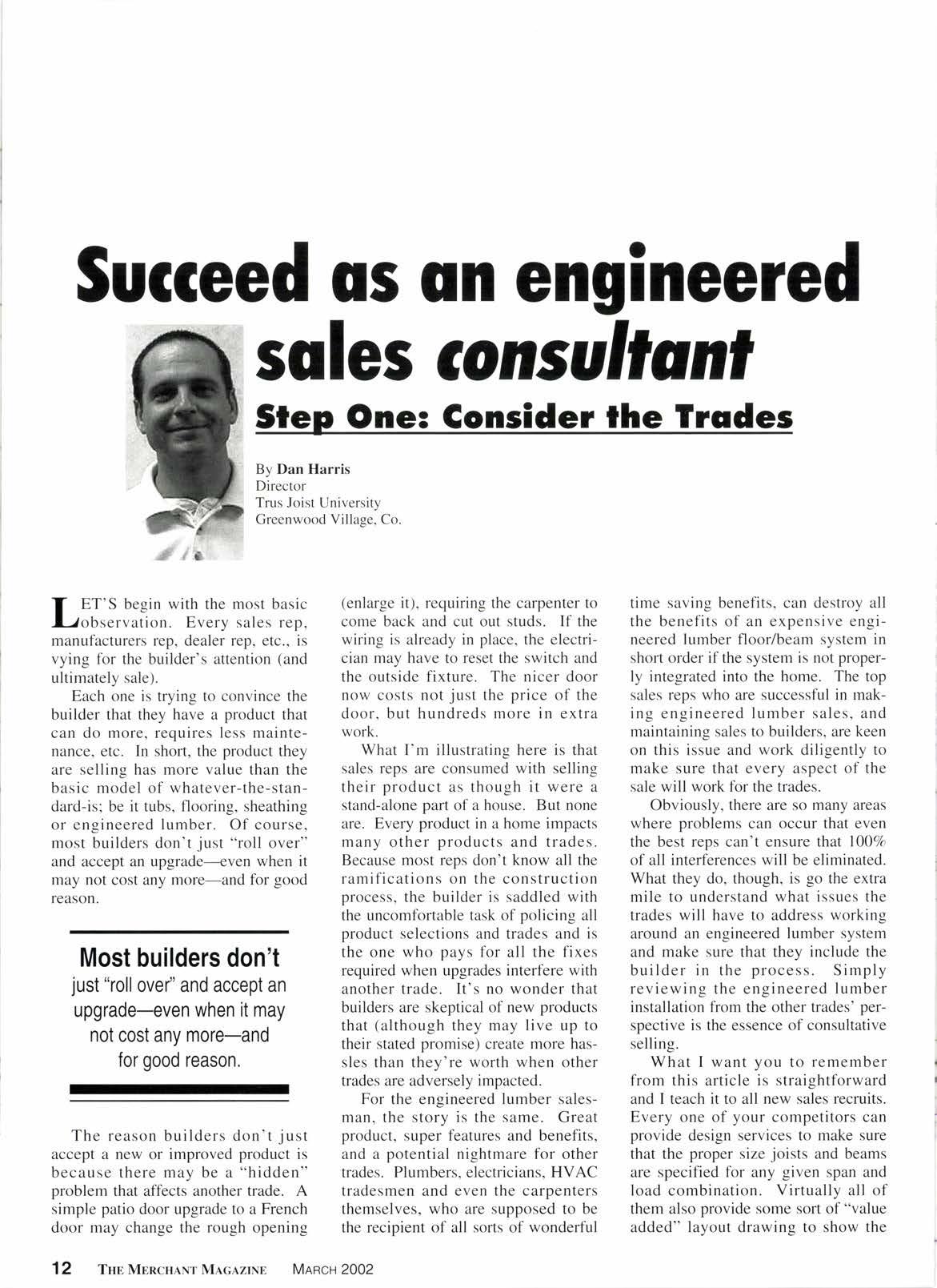
6 minute read
Succeed os qn engineered sqles Gonsullunl
Step One: Consider the lreides
By Dan Harris Director Trus Joist University Greenwood Village, Co.
f ET'S begin with the most basic I--lobservation. Every sales rep. manufacturers rep, dealer rep, etc., is vying for the builder's attention (and ultimately sale).
Each one is trying to convince the builder that they have a product that can do more, requires less maintenance, etc. In short, the product they are selling has more value than the basic model of whatever-the-standard-is; be it tubs, flooring, sheathing or engineered lumber. Of course, most builders don't just "roll over" and accept an upgrade-even when it may not cost any more-and for good reason.
(enlarge it), requiring the carpenter to come back and cut out studs. If the wiring is already in place, the electrician may have to reset the switch and the outside fixture. The nicer door now costs not just the price of the door, but hundreds more in extra work.
