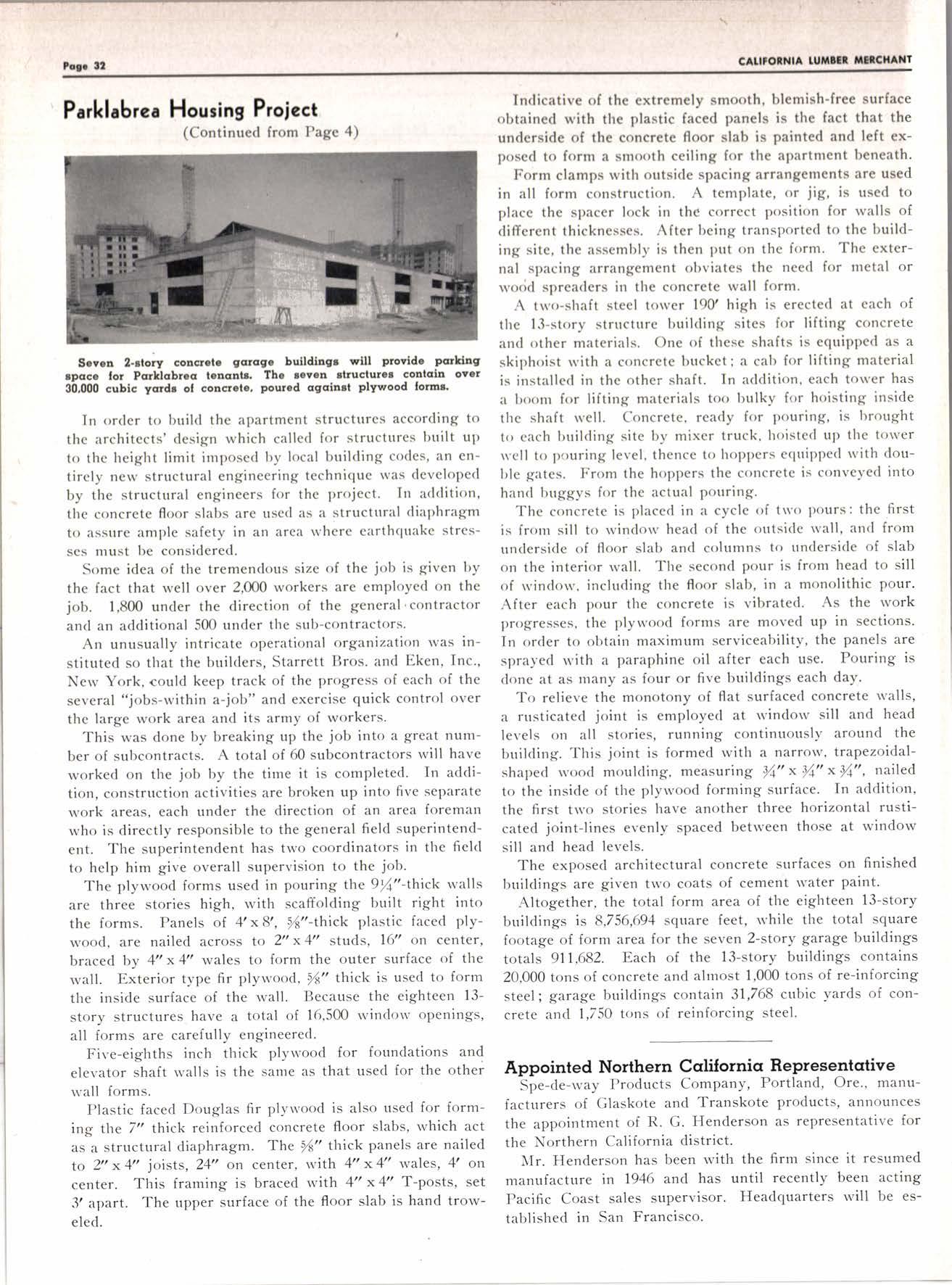
3 minute read
Parklabrca Houring Proicct
(Continued from Page 4)
Indicative of the extremely smooth, blemish-free surface obtainecl with the plastic faced panels is the fact that the undcrside of the concrete floor slab is painted and left exposcd to form a 56ooth ceiling for the apartnrent beneath.
Form clamps rvitlt otttside spacing arrangenrents are used in all form construction. A template, ()r jig, is used to pl;rce the st)acer lock in thc correct position for rvalls of diffcrent thicknesses. After being transportetl to thc building site, the nssemblf is then l)ut ()n the form. Thc external sllacing arrangement obviates thc nee<l for ntetal or rr'<lod spreadcrs iu tlte concrete rvall form.
