has worked from ever since. Over its life, the company has been owned by Rexam, Amcor and most recently, Grove Industries Ltd.
It has grown to become one of the world’s largest single-site metallisation vacuum coating and lamination companies. It places them in a unique market position. Some companies offer metallising or vacuum coating or lamination, but nobody offers all of these services together, in one location.
With 135 employees and a 24-hour-a-day, five-day-a-week shift pattern, Camvac remains an invaluable supplier to the liquid packaging, processed food, and live-in-film markets for fresh foods, as well as some industrial products.
“Each of those markets has different requirements, whether in the form of a barrier film that prevents oxygen or moisture exposure, or a barrier to give you very good resistance to thermal exposure,” explains Greg
Kingham, Camvac’s CEO. “Within our metallising process, we have patented technology that allows us to treat the surface of the films that we process to whatever level we want in terms of achieving a specific barrier level. We are unique in that we can offer a bespoke solution depending on what the customer wants.”
Camvac’s treatments can be found on products ranging from box wines, a big business segment for the company, as well as specialty materials for cold storage, including a special barrier foil for vacuuminsulated panels that have become commonplace for passive transport.
“Where before you would have used a forty-foot container with a fridge unit, you can now pack a container insulated with these panels and it will hold
SRF is a multi-business
SRF is among the pioneer suppliers of
production capacity
films, having
SRF have a diversified range
being
widely used
SRF value preposition has always been
while
SRF packaging films
SRF has been
the temperature for up to 10 days, at minus 20 degrees, with no requirement for topping up,” Kingham tells us. “From a sustainability perspective, it saves the need for fridge units on lorries.”
These panels have seen use in the transportation of Covid vaccines such as the Pfizer vaccine, which needs to be stored below minus 89 degrees centigrade.
While there have been exciting new opportunities for Camvac and its products, there have also been challenges. The last year has been difficult for most businesses in the manufacturing sector, with the recovery from the Covid lockdown meeting a fall in raw materials availability.
“Business was starting up, but the pipeline of supply was empty within a few months of everyone going back to normal,” Kingham points out. “That had an impact on material prices and availability. We have seen that return to pre-covid levels but now energy prices are rising significantly, which is driving raw material prices for resources like resin, although I think polyethene has probably levelled out now. We are still seeing increases in specialist materials.”
None of these factors occurs in isolation, and Kingham points to the ways Covid has changed perceptions on other issues.
“Before Covid, we saw a lot of demand for green materials coming in and industrial materials, but when Covid hit most businesses stopped development of new films. But then everyone woke up to the fact that we need a proper green solution to recycle materials,” he observes. “We have seen a lot of interest and development in postconsumer recycling. The £200
The
a ton tax on plastic packaging came in, so one of the ways that we can help is to provide an end product with over 30% recycled material (Post-Consumer Recycled PCR) already in it, a like-for-like solution to our current lidding film, ExtraPET.”
ExtraPET is Camvac’s marketleading monomaterial lidding film which is used primarily within the food and converter marketplace. The company services the global food packaging marketplace and ExtraPET can be found in supermarkets around the world due to its high gas barrier performance.
While Kingham is the first to admit that these are unpredictable times, and not every eventuality can be prepared for, he insists having a strong continuity plan in place can help a business adapt to the unexpected.
“Sometimes there are curve balls,” he says matter-of-factly. “It is about how quickly you can react to them. I think we have done that as a management team. We have been working closely together during Covid. We kept the site open with the senior management team always on-site, kept the business going, learning to be flexible in areas we had not thought we could before. It is about adapting to what is around you.”
As well as Covid, and volatile prices, Camvac also faced difficulty when a shipment of its raw materials, transported on the container ship Ever Green, got wedged in the Suez Canal.
“We had to find innovative ways to resource other materials to bridge the gap,” Kingham recalls.
“Some of those alternatives proved successful and have been developed in their own right.”
almost
last
As well as looking after its own business, however, Camvac has also responded to changing global events when there is an opportunity to help others.
“When trouble broke out in Ukraine one of our Warehouse Managers said, ‘Is there anything we can do to support these guys?’” Kingham says. “So, I said, ‘What can we do?’ and he suggested we sponsor a truckload of equipment to Ukraine.”
Camvac put the word out, and as part of the Thetford Business Forum, the company looked for donations to take to Ukraine.
“In a strange way, we became the hub for people bringing in donations in Thetford. The response from the local community was one of overwhelming generosity. We have the elder generation donating knitted jumpers and young children donating toys.” Kingham says. “We ended up needing three articulated truck loads and four or five transit van loads of medical equipment. It was a unique experience!”
We are making progress. It has changed our outlook slightly on things, and we are looking proactively at future strategic recruitment strategies.”
This is why Camvac has recently brought on board a new, dedicated HR manager to help manage the growth of the business.
“We’ve used agencies but also done some advertising in the local community,” Kingham says. “Norfolk is a largely agricultural area, so being an engineeringbased packaging company, it is sometimes not easy to get the skills you need. It takes a bit of looking.”
Covid has not just affected the way businesses work, it has affected the way people themselves work.
“Working from home during lockdown caused people to look at their lifestyle and what they want to do,” Kingham points out.
“That has attracted people into other roles. We have lost a few people from Camvac, and finding good quality people, with the right skill set, that is also a challenge.
Camvac will need all the talent it can find, as Kingham has big plans for the company. It has recently invested approximately a million euros in a newly installed lamination line which will add 2,500 tons of extra capacity to Camvac’s factory. It is a bespoke line, specifically built for bag-inbox type applications. The new lamination line further strengthens Camvac position within the Bagin-Box and bulk liquid packaging marketplace. The company’s thermal lamination range provides
excellent seal strength, seal integrity and flexibility, which are key performance parameters in the packaging and transportation of liquids around the globe.
“We are very pleased with it so far. We can see that being a big growth area, with order right up to February 2023, even though we only started commissioning it in August,” Kingham says. “One of the other reasons we’ve invested in a new line was to relieve the capacity on our larger lamination line where we’re looking to do more specialised materials.”
Camvac has seen interesting developments around medical applications that can make use of its wide-width line to laminate substrates up to 2.25 metres wide.
It is all part of a long-term vision for growth and our ambition to double the size of the business in three years.
“When I took over in 2019 sales were at about £16.5 million. The next budget year we aim to have reached £32.5 million,” Kingham tells us. “We are on track to double the size of the business in the last three years, and I can see us having another record year this year.”
“WHEN TROUBLE BROKE OUT IN UKRAINE ONE OF OUR WAREHOUSE MANAGERS SAID, ‘IS THERE ANYTHING WE CAN DO TO SUPPORT THESE GUYS?’”Camvac’s fresh food packaging films are found in a range of Supermarkets globally.
Imprima S.p.A. is a global holding company dedicated to development and innovation in the textile printing and finishing sector. Only established in 2017, the company has bold ambitions with its well-established brands, aiming to set a firm footing in global markets.
The company employs over 400 workers in its production plants in Italy, spread over a total of 40.000 square metres. Following an investment of over €25 million, the plants are equipped with stateof-the-art printing technologies with the capacity to produce more than 35 million metres of fabric. The advanced technology allows them to satisfy every customer requirement in terms of quality, printing type and service.
In addition to the Italian plants, the Group also operates a production facility in Brazil and has strong partnerships in Asia.
“We have a strong culture from an industrial point of view with our digital and rotary printing, and we leverage our product offer based on our capability to be very fast and efficient in fabrics production,” says CEO Federico Benevolo.
The breadth of its offering, covering several brands with an impressive heritage, is one
of the factors that differentiates Imprima from competitors. The group includes Germany-based KBC Fashion with more than 270 years of history and one of the best-known textile printing companies in Europe; Italian textile converters Guarisco and B-Blossom; SET, a promoter of fast fashion.
In 2019 the group added garments to its two key sectors. The garment business is run from Morocco, the group’s base for satisfying demand in Europe.
“Adding garments to our portfolio means that we can now offer solutions, not just products. This provides for more stability and enables further growth,” says Federico Benevolo, affirming that Imprima’s goal is not only to evolve as a company but to be a true game changer within the Italian textile sector.
Each new acquisition has added new skills, quality, creativity, and service. That is how Imprima has become a prominent brand in the market in
ISOCARBO, founded in 1923, is approaching its rst centenary of activity. Today, as then, customer service and evolving product ranges are continuously adapting customers’, markets and regulations’ needs.
Isocarbo decided to relaunch itself in 2013 with the birth of the Isonik® Division dedicated to research, development, in-house manufacturing, and worldwide marketing of digital printing inks for the main technologies available today, ready to anticipate and follow any further development.
Today, Isocarbo o ers Disperse, Sublimation, Reactive, Acid and Pigment digital inks of recent introduction. Without forgetting the relative fabric preparations and post-treatments able to reach the best technical standards required by the market. Isocarbo is the only European manufacturer able to o er a complete gamut of inks for all textile printing production processes.
At the same time the traditional printing and dyeing technologies are served by Kemik® Division with its Disperse dyes, speci c and optimized for each ber and for each type of blend, Reactive, Acids, Premetallized Acids, Cationic and Direct dyes. Also, for traditional textile sectors, the range is completed by a wide series of auxiliaries for pre-treatment, dyeing, nishing.
Isocarbo’s basis for further future growth are the recent developed products, the constant commitment of our R&D laboratories in guaranteeing the proper technical assistance for every type of issue, an ever-growing team of engineers, technicians, experts, and technical-sales o cers to support customers and last but not least a further expansion of the production capacities of the Isonik® and Kemik® lines already in progress.
just a few years. Among leading European textile companies, the Group acts successfully both in the “Collection” and “Fast Fashion” areas, with refined printed fabrics and finished trendy garments.
“In a nutshell, our wide offering, high efficiency and focus on sustainability are the key pillars of our power today, and our key differentiators,” affirms Mr Benevolo.
Imprima is one of the companies that is set to play a major role in the European textile industry, most of which had been relocated to the Far East over the last few decades. Mr Benevolo points out that a reshoring of garments back to Europe can now be observed, as the reliability of deliveries is becoming increasingly important. This opens new opportunities for European companies.
