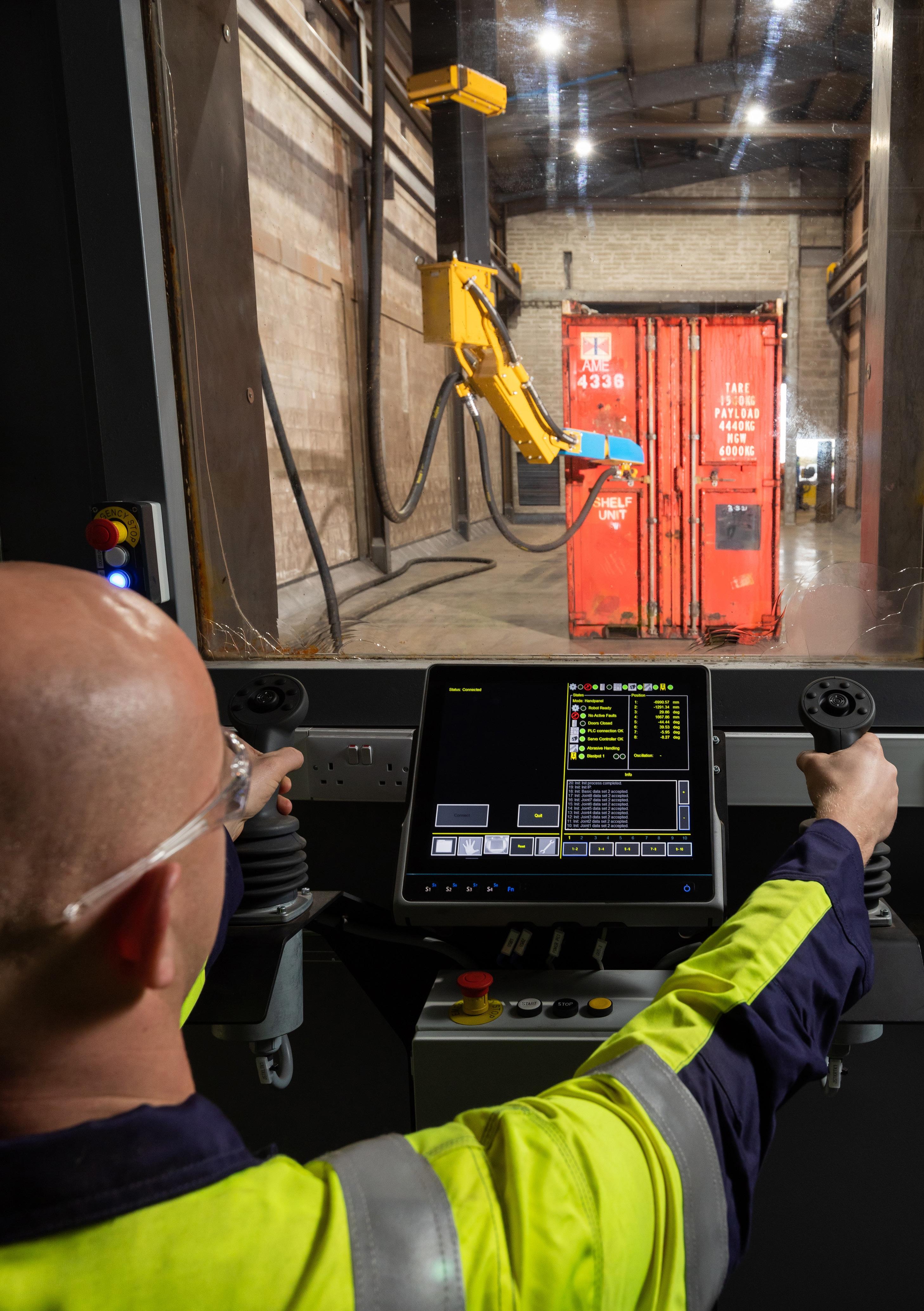
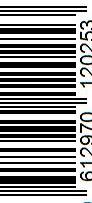
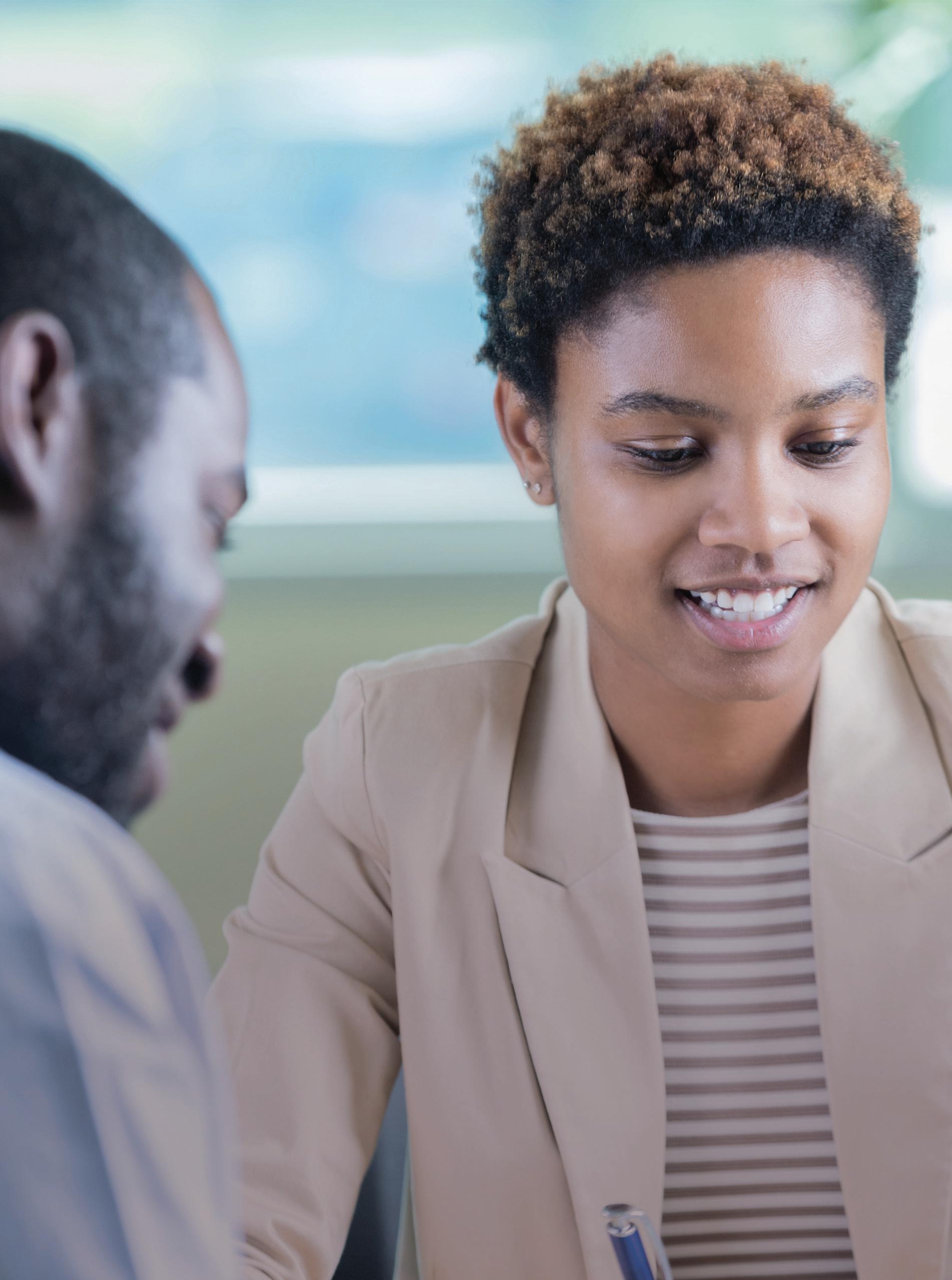
That’s how we help.
Switching your business is one of the most important decisions you’ll ever make. This is why we proactively manage the transition for you, to ensure minimal disruption to your business. We take end-to-end accountability until your business is fully banked, and a Business Banker is in play to look after the day-to-day relationship. It takes a bank that does more to help you start, run and grow your business.
For more information, contact:
Fathima Rahman
Email: frahman@fnb.co.za I Call: 087 328 0280
Eloise Heyduczek
Email: eloise.heyduczek@fnb.co.za I Call: 087 335 6859
- Frederick Wilcox
Published and Distributed by Business Industry Publishing Ltd
For any enquires contact info@business-pursuit.net
Production
Donnie Rust
Editor donnie@business-pursuit.net
Charles Brown
Business Development Manager charles@business-pursuit.net
James Smith Operations Manager james@business-pursuit.net
Harry Lewis Accounts Manager harry@business-pursuit.net
Romain Vaast
Project Manager Romain@business-pursuit.net
Design Felix Baldwin Design Assistant felix@business-pursuit.net
Harvey Tarlton
Graphic Design harveytarlton.co.uk www.business-pursuit.net
If you would like more information about ways in which Business Industry Publishing can promote your business please call +44 (0)20 32878 795 or email | charles@ business-pursuit.net. Business Industry Publishing does not accept responsibility for omissions or errors. The points of view expressed in articles by attributing writers and/or in advertisements included in this magazine do not necessarily represent those of the publisher. Any resemblance to real persons, living or dead is purely coincidental. Whilst every effort is made to ensure the accuracy of the information contained within this magazine, no legal responsibility will be accepted by the publishers for loss arising from use of information published. All rights reserved. No part of this publication may be reproduced or stored in a retrievable system or transmitted in any form or by any means without the prior written consent of the publisher.
