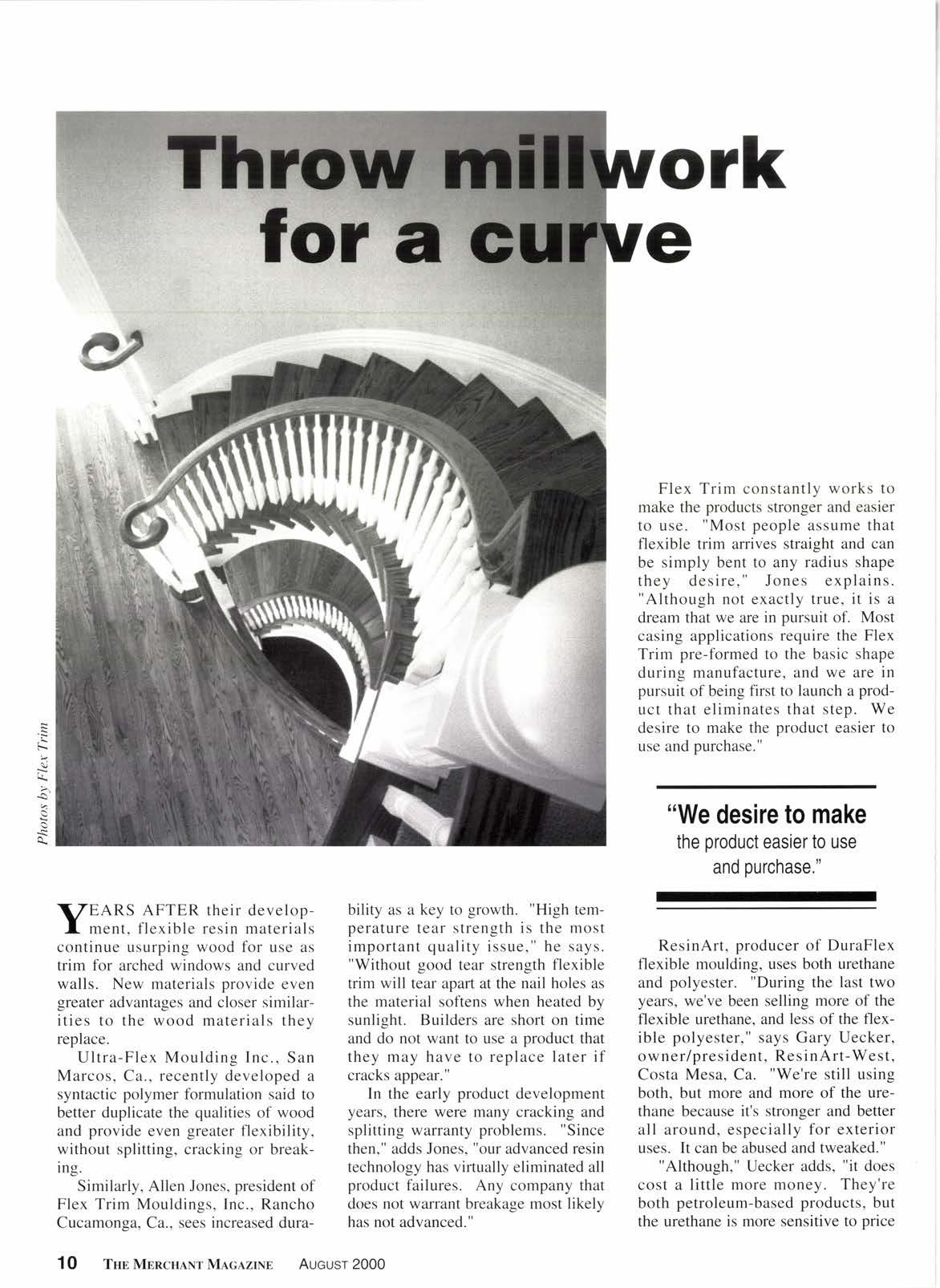
2 minute read
ork
bility as a key to growth. "High temperature tear strength is the most important quality issue," he says. "Without good tear strength flexible trim will tear apart at the nail holes as the material softens when heated by sunlight. Builders are short on time and do not want to use a product that they may have to replace later if cracks appear."
In the early product development years, there were many cracking and splitting warranty problems. "Since then." adds Jones. "our advanced resin technology has virtually eliminated all product failures. Any company that does not warrant breakage most likely has not advanced."
Flex Trim constantly works to make the products stronger and easier to use. "Most people assume that flexible trim arrives straight and can be simply bent to any radius shape they desire," Jones explains. "Although not exactly true. it is a dream that we are in pursuit of. Most casing applications require the Flex Trim pre-formed to the basic shape during manufacture, and we are in pursuit of being first to launch a product that eliminates that step. We desire to make the product easier to use and purchase."
ResinArt, producer of DuraFlex flexible moulding, uses both urethane and polyester. "During the last two years, we've been selling more of the flexible urethane, and less of the flexible polyester," says Gary Uecker, owner/president, ResinArt-West, Costa Mesa, Ca. "We're still using both, but more and more of the urethane because it's stronger and better all around, especially for exterior uses. It can be abused and tweaked."
