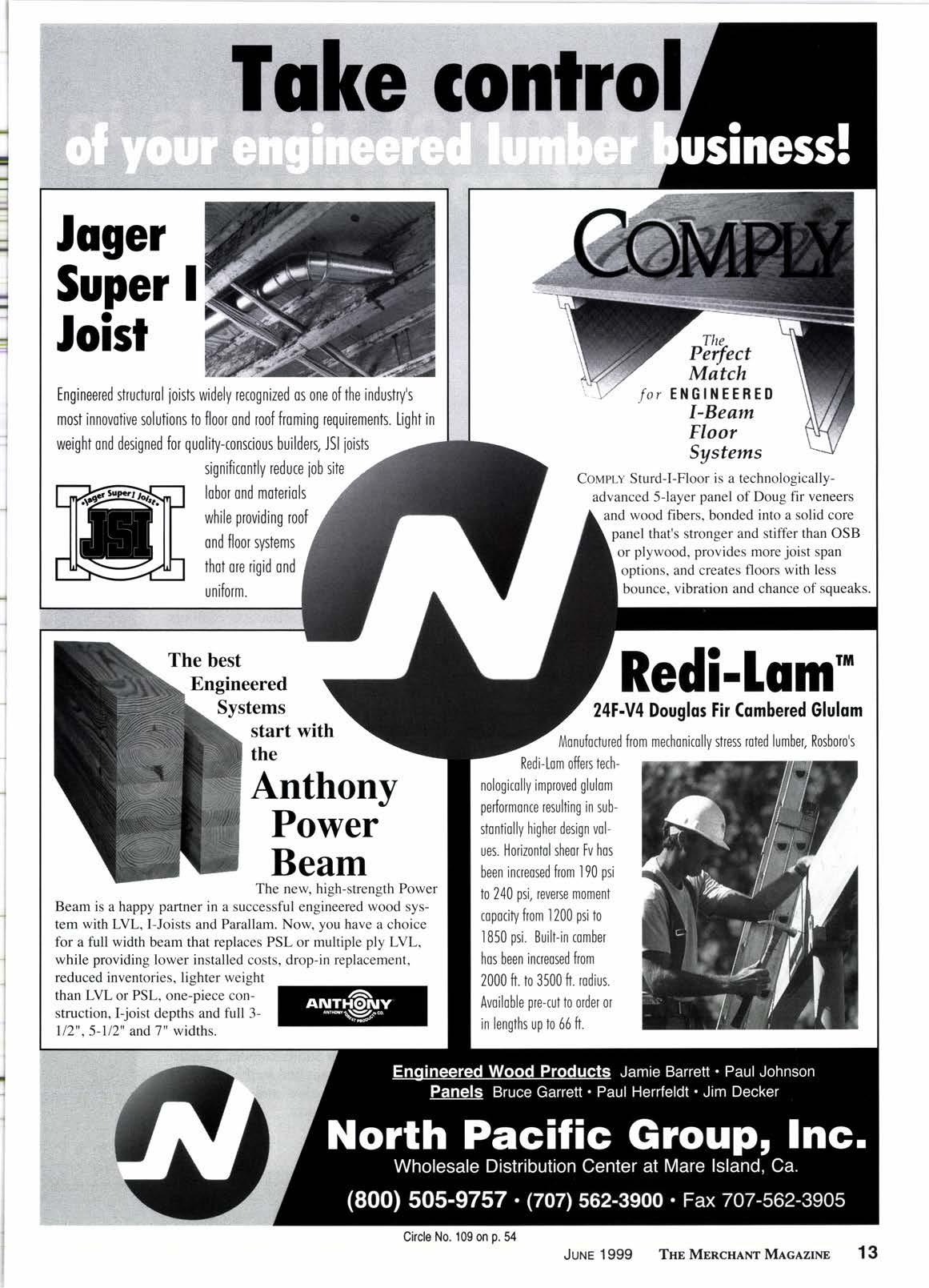
4 minute read
foger Super I foist
Engineered structurol ioi$s widely recognized os one of the industry's most innovolive solutions to floor ond roof froming requirements. Light in weight ond designed for quolity-conscious builden, JSI ioi$s significontly reduce iob site lobor ond moteriols while providing roof ond floor systems
The best Engineered Systems start with the Anthony Power Beam
The new, high-strength Power Beam is a happy partner in a successful engineered wood system with LVL, I-Joists and Parallam. Now, you have a choice for a full width beam that replaces PSL or multiple ply LVL, while providing lower installed costs, drop-in replacement, reduced inventories, lighter weight than LVL or PSL, one-piece construction, I-joist depths and full 3ll2',5-ll2' and 7" widths.
