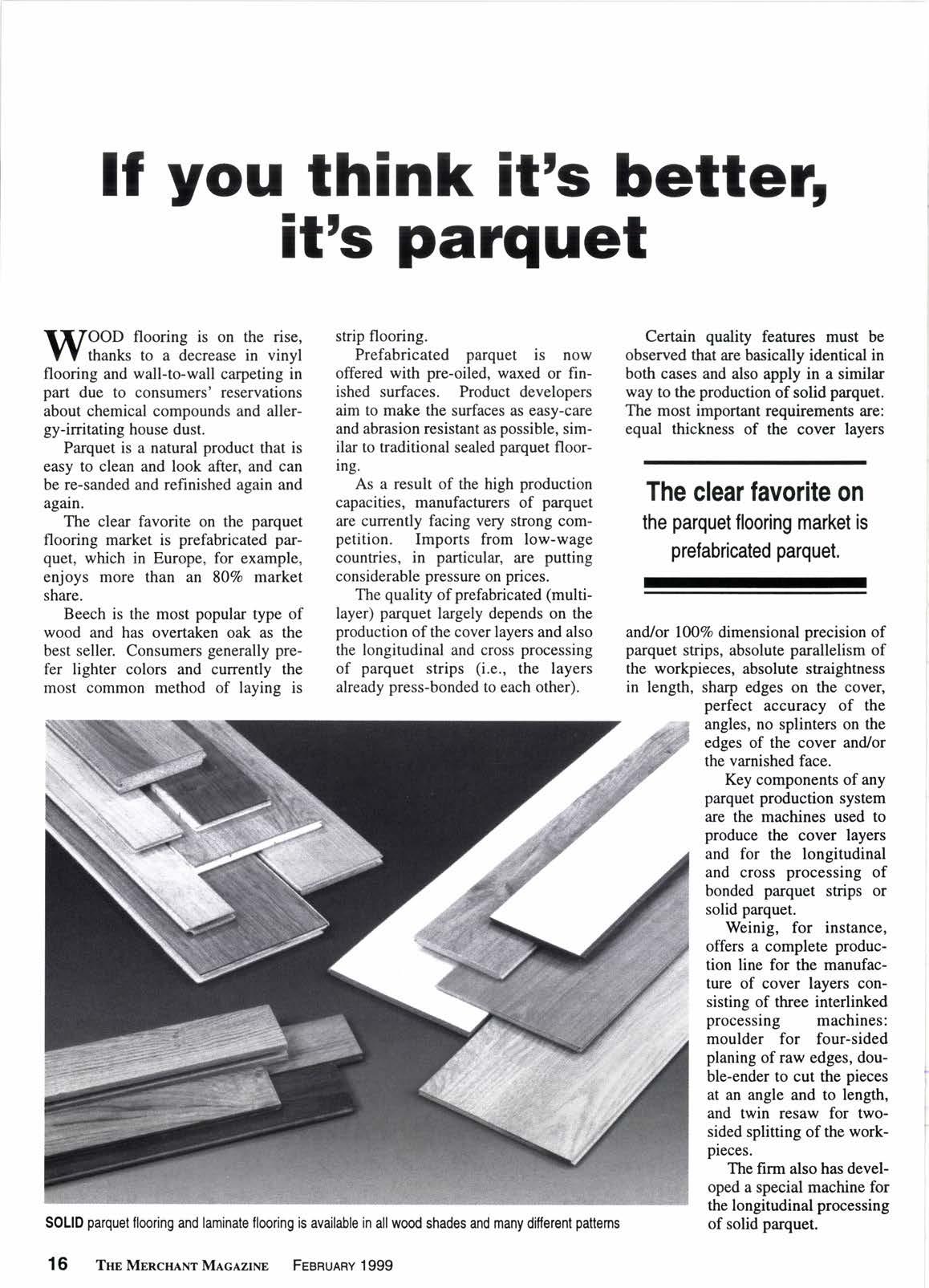
1 minute read
lf you think it's better, it's parquet
II/OOD flooring is on the rise, V Y thanks to a decrease in vinyl flooring and wall-to-wall carpeting in part due to consumers' reservations about chemical compounds and allergy-irritating house dust.
Parquet is a natural product that is easy to clean and look after, and can be re-sanded and refinished again and again.
The clear favorite on the parquet flooring market is prefabricated parquet, which in Europe, for example, enjoys more than an 80Vo market share.
Beech is the most popular type of wood and has overtaken oak as the best seller. Consumers generally prefer lighter colors and currently the most common method of laying is strip flooring. Prefabricated parquet is now offered with pre-oiled, waxed or finished surfaces. Product developers aim to make the surfaces as easy-care and abrasion resistant as possible, similar to traditional sealed parquet flooring.
As a result of the high production capacities, manufacturers of parquet are currently facing very strong competition. Imports from low-wage countries, in particular, are putting considerable pressure on prices.
The quality of prefabricated (multilayer) parquet largely depends on the production of the cover layers and also the longitudinal and cross processing of parquet strips (i.e., the layers already press-bonded to each other).
Certain quality features must be observed that are basically identical in both cases and also apply in a similar way to the production of solid paxquet. The most important requirements are: equal thickness of the cover layers and/or 1007o dimensional precision of parquet strips, absolute parallelism of the workpieces, absolute straightness in length, sharp edges on the cover, perfect accuracy of the angles, no splinters on the edges of the cover and/or the varnished face.
Key components of any parquet production system are the machines used to produce the cover layers and for the longitudinal and cross processing of bonded parquet strips or solid parquet.
Weinig, for instance, offers a complete production line for the manufacture of cover layers consisting of three interlinked processing machines: moulder for four-sided planing of raw edges, double-ender to cut the pieces at an angle and to length, and twin resaw for twosided splitting of the workpieces.
The firm also has developed a special machine for the longitudinal processing of solid parquet.