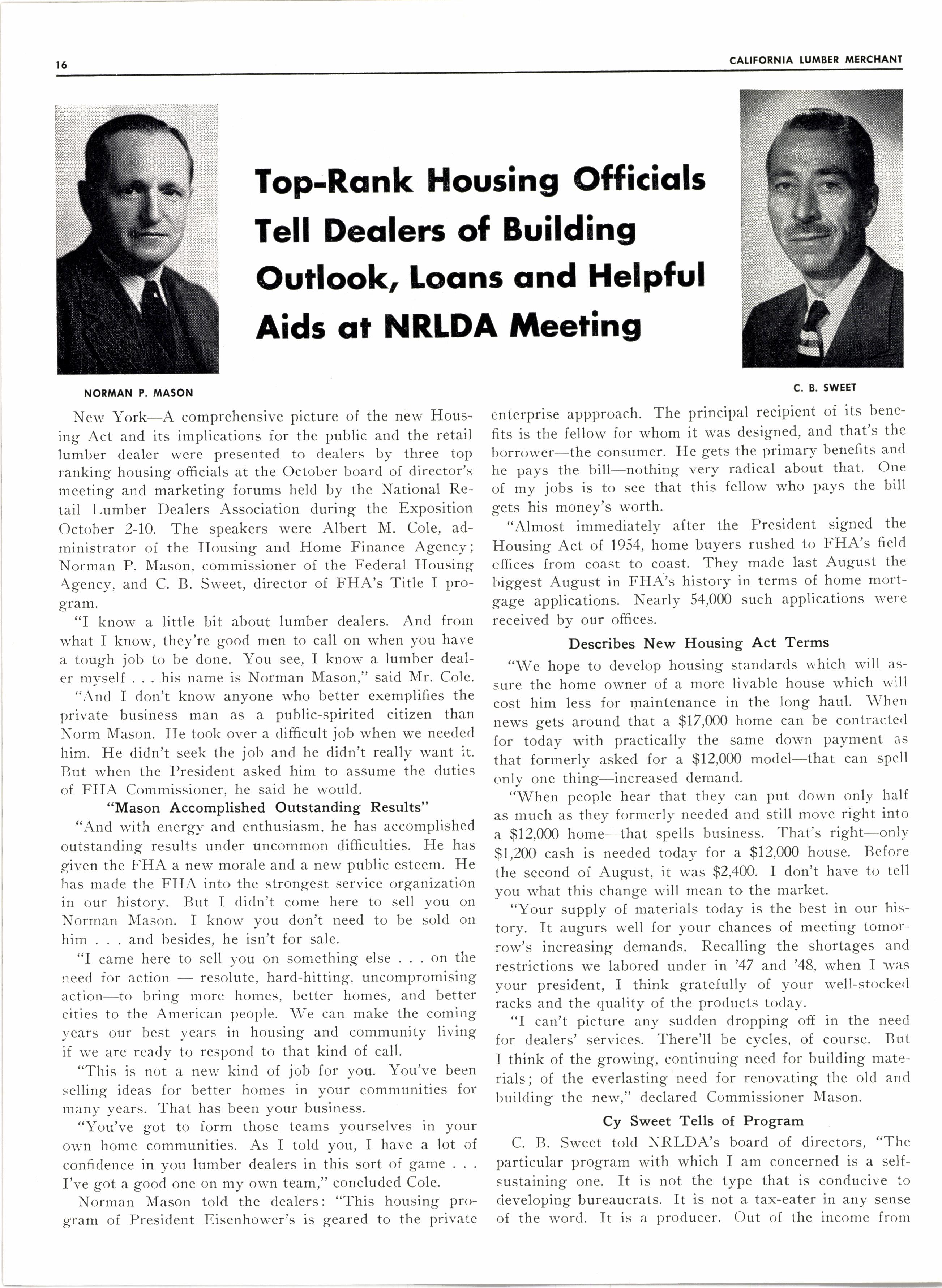
11 minute read
Top-Rqnk Housing Officiols Tell Decrlers of Building Outlook, Loclns clnd HelPful Aids crt NR.LDA Meeting
NORIIAAN P. TAASON
New York-A comprehensive picture of the new Housing Act and its implications for the public and the retail lumber dealer were presented to dealers by three top ranking housing officials at the October board of director's meeting and marketing forums held by the National Retail Lumber Dealers Association during the Exposition October 2-10. The speakers were Albert M. Cole, administrator of the Housing and Home Finance Agency; Norman P. Mason, commissioner of the Federal Housing Agency, and C. B. Sweet, director of FHA's Title I program.
