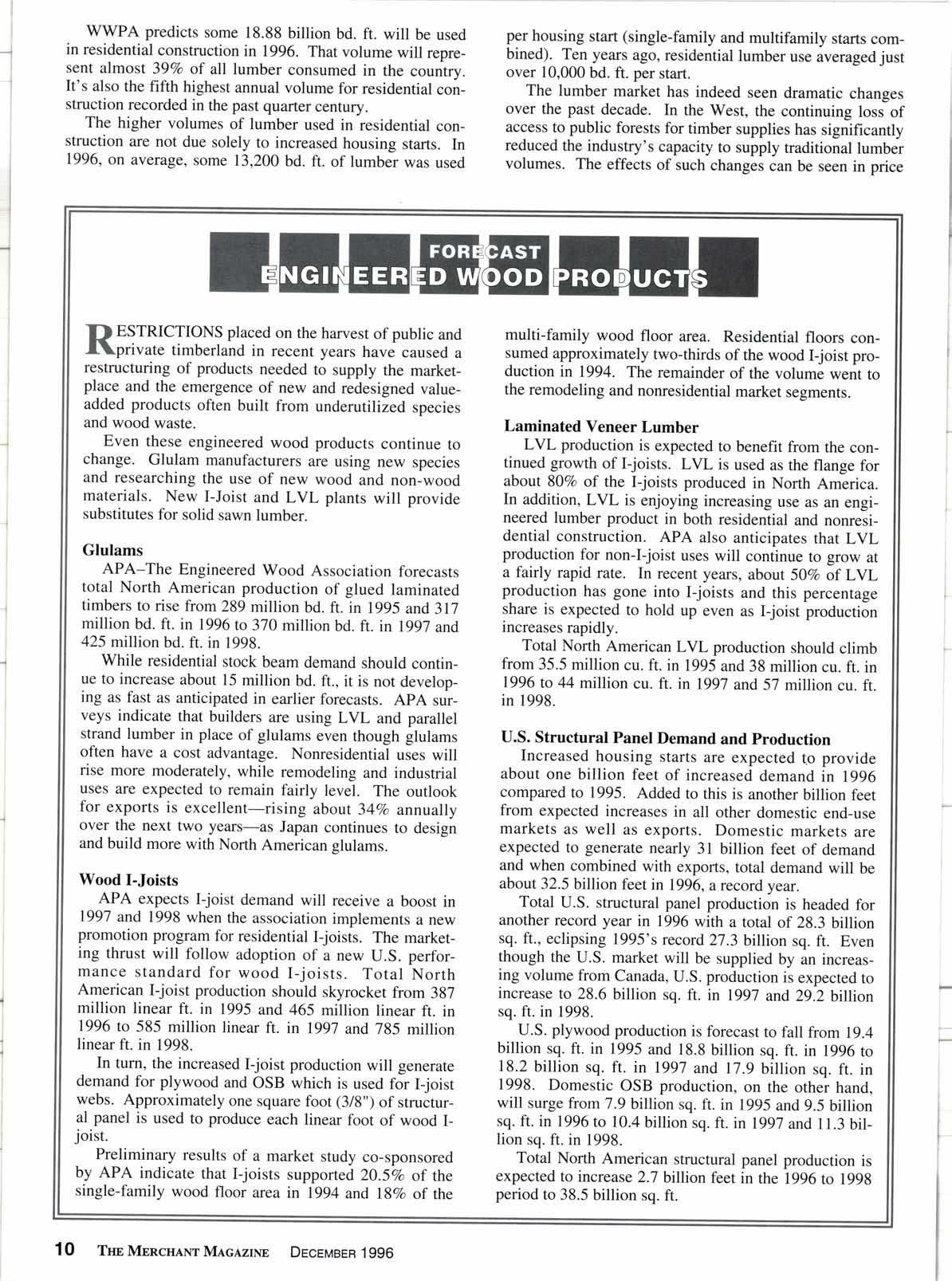
14 minute read
CCTT#ffiffiilGGil
ESTRICTIONS placed on the harvest of public and l\private timberland in recent years have caused a restructuring of products needed to supply the marketplace and the emergence of new and redesigned valueadded products often built from underutilized species and wood waste.
