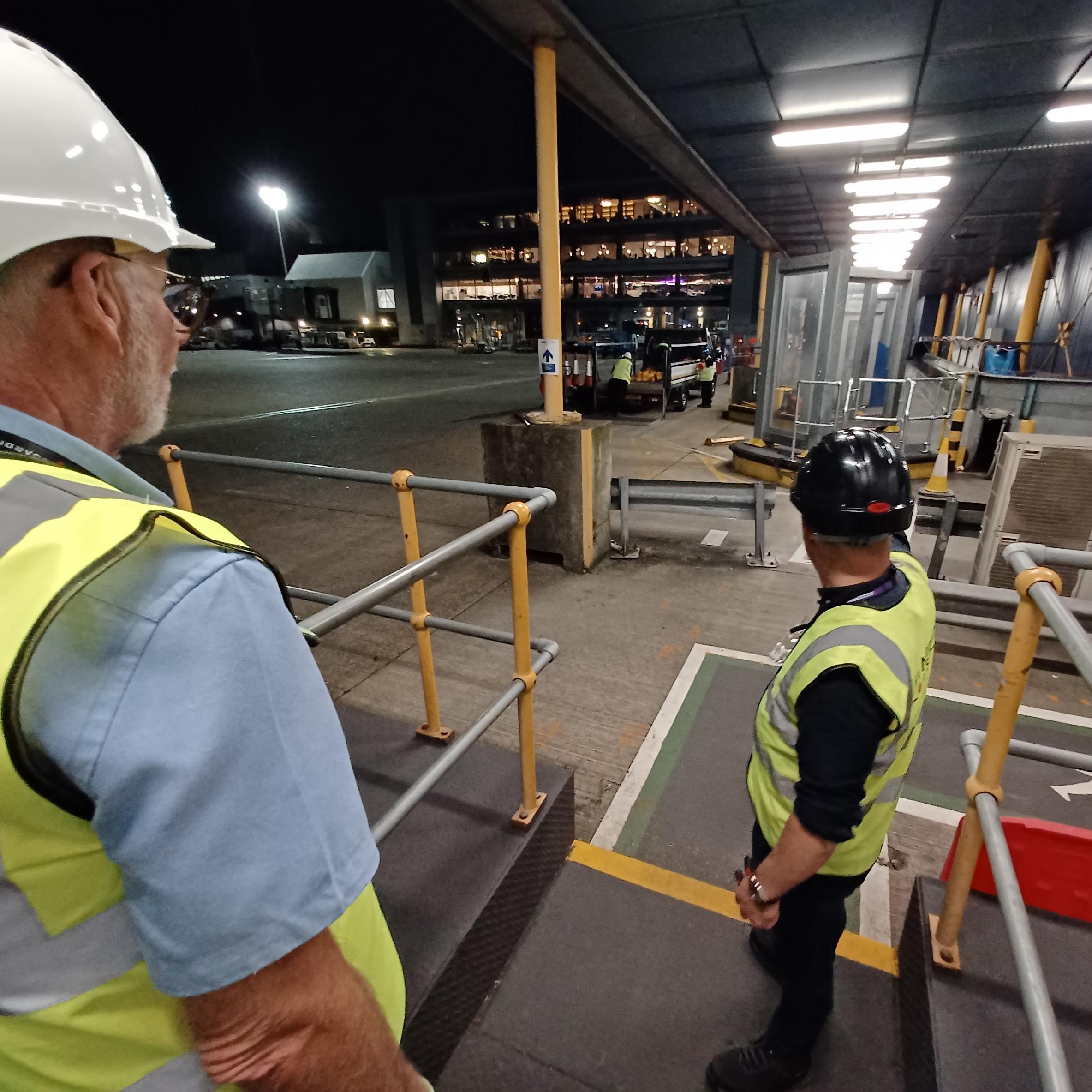
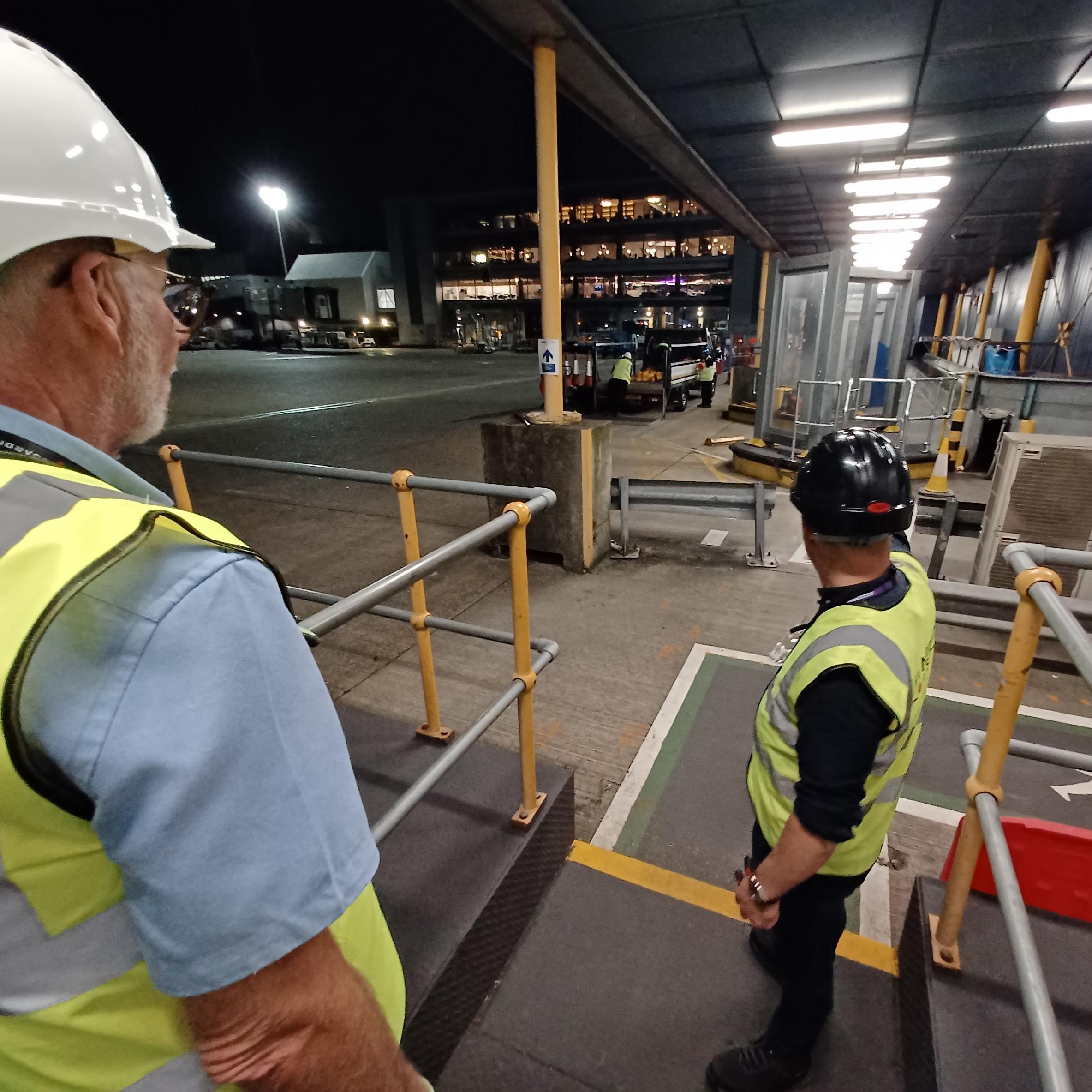
BBS BEHAVIOUR BASED SAFETY
For two decades, Guardior has established itself as a trusted name in the security industry.
We have built our reputation on a strong commitment to professionalism, reliability, and quality service delivery.
Chris Hope Managing Director (Guardior)
m: 07734 905 011
t: 020 8278 7068
e: chris.hope@guardior.com w: guardior.com
Frazer Serrano Director of Operations (Security)
m: 07596 548 434
t: 020 8278 7068
e: frazer.serrano@guardior.com w: guardior.com
Martin Allum Director of Operations (Logistics)
m: 07845 652 006
t: 020 8278 7068
e: martin.allum@guardior.com w: guardior.com
What is Behaviour-Based Safety (BBS)?
A behaviour-based safety programme is designed to modify a person’s behaviour whilst working, leading to a ‘total safety culture’ and performance.
A total safety culture is a culture in which:
» Individuals hold safety as a ‘value’ and not just a priority.