"I know a little bit about lumber dealers. And froin what I know, they're good men to call on when you have a tough job to be done. You see, I know a lumber dealer myself his name is Norman Mason," said Mr. Cole.
"And f don't know anyone who better exemplifies the private business man as a public-spirited citizen than Norm Mason. He took over a difficult job when we needed him. He didn't seek the job and he didn't really want it. But rvhen the President asked him to assume the duties of FHA Commissioner, he said he would.
"Mason Accomplished Outstanding Results"
"And rvith energv and enthusiasm, he has accomplished outstanding results under uncommon diffrculties. He has given the FHA a new morale and a new public esteem. He I.ras made the FHA into the strongest service organization in our history. But I didn't come here to sell you on Norman Mason. I know you don't need to be sold on him . and besides, he isn't for sale.
"I came here to sell you on something else . . on the leed for actionresolute, hard-hitting, uncompromising action-to bring more homes, better homes, and better cities to the American people. We can make the coming )/ears our best years in housing and community living if rve are ready to respond to that kind of call.
"This is not a nerv kind of job for you. You've been selling ideas for better homes in your communities for lnany years. That has been your business.
"You've got to form those teams yourselves in your olvn home communities. As I told you, I have a lot of confidence in you lumber dealers in this sort of game I've got a good one on my own team," concluded Cole.
Norman Mason told the dealers: "This housing program of President Eisenhower's is geared to the private enterprise appproach. The principal recipient of its benefits is the fellorv for r,vhom it was designed, and that's the borrower-the consumer. I{e gets the primary benefits and he pays the bill-nothing very radical about that. One of my jobs is to see that this fellow who pays the bill gets his money's worth.
"Almost immediately after the President signed the Housing Act of 1954, home buyers rushed to FHA's field cffices from coast to coast. They made last August the biggest August in FHA's history in terms of home mortgage applications. Nearly 54.000 such applications r'vere received by our offices.
Describes New Housing Act Terms
"We hope to develop housing standards which will assure the home owner of a more livable house r.vhich will cost him less for gtaintenance in the long haul. When news gets around that a $17,000 home can be contracted for today with practically the same down payment as that formerly asked for a $12,000 model-that can spell only one thing-increased demand.
"When people hear that thev can put dorvn only half as much as tl-rey formerly needed and still move right into a $12,000 home-that spells business. That's right-only $1,200 cash is needed today for a $12,000 house. BeIore the second of August, it was $2,400. I don't have to tell you what this change rvill mean to the market.
"Your supply of materials today is the best in our history. ft augurs well for your chances of meeting tomorrorv's increasing demands. Recalling the shortages and restrictions we labored under in '47 and '48, when I rv:rs your president, I think gratefully of your rvell-stocked racks and the quality of the products today.
"I can't picture any sudden dropping off in the neecl for dealers'services. There'll be cycles, of course. Bu,t I think of the growing, continuing need for building materials; of the everlasting need for renovating the old and building the new," declared Commissioner Mason.
Cy Sweet Tells of Program
C. B. Sweet told NRLDA's board of directors, "The particular program with which I am concerned is a self-.ustaining one. It is not the type that is conducive io cleveloping bureaucrats. It is not a tax-eater in any sense of the rvord. It is a Droducer. Out of the income from insurance charges the program not only has produced enough money to pay all claims and operating costs since 1939, but it has made full return to the Treasury of the 8 1/3 million dollars originally advanced for operating capital and, in addition, it has built up a surplus of over 30 million dollars in the Title I fnsurance Reserve Fund.
"While I am on this point, I may add, too, that the over-all activities of FHA for the fiscal year 1954, for instance, produced an income of 128 million dollars while the outlay was only 74 million, leaving a net earned income for the year of about 54 million.
"For the past two years repair and modernization loans insured under Title I have exceeded one billion dollars annually. Practically all of these loans involve materials which are stocked by the local retail dealers.