D)
Even these engineered wood products continue to change. Glulam manufacturers are using new species and researching the use of new wood and non-wood materials. New I-Joist and LVL plants will provide substitutes for solid sawn lumber.
Glulams
APA-The Engineered Wood Association forecasts total North American production of glued laminated timbers to rise from 289 million bd. ft. in 1995 and 3lj million bd. ft. in 1996 to 370 million bd. ft. in t99i and, 425 million bd. ft. in 1998.
While residential stock beam demand should continue to increase about 15 million bd. ft., it is not developing as fast as anticipated in earlier forecasts. ApA surveys indicate that builders are using LVL and parallel strand lumber in place of glulams even though glulams often have a cost advantage. Nonresidential uses will rise more moderately, while remodeling and industrial uses are expected to remain fairly level. The outlook for exports is excellent-rising about 34Vo annually over the next two years-as Japan continues to design and build more with North American slulams.
Wood l-Joists
APA expects I-joist demand will receive a boost in 1997 and 1998 when the association implements a new promotion program for residential I-joists. The marketing thrust will follow adoption of a new U.S. performance standard for wood I-joists. Total North American I-joist production should skyrocket from 387 million linear ft. in 1995 and, 465 million linear ft. in 1996 to 585 million linear ft. in 1991 and 785 million linear ft. in 1998.
In turn, the increased I-joist production will generate demand for plywood and OSB which is used for I-joist webs. Approximately one square foot (3/8") of structural panel is used to produce each linear foot of wood Ijoist.
Preliminary results of a market study co-sponsored by APA indicate that I-joists supported 20.5% of the single-family wood floor area in 1994 and lSVo of the multi-family wood floor area. Residential floors consumed approximately two-thirds of the wood I-joist production in 1994. The remainder of the volume went to the remodeling and nonresidential market segments.
Laminated Veneer Lumber
LVL production is expected to benefit from the continued growth of I-joists. LVL is used as the flange for abofi 80Va of the I-joists produced in North America. In addition, LVL is enjoying increasing use as an engineered lumber product in both residential and nonresidential construction. APA also anticipates that LVL production for non-I-joist uses will continue to grow at a fairly rapid rate. In recent years, about 50Vo ofLyL production has gone into I-joists and this percentage share is expected to hold up even as I-joist production increases rapidly.
Total North American LVL production should climb from 35.5 million cu. ft. in 1995 and 38 million cu. ft. in 1996 to 44 million cu. ft. in 1997 and 57 million cu. ft. in 1998.
U.S. Structural Panel Demand and Production
Increased housing starts are expected tp provide about one billion feet of increased demand in 1996 compared to 1995. Added to this is another billion feet from expected increases in all other domestic end-use markets as well as exports. Domestic markets are expected to generate nearly 31 billion feet of demand and when combined with exports, total demand will be about32.5 billion feet in 1996. a record vear.
Total U.S. structural panel production is headed for anorher record year in 1996 with a total of 29.3 billion sq. ft., eclipsing 1995's record27.3 billion sq. ft. Even though the U.S. market will be supplied by an increasing volume from Canada, U.S. production is expected to increase to 28.6 billion sq. ft. in 1997 and Zg.Z Ailion sq. ft. in 1998.
U.S. plywood production is forecast to fall from 19.4 billion sq. ft. in 1995 and 18.8 billion sq. ft. in 1996 to 18.2 billion sq. ft. in 1997 and 17.9 billion sq. ft. in 1998. Domestic OSB production, on the other hand, will surge from 7.9 billion sq. ft. in 1995 and 9.5 billion sq. ft. in 1996 to 10.4 billion sq. ft. in 1997 and I1.3 billion sq. ft. in 1998.
Total North American structural panel production is expected to increase 2.7 billion feet in the 1996 to 1998 period to 38.5 billion sq. ft.
fluctuations, where, unlike the past, the lumber industry has a limited ability to increase production when lumber demand accelerates.
Despite such changes, demand for lumber in the U.S. has continued at high levels. Total U.S. lumber consumption over the decade from 1986-1995 averaged 46.9 billion bd. ft., 227o more than the average annual usage during the previous l0 years.
Discussions about replacing lumber with other materials often pick up when lumber prices rise. It's important to remember, however, that competing against lumber requires more than just a better price. Unlike other materials, lumber is produced under industry standards that are enforced through a third-party quality control system. This system assures users the lumber they buy will meet the specifications indicated for the grade marked on the product.