» Individuals take responsibility for the safety of their co-workers in addition to themselves.
» All levels of employee are willing and able to act on their sense of responsibility – they can go ‘beyond the call of duty’.
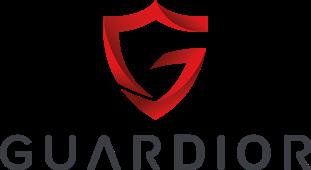
A BBS approach can be further described as one which:
» Is based on solid principles about engaging, motivating, assisting, reinforcing, and sustaining safe behaviours.
» Takes a systematic approach, examining the motivation underlying behaviours, in order to increase safe behaviour.
» Is an ongoing effort; not ‘once-off’ provisions, but a new way of working that the safety leader must continually promote for sustainable, positive results.
» Takes time to achieve; however, results can be observed immediately due to the nature of measurement involved.
» Emphasises increasing safe behaviours rather than focusing on length of time without injury. BBS programmes do not depend solely on ‘lagging indicators’ (after the fact), and instead shift the focus to ‘leading indicators’ (preventative).
» Is not a substitute for an already existing comprehensive health and safety programme; it is a supplementary tool that will enhance the ~effect of already existing practices, and will allow for an objective measurement system.
» Aims to understand causes of incidents and near misses and correct them through the behaviour of relevant people. For example, reducing hazards often requires behaviour change of managers and frontline workers, and equipment redesign involves behaviour change of engineers.
Why is BehaviourBased Safety commonly used?
» A significant number of accidents are reportedly caused by inappropriate behaviour.
» It is a good vehicle for management and workforce participation.
» It can improve the visibility of managers.
» Behaviours and actions influence culture through attitudes and perceptions.
» Behaviours determine the performance of systems.
Key features
» It helps to clearly define what ‘safe’ and ‘unsafe’ behaviours are.
» All involve observation of behaviour in the workplace
• By managers and/or peers.
• With/without targets.
» Provides feedback
• Reinforces safe behaviour.
• ‘Re-educates’ on unsafe behaviour.
» Feedback ranges from on-the-spot specific feedback and discussion, to impersonalised general data.
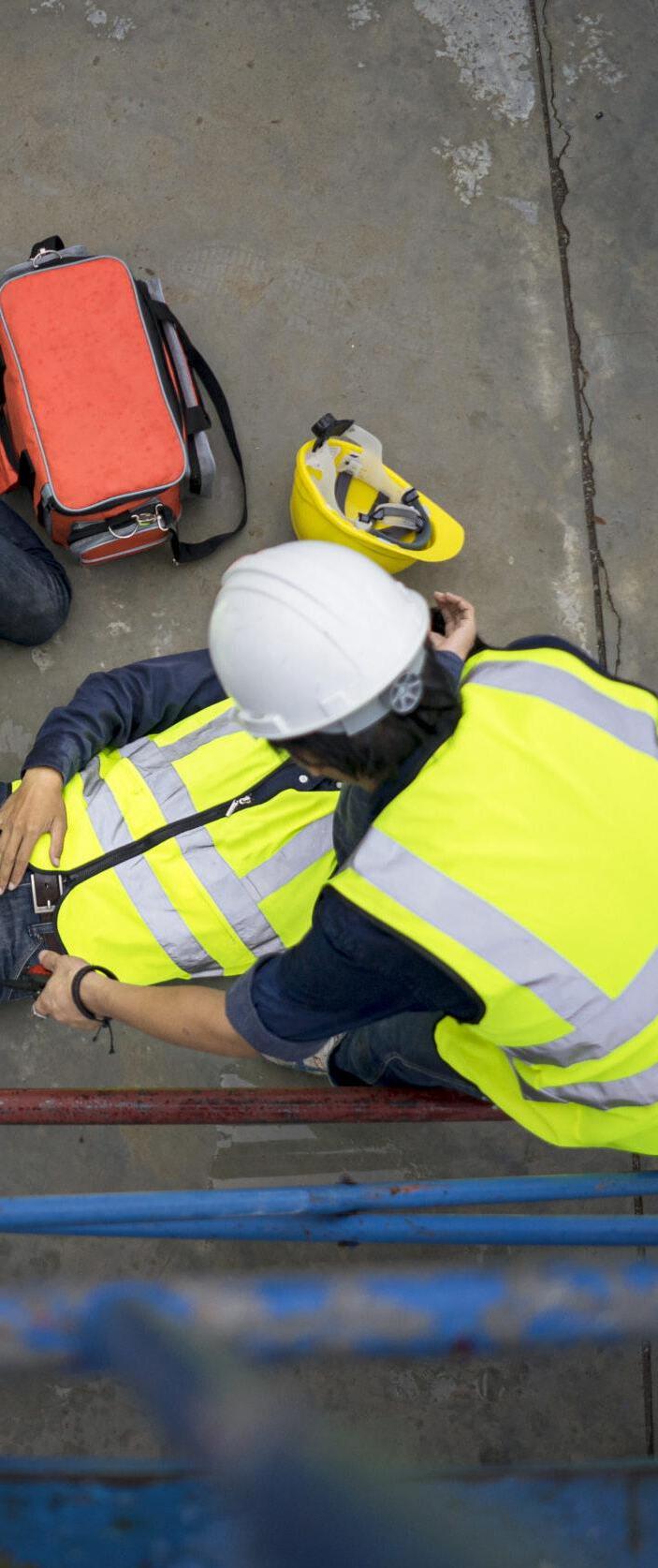
Requirements
The following are some requirements for any approach to safety at work that brings about noticeable, lasting results and contributes to a total safety culture:
» A strong management commitment towards maintaining and improving behavioural safety, witnessed in the regular acts of individuals at management level.
» Respectful, trusting, open communication between management and employee groups about all aspects of safety in the workplace.
» An open, feedback-rich culture among employees, which enables employees to consistently learn and grow.