1,500,000 Title I Loans Annually
"Title I loans are now being made at the rate of a million and a half annually, the average of which is about $600. There are two types of loans made-(l) direct-toborrower, and (2) dealer-originated loans. Between 80 end X)/o are of the dealer-originated type.
"There are six principal steps the dealer takes in the origination and consummation of a Title I loan transaction: First, he computes the total cost of the job; Second, he has the customer complete the credit application; Third, he sends the completed credit application and copy of the contract to the lending institution; Fourth, he does the work; Fifth, he has the loan papers executed, including a completion certificate signed by the customer; Sixth, he presents the note and related papers to the lending institution and receives cash in full payment for his services,,' pointed out Cy Sweet.
"fn my opinion, we now have the most practical housing legislation this country has ever known. I am confident it will stimulate record activity both in the construction 'rf new homes and in the rehabilitation of existing homes. It will permit you to expand your operation. It offers you the opportunity to do a better job than ever of serving your own people.
Rely on Dealers for Home fmprovements
"The elimination of the crooked salesman and fly-bv- night dealer will greatly improve the position of the established retail lumber dealers in the local communities. And it is here where you, if you are not already participating in the program, may step in and better your own respe,ctive communities. They, in turn, will learn to rely on you for home repairs and modernization rather than rx glib salesmen from out of town who seek to get their money for shoddy work and inferior materials rvithout giving value for the money received,,' continued the Cali_ fornian.
"ft has been estimated that to meet adequately the real housing needs of our people it will require an average an_ nual construction of 1,400,@O new homes, and the new conditioning of another 600,000 existing dwellings each year for the next ten years. The new Housing Act will be of tremendous help along this line. And in another five or six years it is quite likely that our current housing sights r,vill have to be raised still further," concluded Mr. Sweet.
lumIer two
'We now carry the following Baxco Pressure Tieated Foundation Lumber in stock at Alameda and Long Beach for immed.iate sbipment to dealers: Douglos Fir 545 ALS 2x4,2x5,2x8,2x70, 3x4,3x6,4x4ond4x6.
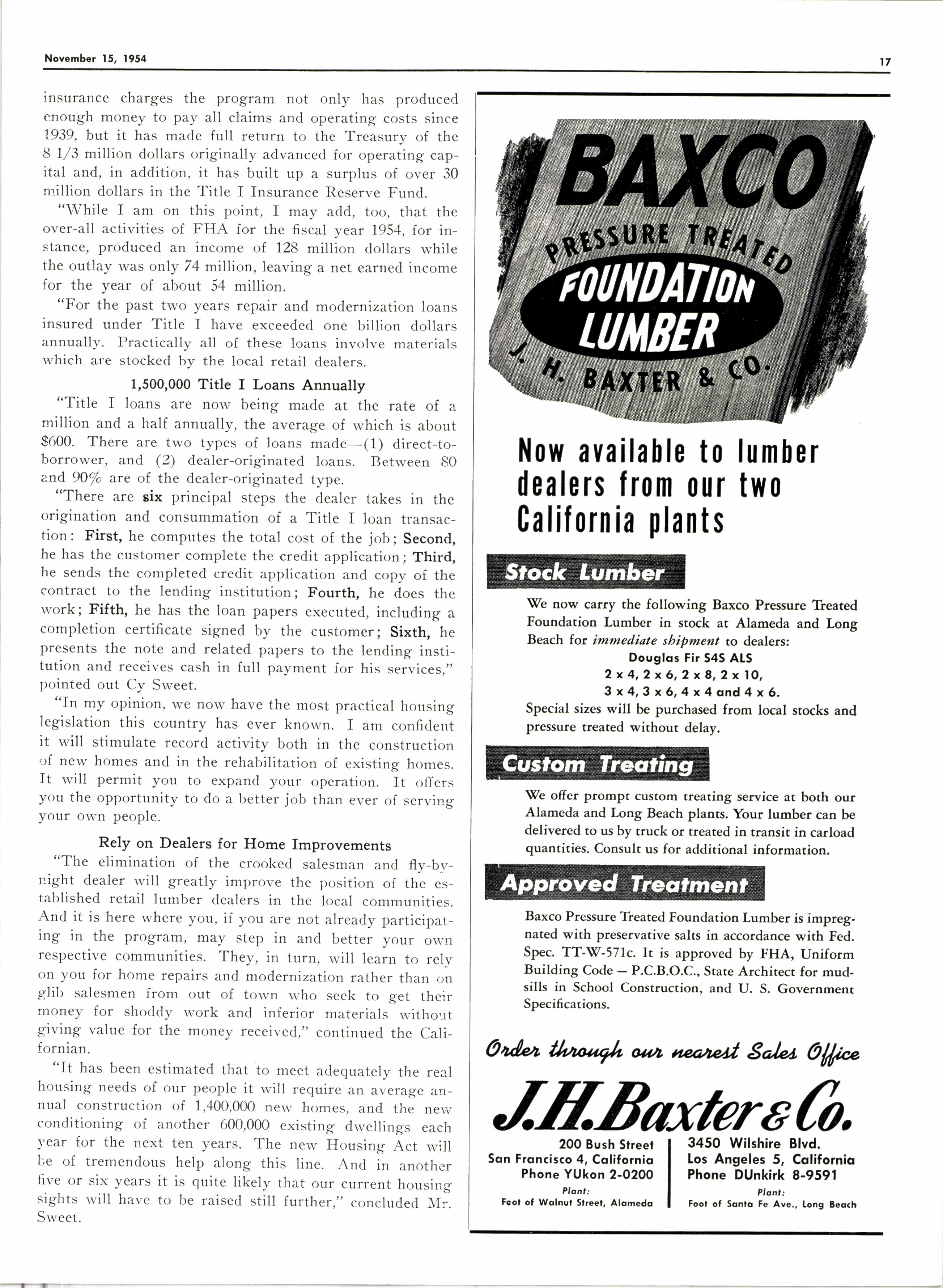
Special sizes will be purchased from local stocks and pressure treated without delay.