Lumber also is sold via an extensive distribution network, with wholesalers and retailers able to serye communities throughout North America. Customers in virtually any town can easily find the lumber products they need.
Wood-frame construction is commonly accepted by building officials, with prescriptive requirements available in the codes. Other materials may require engineering and other design work to gain the necessary code approvals.
And, of course, wood remains the most environmentally sound building material available today. It is renewable, durable, safe to handle and easy to work with.
Any piece of the market competing materials wish to take will have to be earned. WWPA, on behalf of its member producers, will continue to educate customers on how to best select and use lumber. The association will refute misleading statements about lumber made by competitors, assuring that customers have the proper information on which to base buying decisions. And it will continue to offer the field and technical support users demand today.
cials, and readily available. Labor must be comfortable with its use and be prepared to respond to demand as consumers understand the benefits of steel framing.
Fortunately, we have seen tremendous progress in each of these areas to give us confidence in our ability to achieve a 25Vo share of the market by the year 2000.
This year, agreement was reached among manufacturers to standardize the grades and dimensions of framing sections. These were incorporated into our 1996 CABO submittal, approved in October, which created the prescriptive standards needed to simplify the design and construction of steel-framed walls and floors. HUD has published a broader prescriptive method which will be the basis for future code submittals so that the code can apply to more and more residential projects.
While standards are expanding in generic products, we've also seen a surge in proprietary solutions to specific market demands. Design, engineering and cut list software have been developed to support the sales and manufacturing effort. New steel truss products are available for roofs and floor systems. Innovations now under development in connection and cutting tools will have a dramatic impact on job site productivity. The increased use of panelization, possible from steel's consistent quality, will further reduce the cost ofjob site labor.
In distribution, we are seeing progressive commercial roll formers teaming up with major drywall wholesalers to meet the needs of the residential and commercial builder. Smaller roll formers are proliferating who are combining design, production, distribution, and panelization in an effort to compact the supply chain. As these companies establish themselves, we can expect costs and service to continually improve to the benefit of the builder and buyer alike. Even to the most traditional lumberyards and home centers, the prescriptive standards can provide the guidance on what to stock for the builder or the remodeler.