» A commitment to improving the profile of and attitude to health and safety, and increased employee engagement in safety.
» An emphasis on safe and unsafe behaviour; not a sole dependence on lagging indicators such as safety statistics.
» A strong, consistent, timely reaction to the discovery of unsafe acts, whether they result in injury or not. Safety incidents are viewed as an opportunity to learn and improve.
» Generally transparent and fair leadership from all, including managers, supervisors, and owners.
» Awareness amongst all staff of different ways to consider or query human factors – how we do what we do, and why.
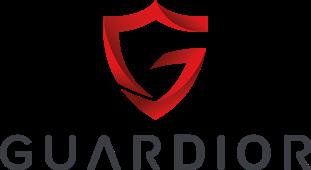
Pitfalls
» Rule violation vs good rules?
» Big, disciplined effort required.
• Very often fails through lack of real commitment or discipline.
• Some changes will be expensive.
» Not ‘owned’ by everyone.
» ‘Off the peg’ or consultant-led programmes can fail because of poor fit with local style/culture (UK/US).
» Trust levels amongst management and employees must match.
» Lack of friendly communication/Directive style of management.
More pitfalls
» May not be compatible with other messages.
» Focus on easy, intuitive issues.
» Tend to ignore low probability, high consequence risks. ‘Boots not leaks’ - can draw attention away from process safety.
» Can shift onus away from management onto individual.
» Don’t address significant impacts of management behaviour.
» ‘Big brother’/blame culture/Oh no, not another programme.
» High short-term expectations.
» Failed programme = worse situation than start.
BehaviourBased Safety
This guide is informed by the field of BehaviourBased Safety (BBS), which is often described as a bottom-up approach (frontline employees), with top-down support from safety leaders.
A behaviour-based safety approach promotes interventions that are people-focused and often incorporate one-to-one or group observations of employees performing routine work tasks, setting goals carefully and giving timely feedback on safetyrelated behaviour, coaching and mentoring.
The initiatives have a proactive focus, encouraging individuals and their work groups to consider the potential for incident involvement, (accidents) and to assess their own behaviour as safe or unsafe always, no matter what.
When we examine an incident report and ask questions around why a person behaved in a certain way, we tend to look at antecedents, or what occurred to ‘set off’ the behaviour.
However, if we examine the report with a view to consequences, we will gain a clearer picture of why the behaviour occurred.
For example, if an eye injury occurred and the individual was not wearing PPE, we need to examine what were the consequences for wearing the PPE (e.g., possible but not definite reduction of injury) and what were the consequences for not wearing PPE (e.g., immediate comfort, better vision on the job).