Most
builders don't just "roll ove/'and accept an upgrade-even when it may not cost any more-and for good reason,
The reason builders don't just accept a new or improved product is because there may be a "hidden" problem that affects another trade. A simple patio door upgrade to a French door may change the rough opening
What I'm illustrating here is that sales reps are consumed with selling their product as though it were a stand-alone part of a house. But none are. Every product in a home impacts many other products and trades. Because most reps don't know all the ramifications on the construction process, the builder is saddled with the uncomfortable task of policing all product selections and trades and is the one who pays for all the fixes required when upgrades interfere with another trade. It's no wonder that builders are skeptical of new products that (although they may live up to their stated promise) create more hassles than they're worth when other trades are adversely impacted.
For the engineered lumber salesman, the story is the same. Great product, super features and benefits, and a potential nightmare for other trades. Plumbers, electricians, HVAC tradesmen and even the carpenters themselves, who are supposed to be the recipient of all sorts of wonderful time saving benefits, can destroy all the benefits of an expensive engineered lumber floor/beam system in short order if the system is not properly integrated into the home. The top sales reps who are successful in rnaking engineered lumber sales, and maintaining sales to builders, are keen on this issue and work diligently to make sure that every aspect of the sale will work for the trades.
Obviously, there are so many areas where problems can occur that even the best reps can't ensure that 1007o of all interferences will be eliminated. What they do, though, is go the extra mile to understand what issues the trades will have to address working around an engineered lumber system and make sure that they include the builder in the process. Simply reviewing the engineered lumber installation from the other trades' perspective is the essence of consultative selling.
What I want you to remember from this article is straightforward and I teach it to all new sales recruits. Every one of your competitors can provide design services to make sure that the proper size joists and beams are specified for any given span and load combination. Virtually all of them also provide some sort of "value added" layout drawing to show the carpenter where to put each piece. YOUR job is to make sure it can work in the house-for the electrician, plumber and HVAC trades, and to be able to make a convincing argument to the builder that you've considered the specific needs of each home so that the builder will not have problems.
Let's look at a typical engineered lumber sales scenario so you can see what we're talking about. The specific issues we'll address are: stool flanges, tub drain and waste, canned light fixtures, flue "B" vent, and floor registers.
The engineered lumber salesmen returns a set of plans with the basic structure designed as such: I-joists at 16" o.c. with no interruptions to the spacing. Because of the length of the house, the lastjoist space is 12" (center to edge of wall). In the great room, the sales rep changes the spacing to 12" o.c. and uses a wide flange I-joist for a long span. Structurally this is a good design and this is traditionally considered the value-added approach. But it fails. Here's why: the carpenter gets to make an easy decision. Because he's handed an official layout drawing with the manufacturer's warranty, he doesn't need to adjust spacing for any floor penetrations. The joists will be cut when they interfere with the stool, tub drain and waste, and flue chase. And from the carpenter's perspective, well... too bad. His obligation is to follow the directions. i.e. exact centers. If he varies it, he becomes responsible for any interference. Some designers try to solve this problem by stamping drawings with a note 'Joists may be moved up to 3" to avoid plumbing drops," but this is just a feeble excuse to not get involved and learn how to properly design.
Here is the sequence of what happens once the rough framing is complete: The HVAC tradesman is dropped off at the house with a pickup truck of tin; enough to do the house and instructions that he has two days to get in and out. When he cuts a 10" slot for a 10" register under the great room windows, the wide flange joists are cut. (From the designer's perspective, the joists are just lines on a piece of paper, but to a tinner, the joists are 3-l/2" wide, so 12" centers minus 3-112" flanges means he has only 8-l/2" of width to put in a 10" register. He probably won't change the register because he has to add extra time, order extra material, and ultimately, the registers would look different than every other one in the house.
The 6" supply line to the heat register against the gable end wall will be crushed to fit into the remaining joist space resulting in poor airflow and a colder room. Again, the designer sees only that the maximum spacing hasn't been exceeded:12" is less than 16", but to the tinner, the space is a lot less than 10" because the space is actually 12" minus 8" (the thickness of the foundation wall). The insulator is totally confounded at this point, because he has no way to physically get insulation through the tiny 4" gap.
The space allocated for the B vent in the floor plan may have a joist in it. The tinner can't move the vent to be outside the chase. so out comes the Sawzall and within 60 seconds this joist is cut to make room for the flue.
The plumber is next in line. He has almost no flexibility in setting fixtures. The toilet has to be centered in its assigned space or 1 5" from a vanity or wall (otherwise the homeowner won't be able to reach for paper comfortably when it's most needed).
The same is true of the tub. There is a spot that is exactly 30"x60", and the water and waste lines will only be on one side. If the joists are not offset for these fixtures, they'll be notched until there's space to get the piping in.
Last up is the electrician. He lays out the canned lights nicely centered in the room, plumbs up and finds a joist smack dab in the way. He won't cut the joist out, he'll just modify the lights so they won't be perfectly centered in the room and let the builder know. Don't be surprised if you're the carpenter and get a call to cut the joist out and move it so the lights can be installed the way the architect intended.