In the area of training, we still have a big job ahead of us, but we are enthused at the increased number of vo-tech programs that are incorporating steel into their curricula. The carpenters union has launched an aggressive training program for its members, and the American Iron & Steel Institute and National Association of Home Builders continue to support training for builders and framers through our regional training centers and traveling seminars.
By Michael N. Meyers U.S. Steel Residential Advisory Group Chairman American Iron & Steel Institute
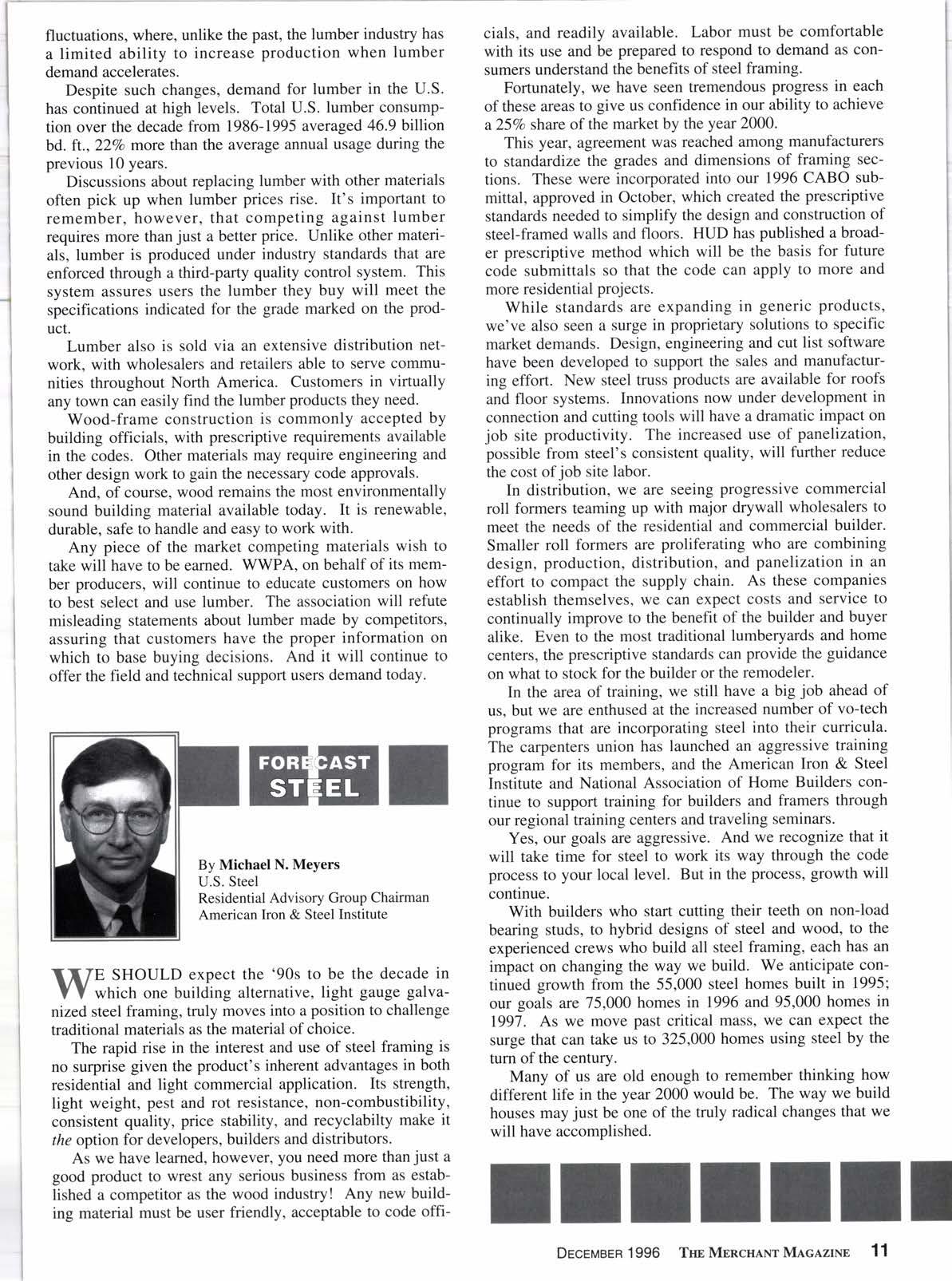
IXIE SHOULD expect the '90s to be the decade in V Y which one building alternative, light gauge galvanized steel framing, truly moves into a position to challenge traditional materials as the material of choice.
The rapid rise in the interest and use of steel framing is no surprise given the product's inherent advantages in both residential and light commercial application. Its strength, light weight, pest and rot resistance, non-combustibility, consistent quality, price stability, and recyclabilty make it the option for developers, builders and distributors.
As we have leamed, however, you need more than just a good product to wrest any serious business from as established a competitor as the wood industry! Any new building material must be user friendly, acceptable to code offi-
Yes, our goals are aggressive. And we recognize that it will take time for steel to work its way through the code process to your local level. But in the process, growth will continue.
With builders who start cutting their teeth on non-load bearing studs, to hybrid designs of steel and wood, to the experienced crews who build all steel framing, each has an impact on changing the way we build. We anticipate continued growth from the 55,000 steel homes built in 1995; our goals are 75,000 homes in 1996 and 95,000 homes in 1997. As we move past critical mass, we can expect the surge that can take us to 325,000 homes using steel by the turn of the century.
Many of us are old enough to remember thinking how different life in the year 2000 would be. The way we build houses may just be one of the truly radical changes that we will have accomplished.
By Alan E. Robbins
The Plastic Lumber Co., Inc. President Plastic Lumber Trade Association
rFHE $40 to $60 million Recycled Plastic Lumber (RPL)
I industry is showing emerging growth. Manufacturers are feeling their way through a myriad of issues as technologies compete to find market areas where their products' physical property strengths and weaknesses are appropriately matched. In addition, manufacturers must find a distribution channel that will not only work for today but tomorrow as well. Not easy tasks for an industry predominately made of small entrepreneurial companies.