Examination of consequences can reveal that in some instances it is actually more preferable to not wear safety equipment. It is the job of a safety leader to ensure that it is more preferable to engage in safe behaviour.
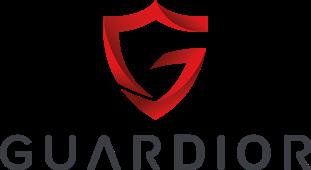
With BBS, behaviour is explained in terms of ABC model (Antecedent, Behaviour. Consequences).
ANTECEDENT
BEHAVIOUR
CONSEQUENCE
A stimulus or event that occurs before a behaviour in time. This stimulus or event may result in the behaviour. Work examples include goals, policies, training, job aids, guides.
Anything that we can see an individual do, or say.
A stimulus or event that occurs after a behaviour in time. This consequence could increase or decrease behaviour in the future, depending on its reinforcing or punishing properties. Work examples include feedback, recognition, task completion, goal achievement, rewards.
Reinforcement
Reinforcement occurs when a consequence that follows a behaviour makes it more likely that the behaviour will occur again in the future. Therefore, a reinforcing consequence is one that causes behaviour to occur more frequently.
For example, the behaviour of putting money in a snack vending machine and pressing a button has the consequence of the chosen food item being distributed. The presentation of the food item functions as reinforcement for putting the money in and pressing the button. If the person using the vending machine actually wanted the food item then they will repeat this behaviour in the future (because it was successfully accomplished).
