
2 minute read
Sandwich Panels Ready To Take Bite Out of Structural Market
Use of structural insulated panels is spreading fast with the increasing awareness of these energy saving building components. Some even forecast they will eliminate framing crews.
Also called foam core, stress skin or sandwich panels, structural insulated panels have an expanded polystyrene core pressure bonded between skins of plywood or oriented strand board.
They provide incredible strength, cost saving installation and, best of all, excellent insulation, reducing heating and cooling costs. The foam core acts like an ice chest, virtually eliminating air and moisture infiltration. Panels range from 4' x 8' up to 8' x 28'.
While sandwich panels were first introduced in the 1920s, they weren't used in quantity until about World War II, when they were especially useful in the aircraft industry. Mobile homes became a primary user and, by the 1980s, they were being used for walls, floors, roofs and ceilings in residential and commercial buildings.
While the push is on to get retailers to stock 4 x 8's, panels are currently sold direct from the distributors.
The Merchant Magazine
Manufacturers admit public acceptance will be gradual. "The old ways die hard," explains Stan Dimmick, president of Korwall Industries. "The building industry has used 2 x 4's and 2 x 6's for many years. The building officials also are very wary of anything new or different. Trade unions are very skeptical of anything they don't control. The sandwich type construction does away with a framing crew altogether."
Company Promotes Wellness
In an effort to promote good health awareness and physical well being, Western Lumber Co., National City, Ca., recently held a half day health and wellness fair for employees and members of the community.
Service providers presented information relating to nutrition, physical fitness and medical health with blood pressure and cholesterol testing available. Displays included lectures, promotional material, prizes and give-aways.
(See editorial, p. 6 for some comments on wellness fairs.)
Rrfuod lur urlvrbd nriln| ptwcth that endow it with adunbges oor other wood specles. Now we haw improwd on the selectbn, soasoning, manufacturing and protectiw packaging of this spcies to deliwr Prcmhn l$ptty-the elil6 among tight knot redwood sillings.
>Eadr @ d Pnmhrm l(nfi is inrlMdually machins monitorcd b a$suro a moisturc mnlenl of €% or bss.
well as relieving drying strcses contribute to checking and lo knots.
>Tlgfrbr sbndrds of selection and gnding have also eliminated all cutouts formerly allowed.
>lnpmd pnbciln ond cap assures that all the values added at the mill are delhored to the pbsite. The end cap carries storago, application and finishing instructlons to enable those values to be properly utilized.
A handromoly rrw-toxturod nngo of available patterns includes Thick Butt Rabbot€d Bevel, V-Joint Tongue and Gpove, 1" Channel Shlplap, V-Shlplap, and trlm. Vlrtually all pattems haw undergone perfornance enhancflients including among others, increasing to %" the lap of the rabbet on the Thick Butt Bwel siding pattern.
ftopody llnlshd, Premlum Knot$ will provide attractive, affwdabb, longlasting perfonnancs. So rHexdthtln bostPromftrm Knony Sil kno[ rodxmd rldlry. Tlp obrhn duh. lltilnlly.
For information on avallabllfi and the name of your nearest source ol supply call:
Toll tno Pnmtum l(ndty Hofi Unr 1-800-63 7 -7 477
FAx707-822-7A89
The Redwood People
Simpson Timber Company Redwood Division P.O. Box 1169
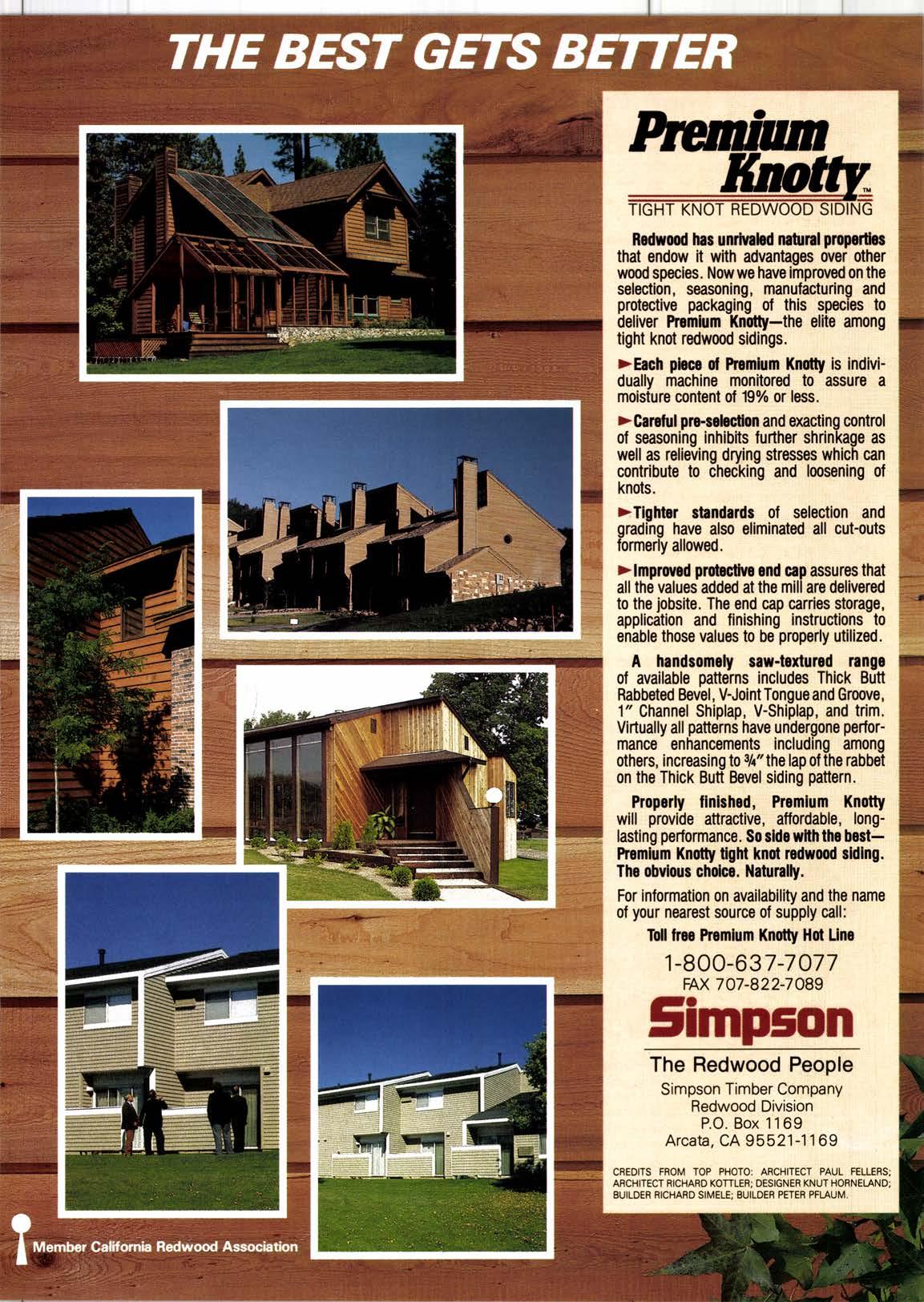
Arcata, CA 95521-1169
CREDITS FROM TOP PIIOTO: ABCHITECT PAUL FELIERS; ABCHITECT FICHAFD KOTTLER; DESIGNER KNUT HOFNELAND; EUILDER RICHARD SIMELE: BUILD€R PETER PFLAUM.