What? Basically, there are four technologies currently competing in the marketplace: single polymer systems made from recycled high density polyethylene, mixes of recycled polyethylene and/or other recycled plastics (known as commingled plastics), fiberglass reinforced polyethylene, and wood/thermoplastic composites. These technologies produce over 50 different lumber look dimensions and shapes from formulations ofrecycled plastics.
Park & Recreation: The largest single market segment has been the commercial park and recreation industry, which has consumed 50Vo to 70Vo of the product sold. The maintenance issues associated with wood materials, risks to children from splinters from treated lumber, the cost of redwood or alternate materials, and the ability to creatively design "effective" products and quickly deliver them to the marketplace result in a large and responsive market. The commercial park and recreation industry also understands the "true costs" of maintenance, and has readily embraced the durability and environmental issues of RPL materials.
Building Products: Plastic Lumber Trade Association has initiated an alliance with Battelle, a Columbus, Oh., think tank, for "application specific" product development of technologies for structural uses of RPL. In cooperation with the ASTM D20.20.01Committee on Recycled Plastic Lumber & Shapes, they selected three initial markets to develop product standards and optimized design guidelines:
(l) Residential Decking: Wood is not holding up well in service. The rapid cultivation of today's softwood lumber product, when cut into a plank board, exposes wide growth rings which deteriorate more quickly in outdoor weathering environments when compared to their original virgin grown timber counterparts or hardwood materials. No matter what the warranty from the pressured treated wood industry, decking is identified as a leading headache for homeowners and builders alike. So bad are the options to the builder/subcontractor, that they are picking materials for a deck on a $400,000 home or the porch of a mobile home from the same lumber pile. Today's customer doesn't want to perform annual maintenance and, even then, there may be significant board replacement-in just two to five years. Quite simply, the market wants a better mousetrap. The ever increasing number of new products on the market designed to preserve your deck substantiates that traditional materials are not doing the best job.
While the current use of RPL in residential decking has been 5Vo or less, adding commercial decking for boardwalk and walkway applications could elevate the current usage percentage another l0vo to 20Vo.
(2) MarineAVaterfront: The growing market for bulkhead, breakwall and pier applications has also been fostered by traditional materials not performing well in service, especially in saltwater environments where marine borers destroy wooden materials at an incredible rate. Some states have banned the use of pressure treated lumber in direct contact with water, creating new market opportunities for substitutes, especially "fiberglass reinforced" materials.
(3) Material Handling: RPL will find its place in areas where durable returnable pallets or special material handling applications can meet the customer's needs. The technology evolution for innovative weld joints will reduce costs and further enhance penetration into this marketplace.
Aside from the targeted markets of the Battelle project, there are significant fractional markets in various industrial and agricultural applications which represent 207o to 30Vo of overall sales. Fencing is also an area where many new polymer based materials are taking over market share.
Who? The 27 PLTA member manufacturers are most highly concentrated in the Midwest. New operations are constantly springing up. The new business casualty rate is beginning to slow.
How Much? The overall RPL industry has been growing at a 3O7o to 4O7o annualized growth rate which, given stable raw material costs, should continue. Explosive growth could come to certain segments, such as residential decking and marine/waterfront, given their ability to work through the various technical, market, distribution, capital and profitable pricing issues.
Market (share)
Park & Recreation (50-70Vo)
Decking (lO-2OVo)
Marine/Waterfront (5 - I 5 7o )
Material lJandling (2 - 5 Vo)
IndustriaUA gricultural (2O -30Vo)
Fencing (l-57o)
Sales (S40 Million) ($60 Million) 20-28M 30-42M 4-8M 6-t2M 2-6M 3-9M .8-2M r.2-3M 8-l2M l2-t8M
By Richard Schmickle Director, Residential Programs Portland Cement Association Skokie, Il.
