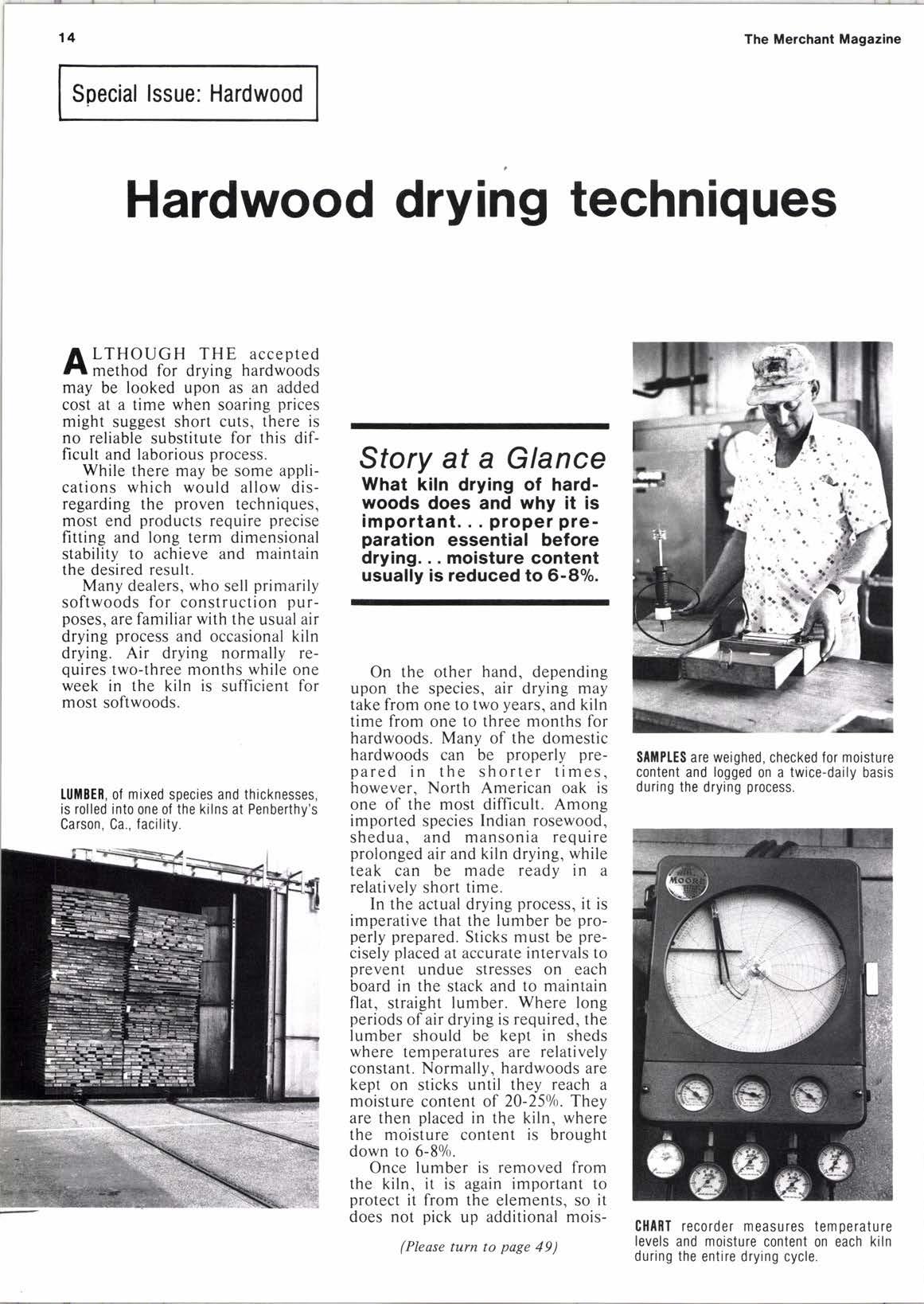
1 minute read
Hardwood drying techniques
A LTHOUGH THE accepted
Fl method for drvins, hardwoods may be looked upbn -as an added cost ata time when soaring prices might suggest short cuts, there is no reliable substitute for this difficult and laborious process.
While there may be some applications which would allow disregarding the proven techniques, most end products require precise fitting and long term dimensional stability to achieve and maintain the desired result.
Many dealers, who sell primarily softwoods for construction purposes, are familiar with the usual air drying process and occasional kiln drying. Air drying normally requires two-three months while one week in the kiln is sufficient for most softwoods.
Sfory at a Glance
is reduced to 6-8o/o.
On the other hand, depending upon the species, air drying may take from one to two years, and kiln time from one to three months for hardwoods. Many of the domestic hardwoods can be properly pre- pared in the shorter times, however, North American oak is one of the most difficult. Among imported species Indian rosewood, shedua. and mansonia require prolonged air and kiln drying, while teak can be made ready in a relatively short time.
In the actual drying process, it is imperative that the lumber be properly prepared. Sticks must be precisely placed at accurate intervals to prevent undue stresses on each board in the stack and to maintain flat, straight lumber. Where long periods of air drying is required, the lumber should be kept in sheds where temperatures are relatively constant. Normally, hardwoods are kept on sticks until they reach a moisture content of 20-250/0. They are then placed in the kiln, where the moisture content is brought down to 6-80/0.
Once lumber is removed from the kiln, it is again important to protect it from the elements, so it does not pick up additional mois-
(Please turn to page 49)