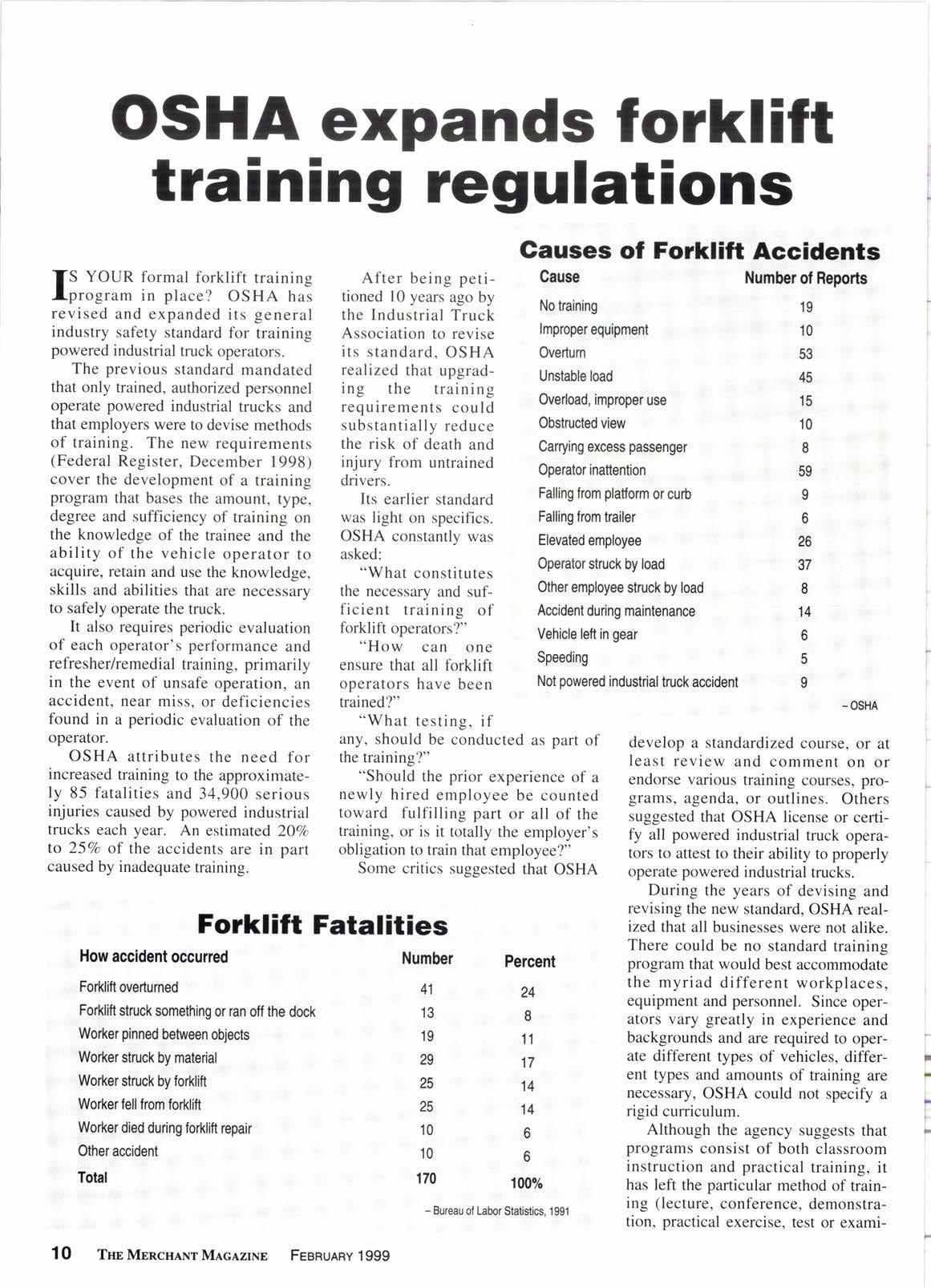
5 minute read
OSHA expands forklift training regulations
Gauses of Forklift Accidents
fS YOUR formal forklift training Iprogram in place? OSHA has revised and expanded its general industry safety standard for training powered industrial truck operators.
The previous standard mandated that only trained, authorized personnel operate powered industrial trucks and that employers were to devise methods of training. The new requirements (Federal Register, December 1998) cover the development of a training program that bases the amount, type, degree and sufficiency of training on the knowledge of the trainee and the ability of the vehicle operator to acquire, retain and use the knowledge, skills and abilities that are necessary to safely operate the truck.
It also requires periodic evaluation of each operator's performance and refresher/remedial training, primarily in the event of unsafe operation. an accident, near miss, or deficiencies found in a periodic evaluation of the operator.
