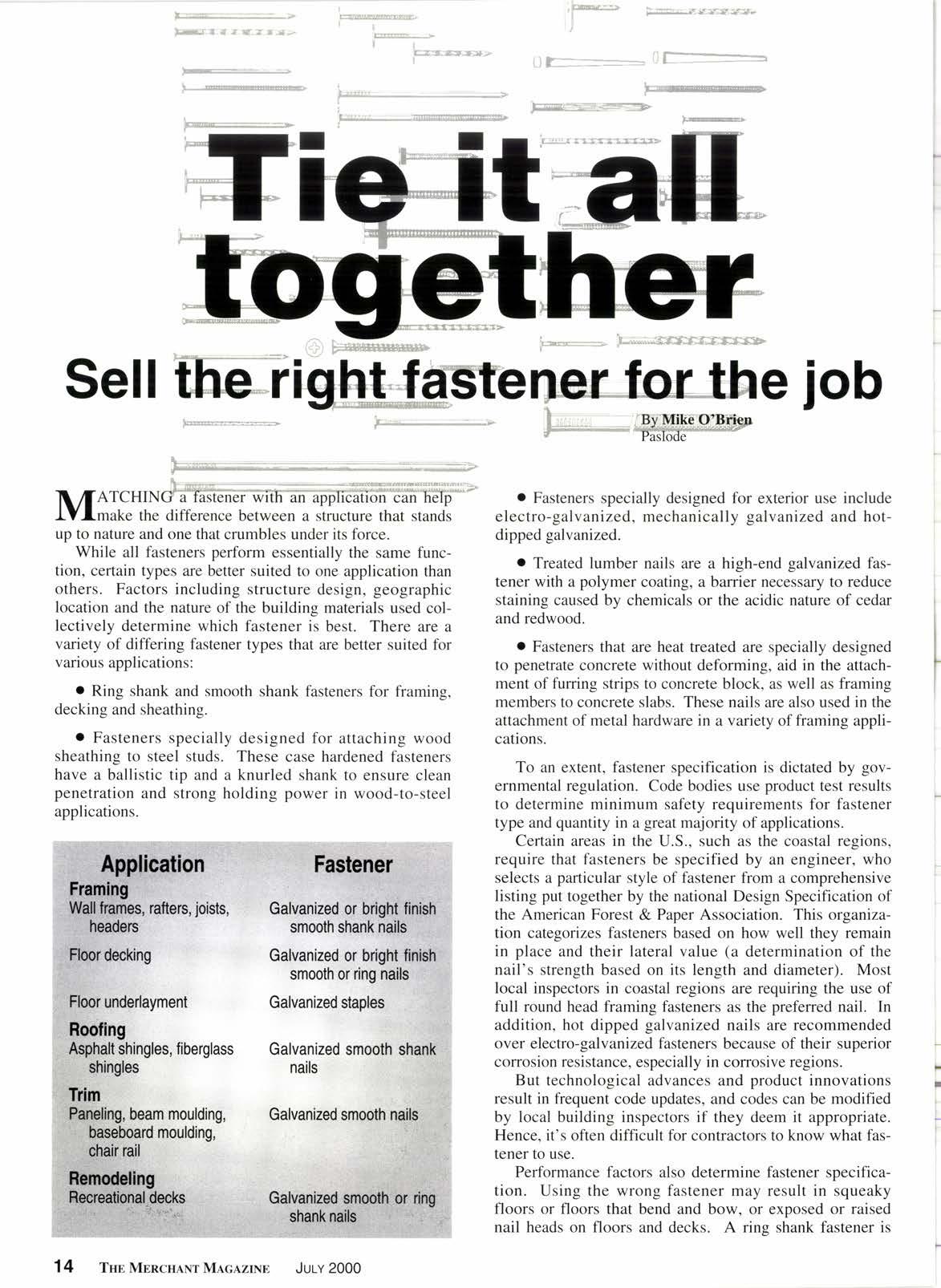
4 minute read
Sell tffififfi
While all fasteners perform essentially the same function, certain types are better suited to one application than others. Factors including structure design, geographic location and the nature of the building materials used collectively determine which fastener is best. There are a variety of differing fastener types that are better suited for various applications: o Fasteners specially designed for attaching wood sheathing to steel studs. These case hardened fasteners have a ballistic tip and a knurled shank to ensure clean penetration and strong holding power in wood-to-steel applications. o Fasteners specially designed for exterior use include electro-galvanized, mechanically galvanized and hotdipped galvanized. o Fasteners that are heat treated are specially designed to penetrate concrete without deforming, aid in the attachment of funing strips to concrete block, as well as framing members to concrete slabs. These nails are also used in the attachment of metal hardware in a variety of framing applications.