#lfect Match
I-Beam Floor Systems
Colrpr-v Sturd-I-Floor is a technologicallyadvanced 5Jayer panel of Doug fir veneers and wood fibers, bonded into a solid core panel that's stronger and stiffer than OSB or plywood, provides more joist span options, and creates floors with less bounce, vibration and chance of squeaks.
nologicolly improved glulom performonce resulting in sub$ontiolly higher design volues. Horizontol sheor Fv hos been increosed from 190 psi to 240 psi, reverse moment copocity from 1200 psi to 1850 psi. Built-in comber hos been increosed from 2000 fr. ro 3500 ft. rodius. Avoiloble pre-cut to order or in lengihs up to 66 ft.
D OOF coatings aren't just for emerl\gencies. Regularly applied, they can improve the roofing system's thermal performance r well as extend its lif'e.
"Most people misinterpret a coating as only a short-term fix for a leak," said Brian Anthony, PRI Asphalt Technologies Inc., Tampa, Fl.
As such, property owners don't periodically reapply coatings-essential for keeping structures dry and operating. "By overlooking coatings, overall cost goes up because you're replacing the roofing system sooner," said Lewis Ripps, Palmer Asphalt Co., Bayonne, N.J.
Added Don Portfolio, Tremco, Inc., Cleveland, Oh.: "They may not have a good feel for what a high-quality roof caused by ultraviolet rays and water. coating can do for them.
Manufacturers of cold-applied roof coatings have responded by making their products perform even better. "One trend with significant impact on the future of the roof coatings industry is the energy efficiency movement," said Roof Coatings Manufacturers Association president Richard Zegelbone, Tropical Asphalt Products, Hallandale, Fl. "Although customer demand for 'blackline'products such as resaturants, asphalt coatings, waterproofing coatings, asphalt quick-dry cements and aluminum coatings will continue into the next millennium, 'white' and highly reflective coatings may account for faster product growth."
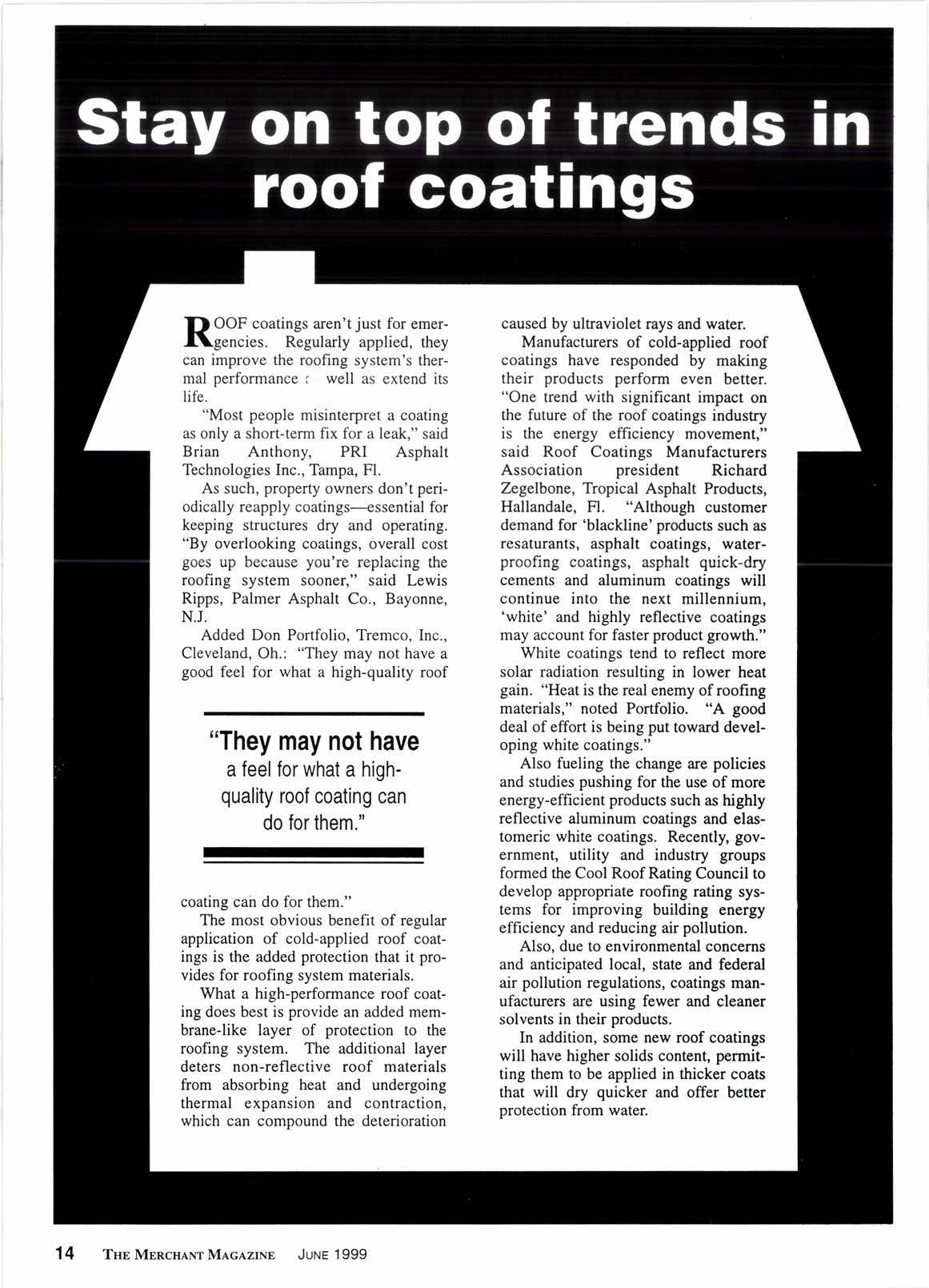
White coatings tend to reflect more solar radiation resulting in lower heat gain. "Heat is the real enemy of roofing materials," noted Portfolio. "A good deal of effort is being put toward developing white coatings."
The most obvious beneflt of regular application of cold-applied roof coatings is the added protection that it provides for roofing system materials.