© Business Industry Publishing Ltd 2025
Business Industry Publishing
Welcome to the June 2024 edition of Business Pursuit Europe & Middle East, where we highlight the companies and leaders setting new standards for excellence across the region.
This month, we feature Swire Energy Services in our lead article, “Being the Easiest Company to Work With.” Discover how this global leader is redefining customer experience through efficiency, innovation, and a commitment to seamless partnerships in the energy sector. Their approach proves that in a complex industry, simplicity and reliability make all the difference.
We also turn the spotlight on EE Smith in “Attitude Makes the Difference.” With a reputation built on craftsmanship, dedication, and an unwavering pursuit of quality, EE Smith demonstrates how the right mindset can shape not only a company’s success but also the industries it serves.
As we explore the strategies and innovations shaping business in Europe and the Middle East, we hope these stories inspire and inform your journey. Enjoy this issue of Business Pursuit Europe & Middle East!
Donnie Rust Editor
Don Campbell
Aformidable entity within the energy sector, notably recognized for their enviable standards even by the energy levels, Swire Energy Services (SES) have effectively written the book on quality, innovation, and sustainability. Founded in 1979, SES have spent over forty-five years establishing itself as the world’s largest supplier of specialist offshore containers and integrated services tailored to the oil, gas, and renewable energy sectors. Operating in thirty-two countries, leveraging a fleet of over 52,000 DNV-certified offshore containers and a dedicated workforce of more than 500 employees, this is a company that has many of their competitors sitting in their shadow.
As Chief Executive Officer Manfred Vonlanthen points out, the driving force behind SES is neither their sophisticated machinery nor their impressive technology. Instead, at their core the thing that drives the company is their people. As he puts it, if the company is known for anything, they are known for their steadfast commitment to their employees.