"Although," Uecker adds, "it does cost a little more money. They're both petroleum-based products, but the urethane is more sensitive to price increases in raw materials. The more economy-minded buyer who just wants a simple curve will stick with polyester. "
He points to the strong economy to help explain the growth in urethanes: "People are in a hurry to complete jobs, so they say, 'We don't even want to mess with it. We want something that's real durable. Let's get the better product."'
Flex Moulding Inc., Hackensack, N.J., has stayed with polyester to manufacture its Flex Moulding and SuperFlex. "There are urethanes and other newer casting materials out there, but we're sticking with the tried and true," says general manager Miguel Dominguez. "We prefer the performance of polyester resins. One of the reasons is their superior compatibility with finishes."
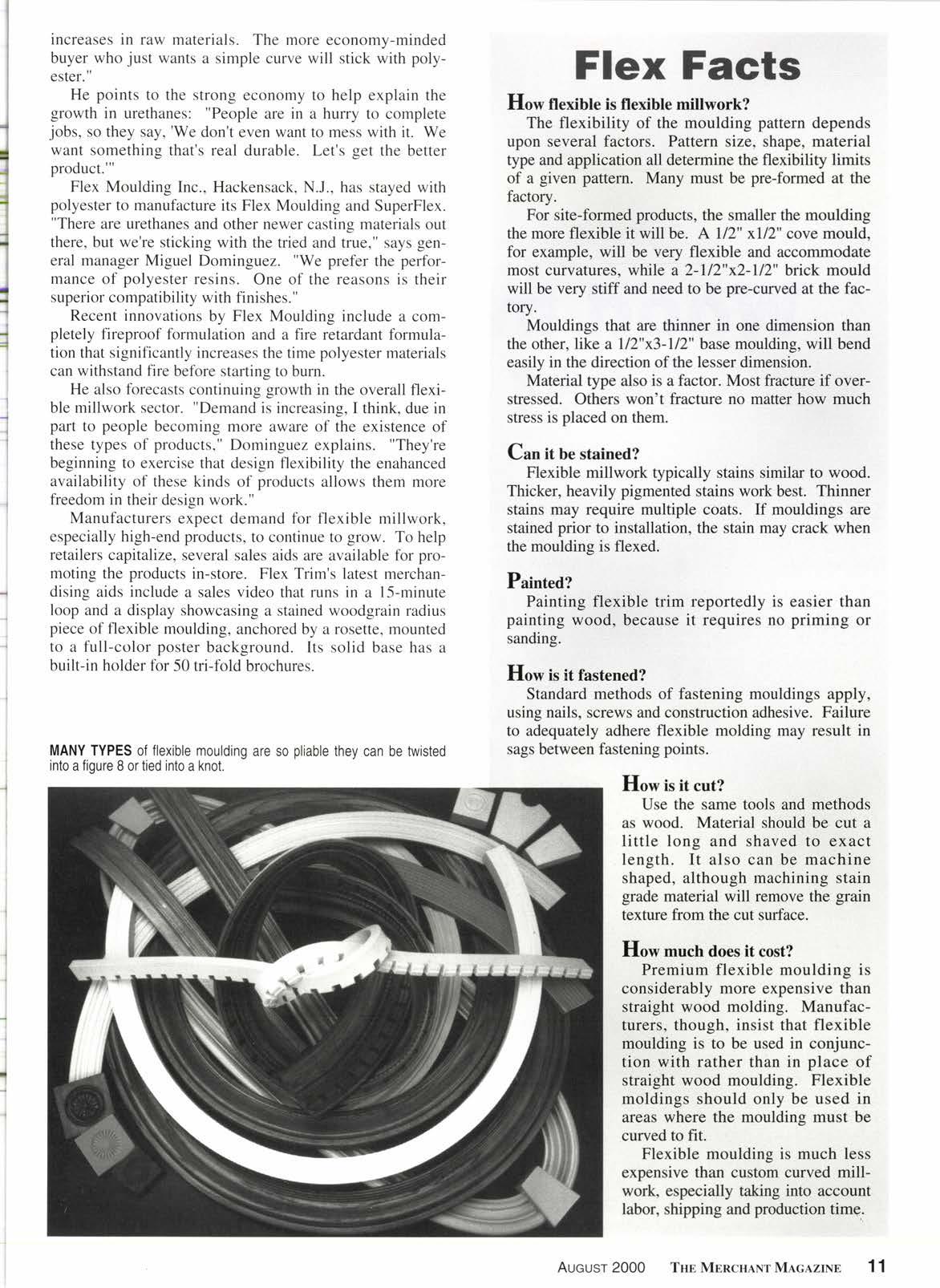
Recent innovations by Flex Moulding include a completely fireproof formulation and a fire retardant formulation that significantly increases the time polyester materials can withstand fire before starting to burn.
He also forecasts continuing growth in the overall flexible millwork sector. "Demand is increasing, I think, due in part to people becoming more aware of the existence of these types of products," Dominguez explains. "They're beginning to exercise that design flexibility the enahanced availability of these kinds of products allows them more freedom in their design work."
Manufacturers expect demand for flexible millwork, especially high-end products, to continue to grow. To help retailers capitalize, several sales aids are available for promoting the products in-store. Flex Trim's latest merchandising aids include a sales video that runs in a l5-minute loop and a display showcasing a stained woodgrain radius piece of flexible moulding, anchored by a rosette, mounted to a full-color poster background. Its solid base has a built-in holder for 50 tri-fold brochures.