What a high-performance roof coating does best is provide an added membrane-like layer of protection to the roofing system. The additional layer deters non-reflective roof materials from absorbing heat and undergoing thermal expansion and contraction, which can compound the deterioration
Also fueling the change are policies and studies pushing for the use of more energy-efficient products such as highly reflective aluminum coatings and elastomeric white coatings. Recently, government, utility and industry groups formed the Cool Roof Rating Council to develop appropriate roofing rating systems for improving building energy efficiency and reducing air pollution.
Also, due to environmental concerns and anticipated local, state and federal air pollution regulations, coatings manufacturers are using fewer and cleaner solvents in their products.
In addition, some new roof coatings will have higher solids content, permitting them to be applied in thicker coats that will dry quicker and offer better protection from water.
Itr/HEN selling siding, make sure Y Y your customers know that, while it is a /ow-maintenance product, it is not a no-maintenance product. Cedar, hardboard, plywood, brick, synthetic stucco, vinyl and fiber cement siding all require at least annual check-ups.
Gonstant moisture
can rot wood or fiberboard siding.
Suggest that the following are periodically inspected:
(l) Check the installation. The bottom lap of the siding should be no closer than 6 inches to the ground and no closer than I inch from surfaces where puddles may form, such as driveways or concrete patios.
(2) Check the nearby mulch, bushes and other landscape materials that may contribute moisture. Such materials should be at least a foot away from the siding.
(3) Check the air conditioner. Moisture must run away from the siding.
(4) Check the gutters and drains. Leaks are not to run down siding.
(5) Check sprinklers near the home. Make sure that spray does not hit the siding. Spray from below gets moisture up underneath siding. Chemicals and minerals in the water may rust, decay or discolor siding. Constant moisture can rot wood or fiberboard siding.
(6) Check the paint.
Immediately attend to chalking (by washing), cracking (by sanding, priming and repainting), and lack of paint (if primer is visible through fine cracks, the siding will soon need to be washed and repainted).
(7) Check the caulking.