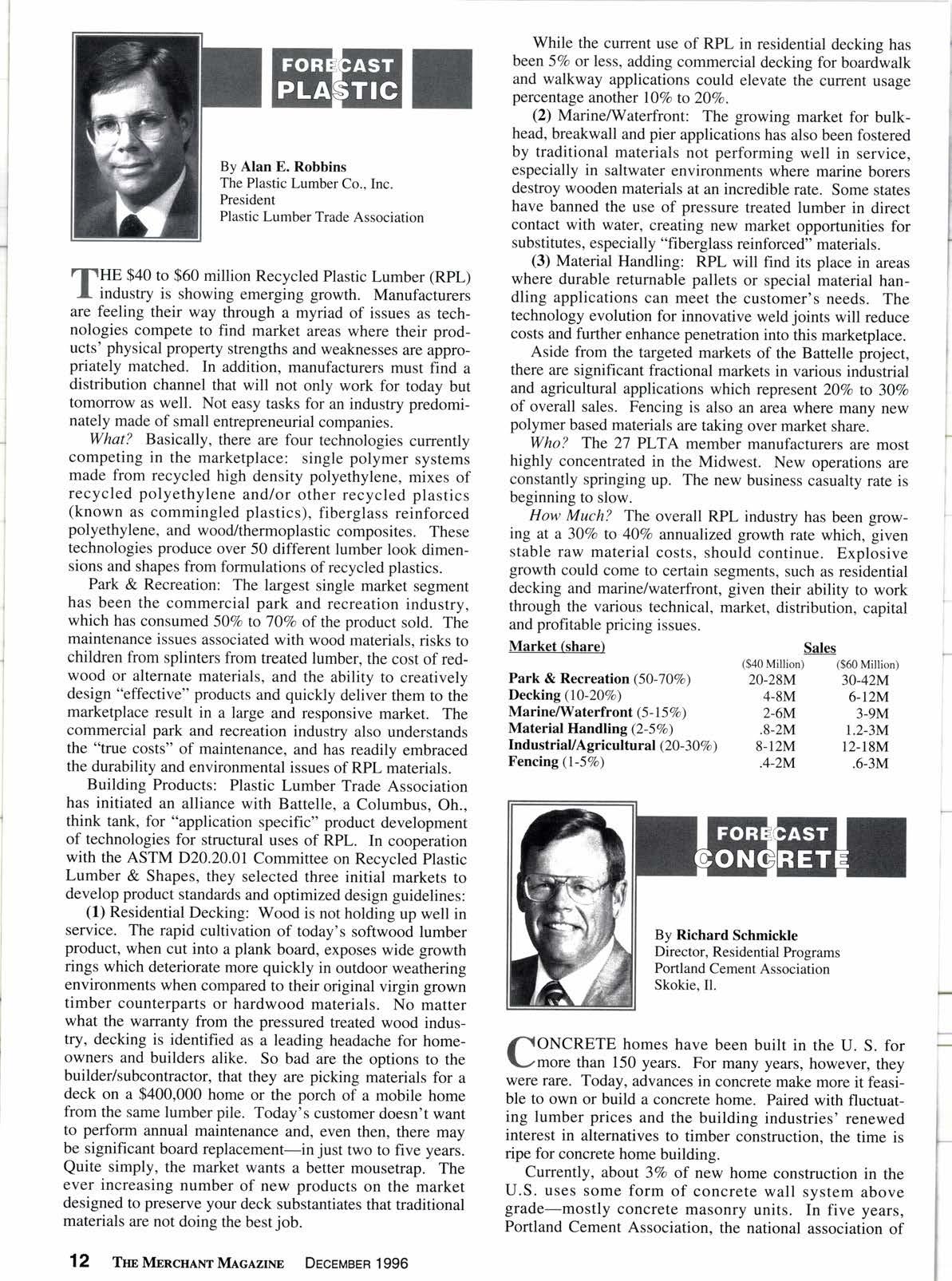
flONCRETE homes have been built in the U. S. for \-rmore than 150 years. For many years, however, they were rare. Today, advances in concrete make more it feasible to own or build a concrete home. Paired with fluctuating lumber prices and the building industries' renewed interest in alternatives to timber construction, the time is ripe for concrete home building.
Currently, about 37o of new home construction in the U.S. uses some form of concrete wall system above grade-mostly concrete masonry units. In five years, Portland Cement Association, the national association of cement producers, predicts that l5%o of new homes will use one of the many concrete wall systems available today.
In the past, home builders adopted certain "evolutionary" methods and products with obvious benefits' Things like drywall, rvc pipe and novrx wiring are now standard. But builders tend to be cautious about adopting new products and methods that may have benefits, but may disrupt their accustomed way of building. This, coupled with a complex network of local and regional building codes, drags the rate of adoption of innovations.