In or<ler to lruild the apartment structtlrcs according to thc architccts' design which called for structttres built u1r to thc height limit irrrposed by local builtling codes, an cntircly new structural engineering tcchnitluc lvas devclope<l by the structttral engineers for the project. In a<l<litiorr, the concrete floor slalls are ttsctl as ;t structtlral diaphragm t() assure ample safety in an arca rvherc earth<ltrakc strcsses nrust be considered.
Some idea of the tremendous size of thc job is given by the fact that well over 2,000 workers are employed on the job. 1,800 under the direction of the gencral'contractor and an additional 500 under the sttb-contractors.
An unusually intricate operational organizati<ln rvas instituted so that the builders, Starrett Rros. and Eken, Inc., Nerv York, could keep track of the progress of each of the several "jobs-rvithin a-job" and exercise quick control over thc large rvork area ancl its army of workers.
This was done by breaking up the job into a great number of sultcontracts. A total of 60 subcontractors will have worked on the job by the time it is completed. In additior.r, constrttction activities are broken up into frve separate rvork areas, each under the direction of an area foreman rvho is directly responsible to the general field superintendent. The superintendent has tr'r''o coordinators in the fiel<l to help him give overall supervision to the job.
The plywood forms used in pouring the 9tl"-thick walls are three stories high, rvith scaffolding built right into the forms. Panels ol 4'x8', s/"-thick plastic faced plyr,r'ood, are nailed across to 2" x 4" studs, 16" <';n center, braced by 4" x 4" wales to form the outer surface of the rvall. Exterior type fir plywood, sf" thick is used to forn-r the inside surface of the wall. Because the eighteen 13story structures have a total o{ 16,5@ lvinclo'lv openings, all forms are carefully engineered.
Five-eighths inch thick plyr,r'ood for foundations and elevator shaft rvalls is the same as that usecl for the other rvall forms.
Plastic facecl Douglas fir plyrvood is also used for forming tlre 7" thick reinforced concrete floor slabs, which act as a structural diaphragm. The 5/t" thick panels are nailed to 2"x4' joists, 24" on center, r.r'ith 4"x4'wales, 4' on center. This framing is braced with 4" x 4" T-posts, set 3' apart. The upper surface of the floor slab is hand troweled.
A tu'o-slraft stcel torver 190' high is erected at each of the t3-story structure buil<ling sites for lifting concrete and other nraterials. One of these shafts is eqtrippc<l as a skiphoist u'ith a concrete lrttckct ; a cab for lifting material is installed in the other shaft. In atlclition, each tou'er has :r lroonr for liftirrg matcrials to<t llulkv for hoisting irrside thc shaft u'ell. Cloncrete, ready for prturing, is llrotlght to cach lruilding site b-v mixer truck, lroistcd up the to\\'er u'cll to llouring level, thencc to lto;tpcrs erltrippe<l lvith doulrlc g:ttes. Ii'ronr the h<tplters the cotrcrctc is cotrvel'ed into han<l lruggvs for the actual potrrir.rg.
Thc concretc is placed in a cycle of tu'tt lx)urs: the first is frour sill to rvin<lon' hea<l of the otttsidc 'rvall, an<l from turrdersi<le of floor slatr and coltttttns to trndersi<le of slab on the interior rvall. The second pour is fror.n head to sill of s'indou'. including the floor slab, in a monolithic pour. After each llour the concrete is vibrated. As the lvork I)r()gresses, the ltlywood forrrrs are moved up in sections. Irr order to obtain maximttm serviceability, the panels are spra)'ed u'ith a paraphine oil after each ttse. Pouring is donc at as rnany as four or five buildings each day.
Trl relieve the monotony of flat surfaced concrete lvalls, :r rrrsticated joint is employed at u'indorv sill and head levels orr all stories, running continttottsly arouncl the buil<ling. 'I'his joint is formed rvith a narro\\', trapezoidalshalred rvood moulcling, measuring fu"x%"xfo,", nailed to the inside c,f the plywood forming sttrface. In addition, the first tlro stories l.rave another three horizontal rusticated joint-lines evenly spaced betrveen those at r'l'indow sill and head levels.
The exposetl architectural concrete sttrfaces on finished brrilclings are given trvo coats of cement n'ater paint.
Altogether, the total form area of the eighteen 13-story brrildings is 8,756,694 sqtlare feet, rvhile the total square footage of form area for the seven 2-story garage buildings totals 911,682. Each of the 13-story buildings contains 20,000 tons of concrete and ah.nost 1,000 tons of re-inforcing steel ; garage buildings contain 31,768 cubic yards of concrete and 1,750 tons of reinforcing steel.
Appointed Northern Calilornic Representqtive
-Spe-de-rvay Products Company, Portland, Ore., manufacturers of Glaskote and Transkote products' announces the appointment of R. G. Henderson as representative for the Northern California district.
I\fr. Henderson has been rvith the firm since it resumed manufactttre in 1946 and has until recently been acting Pacific Coast sales supervisor. Headquarters will be established in San Francisco.