The company invests significantly
in staff development, ensuring that their personnel are well-trained and equipped to meet the challenges of a rapidly evolving industry. Supporting them they emphasize safety, diversity, and inclusion, fostering a workplace culture that values every team member’s contributions.
“The whole leadership team are deeply engaged in promoting a culture of resilience and adaptability,” he says, “Under my guidance, the company has focused on enhancing its operational efficiency through technology and innovation, resulting in a workforce that is both skilled and motivated.”
Vonlanthen himself notes that the commitment and adaptability of the team have been pivotal in navigating the challenges posed by global supply chain issues and market volatility, “When the seas are rough you have only the training and dedication of your crew to keep your vessel afloat.”
It is a well-known formula: look after your staff and they will look after your clients. And, from the outside looking in Swire Energy Services maintains a very client-centric approach, providing tailored solutions that
cater to the unique needs of its diverse customer base. They serve clients across multiple sectors, including offshore oil and gas, offshore wind, and marine operations, ensuring they receive reliable, safe, and costeffective services. Their mission is clear: to be the easiest company to work with, which speaks volumes about their commitment to
The whole leadership team are deeply engaged in promoting a culture of resilience and adaptability
customer satisfaction.
This focus is exemplified by their integrated service offerings, which encompass not just equipment supply but also integrity services, aviation support, and chemical management solutions. Such comprehensive services enable clients to streamline their operations and enhance their operational safety.
As we look toward the future, Swire Energy Services is embarking on several new initiatives that underscore its commitment to innovation and sustainability. Vonlanthen tells us that a major focus is the implementation of advanced technologies to enhance operational efficiency and reduce environmental impact. The company’s ambitious goal is to achieve net carbon neutrality by 2030, reflecting a proactive stance in the face of climate change.
One notable development is the expansion of their aviation services. SES has rolled out end-to-end aviation services globally, providing critical support for helicopter operations and refuelling. This strategic move not only diversifies their service portfolio but also positions SES as a key player in the burgeoning market for offshore wind and renewable energy support.
In addition to these expansions, SES has made significant strides in sustainability. The company achieved a 56% reduction in carbon emissions since 2019 and continues to implement initiatives aimed at further
minimizing its environmental footprint.
Swire Energy Services offers a comprehensive range of products tailored for offshore operations. Their inventory includes offshore containers for equipment storage and transport, offshore baskets and tanks for safe handling of supplies and fluids, and award-winning tubular handling systems for the efficient transportation of pipe casing. Additionally, they provide aviation refuelling systems to ensure safe and compliant helicopter operations. These products are essential for maintaining safety and operational efficiency in offshore energy operations, solidifying Swire Energy Services’ leadership in the industry.
...we are dedicated to providing the highest quality products and services to meet the safety and operational challenges of offshore energy production
Swire Energy Services (SES) holds a prominent position as a global leader in the offshore energy services industry. Specializing in logistics, modular systems, and maintenance solutions, SES operates in more than 30 countries, delivering essential services and products to support offshore operations. Their diverse product portfolio, which includes offshore containers, tubular
handling systems, and aviation refuelling solutions, plays a critical role in ensuring the operational integrity of offshore projects.
The company’s annual turnover has exceeded $200 million, reflecting its extensive market reach and successful business model. SES is known for continually enhancing its products and services to adapt to the evolving needs of the energy sector. SES has built a strong reputation by prioritizing safety and compliance, which is reinforced by its leadership team.
Richard Sell, Managing Director of SES, has emphasized the company’s commitment to innovation and safety, stating, “At Swire Energy Services, we are dedicated to providing the highest quality products and services to meet the safety and operational challenges of offshore energy production.” This dedication to operational excellence has helped SES maintain its competitive edge, allowing the company to serve major players in the global energy sector and remain a trusted partner for offshore logistics and maintenance.
Swire Energy Services continues to be a key player in the offshore energy industry, providing critical services and products that ensure the safety and efficiency of operations. With a strong global footprint in over 30 countries, SES offers essential solutions, including offshore containers, tubular handling systems, and aviation refuelling systems, which help energy companies maintain operational integrity.
The company’s focus on innovation and safety has earned it a trusted reputation. Sell highlights this commitment: “Our goal is to continually push the boundaries of safety and innovation to meet the evolving needs of our clients.” This drive makes SES an indispensable partner for major offshore energy companies, supporting operations with cutting-edge solutions tailored to the unique challenges of the industry.
EE Smith
Donnie Rust
It has to be said that having the right kind of attitude stands for a lot. A reputation for style, confidence and a “must-do” approach are what the business world has always run on. Donnie Rust explores EE Smith.
The company, EE Smith was founded in 1897 by Edward Elijah Smith who ran his business from a small shop on Canning Street, Leicester. The self-proclaimed, ‘Master Craftsman’ was skilled as a plumber, gas and bar fitter and supplied and repaired gas stoves and gas chandeliers, proclaiming with understated professional pride, that all kinds of repairs would be ‘neatly executed’.
During these early years, EESmith took on a number of young apprentices to aid his flourishing business and as the business prospered, it moved to new premises in 1937. In the same year, 14-year-old Basil
Richardson was taken on as an apprentice, making pewter basins.
Although many of EE Smith’s apprentices who fought in the Second World War did not come home, following his wartime service in the Royal Navy, Basil Richardson returned to Leicester to find Edward Elijah Smith in poor health and the business in decline. At the age of 24, Basil became EE Smith Contracts’ Managing Director, foreman and entire workforce. However, in an age of heroes he did not wilt under the challenge but grabbed and ran with it.
We are experts in fitting out some of the world’s most prestigious hotels, commercial interiors and private residences
Since then, the company has had the opportunity to shift and change with markets and ride on the momentum of just getting things done. After turning down interest from market leaders, 2016 began an exciting new era when a management buy-out saw four of the long serving team take over the ownership of the business, with Neil Bottrill at the helm as the new Managing Director.