The "lumber crisis" that began in the late 1980s and has carried on till now has been a catalyst for change' At first, the price of dimensional lumber skyrocketed ovemight to levels 507o to l00Eo above previous levels, even as the quality of lumber severely deteriorated. Although prices liave come down, they still fluctuate, making it hard to secure lumber contracts more than 30 days out'
Newer concrete technologies, such as insulating stay-inplace forms and lightweight autoclaved cellular block, overcome many barriers to building concrete homes. These products make concrete-for the fust time---+ost competiiive with 2x6 wood frame construction. A home built with insulating concrete forms typically costs only 3Vo to 5Vo more to frame than a 2x6 wood frame home.
Two years worth of hurricanes, earthquakes and fires added momentum to consumers' demands for higher quality homes. The perception that "they don't build 'em like they used to," plus demands for energy efficient housing are favorable to concrete building systems. In places like Florida and California, consumer demand for fire and hurricane resistance in new home construction is strong. Builders now see stricter building codes in many places, such as in Dade County, Fl.
To help the market for concrete homes grow, the PCA conducts research and marketing activities, such as working with Construction Technologies Laboratories, Skokie, Il., to perform lab testing and analytical studies that address issues of structural performance for insulating concrete form systems. In particular, they analyze issues of wall thickness and rebar requirements in order to reduce overengineering in the field. They have also tested thermal qualities of the systems.
A three-year program using builders around the U.S. will gather field data on constructing homes using insulating concrete forming systems (ICFs). The National Association of Home Builders Research Center will study construction methods and finished house performance characteristics and building code considerations for ICFs.
Sponsored jointly by the Portland Cement Association and the U.S. Dept. of Housing & Urban Development's Office of Policy Development and Research, the program will use four builders in each year of the study. The frst year will include Dominion Building Groups, Virginia Beach, Va.; John Weaver Custom Homes, Austin, Tx.; Lite-Form Construction Division, Sioux City, Ia., and Womak & Associates, Chestertown, Md.
ICFs use foam blocks or foam panels that are erected, filled with concrete, and left permanently in place. The interior and exterior can be finished with familiar material to provide a readily marketable home.
A new concrete information clearinghouse will give builders a chance to call toll-free and learn more about insulating concrete forming systems.
These programs are now in place. Coupled with builders' renewed interest in alternative building systems, the use of concrete should accelerate in the next few years.
"A new agreement on Canadian softwood lumber means U.S. builders should seriously explore alternative materials, including steel studs and insulating concrete forms. Everyone stopped worrying about finding lumber alternatives after prices came down. But the mills are very worried about the tariff and it's creating some price movement in the market."
- David Seiders, National Association of Home Builders
"(The complex assembly of steel studs and trusses makes steel framing) much too costly to be a viable alternative for high-volume residential construction. It took three trucks to carry the steel trusses for our demonstration house; we could have transported the wood trusses in one truck. And it's a simple fact that all those screws take longer to set than driving nails."
- Craig Steele, Schuck Component Systems, Phoenix, Az'
"There is little doubt that steel roofing is making inroads in the residential marketplace, with tremendous growth potential. Roofing contractors that step up to the plate first are going to reap the benefits of this fast-growing market."
- Richard Haws, American lron & Steel Institute
"Builders seeking to save a few dollars by switching from wood to steel framing could have their workers reclassified and their (workers' compensation) premiums soar into orbit. The increase would more than wipe out any saving from building with steel."