“We now receive a lot of requests from retailers for garment solutions, and not only from European customers but also from companies in North America. We can deliver in two weeks to the East Coast, something which is not achievable from China.”
Imprima’s success is even more impressive given its short existence. The company started operations just before the global pandemic when it was developing its plants from scratch. Covid-19 brought everything to a halt. “We had to completely re-think our operation in terms of reorganising the two Italian plants, but also our internal structure in terms of positioning of the brands, as well as the internal synergy,” says Mr Benevolo.
“Our teams did great work during the pandemic and all credit goes to them. We are very proud of what has been achieved in such challenging circumstances. Our people have made sure that we are operating, making revenues and profits. That is very positive.”
He points out that Imprima has invested heavily in the Industry 4.0 concept as well as in environmental protection. “We have completely refurbished our plans and are now aiming for ISO 50 000 certification, developed for organisations committed to addressing their impact, conserving resources and improving the bottom line through efficient energy management.”
“Globally, the fashion industry is the second worst in the world for air pollution and environmental impact. In fact, 10% of the carbon dioxide emissions released to the atmosphere comes from this segment.”
Conscious of this, Imprima Group has set for itself and its brands the ambitious and expensive goal of reaching net-zero GHG emissions by 2023, as part of its sustainable programme. The ambition is to become a world textile company with zero impact and the company has already started implementing actions towards this goal.
Mr Benevolo explains that the biggest challenge is water consumption – zero water is quite impossible with the current technology in the textile printing industry, but the company is striving to develop pigment production that does not need water. “We are not there yet but the situation may be very different in 12 to 18 months.”
differently, with a fresh approach and new ideas. We want people bringing innovation, bringing motivation to revive the sector that has suffered a lot over the few decades.”
With the right people, the company is set to regain its pre-pandemic market share, he affirms. “We are now thinking of investing in the US market and reinforcing our operation in Brazil.”
The company is aware that to move the business forward, having the right talent on board is crucial. Mr Benevolo says: “While the textile industry in Europe is very old with a sound legacy of technologies and know-how, we want to have people on board that see the textile business
“And, of course, we are looking intensively at the Asian market; as a textile company, we have to be there. We cannot export to China from Europe. In any case, our growth strategy is clear – we want to drive the garment business in the United States, conversion in Brazil and reproduction in Asia. At the same time, we will strive to be a zeroimpact textile company.”
TO REVIVE THE SECTOR THAT HAS SUFFERED A LOT OVER THE FEW DECADES.”Federico Benevolo, CEO & Chairman, Imprima Group.
Ken Baker, CEO, NewAge Industries.
US-based NewAge Industries is a leading independent manufacturer of fluid transfer systems including thermoset and thermoplastic tubing, hose, fittings, clamps, single-use systems as well as RFID tagging solutions. The products are supplied to biopharmaceutical, food and beverage as well as industrial applications.
The company was founded by Raymond Baker in 1954 and gradually established a firm position selling and distributing flexible PVC hose imported from Europe. In 1984, the founder’s son Ken Baker joined the family business, to eventually become the sole owner of the company, remaining its CEO until today.
Speaking about the business’s development and its key milestones, Ken explains that in the 1990s the company started manufacturing its own PVC and polyurethane tubing – a major investment and a significant turning point for the future of the business. A few years later, silicone tubing was added to the portfolio.
“In 2000, the company experienced another significant change with the introduction of our AdvantaPure® brand; a line of high purity flexible silicone tubing and hose designed to aid pharmaceutical and biopharma manufacturers,” he says. “That really rocketed the organisation, with the AdvantaPure line taking over as the major revenue stream of the company.”
In 2006, Ken Baker completed another significant step. He established the ESOP – Employee Stock Ownership Plan – giving team members a 30% stake in the company at no cost to them. By 2019, Ken had sold the remaining company shares, making NewAge Industries 100% employeeowned.
“The change in ownership resulted in a true business metamorphosis and fundamentally changed the company culture, as the employees started thinking about the company as well as its customers from an owner’s perspective,” he says.
Today, the business is stronger than ever, serving a wide customer base around the world. Right now, NewAge is expanding its presence in Europe with a brand-new factory that is being built in the Netherlands.
On its home turf, NewAge has proudly opened its newest facility in Warrington, with seven new ISO Class 7 clean room suites, totalling 22,000 square feet, designed for controlled silicone and TPE tubing extrusion. Further afield, the company is eyeing China as a potential location for its next factory in the future.
So, what is its recipe for the company’s success? “In addition to top quality, what makes us different from competitors is that we truly partner with our customers, we really try to understand their current and future needs and come up with systems that match those needs. I think our secret lies in having owners that really take care of customers,” says Ken Baker.
That attitude also helped the company sail through the two years of the pandemic. When Covid-19 struck in 2020, NewAge’s AdvantaPure products were designated “essential” in the battle against the virus.
“Our tubing is used in the pharmaceutical and biological processes within the production of vaccines,” Ken explains, adding that the company was faced with the challenge of satisfying the new demand while keeping existing customers happy.
That challenge was handled by introducing extra overtime and purchasing a second facility within seven miles of its corporate headquarters with 97,000 additional square feet, in line with the company’s plans to double and triple capacity.
“We continue to supply Moderna, Pfizer, Johnson & Johnson with tubing and hose for making the Covid-19 vaccine, but we also supply other vaccine and drug manufacturers, such as Merck, Sanofi, GSK, Amgen, basically the whole of Big Pharma. We help the pharma and biotech companies to make their medicines and that will continue.”
In 2021, the company achieved yet another milestone – B Corporation™ certification. “It is a very special certification, which says that we believe in taking care of our employees, taking care of our customers, taking care of the community and the environment,” says Ken.
“That’s why we operate using sustainable energy, embrace a zero-landfill initiative, and invest in our people to produce better outcomes for end users,” he continues, explaining that over the last decade, the company has installed over 4,000 solar panels on the roof of the company’s headquarters, and the power system has the capacity to produce up to
one megawatt continuously. NewAge also recycles its silicone scrap as well as its PVC scrap.
Ken affirms that the whole business model is sustainable.
“We have a saying that we will not be sold in 100 years; we will be an independent employeeowned business 100 years from now. Sustainability is not just environmental, we’re also talking about the sustainability of the business. Our purpose statement is ‘in business to do good, driven to excel’.
“To this end, we are involved in many social initiatives: we have people volunteering in the community, we support food banks, and we have sent tonnes of products to Ukraine. A lot of these initiatives happen without me, the CEO, talking about it –it’s part of the company culture,” he affirms.
Ken Baker reflects that over the years, he has given a lot of thought to the role of a business should be for society. “I don’t buy the ‘greed is good’ idea,” he says. “I think that business has a responsibility and an obligation to do good for society. I have learned from employee ownership that it brings a real business transformation, it makes a business what it really should be –doing good for the employees/owners as well as for the community.”
“That’s why I have started to promote the idea of employee ownership across the country. I have also started the ‘Baker’s
Centre of Excellence for Employee Ownership and Business Transformation’ at a local college to educate people like myself, and employees about this concept.”
“The benefits are clear for all. Out of our 300 employees, we have 54 millionaires working here, and of those 32 are multimillionaires. Some of those millionaires are on our factory floor making $18-19 an hour, but they have a retirement –they are creating wealth while they’re working. We have people that leave here with a lot of money. I want them on the cruise, not the couch when they retire, and I tell them so.”
“I HAVE LEARNED FROM EMPLOYEE OWNERSHIP THAT IT
BRINGS A REAL BUSINESS TRANSFORMATION, IT MAKES A BUSINESS WHAT IT REALLY SHOULD BE –DOING GOOD FOR THE EMPLOYEES/OWNERS AS WELL AS FOR THE COMMUNITY.”
In business since 1954, NewAge Industries is a manufacturer and fabricator of unreinforced tubing and reinforced hose for use in applications ranging from industrial to food and beverage. AdvantaPure®, NewAge’s high purity products brand, addresses the needs of the pharmaceutical and biopharm industries. In 2006, NewAge Industries initiated an ESOP and became 100% employee-owned in 2019 for the benefit of both its employees and customers. NewAge is a solar powered, zero landfill, Certified B Corporation™ committed to continually minimising its environmental impact.
US-based Printronix’s purpose is to be a trusted global leader for highly reliable, innovative printing products, solutions, and services to support and improve businesscritical applications in industrial environments.
Printronix manufactures a line of heavy-duty impact printers, used across the globe in automotive, retail, food & beverage, pharma distribution, transportation & logistics enterprises, government services and utilities.
“Printronix is a global provider of industrial print solutions, with a direct market presence in North America, Latin America, Europe, Middle-East, Africa, China, South-East Asia, Korea, Taiwan and India,” says CEO Werner Heid, explaining that the company’s solutions are designed for mission-critical applications, especially in harsh environments.
Key applications include just-in-time build sheets for production (automotive) and documentation for the last mile (from palette configuration to the truck) in the warehouse environment.
“For example, we have customers all over the world in the pharmaceutical distribution, supplying pharmacies, hospitals and retirement homes. They have short delivery windows and if the paperwork is not ready, the truck cannot leave the warehouse. The whole process is supported by our equipment and if stopped, the entire operation stops. That’s what mission-critical means in our context.”
The quality, reliability and robustness of the equipment provided make Printronix stand out in the marketplace, says Mr Heid. “We have a long-standing tenure with leading F500 global customers, with an average customer tenure of 24 years.”
“How have we achieved this? We offer the most reliable printer solutions & service to guarantee maximum product uptime, in line with our brand slogan ‘When Reliability Counts’. We also provide best-in-class lifetime total cost of ownership – our impact printing technology has the lowest total cost of ownership in the entire printing industries.”
“And, last but not least, we have the ability to adapt to customer-specific needs and can provide highly customised solutions. We are very close to our top-end users; we have a very good understanding of their document management needs within their factories or within their warehouses, and we are willing to adapt the equipment to fit better into their production or warehouse application processes.”
Mr Heid admits that continuing to provide reliability and consistency at every touch point of the company in uncertain times when inflation threatens demand, Covid-19 remains an issue, global conflicts hinder supplies and material price pressure increases present a significant challenge, but ones that Printronix has been managing well.