OSHA attributes the need for increased training to the approximately 85 fatalities and 34,900 serious injuries caused by powered industrial trucks each year. An estimated 2O7o to 257o of the accidents are in part caused by inadequate training.
injury lrom untrained
Its earlier standard was light on specifics. OSHA constantly was asked:
"What constitutes the necessary and sufficient training of forklift operators?"
"How can one ensure that all forklift operators have been trained?"
"What testing, if any, should be conducted the training?" as part of
"Should the prior experience of a newly hired employee be counted toward fulfilling part or all of the training, or is it totally the employer's obligation to train that employee?"
Some critics suggested that OSHA
Forklift Fatalities
How accident occured
Forklitt overtumed
Forklitt struck something or ran off the dock
Worker pinned between objech
Worker struck by material
Worker struck by torf<m
Worker fell from lorklift
Worker died during forklift repair
Oher accident platlorm or curb
-OSHA develop a standardized course, or at least review and comment on or endorse various training courses, programs, agenda, or outlines. Others suggested that OSHA license or certify all powered industrial truck operators to attest to their ability to properly operate powered industrial trucks.
During the years of devising and revising the new standard, OSHA realized that all businesses were not alike. There could be no standard training program that would best accommodate the myriad different workplaces, equipment and personnel. Since operators vary greatly in experience and backgrounds and are required to operate different types of vehicles, different types and amounts of training are necessary, OSHA could not specify a rigid curriculum.
Although the agency suggests that programs consist of both classroom instruction and practical training, it has left the particular method of training (lecture, conference, demonstration, practical exercise, test or exami- nation, etc.) to the employer. Length of training must be based on the employee's experience and other qualifications and the nature of the work. The employer also chooses the instructor and the progfam developer (from within the company, outside training firm, forklift manufacturer, association, etc.).
The National Lumber & Building Material Dealers Association has just unveiled an operator haining program custom designed for the lumber industry, '"The Forklift and You." The kit, available from NLBMDA or any of its 22 rcgional federated associations at $199 for association members and $349 for non-members, includes a 30-
During the years of devising and revising the new standard, OSHA realized that all businesses were not alike. minute video, fiainer's guide, "Safety, Efficiency, Professionalism" poster, authorized operator poster, and five operator workbooks, ID cards, certificates and examinations. The components are also sold in a trainer package and an operator package.
While the kit provides "everything your on-site supervisor needs," it still takes effort to implement. Says NLBMDA director of public affairs Vicki Worden: "We provide all the tools dealers need to comply, but ultimately it's up to them to follow through and use them properly. It's notjust pop in a video and you're certified."
OSHA requires that there be some means to verify that training was conducted, such as mandating documentation of the training, producing and retaining plans, keeping attendance rosters, or issuing training certificates.
When refresher training is required, a set amount of naining must be conducted at a regular interval (for example, x number of hours of retraining annually). A designated person must evaluate and certify that each employee has taken the training and can competently operate the truck. Course malerials must be kept.
Each potential operator of a powered industrial truck must be capable of performing the duties that are required after training and appropriate accommodation. This includes being able to climb onto and off of the truck, to sit on the vehicle for extended periods of time, and to turn his or her body to be able to look in the direction oftravel when driving in reverse.
Operator evaluation should continue on a periodic basis to ensure that knowledge and skills are retained. Employers must certify that the required training and evaluations have been conducted. To minimize paperwork, certification need consist only of the name of the employee, the date of the training or evaluation, and signature of the person conducting the training or evaluation.
The employer should identify all the aspects of the job that the employee must perform, including the level at which the employee must see and hear, the physical demands, and the environmental extremes of the job.
Employers can forgo portions of the instruction that an employee previously learned, if he or she has been evaluated and has proven to be competent in those duties.
Methods of initial evaluation include having the employee fill out a questionnaire, by an oral interview, or by a combination of mechanisms.
Refresher training consists mostly of on-the-spot correction. The person making the correction should point out the incorrect manner of operation of the truck or other unsafe act being conducted, tell the employee how to do the operation correctly, and then ensure that the employee does the operation correctly.
More general, structured retraining programs might address common unsafe situations encountered in the workplace, unsafe methods of operating observed or known to be used, and the need for constant attentiveness to the vehicle, workplace conditions and how the vehicle is operated.
All training programs must cover:
(l) the characteristics, operation and limitations of the vehicles to be operated; (2) the hazards due to the characteristics of the workplace where these vehicles operate, and (3) the general safety rules that apply to these vehicles and their operation.
As an example, OSHA provided the following outline of a generalized forklift operator training program.
