
3 minute read
MMM – Münchner Medizin Mechanik GmbH
Name ›
Address/P.O. Box › Postal Code/City › Country › Contact Person › Telephone › Fax › Email › Website › Social Media › Number of Employees › Founded (year) ›
Areas of Activity ›
Annual Turnover › Relevant R&D budget ›
External ›
Collaborations Mikron GmbH Rottweil Abteilung Werkzeuge
Berner Feld 71 78628 Rottweil Baden-Wuerttemberg Simon Sprissler +49-741-5380-450 +49-741-5380-480 info.mtr@mikron.com www.mikrontool.com
I
245 (worldwide) 1998
Development and fabrication of cutting tools
€45m €1.4m
DMQP (DMG MORI Quality Products)- Programme
Tools are our passion, small dimensions are our specialty, and hard-to-machine materials are our challenge. Every day at Mikron Tool is dedicated to achieving the best possible results in these areas.
Mission – Mikron Tool
We are working daily to achieve a leading position worldwide in the high-precision machining of small dimensions and challenging materials. This includes the regular development of new and unique tools as well as customer-specific solutions. In everything we undertake, a high level of competence is important. Focusing on our strong points is the key to our success. These include our well-trained and motivated employees, intensive development activities and investment in the most advanced production technologies.
MedTech Solutions – the tool range
The highest quality, precision, and process reliability are some of the main criteria when manufacturing medical devices, wether you are speaking about implants (trauma, prostheses or screws), instruments, or devices. This is exactly where our strength lies: in the development of carbide cutting tools for machining high-quality and biocompatible materials such as stainless steels, titanium, or chrome-cobalt alloys. We offer standardised tools for drilling, milling, and deburring in a diameter range from 0.1 to 8 mm as well as customised solutions up to 32 mm for all machining operations.
Latest innovations
A product is considered NEW at Mikron Tool only when it is unique and with high added value for the user. Without a doubt, this is true for every single CrazyLine product. For example:
Machining hexalobular sockets for bone screws CrazyTool Hexalobe is a new concept for machining hexalobular sockets on medical screws (better known as Torx® sockets) made of stainless steel or titanium. A combination drill and a milling tool is all you need to
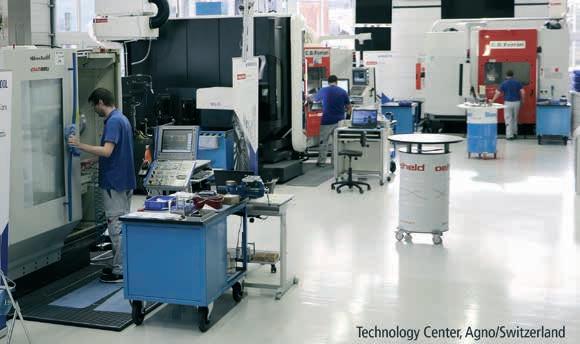
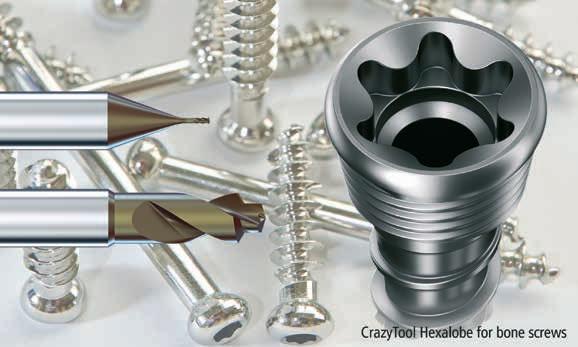
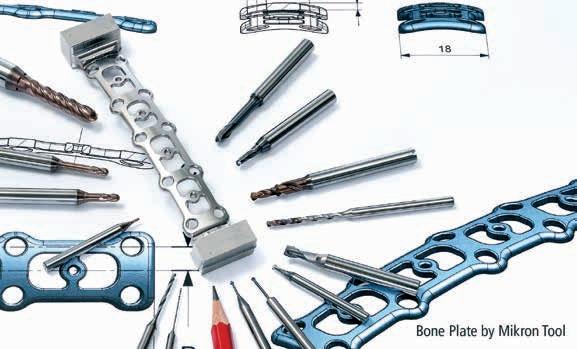
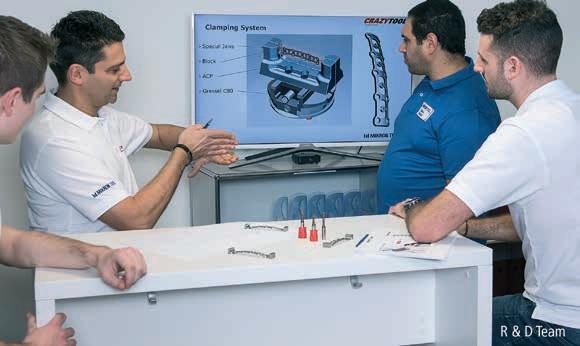
complete the four operations (predrilling – chamfering – milling – deburring). In three steps you reduce the cycle time by 50% whilst achieving a highly precise profile and an excellent surface quality.
Reducing machining time for bone plates Integrated cooling, high- performance coating and carbide, adapted cutting geometry, all combined with an optimised cutting strategy – these are some of the features of our performance cutting tool package (CrazyDrill and CrazyMill product lines). With this we are able to reduce the machining time from two hours to 48 minutes for a distal radius plate made of titanium.
Technical support
How to produce a new part with the best adapted tools? What is the right tool for a new material? How to optimise quality and cycle time in an existing process? How to be more efficient and maximise my possible cost saving? Shall I use standard tools or rely on a special solution with combined tools? To answer all these questions, we are at your disposal with our Technology Centre and our specialised cutting tool team!
Quality made in Switzerland and Germany
All our tools are produced in Switzerland or Germany, where identical production facilities, machine programmes, measuring instruments, and skilled tool grinders guarantee the same level of quality for all our products.