“We have sound relationships not only with our customers but also with our suppliers. We are flexible, trying to accommodate their needs and willing to optimise our purchasing practices towards our suppliers’ manufacturing processes although this means carrying higher levels of materials. Any crisis highlights the true value of partnerships.”
As in any industry, environmental protection is a key topic in the printing business. Mr Heid affirms that Printronix’s high-performance impact printing solutions are based on a technology which is very sustainable and environmentally friendly in terms of product life and low power consumption.
“Although it is impossible to beat certain limiting factors of the technology, you can always improve certain aspects. Our products last a long time. It is a very different story to replace a machine only every 10 years as opposed to every three years. As for new products, we are focusing on equipment with high life cycles of 300,000 to 1,000,000 pages.”
He explains that the company is also launching a new, cloudbased Fleet Care Industrial Print Management System, a cloud IoT tool enabling customers to do analysis and manage their entire print fleet across the globe to achieve maximum uptime for their equipment and uninterrupted performance.
The tool enables usage balancing, an important factor for efficiency optimisation, as well as proactive maintenance and printer health analytics to reduce consumables waste and unneeded service visits.
“The system actually enables customers to stretch the equipment life with better service and maintenance. All this has a direct, positive impact on the environment,” he points out.
Printronix operates in an environment where its customers strive for continuous productivity improvements, in order to support continuous supply chain growth without increasing warehouse
uncertain times, they shy away from major investments in increased physical capacity. Instead, they are looking for ways to accommodate increased demand with improved efficiency from existing assets. These requirements are the primary driver of Printronix’s future growth and development plans.”
He explains that one solution is the use of colour, instead of black and white printing, allowing the customers to increase warehouse material labelling efficiency. Many warehouses have started to adopt colour, as well as use cloud-based print usage data analytics in warehouses and production to increase productivity and/or reduce human error.
“End-users deploy different industrial print technologies and brands, which have different duty and maintenance
cycles, different usage patterns and inconsistent service levels, which makes managing industrial print fleets timeconsuming and costly.”
“Our customers desire to simplify their operations by engaging vendors and solutions which provide a broad, brand- & technology-agnostic solutions covering. Our FleetCare solution will be able to satisfy this demand and help them increase productivity with the equipment they already have from different manufacturers.”
Mr Heid affirms that the company is in growth mode. In October 2021, Printronix was acquired by Acacia Research Corporation, a publicly traded corporation that acquires undervalued businesses with a primary focus on mature technology, life sciences, industrial and certain financial services segments, and pursues opportunities for value creation.
The new owner is excited to support Printronix’s growth initiatives, including enabling M&A as an additional tool for growth.
“In 2022 we started Year One of a three-year growth strategy, evolving Printronix from the
leading impact printing solution provider to the leading allindustrial print solution provider. As such, we are investing in an expansion of our industrial printer solution portfolio.”
In July Printronix announced the launch of the first two models of an industrial-grade laser printer, and over the next nine months is planning to launch an additional six models to complete the portfolio. “We understand what it takes to make our industrial customers successful, and that knowledge is reflected in the new portfolio of products.”
The FleetCare Fleet Management system is also going to be launched shortly, and the company is ready to expand its existing multi-vendor service offering to enable consistent service management regardless of brand and technology.
“Our objective is to become the leading industrial print solution provider for all our customers’ industrial printing needs. Initially, the focus will be on the Americas and EMEA, which will be followed by expansion into key Asian markets,” concludes Mr Heid.
Westley Group exists to provide engineering solutions, particularly in the provision of high integrity cast components with tight tolerance machining solutions for mission-critical hardware.
We’re a special alloy engineering solutions provider, with key competencies in producing castings in our foundries and finish machining in our two machine shops,” says James Salisbury, CEO of the Group. “We offer a fully integrated supply chain to our customer base operating from four different strategic divisions.”
Westley Group has become trusted experts in heat, wear, and corrosion-resistant alloys for a huge range of safety-critical applications.
The Group’s customers depend on it for its unrivalled experience in delivering extraordinarily certified and quality-assured projects.
“We are producing castings in copper and nickel-based alloys that commonly have very demanding integrity and quality assurance requirements, any of which we can supply fully
machined, tested, and certified,” Salisbury tells us. “We supply to very bespoke requirements with small batch sizes and responsive lead times.”
Both the quality standards and the delivery times are absolutely critical, given the kinds of customers that Westley Group works with.
“Nearly half of what we do is supplied into Naval programmes around the world, specifically submarine programmes,” says Salisbury. “A lot of those components are mission-critical components. If they were to fail, which obviously they do not, they could jeopardise the submarine’s integrity, so we take huge pride and responsibility in what we do.”
That Westley Group can meet these standards has led to it supplying programmes in the UK, US and further afield. The company works across four distinct business divisions. The first of these is Spunalloys, the UK’s largest, most diverse nonferrous and ferrous centrifugal
castings foundry. It is joined by Meighs & Westley, one of the largest and most experienced non-ferrous foundries in Europe, which is the result of a strategically consolidated consortium of sand-casting foundries. The Group also comprises Francis Birkett, an extensive precision machine shop that has invested heavily in suites of CNC machining centres and lathes. Finally, there is Walter Frank, which manufactures a comprehensive range of fittings and hydrant valves in non-ferrous alloys to all international standards, including its PRV9i valve range. These divisions are served by 280 committed employees, generating revenue of roughly £33 million.
Meeting the exacting standards within tight time frames is no small task, however.
“The biggest challenge is being able to offer a manufacturing service that by its very nature is entirely bespoke,” Salisbury tells us. “We literally do not get the opportunity to prototype in many cases. When that is coupled with our customer base’s understandable expectations for on-time delivery and quality, that creates a challenge in achieving everything the customer and the supply chain require. Our customers trust us to achieve what they need, even though the complexity of what we do is not always obvious.”
This is made possible through robust, tried, and tested manufacturing systems, with very experienced personnel in all areas of the business, and clear standard operating procedures for each and every process that the company follows.
New CNC machinery finishing product destined for the US Navy.
“Recruitment’s very difficult where that top-level knowledge is required. The majority of our staff have gone through vocational training within our business sometimes for up to 40 years,” Salisbury says. “Our staff retention is very high, allowing us to then backfill positions through employees who have the highlighted qualities and the desire to learn and progress.”
Nurturing new talent is not only essential to the business but also something Salisbury has come to take pride in.
“We’re very proud that we’re on a journey with an apprenticeship programme, with apprentices in all levels of the business,” Salisbury says. “We are running at over 10% apprentices in the business vs employee numbers. That creates its own complexities, but we are very aware that the best way to get the people you ultimately want is to train from within. There is simply nobody better than us to provide that training because, ultimately, we are the best at what we do.”
“We micromanage our order book on a daily basis, to understand what’s required and what needs to be considered,” Salisbury says.
Ultimately, most of what Westley Group does is “Built to Print.”
“We’re supplied with a suite of drawings for a component as well as the quality requirements associated with the product,” explains Salisbury. “We will analyse the detail at the enquiry stage, robustly interrogate what is required in terms of tooling to produce it and whether those tools already exist. The project will then go through a very rigorous contract review process from an engineering and quality assurance perspective.”
Dependent on the specification of the product, Westley Group follows their proprietorial standard operating procedures to produce each component, subject to stringent non-destructive testing processes such as in-house radiographic examination & CNC CMM geometrical confirmation.
“On many occasions, we fully machine and test the component, which provides the customer with a full turnkey solution,” Salisbury says. “They’re getting something delivered that they can go straight to assembly with.”
Carrying out these procedures to the required standard requires talent and experience, and Westley Group requires that its people be trained by the best.
Making sure a special alloy Naval shaft liner is perfect for release.
“WE ARE TRUSTED TO DO THE DIFFICULT THINGS, SO WE SHOULD DO THE RIGHT THING AS WELL. WE ARE PLEDGING TO BECOME CARBON NEUTRAL BY 2040. WE ARE GOING TO PLANT A MILLION TREES IN THAT PERIOD.”
As well as manufacturing bespoke products to the highest standards, and building talent, Westley Group is also dedicated to creating sustainable value not just for its stakeholders, but for society at large.
The company incorporates economic performance and environmental and social responsibility into its CSR strategy. Westley Group has moved beyond simple and traditional profit generation objectives to leverage its economic performance and direct it towards environmental and social governance.
“We have just launched a sustainability drive in terms of emissions and our carbon footprint. That is difficult to do in manufacturing industry such as ours,” Salisbury admits. “We are trusted to do the difficult things, so we should do the right thing as well. We are pledging to become carbon neutral by 2040. We are going to plant a million trees in that period.”
By integrating ESG into Westley Group’s CSR strategy, the company has created a profitable model that provides long-term value for all stakeholders. The Group aims to reduce its impact on the environment, protect its employees, and improve the way it operates as a business.
Constant improvement remains a central part of Westley Group’s outlook.
“We plan to continue to evolve, to get better. You can always look for improvements and that is inherent in all that we do,” Salisbury insists. “We are increasing our footprint into key naval and defence markets and continue to invest in growing our capabilities and capacity to machine everything that we cast.”
“OUR STAFF RETENTION IS VERY HIGH, ALLOWING US TO THEN BACKFILL POSITIONS THROUGH EMPLOYEES WHO HAVE THE HIGHLIGHTED QUALITIES AND THE DESIRE TO LEARN AND PROGRESS.”
© BAE Systems
© BAE Systems
MADE BESPOKE. BUILT WITH PRECISION.
Westley Group produces high-intensity cast components and tight-tolerance machining solutions in a fully integrated supply chain.
Westley Group produces high-intensity cast components and tight-tolerance machining solutions in a fully integrated supply chain.
Unrivalled experts in heat, wear, and corrosion-resistant alloys, we supply fully machined, tested, and certified components for safety-critical applications.
Unrivalled experts in heat, wear, and corrosion-resistant alloys, we supply fully machined, tested, and certified components for safety-critical applications.
With our bespoke service, no project is too big or small.