The £11.1 million buyout was made possible thanks to funding from Maven Capital Partners, an investment that reflected the confidence in Bottrill’s leadership qualities.
Bottrill, who has been with the firm since 1990 in a variety of estimating and commercial management roles, joined the board of directors in 2008 as commercial director. Even after becoming MD in 2016 following the buyout, he has continued the company’s spirit of driving hard into the future and always leading by example.
Having climbed up through the ranks and firmly established himself as the leader of the company, Bottrill reveals that EE Smith, still one of the UK’s leading privately owned specialist interior fit-out contractors, have been setting the industry standard for over 100 years.
“We are experts in fitting out some of the world’s most prestigious hotels, commercial interiors and private residences,” he says, “Our interior solutions are engineered to the finest tolerances, ensuring the finished product perfectly matches the designer’s vision.”
Further to this, EE Smith Contracts is also one of the UK’s leaders in training apprentice joiners and cabinet makers, taking on new applicants every year, and have seen over 200 apprentices successfully pass through their programme. Bottrill explains that it is this marriage of technology and tradition
that allows his company to deliver highquality solutions to design briefs without compromising on aesthetic requirements.
“Our outstanding level of project management is one of the key elements which sets us apart within the saturated industry,” he says, “ With an in-house team of directly employed design managers, technical services managers and preconstruction coordinators, we are able to seamlessly take a project from tender stage to completion, whilst providing a consistent project management team to the client.”
And according to him, it is this ethos that is the core to their success and one of the many reasons they have such a longstanding rapport with their repeat clients. This close control over every detail makes them proud
EE Smith Contracts has a long history of training youngsters, and a significant number of our current employees are former apprenticeships
to be one of the UK’s very few contractors with a turnkey offering.
Regardless of circumstances, EE Smith has a reputation for being outstanding, for example in 2022 when many companies were still struggling to recover from the ripples of Covid, they posted the highest annual revenues in the company’s history, with an
additional £60 million of secured work for the new financial year.
It was fitting as they also celebrated their 125th birthday in 2022. Bottrill explains that the record-breaking activity was secured partly by working on multiple prestigious developments including the luxurious Peninsula London hotel overlooking Hyde Park Corner and the completion of 15 super-prime apartments in Knightsbridge in London. Profits have bounced back strongly following Covid-19 and are forecast to exceed pre-pandemic levels for the year ahead.
Generally working with around £60 million worth of secured work, EE Smith Contracts enters 2025 with their usage aplomb and confidence. But have gone a step further as pioneers in their business with a focus on sustainability.
The business, which employs 285 staff, has reduced carbon emissions by over 20 per cent in the last year despite the growth in activity at its sites in Leicester and London by investing in a new £125,000 extraction system. There is also continued growth in long-established apprenticeship programmes, with 35 new apprenticeships having been recruited since the outbreak of Covid-19.
Neil Simpson, Finance Director, says, “EE Smith Contracts has a long history of training youngsters, and a significant number of our current employees are former apprenticeships who have stayed with us because it is a family environment. We have established great links with London colleges and have thirty apprentices on our sites in London learning from among the finest craftspeople in the country. The London labour market is very dynamic and we’re building the EE Smith Contracts family environment on those sites as well to retain our apprentices and provide a pathway for their career. Further reductions are forecast in our carbon emissions following significant investment in carbon saving technology in the last six months because this is an area which is really important to us.”
Donnie Rust
Biennially, WindEnergy Hamburg brings together the most prominent and promising businesses within the eco-sphere of green energy and has become the global flagship event for the wind energy sector. Having took place in late September, it once again offered businesses unprecedented opportunities for growth, networking, and innovation. Enjoying over 1,500 exhibitors from 40 countries, the event remains a major destination for companies involved in both onshore and offshore wind energy looking to network and gain access to new ideas. However, as we discovered, while the event promises numerous advantages for businesses, it also comes with unique challenges that require careful planning and strategic execution.
A common consideration is the real-world benefit of networking events with some people questioning the value of them compared to online presentations and video calling. However, for businesses involved in wind energy, WindEnergy Hamburg presents several compelling advantages. First and foremost, it serves as a platform for connecting with key stakeholders across the entire value chain. From turbine manufacturers and component suppliers to financiers, policymakers, and service
providers, the event brings together all major players under one roof. Then, the event also creates an ideal environment for networking, deal-making, and discovering new business opportunities.
One of the most significant advantages for companies is the event’s focus on both established markets and emerging sectors within wind energy. Offshore wind, in particular, is expected to see explosive growth over the next decade. According to recent data, global offshore wind capacity reached 75.2 gigawatts in 2023, with projections showing that this figure will triple by 2028. The European Union’s “Wind Power Package” is designed to accelerate this expansion by streamlining permitting processes and expanding grid infrastructure. For companies seeking to enter or expand in this lucrative market, WindEnergy Hamburg offers access to the latest developments, cutting-edge technologies, and critical policy updates.
Moreover, the event caters to businesses of all sizes, from multinational corporations to innovative start-ups. In fact, 2024 saw the introduction of the AI Centre in Hall A3, a dedicated space for showcasing the role of artificial intelligence (AI) in wind energy. Artificial Intelligence is increasingly being used to optimize turbine performance, predict maintenance needs, and streamline
While it is true that for smaller companies with limited budgets, securing a prominent position and attracting attention amidst the 1,500 exhibitors can be daunting
project development. At the event, companies specializing in digitalization, data analytics, and AI-driven solutions found a welcoming environment to showcase their products and explore new partnerships.
Then, for smaller businesses, WindEnergy Hamburg also provides a unique opportunity to compete on a global stage. The inclusion of a joint exhibition stand for young, innovative enterprises means that start-ups can present their solutions to an international audience, gaining exposure that would be difficult to achieve elsewhere.