I Ring shank and smooth shank fasteners for framing, decking and sheathing.
Treated lumber nails are a high-end galvanized fastener with a polymer coating, a barrier necessary to reduce staining caused by chemicals or the acidic nature of cedar and redwood.
To an extent, fastener specification is dictated by governmental regulation. Code bodies use product test results to determine minimum safety requirements for fastener type and quantity in a great majority of applications.
Certain areas in the U.S., such as the coastal regions, require that fasteners be specified by an engineer, who selects a particular style of fastener from a comprehensive listing put together by the national Design Specification of the American Forest & Paper Association. This organization categorizes fasteners based on how well they remain in place and their lateral value (a determination of the nail's strength based on its length and diameter). Most local inspectors in coastal regions are requiring the use of full round head framing fasteners as the preferred nail. In addition, hot dipped galvanized nails are recommended over electro-galvanized fasteners because of their superior corrosion resistance, especially in corrosive regions.
But technological advances and product innovations result in frequent code updates, and codes can be modified by local building inspectors if they deem it appropriate. Hence, it's often difficult for contractors to know what fastener to use.
Performance factors also determine fastener specification. Using the wrong fastener may result in squeaky floors or floors that bend and bow, or exposed or raised nail heads on floors and decks. A rine shank fastener is recommended for floor decking, wall sheathing and roof decking because it will add to the overall performance. When nailing subfloors, squeaks can result when the subfloor is not held tight to thejoists.
Ring shank nails should also be used in areas subject to extreme weather conditions because they grip the wood better than smooth shank. The head of the fastener is also a determinant, especially in earthquake-prone areas, because it is a significant factor in preventing "pull though," where the wood is literally ripped from the fastener.
Electro-galvanized nails have a very bright, shiny and expensive looking appearance, however the nail will not last very long if used in cedar, redwood or CCA treated lumber. The acids and chemicals in these types of woods will eat away at the zinc, causing the nail to rust and leave black streaks in the wood around the nail. Electro-galvanized nails are better for use in woods that do not have acids such as spruce, pine and fir.
Mechanically galvanized nails offer better corrosion protection than electro-galvanized because the amount of zinc per square foot is greater. The nail has a dull, gray appearance and performs best in cedar, redwood and CCA treated lumber.
Hot-dipped galvanized nails are dipped into molten zinc. The corrosion protection can be as much as two times that of the mechanical galvanized fasteners. It all depends on how much zinc is applied to the nail. Some companies even advertise double-dipped nails.
Power fastening is the preferred method of a wide majority of professionals and remodelers because of the speed and consistency of fastener application. In deciding
To an extent, fastener
specification is dictated by government regulation.
and usually hold about 100 fasteners. Coil nailers are useful for roofing and decking applications because they hold 225-275 nails in a coil and require less reloading.
Cordless framing nailers are the ideal choice when the volume of nails in a job doesn't warrant the one to two hours involved in setting up and putting away the hoses and compressor necessary to operate pneumatic systems. Compact and lightweight, cordless framing nailers are well which to use, one should consider the nature of the task at hand, for cordless and pneumatic nails each are suited to specific applications.
Pneumatic nailers can perform at high speeds for long periods of time, and are ideal for heavy, high-volume framing and commercial jobs. They can fire up to 20,000 nails per day at a rate of up to six nails per second, compared to cordless nailers which are designed to fire roughly 8,000 nails per day at three nails per second.
Pneumatic strip and coil nailers provide power and speed for decking, sheathing and subassembly applications. Strip nailers are preferred for framing applications suited to nailing applications in attics, basements, tight spaces and overhead work on ladders. These nailers also are great for remodeling and light framing such as joist and rafter work, bridging, subassemblies, soffits, stairs and pick-up and service work.
Many 30" power fasteners use "D" head nails or nails that are clipped at the head for easier collation. Full-headed nails are required by code in extreme weather areas, including both U.S. coasts.
When fastening, it is important to consider not only the tool used, but the method of fastener collation. There are three main collating types. One type is paper tape collation. These fasteners are generally more expensive but are advantageous because they can be used in any weather condition from wet and cold to dry and hot. In addition, this method of collation generates virtually no on-site debris, decreasing safety concerns.

Another type of nail collation is plastic laminating or nails that are attached to a strip of plastic. This type is not preferable in cold weather and can also generate more debris that can cause slipping, cuts and damage to eyes.
Wire collated nails are yet another type of fastener collation. These nails are advantageous because nails can be put on a coil which offers more nails per application. However, they typically generate hot debris when the nails are fired, resulting in increased safety concems.