With our bespoke service, no project is too big or small.
For a wide range of industries, where safety is of the utmost importance, our robust manufacturing expertise and qualified personnel deliver exceptionally certified and quality-assured products.
For a wide range of industries, where safety is of the utmost importance, our robust manufacturing expertise and qualified personnel deliver exceptionally certified and quality-assured products.
GROUP. TRUSTED TO DO THE DIFFICULT THINGS.
WESTLEY GROUP. TRUSTED TO DO THE DIFFICULT THINGS.
MADE BESPOKE. BUILT WITH PRECISION.
Yamato is a leading global manufacturer of multi-head weighers, commercial scales and product inspection equipment. With a track record going back more than 100 years, Yamato weighing solutions enhance production processes in a range of industrial food sectors from granulated products, confectionery and snacks to fresh produce, IQF (individually quick freezing) products, fish and meat.
Yamato was founded as the Kawanishi Machinery Co. Ltd. in Japan in 1920 and became Yamato in 1945. “At first, we became known for making heavy-duty weighing technology across many industries including steel, automobile, and highway construction,” says Mr Chun Ha, Managing Director of the British subsidiary Yamato Scale Dataweigh UK.
“As the company developed, its focus shifted. Yamato was one of the first companies to realise the true potential that lay in the technology of multihead weighing – in the late 1970s, Yamato developed the first multi-head weigher and focused its efforts on serving the food processing industry. This was the beginning of the company’s global expansion.”
Since then Yamato has continued to innovate in the industry developing ‘double shift operation’, introducing a
16-head multi-head weigher with memory buckets, and developing mixing software and a touch screen command module in the 1980s.
The launch of the Sigma F1 Frontier series in 2005 revolutionised multi-head weighing technology, enabling quick, precise and safe weighing in new and previously unforeseen applications. In 2008 Yamato introduced a completely new concept for a 28-head multi-head weigher.
Today, Yamato holds over 400 patents worldwide and is continuously developing new technologies to provide better weighing solutions for its customers.
Mr Chun Ha says: “Yamato is highly technically oriented on its core weighing technology, serving a well-developed customer base. Yamato
ENE Group has been designing and manufacturing bespoke processing line machinery for over 25 years. We operate from four sites throughout the UK and EU and can provide a full package of stainless steel conveyor systems, labelling systems, production line equipment and conveyor belting.
ENE Group has undertaken projects across the globe working with many of the world’s leading food and drink processors. We take great pride in our reputation for engineering excellence and innovation. Our engineering team has a wealth of experience which paves the way for cutting edge practical solutions. We understand that each industry sector can have a different set of requirements, standards and processes. This is why we provide bespoke and tailor made solutions which meet the needs of each of our customers individual requirements. ENE Group leads the way in bringing new solutions to the industry through extensive research and development. We have continually invested in our manufacturing technology and skills, supporting a culture of ongoing innovation.
With our extensive knowledge of the food industry, ENE Group has worked in partnership with Yamato Scale to deliver an innovative food processing package to feed into their multi-head weigher. This bespoke solution included a swan neck conveyor, wire belt conveyor, hoppers and indexing conveyors. Our unique automated system ensured continuity of process, speed, accuracy and productivity. Through this partnership, Yamato Scale and ENE Group have achieved a system that delivers outstanding performance, advanced hygiene and flexibility to all production line requirements.
continues to be a privatelyowned company, and with a total workforce of around 1100, has subsidiaries and branches in 12 countries.”
Mr Chun Ha brings a wealth of experience to the Yamato Scale Dataweigh team. He joined Yamato in Japan from Schneider Electric where he undertook a number of senior roles from business development manager to the business unit director. With a Doctorate in Economics, Chun Ha has gained significant management experience both in Japan and worldwide, including overseeing the operation of multiple sites.
He joined Yamato’s UK operation from Japan where he had served as general manager for global sales since joining Yamato in July 2015, and more recently, as executive officer and managing director of Yamato Scale Gmbh.
Explaining the development of the British business, he says: “Yamato UK was founded as our second subsidiary in Europe (after Germany) in 1994. We basically focus on two business lines: weighing equipment for the food industry and product inspection equipment. Following a recent restructuring, we are now well-placed to provide superb customer care –the customer is at the very top of our business priorities.”
The multi-head weighers are the company’s flagship product range, and Mr Chun Ha highlights the Dataweigh Epsilon in particular – a revolutionary mid-range solution that delivers excellent performance at an
affordable price. The range has 10-, 14-, 16-, 20-, or 24- head models available, with userfriendly icons enabling effortless operation, and 100 pre-set programs that can be stored in memory. The Epsilon is the ideal solution for weighing bulk loose products in a range of food and non-food applications.
“Our core R&D capability is based in Japan, but in the UK, we have design engineers for specific applications and for customising the machines for each particular client. The UK market is not that different from other regions in terms of requirements, but there is a wide variety in the food sector in terms of different product
characteristics, so ultimately, the weighing equipment needs to be adapted to particular needs. These may be just minor changes but design flexibility is quite important for us.”
“FOLLOWING A RECENT RESTRUCTURING, WE ARE NOW WELL-PLACED TO PROVIDE SUPERB CUSTOMER CARE – THE CUSTOMER IS AT THE VERY TOP OF OUR BUSINESS PRIORITIES.”
He reveals that the company has just secured a major project for a prime UK customer, an important achievement that will move the business further on again, fully in line with current market trends.
“The general trend postpandemic in the UK, but also globally, is towards increased automation driven by the need for accuracy and the sparseness of skilled labour. Automation, while requiring initial investment, ultimately lowers costs and enables highly efficient and faster operation.
This trend will bring us more and more business.”
The company is set to invest in its UK facility, specifically in increasing its customer demonstration capacity, in line with the parent company’s plans to expand its global footing in the longer run, both in Europe and in the Far East, says Mr Chun Ha.
“AUTOMATION, WHILE REQUIRING INITIAL INVESTMENT, ULTIMATELY LOWERS COSTS AND ENABLES HIGHLY EFFICIENT AND FASTER OPERATION. THIS TREND WILL BRING US MORE AND MORE BUSINESS.”
“Yamato is a unique company, with its specialisation in the food industry and its firm business base. An interesting, and impressive point is that, unlike our competitors, we have been increasing our global presence purely by organic growth, never by M&A as is customary in our industry.”
In conclusion, he affirms that the company has withstood the current market challenges in good shape and is ready to make use of emerging opportunities:
“Both Yamato UK and Yamato Japan have hit historical records in terms of business revenue during the global pandemic.”
“Our level of expertise and our dedication to providing a range of added-value services to our customers make us unique. We have a good market position in the US and Europe, and will now build the business in Asia, drawing on our successful history, top quality and customer-centric approach.”
NAMCOR, THE NATIONAL PETROLEUM CORPORATION OF NAMIBIA, WHICH OPERATES ACROSS THE OIL & GAS VALUE CHAIN, IS SET TO MOVE THE COUNTRY FORWARD WITH NEW OIL DISCOVERIES.
The National Petroleum Corporation of Namibia – NAMCOR, is a legally incorporated entity with the Government of the Republic of Namibia as its primary stakeholder. The company is active in the oil and gas sector and serves a variety of customers including the government and parastatals, as well as private companies in the mining, transport, and other industries.
We are fully owned by the Namibian government, and operate as the state’s vehicle to participate in both the upstream and downstream sectors,” says the company’s Managing Director Immanuel Mulunga.
He explains that in 2021, the company was also awarded the operatorship of the National Oil Storage Facility (NOSF) and Jetty at Walvis Bay, which was constructed with the aim to improve Namibia’s security of supply of petroleum products. Most recently, NAMCOR has entered the downstream retail sector, having opened 11 service stations at strategic locations around the country.
“On the upstream side, we have been going through an evolutionary process, initially playing the role of the government advisor on
upstream regulations as part of our mandate under the Petroleum Exploration and Production Act, which is our enabling legislation,” adds Mr Mulunga. “The same law allows us to participate in the entire oil and gas value chain.”
Within that mandate, NAMCOR is participating in the exploration and production of oil and gas in Namibia and outside, an area which is now set to be a driving force for both the company and the country’s economic development.
After decades of exploration, in February 2022 NAMCOR and its partners, Shell Namibia Upstream B.V and Qatar Energy, announced the discovery of light oil in both primary and secondary targets at their Graff-1 deep water well in the
Orange Basin, offshore Namibia. This was followed by another major light oil and associated gas discovery on the Venus-1X prospect, also located in the Orange Basin in partnership with TotalEnergies.
“Following the recent success of the Graff-1 well for Shell, this second light oil discovery by TotalEnergies has demonstrated the world-class potential of this new play in the deep-water of the Orange Basin, which could be a major game changer for Namibia’s economy and its people,” says Mr Mulunga.
“With regard to their size, these two discoveries are probably in the top 20 discoveries made in Africa in the last couple of decades and are going to make a huge impact on the economy of Namibia, as well as a huge impact on NAMCOR, likely to transform the company into the biggest corporation in the country.”
“We are looking forward to the appraisal programme that is currently taking place, and we hope to accelerate the development and the ultimate production of oil in the next five years.”
Under Mr Mulunga’s management, the company has already experienced major development over the last five years, having grown from a business with under 85 people to a company of approximately 200 permanent and temporary employees. NAMCOR has also grown in financial terms, increasing its revenues by 394% and more than doubling its net balance sheet assets over the same period.
For his exemplary leadership, Immanuel Mulunga was honoured in June with an award and Certificate of Excellence after being voted Namibia’s Executive of The Year for 2021 by the readers of Executive Magazine.
“It is very humbling to be part of NAMCOR’s growth, and part of the creation of a worldclass national oil company,” he says.” We expect to grow exponentially over the next two years, on the route to becoming the biggest company in the whole of Namibia, as a result of the equity holdings in the oil discoveries that we have made.”
“We believe, though, that the role of NAMCOR should be wider – namely in supporting the communities that we operate in. Right now, we are increasing our corporate social responsibility budget, and looking at creating a foundation for NAMCOR so that we can give back more to the communities. Our focus will be primarily on education, community development and health, and also sports.”