While the advantages are clear, setting up a presence at WindEnergy Hamburg is not without its challenges. Andreas Arnheim, who is the Director of WindEnergy Hamburg appreciates that the sheer scale of the event means that businesses must carefully plan their participation to make the most of the opportunity. After all, exhibiting at such a large event requires significant resources, including financial investment, logistics, and manpower.
“While it is true that for smaller companies with limited budgets, securing a prominent position and attracting attention amidst the 1,500 exhibitors can be daunting,” he says, “It does mean that our exhibitors are those companies that offer real benefits in networking and technology.”
Additionally, businesses must navigate the technical complexities of the wind energy sector. Offshore wind, while offering tremendous potential, also presents unique logistical challenges. For instance, companies like Vattenfall and JDR Cable Systems have had to overcome significant engineering hurdles to develop and
implement their cutting-edge technologies for offshore wind farms. Vattenfall’s work on the Hollandse Kust Zuid project, the world’s largest offshore wind farm, involved innovative solutions such as the use of recyclable rotor blades and noisedampening technologies. For businesses aiming to break into the offshore wind market, understanding and addressing these challenges is crucial to success.
Another challenge relates to the energy grid infrastructure. As the wind energy sector grows, so does the strain on existing electricity networks. Smart grid solutions and enhanced transmission capacity are essential to ensure the reliable integration of large-scale wind farms. For many businesses, particularly those involved in grid infrastructure and energy storage, WindEnergy Hamburg offers a forum to explore these challenges and collaborate on innovative solutions.
“There is no substitute for being able to discuss issues and solutions in a face-to-face manner,” says Andreas, “Networking in real life repeatedly proves to be the best way to form partnerships and share ideas.”
One of the key benefits of WindEnergy Hamburg is the event’s extensive conference program, which features around 150 sessions spread across five open stages. These sessions offer a platform for national and international experts to discuss the most pressing issues facing the wind energy industry today. From market expansion strategies to financing models and technological advancements, the conference sessions are designed to foster knowledge exchange at the highest level.
In particular, businesses can benefit from discussions on how to tap into new markets, improve competitiveness, and navigate the regulatory landscape. For example, with offshore wind poised for significant growth, businesses will need to stay informed about developments in permitting processes, regulatory frameworks, and grid expansion efforts. The event’s focus on these critical topics provides companies with the insights they need to make informed decisions and strategically position themselves for success. As Andreas alludes, the industry is a competitive one and businesses that have access to events such as these, where they can stand shoulder to shoulder with the movers and shakers of the industry have a distinct advantage over their competition.
While another challenge businesses must
contend with is the logistical complexity of exhibiting at a large-scale international event, where the process of setting up an exhibition booth, coordinating staff, and ensuring a seamless experience for attendees requires careful planning and execution. WindEnergy Hamburg offers a range of services to help exhibitors navigate these challenges in particular.
“Much of our time is spent helping businesses, of all sizes, from startups to multinationals, construct suitable stands and set up technical support,” Andreas says, “We also offer marketing packages and advertising opportunities and provide exhibitors and sponsors the tools they need to make the most of their participation.”
As the world continues to transition towards renewable energy, the role of wind energy will only become more important. The Global Wind Energy Council (GWEC) predicts that to meet the goal of limiting global warming to 1.5 degrees, the global wind industry must continue to scale rapidly. This requires not only increased investment in wind energy projects but also significant advancements in technology and infrastructure. WindEnergy Hamburg is uniquely positioned to facilitate this growth by providing a platform for businesses to engage with the latest innovations and form strategic partnerships. However, success requires careful planning, a clear understanding of the industry’s challenges, and the ability to adapt to a rapidly changing market.
Jonathan Cole, Chairman of the Global Wind Energy Council, emphasized the importance of timely investments and streamlined regulatory processes in driving the energy transition. “Countries must take action to accelerate the use of renewable energy by prioritizing timely investments in grid and transmission infrastructure while simplifying permitting procedures quickly,” he said, “For businesses, this means staying ahead of regulatory changes and positioning themselves to capitalize on emerging opportunities.”
From AI-driven solutions and digitalization to the rapid expansion of offshore wind, WindEnergy Hamburg provides a comprehensive platform for companies to position themselves for success in a rapidly evolving industry. However, like ships on the sea, businesses must also be prepared to address the logistical and technical challenges of participating in such a large-scale event. To get the wind in your sails, you have to have the sails first
Allianz Insurance is one of the largest general insurers in the UK and part of the Allianz Group, who are one of the leading financial services providers globally. With around 147,000 employees worldwide, the Allianz Group serves over 100 million customers in more than 70 countries. Allianz Insurance handles Commercial, Engineering, Legal Protection and Premierline Business on their business insurance section. Meanwhile Petplan, Petplan Equine and Allianz musical insurance on their personal insurance section.
At the heart of the business is the focus on their customers and guided by the principles of their parent group, Allianz Insurance strives to be a trusted partner for their customers and to put them centrestage. By working to continually improve the quality of their service, incorporating sustainable and responsible business practices into their products and services, and combating insurance fraud, they aim to meet the needs of their customers now and into the future.
“We want to build relationships with our customers that are based on trust, so that
they recommend us to others,” says Graham Gibson, chief claims officer of Allianz Insurers. He goes on to explain that along with this customer centric approach is their management of customer feedback be it in the form of reviews or complaints. Swift action being the top priority for them. He says, “We ensure that Group-wide quality standards are met in handling complaints and that our customers are treated fairly. We also regard complaints as another important source of customer feedback, so we analyse them to implement improvements.”
