The Versatility and Precision of PCD End Mill Cutters
End mill cutters are indispensable tools in the machining industry, used for milling, drilling, and other complex operations. Among the various types of end mills, Polycrystalline Diamond (PCD) end mill cutters stand out for their remarkable versatility, precision, and durability. This article explores the unique features of PCD end mill cutters and why they are a valuable addition to any machining process.
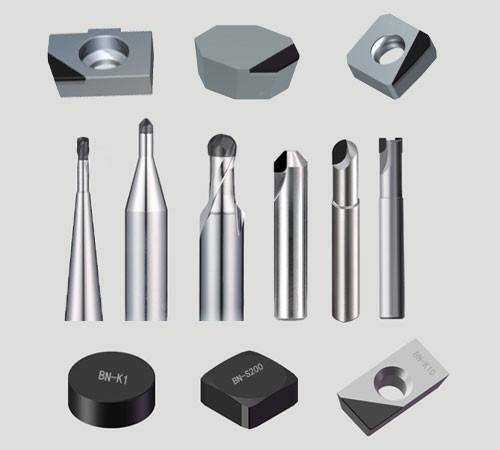
What Are PCD End Mill Cutters?
PCD end mill cutters are tools with cutting edges made from polycrystalline diamond, a synthetic material composed of diamond particles bonded together. This bonding creates a highly durable and wear-resistant tool, suitable for cutting various hard and abrasive materials. The versatility of PCD end mill cutters allows them to be used across a wide range of applications, from aerospace and automotive to electronics and medical manufacturing.
Related post: https://www.halnncbn.com/News/Industry_News/585.html
Key Advantages of PCD End Mill Cutters
The benefits of using PCD end mill cutters in machining processes are numerous. Here are some of the key advantages that set them apart from other end mill cutters:
1. Superior Hardness
Polycrystalline diamond is one of the hardest known materials, providing exceptional durability and resistance to wear. This hardness allows PCD end mill cutters to maintain their sharp cutting edges for extended periods, reducing the need for frequent tool changes and minimizing downtime.
2. High Precision
PCD end mill cutters are engineered for precision. Their sharp cutting edges and stable geometry enable them to produce intricate cuts with tight tolerances. This makes them ideal for machining complex shapes and patterns in materials where precision is crucial.
3. Excellent Surface Finish
Due to their hardness and precision, PCD end mill cutters can achieve high-quality surface finishes. This reduces the need for additional finishing processes, saving time and resources in the manufacturing workflow.
4. Enhanced Productivity
The longevity of PCD end mill cutters and their ability to cut at high speeds result in enhanced productivity. Manufacturers can increase production rates and achieve higher throughput without compromising on quality.
5. Versatility in Applications
PCD end mill cutters are versatile tools that can cut a wide range of materials, including aluminum, composites, graphite, and other non-ferrous materials. This versatility makes them a popular choice for various industries.
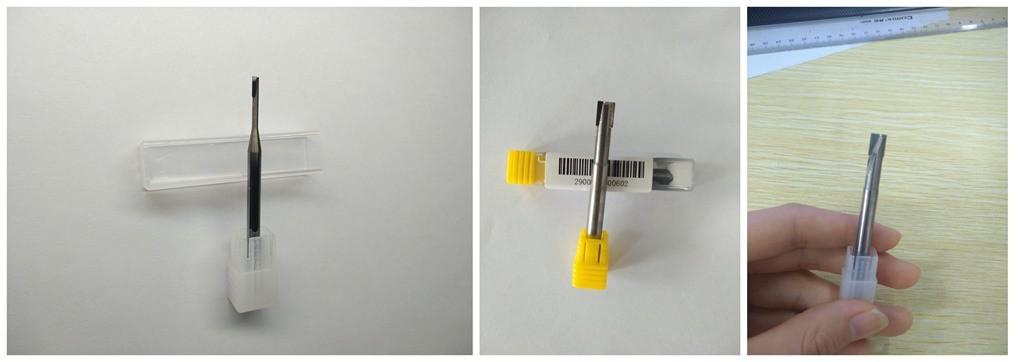
Applications of PCD End Mill Cutters
The unique characteristics of PCD end mill cutters make them suitable for a variety of applications. Here are some examples of industries that benefit from their use:
Aerospace
In the aerospace industry, precision and durability are essential. PCD end mill cutters are used to machine complex components made from aluminum and composite materials. Their high precision ensures that parts meet stringent industry standards.
Automotive
PCD end mill cutters are ideal for machining automotive components, where efficiency and accuracy are critical. They are used to cut engine parts, transmission housings, and other complex components.
Electronics
In the electronics industry, PCD end mill cutters are used to machine circuit boards and other delicate components. Their precision and ability to create smooth surfaces make them suitable for this industry.
Medical
PCD end mill cutters are also used in the medical industry, where precision is paramount. They can machine medical devices and implants with high accuracy, ensuring patient safety and product reliability.
Conclusion
PCD end mill cutters offer a range of advantages, from superior hardness and high precision to enhanced productivity and versatility in applications. These unique features make them a valuable tool in various industries, enabling manufacturers to achieve high-quality results efficiently.
Whether you are in aerospace, automotive, electronics, or medical manufacturing, PCD end mill cutters can provide the precision and durability needed for your machining processes. Their ability to cut complex shapes and maintain sharp edges over extended periods makes them an essential component of modern manufacturing.