Essentially, everything we do changes our environment in some way (consequences). When the environment changes in a way that we like, then we will repeat the behaviour that led to the change (reinforcement).
When we talk about reinforcement, we refer to the consequence that increases behaviour as a reinforcer.
A reinforcer is anything that is added following a behaviour that increases that behaviour in the future.
This could be recognition, praise, money, or anything at all that is provided after our behaviour.
As a basic example, when two people are having a conversation, they are reinforcing each others ‘conversation’ behaviour. If one person stopped talking, then reinforcement would no longer be present and the conversation would cease. Reinforcers are around us in our environment and maintain our behaviours all of the time.
A successful leader will identify their employees reinforcers through observing what motivates their employees, and by trying out potential reinforcers, for example, increasing positive feedback to see if that increases safe behaviour.
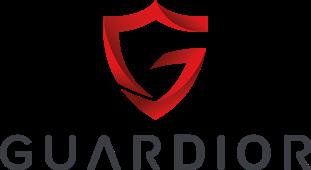
Inspection and assessment issues
» What is the evidence that behaviour change will improve safety? (as opposed to better procedures or easier to use equipment for example).
» How is the programme linked to the Safety Management System (SMS)?
» How do they address tough issues? (ie costly remedial work, time pressure).
» Do they understand the programme and its strengths and weakness (ie competence)?
» Are programme goals linked to other goals, ie team working?
» What happens when an observation card is completed? (workforce experience vs. management view).
» Are they knowledgeable, intelligent customers?
Advice for companies considering behavioural approaches
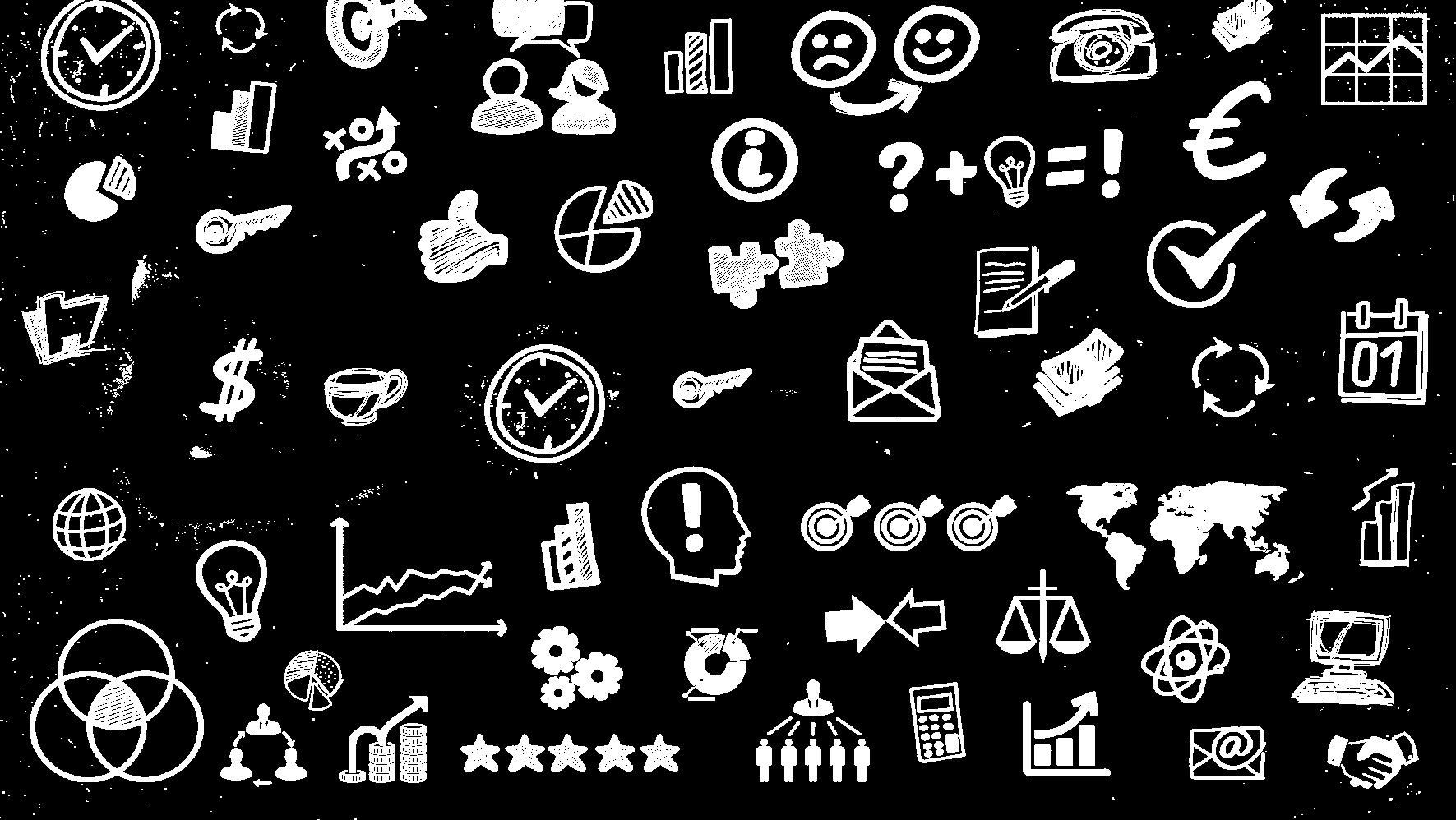
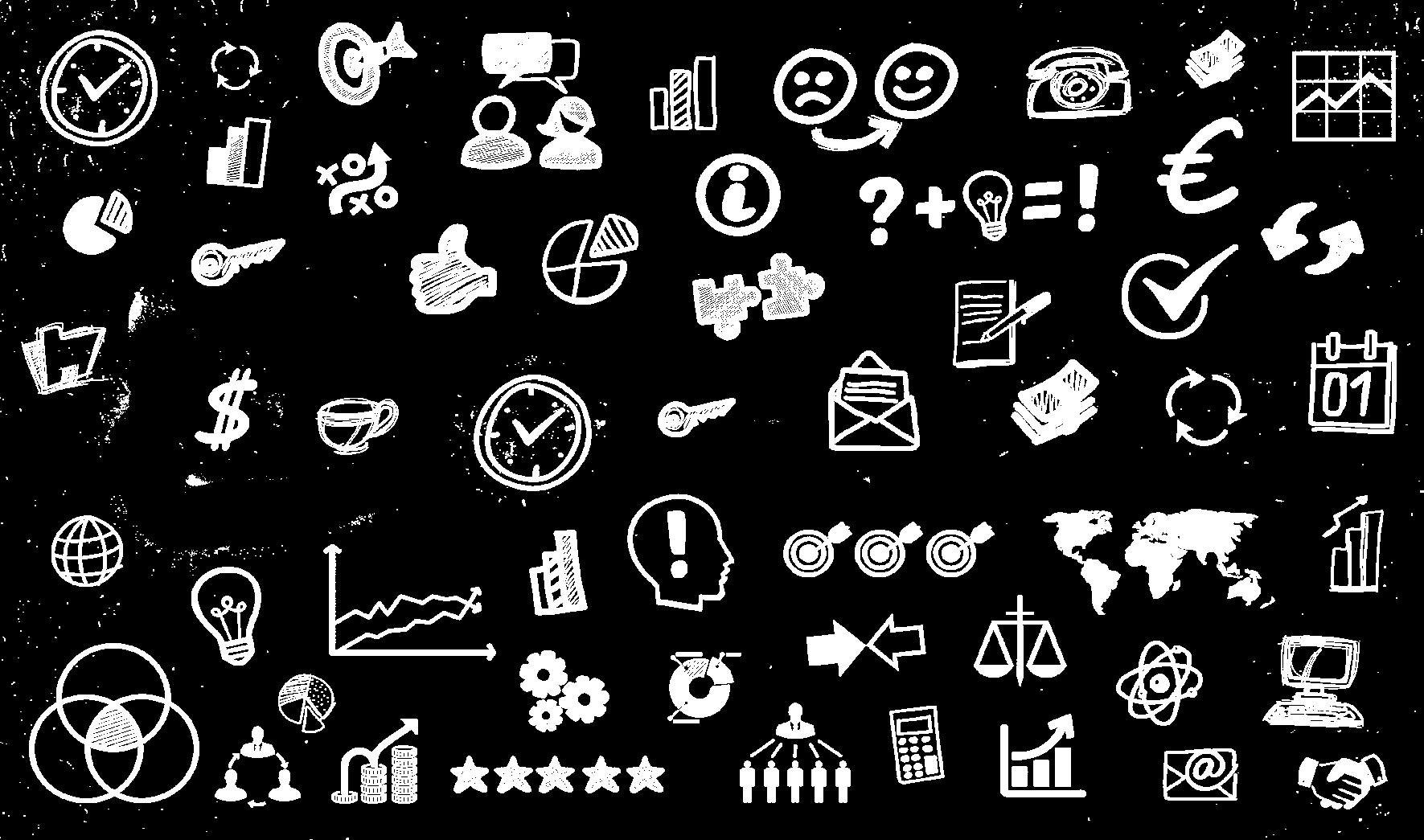
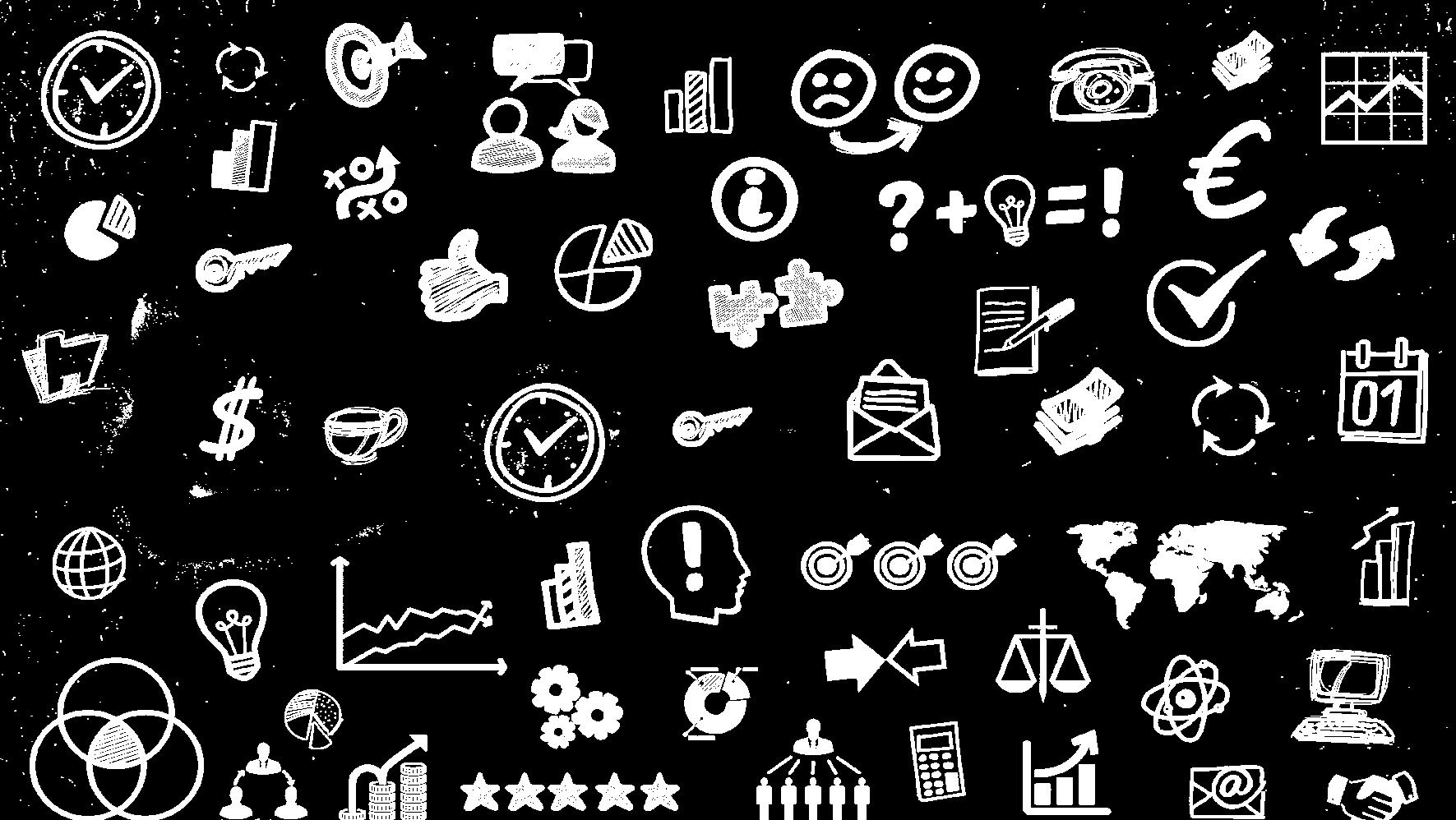
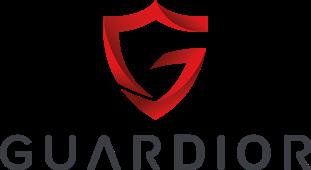
Do
» Be sure that it is really what you need right now.
» Find out (from employees) whether signals they get from management about safety are the first issue to address.
» Network with others - not only those suggested by the consultants.
» Learn what you can from alternative techniques available.
» Make sure the system is your own, in style, language, presentation etc.
» Pilot, and only roll-out when confident of success.
» Use it as a dialogue – and that means LISTEN to your employees!
» Spend considerable effort to get good, strong facilitators who understand safety.
» Make sure that participants focus on root causes of behaviours.
Don’t
» Underestimate the effort and planning required.
» Be over-optimistic.
» Get carried away and lose focus on other aspects of safety.