Offering peace of mind through their products and services allow the customers to know that, in moments that matter, Allianz deliver on their promises. Along with this, they maintain solid underwriting practices and ensure that insurance transactions in 13 sensitive business areas are screened and assessed for ESG risks. Additionally, every employee must complete annual compliance training and regulatory testing to uphold the ethical standards and behaviours required
of all of them to carry out their day to day business.
Graham says, “We ensure our products are clearly explained and honestly marketed so our customers and their broker partners can make informed decisions and choose solutions that are relevant to them.”
Interestingly, the company also does all it can to support a low-carbon society and social inclusion. In 2021, Allianz had over 162 sustainable insurance solutions globally including their products in the UK covering renewable energy instalments. Globally the business supports emerging customers through their micro insurance products, giving protection to 62.2 million customers in 2021, in the poorest 60% of developing countries in Asia, Africa, and Latin America.
It is Graham’s belief that by supporting employees, they become resilient both at work and in their personal lives. He wants their employees to be able to come back from life’s setbacks stronger than ever and to have the courage to move forward. This makes
One of the UK’s leaders in workplace fire prevention and suppression, Nobel Fire Systems offer a comprehensive suite of fire suppression systems with a focus on two main products. These include their own proprietary K-Series commercial kitchen fire suppression system, which comes recommended by Allianz (and includes a discount for Allianz customers) and Stat-X, a condensed aerosol fire suppression system suitable for ‘special risk’ commercial and industrial plant locations.
In recent years, an area of growth for Stat-X has been the protection of Battery Energy Storage Systems (BESS), which contain lithium-ion batteries. These batteries, found in many, if not most, of today’s devices and electric vehicles are often stored together but if damaged can enter a “thermal runaway” reaction that poses a danger to health and safety and through the chain reaction, destroy all of the battery cells and any devices/components within the BESS, attached to it or within their vicinity. BESS facilities were initially found in relatively remote locations linked to major substations at the grid-scale level, however smaller systems are increasingly being installed in commercial and industrial locations, within or adjacent to buildings, such as hospitals, schools, leisure centres, shopping centres and arenas.
There is no system or suppression agent that is guaranteed to put out a lithium-ion battery fire, therefore Nobel recommends a 3-stage BESS fire protection system, including Prevention via Li-ion Tamer® off-gas detection, Containment via Stat-X fire suppression, and back-up Cooling with Watermist. Their BESS page offers a complete overview of this approach (see link).
Forward thinking companies, like Nobel Fire Systems, who can calculate potential risks and take meaningful action to meet and mitigate them, is what helps keep Allianz Insurers ahead of the game for their customers.
the business stronger, and employees who are proud to work for a company are always going to be better brand ambassadors when serving customers.
As part of the above, Allianz Insurers believe that the difference in their people makes the difference to their business and they embrace the uniqueness of their employees because they understand the strength of their business lies in the diverse contributions everybody can make.
“We’re inspired to create a workforce which reflects our community and customers,” says Graham, “We champion environments where we celebrate diversity and people are encouraged to share their thoughts and ideas with confidence to help us arrive at excellent solutions for our customers.”
This includes equality of opportunity where they are committed to creating a fair environment where people can succeed regardless of race, gender, age, disability, religion, sexual orientation, or ethnic background.
Providing personal development and career fulfilment for all employees is a top priority for the company management. Allianz invested 106.3m euros in training of their employees across the globe in 2022 making sure they are equipped with the skills and knowledge to carry out their role and to take on new responsibilities in the future.
Developing their inhouse talent is a very important success factor for their business, both locally and globally. Their internal talent programmes help to move people up through the business using performance management, succession planning and leadership development while their external recruitment activities help them find the best people for critical roles through search agencies and market mapping.
In 2022 across the Allianz world, they invested €719 per employee in development and training, each employee averaged 45.2 hours of training and the company had 83,529 learning users who logged into their AllianzU platform.
Insurance consultancy Gracechurch has awarded Allianz Commercial its Service
I’m thrilled to secure this award for the eighth year in a row, which is a significant achievement and I’m proud of the team
Quality Marque (SQM) for the eighth year in a row and is the only insurer to receive this accolade.
Insurance consultancy Gracechurch has awarded Allianz Commercial its Service Quality Marque (SQM) for the eighth year in a row and is the only insurer to receive this accolade.
Run annually, the independent research found Allianz to be particularly strong for its personalised service, with the commercial insurer striking the right balance between expert assistance and online capability through its Claims Hub and Live Chat functionality.
The net promoter score (NPS) for Allianz is at its highest since 2018, with a marketleading position maintained throughout 2023 retaining its number one spot throughout the year according to the Gracechurch survey.
“I’m thrilled to secure this award for the eighth year in a row, which is a significant achievement and I’m proud of the team. Our aim is to constantly improve the service we provide, and our strong customer-first focus in claims management has strengthened our relationships with broker partners,” says Graham, “With a strong team of claims experts and a mixture of digital services, our people and service make a difference and winning this highlights that. However, this doesn’t mean we won’t rest on our laurels, as we constantly strive to maintain and improve how we support our broker partners in the best way.”
The journey that Macdonald Hotels took to become one of the UK’s leading privately owned hospitality businesses, began in 1990 when Donald Macdonald, who was the managing director of Stakis Hotel at the time, created the brand by purchasing a pair of Scottish hotels. Since then, the company has continued to grow through various acquisitions and developments. Including the purchase of properties formerly owned by De Vere Hotels and The Rank Organisation and the takeover management of Spanish resorts under the popular time-share umbrella contract with Barratt Resorts.
While the United Kingdom has seen notable hotel chains crumble over the first decades of the 21st century, The Macdonald Hotels Group remains one of the UK’s leading privately owned hospitality businesses with over thirty hotels and resorts in the UK and Spain. Headquartered in Bathgate, West Lothian Scotland the company has spread good ol’ Scottish hospitality across borders and the sea. How do they do it?