With its latest development, NAMCOR is transforming from a national oil company into a national energy company, set to play a meaningful role in the global energy transition. The
sustainability agenda is part of the corporate strategy, affirms Mr Mulunga, and includes electric vehicle charging points at service stations as well as solar energy to power the headquarters building and the service stations later on. There are also plans to participate in the green hydrogen economy as an equity holder in some of the upcoming hydrogen initiatives.
Immanuel Mulunga admits that managing this exponential business growth has been not only rewarding but also challenging, making sure that the company attracts and
retains the talent it needs, and puts measures in place to remain competitive with international companies operating in Namibia.
“Namibia is not a traditionally petroleum-producing country. We, as a national company, have to make sure that this development takes place sustainably, without undue political influence derailing the production of oil and gas over the next five years. Taking and mitigating all the risk is a challenge, but we believe we have what it takes.”
“We will need to hire new people, develop our resources internally but also bring in external expertise to allow for knowledge transfer. We don’t need to reinvent the wheel but bringing in the right skills is something that’s critical, and a key success factor.”
In concluding, he affirms that NAMCOR wants to continue to play a central role in the Namibian economy, to make sure that the recent oil discoveries benefit the entire country, as well as making sure that government continues to play a central role in the oil and gas space. “NAMCOR and Namibia are in a good place, so I’m really looking forward to the future.”
“WE EXPECT TO GROW EXPONENTIALLY OVER THE NEXT TWO YEARS, ON THE ROUTE TO BECOMING THE BIGGEST COMPANY IN THE WHOLE OF NAMIBIA, AS A RESULT OF THE EQUITY HOLDINGS IN THE OIL DISCOVERIES THAT WE HAVE MADE.”
Prairie Provident Resources is a Canadian junior oil & gas company operating exclusively in Alberta with over 375,000 net acres. Based in the city of Calgary, Prairie Provident Resources is engaged in the exploration and development of Alberta’s oil and natural gas properties, optimising cash flow from its existing assets while growing a base waterflood business at its Evi (Slave Point Formation) and Michichi (Banff Formation) assets. This allows the firm to provide low decline production & stable cash flow while organically developing a new complementary play to facilitate reserves and production growth. The firm is also providing short cycle returns through the successful development of the Glauconite and Ellerslie formations in the Princess area of Southern Alberta.
With a small Calgarybased technical team and a revitalized field operations team, Prairie Provident Resources has achieved production levels of 4,500 barrels of oil equivalent a day.
As company President and CEO, Tony Berthelet tells us, “We are an energy company where all things are possible. We have a team of like-minded individuals focused on responsible energy development.”
“We have the potential to add significant reserve growth through waterflood expansion,” Berthelet explains. “Our assets have the capability to repay debt and continue to provide a return on investment to shareholders with an improved balance sheet.”
The balance sheet is the biggest challenge Prairie Provident Resources currently faces, but
it is a challenge Berthelet has been ready to handle from the outset.
“We came into these resources with a challenging debt position, and we’re setting the company up for a sustainable future, but the price collapse in 2020 has been a barrier to growth,” he says. “In this current commodity cycle, we are taking the opportunity to address our balance sheet and set the company up for success.”
It is a process that will involve bolstering Prairie Provident Resources’ ability to manage its liabilities. The company has a team specifically focused on liability management, and over the last 14 months, it has made significant progress through area-based closure work. The firm has made a 13% reduction in its inventory of inactive wells, which it intends to build on with a further 15% reduction this year.
“We’re building trust with our regulators and stakeholders through liability reduction as part of our ESG commitment,” Berthelet says.
As part of this process, Prairie Provident Resources is renegotiating its debt over the third and fourth quarters, exploring all possible opportunities to address the balance sheet.
“We’ve partnered with leading industry advisors and are looking forward to sharing developments with shareholders,” Berthelet tells us. “In terms of liability reduction, our entire team is addressing the whole lifecycle from exploration, to production, to abandonment and reclamation. If the well isn’t profitable it is added to abandonment inventory. Almost every person in the organisation has some involvement with each well, so we don’t miss any opportunities with existing wells.”
Berthelet has not been with Prairie Provident Resources for long, taking up his position only last year, but one of the first things he did on joining the company was to overhaul the company’s leadership team to help shape the culture of the company.
“ONE OF THE FIRST THINGS WE DID AS A NEW LEADERSHIP TEAM WAS TO INITIATE A CULTURE JOURNEY TO HELP US EXPLORE WHAT OUR CORE VALUES ARE.”
“One of the first things we did as a new leadership team was to initiate a culture journey to help us explore what our core values are,” Berthelet recalls. “We asked what key attributes were needed to address our challenges, and how we could create an environment where we can have fun and hold each other accountable in our pursuit of excellence. We have established a shared understanding with our staff who share those values.”
Berthelet uses those shared values and culture as a lens to view the firm’s recruitment process and to find recruits who align with those values to ensure the company’s best chance of retention.
“I’m a firm believer in diversity, I believe we make better decisions with different perspectives,” Berthelet insists. “We have 61% female representation in
head office and 20% on the board of directors. As part of that culture, we’ve invested in staff across all disciplines. They are responsible for leading our quarterly review meetings, sharing knowledge with the rest of the company related to their job function.” This improves a common understanding of the business & highlights our interdependencies.
The company also has annual cross-company strategy sessions, and each employee builds the targets that come out of those meetings into their individual performance targets.
“When you think about retention, one of the biggest retention tools is employees knowing they contribute to something bigger than they are,” Berthelet says. “We hold each other accountable and build a sense of commitment to the corporate vision.”
As well as ensuring that the resources they are operating generate profit for the company, Prairie Provident Resources also makes reclamation a priority across Alberta and Western Canada in general.
“We have created a specific team to address liabilities, working with our stakeholders to find ways to ensure we’re maximising our opportunities by addressing issues specific to stakeholders,” Berthelet points out. “Last year we launched an initiative to go back to unreclaimed sites, restoring them as closely as possible to their original specifications. We sat down with landowners to ask them to prioritise which leases they would like us to focus on. It has been a great opportunity to win hearts and minds. We’re saying look, tell us which of these areas we should be looking at first, then we look at those sites for new reclamation opportunities.”
The company has engaged local landowners so that their voice has been at the heart of Prairie Provident Resources’ approach. It has been a key initiative for the company, keeping it tuned into the key issues of the community.
Community involvement & stakeholder engagement are key factors in responsible energy development, and Prairie Provident Resources recognises that each group has its own unique culture and circumstances; and therefore, its own process preferences. The company builds mutually beneficial relationships through respect, understanding and cooperation with indigenous & non-indigenous communities.
“In 2022, we launched our inaugural ESG report for the company, created an ESG
committee at the board level, and with the Chair’s support we created a policy with focus areas related to climate change, community and indigenous relations, asset management and diversity targets at the board level,” Berthelet tells us. “This ESG policy aligns our strategy with all stakeholders. This is a key achievement for us in 2022. It really does provide shareholders and all stakeholders with assurance that we’re focused on setting targets which we will report on and update every year.”
This is a special year for Inchcape Shipping Services. The maritime service provider, primarily focusing on port agency, is celebrating 175 years of business in 2022. In those 175 years, Inchcape Shipping Services has grown to employ over 3,000 people, across 240 offices in 60 countries.
But that is not the only reason that 2022 is a special year for the company. It also marks Inchcape Shipping Service’s first year under its new owners, the London-based private equity firm, Epiris.
“Inchcape has arguably the largest and most extensive port agency network in the world,” explains company CEO, Frank Olsen. “Literally wherever you might have a ship calling, almost regardless of the services you require, we’re there on the ground and can support your business. We offer a global platform of governance, compliance, ethics, health and safety, and of course ESG where the E becomes more and more important. It is a seamless global network.”
Whether customers are looking for support with their crew, cargo, or the vessels themselves, Inchcape is ready to provide support.
That wide array of services has also ensured that Inchcape has remained robust in the face of repeated global crises.
“Serving all these customer segments means we are well protected against swings within specific markets, often leaving us unaffected by events like financial crises, Covid, and geopolitical turmoil,” Olsen points out.
“Having a global network and being activity agnostic means we’re well-suited to always deliver good results despite the market.”
Frank Olsen, CEO, Inchcape Shipping Services.
Inchcape is capable of serving vessels from every sector imaginable, including cruise ships, container vessels, tankers and military vessels.
Even with 175 years of history behind it, Inchcape Shipping Services has faced few periods quite as eventful as our current times.
Belle Chasse Marine Transportation, LLC, is a familyowned and operated business, founded more than 45 years ago. Headquartered in New Orleans, Belle Chasse Marine has grown into the largest launch service on the lower Mississippi River. It is able to efficiently serve its customers by utilizing 35 launch boats, seven launches and four smaller-foot docks. In addition to launch services, Belle Chasse Marine delivers marine lubricants to deep-draft vessels along the lower Mississippi River and in the Houston Ship Channel and Galveston Bay. Belle Chasse Marine delivers these lubricants using a fleet of 20 trucks, six oil barges and one offshore oil tanker. Belle Chasse Marine employs more than 225 employees and operates on a 24/7 schedule, 365 days a year.
“There is a tremendous amount of noise in the shipping market and the world in general,” Olsen admits. “There is tension, the war in Ukraine, political unrest, we are in a high inflation market and the macro-economic outlook is very uncertain. The global supply chain is to a large extent broken and struggles to recover, and covid continues to affect a large part of the world. So that combination of noise and uncertainty and tension is a challenge for everyone.”
Inchcape in particular has been navigating challenges around Covid restrictions in North Asian countries, as well as a high inflation environment where 90% of the firm’s operating costs are in manpower.
“When it comes to Covid restrictions- unfortunately, we now have well over two years’ experience dealing with that. We are used to navigating the various restrictions and have learned to adapt and deal with those challenges,” Olsen points out. “We actively advise our customers on how to perform crew changes and other vessel-related operations. That is almost business-asusual by now, but it still creates complexity. In terms of inflation, there is not much we can do but constantly look at how to work more efficiently. We increase the efficiency of our network, but primarily we are focusing on how to add new business, and new revenue, without increasing our headcount.”