'We offer prompr custom treating service at both our Alameda and Long Beach plants. Your lumber can be delivered to us by truck or treated in transit in carload quantities. Consult us for additional information.
Baxco Pressure Treated Foundation Lumber is impregnated with preservative salts in accordance with Fed. Spec. TT-W-571c. k is approved by FHA, Uniform Building Code - P.C.B.O.C., State Architect for mudsills in School Construction, and U. S. Government Specifications.
TilC SfeffORD SUDI: A'IIERICA'S DEMAND FOR WOOD
1929 - r97s
Summary of a report by Stanford Research Institute, Stanford, Calif., to Weyerhaeuser T'imber Company, Tacoma, Ilash., 1954.
Part IV
The roof is now the most important component of the dwelling unit in terms of actual lumber consumptionl Next is the floor, followed by exterior and interior walls. These four components account for more than 7O/o of. the lumber consumed per dwelling unit.
Offsetting the shrinkage in the roof market due to decreasing dwelling-unit size and lower roof pitch has been a change in lumber consumption in roof sheathing due tc the trend from stiff wooden shingles, which required only ligh't, spaced sheathing, to limp coverings such as asphalt shingles and composition roofing, which require solid sheathing. Furthermore, as pitch decreased, the size of supporting members increased, which aided lumber's market for roof framing. The increased proportion of onestory houses also increased average roof area per unit. The decline projected to 1975 in lumber consumption in roofs reflects expected increasing competition from sheet materials.
TOTAL CONSUMPTION OF LUMBER PER DWELLING UNIT BY TYPE OF LUMBER
Lumber consumed in floors dropped more than 50o7b irom 1920 to 1953 due to inroads made by slabs, the decline in the percentage of dwellings having any subfloor, aind increasing competition from plywood and hardboard subflooring. Lumber's share of the potential floor market declined from about 96/o in 1920 to about ffi/o in 1953. By 1975, lumber is expected to have about 37/a of its ,inaximum possible usage in floors.
The 360/" drop in lumber consumption for exterior walls between 1920 and 1953 was due primarily to the shrinkirrg size of dwelling units and the shift toward single-story construction. Offsetting losses in sheathing, caused by inroads of sheet materials, has been the increase in the proportion of frame structures to total structures. The expected continued decline to I97S is a result of the anticipated increase in masonry construction, a decline in the percentage of dwellings using sheathing materials of any type, further losses in the participation of lumber in the sheathing market, and a drop in the share of the exterior facing market taken by wood siding.