» Believe that the ‘Heinrich triangle’ works for occupational ill-health, minor personal injuries and major accidents.
» Bother at all unless -
• You’re confident that you already have a strong SMS and a safe workplace.
• Senior management can be made to think it was their idea all along.
Increasing the effectiveness/ chance of success
1
Ownership - developed inhouse is best.
2
Good fit with organisations needs, culture and SMS.
3
Commitment (involvement is better) from management.
4
Good communication and understanding of programme.
5
Approach seen as ‘fair and just’ - trust.
6
Managers act as role models.
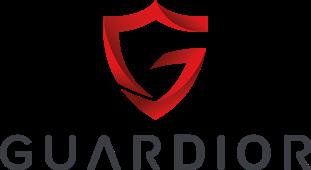
Summary
There are many advantages to undertaking and implementing BehaviourBased Safety protocols but these programmes (and cultural change) take time, resources and a concerted effort and senior management commitment.
BBS initiatives are a useful addition to the toolkit for occupational safety, but it should be noted that they still offer limited benefits for the control of major hazards.
A bias towards measurable success, can pull focus away from the basics of a business’ SMS and process safety. Additionally, all aspects of engineering and systems must be similarly considered and addressed. Both workforce and management behaviours must be included and there must be an awareness that the effectiveness of a programme largely depends on the existing cultures within a business.
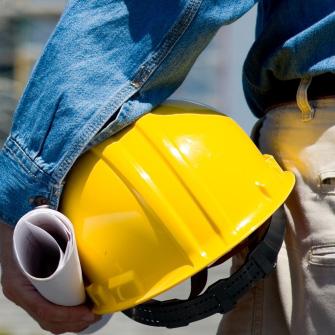