“HAVING A GLOBAL NETWORK AND BEING ACTIVITY AGNOSTIC MEANS WE’RE WELLSUITED TO ALWAYS DELIVER GOOD RESULTS DESPITE THE MARKET.”
While Inchcape is not looking to increase its workforce by more than necessary, it is clear from talking to Olsen that holding onto the company’s existing talent is one of his top priorities.
“The most important task is retaining the good people we have in the company,” he says. “There is a lot of attrition right now. People are moving jobs and it is a tight labour market. So, it is important not to lose someone who might go to a competitor. We focus on providing a fair and attractive salary and remuneration, but also continuous learning, development, and career progression so that people feel they’re developing while they’re with us. If someone
Horizon Air Freight is a proud partner of Inchcape Shipping Services. Providing door-to-deck delivery and last-mile logistics, Horizon shares Inchcape’s commitment to do whatever it takes to keep ships sailing safely and on schedule.
We are one of the largest
waste
Antwerp in the field of liquid & hazardous waste from Annex I to
the port of Rotterdam, Amsterdam
VI.
Because of the strategic alliance with port reception facility MTD in Antwerp, we are able to operate in the entire port area of Rotterdam, Amsterdam & Antwerp. This allows us to work efficiently & environmentally friendly.
For the collection of liquid hazardous waste, we use the most modern vessels & highly trained personnel. We are the only collector in the port of Rotterdam, Amsterdam & Antwerp, which features 3 C type barges. Therefore we are fully equipped for future legislation & regulations in our field, our total collection capacity is 8,500 tons. We always try to bear in mind the requirements & needs of our stakeholders, we find it very important to work closely with our clients. For the collection as well as with our outlets to make sure waste processing takes place efficiently & in an environmentally responsible manner.
Global, cost-effective, time-sensitive marine supply chain solutions.
You move the world. We’re here to help.Kenny, Warehouse Manager Horizon Air Freight Warehouse,
is with us on a salary, the cost of replacing them is higher. So, retention is crucial.”
To ensure Inchcape remains an appealing place to work, the company has adopted flexible working and hybrid working solutions, offering employees a certain amount of freedom in how much they work from home, and how much they work in the office.
“Home working is part of the new way of working,” Olsen acknowledges.
Of course, recruitment remains an essential task in a competitive employment market, and to meet those
needs Inchcape is trying something new.
“We have hired several internal recruiters, something we’ve never done before,” Olsen says. “Previously, we relied on recruiting agencies. We have now added two recruiters and plan to recruit two more, and we are actively marketing ourselves as an employer.”
While Inchcape still uses agencies, Olsen wants to build an in-house pool of talent, while welcoming speculative CVs and keeping a database of candidates who have expressed an interest in joining Inchcape.
“However, we still have a few key recruitment agencies we know and have worked with who understand our culture for senior positions,” Olsen points out.
As well as attracting and nurturing talent within the company, Inchcape aims to empower its people, and its customers, with the latest technology.
“We’re not a technology company and never will be, but we need to leverage technology and digital solutions to drive increasing value in our network,” Olsen says. “When we talk and think about technology, we focus on making it easier to do business with us, improving productivity and quality so that we can provide superior service.”
It is an approach that prioritises transparency, information, data collection and analytics.
“If we get all of this right the ambition is to provide a high level of predictability. If a customer contracts Inchcape we can provide a good estimation of what is going to happen before it happens,” Olsen tells us. “We handle a tremendous amount of port calls, more than 100,000 port service jobs per annum, so we are using technology to give customers a clear picture of what will and might happen in the future.”
Olsen, meanwhile, has his own opinions about Inchcape Shipping Services’ future.
“With new ownership, private equity-backed as of July, we see a strong focus on growth from three main pillars,” he says. “The first is organic growth, growing with existing customers, and winning new business, closely linked to our value proposition and unique attributes as a global network.
Secondly, we see growth and additional revenue from new services and product offerings. We are expanding our service portfolio in and around the port. The third and final pillar is inorganic growth through acquisitions.”
With 175 years of history and a new owner behind it, and a clear vision of the future, Inchcape is ready for the next 175 years.
“WE HANDLE A TREMENDOUS AMOUNT OF PORT CALLS, MORE THAN 100,000 PORT SERVICE JOBS PER ANNUM, SO WE ARE USING TECHNOLOGY TO GIVE CUSTOMERS A CLEAR PICTURE OF WHAT WILL AND MIGHT HAPPEN IN THE FUTURE.”
Viken Group is made up of several companies, but the Group’s main company is Tillberg Design of Sweden (TDoS). This firm was founded in 1964 by the industry pioneer Robert Tillberg. It became a famous name in interior design, working mainly on cruise ships as well as super yachts and ferries. TDoS thrived in that sector for 50-odd years. Then the pandemic hit, and the cruise lines had close to 0 revenue for more than one year.
We realised we needed to adjust to a new normal and the future that followed,” says Stefan Nilsson, CEO of Viken Group as a whole. “We also realised we could not do it ourselves. We needed to look at our community within the marine industry.”
Nilsson quickly determined that his clients’ priorities were health and safety, but also that they now had limited funds to invest over the years to come.
“They were in survival mode. That is when we started to think about creating a group of
companies,” Nilsson points out. “We founded the Viken Group, of which I am the CEO. Tillberg Design of Sweden became the main brand underneath it, and we looked at how we could strengthen our services while solving problems like health and safety by smart design. We continued adding a company of a technical nature, Thalia Marine based in Trieste, to help with Naval architecture, Surveying and inspections, Project management and the more technical aspects of design.”
It was a process that involved rigorous consultation with TDoS’s target markets.
“We spoke to a lot of brokers, financial experts, and clients, including current and former executives in the cruise industry. We found almost everyone felt they were in need of someone who could take on the whole design process, particularly for new cruise ships,” Nilsson recalls. “Today there are over ten specialist consultancy firms that all have separate scopes of work and contracts. Examples are that the client would have different companies doing interior and exterior design, signage, artwork, lighting design and the galley etcetera. So that is when we picked up the pace, making acquisitions and partnerships in our ambition to solve the problems our current and future clients have. Long-term, we should be able to provide everything between the shipyard and the client, and where we cannot, we have partners who can.”
By carefully acquiring and combining capabilities, Viken Group has become the only firm capable of providing both naval architecture and interior design for cruise ships and yachts. By acquiring a very well-known Milano-based yacht design company, Hot Lab, Viken Group can do this all the way down to 20-metre yachts. It is unique in being able to provide
that combination in-house, alongside an extensive network of partner companies, including ship management company Columbia Blue.
It has created a powerful tool for navigating the industry in a post-Covid environment, but the pandemic is not the only world crisis affecting the market.
“Nobody knows what will happen with Ukraine. The war there is horrible,” Nilsson says.
“We had partners directly affected, as Ukrainians and Russians made up a lot of their crew. What we have also seen over the last few months is the energy crisis, which directly affects the fuel crisis for ships. Then the recession comes, and it is difficult to say what to do.
In the yacht industry, our target market will stay solvent, but it is difficult going straight from a pandemic into a world with war in Europe. We are riding the storm, so to speak.”
At the same time, Viken Group’s companies are taking steps to look after its own people who have been affected.
“Within the company, a lot of our staff are hurting on a personal level because they have friends and business partners from Ukraine,” Nilsson says.
Human resources have always remained central to Viken Group’s strategy. The Group has a strong HR team, with talent management programs spread across the Group’s different design studios for cruise ships, yachts, exterior design, and R&D.
“Our managers are very present, and each person gets their own personal development plan, and that can go in very different ways,” Nilsson says. “We have the ability to let staff swap company, so one employee can go from working on smaller yachts to bigger yachts and cruise ships. You can learn skills within the group, which is a selling point to employees.”
When Nilsson helped to create the Viken Group, he did it with the goal of bringing together companies that could work together for their clients and employees, but he also wanted to do good beyond that. While there is little the company can do directly to drive sustainability, it has made a significant focus on environmental issues. This is why we say we are “Better together.”
“We can influence clients and show them ways to be on top of that,” Nilsson says. “The recent heat wave demonstrates how urgent it is to innovate and work on that.”
Innovation continues to be a watchword for the Viken Group. Building on the plan established in 2020, Viken will continue to focus on the technical side of the industry through its subsidiary, Thalia Marine, with an increased focus on effective technical solutions from a sustainability point of view.
“We are diversifying and seeing that the need in the market is there already,” Nilsson tells us. “We are also continuing to diversify through our other subsidiary, Hot Lab, a firm that works mainly on 20 to 80-metre yachts. They are working in a different space from the rest of the Group, but we can share resources and together we have a strong management structure to
support the team, focussing on excellent design and meeting the client’s needs.”
To help build that future, Nilsson is drawing on the best talent available.
“Besides the best company management in TDoS, Thalia and Hot Lab we also have a brilliant IT manager in the Group, an expert who tells me where to look, speaks to people within the industry and attends technical exhibitions like the one in Dubai,” Nilsson says. “My job is to meet as many potential partners as possible, sometimes to say hello, sometimes to make an acquisition. Sometimes we will not talk for two years but then realise there is something we can work together on.”
This growth into the technical side of the market is a major
part of Nilsson’s plans for the Group’s future. As well as the technical services the Group acquired in Italy with Thalia, Nilsson is also excited about making future acquisitions over the next couple of years in the technical field.
“On a longer-term basis we believe the way of designing and working, in general, will move in the direction of digitalisation with AI support,” Nilsson says.
“Artificial intelligence and augmented reality are becoming more relevant in their field.
We are working to understand what we need via acquisition or partnerships. We always improve our way of working continuously. Digitalisation is not just doing CAD drawings. There is so much more in our future.”
West Africa Container Terminals is a 100-person facility owned by APM Terminals, in the ports and terminals division of the Maersk Group. Located in the oil and gas free zone in Rivers State, in the Southern part of Nigeria, the facility was established at the turn of the century, building on Maersk’s long history in the region.
Despite having the backing of the international Maersk Group behind it, West Africa Container Terminals began from relatively humble beginnings.