As they say on their website, “The focus of our business is people,” and this begins with the way they treat their staff and invest in their potential through training and personal development. The business relies on the services of around 3,000 workers spanning food and beverage operations, these include housekeeping and guest service operations, kitchen operations and recreational operations. Not to mention commercial and finance staff, hotel operations which include general managers, administration, IT and HR.
An important aspect of running a successful hospitality business is directing the focus of management. Those at the top do not need to be as concerned with guests as they should be with staff. Happy staff mean happy guests.
Keeping ahead of market developments, The Macdonalds Hotel Group have pioneered a number of technological developments that helped them stay ahead of their competition. For example, while it is by far the norm today, in 2005 they were one of the forerunners for the online booking of hotels, and that year boasted a 600% web revenue increase, attributed not only to pioneering updates to their website but also a new online marketing strategy.
Comprising of a selection of hotels and selfcatering resorts across the UK and Spain, each of the properties enjoys its own unique style, charm and character. Instead of the templated-one-sock-fits-all approach of many hotel chains, the Macdonald brand accentuates the style and aesthetic of its locality. Furthermore, each of the hotels from Scotland to the South of England are managed by real hoteliers with experience and passion for the trade, allowing the group to rely heavily on their professional expertise and calibre.
With the support of their dedicated workforce, Macdonald Hotel & Resorts has become one of the UK’s best-loved hotel
While it is true that for smaller companies with limited budgets, securing a prominent position and attracting attention amidst the 1,500 exhibitors can be daunting
companies. They value the diversity of their workforce and believe that the best results are achieved from committed people from a variety of diverse backgrounds, ethnicities, and genders.
As reported in the 2022/23 details of the gender pay gap for Macdonald Hotels Limited and Macdonald Resorts Limited, both of which employ more than 250 people, any gender pay gap does not stem from paying men and women differently for the same or equivalent work. Instead, it is the result of the roles in which men and women work within the company and the salaries that these roles attract in the labour market.
And, as part of their zero-tolerance approach to slavery and human trafficking,
Macdonald Hotels will only work with those who provide assurances on their working practices and commitment to combating slavery and human trafficking in their own businesses and supply chains.
Besides the hotels, there are nine holiday resorts in the most wonderful locations in the UK and Spain, with each of the UK resorts located within a national park offering stunning scenery and opportunities for adventure. In Spain they are in the heart of the Costa del Sol with three resorts on the Mediterranean coast near Marbella and one just north of the coast in the beautiful village of Mijas. But the question must be asked, which is better, self-catering resort or a hotel stay?
When travellers embark on a journey to explore new destinations or indulge in a relaxing getaway, accommodation plays a pivotal role in shaping their overall experience. Two distinct options that travellers often consider are self-catering resorts and old-fashioned hotels. Each offers a unique set of features, catering to diverse preferences and travel styles.
One of the prominent distinctions between self-catering resorts and old-fashioned hotels lies in the level of autonomy they offer. Self-catering resorts, as the name suggests, provide travellers with self-contained units equipped with kitchen facilities. This grants visitors the freedom to prepare their meals according to their dietary preferences and schedules. On the other hand, old-fashioned hotels, like those within the Macdonald Hotels chain, typically offer dining options through on-site restaurants or room service, limiting guests’ culinary choices.
When it comes to privacy, self-catering resorts often provide more spacious accommodations than traditional hotel rooms. These resorts frequently feature apartments, cottages, or villas, offering separate living areas and bedrooms. This arrangement is particularly appealing to
families or groups seeking communal spaces and enhanced privacy. In contrast, hotels provide smaller, more standardized rooms with limited private living space.
Old-fashioned hotels are known for their comprehensive services and amenities, such as concierge services, fitness centres, and spas. These establishments encourage social interaction by hosting events, creating a lively atmosphere for mingling with fellow travellers. Macdonald Hotels, for instance, often prioritize such offerings to enrich the guest experience. Conversely, self-catering resorts may offer fewer shared amenities, placing more emphasis on personal leisure and relaxation within individual accommodations.
While hotels can and do often boast fine dining establishments highlighting local and international cuisines, self-catering resorts provide an opportunity for travellers to explore local markets and create their culinary experiences. Guests can shop for fresh ingredients, learn about regional cooking techniques, and immerse themselves in the destination’s food culture.
Self-catering resorts can be budget-friendly, especially for longer stays or for those traveling in groups. The ability to cook inhouse reduces dining expenses and allows for a more economical approach to meals. On the other hand, old-fashioned hotels might entail higher food costs due to dining at on-site establishments.
With a legacy extending to nearly thirty years, guests can be confident that their stay at any of the Macdonald hotels or resorts will be filled with a Scottish standard of guestattention that has made the country famous worldwide.
Donnie Rust
IMI Critical Engineering are a global leader in engineered solutions for severe service applications requiring valve and flow-control manufacturing. Providing innovative and efficient solutions to various industries such as power generation, oil and gas, petrochemical, pharmaceuticals, and industrial manufacturing. Over 150 years old, the company has an interesting history that has deeply influenced their approach to business today.
Based in Birmingham, United Kingdom, IMI Critical Engineering have always offered cutting-edge technologies and comprehensive solutions and their renowned team of experts have been setting the industry standards in the UK since they were founded in 1862. Originally a percussion cap manufacturer, the company’s growth was rapid and diverse as they entered other prominent areas of the time including printing, brass rolling, bicycle components and manufacturing.