In addition to the decline in perimeter of interior walls, owing to the decline in average size of dwelling units, a drop in average ceiling height has accounted for a market loss. The consumption of lumber in interior walls is expected to remain at about today's level for the next 25 years, however, as the average cubic footage of dwelling units is expected to remain virtually unchanged. Lumber will probably continue its dominant position in the interior wall framing market. In interior wall surfacing, dry-wall construction increased ftom 20/o of the market in 1940 to 7O/o in 1953. Gypsum board is the dominant dry-wall material, accounting for more than 9O/o of the dry-wall potential.
Framing lumber had about 62/o of its maximum possible market in 1920, as compared with about 53/o in 1953. By 1975, f.raming lumber is expected to have abofi 48/o of. its possible maximum market. (This includes a minor quantity of finished boards used for interior walls and ceilings.)
Sheathing lumber accounted for about 8O/o of. the sheathing market in 1920, but only about 58/o in 1953. It rs estimated that by 1975 sheathing lumber will have only about 43/o of the potential sheathing market.
Although lumber siding increased its part in the exteriorfacing materials market from about 2l/o to about 281/o between 1920 and 1953, total consumption of siding per TABLE 7
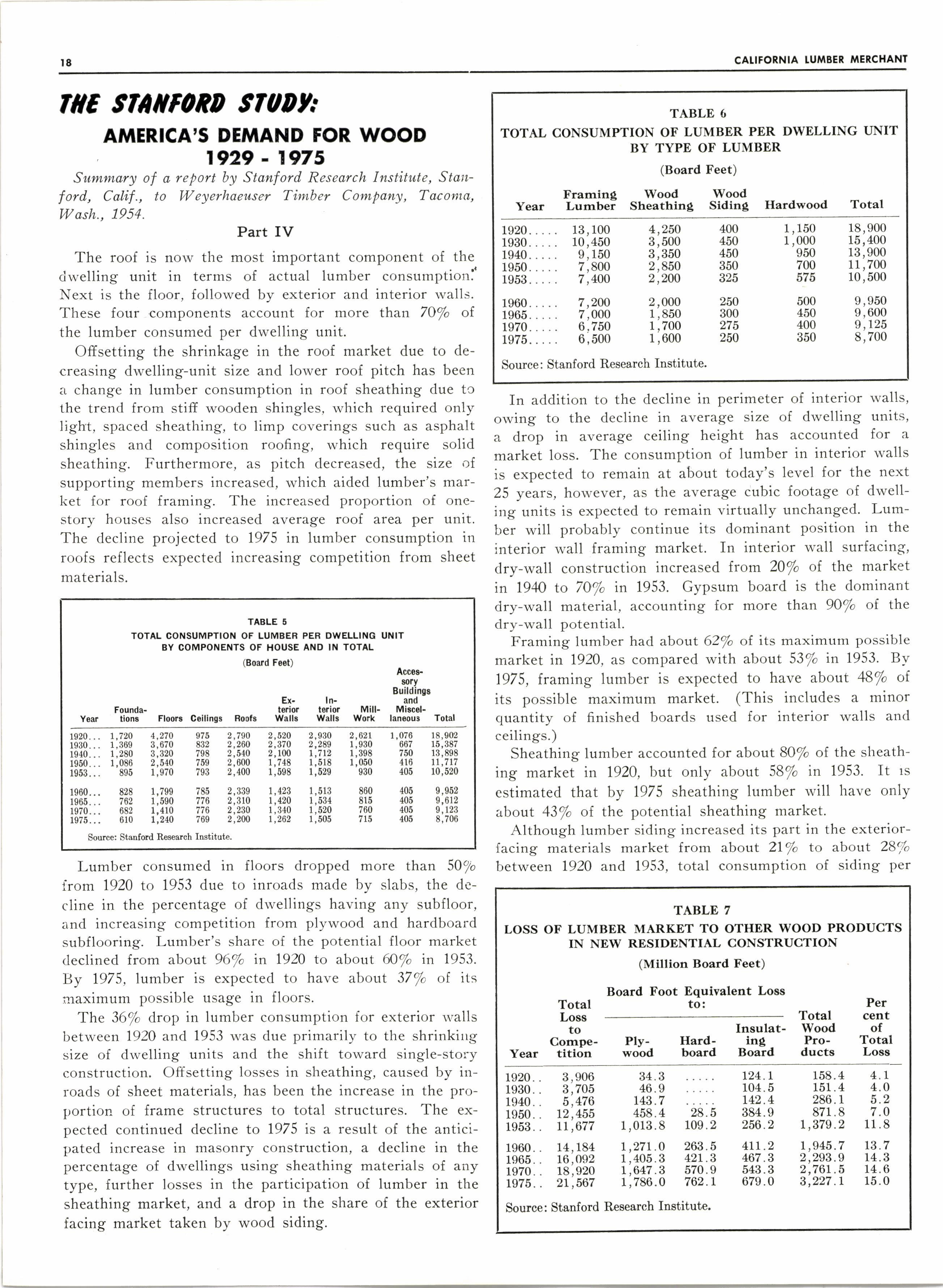
LOSS OF LUMBER MARKET TO OTHER WOOD PRODUCTS IN NEW RESIDENTIAL CONSTRUCTION (Millton Board Feet)
Board Foot Equivalent
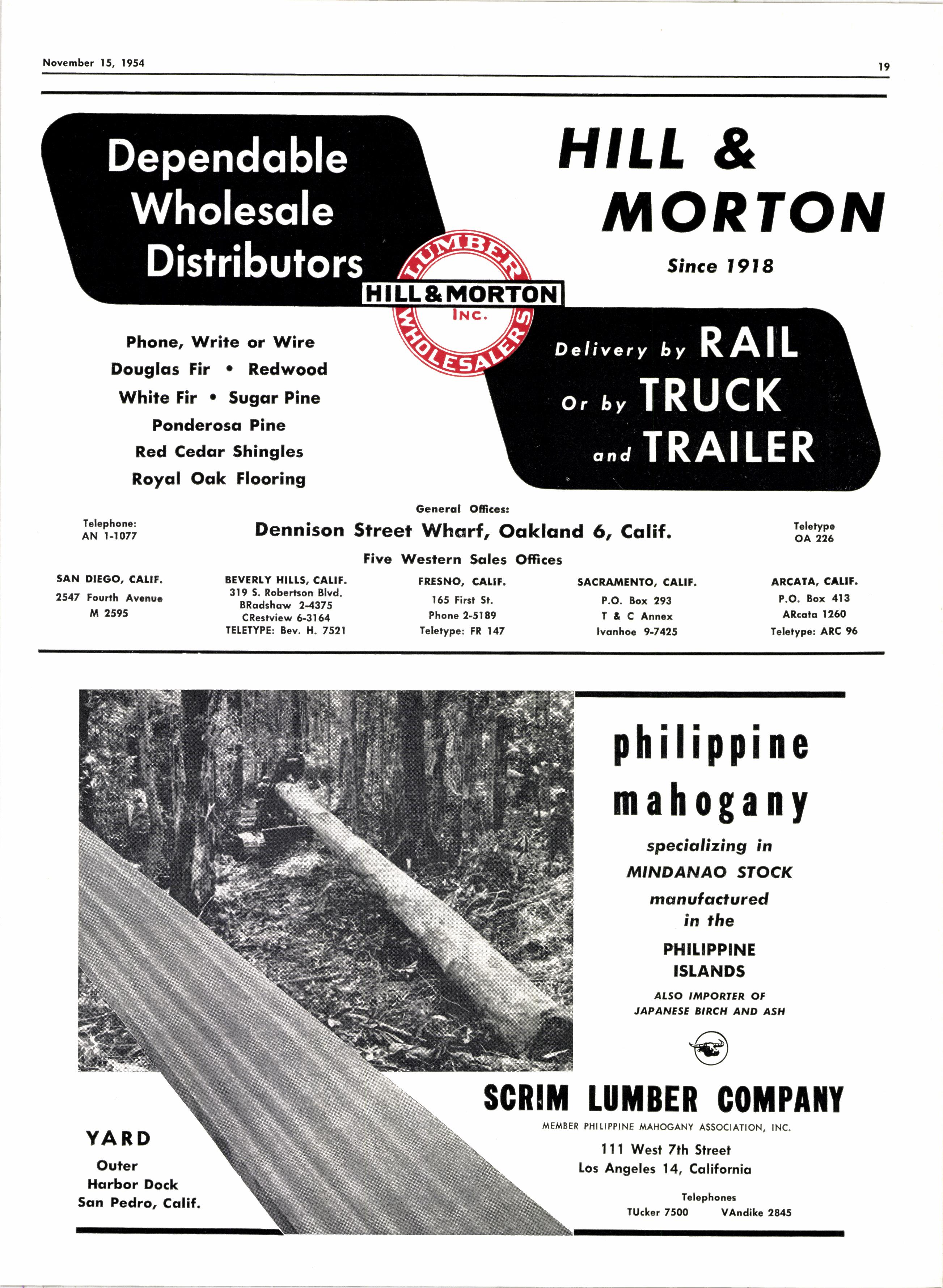
<iwelling unit has slumped from about 400 board feet to about 325 board {eet. It is estimated that about 250 board Ieet of siding rvill be used per dwelling unit in 1975, representing about 23/o of total siding potential.