Now that we can see how our engineered lumber layout is used and how other trades see their place, let's redo the plan as a sales rep/consultant. Put the joists at 16" o.c. starting from one side. The second-to-last space is 12" and the last joist space is again 16". Joists are offset to miss plumbing fixtures, the canned lights, and the B vent. and the offset dimensions are shown on the plan. The builder is consulted about the 12" o.c. spacing for joists in the great room. Should he keep the wide flange joist and use different size vents or narrower flange joists that are deeper to would allow the standard 10" register? Of course changing to a different depth joist means that the carpenter must modify the bearing, so the options to fix this are reviewed well in advance of the carpenter ever showing up on the site. What we've done with this second solution is try to predict with relative certainty the trades that will be impacted in order to save the builder a lot of nightmares. Nightmares that he's dealt with a hundred times before... until now, when you take the initiative to learn the trades and become his engineered lumber "framing consultant."
(Series to tnntinue in.future issues)
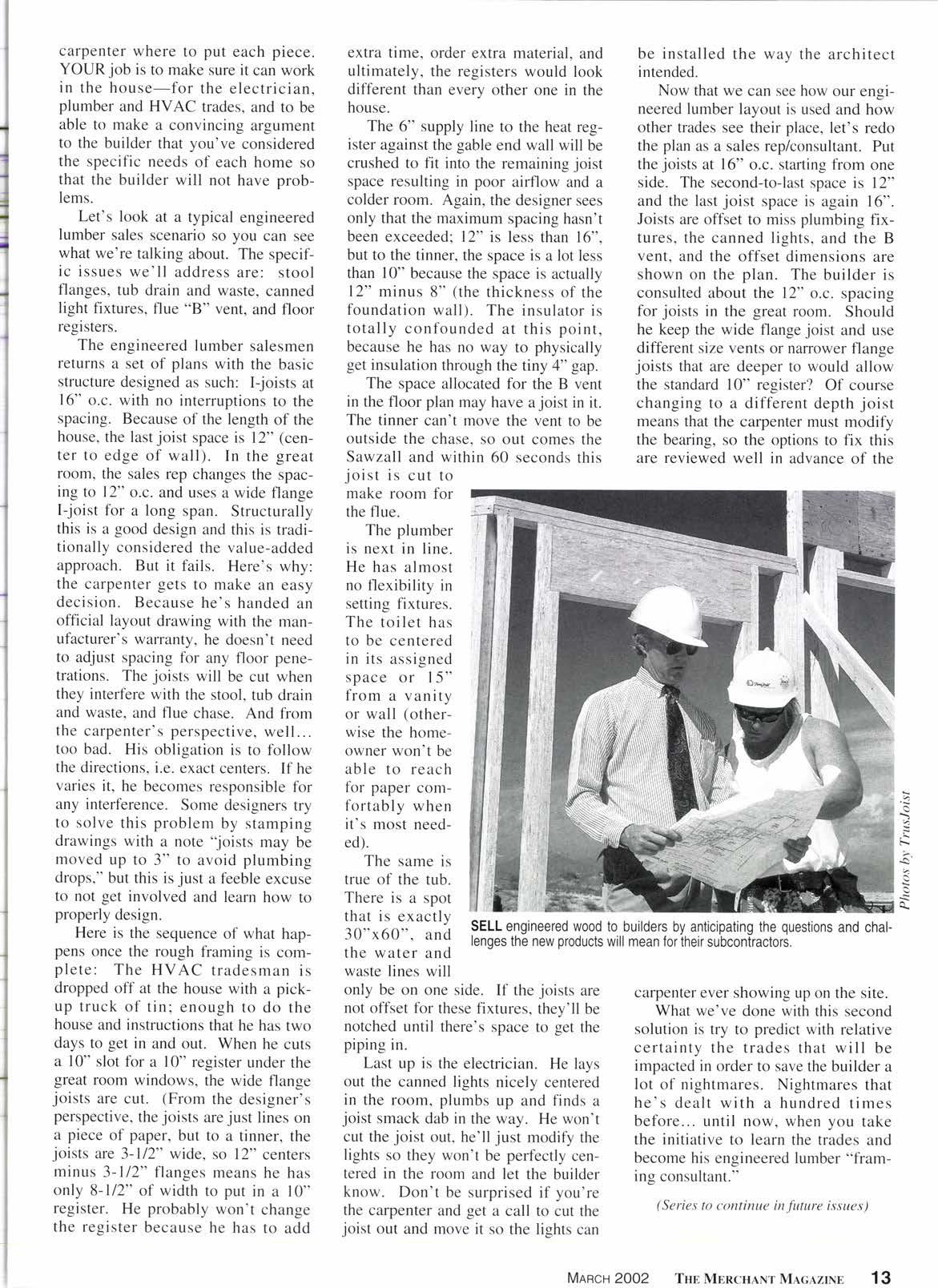