During those early fledgling days, the company honed its expertise in metallurgy and at the turn of the 20th century opened its first metallurgy laboratory. Bringing a series of never-seen-before technological advances to the industry they were soon a globally recognised mover and shaker in the
engineering world. Amid the tremendous technological advances that were seen in the 20th century, a new company IMI CCI was founded in 1961 that focused on the development and manufacturing of a new type of control valve. By 1981 IMI CCI had joined IMI and through successful acquisitions and pioneering endeavours established the current IMI Critical Engineering and took podium position as a major, worldwide valve manufacturer.
Building on such a rich heritage spanning over a century, the company has and continues to build a reputation for excellence and innovation in industries where safety and reliability are paramount. As the trusted partner to major industrial and infrastructure sectors, IMI Critical Engineering deliver advanced technologies, including valves, actuators, and related services, that ensure the smooth and efficient operation of critical systems.
The comprehensive portfolio, combined with their deep engineering expertise, enables IMI to tailor their solutions to meet unique industry
During those early fledgling days, the company honed its expertise in metallurgy and at the turn of the 20th century opened its first metallurgy laboratory
challenges and turn them into development opportunities. At IMI Critical Engineering, there is an unwavering commitment to quality, performance, and customer satisfaction that has positioned them as a global leader and set the benchmark for best practice in the industry.
Part of this are comprehensive lifecycle
maintenance programmes that are on offer covering work and expertise needed during projects and support afterwards. Maximising valve reliability and performance is prioritised, ensuring smooth operation, minimising downtime, and providing peace of mind to customers.
People make a company great. Front and centre of IMI are the 2,900 talented and diverse individuals committed to delivering precision-engineered flow control solutions, expert installation, and lifetime servicing. Alongside this, the company utilises manufacturing facilities in twelve countries and a global service network.
IMI Critical Engineering are known to invest heavily in training and development to deliver a deep understanding of their solutions, their functionalities, and the industries they serve. This expertise allows them to offer comprehensive design and installation guidance, troubleshoot effectively, and provide valuable insights empowering the customer to leverage their solutions to the fullest potential.
The United Kingdom, and indeed the world, has seen a great deal of change to the workplace since the 1860s and IMI Critical Engineering have always found that if you plan to lead the change in industry, you must do it from the front. As such, they continue to believe all companies must take their role seriously in preventing modern day slavery and human trafficking. For themselves, IMI utilises a combination of general corporate responsibility policies and specific supply chain compliance actions to combat modern slavery in its supply chain. These include processes and codes of conduct that affect the company at all levels from management down to staff training.
Above all else, their flow control solutions are designed to enhance safety, plant performance, and environmental standards. IMI are specialists in working closely with process licensors and electronic pressure controllers (EPCs) to create innovative products that address the evolving needs of the oil and gas industry. Their unique, experiencebased expertise enables them to play a critical role across the entire industry value chain, from upstream gas production and midstream processing
to downstream distribution, as well as every aspect of the liquified natural gas (LNG) process.
The application of their technology is far reaching and connects many different industries sectors such as petrochemical, nuclear, hydrogen power and renewables, process industries, marine, sanitary solutions for pharma, biotech, food, and beverage industries. Not to mention iron and steel metallurgy, desalination, and potable water solutions.
In a recent case study, A leading energy provider had significantly increased oil production from a field in the Arabian Gulf. Higher production increased the pressure of the flow passing through its water injection system beyond its capability and multiple control valves began to fail after a short period of operation, with severe cavitation damage to the valve trim. This calamity resulted in high costs due to the need for frequent maintenance and trim replacement. The client asked IMI Critical Engineering to investigate and recommend a solution.
Team engineers were sent in to analyse the current process conditions in the plant, including production volumes, the properties of the injected water, pressure, and temperature ranges.
Interestingly, valve problems are often wrongly attributed to component and plant age, however this is usually due to the operating conditions changing. Valves are precision components designed for specific conditions. When process conditions change, problems can arise, including excess vibration and noise, cavitation, and leakages, as well as reduced control over the flow through the valve.
In this instance, IMI’s team of engineers identified a change in the inlet pressure as the root of the problem. During earlier periods of operation, inlet pressure had been below 1000psig, but when production from the field increased significantly, inlet pressures rose to 2500psig, putting stress on the internal parts of the valve. Furthermore, water saline content is double that of seawater (70,000 ppm), as the plant pulls injection water from the reservoir the fluid velocity exceeds 100 ft/sec through the valve.
In the past, operators would have had to replace the whole valve with a new one customised to the current process conditions, attracting significant costs and disruption. Now, with the advent of additive manufacturing – 3D printing – it is
The application of their technology is far reaching and connects many different industries sectors
possible to retrofit a new valve trim to the existing valve.
A ‘drop-in’ solution for valve problems, IMI Critical Engineering’s Retrofit3D provides a speedy and cost-effective solution to many valve problems, including those arising from a change in the process conditions.
Retrofit3D combines additive manufacturing, also known as 3D printing, and traditional manufacturing techniques to engineer valve trims that are optimised for the process conditions.
Unlike traditional manufacturing techniques which are subtractive and remove material, additive manufacturing works by building components by ‘printing’ layer upon layer. This provides extra flexibility in valve design, as internal features and complex geometries can be incorporated that would be impossible to achieve with traditional manufacturing techniques. Additive manufacturing also allows for more efficient use of space, with disk stacks up to 40% smaller, which can be retrofitted into a wide range of valve bodies.
Additive manufacturing is a widely used term, but covers many different, sophisticated techniques with new methods being developed constantly. Laser Powder Bed Fusion (LBPF) or Direct Metal laser Sintering (DMLS) are among the most known technics for stainless steel and nickel-based alloys printing, but IMI Critical Engineering also uses Binder Jetting techniques for specialist applications requiring specific materials such as Stellite6.
IMI Critical Engineering is at the forefront of additive manufacturing, having successfully used the technology for over ten years, and playing an active role in the industry, from the development and testing of materials, parts qualification, to standards development.