- Mid America Lumbermens Association newsletter
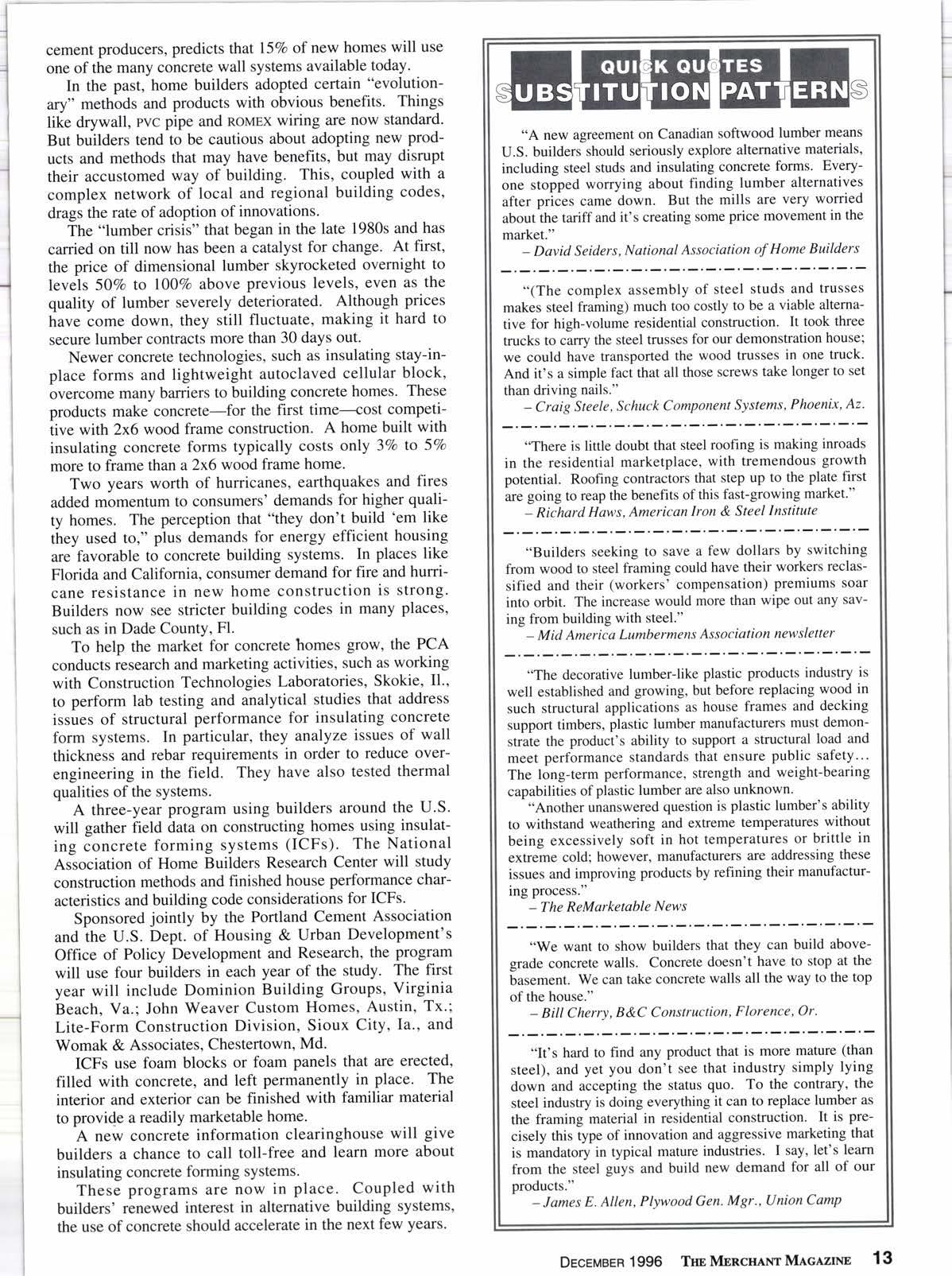
"The decorative lumber-like plastic products industry is well established and growing, but before replacing wood in such structural applications as house frames and decking support timbers, plastic lumber manufacturers must demonstrate the product's ability to support a structural load and meet performance standards that ensure public safety... The long-term performance, strength and weight-bearing capabilities of plastic lumber are also unknown.
"Another unanswered question is plastic lumber's ability to withstand weathering and extreme temperatures without being excessively soft in hot temperatures or brittle in extreme cold; however, manufacturers are addressing these issues and improving products by refining their manufacturing process."
- The ReMarketable News
"We want to show builders that they can build abovegrade concrete walls. Concrete doesn't have to stop at the basement. We can take concrete walls all the way to the top of the house."
- Bill Cherry, B&C Construction, Florence, Or.
"It's hard to find any product that is more mature (than steel), and yet you don't see that industry simply lying down and accepting the status quo. To the contrary, the steel industry is doing everything it can to replace lumber as the framing material in residential construction. It is precisely this type of innovation and aggressive marketing that is mandatory in typical mature industries. I say, let's learn from the steel guys and build new demand for all of our products."