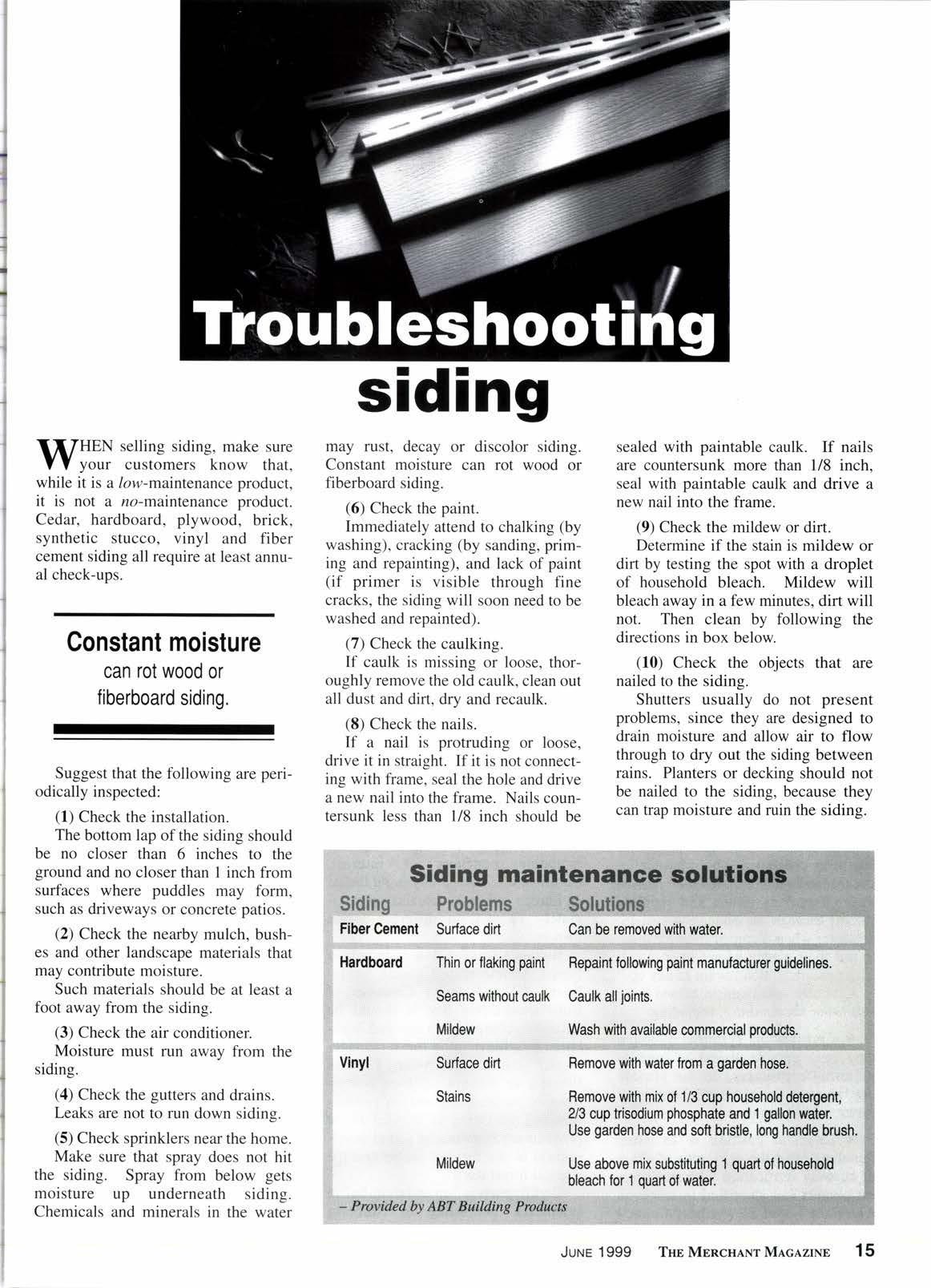
If caulk is missing or loose, thoroughly remove the old caulk, clean out all dust and dirt, dry and recaulk.
(8) Check the nails.
If a nail is protruding or loose, drive it in straight. If it is not connecting with frame, seal the hole and drive a new nail into the frame. Nails countersunk less than 1/8 inch should be sealed with paintable caulk. If nails are countersunk more than l/8 inch, seal with paintable caulk and drive a new nail into the frame.
(9) Check the mildew or dirt.
Determine if the stain is mildew or dirt by testing the spot with a droplet of household bleach. Mildew will bleach away in a few minutes, dirt will not. Then clean by following the directions in box below.
(10) Check the objects that are nailed to the siding. Shutters usually do not present problems, since they are designed to drain moisture and allow air to flow through to dry out the siding between rains. Planters or decking should not be nailed to the siding, because they can trap moisture and ruin the siding.