“In 2000 we started from a very smallish team doing set-up to handle Maersk ships in the Eastern part of Nigeria,” says Naved Zafar, Managing Director of the firm. “From there we gradually grew the core staff, not just developing the company and the terminal business but also developing a pivotal role for the entire Eastern Nigerian market. We are offering an alternative and additional gateway to the Nigerian business and trading community.”
From the beginning, West Africa Container Terminals’ facility was aptly positioned as an alternative to the Lagos port terminal’s structure, which has often been under pressure from supply chain and infrastructurerelated challenges. It was a great position to grow from.
“It has been a great story since our inception,” Zafar tells us. “We started with one shipping line, then took on additional shipping lines as new companies came over. A major expansion plan was put in place in 2018 when we started modernising our terminal facility by bringing in mobile crates to improve efficiency and capacity. We also took part in a major upgrade, transformation, and expansion of our facility.”
Key components of the project include an additional ten hectares being added to the site, a brandnew yard, and the deployment of additional terminal cranes that will forever change the way cargo is handled inside the yard. The business is investing $112 million into civil works and expansion, new cranes and upgraded equipment. And it could not have come at a better time.
“It was a major milestone,” Zafar says. “Until last year we were the only major terminal operator in the region with only two small basic competitors. Last year another company started their operations near our facility. So, we have focussed on efficiency and digitalisation, which has really become a key differentiator.”
INTELS NIGERIA LIMITED PROVIDES COMPREHENSIVE INTEGRATED LOGISTICS SERVICES FOR THE NIGERIAN OIL AND GAS INDUSTRY AND BEYOND. THE COMPANY ENJOYS 30 YEARS OF EXPERIENCE IN PORT MANAGEMENT AND SUPPORT SERVICES IN SHORE BASES ACROSS NIGERIA.
Intels is offering comprehensive support at any type of port facility, the wide offer includes pipe racks, stacking areas, warehousing, dedicated enclosed areas, jetties, offices, tanks, workshops, and a variety of other services and facilities as required ad-hoc. Intels’ logistics areas have a direct connection to the quay, offering an ideal solution and our customers can operate in total security within their dedicated area, whose surveillance is on duty 24/7. Moreover, baing inside the Onne Oil & Gas Free Zone offer many advantages.
Receiving and dispatching goods, while providing localized services and supplies, is one simple concept behind Intels’ success. This enables our clients to reduce significantly transport and handling costs, and minimize any risk of cargo damage. Intels provides facilities, equipment and personnel to manage and supervise the logistic requirements of oil producing, service and project companies. The core of the offer is assistance, from cargo arrival in IMPORT, through the stacking/ racking stage, until the final delivery of materials to the designated transportation medium (support vessels, barges or trucks).
Intels can provides DEDICATED PERSONNEL available 24/365 if required. Upon clients’ needs, specialized services can be provided on a monthly basis, whether the need is for unit or team managers, supervisors or clerks.
Intels can provide DEDICATED EQUIPMENT or service with pool equipment for any necessary logistic operation. Having many agreements with the world leading manufacturers, our customers will be able to take advantage of state-of-the-art machinery and vehicles, increasing their working performances due the efficiency of our service.
Intels is a multi-sector entity able to provide its customers with a full-spectrum range of services, from logistics to accommodation. Our lodgings are located in modern and stylish estates, near the port complexes, with the highest security standards, and to assure all the comforts, every site comes with sports and leisure facilities.
The Multi Center complex is offering the possibility to host congresses, exhibitions, parties, dedicated events, fairs. While the main hall can be set-up as a cinema, conference etc. In the bright hall, guests are welcomed by a modern lounge bar and a relax area. Security within the buildings takes on a vital role, and Intels considers this a key aspect in its facilities. Complementary to the conference centre is the Heliconia Park Hotel, an exciting fusion of luxury, efficiency, and technology. Among the other services it provides its guests with an international restaurant and a lounge bar.
West Africa Container Terminal differentiates itself from this new competition with its long history and strong legacy.
“We started here from scratch. There was no container market here 20 years back,” Zafar tells us. “We played a key role in developing this market. We have been working hand-to-hand with all our key customers, cleaning agents, and forwarding agents, facilitating their use of the port.”
It is a role Zafar intends for West Africa Container Terminals to continue to play. From an operational point of view, the facility’s new upgrade has provided much greater capacity, with four mobile cranes and the fifth one on its way.
“With five cranes across two quays our productivity and time to move containers are much faster compared to anyone else in the entire region,” Zafar says. “Ships do not make money while they are in port. Their job is to move from port to port and it costs the entire supply chain if they stay longer on the quay than necessary.”
As well as building capacity and efficiency, West Africa Container Terminals is improving its digital offering to further empower its stakeholders.
“When it comes to handling customers, we are very advanced. 24/7 our handling is online and digital, supporting customers in seamless handling,” Zafar says. “We have also provided office facilities to our shipping line customers on site, to create smooth interactions.”
West Africa Container Terminals is adding to this with its pilot Container Freight Station Project, to support customers in the agriculture sector. Nigeria has a strong offering of agricultural products, but in the past has been frequently let down by the supply chain.
“This region produces a lot of agricultural commodities, but supply chain issues make it hard to export them,” Zafar says. “We felt that we could support these producers by facilitating that.”
Zafar is no stranger to deficiencies in infrastructure, and it is one of the things that drives him to ensure West Africa Container Terminals is a reliable and sophisticated gateway to the East Nigerian economy.
“It is an area that has been somewhat neglected by various successive governments, even though it is generating revenue for the country, there is no
investment here,” Zafar tells us.
“There are bad roads and a lot of infrastructure challenges. Our staff have to commute every day and can be stuck for hours in congestion, which all has a major impact on our business. The region also faces record
poverty, and unemployment, and that has accelerated with the oil price crisis.”
Zafar sees West Africa Container Terminals as a business that can play a valuable role in helping rectify these problems.
“THIS REGION PRODUCES A LOT OF AGRICULTURAL COMMODITIES, BUT SUPPLY CHAIN ISSUES MAKE IT HARD TO EXPORT THEM. WE FELT THAT WE COULD SUPPORT THESE PRODUCERS BY FACILITATING THAT.”
VITA CONSTRUCTION is one of the largest construction companies in Nigeria with over 41 years of experience in providing professional services, in engineering and construction, as well as maintenance operations. Delivering world-class projects of every size in numerous fields including industrial, commercial as well as residential. We strive for excellence in the construction industry and focus on serving our clients.
We are proudly certified with ISO 9001-2015, ISO 14001-2015, ISO 45001-2018 and thus adhere to high standards of quality, health & safety, and environmental protection and support social and local community relations throughout our operations.
Vita Construction Ltd has been appointed as the principal contractor for the development of the West Africa Container Terminal (WACT) Onne Expansion & Improvement Project, located within Onne port, in Port Harcourt, Nigeria.
In order to accommodate the increasing trade demands, WACT decided to expand the existing terminal to include an additional 142,000 m2 of concrete hardstand at the rear of the existing terminal, as well as changes to the yard operation from reach stacker (RS) to rubber tired gantry crane (RTG).
Part of the project included the construction of stormwater drainage along the entire rear side and the construction of a culvert leading to a new gate entrance to the terminal.
In addition, the expansion includes the introduction of steel reefer racks to accommodate 665 refrigerated containers and a 5000 m2 steel building that comprises a modern workshop able to accommodate 7 reach stackers at the same time, fully fitted offices, and a canteen. The project scope covered the upgrade of the lighting lux level of the entire Maersk terminal. This was accomplished with the introduction of 16 no 45-meter-high masts to provide sufficient lighting inside the terminal for port operations to run 24 hours.
Finally, the entire terminal security and telecommunication systems have been upgraded to the most modern systems currently available, including the installation of ISPS fencing and access control systems.
“We have to deal with all these issues, so our focus is to complete this $112 million modernisation project, which is almost 80% done,” Zafar says. “By the end of the year we hope it will be complete, and we will focus on our valueadded service project, working closely with our shipping lines and landside customers to further grow this market. We are working with shipping customers to get that growth back into the East Nigeria market.”
The firm is also investing in further training and development programs for its teams, including its supervisors and leadership.
“They are the agents of change, driving operational efficiencies and major improvements,” Zafar insists.
While West Africa Container Terminals is not a large facility in the grand scheme of things, Zafar has high hopes for its future.
“WE ARE WORKING WITH SHIPPING CUSTOMERS TO GET THAT GROWTH BACK INTO THE EAST NIGERIA MARKET.”
“We are not a very big terminal. We have two births and a 40-hectare yard. Our focus right now is on efficiency,” he reflects. “We are using leading methodologies to improve our productivity, reduce waste and cut idle time for vessels. We are also working very hard on digitising our terminal operations, including our trucking system so truckers can book delivery times online. This allows us to serve customers efficiently and cut down on delivery time. It used to be a process taking a number of hours, but the latest status is we are serving them in under 60 minutes.”
In the long term, Zafar’s goal is not only to improve the facility but also to grow its service offering.
“We want to offer value-added services to our clients that go beyond our core business,” Zafar says. “We’re seeing what we can do to further expand and deliver for our clients.”
Heartland Express was founded in 1978 and gone public in 1986. At the time it went public the firm had $20 million in revenue and a fleet of 125 trucks. From there Heartland Express has grown and spread, focussed on truckload and A-to-B-and-back and collect-to-freight business, doing the best it can by customers and drivers every day.
Throughout all those trips, Heartland Express differentiates itself through one crucial ingredient: Service.
“We do a lot of just-in-time freight, we do a lot of production line freight,” says Mike Gerdin, Heartland Express’s CEO. “We haul a lot for FedEx, DHL, and UPS. We haul freight that is very time sensitive, so our
calling card has always been service and taking care of our customers.”
And it is a good thing too, as Heartland Express’s services have never been in more demand.
“For the last two years, we’ve had more freight to haul than we can think about hauling,”
Gerdin says. “Everyone was afraid of running out of things during Covid so there was so much over-ordering by so many companies that we were jammed with freight, which is where the supply chain issues came in.”