Hardrvood lumber consumption in 1953 accounted for only about 64/o of the maximum possible hardwood lumber market (flooring and millwork), as compared 'ivith a.bout 9B/o in 1920. It is estimated that by 1975 hardwood lumber rvill have 39/. of its total market, due largely to the loss of flooring markets, but also to stiff competition from other materials in millu'ork markets.
Some of the loss o{ lumber markets in residential building is to other forest products such as plywood, hardboard, and insulating board. These products accounted in 1953 for a little less than 72a/o of lumber's total loss of markets to competing materials. All three are expected to shorv substantial growth in residential building uses by 1975, and they are expected to account by that time for about l5/o of the total loss of lumber markets to competing materials.
Nonhousekeeping Units
The bulk of expenditures for nonhousekeeping units is for larger structures such as hotels and motor courrs. Lumber constumption per dollar of expenditure for such units has declined from 3 board feet in 1920 to 1.5 in 1952. It is estimated that by 1975 about 1.1 board feet of lumber lvill be used per dollar spent for new nonhousekeeping rrnits.
By ,combining this lumber-use factor with estimated ex1'renditures, 274 million board feet of lumber are expected to be used in new nonhousekeeping units by 7975. This is about the same as the 278 million board feet consumed in 1952.
Additions and Alterations
Consumption in additions and alterations in 1953 represented about 4/o of total lumber consumption in construction of all types.
It is estimated that about one board foot of lumber was consumed per dollar of addition and alteration expenditures in 1953 ; it is expected that this lumber-use factor rvill decline by 1975 to about 0.85 board feet per clollar. Competition from ply'rvood, hardboard and insuiating board rvill tend to reduce the boards consumer per dollar of expenditure, but the quantity of dimension lumber consumed per dollar will probably remain at present levels.

The expected decline in the lumber-use factor, however, is offset by probable increases in total expenditures for this type of construction, from $1.1 billion in 1953 to $1.25 (at 1952 prices) by 1975. As a result, lumber used in additions and alterations is expected to remain close to present levels (about 1.i billion board feet annually) throughout the period to 1975.
Lumber Used in Nonresidential Construction
A special survey made in 1953 by Stanford Research Institute of 1,000 large non-residential contractors sholvs that lumber consumption in non-residential construction of all types can be allocated by end-use as follows: don't you think
Lumber is used in preference to plywood, hardboard, or steel in concrete forms because it is more economical when large, smooth surfaces are not required. Lumber can be re-used for concrete forms and later utilized for bracing, shoring, or for temporary buildings and fencing. Because of the many possible re-uses, it appears likely that lumber will retain a portion of the concrete form market in future years. Plywood and hardboard provide the greatest competition in concrete forms where smooth surfaces are desired.
The closet competitors of lumber for framing, scaffolding, bracing, shoring, and decking are steel or concrete and steel. The principal advantage of lumber is its lower cost and its workability, resulting in lower total installed cost or total use cost. In many cases, however, steel or steel together with concrete are used because they offer additional strength.
An over-all decline of about 45/o in the board feet of lumber consumed per dollar of nonresidential construction is expected in the period between 1953 and 1975. These declines in lumber-use factors range from about 25/o in institutional building to 50/o in highway construction.
By combining these lumber-use factors with estimated expenditures for each type of nonresidential construction, estimates were made of lumber consumption for each of the target years. Estimates for 1953 and 1975 are shown below.