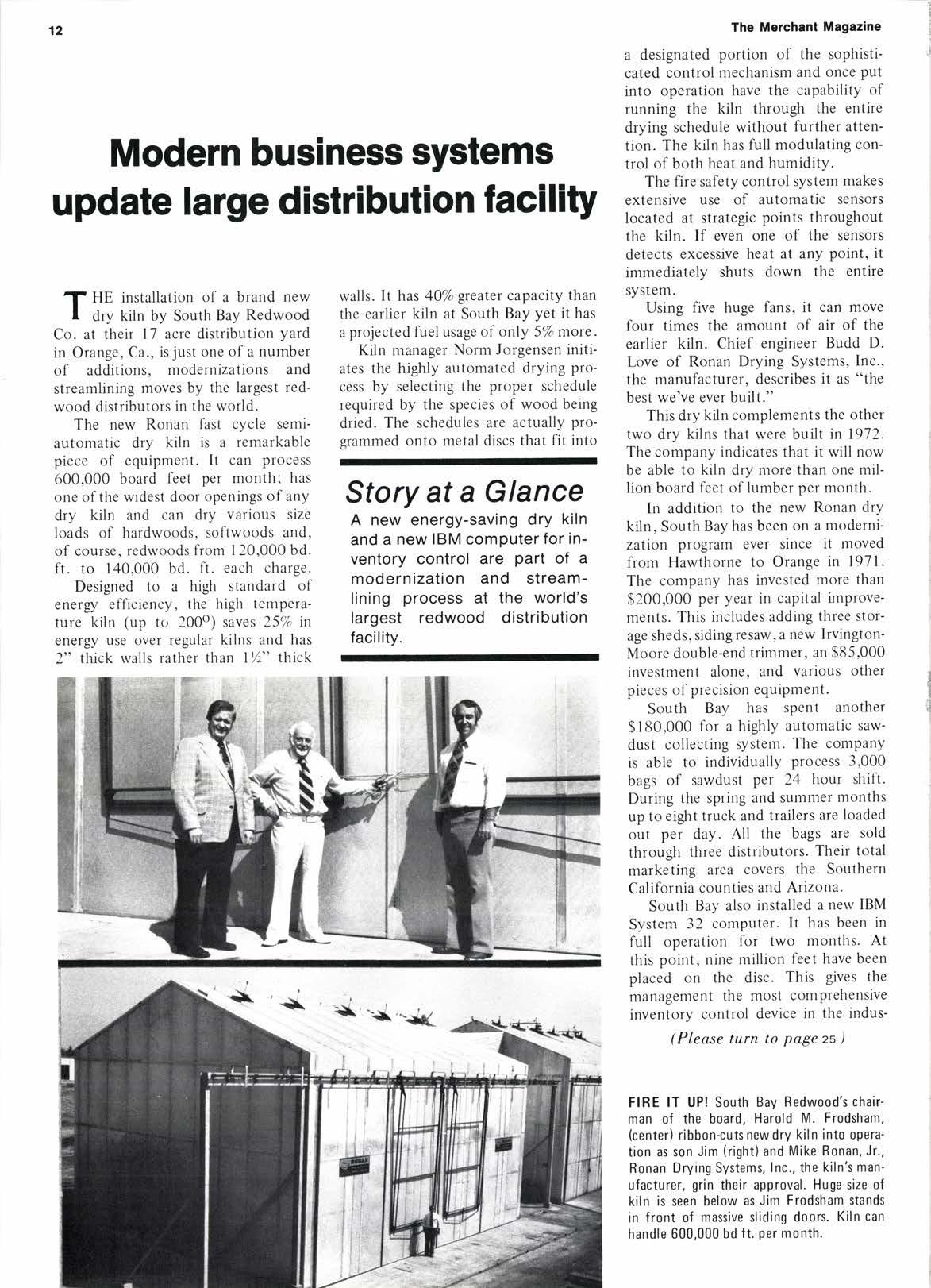
2 minute read
Modern business systems update large distribution facility
T HE installation of a hrand new I dry kiln by South Bay Redwood Co. at their 17 acre distribution yard in Orange, Ca., is just one of a number of additions, modernizations and streamlining moves by the largest redwood distributors in the world.
The new Ronan fast cycle semiautomatic dry kiln is a remarkable piece of equipment. It can process 600,000 board feet per monthl has one ofthe widest door openings ofany dry kiln and can dry various size loads of hardwoods, softwoods and, of course, redwoods from 120,000 bd. ft. to 140,000 bd. ft. each charge.
Designed to a high standard of enerS/ efficiency, the high temperature kiln (up tr.r 2000) saves 25% in energy use over regular kilns and has 2" thick walls rather than I %" thick walls. It has 40% greater capacity than the earlier kiln at South Bay yet it has a projected fuel usage of only 5% more.
Kiln manager Norm Jorgensen initi ates the highly automated drying process by selecting the proper schedule required by the species of wood being dried. The schedules are actually prosrammed onto metal discs that fit into
Story at a Glance
A new energy-saving dry kiln and a new IBM computer for inventory control are part of a modernization and streamlining process at the world's largest redwood distribution facility.
The l$erchanl Magazlne a designated portion of the sophisti cated control mechanism and once put into operation have the capability of running the kiln through the entire drying schedule without further attention. The kiln has full modulating control of both heat and humidity.
The fire safety control system makes extensive use of automatic sensors located at strategic points throughout the kiln. If even one of the sensors detects excessive heat at any point, it immediately shuts down the entire system.
Using five huge fans, it can move four times the amount of air of the earlier kiln. Chief engineer Budd D. Love of Ronan Drying Systems, Inc., the manufacturer, describes it as "the best we've ever built."
This dry kiln complements the other two dry kilns that were built in 1972. The company indicates that it will now be able to kiln dry more than one million board feet of lumber per month.
In addition to the new Ronan dry kiln, South Bay has been on a modernization program ever since it moved from Hawthorne to Orange in 1971. The company has invested more than $200,000 per year in capital improvements. This includes adding three storage sheds, siding resaw, a new IrvingtonMoore double-end trimmer, an $85,000 investment alone, and various other pieces of precision equipment.
South Bay has spent another $180,000 for a highly automatic sawdust collecting system. The company is able to individually process 3,000 bags of sawdust per 24 hour shift. During the spring and summer months up to eight truck and trailers are loaded out per day. All the bags are sold through three distributors. Their total marketing area covers the Southern California counties and Arizona.
South Bay also installed a new IBM System 32 computer. It has been in full operation for two months. At this point, nine million feet have been placed on the disc. This gives the management the most comprehensive inventory control device in the indus(PLease turn to page zs )