For two years Heartland Express, and the industry as a whole, faced a huge influx of freight, and while it kept the company’s drivers busy and was good for business, the aftereffects of that rush have left lingering issues on the supply chain. To start with, Heartland Express needs to keep its trucks on the road.
“Our current challenges are tuned towards trucks and trailers and getting components,” Gerdin says. “OEMs are struggling to manufacture enough trucks for the industry. All across the world trucks need different components and a lot of the companies building those components are out of workers or shut down for Covid. So now this is the supply chain issue that is hitting us in terms of getting enough trucks or parts to keep trucks running.”
Fortunately, Heartland Express has a very new fleet, something that has always been a hallmark of the business.
“We have fewer breakdowns than a lot of trucking companies out there running older equipment. We intend to keep that going, because I hear a lot of nightmare stories in the industry about when parts break down and you can’t find replacements,” Gerdin points out.
Maintaining a young fleet has also proven to be a vital boon at a time when sustainability is at the top of everybody’s agenda.
“Having a new fleet helps in staying up-to-date on sustainability and green items and initiatives,” Gerdin says.
“We don’t build the trucks, we just drive them, but we have always had the newest technology that’s available
in the industry. We have the cleanest engines that have ever been produced. We have always been on the front end of these sustainability issues and greenhouse gas issues as well. We have invested in that technology in the past, staying ahead of the latest benchmarks set by the EPA.”
Having fresh, high-quality vehicles also helps Heartland Express with one of the other biggest challenges facing the freight industry at the moment.
“Drivers want to be driving a good quality truck, and we’ve covered that. That is important for retention,” Gerdin tells us.
Recruiting drivers is a certainly hard nut to crack for everyone in the road freight business right now. As Gerdin says, “There is a lot of freight out there, and it all has to move, and people need to drive trucks to do that.”
But the industry needs more than people who can drive, the job demands a very specific set of qualities.
“It is not an easy job and the drivers we have to do a great job, but it’s not for everyone. It takes a special person to do that job and it is a challenge for our industry going forward because the freight keeps coming and has to move,” Gerdin says. “People need to eat and the only way to do it at this point is trucks.”
Heartland Express is nurturing its own new generation of drivers, with its own driving schools to take people without a CDL and turn them into certified truck drivers.
“We do the classes, the paperwork, road tests, everything needed to get a man or woman to have a CDL and be qualified to drive a truck,” Gerdin says. “That has helped to bring
new blood into the industry. A lot of other companies are doing the same thing. A lot of drivers are reaching the end of their careers, so we need more new blood coming into the industry.”
And it is in a hurry to find that new blood, as Covid-19 and the lockdown have put the entire industry’s training programme back almost two years.
But it is not enough to simply train drivers, driving has to be seen as an appealing career path. Heartland Express’s young fleet of high-quality vehicles is only part of that.
“It also means having facilities they can rest at and terminals and facilities with showers and drivers lounge and nice amenities,” Gerdin says. “We are trying to make their lives comfortable for the job that they do every day.”
Alongside amenities, Heartland Express also allows its drivers the flexibility to fit their driving to their lifestyle.
“There are all different kinds of drivers in the industry,” Gerdin reflects. “Some want to be gone for a month and just work, some want to be home every single weekend, and some want to be home every single day. We have provided a lot of different avenues to accommodate drivers and the kind of driving they want to do.”
As well as growing and taking care of driving talent within the company, Heartland Express has also been expanding through other means, including its recent acquisition of Contract Freighters Inc.’s (CFI) truckload unit and its logistics unit in Mexico from TFI International for $525 million.
“CFI is a company we have admired for a long time. They do the same things we do,”
Gerdin tells us. “They provide high service, great drivers. They are an irregular route truckload carrier just like we are. Our cultures and company goals match in a lot of different areas. We are thrilled to have them come aboard and truck with us.”
The deal will put Heartland Express in ownership of the eighth largest freight fleet in the USA. It is the kind of fleet that the industry needs right now.
“We’re in such a big industry, and there’s so much freight to be hauled,” says Gerdin. “We are just a small portion of this industry and supply chain, so being able to grow in the future is not a question. But being disciplined and growing in the right markets is very important. We have always considered ourselves a longterm investment, and our track record shows what we’ve done over the long-term.”
LBC Tank Terminals is a top-tier global independent operator of bulk liquid storage facilities for chemicals, petroleum, and base oils. The firm owns and operates a global network of seven state-ofthe-art, flexible storage terminals at strategic locations across the United States and Europe, offering loading and unloading services for transportation modes including pipelines, vessels, barges, rail tank cars and trucks from terminals connected to vital chemical process plants via pipeline infrastructure networks.
We form an integral part of our customers’ supply chains,” says Frank Erkelens, LBC Tank Terminals’ CEO. “We store and handle products that meet essential consumer needs of everyday life. These products make their way into the healthcare and personal care sectors, construction and housing, the food industry, and other essential markets.”
The company safeguards its long-term relevance by offering integrated services which respond to its stakeholders’ expectations and anticipates evolving environmental, social, and governmental requirements.
“We invest in a digital, efficient, and sustainable future, serving markets and customers with storage solutions that contribute to a better tomorrow,” Erkelens tells us.
of being the most sustainable chemical storage company on the market. This goes far beyond guidelines and procedures.
“It is about creating awareness on these topics and engaging more and more people inside and outside of LBC to participate in sustainability improvement initiatives and to take ownership in them,” Erkelens explains.
This focus on sustainability is part of a long-term outlook to create a meaningful future for LBC and its stakeholders by anticipating global trends and developments, staying agile, and being open to change. It is a group effort supported by the entire company’s leadership and ownership.
Frank Erkelens, Group CEO, LBC Tank Terminals.At the core of LBC Tank Terminals’ offering is the goal
“Our strategy and objectives are highly supported by our shareholders,” Erkelens says. “They have strongly contributed to the growth of LBC and empower us to make longterm decisions and investments aligned with our strategy.”
LBC Tank Terminals needs every bit of that agility to take on the challenges facing the sector right now. The firm’s focus on sustainability is a recognition of the fact that climate change is the defining issue of our time.
“The energy transition is aimed to develop and use alternative energy sources for hydrocarbons to reduce our CO2 footprint and the environmental impact that we all have,” Erkelens points out. “We are part of our customers’ supply chains, and we are
part of their CO2 footprint. Greater energy security and sustainability is now a priority combination.”
The energy transition is not the only big change hitting LBC’s sector, however.
As Erkelens puts it, “Digitization is gaining importance, matching the operating systems in the supply chain integration between tank storage companies and their customers. The same technology that we are all used to when we order something online, has reached our professional lives.
Customers expect real-time data on their products and orders and expect us to be integrated with other supply chain parties.”
Erkelens’ strategy is focused on growing LBC by being the connected partner, offering superior service and sustainable storage solutions to its customers.
“We continuously optimize our core business and current operations so that we remain best in class in service, safety and sustainability, and efficiency, and that we retain and grow with our customers,”
Erkelens tells us. “LBC already has a firm ambition and an implementation plan to become CO2 neutral by 2030 on scope one and scope two emissions. Additionally, LBC is looking to go beyond its own net-zero target by actively contributing to its customers becoming net-zero supported by LBC’s infrastructure.”
As well as the energy transition, LBC Tank Terminals has also seen the reverberations of the energy crisis brought on by global political events.
“We have contingency plans in place for unpredictable factors such as the gas supply,” Erkelens says. “’We anticipate’ is one of our company values, and by, for instance, studying the impact on product flows, we aim to do just that.”
In making those plans a reality,
LBC Tank Terminals has a powerful resource on its side.
“Our team is our greatest asset. The diversity of our organization provides us with different perspectives and better decision-making. We are all LBC,” Erkelens insists.
“The quality, leadership and commitment of our team are something we are very proud of. Our employees each have an extensive skillset, and, thanks to our open company culture, they are empowered to contribute to realising our vision.”
LBC Tank Terminals’ strategy is built around connected partnerships, supported by a dedicated LBC team that makes a real impact. But at every step of the way, the firm takes care
It is our duty to put sustainable business practices at the heart of what we do.
We continue to play an active role in the energy transition and keep a close eye on the future developments and the potential role we can play in transforming the energy landscape towards more sustainable alternatives.
of the people that make that strategy possible.
“We consider diversity an asset and believe that all employees have a right to be treated with dignity and respect and to work in a non-threatening environment,” says Erkelens.
“We trust that our goals can only be reached by fostering a work environment where everyone feels inspired and confident to collaborate in a transparent, respectful, and inclusive way. We empower each other to make responsible decisions and to take ownership of our actions.”
With a flat organisational structure and an open culture, Erkelens’s door is always open to his team.
As he says, “If you have a good idea, you can make it happen.”
And Erkelens should know- he has plenty of ideas for the future of LBC.
“We aim to grow within and beyond the footprint of our terminals on the USGC and in North-western Europe focused on chemicals and products
related to the energy transition, such as liquid organic hydrogen carriers, ammonia, methanol, and renewables,” he says. “On the one hand, we will focus on growth at our existing locations in key hub markets and our customers’ supply chains. On the other hand, we aim to expand our global footprint in new locations and offer storage solutions in growing markets. We see that our customers are changing their products and supply chains to meet the Paris Climate Agreement’s objectives and we believe that, with our investments in sustainable liquid bulk infrastructure, we can help them achieve these objectives.”
LBC will continue to optimize its performance through operational excellence, focussing on sustainability and efficiency to provide customers with sustainable, reliable, and efficient tank storage infrastructure and services.
“We continue to play an active role in the energy transition and keep a close eye on the future developments and the potential role we can play in transforming the energy landscape towards more sustainable alternatives,” Erkelens says.
LBC provides vital infrastructure to store and handle liquids that are used to create products that have a positive impact on people’s lives. By designing, building, operating and continuously improving this infrastructure against the highest standards and by implementing the latest technologies, the firm will continue to improve its operations, minimize its environmental impact, and ensure the safety of the people at LBC’s terminals and neighbouring communities.
As Erkelens concludes, “In short, we work hard on our progress and continue to explore opportunities to improve.”
In making an impact & in driving change, our team is our greatest asset.