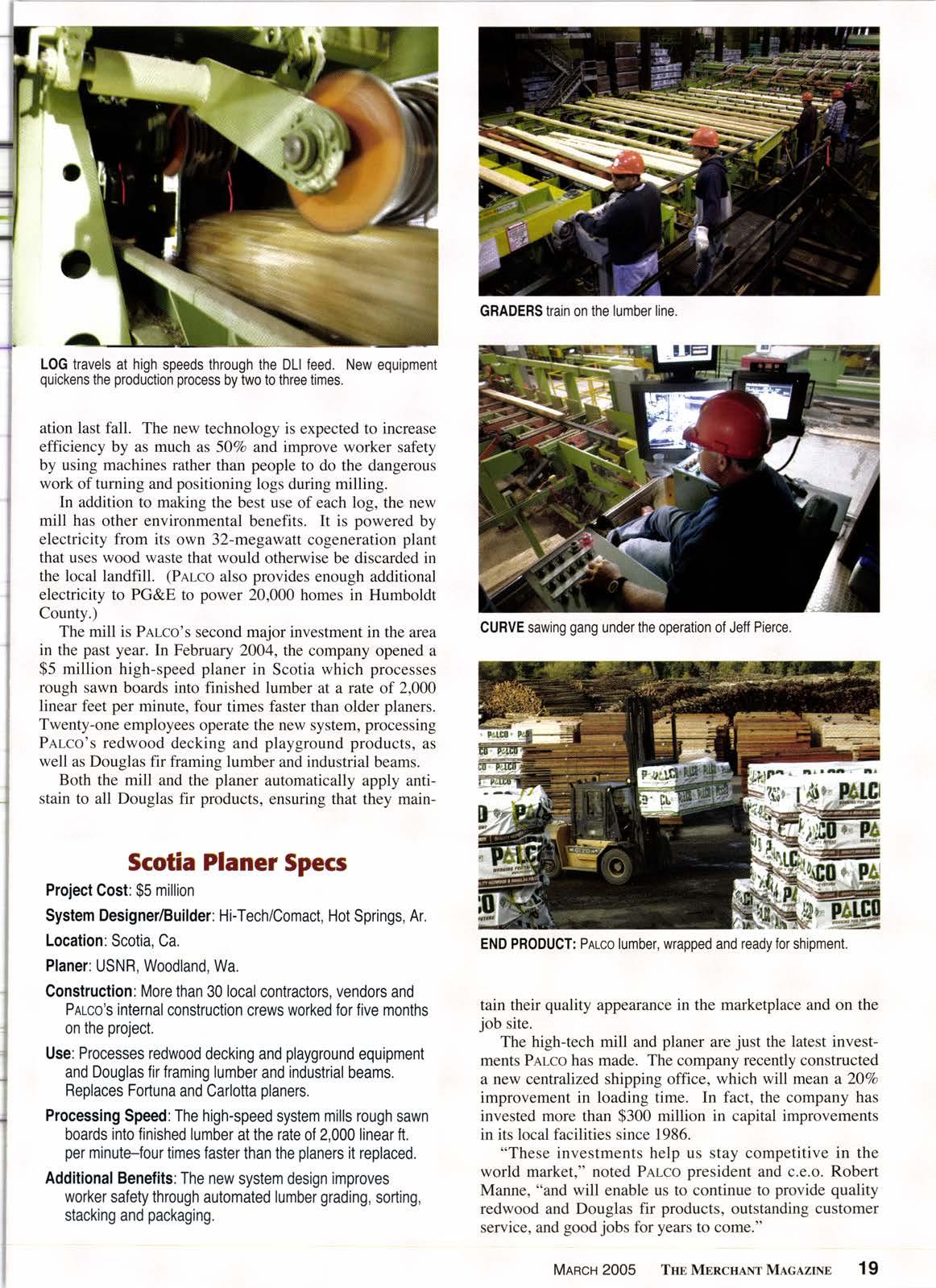
2 minute read
rolls out high-tech sawmill
pelco is on the move. The historic 140-year old I Norrhem California timber company is still headquartered in the picturesque community of Scotia, but Per-co's recent investment of $30 million in a new high-tech sawmill and state-of-the-art planer is designed to move the company into the ranks of the nation's premier wood products companies.
The new mill, located at PALCo's Scotia facility, is the first major sawmill built in California in a decade. Utilizing laser beams and computers, the high-tech mill processes logs two to three times faster than standard mills, increasing productivity, enhancing worker safety, and reducing waste.
The mill will ensure top quality redwood and Douglas fir products for PeLco's customers. In addition, its ability to mill smaller second-growth logs will help keep Pelco's competitive far into the future.
As each log enters the mill, multiple laser beams take readings every _ inch to map its shape and wood volume. That information is sent to a computer that factors in current market prices and customer preferences to determine the cuts and dimensions that will produce the most usable lumber or the best market return. The logs are then automatically positioned, milled, graded, and sorted.
The technology allows Pnlco to instantly respond to changes in market conditions and customer preference.
The mill can easily process 15 20-ft. logs per minute and has operated at or near capacity since it went into oper- ation last fall. The new technology is expected to increase efficiency by as much as 5OVo and improve worker safety by using machines rather than people to do the dangerous work of turning and positioning logs during milling.
In addition to making the best use of each log, the new mill has other environmental benefits. It is powered by electricity from its own 32-megawatt cogeneration plant that uses wood waste that would otherwise be discarded in the local landfill. (Perco also provides enough additional electricity to PG&E to power 20,000 homes in Humboldt County.)
The mill is Pnlco's second major investment in the area in the past year. In February 2004, the company opened a $5 million high-speed planer in Scotia which processes rough sawn boards into finished lumber at a rate of 2,000 linear feet per minute, four times faster than older planers. Twenty-one employees operate the new system, processing PALCo's redwood decking and playground products, as well as Douglas fir framing lumber and industrial beams. Both the mill and the planer automatically apply antistain to all Douglas fir products, ensuring that they main-
Scoffa Planer Spect
Project Cost: $5 million tain their quality appearance in the marketplace and on the job site.
System DesignerrBuilder: Hi-Tech/Comact, Hot Springs, Ar.
Location: Scotia, Ca.
Planer: USNR, Woodland, Wa.
Construction: More than 30 local contractors, vendors and PRLco's internal construction crews worked for five months on the project.
Use: Processes redwood decking and playground equipment and Douglas fir framing lumber and industrial beams. Replaces Fortuna and Carlotta planers.
Processing Speed:The high-speed system mills rough sawn boards into finished lumber at the rate of 2,000 linear ft. per minute-four times faster than the planers it replaced.
Additional Benefits: The new system design improves worker safety through automated lumber grading, sorting, stacking and packaging.
The high+ech mill and planer are just the latest investments PeLco has made. The company recently constructed a new centralized shipping office, which will mean a ZOVo improvement in loading time. In fact, the company has invested more than $300 million in capital improvements in its local facilities since 1986.
"These investments help us stay competitive in the world market," noted Pnlco president and c.e.o. Robert Manne, "and will enable us to continue to provide quality redwood and Douglas fir products, outstanding customer service, and good jobs for years to come.o'