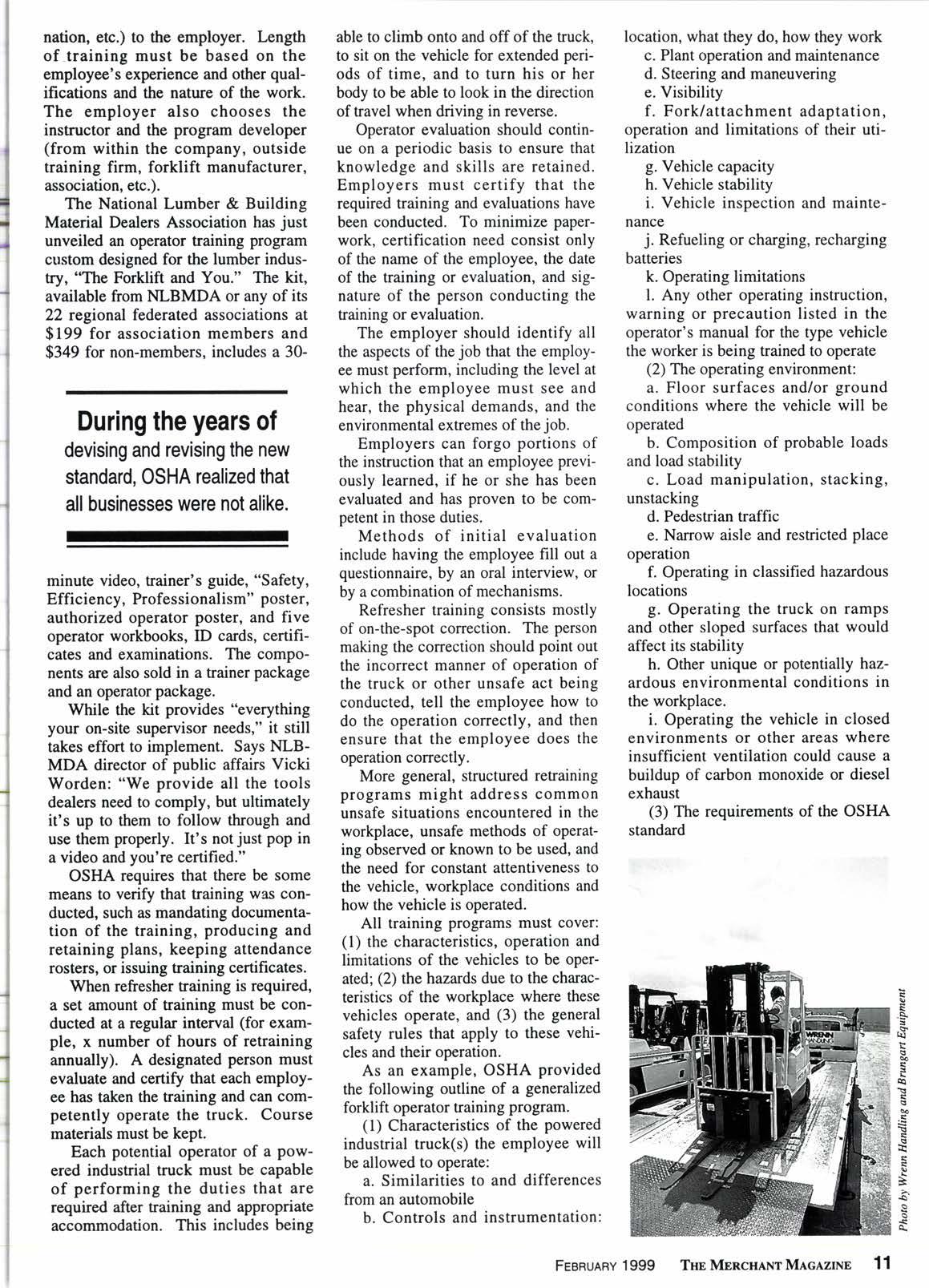
(l) Characteristics of the powered industrial truck(s) the employee will be allowed to operate: a. Similarities to and differences from an automobile b. Controls and instrumentation: location, what they do, how they work c. Plant operation and maintenance d. Steering and maneuvering e. Visibility f. Fork/attachment adaptation, operation and limitations of their utilization g. Vehicle capacity h. Vehicle stability i. Vehicle inspection and maintenance j. Refueling or charging, recharging batteries k. Operating limitations
L Any other operating instruction, warning or precaution listed in the operator's manual for the type vehicle the worker is being trained to operate
(2) The operating environment: a. Floor surfaces and/or ground conditions where the vehicle will be operated b. Composition of probable loads and load stability c. Load manipulation, stacking, unstacking d. Pedestrian traffic e. Narrow aisle and restricted place operation f. Operating in classified hazardous locations g. Operating the truck on ramps and other sloped surfaces that would affect its stability h. Other unique or potentially hazardous environmental conditions in the workplace. i. Operating the vehicle in closed environments or other areas where insufficient ventilation could cause a buildup of carbon monoxide or diesel exhaust
(3) The requirements of the OSHA standard